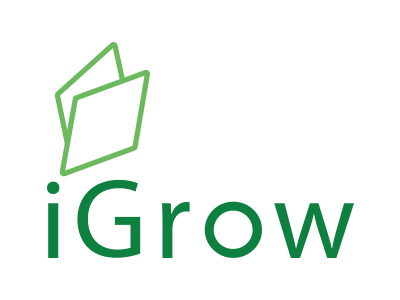
Welcome to iGrow News, Your Source for the World of Indoor Vertical Farming
Can Artificial Intelligence Do As Well As Farmers In The Future?
Cucumber plants to enter autonomous greenhouse of Wageningen University & Research
Tuesday 14 August marked the start of the Autonomous Greenhouses Challenge as five international teams try to grow cucumbers at a distance with the use of artificial intelligence at the facilities of Wageningen University & Research (WUR). “The goal is to convert knowledge about cultivation into algorithms that can enable computers to regulate cultivation automatically in the future, even in places where such knowledge is lacking. So the question is: can computers do as well as farmers?”
The five international teams will have four months to produce a cucumber yield remotely and without human intervention, using as little water, nutrition and energy as possible while achieving the highest possible output (i.e. production). Each team has been allocated 96 square metres in the facilities of WUR’s business unit Greenhouse Horticulture in Bleiswijk.
“The teams have partly developed their own algorithms and used them to determine output settings such as temperature, light quantity, CO2 concentration, fertilisation and several cultivation-related parameters such as plant and stem density,” says the head of the Horticulture Technology research team Silke Hemming. “The sensors and cameras – which they will be installing themselves in the week of 20 August – measure some of these cultivation data. The sensors send the information to the computer systems, allowing them to control the climate and fertilization in the greenhouse. The teams will not be allowed to enter the greenhouses apart from to install the equipment.”
The teams will collect all data remotely and be able to continuously adjust their algorithms for the software. Hemming: “The software itself will adjust the output settings like temperature where necessary. The goal is that the self-teaching software gradually takes over human decision-making.”
The challenge was organized by Wageningen University & Research Greenhouse Horticulture and the internet company Tencent. “We think we can further improve food production in greenhouse horticulture by introducing artificial intelligence,” Hemming continues. “This unique challenge lets us connect with international partners and make major strides forward. Although they are already global leaders in cultivation expertise, we believe even Dutch breeders will benefit from results of the challenge, as it will enable them to make decisions based on more carefully considered information.”
According to Hemming, the use of artificial intelligence will have an even greater impact globally. “In many countries, there is very little knowledge about complex plant production. Artificial intelligence can help people make complicated decisions, so they can locally produce vegetables and fruit with fewer means. The higher yield and production are especially important in view of the growing global population.”
Cucumber, the crop of choiceIn addition to the autonomously controlled greenhouses, the challenge will comprise a reference greenhouse where the chief grower of WUR Greenhouse Horticulture and several Dutch growers will cultivate cucumbers in an authentic way. “We settled on cucumbers as our crop of choice because they grow fast,” says Hemming. “This will enable us to obtain lots of information in four months. Cucumber plants are also very quickly affected if something is done incorrectly during cultivation. A breeding company cultivated the plants for the teams, and people from the test company of WUR Greenhouse Horticulture will put the plants in the greenhouses. The yields, their value and the associated costs and sustainability factors will be compared to the reference greenhouse.”
Supervisors from WUR Greenhouse Horticulture will provide the teams with the required digital information. Information will be shared with and output settings received from the teams via an interface produced by LetsGrow.com, one of WUR’s tech partners. WUR employees will be responsible for harvesting and communicating standard crop information, including yield weight, to the teams. An international jury will oversee the process and award points.
“Most of the points will be awarded for maximization of net profit,” Hemming explains. “Another criterion will be sustainability: energy & water consumption, CO2 levels and the use of crop protection agents.” Teams will also receive points for the use of artificial intelligence. Questions such as ‘how autonomous was the teams’ actual approach?’ and ‘how realistically could this system be applied on a large scale?’ will be the main issues evaluated by the jury in the final stage.
An exciting competition
“We expect an exciting competition in which the teams – deep_greens, AiCU, The Croperators, Sonoma, and iGrow – apply different approaches,” Hemming concludes. “For one team, for instance, the focus will be on artificial intelligence, while another team will highlight cultivation expertise.” The winner will be announced in the second week of December during the AgriFoodTech trade exhibition. “We will gain lots of new knowledge for a new cultivation method for the future.”
For more information:
Publication date: 8/15/2018
Q&A: UVA i.Lab-Supported Indoor Farming Startup Beanstalk Still Growing After Y Combinator
Q&A: UVA i.Lab-Supported Indoor Farming Startup Beanstalk Still Growing After Y Combinator
3-May-2018
Source Newsroom: University of Virginia Darden School of Business
Beanstalk Farms founders Jack and Michael Ross are building their first production facility in Northern Virginia.
