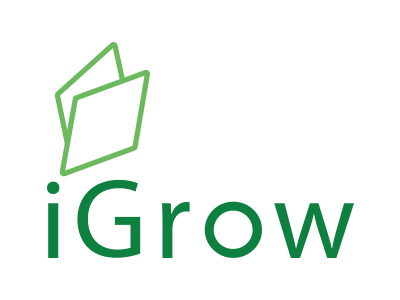
Welcome to iGrow News, Your Source for the World of Indoor Vertical Farming
Vertical Farming Kit Recognised by Manufacturers' Association
In May the company was awarded £340,000 from the government's Agri-Tech Catalyst fund to develop the format.
Vertical Farming Kit Recognised by Manufacturers' Association
15 November 2016, by Gavin McEwan
Coventry-based hydroponics developer HydroGarden's vertical-farming system VydroFarm was among the winners in the Future of Manufacturing Regional Awards, presented by EEF, formerly the Engineering Employers Federation.
The firm will now go on to represent the Midlands in EEF's National Awards, the winners of which will be announced on 31 January 2017 in London.
HydroGarden says it intends to "maximise VydroFarm's significant growth and sales potential, especially via export".
In May the company was awarded £340,000 from the government's Agri-Tech Catalyst fund to develop the format.
OPCOM Farm Makes Indoor Gardening As Easy As Plant, Pick and Plate
OPCOMLink USA announced today its OPCOM Farm indoor gardening systems, which enable anyone to easily grow their favorite vegetables, herbs, sprouts and fruits inside their homes, year-round
Our gardening systems combine advanced lighting, water management, and horticulture know-how, making it easy and fun to grow produce that is even fresher than farm-to-table; we call it Farm-on-Table.
LOS ANGELES, CA (PRWEB) NOVEMBER 14, 2016
OPCOMLink USA announced today its OPCOM Farm indoor gardening systems, which enable anyone to easily grow their favorite vegetables, herbs, sprouts and fruits inside their homes, year-round.
The GrowBox and GrowWall models couple OPCOM’s soil-free, hydroponic growing technology with proprietary color LED lighting tuned for optimal plant growth. These next generation indoor gardens enable 25 percent faster growth cycles, and eliminate the challenges of weeding, pests and weather normally associated with outdoor gardening.
GrowBox, a tabletop system incorporating four multi-wavelength LED lamps, is able to grow up to 50 plants at a time. GrowWall offers a space-saving vertical design with advanced LED tubes that support up to 75 plants displayed on five different levels. Both models use approximately 90 percent less water than traditional outdoor gardening, offering an environmentally friendly way to grow.
“Our gardening systems combine advanced lighting, water management, and horticulture know-how, making it easy and fun to grow produce that is even fresher than farm-to-table; we call it Farm-on-Table,” said Rajeev Mishra, Vice President and General Manager of OPCOMLink USA. “Given the overall concerns around eating safe and healthy fruits and vegetables, OPCOM Farm offers customers convenient and affordable solutions to personally grow clean and fresh food the entire year.”
The GrowBox and GrowWall are priced at $499 and $599 respectively, and are available on http://www.OpcomFarm.com and Amazon, right in time for the holiday season.
“You don’t have to be a gardener to enjoy our products,” Mishra says. “We are finding a lot of interest among urban dwellers, conscious consumers looking for pesticide free and non-GMO produce, and parents wanting to nurture an interest in their kids for healthy eating. It’s also a great option for seniors and others who would like to garden without the physical toll.”
Given their impressive water conservation and zero carbon footprint, such systems are considered a highly sustainable way to grow.
“Hydroponics is the future of farming and food production,” Mishra maintains, “and OPCOM is committed to being at the forefront of this revolution.”
For more information and videos about OPCOM Farm indoor gardening products, visit http://www.OPCOMFarm.com.
About OPCOM
OPCOMLink USA Inc., based in Costa Mesa, Calif., is OPCOM’s regional sales and marketing headquarters for the Americas. The company was established in 2014 to introduce advanced imaging and lighting technologies in products that help people achieve smart, healthy, and simple lifestyles. OPCOM is a global technology pioneer of advanced imaging and lighting solutions, delivering breakthrough technologies and quality products to the world’s top brands for over 20 years.
Modular Farms Announces First Modular Farm Unit
Modular Farms Inc, a Canadian start-up founded in 2015, announced the release of the first modular farm unit in press release
Modular Farms Announces First Modular Farm Unit
Set for a 2017 release, the product is a portable container farm designed for harsh weather.
November 14, 2016
Press Release
BRAMPTON, ONTARIO, CANADA - Modular Farms Inc., a Canadian start-up founded in 2015, announced the release of the first modular farm unit in press release. The portable container farm, which is designed to grow lettuces, leafy greens and herbs in the harshest and most remote environments, is available for showcase at their Brampton offices.
“Indoor agriculture is becoming a very important trend in the food market and Modular Farms is poised to be a leader in this field moving forward,” said Eric Amyot, the company’s co-founder and CEO. “We’ve designed a scalable, modular, portable and self-contained indoor farming system that literally gets delivered on a truck and plugged in to start growing, with yields twice as high as any other farming system we’ve seen to date.”
“We specifically designed the farm system to work in the north of Canada. The food security problems there are problems we think we can help solve,” said Amyot according to the release. “By doing so, we’ve created a product that can work virtually anywhere in the world.”
The Modular Farm allows farmers to add on new growing modules in the future, such as a water-capture module, a storage module, a vestibule, a micro-green module and a micro grid module.
“We want our farmers to know that they are capable of growing their business and adding modules in the future,” said Eric Bergeron, the company’s other co-founder and lead farmer. “The modules, which will be released in 2017, are specifically designed to allow farmers the flexibility to scale their business as needed.”
Modular Farms works with industry leading experts such as Intravision Light Systems of Norway and Canada, as well as Bright Agrotech from the U.S.
“The light system in our farm was specifically designed to maximize yields in the enclosed environment but also to work with the proven ZipGrow Tower growing system from Bright Agrotech,” said Amyot.
The farms, which retail for between $125,000 and $150,000 CDN are ready for production and the company has already landed 32 units to manufacture in the coming year.
GE Forges Ahead With World’s First Wind + Hydro + Storage Project
Here’s a view of the interior: That’s a lot of useful space, right? The polyvinyl cladding allows daylight to filter through, so you could imagine indoor farming among many other options
GE Forges Ahead With World’s First Wind + Hydro + Storage Project
November 14th, 2016 by Tina Casey
Trump or no Trump, the global clean energy train has left the station. A case in point is a new wind, hydropower, and energy storage collaboration between US-based GE and Germany’s Max Bögl Wind AG. The project is on track to connect its four wind turbines to the grid next year, with the hydropower component coming online in 2018.
The project represents an innovative combo of two different forms of renewable energy with an energy storage bonus thrown in.
Wind turbines and real estate
GE dropped a bit of a clue regarding one aspect of the project a couple of years ago, when it introduced its “space frame” turbine tower.
The company invited me to take a sneak peek of its prototype in California on behalf of CleanTechnica, and one thing I learned is that GE was beginning to think of wind turbine towers in terms of their footprint.
Our guide on the tour pointed out that the hollow design of the turbine tower provides the potential for piggybacking other uses inside the frame. Here’s a view of the interior:
That’s a lot of useful space, right? The polyvinyl cladding allows daylight to filter through, so you could imagine indoor farming among many other options.
Wind power and energy storage
GE’s new project takes the piggyback idea to a whole new level.
The project is located at the Gaildorf wind farm. It includes four wind turbines with a combined capacity of 13.6 megawatts. The base of each turbine will double as a water storage reservoir, for a total of 1.6 million gallons (to be clear, these are not GE space frame towers — for obvious reasons, they are fully enclosed).
These storage units will interact with a nearby lake with a 9 million gallon capacity, and a 16 megawatt hydropower plant. In effect, the turbines will act as giant batteries and provide an opportunity for the hydroplant to operate economically:
During times of peak demand and high electricity prices, the hydro plant will be in production mode. During times of low electricity demand and lower prices, the hydro plant will be in pump mode, pumping and storing water–and hence energy–in the upper reservoir for later use.
Here’s a schematic representing how the storage will help ensure the reliable delivery of electricity from the system:
To ice the renewable energy cake, the added storage raises the height of each turbine tower by 40 meters.
The end result is a “record-breaking” height of 246.5 meters, making these turbines the tallest in the world.
GE will contribute its new 3.4-137 (3.4 megawatts, 137 meter rotor diameter) wind turbines to the project. That includes the company’s Digital Wind Farm platform with Predix* software to maximize efficiency.
For those of you new to the wind energy topic, stronger, more consistent winds are located at higher altitudes. So, the taller the wind turbine, the better.
When the wind is blowing strong, excess energy from the turbines will go directly to the grid. During lulls, the hydropower plant will draw additional water from the turbine towers as needed.
Onward And Upwards For Pumped Storage
Compared to other forms of energy storage, conventional pumped hydro has a limited opportunity for global application. Geography is the main limiting factor because two reservoirs are required, and one must be located higher up than the other.
