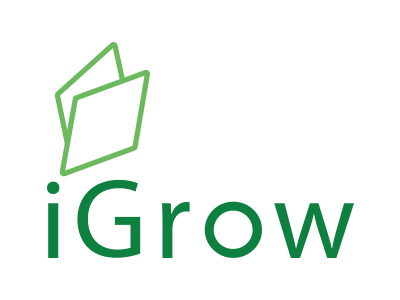
Welcome to iGrow News, Your Source for the World of Indoor Vertical Farming
Central Minnesota Research Project Growing Kale Indoors
The project is a partnership with Todd-Wadena Electric Cooperative, Central Lakes College, Lakewood Health System, Great River Energy and the Electrical Power Research Institute
The project is a partnership with Todd-Wadena Electric Cooperative, Central Lakes College, Lakewood Health System, Great River Energy, and the Electrical Power Research Institute.
Written By: Rebecca Mitchell
July 21, 2021
Central Lakes College research analyst Noah Boetler shows a panel of kale plants in the Sota Grown pod during a virtual tour on July 13, 2021. Rebecca Mitchell/Pioneer Journal
STAPLES, Minn. — A community research project in Staples involving indoor gardens is set to continue growing.
The hydroponics project started in 2020 with Great River Energy, Todd-Wadena Electric Cooperative, and the Electrical Power Research Institute hoping to learn new technology and increase access to fresh produce. And even with kale as the chosen plant, local organizations rooted for the success of the hydroponics pod. The pod, planted at the Central Lakes College Staples campus, is a shipping container with room for 5,820 kale plants.
“I didn’t know how things were going to grow in here, it’s kind of a weird concept with there being no sunlight and things like that, so just seeing it go from a little seed to your big plant and harvesting it, I think that has been the coolest aspect,” CLC research analyst Noah Boelter shared with Minnesota educators in a virtual tour on July 13.
The partnership is called "'Sota Grown" and has helped develop a fully enclosed hydroponic container for growing fresh plants all year long — to supplement existing agriculture practices in communities across the state.
The pod, equivalent to one acre of crops, is a supplement to traditional farming, not a replacement, as TWEC member service manager Allison Uselman said. Although kale is the focus of the two-year project, the team has experimented with growing basil, swiss chard, lemon balm, and chives. Romaine lettuce, butterhead lettuce, and salad mixes are next on the list — and after a year of only kale, Boelter is excited for the new opportunities.
Each kale seed, planted by hand, starts in the nursery before being transplanted to vertical panels. The kale takes 12 weeks to reach maturity. The team of four staff members and interns plant and transplant on Wednesdays and harvest on Mondays.
“Kale is pretty forgiving, which is very fortunate for us,” Boelter said after sharing about a frozen pump during the winter. The kale wilted and bounced back in a matter of days. The team is also learning about flooding and nutrient dosing in the pod.
With the expected growth of indoor agriculture, Uselman said electrical companies will need to prepare for the change. For example, the pod uses the most energy when most other customers could have off-peak rates. The light and water systems run from 4 p.m. to 8 a.m. daily. The kale is watered for five minutes every 45 minutes. The electricity is about $600 a month.
“It’s education with students, it’s giving back and feeding our communities, and Todd-Wadena has the opportunity then to research all the electrical side of things and really understand this industry before it grows to a larger state,” Uselman said.
The pod’s water usage depends on the humidity levels outside, with the most water used in the winter — about 10.5 gallons every day—and about five gallons a day in the summer. The two water tanks deliver water above the panels and water behind the plants. There are also several different nutrients added, such as one to adjust pH levels.
“In the summertime, the pod does not use a whole lot of water because the HVAC unit has a dehumidifier built into it and that’s recirculating around a gallon of water an hour that gets dumped back into the pod, so it’s really efficient in the summer,” Boelter explained. “But when it’s winter, the air is so dry that’s when we use the most water.”
The indoor pod means the ability to regulate the temperature, which is a cool 65-68 degrees and having no pesticides or herbicides used on the plants since most bugs remain outside. There are some drain flies due to the algae.
The red LED lights in the Sota Grown pod at Central Lakes College are the only source of heat. The lights and water run from 4 p.m. to 8 a.m. daily. Rebecca Mitchell/Pioneer Journal, July 2021
As for sunlight, the LED lights are the only heat source in the pod, as Boelter said, though it is also insulated. The red and blue lights support stem growth and leaf density.
The process yields about 20 pounds of kale a week — and on a record week 43 pounds — or over 1,000 pounds as of July 5. All of the kale is donated to Lakewood Health System, who shares the kale through the Food Farmacy and Hilltop Regional Kitchen. The Kitchen uses the kale in specific meals for those who have tested positive for COVID-19 and people being discharged from the hospital. People can also receive free kale at the summer farmer’s market on Thursdays.
As Lakewood’s Community Health Coordinator, Amy Wiese works with about 70-100 bags of kale a week to find where it can best be served. She said the kale lasts about two weeks in the fridge.
People also receive kale recipes for new ways to enjoy the vegetable. Wiese enjoys massaging the kale to break down the bitterness and then eating it in a salad. Other favorites are kale chips and soups.
“We just see the benefits of this project and recognize the positive impact that healthy food can have on individuals and in the community,” Wiese said. The organizations also hope to address local food deserts. “It’s really amazing that we are able to provide fresh produce all year with this pod” even with snow on the ground for six months of the year.
The seeds grown and sown in the community have finished their process with new seeds set to germinate, grow to maturity, and be harvested and packaged in four to eight hours for their short drive up the road.
Photo: 1 - The kale seeds are planted in peat moss plugs and stored in the nursey for three weeks before being transplanted to the indoor panels. The planting process takes about an hour. Submitted photo
Photo: 2 - The shipping container contains an acre of kale growing hydroponically with LED lights. Photo courtesy Todd-Wadena Electric Coop
Photo: 3 - Each section has 22 panels with space for 5,820 kale plants or the resemblance of one acre of crops. Rebecca Mitchell/Pioneer Journal, July 2021
Vertical Farming For The Future
Beyond providing fresh local produce, vertical agriculture could help increase food production and expand agricultural operations as the world’s population is projected to exceed 9 billion by 2050
Posted by Sarah Federman, AAAS Science and Technology Policy Fellow, Office of the Chief Scientist andPaul M. Zankowski, Senior Advisor for Plant Health and Production and Plant Products, Office of the Chief Scientist in Research and Science
Aug 14, 2018
Indoor And Vertical Farming
May Be Part of The Solution To Rising Demands
For Food And Limited Natural Resources
Imagine walking into your local grocery store on a frigid January day to pick up freshly harvested lettuce, fragrant basil, juicy sweet strawberries, and ripe red tomatoes – all of which were harvested at a local farm only hours before you’d arrived. You might be imagining buying that fresh produce from vertical farms where farmers can grow indoors year-round by controlling light, temperature, water, and oftentimes carbon dioxide levels as well. Generally, fresh produce grown in vertical farms travels only a few miles to reach grocery store shelves compared to conventional produce, which can travel thousands of miles by truck or plane.
Beyond providing fresh local produce, vertical agriculture could help increase food production and expand agricultural operations as the world’s population is projected to exceed 9 billion by 2050. And by that same year, two out of every three people are expected to live in urban areas. Producing fresh greens and vegetables close to these growing urban populations could help meet growing global food demands in an environmentally responsible and sustainable way by reducing distribution chains to offer lower emissions, providing higher-nutrient produce, and drastically reducing water usage and runoff.
Recently, USDA and the Department of Energy held a stakeholder workshop focused on vertical agriculture and sustainable urban ecosystems. At this workshop, field experts shared thought-provoking presentations followed by small group discussions focusing on areas such as plant breeding, pest management, and engineering. Workshop attendees from public and private sectors worked together to identify the challenges, needs, and opportunities for vertical farming. A report on this workshop will be released to help inform Departmental strategic planning efforts for internal research priorities at USDA and external funding opportunities for stakeholders and researchers.
We’re excited about the potential opportunities vertical agriculture presents to address food security. That’s why USDA already has some of these funding and research opportunities in place. The National Institute for Food and Agriculture has funding opportunities (PDF, 1.22 MB) that could support future vertical agriculture conferences and research. Similarly, the Agricultural Research Service is working on a project to increase U.S. tomato production and quality in greenhouses and other protected environments. We look forward to continuing our partnership with our customers, both internal and external.
Lead Photo: Photo credit: Oasis Biotech
Category/Topic: Research and Science
Tags: Office of the Chief Scientist National Institute of Food and Agriculture NIFA Agricultural Research Service ARS Department of Energy vertical farming
USA - Orlando, Florida: No Better Time Than Now
Kalera, one of 2020’s biggest headline makers in vertical farming, has even bigger plans for its still-under-construction nationwide network, and there’s nothing that can slow it down.
Kalera, one of 2020’s biggest headline makers in vertical farming, has even bigger plans for its still-under-construction nationwide network, and there’s nothing that can slow it down.
