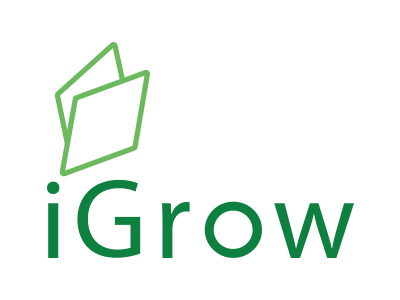
Welcome to iGrow News, Your Source for the World of Indoor Vertical Farming
US (CO): Container Farm at Historic Ranch to Grow Restaurant's Produce
A historic ranch in the mountains of Colorado is using a high-tech container farm to broaden its focus on farm-to-table options for guests.
August 10, 2021
A historic ranch in the mountains of Colorado is using a high-tech container farm to broaden its focus on farm-to-table options for guests.
Having been in business for 102 years, C Lazy U Ranch in Granby has a storied reputation as a luxurious, year-round mountain getaway with 8,500 acres of land for a multitude of activities. The ranch’s culinary program will soon be complemented by fresh leafy greens and herbs. The produce will be grown on-site in an automated container farm, built by Colorado-based FarmBox Foods.
“We saw an opportunity with FarmBox Foods to essentially have a year-round farm-to-table option,” said Paul Klees, assistant general manager of C Lazy U Ranch. The container farm is scheduled for delivery in mid-August.
Container purposes
Guests and members will have the opportunity to tour the farm. C Lazy U Ranch is planning to grow lettuce and culinary herbs inside the 320-square-foot farm. The sensor-based technology and insulation in the container farm are superior to greenhouses, which are susceptible to the bitter cold of the Colorado Rockies, Klees said.
The container farm is slated to be the next hands-on attraction at the ranch, where guests and members could have the opportunity to harvest their own veggies and prepare meals with a chef. “It’s interactive, it’s educational, and it builds into our vision and mission statement of having a sustainable model,” Klees said.
Purchasing a container farm is “just another step in the ranch’s continuing effort to create authentic farm-to-table dining,” Klees said.
“There are economic aspects to it because we’re shipping in all of the food, including produce,” he said. “When guests eat at our restaurants, we want the meals to resonate with them, and what people are looking for is healthy organic fresh produce.”
Horses get their share
The 200 horses on the property already benefit from C Lazy U’s sustainable approach to food sourcing; most of the hay they eat is grown on the ranch. C Lazy U is also supplied with water by its own spring and operates its own wastewater facilities.
The exterior of the container farm will be finished with a rustic scheme so it will easily blend in with its natural surroundings, which include a creek and historic structures.
For more information:
FarmBox Foods
www.farmboxfoods.com
USA - FLORIDA: Brick Street Farms Was On A Podcast!
What an exciting opportunity we had this week to sit down with Feeding Tampa Bay to record a podcast episode about how we grow our produce and our dedication to sustainability
Farm in a Box with Shannon and Maddy of Brick Street Farms
What an exciting opportunity we had this week to sit down with Feeding Tampa Bay to record a podcast episode about how we grow our produce and our dedication to sustainability.
We also got a chance to discuss how our non-profit organization, Desert Farms, is partnering with them to work towards a hunger-free Tampa Bay. Click below to listen to the full podcast.
Listen
Freight Farms And CEO Vanzura Set To Reinvent Container Farming
June 17, 2021
The global pressures exacerbated by COVID-19 and the rippling toll it takes on the international community has made one thing clear: preparedness is everything. The Coronavirus has exposed vulnerabilities in the global health network that no one could have imagined. Food production and distribution must now reset their agendas to prepare for catastrophe.
Freight Farms, a 2011 Agtech company that pioneered hydroponics-based container farming, is committed to preparing the world for the next disaster by reinventing the way we grow food.
“Fill in the blank with the institution, how prepared are you for the emerging trends that are impacting the world,” Freight Farms CEO Rick Vanzura explained. “Sustainability issues, land availability, water availability; those issues obviously preceded COVID-19, but we think there’s going to be a greater sense of urgency around folks expecting us to have an answer and be prepared for these global trends, as opposed to being reactive.”
Vanzura looks to channel his decade of experience as a restaurant executive, growing Wahlburgers from a single restaurant to a $100 million dollar institution, as well as greatly expanding Panera Bread, to redefine food production and distribution as a whole.
Freight Farms uses container-based “vertical farming” to do just that, allowing farmers to produce hundreds of high-quality local crops from a 320 square foot shipping container which automates the farming process for maximum efficiency.
Vanzura plans to expand and distribute these self-contained, sustainable farms to a wide diversity of industry segments. The priority will of course be the global communities that need them the most. “We see the Freight Farm as a perfect fit for countries with food access difficulties, short growing seasons and inherently challenging climates. There’s probably no location where having a hyper-local, highly traceable, always available solution isn’t going to make sense in some way,” he added.
In the name of access to high-quality food, in a sustainable model built to withstand a natural disaster, Freight Farms has now distributed their automated, hydroponic farms to 48 U.S states and across the world to 32 different countries, boasting success and efficiency from the Arctic wilderness, to the desert, and to concrete jungles.
Freight Farms believes that its emphasis on access, preparedness, and sustainability will be more necessary than ever in the wake of COVID-19, as well as global trends of food insecurity and environmental uncertainty. Vanzura explained that the company has already reacted to shifting demands by supporting small-scale farmers as they set up drive-through produce stations to reach customers directly.
Freight Farms CEO Rick Vanzura
“Demand during this time for that hyper-local, fresh product has certainly ramped up,” Vanzura added. “Hopefully, once people get a taste of it, they will understand the difference, and post Covid, our containers will become an industry staple.”
Vanzura sees his role as not only expanding to agriculturally vulnerable countries abroad but also increasing access to high-quality food across institutions in the United States. He wants to specifically target universities and has partnered with foodservice provider Sodexo to ensure local food is available to as many people as possible.
Vanzura says he was forced by his children to move beyond the world of crafting a restaurant chain’s vision and use his knowledge to make the world a better place. Freight Farms, with Vanzura’s leadership, has the ability to change the way we think of farming and change the world.
Freight Farms hopes to combat international uncertainty, face the threats of climate change, and provide people with fresh produce regardless of climatic constraints and difficulties. “Healthy food is a right, not a luxury,” and Freight Farms is helping make this mission statement a reality.
Lead photo: A Freight Farms container has unprecedented environmental control and exceptional ease-of-use to unlock your growing potential.
To learn more about Freight Farms and how they are reinventing container farming, visit their website.
Total Food Service is a monthly B2B foodservice publication and website covering foodservice and hospitality news, industry trends, and exclusive interviews.
USA - ALABAMA: Auburn College of Agriculture Using High-Tech Shipping Containers To Grow Produce For Campus Dining
Unique ‘Vertical’ Farms part of Planned 16-Acre Transformation Garden On Campus
High-tech Horticulture
Unique ‘Vertical’ Farms part of Planned 16-Acre Transformation Garden On Campus
June 10, 2021
Josh Woods | College of Agriculture
Recycled shipping containers have gained popularity in recent years, being converted into everything from houses to small stores—but the Auburn University College of Agriculture, in partnership with Campus Dining, is using them as self-contained “vertical” farms to grow produce to serve to students.
In April, the college acquired two Freight Farms shipping containers that have been converted into technologically advanced hydroponic growing stations in which plants grow vertically indoors without soil, getting their nutrition from water and light energy from powerful LEDs.
Now, the farms are producing the first crop of lettuce.
“This is state of the art,” said Desmond Layne, head of the Department of Horticulture. “We're talking growing from seed to fork in four to six weeks, depending on whether it is lettuce, arugula or another vegetable crop that can grow in there. And we can produce 15 times as much per year as we could outside in the same exact spot.”
Associate Professor of Horticulture Daniel Wells taught a vertical farming course this spring and leads operations of the vertical farms.
Wells said the containers are outfitted with a complete climate control system, which includes air conditioning and humidity control. Because they are highly insulated, the system ensures the same climate 365 days a year.
The converted containers also have an elaborate lighting system, giving all the light the plants need from two color LEDs.
“We can do any number of colors of lights,” he said. “But it turns out for photosynthesis, plants use mostly red and blue light. What’s neat about that is you can cut out a lot of the other color spectrum, creating far less heat energy. That's very efficient. It means more of the energy used is turned into light than heat.”
The containers also allow for controlled carbon dioxide levels, which accelerates plant growth.
“Ambient CO2, what you and I are exposed to every day, is about 400 ppm [parts per million],” he said. “And that’s fine, plants can grow there. But if we boost the CO2 to 1,000 ppm, they’ll grow faster. And because we’re containing the CO2, the plants can really use it. And it’s not dangerous for humans at all.”
