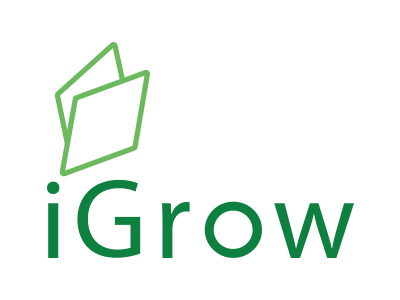
Welcome to iGrow News, Your Source for the World of Indoor Vertical Farming
Vertical Farming
It is now a well-known and recognized fact that our societies are becoming increasingly urbanised. It is also well established that our population as a whole is growing rapidly, expected to peak at around nine billion by 2050
Vertical Farming
09/03/17
Mark Horler of the Association for Vertical Farming sets out the role urban agriculture could play in smart cities of the future
It is now a well-known and recognized fact that our societies are becoming increasingly urbanized. It is also well established that our population as a whole is growing rapidly, expected to peak at around nine billion by 2050. In the light of these facts, it is becoming ever clearer that our current linear economic model is not sustainable. The take, make and waste model cannot continue to be the foundation of our economy, if we are to have and live in resilient and sustainable societies.
What is needed instead is a circular economy, whereby resources are reused, repaired and recycled. It follows from this that we would design products and systems to be durable, rather than disposable. This simple-seeming shift in priorities would have a profound effect on the whole way that our production systems operate, and therefore an equal knock-on effect on society as a whole. Finally, this would result in an enormously positive reduction in the harm we cause to the ecosystems upon which we in turn depend.
How does this pertain to the production of food?
The existing agricultural model has, since the so-called ‘green revolution’, achieved enormous gains in productivity. But those gains have come at a substantial cost to ecosystems and the services they provide us. With 70% of all available fresh water now used to irrigate crops, much of that is lost to evaporation and surface run off. This latter leads to a second problem in that the pesticides and fertilisers we use also run off in that water, causing untold damage to the environment around them and even getting into drinking water supplies, from which they must be removed.
Moreover, those pesticides and fertilizers are derived from natural sources, which must be mined, alongside all of the consequences that entail. To then allow those precious resources to be wasted as run-off makes little sense from either an environmental or economic perspective. Once all that food is grown, it must be transported to market. This utilizes yet more resources, particularly fossil fuels. The advent of globalized food systems means that enormous amounts of these resources are now used to transport food products.
We also have waste. Much of this happens during the transportation and storage phase, but it is also present in the supermarkets that stock the food and at the level of consumers in their homes. In the end, around one-third of all the food we produce is wasted.
The defining principles behind vertical farming
Vertical farming was established to help address these challenges via a series of simple premises. The first and defining principle is that the food should be grown as close as possible to where the people who will consume it live. This means that, instead of only growing in rural areas, we should, wherever possible, also grow in urban and peri-urban areas. Doing so removes, at a stroke, the majority of problems associated with transport. It also substantially reduces wastage. However, land is expensive in urban areas, so conventional farming in cities is simply not realistic economically. As with all urban developments, then, the guiding principle is to go upwards rather than outwards. Thus vertical farming came to be.
The second principle is that growing the food should use as few resources as possible. It follows that not only is a minimal degree of input necessary but that those inputs should be recycled and reused wherever possible. From this came controlled-environment agriculture. Many vertical farms now operate this way, in an entirely enclosed environment, with artificial lights specially designed for maximum benefit to plants, and with controlled heating and ventilation systems. These vertical farms also use soil-less growing systems such as hydroponics and aeroponics, the result being a water use reduction of between 75% and 95%. Pesticides are entirely unnecessary in such a system, and what small amounts of nutrients are required can be dissolved into the water, which is recirculated around the system.
This leads to the final principle, which is that waste outputs should be eliminated wherever possible and limited to the greatest possible extent where they are unavoidable. From these three principles then, a complete, circular, closed-loop system has been derived. This is vertical farming.
The Association for Vertical Farming
The Association for Vertical Farming (AVF) was set up to lead the vertical farming movement to facilitate healthy food, green jobs, environmental protection and climate change resilience by fostering the sustainable growth and development of the movement through education and collaboration. To achieve this, the AVF has focused on four key areas: education and awareness, industry standardisation, sustainability and the circular economy, and policy advocacy.
In turn, this has led the structuring of the association into seven divisions: education; research; standardization and certification; events, policy and advocacy; press and communications; and finance and business models. These divisions are then subdivided into project groups. Each PG is designed to address a specific challenge within the vertical farming world, with divisions therefore acting as communities of PGs, united by a common purpose.
Pursuing our four key areas via this structure has yielded a variety of interesting and exciting projects. We hold events of our own such as the yearly AVF summit, and we frequently partner with other major events to promote the cutting-edge world of vertical farming. We have an education programme in which, by collaborating with major education institutions, we will help to train the next generation of urban vertical farmers. We have a specially designed, first-of-its-kind sustainability certification scheme for vertical farming in development, which will allow the industry, governments and wider society to see exactly how sustainable vertical farming truly is.
Of course, the association, as the name suggests, is primarily made up of its members and, as a result, all of these efforts are dependent upon their support and engagement. We are very fortunate to work in an exceptionally forward-looking movement, where our members do indeed support, engage and collaborate with us in everything we do. Those numerous members, not incidentally, also represent an important counterpoint to those who would argue that vertical farming is not economically viable.
As in any young industry, the failure rate of start-ups was initially high, but the market is now expanding rapidly and, with the support of the AVF, is becoming more stable, with fewer barriers to entry.
Accommodating vertical farming within EU policy
This brings us to what the EU can do to help. One of the greatest barriers to the development of the industry, both in Europe and worldwide, has been the difficulty of placing vertical farming within existing categorisations. As a result, it has been hard for governments and planners at all levels to recognise it as a legitimate agricultural and business sector. Because vertical farming is agriculture, but takes place within a building in an urban environment, currently accepted classifications do not adequately cover all areas of the business. Put another way, vertical farming overlaps several categories.
In Europe especially, most agricultural and agri-tech policy is made at the EU level, for example via the Common Agricultural Policy (CAP), and then filters down to the various levels below. As such, it is imperative for the development of this industry in Europe that the EU recognises the unique nature of vertical farming and designs policy to accommodate it. From this would follow EU support for what is a true circular economy food system and industry, in line with its own stated goals of promoting those same objectives, of protecting our natural world, and of increasing human wellbeing via a sustainable and resilient economy. More practical support would also include clear financial incentives and grants to incentivise growth.
Vertical farming is a nascent industry and, if the EU wishes not only to keep up with the rest of the world, but to lead the way, such support is going to be crucial in achieving that goal.
Mark Horler
The Association for Vertical Farming
This article first appeared in issue 21 of Pan European Networks: Government, which is now available here.
Military-Grade Tech to Monitor Eggplants Rather Than Explosives
Military-Grade Tech to Monitor Eggplants Rather Than Explosives
by: Gwen Ackerman
March 9, 2017, 12:00 AM CST
Israel army know-how used to build robot for hydroponic farming
Founders hope tech will be used in outer space to grow food
On a rooftop in the Jewish-Arab Tel Aviv neighborhood of Jaffa, a former military technologist and an ex-journalist sit in a transparent bio-dome where their robot is busy learning how to grow food.
Flux IoT’s Eddy, a robot measuring less than a foot tall and resembling a life buoy, is built with military-grade sensors and armed with image-processing technology.
Its inventors intend it to become the industry standard for commercial and amateur indoor farmers who want to grow pesticide-free, water-efficient crops via hydroponics -- a method of growing plants without soil. Eddy sits in the growing reservoir, and users can stay updated on their crops’ progress via a mobile app, where information gleaned from fellow farmers can help them know when to change the lighting or add nutrients.
Currently closing a $2 million seed funding to start manufacturing, Flux is planning another financing round of as much as $8 million later this year, its size dependent on how many robots sell on crowdfunding platform Indiegogo Inc., said Chief Executive Officer Blake Burris. It’s also growing its U.S. team, primarily based in Colorado, while research and development will remain in Israel. The Israeli team is led by co-founder and Chief Technology Officer Amichai Yifrach, who previously built nano sniffers to detect explosives and image processing tools to protect U.S. troops at checkpoints in Afghanistan and Iraq.
“In the army you build perimeter security using imaging processes and webcams that can see things the human eye can’t,” said Flux VP of marketing and co-founder Karin Kloosterman, a former journalist. “With that technology Eddy can look at a plant and detect nutrient deficiency and tell you what it is. Right now you have to be a trained agronomist to know.”
