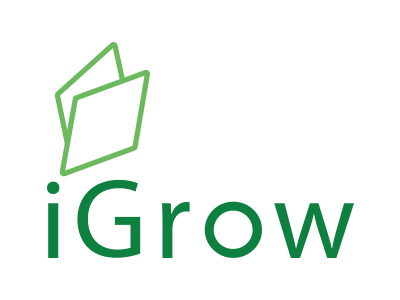
Welcome to iGrow News, Your Source for the World of Indoor Vertical Farming
Ushering In The Future
Why thermal management is critical to the evolution of LED grow lighting
Ushering in the future
Why thermal management is critical to the evolution of LED grow lighting.
November 10, 2016
John Cafferkey
The world is undergoing a revolution in horticultural lighting that will have wide-ranging implications in terms of how and where we grow, and what crops we consume. The move from high-intensity discharge (HID) lighting to LEDs is slashing electric bills for indoor farmers. Alongside cost, the reliability and longevity have both improved, reducing maintenance requirements.
The “instant on-and-off” aspect of LEDs makes them easily integrated into automated growing cycles to maximize plant growth. And with wavelengths optimized for different crops, power usage can be reduced further. The lower heat output of LEDs means plants can be grown closer to light sources, allowing for better use of space.
Analysts LED Inside predicts the market will reach USD $500m by 2017, while WinterGreen Research sees it reaching $1.8 billion by 2021.
LED technology is likely to transform the horticultural industry
The argument for LED grow lighting is increasingly one of economy. The reduced running costs of LEDs has moved the market from high-value crops like cannabis, to lower-value fruit and vegetables, which is having a transformative effect on the industry.
LEDs allow affordable cultivation in previously inaccessible places such as tower blocks in city centres, extreme climates or areas lacking natural light such as the Arctic Circle in winter. Innovations like vertical farming, where plants are tightly stacked on floor to ceiling shelving with closely positioned LED lights, make enormous crop yields from a small footprint possible. Such techniques improve the consistency and standardization of crops while reducing pesticide use. And locating farms close to consumers cuts transport and storage costs.
The societal implications are enormous. In enabling the affordable growth of a diverse range of crops, LED technology has the potential to improve worldwide nutrition, as well as to offset food inflation as populations increase. By enabling crops to be grown close to consumers, LED technology could offset ecological and ethical issues associated with the over-farming of high-value crops (such as avocados and quinoa) within highly localized regions.
Thermal management is a critical factor in the further evolution of LED grow lights
However, LEDs do have one issue: thermal management.
The type of LEDs generally used in horticultural lighting are high-brightness LEDs (HB LEDs), between 1–5W. Although massively more thermally efficient than HIDs, most HB LEDs are still only around 40 percent efficient, so 60 percent of the energy comes out as heat rather than light. Horticultural LED modules often have hundreds of HB LEDs mounted onto a printed circuit board (PCB), creating a considerable thermal challenge. If heat isn’t removed effectively it can have a negative impact on the LEDs, reducing lifetime and light quality and ultimately leading to the LED’s failure, and the plants themselves.Another factor to improve thermal management is growers’ desire to place plants closer to the light source without heat affecting the crop, thus allowing for tighter spacing and greater economies of scale.
There are two fundamental types of thermal management — active and passive. Active thermal management uses fans and pumps to push air or liquid through the LED module. Heat is conducted into this medium (air or water) and drawn away from the LEDs where it is radiated out into the atmosphere or used to warm soil. Passive thermal management uses materials to conduct the heat away. A heatsink is a good example.
Most designers are familiar with active cooling systems. However, heat must be removed at the level of the LED chip itself. If heat is not effectively conducted away from the LED chip, the whole system will fail.
How LED heat extraction works (at the chip and board level)
An LED module will, depending on the device, generally feature either “packaged” or bare HB LED dies mounted on a PCB. To keep this simple, let’s assume the use of packaged LEDs.
A packaged HB LED cannot radiate heat directly into the air due to the surrounding encapsulant. Heat must be conducted through the bottom of the LED, - usually via a ceramic mount that is part of the HB LED ”package” – through the PCB and then out to the thermal management system.
Traditional PCBs, such as FR4, are not sufficiently thermally conductive for HB LEDs. Instead, HB LEDs are mounted onto metal-clad PCBs (MCPCBs), a PCB that incorporates a metal heat spreader. Critically, this MCPCB must also feature a dielectric (electrically isolating) layer that sits between the metal board and the circuit layer to prevent the LED shorting. This dielectric layer must be sufficiently thermally conductive to conduct heat effectively to the metal layer beneath it.
Traditionally, MCPCBs use a layer of epoxy resin between the metal base and the copper circuit as the dielectric. As resins are poor thermal conductors, the epoxy is usually laced with grains of ceramic to improve its performance. However, ceramic-loaded epoxy resin cannot achieve really good thermal conductivity because individual ceramic grains must be separated from each other by epoxy to hold the material together. As the need to remove heat increases, existing MCPCB solutions are unable to meet the challenge.
A new approach is required — one that enables MCPCBs to reach a significantly higher level of thermal conductivity.
Nanoceramics — a new approach to MCPCBs
A new approach to MCPCBs has been developed that delivers thermal performance suited to the demanding needs of horticultural lighting. This approach uses a patented electro-chemical oxidation process to convert the surface of aluminium into a nano-grain alumina (nanoceramic) dielectric layer.
The thinness of this alumina layer (10–30 microns) is critical as it creates an extremely short, uninterrupted thermal path which the heat can move quickly. This gives nanoceramic a composite thermal performance of 115 W/mK. This is much higher than anything else available.
This performance enables horticultural grow light designers to push the limits of lumen density, squeezing more light out of smaller modules. Indoor farms can be built to a higher density helping to achieve higher yields on the same footprint, ultimately driving the economies of scale that are the critical factor for this new wave of farming to fulfil its potential.
John Cafferkey is Marketing Manager at Cambridge Nanotherm, an innovative company employing nanotech for the thermal management of LEDs headquartered in Haverhill just outside of Cambridge. John is responsible for developing and communicating Cambridge Nanotherm’s proposition to global LED manufacturers and designers.
Vertical Farming: What Is It, And What’s Fueling Its Growth?
80% of the earth’s population will live in urban areas by the year 2050.
Vertical farming, or urban farming, is becoming more prevalent in the agribusiness sector. Experts predict that almost 80% of the earth’s population will live in urban areas by the year 2050, so developing and maintaining sustainable supplies of fresh food in large cities is increasingly important–and profitable.
By cultivating plants inside a skyscraper greenhouse, utilizing natural sunlight and artificial lighting, vertical farmers are able to produce fresh food while minimizing land usage and transportation costs. Droughts, floods and other weather-related issues are a thing of the past, and a controlled indoor climate carefully regulates ideal growing conditions year-round.