May 21, 2021
Matthew J. Grassi || Photos by Connor Barber
Kalera, based in Orlando, Florida, is taking the local indoor farming concept and stretching it from coast to coast during a nationwide pandemic. This all while turning out flavor and nutrient-packed and conventional crop price-competitive lettuce and leafy greens in a zero-pesticide, 95% less water-requiring closed-loop automated production system.
The highly automated vertical grower (with the slogan The Science of Great Greens) operates three indoor vertical farms, two of which are situated near its corporate headquarters in Central Florida.
The operation’s third vertical farm, located in Forest Park, Georgia, recently completed its inaugural lettuce harvest. This farm is one of the largest indoor farms in the U.S. Southeast at 77,000 square feet and is reportedly capable of churning out 10 million heads of lettuce to local Atlantans and foodservice distributors annually. Heads of lettuce pulled out of the new Atlanta facility have already made their way to local operators like Publix, Sysco and Fresh Point.
With the first harvest in Atlanta now under its belt, the nationwide farm network rollout rolls on into the summer.
The latest scoop: Kalera is pursuing a whirlwind agenda for the home stretch of 2021 and into the next year, opening new, modular farms in places like St. Paul, Houston, Denver, Columbus, Seattle and Hawaii. There, the company says the farm will be the island’s first operable commercial indoor farm when launched.
The new farm building campaign is not the only big news with Kalera. The group recently made waves by acquiring Vindara, an up-and-coming disruptor in the plant breeding world. The operation says it leverages machine learning and AI alongside traditional breeding techniques to drastically shorten the development window of new seed varieties and traits bred specifically for indoor vertical farming.
Leading and innovating
While the Kalera name is fairly new, the group is not some fly-by-night operator that just sprang up in a retrofitted warehouse one day. CEO Daniel Malechuk says the group worked for 10 years “behind the scenes in stealth mode” to develop the coast-to-coast indoor farm network concept.
“For the first time ever, an indoor farming company can offer you something from Hawaii to Seattle to Florida, and everywhere in between — which is exactly what the foodservice companies want — and it’s a consistent, quality product,” he says. “We’re bringing scale and unit economics and high yields unseen to this point in the vertical farming world, a couple of years ago people laughed at this concept, but clearly this is no longer a pipe dream.”
Malechuk has been with Kalera for just about a year now, having spent the bulk of his career in supply chain and retail purchasing across the food industry. The former VP of the supply chain for Mastronardi Produce has a firm grasp on what consumers want from an indoor produce company, and how to make that a reality in today’s world of segmented supply chains and COVID-closed borders.
“I have a lot to learn [about vertical farming] and I still do, and honestly that is what is most exciting for me — solving some of these challenges of ‘this is how we do it now, but can we do it this way’,” he says. “Can this be done at scale and with profitability? Those are the burning questions in this industry right now, and at Kalera we are answering those questions in a big way.”
Answering those questions by staying focused on providing a phenomenal produce product at a reasonable price is what sets Kalera apart in a crowded segment, according to Malechuk. “[Growing] something people can afford and not have to splurge to purchase this premium product, that is really what drives. Of course, our robotics and advanced technology is part of that focus, too, but our customer and what they care about — quality grown and sustainably produced, and at what price — that’s what gets us out of bed every morning.”
Kalera's closed-loop growing system produces crops with 95% less water used than field growing, according to the company.
Building out during a shutdown
Austin Martin is Kalera’s chief operating officer, based at the group’s first farm outside Orlando. The former big-box retail logistics professional oversees all of the far-reaching tentacles of the Kalera nationwide expansion strategy, managing the various farm buildouts as well as many aspects of the farm operations themselves.
“For those that were willing to work really hard and push the envelope to make things happen, [COVID] was actually a great opportunity for us to focus and get ahead,” Martin says when asked what it has been like managing such an ambitious rollout throughout the pandemic.
COVID did in fact alter Kalera’s go-to-market slightly. Initially, management was keenly focused on the food service retail segment as its primary customer. Then COVID hit and the bars, restaurants and local distribution networks that serve them practically grounded to a halt. Martin and his team had to quickly pivot to consumer-facing food retail to ensure a mixed-channel distribution strategy which the company will stick with once normalcy returns.
“These food retailers want to partner with a more sophisticated provider who can guarantee continuity in supply across a wide geography, yet still maintain that same level of focus on food safety,” Martin says. “They deal with a lot of regional growers and that’s really just because they don’t have another choice. They want the redundancy that a larger-scale operation can provide.”
The indoor farm's acquisition of a vertical farming genetics startup allows for customized hybrids brimming with nutrients, taste, and texture.
Seed acquisition
While Kalera’s scale and approach to vertical farming are attention-worthy attributes, what put the operation over the top was the acquisition of indoor seed genetics provider Vindara. It’s not every day that a farm can buy the company and infrastructure that provides arguably the most crucial link in the production chain.
The collaboration was born out of both familiarity and need: both companies have close ties to North Carolina State University’s ag programs — Malechuck is an alumnus — and Kalera’s leadership had realized a glaring need for genetics tailored specifically to indoor production systems.
Add Vindara president and co-founder Jade Stinson to the list of Kalera-connected executives with an interesting background. Stinson has worked in agriculture for decades, having helped with uncovering the link between mad cow disease and humans in the United Kingdom before joining BASF after college.
Vindara was founded in 2018 on the back of Stinson’s vision of becoming the premier provider of elite genetics for the vertical farming space. The fact that they figured out how to accelerate the seed trait breeding cycle from a ten-year lead time down to 18 months, while maintaining and even offering customizable yield and flavor profiles, simply cannot be oversold.
We're bringing scale and unit economics and high yields unseen to this point in vertical farming ..."
“Say we develop a new indoor lettuce seed variety today with higher yield. Ok, that’s great, but that can’t be it,” Stinson says. “LED lighting technology will evolve, there’ll be more automation and more hands-off growing style, different plant architectures. This industry is moving too fast for traditional breeding to keep up, and when you can leverage deep machine learning and analytics, you can really dive into the genetics and really start leveraging genetic diversity.”
What today’s vertical farming space requires is what Stinson calls a “systems approach” to breeding. “It’s not a one seed fits all approach. The production systems from grower to grower are so disparate, one seed in one system won’t move the needle,” she adds.
The partners share a focus on democratizing their own corners of the ag universe. Vindara is wholly-owned by Kalera, yet operates autonomously and will continue serving genetics to the entire CEA industry. Kalera wants more access to fresh, nutritious and affordable food, and Vindara wants the same for the breeding innovations side of the coin, too.
“Let’s democratize and have growers be able to call us up and say ,‘Ok I want a lettuce with dark purple color, high yield and nutrition, and it has to stay crispy in transport,” she envisions. “The Kalera vision is why should just the top 5% of the world population have access to the most nutritious food? And that’s what we believe in, too.”
Automation and technology
Having launched its first facility located at Orlando, Florida’s Marriott World Center convention area (which has a commercial irrigation and climate control system) Kalera’s chief technology officer and co-founder knew the operation required more precision and customization.
“Development and implementation of our automated HyCube growing system has been a tremendous advantage for our production cycles,” says Cris Toma, co-founder, and chief science officer. “It’s something we started to develop a couple of years ago because those off-the-shelf systems didn’t meet the requirements of our vertical farming operation and it was too difficult to extract the data.”
Today, the system is a cloud-based, mobile-optimized ecosystem of sensors and controllers and irrigation modules that are in constant interaction with the group’s closed-loop production systems.
By developing and launching its own system, the operation has cultivated a unique approach to technology via its experiences thus far.
“We like to say that we are farmers who use technology, rather than being a technology provider looking for an application in farming,” Toma says. “And that’s coming from somebody like myself with a machine learning and digital imaging processing background.”
By establishing indoor farms from coast to coast (and beyond) Kalera can offer its customers a consistent product from California to Maine.
“We do not make these statements because we do not understand technology, or have trepidation in dealing with it, rather it’s been my entire professional life,” he continues. “Yet, at the same time we need to be very careful that we don’t destroy the ROI and economic performance of each project with how we integrate technology.”
Once Kalera’s farm network is built and fully operational, the built-in advantage provided by all that aggregated production data will be a massive enablement piece for the head growers at each facility.
“We’ll create a digital data warehouse and implement big data analytics and algorithms, and those activities will drive our sensors with computer visions and AI for tracking plant health and development across all facilities,” Toma says.
While that data is important to what Kalera plans to do in 2021 and beyond, it will still rely on the tried-and-true head grower structure.
“The AI is not quite there yet for full automation, but the trend is there and will only continue to grow. And yet we still need a human in the loop for certain tasks, for the more complex tasks you still need the expert in there monitoring and making adjustments, and then you hope to build on the expert with data and analytics,” Toma says.
Bottom line
Kalera isn’t settling down anytime soon.
“I envision our expansion plans are going to continue, and we are also looking at international expansion in the years ahead,” Toma replies when asked what’s next for the operation. “We’ve got a deep pipeline of opportunities to capitalize on.”