Zirra.com Ltd., an Israeli startup that uses artificial intelligence and machine learning to analyze the private tech market, says Flux’s offering “poses significant disruption in their relevant space,” but that the price of the robot could be a “showstopper.”
Burris says they plan to sell Eddy for $179, and expect to sell anywhere between 10,000 to 25,000 robots this year. Rival SmartBee Controllers, which provides water content sensors, sells starter systems starting at $2,500. A water content sensor alone costs between $350 and $400.
Green Shoots
Hydroponic farming is growing in importance as government agencies such as the U.S. Department of Agriculture reflect on the potential impact of industrial or conventional farming, including soil productivity decline, pollution and depletion of natural resources such as water.
According to global market research firm IBISWorld, the U.S. hydroponic industry alone will reach $856.8 million by 2021, from $821 million in 2016 and the number of businesses will jump from 2,347 to more than 3,000. Flux sees home gardeners as a target market, and in the U.S. 42 million households grow food at home, according to The National Gardening Association.
Scotts Miracle-Grow Co., the world’s largest seller of lawn and garden products, bought an Arizona-based company in October to boost its hydroponics offering. New Zealand-based Bluelab, a global supplier of testing and control equipment for hydroponics, gives basic readings that are linked to a computer and is also working on a mobile app. One of the big markets for hydroponic equipment are cannabis growers.
Flux will assemble the first few thousand robots in Israel, and if demand expands as expected, manufacturing will move to China shortly thereafter.
The intersect in hydroponics is also spreading between worlds. Elon Musk has plans for a Martian colony, NASA is trying hydroponics out in space, and the European Space Agency is cooperating with the Space Farm Collective led by a Netherlands Border Labs team on ways to grow food on planets other than Earth. Thieme Hennis, head of the Space Farm Collective, is testing out Eddy to see how it might help a citizen science project called Watch Me Grow, aimed at finding plants that will grow best in space, and improve ways even the public can grow their own food on Earth.
“Eddy has to prove itself on a larger scale, but something like this is necessary and offers an interface for non-professional and professional growers alike to understand and ‘talk’ with plants,” said Hennis.
Urban Vertical Farming Helps, Inspires, Grows The Green Wave
Urban Vertical Farming Helps, Inspires, Grows The Green Wave
By Eliza Grace | Thursday, March 9
Last week, I went to catch up with an old friend who graduated from Duke last spring. Dr. Spencer Ware, a major in Environmental Science, found his new job by researching urban gardens in the greater Raleigh/Durham area. He stumbled across a small but productive operation called Sweet Peas Urban Gardens. This haven, created by Tami Purdue, takes up an average size plot in the middle of a residential area that features a greenhouse, outdoor garden and a Crop Box. You may not recognize the term "Crop Box," as the concept is quite new. Sweet Peas is home to the fifth one ever created!
The Idea of the Crop Box originated when a few people realized how many empty shipping containers there were laying around. These large metal boxes take up space without a purpose. The solution proposed by Crop Box was to make these spaces into small vertical urban farms. From the ideas conception in 2012, the first model took two years to perfect. As of now, a fully-functioning, fully green Crop Box would cost you about $75,000. Purdue pointed out that the high cost is due to the 50 LED lights that Sweet Peas purchased to grow each layer of produce. LED lights are four times the price of fluorescents, but in the long run save electricity costs that would be needed to ventilate the heat produced by cheaper fluorescents.
The entire container comfortably hosts four layers of a variety of soil-free growing plots. The Crop Box could also feature soil, but Sweet Greens uses a hydroponic system instead, because, why use an unnecessary resource? Their soil-free (hydroponic) growing system uses only decomposable materials which are later composted, and so little water that Sweet Peas water bill went up only four to six dollars per month once the Crop Box was up and running.
The early adaptors of this new system have so-far found that the way to make the fastest profits is through growing micro-greens. Micro-greens have a growing cycle of only 10-14 days. They are packed with flavor, nutrients(up to 40 time higher levels of vital nutrients than their mature counterparts) and are part of a growing market. This means produce can be churned out in a quick and efficient manner. The system is also made more cost-effective and sustainable by thriving without the need of any chemical fertilizer inputs. The more difficult part has been finding the market to sell to.
Sweet Peas made their mark by starting at the local farmers market in Raleigh. Until recently, micro-greens have gone underutilized and under cultivated in the kitchen. However, with a growing trend towards eating healthy and local, people have started to recognize micro greens as a perfect garnish with lots of different flavors. Sweet Peas alone harvests a large variety. When I visited, Purdue and Spencer showed me varieties of wheatgrass, radish, broccoli, kale, cilantro and much more than was all soon to be harvested. The whole operation was diverse, concise and beautifully efficient in producing delicious organic micro-greens.
While the whole operation requires a large investment to get started, Sweet Peas Urban Garden made its money back in just two years. This includes the time it took to get Sweet Peas recognized as a supplier to the area. After spending time at the farmers market, local chefs caught on to the Sweet Peas mission and fell in love. These gourmet, farm-to-table chefs are the backbone of the micro-green business, a small but budding market in the N.C. triangle.
While the Crop Box also takes work to maintain, Purdue has found a lot of free help, and new friends, through using the website WWOOF (Worldwide Opportunities on Organic Farms), which lists farms worldwide where people are welcome to live for free in exchange for farm work. In addition to this money-saving tactic, Sweet Greens makes local deliveries by bicycle. Both of these methods are not only good for business, but good for the health and spirit of those running the business.
Because of the success Sweet Greens has seen, Purdue is considering investing in a second Crop Box. There is a possible deal in the works with Whole Foods that could launch their operation to a much larger scale, and even without Whole Foods the demand has still been continuously growing.
While a growing desire for fresh local foods exists, many urban areas continue to lack initiative. When exceptional people such as Purdue of Sweet Peas decide to take action and start a project, people notice. No matter how small the operation, a new trend can be created through a growing appetite and awareness for local, organic food. Every individual with any size plot of land has the power to grow their own food, and Sweet Peas is a larger symbol of that. If this small shipping container can be turned into a profitable farming project in two years, we should all spend more time thinking about the future possibilities of urban and vertical farming. People from around the world have traveled to Raleigh to see Sweet Peas Urban Farm and it’s Crop Box initiative. If their little box can serve as a model for the rest of the world, then no effort is too small to help innovate new models to feed an ever-growing population.
Many Thanks To Dr. Spencer Ware and Tami Purdue for welcoming me on their farm and talking to me about the project!
Eliza Grace is a Trinity junior. Her column, "the green wave" runs on alternate Thursdays.
Urban Crops Announces Corporate Name Change to Urban Crop Solutions
March 9th, 2017 11:16
Urban Crops Announces Corporate Name Change to Urban Crop Solutions
As of today Urban Crops will change its name to Urban Crop Solutions, highlighting the core of the company being a global turnkey solution provider in automated plant growth infrastructure and plant growth recipes. In alignment with the adoption of the new name Urban Crop Solutions has also launched a new website: urbancropsolutions.com.
“We are very excited about the introduction of our new company name and believe that the name Urban Crop Solutions allows us to better represent our business model, being an independent turnkey vertical farming solution provider with an extensive after sales model”, explains Maarten Vandecruys, co-founder and managing director of Urban Crop Solutions. “Being categorized as a solution provider better aligns with our philosophy and core values of delivering reliable and qualitative products and services” adds Frederic Bulcaen, co-founder and chairman of Urban Crop Solutions. “All our products and installations are engineered and manufactured to be industry-proof.”
We are very excited about the introduction of our new company name and believe that the name Urban Crop Solutions allows us to better represent our business model, being an independent turnkey vertical farming solution provider with an extensive after sales model.
Maarten Vandecruys, co-founder and managing director
Urban Crop Solutions with headquarters in Beveren-Leie (Waregem, Belgium), in the middle of the Western European vegetable industry and surrounded by international well-reputed machine building companies, develops since 2014 tailored plant growth installations. These systems are turnkey, robotized and able to be integrated in existing production facilities or food processing units. Urban Crop Solutions also has its own range of standard growth container products. Being a total solution provider Urban Crop Solutions can also supply seeds, substrates and nutrients for clients that have limited or no knowledge or experience with farming. Currently the company has a growing list of more than 180 varieties of crops that can be grown in closed environment vertical farms and that have been validated. These plant recipes (ranging from leafy greens, vegetables, medicinal plants to flowers) are developed specifically for indoor farming applications and sometimes exclusively for clients by its team of plant scientists. Urban Crop Solutions has started activities in Miami (Florida, US) in 2016 and expects to have an own subsidiary in Japan in Q2 2017.