Wells and Director of Dining and Concessions Glenn Loughridge first initiated a partnership between the College of Agriculture and Campus Dining five years ago through the Auburn Aquaponics Project, which uses hydroponics and aquaculture technologies to provide a system in which nutrient-laden wastewater from fish production is used as a food source for plant growth. Today, fish from this effort are served in dining facilities on the Auburn campus.
The new vertical farms build on that effort.
“We're in the process of finishing a $26 million dining hall in the center of campus,” Loughridge said. “It has always been foremost in my mind that we would have the opportunity to feature produce grown here on campus in that dining hall. In our biggest location, our biggest asset, we want to bring our A-game.
“This is hyper-local, on-campus sourcing,” he added. “Can you imagine being a potential student coming to tour, seeing where these products are grown, and then going to eat there? It’s incredible. We truly believe this elevates our dining experience.”
The converted shipping containers were manufactured by Freight Farms, a Boston-based company operating in 45 states and 28 countries.
“There are a few different companies out there doing this,” Layne said. “But Freight Farms is the most sophisticated. They’re the ones who have both the best product on the market and the largest production of these containers. It’s really a best-case scenario.”
Adam Lenhard, a rising senior majoring in biological agricultural technology management, said Wells’ course has been one of the most influential courses he’s taken at Auburn.
“It has been very helpful, not just in preparation for the arrival of the freights, but also in learning all about new hydroponic technologies and growing techniques,” Lenhard said. “Post-graduation, I plan to continue to work with these types of indoor, LED hydroponic systems. My primary goal after college is to normalize urban hydroponic farming, provide large, consistent yields of fresh vegetables and provide food to those in need who do not have as much access to fresh produce.”
Transformation Garden
The vertical farms are located on the College of Agriculture’s planned 16-acre Transformation Garden on the south end of the university’s campus, near the intersection of Lem Morrison Drive and Duncan Drive. The goal of the garden is to encompass every aspect of plant-based agriculture, including everything from fruits and vegetables to ornamentals to grow crops and more.
The Transformation Garden will showcase new technology and the history of agriculture, as it envelops Auburn’s Old Rotation, a single-acre research plot created in 1896. Continuously since that year, the historic landmark has been the site for testing and advancing transformative ideas that are now commonplace—ideas like crop rotation, cover crops, and low- and no-till farming.
(Written by: Kristen Bowman)
HELP DEVELOP THE TRANSFORMATION GARDEN
To help develop the new Transformation Garden, you can give online or contact Phillip Cowart, College of Agriculture director of development, at poc0001@auburn.edu or 334-844-1198.
Auburn University is a nationally ranked land grant institution recognized for its commitment to world-class scholarship, interdisciplinary research with an elite, top-tier Carnegie R1 classification, life-changing outreach with Carnegie’s Community Engagement designation and an undergraduate education experience second to none. Auburn is home to more than 30,000 students, and its faculty and research partners collaborate to develop and deliver meaningful scholarship, science and technology-based advancements that meet pressing regional, national and global needs. Auburn’s commitment to active student engagement, professional success and public/private partnership drives a growing reputation for outreach and extension that delivers broad economic, health and societal impact.
Latest Newsroom Articles
It's Harvest Time! Yukon's 1st Off-Grid, No-Dirt, Hydroponics Farming Unit Produces Crops
The unit is 8 by 40 feet and can hold up to 2,800 mature plants and 1,000 seedlings
The First Harvest of Crops Comes After Only 6 Weeks of Planting The First Round of Seeds
Chris MacIntyre · CBC News · Jun 06, 2021
'It's awesome to see what you put into the project, you get out,' said Brittany Weber, the agricultural operations coordinator at the Kluane Lake Research Station. (Chris MacIntyre/CBC)
The Kluane Lake Research Station located between Haines Junction and Destruction Bay is known for its studies on climate change and the impacts it has on wildlife and the ecosystem.
Now, they're taking a look at food sustainability in the North.
It's been months of work but their off-grid hydroponic containerized farming unit is now producing leafy greens and herbs.
The first harvest of crops comes after only six weeks of planting the first round of seeds.
Brittany Weber is the agricultural operations coordinator for the research station.
And she's responsible for taking care of the crops.
'It's kind of a bit of an optical illusion when you walk in. It's super cool,' says the station's agricultural operations coordinator, Brittany Weber. (Chris MacIntyre/CBC)
"We grow plants without the use of dirt," she explained.
"Instead we use this nutrient-rich water solution. Using pumps and gravity, we wash the water over the roots of the plants and that provides them with everything they need.
Weber says because the system is containerized it is a controlled environment so pesticides and herbicides aren't used.
Inside the container
The unit is 8 by 40 feet and can hold up to 2,800 mature plants and 1,000 seedlings.
"We have six shelves going all the way from the floor to the ceiling," said Weber during the tour of the unit.
Entering into the container is described as an optical illusion.
"The trays are actually sloped so you'll stand there and see the next tray in the back row and it'll be a foot off of the first tray but really that's the gravity so the water can flow naturally down these trays," Weber said.
The plants are arranged in a "cascading of age".
The front of the container holds the big greens while the back of the unit will have the newly planted seedlings.
"You'll be able to see the different life cycles of the plants," Weber said.
A look inside of the off-grid hydroponic containerized farming unit. (Chris MacIntyre/CBC)
The entrance of the container has been made into a processing area called an Arctic entrance.
This allows the vegetables and greens to be processed in freezing temperatures, without worrying about frostbite or losing any leaves.
"We have a little bit of a processing area called an arctic entrance,"
Harvesting the crops
Approximately 350 plants will be harvested next week.
Produce include kale, lettuce, spinach, Swiss chard, basil, cilantro, and dill.
Henry Penn, manager of the research station and the project lead, says the next step is to get the produce out into the community.
"The plan for the first number of harvests, they will be gathered up into a few small sample bags," Penn said.
"We'll be bringing them to locations around the Kluane region and offering them up to anyone that would like one free of charge."
'People are more than welcome to come by the Kluane Lake Research Station and have a tour, see the facility and learn all about the project,' said manager Henry Penn. (Chris MacIntyre/CBC)
The goal behind this is to let people try the product, understand how it is grown, and to provide feedback on what sort of produce is needed and wanted in the community.
Penn says now that the project is up and running, the public is invited to visit the station and see how everything works in person.
"People are more than welcome to come by the Kluane Lake Research Station and have a tour, see the facility and learn all about the project," Penn said.
Shipping Container Farm by CropBox
Lead photo: Yukon's first off-grid hydroponic containerized farming unit. This unit can hold up to 2,800 mature plants. (Chris MacIntyre/CBC)
CBC's Journalistic Standards and Practices|About CBC News
Report Typo or Error
Modular Hydroponic Growing Spaces In Freight Containers For Local Food Production
Freight Farms’ design was the first containerized vertical growing environment using hydroponic technology
May 17, 2021
Southeastern Pennsylvania Correspondent
A Massachusetts company has developed a unique, hydroponic growing environment in closed 40-foot freight containers that are being used world-wide to grow produce in areas with bad soil or weather conditions not conducive to outdoor growing.
Bay State natives Jon Friedman and Brad McNamara were developing rooftop greenhouses in the early 2000s when they realized a modular, hydroponic container might be a more viable solution.
Hydroponics wasn’t something new. Historians believe this soilless gardening can be traced back to hanging gardens of Babylon in Iraq built by King Nebuchadnezzar about 600 BC. Nutrient-rich water was pumped to the gardens from the Euphrates river to sustain its plants. A water-based growing thread continued through history and in the 1930s a University of California scientist, William Gericke, coined the term from the Greek word “hydro” (water) and “ponics” (work).
Friedman and McNamara, who were building outdoor, roof-based gardens on older residential buildings, looked outside the box, and turned their focus to widely available shipping containers.
They thought they could provide the equivalent of 2 acres of growing space in traditional 40-foot-by-8-foot containers and extend growing seasons year-round everywhere — especially in areas that couldn’t support traditional outdoor agriculture or in parts of the world affected most by climate change.
They named their company Freight Farms and placed their first container less than a decade ago. Now the concept is catching on worldwide.
View Photos From Freight Farms
Freight Farms’ design was the first containerized vertical growing environment using hydroponic technology. It was initially funded by a Kickstarter campaign in 2012, where they raised the funds to build a prototype to allow local food production to be available to everyone, anywhere.
The first commercial unit was installed at Boston Latin School, the oldest public school in the U.S., to produce fresh produce for the school cafeteria as well as serving as a teaching classroom for high school students.
