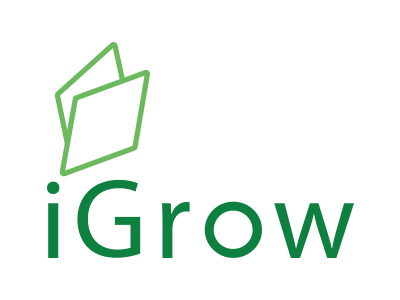
Welcome to iGrow News, Your Source for the World of Indoor Vertical Farming
Tri-State, EPRI Team To Officially Bring ‘Farm In A Box’ Program To Moffat County School District
Tri-State will install one of EPRI’s cutting-edge indoor agriculture facilities on the grounds of Moffat County High School later this year, according to a press release from Tri-State
09-23-20 | Joshua Carney | Follow
Tri-State Generation and Transmission Association’s decades-long relationship with the Electric Power Research Institute is about to bear fruit for Moffat County School District students and the Craig community as a whole as the “Farm in a Box” project moves forward.
Tri-State will install one of EPRI’s cutting-edge indoor agriculture facilities on the grounds of Moffat County High School later this year, according to a press release from Tri-State.
The “Farm in a Box” is valued at $250,000 – which is covered as part of Tri-State’s EPRI membership – and will provide a new source for fresh produce in the region and educational opportunities for MCSD students. Moffat County High School Business Teacher Krista Schenck presented the project to City Council in early September. The project has the capability to produce various crops, such as lettuce, kale, arugula herbs, flowers, carrots, and radishes, year-round inside the shipping container.
“Tri-State invests in its EPRI membership and is keen to find immediately applicable uses for the remarkable technologies that emerge to benefit the electric sector and society at large,” said Tri-State CEO Duane Highley in a press release. “We also recognize that the transition brought on by our Responsible Energy Plan will have a major impact on coal-dependent communities, so if we can leverage a program to bring new educational, economic, and lifestyle benefits to support Moffat County schools, we are proud and eager to do so.”
An EPRI-led team is constructing the facility – a 40-foot long shipping container equipped with efficient lighting, temperature control, and plumbing infrastructure needed to grow crops inside the container on a year-round basis.
Since 2015, EPRI has been examining the operational, technological, sustainability, and environmental characteristics for indoor agriculture, by installing container farms across the United States and assessing their performance with local electricity providers, academic institutions, and other community organizations.“
As an emerging industry in urban and rural areas throughout the United States, indoor farming can help us use our energy and water resources more efficiently,” said EPRI President Arshad Mansoor. “EPRI’s indoor food production research aims to help electric utilities better understand, plan for, and engage with this novel enterprise while also offering educational opportunities for project collaborators, the local community, and the next generation of farmers to address food availability challenges.”
According to Tri-State, EPRI staff will monitor the container to evaluate nutrient quality of the produce, utility program compatibility, community impacts, sustainability performance, technology trends, market drivers, electricity load profiles, and other broader environmental and economic aspects of indoor food production for the first two years following installation. EPRI will conduct research on the container and MCSD will be the sole owner and operator of the equipment.
“Moffat County School District is excited about the learning potential this program affords its career and technical education students in our community,” said Principal Sarah Hepworth of Moffat County High School.“
Through the collaboration between agricultural, business, marketing, and culinary programs, the opportunities to learn about horticulture, conservation, food regulations, business, and project management, marketing, sales, and food preparation are endless for MCSD students,” said Schenck. “Students and faculty look forward to utilizing this partnership and the technology of ‘Farm in a Box’ to grow crops from microgreens to lettuce and carrots.”
Preparing the container farm will take several weeks and involve manufacturing and a customized graphic treatment of its exterior. School officials are targeting early to mid-November for its arrival in Craig. The EPRI team will consult with the school district on installation and operation.“
This is a true team effort,” added Highley. “One of the seven cooperative principles under which we operate is ‘Concern for Community,’ so we’re excited to see the school district adopt this project and turn it into a real asset for community betterment.”In January, Tri-State announced its Responsible Energy Plan, which will transition the company to more renewable energy production for its members to address changes in the industry and to support new state requirements for clean energy. The effort will result in the closure of the Craig Generation Station by 2030, and Tri-State has been working with state and local officials to support transition efforts in the community.jcarney@craigdailypress.com
Latest ZipGrow Inc. Product Introduces Vertical Indoor Farming To New Growers
Controlled Environmental Agriculture (CEA) is currently undergoing an upturn in public interest as the general population begins to appreciate the importance of locally produced food from sustainable sources
September 9, 2020
ONTARIO, CA - Controlled Environmental Agriculture (CEA) is currently undergoing an upturn in public interest as the general population begins to appreciate the importance of locally produced food from sustainable sources. ZipGrow Inc.’s new product offering, the Introduction to Commercial Growing package, is designed to make commercial growing more accessible to farmers and businesses wanting to get into the CEA industry.
