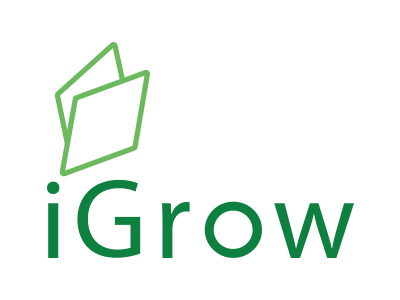
Welcome to iGrow News, Your Source for the World of Indoor Vertical Farming
Organic Industry Is Not Giving Hydroponic, Aquaponic Growers A Warm Embrace
The litigious Center for Food Safety two weeks ago filed a rule-making petition with U.S. Department of Agriculture, demanding new regulations prohibiting organic certification of hydroponic agriculture production
By Dan Flynn on February 8, 2019
Some fresh produce from hydroponic growers has been approved for and is being sold under USDA’s organic seal, but farmers who grow their organic crops in the soil don’t like the competition.
The litigious Center for Food Safety two weeks ago filed a rule-making petition with U.S. Department of Agriculture, demanding new regulations prohibiting organic certification of hydroponic agriculture production. The 22-page petition also asks USDA to revoke any existing organic certification previously issued to hydroponic operations.
Food safety comes into play in the petition in only one way. Hydroponics doesn’t have soil, so they come up a little short because they do not provide soil samples as a measure of testing compliance. The CFS points out that regulations implementing the Organic Foods Production Act of 1990 “consistently suggest soil samples as a measure for testing compliance.”
Agents who review operations as part of the USDA’s organic certification process “must conduct periodic residue testing of agricultural products,” with soil samples suggested as a method for testing, CFS’s petition says. “Many hydroponic systems would not contain soil for sampling, as suggested in the OFPA regulations.”
Hydroponic, aquaponic and aeroponic growers currently can earn organic certification. It is allowed by USDA so long as the certifier can show there is compliance with the organic standard. One industry supplier says hydroponics, by definition, is a method of growing plants in a water-based nutrient-rich solution that does not use soil. Instead of plants root in a nutrient solution with access to oxygen.
A year ago, USDA’s Agriculture Marketing Service (AMS) tried to settle some issues concerning organic certification of hydroponic and aeroponic growing operations. The AMS action came after USDA’s advisory National Organic Standards Board (NOSB) recommended banning the non-soil systems from being called organic production. USDA only briefly pondered that one before saying “thanks, but no thanks” to NOSB for the recommendation.
Aquaponics refers to growing crops in a system with farmed fish that supply nutrients for plants. Greenhouse growers and urban farmers using vertical growing systems use hydroponic and aeroponic methods — all without soil. The organic industry has been rocked with debate about these hydroponic methods for nearly a decade.
CFS wants a flat prohibition on hydroponic operations ever being allowed to use the USDA organic label. It claims hydroponic production systems that do not use soil do not meet federal organic standards and violate organic practices, which require that organic farming include soil improvement and biodiversity conservation.
Joining the CFS petition are more than a dozen other organic farmers, consumer, retailer, and certifying organizations, including the Organic Farmers Association, Northeast Organic Dairy Producers Alliance (NODPA), PCC Community Markets, and the Cornucopia Institute.
“Mislabeling mega-hydroponic operations as ‘organic’ is contrary to the text and basic principles of the organic standard. Right now there is a pitched battle for the future of organic, and we stand with organic farmers and consumers who believe the label must retain its integrity,” said George Kimbrell, CFS legal director.
The petitioners say consumers trust the organic label and pay extra for the assurance that it indicates a more healthful and environmentally-friendly way of producing the food they buy.
Since the federal Certified Organic label was introduced more than 20 years ago, CFS says the organic food market has grown exponentially and is now a $60 billion industry in which multinational corporations have bought organic brands and compete with small food producers who use environmentally-friendly methods.
“Allowing hydroponic systems to be certified as organic undercuts the livelihood of organic farmers that take great lengths to support healthy soil as the bedrock of their farms,” stated Kate Mendenhall of the Organic Farmers Association. “Hydroponic producers getting the benefit of the organic label without actually doing anything to benefit the soil undermines the standard and puts all soil-based organic farmers at an untenable economic disadvantage.”
The petition argues that organic agriculture has traditionally been defined as using soil requirements such as fostering soil fertility, improving soil quality, and using environmentally beneficial farming methods such as proper tillage and crop rotation.
USDA continues to allow hydroponics, which goes against the advisory NOSB’s recommendation that organic certification not be extended to the non-soil growing methods.
Canada and Mexico prohibit hydroponics for organics, and the European Parliament voted to end the organic certification of hydroponic products in April 2018.
“Corporate agribusiness lobbyists have been working to water down the organic standards for decades,” said Mark Kastel, executive director for the Cornucopia Institute. “In this case, the careful stewardship of soil fertility is not only a philosophical precept, but it’s also codified in federal law.”
And while CFS is often successful with its legal strategies, the current petition to USDA may not get too far. Jennifer Tucker, the deputy administrator of USDA’s National Organic Program, recently said organic certification of hydroponic operations is “a settled issue.”
“Last year we issued an Organic Insider (e-mail newsletter) that indicated that hydroponics had been allowed since the beginning of the program and that (they) are still allowed,” Tucker said. “We consider that a settled issue.”
The Packer, the produce industry publication, reported Tucker’s comments to the 2019 Global Organic Produce Expo.
“There are some certifiers that certify hydroponics, and there are some that do not; they are all bound by a common set of regulations,” Tucker added.
Tags: Center for Food Safety, hydroponic, Jennifer Tucker, NOP, NOSB, organic certification, organics, USDA Organic
Introducing Living Food Company: The Future of Food
India’s Food Supply Chain is Not Working
Why is India, one of the fastest growing economies, undergoing a nutrition and health crisis? India has the largest micronutrient deficiency among all countries and among the highest disability-adjusted lost years of life from micronutrient deficiencies. Diets low in nutrition are the leading cause of this current health and nutrition crisis. Fresh food that is nutrient-dense is surprisingly difficult to find in India, particularly for the urban consumer.
We don’t know where our food comes from, what it contains and how long it takes to reach us.
The food we consume has been designed to be stored and shipped in containers over long distances. The industrial food supply chain is extremely complex and is plagued by inefficient supply management and wastage at the distribution stage. The agriculture system is failing us by producing food that contains harmful chemicals in the form of pesticides and fertilizers.
On an average, Indians consume close to 42000 metric tonnes of pesticides in a year, including those that are banned in other countries for their carcinogenic effects.
In June 2017, more than 40 cotton farmers died after inhaling chemicals while spraying pesticides in Maharashtra in one agricultural season.
Micronutrient deficiency in India. Source: http://unicef.in/Whatwedo/8/Micronutrient-Nutrition
We now depend upon cheap, low-nutrient food that sacrifices quality for quantity at the cost of our health and the environment. Global crop production has more than tripled since the 1960s. This has led to the depletion of water resources for irrigation, soil pollution from overwhelming fertilizer application and rising greenhouse gas emissions.
The average concentration of pollutants in the Indian soil is almost twice the amount found globally.
Such high levels lead to long-term damage in the central nervous system, immune and reproductive systems, while also being one of the leading causes of cancer.
The organic food movement, tries to address some of the health risks by eliminating the use of fertilizers. Yet, organic produce that is grown in soil can’t prevent harmful chemicals from entering our bodies. Contaminated groundwater containing dangerous proportions of heavy metals such as Arsenic is still used in organic farming and can cause long-term damage to our cells and immune systems. Simply put, organic food doesn’t solve the problem.
We are what we eat
In June 2017, my life took a drastic turn. My mother was diagnosed with Thyroid cancer and had to undergo a painful surgery. Less than a year later, on 20th March, my father was diagnosed with Stage 4 Peritoneal cancer.
This personal tragedy shook me to the core and I started investigating into this deadly disease. The more I read, I found out — how less I knew. I had never imagined that the everyday food that we eat can either strengthen our immune system or completely break it down making us susceptible to life threatening diseases, such as cancer. Everything I read brought me to the same point — we are what we eat.
Real food is about trust and transparency. It is also about ensuring quality and traceability at every step. Living food Company was born to provide food that we can trust. Our produce is grown with passion, care and precision and by controlling the entire process we guarantee high quality produce that can be traced at every step.
Living Food Company: The Future of Food
Living Food Company was born from the need to take control of our food production systems. We decided to grow microgreens, 10–12 day old baby plants that are extremely rich in nutrients, anti-oxidants and essential vitamins and minerals. They contain upto 40 x the nutrition found in their mature counterparts.
We focus on growing extraordinarily highly nutritious microgreens such as Kale, Broccoli, Mizuna (Japanese mustard), Pink Radish, Red Chard and 15 other powerful varieties. We make these nutrient rich foods affordable and accessible for the average urban Indian consumer and democratize access to superfoods.
Akash K. Sajith
CEO & Founder at @LivingFood, building the future of food.
AEssenseGrows Introduces ‘The Perfect Grow Light’ For Cannabis
AErix Line Brings Broad Spectrum and High Photon Efficacy
that Help Plants Grow Superior Buds
SUNNYVALE, Calif., Nov. 12, 2018 -- AEssenseGrows, an AgTech company specializing in automated precision aeroponic platforms for consistent high-yield plant production, today introduced a unique new line of grow lights optimized for premium value plants like cannabis. The AErix LBR003 grow light delivers the specifications required to improve the quality of buds grown indoors along with all of the automation features large cultivation facilities desire.