“The company has placed 350 units in 48 states and 32 foreign countries,” Friedman said.
The company also introduced proprietary software called “farmhand” to help automate many farm processes, and is manufacturing its 10th generation container, the Greenery S, incorporating the latest technology and automation for vertical, hydroponics growing.
Growing Strong
Hydroponic Operation Supplies High-End Restaurants
Art Petrosemolo, Southeastern Pennsylvania Correspondent
Although the Freight Farms container units are capable of growing a variety of produce, leafy greens are its specialty and the best choice for farmers looking to sell their harvests year-round.
Containers also have been embraced by educational institutions to supply fresh vegetables for cafeterias and serve as learning and teaching space.
St. Joseph College in Standish, Maine, has been operating a Freight Farms unit for years to both supply fresh vegetables to its dining facilities as well as for student employment.
The site also has been a tool for community involvement with St. Joseph students working with a town Institute for Local Food System Innovation utilizing the Freight Farms container in partnership with a large hydroponic farm and commercial processing kitchen for events and agritourism.
With a decade head start in the business, Freight Farms does not have major competition in hydroponics container gardening production, although, in recent years, it has seen significant growth in multiple indoor soil- and water-based farming formats including warehouses, greenhouses and pods that are addressing growing produce year-round.
Climate change has increased concern about food production for growing populations worldwide with extreme weather conditions and higher levels of carbon dioxide in the atmosphere.
Friedman and McNamara have always been aware that the challenge to expansion for stand-alone, container gardening is the cost of power and each new rendition of their growing units has addressed both power consumption and automation to be more efficient.
Their latest Greenery S model uses growing lights that are 50% more efficient than previous models and the technology allows farmers to choose pre-set growing modes to maintain higher yields — 20% higher than earlier models — while prioritizing energy use.
Addressing affordable and clean power for customers, Freight Farms recently partnered with Arcadia, a Washington, D.C., energy company to offer affordable, renewable power options for customers.
Going forward, Friedman said growing container units will continue to become more efficient, allowing owners to increase their growing yield while having more control of their energy use to power the unit.
Slide Show Photos:
Lights and plant arrangements in Freight Farms new Greenery S model container.
Photo provided by Freight Farms
Leafy greens grow in Freight Farms’ own Greenery Farm container.
Photo provided by Freight Farms
This Freight Farms container is ready for shipment.
Photo provided by Freight Farms
Freight Farms' containers under construction in their Vermont facility.
Photo provided by Freight Farms
Lexy Basquette, Freight Farm’s on-site farmer, checks on some of her growing plants.
Photo provided by Freight Farms
Greenhouses, Vertical Farming and Urban Ag: Controlled-Environment Agriculture Has Growth Potential
Paul Post, New York Correspondent
More Than Simply Housing
While “Housing” is in our name, CASS isn’t just about building homes. CASS is about holistically partnering with people with developmental disabilities to create opportunities that wouldn’t otherwise exist
While “Housing” is in our name, CASS isn’t just about building homes. CASS is about holistically partnering with people with developmental disabilities to create opportunities that wouldn’t otherwise exist.
Employment for people with disabilities is one of the largest hurdles that many folks will ever face. Whether it is obtaining a job, the workplace environment, or transportation to and from the workplace, the enjoyment, meaning, and income that comes from a job is not available to millions of people with disabilities across the nation.
In Summer 2020, we were introduced to a company called Freight Farms out of Boston. Freight Farms converts shipping containers into hydroponic gardens. In these 10’x40’ climate-controlled boxes, over an acre’s worth of produce can be grown year-round. Leafy greens, herbs, root vegetables, and flowers grow extremely well in these containers.
image courtesy of freightfarms.com
As we looked further into Freight Farms, we realized that not only would these container gardens create employment opportunities for our Core Members, but they would give them access and working knowledge of produce, local food, gardening, and more.
image courtesy of freightfarms.com
By the end of April, our first 2 containers will be delivered to our existing neighborhood on Constance Ave. (just north of Turnstone). We expect produce to be available by mid to late summer 2021.
Are you a restaurant, business, or grocery store interested in sustainable, year-round, local greens and herbs with a greater cause? Reach out to us by emailing robert@casshousing.org today.
How COVID-19 Fed The Dream of Growing Food At Home
Sales of hydroponic gardens boomed during the pandemic, but do high-tech solutions like those only further fuel inequality?
04-28-21
Sales of hydroponic gardens boomed during the pandemic, but do high-tech solutions like those only further fuel inequality?
This story is part of Home Bound, a series that examines Americans’ fraught relationship to their homes—and the once-in-a-lifetime opportunity to hit the reset button. Read more here.
When COVID-19 struck the United States, people rushed to grocery stores to stock up on food, only to find that many shelf-stable items like beans, rice, and flour were sold out. It was the first time many of us were forced to consider where our food comes from—and how vulnerable the global food system really is.
These food shortages spurred many Americans to consider growing their own food for the first time. Some planted vegetables in their backyards and windowsills, while others went for high-tech hydroponic gardens.
In the years before the pandemic, startups developed these compact self-watering, self-fertilizing, gardening machines that were aesthetically pleasing, to boot. During the lockdowns, sales of these products—which start around $800—spiked, prompting venture capitalists to pour millions into the industry.
But as the COVID era comes to an end, it remains to be seen whether these high-tech gardens have staying power or whether they were just a short-lived novelty. And more broadly, it’s worth asking whether these devices can be a tool for making agriculture more sustainable and equitable, or whether they’re just another toy for the Whole Foods class.
[Photo: courtesy of Freight Farms]
THE HYDROPONICS REVOLUTION
Hydroponics, which simply means growing plants in a solution of water and nutrients instead of soil, have been around since at least 600 BCE. But in the late 1920s, William Gericke of the University of California modernized these techniques, creating farms that require less space and up to 95% less water than soil-based farms but yield much bigger harvests by optimizing light, water, and nutrients. During World War II, the U.S. military built hydroponic gardens to grow vegetables for troops in locations that weren’t suited to traditional agriculture, such as Ascension Island, a refueling station in the Atlantic Ocean, where soldiers grew thousands of pounds of cucumbers, tomatoes, lettuce, and radishes each month, staving off malnutrition.
COVID-19 prompted some countries to use hydroponics to deal with disruptions in the global supply chain. The Netherlands and Singapore, which have limited agricultural land and rely largely on imports, invested billions during the pandemic to build industrial hydroponics farms on rooftops and parking lots. In the United States, hydroponics are still a small business, with about 3,000 businesses generating around $800 million in revenue, a small sliver of the $451 billion from traditional farming. But analysts are banking that the industry is poised to grow.
Over the last five years, a bevy of startups—including Rise Gardens, Gardyn, Lettuce Grow, Aerogarden, and Click-and-Grow—have launched to create hydroponic systems that can fit inside a home. That’s a departure from the focus over the past century on large-scale hydroponics farms.
The devices are expensive, and before the pandemic, it was a tough sell convincing consumers to spend nearly $1,000 on a machine that might take years to pay off. But COVID-19 changed the game, as people around the world worried about food shortages. “The pandemic made people pay attention to where their food comes from and accelerated their interest in producing their own food,” says Nina Ichikawa, executive director of the Berkeley Food Institute, which promotes food equity. “This new awareness is a good thing.”
Many of these startups doubled or tripled their sales over the past year, and some investors are capitalizing on this interest. True Ventures, which funds Peloton and Blue Bottle, invested $2.6 million in Rise Gardens; Gardyn raised $10 million from JAB Holding Company, the largest shareholder in Keurig. And right before the pandemic, Estonia-based Click & Grow received $11 million in funding from Y Combinator and Ingka Group, which operates 367 Ikea stores in Europe.
[Photo: courtesy of Lettuce Grow]
A PERSONAL HYDROPONIC GARDEN
Despite my lifelong black thumb, I decided to test Lettuce Grow, a six-foot tall hydroponic garden that looks like a white sculpture with plants artfully growing on it. I’m shocked by how much food I’ve grown: My family of three now eats freshly plucked lettuces with each meal and yet our harvest is so plentiful, we’ve had to share our veggies with neighbors.
The beauty of hydroponic systems is that they’re designed to run on their own, with minimal intervention from the owner. My machine automatically waters and fertilizes the plants by pumping a nutrient-rich solution through the system for 15 minutes every hour. The high-efficiency LED light rings control how much light the plants receive, adding only a few dollars to our monthly electricity bill. All I have to do is top up the water in the base and add a few spoonfuls of plant food every week.
