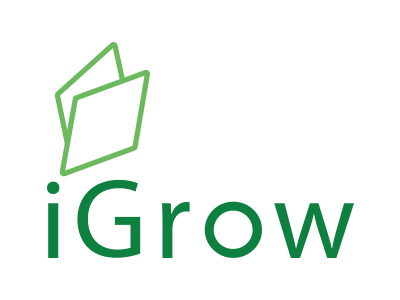
Welcome to iGrow News, Your Source for the World of Indoor Vertical Farming
Dene High School in La Loche, Saskachewan Gets A Modular Farm
Last month, students and teachers from Dene High School in La Loche, Saskatchewan, visited our Modular Farm located at The Food Dudes HQ in Toronto.
The students received hands-on training on how to grow and harvest fresh foods in a purpose-built container. With the help of President’s Choice Children’s Charity, the school will be getting its very own modular farm, where the produce grown will be used for the school’s lunch program and potentially for the greater La Loche community.
Food inaccessibility is becoming a bigger issue in La Loche especially after a recent grocery store fire that moved the community, leaving only one shop to provide fresh foods to the entire community. Locals are being pushed to their limits with some having to travel to Saskatoon for groceries as all options have run out in the remote Northern Canadian city.
The small prairie town is located six hours away from Saskatoon and often has a limited supply of fresh produce. Adding in high shipping costs, the cost of available produce is outstandingly more expensive compared to Toronto. With a small population of approximately 2,600 people, inaccessibility to fresh, healthy meals can pose a real food security issue. However, with the future installation of a modular farm at Dene High School, the move is a real game-changer for the community.
With the state-of-the-art modular farm, students will be able to actively contribute to their community and school’s food system. The concept to have the students become self-sufficient buyers and growers of local foods aligns directly with Modular Farms’ vision to eliminate a dependency on fresh food imports. Students will be able to taste their hard work with each harvest and take ownership in what they eat, understanding how and where foods come from. Not only will students reward themselves with the food they grow, but the farm also acts as an educational tool to teach them about topics like entrepreneurship, health, biology and nutrition. In many ways, the modular farm will be a “classroom” of sorts for students.
To spark the students’ creativity, the farm’s exterior will serve as an art canvas for students, thus allowing the personalized farm to be representative of the community it is run and led by. This initiative was made possible by President’s Choice Children’s Charity. Thank you PC! We hope to see more opportunities arise for Modular Farms to aid cites in Northern Canada by providing a vertical farm to grow fresh foods for nutritious meals year-round.
Have a question now? Contact our Customer Empowerment team at sales@modularfarms.co or read our FAQ section.
n.thing Gives Visitors A Taste of High-Tech Smart Farm
n.thing Gives Visitors A Taste of High-Tech Smart Farm
April 5, 2018
By Ko Dong-hwan
Agritech company n.thing revealed its groundbreaking automated smart farm methods for growing plants to a select few invited guests Thursday.
The startup company, established in 2014, is growing romaine lettuce in one of three refurbished shipping containers that it calls "Planty Cubes" in Mia-dong, Gangbuk-gu, in northern Seoul.
The lettuces are grown in "pickcells," 125-cubic-centimeter plastic pots filled with water-soaked decomposable sponge. The plants were at various stages of development ― from one week to maturity.
Hundreds of pickcells in three rows on five tiers filled each cube, spanning 27.6 square meters. Each row was under an LED tube that produces different colored light. The tubes are turned on and off and the color changes using the company's smartphone app.
"The cube is completely isolated from outside, with its ventilation system bringing air from outside and circulating it inside," Tony Baik, the company's CTO, told a group of guests inside a cube.
"Mid-air moisture vaporizing from the plants gets sucked up by dehumidifiers and is reused to replenish water troughs running below pickcells. This water amounts to as much as 100 liters."
Next to the lower cube is another that the company kept closed to visitors. CEO Leo Kim said an experiment in growing strawberries was going on there.
"People in this neighborhood love our cubes," said Kim, who refurbished the white-painted cubes in a dense low-rise commercial district in Mia-dong in January. "Once they found the structures were growing plants inside, they embraced the venues."
Thursday's invited guests included n.thing investors, the company's partners who provided seeds for the cubes, and people interested in investing. Previously, no one but company researchers had been allowed inside the cubes.
The cube, a vertical farm, is the company's main product. It has state-of-the-art technologies for growing leafy and herb plants in an automated indoor space away from outside influences.
Because of the controlled environment, a cube can provide ripe plants 14 times a year. For some crops, the yield can be 400 times that of traditional farm fields, according to Kim.
When a guest asked about the plants' taste, Kim said a test proved that they tasted better than traditionally grown ones.
"Some believe that plants that grow outside weathering different climate seasons taste better," said Kim in an orientation session in Y Square, a shopping mall near the cubes.
"It is the taste of 'stress' the plants go through to defend themselves from the environmental influences. The stress is reflected by not just the taste but their color and texture. The cubes can re-create those environments, or even enhance them to more ideal conditions. The question of whether they taste good is already past our consideration."
The company exported two cubes to Poshtel, a hostel in Copenhagen, Denmark, in January. It has also sold "Planty Squares," modular pots with multiple pickcells, to about 30 countries through crowd-funding site Kickstarter.
Romaine lettuces grow inside one of n.thing's three 'Planty Cubes.' The smart farm developer unveiled two of the three cubes to selected guests Thursday. / Korea Times photo by Ko Dong-hwan
Freight Container At Yellow Bay Grows 'Smart Crops'
The future of farming, according to Pamela Marks and Wade Young, sits in a refrigerated freight container amid the cherry trees freckling their property near Yellow Bay.
Freight Container At Yellow Bay Grows
'Smart Crops'
May 21, 2018 at 10:08 am | By MARY CLOUD TAYLOR Daily Inter Lake
The future of farming, according to Pamela Marks and Wade Young, sits in a refrigerated freight container amid the cherry trees freckling their property near Yellow Bay.
Inside that box, a hydroponic garden grows a variety of lettuces, herbs and other leafy greens without sunlight, soil, chemicals or pests.
The second to enter service in the state, Marks and Young’s Freight Farm was developed by Brad McNamara and Jon Friedman, two innovators from Boston bent on pioneering the agriculture technology industry with their systems designed for “big production in a small footprint.”
Each 40-foot shipping container can sustain 8,000 plants at a time and produce enough food to feed around 200 people a week, the equivalent of a solid planted acre of crops, Young said.
At full capacity, each unit can produce 500 full heads of lettuce, 60 to 100 pounds of “hearty greens” or 35 to 80 pounds of herbs a week, according to the Freight Farms website.
Growers need only get their hands dirty for the planting and harvesting, dropping a single seed into a cork-like seed pod and placing it into a seedling container until the plant grows big enough to be moved into one of the hanging columns to grow to its full size.
The rest, including watering cycles and sunlight hours, can be monitored and controlled remotely via a smart device such as an iPad or smartphone.
“Here, Mother Nature has to cooperate with you,” Young said.
Pumps and filters cycle water from a mountain spring near the property into the unit and then recycle the runoff to be filtered, infused and used again, allowing the system to use less than 5 percent of the water needed for traditional farming methods.
Each plant is fed automatically through the water, which is monitored by a computerized system that measures pH balance and nutrient levels, adding whatever the plants need as they grow and eliminating the need for soil.
A dehumidifier regulates the humidity, an air-conditioning unit regulates the temperature and strands of purple LED lights hang from the ceiling directly in front of each hanging column of crops, simulating sunlight and allowing the plants to grow straight out instead of curving upward.