AErix lights offer a balanced broad spectrum coupled with high photon efficacy, making them ideal for premium leafy plants. The lights will be showcased Wednesday through Friday at MJBizCon in Las Vegas at the AEssenseGrows booth, #2473.
“Science has come a long way in pinpointing the role lighting plays in plant growth, and our new AErix line is built around these findings,” said Phil Gibson, AEssenseGrows’ vice president of marketing. “The best quality buds grow under balanced broad-spectrum light--light that contains sufficient amounts of blue, green, yellow, and red—and that’s what AErix lights deliver. That’s why we call them the perfect grow light.”
AErix lights (dimensions: 40”x50”) provide intense output with wide wavelength coverage and full light spectrum with an average PPFD of 1,000 µmol/s/m2 when placed 6 to 12 inches above the plant canopy—optimal for cannabis. With a maximum power usage of 700W, the lights are less than 3 inches thick including the power supply with no fan required. All AErix lights include an IP65 water repellant rating covering everything you want in a high humidity-intensive grow room.
The AErix lights drew praise from Joel Cuello, professor of Agricultural and Biosystems Engineering at the University of Arizona and a global expert in indoor farming.
“The AErix LBR003 indoor grow light spans the wavelength range of the photosynthetically active radiation with a spectral output distribution that remarkably conforms with the significant portions of the average plant's photosynthetic response curve to light,” Cuello said. “Its excellent spectral quality distribution combined with its high photon flux output makes it a superior indoor grow light.”
The new networked lights include many automation features and are optimized for the AEssenseGrows AEtrium-4 Bloom System. Fully controlled by the Guardian Grow Manager central control system software, the AErix lights include 0-100% dimming through an integrated AES link for complete scheduling and intensity automation. When connected, the lights automatically daisy chain to the network and can be sequenced in massive grow rooms to soft-start, one row at a time, without complex relays or programming.
Also included is a wide range 100-277V universal input power connection so the light is ideal for all power grids and geographies. The AErix lights will deliver as much as 16-24 pounds of dry trimmed bud per light per year, at below $150 per pound at scale. The complete AEssenseGrows system will be on display this week at MJBizCon Las Vegas.
The lights are automated to enable scheduling at various intensity levels. They are built for longevity and require little to no maintenance. The AErix light is verified by the Electrical Testing Laboratories (ETL) safety certification, exceeding or surpassing all Standards for Safety published by UL and other standards bodies.
For more information about the AErix lights, including a data sheet and user manual, visit the AEssenseGrows website or contact Gibson at pgibson@aessensegrows.com or 669.261.3086.
Ackrell Capital listed AEssenseGrows as one of the firm's Top 100 Private Cannabis Companies for 2018.
AEssenseGrows (pronounced "essence grows"), founded in 2014, is a precision AgTech company based in Sunnyvale, CA. AEssenseGrows provides accelerated plant growth SmartFarm platforms and software automation delivering pure, zero pesticide, year-round, enriched growth to fresh produce and medicinal plant producers globally. With AEssenseGrows, you can precisely control your production operations at your fingertips from anywhere in the world.
A ‘Fresh’ Look At Indoor AgTech
ndoor production of fresh fruits and vegetables leveraging aeroponic and hydroponic growing techniques has gained meaningful investor momentum in recent years.
Kenneth Scott Zuckerberg, AIF® AFA®, Wells Fargo Sector Manager, Agrifood Technology and Packaged Foods
Indoor production of fresh fruits and vegetables leveraging aeroponic and hydroponic growing techniques has gained meaningful investor momentum in recent years. The simplistic bull case for sector investment is that indoor farming operations provide direct exposure to a growing consumer demand for healthy, local, farm-fresh produce. Unfortunately, the defendable bear case is that indoor farms are expensive to build and operate, lack full automation, and do not command a pricing premium over outdoor-grown, organically produced crops.
In my opinion, the path to greater value creation lies in the partnership between indoor farms and food retailers. I think this can be accomplished by: 1) creating a branded ultra-premium offering; 2) creating private-labeled products leveraging the retailer’s brand name; and/or 3) installing living breathing vertical farms inside the produce section of the grocery store. Can anyone say craft produce?
I commenced a deep-dive into indoor farming prior to moderating a panel at the Indoor AgTech Innovation Summit sponsored by Rethink Events, Ltd., this past June. The event afforded me the opportunity to gain perspectives from the leading players in the space, including AeroFarms, Bowery, Bright Farms, 80 Acres Farms, Gotham Greens, Plenty, and Uriah’s Urban Farms, as well as greenhouse data service providers such as iUnu, and academic experts from Cornell University. The knowledge gained augments existing Wells Fargo Food and Ag Industry Advisor subject matter expertise.1
Defining indoor farming and Controlled Environment Agriculture
Indoor farming is actually a sub-segment of a much broader segment of farming called Controlled Environment Agriculture. The New York State Energy Research and Development Authority’s definition reads as follows:
Controlled Environment Agriculture (CEA) is the combination of engineering, plant science, and computer managed greenhouse control technologies used to optimize plant growing systems, plant quality, and production efficiency. CEA systems allow stable control of the plant environment, including temperature, light, and CO2, and provide separate control of the root-zone environment.
In simple terms, indoor farming can be seen as an innovative, conservation-oriented method of growing high-quality produce such as lettuces, microgreens, tomatoes, and other fruits and vegetables on a year-round basis in local communities. Currently, a large amount of the fresh produce consumed in the U.S. is grown on the West Coast and shipped cross country, or imported from other farming regions such as Mexico.
To be clear, CEA is not a new concept as evidenced by the fact that mushrooms have been grown indoors in the U.S. for approximately 100 years, and edible plants and decorative flowers have been grown in greenhouses and nurseries in Holland for approximately 50 years. Tomatoes are another important crop grown in greenhouses. Additionally, NASA has claimed to pioneer the process of growing plants utilizing LED lights as far back as the 1980s. What is new, however, is the combination of more powerful and energy efficient LED lights coupled with improved controls on temperature, humidity, and sensors, tied into a plant growing system on warehouse vertical racks, in shipping containers, or on rooftop farms.
Investor interest in indoor agriculture
In recent years, more than $500 million of capital has been deployed by investors in indoor AgTech startup companies based on the simple thesis of high-return potential resulting from the intersection of declining prices for LED lighting technologies and the growing consumer demand for fresh produce grown with limited use of traditional crop inputs. The capital has come from socially responsible funds and others seeking returns from companies that use clean technology and emphasize sustainable business practices.
The following table presents a snapshot of the competitive landscape for the indoor AgTech Industry. It should be noted that this snapshot excludes traditional nurseries and greenhouses along with certain technology robotics companies. (The latter happens to be a very interesting category, including startups such as AgriLyst, Arable, FoodLogic, Harvest Automation, and iUnu, that I’ll cover in a future blog.)
A theory on how indoor Ag retailers and consumers can all win
To recap several of the points above, produce grown in indoor farms provides an interesting alternative to outdoor-grown fruits and vegetables. That being said, I struggle with the notion that indoor farming will fully disrupt the existing outdoor growing regions and seasonal migration of growing operations between central, coastal, and desert valleys in the Western U.S. and Mexico. My reasoning is as follows:
- Many, not all, business models are capital intensive, and could be challenged to scale profitably in local regions.
- Local indoor farms typically offer high-quality produce delivered to grocers more quickly than many Californian or Mexican producers can, however the industry is not achieving additional compensation for this perceived competitive advantage.
- Existing industry players are generally low-cost, high-efficiency operators with long-established relationships with food distributors and retailers. Without a large scale national player, the incumbent players will remain in control of the terms of trade.
- Indoor farming operations have not yet proven they can fully insulate themselves from a disease outbreak such as the recent outbreak of the E.coli virus in Romaine lettuce, even though growing in a controlled environment.
- Indoor-grown lettuces, microgreens, arugula, and tomatoes lose flavor and remain highly perishable once harvested, packaged, and shipped to product sellers.
Notwithstanding this backdrop of challenges, I remain intrigued by the idea that closer alignments and joint ventures between indoor farmers and food retailers can create and deliver significant value. How can this be accomplished? Here are a few tactical ideas:
- Creation of an ultra-premium line of produce – Working directly with retailers, indoor farming operations can better message key product attributes: high-quality consistent products, year-round availability, and local/sustainable production. Wendy’s recent announcement to eventually source 100% of its tomatoes from indoor greenhouses would seemingly provide a positive tailwind for marketing indoor-grown produce.
- Installation of vertical farms in or on top of the grocery store – The difference in quality is noticeable between produce harvested immediately prior to consumption as compared to packaged, post-harvest produce. Again, the taste and quality attributes need to be properly marketed to achieve better pricing, however, the idea of produce harvested on-demand should theoretically de-risk the stand alone indoor ag business model from the perspectives of efficiency and waste reduction.
Parting thoughts
Personally speaking, nothing makes me happier than starting a meal with a healthy salad filled with fresh, peppery arugula, leafy spinach, and flavorful, red tomatoes, and cucumbers. Based on ongoing sector research and visits to several indoor farming facilities, I believe that indoor AgTech offers a compelling method to extend the seasonality of domestically-grown produce to 12 months of the year. I look forward to further exploring the issues raised in this blog in a future webinar on indoor farming and Controlled Environment Agriculture.