For the CEO, it’s all about continuous improvement and never growing complacent.
“We never want to be flat organizationally, we are constantly striving to get better, learn, refine, and innovate within our business model,” Toma says. “And, if it adds value to our customers, then we’re going to do it.”
USA - KENTUCKY: Elliott County High School Receives New Container Farm Through AppHarvest
The curriculum provided by AppHarvest will cover topics such as high-tech growing and an introductory course on local food systems and food resiliency
May. 29, 2021
SANDY HOOK, Ky. (WSAZ) - Some students at Elliott County High School will soon be able to help grow food -- not only for themselves but for the entire region.
The Elliott County High School container farm is the fourth addition to AppHarvest’s program in 2021 and the sixth educational container farm to date.
The container farm program was launched in 2018 and demonstrates AppHarvest’s ongoing commitment to cultivating interest in high-tech farming as it seeks to create America’s AgTech capital from inside Appalachia. Each retrofitted shipping container acts as a hands-on agricultural classroom for students, allowing them to grow and provide fresh leafy greens to their classmates and those in need in their communities.
AppHarvest has opened container farms in Eastern Kentucky at Madison Central High School in Richmond; Breathitt High School in Jackson; Shelby Valley High School in Pikeville; and Rowan County Senior High School and AppHarvest’s flagship farm at Rockcastle County High School in Morehead.
Elliott County High School’s container farm includes space to grow up to 2,760 seedlings and 2,960 mature plants, all at once in a nutrient film technique (NFT) system. NFT is a water-saving system in which plant roots are continuously fed all necessary water and nutrients by a shallow stream, also called “film.” Excess water drains to a holding tank and is then recirculated. This system of high-tech growing sets the Elliott County container apart from AppHarvest’s other educational containers, which have operated hydroponically and vertically.
“One of our goals at AppHarvest is to build an AgTech capital right here in Appalachia,” said Jonathan Webb, AppHarvest Founder, and CEO. “We want to see communities across the region use technology to bring farms to life. And in five years from now, it’ll be leaders from these very programs coming to us with ideas on how we continue to evolve and change agriculture.”
Makayla Rose, Elliott County High School agriculture teacher, will lead the newest container program.
The curriculum provided by AppHarvest will cover topics such as high-tech growing and an introductory course on local food systems and food resiliency.
“This is exciting. Some students who might not like to get in the dirt have a different way of growing vegetables,” said Garret Barker, president of Elliot County’s FFA chapter. “It’s different than my farm at home. It doesn’t depend on outside factors like the rain. It’s all controlled by an app.”
Lead Photo: Elliott County High School receives new container farm through AppHarvest (Kimberly Keagy/ WSAZ)
Modular Hydroponic Growing Spaces In Freight Containers For Local Food Production
Freight Farms’ design was the first containerized vertical growing environment using hydroponic technology
May 17, 2021
Southeastern Pennsylvania Correspondent
A Massachusetts company has developed a unique, hydroponic growing environment in closed 40-foot freight containers that are being used world-wide to grow produce in areas with bad soil or weather conditions not conducive to outdoor growing.
Bay State natives Jon Friedman and Brad McNamara were developing rooftop greenhouses in the early 2000s when they realized a modular, hydroponic container might be a more viable solution.
Hydroponics wasn’t something new. Historians believe this soilless gardening can be traced back to hanging gardens of Babylon in Iraq built by King Nebuchadnezzar about 600 BC. Nutrient-rich water was pumped to the gardens from the Euphrates river to sustain its plants. A water-based growing thread continued through history and in the 1930s a University of California scientist, William Gericke, coined the term from the Greek word “hydro” (water) and “ponics” (work).
Friedman and McNamara, who were building outdoor, roof-based gardens on older residential buildings, looked outside the box, and turned their focus to widely available shipping containers.
They thought they could provide the equivalent of 2 acres of growing space in traditional 40-foot-by-8-foot containers and extend growing seasons year-round everywhere — especially in areas that couldn’t support traditional outdoor agriculture or in parts of the world affected most by climate change.
They named their company Freight Farms and placed their first container less than a decade ago. Now the concept is catching on worldwide.
View Photos From Freight Farms
Freight Farms’ design was the first containerized vertical growing environment using hydroponic technology. It was initially funded by a Kickstarter campaign in 2012, where they raised the funds to build a prototype to allow local food production to be available to everyone, anywhere.
The first commercial unit was installed at Boston Latin School, the oldest public school in the U.S., to produce fresh produce for the school cafeteria as well as serving as a teaching classroom for high school students.
“The company has placed 350 units in 48 states and 32 foreign countries,” Friedman said.
The company also introduced proprietary software called “farmhand” to help automate many farm processes, and is manufacturing its 10th generation container, the Greenery S, incorporating the latest technology and automation for vertical, hydroponics growing.
Growing Strong
Hydroponic Operation Supplies High-End Restaurants
Art Petrosemolo, Southeastern Pennsylvania Correspondent
Although the Freight Farms container units are capable of growing a variety of produce, leafy greens are its specialty and the best choice for farmers looking to sell their harvests year-round.
Containers also have been embraced by educational institutions to supply fresh vegetables for cafeterias and serve as learning and teaching space.
St. Joseph College in Standish, Maine, has been operating a Freight Farms unit for years to both supply fresh vegetables to its dining facilities as well as for student employment.
The site also has been a tool for community involvement with St. Joseph students working with a town Institute for Local Food System Innovation utilizing the Freight Farms container in partnership with a large hydroponic farm and commercial processing kitchen for events and agritourism.
With a decade head start in the business, Freight Farms does not have major competition in hydroponics container gardening production, although, in recent years, it has seen significant growth in multiple indoor soil- and water-based farming formats including warehouses, greenhouses and pods that are addressing growing produce year-round.
Climate change has increased concern about food production for growing populations worldwide with extreme weather conditions and higher levels of carbon dioxide in the atmosphere.
Friedman and McNamara have always been aware that the challenge to expansion for stand-alone, container gardening is the cost of power and each new rendition of their growing units has addressed both power consumption and automation to be more efficient.
Their latest Greenery S model uses growing lights that are 50% more efficient than previous models and the technology allows farmers to choose pre-set growing modes to maintain higher yields — 20% higher than earlier models — while prioritizing energy use.
Addressing affordable and clean power for customers, Freight Farms recently partnered with Arcadia, a Washington, D.C., energy company to offer affordable, renewable power options for customers.
Going forward, Friedman said growing container units will continue to become more efficient, allowing owners to increase their growing yield while having more control of their energy use to power the unit.
Slide Show Photos:
Lights and plant arrangements in Freight Farms new Greenery S model container.
Photo provided by Freight Farms
Leafy greens grow in Freight Farms’ own Greenery Farm container.
Photo provided by Freight Farms
This Freight Farms container is ready for shipment.
Photo provided by Freight Farms
Freight Farms' containers under construction in their Vermont facility.
Photo provided by Freight Farms
Lexy Basquette, Freight Farm’s on-site farmer, checks on some of her growing plants.
Photo provided by Freight Farms
Greenhouses, Vertical Farming and Urban Ag: Controlled-Environment Agriculture Has Growth Potential
Paul Post, New York Correspondent
USA: NEW YORK - When A Shipping Container Becomes A Farm
Compact, enclosed vertical farms are making their way to Hudson Valley's urban areas
Compact, Enclosed Vertical Farms Are Making Their
Way To Hudson Valley's Urban Areas
May 3, 2021
John Lekic is the chef and owner of Farmers & Chefs in Poughkeepsie and vertically grows his own produce for his restaurant in a shipping container on site. He came across the concept of shipping container farming at an exhibition at the Culinary Institute of America in 2019. Aaron Lacan
The Hudson Valley is quite familiar with what it means to be farm-to-table, but what if the farm is also practically right next to the table, even in the more urban and metro areas?
Vertical farming via high-tech shipping containers is emerging as a new solution for businesses seeking to grow their own produce in a way that shrinks the necessary agricultural footprint while maximizing yield and reducing produce travel time. Here in the Hudson Valley, a 20 by 20-foot shipping container is being used to grow up to 400 pounds of fresh produce a month at Farmers & Chefs restaurant in Poughkeepsie.
Last year, the restaurant partnered with an Israel-based agro-tech company Vertical Field to grow herbs and vegetables for its dishes in a new and innovative way. The startup, established in 2006, uses technology to create innovative growing methods to improve food supplies in urban areas around the world, working mostly in the Middle East and Europe but also recently in the United States — including right here in Dutchess County.
Poughkeepsie's Farmers & Chefs is one of the first businesses in the Hudson Valley to try shipping container farming. The restaurant's 20 by 20-foot climate-controlled container (pictured above) produces about 400 pounds of fresh produce a month. Aaron Lacan
John Lekic, chef and owner of Farmers & Chefs, grows everything from buttercrunch lettuce, kale and baby arugula to herbs like rosemary, sage and basil in his enclosed vertical farm. The container is divided into four growing fields and is set on the restaurant’s property for customers to see, which has drawn even more interest to Farmers & Chefs as of late.