“It’s one smart machine,” Marks said. “We think that with what’s going on with the climate, indoor [farming] may just be the wave of the future.”
The growth period for the plants mirrors that of traditionally grown crops, and because it is completely self-contained and sustained, Young said, the system can continue producing at a steady rate year-round, regardless of temperature and other outside factors that limit the growth and production of traditional farms.
MARKS SAID they made the jump into freight farming when local groceries — to which they were already delivering wheatgrass and pea sprouts — began requesting more diversity in their crops.
Faced with the decision of having to add on to their home again after having already added on their wheatgrass/sprout room, they began to look into alternative options online.
Their search led them to the Freight Farms website and then to the only other unit in Montana, owned by a Bozeman woman who uses hers to grow specialty lettuce for high-end restaurants.
If chefs and restaurateurs liked the product, Marks said she felt confident they would, too, especially after tasting it themselves.
Marks and Young felt a Freight Farms unit would provide the perfect alternative to a home addition and made an $80,000 investment in their first unit.
The unit arrived this winter and is now up and running with its first batch of leafy greens growing rapidly. Marks and Young currently have arugula, basil, kale, parsley, stevia, wasabi and more growing from their hanging columns, with plans to include a greater variety and number of plants as they get the hang of things.
Marks said the farm will take about two years to pay for itself, but a recent edit to the USDA’s standards for organically grown produce has the potential to expand their market.
A meeting of the National Organic Standards Board in the fall of 2017 decided that as long as hydroponic farmers are certified by a United States Department of Agriculture agent and comply with federal standards, they can label their products as organic, meaning the produce that comes from Marks’ and Young’s freight farm can be sold on the organic market.
Local health-food stores, groceries and other stores in the area have already begun to express an interest in the prospect of buying locally from a source that will deliver a variety of products to them year-round.
Depending on how much demand they have for their “smart crops,” Young said they might consider adding more units in the future.
Marks hopes the Freight Farms unit will eventually provide opportunities for school field trips, interns from the community college, specialty growth for herbal and homeopathic retailers and donations of fresh produce to local food banks and other nonprofits in the future.
“We’re here to make a contribution,” Marks said. “This just allows us to contribute more to this section of the local economy.”
For more information about Freight Farms, visit https://www.freightfarms.com/home/#ready-set-grow.
Mary Cloud Taylor can be reached at 758-4459 or mtaylor@dailyinterlake.com.
Social Innovation Challenge Winner Building Food Growing Facility In Shipping Container
Social Innovation Challenge Winner Building Food Growing Facility In Shipping Container
May 14, 2018
A MUN student and entrepreneur is building his first shipping container food growing facility after winning a pitch contest at Memorial University over the weekend.
20-year-old Bennett Newhook won the 2018 Social Innovation Challenge this weekend for his social enterprise Green Space Farms. His partners were Justin Elliott, Sonya Killam, and Draco Dunphy.
The group’s goal is to lower the cost of alternative farming methods for communities across the province.
Bennett says he’s always had a keen interest in food sustainability on the island.
He says he and his team were shocked to find out Newfoundland only produces ten percent of the food that’s consumed while Labrador only produces one percent, so they decided to try and make a positive impact by coming up with Green Space Urban Farms.
The group is proposing to build food farms out of 20-foot shipping containers constructed with post-consumer materials.
Green Space Urban Farms won $1,500 cash and $2,000 in business support for market research and product development.
Newhook would like to see the idea brought to rural communities to help residents access fresh, local produce year-round. He expects to see the first unit up and running within the next few months.
You can find out more here.
PC® Children's Charity Plants Modular Farm in La Loche, Saskatchewan
PC® Children's Charity Plants Modular Farm in La Loche, Saskatchewan
NEWS PROVIDED BY Loblaw Companies Limited
May 17, 2018
Inaugural Innovation Grant supports groundbreaking project, providing local, fresh produce year round and the opportunity for students to learn and grow
BRAMPTON, ON, May 17, 2018, /CNW/ - Today, students from Dene High School in La Loche, Saskatchewan, started training to grow and harvest a variety of produce in a farm the size of a shipping container. Made possible by a new Innovation Grant from President's Choice® Children's Charity, the $220,000 state-of-the-art modular farm will soon arrive in La Loche. By autumn, the student-managed farm will be bursting with fresh, locally-grown produce for the school's lunch program and potentially the wider community, where at times food access can be an issue.
Students from La Loche Saskatchewan train to grow and harvest their own produce in the purple glow of a state-of-the-art modular farm. The $220,000 farm was granted to them by PC Children’s Charity as the first of a new series of innovation grants which award transformative Canadian projects that combat childhood hunger and poor nutrition. (CNW Group/Loblaw Companies Limited)
"In the wake of the tragic events at the school in 2016, we were asked to do our small part to help restore the health of the school kids and their community. Our PC Children's Charity began to fund the school lunch program, but we thought we could do more," says Sarah Davis, Chair, PC® Children's Charity and President, Loblaw Companies Limited. "This project is funded by our new Innovation Grant, which was developed to really expand our impact in communities, through unprecedented opportunities to make change."
PC® Children's Charity, established and funded by Loblaw Companies Limited, has committed $150 million over the next 10 years to tackle childhood hunger and deliver nutrition education. Stemming from the belief that well-fed kids learn better and contribute more to a better Canada, this initiative is the first of the Charity's new Innovation Grants which support transformative projects to combat childhood hunger and poor nutrition.
Today, five Dene High School students and three staff are in Toronto to receive hands-on training in a modular farm, which looks like a large shipping container. The unit, developed by Modular Farms Co., contains a workspace for learning, planting, and harvesting as well as four vertical walls of produce sustained by automated lighting, heating and watering systems. The unit is purpose-built for a northern environment. Its closed-loop system uses 95 percent less water than a typical farm and may produce up to 1,000 heads of lettuce or 6,000 plum tomatoes per week.
"The farm will help students develop a stronger relationship with food and serve as a valuable teaching aid on subjects like nutrition, business, math and biology to set them up for future success," says Greg Hatch, Principal, Dene High School. "When we asked our students how we could become better and move forward, they suggested a greenhouse. I don't think any of us imagined PC Children's Charity giving us a state-of-the-art modular farm."
"This is a huge opportunity for us," says Danisa Petit, Grade 12 student at Dene High School. "We're going to learn a lot by managing the farm and we can't wait to have more fresh, local produce for our school meal program."
In preparation for growing in September, the farm's exterior will serve as the canvas for art students who will be given the opportunity to personalize it.
About PC® Children's Charity
PC® Children's Charity believes nothing will create better conditions for success than nourishing our kids, which is why we've committed $150M over the next 10 years to tackle childhood hunger and deliver nutrition education to children across Canada. Well-fed kids will change our world for good, and we pledge to provide them with the nourishment to learn, to grow, and to succeed. For more information on PC® Children's Charity or to donate online, visit pc.ca/charity.
About Dene High School
Dene High School offers a quality education for over 350 students in La Loche, Saskatchewan. The school has a big gymnasium, science lab, home economics lab, commercial food preparation facility, industrial arts shops, library, computer lab, and many large, well-equipped classrooms. This is a school with a motivated staff who are always engaged in implementing innovative and creative programs that are found nowhere else in the country.
