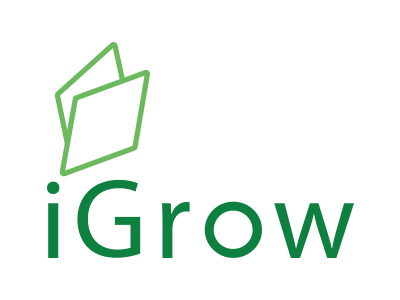
Welcome to iGrow News, Your Source for the World of Indoor Vertical Farming
Grant Supports Urban Farming Initiative In Holyoke, Massachusetts
Governor Charlie Baker speaks at the 2018 Small Business Day at the Omni Parker House on Tuesday, April 10, 2018. Staff photo by Matt Stone
Grant Supports Urban Farming Initiative In Holyoke, Massachusetts
April 29, 2018 | Associated Press
HOLYOKE, Mass. (AP) — State and local officials are teaming up with a community group to help create a new city farming program in western Massachusetts.
Republican Gov. Charlie Baker's administration says the state will invest $200,000 in two Holyoke container farms that will be managed by Nuestras Raices, an organization that supports urban agriculture.
The farms will be located next to the recently-opened Culinary Arts Institute at Holyoke Community College. Officials say interns from the college and apprentices nearby neighborhoods will be taught hydroponic food production and grow leafy greens — such as lettuce and spinach — that will be sold to the college and local restaurants.
The farms are part of a new "transformative development" district in the city.
The state is also spending $1.6 million to help make the district safer for pedestrians.
Elon Musk's Younger Brother Kimbal Founded A Company Called Square Roots
Elon Musk's Younger Brother Kimbal Founded A Company Called Square Roots
- Brooklyn-based Square Roots 'farmers' grow greens in shipping containers
- The greens can be sent to local establishments that lack access to fresh food
- Kimbal Musk is auctioning off his Tesla Model 3 to fund the project
- It is the sixth Tesla Model 3 created and is 'mostly handmade', Musk said
By Maggie O'Neill For Dailymail.com
5 April 2018
Elon Musk's younger brother Kimbal is trying to revolutionize food production, and is auctioning off his Tesla Model 3 to do so.
The 45-year-old chef is the founder of urban farming company Square Roots, based in Brooklyn, and is trying to get the project off the ground by letting go of the sixth Model 3 made by his brother's company.
Kimbal Musk went on Megyn Kelly TODAY to talk about how he came up with the idea of auctioning off the car in order to fund Square Roots and what he hopes his company will do for the future of urban food production.
Musk's firm uses 320-square-foot shipping containers to produce roughly the same amount of food as two acres of farmland annually but in a fraction of the space.
Square Roots grew out of Musk's search for food that tastes good.
The chef told Megyn Kelly that while working on developing one of his restaurants in Colorado, called The Kitchen, he realized his team was having trouble finding 'good food' to use at the establishment.
Musk said: 'We started about 15 years ago, [and] we really struggled to find food that tasted good.'
He explained his frustration over a system that has been designed to exclude local farmers.
'The industrial food system is literally designed for food to ship thousands of miles. It's not designed to taste good,' Musk said.
RELATED ARTICLES
- Billionaire Elon Musk says he is sleeping on Tesla's factory...Tesla says it churned out over 2,000 Model 3 sedans in the...
Kimbal Musk got the idea for Square Roots while developing a restaurant in Colorado called The Kitchen. Musk, a chef, found that getting fresh food that tasted good was challenging for his staff members. Pictured is the inside of a Square Roots shipping container
He added that most foods used by restaurants are high in calories but do not have the benefit of high nutritional value, which renders them basically useless - and possibly harmful - to the body.
'It causes a lot of problems we have in food today,' Musk said.
This conundrum led to the development of shipping containers designed to grow food for local use.
Musk emphasized that he was only trying to engineer food that tasted good when the idea came to him. He said: 'If you can grow the food really close to home - to the restaurant - the food tastes so much better. It is absolutely delicious.'
Musk says that Square Roots can give local establishments access to fresh food that tastes good. Additionally, no pesticides are used during the production process, Musk said
HOW DOES KIMBAL MUSK'S URBAN FARMING TECHNOLOGY WORK?
Elon Musk's brother founded a company called Square Roots that he hopes will revolutionize urban farming.
Square Roots 'farmers' grow greens in shipping containers without using any pesticides.
The food can be sent to local establishments that otherwise might not have access to fresh, locally-grown greens.
Kimbal Musk explained on the TODAY Show that one 'farmer' at his company specified the conditions within a shipping container to try to replicate a certain crop of basil from 2009.
Pictured is a Square Roots shipping container around New York City. For now, Square Roots is producing mostly just greens
He explained: 'We have one farmer who - this is so cool - he took his container and he is able to control the weather.
'So he can decide what time the sun rises, what time the sun sets, everything.
'And in Italy in 2009 there was this vintage of basil - just the basil that we normally eat.
'But that particular year is quite a famous year for basil in Italy, and he went into the weather records and recreated the summer of Italy 2009 inside of his container: what time the sun came up, what time the sunset, what days did it rain, how much oxygen was in the air, what was the temperature, what was the humidity, everything.
'And now [he] sells the most premium basil in the whole city of New York because it just tastes so much better!'
And the food is safe, Musk reassured a hesitant Kelly, saying no pesticides are used during the production process.
'Am I eating computer-generated leaves?' Kelly asked skeptically.
But her guest told her that no artificial ingredients are used at Square Roots.
He took it a step beyond that, promising: 'It is the cleanest food you can possibly eat.'
But there is no doubt about the model's sustainability benefits. One of Square Roots's 320-square-feet shipping containers can produce the same amount of food as two acres of farmland annually.
Musk pitched the project as an answer to urban environments that do not have great access to fresh food.
And Square Roots 'farmers' can even produce foods that have specific tastes for certain restaurants. 'They can design it the way a chef might like it,' Musk said.
The company is, at the moment, producing mostly just greens.
Musk also mentioned on the TODAY Show segment that Square Roots is in the business of hosting farmers markets within New York City office spaces.
He then explained how he plans on expanding the company: by selling the sixth ever made Tesla Model 3.
Musk said: '[The early cars] are mostly handmade. Only very, very close friends of the company get access to the early cars.
'I have it, and when I got the Model 3, I just thought how much more special it would be for someone who's a big green supporter to have it.
'It's so special to have one of the first cars off the line.'
Read more: http://www.dailymail.co.uk/sciencetech/article-5582987/Kimbal-Musk-unveils-urban-farming-plan-produces-2-ACRES-worth-food-shipping-container.html#ixzz5DQupY3hN
Follow us: @MailOnline on Twitter | DailyMail on Facebook
Contain Inc And InterWest Collaborate To Offer First-of-its-Kind Insurance For Container Farmers
Contain Inc And InterWest Collaborate To Offer First-of-its-Kind Insurance For Container Farmers
Contain Inc has collaborated with InterWest Insurance & a leading national insurance firm to launch a comprehensive, flat-rate insurance for container farms.
Growers have sometimes found that they’re not covered for key risks, such as losing a crop to an HVAC unit’s breakdown”
— Rick Harrison, Vice President at InterWest Insurance
RENO, Nevada, USA, May 2, 2018, /EINPresswire.com/ -- Indoor agriculture - the practice of raising crops in warehouses, containers, and greenhouses using hydroponics, aquaponics and aeroponic techniques - is one of the fastest-growing practices in global farming. The number of commercial indoor farms in the US has more than doubled in the past two years as growers use the practice to deliver safe, fresh, local produce to consumers year-round. To date, indoor farmers have lacked the same access to financial tools enjoyed by their outdoor counterparts. This morning, Contain Inc and InterWest Insurance are announcing a first-of-its-kind collaboration to rectify one aspect of that inequity.
Indoor growers have different insurance needs to their outdoor counterparts; their operations rely on climate control equipment, and some crops are so delicate that they can perish in as few as two hours if not kept in the correct environment. Yet, workers in indoor farms typically have more variety in each day’s work, and so, we expect that they will see fewer repetitive strain injuries over time. Their customers are typically nearby, so they have less post-harvest risk of losing a crop. Current insurance options don’t take account of these differences. Instead, indoor growers all too often find themselves with insurance that does not meet their needs. “Growers have sometimes found that they’re not covered for key risks, such as losing a crop to an HVAC unit’s breakdown” commented Rick Harrison, Vice President at InterWest Insurance.
To remedy this, Contain Inc is collaborating with leading regional insurance broker InterWest Insurance and a major national insurance carrier to offer insurance designed specifically for indoor growers. Its first product is targeted at container farmers and offers a “one-stop shop” package for their insurance needs. It combines property coverage, farm liability insurance, crop loss and equipment breakdown coverage. The coverage package is available at a premium of approximately $1,500 per container for up to five containers. Those farming more than five containers will be serviced on an individual basis by InterWest Insurance agents, and the broker is equipped to work with indoor growers utilizing other forms of equipment, such as warehouse farms, plant factories and greenhouses in addition.
