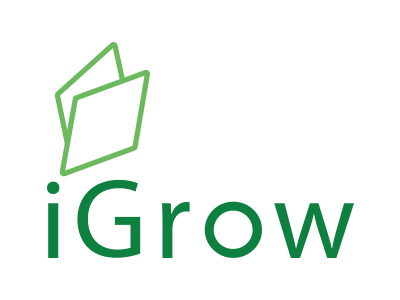
Welcome to iGrow News, Your Source for the World of Indoor Vertical Farming
I Was Wrong About Vertical Farms; Aerofarms Shows How To Make Them Really Work
For a long time this TreeHugger was dismissive of vertical farms, agreeing with Adam Stein who wrote that "Using urban real estate in this manner is incredibly wasteful: bad for the economy and bad for the environment. Local food has its merits, but that's what New Jersey is for." As recently as a year ago I was calling them wrong on so many levels.
I Was Wrong About Vertical Farms; Aerofarms Shows How To Make Them Really Work
Lloyd Alter (@lloydalter)
Living / Green Food
January 9, 2017
For a long time this TreeHugger was dismissive of vertical farms, agreeing with Adam Stein who wrote that "Using urban real estate in this manner is incredibly wasteful: bad for the economy and bad for the environment. Local food has its merits, but that's what New Jersey is for." As recently as a year ago I was calling them wrong on so many levels.
I was wrong.
At the time, almost eight years ago, when we were dissing vertical farms, it was all about visions of new towers in the city, expensive purpose-built structures that I thought were "good drawings, lots of ideas and great fun" but unrealistic, like Vincent Callebaut's silly Farmscrapers. I was probably right about that, and Adam Stein was right about New Jersey.
The vertical farm that is changing the way we think about vertical farms is in fact in Newark, New Jersey, inside an existing old steel warehouse that has been converted rather than an expensive new facility. It's called Aerofarms, and Margaret wrote about it when it was proposed two years ago.
When TreeHugger friends Philip and Hank complained about the economics of vertical farms, they noted in EcoGeek:
A farmer can expect his land to be worth roughly $1 per square foot...if it's good, fertile land. The owner of a skyscraper, on the other hand, can expect to pay more than 200 times that per square foot of his building. And that's just the cost of construction. Factor in the costs of electricity to pump water throughout the thing and keep the plants bathed in artificial sunlight all day, and you've got an inefficient mess. Just looking at those numbers, you need two things to happen in order for vertical farms to make sense. You need the price of food to increase 100 fold over today's prices, and you need the productivity of vertical farms to increase 100 fold over traditional farms. Neither of those things will ever happen.
But if you read Ian Frazier's wonderful article in the New Yorker, The Vertical Farm, you find that they did actually solve most of those problems at Aerofarms. The cost of the real estate per square foot is irrelevant, because the plants are stacked in trays eight high.
They are set in a repurposed old building in a city that's very close to New York city but has relatively cheap industrial real estate.
Then there are the changes in technology. LED lighting has evolved to where they can tune the lighting to the exact colours that the plants need for photosynthesis, saving huge amounts of electricity and excess heat over the broad fluorescents and metal halide lights of a decade ago.
And water? Using technology developed by inventor Ed Harwood of Ithaca, New York, the plants are suspended in a fabric made from old pop bottles. Frazier writes:
The fabric is a thin white fleece that holds the seeds as they germinate, then keeps the plants upright as they mature. The roots extend below the cloth, where they are available to the water-and-nutrients spray.
The air in the building is rich in CO2, the lighting is just right, the nutrients are fed at just the right rate using seventy percent less water, and it is all carefully monitored by computers and technicians.
... each plant grows at the pinnacle of a trembling heap of tightly focussed and hypersensitive data. The temperature, humidity, and CO2 content of the air; the nutrient solution, pH, and electro-conductivity of the water; the plant growth rate, the shape and size and complexion of the leaves—all these factors and many others are tracked on a second-by-second basis. AeroFarms’ micro-, macro-, and molecular biologists and other plant scientists overseeing the operation receive alerts on their phones if anything goes awry. A few even have phone apps through which they can adjust the functioning of the vertical farm remotely.
Ten years ago, we showed visions of people in lab coats walking around plants in soil many storeys up in the air. The reality today is very different, using rehabilitated buildings, high density planting, almost no water and LED lighting. It makes so much more sense. Ian Frazier concludes:
I thought of the tenderness of the greens this device produces—a natural simplicity elicited mainly from water and air by high-tech artifice of the most complicated and concentrated kind. It seemed a long way to go for salad. But if it works, as it indeed appears to, who knows what might come of it when we’re nine billion humans on a baking, thirsting globe?
A decade ago we called them pie in the sky, and thought nothing would come of it. Today, I am not so sure. I think I have to eat my words, along with some Aerofarms baby greens the next time I am in New York.
Related on TreeHugger.com:
- Adam Stein on Vertical Farms: "Pie in the Sky"
- Do Vertical Farms Make Sense?
- Futurama Farming in New York
- Gordon Graff Demonstrates That Vertical Farms Can Actually Work
- Vertical farms: Wrong on so many levels
- Fix Our Horizontal Farms Before We Go Vertical
Tags: Food Miles | Food Security
The Great Indoors
The Great Indoors
You’ve heard of recipes for food, but have you heard of a grow recipe? That’s exactly what Philips Grow Wise is developing with partners such as Grow Up Urban Farms in London. Together they are pioneering city farming in the U.K.
By Pithrika Nair.
Any Smart City vision is incomplete without smart food. The current world population of 7.3 billion is projected to reach 9.7 billion in 2050. Of that population 7.7 billion (80 per cent) are expected to live in cities. The UN Food and Agriculture Organization (FAO) also estimates that farmers will have to produce 70 per cent more food by 2050 to meet the needs of these 9.7 billion. Notwithstanding the fact that the quantity of food produced isn’t a safeguard against world hunger (we currently produce enough food to feed the world’s population, but 795 million people still go hungry due to poverty), there is a pressing need to produce more food, with greater efficiency, and a lower carbon footprint.
A potential answer to the problem of food production is urban indoor agriculture, the growing of crops in a building within or near a city, using artificial light to stimulate photosynthesis. The controlled system helps growers reduce or eliminate pesticides and other chemicals, and its proximity to the end consumer ensures fresher produce with greatly reduced food miles. The quality of the solution is driven by how lighting, climate control, software controls, sensoring and logistics work together.
Kate Hofman and Tom Webster founded Grow Up Urban Farms in 2013 as London’s first commercial urban farm. Housed inside an industrial warehouse, the farm combines aquaculture (fish farming), with hydroponics, the practice of growing plants in a nutrient solution with no soil. This is a symbiotic system with one product, the fish, providing fertilizer for the second product, the plants.
With a year round growing season, the 6,000 sq. foot urban farm produces 20,000 kg of salad greens grown in vertically stacked trays under Philips LED lighting. Researchers at Philips GrowWise Center have developed precise ‘growth recipes’ for each product. Just like a cooking recipe, a growth recipe includes an ingredients list and a method, and Philips provides extensive support in both areas to ensure the end result meets the customers’ exact needs.
The ingredients list is the lighting system itself: the type and number of LEDs and where to place them to deliver the optimal lighting conditions and coverage for the plant type and greenhouse set-up, and the growth system.
The full package includes the technology hardware such as racks and automation and software like climate (temperature, humidity, CO2) as well as plant material, fertilizers and growth media. A ‘growth recipe’ helps farmers to optimise their farm systems for productivity.
According to Gus van der Feltz, director of City Farming at Philips, “Indoor growing systems based on LED lighting can maximise plant photosynthesis, for the most delicious and nutritious vegetables grown in a sustainable manner. Growing crops vertically makes it possible to pack more plants per acre, in a much faster way, than would be possible with a field farm, which means more harvests per year. With little waste, no agricultural run-off and more than 90 per cent reduction in the water used to grow clean and healthy food.”
This hyper-controlled growing environment enables better, faster, tastier, cleaner plants through light recipes, in clean air with no pesticides or crop protection.
At the Philips GrowWise research facility in Eindhoven, growers and plant specialists trial a variety of crops under different lighting and climate conditions for a variety of purposes.
“At Philips, we are teaming up with partners to bring this new innovation to the next level,” says Gus van der Feltz. “We are also looking forward to discovering what else can be achieved through this new form of high-tech horticulture. We have already seen that we can increase the amount of vitamin C in tomatoes, colour lettuce, and affect the taste and smell of basil through the smart use of LED light and growth recipes. And it’s possible to grow different varieties indoors. So we certainly have an interesting future ahead of us.”
Does this mean we’ve found the solution to the population-food-location quandary? Not yet. Although the potential unlocked by the LED technology is promising, urban indoor farming still faces several challenges before it starts producing significant, sustainable, and affordable food on a large scale.
A critic of indoor growing systems, Louis D. Albright, programme director of Controlled Environment Agriculture at Cornell University, estimates the high amount of energy required to provide 100 per cent of the light and heat needed doesn’t result in environmental benefits. He found one kilo of tomatoes farmed indoors produces 11-13 kg of CO2 (2-4 kg CO2 in production and 9kg of CO2 in lighting), while tomatoes farmed and transported from California to New York produced 0.6 kg of CO2 (0.3 Kg of CO2 in Production + 0.3 Kg of CO2 in Transport).
What if that energy came from renewable sources? Bruce Bugbee, director of the Plants, Soils & Climate department at Utah State University says, “If we’re going to use solar panels, we’d need 5.4 acres of solar panels to provide 1 acre of sunlight equivalent.”
