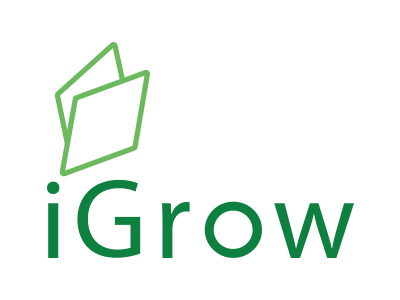
Welcome to iGrow News, Your Source for the World of Indoor Vertical Farming
Will Vertical Farming Continue To Grow, Or Has It Hit The Greenhouse Ceiling?
Will Vertical Farming Continue To Grow, Or Has It Hit The Greenhouse Ceiling?
Agriculture has come a long way in the past century. We produce more food than ever before — but our current model is unsustainable, and as the world’s population rapidly approaches the 8 billion mark, modern food production methods will need a radical transformation if they’re going to keep up. But luckily, there’s a range of new technologies that might make it possible. In this series, we’ll explore some of the innovative new solutions that farmers, scientists, and entrepreneurs are working on to make sure that nobody goes hungry in our increasingly crowded world.
A pair of lab workers, dressed head to toe in bright white biohazard suits, patrol rows of LED-lit shelves of lettuce, quietly jotting down a series of numbers and readings. Stacked some 15 to 20 feet high, the shelves cover nearly every inch of a massive 25,000-square-foot facility. As the lab hands pass by each row of lettuce, some in the germination phase, some ripe for picking, a psychedelic pink glow wraps around them, painting an almost extraterrestrial setting.
This isn’t a scene plucked from Alfonso Cuarón’s latest blockbuster; it’s an everyday occurrence at a vertical farm in eastern Japan.
The farm was built in the wake of a devastating magnitude 9.1 earthquake that rocked Japan in 2011 and led to a temporary food crisis in the affected area. After seeing the chaos, Japanese plant physiologist Shigerharu Shimamura decided to develop a more consistent, reliable model for manufacturing lettuce. He ended up turning an old Sony-backed semiconductor facility into the planet’s largest vertical farm – a huge operation that now churns out an astounding 10,000 heads of lettuce per day.
“We’re talking coming in and supplying 10, 20, 30 percent of the food supply of an entire city.”
Recently, the facility (and others like it) has become a poster child for indoor farming. There’s now a rapidly expanding movement to bring this type of food production to urban centers all over the globe.
It’s easy to see the appeal. In theory, indoor farms could allow us to grow food 24 hours a day, protect crops from unpredictable weather, and even eliminate the use of pesticides, fertilizers, and herbicides. If these farms were built in cities, we could potentially mitigate crop loss due to shipping and storage, and cut down on fossil fuel usage because food wouldn’t need to be transported very far after harvest.
But of course, the idea of indoor farming isn’t without its detractors. Critics are quick to point out the method’s shortcomings when it comes to efficiency, effectiveness, and cost. In their eyes, vertical farming simply isn’t something that can be deployed on a large enough scale, and therefore isn’t a viable solution to our problems.
So, who’s right? Should we start building giant, garden-stuffed skyscrapers in our cities, or abandon the idea and devote our efforts to improving existing (horizontal) farms? Could vertical farming legitimately help us meet the world’s growing demand for food, or are we chasing the proverbial pie in the sky?
Upward trajectory: the benefits of growing vertically
In his seminal book, The Vertical Farm: Feeding the World in the 21st Century, Dr. Dickson Despommier puts forth the theory that vertical farming is a prime candidate to help solve the growing food, water, and energy crisis in the United States.
As populations continue to rise in urban centers around the globe, Despommier sees no other solution.
“As of this moment, the WHO (World Health Organization) and the Population Council estimate that about 50 percent of us live in cities and the other half, of course, live somewhere else,” Despommier said in a video. “Another thing we can learn, from NASA of all places, is how much land those 7 billion people — half urban, half rural — actually need to produce their food every year. It turns out to be the size of South America. So, the size of South America, in land mass, is used just to grow our crops that we plant and harvest. I’m not even talking about herbivores like cows, goats, or sheep.”
When the book was first published in 2011, the indoor farming industry essentially stood as a barren landscape, with few companies setting out to literally put vertical farms on the map. Now, with Despommier’s written blueprint in the wild, the concept has recently gained a good deal of popularity.
“It’s estimated that by around 2050, roughly 80 percent of the world’s population will reside in urban city centers.”
Aside from Despommier, a growing number of people strongly believe in a prominent future for vertical farms. Today, there exist throngs of vertical farming companies all geared toward making this innovative technology a reality. Unsurprisingly, it’s with Despommier and these upstart companies that the industry’s appeal rings the loudest.
Companies such as Bright AgroTech and AeroFarms have set out to educate and inform small farmers to grow locally in urban areas, while other firms like Freight Farms and Edenworks lean on unique and innovative growing concepts — such as shipping containers or rooftop aquaponics — to bring the idea to life. Thus far, there’s no real right or wrong way to go about it, and the recent influx of startups should only prove advantageous to the industry in the long run.
“I do believe there are a few players coming to the table that look poised to supplement local food supplies to a really significant degree,” aquaponics expert Dr. Nate Storey told Digital Trends. “We’re talking coming in and supplying 10, 20, 30 percent of the food supply of an entire city. So, you have this future where you have indoor growers taking on that task, and you have small guys that are kind of collaborating and cooperating to sell to niche markets, really high-value products. Then you have the big boys who are really kind of going head-to-head with some of your field producers, who are growing at much larger scales and interested in replacing that wholesale product.”
As Despommier states on his website, it’s estimated that by around 2050, roughly 80 percent of the world’s population will reside in urban city centers, with the population of the world ballooning by an additional 3 billion people over that time. To Storey’s point, the diversity of vertical farms should allow these urban areas to continue to function as they do today. That is, access to food should remain a basic function of society, as opposed to it serving as a luxury should food production dwindle in the future.
Like the Green Revolution from the 1930s to the 1960s, Storey believes the world sits poised for yet another research and development breakthrough regarding vertical farming.
“When you step back a bit, you begin to realize that we’re kind of on the verge of another Green Revolution,” he added. “I think that indoor agriculture plays a huge role in that. So, the 40,000 feet in the air perspective is it’s not just about supporting local demand for food, it’s about controlling the environment completely. This means eventually taking things out of the field entirely and putting them indoors.”
Bringing a high-flying idea back down to Earth
While the upstart vertical farming community largely agrees with Storey’s stance, there also exists a wing of detractors who point to indoor farming’s inefficiencies.
The loudest voice among these critics is former United States Department of Agriculture biologist Stan Cox. After serving for the USDA for 13 years as a wheat geneticist, Cox joined the Land Institute as a senior scientist in 2000, specifically focusing on plant breeding in greenhouses and fields. An author of several books looking at the past, present, and future of all things agriculture and food, Cox is an expert in the field — which is why his view of vertical farming as a scam is a perspective that should give anyone pause.
“This will never be able to supply any significant percentage of our food needs.”
Vertical farming’s largest hurdle — a concept Cox thinks should’ve “collapsed under its own weight of illogic” and that he says remains incredibly difficult to overcome — concerns its scale. Cox posits that to be truly effective, vertical farms would require an incredible amount of floorspace. Despommier envisions indoor farming as a means to avoid the degradation of soil, but turning currently cultivated land into soil-preserving indoor farms would require an almost unfathomable amount of space.
To get a true picture of this, Cox breaks down the floorspace requirement for growing just vegetables — which clocks in at roughly 1.6 percent of cultivated land in the U.S.
While that number may not sound like much, turning that 1.6 percent of cultivated land into a functioning indoor or vertical farming operation demands the relative floorspace of around 105,000 Empire State Buildings. As Cox also points out, even with that much dedicated space, 98 percent of U.S. crops would continue to grow at outdoor farms.
“A colleague and I originally did some back of the envelope calculations that show if we grew grain- or fruit-producing crops [in vertical farms], it would take half of the country’s electricity supply or tens of thousands of Empire State Buildings,” Cox told Digital Trends. “These huge numbers would show that this may be fine for growing, on the small side, fairly expensive leafy greens to be used in restaurants or local areas. But the two things we have to always keep in mind is the amount of energy and resources being put into each unit of food, and the second is the scale. This will never be able to supply any significant percentage of our food needs.”
Despite Cox’s calculations painting a grim picture for large-scale urban production of grain or vegetables, he did emphasize that he’s “all for” urban gardening, or growing food as close to a population center as possible. To Cox, it just “makes sense.” Unfortunately, small urban gardening operations won’t likely have any shot at replacing the more than 350 million acres of rural U.S. cropland that consistently churn out America’s food supply.
“We can only grow enough crops within cities to substitute for a very tiny portion of [our food supply],” Cox added. “We’re still going to depend on rural America for growing the bulk of our food. There’s no big problem with that, really. We certainly want for perishable food, like fresh produce, to grow as much as we can close to where we live. But for grains, dry beans, food legumes, oil seeds, quinoa, all of these dry, nutrient-dense foods with a lower moisture content that can be shipped with very little energy or cost (by rail), that’s still going to be grown around our rural areas.”
Plain and simple, Cox doesn’t see a way around the issue of energy as it pertains to vertical farms — at least for the sustained growth of something like grains or fruit. Because leafy greens require less light to grow sufficiently, it makes much more sense to operate vertical farms geared solely around these foods. Conversely, growing something like corn or wheat — which produce much more dry matter — just doesn’t seem like a feasible option if there’s an intention to keep energy, production, and food costs down.
