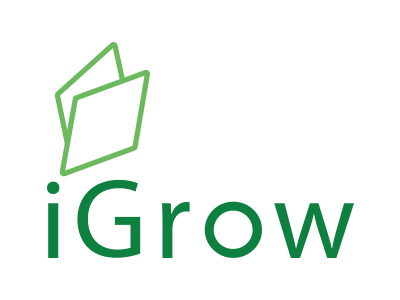
Welcome to iGrow News, Your Source for the World of Indoor Vertical Farming
Bringing Energy Management And Automation Opportunities To Indoor Farming
“We can’t be the most sustainable company in the world if we don’t work on the world’s biggest sustainability challenges,” says Travis Graham, international account manager at Schneider Electric. Schneider provides a vast array of digital technologies to multiple sectors, including horticulture
By Rebekka Boekhout
July 14, 2021
“We can’t be the most sustainable company in the world if we don’t work on the world’s biggest sustainability challenges,” says Travis Graham, international account manager at Schneider Electric. Schneider provides a vast array of digital technologies to multiple sectors, including horticulture. However, the company recently decided to strategically address the indoor farming segment and partner with growers to improve energy efficiencies within the sector.
As a global specialist in energy management and automation, Schneider’s goal is to empower the global population to improve their energy and resource use efficiency. This purpose, coined “Life is On”, aligns strongly with the spirit of indoor agriculture whose goal is to produce food and medicinal crops in an environmentally sustainable manner.
Named the world’s most sustainable company in 2021 by Corporate Knights, Schneider holds sustainability at its core and uses its century-long experience in energy management to help growers improve the energy efficiency of their facilities.
Read the rest of the article here
For more information:
Schneider Electric
www.se.com
Nature Fresh Farms And The University of Windsor Looks To Bring Clean Transportation In New Partnership
Nature Fresh Farms joins the University of Windsor in their long-haul vehicle transportation sustainability project to help achieve new advancements in energy efficient shipping.
July 5, 2021
Leamington, ON – Nature Fresh Farms joins the University of Windsor in their long-haul vehicle transportation sustainability project to help achieve new advancements in energy efficient shipping.
The purpose of this $160,000 project is to determine the impact of long-haul electric vehicles (LHEV) on Ontario’s electric grid. They will create an archetypal routing network by determining the most frequently traveled routes and then overlay the electric grid which will help determine how it will perform when managing a fleet of electric trucks. Being battery operated the trucks will look, haul, and perform similarly to diesel trucks but with zero emissions. By drawing power from the electric grid, the transport trucks would not only be able to sustainably deliver goods but also allow for the transferring of electrons back to the grid at strategic locations and times.
The project is spearheaded by Dr. Rupp Carriveau, of the Environmental Energy Institute, and his associate Dr. Hanna Maoh, of the Cross Border Institute, with the assistance of several graduate students. In addition, they are developing various industry related partnerships that will assist in different facets of their project, including Nature Fresh Farms.
“We needed a partner to help pilot our project and potentially test and Nature Fresh Farms came to mind. They are a very progressive company and are calculated risk takers that push boundaries with new technologies.” – Rupp Carriveau
The analytics and case studies are where Nature Fresh Farms comes in. The company will be able to send information from its operations which will include shipping schedules, power use, and utility costs to provide the research team with data that will determine the strengths and weaknesses of converting its fleet to electric vehicles. This information will help to examine the opportunities of electric trucks in the greenhouse industry.
“As an innovative company we are always thinking ‘what is next?’, whether its developments in product varieties, technology, or sustainability. Green transportation is the next big focus,” shared Nature Fresh Farms CEO, Peter Quiring. “We were given the opportunity to work closely on this project and offer our operations as a case study to see how we can find feasible alternatives, not only for Nature Fresh Farms or even for companies in agriculture, but for every industry that relies on the transportation of their goods.”
