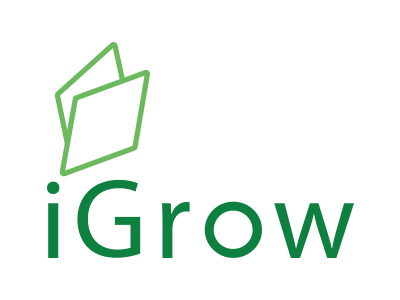
Welcome to iGrow News, Your Source for the World of Indoor Vertical Farming
Who Will Create The First Self-Cultivating Greenhouse?
Who Will Create The First Self-Cultivating Greenhouse?
Wageningen University & Research organizes an international challenge to boost vegetable production using artificial intelligence and autonomous greenhouses. The challenge is sponsored by Tencent, a leading provider of internet services in China and David Wallerstein, Chief Exploration Officer (CXO) of Tencent. The world is facing a rapid increase in human population and Wageningen University & Research is working with Tencent to explore breakthroughs that can help feed more people, deliver greater food security and create more food with fewer resources.
Open for registration
The challenge is open for multi-disciplinary teams from all over the world. Teams can subscribe from 19 March to 15 April at www.autonomousgreenhouses.com and can consist of people like scientists, R&D specialists, and students, from different disciplines like artificial intelligence, sensor technology, and crop physiology.
The teams participating in the challenge will run a greenhouse compartment in which a computer and machine learning algorithms or computer models make all kind of decisions on distance with limited human interaction.
Safe products without residues
In order to supply consumers with fresh products produced close to large cities, greenhouse production is a very efficient way to supply fresh vegetables and fruit with a high content of vitamins and minerals requiring only a small production area. Production in greenhouses is typically up to 10 times higher than in open field and uses much less water. Recent research results of Wageningen University & Research have shown that in extremely controlled greenhouses only 5 litres of water is used to produce 1 kilogram of tomatoes, while it would be up to 40 more litres in open field production. The controlled environment enables the reduction of pesticide use to a minimum and leads to the production of safe products without residues.
In the future even more greenhouses are needed to produce our food. For that the “green fingers”, or the knowledge and experience of a grower, is essential. At the same time, it is hard to find enough skilled workers in many countries worldwide. Automation, ICT and AI can help the grower to oversee all the information needed and help to make complex decisions.
Tencent and Wageningen University & Research believe that autonomous greenhouses can boost vegetable production and bring greenhouse production to a next level. Autonomous greenhouses can bring further improvement to yield and quality of greenhouse vegetable crops and a substantial reduction of the needed input in terms like energy, water, and crop protection at the same time.
In autonomous greenhouses the computer will decide about the optimum greenhouse climate set points, based on a wide range of sensors and cameras, self-learning software will partly take over human decisions. AI will help the grower to run the greenhouse in an optimal way, enable him to manage his greenhouses at a distance in various parts of the world.
Start in June
The first part of the challenge will start in June to select the five best teams and will run May-December 2018. From August till the end of December, five selected teams will run their own crop in their own greenhouse compartment at the greenhouse facilities of Wageningen University & Research. The experts of Wageningen University & Research will monitor the results of the teams: resources input and crop production output.
Source: Wageningen University & Research
Publication date: 3/20/2018
Photo Report: A Hat-Trick In Tunisia
Photo Report: A Hat-Trick In Tunisia
Building greenhouses in the Tunisian desert can be quite a challenge. The temperatures rise during the day but in the nighttime it's really cold. Combined with the dust and the distances to projects, it's not an easy topic at all. On the other hand, for growing this climate is ideal. That's why over the last couple of years more and more greenhouses have been erected in the country.
Since the rise of the horticulture in Tunisia, the Serbian building company Agrikol is one of the leading building companies in the market. Agrikols Nikola Petković, browsed through his photo album and showed us the hat-trick they made here last year.
Desert Joy
It was only 4 years ago when the first 2.5 hectares of the modern Desert Joy tomato farm was prepared in 2013. The company is located a half hour drive from the coastal city of Gabes, in southern Tunisia. The expansion has continued ever since. The fifth phase was realized last year and concluded 5.4 ha greenhouse and 2 technical rooms. Agrikol provided the supervision and the turn-key overview for this project. In Tunisia, another 6 greenhouses will be erected in the near future.
Agrikol is active more often in Tunisia. Also, Rainbow Horticulture Tunisia, Tunisian-Dutch pepper producing company created in 2015, took advantage of their activities. Last year they extended their facilities with 2.5 hectares. Agrikol facilitated the supervision of ground leveling and foundation and the construction team for the turn-key greenhouse.
The third project realized last year in Tunisia is a bit of a stringer in the midst. This concerns the construction of an algae farm in Tunisia! Also, this crop is being grown more and more in greenhouses and Tunisia holds one of the farms.
Larry Ellison Says His $15M Hawaii Project Can ‘Transform Agriculture’
Billionaire Larry Ellison says he plans to use his Hawaiian island of Lanai as the first step toward transforming agriculture by growing fresh produce using automated hydroponic cultivation inside a $15 million greenhouse operation.
Larry Ellison Says His $15M Hawaii Project Can ‘Transform Agriculture’
arry Ellison, seen in this file photo, is planing to build a $15 million greenhouse operation on the Hawaiian island of Lanai that could "transform agriculture." Ellison bought 98 percent of Lanai in 2012 for some $300 million.
David Paul Morris/Bloomberg
By Janis L. Magin – Real Estate Editor, Pacific Business News
Aug 6, 2017
Billionaire Larry Ellison says he plans to use his Hawaiian island of Lanai as the first step toward transforming agriculture by growing fresh produce using automated hydroponic cultivation inside a $15 million greenhouse operation.
In an interview with the Honolulu Star-Advertiser, Ellison said he and his team “think we can transform agriculture” with the Lanai Farms project, which will rely on renewable energy to grow tomatoes, lettuces, cucumbers, and herbs that will result in the “highest-quality food at the lowest prices” grown on the island whose land was once primarily used as a pineapple plantation.
Ellison spoke to the newspaper at the Four Seasons Resort Lanai at Manele Bay on Saturday, the same day some 80 residents, most from Lanai, attended a presentation in the island’s movie theater by a cancer specialist and Ellison friend David Agus on Ellison’s agriculture plans and health initiatives.
He also told the newspaper that his team is working with the University of Hawaii and has applied for a $10 million grant from the National Institutes of Health to research the nutrition and conservation work to be done at the greenhouse complex, which will include 10 greenhouses, each 20,000 square feet.
Ellison told the newspaper that the $75 million renovations of the Lodge at Koele will transform the resort into a wellness retreat that will include more than the typical spa features, such as nutritional consultations and meditation.
Ellison, the co-founder of Oracle Corp., bought 98 percent of Lanai in 2012 for about $300 million from fellow billionaire David Murdock of Dole Food Co. and Castle and Cooke.
NatureFresh™ Farms Shines Light on Tomatoes in Leamington, Ontario Expansion
NatureFresh™ Farms Shines Light on Tomatoes in Leamington, Ontario Expansion
Leamington, Ontario | March 25th, 2018
John Ketler, General Manager at NatureFresh™ Farms, is excited to announce the newest NatureFresh™ Farms greenhouse expansion taking place in Leamington, ON later this year. Construction of a new 32-acre greenhouse facility will commence in the summer of 2018, with production scheduled to begin in 2019. This facility will house a range of Tomato varieties to be grown using supplemental lighting, allowing for year-round production of fresh, Canadian-grown Tomatoes!
With construction beginning in the summer of 2018, NatureFresh™ Farms will further increase its presence within the Tomato category by 2019. In this new facility, there will be a variety of Tomato crops being grown, including TOMZ® Snacking Tomatoes, Tomatoes-on-the-Vine, and Beefsteak Tomatoes. A greater supply of Canadian-grown Tomatoes produced year-round will ensure that NatureFresh™ Farms successfully meets increased market demands within the Tomato category with consistently fresh and high-quality products.
NatureFresh™ Farms expanded its greenhouse production into the United States in 2015 with the construction of a 45-acre facility in Delta, OH. In Ohio, NatureFresh™ Farms also grows TOMZ® Snacking Tomatoes, Tomatoes-on-the-Vine, and Beefsteak Tomatoes, but these crops are grown using High-Pressure Sodium (HPS) lighting, allowing year-round availability of Ohio-grown Tomatoes.
With supplemental lighting and other innovations being launched in the new facility, the Leamington, ON greenhouse will be equipped with the same state-of-the-art growing technologies as seen in Ohio. Matt Quiring, Executive Retail Sales Accounts Manager at NatureFresh™ Farms, is expecting great success from the expansion: “The first full growing season in our Ohio greenhouse has been very successful so far, so with the same technology that we use in Ohio being implemented in our new Leamington greenhouse, we expect similar success. We should see higher production, greater efficiency in the growing process, and consistently high-quality products from our new Canadian greenhouse.”
NatureFresh™ Farms continues to grow its acreage with this exciting Canadian expansion. Once construction is complete on the new facility, NatureFresh™ Farms will be growing flavorful, high quality Tomatoes across over 90 acres of greenhouses! With exciting times ahead, the NatureFresh™ Farms team is looking forward to further development as a leader within the industry.
-30-
About NatureFresh™ Farms -
NatureFresh™ Farms has grown to become one of the largest independent, vertically integrated greenhouse vegetable growers in North America. Growing in Leamington, ON and Delta, OH, NatureFresh™ Farms prides itself on exceptional flavor & quality. Family owned NatureFresh™ Farms ships fresh greenhouse grown produce year-round to key retailers throughout North America.