The innovative approach offered by the GE – Bögl collaboration expands those opportunities to more sites, where an in-ground upper reservoir is otherwise unfeasible.
According to GE, Bögl is already anticipating that it will engage in one or two similar projects in Germany annually after the Gaildorf project goes online.
As for GE, the company’s GE Renewable Energy arm has been front and center in the clean energy revolution, especially in the area of wind turbine technology.
The company positioned its wind turbine business to take full advantage of the federal Production Tax Credit for wind, and now it has been expanding into the wind transmission sector.
GE recently got back into the high voltage converter business after a 20-year hiatus, just in time to hook up with the proposed 720-mile Plains & Eastern wind transmission line. The company will provide three converter stations for the project, which also has the support of the Energy Department.
State of Indoor Farming 2016
There are many unknowns and misconceptions about the indoor farming market
State of Indoor Farming 2016
The Landscape
Responses came from growers around the world, including the United States, Canada, the Caribbean, Slovakia, Taiwan, Bahrain, Dubai, Tunisia, Finland, Belgium, China, and Japan.
Indoor vertical farms and hydroponic greenhouses were the most prominent primary facility type of survey respondents. Small farms primarily consisted of indoor vertical farms while larger farms primarily consisted of hydroponic greenhouses.
Any crop can be grown indoors. The more common crops grown indoors are greens, microgreens and herbs, vine crops, cannabis, some fruits, and flowers or nursery crops. Survey respondents also reported growing tubers, mushrooms, insects, hops, algae, and commodity crops (corn and wheat).
Survey respondents are growing greens, microgreens, and cannabis in greenhouses, vertical farms, and container farms, while they are growing vine crops and flowers predominantly in greenhouses.
For the most part, indoor farmers believe that the products they’ve chosen to grow are the most profitable and they plan to continue growing those crops in the future. Cannabis and microgreens top the list of crops growers believe are most profitable to grow.
Though many growers agree that cannabis is the most profitable crop, most do not plan to grow it in the next five years.
When asked about annual production and revenue capacity, cannabis topped the list of highest revenue generating crops at about $112 per square foot or about $4,800,000 per acre. Greens were the next highest revenue generating crop at $64 per square foot or about $2,800,000 per acre. The lowest revenue generating crops reported were strawberries at about $22 per square foot or $1,000,000 per acre.
Production & Operations
One of the reasons indoor farming is gaining significant traction in the United States is the ability to produce more while using less resources. According to the United States Department of Agriculture’s (UDSA) July projection for the 2016 - 2017 growing year, corn prices range from $3.10 - $3.70 per bushel and farms are producing an average of 168 bushels per acre; conventional lettuce and tomatoes are between 23 and 25x more productive at about $12,000 and $13,000 per acre respectively. In comparison, on a revenue basis alone, indoor horticulture is about 4,000x more productive than conventional outdoor commodity farming; indoor cannabis is about 9,000x more productive.
The higher revenues realized by indoor farming are driven by three factors: (a) year round production capability, (b) higher yield, and (c) higher retail pricing.
Year Round Production
In a given year, assuming there are no weather-related incidents, outdoor conventional lettuce farmers will be able to harvest their entire farm 4–5 times. In comparison, indoor farmers will be able to harvest their entire farm an average of 18 times in a given year.
Yield
According to the USDA, the average yield for outdoor conventional lettuce production in 2015 was about 30,000 pounds per acre. Indoor greens growers reported growing an average of 340,000 pounds per acre annually. The 11x increase in yield over conventionally grown lettuce is partially due to faster growth times and additional crop turns. After removing the benefit from cyclical advantages, the increase due to indoor productivity alone is 2.8x.
Higher Retail Prices
According to the USDA, the average price per pound of conventionally grown head lettuce was $0.29 in 2015. In the same year, the price of leaf lettuce was $0.58, the price of romaine lettuce was $0.39, and the price of tomatoes for the fresh market was $0.46 per pound.
In comparison, indoor greens growers reported revenues of $6.00 per pound and indoor vine crops growers reported revenues of $1.13 per pound. Even compared to the highest priced conventional lettuce crops, indoor greens farmers are seeing 10x increases in pricing and indoor tomato growers are seeing 2.5x increases in pricing.
Organic Certification And Local Production
Half of survey respondents reported growing organically though only 8% of growers answered that they were certified as USDA Organic. When asked if growers who weren’t certified wanted to achieve the certification, 47% of growers indicated interest in the certification.
Operating Costs
When asked about their biggest challenges, growers reported managing operating costs as the most difficult - their highest priorities were both reducing and predicting/stabilizing operating costs.
Labor is one of the most costly components of indoor farming operations. Large farms reported employing an average of 24 full time and 12 part time employees. Small farms reported an average of two full time and two part time employees.
On average, data collection and analysis account for about 9% of a farm workforce’s weekly labor hours and 27% of respondents spend 20 or more hours per week on data collection and analysis.
Cannabis growers, whether small or large, spend the most time working with data (about 30 hours per week on average). Large cannabis growers also have the largest reported workforce, and growers of greens and microgreens/herbs have the smallest, comparatively.
Technology
A climate control system is one of the most critical pieces of technology for an indoor farm. This system comprises of sensors (typically recording light, temperature, humidity, CO2) and some level of control for HVAC and lighting equipment.
Of those surveyed, 54% of farms have climate controls systems and 74% of those systems are connected to the internet. There are a handful of leaders in the climate controls market, including Priva, Argus, Link4, Hortimax, and Hoogendoorn; 45% of respondents have one of these systems. Of respondents, 29% have a custom system, ranging from HVAC systems on timers to proprietary sensor and controls systems developed in partnership with universities.
On average, growers have an annual budget of $12 per square foot to invest in technology for both increasing plant yields and managing operations more efficiently. Growers have an annual budget of $15 per square foot to invest in technology to improve crop quality.
Topping a list of new technologies of interest to farmers, 39% of growers are interested in purchasing a farm management system in the next year; 28% of growers are interested in purchasing post-harvest automation systems, 28% are interested in purchasing LED lighting, and 27% are interested in purchasing climate control systems. The lowest priority item listed was organic nutrients. (Note that respondents could select more than one item.)
Farm management systems help growers cut down on the time spent collecting and analyzing data as well as the cost of hiring a growing consultant. Of the 38% of respondents who reported hiring a growing consultant, about half spend between $5,000 to $20,000 in a given year on such consulting.
With farm management systems, growers have access to data and insights into their operations, and they see the value in such analytics. Of those surveyed, 90% of growers believe they can increase crop yields with data analytics.
When asked to rank the operational processes on which data would have the largest impact, growers ranked crop quality and energy/climate control first. Impact is defined here as cutting costs and/or increasing yields.
Growers recognize the amount they could save with both hardware and software upgrades. Small vertical indoor farms report large savings expectations — on average, microgreen/herb farmers reported possible software savings of $71 per square foot. Larger farms show a range of $0.05 up to $7.00 in savings per square foot with software and hardware improvements. Cannabis growers estimate the largest benefit from technology improvements. As yield efficiency increases, so does the impact of technological improvements.
Market & Future
The vast majority of growers, 86% of survey respondents, are planning to expand their facilities in the next five years and they’re planning on growing significantly. The minimum planned expansion is 4.7x larger than current farm size.
Small farms have big plans — farms less than 1,500 square feet have a planned minimum expansion of 179x the sum of their current square footage. For large farms, the minimum planned expansion is 2.7x the sum of current square footage.
Based on current reported revenue and the expected expansion area, these farms will add to the market between $336 million and $610 million in revenue in the next five years. From all existing indoor farms then, this means a market expansion of between $3.7 billion and $6.8 billion during the same period.
Based on current reported revenue and expected expansion area, reporting cannabis growers will add between $102 million and $153 million in expansion revenue to the market in the next five years.
HATponics: How To Feed 20 Million People By 2020
The goal of this organization, named HATponics, is to feed 20 million people with sustainable farm systems by the year 2020
HATponics: How to Feed 20 Million People by 2020
Posted by Amy Storey on Nov 4, 2016 9:06:10 AMFind me on:
At some point, you must stop talking and start doing.
HATponics is what happened when somebody took that realization to heart.
Ryan Cox, CEO and founder of HATponics (hydroponics, aquaponics, terraponics) realized the need for action in 2012.
He heard a lot of talking about solving global and domestic hunger problems, but not many people were taking action to solve the problem.
The people that were doing something were focusing on ineffective measures; movie stars and philanthropists spent millions on transporting food to the hungry, but troubles encountered en-route caused waste.
The food that did arrive at its destination was only a temporary solution. It’s used up, and then what? People are hungry again. “Give a man a fish, he eats for a day. Teach him to fish, he eats for a lifetime.”
Ryan saw a problem with this mainstream solution. He decided to do something different. So he started a non-profit called Inner City Aquaponics to prototype a farm.
Then in 2013, he gathered a team of competent, like-minded people around him, and he started to execute on better ideas on a wider scale.
The goal of this organization, named HATponics, is to feed 20 million people with sustainable farm systems by the year 2020.
