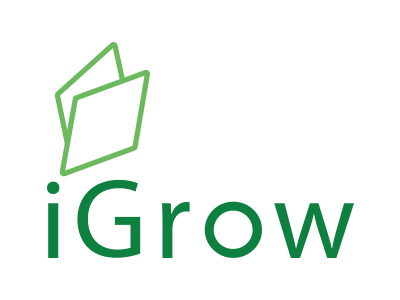
Welcome to iGrow News, Your Source for the World of Indoor Vertical Farming
Hydroponics Firm Launches Urban âFarm-In-A-Boxâ
Tuesday 21st March 2017, 16:38 London
Hydroponics Firm Launches Urban âFarm-In-A-Boxâ
Company aims to reduce food miles and boost nutritional value with hydroponic farming equipment for grocery stores, restaurants, and schools
Urban farming company groLOCAL is launching equipment to enable businesses to cut food miles and grow their own fresh produce on site.
The groTAINER shipping container - which the company describes as a fully-configured "farm-in-a-boxâ - allows grocery retailers, restaurants and schools among other businesses to grow produce such as herbs, spices and micro-greens on their own premises.
This ensures that produce maintains its nutritional value, according to the company, which highlights the fact that a tender soft tissue plant loses 80 per cent of its essential oils and half of its vitamin and mineral content within the first day after picking.
âItâs possible for businesses to grow highly nutritious produce at just a fraction of the cost of buying from suppliers,â the firm added in a press release.
David Charitos, managing partner of groLOCAL, said: âStanding out from the crowd in the food market can be a challenge. But having the ability to grow your own spice, greens, and herbs can mean you have something different to offer customers and really gives you the flexibility to try different flavours, knowing that all the ingredients are fresh.
âHaving the option to grow some of the produce used means cutting down on expenses in the long run too."
The team behind groLOCAL are experts in hydroponic farming â the process of growing plants without soil, using nutrient solutions instead. This farming method makes it possible for businesses to grow plants anywhere, including urban environments.
The farm containers come with a fully-fitted production unit, including preparation and packing areas, meaning businesses do not need to find further space in their existing premises to accommodate hydroponic farming.
groLOCAL offers businesses the choice of either purchasing a groTAINER outright or leasing the equipment.
Vertical Farming, The Future of Crop Growth
Vertical Farming, The Future of Crop Growth
By Riana Soobadoo -
March 21, 2017
The future of farming is on the up and up, literally. With todayâs society constantly changing, progressing, and evolving, everything that can be revolutionized will be. Now, with the emergence of vertical farms on the rise, it seems that the future of urban farming is here.
Vertical farming refers to when food is produced in vertically stacked layers, usually in a greenhouse or warehouse. These farms use indoor farming techniques and a variety of controlled environmental agriculture technology to control environmental factors in their favor. Such as the use of LED lights to substitute natural light that is missing indoors. Never having to be subjected to the elements, or worrying about what season it is, indoor farming allows for completely controlled growth of produce.
Because of its potential to transform agriculture globally, vertical farming is quickly becoming the next step forward in agricultural production. Although the produce cannot technically be labeled as organic, because it is not grown in soil, vertical farming processes are completely pesticide free, require no sun, and use 95% less water than traditionally field-grown crops. Additionally, due to the faster harvest time, crops grown through vertical farming produce a higher annual yield than those grown through traditional agriculture methods. The increased popularity in the sector has led to a surge in numbers of companies looking to make their mark on the industry.
The first of these, AreoFarms, is the one of the worldâs largest indoor vertical farms. Based in Newark, New Jersey, USA, AreoFarms has been farming indoors since 2004. AreoFarms uses a technique called aeroponics. Aeroponics uses 40% less water than traditional hydroponic farming. It also utilizes smart LED technology to customize the amount of light used for each plant type. This energy efficient process has the potential to change the farming industry forever. Mark Oshima, a co-founder of AeroFarms explains that they use:
âIN-DEPTH GROWING ALGORITHMS WHERE WE FACTOR IN ALL ASPECTS FROM TYPE AND INTENSITY OF LIGHT TO NUTRIENTS TO ENVIRONMENTAL FACTORS LIKE TEMPERATURE, HUMIDITY, AND CO2 LEVELS, AND WE CREATE THE PERFECT RECIPE FOR EACH VARIETY.â
Another emerging vertical farm is Bowery Farming. Based in New York, New York, USA, Bowery Farming first opened their doors in 2015 and has recently opened another location in New Jersey, USA, to increase their reach. Labeled as post-organic, Boweryâs products never travel more than 100 miles to guarantee freshness. Attracting increasing interest of new Investors, Bowery Farming has quickly become a big name in the vertical farming industry. They currently produce five leafy vegetables, including baby kale, lettuce, and arugula, and one type of herb, basil. These greens are non-GMO and do not need to be washed when taken home.
In Japan, the Pasona O2 building is yet another example of vertical farming; with 6 rooms of farms, 100,000 square meters, and growing over 100 different types of produce, this farm employs young men and woman who are struggling to find jobs or have an interest in farming. The company advocates the individual development of these men and woman, passionate about seeing them succeed in their industry. Each room at Pasona O2 houses something different: room 1 houses a flower field, room 2 is a herb field, room 3 a rice field, room 4 a fruit and vegetable field, room 5 is vegetables, and room 6 is for lettuce and the seeding room. Each room is set to the proper environmental specifications needed to grow and sustain the crops.
Unfortunately, as revolutionary as vertical farming is, the start-up costs are astronomical, which can be a problem for companies trying to expand. One company in particular, the Atlanta based PondPonics, was able to get their productions costs down lower than anyone else. Unfortunately, when offered a $25 million dollar annual contact with Kroger they could not get the funds to build the necessary facilities to grow in such volumes. Ultimately, PodPonics was forced to close their doors as the running costs became too high.
This is not the case for every company. As time moves forward we will begin to see a shift in the attitudes of investors, and interest in vertical farming will continue to grow. The future of agriculture is looking greener and greener. With vertical farming on the rise, we can expect to see a change in the industry unlike ever before.
Urban Farmers Grow Veggies In Freight Containers
Urban Farmers Grow Veggies In Freight Containers
Kara Carlson, The Arizona Republic
9:10 a.m. ET March 21, 2017
(Photo: Kara Carlson/Arizona Republic)
PHOENIX -- The future of urban agriculture might require farmers to think inside the box.
Farmers here are growing vegetables here in converted freight shipping containers equipped with the latest hydroponics and automated systems equipment. They are provided by a Boston-based firm, Freight Farm.
âThe farm of the future,â said Mark Norton of Phoenix, whose Picked Fresh Farms grows kale and lettuce in one of the containers.
Freight Farms started in 2010 with the goal of bringing viable, space-efficient farming techniques to all climates and skill levels year-round. It recently expanded to Arizona.
The cars are not cheap. Each container -- the kind commonly seen on trains, trucks or ships -- costs $85,000, not including shipping. Freight Farms calculates annual profit for each container to be an average of $39,000 annually.
Caroline Katsiroubas, marketing director for Freight Farms, said urban areas are the most popular destinations for its equipment and expansion has been nationwide.
Norton of Picked Fresh Farms isnât what most people would picture as a farmer. The closest anyone has come to farming in his family was his grandfather, who farmed as a child, but that didnât deter Norton.
âIf I can get a better environment, better food, help people with their food, and still help people with their health, thatâs where it all fits,â Norton said. âIt aligns with my core values.â
He recently had one of his first successful harvests of lettuce, but heâs already looking to the future, with a 10-year goal to expand to 10 containers.
Mark Norton of Picked Fresh Farms closes the container where he grows kale and lettuce.
(Photo: Kara Carlson, Arizona Republic)
âI was just going to do it as like a hobby, but these things, thereâs a need and nobody's really filling it,â Norton said.
Norton is one of only two freight farmers in Arizona, but the thought of competition doesnât bother him.
âI think thereâs enough space to have a bunch of these,â he said.
Heather Szymura, who co-owns Twisted Infusions Farms with her husband Brian, agreed. The Glendale, Ariz., company was the first in the Grand Canyon State to freight farm, and Szymura said she wants to see more of the farms come to Arizona because there is no way her company alone can feed everybody.
She has been urban farming for 12 years, with gardens and walls of plants in both her front and back yards. The latest edition, the 7œ-ton container is nestled on the side of her house.
In a year, the 320-square-foot container can produce the equivalent of a three-acre farm. It also saves water, using five to 10 gallons of water a day, 95% less than traditional farms, Freight Farms said. The water is delivered in a nutrient-rich system based on hydroponics, a method to grow plants without soil.
