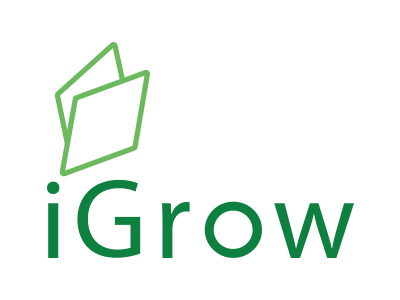
Welcome to iGrow News, Your Source for the World of Indoor Vertical Farming
Smart Home Farms To Enhance Food Security In The UAE
July 31, 12018
The UAE Office for Future Food Security and Masdar (Abu Dhabi Future Energy Company) have announced a strategic partnership to enhance food security in the country.
The collaboration aims to address future challenges by developing joint initiatives that enhance the country’s capacity and competitiveness in critical sectors related to future food security.
Mariam bint Mohammed Saeed Hareb Almheiri, Minister of State for Future Food Security, and Mohamed Jameel Al Ramahi, Masdar
The agreement was signed at the Masdar headquarters in Masdar City, Abu Dhabi by Mariam bint Mohammed Saeed Hareb Almheiri, Minister of State for Future Food Security, and Mohamed Jameel Al Ramahi, Chief Executive Officer of Masdar.
“This strategic partnership is the cornerstone of achieving future food security objectives – an important step in activating plans to meet the challenges of this vital cause and invest in its opportunities,” said Almheiri.
“Masdar was a natural partner, given its experience working in sustainability through tangible projects in Masdar City and their renewable energy assets globally.
“This collaboration signifies an important step towards advancing innovations in agricultural production mechanisms and sustainable solutions to the challenges facing the agriculture industry in the UAE. It will also contribute to raising awareness about new, innovative solutions to enhance food availability and sustainable agriculture, and support emerging companies in the sector, boosting future food security in accordance with the UAE Vision 2021.”
According to Almheiri, future food security is a key focus of the UAE government, a reflection of the leadership’s far-sighted vision, which sets the well-being, prosperity and food availability of its citizens and residents at the top of its agenda. “This has led to close cooperation between the government and private entities to achieve the objectives of future food security, through an integrated system of joint work. The outcome aims to develop the necessary infrastructure, and implement practical approaches based on the latest scientific research findings.”
The Memorandum of Understanding (MoU) focuses on two major initiatives, a vertical farming container pilot project, and a smart home farm.
The vertical farming container programme will see a pilot facility established in Masdar City, where the latest technologies and best practices in controlled environment farming will be tested. The project will also contribute to defining the business and regulatory guidelines for the development of vertical farming in the country.
Meanwhile, the Smart Home Farm is an initiative to be developed in connection with Masdar City’s Eco-Villa, conceived as a template for affordable and highly energy- and water-efficient residential villas in the UAE.
The Smart Home Farm initiative will help showcase emerging sustainable home and urban farming technologies and solutions from local and international suppliers.
Masdar’s Al Ramahi, said, “Masdar City in Abu Dhabi is already a highly successful testbed for research into sustainable food production and today, as the city’s community of residents, office workers and visitors continues to grow, we are exploring further opportunities to combine sustainable farming with low-carbon urban development, including vertical farming methods and home farming technologies integrated within our Eco-Villa concept.”
Collaborating with the UAE Office for Future Food Security will help to raise awareness of these efforts and the benefits of sustainable food produce, encourage innovation, and promote further public-private involvement in food security projects.”
Why I’m Empowering A New Generation Of Farmers To Transform America’s Food System
Applications now open to be a Next-Gen Farmer at Square Roots.
Applications are now open for the third season at Square Roots, on our Brooklyn farming campus. Join a unique program that trains and empowers the next generation of leaders in urban farming.
We need new leaders to forge a new food system
Consumers across the world are demanding greater transparency into where and how their food is grown. Yet most people in cities are tethered to an industrial food system that ships in high calorie, low nutrient food, often from across the globe. It’s harmful to the health of the planet and its populations, and leaves us completely disconnected from the people who grow our food.
We need to act now — as urban populations keep rising and global temperatures continue to climb. The next generation has an incredible opportunity to re-envision a food system that implements responsible farming practices, leverages new technologies, works together to value everyone from the farmer to the consumer, and rebuilds the connections between people and their food.
We launched Square Roots two years ago to start playing our part in this new system.
Bringing the Farm to the City
Square Roots is an urban farming company. We grow nutritious food, year round, using indoor vertical farming systems. Our farms are non-GMO, pesticide-free, and use 90% less water than their outdoor equivalents. We continually work to improve the technology in our farms to grow more (and higher quality) food, with less resources, giving the farmer more time to expand their knowledge and get connected with local communities. Customers are often eating our food within hours of harvest — and because it’s so fresh, it tastes delicious.
The Square Roots farms, built inside refurbished shipping containers, have programmable climates — this allows our farmers to grow food from all around the world, all year round, right in the heart of NYC.
Our first farm in Brooklyn is just a subway ride away from over eight million New Yorkers, making it easy for urbanites to get connected to their local farmer. We hold workshops, open community tours, and pop-up markets for foodies, tech-lovers, and passionate real food advocates. The farm is a space to connect with community and share thoughts; and at the heart of it are the farmers.
The Next-Gen Farmer Training Program
If we’re going to change the food system, we simply need more young farmers. The average age of the American farmer is 58, there are huge obstacles to start farming, and making a livable income can be challenging. We need to create more pathways for young people to launch successful careers in farming. And we need many of them to understand the nuances of urban farming business — to bring fresh, local food to ever-increasing populations in cities.
Our mission at Square Roots is to bring local, real food to people in cities by empowering a whole new generation of leaders in urban farming — because the more of us working to shape the future of food, the better.
Integral to that mission is our Next-Gen Farmer Training Program — a year-long program that puts participants at the forefront of indoor urban farming. After an initial period of hands-on training in our farms, Square Roots Next-Gen Farmers grow food year-round for customers across NYC. No previous farming experience is necessary to apply — just the passion and entrepreneurial spirit to jump in and start learning. Our intuitive farming technology and expert team combine to help participants become the best urban farmers they can be. The opportunities in front of successful graduates are endless.
Next Gen Farmers have the passion and entrepreneurial spirit to jump in and start learning.
Impacting People, Planet, and Profits
Next-Gen leaders in urban farming understand the importance of equally-weighted social, environmental, and financial success. We’re a young company ourselves, and we are building these measurements into every aspect of our business. Throughout the year the farmers are involved in the entire process.
Built into the second half of the program are two multi-month, project-based learning experiences. A business-focused project introduces entrepreneurial frameworks and further develops farming business knowledge; while a community-oriented project is focused on creating more pathways for even younger generations to get connected to their food. These projects are integrated into the farmer’s 40-hour work week, alongside ongoing farming responsibilities.
The Many Faces of Urban Farming
Square Roots program alumni have gone on to start their own urban farming businesses, take incredible jobs at other forward-thinking companies in urban ag, and moved into permanent positions on the Square Roots team. Our Next-Gen Farmer Training program provides unique experience and insight into the many roles for leaders in the future of food.
The Next-Gen Farmer Training Program is a year-long, full time position, based on our Brooklyn farming campus, starting November 2018. The next round of applications opens today! If you want to start making a massive impact — socially, environmentally and economically — in urban farming and the future of food, let us know right here. We can’t wait to talk with you.
Kimbal Musk
My mission is real food for everyone. Co-founder of The Kitchen #realfood restaurants, Big Green teaching kids about food & Square Roots mentoring young farmers
Edmond, Oklahoma - Native NBA Player Officially Launches Hydroponic Farm In Edmond
Edmond, Oklahoma Native NBA Player Officially Launches Hydroponic Farm In Edmond
JULY 22, 2018, BY SARAH STEWART
EDMOND, Okla. - This weekend, Edmond native and Utah Jazz Center Ekpe Udoh has officially launched his company, LGR Farms, in Edmond.
Oklahomans attended the Saturday night launch party, getting a hands-on tour, even planting some seeds that will eventually grow into crops.
“It’s been four years in the making,” Udoh said.
It’s a hydroponic farm that literally sits in a shipping container. The crops grow vertically with filtered water and nutrients instead of soil and blue and red LED lights instead of sunlight.
It’s herbicide- and pesticide-free for the leafy greens and herbs grown there. And, the “farmer” can control everything from a phone.
“I can turn on and off the lights with the touch of my phone, and it controls like literally everything,” said LGR Farms Vice President Erica Young. “We have in, our farm, approximately nine to 10 different crops being grown currently. We have four or five lettuces, herbs right now, different leafy greens that we’re growing.”
Udoh hopes his farm can make a difference in inner city communities.
“There’s higher rates of obesity and such in inner city, inner city areas. As you can see just going around, fast food’s on every corner in those neighborhoods, unfortunately. And, this is just something different, you know, be able to get them fresh produce and, then, try to educate them along the way,” Udoh said.
One of Udoh’s goals is to provide food for public schools, especially inner city schools.
“Growing up in Edmond, we had salad bars. I didn’t appreciate it back then, you know, being a knucklehead. But, now, I understand it. With all the pictures that have been going viral, Oklahoma City public schools, just want to give them a choice,” Udoh said.
Udoh plans to expand his Edmond operation and go into other states as well, eventually selling to chefs and grocery stores also.
He also announced he’s partnered with Magic Johnson’s food service company, Sedexo MAGIC, to provide produce to kids in inner city schools. And, he said he’s in talks with Oklahoma City public schools to provide food for them as well.
Nova Scotia: Tiny Farm Grows Giant Crop In Old Dartmouth Shipping Container
Nova Scotia
Tiny Farm Grows Giant Crop In Old Dartmouth Shipping Container
Phil Hatcher quit film industry to start his own high-tech urban farm
Emma Smith · CBC News · Posted: Jul 21, 2018
Very Local Greens leases a small parcel of land from King's Wharf development on the Dartmouth waterfront. (Emma Smith/CBC)
A 12-metre shipping container that once sent goods overseas is now an urban farm on the Dartmouth waterfront that's feeding customers closer to home.
Very Local Greens planted itself in a large parking lot across the street from the King's Wharf development. The industrial location is in stark contrast to what's inside — a tiny, high-tech farm teeming with life.
"The container can essentially hold the same amount of leafy greens as would a traditional two-acre farm," said Phil Hatcher, who founded what he believes to be Nova Scotia's first freight farm this spring.