Growing up: The future of vertical farming
With the vertical farming industry still very much in its infancy, its future remains somewhat murky. Despite the growing number of startups committed to nurturing the idea, its hindrances and drawbacks pointed out by critics like Stan Cox carry just as much clout. Because of this, it’s hard to confidently put stock in either its failure or success.
“The Achilles’ heel of vertical farming or gardening is that it just does not work out energetically.”
Vertical farming’s best shot at a lasting legacy may be to simply pump the brakes on continued advancement. As it stands today, the startups that currently run operations geared toward producing heaps of leafy greens might want to think long and hard about introducing anything capable of completely shutting down momentum — i.e., fruits, grains, etc. In this case, energy usage is the bane of vertical farming’s existence.
“The Achilles’ heel of vertical farming or gardening is that it just does not work out energetically,” Cox points out. “The amount of energy put into [vertical farming] per unit of food you get out of it is very tiny. That’s why almost everything you see being grown this way is some type of leafy green that doesn’t require as much light to produce.”
Now, this isn’t to say vertical farming won’t continue to exist, or even that any of the startups dedicated to its advancement won’t try to introduce fruit or grain to their production. Perhaps there comes a time when someone finds a solution to the energy dependence issue, but for now, leafy greens are the vertical farming industry’s ceiling.
Dr. Nate Storey is the founder of BrightAgrotech — a company that designs and develops vertical farming technologies, such as the ZipGrow hydroponic system pictured above. (Credit: Bright Agrotech)
First Large Scale Commercial Vertical Farm in Europe To Be Set Up in The Netherlands
First Large Scale Commercial Vertical Farm in Europe To Be Set Up in The Netherlands
Farm to serve one of Europe’s biggest supermarket chains with fresh-cut lettuce grown using LED horticultural lighting
Eindhoven, the Netherlands – Philips Lighting (Euronext Amsterdam ticker: LIGHT), a global leader in lighting, today announced that Staay Food Group, a leading fresh fruit and vegetables company, is building the first of its kind vertical farm in Europe, in Dronten, the Netherlands, which will use Philips GreenPower LED horticultural lighting. The facility will serve one of Europe’s biggest supermarket chains and will be used for testing, and optimizing processes for future, large vertical farms.
Ahead of new legislation
The 900m2 indoor vertical farm will have over 3,000m2 of growing space and produce pesticide-free lettuce. With upcoming stricter regulations on the residual pesticide levels in a bag or bowl of lettuce, retailers will need to provide exceedingly high quality, pesticide-free lettuce.
Defining growth recipes
Staay, Philips Lighting and vegetable breeder Rijk Zwaan collaborated and undertook intensive research over the past three years to determine the best combination of lettuce varieties and growth recipes to improve crop quality and yields. Having the right growth recipe prior to the start of operations at the vertical farm will help Staay achieve a faster return on investment.
“Our plant specialists at our Philips GrowWise research center in Eindhoven are testing seeds from a selection of the most suitable lettuce varieties, to define the best growth recipes and to optimize crop growth even before the farm is running,” said Udo van Slooten, Managing Director of Philips Lighting Horticulture LED Solutions.
Sustainable growth
“Producing lettuce for the fresh-cut segment indoors not only means avoiding all pesticides, it also means a much lower bacterial count and therefore longer shelf life at the retailers. With the lettuce being packaged at the same spot as where it is grown, we save on transport before distribution to retailers,” says Rien Panneman, CEO of Staay Food Group. “Also, by avoiding weather fluctuations, we maintain an optimized and stable production environment to guarantee consistent and optimal product quality.”
Looking for the best varieties
Wim Grootscholten, Marketing and Business Development Manager of Rijk Zwaan, worldwide market leader in lettuce seeds said: “The tests we are conducting within this project are enabling us to identify which varieties are optimal for growing in a vertical farm, and also which varieties offer the best taste and texture. It will help us with our continuous challenge to offer solutions for the growing world population. We believe that vertical farms will become increasingly important, because in the future we see more economic and environmental pressure to produce fruit and vegetables, such as lettuce, closer to where end-customers are located.”
First of its kind
The vertical farms in Europe, using LED-based lighting have so far been research centers or specialist producers serving restaurants. The new Staay facility in Dronten will be the first in Europe to operate commercially, serving large-scale retail. The facility will start operations in the second half of 2017.
About Philips GrowWise
Philips GrowWise Center in Eindhoven, the Netherlands, is the largest research facility of its kind with a total growing surface of 234m2. Here, Philips Lighting’s researchers trial a variety of crops under different LED lighting and climate conditions to help determine their economic potential. Vertical farming investors and operators can visit the facility to see demonstrations of different vertical farm technologies, taste crops grown under LED lighting and discuss the economic viability of the technology used.
For further information, please contact:
Philips Lighting Global Media Relations
Bengi Silan Genc
Tel: +31 6 25441798
E-mail: bengi.genc@philips.com
Philips Lighting; Horticulture LED Solutions
Daniela Damoiseaux, Global Marcom Manager Horticulture
Tel: +31 6 31 65 29 69
E-mail: daniela.damoiseaux@philips.com
Fresh-Care Convenience (member: Staay Food Group)
Marco Kleijn, Managing director Fresh-Care Convenience
Tel: +31 321 382 308
E-mail: marco.kleijn@fresh-care.nl
www.staayfoodgroup.com
Rijk Zwaan
Ton van Leeuwen, Communication Specialist
Tel: +31 174 532 487
E-mail: t.van.leeuwen@rijkzwaan.nl
www.rijkzwaan.com
About Philips Lighting
Philips Lighting (Euronext Amsterdam ticker: LIGHT), a global leader in lighting products, systems and services, delivers innovations that unlock business value, providing rich user experiences that help improve lives. Serving professional and consumer markets, we lead the industry in leveraging the Internet of Things to transform homes, buildings and urban spaces. With 2016 sales of EUR 7.1 billion, we have approximately 34,000 employees in over 70 countries. News from Philips Lighting is located at http://www.newsroom.lighting.philips.com
About Staay Food Group
Staay Food Group is the fresh fruit and vegetables company in which centralized policy, marketing and sourcing control is supplemented by local expertise in growing and sales. Since 1946, we have delivered a wide range of excellent quality fresh fruit and vegetables worldwide. In response to supply chain integration, Staay Food Group positions itself closer to the growing process by cooperation and participation. Our regional offices closely monitor the growing process and the direct deliveries to customers.
About Rijk Zwaan
Rijk Zwaan develops vegetable varieties and produces seeds, which it sells in more than 100 countries. The family-owned company is amongst the top five in the global vegetable seed market and is characterized by a people-focused approach. More than 2,600 employees in over 30 countries work enthusiastically to provide products and services that add value for the market. The company has its headquarters in De Lier, The Netherlands.
Vertical Farming Grows Up And Comes Of Age
Vertical Farming Grows Up And Comes Of Age
Growing food without sunlight or soil is now a reality, but the economics leave little room for error
By Jennifer Blair Reporter
Published: April 25, 2017
Partners Wayne Lohr and Ulf Geerds have turned their extensive experience in agriculture and horticulture into a growing vertical farming venture near Olds. Photo: Jennifer Blair
Olds-area greenhouse operator Wayne Lohr and business partner Ulf Geerds are dreaming big — they want to grow an acre of strawberries.
That may not sound like a big deal until you consider that acre will take up just 360 square feet and produce strawberries year round. And even though they’re grown in racks on a shed, these berries will, the duo says, taste just as good as ones picked fresh in the field on a nice summer day.
“They taste like they’re from the field because they actually get the same treatment as from the field. We mimicked the environment that’s outside,” said Geerds.
“At the end, you’ll end up with a crop that has the same taste as from the field, but you can have it year round.”
The duo is talking about vertical farming, a relatively new industry birthed by the advent of LED lights and ‘aeroponics’ — rather than soil and sunlight — to produce fruit and vegetable crops in a small indoor area.
What was, until fairly recently, the stuff of science fiction is now a reality. Sales of produce grown via this method topped US$1 billion in 2015, and with production increasing by nearly 30 per cent annually, sales are forecast to surpass $15 billion by 2025.
And although it’s touted as a way to grow food in cities (as well as in countries where land is in short supply), vertical farming has also arrived in Alberta. And it’s winning over traditional growers such as Lohr and wife Carolyn, who have been in the greenhouse business (mostly growing ornamentals) since 1982. They got into vertical farming a year and a half ago, forming Lohr-A-Lee Indoor Gardens with Geerds and his wife, Sangeetha Varghese.
They started small, with two integrated upright systems purchased from Indoor Farms of America. The vertical panels take up a floor area of about 16 square feet in one of Lohr’s outbuildings, and have 650 plants in total. That’s an incredibly dense 40 plants per square foot of floor space — normally strawberries need one square foot per plant. At that density, their plan to scale up to 360 square feet will give them the equivalent of an acre of strawberries. (Aeroponics means there is no growing medium and roots are kept moist by misting.)
Lohr-A-Lee Indoor Gardens started small with its system, with plans to scale up with an additional 24 panels in the next few months.photo: Jennifer Blair
The pair has tried their hand at lettuce, basil, kale, arugula, Swiss chard, and bok choy, but so far, strawberries are the real star. There are no weather, disease, weed, or insect pressures, and with “total control of the environment,” the strawberry plants will grow for up to 14 months before needing to be replaced. Normally, the growing season for strawberries is two months, so the potential yield per plant is much higher.
“Effectively, you create an environment that’s consistent, so as far as this plant’s concerned, it’s July 15 every day,” said Lohr. “The target is to get four pounds per plant per year. We feel that that’s more than achievable. That’s the target. The goal is to beat it.