Curious about opportunities in vertical farming? Here are 10 things you need to know about this growing industry.
History of Vertical Farming
1. Vertical farming is regarded as a fairly new concept, but the idea has been around for a long time. In 1915, American geologist Gilbert Ellis Bailey wrote a book called Vertical Farming, and while it mostly dealt with using particular types of soils to grow crops, the idea for today’s vertical farm was born from his theory.
2. The first practical example of a vertical farm dates back to the 1950s, with an attempt at growing cress indoors at a large scale.
3. In 1999, students in a university classroom were discussing the idea of rooftop farming to produce rice. Dr. Dickson Despommier then took the discussion to the next level: what if crops were grown inside buildings?
How Vertical Farming Works
4. Using Manhattan as an example, Dr. Despommier’s class estimated that one 30-story vertical farm could produce enough food for more than 50,000 people, and 160 such farms could feed the entirety of New York City.
5. The plants that thrive best in vertical farms are nutritious types of produce, like green veggies and tomatoes. Crops like wheat and rice will be more difficult to grow in a vertical farming environment because of the amount of biomass required for them to thrive.
6. Vertically farmed crops can be grown hydroponically or aquaponically (in water) or aeroponically (in the air), without any soil. The biggest need is for a light source throughout the farm. Typically, prototype vertical farms use a combination of natural and artificial light for photosynthesis.
7. Because vertically farmed crops are produced indoors, in a controlled environment, people would have access to locally grown fresh produce year round – no need to purchase imported fruits and vegetables or prepared or frozen foods during the winter months, when those crops typically aren’t in season.
8. Another benefit to vertical farming? Produce grown indoors is organic and chemical-free, as no herbicides or pesticides are required.
The Future of Vertical Farming
9. By 2050, the world’s population is estimated to swell to 9 billion people, and experts guestimate that 80 percent of them will reside in urban areas. As the population grows, there will be less land mass available for farmland and growing food.
10. The world’s largest vertical farm is scheduled to open in Newark, NJ, this year. Set up in an old steel factory, it’s estimated to be 75 times more productive than a traditional farm of a similar size, and it requires no soil and 95 percent less water.
USA Subterranean Farm
About two years ago, before I was really ready, I proposed the development of a subterranean indoor farm in a major metropolitan area in the mid-western United States
USA Subterranean Farm
- Published on July 6, 2015
Glenn Behrman
FollowingUnfollowGlenn Behrman
CEA Advisors,GreenTech Agro LLC, Developers of The Growtainer™ & Growrack™. Indoor Farming Experienced Professional
About two years ago, before I was really ready, I proposed the development of a subterranean indoor farm in a major metropolitan area in the mid-western United States.With a population of 2.75 million, access to four major highways and a food deficit over 2 billion dollars per year, this was and still is an excellent opportunity.
Although I've been in the horticulture industry for almost 45 years, two years ago I was still connecting the dots and certainly didn't know then what I know now about indoor farming, controlled environment agriculture and technology based production but my proposal was well received by the local and state government officials that I came in contact with and they were behind the project 100%. The city and state offered substantial assistance, including access to various economic incentives, a preferred "local grown" purchasing initiative and assistance with developing strategic relationships with C level executives at local Fortune 500 businesses, local hospitals and universities, non-profits, schools, etc.
Since that time I've developed and nurtured relationships with the right people, further evaluated the site that I have in mind, met with the leasing people and found a subterranean site that is affordable, has a great infrastructure in place and is guaranteed to be front page news for a number of reasons.
Fast forward to today: Now I've spent the past four years laser focused on indoor farming, learning a lot from a lot of really qualified people. I've designed, built and operate two successful container based indoor farms, picked the brains of the most knowledgeable people in the industry, established a network of experts in every necessary component and facet of indoor production, spent 1000's of hours focused on site design, automation, production, technology and economics and now I'm ready to pull the trigger on the development of the most unique state of the art indoor farm in the world.
Fast Forward to November 2016. I'll be in Kansas City next week for the kick off of this fantastic project. Watch as it unfolds.... gb@cea-advisors.com
Five Vertical Farms that Capture the Imagination and Profit
Vertical farms: the idea captures our imagination.
May 17, 2015 | Rose Egelhoff
Vertical farms: the idea captures our imagination. We envision their upward-twisting frames nestled between the steel and chrome skyscrapers of the big city. Each floor overflows with fruits and vegetables brought to life by hydroponic or aquaponic growing systems, bringing local food and a breath of fresh air to cities with a footprint smaller than any “horizontal” farm.
Harvesters Alejandra Martinez (front), Steve Rodriguez, and Marquita Twidell cut basil grown in an aquaponic system at FarmedHere, a vertical farming operation based in Bedford Park, Illinois. Image courtesy of FarmedHere.
While setup and electrical costs remain expensive, a wave of vertical farmers around the world has been finding new ways to cut costs and streamline systems to make vertical farming a reality. They may not be ‘farmscrapers’, but these five vertical farms achieve production rates up to 100 times more efficient per square foot than traditional farming while bringing year-round local produce to their communities.
FarmedHere
FarmedHere’s huge, 90,000 square foot facility features an aquaponic setup lit by specially designed magenta and blue LEDs, developed through a partnership with the LED lighting manufacturer Illumitex, Inc. The lights emit only the frequencies of light that plants utilize, reducing energy costs. Roots dangle in trays of water fertilized with waste from tanks of tilapia and closed, soil-free systems minimize exposure to pests and disease, making their organic certification an easy achievement.
FarmedHere grows microgreens, basil and mint—staple crops for vertical farmers because they can be ready in as little as 14 days (that’s 26 harvests every year!). They sell to the big names, including more than 50 Whole Foods Markets and many other Chicago grocery stores.
This Singapore farming company exemplifies the potential for vertical farming to thrive in urban spaces. Real estate prices are sky-high on the densely-populated island, and access to fresh food is limited. Singapore imports most of its produce from China, Malaysia or the U.S.
Jack Ng saw the potential demand for fresh, local produce and created Sky Farms. He designed a growing system called A-Go-Gro. Thirty-foot A-frame towers rotate plant troughs up and down on a hydraulically powered belt to provide equal exposure to sunlight. Though Sky Greens grows hydroponically, these systems can also be adapted to soil growing.
Sky Greens currently produce ten varieties of greens including bok choi, lettuce, kang kong (water spinach) and bayam (amaranth). The product ends up costing about 10% more than imported greens but according to Permaculture News, Sky Greens’ extra- fresh veggies are “flying off the shelves.”
Another Chicago enterprise, the Plant describes itself as “part vertical farm, part food business incubator, part research and education space.”