“As interest grows in improving food security, we wanted to make commercial growing more accessible to newcomers to the hydroponics world”, explains Eric Lang, President of ZipGrow Inc. “This new package is an accessible, and affordable entry-level product for anyone interested in testing out if controlled environmental agriculture is right for them.”
The new product package includes a discounted set of everything you need to get started, including 90 patented 8’ ZipGrow™ Towers, steel ZipRacks, LED growing lights, a seedling area, a comprehensive plumbing system, and an automatic doser from Atom Controllers. This package is not only all-inclusive, but also modular to be able to expand as the operation grows.
“This package can set someone up to produce up to 100 pounds of leafy greens or herbs such as lettuce or basil each week, and is a great way to test a pilot system in your local community”, adds Lang. “Since the start of COVID-19 we have seen interest in sustainable food sources skyrocket, and this is one way we are trying to encourage more people to see if hydroponic farming is right for them.”
The Introduction to Commercial Growing package has a flat rate shipping option for all locations within Canada and the continental United States, with shipping to other locations available at custom rates. The package will be fully installed on-site, with costs varying dependent on location. ZipGrow team members will work with customers to ensure the product is the right fit for them and ensure all training and ongoing education needs are fulfilled.
ZipGrow Inc. is an international leader in indoor, vertical farming technology. Our flagship product, the ZipGrow™ Tower, is a core component of many of the world’s most innovative farms; from indoor hydroponic warehouses to vertical aquaponic greenhouses and high-density container farms.
For more information contact Gina Scandrett at hello@zipgrow.com or at 1-855-ZIPGROW.
LIVE Virtual Tour - Inside the Greenery Container Farm with Freight Farms' Lead Designer - Thurs, Sept 10, 2020 - 4:30 PM EST
Explore the technology behind our Greenery container farm that allows farmers to grow food anywhere in the world!
Take a Virtual Tour of the Freight Farms Greenery™
Explore the technology behind our Greenery container farm that allows farmers to grow food anywhere in the world!
Farm expert Derek will explain the ins and outs of the Greenery using a live video stream inside the farm. He’ll cover the basics of controlled environment agriculture, hydroponics, vertical farming, and how all those work together inside the Greenery to create the perfect conditions for crop growth regardless of geographic location.
To Register For This Free Zoom Virtual Live Tour
Thursday, September 10, 2020 - 4:30 PM
Freight Farms in Montrose Colorado - Eatin' Greens Farm - Locally Grown Produce
“We have been container farming for 3 years now and we were in agriculture in this area since 1970, so we have been through a few cycles of wet and dry years. We are able to grow consistently all year long no matter what the weather is like. We only use about 3 or 4 gallons of water a day, so drought or no drought we aren’t affected.”⠀
The deserts of the west meet the Rocky Mountains, blocking any rainfall that might come their way. ⠀
Instead, the town relies on snowmelt to irrigate their valley so they can grow beautiful crops of corn, alfalfa, peaches, apricots and apples, and more.⠀
But for the past 2 years, the area has been experiencing a drought and the availability of water for next year depends entirely on the amount of snowfall the mountains receive this winter.⠀
“These cycles certainly make my wife and I appreciate the Freight Farm," says Steve Arnold of @eatingreensfarm. “We have been container farming for 3 years now and we were in agriculture in this area since 1970, so we have been through a few cycles of wet and dry years. We are able to grow consistently all year long no matter what the weather is like. We only use about 3 or 4 gallons of water a day, so drought or no drought we aren’t affected.”⠀
Future of Food Is Fresh And Green For Manitoulin First Nation
Launched in 2015, The Growcer adheres to other models of container farming that start with a shipping container and add hydroponic growing equipment and LED lights to create a self-contained, closely monitored system that allows for growing year-round
Sheshegwaning First Nation Takes High-Tech Step
Toward Food Security
Jul 22, 2020
By: Lindsay Kelly
Last February, April Folz was attending a conference in Québec with a team from Sheshegwaning First Nation when a tradeshow display caught her eye.