1. Article input provided by David Branch, Wells Fargo Sector Manager, Specialty Crops, Matt Dusi, Wells Fargo Sector Manager, Fresh Produce, and Karol Aure-Flynn, Wells Fargo Senior Sector Analyst, AgriFood Technology and Packaged Foods
Using A Hydroponic System Vs Growing With Soil
by Stephen Campbell
June 08, 2018
Ah, one of life’s great debates: growing with a hydroponic system or with soil, an especially difficult question to answer for your first grow.
History has given us great success using dirt as a base, and in 1953, Austin Miller referred to soil as ‘the skin of the earth’. Throughout the years, the soil community has learned a few tricks. By adding nutrients, balancing pH, and enriching soil with organic ingredients, producers have made advanced planting mixes to ensure healthy plant growth.
So why consider a hydroponic system at all if soil has come so far? Well for starters, the advantages of hydroponics include offering the grower higher plant yields and automation, which for most people, are two very powerful motivations to switch away from the past, and move into the future. Let's take a more in-depth look at the two mediums:
HYDROPONICS
In a nutshell, a complete hydroponic system is simply growing plants without soil. There are many different types of hydroponic systems, we've listed some of these techniques below.
Aeroponics - The process of growing plants in an air or mist environment, without the use of soil or aggregate medium. Plant roots hang in the air, and a mist of nutrient-rich water is sprayed onto the roots periodically.
Aquaponics - The combination of aquaculture (raising aquatic animals such as snails, fish, or prawns in tanks) and hydroponics (cultivating plants in water) in a symbiotic environment. The waste produced by aquatic animals supplies nutrients for the hydroponic plants. In turn, these plants purify the water for the animals.
Drip Irrigation - Also known as micro or localized watering, small drip emitters deliver a constant drip directly to the soil. This ensures that the soil is always moist, but not over watered.
DWC (Deep Water Culture) - A type of hydroponics system where plant roots continuously sit in a highly oxygenated water and nutrient solution. Oxygen is usually supplied using an airstone that pumps air to into the water.
Ebb & Flow - In this process, plant roots sit in a coarse growing medium for support, while a water and nutrient solution periodically flows past the roots on a set time schedule. This is similar to the ocean's rising and receding tides. This allows for the aeration of the roots, while automating the job of watering the plants by hand.
Nutrient Film Technique - This technique involves running a continuous oxygen and nutrient rich film of water over the plants roots in an enclosed space or tube.
All of these different techniques have one thing in common: they don’t need the roots to spread out in soil to absorb nutrients. Instead, they are fed a concentrated solution of oxygen and nutrients. This allows the roots to be packed into much smaller spaces.
All of these systems allow you to be creative and in control. You decide what nutrients to add, how much, and when. This control contributes to the increased speed and yield of growth you will experience.
There are additional benefits to going the hydro route. With a hydroponic system, you are using less water, as it is being recirculated to your plants and only changed out every 7-12 days. No more watching 10% of your runoff go to waste each watering. You also have a secret weapon in your battle against bugs, since eliminating soil from your operation will also eliminate certain bugs that can attack your plants.
SOIL
When it comes to soil, there are many different types and blends of soil available. So what's what?
Sand - Formed from bits of rock including limestone, quartz, granite, and shale. Drains water quickly.
Silt - Fine particles of organic material combined with sand. Very fertile, drains water well.
Muck - Primarily humus from drained swamps or bogs. Dense with little potassium.
Clay - Fine crystals formed by chemical reactions between minerals. Very poor draining.
Loam - A combination of the above. Organic loams must contain at least 20% organic matter.
Compost - Decayed organic matter. Can contain good bacteria, fungi, insects, worms, and microorganisms.
So head outside with a bucket and shovel right? Yeah, not so fast.
You should always ensure that you are buying your soil from a bag and not just getting it from outside, as store bought product has been treated to remove all of the bugs and critters that can tear-up your garden.
Soil not only provides a secure anchor for your plants and it’s roots, but it also aids in the retention and delivery of nutrients. Soil can act as a buffer for those nutrients, making it easier for the gardener to maintain a perfect nutrient balance.
One thing to watch out for is watering soil, as it can be surprisingly tricky. The number one issue new growers have is overwatering their precious plants.
New growers will try to be extremely attentive to their plants, and they normally want to get the most growth possible. This causes them to water too much and results in killing their plants. Over watering is dangerous because plant roots need to eat and breathe. Too much water logged in soil depletes oxygen, and thus the roots do not get enough oxygen to survive.
When you water your soil, it’s helpful to have some water runoff to ensure you have fully saturated your medium. Once watered, the soil needs to dry out, allowing the roots access to air before letting them drink again. It is a balance that once achieved, will produce consistent healthy results.
The Final Choice
In the end, whether you choose to use soil or hydroponics is, of course, up to you. There really is no right or wrong answer. Just weigh the pros and cons of each style and method, make a decision that works best for you, and then get growing!
How Does Aeroponics Work?
Aeroponic systems nourish plants with nothing more than nutrient-laden mist. The concept builds off that of hydroponic systems, in which the roots are held in a soilless growing medium, such as coco coir, over which nutrient-laden water is periodically pumped.
By Brian Barth on July 26, 2018
Towers and other vertical approaches are increasingly popular for aeroponics systems. Since the roots have a need to spread out, this is a clever way to save space. A vertical setup also allows misting devices to be placed at the top, allowing gravity to distribute the moisture.
By Globe Guide Media Inc / shutterstock.com
You finally wrapped your mind around the concept of Hydroponics
(soilless growing). Then all your horticulturally-savvy friends started carrying on about Aquaponics
(raising fish in a hydroponic system) So here’s a new buzzword for you: aeroponics. It has nothing to do with raising vegetables in airplanes, though it has been used to grow beans in the zero-gravity confines of the Mir space station
So what is it? Let’s investigate.
Aeroponics Defined
A simplified diagram of an aeroponic system. By Lilkin / shutterstock.com.
Aeroponic systems nourish plants with nothing more than nutrient-laden mist. The concept builds off that of hydroponic systems, in which the roots are held in a soilless growing medium, such as coco coir, over which nutrient-laden water is periodically pumped. Aeroponics simply dispenses with the growing medium, leaving the roots to dangle in the air, where they are periodically puffed by specially-designed misting devices.
In aeroponics systems, seeds are “planted” in pieces of foam stuffed into tiny pots, which are exposed to light on one end and nutrient mist on the other. The foam also holds the stem and root mass in place as the plants grow.
The Advantages of Aeroponics
Who knew naked roots could survive, much less thrive? It turns out that eliminating the growing medium is very freeing for a plants’ roots: the extra oxygen they are exposed to results in faster growth. Aeroponic systems are also extremely water-efficient. These closed-loop systems use 95 percent less irrigation than plants grown in soil. And since the nutrients are held in the water, they get recycled, too.
In addition to these efficiencies, aeroponics’ eco-friendly reputation is bolstered by the ability to grow large quantities of food in small spaces. The approach is mainly employed in indoor vertical farms, which are increasingly common in cities—cutting down on the environmental costs of getting food from field to plate. And because aeroponics systems are fully enclosed, there is no nutrient runoff to foul nearby waterways. Rather than treating pest and disease with harsh chemicals, the growing equipment can simply be sterilized as needed.
Drawbacks of Aeroponics
Aeroponics systems require a bit of finesse to operate effectively. The nutrient concentration of the water must be maintained within precise parameters and even a slight malfunction of your equipment can cause the loss of a crop. If the misters don’t spray every few minutes—maybe because the power goes out, for example — those dangling roots will quickly desiccate. And the misters need regular cleaning to keep them from becoming clogged by mineral deposits in the water.
There is also one major drawback, environmentally-speaking: aeroponic systems rely on electrical power to pump water through the tiny misting devices. And while they can be employed in the natural light of a greenhouse, they are more often used with energy-intensive grow lights. Solar power or other alternative energy sources can be harnessed to eliminate this drawback, however.
How Much Does an Aeroponics System Cost?
DIY models can be made for less than $100, but good quality professional systems with automated nutrient monitoring and a backup power supply start in the four-figure range.
Equipment Considerations
All aeroponics systems require an enclosure to hold in the humidity and prevent light from reaching the roots (this is typically a plastic bin with holes drilled for each plant), plus a separate tank to hold the nutrient solution. Beyond these basic components, there are a few other things to consider in devising an aeroponic system to suit your needs.
Some aeroponics systems are designed to be used horizontally, like a traditional planting bed. But towers and other vertical approaches are increasingly popular — since the roots need to spread out, this is a clever way to save space. Vertical systems are also popular because the misting devices may be placed at the top, allowing gravity to distribute the moisture.
Another dichotomy in aeroponic equipment: high-pressure versus low-pressure systems.
Low-pressure systems, which rely on a simple fountain pump to spray water through the misters, are inexpensive and suitable for DIY construction. This approach is sometimes called “soakaponics,” as low-pressure misters are capable of producing only a light spray, kind of like a tiny sprinkler, not true mist.
For true mist—meaning moisture floats in the air and more effectively delivers nutrients to the roots—you need higher water pressure than an ordinary pump can provide. Thus, professional aeroponics systems rely on a pressurized water tank capable of holding 60 to 90 psi, along with top-quality misters capable of delivering the finest possible puff of moisture.
National Organic Standards Board Decrees That Hydroponic Can Be Organic
Can Hydroponic Farming Be Organic? The Battle Over The Future Of Organic Is Getting Heated
A Hydroponic Rooftop Farm Grows in the Bronx
Dirt-Free Farming: Will Hydroponics (Finally) Take Off?