Growing crops in a climate controlled multi-layer environment with own developed LED lights achieves shorter growth cycles, higher water efficiency, flexible but guaranteed harvests and safe and healthy crops (no pesticides or herbicides needed). The grow infrastructure can be installed in new buildings, as well as in existing (industrial) buildings or unused spaces. Above all, it gives the clients the possibility to grow, harvest and consume locally, every day and in any chosen quantity.
Facebook: www.facebook.com/urbancropsolutions
Twitter: www.twitter.com/U_C_Solutions
LinkedIn: bit.ly/UrbanCropSolutionsLinkedIn
YouTube: bit.ly/UrbanCropSolutionsYouTube
Indoor Farming Takes Root At U of T Mississauga
Indoor Farming Takes Root At U of T Mississauga
Student startup, Just Vertical, is growing an indoor farm wall hydroponically at U of T Mississauga – with nutrient solution, instead of soil
At University of Toronto Mississauga, a plastic tower sprouts produce including curly starbor kale, buttercrunch and collard greens.
Rising almost six feet off the ground and illuminated by high output fluorescent bulbs, the indoor farm wall grows plants hydroponically – with nutrient solution, instead of soil. The water nourishes the roots, collects in a gutter and then recirculates back to a nutrient tank that feeds back into the hydroponic system.
The farm wall was the idea of Master of Science in Sustainability Management (MScSM) students Conner Tidd and Kevin Jakiela who partnered with Modular Farms Co., which specializes in vertical farming systems, to create distribution channels and services.
“You can grow pretty much anything,” Jakiela says. “Here, we’ve already grown three different types of lettuce, Genovese basil, joi choi, peppermint and parsley.”
From seed to harvest, it takes about four weeks to grow leafy greens and herbs.
“If you stagger it correctly, you can harvest it almost every day,” Tidd adds.
The wall costs just under $25 a month in electricity.
The seedlings, nestled in plugs made of peat moss, begin in a tray and are placed under a humidity dome where they germinate and are fed different levels of nutrients and pH. After a couple of weeks, they're ready to be transplanted into the tower.
Wicking strips help water find the path of least resistance by controlling the water flow and taking the water directly to the seedling roots.
“It’s a white cloth that you open up, put the plug in, then you close it like a sandwich, and put it into the tower,” Jakiela says.
Although the produce the farm wall yields is not organic-certified yet, the students' startup company, Just Vertical, uses organic-based practices, foregoing herbicides and pesticides.
“When you’re outside, you’re exposed to pests and fungi,” Tidd says. “Unless you’re using herbicides and pesticides, it’s going to be a problem especially when you’re growing strawberries and tomatoes.”
“With Just Vertical, Kevin and Conner have a great product in place, and manufacturing is lined up so now the initial focus will be on market validation,” says Sam Dumcum, the programs, strategic relationships and innovation lead at ICUBE, U of T Mississauga's incubator that provides startup support to new ventures at any stage.
Dumcum says that by focusing on market research during the next phase of their startup, Just Vertical will be able to have a solid base with which to advertise and sell their product but also to appeal to investors.
Harnessing Local Food Production
Harnessing Local Food Production
By Drs. Robert & Sonia Vogl
Contributors
In our efforts to promote sustainable living we have used several approaches: offering classes on gardening and hoop house construction at IREA Headquarters; workshops and booths related to organic gardening; sales of organic produce from local producers; hydroponics and fish farming at the Renewable Energy and Sustainable Lifestyle Fair; and building a demonstration solar greenhouse which we later donated to the Oregon High School agricultural program with modifications gained from our experiences with it.
We initiated a prairie project on the roof of the building occupied by Freedom Field at the Rock River Water Reclamation Campus in Rockford. We called attention to the hydroponics project at Auburn High School developed by Tim Bratina, who took his students on field trips to Chicago and Milwaukee to stimulate their interest in developing a small scale project at the high school. Bratina advocated the utilized of empty factory facilities in Rockford to house what amounts to vertical farms. We were involved in a series of meetings with YouthBuild In Rockford exploring the potential of utilizing their facilities as a site for what would be considered a vertical farm.
Sadly, none of these efforts succeeding in stimulating the utilization of available space as a site for an indoor organic farm in Rockford.
While gardening programs operate in communities in the area, an outstanding one has operated for several years in the DeKalb Schools under the leadership of Dan Kenny. He has agreed to make a presentation at this year’s IREA Fair, providing insights into the nature of his program and its future directions. His is an excellent model of what can happen in a community under effective leadership.
Vertical farming is another sustainability option to investigate. Although it is a relatively new, growing industry, it was suggested as long ago as 1909. Plants are raised indoors in layers, avoiding the extremes of weather. It generally uses hydroponics, the technique used by Bratina’s students. Vegetables are grown in nutrient rich waters and often include fish growing operations as well. Some use aeroponics, growing plants with only misting roots. Being indoors, LED grow lights are used to replace sunlight. Although it is an efficient use of resources, artificial light, heat and power are needed.
Recently some large-scale indoor gardening operations raising produce on a year-round basis and marketing through local supermarkets have been established in Chicago and Rochelle.
Mighty Vine in Rochelle grows tomatoes in a greenhouse operation and markets them through regional supermarkets. Bright Farms, also in Rochelle, offers a broader range of greens. Both of these operations are backed by outside interests and provide their produce on a year-round basis.
Chicago’s The Plant has been in operation for several years. It combines aquaculture, produce production, a brewery and an algae bioreactor. They are installing a biogas operation to reduce electricity costs. When it opened, the 90,000 square foot facility was the largest in the world. It is expected to produce one million pounds of organic greens including lettuce, spinach, basil and mint annually. It also expects to provide hundreds of jobs.
Although these farms are growing, Farmed Here in Bedford Park, formed in 2013 and billed as “the world’s largest indoor vertical farm,” closed its growing operations this year. It is, however, still producing food products.
Vertical farms are seen as an integral component in providing some of the food needs of urban populations and jobs for the communities. Such installations are expected to expand rapidly in urban centers around the world in response to the ravages of climate change, ongoing population growth and the desire to consume cleaner organic foods.
Drs. Robert and Sonia Vogl are the President and Vice President of the Illinois Renewable Energy Association.
Valoya Launches "Heavy-Duty" Tube LED for Vertical Farms
Valoya Launches "Heavy-Duty" Tube LED for Vertical Farms
8 March 2017, by Gavin McEwan, Be the first to comment
Finnish specialist lighting manufacturer Valoya has extended its L range of LED tube lights for vertical farms.
With a 40W power consumption, the 18.m-long L40 tube is described by its manufacturer as a heavy duty fixture.
It has the same dimensions of standardised T8 tubes meaning it can be retrofitted into existing structures.
The fully enclosed L-Series has low power consumption, cool running temperature and maintenance-free lifetime of at least 50,000 hours.
They are dust-proof and can withstand submerging in water to a depth of 1m. They are available with all of Valoya's proven wide light spectra.
Current users include London's Growing Underground where Valoya's L-Series lights are used to cultivate a range of leafy greens and herbs.
- Read more on LED Lighting Systems
Local Roots Hits The Road To SXSW With World’s First Traveling Indoor Farm
Local Roots Hits The Road To SXSW With World’s First Traveling Indoor Farm
Launch of National Tour Features Newest Methods in High Tech Agriculture Production
March 08, 2017 12:11 PM Eastern Standard Time
LOS ANGELES--(BUSINESS WIRE)--Local Roots Farms will debut the world’s first traveling indoor farm at SXSW, March 11-15, 2017. Built inside a 40’ shipping container, the mobile farm uses a proprietary form of hydroponic technology to grow leafy greens equal to five acres of land, 365 days a year, with up to 99% less water than conventional agriculture and is pesticide and herbicide free. The farm departed from the Local Roots headquarters in Los Angeles today to set up residency at the SXSW Festival in Austin, Texas.
@LocalRootsFarms to debut world’s first traveling indoor farm at SXSW! Follow our #lettuceadventures at #sxsw2017
Tweet this
Centrally located in the main SXSW exhibition hall (Booths #2011-2015), festival-goers will have an opportunity to tour inside the high tech farm. The tour focuses on the Local Roots proprietary approach to indoor farming, including the design and engineering of their modular indoor farms- see video. Capitalizing on both traditional farming methods and scientific breakthroughs at NASA, the Local Roots traveling farm features the newest methods of agricultural production.