SOURCE Loblaw Companies Limited
Related Links
Organization Profile
Loblaw Companies Limited is Canada’s food and pharmacy leader, the nation’s largest retailer, and the majority unitholder of Choice Properties Real Estate Investment Trust. Loblaw provides Canadians with grocery, pharmacy, health and beauty, apparel, general merchandise, banking, and wireless mobile products and services. With more than 2,300 corporate, franchised and Associate-owned...
Also from this source:
Qatar Could Export Vegetables In Future: US Agriculture Expert
Glenn Behrman; Some of the leafy vegetables produced through indoor farming
Qatar Could Export Vegetables In Future: US Agriculture Expert
Qatar could become an exporter of several agricultural products at some point in the future, an expert from the US told Gulf Times.
“There are tremendous opportunities for the country,” claimed horticulture specialist Glenn Behrman, a proponent of controlled-environment indoor farming concept called 'Growtainer'.
It features a container - a highly engineered modular and mobile vertical production environment, custom-built for a wide variety of crops, botanical products, and business models. In the high tech facility, plants are grown in nutrient-enriched water through vertical farming. They can be grown in shipping containers, warehouses or such enclosed areas.
“We can recreate nature. If the plants want rain, there will be rain, if there is no need of wind, there will be no wind and can even provide the best light for the plant. It is fully controlled by computers. Some crops grow 18- 20 hours a day and the yield is dramatically higher,” said Behrman.
In Qatar to explore the possibilities of introducing the new method, the expert had several rounds of meetings with the royal family members, government officials, potential partners, and investors as well as business people in the country.
“We have had several rounds of discussions. They had visited me in the US and invited me to come over here. Now, we are moving into the next stage of co-operation. I am hopeful that we will be able to start the project in less than six months,” noted Behrman.
According to Behrman, most types of vegetables can be grown using the technology. “The normal space between the rows in a shipping container is about 18-20 inches. You can grow anything with shallow roots. Lettuce, tomatoes, radish, herbs, spices and leafy vegetables are some of them,” he explained.
The expert also pointed out that the produce from the system are healthier and cleaner than organic products. “It is also less expensive than organic food. They grow 30 to 40% faster than other food items,” he described.
“The technology is very much water conserving and does not waste any water. It uses about 750 gallons of water for a certain number of plants whereas in a farm the same number might need 60,000 gallons of water. We can also grow many vegetables that are yet to be grown in Qatar,” he added.
San Antonio, Texas - How Does Your Garden Grow? At IDEA Eastside, In A Freight Container
(from left) IDEA Farm Coordinator Cecile Parrish; students Briana Perez, David Jones, and Laila Rodriguez; and IDEA Child Nutrition Program Farm Manager Hernan Colmenero stand outside the shipping container that houses a hydroponic garden. SCOTT BALL / RIVARD REPORT
How Does Your Garden Grow? At IDEA Eastside, In A Freight Container
EMILY DONALDSON May 13, 2018
SCOTT BALL / RIVARD REPORT
(from left) IDEA Farm Coordinator Cecile Parrish; students Briana Perez, David Jones, and Laila Rodriguez; and IDEA Child Nutrition Program Farm Manager Hernan Colmenero stand outside the shipping container that houses a hydroponic garden.
With purple LED lights, a sound system that blasts music, and vertical crop columns, the hydroponic shipping container that arrived at IDEA Public Schools’ Eastside campus about three months ago isn’t what most people picture when they think of a farm.
The 40-foot shipping container – what IDEA Farm Coordinator Cecile Parrish calls “an acre in a box” – will grow 500 heads of lettuce, about 50 pounds of greens, and just under 45 pounds of herbs a week at full capacity. The produce will go directly into the kitchens of the charter-school operator’s 11 San Antonio campuses and onto students’ lunch plates.
A shipping container on the campus of IDEA Eastside is used to grow lettuce and other crops hydroponically. SCOTT BALL / RIVARD REPORT
Hydroponic farming is a cultivation method by which plants grow without any soil, instead obtaining needed nutrients from the water. At IDEA Eastside, plants grow inside an industrial shipping container that mainly uses water to grow produce such as kale, lettuce, spinach, basil, cilantro, thyme, and mint.
The container is water-efficient, using 10 gallons of water a day, or about as much as is used during a five- to 10-minute shower, Parrish said. Caring for the container’s crops is less labor-intensive than an open acre of land, she said, requiring just 20 hours a week.
While many schools use gardens both for producing food for their lunchrooms and as an educational tool, IDEA Eastside is one of fewer than 10 K-12 schools nationwide to use a freight farming system. Parrish pitched the idea to students as a “high-tech computer that grows salad.”
It took three months to get what the school calls the Leafy Green Machine up and running and get water and power to the container, which is air-conditioned. Four students, who last year were certified as Junior Master Gardeners through an educational program on best practices of gardening, started cultivating the container crops, and Parrish said that she plans on teaching others about sustainable food growth in the next school year.
Related: LocalSprout: Inside an Urban Farm on San Antonio’s Eastside
Students can change the internal temperature of the container, adjust carbon dioxide levels to optimize growth, and select a music playlist through an application on their phones. The music, however, is more for the students than for the plants.
Eighth-grader Laila Rodriguez said she works in the container on free periods and after school, and she loves it because it reminds her of her grandfather’s garden.
“Ever since I was little, I would like helping my grandpa in his garden because he has one, so that’s kind of what got me into it,” she said. “I had never seen anything like this. … [my grandpa] is happy and he thinks it’s cool.”
David Jones, eighth-grade student, stands inside the hydroponic shipping container at IDEA Public Schools’ Eastside campus.
SCOTT BALL / RIVARD REPORT
Eighth-grade student David Jones didn’t have much experience gardening before attending IDEA Eastside, but he said he was excited to get involved with an after-school activity.
Parrish said her goal is for students to learn the entire process of growing food: planting the seeds in coconut coir, which is used in hydroponic gardening as an alternative to soil; taking care of the seedlings; and transferring them into vertical columns to grow until harvest.
“Schools go through tons of lettuce, [and] in South Texas we are really limited seasonally for when we can grow [it],” Parrish said. “So this is kind of our answer for how we can sustainably provide a large, significant amount of the lettuce that IDEA uses.”
The herbs also will be used to support IDEA’s efforts to serve healthier lunches to its students. In IDEA cafeterias, Parrish said, students don’t have access to salt or pepper. The school plans to use the container-grown herbs to make a seasoning mix that provides a healthier alternative to salt.
Jones, whom Parrish calls the official taste tester for the freight farm’s products, said so far, the produce has been “pretty good.”
The first crop from the container will be delivered to IDEA kitchens in about two weeks, just in time for the end of the school year. Over the summer, Parrish plans to streamline the growing process so students can eat the Leafy Green Machine’s produce on the first day of school.
The container will be able to produce crops year-round, regardless of outdoor weather conditions.
Parrish said IDEA plans to add a second freight farm unit to another campus, although timing and location haven’t yet been determined.
ABOUT EMILY DONALDSON
Emily Donaldson reports on education for the Rivard Report.
3-Minute Survey: Growing Produce At The Grocery Store
According to a recent survey, grocery shoppers aren’t too keen on mixing technology and food, despite wanting technology in every other aspect of their lives. So how do they like the idea of their local grocery store growing produce indoors? While some level of wariness is to be expected, the vast majority of shoppers actually embraced the idea, particularly if they had seen indoor growing at work.