Growing the leafy greens inside seem unnatural, but the farmers maintain not only is the process natural, itâs optimal.
Norton prides himself in using no GMOs, no pesticides and no herbicides. The environment is controlled, so thereâs no reason for it. The container can put out 50 to 100 pounds of lettuce a week.
The farm uses strips of red and blue lights, the spectrums used in photosynthesis, to make it as efficient as possible. Machines automatically dose the plants with water and nutrients. All notifications lead back to an app on phones, which allows farmers to track everything from seeding to harvesting. On average the process takes about seven weeks and, depending on the environment, this can actually be almost twice as fast as a traditional farm, Freight Farms said.
This optimization allows for a greater variety than a grocery store might offer. Katsiroubas of Freight Farms said it allows farmers to focus on the characteristics they want because of the efficiency.
This is an aspect of farming the Szymuras enjoy, and itâs allowed them to be more experimental and try different plants and techniques.
Kale growing inside a temperature-, water- and light-controlled freight car makes the plant sweeter, and softer, Norton said. He said itâs also healthier because itâs traveling less distance and keeping produce local.
The ability to support local is part of what appealed to the Szymuras. They get as much of their farming products and water supplies as possible from local suppliers.
The produce is all sold locally, and the container allows them to easily educate people on urban farming and the seed to harvest process.
Szymura especially enjoys the ability to watch the process from start to finish. Seeding starts in trays kept at optimal light and temperature and then moves to the towers, which contain rows and surround more LED lights.
Itâs something her clients like seeing as well. Many of Twisted Infusionâs customers are chefs and caters who come in to see what will be harvested next and appreciate being able to even pick the produce themselves. The caters can have their produce from farm to table in the same day.
The system, and the ability to switch crops easily, also allows chefs to put in specific orders and know it will be ready when they need it.
Norton is focused more on restaurants and individuals through members of Community Supported Agriculture, a subscription-like system that lets customers buy shares of local food. Norton expects most of Picked Fresh Farms' business to come from this, but he also has started to reach out to restaurants with samples of his product.
Five of Brooklyn's Most Innovative Urban Farms
It may be a cliché to lament the loss of farms in New York City. These five Brooklyn-based urban farms, mostly co-founded by former Wall Street professionals, are using the most creative and entrepreneurial techniques, from aquaponics to vertical growing, to bring fresh, locally grown produce to New Yorkers.
FIVE OF BROOKLYN'S MOST INNOVATIVE URBAN FARMS
New YorkSustainability Mar 16, 2017 Kouichi Shirayanagi, Bisnow
It may be a cliché to lament the loss of farms in New York City. These five Brooklyn-based urban farms, mostly co-founded by former Wall Street professionals, are using the most creative and entrepreneurial techniques, from aquaponics to vertical growing, to bring fresh, locally grown produce to New Yorkers. Beyond the health benefits of eating fresher produce, locally grown food benefits the environment by cutting out the need to transport and preserve perishable fruits and vegetables, which can take more than a week to get from the farm to a New York City dinner plate.
Gotham Greens Location: 810 Humboldt St., Greenpoint Co-founded in 2009 by a sustainable development manager and an ex-JP Morgan Chase private equity fund manager, Gotham Greens produces organic leafy greens, lettuces and tomatoes from the tops of buildings in Greenpoint and Gowanus as well as in Hollis, Queens. Early in the business, partners Viraj Puri and Eric Haley developed a relationship with Whole Foods to distribute their produce. In 2013, Gotham Greens built a 20K SF greenhouse on the roof of the Whole Foods store in Gowanus. The project marked the first time a greenhouse integrated with a major grocery store. The first Gotham Greens greenhouse, built in 2009 in Greenpoint, is 15K SF and produces 100,000 pounds of produce a year.
Red Hook Community Farm Location: 560 Columbia St. and 30 Wolcott St., Red Hook Managed by environmental educator Saara Nafici, Red Hook Community Farm produces more than 20,000 pounds of produce a year from two Brooklyn sites. The 120K SF farm on Columbia Street uses ground compost two-feet deep to create a diverse environment of microorganisms and insects that nourish the produce. Red Hook Community Farm also built a 48K SF site on Wolcott Street in collaboration with the New York Housing Authority. Members of Green City Force, an AmeriCorps program, maintain the farm. The organization maintains a Saturday farmers market at the Columbia Street site between June and November to sell the farm's produce.
Eagle Street Rooftop Farm Location: 44 Eagle St., Greenpoint Managed by educator and journalist Annie Novak, the Eagle Street Rooftop Farm occupies 6K SF on top of a warehouse in Greenpoint. The farm grows a wide variety of vegetables, spices and greens, including hot peppers, eggplants, sage, parsley, cilantro and dill. Novak sells produce from the farm at an on-site Sunday farmers market.
Brooklyn Grange Location: McGolrick Park, Greenpoint Co-founded by former E*Trade Financial consultant Ben Flanner and longtime sustainable food advocate Gwen Schantz, Brooklyn Grange grows over 50,000 pounds of produce per year in over 87K SF on two rooftops, one in Brooklyn and one in Queens. The Brooklyn Grange education program brings 17,000 New York City youths each season for tours through their farms. The organization is supported by a produce share program in which members subscribe to weekly deliveries of fresh produce. The farm grows a variety of produce, including from salad greens, mix herbs, eggplants, chard, carrots, peppers and flowers.
Square Roots Location: 630 Flushing Ave., Sumner Houses Square Roots operates vertical farms from shipping containers. Specializing in greens and herbs, the indoor growing process allows for year-round growing using 80% less water from traditional outdoor farms. Like Brooklyn Grange, Square Roots is funded by a food-share program where members can buy in $7, $15 and $35 per week packages. The working collective also has an active, year-round events business.
McNamara: âTo Fix The Food System, Move It Back Into The Hands of More Peopleâ
Brad McNamara, CEO and co-founder of Freight Farms, is speaking at the inaugural Boston Food Tank Summit, âInvesting in Discovery,â which will be held in collaboration with Tufts University and Oxfam America on April 1, 2017.
Brad McNamara, CEO and co-founder of Freight Farms, is speaking at the inaugural Boston Food Tank Summit, âInvesting in Discovery,â which will be held in collaboration with Tufts University and Oxfam America on April 1, 2017.
Freight Farms is an agriculture technology company that provides physical and digital solutions for creating local produce ecosystems on a global scale. Brad and his co-founder, Jon Friedman, developed the companyâs flagship product, the Leafy Green Machine, to allow any business to grow a high-volume of fresh produce in any environment regardless of the climate. His hope is for Freight Farms to be scattered across the globe making a dramatic impact on how food is produced.
Food Tank had the chance to speak to Brad about his work developing Freight Farms and his vision for the future of our food system.
Brad McNamara, CEO and co-founder of Freight Farms, is speaking at the inaugural Boston Food Tank Summit, âInvesting in Discovery.â
Food Tank (FT): What originally inspired you to get involved in your work?
Brad McNamara (BM): It was a coming together of many different factors. My co-founder, Jon, and I had worked together in the past, and we were both intrigued by the food system and how we could make a difference. Around 2009, Jon was focused on food systems and system design, and I was passionate about the purity of food and the increasing trend towards food awareness. When the two of us first reconnected over a cup of coffee (and then a beer), we got to talking about the complexity of the food system and what we could do to combine our interests. With backgrounds in design and environmental science, our goal was to research methods to allow urban agriculture to emerge as a competitive industry in food production. We mainly focused on rooftop development, then determined the criteria for success and scale to be outside the realm of possibility with agricultural installations that were already in existence. When costs and logistics soared, we turned to shipping containers (thereâs Jonâs design background coming into play), and the idea for Freight Farms took off with the goal to build farms in areas that couldnât support more traditional methods.
FT: What makes you continue to want to be involved in this kind of work?
BM: Our world and our climate are changing, and it is so apparent that there is more work to be done. According to the U.N., food production needs to increase 70 percent by 2050, to feed an ever-urbanizing population. Land and water scarcity take on even more pressing importance, as does urban agriculture. The future is so much bigger and more complex than we could have ever imagined. Over the past few years, weâve gotten to witness the emergence of a new industry of agriculture technology, and itâs poised to make a dramatic impact on the food system. One of the most amazing things weâve been able to watch is how many are interested in joining the movement towards a better future. Our network of freight farmers are making dramatic impacts on their local food systems every day, drastically improving food security in their community. They inspire all of us to continue this work.
FT: Can you share a story about a food hero who has inspired you?