“There is nothing like experiencing the farm firsthand,” says Local Roots VP of Business Development Brandon Martin. “We’re excited to make this unique experience available to the public with the launch of our cross-country tour. The interactive experience is truly unique and provides a profound understanding of the impact this technology will have on the future of farming.”
During the SXSW Festival, Local Roots Founder and CEO Eric Ellestad will speak on the Funding the Future of Food Tech panel on March 12. Local Roots will also be on display at the Food and Tech Innovation Spotlight on March 11. The program will explore the practical applications for this new form of growing food, including urban development and the creation of a more sustainable food system.
SXSW is the first of a series of road trips, with plans for the traveling farm to make quarterly tours throughout 2017. Additional dates and cities will be announced in May 2017. The farm will be used as an educational tool to inspire consumers about agriculture science & technology with stops at schools, corporate campuses, restaurants, and festivals throughout the U.S.
About Local Roots Farms
Local Roots designs, builds, deploys, and operates controlled-environment farms that yield the highest quality, locally-grown produce using breakthrough technologies. These farms, called TerraFarms, grow with up to 99% less water, 365 days a year, without pesticides or herbicides. Headquartered in Los Angeles, CA, Local Roots is a portfolio company of the Los Angeles Cleantech Incubator (LACI). The Local Roots R&D team, comprised of plant science, botany, agronomy, design and engineering specialists, utilizes a vast body of data to grow better-tasting and nutrient-rich produce with guaranteed harvests and yields. Visit http://www.localrootsfarms.com and follow our #lettuceadventures on Twitter, Facebook and Instagram.
Contacts
Local Roots Farms
Allison Towle, 310-779-6993
Director of Corporate Development
a.towle@localrootsfarms.com
or
LACI
Laurie Peters, 818-635-4101
Communications Director
lpeters@laci.org
Are Urban Farms The Wave Of The Future?
Are Urban Farms The Wave Of The Future?
7 March 2017
The farm of the future may not be the traditional kind with crops planted in vast fields and serviced by tractors and subject to the vagaries of weather and soil quality. According to Buzzfeed, the farm of the future will be in warehouses in the middle of the city, with crops #Growing in nutrient baths and temperature, light, and even the atmosphere tightly controlled.
Right now these urban farms are producing trendy salad greens such as arugula and kale favored by fashionable foodies. The product is more expensive currently than naturally grown produce, but the potential for significant cost savings are apparent as the urban farms scale up.
The urban farms are far more productive than the rural kind. The growing season is year-round, 24/7. The warehouses where the food is being produced are near enough to restaurants and supermarkets so as to keep transportation costs low. The urban farms require less water than the natural, rural kind, a consideration where clean water has become scarce in certain parts of the world.
One of the factors that are holding back the proliferation of these facilities is high startup costs. Some existing agricultural factories, as some people have called them, have failed for various reasons. Nevertheless, some entrepreneurs are planning to expand the crops being grown, to cucumbers, peppers, and various berries.
The technology for these types of farms will certainly be adapted as people begin to settle other planets. No one is going to plant crops on the moon or Mars (at least until terraforming takes hold on the Red Planet.) But a dedicated agriculture facility would provide all the needs for future space settlers
The question also arises, what to call these new factory grown food. It cannot, at least according to current law, be called “organic” despite the fact that the method uses no pesticides. Call it “post-organic.” The crops are generally not genetically modified because the environment is altered to suit the plants and not the other way around.
Are these type of vertical farms the wave of the future? Very likely, sooner rather than later, a lot of food we eat will be grown indoors, with LED lights rather than the sun.
The Urban Farming Pioneer Who Wants To Feed The City’s Soul
The Urban Farming Pioneer Who Wants To Feed The City’s Soul
Bjorn Low made the work of growing food in urban spaces ‘sexy’, but his other mission is to help city-dwellers reconnect with life. His story on Game Changers.
By Steffi Koh
- Posted 05 Mar 2017 10:15
SINGAPORE: For four years after giving up his corporate job which was making him miserable, Bjorn Low spent a happy four years working on organic farms in far-flung places such as Scotland, Spain and Japan.
But when he returned to Singapore to start up a farm here, he hit a costly roadblock – he could ill-afford the land he needed. “I wasn’t shocked but surprised,” he said.
“To buy 10 acres of land (about the size of 10 football fields) in the middle of Wales with a river running through, with a farmhouse, cost less than a HDB flat in Singapore then.”
How could one farm without land? While looking around Singapore, the many green spaces in the midst of urban development triggered an epiphany – why not make use of the many under-utilised spaces to grow food?
That’s when the mission of turning Singapore into an “edible garden city” – which eventually became the name of his enterprise – took shape.
GETTING CHEFS TO CHOOSE LOCAL
Inspired by what he called a “global movement” of chefs wanting to connect with local farmers, Mr Low started out setting up edible herb gardens - initially using something as simple as stacked wooden boxes - and was soon approached by various hotels and restaurants.
But to grow his business, he needed international chefs and bartenders here to demand locally-grown herbs too.
Convincing them proved to be a challenge. “A lot of the chefs are very used to using Western herbs but they don’t grow very well in our climate,” said Mr Low.
“You need to spend millions of dollars to set up that infrastructure. Using a lot more local herbs and vegetables allows us scale up our operations much faster with lower infrastructure costs.”
An opportunity arose when Spa Esprit Group’s CEO Ms Cynthia Chua approached Mr Low, 36, and together with French chef Benjamin Darnaud – a believer in growing one’s own vegetables – they started Open Farm Community, a restaurant set in an urban farm on Minden Road.
“Urban farming in Singapore was previously unheard of,” said Ms Chua. “But now there is a momentum, there is a rhythm, and it was started because of people who are passionate about it like Bjorn.”
As Mr Low’s business partner, she helped put Edible Garden City on the radar of dining establishments such as the Tippling Club and Jamie’s Italian, encouraging them to use herbs grown in Singapore like cinnamon basil and white pea flowers.
FOOD FOR THE SOUL
But for Mr Low, the success of Edible Garden City goes beyond being a movement for locally-grown ingredients, to something almost existential in nature.
He described how working on overseas farms had helped his wife, Crystal, and him to escape the accumulated stress of working in the advertising industry.
“Working on the farm made me realise that actually, there is more to life than material wealth,” said Mr Low. “Being in touch with nature, and growing (my) own food, was able to fill up the void in my soul.”
He noted how “being able to nurture something to life” has been observed to help people out of depression. He added: “I’ve a history of depression in my family, so there’s multi-layered motivation for me to continue to do this - not just myself but for everyone in the community.”
His simple and wholesome outlook on life turned out to be contagious.
His employee, Mr Christopher Leow, 29, never thought that he could be a farmer in Singapore until he stumbled upon Mr Low at one of his talks.
“He made farming attractive to young people. He made it very sexy,” said Mr Leow, who used to manage a mobile coffee business. He is now one of 22 employees at Edible Garden City, which had started out with a staff of just three in 2012.
MUSHROOMING SUCCESS
The company’s revenue has since quadrupled to S$800,000 annually in the last four years, a point of success which has helped bury Mr Low’s family’s initial doubts.
“They realised that it’s become a career for me and a business that’s sustainable,” said Mr Low.
Edible Garden City now operates from an 8,000-sqm plot of land in Queenstown. Calling the place “home”, Mr Low said that with the security of a nine-year lease, his team can now “go full steam ahead with experiments” to show how under-used spaces can produce food and add to the aesthetics of the area.
The company is also working with the Spa Esprit group to create skincare and beauty products out of organic herbs. Calendula flowers with their anti-microbial and anti-fungal properties, for instance, can be made into creams, soaps and tea, said Mr Low.
“We have to innovate and add value to the crops we are growing so that we can make it a more sustainable industry,” he said.
One project will see Edible Garden City training and employing adults with Down Syndrome to grow mushrooms out of coffee and food waste, as part of their exploration into “closed-loop” farming.
“Essentially, we’re able to deal with the food waste problem in the city itself, and not having to cart it to a landfill,” explained Mr Low. He hopes this model can be scaled into other sites and even abroad - creating employment for slum-dwellers like those in Bangkok and Jakarta.
“It’s really important for me that it takes off, because I feel that, inherently, we can help urbanites reconnect with nature,” said Mr Low. “Gardening and horticulture has a way to let people understand what life is about.”