“We don’t need to import this stuff. We can grow it here.”
‘Lots of unknowns’
Despite their belief in vertical farming’s future, both men warn that this is not a way to make a quick buck.
That view is echoed by horticulture consultant Cees VandenEnden, owner of HortiSource Consulting in Mountain View County.
“I truly believe that 50 per cent — or maybe even more — of the startups will not see their fifth anniversary,” VandenEnden said at a workshop last month. “There are plenty of opportunities. I’ll be the last one to say this is not working. But there are some big question marks.”
But VandenEnden is being “optimistic,” said Lohr, who expects 80 to 90 per cent of startups will fail in their first year.
While vertical farming has many attributes — including a reduced carbon footprint, zero pesticide use, high nutritional value, good water-use efficiency, and local production — anyone taking a “romanticized” view will be in for a rude awakening, said Geerds.
VandenEnden agrees.
“There’s a lot going on, and I think it has a lot of potential — it’s ‘sexy,’” said VandenEnden. “In the public mind, local produce and knowing your producer is good.
“(But) this piece of the industry is attracting people who have no agricultural background and no growing knowledge. Your learning curve is tremendous and very costly. There are hyped-up expectations, and your startup cost is high. Making an income is not easy.”
In addition to the typical challenges associated with agriculture, such as labour and marketing, vertical farming comes with its own set of problems, including picking the right growing system, climate controls, light sources, watering systems, and product mixes.
“There’s a lot of thinking and problems to solve,” said VandenEnden.
“At this point in time, it’s new, so we do not know what works and what doesn’t,” added Geerds.
Ready for takeoff
Figuring out the market is even trickier. Geerds points to lettuce, which is an “easy” crop to grow.
“Lettuce grows very well in here. In 26 days, we have a crop that we can sell, but the demand is not there,” said Geerds. “We want to grow what the market wants. Strawberries make a lot of sense to us because there’s a high demand and the quality is very poor from the imports.”
Lohr and Geerds have partnered with a retailer for “significant volumes of strawberries weekly” for a small price premium.
“We’re getting a reasonable premium over what they’re paying wholesalers, but it’s not huge,” said Lohr. “Economics will ultimately take the premium away, so it comes down to production efficiencies and cost efficiencies.”
VandenEnden predicts the fledging industry will quickly scale up.
“It took over 100 years for the greenhouses to go from small entities to the big greenhouses you see nowadays,” he said. “But (vertical farming) will not take 100 years to get to that point. It’s probably closer to five years or maybe even faster.
“When that volume comes on the market, your premium prices are gone. You’ll have to produce for regular market prices.”
Competition is already growing in Alberta, he added.
“I was surprised to learn how many people are already doing this in Alberta. That will only increase,” said VandenEnden. “Big producers will develop fairly soon, and they will basically drive the prices.”
When that happens, production will be “the least of your problems” when compared with marketing, he said.
“It takes time to grow, but it takes a lot of time to market as well,” he said. “I’ve seen very few people who are excellent at growing and do a good job of marketing, too. Most of the time, one of the two is mediocre.”
But ultimately, marketing vertically farmed produce is much the same as marketing any other crop, said Lohr.
“Know what it costs you to produce it, know what kind of returns you want, and that tells you what price you need to make money.”
A costly venture
Production costs will vary based on the crop and the system used to grow it.
“If a traditional crop costs $1 to produce, the closed environment systems are costing between $1.40 and $2,” said VandenEnden. “That’s something we have to work on because that is not sustainable.”
Generally, the cost of equipment is related to the size of the system, he added, and there will be power and labour costs on top of that.
“With the right setup, there are good prospects, but what is the right setup? You need to go over that in your mind to make the right decision,” said VandenEnden.
Geerds agrees.
“You can pretty quickly sink a lot of money into the system, and if you don’t do it right, you will definitely lose.”
Producers should look at the price per square foot of growing area rather than simply the price per square foot when costing out a system, said VandenEnden. Because vertical panels do more with less space, the growing area square footage is typically about double the actual square footage. The panels at Lohr-A-Lee Indoor Gardens cost $8,800 each, and Lohr and Geerds are in the process of scaling up with an additional 24 panels.
“It’s not cheap, and it does scare the financial world. The big system that would go in the whole building is about the same dollars as a new combine today,” said Lohr.
Each vertical panel, which costs $8,800 each, can accommodate around 325 plants, or 40 plants per square foot.photo: Jennifer Blair
“We’ve done some pretty elaborate cash flow projecting but again, you’ve got to look at this on a per-plant basis. They’re still big numbers and the bill still has to be paid, but on a per-unit basis, it’s not near as scary.
“The ROI is definitely there. You’ve just got to make it produce.”
The test unit they’ve been running for the past year has helped them verify their cost of production — data that isn’t available for this new type of farming.
“Because it’s the first commercial system that we’ll have, the next system will tell us, do we make money or don’t we?” said Geerds, adding they have a few other ideas of crops they can try if strawberries don’t pan out.
“We’ve talked to a lot of people who want to grow very big very fast. I don’t think that’s the right way to approach it. You have to find the sweet spot. You don’t want to be too small but because the science is just developing, we have to really see where the sweet spot is. We’re not sure what that is yet.”
Lohr’s advice is to “start small and learn as you go.”
“Do your homework. Otherwise, there’s going to be a lot of roadkill.”
Vertical Farming: A Better Option
Vertical Farming: A Better Option
By Emily Williams, Columnist | Apr 25, 2017 | Opinion, Opinion Columns |
We need to rethink industrialized factory farming and quick. The agricultural revolution boomed back in the 18th Century which allowed the industrial revolution to change the world we lived in. So, this is a good thing with more access to food, food produced on higher levels and a decline in world hunger, right?
Wrong.
The agricultural revolution not only ruined the society humans had been living in for thousands of years, but it took our environment into a downward spiral that we may not fix in time. The agricultural revolution sparked war between mankind on drastic levels since it was one of the first times we as a species started assigning ownership to land.
If we weren’t killing each other, the diseases spread by factory farming were. The domestication of animals was needed for living purposes, but on the massive levels we’ve allowed to be perceived as appropriate have caused an influx of diseases carried by our animal friends.
Influenza, TB, smallpox, Measles and even the common cold are all linked back to the domestication and farming of livestock. But let’s argue for a second, the domestication and cultivation of animals in small populations allowed the human population to grow. That’s great, we’re living and able to reproduce at rates higher than we were dying.
But we were still dying. Hunter and gatherers shifted camps quickly and effectively. The quick rise in populations allowed us to establish villages and cities which ended up doing more harm than good. We created perfect living petri-dishes for microbes and diseases to spread. We may have been reproducing at large rates due to the advancements made with farming and domestication of meat, but death was occurring at the same rate. Our life-span declined drastically for a long time.
Sounds great.
We’ve moved on from disease altering life-spans and have outsmarted microbes like the common cold and smallpox for the most part. What has factory farming done to the environment? Not only did we introduce foreign species of plants and grasses but we allowed our carbon footprint skyrocket with meat production worldwide having quadrupled in the last 50 years.
Globalagriculture.org breaks it down for us easily: in 2014 meat production reached a high of around 315 million tons. An estimation of 450 million tons will be produced by 2050 yearly. Cows, pigs and chickens, the top three livestock handled in factory farming, have increased by over 50% percent in population for each animal, chicken an upward of 114%.
In 2016, 164 million metric tons of CO2 and methane gasses were produced by livestock in the world, and meat makes up 47.6% of greenhouse gasses from average food consumption based on the factsheet produced by the University of Michigan in August 2016 for U.S. households.
So, what is the future of farming if we want to somehow protect our environment that is deteriorating away? The future of farming is: well… not any kind of farming we’ve become comfortable with. Farms are businesses, and ones that are becoming less and less valuable unless you’re at the head of a factory farm rolling in the bundles of money you make. It’s also clear that as a society we are obsessed with technology.
Our world is crying out for help in the way we’ve destroyed it, and our global size is demanding a new revolution in our agricultural system. The technology is here, we just need to stand behind it and support it. Companies like AeroFarms, FreightFarms, and BoweryFarming have the right idea.
They’ve taken farming on land and put it inside. Vertical farming is what we need, and it works. It allows produce to be aligned in a systematic way for the purest and cleanest forms to be grown. Conditions can be manipulated for produce to be grown all year long and without the use of pesticides and fertilizer since variables can be changed and controlled easily.
These farms are able to exist in any urban environment, unlike the agricultural system we have now that takes up hundreds of acres. Not only is it using less space, farming like this uses less resources too. Bowery states they use 95% less water than traditional agricultural farming and produce 100x more on the same footprint of land.
Less CO2 emissions, less harm with fertilizers and pesticides and a more effective urban setting with farming is what we need to help the environment. There would be less demand for deforestation, and species affected by pesticides like the bees and butterflies would be able heal.
Let’s take a stance against factory farming and look at what we can do to change the way we’re treating the world. Start buying from your local farmer’s market, Oxford is a fantastic place to start. Findley Market isn’t a far drive either! Decreasing your meat intake by even one day a week and combining it with buying produce at a local market and these steps with help us heal the environment we’ve … well, trashed.
taylo193@miamioh.edu
This Incredible Vertical Farm Skyscraper Could Feed An Entire Town
Every year, the design magazine eVolo holds a competition for the most ground-breaking skyscraper concepts.
This year's first place winner is the Mashambas skyscraper, a vertical farm tower that would be able to feed an entire town in sub-Saharan Africa. The conceptual skyscraper could also be disassembled, and moved to different locations where communities need it.