Ten local food businesses, including several vertical farming operations, a sustainable prawn grower and a bakery, are located inside The Plant. The building is an abandoned pork packing facility in Chicago’s Back of the Yards neighborhood, retrofitted by crews of volunteers to fit the needs of local food producers. One business uses the roof space for good old soil farming while indoor operations employ hydroponics and artificial light. Plans for a shared kitchen are in the works, and The Plant eventually hopes to achieve net-zero energy use by harvesting biogas from their anaerobic digester, eliminating the high electricity costs that plague vertical farmers.
In Japan, the aftermath of the Fukushima crisis left in its wake both abandoned buildings and farmland devastated by radioactive contamination. Vertical farms like Mirai (“future” in Japanese) helped replace the lost food production capacity. Shigeharu Shimamuru, plant physiologist and president of Mirai, collaborated with GE Japan to design a state-of-the-art LED hydroponic system with carefully controlled wavelengths and dark periods. This means plants can photosynthesize at maximum capacity during the day and rest or “breathe” at night.
The combination makes for both fast-growing plants, and efficient resource use. Compared to conventional farming, the setup cuts produce waste by 50 percent, reduces water use by 99 percent and is 100 times more productive per square foot. The system operates in 12 locations around Japan, including a 25,000 square foot farm in the Miyagi prefecture just north of Fukushima, which can produce 10,000 heads of lettuce a day at full capacity. Mirai has recently begun another project in Korea.
Instead of growing in water, Aerofarms takes things another step away from conventional soil farming and grows plants in the air. Seeds germinate in a reusable fabric layer and suspended in stacked trays. The roots are sprayed with water and nutrients and LED lights fuel photosynthesis. Ed Harwood, a former Cornell professor who founded Aerofarms with his partners Marc Oshima and David Rosenberg in 2004, designed the system.
Aerofarms started off producing greens and herbs for farmers’ markets in upstate New York, including the prestigious Ithaca Farmers’ Market. They also sell their technology to other indoor farmers. Though not yet profitable, they are planning to expand. The project: a 69,000 square foot custom-built vertical farm in Newark, NJ. The $39 million development project, which is scheduled for completion in 2016, is being financed primarily by Goldman Sachs’ Urban Investment Group. Additional funds from Prudential Financial and the city of Newark supplement Goldman Sachs’ investment.
City of Vancouver Still Paying for Failed Urban Farm
A failed urban farm located in a downtown Vancouver parkade continues to be a costly headache to the City of Vancouver.
According to documents filed in a continuing lawsuit against the city, a greenhouse and equipment from the farm is still located in the parkade, over a year after the company operating the farm went bankrupt.
In a counterclaim filed April 20, EasyPark, a non-profit authority that manages parkades owned or leased by the city, claims it has been unable to use the roof of the parkade or make any income from the space.
EasyPark alleges the greenhouse is a safety risk because it could collapse in a heavy snowfall, and it continues to pay for security and maintenance related to the greenhouse, according to court documents.
EasyPark is asking for an injunction requiring the farm’s current owners to either remove the greenhouse from the roof of the parkade, or permit EasyPark to remove and dispose of the structure.
The counterclaim follows an initial lawsuit filed by Clay Haeber and a numbered company on March 3. In that claim, Haeber alleges the City of Vancouver’s refusal to transfer a licence to operate the farm in the parkade to his company is breach of contract.
Meanwhile, Donovan Woollard, one of the proponents of the high-profile vertical farm that went bankrupt in 2014, says he still believes in the concept and is now working with an Australian company on a new project.
Home of the lettuce-eaters
In 2012, Alterrus, a company trading on the Canadian Securities Exchange (CSE), signed a licence agreement with the City of Vancouver and EasyPark to use space in the parkade at 535 Richards Street.
Alterrus and its subsidiary, Local Garden Vancouver, operated the vertical farm in the parkade. It used a system involving stacked trays that moved automatically “to maximize exposure to natural light,” according to court documents.
The business model for the farm involved selling pesticide-free greens and herbs to high-end restaurants. Local Garden hired people with barriers to employment and planned to deliver by bicycle, according to media reports from 2012.
Alterrus' vertical farm on the top floor of a parkade at 535 Richards Street in 2012 |Dan Toulgoet, Vancouver Courier
At the time of its launch, Vancouver Mayor Gregor Robertson said the project showed “the innovative spirit in our city’s booming clean tech sector,” according to Business in Vancouver’s sister paper, the Vancouver Courier.
Public filings for Alterrus show the company tried several business ideas from the time it was incorporated in 1996, from bicycle rentals for hotels to online dating to skin care. By 2007, the company was focused on vertical farming, and in June 2012, changed its name from Valcent to Alterrus.
Alterrus’ 2012 annual financial statement showed an accumulated deficit of $52 million.
In 2014, both Alterrus and Local Garden Vancouver went bankrupt. The companies owed over $4 million, including $1.2 million to the largest creditor, Vancity Credit Union, and were behind on rent payments to EasyPark.
As the owner of sustainable business consulting company Transom Enterprises, Woollard partnered with Alterrus to launch Local Garden.
Woollard is also director of Radius Ventures, a socialenterprise program at Simon Fraser Univerity’s Beedie School of Business.
“For various reasons which I’d rather not get into, Alterrus as a company went bankrupt,” Woollard said. “At the end of the day there were a number of creditors of which I was one. I am hopeful for the space and [I] continue to do work in the vertical farming space and would love to see that facility open up again.”
Woollard is working with a potential business partner in Australia on another vertical farming project, although the venture is in a preliminary stage, he said. It’s possible the project may be based in Vancouver.
Strawberries, not marijuana
Haeber was appointed to Alterrus’ board in November 2013. In his lawsuit, Haeber claims he incorporated a numbered company because he wanted the vertical farming operation to continue and he was “keenly interested in the urban gardening concept.”
Haeber did not respond to interview requests from BIV.
Haeber is currently head of information technology for Kit and Ace, a clothing firm started by the son and wife of Lululemon (NASDAQ:LULU) founder Chip Wilson. According to his LinkedIn profile, Haeber worked at Lululemon between 2007 and 2013.
Haeber’s numbered company purchased the loans owed by Alterrus and Local Garden and became owner of the farm in July 2014, but still had to negotiate with the City of Vancouver and EasyPark for a licence to operate.
Haeber claims he told the city that once he got the licence, he would sell all his shares in the numbered company to Affinor Growers Inc., a company with experience growing medical marijuana in a vertical farming format. Like Alterrus, Affinor trades on the CSE, an exchange with simpler reporting requirements and lower fees than the Toronto Stock Exchange or the TSX Venture.
According to Haeber’s claim, Affinor confirmed to the city in writing that it would only grow vegetables such as strawberries in the parkade, not marijuana.
