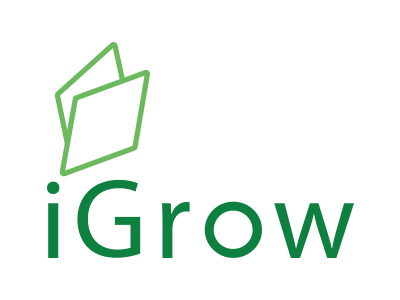
Welcome to iGrow News, Your Source for the World of Indoor Vertical Farming
USA - MARYLAND - Father, Daughter Launch Hydroponic Farming Operation In Montgomery County
With lettuce regularly being in the news related to an outbreak of disease, father and daughter Rod Kelly and Alex Armstrong concluded that there has to be a better way to purchase fresh produce
By Sondra Hernandez, Staff writer
September. 28, 2020
With lettuce regularly being in the news related to an outbreak of disease, father and daughter Rod Kelly and Alex Armstrong concluded that there has to be a better way to purchase fresh produce.
“It’s really hard to get fresh produce,” Armstrong said. “About 80 percent of lettuce comes from California. It’s hard to find locally grown produce.”
It was also concerning to her that consumers don’t quite know what they are getting with lettuce brought in from another area. Is it pesticide-free? Was there any contamination from livestock waste runoff?
“People are more aware of what’s in their food and they are more concerned about it,” she said.
To offer a fresh, locally grown option, the two have turned to a climate-controlled, vertical, hydroponic farming operation set up in a shipping container on property in South Montgomery County.“It’s an amazing technology,” Kelly said. “It’s a perfect climate-controlled environment for growing leafy greens.”
Kelly is a petroleum engineer and Armstrong has a marketing background. Kelly also owns several businesses and was looking for a project that he and his daughter could work on together.
They found the technology behind hydroponic farming fascinating.
The farm is contained in a custom-built, insulated shipping container. Kelly and Armstrong worked with Freight Farms in Boston for their operation.
The shipping container came from Boston by 18-wheeler and was delivered in late June. They planted their first crop in late July.
The message of Freight Farms is that fresh produce can be grown anywhere regardless of the climate.
Seedlings begin growth in trays under red and blue LED lights. Once the seedling grows larger, it’s transferred to a vertical tower for growing until its ready to harvest.
Water flows from the top of the container down through the roots and is collected at the bottom of the tower before being recycled to use again. These methods use about 90 percent less water than conventional farming. A panel of red and blue LED lights help the plants to grow into nutrient-rich food.“It’s cool technology and as an engineer, I appreciate that” Kelly said.
Fare House Farms grows a variety of lettuce and herbs.
They offer a wide array of lettuce like butterhead, bibb, romaine, Summer Crisp, and Oakleaf just to name a few. They offer leafy vegetables like arugula, cabbage, collards, kale, mustard greens, spinach, and chard. They also offer a variety of herbs like basil, cilantro, chives, dill, and more.
See their website at farehousefarms.com for a full menu.
Before this experience, Armstrong said she never knew what truly fresh lettuce and herbs tasted like.
She said the hydroponically grown lettuce was sweeter and crunchier. Kelly added the lettuce was prettier too.
The lettuce is sold with the peat moss plug still on so it will stay fresh for longer.
Kelly said they will spend the rest of 2020 experimenting with what grows best and studying the produce preferences of local buyers.
They plan to participate in local farmer’s markets to get their start.
They harvest on Fridays before the Saturday farmer’s markets.“You’re getting the freshest crop that you can get,” Kelly said.
Visit the Fare House Farms page on Facebook for more information and to see the farmer’s markets that they’ll be at.shernandez@hcnonline.com
Photos:
Alex Armstrong left, shares a laugh with Jane Pope after handing her a bag of freshly harvested lettuce at Fare House Farms, a hydroponic farming operation, Wednesday, Sept. 23, 2020, in Oak Ridge. Hydroponic farming is a type of horticulture where indoor crops are grown without soil by using a nutrient-rich and climate-controlled
Photo: Jason Fochtman, Houston Chronicle / Staff photographer
Rod Kelly and Alex Armstrong run Fare House Farms, a hydroponic farming operation in Oak Ridge. Hydroponic farming is a type of horticulture where indoor crops are grown without soil by using a nutrient-rich and climate-controlled environment.
Photo: Jason Fochtman, Houston Chronicle / Staff photographer9of10Alex Armstrong, and Rod Kelly are lit with panels of red and blue lights Alex Armstrong and Rod Kelly at Fare House Farms, a hydroponic farming operation, Wednesday, Sept. 23, 2020, in Oak Ridge. Hydroponic farming is a type of horticulture where indoor crops are grown without soil by using a nutrient-rich and climate-controlled environment.
Alex Armstrong and Rod Kelly make their way past pannels of red and blue lights, which encourage strong plant health and production, at Fare House Farms, a hydroponic farming operation, Wednesday, Sept. 23, 2020, in Oak Ridge. Hydroponic farming is a type of horticulture where indoor crops are grown without soil by using a nutrient-rich and Photo: Jason Fochtman, Houston Chronicle / Staff photographer
Fresh Hydroponic Produce In A Swedish Ski Resort
ICA Åre, located in one of the leading Scandinavian ski resorts, is the second ICA supermarket store in Sweden to install a hydroponic vertical container farm from Boston-based Freight Farms – providing its customers with just-picked leafy greens grown onsite, year-round
ICA Åre, located in one of the leading Scandinavian ski resorts, is the second ICA supermarket store in Sweden to install a hydroponic vertical container farm from Boston-based Freight Farms – providing its customers with just-picked leafy greens grown onsite, year-round.
Housed inside a 13-meter long shipping container, the onsite Freight Farm will reduce ICA Åre’s reliance on transported produce shipped long-distance into the mountain region, while providing pesticide and herbicide-free greens to customers at the peak of freshness year-round.
The initiative, Åre Byodling, was led by ICA Åre store owner Lars Ocklind and real estate company Diös Fastigheter, who recognized the benefits Freight Farms’ environmentally-controlled technology can have in the Nordic climate, particularly within the resort community hub that’s home to ICA Åre, the main train station, and other surrounding stores and restaurants. Ocklind believes that the store’s ability to grow its own crops is an investment in its future and that of its community.
Freight Farms, founded in 2010, pioneered hydronic vertical container farming and has a large network of IoT-connected farms in the world. The container farms, integrated with IoT data platform, farmhand, creates and maintains the optimal growing conditions to harvest crops year-round using less than 5 gallons of water per day. The technology has empowered ICA Åre and ICA Maxi Högskolan to create closed-loop food systems onsite, eliminating transportation emissions. Harvesting crops onsite also keeps crops fresh and nutrient-dense for longer, significantly reducing food waste for both sellers and consumers.
ICA Åre’s first farm harvest is scheduled for mid-October. The supermarket will begin by selling a selection of lettuce, kale and herbs in-store, and crops will also be used in their own restaurant and sold to other restaurants in the village. The range of crop offerings will continue to develop and expand – there is already great interest in collaboration from local restaurateurs for special lines of locally-grown crops.
For more information:
Freight Farms
www.freightfarms.com
Publication date: Fri 2 Oct 2020
“We Are Developing A Sustainable Technology That Uses 75% Less LED Lighting”
Verde Compacto, a Mexican start-up, producer of container farms and indoor farming growing technologies, has seen significant demand for their growing systems during the pandemic
Verde Compacto, a Mexican start-up, producer of container farms and indoor farming growing technologies, has seen significant demand for their growing systems during the pandemic.
"COVID is driving this market forward because people want to know what is behind their food and their diets. Logistic chains in countries like South Korea and Arab countries are really dependent on imports. They are trying to implement urban technologies to strengthen their supply chains. As we’re focusing on growing systems, we are trying to turn this into reality. We are growing food in a more sustainable way where everyone can benefit from it”, Juan Gabriel Succar, Co-Founder and CCO of Verde Compacto says.
The company has an R&D container farm, Huvster, with several labs and small scale systems. The company sells some of its crops locally to better understand the urban business model, as Verde Compacto is educating the future indoor growers.