New Climate Screen Offers More Light And Lower Energy Costs
New Climate Screen Offers More Light And Lower Energy Costs
Ridder Climate Screens introduces a new energy-conserving screen fabric that offers 2% more light transmission – without detriment to its energy conservation properties.
More light
Ridder Climate Screens’ new RES 10+ FR climate screen fabric has been developed in response to the demand for more light in dark, cold growing periods.
Ridder's Mario Scherpenzeel explains: "Obviously, growers use energy-saving screens to minimize heat losses from their greenhouse in the winter. However, they also want to let the maximum possible light into the greenhouse that their crops need to achieve optimum growth and yields. These needs gave us cause to give careful consideration to the available technological options for the optimization of our Ridder Energy Saving (RES) screens. Our efforts have resulted in the development of a new type of screen fabric that offers growers the same energy conservation properties together with an increase in light transmission of no less than 2%."
Extra energy savings
Growers opting for RES 10+ FR screens are able to lengthen daytime screening periods in the darker seasons of the year and benefit from the extra energy savings. Vegetable growers, in particular, can also achieve higher winter yields. Moreover, the additional amount of light ensures that new, young plants become productive earlier in the cultivation period.
Moisture balance
Mario Scherpenzeel adds that the RES 10+ FR screen fabric not only increases light transmission by 2%, but also improves the climate in the greenhouse. "The screen fabric's moisture permeability properties enable growers to retain adequate control of the moisture balance in the greenhouse. This is also beneficial to crop yields."
RES 10+ FR will be available from Ridder Climate Screens, from stock, as from July of this year. Contact your installer or greenhouse builder for more information about the benefits of this new translucent, energy-conserving screen fabric.
For more information:
Ridder Climate Screens
Honderdland 131 – 2676 LT
Maasdijk – The Netherlands
T +31 858 338 333
info.rcs@ridder.com
www.ridderclimatescreens.com
BrightFarms Hydroponic Greenhouse Coming To Abilene, Texas
BrightFarms Hydroponic Greenhouse Coming To Abilene, Texas
by Lindsey Ragas
Thursday, March 22, 2018
ABILENE, Texas — A new business is coming to Abilene and it's expected to bring in more than a dozen new jobs to the Big Country.
BrightFarms, a company looking to build a state-of-the-art hydroponic greenhouse, is behind what KTXS News referred to last week as Project Ladybug.
BrightFarms choose Abilene as the place for its first hydroponic greenhouse farm in Texas, which will not be a traditional greenhouse because it will grow food that people can buy at local grocery stores.
"[This greenhouse will be] a very large glass structure that produces consumable greens: foods, spinach, lettuce, herbs, things of that nature," said Justin Jaworski, Executive Director of the Abilene Industrial Foundation.
“The plants themselves are suspended above a water basin that is nutrient-rich and only the roots touch," said Kim Tarrant, Chief Administrative Officer of the Development Corporation of Abilene.
The greenhouse will be built at Access Business Park, which is located right across the street from Abilene Regional Airport.
The Abilene City Council gave the approval on Thursday and the DCOA approved $2.3 million for this project last week. The DCOA asked BrightFarms to invest $17 million, with the DCOA matching 10% of the company's investment, along with 21 acres of land worth $600,000.
The new hydroponic greenhouse is expected to bring jobs to Abilene and offer health benefits for its employees.
"We'll include a creation target of approximately 24 jobs in year one and we hope by year three we'll grow a little bit more in those terms, but those jobs are on average paid in the $18 range."
By 2023, they hope to create and maintain up to 34 jobs. Construction on the hydroponic greenhouse might begin this summer and it's expected to be fully operational by next year.
Urban Agriculture Firm Gotham Greens Will Double Its Footprint In Chicago
The site is near Gotham’s existing rooftop greenhouse, the largest commercial one of its kind in the world, on top of the Method soap factory in Pullman Park which opened in 2015.
Urban Agriculture Firm Gotham Greens Will Double Its Footprint In Chicago
March 16, 2018 | Staff Writer
A rendering of the 140,000-square-foot commercial greenhouse now under construction in Chicago’s Pullman neighbrohood.
Chicago Mayor Rahm Emanuel and Gotham Greens broke ground yesterday on the first phase of a 140,000-square-foot greenhouse facility in the Pullman neighborhood on Chicago’s south side. The state-of-the-art indoor farm will be built on vacant land at the former Ryerson industrial site, which is being acquired from Chicago Neighborhood Initiatives (CNI), the Pullman-based nonprofit developer.
The site is near Gotham’s existing rooftop greenhouse, the largest commercial one of its kind in the world, on top of the Method soap factory in Pullman Park which opened in 2015. CNI could receive up to $3.35 million in tax increment financing for site preparation and infrastructure. “These are exciting days for Pullman,” said David Doig, president of CNI who credits Pullman’s renaissance with “good bones and great energy.”
Once completed, the greenhouse facility would be the largest ever built in Chicago and will create 60 full-time jobs. The expansion reflects the company’s success growing and selling premium quality produce year-round in technologically advanced indoor farms. The company’s greenhouses yield 30 times more produce per acre than conventional field production while using 10 times less water.
“Thanks to the leadership and hard work of Mayor Emanuel, Alderman Beale, the City of Chicago, CNI and all of our community partners, Pullman has been a great place to innovate and do business,” said Viraj Puri, co-founder and CEO at Gotham Greens. “We’re producing millions of pounds of fresh produce annually for national and local grocery stores and foodservice operators across Chicagoland, far exceeding our expectations. This is the ideal time for us to expand our presence in the Midwest, and Pullman is the ideal place for us to do so.”
“With unparalleled road, rail infrastructure, abundant vacant land, 20-minute proximity to the Loop, complemented by the venerable housing stock and historic buildings, Pullman is becoming the destination where more people are choosing to go to live and work,” said Doig. “Along with great leadership from Alderman Beale and a great partnership with Mayor Emanuel, Pullman is the ‘ultimate comeback’ community.”
Attending the groundbreaking for Gotham Greens’ new 140,000-square-foot greenhouse were (from left to right, starting third from the left) Illinois State Representative Nick Smith, 9th Ward Alderman Anthony Beale, Mayor Rahm Emanuel, Gotham Greens CEO Viraj Puri, Gotham Greens CFO Eric Haley, Pullman resident and Gotham Greens employee Jenny Mitchell, CNI President David Doig and CNI Board Chair Pastor Merlon Jackson.
TAGS
ILLINOISCHICAGOGOTHAM GREENSPULLMANCHICAGO NEIGHBORHOOD INITIATIVESMETHOD
The Green Revolution In Controlled-Environment Agriculture
The Green Revolution In Controlled-Environment Agriculture
"Nectar Farms And Sundrop Farms are Blazing A Trail"
Vertical farms are popping up left, right, and center. Shipping containers full of purple lights and heads of lettuce dot the North American landscape, while in Asia, so-called 'plant factories' (indoor cultivation facilities) show no sign of letting up. Meanwhile, in Australia, they're taking controlled-environment agriculture in a slightly different direction. We spoke to John Mathews, Professor in Management at Macquarie University, about this.
In his book, Global Green Shift, John draws attention to the links between vertical farming, controlled environment agriculture, building-integrated agriculture and simple urban farming. The basic idea is that a new IT-enhanced platform is emerging based on food production in urban, controlled environments, which is quite different from conventional farming - while still using established varieties, so despite the high tech factor, there's no need to resort to genetic modification.
While most of the discussion on these emerging “plant factories” (to use the term employed in Japan, Taiwan and China) is focused on technology, the real issue is market access, John says. "Some of the VF initiatives in the US and Canada have gone bankrupt because their costs were too high (paying inner city rents for premium locations) while their market was not guaranteed." John points out two Australian examples where market access has been made fundamental to their design.
One of them, Sundrop Farms, has a 10-year offtake agreement with the national grocery supermarket chain Coles to take all the tomatoes produced. "This was crucial to gaining finance for the venture, and to ensuring its viability over its first decade of full commercial operation (since 2016)", John says. "Likewise Nectar Farms has an offtake agreement with the national food wholesaler Costa, which supplies supermarkets and other outlets, and also exports to the Asia-Pacific region.
"These offtake agreements guarantee a market for the produce of these green initiatives – the element that has been missing in many of the recent initiatives some of which have gone bankrupt."
Vertical farming... without the verticality
Vertical farming is a generic term used to capture aspects of the new wave of horticultural innovations. Both Sundrop Farms and Nectar Farms embody all these features – and yet both are single-story operations that cannot be described as “vertical farming”.
John sees these operations as examples of a new green revolution that imports to the ag sector the IT-enhanced innovations that we associate with platforms. "I call them instances of controlled environment food production platforms. The lead countries are Japan, Taiwan and China – although it must be conceded that in Taiwan the examples are still very small in scale. (In 2018 Taiwan has a reported 120 plant factories producing 2,500 tonnes of fresh veges each year. That has to be compared with the output from Sundrop Farms of 15,000 tonnes fresh tomatoes each year – six times the output of the entire Taiwan industry.)"
Green tigers
John believes Asia will lead in this new urban-based high-tech ag revolution, "because that is where the new population will be added – in the cities of China, India and elsewhere. The old agricultural model that was introduced 10,000-12,000 years ago and was industrialized by the 'green revolution' is now proving to be completely unsustainable, given the fact that it is completely dependent on fossil fuels both to run the mechanization and to provide feedstock for fertilizers, herbicides and pesticides."