This Incredible Vertical Farm Skyscraper Could Feed An Entire Town
- Leanna Garfield
- Apr. 25, 2017, 10:58 AM
Pawel Lipiński and Mateusz Frankowski
Every year, the design magazine eVolo holds a competition for the most ground-breaking skyscraper concepts.
This year's first place winner is the Mashambas skyscraper, a vertical farm tower that would be able to feed an entire town in sub-Saharan Africa. The conceptual skyscraper could also be disassembled, and moved to different locations where communities need it.
Designed by Polish architects Pawel Lipiński and Mateusz Frankowski, the tower would grow produce on the upper floors and would come with fertilizer and seeds. The other floors would feature kindergarten classrooms, a doctor's office, and even a docking port for drones that would deliver food to hard-to-reach areas. The ground floor would include an open-air market, where farmers could sell their crops.
Part of the tower would be made of modular pieces, which would allow it to be taken apart and transported somewhere else. (Though, the designers do not say how long that process would take.)
Pawel Lipiński and Mateusz Frankowski
"The main objective of the project is to bring this green revolution to the poorest people," Lipiński and Frankowski write. "Giving training, fertilizer, and seeds to the small farmers can give them an opportunity to produce as much produce per acre as huge modern farms."
Its name, Mashambas, is a Swahili word that means cultivated land, Lipiński and Frankowski write. The goal of the tower would be to bolster agricultural opportunities and fight hunger in impoverished towns in African countries.
Pawel Lipiński and Mateusz Frankowski
"When farmers improve their harvests, they pull themselves out of poverty. They also start producing surplus food for their neighbors. When farmers prosper, they eradicate poverty and hunger in their communities," the designers write.
Though he share of Africans living in poverty declined from 56% to 43% from 1990 to 2012, many more African people are poor today due to population growth, according to a recent World Bank report.
"Today hunger and poverty may be only African matter, but the world’s population will likely reach nine billion by 2050. Scientists warn that this would result in global food shortage," the designers write. "Africa’s fertile farmland could not only feed its own growing population, it could also feed the whole world."
Pawel Lipiński and Mateusz Frankowski
Announced April 10, the tower was chosen from a pool of over 400 entries. Though the designers did not name an exact site for a Mashambas skyscraper, they said the first one could be in a town south of the Sahara desert. The design is merely a concept right now, and there are no plans to actually build one.
Though the design is certainly far-fetched, the vision behind it explores what rural farms of the future could look like.
Indoor Farmers Face Uncertainty Over Organic Labeling
The National Organic Standards Board have kicked the can down the road on hydroponic and aquaponic farming. The group was supposed to decide on April 21 if the systems can be considered organic. The only decision they made was to learn more about the farming process and have pushed their decision until the fall.
APR 24, 2017 @ 06:03 PM
Indoor Farmers Face Uncertainty Over Organic Labeling
Debra Borchardt , CONTRIBUTOR
Opinions expressed by Forbes Contributors are their own.
Indoor farms can stack plants vertically and grow more crops than a traditional outdoor farmer. (Photo by Shutterstock)
The National Organic Standards Board have kicked the can down the road on hydroponic and aquaponic farming. The group was supposed to decide on April 21 if the systems can be considered organic. The only decision they made was to learn more about the farming process and have pushed their decision until the fall.
This has left current hydroponic and aquaponic farmers that consider themselves organic in limbo. They can continue to call themselves organic until a decision is reached, but in the meantime the uncertainty is troubling.
“It's more about organic, certified farmers wanting to maintain their market share,” said JP Martin of GrowX, an aeroponic farming system. “The fertilizers are identical,” he said, “So the argument that they use different nutrients breaks down.”
Terra Tech is an indoor farming company that grows leafy greens and its crop that has some soil exposure has been certified organic. Chief Executive Officer Derek Peterson said, "If they came back and had some sort of ruling that disallowed organic, it would be tremendously hurtful. We would lose shelf space." He noted that the demand for non-organic produce continues to drop because the price premium is down for organic. "It's more affordable so the demand has increased," he said.
He's right. The market has grown tremendously. The USDA said that there was a 13% increase between the end of 2015 and 2016 of organic farms. This is the highest growth since 2008.
The point of contention is whether food grown without soil can be considered organic. The USDA admits that obtaining organic certification for crops is challenging and the guide is over 60 pages long. There is a lot of detail regarding the soil, but there isn't a hard and fast rule that the food must be grown in soil.
“It's really about where the nutrients are coming from and less about the methodology,” said Martin. He said it just boils down to money and market share because hydroponic farming has been around for years. If anything, the indoor farming is much more organic than outdoor farming according to Martin.
5 Control System Questions With Darryn Keiller of Autogrow
5 Control System Questions With Darryn Keiller of Autogrow
Darryn Keiller, CEO of control company Autogrow, came to the company from a consulting background, and has led the New Zealand-based company to a sub $3mn equity raise since taking the helm. Ahead of his presentation at Indoor Ag-Con on May 3-4, we caught up with Darryn to ask him about big data and the future of controls in controlled environment agriculture.
1. Autogrow has created a dedicated system – RoomBoss – for controlled environment applications. What drove you to do that?
Market need. Urban and vertical systems are on the rise; from a control and automation perspective innovators in this space have either a) been sourcing from industry vendors existing technology created for Greenhouse production or b) building their own. What is needed is a technology approach that is purpose designed for systems using LED / HPS grow lights, CO2 management and integrates dosing control and all other automation requirements. The Room Boss is a Beta product that also anticipates controlling automated harvesting and robotics. It’s an Internet of Things based platform, not just a device.
2. How much of the hoopla over the application of big data in the industry is well-founded and how much is just hype?
Certainly, there is no shortage of hype. Along with machine learning, deep learning, etc. in every other sentence. The opportunity to apply these data methodologies and techniques to solve real world problems in agriculture is real. The time-line to make these effective and beneficial on a prolific basis is a lot longer than everyone would like. Part of this is due to the slow rate of market adoption and part of it is the technology development itself. Its potential is well-founded.
3. What’s the most common mistake you see beginning farmers make when picking a control system?
The first thing is considering the control and automation side of things last – this happens all the time. And it then leaves the farmer trying to find a solution with what’s left of their budget. Automating your production is key to consistently great crops and profitability through using less labour and managing inputs like water, energy and nutrients. The second part is thinking ahead – if you purchase a limited system now, then what happens when you decide to scale your operations? Sometimes spending a little more now is better than having to “rip and replace” technology later. The approach is to obtain technology that is flexible and modular, that grows as you grow.
4. What do you expect control systems to look like in five years’ time?
I expect most indoor growing environments will be fully automated with no human component except pre-planting and post-harvest. All automation and control to be cloud delivered and all physical automation will be carried out through a variety IoT devices and multi-functions sensors. This will include automated robotic harvesting – it’s already here when you look at examples like Urban Crop Solutions of Belgium or integration of machine vision solutions for crop monitoring, pest and pathogen detection as examples.
5. What’s the biggest advantage that being a Kiwi gives you?
We’re a nation of innovators, inventors and entrepreneurs – it’s how Autogrow began 24 years ago. As a nation, we have a deep history in horticulture, agriculture and pastoral production including R&D in genomics, biologics and technology. We even have our own Rocket company which despite the name was founded and is based in New Zealand. A nation of 4.5m we feed 40m people, exporting 95% of what we produce to 100 countries, every month, including beef, wool, seafood, dairy products and fruit. Because of our location, we travel the World and we embrace the idea of boundarylessness – no limits! Autogrow now exports to 30 countries around the globe.
SEE DARRYN SPEAK AT THE 5TH ANNUAL INDOOR AG-CON ON MAY 3-4, 2017
Indoor Ag-Con Features Container Farm Tours From Indoor Farms of America & Modular Farms
Indoor Ag-Con Features Container Farm Tours From Indoor Farms of America & Modular Farms
Indoor agriculture's premier conference now features tours of live vertical farming operations on site, as well as 50+ exhibition booths & 40+ speakers
We’re excited to have our participants experience these farms on site”
— Nicola Kerslake, Founder, Newbean Capital
LAS VEGAS, NEVADA, USA, April 24, 2017 /EINPresswire.com/ -- Farm tours are a popular feature of agriculture trade shows, but Indoor Ag-Con – the indoor agriculture industry’s premier conference – likes to do things a little differently. It will instead be featuring two container farm tours at its next event, at the Las Vegas Convention Center on May 3-4, 2017.
The tours will be operated by two leading container farming equipment suppliers, Indoor Farms of America and Modular Farms. Their staff will be on hand from 8.30am to 5.30pm on each of May 3 and May 4 to walk participants through the farms and answer questions about their equipment. Their farming approaches are quite different from one another, and will allow participants to identify the best fit for their vertical farming needs. “We’re excited to have our participants experience these farms on site” commented Nicola Kerslake, founder of Newbean Capital, the event’s host.
Indoor Farms of America is based in Las Vegas, NV, and utilizes vertical aeroponic technologies in its container farm products, which range from the truck-mounted farm that it will be showcasing at Indoor Ag-Con to a farm specially adapted to meet the needs of disabled veterans. The farms offer 40 plants/ft2 of grow area, are designed to be used in both controlled environment and greenhouse settings and use just 3% of the water of a traditional farm. It recommends that customers grow leafy greens, herbs, chili & sweet peppers, peas, strawberries, cherry tomatoes and beans in its systems, and is continually adding more crops to the list. The Company’s website is at www.indoorfarmsamerica.com.