BM: My food hero is a customer of ours. His name is Ted Katsiroubas, and he runs Katsiroubas Bros. Fruit and Produce, a wholesale produce distribution company located in the heart of the city of Boston. The business is over 100 years old and was handed down from generations before. I admire how Ted has innovated in the face of a dramatically changing food landscape. As the demand for local, fresh produce has risen, the company expanded to begin working with local farms in the region to meet demand. For those familiar with wholesale distribution, sourcing locally can be a difficult task especially when you are restricted by the growing seasons and volume constraints of small local farmers. Thatâs why traditionally wholesale distributors rely on shipping produce long distances from warmer climates. But Ted brings a fresh approach to an old school industry. He continues to push the envelope and propel the industry to stay on top of the latest technology through collaboration with other distributors. If anyone were to fall into the category of my food hero, it would be Ted because of his willingness to look to the future and go against the conventional wisdom of how the food industry tells him to conform.
FT: What do you see as the biggest opportunity for fix the food system?
BM: I think the biggest opportunity to fix the food system is to bring it back into the hands of the people. By transitioning to a more decentralized food system, and minimizing the gap between consumers and producers, we will take a critical step towards an environmentally and economically sustainable food system. I think all the various types of technology, the hardware, the software, and the social awareness, all point in the direction to empower the individual. So the real opportunity to fix the system is to utilize what we know to be trueâwhen you give opportunity and power to regular people from all walks of life, thatâs when you can change a whole system.
FT: What would you say is the most pressing issue in food and agriculture that you would like to see solved?
BM: There are so many people advocating for a better food system, and we all must be better at communicating and cooperating if we want to make an organized effort to challenge the way things operate currently. From small farmers and producers to organizations and companies. What has become incredibly apparent in the past couple decades is that there is no one size fits all solution. Whether itâs urban or indoor agriculture, hydroponics, aeroponics, aquaponics, or traditional soil-based farming, we all play an important role. We need to have a more holistic view of the food system and how each method can contribute to a better future. If we donât all work together, itâs going to be difficult to disrupt BigAg. I think taking a broader view is key. There has been so much progress made in agriculture, but we still have a long way to go to create a food system that will serve future generations. It is important to continue working with and connecting with each other to empower and support the next generation of farmers.
FT: What is one small change everyone can make in their daily lives to make a difference?
BM: Maybe it is a bit clichĂ©, but the notion of voting with your dollars. Iâm sure others have said it, but it is so important. If every consumer changed 5 percent of their food shopping habits by buying more seasonal and local produce, the impact would be enormous in changing the landscape of the local grocery store.
FT: What advice can you give to President Trump and the U.S. Congress on food and agriculture?
BM: My advice is to be conscious of all the complexities present within the food and agriculture system. There are so many moving pieces that small shifts in the workforce, water use, and the climate have a massive impact throughout the entire system. It is essential to keep a holistic understanding of the relationships between all the components in our food and agricultural system and to consider the ripple effect policy decisions will have on the smaller players involved.
Click here to purchase tickets to Food Tankâs inaugural Boston Summit.
Brad McNamara, CEO and co-founder of Freight Farms, is speaking at the inaugural Boston Food Tank Summit, âInvesting in Discovery.â
SXSW Just Showcased The First-Ever Traveling Indoor Farm
SXSW Just Showcased The First-Ever Traveling Indoor Farm
March 16, 2017
Each year some of the most imaginative and innovative minds from all over the world gather at South by Southwest (SXSW) in Austin, Texas. The first-ever traveling indoor farm was presented this week.
The SXSW trade show offers exhibitions that range from promising startups to well-established global corporations, affiliate KEYE reported. Companies from across the world descend on Austin to display their products in hopes of catching the eye of an investor, networking or just showing what they have to offer.
Local Roots has created a traveling indoor farm that uses a scalable, proprietary growing system that promises to provide "predictable production and quality."
"We have a circulating irrigation system and we recapture all of the water that flows through the system to reduce our water consumption down just what the plant needs to be able to grow," said founder and CEO of Local Roots Eric Ellestad.
Ellestad said his company is proof that technology is needed everywhere.
"The root zone lives down in the irrigation system drinking its nutrient-filled water day in and day out," Ellestad said.
Local Roots compares their technique almost the same as outdoor farming since they are using the same seeds, nutrients, minerals and light to activate photosynthesis. The major differences are that the light is supported by LED lights instead of the sun. The soil has also been removed in order for plants to be able to collect dissolved nutrients in the water.
The California-based company promises that their plants grow twice as fast and plants grow with much higher nutrient densities.
This Bronx Distribution Hub Could Help Local Farmers Reach More Tables
This Bronx Distribution Hub Could Help Local Farmers Reach More Tables
GrowNYC's Marcel Van Ooyen is working to launch a 75,000-square-foot food distribution hub in Hunts Point
By Cara Eisenpress
Van Ooyen wants to serve local and midsize farmers in the state.
The popularity of farm-to-table eating has created demand in the city for a local farmersâ wholesale market. Gov. Andrew Cuomo in August committed $20 million to fund a 75,000-square-foot food-distribution hub in Hunts Point and chose GrowNYC to develop and operate it. The 40-year-old nonprofit runs farmersâ markets and community gardens as well as recycling, composting and education programs. The Bronx distribution hub is the biggest project Marcel Van Ooyen has taken on in his 10 years as GrowNYCâs head. He said he hopes it will open in early 2019.
What's the purpose of the hub, and how will it work?
The hub will source, aggregate and distribute locally grown produce to food-access programs and like-minded restaurants and retail outlets. We anticipate well over 100 farmers will benefit. Farmers who grow for the wholesale markets will deliver large quantities to us. We'll break it up and distribute to public and private buyers. We'll have additional space for farmers to store food, and eventually light processing.
Why build it?
Ninety-eight percent of what we eat comes through wholesale channels. The current hub for local farmers is only 5,000 square feet, so we will replace it to serve more of them.
The limiting factors to supporting local, midsize farmers are having the infrastructure for them to drop produce off and us to deliver it and to be able to pay them a real return on what they're growing. It's difficult for these farmers to compete with the huge farms in California.
So how do you pay farmers a real return?
We let them set the price. By being a nonprofit and not trying to make any money other than [to cover] our operating costs, GrowNYC is able to even the playing field.
How do you get fresh, local food to underserved New Yorkers?
We worked with the Department of Health to create Healthy Bucks, a food stamp incentive program that has become a national model. Through our programs, like Youthmarket, we can distribute in areas that haven't been traditionally served. The same kale that is going into Gramercy Tavern is at a farm stand run by teens in Brownsville, Brooklyn, on the same day.
Is the obsession with farm-to-table more than a trend?
It's the last frontier for environmentalism. We spend millions of dollars protecting the watershed around New York City and building the infrastructure to keep water clean and safe and deliver it to everyone at a reasonable price. We spend a lot of time regulating the air. But food is something we've left to private industry.
Is there enough local food to serve restaurants that say their food is local?
Consumers have to be skeptical and ask. We need to make sure that people are living up to their promises. With more local wholesale, the issue of "faux-cal" may disappear because there's access to that product on a consistent basis.
What does the White House's environmental position mean for the city?
Cities have been the innovators in fighting global climate change. As a citywide organization, we provide an outlet to create change in communities even if they can't get it on a federal level. You're not going to be worried about Trump's tweets while you're shopping in a Greenmarket. Hopefully, you're thinking good thoughts.
Van Ooyen wants to serve local and midsize farmers in the state
Mother Nature Gives Indoor Farms A Boost
Mother Nature Gives Indoor Farms A Boost
By Tom Karst March 14, 2017 | 10:00 am EDT
Tom Karst, national editor
There are times that Mother Nature is just too darn unpredictable.
When everything goes without a hitch, the U.S. typically has an abundant supply of vegetables. But throw in rainy weather, delays that move back planting and harvesting, and all of a sudden you have a case of panicky buyers who are keen to look for more predictable and nearby sources of supply.
Retailers and consumers in the United Kingdom in February suffered a shock when rains in Spain caused some stores to ration their supply of greens. Some California companies saw an opportunity and shipped lettuce to the U.K.
Now itâs California facing rain-related production problems. The Packer has covered the gaps in vegetable supply in California, and various marketers predict it will get worse before it gets better. The rains that brought relief to the Golden State could give buyers a roller coaster ride later this spring.
In the context of these issues, we are reminded of the conviction that one regionâs disaster is an opportunity for someone else.
The Packerâs Ashley Nickle covers the issue this week in a story that reports indoor farms are seeing increased demand as weather-related production issues in Arizona and California have affected the supply of leafy greens.