China is tackling all aspects of green industrialization, because this is the only form of industrialization that will scale and give the country the energy security (through renewable, products of manufacturing) and resource security (through the circular economy) that it needs. The latest wave of this modernization and industrialization of China is fresh food production in cities.
So, should other vegetable-producing countries get nervous? Well, no. "I don’t see China becoming a major vegetable exporter", John says. "It will be focused on establishing huge numbers of CEA food production systems close to cities to supply fresh produce locally and at a scale that can meet the needs of a burgeoning urban population. Exports will be a minor consideration."
Schumpeterian Surge
This doesn't mean the traditional greenhouse vegetable-producing countries can rest on their laurels though. "The big greenhouses in Canada and the Netherlands and elsewhere are products of fossil fuels. They use fossil fuels for heating, for mechanization, for transport and logistics."
There's still time for them to join the green revolution though, as John analyzes: "They can be made sustainable by harnessing renewable energy as a power source and controlling water circulation (supplemented as in Sundrop Farms by desalination, again using renewable power). If new ventures emerge utilizing these technologies, such as PlantLab in the Netherlands, then the new wave will propagate via Schumpeterian competition."
This Schumpeterian Surge (named for Joseph Schumpeter, whose concept of creative destruction is all about sudden changes in economic dynamics following revolutionary innovations), as John calls it, involves propagation of a new IT-enhanced food production platform. He says it will provide the fresh veges needed by expanding urban populations throughout Asia and eventually Africa, Latin America and the rest of the world.
"The platforms will then diversify to the production of fruits, berries, nuts, funghi and other plants, and then perhaps aquaponics. The final frontier will be broad-acre crops like wheat, rice, soybeans etc – a huge issue that needs to be tackled by the combined resources of the Gates Foundation, the Clinton Foundation et al."
So in short, no less than a green revolution. A bold vision indeed, but as John says: "What is the alternative? More fossil-fuelled farming that is destroying the earth? Look closely at Nectar Farms and Sundrop Farms – they are blazing a trail for others to follow." Whether you agree with John's words or not, the idea of a green revolution is certainly interesting.
Publication date: 3/16/2018
Author: Jan Jacob Mekes
Copyright: www.hortidaily.com
"The Technology of Cultivating on Water is Fascinating"
Botman Hydroponics
"The Technology of Cultivating on Water is Fascinating"
"A solid belief in yourself and an even greater belief in technology, that’s the formula for Botman Hydroponics, the ultimate floating cultivation system." The company spent more than ten years on development and research. "It was a necessary period for refining and optimizing every aspect. Now the real action starts", said Jan Botman, company founder.
Until about five years ago people were still often skeptical to the ideas of crop cultivation on water, but you can’t ignore it anymore. The concepts have been refined and thorough research is being done. Hydroponic cultivation has finally become a reality. Jan: "The technique of hydroponic cultivation grabbed me years ago and it has not let go, I have worked for about twenty years as an exporter of produce, especially overseas.
"I decided I wanted to do something else and I read about the program called "Teelt de Grond Uit” (Cultivation Out of the Ground) from Wageningen UR. In this program, cultivation systems for open-field horticulture are being developed that comply with European regulations for water quality. This is done in cooperation with Proeftuin Zwaagdijk and others. Back then, I had already visited a hydroponic project in Belgium that used gutters. I contacted Wageningen and got on board as an entrepreneur. In the meantime, I was already involved in a program of growing leek on water at the testing company of Applied Plants & Environment in Vredepeel. In 2012 I got more deeply involved."
Crop level sub-climate
"Proeftuin Zwaagdijk conducts applied research and I developed the Botman Hydroponics system. The nice thing is that the further development of the system ran parallel to the tests that were being done. Many other systems of cultivating on water work with styrofoam, for example. I absolutely wanted the materials of my system to be 100% food safe, which is why I opted for plastic. In 2013 I made the first Botman Drijverbak model, for both leaf crops and ornamental plants. After several years of testing and research, we gained a deeper insight into how the system works and how crops can grow optimally."
"The nice thing about plastic is that it lets the temperature though because it doesn’t insulate. Contrary to what is sometimes thought, this offers great advantages: the water that the container floats on can act as a type of floor heating - or as cooling. This allows us to create a sub-climate at the crop level, without the entire room has to be a certain temperature. This is much more sustainable. This system also does not leave any waste. The plastic can be recycled and the plant containers are biodegradable. All components have been thought through in detail in order to achieve the most efficient result possible."
Oxygen-rich water
"Another long-held assumption was that the oxygen content of water was unimportant. The opposite is true. The presence of oxygen is essential for the absorption of nutrients by the plant. I, therefore, developed a system for this as well, that’s been studied for three years now. All the results indicate that we are on the right path. In oxygen-depleted water, disease also becomes more likely. This is also the biggest risk of cultivating on water. If things go wrong, then a bacteria can spread rapidly through the water, so you have to make sure that it can’t go wrong. We’ve been successful so far.
The next step is to control the water temperature with a heat pump for both heating and cooling. I have been working on this for ten years, but to me, it’s really only about to start now. The actual production is going to begin, I'm really looking forward to that. It takes a lot of time and attention to think of every step. I stand up and I go to bed with them. But with a smile. "
LivingLab
"From LivingLab EVERGREEN I made a test setup for Clusius Lab, the practical teaching facility at the Clusius College in Hoorn that allows students to do tests on behalf of entrepreneurs. I facilitate the hydroponics system that students can use to find answers to various research questions. While the system of Botman Hydroponics has my name, I, of course, can’t do it all alone. I also work gratefully together with different companies and people. Students can make valuable contributions through smaller, very concrete studies. For example, calculating working with heat pumps or researching an idea for supporting the stems of chrysanthemums. Because they naturally go vertical, you need crop support. And even though some studies do not seem that important, often they are very necessary to get a step further. I can imagine that it would be fun as a student if you could contribute to that."
EFRO EVERGREEN
"In the collaboration with organizations such as Proeftuin Zwaagdijk, like now with the EFRO EVERGREEN project, there is a mutual benefit. They offer the location and a number of facilities, but the input of knowledge comes from two sides, just like the sharing and building on it. I am also a client of Proeftuin Zwaagdijk: partly we work together, other things I take care of myself. The most important thing is the link to the experiments: we have already achieved so many good results. I’m also not the only one working on floating cultivation, other parties are working from their approach. And that we meet each other is only a benefit I think.”
For more information:
GreenPort NoordHollandNoord
www.greenportnhn.nl
Botman Hydroponics
www.botmanhydroponics.com
Publication date: 3/12/2018
KDV Built A Greenhouse Complex For 2.7 Billion Rubles In The Kemerovo Region
KDV Built A Greenhouse Complex For 2.7 Billion Rubles In The Kemerovo Region
TV2
03/01/2018
Tomsk Holding "KDV-Group" opened a modern greenhouse complex in the Yashkinsky District of the Kemerovo Region. For the enterprise, this is a technical launch, necessary to verify the operation of all systems.
"Yashkinskiye Teplitsy" LLC is one of the largest specialized enterprises beyond the Urals, which brings the process of growing vegetables to a new higher level, - the KDV-Group press service reports.
Yashkinsky greenhouses | Photo: KDV-Group
The greenhouse complex is built from scratch. The total area of the enterprise is 9.8 hectares.
The implementation of the "KDV-Group" project took two years and more than 2.7 billion rubles.
KDV Yashkinsky Teplitsy LLC is an autonomous enterprise with high-tech production. To ensure the life of the complex works Energocenter, in its composition - gas piston plants that produce electricity, heat, and gas boilers provide greenhouses with heat and carbon dioxide, so necessary for plants.
Water for production needs comes from its own well. To clean it, a reverse osmosis plant is used to bring the water quality to the desired level. For pouring rainwater near the greenhouses, two storage ponds are organized.
The greenhouses are built on Dutch technology. Equipment that makes it possible to grow quality and delicious vegetables, greens, preserving the maximum of useful substances - German and Finnish. - The general director of the enterprise Alexey Rogov told.
Photo: KDV-Group
In the new modern greenhouse complex, the greenery is grown on a peat substrate, adopting the Finnish technology of flow hydroponics. The technology makes it possible to automate the growing process as much as possible, ensuring a high level of product quality.
Vegetables are grown using technology of low-volume hydroponics. Cucumbers and tomatoes grow not in the ground, but on a special mineral-like substrate, into which, with the help of droppers, the macro and microelements necessary for the plant come in, " Vladimir Bulanov, agronist of Yashkinsky Teplits, explains . - When the plant is in a natural environment, there may be a shortage, an excess of substances, pests and temperature changes pose a threat. Using this technology allows you to monitor and regulate the conditions for growing vegetables. For example, to ensure that the root system is fed with the necessary composition for a balanced growth, the plant nutrition regime is automatically set, which ensures the need for future cucumbers and tomatoes in nutrients.
The microclimate is automated - we set the necessary temperature, humidity, water temperature for irrigation, as well as the concentration of carbon dioxide in the air , the most favorable for photosynthesis, the intensity and duration of illumination, "Bulanov added.
The high degree of automation of "Yashkinskiye Teplits" concerns not only the plant care system, but also the whole equipment of the greenhouse complex. In particular, in the seedling department of greenhouses, where tomato seedlings are already being prepared for planting, the sections of the line can move, as if in a "patchwork" game.