The package was designed with input from indoor growers and container farm equipment suppliers. “We’re excited to bring container farmers an easy, fast way to meet their insurance needs” added Nicola Kerslake, founder of Contain Inc. Further information on the package is available at the Contain Inc website at contain.ag.
About Contain Inc
Contain Inc is an alternate finance company focused exclusively on indoor agriculture. It works with more than a dozen leading indoor agriculture suppliers to aid growers in securing lease financing for their farm equipment and with leading regional insurance broker InterWest Insurance for their insurance needs.
About InterWest Insurance
InterWest was founded in 1992 as a result of the merger of three large successful insurance brokerage firms in Northern California. Through aggressive marketing and acquisition efforts, its influence has expanded and it is now a recognized leader in providing comprehensive insurance solutions for the Agribusiness community. Although headquartered in California, InterWest is licensed in all states and has a depth of expertise and professional in-house claims and risk control resources to serve clients nationwide.
Nicola Kerslake
Contain Inc.
7756237116
email us here
The Current State of Indoor Farm Economics
THE CURRENT STATE OF INDOOR FARM ECONOMICS
Our sibling company, Contain Inc, is providing the white paper that will be provided in hard copy exclusively to participants in this week’s Indoor Ag-Con. Ahead of that, they have provided us with a sneak peak of its contents:
Contain Inc is an alternate finance company focused on the indoor agriculture market. It solves one of indoor farmers’ most pressing issues as it cuts initial farm build costs by 80% by utilizing 3-5 year equipment leases. As a provider of capital to the industry, Contain Inc has a keen interest in better understanding how and why indoor farms are successful. Its team spends a good deal of time attempting to understand the drivers of farm economics, and it is this theme that we cover in the white paper that will be released at Indoor Ag-Con this week.
What’s the Current State of Indoor Farm Economics?
THIS BLOG POSTING PROVIDES AN EXCERPT FROM THE CONTAIN INC WHITE PAPER THAT WILL BE RELEASED AT INDOOR AG-CON ON MAY 2-3, 2018
The greatest criticism of indoor farms has long been that they are not economically viable, and – in the view of some – never will be. Professor Albright of Cornell University created the most often cited criticism of industry economics, arguing in 2014, that widespread adoption of controlled environment agriculture would increase the cost of certain foods beyond market acceptance. The failure of some of the first generation of North America’s indoor farms seemed to confirm this skepticism, even though most fast-growing young industries are characterized by high startup failure rates.
Yet, software firm Agrilyst found that just over half of respondents to their survey of indoor farms said they operated profitably, and market forces are driving more towards this benchmark. New technologies, falling costs for existing technologies, economies of scale, and better access to capital, along with time itself, all have a part to play.
What do we Know so Far?
As it is young as a commercial industry, we are only beginning to see trends in indoor farm economics. For example, there is some evidence that longer standing farms are more likely to be profitable than newer ones, though there is likely to be some survivorship bias in the data. All else being equal, larger farms are more profitable than smaller ones.
One of the long-observed aspects of agriculture is that it’s a cyclical industry, contributing to booms and busts throughout history. From an economist’s perspective, one of the attractions of indoor agriculture is that it offers the possibility of a less cyclical way of farming. Though the industry is too young for any trend to have developed, theoretically, the steady income stream from indoor farms – which harvest daily rather than periodically – should aid in smoothing long-observed farm business cycles.
To inform our work at Contain Inc, we have developed a proprietary model of the exogenous factors – influences that are not in the control of the grower – that impact indoor farm economics. In this multivariate model, the two indicators proving the greatest significance with p-values < .05 are industrial rents and population density, each of which are location-dependent variables. Consequently, our current “top ten most favorable” indoor farm locations are biased towards larger urban conurbations. We note that this model is dynamic and that we moderate it frequently as we capture new data.
What Trends are Driving Farm Economics?
We see indoor farm economics continuing to improve as:
Moore’s Law is at work in the industry – Indoor farming is benefiting from falling capital expenditure costs, particularly for LED lighting. As LED prices have fallen by 85% in the last five years, they are forecast to fall from over 60% of capex costs in 2011 to under 15% by 2026.[1]
Automation & AI – Growers are increasingly adapting automation to improve nursery, harvesting and post-harvesting operations, improving yields and cutting costs as a consequence.
Plant Genomics – Indoor farmers are turning their attention to breeding seeds that are designed to work better in indoor systems to provide higher yields, better taste and better nutrition.
Lower Cost of Capital – As funding options like lease financing from Contain Inc become more prevalent, growers can afford larger, more efficient farms. As indoor agriculture becomes more mainstream, we anticipate that average interest rates will fall as lenders recognize the lower risk inherent in the practice. Better insurance rates, such as those offered by Contain Inc’s collaboration with InterWest Insurance will also help to reassure lenders that indoor agriculture is bankable.
Beyond the technical and scientific barriers that indoor growers, academics and equipment suppliers break each day, better and more nuanced understanding of the economic factors that underpin indoor agriculture can help to drive the industry further towards profitability. This remains an important aspect of Contain Inc’s mission to support indoor growers.
JOIN US AT THE 6TH ANNUAL INDOOR AG-CON ON MAY 2-3, 2018
REGISTER TODAY
Coalition for Sustainable Organics Continues Efforts to Ensure Participation of Containers and Hydroponics in the National Organic Program
Coalition for Sustainable Organics Continues Efforts to Ensure Participation of Containers and Hydroponics in the National Organic Program
TUCSON, ARIZONA - April 25, 2018 - Led by executive director Lee Frankel, the Coalition for Sustainable Organics (CSO), continued its advocacy efforts at the National Organic Standards Board (NOSB) Spring meeting to ensure the National Organic Program remains open to producers using containers and hydroponic cultivation methods.
Frankel testified, “Comprised of growers big and small, we [the CSO] advocate for the continued allowance of containerized growing methods under the National Organic Program while enabling growers to select the most appropriate production system for their specific site and commodity needs.”
“In addition, the CSO was pleased to receive confirmation from the U.S. Department of Agriculture that of the legal basis for these methods via Sections 6503 and 6512 of the Organic Foods Production Act,” stated Lee Frankel. “CSO has long argued that OFPA and the accompanying regulations do not prohibit containers and hydroponics from the organic program.”
“Thanks to USDA’s strong statement, producers can continue to meet the rising demand for fresh organic produce using a wide variety of environmentally sound and sustainable farming methods such as containers and hydroponics,” continued Frankel.
Following a presentation by Undersecretary Ibach on USDA efforts to increase organic integrity, members of the CSO as well as Frankel testified today in Tucson, Arizona at the meeting of the National Organic Standards Board to show continued support for efforts to further strengthen and clarify the USDA organic regulations and ensure integrity in the USDA Organic Seal.
#######
FOR MORE INFORMATION:
Lee Frankel, Executive Director
The Coalition for Sustainable Organics
info@coalitionforsustainableorganics.org
619-587-4341
Very Local Greens' Very Urban Farm
Very Local Greens' Very Urban Farm
Phil Hatcher wants to make friends with salad via his shipping container crops.
Posted By Allison Saunders on Thu, Apr 19, 2018
Phil Hatcher will soon be planting his first round of seeds on the Dartmouth waterfront. | LENNY MULLINS
"My agricultural background is planting peas and stealing peas from my grandfather’s garden growing up,” says Phil Hatcher with a laugh. After 18 years in the film industry, he’s switching gears and getting back to the land. Sort of. This summer Hatcher will launch Very Local Greens, a farm that lives inside a repurposed shipping container that’s been plunked at King’s Wharf on the Dartmouth waterfront.
“This was something I haven’t seen before, something Halifax doesn’t have,” he says of the project, which was inspired by a viral video that lead Hatcher to Freight Farms, makers of the “Leafy Green Machine” AKA Very Local Greens’ home. Aiming to create a local version of Brooklyn’s popular curated (indoor) greens farm, Square Roots, he started crunching numbers.
“I’m kind of going through a little fairytale in my head. I had a dream list in my mind and King’s Wharf was one of my first thoughts,” he says. “I wanted to utilize an unused space. We’re portable, we’re mobile, we’re a crane lift away. We have the privilege to be able to move and adapt with the development.”
Very Local Greens’ sustainable space offers a hydroponic, climate-controlled system that grows its herbs and various greens in vertical towers, watering and feeding them on a schedule. It can help 500-1,000 heads of lettuce grow per week.
“The whole thing is 100 percent traceable and trackable and controllable by an app,” says Hatcher. “The great thing is when I’m at home I can see security footage, adjust my lights, temperature, humidity...right in the palm of my hand. It’s just really smart.”
The aim is for his container farm to work with restaurants, not just providing them locally grown greens, but also growing based on need—and want—if there’s a particular, let’s say, arugula a chef is after. A CSA of some kind is also on the to-do list. Mostly, Hatcher says, he’s just excited to see where the project takes him. (Which is, hopefully, the addition of another container.)
