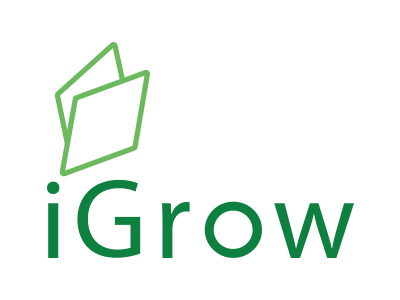
Welcome to iGrow News, Your Source for the World of Indoor Vertical Farming
Urban Crop Solutions Wins the FoodNexus Innovation Award in Belgium
Urban Crop Solutions Wins the FoodNexus Innovation Award in Belgium
Urban Crop Solutions was awarded on Thursday evening October 26th the FoodNexus Innovation Award. Out of many innovative companies, a jury of experts in the agriculture and food industry selected Urban Crop Solutions as the most promising company in the Belgian agri-food industry. Urban Crop Solutions will defend Belgium in the European FoodNexus competition, together with another Belgian company from the French-speaking part of the country, during an event in Wageningen (the Netherlands) on December 13th.
FoodNexus is a European consortium of international food companies and leading knowledge institutions that strives to create a robust and sustainable European Food System. The Belgian FoodNexus challenge was organized for the first time in collaboration with Flanders’ FOOD, the Universities of Ghent and Liège, Food2Know and many other partners. The core business of the young, participating companies must be related to one of the three following areas: food safety and sustainability, food quality, and health and well-being. The aim of the challenge is to identify and stimulate the most promising young companies, and connect them to leading European corporates in the agri-food industry. This allows the companies to scale their innovations to benefit people and planet, with the support of these partners. Urban Crop Solutions was chosen as the young company of the year by a panel of corporate and scientific experts from the agricultural and food industry.
“This award is yet again a highlight for our company. It’s a valuable recognition of the efforts that our team has already made for Urban Crop Solutions. We thank this award to their infinite commitment We want to keep on improving and creating the best indoor vertical farming solutions for our customers everywhere in the world”, says Maarten Vandecruys, CEO of Urban Crop Solutions. “This award is also a recognition for our business model and our global approach. We commit ourselves to bring to our clients Belgians top expertise in growing crops and automation and robotics”, adds Frederic Bulcaen, Chairman of Urban Crop Solutions, with a big smile.
Since 2014 Urban Crop Solutions develops for its client's tailored plant growth installations. These systems are turnkey, robotized and able to be integrated into existing production facilities or food processing units. Urban Crop Solutions also has its own range of standard growth container products. Being a total solution provider Urban Crop Solutions can also supply seeds, substrates, and nutrients for clients that have limited or no knowledge or experience with farming. Currently, the company has a growing list of more than 200 varieties of crops that can be grown in closed environment vertical farms and that have been validated. These plant recipes (ranging from leafy greens, vegetables, medicinal plants to flowers) are developed specifically for indoor farming applications and sometimes exclusively for clients by its team of plant scientists. Urban Crop Solutions has started activities in Miami (Florida, US) in 2016 and is soon to open a division in Japan.
For more information on this press release, on Urban Crop Solutions or on the products and services of Urban Crop Solutions you can contact Maarten Vandecruys, Co-founder and Managing Director (mava@urbancropsolutions.com), Frederic Bulcaen , Co-founder and Chairman (frbu@urbancropsolutions.com ) or visit our website (www.urbancropsolutions.com):
Company headquarters:
Grote Heerweg 67
8971 Beveren-Leie (Waregem)
Belgium
Regional headquarters:
800 Brickell Avenue, 1100 Suite
Miami (FL 33131)
Facebook: www.facebook.com/urbancropsolutions
Twitter: www.twitter.com/U_C_Solutions
LinkedIn: bit.ly/UrbanCropSolutionsLinkedIn
YouTube: bit.ly/UrbanCropSolutionsYouTube
Green Sense Farms to Expand Its Vertical Farming Operations In The U.S. and China
Green Sense Farms to Expand Its Vertical Farming Operations In The U.S. and China
OCTOBER 24, 2017 URBAN AG NEWS
Originally published in Issue 13, April 2016
To meet the increasing demand for clean, safe produce in both the U.S. and China, Green Sense Farms looks to open additional vertical farming operations along with a training facility to create job-ready graduates to grow in controlled environments.
Robert Colangelo, founding farmer and CEO at Green Sense Farms, in Portage, Ind., knows what it takes to be successful in emerging markets.
“I have been very fortuitous in my career,” Colangelo said. “I have been at the forefront of three emerging markets. In the 1990s I operated one of the first companies in the Soviet Union and rode that wave of democratization and privatization of state-owned Russian businesses.
“I was at the forefront of the brownfield industry. Redeveloping contaminated properties, repositioning them for new and productive use. And now I have been lucky to be at the forefront of the emerging vertical farming market.”
Colangelo said all of the new markets he has been involved with have very similar patterns.
“They all require tenacity as the early phase of the market ebbs and flows until it reaches a critical mass,” he said. “They require flexibility and the ability to manage technology. It’s the culmination of my previous experiences that have allowed me to have a diverse amount of skills required to make vertical farming work. This is probably one of the more complex ventures I have ever undertaken, but I love it. I also have a great partner, Carl Wenz, who is a CPA and has complementary skills to mine.
“To be successful in vertical farming, you really have to understand the produce business, have a good understanding of fundamental business operations and be able to integrate many different technologies into a working system. You have to understand plant physiology, packing and post-harvest processes. And you have to have marketing and sales skills and be able to raise capital. That is a unique skill set for one person and requires an experienced team. If you’re not good at all of those areas of expertise, then you’re going to have a real challenge succeeding in the vertical farming market.”
Starting out with “big” partners
Even though Green Sense Farms has only been producing crops since 2014, the company was formed in 2012 and has been doing research and development since 2009. The company’s vertical farm operation is located in a 120,000-square-foot industrial warehouse building. It leases 20,000 square feet in a multi-tenant building.
“We have two grow rooms,” Colangelo said. “Each room measures 60- by 60- by 25-feet tall. One room is dedicated to lettuce. It has nine vertical towers that are 14 levels high. The second room has seven towers with 10 levels in which we produce baby greens, including kale, arugula, bok choy, watercress, upland cress and culinary herbs. About 80 percent of the product goes to grocery stores and 20 percent goes to produce companies, which service restaurants and institutions.”
Colangelo said in order for his company to be a major player in the vertical farming industry required picking “big” partners.
“We looked at lighting and picked a lighting partner,” he said. “This allowed us to focus on building the best vertical farm and our lighting partner can provide us with constant R&D on LED lights. We picked a fertigation partner that could take a well-defined fertigator from the greenhouse industry and customize and tweak it so that it would work in an indoor vertical farm and create the automation controls that link all the different systems together. We formed a partnership with a climate control company so that we just don’t treat our air and filter it and cool it, but we also adjust the humidity because plants transpire and put a lot of moisture in the air. Lastly, we are working with a seed company that together with our LED company can breed non-GMO seeds that grow best under LED lights in indoor controlled environments. This enables us to not only maximize our yields, but through using the right seed with the right LED light recipe, we can double our yields and productivity. This is complex stuff and you have to pay attention to the details. And you have to be at a scale that is big enough to make this economical.”
Expansion in the U.S.
Green Sense Farms is in the process of building additional farms in the U.S.
“We have formed a partnership with Ivy Tech Community College in South Bend, Ind., to build a hands-on training center on the campus,” Colangelo said. “This will be a working commercial farm.
“One of the challenges in this industry is that there are not enough trained people. So we are creating our own “farm team” to mine talent. The training center will be similar to McDonald’s Hamburger U. in Oak Brook, Ill. We plan to train 15 students every six months. At the end of the six months the students are job-ready to work in the ag industry and to also work in vertical farms. We call it “earn to learn.” The students will be paid to work at the farm. This facility will be larger than the one we are operating in Portage.”
Green Sense Farms produces lettuce, baby greens, including kale, arugula, bok choy, watercress, upland cress, and culinary herbs. About 80 percent of the product goes to grocery stores and 20 percent goes to produce companies, which service restaurants and institutions.
Green Sense Farms is also in discussion to put a vertical farm at distribution centers in the Indianapolis area operated by grocery store chains.
“Our goal is to blanket the Midwest,” Colangelo said. “Our strategy is to put these vertical farms at the points of consumption and distribution. We are planning to build farms at perishable food distribution centers and at institutional campuses, including hospitals, colleges, corporate campuses and military bases.
“After Chicago, Indianapolis is the next up-and-coming Midwest city. There is a great food scene. It is also an entrance to the South. The Midwest is a good location because of its short growing season and its cold winters. With the vertical farms we can grow indoors 24/7 and harvest 365 days a year.”
Expansion in China
At the same time that Green Sense Farms is expanding its vertical farms in the U.S., it is also building a network of farms in China. The company’s goal is to build 100 farms in China with its local operating partner Star Global Agriculture. It began work on its first China facility in March 2015. Located in the city of Shenzhen, the vertical farm is expected to start growing produce in June.