The Huvster growing container
Succar continues: “We are providing the knowledge to any grower that wants to have an urban farm and we are helping them throughout the process by constructing a farm to their needs.” The company does not only build container farms, which is their standard model but also provides custom made projects such as warehouses or buildings. Or on a smaller scale like supermarkets and restaurants. “We provide the knowledge to install a farm at any size”.
Decreasing LED use
Verde Compacto is looking to improve the electricity use for its growing solutions. “We are developing a sustainable technology that uses 75% less LED lighting, which is part of a sustainable R&D project. The tests are still running but they have delivered positive results. In the end, our technology used for indoor farms allows us to rotate the lamps. Rather than using four lamps at one spot, Verde Compacto can use one light that is constantly rotating. That's why we can make such a big impact on light usage”, Succar affirms.
Lack of quality and water
“Every business model and location has different benefits. As we are one of the largest agricultural countries in the world, we can offer excellent fresh produce quality. The sad story is that all the good fruits and vegetables are exported, thus there is a lack of quality products here in Mexico”, Succar says.
Succar says that Verde Compacto’s technology can build a profitable business model to deliver excellent quality and healthy food to the Mexican society. He notes that the central Mexican region sees a big challenge: a large water shortage. “With our solution, companies still see an opportunity to grow food and maintain their quality by using fewer resources”, Succar notes.
Sustainability
“We always try to give the best options possible regarding our client’s budget, business model, and capabilities. Verde Compacto is cooperating with solar panels to give access to clients for installing these solutions. “Renewable energy, in the end, really depends on the client. Our goal is to make vertical farming as sustainable as we can”, Succar states. At the end of October this year the company will install the first urban farm in Salamanca, Mexico which will be run on 100% solar energy.
Price opportunities
Succar: “In Mexico, we provide our produce at a lower price level than supermarkets. This is done on purpose, to get people to know about vertical farming. Sometimes we are on the same price level.”
Olivier Kappetein, EU representative at Verde Compacto notes: “We have a financial stimulator and we found out that we can bring product prices down. Consumers would pay less compared to supermarket prices as they are unbelievably high. In the United Arab Emirates, locally grown products are unfindable. An iceberg lettuce costs around €7.60 (9 USD) or more. We could get that price down by at least 350% and still make a profit if we were to sell our produce there. We are aiming to sell high-quality food and that’s what they are looking for.”
Pre- and post COVID story
Verde Compacto has a pre- COVID story and a post-COVID story regarding any company expansions. The pre-COVID story was to expand to all Latin American countries, as a priority. They started several alliances and promoted the Verde Compacto technology in Latin America. However, the economy in Latin America was really affected during the pandemic.
“Thus, countries depending on imports saw a great opportunity in our technology for constant production. We didn’t get behind on the expansion actually. Right now, we are working with associations to open different commercial offices in several countries in Latin America. We will be expanding there at the beginning of next year. We are also exploring different options in different parts of the world, expanding globally. One of the regions is Northern Europe because we saw the need for farming technology in those countries. Especially in Luxemburg, where there’s limited fresh produce available.
“The most common problem in vertical farming is the unawareness of the consumer”, Kappetein adds. “They don’t know what it has to offer. It’s still an investment that needs to be made. There is still a greater focus on organic produce as they are aware of the great benefits that come along.”
The Verde Compacto team
Forage
Verde Compacto has been developing its own R&D department, generating knowledge that is also used for new product lines. Succar continues: “We are developing indoor farming systems that are not limited to leafy greens and herbs, but also for forage e.g.. Forage is eaten by grazing cattle mostly. With our hydro system, we can feed cows e.g. with using fewer resources in a more profitable way. The meat and milk industry is impacting the ecosystem significantly. Implementing this technology will help us to make this type of agriculture more sustainable.” The company is also exploring the opportunities of launching indoor strawberries, with the greatest focus on Europe.
For more information:
Verde Compacto
Juan Gabriel Succar, Co-founder, and CCO
juan.gabriel@verdecompacto.com
Olivier Kappetein, EU representative
olivier.kappetein@verdecompacto.com
Phone: +316 14 62 13 10.
www.verdecompacto.com
Publication date: Tue 8 Sep 2020
Author: Rebekka Boekhout
© HortiDaily.com
Housing And Food Services, Along With The Student Organization OUr Earth, Have Joined Together To Bring The Leafy Green Machine To Campus.
Environmental sensors balance temperature, humidity and CO2 levels to ensure a perfect growing environment
Freight Farms
Housing and Food Services, along with the student organization OUr Earth, have joined together to bring the Leafy Green Machine to campus.
Housed in an upcycled shipping container, it is the first hydroponic farm at a Big 12 university. Produce grown is served in on-campus dining locations.
Happy, Healthy Plants
Environmental sensors balance temperature, humidity and CO2 levels to ensure a perfect growing environment. A nutrient-rich water solution is distributed directly to the roots of the produce from a closed-loop hydroponic system.
'Wall Farm" Allows Shoppers To Pick Their Own Produce in Store
"We are gratified to be the first kosher supermarket in the country to introduce the Vertical farm," said Malki Levine of Evergreen
'Wall farm' allows shoppers to pick their own produce in store
A new vertical field urban farm system at New York-based Evergreen Market makes tasty, healthy, sustainable, and pesticide-free produce available to consumers 365 days a year.
Jul 27, 2020
The world of freshly harvested greens and herbs is looking up—literally—in Monsey, New York. Evergreen Kosher Market is debuting a revolutionary 20-foot-high geoponic (soil-based) wall farm that lets customers choose clean, fresh-picked produce and see exactly where it comes from.
The pesticide-free lettuce, kale, arugula, basil, and cilantro from Evergreen's on-site farm are sold at in individual pots, making the "buying local" experience more convenient than ever. Pesticide-free and grown in soil that is never exposed to bugs, all products are Star-K Kosher Certified for purity.
"We are gratified to be the first kosher supermarket in the country to introduce the Vertical farm," said Malki Levine of Evergreen. "Our customers are very much looking forward to buying fresh produce that is grown in our own backyard rather than being transported on long hauls from farms across the country. They will also appreciate the significantly reduced level of infestation, a major concern of kosher consumers."
Shoppers can visit the vertical farm when they visit the store. The system features a controlled, sterile environment with soil beds containing a proprietary mix of minerals and nutrients. Advanced sensors constantly monitor, irrigate, and fertilize the crops throughout every growth stage.
Evergreen's wall farm is the latest installation from Vertical Field, an Israeli ag-tech company that produces innovative vertical agricultural solutions that help the environment, improve human health conditions, and make fresh produce available all year round.
Geoponic (soil-based) vertical farming yields a new crop every few days, ensuring that fresh greens and herbs will always be in season in Monsey. The sustainable and eco-friendly method produces cleaner, healthier, tastier veggies than those shipped from miles away. And reduced soil-to-plate time means a longer shelf life and fewer hands involved—a welcome benefit in the age of COVID-19. "We are extremely excited about the partnership with Evergreen," said Guy Elitzur, CEO of Vertical Field.
They are precisely the type of supermarket that has the right customer base and will successfully integrate the latest technological advances in geoponic farming."
Source: Evergreen Kosher Market
MarketTAGS: RETAILER AND DISTRIBUTOR
Welcome To Robbinsville, NJ–Home of The First Municipal Freight Farm!
Since Freight Farms sold its first farms in 2013, we have had farmers join our community from all over the world, with a range of backgrounds and business models. Yet, the Robbinsville Farm stands out from all of them because it is the first and only Freight Farm owned by a whole town
A One-of-a-Kind Town Farm
Since Freight Farms sold its first farms in 2013, we have had farmers join our community from all over the world, with a range of backgrounds and business models. Yet, the Robbinsville Farm stands out from all of them because it is the first and only Freight Farm owned by a whole town.
That’s right! The Robbinsville Township of New Jersey came together to bring the Leafy Green Machine™ (the fore-bearer of our current Greenery™) to their town, and the farm operations and distribution has remained a town activity ever since.
We spoke with farm coordinator, Hope Cahill, about her role at the one-of-a-kind Robbinsville farm and how the project gets the entire community–from student to senior citizen–involved.
The Robbinsville Farm on location at the Senior Center.
Image | Robbinsville Hydroponic Farm on Facebook
The town hydroponic farm
A fresh take on a public service.
