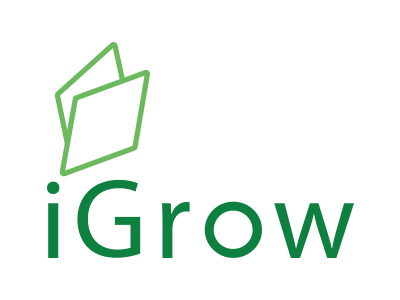
Welcome to iGrow News, Your Source for the World of Indoor Vertical Farming
What Are Novel Farming Systems?
What Are Novel Farming Systems?
AUGUST 29, 2017 | LOUISA BURWOOD-TAYLOR AND EMMA COSGROVE
Novel farming systems are new methods of farming living ingredients, many of which are traditionally grown outdoors.
Consumers are scrutinizing the agrifood industry more than ever for its widespread use of natural resources such as water and arable land, and for its negative impact on the environment. The agrifood sector is neck and neck with heating and cooling as the global industry producing the most greenhouse gases. Industrial farming can also have a damaging environmental impact with the application of chemicals and fertilizers contributing to soil degradation, drinking water contamination, and run off harming local ecosystems.
As a planet, we are also faced with the challenge of increasing food production despite decreasingly nutrient-dense soil and a warming planet. While some are attempting to lessen the extractive nature of conventional farming in soil, or to create seeds and crops that can thrive in these new conditions, others are working on removing land and soil from the equation altogether.
To alleviate these pressures, startups and innovators are finding new ways to produce food and ingredients with novel farming systems in the hope of doing so more sustainably, using fewer natural resources.
Further, many novel farming systems focus on the farming of fish, insects, and algae which have the potential to alleviate the environmental pressure of increasing global demand for protein, where cattle farming is bearing the majority of the burden.
Novel farming systems have also emerged as a captivating solution in the eyes of the public and investors precisely because they could change the paradigm of traditional agriculture so dramatically. Though, as we will explore in our upcoming agrifood tech investing report, public and media excitement are not always met with equal investment.
Novel farming systems, as a category of agrifood tech, includes:
- Indoor farms — growing produce in hi-tech greenhouses and vertical farms
- Insect farms — producing protein alternatives for animal and aquaculture feed and for human food
- Aquaculture — producing seafood and sea vegetables including algae
- New living ingredients such as microbes for use in food, as well as for other industries and applications
- Home-based consumer systems using the technology of any of the above
Here is a closer look at the components of our novel farming systems category of startups ahead of the AgFunder MidYear AgriFood Tech Investing Report.
Controlled Environment Agriculture (CEA) or Indoor Agriculture
The concept of farming indoors in not new; greenhouses have been around for centuries. But in recent years, greenhouses and more insulated indoor spaces like warehouses and shipping containers are rapidly picking up pace as a means to grow food closer to consumers, remove many of the unpredictabilities of outdoor agriculture, and drastically reduce the inputs necessary for outdoor farming.
There are only a few key ingredients needed to grow food: light, water, and nutrition. By growing food in a controlled environment, indoor farmers aim to give plants the perfect amount of each, reducing waste, but also maximizing yields. They can also manipulate the doses of each of these ingredients to impact flavor, color, and texture.
Tomatoes, strawberries, peppers, leafy greens, herbs, flowers, and cannabis are all frequently grown in controlled environments. Greenhouses specifically are also an important part of the tree crops industry as most rootstock starts in a greenhouse.
By some estimates, there are more than 40,000 indoor farming operations in the US alone, producing food worth more than $14.8 billion in annual market value. These numbers exclude the cannabis industry, which brings in an additional $6.7 billion in sales.
The different configurations of CEA include greenhouses and indoor vertical farms, and within these two categories, there is much variation in terms of physical growing structures and architecture, delivery systems for light, water, and nutrients, light source, growing medium, automation, data collection, and environmental controls.
Greenhouses
Greenhouses are covered structures made of glass or plastic that allow sunlight to get in but offer varying degrees of temperature control. They have been used commercially to grow fruits and vegetables for decades, but there are various ways greenhouse technology is being used today beyond its simplest form of growing plants under glass in pots of soil.
Soilless hydroponic growing systems — where the plants are grown in a watery medium as opposed to soil — have been used in greenhouses for more than a decade by major growers like Village Farms and Backyard Farms. And today, computer vision, artificial intelligence, automation, and precision agriculture techniques are arriving at the greenhouse. Some greenhouses are fully kitted-out with sensors using machine learning to detect disease, facilitate efficient use of space, and identify anomalies both within the environment and with individual plants.
Some greenhouse technology has come a particularly long way, with incidences of hybrid greenhouse and indoor operations growing cannabis, like Supreme Pharmaceuticals, as well as innovative locations — like Gotham Greens above Whole Foods in Brooklyn, New York — and business models.
Main greenhouse crops today include lettuces and, leafy and micro greens, tomatoes, peppers, and cannabis.
Vertical Farms
Ranging from as small as a shipping container to as large as an airplane hanger, indoor vertical farms are growing steadily in number, although some have already failed in what’s a capital intensive field.
Most operating vertical farms today are growing only leafy greens and microgreens due to the short growing cycles and high yields. There are a few growing strawberries such as Japan’s Ichigo Company.
Vertical farms use LED lights for photosynthesis and some form of hydroponics for water and nutrition. The fairly simple equation is nutrient-enriched water, moved either in a mist or through channels or tanks around the roots of plants. The roots are planted in various media ranging from spun concrete to coconut husks to cloth, which are submerged in the water or mist.
Every one of the elements involved in growing the plants can be manipulated precisely to influence the outcome — such as lighting wavelengths, timing, the types of nutrients, and so on. This can be particularly effective if sophisticated data collection and analytics are in place; many farms claim that their own internally-created software and hardware tools enabling this are their main differentiator.
The largest vertical farms by capital raised include AeroFarms, Bowery Farming, and Plenty which are all starting to use artificial intelligence and machine learning to manage their plants and boost yields.
Robotics are also slowly making their way into indoor agriculture, though they are currently only used for crops that grow in containers such as rootstock for apple, cherry, and almond trees, and in these cases, the robots move the containers as opposed to more complicated tasks. But fruit-picking and sorting robots are on the way with several startups in the space making advancements and raising funding. (Stay tuned for our Farm Robotics deep-dive article coming soon!)
Aquaponics
Aquaponics is a smaller subset of indoor farming where farmers grow vegetables integrated with, and on top of, fish farms, so that the waste generated by the fish can fertilize the plants. The technology set up is very similar to a vertical farm, but the monitoring of the input composition and the physical layout differ greatly from operations purchasing plant nutrition. Aquaponics operations, like Edenworks in New York and Organic Nutrition in Florida, sell both vegetables and fish.
Aquaculture
Aquaculture is the cultivation of sea creatures and vegetables for human and animal consumption.
According to United Nations Food and Agriculture Organization data from 2010, aquaculture makes up half of the seafood consumed by humans today. This includes the farming of all varieties of fish, along with oysters, scallops, shrimp, mussels, and other shelled creatures. Most of the innovation in this space is currently geared towards fish feed for farmed fish rather than the technology used at the farms themselves. Fish feed is a particularly crucial challenge as currently 30 million tons of wild caught fish per year are used to feed farmed fish, which is a third of global wild fish harvest. With global stocks of wild fish declining, and some sources pointing to the crash in some forage fish populations, this is an unsustainable source of food for farm-raised fish long-term, even with increasingly sustainable practices employed by the fishmeal and fish oil industry. This problem, valued at $100 billion, will likely be solved at least in part by some of the other types of novel farming systems listed here, especially insect farming.
Algae farming represents an underdeveloped sector within novel farming systems but has great market potential. It has been estimated that the algae market will reach $45 billion by 2023 and algae, especially macro algae like edible seaweeds, are farmed in most cases completely without technology or digitalization. Macroalgae can be grown in open water as well as in tanks while most microalgae, which are single-celled, must be grown in a controlled setting. Algae farming startup EnerGaia is growing spirulina (microalgae) on rooftops in Bangkok, Thailand.
Microbe farming
Microbe farming is another emerging field with various applications. Ginkgo Bioworks, for example, genetically engineers microbes for partner companies in the flavor, fragrance and food industries. These microbes are primarily forms of yeast or bacteria that can be designed to replace a natural alternative; rose oil, for example, would be expensive for some companies to manufacture as an ingredient given that roses are not a commodity crop. But Ginkgo can manufacture that fragrance or flavor in-house by writing new DNA code to re-program the genome of a microbe to have it do what customers want. These DNA designs are proprietary to Gingko, as well as the robotics and other technology the company uses to culture the microbes, mostly through a fermentation process. Zymergen and Novozymes are other startups growing microbes, in these cases to make agricultural inputs.
Insect & worm farming
Insects and worms are set to become an increasingly important protein source for both animals and humans with demand far outpacing supply. Insect farming is mainly touted as a more sustainable alternative to animal protein, particularly as the quality of the protein insects offer is actually quite high. According to the Food and Agriculture Organization of the UN (FAO), “insects have a high food conversion rate, e.g., crickets need six times less feed than cattle, four times less than sheep, and twice less than pigs and broiler chickens to produce the same amount of protein.” Further, insects require very little land or energy to produce, and they can be produced quickly and all year round, unlike other animal feedstock such as soybeans. Insects can serve as a protein-rich substitute for the aforementioned wild-caught fish that are often used as aquaculture inputs, potentially turning aquaculture into a sustainable solution to overfishing. Netherlands-based Protix makes animal and fish feed as well as fertilizer from black soldier flies.
Crickets, fruit flies, grasshoppers, and mealworms are all also being cultivated for inclusion in consumer products in this nascent industry. Grasshopper farms like Israel’s Hargol, are racing to get their production capacity up since the demand for alternative proteins for both animals and humans remains much higher than current supply. While very secretive about their designs, many insect farming groups claim to have very high-tech operations using robotics, to create automated insect farming factories, such as Ynsect in France.
Consumer growing systems
Home paramours for almost every novel growing system exist, whether or not they’ve gone mainstream (yes even insect farms). Tabletop hydroponic systems like Plantui, aquaponic systems that have decorative fishtanks topped with produce like Grove, and even mini refrigerator-sized growing towers like Hydro Grow, are available for the shortest farm-to-table experience out there.