“Shenzhen is located right across the border from Hong Kong,” Colangelo said. “There are 48 million people within 50 miles of our farm. Our plan is to build 10 farms in the city in the next 24 months. They would serve Hong Kong and Macau, which is considered the Las Vegas of the East.
“China has 1.4 billion people. The country is transforming from a manufacturing economy into the largest consumer economy. In a very short time China is going to have incredible buying power. As a middle class emerges, Chinese consumers are demanding higher quality food.”
Colangelo said China’s transformation over the last 25 years into one of largest industrial manufacturing economies ate up a lot of farm land and produced heavy pollution.
“A lot of the food supply has been affected by the industrialization,” he said. “There is heavy air pollution, ground water has been contaminated in the large cities and there are terrible traffic jams. Putting vertical farms in the cities close to the people reduces congestion, controls the cleanliness of the food, and supplies emerging markets that want to eat healthy, fresh greens.
“There is a tremendous amount of capital available. In China there aren’t as many rules and regulations as we have had to deal with in the states so we can move much more quickly. Even though we started in the U.S. and we will continue to build our network here, with the availability of capital and less regulations to deal with in China, we feel that we can build a network of farms much more rapidly there.”
Colangelo said the company’s goal in China is to pioneer the lettuce market.
“We know there is an emerging lettuce market. We feel that we can dominate that,” he said “But we also know that we have to grow different greens for the Chinese palette. Some of the crops include Chinese onions, baby bok choy and mustard greens. Some of the herbs will also be different such as coriander.”
Colangelo said with China’s population the potential market is immense.
“Initially we will put as many farms as we can in Shenzhen,” he said. “Then we’ll blanket Shanghai, Beijing and Chengdu. Those cities have large population centers (20 million plus) where we can build a circle of farms around the cities.
“The traffic congestion is so bad in China that it would be better to build smaller farms closer to consumers. Even in a small area it takes a long time to go a short distance during rush hour. It’s better to have several small farms then to have a big farm in a central location.”
The future of vertical farming
Colangelo said the indoor vertical farming market in the U.S. is a rapidly emerging market.
“There are a lot people rushing into vertical farming either because they see it as a way to stop world hunger, as a lifestyle change or they see it as a responsible and sustainable way to grow,” he said. “All those things are great. Vertical farming can help those things, but it is not a panacea.”
He said vertical farming has raised the bar for sustainable farming.
“You are seeing some field farmers becoming much more sustainable, as they use precision farming techniques to conserve water, fertilizer and pesticides,” he said. “Greenhouse growers are also becoming much more responsible on how they minimize water and fertilizer use.
“Each of those methods of farming are targeted to grow different crop types better. Field farming is fantastic for commodity crops like corn, wheat and soybeans. Greenhouses are great for tomatoes, cucumbers and peppers. Vertical farming is a great way to grow leafy greens. Vertical farming really takes a skilled practitioner with a good management team, a good understanding of the produce business and good understanding of controlled environment agriculture and patient capital.”
Colangelo sees more people rushing into vertical farming which will result in a high failure rate.
“I expect that eventually a few companies will emerge in the long run that will be large scale companies,” he said. “Internationally I see vertical farming growing in constrained markets where produce travels great distances. There is either a lack of water, a lack of land or heavy pollution that drive the creation of farms.”
Colangelo said the vertical farming market is rapidly expanding at the same time it is maturing quickly.
“When I started in this industry in 2009, it was a cottage industry,” he said. “Today you really need to bring your A team to start a vertical farm. You have to have a strong management team. You have to be well capitalized. You have to be strategically focused with a cogent business plan. You have to have an experienced growing team in place. You have to have a good command of the technology that’s ever changing. And you have to be willing to constantly innovate and be agnostic towards your current technology.
“Our first grow room is going on three years old and it’s already a museum. We have already retrofitted it with new technology. We have farm designs that go way beyond where we’re at now and we’re just getting started. The only constant in life is change, either be the catalyst for change, be changed or die.”
Saudi Arabia Is Building a Futuristic Mega-City That Will Cost $500 Billion
Saudi Arabia Is Building a Futuristic Mega-city That Will Cost $500 Billion
It'll be 33 times the size of New York City.
TALIA AVAKIAN
OCTOBER 25, 2017
Saudi Arabia is building a mega-city that will span three different countries.
The country’s Crown Prince, Mohammed bin Salman, announced the $500-billion plan, which will create a futuristic city in the northwestern region of the country.
Dubbed NEOM, the mega city will cover 26,500 square kilometers in total, spanning territory within Egypt and Jordan as well.
The city is set to be the world’s first independent economic zone, operating with its own laws, taxes, and regulations.
NEOM will be powered completely by renewable energy from solar and wind panels, with its transport system also running on 100 percent green energy.
Vertical urban farms, seawater farming, and solar-powered greenhouses will help provide residents with fresh food supplies, and the zone will also be a space to test out new technological advances like passenger drones and self-learning traffic systems.
Located next to the Red Sea and the Gulf of Aqaba, the massive city will also provide a serene landscape composed of more than 290 miles of coastline and vast desert terrain.
The city's coastline includes a variety of untouched beaches and coastal reefs and its valleys are cradled by mountains, creating a more moderate climate than that of nearby areas.
Plans also include the creation of sports and visual arts venues, a variety of marinas and waterside restaurants, record-breaking theme parks, natural parklands, a water park with a wave pool where Olympians will practice, and what officials say will be the world’s largest garden.
The move comes as the world’s largest oil exporter looks to boost its economy after falling oil prices.
Construction is already set to begin, with the first phase planned for completion by 2025. You can follow the progress of NEOM’s development through an interactive map on the project’s website.
IKEA & Top Chef David Chang Round Out Financing for $40 Million Series D Round for AeroFarms
AeroFarms just built its ninth farm to date in Newark, New Jersey that is the world’s largest indoor vertical farm based on annual output. Having raised in total over $100 million in corporate and project financing, AeroFarms will used the latest round of funds for continued investment in leading R&D and technology and additional farm expansion around the world.
IKEA & Top Chef David Chang Round Out Financing for $40 Million Series D Round for AeroFarms
October 27, 2017
AeroFarms, the pioneer and leader for indoor vertical farming since 2004, closed $40 million in Series D financing led by an international
Vertical Farming: Key to Meeting Princeton University Sustainability Plan
Dr. Paul Gauthier, a postdoctoral research associate in the geosciences department, created the Princeton Vertical Farming Project (PVFP) this past April. The project is situated in Moffett Laboratory, which adjoins Guyot Hall, and was funded by the University’s Office of Sustainability and is directly related to the University’s SustainabilityPlan.
In 2008, as part of the a larger plan to promote sustainability, the University committed to reduce its overall carbon dioxide emission levels to those of 1990 by 2020. The University's plan also set several more goals in the area of environmentalism and sustainable energy meant to address pressing environmental issues such as climate change, water scarcity, and air pollution.
According to Gauthier, the PFVP is a present-day attempt to expand upon these goals from almost a decade ago. Indeed, Gauthier identified the project as a key addition to the University’s larger sustainability plan.
“The goal of the project [PFVP] is to help students familiarize themselves with vertical farming here [at the University] and eventually create start-ups that employ the technique outside of the University,” explained Gauthier, adding that another goal of the project is to eventually provide produce to the dining halls as a step towards the University becoming completely self-sustaining.
Gauthier explained that, globally, the majority of start-ups utilizing vertical farming shut down after only a couple of years. This short life, he said, stems from the startups' inability to generate enough profit to meet the costs of applying vertical farming to produce farming. PFVP, he hopes, will help advance vertical farming technology from a scientific standpoint to remedy this problem. This kind of technological advancement, he added, will encourage students to build their own start-ups utilizing vertical farming technology.
Gauthier noted that the issues with popular use of vertical farms include a shortage of adequate technology as well as a lack of proper experimental data on the optimization of vertical farming efficiency. To study these problems, Gauthier's team is currently measuring the effectiveness of different vertical farming settings by testing how different lighting and water environments impact plant growth.
As a result of months of experiments and research, Gauthier and his team have enhanced the efficiency of vertical farms in a number of ways, such as reducing water usage and utilizing LED lights instead of sunlight to provide photosynthetic catalyst.
“We are using approximately 0.5 gallons of water for every kale plant,” noted Gauthier. “This is considered very efficient, and will save a significant amount of water when applied to large-scale fields.”
Gauthier added that vertical farming can be utilized not only as a reliable source of food in the future, but also as a means for capturing carbon dioxide emissions.
According to Gauthier, vertically farmed produce is not only sustainable and efficient, but grows rather quickly and is comparable in taste to commercial produce. Gauthier explained that basil plants in the vertical farm take approximately a month to grow, and with the use of special LED lights, are almost indistinguishable from basil sold in markets. According to Gauthier, this is attributable to his focus on the taste and quality of the vertical farm products rather than the quantity.