When the Robbinsville Farm arrived at the local Senior Center in November 2017, Robbinsville became the first municipality in New Jersey (and in the world!) to install a vertical hydroponic Freight Farm. For the town, it was about more than bringing healthy and local food to the community. Robbinsville quickly made their Freight Farm a key piece in education, volunteer, and food access initiatives. The farm’s location on site at the Senior Center was no coincidence either, with a large part of the harvest dedicated to the center’s dining operations and the local chapter of Meals on Wheels.
The initiative was spearheaded by the Robbinsville mayor, Dave Fried, who–upon seeing a similar type of container farm–sent the Robbinsville Recreation Manager a message saying ‘I would love this for the township. Let’s figure out how to do this’. After a long research phase, the town found Freight Farms. For the town, Freight Farms was the perfect choice since they were able to get everything they needed to run the farm–from purchase to supplies, to training, to customer service–in one. To this day, Mayor Dave is one of the farm’s staunchest supporters.
Nearly three years after its installation, the Robbinsville Farm is still serving its community faithfully. The produce goes directly to the seniors at the Robbinsville Senior Center, Meals on Wheels, and the food bank at Mercer Street Friends (a New Jersey non-profit that offers school and employment opportunities and hunger relief programs). In this way, Robbinsville is able to improve food security, increase access to fresh food, and reduce the risk of obesity and obesity-related diseases.
Hope explains the additional value of having a farm directly in Robbinsville
“Because we are distributing so local, we are able to reduce “food miles” that are required to transport nutritious food...Many who volunteer say how relaxing it is therefore we are also improving mental health and promoting relaxation. We also offer field trips to schools, businesses and families to educate people about healthy eating, sustainable agriculture and [hydroponics].”
Town-owned, community-operated
Farm Coordinator, Hope Cahill
It takes a village to raise a farm.
With so many important outlets for the produce, one challenge for Robbinsville was to ensure the farm ran smoothly while also engaging as many community members as possible. For that, Robbinsville hired Hope to manage the operations and the large group of volunteers that run the farm. Unlike many of our farmers for whom hydroponics is their first foray into agriculture, Hope came to the Freight Farm a seasoned expert.
While attending a vocational high school, Hope took courses in Horticulture and Landscape Management which exposed her to a range of plant-related topics, with everything from floral design and landscaping, to pest and greenhouse management. With this experience, she was able to join the Future Farmers of America after graduating; In the years following high school, Hope got certifications from Rutgers University in fields like beekeeping, landscape management, and aquaponics. During that time she served as the New Jersey FFA State Reporter and then State President, which gave her the opportunity to travel the whole state teaching students the importance of agriculture. All this combined experience made her eager to join the Robbinsville Farm team, seeing it as a perfect way to combine her passion for agriculture with her desire to teach and help fight hunger in the local community.
While Hope is the mastermind behind the farm operations, it is the volunteers who really give the farm program life, and capture the whole scope of the Robbinsville community. Volunteers include the seniors who attend the senior center, Meals-on-Wheels recipients, students–and anyone else with the interest and willingness to learn more about hydroponics.
Together, Hope and the volunteers grow a variety of lettuces, such as Butterhead, Bibb, Red and Green Leaf Romaine, Summer Crisp, Oakleaf, Lollo Rossa, and the occasional herbs. The community reaction? They love it.
Hope explains how she manages her large group of volunteers
“Monday and Tuesday are Harvest and transplant days. Wednesday’s, we seed, rotate the towers and do farm maintenance such as cleaning and mixing fertilizers...As Farm coordinator I oversee everything that goes on in the farm and schedule the volunteers. Every Monday I send out the following weeks farm tasks listing jobs to be done and time slots. Then the volunteers will sign up and I will schedule them in.”
COVID-19 had an obvious impact on the volunteer workforce that drives the Robbinsville farm. When the virus reached New Jersey, only Robbinsville Township paid staff were able to run the farm for the purposes of health and safety. This led Hope and her coworkers to change their operations to best meet the needs of a community in crisis. A simple change, like eliminating a Spring Harvest mix, helped them maximize their weekly harvest and reduce time spent in the small space farm.
In spite of all this, Hope believes that the volunteer program will bounce back after the pandemic thanks to the hard work she and her team have done to get the whole community invested in the farm’s success over the years.
Get to know Hope as she shows us how she plants seeds at the Robbinsville farm!
Interested in starting a farm in your town? Get in touch.
VIDEO: May 2020 - Indoor Science Cafe Recording is Now Available - How to Fund Your Indoor Farm
This presentation 'How to Fund Your Indoor Farm' was given by Nicola Kerslake (Contain Inc.) during our 19th cafe forum on May 26th, 2020. Indoor Ag Science Cafe is organized by the OptimIA project team funded by USDA SCRI grant program.
This presentation 'How to Fund Your Indoor Farm' was given by Nicola Kerslake (Contain Inc.) during our 19th cafe forum on May 26th, 2020. Indoor Ag Science Cafe is organized by the OptimIA project team funded by USDA SCRI grant program.
Indoor Ag-Con Kicks Off New Webinar Series With United Fresh Produce Association Panel
Indoor Ag-Con LLC, producers of the premier event for the indoor|vertical farming industry, is launching a free monthly webinar series to share content originally planned for its May 2020 in-person annual conference that has been postponed due to the Covid-19 pandemic
INDOOR AG-CON KICKS OFF NEW FREE WEBINAR SERIES WITH UNITED FRESH PANEL DISCUSSION ON PRODUCE TRENDS, BUSINESS OPPORTUNITIES FOR INDOOR GROWERS
Free Monthly Virtual Events To Share Content Originally Planned For May 2020 Annual In-Person Conference Postponed Due to Covid-19 Pandemic
LAS VEGAS ( May 20, 2020) – Indoor Ag-Con LLC, producers of the premier event for the indoor|vertical farming industry, is launching a free monthly webinar series to share content originally planned for its May 2020 in-person annual conference that has been postponed due to the Covid-19 pandemic. Titled “Indoor Ag-Conversations,” the new virtual event series kicks off with the United Fresh Produce Association Panel: Produce Trends & Business Opportunities For Indoor Growers Emerging From Covid-19 Pandemic on Wednesday, June 3 at 4 pm EST.
Moderated by United Fresh President and CEO Tom Stenzel, the panel will include Alex DiNovo, President and COO, DNO Produce and Paul Lightfoot, President and Founder, BrightFarms.
“While Covid-19 has temporarily halted our opportunity to gather face-to-face for Indoor Ag-Con, it has not stopped us from sharing the incredible innovations and business-building opportunities our vibrant industry offers,” says Brian Sullivan, co-owner of Indoor Ag-Con. “We’re honored to have the United Fresh Produce Association kick off our first webinar with such a dynamic panel of industry leaders talking about the unprecedented challenges and opportunities we’re facing today.”
“Now more than ever it’s critical that we continue to find new ways to connect with industry peers to share industry ideas and experiences,” adds Tom Stenzel, President & CEO, United Fresh Produce Association. “Indoor growing is an important component of the fresh produce industry, and we’re excited to lead the first Indoor Ag-Con webinar on June 3 as we look ahead to our own new free virtual event, United Fresh Live!, coming the week of June 15.”
With plans to feature one to two sessions each month, the new Indoor Ag-Conversations webinar series will feature content originally planned for the now postponed Indoor Ag-Con 2020 Conference line-up, as well as new sessions designed to help industry members find new ways to grow their business.
Scheduled for June 3 at 4 pm EST, the Indoor Ag-Conversations United Fresh panel will share insights from (pictured clockwise from top left):
Moderator Tom Stenzel, the President and CEO of the United Fresh Produce Association, is a frequent speaker on industry issues and has been recognized for his leadership frequently throughout his career. Tom has testified numerous times before Congress, and works closely with leaders at the White House, USDA, FDA, and other U.S. regulatory agencies. He also leads the United Fresh Start Foundation, the association’s charitable foundation focused on increasing children’s access to fresh fruits and vegetables. The Foundation and its partners have donated more than 5,000 salad bars to schools in all 50 states.