Canadian Modular Farms has developed a series of modular units, such as, ones for refrigerated storage and for growing microgreens, that work with its primary unit, a specially designed 40’x10’x10’ composite steel box. The eight unit options can be combined to create the optimal farm for each customer. Its units are based on hydroponic growing and include ZipGrow towers, with over 300 towers packed into its production-only macro farm unit. The Company’s website is at www.modularfarms.co.
The farms will be displayed at Indoor Ag-Con, a two-day event held at the Las Vegas Convention Center, and tailored toward corporate executives from the technology, investment, vertical farming, greenhouse growing, and food and beverage industries, along with hydroponic, aquaponic and aeroponic startups and urban farmers. The event is unique in being crop-agnostic, covering crops from leafy greens and mushrooms to alternate proteins and legal cannabis.
The farms will join industry majors such as Argus Controls, Autogrow, BrightFarms, Certhon, Dosatron, DRAMM, Hort Americas, Philips Lighting, Priva, and Transcend Lighting in a 50+ booth exhibition hall. The event includes two full days of speakers, including executives from CropKing, Driscoll’s, Fresh Box Farms, Grobo, Helical Holdings, Intravision, Kalyx Development, MedMen, Plenty, Shenandoah Farms and Village Farms among a 40+ strong speaking faculty.
Indoor Ag-Con has also hosted events in Singapore, SG and New York, NY in the past year, and is currently planning its first event in Dubai. Since it was founded in 2013, Indoor Ag-Con has captured an international audience and attracted some of the top names in the business. Events have welcomed nearly 2,000 participants from more than 20 countries.
Newbean Capital, the host of the conference, is a registered investment advisor; some of its clients or potential clients may participate in the conference. The Company is ably assisted in the event’s production by Rachelle Razon, Sarah Smith and Michael Nelson of Origin Event Planning, and by Michele Premone of Brede Allied.
5th Annual Indoor Ag-Con
Date – May 3-4, 2017
Place – South Hall, Las Vegas Convention Center, Las Vegas, NV
Exhibition Booths – available from $1,499 at indoor.ag
Registration – available from $399 at indoor.ag
Features – Two-day seminar, an exhibition hall, and after-party
For more information, please visit www.indoor.ag/lasvegas or call 775.623.7116
Nicola Kerslake
Newbean Capital
775.623.7116
email us here
Rice U. Team Cultivates Ideas For Indoor Farming
Rice U. Team Cultivates Ideas For Indoor Farming
APRIL 12, 2017POSTED IN: NEWS RELEASES
David Ruth - 713-348-6327
david@rice.edu
Mike Williams - 713-348-6728
mikewilliams@rice.edu
Rice U. team cultivates ideas for indoor farming
Hydroponic garden graces university’s Oshman Engineering Design Kitchen
HOUSTON – (April 12, 2017) – Some engineering design projects click, hum or make no sound at all. Lettuce Turnip the Beet may be the first at Rice University to gurgle.
“The pumps are always going,” said design team member Dominique Schaefer Pipps. “The water never stops moving, keeping the plants alive.” The punningly named Team Lettuce Turnip the Beet has designed and built what is known technically as a “produce cultivation machine,” which resembles an oasis of greenery at Rice’s Oshman Engineering Design Kitchen (OEDK).
Sprouting from tiers of PVC pipes are lettuce, garlic and other vegetables, grown hydroponically — that is, without soil — and kept fresh by a pump circulating 55 gallons of water. The project was commissioned by a “zero-resource house” on the campus of Chalmers University of Technology in Gothenburg, Sweden. Previously, Chalmers partnered with another Rice team to create BioBlend, a variation on the in-sink garbage disposal that separates food waste from water and simplifies the composting process.
“The emphasis is on using as few resources as possible, using little energy and wasting nothing,” said Sanjiv Gopalkrishnan. He and Schaefer Pipps, along with team members Jared Broadman and George Dawson, are all seniors in mechanical engineering at Rice.
Dominique Schaefer Pipps tends to her team’s hydroponic experiment, a capstone design project required of most senior engineering students at Rice. Photo by Jeff Fitlow
The team achieved its goal to produce sufficient food to make one salad per week for one year, all in an apartment environment. The original prototype was built last November after two months of brainstorming. It’s a much bulkier, space-consuming model and has been moved outdoors to a fenced-in area behind the OEDK. It remains overgrown with sprawling tomato plants, broccoli and Swiss chard.
“We wanted to minimize power consumption and environmental impact, but maximize nutritional content and yield,” Dawson said. “The machine should coexist with humans in a rather small living environment. Noises, lights and smells shouldn’t interfere with the sleep cycle or life in general, and basic maintenance should be kept simple.”
According to the team, the device consumes about 900 watts, about as much power as a microwave or medium window air conditioner, and runs off one outlet even after replacing fluorescent lights with LED growing lights to improve the health of plants farther away from the fixtures.
The new prototype stands 8 feet tall, but its wooden frame and six levels of vinyl pipes are nearly flush with the wall. The biggest change is using square rather than round plastic pipes, which have a larger internal surface area and move more water. The frame is held together with pegs and friction and uses no glue or nails; the entire device weighs around 70 pounds.
George Dawson, a member of Lettuce Turnip the Beat, a senior engineering design team at Rice, works on its hydroponic garden. The team’s initial goal was to produce sufficient food to make one salad per week for one year in an apartment environment. Photo by Jeff Fitlow
“That makes transporting it easy. We have to get it to Sweden. This is like Ikea for toddlers, with really big parts,” Broadman said.
The team will install sensors to automatically monitor pH levels, nutrients, temperature and other factors before the device is installed in Sweden. The current setup uses one reservoir but the students expect a multiple-reservoir system, each with varying levels of nutrients, could permit fine-tuning the nutrient requirements of various plants.
The team is advised by Matthew Elliott, a lecturer in mechanical engineering, who said, “My job is easy. We meet once a week for updates. The students have taken care of everything.”
Team Lettuce Turnip the Beet will compete in the annual George R. Brown School of Engineering Design Showcase at Rice University’s Tudor Fieldhouse April 13. The showcase opens to the public at 4:30 p.m.
-30-
See the team’s web page at http://oedk.rice.edu/Sys/PublicProfile/34366121/4029765
Follow Rice News and Media Relations via Twitter @RiceUNews
Video:
Video produced by Brandon Martin/Rice University
Related materials:
Oshman Engineering Design Kitchen: http://oedk.rice.edu
George R. Brown School of Engineering: https://engineering.rice.edu
Images for download:
http://news.rice.edu/files/2017/04/0417_LETTUCE-1-web-1knd3s0.jpg
Rice University engineering students created a produce cultivation machine at the Oshman Engineering Design Kitchen on campus. From left: Jared Broadman, George Dawson, Dominique Schaefer Pipps and Sanjiv Gopalkrishnan. (Credit: Jeff Fitlow/Rice University)
http://news.rice.edu/files/2017/04/0417_LETTUCE-2-web-19ebcxm.jpg
Rice University engineering students expect to bring their hydroponic experiment to a “zero-resource house” on the campus of Chalmers University of Technology in Gothenburg, Sweden. (Credit: Jeff Fitlow/Rice University)
http://news.rice.edu/files/2017/04/0417_LETTUCE-3-web-1ep5mws.jpg
Dominique Schaefer Pipps tends to her team’s hydroponic experiment, a capstone design project required of most senior engineering students at Rice University. (Credit: Jeff Fitlow/Rice University)
http://news.rice.edu/files/2017/04/0417_LETTUCE-4-web-14oa51u.jpg
George Dawson, a member of Lettuce Turnip the Beat, a senior engineering design team at Rice University, works on its hydroponic garden. The team’s initial goal was to produce sufficient food to make one salad per week for one year in an apartment environment. (Credit: Jeff Fitlow/Rice University)
Located on a 300-acre forested campus in Houston, Rice University is consistently ranked among the nation’s top 20 universities by U.S. News & World Report. Rice has highly respected schools of Architecture, Business, Continuing Studies, Engineering, Humanities, Music, Natural Sciences and Social Sciences and is home to the Baker Institute for Public Policy. With 3,879 undergraduates and 2,861 graduate students, Rice’s undergraduate student-to-faculty ratio is 6-to-1. Its residential college system builds close-knit communities and lifelong friendships, just one reason why Rice is ranked No. 1 for happiest students and for lots of race/class interaction by the Princeton Review. Rice is also rated as a best value among private universities by Kiplinger’s Personal Finance. To read “What they’re saying about Rice,” go to http://tinyurl.com/RiceUniversityoverview.
- See more at: http://news.rice.edu/2017/04/12/rice-u-team-cultivates-ideas-for-indoor-farming/#sthash.yBzLqW2o.dpuf
For Earth Day, A Look Back At Some of The Best Green Building Designs
For Earth Day, A Look Back At Some of The Best Green Building Designs
April 22, 2017 04:00PM
It’s Earth Day, and there are plenty of ways to celebrate across the city. But while we’ve got you here, why not have a look back at some the most interesting green developments out there?
1. A proposed vertical farm on the High Line
This mixed-use concept at the Rem Koolhaas parcel at 511 West 18th Street would include residences, an art gallery and the kicker: 10 levels of indoor farming terraces. You can read more about the project here.
2. A “net-zero” public school
In 2015, city built a 444-seat Staten Island elementary school that runs solely on the energy it produces, in a project the developer calls a “laboratory for ideas for future construction.” Learn more here.
3. Green architecture
The infamous New York architect Robert Scarano, once banned from building in NYC after making false statements to the city to dodge zoning laws, is back and now he is building green. In 2014, his Brighton Beach project attempted to become the first multifamily structure to score a Living Building certification.