In "Yashkinsky Teplice" they expect that by creating modern production, the enterprise can grow from one square meter per year: more than 65 kg of tomatoes, about 100 kg of cucumbers, not less than 60 kg of greens.
Now in "Yashkinsky Teplice" planted seedlings (for 50 thousand plants) of tomatoes and cucumbers, which occupies an area of 2 hectares for each crop, respectively. In general, these vegetables are provided with a space of 4 hectares.
1 hectare is intended for growing seedlings and greens: lettuce, dill, basil, parsley, and arugula - these plants are already gaining strength and in the very near future will go on sale.
The first harvest in "Yashkinsky Teplice" will be picked up in a week: by March 8, a brighter salad will be delivered to the network "Brighter!". By the way, all modern vegetables and greenery will be grown all year round only for this trade network.
At full production capacity - and this is not less than 7 thousand tons of fresh vegetables annually, the company plans to leave in the fall of 2018.
This Local AGTech Startup Wants You To Forget Everything You Know About Farming
This Local AGTech Startup Wants You To Forget Everything You Know About Farming
By Andrew Moore
March 15, 2018
In November 2016, Tyger River Smart Farm constructed a 13,000-square-foot greenhouse and 3,500-square-foot harvesting facility on 30 acres in Greer. The expansion has increased the farm’s production capacity tenfold. Photo by Will Crooks.
Industrial agriculture has allowed farmers to maximize the potential yield of their crops for centuries. But it has done so at a major cost to the environment — a cost characterized by a steady decline in soil productivity, reduced water quality, elevated levels of carbon dioxide, habitat loss, and more.
Unfortunately, the negative consequences of industrial agriculture are set to worsen in the coming decades as the national population grows and urban sprawl continues to swallow large swaths of productive farmland. The American Farmland Trust, a group working to promote healthier farming practices, estimates that 24 million acres of agricultural land have been developed since 1982.
As a solution, an increasing number of entrepreneurs are turning to controlled-environment agriculture (a combination of engineering, plant science, and computer-managed greenhouse control technologies) to optimize plant growing systems, plant quality, and production efficiency.
One company that’s leveraging the power of CEA is Tyger River Smart Farm.
The Greer-based operation grows a variety of lettuces, chard, kale, and basil through the use of hydroponics — the method of cultivating plants without soil by instead using a nutrient-rich solution to deliver water and minerals to their roots.
“I don’t have a problem with people who adhere to conventional farming methods,” said Ryan Oates, owner and founder of Tyger River Smart Farm. “But I do think growing crops with hydroponics is more beneficial to both the consumer and the environment.”
Growing a business
Despite being the first person in his family to farm, Oates is no stranger to plants.
Oates studied plant biology at Clemson University and conducted numerous research projects at the Genomics Institute. He then enrolled at Miami University in Ohio to pursue a graduate degree in plant molecular biology but decided to drop out after becoming disenchanted with academia.
Upon his return to the Palmetto State, Oates spent several years as a financial planner in his father’s business. He then worked in commercial cabinetry for nearly a decade. In 2012, Oates stumbled onto the concept of hydroponic farming and decided to install a system in an existing greenhouse behind his parents’ home in Duncan.
“My mom loves to garden, so she built the greenhouse as a hobby,” Oates said. “But she was no longer using it, so I thought I would give hydroponics a try. It just seemed like something I would enjoy doing as a full-time job.”
Ryan Oates
Oates eventually outfitted his mother’s 1,300-square-foot greenhouse with fans, an evaporative cooling system, a propane heater, overhead LED lights, and hydroponics equipment. He officially launched Tyger River Smart Farm in August 2013. But the new venture didn’t come without challenges, according to Oates. A power outage, for instance, stopped the flow of water for about two hours and decimated about 70 percent of his crop. Oates outfitted the greenhouse with a generator shortly after.
Following the first harvest in February 2013, Oates had to give away most of his produce to neighbors due to a lack of customers. But then Tyger River Smart Farm was accepted into the TD Saturday Market in downtown Greenville. The market, which runs on Main Street on Saturday mornings from May 6 through Oct. 28, has become a signature event since its launch in 2002 and typically features more than 75 vendors that sell farm-fresh produce, baked goods, meats, cheeses, seafood, and other specialty foods.
“We owe a lot of our success to the TD Saturday Market,” Oates said. “The market not only helped us sell our produce that summer. It also helped us get our name out there and gain new customers.”
Tyger River Smart Farm has since become a vendor at the Greer Farmers Market and Hub City Farmers Market in Spartanburg, according to Oates.
The farm also sells fresh produce to a variety of local restaurants and grocers, including the Swamp Rabbit Café and Grocery in Greenville, Tandem Creperie and Coffeehouse in Travelers Rest, The Farmer’s Table in Spartanburg, Stella’s Southern Bistro in Simpsonville, Cribbs Kitchen in Spartanburg, Restaurant 17 in Travelers Rest, Adam’s Mobile Market in Easley, and GB&D in the Village of West Greenville.
Farming as a science
As the farm’s reputation and customer base continued to grow over the years, Oates realized that Tyger River Smart Farm would need to scale to survive.
In November 2016, Oates expanded his operation by constructing a 13,000-square-foot greenhouse and 3,500-square-foot harvesting facility on 30 acres in Greer. The expansion has increased the farm’s production capacity tenfold, according to Oates.
Oates said the new greenhouse relies heavily on automation. The facility features natural gas heaters, recirculating fans, exhaust fans, mechanical vents, and an evaporative cooler that aids in controlling the temperature and humidity. It also features a retracting shade system that helps with temperature control and light levels.
“Traditional farming isn’t easy,” Oates said. “But our CEA system requires us to monitor our plants on a real-time basis and watch how they react to different conditions. It’s much more process-oriented, so all the automation really helps.”
He added that the farm’s greenhouse uses carbon dioxide generators, which enrich the surrounding air if the levels become low, and more than 100 LED lights, which provide supplemental lighting during the winter months when solar light levels are too low for growing crops. It also uses an environmental controller, which is responsible for sensing environmental conditions and integrating all of the equipment through computer logic to produce a consistent environment year round.
As for growing the produce, Tyger River Smart Farm employs a Nutrient Film Technique (NFT) system, a soilless technique that bathes the roots of the plants in water infused with carefully monitored nutrients.
Tyger River Smart Farm uses over 100 LED lights to provide plants with supplemental lighting during the winter months when solar light levels are too low for growing crops. Photo by Will Crooks.
Oates typically begins the process by purchasing seeds from Johnny’s Selected Seeds in Maine or Paramount Seeds in Florida. The seeds are then germinated in a propagation room, which is completely enclosed and controlled with central heat and air.
After basking in the pink glow of LED lights for one to two weeks, the seedlings are relocated into nursery channels in the greenhouse, which sits on a well and 600-gallon underground tank. The water from the tank is then mixed with nutrients and sent down the channel, where it flows over the roots of the plants. Excess water is then collected at the end of the channels and returned to the water tank.
The nutrient water is then pumped from the main storage tanks back into the plastic channels, according to Oates. Thus, no water or nutrients is ever wasted. The same environmental controller in the greenhouse is responsible for maintaining optimum nutrient and pH levels in the storage tanks.
When the produce is harvested, it is packaged and sold with the roots in order to maintain the plant’s lifespan and nutritional value. During the peak of the season, Oates harvests between 8,000 and 9,000 plants a week, but he continues to produce plants all year round.
“The best part about hydroponics is that I get to harvest plants during the winter months when other farms are buried under the snow,” Oates said. “It definitely helps me stay ahead of the competition.”
The farm’s hydroponic system also has various environmental benefits, according to Oates. About 1,500 square feet of the greenhouse, for instance, is dead space reserved for an insect screen, which allows the farm to not use any toxic pesticides, insecticides, or herbicides during the growing process. And the recirculation process from the farm’s NFT system uses about one-tenth of the water a traditional farm usually uses. And since soil is not used, there is no chance of contamination through runoff.
Tyger River Smart Farm also utilizes various methods to conserve energy. Last year, for instance, Oates purchased and installed a large solar array behind the greenhouse that’s capable of producing enough electricity to power the entire operation.
Planning for the future
While hydroponic farming can be more lucrative than traditional farming and beneficial to the environment, it can also be challenging. Plants, for instance, require over a dozen essential nutrients that must be administered according to species, growth stage, and local conditions, such as water hardness.
“Hydroponic farmers have to understand how plants and nutrients interact in order to be successful,” Oates said. “We use a lot of automation, but we’re still dealing with living things that react to the environment. Luckily, I have a background in plants and can tell pretty quickly whether or not I need to make an adjustment to the system.”
Oates has hired three full-time employees since launching the farm in 2012, but he still spends up to 70 hours a week tending to plants in the greenhouse. “Hydroponics is a double-edged sword,” he said. “We get to farm year-round, which gives us a leg-up on the competition. But we don’t really get vacations or holidays because we have to get the work done when the plants demand it.”
Tyger River Smart Farm grows a variety of lettuces, chard, kale, and basil through the use of hydroponics — the method of cultivating plants without soil by instead using a nutrient-rich solution to deliver water and minerals to their roots. Photo by Will Crooks.
The industry forecast, however, makes all the hard work worthwhile, according to Oates.
The U.S. hydroponic industry has grown consistently the past five years and is projected to continue into 2022, according to market research group IBISWorld. Industry revenue rose 3.4 percent to a total of $848 million the past five years ending 2017. Its outlook declined to a yearly rate of 0.2 percent until 2022.