Based on the current technology and energy options, it’s high end, expensive crops such as herbs and microgreens that offer the best business options for indoor farming. These are the limitations Jeremy Rifkin pointed out (in his presentation to the government of Catalunya), in attempting to plug smart city solutions into a fossil fuel infrastructure.
In an ideal future, a digitised internet of energy would be able to provide renewable energy at the price and efficiency needed to make indoor urban agriculture a viable production option.
The area where high efficiency agricultural LEDS such as those developed at Philips Grow Wise are able to have the most significant impact is as supplementary lighting in greenhouses.
Brookberries Venlo BV grows and supplies strawberries in Venlo, Netherlands. It previously used incandescent lamps to elongate the strawberry plant and encourage growth, but the sale of many types of incandescent lights was banned in the EU from 1 September 2012.
Owners Marcel Dings and Peter van den Eertwegh used the opportunity to trial different technology options, deciding finally to deploy the Philips GreenPower LED flowering lamp on their farms. This has resulted in a staggering 88 per cent reduction in their energy consumption as well as the ability to start harvesting earlier in the year (February and March, rather than in May).
Improved temperature control is also a big plus for Dutch tomato grower Jami. Its grow recipe combines overhead high-pressure sodium lamps with LED lamps hung among the crop to illuminate the lower parts of the plant. The LED lamps can be placed close to the plants without damaging them but also add a little bit of warmth – which the tomato plants thrive on.
Through the placement and monitoring of the LEDs the temperature in the greenhouse is carefully controlled, lengthening the growing season into an all year production. Jami has seen its energy bills fall by 10 per cent, while yields have risen by 35 per cent. Thus, although its energy consumption is high, urban agriculture also benefits greatly from increased control and efficiency.
Citizens within the smart city communities have the chance to gain an understanding and sense of connection with their food, as well as the chance to eat high quality products which have been naturally optimized through light control. Hofman from Grow Up Urban Farm says, “With the lighting we get really good color across the leaf, really good shape, and a really strong and solid product. Everything is delivered to local customers within 12 hours after harvest.”
Twelve hours from harvest to your plate in the heart of London is a significant step in the direction of smart, sustainable food.
If you enjoyed this, you might wish to look at the following:
Philips Lighting looks to the future
Future innovation has its roots in real life projects that are happening right now
smartcitiesworld.net/news/news/philips-lighting-looks-to-the-future-1129
Kimbal Musk Just Launched A Revolutionary Shipping Container Farm Initiative In Brooklyn
"Square Roots is an interactive campus of sorts, where each entrepreneur accepted to the one-year program is able to leverage hands-on experience and receive guided mentorship in running a vertical farm and agriculture business"
Kimbal Musk Just Launched A Revolutionary Shipping Container Farm Initiative In Brooklyn
by Jennifer Lauren, 01/06/17
Near Jay Z’s childhood home and an old Pfizer factory, you will find a set of ten steel shipping containers. Inside those seemingly innocuous containers lies a lush urban farm. Launched by Tobias Peggs and Kimbal Musk, brother to Elon, the containers are part of a project called Square Roots, an urban farming incubator created to support emerging entrepreneurs as they develop their own vertical farm start-ups, which Musk hopes will create a food revolution.
Square Roots is an interactive campus of sorts, where each entrepreneur accepted to the one-year program is able to leverage hands-on experience and receive guided mentorship in running a vertical farm and agriculture business. Vertical farms are ideal for urban settings because they require less space, are able to grow soil-free crops indoors under LED lights and expend markedly less water than traditional outdoor farms. Each 320 square foot shipping container-turned-farm can yield crops that would be the equivalent of two acres of farmland. For all these reasons, exploring the potential of vertical farms is a priority for many –including Square Roots investors such as FoodTech Angels and the USDA.
RELATED: Wind-powered vertical Skyfarms are the future of sustainable agriculture
This November, 10 applicants were selected out of over 500 applications, each coming from different backgrounds and experience levels. While each entrepreneur will not only be able to access invaluable farming know-how and business expertise, the incubator also can serve as a testing ground for the future of vertical farms. For example, exploring how to utilize solar power rather than LED lights, which some say is a drain on electricity. Entrepreneurs received funding and loans from the USDA, Powerplant Ventures, GroundUp, Lightbank, and FoodTech Angels.
The endeavor is one of several of Kimbal Musk’s that are designed to shake up the way we grow and eat food. His other projects include The Kitchen and Next Door, both restaurants that serve dishes from local sources only, and the non-profit The Kitchen Community, which has installed “learning gardens” in over 300 schools. While Square Roots is currently only underway in Brooklyn, the founders aspire to bring the concept to more cities in the near future.
How Elon Musk's Brother Kimbal Musk is disrupting Farming With 'Food Revolution'
How Elon Musk's Brother Kimbal Musk is Disrupting Farming With 'Food Revolution'
Leanna Garfield and Sarah Jacobs
Kimbal Musk - the brother of Tesla Motors chief executive Elon Musk - is trying to change the way we eat by creating what he calls a "real food revolution".
For over a decade, he has run two restaurant chains, The Kitchen and Next Door, which serve dishes made strictly with locally sourced meat and veggies.
Samsung started off its CES event in Las Vegas with a mea culpa over its exploding Galaxy Note 7 smartphones.
In 2011, he started a non-profit program that has installed "Learning Gardens" in more than 300 schools, with the intention of teaching kids about agriculture.
His latest food venture delves into the world of local urban farming.
In early November, Musk and fellow entrepreneur Tobias Peggs launched Square Roots, an urban farming incubator program in Brooklyn, New York.
The setup consists of 10 steel shipping container farms where young entrepreneurs work to develop vertical farming startups.
Unlike traditional outdoor farms, vertical farms grow soil-free crops indoors and under LED lights.
Six weeks into the 12-month program, just after the entrepreneurs completed their first harvests, Business Insider got a tour of the farms.
They are vertical farms — everything grows inside 320-square-foot (30 sq m) steel shipping containers. Each container can produce about 50,000 mini-heads of lettuce a year.
- The United States Department of Agriculture (USDA) gave the Square Roots entrepreneurs small loans to cover preliminary operating expenses.
Other investors include Powerplant Ventures, GroundUp, Lightbank, and FoodTech Angels.
The Square Roots farms sit between an old Pfizer factory and the apartment building where rapper Jay-Z grew up in Brooklyn. Photo: Sarah Jacobs, Business Insider
On four parallel walls, leafy greens and herbs sprout from soil-free growing beds filled with nutrient-rich water. Instead of sunlight, they rely on hanging blue and pink LED rope lights.
About the size of the standard one-car garage, each shipping container can produce the same amount of crops as two acres of outdoor farmland.
Musk and Peggs chose Square Roots' first class of 10 young entrepreneurs from over 500 applications.
Peggs says they represent the next generation of farmers — though not all came to NYC with farming experience.
Another 27-year-old farmer, Electra Jarvis, comes to Square Roots three days per week. On Wednesdays, she spends four hours meticulously placing 800 seeds inside small troughs. Photo: Sarah Jacobs, Business Insider
Before Josh Aliber, 24, moved from Boston to Brooklyn to join Square Roots, he had never farmed. Now he's starting up his own specialty herb business and running a vertical farm.
Last year, while Aliber was recovering from a concussion, he learnt about urban farming from a podcast. He started researching it from his bed, and found out about the Square Roots program.
His shipping container farm runs on 10 gallons of recycled water a day, which is less than the average shower's worth.
Aliber can monitor everything from the oxygen level to the humidity — which affects the plants' taste and texture — using "the computer panel" near the door and sensors in the growing beds.
If he wants a tropical or northeastern climate, he can control that too.
Aliber is selling his specialty herbs and basil primarily to upscale Italian and pizza restaurants in NYC.
All the Square Roots farmers sold their first harvests at a recent local farmer's market. Through the program, he has had the opportunity to work with numerous mentors. Square Roots has 120 mentors so far.
"Yes, I have the ability to make money, but yes, I also have the ability to change the world," he says.
Another 27-year-old farmer, Electra Jarvis, comes to Square Roots three days a week.
On Wednesdays, she spends four hours meticulously placing 800 seeds inside small troughs.Two weeks later, she transplants them to the walls.
"We should be growing closer to us in cities," she says.
Aliber, Jarvis, and the other eight entrepreneurs are not just learning how to grow plants, but also how to grow their businesses. A large part of the program is learning about branding and "how to tell our stories", Jarvis says.
The larger goal of Square Roots, Musk tells Business Insider, is to create "a real food revolution".
In the late 1990s, following the tech boom, the Musk brothers moved from South Africa to Silicon Valley. They invested in X.com, which later merged with PayPal and was acquired by eBay.
Kimbal Musk has known Peggs, who previously worked on tech start-ups sold to Walmart and Adobe, for a decade.
Before Square Roots, they worked together at The Kitchen, where Peggs served as the "President of Impact" and helped expand the chain to new cities.
When asked how his experience in tech translates to running a vertical farming accelerator, Peggs says the two fields share the same motivation.
"You learn how to execute impossible dreams. This was all just a Powerpoint presentation six months ago," says Peggs, pointing to the farms behind him.
"Today's consumer wants to know they are supporting companies that are doing something good for the world," Peggs says. "This not just a Brooklyn foodie trend."