Philips Lighting Horticulture LED Solutions adds BWI Grower Technical Sales to North America Partner Network
“We recognize the value of partnering with well-established horticulture suppliers and manufacturers to support our efforts to bring Philips Horticulture LED to greenhouse growers in a highly efficient manner,” said Ron DeKok, Philips Horticulture LED Business Development Director.
September 8, 2017
Philips Lighting Horticulture LED Solutions adds BWI Grower Technical Sales to North America Partner Network
Eindhoven, The Netherlands – Philips Lighting (Euronext Amsterdam ticker: LIGHT), a global leader in lighting, has signed a partnership agreement with BWI Grower Technical Sales. BWI Grower Technical Sales, a division of BWI Companies, provides BWI customers with technical sales and support in the areas of greenhouse design and construction, irrigation design, automation, and greenhouse equipment. With the addition of the Philips Lighting Horticulture LED product offering, BWI Grower Technical Sales can now bring to their customers a broader offering of technical solutions.
“We recognize the value of partnering with well-established horticulture suppliers and manufacturers to support our efforts to bring Philips Horticulture LED to greenhouse growers in a highly efficient manner,” said Ron DeKok, Philips Horticulture LED Business Development Director. “BWI is a well-established supplier in the south and southwestern United States. Now, with the addition of Philips Horticulture LEDs to their product offering, the Grower Technical Sales division can offer a more complete package of technical products and services to their customers. And with the depth of BWI’s technical expertise, the partnership between Philips Lighting and BWI is a great fit and will help customers of BWI capitalize on the many benefits that come with growing under LEDs.”
About Philips Lighting
Philips Lighting (Euronext Amsterdam ticker: LIGHT), a global leader in lighting products, systems and services, delivers innovations that unlock business value, providing rich user experiences that help improve lives. Serving professional and consumer markets, we lead the industry in leveraging the Internet of Things to transform homes, buildings and urban spaces. With 2016 sales of EUR 7.1 billion, we have approximately 34,000 employees in over 70 countries. News from Philips Lighting is located at the Newsroom, Twitter and LinkedIn. Information for investors can be found on the Investor Relations page.
About BWI
Founded in 1958, BWI Companies currently distributes products and services for numerous segments, both wholesale and retail, in the horticulture industry including greenhouse growers, nursery growers, garden centers, and more in the mid-south and southeastern United States. The Grower Technical Sales (GTS) division is focused exclusively on technology solutions for greenhouse growers and includes greenhouses, irrigation, equipment, automation, coverings, chemical applicators and greenhouse lighting.
Wisconsin Indoor Fish Farm Uses Water for Greenhouse
Wisconsin Indoor Fish Farm Uses Water for Greenhouse
Sept. 1, 2017, at 12:04 p.m.
Wisconsin Indoor Fish Farm Uses Water for Greenhouse
NORTHFIELD, Wis. (AP) — A new fish farm and greenhouse operation in western Wisconsin is promising to change the seafood industry with its indoor aqua-hydroponics system.
The Leader-Telegram reports that fish farm-greenhouse enterprise Superior Fresh in Northfield opened its indoor Atlantic salmon farm Thursday.
The 1-acre fish farm can produce up to 120,000 pounds (55 metric tons) of Atlantic salmon and 40,000 pounds (18 metric tons) of rainbow trout each year.
The nutrient-rich water that the fish create is transported to a nearby 123,000-square-foot greenhouse to help grow leafy greens. At full production, the farm is expected to grow about 2 million pounds (907 metric tons) of fresh greens annually.
The operation holds about 1.4 million gallons of water.
Company chief operating officer Brandon Gottsacker says the enterprise needed a nearly $20 million investment.
Information from: Leader-Telegram, http://www.leadertelegram.com/
Copyright 2017 The Associated Press. All rights reserved. This material may not be published, broadcast, rewritten or redistributed.
Aquaponics Farmers Band Together to Set Their Industry Apart
Aquaponics Farmers Band Together to Set Their Industry Apart
Growers that add fish to their vegetable mix say they're combining the benefits of an ecosystem with the resource-efficiency of an water-based operation.
BY LELA NARGI | Agroecology, Climate, FARMING, Seafood
08.30.17
Kimberly Aney, a recent graduate of the agriculture program at SUNY Cobleskill in Upstate New York, has dreams of building a small farm that grows fish and lettuce in concert with one another. She says she sees the practice, known as aquaponics, as a cheap, clean, and compact alternative to the inefficiencies she observed on the dairy farm on which she grew up.
In southern Oregon, Michael Hasey extends the growing season of his 40-acre organic farm with an aquaponics system that produces greens and tilapia throughout the winter. It’s a way to squeak out an extra margin, rest his fields, and, he believes, improve both his own soil and the environment at large.
And, in New Orleans, Marianne Cufone uses her in-ground aquaponics system—in which ponds full of fish provide nutrients for the trays of herbs, cucumbers, and melons floating above them, and vice versa—partly as an educational tool. She wants more people to know about the myriad benefits she’s reaped while farming this way: about the hyper-local crops, the reliable fresh food in flood-prone regions, and the minimal waste inherent in the system.
Diagram courtesy of Aquaponics Phillipines. (Click image for a larger version.)
Unlike modern hydroponic farms, which can feed plants regular quantities of synthetic fertilizers, aquaponics harks back to early growing methods developed in Asia and South America that blend aquaculture (or fish farming) with agriculture. The practice functions in an ecosystem in which the fish eat things like duckweed and, when they’re housed outside, insects; their waste feeds the plants; and the plants filter the water for the fish. Any remaining waste is composted and, as in the case of Hasey’s farm, added back to the soil in which he grows his row crops.
Cufone also has a larger goal. What began as a community-based mission has expanded into a national effort as she seeks to drum up awareness about aquaponic farming in her role as executive director of the Recirculating Farms Coalition (RFC), and to mobilize other farmers using the technology to become more vocal about its virtues and its future.
First, though, she has to find them.
Marianne Cufone. (Photo by Dulce Fernandes)
“Even though [aquaponic farmers] have been operating in the U.S. for more than 30 years, we don’t have a good count,” Cufone says. That applies both to commercial operations such as Hasey’s that sell to regional supermarkets and also to backyard, or “recreational,” farms like the one Aney would like to set up. The latter are especially difficult to track. RFC wants to see aquaculture acknowledged as a positive addition to American agriculture and thereby boost its lobbying power. Haney, an RFC member, calls aquaponics, “the answer” to generating year-round income for farmers constrained by the seasons.
Cufone is currently working on a map of the larger outfits, and reaching out to organizations that keep track of the smaller ones. So far, estimates put the number of commercial aquafarms operating nationally at between 40 and 100, although Cufone says it’s likely higher if one includes backyard operations.
Cufone’s work comes at a critical juncture for American aquaculture. For over a decade, the USDA Organic label, through some third-party licensing organizations like Oregon Tilth, has been conferred upon compliant aquaponic and hydroponic farms. Recently, traditional “dirt first” organic farmers have been pushing the USDA’s National Organic Standards Board (NOSB) to make aquaponics and hydroponics ineligible for the Organic label.
Some opposed to the change, such as Maine farmer and author Eliot Coleman, say that food that isn’t grown in “biologically active, fertile soil” doesn’t deserve to use the moniker for which generations of farmers have built up a market.
One of the biggest targets of some dirt-first lobbyists is scaled-up operations that raise hydroponic produce in places like Mexico. They say these vast international operations siphon off revenue from American farmers as they drive down the price of organics. Aquaponic farmers, who claim to use best organic practices and challenge the assertion that their farms do not give back directly to the soil, may be caught in the crossfire of a bigger, thornier debate.
“Aquaponic farmers employ microbiology in their systems, in the same way dirt farmers do, and the waste [from it] builds beautiful topsoil,” says Hasey. In the process, “We grow copious amounts of food without taxing the land. It’s incredibly sustainable.” Sustainability is also Cufone’s virtue of choice when discussing aquaponics—both for lowering water and energy usage in produce growing as well as for raising fish. Cufone began her career in fisheries management and has seen aquaponics develop to the point where she thinks it now provides a viable, clean way for fishermen to grow some of the protein they can no longer catch in depleted oceans.
Stacy Tollefson is a professor of agricultural and biosystems engineering at the University of Arizona. Along with Cufone, she was part of the most recent task force advising NOSB on the organic certification of aquaponic and hydroponic farms. The way she sees it, what organics-seeking consumers want most of all is pesticide-free produce.
And water-based systems “open the doors to more people getting access to that,” she says. “The traditional agriculture approach says organics have to be grown in soil—but that was when there was no other way to do it. There are still old-school philosophical folks who say, ‘You’re not saving the soil!’ But I think we are doing a lot to not damage the earth.” (The dirt first response to this: That still doesn’t mean it fits the historical definition of organic; they’re contemplating changing their own labeling if hydroponic and aquaponic farmers continue to be able to earn “organic” status.)
Cufone agrees with Tollefson, and also cites what she sees as another overlooked benefit to aquaponics. “The U.S. Department of Agriculture is always talking about attracting new people to farming. Well, this is one part of the industry that’s growing,” she says. She hopes RFC will play a pivotal role in bringing aquaponics further into the mainstream. “When I first learned about recirculating systems, I brought a bunch of people together in a room and had a conversation about the viability of the industry. At the end of two days I asked, ‘If you had $1 million, what would you do?’ And every one of them said, ‘Start an organization that would advertise our industry, and help change policy about it.’”
In the six years since RFC was founded, Hasey has come to rely on it to represent him and his needs. “As a farmer, I spend all day with my head in the plants. I just don’t have time to go out and campaign and get involved in issues,” he says. Both he and Cufone hope the organization will provide their segment of the farm industry with the necessary traction to grow, and thrive.
Top photo courtesy of Recirculating Farms Coalition.
Safe Water Sources For Hydroponic Food Production
Safe Water Sources For Hydroponic Food Production
Whether using municipal or well water, monitoring and testing are important to ensure successful production of greenhouse hydroponic lettuce and leafy greens.