Oates hopes to reach new customers in the coming years by selling produce through local distributors. The farm has already partnered with a wholesale distributor to sell basil at numerous Ingles supermarkets across the Upstate and Western North Carolina.
He also plans to expand the farm by constructing another 13,000-square-foot greenhouse in 2019. “It will just be an addition to what we have now,” Oates said. “We really want to become an industrial operation, and we’re pretty close to that now, but this addition will pretty much complete that transition.”
Five Indoor Farming Question With Paul Brentlinger of Cropking
Paul Brentlinger grew up aroundCropKing, a greenhouse service company founded by his parents Dan and Marilyn in the early 1980s. He grew his first hydroponic greenhouse crop before he was ten. Known for their personal service,
Five Indoor Farming Question With Paul Brentlinger of Cropking
Paul Brentlinger grew up around CropKing, a greenhouse service company founded by his parents Dan and Marilyn in the early 1980s. He grew his first hydroponic greenhouse crop before he was ten. Known for their personal service, CropKing now services nearly 700 commercial hydroponic growers throughout the country. Ahead of his presentation at Indoor Ag-Con in May, we asked Paul five questions about indoor farming.
1. CropKing is known for its longstanding relationships with family farms. How have your family farm customers’ needs changed over the years?
I don’t know if the needs have changed…if anything the needs have become amplified. A constant focus for CropKing is providing a complete option for a new grower to enter the hydroponic controlled environment ag market. A big component of that complete option is the ongoing technical support, understanding the systems, the environment, and how those things will work together in a greenhouse. CropKing has always offered it’s customers this training and technical support and in the past 5 to 7 years you are starting to see a few other companies in the space start to offer similar options, I think it was Albert Einstein who said “the only source for knowledge is experience”. At CropKing we have been conducting ongoing trials and testing in an effort to benefit our customers in our own greenhouses for over 30 years.
2. We see a number of new farmers entering the hydroponics growing space. How do you recommend that they learn about the industry?
Great questions, of course, we offer our monthly Grower Training Workshops usually at our facility here in Ohio. We realize as much as anybody that a two-day course is not enough time to completely prepare someone to become a qualified new, commercial, hydroponic food producer, but it does give a prospective hydroponic farmer a good overview of owning a hydroponic greenhouse. There are Universities across the country that are focusing on controlled environment agriculture and some that offer hydroponic training courses. We are currently working to develop and ideally this summer will start accepting interns for our 1-2 week long internship program taking interested participants much deeper into the day to day activities that are required to run a successful greenhouse operation. This will help to flatten out the learning curve that all new growers experience.
3. How long does a typical greenhouse build take? At what stage do you suggest that potential farmers contact you?
There is no such thing as a typical greenhouse build! Every build will have its challenges and unique issues to deal with. We do suggest that when conditions are optimum it generally requires about 6 weeks to 2 months to build a CropKing 2 bay (44′ x 128′ gutter connected greenhouse) on a prepared site. A prepared site would be defined as a graded pad with utilities available. So many things play into this answer like the weather and how many people are in your crew. CropKing starts talking to many growers years before they are ready to jump into this space, and that is what we want. This is a very long process to get everything in place especially for the family farms were this means taking out a mortgage on their home or against their retirement, we want people to spend the time researching and studying their local markets to ensure they have an outlet for the volume of produce they are about to grow. We want them to be completely comfortable with the process before putting down a deposit on their future.
4. Your parents started CropKing. How do you expect the indoor growing industry to change by the time your children are old enough to join the business?
I think hydroponics and CEA will become even more commonplace than it is today. As consumers continue to demand access to healthy, local, sustainable, fresh produce controlled environment agriculture and specifically hydroponics will continue to flourish.
5. What’s the coolest crop that anyone’s ever grown with your NFT system?
This is certainly a matter of opinion and we’ve seen everything from cannabis and peppers to carrots and corn being grown in NFT channels, but if I have to pick I think it’s carrots…when the root tip hits the bottom of the channel it fingers out and looks like a mutant hand when you harvest it. You have to open the channel and harvest from the bottom because you can’t pull it back through the hole in the top cover. (That’s right, CropKing’s channel has a removable top cover which also makes it easy to clean).
JOIN US AT THE 6TH ANNUAL INDOOR AG-CON ON MAY 2-3, 2018
REGISTER TODAY
New York - Cornell University Small Farms Program - Lucrative Mushroom Enterprises
New York - Cornell University Small Farms Program
Seeking Northeast Grower Input For Lucrative Mushroom Enterprises
People may not think of growing specialty mushrooms on logs, in barns, high tunnels or greenhouses as a profitable enterprise. But fresh shiitakes and dried mushrooms are getting really good prices. And you don’t need a huge investment to reach these lucrative markets. Learn more about commercial specialty mushroom cultivation at cornellmushrooms.org.
Grower input sought
The Cornell University Small Farms Program is seeking survey input from farmers who have grown and sold specialty mushrooms commercially during 2017 in Maine, Vermont, New Hampshire, Connecticut, Rhode Island, Massachusetts, New York, New Jersey, Maryland, Delaware and Pennsylvania. The goal is to get a pulse on the state of specialty mushroom production in the Northeast and track this budding industry’s growth.
According to americanagriculturist.com, the survey asks about harvest numbers, sales, and marketing strategies. Producers are asked to respond by March 23 at CUSFP's Mushroom Growers Survey 2017.
After the results are compiled, the program will offer a summary of the data via a public webinar, which can be useful to individuals and institutions for grants, market assessment and other uses for a growing industry.
Publication date: 3/15/2018
New Yorkers Plan Major Greenhouse Farm At SUNY Cobleskill
New Yorkers Plan Major Greenhouse Farm At SUNY Cobleskill
Produce will be sold in Northeastern markets
Zachary Matson | @zacharydmatson
March 10, 2018
Nearly 300,000 square feet of greenhouse space is planned to be built on SUNY Cobleskill land between campus and I-88. | PHOTOGRAPHER: PETER R. BARBER
Manhattan-based Chobe Advisers are working with SUNY Cobleskill to build nearly 300,000 square feet of greenhouse facilities on college land near I-88.
The project is the first development the finance, commodities, and renewable energy consultants plan to own and operate outright. Utilizing renewable energy and high-efficiency water systems, the developers are making use of various state and federal incentive programs to establish themselves as large-scale growers of produce that qualifies as local, with the goal of providing that produce to large Northeastern markets, including New York City.
Two of the firm’s partners, Louis Ferro and Rob Parker, were interviewed when they were in Cobleskill for meetings earlier this winter. The following has been edited for clarity and length:
Q: Tell me about your company, Chobe. Is this the biggest project you have going now, or do you have other projects like this?
Louis: This is the biggest project we’ve got going right now.
Rob: We had some other more prominent things going… really once we sat down with the university, this one moved to the front of the pack.
Q: Walk me through what it will look like, what will make it special, what types of technologies will be employed there?
Louis: The best way to describe this is going to be commercial-scale, organically-grown greenhouses utilizing vertical agriculture and leveraging renewable energy. There will be net-zero energy, using a combination of solar as well as a biogas digester and geothermal. The idea really is to grow organic food on a very large scale and get it out to the metropolitan area of New York City and the Northeast, usually through large-scale distributors. We are not going to be going direct-to-consumer, and we’re also going to be focusing on working with the state of New York in terms of selling food to SUNY or many other state agencies. The long-term goal is really to provide organic food -- healthier food -- to as many people as possible at a lower cost.
Rob: We can grow roughly up to 50 different types of crops. We have the ability to rotate those to take advantage of some seasonal price spikes. One of the advantages to that is we are not competing with any of the local growers. If something is in season, it makes more sense for us to provide facilities for them for packing and processing, while we are growing something else. Between that and the waste-energy solution… we think that will be a nice asset for farmers in the local community.
Q: So you will be able to provide services to local farmers?
Rob: If they are interested. We will be selling to larger wholesalers and distributors, so we are happy to provide that as a conduit, and/or just through the packing facilities.
Q: People will be able to bring their waste to you?
Rob: Most farmers already have to use spreaders and other services to process (waste)… instead of having to do that or build six months worth of storage on their farm, yeah, it can be trucked into our facility, and we get energy and natural gas, and they will get some fertilizer in return.
Louis: For example, the college produces roughly 10 million gallons of waste on an annual basis, and so from our perspective having the biogas digester there, that amount of waste is probably equivalent to five or six truckloads a day of waste that the college produces and there are many other farms, the dairy farms in the region, that produce a bunch of waste that right now are stuck… so we would be helping provide a solution to that particular issue.
Q: And that’s the source of your energy?
Louis: Yes, that’s one of them, one of the three sources of net-zero energy. The biogas digester essentially just converts the waste or any organic matter into methane gas, and we use that for our purposes to power the greenhouses and operations and whatever extra we convert to natural gas that can be sold back into the market.
Q: What are the actual products that will be produced? Lettuce, tomatoes, what?
Rob: The four categories are fruit and crops, leafy greens, herbs and medicinals, and mushrooms. In the winter, we might grow fresh tomatoes. During the summertime, we might be growing things that are less seasonal. We grow off-season: it’s more profitable for us. We have enough crops to vary that around, and it makes sure that we won’t disrupt the markets for any of the local farms.
Louis: That’s one of the things we are aware of. We don’t want to compete against the local farmers, so because we can grow different types of crops, and the crops are growing 24 hours a day, we are able to ensure we aren’t competing against the local farmer.