Nickle reports New York, N.Y.-based BrightFarms, which has greenhouses in Illinois, Virginia and Pennsylvania, has seen retail orders rise in recent weeks.
Likewise, Buffalo, Mich.-based Green Spirit Farms and Portage, Ind.-based Green Sense Farms reported a jump in interest because of supply glitches in the West.
The latest supply disruption helps make the case for indoor farming operations.
The rains that brought relief to the Golden State could give buyers a roller coaster ride later this spring.
I recently visited with Paul Lightfoot, CEO of BrightFarms about this issue. He said leafy greens buyers are looking for locally sourced and stable leafy greens supply for a number of reasons, including supply disruptions caused by rain and mildew, the pull of overseas demand on U.S. product and even worries about the potential shortage of labor in growing regions.
Supply chain disruptions, combined with what Lightfoot believes is a consumer-led transition from âlong distanceâ to local supply of food makes him optimistic about the future.
BrightFarms secured $30 million in financing last fall that he said will allow the company to expand into about 14 markets over the next four years, growing from three facilities now to 17 facilities in five years. On the immediate horizon is a project in Ohio, he said, followed in short order by a facility in Kansas City.
âWe really view that (financing) as our opportunity to build a national platform, to build out in every major market in the Midwest and the Northeast,â he said.
After building out production facilities over several years, Lightfoot said the company may considering expanding commodities offered beyond the current lineup of leafy greens and selected tomato varieties, perhaps to include cucumbers, peppers and even strawberries.
Even if BrightFarms does have a âtiger by the tail,â as Lightfoot says, it is hard to say how much the local indoor farm trend will play out over the next decade.
For now, unpredictable Mother Nature is giving BrightFarms and similar farms an assist.
Tom Karst is The Packerâs national editor. E-mail him at tkarst@farmjournal.com.tkarst@farmjournal.com
New Technologies Are Creating New Ways To Grow Fresh Produce
New Technologies Are Creating New Ways To Grow Fresh Produce
Vertical farming operations are popping up everywhere and this new technology can complement traditional agricultureâ©
AF Columnist
Published: March 13, 2017
Opinion
We were in Holland and our group stood in amazement at the growing capabilities of Koppert Cress.
Owner Rob Baan, a policemanâs son turned world entrepreneur, was emphatic that neither soil nor light is needed to grow food â only heat. And all of those components could be provided by technology, he said.
In a large glasshouse Baan grew microgreens in cellulose under LED lights. In the vast kitchen on site, we tasted the bounty and I remember it still: an absolute bursting of flavour and texture exploding on the palate.
The Business Plan Was Simple.
Take the product to the chef first, ask them what they liked, disliked, and were looking for in food trends. Go home, turn on some LED lights, and grow what the chef wants. Baanâs global empire (Koppert Cress distributes microgreens across Europe and has a U.S. division) is proof that fresh food can be grown inside. It is the ultimate urban farm.
Later, in a cooking class in Canada, I noted that chefs had microgreen boxes or microgreen appliances in the kitchen. Again, no natural light and no soil were present, and the greens were grown in stacked trays. But it made a huge difference to a dish when that fresh green top was pruned off the tray from the inside of that black box. A variety of these are now available for home kitchens. Retail stores in the U.K. introduced living vegetable aisles where the food was grown on site and the customer picked it from the vertical display.
And in travel, Iâve found hotels now boast rooftop gardens and restaurants are quick to highlight their little herb patch. Thatâs good news because it means we have a movement to grow food that has been unmatched in recent history. How far we go is really limited only by imagination. We can grow food in a field or black box, and both will metabolize similarly.
European scientists have long been curious about food produced in a black box. Their quest for perfection demands vegetables and fruit be fresh and without blemish. Not only must the shape and colour be right, but so must the degree of ripeness. Just as the Chinese form the square watermelon in a box, growing food in black boxes allows for the perfect product every time.
Why is This So Important To Traditional Farmers? And Why is it a Threat?
While it is true that farming is truly evolving on many technical platforms, the idea of food production indoors and without soil or light is leaping ahead in the area of vegetable and biomedical production. The yield is 20 to 30 times that of a conventional field, variety dependent, and the crop is not under weather distress as the environment can be remotely controlled. Lufa Farms, headquartered in Montreal, started the rooftop movement now popular around the world. But it was Vancouver that got folks thinking about filling the space on every floor with food all the way to the roof. Canada started thinking about going vertical.
As cities develop, food policies and municipalities enacted bylaws restricting chemical usage, the natural progression has been to move farms in and up. Touring the Delta area of British Columbia and the Golden Horseshoe in Ontario are jaw-dropping farming experiences. The agricultural output is staggering.
Vertical farming goes a little further and takes those huge flat areas often seen in greenhouses and tiers them with suspending boxes that grow food, particularly leafy greens. These products are often organic, or at least chemical free, saving that production cost while responding to consumer demand.
Some of the designs I researched took advantage of the moderate climate and were glass structures that allowed for natural light. None used soil and either had a growing medium or were hydroponic. A new structure in Canada based out of Truro, Nova Scotia is a closed system based on LED lighting that was built on the premise of food that is nutrient dense, fresh to use in the culinary world, and the structure itself can be built almost anywhere.
One of the challenges in this vast nation is the development of a delivery system that can get perishable, nutrient-dense foods to rural and remote communities. Vertical farming offers a solution to these issues â and creates jobs for the local people, attracts local distributors, and makes good food affordable.
A sack of seed could feed a village and that is an important consideration as we move forward in food policy. Another area of interest for me is the biomedical component as it complements natural health and there is an assurance of purity that we cannot confirm from imported product.
Vertical farming does not threaten agriculture, but it does change it. New technologies will continue to enhance farms in Canada, secure food in urban spaces, and allow our nation to be a world leader in terms of technology and health.
From Shipping Container Farm, Casper, Wyo. Pastor and Hydroponic Lettuce Grower Preaches Local
From Shipping Container Farm, Casper, Wyo. Pastor and Hydroponic Lettuce Grower Preaches Local
March 13, 2017 | Trish Popovitch
Matt Powell opens the door to his hydroponic lettuce farm, housed in a used refrigerated storage container on the corner of his Casper, Wyoming property, and the Marriage of Figaro fills the air.
âMy little Mp3 there is loaded up with Mozart and Bach. The study I heard said they tested growing plants in three sound proof environments. They had classical in one, death metal in another and silence in a third. Classical did the best, death metal did the second best,â laughs Powell explaining how his fresh hyperlocal greens are grown with the aid of some classic tunes as they stay cool in their farm-in-a-box environment.
The enclosed vertical farm, Skyline Gardens, came with the hydroponics already in place from Boston-based Freight Farms. This made it a little easier for Pastor Matt Powell, former computer salesman and current professional theologian, to find his way to a sustainable side business in an area in need of sustainable businesses. Using filtered water, nutrients, red and blue grow lights and of course, classical music, Powell will produce, at capacity, approximately 500 heads of fresh greens for the people of Casper every week. Business is growing steadily and a few harvests have already occurred.
Each variety of lettuce, Swiss chard and culinary herbs grows in isolation in one of the easy to remove and handle vertical growing towers. Powell labels the towers with dry erase marker to keep track of varieties, planting time and harvest requirements. As Powell explains, shipping container farms are ideally suited to the short growing season and temperamental weather of the Equality State. âItâs an enterprise thatâs really custom suited to this area and just the lifestyle around here. People have land and itâs fairly easy to put one of these boxes down,â says Powell.
The company is still in its infancy with just six months under its belt. Most of that time was spent training in hydroponics, learning the equipment and realizing the substantial amount of legwork and marketing even the most tasty lettuce line needs to grow. âThere is the barrier to entry: itâs expensive. And itâs definitely a learning curve,â says Powell. âYouâve got to be a problem solver and you got to be flexible and willing to learn. Thereâs a lot to learn on the farming end of it and thereâs a lot to learn on the marketing end of it.â
Freight Farms uses discarded and retired refrigerated storage containers to build their hydro farms. Powellâs was the first one they sent to Wyoming so they had to add a wind barrier to the outside of the fan so it wouldnât be pulled off or damaged by the high winds. The container ships out of Boston but the ZipGrow vertical hydroponic towers inside come from the folks at Bright Agrotech in Laramie, another indoor agriculture-focused Wyoming company.
Skyline Gardens will produce approximately 500 heads of lettuce per week at capacity.
Skyline is almost at profit level on the month to month books, but Powell predicts three years at this rate of growth to pay startup costs back in full. Self-funded, Powell realizes the wariness of banks, especially in a place like Wyoming where sustainable agriculture is still finding its feet, to fund container farms and similar new social enterprise style businesses.