The world's largest vertical farm, Aerofarms, launched this year in Newark, New Jersey. In late 2015, urban farming company Gotham Greens opened the world's largest rooftop farm in Chicago.
Square Roots hopes to expand to 20 cities by 2020.
Vertical farms can grow all year, using significantly less water and space than outdoor farms.
Critics of vertical farms point out that the LEDs drain a lot of electricity. Peggs says Square Roots is exploring how the farmers can switch to solar power in the future, since electricity is the biggest cost for the farms.
Square Roots' lights are only on in the evening and night, so they don't run 24-7 like some other vertical farms.
Square Roots will build offices inside the Pfizer factory in the coming months. In its past life, the building produced ammonia, a chemical that's sprayed on plants and became vital to the industrial food system after WWI.
In 2017 and beyond, sustainable food start-ups will do business there. "It's an act of poetic justice," Peggs says.
This story first appeared in Business Insider. Read it here or follow BusinessInsider Australia on Facebook.
Agricultural Revolution 2.0
"A revolution in food has begun unlike any since the development of agriculture"
AGRICULTURAL REVOLUTION 2.0
How everything you eat is about to change forever. Say goodbye to farmers and ranchers!
By Marshall Connolly (CALIFORNIA NETWORK)
1/6/2017
A revolution in food has begun unlike any since the development of agriculture.
When You Can Farm Indoors, Who Needs Sunlight Or Soil?
In about a decade or so, your food is going to be a lot different. For the first time since humans began farming and ranching, the way we grow and produce food is about the change --dramatically. Farmers and ranchers, your days are numbered.
Vertical farms already exist on small scale, but their popularity is catching on and rapid expansion and development is expected within the next decade.
LOS ANGELES, CA (California Network) -- Around 10,000 B.C., our ancestors changed the way they ate and thereby changed the world. Before that time, our ancestors were forced to hunt and gather for their food. This meant people lived in small wandering bands, probably not exceeding 200 people. Their only job was to find their next meal, a laborious process that often required lengthy periods of walking and running.
Around 10,000 B.C., our ancestors figured out they could domesticate animals and crops. They learned how to plant and harvest. These advancements were so incredible, historians dubbed the change the "Neolithic Revolution."
It changed everything. With the need to chase their next meal eliminated, humans were able to settle down and build villages, towns and eventually cities. Labor was divided among the people, religion flourished and bureaucracy developed.
For 12,000 years or more, this is the way the world has worked, thanks entirely to farming and ranching. Even today, wars are fought over control of lands that produce food. Much of the land area on our planet is dedicated to growing food.
But all this is about to change again, right before your eyes.
In the next decade, what you eat will change. The first change has already arrived, vertical farming.
Farming is about to move from rural farms to tall factories called vertical farms. These factories are not run by farmers, but by industrialists who grow greens instead of forge steel. Tall racks, several stories high, are filled with soil, or a soil substitute, planted and watered. The racks rotate, and a new crop is harvested every day. This means produce will be grown year-round, under controlled conditions, using a minimum of resources. This will reduce food costs by improving efficiency and increasing supply.
At the same time farming moves indoors, so too will ranching. In fact, ranching will undergo the greatest change as we move from growing live animals to simply growing their meat in an industrial setting.
Scientists have developed what is called "cultured meat." Cultured meat is real meat, grown from stem cells of an actual animal, in a laboratory. The meat is real, but it is grown outside of a living animal, probably in a special tray or vat. At present, the process is difficult and expensive but it's developing. Hamburger patties and meatballs have already been grown, cooked and tsted. There are problems with flavor and texture, but these will be overcome.
Several startups as well as Tyson Foods have started to pour money into the development of this new source of protein.
The cost savings are huge. If meat can be grown in a factory, ranchers will not need millions of acres of land. A lot less water can be used. Feed will not be needed, although a synthetic replacement will be required.
As an added benefit, the meat can be genetically altered to govern its characteristics, such as fat content. It also eliminates the need for additives such as antibiotics and other drugs often administered to ranched animals. The cost of cultured meat will be far below the cost of ranch-raised meats, and ranched meat will become an expensive delicacy.
The third and final major change in our food supply will be the development and use of genetically modified organisms, often referred to as GMOs. While GMOs have been the subject of controversy, they are here to stay. Most of our foods are already genetically modified. As food production moves from the farm to the factory, and genetic modification becomes easier, its use will expand. Like it or not, the food of the near future will not be like the food of the recent past.
The timeline for these changes is very short. Vertical farms are already in use and should catch on quickly. GMOs are already in widespread use. And cultured meats are between five years to a decade away, and it may take 20 years before the product is perfected and becomes competitive with ranched meats. But the incentive to make the change is massive, so investment and development are accelerating.
Perhaps the greatest question of all is how will consumers feel about these changes? Vertically farmed vegetables are already being consumed without complaint. GMOs are also widely consumed although there is some pushback from consumers who fear they are unsafe. Such controversy will probably persist, but the new foods will enter the market anyway. The greatest hurdle is faced by cultured meats, which will be faced with skepticism by consumers who might not trust meat grown in a lab. However, competitive pricing, marketing, and time will ensure cultured meats become the norm of the future.
Today, we look at 10,000 B.C. as a time of dramatic change for humanity. It now appears that the early 21st century will be seen in much the same way.
The Rise of the Vertical Indoor Farm
The New Yorker’s Ian Frazier with a very interesting look at the folks who are growing crops in the city: The Vertical Farm.
The Rise of the Vertical Indoor Farm
A Green Thumb (drive)
“The technology it uses derives partly from systems designed to grow crops on the moon. The interior space is its own sealed-off world … Countless algorithm-driven computer commands combine to induce the greens to grow, night and day, so that a crop can go from seed to shoot to harvest in eighteen days. Every known influence on the plant’s wellbeing is measured, adjusted, remeasured. Tens of thousands of sensing devices monitor what’s going on.” Welcome to what could be the future of the world’s produce supply. And unlike today’s messy farms, it won’t require soil, sunlight, or nearly as much water. (Add in a couple quarts of coffee, and that’s basically the environment in which NextDraft grows.) The New Yorker’s Ian Frazier with a very interesting look at the folks who are growing crops in the city: The Vertical Farm.
+ If you can raise crops indoors in the city, then you can go fishing in a barn in Iowa. From MoJo: A Fish Out of Water. Can farmers in Iowa help save the world’s seafood supply?
Vertical Farms: Smart Food Solutions
“Agricultural runoff is the main cause of pollution in the oceans; vertical farms produce no runoff"
Vertical Farms: Smart Food Solutions
Posted on January 6, 2017 by Danielle Park
Great article in The New Yorker January 9 issue on Vertical Farming and innovators in Newark who are growing fresh vegetables with a fraction of the water, no soil or chemicals, nor cross-country transport.
This is the ‘buy local’ movement personified and it is perfectly timed to meet our simultaneous needs for plentiful, fresh, healthy food and a sustainable environment. See: The Vertical Farm, growing crops in the city, without soil or natural light:
“Agricultural runoff is the main cause of pollution in the oceans; vertical farms produce no runoff. Outdoor farming consumes seventy per cent of the planet’s freshwater; a vertical farm uses only a small amount of water compared with a regular farm. All over the world, croplands have been degraded or are disappearing. Vertical farming can allow former cropland to go back to nature and reverse the plundering of the earth…
Today in the U.S., vertical farms of various designs and sizes exist in Seattle, Detroit, Houston, Brooklyn, Queens, and near Chicago, among other places. AeroFarms is one of the largest. Usually the main crop is baby salad greens, whose premium price, as Ed Harwood realized, makes the enterprise attractive. The willingness of a certain kind of customer to pay a lot for salad justifies the investment, and after the greens get the business up and running its technology will be adapted for other crops, eventually feeding the world or a major fraction of it. That is the vision.”
Feel-Good Story About The Future of Vertical Farms
Feel-Good Story About The Future of Vertical Farms
There's really nothing not to love about vertical farms -- multi-story hydroponic operations, usually sited in dense urban areas -- they borrow their best tech from the space program, they're water-conserving, they don't have runoff, they're energy efficient, and they're super land-efficient, meaning we don't need to turn forests or wetlands into fields.
The New Yorker's profiles of the inventors of modern vertical farming has the usual New Yorker lyricism and slightly-too-long-ism, and is a little short on technical details, but it left me with a warm glow this morning. It's a good example of bright green tech, the kind of thing we'll need as our population stabilizes at 9 billion -- the alternative being the "de-growth" dystopia that starts with 4-6 billion people somehow departing the planet.
For now, vertical farms focus on selling high-margin/high-ticket baby greens in fancy grocery stores, but its proponents argue that they'll scale up through luxury goods, then Moore's Law their way down to the rest of the world. There's also a curious note about a secret process for misting or steaming the veggies that uses a proprietary and unpatented system that the inventor believes no one will ever be able to figure out, which is a claim that the writer allows to pass without comment, despite its extreme implausibility.
AeroFarms occupies three other buildings in Newark aside from the main vertical farm, on Rome Street. At 400 Ferry Street, it has a thirty-thousand-square-foot space whose most recent previous use was as a paintball and laser-tag entertainment center called Inferno Limits. The graffiti-type spray-painted murals and stylized paintball splatters of that incarnation still cover the walls. AeroFarms’ headquarters—sometimes referred to as its “world headquarters”—are in this building, some of which is taken up by a multiple-row, eight-level vertical farm that glows and hums. Technicians in white coats who wear white sanitary mobcaps on their heads walk around quietly. Some of these workers are young guys who also have mobcaps on their beards. The salad greens, when you put on coat and mobcap yourself and get close enough to peer into the trays, stand in orderly ranks by the thousands, whole vast armies of little watercresses, arugulas, and kales waiting to be harvested and sold. For more than a year, all the company’s commercial greens came from this vertical farm.