“I think it’ll adapt and become its own thing. We’re just trying to find out where our niche is going to be and grow with it. There’ll be surprises along the way.”
Hydroponic Container Farm Company Starts Growing Its Own Hyper Local Produce
A new custom partnership between retail foodservice business B.GOOD and Freight Farms will result in hyper-local produce available for use in their New England locations. The partnership is maximizing on Freight Farms’ food production capabilities with B.GOOD’s philosophy of providing a commitment to fresh and local produce year-round at a consistent quality and quantity.
Creating local food availability
Until now Freight Farms has been primarily developing hydroponic shipping container farms (the Leafy Green Machine™) and its associated software (farmhand®) but this will be their first food production venture. Brad McNamara, CEO of Freight Farms, says they’ve already had a connection with B.GOOD for several years. "Discussions of supply chain trials and tribulations and wanting to have a truly local program were an ongoing topic. They’ve always been very forward thinking,” McNamara says of B.GOOD. “They’re about transparency, traceability and striving to find a way to do local in a true way. It’s made for easy mutual learning and good conversation.”
Local lettuce for a signature menu item
There are approximately 30 locations dispersed throughout New England alone. “I think that’s where the conversation started to get really interesting,” says McNamara. “For them, finding a way to do local in all the different places they want to expand B.GOOD is an issue: i.e. your local scene in the Boston area is very different than the scene in Springfield or Connecticut.” By using Freight Farms’ containerized hydroponic system, it doesn’t matter where the ‘farm’ is located. Freight Farms will be growing 600-700 heads of bib lettuce a week for B.GOOD’s signature Cousin Oliver burger menu item for about 17 or 18 of its stores.
Growing food ourselves
McNamara says the Freight Farms team is excited to get right down to the business of actual farming. “This is something that we’ve never officially done before in terms of us running our own facilities and growing the food ourselves. The partnership and the timing is right, he says and with the technology, training and experience Freight Farms already has, it was easy to take that last step and branch out into growing as well.
Hydroponic lettuce supply
Determining production, demand and supply won’t really be an issue with the detailed growing data Freight Farms already has access to. “We’re running on the same platform with the same data set and software as our other 200+ growers around the globe so when it comes to production, we know it down to a T,” McNamara says. The partnership officially began April 10th, 2018, as trucks distributing Freight Farms hydroponic lettuce spread across New England to the majority of B.GOOD’s locations.
Immediate cold supply chain availability
Distribution also remains local: Freight Farms has set up a farm collocated at B.GOOD’s existing distribution facility. “We can provide turnkey distribution as well. The distributor has refrigerated trucks that are already going to all locations in the area on a bi-weekly basis. By locating our farm there we take our food safety to another level by immediately harvesting and packing the lettuce: we never break the cold supply chain before it gets to the kitchen.”
For more information:
Elizabeth Yekhtikian
Freight Farms
Tel: (+1) 781-966-4145
Publication date: 4/11/2018
Author: Rebecca D Dumais
Copyright: www.freshplaza.com
CEA Advisors Is Pleased To Announce That Hort Americas Will Be Working With Them As The Exclusive US Distributor For Growracks™
CEA Advisors Is Pleased To Announce That Hort Americas Will Be Working With Them As The Exclusive US Distributor For Growracks™
Growracks™ are a fully customizable vertical rack system built specifically for vertical farming. Units are available with 1 to 5 growing levels and include leak proof ABS trays. Lighting and or irrigation is also available and very easy to install.
I am very pleased to be working with Chris Higgins and the dedicated and knowledgeable team at Hort Americas”, said Glenn Behrman, President of CEA Advisors. “Their comprehensive catalog of LED lighting products and horticulture supplies makes Hort Americas the perfect partner. Not only for CEA Advisors but also for the growers they serve”.
Chris Higgins commented that “Growracks are appropriate for schools as a tool to teach young people about hydroponics, sustainability, and healthy eating. They’re also perfect for small-scale production, hobby growers or vertical farming research for industry and academia”.
For more information: chiggins@hortamericas.com or gb@cea-advisors.com
Vertical Farm In Shipping Container Solving Problem of Land Loss
FRANK Donato opened the doors to his trial vertical farm, a shipping container on his 4ha Mornington Peninsula Hydroponics business. “These are the LED lights, worth $200 each but last for 50,000 hours,” he said, pulling out a 1.5 metre long beam, designed to project 700 nanometres on the light spectrum.
Vertical Farm In Shipping Container Solving Problem of Land Loss
SARAH HUDSON, The Weekly Times
April 3, 2018
FRANK Donato opened the doors to his trial vertical farm, a shipping container on his 4ha Mornington Peninsula Hydroponics business.
“These are the LED lights, worth $200 each but last for 50,000 hours,” he said, pulling out a 1.5 metre long beam, designed to project 700 nanometres on the light spectrum.
“That’s on the red/pink spectrum, which is required for plant photosynthesis.
“And this,” he said, pointing to a door-mounted machine, “is another expensive piece of equipment, a carbon dioxide injector imported from New Zealand.”
Five years ago, prompted by the annual summer loss of greenhouse crops to extreme temperatures, Frank ran his $20,000 shipping container trial for about four months, proving he was able to grow 1200 basil plants at a time in different seasons to maturity in just over two weeks (compared to up to five weeks in winter).
“The plants even met Coles specifications,” the 60-year-old added.
So impressed was he by the results, he is now planning to transform his farm.
Currently Frank and his wife Luana have seven igloos and a total growing area of more than 3000 square metres at Mt Martha. It is a mix of plastic and shade cloth, with one “smart” computer-controlled glasshouse that has a roof opening to allow heat to escape.
Year-round they grow more than 10 hydroponic herbs, including 2000 basil plants weekly, and 2000 coriander plants, as well as a range of micro-herbs.
They grow eight lettuce varieties, with the most popular being 1000 plants of green oak weekly.
And there are about 400 plants each of two tomato varieties, yielding 8kg per plant.
The Donatos have a nursery growing out their own seedlings under LED lights, planting out after an average of two weeks’ germination.
HEAT IS ON
THE hydroponic system is conventional, using rock-wool as a media, and coconut fibre for tomatoes. Mains gas is used for heating, with the carbon dioxide pumped back in to igloos to encourage plant growth.
To minimise inputs they use biological controls, introducing predatory mites and wasps to control two-spotted mite, aphids and thrip; only once has he had to use sprays to combat downey mildew.
The majority of their stock they sell to Richies supermarkets, as well as having stalls at the Victorian and South Melbourne markets, with a small amount through their on-farm cafe, open seven days a week, which is run by one of their two sons, Nick.
At their peak about two years ago they sold 10,000 basil plants a week to Coles.
However the Donato family have this year sold off 3ha of their property for housing development, retaining 1ha on which Frank plans to demolish his current igloos within the next year and rebuild a 330sq m enclosed warehouse for vertical farming, using LED lights.
Vertical farming, also called controlled-environment agriculture, uses indoor farming techniques where all environmental factors are controlled, using artificial light and vertically stacked layers.
Frank said once the new system was up and running he would grow about four tiers of plants, producing more than five times as much as a conventional greenhouse of the same size, growing at a lower cost, able to control the amount of light and maintain a steady temperature of 21C.
“Every summer I lose crops to heat — this year alone it got up to 53C in the igloos on one of the very hot days,” he said.
“Whereas with LED it will be a fully controlled atmosphere and I’ll have no losses — including no losses from disease or pests.
“I will be able to exactly predict what product will be available and when.”
He plans to introduce automated systems — connected remotely to his mobile phone — such as humidity-controlled reverse cycle airconditioning, automated dosing for fertigation, and carbon dioxide injections, all fully solar-powered.
BOOK WORM
FRANK has closely followed overseas developments in vertical farming through reading widely, subscribing to hortidaily.com, as well as regular trips abroad. While he was conducting his shipping container trials he travelled to the UK; last year a Swedish company visited his farm to trial LED lights.
This year he will travel to the Netherlands to visit the Philips lighting research facility.
“In the past two years alone their lights have become 30 per cent more efficient,” Frank said. “I was the first person in Australia to bring in Philips LED lights five years ago.
“I’ve waited all this time because the technology has been rapidly advancing. It’s now got to a point where the technology is accessible. Maybe from now on costs might come down.
“One of the problems with my shipping container trials was that I couldn’t get the red into the red lettuce and now they’ve developed technology that enables that.”
Frank studied agricultural science at LaTrobe University, graduating in 1980. He immediately started on the Mount Martha property with his father Nick, initially farming 21,000 cage laying hens.
When the egg industry deregulated, the father and son moved to hydroponics.
“We lost a lot of money with the licences. We paid $250,000 in 1980 and with deregulation they gave us back $26,000.”
With little horticultural knowledge, Frank and Nick started growing strawberries and tomatoes.
Frank said while he loved farming, he conceded that growing crops in an enclosed building with artificial lighting diminished the outdoor experience.
“The thing is, you’ve got to imagine how we’re going to feed the world’s population, because we’re increasing at such a rapid rate and we’re using all our farm land for housing.”