Farming inside shipping containers is the latest trend in urban agriculture, a way to get fresh, local produce even in the dead of winter. Containers are proving to be fertile locations because they provide moveability, sustainability and availability.
There are about 5,000 plants growing vertically in a shipping container that's located on the Dartmouth waterfront. (Emma Smith/CBC)
"We can grow from – 50 C to plus 50 C," said Hatcher. "It doesn't really matter, and that's definitely the goal, is to kind of ramp up for the fall and go right through the winter."
Step inside the container and you'll hear the gentle whir of fans and smell an earthy mix of cilantro, basil and kale. There's room for about 5,000 plants, said Hatcher, all grown using hydroponics, so there's no soil, just water.
The plants grow sideways out of slim columns that hang from the ceiling. Between the columns are LED lights, which when turned on make the space feel more like a nightclub than a farm.
Hatcher said the operation uses about 95 percent less water than a traditional farm.
"We reclaim all of our water from our air conditioning and we reclaim all of our water from our dehumidifier, so we're actually producing more water than we need right now," he said.
Hatcher doesn't have a background in farming. In fact, he spent 15 years working in the film industry before making a drastic career change and buying a shipping container.
It cost about $150,000 to set up the operation thanks to Freight Farms, a Boston-based business that started manufacturing and selling the units in 2010.
One of the selling points is the farmer's ability to control everything — from lighting to nutrient levels — remotely from a cellphone.
"Yes, it's high-tech in the way that it's computer controlled and the sensors are all reading different things and crunching numbers, but at the same time it's pumps and it's water and it's tanks and it's air and it's light," said Hatcher.
Hatcher came across a video of freight farms online and was intrigued. It didn't take him long to buy his own. (Emma Smith/CBC)
Robert France, a professor in the faculty of agriculture at Dalhousie University, said one of the major hurdles for urban agriculture is lack of space.
"The advantage of having various containers are that you can just pick up your production system and move it somewhere else should another use come in to dictate the previous site you were in," said France, who co-edited a book on urban agriculture.
He said farms like this have been able to take off thanks to two major developments in the last five years — LED lights and hydroponics.
France says given the growing demand, he wants to see municipalities develop bylaws that are even more welcoming to urban farms like Hatcher's. (Robert Short/CBC)
He teaches an online course on urban farming and says it's attracting people like Hatcher, who've become disillusioned with their first careers and are looking for a sustainable way to grow their own food.
People like chef Dwayne MacLeod are benefiting from the trend. He's one of Hatcher's first customers. He can practically see the farm from his restaurant, Cut Steakhouse, on Lower Water Street in Halifax.
He said in the past, finding produce that's harvested the same day was a challenge. Now, he just has to drive across the bridge. He's been working with Hatcher to get some of his favourite plants in the farm's growing rotation.
MacLeod said greens grown in containers have a stronger flavour and are also more delicate.
Dwayne MacLeod, chef at Cut Steakhouse, says it's exciting to work with produce that's grown so close to his restaurant. (Robert Guertin/CBC)
"It's a very interesting contrast between the two of them and I find the shelf life on these products probably three times longer than any I've used previously and the yield you get out of it is just phenomenal," MacLeod said.
Right now, Very Local Greens is a one-man, one-shipping-container operation, but Hatcher plans to hire staff later this summer.
And if all goes well, he hopes to add a second shipping container to his fleet soon.
"I don't think people realize how easy it can be," said Hatcher. "It's a lot of fun so I think anybody who's thinking of hobby urban farming should go for it."
Hatcher says he wants to work with chefs to grow new and innovative crops at the farm. (Emma Smith/CBC)
Adventist Academy Introduces Innovative Farming Into Its Curriculum
Adventist Academy Introduces Innovative Farming Into Its Curriculum
State-of-the-art initiative includes greenhouses, hydroponics, and microgreens.
By: Shelley Bacon, North Pacific Union Conference News
What is green on the inside, metal on the outside, and high-tech all over? A container full of microgreens.
A new agriculture program has begun at Upper Columbia Academy(UCA) in Spangle, Washington, United States.The era of farms atSeventh-day Adventist schools was thought to be long past, but in an era of new agriculture techniques,UCA is taking a step back into this growing field.
The school had to answer the question, how does one go about establishing a viable agriculture program in today’s market?
Academy leaders found their answers in visionary donors, altruistic alumni, and dedicated staff. Two donors who had long believed in the power and importance of students working in the soil each gave $100,000 toward the development of the program, intending for modern agriculture to be incorporated into the curriculum.
Alumnus Peter Vercio, who is part of a company that sets up farms and agriculture systems like that envisioned for UCA, stepped in to set up the operation. UCA staff will be operating the agriculture program and integrating it into the curriculum.
Vercio was headed toward law school when his life took a detour. After a stint working for a business in the oil field of North Dakota, and realizing he liked the idea of working in a business, he went to work for a solar panel company in California. However, he soon realized his work wasn’t making the difference he wanted it to.
At the same time, Vercio began to recognize the gift of health he had been given as he grew up in an Adventist family. He saw firsthand the effects of poor health as he interacted with colleagues who didn’t have the knowledge of healthy eating and living he had received. As his desire to make an impact with his time and talents converged with his emerging interest in healthy foods, he relocated to Colorado and started Sirona Life, a vertical farming business.
At UCA, Vercio will be combining his expertise in business, his desire to make an impact with his work, his passion for giving students an edge by providing healthier food options and taking an active role in the growing process, and his love for his alma mater to kick off a state-of-the-artagriculture program. Vercio plans to develop the greenhouse and incorporate multiple kinds of growing apparatus, including hydroponic gardening equipment.
He will also set up a container “farm,” which will mostly be used to grow microgreens — an up-and-coming food product. “There are huge amounts of money flowing into the agriculture technology field right now,” says Vercio. “We can give UCA students the tools for big job possibilities for the future.”
UCA staff member Ted McConnachie will move from the maintenance department to the role of farm manager in summer 2018 as he develops the program. He will be responsible for overseeing student labor as well as marketing the agriculture program's harvest. He is excited about the future. “This will be a fantastic place for kids to learn a completely new way of growing food,” he says.
In conjunction with Andrews University in Berrien Springs, Michigan, UCA will offer a related dual-credit class, “21st-Century Agriculture.” Additionally, all teachers will be encouraged to integrate the agriculture program into their curriculum.
Biology teacher Judy Castrejon is planning the integration possibilities in her classes, and chemistry teacher Charles Hartman says that he has a vision of having his students conduct soil analyzation experiments and discover what various soil treatments do to their original numbers.
The agriculture program is a significant reason that UCA is “a place to grow.”
This article by Shelley Bacon, Upper Columbia Academy recruiting and communication director, was originally published by North Pacific Union Conference (NPUC) Gleaner/GleanerNow.com and is reprinted here with permission.
Hydroponics Farm In Shipping Container Seeking Ann Arbor Restaurants
Hydroponics Farm In Shipping Container Seeking Ann Arbor Restaurants
July 9, 2018
By McKenzie Sanderson MSanderson@mlive.com
ANN ARBOR, MI - Hidden inside an upcycled shipping container tucked away in the corner of an industrial plaza parking lot is a fully functional hydroponics farm.
Crop Spot Farms is essentially a two-acre farm retrofitted inside a 320-square foot container that was previously used for transporting meats, fruits and vegetables.
The recycled container now shares space with vehicles in the parking lot of the Michigan Innovation Headquarters on 600 Wagner Rd.
Inside the farm are rows of leafy greens -- lettuce, arugula, swiss chard, kale, and herbs - nestled inside vertically hanging tubes, each connected to a controlled water source and surrounded by strips of grow lights.
Crop Spot Farms brings hydroponic farm tech to Ann Arbor inside a shipping container
Founder and lead farmer Nabeel Kasim can control the farm's climate and irrigation through a mobile phone application, which is connected to the main power source inside the container. The controlled environment allows for more consistency in plant production and a better tasting, more nutritional product, Kasim says.
"Using the (hydroponics system) indoors is more environmentally-friendly because it requires 95 percent less water," Kasim said. "Growing outdoors brings about the issue of bugs and pesticides, so this system reduces the pollutants and toxins that come with that. It also allows the produce to be available year-round, which is why it's so great to have in Michigan where there are limited harvest seasons."
After graduating from the University of Michigan in 2015, Kasim picked up an interest in hydroponics during a trip to a remote village in Cambodia, where he encountered a family using a soil-free farming technique.
The technique, collectively known as hydroponics, was successful in an area with sporadic rainy weather, which inspired Kasim to experiment with it in Michigan.
Kasim hopes Crop Spot Farms will foster engagement and educational opportunities with Ann Arbor restaurants, schools, and the community.
"I want to help people realize the value of healthy, good-tasting food," Kasim said. "It's all about giving back to the community and make people aware of locally-sourced, environmentally-friendly food. I also hope to supply local restaurants so they can have at-scale, quality produce year-round."
Crop Spot Farms has been in operation since the beginning of May. Kasim said the farm's first major harvest was expected to begin this month.
A launch party for Crop Spot Farms is set from noon to 7 p.m. Sunday, July 15 outside the Michigan Innovation Headquarters building on Wagner Road. There will be produce samples and informational tours of the farm.
"Typically, restaurants are less busy or closed on Sundays, so this event will give them the opportunity to learn about the farm and see it in person," Kasim said. "I'll have some yard games and samples for people to try or take home. I also plan on giving tours every half hour as people start to arrive."
The launch event is free and open to the community. More information can be found on the Crop Spot Farms website.
Jacob Hamilton
Owner Nabeel Kasim poses inside Crop Spot Farms, a hydroponic farm in a recycled shipping container at MI-HQ, 600 S. Wagner Rd. In Ann Arbor on July 5, 2018. Kasim started off gardening as a hobby before realizing he could apply his engineering and logistics skills to hydroponics - a technique he discovered on a trip to Cambodia. "Gardening was dirty," Kasim said. Now he plans to make a business selling heirloom variety leafy greens to Ann Arbor restaurants and hopes to turn the operation into an educational example of future farming techniques.
Jacob Hamilton
Lettuce plants grow from hanging hydroponic columns at Crop Spot Farms, a hydroponic farm in a recycled shipping container at MI-HQ, 600 S. Wagner Rd. In Ann Arbor on July 5, 2018.
Jacob Hamilton
Lettuce plants grow under violet-and-blue LED lights at Crop Spot Farms, a hydroponic farm in a recycled shipping container at MI-HQ, 600 S. Wagner Rd. In Ann Arbor on July 5, 2018.