Powellâs background in sales has certainly aided him in selling the idea of hyperlocal lettuce to Casperâs farmersâ market attendees as well as a few area restaurants. Although some early leads grew cold due to, in Powellâs assessment, the difference in price between his product and other wholesalers. âA lot of them want me to meet the price points of [their current suppliers] but I always say itâs a whole different product. When you have to deal with corporate offices out of stateâŠthat always makes it harder, so Iâm working on that. I mean direct sales has a lot to be said for it. I get the whole profit to myself. I can control the way and time that I sell it.â
Powell has several direct sales customers who buy CSA style as well as his wholesale contracts. He also sells through a local aggregation group, Fresh Foods Wyoming, which takes his produce to the farmers market for him. Deliveries have proven the most time consuming aspect of the business so far and for now Powell wants to concentrate on solidifying his customer base with no plans to expand.
âRight now I think this is enough for me. I have my main job and Iâm not planning on leaving that any time soon. Even now, in the startup phase, the time commitment is substantial,â says Powell.
As the âgrow localâ and âsustainableâ concepts continue to build traction in Wyoming, Powell says heâs not worried about a crowded market just yet. âIâm not too worried about competition,â says Powell as he explains how his one container farm could supply a single local restaurant completely and exclusively. âThereâs plenty of room in town for competition.â
Pastor Matt Powell, the owner of Casper, Wyo.-based Skyline Gardens. Photo courtesy of Skyline Gardens
Newbean Capital and Local Roots Jointly Authored A White Paper Entitled âIndoor Crop Production
Newbean Capital and Local Roots jointly authored a white paper entitled âIndoor Crop Production: Feeding the Futureâ which can be downloaded in full below by entering your name and email address. The paper was launched at the 3rd Indoor Ag-Con on March 31, 2015
Livewell Northwest Colorado: Bring Growing Back Home
Livewell Northwest Colorado: Bring Growing Back Home
Andy Kennedy/For Steamboat Today
Saturday, March 11, 2017
In a TEDx Mile High Talk, former three-time Olympian and health expert Jeff Olson described the call of duty during World War II, when Americans bonded together to grow more than 40 percent of the countryâs fruits and vegetables in victory gardens. The premise was that larger agriculture ventures could go toward feeding our troops overseas.
But, when the war was over, the gardens withered, and during the next two decades, when the American family working-dynamic began to shift, there was another more toward agricultural imperialism. This imperialism birthed a larger global agriculture, as the U.S. government emphasized to its small farmers to âget big or get out,â for high-production and low-margin growing.
Olson warned that modern âindustrialized food is a tragedy of human health, an irony of ecology and a paradox of economics.â
Olson elaborated that the solution to this terrible trifecta is the future of âclosed-environment agriculture,â or greenhouses with a vertical twist.
Pioneered by the Dutch and now adopted by most industrialized nations â including 2.8 million acres of greenhouses in China â greenhouse growing is, indeed, feeding the world, and sadly, the U.S. is dead last in this effort. We used to be a net exporter of fruits and vegetables, and we are now a net importer of produce.
While greenhouses can be a viable solution, a better solution could be indoor vertical growing â a marriage of Jetson-like food technology with design wizardry of Steve Jobs.
We stand at the convergence of humanities and technology, and vertical aeroponics serves as nature with aerodynamic design. Imagine 43,000 square feet â about an acre â of your favorite greens. Vertical aeroponics can do it in 4,000 square feet. Thatâs 90 percent less space, with 90 percent less water, giving three times the nutrient density in the plant. Used by NASA and studied by universities around the world, vertical growing has proven efficient time and again.
I recently traveled to Florida to see the start of this revolution at Living Towers Farm, just north of Orlando. For more than six years, Jan Youngâs organization has been growing âbeyond organicâ food for those in need, teaching the techniques of vertical growing to students and in-home gardeners and selling quality food that âdoesnât have to cost the Earth or have a negative impact on it.â
Even though Florida has the weather for outdoor gardening, it does not have the soil for it. Growing vertically yields more and healthier plants. Youngâs eggplants, for instance, yield 8 to 10 fruits on a regular basis â about 30 percent more yield than traditional gardening.
Seeing the vision of Living Towers in person and pondering the economics of vertical growing spins my imagination to what this could mean for a local economy. For example, an acre of commodity corn earns a farmer $1,200; an acre of traditionally grown, organic food earns $12,000; and an acre of vertical aeroponics earns a quarter of a million dollars in revenue for one harvest, according to Olson.
Bringing the concept of Victory Gardens full circle, Olson has teamed up with an organization called Veterans to Farmers, which turns protectors into providers with an urban agricultural training program, creating âagropreneurs.â One of the programâs graduates launched the first vertical growing farm on the Front Range that sold out within a year of production, selling produce to fine dining restaurants on the Front Range.
âPeople are hungry for beautiful food,â Olson said.
Despite being known as an agricultural state, 97 percent of Coloradoâs leafy greens are imported from thousands of miles away. With only a 25 percent increase in Colorado-grown food shift, weâd see 31,000 new jobs, generating more than $1 billion in new wages.
In my own home, we have two commercialized, state-of-the-art vertical growing systems, as do many other friends and peers in town â the Tower Garden has been around six years and is fairly well-known by now as an in-home solution to one of the shortest growing seasons on the planet.
However, itâs the larger installations that now inspire me. The vertical farms popping up around the country are something I would like to emulate. For several years, I have been inspired by the OâHare Airport installation â more than 100 vertical towers in terminal D that outgrew their mission to feed the restaurants so quickly, they now offer a farmers market for travelers, as well.
I have brought this inspiration to several local nonprofits to start working on a project I hope will soon be growing local food on a larger scale, both for families in need and for those who want fresh produce. For more information, contact Andy Kennedy at andyjkennedy@gmail.com.
To view Jeff Olsonâs full TEDx Talk, visit youtube/ttvIeugcigk.
Andy Kennedy a member of the Northwest Colorado Food Coalition
Indoor Ag-Con Returns to Las Vegas to Discuss Farm Economics and New Technology Trends in Hydroponics, Aquaponics & Aeroponics
Indoor Ag-Con Returns to Las Vegas to Discuss Farm Economics and New Technology Trends in Hydroponics, Aquaponics & Aeroponics
Indoor Ag-Con â the indoor agriculture industryâs premier conference â will be returning to Las Vegas for the fifth year on May 3-4, 2017 to discuss the prospects for this increasingly important contributor to the global food supply chain.
LAS VEGAS, NV (PRWEB) MARCH 10, 2017
Indoor agriculture â growing crops using hydroponic, aquaponic and aeroponic techniques â has become popular as consumer demand for âlocal foodâ leads growers to add new farms in industrial and suburban areas across the country. Indoor Ag-Con â the industryâs premier conference â will be returning to Las Vegas for the fifth year on May 3-4, 2017 to discuss the prospects for this increasingly important contributor to the global food supply chain.
The two-day event will be held at the Las Vegas Convention Center, and is tailored toward corporate executives from the technology, investment, vertical farming, greenhouse growing, and food and beverage industries, along with hydroponic, aquaponic and aeroponic startups and urban farmers. It is unique in being crop-agnostic, covering crops from leafy greens and mushrooms to alternate proteins and legal cannabis. Participants will receive an exclusive hard copy of the newest edition in a popular white paper series, which is sponsored by Urban Crops and will focus on the US industryâs development.
The event will consist of keynotes from industry leaders and extended networking breaks, along with a 50+ booth exhibition hall. This already includes industry majors such as Certhon, Dosatron, DRAMM, Hort Americas, Philips Lighting, Priva, and Transcend Lighting. A new addition for 2017 is âlunch and learnâ sessions covering practical topics such as health and safety. Confirmed speakers include executives from Argus Controls, Autogrow, Bright Agrotech, CropKing, Fresh Box Farms, Grobo, Intravision, Plenty, Priva, Shenandoah Farms and Village Farms among many others. âWeâre expecting that the big themes for this year will be farm economics and the commercialization of newer technologies such as machine learning, and are excited to have gathered experts from across the world to speak. The entrepreneurs in our funding session have raised more than $50mn for their indoor farms in the past year alone, and one speaker is operating a 100k ft2 commercial controlled environment farmâ commented Nicola Kerslake, founder of Newbean Capital, the eventâs host.
Agriculture technology companies, suppliers and automation companies will have the chance to meet and mingle with leading vertical farmers and commercial greenhouse operators at a drinks party on the first evening of the event. Event sponsors include Autogrow, Urban Crops, Kennett Township, Freight Farms, Grodan, Joe Produce, Crop One Holdings and Grobo.
