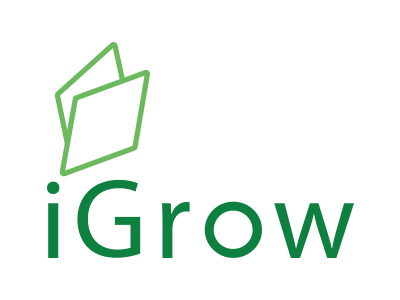
Welcome to iGrow News, Your Source for the World of Indoor Vertical Farming
2021 Virtual Plant Lighting Short Course
In each sequential module, attendees will use interactive tools to define their specific lighting requirements, hear from industry experts about available horticultural lighting systems, and learn how to compare different lighting strategies
Now Open For Registration!
Working in partnership, GLASE, OptimIA, and LAMP are excited to announce the first annual Plant Lighting Short Course! This 6-week modular short course is designed to provide participants the opportunity to learn about all aspects related to the selection, implementation, and benefits of plant lighting systems.
In each sequential module, attendees will use interactive tools to define their specific lighting requirements, hear from industry experts about available horticultural lighting systems, and learn how to compare different lighting strategies. By the end of the course, participants will be equipped to make informed decisions about the best options to meet their lighting needs.
More Info & Registration
Media Partners
Recordings Now Available
Optimizing Resource Use Efficiency in CEA Systems - July Webinar
New CEA Research Programs in the U.S. - June Webinar
GLASE Webinar Series
This short presentation will cover the history of research on photosynthetic responses to light spectrum, recent work on the importance of far-red photons, and a discussion of the implication of (not) extending the definition of PAR
The photosynthetic activity of far-red photons was discovered 70 years ago, but has largely been ignored since then. Recent research has drawn new attention to the importance of far-red photons.
This short presentation will cover the history of research on photosynthetic responses to light spectrum, recent work on the importance of far-red photons, and a discussion of the implication of (not) extending the definition of PAR. There will be ample time for discussion following the presentation.
Register Here - August 26 • 2-3 p.m. EST
iUNU Announces Acquisition of CropWalk, Significantly Expanding The Consulting Capacity For Both
iUNU (“you knew”) is an agricultural machine vision company headquartered in Seattle, with satellite offices in California, Florida, and Toronto as well
iUNU (“you knew”) is an agricultural machine vision company headquartered in Seattle, with satellite offices in California, Florida, and Toronto as well. Founded in 2013 and currently with over 40 employees across the world, the company leverages computer vision and machine learning to allow farms to better manage crop issues and optimize growth cycles. The LUNA system focuses on identifying growing maladies before the crop is affected and promotes better accountability of growing practices through the workflow management application.
In making the announcement, Adam Greenberg, CEO of iUNU, said: “Rising consumer demand is accelerating the growth of the greenhouse industry, but the massive shortage of both growers and manual labor requires a scalable machine vision solution to further produce supply. Having a renowned agronomy team to assist in deploying state-of-the-art technology like LUNA will have a profound impact on our constantly improving capacity to help growers increase quality, yields, and profits. 65% of growers are above the age of 55, and the shortage of qualified people is hitting the fast growing industry hard. Something has to give, thus the future is the centralized management of distributed facilities.”
CropWalk is an integrated pest management (IPM) company that was founded in 2019 and has an expanding team with employees located in key regions across North America, including their Founder and Director of Partnerships, Charlie McKenzie, in the US Southeast, and the CropWalk Director of Operations, Robert Shearer, and Director of Science, Education, and Strategic Development, Ayana Stock, along the US West Coast.
They are a widely recognized name in the horticultural industry for their unbiased approach to empowering growers of high-value crops with the knowledge and resources to prevent and manage pests and plant pathogens. With plans underway to expand their crop care services, CropWalk is well-known for how they customize a unique suite of services for operations of various kinds, offering risk assessments, IPM program development, training sessions, the online CropWalk Academy, and more, including remote monitoring services, the capacity of which are now dramatically enhanced by iUNU’s LUNA system.
Charlie McKenzie, CEO of CropWalk, said: “We’ve always used remote monitoring technology to identify and mitigate conditions that foster plant pathogens. The mantra we live by at CropWalk is ‘Start Clean, Stay Clean.’ Working with the iUNU team and using LUNA, we can digitally walk a crop from anywhere at any time allowing our team to effectively prevent problems before they result in economic injury. Our clients want us around more often, with LUNA, we can be there all the time. It’s a win for growers, a win for CropWalk, and a win for iUNU.”
LUNA, iUNU’s chief product, is an AI tasked with connecting plants, facilities, and people through a single interface. LUNA runs on computers or mobile devices and turns commercial greenhouses into precise, predictable, demand-based manufacturers. LUNA was born in the heart of Seattle, trained in Silicon Valley and the greenhouses of Washington, and is accessible from everywhere.
The future of crop care in modern greenhouses that will feed families for generations involves both people’s human expertise and the best available technologies. The union of iUNU and CropWalk is great news for CEA crop producers seeking the advantage of cutting-edge artificial intelligence, computer vision, and machine learning coupled with industry-leading IPM & biological services. Two companies that were excelling independently have joined forces to set a new standard for the remote monitoring of crops. Services of both companies will still be available for clients independent of one another but will have expanded resources at their disposal.
iUNU’s acquisition of CropWalk helps both companies become more effective in their work towards an important common goal: reducing the cost of nutrient-rich food reaching urban centers while helping growers thrive.
Working In Partnership, GLASE, OptimIA, And LAMP Are Excited To Announce The First Annual Plant Lighting Short Course!
This 6-week modular short course is designed to provide participants the opportunity to learn about all aspects related to the selection, implementation, and benefits of plant lighting systems
Dates: October 14 - November 18, 2021
Time: Thursdays 2 p.m. - 4 p.m. EDT
Presented by: GLASE, LAMP, OptimIA
More Info and Registration
About the Course
Working in partnership, GLASE, OptimIA, and LAMP are excited to announce the first annual Plant Lighting Short Course! This 6-week modular short course is designed to provide participants the opportunity to learn about all aspects related to the selection, implementation, and benefits of plant lighting systems. In each sequential module, attendees will use interactive tools to define their specific lighting requirements, hear from industry experts about available horticultural lighting systems, and learn how to compare different lighting strategies. By the end of the course, participants will be equipped to make informed decisions about the best options to meet their lighting needs.
Speakers
Bruce Bugbee (Utah State University)
Erik Runkle (Michigan State University)
Roberto Lopez (Michigan State University)
Neil Mattson (Cornell University)
Marc van Iersel (University of Georgia)
Jim Faust (Clemson University)
Kale Harbick (USDA ARS)
A.J. Both (Rutgers University)
Paul Sellew (Little Leaf Farms)
Travis Higginbotham (Harborside Group)
Paal Elfstrum (Wheatfield Gardens)
Tessa Pocock (Shenandoah Growers)
Drew Koschmann (Walters Gardens)
Kenneth Tran (Koidra)
Mark Blonquist (Apogee)
Michael Eaton (Cornell University)
Trevor Burns (PL Lighting)
Joe Sullivan - (Franklin Energy)
David Hawley (Fluence Bioengineering)
Ben Campbell (University of Georgia)
Tim Shelford (Cornell University)
Erico Mattos (GLASE)
Special Thanks To Our Industry Partners
If you have any questions or would like to know more about GLASE, please contact its executive director Erico Mattos at em796@cornell.edu
By the end of the course, participants will be equipped to make informed decisions about the best options to meet their lighting needs.
Event Webpage
Philips LEDs Contribute To A Higher Winter Production of Excellent Quality Cucumbers
LED systems clearly add value to year-round growth concepts for cucumbers. Jan Biemans of Tielemans Groentekwekerij from Boekel, the Netherlands and Eric van den Eynde from Kontich, Belgium have determined this after their first growth under a hybrid grow light solution.
July 21, 2021
LED systems clearly add value to year-round growth concepts for cucumbers. Jan Biemans of Tielemans Groentekwekerij from Boekel, the Netherlands and Eric van den Eynde from Kontich, Belgium have determined this after their first growth under a hybrid grow light solution. In 2020, they both upgraded their existing HPS installations with Philips LED toplighting systems from Signify. Despite the differences in their greenhouses, installations, and goals, their conclusions were unanimous: LED contributes to an efficient, high winter production of excellent quality.