It was unusual to see shoots of fresh, edible greens in amongst the displays, especially at that time of year, but there they were, at an exhibit for The Growcer, an Ottawa-based company that develops hydroponic container farms.“
It was winter, and it was snowing,” recalled Folz, Sheshegwaning’s economic development director. “It was so neat that it was growing in the middle of winter – there were snowstorms.”
The community’s interest in the farming system was piqued but wasn’t given any serious consideration until a few weeks later, Folz recalled.
When COVID-19 arrived in Northern Ontario in March, members of the outlying community, which is situated on the far west end of Manitoulin Island, began to worry about food chains being interrupted and how they would continue to enjoy a supply of fresh produce when the nearest grocery store is about 45 minutes away in Gore Bay.
Fears were further exacerbated with talk of closing off access to the swing bridge at Little Current, which, during the winter months, provides the sole route on and off the island that’s situated in the upper end of Georgian Bay in Lake Huron.“
This pandemic happened and people were complaining that they couldn't get anything at the grocery store, and they couldn't get any of the fresh produce in at the store here (in Sheshegwaning),” Folz said.“We were having a hard time supplying that for our people.”
The community of 118 quickly made a decision to take the plunge into container farming, taking out a loan to purchase their very own Growcer farm, and the unit arrived in the community on June 22.
Launched in 2015, The Growcer adheres to other models of container farming that start with a shipping container and add hydroponic growing equipment and LED lights to create a self-contained, closely monitored system that allows for growing year-round.
Seeds are nurtured with a tailored combination of nutrients, water, and lighting, and crops are ready to be harvested after about four to six weeks. With a staggered planting system in place, crops are always growing.If something goes wrong – the temperature gets too high, for example – the sophisticated monitoring system will alert staff through their phones so they can visit the farm and adjust accordingly.“
Growcer also has access to our system,” Folz said. “So they get alarms as well, and they can regulate it from Ottawa.”
The company provides full training and ongoing support as part of the purchase agreement.
There are even some job opportunities for those enterprising community members with an interest in agriculture. Folz is currently hiring for a full-time systems manager, who will be responsible for planting and harvesting, cleaning, and calibrating the Growcer system, as well as two part-timers, who will help with monitoring the crops.
Growcer farms are now successfully producing fresh greens every week in communities as far-flung as Kugluktuk, Nunavut, and Churchill, Man.
Conditions in Sheshegwaning aren’t nearly as harsh or rugged as in those more remote regions, but the arrival of their own container farm has generated buzz amongst the many avid salad-eaters in the community.
For $10 a week, residents who want a take of the harvest sign up for a subscription box, which guarantees them five heads of greens of their choice delivered to their door. A portion of the harvest will also go to local business Mkwa Catering for use in their dishes.
The first seeds were planted during the week of July 20, and Folz expects to reap the harvest in mid-August. Products will be marketed under the Odawa Freshwater brand.
She’s calculated that if they sell out weekly, the community will break even on its loan for the project.
So far, the community has planted Monte Carlo romaine lettuce, red Russian lettuce, Tuscan kale, wildfire lettuce, and win-win choi, along with basil, parsley, and mint.“
People want spinach, so they’re going to send us some spinach seeds and get that going,” Folz noted.
Folz said 450 heads of greens will be harvested weekly, while the herbs can be cut back each week and will self-replenish until they reach the end of their lifecycle, which she estimates will be some time in October.
An ongoing experiment with different lighting and growing conditions aims to see if there's any success with strawberries.
Known in many Indigenous cultures as the “heart berry,” strawberries are celebrated as a marker of spring, help promote health and well-being, and signify friendship and reconciliation.“
Strawberries are very important for Native culture for ceremonies, and it would be fantastic to get them fresh year-round if we could do that,” Folz said.“
This (container) is specific for greens, and it will probably stay that way. Maybe down the road, we’ll get one for strawberries.”