Jacob Hamilton
Plants grow from hanging columns on either side of UV and infrared LED strips at Crop Spot Farms, a hydroponic farm in a recycled shipping container at MI-HQ, 600 S. Wagner Rd. In Ann Arbor on July 5, 2018.
Jacob Hamilton
Plants grow from hanging columns on either side of UV and infrared LED strips at Crop Spot Farms, a hydroponic farm in a recycled shipping container at MI-HQ, 600 S. Wagner Rd. In Ann Arbor on July 5, 2018.
Jacob Hamilton
Plants grow from hanging columns on either side of UV and infrared LED strips at Crop Spot Farms, a hydroponic farm in a recycled shipping container at MI-HQ, 600 S. Wagner Rd. In Ann Arbor on July 5, 2018.
Jacob Hamilton
Plants grow from hanging columns on either side of UV and infrared LED strips at Crop Spot Farms, a hydroponic farm in a recycled shipping container at MI-HQ, 600 S. Wagner Rd. In Ann Arbor on July 5, 2018.
Jacob Hamilton
A drip regulator provides the water for a hydroponic column planter at Crop Spot Farms, a hydroponic farm in a recycled shipping container at MI-HQ, 600 S. Wagner Rd. In Ann Arbor on July 5, 2018.
Jacob Hamilton
Owner Nabeel Kasim peers between vertical hydroponic columns at Crop Spot Farms, a hydroponic farm in a recycled shipping container at MI-HQ, 600 S. Wagner Rd. In Ann Arbor on July 5, 2018.
Jacob Hamilton
Owner Nabeel Kasim peers between vertical hydroponic columns at Crop Spot Farms, a hydroponic farm in a recycled shipping container at MI-HQ, 600 S. Wagner Rd. In Ann Arbor on July 5, 2018.
Container-Grown Vegetables A 'Gardening Revival,' Says Horticulturist
Container-Grown Vegetables A 'Gardening Revival,' Says Horticulturist
Grant Wood says container gardening is an easy way to grow your own food no matter the conditions
Ashleigh Mattern · CBC News · Posted: Jul 07, 2018
Chef James and Chef Ahmed from Culinary Services at the University of Saskatchewan. (Submitted by Grant Wood)
Gardening season is in full swing, but what if you don't have space for a garden?
Grant Wood, who works at the University of Saskatchewan College of Agriculture and Bioresources, says container gardening could be the answer.
He cultivates a rooftop vegetable garden at the University of Saskatchewan, growing everything from tomatoes to cucumbers to herbs.
Wood has heard a range of excuses for why people don't grow their own vegetables: They haven't got room for it, the soil is bad, or it's too much work, to name a few.
"Actually, if you grew things in containers, that could solve a lot of the problems," said Wood to CBC's Saskatchewan Weekend.
Chef Dave and Chef Matt from Louis' at the University of Saskatchewan. (Submitted by Grant Wood)
Don't make rookie mistakes
One of the biggest rookie mistakes people make is not having a hole at the bottom of the container, according to Wood.
"Roots need air. If the roots are sitting in water they tend to rot."
At the same time, plants in containers dry up and get hot faster, which isn't ideal for many plants.
"Warm season crops, things that like heat, they do well, but not necessarily things that like cool soil, like the cabbage family likes a nice cool soil, and they tend not to do well in containers."
If you're not having fun gardening, you're doing something wrong.- Grant Wood, assistant professor of Plant Sciences in the College of Agriculture and Bioresources at the University of Saskatchewan
Another mistake is using garden soil in containers. Garden soil tends to have a high clay content, which makes it harder for water to reach the lower levels of the pot.
He said the best mix for container gardens is 30 to 40 percent compost and the rest a soilless media — mostly peat moss, vermiculite, and perlite.
Also, try to keep it simple at the beginning. Don't plant too many containers and get overwhelmed.
A view of the south roof of the container garden at the University of Saskatchewan. (Submitted by Grant Wood)
Produce fit for a chef
Tomatoes, peppers, cucumbers, lettuce, spinach, dill — and more — can be found on the roof of the Ag-Bio building at the university.
Wood says the vegetables he grows are often used by chefs at the university in the meals they prepare.
"The chefs absolutely love it," he said.
Wood has also experimented with ethnic foods like Malabar spinach.
"For people who have just moved to Saskatoon, you've moved here, this is your new home now and let's try and make your new home a little bit more like your old home. So you can grow certain vegetables just like you did at home," he said.
Wood said people are wanting more control of the food they're consuming. He calls it a "gardening revival" and encourages everyone to give it a try.
"If you're not having fun gardening, you're doing something wrong."
Wood is hosting workshops this week in Saskatoon as part of Hort Week.
There will be a tour of his rooftop garden on Tuesday night.
ABOUT THE AUTHOR
Ashleigh Mattern
Ashleigh Mattern is a web writer and reporter with CBC Saskatoon. Email: ashleigh.mattern@cbc.ca
Modular Farms Now Made In Dalkeith, Ontario, Canada
Modular Farms Now Made In Dalkeith, Ontario, Canada
Lynn Macnab - Dalkeith, Ontario, Canada
In good farm country like Dalkeith, where soil is abundant, it seems unusual to introduce vertical farming. But Eric Amyot, CEO of Modular Farms Inc., believes he’s found the perfect location to build the modular farm that are being shipped worldwide. These metal boxes — some say they look like ATCO storage containers — are now being produced at the old MacLennan sawmill in Dalkeith. The sawmill was purchased 10 years ago by Carter Shows owners Bruce Brock and Geordie Todd.
“I wasn’t planning on selling the place, but they made me an offer I couldn’t refuse,” says Brock, speaking of the farm company that’s interested in purchasing the nearly 10-acre property.
“Right now we have a lease-to-own in place, and because we’ve already started the show season, rides like the Tilt-A-Whirl and Merry-Go-Round will be on the road while others are being stored in the back. That makes the main building available for the farms manufacturing.” He explains that some of their 20 rides can be stored outside, making room for the seven farm employees to work on farm container production in the main storage facility.
Vertical farming occurs in sealed containers and is done hydroponically, without soil. Seeds are started in a nutrient-rich culture and are then transferred to an area where the plants grow vertically on walls of the unit. There are no windows and temperature and humidity are controlled. The company has partnered with a world-leader in LED light. The building is completely self-contained and sterilization means there’s no need for pesticides, herbicides or other chemicals, making the ‘farm’ ideal for areas where traditional crop-growing is almost unthinkable.
The 10’4’’ by 10’4’’ by 40’ containers are used to grow mostly green leafy vegetables and herbs, such as kale and basil. The dimensions were established according to road and rail demands for shipping, and each unit costs an average of $155,000. According to CEO Amyot, the measurements meet highway and rail standards in order to be shipped to communities around the world and remote Northern Canadian areas with little problem. He explains that one of his first concerns when setting up the business, that he started in Cornwall a few years ago, was that container measurements met traffic standards.
Devin Lamb, of Alexandria, has been operations manager at the modular farm business for nine months. Lamb believes the old sawmill is a great location not only for the construction of the farms, but also for research and development. “Our goal is to increase ‘R and D’ here in Dalkeith and continue to build. This farm is going to Alaska,” he says, pointing to the container currently in construction at the Dalkeith facility. “Modular farms are the gateway to indoor agro-technology.”
This Article Has Been Curated From The Review
Next-Gen Leaders In Urban Farming - Josh Aliber
Next-Gen Leaders In Urban Farming - Josh Aliber
Josh joined Square Roots in 2016 as one of ten farmers in the inaugural season of our Urban Farming and Entrepreneurship Program. He’s now part of the R&D team, helping to design our future farming technology. We asked him to share a bit about his journey to become a next-gen leader in urban farming.
Josh Aliber with his thai basil during season one of the Square Roots farming program.
SR: How did you get started in urban farming?
JA: My first time growing a plant was a gardening course in college. I signed up hoping to satisfy some credits not expecting the joy I’d receive from growing food. I had a 5’ x 5’ plot that I decided to fill with broad-leaf mustard. Every week, I returned to my dorm with a bundle of mustards to share with my roommates. They always accepted my greens but never knew what to do with them!
I finished school with a degree in entrepreneurship and spent some time afterwards at a clean-tech startup in Boston before embarking on a multi-month long journey in Central and South America. My travels opened my eyes to the opportunities of sustainable food systems and the perils of processed foods. I remember traveling to Nicaragua, where I was shocked by the rate of obesity. There, it occurred to me that processed foods were cheaper and more readily available than fresh, local food. The longer I traveled, the more I started to observe and analyze the food of different cultures and people.
I returned home to the United States prematurely after injuring myself hiking. During my next six months in recovery, I decided I was going to start my own business when I returned to full health. I started listening to podcasts, because I was not able to read or a use a computer. That’s when I found “Urban Agriculture” — a podcast about vertical farming. I became fascinated and obsessed with the idea of vertical farming — excited by its intersection of technology, social impact, and economics. I spent the following six months studying, networking, and preparing to apply to graduate school to learn controlled environmental agriculture, thinking it’d enable me to start my own farm. This is when I found Square Roots.
“I became fascinated and obsessed with the idea of vertical farming — excited by its intersection of technology, social impact, and economics.”
SR: Tell us about your experience in season one of the Square Roots program.
JA: Rewarding, challenging, and enlightening.
I joined Square Roots with minimal experience in agriculture — hoping to finish the program and start my own farm. I spent the next twelve months effectively learning how to grow and build a small business selling herbs to retail stores and restaurants in New York City. I learned to operate an indoor farm and practice the fundamentals of entrepreneurship. My greatest experiences were in the lessons I learned through failure.
SR: Now that you’ve joined the Square Roots team post-program, what are you up to?
Josh Aliber transplanting basil seedlings in our R&D farm.
JA: I currently work on the R&D team as a farmer. I joined Square Roots at the end of season one to become one of the first members of our R&D team tasked to build new technology, specifically optimizing for healthy plant growth. Today, I work alongside our engineers to beta-test all the hardware and software they build. I build processes to grow food better.
SR: How do you relate to the concept of next-gen leadership in urban farming?
JA: I identify with our next generation of farmers, because I believe that young people have a responsibility to reduce our society’s carbon footprint. I am optimistic that as technology in indoor farming improves, it’s a method through which we can grow food with minimal resources and allow our land to restore itself and heal.
SR: What excites you about future of urban farming?