Uniform distribution
Eric and Lander van den Eynde’s company close to Antwerp consists of 2 ha of unlit tomatoes and 2,1 ha of lit, high-wire cucumbers. “We have been growing under HPS lights for two years already, which complemented the natural light with 180 µmol/m²/s”, says Eric. “However, in winter the fruits did not reach the desired weight of 350 to 400 grams. Therefore, light had to be added and LED is the most efficient solution for that. Our question to Signify was how we could fulfill that in the smartest way.” Multiple light plans were calculated in consultation with their installer and the plant specialists from Signify. Because of the limited height of the greenhouse (gutter height 5 meters), the Philips GreenPower LED toplighting linear was chosen, because that gives the most uniform light distribution.
Half of the HPS lamps were removed, and for each removed lamp 2,9 linear LED modules were installed. This brought the total light intensity to 223 µmol/m²/s, divided between 87µmol/m²/s HPS and 136 µmol/m²/s LED in red, blue and a bit of white working light. The total installation gives 24% more PAR-light, while the energy usage (at equal lighting hours) is about 7% less.
“The light division is nice and equal, even when only the LED lights are on”, the grower continues. “The latter is the case every now and then in the Spring and Autumn especially, when the heat radiation from the HPS lights is not always wanted.”
More and heavier fruit
The new installation was ready in September of 2020. To take maximum advantage of the higher light level, a planting distance was chosen of 50 cm (2,5 plant/m2). Lighting was begun directly after planting on October 2nd. Van den Eynde: “The plants reacted well. Our goal is to have a growth speed of six new leaves per week, and we could keep up with that pace effortlessly. The higher density of the stalks did ask for an altered pruning policy, but that did not have any effect on our labor planning. The most important goal was a higher average fruit weight. That was realized right away. Furthermore, we cut more cucumbers and they were of a good color. Our customer is very satisfied, and therefore so are my son and I.”
Winter production
Tielemans Groentekwekerij consists of 12 ha of greenhouses at two locations in Boekel. Cucumber is the most important crop. The company realizes two high-wire growths per year, from the beginning of January till the end of November, which formerly received 95 µmol/m²/s extra PAR-light from HPS lamps during the lighting season.
“In 2020 we received the request from our producers’ association to adapt 3,0 ha for winter production”, says growth manager Jan Biemans. “In order to realize sufficient production, weight, and quality in the darkest period, quite some additional light had to be installed. We looked at different options and made calculations. The choice was made for Signify’s Philips GreenPower LED toplighting compact, in combination with the GrowWise control system. With that we can dim the LED installation and tune the light level even better to the crop’s needs.”
Longer light in the evening
According to the light plan, the toplighting compact grow lights (providing 2.600 µmol in red and blue for optimal efficiency) were attached to the trellis in between the rows of HPS lights, raising the light level with 144 µmol/m²/s to 240 µmol/m²/s. The stalk density was chosen at 2,25 stalks per m2. Biemans: “We are content with the achieved winter production, and I am happy with this hybrid solution’s flexibility. The LED installation enables us to continue lighting longer in the evening without the additional heat. The plants did fine and got through the winter well.”
The growth manager thinks he can get even more out of it by decreasing the width of the row distance. “In the future I think we can benefit even more by adding far-red light”, he adds. “One variety showed some contracted leaves in darker periods, but the other variety did not do this at all. Overall, we are happy with the results.” Erik Stappers, plant specialist at Signify adds: “Full LED with far-red has proven itself by now. The role of far-red light in a hybrid installation with more LED than HPS is being investigated at the moment. Indeed, we do see differences between the varieties there.”
Let me know in case you have any questions.
Two New Hirers For Horticultural Lighting Specialist
Vertically Urban is excited to welcome Jon Potter and Phoebe Sutton to the team. The two recruits have been bought on board to meet the brand's growth objectives and further improve its scientifically based development process
Vertically Urban, the Leeds-based manufacturer of LED solutions, has welcomed two new specialists to its growing team.
Vertically Urban is excited to welcome Jon Potter and Phoebe Sutton to the team. The two recruits have been bought on board to meet the brand's growth objectives and further improve its scientifically based development process.
Jon joins as Business Development Director, with a wealth of LED lighting and controls knowledge gained from his time with Philip's Lighting and the Aurora group.
In his new role, Jon will be helping to grow the Vertically Urban brand working directly with growers, partners, and system integrators to bring horticultural lighting solutions into several application areas.
Phoebe enters the newly-created position of Plant Biologist, bringing a plethora of research experience in plant photobiology. She has a specific interest in integrating her research and expertise into the vertical farming industry.
Currently, Phoebe is completing a Ph.D. in the optimization of LED lighting regimes to increase the phytonutrient content in hydroponically grown herbaceous crops. In the new role, she will be managing the brand's onsite laboratories to ensure the optimum formula for LED grow lights.
Andrew Littler, CEO of Vertically Urban, says:
"We are thrilled to have both Jon and Phoebe on the team. Following our successful Seedrs campaign last year, we set some ambitious growth plans to help us meet the fluctuation in industry demand for sustainable, efficient LED horticultural lighting solutions. We pride ourselves on our standard and bespoke products, which we scientifically fine-tuned to specific crop requirements. With Phoebe in place, we are certain to improve our formulas further, and with Jon growing our customer bases, tapping into new markets, we are sure to hit our targets."
ENDS
About Vertically Urban
Vertically Urban is a specialist horticultural lighting manufacturer based in Leeds. It designs and manufactures its products in the United Kingdom using the highest photon yielding LEDs available. The Leeds-based factory has full manufacturing capabilities. Using its bio-science know-how, they aim to light the farms of the future by providing efficient LED lighting solutions that are easy to install and set up.
Philly Start-Up GrowFlux Tweaks Lighting For Growing Indoor Agriculture Industry
The University City company has received a $250,000 grant to conduct research at the National Renewable Energy Laboratory in Colorado.
The University City company has received a $250,000 grant to conduct research at the National Renewable Energy Laboratory in Colorado.
GrowFlux offer technology and software to control lighting for indoor farms. Shown here is Second Chances Farm in Wilmington, an early customer. GrowFlux
07-12-21
Crops in greenhouses — an increasingly popular way to supply year-round fresh greens and other produce to places with cold winters — are most productive when they receive the right amount of light at the right time.
But there’s a downside. Greenhouses are energy hogs and typically generate more gasses than traditional field agriculture because of their lighting and heating needs. Those are terrible characteristics for a burgeoning industry at a time of growing concern over global warming.
GrowFlux, a Philadelphia agricultural technology start-up that is trying to make the industry more efficient, won a $250,000 grant last week from the Wells Fargo Innovation Incubator for research at the National Renewable Energy Laboratory (NREL) in Colorado. The aim is to reduce energy consumption in greenhouses by fine-tuning the amount of artificial light that crops receive.
GrowFlux sells sensors that measure the amount of light, carbon dioxide, temperature, and humidity in indoor farms.GrowFlux
Simple timers are traditionally used to turn lights on and off in greenhouses, said Eric Eisele, GrowFlux’s chief executive, and cofounder. “They’re not dialing in the light in accordance with when the crop is actually using light most efficiently,” he said. “It results in a fair bit of energy that’s wasted.”
The GrowFlux system — to be further developed with the help of researchers at NREL and the Donald Danforth Plant Science Center in St. Louis — measures the natural light available and then adjusts the artificial light to add more when needed.
GrowFlux estimates that it can cut energy use by 20% to 30%.
While the grant, funded by the Wells Fargo Foundation, involves GrowFlux’s lighting controls, the University City company has a broader target with sensors that monitor carbon dioxide levels, humidity, temperature, and other factors that determine how well plants grow.
“They were one of the very first companies that were trying to essentially make farms like ours smart farms by using technology,” said Ajit Mathew George, founder and managing partner at Second Chances Farm in Wilmington, an indoor vertical farm that employs formerly incarcerated individuals.
“You don’t think of indoor vertical farms as being a place where technology plays an important part,” said George, who uses a GrowFlux app on his phone to monitor Second Chances Farm. “It does, and the more it does, the better our production is.”
Investor interest in indoor agriculture surged last year, with $929 million going into 41 deals in the United States, according to PitchBook Data Inc. That’s twice the amount invested the year before. Most of the money went into producers rather than into makers of components and technology like GrowFlux.
Eisele, 35, and Alexander Roscoe, chief technology officer, founded GrowFlux in 2017. Both are Drexel University graduates.