Paul Lightfoot, President and Founder of BrightFarms, is creating the first national brand of locally grown produce. In four years, Lightfoot has led the company from a proof-of-concept to operating four greenhouses in key markets like Washington, D.C., Chicago, Cincinnati, and Philadelphia. BrightFarms was named 235th on the 2017 Inc. 500 list of fastest-growing private companies, ranking 10th among all food companies and the only produce company featured on the list.
Alex DiNovo is President and COO of DNO Produce Group of Companies, a rapidly growing family-owned group of businesses located in Columbus, Ohio. DNO is a fresh fruit and vegetable processor, as well as a distributor, with a distribution network throughout the Midwest, Great Lakes, and the southeastern United States. DNO distributes to customers both directly and indirectly through its network. Alex is a fourth-generation family member who has been involved in the produce business from a young age. He has knowledge and experience in many areas of the produce supply chain.
Indoor Ag-Conversation webinars are free to industry members. To register for the upcoming June 3, 2020 session, visit www.indoor.ag/webinar. In addition, the Indoor Ag-Con team is currently exploring dates and options for its postponed May 2020 in-person event and will be providing updates soon.
ABOUT INDOOR AG-CON LLC
Founded in 2013, Indoor Ag-Con touches all sectors of the business, covering produce, legal cannabis, hemp, alternate protein and non-food crops. In December 2018, three event industry professionals – Nancy Hallberg, Kris Sieradzki and Brian Sullivan – purchased Indoor Ag-Con LLC, setting the stage for further expansion of the events globally. For more information, visit: https://indoor.ag
ABOUT UNITED FRESH PRODUCE ASSOCIATION
United Fresh brings together members across every segment of the supply chain to build relationships that are as solid with a handshake as with a contract. We empower industry leaders to join forces to shape sound government policy. We deliver the resources and expertise companies need to succeed in managing complex business and technical issues. For more information, visit: https://www.unitedfresh.org and to learn more about United Fresh LIVE! Visit www.unitedfreshlive.org
SPECIAL THANKS TO INDOOR AG-CON 2020
SPONSORS, EXHIBITORS MEDIA ALLIES & INDUSTRY PARTNERS
In addition, Indoor Ag-Con is proud to be a member of the Hemp Industries Association.
Shipping Container Farm, Vertical Roots Hires Displaced Restaurant Workers To Help Fill Growing Retail Demand
Since launching in 2016, Vertical Roots has expanded from a single hydroponic garden container to a current operation of more than 130, each filled with leafy greens
Vertical Roots hires displaced restaurant workers to help fill growing retail demand
Vertical Roots grows leafy greens in hydroponic gardens inside custom-outfitted shipping containers
With the restaurant and hospitality industry under duress and thousands out of work, container farm company Vertical Roots stepped up to the plate, offering jobs to displaced employees.Since launching in 2016, Vertical Roots has expanded from a single hydroponic garden container to a current operation of more than 130, each filled with leafy greens. For co-owners Andrew Hare and Matt Daniels, their mission is two-fold: delivering a local, pesticide-free product and developing community relationships to serve those in need."I have been in the restaurant industry for most of my adult life, including eight years right here in Charleston," said Hare. "It really hits close to home for me, witnessing this incredible industry turned upside down so quickly by this pandemic."According to Hare, Vertical Roots hired about two dozen chefs, cooks, dishwashers, servers and managers since the COVID-19 pandemic began. In all, employees displaced by the outbreak made up about 25 percent of their 100-employee team split between their two locations in Charleston and Columbia when we spoke in April."We are helping these people get a paycheck and they are helping us get product out of the door," said Hare. "They have been eager, fast learners, which has made the whole process seamless."Many of the new hires have worked with the non-GMO produce in the past. Vertical Roots supplies many local kitchens with their one- or two-day old living baby Romaine, arugula, bibb and butter lettuces.After a food safety course, most new employees started in the "pack room," where Hare said "all the harvested products flow to cool down and be processed for each customer, whether it's making a spring mix of cut leaves or taking living heads of lettuce to clamshell or case."Many of Vertical Roots' newcomers will return to their kitchens as restaurants reopen, but at least one downtown chef currently working with the company said some workers may continue to work at the container farm.For Vertical Roots, the growing season never ends inside their compact, LED-lit shipping containers. The company currently supplies more than 400 stores, mostly in the Southeast. And the customer base is growing, Hare reports."We are 98 percent focused on retail right now," said Hare, who points out that the closure of restaurants in the Charleston area led to an influx of large retail orders.With a hand in every part of the supply chain, Hare knows exactly what's going on with each crop at any given time, and the farm sites' geographic positioning allows the greens to arrive at their final destination within 24 hours of harvesting. Large-scale commercial farms, on the other hand, must contend with corporate concentration, leading to less quality control in a practice where several uncertainties such as soil contamination and water runoff already exist.According to Hare, 95 percent of the leafy greens in grocery stores come from two areas, Yuma, Arizona and Salinas, California. "These products can sometimes have three weeks of travel time," Hare said. "With us, you are dealing with a young, vibrant product filled with calcium and potassium. I would definitely stress how important it is to eat something clean right now."Hare said he feels fortunate for the added business, and they were in need of some help prior to the arrival of their new crew. "What a mutually beneficial thing for us to be able to go out and hire some of our customers who are familiar with our products," Hare said. Having people on staff who know how to use the product is enabling Vertical Roots to meet the growing demand for their seven lettuce varieties," he added.
Create Multiple Streams of Income With Container Farming
Right now, despite COVID-19 repercussions, food remains a necessity, and there exists an opportunity to build resilience into our business models. As a result, many businesses, food-related or not, can create a viable new stream of income by growing your own produce with a container farm
CURRENT CHALLENGES
Right now, despite COVID-19 repercussions, food remains a necessity, and there exists an opportunity to build resilience into our business models.
As a result, many businesses, food-related or not, can create a viable new stream of income by growing your own produce with a container farm.
WHAT IS CONTAINER FARMING?
Container farming uses a hydroponic growing system to commercially grow a variety of fresh produce more sustainably and year-round. This type of growth is done in a controlled environment that is time, space, and resource-efficient.
The real value is not only the produce grown, but the ability for a container farm to offer a community or business a local source of produce, a source of employment, and an additional stream of income.
GROWING FOR THE LOCAL COMMUNITY
Those who work closely with our food systems know that growing your own food is not going to solve food security immediately. However, we can’t dismiss the benefit of growing food closer to the people who consume it.
If you’re a co-op store, the container farm is behind your store and ready to fill your shelves. If you’re a nonprofit that cooks meals, sourcing produce is one logistic you can cross off your list. If your community is remote, or further from city centers, the importance of having a local source of food is not lost on you. Access to local food becomes even more critical in light of current events that have shaken our supply chains.
Abbey Gardens purchased a Growcer to ensure that they were able to generate revenue year-round instead of seasonally.
YEAR-ROUND RELIABILITY
Growcer systems are plug-and-play systems built to operate year-round among all conditions. The system allows you to consistently harvest produce and benefit from this stream of income year-round.
If you rely on a seasonal bump for a boost, this consistent source of income increases the foundation you have to work with.
The hydroponic growing system also allows multiple types of crops can be grown at once from over 140 different varieties of produce and the ability to swap what you’re growing to meet demand.
The Yellowknife Co-op has created their own produce line and branding for their Growcer greens.
PROOF OF CONCEPT
Can a container farm really be an extra source of income? We know it can. We’ve collaborated with many diverse communities and organizations that have tailored a Growcer system to work for them.
For example, businesses like Abbey Gardens and The Yellowknife Co-op used the Growcer system to add extra revenue to their main line of business. For the Gitmaxmak’ay Nisga’a Society, they are adding the system to create an entirely new source of revenue for their non-profit.
While a container farm can be a source of extra income, it has to be feasible first. You must factor your situation, your market, and your financial options when investigating if this is a fit.
Take the first step and plug in your specifics into our ROI calculator to evaluate the feasibility of a container farm for you.
StephanieMay 4, 2020
US: “We Are Increasing Any Kind of Digital Experience.”