By Dave Hendrick
Newswise — Indoor farming startup Beanstalk Farms has come a long way in a short period of time. Jack Ross, a 2017 graduate of the University of Virginia’s School of Engineering and Applied Science, and brother Michael Ross started their venture in the incubator program at the Darden School-hosted W.L. Lyons Brown III i.Lab in 2017, building a prototype and learning as much as they could about the complicated world of fresh produce.
After the i.Lab, the Ross brothers — both of whom trained as engineers — successfully applied for a spot at Y Combinator, the Silicon Valley-based accelerator that has helped launch companies like Dropbox, Airbnb and Instacart, among hundreds of others.
Now back on the East Coast, Jack Ross recently spoke about his experience launching Beanstalk; the UVA network on both coasts; and his quest for faster, cheaper and better-tasting lettuce and spinach.
An edited transcript of that conversation follows:
Give us the pitch for Beanstalk.
Beanstalk Farms grows heirloom produce in automated indoor farms. What that means is we bring the field inside and that allows us to control absolutely everything around the growth of the plant. We like to say it’s always 65 and sunny in our facility.
So we can grow the highest-quality food, all-year-round, and we can actually grow it faster than you can outside because it’s a perfect environment. And we can grow it anywhere, so it can be produced very close to the end consumer.
What’s the innovation you are bringing to the table? What’s different?
Beanstalk’s greatest innovation is our automation of the indoor farming process. We are not the first to grow inside. That’s been done for quite some time. It has, up to now, been very expensive. Food grown indoors has not been able to compete with the price of produce grown in the field, and the biggest reason for that is labor goes up when you grow inside. Indoor farms lose all of the technology that a company like John Deere brought to the field.
My brother and I are engineers, and we took a very different approach to farming. We created a manufacturing line that grows a plant. So the labor is very, very low.
It’s a highly automated process and, on top of that, because we don’t have to design for human labor to tend to the crops, it’s much, much denser. So, in a very small amount of space, we can grow food to feed cities.
We can put that farm right in the city, and we can grow the highest quality food, using heirloom seeds that have been cultivated for thousands of years to be incredibly tasty and very nutritious. Also, unlike field-grown food, even some organic food, we do not use pesticides. This means our food is always clean and ready to eat.
Essentially, our automated systems allow us to sell at prices competitive with traditionally farmed food, and our precise indoor environment ensures we can grow the highest quality food anywhere in the world.
What was your experience in the i.Lab like?
It was great. It’s a wonderful time when you don’t really have anything set in stone. The community was very close knit and attentive. We were just starting out as a company, and learning who we should talk to and who could help us learn more about the problem we are trying to solve. Jason [Brewster], David [Touve] and Sandra [McCutcheon] were incredible in brainstorming solutions, refining our pitch, and connecting us to people that could help us better understand the food system. The i.Lab helped us get on our feet.
During the program, we spent most of that time trying to grow plants quickly and consistently. We knew that if we could do that, the rest of it would fall in line, as the engineering is our sweet spot. The rest of time was talking to customers. We were out talking to people from all different parts of the food system.
The food system is a really complex beast. From food getting off the field, it may change hands over half a dozen times. So we wanted to talk to chefs, restaurant owners, and distributors to understand the system. We found a couple of huge problems for all people involved.
First, finding a consistent source of quality produce is a really big problem.
People are looking for local produce and it just doesn’t exist everywhere. So sourcing was a big problem. And then just the volatility of the market. From week-to-week, prices can go up 800 percent. So that kind of volatility for a restaurant owner is awful.
To us, it was pretty clear we just needed to find a way to create a consistent, high-quality product and remove the risk factors.
So the i.Lab really pushed us to get out and talk to people. Thankfully, our hypothesis was verified and we graduated from the i.Lab Incubator knowing clearly what the problem is and having a rough idea of how we wanted to solve it. So that set us up perfectly for Y Combinator.
What’s the process like for getting into Y Combinator?
It’s quick.
The application is not terribly long. It’s about half a dozen questions on the business. They wanted to know a lot about the founding team. We heard back about a month later and they basically said, “You have an interview spot; it’s in a week for 10 minutes.”
So you have to drop everything you’re doing and fly out to Mountain View for a 10-minute interview. We got organized, and the i.Lab actually helped us get out there and coordinate with people while we were out there.
I thought it was going to be more Shark Tank-style, with a lot of accusatory questions. Not at all. They asked a few hard questions, and then it turned very quickly into brainstorming. What do you guys think you can do in the program while you’re here? What’s next for you?
It was a much warmer conversation than I anticipated.
What’s the program like once you’re in it?
It’s pretty hands-off. The biggest thing they do is they want you to pick a metric, a single metric for your business. And that is kind of your guiding light for three months of the program.
We picked cost because cost is really what drives purchasing decisions. So we focused on getting the cost of production to that of the field. We said if we can reach price parity with food purchased off the field, we can put this anywhere and maintain a profit.
You meet twice a week with your partners at YC and a group of other companies and talk about what you’re doing to hit that metric and what kind of stuff is blocking you.
Was it intimidating to be in this incubator that has launched so many household names?
Intimidating is probably not far off at the beginning, because expectations are very high.