After responding to attitudes on benefits, drawbacks, interests and concept names, respondents were asked one last “overall impression” question summarizing their feeling on growing produce at their grocery store, be it in the store itself, in growth containers behind the store or in the store’s produce warehouse. The bottom line? Many more shoppers showed enthusiasm for the concept than wariness.
· 57 percent believe indoor, on-premise growing makes total sense.
· 38 percent are not sure.
· 5 percent believe it sounds like a terrible idea.
An ironman in the store talks about the benefits of produce grown at the store.
While among some population groups there is a little more uncertainty or wariness, across most population groups the majority believe indoor growing makes total sense. The concept is met with greater enthusiasm among men, older Millennials (ages 27-38), families with kids, urban shoppers and highly educated, high-income shoppers.
Parents added comments about the ability to show their children how produce is grown. Shoppers talked about how beautiful it would look in their store. Others thought it could help educate produce clerks along with shoppers and bring the farm closer to the fork. As for “seeing is believing,” 84 percent of those who have seen the concept at work believe it makes total sense vs. 45 percent who had neither seen nor heard about it.
Retailers, what do you think? Take a quick three-minute survey:
https://www.surveygizmo.com/s3/4276427/Indoor-farming-Produce-Retailer.
NBA Player Builds A Modern Alternative Farm In Oklahoma
NBA player Ekpe Udoh is keeping busy during the off-season.
NBA Player Builds Modern Alternative Farm In Oklahoma
MAY 25, 2018, BY LACEY LETT
NBA Player Builds A Modern Alternative Farm In Oklahoma
EDMOND, Okla. - NBA player Ekpe Udoh is keeping busy during the off-season.
He's back in his hometown of Edmond working on his new urban farm.
"Welcome to LGR Farms,” said Ekpe Udoh, owner of LGR Farms.
Ekpe Udoh stands inside his hydroponic garden located in south Edmond. Udoh is the first National Basketball Player to purchase and use a hydroponic vertical container farm.
A hydroponic container farm that grows vertical crops.
It's herbicide and pesticide free and uses filtered water instead of soil to grow leafy greens and herbs.
"For our crops, we will be doing butterhead lettuce, arugula, Swiss chard, spinach, collard greens, kale and romaine lettuce,” Udoh said.
Udoh started the process four years ago.
Since then, he's become an expert in modern farming.
After the seeds harvest, they grow on a vertical crop.
LGR Farms is high-tech, too, using an app to control the system.
"We can control the temperature, the water here on the table, the main towers," he said.
The main benefit?
A 40-foot shipping container can yield huge results.
"This probably has the footprint of an acre and a half, and I'm turning it over every four to six weeks and in the winter it's still growing,” Udoh said.
Starting in July, Udoh plans to sell to chefs, grocery stores and at the same time, give back to inner city school children.
"I'm from Edmond, Oklahoma, so we were afforded the luxury of a salad bar. Hopefully, I can introduce that into schools and give kids something else as a choice to be much healthier than what they might be eating,” he said.
A healthy lifestyle is something very important to Udoh.
Eventually, he'd like to have five of these shipping container farms in operation, adding in herbs and greens from all over the world.
"Find these powerful herbs that can be for medical or just for your food. Just make it taste better,” Udoh said. "Keep people dancing and eating salads."
It will take four to six weeks to yield the first crop, but plans to eventually produce 500 heads of lettuce a week.
Click here for more information.
Kimbal Musk, Elon Musk's Brother, On Mission To Revolutionize How Americans Eat
CBS NEWS May 12, 2018
Kimbal Musk, Elon Musk's Brother, On Mission To Revolutionize How Americans Eat
On a crisp Denver morning, middle school students were discovering how to develop a green thumb with the help of Kimbal Musk, the brother of Tesla CEO Elon Musk. In the 90s, he helped his older brother launch Zip2 and the company that would become PayPal. These days, the entrepreneur is on an entirely different mission.
"Real food is the new internet means that young entrepreneurs getting into food today, where they're bringing real food that just taste much better. That's food that you trust to nourish your body, trust to nourish the farmer and trust to nourish the planet is the opportunity of our generation," Musk told CBS News' Barry Petersen.
Kimbal Musk CBS NEWS
Musk still works with his brother's ventures Tesla and SpaceX. But his personal venture has become a life's work: replacing high-calorie foods with healthier ones. Musk always had an interest in cooking, attending culinary school after making it big in tech. But in 2001, he found purpose in tragedy.
"I graduated from cooking school just before 9/11. I woke up to the sounds of the planes hitting the building. I lived very close to the World Trade Centers and looked out the window, saw the towers fall, escaped that area was really intense and one of the hardest things I'd ever been through. But in that process I got invited to volunteer to cook for the firefighters," Musk said. "It taught me the power of community, taught me how food brings communities together, how real food can revitalize people even in the most traumatic circumstances."
Alongside his business partner, Hugo Matheson, Musk opened his first restaurant, The Kitchen, in 2004. After rave reviews, The Kitchen expanded to the Kitchen Restaurant Group, serving up high-end dining at Hedge Row and affordable farm-to-table dishes at Next Door.
Kimbal Musk's startup Square Roots turns shipping containers into vertical urban farms CBS
"Local to us primarily means knowing your farmer and trusting where your food comes from. And for us that Next Door that means a farmer gets to know us directly. So the drive here we get to know them we visit their farm," he said.
Musk wants to make sure that no matter where you live, a farmer is never too far away. He's trying to make that a reality with his Brooklyn startup Square Roots, which turns shipping containers into vertical urban farms that fit two acres of outdoor growing space into 320 square feet.
With the amount of American farmers declining steadily, Musk isn't just investing in the technology to move farming into the future, but in future farmers themselves. In 2011, Musk co-founded his non-profit Big Green, bringing edible and educational nourishment to schools that need it most.
Kimbal Musk with some of the students involved in his Big CBS NEWS
"The idea behind the learning gardens is to connect kids to real food. ... They'll take that back to their home. They may get their parents to buy more nutritious food at the grocery stores but they'll make better decisions for the rest of their lives around real food. We're not here to tell them what to do but we want them to know what real food is," Musk said.
Big Green is currently serving 460,000 students in seven states and the hope is to reach 1 million children by the year 2020.
"I would say at times as much as 90 percent of the kids have never put their hand in soil, have never pulled a carrot out of the ground, have never grabbed a cherry tomato off its vine," he said. "And when they do do that and they try it for the first time it's like a magic trick for them. ... Their senses come alive to understand what real food can taste like."
For kids like eighth-grader Paige Davis, Musk is planting the seeds of passion for real food.
"It just makes me happy to think that someone enjoyed planting that tomato and then I'm eating, like, their happiness," Davis said.
A whole new meaning to an old truism: You can be what you eat.
Are Container Farms The Future of Urban Agriculture?
Are Container Farms The Future of Urban Agriculture?
Launched in 2015, the start-up company Agricool, which grows strawberries in diverted shipping containers, today goes to the assault in Dubai. This type of urban agriculture project is a positive complement to conventional crops ....
Fabrice Pouliquen | Posted on 16/05/18
Agricool has one of its contents installed in the park of Bercy. - / Photo Agricool
In three years, the start-up Agricool, which grows strawberries in containers, has grown well. It has four containers that each produce seven tons of strawberries a year.
- Since it works, Agricool wants to deploy abroad in cities where his project makes sense. As in Dubai forced to import the strawberries that its population consumes. A first container Agricool is on the way and must arrive in the coming weeks.
- It is unlikely that these urban agriculture projects will ever be able to feed cities alone. But this complement to conventional farming is more and more welcome.