Affinor is not a party in the lawsuit.
Haeber alleges that both EasyPark and the city, along with Alterrus and Local Garden’s bankruptcy trustee, agreed to the terms of the licence agreement, prompting Haeber and Affinor to ink a $1.4 million deal for the operation, which included $500,000 in cash and the rest in Affinor stock.
The city’s refusal to grant the licence meant Haeber lost $1.4 million, he alleges. Haeber is now searching for a new buyer.
In a response, the City of Vancouver claims that city solicitor Heidi Granger made it clear to Haeber that final authority to sign a licence agreement rested with either the city’s director of legal services or city council.
The city alleges that while Haeber advised them he planned to sell the business to a third party in April 2014, he didn’t tell the city the identity of the buyer until the following August.
When the city did due diligence on Affinor, the response claims, it learned the company was in the business of growing medical marijuana. Affinor’s financial statements “raised concerns with respect to Affinor’s financial circumstances,” according to court documents.
“Ultimately, the City rejected the plaintiff’s proposal that Affinor be substituted in place of Haeber,” states the city’s response.
Now Affinor is considering launching its own lawsuit, said Nick Brusatore, the company’s chairman. He said his company lost $210,000 when the deal fell through.
“I feel borderline discriminated against,” he said.
Affinor has several projects in the works for both vegetable and medical marijuana production, Brusatore said. None of the farms is yet operational.
Brusatore doesn’t believe a vertical farm in the downtown parkade is viable as a business. His aim was to use the farm as a demonstration project to “have something pretty for the city so we could brag about what we did.”
The City of Vancouver declined, and EasyPark did not respond to, interview requests for this story.
With files from the Vancouver Courier
jstdenis@biv.com
@jenstden
5 Ways Vertical Farms Are Changing the Way We Grow Food
No soil? No problem. Vertical farms are sprouting around the world.
No soil? No problem. From Japan to Jackson, Wyoming, plucking fresh lettuce is as easy as looking up. Vertical farms have been sprouting around the world, growing crops in places where traditional agriculture would have been impossible.
Vertical farms are multiple stories, often have a hydroponic system and some contain artificial lights to mimic the sun. These green hubs are attractive in a variety of ways since food can be produced with less water (since it just recirculates), creates less waste and takes up less space than traditional farming, ultimately leaving a smaller footprint on the environment.
Additionally, the United Nations projects that the world's population will reach 9.6 billion people by 2050, 86 percent of whom will live in cities. For swelling cities, these urban farms give city dwellers greater access to fresh, nutritious food-year round, reducing the distance it has to travel to get to forks. Here are five more reaons why the sky's the limit with vertical farms.
1. Vertical farms can defy any weather: In perpetually wintry Jackson, Wyoming, residents will soon be able to find fresh tomatoes, lettuce and other produce that's not hauled in by delivery trucks. The Vertical Harvest farm is a three-story 13,500 square foot hydroponic greenhouse that will sit on a mere 30 by 150-foot plot adjacent to a parking lot. Utilizing both natural and artificial lighting (especially since the area is blanketed in snow most of the year), three stories of plant trays will revolve inside the building as well as the ceiling in a carousel-like system to maximize light exposure. The company aims to supply 100,000 pounds of year-round produce that's pesticide-free, and will use 90 percent less water than conventional farming because it recycles its water.
Construction of the $3.7 million greenhouse kicked off last November and has already pre sold crops to restaurants, grocery stores and a hospital. In the video below, E/Ye Design architects and Vertical Harvest co-founders Penny McBride and Nona Yehia talk about their innovative building and their mission to hire adults with developmental disabilities to spur local employment.
2. Vertical farms are a great response to climate change: Urban farming has been touted by many as a solution to increasingly extreme weather caused by warmer global temperatures. In very parched California, the Ouroboros Farms in Pescadero employs an unusual group of farmers: Catfish. The farm uses an "aquaponics" system, where 800 catfish swim and dine on organic feed, and as they create waste, the crops above suck up this nitrogen-rich fertilizer. All this means no soil, pesticides or other toxins are required for the stunning variety of vegetables that are produced at the farm, from spicy greens to root vegetables. In case you're wondering, nothing goes to waste; these fish are also sold as food. The farm also saves 90 percent less water than traditional farming.
"I honestly believe [aquaponics] is the evolution of farming," Ken Armstrong, the founder of Ouroboros Farms, said in the video below, "because of its ability to grow faster and more densely with fewer resources it will be the methodology of growing in the future."
3. Vertical farms adapt to disaster: We previously featured Japanese plant physiologist Shigeharu Shimamura, who converted an abandoned, semiconductor factory into the world’s biggest indoor farm, Mirai. Shimamura built the farm in 2011 in response to the food shortages caused by the Tohoku earthquake and tsunami that devastated Japan, and sparked the Fukushima nuclear disaster which irradiated much of the region's farmland.
At 25,000 square feet, the farm can yield up to 10,000 heads of lettuce a day. That’s 100 times more per square foot than traditional methods, and uses 99 percent less water usage than outdoor fields.
A press release said that the building is powered by special General Electric LEDs that “generate light in wavelengths adapted to plant growth. While reducing electric power consumption by 40 percent compared to fluorescent lighting, the facility has succeeded in increasing harvest yields by 50 percent,” and meant that Mirai was able to offset the cost of pricy LEDs. Watch how it all works:
4. Vertical farms are becoming more advanced: It's only the beginning for vertical farms in terms of technology. At the New Buffalo, Michigan branch of Green Spirit Farms, some plants grow under pink-tinted LED lights which "provide the correct blue and red wavelengths for photosynthesis," according to Harbor Country News. It's so efficient, the farm can currently grow 10 tons of lettuce in only 500 square feet of space. Green Spirit Farms president Milan Kluko also told New Scientist that he and his colleagues are developing a smartphone or tablet app that can adjust nutrient levels or soil pH balance, or sound an alarm when a water pump is malfunctioning, for example. "So if I'm over in London, where we're looking for a future vertical farm site to serve restaurants, I'll still be able to adjust the process in Michigan or Pennsylvania," he said.
Farm Manager Mike Kennedy making sure our fresh & local veggies (kale) are on the right time zone - they are now! pic.twitter.com/V4sNEzd6HR— Green Spirit Farms (@greenspiritfarm) March 8, 2015
5. Vertical farms are saving lives: Vertical farms are being used beyond food. In fact, they're being used to aid human health. Caliber Biotherapeutics in Bryan, Texas is home to the world's largest plant-made pharmaceutical facility. This 18-story, 150,000 square foot facility contains a staggering 2.2 million tobacco-like plants stacked 50-feet high, that will be used for making new drugs and vaccines. Because the indoor farm is so carefully monitored and tightly controlled by technicians, these expensive plants are shielded from possible diseases and contamination from the outside world.