Meet Herbert, The Vertical Hydroponic Wall Garden
Meet Herbert, The Vertical Hydroponic Wall Garden
Derek Markham (@derekmarkham)
March 3, 2017
The latest edition of YAIGU (yet another indoor grow unit) brings you Herbert, an LED-powered indoor "farm" that grows greens & veggies on your wall.
There's nothing like fresh homegrown produce, but if you don't have an outdoor garden space, or you want a year-round supply of greens and veggies, you're gonna have to bring the 'farm' indoors. And the recent explosion of indoor grow unit products seems to suggest that there are a lot of people who are willing to do so, which might speak more to the desire for high-tech solutions than it does for the desire for local food (but which is probably a combination of the two).
The latest entry to the indoor growing gadget scene is Herbert, which is designed to be a space-saving solution, as it hangs on the wall, as well as a highly efficient one, as it incorporates both hydroponics (for fast growth) and LED lights (for energy-efficient illumination). While there's no indication of where the product's name comes from (Was Herbert a fantastic gardener? Is Herbert a strange portmanteau of herb + robot?), what's clear is that people dig the concept, as the Kickstarter campaign has already quadrupled its crowdfunding goal, with three weeks still to run.
At the core of Herbert is a hydroponic growing system, which grows the plants in a water-based solution (water plus nutrients) instead of soil, allowing for a smaller grow unit (plants need less space for growing medium) as well as more control over nutrient delivery, while also using 90% less water than soil-based systems. Driving the plants' growth is a 60W LED lighting unit, which is said to have been developed specifically for optimal growth, and between the hydroponic system and the lighting, Herbert is said to be "40% faster compared to traditional farming methods."
"Plants use sunlight to convert CO₂ into sugar and other organic compounds. With our lighting solutions you are not only not dependant on daylight anymore and require less thereof, with Malina, our adaptive LED, it is possible to change the light spectrum to meet the specific requirements of plants and their different growth stages. Taste, yield, resilience towards pest problems, surface feel, and growth - all these factors can be influenced by using an optimal lighting system!" - Ponix Systems
15 plants can fit into Herbert, ranging from salad greens to herbs to strawberries, and the initial purchase includes 30 biodegradable sponges (which are used instead of a pot with soil), as well as starter set of seeds and fertilizer. And seeing as it's 2017, a subscription model will have new seeds, sponges, and fertilizer shipped direct to your door if desired.
The units measure 32.3 x 22.0 x 4.5 inches (820 x 560 x 115 mm) and weigh 26.5 lb (12 kg) when fully loaded with plants and water. And BECAUSE APPS, Herbert also integrates with an iOS or Android application that can be used to adjust the lighting settings, as well as "guide you through the growing process."
Here's the kicker, though, which may be a deal-killer for some: Herbert costs almost $400 for backers of the campaign, which is said to be 25% off the future retail price. That's a lot of green for growing green on your wall, but it could be an even trade-off for those who value homegrown produce. The other potential downside to Herbert is the grow light, which is essential to its operation, but which could also be too much light for people in some rooms of the house (your mileage may vary, but I've got an LED grow light that's about double the wattage, and it's intensely bright).
Find out more about this vertical hydro unit at the Herbert Kickstarter page or at Ponix Systems.
Indoor Farming Takes Root At UTM
On the second-floor lobby of the Innovation Complex at the University of Toronto Mississauga, a plastic tower sprouts a variety of produce including curly starbor kale, buttercrunch and collard greens
Indoor Farming Takes Root At UTM
Friday, March 3, 2017 - 4:16pm
Sarah Jane Silva
On the second-floor lobby of the Innovation Complex at the University of Toronto Mississauga, a plastic tower sprouts a variety of produce including curly starbor kale, buttercrunch and collard greens.
Rising almost six feet off the ground and illuminated by high output fluorescent bulbs, it gives the often high-traffic, student-centred space a futuristic feel.
As part of their final capstone project, Master of Science in Sustainability Management (MScSM) students, Conner Tidd and Kevin Jakiela have partnered with Modular Farms Co., a startup company that specializes in vertical farming systems, to create distribution channels and service packages for their indoor gardening farm wall.
“You can grow pretty much anything,” said Jakiela. “Here, we’ve already grown three different types of lettuce, Genovese basil, joi choi, peppermint and parsley.”
From seed to harvest, it takes about four weeks to grow leafy greens and herbs. “And if you stagger it correctly you can harvest it almost every day,” added Tidd.
But it’s more than what they’re growing that sets them apart. It’s also how.
The farm wall grows plants hydroponically — that is, with nutrient solution instead of soil. The water nourishes the roots, collects in a gutter and then recirculates back to a nutrient tank that feeds back into the hydroponic system. It costs just under $25 a month in electricity.
The seedlings, nestled in plugs made of peat moss, begin in a tray and are placed under a humidity dome where they germinate and are fed different levels of nutrients and pH. After a couple of weeks, they're ready to be transplanted into the tower.
Found within the tower, wicking strips help water find the path of least resistance by controlling the water flow and taking the water directly to the seedling roots. “It’s a white cloth that you open up and put the plug in and then you close it like a sandwich and put it into the tower,” said Jakiela.
Although the produce the farm wall yields is not organic-certified yet, Just Vertical uses organic-based practices, foregoing herbicides and pesticides. “When you’re outside, you’re exposed to pests and fungi,” said Tidd. “Unless you’re using herbicides and pesticides, it’s going to be a problem especially when you’re growing strawberries and tomatoes.”
“With Just Vertical, Kevin and Conner have a great product in place, and manufacturing is lined up so now the initial focus will be on market validation,” said Sam Dumcum, the programs, strategic relationships and innovation lead at ICUBE, UTM's on-campus incubator that provides start-up support to new ventures at any stage.
“Who are the customers that want to grow fresh produce in their home with organic practices and how do we find them?”
Dumcum says that by focusing on market research during the next phase of their startup, Just Vertical will be able to have a solid base with which to advertise and sell their product, but also to appeal to investors.
“And as far as being part of an incubator goes, when you’re around other entrepreneurs, other ideas just pop up.”
Vertical Farming: Is This The Answer To The World’s Food Shortage?
Science stacks up in favour of high-rise farms as a sustainable food source – essential as the world’s population rockets
Vertical Farming: Is This The Answer To The World’s Food Shortage?
Science stacks up in favour of high-rise farms as a sustainable food source – essential as the world’s population rockets
At the turn of the millennium, a professor of environmental science at Columbia University in New York took a detour from the curriculum. He asked students what the world would be like in 2050. Dickson D Despommier’s class estimated its population would swell to nine billion people making food production a huge issue.
One solution they considered was to grow crops on every rooftop in New York City. After a lengthy process of studying aerial maps and working out which crops were most efficient, students judged rooftop gardens could feed only about 2 per cent of the 2050 population of New York. “They were terribly disappointed,” Despommier told The New Yorker.
But he got thinking: what if you could stack crops on top of one another like shelves in the fridge, or the floors of a building? The following year he coined the term “vertical farming”. But it would take several years for light technology to make these vertical farms possible.
With scientists having worked out how to manipulate the light spectrum to help plants grow, hundreds of vertical farms have cropped up in Asia and several large farms have been established in the US. Now vertical farming is coming to the UK. Supporters say it will address food supply issues as the world’s population becomes increasingly urban.
“Vertical farming has been born out of the challenges facing modern society,” says Henry Aykroyd, chief executive of Intelligent Growth Solutions, a company building a £2.5m vertical farm at the James Hutton Institute in Invergowrie near Dundee. As the city-dwelling population of the world increases to more than 70 per cent by 2050, people will find themselves further than ever from the places where cattle grazes and food is grown.
Workers at AeroFarms in Newark, New Jersey where LED lamps nourish plants in a former paintballing venue (Reuters)
A new solution is needed to keep up with year-round demand for everything from humble salad leaves to exotic produce like pineapples and avocados. According to Aykroyd, that solution is vertical farming.
Phillip Davis, a scientist from Stockbridge Technology Centre, has been helping the first vertical farms in the UK get off the ground. “The science behind it has been going on since Darwin was doing light measurements but it’s only in the last five or six years that the LEDs are bright enough to grow plants,” he said.
In the millions of years that plants have grown under sunlight, they’ve learned to sense different qualities of light to turn into energy using photoreceptors as their “eyes”. These photoreceptors only “see” blue or red light. It’s now possible to make LEDs that emit the blue and red light the plants need, excluding other parts of the spectrum. “By changing the light quality we can change the way the plant grows,” Dr Davis explained. “You can change how tall it grows, how fast it grows and when it flowers using spectrums of light.”