When it comes to seeds, all of these hydroponic startups are also, effectively, subscription programs. You need to buy seeds or seedlings from the company for about $2 apiece to replace the plants you’ve fully harvested. This takes anywhere from three weeks to several months depending on their growth cycle. “You get to enjoy the beauty of watching living things grow, without needing any expertise in farming,” says Jacob Pechenik, who co-founded Lettuce Grow in 2019 with the actress Zooey Deschanel.
And these startups aren’t just focused on making the machines smaller, they’ve also made them beautiful. Lettuce Grow, for instance, worked with the designer Pip Tomkins—who previously designed the Nokia M Series—to create a stand with vegetables and herbs cascading from the sides, much like you’d see on a plant wall. Rise Gardens partnered with TBD Innovations, a firm made up of former IDEO designers, to create a system that looks like a white cabinet with rows of plants above it. “We knew that our garden needed to look attractive for people to consider bringing them into their homes,” says Hank Adams, founder and CEO of Rise Gardens. “We wanted it to be beautiful and minimalist, so you’d be happy to have it whether you live in your studio apartment or large home.”
Rise Gardens, Gardyn, and Lettuce Grow all created modular systems, so customers can start with just a few levels of plants and expand over time. Pechenik says his goal was for Lettuce Grow to replace up to a fifth of a household’s produce. (I can attest that our 24-plant unit easily achieves this for a family of three.) For those who can afford it, these machines generate fruits and vegetables that are far tastier and more nutritious than what you’d normally buy at a store. Studies show that most produce loses 30% of its nutrients three days after harvest, and much of what we find in the grocery is much older than that.
Hydroponics provides an alternative to industrial agriculture, which has dominated our food system since the 1960s. Factory-like farms are bad for the planet because they deplete the soil, consume a lot of water, spew toxic pesticides into the environment, and contribute to deforestation. Transporting food around the country also generates carbon emissions and creates a lot of waste, since produce goes bad along the way. Half of all U.S. produce is thrown out. For me, one of the best parts about having a hydroponic garden at home is that we’ve virtually eliminated waste and have to make fewer trips to the grocery store.
FOOD INEQUITY
For now, most of these devices have gone to people interested in small-scale gardening. But the founders believe their products have the ability to disrupt our broken food system, if they’re able to scale. “We are not in the gardening business,” says FX Rouxel, Gardyn’s founder and CEO. “We’re trying to reinvent how people can grow their own food at scale. If we have solutions that are compelling enough, we believe we can change people’s food habits and reduce their dependence on the grocery store.” Gardyn launched in early 2020, and in its first year, Rouxel says its hundreds of customers grew 70,000 pounds of produce.
But Berkeley Food Institute’s Ichikawa argues that we should be skeptical about whether these high-end hydroponic systems can actually change the food system. Most people don’t have the money to invest hundreds of dollars in this hardware, and those are exactly the people who could most benefit. A tenth of households experience food insecurity and more than 23.5 million Americans live in neighborhoods without easy access to a supermarket. “Rich people are willing to spend their money on many new-fangled technologies that don’t necessarily impact the rest of the industry for better or for worse,” she says. “It’s just a new business opportunity for these startups.”
She points out that hydroponics don’t have to be so expensive or complicated. In fact, a lot of innovation around cost-effective small-scale hydroponics came from cannabis growers, many of whom were people of color operating underground. Entrepreneurs and scientists have been developing affordable DIY hydroponics in Africa, particularly Kenya. Startups like Hydroponics Africa have built systems that don’t require electricity and use inexpensive, locally available materials, including fungi-resistant aluminum trays. “These [U.S.] startups are creating a flashier, fancier version of systems that have actually been around for a long time,” Ichikawa says. “There are a lot of low-cost solutions that have emerged from the ground up, from the communities that depend on these technologies to survive.”
For now, Pechenik tries to make his technology available to more people by donating one Lettuce Grow machine for every 10 sold to schools, nonprofits, and community organizations. He says they’ve distributed several hundred already, along with $1 million in donations. Rise Garden, meanwhile, has launched a smaller machine that starts at $279. “I compare this to the early days of personal computing when a laptop was very expensive, and yet now, laptops are widely available,” Adams says. “As hydroponic gardens scale, the cost of manufacturing will go down.”
One answer might come from systems that are large enough to feed a community, rather than a single family, and thus are more cost-effective. Take, for instance, Freight Farms, which debuted the first hydroponic farm inside a shipping container in 2012. The company sells $130,000 containers that can generate the same amount of food as three and a half acres of farmland, enough to feed hundreds of people. Long-term, these systems are more economical given their scale and could help solve food insecurity problems. The city of Boston, for instance, bought five Freight Farm systems in Mattapan, where 20% of the population lives below the poverty line, to create a high-tech farming co-op. “Our farms are being used as part of community redevelopment,” says Rick Vanzura, Freight Farms’ CEO.
[Photos: courtesy of Freight Farms]
During the pandemic, Freight Farms’ sales tripled, and the company expects business to triple again in 2021. Last year, it landed $15 million in Series B funding, bringing its total to $28 million. Vanzura believes that for hydroponics to have an impact on agriculture, there will need to be farms of different sizes, ranging from individual gardens to industrial farms. In fact, Freight Farms advised Lettuce Grow about growing techniques, drawing from its decade-worth of data. “We need to cooperate as an industry to take the best of what we each do and help each other get better,” he says.
As hydroponics grow in popularity, Ichikawa says that it’s important to remember that it is not the only, or best, solution to cultivating food for a community. The poor tend to be most impacted by problems in the food system and suffer from health issues due to lack of access to nutritious food. This is why organizations like hers advocate for food sovereignty, which means empowering communities to take charge of their own food supply through things like local ownership of grocery stores and backyard or community gardening.
While midsize hydroponic systems could be a tool for tackling food insecurity, she worries that it could create a new barrier to entry, making access to fresh food seem even more out of reach. “Food sovereignty can absolutely protect us from the instabilities from pandemics or climate change, so any way that folks can feel autonomy over their food supply is a good thing,” Ichikawa says. “But you don’t need a fancy hydroponic system to do this. You could do it just as easily with a bucket of soil by a window.”
ABOUT THE AUTHOR
Elizabeth Segran, Ph.D., is a senior staff writer at Fast Company. She lives in Cambridge, Massachusetts
[Source Images: courtesy of Lettuce Grow]
Square Roots Opens New Indoor Farm, Produces First Harvest
The farm’s first locally grown harvest of herbs and greens that includes basils, arugula and radish microgreens will be available for consumers to purchase on e-commerce platforms, restaurants and grocery stores across the Great Lakes region in the coming weeks
April 15, 2021
New York-based Square Roots, an urban indoor farming company, opened a two-story indoor farm located at Gordon Food Service headquarters in Wyoming.
The farm’s first locally grown harvest of herbs and greens that includes basils, arugula and radish microgreens will be available for consumers to purchase on e-commerce platforms, restaurants and grocery stores across the Great Lakes region in the coming weeks.
Construction on the indoor farm began in December and the first seeds were planted in March. The farm is cloud-connected and is managed by Square Roots’ farmers and in-house software.
“COVID-19 exposed major weaknesses in the industrial food supply chain and accelerated the already fast-growing local farming movement,” said Kimbal Musk, co-founder and executive chair of Square Roots. “Square Roots can now deploy commercial-scale, controlled-climate farms, fast, in locations across America to meet the demand for local food, all year-round. My wider mission is to bring responsibly grown, local food to everyone in America.”
A farmer harvest basil. Courtesy Square Roots
The farm’s proprietary OS, otherwise known as The Square Roots Farmer Toolbelt, provides day-to-day guidance to farmers while capturing millions of data points throughout growing cycles. The data can then be analyzed to determine how changes in certain environmental parameters impact factors like yield, taste, and texture.
In addition to the technology that drives its operation, there also are cold storage, biosecurity, climate-controlled packaging space, and distributor loading docks, among other things in the farm that ensures food safety.
The new indoor farm is Square Roots’ third commercial facility.
Lead photo: Construction on Square Roots' indoor farm began in December and the first seeds were planted in March. Courtesy Square Roots
USA: BALTIMORE - Hydroponic Operation Supplies High-End Restaurants
Growing vegetables in a shipping container have opened new marketing opportunities for a Baltimore County farm
Art Petrosemolo, Southeastern Pennsylvania Correspondent
Apr 23, 2021
Growing vegetables in a shipping container have opened new marketing opportunities for a Baltimore County farm.
The hydroponic growing system has allowed Karma Farm to sell fresh produce regardless of the season to high-end restaurants in Baltimore and Washington.
“Today we are delivering leafy greens and herbs year-round to a growing customer base,” said Jon Shaw, founder of the family operation.