Hydroponics suppliers increasingly stock a full-line of aeroponics equipment, from the nutrients, pots, pumps, timers, and tubing you need for a DIY system to fully-automated turnkey aero-farms.
What Can You Grow with Aeroponics?
Anything, in theory. In practice, aeroponics systems are primarily used for the same applications as hydroponics systems, including leafy greens, culinary herbs, marijuana, strawberries, tomatoes, and cucumbers. One exception is root crops, which are impractical in a hydroponic system, but well-suited to aeroponics, as the roots have plenty of room to grow and are easily accessible for harvesting.
Other vegetable crops are possible but have more complex nutrient requirements. Fruiting shrubs and trees are impractical in aeroponics systems due to their size.
New Commercial Aeroponic Systems
New Commercial Aeroponic Systems
Pure Grows Aeroponics is launching three new product choices, Commercial Aeroponic System, Intelli Tissue Culture Clone Nursery and a 40 Foot Smart Grow Aeroponic Container.
“We keep a close eye to what our clients require for their cultivation needs and aim to meet these requirements with the latest, proven technology at affordable price points,” commented a spokesperson from the company. “Our latest additions are sure to cause excitement among commercial cannabis growers looking to take things to the next level.”
Pure Grows Aeroponic Systems are custom designed for every client. Pure Grows is built on a module based system, where each module produces 416 healthy, fast-growing plants. Modules could be used independently or as part of a larger growing operation where many modules are connected together to cultivate thousands of plants maximizing the use of available space.
Pure Grows Aeroponic Systems are designed for simplified and controlled commercial cultivation of ecologically pure plants, while creating the ideal growing environment with up to 40% shorter maturation times, providing 6 healthy harvests per year, up to 55% more yearly harvest output versus any other growing methods.
Another addition to the Pure Grows catalog is their 40 Foot Smart Grow Container. The 40 Foot Smart Grow Container is an automated aeroponics greenhouse, packaged in its own 40-foot shell, making it an ideal place to grow a wide range of plants, in a 100% turn-key way.
For more information:
Pure Grows
917-755-2446
info@puregrows.com
puregrows.com
Publication date: 5/22/2018
Lettuce Abound Farms Serves Up First Harvest From New London Aeroponics Operation
Lettuce Abound Farms Serves Up First Harvest From New London Aeroponics Operation
By Carolyn Lange on May 4, 2018
NEW LONDON — With plates heaped high with at least five varieties of lettuce picked that morning at an aeroponics farm a couple miles away, restaurant owners and volunteers working to bring a food cooperative to New London were clearly enjoying their salads.
They were also talking with the farm's owners about getting the fresh greens on the menu and on the shelves.
"Absolutely," said Leah Michaelis, owner of Lake Affect Coffee in New London, when asked if she would consider purchasing the leafy greens from Lettuce Abound Farms. "It's good and nearby and fresh."
Mateo Mackbee and his partner Erin Lucas, who will be opening Model Citizen Restaurant this month in the Goat Ridge Brewery in New London, said the locally grown greens will fit perfectly with the farm-to-market emphasis of their menu.
That's exactly the kind of reaction Kevin Ortenblad and Brian Dengler were hoping for when they invited several business owners and business leaders on a tour last week to see how their aeroponics lettuce is grown and to serve up a meal featuring their first harvest.
When Ortenblad and Dengler, along with their wives Julie Ortenblad and Melody Dengler, started the process 16 months ago to build the region's first commercial-scale aeroponics lettuce farm, they asked local grocery stores and restaurateurs if they would be interested in buying lettuce grown year-round in rural New London.
"They told us, 'let us know when you have something to taste,'" said Dengler, who is Ortenblad's son-in-law.
That time has arrived.
To show people how the lettuce is raised, how it tastes and how much it costs, the family-owned farm is giving tours and giving potential customers a taste of the product.
While building up their wholesale commercial base, individuals can purchase the lettuce from 9 a.m. to 4:30 p.m. directly from the farm site, 3825 County Road 40 N.E. The price is $2.25 a head.
"You pray at the end that people want it," said Dengler, who is also setting up private meetings with local grocery stores. Their goal is to sell their product to local vendors.
"We're very optimistic," Dengler said.
They're hoping that once people taste the greens, they'll be hooked.
"My life was rocked when I found out what real lettuce can taste like," Dengler said.
Lettuce Abound is the first franchise operation of the Faribault-based Living Greens Farm, which developed this type of aeroponics system.
Ortenblad and Dengler modified the system and, despite some challenges that delayed the start-up, they said the system is working flawlessly and plants are growing faster than expected.
The facility is housed in a farm machine shed they turned into an immaculate indoor farm that meets federal vegetable production and packaging standards.
After suiting up in a white jacket and hairnet, washing one's hands and stepping in a shallow shoe wash before entering the indoor farm, visitors see vertical walls of lush green lettuce.
The quantity and vibrancy of the edible greens stops visitors in their tracks.
When the facility is eventually in full year-round production, the 102- by 50-foot building will produce the equivalent of a 180-acre farm.
But these plants are grown without one grain of soil.
Instead, seeds for the greens — including butter lettuce, red and green oak leaf lettuce, romaine, arugula and microgreens — are hand-seeded in a product called "rock wool" that Dengler describes as crushed volcanic rock "spun like cotton candy."
After the seeds germinate and plants are a couple inches high, the chunks of rock wool are placed into panels with cup-like plastic containers and attached to 12 stainless steel A-frame units that are eight feet high and 32 feet long.
Each unit holds 1,536 lettuce plants.
The roots of the plants dangle in the air underneath the frame and are spritzed every 12 minutes with a mist of reverse osmosis water and fertilizer delivered through mechanical sprayers run by a complex computer program.
The water does not touch the leaves of the lettuce, and there are no pesticides used.
Banks of intense lights — which are so strong sunglasses are needed to work among the plants — help fuel the plants' rapid growth. (The lights are turned down during tours.)
The carbon dioxide level is carefully measured, the temperature is kept at 70-72, the humidity is at 55-65 percent and a fan blows air to mimic the wind and makes the indoor farm "smell amazing," Dengler said.
"Schedule is king," Dengler said of the enclosed system and computer program that controls nearly every aspect of the growing process.
It takes about a month from when seeds are started to when plants are harvested. During peak capacity, they will harvest three units, or about 4,600 heads of lettuce, every week, Ortenblad said.
The plan is to harvest lettuce on Thursday, and get it packaged and cooled and delivered on Friday.
They are gradually increasing the number of varieties of lettuce and will grow specific types of greens requested by large-scale customers, Dengler said.
While they're growing just lettuce now, they have already laid the groundwork for a potential expansion in a couple years for a new building to grow aeroponics strawberries and small cherry tomatoes.
Ortenblad, a retired farmer who raised organic soybeans in traditional fields near Willmar, said he is "having a ball" with this new project, in part because he gets to work with his family, including grandchildren, who help plants the seeds.
During the April blizzard, he teased his farmer friends that he was already working in his fields in a perfect climate-controlled environment surrounded by sumptuous green leaves ready to eat while they were waiting out the storm.
US (CO): Aeroponic Garden Provides Students With Fresh Greens
US (CO): Aeroponic Garden Provides Students With Fresh Greens
A new aeroponic garden in the Village Center Dining and Community Commons is the first in the nation to provide students, staff and faculty with fresh salad greens grown on site in a high-tech greenhouse attached to a dining hall.
The “air garden” will help the university reduce its carbon footprint, cut energy costs and eliminate the need for harvesting, cleaning, packing and transporting food from outside farms.
The greenhouse in CU Boulder’s Village Center Dining and Community Commons occupies nearly 3,000 south-facing square feet and consists of 137 grow towers able to produce 44 plants each without soil.
“Locally grown food just tastes better,” said Farm Manager Alex Macmillan, a horticulturalist and organic farmer who will oversee the greenhouse and its production schedule.
Macmillan and student-assistants will start by growing romaine lettuce and other vegetables in stages to ensure a continuous supply of fresh greens.
The inaugural harvest in March produced 15 pounds of kale, 10 pounds of all-star lettuce and 10 pounds of arugula that dining hall employees served to students, staff and faculty.
The aeroponic system at CU Boulder relies on water and “soilless media” to provide nutrients to plants, allowing them to grow faster and produce greater yields on average.
Vertical farming allows for better space usage and efficiency, and automated operations help maintain optimal sunlight, shade, temperature and humidity levels, creating the best year-round growing conditions.
Sensors will monitor conditions to prevent fans, lights and other equipment from running unnecessarily when natural sunlight and other conditions are sufficient.
“I’m excited to get growing and hope this new greenhouse inspires people to be informed about where their food comes from,” Macmillan said. “It’s not grown by someone you’ve never met on some faraway farm with unknown farming practices. It’s me, right here, and you can literally see how I’m growing your food.”
Source: University of Colorado Boulder
Publication date: 5/2/2018
"50% Higher Clone Production With New AEtrium-2.1 SmartFarm-72"
"50% Higher Clone Production With New AEtrium-2.1 SmartFarm-72"
In advance of next week's MJBizConNEXT conference, AEssenseGrows introduced last Monday the AEtrium-2.1 SmartFarm-72, enabling 50 percent higher clone production than prior versions of the aeroponics system. The new 72-tray configuration increases yield to 13,500 per month from the prior version's 9,000 per month.