Eisele’s background is in interior lighting for humans. He worked for seven years in the research group at KieranTimberlake, a Philadelphia architecture firm. Rosco, 36, worked at Comcast on the build-out of national internet architecture.
GrowFlux’s first products, launched in 2018, were horticultural lights with built-in wireless technology. “The lighting space got very competitive in horticulture due to legalization of cannabis,” Eisele said.
The start-up, which now employs four, was competing with “the likes of Philips and General Electric and Osram,” Eisele said. GrowFlux dropped its lights in 2019 but kept developing its controllers.
Eisele and Roscoe declined to disclose their annual revenue but said they have raised close to $2 million from investors. The company has products in more than 100 farms, including indoor cannabis producers and greenhouses growing food like tomatoes and strawberries. The products are also used overseas, in Iceland and in an indoor vertical farm in Singapore that grows strawberries, Eisele said.
Trish Cozart, NREL’s program manager for the Wells Fargo Innovation Incubator, which in the past has worked with companies involved in traditional farming, said that over the next 30 years, global food production will have to increase by 60% to meet demand. NREL is part of the U.S. Department of Energy.
“It might not be possible to meet that demand through field-grown agriculture. Indoor agriculture is going to play a part. We don’t know how big of a part,” she said. But because indoor agriculture consumes so much energy, “we want to figure out how to combat that using innovative companies,” Cozart said.
Published July 12, 2021
I write about the business side of health care and the nonprofit sector.
VIDEO: Signify Expands LED Installation At Walters Gardens With Philips GreenPower LED Toplighting Compact
“It was a really easy decision to go with the Philips LED toplighting compact”, says Aren Philips, finishing lead grower at Walters Gardens. “The tops are fuller, the roots are more active, we are able to finish our hostas product 1 to 2 weeks ahead of schedule.”
July 6, 2021
Eindhoven, the Netherlands – Signify (Euronext: LIGHT), the world leader in lighting, is supplying Walters Gardens with the Philips GreenPower LED toplighting compact to expand their existing lighting installation. Walters Gardens is a market leader in the ornamental industry from Zeeland, Michigan, in the United States.
They first trialed Philips GreenPower LED toplighting in 2014 - one of the first growers in North America to install Philips horticulture LED grow lights over ornamental crops, with the aim to jump-start their spring perennial production.
As a result of the trial’s success, Walter’s Gardens partnered with Signify again, when expanding their lighted growing areas in 2019 - 2020, with the Philips GreenPower toplighting compact.
“It was a really easy decision to go with the Philips LED toplighting compact”, says Aren Philips, finishing lead grower at Walters Gardens. “The tops are fuller, the roots are more active, we are able to finish our hostas product 1 to 2 weeks ahead of schedule.”
Together with the high efficacy of the toplighting compact, and the easy 1:1 replacement of the HPS, leading to a great ROI, Walters Gardens knew the expansion would pay off.
Learn more about the Philips LED grow lights for floriculture here.
--- END ---
For more information:
Global Marcom Manager Horticulture at Signify
Daniela Damoiseaux
Tel: +31 6 31 65 29 69
Email: daniela.damoiseaux@signify.com
About Signify
Signify (Euronext: LIGHT) is the world leader in lighting for professionals and consumers and lighting for the Internet of Things. Our Philips products, Interact connected lighting systems and data-enabled services, deliver business value and transform life in homes, buildings, and public spaces. With 2020 sales of EUR 6.5 billion, we have approximately 37,000 employees and are present in over 70 countries. We unlock the extraordinary potential of light for brighter lives and a better world. We achieved carbon neutrality in 2020, have been in the Dow Jones Sustainability World Index since our IPO for four consecutive years and were named Industry Leader in 2017, 2018 and 2019. News from Signify is located at the Newsroom, Twitter, LinkedIn, and Instagram. Information for investors can be found on the Investor Relations page.
Why Does Energy Efficiency Matter When Selecting LED Grow Lights?
Learn the 3 things to consider when choosing energy-efficient lighting in your greenhouse or vertical farm.
Before we get started, let’s set some ground rules for this article.
1. I want to believe that everyone wants to do what’s right for the planet as long as they think their business can afford it, so we will not focus on energy efficiency and its impact on sustainability.
2. In this article I will not post the name of suppliers or the price of the lights. The price of the light will definitely impact people’s decisions and will vary widely based on the volume of lights being purchased and the supplier providing it.
3. This article is not about light quality or light spectrum. To look for information on spectrum please read this article: Why I Still Believe in Red/Blue LED Grow Lights
4. This article is written with commercial greenhouse produce growers in mind, but we do include a model which shows high output led grow lights running for long hours per day which could imply a greenhouse cannabis crop.
5. We are fully aware that when you change the amount of energy going into the light as well as the type of electric light (HPS vs LED) one is using, it will have an impact on the climate in the growing/production area. Factors like heat and relative humidity would need to be taken into consideration if one was taking a holistic approach to energy savings on the farm.
6. All lights have different output (measured in PPF.) In this article we are going to make the assumption that a grower is using the same amount of fixtures per acre regardless of output. For simplicity we are also going to assume that the grower is running the lights for the same amount of time. We are fully aware that this will have an impact on the potential yield of the crop.
7. All greenhouses can require a different amount of lights per acre to achieve the target light intensities. I am using an average of the amount of lights per acre. Height of the greenhouse, width of the bays, placement of walkways, crop layout, crop density, as well as many other variables will impact the exact number of lights per acre.
__________
There is a growing amount of discussion around the environmental sustainability of a greenhouse or a vertical farm. Much of this discussion is being driven by two or three big energy hogs inside these production facilities. This includes the grow lights and climate management equipment like heaters and cooling units.
We all know that LED grow lights are more efficient than the older HPS lights that growers have used for decades, but do we know just exactly how to measure that? And do we understand how that will have a direct impact on not only energy savings but the operational cost at the farm? For those growing in a greenhouse, understanding these numbers during dark winter months can have a huge impact on electricity bills.
3 FOCUS POINTS
1. Start by understanding the amount of light you need.
Urban Ag News recommends going to websites like Suntracker or the ESRI DLI maps site. These websites allow anyone to determine the historical DLI monthly averages for their individual locations. For this example I am going to use the area where my grandparents farm is located in southwestern Michigan. As one can see this is an area of the United States that has very dark winters.
2. Work with a trusted advisor or extension specialist to determine the amount of hours your crop needs to grow consistently year round. Remember not all crops have the same light requirements and some crops have very specific photoperiods which can determine the amount of hours one can light their crops. Use all of this information to see when you will need supplemental light and how much light you will need to supplement with.
For this example I am going to use 1 acre of greenhouse tomatoes in a glass greenhouse located in southwestern Michigan.
3. Now let’s calculate how much it’s going to cost you to run the grow lights for the estimated hours you and your advisor determined were needed per year to get the desired yields.
a) To provide a baseline, we started with traditional 1000w HPS lights which are highlighted in yellow.
b) Then we chose six different LED grow light fixtures. Because the light spectrum has an impact on how efficiently the lights run, we chose three broad spectrum fixtures and three that are red and blue only.
c) Since HPS is the baseline, the final column labeled “savings” shows how much the total savings per year one would achieve when replacing traditional HPS with the latest LED grow light technology.
d) We made a few important assumptions in this example. First, the cost per kwh is around the USA national average of $0.09/kwh. Second, the same amount of grow lights would be used even though there would be some relative differences in umols/m2/s measurements for two of the samples. We decided not to change them because that would have an impact on uniformity (the even spread of the light over one’s entire crop) and associated capital cost not addressed in this article.
IMPORTANT NOTES!
It’s important to remember the 7 assumptions made at the beginning of this article and that lights are not equal. This chart only compares ppf (output) and w (watts). We elected to account for the difference in output by changing the amount of hours we estimated you would need to run the lights. Another way to look at this would be to remember the Golden Rule of Light in which 1% increase in light is equal to 1% increase in yield.
Running these simple calculations will show you why you need to look at energy efficient lighting and in general the importance of researching energy efficient equipment in general. What these calculations do not show is the quality of some fixtures over others. Buyers must always be aware of the value of warranties, ease of returns, durability and quality of product plus accuracy of your vendor to create detailed information on the best way to use and install fixtures. We understand that this topic is intimidating for most, but this is a major purchase for your farm. Make sure to take the time to learn the math and do your homework before purchasing.