Barry Holtz, the CEO of Caliber, told NPR that the facility is also efficient when it comes to water and electricity: "We've done some calculations, and we lose less water in one day than a KFC restaurant uses, because we recycle all of it."
Plants at Caliber Biotherapeutics grow in a "pink house" under blue and red LED lights. The tobacco-like plants will be used for making new drugs and vaccines. Photo Credit: Caliber Biotherapeutics
This vertical farm will provide Wyoming residents with 100,000 lbs of fresh produce each year
Not only will the Vertical Harvest provide fresh produce for Jackson, it will also serve as an educational facility, with a “small but functional ‘living classroom’” and access for visitors to view the growing areas without contaminating the crops
A 30 foot by 150 foot sliver of land located next to a parking lot in Jackson, Wyoming is set to be transformed into a vertical farm that will produce up to 100,000 lbs of produce each year. Using 90 percent less water than conventional farming, and absolutely no pesticides, the three-story Vertical Harvest greenhouse will enable the cold, land-locked city to provide locally-grown produce for its residents all year round.
The Vertical Harvest farm is designed by E/Ye Design and utilizes a 30 by 150-foot plot of unused city land that sits next to a parking lot in Jackson, Wyoming. Through an efficient building design, and the use of hydroponic farming techniques, the 4,500 sq ft footprint will have 18,000 sq ft of growing area. Within this area, the farm will produce over 37,000 pounds of greens, 4,400 pounds of herbs, and 44,000 pounds of tomatoes.
This is a significant amount of fresh produce for the town of 9,577, and provides residents with a locally-grown alternative thatJackson’s climate previously prevented. Located one mile above sea level, the town is blanketed in snow for months on end, and is therefore forced to import much of its food. In addition, the developers behind the farm have been careful to plan to grow only produce that is currently imported—thereby not competing with local farms, but rather bolstering local businesses by saving on transportation costs.
The 150-foot-long greenhouse facade of the building optimizes the potential for natural light, which both improves photosynthesis and cuts down on energy costs for the facility. There will be times when artificial light is required—for instance, it is impossible to grow tomatoes during a frozen winter on natural light alone—and so grow lights will be installed in order to ensure that the farm meets production goals.
Although the grow lights will require a certain amount of energy, Vertical Harvest founders Nona Yehia and Penny McBride have stated that it still constitutes net energy savings over imported produce, and while HPS (High Pressure Sodium) bulbs will be used for the tomatoes, LEDs will be utilized for the “lettuce varietals, microgreen and propagation areas.”
Not only will the Vertical Harvest provide fresh produce for Jackson, it will also serve as an educational facility, with a “small but functional ‘living classroom’” and access for visitors to view the growing areas without contaminating the crops. Vertical Harvest recently broke ground, and growing will commence later this year.
Vertical farms: "Making Nature Better"
The entire operation is indoors, and it's a trend that could turn urban areas into agricultural hotbed
By DEAN REYNOLDS CBS NEWS December 27, 2014, 7:04 PM
Vertical farms: "Making Nature Better"
- PORTAGE, Indiana -- Do not be confused by the drab facade of the warehouse in this Northwest Indiana industrial park. It's a farm... and it could well be the future. They're called "vertical farms" -- The entire operation is indoors, and it's a trend that could turn urban areas into agricultural hotbeds.
You'll find arugula and parsley, basil, kale and other greens that grace our plates.
"We are growing nine varieties of lettuces,'' said Robert Colangelo, the founder of Green Sense Farms.
Or you could call him Mr. Salad.
"I guess. I'll take that. I could be called worse," says Colangelo.
This is how he does it, with a pink light from a light-emitting diode, or LED
"It gives you a very concentrated amount of light and burns much cooler. And it's much more energy efficient," says Colangelo.
No sun? No problem.
Researchers believe plants respond best to the blue and red colors of the spectrum, so the densely-packed plants are bathed in a pink and purple haze. They're moistened by recycled water; bolstered by nutrients; and anchored in a special mix of ground Sri Lankan coconut husks.
"We take weather out of the equation," says Colangelo. "We can grow year round and we can harvest year-round."
This abundance keeps the prices consistent year-round at local groceries.
Scott Hinkle, a local chef, says the sunless harvest tastes great. Hinkle shows off a "blossom salad" he serves which can include watercress, micro-arugula or kale.
With less water and fertilizer, fewer workers and no gasoline, it's more economical to grow greens this way than on a traditional farm.
Since there are no bugs, there's no need for pesticides. No weeds, so no need for herbicides.
And Colangelo really knows his plants. He says workers play classical music to create happy vibes for the flora.
Is there a composer the plants prefer? If it's Metallica, we don't want to eat it.
As to whether he's cheating nature...
"We're making nature better," says Colangelo.
There's no need for insecticides or herbicides inside the warehouse.
CBS NEWS
© 2014 CBS Interactive Inc. All Rights Reserved.
Urban Farms Build Resilience Within Singapore's Fragile Food System
"For every 2.5 acres, we should be able to produce 1,000 tons of vegetables per year — or about 1 percent of Singapore's needs for leafy green vegetables
Urban Farms Build Resilience Within Singapore's Fragile Food System
August 20, 20147:17 AM ET
At a local FairPrice Supermarket in central Singapore, you'll find baby carrots grown in Bakersfield, Calif. — the same ones for sale at my local grocery store in Washington, D.C.
Such well-traveled vegetables aren't unusual in the tiny island state, which imports more than 90 percent of its food from some 35 countries. Singapore may be one of the most affluent countries in the world, but it depends heavily on others for basic foodstuffs.
A new crop of farmers is trying to change that. Just as property developers build up when they can't build out, so, too, are these agricultural pioneers. Vertical farming is taking hold across Singapore — not only in greenhouses in the vanishing countryside but also on rooftops in the heart of the city, amid soaring skyscrapers and housing blocks. The goal is to farm as efficiently as possible and maximize the remaining land — as well as abandoned and under-utilized spaces — and improve Singapore's ability to provide more of its own food.
In the 1960s, farms occupied about 10 percent of Singapore's 280 square miles, says Ngiam Tong Tau, a former government official who now is chairman of Sky Greens, one of Singapore's vertical farms.
Today, it has shrunk to less than 1 percent to make way for housing and industry.
Not only is land in short supply, but water is, too. Singapore imports an estimated 30 to 40 percent of its water from neighbor Malaysia.
All this means that these new rooftop and vertical farms could make a big difference for Singapore, helping to insulate it from both natural and man-made threats to its food supply that result in periodic food shortages and price spikes.
"In times of emergencies or food shortages around the world, [if] our neighbors ... don't want to export to us, we still have some food left for certain short periods of time until the food emergencies subside," Ngiam says.