Beginning farmers, chefs and entrepreneurs can apply for passes to the event through the Nextbean program, which awards a limited number of complimentary passes to those who have been industry participants for less than two years. Applications are open through March 31, 2017 at Indoor Ag-Conâs website. The program is supported by Newbean Capital, the host of Indoor Ag-Con, and by Kennett Township, a leading indoor agriculture hub that produces half of the USâs mushrooms.
Indoor Ag-Con has also hosted events in Singapore, SG and New York, NY in the past year, and will host its first event in Dubai â in partnership with greenhouse major Pegasus Agriculture â in November 2017. Since it was founded in 2013, Indoor Ag-Con has captured an international audience and attracted some of the top names in the business. Events have welcomed nearly 2,000 participants from more than 20 countries.
Newbean Capital, the host of the conference, is a registered investment advisor; some of its clients or potential clients may participate in the conference. The Company is ably assisted in the eventâs production by Rachelle Razon, Sarah Smith and Michael Nelson of Origin Event Planning, and by Michele Premone of Brede Allied.
5th Annual Indoor Ag-Con
Date â May 3-4, 2017
Place â South Hall, Las Vegas Convention Center, Las Vegas, NV
Exhibition Booths â available from $1,499 at indoor.ag
Registration â available from $399 at indoor.ag
Features â Two-day seminar, an exhibition hall, and after-party
For more information, please visit http://www.indoor.ag/lasvegas or call 775.623.7116
Are Indoor Farms The Next Step In The Evolution of Agriculture?
Youâve probably heard of farm-to-table, or even farm-to-fork, agricultural movements that emphasize the connection between producers and consumers. But what about factory farm-to-table?
Are Indoor Farms The Next Step In The Evolution of Agriculture?
SPECIAL TO THE JAPAN TIMES
MAR 10, 2017
Youâve probably heard of farm-to-table, or even farm-to-fork, agricultural movements that emphasize the connection between producers and consumers. But what about factory farm-to-table?
Spread, a giant factory farm that grows lettuce in Kameoka, Kyoto Prefecture, is just one of more than 200 âplant factoriesâ in Japan capable of harvesting 20,000 heads of lettuce every day. Their lettuce, which includes frilly and pleated varieties, is grown in a totally sterile environment: Thereâs no soil or sunlight, no wind nor rain.
The rich, dark-brown soil in which produce has traditionally been grown is utterly alien inside the factory. Instead, the lettuce is grown hydroponically, in a nutrient-rich gelatinous substance. The vegetables grow in vertically stacked trays under LED lights timed to come on during the day and switch off at night.
The lettuce Spread grows in Kameoka â which takes about 40 days from planting to harvest â is packed into bags and shipped to over 2,000 supermarkets across the country. The product also makes it into airline meals, although the company wouldnât reveal which ones.
At a time when Asian countries are scrambling to deal with the surges and declines in population as well as the effects of climate change, factory farming is a burgeoning business. In Japan, for example, the number of farmers has dropped from a high of over 7 million in the 1970s to under 2 million, and today the average age of Japanese farmers is 67.
Spread, however, is about as far from the pastoral image of a vegetable farm you can imagine. While the facility, and even the concept, sounds futuristic, Spread has been growing lettuce in these conditions since 2006 at its Kameoka base.
This year, it will open another plant factory at Kansai Science City, on the borders of Kyoto, Nara and Osaka prefectures. Between the two factories the company will be able to produce 50,000 heads of lettuce each day.
What makes the new facility different is the level of automation: tasks such as raising seedlings, replanting and harvesting will be done by machines and guided by artificial intelligence, a move that will cut labor costs by 50 percent and boost profitability. In 2016, Spread was awarded a gold medal at the Edison Awards in recognition of its role in agricultural innovation.
On a recent tour of Spreadâs facility in Kameoka participants viewed the lettuce through an observation window, while factory manager Naohiro Oiwa communicated via telephone with a worker dressed head to toe in white protective clothing. âWhen our products first appeared in supermarkets, plant factory-grown vegetables werenât yet recognized by many people. Our sales staff had a very hard time selling them to retail stores,â Oiwa said.
People wanted to know if vegetables grown without sunlight are safe to eat, he added. Spread has since assuaged some of those anxieties by emphasizing the safety of its growing environment and the quality of its crops.
It also helps that Spread can compete on cost: a bag of its lettuce sells for „198, a price the firm can maintain. Field-grown lettuce, by contrast, is subject to the vagaries of the weather, and therefore to fluctuations in price.
So-called vertical farms, such as Spreadâs facility in Kameoka, are also able to use water in an extremely efficient way. The company would not disclose, however, how much it spends on something that is essentially free to conventional farmers, sunlight, or, in Spreadâs case, LED lighting.
Spread spokeswoman Minako Ando said that the firmâs operations received a boost in the aftermath of the nuclear disaster in Fukushima Prefecture following the Great East Japan Earthquake, which struck six years ago today. Amid widespread fears that traditionally grown produce could contain radioactive fallout, factory farming, which is mostly done indoors, suddenly looked like a safer option.
Itâs important to remember that, while Spread is at the vanguard of technological developments in farming, the history of agriculture has always been characterized by innovation in its tools.
Spread doesnât see its role as replacing farmers; it seeks to complement and support the agricultural industry as a whole, Oiwa said.
Along the way to profitability â Spread started operating in the black in 2013 â it has developed several patents and is now in talks with partners around the world to set up similar ventures.
With the know-how it has gathered from growing lettuce, Oiwa said, Spread could start mass-producing other vegetables, such as tomatoes, in giant plant factories in the years to come.
Michael Blodgett, an organic kale farmer in Wazuka, a picturesque tea-producing town in southern Kyoto Prefecture, echoes the notion that, when it comes to farming, innovation is nothing new. âFrom that viewpoint, new and sustainable techniques for growing healthy vegetables are certainly welcome,â Blodgett said.
He noted, however, that the type of farming he and his neighbors practice engenders a sense of community. Advice is solicited from older farmers, and at harvest time neighbors share what they bring in from the fields.
âThere is something special about planting seeds in the ground, taking care of the plants by weeding, watering, and love,â Blodgett added.
In the near future it will increasingly be the charge of robots and AI systems to plant, weed, water and harvest the food that ends up on our table. Where exactly that leaves the farmers, or the land itself, remains to be seen.
Food factory: At Spread's facility in Kameoka, Kyoto Prefecture, lettuce is grown hydroponically using timed doses of LED light. | J.J. O'DONOGHUE
The Farm of The Future? (Video)
The Farm of The Future? (Video)
AMERICAN CHEMICAL SOCIETY
WASHINGTON, Feb. 28, 2017 -- There's a new trend in agriculture called vertical farming. As humans learned to farm, we arranged plants outside in horizontal fields, and invented irrigation and fertilizer to grow bumper crops. But with modern technology and farmers' cleverness, we can now stack those fields vertically, just as we stacked housing to make apartment buildings. Moving plants indoors has many benefits: Plants are not at the mercy of weather, less wilderness is cleared for farmland, and it's easier to control the runoff of fertilizer and pesticides. But the choice of lighting can make or break the cost of a vertical farm and affect how long it might take for urban agriculture to blossom. Watch the latest Reactions video here: https://youtu.be/rEw-VfFkUik.
Growing In Vertical Farms Around The World With Philips LED Systems
Following on from partnering with the Staay Food Group to build Europeâs first large-scale commercial vertical farming specifically supplying retail, city farm project manager for Philips Lighting, Roel Janssen, takes PBUK through the âgrowing recipesâ behind the LED systems and examines the needs of different vertical farming markets around the world
10 March 2017
Growing In Vertical Farms Around The World With Philips LED Systems
Following on from partnering with the Staay Food Group to build Europeâs first large-scale commercial vertical farming specifically supplying retail, city farm project manager for Philips Lighting, Roel Janssen, takes PBUK through the âgrowing recipesâ behind the LED systems and examines the needs of different vertical farming markets around the world.
The outdoor temperature in the remote regions of Saskatoon, Saskatchewan Canada have recently been around the minus 30 degree mark - but inside its high-tech greenhouse herb growers Ecobain Gardens is witnessing dramatic changes in its crops as well as big energy-saving impacts, following the Philips LED system installation.
By upgrading the fluorescent lighting previously used in the facility to LED, Philips Lighting is helping the vertical farming pioneer to produce at commercial scale, accelerate growing cycles and grow healthier, more consistent plants, while saving up to CAN $30,000 per year.