So why vertical farming?
Vertical Field is just one manufacturer specializing in reimagining steel shipping containers into enclosed, climate-controlled farms that are powered by LED lights instead of the sun, essentially supercharging a growing environment. Freight Farms and Grow Pod Solutions, other manufacturers, also tout this farming approach for its lower burden on farm labor and land, and for the higher output per square foot.
Shipping container farming is climate-controlled, powered by LED lights instead of the sun, and can produce high yield in a small space. But humidity and start-up infrastructure costs can be challenges. Aaron Lacan
“It’s a dream come true for chefs to be involved from the seed to the plate,” said Lekic. “It’s a great experience when you grow your own ingredients.”
Lekic pursued vertical farming after coming across Vertical Field during an exhibition showcasing a number of Israeli-based companies involved in food and agriculture at the Culinary Institute of America in late 2019.
Before the shipping container arrived at the Poughkeepsie restaurant, Lekic sourced vegetables from nearby farms and grew herbs in small outdoor gardening beds on site. However, Lekic found that it wasn’t enough yield, especially in the summer, and he often collaborated with additional farms to fill the gap. With a shipping container for growing, the restaurant is able to produce enough of what they need and on site – a key benefit for Lekic.
“There is a huge importance of having urban farms where the demand is,” said Lekic. “The problem with today’s agriculture is that everything has to travel. Most people are not aware of it, but depletion of the nutrients in our food is a huge issue.”
If you harvest spinach, it would be full of vitamin C that same day, Lekic said. But that changes dramatically just 48 hours later, when that nutrient is mostly gone. (A 2013 study by the University of California showed that spinach could lose as much as 90 percent of vitamin C in a single day.)
Farmers & Chefs restaurant grows everything from buttercrunch lettuce, kale, and baby arugula to rosemary and sage in its on-site shipping container. Aaron Lacan
By growing the restaurant’s produce steps away from the kitchen, “it’s as fresh as it gets,” said Lekic.
Farmers & Chefs received its shipping container farm right around the same time that COVID-19 hit last year, which Lekic said actually worked out well, as it gave him a chance to learn the ins and outs of vertical farming during a period that was quiet for his restaurant. By April, he was harvesting the first crops.
“Overall, the goal of vertical farming is to reduce the cost of healthy and fresh food to the retailer and to the end buyer as well,” said Vertical Field marketing director Noa Winston. “Since vertical farming reduces transportation costs, food losses, inventory inconsistencies, and price fluctuations due to climate, natural disasters, and other crises that create shortages, the retailer with vertical farming can benefit from consistency, security, and ownership over the entire supply chain.”
In another regional example, Evergreen Market, a grocery store in Monsey in Rockland County, partnered with Vertical Field to grow vegetables that ultimately stocked the store’s produce aisles, while also inviting customers to view its micro-farm when they visit the store.
Cost and maintenance concerns
This farming approach isn’t for everyone and there are drawbacks. “While it does offer some solutions to things like land access — which is, frankly, a huge barrier to the farming we advocate for here in the Hudson Valley — there is a lot of infrastructure needed,” said Kathleen Finlay, president of Glynwood, a center for regional food and farming based in Cold Spring.
“That brings a whole other set of challenges — how to create enterprises with a high capital upfront cost, how to get sustainable systems. It’s a different suite of challenges than more land-based production.”
Indeed, the start-up costs for an on-site shipping container farms aren’t cheap, although businesses say savings can be realized downstream by the reduced costs of paying produce purveyors for food that a restaurant or business is now growing itself.
Freight Farms' 2021 Greenery S model costs $149,000, which doesn’t include the shipping fee. Additional start-up costs can vary depending on where its being shipped, training packages selected, and any extras. Vertical Field would not disclose the fees associated with its model.
Plus, there is a bit of a learning curve when farming in a shipment container. Lekic played around with different variables, like what was best to grow at the same time, to see what would produce the highest yield.
"It's as fresh as it gets," said John Lekic of Farmers & Chefs, pictured above, about the new way of farming. Aaron Lacan
“For my purposes, I learned to stick with only two to four items – mostly greens,” said Lekic about his growing. “It makes the most sense based on my demand.”
Maintenance is an ongoing effort with an enclosed growing system that requires constant electricity and temperature controls to assure optimal growing conditions. “It’s always work,” said Lekic.
Over the past year, Lekic had to work out some kinks and issues, like making sure the air conditioning and heat levels were favorable to growing produce year-round. Just like traditional farming, some seasons might require more work — a vertical farm in the summer, for example, would have increased humidity that could negatively affect plants if not properly controlled.
While some growers may need back-up plans for electricity outages, Lekic doesn't foresee issues there because he is connected to the main restaurant building, which runs on a hospital-grid electricity system. Just in case, he has two generators that he could connect to if needed.
These drawbacks are outweighed by the ability to grow such consistent produce yield himself on site, he said, and the built-in technology features like being able to water plants by pushing a button on his phone. Lekic said overall it’s pretty easy to operate and monitor, so much so that the restaurant is looking into upgrading its original container to the newer version of the same size, and purchasing a second container.
“I’m interested in doing a mushroom container,” said Lekic. “There is the possibility of that. It’s a completely different kind of experience, but we would be super excited.”
DIY shipping container farming
While the hefty price tag of some farming shipping containers might be too prohibitive for some, others are riffing off of elements of tech-first farming for their own DIY growing methods.
KC Sullivan, a New Jersey-based mushroom farmer, created his own vertical farming environment out of an abandoned 40-foot-length shipping container that was used for storage at the Whitechapel Projects in Long Branch. Sullivan, who often collaborates with Tivoli Mushrooms here in the Hudson Valley, decided to create his own container farm by spray foaming it, sealing the floors, putting in an HVAC system, adding lighting and installing a misting mechanism.
He estimated the costs to be between $15,000 and $20,000 — not insignificant but far cheaper than a new shipping container already turbo-charged for farming.
“It was challenging,” said Sullivan. “There is no real guidebook or instruction manual on how to create a container mushroom farm. It was all about brainstorming how we wanted it to be.”
While it’s only been a year since mushrooms have been grown out of this urban shipping container, Sullivan is happy with the high-yield results: he's growing around 400 to 500 pounds of mushrooms a week. Mushroom container farming is slightly different from growing vegetables or herbs; for example, Sullivan doesn’t grow compost mushrooms, so there is no dirt necessary.
“We grow hardwood varieties, so it’s exclusively on red oak saw dust that is supplemented with agricultural byproducts,” said Sullivan. “You mix the two together with water, pasteurize it to kill off any pathogens, inoculate it with the strain of mushroom you’re looking to grow. It goes through an incubation period in a separate room [outside of the container], and then it goes to the fruiting room, which is the container and where it will be harvested.”
Just like Lekic, Sullivan also has run into some maintenance hiccups. The waterlines froze during the winter, which was a “big challenge and setback,” leading to a starved off humidification system, costing him around 100 to 150 pounds of crop.
Despite that hurdle, Sullivan also says the container can stand up against storms because it’s “built like a tank,” while regular farmland could be vulnerable to severe thunderstorms and potential flooding.
“One tool in the toolbox”
While an exciting option for some, vertical farming is “one tool in the toolbox” and it’s important to not forget about the benefits of traditional farming, said Finlay of Glynwood.
Finlay applauds any effort to produce food “that aligns with environmental sustainability,” but doesn’t think vertical farming will ever replace traditional farming or even fix the lack of land available for production.
Still, any effort to grow fresh food for more people is a win overall.
“We need more healthy food, accessible and affordable to more people,” said Finlay. “As much as vertical farming can play a role to that, I think that’s wonderful.”
Written By
Cloey Callahan is a lifelong Hudson Valley resident who was born and raised in Brewster, lived in New Paltz for four years while she attended college, and now resides in Newburgh on Liberty Street. On a sunny day, she strolls through Newburgh enjoying the 19th-century architecture on her way to the Hudson River waterfront. You can reach her at cloey.callahan@hearst.com to say hi or with pitches.
VIDEO: One Sure Way To Save Our Soil – Don’t Use Any
The advantage of container farming is the ability to create commercial-scale production within a small space the size of your standard 40-foot shipping container through vertical farming techniques
In the push for regenerative agriculture and soil rehabilitation, container farming has an important role to play.
The idea behind regenerative agriculture isn’t new, but this year it is front and center as one of the key initiatives of the official Earth Day 2021 campaign: Restore Our Earth™.
According to the Earth Day organization, overfarming has caused soil capacity in the U.S. to decline dramatically, losing soil 10 times faster than it can be replenished. The result is that in many places, the land has as few as 60 harvests left before it is completely depleted. Unfortunately, with ownership of farms increasingly concentrated in the hands of industrial or foreign producers, the promise of short-term profits wins out over long-term solutions that would prioritize soil health.
What is regenerative agriculture?