Kyra Gregory ‘19, a communications assistant for the Office of Sustainability and PVFP website manager, has been working with Gauthier from the start of the project and believes it will contribute to the University’s larger sustainability initiatives.
“Overall, seeing the vertical farm progress from its initial stage to where it is now is very inspiring for me. The amount of growth and student interest gives me hope for sustainability efforts at Princeton and in our generation in general,” said Gregory. She also explained that the PVFP team, which includes other students, hopes to make a meaningful impact on sustainability at Princeton and to highlight the benefits of vertical farming.
In addition to being a great chance to improve sustainability on campus, PFVP has left a mark on the team members for other reasons. “It's wonderful being involved with a team where people from different academic and social backgrounds can come together to work on this project that we all care deeply about,” Gregory said.
Reached out to Dr. Shana S. Weber, Director of Sustainability Office, and Ms. Kristi Wiedemann, Assistant Director of Sustainability Office, were unable to be reached for comment before publication.
Urban Farms Gain Support
In this 2014 photo, urban gardener Jo Bartikoski picks dill from her garden patch at the Dundee community garden in Omaha, Nebraska. Some are looking to expand so-called urban farms to produce more healthy food for city residents. (AP Photo/Nati Harnik)
Urban Farms Gain Support
October 15, 2017
New York City is known for its tall buildings, financial markets and centers for the arts.
But America’s most populated city is becoming known for something you might not expect -- farms.
New York City’s government announced last month that it is providing $500,000 to create two urban farms. Both will use space in New York public housing developments. The new farms will join four other farms already operating with city government help.
The idea is to get more fresh fruits and vegetables to communities in the city. City officials see it as a public health issue.
“These new urban farms will not only provide access to healthy produce, but also provide jobs to young residents,” said New York City Councilman Ritchie Torres.
The new farms will be in the New York City boroughs of Staten Island and the Bronx.
Farming businesses in the city?
These farms are supported by the local government. But, there are also privately run farms in the city.
In the New City neighborhood of Tribeca, Robert Laing has opened up a privately-run indoor farm called Farm.One. He grows many kinds of herbs. His customersinclude well-known restaurants in New York City.
The restaurants can pick up fresh herbs hours before they are needed for that night’s dinner because his “farm” can be reached by bicycle from much of the city. Laing's website tells customers that they can buy fresh herbs, even in a snowstorm.
Farm.One is very different than farms in less populated communities. The major difference is size. It is only 112-meters. The U.S. Department of Agriculture says the average farm in America is 176 Hectares.
Farm.One’s crops are grown on vertical shelves so more can be grown in less space.
“The nice thing about farming vertically indoors is that you don’t need a lot of space,” Laing said. “I can see some bodega (a small grocery story) setting one up on the roof.”
Robert Laing of Farm.One.
Urban farms are growing in other cities besides New York City.
The website Inhabitat.com recently released a list of the top four U.S. cities for urban farms. They are Austin, Texas; Boston, Massachusetts; Cleveland, Ohio and Detroit, Michigan.
Urban farms still need to develop more
The Johns Hopkins Center for a Livable Future released a report on urban farms in 2016. It said there are important benefits to turning unused land into sources of healthy food.
But it said that urban farming still has a long way to go to produce the environmental and health benefits claimed by supporters.
“In some cases, the enthusiasm is ahead of the evidence,” the Johns Hopkins research said.
For example, the report said that supporters of growing food close to the people who eat it claim that it reduces pollution compared to transporting food long distances.
But the researchers found that smaller farms do not do as a good a job as larger farms in reducing use of water and other natural resources.
Indoor farms: a controlled environment
The Foundation for Food and Agriculture Research based in Washington D.C. wants more urban farms. It said the benefits are almost unlimited.
The group announced last month that it will give $2 million to help pay for a new farm in Newark, New Jersey, just outside of New York City.
Aero Farms will work with scientists from Cornell University in New York State and Rutgers University in New Jersey. The goal is to grow salad greens with improved taste and color.
The funding announcement said that because the farm is indoors the farmers can control the environment, including temperature, to improve their crops.
Sally Rockey is executive director of the Foundation for Food and Agriculture.
She said that more than half the world’s population lives in cities and that it is important to provide healthy food to this population. Whenever possible, Rockey said, food should be “grown locally.”
Brian Massey writes and farms. He recently wrote about managing an urban farm in a Washington D.C. neighborhood near Howard University. His report appeared on the website, civileats.com.
He said that a lot of people liked the fresh fruit and vegetables his farm produced. But he said others worried the farm was there to help the newly arrived, wealthier residents, not the poor.
There was a concern that the farm would add to Washington’s continuing shortage of low-income housing, Massey wrote.
I’m Jill Robbins.
And I’m Bruce Alpert.
Bruce Alpert reported on this story for VOA Learning English. Mario Ritter was the editor.
Trending: Spiders, Butterfly Wings Inspire New Solutions for Urban Agriculture, Renewables
Trending: Spiders, Butterfly Wings Inspire New Solutions for Urban Agriculture, Renewables
October 23, 2017
Image Credit: Boris Smokrovic
Innovators continue to look to nature to create new solutions to tackle everything fromwater scarcity and depletion to climate change.
An international team based in New York City has developed a prototype product that mimics the way living systems capture, store and distribute water, which could be deployed to help meet growing demand for sustainable, local food production. Designed by NexLoop, the prototype has been awarded the 2017 $100,000 Ray C. Anderson Foundation Ray of Hope Prize in the Biomimicry Global Design Challenge. The challenge is an international design competition and accelerator program that crowdsources nature-inspired climate change solutions for issues such as food systems, water management and alternative energy.
Dubbed AquaWeb, the product aims to help urban food producers collect, filter, store and distribute atmospheric moisture with a modular, all-in-one water sourcing and management system. Instead of drawing on groundwater, AquaWeb harnesses rain and fog and uses passive strategies to distribute water so that urban farms, including greenhouses, indoor vertical farms and container farms can save energy and become more resilient to disturbances.
Natural systems inspired each design element of NexLoop’s solution: It borrows heavily from the examples of cribellate orb weaver spider webs that collect fog from the air, drought-tolerant plants such as the crystalline ice plant that stores water and mycorrhizal fungi such as the Jersey cow mushroom which distributes water. The team also looked to the dwarf honey bee’s hexagonal nest structure for AquaWeb’s efficient and modular design.
“NexLoop is an impressive team across the board,” said John A. Lanier, Executive Director of the Ray C. Anderson Foundation. “They have a deep understanding of how biomimicry aids in the design process and their plans for hyperlocal water capture and storage in urban settings could play a crucial role in scaling local, sustainable agriculture. We are proud to award them this year’s Ray of Hope Prize.”
The trustees of the Ray C. Anderson Foundation also awarded a $20,000 prize to second place team Windchill from the University of Calgary, Canada, which created an electricity-free refrigeration system inspired by how animals regulate body temperature. The $15,000 third place prize went to Evolution’s Solutions from theUniversity of California, San Diego, which created a food waste nutrient recycling and supply system inspired by bacteria that helps hydroponic farmers grow food more efficiently and sustainably.
A total of six international teams spent the past year in the world’s only Biomimicry Accelerator program, developing working prototypes with the help of biomimicry experts and business mentors in order to create viable, market-ready solutions. The Biomimicry Accelerator is a commercialization platform for biomimicry entrepreneurs to bring needed sustainability solutions to market faster.
“Our vision moving forward is to help seed biomimicry and biomimetic thinking as the default position for design, industry, economy and culture,” said Kenny Ausubel, Co-Founder and CEO of Bioneers. “The Biomimicry Global Design Challenge doubles down on innovation, providing a business incubation process as potential investment capital for the finalists to accelerate market-ready, scalable biomimetic solutions to our greatest challenges. As such, we are honored to be continuing and deepening our partnership with them.”
Meanwhile, researchers at the California Institute of Technology and Karlsruhe Institute of Technology have developed thin film solar cells that mimic the delicate black wings of the rose butterfly to better absorb light. According to reports, the solar cell is capable of gathering light two times more efficiently than traditional solar cells.
The key to the discovery, the results of which are published in the journal Science Advances, are the disordered nanoholes in the wings’ scales, which not only allow the wings to be lighter, but allow the butterfly to better absorb heat. The random ordering, in particular, is what makes the technology tick. After studying the butterfly’s wings under a microscope, researchers discovered the position and order are important for absorbing light. They then used the model to recreate the structure with thin sheets of hydrogenated amorphous silicon sheets with similar holes that scatter light onto a silicon base. In addition to collecting twice as much light as conventional solar cells, they can also be created quickly — in the range of five to 10 minutes, to be exact.
Another advantage of the team’s discovery is that the sheets have the capacity to expand the capabilities of existing solar systems. Solar panels are typically installed on an angle and therefore capture sunlight only during a specific time window. Solar panels equipped with this new technology could generate for longer periods of time, and ultimately take solar technology to the next level.