From less than 1,400 square feet, the facility produces approximately 18,000 pounds (8,164 kilos) of produce each year through farming methods which use up to 98% less water, no pesticides and now the latest LED technology.
âSaskatoon is really in the middle of nowhere with extremely low temperatures, so for Ecobain CEO Brian Bain, the key was to supply basil and other produce throughout the whole year, even while it was well below zero degrees outside,â Janssen tells PBUK.
âThe big advantage now for his operation is year-round supply which is premium quality, has uniformity, looks the same and tastes the same, and has the same nutrient content.
âAt Ecobain, growing cycles are now considerably shorter and they are producing commercial scales of produce like basil, where now more than 10,000 plants are produced a week.â
A value-added aspect of Philips LED from a growers point of view is the low heat output which produces a healthier, more consistent plant growth by reducing the heat stress on the plant canopy and root zone as well as providing uniform lighting.
Light Recipes
âWhen a plant is growing it uses red and blue lights most optimally and if you start trialling LED lights itâs fairly difficult to see what is the best combination of red and blue. Weâve been active in the LED lighting industry for horticulture for the past 9 to 10 years looking at that specific combination of colours that are what we call âlight recipesâ and they can be optimised for a specific crop or sub-optimised for a range of crops or leafy greens,â adds Janssen.
âIf you look specifically at growing without daylight, there are three main advantages for growers; the first is reliability because it's a controlled production cycle so that when everything functions in the right way - the climate, the carbon dioxide, irrigation, the right seeds, the right lighting - itâs always the same production cycle.
âThere is no pressure from disease or pests and itâs basically always summer inside. And because you grow in a controlled environment itâs always free from pests so you donât need any pesticides to get rid of the disease compared with outside where you cannot control the environment and are exposed to the risks of disease and pests.â
The second advantage, Janssen, explains is quality; because of the uniformity a controlled environment under LED offers, plants can be optimised for taste, colour and nutrient content with more than 90% less water because its easier to recycle resources when growing indoors.
The Third Plus Point - And Itâs A Big One - Is Yield.
âYields can vary depending on the light levels and the varieties that you use, but for example, in open field production if you talk about head lettuce, you would go to 15 to 20 kilograms per square metre of growing area per year to, in the most advanced high-tech greenhouse, 60 to 65 kilograms. And if you grow without daylight, you could grow above 100 kilograms per square metre per year.
âThatâs growing square meters so if you do that in ten layers, you could go for one square metre of floor space and get 1,000 kilograms of production.â
Ecobain Gardens has partnered with Star Produce to distribute its produce throughout Canada to retailers like Loblaws, Federated Co-op, Safeway and Sobeys, as well as other local grocery stores.
The differences in vertical farming around the world
The Ecobain Gardens project is about locally-produced crops being grown year-round in an area not ordinarily associated with growing herbs and microgreens.
Part of Janssenâs job is to travel the world investigating the specific growing recipes for a myriad of vertical farming growers who want to tap into the potential of LED. Heâs the man behind the Eindhoven-based GrowWise Research Centre facility - where R&D teams work in eight âclimate cellsâ researching how to optimise crops further and streamline light recipes.
Since GrowWise first opened in July 2015, Janssen explains how he has witnessed quite a big shift in the interest from industry.
âAt first, there were a lot of entrepreneurs wanting to do something within horticulture. They didnât necessarily have a horticulture background or sufficient knowledge to build a greenhouse, but they saw indoor controlled environments as a an opportunity and if the technology functions in the way it should do, anyone can be a grower.
âBut you still need horticulture knowledge and green fingers because if something in the system doesnât function, you really need someone who can steer the product in the right way.
âWhat you see in North America and Canada, which are big markets for us, is that most of the lettuce, leafy greens and salad that is produced comes from California. The produce is in a truck for five days before it reach cities like Chicago and Saskatoon in this case, and itâs not as fresh as if you would harvest it on demand and then straight away give it to the consumer. Thatâs a big advantage when youâre in a remote area.â
In contrast, the indoor vertical farms of the US and Europe, are known as âplant factoriesâ in China and Japan, where the focus is more about food safety and getting access to fresh produce in massively populated urban areas like Singapore and Tokyo.
âIn Asia they typically talk about âplant factoriesâ and like the controlled conditions and the safety aspects. Thatâs basically the idea; they want to push food safety and accessibility.
âWhereas in the US it's more about being local, in Asia the focus is on food safety and accessibility to food is really important.
âWe had a lot of customers in Japan with a lot of operational indoor farms.â
Over the last two years, Philips Lighting has seen increasing interest, not just from growers supplying the market, but from retailers and food processors.
Last month during Fruit Logistica, Philips Lighting and the Staay Food Group announced Europeâs first large-scale vertical farm will be built in Dronten, the Netherlands, to serve supermarkets with fresh-cut lettuce grown using LED horticultural lighting.
The indoor vertical farm will have more than 3,000 squared metres of growing space to produce its pesticide-free lettuce - something that appeals to retailers who need to provide high quality bagged or loose lettuce with zero contamination issues.
âWhen we first met the owner of Staay he wanted to tap into the possibilities of growing in an indoor farm and we started discussing it. Eventually he decided to build a farm and his key reason was that so he could grow locally in the facility where he also uses his pre-cuts salad.
âThe level of MRLs on the leaves is really low which is a big added value for them going forward with stricter rules from retail and of course there are no bugs.
âIf we play with our grow recipes, we can also extend the shelf life of lettuce, get more dry matter into the lettuce, get it crispier; itâs exactly the same process as growing outside but itâs controlled so if we know what triggers red colouration in a plant for example, we can use a specific light recipe to trigger that colouration and get a nicer colour or trigger dry matter so the shelf life is extended.â
Once the facility is complete, the Staay Food Group can do everything under one roof; grow, pack, process with very low risk of contamination from the pesticide-free lettuce.
UK Loves âHome-Grownâ
Janssen explains, UK-based growers like to market produce as âhome-grownâ, something that particularly resonates with the British market. But why do vertical farms tend to focus on salad crops, microgreens and herbs?
âIn the UK we also see that itâs a real added value to have UK-grown products and there are companies growing other crops apart from lettuce and herbs such as Flavour Fresh which grows tomatoes year round using our LED solutions.
âTypically a leafy green is produced within three to five weeks and cucumbers after a few weeks already started giving fruits. Weâre also investigating growing fruiting crops but because of the speed or the short crop cycles, at least at this point in time, the main focus is on leafy greens because they offer the biggest opportunities.
âWe managed to grow strawberries in our GrowWise facility, but the difficulty of growing completely without daylight is that itâs better to have fast rotating crops with really high yields that you can improve because the economics around it are much more interesting.â
Taking the case of strawberries, Janssen, explains the challenges associated with growing this kind of fruit.
âIf you put the seed into a substrate and the strawberry needs two months before it starts fruiting, during those two months you need to put on your lights and climate system, whereas with lettuce, leafy greens and short cucumbers, theyâre really fast in how they rotate.
âWeâre not saying that we can feed the masses with this but it is a market where there is added value to be found. In Asia itâs mostly about food safety and availability, in the US itâs mostly about the local movement and pesticide-free production, but in Europe itâs for processed optimisation.
âGrowers in Europe are triggered by retail to look into this technology and they are stepping into the business. We expect this to grow when Staay is operational later this year because I think they will set the standard in the level of contamination you can have on a leaf which is very close to zero at that point.â
- See more at: http://www.producebusinessuk.com/insight/insight-stories/2017/03/10/growing-in-vertical-farms-around-the-world-with-philips-led-systems#sthash.s0Y5YKCx.dpuf
Indoor Farming Takes Root At U of T Mississauga
At University of Toronto Mississauga, a plastic tower sprouts produce including curly starbor kale, buttercrunch and collard greens
Indoor Farming Takes Root At U of T Mississauga
At University of Toronto Mississauga, a plastic tower sprouts produce including curly starbor kale, buttercrunch and collard greens.
Rising almost six feet off the ground and illuminated by high output fluorescent bulbs, the indoor farm wall grows plants hydroponically â with nutrient solution, instead of soil. The water nourishes the roots, collects in a gutter and then recirculates back to a nutrient tank that feeds back into the hydroponic system.
The farm wall was the idea of Master of Science in Sustainability Management (MScSM) students Conner Tidd and Kevin Jakiela who partnered with Modular Farms Co., which specializes in vertical farming systems, to create distribution channels and services.
âYou can grow pretty much anything,â Jakiela says. âHere, weâve already grown three different types of lettuce, Genovese basil, joi choi, peppermint and parsley.â
From seed to harvest, it takes about four weeks to grow leafy greens and herbs.