Regenerative farming takes an opposite position. As a school of thought, it is a method of farming that actively fights soil degradation by restoring carbon to the soil, which has a double benefit of renewing the viability of the land while simultaneously removing carbon dioxide from the atmosphere. There are many different types of regenerative agriculture, here’s a helpful video to explain the main three:
But between destroying the soil and saving the soil, there’s a third option: not using any soil at all. This is the premise behind container farming.
Container farming to save soil.
Container farming is a subset of the indoor farming industry, which includes everything from greenhouses and warehouses to at-home tabletop setups. The advantage of container farming is the ability to create commercial-scale production within a small space the size of your standard 40-foot shipping container through vertical farming techniques. Inside the container, plants are protected from the external elements and nurtured using nutrient-enriched water, powerful red and blue light, and optimal temperatures.
Notice anything missing? Oh yeah–soil!
Container farming with hydroponics completely eliminates the need for soil to grow food, which is great news for the whole regenerative agriculture movement. Since regenerative farming is based on the idea of protecting soil, container farming is able to take the whole idea to the logical extreme by not using any soil–period.
Not only does container farming prevent the further degradation of soil, but it actually frees up land to be actively regenerated. At Freight Farms, our containers (each capable of growing an average of 2 acres of food) have already saved 700 acres of land… which’s equal to about 530 football fields!
Additional sustainability benefits
Beyond regenerative agriculture, which is primarily focused on soil, container farming brings many additional sustainable benefits. The Greenery S is able to save:
Water: 99% less water than is used in conventional agriculture.
Food miles: we move the farms, not the food. Instead of trucking/shipping food from a centralized location, we put the farm as close to the final consumer as possible.
Carbon emissions: in addition to reducing food miles, we’ve partnered with Arcadia to make it easy and effective for our farmers to get onto the renewable energy grid and make their carbon footprint just one-quarter of what it would be if they were farming using industrial farming methods.
Regenerating communities
While regenerative agriculture may start with soil, the implications on climate change, food access, and food security are clear. In the same way, container farming is also more than just improving the sustainability of our agriculture system. In addition to saving soil, land, water and reducing food miles and carbon emissions, container farming unlocks many important social gains:
Independence: when we are not reliant on soil, land, and climate, we can make any place a farm. This makes it possible for us to create the distributed system we need to combat the harmful effects of industrial farming and centralized food systems.
Equality: independence from soil and land also creates more food equality, since individuals and communities need fewer resources (money & land) to create commercial-scale farms.
More farmers: Soil is complicated and nuanced, it takes huge amounts of experience and education to know how to do regenerative agriculture properly. With container farming, everyone can be a low-impact farmer.
More varieties: Conventional agriculture is beholden to monocropping, which improves the unit economics of growing food but also increases the risk of crop failure, blight, and soil degradation. Container farming makes it possible to grow hundreds of plant varieties, introducing people to new types of plants and growing public perception of the diversity you can have with fresh greens. This can have an overall positive effect on market demands and help move the whole system away from relying on mono-cropping.
Learn more about the Earth Day Restore Our Earth™ campaign and check out how Freight Farms is helping support the regenerative farming movement with container farming!
Freight Farms
Empowering anyone to grow food anywhere. Freight Farms makes local food accessible in any climate with the Greenery™ container farm.
April 23, 2014
Follow Earth Day Earth Day 2021 Sustainability Regenerative Agriculture Agriculture
USA: This Colorado Company Is Building Farms In Shipping Containers To Help Feed People In Need
FarmBox Foods wants people to be able to farm anywhere, allowing them to access fresh food they otherwise wouldn't be able to
Author: Jeremy Moore
April 19, 2021
FarmBox Foods Wants People To Be Able To Farm
Anywhere, Allowing Them To Access Fresh Food
They Otherwise Wouldn't Be Able To
SEDALIA, Colo. — A three-year-old Colorado company has an ambitious goal: to bring food security, safety, and sustainability to communities in need around the world.
FarmBox Foods aims to achieve that goal by connecting those communities to sustainably sourced food that's grown locally inside one of their container farms.
Their first product was a vertical hydroponic farm, or VHF, built inside a shipping container.
The company has since developed a second product: a gourmet mushroom farm, or GMF.
So far, customers in Colorado include Centura Health, Vitamin Cottage Natural Food Markets, and the C Lazy U Ranch in Granby.
FarmBox CEO Rusty Walker and COO Jake Savageau joined 9NEWS to talk about how they hope to change the way the world thinks about farming.
9NEWS also spoke with a prospective customer of FarmBox, Cori Hunt of the Denver restaurant group Edible Beats.
(Editor’s note: Responses have been edited for context and clarity.)
As a mission-driven company, what is the mission of FarmBox Foods?
Walker: Our goal and our mission is to get our products out into the communities where we can help develop food security programs. We’re looking to get into food deserts, opportunities where folks in the world might not have access to good, clean nutritional food. And so we kind of strive as a company that’s driven to feed the world one container at a time. And we’re ready to go out and manufacture thousands of these if we can.
We’re able to decentralize growing food by being mobile – being able to deploy these by just having a semi come in. We can then lift it up on a flatbed and take it to anywhere in the world. We’ve got two containers going to islands. We’ve got our first container that took off for the island of Jamaica. It’s going to Montego Bay where it’s going to be used behind mega marts on the island. And then we have another container which is our gourmet mushroom farm that’s going to be going to Tahiti where they’re going to be using that to feed the island population which does not have access to that type of food.
One big area that we’re really focusing on is the urban areas throughout the U.S. where they don’t have a lot of land to grow. These farms can go right into the parking lots, behind a church for example. We’re working with a community church on the south side of Chicago that’s looking at placing two of these containers – a vertical hydroponic farm and a mushroom farm – right outside in the parking lot outside the church.
And we think we could bring an educational spin to this where we can have the community grow their own food and supply the community themselves with highly nutritional food that ordinarily they just would not be able to get their hands on. So, we’re thinking that if this pilot program goes well this would be an application that would apply to every inner city throughout the U.S.
Farmbox Foods grows vegetables in shipping containers. Credit: Jeremy Moore, KUSA
Savageau: The mission’s always been to create products that are for the decentralized food insecurity industry. So, we want to create a product that can be deployed anywhere in the world, can run off-grid, and can feed communities. So, we have two different products – the VHF and the GMF. Every product that we develop gets us one step closer to being able to feed a community with everything they need, because you can’t feed communities forever just on leafy greens.
So mushrooms, they’re more nutrient dense, that gets us one step closer. There’s other products that we’re going to develop to get us to that point. But, I think the mission for the company is to be able to deploy these farms into communities where they’re needed, whether that’s a rural area, a food desert in the U.S., an inner city, or somewhere in Africa like Ghana or the Sudan.
We want to align with big ag and we want to help the industry get better. So we want to get food to where it’s needed. We’re looking at doing stuff with food insecurity and food inequality. That’s big with what we’re doing. So, that kind of aligns with our mission. If you look at our food system – just take for instance – you know if you look at a SNAP program or food subsidy program – you’re taking food and giving it to somebody or they’re purchasing it.
But, a lot of that food that they’re purchasing is processed, sugar – I mean, it’s poison. And if you go on a military base anywhere in the U.S., there’s fast food on the base. It’s really what you see. So, there’s a lot of reasons why we’re doing this I think. We can help fix our food system. And we can help educate the youth on how they should eat. We’re doing some stuff with an Inuit community in Alaska. They don’t necessarily know how to fix this food or prepare it or use it. So, I think education is a big part of what we’re doing.
How do these container farms work?
Savageau: When people think of farms, they don’t think of agriculture like this. Vertical hydroponics and indoor ag and controlled environments – it’s been around for a long time. I think that the way that this one works is pretty simple. The water gets fed into a tube system and the water trickles down and goes back into the tank. And where you’re standing – the seedling tray area – the water goes into a tank, into the seedling trays, gets flooded, and then back into the tank.
There’s a software that we use called Agrotech that monitors the temperature, the humidity, the lights – basically, all automated. So, it’s fairly easy to run. You need about 15 to 20 hours a week to run one farm. The GMF farms takes about 25 hours a week. It’s a little bit more intensive. The VHF is the vertical hydroponic farm and that’s the farm that we’re standing in. The GMF is the gourmet mushroom farm, which is the one that you went through earlier. You want to just keep things as clean as possible. The cleaner that you keep it the better it’s going to run.
So, we have a standard SOP, you know, that we implement with our training. Cleaning the floors. Cleaning the tubes. You don’t clean them every time. But, usually, every couple harvests you’ll take the tubes out, wash them out. You’re cleaning the tanks about every 60 days.
But, on average it’s pretty easy to maintain if you’re doing the daily checklist. The seeds are going to be in the seedling tray for about two weeks. Then, they go into the wall. And then they get harvested about 60 days after they start in the seedling tray. So, on average you’re about 60 days from seedling to harvest depending on what you’re growing.