Nobody in the building appears to have an actual office. Employees are distributed in more or less open spaces here and there. In a dim corner of the area with the vertical farm, where the fresh, florist-shop aroma of chlorophyll is strong, young graduates of prestigious colleges confab around laptop screens that show photos of currently germinating seeds and growing leaves. Folding tables burgeon with cables, clipboards, and fast-food impedimenta. David Rosenberg, the C.E.O., who hired Ingrid Williams last year, is the boss. This distinction is hard to notice, because he looks more or less like anybody else.
Urban Farming Today Is Like the Internet More Than 20 Years Ago
As Kimbal Musk puts it, “the opportunity in front of entrepreneurs in real food today is bigger than the internet was to my generation in the mid-90s.” That’s one of the reasons we set up Square Roots — to empower the next generation to become entrepreneurial leaders in the coming real food revolution
tobias peggs |Cofounder & CEO at Square Roots.
Urban Farming Today Is Like the Internet More Than 20 Years Ago
The first Square Roots Urban Farming Campus, Brooklyn, New York.
As Kimbal Musk puts it, “the opportunity in front of entrepreneurs in real food today is bigger than the internet was to my generation in the mid-90s.” That’s one of the reasons we set up Square Roots — to empower the next generation to become entrepreneurial leaders in the coming real food revolution.
Hopefully some of the stuff we learned about making the internet work back then is helpful to the next generation as they tackle the opportunity in real food right now.
Some parallels hit home one morning this week when I bumped into Maxwell as I arrived on the Square Roots farm in Brooklyn. He was just heading home for some sleep after harvesting all night. Max is one of the first ten entrepreneur-farmers at Square Roots. His cohort classmate Electra had also pulled a late one — and this incredible time lapse video shows how hard they have to work in the farms today, and how manual the harvesting process is right now.
I got an instant flash back to 1994. I was working on the student newspaperat Cardiff University, doubling up as Music Reviews Editor and ‘That Crazy Internet Guy’. Once the newspaper had been put to bed, I would save all the Quark Xpress* files on to mountain of floppy disks, put them in my backpack, and walk home via a convenience store to stock up on Redbull. Then I would stay up all night, inserting floppy disk after floppy disk into my own 386 computer, manually copying and pasting article after article into a rudimentary text editor where I would painstakingly markup thousands of headlines, bylines, photo captions and article text with hardcoded HTML, before “dialing up the internet” with a 28.8 kbit/s modem connected to a landline, and sit there for hours pushing up webpages… all to create the first online student newspaper in the UK!! It didn’t matter how much of a pain in the ass that whole process was, the energy and ideas I got from glimpsing at the future was incredible.
While going through those efforts, you were constantly thinking about ways to improve, ways to automate, ways to scale… ways to bring the internet to everyone. And we’re seeing Max and Electra and all the other Square Roots entrepreneurs going through that same thought process right now. The energy and ideas flying around the Square Roots Slack channels on a daily basis are incredible. And as we start to turn those ideas into realities, we march ever closer towards the big idea of bringing real food to everyone.
It’s happening.
If you want to learn more about Square Roots, come to our farm tour and farmers market on Tuesday! See the farms, meet the farmers — and taste the freshly harvested food. Details on our website.
What Will 2017 Bring For Indoor Ag?
What Will 2017 Bring For Indoor Ag?
JANUARY 4, 2017 NICOLA KERSLAKE
Editor’s Note: Nicola Kerslake is the founder of Newbean Capital, a registered investment adviser that manages early stage venture capital mandates and that has a particular interest in indoor agriculture. It owns the Indoor Ag-Con events business as well as an indoor agriculture alternate financing business Contain that is currently in pilot stage. The next Indoor Ag-Con event will be held in Singapore on January 24-25, 2017.
Here Kerslake offers some predictions for the indoor agriculture industry in 2017.
For all of the year’s many horrors, 2016 was a banner year for indoor agriculture, the practice of growing crops in hydroponic, aquaponic and aeroponic systems in greenhouses, warehouses, and containers. The fledgling industry saw record investment fueling a wave of new indoor farm builds, innovative business models, and technology introductions.
Highlights included the launch of Square Roots, a Kimbal Musk-backed social-benefit endeavor to incubate new urban farmers utilizing Freight Farms’ container farms, and the inauguration of Aerofarms’s long-anticipated Camden, NJ vertical farm. The latter is notable because it uses aeroponics — misting plant roots with a nutrient-rich solution, rather than submerging them in water – and this is typically considered a trickier technology to implement commercially than the more common hydroponics. The upside is, in theory at least, more efficient growing. Both Freight Farms and AeroFarms raised equity from private investors during 2016, contributing to the $50m+ raised from private investors in the US last year.
We expect to see accelerating activity in 2017 thanks to better economics and more farm and technology launches. Here are six ‘big themes’ for the year ahead:
1. The First of the Mega Farms
Indoor farms run the gamut from a basic home-built set up using equipment bought at Home Depot to custom engineered 100,000 ft2 facilities. With a few notable exceptions – such as those growing for the pharmaceutical industry – the US market has mostly used vertical farms to date; mid-sized farms that stack growing racks to maximize space in a warehouse or repurposed building.
Their cooler cousin is the ‘plant factory,’ a term coined in Japan to describe multi-layer growing in clean room conditions using increasingly sophisticated monitoring and control systems to optimize growing conditions. These are large-scale operations, “farming as manufacturing.” The Japanese company, 808FACTORY, has its own data server running at its plant factory, for example. Plant factories are commonplace in the more advanced Asia market – Japan has more than 200, China more than 80 – and we expect them to become a feature of the US one in 2017. For instance, Japanese plant factory company Spread has publicly discussed its search for US partners, while Middle Eastern greenhouse company Pegasus Agriculture leased a large parcel of land in Florida in 2016, though the latter will more likely be used for next-gen greenhouses than for plant factories.
Funded by low-key rounds or by overseas parent companies, new mega-farmers are typically shyer than the likes of BrightFarms or AeroFarms. A few will eventually discuss their work in public, but the majority will stay on the downlow, focused on the complex business of adapting new crops to indoor systems or applying machine learning techniques to improve yields.
2. Indoor Ag goes Mainstream
When we first got involved with the indoor agriculture industry nearly six years’ ago, we spent a good deal of our time explaining the sector to other investors. The vast majority saw it as too small, too niche and too risky to be of interest. A combination of time, technology advances, and a halving of the price of the LED lights — they make up around half of a farm’s capex — has made a big difference. The attention paid to legal cannabis has also helped; its newfound respectability has a halo effect for other crops grown in indoor farms. Now, we receive a couple of inbound calls a week from new investors looking to get into the sector, one of the reasons that we have authored five white papers on various aspects of the industry.
In turn, this influences the kinds of companies that become involved in the sector. Recently, big box retailer Target announced its plans to test in-store vertical farms in the spring, and telecoms major Ericsson demoed an aquaponics project utilizing its IOT-based controls. We expect to see more “big names” announcing their involvement in indoor agriculture this year, whether that’s large produce buyers, technology providers, or long-established farming majors diversifying their growing techniques.
3. IoT Everything
Given the controlled environment in which they operate, indoor farms are well suited to the application of ‘big data’ techniques and a range of startups are joining established industry players in introducing these. Agriculture control majors – Argus Controls, Hortimax, Priva – benefit from long histories of working with customer data, and others are taking innovative approaches to pilot new products. For example, New Zealand-based Autogrow raised a sub-$5m round in 2016 to create an open platform for its controls products and TechCrunch Disrupt winner Agrilyst launched a greenhouse management platform. Up next, we expect to see machine learning-based approaches launching commercially.
4. In-Home Growing
Ubiquitous furniture retailer IKEA has been rolling out an in-home hydroponic range recently and is about to see competition from a wave of in-home growing startups. Some examples of the next generation include SkyDeck graduates Verdical and app-controlled Grobo. We expect that those that gain market traction will be looking for seed and A rounds in 2017, following in the footsteps of an earlier wave of strategic and VC-backed in home systems, such as Scott’s Miracle Grow’s AeroGardens and Upfront Ventures’ Grove Labs.
5. The Crickets are Coming
As alternative proteins – plant-based meat, insects – become commercially available, we anticipate that indoor agriculture will be a part of figuring out the supply chain for these approaches. For instance, cricket farmers, including equipment provider Bitwater Farms, super-angel backed Tiny Farms and Thailand’s Eco Insect Farming, are already adopting and adapting indoor farming techniques.
6. But It Won’t All Be Roses…
A high business failure rate is one of the characteristics of startups, and indoor agriculture is far from immune. This is especially true for the mid-sized vertical farms that make up the bulk of the US market, some of which have yet to hit a scale or figure out a business model that allows for a decent operating profit. If the trajectory of analogous industries – such as solar – is anything to go by, some will merge, others will pivot to new business models, and some will fail. While wretched for the hard-working farmers involved, we view these failures as a necessary part of the industry’s rapid growth. Private and VC investor-backed indoor farmer PodPonics, for instance, shuttered its Atlanta, GA, farm this year to focus on its Middle East technology operations, and we expect to see more of the same as indoor agriculture matures.