AEssenseGrows is an ag-tech company specializing in automated aeroponic platforms for high-yield plant production. The company has developed advanced grow systems featuring sensor-driven software that monitors and automatically adjusts the ingredients for specific grow recipes. The four-layer high-density AEtrium-2.1 SmartFarms are designed for high-volume cultivators and come in 24-, 48-, and now 72-tray configurations.
"The pressure on growers in the burgeoning cannabis industry is intense and will only increase as laws evolve and the market grows," said Phil Gibson, vice president of Marketing at AEssenseGrows. "AEssenseGrows' latest version of its SmartFarm cloning product helps give growers greater control over their fates by delivering fast, safe and reliable clones in volume."
AEssenseGrows will showcase its grow systems at MJBizConNEXT, May 9-11, at the New Orleans Morial Convention Center. The company will also participate in the National Cannabis Industry Association annual Lobby Days, May 21 to 23 in Washington, D.C.
And in mid-June, AEssenseGrows will co-sponsor the 2018 International Indoor Plant Factory Symposium with the Shanghai Academy of Agricultural Sciences (SAAS). The symposium, running June 12-15 at the Blue Palace Hotel in Jiading, Shanghai, brings together some of the world's leading experts in commercial indoor cultivation for an exchange of ideas and information about the latest innovations, technologies and research in the field.
More information:
www.aessensegrows.com
Publication date: 5/2/2018
"Customers Can Harvest Lettuce At Dutch Retailer Albert Heijn"
"Customers Can Harvest Lettuce At Dutch Retailer Albert Heijn"
Michiel van Zanten, Hrbs:
Consumers seem to prefer convenience and pre-packaging. There is, however, a growing counter-movement. Starting this week, Albert Heijn Gelderlandplein in Amsterdam boasts a harvest stand. It has an assortment of lettuce with their roots still attached. "It looks like a large lettuce bouquet", says Michiel van Zanten, of the Dutch company, Hrbs. "A very different sight to the lettuce in bags of which as many as possible are crammed into a crate.
The stand looks good. People regularly take photos of it. It is also going well regarding rotation. I often see people harvesting a head of lettuce." How successful this self-harvesting of lettuce will be, will only become evident at the end of the project. Michiel is, from what he has observed, pleased with it.
Lettuce on water is a co-creation of Albert Heijns Food Rebels, Hrbs' green design, and the products of AH's permanent lettuce suppliers. "We chose to offer different kinds of lettuce, not just butter lettuce. There is also tricolour, curly leaf and oak leaf lettuce. It is also a good test for the fresh fruit and vegetable teams to see how these new lettuce varieties catch on with customers when they are presented in this way.
There are buckets with holes in for a total of 35 heads of lettuce in the viewing, selection and packing stand. Here the lettuce stand, with their roots still attached. In this way, the lettuce's roots lie in nutrients, keeping them fresh and lovely. Customers can easily grab the lettuce and put them in the supplied cups. The lettuce then does not drip all over the shop floors. The stand looks at its best when it is fully stocked. Attentive fruit and vegetable staff need to fill the stand up when they become 10% empty.
It is an experiment for AH as well as Hrbs. The company is a service model for fresh herbs and crops. It has, up to now, focused on companies and the catering industry. "Hrbs wants to bring the world of fruit and vegetables as close to the ordinary person as possible. We want to integrate them into everyday life. We supply stands, for inside and outside, with trays for different kinds of mini-vegetable crops and herbs. Chefs and clients can then harvest these themselves. When the crops have all been harvested, or are old, we deliver a new tray and take the old one along for reuse", says Michiel. Before he started working at Hrbs, he was a buyer at Albert Heijn. Her reconnected with this retail shop with this idea. "I know how they think, and what is important to them. We will see how it goes. We consciously opted for co-creation. Lettuce is a new product for us. We are certainly open to the idea of including collaborations to also provide services to retail", he says.
For more information:
Hrbs
Michiel van Zanten
400 Johan Huizingalaan
Amsterdam
T+31(0) 610 247 253
info@hrbs.com
www.hrbs.com
Nebullam: Indoor Farming
What started seven years ago as a way to address food security, production and sustainability led to 13 different prototypes and a model farm near Nevada. And if all goes according to plan in 2018, Nebullam will have a second model farm near Ames and additional capital to help send a product to market by 2019.
Nebullam: Indoor Farming
Lettuce that was grown and harvested last Friday from inside the Nebullam model farm near Nevada. Photo courtesy of Clayton Mooney
For the founders of Nebullam, they hope 13 is a lucky number.
What started seven years ago as a way to address food security, production and sustainability led to 13 different prototypes and a model farm near Nevada. And if all goes according to plan in 2018, Nebullam will have a second model farm near Ames and additional capital to help send a product to market by 2019.
The Ames-based agtech startup pairs high-pressure aeroponic technology and software to grow different types of leafy greens indoors.
The company was founded by Clayton Mooney and Danen Pool, who first met while attending Indian Hills Community College. They stayed in contact and three years ago, Pool contacted Mooney to run a business idea by him.
“He started tinkering on hydroponic systems which led into aeroponic systems,” Mooney said of Pool. “He was very intrigued by the early research NASA had done on aeroponic systems back in the 80’s. Throughout the first half-dozen prototypes, he (Pool) was able to grow tomatoes, basil and lettuce varieties. One winter, he took tomatoes into his coworkers and got great feedback.”
Aeroponics is a method of growing plants in a water-based, nutrient-rich solution without using soil. And when those tomatoes—that were grown indoors—tasted like they were from the garden, a business idea formed.
It was no longer a hobby.
“We thought our original business model was to go around Iowa, set up in warehouses, grow leafy greens and get them into grocery stores,” Mooney explained. “The more feedback we received, it really came back to the technology and that was more interesting to scale than just the production side.”
Mooney said along with Pool and third co-founder Mahmoud Parto, they realized the industry needs to be automated.
“Eventually you need an indoor, vertical farm producing at full capacity without any human interaction,” Mooney says. “We are trying to bring it to the forefront so if we have to trail blaze a little bit, we’re ready.”
To fund Nebullam, Mooney said they raised a “friends and family” round of investment last year and received some funding from through the Iowa State Ag Startup Engine last year when they were going through the program. Nebullam also received a $25,000 loan from the Iowa Economic Development Authority.
This year Mooney said they hope to raise $1 million by the end of June.
Fewer parts, fewer problems
With high-pressure aeroponic expertise and startup experience, Nebullam was looking for a partner who had a background in software and automation.
Mooney said that’s when Nebullam hired Parto, who has helped implement software and automate as many of the processes between germination and harvest as possible.
“From there we’ve considered ourselves a 50 percent hardware and 50 percent software company,” Mooney says.
In total there are six employees working for Nebullam in some capacity, with interns to be hired this summer. Mooney said the team should reach ten people.
Nebullam partnered with LongView Farms in Nevada to create a 300 square foot model farm.
“Hardware is tough and the more pieces you have in a product, the more that can go wrong,” Mooney explains. “In our model farm location, we have just under 5,000 parts total. And that’s across four growing units.”
But Mooney said they’ve streamlined the process to get it to 5,000 parts.
“For the 13th prototype that was our entire focus, how do you reduce the required labor?” Mooney asks. “We think we’ve figured that out. We see ourselves as a technology provider to new, indoor growers.”
He said the hardware, software and inputs such as nutrients and seeds are bundled into a monthly price. And over an 18-24 month contract, the grower pays off the hardware and reoccurring revenue comes from seeds, nutrients and an annual licensing fee for the software.
Mooney said they are in negotiations for a second model farm that would be nearly 1,500 square feet and serve as a showcase for potential customers.
“Do we see corn and soybeans being grown aeroponically? Not at this time,” Mooney says. “But leafy greens, herbs, micro greens, flowers and cannabis, we feel pretty good about those segments.”
IndoorFarming Company Bringing News Jobs To Breathitt County, Kentucky
Indoor Farming Company Bringing News Jobs To Breathitt County, Kentucky
By Morgan Henry
March 29, 2018
FRANKFORT, Ky. (WTVQ)-Governor Matt Bevin announced Thursday that startup indoor farming company Hydroponic Farms USA will invest more than $44.5 million in Eastern Kentuckys Breathitt County and create 121 jobs with the construction of a new facility on a reclaimed mine in Jackson.
Bevin says “The announcement of 121 full-time jobs in Breathitt County is wonderful news for Eastern Kentucky and its skilled workforce. It has been our administrations mission to provide better job opportunities in every part of our state, and this investment is evidence that we are achieving that goal. We are truly grateful for this vote of confidence in the commonwealth. Hydroponic Farms USA will be a great fit for the Jackson community, and continues the economic momentum that is building in Eastern Kentucky.”
Hydroponic Farms USA will build a nearly 42-acre facility with 35.5 acres of production space. The facility will use hydroponic and aeroponic technology to grow leafy greens, tomatoes, peppers and other produce. The 121 jobs will include leadership, production and post-production roles. Company leaders plan to break ground following their land purchase and approval of permits.
Tim Davis, the managing member of Hydroponic Farms USA, says “Appalachia has much to offer the world in terms of natural beauty and abundant resources, but what really makes this place special is its people. We knew the moment we set foot in Breathitt County, that this was not only a perfect place to build our business, but also a place we could proudly call home. Our investors have been humbled by the overwhelming support of Kentucky's state and local government representatives. Moving forward, we are committed to building positive relationships with all of our new neighbors in Breathitt County and doing our part to create real opportunities for people. With the agronomic and technological expertise provided by our partners at Green Ag Technologies, we are proud to bring the future of farming to the area and make a significant impact on the produce industry.”