Q: What markets are you eyeing?
Rob: Our customer is really about a wholesaler, food distributor. They are going to come and pick up the product, and if their customer is a grocery store in Albany or a distributorship nearby… or if their market is New York City, (that's where the produce goes).
Louis: One of the key things to consider is some of the basic elements of the food-supply chain right now. Typically you buy an heirloom tomato in California, usually that heirloom tomato actually may have originated in China, it’s flash frozen and sent by vessel. It arrives in California… We are going to be able to ship it from Cobleskill, say, down to New York City same day that it’s picked, so you have an extra week, week-and-a-half of shelf life for a product, which we think is really important.
Rob: It gives us some ways to carve out some of that margin, still charge good prices and have good-paying jobs in the process of having good margins.
Q: It’s going to be three separate facilities built over a period of time?
Rob: There are three individual units within one overall structure. Each unit is essentially modular; it can start producing on its own. Hopefully, if we stay on our schedule, we should have the first unit complete toward the end of 2018. And while completing the second and third units, the first unit can be growing and generating crops and some revenue.
Q: What is the ultimate volume of production or potential volume of production?
Louis: I think the way to look at it is, in order for us to achieve our goals, to be able to sell to the large distributors that are out there, we want to be producing roughly a container a day -- a truckload, which is roughly 25,000 pounds of product. That’s usually what large-scale wholesale distributors require in order to actually do business with them. So that’s what our target ultimately will be: to produce that volume on a regular basis. It’s going to take us a while to scale up to that, obviously, but the capacity will be there.
Q: Will you need local contractors?
Rob: We don’t plan on trucking in construction crews from out of state or anything like that. Some project managers or perhaps some of the design engineering will be more foreign, but on the construction side, we anticipate mostly local unless there is some need.
Q: How did you come to the Cobleskill area?
Louis: We actually were looking at several locations initially that met our overall criteria for locally grown. In the last three years, as we have been developing this project -- we’re New Yorkers, we live in New York -- and we realized that New York was a great place for us to develop a public-private partnership.
Rob: We had been looking at other parts of the country.
Louis: We also realized that we had an opportunity to work with START-UP NY program, which is a huge advantage. We actually originally looked at Cornell as being one of the possibilities, being an ag school, Cobleskill being another. Cornell did not have the available land. About a year ago we reached out to Cobleskill, and they were really receptive and willing to work with us. We just felt it was a really good fit all the way around.
Q: Is a project like this viable without all the different incentive programs?
Louis: Absolutely.
Rob: It is but because there are a lot of different moving parts, it makes it a lot easier. None of what we ware doing is new but integrating and scaling them in the way we are is pretty innovative, and it's tougher to be first in a lot of things, so having that type of support at various levels makes a difference. But it would be viable regardless… we are cutting out a lot of the embedded costs that get added as a lot of produce makes it way to the northeast. For most crops, roughly 90 percent of it comes from the southwest and Latin America.
Louis: It makes perfect sense to be able to locally grow produce and be able to distribute it locally and have it that much fresher the next day it’s available.
Rob: With the declining costs of renewables, even with paying strong wages across the board, our margins will be solid regardless of whether these subsidies are there or not... But without a variety f the state and federal incentive programs it would be tougher to pull off.
Q: Walk me through the different types of jobs there will be once operating?
Louis: You start out with truck drivers who will be driving trucks, particularly for the digester. You are going to have some managerial positions, some project managers.
Rob: Some scientific-based positions, biologists, chemists, technicians. The rest is growers and greenhouse technicians of various levels. It’s pretty widespread, we think all are regular jobs, full-time, benefits and it’s one of those things as we move it forward, some of it will evolve on different things, what products we are growing. We plan on being here for a while so we expect them to be pretty steady jobs. For the jobs that require more skills… some it will require training, the university is a good partner on that…. I know the university is going to be a great source of potential employees but as well as other people from throughout the region.
Louis: We also plan on working closely with the college to possibly tailor or create some courses around what we are doing, incorporating internships maybe even some classroom lectures. Both Rob and I are adjuncts, so we certainly embrace the whole idea of working closely with education facilities like SUNY-Cobleskill, and it’s something we’ve actually spoken to the school about.
Rob: And we benefit just from the expertise of the university faculty as one of the leading ag schools in the country, so that’s an asset for us definitely.
Q: As net-zero are you off the grid?
Rob: We could be but it’s a grid-tied system. It’s just easier from a variety of standpoints, there is storage, energy storage is part of the mix, but for the excess natural gas, we are producing it’s a lot easier to be tied into all of the grid systems for that. One of the programs we’ve been accepted to is Recharge New York, that gives us seven years of discounted power prices. Obviously, once we are fully operational, we should be pretty much set, but while the building is under construction and while we begin our operations some crops are more energy-intensive than others, it gives us a nice fall back to make sure that we get that mixture right… It gives us the ability to keep our costs low while the project is in development.
Q: How does the water system work?
Rob: Once the tanks are filled, it exceeds 95 percent water efficiency. It’s using technology like micro-targeted misters, so when water is delivered to the different crops it’s done as efficiently as possible. There have been a lot of advances in those technologies over the last few years, so it enables us to be that much more efficient with our water use, which is good for the environment and good for our bottom line.
Q: Do you see this as the direction in which agriculture is heading?
Louis: There is already a movement to locally grown around the country. The problem is in the northern climate where you have harsh winters, the traditional greenhouse model doesn’t work, because of the energy usage, the costs are too high. We do think that being able to leverage renewable energy is one way to deal with this issue. We do think this is going to set forth a new trend where other states, other locations, and not just in northern climates… those areas that have issues with water, this types of solution is a huge advantage for them… We hope this is going to be a long-term trend in agriculture, at least on the produce side.
A Des Moines Couple's Urban Farm Runs Into An Expensive Roadblock of Polk County Regulations
A Des Moines Couple's Urban Farm Runs Into An Expensive Roadblock of Polk County Regulations
Lee Rood, lrood@dmreg.com
March 13, 2018
Eric and Jenny Quiner, owners of Dogpatch Urban Gardens have been told by the county that their farm stand must meet commercial building requirements which means $75,000 worth of changes to their 2-year-old business. Kelsey Kremer/The Register
(Photo: Kelsey Kremer/The Register )
Spring planting is underway inside the greenhouse at Dogpatch Urban Gardens, marking what should be the most hopeful time of year for owners of Des Moines' only urban farm.
But when Eric and Jenny Quiner talks about all the changes they have to make this year on their acre lot on Meredith Drive to stay in business, the strain is palpable.
"The stress has almost been the biggest hardship in all of this,” Eric Quiner said, his voice quivering.
A March 19 meeting may tip the scale on whether the couple’s two-year-old business ultimately succeeds or fails. That's when Polk County’s Board of Adjustments will weigh in after planning and development staffers determined the Quiners’ new building amounts to a commercial storefront, not just a farm stand.
With that change comes a mix of building, landscaping, health and safety requirements for the Quiners that they say have necessitated spending about $75,000 more than expected.
2018 PEOPLE TO WATCH: Urban farmers hope to change Des Moines foodscape
The Quiners’ larger-than-a-pumpkin patch business is unique to Des Moines, but their struggle is not.
As bootstrap urban farm businesses and nonprofits have sprouted up around the country in urban centers, some have run afoul of local requirements guiding everything from food sales to water runoff to building codes.
Some cities and counties in recent years have enacted urban farming ordinances or zoning codes because the operations don’t neatly fit into regulations for residential, commercial or agricultural land.
Boise, Idaho, Denver and Kansas City, Mo., have made urban farming a permitted land use. As yet, Des Moines and Polk County have not.
Photos: Urban Garden showing local food impact in the Dogpatch
New territory, lots of questions
The Quiners feel they were open and thorough, asking questions about what they could do with the land when they first explored buying a house (now rented as an Airbnb) and property in an unincorporated part of Polk County in 2015.
That fall, Jenny sent an email to Bret VandeLune, planning and development services manager for Polk County public works, saying she and her husband wanted to grow food, sell on site, distribute to local restaurants, participate in farmers markets and start a CSA down the road.
In the spring of 2016, county building inspectors approved the couple’s plans to build a pole barn on the site to wash, sell and display Dogpatch produce.
In August, the couple asked if they would need a public restroom if they also decided to sell prepackaged meat out of that building.
VandeLune said they did not, as long as they still met requirements for a farm stand, which primarily meant that at least 50 percent of the products sold had to be grown on site and that the business did not stay open more than half the year.
“For a farm stand, selling produce and other products we will not require a public restroom,” VandeLune wrote. “Adding the sales of prepacked pork would not change that requirement, as long as the farm stand requirements are being met.”
VandeLune's email did not address the on-site pole barn, where neighbors came to buy produce.
The county's demands grew, however, after the couple applied for a conditional-use permit that would allow them to have a sign and hold special events (such as weddings) at the farm.
(A 2010 agricultural tourism ordinance allows people living in residential districts to sell vegetables and hold special events.)
Eric Quiner said they were required to hire an engineer to do a professional site plan, at a cost of about $13,000.
After that plan was completed, planning and development staffers realized the business was more than a typical Iowa farm stand.
After that, they say, the Quiners were told they would have to add restrooms and paving and parking to comply with the Americans With Disabilities Act.
They also were told they’d have to add a septic system and fencing and plant dozens of trees when their produce needs as much sun as possible.