And this farm is really setup for vertical hydroponics. So, it’s leafy greens. You can do hundreds of different types of lettuce. You can do cherry tomatoes, strawberries and peppers. There’s a lot of different things that you can grow in here. Most of our clients are only growing a couple things at one time. You don’t have to worry about weather. You don’t have to worry about if this is in a cold climate like the arctic. You know, they can’t grow food. If it’s in a desert, they can’t grow food. If it’s on an island, they can’t grow food. So, these can be deployed anywhere. And they grow 365, all day, every day. Also, the yield is very high for the square footage. So, you can put these on top of a building, inside of a building. It only takes up 320-square feet. You don’t have any pesticides. So, you don’t have to worry about pests, bugs, mildew, stuff like that’s going to effect the plant as it’s growing. It’s also decentralizing the food system.
So, you’re not having to ship food hundreds of thousands of miles from point A to point B. So, the food is right there. And the nutrients that we use are organic plant-based nutrients. And there’s no pesticides. So, the nutrient density is extremely high compared to something that you would buy – even organic – in a store.
Walker: We grow a variety of vegetables and lettuces. I believe that we’re somewhere in the area of 30 to 40 different types of vegetables and lettuces that we can grow in our farms. And, then of course we’ve got our gourmet mushroom farm which we’re currently growing anywhere from eight to nine different varieties of mushrooms. We’re in the startup phase of running that farm ourselves. So, we’re exploring the different types of mushrooms that we can grow. But, we’re very proud of the folks that are actually running these farms – our staff, very knowledgeable and they do a great job. We’re going upwards to 300 to 400 pounds a week now. We’re not competing with traditional farming. We’re actually a compliment.
Who are your customers?
Walker: One of our first customers is Centura Health. They purchased their first container – which is now sitting at St. Mary’s in Pueblo. They ordered two more containers after seeing how the first container behind their hospital worked. We actually started up a pilot program with Centura Health where we’re now running them as the FarmBox family.
We’re working with Centura Health in identifying not only their hospitals and the patients who are going to be fed through our vertical farm – but then we’re also identifying where the food deserts are and Centura Health will then help us with what we’re going to be growing, and then the communities that we’re going to be serving from those, those particular crops.
We do have a couple that’s looking at doing some farming right here in Sedalia. They’re going to use it to supplement their traditional farming, which will be an interesting pilot program for us to work with them on. We’re working with C Lazy U Ranch out of Granby, Colorado. They’ve ordered a hydroponic farm and we’re going to be manufacturing that. And they’re going to place that at the ranch. They don’t really have access to a lot of good food as far as having it grown right there on the property. So, this will be a nice compliment to the services and the customer experience that they provide their customers by having one of our farms right on site.
Centura Health is one of FarmBox Foods' first customers. Credit: Jeremy Moore, KUSA
One big area that we’re really focusing on is the urban areas throughout the U.S. where they don’t have a lot of land to grow. These farms can go right into the parking lots, behind a church for example. We’re working with a community church in the south side of Chicago that’s looking at – we’re looking at placing two of these containers – a vertical hydroponic farm and a mushroom farm right outside in the parking lot outside the church.
We can have the community grow their own food and supply the community themselves with highly nutritional food that ordinarily they just would not be able to get their hands on. So, we’re thinking that if this pilot program goes well this would be an application that would apply to every inner city throughout the United States.
Savageau: We have a customer here in Lakewood that’s going to put one in their backyard. They run a small organic farm. We’re looking all the way up into federal government and military, and everything in between.
So, Rusty was talking about FEMA, the UN, UNICEF, those are the big customers that take a long time to build a relationship with. And then we have customers that are all the way down to just an individual that wants one for their property or maybe a couple of people are going to run one for a restaurant or a developer wants one for a small development that he’s doing.
We’re working with a group in New Mexico and they’re building a huge development of about 45,000 houses. So, we’re talking about 100 of these units that are going to be deployed in that area right outside Albuquerque to feed those communities within that area over the course of about two years. We work with a grocer that’s regional. And we work with some other customers that are kind of at a government, federal government level.
I think we’ve done a lot in the last three years. I mean we haven’t gone out and raised any capitol. So, we’ve self-funded it. And I think from that point of view you know we’ve done a lot. We’re kind of at the point right now where we’re just starting to scale. So, we’ve just started our social media. You know SEO (search engine optimization), SEM (search engine marketing). We have a sales team. And orders are starting to come in. We’ve partnered with RK which is manufacturing our units. That’s giving us the ability to scale. Because before that we were building these one or two at a time in Sedalia and now we can build 100 of them. So, that’s really been a huge part of us being able to scale is the manufacturing side.
How much does it cost to purchase and operate the farms?
Jake: This VHF farm – vertical hydroponic farm – starts at $140,000. The GMF starts at $150,000. Then, you have training and deploy, getting it there. So, usually, you’re over $150,000 for a farm. So, your ROI (return on investment) in this product is going to be about 12 months to 24 months depending on what you’re growing and where it is in the world.
The GMF is going to be closer to 12 months because mushrooms tend to be more expensive – again – depending on where it’s going. We have a unit that’s going to Tahiti for example. That ROI is going to be extremely fast because they ship everything in. If there’s a market for mushrooms there, which there is with a grocer, it’s going to be quick. So, the cost of running it with labor and everything you need to grow the plants, usually around $20,000 to $40,000 a year. We’re a mission-driven company. So, money isn’t the first thing that’s important. We want to build a certain amount of these and then every x amount that we build, we build one for free and we send it to a community that maybe our social media has engaged with or given us an idea that ‘hey, this would be a good community.’ And then, we send it there. We pay for it. We train people. And that’s something that we want to do. We can’t do it yet. But, I think that’s coming in the next year.
Why is Edible Beats interested in working with FarmBox?
Hunt: We try to be as local and organic as possible and that’s what brought us here to FarmBox. We can put a box behind a restaurant and have lettuces cut and washed and put on the plate the next day.
Just to have that connection with our food and know exactly where it’s coming from and how it was produced. It’s going to be better quality because it’s not traveling. It’s not ripening in a truck coming from Mexico. Economically, what we can do to not pay the mileage on the vehicles and the gas, the inputs, the emissions, the extra packaging, the plastics.
That’s one of the best things about FarmBox – that what we can do is – if we produce food for our restaurant group – I’m not going to have to buy packaging that’s going to go into a landfill or even need to be recycled. It’ll go directly into the vessels that we’re going to store them in the cooler. We don’t have to worry about marketing and labeling and you know stickers and plastics and all this extra stuff – this hoopla that we don’t need – because FarmBox is a possibility now.
The Farmbox Foods containers allow leafy greens to grow vertically, maximizing space.
Credit: Jeremy Moore, KUSA
We are looking at lettuces and herbs, leafy greens. So yeah, like basils, sage, leaf lettuces, butter lettuces, arugula – these kinds of things that we use that could greatly help our impact. Essentially it’s a self-contained box that you can grow fruits and vegetables in – most likely leafy greens – and it’s a soilless or near soilless medium.
So, essentially you plant your seed in a very small amount of coconut core or soil or peat moss – something to hold the root structure – and that, according to with FarmBox, they’re system is a vertical farming.
So, they have vertical towers and then they put the lettuces in the towers in their small soil medium and then they drip water with enhanced nutrients mixed into the water specifically built for those vegetables. It doesn’t have a lot of soil waste.
For the amount of the surface area you can get way more production out of it and the water that goes through is recycled. Per plant, it uses far less water than any other type of growing system.
RELATED: Why Colorado agriculture groups oppose Initiative 16, an animal cruelty proposal
MALAYSIA: Turn Empty Spaces Into Urban Farms To Grow Food
WITH the Covid-19 pandemic highlighting the importance of food self-sufficiency, it is probably time for Malaysians to turn empty urban spaces into farms. Urban farming is the practice of cultivating, processing and distributing food in or around urban areas
17 Apr 2021
WITH the Covid-19 pandemic highlighting the importance of food self-sufficiency, it is probably time for Malaysians to turn empty urban spaces into farms. Urban farming is the practice of cultivating, processing, and distributing food in or around urban areas.
Although our country is rich in natural resources, we are still highly dependent on high-value imported foods. Currently, our self-sufficiency level (SSL) for fruits, vegetables, and meat products is 78.4%, 44.6%, and 22.9% respectively.
With a lower occupancy rate in both retail and office space after businesses folded due to the pandemic, property owners could perhaps be induced into redeveloping their buildings for urban or vertical farming. This is being done in Singapore with tremendous success.
According to the National Property Information Centre (Napic), the occupancy rate for shopping malls in Malaysia has dropped steadily for five consecutive years, declining from 79.2% in 2019 to 77.5% in 2020, the lowest level since 2003.
And, according to the Valuation and Property Services Department (JPPH), the occupancy rate for privately-owned office buildings is lower now compared to the pre-pandemic era.
Aquaponics, a pesticide-free farming method that combines aquaculture (raising fish) and hydroponics (growing plants without soil), would be one of the ways forward in food production. In aquaponics, the nutrient rich aquaculture water is fed to the hydroponic-grown plant.
This method of farming could be the economic livelihood for many, particularly the underprivileged and disabled communities as well as fresh graduates who are still struggling to secure a decent job.