Launched in 2006, Sustainable Brands has become a global learning, collaboration, and commerce community of forward-thinking business and brand strategy, marketing, innovation and sustainability professionals who are leading the way to a better future. We recognize that brands today have… [Read more about Sustainable Brands]
AeroFarms Upcoming Events
AeroFarms Upcoming Events
On October 31st, AeroFarms Co-Founder & CMO, Marc Oshima, will be presenting at the London Food Tech Summit! He will be sharing the AeroFarms story on "The Future of Our Food Tech Reality" panel. For more information about this event, click here.
Are you in the NYC Area? Join us at Food Loves Tech! This two-day innovation expo will take place at Brooklyn's Industry City on November 3-4 and will feature the latest innovations happening in the food & drink industry. AeroFarms Co-Founder & CMO, Marc Oshima, will help kick off this event, speaking on the opening panel Friday morning. You don't want to miss this! Click here for tickets.
On November 6th, AeroFarms Co-Founder and CEO, David Rosenberg, will be the keynote speaker at the AT&T Mobile TUN Gala in Vienna, Austria. This event will highlight various projects that contribute to energy efficient, environmentally conscious use of telecommunications and the conservation and protection of the environment, nature and species.
On November 8th, AeroFarms will be participating in The Slow Down - Slow Food NYC's 6th Annual Party! This year's Slow Down will be a one-of-a-kind celebration hosted at Grow NYC's Project Farmhouse, with a delicious menu featuring AeroFarms greens throughout! Click here for tickets.
On November 13th, AeroFarms CTO, Roger Buelow, will be speaking at the FFAR Crops in Controlled Environments Convening Event in Yorktown Heights, New York. Click here for more event information.
On November 14th, AeroFarms CMO, Marc Oshima, will be speaking at the Forbes AgTech Launch Event in NYC. Register for the event here
On November 15-16th, David Rosenberg, will be traveling back to Saudi Arabia, to speak at the Misk Global Forum. This event is an ongoing platform that brings young leaders, creators and thinkers together with established global innovators to explore, experience and experiment with ways to meet the challenge of change.
AeroFarms Brings in IKEA and David Chang to Close $40m Series D
US indoor agriculture group AeroFarms has closed a $40 million Series D round, adding IKEA Group and David Chang, chef and founder of the Momofuku Group, and retired US Army General David Petraeus to a previously released list of international investors.
AeroFarms Brings in IKEA and David Chang to Close $40m Series D
OCTOBER 27, 2017 LOUISA BURWOOD-TAYLOR
*First Published May 30, 2017. Updated October 27 to reflect final close on $40m.
US indoor agriculture group AeroFarms has closed a $40 million Series D round, adding IKEA Group and David Chang, chef and founder of the Momofuku Group, and retired US Army General David Petraeus to a previously released list of international investors.
A May Securities & Exchange Commission Filing indicated that AeroFarms had raised $34.3 million of a targeted $40 million.
AeroFarms grows leafy greens using aeroponics –- growing them in a misting environment without soil –- LED lights, and growth algorithms.
The round takes AeroFarms’ total fundraising efforts to over $130 million since 2014, including a $40 million debt facility from Goldman Sachs and Prudential.
AeroFarms attracted new, international investors in this latest round, including Meraas, the investment vehicle of Sheikh Mohammed bin Rashid, vice president of the United Arab Emirates and the ruler of Dubai.
The round marks the first investment for ADM Capital’s new growth stage agriculture-focused Cibus Fund, and global asset management firm Alliance Bernstein also invested. Existing investors Wheatsheaf Investments from the UK and GSR Venturesfrom China also joined the round.
The filing also revealed that AeroFarms had renamed its holding company to Dream Holdings, as part of its move from an LLC to a C-Corp, referencing its new retail brand Dream Greens. The Dream Greens brand hit the shelves of ShopRite, Whole Foods, FreshDirect, and Newark chain Seabras in February. Before that, the business was selling its greens into food service under the AeroFarms brand.
AeroFarms’ global list of investors is representative of its plans to expand globally, David Rosenberg, CEO, told AgFunderNews.
“We want to expand domestically and overseas, and we are excited about the potential for Meraas to help us expand into that region,” he said.
AeroFarms is not the only group to consider building indoor farms in the Middle East; Pegasus Agriculture Group, is a hydroponics-based indoor ag company that is based in Abu Dhabi, with facilities across the Middle East and North Africa.Egyptian Hydrofarms is another local example, and Indoor Farms of America recently made its first farm sale in the region.
AeroFarms also wants to add to its 120-strong team of plant biologists, pathologists, microbiologists, mechanical engineers, system engineers, data scientists and more. In particular, the company wants to add team members to its research & development department, with a view to improving the quality and operating costs of the business, according to Rosenberg. “This is where the data science and software platforms we’re using can really pull the business together.”
AeroFarms just completed construction of its ninth indoor farm, with four in New Jersey including its state-of-the-art 69,000 square foot flagship production facility in Newark. It also has plans to build in the Northeast of the US.
For more about AeroFarms, read our earlier interview with CEO David Rosenberg here.
Toronto Entrepreneur Brings Vertical Farms to Windsor
The old Forster high school’s computer lab houses the steel frame work for four vertical farms, including one that’s teeming with several types of kale and lettuce along with thyme, arugula and Italian dandelion. It has the potential to grow 70 plant varieties year round.
Toronto Entrepreneur Brings Vertical Farms to Windsor
MARY CATON
Published on: October 18, 2017 | Last Updated: October 18, 2017 8:27 PM EDT
Vertical Farm Inside Old Forster H.S. Click Here to View Video
The future of indoor farming is held together with zip ties, powered by extension cords and aerated by bathroom exhaust fans.
Toronto area entrepreneur Zale Tabakman has brought his budding vertical farming business to Windsor through a collaboration with Canada South Science City and support from Unifor Skilled Trades.
Tabakman’s agriculture and technology company — Local Grown Salads — is taking root inside the Forster Community Hub.
The old Forster high school’s computer lab houses the steel frame work for four vertical farms, including one that’s teeming with several types of kale and lettuce along with thyme, arugula and Italian dandelion. It has the potential to grow 70 plant varieties year round.
Because of the density of the plantings, each 32-square-foot unit can produce the equivalent of one acre of land over the course of a year.
“So I’ve got four acres of land here that don’t even take up a classroom,” Tabakman said.
Tabakman is fiddling with prototypes which is why the units still feature zip ties and bathroom fans.
“There’s nothing fancy here,” he said.
The roll-up shades contain the LED lighting necessary for growing while the base holds water and the white square-shaped towers contain an organic soil mix and the root system. The exhaust fans mounted at the top attach to flexible vent hoses punctured with holes so that air is pushed down on the plants.
It’s almost a closed-loop system that recycles water and nutrients to make it environmentally sustainable.
Eventually, Tabakman hopes to grow, harvest and package all in one location — so you can serve a salad harvested that morning.
Zale Tabakman checks on seedlings at Local Grown Salads, a business specializing in vertical growing located inside the Forster Community Hub on Oct. 18, 2017. NICK BRANCACCIO / WINDSOR STAR
Bill Baylis, left, of Science City, and Zale Tabakman, owner of Local Grown Salads, a business specializing in vertical growing, examine fresh lettuce, thyme and kale inside the Forster Community Hub. NICK BRANCACCIO / WINDSOR STAR
Zale Tabakman samples lettuce, thyme and kale at Local Grown Salads. NICK BRANCACCIO /WINDSOR STAR
At Science City, he will offer an education component explaining the process and even providing information on how to set up a home hydroponic growing unit.
Plans also call for a commercial grade farm in the old school cafeteria. Produce could be sold at local markets with the proceeds helping to sustain the Forster Hub.
A second non-profit community farm would be operated elsewhere in the building to provide fresh produce at low cost to the Sandwich community.
“It’s got a lot of potential,” Science City president Bill Baylis said.
“This food initiative captured Unifor’s attention,” said Ken Lewenza Jr. “There’s no pesticides, it’s more nutritious and better for the environment because it’s not being transported to Windsor-Essex from California.
“This is not your grandpa’s farm.”
LiUNA is another supporter of the venture and Lewenza Jr. anticipates a number of partnerships being forged in the coming months to bring vertical farming to different sectors.
“I think academic institutions could play a role in developing this,” he said. “We can develop interconnected strategies for social, economic and ecological development and think about how new technology can be owned, operated and directed by communities.”
Lewenza Jr. wants to work in partnership with traditional agricultural and green house sectors.
He calls the vertical farm “a game-changer in terms of thinking about schools and under-utilized community spaces we can make into sustainable hubs.”
Tabakman’s system economically grows vegetables free of insecticides or herbicides.
As for its home inside the Forster Hub, it’s been a slow ramp up since the idea of a community-based co-op first surfaced in May 2016.
The building is owned by Matty Maroun’s Canadian Transit Co.
Baylis said all the legal details have yet to be finalized and the 94-year-old building is still in need of a new roof.