We had left Guillaume Fourdinier in December 2015, at the foot of a 30 m² maritime container just laid in the park of Bercy in Paris. This farmer's son, with his counterpart Gonzague Gru, had just turned him away to launch a first strawberry crop in the middle of Paris .
From a container to 1,500 m² of workshops
Three years later, Agricool , their start-up, grew up well. It is enough to realize to put a foot in the rear base of the company, 1,500 m² of workshops and offices at the bottom of a business area of La Courneuve (Seine-Saint-Denis). Agricool employs 55 people, including a team of agronomists, designers, and developers to further improve both the containers and the quality of strawberries produced.
"In December 2015, we were at the beginning of a bet, says Guillaume Fourdinier. We were happy with the taste of strawberries produced in this first container, but we had only a very low yield. Just enough to take out a tray a day. We still had a lot of technology to invent. "
Since then, Agricool has gleaned some certainties and spread its containers in the capital and its surroundings. "We have four in operation now, says Guillaume Fourdinier. At Parc de Bercy still, but also at Station F (13th) , Stade France and Asnières (Seine-Saint-Denis). In these boxes 12 meters long and 2.5 meters wide, strawberries grow vertically along towers placed in front of low-power LEDs (LEDs).
In these containers, the strawberries grow vertically along towers placed in front of light-emitting diodes (LEDs). - / Photo Agricool
Productivity, a settled business ...
Strawberries grown above ground and without seeing the light of day will tick some. "But strawberries with high nutritional value and very low carbon output", Guillaume Fourdinier replies. Agricool does not use any pesticides. "Just organic fertilizers and optimized LED technology that we have developed ourselves," he says.
The containers are supplied with electricity by Enercoop, a renewable electricity supplier. As for the water, it follows a closed circuit. Stored initially in a large tank, it is taken to drips placed above the towers, flows along the roots to be collected in gutters. She then arrives at a pump that takes care of bringing the water back to the tank of departure. "In other words, the water goes completely strawberry, we have very little loss, says the urban farmer. We use even less water here than in a greenhouse for example. "
As for productivity, it's a settled matter. The four containers make it possible to take out seven tons of strawberries each year. "Or 60 trays of strawberries a day," explains Guillaume Fourdinier. Until then, they had only been sold directly at the foot of the containers. But since this spring, they are also sold in two stores Monoprix, Beaugrenelle and Asnieres.
In short, it's a business that rolls. Agricool probably says it can still improve its technology. "But we will surely be working on other fruits and vegetables soon," he says.
And now strawberries produced in Dubai
Above all, Agricool wants to expand its horizons and not be limited to Paris and its suburbs. One of its containers went to sea last week. Head to Dubai in the United Arab Emirates where it should arrive within three weeks. "We thought for some time to develop abroad but we wanted to choose a city in which our mini urban farms would really make sense, says Guillaume Fourdinier. That is to say in a region where it is very difficult to produce locally, either because of the climate or because of the lack of space, and where most of the food consumed must be imported. In Dubai, strawberries come for most of the United States, France and Japan. The carbon footprint is deplorable and the prices exorbitant. "
This new container will take place in The Sustinable city , a futuristic neighborhood project in Dubai where already 2,500 inhabitants live. "They have all designed to have a carbon footprint closer to zero, says Guillaume Fourdinier bluffed by his visit. They are self-sufficient in energy, the sewage is filtered by plants, they produce fruits and vegetables locally in biodomes, bioclimatic greenhouses ... "
The perfect place for Agricool. The Parisian start-up is not putting pressure but hopes ideally to taste the first strawberries to the local population by the end of the year. And if this first experience abroad works, why not decline it in other parts of the world that import until now all the strawberries that their populations consume. For example, Guillaume Fourdinier cites Iceland and most major Asian cities, starting with Singapore.
Maybe not feeding the cities of tomorrow ...
Agricool is not the only start-up to have sniffed this vein of agricultural production in containers. In the Rennes region, Urbanfarm cultivates salads and aromatic herbs . The ECF company is also on the spot in Berlin as well as the vegetable box in Laval (Quebec) to name a few. The ADEME (Environment and Energy Management Agency)classifies these projects in the category of urban technological agriculture , one of the parts of urban agriculture, alongside vertical farms, greenhouses on roofs, aquaponics, above ground crops ...
Ideas abound but Jérôme Mousset, head of the service "forest, food and bioeconomy" at the Ademe, remains cautious. "For every project, it is important to make a global environmental assessment, objective, and analyze the strengths and weaknesses according to the local context," he says. Environmental analyzes show that the impact of transport is often lower than that of production when it is done out of season. In addition, technological urban agriculture alone will not be enough to feed cities one day. There will always be the question of volumes and this urban agriculture does not cover the entire category of food products. There are many vegetables, but few products of animal origin and cereals. As such, the preservation of agricultural land remains a priority issue. "
... But start-ups who have their place
If urban technological agriculture has no answer to everything, "it still has its place today, continues Jérôme Mousset, especially in regions of the world where climatic conditions or available space are not conducive to urban development. 'Agriculture. It can also recreate the link between consumers and producers, and because of its location, have a pedagogical vocation. "
A role on which also insists Luc Smessaert, vice-president of the FNSEA, first agricultural union, a farmer in the Oise and responsible for the #agridemain platform . "Many of the urban agriculture projects have a social dimension, either through direct sales or through the involvement of neighborhood residents or school groups," he observes.
Luc Smessaert also points to another reason for satisfaction in the development of urban farming solutions. "They bring start-ups to take an interest in agricultural issues," he says. Often, they are launched by young agronomists in teams with specialists in new technologies. These duets regularly lead to innovative solutions that benefit all agriculture. "
KEYWORDS: Planet Paris Agriculture startups innovation city dubai
Eco-Friendly Farming In A Shipping Container
May 11, 2018
The vertical farming market in 2016 was valued at somewhere between $1.5-$2 billion and it has people growing food in places like skyscrapers, warehouses, and yes, shipping containers, which is just what Boston-based Freight Farms is doing. Bloomberg's Caroline Hyde looks at what it's like to farm in a box. (Source: Bloomberg)
New Commercial Aeroponic Systems
New Commercial Aeroponic Systems
Pure Grows Aeroponics is launching three new product choices, Commercial Aeroponic System, Intelli Tissue Culture Clone Nursery and a 40 Foot Smart Grow Aeroponic Container.
“We keep a close eye to what our clients require for their cultivation needs and aim to meet these requirements with the latest, proven technology at affordable price points,” commented a spokesperson from the company. “Our latest additions are sure to cause excitement among commercial cannabis growers looking to take things to the next level.”
Pure Grows Aeroponic Systems are custom designed for every client. Pure Grows is built on a module based system, where each module produces 416 healthy, fast-growing plants. Modules could be used independently or as part of a larger growing operation where many modules are connected together to cultivate thousands of plants maximizing the use of available space.
Pure Grows Aeroponic Systems are designed for simplified and controlled commercial cultivation of ecologically pure plants, while creating the ideal growing environment with up to 40% shorter maturation times, providing 6 healthy harvests per year, up to 55% more yearly harvest output versus any other growing methods.
Another addition to the Pure Grows catalog is their 40 Foot Smart Grow Container. The 40 Foot Smart Grow Container is an automated aeroponics greenhouse, packaged in its own 40-foot shell, making it an ideal place to grow a wide range of plants, in a 100% turn-key way.