Driven by a strong vision, lots of hard work, and partnerships made with hundreds of schools on the east coast, HATponics started accomplishing their goal.
The company takes two approaches to feeding people. The first is by teaching students to grow food in their schools, and the second is partnering with schools to build sustainable farms internationally.
Their core tools to feeding people are:
- Aquaponic, hydroponic, and terraponic systems being used to feed and teach U.S. students
- The Global Challenges program.
How US Schools play a role in feeding people
A key trait of sustainability is creating solutions that function now and in the future. For HATponics, this means both building systems now and giving future farmers the tools to do the same.
To date, HATponics has partnered with over 1000 schools across the eastern coast of the US.
Schools with hydroponic or aquaponic systems give their students and parts of the community an opportunity to eat healthy produce and learn to grow it themselves.
Each school’s farm system is custom-made to fit the school's goals. Some schools focus on feeding students and the community, others on integrating the systems into lesson plans. Most schools use systems for both.
Malcolm Bridge Elementary in Bogart, Georgia outfitted their first system this September.
Less than two months ago, the HATponics crew built an aquaponics system for the 5th grade class taught by Merritt Arnold. The vertical aquaponic garden uses a zero-gravity fish tank and 16 ZipGrow Towers.
The system is still cycling (microbes are establishing over the course of a few months which will power nitrification), but he’s already using the system to work through the scientific process with his students.
Mr. Arnold hopes to eventually contribute fresh, nutritious produce to the school cafeteria and the community.
The future is exciting for Malcom Bridge's farm. Dedication of teachers like Mr. Arnold combined with the support of HATponics allow schools to feed current and future students.
Many schools take this goal a step further by participating in the Global Challenges program.
Global Challenges: building beneficial partnerships
Through Global Challenges, schools have the opportunity to meet the specific needs of a community elsewhere in the world.
For instance, a village in Ethiopia may need an aquaponic system that they can use to grow food and fish, but they need it to be powered by solar panels.
HATponics would take this need, connect it with a school, and work with a class to design the system that the village needs. Then if possible they would take the class to Ethiopia to install the system.
Most recently, students designed a vertical axis wind turbine to power an aquaponics system in Swaziland, Africa.
In total, HATponics has guided three student challenges and fifteen global builds, and have reached many other countries with consulting, training, and design.
In just three years, HATponics has accomplished a significant portion of their goal. They estimate that through their systems around the world 5 million people are being fed with fresh food.
Take action in your community.
One thing that everybody who has worked with HATponics stresses is that you don't have to know everything. Growing food is a learning curve, and the folks of HATponics are there to help people learn their systems.
Ready to stop talking and start doing? Get connected with HATponics and make it happen!
Over One Million Grown!
Over One Million Grown!
Green Sense Farms has just announced that they have grown 1.4 million plants using their innovative vertical farming technology.
Headquartered in Portage, IN, Green Sense Farms is the largest indoor vertical farm network. These progressive farms grow leafy green vegetables (micro greens, baby greens, culinary herbs and lettuces) indoors in stacking hydroponic towers in a controlled environment year-round, without the use of pesticide, herbicides, and GMOs.
Using sustainable farming practices, Green Sense Farms can grow vegetables, using much less land, water and fertilizer than traditional field farms. They conserve resources, which is good for the environment and the bottom line. Green Sense Farms is working towards zero net energy use, and zero waste, recycling all water.
Green Sense Farms has launched an Equity Crowd Funding campaign.
To learn more about this investment opportunity, please visit StartEngine: https://www.startengine.com/startup/green-sense-farms-llc
Trendy Indoor Farms Will Allow You To Have Personal Produce
Trendy Indoor Farms Will Allow You To Have Personal Produce
Eve Turow Paul, I write about Millennials and food culture.
Opinions expressed by Forbes Contributors are their own.
Now, what if this simple houseplant could feed you too? Companies like Grove, SproutsIO, Aerogarden and Replantable are working to make your in-home edible garden a reality, with compact aquaponic, aeroponic and hydroponic systems that will seamlessly integrate into your living room, kitchen, or wherever your green-thumb strikes you.
With rising rates of “nature deficit disorder,” a raucous Millennial obsession with food, only 2% of Americans living on farms, and skyrocketing rates of stress, distraction, and anxiety, many entrepreneurs believe that in-home “farming” can alleviate many of modern society’s pain points . The goal is not necessarily to feed people exclusively from their countertops. The mission, instead, is far more philosophical. And a bit political.
“ I really believe that people need to have more of a connection to their food ,” states SproutsIO co-founder Jennifer Farah. Farah began her journey to in-home gardening via architecture, designing grow-walls and other mechanisms to bring nature into cities. Then, as a Masters candidate at MIT, Farah was able to observe the benefits of taking this concept down to a more personal level, as she watched young students interact with an early prototype of a SproutsIO growing system.
First and foremost, Farah believes that we, as a society, a better understanding of our food will ultimately lead to greater respect for produce and thus improve diets. But overall, Farah focuses more on the fun and creativity generated by putting seeds into the eater’s hands.
Grocery store produce sections are limited by the current supply chain: what produce can survive the travel time, the refrigeration, what’s worth the shipping and handling costs, what can be harvested in bulk, etcetera. Indoor growing systems allow consumers to explore thousands of varietals of tomatoes or lettuce or basil that simply aren’t available at the local supermarket.
And with Sprouts IO, users can even customize the environment of a plant to grow a product exactly as they want it. Think of it as personal produce. For example, if you like a more peppery arugula or a sweeter tomato, you can adjust the nutrient levels and misting of your SproutsIO system to cultivate ingredients with your desired characteristics. “These things are allowing us to get more nuanced flavors,” explains Farah. It’s for this reason that SproutsIO launched first with chefs. And it’s also part of what excites users: putting all the control and creativity into their own hands. It’s like building a recipe far before the measuring cups are taken out of the drawer.
Both Grove and SproutsIO put the act of “farming” into a plug-and-play setting, utilizing the benefits of technology to connect people with something truly un-digital: plant growth and the act of harvest. Both Grove and SproutsIO are regulated by app, allowing users to monitor and assess their units even while away from home. It also relieves the user of many of the unknowns and uncontrollable elements of traditional farming.
“When the microwave came out people didn’t know why they needed it or what to do with it,” says Farah, “but soon people gravitated towards it.” Why, Farah ponders, shouldn’t growing produce become ubiquitous in our lives? “When we’re cooking for friends and family, why shouldn’t some of that produce be grown in your home? I do think it will become more a part of people’s everyday experiences.”
The transparency and interactive design of these in-home units also encourage education and conversation, notes Grove co-founder Jamie Byron. “It’s social. The entire family,” he says, or your group of friends or a classroom, “really come together around this experience. It’s a shared responsibility.”
As an undergraduate student at MIT, Byron was able to witness the communitarian, as well as health aspects, of in-home gardens. Back in 2013, Byron built an aquaponic system with a “Rube Goldberg Machine”-like contraption of PVC pipes, lights, and bins that balanced in the window of his fraternity house where he shared a bedroom with Grove co-founder Gabe Blanchet. The eye-sore experiment eventually flowered into a mass of peas, chard, tomatoes, kale and more.
Though Blanchet was at first skeptical of his roommate’s fish and greenery creation, the benefits of his little jungle were obvious. While the fraternity hallway smelled like beer and body odor, Byron and Blanchet’s room provided an oasis of oxygen-rich air and attractive foliage. The two found themselves grazing on their home garden daily, thus increasing their vegetable intake. Inspired by this makeshift garden, the roommates graduated and founded Grove to create a clean-cut product that has already found its way into some school and homes. Byron hopes that one day they can put their indoor gardens in prisons and hospitals to offer not just physical benefits, but the positive emotional experience as well.
“There’s this joy that people don’t talk about,” says Farah. “When you’re planning your vacation, there’s a joy in setting up that experience, and then the vacation is the culmination of that. Growing your own produce can provide a similar joy. When I can also incorporate produce I’ve grown to make a dinner, it’s even more special.” Both founders, independently, observed that the true benefit of their products is actually not what they had originally thought it would be, that growing produce at home has ramifications far beyond great tasting food. Ultimately, they hope these units will become touchstone items for creativity, connection to nature, and perhaps, an tool for taking a deep breath of fresh air and enjoying the roses…or wheatgrass…or whatever you have growing in your kitchen corner.
Local Farms Urged To ‘Embrace Technology’ To Increase Food Supply
Embracing technology could help Singapore farms “make a quantum leap in our food production levels”
‘S’pore can make a leap in food production levels, new innovation could be shared’BY
PUBLISHED: 4:00 AM, NOVEMBER 3, 2016
SINGAPORE — With increasing stress on global food supply brought on by growing demand and degrading conditions for producing food, farms — including those in Singapore — should take steps such as embracing technology to increase food supply, said Minister for National Development Lawrence Wong.
Embracing technology could help Singapore farms “make a quantum leap in our food production levels”, and new technologies could be shared with other countries that are urbanised like Singapore, Mr Wong said, speaking at the 27th Commonwealth Agricultural Conference yesterday.