PHOTOS:
1 / 6 Crops being grown by Sheshegwaning First Nation in its new container farm include kale, lettuce, parsley, mint, and basil. (Supplied photo)
2 / 6 Sheshegwaning First Nation took delivery of its Growcer container farm on June 22. Its first crops will be ready in mid-August. (Supplied photo)
3 / 6 Container farms use a customized combination of water, nutrients, and lighting to get the maximum yields per crop. (Supplied photo)
4 / 6 Ottawa-based The Growcer uses a shipping container, outfitted with LED lights and a hydroponic growing system, as the base for its container farms, which allow year-round growing. (Supplied photo)
5 / 6 Seeds are put into a growing medium to get started. Crops are ready in four to six weeks. (Supplied photo)
6 / 6 Sheshegwaning's Growcer container farm will create jobs for three community members, who will plant seeds, harvest crops, and clean, calibrate, and monitor the system. (Supplied photo)
NEW YORK: Vertical Farming Takes Root in Hudson Valley
Vertical Field launched in Israel in 2006 as an agricultural supply solution for the nation’s urban markets. Miner stated the firm began as a “green wall company” that took the horizontal aspect of rooftop gardens and switched it on its side
By Phil Hall
June 20, 2020
Among the more disturbing aspects of the COVID-19 pandemic involved food costs and supplies. The U.S. Department of Agriculture reported a 2.6% increase in food prices nationwide from March to April, marking the largest monthly increase in 46 years. These increases have been fueled by disruptions in the supply chain due to worker illnesses in processing plants.
For restaurants and food retailers, not being able to access materials or being charged higher-than-normal exacerbates an already acute problem of trying to maintain revenue streams during the pandemic.
However, a pair of regional businesses have begun using agricultural technology from the Israeli company Vertical Field that takes the farm-to-table concept and turns it into a container-to-table approach.
“The way it works is that we take a container, just the standard shipping container,” explained Sam Miner, Vertical Field’s U.S. launch manager.
“And the main thing that we do is we put these modules on the wall that have irrigation lines behind it. We simply fill those modules with soil and we put in the right lighting equipment. And once you put plants in there, they just grow fairly simple.”
John Lekic, chef and owner of Poughkeepsie’s Farmers & Chefs restaurant, poses in front of his Vertical Field container used for growing greens and herbs. Photo courtesy Vertical Field.
Vertical Field launched in Israel in 2006 as an agricultural supply solution for the nation’s urban markets. Miner stated the firm began as a “green wall company” that took the horizontal aspect of rooftop gardens and switched it on its side.
The company now has 400 projects around the world, including a massive installation in Vietnam that Miner described as being “tremendous, like a football field.”
This spring, Vertical Field made its way into the U.S. market through a pair of Hudson Valley installations. John Lekic, chef and owner of Poughkeepsie’s Farmers & Chefs restaurant, learned about the technology at a Culinary Institute of America symposium in late 2019 and was intrigued about operating his own food source.
“We were planning to bring in the container in March and we actually brought in a container days after the emergency thing was declared in New York,” he said. “It was a perfect timing. Ten days later, we planted our first crop, mostly salad greens, and in the middle of May we already had to harvest. We are going to have a third one this week.”
Lekic praised the technology for allowing several harvests per week, noting the ability to “harvest them the day of serving.” He also praised the user-friendly aspect of the 20-foot containers.
“It’s super easy to maintain,” he said. “Once the container is set up and the mechanism is in place, you have an app that does the irrigation and controls the temperature and the humidity. It’s not really complicated — after you do it once or twice, the planting and everything else becomes really easy to maintain. It does not require a lot of time.”
Lekic is now growing herbs and leafy vegetables in the containers, adding “it’s still a playground for us.”
Another Hudson Valley business that has Vertical Field’s technology in place is the Evergreen Kosher supermarket in Monsey, which installed its containers at the end of May. Menachem Lubinsky, president of Brooklyn-based Lubicom Business Consulting and marketing director for Evergreen, praised the product for creating a speedy supply of produce.
“If something takes normally three months to grow, the technology can accelerate that to three weeks,” he said. “A restaurant or a supermarket can be in control of their supply.”
Lubinsky said he reached out to Vertical Field following news reports during the pandemic of truckers not being able to deliver goods and farms destroying crops because they suddenly had no outlets for selling. Besides selling the harvested crops, Evergreen is planning to make the containers a visitors’ attraction.
“The customer will be able to see the process of how it grows because one of the walls of the container is glass,” he said. “It’s kind of like an educational experience just for a family to go over to see how this whole process grows. And there’s a very large kosher constituency there who are concerned about consuming insects. This eliminates that concern because of the way it grows — it is insect-free.”
Lubinsky said that Vertical Field is planning to build on its technology to accommodate the growing of a wider variety of items, including strawberries and vegetables.
Localization is Seeding Innovative Produce Supply Chains
The COVID-19 crisis is shining a light on the vulnerabilities of food supply chains, as well as opportunities to develop inventive ways to deliver fresh foods such as fruit and vegetables from farm to table
A Key Theme of These changes is Localization – An Increasing Reliance on Local Growers to Supply Produce To Retail Outlets.