4. Hipster farmers
Eight floors above the ground at Barclays Center in downtown Brooklyn, workers at the condo building at 550 Vanderbilt Avenue are installing plots of soil on a south-facing terrace. The plots will allow residents to grow their own vegetables.
5. Design for modular green skyscraper wins competition
A conceptual high-rise intended for use in sub-Saharan Africa would taking farming vertical and help eliminate hunger. Now, the architects behind the tower, Pawel Lipiński and Mateusz Frankowski, have won the the eVolo Skyscraper Competition for their design. Check it out here.
6. A Parisian garden on top of an old car plant
Parc André Citroën opened for public use in 1992 and was built atop the old André Citroën car manufacturing plant, which functioned from 1915 to 1970. A large lawn anchors the park, while smaller structures like gardens, greenhouses, and meditative spaces act as the park’s border. It’s really beautiful as well.
7. A wooden skyscraper in London
London Mayor Boris Johnson just received a proposal to solve London’s eco-crisis: an 80-story eco-friendly skyscraper made of wood. The project would house hundreds of units of low-cost housing while becoming the second-tallest building in London behind the Shard.
8. A sustainable home within a greenhouse
Stockholm residents Marie Granmar and Charles Sacilotto live in what they call Naturhus – an environmentally friendly house built within a functioning greenhouse.
Civic Farms To Break Ground On 20,000 sq.ft. Vertical Farm At Biosphere 2
Civic Farms To Break Ground On 20,000 Sq. ft. Vertical Farm At Biosphere 2
Vegetables can soon be reaped again from the Biosphere 2 complex of the University or Arizona. Tomorrow, on Earth Day, Civic Farms will break ground for anew 20,000 sq. ft. vertical farm inside Biosphere 2’s West Lung.
Civic Farms has come to an agreement with the University of Arizona to lease the cavernous space for a nominal fee of $15,000 a year. The new vertical farming operation has announced that it will invest more than $1 million in the facility and dedicate $250,000 over five years to hire student researchers in conjunction with the UA’s Controlled Environment Agriculture Center.
The brain behind the project is Paul Hardej, Illumitex' VP of Turnkey Horticulture Lighting Solutions and former co-founder of the recently dissolved indoor grow op FarmedHere. Hardej unraveled his new plans this week in an article on Tucson.com. "Half the 20,000-square-foot space to be devoted to production, with areas given over to research and scientific education. A variety of leafy greens and herbs such as kale, arugula, lettuce and basil will be packaged and sold to customers in Tucson and Phoenix"
In the article on Tucson.com, Hardej furthermore said that he recognizes the irony of growing food in artificial light at the giant Biosphere 2 greenhouse. He is convinced, however, that growing plants with artificial lighting can become as economical as growing them in sunlight. "[Indoor] Farming is much more productive and much more predictable than in a greenhouse [...] A vertical farm can be 20 to 100 times more productive. The overall direction globally is indoors".
The Civic Farms groundbreaking ceremony will take place tomorrow the special Earth Day event at Biosphere 2.
Click here for the complete article on Tucson.com, which also features CEAC's Gene Giacomelli and Murat Kacira.
Publication date: 4/21/2017
This Japanese Smart Farm is Getting Even Smarter
This Japanese Smart Farm is Getting Even Smarter
By John Hopton
April 21, 2017
Perfect lettuce is grown with help from robots and the Internet of Things
For all Japan’s advancements, it is still common to see older people in the country bending over awkwardly in fields, picking crops by hand – a vision of the past. Twenty miles west of Kyoto, though, stands a smart farm that’s very much a vision of the future.
SPREAD‘s Kameoka Plant grows 21,000 heads of lettuce a day using multistage hydroponics and artificial lighting.
A network of connected devices, the Internet of Things at work under the roof of one slick indoor farm, ensures full control and data analysis of variables like lighting, temperature and humidity, as well as the flow of liquid nutrients.
But, if this smart farming is not smart enough, it will soon get considerably smarter. Before the end of 2017, SPREAD will open the Techno Farm™.
The world’s first robot farm
The company envisages that its super high-tech farm will reduce running costs by around 30 percent. Most impressively, though, it will be run almost entirely by robots.
The new plant in Kizugawa, Kyoto prefecture, will produce 30,000 heads of lettuce per day, which will be tended to by robots that have been brought lettuce seedlings by stacker cranes.
The robots will take care of tasks like trimming and watering, before making sure that fully grown lettuce is harvested and delivered to the factory’s packaging line.
Several countries now have smart farms, but this will be the world’s first robot farm.
A vision of the future? Source: Wide Open Country/Twitter
SPREAD says it has, “developed the most advanced vegetable production system created by
taking advantage of the cultivation techniques and accumulated know-how with the cooperation of technology equipment manufacturers.”
The company showcased that production system at CeBIT 2017 in Hanover, Germany, last month. The opening of the plant is scheduled for winter 2017.
Is a smart farm an ethical farm?
Despite the obvious cost to jobs in the local area, SPREAD believes its methods will contribute to humanity, as well as, to technological advancement (and not just by giving us more lettuce).
SPREAD claims its mission is to “create a sustainable society where future generations can have peace of mind.”
“By developing a system that can produce high quality food, rich in nutritional value anywhere in the world in a stable way, we will build an infrastructure that can supply food to all people equally and fairly around the globe,” says the company site.
Spread says lettuce costs will be the same as regular produce. Source: Spread
Japan probably has more of a need to develop an automated labor force than most other countries do, given that its population is actually declining. Japanese people famously live long, and a future in which there are not enough younger workers to support older, retired people looms large.
Nevertheless, Spread’s global marketing manager, JJ Price, told the Guardian: “Our new farm could become a model for other farms, but our aim is not to replace human farmers, but to develop a system where humans and machines work together. We want to generate interest in farming, particularly among young people.”
The company hopes eventually to take its technology around the world. Meanwhile, Japanese shoppers can rest assured that even lettuce produced by such a futuristic smart farm will cost the same as lettuce always has.
[See More: How Agriculture Technology Has Helped Feed Our Growing Population]
How Vertical Farming Could Save the Planet
How Vertical Farming Could Save the Planet
Inside the growing trend of indoor urban farms
4/21/17
"Take a leaf; just use your hand." Tom Colicchio directed a group of guests at dinner at River Park, instructing us to smell then take a bite of a garnish adorning our plates of tuna crudo. "That's amazing—something I hadn't seen before. That's wasabi arugula." The spicy, acidic burst from those leaves hushed the room. In a single bite, the chef explained why he's chosen to be a part of Bowery Farming, a modern farming company that just put its produce on the market.
The three-course meal showed off everything from three kinds of basil—lemon, Thai and Genovese—to pac choy (i.e., bok choy) and the startlingly good wasabi arugula, which Colicchio serves at his recently opened Fowler & Wells. It was all grown inside a New Jersey-based warehouse, using LED lights and zero pesticides. Bowery is just one of the many vertical farming companies that has sprouted up over the last few years. With Earth Day upon us, we're taking a peek inside this growing trend, which just might be the future of farming as we know it.
RELATED How Rooftop Farm Brooklyn Grange Got off the Ground »
Having truly landed only five months ago—first at NYC's Foragers Market and recently launching in tri-state area Whole Foods, where it sells two kale varieties, lettuce, arugula, basil and a spring mix—Bowery has already started to take off. It's also planning a new farm in the tristate area, with long-term goals to expand country- and eventually worldwide, making its greens local for customers everywhere. And though it might be one of the most ambitious, Bowery is definitely not alone.
There's AeroFarms, also based in New Jersey, Edenworks in Brooklyn, FreshBox Farms in Massachusetts and Green Sense Farms in Indiana, to name a few. Vertical farms have been cropping up at a rapid pace, and as the world's population continues to rise while also becoming increasingly urban, this indoor agriculture will undoubtedly become more crucial.
"How do you provide fresh food to urban environments in a way that's more efficient but sustainable?" That's the question that led Bowery cofounder Irving Fain to start the company with Brian Falther and David Golden. Sure, Fain admits there are many pieces to this complicated puzzle, rattling off issues like limiting food waste, eating less meat and helping developing countries increase their yield. But he believes his farm's proprietary hardware and software, which helps them to track and fine-tune their processes in real time, can effectively provide quality produce to our urbanizating population.
Though each organization has its own approach, the basic premise is to grow produce in a regulated, indoor environment, stacking beds on top of each other to maximize square footage. By controlling the plants' temperatures, airflow, water, nutrients and growing mechanisms, these farms are able to cultivate their crops much more efficiently than standard outdoor farms. And thanks to these ideal conditions, their growing season lasts an astounding 365 days a year.
"We're over 100 times more productive than the same square footage of farmland," Fain notes.
Falther calls Bowery a hydroponic farm, which means its plants are grown in water fortified with specific nutrients. Edenworks uses a version of this method called aquaponics, creating an ecosystem of aquatic animals and produce working to feed each other.
"Our fish generate manure, which is naturally broken down by a microbiome of soil bacteria into the nutrients that our vegetables need. The vegetables filter the water as they grow, then clean water is sent back to the fish, and around it goes," Edenworks cofounder and CEO Jason Green explains. Over at AeroFarms, they use an aeroponic mist on their plants.
Figuring out how best to grow produce in an environment devoid of natural light and soil is an issue all of these farms face.
But, as Fain points out, "the reality is that organic standards were written at a time when a lot of the technology we have access to today didn't even exist." He urges people to rethink agricultural possibilities, describing Bowery as "post-organic."