Diving into these calculations will also highlight how much energy will be required to grow a wide variety of crops consistently with uniformed yields year round in climates with low light. Hopefully in articles to come we can discuss what this means for our environment and how we might develop additional ways to lower that ecological footprint.
For help in calculating the energy efficiency of grow lights you are considering, please email us and we will connect you with professionals capable of helping you make an informed decision.
Chris Higgins is the founder of Urban Ag News, as well as General Manager and co-Owner of Hort Americas, LLC a wholesale supply company focused on all aspects of the horticultural industries. With over 20 years of commercial horticulture industry experience, Chris is dedicated to the horticulture and niche agriculture industries and is inspired by the current opportunities for continued innovation in the field of controlled environment agriculture. Message him here.
Tagged GreenhouseGreenhouse TechnologyIndoor Ag TechnologyTechnologyVertical Farming
Research Signify And Fragaria Innova Into Growing Strawberries With LED Bears Fruits
“Extra growth light is needed to realize sufficient yield and quality in winter”, according to plant specialist Peer Hermans, who conducts the research on behalf of Signify
June 15, 2021
· Provides better steering of the plants
· Optimizes winter growth
· Helps growers realize a stabile production pattern with high yield and good quality strawberries
Eindhoven, the Netherlands – Signify (Euronext: LIGHT), the world leader in lighting, has worked together with Fragaria Innova to develop specific light recipes for strawberries, resulting in a steady production pattern with high yield, and good quality strawberries in wintertime. The joint research over the past year helps to further optimize the winter production of the so-called ‘June bearers’, a strawberry cultivar known for relatively short peaks in production.
Within Fragaria Innova, progressive strawberry growers commit themselves, together with external partners, to innovation surrounding the themes of growing under light and plant health. For growing under light, Fragaria Innova and market leader Signify conduct a multi-year program with participating growers/propagators. At one of the production companies, a special compartment has also been equipped with separate climate control, this enables the testing of several growth- and light strategies for multiple cultivars under full LED. One of the main goals of the research is realizing a (more) stable production pattern during wintertime.
Current winter productions usually take place with June bearers with a short production period of 8 to 10 weeks, after which a new planting in another section takes over production to create a stable, flat production. Unlit cultivation dominates before- and after the winter production.
“Extra growth light is needed to realize sufficient yield and quality in winter”, according to plant specialist Peer Hermans, who conducts the research on behalf of Signify. “The trials have shown that you can influence the plant build-up somewhat with specific light recipes, for which LED is ideally suited.” By accurately tuning the light intensity and spectrum offered to the developmental stage of the plant, you can optimize the leaf surface and stretching of the flower trusses and leaf stalks. A better plant build-up can benefit the production. The idea is to raise the production quality through light optimization.
Grower Marcel Dings from Brookberries, co-initiator behind Fragaria Innova, noticed some influence on the plant build-up, but the extra assimilates that came with it, went mostly to the crop and less to the fruits. Dings: “Next season will focus on how we can further optimize the division of the assimilates in the plant, and how we can get the assimilates to the fruits”. The grower notices that there are a lot of variables at play, such as: cultivars, planting times, cultivation goals, light spectra, light intensity, and the balance between natural daylight and artificial lighting. “The benefit of this new generation of LED grow lights is that we can play with lighting efficiently and that we can finetune the recipe to our own wishes and possibilities. Within this project, together we can achieve faster and more progress. I am satisfied with the results of this first year, but there is definitely room for further optimization. Hopefully, we can keep this going in the coming years.”
Grower Dave Linssen, a participant within Fragaria Innova (cultivar: Malling Centenary), had a trial with different spectra at one company location, planted in August just like his unlit crop. “The lit plants went into production earlier in winter, as expected. When it came to kilos and plant build-up, we hardly noticed any difference between the light spectra”, he concludes. “We may need to tinker a little to get the ideal light recipe for our company. It seems obvious to me that growing under LED is a desired addition.”
Based on these encouraging results, the trial set-up for the coming season will be determined. Spectrum research and testing different cultivars will be part of this research. For more information on growing strawberries with LED grow lights, please go to www.philips.com/horti.
--- END ---
For further information, please contact:
Global Marcom Manager Horticulture at Signify
Daniela Damoiseaux
Tel: +31 6 31 65 29 69
E-mail: daniela.damoiseaux@signify.com
About Signify
Signify (Euronext: LIGHT) is the world leader in lighting for professionals and consumers and lighting for the Internet of Things. Our Philips products, Interact connected lighting systems and data-enabled services, deliver business value and transform life in homes, buildings and public spaces. With 2020 sales of EUR 6.5 billion, we have approximately 37,000 employees and are present in over 70 countries. We unlock the extraordinary potential of light for brighter lives and a better world. We achieved carbon neutrality in 2020, have been in the Dow Jones Sustainability World Index since our IPO for four consecutive years and were named Industry Leader in 2017, 2018 and 2019. News from Signify is located at the Newsroom, Twitter, LinkedIn and Instagram. Information for investors can be found on the Investor Relations page.
About Innoveins | Fragaria Innova
Innoveins is an ecosystem where organizations cooperate at the cross-over between plants and technology to develop innovations through co-creation and bring them to the market.
Within Innoveins, Fragaria Innova unites ambitious strawberry growers to jointly tackle challenges in the areas of labor, upscaling, efficiency, plant health and resilience, biodiversity, growth media, product quality, continuity, delivery reliability and smart farming.
5 Things To Check When Comparing Lighting Designs For LED Grow Lights
As a grower, you invest in supplemental LED grow lights because they power the yield and quality of your crops.
May 17, 2021
· When you compare different lighting designs, make sure to compare apples with apples.
· These are the 5 things to check when comparing lighting designs for LED grow lights.
Eindhoven, the Netherlands – As a grower, you invest in supplemental LED grow lights because they power the yield and quality of your crops. In fact, the rule of thumb is that 1% light output equals 1% crop yield. So, it is vital that your LED lighting investment delivers the full performance you paid for.
The performance is determined by the light intensity and light uniformity of the LED grow lights you use. If the installed light intensity is lower than what has been designed, there will be less yield. If the uniformity is inconsistent, individual plants will grow and develop at different rates and there will be uneven production in your greenhouse.
Before you start
When you compare different lighting designs, make sure to compare apples with apples. This means taking 3 things into account:
1. Verify the credibility of the performance claims that manufacturers make
2. Make sure that DIALux calculation software is used for the lighting design. This calculation software is independent and commonly used in the horticulture market.
3. Check which input parameters have been used for each lighting design. It is easy to tweak the input parameters and give the impression of a more positive light level and uniformity within the lighting design. So which parameters are crucial?
Most important input parameters to check
• Is the right product specified? Check if the exact product that you have selected for your project has been used in the lighting design; with the right light output (PPF in µmol/s) and spectrum (blue/red/white/far red/…)
• Are your specific design values used like the average light level at your crop (PPFD in µmol/m2/s) and the overall light uniformity?
• What are the standard settings? The height of the grow light and crop (free height), reflection factors, and size and position of the area that is used in the uniformity calculation have an impact on the average light level and overall uniformity.
#1 Check the free height
The first input parameter to check is the free height specifying the distance between the LED module and the head of the crop. The free height can seriously impact the overall uniformity value. In case of high-wire tomato crops, with a limited free height of 1.50 to 2.50m, realizing a good overall uniformity value can be a challenge. An optimistic free height or calculating uniformity on floor level as if there is no crop will positively impact the overall uniformity value.
The free height is calculated by measuring the eventual top of the crop and the mounting height of the LED grow light.
#2 Check the reflection factors
Another important parameter to check, are the reflection factors used in the lighting plan. A reflection factor indicates the amount of light that is reflected by walls and other objects in a space. DIALux calculation software has originally been designed for indoor spaces like offices, where you will get reflection off the walls, ceiling, and floors that impact the light level on your desk. To avoid being too optimistic about the outcome, the reflection values in DIALux are set at 0% for a greenhouse lighting design, because the glass in a greenhouse does not reflect the light from the grow lights.
#3 Check the area that has been used to make light intensity calculations.
The next thing to check is the defined calculation surface. The size of the calculation area and the position of the grow lights within that area will seriously impact the average amount of active photons that reaches the surface of the crop (PPFD value in µmol/m2/s). When comparing lighting design results from different manufacturers, make sure that the calculation surface shows an equal number of maximum (peaks) and minimum (dips) light intensity values. Only then you receive a realistic average PPFD value in the lighting design.