Sunway FutureX Farm, Kebun-Kebun Bangsar (KKB) and Urban Hijau are examples of good urban farming initiatives in the Kuala Lumpur city centre.
Perhaps Malaysians could adopt Singapore’s approach by setting up aquaponics farming systems on roofs of car parks and opening urban farms in unused buildings.
The vertical rooftop system is another way of increasing our food production capacity. This system requires only a quarter of the size of a traditional farm to produce the same quantity of vegetables. At the same time, it also reduces the need to clear land for agricultural use.
The government should provide incentives for farmers and the relevant stakeholders who are interested in venturing into urban farming. This would enhance the supply and affordability of a wide range of minimally processed plant-based foods, as suggested under the latest Malaysia Economic Monitor “Sowing the Seeds” report by the World Bank.
With the current administration’s laudable commitment to tackling food security issues, this would provide the opportunity for Malaysia to review the current national food security policy by addressing productivity, optimization of resources, sustainable consumption, climate change, and water and land scarcity. By putting greater emphasis on urban farming, the government could encourage farmers to plant more nutritious and higher-value crops.
Given that the involvement of youths in the agriculture sector is only 240,000 or just 15% of the total number of farmers in Malaysia, as noted by Deputy Minister of Agriculture and Food Industries I Datuk Seri Ahmad Hamzah, the Entrepreneur Development and Cooperatives Ministry and Youth and Sports Ministry would need to come up with training programmes and develop grant initiatives to attract the younger generation to farming, in this case urban farming.
These ministries can also work with the Agriculture Department, Malaysian Agricultural Research and Development Institute (Mardi), and Federal Agricultural Marketing Authority (Fama) to develop more comprehensive urban farming initiatives.
The upcoming 12th Malaysia Plan (12MP) would also provide opportunities for the government to turn empty spaces into urban farming. In a nutshell, every Malaysian can do their part to help the country become more food resilient by converting empty spaces into farms.
Lead photo: Vertical farming systems can maximize use of space in an urban context.
AMANDA YEO
EMIR Research
Kuala Lumpur
TAGS / KEYWORDS: Letters & Opinion,
How Square Roots Is Training Next-Gen Farmers During A Pandemic
The average age of the American farmer is 58 years old. If we're going to change the food system, we need to create more pathways for young people to launch successful careers in agriculture
Square Roots
10.08.20
The average age of the American farmer is 58 years old. If we're going to change the food system, we need to create more pathways for young people to launch successful careers in agriculture.
One of the many ways Square Roots invests in the future of farming is through our Next-Gen Farmer Training Program—aimed at new farmers or those at early stages in their careers. Farmers initially join Square Roots as Apprentice Growers. Through our proprietary training methodology—supported by our intuitive technology platform—Apprentice Growers rapidly learn the essential farm skills needed to move into permanent roles on the farm team and accelerate their careers.
We continuously evolve our training program to zero in on the skills and experiences that help employees become the best indoor farmers they can be. Throughout COVID-19, we have been committed to prioritizing people safety and plant safety which has led to changes in our day-to-day farming operations, as well as rewiring our in-flight farmer training programs in May and adapting how we run the Square Roots Next-Gen Farmer Training Program going forward. Also, after several years of training farmers, we’ve listened and learned to what farmers value from their experience at Square Roots and have incorporated that into our program going forward. Read more about what it’s like to be a grower at Square Roots and how the program has evolved:
Individual Pathways
Based on the needs of our farm production teams, apprentices are hired and onboarded, either individually or in pairs, on a rolling basis. By spacing out onboarding and training, our team is able to provide more attention and support to apprentices, allowing them to move more quickly through the training program and into permanent positions on our team. We expect most apprentices will complete their training in three to six months, but each will advance at their own pace.
Foundational Remote Learning
We have moved our training materials onto a virtual learning platform, which houses videos, interactive presentations, animated diagrams, virtual tours, and other types of content that can be brought to life beyond a typical presentation. Since COVID-19 restricts our ability to hold classroom-style learning, online learning can be self-serve, supporting different types of learning styles. It also drives consistency in training and terminology, reducing the burden on managers responsible for administering it.
Intensive ‘Boot-Camp’ Style Farm Immersion
Training for Apprentice Growers is laser focused on the skills required for new farmers to quickly become the best indoor farmers they can be. After the initial foundational onboarding, apprentices will jump into production, and, in parallel, will be equipped with the necessary context and complementary training to support expanded learning and competency much sooner. Apprentices will be supported by our software operating system the Farmer Toolbelt, empowering them to get up to speed much faster, engaging with data, and ultimately helping them become better growers. Throughout the training process, farmers will receive direct supervision by one of our experienced farm team members who will act as their training guide and provide professional and moral support.
Pathway to Permanent Employment at Square Roots
Central to Square Roots is our mission to empower Next-Gen leaders in urban farming, and the Next-Gen Farmer Training Program is one of the most direct ways we do that. The program is designed to bring young people with little or no experience up to speed in our proprietary indoor farms as quickly as possible and on to their careers in indoor farming—acting as an internal training program for permanent full-time employees on the Square Roots farm team.
The Apprentice Grower role is the first step in a career path to indoor farming at Square Roots. To start, apprentices will earn an hourly rate indexed to the area’s living wage, and receive 100% covered health benefits and equity in Square Roots. Once they’ve successfully mastered indoor growing fundamentals (we expect this to take three to six months), apprentices will be eligible to move into Associate Grower positions.
For more information and to learn about new open positions on our farm teams, follow us on social media and sign up for our newsletter for updates.
Tags: Next-Gen Farm / Farmer Training / COVID-19 Response / Updates
US - NEW MEXICO: ‘Farm in a Box’ Coming To Grants
The Farm in a Box operates inside a 40-foot shipping container, shown here in Moffat County, Colo. A similar one will be set up at New Mexico State University branch campus in Grants. (Courtesy of Tri-State Generation and Transmission)
ALBUQUERQUE, N.M. — Fresh, locally produced vegetables will soon sprout from hydroponic beds in an enclosed, converted shipping container parked at New Mexico State University’s branch campus in Grants.
The 40-foot “Farm in a Box” will provide hands-on education and workforce training for local students and others interested in studying the emerging science of “indoor agriculture” as a new, potentially sustainable, enterprise that could offer fresh economic development opportunities and job creation in an area hard hit by the transition from fossil fuels to renewable energy.
NMSU, the Tri-State Generation and Transmission Association, and the National Electric Power Research Institute (EPRI) are collaborating on the project.
It’s one of several initiatives under development with local, state, and federal backing to diversify economic activity in Cibola, McKinley, and San Juan counties, where coal-fired power plants and associated mining have provided a financial mainstay for workers and communities for decades.
Both Cibola and McKinley counties are reeling from last year’s shutdown of the coal-fired Escalante Generating Station near Grants, plus the closure of Marathon Petroleum’s oil refinery in Gallup, which together eliminated hundreds of stable, high-paying jobs in those northwestern communities.
Unemployment hit 10.8% in Cibola County in December and 10.2% in McKinley County, according to the state Department of Workforce Solutions. That compares to an 8.2% average statewide unemployment rate.
To ease the impact of Escalante’s closure and assist in transitioning local communities, Tri-State provided $5 million in grants in January to four local economic development organizations. It is also now sponsoring the Farm in a Box initiative, providing $250,000 to set up and equip the high-tech container unit that houses the indoor agricultural operation, with forthcoming grants for NMSU faculty and student assistants to work on the project.
“We realize that closing such coal facilities as the Escalante plant that have traditionally employed significant workforces creates very difficult challenges for local communities to replace those jobs,” Tri-State spokesman Mark Stutz said. “Our goal is to find opportunities in support of economic development with new technologies when we can.”
Tri-State permanently closed the 253-megawatt Escalante power plant in Pruitt last summer as part of the association’s long-term plan to completely withdraw from coal generation over the next decade. It laid off about two-thirds of the plant’s 107 employees, Stutz said.
TriState also plans to close a much larger, 1.3-gigawatt coal facility in Craig, a municipality in Moffat County, Colorado, where the company sponsored another Farm in a Box project that EPRI set up last November.
“We don’t want to just walk away from these communities that we’ve been a part of for decades,” Stutz said.
High tech
EPRI has set up similar Farm in a Box projects in 13 states, said its principal technical leader Frank Sharp, project manager for the institute’s indoor agriculture-and-lighting research efforts.
It’s part of an emerging concept of indoor farming for urban areas and isolated rural communities where food could be grown year-round right where it’s consumed. It could lead to huge energy and water savings through efficient, high-tech growing processes, contributing to carbon reduction by using electricity rather than fossil fuels in agricultural operations and by eliminating long-haul transport of produce to market.
For economically stressed communities such as Cibola and McKinley counties, it could be scaled beyond shipping containers to retrofit under-used or abandoned buildings and to construct new facilities, such as greenhouses, on empty plots, Sharp said.