An increasing number of ornamental plant growers are looking to take advantage of the growing interest in local food sales by expanding their production with seasonal crops of lettuce, leafy greens and herbs. Unlike ornamental plants, growers of edible crops have the added concerns of food safety.
“If growers are using municipal water for growing ornamental crops and then add lettuces and leafy greens, there should be no concerns related to water quality from the standpoint of human pathogens that might be associated with surface water,” said horticulture professor Sarah White at Clemson University. “There are pH issues associated with municipal water because most municipal water is neutral or alkaline to prevent the corrosion of pipes. Ornamental growers would likely need to acidify their water if the pH is above 7.5, especially for leafy greens and lettuces. These growers may already be acidifying their water for the ornamental plants they are producing.
“For new growers who are planning on using municipal water, they need to know what the water pH is. Because the pH is likely to shift during the year, growers need to be cognizant of the shifting pH and how injecting acid needs to be responsive to these changes. Some bedding plant crops may require more or less acid injection than lettuces and leafy greens.”
White said most municipal water sources are drawn from surface water reservoirs, which can cause some seasonal variation in water pH.
“Usually during the winter the water source quality is consistent,” she said. “If growers are producing during the winter and carrying production into spring there might be some changes in the water source that can affect the pH.
Ornamental plant growers using municipal water who add lettuces and leafy greens should not be concerned with water quality from the standpoint of human pathogens.
Photo courtesy of Tyler Baras, Hort Americas
“Regardless of whether growers are producing lettuce and leafy greens in nutrient film technique (NFT) or deep water raft systems, they need to actively monitor pH year round. There are Bluetooth pH meters that can be stuck into a water source that will log pH. It’s easy to do. Growers should monitor and track their pH and know what they have to do to adjust it.”
White said for ornamental growers looking to add lettuces and leafy greens, it isn’t going to matter what type of acid is used to lower the water pH.
“Growers should be able to use the same acid for both ornamental and edible crops,” she said. “Usually they pick an acid based on the cost. If they are going to adjust the water pH they should inject fertilizers after the water pH has been adjusted.”
White said municipal water usually has a pH of 7.5 to 8. Most plants grow best at a pH of 6 to 6.5.
“Nutrient availability changes with different pH,” she said. “That is why the pH needs to be adjusted in order for the nutrients in the water to be available to the plants.”
White recommends if growers have never produced lettuces and leafy greens that they monitor the water pH more often.
“If growers don’t know how sensitive these new crops are to pH, they might try doing some trials with lettuces, leafy greens or herbs,” she said. “This will enable growers to determine the best pH for producing these new crops before they invest in filling a whole greenhouse.”
Adjusting water alkalinity
White said depending on where growing operations are located in the country, municipal water sources can have different alkalinities.
“In some western states and coastal regions of the United States, alkalinity issues are more likely,” she said. “In locations with higher alkalinity, more acid is required to get the water pH to the desired range for crop production. A lot of plants don’t do well with high alkalinity vs. low alkalinity. If the pH is being adjusted by injecting acid this coincidentally manages the alkalinity level as well. It typically requires more acid to accomplish the same pH change in water with higher alkalinity. Water that has high alkalinity will also have a high pH.
“If growers have a water source that is highly alkaline in a certain region of the country, chances are it won’t matter what source growers pull from because there are going to be alkalinity issues. The only thing they could do differently is if they capture rain water, filter it, and then blend it with their other water source.”
A rapid sand filter removes organic matter and other debris that might get into recycled irrigation water. This filter might remove some disease organisms, but it’s not 100 percent.
Photo courtesy of Sarah White, Clemson Univ.
Well water
White said well water is the most common water source used by growers.
“We have done two surveys in the last 10 years and about 65 percent of all growers indicated they use well water,” she said. “The reason is because it is a clean water source and there are not usually any issues with plant diseases. The contaminants that most growers might encounter are salinity and iron. If growers have a lot of salts in their water, how it is managed becomes very critical. Many Southwestern growers deal with this issue.”
White said water with a high salt level can be caused by a mix of elements and it is regionally specific.
“Sodium, chloride, calcium and magnesium are the biggest contributors to high salinity water sources,” she said. “If growers are having high salt issues, it’s probably caused by chlorine or sodium. Growers can manage fertilizers to help balance the high salts.”
White said the other contaminant growers might find in well water is iron depending on the region of the country where they are located.
“There are typically problems with iron and iron-oxidizing bacteria associated with well water use. If there is iron in the water, growers should aerate it before they use it. Aerating the water oxidizes the iron so that it precipitates out. The aeration should be done before the water goes into the fertilizer tank and before growers start adding salts. Once fertilizers begin to be added it might be more difficult to remove the iron.”
White said the pH for well water is usually in a good range for growing plants. She said growers should still test the pH of their water.
“If growers are drawing from a salty water source, chances are they are going to have alkalinity and pH issues. If growers are using salty water sources on ornamental plants and decide to try growing lettuces, leafy greens and herbs, whether they can use that water and how it is being treated will depend on the type of ornamental plants being grown. Some ornamental plants tolerate salts more than others. Growers may not have to do much to bring the salts to an acceptable level for lettuces, leafy greens and herbs.”
White said most growers won’t put in a reverse osmosis system to remove high salts because of the high cost associated with the equipment and having to manage it along with the waste water it produces.
“Growers are more likely to manage high salts by blending water sources, by heavily irrigating the crops or by their choice of which plants to grow,” she said. “Growers may want to use a municipal water source to blend with well water so that salts are at a manageable level for the plants. I highly recommend that growers get water quality analyses done periodically. They should also have an inline monitoring system if they chemically treat the water so that they know the real-time pH and salinity (electric conductivity is a proxy) levels of their water.”
Growers concerned with plant diseases can pair a rapid sand filter with a sanitizer such as a chlorination system like Accu-Tab.
Photo courtesy of Sarah White, Clemson Univ.
Water filtration
White said there really isn’t a need to filter municipal or well water unless growers are recirculating the water.
“A rapid sand filter, which is cheap and fast, will remove organic matter and other debris that might get into the water,” she said. “This filter might remove some disease organisms, but it’s not 100 percent. If growers are concerned with plant diseases, they are going to need to add a sanitizer like chlorine, ultraviolet light or ozone. A rapid sand filter is easy to pair with a chlorination system like Accu-Tab.
“Growers could also use a slow sand filter. This is a biologically-based system, but it just takes longer to filter the water. The slow sand filter removes both particulate and plant disease propagules. Depending on what a grower’s goal is, a slow sand filter would accomplish the same thing as a sanitizer.”
White said a lot of ornamental plant growers who use well water route it into an open containment pond.
“Most growers have a pond that they pump the well water into before irrigating their crops,” she said. “These growers might have an issue with using that water to irrigate edible crops. They would need to use a sanitizer, which would take care of plant pathogens as well as potential human pathogens such as Salmonella and E. coli. Those are the main pathogens growers would have to be worried about.”
For more: Sarah White, Clemson University, Plant and Environmental Sciences Department, (864) 656-7433; swhite4@clemson.edu; http://www.clemson.edu/cafls/faculty_staff/profiles/swhite4; http://cleanwater3.org.
David Kuack is a freelance technical writer in Fort Worth, Texas; dkuack@gmail.com.
USDA Secretary Impressed By NH Agriculture Innovation
September 2, 2017 | CONCORD, N.H. | The Associated Press
USDA Secretary Impressed By NH Agriculture Innovation
New Hampshire may not be part of the nation's farm belt, but U.S. Agriculture Secretary Sonny Perdue says he's impressed with what he saw in the Granite State.
Perdue on Friday toured Lef (pronounced Leaf) Farms to learn how year-round, indoor farming can be far more efficient than traditional agriculture operations. The Concord Monitor reports (http://bit.ly/2eOsXx1 ) that the hydroponic farm aims to produce 3,000 pounds of leafy greens every 24 hours.
Perdue says New Hampshire farmers are taking "two- and twenty- and hundred-acres and making a sustainable lifestyle out of a product that we all need."
Perdue was in New England on a two-day "Back to Our Roots" trip to discuss the 2018 Farm Bill with farmers and other agriculture producers.
Walker Celebrates Opening Of Aquaponics Facility
Walker Celebrates Opening Of Aquaponics Facility
Gov. Scott Walker Thursday joined employees of Superior Fresh LLC. to celebrate its grand opening.
Owners say the 3.75-acre aquaponics facility will produce more than 2 million pounds of fresh Atlantic salmon, rainbow trout and leafy green vegetables annually.
“The complexity of the farm, ranging from automation to water chemistry and biology, has created some very exciting, high-end jobs,” said Walker.
The facility combines aquaculture and hydroponics whereby waste from fish will be used to supply nutrients for plants grown hydroponically. 99 percent of the purified water is recirculated.
Owners, Todd and Karen Wanek stated, “We want to lay the groundwork for sustainable food production, not by reinventing the wheel, but by refining processes and lessons learned to create a one-of-a-kind business.”
Superior Fresh has partnered with UW-Madison, UW-Stevens Points, UW-La Crosse, and UW-River Falls for research opportunities for students. The facility includes the first indoor Atlantic salmon farm in the United States and a 123,000-square foot greenhouse. The company employs nearly two dozen people and plans to expand operations throughout the world once the Northfield facility becomes fully operational.
Israel Agritech Market Map: 400 Startups Putting The Tech in Agritech
There are now more than 400 Israel agritech startups working on innovations for the global agriculture sector, according to new research from Start-Up Nation Central, an Israeli NGO and Greensoil Investments, a local agritech venture capital firm.
Israel Agritech Market Map: 400 Startups Putting The Tech in Agritech
AUGUST 10, 2017 LOUISA BURWOOD-TAYLOR
For a young nation built on the collectivist agricultural ethos of the Kibbutz movement, it’s perhaps no surprise that Israel’s agricultural technology startup ecosystem is booming.
There are now more than 400 Israel agritech startups working on innovations for the global agriculture sector, according to new research from Start-Up Nation Central, an Israeli NGO and Greensoil Investments, a local agritech venture capital firm.
These agritech startups are innovating across a range of challenges such as drought and water efficiency, as well as crop productivity and waste.