With Singapore’s agricultural sector playing an important role in the food system here, the Government will continue to ensure “sufficient agriculture land for farms that are able to harness technologies, leverage on innovation and maximise their productivity,” said Mr Wong, addressing an audience of about 250 farmers and regional government officials.
“The Government is also supporting these farms with funding for technology adoption and R&D. So while we may be small in size, we believe that we can be a useful ‘living lab’ for urban farming solutions and new technologies,” he added.
For example, in the area of vegetable farming, Singapore now produces about 10 per cent of local demand. “But we have farmers who are starting to try out new technologies and different ways of farming.
“One of them is Sky Greens, which is the world’s first commercial vertical vegetable farm. Its hydraulic water-driven vertical farming system enables it to be resource-efficient and produce up to five times more than traditional vegetable farms,” noted Mr Wong.
Agri-Food & Veterinary Authority of Singapore (AVA) chief executive Tan Poh Hong, who also spoke at the conference, noted the growing support in promoting local produce.
Going forward, the farming sector could be “branded” differently to attract the next generation of young farmers.
“Someone in (the) computer (field) could decide to do fish farming, and use his knowledge to design a water-monitoring system that he can monitor from his iPhone,” she said.
Responding to questions from the audience on how Singapore deals with matters of limited land and short leases of 20 years, leaving farmers with little certainty, Ms Tan said that they are issues the authorities are still “mulling over”.
“We’ll be talking to the (Kranji Countryside Association), and to many of the farmers … (to discuss) what happens after 20 years.
“Our premise has always been if the land is meant for agriculture, and you use it for agriculture productively … it is likely you could get an extension on your own land, or on replacement land … We always premise on the fact productivity will be one of the key considerations in (ensuring) tenure of land,” she said.
Kranji Countryside Association president Kenny Eng was optimistic about the local agricultural community’s ability to innovate, but felt the Government needed to provide more certainty, such as with a ten-year masterplan, and keeping farmers in the loop.
Referring to the 62 farms in Lim Chu Kang which will have to make way for redevelopment plans, Mr Eng acknowledged the authorities had not been turning a “deaf ear” to their sentiments. For the 62 farms with leases due to expire next year, AVA has granted a reprieve by extending them to 2019.
New sites nearby would be opened for bidding, and in June, the AVA announced that all new agricultural land will be tendered on 20-year leases, instead of 10 years.
Mr Eng told reporters yesterday: “If we have a proper plan, then we won’t rush (things) as we know the next step is the right move and everyone will (follow) happily.
“But the frustration on the ground is that we are unsure, everyone is worried that we might (be told to shift again) … Careful thought has to be put into this industry.”
Agreeing, Ms Chelsea Wan, director of Jurong Frog Farm, said: “You can’t (just) tear down and rebuild agriculture. It takes time for people to build up an area, a reputation.”
Sky Greens founder Jack Ng felt there was no lack of government grants to draw on to boost the firm’s productivity, but there are too few specialists to guide farmers on issues such as disease management, for instance.
What's Indoor Farming All About?
For a lot of folks, the idea of growing plants indoors on a [relatively] large scale is a little mind boggling
What's indoor farming all about?
Chris Michael
Co-Founder and CMO at Bright Agrotech
If you've found yourself asking this question in the past few months, you're not alone.
For a lot of folks, the idea of growing plants indoors on a [relatively] large scale is a little mind boggling.
And rightly so.
At first, it's hard to understand why anyone would want to give up the beautiful, life-giving sunshine and start a farm in a warehouse, shipping container, or even their garage saying things like....
Sure the technology is fascinating and all, but sunlight is free! How could indoor farms ever justify the additional lighting cost?
I'm going to stop you right there.
As all farmer's know, there's a cost to everything. Including sunlight.
That's because sunlight (assuming you actually have enough where you're trying to grow crops) comes with its own set of limitations.
For instance, relying on the sun means you need to grow outdoors or in a greenhouse, both of which also constrain you to specific sets of conditions, crops, and costs.
Growing outside without a greenhouse of any kind means you have to live in a location with the optimal temperature range and enough quality light to grow your crops effectively. And without a covering, you're subject to temperature fluctuations and/or weather events like hail or strong winds - all of which can damage crops due to shock.
Maybe that doesn't sound devastating enough to make you want to grow indoors, but you're probably not relying on the successful sale of these crops for your livelihood either. Remember today's small farmers are largely bootstrapping their operations their ability to not only grow but sell their food means staying in business or closing their doors. No farm subsidies here either.
Growing in a greenhouse also allows you to leverage "free" sunlight as well, but don't forget about the seasons! Depending on your location, you may actually have too much sunlight in the summer and not enough in the winter (you know, like most places in the northern hemisphere). That means you have to factor in the added costs of dealing with too much heat in your growing environment (e.g. fans, cooling walls or even HVAC systems that all suck up electricity at alarming rates).
And unless you're planning on closing up shop for the winter, you're going to need to think about how to give your plants the optimal amount of light when the sun angle is too low and your light quality/duration drops significantly.
All of this assumes you have the land (and zoning approval) needed to grow crops in your city or other urban/suburban environment.
You see, nothing - including the sun - is without tradeoffs. That's how life works. That's how farming works.
Indoor Farming Helps Control the [Climate] Chaos
Now I know what you're thinking...
"If growing outdoors or in a greenhouse cost money, then growing in a warehouse must be crazy expensive!"
Maybe, but you're really thinking about this the wrong way.
The cost of farming depends on a wide variety of factors from the growing technology you use to the cost of real estate/rent, to electricity prices and market demand, but these are factors all growers, regardless of technique have to think about.
That said, once you understand the tradeoff between the benefits of natural light vs. the benefits of increased control, it's pretty easy to see all the advantages growing indoors gives modern growers and subsequently the communities they serve.
The benefits mostly come in the form of optimizing the environment to stabilize temperatures, humidity levels, lighting quality and duration, and much more. Optimizing all of these variables allows tech-savvy indoor farmers to maintain better plant health, with faster, more consistent yields.
More control also means more flexibility in terms of where farmers grow food. Barring any type of natural disaster, indoor farms aren't nearly as susceptible to the climate constraints or variability that conventional farms are, giving them the ability to grow all year long.
Because of that, I believe we're rapidly approaching a reality where fresh crops can be grown and sold anywhere, regardless of climate or conventional food distribution capabilities.
And these are just the benefits we know about... Don't even get Dr. Storey started about the ones we haven't discovered yet.
"But, what's in it for me?"
Most people who read this may not have any current connection to farming or a farmer and may be wondering why this all matters.
Well for one, it matters because our food system is broken... and chances are, you eat food.
Broken not just in terms of the 1,500 miles from farm-to-plate, the depletion of precious soil nutrients, the rampant pesticide use, the massive factory farms owned by just a few food conglomerates exploiting low-wage labor, and don't forget about the chronic droughts in parts of the country that historically have grown most of our produce... but broken in terms of the transparency and accountability that existed when agriculture was relational.
For some, the idea of "shaking your farmer's hand" might sound a little overly romanticized. And, that's fine, but can't we have some middle ground? Wouldn't you feel better about the lettuce you buy if you knew who grew it and how it was grown at the very least?
It's like they took our most basic relational (i.e. human) elements of communication, trust and accountability. All we got in return was an empty "O" label.
But indoor farming is changing all that.
One small farmer at a time.
Thanks to the bold, yet generous modern farmers around the country like Localize Farm, more and more people are getting greater access to better food everywhere.
Soon we can all have the option of feeding our families fresh, healthy food regardless of whether you live in the light-deprived tundra or the water-starved desert.
If you don't have one of these innovative farmers in your city yet, don't fret.
You will soon enough. 😉
[This article expands on a recent Instagram post I created on behalf of Bright Agrotech. If you want a glimpse inside some of the world's most innovative farms, you should totally be following us.]
Chris is the Chief Marketing Officer and Chief of Staff at Bright Agrotech. He believes strongly in the power of small farmers and small businesses to impact their communities in meaningful ways and loves playing a small role in their ability to be successful.
Affinor Growers’ (RSSFF) Vertical Farming System Has Many Advantages
Agriculture is one industry that will always be a major part of our global economy for obvious reasons of course… We all gotta eat
Affinor Growers’ (RSSFF) Vertical Farming System Has Many Advantages
Bolton Flautt Follow | Wednesday, 02 November 2016 16:48 (EST)
Agriculture is one industry that will always be a major part of our global economy for obvious reasons of course… We all gotta eat. A growing world population is a concern that our demand will be greater than our supply. Affinor Growers (RSSFF) is a farming technology company, engaged in designing, patenting, and commercializing vertical farming technology for indoor controlled environment and outdoor greenhouse agriculture industry in North America. It produces strawberries and other crops, such as romaine lettuce and herbs using vertical farming technology. The company is headquartered in Vancouver, British Columbia, Canada and is led by Chief Executive Officer, Interim President, and Chief Operating Officer Mr. Jarrett Malnarick.