With the first step of the project working towards establishing an electrical grid that will manage a fleet of electric vehicles, phase two is the potential pilot study of developing and using electric long-haul vehicles for that grid. Nature Fresh Farms looks forward to the continued partnership and progression of their project with the University of Windsor and the future in the sustainable shipping of goods.
About Nature Fresh Farms - Continuously expanding, Nature Fresh Farms has become one of the largest independent, vertically integrated greenhouse vegetable farms in North America. As a year-round grower with farms in Leamington, ON, Delta, OH, and Mexico, Nature Fresh Farms prides itself on consistently delivering exceptional flavor and quality to key retailers throughout North America, while continuing to innovate and introduce more viable and sustainable growing and packaging solutions.
SOURCE: Nature Fresh Farms | info@naturefresh.ca
T: 519 326 1111 | www.naturefresh.ca
Lead Photo: CEO, Peter Quiring (Left) & Dr. Rupp Carriveau (Right)
A High-Yield Indoor Farming System Ideal For The City
According to Pollard, the evolution of new technology, such as LED grow lighting and the Internet of Things (IoT), has complemented the development of indoor soilless cultivation systems
As prolonged droughts occur more frequently in South Africa, some entrepreneurs are investing in and developing new technology and farming methods, such as indoor growing systems, that ensure consistent, high-quality food production. Juan-Griffith Pollard, CEO of Urban Cultivation International, spoke to Pieter Dempsey about his scaleable hydroponic farming system.
More frequent and long-lived droughts. Global warming. Water scarcity. Higher input costs.
These are some of the factors driving the growing interest in new technology that enables a farmer to produce the same quality and yields as conventional farming, but using indoor farming systems instead.
Hydroponics, or indoor soilless cultivation, as Urban Cultivation International (UCI) calls it, is a method of growing plants in a water-based, mineral- and nutrient-rich solution instead of soil, and under artificial LED lights instead of sunshine.
According to Juan-Griffith Pollard, the CEO of UCI, indoor farming uses up to 90% less water than traditional farming practices, and far less space. In addition, plants can be grown pesticide-free and closer to high-consumption areas, such as densely populated cities.
These reasons, and more, explain why an increasing number of growers have begun exploring indoor soilless cultivation.
Precision growing
The system provides the optimal growing conditions for plants, enabling them to develop much faster and be far healthier than is the case with traditional outdoor cultivation.
According to Pollard, the evolution of new technology, such as LED grow lighting and the Internet of Things (IoT), has complemented the development of indoor soilless cultivation systems.
“IoT can be used to automate and regulate indoor farming by monitoring water levels, nutrient levels, pH levels, and temperature and light requirements of plants. “A farmer can be in control of the harvest at all times, wherever he or she is physically present.
“One of the biggest benefits of indoor farming is that produce can be farmed at any time of the year. Thus, a farmer can sell produce at out of season prices, and supermarkets can stock fresh local produce all year around,” says Pollard.
No-soil farming
Pollard started investigating various methods of indoor soilless cultivation in 2016 and fine-tuned them in 2019 to create a healthy, productive indoor farming system.
An entrepreneur by nature, he took note of the various challenges in traditional South African agriculture, including water scarcity and security risks. He also noticed the demand for certain leafy greens and microgreens in cities.
Thereafter, he traveled to the US, Europe and Asia to research systems that could be applied in the South African agricultural environment.
He went on to establish UCI at the N4 Gateway Industrial Park in Pretoria East.
“What makes UCI’s technology different from most other indoor systems is that a farmer can start small and expand by adding additional racks to the system. So there’s no need to commit to a huge capital investment to get started,” Pollard explains.
The UCI model enables the farmer to control the light hours, nutrients and moisture. It is automated to produce rapid harvest cycles with predictable results, and can be used in a small space. Crucially, it is also affordable.
A key advantage is that the plants can be grown without the use of insecticides and herbicides, as the crops are grown in a controlled environment.
Pollard predicts that farms of the future will be urban-based, and crop cultivation will have to become far more sensitive to water and energy usage. There are many cost-effective options for indoor, soilless cultivation, and these allow farmers to move from the fields to the city.