By the end of 2017, we expect to see a larger, and stronger, US indoor agriculture industry, able to benefit from a wider variety of technologies and anchored by the beginnings of its own plant factory revolution.
Planned Vertical Farm in East Baltimore Aims To Train Ex-Offenders
Baltimore Business Journal
Morgan Eichensehr Reporter
Planned Vertical Farm in East Baltimore Aims To Train Ex-Offenders
A Canadian agriculture technology company is partnering with CBO Financial Inc. and Volunteers of America Chesapeake to develop a $6 million indoor urban farm in East Baltimore, part of a new program to give workforce training to ex-offenders.
Arcturus Growthstar Technologies Inc. signed a letter of intent last month to lease 25,000 square feet from local nonprofit Volunteers of America Chesapeake at one of its centers at 5000 E. Monument St. Part of the building will be renovated to accommodate Arcturus’ "controlled environment agriculture" technology, which uses LED lights to grow plants indoors on vertically-stacked levels. The farm will vertically grow produce like lettuce, basil, cilantro and oregano.
And though the company is involved with marijuana growing efforts in other markets like Florida, Russell Snyder, CEO of Volunteers of America Chesapeake, said that will not be part of the Baltimore operation.
The renovation is expected to be finished in 2018.
Volunteers of America Chesapeake currently uses the building as a residential re-entry center to help ex-offenders rejoin society and the workforce after serving prison sentences. The new partnership will be utilized to provide workforce development opportunities for residents of the re-entry program — the center serves about 150 residents at a time — in the area of urban farming, Snyder said.
"The job training and jobs created by this social enterprise will allow the resident to gain a skill that can be applied in the workplace once they successfully leave our program," he said. "VOAC is all about empowering individuals who have struggled in life to be independent and inspire hope in a new direction with their lives."
Columbia-based CBO Financial Inc. is helping to arrange financing for the project. Financing will be sought through the federal New Markets Tax Credit program, a $65 billion program designed to incentivize private investment in low-income communities.
The Baltimore farming operation is expected to serve as a model for expansion of Arcturus' technologies and training programs across the country and one of several projects Arcturus, CBO and Volunteers of America will work on together going forward.
William Gildea, CEO of Arcturus, said if the program is successful, it could serve as a bellwether for other public-private partnerships within the urban farming industry.
“Our goal was always to create impactful social and corporate programs that are mutually beneficial for all involved, from the community, to the company and our shareholders," he said in a statement. "Partnering with Volunteers of America Chesapeake and CBO Financial puts us in the position to achieve that goal.”
Morgan is a reporter for the Baltimore Business Journal. She covers technology, education and health care.
Kimbal Musk, Elon’s Brother, Grows Food In Brooklyn Shipping Containers
"Whereas Elon Musk is determined to colonize space with SpaceX, his brother Kimbal Musk is equally determined to leave the earth behind"
Kimbal Musk, Elon’s Brother, Grows Food In Brooklyn Shipping Containers
by 2Paragraphs in Business Spotlight | January 4, 2017
Whereas Elon Musk is determined to colonize space with SpaceX, his brother Kimbal Musk is equally determined to leave the earth behind. But in Kimbal's case, earth means the soil, not the whole planet. Kimball, a restaurant and sustainable foods entrepreneur and venture capitalist, is helping urban farmers grow soil-free crops -- crops that grow vertically indoors in giant shipping containers, nourished by LED lights and nutrient-rich water instead of earth. Leafy greens, basil and other herbs are the crops.
In the fall, Musk and his business partner Tobias Peggs set up a shipping container farm complex in Brooklyn -- creating small vertical farms that thrive in one of the least bucolic places on earth. Each farm is individually managed by selected farmers/entrepreneurs. The business is called Square Roots, and it's as radical an idea as SpaceX or Tesla -- and like Tesla, it really starts to work if the practice scales. The advantages are tantalizing. The farms are closer to the customer base in New York City. They save transport time and expense. They use less water. They grow year-round. And one container can produce as much in crops as two acres of land. If you want to know more about the kind of food Kimbal and Peggs believe in, check out The Kitchen.
Kimbal Musk — Elon's brother — Just Opened A Shipping Container Farm Compound In New York City
Business Insider
01.04.17
- and Sarah Jacobs
Kimbal Musk — Elon's brother — Just Opened A Shipping Container Farm Compound In New York City
For over a decade, he has run two restaurant chains, The Kitchen and Next Door, which serve dishes made strictly with locally-sourced meat and veggies. In 2011, he started a nonprofit program that has installed "Learning Gardens" in over 300 schools, with the intention of teaching kids about agriculture.
His latest food venture delves into the world of local urban farming.
In early November, Musk and fellow entrepreneur Tobias Peggs launched Square Roots, an urban farming incubator program in Brooklyn, New York. The setup consists of 10 steel shipping container farms where young entrepreneurs work to develop vertical farming startups. Unlike traditional outdoor farms, vertical farms grow soil-free crops indoors and under LED lights.
Six weeks into the 12-month program, just after the entrepreneurs completed their first harvests, Business Insider got a tour of the farms. Take a look below.
View As: One Page Slides
The Square Roots farms sit between an old Pfizer factory and the apartment building where Jay-Z grew up in Brooklyn.
They are vertical farms — everything grows inside 320-square-foot steel shipping containers. Each container can produce about 50,000 mini-heads of lettuce per year.
The USDA gave the Square Roots entrepreneurs small loans to cover preliminary operating expenses. Other investors include Powerplant Ventures, GroundUp, Lightbank, and FoodTech Angels.
On four parallel walls, leafy greens and herbs sprout from soil-free growing beds filled with nutrient-rich water. Instead of sunlight, they rely on hanging blue and pink LED rope lights.
About the size of the standard one-car garage, each shipping container can produce the same amount of crops as two acres of outdoor farmland.
Musk and Peggs chose Square Roots’ first class of 10 young entrepreneurs from over 500 applications. Peggs says they represent the next generation of farmers — though not all came to NYC with farming experience.
Before Josh Aliber, 24, moved from Boston to Brooklyn to join Square Roots, he had never farmed. Now he’s starting up his own specialty herb business and running a vertical farm.
Earlier this year, while Aliber was recovering from a concussion, he learned about urban farming from a podcast. He started researching it from his bed, and found out about the Square Roots program.
His shipping container farm runs on 10 gallons of recycled water a day, which is less than the average shower’s worth.
Aliber can monitor everything from the oxygen level to the humidity — which affects the plants’ taste and texture — using “the computer panel” near the door and sensors in the growing beds. If he wants a tropical or northeastern climate, he can control that too.
Aliber is selling his specialty herbs and basil primarily to upscale Italian and pizza restaurants in NYC.
All of the Square Roots farmers sold their first harvests at a recent local farmer’s market.
Though the program, he has had the opportunity to work with numerous mentors, including Tom Colicchio, a restaurateur and judge from “Top Chef."
“Yes, I have the ability to make money, but yes, I also have the ability to change the world,” he says.
Another 27-year-old farmer, Electra Jarvis, comes to Square Roots three days per week. On Wednesdays, she spends four hours meticulously placing 800 seeds inside small troughs.
Two weeks later, she transplants them to the walls. “We should be growing closer to us in cities,” she says.
Aliber, Jarvis, and the other eight entrepreneurs are not just learning how to grow plants, but also how to grow their businesses. A large part of the program is learning about branding and “how to tell our stories,” Jarvis says.
The larger goal of Square Roots, Musk tells Business Insider, is to create “a real food revolution.”
In the late ‘90s, following the tech boom, the Musk brothers moved from South Africa to Silicon Valley. They invested in X.com, which later merged with PayPal and was acquired by eBay.
Kimbal Musk has known Peggs, who previously worked on tech startups sold to Walmart and Adobe, for a decade. Before Square Roots, they worked together at The Kitchen, where Peggs served as the "President of Impact" and helped expand the chain to new cities.
When asked how his experience in tech translates to running a vertical farming accelerator, Peggs says the two fields share the same motivation.
“You learn how to execute impossible dreams. This was all just a Powerpoint presentation six months ago,” says Peggs, pointing to the farms behind him.
“Today’s consumer wants to know they are supporting companies that are doing something good for the world,” Peggs says. “This not just a Brooklyn foodie trend.”
The world’s largest vertical farm, Aerofarms, launched this year in Newark, New Jersey. In late 2015, urban farming company Gotham Greens opened the world’s largest rooftop farm in Chicago.
Square Roots hopes to expand to 20 cities by 2020.
Vertical farms can grow all year, using significantly less water and space than outdoor farms.
Critics of vertical farms point out that the LEDs drain a lot of electricity. Peggs says Square Roots is exploring how the farmers can switch to solar power in the future, since electricity is the biggest cost for the farms.
Kimbal Musk — Elon's brother — Just Opened A Shipping Container Farm Compound In New York City.
Square Roots will build offices inside the Pfizer factory in the coming months. In its past life, the building produced ammonia, a chemical that’s sprayed on plants and became vital to the industrial food system after WWI.
In 2017 and beyond, sustainable food startups will do business there. “It’s an act of poetic justice,” Peggs says.
Copyright © 2017 Business Insider Inc. All rights reserved. Registration on or use of this site constitutes acceptance of our Terms of Service, Privacy Policy, and Cookie Policy.
To Grow Community and Jobs of the Future, Suburbanite Launches Vertical Farming Enterprise in Detroit
After spending time with street children in Brazil as part of a missionary trip, Jeff Adams, founder of Detroit, Michigan-based urban vertical farming enterprise Artesian Farms, felt compelled to change his community. “If we can go 7,000 miles to work with young people we won’t see again, what can we do in our own backyard?