How Elon Musk’s Brother Kimbal Musk Is Reimagining Farming
April 5th, 2018
How Elon Musk’s Brother Kimbal Musk Is Reimagining Farming
Kimbal Musk, brother of Tesla founder Elon Musk, has set up 10 sustainable farms in shipping containers that produce 50 to 100 pounds of food every week, the equivalent of that traditionally produced by 2 acres of farmland. He talks about his Square Roots urban farming project and reveals how you could enter a raffle to win his Tesla Mode
In Antarctica For The First Time Gathered The Harvest of Vegetables
IN ANTARCTICA FOR THE FIRST TIME GATHERED THE HARVEST OF VEGETABLES
magictr | April 8, 2018
A greenhouse that uses hydroponics led lighting and feeding system allows you to collect 4-5 kg of vegetables weekly.
Team polar station Neumayer III in Antarctica for the first time gathered crops grown in greenhouses without soil and a Sunny light: 3,6 kg salad cucumbers 18 and 70 radishes.
In the high-tech greenhouse, the walls of which had temperature — 20 °C, used reusable water cycle system, nutrients, led lighting and careful control of carbon dioxide. Based on a method known as hydroponics. Scientists from the German aerospace center, which is coordinating the project, said that by may I hope to collect 4-5 kg of vegetables per week.
On the International space station (ISS) salad how to grow in 2015, but the project focused on the production of a wider range of vegetables: radishes, tomatoes, cucumbers, pepper, greens and berries. Technology develop in the future, astronauts space stations and colonizing other planets could use it for growing a sufficient number of provisions.
Team polar station Neumayer III in Antarctica for the first time gathered crops grown in greenhouses without soil and a Sunny light: 3,6 kg salad cucumbers 18 and 70 radishes.
In the high-tech greenhouse, the walls of which had temperature — 20 °C, used reusable water cycle system, nutrients, led lighting and careful control of carbon dioxide. Based on a method known as hydroponics. Scientists from the German aerospace center, which is coordinating the project, said that by may I hope to collect 4-5 kg of vegetables per week.
On the International space station (ISS) salad how to grow in 2015, but the project focused on the production of a wider range of vegetables: radishes, tomatoes, cucumbers, pepper, greens and berries. Technology develop in the future, astronauts space stations and colonizing other planets could use it for growing a sufficient number of provisions.
Team polar station Neumayer III in Antarctica for the first time gathered crops grown in greenhouses without soil and a Sunny light: 3,6 kg salad cucumbers 18 and 70 radishes.
In the high-tech greenhouse, the walls of which had temperature — 20 °C, used reusable water cycle system, nutrients, led lighting and careful control of carbon dioxide. Based on a method known as hydroponics. Scientists from the German aerospace center, which is coordinating the project, said that by may I hope to collect 4-5 kg of vegetables per week.
On the International space station (ISS) salad how to grow in 2015, but the project focused on the production of a wider range of vegetables: radishes, tomatoes, cucumbers, pepper, greens and berries. Technology develop in the future, astronauts space stations and colonizing other planets could use it for growing a sufficient number of provisions.
Loveland, Colorado, Fyn River Farms Prototype Grows Basil With Nutrients Produced By Fish
Loveland, Colorado, Fyn River Farms Prototype Grows Basil With Nutrients Produced By Fish
By Craig Young | Reporter-Herald Staff Writer
POSTED: 03/31/2018
Jason Rider, co-owner of Fyn River Farms, clips basil from some plants Tuesday at the indoor farm on the outskirts of Loveland. Goldfish provide most of the nutrients for the hydroponically grown basil plants. (Jenny Sparks / Loveland Reporter-Herald)
The farmers at Fyn River Farms near Loveland don't have much acreage to speak of, and their hired hands don't even have hands. That's the way of this aquaponic operation: The field is inside a building, and most of the workers are goldfish who create the nutrients to feed the crops.
Business partners Jason Rider and Mike Bennett have converted a 2,400-square-foot shop building just east of Loveland into an indoor growing operation that they call a farm. The system was ready to go in mid-January, and they are harvesting basil leaves as big as their hands now.
Fyn River Farms' prototype farm is an aquaponic operation, combining aquaculture — the growing of aquatic animals or plants — with hydroponics, the growing of crops in water.
The company's name is a nod to both aspects: Fyn is pronounced like the fin of a fish, and River refers to the water running through.
They grow their crops in a small amount of peat moss inserted into holes in a four-level system of blue plastic pipes, almost 2 miles' worth, filled with continuously running water. Grow lights hang over every section of pipe.
At the end of the building sits a 5,000-gallon tank housing goldfish and koi. The ammonia-rich droppings from the fish provide the nutrients for the plants — after the waste is run through a biofilter to produce nitrates. That water is pumped slowly through the pipes, nourishing the crop.
Fish are "workers on the farm"
Unlike in some aquaponic operations, Fyn River's fish aren't harvested for their meat because federal regulations would make a much larger operation necessary to maintain profitability, Bennett said.
"They're just workers on the farm," he said of the fish. "They get room and board."
The four-level setup enables the farm to fit a large number of plants in a small footprint. Scaffolding allows workers to reach the crop without bending. And the farm can grow almost any kind of crop — the basil is just an easy one to start with, the owners said.
Bennett, who represents the sixth generation of a farming family in Colorado's San Luis Valley, said his interest in the unusual indoor farm is all about sustainability.
"Farming has always been something I loved, but it's always been inefficient," he said. "In the pit of my stomach, I knew how inefficient we were in using our land and water resources."
For example, he said a center-pivot irrigation system requires almost 1,000 gallons of water a minute to operate, and some fields are irrigated 17 hours a day.
"We'll use less than 200 gallons a day," he said of the first Fyn River farm, which holds 7,000 gallons total. The pipes have spaces for more than 14,000 plants; an equivalent amount of basil grown on a traditional farm would need 10 acres, he said.
"We have optimized every inch of space in this building," he said.
That many basil plants will produce a harvest of 10,000 to 15,000 pounds each month year-round, regardless of the season, Rider said.
Bennett said he has been involved in a variety of agricultural operations over the years. Most recently, he owned KM2 Farms, a similar but smaller operation in Fort Collins.
When Rider was working on the idea of an aquaponic farm last spring, he contacted Bennett, for whom he had consulted at KM2. The two decided to partner in the new venture.
Relying on technology
Although the use of aquaculture dates back thousands of years, Fyn River's operation would not be viable without the technology developed in the past 10 years, Bennett and Rider said.
In fact, the partners said, they are reaping the benefits of innovations developed by black-market marijuana growers.
One way that law-enforcement investigators have found illegal indoor pot-growing operations is by looking for suspiciously large electricity bills, Bennett said. So growers figured out how to more efficiently use electric power. Grow lights have become more efficient, too, he said.
Fyn River has two propane burners suspended from the ceiling that give off carbon dioxide to help with plant growth, another technique used by indoor marijuana operations.
An automation system designed by Colorado Controls in Fort Collins allows the owners to monitor energy and water use, water temperature and pH, humidity in the building and more, Rider said. Using a mobile app, he can turn lights and fans on and off remotely.
"We create an environment that's perfect for growing, an ecosystem that allows the plants to thrive," Bennett said.
Though the relatively small space is packed with equipment and technology, the system is so efficient that Fyn River can compete with large farms in Mexico, California and Hawaii, Rider said.
"We run our farm with only a fraction of the human resources" of a traditional farm, he said. "Three people can run this farm full-time."
A global impact
So far, Rider and Bennett have been providing basil just to some local restaurants as they fine-tune the operation. But their real aim is to connect with distributors who can take their produce to a regional and national market.
If a market develops somewhere else in the country, the partners said they could set up a farm in the space of a few months to supply that area, at the fraction of the cost to start a traditional farm.
Having the farm close to the consumers is important in today's world, they said, when "local, fresh and real" are important to shoppers.
And if the bottom falls out of the market for a certain kind of produce, they can change out an entire crop and be heading to harvest in six weeks, Bennett said.
Bennett and Rider say the feasibility of their system would allow it to be used in areas of the world where food security is a problem.
"Agriculture is not sustainable the way we grow right now. A system like this can literally change the world hunger problem, to be honest with you," Bennett said. "This empowers people to have food. That's important to me."
Craig Young: 970-635-3634, cyoung@reporter-herald.com, www.twitter.com/CraigYoungRH.
Goldfish swim in a tank at Fyn River Farms on Tuesday. The fish — about 5,000 right now — provide most of the nutrients for the Loveland farm's hydroponically grown plants. (Jenny Sparks / Loveland Reporter-Herald)
Shipping Container Farms Bring Food Source Closer To City Dwellers
Shipping Container Farms Bring Food Source Closer To City Dwellers
By Jessica Schremmer
April 15, 2018
Growing herbs and vegetables vertically in shipping containers is a rising trend in Australia and aims to reduce food waste and food miles.