While Israel’s agritech funding footprint might look relatively small compared to other leading markets such as the US — according to AgFunder, Israeli agritech startups raised just 2% of funding dollars in 2016 ($51.7m), accounting for 3.3% of deal-flow (19 deals) in 2016, while US startups raised 58% of funding dollars and 48% of deal-flow — this is still impressive with a population of 8.5 million next to the US’s 323 million.
Israel is undoubtedly an innovation hub, and there are many serial entrepreneurs moving into agritech bringing experience, tech, methodologies, and connections from other sectors into the agritech vertical.
Companies like ATP Labs and Agritask were founded by people moving from military data analytics and sensor technology, respectively, into the peaceful and impactful area of agritech.
Israeli agritech is also growing in terms of incoming investments. Since the beginning of 2017, there have been many large investments such as Prospera’s $15 million Series B financing, Taranis’ $7.5 million Series A, a strategic $15 million investment in Hinoman, and others.
Currently, Start-Up Nation’s online, searchable startup database includes more than 5,500 profiles of active, innovative startups across all tech verticals, including agritech.
Along with Greensoil Investments, Start-Up Nation Central has used the Start-Up Nation Finder platform to build a taxonomy that identifies different sub categories in agritech. This has been visualized in an Israeli agritech market map along with a representative, and non-exhaustive, selection of companies in each category.
Here is a description of each category according to Start-Up Nation and Greensoil, and some company examples.
• Biotech – Typically involves breeding of plants and bacteria with improved traits to help plant growth. Some companies use genetic technologies for that. These include companies such as Groundwork BioAg, Rootility, and Kaiima.
• Smart farming – Data-based technologies making use of big data and predictive analytics to help farmers make better decisions on daily farm issues (irrigation, pest management, risk management, etc). Some of the more known companies are Taranis, Phythech, Cropx, and Prospera
• Crop protection – Biological or chemical substances used for protecting the crops from pests & diseases, nontoxic and environmentally friendly. Companies like Biofeed which lures insects away or EdenShield.
• Machinery and Robotics – Companies that build all kinds of robotics, machinery, and equipment used primarily to automate farm work, harvest crops and to sort it. Metomotion is one example with a robotic system developed for greenhouses.
• Irrigation & water management – Israel is well known for water innovation, but there are new companies that are creating innovative irrigation methods and water efficiency, such as Neotop which covers water reservoirs and Emefcy which created an Energy-efficient Wastewater Treatment.
• Post-harvest – Technologies to reduce post-harvest losses in diverse ways (e.g. storage, packaging, treatments and climate management technologies). An example for these companies can be found in Amaizz which deals with drying produce or Valentis Nanotech, which produces polymeric films for coating.
• Farm to consumer – Companies that leverage new business models to shorten and simplify the supply chain by connecting the farm to the end consumer. Usually done through digital platforms. A good example would be Avenews-GT, which builds a digital trading platform connecting food wholesalers with producers.
• Novel farming systems – Innovative systems for growing plants, new types of greenhouses, urban farming, hydroponics, and aquaponics. It could be small scale growing in the case of Flux or lighting solutions for farmers such as FloraFotonica.
• Livestock – Companies that create technology for farm animals and pets. With mass vaccination companies such as adst Technologies and Eggxyt’s pre-hatch sex detection for chicks
• Waste technologies – Processing livestock manure, fertilizer run-off, harvest, and food waste to reduce harmful substances and reuse the materials. Companies like 3PLW and HomeBiogas which convert organic waste to bioplastic and cooking gas, respectively.
• Special crops – Companies which deal with medicinal plants from growing human tissue repair plants, such as Collplant to cannabis-based products, in the case of Corsica Innovations
• Aquaculture – These are companies that develop technologies to grow things in water – algae (e.g., Algalo), fish or sea food (e.g., BioFishency)
“The Israel agritech market map displays the wide variety of Israeli agritech innovation and the growth of this sector”, says Eitan Elkin, Start-Up Nation Central’s director of marketing, “The number of companies behind it and the fact that most of them were founded in recent years really brings to attention of the boom which this industry enjoys in Israel and the appeal it has to many entrepreneurs.”
Click here to download your own free copy of the Israel Agritech market map.
About Start-Up Nation Central
Start-Up Nation Central is an independent, nonprofit and nonrevenue organization committed to leveraging deep knowledge of the Israeli innovation ecosystem to connect business, government, and NGO leaders from around the world to people and technologies in Israel to help them solve their most pressing challenges while creating value for the Israeli innovation ecosystem.
Start-Up Nation Central has curated the largest and most up-to-date collection of Israeli innovators and entrepreneurs, providing critical information on over 6,000 companies across dozens of industries. To search Start-up Nation’s Finder, click here.
About Greensoil Investments
With offices in Raanana and Toronto, and $100m under management, GreenSoil Investments funds companies in the agro & food technologies and building innovation sectors. Founded in 2011, GreenSoil’s agro & food technologies fund has a portfolio of six promising companies and is the largest dedicated fund in this space in Israel.
Philips Lighting Signs New Horticultural LED Lighting Project With Longtime Partner Wim Peters
In total, Philips Lighting will install over 26,000 GreenPower LED interlighting modules in the two rebuilt greenhouses and the greenhouse that is scheduled to be built in October 2017.
Philips Lighting Signs New Horticultural LED Lighting Project With Longtime Partner Wim Peters
August 24, 2017
Wim Peters rebuilds two greenhouses after hail storm and chooses for GreenPower LED interlighting
The higher light level gives him more uniform production in winter and better quality and taste
Eindhoven, The Netherlands – Philips Lighting (Euronext Amsterdam ticker: LIGHT), a global leader in lighting, today announced it has been awarded a new project with longtime partner Wim Peters, one of the largest high wire tomato growers in The Netherlands. Philips Lighting will again provide Peters with LED lighting for two greenhouses that he’s rebuilding after they were destroyed during a hailstorm in June 2016. The company will also provide LEDs for one new greenhouse that Peters is building to expand his business and meet the growing demand for LED grown tomatoes by his customers. The LED lighting will have higher light levels than the twenty kilometers of LED grow lights that Philips Lighting installed in the two greenhouses in 2013.
Higher light levels
Over the last 10 years, light levels in tomato cultivation (actually all vegetables) have continued to rise. In his previous installation, Peters had a light level of 55 µmol/m²/s LED interlighting. With the new project, he chose for 75 µmol/m²/s LED interlighting, a significant increase in light level. “A higher light level gives me more uniform production in winter and better quality and taste,” Peters said. “It also gives me a better balance between vegetative and generative phases, so leaf versus production.”
“This is in line with the trend we are seeing from other tomato growers who want to go to higher light levels,” said Udo van Slooten, Managing Director of Philips Horticulture LED Solutions. “To meet this demand, we launched the new Philips GreenPower LED interlighting module earlier this year with a system efficacy of up to 3.0 µmol/J. The modules are easier to install and maintain, bringing the total cost of project installation down significantly.” Several other Belgian, Russian and French tomato growers have recently moved to higher light levels as well.
Over 26,000 GreenPower LED interlighting modules
In total, Philips Lighting will install over 26,000 GreenPower LED interlighting modules in the two rebuilt greenhouses and the greenhouse that is scheduled to be built in October 2017. The new hybrid lighting installation combines HPS toplighting with Philips GreenPower LED interlighting High Output, spanning a total area of 10.6 hectare. The entire lighting installation will be installed by Philips Lighting’s Horti LED partner Codema B-E de Lier, who has been working with Horti LED partner Agrolux to come up with the best hybrid lighting system for the customer.
For further information, please contact:
Daniela Damoiseaux, Global Marcom Manager
Philips Horticulture LED Solutions, Nederland
E-mail: daniela.damoiseaux@philips.com
www.philips.com/horti
About Philips Lighting
Philips Lighting (Euronext Amsterdam ticker: LIGHT), a global leader in lighting products, systems and services, delivers innovations that unlock business value, providing rich user experiences that help improve lives. Serving professional and consumer markets, we lead the industry in leveraging the Internet of Things to transform homes, buildings and urban spaces. With 2016 sales of EUR 7.1 billion, we have approximately 34,000 employees in over 70 countries. News from Philips Lighting is located at the Newsroom, Twitter and LinkedIn. Information for investors can be found on the Investor Relations page.
Dean Martel Joins BrightFarms as Vice President of Sales
Dean Martel Joins BrightFarms as Vice President of Sales
BrightFarms is pleased to announce that Dean Martel has joined the company as Vice President of Sales. Martel will lead supermarket partnership business development, sales and account management.
Martel has more than 25 years of experience leading category growth in the consumer packaged goods industry. Most recently, he served as the Director of U.S. Retail Sales for It’s Fresh!, a food freshness technology company. Prior to his tenure with It’s Fresh!, Martel spent 16 years in category management and sales leadership positions at Fresh Express, which at the time was the nation's leading fresh salad brand. He began his career in the food industry at Kraft Foods, where he served in a variety of sales and supply chain roles.
Martel’s experience ranges from category management best practices to expertise in value added salads. He is known for building strategic relationships with key retailers in the U.S., which well-positions him to add value to the BrightFarms team during this growth phase.
With greenhouse farms built in close proximity to major metropolitan markets like Chicago, Washington, D.C. and Philadelphia, BrightFarms is currently the leader in producing local produce for supermarkets. The company plans to construct more than a dozen greenhouse farms across the country in the next three years.
“We are on a fast-track to becoming the country’s first national brand of local produce,” said BrightFarms CEO Paul Lightfoot. “Dean’s background leading high-profile teams and growth initiatives within the category adds immeasurable value to our team. We’re entering a period of serious growth as we look to bring fresh, local produce to more grocery store shelves. We are very happy to have Dean in our corner.”
This hire also allows for Abby Prior, another key member of BrightFarms leadership team, to shift into a newly created role as the Vice President of Marketing. Before joining BrightFarms, Prior served as a Director of Marketing for Bimbo Bakeries, USA.
“Joining Paul and the BrightFarms team is an incredible opportunity to be part of a leading-edge company with innovative greenhouse farming technologies and practices to help solve the lengthy food supply chain problem,” said Martel. “At the end of the day, we’re helping to deliver fresher, higher-quality produce to the grocery shelves of consumers every day, and that is something to feel good about.”