To Grow Community and Jobs of the Future, Suburbanite Launches Vertical Farming Enterprise in Detroit
January 3, 2017
Trish Popovitch
After spending time with street children in Brazil as part of a missionary trip, Jeff Adams, founder of Detroit, Michigan-based urban vertical farming enterprise Artesian Farms, felt compelled to change his community. “If we can go 7,000 miles to work with young people we won’t see again, what can we do in our own backyard?”
13 years ago Adams moved from the suburbs of Detroit to the urban neighborhood of Brightmoor—roughly four square miles on the outskirts of Detroit full of abandoned homes and derelict industrial buildings.
“My wife and I sold our house in the suburbs and moved to the Brightmoor neighborhood in the city of Detroit. What I noticed was in our community there was a lack of jobs for people who are 18 to 30 years old that had some limited skills and limited availability to transportation to get to a job,” says Adams. “I started looking for opportunities to employ people. I set up a business incubator and started looking around to see what we could do.”
What Adams discovered is what many have found in the rehabilitated Motor City – a well established urban farming movement with support from local businesses and city officials that was growing jobs and revitalizing communities. Adams wanted more opportunities like that for the neighborhood of Brightmoor.
After researching the state of urban agriculture in the city and determining that seasonal jobs wouldn’t cut the mustard, Adams bought a warehouse in August of 2014, unoccupied since 1998, on a local industrial complex and set up the shell of a indoor vertical hydroponics farm. “We set up this business as a social enterprise, a limited liability corporation with the social cause of employing people who are difficult to employ, bringing blighted structures back to life and making a vibrant opportunity for our neighborhood,” says Adams.
By March of 2014, the warehouse was renovated enough to set up shop. The farm sits inside a 7,000 square feet warehouse. Using artificial light and seven 20 foot high vertical towers and racked trays, Adams’ workers produce around 75 pounds of lettuce and kale a week, and approximately 40 pounds of basil per week. Adams has recently received funding to install an additional 35 vertical growing systems in the rest of the space, which will serve to increase output as well as his customer base.
Adams sells to local businesses, mostly restaurants and grocery stores. With some proactive self promotion and good old fashioned cold calling, he managed to get Artesian Farms produce into a regional chain with 15 stores as well as one local branch of Whole Foods. One growing contract took an hour while another took 18 months to negotiate. For Adams it’s about having the right product and understanding how to sell your company’s narrative.
“You have this product that people consume, but you also have this background story about growing local and what it means to the city of Detroit. It makes for a compelling combination of good food with a social cause behind it and people gobble that up,” says Adams. “Our branding is all about growing in Detroit for ‘goodness’ sake.’ It’s a great product offering great services to our community.”
Adams introduced his product to the local community on Earth Day last year, gathering locals to celebrate and experience their growing unit’s food. The positive feedback provided the farm with early momentum. Artesian Farms also markets through the local farmers’ markets.
Currently Artesian Farms has two full-time workers, one part-time, and Adams. Having felt the brunt of the mass layoffs in Michigan on a personal level after leaving his job in tech after 30 years, Adams can relate to many of the social and emotional stresses his workers and the locally unemployed face and feel. “There are a lot of issues that go along with hiring under resourced folks. I tell people as long as you can read and follow directions you can do this job. It’s a great way to make a salary.”
Artesian Farms is very aware of the potential issues facing urban employees such as lack of transportation, child care, and background checks that prevent many people from making a fresh start or finding gainful employment. Adams offers his employees a salaried wage and accommodates their scheduling needs as much as possible.
Just recently, Adams installed 15 additional growing towers although they are not yet active. “Now is the time for us to go out and create the volume to fill that up,” says Adams. “Then as we fill this up, then we will look for another space in Detroit to be able to continue that growth.”
Indoor Harvest Corp and Alamo CBD Enter Into Discussions to Combine and Ultimately Create Medical Cannabinoids Pharmaceutical Group
Indoor Harvest Corp and Alamo CBD Enter Into Discussions to Combine and Ultimately Create Medical Cannabinoids Pharmaceutical Group
January 03, 2017 13:39 ET | Source: Indoor Harvest Corp
HOUSTON, Jan. 03, 2017 (GLOBE NEWSWIRE) -- Indoor Harvest Corp (OTCQB:INQD), through its brand name Indoor Harvest®, is a full service, state of the art design-build engineering firm for the indoor and vertical farming industry. The Company provides production platforms, mechanical systems and complete custom designed build outs for both greenhouse and building integrated agriculture grows.
The Company is pleased to announce it has entered into discussions to acquire 100% of the member interests in Alamo CBD, LLC. (“Alamo”), a Texas Limited Liability Company. Upon closing of the acquisition, it is intended that Indoor Harvest shareholders would retain 40% and Alamo shareholders would retain 60%, of the total issued and outstanding common stock of Indoor Harvest. It is contemplated that at or subsequent to the acquisition of Alamo by Indoor Harvest, Indoor Harvest will spin-off its vertical farming operations including its produce and engineering, procurement and construction related operations to Indoor Harvest shareholders at the closing of the acquisition. The Company’s remaining cannabis related assets, agreements, intellectual property and operations will remain with Indoor Harvest/Alamo.
Alamo has signed an agreement with Vyripharm Enterprises, LLC. ("Vyripharm"), a Delaware limited liability company, to form a Joint Venture for pharmaceutical cannabinoids research (“Joint Venture”). Under the proposed joint venture with Vyripharm, Alamo will provide pure medical cannabis oil/product to Vyripharm in order to provide specific chemical profiles needed for Vyripharm’s research and patient treatments. It is planned that Alamo will, as a result of the acquisition by Indoor Harvest described above, have the right to Indoor Harvest’s patent pending biomanufacturing platform which it will then use in connection with the planned Joint Venture. The Joint Venture’s business plan is to develop specific process IP to achieve specific chemical profiles to treat various medical conditions such as epilepsy or PTSD, custom tailored to each patient.
It is anticipated that a condition precedent to the closing of the acquisition will be that Indoor Harvest must raise sufficient capital to repay all existing Company debt and pay for the expenses necessary to complete the spin-off of its vertical farming operations and to complete the proposed acquisition, currently anticipated to be approximately $1,000,000 in the aggregate. John Choo, Chief Executive Officer of Indoor Harvest noted, “The acquisition and spin-off transaction currently contemplated would, if all aspects of the transaction are effected as currently planned, complete Indoor Harvest’s previously announced plan to separate our cannabis and produce related operations.”
Chad Sykes, founder and Chief Innovation Officer of Indoor Harvest, added, “It will be the aspiration of our Company after acquisition of Alamo and thus becoming a joint venture partner with Vyripharm Biopharmaceuticals, to become a leader in the medical cannabinoids pharmaceutical space. Our aeroponic biomanufacturing platform allows for very precise control of plant expression, which allows a producer to create repeatable, consistent chemical profiles. We believe that unlike the small number of pharmaceutical groups operating in cannabis today, which use less precise cultivation methods and isolate certain chemical compounds, we can harness the benefits of the full entourage effect through the actual cultivation process. The planned Joint Venture that we’ll become part of our acquisition of Alamo has the potential to leverage our individual entities’ IP, agreements and relationships and would position us to become a major part of a serious player in the pharmaceutical space and medical cannabis research.”
Alamo’s current business plan is to use ten (10) acres of land, to include water rights, in La Vernia, Wilson County, Texas, to construct a 17,500 square foot cannabidiol pharmaceutical production facility. Alamo plans to seek a license to operate their facility under the Texas Compassionate Use Act. The Texas Compassionate Use Act (Senate Bill 339) was signed by Gov. Greg Abbott and became effective June 1, 2015. The bill requires the Department of Public Saftey (“DPS”) to create a secure registry of physicians who treat epilepsy for the purpose of prescribing low-THC cannabis to patients who have been diagnosed with intractable epilepsy. In addition, the bill requires DPS to license at least three dispensing organizations by Sept. 1, 2017. In addition to plans to file an application to operate under the Texas Compassionate Use Act, Alamo also plans to file an application with the DEA and register to become an authorized producer of medical cannabis and medical cannabis extracts for pharmaceutical research and clinical trials within the United States.
Vyripharm has advised us as follows: It is a biopharmaceutical company with a goal of improving clinical management through diagnosis and treatment with botanicals, synthetic pharmaceuticals and drug delivery systems. Vyripharm is reformulating its patented In-Situ Hydrogel, N4 Technology and Oligosaccharide (Dual Agent) Technology to develop applications in combination with medical cannabinoids for nuclear imaging and treatment for neurologic disorders including, but not limited to, post-traumatic stress disorder, epilepsy, acute/chronic disorders, cancers, metabolic disorders, and microbiome. Vyripharm is working diligently to prepare and file a range of new patent applications covering what it has described to us as being breakthrough work on medical cannabinoids (synthetic/natural).
Dr. Elias Jackson, Vyripharm’s Director of Scientific Public Relations said, “Early studies have shown a positive impact on certain resistant forms of cancer. We are carefully analyzing these results before we formally release this data. Based on the strength of these early studies, we believe that medical cannabis will play a vital role in the treatment regimen addressing a range of cancers, and that Texas and the Texas Medical Center could become a focal point for this important research.” Vyripharm has entered into sponsored research agreements for its core platforms with the University of Texas Medical Branch Galveston, The University of Texas Health Science Center at Houston – Institute of Molecular Medicine Sponsored Research and The University of Texas M.D. Anderson Cancer Center. There is also an agreement with the National Institute of Drug Abuse and has pending agreements with Baylor College of Medicine and the VA Hospital in Houston, TX.