The Canadian company Modular Farms Co. launched its first vertical hydroponic farm in Brisbane last month, and not only supplies food vendors at the city's Eat Street Northshore markets with fresh 'farm to plate' produce, but also helps food rescue organizations like OzHarvest to provide food for people in need.
Modular Farms Australia director James Pateras is a third-generation farmer who experienced the devastating impact of drought on his family farm in Victoria and decided to find new ways to farm, integrating technology.
"Going through drought was one of the biggest pains with this type of agriculture," he said.
"I realized then that the techniques used in traditional agriculture were something that had to change, especially if we wanted to continue for the next 100 years and be able to feed the planet.
"I think the climate and adverse weather events are the biggest challenges to traditional farming, followed by disease."
Mr Pateras said the motivation behind the new farm project was to reduce food waste and create food security.
"We want to reduce food miles and give people a fresher product on their plate by being able to take the farm to the cities," he said.
"We can grow 365 days a year and are able to control the plants' biology and environment, so by doing that we are eliminating the possibility of any pathogens coming into the farm and don't have to rely on the next rain event.
"In the farm itself we can grow up to 1,000 heads of lettuce a week, so about 52,000 lettuce heads a year."
The vegetables and herbs are grown in recycled plastic in a closed loop system, with LED lighting, recycled air and 40 litres of water a day.
Expertise needed to grow safe produce
Protected cropping is one of the fastest-growing areas of food production in the country, with almost 30 percent of all Australian farmers growing produce in some form of a soil-less culture system. according to peak vegetable industry body Ausveg.
Ausveg CEO James Whiteside said the organisation supported innovation in growing vegetables.
"This [the modular farm] is a prime example of thinking outside the box and using recycled material to create a new environment to grow fresh produce," Mr Whiteside said.
"It is an innovative way to close the gap between the farm gate and a consumer's plate, as urban growers and the general public have an opportunity to see how vegetables can be grown in this new environment.
"Containerised farming is another way of producing vegetables and it has the potential to work well in urban environments."
However, a hydroponic farm owner in far north Queensland is warning people about growing herbs in containerised farming systems without expert knowledge.
Neil Carpenter, owner of the Village Herb Farm in Kuranda, said it was very important to produce a safe product.
"If you think containers are a 'put chemical in one end and get herbs out the other' then you are endangering the public," he said.
"Sterility, seed control and disease checking are the three fundamentals for anyone going into urban farming."
Potential markets in Asia
Mr Carpenter said he did not see containerized farming as a major competitor in the market space in Australia.
"In Australia, power is very expensive and that is one of the major challenges to containerized farming," he said.
"I think they could be a big deal in Hong Kong, where people are prepared to pay a premium to be reassured that the risk of travel-related disease is reduced.
"In Australia it's only a niche market."
Poulet & Porc director and chef Peter Dressler has a food stall restaurant at Eat Street Northshore and uses some of the freshly produced herbs from the onsite modular farm.
He said it was great to get produce that he was not able to source from Brisbane's major fruit and vegetable wholesaler.
"It's really impressive what can be grown is such a small space.
"I think it would be quite hard for them to compete for price with Brisbane's major fruit and vegetable wholesaler in Rocklea," Mr Dressler said.
"Their niche will be building relationships with all the food vendors.
"I have tried the modular farm's basil, varieties of kale and coriander and they got the tick from me.
"We yet have to see if it all works but for us, it's about getting the consistency."
Mr. Pateras said it was his aim to broaden people's perspectives on agriculture.
"There will be skeptics of containerized farming out there," he said.
"But in this modern day and with a lot of countries, especially in Asia, turning towards factories to farm produce in, I think containerised farming definitely will have a long future."
Topics: herbs, science-and-technology, food-and-beverage, horticulture, food-and-cooking, agricultural-crops, australia, canada, qld, asia, brisbane-4000
CAN: Hydroponics Is Blooming In The North
CAN: Hydroponics Is Blooming In The North
As in most northern towns, the concept of "locally grown" is exotic in Churchill, Man.
So when Carley Basler shows up at people's homes with a big bags of fresh vegetables, it's little wonder people get excited.
"It's fresh food, fresher than probably anything that Churchill has ever experienced," Basler said.
She knocks on a door, and inside seven-year-old Karalina Burke is excited. As the door opens, she declares: "I ate three heads of lettuce!"
Her mother, Sandra Cook, is subscribing to Basler's Rocket Greens, Churchill's first locally grown produce.
"It's really remarkable we can have this here," she said.
In the town of 800, perishables need to be flown in, making produce expensive. A head of lettuce at the grocery store can cost up to $7. By the time it arrives, it's often wilting, and its freshness and nutritional value have diminished.
Basler's produce is fresher — and she's getting prices down to $3.50.
FOOD SECURITY
Food security is a problem across Canada's North, where climate and geography make it impossible for most communities to grow their own produce.
Three months ago, the Churchill Northern Studies Centre started growing vegetables hydroponically as an experiment to see if it could address local food security on a commercial scale.
It's turning into a fledgling business.
Rocket Greens is named for the old rocket testing range where the Northern Studies Centre is set up.
As winter wind whips up a windchill that feels like –50 C outside, Basler is tending to her soil-less hydroponic garden in a computer-controlled climate. She's harvesting giant plants of lettuce, arugula, spinach, and kale.
"What we are doing is growing about 400 to 450 units of produce that we can harvest weekly and make available in our community," said Basler, an electrician who took on the role of system manager.
She's already supplying two grocery stores and a few restaurants while running her weekly subscriber program.
Eighty dollars a month gets each subscriber a weekly Launch Box, a bag full of greens guaranteed fresher than any southern grocery store. It's delivered the same day it's picked, she said..
It's also putting some variety into people's diets. Basler is growing items like pak choi, a Chinese cabbage and close cousin to the more widely known bok choy.
"We've been showing people how to cook it, they're putting it in stews," she said. "It goes great with caribou."
Originally set up as a break-even proposition, Rocket Greens is already talking about expanding by potentially adding another farm.
NO REASON NOT TO GROW FOOD IN NORTH
The "farm" is built into a shipping container also known as a sea can. Seedlings grow without any soil under LED lights in the nutrient-enriched water.
It was designed by Growcer Modular Food Solutions, an Ottawa company focused on northern food security.
The Churchill system is the first of its kind in Canada. Growcer has six others in Alaska, all growing food on a commercial scale.
"We really think there is no reason why every community shouldn't be growing their own food," said Corey Ellis, Growcer's co-founder, and CEO.
While hydroponics have been tried in the north before with little commercial success, Ellis says Growcer is designed to turn a profit by letting growers start small and scale up. Each unit costs about $210,000 and is basically plug-and-play, requiring only electrical and water connections.
Ellis says each unit has the potential to turn a profit of between $30,000 and $40,000 a year.
"Many communities want to create jobs and economic development, they want to produce food so they don't have to rely on the south, but not in a way where they have to depend on grants," he said.
The one thing it can't do right now is grow a root vegetable like a potato. Ellis says Growcer is working on it.
The company plans to add half a dozen systems in Northern Canada this year, including one at Manitoba's Norway House.
Click here to read the full article and to watch a related video.
Photo credit: Carley Basler
03/23/2018 - CBC/Radio-Canada
Hydroponic Produce Is Blooming In Churchill, Manitoba
Hydroponic Produce Is Blooming In Churchill, Manitoba
Company raising northern veggies in a shipping container sees room to grow
By Cameron MacIntosh, CBC News Posted: March 20, 2018
Carley Basler, system manager of the Growcer system at the Churchill Northern Studies Centre, delivers fresh produce around Churchill, Man., the same day she picks it. (Warren Kay/CBC)
Cameron MacIntosh
Senior reporter
Cameron MacIntosh is a senior reporter with CBC National News based in Winnipeg.
As in most northern towns, the concept of "locally grown" is exotic in Churchill, Man.
So when Carley Basler shows up at people's homes with a big bags of fresh vegetables, it's little wonder people get excited.
"It's fresh food, fresher than probably anything that Churchill has ever experienced," Basler said.
She knocks on a door, and inside seven-year-old Karalina Burke is excited. As the door opens, she declares: "I ate three heads of lettuce!"
Her mother, Sandra Cook, is subscribing to Basler's Rocket Greens, Churchill's first locally grown produce.
"It's really remarkable we can have this here," she said.
The produce grows in a hydroponic farm inside a repurposed shipping crate while chilling winter winds swirl outside. (Carley Basler)
In the town of 800, perishables need to be flown in, making produce expensive. A head of lettuce at the grocery store can cost up to $7. By the time it arrives, it's often wilting, and its freshness and nutritional value have diminished.
Basler's produce is fresher — and she's getting prices down to $3.50.
Food security
Food security is a problem across Canada's North, where climate and geography make it impossible for most communities to grow their own produce.
Three months ago, the Churchill Northern Studies Centre started growing vegetables hydroponically as an experiment to see if it could address local food security on a commercial scale.
The seedlings do not require soil in order to grow. (Cameron MacIntosh/CBC)
It's turning into a fledgling business.