As the situation around COVID-19 worsens in the USA, Freight Farms has still been able to continue its momentum in a meaningful way
As the situation around COVID-19 worsened in the USA, Freight Farms has still been able to continue its momentum in a meaningful way. With the company’s team working remotely during this crisis, demand for Freight Farms’ Greenery has continued to grow, resulting in the team exceeding its sales goals for the first and second quarter of the year. Brad McNamara, President of Freight Farms mentions: “There are a lot of people coming to us seeing the urgency of the food supply.”
The company’s customers are also responding to the crisis in various ways. Many of Freight Farms’ small business customers have been able to quickly pivot from supplying restaurants and foodservice to consumers in their communities directly via CSA, delivery, and drive-through models. CEO Rick Vanzura says that there has been a lot of discussion on how countries' food supply chains were or weren’t prepared for COVID-19. “The situation has spotlighted urgent supply chain challenges faced around the world, and we want to help provide solutions wherever we can.”
The Freight Farms Greenery cultivation area
Business past weeks
Caroline Katsiroubas, Director of Marketing & Community Relations states, “There has been an increase in consumers researching how to grow their own food that’s highlighting a heightened interest in local sourcing and the need to shorten supply chains. People are also searching for food production technology – we’ve seen a significant increase in visits to our website, as well as in inbound inquiries.” The company receives many messages of people that are interested to create a reliable source of food for their communities. “Our small business customers sell their produce directly to consumers in their local communities, as well as to local restaurants and foodservice groups.
Those who relied heavily on restaurant and foodservice sales prior to the pandemic have been nimbly pivoting their business models to reach consumers in their local communities directly through contactless CSAs, drive-through farm stands, and delivery models. And the communities have very receptive – they want access to fresh produce without having to go to the grocery store right now, they want to support local business, and they like knowing their food has been in contact with fewer people – just them and their farmers.”
At the moment Freight Farms is scheduling live videos for social media and online webinar presentations to highlight Freight Farms’ customers. There will continue to be webinars for customers to share their experience and learn new farming and business tactics. “We are increasing digital experiences for our existing farmers and those interested in learning more about our farming technology.”
The leafy green machine, succeeded by the Greenery
Freight Farms supporting farmers
McNamara: “We are working on initiatives to support our community of farmers around the globe and domestically. We’re offering free access to our IoT platform Farmhand Connect to support their remote access to their farm operations. We’re also helping to connect farmers in our network who have extra produce to nonprofit organizations seeking donations.” Freight Farms is also supporting its customers by ensuring access to its service and technical teams. “We’ve increased our customer service and engineering support,” Vanzura mentions. We also have an online platform where our farmers share tips and tricks, and we are helping facilitate that conversation, even more, to promote best practices to respond to this crisis.” “For some of them, it’s pivoting to a more B2C model and we want to help them achieve that,” Katsiroubas notes.
Freight Farms' Greenery Farmhand
Locals are helping out
Katsiroubas: “Some of our institutional customers, like schools which are of course now closed, are donating the produce they’ve been growing for the dining hall to food banks or nonprofit organizations that are lacking fresh produce. Our customers at Saint Joseph's College have been continued growing despite the COVID-19 to deliver their supply to the local elderly population in the community.” “Our customers have the power to grow food in minimal time and pivot supply to where it needs to be in the community. I am so proud of our community of farmers as they’re using our technology to do what they can to help others in this time of crisis,” McNamara notes.
A St. Joseph's student farmer
Pushing forward developments
McNamara states that the company’s resources are ramped up, for the current situation and for continued product development. “Fortunately, our supply chain is in good shape, so we are in a good position not only to support the current network, but also the new farmers coming on board in the upcoming months.” Freight Farms recently hired automation and robotics specialist Jake Felser, as the new head of engineering. “Having Jake onboard has been great. We have a dream team pushing development forward, especially from an automation perspective. We are moving forward constantly and have never been better positioned.”
Freight Farms Greenery calendula
Crispr tomatoes
“We’re always pushing forward on collaborative research, and recently worked with Cold Spring Harbor Laboratory as they explored how seed genetics and vertical farming can work together for efficiencies in food production, especially in confined environments. Our farm was used to create optimal growing conditions to unlock unique characteristics of their gene-edited tomato seeds,” McNamara states. The launch of the Greenery last year has proven to be more powerful with 70% more linear growing room in the same 320 sq. footprint as its flagship farm. “The interior flexibility of the Greenery supports efficient growth of more than 500 varieties of crops, and farmers are able to increase yield overall. With our integrated IoT platform farmhand, these farms will only continue to be more efficient.”
Freight Farms Greenery stacked crane lot
Investment
In February the company raised $15 million in their series B funding led by Ospraie Ag Science. McNamara says, “Ospraie Ag Science is a great investor and focused on agricultural and environmental sciences. It’s important for us to have our mission in line with whomever we work with on the investment side. We are using the funding to push ongoing technology development for our growing customer community.” “The partnership with Sodexo was a milestone moment for the company. By being a key player in their foodservice program, integration of our Greenery farms onto more campuses across the country will accelerate.” “It’s an important time to invest in agtech and to empower food production on a local level everywhere.”
For more information:
Freight Farms
www.freightfarms.com
Publication date: Wed 29 Apr 2020
Author: Rebekka Boekhout
© HortiDaily.com
Vertical Field's New Portable Farms Are Making The World More Sustainable - And Better Fed
Vertical Field’s Urban Crops offers an ideal alternative to traditional agriculture, especially in urban settings where space is scarce. The soil-based platform can grow hundreds of types of crops – pesticide-free, indoors or outdoors – and requires no training to operate
REVIVING URBAN LIFE – AN INNOVATIVE SOIL-BASED INDOOR
VERTICAL FARM THAT BRINGS THE PRODUCTION OF FOOD
TO THE PLACE IT IS CONSUMED
• Consistent Supply
• Reduces Inventory Waste
• Less Human Handling
• More Sterile Environment
APRIL 28, 2020, New York/Rana’na, Israel
Urban areas contain more than half the world’s population and contribute to some 70% of the planet’s energy emissions. Cities guzzle the bulk of Earth’s resources and produce more waste. Many residents live in “urban food deserts.” And buildings are literally making their occupants sick.
Our planet is home to some 7.7 billion people. In many places, hunger is a reality. Unpredictable climate patterns are threatening the availability and stability of fresh produce. Yet the global population is rising. How will we feed the world by the mid-21stcentury, when an expected 10 billion of us need food? And now in-light of the COVID-19 pandemic, the food supply chain is in jeopardy more than ever before -- the need to bring food easier and faster directly to consumers is more important than ever.
One revolutionary agro-tech company, Vertical Field (www.verticalfield.com), is harnessing the power of geoponic technology, agricultural expertise, and smart design to tackle all of these issues and more. The Israeli startup – cited by Silicon Review as a “50 Innovative Companies to Watch in 2019” and named by World Smart City in 2019 as “Best Startup” – produces vertical agricultural solutions that help the environment, improve human health conditions, cut down on human handling, reduce waste, and make fresh, delicious and more produce available 365 days a year locally and directly to consumers and other end users.
“Vertical Fields offers a revolutionary way to eat the freshest greens and herbs, by producing soil-based indoor vertical farms grown at the very location where food is consumed,” said Vertical Field’s Chief Executive Officer, Guy Elitzur of Ra’anana, Israel who is hoping to place his ‘vertical farms’ in retail chains and restaurants establishments in cities throughout the US.
Vertical Field’s Urban Crops offers an ideal alternative to traditional agriculture. The soil-based platform can grow hundreds of types of crops – pesticide-free, indoors or outdoors – and requires no training to operate.
“Not only do our products facilitate and promote sustainable life and make a positive impact on the environment, we offer an easy to use real alternative to traditional agriculture. Our Urban farms give new meaning to the term ‘farm-to-table,’ because one can virtually pick their own greens and herbs at supermarkets, restaurants or other retail sites,” he adds.
Vertical Field’s Urban Crops offers an ideal alternative to traditional agriculture, especially in urban settings where space is scarce. The soil-based platform can grow hundreds of types of crops – pesticide-free, indoors or outdoors – and requires no training to operate.
From Wall to Fork
Vertical farming in cities is an energy-efficient, space-saving, farming alternative to traditional crops grown in acres and fields. Thanks to Vertical Field, everyone from city planners and architects to restaurants, supermarkets, hotels are using vertical farming to create lush, green edible spaces in congested areas around the world.