Mr. Malnarick commenting on Affinor Growers’ purchase agreement with THC BioMed to install Affinor’s tower vertical farming system, "Affinor Growers looks to align itself in all agriculture sectors such as fresh produce, fruiting plants, and flowers. As a technology seller of vertical growing systems, this new relationship with THC BioMed allows us to continue business development within different sectors pertaining to plants and demonstrate the diversity of the technology in the vertical farming space. Affinor will now have several installations of the technology within commercial settings actively growing different crops."
Technological advancements have occurred in every industry except agriculture. However, new challenges in food security, dwindling natural resources and population growth have created agricultural problems that can only be solved through the use of technology. As a practice, traditional farming is not going to disappear, but it is crucial that alternative agricultural practices be devised to alleviate the pressure imposed by conventional farming methods.
As a solution, Affinor Growers offers patented agricultural technology and proprietary cultivation systems for vertical farming and controlled environment agriculture. Controlled Vertical Farming has a number of inherent advantages. Compared to conventional farms, it is significantly more efficient in terms of usage of space and reliance on water. Vertical farming also enables foods to be are grown in soils without the use of pesticides, nutrient rich and free from chemical contaminates. Because they can be implemented virtually anywhere, Controlled Vertical farming systems can serve communities where certain foods are not normally grown.
The fresh food organic produce is a $33.8 billion industry and is expected to nearly double by 2020. In continental North America, there are over 17,000 hectares of greenhouse farms. Affinor is the only company to offer patented vertical farming technology to both the indoor controlled environment and outdoor greenhouse industries. Affinor’s vertical farming technology will help farmers gain certain advantages by optimizing growing conditions, extending growing seasons year round and improving yields of production per square foot, as well as by improving quality through automated harvesting, handling and packaging systems.
Vertical Farming Innovator Urban Crops Opens U.S. Regional Headquarters
Urban Crops, a Belgian agriculture technology company, recently established operations in the U.S.
November 1, 2016
Vertical Farming Innovator Urban Crops Opens U.S. Regional Headquarters
Posted By: Rosemary Gordon | Email
Growing crops in a climate controlled multi-layer environment with the LED lights achieves shorter growth cycles, higher water efficiency, flexible but guaranteed harvests and safe and healthy crops. Photo courtesy of Urban Crops.
Urban Crops, a Belgian agriculture technology company, recently established operations in the U.S. The company opened an office in Miami, FL, that will be responsible for North and South America.
Urban Crops is a solution provider in the closed environment, vertical farming industry and is expanding its business globally through its own offices as well as a network of sales agents. Pieter De Smedt is leading the U.S. operations for Urban Crops.
The company creates tailored growth infrastructures, which are turnkey, automated, robotized, and able to be integrated into existing production facilities or food processing units. Urban Crops also has its own range of growth container products.
The company also can supply seeds, substrates, and nutrients for all its growth recipes. Currently, more than 160 varieties of crops that can be grown in Urban Crops’ systems using growth protocols developed specifically for indoor farming by the company’s team of plant scientists.
Growing crops in a climate controlled, multilayer environment with LED lights achieves shorter growth cycles, higher water-use efficiency, flexible but guaranteed harvests, and safe and healthy crops, according to Urban Crops. The grow infrastructure can be installed in new buildings, as well as in existing (industrial) buildings, or unused spaces. The grow infrastructure also gives the clients the possibility to grow, harvest, and consume locally, every day, and in any chosen quantity.
Urban Crops’ main office is in Belgium, where the company has built the largest European automated growth indoor farm to date, which is used mainly for R&D purposes and test runs for potential customers.
“Opening an office in the U.S. became a necessity as we received numerous requests in the past months from the American continent,” says Maarten Vandecruys, Managing Director of Urban Crops. “Our grow systems and business model make it possible for all people that have interest in the agri-food, medicinal industry, or any other industrial crop production to start its own production activities, leveraging on our proven know-how of plant science and plant grow infrastructure.”
De Smedt adds: “Supplying innovative and high-quality solutions, products, and services is our core strength. Our U.S. presence is thus a very important factor if we want to service our clients and sales agents from this continent.”
Urban Crops is currently looking for sales agent candidates. For more information, contact Pieter De Smedt at pieter.desmedt@urbancrops.be, or 786-479-8902.
Can Vertical Farming Sustain Food Demands in the Wake of Climate Change?
Posted by Guest Blogger on October 31, 2016
By Robert Colangelo
According to a 2015 report by the United Nations, the world’s population is expected to reach 9.7 billion by the year 2050. While those numbers are set to increase, so are rising surface temperatures and worsening droughts caused by severe weather patterns. Changes in climate are already reducing the amount of arable land and rising urban populations are depleting aquifers, creating a need for more sustainable farming solutions.
Indoor vertical farming is the practice of growing plants indoors in a controlled environment in stacking hydroponic towers. These farms produce a consistent, high quality crop year-round in a small footprint. By growing indoors, weather and climate change is taken out of the equation. Over time these farms will produce zero waste by recycling all water with net zero energy use.
Green Sense Farms grows leafy green produce indoors using sustainable farming practices with minimal impact to the environment. They can grow vegetables faster than field farms using less land, water and fertilizer- free of pesticides, herbicide and GMOs. By locating these farms at or near produce distribution centers and on institutional campuses wherever large volumes of meals are served daily, they are transforming farming. The produce is fresher and the miles food travels from the farm to the table is reduced. This truly is the future of not just sustainable farming, but a farming solution to meet growing populations and changing global weather patterns.
Green Sense Farms is building a network of indoor vertical farms around the world. By farming smarter and providing consumers with access to fresh leafy greens, communities become healthier. Research has shown that a diet filled with leafy greens is rich in antioxidants and enzymes that reduce heart disease and cancers.
Green Sense Farms has been the fortunate recipient of numerous stories about our exciting innovative indoor vertical farming technology. All this press has generated many inquiries from individuals asking how they can invest in our sustainable farm. We’re pleased to announce that the recently released crowdfunding regulations now allow for individuals to make direct equity investments in growth companies like ours. Just as Green Sense Farms has disrupted produce distribution and cut out the middleman, the new crowdfunding regulations have democratized the capital markets, allowing individuals the opportunity to take advantage of public offerings without the use of traditional stock brokers.
Green Sense Farms, the country’s largest network of commercial indoor vertical farms is an early adopter of technology and employed a new strategy to finance its growth through equity crowd funding. We launched this equity crowdfunding campaign to share the unique offering with our community. The 60-day campaign which launched in early September reached its $100,000 goal in just one day and has accumulated over $360,000 to date. The campaign, ending October 31st, can be found here: https://www.startengine.com/startup/green-sense-farms-llc.
ABOUT GREEN SENSE FARMS:
Green Sense Farms is the country’s largest commercial indoor vertical farm. The company provides nutritious and delicious produce that’s good for people and the planet. Because Green Sense Farms creates conditions that are always perfect for growing, they’re able to harvest year-round, using a fraction of the land, water, and fertilizer of traditional field farming. These sustainable farming practices make Green Sense Farms a local solution to a global challenge.Green Sense Farms is located in Portage, Indiana—40 miles outside of Chicago and has created innovation partnerships with Philips, Hortimax, Rijk Zwaan, Desert Aire and Dramm. We have also formed a business partnership with Infinite Herbs. Find more information on their website at greensensefarms.com.
Size Isn’t Everything. Here’s a Farm That Fits in Your Kitchen
It's like a microwave that grows food!
Image courtesy of Replantable
You’ve got a microwave, a toaster oven, and a myriad of other kitchen appliances, none of which actually grow food. That could change thanks to a Georgia-based startup Replantable. They've created Nanofarm, an almost completely automated system that grows vegetables and herbs in a unit small enough to fit on your kitchen counter.
The key to Nanofarm, which is smaller than a mini-fridge, are its patent-pending plant pads, which are made out of multiple layers of fabric and paper. The pads contain the seeds and the same kinds of plant nutrients used in traditional hydroponics—elements like nitrogen, phosphorus, and potassium—that are culled from sustainable sources like compost tea and aquaculture waste. The pads sit on top of a water-filled reservoir.
The Nanofarm only has two knobs: a dial to control the grow cycle and a start button. Theoretically making it more straight-forward to grow your own vegetables than defrost leftovers in a microwave.
To start a grow cycle, just turn the dial labeled “weeks” to the number indicated on the plant pad and then push start. The “harvest” light turns on when your plants are grown. You then have about two weeks to pick your veggies or herbs. The used pads are biodegradable and can be composted. The company offers a variety of vegetables, like romaine lettuce, radishes and kale; and herbs like basil, thyme, and cilantro.
One Nanofarm can produce around 12 ounces of romaine lettuce or four ounces of basil (about five and a half packs of what you would find at the grocery store). The growing space is comparable to a good-sized windowsill planter, but the produce only takes between two to four weeks to grow thanks to the daylight spectrum LED lights that provide as much light as a California summer day, but consume less than a dollar of electricity per month, according to the company. The smoked glass front of the Nanofarm keeps the light from being annoyingly bright on the outside of the device.
The estimated retail price of the Nanofarm is $400, but you can pre-order one on the company’s website for $350. The plant pads are $8 each or $5 if you buy five or more at a time.