JA: Circular economies. In regenerative soil farming, inputs are a function of outputs: no resources are wasted. I’m excited by the opportunities of indoor farming to follow a similar approach to build circular systems, to build farms using recycled materials, and to use renewables and waste for power.
SR: What favorite plant are you currently growing?
JA: Stevia! Many people don’t know that stevia is a plant! It’s super sweet and tastes better than the artificial sugar we put in our coffee. I love growing plants that WOW people. I’m excited to see stevia used in a cocktail at a bar. It’s going to be a bestseller!
You can follow along with Josh Aliber on Instagram @joshaliber.
Agriculture Real Food Urban Agriculture Technology Urban Farming
Freight Farming Over Freight Shipping: Bringing Local Back To The Island
June 25, 2018
Can modern container farming technology reduce island dependence on imported food?
We think it can! First, however, we need to be able to understand the issue at hand.
While we usually associate islands with beautiful beaches and relaxing vacations, there is a more sinister side to everyday island life. One of the most pressing issues is the lack of local, on-island food production due to space, climate, and weather restrictions. As a result, many island nations rely on imported food that degrades the local culture and introduces unhealthy food products to island communities. Furthermore, it creates great instability for regions that will likely be the most affected by climate change in the years to come.
Here are just some limitations to island food production...
Limited space
One of the greatest limitations to island food production is simply the lack of space! Many islands or archipelagos are tiny, with not enough land available to hold residents, tourists and visitors, the necessary infrastructure, AND productive farmland.
Three examples of tiny islands
The Marshall Islands in the Pacific Ocean (69.8 sq. mi/ 181 sq. km.)
The Maldives in the Indian Ocean (115 sq. mi./298 sq. km.)
Malta in the Mediterranean Sea (122 sq. mi./ 316 sq. km.)
To compare just how small these islands are, the tiny state of Rhode Island in the U.S. is 1,212 sq. mi, or 3,139 sq. km!
High population density
Another largely limiting factor aside from size is population density. While an island can be large enough to host farmland, the space is not necessarily available, or even large enough, to support the dense local populations.
Islands with the highest population density
Singapore: 20,169 people/ sq. mi. (7,788 people/ sq. km.)
Bahrain: 4,822 people/ sq. mi. (1,863 people/ sq. km.)
Malta: 3,581 people/ sq. mi (1,383 people/ sq. km.)
Source: 2016 population data from the World Bank
Unsupportive climates
While we usually think about islands located in the warmer regions of our planet, some of the largest islands–like Iceland, Greenland, and parts of Canada–have very cold climates. This doubles the pressures of importing food, as there’s a large part of the year where nothing can grow!
Unfortunately, tropical islands also have problems with growing food locally. The hot and humid environments are breeding grounds for destructive plant pests and diseases that have only become more aggressive with climate change.
Changing environment and natural disasters
Speaking of climate change, many island nations near the equator are extremely vulnerable to worsening climate and weather patterns (Madagascar, Malaysia, and Indonesia are amongst the most vulnerable). The United Nations Framework Convention on Climate Change (UNFCCC) also identified Haiti, Fiji, the Dominican Republic, St. Vincent and the Grenadines, and the Bahamas as the most affected by climate change in 2016, with millions of dollars lost in infrastructure due to natural disasters (major cyclones, hurricanes, storm surges, and flooding).
Puerto Rico is a grim example of the vulnerability of islands in the face of natural disasters made more common by global climate change. In the aftermath of Hurricane Maria in September 2017, Puerto Rico not only suffered from destroyed infrastructure, but also lost 80% of the island’s crops and $780 million in agricultural yields. It could take years for farmers to recover as the island struggles to rebuild even the most basic infrastructure.
So, what are the repercussions?
As a result of these limiting factors–space, population, climate, and weather– many island nations rely on imports to feed their residents. Unfortunately, this causes a lot of stress on island food systems as communities have abandoned their local production in favor of importing, creating a negative food trade balance and high dependency. Climate change and natural disasters have only exacerbated the problem as local options become less and less dependable.
Hawaii endures the stresses of an import-based food system. With a booming tourism industry, Hawaii imports 6 million pounds of food by ship to feed the 1.4 million residents and 8 million annual visitors (this doesn’t even include perishables that are delivered by airplane!). As the world’s most isolated island chain, Hawaii imports almost 90% of its food for $3 billion a year. This dependence on imports is highly vulnerable: if Hawaii is subjected to any severe weather, food stores would last less than a week and leave residents and visitors stranded without access to food.
A side-effect of the high import island food systems has also been a rise in diet-related health issues in many island nations. With the majority of imported foods being highly processed packaged goods, island communities are seeing drastic increases in obesity rates. In fact, nine of the most obese territories in the world–American Samoa, Nauru, the Cook Islands, Tokelau, Tonga, Samoa, Palau, Kiribati, and the Marshall Islands– are all islands located in the South Pacific. Sadly, this is also tied to a decrease in the industries and diets that have been part of islands’ identities for centuries. As fishing and local food production decreases, much of the rich food culture is being replaced with an imported Western diet.
How can hydroponic container farming be a viable solution?
Small footprint
We built the Leafy Green Machine for people looking to grow with limited space. At just 320 square feet, the container farm uses vertical hydroponic growing technology to produce 2-4 tons of produce every year (the rough equivalent to 1.8 acres of traditional farmland, although this varies based on the crops being grown). Small space agriculture practices such as these create dense growing spaces that can support entire communities with fresh produce year-round. Furthermore, the farm’s modular design (and past life as a freight container) means that they’re easily stackable to get even more food per square foot.
Protection from the elements
The Leafy Green Machine also creates a fully climate controlled and protected environment for plants to grow. Thanks to farmhand® technology, every component in the farm is automated, with the farmer able to monitor and control the farm remotely. This means full control over water and nutrient dosing, light exposure, indoor temperature and humidity, and CO2 levels. Not only does this create a consistent climate regardless of high or low outdoor temperatures, but it also keeps plants protected during droughts, storms, or floods. The 7-ton container was built to withstand all types of extreme weather on the high seas, and is equally impenetrable on land. One of our existing farmers in Houston, Texas, was able to keep his crops safe during Hurricane Harvey in 2017, which was the “the most significant tropical cyclone rainfall event in United States history,” after which he was one of the only local suppliers still operating in the area.
Healthy food options
As the name suggests, the Leafy Green Machine is optimized to grow leafy greens (along with lettuces, herbs, flowers, and root vegetables–see the full crop guide). These crops are cornerstones to a healthy diet: They’re high in vital vitamins and minerals and low in calories. Additionally, thanks to the container farm’s climate control, it is possible to introduce nutritionally rich crops such as kale or a variety of lettuces–typically colder weather crops–to tropical regions or, vice versa, bring warm weather crops like arugula and basil to cold regions.
Local flavors
Here at Freight Farms, we see monocultures as destructive to not only the land, but many rich food traditions that exist around the world. The Leafy Green Machine is a way to promote culturally-diverse plants to be grown and used in local cooking as a means of staving off the effects of a Western diet on local cuisine.
Meet some existing island farmers!
Bee’s Greens Co. in Hawaii
HerbanLeaf Farms in Cyprus
Sprout Farm in Trinidad & Tobago
Ino-Gro in Barbados
"A Good Growing Recipe For Every Crop"
Light4Food inovates with smart indoor growing system
"A Good Growing Recipe For Every Crop"
It all starts ten years ago with a shipping container in which LED lights were installed in layers. Leafy vegetables can be harvested year-round in these layers as is the idea. Led technology isn’t as efficient as we might want but entrepreneurs Peter Christiaens, René van Haeff and Michel la Crois see its potential. Experiments are being done with crops like spinach and other types of lettuce in association with partners like Van Dijck Groenteproducties who are members of growers association Fossa Eugenia.
In doing so Light4Food can gather the necessary experience for growing in an indoor environment. Light, climate, and air are being kept in the optimum balance in a computer-controlled environment. The first indoor growing facility is born.
Mobile climate chamber for rent
The innovation gets a lot of interest mainly from companies in seed breeding. The initial investment for a fixed installation, however, is quite high which still holds companies back on buying them. For this the entrepreneurs thought up a solution; they are developing a Mobile Climate Chamber to rent out for plant related research looking at possibilities of indoor growing.
In the following years, renting will soon change into buying. Mainly seed breeders both national and international are interested in these Mobile Climate Chambers for their own research. The most notable renter might just be Ciris in Norway, where they use the Mobile Climate Chamber for the International Space Station (ISS).
Growing vegetables on Mars: is also possible.
First green thumbs
Light4Food might be a technology company but it is starting to get green thumbs. This is the reason for their success tells Van Haeff. “Many companies start in technique. But technique is not good if you don’t know what the plant needs. That’s why we have botanists in our company that, together with our clients, look at the specific trades and needs of certain crops. Having this information allows us to change the lighting, climate, and nourishment to increase efficiency.”
Own research and engineering
Light4Food invests in their own botanist research besides the production of their installations. Van Haeff tells us why. “Every crop requires a different spectrum of light, climate needs, air flow and nourishment. For every crop, we go look for the right botanist growing recipe and in which installation this recipe will work the best. The technical growing recipe. By researching this ourselves we can develop better products.” The botanists are also researching the ideal growing recipe for high wire crops like cucumbers and tomatoes.
Christiaens explains: “A tomato plant is obviously much larger than a lettuce and produces more moisture. This, for instance, requires a different division of light and air flow. All of our research leads to a new type of installation.”
The first test installation for indoor growing of high wire crops is built in what used to be a spraying booth. Soon more advanced installations can be built.
Extreme climate is an opportunity
Advantages of the new solutions mainly are in regards to efficiency. Van Haeff: "The time of the breeding cycle can be greatly reduced by this. The growth quality is more stable due to optimal growing conditions and the growing itself becomes much more sustainable because of recirculation and regeneration of warmth and water. These are important components when it comes to costs in horticulture.” At first, Light4Food will serve the seed breeding companies in the Netherlands. Later even countries with extreme climate conditions for growers like Russia and Saudi Arabia will come into the picture. The reputation of the Netherlands will make it so that the market will be able to find them.
Christiaens: "You can imagine how important it is in desert areas to absorb sunlight and water to re-use. In countries with extreme cold, you want to be able to heath in an energy efficient way. By growing in one controlled environment you take away a lot of uncertainties and give sustainability.”