Rocket Greens is named for the old rocket testing range where the Northern Studies Centre is set up.
As winter wind whips up a windchill that feels like –50 C outside, Basler is tending to her soil-less hydroponic garden in a computer-controlled climate. She's harvesting giant plants of lettuce, arugula, spinach, and kale.
"What we are doing is growing about 400 to 450 units of produce that we can harvest weekly and make available in our community," said Basler, an electrician who took on the role of system manager.
She's already supplying two grocery stores and a few restaurants while running her weekly subscriber program.
Rocket Greens has only been up and running for a few months, but there is already talk of expanding. (Cameron MacIntosh/CBC)
Eighty dollars a month gets each subscriber a weekly Launch Box, a bag full of greens guaranteed fresher than any southern grocery store. It's delivered the same day it's picked, she said..
It's also putting some variety into people's diets. Basler is growing items like pak choi, a Chinese cabbage and close cousin to the more widely known bok choy.
"We've been showing people how to cook it, they're putting it in stews," she said. "It goes great with caribou."
- Food insecurity in Nunavut 'a national crisis'
- Amazon Prime better for fod security, say Iqaluit residents
- Food Secure Canada defends Ontario nutrition report
Originally set up as a break-even proposition, Rocket Greens is already talking about expanding by potentially adding another farm.
No reason not to grow food in North
The "farm" is built into a shipping container also known as a sea can. Seedlings grow without any soil under LED lights in nutrient-enriched water.
It was designed by Growcer Modular Food Solutions, an Ottawa company focused on northern food security.
The Churchill system is the first of its kind in Canada. Growcer has six others in Alaska, all growing food on a commercial scale.
"We really think there is no reason why every community shouldn't be growing their own food," said Corey Ellis, Growcer's co-founder and CEO.
The company is named for the Black Brant rocket, which marks the location of the former Churchill rocket range. (Cameron MacIntosh/CBC)
While hydroponics have been tried in the north before with little commercial success, Ellis says Growcer is designed to turn a profit by letting growers start small and scale up. Each unit costs about $210,000 and is basically plug-and-play, requiring only electrical and water connections.
Ellis says each unit has the potential to turn a profit of between $30,000 and $40,000 a year.
"Many communities want to create jobs and economic development, they want to produce food so they don't have to rely on the south, but not in a way where they have to depend on grants," he said.
The one thing it can't do right now is grow a root vegetable like a potato. Ellis says Growcer is working on it.
The company plans to add half a dozen systems in Northern Canada this year, including one at Manitoba's Norway House.
Fight over fixing rail line
It all comes at a good time for Churchill.
Last May, record flooding washed out portions of the rail line that was its only land link to the south, driving up the costs of goods that now need to be flown in.
It's unclear when or if the service will be restored. The rail line's owners and the federal government are in court fighting over who will fix it.
- Omnitrax Inc.'s name scratched off federal lawsuit
- Churchill cheers as goods arrive after 25-hour ice road journey
- Residents face rising cost of food after rail line suspended
In the meantime, Churchill has been put on federal Nutrition North subsidies, which cover some of the costs of transporting essential groceries.
Operating locally, with virtually no transportation costs, the Growcer system has the potential to relieve that vulnerability.
"It's available weekly regardless of rail service or air service or weather," Basler said.
"It's a lush green garden in the dead of winter, so that's pretty unique."
A Growing Concern
A Growing Concern
The Junior League of Richmond is raising $35,000 to buy a container-enclosed garden for residents in the city's East End
March 23, 2018
richmag
Developed by Envirable Grow Systems LLC, the EnviraGrow center will operate inside a 20- to 40-square-foot trailer.
Through midnight on March 23, the Junior League of Richmond is raising funds to purchase an EnviraGrow Mobile Learning Center — essentially a garden within a trailer similar to a shipping container — to be placed in the city’s East End.
“It’s being built and retrofitted in order to have an eternal garden,” says Kasey Hayes, a spokeswoman for the Junior League.
Developed by Envirable Grow Systems LLC, the sustainable community farming initiative focuses on providing access to more than 6,000 pounds of fresh produce per year while providing education and training on how to build and maintain an indoor farming system. The 20- to 40-square-foot EnviraGrow center is expected to open in June at the Virginia Cooperative Extension Center on 25th Street.
The Junior League hopes to raise $35,000 for the project through its “Little Black Dress Initiative,” in which participating members wear the same black dress for five days in recognition of the lack of choices people in poverty face. The organization notes that Richmond has one of Virginia’s highest percentages of residents living below the federal poverty threshold, nearly 25 percent, and about 40 percent of the city’s school-age children live in poverty.
Lewis Ginter Botanical Garden is also working on opening an EnviraGrow centerin collaboration with the Richmond Office of Community Wealth Building’s Conrad Culinary Training Center program. Expected to open in two or three weeks, it will have wheels, allowing movement around the city.
Based in a warehouse in Richmond’s East End, Envirable Grow Systems LLC was started by Sean Jefferson with a goal of creating controlled environment systems with integrated grow lighting, shelving and a self-contained water reservoir. Jefferson says Envirable also has a location in Washington, D.C.
This model shows what the inside of an EnviroGrow center will look like. (Photo courtesy Sean Jefferson/Envirable Grow Systems)
Junior League of Richmond Anti-Poverty Commission Duron Chavis poverty urban farmingfood deserts Lewis Ginter Botanical Garden
Hydroponic Lettuce Coming Soon To Saranac Lake, New York
Hydroponic Lettuce Coming Soon To Saranac Lake, New York
March 31, 2018
GLYNIS HART | Staff Writer | ghart@adirondackdailyenterprise.com
SARANAC LAKE — Jennie Evans and Aurora White may have the solution to a problem that has long frustrated farming in the Adirondacks: the short growing season.
In mid-April, Evans and White hope to start Saranac Lake’s first hydroponic container farm on the site of the old municipal dump near McKenzie Pond Road.
“It’s a great opportunity for the village to support an environmentally friendly business,” said Saranac Lake village Mayor Clyde Rabideau. At the next village board meeting, he will ask the trustees to approve letting Dandelion Farm place the container near the old landfill.
Evans and White said the site is ideal for two reasons: it’s flat, and it’s close to where they want to sell their produce.
“One of our goals is to be hyper-local,” said White. “The idea is to distribute your product as close to where it’s grown as possible.”
The hyrdroponic farm is a 40-foot shipping container sold by Freight Farms, which comes complete with the hydroponic systems installed.
Plants are grown vertically inside the container, which uses no outside light. Evans estimates the yield from one container to be the equivalent of 1 to 3 acres of soil.
The farm needs water and electricity to function. It runs year-round, keeping an indoor temperature between 60 and 65 degrees F.
“It uses 90 percent less water than traditional farming,” said White. “We’re using much less water, and not adding anything dirty to the environment.”
The water inside the container is recycled. Dehumidifiers remove water from the air when it’s too humid, and air conditioners kick on when it gets too hot inside. Water use can be as little as 5 gallons a day.
Electricity use is estimated at around 125 kwh (kilowatt hours) per day. For comparison, National Grid estimates the monthly kilowatt hours needed to run an electric water heater is 100 kwh; a 17 cubic foot refrigerator uses up to 190 kwh per month.
“That will be our greatest expense,” said White. “The lights are using most of the electricity.”
The container farm uses no pesticides. Plants are grown in nutrient-rich water rather than soil. Different nutrient mixes are available according to the product the grower is planning on.
Evans said the short-term plan is to grow head lettuces and loose-leaf lettuces, kale, and herbs. “We’ll just start with some basic lettuce varieties,” she said. “Hopefully, we’ll be selling to a lot of the local restaurants and Nori’s as well.”
“Once we start growing our first harvest is about seven weeks out,” said White. “So we hope to be at the farmers market in June.”
CEO Eric Amyot on Smart Cities Through The Lens of a Farmer
As Modular Farms gears up for a new year of innovation, we caught up with CEO Eric Amyot to gain perspective on Smart Cities, the advancing urban farming industry and what Modular Farms has in store for 2018. Find out what Eric has to say in this in-depth interview on the future of farming and living.
Eric Amyot, CEO of Modular Farms Co
What was your first introduction to the idea of a Smart City?
In all honesty, the idea of a Smart City was introduced to me as a child watching the cartoon show The Jetsons. Although the program seemed like science fiction when I was young, it was my first opportunity to explore and imagine life in the future. Fast-forward a couple years and I’m realistically thinking about how advancements in robotics, autonomous transport and artificial intelligence might shape a family's lifestyle and individuals' work habits. Imagine only having to work three days a week and having an AI enhanced robot as a maid!? Cool, right?
Who is a thinker or leader that inspires you?
There are a few agricultural and technological leaders who give me inspiration. First I’d like to shout-out Ron Finley for knowing how to get his hands dirty, putting in work and getting shit done in urban agriculture. Second, Stephan Ritz is inspiring for just being so damn passionate and genuine. Finally, Elon Musk (sorry, had to) for reminding me there's simply too much stuff to get done in a single lifetime to focus on just one thing.