For more information:
Pure Grows
917-755-2446
info@puregrows.com
puregrows.com
Publication date: 5/22/2018
A Revolution In Farming
Caroline Katsiroubas/Freight Farms
May 21, 2018
On a recent walk one afternoon in Manhattan, I stumbled upon a shipping container. Parked on a small patch of concrete next to a subway exit in Soho, the steel box took up about the same amount of space as several parked cars. It was noticeable for its novelty but otherwise unobtrusive. I peered inside and saw electric pink lights and column after column of leafy greens.
The shipping container, it turns out, contained a hydroponic farming system capable of producing between two to four tons of produce each year. I turned the corner to the other side of the container and was promptly handed a bag of dinosaur kale, plucked just the day before from inside that very shipping container.
Have you seen the #urbanfarm growing in #NYC? It’s on the corner of Lafayette and Houston St. until May 10th! #wsjfuturefest #verticalfarm
This particular container was created by a company called Freight Farms. According to its website, the box, called a Leafy Green Machine, "is capable of growing lettuces, herbs, and hearty greens at commercial scale in any climate or location." Produce can be grown year-round, using less than five gallons of water a day.
The farms are hydroponic systems, which means the plants are grown in liquid nutrients rather than in soil. The low water usage of the containers is partially due to the fact that leftover water gets recirculated. The neon pink lighting I noticed were the LED lamps that provide the plants with the right amount of light and can even affect how the plant looks and tastes. The light tends to appear pink or purple because chlorophyll, the pigment in plants that soaks up energy from light, absorbs red and blue light.
While the concept of shipping container farms was novel to me, they aren't new — and Freight Farms is far from the only company selling these farms-in-a-box to hopeful growers. Local Roots, Modular Farms, and Growtainer are just a few of the other major players in the space. Though these farms seem a natural fit for urban environments that are short on space, they aren't just cropping up in New York City. One farmer purchased a shipping container farm for her plot of land in Montana — a place with significantly more space than downtown Manhattan — because she says it allows her to grow fresh food year-round despite Montana's cold winters. Shipping containers are also getting parked in the Arctic, allowing people to grow fresh produce in the frigid climate and avoid the high costs and long waits associated with shipments from far-away farms. Furthermore, the food they are getting is more nutrient dense, as food can lose up to 45 percent of its nutritional value during transport.
Recently, NASA awarded a grant to Freight Farms and Clemson University to look into the possibility of growing food in space. Freight Farms says the innovations "could also be applied to other industries in need of a stable food supply, such as disaster relief, military bases, mining, and offshore industries." The Washington Post's Maura Judkis pointed out that "the flexibility and scalability of the farms has huge implications for food desserts" as well.
While these farms boast compactness, transportability, ready availability, and sustainability, there are challenges associated with them. Though shipping container farms seemingly make it easy for novice farmers to become green thumbs, these farms aren't an inexpensive investment — and it isn't always paying off, Vox reported recently:
Farming well requires deep know-how and expertise; it has proven extraordinarily difficult to expand vertical farms in a way that holds quality consistent while driving costs down. Optimizing production at a small scale is very different from doing so at a large scale. The landscape is littered with the corpses of vertical-farming startups that thought they could beat the odds (though several are still alive and kicking). [Vox]
Another issue is that not all fruits and veggies can be easily grown in a shipping container system. "Hydroponics and controlled-environment agriculture lends itself to certain types of produce, like highly perishable leafy greens, salads, herbs, and vining crops like tomatoes, cucumbers, and peppers," Viraj Puri, CEO of Brooklyn-based urban farming company Gotham Greens, told The Wall Street Journal. "But a lot of other ag staples can't be grown in a commercially profitable way, like grains, root vegetables, and tropical fruit." Puri predicts that these shipping container farms would be more of a complement to traditional farms rather than a replacement.
But even still, with a projected 2.4 billion more mouths to feed by 2050, an alternative source of fresh produce is certainly a mouthwatering prospect.
of The Week magazine.
Why You Should Eat Dockery's Shipping Container-Grown Greens
Why You Should Eat Dockery's Shipping Container-Grown Greens
From Container to Table
Posted by Mary Scott Hardaway May 10, 2018
Tiger Corner Farms' aeroponic farming systems prove that eating farm to table is not some halcyon, hippie dream. In fact, TCF, local farmers Vertical Roots, and Dockery's on Daniel Island take the dream to an even sweeter reality. They provide diners with container-to-table leafy greens, grown a stone's throw from the restaurant's dining room.
Last night at Lowcountry Local First's May mixer, LLF members and first-timers were treated to the coolest science fair this side of sixth grade. With Dockery's in-house brews flowing, mixers mingled with Tiger Corner Farms, Vertical Roots, and Boxcar Central — the software development company that provides the integrated platform sensors, controllers, and business software to the indoor farming market — employees. The lettuce that Dockery's uses in their salads, from arugula to butter lettuce, is grown by Vertical Roots in TCF containers run by Boxcar Central software. Pretty neat, huh?
We first learned about (and geeked out over) TCF last spring when we wrote an article on the aeroponic container farms for our Dirt issue. TCF general manager Stefanie Swackhamer, a former Latin teacher lacking a traditional ag background but possessing some serious business savvy, told us then that the end goal of creating and selling these containers is that a customer — be it a restaurant, a University, a hospital, or maybe even just a family — would ask "how do we grow blank?"
And Swackhamer could answer with "here's the framework, if you want bok choy you need to use this light integral, for arugula set these CO2 levels.' We're taking the automation of an algorithm and breaking it down."
With three local companies working so symbiotically, producing fresh produce for a new, local restaurant, you've got a new incentive to visit Daniel Island. Years from now, you'll be able to say you witnessed the future of farming at its nascence. And you'll get to sip on some pretty solid brews, too.
The Dallas Morning News features Dallas’ Central Market For Growing Their Own Salad
The Dallas Morning News features Dallas’ Central Market For Growing Their Own Salad
By urbanagnews April 10, 2017
Published by the Dallas Morning News
You want fresh? Dallas’ Central Market is growing salad behind the store
Fresh is a word that’s used loosely in the grocery business.
To the consumer, everything in the produce section is fresh. But most fruits and vegetables are picked five to 21 days earlier to make it to your neighborhood grocery store.
Central Market wants to redefine fresh when it comes to salad greens and herbs. It also wants to make available to local chefs and foodies specialty items not grown in Texas like watermelon radishes or wasabi arugula.
And it wants to be both the retailer and the farmer with its own store-grown produce.
The Dallas-based specialty food division of H-E-B has cooked up an idea to turn fresh on its head with leafy greens and butter lettuce still attached to the roots and technically still alive.
Beginning in May, the store at Lovers Lane and Greenville Avenue in Dallas will have a crop of about half a dozen varieties of salad greens ready for customers to purchase.
The greens will be harvested just a few dozen steps from the store’s produce shelves.
They’re being grown out back, behind the store in a vertical farm inside a retrofitted 53-foot long shipping container. Inside, four levels of crops are growing under magenta and other color lights. In this controlled environment, there’s no need for pesticides and no worries of a traditional farm or greenhouse that it’s been too cloudy outside.
Central Market has been working on the idea for about a year with two local partners — Bedford-based Hort Americas and Dallas-based CEA Advisors LLC — in the blossoming vertical and container farming business.