Indoor growing, not everywhere and all the time
Yet, the partners realise that indoor growing is not always the best solution. Van Haeff: "For the more generic crops like potatoes and grain outdoor growing remains a great way of doing things, especially in Western Europe. This is also something we look at with our partners and clients: when will indoor growing get interesting and how do we get there?” Producing more efficiently and wasting less they see as a theme that is applicable to all agri-food.
Christaens: "Here lies the solution to the worlds food problem. There is still so much being wasted in all phases from farm to table that there is still a world to win over.”
Free thinking and implementation
When talking with Van Haeff and Christiaens: it becomes clear: innovation is in their blood. They both believe you can not learn how to be innovative. Christians: "You must be sort of a hippie and dare to think freely. If you only see bears on the road you won't get anywhere.” At the same time though they believe you can stimulate innovation within a company. Van Haeff: "We have weekly meetings with all of our employees in which we look back at projects and discuss things we can still improve upon. This is how we create a company culture that keeps on evolving.”
By now they know that only innovating won't work. “if you only want to think of new ideas and not about implementation you cant build a good company. The art is in finding the balance.”
Innovation tips
The entrepreneurs have tree tips for innovation-seeking companies in the agri-food sector.
- Combining young talent with people who have been in the business for a long time. “We have a couple nearly retired employees with years of experience in things like lighting and growing, air treatment or engineering. This can be very useful if you want to be able to test out a new idea and eventually make a real product. The younger generation, on the other hand, is super-fast with computer technology.”
- Find suitable partners and allow each other to do things. “don’t try to do everything by yourself, together you can figure things out much faster. But you have to allow each other this and share your knowledge freely amongst each other. You will know rather quickly if this is possible. The give and take must be in balance.”
- Innovate from a demand or need. “Innovation without demand has no use, then it becomes just a gimmick. Do some research on the market. Talk to people and discover what it is they want.”
Source: Kiempunt-Limburg
FOR SALE: (SOLD) 2016.5 Freight Farm-Computer Controlled Hydroponic Grow System
The Leafy Green Machine is a complete hydroponic growing system built entirely inside a shipping container with all the components needed for commercial food production. The system is designed and engineered for easy operation, allowing users of all backgrounds to immediately start growing.
FOR SALE (SOLD)
2016.5 Freight Farm-Computer Controlled Hydroponic Grow System
Guilford County, NC (Relocatable)
Asking Price: $65,000
2016.5 Freight Farm Leafy Green Machine (LGM)
The Leafy Green Machine is a complete hydroponic growing system built entirely inside a shipping container with all the components needed for commercial food production. The system is designed and engineered for easy operation, allowing users of all backgrounds to immediately start growing.
Current Uses
• Perfect for starting a small produce business, growing for restaurants or supplementing existing produce production.
• Restauranter who wants to grow custom greens for rotating menus 365 days a year. Farm to Table? How about Parking Lot to Table!
• Universities and schools have created programs for students to learn to grow while supplementing dining facilities with fresh greens.
The Highest Standard in Controlled Environment Agriculture
• Pre-built system designed to maximize operational efficiency and streamline workflow
• Perfect environment is achievable 365 days a year, regardless of geographic location
• Automated scheduling reduces the amount of labor required to operate
• Remote monitoring & control capabilities through the Farmhand AppTM
Operation Requirements
Space- The LGM dimensions are 40’ x 8’ x 9.5’. We suggest putting the farm on either trap rock or a concrete pad.
Electrical- 60 amp, 120/240-volt single phase or 120/208V three phase connection.
Water- A designated water source is suggested such as a garden hose or hardline water plumbing.
Labor- 15 to 20 hours a week for farming and upkeep.
It is recommended growing smaller compact crops with a high turnover rate, like head and loose leaf lettuces, herbs and heartier greens like kale and swiss chard.
Crop Examples
Butterhead lettuce, Oakleaf lettuce, Swiss Chard, Mustard Greens, Cabbage Leaves, Arugula, Cilantro, Mint, Dill, Oregano, Kale, Endive, Basil, Chives and Thyme
Yields
800+ heads of lettuce weekly
12 heads per tower (256 vertical towers)
1 LGM= 1.8 acres
This LGM is only 1 yr old. It was put in production 11/9/2016.
Training and ongoing support available through Freight Farms.
Visit www.freightfarms.com for more information.
How To Grow Farm-To-Table Food And Where To Find It Ready-Made In Toronto
June 18, 2018
How To Grow Farm-To-Table Food And Where To Find It Ready-Made In Toronto
(All photos courtesy of Modular Farms Co.)
Let’s face it, none of us are Gwyneth Paltrow, the Goop guru and winner of everything organic and healthy. But with her inspiration and some easy life changes, we can come somewhat close. And in Toronto, this can be done thanks to Modular Farms Co. — a Canadian design and engineering company.
The company has made its mark by creating purpose-built container farms and delving into food research and development, using vertical farming solutions.
Its scalable and modular farming systems are capable of growing fresh foods virtually anywhere, in any climate.
Currently, Modular Farms is experimenting with vertically growing quinoa, blueberries, raspberries, lavender, and dandelion.
Dandelion processed with VSCO with fr4 preset.
Its CEO Eric Amyot is all about local eating.
He believes changing the global food system takes more than just funding from large corporations; it boils down to individuals.
Amyot says, “I want to not only expose people to the capabilities of what vertical farming can do but also teach others the tools that will enable them to grow local produce in their own backyards.”
Now that the weather is heating up, it’s time to get dirt stuck under your nails and bring hyper-local foods into your kitchen.
And so, we had Modular Farms, put together a grow guide so you can get started. Plus, we’ve rounded up some Toronto spots where you can eat a vertical farm-to-table meal.
Winterbor Kale
Whether you eat it in a salad, bake it in the oven, or add it to your morning smoothie, the kale craze is in full force.
Modular Farms grows a unique cool-season variety called winterbor kale, which features thick, curly, blue-green leaves, yielding 300-600 grams per eight-foot tower.
This hardy species of kale can be harvested in cooler months as a microgreen, baby greens (seedlings), mature leaves/leaflets or fully-grown plants, making it an excellent versatile plant to grow even at home.
It is an early-spring and late-fall species and is a popular choice amongst market growers. The variety is tastiest in a salad when the leaves are chopped finely and massaged or baked in culinary dishes.
Tip: Kale tastes sweeter with a touch of frost. Don’t be afraid to grow it through the winter months. Shield your kale during that time with row covers for extra protection.
Bull’s Blood Beet Microgreens
Bull’s blood beet microgreens stand out with colorful purple stems and bright green leaves. This plant is commonly used for garnishing and has a mild spinach-like flavor.
In Modular Farms, these sprouts are grown in trays using hemp mats as the substrate instead of soil or peat moss. However, feel free to use soil at home.
Luckily for all farmers (even home growers), microgreens have a very quick turnover rate (with each harvest taking place each time the plant reaches a height of four to five centimeters.
Tip: When watering, keep the water off the plants — only focus on the medium. This will help it last longer in the fridge. But since this plant degrades quickly, we recommend eating it as soon as possible once harvested.
Rosemary
Who doesn’t love to liven up their dishes with some fresh herbs?
Rosemary is a top choice amongst home growers with its ability to grow indoors and outdoors.
You can dry, freeze, preserve and even use the herb to flavor oil or butter. The best part? Once you cut rosemary, simply repeat the process and let it grow back in again. With ZipGrow towers, Modular Farms is able to grow up to five varieties of herb at a time.
Tip: Hang stems upside down in bunches to dry. Then, strip the leaves and store in a container to use in the kitchen.
Do want to grow? Then go vertical farm-to-table!
Not so into growing or growing impatient waiting for your plants to thrive? You can still make a difference by eating a vertical farm-to-table dish.
The Food Dudes have you covered as they currently receive a weekly batch of Modular Kale from the parking lot Modular Farm at the HQ to use in their vertical farm-to-table dishes. Find it at a couple of their restaurants, including OMAW and Rasa.
OMAW features a Rutabaga dish and chopped salad that contains fresh, modular kale grown in their parking lot (and is legit to die for).
The Food Dudes creative director Brent McClenahan wanted to install a Modular Farm to supply their restaurants because they saw Modular Farms Co. as a “manifestation of forward-looking companies actively trying to tackle the challenges facing our society.”
McClenahan says, “I saw the partnership as a way to get hyper-local food sources for a true farm-to-table experience and as a way to build a community who shares the same vision as my business — to create a food culture based on innovation and efficiency.”
With the capabilities of a Modular Farm, McClenahan and his team can grow produce and take it farm-to-table in a matter of hours. With this, diners are not only able to eat the freshest foods, but also will understand where and how their foods were grown.
This is yet another reason why I’m such a big fan of The Food Dudes — from their grade-A catering to their talk-of-the-town restaurants, they continue to shapeshift the Toronto food scene and set trends that help us grow and flourish.
Tags from the story
Despite Growing Demand For Better Food, China Isn't Quite Ready For Indoor Farming
Despite Growing Demand For Better Food, China Isn't Quite Ready For Indoor Farming
- Jun 25, 2018
Every Monday and Thursday morning, a team of urban farmers go to a high-end restaurant in eastern Beijing. They deliver radish, wheatgrass, and bean sprouts seedlings and place them inside four glass cabinets. The cabinets are automated indoor farms with LED lighting, fresh water and nutrients. About 2 meters tall and have four tiers on which the vegetable seedlings grow, chefs at the hotel will harvest the vegetables from the cabinets throughout the week and the team will restock the cabinet twice a week. They will spot check if the cabinets are functioning properly.
The seedlings the team deliver are cultivated in a shipping container in central Beijing. The containers are indoor farms operated by Alesca Life, an agriculture start-up based in the same city. The company was co-founded in late 2013 by Stuart Oda with the ambition to make cities nutritionally self-sufficient.
The indoor farms provide everything the plants need to mature, but the seedlings need to be grown in shipping containers first. All the factors affecting the growth of the plants can be monitored and controlled by the company’s self-developed technologies, making the vegetables from unfavorable weather conditions, pollution, and pests.
Alesca’s indoor farms at Beijing Marriott Hotel Northeast (Image credit: Alesca Life)
While moderately successful in Beijing, Oda is also trying to realize his vision in a different city: Dubai. Their business in Beijing has expanded too, though in a different direction. Instead of aiming for mass production and competing on price and volume with local supermarkets, the company has cooperated with several high-end hotels, including Marriott, Westin, and Shangri-La, and has provided them with the indoor farms with fresh vegetables that are highly seasonal or imported in China. They have joined China’s consumption upgrade, targeting the rising middle class who are more and more willing to spend on quality food. One serving of the radish they grow is sold for RMB 70 to 80, nearly ten times of that sold at local diners on the streets.