What are the key advantages of vertical farming? How do these advantages align with the goals of Smart Cities and the future of agriculture?
The key advantage I'd like to point out, though there are many, is the ability to make growing and sharing food accessible in any scale, at any location. The potential genius of the Smart City really is its inclusivity. All citizens of a Smart City must have access to essentials like transit, waste reclamation, lifestyle services and, of course, healthy and safe food year-round. If that is accomplished, the possibilities are overwhelmingly positive, particularly for those who are typically or historically at risk of marginalization.
Vertical Farming will play a significant role in the success of Smart Cities, however it is alarming to often hear many planners misunderstanding or altogether discrediting the food production model. The current thought process of feeding people in densely populated city centres still invokes the ideas of raised soil beds, courtyard gardens and rooftop greenhouses. It is unrealistic to expect to feed large populations, (worldwide and all year long) without the adoption of controlled-environment vertical farming. Having said that, there will always be a need for hands-in-the-dirt gardening. In the case of Smart Cities, I believe traditional gardening will play more of a spiritually nourishing role for cities of the future than actually feeding a population.
What are some of the logistical challenges of integrating Vertical Farming solutions, and how can Smart Cities overcome those challenges?
There are a few primary hurdles vertical farming must overcome before it can be expected to be integrated into Smart Cities.
Education:
A large portion of society still lacks an accurate and positive perception of what vertical farming is. Space-age technologies are popularly regarded as a cumbersome mashing of nostalgia and futurism; both are perceived as time consuming and ineffective. Unfortunately, many of today's solutions are just that, well, at least for most individuals and families. While the vertical farming industry is getting closer in defining itself as an appealing option for some people, it must do a better job at honestly communicating the real benefits and challenges it presents before becoming a universal, trusted and commoditized solution.
Acceptance:
While the industry is pushing towards intensive capital to fund large factory farming ventures, acceptance by society will only occur when the individual consumer learns to trust and accept vertical farming as a means to nutritional sustainability, transparency and safety.
Energy:
The vertical farming industry is producing an increasingly prolific amount of food. Unfortunately, as we race to produce more and more lettuce and kale, we continue to place the importance of solving the industry’s high-energy issues as a secondary priority. The net-zero farm isn't very far in the future, in my opinion, but it isn't the focus it needs to be. Simply put, vertical farms consume too much energy to be implemented as a mandatory fixture and amenity in our cities. Another form of energy often overlooked are calories. The labor involved in owning and maintaining a vertical farm, particularly one producing enough food to truly feed a family, is far too labor-intensive and time-consuming to operate. Society barely has time to make kids' lunches, walk the dog, go to work, get to cheerleading practice, and do the laundry, let alone operate a vertical farm. Until vertical farms consume less energy (from the grid and from the people who operate them) they will have issues with broad adoption in Smart Cities. The only strategy for early adoption of vertical farming as a commoditized solution is to make it a mandatory amenity for new developments. Otherwise, as we see now, people will most often opt out.
As you delve further into the R&D side of vertical farming, what makes Modular Farms’ agritech different from other vertical farming systems (now or in future)? How does this fit in with designing the city of the future?
Modular Farms farming system has two distinct competitive advantages – it’s modular and scalable. Providing different models of container farms and farming implements our Growers’ results in a refined and defined solution, not only for crop diversity but also ROI. Just like everything else in life, no single product provides a solution to every challenge. At Modular Farms, we certainly don't believe in pounding square pegs into round holes. This approach speaks well to the challenges of working with Smart Cities of the future. We're container farmers at our core, but our past experience, current design and future Modular approach will allow us flexibility in scale, accessibility and aesthetic. Future Smart City farms will have to be built on the principles we are currently following. Secondly, Modular Farms strongly considers aesthetics and ergonomics. Let's be realistic and honest, working for any period of time inside a shipping container isn't exactly a dream scenario, despite how cool and exciting it can be. While we are still growing food in boxes, it’s important to try making those boxes as bright, cheery and enjoyable as possible. Having spent years farming inside an 8' foot wide container, I can't tell you how much the extra 2' in a Modular Farm means, to both the Growers and the plants. Being inside a Modular Farm is like being in a pre-fab structure, lab or office. It is what it is, a box, but it's so much better in so many ways. Finally, Modular Farms is consistently and actively looking toward the future and for areas of differentiation. Fact: people in Smart Cities won't be fed by lettuce and kale alone. Yes, some container farms are capable of growing fancy herbs and strawberries, but it's still not enough. I won't divulge all of our secrets at this time, but the future of Modular Farms includes precisely what we're doing now and something much different.
We understand that Modular Farms is diving into AI and robotics. What short term/long term goals can we share and how do they integrate into this subject matter?
I've always believed vertical farm companies, at least for the foreseeable future, should be focusing on making better labor assistive tools and technologies before jumping to fully-enabled farming robots. Yes, it would be cool having a farm where simply dropping a seed produces a head of lettuce only a few weeks later, but for now we should be focusing on farms with low costs that grow the foods we need. Modular Farms is taking a close look at robotics and AI in 2018, learning how we can make the process of vertical farming easier for Growers without replacing them.
Name a current city that’s doing Vertical Farming really well. Tell us who’s doing a great job in your eyes (if any).
I'm actually really excited about Alphabet's Sidewalk Labs consultation over the next year with the City of Toronto and its $50 million commitment for the installation and testing of the company’s smart city technology. There’s still a long way to go, it’s noted if the Quayside project is completed the costs would be in the billions, fortunately Alphabet is capable, and Toronto’s tech-focused eagerness gives me hope it might actually happen. Toronto is running behind in established vertical farming infrastructure compared to cities like New Jersey, Boston and even Truro, NS. However, Toronto’s position as the world’s tech centre in AI, Fintech, and other advancing strengths would have me place my bet on Toronto coming away as a leader in the vertical farming race for success. I hope companies like Just Vertical, Waterfarmers, Ripple and of course Modular Farms, among every other vertical farming startup calling Toronto home, continue to shape the future of vertical farming in the city.
Credit: Sidewalk Labs
Can you describe the ideal result for a Smart City for Toronto? What would vertical farming on a grand scale look like here?
Vertical farming will only truly serve a large metropolitan centre like Toronto if solutions like large-scale vertical farming, micro farming (like Modular Farms) and viable residential solutions are considered. The challenge of feeding as many people as possible is only met by matching large-scale production with local distribution or even in-home growing; regardless whether national grocery chains adopt vertical farming. A Smart City in Toronto, if well executed, provides new opportunities for food, energy, health care and transportation inclusivity – helping blur class divisions. Large-scale vertical farming in Toronto means eliminating a dependency on fresh food imports. Incorporating restorative agriculture practices in the city and surrounding areas ensures that preservation and improvement of conventional soil-based farming. Frankly, the fastest approach affecting the largest populations requires an obligation or mandatory measure, ensuring citizens become self-sufficient, confident growers and buyers of locally sourced, distributed and affordable food.
With Sidewalk Labs announcing its creation of a Smart City at Toronto’s waterfront, do you have any final words to share with stakeholders who may read this published piece in future?
We're at a wonderful and pivotal time in the world of vertical farming. Despite all the fantastic technologies assisting the rise of vertical farming as a viable solution, we've got a little way to go before we can provide a solution that is suitable for everyone. As billions of dollars are invested in the grandiose dreams of giant vertical farms feeding global populations, we mustn't forget, food is a fundamental right intended for all citizens and is not a privilege to those solely with the means to afford and access it. The impressive amount of capital pouring into a handful of the now-largest vertical farming companies in the world spurs innovation and produces vast quantities of only some foods. It is important to keep focus, if not an increased amount of focus, on the reason why we are doing this to begin with – to build food secure cities, institutions, schools, homes and families. I maintain my excitement for what is coming across the industry, and I am in awe by the scale of our ambitions. I will however, rest happy when we've taught everyone the value of local, healthy and safe food by giving them tools for growing the essentials themselves.
Published by: Jesse Brito in Farm Resources, News
This Musk — Elon's brother — Looks To Revolutionize Urban Farming
This Musk — Elon's brother — Looks To Revolutionize Urban Farming
This Musk — Elon's brother — Looks To Revolutionize Urban Farming
Zlati Meyer, USA TODAY February 18, 2018
Square Roots urban farming has the equivalent of acres of land packed inside a few storage containers in a Brooklyn parking lot. USA TODAY
(Photo: Jennifer S. Altman, for USA TODAY)
NEW YORK – In sunny California, Elon Musk is upending America's auto and space industries. And here, in a cold, gritty section of Brooklyn, his brother Kimbal has embarked on a project that's just as significant in its own way: Trying to reboot the food system.
The younger Musk is the co-founder of Square Roots, an urban farming incubator with the goal of teaching young people how to farm in cities while preaching the importance of locally sourced, non-processed food.
Having shown its potential during the past two years in the parking lot of a shuttered factory near public housing projects of Brooklyn's Bedford-Stuyvesant, Square Roots is ready to branch out. It is looking to set up plots — each the equivalent of 2 acres of farmland — in cities across the U.S. They're hydroponic, which means the crops grow in a nutrient-laced water solution, not soil.