Farming High In The Heart Of The City
Once lined with plantations, Singapore's Orchard Road is now a sort of Asian Rodeo Drive. But overlooking the commercial mecca is a different kind of oasis: 6,000 square feet of vegetable and fish gardens.
The aquaponic garden features mint, basil and leafy greens growing in clay pellets in rows on vertical A-frames that draw water from tanks filled with fish. The waste from the fish fertilizes the plants; eventually, the tilapia will become another crop — to be sold or donated to charity.
It's an economical system, says Allan Lim, one of the founders of ComCrop, the startup that built this garden. It costs about $1.60 a day to pump the water through the 10-foot-tall frames, which go for about $1,000 each.
This closed-loop irrigation system makes sense in tropical Singapore since it uses less water and loses less of it to evaporation and runoff than traditional soil farming. Still, for now, ComCrop relies on roughly two-thirds tap water — versus harvested rainwater — to replenish what's lost to evaporation.
Electricity costs are fairly low, too, and ComCrop's central location means it doesn't have to spend much to distribute its food to clients. Its vertical system yields eight to 10 times more crops than conventional, soil-based farming, according to Keith Loh, another one of the company's founders.
ComCrop sells its herbs wholesale to a local distributor that supplies high-end bars and restaurants. But one of the macro problems that these entrepreneurs are addressing is how to help Singapore's food supply withstand external disruptions like drought, flooding or trade restrictions due to regional public health issues — for example, when Malaysia halted poultry exports during the country's 2004 outbreak of avian flu.
Next year, they hope to scale up the farm by 10 times at another building that houses 80 food-processing companies, with a goal of producing 23 tons of food per month.
"Our goal is that when a time of need comes, the rooftop farm can convert into something important," Lim says.
From Ghost Town Garage To Showcase Garden
Atop the mostly empty garage of the People's Park Complex, a massive housing and commercial development in Chinatown, is a pop-up boutique, spare with a minimalist color palette and lots of reclaimed wood. It wouldn't look out of place in Brooklyn.
It's an outpost of Edible Gardens, a design firm founded two years ago by Briton Rob Pearce and Singaporean Bjorn Low that does foodscaping and landscaping for hotels and restaurants.
"Space in Singapore has to work really hard," says Pearce, who comes from a family of farmers in Somerset, England. "People see what we're doing, so it has to be beautiful."
The next beautification project is turning half of the garage's 60,000-square-foot roof into a farm. Pearce sees rooftop gardens that use otherwise abandoned or underutilized spaces as a win-win solution for developers and urban farmers.
Reaching Higher In The Countryside
Singapore's vanishing countryside — accessible via a 40-minute ride on the immaculate and ultra-punctual MRT train — is home to Sky Greens, one of the world's first commercial vertical farms.
Though Sky Greens has put down roots on 8.6 acres, its crops grow in greenhouses on 30-foot-high vertical frames with hydraulic rotating troughs that bring the plants down to water and then up to the sun.
This kind of farming, says Ngiam, Sky Greens' chairman, yields five times more food than conventional farming.
"For every [2.5 acres], we should be able to produce 1,000 tons of vegetables per year — or about 1 percent of Singapore's needs for leafy green vegetables," Ngiam says.
With about half of the farm developed, Sky Greens is already producing 1.5 to 2 percent of Singapore's demand for leafy green vegetables such as baby bok choy, Chinese water spinach and Chinese broccoli, he says. Eventually, the farm will have 2,000 A-frames, which cost about $12,000 each.
Like other urban farms in Singapore, one of Sky Greens' advantages is how little water it uses, relying primarily on collected and recycled rainwater. And its system of hydraulic-powered rotating troughs means less spent on electricity, and even less water is wasted.
"The troughs come down and go into the water and go up. So there's no leaching of the water," Ngiam explains. "If you are planting on the soil, what the farmer does is pour a lot of water, and then it just leaches out. For us, every drop is used by the plant."
Another advantage is that Sky Greens products can go from harvest to market within the same day. By comparison, vegetables from Malaysia travel one to two days to market.
Sky Greens vegetables do cost more: up to $2 per 3.5-ounce package, or about 10 percent more than vegetables from Malaysia. But Ngiam thinks some middle- and upper-income Singaporeans are willing to pay that premium.
Despite the challenges — of scale, pricing and sustainability — for each of these vertical and rooftop farms, the trend toward quality and the push toward self-sufficiency all point in one direction: up.
This Vertical Farm Skyscraper May Change Our Cities Forever
The Hive-Inn farm would seriously re-vamp the way urbanites eat, by providing very local produce
The Hive-Inn farm would seriously re-vamp the way urbanites eat, by providing very local produce.
Imagine a future where you could pick fresh produce in downtown Manhattan just by visiting a vertical farm right down the block, or where restaurants could use local ingredients from that same quirky-looking farm skyscraper. That future may be nearer than you think. Meet the Hive-Inn farm by OVA Studio in Hong Kong, a concept that is still just in sketch form, but could be changing the way urbanites eat as soon as the next several years.
The Hive-Inn farm resembles a small skyscraper, and is essentially a vertical farm made up of individual containers, or farming modules. Each unit would play a role either in producing food, harvesting energy from the sun and rain, or recycling waste. Essentially, the whole “green building” would be a living ecosystem. The Hive-Inn farm would produce fruits and vegetables that could be used by downtown Manhattan residents and businesses.
See More Urban Farming News
- World’s First Underground Farm to Open This Fall in London
- Explorations in Urban Farming
- The Case for Connection: Urban Farming Takes Root in Upper West Chicago
- Urban Farming Takes Off in Tokyo
- Changing Lives – Urban Farmers of Nairobi
We spoke with Slimane Ouahes, the director at OVA Studio about the future of the project, and what it could mean for New York. Right now, he said, OVA does not have a client, and the idea is still in the planning stages.
“As [the farm] is local, there is nothing to hide, you can see your food growing, rebuild trust between the food production and your appetite, and it will be an attraction for visitors,” explained Ouahes. “Local restaurants would also produce their veggies in these containers and have much more control over the quality.”
Sky-High Vegetables: Vertical Farming Sprouts In Singapore
Singapore is taking local farming to the next level, literally, with the opening of its first commercial vertical farm
Sky-High Vegetables: Vertical Farming Sprouts In Singapore
November 9, 20123:31 PM ET
Singapore is taking local farming to the next level, literally, with the opening of its first commercial vertical farm.
Entrepreneur Jack Ng says he can produce five times as many vegetables as regular farming looking up instead of out. Half a ton of his Sky Greens bok choy and Chinese cabbages, grown inside 120 slender 30-foot towers, are already finding their way into Singapore's grocery stores.