In the below example, you will see two positions of a calculation area within the same light plan, which will generate far better average light intensity values in the B situation, because the light intensity is calculated with an area that shows more grow light (peaks), and consequently less areas with the minimal amount of grow lights, which will not represent the reality after installation
Position of measurement grid defines the outcome of average light intensity
#4 Check the size of the calculation surface
Another important factor is the size of the calculation surface that will impact the overall uniformity value. When comparing lighting design results from different manufacturers, make sure the same calculation surface has been applied.
To represent a real-life situation, a calculation for the full compartment area should be made that includes the edges of the greenhouse. In case of a typical production area, a centred area is used. You may understand that a full compartment will generate lower uniformity levels, because of the lower light intensities at the edges. So, make sure you always compare either full compartments or smaller areas.
#5 Check the used uniformity
The final parameter to check is the uniformity being used. Uniformity can be expressed in different ways. When you run the DIALux lighting design software, it provides you with different types of uniformity. When comparing lighting design results from different manufacturers, make sure the same type of uniformity is applied. For a horticulture application, we prefer to express uniformity as the average light intensity divided by the maximum light intensity, which represents real-life situations best.
In Summary
When comparing lighting designs there are lots of tweaks that suppliers can possibly make to finetune their plan. In case you want to make a proper comparison, you have to take a few parameters into account.
- Is the specified product with the right spectrum and efficiency used in the calculations?
- Is the right light level for your crop used and the right overall light uniformity?
- Are the settings comparable:
o Is the free height correctly defined?
o Are the reflection factors set to 0%?
o Does the measurement grid have an even number of light and dark spots in it.
o Are you comparing full compartment or small centered area numbers?
o And is the defined uniformity similar in the lighting designs?
Read our other blog and learn how to evaluate the performance claims of an LED grow light.
Grow with the pros
You want to be sure to get a rapid return on your investment and have all aspects of your project carried out professionally. With Signify, your project is in experienced hands. Signify is the global leader in the lighting sector and has built up a substantial track record in more than 1000 projects in the horticultural lighting market since 1995. This includes over two decades of dedicated experience developing tailor-made, LED-based light recipes that help growers speed up growth, increase yield and improve the quality of plants. With cutting-edge LED innovations at our command, we can custom-build a science-based solution for you.
Pascal van Megen is an application engineer at Signify with a background in mechanical engineering. As an application engineer, Pascal ensures that growers are provided with high-end horticulture lighting designs. He is providing internal and external training to customers and partners in the application of the Philips LED Horticulture products and systems. He acts as a consultant to customers and engineers, to drive continuous improvement of Philips LED lighting solutions.
--- END ---
For further information, please contact:
Global Marcom Manager Horticulture at Signify
Daniela Damoiseaux
Tel: +31 6 31 65 29 69
E-mail: daniela.damoiseaux@signify.com
About Signify
Signify (Euronext: LIGHT) is the world leader in lighting for professionals and consumers and lighting for the Internet of Things. Our Philips products, Interact connected lighting systems, and data-enabled services, deliver business value and transform life in homes, buildings, and public spaces. With 2020 sales of EUR 6.5 billion, we have approximately 37,000 employees and are present in over 70 countries. We unlock the extraordinary potential of light for brighter lives and a better world. We achieved carbon neutrality in 2020, have been in the Dow Jones Sustainability World Index since our IPO for four consecutive years, and were named Industry Leader in 2017, 2018, and 2019. News from Signify is located at the Newsroom, Twitter, LinkedIn, and Instagram. Information for investors can be found on the Investor Relations page.
"Together We Are Expanding Our Facility In Sweden"
"Our expansion will enable us to offer our sustainably-grown salads to more Swedish households throughout the year, so we are looking forward to an exciting time," says Andreas Wilhelmsson, CEO of Ljusgårda
"Our expansion will enable us to offer our sustainably-grown salads to more Swedish households throughout the year, so we are looking forward to an exciting time," says Andreas Wilhelmsson, CEO of Ljusgårda.
In April, the first batch of salads was harvested in the company's new premises – and already now, Ljusgårda can deliver significantly more locally-grown salad to Swedish households, all year round. When the new 7000-m2 indoor farm, of which 2500 m2 growing area, is completed in the summer, Ljusgårda will become one of Europe's largest vertical farms.
"We are delighted to help Ljusgårda to produce local, climate-smart salads, says Henrik Nørgaard, Nordic Commercial Director of Agriculture at Signify[1]. "Ljusgårda shares our vision of a sustainable transformation within agriculture and is focusing in particular on quality and flavor."
Supporting the expansion
Andreas continues, "Signify has extensive experience of advanced lighting solutions and works with other large-scale indoor farms. They provide us access to lighting experts who can help us to continuously improve production. Signify is also one of the few suppliers with the capacity to deliver in line with our growth plan. Together we are expanding our facility in Sweden. Signify’s controllable light spectrum enables us to optimize the light for cultivation and produce the highest quality crops," Andreas continues.
Andreas Wilhelmsson
More than 70% of the fruit and vegetables consumed in Sweden today are imported by truck, ship, or plane from other countries. With the aim of making food production more sustainable, Swedish vertical farmer and salad producer Ljusgårda plans to increase its production 20-fold and expand its cultivation capacity to produce at least 60 tons of salads a month, which is the equivalent of around 1 million bags.
Signify is helping the Swedish vertical growers to expand their production facility in Tibro. By expanding its cultivation area from 300 m2 to 2500 m2, Ljusgårda will be able to supply fresh, locally produced salad all year round. Signify is providing the company with its latest high-tech solutions: Philips GreenPower LED production modules and the Philips GrowWise control system. These allow the light spectrum and lighting levels to be controlled, resulting in improved quality and higher yields per square meter.
As a result, Ljusgårda can ensure that its salads are tasty and nutritious. LED lighting also makes it simpler to predict growth levels, which means that it is easier for Ljusgårda to adapt its production to market demand during the season. The lighting is managed by the Philips GrowWise control system to schedule growth cycles well in advance and to allow for greater automation.
Making an impact
Henrik adds, "This is important to Signify because of our strategic goal of helping our customers accelerate the use of sustainable farming to improve agriculture’s impact on climate change. By using the latest lighting systems in vertical farming, Ljusgårda can supply salads that meet the highest food safety standards. The right lighting also results in plants of a higher quality and a higher percentage of crops being consumed, reducing food waste.'
"Additionally, by helping Ljusgårda to grow locally we contribute to significantly reducing the food miles these salads have to travel before making it to Swedish consumers. We are therefore proudly taking part in the journey from the first green shoots to more consumers being able to enjoy Swedish salads all year round," Henrik states.
Today, Ljusgårda's salads are sold in more than 60 ICA supermarkets, mainly in the Swedish regions of Västra Götaland and Småland. With the expansion of the facility and production on a much larger scale, Ljusgårda aims to supply sustainable Swedish salads to stores throughout Sweden.
Supporting food availability through horticulture LEDs illustrates Signify's commitment to supporting good health and wellbeing (SDG3). It is key to Signify's commitment to doubling the percentage of our revenues for brighter lives, which benefit society, to 32%. "This is part of our Brighter Lives, Better World 2025 program, which was launched in September 2020."
For more information:
Signify
Daniele Damoiseaux, Global Marcom Manager Horticulture
For more information:
Ljusgårda
info@ljusgarda.se
www.ljusgarda.se
Sources used:
[1] Climate-smart agriculture is an integrated approach to managing landscapes—cropland, livestock, forests, and fisheries—that addresses the interlinked challenges of food security and accelerating climate change.
11 May 2021
Explore The Sixth Edition of Clima, Powered by IGS
In this edition, we look at why precision farming and Controlled Environment Agriculture (CEA) techniques are becoming more mainstream, and the skills and talent required to make this approach a success
In this edition, we look at why precision farming and Controlled Environment Agriculture (CEA) techniques are becoming more mainstream, and the skills and talent required to make this approach a success. Technology is having a greater impact on agriculture than ever before, and this is only set to increase. It will bring with it a wider and more advanced agricultural ecosystem that requires a skilled, knowledgeable, and committed workforce, with as great an appetite for innovation and capacity to problem solve as any generation before.
Discover more on this topic in the sixth edition of Clima today.