These LEDs make it possible to grow salad and other crops that have a short shelf life in places where there is little space and no natural light. Tom Webster, a biologist, and his business partner Kate Hofman founded GrowUp Urban Farms in a warehouse with no windows in Beckton, east London. “The idea is to grow food close to where it is consumed, in commercial volumes,” says Webster one weekday afternoon as he inspects a control panel showing the amount of water, waste and light in the growing beds. Behind him pea shoots, watercress and baby kale grow on wide metal trays stacked to the roof.
Each metal tray is lined with a mat made of carpet fibres. The crops are hydrated using water from fish tanks next door, which contains nutrients courtesy of the fish poo. Growers control light and heat to simulate night and day. “Even plants like to rest at night,” says Webster. A white sock, running behind each shelf, blows cooling air over the crops to counter the heat and humidity that gathers above the leaves. The system is between 70 and 90 per cent more water-efficient than traditional agriculture and, because the shelves can be stacked 10 high, it is 10 times more productive per square metre of space.
The whole cycle from seed to harvest takes between seven and 21 days, meaning at least one crop a month, regardless of weather or the season, keeping the shelf price of the salad stable. When the shoots are ready for harvesting, one of the farm’s few employees uses a lift on wheels to go between the beds, cutting the greens so they can be sorted into boxes and moved to a small walk-in fridge. From here the microgreens and herbs are transported to retailers ready for sale. It’s always boxes, never bags, as this helps to prolong the shelf life of the greens.
GrowUp supplies salad, including microgreens and herbs, to organic food retailers. Its microgreens are scattered on plates in restaurants across the capital. Sister community interest company GrowUp Box uses smaller, greenhouse versions of the warehouse ‘aquaponics’ system to teach communities how to grow salads on their own roofs, echoing Despommier’s students, who hoped to feed their city this way
Inside The Computerized Lettuce Factory Of The Future
Inside The Computerized Lettuce Factory Of The Future
High-tech farms in urban warehouses can grow 100 times more food using 95% less water than old-fashioned operations depending on soil and sunshine.
Farming, even in its modern, hyper-industrialized form, still relies on some very old-school technology: the sun, dirt, seasons, tractors. It’s all a bit messy and inefficient, at least by the standards of modern technologists, who are more accustomed to server farms that churn through data 24/7.
It’s not that surprising, then, that the self-declared farms of the future look more like an Amazon data center than an organic apple orchard. A wave of companies are rushing to figure out how to grow commercial volumes of food in giant urban warehouses, using LED lights instead of sun, and stacked shelves of nutrient solution instead of soil.
This particularly tech-centric model of urban farming us run by computer systems that monitor thousands of points of data and constantly adjust growing conditions. Marc Oshima, co-founder of AeroFarms, one of the world’s largest vertical farms, says the company uses “in-depth growing algorithms where we factor in all aspects from type and intensity of light to nutrients to environmental factors like temperature, humidity, CO2 levels, and we create the perfect recipe for each variety.”
While conventional agriculture companies engineer their crops to design plants suited to their environment — improving mildew resistance, for example — these companies are engineering the environment to match the plant.
None of this is cheap to set up. New Jersey’s AeroFarms has raised more than $50 million and says it can grow 2 million pounds of food each year in the “growing towers” in its 70,000 square foot facility in Newark. Gotham Green invested $8 million to build a rooftop farm in Chicago’s Pullman neighborhood. In February, New Jersey startup Bowery Farming, which attracted $7.5 million in a seed round, began selling locally grown leaf vegetables at Whole Foods and a few area restaurants, including Tom Colicchio’s Craft in Manhattan.
These high-tech farms — often led by entrepreneurs with backgrounds in finance and other non-farm businesses — are “definitely more expensive, but the expense is balanced out by more productivity,” said Irving Fain, CEO of Bowery and former Citigroup investment banker. Bowery estimates his facility is 100 times more productive per square foot than a typical farm.
Fain said Bowery’s operating system automatically monitors “hundreds of thousands of points of data on plant health, quality, growth, yield, taste and flavor.” Bowery is also designed to “take processes that are manually intensive and automate them” so that “the farm runs itself,” more or less. And because the environment is tightly controlled and there are no seasons, there are more harvest cycles — AeroFarms has up to 30 harvests each year.
So far, these capital-intensive indoor farms have focused on growing trendy greens that can be sold to the area’s salad-eating yuppies — baby kale, butterhead lettuce, arugula, and basil. A box of AeroFarms greens goes for $3.99, and Bowery Farming’s salad greens retail for $3.49, which is a lot more than a head of iceberg lettuce. And that’s the main challenge these startups face: there’s no shortage of cheap produce in supermarkets today.
It’s a pricey, niche product for now, but the companies have bigger plans. “As we scale, we plan to continue to drive down our costs and deliver the highest quality produce at a price that makes it even more accessible to all,” said Fain.
Oshima said AeroFarms is looking at other crops: berries, peppers, and cucumbers. “Our lens is on how we can transform agriculture around the world,” he said.
Realistically, these vertical farms “will never grow enough to feed cities,” said Danielle Nierenberg, cofounder of the nonprofit Food Tank. Grains like wheat, for instance, simply require more space than a warehouse can ever provide. But at the very least, she said, they bring some fresh food to urban communities, and may one day even create a new type of urban green space.
Bowery grows its greens hydroponically in a commercial warehouse in Kearny, New Jersey. The company says its farm requires 95% less water than a traditional farm and uses no pesticides or chemicals — and its location means its greens need to travel less than an hour to make it onto Manhattan restaurant plates.
These products can’t be called organic — that label generally refers to food grown in soil —so Bowery describes the model as “post organic.”
“This is the next evolution in produce,” said Fain. “The USDA’s organic standards were written at a time when the technology that’s available today simply didn’t exist.
The high startup costs associated with these ventures — the lights, the software, the urban real estate — mean the risks are also high. “Unless you’re in a place with geothermal power, this can be very energy inefficient,” said Food Tank’s Nierenberg. “In the same way we romanticize rural agriculture, we can romanticize growing food in urban places.”
In January, the hydroponic farm FarmedHere closed its 90,000 square foot facility in Chicago and pulled the plug on plans to invest $23 million in a new farm in Louisville, Kentucky. The company’s high labor and energy costs meant it needed to sell huge volumes of produce to break even, CEO Nate Laurell told the Chicago Tribune. “The more I learned about the reality of farming, it led to a change of strategy”
Atlanta vertical farm PodPonics closed last year. Its co-CEO Matt Liotta recently spoke of the tough realities of the business at an industry conference. PodPonics achieved a cost per pound of $1.36 — less than the cost of shipping organic lettuce from California. The company had an offer from Kroger to order $25 million woth annually, if it could build the farm to support it.
“This was our wildest dream, we were ready to go, this was everything we wanted. And then we realized how much capital this was going to require, how many people we were going to have to hire,” said Liotta. “We were simply incapable of building everything they wanted.”
“This is really a manufacturing game,” Liotta said. “It is not an art. If you want to do art, get a garden.”
Modular Farms Newsletter #7
February was a very historic month for Modular Farms. We harvested our first batch of fruiting crops, trained our first class of Modular Farmers, put FarmWalls up in schools and food banks, and began wrapping up production of our first set of Modular Farms!
Modular Farms Newsletter #7
February was a very historic month for Modular Farms. We harvested our first batch of fruiting crops, trained our first class of Modular Farmers, put FarmWalls up in schools and food banks, and began wrapping up production of our first set of Modular Farms!
We are extremely proud and thankful for all the tireless work and dedication that has been put forth by our team, our neophyte farmers, and our community partners. Together, our continued efforts are bringing Canada that much closer to having a truly sustainable and secure means of local food production from coast to coast.
Our foray into cultivating fruiting crops on our office ZipGrow towers has been a great success so far. As you can see from the above photos, our daily Tomato harvests are in full swing and the yields have been more bountiful than we initially imagined. Our first big batch of Strawberries are also beginning to ripen and soon Cucumber and Hot Pepper sprouts will find a home alongside them.
We also decided to give our ZipRack a big upgrade this month by swapping out its standard T5 white lights for Intravision Spectra Blades. The Blades are the same lights we chose to utilize inside our Modular Farms, and for good reason - they make a world of a difference. The spectrum variable LEDs add a new depth of flavor and vibrancy to anything being grown beneath them, while simultaneously increasing their photogenicity by 1000%.