The farm, which makes multiple weekly deliveries to 27 customers, has picked up clients through word of mouth and sampling visits arranged with chefs who find the farm on social media.
“Well-known chefs talk and move from restaurant to restaurant ... and they have brought us with them,” Shaw said.
The farm got its start just over a decade ago when Shaw was growing produce on 5 acres, both outside and in hoop houses, for retail sale as well as a nearly 100-member CSA.
Karma Farm purchased a freight container vertical hydroponics Leafy Green Machine from Freight Farms in Boston in 2017. Photo by Art Petrosemolo
Jon’s 28-year old son, Nat, learned the business from his dad as a teenager, and in the past few years he has helped Karma Farm pivot to the new customer base, embracing the new ag technologies.
Nat, now the farm’s hydroponic production manager, researched vertical growing in insulated shipping containers while he was studying entrepreneurship at the University of Baltimore and thought the year-round production method would be a good fit.
“Hydroponic container farming is still relatively new and is being introduced to farmers in parts of the country where short growing seasons, weather, and soil conditions make profitable, small family farming difficult,” he said.
With a feasibility study completed and a new focus for the business, the Shaws purchased a Leafy Green Machine container in 2017 from Freight Farms in Boston. The container is 40 feet long by 8 feet wide.
“These are the insulated type of refrigerated containers used to ship fresh produce across the country,” Nat said.
With delivery and setup, the container cost about $100,000.
Lead photo: Nat Shaw, left, and his dad, Karma Farm owner Jon Shaw, stand in their freight container.
US: KENTUCKY - AppHarvest Continues To Expand Operations, Adds New Container Farm In Madison County
Some Central Kentucky high school students will soon be able to help grow food not only for themselves but the entire region
AppHarvest (WYMT)
By Brandon Robinson
Apr. 22, 2021
RICHMOND, Ky. (WYMT) - Some Central Kentucky high school students will soon be able to help grow food not only for themselves but the entire region.
On Thursday, officials with Morehead-based AppHarvest announced the expansion of their container farm program to Madison County High School in Richmond.
Watch Live Below:
Gov. Andy Beshear, who attended the event, appropriately held on Earth Day, said the move will not only provide food but help students prepare for possible careers in a field with growing demand.
“AppHarvest has been reimagining and reinventing sustainable food production at its state-of-the-art facility in Morehead. With the opening of the company’s container farm classroom at Madison Central High School, AppHarvest is showing its commitment to the Commonwealth runs both strong and deep,” said Gov. Andy Beshear. “This living, teaching lab will inspire and engage Kentucky students to learn about cutting-edge technology that will become the basis of the jobs of the future. Thank you to Founder & CEO Jonathan Webb and his team for making education and Kentucky students a priority in his plans for success.”
The container farm is 2,880 cubic feet, weighs 7.5 tons and includes space to grow up to 4,608 seedlings and 8,800 mature plants all at once using 440 vertical crop columns.
Each retrofitted shipping container serves as a hands-on agricultural classroom for students, allowing them to grow and provide fresh leafy greens to their classmates and those in need in their communities. The company has previously opened container farms in Eastern Kentucky at Breathitt High School in Jackson, Shelby Valley High School in Pikeville, and Rowan County Senior High School in Morehead, the site of the company’s flagship farm.
AppHarvest Founder & CEO Jonathan Webb said the latest expansion will not only help feed Kentuckians but will help Eastern Kentucky’s struggling economy.
“We knew long before opening our Morehead farm that we wanted to invest in the region to help grow our growers and build on the many outstanding community and education programs focused on creating a more resilient Appalachian economy,” Webb said. “The technology in each of these container farms is a good example of what AppHarvest’s modern farmers use daily on a larger scale.”
The Madison Central High School container program will be led by agriculture teacher and FFA adviser Derek Adams.
“Our students are looking forward to getting hands-on experience with state-of-the-art technology that will better prepare them for career opportunities in the agriculture industry,” Adams said. “They are especially eager to see the leafy greens come full circle from farm to table in their own school cafeteria.”
USA: Local Farm Brings Hope To Food Desert
A hydroponic produce farm in Indianapolis is filling a need in food deserts around the city. Food deserts are areas where grocery stores aren’t easily accessible. More than 200,000 people live in food deserts in Indy, according to a study published by SAVI
Q&A: Mario Vitalis
April 13, 2021
Mario Vitalis, farmer, owner, and founder of New Age Provisions, holds plants grown on his farm.
INDIANAPOLIS — A hydroponic produce farm in Indianapolis is filling a need in food deserts around the city.
Food deserts are areas where grocery stores aren’t easily accessible. More than 200,000 people live in food deserts in Indy, according to a study published by SAVI.
Mario Vitalis, farmer, owner, and founder of New Age Provisions farm, uses advanced hydroponics and vertical planting to grow year-round.
It all starts inside a shipping container on an old car lot on East 10th Street. A step inside transports visitors to a lush, green garden of produce. A variety of herbs, leafy greens, microgreens, and hemp are grown inside.
The location allows Vitalis to provide fresh produce to the community, one of the city’s many food deserts. The farm also provides produce to restaurants in Indianapolis.
“I’ve always known the city life — but there is a nagging desire to get back to my roots,” Vitalis said. “As an African American, my roots made it from slaves in the field, to sharecroppers in the South, to farming in the city.
“As a descendent of slaves, this farm enables me to get back to the type of living where our people once lived off the land. Having an urban farm allows me to connect to a long history of farming that has been forgotten.”
Vitalis shared his story with AgriNews.
Tell me a little bit about your farm.
“We are a hydroponic commercial farm. We officially started farming in August 2020.”
What was your inspiration to grow things?
“I wanted to be involved in agriculture, to be able to provide fresh food to the community independent of the supply chain, and independent of herbicides, pesticides, and contaminants.”
Indiana has several food deserts. Did that inspire you to fill a need in the community?
“Yes, it did. It provides us with the equipment to do so, as well. We’re the first company in Indiana to own this piece of equipment, the Freight Farms Greenery. We’re currently the only African American owner of the equipment. We want to be able to provide food and also provide a new way of farming. We want people to see it and have access to it.”
How does the farming system work?
“It’s called a Greenery and it’s built by Freight Farms, based in Boston. It’s essentially a hydroponic farming system in a 40-foot shipping container. If you can imagine those shipping containers that go up and down the highway, you go inside of one of these and grow vegetables. It has everything you need to do that. It has a seedling table and growth tower with different types of hydroponic methods.”
Basil grows at a hydroponic produce farm in Indianapolis.
What are some of the features of the technology?
“It has its own dosing system to control nutrients. You can control humidity, temperature and pH levels. You can check your settings and programming on a computer. There’s an app that goes with it, as well. So, you can control your farm from your phone. The technology is state of the art.”
What are some of the challenges you’ve faced as a new farmer?
“I think the biggest challenge is developing a market and getting our name out there. There’s also a learning curve to farming. I didn’t have any experience. So, I had to learn what to do and how to operate.”
What do you enjoy most about growing things?
“Seeing the plant life cycle from seed to seedling into a full plant. I also enjoy the environment. Since we’re in an enclosed environment, we can grow year-round and it’s always 65 degrees.”
Do you have any advice for minorities interested in farming?
“Right now there are so few minority farmers in general. For African American farmers, the best thing they can do is get land and find ways to cultivate the land or make use of it. Good land is becoming a scarce resource. If they’re interested in farming, there’s funding available from USDA for Black and minority farmers. There are different avenues out there. But it all starts with land and a business plan. After that you just have to have motivation and knowledge to do it.”
Anything else you’d like to share about your farm?
“Our farm is local on the east side of Indianapolis. We grow hydroponically without herbicides, pesticides or contaminants.”
How can people purchase your products?
“They can go online to our website www.newageprovisions.com. We deliver. Or, you can purchase through Market Wagon or Hoosier Harvest Market.”
Polygreens Podcast Episode: 17 - Nicola Kerslake - Contain Inc.
Nicola Kerslake founded Contain Inc, a fintech platform for indoor agriculture, that aids indoor farmers in finding lease funding for their projects
Nicola Kerslake founded Contain Inc, a fintech platform for indoor agriculture, that aids indoor farmers in finding lease funding for their projects. They're backed by Techstars' Farm to Fork program, funded by Cargill and Ecolab.
Latest Episode
VIDEO: A Visit To The ZipFarm - Join The Virtual Farm Tour
Recently, ZipGrow has opened its doors for a virtual farm tour to demonstrate 'how all things are put together'
Recently, ZipGrow has opened its doors for a virtual farm tour to demonstrate 'how all things are put together'. The tour was kicked off at the germ chamber, then, after passing through the vestibule viewers are lead to the indoor farm.