That’s prevented Baylis from re-launching all of Science City’s exhibits, although he is hopeful he will be able to accommodate school tours by the end of November.
“The schools are still calling, so it’s nice that they remember us,” he said.
Foundation for Food and Agriculture Research Crops in Controlled Environments Convening Event
Foundation for Food and Agriculture Research Crops in Controlled Environments Convening Event
MONDAY | November 13, 2017 | 8:30 AM
To advance crop development in controlled systems that will support economic viability, FFAR will host a convening event to help us determine the state of science and, most importantly, the areas where FFAR can catalyze research efforts to advance crop development for controlled environments. At this convening event, we will explore areas of research where joint efforts in research between the public and private sectors will advance the field, such as:
– Advances in the molecular understanding of traits required for controlled environments
– Breeding crops for controlled environments and increasing nutritional content
– Alternative methods for crop adaptation
– Environmental stressors to enhance qualities and nutritional content
FFAR believes that through increased investments from both the private and public sector, we can help put controlled environment agriculture at the forefront of providing food security and economic opportunities in urban centers.
Event Details
Date: November 13, 2017
Time: 8:30 a.m. – 5:00 p.m.
Location: IBM Thomas J. Watson Research Center in Yorktown Heights, New York
Keynote Speaker
Caleb Harper
MIT Media Lab
Contact Details John Reich | FFAR | jreich@foundationfar.org
Melbourne Start-up Farmwall Lets Chefs Harvest Their Own Greens
Melbourne Start-up Farmwall Lets Chefs Harvest Their Own Greens
ROSLYN GRUNDY
October 10, 2017
An artist's impression of the Farmwall vertical farm. Photo: Supplied
It's a plan so cunning you could put a tail on it and call it a fox. Geert Hendrix, Serena Lee and Dr Wilson Lennard, from Alphington-based start-up Farmwall, have devised a small-scale indoor farm for restaurants and cafes that allows chefs to grow and harvest their own herbs and microgreens in a space the size of a bookcase.
Farmwall has crowdfunded its first three vertical farms, which will be custom-designed and installed in restaurant kitchens and dining rooms after consultations with chefs and restaurateurs.
Once chefs have selected the plants they want to serve, Farmwall will take care of the rest, making weekly visits with trays of germinated seeds.
Nathan Toleman is an early adopter of Farmwall's aquaponic vertical garden. Photo: Luis Enrique Ascui
The company's first customer is Nathan Toleman, who is installing vertical farms at his cafes Higher Ground and Top Paddock. Toleman says the cafes spend a fortune on herbs, which often come in individual plastic packets.
"There's so much waste product, and we thought we could firstly save money, and secondly save waste. There's nothing fresher than herbs you grow right there and we can harvest them as we need them."
The herbs grow under lights in trays lined with organic hemp fibre, a waste product. The water that wets the hemp mats and germinates the seeds cycles through a fishtank, with the filtered fish waste feeding the growing plants.
Roasted mushrooms and polenta with lemon balm at Higher Ground. Photo: Supplied
"It's 100 per cent natural," says Geert Hendrix. "It's an ecosystem so we never have to clean the water out, although we have to monitor it to keep the ecosystem in balance."
The company's next step is to build Melbourne's first commercial aquaponic farm at the rehabilitated former tip in Alphington.
What Will it Really Take For Vertical Farms To Succeed?
What Will it Really Take For Vertical Farms To Succeed?
Funders and proponents say vertical farming is the future. But consumer demand may change the nature of what it means to "grow."
October 24, 2017
by Paul Adams
ENVIRONMENT FARM OUTLIERS PLATESCIENCE SHELF TECH
AeroFarms, the world’s largest industrial farm, is contained within a windowless, gray building in Newark, New Jersey. In its 70,000 square feet of floor space—not all of it yet in use—kale, arugula, baby salad greens, and herbs grow in trays without soil; their roots grow down through water-misted air. It’s a clean, painstakingly engineered facility, where outside visitors must go through the hygienic paces before entering, moving through a series of antiseptic footbaths; into a sanitary uniform complete with booties, shopcoat, and hairnet; and finally through a particle-removing blast of pressurized air. Only then can one take in the sight of thousands of plants growing under neon lights in 80-foot-long racks stacked 36 feet high, arranged in aisle after aisle.
Vertical farms like AeroFarms, of course, have their critics. But proponents say they are the future, and judging by the sheer volume of vertical farm-related headlines, you might conclude that those proponents are right—that all we need to do is sit back and watch while conventional agriculture withers away, farms revert to wildland, and sparkling, non-polluting growing facilities become a new part of our cityscapes.
AeroFarms,
It was this summer, after all, that the SoftBank Vision Fund, whose investors include the Public Investment Fund of the Kingdom of Saudi Arabia, Apple, Foxconn, Qualcomm, and Sharp, anted up $200 million—said to be the largest ag-tech investment ever—to help San Francisco-based company, Plenty, realize its vision of building vertical farms in every city with a population of greater than one million. Meanwhile, Global Market Insights, a research firm, recently predicted that the vertical farming market will be worth $13 billion dollars by 2024, with more than 70 percent of that value coming from indoor farming operations like AeroFarms and Plenty.
It’s easy to see the appeal. By isolating themselves from the outside environment, vertical farms can go pesticide-free. They use very little water; AeroFarms claims that it can grow its greens using only five percent as much water as a conventional farm. They can shorten food’s voyage from farm to plate from hundreds or thousands of miles to mere steps. On the downside: Facilities are expensive to build, and they mostly replace free sunlight with expensive electricity—so much electricity that it may well wipe out the carbon advantage of fewer food miles.
Something is going on here. The question is, what?
But they are fabulously productive. That’s partly because they operate year-round, explains Marc Oshima, chief marketing officer of AeroFarms, and partly because they stack growing plants ten or 20 deep. But it’s also that today’s high-tech vertical facilities can fine-tune variables such as airflow, humidity, and the intensity, wavelengths, and duration of light, as well as piping nutrient-enriched water directly to the roots. That allows each plant to “get what it needs, when it needs it. That lets us grow our greens in 12 to 16 days. It takes 30 to 45 days in a field,” Oshima says. “Annualized, we’re 390 times more productive than a field farm.”
Impressive, but not enough to trigger a collapse of conventional agriculture. To date, vertical farms have grown only a limited array of crops. They seem to be nowhere near to growing the corn and soybeans that make up more than half of American ag. And as for the idea of replacing the output of America’s roughly 400 million acres of cropland with indoor facilities, it’s not particularly credible. Let’s say we could reduce the necessary acreage by a factor of 400 because of the increased productivity of vertical farms. (We probably couldn’t, once we started moving into grains and beans and other vegetables.) We’d still need a million indoor acres, or roughly as much space as a thousand World Trade Centers.
So the death of outdoor agriculture isn’t going to happen. But there’s a lot of smart money behind vertical farming, and a lot of tech-trained guys, whose best skill is shifting gears as they learn the ins and outs of a market.
Low light, high density, short turnover
For Chris Higgins, the founder of indoor-farming industry publicationUrban Ag News, the current formula for vertical farming success includes “a low-light-intensity, high-plant-density, short-turnover crop.” That is, a crop that doesn’t use much electricity and produces a lot of pounds of product per unit of space and time. What that means is that, for the foreseeable future, the salad market, with its clamshell boxes of dollar-an-ounce greens harvested as young as possible, is the place to watch for vertical farm growth.
“We’re going to see a lot of failures before things take off.”
Baby greens, says Marc Oshima, “is an $8 billion market – and it’s considered one of the most dangerous to be in.” Leaf vegetables grown in fields, he points out, are highly dependent on vicissitudes of water availability and vulnerable to microbial contamination. Growing them in a controlled indoor environment has the potential to change that equation.
That makes differentiating one’s lettuce in the market more of a challenge, but, according to Robert Colangelo, CEO of Green Sense Farms, the way to succeed in a difficult market is to keep the quality of the end product in the foreground. And the vertical farms, with their tight environmental controls and local delivery, may well have an advantage there.
But is there life beyond greens? There are a handful of crops that may soon be added to the greens-and-herbs rotation, notably strawberries. But, as Higgins points out, the game could change as growers develop strains of plants adapted to indoor farming. “Right now,” he says, “we’re just using field varieties. We won’t see a ton of growth in our industry until we breed lower-light-requiring crops. And that’s very feasible, but people won’t start really developing them until the industry hits a certain critical mass, and it’s hard to say when that will happen. We’re going to see a lot of failures before things take off.”
Strawberries may be the next crop that vertical farm companies aim to grow northward
And Colangelo foresees development beyond the conventional food market in the near future: “The next areas are plant proteins and botanicals for biopharmaceuticals. And crops grown for home delivery, to completely go around brick-and-mortar stores. That will be a huge change over the next five years.”
In search of a business model
Part of that change will be in crops grown. But equally important will be the changes that come as vertical farmers discover business models that work.