Alesca Life’s container farm in central Beijing (Image credit: TechNode/Jiefei Liu)
“The cabinets are more for market promotion and making impressions,” Jannelle Liu told TechNode. She is China Food and Beverage Sales Lead at Alesca. Consumers will be able to see the process of how their food is grown and be reassured about the quality – no pesticides, no soil or water pollution, she explained. Plans for producing plants in larger volumes will mainly happen in Dubai.
Cheap vegetables, expensive electricity
Alesca isn’t the only agriculture start-up that adjusted its business strategy facing China’s current agriculture industry.
When Tristan Lim co-founded Hydra Biotech in Shanghai with two of other alumni from China Europe International Business School, he first wanted to take indoor farming to China but ended up doing the business with US companies, taking advantage of China’s cheap manufacturing costs.
“Food production is a big issue in China and urban residents are willing to pay more for clean and safe food,” Lim told TechNode. This gave him the idea to start the business in China.
Hydra Biotech sells farming containers that have independent climate controlled modules and that can be equipped with hydroponics and aquaponics towers. One complete set, climate controlled module and essential hardware included, is sold for $58,000.
Inside Hydra Biotech’s independent climate-controlled module (Image credit: Hydra Biotech)
Lim knew this was too expensive for individual farmers and so he tried to partner with corporates, but they are not interested. “The agriculture companies have income from the government and have different priorities,” Lim said. “They are more interested in how to get more government subsidies.”
Another reason why this is difficult is that compared with the five-digit equipment Lim provides, agriculture is cheap in China. “Fertilizers, labor, and rent are very inexpensive,” Lim said. Lower-end restaurants don’t care that much about the quality of the food as long as they can have them at the lowest costs.
One of the biggest costs of running indoor farms, Lim said, is electricity, which will add to the overall cost of the vegetables. Electricity makes up 60 to 70% of the overall production costs and it’s not cheap in China or other places around the world, Lim said.
“We trade energy for less pollution,” said Lim. Some of the most notorious issues in China’s agriculture are the overuse of fertilizer and pesticide. They ensure the crop yields, but excessive usage has caused serious environmental problems. The residual pesticide on vegetables not only harms human bodie, but also pollutes the air and water when evaporated or washed into the drains and rivers. High application rates of nitrogen-based fertilizers can bring an excessive richness of nutrients in lakes and oceans, suffocating life living in the waters.
Hydro Biotech is now opening an online store that sells indoor farm grown greens. Similar to Alesca, they are targeting at wealthier Chinese customers, though only in Shanghai for now.
Also, Lim said they took a different strategy: making Hydro Biotech recognizable in international markets and then reintroducing it to China. Plenty, a vertical farming startup backed by SoftBank Vision Fund, is one of the companies that Hydro Biotech sells equipment to.
The San Francisco-based startup Plenty announced early this year a plans to enter China and build at least 300 indoor farms. Although the company declined to comment on its recent progress in Chinese markets, Christina Ra, Head of Communications, told TechNode that “the only way to have true impact is to grow in ways that produce volumes comparable to conventional farm fields, and to do so at a scale where the price is comparable to – or better than – what exists in grocery stores today.” Despite the fact that this isn’t how things are today, Ra added Plenty will continue to work on providing the globe with affordable and clean food.
Importing expectations
“China is a net exporter of vegetables, so it’s not relying on imports,” Oda told TechNode. According to China’s Ministry of Agriculture and Rural Affairs, the country exported $ 15.5 billion worth of vegetables in 2017, 5.5 percent higher than the amount of the year earlier.
The growing middle-class demand products from other parts of the world, such as some specific basil from Japan or Italy, and Alesca will focus more on providing the variety of types of vegetables rather than the quantity, Oda explained.
For Alesca, which not only sells growing equipment but also a vegetable service, human labor is a significant expense. As for now, one person operates one container, but Oda expects one person to operate 5 to 8 in near future. Oda said he has been hiring people with higher education qualification to show them that there’s a career in urban agriculture.
Limited land supply was another issue that Alesca faces when it tries to expand in Beijing.
Alesca wants to build farms in the city center because it’s closer to their customers and will prevent vegetables from losing their nutrients during transport. However, there is very limited space in the city center. Although their farming containers can stack one on another, weight capacity of the building and fire safety regulations are difficult to comply with.
Bigger markets on the horizon
None of these start-ups have given up on China. They are waiting for the right time: serious environmental pollution, more urgent demand for fresh food, decreasing arable land and people’s increasing incomes.
Apart from being able to control factors that affect the growth of the plants, indoor farming systems, in general, consume much less water and can farm all year around when growing seasons in traditional agriculture are usually confined to half a year, depending on the latitudes. According to Ra, Plenty’s yields are up to 350 times more than the conventional field, depending on the crop, and use less than 1% of the water of traditional farming.
As to the electricity consumption that made up most of the costs for operation indoor farms, Dickson Despommier, emeritus professor at Columbia University who developed the concept of vertical farming a decade ago, told TechNode that to compare the energy consumption between indoor farming and traditional farming, one has to include the power consumed in the production of fertilizers, operation of tractors and so on. Thus, in general, indoor farming costs less energy.
Also, progress in the energy innovation will eliminate the power costs, such as improving the LED lighting efficiency or advancement in the field of new energy will lower the electricity price in general.
China’s GDP per capita more than doubled in the recent decade, according to the World Bank, and the country’s middle class is growing at a rapid pace. For modern agriculture startup like Hydra Biotech and Alesca, China still represents a promising market. People have already started to care about food and hopefully, with more education, more of them will join the trend and begin to consider the influence the food they are eating is having on the environment, Lim said.
Although the future seems promising when thinking about how fast technologies such as riding hailing services and e-commerce platforms have changed how society functions, Lim said for now they want to stay “small and practical” and build the business step by step.
Tags: Alesca Life, Hydra Biotech
Jiefei Liu is a Beijing based tech reporter. She focuses on the union of tech and content creation and loves agriculture. You can write to her at Jiefei@technode.com
Lettuce Lads Look To Hydroponics In Valley
Devon DaDalt, left, Kevin West and Caleb Allen hold up some lettuce grown in a high-yield, high-density hydroponic system in Canmore on Sunday (June 10).
Photo credit: Aryn Toombs RMO photo
Lettuce Lads Look To Hydroponics In Valley
BY ROCKY MOUNTAIN OUTLOOK JUN 14, 2018
BOW VALLEY – While fresh, locally grown commercial produce is generally not a feature of Rocky Mountain geography, a trio of valley entrepreneurs are hoping to change that with a new hydroponic operation.
Lettuce Lads – Caleb Allen, Devon DaDalt, and Kyle West – have a provisional patent on a hydroponic system in place, some federal funding, launched a GoFundMe campaign and are working toward making locally grown leafy greens a reality in the valley.
The project has been underway for a while, with each drawing on their own experience in agriculture, business, sales, and marketing.
“We’re always trying new things and looking for ways to improve the area where we live and for the people in the area,” said Allen explaining, initial talks with DaDalt about hydroponics soon included West.
“It turned out he had a hydroponic system working in his hallway. He had vegetables in the system. He had vertical units and plants growing in the summer he covers his deck with a system. He’s got corn over here, other things over there.
“That’s how we met. Then we started kicking around the idea of putting together a Canmore hydroponics operation.”
It quickly became clear that hydroponics can be an expensive process and in Canmore, land costs can quickly go through the roof. “So we started to look at it and realized we can’t do a conventional system, so we started brainstorming.”
Brainstorming resulted in the development of a new system (patent in the works) that would incorporate growing within the enclosed environment of an 8×40-foot shipping container. In the container, all aspects of growing from the medium to watering and light, to delivery of hydroponic nutrients – can be carefully controlled for maximum production.
“We all compliment each other well,” said Allen. “Because I can speak sales and marketing, but I also built the prototype in my garage. We don’t feel we have gaps in our team and we’re able to use momentum from each other to bring up new ideas.”
As Allen explains, hydroponics is not new, it’s a centuries-old concept, but there are different methods of doing it.
As the Lettuce Lads move forward, a single shipping container would be home to about 8,000 plants at any given time, which, with automation, will reduce growing time and labour. Farm to table would be 10 minutes, rather than thousands of kilometres.
“Then it starts to become economically viable in the area,” said Allen. This is also where, with federal Industrial Research Assistance Program (IRAP) funding of $30,000, some private investor funds, donation of a site for a shipping container, plans and a budget, and a distribution partnership with Polar Egg in Hay River, things are moving ahead.
The Lads’ funding campaign is aimed at $50,000 which will put a first prototype container in place.
“We feel this is a start to the solution,” he said. “I get frustrated when people downplay the opportunity and what fresh, leafy greens can add. But change happens one step at a time and we need to be able to work as a community and country of people to change things.
“The first prototype is to prove we can grow and sell in Canada. We want to serve the community we live in and we also believe we can drive the price point down. Our vision is to empower people with access to good food, so they can live healthy sustainable lives.
“That’s where everything stems from. Our starting place is a container, but because of the technology, it can go far beyond that.”
To support the Lettuce Lads’ visit www.gofundme.com/lettucelads.
An Agricultural Revolution
An Agricultural Revolution
JUNE 16TH, 2018 CATHERINE MORRIS0
Ino-Gro Inc. uses high-density vertical farming techniques coupled with automation and remote monitoring software to create a climate-smart food production system.
How GreenTech is transforming the agricultural industry in Saint Lucia and beyond
In the past, successful farmers relied on the land, the weather, their instincts and a little bit of luck. Thanks to a boom in ‘green technology’ there are now a lot more tools at their disposal. The uptake of GreenTech among agricultural pioneers is helping to modernise the industry and streamline farming, as well as aiding the Caribbean in achieving its goal of food security.
CREATIVE TECH
More than US$800m was invested in agricultural technology (‘agtech’) globally between 2012 and 2016, according to research group CB Insights.
“Technology has been the main driver of change in most industries, and agriculture is no different,” says Warren Kellman, Managing Director of Ino-Gro Inc, a hydroponic farm in Barbados. “New technologies are being created every single day around the world and people are coming up with creative solutions [to environmental challenges].”