Bringing future talent to Agriculture 4.0
We discuss the emerging influences on education and skills development across Agriculture and Horticulture with two senior leaders from Scotland’s Rural College (SRUC). We spoke to Professor Fiona Burnett, Head of Connect for Impact in SRUC’s Knowledge and Information Hub, and Ruth Vichos, Lecturer in Horticulture, about the evolution of Agriculture 4.0, and how technology is impacting skills evolution and teaching mechanisms.
Listen To The Full Interview
Vertical Farming Gaining Popularity Among Traditional Growers
They see opportunities in using techniques from vertical cultivation, for example in propagation. “It is not just about improving the quality of the young plants, but above all about the controllability of the cultivation, and thus the speed and quality,” says Koen with Mechatronix
'Where in recent years vertical farming enthusiasts have perhaps been mainly qualified as hipsters with a rather expensive hobby, this new branch of horticultural sport is steadily on the rise and traditional growers are also finding their way to the multi-layer installations.'
They see opportunities in using techniques from vertical cultivation, for example in propagation. “It is not just about improving the quality of the young plants, but above all about the controllability of the cultivation, and thus the speed and quality,” says Koen with Mechatronix.
What is the most expensive greenhouse there is? That would be an empty greenhouse, and that is exactly where, according to Koen van Mechatronix, opportunities lie for vertical farming. “In lettuce cultivation you see many nurseries working with fully automated cultivation systems. With mobile gutters, they can use the available space in the greenhouse as efficiently as possible. However, it remains difficult to adjust the speed of the preliminary cultivation to the available space in the pond. By replacing traditional, unexposed or illuminated cultivation with cultivation that is more controllable in a multi-layer system, you can plan much more precisely how many plants to set up. Accurate to the day, you know how many plants are ready to go in,” he says.
The lighting company developed a multi-layer cultivation system together with Meteor Systems: an automated track, including spray booms. In the past quarter, intensive testing was already carried out with a grower who works with floating gutters. “We have 120,000 cuttings up in the test setup. Multi-layered, of course, because otherwise, it would be too expensive in terms of floor space. Now you can grow enough cuttings on a few square meters to fill 1 / 3rd of the garden,” he shows.
The controlled cultivation makes it possible to use the entire cultivation system more intensively, which shortens the payback period and the depreciation period. “You can get more heads of lettuce from your expensive greenhouse,” Koen summarizes. “In addition, you always send exactly the same quality plants to the pond, which also gives you more control over your outgrowth. If you still adhere to the correct lighting strategy, you can start making a perfect prediction on your planning. This wasn't possible before. ”
Further opportunities
In herbs there are also opportunities for hybrid cultivation, where part of the cultivation will takes in an indoor or multi-layer cultivation system and the outgrowth will take place "as usual" in the greenhouse. “In the classic, fast-growing herbs, a full indoor cultivation is soon done, but in the woody herbs it is purely the rooting that takes place in a VF installation,” says Koen. “Total cultivation is too slow for this. Your turnaround time is too long and that makes the investment per m2 too expensive, but rooting often goes perfectly in a VF system.” In the same way, plant breeders use the techniques in part of the propagation, for example, to improve healing after grafting or to speed up cultivation from mother plants. "Ultimately, propagation is about the controllability of a known phase of the propagation."
All in all, this means that there appear to be more and more surprising opportunities for vertical farming, also in Europe. “The first major projects are starting to arrive, although we also see that people here are even less familiar with the possibilities and often depict it as expensive cultivation,” says Koen. “And of course an economic assessment must always be made. It will not be the case that complete crops will be placed indoors here tomorrow - there is always a reason to look at the sun. Where possible we use the sun, and where necessary the lighting. ”
For more information:
Koen Vangorp
MechaTronix
koen@mechatronix-asia.com
www.horti-growlight.com
8 Apr 2021
Three Way To Maximize A Vertical Farm's Potential
Population growth and urbanization are forcing global food production to a crossroads
17 March 2021
By Abhay Thosar, Ph.D., director of horticulture services for Fluence by OSRAM
Previously published in the February 2021 issue of Inside Grower.
Population growth and urbanization are forcing global food production to a crossroads. Overall, migration to high-density areas increases access to health care, higher-paying jobs, education, and other socio-economic opportunities. But it also places more strain on existing infrastructure and demand for resources, leading to greater water scarcity, energy consumption, waste, and, perhaps most importantly, threats to the food supply, prices, and quality.
The economically disadvantaged will be the first to pay the price of increased urbanization. As prices increase and access to quality food sources decreases, the nutritional health of poor populations will decline. Over the next several years, the responsibility of bridging the gap between projected food supply and demand in urban areas will largely fall on vertical farms, an industry that is expected to nearly quadruple by 2025 to about $16 billion. The COVID-19 pandemic could accelerate that growth rate even further.
The vertical farming industry still has challenges to overcome. Production costs remain relatively high and, as a young market, knowledge gaps in operational best practices in critical areas like facility design and environmental conditions threaten long-term sustainability and profitability. The evolving economic dynamic with supermarkets is forcing vertical farms to scale quickly as they attempt to grow and supply a wider variety of crops while maintaining the buyer’s standards around produce size, quality, and nutritional value.
And, as we look to the future, new innovations in lighting strategies, facility design, cultivation best practices, and automation mean that vertical farming operations have to be constantly adapting and seeking new operational advantages. This is just as true for new market entrants and relatively established players alike, and each will be critical to not only maintaining profitability, but ensuring that food production in urban areas can increase with demand.
With that in mind, here are three critical factors vertical farmers need to consider to meet market expectations, improve efficiency and ultimately grow, cultivate and distribute larger quantities of quality food to more people in a smaller area.
Facility design as a function of market demand
The history and growth of the vertical farming market are largely driven by two trends at the consumer and buyer levels. A decade ago, consumers asking questions about how, where, and when their food was grown was practically unheard of. Things are different today. People want to know the provenance behind the food they buy and ensure it is chemical-free and safe to eat. Every product has become more than a label, it’s become a story that consumers want to hear, and one that has an equally significant impact in where they shop and what they buy.
Supermarkets have taken notice. Beyond that, though, vertical farming operations have given supermarkets one more option in addition to the existing supply chains on which they’ve relied for food production and distribution. Vertical farms play an even more important role during large-scale disruption events like the COVID-19 pandemic or massive recalls. As a result, supermarkets—which value the consistent supply of produce above all—are turning to their local vertical farming operations and, in some cases, even investing in them directly. The increased attention, however, comes at a cost (literally and metaphorically). Supermarkets are demanding that the vertical farms supplying them grow a wider variety of crops—lettuce, tomatoes, cucumbers, leafy greens, microgreens, herbs—more consistently while also meeting unique specifications around weight, aesthetic, nutritional value and a variety of other factors that are ultimately dictated by the vertical farm’s environment and the grower’s expertise.
Vertical farmers are quickly realizing they need to expand their portfolio from potentially a handful of crops to a few dozen or more, raising a range of questions on how to design or retrofit their facilities and adjust environmental conditions that favor any given crop.
The first decision many vertical farmers face is the growing technique that will be most scalable and viable for their operation. Hydroponics, aeroponics and aquaponics have all emerged as viable options with varying degrees of success, but they’re far from interchangeable.
In the end, there is no universal solution for every vertical farm. Cultivators should closely consider their buyers’ expectations, and how those expectations might change over time. Then, cultivators must assess the full range of their crops’ needs and how each might respond differently to various environmental factors and lighting strategies.
Strike a balance between environmental factors
The next set of factors governing facility design, investment and day-to-day operations should always be the environmental conditions themselves.
How air flows into and across each rack of a vertical farm is one of the most unique and important challenges vertical farms have to solve. Ignoring or failing to closely monitor airflow is often a death blow to entire sections of crops and to profitability, yield, and consistency as a result. Air movement helps to maintain temperature, humidity, and transpiration at each rack, and lack of it creates wide temperature swings or large gaps between crops at the bottom and crops at the top. It’s an incredibly fragile balance to strike. Everything from the number of access points into a warehouse—there should only be one access point—to HVAC and circulation systems affect air movement.
As a best practice, the maximum difference between the temperature at the top-most rack and the bottom-most rack should be no more than two degrees Fahrenheit. In practical scenarios, cultivators facing large temperature fluctuations can also consider placing crops that prefer relatively warmer temperatures—such as basil, oregano, chives, sage or thyme—at the top and simply let the laws of thermodynamics do the rest.