We are proud to announce that February 2017 marked the first official month of Modular Farmer training. Over the past few weeks, our first crop of farmers-to-be have made their pilgrimage to Cornwall, where they received some rigorous, hands-on, tutelage from the Smart Greens gurus. All that's left now is for them to receive their farms and begin the rewarding process of reshaping Canada's access to locally grown, sustainable produce one area at a time.
The first few areas to reap the benefits will be Calgary, via the Vertically Fresh Farms team, and Sudbury, via our first Western Ontario-based Smart Greens brand farm, courtesy of Stephane Lanteigne.
The west coast extension of our team - Ethan and Cole - have been doing some incredible philanthropic work within their community. Their company, Living Garden Foods, has recently partnered with the US-based Modern Steader in order to bring their industry leading hydroponic-based classroom curriculum north of the border. They have also help to set up some student-run FarmWalls at the Zion Lutheran Church in Cloverdale, BC, which operates a food bank that is now proud to offer those in need regular servings of fresh salad vegetables.
If you're Canadian, and have found yourself on the fence when it comes to purchasing a FarmWall, now might be the time to pull the trigger. For a limited time, all of our FarmWalls are currently being shipped free of charge to all customers residing in Canada. However, we must warn you that owning and operating a FarmWall will turn you into a snob. You will start questioning the taste and freshness of any other produce you eat that was not directly seeded, grown, and picked by you.
Once again we managed to scrape together some time-lapse footage to get you all quickly brought up to speed on this months transpirings at our office. As you can see, emails were answered, seeds were sown, fruits were ripened, wood was cut, and farms were built; another month in paradise.
Stay tuned for the next installment of our newsletter!
Hungry for more?
Here's some recent updates and tips from our friends at Bright Agrotech -
Learn by Doing: How to Use a Pilot System to Learn Vertical Farming
by: Amy Storey
Modern Hydroponic Production: Why All the Right People Are Wrong
by: Nate Storey
The 6 Main Challenges of Classroom Gardens (And How to Overcome Them)
Wannabe Urban Gardners, How About This Indoor Farm to Get You Started?
If the idea of urban gardening appeals but you're concerned about space, then the Altifarm is definitely worth a look.
Wannabe Urban Gardners, How About This Indoor Farm to Get You Started?
By Trevor Mogg — March 2, 2017 12:40 AM
If the idea of urban gardening appeals but you're concerned about space, then the Altifarm is definitely worth a look.
If you’ve always fancied tending your own vegetable garden but live in a place so small that such a hobby seems impossible, then there may be a solution.
The Altifarm is a modular solution for wannabe urban gardeners that lets you grow vegetables and herbs year-round, inside your apartment.
The Indiegogo project recently blasted through its funding target, so the Altifarm could be in your lounge, or possibly on your balcony if you have one, within months.
Described as “a complete home farm,” the kit comprises four tiers to keep it compact and, according to its Mumbai maker, can be set up in just five minutes. It’s on wheels, too, so you can easily move it around if necessary,
And here’s another bonus: If watering your garden feels like too much effort, or you’re worried about forgetting such duties, then fear not. The setup includes an automatic watering system, with your only responsibility to fill up the reservoir around once a week.
If your apartment doesn’t let in much natural light, the Altifarm also offers a low-power light pack that provides all the necessary light wavelengths to get your greens growing fast. There’s even a purpose-built greenhouse extension pack — essentially a clear plastic covering with a zipper — to protect your plants from extreme weather should you choose to put your Altifarm outside.
If you’re still making excuses about why you can’t grow your own food at home, then consider how everything that you produce will be free from all of those nasty chemicals used in modern-day industrial farming.
More: New farming startup takes agriculture indoors
Of course, as the Altifarm is fairly small, growing large fruit and vegetables would be something of a challenge. But the startup helpfully suggests nourishing edibles such as strawberries, raspberries, bell peppers, lettuce, herbs, and even broccoli and cauliflower. But take note, the setup doesn’t come with soil or seeds, so it’s entirely up to you how you fill it. The green-fingered crew behind the kit has a website providing tips on how to get started with your Altifarm with posts such as “12 awesome foods that are perfect for your indoor garden” and “a guide to growing vegetables and flowers from seeds.”
The Altifarm’s Indiegogo page offers a range of deals depending on how many extras you purchase with the base product. Prices start at $179, offering a decent saving of $70 on the expected retail price.
Read more: http://www.digitaltrends.com/home/urban-gardeners-altifarm/#ixzz4aB3T3NLa
Follow us: @digitaltrends on Twitter | DigitalTrends on Facebook
ICCEA 2017: Dr. Toyoki Kozai’s Take On Vertical Farming
ICCEA 2017: Dr. Toyoki Kozai’s Take On Vertical Farming
The celebrated researcher and ICCEA Panama keynote speaker looks back on his career and toward the future of controlled environment agriculture.
March 2, 2017
Patrick Williams
Also known as the “Father of Vertical Farming,” Dr. Toyoki Kozai, professor emeritus at Chiba University in Chiba, Japan, has been making strides in controlled environment agriculture for decades. From his work on energy savings and artificial lighting to his studies with in vitro plant propagation and medicinal plant production, Kozai has earned the high esteem of controlled environment agriculturalists worldwide.
Kozai, who previously served as president of Chiba University and has edited numerous papers, book chapters and the books “Plant Factory” and “LED Lighting for Urban Agriculture,” will give the keynote speech on May 17, 2017 at the International Congress on Controlled Environment Agriculture in Panama City, Panama. Produce Grower is proud to be a media partner for the event.
As ICCEA Panama approaches, Produce Grower magazine caught up with Kozai to discuss his vertical farming and lighting research, new technologies and methods of production, and which countries and companies are expressing interest in the growing market.
Produce Grower: Your keynote topic is titled "LED lighting for Urban Agriculture." How is LED lighting different for urban agriculture than for agriculture in other types of controlled environments?
Dr. Toyoki Kozai: By using LED, we can choose an optimal light quality for vegetative growth, reproductive (flowering) growth, and/or secondary metabolite production of crops with use of minimum electricity consumption. Inter-crop supplemental lighting can be conducted most efficiently by using LEDs. LED technology has still been advancing rapidly and the cost performance of using LEDs will be improved further in the near future. Optimal LED lighting recipe for value-added plant production will open a new business (cosmetics, medicinal, plant-derived food/soft drink additives).
PG: What else can ICCEA Panama attendees expect from your presentation?
TK: I will talk about the applications of AI (artificial intelligence) with big data mining, ICT (information and communication technology) with camera image processing, and global and local network with open source database.
PG: How has the vertical farming industry changed since you were a keynote speaker at ICCEA 2015?
TK: Many big private companies such as Philips, Panasonic, Syngenta (Seeds), Apple computer, etc. are entering the vertical farming business.
PG: Can you give us examples of some of the research you have done over the years on vertical farming?
TK: Online estimation of rates of photosynthesis, transpiration (water uptake) and respiration in vertical farms.
Reduction in electricity costs for lighting and air conditioning by improving LED lighting system and lighting period scheduling, operation modes of air conditioners, and optimization of environmental factors other than light.
Standardization and guideline drawing-up of units and terminology used in vertical farming.
PG: Which research projects have you found to be most fulfilling?
TK: The most fulfilling project for the next generation of vertical farms is the online estimation of rates of photosynthesis, transpiration (water uptake) and respiration in vertical farms.
PG: What is a Plant Factory with Artificial Light (PFAL), and why is it important for CEA?
TK: PFAL is a group of vertical farms. PFAL is characterized by its high airtightness, high thermal insulation with a high hygiene level, where they can produce clean and high quality vegetables ready to eat without washing. The PFAL is best not suited to maximize the yields with highest quality using minimum resources and minimum emission of wastes currently, but it will become best in the coming decades.
PG: In an interview with Greenhouse Management magazine in 2015, you said Japanese CEA greenhouse innovation is behind the Dutch? Do you still feel that way? Is Japan catching up at all?
TK: Yes, I feel that Japanese CEA greenhouse innovation is still behind the Dutch. Japanese CEA greenhouses are small scaled and cannot invest a lot for innovations. On the other hand, most greenhouse growers are making profits because the retail prices of vegetables are high in Japan. This situation make Japanese greenhouse growers a bit lazy.
PG: What response would you have for a person who does not think that the high cost of vertical farms is worthwhile? What about in regard to LED lighting?
TK: The cost of vertical farms has been decreasing year by year.