In ZipGrow's seedling station plants the crops are propagated until they are suitable for transplantation to the growth section. The plants are given 16-18 hours of light per day. The crops are penetrated through an up-down, siphon system that allows for three times watering a day.
The Atom Doser is the 'brain of the farm' as it controls most growing parameters. It monitors, tracks and controls the hydroponic reservoir with customized recipes and irrigation settings. The 1000 sq. ft. farm allows for several crops to be grown, such as leafy greens.
Have a look at the video below to 'join' the tour.
For more information:
ZipGrow
hello@zipgrow.com
www.zipgrow.com
Publication date: Tue 16 Feb 2021
Author: Rebekka Boekhout
© VerticalFarmDaily.com
Publix And Its GreenWise Stores Go After Hydroponics In Big Ways
Publix partnered with St. Petersburg-based Brick Street Farms on the initiative, a good fit because of Brick Street’s focus on quality and sustainability
September 9, 2020
by: Grier Ferguson
Sarasota-Manatee Editor
The Lakeland-Based Grocery Giant Is
Targeting Customers
Who Want Fresh, Local Products
There was a time when hydroponic farming seemed almost futuristic, like flying cars or underwater houses. But not anymore. The future is now for hydroponics.
Hydroponics, which involves growing plants without soil, is becoming more prevalent, including with Lakeland-based grocery giant Publix and the company’s GreenWise Market stores that sell organic, natural, and specialty groceries. Publix operates GreenWise stores in Lakeland, Tallahassee, Boca Raton, Ponte Vedra, and Odessa as well as in Mountain Brook, Ala., and Marietta, Ga. It closed two GreenWise stores in South Carolina in late August, citing the locations’ space constraints, but it plans to open a store in South Florida in the fourth quarter.
Publix and GreenWise are biting into hydroponics in some big ways, hoping it pays off with customers seeking fresh, local products.
Courtesy. Lettuce grown in the hydroponic container farm at Publix’s GreenWise Market in Lakeland is sold in the store.
In one major move, the company installed a 40-foot hydroponic container farm in front of its Lakeland GreenWise store. The container, added at the beginning of March, uses mineral-rich water instead of soil to grow lettuce plants. Publix partnered with St. Petersburg-based Brick Street Farms on the initiative, a good fit because of Brick Street’s focus on quality and sustainability efforts, Publix Business Development Director for Produce and Floral Curt Epperson says.
One key feature of the container is a viewing window on the side that allows people to see the plants growing. Along with showing off the growing process to customers and store employees, GreenWise also wants to use it during educational tours for schoolchildren. The image of the fresh product is key, Epperson says. “You have a good visual of farming at its best inside a container,” he says.
The hydroponic farm is near an outdoor sitting area, encouraging people to mingle and see what it's all about. “There’s certainly been some interest in that,” Epperson says. People are also attracted to the system’s sun-emulating lighting. “It really has an iridescent grow to it,” he says. “It draws you into the container. It’s hard to walk by it and not say, ‘What is that?’”
The lettuce, which takes about five weeks to grow, is harvested right in the container. GreenWise has a grower on site who works with Brick Street and harvests the product three days a week, amounting to about 720 heads of lettuce each week. The same day it’s harvested, the lettuce is taken into the store to be sold. “It really brings a new level of freshness and sustainability to the customer,” Epperson says.
Sustainability can be a key selling point for consumers who are becoming savvier and more knowledgeable about where their food comes from. Because the lettuce from the hydroponic container only has to travel mere feet to end up on store shelves, the product uses fewer resources and has a reduced carbon footprint.
Customers are already responding well. The lettuce grown in the container has done well at the store, Epperson says, and currently, all of it is purchased at that location. Once the lettuce is harvested, more is planted, continuing the cycle.
Other GreenWise stores are getting in on the hydroponic action, too. Brick Street, for instance, is providing lettuce for other locations. Publix has also worked with South Carolina-based Vertical Roots on a mobile hydroponic farm that it brought to stores, giving people the chance to walk inside the farm. The mobile educational tool is on hold during the pandemic, but it’s expected to come back. “It’s really just a cool opportunity to bring the farming concept to the customers,” Epperson says.
Courtesy. Publix worked with South Carolina-based Vertical Roots on a mobile hydroponic farm that it brought to stores, giving people the chance to walk inside.
In another hydroponic effort, Publix has partnered with vertical farming company Kalera to distribute the lettuce it grows hydroponically in Orlando.
Other crops might be involved in the future as well; growers are working on expanding beyond lettuce. “Each of these growers are looking at other ways to grow other commodities,” Epperson says. “I think you’ll see more trials into tomatoes, cucumbers, and peppers going forward.”
Epperson says Publix is working with more hydroponic growers, too, in states including Florida, Georgia, South Carolina, and North Carolina. “Every day, we’re outsourcing product,” he says. “It’s a great way to support communities that are supporting the growers and us. It’s great for the customer, great for the grower, and great for Publix.”
Is Hydroponic Farming Actually Sustainable?
If you've ever wondered how sustainable hydroponic farming really is—or what exactly is involved in vertical farming—this article is for you.
September 4, 2020
According to the UN, the world is on the brink of its worst food crisis in 50 years.
The global food industry is searching for a more sustainable and accessible system for producing healthy food, particularly fresh fruit and vegetables. Techniques such as hydroponics and vertical farming may provide the solution by maximizing overall output and minimizing the use of space, soil, and other resources.
But what exactly is hydroponic farming? And is it actually sustainable?
Gotham Greens grows fresh produce such as leafy greens in urban greenhouses. | Image/Gotham Greens
What Is Hydroponic Farming?
There are a variety of different approaches to Hydroponic Farming. But they all involve growing plants and fresh produce minus the soil.
There are several main styles of hydroponic systems. One uses an absorbent wick to transfer nutrients from a water reservoir up to the roots of the crop. While others leave an air-gap, allowing part of the root system to absorb nutrients directly while the remainder is exposed to oxygen in the air.
Plants may also be positioned on a floating raft, or grown through a medium, into which water is regularly pumped. Top feeding also requires regular water circulation, while aeroponics involves leaving the roots completely exposed but frequently filling or misting the space with nutrient-enriched water.
Whatever the precise method used, hydroponics involves regular exposure to both air and nutrient-rich water. According to Vertical Roots, a South Carolina-based Indoor Hydroponic Container Farm, there are five core elements to hydroponic farming. These are freshwater, oxygen, root support, nutrients, and light.
By growing crops in water, vertically, and in climate-controlled greenhouses, Vertical Roots and other similar farms are able to produce nutrient-dense food anywhere in the world, at any time of year, and using fewer resources than traditional methods.
Hydroponic farming is more resource-efficient than traditional methods. | Image/Shawn Ang via Unsplash
Is Hydroponic Farming Sustainable?
Soil-less farming techniques, in general, are typically more resource-efficient long term than traditional methods. According to the National Parks Service (NPS), hydroponics can use up to 10 percent less water than field crop watering.
By operating a closed-loop system and recycling rainwater, high-tech greenhouse developer AppHarvest uses up to 90 percent less water than traditional methods.
Most hydroponic farms utilize closed-loop systems, like AppHarvest, that contain and preserve water. This control over the water system also allows for delicate adjustments to the environment. PH levels, amount and type of light, and quantity of nutrients can all be modified to enhance the growth of crops.
Emphasizing perennial agriculture—particularly in combination with vertical farming and hydroponics—can further maximize both production and nutritional content per-plant. Many perennials, which can be maintained all year round with no replanting, are extremely nutrient-dense.
Start-up costs for hydroponic systems are typically greater than for traditional farming. But overall, it produces far greater output with fewer resources. It also allows growers to produce food anywhere in the world. Thereby reducing the carbon emissions generated through transportation, and allowing for year-round production in even inhospitable environments or weather conditions.
In general, hydroponic systems can produce a greater yield of fruits and vegetables. This is in part due to the controlled environment, but also because plants can be housed much more densely than possible using traditional methods. This both increases the overall output and reduces the quantity of land required.
Vertical farming can decrease the amount of land used for fresh produce even further. | Image/Markus Spiske via Unsplash
What Is Vertical Farming?
Vertical farming involves the growing of vegetables in stacked layers, frequently in a controlled environment.
Vertical farming also requires much less land than traditional methods. Typically, it incorporates controlled-environment systems such as hydroponics to maximize output. The primary goal of vertical farming is to increase the crop yield while reducing the space required, much like hydroponics itself.
Vertical farming firm Infarm recently partnered with supermarket chain Marks & Spencer to grow fresh herbs in select stores. The company is also working with several retailers and chefs across Europe who aim to add small vertical farms to their restaurants and stores.