By Chris Mejia Argueta, Alexis H. Bateman, & Ken Cottrill · June 12, 2020
Editor’s Note: Chris Mejia Argueta is a Research Scientist at the MIT Center for Transportation & Logistics and directs the MIT Food and Retail Operations Lab. Alexis H. Bateman is a Research Scientist at the MIT Center for Transportation & Logistics and directs MIT Sustainable Supply Chains. Ken Cottrill is the Editorial Director at the MIT Center for Transportation & Logistics.
The COVID-19 crisis is shining a light on the vulnerabilities of food supply chains, as well as opportunities to develop inventive ways to deliver fresh foods such as fruit and vegetables from farm to table.
A key theme of these changes is localization – an increasing reliance on local growers to supply produce to retail outlets. The movement has gained momentum as a result of shifting consumer buying preferences and the need to make food supply chains resilient to a wide array of risks.
What is localization?
From a global perspective, localization can mean reorienting supply chains towards suppliers in specific countries or regions in any market. In this article, we focus on the localization of fruit and vegetable supply chains in the United States.
There are several definitions of what constitutes a “local” food supply in the US. The United States Department of Agriculture maintains that although “local” connotates short geographic distance between producer and consumer, there is no consensus on what products meet the definition. A government definition assumes that a product can be considered locally or regionally produced if it is less than 400 miles from its origin or within the state in which it was produced. A consumer survey carried out by the research firm Nielsen found that most buyers classify products across various food categories made 50 miles or less from the store, as local.
Local sources of produce are not confined to farms or small-size plots of land; They also include specialist operations such as high-tech commercial greenhouses and urban gardens. The enterprises sell directly to consumers or to retail customers such as supermarkets.
The size of the market for local food is unclear. From an industry standpoint, research from the Congressional Research Service (CRS) estimates that direct-to-consumer food sales account for about 3% of the total US agricultural production value. Up to one-half of the produce industry relies on sales to supermarkets and other chain stores, and the remainder serves foodservice companies (e.g., restaurants) and large consumers of produce such as schools and other institutions.
Pre-pandemic drivers
The localization movement was gathering steam in produce markets before the COVID-19 pandemic.
One of the drivers is the need to make produce supply chains more resilient to disruptions, like market volatility and labor shortages. Local sourcing avoids the risks associated with shipping perishable product long distances from growers to consumers. Also, shorter supply chains are more flexible, require fewer product touches and intermediaries, reduce wastage, and minimize potentially costly and delay-prone cross-border movements. There are cost advantages as well, mainly in the form of reduced transportation and warehousing costs.
Localization is finding support among consumers. Trust in food crops grown on distant, large-scale factory farms has declined as consumer interest in the safety and origins of food products has increased. Another component of this trend is the increased demand for sustainable products. For example, research by The Center for Food Integrity suggests that concepts such as “food miles” are becoming more relevant to consumers, as they place more value on shorter, more carbon-efficient supply chains.
The localization movement also aligns with the need to provide underserved communities with sources of fresh, nutritious food. One way to combat the spread of so-called food deserts – communities where access to fresh fruit and vegetables is limited – is to connect these communities with local growers.
These forces drive demand for locally grown fruits and vegetables and increase the premium that consumers are willing to pay for “locally produced” and “farm to table” product labels.
Coronavirus-related market shifts
Today, the COVID-19 crisis is reinforcing many of these market changes by illuminating weaknesses in produce supply chains. The pandemic shuttered restaurants and other places where large numbers of people congregate such as schools – effectively depriving fruit and vegetable producers of a primary market.
An obvious response was to pivot to other customers, notably supermarkets and other retail outlets. However, these are different channels with distinct specifications for product packaging and unit sizes. Reorienting supply chains geared to foodservice and institutional buyers towards customers in the retail business proved extremely challenging. To solve this issue, some farmers turned to selling their produce directly to the consumer, highlighting the value of locally produced foods as a source of revenue for farmers during supply chain disruptions. Some farmers may never go back to the original model.
The pandemic also exacerbated the labor shortages that plague growers in agricultural regions of the US. Restrictions on migrant workers crimped the supply of labor before the pandemic. The coronavirus’s health threat made it even more difficult to recruit the workers that growers need to harvest and pack food crops.