The idea behind vertical farming is simple: Think of skyscrapers with vegetables climbing along the windows. Or a library-sized greenhouse with racks of cascading vegetables instead of books.
Ng's technology is called "A-Go-Gro," and it looks a lot like a 30-foot tall Ferris wheel for plants. Trays of Chinese vegetables are stacked inside an aluminum A-frame, and a belt rotates them so that the plants receive equal light, good air flow and irrigation. The whole system has a footprint of only about 60 square feet, or the size of an average bathroom.
Advocates, whose ranks are growing in cities from New York City to Sweden, say vertical farming has a handful of advantages over other forms of urban horticulture. More plants can squeeze into tight city spaces, and fresh produce can grow right next to grocery stores, potentially reducing transportation costs, carbon dioxide emissions and risk of spoilage. Plus, most vertical farms are indoors, so plants are sheltered from shifting weather and damaging pests.
But is vertical farming just a design fad, or could it be the next frontier of urban agriculture? That depends on your angle — and location.
Implementing these "farmscrapers" on a commercial scale has been challenging, and making them economical has been almost impossible.
It's still up for debate whether vertical farms are more efficient at producing food than traditional greenhouses, says Gene Giacomelli, a plant scientist at the University of Arizona, who directs their the Controlled Environment Agriculture Center.
The limiting factor is light. The total food produced depends on the amount of light reaching plants. Although vertical farms can hold more plants, they still receive just about the same quantity of sunlight as horizontal greenhouses.
"The plants have to share the existing light, and they just grow more slowly." Giacomelli tells The Salt. "You can't amplify the sun."
For American cities, like New York and Chicago, Giacomelli thinks putting plain-old greenhouses on rooftops could be just as efficient as vertical farms – and a lot easier to implement.
In fact, two companies are already working on that approach. Gotham Greens is producing pesticide-free lettuce and basil for restaurants and retailers from rooftop greenhouses in Brooklyn, while Lufa Farmsgrows 23 veggie varieties in a 31,000 foot greenhouse atop a Montreal office building.
But for the island of Singapore, where real estate is a premium, vertical farming might be the most viable option. "Singapore could be a special case, where land value is so exceptional high, that you have no choice but to go vertically," Giacomelli says.
The Sky Greens vegetables are "flying off the shelves," reports Channel NewsAsia — perhaps because the vertical veggies are fresher than most available in Singapore, which imports most of its produce from China, Malaysia and the U.S. They do, however, cost about 5 to 10 percent more than regular greens.
"The prices are still reasonable and the vegetables are very fresh and very crispy," Rolasind Tan, a consumer, told Channel NewsAsia. "Sometimes, with imported food, you don't know what happens at farms there."
Construction Begins For Plantagon Vertical Farm In Sweden
Although vertical farming has been talked about for over a decade, technical barriers have prevented construction of these unique urban farming solutions. But for the new Swedish company Plantagon, vertical farming is no longer an elusive architectural feat
Construction Begins For Plantagon Vertical Farm In Sweden
by JOSEPH TOHILL on 02/22/2012
in EARTH, LIVING, SOCIAL, TECHNOLOGY
Although vertical farming has been talked about for over a decade, technical barriers have prevented construction of these unique urban farming solutions. But for the new Swedish company Plantagon, vertical farming is no longer an elusive architectural feat. In fact, construction has just begun on the Plantagon vertical farm in Linköping, Sweden, with the hopes that urban dwellers will soon be enjoying food produced on a large-scale in their very own city.
The Plantagon urban greenhouse will achieve a height of 177 feet, and boast 18 levels of vegetable gardens. In addition to providing a source of fresh food, Plantagon will also develop “integrated solutions for energy, excess heat, waste, CO2, and water in cooperation with several partners” said a news release.
Hans Hassle, CEO of Plantagon, stated: “we’re developing and fine-tuning the technical systems required for vertical farming in urban areas, together with several well-known Swedish partner companies. We want to gather expertise in the field, and our long-term objective is to create an international Center of Excellence for Urban Agriculture here in Linköping.”
For years, supporters of vertical farms have been baffled with how to effectively provide an equitable distribution of light to the plants in a tall vertical structure. If the vertical farm were to rely exclusively on natural light, plants on the outside of the structure would receive more light than plants towards the middle. As a result, the crops would grow unevenly.
To get around some of these technical issues, the Plantagon vertical farm situates the plants on a vertical, rotating “corkscrew” platform inside of an enormous curved-glass, geodesic spheroid structure. This design allows the plants to receive an equitable distribution of light. Although the Plantagon may not yet feature the most efficient vertical farm design, it is by far the most effective one to date.
It will be interesting to see where the state of vertical farming will be in another five years.
Vertical Farms: From Vision to Reality
Vertical farming: help feed the growing global population and undo the environmental damage caused by conventional agriculture.
Agriculture
Vertical farm designs by Chris Jacobs, Gordon Graff, SOA Architectes
(Updated October 17, 2011)
Dr. Dickson Despommier laughs when he recalls how crazy people thought he was just a few years ago. But Despommier, the most passionate proponent of vertical farming—the growing of crops indoors in multi-story urban buildings—is now seeing his vision being realized. He believes vertical farming can help feed the growing global population and undo the environmental damage caused by conventional agriculture.
“Farming has upset more ecological processes than anything else—it’s the most destructive process on earth,” Despommier told me. As of 2008, 37.7 percent of global land and 45 percent of U.S. land was used for agriculture. The encroachment of humans into wild land has resulted in the spread of infectious disease, the loss of biodiversity and the disruption of ecosystems. Over-cultivation and poor soil management has led to the degradation of global agricultural lands. The millions of tons of toxic pesticides used each year contaminate surface waters and groundwater, and endanger wildlife.
Agriculture is responsible for 15 percent of global greenhouse gas emissions, and accounts for one-fifth of U.S. fossil fuel use, mainly to run farm equipment, transport food and produce fertilizer. As excess fertilizer washes into rivers, streams and oceans, it can cause eutrophication: Algae blooms proliferate; when they die, they are consumed by microbes, which use up all the oxygen in the water; the result is a dead zone that kills all aquatic life. As of 2008, there were 405 dead zones around the world.
More than two-thirds of the world’s fresh water is used for agriculture. And around the world, farmers are losing the battle for water for their crops as scarce water resources are increasingly being diverted to expanding cities. As climate change brings warmer temperatures and more droughts, the water crisis will worsen.
To feed the growing and increasingly urban global population of 9 billion expected by 2050, we need to boost food production by 70 percent through higher crop yields and expanded cultivation. The FAO estimates that we will need nearly 300 million more acres of arable land to do this, but most of the remaining arable land lies in developing countries, and many of the available land and water resources are currently providing other important ecosystem functions. Pressing them into service to produce food will upset many more of the planet’s ecosystems.