The initial cost per floor area of vertical farms is currently about 10 times higher than that of [a] greenhouse with environment control units. On the other hands, the productivity per unit floor area of leafy vegetables is about 10 times higher than that of greenhouse, meaning that initial cost per production capacity is comparable. Also, the yield in vertical farms is not affected by weather and pest insects. The direct production per kilogram of fresh vegetables in vertical farms and greenhouses is currently comparable in Japan.
However, you need very high skills (knowledge, experience, etc.) to manage the vertical farms.
The price of LEDs has been decreasing year by year. On the other hand, the introduction of LEDs to vertical farms is justified only when they know which LED is best and how to use it.PG: You recently released the book "LED Lighting for Urban Agriculture." What led you to develop this book? How is it different from other books on the market?
TK: Recent technological developments in LEDs, image processing, big data mining, [and] DNA sequencing are remarkable. I intended to include such recent technological developments in "LED Lighting for Urban Agriculture." In “Plant Factory” published by Academic Press in 2015, these technologies were described very little.
PG: What does the future look like for vertical farming?
TK: It is promising. Commercialization of vertical farms started in Asian countries such as Japan and Taiwan since 2010. It is going to be started in the Netherlands this year. Russia has a strong interest in the vertical farming business.
Commercialization of strawberry production in vertical farms started in Japan two years ago. Commercialization of high-wire cherry tomato production has been considered in the Netherlands. Many private companies are interested in the production of medicinal plants in vertical farms.
Patrick Williams is the associate editor of Produce Grower magazine. pwilliams@gie.net
Fish And Fresh Greens At The Farmory in Green Bay
Inside an old armory now called the Farmory - fish swim and greens grow. A collaboration of many aimed at creating this indoor farming system, to eventually help people learn how to help themselves.
Fish And Fresh Greens At The Farmory in Green Bay
By: Kris Schuller
Posted: Mar 02, 2017 07:04 PM CST
Updated: Mar 02, 2017 10:18 PM CST
GREEN BAY, Wis. (WFRV) - An old armory turned into the Farmory continues to move forward in Green Bay. We head inside this indoor farm that one day may provide the perch for your favorite fish fry.
Inside an old armory now called the Farmory - fish swim and greens grow. A collaboration of many aimed at creating this indoor farming system, to eventually help people learn how to help themselves.
“We want to transform the local food economy and show there is an opportunity for Wisconsin residents to grown year-round either in their homes or businesses for themselves.” said Alex Smith, director of the Farmory.
In operation for a year, part of NeighborWorks Green Bay, this non-profit indoor aquaponics farm grows yellow perch in tanks and leafy greens in potted soil.
“It's a symbiotic relationship between the two,” said Jimmy Pandl, a member of the board Farmory. “The fish waste feeds the plants; the plants need the water and it's recirculated to help the fish grow.”
Farmory Director Smith says the goal is to have 50 aquaponic systems in operation by the fall and to grow 173,000 pounds of mixed salad greens each year. In fact, it is a crop that is already bringing in cash.
“February 1st, we actually sold our first batch of mixed greens to The Cannery and they’ve been using them ever since,” said Smith.
As for the perch Pandl expects they'll bring 50,000 fish per year to market.
“We want to do perch because of the history in the community here and because of the demand really - we know we can sell it,” said Pandl.
“People love yellow perch, it's the Wisconsin fish for any fish fry,” said Smith.
But to operate at capacity as an indoor agriculture center the Farmory needs to raise $3.4 million. Smith says those efforts are underway and the goal will be met. She believes the community sees the Farmory's value and the area's need.
“The Farmory is really here for a long-term solution to the food insecurity in this community,” Smith said.
Indoor Farming Company Launches in Kearny
Indoor Farming Company Launches in Kearny
Caitlin Mota | The Jersey Journal
By Caitlin Mota | The Jersey Journal
on March 02, 2017 at 2:34 PM, updated March 02, 2017 at 4:16 PM
KEARNY - A new farming company is growing its produce at a quicker and more cost-effective rate than traditional farms.
The secret to the success? The produce is grown indoors.
Bowery, based in the southern section of Kearny, was founded two years ago by Irving Fain and officially launched last week. The company dubs itself as the first to grow "post organic produce."
"We have completely pure and clean crops," Fain said.
By growing produce - like kale and arugula - indoors, Fain said the company eliminates dealing with harsh weather conditions and is able to bring its products to local retailers quicker then other distributors.
Fain previously worked in software and described himself as an entrepenuer. He wanted to take what he learned in the tech industry and find a way to address agricultural issues.
"I saw the power of technology and the power of innovation technology," he said.
More than 70 percent of the country's water supply is used for agriculture, Fain said, though only a fraction of that is necessary for crops to grow.
Sneak peek: Newark's Whole Foods opening Wednesday
Using hydroponic techniques and software that controls the atmosphere inside the farm, produce crews significantly quicker without using any pesticides.
Bowery currently sells six products in locals stores, including the new Whole Foods that opened in Newark on Wednesday. Celebrity Chef Tom Colicchio uses the produce at his New York restaurant and has made investments in the company, Fain said.
The company currently employees 13 people with more hires expected as the it expands. A second farm is already in the works, though Fain said the exact location in the tri-state area hasn't been decided.
Caitlin Mota may be reached at cmota@jjournal.com. Follow her on Twitter @caitlin_mota. Find The Jersey Journal on Facebook.
The Future Of Urban Farming Might Actually Be Suburban Farming
The Future Of Urban Farming Might Actually Be Suburban Farming
After dealing with the high costs and logistical nightmares of developing in urban areas, one farming startup realized that they could streamline their process by moving just a bit outside the city limits.
- ADELE PETERS 03.02.17 10:30 AM
When the urban farming startup BrightFarms first launched, it envisioned building its hydroponic greenhouses directly on grocery store roofs and on vacant city lots. Now, it says that the smartest place to grow food for cities may be just outside of them.
The company’s newest site will be in the town of Wilmington, Ohio. With a population of only 12,459, it's not the target market. But it's near Dayton, Columbus, and Cincinnati, which together have a population over a million people.
BrightFarms also has greenhouses in Bucks County, Pennsylvania; Culpeper County, Virginia; and Rochelle, Illinois—all also near, but not in, large cities. The new strategy lets the company avoid the costs and challenges of working on urban sites, while still providing a local version of foods like salad greens that would normally travel thousands of miles.
"Like most good strategies, it was driven by some painful experiences," Paul Lightfoot, CEO of BrightFarms, tells Co.Exist. "Basically, we had a couple of failures. We tried to develop a giant rooftop of a building in Sunset Park, Brooklyn, and we also tried to develop an environmentally soiled parcel of land in the city of Washington D.C., owned by the city."
In both cases, the landowners were eager for BrightFarms to build, and they had strong support from the communities and city leaders. But both sites had challenges. In Brooklyn, the roof needed complex engineering work that couldn't be completed on the startup's timeline; in D.C., the city had to do environmental remediation that also took longer that was commercially viable.
Both cities also had complex regulations that weren't created with urban agriculture in mind. "We found ourselves dealing with a regulatory framework that didn't understand us, and didn't have the ability to adapt to us," Lightfoot says. The projects were classified as "industrial" rather than agricultural, which triggered regulations that didn't fit.
In smaller communities, the experience was radically different. In Virginia, because it was considered an agricultural project, it was exempt from the typical permitting process. "I think we got the permit in a week," Lightfoot says. "In D.C., we spent a year getting it."
The company realized that even if it built outside city limits, it could still stay close enough that transportation would be negligible. BrightFarms sells its produce in 150 stores in the D.C. market, and even if its greenhouses were inside city limits, it would still require driving fairly long distances to make deliveries to all of the stores.
"Being in the city center is not logistically a benefit," Lightfoot says. "Being 30 miles out of the city is just as good as being in the city. The extra cost of building in a city has absolutely no benefit except for maybe shallow, fake marketing, but it has a real significance in terms of capital costs, and in some cases, operation costs as well, including utilities and transportation."
BrightFarms' greenhouses often make use of underutilized spaces: In Rochelle, Illinois, they've set up on an empty lot between a distribution center and a factory that was once farmland, then an industrial park.
Even though BrightFarms sometimes establishes its greenhouses near traditional farms, the startup isn't directly competing with the other operations because it's focused on tomatoes and greens that typically come from California or Arizona. The greenhouses grow the food with a tiny fraction of the water, and provide it fresher to customers. Less perishable crops, such as root vegetables and corn, are left to traditional farms.
BrightFarms plans to use the same model, building outside cities, as it moves forward. After closing a $30 million equity round in September 2016, it plans to open 14 more greenhouses over the next four years.