Hydroponic Farms USA says it is working to develop and implement advanced hydroponic and aeroponic technology and innovation. To do so, the company formed a partnership with Oz Agribusiness Projects and Investments Ltd. and Green Ag Technologies LLC to manage and operate the facility.
Hydroponic Farms USA will follow a similar business model to Kentucky Fresh Harvest, which broke ground in Lincoln County in January 2017 and also is managed by OAPI. Currently, the company is working with major retailers and wholesalers to secure contracts to supply their customers with fresh produce year-round.
Kentucky Commissioner of Agriculture Ryan Quarles says the project is a good fit within the commonwealths evolving agricultural profile.
Kentucky has a long tradition of being a leader when it comes to agricultural innovation, Commissioner Quarles said. Whether it is no-till corn, industrial hemp or hydroponic farms like this one, Kentucky agriculture continues to thrive. Todays announcement is the result of the hard work done by Governor Bevin and Think Kentucky to attract new and exciting businesses to our old Kentucky home.
In addition, Hydroponic Farms can receive resources from the Kentucky Skills Network. Through the Kentucky Skills Network, companies can receive no-cost recruitment and job placement services, reduced-cost customized training and job training incentives. In fiscal 2017, the Kentucky Skills Network provided training for more than 120,000 Kentuckians and 5,700 companies from a variety of industry sectors.
One of The World's Largest Indoor Farms Is Located in Faribault, Minnesota
One of The World's Largest Indoor Farms Is Located in Faribault, Minnesota
February 28, 2018
Living Greens Farm's founder, president, and chairman Dana Anderson is the brains behind one of the largest indoor farms in the world. And as it turns out, it's located right here in Faribault! To keep this huge production running, Anderson utilizes a computer system to control different aspects of the farming process such as light, CO2, humidity, and temperature. All of that combined with aeroponics is what makes Living Greens Farm so successful!
For those of you that don't know, aeroponics is when you grow plants upside down and, instead of planting the roots in soil, they are sprayed with a nutrient-rich solution.
Aeroponics was by no means invented by Anderson, but he did invent and patent the vertical growing and traversing misting systems which is a super efficient way of farming. Kind of reminds me of a Miracle-Gro AeroGarden. According to Anderson in his interview with Twin Cities Business, it's "the fastest way to grow plants." Living Greens Farm recently expanded and they have even more room to grow in the future.
Currently, the farm's greens are being sold in Lunds & Byerlys, some Cub Foods, and Hy-vee stores, Fresh Thyme, as well as other food co-ops.
Organic Certification For Hydroponic Systems
Organic Certification For Hydroponic Systems
The U.S. Department of Agriculture has ruled that hydroponic and aquaponic products remain eligible for organic certification.
By Lydia Noyes | Spring 2018
The National Organic Standards Board has ruled that hydroponic and aquaponic products will continue to be eligible for organic certification.
Photo by Getty Images/LouisHiemstra
As hydroponic and aquaponic farms have flourished across the country in recent years, debates about their suitability for organic certification have reached a fever pitch. This past November, the National Organic Standards Board came to a decision on one of the most divisive topics in sustainable farming: Should plants qualify for organic certification if they’re grown without soil? Through a series of close votes, the board — an advisory committee to the U.S. Department of Agriculture (USDA) — ruled that hydroponic and aquaponic products will continue to be eligible for organic certification.
To be clear, this vote doesn’t change the standards in place. Hydroponic and aquaponic systems already qualified for certification, but their increasing prevalence has made this standard controversial among many traditional organic farmers, who argue that the lack of soil used with these growing techniques means they don’t meet the USDA’s definition of organic. (Hydroponic systems grow plants in water-based nutrients, while aquaponic systems combine hydroponics and fish farming. Both techniques often grow produce indoors.)
The subject of organic certification is quite contentious. Conceptualized in the mid-20th century, the organic movement originally idealized a “closed-loop” farm system, or a property that produced almost everything it needed on-site. Based on the notion that a well-managed farm would rely foremost on natural processes, organic farming was fundamentally about maintaining and improving soil health.
Today, organic certification has drifted away from this original premise. The requirements for certification focus less on a natural farming philosophy and more on what isn’t allowed — namely, synthetic chemical inputs, such as fertilizers and pesticides. This creates a considerable gray area for farming practices that technically follow organic certification requirements but ethically and/or technologically may fall short of their original intent. While hydroponics don’t pollute the soil with toxic chemicals, they also don’t improve it, mainly because no soil is involved. This leads to the crucial question: How do you categorize a farm operation that uses sustainable techniques, but doesn’t benefit the land it’s on?
Beyond the philosophical tensions, organic farmers are worried about the financial impacts of making certification more inclusive. Organic food sales reached $43 billion in the United States in 2016. Because large-scale greenhouses are cheaper to operate than soil-based farms, hydroponically-grown organic tomatoes can undercut soil-grown ones and drive down prices. Moreover, because hydroponic operations don’t need to undergo a three-year “transition period,” as field-based farms do before putting certified products on the market, they can benefit from a faster return on their investments.
While the controversy over organic certification ostensibly pits farmers with similar goals against each other, the stakes are high. The recent decision may have awarded hydroponics more credibility in the sustainable-growing sphere, but it hardly signals the end of the debate.
USDA Accused of Disseminating “Corporate Propaganda” Backing Agribusiness Switch of Organics to (Soil-less) Hydroponic Production
USDA Accused of Disseminating “Corporate Propaganda” Backing Agribusiness Switch of Organics to (Soil-less) Hydroponic Production
February 15th, 2018
[Read Cornucopia’s formal request to the USDA’s Office of Inspector General to investigate whether the agency willfully attempted to misinform the public.]
Regulators Bypass Expert Panel, Endorse Organic Practices Banned Worldwide
FOIA Documents, Witnesses Indicate Collusion, USDA Organic Program in Turmoil: Formal Complaint Filed with Office of Inspector General
Hydroponic operations, like this one,
need only change the fertilizer solution to become certified organic
Image source: Horticulture Group
In an affront to the farming pioneers who launched the organic movement, today a $50 billion industry, the USDA announced late last month that the “Certification of hydroponic, aquaponic, and aeroponic operations is allowed under the USDA organic regulations, and has been since the National Organic Program (NOP) began.”
Much of the hydroponic production entering the organic market takes place in large, industrial-scale greenhouses using liquid fertilizers, mostly produced from conventional, hydrolyzed soybeans. Hydroponic produce under the organic label is rapidly displacing fruit and vegetables grown in soil, which is carefully nurtured to improve fertility, by diversified farms. The founders within the organic farming community contend that hydroponics’ cheaper production techniques, employed by huge growers in Mexico, Canada, and Europe, where hydroponics cannot be legally labeled as “organic,” is crushing legitimate soil-based farmers in the U.S.
There is no legal requirement for conventional or organic produce to be labeled as grown hydroponically, so consumers are likely unaware that the production methods, and corresponding nutrient levels, used in the fruits and vegetables they are purchasing have radically changed.
The USDA’s statement was made regardless of the fact that the National Organic Standards Board (NOSB), the governing body that the USDA Secretary is required by Congress to consult on all organic rulemaking, has never voted to legalize soil-less production.
The present federal organic regulations and their enabling legislation, the Organic Foods Production Act (OFPA), both require careful stewardship of soil fertility as a prerequisite for organic certification.
Despite the USDA’s claim that hydroponics has always been approved as part of organics, The Cornucopia Institute, a farm policy research group based in Wisconsin, has obtained numerous internal and external emails exchanged between NOP staff and certifiers expressing their understanding that soil-based production is required. These documents were procured through a Freedom of Information Act request and are dated as recently as 2016.
“The NOP has unilaterally, and in secret, allowed for the certification of soil-less systems without standards, public notice, or opportunity for public comment,” said The Cornucopia Institute’s senior scientist, Linley Dixon, PhD.
Since the seemingly erroneous official statement was released last month, there has been an outpouring of opposition from the organic farming community. Dr. Dixon said Cornucopia has received a flurry of inquiries from organic farmers surrounding the NOP’s statement, some of which called it an “outright lie,” while others referred to it as “a rewriting of history.” The current USDA standards went into effect in 2002.
The nonprofit farm policy research group sent a formal request to the USDA’s Office of Inspector General asking them to investigate whether officials within the agency willfully attempted to misinform the public.
Since 2005, a few organic accredited certifying agents (ACAs), catering to corporate agribusiness, have quietly certified hydroponic production systems based on the USDA’s public silence on the issue. The largest certifier in the country, CCOF in California, is the predominant certifier of hydroponic operations.
Miles McEvoy
Source: USDA
Earlier this month, Miles McEvoy, the official who stealthily approved hydroponic production while running the NOP during the Obama administration, resurfaced as an official representative of CCOF at a national meeting of organic certifiers. McEvoy resigned from his position with the NOP in September 2017 under an ethical cloud, and has since been a speaker at prominent industry conferences focusing on large-scale organic production, including hydroponics.
Meanwhile, the divide in the organic industry has other ACAs choosing not to certify soil-less production systems, based on their straightforward interpretation of current regulatory requirements. To date, the NOSB has never formally made recommendations for how these soil-less systems might operate within the law, as Congress required.
There are several prominent ACAs that have never allowed the certification of soil-less systems and have a reputation for their high organic integrity in other regards, as well. These include OneCert, Vermont Organic Farmers, Maine Organic Farming and Gardening Association, Organic Crop Improvement Association, and Ohio Ecological Food and Farming Association.