Plants are harvested inside a vertical farm in the back of the Central Market store in Dallas, Thursday, April 6, 2017. Central Market is trying out indoor growing, and the crops will be sold in the store beginning in May. (Jae S. Lee/The Dallas Morning News) Staff Photographer
“We’re the first grocery store to own and operate our own container farm onsite,” said Chris Bostad, director of procurement, merchandising and marketing for Central Market.
There’s a Whole Foods Market store in Brooklyn, New York with a greenhouse built on the roof, but it’s operated by a supplier, urban farmer Gotham Greens.
The difference, Bostad said, is that “we can grow whatever our customers want versus someone who is trying to figure out how to cut corners and make a profit.”
Central Market’s new venture is starting out with the one Dallas store, said Marty Mika, Central Market’s business development manager for produce. “But we’ll see what the customer wants. We can do more.”
This has been Mika’s project. He’s itching to bring in seeds from France and other far off places, but for now, he said,“We’re starting simple.” The initial crop included red and green leafy lettuce, a butter lettuce, spring mix, regular basil, Thai basil and wasabi arugula.
The cost will be similar to other produce in the store, Bostad said.
Why go to so much trouble? Why bother with lighting and water systems and temperature controls in what’s become a high-tech farming industry?
“Taste,” Mika said. “Fresh tastes better.”
And the company wants to be more responsive to chefs who want to reproduce recipes but don’t have ingredients like basil leaves grown in Italy that are wide enough to use as wraps.
Tyler Baras, special project manager for Hort Americas, said with the control that comes with indoor farming there are a lot of ways to change the lighting, for example, and end up with different tastes and shades of red or green leafy lettuce.
Butter lettuce is harvested inside a vertical farm in the back of the Central Market store in Dallas, Thursday, April 6, 2017. Central Market is trying out indoor growing, and the crops will be sold in the store beginning in May. (Jae S. Lee/The Dallas Morning News)Staff Photographer
In Japan, controlled environment container farms are reducing the potassium levels, which is believed to be better for diabetics, Baras said. “We can increase the vitamin content by controlling the light color.”
At Central Market, the produce will be sold as a live plant with roots still in what the industry calls “soilless media.”
Central Market’s crops are growing in a variety called stone wool, which is rocks that are melted and blown into fibers, said Chris Higgins, co-owner of Hort Americas. The company is teaching store staff how to tend to the vertical farm and supplying it with fertilizer and other equipment.
“Because the rocks have gone through a heating process, it’s an inert foundation for the roots. There’s nothing good or bad in there,” Higgins said.
Farmers spend a lot of time and money making sure their soil is ready, he said. “The agricultural community chases the sun and is at the mercy of Mother Nature. We figure out the perfect time in California for a crop and duplicate it.”
Growers Rebecca Jin (left) and Christopher Pineau tend to plants inside a vertical farm in the back of the Central Market grocery store in Dallas, Thursday, April 6, 2017. Central Market is trying out indoor growing, and the crops will be sold in the store beginning in May. (Jae S. Lee/The Dallas Morning News) Staff Photographer
He called it a highly secure food source and in many ways a level beyond organic since there are no pesticides and nutrients are water delivered.
Glenn Behrman, owner of CEA Advisors, supplied the container and has worked on the controlled environment for several years with researchers at Texas A&M.
“Technology has advanced so that a retailer can safely grow food. Three to five years ago, we couldn’t have built this thing,” Behrman said.
Mika and Bostad said they also likes the sustainability features of not having trucks transport the produce and very little water used in vertical farming. They believe the demand is there as tastes have changed and become more sophisticated over the years.
The government didn’t even keep leafy and romaine lettuce stats until 1985.
U.S. per capita use of iceberg, that hardy, easy to transport head of lettuce, peaked in 1989. Around the same time, Fresh Express says it created the first ready-to-eat packaged garden salad in a bag and leafy and romaine lettuce popularity grew.
In 2015, the U.S. per capita consumption of lettuce was 24.6 pounds, 13.5 pounds of leafy and romaine and 11 pounds of iceberg.
This Detroit Non-Profit Created A Shipping Container Farm To Feed Their Community
SOURCE CHARLOTTE BODAK
This Detroit Non-Profit Created A Shipping Container Farm To Feed Their Community
May 11, 2018
A charitable grant from the Ford Motor Co. has made possible a "mobile farm" partnership between the automaker and a Detroit charity that promises to educate children on healthy eating, provide food for the hungry, and teach people to be more self-sufficient by growing their own food.
Two essential (if unlikely) pieces required to make this project happen? A 40-foot-long shipping container and an F-150 pickup truck.
The collaboration answers a call to build a “Better World.”
The Bill Ford Better World Challenge distributes up to $500,000 a year to innovative programs that serve communities, from health and safety initiatives to education. Half of the money awarded each year comes from the Ford Motor Company Fund (the charitable arm of Ford), and half comes from Bill Ford personally.
"Our work can be divided into three broad areas," said Todd Nissen, director of communications for Ford Motor Company Fund, in an interview with Green Matters. "Basic needs, economic advancement, and quality of life. We believe it’s important to address all three categories in order for people to move up the social mobility ladder. We group hunger and food insecurity as basic needs. If people are food insecure, they are not able to do well at school or reach their full economic potential."
SOURCE: CHARLOTTE BODAK
A full 50 percent of the 2017 challenge funding went to the Ford Mobile Farm project, an ambitious undertaking that will grow several tons of food every year in a 40-foot shipping container equipped with hydroponics to grow food; and a Ford pick-up truck with plants growing in its bed that will make rounds at local schools to teach students about healthy eating and cultivating a garden.
The mobile farm was conceived of by two Ford employees, Chris Craft and David Root, both of whom are participants in Ford's Thirty Under 30 program. That leadership course educates young Ford employees about philanthropic organizations and design.
Nissen emphasized Detroit as being a perfect city for the mobile farm, saying, "We believe it’s important to add to the enrichment and quality of life where we do business. Detroit is our hometown and southeast Michigan is where a large number of our employees live.
But there’s a bigger issue at work. Although the downtown area has enjoyed a lot of economic success, the neighborhoods face significant challenges. About 40 percent of Detroiters are at or below the poverty line. In southeastern Michigan, nearly 900,000 adults and children are food insecure. In short, there’s a huge need for not just access to food, but education and access to healthy food."
SOURCE; CHARLOTTE BODAK
Cass Community Social Services is rooted in sustainability issues.
Ford’s partner in this project, Cass Community Social Services (CCSS), is a Detroit-based, non-profit entity that has focused its efforts on combating poverty since 2002. The organization's initiatives center around access to food, health, housing, and jobs.
"We prepare and serve 700,000 meals annually, and house 300 homeless men, women and children nightly," said the Rev. Faith Fowler, executive director of CCSS, in an interview with Green Matters. "We operate two free medical clinics, and a day program for 135 adults with developmental disabilities; [as well as provide] recycling jobs [through the organization’s 'Green Industries' program] for 80 adults with significant barriers to employment."
Last year, she said, the Green Industries Program began assembling and installing solar power. "We even took a team to Puerto Rico last November and powered up 50 homes."
The Rev. Fowler also described Cass Community’s tiny home initiative as a "tiny homes campus" of more than two dozen 250- to 400-square-foot houses for homeless individuals, low-income senior citizens, and young adults who have "aged out" of foster care. "They rent for seven years and participate in a program that prepares them for homeownership," she explained. "If they meet the program requirements, they are given the homes." The tiny homes on campus is another of several collaborations between CCSS and Ford.