Another challenge is ensuring the produce grown on these futuristic farms retains its familiar flavor. That wasn't a problem at last night's dinner, though, and if you've picked up a box of greens at Whole Foods lately, you might not even realize it was grown in one of these vertical farms.
"It's a new paradigm for farming," Colicchio said, "and it's something I'm really excited about."
Shanghai Planning Huge Vertical Farm, Looking to change The Way It Feeds Its 24 Million Residents
Shanghai Planning Huge Vertical Farm, Looking to change The Way It Feeds Its 24 Million Residents
BY ALEX LINDER IN NEWS ON APR 21, 2017 3:30 PM
As Shanghai continues to expand outward, replacing agriculture with urbanization, a US-based design firm is looking to reimagine the way that Shanghai grows food to feed its 24 million people.
The Sasaki planning and urban design firm is turning heads with its masterplan for a 250-acre urban agricultural district in Pudong called Sunqiao, which will include, most spectacularly, towering vertical farms that grow lots of leafy vegetables
Sunqiao will include residential, commercial and public spaces integrated with an urban farm spread out across several buildings that will hydroponically produce spinach, kale, bok choi and watercress under LED lights and nutrient-rich water. Those veggies will then be sold to local grocers and restaurants.
Michael Grove, a principal at Sasaki, told Business Insider that the firm expects to break ground on the project by 2018, though there is no timeline yet. Grove said that the biggest problem they will face will be designing buildings that block out as little sun as possible.
While this project may seem ambitious, it's not quite on the level of Italian architect Stefano Boeri who wants to cover China with "forest cities" starting with the smoggy Hebei capital of Shijiazhuang
For China, the future certainly looks green.
[Images via Sasaki]
Netherlands Begins Construction On Europe’s First Commercial Vertical Farm
20 April 2017
Netherlands Begins Construction On Europe’s First Commercial Vertical Farm
Image source: chipmunk_1/Flickr
Europe, Worldwide, Agriculture, Tech. & Innovation, Sustainable Innovation Forum
The farm in Dronten, the Netherlands, will serve one of Europe’s biggest supermarket chains with lettuce grown using LED horticultural lighting.
To date, the only vertical farms in Europe using LED-based lighting have so far been research centres or specialist producers serving restaurants.
The new facility in Dronten – built by fresh fruit and vegetables company Staay Food Group – will be the first vertical farm in Europe to operate commercially.
The facility will serve one the continent’s largest supermarket chains in addition to being used for testing and optimising processes for future, larger vertical farms, and is scheduled to begin operating in the latter half of this year.
The 900 square metre indoor vertical farm will have over 3,000 square metres of growing space, and will use Philips GreenPower LED horticultural lighting.
As the farming happens indoors, any harmful insects or other pests will be prevented from reaching the crops – as a result no pesticides will be required in the process.
Staay and Philips Lighting collaborated with vegetable breeder Rijk Zwaan to carry out the extensive research required to determine the best combination of lettuce varieties and growth recipes in order to improve crop quality and yields
Udo van Slooten, Managing Director of Philips Lighting Horticulture LED Solutions, said: “Our plant specialists at our GrowWise research centre in Eindhoven are testing with seeds of a selection of the most suitable lettuce varieties to define the best growth recipes and to optimise the crop growth even before the farm is running”.
Wim Grootscholten, Manager of Marketing and Business Development at Rijk Zwaan, said: “The tests we are conducting within this project are enabling us to identify which varieties are optimal for growing in a vertical farm, and also which varieties offer the best taste and texture.”
Vertical farming also allows for the locating of food production close to – or even within – urban areas, where food consumption id concentrated.
Grootscholten went on to say: “It will help us with our continuous challenge to offer solutions for the growing world population. We believe that vertical farms will become increasingly important, because in the future we see more economic and environmental pressure to produce fruit and vegetables, such as lettuce, closer to where end customers are located.”
Farms located nearer consumers will help to reduce emissions and transport-related costs.
Similar facilities are also on the rise in the U.S., Vertical Fresh Farms has been farming commercially on a small scale in Buffalo, New York for a few years and Aerofarms in Newark, New Jersey, is currently developing the largest vertical farm in the world, with expected harvests of over 900,000 kilograms each year.
A report by PS Market Research projects that vertically farmed food market will take off in the next few years, generating $6.4 billion of total revenue by the year 2023.
To receive similar news articles, sign up to our free newsletter here.
How Freight Farms Is Taking Off From Boston To Canada
SEB EGERTON-READ · APRIL 19, 2017
Freight Farms sell a solution where 40’ x 8’ x 9.5’ shipping containers are outfitted innovative tools and technologies to produce consistent, high-volume harvests of leafy greens, herbs and a number of other select crops 365 days per year. Based in South Boston, this highly innovative idea was derived by co-founders Jon Friedman and Ben McNamara partly when they discovered that New England, despite its wealth and prosperity, relied on imports from outside the region for close to 90% of its food, while nearly 15% of all households reported not having enough to eat.
Using solar energy to provide the majority of the electricity required to grow crops, the containers are designed to be self-sustaining and are sold to individuals, not necessarily farmers by trade, but people who want to grow food for themselves and/or their community. The freight farm containers are small enough to be squeezed between buildings, placed at the end of parking lots, or almost anywhere in urban terrains.
The Freight Farm equipment set offers a hydroponic system, which they call the Leafy Green Machine, a soil-free growing method that utilised recirculated water with nutrient levels to grow plants. LED lights are optimised for each growing cycle, while a smartphone app called Farmhand allows the container owners to manage conditions remotely and connect with live cameras to monitor the plants.
The idea was simple. Give individuals a base and template to enable a distributed food growing network in cities. Boston may not be the obvious ‘hub’ for farming activity, but Freight Farms has spread across the north-east USA and into Canada, and there are now more than 100 of the company’s containers operating in the US alone.
The container’s growing conditions are controlled via a mobile app. Credit: Freight Farms
Investing and owning a Leafy Green Machine isn’t an inexpensive proposition, rather it’s an entrepreneurial investment opportunity. Purchasing one of the containers reportedly costs a business up to $85,000, while annual operating costs may reach $13,000. However, in a New England context where demand for locally grown food is increasing (close to 150 farmer markets operate in the state of Massachusetts alone), which offers significant business potential for new local growers, especially if they can run on low operating costs with minimal demand for land, water and chemical fertilisers.
In Boston in particular, enabling policy support has been a factor, where a recent mayor legally expanded zoning laws within the city to allow farming in freights, on rooftops and in other specific ground-level open spaces. One of the most overt examples the city’s positive stance on urban farming is at the iconic Fenway Park, where Green City Growers run the 5000-sq ft Fenway Farms above the iconic home of the Boston Red Sox.
There are legitimate questions about the role of urban farming, in particular hydroponic techniques, in the future of food. Will urban farming ever be able to grow the volume and variety needed to account for a significant percentage of the consumption of the city’s inhabitants? The answer to that question is, at best, unknown. However, there’s no doubt that hydroponic, aquaponic and aeroponic urban farming methods are gaining traction because they speak to a new way of thinking about how food is grown, distributed and consumed. In a context where land and water is scarce, and where people are increasingly inquisitive for information about what they eat, it seems increasingly likely that at least some portion of the food consumed within urban areas will be grown by a distributed network across the city in containers, warehouses and rooftops. The story of Freight Farms, and their growth across the north-east USA and Canada is just another hint in that direction.
Vertical Farming Is Taking Off: Europe’s First Commercial Vertical Farm Under Construction In The Netherlands
Vertical Farming Is Taking Off: Europe’s First Commercial Vertical Farm Under Construction In The Netherlands
April 19th, 2017 by Rogier van Rooij
Innumerable layers of vertically stacked crops, growing at insane speeds thanks to the meticulous administration of exactly the right quantities of water, nutrients, and a precise spectrum of light. Vertical Farming has so far been more successful in gaining media attention than in producing food, but this is about to change. Until recently, the only operational vertical farms were small-scale installations in research labs. Facilities aimed at developing the technology were involved, especially in refining the required lighting and climate control equipment. But this year, 2017, appears to usher in the next stage in the development of vertical farming. For the first time, larger scale commercial production is being undertaken.
Vertical Fresh Farms has been farming commercially on a small scale in Buffalo, New York for a few years, but a larger scale commercial facility is currently under construction in the Netherlands. Fruit and vegetables supplier Staay Food Group is erecting a 900 square meter vertical farm, which will have a total cultivation area of 3000 square meters.
Based in the town of Dronten, the facility is producing lettuce for ‘one of the largest supermarket chains of Europe.’ The lettuce is grown using Philips GreenPower LED horticulture lightning technology, and besides tech-multinational Philips, vegetable breeder Rijk Zwaan was involved in the development of the facility. The farm is expected to come online somewhere during the latter half of 2017.
This is good news for the environment because no pesticides are required in the process. Farming happens indoors, preventing any harmful insects or other pests from reaching the plants. Furthermore, vertical farming allows for locating food production closer to, or even in cities, where food consumption is concentrated. As a result, suppliers can save on transport emissions as well as on transport costs. The farm in Dronten packs the lettuce on location, which reduces the shipment distance even further.
The Dutch commercial facility is not the only sign that vertical farming is on the rise. Aerofarms in Newark, New Jersey, is currently bringing online the largest vertical farm in the world, with expected harvests of up to 2 million pounds a year. In Shanghai, plans have just been released for a massive 250-acre city farm, on which construction should start in 2018.
This growth of the vertical farming sector appears to be driven by two key components: an increasing demand for organic, pesticide-free food, and innovation, especially in the power consumption of the LED-technology required to grow indoors. A report by PS Market Research forecasts that the market for vertically farmed food will grow rapidly in the coming years. Their calculations give $6.4 billion of total revenue by the year 2023.