Canadian Greenhouse Cucumber Grower Prepares For Any Eventuality
Canadian Greenhouse Cucumber Grower Prepares For Any Eventuality
From storage capacity for 2 million gallons of fuel oil to multiple boilers
Leamington-based Great Lakes Greenhouses is focused on redundancy and controls to be in place to react to any unforeseen events. “We prepare for any eventuality,” says David Revington with Great Lakes. “Whatever may happen, we will continue to function and supply the highest quality greenhouse-grown cucumber to the customer,” he added.
Bunker oil as a back-up for natural gas
Greenhouses rely heavily on the supply of natural gas, but harsh winters in Leamington, ON sometimes cause interruptions of supply. Therefore, Great Lakes has two back-up tanks on the farm that each hold 1 million gallons of bunker oil. “The cost of bunker oil is four times the amount of natural gas, but security of supply is everything,” said Revington.
A huge room with multiple boilers generates the steam to heat the greenhouses. “It took us 2.5 years to get permission to build it,” shared Revington. The condenser, that was built in the Netherlands, provides significant energy savings. “With one condenser, we save four acres of energy, but now we have three condensers that we can use in the heart of winter,” mentioned Revington. As if this wasn’t enough, three natural gas generators enable Great Lakes to produce hydro. Most of the farm can run on two gas generators, but three is a safety precaution. The company has its own in-house maintenance team of 25 people who make sure everything functions the way it should.
Propagation site
Another way of taking control is a 4-acre propagation site. “The majority of greenhouse growers outsource propagation, but we feel we get to grow a better plant by doing it in-house,” shared Revington. Every two weeks, about 120,000 plants go into the propagation area and fill approximately 20 acres of greenhouses. The showpiece of the propagation area is the flood floor by European design. “It allows us to sterilize the water, which helps in preventing root diseases,” said Revington. The plants are watered as needed and the water comes up through the floor. Sprinklers are used to take the heat off the plants.
Propagation area
Organic expansion
Based on consumer demand, Great Lakes is expanding its organic program. 3.5 acres are being prepared for organic production while trials are done in a small area of the greenhouse. In the trial section, cucumbers are grown next to organic beans. The beans are needed to grow natural bugs such as thrips. Clover is used as underseeding to ‘fix’ nitrogen levels of the cucumber plants. Optimizing nitrogen levels in a natural way can result in significant savings. A unit of conventional nitrogen costs CAD 0.40 per pound whereas the organic counterpart is CAD 6.00 per pound.
Organic greenhouse
30,000 dozen of cucumbers per day
Great Lakes harvests about 30,000 dozen of cucumbers per day and product is moved the same day it is harvested. During peak season, about 250-300 laborers are involved in moving the product. The pickers play an important role and recently, Great Lakes installed scales on the picking carts. “They are tied directly to the labor system and provide the packing shed a more accurate idea of the amount of cucumbers that will come in,” according to Revington. In addition, the scales also support accountability. The system registers how many pounds each laborer picks and a bonus will be paid to the people who score above average. At the packing shed, the cucumbers go through a grading process. Based on their diameter, length and curvature, the grading system determines what packing table they are directed to.
Packing line
In addition to the organic expansion, the company also hopes to expand its conventional production from 90 acres to 120 in the next year.
For more information: David Revington |Great Lakes Greenhouses Inc.
Tel: 519-419-4937 | david@greatlakesg.com | www.greatlakesg.com
Publication date: 8/23/2017 | Author: Marieke Hemmes | Copyright: www.freshplaza.com
Delta Greenhouse Expansion On Hold Thanks To Labor Shortage
Delta Greenhouse Expansion On Hold Thanks To Labor Shortage
ByTyrel Linkhorn | BLADE BUSINESS WRITER
Published on Aug. 17, 2017 | Updated Aug. 18, 2017 6:19 p. m.
NatureFresh Farms has announced that a planned expansion of its greenhouse in Delta, Ohio, has been put on hold.
The owner of NatureFresh Farms said Thursday that a planned expansion of its large commercial greenhouse in Delta, Ohio, is on hold because of the company’s difficulties in finding and keeping employees.
The Ontario-based company came to northwest Ohio in 2015, with plans to build a sprawling, 175-acre greenhouse over the next seven years at a cost of up to $200 million. So far, the firm has spent about $65 million to get the operation up and running and build out 45 acres of growing space under a roof.
And business has been good. Peter Quiring, NatureFresh’s founder and chief executive officer, said he has the customers to support doubling that acreage.
RELATED: Ontario-based grower plans 175-acre greenhouse in Delta
But he’s holding back on an expansion because of the company’s ongoing struggle with finding workers.
“Labor’s the caveat,” Mr. Quiring said in an interview. “It’s not happening unless we figure out the labor situation. It can’t happen. My bank wouldn't even let me do it, not that I would.”
Mr. Quiring was in town Thursday for the Northwest Ohio Ag-Business Breakfast Forum near Bowling Green hosted by the Center for Innovative Food Technology. NatureFresh was this month’s presenter.
Between its greenhouse and a distribution center in Maumee, the company has about 220 full-time employees in northwest Ohio. NatureFresh grows about 10 varieties of tomatoes in Delta, which are shipped primarily to customers across the Midwest and the eastern seaboard.
A 45-acre expansion would require another 90 to 100 full-time, year-round employees.
“The sad reality is Canadians and Americans do not want to do agricultural work. That is just the reality. If they do agricultural work, they want his job,” Mr. Quiring said, gesturing to his chief grower, “or my job, or at the very least they want to be in shipping and receiving. They do not want to pick tomatoes.”
Officials said wages start at more than $12 an hour and can rise to more than $18 an hour for quality employees.
One important source of labor are guest workers from outside the United States. The company currently has 43 employees from Honduras and Guatemala who are here on visas.
The United States does allow companies to bring in foreign workers for agricultural work, but only on a seasonal basis. And while there’s no cap on the total number, workers must go through the application process every year and can’t change employers without a new petition.
Exterior of NatureFresh Farms' greenhouse facility in Delta, Ohio. A planned expansion of its the facility is on hold because of the company’s difficulties in finding and keeping employees.
THE BLADE/JEREMY WADSWORTH
Enlarge | Buy This Image
Mr. Quiring said Canada’s guest worker program is more manageable for operations like his that can grow produce year-round.
“What we need is a better system of getting labor,” Mr. Quiring said. “We need the American program to be year-round. We need to open that up. We need to bring people here legally.”
In a phone interview, Baldemar Velasquez, president of the Toledo-based Farm Labor Organizing Committee, said that, while there have been a number of well-documented problems and abuses within the farm labor visa program, there are legitimate reasons for keeping it.
One of the chief ones, he said, is the fact that many of those workers don’t want to immigrate full-time to the United States, and the ones who do likely wouldn’t want to keep working in what are largely seasonal jobs.
And Mr. Quiring made those same arguments at the forum.
“Number 1 they’re probably not going to stay with agriculture very long. But Number 2, you’re doing a brain drain from that country again,” he said. “That may help our country, but it certainly doesn’t help theirs. When they go back home they educate their children. They’ve got a chance of taking that country out of the third world status that they’re in and making something of it.”
U.S. Rep. Marcy Kaptur (D., Toledo), who was among the crowd at Thursday’s forum, urged during a question-and-answer session that that those in the agricultural industry push for changes that can improve the country’s visa program for employers and workers.
“We have a unique opportunity with the renegotiation of NAFTA, and I just want to get it in your consciousness and the consciousness of every agricultural person here,” she said.
“This is really important,” she continued. “We’ve got 16 members in the House. We’ve got two senators from Ohio, so that’s 18 voices. If Ohio agriculture could be focused on this, I think we could really make a difference.”
Mr. Velasquez said changes to the visa program would need to come from a place where both labor and business are at the table.
“There’s some things you could do, but to make it politically feasible you have to have all segments of the labor market involved,” he said. “If you have the unions involved and you have the employers involved, it makes it much easier politically to make those changes.”
Even so, Mr. Velasquez disputes the notion that Americans won’t work those jobs at all, saying what they won’t do is work for low wages.
“I can understand how NatureFresh, being under the roof and year-round would want year-round workers, but frankly there are enough domestic workers to do something like that,” he said. “That’s a more controlled climate that would attract local workers or domestic workers if they paid a wage that was high enough.”
Mr. Quiring painted a somewhat bleak picture of their efforts to staff the greenhouse.
“We’ve interviewed around 600 people in the last two years. Of that 600 people, about 30 to 40 percent didn’t pass a drug test. And we don’t care about marijuana, by the way. This is heavy drugs we’re talking about,” he said. “It’s a sad fact.”
NatureFresh hired close to 300 from that pool. Some never showed up, about 40 were dismissed, and another 90 quit — many within their first few days.
“I go to a lot of trade shows,” Mr. Quiring said. “The Number 1 topic of conversation for the last five to 10 years has been labor. Now it’s the only topic of conversation. There is nothing else to talk about anymore.”
Contact Tyrel Linkhorn at tlinkhorn@theblade.com, 419-724-6134 or on Twitter @BladeAutoWriter
He’s Spent Most of His Life Perfecting Lettuce
He’s Spent Most of His Life Perfecting Lettuce
Pieter Slaman in the greenhouse at Little Leaf Farms. | JONATHAN WIGGS/GLOBE STAFF
By Cindy Atoji Keene GLOBE CORRESPONDENT AUGUST 17, 2017
Why should a greenhouse worker be granted an 0-1 Visa? The document is granted by the US government only to noncitizens who demonstrate “extraordinary ability or achievement.” For Dutchman Pieter Slaman, it’s because he had proprietary knowledge of commercial horticulture that was needed for a new high-tech lettuce farm in Devens. Slaman is a fourth-generation grower from the Netherlands, where over a century of experimentation has made the Dutch experts in sustainable-agriculture practices. He hails from near the Hague, where an industry cluster of greenhouses gave the area the nickname “Glass City.” Slaman, 50, grew up “between the tomatoes,” starting his first greenhouse when he was just 17 years old. Now he uses his “green fingers” to grow 4 million plants in a 3-acre greenhouse at Little Leaf Farms, an agribusiness that produces arugula and other greens on a relatively small footprint. While the majority of lettuce is shipped in from the West Coast, Little Leaf Farms produce goes from harvest to supermarket shelf within a day of harvest. The Globe spoke with Slaman about how he’s making a life out of lettuce.