âIf you stagger it correctly, you can harvest it almost every day,â Tidd adds.
The wall costs just under $25 a month in electricity.
The seedlings, nestled in plugs made of peat moss, begin in a tray and are placed under a humidity dome where they germinate and are fed different levels of nutrients and pH. After a couple of weeks, they're ready to be transplanted into the tower.
Wicking strips help water find the path of least resistance by controlling the water flow and taking the water directly to the seedling roots.
âItâs a white cloth that you open up, put the plug in, then you close it like a sandwich, and put it into the tower,â Jakiela says.
Although the produce the farm wall yields is not organic-certified yet, the students' startup company, Just Vertical, uses organic-based practices, foregoing herbicides and pesticides.
âWhen youâre outside, youâre exposed to pests and fungi,â Tidd says. âUnless youâre using herbicides and pesticides, itâs going to be a problem especially when youâre growing strawberries and tomatoes.â
âWith Just Vertical, Kevin and Conner have a great product in place, and manufacturing is lined up so now the initial focus will be on market validation,â says Sam Dumcum, the programs, strategic relationships and innovation lead at ICUBE, U of T Mississauga's incubator that provides startup support to new ventures at any stage.
Dumcum says that by focusing on market research during the next phase of their startup, Just Vertical will be able to have a solid base with which to advertise and sell their product but also to appeal to investors.
Student startup, Just Vertical, is growing an indoor farm wall hydroponically at U of T Mississauga â with nutrient solution, instead of soil (photo by Sarah Jane Silva)
Why Large-Scale Indoor Farms Will Be Crucial to Feed Our Fast Growing Cities
Why Large-Scale Indoor Farms Will Be Crucial to Feed Our Fast Growing Cities
SEB EGERTON-READ · MARCH 9, 2017
Technological innovations are enabling a new way of producing food transforming indoor environments into places where fruits and vegetables can be grown without soil, close to the city, with an extremely short supply chain, fully independent of weather fluctuations, while reducing demand on water and chemicals. One of the pioneers of the approach, New Jersey based Bowery, describe it as âpost-organicâ farming, and momentum is growing behind the idea that a sizeable percentage of some of the fruits and vegetables of the future could be grown using this technique.
On the current path, the world populationâs caloric demand will increase by 70%, while crop demand for human consumption and animal feed is expectedl rise by 100%. Meeting these needs with existing agricultural practices will require large areas of additional land, and will increase pressure on the earthâs soil, which has gradually been degraded losing a significant percentage of its nutritional capacity over the last 100-150 years. Meanwhile, the effects of climate change, realised through extreme weather patterns, threaten to negatively impact crop yields and disrupt food supply chains.
Urban agriculture in the form of aquaponics, where fish farming is combined with the growth of vegetables and a self-maintaining system is established has a long history, but the data monitoring and ability to control internal conditions provided by new technologies has enabled the further evolution of hydroponics.
Hydroponic farming involves growing produce in multi-storey warehouses without soil. Seeds are planted in a soil substitute and grown in nutrient-rich water, where water is recirculated, and temperature, salinity and humidity are monitored and controlled to maximise the yield. The method has a number of economic, environmental and social advantages. Hereâs a pretty good initial list taken from SystemIQâs Achieving Growth Within report:
- 90-95% reduction in water demand
- Fertilizer use reduced by 70%
- Use of herbicides and pesticides eliminated
- Food waste at the production stage minimized
- Growing space maximized
- Ability to grow throughout the year
- Shorter supply chain results in lower transport costs and related emissions
Reportedly 100+ times more productive on its land compared against traditional farming, Bowery is one of the most advanced movers in the sector. Theyâre far from alone, Japanâs Spread declared their initial plant profitable in 2013 and now have plans to open an automated plant that could increase their yield to 51,000 lettuce heads per day, and weâve previously told the story of AeroFarms, another New Jersey based firm.
Itâs also a highly efficient technique in terms of resource use. For example, only 5% of the fertilizer used on large fields is actually consumed by people, according to the Ellen MacArthur Foundationâs Growth Withinresearch, the rest of the nutritional value is waste across the value chain.
The new model doesnât come without criticisms. Growing without soil means that there is little opportunity for regeneration or the development of an ecosystem that âfeeds itselfâ, rather the method allows for the development of a large number of linear and separate processes in an ultra-efficient way.
Furthermore, there will always be concerns about the nature of the chemicals needed to grow plants in these conditions, and the types of seeds used. For their part, Bowery take pride in sourcing, âfrom partners who spend nearly a decade developing the ideal seed, rather than relying on GMOsâ. When Circulate asked him about some of the potential trepidations, CEO Irving Fain was quick to highlight that the story of indoor farming is a healthy one, both for crops and people:
âBowery grows its produce under LED lights that mimic the spectrum of the sun. By monitoring the growing process 24/7 and capturing data at each step, we give our crops exactly what they need and nothing more. Because we control the entire growing process from seed to store, our produce is the purest available â food you can truly feel good about eatingâ.
For Irving, who is already planning Boweryâs second farm, scale is the next challenge, âwe plan to continue to build additional farms, keeping them all close to the point of consumption to deliver products at the height of freshness and flavor, and we hope to serve more cities throughout the countryâ.
Up front investment costs are a potential barrier, but thereâs also an increasingly strong business case associated with indoor farming. Besides the growing number of innovators establishing businesses, SystemIQâs research estimated that âŹ45 billion of total investment between now and 2025 could create an economic reward across Europe of âŹ50 billion by 2030 with key benefits including the freeing up of land space and reduced reliance upon fertilisers and pesticides.
Pair the potential economic opportunity with the demands expected by a fast-growing global population, and itâs easy to imagine a future where at least part of the food supplied to the worldâs largest cities comes from indoor farms located inside the city limits.
West Coast Supply Issues Prompt More Demand At Indoor Farms
West Coast Supply Issues Prompt More Demand At Indoor Farms
By Ashley Nickle March 09, 2017 | 2:23 pm EST
Indoor farms are seeing increased demand as weather-related production issues in Arizona and California have affected the supply of leafy greens.
Rain has interrupted planting and harvesting in California throughout the season, and the Yuma, Ariz., deal is expected to finish earlier than previously thought after mildew proved to be a major problem.
With West Coast supplies tight, several indoor farms have reported increased interest from buyers.
New York, N.Y.-based BrightFarms, which has greenhouses in Illinois, Virginia and Pennsylvania, has seen retail orders rise in recent weeks.
âIt has been impacting most of our customers pretty significantly and their availability on items like spinach and arugula and other baby greens items as well,â said Abby Prior, vice president of business development for BrightFarms.
âBecause our crop cycles are relatively short, we have a lot of flexibility to be able to adapt on planting cycles relatively quickly,â Prior said. âThat is really a daily and weekly process with our retailer partners, looking at their forecasted demand, and we can adapt our planting pretty much daily based on their needs.â
Prior said the company will likely be providing higher amounts of product at least through March as crops transition from Yuma to California.
Milan Kluko, CEO at New Buffalo, Mich.-based Green Spirit Farms, said his company has seen an uptick in interest in the last month due to the Western production problems. Green Spirit can only increase capacity at its New Buffalo location â it also has a farm in Detroit â about 20% due to space constraints, but it has been ramping up production as much as it can.
One of the large supermarkets with which Green Spirit works is ordering double what it did a few weeks ago, Kluko said.
Robert Colangelo, CEO of Portage, Ind.-based Green Sense Farms, said the company has been shifting production to meet higher demand. Green Sense grows micro greens, baby greens, herbs and lettuces but will produce about 30% more lettuce and less of other items to address customer needs.
Benjamin Kant, CEO of Chicago-based Metropolitan Farms, said it is hard to tell whether his companyâs current strong demand is a direct result of the West Coast production issues because the company just completed its first full year in operation.
However, Kant said he has heard complaints about higher prices and lower quality of West Coast product.
Marc Oshima, chief marketing officer at Newark, N.J.-based AeroFarms, said demand has âabsolutelyâ increased lately but noted overall interest has been high for a while.
âItâs not just recently,â Oshima said. âThese are ongoing issues that have troubled the industry.â
All five of the indoor farms interviewed for this article have recently expanded or are expanding.
âThe more we (as a country) see challenges in sourcing all of our produce from a relatively small area on the West Coast, farms like ours and companies like BrightFarms will continue to grow and will continue to gain relevance in the produce industry,â Prior said, âand weâre glad to be able to fill the gaps at times like these where retailers are struggling.â