About the Author
Rogier van Rooij Optimistic, eager to learn and strongly committed to society's wellbeing, Rogier van Rooij wants to share with you the latest cleantech developments, focussing on Western Europe. After graduating cum laude from high school, Rogier is currently an honours student at University College Utrecht in the Netherlands.
Innovative, Efficient Indoor Farm In New Jersey
Innovative, Efficient Indoor Farm In New Jersey
By: ALISON MORRIS
POSTED: APR 18 2017 05:41 PM EDT
NEW YORK (FOX 5 NEWS) - Could the answer to the global food crisis be hidden in a warehouse in New Jersey? A local indoor farming startup is producing affordable crops there year-round, independent of the weather.
And food safety is paramount. That means outside clothes or jewelry can't come in. A visit to Bowery's farm starts with a uniform and some hand sanitizer. This vertically integrated farm in Kearny, New Jersey, is producing some seriously clean greens.
CEO and co-founder Irving Fain describes the farm as "post-organic" and says it is completely chemical free: no pesticides, herbicides, fungicides, or insecticides. Fain says it is the purest produce you could possibly get.
Innovative, efficient indoor farm in New Jersey
He founded the farm a few years ago along with David Golden and Brian Falther. They've brought in $7.5 million in funding from some rock star investors, including Top Chef Tom Colicchio.
The farm is now producing crops 365 days a year regardless of the weather, using a lot less water. Fain says it is 100 times more productive than the same square footage of outdoor land. The farm grows twice as fast as the field, with more crop cycles every year, more yield in every crop cycle, and uses 95 percent less water.
Their hope is to help solve the global food crisis. Fain says the planet's population will be 9 billion to 10 billion by 2050, so it will need 50 percent to 70 percent more food to feed everyone.
While that change is happening, 70 to 80 percent of people are living in cities. They saw that urbanization and became obsessed with the question: how do you provide fresh food to urban environments in a more efficient and sustainable way? The answer: start with LED lights. Fain says the lights they use mimic the sun, so it's as if the plant is growing in the absolute healthiest environment for its entire life. He says that the price of those lights dropped while their efficiency went up about 5 years ago, making indoor growing commercially viable.
Fain says Bowery sells 5-ounce clamshells for $3.99 or even $3.49, which is pretty standard, if not lower, than what you find out in the field. Throw in the Bowery Operating System, which creates optimal growing conditions, and Bowery is able to churn out fresh, affordable, and delicious greens.
And the farm is growing. Fain says they're already experimenting with different types of crops and other SKUs outside of the leafy green category.
Right now you can find Bowery lettuce and basil in tri-state Whole Foods and in Foragers Market in New York City. The lettuce you'll find there has often been harvested the same day it hits the shelves.
Elon Musk’s Brother Is Disrupting Farming—One Sprig of Hyperlocal Microgreen At A Time
04.17.17 | 3 HOURS AGO
Elon Musk’s Brother Is Disrupting Farming—One Sprig of Hyperlocal Microgreen At A Time
Elon Musk's brother, Kimbal, cofounded a high-tech company for a very low-tech product—spinach. And also chard and mustard greens and anything else that can be grown in an old shipping container outfitted with $85,000 worth of high-tech farming equipment. Called Square Roots, the idea could shake up the way we think about farming and food production. Its genesis comes from an unlikely source: weed. "Cannabis is to indoor growing as porn was to the internet," says its CEO and cofounder, Tobias Peggs.
Backchannel takes a close look at the new startup that takes the guess work out of growing food. It lets wannabe farmers grow artisanal lettuce in the so-called "nano-climate" of an old shipping container that makes the farms impervious to weather and capable of being run almost entirely via iPhone. The nano-climate has a few other perks, too, including something straight out The Hitchhiker's Guide to the Galaxy: the ability to design a specific taste in a crop thanks to tech that can precisely control growth factors like light and temperature. Check out the full story here while munching on your hyper-local bag of freshly picked microgreens.
New Vertical Gardens At UA's Biosphere 2 Will Provide Produce For Sale
New Vertical Gardens At UA's Biosphere 2 Will Provide Produce For Sale
The University of Arizona-Biosphere’s West Lung. right, will be converted into a “vertical farm” of stacked racks of floating plants under LED lights.
Jill Torrance / Arizona Daily Star 2011
- By Tom Beal Arizona Daily Star
- Apr 17, 2017
Food crops are coming back to Biosphere 2, but they won’t be planted in the 3 acres under glass at the University of Arizona research facility in Oracle.
A company named Civic Farms plans to grow its leafy greens under artificial lights in one of the cavernous lungs that kept the Biosphere’s glass from imploding or exploding when it was all sealed up.
The lungs, which equalized the air pressure in the dome, are no longer needed now that the Biosphere is no longer sealed. The west lung will be transformed into a “vertical farm” that will train LED lights on stacked racks of floating plants whose roots draw water and nutrients from circulating, fortified water.
A variety of leafy greens and herbs such as kale, arugula, lettuce and basil will be packaged and sold to customers in Tucson and Phoenix, said Paul Hardej, CEO and co-founder of Civic Farms.
He also expects to grow high-value crops, such as microgreens, Hardej said.
Hardej said the company plans to complete construction and begin growing by the end of the year.
Civic Farms’ contact with the UA allows for half the 20,000-square-foot space to be devoted to production, with areas given over to research and scientific education.
The UA will lease the space to Civic Farms for a nominal fee of $15,000 a year. In return, the company will invest more than $1 million in the facility and dedicate $250,000 over five years to hire student researchers, in conjunction with the UA’s Controlled Environment Agriculture Center.
Details of branding haven’t been worked out, said UA Science Dean Joaquin Ruiz, but don’t be surprised to find Biosphere Basil turning up in your salad soon.
Hardej said the “brands” established by the UA were lures for his company.
“The UA itself has a brand recognition throughout the agricultural industry and specifically the Controlled Environment Agriculture Center. They have a lot of respect worldwide.”
“Also, the Biosphere itself is a great story,” he said. “The original intent was to develop a self-sustaining controlled environment where people could live, regardless of outside conditions.”
“In a way, this is a fulfillment of the original purpose,” he said.
Hardej said he recognizes the irony of growing food in artificial light at the giant greenhouse. He is convinced, however, that growing plants with artificial lighting can become as economical as growing them in sunlight.
“Decades ago, greenhouses were very innovative. It felt like it allowed the farmer to control the environment. It did not control the light and also the temperature differentials.”
Hardej said indoor growing allows you to control all the variables — the water, the CO2 levels, the nutrients and the light. “Farming is much more productive and much more predictable than in a greenhouse,” he said.
You can’t stack plants on soil, or even in a greenhouse, he said. “A vertical farm can be 20 to 100 times more productive. The overall direction globally is indoors,” he said.
Indoor agriculture is still a sliver of overall crop production, said Gene Giacomelli, director of the UA’s Controlled Environment Agriculture Center and most indoor operations are greenhouses.
“Vertical farms,” account for a small portion of that sliver, but are a fast-growing segment for growing high-value crops with a level of control over the environment that can’t be attained elsewhere, he said.
“Theoretically, we should be able to control everything,” he said.
Murat Kacira, a UA professor of agricultural-biosystems engineering, is already working on systems to do that in a lab at the CEAC center on North Campbell Avenue, where he grows leafy greens and herbs under banks of LED lights.
He can control the wavelengths of light, temperature, humidity, the mix of oxygen and carbon dioxide and the nutrients available to the plants.
Those variables can be tuned to improve the yield, quality and nutritional value of the plants being grown. He is developing sensor systems that allow the plants to signal their needs.
A lot of questions remain, said Giacomelli. Different plants require different inputs. Young plants have different needs from mature ones.
Air handling is a tricky problem, he said. Air flow differs between bottom and top racks and at different locations of a given rack of plants.
It will take “more than a couple years” to figure it all out, said Giacomelli.
Kacira said the Civic Farms installation “is a really complementary facility to the research going on under glass.”
He expects the Biosphere to become a “test bed” for more research on the nexus of food, water and energy.
Ruiz said that “nexus” is the direction for research at the Biosphere for the coming decade.
Contact: tbeal@tucson.com or 573-4158. Follow him on Facebook or on Twitter: @bealagram
Jill Torrance / Arizona Daily Star 2011
Researchers will be able to control the environment inside the “vertical farms.” “Farming is much more productive and much more predictable than in a greenshouse,” said Paul Hardej, CEO and co-founder of Civic Farms.
Jill Torrance/Arizona Daily Star
The tour ended outside “the Lung” at the University of Arizona-Biosphere 2 Tuesday, January 11, 2011. Photo by Jill Torrance/Arizona Daily Star
Mike Christy/Arizona Daily Star
Murat Kacira, professor in the UA’s department of agricultural and biosystems engineering, keeps tabs on readings from the next room where greens are being grown in a multi-level artificial light environment at the Controlled Environment Agriculture Center, 1951 E. Roger Road, on Feb. 9, 2017, in Tucson, Ariz. CEAC is helping NASA develop a sustainable gardening system for the moon and Mars.
Mike Christy/Arizona Daily Star
Murat Kacira, professor in the UA’s department of agricultural and biosystems engineering, shows the floating raft hydroponics greens being grown in a multi-level artificial light environment at the Controlled Environment Agriculture Center, 1951 E. Roger Road, on Feb. 9, 2017, in Tucson, Ariz. CEAC is helping NASA develop a sustainable gardening system for the moon and Mars.