“Both of my grandparents and many other relatives had a greenhouse in the Netherlands, so it’s in my blood. One grew lettuce, and the others, flowers and bulb plants. Dutch farmers have been growing indoors for years, using sunlight and rainwater to compensate for our agriculturally challenged geography.
“I heard stories from my dad about the World War II resistance and how my family hid escaping Jews under the greenhouse floor. The region was the biggest horticultural producer in the world, providing the whole of Europe with vegetables. But times have changed, and I wanted to travel the world to see if I could grow things elsewhere.
“Little Leaf contacted me and said they needed a Dutch grower. They had a greenhouse they were building in New England and wanted to do it ‘right’ — no pesticides, collecting rainwater for irrigation, LED lights.
“When I first arrived in Boston, it was the second week of February, minus 20 degrees Celsius, and very cold and snowy. The first couple of months, I’m thinking in Dutch and talking in English. There were many cultural differences. I had to adjust to working with a Mexican crew instead of a Polish one. I missed having a neighborhood of other growers around me.
“And I quickly learned that if something broke, I couldn’t just jump into the car and go to the nearest greenhouse supplier, especially with metric parts. I had to order and wait, and this could be a problem because a crop can die within six hours without water.
“But we were able to set up a highly advanced, automated hydroponic system. Even with that, it’s not easy to grow lettuce in New England’s erratic weather. But in the end, growing is nothing more than taking the stress away from the crop.
“An expert’s eye, the many years of experience, and a grower’s passion make the difference and can never be taken over by a computer and data. I can just step into the greenhouse and instinctively know whether the humidity or temperature is too high or low. I spend many hours a week, just walking, scouting, and turning over leaves to see what kind of bugs I can find. This is something I’ve been doing my whole life.
“After all, everything around us has a connection. That’s why I pray in the greenhouse and do yoga in my free time. It’s all about time and balance. And that’s true for plants — and for humans.”
Cindy Atoji Keene can be reached at cindy@cindyatoji.com.
Editorial: Research at UMass With Global Reach
Editorial: Research at UMass With Global Reach
Evan Chakrin, a University of Massachusetts Amherst junior studying horticulture, harvests butterhead bibb lettuce from a hydroponic raft bed Aug. 4 at the UMass Hydrofarm he co-founded with Dana Lucas, a senior majoring in sustainable food and farming. GAZETTE FILE PHOTO
August 17, 2017
Two students at the University of Massachusetts Amherst have turned a modest grant and an old greenhouse into the first hydroponic farm on campus to show off sustainable agriculture techniques.
An award-winning geoscientist at UMass will use a $94,375 grant from the Massachusetts Environmental Trust to gather and study water samples with the goal of better understanding the impact of droughts.
Those are examples of research that spills outside the university’s classrooms to address real-world issues such as local food production and climate change.
Evan Chakrin and Dana Lucas are co-leaders of the student-run hydrofarm in a small greenhouse next to Clark Hall in the central residential area of campus. Started last winter, the farm grows food without using soil. Nutrients are dissolved into the water surrounding the plants’ roots, and the system uses less water than an irrigated field. It also keeps nutrients from running off fields to other water sources.
“It’s basically just using chemistry to grow plants,” says Chakrin, a junior studying horticulture. “We can totally control whatever we waste.”
One Friday this month, he harvested 10 pounds of lettuce that he planned to donate to the Amherst Survival Center. Also during its first year, the hydrofarm has supplied food to on-campus restaurants, including the vegetarian Earthfoods Cafe. Other crops include kale, tomatoes and strawberries.
Lucas is a senior majoring in sustainable food and farming. Since it was elevated in 2013 from a concentration to a full-fledged major within the Stockbridge School of Agriculture, enrollment in the major has increased from 50 to 140 full-time students.
She started cultivating the idea for a hydroponic farm on campus in 2015, and with Chakrin received a $5,000 grant and use of the greenhouse from the Stockbridge School in December. They started germinating seeds and later in the winter began selling food they harvested. The revenue is used to buy more seeds and equipment.
In the fall, the pair will teach a course for 12 undergraduate students who want practical experience. “The techniques we use here are are the main hydroponic techniques used,” says Chakrin. “This work is directly applicable to any of their food production goals.”
He hopes to attract students interested in urban food production, even if they are not enrolled in the Stockbridge School. One of the benefits of hydroponics is that it can used almost anywhere to grow food locally.
Chakrin and Lucas also have a consulting service, which they call Farmable, to coach people who want to farm in urban areas. “Anywhere is farmable and this concept will revolutionize how urbanites are able to access food,” Lucas says.
Water is also an important ingredient in the research by hydrogeologist David Boutt, an associate professor in the Department of Geosciences. His grant — funded by the sale of the state’s environmentally themed license plates — will help develop an isotope mapping tool to study the composition of water samples and learn more about the effects of droughts. A public database will help water managers assess the sustainability of freshwater resources.
Boutt says, “By measuring the isotopic composition, we can start to describe the source of that moisture — did it come ultimately from the Arctic? Or the Gulf of Mexico?”
The data is important not just to better assess how droughts may affect an area, but also in relation to global warming. “As the Arctic is warming, more and more of that moisture is moving to New England,” Boutt says. “With this database we can start to track this and understand how the hydrological cycle is changing the source of moisture to the region.”
Boutt is seeking water samples from wells and streams in the region. Anyone interested may call him at 413-545-2724 or email dboutt@geo.umass.edu.
He will have an international forum to discuss his research next year after being named the Birdsall-Dreiss Distinguished Lecturer for 2018 by the hydrogeology division of the Geological Society of America. His topics will include groundwater and climate change, the role of groundwater flow in hydrologic processes and how water and lithium factor in the global transition from fossil fuels to green energy.
Chakrin, Lucas and Boutt put a face on the many people studying and teaching at the university who are determined to make a difference by applying what they learn locally to global problems.
Pure Flavor® To Build 75 Acre Greenhouse Project in Georgia
Pure Flavor® To Build 75 Acre Greenhouse Project in Georgia
Leamington, ON (August 21st, 2017) – With demand for its premium greenhouse vegetables continuing to grow, Pure Flavor® announced recently the investment of more than $105 million USD to build a 75-acre state of the art high tech greenhouse facility & distribution center in Peach County, GA south of Atlanta.
"We at the Georgia Department of Agriculture and Georgia Grown are proud to welcome Pure Flavor® to our great state”, stated Gary W. Black, Georgia Agriculture Commissioner. “I am confident this innovative venture will prove to be a real asset to Peach County and to Georgia's entire agricultural sector. Pure Flavor® has indeed found the ideal location for this type of operation and I look forward to working with them as they continue to grow and expand”, said Black.
The new greenhouse complex, located just 90 minutes south of Atlanta and less than 3 miles from I-75, will grow tomatoes & cucumbers year-round. Coupled with Pure Flavor’s existing farms throughout Canada, USA, and Mexico, growing in Georgia will further expand the company’s reach along the eastern seaboard as far north as Virginia, west to Texas, and all the way down to south Florida with premium greenhouse grown vegetables.
“The strategic investment in Peach County, GA is one that will not only expand our acreage but also creates opportunities to strengthen & grow our retail & foodservice partnerships across the southeast with Georgia grown vegetables”, said Jamie Moracci, President. Moracci & his partners spent nearly 2 years researching locations across the USA for this expansion. With the Midwest region, already over saturated with a variety of projects and an abundance of product, developing in Georgia with the first significant high-tech build of its kind in the state, is going to be a game changer.
Key Project Facts:
- Location: Fort Valley (Peach County), Georgia – 3 miles off I-75
- Start of the art, high tech 75-acre greenhouse complex
- Built in three (3) phases of 25 acres over 5 years
- Investment: $105 million
- Distribution area: Georgia, Florida, North/South Carolina, Alabama, Louisiana, Arkansas, Mississippi, Tennessee, Virgina, Kentucky, Missouri, Texas
- New 75,000 sq. ft. distribution center on site to service the southeast
- Installation of High Pressure Sodium (HPS) lighting to assist with year-round growing
- Phase 1 commodities: Tomatoes & Cucumbers
- Creating 200+ new year-round job opportunities over 5 years
- Largest facility of its kind in southeastern USA
“Built in 3 phases of 25 acres over the next 5 years, the financial investment we are making further demonstrates our goal of growing our business in a significant region and not looking at the investment as just growing in a state”, said Jeff Moracci, Chief Financial Officer. With a potential reach of nearly 80 million people in less than a 24 hrs. drive, a regionally grown message featuring the Georgia Grown emblem will help leverage the brand with consumers. The first phase of the project of 25 acres is due to break ground in September.
International greenhouse manufacturer Havecon has been retained to build the facility in Georgia. Using state of the growing systems, Pure Flavor® will have diffused roof glass installed to take advantage of the southern US, nutrient rich sunlight during peak season. Pure Flavor® will also be installing High Pressure Sodium (HPS) lights to be used as supplemental energy to help grow through the winter months.
““A leader in the global marketplace, Georgia has become a hotspot for international companies who are looking to expand their footprint in the U.S.,” said Pat Wilson, Commissioner, Georgia Department of Economic Development. “Pure Flavor® is taking a highly-specialized, dynamic approach to agriculture that our workforce is well suited to support. With a solid logistics infrastructure and robust network of companies, Pure Flavor® will have all they need to thrive in our state. Congrats to Peach County on this incredible win.”
Under the Pure Flavor® brand, the company grows & markets an extensive variety of greenhouse tomato, bell pepper, cucumber, eggplant, and living lettuce that is grown in Canada, USA, and Mexico. Founded in 2003, Pure Flavor® has experienced significant growth year over year with its expanding product offering. With distribution centers strategically located in Leamington, ON, Detroit, MI, San Antonio, TX, and soon to be Peach County, GA, Pure Flavor® provides year-round availability of premium greenhouse grown vegetables.