The Quiners also had to agree to construct a berm in accordance with a flood plan for the area, although they’d already spent $7,500 adding drainage tile to mitigate the threat of their crops flooding. The couple plans to add a holding tank to capture rainwater for food production.
Jenny Quiner, of Des Moines and owner of Dogpatch Urban Gardens, prepares lettuce plants to be planted in her high tunnel greenhouse on Thursday, March 8, 2018, in Des Moines. (Photo: Kelsey Kremer/The Register )
A plea for help
The unplanned costs and changes forced the Quiners to take out a second mortgage and appeal for help from supporters with a Kickstarter campaign.
Thus far, supporters have invested more than $21,000 to help them succeed.
Still, Eric and Jenny say the stress of having their infrastructure costs double has weighed heavily on them. It's even strained their marriage.
“If we’d have known, we maybe wouldn’t have done this,” said Eric, a Realtor who works in the Beaverdale branch of Iowa Realty. “We don’t have the money.”
VandeLune said the county’s position changed because the couple built a commercial storefront on the property, which comes with specific requirements on how it is finished.
“If all they were doing is growing and selling vegetables, this wouldn’t be a problem,” he said. “They were clear they were building a building. But they weren’t clear they were building a commercial storefront.”
When the couple’s conditional-use permit was approved in March 2017, the Quiners agreed to make the changes necessary, VanderLune said.
“We’ve been working with them,” he said. “We haven’t done any enforcement."
More potentially costly decisions
On March 19, the county’s Board of Adjustments will decide whether to grant the Quiners a series of variances to keep a conditional-use permit.
The variances would allow them to forego some tree planting on the property, skip paving their driveway, increase their height of a fence to keep out deer and bypass setback requirements for the new farm-stand building.
Small-scale growing operations are not new to Polk County. But the Quiners are planning much more on their site. And they are cleared to have as many as 120 people at their special events.
“There’s got to be accommodations for parking so they are safe for the public,” VandeLune said.
In the two years, the Quiners have been in operation, they've gained considerable support from neighbors and restaurants, as well as positive press for their efforts to build community and educate the public.
The couple said revenues grew and are trending the right direction.
The Quiners are hoping all that support will move the Board of Adjustments to work with them as they strive to make their operation economically viable.
Urban farms are not easy to maintain as for-profit businesses. One recent study by a New York University professor found two-thirds of 370 self-identified urban farmers were failing to make a living from farming.
Supervisor Angela Connolly, who lives near the farm at 5085 Meredith, said she believes the Board of Adjustment is poised to approve most of the couple's requests.
"I buy my veggies there, and I think the concept's great," Connolly said. "But what they are doing is not typical. Their business model just kind of grew. And the county still has to assure it's accessible and safe. It's a unique situation."
Lee Rood's Reader's Watchdog column helps Iowans get answers and accountability from public officials, the justice system, businesses and nonprofits. Contact her at lrood@dmreg.com, 515-284-8549, on Twitter @leerood, or at facebook.com/readerswatchdog.
Mucci Farms, A $70M Investment In Huron, Ohio, Continues To Grow
Introduced, developed and entirely paid for by Mucci Farms, the Canada-headquartered company recently finished building its first of three greenhouses after breaking ground in spring 2017. Blueprints show each glass structure totaling 25 acres in size
Mucci Farms, A $70M Investment In Huron, Ohio, Continues To Grow
3/9/2018
HURON
Construction work continues on the first of three planned Mucci Farms greenhouses, each 25 acres large, in Huron near BGSU Firelands. Executives anticipate the process of planting environmentally conscious fruits and vegetables will begin later this month. After a 10-week growth period, the food will be ready for distribution and sent to several supermarket chains across North America. -- Register photo/ERIN McLAUGHLIN
HURON — They’re just days away from planting all-important seeds carrying great weight for the company’s, city’s and cultivation communities’ futures.
Construction work continues on a $70 million privately funded, groundbreaking agricultural venture in Huron.
Introduced, developed and entirely paid for by Mucci Farms, the Canada-headquartered company recently finished building its first of three greenhouses after breaking ground in spring 2017. Blueprints show each glass structure totaling 25 acres in size. There’s also a warehouse, for shipping and distribution purposes, connecting all three greenhouses.
By next week, workers can begin seeding non-GMO crops — namely for tomatoes, cucumbers, peppers, eggplants and strawberries — in the first completed greenhouse. Crews should finish the other two greenhouses within a year’s time.
All food cultivated from the greenhouses will eventually get shipped to major supermarket chains contracting with Mucci across North America. This would include Kroger and Wal-Mart.
Sophisticated, energy-efficient systems for heating and electricity create an ideal environment to grow crops year-round, no matter if it’s 90 degrees and humid in July or 10 below zero in January.
“We have to make sure, especially in the wintertime, that we keep a consistent climate,” said Dave Loewen, Mucci Farms’ general manager who’s helping supervising efforts in Huron. “We are basically trying to create summer inside all year so the crops can grow optimally.”
Then there’s a computer-controlled irrigation program, which knows exactly when an individual plant needs more or less water. Sitting and growing in its own station, a “growing medium,” each crop receives an individual spigot to receive proper nutrients.
Mucci Farms, which operates five facilities and about 175 acres in Canada, incorporates a hydroponic process, meaning it relies on water and not soil to grow crops. With tomatoes, for instance, they need enough minerals so their vines can grow upward of 47 feet tall.
Yet the company doesn’t completely ignore the outdoor elements. Combining both systems, Mucci executives contend, produces better tasting and overall healthier foods.
“Mother Nature is still active in our greenhouse ecosystem,” according to a company statement. “Bees fly around to pollinate the plants and, rather than pesticides, we use a program … where ‘good bugs,’ such as ladybugs, prey on ‘bad bugs.’ Additionally, we’re able to use a fraction of the land and water that traditional farming requires with high yields and by sterilizing and recirculating our run-off water.”
Mucci Farms also does it best to protect the outside environment.
“By growing on elevated benches and troughs, we can achieve a high caliber of cleanliness,” the statement read. “We recycle all of our leachate irrigation water to reduce our footprint on the environment.”
During a recent tour with city officials, Loewen expressed his awestruck emotions for the project in Huron.
“To see this, knowing a year ago we were walking through trees, and being able to walk inside a greenhouse, and how everything else is accomplished, is pretty impressive,” Loewen said.
Many consider Mucci Farms the future of farming and agriculture. Local officials, meanwhile, couldn’t be happier the pioneering project is happening in Huron.
“This is so unbelievable and such a great opportunity to create partnerships for the city and others,” Huron city manager Andy White said. “We are so excited about this and the huge impact it will have on the local economy.”
More about Mucci
Q: What is Mucci Farms?
A: Since the 1960s, Mucci (pronounced moo-chee) Farms has grown non-GMO produce — specializing in tomatoes, cucumbers, peppers, eggplants and strawberries — inside factory-size greenhouses.
A sophisticated, high-wattage lighting system helps products, in a matter of weeks, evolve from tiny seeds to fully grown crops dangling off upward of 47-foot vines.
Mucci Farms, headquartered in Kingsville, Ontario, directly north of Pelee Island, sells its hydroponic crops — a process incorporating mineral nutrient solutions in water and not soil — to wholesalers and major corporations, such as Kroger, Trader Joe’s, Costco, Wal-Mart and others.
“The whole locally grown concept has really taken off,” company CEO Bert Mucci previously told the Register. “That is what the wholesalers and retailers want.”
Q: Why would Mucci Farms want to locate a base in Huron?
A: Bert Mucci explained why Huron represents the perfect location for his company’s first U.S. base.
“It’s a unique opportunity for us because of (Huron’s) proximity to our markets and our headquarters,” Mucci said. “About 65 percent of our production right now is delivered across the border (from Canada to the U.S.). Because of that, being in the U.S. is really attractive to us.”
Q: Are there any other reasons Mucci is coming to Huron?
A: Mucci Farms came to the city because Huron Public Power could promise the company the least expensive electric rate for the greenhouses.
Huron’s publicly managed utility company can provide Mucci with extremely affordable electric rates associated with a large volume of consumption associated with greenhouse-grow lights, officials said.
The company will install blackout curtains to cut down on light pollution, ensuring people aren’t disturbed at night.
Q: Who else benefits from this deal?
A: Several entities stand to reap the windfalls of a $70 million investment.
For starters, Huron Schools would receive an injection of property tax money from new development.
Additionally, BGSU Firelands students could also enroll in special agricultural classes, learning firsthand how a specialized greenhouse operates.
The 100 initial jobs created would also lower unemployment levels and no doubt stimulate the local economy, according to area officials.
Plus retail giants purchasing Mucci-made produce would recognize Huron as a key location for their operations, a possible prelude to more development within the area.
Business brief: Mucci Farms
• What: In Huron, construction continues on the company’s first U.S. base, which focuses on growing crops hydroponically, an energy-efficient, environmentally friendly process incorporating water and not soil.
• Where: It’s being built on a plot of land wrapping around Rye Beach and Bogart roads, beside BGSU Firelands.
• When: The first crops should be planted next week. Workers will care for them over a 10-week period, ready for distribution and consumption this summer.
• How much: The investment in constructing and developing this facility totals $70 million, all paid by company ownership.
• Jobs: Upon starting, the company wants to hire 100 workers and wants to eventually increase the number to 250. People can apply for jobs by visiting muccifarms.com/careers.