At the moment, that is a crying need. Think of AeroFarms, the world’s largest vertical farm at 70,000 square feet. A year ago, the world’s largest vertical farm was even larger: a company called FarmedHere, which grew greens in a 90,000-square-foot warehouse space on the outskirts of Chicago. That farm shuttered in January. The ChicagoTribune wrote that, given the costs of energy and labor, the company’s bottom line “looked significantly better by giving up the farm.” Last year, Atlanta’s PodPonics, which both sold turnkey farm “pods” and grew its own produce, went bankrupt, unable to scale up fast enough to stay afloat.
“The large-scale, that’s where most of the investment is going,” says Henry Gordon-Smith, co-founder of the Association for Vertical Farming. “But in a lot of cases, they’re too new to make profit. You can have all the size and efficiency in the world, but you still have to sell millions of units of produce.”
Numerous containers can be networked together in a single warehouse, to benefit from the economies of scale of a larger installation.
And once you’ve landed a big investment, you’ve lost some freedom. Robert Colangelo’s Green Sense is about to build its fourth farm, in Las Vegas, at a cost under $5 million. “With big investments, you get big investors watching everything you do,” says Colangelo. “Just because you have money doesn’t mean you can expedite your way through the learning curve; you still have to go through the same trial and error, and that takes patience.”
Higgins concurs. “With a bigger farm, logistics becomes more important: distribution, trucks, inputs. If you streamline with automation, and put in the crop that works with your automation, now you need to get access to shelf-space at key grocery stores and focus on sales to turn around on the shelf very quickly.”
By Gordon-Smith’s estimate, there are about 25 vertical farming companies in the United States, with 5,000 or more square feet of growing space, and only about half a dozen, like AeroFarms, operating with 20,000 or more.
Of those 25 medium-scale farms, some are “very healthy,” says Higgins. “It helps that they can live on lower profit margins.”
In a more mature industry, says Colangelo, the larger farms will have some undeniable advantages, but today, with the technology evolving as rapidly as it is, “if you build smaller farms, you’re not as committed. If you bought two million dollars’ worth of lights two years ago, in a short time your big farm will be obsolete.”
A smaller operation is nimbler as well. Green Sense’s business model is to build each of its farms to supply a particular customer, growing the specific crops they want, in the required amount, in the right location. A customer might be a supermarket chain, a college campus, or a military base. “We find out the exact count and cultivar of greens that they use each day, and then we back-build the farm.”
Ideally, vertical farms will would move beyond the herbs-and-leafy-greens outputs
Gordon-Smith cites FarmOne, based in downtown New York City, as another operation that succeeds by focusing heavily on demand. FarmOne targets a specific, finicky niche: high-end restaurants. The farm’s web store lists such grow-to-order specialty crops as micro anise hyssop and over 20 varieties of basil.
FreshBox, near Boston, is proudly among the only commercial farms that are “gross margin positive” according to its CEO, Sonia Lo. Her farms are modular, built in 320-square-foot shipping containers, each with its own temperature, humidity, and airflow customized to the needs of a crop. Numerous containers can be networked together in a single warehouse, to benefit from the economies of scale of a larger installation, while maintaining the flexibility of smaller ones. “There’s a 20-degree difference between what romaine grows at and what basil grows at, so in a single space, you’re not optimized for any one plant. Containerization is our solution for that,” Says Lo. This approach allows crop yields per square foot as much as 2,000 times that of field farms, she says.
And, she adds: “We’re also fortunate to have very patient investors.”
Beyond greens
The next major shift might happen when major fresh produce brands start to move into vertical farming.
Vertical farms are still in their infancy. The presence of high-tech investors and the tech-oriented approach many of them have taken virtually guarantees that many will take the tech industry’s approach to finding their feet—shifting target markets, techniques, and business models fluidly as opportunities present themselves. Some, surely, will end up taking what they’ve learned about small-scale operations and use it to build high-output farm “machines” for restaurants and grocery stores. Some will gravitate to restaurants or growing specialty products. Others will wander further afield.
In the short run, though, to remain sustainable, they need to be good at their current business—growing greens. And that’s not easy.
Colangelo says, “People come in from a tech background and they understand it academically but not from a production standpoint; or they come from the business world, and they don’t understand science and growing.”
“These farms aren’t run by robots, despite what you may believe,” says Gordon-Smith. “Some people think they’re going into the farm business and they create a tech company. You need a grower with a personal touch, and you need that person to be treated with respect, and to stick around.”
Chris Higgins predicts that the industry will continue to grow with cautious investment, but that the next major shift might happen when major fresh produce brands start to move into vertical farming. “They’re paying very close attention. If a big traditional farming company gets in, that will really start to bring it mainstream.”
“Extremely smart people run all of these companies, and they know how to access financing, even based on the small amount of sales they have,” says Gordon-Smith. “Five years from now, if they’re not profitable, they can keep getting that money. Maybe not for 20 years, but for five years.”
ENVIRONMENT, FARM, OUTLIERS, PLATE, SCIENCE, SHELF, TECHVERTICAL FARMING
The Future of Farming May Be Below The Soil
By IRINA IVANOVA MONEYWATCH October 16, 2017, 5:15 AM
The Future of Farming May Be Below The Soil
Think of urban farming and the images that may come to mind are a community garden, vertical greenhouse or even a rooftop garden.
The farm Steven Dring operates in south London isn't like that. In fact, it's not even visible from street level. The operation is situated in an air raid shelter 100 feet underground that has been left vacant since World War II.
Dring, his co-founder, Richard Ballard, and a team of a dozen people grow lettuce and microgreens hydroponically, year-round, in the shelter, which includes two tunnels. The produce is then sold to restaurants and stores around London.
"It does seem completely counterintuitive to build a farm underneath the soil, but it's actually one of the best environments to do it," Dring said.
"You've got that duvet of 100 feet of soil, which insulates the tunnel—it's like someone's built a greenhouse for us. You have LED lights and hydroponics, which has been around forever. We just put it all together and re-purpose an unloved space."
The operation, called Growing Underground, is competitive with traditional farming because their model excludes many of the costs large agribusiness has to contend with, Dring said. The startup sells locally, meaning it doesn't have to ship produce long distances. Another advantage is they don't have to heat or cool the underground tunnel, which stays at steady temperature because it's so far under the earth.
"The one cost that we have consistently all year round is our energy cost, the cost for the LED lighting," Dring said. "Our seeds cost the same, our water costs the same, our nutrients cost the same."
Rows of microgreens at the Growing Underground facility in London | GROWING UNDERGROUND
Hydroponic agriculture grows food without soil, suspending plants in water filled with nutrients. Because the water can be captured and reused, hydroponics uses only about one-third of the water consumed in traditional farming. That's especially important these days because industrial-scale agriculture has severely depleted the soil in many places and caused other environmental harm.
Until recently, hydroponics usually came with high start-up costs, meaning a farmer could wait for years before seeing a profit. Dring, who recently reached a distribution deal with Marks and Spencer, one of the U.K.'s largest retailers, expects Growing Underground to break even later this year.
"I'm going to get drunk for a week when that happens," he joked. "I've already told my investors."
Beyond the novelty of growing food in the bowels of London, Growing Underground's approach shows that it's possible to feed a growing population without the carbon-intensive effects of conventional industrial agriculture, which is in many ways unsustainable.
"They can grow food under deserts, they can grow food in old salt mines, they can grow food in old World War II bunkers," said Daniel Epstein, CEO of the Unreasonable Group. "They can port this model to any town in the world."
The Unreasonable Group incubates and invests in companies tackling social issues, including Growing Underground and other startups growing food with hydroponic and aquaponic technology.
"Urbanization is the largest movement of humans in the history of humankind," Epstein said. "Urban environments are also food deserts, because all the food is grown on the outskirts. That has to stop."
Dring is already scoping out sites in other parts of England, and said he has his sights set on a number of U.S. locations. He doesn't see the group as competitors to traditional farming, but rather as a compliment.
"Farmers are looking at the future," he said, "and they start to look at us, and say, 'Well, if you can use agricultural technology and intensify the yields when you grow produce, can you start to grow in different spaces?'"
Urban Farming? It's Operations, Stupid
Everything in its right place
Urban Farming? It's Operations, Stupid
Published on October 12, 2017
Robert Laing
CEO & Founder at Farm.One
Contrary to most press, the challenges of urban farming are mostly not about high-tech LEDs and patent-pending hydroponics designs - they are about efficient operations.
When you see images of vertical farms, you shouldn't think "Woah, cool" - you should be asking "Does it actually work well?", and "Is it a sustainable operation?"
Vertical farming, and urban farming at small scales, are new practices. There is no rule book. There is no workforce of managers with prior experience to draw on. Everything is being rewritten from scratch.
In this new world, the farmers who will be successful are those who are obsessed with operational efficiency.
The McDonald's brothers established the first rulebook for an efficient, replicable fast-food operation by laying out their draft kitchen over several iterations with chalk on a tennis court (as immortalized recently in The Founder).
Urban farmers should be starting to think in similar terms, understanding how they can operate in new forms of physical space most efficiently, safely and easily.