“Having Pure Flavor invest in Peach County is proof positive that our community is attractive to newcomers and major international companies’, said BJ Walker, Executive Director, Development Authority of Peach County. “It is confirmation that we possess all of the necessary qualities and assets that are ideal for a business to succeed and grow and we are thrilled and excited to welcome Pure Flavor into the Peach County family!”, said Walker.
The first crop of Tomatoes-on-the-Vine and Long English Cucumbers will be planted in Summer 2018 to be harvested in mid fall that year.
“Being strategically located in Georgia with our new greenhouse will enable Pure Flavor® to significantly extend its reach to open more distribution channels along the southeastern seaboard while further supplying existing key retail & foodservice partners across the southern US”, commented Matt Mastronardi, Executive Vice-President.
To learn more about the project, please visit GeorgiaGrownFlavor.com (https://goo.gl/QfKD45 ).
-30-
About Pure Flavor®
Pure Flavor® is a privately held greenhouse vegetable company providing year-round production of premium vegetables to retail & foodservice partners throughout North America.
Founded in 2003, Pure Flavor® grows & markets an extensive variety of greenhouse tomato, bell pepper, cucumber, eggplant, and living lettuce that is grown in Canada, USA, and Mexico.
WEBSITE LINK: https://goo.gl/QfKD45
Exclusive Agreement Between Mastronardi Produce and Golden Fresh Farms
Exclusive Agreement Between Mastronardi Produce and Golden Fresh Farms
Mastronardi Produce and Golden Fresh Farms, located in Wapakoneta, Ohio, are pleased to announce an exclusive agreement between the two companies to bring Mastronardi’s SUNSET® brand produce to more consumers throughout the US. This will be the 5th state that the SUNSET® brand will be grown locally in, allowing the company to reach over 75% of the United States population, delivering a local fruit in less than a 10-hour drive.
“Luis Chibante is a fantastic grower and operator. I’ve known him for years,” stated Mastronardi Produce President and CEO Paul Mastronardi. “His passion and expertise in growing will enable both of us to expand the Ohio footprint together.”
The Ohio Proud program allows loyal consumers to choose great tasting products that help support their local communities and ensures freshness.
“I’m excited to join Paul and the SUNSET® team with our new crop starting this fall,” shared Luis Chibante, President and owner of Golden Fresh Farms. “Mastronardi is the best growing and marketing company in the greenhouse industry, and this will give us the opportunity we need to expand the next 15 acres.”
Currently the greenhouse grows approximately 20 acres of tomatoes year-round with advanced supplemental lighting.
For more information: www.sunsetgrown.com
Publication date: 8/15/2017
This Midwestern Greenhouse Has Perfected The Art Of Growing Quality Tomatoes Year-Round
This Midwestern Greenhouse Has Perfected The Art Of Growing Quality Tomatoes Year-Round
No more ruining deli sandwiches–and no more shipping bad tomatoes across the country. MightyVine’s hydroponic technology produces ripe, red tomatoes, on land close to the city.
“Until someone invents a robot that can gauge which leaves to pluck off and when, there’s going to be a strong human element in tomato growing.”
A few years ago, as a food industry entrepreneur in Chicago, Gary Lazarski started to notice something that bothered him. “My office back in 2010 was in the Loop; there were a bunch of different lunch places around there, and every sandwich and every salad you bought would have these tomatoes on them,” Lazarski tells Fast Company. “They were terrible. You’d see people sitting on a park bench, and without fail, they all do the same thing: Open up the sandwich, look at that sad, orange disk, peel it off like it was a dirty sock, and throw it out.”
We all do it, Lazarski says; when a tomato is subpar, mealy-textured, and weak-colored, we don’t think of throwing it away as wasting food, but rather as salvaging an otherwise acceptable sandwich. But why, Lazarski wondered, could Chicago, a great food city, not equip its lunch options with tomatoes that actually tasted good?
“Open up the sandwich, look at that sad, orange disk, peel it off like it was a dirty sock, and throw it out.” [Photo: MightyVine]
Lazarski and his business partner Danny Murphy were, at the time, piloting a food-distribution company called Local Foods, which is still operational today. Through that enterprise, they connected with some Dutch business partners, Royal Pride Holland, and on trips to the Netherlands, visited their greenhouses. Royal Pride Holland has, since its founding in 1960, been a pioneer in greenhouse growing techniques; their many-acred structures use hydroponics and radiated heat to grow produce year-round. In one greenhouse, Lazarski and Murphy saw bright red, perfect tomatoes growing in the middle of winter. They began to wonder if a glass enclosure on the outskirts of Chicago could supply the city with the elusive, quality tomatoes that would not end up in the trash.
They pulled together around a dozen investors and $11 million to develop a greenhouse built with Royal Pride Holland’s glasshouse and hydroponic technology, where they would, once launched as MightyVine in August 2015, grow both cherry and large slicing tomatoes. In the Midwest, land-grown tomatoes enjoy just a brief season, from midsummer to early fall. The best tomatoes are those that are plucked at peak ripeness and delivered fresh, but the tomatoes populating grocery store shelves in Chicago through the winter have been plucked prematurely to survive a long trip cross-country from warmer climates. MightyVine, with Lazarski as CEO, can grow and ship ripe tomatoes year-round; the produce is grown without pesticides, and the tomatoes can linger on the vine until they’re ready to be plucked. Lazarski knew the operation would fill a void in the Midwestern produce scene, but they needed land to be able to pull it off.
“It’s well suited to get us up into Wisconsin, into Iowa, and into the city itself.” [Photo: MightyVine]
Rochelle, Illinois, a small city 80 miles west of Chicago, was where Lazarski and Murphy landed. “It’s well suited to get us up into Wisconsin, into Iowa, and into the city itself,” Lazarski says. While it would have been appealing for marketing purposes to locate the greenhouse in Chicago proper, logistically speaking, it would’ve been a nightmare, Lazarski says; space constraints would make it difficult to scale, and visions of tomato trucks attempting to navigate the Dan Ryan Expressway during rush hour were enough to cement the founders’ decision to locate on the outskirts.
Rochelle was a city that was poised, in the years leading up to the recession of 2008, for great economic growth, as it sat at the intersection of a number of roads that fanned out into other Midwestern economic centers like Chicago and Milwaukee. When Lazarski put out an RFP to the state of Illinois, seeking a place to site a 15-acre tomato greenhouse, he learned about a parcel that had been bought up by CenterPoint Properties, which intended to build a network of warehouses on the site. They built one, then the recession hit, and they abandoned the plans and sold the property back to its original owner, a local farmer. “You hear a lot of talk about shovel-ready projects around the recession,” Lazarski says. “This was literally shovel ready–CenterPoint had already stripped the topsoil off and run roads, water, and electricity out to the site.”
Because it was already treated for development, the land could not be farmed. When Lazarski and Murphy approached the farmer who owned the property, and explained their idea–to build a greenhouse on top of the wasted land–he was immediately on board; the farmer is now an investor and board member for MightyVine.
“What we found is if you offer people a good tomato, they’re willing to pay for it.” [Photo: MightyVine]
The greenhouse leaves a light enough environmental footprint to allow the farmer to continue working his plots of land around MightyVine’s facility. The Dutch glasshouse model includes rainwater capture capability, which prevents runoff into the field; that rainwater is then used to feed the tomatoes growing inside; MightyVine uses around 10% of the water of conventionally grown tomatoes. And because the tomatoes are distributed only around the greater Chicagoland region, the company is cutting down the carbon footprint associated with long-haul shipping.
Since October 2015, when MightyVine collected its first harvest, it’s been growing continuously. At first, only half of the greenhouse was being used, but the company, in response to demand, brought the other 7.5 acres into production this January. In a given week, MightyVine will harvest and deliver around 120,000 pounds of tomatoes. The approval of well-known chefs like Frontera’s Rick Bayless, who told Modern Farmer that he hasn’t been “so excited about a local product in a long time,” has contributed to MightyVine’s growth.
While indoor vertical farming companies like Bowery and AeroFarms are perfecting automated, data driven hydroponic models that consistently deliver large quantities of leafy greens with minimal labor, tomatoes, Lazarski says, are a more difficult product. “With lettuce, you have to get the nutrient mixture and the lighting down, but once that’s set, they will pretty much grow on their own,” Lazarski says. Tomatoes require constant pruning; there’s a lot of fussing that has to occur around a vine to ensure it grows correctly. “Until someone invents a robot that can gauge which leaves to pluck off and when, there’s going to be a strong human element in tomato growing,” Lazarski says. MightyVine has hired and trained around 80 local people, who have taken to the working conditions, Lazarksi says: The greenhouse is consistently 70 degrees, and because the tomatoes are grown in standardized hydroponic structures, they’re plucked at waist height, negating the need for injury-inducing stooping.
In order to be able to pay their workers a good living wage and benefits, Lazarski says the tomatoes are priced at a premium; while standard tomatoes retail for around $1.24 per pound, MightyVine products sell between $2.99 and $3.99 per pound. “But what we found is if you offer people a good tomato, they’re willing to pay for it,” Lazarski says. Local high-end grocery stores consistently sell the tomatoes (Local Foods, Lazarski’s and Murphy’s original venture, oversees the distribution of the produce), and some of Chicago’s most prominent restaurateurs are sourcing from MightyVine. While Lazarski cannot testify to the fate of the tomatoes once they reach people’s plates, one can only assume that they land in the trash at a much lower frequency than their pale orange competitors.
LumiGrow Partners With CF Industrial For Local Lighting Service in Ontario, Canada
LumiGrow Partners With CF Industrial For Local Lighting Service in Ontario, Canada
Ontario, Canada – July 24, 2017 –
LumiGrow Inc., a smart horticultural lighting company, announced today their partnership with CF Industrial, a lighting and power solutions provider in Leamington, Ontario. The new partnership bolsters LumiGrow’s commitment to their Ontario greenhouse growers, further providing responsive local support for those implementing smart horticultural lighting for precision greenhouse management. The CF Industrial team is yet another addition to LumiGrow’s Ontario-based services, as the company has already deployed plant science research support across the region.