Dickson Despommier.
In 1999, while exploring the negative impacts of agriculture, Despommier, a professor of environmental health sciences at Columbia University’s Mailman School of Public Health, and 105 graduate students came up with the concept of the vertical farm—a multi-story building growing layers of crops on each floor. Vertical farm crops can be grown using hydroponics, where plants grow in water or a growing medium with nutrients delivered directly to their roots; aeroponics, which uses a mist to deliver nutrients to plant roots; aquaponics, when fish are raised concurrently and their waste is used as nutrients for crops; or even in soil if the building is designed accordingly.
At present, lettuce, leafy greens, herbs, strawberries and cucumbers are the most commonly grown crops in vertical farms, but in theory, corn and wheat could be grown, as well as biofuel crops and plants used to make drugs. Hydroponics use 70 percent less water than conventional agriculture; aeroponics use even less; and all water and nutrients not taken up by the plants are recycled.
LED lights. Photo credit: John Abela
Climate controls and LED lights programmed to deliver the wavelengths of light that plants prefer create optimum growing conditions. Methane generated from restaurant or crop waste can supply energy and heat for vertical farms.
As a balanced mini-ecosystem, the vertical farm has many advantages. A vertically farmed acre can produce the equivalent of 4 to 6 soil-based acres, depending on the crop (for strawberries, 1 vertical farm acre produces the same amount as 30 outdoor acres). Plants can be grown year-round, unaffected by weather conditions such as droughts, floods or pests. Vertically farmed food is safe from contamination(for example, from e-coli or radiation), and is grown sustainably and organically without the use of fertilizer, pesticides or herbicides.
Fossil fuel use is minimal because there’s no need for farm equipment, transportation of produce into cities, storage or distribution. Unused urban buildings can be revamped as sustainable centers providing healthy food in neighborhoods where fresh produce is scarce, and also creating new job opportunities. In war or disaster zones or refugee camps, modular vertical farms could provide much needed fresh produce. And if vertical farms were implemented on a large scale, we might one day be able to reclaim farmland and restore our soil, forests and ecosystems. Without fertilizer runoff, coastal waters could be revitalized and our fisheries might once again flourish.
Some skeptics have said that the amount of electricity that would be needed to replace sunlight in vertical farms would be prohibitively expensive and unachievable. But Despommier counters that the cost of LED lighting is offset by savings from the elimination of fossil fuel use in fertilizer, transport, storage and distribution, as well as from less spoilage and waste. This, however, remains to be proven, since no one has yet done a life cycle cost comparison between vertical farm-grown crops and those produced conventionally.
Another criticism, no doubt in response to early designs of futuristic vertical farms towering over a city, is that the steep capital investment needed is prohibitive and doesn’t make economic sense. Despommier himself acknowledges that integrating multiple stories of crop growing presents engineering issues that need to be solved. But why do vertical farms have to be in skycrapers?
One year ago, no vertical farms existed. Today the modestly sized vertical farms springing up around the world are proving the skeptics wrong.
Kyoto, Japan’s Nuvege is growing a variety of lettuces in a 30,000-square-foot hydroponic facility with 57,000 square feet of vertical growing space. Amidst fears of radiation contamination from the Fukushima nuclear plant, Nuvege can tout the safety and cleanliness of its crop. Over 70 percent of its produce is already being sold to supermarkets, with 30 percent going to food service clients such as Subway and Disney.
PlantLab in Den Bosch, Holland, is constructing a three-story underground vertical farm that completely eliminates the wave lengths of sunlight that inhibit plant growth. With the latest LED technology, PlantLab can adjust the light composition and intensity to the exact needs of the specific crop. The room temperature, root temperature, humidity, CO2, light intensity, light color, air velocity, irrigation and nutritional value all can be regulated. PlantLab claims it can achieve a yield three times the amount of an average greenhouse’s while using almost 90 percent less water than traditional agriculture.
Growbeds and fish tanks in The Plant. Photo credit: Plant Chicago
In the U.S., a dilapidated 93,500-square-foot former meatpacking facility in Chicago is being transformed into a net-zero aquaponic and hydroponic vertical farm. The Plant will also include an artisanal brewery, kombucha brewery, mushroom farm and bakery. Waste from the food businesses will be used to generate methane in an anaerobic digester, which will produce enough steam and electricity to meet the full energy needs of the facility.
In Seattle, ecological designer Dan Albert and his wife run a 100-square-foot, two-level vertical farm called Civesca (the name is due to change) in a simple warehouse. They will begin selling their aeroponically grown salad greens, mustard greens, and kale to a few local restaurants on Nov. 1.
Purple basil and mizuna growing in Civesca.
Albert gives high praise to his aeroponics technology, created by Ithaca, NY-based AeroFarms. The modular system incorporates aeroponics, programmable LED lights, climate controls, and a proprietary horizontal cloth conveyor that takes the plants from seed to harvest. AeroFarms says its customizable system increases yield up to 60 times that of conventional agriculture, uses 80 percent less water than hydroponic systems and only 3 percent of the land required by conventional agriculture.
In New York City, Big Box Farms is a hybrid vertical farm, growing salad greens inside a one-story industrial warehouse. It stacks plants between 10 and 20 layers high, up to 20 feet high, and uses a proprietary controlled and automated environment and harvesting system that employs LED lights, hydroponics, and 5 percent of the water used by conventional agriculture. The farms will be built right next to food suppliers and distributors to provide them with “private label,” just-harvested products.
About 3 million New Yorkers have no access to supermarkets or fresh produce in their neighborhoods. Vertical farms and other types of urban farming could help low-income residents shop and eat more healthfully. Despommier was a core member of the Earth’s Institute’s Urban Design Lab, whose fall 2003 Urban Ecology Studio project on remediating the Gowanus Canal in Brooklyn produced the first concrete vertical farm design (called Agro-wanus by Andrew Kranis) based on his ideas. The Urban Design Lab recently published a report examining New York City’s capacity for urban agriculture, ranging from community gardens to rooftop greenhouses.
Kubi Ackerman, project manager at the lab, told me that the report focuses on “existing” and “shorter-term” solutions, only mentioning vertical farms in passing, “But I’m a fan of Dickson Despommier’s. His work is interesting and there’s real value in having that vision out there to grow the discussion.”
And the discussion is indeed growing. Vertical farms are also being constructed in Manchester, England and Milwaukee, WI. And there is interest around the world—from Newark, NJ to Beijing, China, and in Singapore, Doha, Vancouver, Milan, Amman, Riyadh and Las Vegas. As more vertical farms are created, the engineering and technology will continue to evolve. And one day, NYC may well have vertical farms of all sizes in every borough, providing fresh produce to retailers, restaurants, and community residents. I think it’s only a matter of time…
By Renee Cho