Indoor production is also an easier entry into farming; it can be started by any entrepreneur, or even a retiree, he adds.
A wide range
The options offered by UCI range from small household units to large-scale commercial systems. Regardless of size, they can deliver crop yields of up to 10kg/m2.
The household units are small, with just enough space to service the average household and to plant a variety of crops, such as leafy greens, microgreens and berries.
The household system was also developed for educational purposes and can be used as an entry into indoor soilless cultivation before a large capital investment is made in a commercial unit. UCI has developed a curriculum that explains the A to Z of indoor hydroponic farming.
The company’s industrial units include climate control and a lift system, which makes harvesting easier.
Depending on the type of crop, the return on investment is between two-and-a-half and five years, while high-value crops such as microgreens have a payback period of less than a year on capital investment.
Growing with ease
Plants can be grown from seed to harvest in 28 days, three times faster than that achieved with traditional farming.
“The plants are grown in a controlled environment under 12 to 16 hours of LED lights, giving you optimal harvest and zero wastage,” explains Pollard. In addition, produce grown in UCI’s systems has proved to be of excellent quality and offer good taste.
The entry commercial turnkey solution system contains a 10m-long and 1,9m-wide row, and the buyer can choose to fit between three and 12 levels.
For example, a 10m-row, five-level-high farm enables 100m2 to be planted in a floor space of only 20m2. “The higher you go, the more your yield per square metre,” says Pollard. The grow trays and spacing between plants are designed for optimal growing and yield. No sunlight is needed for this method; all the systems use LED grow lighting.
“LED technology provides the best energy efficiency, which saves you money in the long term,” says Pollard.
Production
A 10m-long unit can handle 54 plants per tray. At 12 trays per level and at five levels, this equates to 3 240 plants per unit.
The lighting is usually kept on for between 12 and 16 hours a day, depending on the requirements of the plants.
“The more light they get, the faster they grow,” says Pollard.
The system can handle a variety of crops such as lettuce, spinach, baby spinach, marog (imfino), cherry tomatoes, strawberries, basil, watercress, sage, zucchini, beans, fodder and a range of microgreens and herbs.
To illustrate potential crop yields, Pollard and his team have used the five-level demonstration system at UCI’s premises to grow 250g lettuce heads in 28 days under optimal growing conditions. A yield of more than 18kg per tray has been achieved.
“Compared with traditional farming, the only major cost drivers are electricity and wages,” he says.
Each tray contains about 20ℓ of constantly recirculated water, and total water use is approximately 1 250ℓ/month. The system is extremely water-friendly, as almost all the water is absorbed by the plant.
“No water is wasted, hence the saving of 90% compared with traditional farming,” says Pollard.
He adds that climate and temperature control is a key factor in the grow room, and even the water temperature is cooled or heated as the plants require.
“We can mimic the controlled growing environment of certain crops as they require. “The system works with any water, and tests are routinely conducted to see what nutrients the plants need, and all variables can be adjusted according to the needs of the plants.
“We have a nursery system that grows the plants from seed to seedlings. After about seven days, the seedlings can be transported into the commercial system; the fully grown plant is then ready to be harvested after another 21 days,” Pollard says.
Due to the way in which the system operates, the chances of a pest infestation are very low.
“Biosecurity is crucial and we prevent any pathogens and pests from entering the facility.”
Harvesting a system that is 10m long and has five levels requires about three hours with two people.
With rapid urbanization increasing the demand for food, UCI’s system offers a number of key advantages.
It brings the farm closer to the people, thereby improving food security, and it reduces transport costs, in turn lowering the carbon footprint of supplying food. The system also offers good potential as a job creator.
“Our aim is to get entrepreneurial farmers to start utilizing the empty spaces in cities, such as empty buildings in city centres. Such spaces can be used to grow food, provide jobs and supply retailers directly,” says Pollard.
Visit urbancultivation.co.za.
By Pieter Dempsey | Farmer’s Weekly | May 6, 2020