In our Commercial Urban Farming class, this is one of the aspects we touch on, showing how important efficient operations can be in ensuring you have a profitable farm.
Farm Design
Designing the physical space of a farm is as important as specifying the right pumps and ventilation systems. While building vertically is incredibly space-efficient, it creates problems when it comes to worker access, safety and airflow. Overall, designing with humans in mind is vital. When looking at a farm design, some of the following questions are important:
- Is there wasted space?
- Are crops easily accessible for plant care and harvesting?
- Does equipment require especially tall or skinny staff? (Really!)
- Does everything have a clear place to go?
- Is everything that could be automated, that can be?
- Are spaces designed to facilitate quick movement?
- Are workers able to move items efficiently, without "dangerous carrying"?
- Is it always clear when something is wrong?
- Is it easy to check if equipment is working?
- Is the farm a pleasant place to be?
Managing the team
Managing the workforce is an important practice, both when it comes to tactical efficiency, but also safety, training and other considerations. A poorly-designed, low-tech, but well-managed farm may out-perform a sexy high-tech mess. Think about some of the following questions as you build your idea for farm:
- Is training standardized? How is training assessed?
- Are workers expected to be generalists, or specialized?
- Are there written instructions in relevant places?
- Are there visual or video guides for complex processes?
- Are workers empowered to ask questions?
- Are there clear safety protocols? How are they enforced?
- Is there a culture of safety that encourages honest, prompt feedback?
- Are workers taught how to move efficiently?
Task Management
On a working farm there are dozens or hundreds of specific tasks to perform, in terms of maintenance as well as normal daily operations like planting, transplanting, harvesting. Inexperienced teams may not treat these as carefully as they need. Questions such as the following can expose potential issues:
- Are processes clearly defined and understood?
- Is the state of the farm clear to all workers and management?
- Are problems fixed or escalated at the right levels?
- Are there metrics/SLAs in place for speed-of-answer for problems?
- Are checklists in place for complex tasks?
- Is record-keeping digital? If not, why not?
- Can tasks be tracked back to specific times and individuals?
Ensuring long-term staff retention
Farm work can be physically taxing, under difficult conditions such as elevated temperature, humidity and noise. If farm workers are not motivated sufficiently, this can become a short-term gig rather than a long-term career - which is bad for morale, bad for company training costs, and bad for keeping knowledge within the organization. So careful attention should be paid to questions like these:
- Do management understand the true nature of farm tasks?
- Do management regularly go 'back to the floor'?
- Is the hiring process effective at identifying the right personnel?
- Are farm workers listened to? Are there concerns acted on?
- Are farm workers given a clear career progression roadmap?
- Are farm workers paid an appropriate (not just minimum) wage?
- Are staff retention problems addressed tactically and strategically?
Of course, this is a general, non-exhaustive list. But these kinds of considerations should be on the mind of any team that wishes to build a successful urban farming business. Operations is key!
Find out more about our Commercial Urban Farming class. Next class October 28/29.
First Indoor Vertical Farm in Slovenia
First Indoor Vertical Farm in Slovenia
Slovenia has amazing nature with mountains, lakes, woods, rivers, good fertile land and clean fresh water. Sounds like a fairy-tale, but it is true.
It is also true that we have lots of farms growing different crops and farmers raising livestock and all this you can see when you drive just a few miles from the city. You guessed it. Our country is small. So perhaps we have good soil, good weather conditions, clean fresh water, but the quantity of the fertile land is getting smaller. (And of course, we can't forget that people wants to eat quality and clean food all year.)
So that’s why, we decided to start exploring the idea of indoor vertical farming. We decided to start from scratch. Firstly, with books, YouTube, online courses and then we made a small room for growing microgreens, around 120cm long, 40cm high and 30cm deep with fluorescent lights, thermometer from an aquarium, and seeded our first seeds.
We were so proud!
We quickly found out, the importance of airflow, so we installed a PC fan, which was a simple and amazingly effective solution. In a few days we had our first microgreens crop.
And they were so tasty
So after some more trials and fine adjustments of the parameters, we decided that it is time to start developing larger and more advanced Indoor Vertical Farms and its components.
So in the past two years, we developed and constructed a controlled growing room with multi layers, providing perfect conditions for growing vegetables locally, without using any non natural enhancements.
Our automated control system keeps more than 10 parameters at optimal level all the time, for perfect growing conditions.
Our ventilation system is one of a kind. It solves the problem of even heat distribution between layers, better introduces CO2 to the plants, removes humidity from the leaves and keeps them dry and also keeps roots warm and cools the air, on top of the plants. Basically, it imitates the movement of the air in nature.
We also made our own recipes for optimal growing different plants and we constantly upgrade our software and hardware with better solutions. In the future, we are planning to develop our own fully automated Indoor Vertical Farm.
We presently offer complete construction of vertical farms to the potential buyer, with all our solutions. We are also already selling vegetables, produced in our farm, to local chefs and other markets.
FFAR Makes Grant to Vertical Farming Company
FFAR Makes Grant to Vertical Farming Company
The Hagstrom Report
September 11, 2017
The Foundation for Food and Agriculture Research announced a grant awarded to AeroFarms, an indoor vertical farming company based in Newark, N.J. to improve crop production.
FFAR, a nonprofit set up in the 2014 farm bill to combine public and private research dollars, gave AeroFarms $1 million, and the company will matched that with a $1 million commitment.
Roger Buelow, the company's chief technology officer, will use the grant to collaborate with scientists at Rutgers University and Cornell University to improve crop production by defining the relationships between stressed plants, the phytochemicals they produce and the taste and texture of the crops grown.
The work will result in commercial production of improved leafy green varieties and yield science-based best practices for farming, FFAR said.
The grant was announced at an event in the patio of the Agriculture Department's headquarters attended by FFAR Executive Director Sally Rockey; David Rosenberg, AeroFarms co-founder and CEO; Ann Bartuska, the acting undersecretary for research, education and economics; and Tom Stenzel, president and CEO of the United Fresh Produce Association.
Rockey said vertical farming allows scientists to take advantage of the precision that is possible in indoor systems, where "stressors" from light to humidity to temperature can be controlled consistently and precisely to improve specialty crop characteristics such as taste and nutritional quality.
Rosenberg said "This FFAR grant is a huge endorsement for our company and recognition of our history and differentiated approach to be able to optimize for taste, texture, color, nutrition, and yield and help lead the industry forward."
Stenzel said "Pioneering initiatives like the work by AeroFarms and FFAR will help lead the produce industry with a science-backed approach to understand how to grow great tasting and nutritionally dense products consistently all year. We believe that there is a need for even more public/private partnerships like this to spur breakthroughs."
Senate Agriculture Committee ranking member Debbie Stabenow, D-Mich., praised FFAR for making the grant.
"Urban agriculture has incredible potential to spur economic opportunity, increase access to healthy food, and inspire the next generation of farmers. I'm pleased that the foundation is committed to new techniques to grow food in innovative ways," said Stabenow, who has introduced a bill to establish an office of urban agriculture at USDA and to make urban farms more easily eligible for federal funding.
The grant to AeroFarms was made through FFAR's Seeding Solutions grant program, and is being funded within the Urban Food Systems Challenge Area, which aims to augmenting the capabilities of the current food system to feed urban populations by enhancing urban and peri-urban agriculture.
Are Vertical Farms The Way of The Future?
Are Vertical Farms The Way of The Future?
BY Avlya Jacob 12, OCT 2017
Leafy greens and herbs growing on stacked trays, in a highly-controlled environment like abandoned buildings or used warehouses, with absolutely no sunlight and soil - only LED lamps, a small amount of water, and a little bit of science.
We’re talking about vertical farming.
From a simple idea in Dr. Dickson Despommier’s medical ecology class back in 1999, this method of producing crops is now slowly transforming the way we grow food and is on track to becoming one of the answers to global food shortages. Vertical farming is far from the traditional approach where crops are being grown in huge fields or greenhouses. It's is all about taking advantage of vertical space and creating production efficiencies. Vertical farming uses 40% less power, 95% less water, and can produce crops as fast as 30 days
WHAT’S SO GOOD ABOUT VERTICAL FARMING?
Vertical farming comes with a long list of benefits, and they're beyond the typical “zero sunlight and soil.”
First up, no more seasonal crops. These modern farms are capable of producing traditionally seasonal fruit and vegetables all year-round. There will no longer be a “wrong season” as the crops will be grown inside a facility where environmental factors are completely controlled. Also, there will be less post-harvest spoilage and food waste since most of the produce can be sold in the same building where it is grown. According to estimates, about 30% of harvests are lost each year due to spoilage.
Second, vertical farms are weatherproof. Since the crops are safe and sound in a highly-controlled environment, the entire harvest won’t get affected by extreme weather events like hurricanes, droughts or floods, unlike outdoor farming.