“It all translates into community impact, job creation, and beneficial use of electricity,” Sharp told the Journal. “Vacated buildings with the infrastructure already in place can be retrofitted, with opportunities to also build new facilities.”
Electric Power Research Institute principal technical leader Frank Sharp, left, with Tri-State Generation and Transmission Association CEO Duane Highley, inside the Farm in a Box agricultural container that was set up in Moffat County, Colo., last November. (Courtesy of Tri-State Generation and Transmission)
Research needed
Research is still needed to maximize efficiency and production, measure benefits, make contained farming systems profitable, and train the workforce. That’s where NMSU comes in, said Jay Lillywhite, agricultural economics professor and co-director of NMSU’s center of Excellence in Sustainable Food and Agricultural Systems.
NMSU faculty and students will study the entire container system, which includes vertical, hanging plastic enclosures to grow crops connected to a closed-loop plumbing system to recycle all water. Researchers will monitor all energy and water use, plant productivity, the impact of red and blue LED lighting spectrums on plant growth, and the economics of the whole operation, Lillywhite said.
“We’ll record everything and transmit all the data wirelessly to EPRI,” Lillywhite said. “It needs to be profitable. Indoor agriculture has had mixed reviews in terms of profitability, so we’ll look at a model that makes sense for New Mexico and the Southwest.”
Other applications
Opportunities extend into many disciplines beyond agriculture, including electrical engineering focused on energy efficiency and renewable generation as alternative systems, such as solar panels, are added to indoor operations, said Rolando A. Flores, dean of NMSU’s College of Agriculture, Consumer, and Environmental Sciences.
“The project has excellent potential to address social, environmental, and economic facets of sustainability, and become a resource-efficiency model for urban agriculture, provided that renewable energy can be incorporated from the beginning,” he said.
State Rep. Patricia Lundstrom, D-Grants, said indoor agriculture can offer significant opportunities alongside other initiatives to diversify the local economy.
Lundstrom sponsored legislation last year that now allows counties with coal plants that are closing to set up special economic districts with bonding and taxing authorities to invest in infrastructure, business recruitment, and retention to create jobs and promote economic development.
That led to the launch in December of the McKinley County Electric Generating Facility Economic District, which is focused on converting the Escalante site in Pruitt into a new industrial zone to recruit more businesses to the area.
“Value-added agriculture is one of the opportunities we can work to develop there with help from the partners on this project,” Lundstrom said. “It can have a significant impact as we work to recruit new, sustainable industry to the local community.”
The Farm of The Future Could Be Hiding Inside This Shipping Container
It's called The Cube and could bring farming to urban environments
It's Called The Cube And Could Bring Farming To Urban Environments
The Cube's crops are powered by LED lights. N.Thing
As we head into 2021 facing a number of dire existential threats -- pandemics and climate change to name a few -- one of humanity's encroaching issues is population rise.
How on earth (literally) are we going to feed all these people?
Traditional farming methods could be problematic in the long term. It's not just an issue of space but a problem of sustainability. We're currently damaging our environment with current farming techniques -- and eradicating existing species and their habitats to the point where many are calling it the sixth extinction event.
In short, we have some problems to solve. Part of the solution could be found inside this 40-foot refrigerated shipping container.
They call it The Cube: A modular smart farm, designed to be built in urban spaces in pretty much any configuration you like.
The containers can be stacked vertically or horizontally, with potentially dozens or even hundreds of Cubes fitting together to make one giant farming system, capable of cultivating and growing tonnes of produce. The hope is to bring sustainable, efficient, year-round farming to spaces that can't traditionally support agriculture.
"The human populations are growing quite fast," explains Seungsoo Han, the COO at N.thing, "and we need to come up with some kind of very efficient solution that can actually support that fast-growing population, also at the same time, we shouldn't actually damage the environment that that population lives in."
At the heart of the Cube, the farm is an automated operating system known as Cube OS. The system takes in data from sensors inside each farm, measuring readings like humidity, ph levels in the water, temperature, carbon dioxide -- everything that's needed to grow a healthy plant. And each of these variables can be tweaked and optimized, depending on the plants you're growing.
N.Thing has already partnered with Korea's largest supermarket chain to supply greens and, last year, it rolled out a farm in the United Arab Emirates, where summer temperatures regularly climb over 100. Next, N.Thing plans to expand into other territories like Singapore and Qatar.
Israeli Supermarket Employs Vertical Farm Start-Up For Selling Produce
Vertical Fields, a Ra'anana based agri-tech start-up that creates vertical, sustainable farms using geoponic technology, agricultural expertise, and smart design, teamed up with BIOLED, a Tzuba-based eco-lighting start-up that uses LED lights to create more sustainable, profitable crops in order to erect the growing container
The new technologies eliminate the need to rely on outdoor growers and suppliers while also providing a fresher, more eco-friendly product which needs much less water and land to grow.
NOVEMBER 21, 2020
Produce growing under BIOLED lights. (photo credit: BIOLED)
Rami Levy, one of Israel's largest supermarket chains, has been cooperating with two Israeli agri-tech start-ups to erect large containers to grow fruit and vegetables, which will be sold in the chain's stores.
Vertical Fields, a Ra'anana based agri-tech start-up that creates vertical, sustainable farms using geoponic technology, agricultural expertise, and smart design, teamed up with BIOLED, a Tzuba-based eco-lighting start-up that uses LED lights to create more sustainable, profitable crops in order to erect the growing containers.
According to BIOLED, the first container is already in the process of being set up in Rami Levy's Ayalon Mall branch in Tel Aviv.
Thanks to the rapidly growing worldwide population, the amount of produce must grow by 60% to keep up with demand and overpopulation trends. Current methods of farming require too much water and land to meet that demand.
The new technologies eliminate the need to rely on outdoor growers and suppliers while also providing a fresher, more eco-friendly product that needs significantly less water and land to grow.
BIOLED already produces eco-friendly LED lighting for a wide variety of purposes for companies in Israel and plan to expand to Europe and the rest of the global market. Recently they breezed through their crowdfunding goal, nearly two months before their funding deadline expires in January 2021.
BIOLED also provides agricultural lighting for most of Israel's medical cannabis companies, most famously for the largest cannabis farm in the country, grown by medical cannabis giant INDOOR.
One of the main reasons for this is BIOLED's ability to shorten and stabilize horticultural growth cycles regardless of season, while also eliminating the need for pesticides and the logistical issues that comes with supplying fresh produce to urban areas,
Vertical Fields is a slightly younger company. They recently burst onto the Israeli agri-tech scene with their technology, which allows for produce to be farmed vertically within containers big enough to fit in a parking lot, using only one-tenth the amount of water usually needed.
Tags startup ecology hi-tech israel tech israel technology for agriculture rami levy agriculture Hunger start-up supermarket Farming
FREE ZOOM WEBINAR'S: Perennia's Virtual Field Days - Sept 8, 9 and 10
Virtual Field Days – Sept 8, 9 and 10
Tuesday, September 8, 2020, at noon (ADT)
You’re invited to Perennia’s Virtual Field Day on Insects and Pests. Join us for an online session on Tuesday, September 8, at noon (ADT) to hear from Perennia crop specialists, researchers and producers.
AGENDA
Viticulture Specialists, Francisco Diez, will discuss Grape Phylloxera with guest Dr. Deb Moreau, AAFC
Acting Vegetable Specialist, Caitlin Congdon will present information on a trial for management of cucumber beetle and squash bug, with guest Dr. Suzie Blatt, AAFC
Field Crops Specialist Sonny Murray, Acting Vegetable Specialist Caitlin Congdon and Dr. Jocelyn Smith of the University of Guelph discuss Bt Trials for Control and resistance development of corn insect pests
Wednesday, September 9, 2020, at noon (ADT)
You’re invited to Perennia’s Virtual Field Day on Production Systems. Join us for an online session on Wednesday, September 9, at noon (ADT) to hear from Perennia crop specialists, researchers and producers.
AGENDA
Manager of Horticulture Jennifer Haverstock and Protected Crops Specialist Talia Plaskett will chat about strawberry production substrate with guest speakers Jackson Lore etc.
Protected Crops Specialist Talia Plaskett will discuss shipping container greens with guest speaker Phil Hatcher from Very Local Greens
Thursday, September 10, 2020, at noon (ADT)
You’re invited to Perennia’s Virtual Field Day on Weed Management. Join us for an online session on Thursday, September 10, at noon (ADT) to hear from Perennia crop specialists, researchers and producers.
AGENDA
Wild Blueberry Specialist Hugh Lyu discusses the major weed species in wild blueberries
Tree Fruit Specialist Michelle Cortens talks about weed identification in apple production
Manager of Horticulture Jennifer Haverstock and Gavin Graham, Weed Management Specialist with the New Brunswick Department of Agriculture, discuss weed management in strawberries and a demo trial highlighting the opportunity of fall herbicide application.
REGISTRATION
Registration is required.
Cost: Free
QUESTIONS?
Caitlin Congdon
Phone: 902-698-9473
Email: congdon@perennia.ca