The really amazing thing is the first day they brought in Drew Houston, the founder of Dropbox, and he was gearing up for his IPO. You build up the impression of these people, and he came in and had a very pragmatic approach to how he started Dropbox and how he grew it. He was a regular guy, and he made himself very available. So that kind of demystified it a bit. The biggest thing they stress is to just keep at it. Don’t die, is what they stress. If you can just get through it, the odds are so much better that you’ll be successful.
From that first day on, it was less about meeting these ridiculous expectations and more about just figuring out what kind of support you need for your business to stay alive.
Were you tapping into a UVA or Darden network while you were out there?
Absolutely. We touched back with the i.Lab while we were out there. [BlueRun Ventures General Partner] Jonathan Ebinger (MBA ’93) was my mentor at the i.Lab, and we had connected a few times while we were in Charlottesville. But after moving out there, he helped us understand more of the pacing of these sorts of things. He’s been a venture capitalist for 20 years and has seen a lot of companies come and go, so we were able to go to him with questions. Just having someone with that experience and wisdom helped us a lot. Not to mention he helped us get a place to live while we were there for three months.
Y Combinator just wrapped up in March. Where are you all now?
We moved back just last week to set up what is going to be our first production farm. We’re setting that up in Northern Virginia and looking to go into production in pilot runs at the end of this year. Then we’ll start selling into wholesale next year. That will position us as the first vertical farm to go into wholesale markets.
To us, that’s really important. We view this as an impact or mission-focused business. So being able to sell at wholesale proves to us and to our investors and customers that this is profitable at a mass-market size. So we can sell food that everyone can afford — not just the Michelin-starred chefs.
You have a background starting technology companies. Do you consider this a tech company?
We like to say we are a technology-enabled business, as the core of our innovation is technology. However, at end of the day, we are selling produce. What we focus on day to day is how we build a better manufacturing line that grows better and more affordable food.
As you’ve been through this process, have you keyed on a particular area of weakness to address?
Certainly, continuing personal development is the most important thing. If successful, your business is going to grow exponentially. Humans do not have an intuition for exponential growth, so it’s very important to just be learning as much as you possibly can so that you can try to stay ahead of your business’ growth.
Do you end up eating a lot of your product?
We do. It’s very cool to have a company where you can eat what you work on. The past three months have been largely a salad-based diet. I was not a huge salad aficionado before, but after having tasted these heirlooms seeds and eating our food fresh off the farm, it does taste a world different.
What other lessons stand out for you from these early days?
I think the most important lesson I’ve been learning through these programs is that the time you’re there is valuable, but it’s really brief. The most important thing is the network of people you become a part of and whom you spend your time with. At UVA, I became very close with fellow i.Lab founders including Kevin Eisenfrats of Contraline, Kris Cody of Paka, and Brent Baumgartner of Helme. Even though we all run very different business, we face the same problems. It is the support from this group of fellow founders from the i.Lab, and from YC now, too, that have helped me get to where I am and keep moving forward.
About the University of Virginia Darden School of Business
The University of Virginia Darden School of Business delivers the world’s best business education experience to prepare entrepreneurial, global and responsible leaders through its MBA, Ph.D. and Executive Education programs. Darden’s top-ranked faculty is renowned for teaching excellence and advances practical business knowledge through research. Darden was established in 1955 at the University of Virginia, a top public university founded by Thomas Jefferson in 1819 in Charlottesville, Virginia.
Agriculture, Education, Entrepreneurship, Local - Virginia
KEYWORDS
The Future of Automated Urban Farming by Babylon Micro-Farms
Alexander Olesen is Founder and CEO of Babylon Micro-Farms, developing automated hydroponic systems for the restaurant and hospitality industries that grow fresh, sustainable and organic food on-site.
The Future of Automated Urban Farming by Babylon Micro-Farms
February 17, 2018 AT 12:54 PM / BY ADMIN
Podcast: Play in new window | Download (Duration: 16:00 — 22.2MB) | Embed
Subscribe: Apple Podcasts | Android | Email | RSS | More
Alexander Olesen, Founder, and CEO of Babylon Micro-Farms joins Enterprise Radio to talk about his company and why technology and hydroponics will revolutionize the way we grow food.
Listen to host Eric Dye & guest Alexander Olesen discuss the following:
- What inspired you to start Babylon?
- How do you think hydroponics will change the way we consume food?
- Why should people be paying more attention to hydroponics in 2018?
- You are working on a new product, the Micro-Farm. What can you tell me about that?
- What are you most excited about for where Babylon is headed?
Alexander Olesen is Founder and CEO of Babylon Micro-Farms, developing automated hydroponic systems for the restaurant and hospitality industries that grow fresh, sustainable and organic food on-site. The idea was conceived in a Social Entrepreneurship class at the University of Virginia in 2015. Ever since then Babylon’s mission has been to make urban farming accessible to everyone and ensure a healthier and sustainable future.
Website: www.babylonmicrofarms.com
Social Media Links:
Facebook: www.facebook.com/BabylonMicroFarms
Twitter: www.twitter.com/BabylonMF