Portable Urban Farm
An alternative to the living wall is Vertical Field’s unique Vertical Farm®, which can be placed in either a 20-ft or 40-ft. container equipped with advanced sensors that provide a controlled environment. This technology constantly monitors, irrigates, and fertilizes crops throughout every growth stage. Healthy, high-quality fruits and vegetables flourish in soil beds that contain a proprietary mix of minerals and nutrients.
Advantages of Vertical Field’s Vertical Farm:
● Bug-free and pesticide-free – healthy, fresh, and clean produce
● Less waste – uses 90% less water
● Shorter growing cycles, longer shelf life
● Plants are “in season” 365 days/year - grow whatever you want, no matter the weather or climate conditions of the geography
● Consistent quality
● Modular, expandable, and moveable farm
● Automated crop management
● More Sterile Environment
● Less Human Contact
Creating a more sustainable way of life in cities across the globe has never been more urgent. Vertical Field is responding to the challenge today. Green cities will enrich life in urban areas, provide healthier and better food, and shorten the distance between consumers and their food.
About Vertical Field:
Vertical Field is a leading agro-tech provider of vertical farming and living green wall solutions for urban environments and smart cities. The company is operated by professionals, agronomists, researchers, and a multi-disciplinary team, enabling the development of smart walls that combine the best of design and manufacturing, smart computerized monitoring, soil-based technology, water and lighting technology and more. Vertical Field delivers next-generation vertical farming systems for a global clientele, including Facebook, Intel, Apple, Isrotel, Microsoft, and many more.
For more information:
Vertical Field
www.verticalfield.com
Vertical Farms: The Height of Sustainability In A Post-COVID World
Vertical farms are innovative soil-based indoor farms that bring production of food to the location where it is consumed: supermarkets, local distribution sites, and restaurants
Among the many indelible images of the COVID-19 crisis have been the photos of mountains of surplus produce rotting in fields while millions of Americans go hungry. Urban areas are especially hard hit as supply chains are disrupted due to coronavirus fallout.
Vertical farms are innovative soil-based indoor farms that bring production of food to the location where it is consumed: supermarkets, local distribution sites, and restaurants.
Vertical Field, an Israeli start-up, has a container up and running at a Poughkeepsie, New York, restaurant and arriving soon at Evergreen supermarket in Monsey, N.Y. Its global clientele for its next-gen vertical farming systems includes Facebook, Intel, Apple, Isrotel, Microsoft, and many more.
Benefits include:
Consistent Supply
Reduced Inventory Waste
Less Human Handling
More Sterile Environment
Modular, expandable, and moveable farm
Bug-free and pesticide-free – healthy, fresh, and clean produce
Uses 90% less water
For more information:
Vertical Field
www.verticalfield.com
May 6th, 2020 16:00 CEST Webinar Series 'Eat This' by World Horti Center
World Horti Center and NethWork collaborate in giving a follow up to the exhibition ‘Countryside – The Future’ initiated by the Dutch architect Rem Koolhaas, that was opened on February 20 in the Guggenheim Museum in New York
World Horti Center and NethWork collaborate in giving a follow up to the exhibition ‘Countryside – The Future’ initiated by the Dutch architect Rem Koolhaas, that was opened on February 20 in the Guggenheim Museum in New York. The exhibition among others features the current and future developments in food production, especially what is happening in greenhouses.
Webinar sessions
The exhibition is currently closed, due to the COVID-19 pandemic, but the production of cherry tomatoes in a closed, high tech production unit, situated in front of the museum on Fifth Avenue, continues. Right in the center of the world and the epicenter of the pandemic. The unit, therefore, is a great metaphor and catalyst in the discussion on the consumption of healthy food, produced in a sustainable and affordable way. Therefore, World Horti Center (WHC) took the initiative to facilitate, in cooperation with foundation NethWork, a new series of online events.
Thought leaders
During weekly webinar sessions, thought leaders in the field of food will share their vision on (the future of) healthy food. The kick-off takes place on Wednesday 6 May, 16.00 hrs CEST and features architect Rem Koolhaas, initiator of the exhibition ‘Countryside – The Future’. He will be assisted by Clemens Driessen, a philosopher at Wageningen UR. Both gentlemen will share their vision on current developments and the future of horticulture in the Netherlands and beyond. You can register for the first webinar here.
Eat This
This webinar series, named ‘Eat This’ is a close collaboration between NethWork and World Horti Center. Both organizations want to connect the horticultural sector with the world beyond horticulture. Renee Snijders and Ed Smit of NethWork will present these weekly webinar sessions. After the inaugural session with Rem Koolhaas, 9 webinars will follow. Additional details on guests and themes will follow soon.
For more information:
World Horti Center Europa 1
2672 ZX Naaldwijk
Netherlands
+31 (0)174 385 600
info@worldhorticenter.nl
www.worldhorticenter.nl
NethWork
www.nethwork.info
Publication date: Wed 29 Apr 202
Innovation Consulting Community Team Proposes Sustainable Farming Container At ISU
In just a few months, a team of motivated students put together a proposal to implement a shipping container farm on Illinois State’s campus
Evan Linden April 15, 2020
NOTE: The photos in this story were taken before travel restrictions from coronavirus (COVID-19) were in place.
In just a few months, a team of motivated students put together a proposal to implement a shipping container farm on Illinois State’s campus.
“Self-motivation is impressive to employers,” said Marketing Professor Dr. Peter Kaufman, one of the founders of the Innovation Consulting Community (ICC). “Most students are taught one discipline in school, but world problems are interdisciplinary.”
Kaufman and others founded the ICC in 2016 to provide students with hands-on experiences outside their classes. Each year, teams of students are matched with clients at companies and nonprofit organizations to help solve a current issue they are facing. “It’s a unique experience to tackle both profit and nonprofit projects,” said Kaufman. “This experience helps students enhance their skills all around and helps our clients find solutions.”
This year, the ICC assigned 14 projects to 90 students representing 24 majors. One group of four students tackled an increasingly pressing issue: sustainable farming.
The students assembled in late October, mentored by Elisabeth Reed, director of the Office of Sustainability, and Dr. David Kopsell, assistant chair of and professor in the Department of Agriculture. Ryan Strange, a senior from Bloomington double majoring in business administration and small business management, led the team and collaborated with fellow students Joe Kennedy, Madison Steines, and Joe Quigley.
The project was inspired by the Boston company Freight Farms, urban agriculture innovators who create farms in shipping containers. Kopsell, who is familiar with growing systems, was brought in by Kaufman to be a horticulture mentor.
“I shared some of the ideas that I’d always wanted to investigate, and one that he really liked was the idea of writing a grant for a containerized growing system,” said Kopsell.
From there, the team focused on analyzing the benefits of a containerized growing system on campus.
“Our project was a feasibility study of the purchase of one of these units,” said Strange. “The unit itself is the technology necessary for hydroponic farming, and all of that goes inside an old freight container.”
The inside of a shipping container farm located in Champaign.
To see one of these units in action, the group visited a current model located at the University of Illinois at Urbana-Champaign. “The director there was a tremendous help,” said Strange. “He gave us many details about operations and risk management.”
The team spent weeks finding the right contacts and establishing relationships in order to gather information for the project. “We built this huge network of different partnerships that helped us find out how we would finance this unit,” said Strange.
According to Strange, the purchase of one of these units would cost $120,000, with recurring costs adding up to around $40,000 a year.
“I think the cost is within the reach of a grant program,” said Kopsell. “These containers can operate year-round and provide great teaching and learning tools.”
Most importantly, the containers are both efficient and sustainable. Each container system can produce as much as one acre of field production —up to 13,000 plants depending on the crop. The efficient drip irrigation system uses five gallons of water per day, which is marginally less than a field.
“This is really the forefront of innovation in terms of agricultural production,” said Strange. “It’s going to cut back on a lot of the carbon emissions from transporting the food. It’s really going to cut back on costs also because most of the costs for food come from transportation.”
If installed on campus, the container system could be located next to the South University Street Garage.
Strange’s team presented its project at ICC’s annual symposium. In adherence with social distancing requirements, the symposium took place via Zoom on April 10.