“We are happy to welcome CF Industrial as a LumiGrow Canada Partner. This partnership will ensure that our superior level of technical support can be deployed immediately upon short notice. Our local lighting specialists will be able to personally visit and consult with commercial growers in Ontario, assisting with lighting implementation, as well as environmental and horticultural considerations.” says VP of Sales and Marketing, Jay Albere.
CF Industrial has been a symbol of reliance and service excellence for over 35 years. Jason Papp, CF Industrial Business Operations Manager says, “It’s important for us to find partners that share our values of long-term customer relationships, and we feel that’s exactly what we’ve found. We’ve been involved in the greenhouse industry here in Leamington for many years, and until now we haven’t seen an LED technology work like the LumiGrow solution. Both companies have been in business for a long time and realize that enterprise horticulture takes more than the right tools, but requires top-notch service from experts you can trust. We’re really here to bring this high level of knowledgeable support closer to home for our Canadian growers.”
The LumiGrow Plant Research Group will continue to work with growers in the Ontario region to develop crop-specific adjustable lighting strategies tailored for specific growth goals and financial objectives. “Our research team is already working with Canadian growers to develop custom lighting strategies for cucumber, tomato, pepper, leafy green, and strawberry cultivation.” says Jay Albere. “The ROI is proven and the crop-benefits are well-known. We’re just expanding our local support to offer a full breadth of sales, infrastructure, and research service so that greenhouse business owners, facility managers, and growers alike have access to LumiGrow lighting resources when their operations most depend on it.”
About LumiGrow Inc.
LumiGrow, Inc., the leader in smart horticultural lighting, empowers growers and scientists with the ability to improve plant growth, boost crop yields, and achieve cost-saving operational efficiencies. LumiGrow offers a range of proven grow light solutions for use in greenhouses, controlled environment agriculture and research chambers. LumiGrow solutions are eligible for energy-efficiency subsidies from utilities across North America.
LumiGrow has the largest horticultural LED install-base in the United States, with installations in over 30 countries. Our customers range from top global agribusinesses, many of the world’s top 100 produce and flower growers, enterprise cannabis cultivators, leading universities, and the USDA. Headquartered in Emeryville, California, LumiGrow is privately owned and operated. For more information, call (800) 514-0487 or visit www.lumigrow.com.
Mucci Farms Announces 60-Acre Expansion Into Ohio
Mucci Farms Announces 60-Acre Expansion Into Ohio
Mucci Farms (the “Company”) yesterday announced a large-scale, multi-year investment in Huron, Ohio. The Company confirmed that it was starting a multi-year, three phase construction project which will cover a total of 60 acres and feature the newest and latest state of the art greenhouses equipped with grow lights which extend the growing season. The constructed facility will also include a 272,000 sq. ft. distribution warehouse to support the Company’s growing US customer base.
The Company has already broken ground on the first phase which is the construction of a 24 acre range and the Company expects produce from this facility will be available as soon as March 2018.
This new, state of the art facility, will include the latest grow light technology which simulates sunlight by providing or supplementing the necessary light to optimize plant growth. The use of this grow technology allows for year-round production, keeping our produce -”always in season”.
Mucci Farms already has a sustainable, successful business with a well recognized brand in a number of large US retailers.
Expanding our operations to include a US growing facility was strategically done to meet our US customer demands for locally grown, year-round, fresh and flavourful produce.
Making this investment in Ohio allows us to reduce the food miles for our US retailers and gives our US consumers the confidence that they can bring fresh and flavourful Mucci Farms’ produce into their homes all year round.
The Company has been actively exploring a number of US expansion opportunities for the past 18 months and the site located in Huron, Ohio was a perfect fit due to its easy access to a number of current and potentially new retailer distribution facilities as well as its proximity to our Corporate headquarters in Kingsville, ON.
The Company has enjoyed establishing a number of working partnerships during the development stages of this expansion with the City of Huron and Erie County officials and the Company looks forward to what it expects will be a number of promising opportunities for continued community partnerships ahead.
As Mucci Farms continues to grow so will its work in the communities the Company is a part of. Mucci Farms understands the value of supporting all local communities in which it operates and it places equal emphasis on social interests as business interests. The Company is confident that there are a number of inspiring things to come with this investment in Ohio and Mucci Farms looks forward to growing with the City of Huron, Huron Township and Erie County.
“The City is excited to collaborate with Mucci Farms in bringing a new, advanced technology to the region. The impact to this area is expected to be profound and transformational. Welcome.” Andy White, City of Huron, Manager.
“We are extremely pleased to be a part of this next step for Mucci Farms. The Company’s advanced practices and reputation is well suited for our region and business community.” Abbey Bemis, Executive Director, Erie County Economic Development Corporation.
Potential Employment Opportunities
The Company anticipates that when the first phase of construction is completed it will be looking to employ up to 100 full-time positions. The Company expects this number will increase to 250 full-time positions by the completion of the third phase of construction.
These positions will capture many different levels between professional and general labourer positions. Some key positions the Company is looking to hire right away include growers, assistant growers and greenhouse labour supervisors. For more information, please contact Carol Bendo, HR Manager.
Contact: Ajit Saxena
Mucci International Marketing Inc.
Tel: 519-326-8881
Publication date: 8/9/2017
This Company Wants to Bring Soil-Free Farming to Restaurant Kitchens
Hydroponics have allowed garden vegetables to grow in novel places—from a pillar inside a Berlin grocery store to a veritable skyscraper of plants in Singapore.
This Company Wants to Bring Soil-Free Farming to Restaurant Kitchens
by Cathy Erway • 2017
Hydroponics have allowed garden vegetables to grow in novel places—from a pillar inside a Berlin grocery store to a veritable skyscraper of plants in Singapore. The fast-growing, soil-free farming method has been well-embraced in urban areas to produce crops using less water and space, since the plants are grown in a nutrient water solution, rather than in-ground. But rarely is it done within some of the buzziest places for the farm-to-table movement: a restaurant.
The team behind Farmshelf hopes that will soon change, and recently debuted three indoor hydroponic growing units at Grand Central Station’s Great Northern Food Hall. There, the chefs at the busy food market’s Scandinavian restaurant Meyers Bageri reach into the glass-walled cubicles to pick lemon basil for a garnish on their zucchini flatbread, and nearly a dozen varieties of baby lettuces are plucked for salads at the neighboring Almanak vegetable-driven café. And, as it would appear on recent visits, curious bystanders peer through the glass, agape at the billowy mixture of herbs and greens, illuminated by a ceiling of LEDs. Unbeknownst to the casual observer, the units are also outfitted with five cameras along every shelf, so that the Farmshelf team can monitor the plants’ progress from afar and adjust the system via a web application.
“The more plants we grow, the smarter we are about plants,” said Jean-Paul Kyrillos, Farmshelf’s Chief Revenue Officer. He explained that through their data collection, Farmshelf can optimize the growth and flavor of any plants that a client may want. “This is for someone who doesn’t want to be a botanist, or farmer. The system is automatic.”
“Plants can grow two to three times as fast using 90% less water than traditional in-ground farming”
That’s why Farmshelf hopes its units will be a boon for restaurants serving greens galore. Founded in 2016 by CEO Andrew Shearer, Farmshelf is just planting its roots in the New York City restaurant industry with its first partner, Meyers USA hospitality group. The startup was in the inaugural lineup of the Urban-X accelerator and is part of the Urban Tech program at New Lab. The company is looking to partner with more restaurants soon, and Kyrillos mentioned a restaurateur who was excited about the idea of placing a Farmshelf unit right in the dining room, as a partition.
Distribution is the last challenge of getting local food onto plates, and Farmshelf eliminates that entire process—no middleman, forager, or schleps to Union Square Greenmarket. Kyrillos is hopeful that the efficiency of hydroponics—where plants can grow two to three times as fast using 90% less water than traditional in-ground farming—will also convince restaurants of the value of placing such a system on-site. Then, there is the potential of growing ingredients that you could never get locally, like citrus; or mimicking the terroir of, say, Italy, through a special blend of nutrients and conditions within the units.
Green City Growers in Cleveland, OH, has a 3.25-acre hydroponic greenhouse. Photo by Flickr/Horticulture Group
With hydroponics, you can grow a plethora of vegetables, even root vegetables like turnips, carrots, radishes, but these take much longer, and thus not suited to the fast-paced restaurant environment Farmshelf is trying to service. Crops that take up a lot of space, like watermelon and pole beans, are also not ideal, as the point is for these systems to use space efficiently (though future designs of hydroponic units might be able to tackle this challenge). It's most cost-effective to grow delicate, highly perishable, expensive leafy greens than roots, which are quick to grow and easy to ship and store.
The possibilities seem endless. But, in an age when the small family farm is rapidly disappearing in the US—and faces further threat from a recent White House budget proposal that would eliminate crop insurance—would this technology take away business from local farms, which restaurants might otherwise buy from?
Hydroponics—The Future of Farming in Detroit?by Lindsay-Jean Hard
Kyrillos doesn’t see Farmshelf as a replacement for the local farmer. There are some six to eight months of the year where traditional farms can’t grow too many crops, so restaurants would buy leafy greens and other warm-season produce elsewhere. If anything, Kyrillos posited that it might chip away at business from some of the bigger food distributors.
But time will have to tell what best works for the soon-to-be users of Farmshelf. Right now, the company is hoping to sell restaurants at least three growing units to make a significant enough impact on its kitchen orders. Rather than leaving it at that, Farmshelf wants to work with restaurants through a sort of subscription-based service, supplying seeds for crops that the restaurant would like to grow and monitoring the growing process consistently. Could a chef go rogue, and use the unit to plant and harvest whatever, whenever he pleased? Perhaps—but that wouldn’t really be taking advantage of the full product, which the team estimates might cost around $7,000 per unit (a medium-sized restaurant might need three units, at $21,000), which would pay off in ingredient costs.
And how about home chefs? When will average consumers be able to place Farmshelf inside our cramped, outdoor space-free apartments? That’s in the vision for Farmshelf someday. Not just homes, but school classrooms or cafeterias could be future sites of these hydroponic shelves, Kyrillos suggested, offering an easy, indoor way to connect youngsters to the food on their plates. “Imagine children were watching food grow, all the time.”
TAGS: HYDROPONICS, TECHNOLOGY, ENVIRONMENT, GRAND CENTRAL