Ino-Gro Inc is one of those creative solutions. Launched in 2016 by Kellman and a friend, the farm is the first of its kind in Barbados and consists of a 40ft shipping container stacked with walls of leafy greens and operated through a fully automated, online system. Kellman and his team can monitor and control the environment – temperature, humidity, LED lighting – within the container through an app downloaded to their smartphones. Sensors, timers and alerts feed them information in real-time, with all data available via the cloud.
The vertical farming model allows Ino-Gro Inc to practise high-density farming in a relatively small area. Kellman says the container is equivalent to one acre of farmland and produces around 40kg of produce a week, including three different types of lettuce, mint, basil and edible flowers. Demand is high and the produce sells out every week, with hotels, restaurants, chefs and the general public eager to buy local.
Ino-Gro Inc’s success, however, was not guaranteed. There were challenges along the way but Kellman says he was not just motivated by turning a profit. “When we started, we wanted to find a way to make money but also do something good. We import too much. The population of the Caribbean is only going to grow, we need to find more sustainable ways to produce enough food.”
PRECISION FARMING
One of the biggest obstacles for Ino-Gro Inc was the initial expense. “These are high tech systems; the main challenge is the cost associated with them. It is one thing to buy them in the United States, but then you have to get them to the Caribbean,” says Kellman.
Ino-Gro Inc’s computerised container was developed by US firm Freight Farms but Kellman would like to see the Caribbean develop its own agtech industry. He is working as a consultant with Saint Lucia’s TeleCarib Labs, Inc to help develop a model, climate-controlled, indoor farm. “We are working on being the first to create, design and build this type of model farm. We want to find a more affordable solution so we can overcome the challenges of cost and, from there, we can approach other countries who are interested. Our aim is to manufacture in the Caribbean, reduce the cost of these systems and enable a lot more people to grow their own food.”
A prototype for the farm will be established before the end of the year at the TeleCarib Labs’ campus, and will be “data-centred”, according to Kellman who says sensors will collect information that can be analysed to maximise productivity. “It allows for more accurate farming. We can analyse the data and make calculated decisions.”
VIRTUAL HUB
When the TeleCarib Labs farm becomes operational, it aims to sell directly to consumers through a virtual platform created by Tri Farms Ltd, a Saint Lucia company founded by local entrepreneur Garvin Francis.
Tri Farms’ eCrop is the region’s first virtual agricultural hub where producers and buyers can connect online. Producers simply log on, create a profile for their farm and let potential buyers know what they are selling and when it will be available. This direct service allows farmers to pre-sell their goods and gives buyers certainty so they can plan their purchases and minimise supply chain risks.
The system, which went live in January 2017, is used by the Saint Lucia Hotel and Tourism Association to host its Virtual Agricultural Clearing House (VACH) which encourages hotels, restaurants and food and beverage distributors to buy local. Francis says that helping Saint Lucia limit its food import bill was the impetus for Tri Farms Ltd when he first began brainstorming the idea over a decade ago. “Agriculture has been lagging in Saint Lucia and tourism provides an opportunity for local producers,” he says. “It sounds simple on paper but it’s not that easy – the market is so fragmented. There was a disconnect in terms of information; you could have a glut of one item one week and the next you might not find it on the island.”
Francis, who has previously worked in both the tourism and agricultural sectors, teamed up with Melvin Felicien whose background is in IT. Together they developed Tri Farms’ forecasting tool which is primarily aimed at buyers in the tourism industry. “Availability and consistency are very important in the tourism sector. Those buyers needed a tool that could predict what was coming on the market,” says Francis. “There is no reason why the hotels should be importing any produce that can be grown locally.”
There are now around 80 farmers registered with Tri Farms’ eCrop service. The company is looking to acquire more capital so it can scale up operations to make the system more intuitive and offer users an app. Francis says: “As with any tech company, capital is our biggest restriction, but this product has so much potential. There is quite a bit of focus now on building these platforms to create linkages. That is the future of agriculture – the availability of information through the use of technology. I anticipate a huge buzz and some creativity coming out of the Caribbean.”
THE NEXT GENERATION
If the agricultural industry is to reach its potential, however, the next wave of entrepreneurs has to be engaged. “The awareness is there but it’s not where it needs to be, especially when it comes to the younger generation,” says Kellman who wants to see more technology in schools and regularly invites kids to Ino-Gro Inc to show them how the system operates and spark their interest. “They come to our farm so they can get introduced to this new technology and become familiar with the way farming will be in the future. That is part of our mission – to not only grow and supply food, but also to educate people and let them know the importance of food security.”
It’s also the goal of TeleCarib Labs, which aims to launch its Future Farmers Entrepreneurship Programme next year. This initiative will give students the opportunity for hands-on experience at the model indoor farm, as well as skill development workshops and online learning.
“TeleCarib Labs will transform farming by linking innovation with education,” says Kellman. “There is plenty of opportunity in the agricultural industry. I would encourage young entrepreneurs to never settle, never give up and keep up to date with the technology that’s out there, not just in their own country but all over the world.”
To learn more, visit:
Whitehorse Firm Solvest Hopes To Grow Business With Hydroponic Farms
LED lights are used to grow leafy greens inside the CropBox - a refurbished shipping container turned into a hydroponic farm. The Whitehorse-based solar energy company, Solvest, is a distributor. (Mike Thomas/Yukon News) Mike Thomas/Yukon News LED lights are used to grow leafy greens inside the CropBox — a refurbished shipping container turned into a hydroponic farm. The Whitehorse-based solar energy company, Solvest, is a distributor.
Whitehorse Firm Solvest Hopes To Grow Business With Hydroponic Farms
‘When you take produce 2,000 km up the highway, you lose some nutrition’
- AMY KENNY Jun. 14, 2018
Stepping into a CropBox feels like walking onto a Star Trek set.
The all-white interior of the long, narrow unit glows like it’s a sci-fi flight deck.
“They’re LED lights,” says Danny Ghul, gesturing to the hundreds of mini-lights shining down on rows of perfect leafy greens, sprouting from holes in smooth white shelves. “The reason they’re red, green and blue is those are the only values of the light spectrum that the plants need to produce.”
Guhl is the business development manager for Solvest — a solar energy company in Whitehorse that specializes in remote energy generation. Last year, Solvest became the Canadian distributor for the North Carolina-based company that developed CropBox — a refurbished shipping container that serves as a hydroponic farm.
One of Solvest’s contributions to the system is the PowerBox, a unit that stores solar energy so a CropBox can be maintained off-grid.
Next, it will “northernize” its test unit by increasing insulation from R20 to R60, so it can maintain growing conditions even in -45 C weather. Solvest will also add an Arctic entrance to make it easy for CropBox owners to harvest and package produce.
With a $150,000 price tag for a standard CropBox and $200,000 for a winterized version (plus an additional $220,000 if you want the PowerBox), this isn’t the kind of set-up your average backyard gardener can afford, but it’s easy enough for a beginner to operate, says Sabrina Clarke, CropBox operator for Solvest.
“It sounds gimmicky, but I came into this job having no hydroponic experience,” says Clarke, who’s also a chemical and environmental engineering student at McGill University. “And you get kind of all the nutrients that you need to grow, you get a manual saying ‘if you want to grow lettuce, have the water at this pH.’ So it’s really accessible to anyone who wants to learn.”
On June 7, Lana Selbee, operations director of YuKonstruct, toured the CropBox. She says YuKonstruct is looking at ways to offer hydroponics workshops in partnership with Solvest.
Clarke says the Kluane Lake Research Station has also expressed interest in testing a CropBox this winter. As well, representatives of mining sites have been in touch about the option to lease CropBoxes for temporary sites. And while Cold Climate Innovation at Yukon College won’t be directly involved in the day-to-day operations, CCI did provide funding for the project.
“This ticked a lot of our boxes,” says Eoin Sheridan, Project Officer at CCI, whose areas of interest include cold climate innovation, alternative energy, and food security in the North.
“There’s nothing like this in the Yukon yet. (CropBoxes) have been more or less successful in other places, but as yet there’s nothing operating in the Yukon,” he says.
Special conditions in the North, from its remote location, to its climate and soil conditions, all have implications when it comes to food production.
“This skips around that,” he says.
“This is part of a continuum of solutions.… It’s not a one size fits all solution, but it’s part of a broader solution.”
Guhl says that’s the hope.
“When you take produce 2,000 km up the highway, you lose some nutrition,” he says. “With the CropBox, not only do you only ship it up once, you can increase the shelf life of produce. You can add weeks.”
And, says Clarke, while there are no concrete numbers yet on what it will cost to power a CropBox for a year, the process is low-maintenance.
Seedlings are started in tiny compostable sponges, then transferred into one of the CropBox shelves. There, two 378-litre tanks circulate water to the plants. Because the water is recycled through the reservoirs, the CropBox uses around 100,000 litres annually compared to 10 times that in traditional farming.
Nutrients can be added to the water, depending on the balance needed for any given crop. The LED lights cycle on for 16 hours a day and off for eight, to mimic a natural cycle. Water and temperature can be monitored and controlled by way of a smartphone.
So far, Solvest has seen one crop come to the point where it can be harvested. Lettuce, swiss chard, and watercress planted at the beginning of May are ready for harvest by the beginning of June.
Guhl says Clarke will try out other plants in the coming weeks, to see how quickly they grow, and what the optimal conditions are.
Contact Amy Kenny at amy.kenny@yukon-news.com
Brooklyn Urban Farming Program Cultivates Opportunity In The Projects
Brooklyn Urban Farming Program Cultivates Opportunity In The Projects
Linked by Michael Levenston
Paul Philpott preps kale to be packaged and distributed. Photo: Kellyann Petry For The Wall Street Journal.
After graduating from an Urban Farm Corps program, Paul Philpott is running his own hydroponic farm business out of a shipping container in a Brooklyn parking lot
By Anne Kadet
Wall Street Journal
June 12, 2018
At age 24, Paul Philpott wasn’t exactly riding high. He’d just quit a job at Walmart and moved back in with his parents in the projects. So while he had no clue what to expect, he was happy to check out a job-training program suggested by his mother.
“You’re going to farm in the hood?” he recalls thinking after meeting a recruiter. “I don’t think that’s going to work!”
Eighteen months after graduating from the program, Mr. Philpott is running his own hydroponic farm business out of a shipping container in a Brooklyn parking lot.
“Farming in the city is nothing I’d ever thought I’d say I’d do,” he says.