“Our vertical farms can be installed directly in any urban space,” said Emmanuel Evita, global communications director at Infarm. “Which is where the majority of the global population will live in the next few decades.”
It is particularly useful for growing produce in areas where there is a lack of arable land. In Abu Dhabi, where there are extremely high temperatures and increasing water scarcity, the government is investing $100 million in indoor farming.
Inner-city gardening, in general, also lends itself to vertical farming. While harder to create a controlled environment, guerilla gardening and other community-based projects have also made use of the vertical system. This enables greater access to fresh produce and reduced mileage overall, even with rudimentary systems in place.
Emphasizing perennial vegetables could also maximize nutrients, increase production, and reduce the consumption of resources.
Why Do We Need Alternative Farming Methods?
Studies indicate that the suburbanization of major supermarkets has led to food deserts within cities. This disproportionately impacts low-income people and those who live in urban areas. Traditional malnutrition affects around two billion people worldwide. But the Standard American Diet (SAD) and lack of access to fresh food is also responsible for chronic deficiencies.
Access to fresh fruit and vegetables is likely to become even more restrictive in the recession following the COVID-19 coronavirus pandemic. And even in countries with plenty of food, there will likely be further disruptions in the food supply chain.
In order to provide enough vegetables for the global population to maintain a healthy diet, food production would need to triple. Alternative methods such as vertical farming and hydroponics could provide a resource-efficient and accessible way of revolutionizing the global food industry.
Gotham Greens, a fresh food farming company, specifically choose to build sustainable greenhouses within cities. Local cultivation helps the company deliver products quickly and with minimal energy expenditure. This also allows those who live within urban areas access to fresh, nutrient-dense food, and to agricultural jobs.
AppHarvest is also creating jobs, minimizing its carbon footprint, and increasing its output with its choice of location. By opening a new facility in Morehead, Kentucky, the company is both tackling high local unemployment rates while placing itself less than one day’s drive from 70 percent of the U.S. population. This reduction in travel for delivery has dropped its overall diesel costs by 80 percent.
“It’s time for agriculture in America to change,” said Johnathan Webb, the founder, and CEO of AppHarvest. “The pandemic has demonstrated the need to establish more resilient food systems, and our work is on the forefront of that effort.”
STAFF WRITER | BRISTOL, UNITED KINGDOM | CONTACTABLE VIA: LIAM@LIVEKINDLY.COM
Liam writes about environmental and social sustainability, and the protection of animals. He has a BA Hons in English Literature and Film and also writes for Sustainable Business Magazine. Liam is interested in intersectional politics and DIY music.
Lead photo: How sustainable is hydroponic farming? | Image/Gotham Greens
What Is Hydroponic Farming?
It is the process of growing crops with nutrient-rich water kept in contact with the plant roots without using soil. This process is touted to significantly reduce the risk of wastage and pollution that can harm the produce and cause diseases, making it popular to health-conscious consumers
Kemkar wants to make a difference through urban farming by introducing the technique of hydroponic farming to all so that they have access to grow their own vegetables at home.
Manjula Ramakrishnan, Gulf Today
The science of urban farming has become hugely popular in recent times and hydroponics is leading the way in this green revolution. Jui Kemkar, a passionate young entrepreneur with a quest to make a difference through urban farming co-founded Waves Enterprises with a vision to introduce the technique of hydroponic farming to all, such that they have access to grow their own vegetables at home.
“From residential balcony gardening, community farming, or indoor/outdoor commercial farming, hydroponic farming methods prove to be beneficial for all. Residential enthusiasts of hydroponics can grow herbs, green leafy vegetables, tomatoes, cumbers, and even small plants or flowers in the comfort of their own homes,” explains Jui.
Jui’s impressive repertoire of work comprises humanitarian work in rural, urban farming projects in India and empowerment of women. It was when she moved from India to Dubai that she chose to promote hydroponic farming in order that healthy food supplies can either be grown by families in their own homes or produced by companies and supplied at affordable rates in the UAE.
Jui talks about her conviction that the future of farming lies in hydroponics.
What is hydroponic farming?
It is the process of growing crops with nutrient-rich water kept in contact with the plant roots without using soil. This process is touted to significantly reduce the risk of wastage and pollution that can harm the produce and cause diseases, making it popular to health-conscious consumers. This method saves up to 70 percent of water while allowing for a longer growing season and avoiding harmful chemicals.
Jui Kemkar, co-founder of Waves Enterprises.
How suitable is this for Middle East consumers?
The extreme climatic conditions and limited agricultural land availability in the Middle East makes hydroponic farming an excellent agro-solution as it increases farming capability. The absence of soil in the growing process makes it conducive for this method of growth to be used in an indoor or outdoor setting.
Can you explain the actual process behind this?
Plant growth happens through a combination of water, sunlight, carbon dioxide, and mineral nutrients. In traditional farming, these nutrients are derived from the soil. Through photosynthesis, plants transform light energy into chemical energy to form sugars that allow them to grow and sustain themselves. This is the basic premise behind hydroponics where all the elements required for plant growth are the same as with traditional soil-based gardening but only taking away the soil requirements, hence making it convenient to perform the farming process anywhere within a controlled environment.
What are the advantages of this kind of farming?
For one, plants can grow both indoor and outdoor and there is growth observed throughout the year. There is complete control over the nutrient balance with a proven technology that ensures high yield. Research shows that growth is faster with hydroponics and 70 percent less water is consumed in the farming process. No harmful contents enter the plant, as no soil or fertilizer or other harmful chemicals are used. The overall economy of a nation will benefit by promoting local farming and reducing the import of vegetables from other countries.
How affordable is this type of farming?
Residential setups are affordable and can be customized to individual budgets; however, commercial farms can be expensive depending on the extent of growth required. But despite the heavy investments for commercial set-ups, profits of up to 60 percent or more are visible in a short period of time. Profits will vary and depend largely on the type of crop cultivated. For example, due to low operational costs, green leafy vegetables yield more profits.
What kind of environment protection does this offer?
As global warming becomes a bigger issue for the world, there is a constant need for better ways to cut down on CO2 emissions to help the environment thrive. Perhaps one of the greatest ways countries can cut back on harmful greenhouse gasses is through examining how they produce and distribute their food supply. Hydroponic growing has numerous possibilities to produce larger, better-tasting vegetables. This method of growth uses less land, 70 percent less water, and minimum to no use of pesticides or herbicides.
Due to controlled growing environment, growth is possible in all types of climatic conditions. Dry and arid climates are not conducive to the growth of berries, bananas, and citrus fruits; however, one country was able to successfully adopt the hydroponic growing process on a large scale. The produce was grown in 40ft large containers and transported to consumer markets for sale.
What is the future of hydroponic farming?
Hydroponics is the fastest growing sector of agriculture, and it could very well dominate food production in the future. As population increases and agricultural land declines due to poor land management, people will turn to new technologies like hydroponics and vertical farming to create additional channels of crop production.
CubicFarms Announces Sale of Control Rooms To Global Agtech Leader, Terramera
In June, CubicFarms offered its Control Room system for sale to growers requiring complete control over the growing environment that is so crucial for high crop yields and quality
VANCOUVER, BC, AUGUST 31, 2020 – CubicFarm® Systems Corp. (TSXV:CUB) (“CubicFarms” or the “Company”) is pleased to announce the sale of three Control Rooms to Terramera, a global agtech leader transforming how food is grown and the economics of agriculture. Terramera is a British Columbia-based company on a mission to reduce global synthetic pesticide use 80 percent by 2030 with its revolutionary Actigate™ technology platform, named a 2020 World-Changing Idea by Fast Company.
In June, CubicFarms offered its Control Room system for sale to growers requiring complete control over the growing environment that is so crucial for high crop yields and quality. Each CubicFarms Control Room is assembled inside a proprietary stainless steel, fully insulated growing chamber with the option to customize features such as lighting, automated irrigation, and nutrient delivery, providing full climate control for temperature, humidity, and carbon dioxide levels. The system has a variety of sensors available, all of which can be remotely monitored and controlled.
Dr. Travis Good, Terramera’s Chief Technology Officer commented, “We required a closed space with precise controls to isolate each environmental variable and produce uniform, plentiful and high-quality plants for our research. CubicFarms’ Control Room system is an ideal solution and helps us scale our Actigate™ technology with the goal of dramatically reducing the use of synthetic pesticides in agriculture.”
CubicFarms CEO Dave Dinesen commented, “We are pleased to call Terramera a customer as we share the same strategic investor, Ospraie Ag Science, and vision to transform how food is grown with the use of leading-edge technology. Terramera is a natural fit for a synergistic partnership in the future as both companies look to develop our machine learning and AI capabilities to further advance our respective technologies.”