Strange and his team noted that the ICC experience greatly benefited them as professionals. “It opens up a lot of doors and you have to teach yourself a lot,” said Strange. “Our mentors were definitely there for help, but it was mostly our group that set up all of the meetings and held ourselves to the deadlines. All of those things are fundamental skills that you’ll need when you move on to the professional workforce.”
Reed and Kopsell were impressed by the group’s work ethic and commitment.
“This student group was very well organized and stayed on task throughout the entire semester,” said Reed. “They communicated well with each other.”
“For me, this project represents the best of Illinois State University,” said Kopsell. “It allows students to find their passion and provides them an avenue to learn how to overcome challenges, solve problems, and make a difference.”
Students interested in participating in the Innovation Consulting Community for the next academic year can email innovationconsulting@IllinoisState.edu for more information.
Lead Photo: The ICC team visits a shipping container farm in Champaign. Pictured from left to right: Ryan Strange, Joe Quigley, Madison Steines, James Smith, Phoebe Naylon, Brennan Douglas, Alicia Chiakas, Aviv Zelniker, Max Snyderman, Bill Bagby with Central Illinois Produce, Dr. Eric Godoy, and Joe Kennedy
Filed Under Agriculture Center for Community Engagement and Service Learning College of Business Office of Sustainability
Are Container Farms The Solution To The Coronavirus Food Supply Problem?
As people run to grocery stores to stock up on food and supplies during a time of quarantine, the $899 billion restaurant industry is collapsing, raising questions about the economic security of the nation’s food supply industry in the time of COVID-19
April 13, 2020
As people run to grocery stores to stock up on food and supplies during a time of quarantine, the $899 billion restaurant industry is collapsing, raising questions about the economic security of the nation’s food supply industry in the time of COVID-19.
Dairy farms are already seeing the effects of nationwide school and restaurant closures in the wake of the coronavirus.
About one half of the normal demand for dairy has disappeared since the start of the United States’ social isolation period.
As a result, dairy farmers have had to throw out thousands of pounds of excess milk.
The agricultural side of the farming industry faces similar threats.
Food distributors and wholesalers are scrambling to redirect products from restaurants and other affected businesses to grocery stores.
But grocery stores desire different things than restaurants and schools, making it difficult to fully solve the problem.
Meanwhile, farm suppliers are racing to ship out fertilizers, seeds, and chemicals before the deadly virus disrupts the truck delivery industry.
Without these essential supplies, agriculture farmers won’t be able to produce enough food to meet demand in the States, especially as trade with other countries decreases.
The result could be a wide-scale food shortage.
Labor is also threatening agriculture as many field workers cannot afford to take time off, increasing potential for rapid spread throughout farms.
It’s a problem threatening to cause a significant labor shortage, lowering production and contributing to a potential food shortage.
Experts predict that our food security this fall and next year will be determined by how well these next harvests go.
With shortages in the food supply comes price gouging, leaving the world’s most vulnerable even more so.
The price of global food staples such as wheat and rice are already rising worldwide. Meanwhile, egg prices reached a record high in the US, as grocery stores reported a demand of six times the normal amount.
With more and more people facing unemployment and economic insecurity due to the effects of the global pandemic, increased food prices can make food insecurity worse.
Food security refers to the ability to obtain affordable, nutritious food.
In 2018, 5.6 million households in the US had very low food security.
Plus, as safety concerns skyrocket, consumers are becoming more conscious of how many hands have touched the food they’re about to take home and eat.
As a result, at-home solutions are seeming more appealing.
Since the beginning of March, Google searches for words related to “gardening” and “hydroponics” have increased.
In this time of uncertainty, small-scale indoor farming, like container farms, could prove to be an emergency solution.
Container farms are small indoor farms built inside of repurposed shipping containers.
They have the potential to easily provide food to urban areas, which tend to have the highest populations of food-insecure households, as they don’t require any farmland, only electricity, water, and internet connections.
Container farms also won’t be too affected by labor problems, as they’re fairly self-sufficient, meaning it doesn’t require too many laborers to ensure a bountiful harvest.
Higher tech containers, like our Pure Greens Container Farms, use controlled environment agriculture technology that’s automated and controllable through a smartphone app.
This allows for a more hands-off approach than traditional agriculture.
It also means the growing environment simulates perfect conditions for crops, resulting in more consistent and reliable yields.
Container farms are also able to yield quite a lot while being compact in size, which could help ease some of the burden of a global food shortage.
We’ll have to wait to see how well the agriculture industry adjusts to the pandemic, but it’s worth it to be proactive by looking into possible solutions as soon as possible.
If you’re interested in learning more about starting your own container farm, visit our website or call us at 602–753–3469 to get started!
WRITTEN BY Pure Greens Arizona LLC
Pure Greens’ container-based grow systems offer a variety of interior layouts, sizes, and options so customers can create a farm that meets their needs.
Tags: Container Farming Farming Covid 19
Clawson Greens Supplies This Snowy Tourist Town With Local Produce, Year-Round
Dave Ridill of Clawson Greens shares his farming unique experiences farming in snowy Tetonia, Idaho.
March 17, 2020
Dave Ridill of Clawson Greens shares his farming unique experiences farming in snowy Tetonia, Idaho.
Dave Ridill from Clawson Greens has made the impossible possible: in an area with a growing season that lasts less than three months (and is known for avalanches!), he has created a thriving year-round farming business that keeps surrounding restaurants flush with fresh greens even in the snowiest weather.
Download our interview with Dave to hear about his experiences!
CLAWSON GREENS WEBINAR
Or, keep reading to a re-cap of the webinar and Q&A with Dave.
Photo by Camrin Dengel, Teton Valley Magazine
Freight Farms: What’s the story behind your Freight Farms project?
Photo by Camrin Dengel, Teton Valley Magazine
Dave Ridill: Long story, short–my neighbors discovered Freight Farms while doing consulting work for Yosemite National Park. They were putting together a proposal for Yosemite to cut down on transportation costs and offer a new plan for food options inside the park. Yosemite didn’t end up going with their bid, so they approached me about starting a hydroponic farm business together. At the time, I was in the process of moving to Boston to go to paramedic school. However, after visiting Freight Farms, I decided to leave the Fire Department, where I was working at the time, and become a lettuce farmer.
FF: Who do you sell to and how do you do it?
DR: Our business model was focused on the restaurants in both Teton Valley and Jackson Hole, Idaho. The restaurant industry in our tourist town is booming. Despite highs and lows with seasonality, restaurants were the main focus in the inception of Clawson Greens.
We also tried a direct to consumer route (CSA) and the local natural food store. Due to time and labor increase, the CSA was not as profitable. We also have a very strong farmers market in both Teton Valley and Jackson so there was never a plan to try and compete with our local farmers. With an 85 day growing season, the local organic farmers already have a very short growing/selling season so adding another vendor to that market would just dilute an already competitive and small market. Our focus was on a market that no other local grower could tap into, year-round tourism.
“Our focus was on a market that no other local grower could tap into, year-round tourism.”
— Dave Ridill
FF: Do you find that customers are willing to pay more for your premium product?
DR: This question reminds me of a meeting with the restaurant manager of our local pub. We sat down and looked over a year’s worth of invoices from his distributors and the price fluctuation that the seasons had. We also looked at his total costs after he factored in waste due to buying in bulk to get the best pricing. With price changes and waste, my higher-priced product that I guarantee was not much more expensive than Sysco.
What I’m trying to say, is chefs will choose fresh local ingredients any day over large scale commercial produce. For them, it’s a selling opportunity: They market it by advertising the local farms/producers on their menus and have servers talk about the local products which are used in the specials. Consumers are willing to pay more for quality and to support local businesses.
“Chefs will choose fresh and local ingredients over large scale commercial produce any day. ”
Photo by Camrin Dengel, Teton Valley Magazine
— Dave Ridill
FF: How do you package your crops?
DR: From the start, Clawson Greens has made a point to not use single-use plastic clamshells or plastic bags. We use compostable corn-based bags for all our deliveries. On average, I put about 30 mini heads into 23-gallon compostable bags.
FF: What was the most challenging part of becoming a Freight Farmer and how were you able to overcome it?