The sites in contention, all of which had to pledge support from local governments and businesses, are in Chicago, Denver, Memphis, Indianapolis, Pittsburgh, Boston, Detroit, Los Angeles, Tampa, Atlanta, Dallas, Cincinnati, St. Louis, Washington, D.C., and a second site in New York. Musk and Square Roots CEO Tobias Peggs will narrow the list down to 10 later this year.
In Brooklyn, budding agricultural entrepreneurs set up year-round farms inside 10 retired metal ocean shipping containers and grow crops like microgreens, herbs and strawberries.
"I want them to get to know entrepreneurship through food," said Musk in a phone interview, who counts both growing business and food as big passions.
Kimbal Musk is a co-founder of Square Roots. (Photo: Neilson Barnard, Getty Images for New York Times)
In 2004, Musk co-founded The Kitchen Restaurant Group, which opened eateries in Colorado, Tennessee, Illinois and Indiana. Musk, who sits on the board of directors of his brother's electric car and solar power provider maker Tesla, also co-founded Big Green, an organization that installs gardens in underserved schools and teaches children about the importance of eating natural food.
With so much on his plate, Musk leaves the day-to-day running of Square Roots to Peggs. They usually talk twice a day, Peggs said. The two met while working at OneRiot, a social media target-advertising company in Colorado, which Walmart acquired in 2011. Peggs has a doctorate from Cardiff University in Wales in artificial intelligence but can just as easily switch to extolling the virtues of freshly-picked peppery arugula.
"By 2050, there’ll be 9.6 billion people on the planet and 70% of them in urban areas. That’s driving a lot of investment and interest in urban farming. Our thinking was if we start in New York and we can figure out solutions ... then we’ll be able to roll out those solutions to the world," he said.
To initially get set up in Brooklyn back in 2016, Square Roots raised $5 million in — no pun intended — seed money, Peggs explained. For each of the 10 new locations around the country, slightly more than $1 million is needed.
Peggs said the farmers find buyers for their produce, like stores, restaurants, and individuals, though they also inherit the client's list from previous Square Roots participants. Some of Square Roots' staff of 14 help generate leads, too. Thirty percent of what they earn goes to Square Roots, and expenses are another $30,000. That leaves them with an annual profit of $30,000 to $40,000.
A single 40-foot container provides 320 square feet of growing space. It is outfitted with long, narrow towers studded with crops that are hung on tracks from the ceiling in rows, like vertical blinds. The plants get their water and nutrients from irrigation pipes running along the tops of the towers and their sunlight from dangling narrow strips of LED lights. Besides arugula, crops include kale, radicchio, and pak choi.
More: Urban farmers grow veggies in freight containers
More: Farm on wheels will deliver fresh produce to food deserts
"What we’ve proven in the first phase is we can take young people with no experience in farming and get them very, very quickly to grow really high-quality food that people want to buy," he said.
Over the year-long program, the young, mostly 20-something farmers learn about not only agricultural science and farm management but also marketing, community outreach, leadership, and business, according to Peggs. During a typical week, they spend about 15 to 20 hours doing farm work, 10 hours handling the business side and 10 hours getting coached by Square Roots' in-house agriculture expert and the team of mentors the company has assembled.
Last year's group was comprised of 10 people, and this year has six. More than 1,500 individuals have applied to Square Roots, the company said.
The program has attracted participants like Hannah Sharaf, who sells her weekly yield of 25 to 30 pounds of microgreens to office workers for $7 per 2.25-ounce bag. Sharaf, 27, said she is fascinated by "how food affects the body," prompting her to give up a career in international marketing. "I really want to be a farmer. I'm exploring both urban and soil."
"High-profile, really cool projects are important because they draw attention to urban agriculture. They fascinate people. They attract capital, and that helps to grow the sector," said Nevin Cohen, research director of the City University of New York's Urban Food Policy Institute.
Part of the draw is the bold-faced name attached to it: Musk. That could make urban farming a bigger topic in the national conversation about local and fresh food, which also is driven by thousands of small activists, some of whom have been advocating for decades.
"I don’t enjoy the industrial food system. It's definitely not good for America or the world," Musk said, citing high obesity rates, the thousands of miles food has to be shipped and the lackluster taste. "We're very excited to teach America about real food."
But Musk acknowledged that not everyone can afford that — including some of Square Roots' neighbors. At least, not right now.
"It's not something restricted to the urban elite," he said. "Our mission is real food for everyone. We need food to be delicious and young entrepreneurs to be empowered."
Modular Farms Co Adopts Brisbane's Eat Street As Home
BRISBANE is now home to the first “modular farm” in Australia. And it’s just a stone’s throw from the CBD. Modular Farms Co opened its first permanently located herb and vegetable production facility, housed within a shipping container, at the popular food precinct, Eat Street Northshore.
Modular Farms Co Adopts Brisbane's Eat Street As Home
31 Mar 2018
INSTALLATION: The final piece to the Modular Farms Co vertical farm being installed at Brisbane’s Eat Street Northshore food precinct, earlier this month.
BRISBANE is now home to the first “modular farm” in Australia.
And it’s just a stone’s throw from the CBD.
Modular Farms Co opened its first permanently located herb and vegetable production facility, housed within a shipping container, at the popular food precinct, Eat Street Northshore.
The vertical hydroponic farm will help provide fresh herbs and vegetables to the numerous food vendors located within the precinct.
With access to power and water, Modular Farms can grow fresh produce nearly anywhere in the world and in any climate.
RELATED READING
- Vertical farming could take horticulture higher
- LEDs let growers "pull strings" in plants
- Vertical farming could work for Aussie farmers
The facility is a vertical hydroponic system inside shipping containers with the idea being to blend into the landscape that is synonymous with Eat Street’s aesthetic.
Modular Farms says the system is able to grow food sustainably and cleanly for everyone to enjoy and can be utilised anywhere, including those regions prone to devastating droughts.
Modular Farms has based its new Australian headquarters in based in Brisbane, where it will manufacture its state-of-the-art farming systems and modules designed for scalability and maximum “return on investment” for agriculturalists.
GOING UP: The vertical farming system allows for more growth in tighter spaces, ideal for shipping containers.
At the helm
LEADING Modular Farms Co in Australia are James and Prue Pateras, who aim to connect with local businesses, entrepreneurs and farmers, including those still recovering from, or experiencing drought.
"Having grown up on a farm near Melbourne and having experienced first-hand the distressing effects of drought, I wanted to create a new business model for farming, based on a concept of doing more with less,” director Jame Pateras said.
“With an invested interest in technology I knew it had the capability of improving productivity, sustainability and farming life. This is ultimately what I feel we have achieved.”
RIPE: A strawberry produced from within a modular farming system.
“Current farming practices are over 100 years old and are unsustainable for the next 100 years. Using Modular Farms technology, we are reducing food waste, increasing food security, and eliminating supply chain logistics to cut food miles.
“We are excited to be able to showcase what this amazing product can do by partnering with Eat Street Northshore and are so grateful for the opportunity it has afforded us.
“We welcome people to come and taste our produce in the delicious food being served at ESN.”
One of the partners in Eat Street, John Stainton, said he was thrilled to have a Modular Farm onsite.
“James and the modular team are now part of the family and the produce they are able to supply ensures we have a constant, and consistent supply of high quality, fresh food for our customers without the food miles,” Mr. Stainton said.
“You can’t get much fresher than having a farm on-site.”
HEALTHY HARVEST: Modular Farms says given access to water and power, the vertical farming system is able to produce food in all climates and areas, possibly helping drought-affected areas.
The Modular Farm will supply the Northshore precinct and OzHarvest with some of their fresh produce needs and will also provide the opportunity for potential Modular Farmers to see the technology in action.
What is Modular Farms Australia?
MODULAR Farms Australia is the first Modular Farming operation outside of North America providing fully engineered units compatible with multiple terrains, weather conditions and a focus on plant health.
Current modules include Primary and Vestibule with the Macro coming soon.
The Modular Farms App allows users to monitor and control their farm in real time from their smartphones.
By partnering with experts in LED lighting, plant health sciences and indoor agriculture, Modular Farms Australia brings opportunity for expansion and growth in the agricultural industry.
GOOD GLOW: Modular Farms Co director, James and Pateras, says vertical farming reduces food miles, cuts back on waste and increases food security.
To improve upon the first-generation shipping container concept, the research and development was jointly conceived by a team diversely educated farmers and engineers, including Mr Pateras, which resulted in the founding of the technologically advanced Modular Farms Co in Canada in 2015.
Its engineered farming units are designed with modularity and scalability in mind, taking Modular Farms to new terrains and markets.
According to the company, modular farming is suitable for remote and island communities, grocery stores, food services, agribusinesses and educational facilities wanting access to freshly harvested, sustainable food.
By doing so Modular Farms reduces food waste and transportation while increasing food security.