Carbon dioxide enrichment is a slightly easier condition to manage but no less important and changes based on temperature and lighting strategy. CO2 enrichment, too, can fluctuate based on the number of access points into a warehouse (again, there should only be one). Enriching a cultivation environment with carbon dioxide stimulates photosynthesis and plant growth, the rate of which is critically dependent on the difference between CO2 concentrations in the air and in the leaf cells.
The law of diminishing returns puts a cap on the amount of carbon dioxide cultivators should be introducing. CO2 is by no means the only factor governing plant growth, but vertical farms have the advantage of being able to closely monitor and control CO2 levels. To do so properly, however, they shouldn’t shy away from significant investments in both handheld devices—which allow cultivators to measure carbon dioxide levels at each rack, each plant, and each leaf—but also large-scale control systems that can measure and track CO2 throughout the entire warehouse.
Humidity levels govern a plant’s transpiration rate and the aperture sizes of its stomata, ultimately affecting how much water it moves from its root zone to release back into the warehouse. When a plant’s stomata open, they release water while also collecting carbon dioxide, making the balance of humidity, temperature, and carbon dioxide all the more crucial. Different plant types in different growth stages have different transpiration rates, adding even more complexity to how a vertical farm is designed and managed. The most common way to express humidity is relative humidity, the percentage of water vapor in the air at a given temperature compared to the total amount of water the air can hold at that temperature. In vertical farming, however, vapor pressure deficit (VPD) is the more accurate way to gauge humidity’s effect on plant growth. VPD remains an interesting discussion among researchers as the industry seeks to understand the differences between VPDs for air and leaves as well as exact VPD calculations.
Every environmental factor in a vertical farm affects the others to some degree. Nearly everything can be controlled; it’s both the advantage and the challenge native to the market. No factor, however, is more important to photosynthesis than its primary driver: light. Each factor—CO2, temperature, airflow, humidity, fertilizer, irrigation, VPD—need to be fine-tuned with changes to light quantity and quality to optimize plant performance and response.
Designing an effective lighting strategy
The design and implementation of an effective lighting strategy is and always will be the primary driver of your vertical farm’s success. In environments as complex as vertical farms, identifying the correct light intensity, spectra, photoperiod, and configuration will determine how other environmental factors work together to optimize a facility for plant yield and quality.
The first of these, the fixtures themselves, carry more implications for vertical farms than other cultivation spaces; in a vertical farm, plants receive no other source of light. The sun isn’t the safety blanket that it is for greenhouses. This simple and obvious fact means that vertical farmers have to find efficiencies in ways others don’t, which can manifest across a variety of operational metrics. Light efficacy, for instance, becomes more important. Most vertical farms are located in urban areas and are likely paying a premium for electricity. Maximizing micromoles per watt and reducing energy waste becomes more than a sustainability initiative, it’s critical to overall profitability.
Similarly, vertical farms operating warehouses measuring in the tens of thousands of square feet need fixtures with a good form factor without sacrificing light intensity. The right configuration means vertical farms can squeeze more racks into their facilities while also putting the lights closer to the plants for better results.
Beyond the hardware specifications, lighting design and strategy consist of several key factors: light intensity, light quality (or spectra), and light bar configuration. Each should be rooted in a facility’s overarching goals—typically defined by the consumer or buyer. Lighting strategies can be customized by crop, yielding specific plant chemistries or changes in biomass. Differences in spectra and light intensity can affect a crop’s coloration, shelf life, taste, and smell. Desired crop characteristics should be determined upfront in conjunction with the prospective buyer, therefore guiding a lighting designer to identify the optimal strategy to accomplish a facility’s goals.
Light quantity is the first and foremost aspect when it comes to optimizing the productivity of the crop. It is important to target the correct mols/day for each crop. Light quality (or spectra) is defined by measuring light’s wavelength in nanometers (nm). Wavelengths of light that drive photosynthesis are primarily found within 400 to 700nm—a range identified as photosynthetically active radiation (PAR). In a vertical farming environment, broad, white light has proven effective for tissue culture, propagation, and vegetative growth—while also serving the more practical function of making it easier for human eyes to diagnose and observe crops day in and day out. As the body of research into LED applications has expanded, it’s become clear that lighting strategies need to shift based on the growth stage. The days of bombarding plants with the same intensity and spectra are quickly fading. More and more research is showing that different cultivars respond to different lighting strategies at different stages of their maturation. More nuanced, customized lighting strategies are increasingly leading to tangible business outcomes for cultivators: longer shelf life, improved aesthetic, enhanced nutritional value, faster cycle times, and higher yields.
LED improvements will continue to drive costs down, while more in-depth research will discover and confirm a new set of lighting strategies and operational best practices to help vertical farmers meet future market demand for increased food production while also improving profitability. Overall, the future for vertical farms is bright and ripe for even broader innovation. Automation—the final frontier of food production—will mean even greater control of agricultural environments. That future is on the horizon. For now, though, vertical farms just need to stick to what they can control, which is pretty much everything else.
About Abhay
Abhay Thosar is the director of horticulture services at Fluence by OSRAM, where he is responsible for managing a team of horticulture specialists that enhances how cultivators grow their crops, optimize their lighting strategies and increase profitability in their operations. He holds a Ph.D. in plant physiology from Gujarat Agricultural University and spent more than a decade at leading greenhouses and nurseries throughout the U.S.
Lumileds Addresses Industry Growth With LUXEON 3030 HE Plus Horticulture
The new LEDs are engineered for robust sulfur protection – critical for long and stable lifetime in warm and humid environments
Broad spectrum white LEDs are widely available
San Jose, CA – February 2, 2021 – Lumileds today announced immediate high quantity availability of its LUXEON 3030 HE Plus Horticulture LEDs. Based on the company’s leading 3030 LED portfolio and characterized for horticulture, the new options offer high PPF/W, broad-spectrum white light that enables grow lights that are productive and economical.
“In horticulture applications growers are looking for time tested, top performance and reliability, the LUXEON 3030 HE Plus Horticulture delivers the photons that enable consistent and high growth output with the highest of efficiencies,” said Mei Yi, Product Manager.
The new LEDs are engineered for robust sulfur protection – critical for long and stable lifetime in warm and humid environments – and are specified for horticulture at 65mA and Tj= 25°C with CCTs from 2200K to 6500K and CRI of 70, 80 or 90. When matched with LUXEON Deep Red and Far Red options a complete horticulture illumination solution is at hand.
LUXEON 3030 HE Plus Horticulture is available in manufacturing quantities today. It offers a 0.1V forward voltage bin, quadrant color bin inside 3SDCM, and a maximum drive current of 480mA. Detailed product information can be found at https://lumileds.com/3030Horticulture.
About Lumileds
For automotive, mobile, IoT, and illumination companies that require innovative lighting solutions, Lumileds is a global leader employing more than 7,000 team members operating in over 30 countries. Lumileds partners with its customers to push the boundaries of light.
To learn more about our portfolio of lighting solutions, visit lumileds.com.
For further information, please contact:
Steve Landau, Director Marketing Communications
+1 408 710 4090
Year-Round Under-Glass Herb Cultivation In The Heart of Berlin
ECF Farmsystems uses innovative LED lighting solutions from Fluence for today’s herb cultivation in the heart of Berlin
Urban Farming Using LEDs From Fluence by OSRAM
ECF Farmsystems uses innovative LED lighting solutions from Fluence for today’s herb cultivation in the heart of Berlin. An innovative urban farm, ECF Farm Berlin (ECF Farmsystems) uses techniques for greenhouse and vertical cultivation of basil. The farm also uses aquaponics to naturally fertilize the crops, the produce of which then goes to Rewe, Germany's second-largest supermarket chain.
Less space and more production is the name of the game at ECF Farmsystems: comprehensive lighting solutions, from growing to greenhouse culture, enable the year-round production of uniform, aromatic basil plants.
Modern agriculture thanks to LED lighting / Image: Osram
Urban cultivation from seed to finished product
On-site propagation on VertiCCs, a racking system for vertical cultivation developed by ECF Farmsystems, increases production by 35% with the same footprint and optimized supply chain from seed to finished product.
The system also ensures consistent, uniform products. This is because ECF Farmsystems completely controls the entire growing cycle with less pest infestation and more accurate yield forecasting. In addition, the VYPR lighting systems offer higher-quality light spectra compared to conventional lamp systems. In addition, thanks to VYPR solutions, greenhouse growing is no longer seasonal, as efficient crop lighting provides uniform plants with consistent productivity, regardless of local weather.