Sam Welsch, the president of the USDA-accredited certifier OneCert, responded to NOP’s notice stating, “There are two parts to the NOP’s lie. The first is that hydroponic operations are allowed by the regulations. The second is when that was allowed. The certification of hydroponics was not even considered an option until September 2006 when the NOP sent certifiers a survey on the topic.”
FOIA documents indicate that, as of 2016, 41 ACAs had responded to a survey stating that they do not certify hydroponics, while only 18 ACAs said that they do.
Dixon referred to the NOP’s statement as “revisionist history” and said that The Cornucopia Institute currently has their legal team researching the filing of a federal lawsuit challenging the agency. The farmer outcry in response to NOP’s position signals that many certified organic growers do not believe that soil-less systems meet the organic standards.
“The USDA’s crude rewriting of history is in keeping with the Trump administration’s attitude towards reality. They seem to believe that if they say something loud enough, we will all believe it,” said Dave Chapman, a 40-year organic farming veteran who has been working to raise awareness around the corporate-hydroponic takeover of organics.
Chapman continued, “The clumsiness of this fake news reveals the current NOP’s disconnect from the organic community. They seem intent on pushing away the very people they were created to serve.”
The Perdue/Trump administration at the USDA has also recently come under fire for scuttling new benchmarks that would have made it easier to enforce animal welfare standards in organic livestock production. That, too, was viewed as an affront to organic stakeholders, as tens of thousands of farmers and consumers formally commented in support of the rulemaking after the NOSB voted unanimously for its adoption. The rules were set aside after heavy lobbying from a few giant, predominantly conventional, egg and poultry producers defending confinement practices.
Whether producing meat, milk, eggs, or produce, many certified organic farmers are becoming aware of the fact that the certifiers they employ are ultimately hurting their bottom line when they certify operations that skirt organic standards, regardless of what the NOP permits.
“More and more growers are recognizing that they are being placed at a competitive disadvantage by the very certifiers who we have been paying thousands of dollars to over decades, assuming they were defending the integrity of organic production,” said Tom Beddard of Lady Moon Farms, the largest organic grower east of the Mississippi with farms in Pennsylvania, Georgia, and Florida.
The USDA’s announcement comes on the heels of a year of controversy surrounding the regulatory agency’s oversight of the organic industry. A series of damaging investigative stories in The Washington Post highlighted allegedly illegal “factory farms” producing organic eggs and dairy products and the failure of the NOP to investigate and control illegal and fraudulent grain imports.
“It’s now more important than ever for organic consumers to do their homework, making sure they receive the safest, nutrient-dense food for their families while simultaneously rewarding the true heroes in the organic movement,” Dixon added.
The Cornucopia Institute maintains scorecards rating organic brands based on their legal/ethical approach to organic production.
MORE:
According to Freedom of Information Act (FOIA) documents obtained by The Cornucopia Institute, NOP staff and some certifiers were still uncertain, as recently as 2013, that hydroponic operations were legally certifiable as organic even while other certifiers, including the nation’s largest, CCOF, were profiting by certifying many large operations.
NOP staff member Renee Mann was asked to respond to a question from a certifier and another NOP staff member seeking clarity on whether or not hydroponic operations could be certified as organic. In a 2013 email, Mann stated, “I don’t know … I seem to remember a time when the NOP said that hydroponic operations could not be certified because they could not meet the requirements for 205.203 (a‐c) to maintain or improve physical, chemical & biological aspects of soil.”
Another certifier contacted the NOP that same year, complaining that they were losing business because it was their understanding, from information provided to them previously by USDA regulators, that hydroponic operations were not eligible for certification. As a result, the hydroponic operators found other certifiers that were willing to deem their operations organic. The certifier called the situation “unfair” and requested additional information.
In addition to asking the OIG to investigate the intent to mislead the public on the legality of hydroponics and the history of the controversy at the NOP, Cornucopia has asked the independent agency watchdog to also look into the chronology of the former top organic regulator, Miles McEvoy, and his waltz through the proverbial revolving door to his current position with CCOF, the nation’s largest organic certifier. McEvoy previously was charged with directly overseeing all certifiers, including CCOF. It should also be noted that CCOF certifies, by far, more hydroponic operations than any other single accredited certifying agent and has profited handsomely from the decision McEvoy made to sidestep NOSB deliberation on the issue and, in a stealthy manner, allow certification of soil-less operations.
Recent high-profile scandals at the National Organic Program, including a series of critical investigative reports in The Washington Post profiling alleged illegal factory dairy and egg operations and fraudulent imports, along with a damning audit by the OIG, immediately preceded McEvoy’s “retirement.”
Furthermore, reports illustrate that during the last years of his tenure, the NOP was a program in crisis, with attrition reducing the staff from approximately 45 down to the current 35.
That staff reduction took place in a program that was already thought to be seriously understaffed, given the magnitude of supervising a $50 billion global industry. “Exacerbating the problem was the unwillingness of Mr. McEvoy to make NOP enforcement documents public and legally fighting their release when receiving requests under the Freedom of Information Act. He had previously stated that over 10% of the diminished staff (four staff members) were strictly involved in reviewing and releasing FOIA documents,” said Mark Kastel, Cornucopia’s senior farm policy analyst.
Many industry observers and certifiers claim organic certification of hydroponic production systems violates several sections of the Organic Foods Production Act of 1990 (OFPA), especially §6513(b)(1):
“An organic plan shall contain provisions designed to foster soil fertility, primarily through the management of the organic content of the soil through proper tillage, crop rotation, and manuring.”
The final NOP rule, adopted under OFPA, and effective in late 2002, mentions soil over fifty times, affirming the central role of soil in cycling organic matter, a practice that is fundamental to organic agriculture.
“The operative legal question is, ‘How can you foster soil fertility without soil?’” stated Cornucopia’s Kastel.
The Cornucopia Institute brought up one final concern in their communication with the Office of Inspector General: the current vacancy on the National Organic Standards Board.
Dr. Francis Thicke, a past board leader who has aggressively challenged the legality of certifying hydroponic production, left the board when his five-year term expired at the end of January. The official posting in the Federal Register announcing nominations to fill the vacancy stated that the term of the new NOSB replacement would commence on January 24, 2018.
It is the contention of The Cornucopia Institute that Congress carefully designated certain seats on the NOSB to assure diversity in knowledge for decision-making by the board (the one held by Thicke was for a conservationist). The organic industry watchdog contends that, based on the clear Congressional intent for seats held by specific industry stakeholders, no official business can transpire without a full complement of members. It is hoped that this deficiency will be resolved before the NOSB’s next official meeting in Tucson, Arizona this April, forestalling potential legal action.
Aeroponics Farm Near New London, Minnesota Will Produce Leafy Greens Year-Round
Aeroponics Farm Near New London, Minnesota Will Produce Leafy Greens Year-Round
By Carolyn Lange / Forum News Service | February 13, 2018
NEW LONDON, Minn. — What had been a large, empty pole barn on a farm in rural New London last year is now becoming a climate-controlled maze of computer-operated, high-powered lights and a water misting system housed on a dozen massive stainless steel frames.
By early spring, the building will be filled with lush, fresh lettuce and other leafy greens.
Grown without soil, pesticides or herbicides, the greens will taste "like a treat," said Kevin Ortenblad, who along with his wife, Julie, and daughter and son-in-law, Brian and Melody Dengler, are launching Lettuce Abound Farms LLC.
It will be the region's first large-scale, commercial indoor aeroponics growing system that will produce fresh greens year-round.
They intend to market the high-end produce to restaurants and other outlets, like food co-ops.
"Our goal is to be able to supply this part of the state with all of the leafy green products," Ortenblad said.
Because plants are grown in numerous trays that are stacked vertically in rows that are 8 feet high and 32 feet long, the growing capacity of the building is the equivalent of 180 acres of cropland, Ortenblad said.
Fed with a nutrient-rich mist that's continually sprayed on the roots by a trolley system that traverses back and forth along the rows, the aeroponics method will use about 5 percent of the water used in conventional farming, he said.
The science of farming
Ortenblad is no stranger to farming.
For more than 30 years he farmed in Priam, near Willmar, and found a niche market of selling organic soybeans to Japan.
The family then moved to Colorado, where he and his wife were involved with Christian ministries. They moved back to Minnesota a year ago to be closer to family and began looking for a business venture.
That's when they heard about a Faribault company, called Living Greens Farm, that developed the technology to grow aeroponic greens on a commercial level.
"I thought, 'I can do that,'" said Ortenblad, 62, who confesses the learning curve has been steep, especially when it comes to the computer programming of the automated systems.
Ortenblad and Dengler worked at the Faribault facility for six weeks learning the ropes.
"They shared a lot of secrets with us," said Ortenblad, adding that they have a "sister farm" relationship with Living Greens Farm.
"They've been very helpful," he said of the crew at Living Greens, which includes New London-Spicer graduate Dana Anderson, who is president and chairman of the Faribault company.
After purchasing the equipment and patented technology from Living Greens Farm, Ortenblad and Dengler began assembling the system at their farm in New London.
"It's been an enormous amount of work," Ortenblad said.
The investment of up-front time and money has been more than what he had initially expected, but Ortenblad said the complex system is nearly complete and seeds will be planted this month.
When seedlings are moved from the nursery into the vertical trays, they will be anchored with a product called "rock wool" but the roots will dangle in the air and be spritzed with a mist every five or six minutes.