NatureFresh Continues Expansions And Increased Efficiencies
NatureFresh Continues Expansions And Increased Efficiencies
BY CHRISTINA DIMARTINO | MARCH 08, 2018
Leamington, ON-based, NatureFresh Farms markets year-round greenhouse Bell peppers, tomatoes, and cucumbers, as well as organic Bell peppers and cucumbers. Kara Badder, the marketing project manager for the greenhouse producer and shipper, said the company is currently shipping from multiple locations.
NatureFresh Farms’ tomato mix.
“Both our Canadian and Ohio greenhouse production facilities are supported with shoulder season supplies from Holland, Spain, Israel, and Mexico,” said Badder. “We plan to continue expanding our organic acreage to meet increasing demand within this category,” she continued. “Last summer we also opened a new modern distribution center in Leamington, which has further increased the efficiency across all of our facilities.”
NatureFresh Farms’ popular items include Ohio Red and TOMZ Snacking tomatoes. It has also increased its organic bell pepper production to 15-acres, with additional expansions planned for 2019. The company also produces red, yellow and orange Bell peppers in Leamington. Its cucumber line includes long English and mini seedless options.
In late 2016, NatureFresh Farms opened a 40,000-square-foot distribution center in the Toledo, OH, area to help to fulfill the increase in demand for its greenhouse produce. The facility operates year-round to support the company’s business on both sides of the border.
The company is also strong in its U.S. Department of Agriculture certified organics. Its organic line includes red, yellow, orange and green Bell peppers, tomatoes-on-the-vine and red grape tomatoes.
“NatureFresh Farms’ Delta, OH, the facility produces numerous tomato varieties, including OhioRed tomatoes-on-the-vine; OhioRed red beefsteak; OhioRed Roma TOMZ grapes in red, yellow and orange; TOMZ red cherry; TOMZ mixed snacking; TOMZ sweet red cocktail; heirloom; and green beefsteak,” Badder pointed out. Early last spring, the company broke ground on a 106,000-square-foot warehouse and distribution center in Leamington.
The new center will help the company increase its volumes to accommodate the increase in business.
North American Growers Welcome New Tool To Manage Light
North American Growers Welcome New Tool To Manage Light
JANUARY 26, 2018 URBAN AG NEWS
“Giving growers the tools to manage light quality is one of our specialties,” says Chris Higgins, General Manager of Hort Americas. “For example, we were one of the first suppliers of LED grows lights in the US. At that time, we saw the crop advantages that growers realized when they had the ability to manipulate spectrum along with intensity.”
The company recently started a partnership with Sudlac. Sudlac’s shading products were introduced in the US last year and received much interest from a wide variety of growers. “We’re giving North American growers a new tool to manage light.”
Hort Americas was founded in 2009 although the team has been actively involved in commercial horticulture for much longer. Strategically positioned in Dallas, it is centrally located to serve its customers in the US, Canada, Mexico and the Caribbean. It has also partnered with the Dutch supplier Horticoop which provides access to knowledge and products developed by leading European horticulture companies.
Proven products
The decision to partner with Sudlac was based on the European manufacturer’s proven ideas and concepts to manage light and protect the greenhouse structure, says Chris. “As a company, we spend a significant amount of our time managing light in greenhouses and other horticultural production facilities.”
In the past shading, products were designed to reduce the amount of light when the sun was at its brightest. “However, when we started talking to Sudlac we weren’t only looking at shading products. Additionally, we were looking at tools that would complement our product range and that would allow growers to manipulate light quality as well as light intensity in the greenhouse. Sudlac’s product portfolio includes such products and as a result, has been enjoying growing success in Europe,” says the general manager.
Once Chris and his team had indeed established that Sudlac had the sort of high-quality products they were looking for the decision to form a partnership came down to people. “We also considered competitive products but ultimately it was Sudlac’s team that won us over. They are very open and easy to talk to. They have a simple philosophy when their business partners do well, they do well. And working together for shared goals is something we always strive for.”
Wide range of climates
The main shading products imported to North America from Europe are Eclipse LD, Optifuse and Transpar. Eclipse LD is a removable shading agent that protects crops against excessive light and heat; Optifuse is a removable diffuse coating; while Transpar is a shading agent that reflects heat radiation.
“Our growers experience a vast variety of climate conditions and grow a wide variety of crops. These products are best suited to cover all possibilities,” says Chris.
The customers also range from very large to small growers with high value crops. “We want all growers to be able to enhance their crops using shading products. Early interest has come from growers with high value crops such as tomatoes, cucumbers, leafy greens and herbs as well as ornamental potted crops. We are also hearing from growers with a wide variety of niche crops that range from general ag research to high end medicinal and biopharmaceutical crops.”
Hort Americas introduced the first products to the North American market in the middle of 2017. “We are still in the process of convincing growers that this technology is going to work, and we have had a huge amount of interest so far. We expect demand to take off when the shading season starts this year!”
For more information:
Hort Americas
2801 Renee St
Bedford, Texas 76021
469-532-2383
hortamericas.com
Ontario Greenhouse Grower Wins PAC Award For Veggies To Go
Ontario Greenhouse Grower Wins PAC Award For Veggies To Go
Mucci Farms announces that they have been awarded a Best In Class Award in the New Brand – Food & Beverage category at the 2018 Packaging Consortium (PAC) Awards. Highly regarded as a global industry leader, PAC is a not-for-profit corporation that includes over 2,500 members throughout the packaging value chain. Their networking process includes webinars, seminars, conferences, competitions, facility tours, education programs, trade shows, technical work groups and social activities throughout the year.
“We are excited and honoured to receive another award for Veggies To Go™," said Emily Murracas, Director of Marketing. “Having been recognized within the produce industry for this product and package, it’s particularly exciting to be recognized in a broader context amongst well established world class brands and packages.”
From left to right Ajit Saxena – Digital Media Coordinator, Fernanda Albuquerque – New Product Development Manager and Wayne St-Denis – Senior Graphic Designer
The annual PAC Awards were judged by a panel of international brand design packaging experts from around the world. Well over 200 entries were judged on a variety of criteria requiring entrants to submit detailed responses to several questions pertaining to sustainability, food safety, cost, packaging material, graphic design, print process, practical usage and the story of the product from inception to market.
“Veggies to Go™was an exciting and challenging project that took us three years to bring to the market, so it’s very rewarding to have it received so well by retailers, consumers and now industry packaging experts” said Fernanda Albuquerque, New Product Development Manager.
Veggies to Go™has received several awards including the Freggie Approved award at the Canadian Produce Marketing Association’s Convention & Expo recognizing the best kid-centric product and package, and most recently won the Award for Best New Package Promo at the PMA’s 2017 Fresh Summit Conference and Expo. The PAC Awards were presented at Brand Experience Magazine’s BXP Live! Conference in Bonita Springs, Florida on Tuesday February 27th, 2018.
A team from Mucci Farms was on hand to accept the award. Veggies to Go™ will be featured in the new product showcase at the SEPC’s Southern Exposure Conference this week in Tampa, Florida.
Canadian Greenhouse Expert Partners With Cannabis Company
The list of Canadian companies planning to grow and market cannabis is increasing, and greenhouse vegetable veterans play a key role.
( File photo )
Another greenhouse vegetable grower is lending his expertise to the growing number of companies with plans to produce medical marijuana in Canada.
Peter Quiring, owner, and CEO of NatureFresh Farms, Leamington, Ontario, is the CEO of GreenhouseCo., a joint venture with Quiring and Wheaton Income. Quiring, who also founded greenhouse fabricating company South Essex Fabricating Inc., will oversee construction of the new company’s 1.4-million-square-foot cannabis greenhouse in Leamington.
The 102-acre site has room to double to 2.8 million square feet of production, according to a news release.
Quiring said the partnership is separate from NatureFresh. Harvest of the first crop, from 30-35 acres of new greenhouse construction, should be in late summer 2019.
Quiring said the large scale of the operation and the fact it’s in a new facility and not a retrofit of a vegetable greenhouse, sets the new venture apart from similar Canadian operations. The new operation takes no vegetables out of production.
Quiring’s expertise will be used for building the facility, not overseeing production.
“It’s a very different crop — there’s not like there’s 10 years or 20 years of history on this,” he said. “ ... The fit is really good because I bring strengths they (Wheaton) don’t have, and they have strengths I don’t have.”
The company will also seek “international cannabis-related greenhouse cultivation opportunities for joint development” and license GreenhouseCo.’s intellectual property for facility design and operation information, according to the release.
The company will also seek “international cannabis-related greenhouse cultivation opportunities for joint development” and license GreenhouseCo.’s intellectual property for facility design and operation information, according to the release.
“In getting to know Peter during this transaction it has become clear that he possesses exceptional greenhouse and operational knowledge and his track record as one of North America’s most accomplished greenhouse builders and operators speaks for itself,” Hugo Alves, president, and director of Cannabis Wheaton, said in the release.
Quiring isn’t the only greenhouse vegetable grower who’s applying greenhouse production expertise to help medical marijuana businesses. Casey Houweling, chairman of Houweling's Group, is also CEO of Glass Investments Inc., a consultancy focused on expanding greenhouse technology. He and Peter Cummings, who has worked with Houweling for two decades, are consulting for PUF Ventures Australia, which is building a 1.2-million-square-foot cannabis facility in New South Wales in Australia. Houweling's Group is not affiliated with the project.
Another greenhouse grower recently announced plans to turn a 540,000-square-foot cucumber facility into a medical marijuana production facility. In mid-February, the Ottawa City Council gave grower Peter Abboud approval for the transition. Abboud is the co-CEO of the company, LiveWell Foods Canada.