With Fluence's RAZR Series, ECF Farmsystems achieves more effective operations and a 35% increase in production without the need for new construction or remodeling. By expanding vertical growing in the plant nursery, which eliminates the need to invest in additional growing space/facilities, ECF Farmsystems saves important emission costs. Propagation on VertiCCs systems with RAZR exposure allows ECF Farmsystems to control the entire growth cycle, better manage pests, and now calculate yields more accurately.
The new RAZR module will be available in January 2021.
For more information:
fluence.science/webinars
https://en.ecf-farm.de/
https://www.osram.com/os/applications/horticulture-lighting/index.jsp
Publication date: Thu 7 Jan 2021
Improving The Profitability And Economic Sustainability of Vertical Farms
“According to our research, most vertical farms are focused on lighting as a means of improving yield and growth speed,” says Rob Agterberg, Partner at Back of the Yard Algae Sciences (BYAS)
“According to our research, most vertical farms are focused on lighting as a means of improving yield and growth speed,” says Rob Agterberg, Partner at Back of the Yard Algae Sciences (BYAS).
“However, not enough vertical farms are looking at innovative ways of growing faster and better. Through our research, we’ve discovered that certain algal proteins improve the photosynthetic process and this results in a biostimulant effect and also improves taste, aroma, shelf life and nutrient value in vertically farmed crops such as lettuce."
The biostimulant research
Algae biostimulant
“At BYAS we’re creating ingredients such as alternative proteins, food colorants, made from microalgae. We have a patented, unique, zero-waste production process that enables us to extract food ingredients and alternative proteins from microalgae,” says Marc Peter Geytenbeek, Partner at BYAS. The company has been researching its biostimulant for vertical farming the past 2 years and recently published a scientific article outlining a number of breakthrough results. Currently, the biostimulant is being tested by vertical farming companies, including across the world.
Saving time and money
Rob states that about two-thirds of vertical farms are struggling to be economically viable, due to their high capital expenditures. He says: “Our research has shown that lettuce growth increases after adding the biostimulant. This increase results in up to 20% shorter growth cycles, saving on lighting and therefore energy and labor costs. We think that our biostimulant can be a huge boost to make vertical farms more economically sustainable.”
Sustainable works
“Surprisingly, the biostimulant can be made from algae grown on agriculture waste streams,” says Rob. The biostimulant is organic and GRAS (generally recognized as safe). What is particularly interesting to vertical farming is the fact that the biostimulant is an extract, so there is no need to administer a live bacteria or fungus into a hydroponic system. BYAS is committed to the circular economy - sustainable re-use of resources. This can be found in the production processes that are zero-waste and use very little energy.
For more information:
Back of the Yard Algae Sciences
Marc Geytenbeek, Partner
marc.geytenbeek@algaesciences.com
www.algaesciences.com
Rob Agterberg, Partner
rob.agterberg@algaesciences.com
www.algaesciences.com
Publication date: Wed 6 Jan 2021
Author: Rebekka Boekhout
© VerticalFarmDaily.com
Signify Adds Artechno To Its Philips Horticulture LED Partner Network To Lower Bar For Future Vertical Farmers
“Partnering with Signify is a logical choice for us,” said Art van Rijn, Owner of Artechno
January 4th, 2021
Signify Chooses Artechno As its New Philips
Horti LED Partner For The Unique Modular
Turnkey Vertical Farming Solutions That it Provides
· Lowers bar for growers and entrepreneurs to start a new vertical farm
· Helps to automate the production process for diverse crops from seed to harvest
Eindhoven, Netherlands – Signify (Euronext: LIGHT), the world leader in lighting, has signed a partnership agreement with Artechno, global provider of scalable Automated Vertical Farming systems, to make it easier for growers and entrepreneurs to start a state-of-the-art vertical farm using Philips GreenPower LED lighting. Artechno, headquartered in De Lier, the Netherlands, is an engineering company that develops and realizes unique automated cultivation systems based on hydroponic substrates for clients across the globe.
“Partnering with Signify is a logical choice for us,” said Art van Rijn, Owner of Artechno. “We’re a winning combination as we offer our customers the highest efficiency and highest reliability, while Signify provides energy-efficient lighting solutions that perform 24/7, 365 days a year. Together this will help our customers to grow tasty, high-quality produce year-round.”
Artechno has channeled 100+ years of combined experience in horticulture into its flagship product, Automated Vertical Farming, or AVF+. It offers a fully automated solution for producing a variety of crops from seed to harvest. Artechno has automated all processes to ensure low labor costs and consistent crop production. AVF+ is a modular system that can be customized to the needs of the crop, available space, or desired production volume. Growers and entrepreneurs can start with a few key components and scale up their automation and operation as they grow.
“We’re proud to expand our partnership network with the knowledge and expertise of Artechno,” said Udo van Slooten, Business Leader Horticulture at Signify. “They share our values of innovation, quality and reliability. This partnership will help us lower the barriers for growers and entrepreneurs who are considering a vertical farm by enabling us to offer Philips GreenPower lighting within fully modular and automated systems for every aspect of their operations.”
Signify continues to expand its horticulture partner network, further demonstrating its commitment to lead the horticulture industry as the innovative LED lighting systems provider for the indoor farming industry.
--- END ---
For further information, please contact:
Global Marcom Manager Horticulture at Signify
Daniela Damoiseaux
Tel: +31 6 31 65 29 69
E-mail: daniela.damoiseaux@signify.com
About Signify
Signify (Euronext: LIGHT) is the world leader in lighting for professionals and consumers and lighting for the Internet of Things. Our Philips products, Interact connected lighting systems and data-enabled services, deliver business value, and transform life in homes, buildings, and public spaces. With 2019 sales of EUR 6.2 billion, we have approximately 37,000 employees and are present in over 70 countries. We unlock the extraordinary potential of light for brighter lives and a better world. We achieved carbon neutrality in 2020, have been in the Dow Jones Sustainability World Index since our IPO for four consecutive years, and were named Industry Leader in 2017, 2018 and 2019. News from Signify is located at the Newsroom, Twitter, LinkedIn and Instagram. Information for investors can be found on the Investor Relations page.
Unleashing The Potential of Indoor Sole-Source LEDs on Tomato Production
Enlightening collaboration between Heliospectra and the University of Tokyo
Enlightening Collaboration Between Heliospectra And The University of Tokyo
Heliospectra announced a collaboration with the Institute for Sustainable Agro-ecosystem Services (ISAS), the University of Tokyo. In an effort to redefine and unleash the potential of indoor tomato production, this will be a joint research project with the University’s Institute for Sustainable Agro-ecosystem Services (ISAS), in collaboration with Associate Professor Wataru Yamori at the Agricultural Biology and Biogeochemistry Group, and Heliospectra Japan.
With the average age of Japanese farmers reaching 67 years old and younger generations migrating to cities, traditional farming is facing a crisis. This is forcing the country to investigate new ways to produce food. Plant factories are scaling to meet consumer food demand, mainly in vegetable cultivation in both solar and artificial light environments, and the industry is growing. Japan already has approximately 200 lettuce factories using artificial light, and that number is expected to double by 2025. However, to-date, plant factories have been unsuccessful in cultivating light-hungry vine crops such as tomatoes in indoor artificial light. Heliospectra and the University of Tokyo want to challenge this.
Working together, they are looking to build a business model for Japan’s plant factories and PFAL (Plant Factory with Artificial Lighting) organizations for indoor tomato cultivation. In the University lab, the Professor and his students will be using Heliospectra’s MITRA linear, the horticulture market’s first truly modular LED light. Designed by growers for growers, MITRA is a solution for high-light crops, with high-intensity light output and electrical efficacy of up to 2.8 µmol/J.
“We are very excited to be a part of this research together with Dr. Yamori and the ISAS at the University of Tokyo. Over the years, Heliospectra has conducted research on light’s effect on tomatoes in indoor facilities with great results,” comments Yasuhiro Suzuki, General Manager of Heliospectra Japan. “We now look forward to further expanding our knowledge and developing more effective indoor cultivation of tomatoes for commercial use. We look forward to collaborating with the university and sharing with the world our knowledge of growing tomatoes indoors.”
For more information:
Heliospectra
info@heliospectra.com
www.heliospectra.com
Publication date: Thu 29 Oct 2020