The Ford Mobile Farm's shipping container's food will supplement CCSS' community gardens, serving up food for the hungry year-round in the organization’s community kitchen. Produce will also be sold to local restaurants, creating an income stream to keep the freight farm afloat.
'Ford Mobile Farm' is an exercise in green innovation.
The shipping container, built by Freight Farm, is dubbed the "Leafy Green Machine." The system arrives from Freight Farm fully assembled, with 256 irrigated vertical towers and thousands of growing sites, custom workbench, automatic nutrient and pH dosing, and insulated padlocked entry. Plants are irrigated by captured rainwater, with LED lighting powered in part by solar to stimulate plant growth.
"We’re excited to expand what we are doing with solar energy," the Rev. Fowler said. "The use of solar with the shipping container fits in nicely with what we are doing with renewable energy and employment."
CCSS is expected to harvest weekly from the shipping container once it is up and running, amounting to several tons of produce grown every year. "We will also be able to monitor and control the lighting, and can water remotely thanks to specially designed software," the Rev. Fowler said. The system is expected to produce the same volume of food as a 1.8-acre farm, with solar power and 90 percent less water than a traditional farm.
The biggest plus next to the system's compact design is its predictability. "We will be able to grow no matter what the weather is like outside," the Rev. Fowler said.
As for the pick-up truck, CCSS will likely hire someone to take the Ford F-150 to area schools, where he or she will be working alongside members of Ford Motor Co.'s Thirty Under 30 team, as well as other volunteers from Ford. The program will reach about 2,250 Detroit-area students in its first year.
The freight farm is expected to be fully operational by August.
The shipping container farm is being installed at Cass Community’s World Building site in downtown Detroit, a move the Rev. Fowler said will allow the organization to "utilize volunteers as part of the gardening."
That shipping container is slated for arrival in July and will be followed by a few cycles of harvesting produce before opening the site up to the public. "This is the first time we will have grown anything vertically or hydroponically," the Rev. Fowler said, "and we expect there will be a steep learning curve."
It's hard to overemphasize the impact of year-round, on-site food being produced at CCSS — and the reach of the new educational component with the traveling Ford truck. "The greatest feature for us is the ability to have fresh, free, organic food all year long," the Rev. Fowler said. "Up until now, this was limited to June through September utilizing our gardens. In terms of the school outreach component, we believe that teaching children about healthy alternatives to snacks and meals full of salt and sugar is extremely important. Our food choices are as critical as our exercise habits in terms of health."
Nissen said Ford doesn’t have any specific plans to repeat the freight farm and mobile farm project elsewhere just yet, but "we always look for opportunities to replicate successful programs elsewhere."
CCSS recently made a trial run with the truck to a Detroit-area pre-school to see how the project might be received. According to the Rev. Fowler, that excursion ended with one of the students gobbling up seven crackers piled high with cream cheese and fresh-cut basil. "I have no idea if she ate her dinner that night," the Rev. Fowler said.
These Shipping Containers Have Farms Inside
These Shipping Containers Have Farms Inside
A startup called Local Roots is supplying its TerraFarms to restaurants, SpaceX, and the UN.
By Adam Popescu | May 9, 2018
Baby lettuce grows in a Local Roots TerraFarm. SOURCE: LOCAL ROOTS
Los Angeles startup Local Roots retrofits 40-foot-long shipping containers, turning them into “TerraFarms” that yield as many leafy greens as five acres of farmland—only faster, using as little as 1 percent of the water. The company leases TerraFarms to wholesalers, restaurant chains, and SpaceX. The United Nations is preparing to field-test them, too. Chief Executive Officer Eric Ellestad, a venture capitalist who’s raised about $11 million for Local Roots, says he’ll stand by the taste of the greens grown in the former containers, no salad dressing required. “Chefs we work with,” he says, “that’s what sells them.”
Irrigation
SOURCE: LOCAL ROOTS
Twenty-five gallons of water a day is all each TerraFarm’s hydroponics needs. Climate controls and LED grow lights also help nurture crops including butterhead lettuce, baby kale, Italian basil, and arugula with a wasabi-like kick.
To maximize water efficiency and recirculation, hundreds of sensors track such factors as airflow and water temperature and feed the data to TerraFarms staffers for real-time tweaking.
Yield
Four thousand heads of lettuce can come from a single TerraFarm every 10 to 12 days. They grow from seed to full maturity in 30 days. Outdoor farming takes at least 60 days.
Overhead
Local Roots buys old containers from the Port of Los Angeles for about $5,000 and retrofits them for more than double that. It owns the farms and contracts with clients for a set period of use.
SOURCE: LOCAL ROOTS
Efficiency
Customers place the container farms at food distribution centers so they can cut out days or even weeks of produce travel time.
TerraFarms Reduce Food Miles by 93%, Nix Supply Chain Risk
Product Announcement: TerraFarms Reduce Food Miles by 93%, Nix Supply Chain Risk
A Los Angeles start-up aims to revolutionize the food industry by eliminating supply chain risks for mass market grocers, big box retailers, universities, hospitals and medical centers, food service distributors, and more, by delivering a “farm” for vegetable crops right to the company’s door. The company says that by bringing the farm closer to the consumer, it reduces food miles by up to 93%.
How? Local Roots retrofits shipping containers to create a TerraFarm – an indoor growing system that yields predictable harvests and volumes, 365 days a year, the company says. The shipping containers are outfitted with sensor systems to create the right climate, LED lighting, and efficient irrigation systems. The company delivers the TerraFarm to wholesalers, restaurant chains and the like, and provides a farming team to manage the entire growing and harvesting process. “This farming solution allows us to grow consistent yields, eliminating supply chain volatility while maintaining excellence in quality and taste,” according to the company’s website.
Local Roots buys 40-foot long shipping containers from the Port of Los Angeles for about $5,000, then retrofits them and contracts them to clients for a set period of time, according to Bloomberg. A single TerraFarm can produce up to 4,000 heads of lettuce every two weeks, growing from seed to maturity in 30 days, compared to the 60 days or more than it takes in an outdoor farming environment.
“We believe the key to a more sustainable future requires eliminating supply-chain risks and undoing the commoditization of the food industry,” the company says. Local Roots hopes to do so by building its distributed network of farms throughout the word to grow fresh and healthy food.
Crops are grown with up to 99% less water than conventional agriculture, with no pesticides or herbicides, and no agricultural run-off.
Categories Environmental Management, Feature, Sphera Must Read, Transportation, Water
Tags agriculture, farming, food industry, supply chain, Sustainability
San Antonio, Texas - Idea Public Schools Program Shows Middle School Students Hydroponic Farming
Idea Public Schools Program Shows Middle School Students Hydroponic Farming
Idea East Side is the first K-12 school in the nation to have the program
Posted: May 03, 2018
SAN ANTONIO, TEXAS - Idea Public Schools unveiled its first “Leafy Green Machine” on Thursday in an effort to connect school cafeterias and students with local farmers and ranchers.
The modified shipping container grows various kinds of crops using minimal electricity and water. All the produce goes to the school cafeteria.
The machine is part of a pilot program for hydroponic farming. Officials said the technology will engage students, especially those in sixth, seventh and eighth grades.
The program goes hand-in-hand with classes such as biology, chemistry and math.
“It’s a great addition to our program because it's showing students the tech side of agriculture, fully automated. Students are able to see firsthand how tech plays a role in agriculture by using computers (and) chemistry of chemicals,” said Hernan Colmemero, CNP farm manager for Idea Public Schools.
Idea East Side is the first K-12 school in the nation to have this kind of program