The 40-foot container, with its metal walls and pink LEDs, looks more like a lab than a farm. There’s no dirt. A programmed system dispenses a nutrient cocktail, controls water flow and monitors the temperature. Rows of kale, chard and romaine grow on sliding columns suspended from the ceiling.
Mr. Philpott is not a big greens guy. Lettuce, he says, is best served atop a burger: “If I’m really bored, I’ll eat a salad.”
But the profits on these nutrient-dense greens are lucrative. While growing costs are astronomical—$10 to $15 a pound—high-end restaurant customers pay double, says Mr. Philpott.
“It’s very crazy,” he says. “But we have very premium ingredients, and grow it and deliver it to you directly.”
Customer Patrick Connolly, chef-owner of Rider, a bistro in Williamsburg, Brooklyn, says he’s not a big fan of hydroponic crops, but Mr. Philpott’s greens are exceptional. “The kale has spice to it,” he says.
Mr. Philpott says that despite growing up in the projects, he enjoyed a sheltered childhood. “My mom was extremely protective,” he says.
But then he attended high school far from home and fell in with the wrong crowd. “I can’t lie,” he says. “I did a lot of dumb things.”
There was a lot of drinking and fighting. “I hung around people who went stealing and robbing places,” he says.
He didn’t graduate from school until he was 20, and things went downhill from there. “I’d be on the streets getting drunk all day with my friends,” he says. “Especially if I lost my job. The week after, my check would go to bottles and bottles.”
Green City Force, a nonprofit which recruits young adults from the city’s 15 highest-crime public-housing developments, offered Mr. Philpott a spot in its 10-month Urban Farm Corps program.
Earning a $1,200 monthly stipend, Mr. Philpott learned the basics of farming and tending a produce stand, distributing free vegetables at a housing project in Red Hook, Brooklyn.
Early on, he aimed for a spot on the infrastructure team and initiated projects like repairing a dilapidated greenhouse. “I stepped up and showed I know what I’m doing,” he says.
He soon joined the team building new farms at housing projects in Harlem and Canarsie, Brooklyn.
By the time he finished in early 2017, he had landed a coveted spot in the entrepreneurship program at Square Roots, the urban farm incubator currently hosting his business.
Not all his peers fared so well. Among the 24 trainees in his cohort, only 16 graduated. This year, 28 of 40 made it to the finish line, the nonprofit says.
But these graduates have enjoyed a 95% job-placement rate, in occupations ranging from landscaping to working as a chef’s assistant.
It’s a fine accomplishment considering the 75% unemployment rate among young adults in city public housing.
Mr. Philpott says the experience gave him a new identity as a community leader. When he’s not tending crops these days, he’s giving tours, supervising apprentices and volunteering at a community garden in the Bronx.
When younger guys on the block ask if he’s dealing, he tells them the cash in his wallet is from his business. “I pull out my Instagram and show them the farm,” he says.
Brandee McHale, president of Citi Foundation, which focuses on economic opportunity, says the foundation donated $1 million to Green City Force because it’s not just another job-training program—participants contribute to their community and become role models. “It has a multiplier effect,” she says.
Mr. Philpott’s stint with Square Roots will end in October. What’s next? “I have no idea,” he says.
But it’s a happy dilemma, he adds, induced by the skills he’s learned and contacts he’s made: “The weird thing is, now I have so many opportunities, I don’t know which I want to do.”
Driverless Cars And Climate Change Prompt Push For Urban Farming
Driverless Cars And Climate Change Prompt Push For Urban Farming
Modular Farms. Image: Chris Jack
Cameron Jewell | 4 June 2018
Five kilograms of mushrooms, 100 heads of lettuce and 25 trays of micro-greens. These are the spoils so far from Mirvac’s urban farm pilot set up in the basement of its 200 George Street HQ in Sydney.
The pilot program, Cultivate, has been operating for about six weeks, and has seen 200 staff sign up to get involved in fresh food production.
The farm includes veggie patches and hydroponic vertical farms, as well as mushrooms grown in coffee grounds diverted from landfill. Special grow lamps are used to stimulate plant growth in the basement environment.
The pilot could be a sign of the future for commercial office basements, as technology such as autonomous vehicles promises to make traditional car parks all but redundant.
Mirvac’s cultivate pilot
Real estate services firm JLL last year predicted that adaptive reuse of basement car parking could see urban farms sprout up all over cities.
“An urban farm could be created in a building’s redundant car park and the produce used to service local kitchens and cafes within that proximity,” JLL head of property and asset management – Australia Richard Fennell said.
“Urban farming is yet to be embraced by mainstream property companies, no doubt due to the traditional concepts of value and property best use, but we believe this could change.”
The report said developers needed to be designing new buildings with adaptive reuse in mind.
Mirvac’s Cultivate pilot
Mirvac group general manager of innovation Teresa Giuffrida said the company was thinking seriously about future transport’s effects on the built environment.
“We are starting to make step changes towards a time when we need to think differently about using assets like car parks,” she said.
“We will be looking at the long-term advantages of this, while assessing the health and wellbeing benefits of nurturing urban farming skills within the busy office environment,” she said.
Mirvachead of office and industrial Campbell Hanan said the trial was already seeing changes in staff behaviour, with some even coinducting meetings in the basement.
“People are telling us that it gives them a peaceful break in the middle of the working day, as well as a way of learning more about growing food.”
New technology opening the door to wider take-up
The technology has been provided by start-up Farmwall. Its chief executive Geert Hendrix said having urban farms eliminated transport and packing waste while reconnecting people to the process of growing.
“We have started supplying some produce to nearby cafés, including Avenue On George cafe, and it can basically get from farm to plate in about seven minutes.”
Co-founder Serena Lee said at the end of the experiment there would be data generated on interest, effects on mental health and wellbeing, and whether it could be a replicable business model.
Farmwall has also set up its vertical farming systems in Melbourne restaurants and cafes, allowing chefs to grow and harvest their own greens. It uses an aquaponics system where water used for the plants is fed through a fish tank, and the filtered fish waste recycled back to feeding the plants.
Another business launched this year is Modular Farms Australia, which uses converted shipping containers for its modular farming systems, which it says can be deployed in any environment regardless of climate. Energy and water supply are the only necessities.
The Brisbane-headquartered company says its technology can see a 5-10 time higher output than traditional farming, an 80 percent increase in yield compared with standard shipping container farming, and can grow 50,000 heads of lettuce a year with as little as 40 litres of water.
The systems could have particular applications in “remote and island communities, grocery stores, food services, agribusinesses and educational facilities wanting access to sustainable healthy produce”, the company says.
“The main goal is to reduce food waste, increase food security and eliminate supply chain logistics to cut food miles.”
A Modular Farms module. Image: Modular Farms Australia
Modular Farms Australia director James Pateras said being brought up on a farm and witnessing the impact of drought was key to creating the product.
“As a third generation farmer, I felt that doing what we have done for the past 100 years will not suffice for the next 100 years,” he said.
As climate change impacts become more pronounced, such solutions could become more widespread as cities move to increase resilience and self-sufficiency.
Tags: Cultivate, mirvac, urban farming
Whitehorse Company Pitches Off-Grid hydroponics To Improve Northern Food Security
Whitehorse Company Pitches Off-Grid Hydroponics To Improve Northern Food Security
Solvest partners with Cropbox to test winterized, off-grid, hydroponic setup in a shipping container
Jackie McKay · CBC News · Posted: Jun 01, 2018
Sabrina Clarke, Cropbox operator for Solvest, has been growing different kinds of produce such as lettuce, cilantro and mint in this container. (CBC/Jackie McKay)
A Whitehorse solar energy company is expanding its business to included hydroponic farming.
Solvest Inc. has partnered with Cropbox, an American company that refurbishes shipping containers to grow produce.
Solvest is taking the product a step further by revamping the containers with cold-weather modifications in order to grow fresh produce in Northern climates.
"What we've discovered [in] the more remote Northern communities that we work in when we are trying to help them with their energy needs is ... a profound problem with food security and food supply," said Ben Power, Solvest vice president and co-founder.
Each refrigerated container is outfitted with plastic pipe shelving that holds growing trays. Pipes pump nutrient rich water into the trays so no soil is needed to grow produce. LED lighting replaces sunlight.
A container now on the Solvest compound is for demonstration only, and not equipped with the features needed to grow produce in temperatures as cold as –50 C. The company is monitoring the container's energy consumption without arctic features to compare to the energy it will use once the features are added in the fall.
Cold weather features would include an arctic entrance to protect plants from frigid outside temperatures, and an extra layer of insulation.
Ben Power, Solvest Inc. vice president and co-founder, believes the modified Cropboxes will help fill a gap in Northern food security. (CBC/ Jackie McKay)
According to Power, the containers require as much energy in one day as would power up to four homes.
Solvest has created a second container to power the Cropbox off-grid using a combination of solar panels, batteries, and diesel fuel.
"That allows a remote diesel community to operate this ... and not stress the local grid," said Power. "If you don't have that power box in a remote setting you may be solving one problem of food security and adding to another problem of diesel consumption in a community."
Economic benefit to be determined
The container grows 2,700 plants cultivating about 400 heads of lettuce a week.
"It would feed a small community in the north," said Sabrina Clarke, Solvest's Cropbox operator.
The unit has yet to be tested in a Northern winter.
The Kluane Lake Research Station, 60 kilometres north of Haines Junction, Yukon, has applied for grants to field test a unit this winter.
The unit is hydroponic meaning the plants grow in nutrient-infused water instead of soil. (CBC/ Jackie McKay)
Researchers will work with the Kluane First Nation and Champagne-Aishihik First Nation to create a public report on the Cropbox's suitability for use in the region, including a cost-benefit analysis.
"What does a head of lettuce that comes out of the container cost? What does it cost in comparison to what you can buy in Whitehorse?" asked Henry Penn, a researcher with the station.
Solvest's Cropbox was partly funded with $24,000 from Cold Climate Innovation at Yukon College.
A Cropbox with the arctic insulation package costs $150,000 before shipping. The external power box raises the cost to about $400,000.
"This is technology that can make a huge difference for food security," said Eoin Sheridan, project officer with Cold Climate Innovation.
"On the cautionary side, it's not something that people want to jump into without doing their due diligence ensuring they have a market for the food and will be able to utilize the amount they produce."
Sheridan said similar growing systems have been successful in Alaska and are likely to benefit the Yukon as well.
"There is a huge number of different aspects to Northern food security, this alone [isn't] a one size fits all solution but it's definitely part of a broader solution," Sheridan said.