Cynthia Cortez, Alamo’s Marketing Director said “Alamo together with Indoor Harvest after the planned acquisition transaction and through the Joint Venture will have complete control over the entire grow process to ensure consistent high quality medical cannabis. Utilizing Indoor Harvest’s state-of-the-art cultivation process will maintain a clean product for patients. In addition, Alamo looks forward to working with Vyripharm to provide what is intended to be high-quality medical cannabis for their research and development studies. We believe that Vyripharm, Indoor Harvest and Alamo share the same goal of becoming recognized as the global leaders in comprehensive cannabis product testing, certified pure cannabis oil, and evaluating the efficacy of certified pure cannabis in humans.”
Alamo and Indoor Harvest are currently completing customary due diligence and it is expected a definitive acquisition agreement will be agreed upon on or before February 15, 2017. We understand that Alamo and Vyripharm are also completing customary due diligence regarding the proposed Joint Venture which the parties expect to complete a definitive agreement prior to the closing of our acquisition of Alamo.
Consistent with the SEC’s April 2013 guidance on using social media outlets like Facebook and Twitter to make corporate disclosures and announce key information in compliance with Regulation FD, Indoor Harvest is alerting investors and other members of the general public that Indoor Harvest will provide weekly updates on operations and progress through its social media on Facebook, Twitter and YouTube. Investors, potential investors and individuals interested in our company are encouraged to keep informed by following us on Twitter, YouTube or Facebook.
ABOUT ALAMO CBD
Alamo CBD, LLC is dedicated to producing high quality CBD products in service to the patients of South Texas. The company is based in the San Antonio metropolitan area and was founded by a qualified team consisting of a pharmacist, a neuropsychologist, a microbiologist, a horticulturalist, and a dietitian. For more information, please visit http://www.alamocbd.com.
ABOUT VYRIPHARM BIOPHARMACEUTICALS
Vyripharm is a biopharmaceutical firm focused on natural products, regulatory testing, pharmaceutical drug development, data storage, monitoring technology, development of imaging agents, and drug delivery systems. The aim of Vyripharm is to improve clinical management through diagnosis and treatment with botanicals, synthetic pharmaceuticals, and drug delivery systems.
ABOUT INDOOR HARVEST CORP
Indoor Harvest Corp, through its brand name Indoor Harvest®, is a full service, state of the art design-build engineering firm for the indoor farming industry. Providing production platforms and complete custom designed build outs for both greenhouse and building integrated agriculture (BIA) grows, tailored to the specific needs of virtually any cultivar. Our patent pending aeroponic fixtures are based upon a modular concept in which primary components are interchangeable. Visit our website at http://www.indoorharvest.com for more information about our Company.
FORWARD LOOKING STATEMENTS
This release contains certain “forward-looking statements” relating to the business of Indoor Harvest and its subsidiary companies, which can be identified by the use of forward-looking terminology such as “estimates,” “believes,” “anticipates,” “intends,” expects” and similar expressions. Such forward-looking statements involve known and unknown risks and uncertainties that may cause actual results to be materially different from those described herein as anticipated, believed, estimated or expected. Certain of these risks and uncertainties are or will be described in greater detail in our filings with the Securities and Exchange Commission. These forward-looking statements are based on Indoor Harvest’s current expectations and beliefs concerning future developments and their potential effects on Indoor Harvest. There can be no assurance that future developments affecting Indoor Harvest will be those anticipated by Indoor Harvest. These forward-looking statements involve a number of risks, uncertainties (some of which are beyond the control of the Company) or other assumptions that may cause actual results or performance to be materially different from those expressed or implied by such forward-looking statements. Indoor Harvest undertakes no obligation to publicly update or revise any forward-looking statements, whether as a result of new information, future events or otherwise, except as may be required under applicable securities laws.
Contacts: Indoor Harvest Corp CINO, Mr. Chad Sykes 713-410-7903 ccsykes@indoorharvest.com
Vertical Farming Campaign Kicks Off
LAFAYETTE, Ind. — Austin Kasso, executive director of Red Giant Union, has a towering vision for Greater Lafayette's food production and consumption future, and the vision is vertical, so to speak
Vertical Farming Campaign Kicks Off
Emma Ea Ambrose , eambrose@jconline.com4:10 p.m. EST January 2, 2017
LAFAYETTE, Ind. — Austin Kasso, executive director of Red Giant Union, has a towering vision for Greater Lafayette's food production and consumption future, and the vision is vertical, so to speak.
On Monday Red Giant Union, a charity to further urban agriculture, in partnership with local startup Hydro Grow, launched a campaign to raise $30,000 to start a vertical farm in downtown Lafayette called The Tower Farms.
The vision is to take over a space at 419 North 3rd Street and install vertical tower growers that will generate fresh produce to supply the juice and salad bar that will operate at the same location.
The long term goal is to convert this space into a place where local chefs, food entrepreneurs and farmers can innovate and collaborate on issues of food security and sustainability.
“We transport most of our produce from Arizona and California, which in this day and age is not necessary anymore because we have the means and infrastructure to grow our own produce within our community,” Kasso said.
Kasso said he thinks Lafayette is ready for a vertical tower farm and doesn’t anticipate any issues fundraising the capital required to start the endeavor.
“Lafayette is ready for this. … It’s all about finding ways to engage the community,” he added.
Roughly 300 people are involved with the campaign in some fashion, according to Kasso, and he expects those numbers to grow.
The campaign goal is to raise 75 percent of the funds within two weeks and be fully funded within the month. From that point, it will take two months to set up the farm space.
Projects like this have been successful elsewhere in the country, Kasso said, referencing the Green Bronx Machine project, which takes urban agriculture techniques to children in Bronx school systems.
Urban farming practices, Kasso said “creates economic growth, healthier minds and bodies and an overall healthier community.”
The campaign went live on crowdfunding website Barnraiser and Kasso said they are still looking for corporate partners and sponsors in the community.
Call J&C reporter Emma Ea Ambrose at 765-431-1192. Follow her on Twitter: @emma_ea_ambrose.
Major Vertical Farm Operator Builds Productivity, Scale and Scope
Climate change, water scarcity and a soaring global population are among the key reasons why vertical indoor farming is taking off around the world. Here at www.freshfruitportal.com we recently visited one such facility belonging to U.S.-based AeroFarms, and learned about the extensive international growth plans for its ‘game-changing’ proposition
Major Vertical Farm Operator Builds Productivity, Scale and Scope
January 03 , 2017
Climate change, water scarcity and a soaring global population are among the key reasons why vertical indoor farming is taking off around the world. Here at www.freshfruitportal.com we recently visited one such facility belonging to U.S.-based AeroFarms, and learned about the extensive international growth plans for its ‘game-changing’ proposition.
One could be forgiven for thinking they had come to the wrong location when arriving at AeroFarm’s 30,000-square foot vertical farm in Newark, New Jersey. The unassuming building had operated as a paintball and laser tag arena prior to the company acquiring it, with much of the old business’ artwork still on display outside.
Upon entry I am met with a humid waft of fresh leafy greens, rows upon rows of LED-covered vegetables, and the company’s chief marketing officer Marc Oshima.
AeroFarms started out in 2004 in upstate New York selling to the Ithaca Farmers Market, and has since invested heavily in its R&D and technology.
Over the years it has built and operated numerous vertical farms while continuing to optimize its technology, and has grown more than 250 vegetable varieties.
I am told around 10-15 types of leafy greens are grown at this facility – its eighth in the company’s history. The vegetables have an extremely short crop cycle of just 12-16 days, while using 95% less water than conventional growing methods and no pesticides.
The seeds are germinated and grown on a cloth made from recycled BPA-free plastic bottles and then loaded into one end of the production row.
Over the course of their growing cycle they are moved further down the row, receiving specific intensities and spectrums of light and a nutrient mist sprayed in precise amounts onto the roots hanging below the cloth. Many factors like temperature, humidity, and Ph and CO2 levels are also closely monitored and modified.
“Everything has been measured down to the micron of the misting droplet. This is really taking farming to a whole other level of precision and performance,” Oshima says.
He explains AeroFarm’s technological developments are happening at such a pace that while just one year ago the vertical farm was around 75-times more productive than an open field farm – due to aspects like crop cycle and density – that figure has now shot up to 130 times.
No dressing needed
The various greens I am given to sample pack a flavor punch – a focus of the company’s R&D process. From baby Bok choy to Ruby Streak mustard greens to baby kale and arugula, each item’s flavors are strongly accentuated.
“No dressing is needed for these. What’s been exciting is that the key taste makers like top chefs say they feel like their pallets are being woken up again,” Oshima says.
“At the end of the day we’re a technology company, but we’re also a food company passionate about how we can change behavior. You have to make it taste good – that’s how you change consumption and how you get opportunities to be able to expand category.”
The short crop cycle afford the R&D team ample learning opportunities to optimize the taste and production technology.
“Out in the field you may only have one harvest a year, so you have to get it right. But here we have around 30 harvests a year, or 30 learning opportunities,” Oshima says.
He adds there are more employees with PhDs in the company than just about any other farming operation, and that staff includes the likes of a chief science officer, a chief technology officer, and an Oxford University-educated chief operating officer with a deep background in operating large-scale controlled growing environments.