But it may be a while before you can get one for your own kitchen. While the company has created beta versions of the Nanofarm, the product won’t be available to consumers until late next year. Ruwan Subasinghe, the company’s co-founder, tells Modern Farmer they are currently getting samples of the parts that go into the Nanofarm and once approved, they can move into prototyping units for mass production, then onto actual production.
Dirt-Free Farming: Will Hydroponics (Finally) Take Off?
The Amazing New Way To Grow Tomatoes: In Tomato Waste
The Ultimate Ikea Hack: A Hydroponic Farm
The FarmBot Genesis Brings Precision Agriculture To Your Own Backyard
A Hydroponic Rooftop Farm Grows in the Bronx
The company just finished a Kickstarter campaign that raised about $61,000, $11,000 more than their goal. Subasinghe says they were “quite surprised” by the support they received—and not just financially. He says they got a ton of messages from people who enthusiastically believe in what they were doing. The Kickstarter contributors get the first mass-produced models that are tentatively set to be shipped next October. It will be a few more months after that when the general public will be able to get one.
Subasinghe and his business partner, Alex Weiss, met when they were attending Georgia Tech, in Atlanta, where they were working on projects involving hydroponics and issues of food waste. They realized that the produce you get at grocery stores tends to have travelled thousands of miles to reach the store’s shelves, which leaves only a small window of time before the produce goes bad, leading to food waste. They joined forces with the idea of combatting food waste and last year started Replantables following their involvement in a startup accelerator through the school. “We saw the potential for hydroponics to allow people to grow their own food at home,” says Subasinghe.
The initial prototype was just a souped up hydroponics system made out of PVC pipes with running water, filters and pumps that needed to be cleaned by the user, according to Subasinghe. They quickly realized that consumers wanted something simpler and easier to use. By the time they were done with the beta version, it was almost completely automatic and no longer resembled a typical hydroponic system since they’d ditched the pump, liquid nutrients, and inert growing medium.
“We hope that by providing technology that allows people to easily grow their own food while using fewer resources, we’re allowing the future of food to be more earth-conscious.” says Subasinghe.
Trials See Cucumbers Gain From LED Lighting
Recent trials of supplemental LED lighting in cucumber glasshouses show they can increase both productivity and sustainability
Trials see cucumbers gain from LED lighting
28 October 2016, , Be the first to comment
Recent trials of supplemental LED lighting in cucumber glasshouses show they can increase both productivity and sustainability, Philips Horticulture high-wire crops specialist Piet Hein van Baar told the Cucumber & Pepper Growers Day.
Trials show how LED lighting in cucumber crops boosts productivity and sustainability
One trial compared growing midi cucumbers on a high-wire format in Poland under three lighting regimes: high-pressure sodium (HPS) toplighting and LED interlighting; both LED topand interlighting; and only HPS toplighting, each in a 60 sq m compartment at 3.14 plants per square metre.
These were first planted in December 2014. Over the four months of the trial, the all-LED plot yielded 43.1kg of fruit, compared to 40.6kg for the hybrid format and 34.7kg for the HPS-only control - indicating an uplift of 24 per cent for the all-LED format.
A further crop begun in December 2015 then tested the proposal that higher planting densities, hence higher yields, would be possible under LED lighting. Indeed at 3.66 plants per square metre, the all-LED format yielded 54.3kg in four months, and the hybrid 47.5kg, while at the lower density the yield under HPS also improved to 39.6kg, but this still left the all-LED system 37 per cent ahead.
"With 100 per cent LED the fruit development is also faster while the water use is nearly 14 per cent lower," Van Baar added. "But adding LED interlight to an existing HPS system can also give you more grams per mol of light."
A separate trial at a Dutch commercial grower in a glasshouse too low for overhead lighting assessed what benefits if any are brought by double LED interlighting booms between high-wire long cucumber aisles.
"With 18 hours of lighting there was significantly more production," said Van Barr, adding that this had the side-effect of raising temperature over much of the trial period. The interlighting appeared to promote earlier production, gave fewer signs of Mycosphaerella infection and yielded fruit with five-to-seven days longer shelf life.
Trials are also ongoing to ascertain the value of LED lighting in pepper production, he said. "Interlighting appears to strengthen the pepper plant and boost production by seven-to-10 per cent, but it takes two months for the crop to grow high enough to fully benefit." LED toplighting remains another area for further work, he added. "It should make winter pepper production possible - you can't do it with just interlighting."
He estimated that around two per cent of the Netherlands' glasshouse area now uses some form of LED lighting, but pointed out: "You need a specialist to work out the most efficient light distribution for your crop."
CGA technical officer Derek Hargreaves noted: "HPS is effective but not profitable - not due to the lighting, but to the price of cucumbers."
LED lighting further complicates the already complex interactions of factors governing the behaviour of pests, beneficial insects and the growing environment, Stockbridge Technology Centre (STC) director of entomology and sustainable agriculture Dr David George told the conference. These include visual, chemical and physical cues, he said. "Plants alter their chemistry in response to pests, to limit damage and attract biocontrol agents, and the nature of this response can be affected by the type of light."
Enclosed LED systems such as the LED4Crops facility at STC "require back-to-basics thinking" to optimise pest monitoring, choice of beneficial insects and pollination, he said. "Supplemental lighting in glasshouses and polytunnels could present similar opportunities and challenges."
His STC colleague Dr Phillip Davis, who manages LED4Crops, explained the growing understanding of individual crops' lighting needs. "Light colour influences leaf pigmentation and morphology," he said. "Flowering is inhibited by red light but promoted by far-red light. Under blue light you can get lettuces that are almost black, and so high in anthocyanins. Blue also helps to open stomata, though there is a trade-off between biomass and quality. Plants are very sensitive to UV-B light as it's very damaging."
With all this in mind "we can start to design a lighting regime that gives you the kind of plant you want, including by supplementing sunlight in a glasshouse", he said. "Selecting light spectra can improve quality and efficiency, and plants will benefit from different spectra at different stages of growth."
He added: "We are hoping to look next at the interaction of light and pathogens - but informally we seem to be enhancing plant immunity with LEDs."
This Farm Uses Only Sun and Seawater To Grow Food
Sundrops Farms in Australia uses solar power to convert seawater into usable water for crops, which are grown in coconut husks instead of soil
In the arid desert of coastal South Australia, a new indoor farm is using the two most available resources, that also happen to be free—sun and seawater—to grow tomatoes. Lots and lots of tomatoes.
Sundrop Farms, located near Port Augusta in South Australia, is the first commercial agricultural system of its kind: It doesn’t use groundwater, soil, pesticides, or fossil fuels to grow crops. The project has been a six-year odyssey that began with a pilot greenhouse in 2010, followed by the construction of a nearly 50-acre facility in 2014 that, as of earlier this month, is now fully up and running with a projected capacity of 18,000 tons of tomatoes —the crop the company is focused on at this facility—a year, according to Sundrop.
Here’s how the company explains it: Seawater is pumped from Spencer Gulf, located about a mile and a half away from the facility, where it’s desalinated through a solar powered thermal unit. “Sustainably sourced” fertilizers and micronutrients are added to the water (they won’t give details regarding their nutrient mix), which is then used to hydrate the tomato plants, which are grown in coconut husks instead of soil (a renewable resource), which also aids in root growth due to their natural hormones. According to Philipp Saumweber, Sundrop Farms CEO, the they don’t have to use pesticides the they pump seawater through the facility’s air filters, which kills insect pests due to the high salt content in the water-saturated air.
The farm’s solar power is generated by 23,000 mirrors that reflect sunlight to a more than 375-foot high receiver tower. On a sunny day, it can produce up to 39 megawatts of electricity, which is more than enough to power the desalination system and the rest of the facility’s power needs. Excess thermal heat and water are kept in storage facilities on the farm to use when needed, according to Saumweber. That said, the facility remains on the electrical grid as a back up for 10 to 15 percent of its power needs when weather makes it difficult to rely solely on solar power.
The company spent about $200 million on the project, with $100 million coming from the global investment firm KKR, a larger outlay than a typical hydroponic greenhouse system, which can run about $1 million an acre. But, according to Saumweber, who spoke to New Scientist, the seawater system will pay off in the long run since conventional greenhouses are more expensive to run on an annual basis since the rely on the power grid, which is powered by fossil fuels.
The price tag isn’t stopping the company from building another farm in Australia, one in Portugal, which was recently completed, and one in Tennessee, which broke ground this year. While not all of them may use seawater or a solar tower, they will all have some “sustainable resource angle,” according to an Australian Broadcasting Corporation interview with Reinier Wolterbeek, the chief technology officer for Sundrop Farms. When Modern Farmer asked Saumweber whether he could be more specific, he answered that he couldn’t “at this stage,” and added “that we will always use sustainable inputs to dramatically reduce our reliance on finite natural resources.”
The company partnered with a large Australian grocery retailer, Coles, with whom they have a ten-year contract. Tomatoes from their pilot program, which started before the larger facility came online, are already on grocery store shelves.