Computers programmed with exactly what nutritional balance plants need at each phase of the growing season will spoon feed liquid fertilizer, micronutrients, macronutrients and filtered water into tubes and sprayers that will glide along on tracks to steadily mist the roots of the plants.
Any excess water that drips down will be returned to the tanks in the closed-loop system.
"This is not farming. This is science," Ortenblad said. "This is science and computer automation is what this is, with farming a cool side part of it."
With a constant temperature of 70-72 degrees and humidity of 60-65 percent, he said farming indoors will have its advantages.
"No hail, no dust, no wind, no cold," he said. "That's the environment I'll get to farm in."
There is about four pounds of pressure in the building, which will help prevent dust and bugs from entering the environment, he said. If aphids do enter, beetles will be released to eat them.
Fans will be used to replicate air flow to help strengthen plants and the system also includes 126,000 watts of light bulbs that will replace the sunshine.
"The power company is going to be our best friend," Ortenblad said.
To augment the science, Ortenblad said he intends to play Christian music in the indoor garden to help inspire the plants to grow. He also said there are hundreds of handwritten Bible verses inside the walls in a nod to the family's core values for their new business.
Year-round greens
The variety of greens that will be grown at Lettuce Abound Farms, like oak leaf lettuce, arugula, and butter lettuce, will be harvested about four weeks after germination.
Microgreens — young, tender plants with intense flavor — will be harvested about two weeks after germination.
Because they are herbicide- and pesticide-free, Ortenblad said the greens don't need to be washed before being put on the table, which he said also extends their shelf life.
"I've never tasted lettuce as good as what Living Greens gave us and what we will be growing," he said.
Ortenblad said he hopes others will also appreciate the flavor and having year-round, locally grown produce raised without pesticides or herbicides.
The cost of the fresh greens will likely be more than typical grocery store prices, but Ortenblad said it will be worth it.
Tags:
Business, Agriculture, Agriculture, Aeroponics, Minnesota, leafy greens, New London
Stop the Presses: Hydroponics Certified Organic
While both sides still feel they’re in the right as to whether or not hydroponic produce should be certified as organic, that argument ended on November 1, 2017, with an industry decision that such certification was allowable.
Stop the Presses: Hydroponics Certified Organic
Lee Allen | February 15, 2018
Takeaway: Until November of 2017, growers debated the organic certification of hydroponics. Now, the verdict is in.
While both sides still feel they’re in the right as to whether or not hydroponic produce should be certified as organic, that argument ended on November 1, 2017, with an industry decision that such certification was allowable.
The highly emotional status declaration came down at the Fall 2017 NOSB meeting in Florida, where the advisory body to the USDA ruled that hydroponic and aquaponic farms could carry the organic label. They’ve been allowed to be called organic for a number of years, but now it will be official.
Still, the proverbial Hatfield and McCoy battle on the issue remains pretty heated. Both sides still believe they have the best idea.
The Coalition for Sustainable Organics put the approval in the win column for them, pleased that NOSB rejected a number of proposals that would revoke the certification of many hydroponic, aquaponic, and container growers. President Lee Frankel’s contention was that more, not less, the organic product was needed to feed a hungry world. “Everyone deserves organic, and this proposal would have made it harder for consumers to access organic produce as a meaningful solution to environmental challenges faced by growers (who) need to adapt to site-specific conditions,” he says.
Another supporter, the Recirculating Farms Coalition, was equally pleased with the vote. “NOSB made the right decision,” says executive director Marianne Cufone. “Many products already carry a USDA Organic label and to now withdraw that would be irresponsible and confusing for both farmers and consumers.”
Conversely, The Cornucopia Institute group had sought rejection of what they called a “watering down” of organic standards supported by “big money and powerful corporate lobbyists who want their piece of a growing organic pie.” They advised a “no” vote to “protect soil-based farmers who raise fruits and vegetables in a sustainable, healthy fashion.”
The NOSB ballot count wasn’t an overwhelming landslide but a squeaker win with an eight to seven final tally to reject proposals prohibiting hydroponic/aquatic production certification. By a much larger margin (14 to zero, with one abstention), however, aeroponics was denied the organic certification.
Biosystems engineer Dr. Stacy Tollefson of the Controlled Environment Agriculture Center at the University of Arizona, a member of the Hydroponic and Aquaponic Taskforce, says she’s dumbfounded the NOSB didn’t support aeroponics. She asks, “If they support aquaponics and liquid systems, why not aeroponics?”
The NOSB recommendation is now in the hands of USDA. The federal agency and the staff of the National Organic Program will decide on the rules to modify existing organic standards. Once that is done, there will be a public comment period and a regulatory review before the new classifications become regulation.
Going forward, “This decision should promote more innovation in organic production,” Tollefson says. “There may be increasing pressure to be more transparent within the USDA Organic label, perhaps a push for mandatory labeling that differentiates ‘soil grown’ versus ‘container grown.
USDA Reaffirms Organic Certification for Container Production Systems
In the most recent edition of the Organic Insider newsletter, USDA states, “Certification of hydroponic, aquaponic, and aeroponic operations is allowed under the USDA organic regulations, and has been since the National Organic Program began.”
USDA Reaffirms Organic Certification for Container Production Systems
The United States Department of Agriculture (USDA) clearly reaffirmed its position this week on the inclusion of hydroponic, aquaponic, and aeroponic within the organic program. In the most recent edition of the Organic Insider newsletter, USDA states, “Certification of hydroponic, aquaponic, and aeroponic operations is allowed under the USDA organic regulations, and has been since the National Organic Program began.”
This is a significant victory for farmers and producers across the country to provide more certainty over certification standards. The Coalition for Sustainable Organics, a group of environmentally and socially responsible growers committed to maintaining USDA’s current high standards, thanks USDA for its thoughtful approach on this issue. In addition, CSO thanks all the growers, consumers, farm workers, marketers, input suppliers, auditors, and others who took the time to participate in the debate by submitting comments, providing testimony, speaking with your customers and consumers, and reaching out to government officials to help educate members of the NOSB as well as the broader organic community regarding the benefits and legitimacy of organic container production methods.
The Organic Insider is a routine publication of the USDA to inform the organic community and industry on a range of topics related to organic agriculture at USDA, including regulatory updates, requests for public comments, and notices about upcoming activities. This edition also includes links to the materials from the Fall 2017 National Organic Standards Board meeting such as transcripts,presentations made by the USDA, votes, formal recommendations and USDA’s initial responses to the recommendations.
While this publication is important, growers are still reporting wide differences in how individual auditors are evaluating their organic operations with frequent changes to their reviews despite USDA’s consistent policy. In addition, the National Organic Standards Board’s (NOSB) Crops Subcommittee continues to discuss additional regulations for container production systems. It remains unclear how these efforts may unfold moving forward. In addition, USDA acknowledged it received NOSB’s recommendation to prohibit aeroponics from certification.
CSO continues to work with its members to ensure the organic community remains open to a wide diversity of participants in order to provide organics to all and ensure regulatory certainty.
Living Greens Farm is Hooked on Aeroponics
Living Greens Farm is Hooked on Aeroponics
The Faribault company produces lettuce year-round, 21 days from seed to salad.
JANUARY 23, 2018
KATE LERETTE
What do popcorn and lettuce have in common? Nothing, really. It’s how Dana Anderson describes how produce is grown at Living Greens Farm: “It’s like pushing the popcorn button on the microwave,” he says.
Based in Faribault, Living Greens Farm is one of the largest indoor farms in the world, according to Anderson, who is the founder, president, and chairman. The company uses a computer system to control elements such as light, temperature, humidity, and CO2, combined with aeroponics—a method of growing plants by suspending their roots in the air—to grow lettuce, herbs, and microgreens. Rather than using soil, plants are sprayed with a nutrient-rich solution.
“Aeroponics is the fastest way to grow plants,” says Anderson. “Harvest is less than 21 days for a head of lettuce. It’s about two times faster than traditional farming.”
While Living Greens Farm didn’t invent aeroponics, it did develop its own vertical growing and traversing misting systems. The patented systems use 200 times less land and 95 percent less water than a traditional farm, says Anderson, which is huge, given that “70 percent of the world’s fresh water is used for agriculture.”
Anderson launched Living Greens Farm in 2012 after working out of his garage for three years. He and his team raised $8 million from friends and family to help get the company off the ground.
In October, Living Greens Farm completed its first expansion, increasing growing space from 5,000 square feet to 21,000. With the additional space, the company added 32 growing units to its existing 10, increasing its production to 1 million heads of lettuce per year.
Living Greens still has plenty of room to grow; right now it’s using only about 35 percent of its space. Once the company reaches max capacity, it will have 60,000 square feet of growing space. “When all is said and done,” says Anderson, “we will be able to produce a head of lettuce for every person in the entire MSP metroplex.”
The company currently sells greens at Lunds & Byerlys, a handful of Cub Foods and Hy-Vee stores, Fresh Thyme and other major co-ops. A few stores in Iowa will begin carrying its products this year. In addition to growing its grocery-store base, Living Greens Farm is working on adding accounts with food services at local colleges and corporate offices. Anderson also is exploring licensing opportunities worldwide and expanding its operations in other markets.
“There are hundreds of people who do this type of farming as a hobby, but in terms of large commercial companies, we only have three or four major [U.S.] competitors,” says Anderson. “What makes us different is our patented systems and our impact on the economy; we keep more dollars in the state.”