Third, they consume less water. Vertical farms use a minimal amount of water compared to normal farms. The methods used are either hydroponic, where plants are grown in a basin of water with nutrients, or aeroponics, where the roots of the crops are sprayed with nutrient-filled water or mist. These two methods use far less water, as all water is taken up directly by the plants - with no wastage as a result of water being spread out in soil. The exact amount of water needed by the plant is the exact amount used. Vertical farming even promotes water recycling. Urban waste, including black water, can be composted and used for farming inside the facility.
Lastly, vertical farms can grow produce twice as fast. This is the main reason it has been touted as the ideal solution to the food crisis some countries are facing. The world’s population is expected to balloon to 10.5 billion by 2050. Which means we have to increase our food supplies by at least 60% to be able to meet demand. To make this possible, a food production system that requires low water consumption, less resources, and less land space is critical. Vertical farming ticks these boxes. The method can yield more plants per square metre than outdoor farms or greenhouses simply because the crops can be stacked as high as the building or the facility.
On the whole, there’s no question to what vertical farms can do. A lot of advocates and agriculture analysts today are seeing the huge potential of this modern method and there are plenty of examples of it working really well.
VERTICAL FARMS AROUND THE GLOBE
The first low-carbon, hydraulic driven vertical farm in the world was Sky Greens.
Located in Singapore, a small island city with a population of more than 5 million that relies heavily on food imports from other countries, the farm grows veggies in A-shaped aluminum towers about nine meters tall each. Sky Greens calls its technology the “A-Go-Gro”. Each tower has 22-26 tiers, which are rotated at a rate of 1mm/second for an equal distribution of natural sunlight and airflow. Sky Greens is capable of growing 800 kilos of Chinese cabbage, kai lan, spinach, and other leafy greens every day. It has been producing these crops commercially since the year 2012.
Photo: Sky Greens vertical farm
In Japan lies one of the largest vertical indoor farms in the world, built by the Mirai Corporation, founded by plant physiologist Shigeharu Shimamura. With a 25,000 square feet bacteria-free and pesticide-free space equipped with 17,500 LED lights, the farm can grow up to 10,000 lettuce heads per day.
For other crops apart from lettuce, Shimamura explains: “I believe that, at least technically, we can produce almost any kind of plant in a factory. But what makes most economic sense is to produce fast-growing vegetables that can be sent to the market quickly. That means leaf vegetables for us now. In the future, though, we would like to expand to a wider variety of produce." Currently, Mirai has two additional factories located in Mongolia. It is also planning to expand in Russia and Hong Kong in the near future.
The U.S is home to several vertical farms as well. The biggest ones can be found in New Jersey, operated by the well-known firm, AeroFarms. Its global headquarters (and 9th farm) in Newark is a 69,000-square-foot indoor farm that can harvest up to 2 million pounds of leafy greens and herbs a year. It is currently the largest indoor vertical farm in the world.
By 2018, AeroFarms is expecting to have its 10th farm built in Camden. This will be a 78,000 square feet space and will supply produce to Philadelphia and South Jersey.
Meanwhile, a 900-square meter vertical farm is presently being constructed in Dronten, Netherlands. When finished later this year, it will be the largest commercial vertical farm in Europe. Fruit and vegetable supplier Staay Food Group was involved in the development of the Dronten facility along with Philips, the global leader in lighting who will be providing the facility’s GreenPower LED horticultural lighting.
VERTICAL FARMING IN AUSTRALIA
Unlike in Asia and the United States, Australia doesn’t have many commercial vertical farms. We have one private facility based in Queensland: Vertical Farm Systems. This firm produces commercial leafy greens like baby spinach and rocket, and has developed its own automated growing system, the XA series, which is being offered to buyers in Malaysia and Canada and to those wanting to grow vegetables and herbs commercially.
Photo: Vertical Farm Systems XA series automated growing system
Though it was able to successfully enter the commercial market, Vertical Farm Systems thinks it will be challenging for Australia to thrive on vertical farming on a commercial scale. This isn’t just because we’ve got plenty of land space available for farmers to grow what they need to grow (the problem countries like Singapore and Japan are facing), but largely because of our country’s expensive real estate. Our high property rates may result in high retail product prices.
"At the end of the day, the market will buy the cheapest food the market can get and you can't charge a premium for lettuce just because it was grown in a vertical farm,” Vertical Farm Systems’ managing director, Ashley Thomson, pointed out. “A lettuce is a lettuce and it sits on the table and people don't care if it is hydroponic, grown in a paddock or a vertical farm, they ask: 'How much is it?'"
Chris Wilkins of Sydney-based vertical growing systems company PodPlants, however, believes that vertical farming still has a place here in Australia because it can help produce best-quality vegetables.
“Consumers here share the same concerns about food safety and sustainability that have made the practice so popular in the US and parts of Asia," Wilkins said. "Australian cities are not so different – people simply care about where their food comes from and place a higher value on food they know was grown locally.”
PodPlants develops portable and lightweight vertical gardens. In 2014, the unique technology won the Australian Innovation Challenge.
As you can see, vertical farming has a plethora of potential benefits and a bright future ahead of it. But, it’s not all rainbows and butterflies when it comes to this trendy practice. This modern method of growing food still comes with some downsides.
WHAT’S NOT SO GOOD ABOUT VERTICAL FARMING?
One is it needs a lot of energy. Vertical farming doesn’t use natural sunlight to grow plants, it uses artificial lighting which requires high energy. According to a report, it would take about 1,200 kilowatt-hours of electricity to run the LED lights needed to produce 2.25 pounds of crops.
Also, vertical farms cannot yield all types of vegetables. Usually, they can only produce leafy greens, herbs, and tomatoes because these grow quickly. Other crops like potatoes, wheat, and rice have no place in such farms because they weigh more and require a larger space for growing.
Another disadvantage is the greens produced in these vertical farms are (currently) far more expensive than those produced traditionally. This is because they require high setup costs - with all the lighting, technology, and experienced “growers” needed. Let’s take Sky Green’s produce as an example. A 200-gram pack of Sky Greens bok choy is worth $1.25, while a 250-gram bag of bok choy produced on a traditional farm in Singapore only costs 80 cents.
Given these factors, it's evident that vertical farming is still in its infancy and more research, development and market testing is needed to get a clear picture of how it can be commercially viable in other dense areas and how it can produce a variety of crops beyond the typical lettuce and tomatoes. We’ll also need to see first a lot more companies being successful before we can say it will completely change the way food gets to our table. Right now, vertical farming cannot feed the world YET; but with its long list of benefits and its huge potential, there’s no doubt it could be the future of agriculture.
Have thoughts about vertical farming you want to share? Leave a comment below.
In the meantime, if you want to read more industry insights from us, you can check out our blog.
AVLYA JACOB
Avlya Jacob is a content writer at Ordermentum. When not working, she enjoys writing online novels and spending time with her husband.
High-Tech Farm Spreads to Middle East
BY GABRIELLE EASTER | @gab_produceplus
Tuesday 17th October 2017, 12:12 Hong Kong
High-Tech Farm Spreads to Middle East
Japan’s Spread will launch its vertical farm business in the UAE with Madar Farms and Toyo
Kyoto-based vertical farm business Spread has partnered with UAE business Madar Farms and Japan’s Toyo Engineering to launch in the Middle East.
The Japanese high-tech farm business is constructing a Techno Farm in the arid, water-sparse region that relies heavily on imported vegetables. Spread’s systems are almost fully automated, use recycled water and save on energy costs, with the new partnership aiming to supply safe, high quality vegetables to the Middle East. Once the UAE Techno Farm is completed in 2019, it will be capable of producing up to 30,000 lettuce heads a day.
The UAE farm will be the first of around 20 Spread facilities in the works for the Middle East, according to Spread.
Spread operates high-tech farms in Japan, opening the world’s largest automated vertical farm in Kizugawa, Japan.
New Downtown Restaurant to Grow its Own Produce at Indoor Urban Farm
New Downtown Restaurant to Grow its Own Produce at Indoor Urban Farm
Friday, October 13th 2017, 7:37 pm CDT | By WTOL Staff
New location for Balance Pan-Asian Grill (Source: WTOL)
TOLEDO, OH (WTOL)
Business continues to boom in downtown Toledo, especially when it comes to food.
Balance Pan-Asian Grille began construction on Friday on its new downtown Toledo location.
The restaurant will be at the corner of Summit and Jefferson.
It's not only a restaurant though.
They are also building an indoor 8,000 square foot urban farm that will grow seventy percent of the produce for their restaurants.
"This is location number four for the restaurant and our very first attempt at urban farming,” said co-founder Prakash Karamchandani.
The restaurant wanted to find ways to bring locally grown produce to their diners year-round.
"In the midwest, living somewhere like we live here with the inconsistency of the weather, we couldn't find a better idea to continue to grow local, fresh produce and be able to utilize it in our own restaurant,” said co-founder Hochan Jang.
Owners said they've loved working with the city to get the project going.
They are so excited that they're working hard to open the new restaurant before the new year.
https://balancegrille.com/ | eat@balancegrille.com