Not everyone feels the system makes economic or environmental sense, at least in regard to the project in Australia. Paul Kristiansen, a professor at the University of New England, Australia, told New Scientist, that since there wasn’t a problem growing tomatoes in other parts of Australia, the need to grow tomatoes in a desert was a “bit like crushing a garlic clove with a sledgehammer.”
Environmentalists have taken issue with desalination due to the amount of energy it takes to produce potable water, and the problem of the disposal of the highly concentrated salt brine that’s dumped back into the ocean, which can be too salty for marine life to inhabit.
Sundrop Farms’ technology answers the energy question with its use of solar power. As to concerns about impacts on marine life, Saumweber says their system doesn’t result in water with high levels of salinity. According to Saumweber, cooled seawater from the greenhouse cooling system is mixed with warm elevated salinity seawater in a large lined storage tank for discharge back to the ocean.
“The large size and surface area of the storage and the mixing of warm and cool streams results in a seawater that is only slightly more concentrated and at a similar temperature to the ocean,” he tells Modern Farmer in an email. “The minor increases in salinity at the discharge location as approved by the Environmental Protection Authority.”
In the face of the high loss of groundwater worldwide and other problems associated with climate change, Sundrop Farms’ technology may prove to be helpful in combating these issues as we try to figure out how to provide enough food to feed the world’s growing population, estimated to be 9.6 billion people by the year 2050.
Growing Up…Vertical Farming
Dickson Despommier, a professor at Columbia University, talks vertical farming
Vertical farming–as the name suggests–refers to cultivating crops in multi-story greenhouses. These vertical farms are fitted with modern technology (hydroponics, aeroponics and aquaponics) and enable crops to be grown in the center of urban areas. Being a closed-loop agricultural system, it's the cleanest industry you can imagine, filtering dirty air and rain water during the process.
The concept of vertical farming has been around since the 1980s–when we started to realize a change was necessary–but didn’t evolve into a viable solution until the late 1990s, thanks to technical advances.
However, today we can no longer avoid the need to find new solutions. One example are wine growing regions which can be used as a barometer to measure climate change as grapes require such a specific regime of humidity and temperature to grow. In fact, according to wineologists, in 50 years wine growers in Bordeaux will no longer be able to grow grapes in the region. We can see in many regions that optimal wine growing conditions are moving north in the northern hemisphere and south in the southern hemisphere–for example, ideal climatic conditions for growing the Pinot Noir grape are shifting steadily north from the Napa Valley, towards northern California and even into Oregon.
These changes are also having a tangible impact on corn, wheat, barley, rice and other cash crops. As our populations expand we will need to start growing crops in new regions that don’t necessarily have the correct soil types. Vertical farming provides the opportunity to bypass these regional environmental hurdles by creating prime exterior conditions indoors.
Benefits of vertical farming
- Year-round crop production – there are no seasons in a vertical farm, so any crop that can be grown indoors can be produced year-round, locally
- Requires very little water – water is scarce in many locations but water used in vertical farming is recycled in a closed loop cycle which means availability and waste of resources is not a problem
- Employment opportunities – vertical farms are located in the city and therefore provide employment, in a pleasant environment for urban dwellers
- No soil contamination – with no agricultural run-off, need for fertilizers or heavy metal contamination, vertical farming eliminates the usual pitfalls associated with outdoor traditional farming
- Repurposes old buildings – warehouses equipped with the right infrastructure make the ideal vertical farm, negating the need to destroy old buildings
Encouragingly, an increasing number of big companies are now getting on board with vertical farming and developing the idea at a corporate level, including Toshiba, Panasonic and Goldman Sachs–who are funding a large vertical farm in Newark, New Jersey. A clear demonstration that vertical farming is a viable and efficient way of growing food for urban populations and industry will have a core role in making this happen.
Vertical farms are also beginning to harness the power of natural energy sources. For example, the power of geothermal energy is being harnessed in places like Italy, USA, Iceland, New Zealand and Japan. Huge opportunities also exist in places like Australia where the climate is favorable and solar energy could be used. There will be a whole host of alternative energy solutions to generate electricity for these farms, meaning the more we invest in thinking about how to do things ecologically, the more economical the process of vertical farming will become.
Vertical farming presents a huge investment opportunity, and as you would expect, the concept is now gaining extensive global interest thanks to the possibility of creating inexpensive, healthy and locally produced food.
For example, we only need to look to China which has employed US company, Green Sense Farms, to develop 20 vertical farms across major cities in the country.
Farms of the Future
Solar powered irrigation system
SunCulture is providing solar-powered irrigation systems for farmers in Kenya, enabling them to grow additional fresh fruits and vegetables at less cost. The system–delivering water directly to crop roots–provides yield gains of up to 300 percent and 80 percent water savings.1In areas of low and unpredictable rainfall, this system is proving invaluable and ensuring farmers can avoid high fuel costs, negating the need for diesel-powered generators.
Drones for crop management
Start-up PrecisionHawk has created a lightweight drone to gather high-resolution aerial data enabling the agriculture industry to “optimize area usage and increase land use efficiency”. The system–integrating drones and software–provides information on “the status and health of crops and soil”, enabling maximum crop yield. Going one step further, the drone can also identify areas at risk of drought, detect disease (in plants and animals) and estimate growing time for crops. A highly useful tool for drought affected regions.
Dairy hubs
A dairy hub refers to community dairy “development programs” which have been launched successfully in Bangladesh and Pakistan and are currently being piloted in East Africa and India. Linking smallholder farmers to dairy processors, this model enables cost cutting, higher incomes, healthier livestock as well as access to proper infrastructure. With milk being an important source of energy,
vitamins and minerals, it also increases the availability of a long term supply of safe, affordable and local milk in these regions.
CONTRIBUTORS
Dickson Despommier Microbiologist and Ecologist
As an Emeritus Professor of Microbiology and Public Health at Columbia University, Despommier conducted laboratory research for 27 years, which he left in order to focus on globally relevant projects, such as parasitism and its impact on societies living in the tropics. In “Growing Up…Vertical Farming”, IN spoke with Despommier about vertical farming, and its critical role in achieving agricultural s
How Two IIT Scientists Are Using Food Waste To Revolutionize Indoor Farming
Two scientists at Illinois Institute of Technology may have solved one of the biggest inefficiencies in aquaponic farming -- the abundant use of energy that it requires...
10/18/16 @10:28am in Tech
Two scientists at Illinois Institute of Technology may have solved one of the biggest inefficiencies in aquaponic farming -- the abundant use of energy that it requires.
Elena Timofeeva, a research professor in chemistry, and John Katsoudas, a senior research associate in physics, have developed a system that uses organic food waste -- rather than electricity -- to generate a mobile, containerized aquaponics farm that will bring locally produced food to food-poor areas while also cutting down on the pollution that contributes to global warming. The team was recently selected as a semi-finalist in the 2016 Cleantech Open Accelerator Program, which identifies promising early-stage clean technology companies and provides them with six months of educational and mentoring support. Now, they're working with Cleantech adviser on market research, business strategy and fundraising, and they plan to have the full-scale prototype finished in the next 18 months.
The two explained that in a traditional aquaponics farm, the fish in the tank produce waste that is converted into a natural fertilizer for the plants. In turn, the plants keep the water clean for the fish. It's a system that requires about 80 percent less water than traditional farming, Katsoudas said.
However, it's not a perfect system. There are at least two popular methods of aquaponics farming -- completely enclosed units where artificial light is brought in to do year-round growing or operating one within a greenhouse. In both cases, energy is consumed for the electricity, heating or cooling of the enclosed environment.
"[Aquaponic farming] has really started to take off now in the modern age because of the stresses being put on the environment. From increased farming to increased population density, it’s been identified [that] the production model for food needs to change," Katsoudas said. "The problems with aquaponics ... is that they consume a lot of energy. What AquaGrow Technology does is [identify] a way to bring in bio-digestion."
Biodigestion is where food waste, which comes from outside sources like cafeterias, food processing plants, food banks or anywhere else organic waste is generated and destined for landfills, comes into play, Katsoudas said.
"[Food waste] is introduced into the biodigester through an external chute and then over the period of about 21 days it's converted into methane," he later explained in an email to Chicago Inno. "We then pipe that methane into an electric generator and produce electricity and CO2. The electricity is what we use to power the aquaponics systems, i.e. the grow lights, heaters, pumps, air conditioners, control systems, life support for the fish, etc. The byproduct of generating electricity using methane is CO2."
Simply put, the aquaponics farm that Timofeeva and Katsoundas have developed replaces electricity with organic food waste as the energy source for the lights and other technologies that support the system.
The other key difference to their system is the size, according to Timofeeva. The container will come to a total size of 10 feet wide, 10 feet deep and 45 feet tall.
"[The size] also enables smaller players -- like individual families, individual churches, individual communities -- to get into this farming locally," she said. "If it’s a huge farm, you need a large investment to get involved in this. Having a containerized farm that can be located in small plots of land would enable local farming and engaging pops in farming as well."
They estimated that the cost of such a unit would come to about $150k, and it would produce an annual profit of $40-$80k, depending on the plant or crop harvested.
"The investment [an individual family] would make would pay back in 2-3 years," Timofeeva said. "They can locally produce food and make money off of it ... It works really well economically … by minimizing operational expenses on site."