“It’s a symbiotic relationship between our growing system, environment and product. At the end of the day it’s biology, but it’s also about how we mange and optimize that. And because it’s all our own technology, we understand very clearly how to optimize for these different characteristics.”
The products are sold to retailers within around 50 miles, including ShopRite – one of New York’s leading supermarket chains – and foodservice companies including the Compass Group, one of the world’s leading foodservice operators.
Local schools and restaurants are also supplied, and every week the production facility opens up its doors for local residents to buy from its farm stand.
Oshima says having a connection with the local communities in which AeroFarms operates is important to the company and its ethos of responsibility.
“We think a lot about our local footprint – serving the local communities and hiring locally. Over 40% of our team here lives in Newark, and over 85% live within 15 miles, so there’s a tremendous connection with the community overall.”
A couple of years ago the New York Times hailed the Newark vertical farm as helping to drive the revival of the Ironbound local area, which has been troubled over recent decades with severe economic and social issues.
An ambitious pipeline
With AeroFarms having invested a significant amount of time and money optimizing its business model and production operations, the organization is now in the midst of a major expansion, both in the U.S. and overseas.
Half a mile away from its Newark operation I visited, AeroFarms is building what is claimed to be the largest vertical farm in the world, which will also serve as its global headquarters.
I am given a sneak peek of the 70,000-square-foot operation in a former steel mill, which has started production and is due for its first sales in the first quarter of 2017.
With 35 rows and 12 levels of vertically growing leafy greens, the farm’s growing capacity is far higher than any other facility, and is complete with full automatization for the harvesting and packaging process.
Despite the impressive size of that farm, Oshima tells me soon it will no longer be the biggest, as the company rapidly rolls out major new projects in other locations.
“Our whole focus as a company has been local – thinking how do we disrupt what is often a very complex supply chain involving produce that is grown remotely?”
He says the crop’s high quality has led to interest from international retailers. Supplying to them from afar would mean going against the company’s focus on supplying locally, but inquiries have served as a strong indicator of the level of demand out there.
“It’s opened our eyes about a completely different part of a business opportunity. Our core focus though is about how do we serve the local communities that we have, and what we want to do is build responsible farms in all the major cities around the world.”
The next two major projects in the pipeline in the U.S. are in Camden, in southern New Jersey, and Buffalo, in upstate New York, and development is underway to roll out new projects in overseas locations.
“Our CEO just got back from China last week where he was for development talks, and then there are other markets we are looking at as well,” he says.
“We’ve had a working demonstration farm in Saudi Arabia since 2011, to show we are able to grow in different challenging environments. So the GCC [Gulf Cooperation Council] countries are an option, and we also have development in Africa and northern Europe, along with a tremendous amount of interest in the U.S.”
Aspects relating to the weather, climate change, pest pressure, water scarcity, food safety and urban density were all among the issues addressed by AeroFarms when decided where to establish new projects.
The entity has been working closely with Goldman Sachs and Prudential Financial on project financing for its farms.
“Each farm in and of itself has the right kind of economic profile that an investor like Goldman Sachs looks for, and they’re very much interested in being part of the next farm and the next farm,” he said.
The company had earlier mentioned its plans to carry out 25 projects over the next five years, and while Oshima explains this figure may end up being higher or lower than estimated due to varying sizes of the operations, he emphasized there was an ‘ambitious pipeline’ based on demand.
“Our organization is very much set up in terms of building the next farm,” he says, adding the operation and technology are very easy to deploy.
“We’re just trying to have very measured growth so that we can make sure we execute and deliver what we think is a game-changing proposition.”
US: Food Retailer Starts With On-Site Production in Growtainer
"In 2016 we saw the successful Growtainer launch in the UK and the expansion of their European presence at a Spanish biotechnological giant. CEA Advisors & Growtainers® promises, even more, global excitement in Indoor Farming and Controlled Environment Agriculture in 2017"
US: Food Retailer Starts With On-Site Production in Growtainer
In 2016 we saw the successful Growtainer launch in the UK and the expansion of their European presence at a Spanish biotechnological giant. CEA Advisors & Growtainers® promises even more global excitement in Indoor Farming and Controlled Environment Agriculture in 2017.
After more than a year of meetings with the Produce Marketing team at a major US food retailer, the first custom built for onsite production Growtainer® has been delivered and will begin production in Q1, 2017. “We spent over a year discussing the retailer’s concerns and objectives and when I was sure we were all on the same page we began the design and manufacturing process” said Glenn Behrman, founder of Greentech Agro LLC and CEA Advisors LLC.
Growtainers® have come a long way from those first two prototype models built about 4 years ago and recently donated to Texas A & M Agrilife Research Center in Dallas. LED costs have come down and their efficiency has improved. "Our understanding of the critical importance of the growing environment and the need for intuitive control systems has increased. We’re collaborating with more industry experts in all areas that are critical to the development of a well-balanced successful production environment”.
According to Behrman, increasing global awareness of indoor local vertical production has been the driver in the laser focused pursuit of new, modern and sustainable indoor farming practices. "On site production in the Growtainer® to produce the freshest, unique, gourmet leafy greens and herbs for their customers at the retail level is the objective of the retail partner. They are the first in the nation to train their team members in a food safety compliant, climate controlled, LED lit multi-layer vertical indoor production environment. "
"CEA Advisors is proud to be working with a forward-thinking food retailer that is committed to innovation and focused on food safety, unique products and the customer experience” said Behrman.
For this project, CEA collaborated with a McKinney Texas based water management firm, whose team assisted in the design and installation of a state of the art irrigation system. "The container modifications were carried out by the largest and most experienced group in the USA. North America’s leading horticultural supplier of goods and services provides their expert and ongoing consultation to the project, as well."
The state of the art 53’ custom built Growtainer® has a separate utility area and provides 480 square feet of climate controlled vertical production space, specially designed for maximum efficiency and food safety compliance. Besides having a dedicated proprietary technology for ebb and flow irrigation installed, these Growracks® are also equipped with energy efficient LED production modules, specifically designed for multilayer cultivation. The irrigation system is divided into separate zones to provide flexibility and allow a wide variety of production of crops at various growth stages. Behrman worked closely with the irrigation engineers to design a sophisticated control system. The proprietary irrigation system is constantly monitored and any corrections to EC or PH are made immediately. Every irrigation event is perfect for the plants optimum growth.
For more information on this and other exciting innovations in Indoor Vertical Farming
visit www.growtainers.com or email gb@cea-advisors.com
Publication date: 1/2/2017
A barely-used high-tech food-growing and production line is to be pressed into greater service: making soup for Wigan’s homeless and needy. Wigan University Technical College is the proud owner of Britain’s only “vertical farm” and process hall
College Vertical Farm to Help Feed Homeless
Saturday 31 December 2016
A barely-used high-tech food-growing and production line is to be pressed into greater service: making soup for Wigan’s homeless and needy. Wigan University Technical College is the proud owner of Britain’s only “vertical farm” and process hall.
When installed three years ago they were to be used to train up would-be engineers to learn the entire food creation process from seed to container.
But the UTC has struggled to attract the desired number of students to date to get it all running very often. There are plenty of other plans from millionaire backer Martin Ainscough, whose brainchild the UTC was, in order to turn round the college’s fortunes.
But his first mission is to help the borough’s neediest. Students, helped by Groundwork Trust Prince’s Trust participants and experts will grow and process various foods to produce around 60 gallons of soup a week: or, to put it in drinkable sizes, around 500 half-litre pouches.
And Mr Ainscough intends to the give the soup, free of charge, to the Wigan-based charity The Brick. Some of it will be given out free to the homeless, some will be sold at discount at its food banks and also given to volunteers. Mr Ainscough, who recently received a CBE for his services to charity and is a major supporter of the Prince’s Trust and the neighbouring Wigan Youth Zone, said he was keen to forge partnerships.
He added: “The vertical farm is a great piece of machinery. They are used a lot abroad already, but this is the only one in this country and it has been a great shame that it hasn’t been put to use more often since it was installed. “With this in mind I want it to be used to make soup for a charitable cause and there are few more deserving than The Brick. “I think businesses, charities and those in training should work together far more often. “We put the equipment to good use, we educate people and we help those less fortunate.
The farm can grow the equivalent of two acres of greenhouse produce.” Mr Ainscough said that some of the produce for the soup will come from the My Life charity project at Standish (which he also founded) and talks were under way with other organisations to sponsor the UTC to produce the vegetables.
Kathleen Pitt, chief executive of Queen’s Hall Action on Poverty which runs The Brick, said: “Martin Ainscough is keen to get this soup facility up and running and we are equally keen to receive the soup! It would be given out at the food bank at the Brick in Rowbottom Square. “We also have a kitchen and we provide a lunch for the people who work with us.
We have a community warehouse where we help people to learn how to get into employment and we have a kitchen and cafe there too. We could also sell the soup in our charity shop.
We cannot wait for the project to start.” Colin Greenhalgh, programme director, employment and skills at the Groundwork Trust, said: “We run a Prince’s Trust programme, part of which includes a community project which benefits the local community. This soup production idea links up perfectly with the UTC.
It helps them develop new skills and confidence and that looks good on a CV and it is good to give something back to society. “Initially it would be young people learning about food production and distributing the soup. But in the longer term it might also be about growing produce as well because we run a number of community allotments and gardens. This idea is perfect for the community project and it’s right on our doorstep.”