Photos: The CubicFarms Control Room, complete with LED light fixtures, an automated heating, cooling and ventilation system, and wired environmental controls.
Neither the TSX Venture Exchange nor it’s Regulation Services Provider (as that term is defined in the policies of the TSX Venture Exchange) accepts responsibility for the adequacy or accuracy of this release.
About CubicFarm® Systems Corp.
CubicFarm Systems Corp. (“CubicFarms”) is a technology company developing and deploying technology to feed a changing world. Its proprietary technologies enable growers around the world to produce high quality, predictable crop yields. CubicFarms has two distinct technologies that address two distinct markets. The first technology is its patented CubicFarms™ system, which contains patented technology for growing leafy greens and other crops. Using its unique, undulating-path growing system, the Company addresses the main challenges within the indoor farming industry by significantly reducing the need for physical labour and energy, and maximizing yield per cubic foot. CubicFarms leverages its patented technology by operating its own R&D facility in Pitt Meadows, British Columbia, selling the system to growers, licensing its technology, and providing vertical farming expertise to its customers.
The second technology is CubicFarms’ HydroGreen system for growing nutritious livestock feed. This system utilizes a unique process to sprout grains, such as barley and wheat, in a controlled environment with minimal use of land, labour and water. The HydroGreen system is fully automated and performs all growing functions including seeding, watering, lighting, harvesting, and re-seeding – all with the push of a button – to deliver nutritious livestock feed without the typical investment in fertilizer, chemicals, fuel, field equipment and transportation. The HydroGreen system not only provides superior nutritious feed to benefit the animal, but also enables significant environmental benefits to the farm.
About Terramera
Terramera is a global agtech leader fusing science, nature, and artificial intelligence to transform how food is grown and the economics of agriculture in the next decade. With its revolutionary Actigate™ technology platform, which was recognized by Fast Company as a 2020 World Changing Idea, Terramera is committed to reducing the global synthetic pesticide load 80% by 2030 to protect plant and human health and ensure an earth that thrives and provides for everyone. The privately-held, venture-backed company was founded in 2010 and has grown to include a world-class bench of engineers, scientists, advisors, and investors. Terramera is headquartered in Vancouver, British Columbia, with integrated operations in Canada, the US, and India that include research labs, a greenhouse and farm, and more than 240 patents in its global IP portfolio. For more information, please visit terramera.com
Cautionary statement on forward-looking information
Certain statements in this release constitute "forward-looking statements" or "forward-looking information" within the meaning of applicable securities laws, including, without limitation, statements with respect to CubicFarms’ future partnership with Terramera; and the development of machine learning and AI capabilities by CubicFarms. Such statements involve known and unknown risks, uncertainties, and other factors which may cause the actual results, performance, or achievements of CubicFarm Systems Corp., or industry results, to be materially different from any future results, performance, or achievements expressed or implied by such forward-looking statements or information including the Company obtaining the approval of the Offering from the TSX Venture Exchange. Such statements can be identified by the use of words such as "may", "would", "could", "will", "intend", "expect", "believe", "plan", "anticipate", "estimate", "scheduled", "forecast", "predict", and other similar terminology, or state that certain actions, events, or results "may", "could", "would", "might", or "will" be taken, occur, or be achieved.
These statements reflect the Company's current expectations regarding future events, performance, and results and speak only as of the date of this news release. Consequently, there can be no assurances that such statements will prove to be accurate and actual results and future events could differ materially from those anticipated in such statements. Except as required by securities disclosure laws and regulations applicable to the Company, the Company undertakes no obligation to update these forward-looking statements if the Company's expectations regarding future events, performance, or results change.
Information contact:
Kimberly Lim
VP, Corporate Communications & Investor Relations
Mobile: 236.858.6491
Office: 1.888.280.9076
Email: kimberly@cubicfarms.com
Freight Farms in Montrose Colorado - Eatin' Greens Farm - Locally Grown Produce
“We have been container farming for 3 years now and we were in agriculture in this area since 1970, so we have been through a few cycles of wet and dry years. We are able to grow consistently all year long no matter what the weather is like. We only use about 3 or 4 gallons of water a day, so drought or no drought we aren’t affected.”⠀
The deserts of the west meet the Rocky Mountains, blocking any rainfall that might come their way. ⠀
Instead, the town relies on snowmelt to irrigate their valley so they can grow beautiful crops of corn, alfalfa, peaches, apricots and apples, and more.⠀
But for the past 2 years, the area has been experiencing a drought and the availability of water for next year depends entirely on the amount of snowfall the mountains receive this winter.⠀
“These cycles certainly make my wife and I appreciate the Freight Farm," says Steve Arnold of @eatingreensfarm. “We have been container farming for 3 years now and we were in agriculture in this area since 1970, so we have been through a few cycles of wet and dry years. We are able to grow consistently all year long no matter what the weather is like. We only use about 3 or 4 gallons of water a day, so drought or no drought we aren’t affected.”⠀
10 Questions to Ask Before Starting a Container Farm
If you’ve been looking into indoor farming from home, you’ve probably come across a container farm as a sustainable option. A container farm is an indoor vertical farm, that operates inside of a repurposed shipping container
If you’ve been looking into indoor farming from home, you’ve probably come across a container farm as a sustainable option.
A container farm is an indoor vertical farm, that operates inside of a repurposed shipping container.
These farms grow crops using hydroponic systems, artificial lighting, and controlled environment agriculture (CEA) technology.
Container farms are popular for their ability to yield a lot of produce in a compact space.
But before you get started, there’s some vital information you should learn.
In this article, you’ll learn what you should find out before starting a container farm.
1. What type of hydroponic system does it use?
There are many different types of hydroponic systems.
The type of hydroponic system a container farm uses will influence compatible crops, maintenance, and its advantages and disadvantages.
For example, recirculating systems like nutrient film technique (NFT), allow the farm to reuse water, cutting back on water use, and work best with quick-growing leafy greens.
2. How is the hydroponic system controlled?
How the hydroponic system is controlled, will determine how much additional labor you need in order to operate it.
If it’s an automated system, like our Pure Greens Container Farms, you’ll save time and energy.
If it’s a more basic system, you’ll have to put in more work to get the results you desire.
3. How is the environment controlled?
How the inside environment of the container farm is controlled, depends on the level of CEA technology that’s been installed.
A basic refrigerated container, with no modifications, will regulate indoor temperature to some degree, but it won’t be easily adjustable or precise.
On the other hand, more controls like temperature, humidity, and carbon dioxide will result in perfect growing conditions for your crops, improving quality and yields.
4. Where can you put it?
One of the benefits of container farming is the ability to grow food in any climate and in densely populated urban areas.
But before starting your container farm, you’ll need to know if you have the proper space for it.
You need to make sure you have enough room on all sides of the farm, level ground, a proper connection to water, and an electrical source.
5. What preparation do I need to do before starting?
The preparation you put into starting a container farm will depend on your personal situation, such as whether you already have the proper space, tools, and materials for it.
Additionally, you’ll want to consider preplanning your budget and what crops you’d like to grow so that you can adjust your expectations accordingly.
6. What do I need to buy separately?
Whether you’re renting or purchasing your container farm, you’ll need to know what materials and equipment it comes with, so you can plan to purchase anything else separately.
These things will need to be accounted for in your budget, and it’s best to know before starting in order to minimize financial surprises.
7. How much work does operating one unit require?
If you already have plenty of time on your hands, this might be less of a concern.
But if you’re only going to be able to put in a few hours of work each week, you might want to look into getting some help.
In general, you should budget for at least 20 hours of work time for your container farm each week.
8. Who will do the labor?
As mentioned in the previous section, if you can’t fully commit your time to maintaining your container farm, you should look into hiring someone.
If you plan to hire someone, you’ll have to make sure to include that in your budgeting as well.
And if you’re going to take on the work all on your own, you should ensure that you’ll have enough time to do so before you start.
9. What plants can I grow in it?
Before starting a container farm, you should know what crops you’re most interested in growing.
Container farms grow a lot of different types of crops, but the most ideal ones will depend on what type of hydroponic system it uses.
You’ll want to make sure your desired crops align with what you’ll actually be able to grow.
10. What are the expected yields?
Whether you’re using the container farm to feed people or to sell your produce, knowing what to expect is important.
You should make sure the farm has the ability to yield enough to match your needs, both in terms of mouths to feed and profit.
Now that you know what questions to ask, you can start finding the answers!
Check out our container farming guides on our website puregreensaz.com or call 602–753–3469 for more information.
WRITTEN BY