DR: Becoming a Freight Farmer has many challenges much like starting any new business. There’s a steep learning curve but I enjoyed that process. The hardest part for me was understanding when to expand and how to grow with the business as it expanded. It was easy to transition from a full-time ski patroller to a part-time patrol/part-time farmer. However, as I added farms to grow the business, I found it hard to dive in and become a full-time farmer and business owner.
Being thrown into the deep end of the pool overnight was the hardest and easiest way to become a business owner. When your only option is to sink or swim, you do everything you can to make it work. Failure was never an option so by taking that off the table, you’ve got one direction, forward!
Implementing the ‘Profit First’ system is what really changed Clawson Greens. I went from a business that had money in the business account and was blindly throwing money around to pay bills, payroll and occasionally paying myself, to a business that knows exactly how much money to put towards operational expenses, taxes, owners’ compensation and most importantly, profit!
Photo by Camrin Dengel, Teton Valley Magazine
FF: What’s the best piece of advice you can give to people interested in becoming Freight Farmers?
DR: My advice is to hire the right people and acknowledge that you (the owner and operator) deserve to be paid accordingly.
“You are the one who puts in the most time, works late, lays awake at night thinking about the business.”
— Dave Ridill
This is where the profit-first system comes into play again. Being a farmer is hard, being a business owner is even harder. Being the owner and operator of a Freight Farm is very challenging and making a living at it can be a huge challenge. You can hire great employees but they will never go the extra mile that you the owner does. Over the past few years as an employer I’ve learned that you can teach people skills and procedures, but you can’t teach someone to care about your business. Only you can do that: you are the one who puts in the most time, works late, lays awake at night thinking about the business and at the end of the day, is the one who answers to whether the business is a success or failure. You need to pay yourself accordingly. Don’t start a business to make a living for someone else until you can make a living for yourself. When you are ready to start hiring, find an employee that’s financially invested in the business. Their effort and quality of work has a direct impact on their income
Interested in learning more about Clawson Greens?
Hear how Dave created his thriving farming business in some of the harshest conditions in the U.S. when you sign up for our upcoming webinar!
SIGN UP
Coronavirus Is Teaching Us That Our Supply Chain Is Flawed
America’s supermarkets are the tip of an enormous iceberg that represents a complicated logistics network. On a good day, this system works
The world is unpredictable–the past few months have made this abundantly clear. Since January 2020, the global community has had to grapple with the unprecedented COVID-19 pandemic. The virus’s trajectory has been closely followed by drastic and disruptive measures around the world. Words like “social distancing”, “shelter in place”, and “quarantine” are new additions to our common lexicon and everyday reality. Businesses are shuttered, schools are closed, and the global economy is wobbling dangerously.
For many, a trip to the grocery stores represents one of the last ties to normalcy–and a needed break from the cabin fever of lockdown. But even in this essential industry, long-hidden cracks are beginning to show. Panic buying has brought on the near extinction of many familiar products (toilet paper, cleaning supplies, hand sanitizer) and the endangerment of several kitchen staples (chicken, baking goods, and, increasingly, fresh produce).
As the pandemic exacerbates the issues in our global food system, we wanted to understand why the system is failing, and how we can build a more resilient one in the future.
Complete Story Here
Is Containerized Blackberry Production-Ready For Prime Time? By e-GRO
Growing small fruit crops in containers requires additional capital and effort compared to field production, but has some potential benefits
By urbanagnews
April 6, 2020
Ryan Dickson and Leala Machesney
University of Arkansas
Blackberries and other small fruits are increasingly being grown in soilless substrate and containers versus field soil.
Growing small fruit crops in containers requires additional capital and effort compared to field production, but has some potential benefits.
e-gro Edible Alert: Containerized Blackberry Production
Download
Freight Farms Expands Leadership Team with New CEO and Head of Engineering as Business Scales to Meet Growing Global Interest in Decentralized Food Production
Freight Farms, the global innovation leader of containerized vertical farming with the world’s largest network of IoT-connected farms, announces today that it has hired veteran consumer brand executive Rick Vanzura as CEO who will also join the company’s Board of Directors, while cofounder Brad McNamara will remain as Freight Farms’ President
Freight Farms Produce March 27, 2020
BOSTON — Freight Farms, the global innovation leader of containerized vertical farming with the world’s largest network of IoT-connected farms, announces today that it has hired veteran consumer brand executive Rick Vanzura as CEO who will also join the company’s Board of Directors, while cofounder Brad McNamara will remain as Freight Farms’ President. The company also welcomes automation and robotics specialist Jake Felser as Head of Engineering.
The need to simplify supply chains and ensure reliable access to healthy, traceable food at a local level has become more crucial for communities worldwide. Expansion of Freight Farms’ team follows a year of strong momentum for the company as forward-thinking organizations, particularly at the institutional level, recognize the benefits of a secure, distributed, and transparent food supply. As the company scales for growing demand at speed, expansion of Freight Farms’ leadership is positioned to quicken new extensions of its technology platform and deepen market reach.
“What excites me about Freight Farms is the ability to join a passionate, mission-driven business that is already perfectly positioned to address the growing critical need for sustainable, hyper-local food production,” says Vanzura. “Freight Farms has an incredible technology platform as the originator of container farming, as well as a global footprint driving numerous sources of value. Beyond providing a meaningful solution across industries, Freight Farms’ innovation addresses issues like urban land scarcity, traceability and the need for hyper-local solutions with speed to market. The current environment demonstrates more than ever the value of Freight Farms’ offerings.”
Vanzura has driven value for companies from start-up to Fortune 5 across technology, restaurant, retail, and entertainment sectors. With a focus on leveraging innovation and developing new market channels, he led strategy for Panera, General Motors Information Services and GameStop, and as the original CEO of Wahlburgers, he built the company from a single unit into one of America’s fastest-growing restaurant brands. Vanzura’s 20 years in President and C-level roles include a decade in food service working with markets central to Freight Farms’ business. He also brings significant international experience to his role, having run Borders Group’s nearly $1 billion International business.
“As cofounders, Jon Friedman and I have taken Freight Farms from an idea to help decentralize the food system to being the leader in containerized vertical farming that’s truly putting the power of hyper-local food production into people’s hands,” said McNamara. “Rick has amplified growth across interconnected industries, and his international experience lends itself to our ongoing global expansion. His personal alignment with Freight Farms’ mission was crucial for us as well—he’s a welcomed addition to the team as we scale.”
“The potential is extraordinary,” Vanzura added, “I’m excited to be working with Brad, Jon and the team on the spectacular opportunities ahead, all while doing our part to help build a better, more sustainable food system for all.”
Jake Felser, former VP of Engineering for eatsa (now Brightloom), has also joined the Freight Farms team as Head of Engineering. With teams across hardware and software, Felser led robotics R&D and the development of eatsa’s shelf-style pickup system from conception to deployment across the company’s network of partners. Prior to eatsa, Felser was Senior Engineer and Product Manager at Cooper Perkins and has worked in hydraulics, refrigeration, structural optimization, design for development, and agriculture for companies including Blue Origin, Promethean Power Systems, and AGCO. With a passion for sustainable development, Felser is focused on automation, IoT, and machine learning-based integrations for Freight Farms growing technology portfolio.
Company growth, including ten new roles across all departments in Q1, also follows Freight Farms’ recent launch of the Greenery. Nearly 100 have been adopted by customers in 9 countries to date, bringing Freight Farms’ global footprint to more than 300 container farms around the world. The innovation also spurred interest from Sodexo in a strategic national partnership to grow food onsite at educational and corporate campuses nationwide and new investment from Ospraie Ag Science.
About Freight Farms
Founded in 2010, Freight Farms debuted the first vertical hydroponic farm built inside an intermodal shipping container—the Leafy Green Machine—with the mission of democratizing and decentralizing the local production of fresh, healthy food. Now with the Greenery and integral IoT data platform, farmhand®, its technology empowers people anywhere in the world to grow more than 500 varieties of pesticide and herbicide-free produce, from leafy greens and herbs to root vegetables and vine crops, with 99.8% less water—onsite, year-round. Freight Farms’ network of IoT-connected container farms is the largest in the world, with more than 300 operating in 25 countries and 44 U.S. states. Customers range from small business farmers to the corporate, hospitality, retail, education, and nonprofit sectors.
To learn more, please visit freightfarms.com,