While localization does not address all pandemic-related supply chain issues, it does promote the flexibility, agility, and resilience needed to mitigate the risks associated with COVID-19 disruptions. This is one reason why the pandemic has underscored the advantages of local sourcing, especially for perishable products such as fruit and vegetables.
Moreover, preference for neighborhood markets may grow beyond food deserts. A recent study from mathematician Elena Polozova indicates that buying in corner stores is less risky than in big retail formats.
Innovations hone local models
The localization movement also benefits from a number of supply chain innovations in the agricultural industry. Here are some notable examples.
Local supply programs. As NPR reported recently, the movement known as community-supported agriculture (CSA) is experiencing growth in various parts of the country. Members of CSA programs typically commit to buying regular deliveries of fresh produce from local growers. The coronavirus pandemic has raised the profile of CSAs for the reasons described above, although the model is mainly growing in wealthy communities.
Veggie box models. The so-called veggie box model is an evolution of the CSA movement. In this variation, groups of farmers create boxes of produce items in accordance with consumer preferences.
Commercial veggie box models such as HelloFresh are expanding, and provide a new buying channel for fresh produce. However, they do not offer the variety and quantity that most customer segments need. In addition, these services are configured for middle-to-high income population segments and assume that there is enough last-mile delivery capacity to perform dozens of deliveries effectively. However, the capacity is not always available, a problem exacerbated by the COVID-19 crisis.
Dr. Chris Mejia, Dr. Lars Sanches, along with master’s students Jamal Taylor and Luiz Barreto from the MIT Food and Retail Operations Lab have collaborated with colleagues from Tufts University, and the City of Somerville, MA, to explore the veggie box model, in underserved communities. The options under review use neighborhood markets as pickup points for veggie boxes, analyze the impact of ride-sharing systems, and extend the impact of grocery delivery models in the city. Despite its complex design, the researchers found that the veggie-box model can support a local economy, decrease food insecurity, and address shortages of healthy food items. However, neighborhood market owners or managers need to widen the choice of produce, promote the veggie box service to the appropriate customers, and allocate space to store the boxes of produce.
A future article in this series on food supply chains will give a detailed account of the veggie box research described above.
Innovative growing models. Growers are harnessing novel agricultural methods such as hydroponics, advanced sensing, and information technologies to develop alternatives to traditional farms. An example is BrightFarms, a company that grows produce sustainably in high-tech, hydroponic greenhouses located in Pennsylvania, Ohio, Illinois, and Virginia. The greenhouses typically supply local supermarkets. In January 2020, the company opened a 280,000 sq. ft facility in Selinsgrove, PA, that can deliver over 2 million pounds of fresh, local produce year-round in PA and the PA-NJ-DE tri-state area. It has partnered with local supermarkets, including the Giant chain.
Urban and Container Farms. Small urban farms that sell to retail, food service, or restaurants have also become increasingly common with open fields, rooftops, brownfields, and other open spaces being utilized in cities to grow fresh fruits and vegetables. Urban farms that serve public demand reduce product transit and storage needs and increase food freshness in most cases.
Container farms use shipping containers to create self-contained growing environments for fresh produce, often in urban settings. One example is FreightFarms, which provides the container and set up that enable people to grow produce anywhere in the world.
Diversity programs. Traditional farmer’s markets allow residents to shop for a variety of produce items at specific locations in city locations at weekly times. However, these markets may not cater to the fruit and vegetable needs of ethnically diverse communities. World Farmers Organization in Massachusetts is implementing an innovative strategy to support culturally diverse farmers who grow their preferred products in small parcels and connect them to retail outlets. Some of these outlets are located in neighborhood markets.
Small growers, big potential?
While the localization of fruit and vegetable supply chains is attracting interest, most conventional, large-scale growing operations are not under threat.
Not all food crops are viable candidates for small, local suppliers. Moreover, the competitive advantages of localization are subject to tradeoffs between economies of scale, the capital cost of growing facilities, and transportation costs. Also, more emphasis on locally grown produce increases the importance of supply chain transparency. Consumers who buy local produce want to be reassured that their purchases are sourced locally, and this will require relevant sourcing information at the point of sale. The availability of investment funds also influences the commercial success of localization – a factor that could become more critical while the US economy remains mired in recession.
Still, consumers switching to local growers pre-COVID, in combination with the changes wrought by the pandemic, are creating a significant market for locally sourced produce that poses new supply chain challenges and opportunities. Researchers across MIT CTL are working on research projects to better understand this trend.