Katsoudas also said that the mobility of these containers would prove especially useful in communities after national disasters where there is no access to food, or in underserved urban communities
"We have to believe that when there’s a good investment made, there will be resources available to make it," he said. "When you look at the nature of the grants coming out, there is a whole new movement of grant money that's coming to bear for social impact."
He explained that there is a direct correlation between the level of crime in an urban area, and the amount of nutritional food in that area.
"You look at the dollars that society spends on police forces and incarceration ... If you were able to bring the crime down but supplying a nutritional value, an asset to the local community, those are dollars better spent.," he said, explaining that after obtaining grants, ministries, congregations and social organizations would likely be the first adopters of their aquaponics farm.
"I think that’s a good investment," he said. "I do believe there are organizations and people that will see that."
The Potential of Urban Agriculture Innovations in the City, from Hydroponics to Aquaponics
How large a role will local food demand play with respect to the growth of indoor and controlled environment urban farming ventures?
The Potential of Urban Agriculture Innovations in the City, from Hydroponics to Aquaponics
October 18, 2016/in aquaponics, Local Food, Sustainable Agriculture Conference, Urban Agriculture /by Robert Puro
How large a role will local food demand play with respect to the growth of indoor and controlled environment urban farming ventures? What are the costs involved in starting a small scale commercial hydroponic/aquaponics farm? What are the opportunities (community and economic) for high-tech controlled environment growing in urban environments such as Orange County? What tools or assets would give an entrepreneur the best chance for success in launching a vertical farming venture in the city?
To learn the answer to these questions, and more, you won’t want to miss the ‘The Potential of Controlled Environment Agriculture in the City’ panel at the upcoming Grow Local OC: Future of Local Food Systems slated for Nov. 10 at California State University, Fullerton. The following expert speakers will address the challenges and opportunities present in employing innovative agricultural growing systems in cities:
Erik Cutter is Managing Director of Alegría Fresh, an urban farming company engaged in promoting and deploying zero waste regenerative food and energy solutions using hybrid soils and integrated technologies. In 2009, Mr. Cutter founded EnviroIngenuity with a group of forward-thinking professionals to take advantage of the growing demand for more efficient, cost effective sustainable energy solutions, employing solar PV, hi-efficiency LED lighting, green building and zero waste food production systems. More than 35 years of travel throughout the US, Mexico, South America, Africa, French Polynesia, the Peruvian Amazon, Australia and New Zealand gave Mr. Cutter expert insight into the unique investment opportunities that exist in each region, focusing on sustainable living models and the increasing availability of super foods as a major new market opportunity.
Chris Higgins is General Manager of Hort Americas, LLC (HortAmericas.com) a wholesale supply company focused on all aspects of the horticultural industries. He is also owner ofUrbanAgNews.com (eMagazine) and a founding partner of the Foundation for the Development of Controlled Environment Agriculture. With over 15 years of experience, Chris is dedicated to the commercial horticulture industry and is inspired by the current opportunities for continued innovation in the field of controlled environment agriculture. Chris is a leader in providing technical assistance to businesses, including commercial greenhouse operations, state-of-the-art hydroponic vegetable facilities, vertical farms, and tissue culture laboratories. In his role as General Manager at Hort Americas he works with seed companies, manufacturers, growers and universities regarding the development of projects, new products and ultimately the creation of brands. Chris’ role includes everything from sales and marketing to technical support and general management/owner responsibilities.
Ed Horton is the President and CEO of Urban Produce. Ed brings over 25 years of experience from the technology industry to Urban Produce. His vision of automation is what drives Urban Produce to become more efficient. With God and his family by his side he is excited to move Urban Produce forward to provide urban cities nationwide with fresh locally grown produce 365 days a year. Ed enjoys golfing and walking the harbor with his wife on the weekends.
Chef Adam Navidi – In a county named for its former abundance of orange groves, chef and farmer Adam Navidi is on the forefront of redefining local food and agriculture through his restaurant, farm, and catering business. Navidi is executive chef of Oceans & Earth restaurant in Yorba Linda, runs Chef Adam Navidi Catering and operates Future Foods Farms in Brea, an organic aquaponic farm that comprises 25 acres and several greenhouses. Navidi’s journey toward aquaponics began when he was at the pinnacle of his catering business, serving multi-course meals to discerning diners in Orange County. Their high standards for food matched his own. “My clients wanted the best produce they could get,” he says. “They didn’t want lettuce that came in a box.” So after experimenting with growing lettuce in his backyard, he ventured into hydroponics. Later, he learned of aquaponics. Now, aquaponics is one of the primary ways Navidi grows food. As part of this system he raises Tilapia, which is served at his restaurant and by his catering enterprise.
Nate Storey is the CEO at Bright Agrotech, a company that seeks to create access to real food for all people through small farmer empowerment. By focusing on equipping and educating local growers with vertical farming technology and high quality online education, Nate and the Bright Agrotech team are helping to build a distributed, transparent food economy. He completed his PhD at the University of Wyoming in Agronomy, and lives in Laramie with his wife and children.
Register here: http://growlocaloc.eventbrite.com
From A Closet To Five Acres: How Motorleaf Aims To Boost Indoor Growing
A year ago, Alastair Monk and Ramen Dutta had a seedling of an idea: If you can automate a home, why not a greenhouse?
A year ago, Alastair Monk and Ramen Dutta had a seedling of an idea: If you can automate a home, why not a greenhouse?
The two entrepreneurs and residents of Sutton, in Quebec’s Eastern Townships, were not professional farmers by any stretch of the imagination — but they were hobby growers in the middle of Quebec’s breadbasket.
Dutta, an agricultural engineer, programmer and tinkerer, put together his first prototype of the connected greenhouse’s central nervous system last November. He called it the HUB, short for “huge, ugly box.”
Fast forward to today, and Monk and Dutta’s company, Motorleaf — a name inspired by British rock ‘n’ roll band Motörhead — is filling orders, meeting with major company bigwigs and is closing in on a $1 million seed investment round.
“A year ago, our objective was to see if what we had built should and could be made available to other indoor growers,” says Monk. “Since then our ambition has grown significantly, mostly in part because of our participation in the FounderFuel accelerator program.”
Motorleaf’s founders participated in last spring’s cohort of the FounderFuel accelerator, a boot camp of sorts to help technology startups speed up the process of forming profitable companies.
In Motorleaf’s case, it happened at a breakneck pace.
Dutta’s original HUB was meant to be one piece of hardware to rule the greenhouse. But during the accelerator program, the design was revised and separated into four parts to create a modular, scalable approach.
Monk likes to boast that Motorleaf’s network can now be scaled for growing spaces as tiny as a closet, up to five acres. The pitch has clearly worked: Monk says he’s got thousands of dollars of sales lined up already.
The HUB is now called “the heart” — a piece of hardware that communicates with other elements of Motorleaf’s product suite, forming a wireless mesh network. The network, in turn, can monitor and control a couple dozen growing factors, including pH level, nutrients, humidity, temperature, lighting and reservoir water level.
Growers can then use a desktop or mobile app to remotely monitor and control growing conditions. Meanwhile, artificial intelligence and machine learning components baked into the process can learn from the plants, self-correcting to eventually optimize a perfect nutrient and atmospheric cocktail for each crop.
“The idea is not to replace people, but to take the guessing out of growing and prevent mistakes from happening,” Monk says.
Motorleaf’s solution may be ripe for the marijuana biz; certainly, growing weed is often an indoor activity across surface areas that would be well-served by what Motorleaf makes.
Monk shrugs that idea off. He says there are plenty of legitimate businesses, particularly in the technology sector and urban-farming movement, that are seeking his company’s services.
“Our goal is to be the default operating system for indoor growers around the world,” he says.
Over the summer, Motorleaf installed its system in a tomato-growing display case inside an upstate New York Price Chopper grocery store. Now it’s working with the same company, Vermont Hydroponic Produce, on a series of installations in Sutton and in New England that will allow students to grow food inside their schools.
“The Motorleaf system is a great tool for the kids to get involved in the actual processes of the growing method,” says Jeff Jones of Vermont Hydroponic, a subsidiary of Upper Valley Produce Group.
Jones backs up Motorleaf’s claims that it offers a unique product to relatively small-scale growers.
“When we were looking for automation, we went through three different small companies that provided aspects of what Motorleaf provides, and we were disappointed with all of them,” he says.
Although Motorleaf is still a small operation — currently with four employees, it’s looking to add another dozen staff with its seed money — it’s been making some big moves.
With little funding and exposure to date, the startup has received inbound inquiries from potential customers in 20 countries since July, and has letters of intent to purchase from growers from the Canadian Arctic to South America.
At this point, the company is focused on responding to demand by stepping up production. Monk says manufacturing will soon move from an in-house environment to a Canadian manufacturing facility. New and prospective partnerships with established greenhouse-automation companies, tech giants and other startups, have propelled the company forward, as well.
“All of their prospective customers know that it’s more efficient to grow year-round in a controlled environment than to roll the dice with changing weather patterns and unpredictable factors that are out of their control,” Monk says.