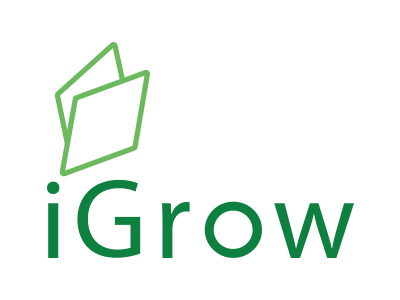
Welcome to iGrow News, Your Source for the World of Indoor Vertical Farming
More African Farms Turning To Hydroponics
More African Farms Turning To Hydroponics
As climate change begins to pose new challenges for conventional outdoor food production methods, hydroponic farming is fast gaining popularity in South Africa. Considering the current drought in the Western Cape and other parts of South Africa, you may say it is a forced shift, but it does bode well for the environment and our scarcest resource on planet earth – water.
For anyone who cares about our resources, it’s not difficult to obtain research about the “carbon footprint” of food transportation and the many other ways in which we harm our environment through producing our food. It is clear that we cannot continue on the way we have always produced food.
NFT Hydro, as the manufacturers and suppliers of Hydroponic NFT Systems and equipment, has become a key part of this shift change in South Africa & Africa. We have seen a significant up-take in growing hydroponically from our South African urban farmers, rooftops growers in our cities and commercial farmers searching for alternative methods of farming to meet the demand for higher yield and the consumers’ concern for the environment.
These urban growers and emerging farmers in South Africa are able contribute to food security through the KHULA farmers App (meaning GROW) which allow farmers to list their produce and track real time inventory levels from emerging farmers as well as basic production forecasting. The App also includes a crowd-sourcing marketplace where farmers can satisfy market demand and incoming orders.
That being said, some of our African neighbours have been even quicker on the uptake of Hydroponics than South Africans, the vast majority of whom, not surprisingly, are women.
NFT Hydro export on a regular basis into Africa as well as the rest of the world, attesting to the quality of our products proudly manufactured here in South Africa.
For more information:
Lynn Gunning
NFT Hydro
Tel: +27 (0)83 737 8602
Lynn@nfthydro.co.za
www.nfthydro.co.za
Publication date: 4/4/2018
Fishers Startup Says Its Indoor Veggie Farms Can End Hunger
Fishers entrepreneur is bringing farms into the kitchen. And the garage. And the closet. And anywhere else at home one might have room indoors for small planters of lettuce, carrots or tomatoes.
Fishers Startup Says Its Indoor Veggie Farms Can End Hunger
John Tuohy, john.tuohy@indystar.com
April 6, 2018
FacebookTwitterGoogle+LinkedIn
This veggie farm fits in your apartment
A Fishers entrepreneur is bringing farms into the kitchen. And the garage. And the closet. And anywhere else at home one might have room indoors for small planters of lettuce, carrots or tomatoes.
Jonathan Partlow, founder of Aggressively Organic, sells small hydroponic plant growing systems that don’t need sunlight, dirt or pesticides and are grown indoors using just water, nutrients and LED lamps.
Partlow says he has the modest of goal of ending hunger. And he’s being taken very seriously.
The bioscience company last month won two awards at the SXSW (South-by-Southwest) convention in Austin, Texas, the first contestant to win both the Food+City Challenge Prize and the People’s Choice Award.
“One of our biggest goals is to end food insecurity within our lifetime,” said Partlow, 49, an Indiana University graduate from Anderson. “We had to create a system that anyone could afford and use.”
Partlow started Aggressively Organic at Launch Fishers, the tech- and app-focused shared workspace that in just a few years has paved the way for several successful startups.
Now, Aggressively Organic is preparing to move into its own 40,000-square-foot building at 9160 Ford Circle later this month, where it will grow 6 million plants each year. It hopes to hire 200 employees within five years and have 42 indoor farms of various sizes across the country.
The concept is the same as hydroponic systems, also known as vertical farming, that are sprouting around the country and grow crops indoors year-round in controlled settings. But unlike those farms, in which thousands of shelves are stacked in large warehouses for wholesale distribution, Aggressively Organic’s plants are tailored for the individual, with the plants grown in cardboard, flower pot-sized containers.
“They are cheap and so easy a kindergarten student can learn it,” Partlow said. “In fact, we have taught kindergartners to use it in Fishers schools.”
Schoolchildren and various Indiana 4-H clubs already are learning the system, and there are plans to distribute the plants to food banks. More broadly, Aggressively Organic launched a crowdfunding campaign to send 50,000 plants to Puerto Rico to aid Hurricane Maria victims.
The plants need only 16 ounces of water and a patented nutrient mixture that permits them to grow rapidly for harvesting in about 30 to 60 days. Replenishing leafy plants, such as arugula and kale, grow fastest and can be plucked and eaten for weeks. But even cherry tomatoes grow quickly and can last a couple of growth cycles.
“I’ve been eating from the same head of lettuce for a month,” Partlow said.
The plants, which include herbs like basil, can be kept anywhere in the house where there’s extra space. They also take a minimum of supervision.
A built-in advantage to Aggressively Organic’s individual system, compared to large systems, is that each box and plant is self-contained. So, a flaw in the balance of nutrients in a water-recirculating system won’t affect an entire supply of plants, said Chris Chick, Aggressively Organic’s plant physiologist.
Chris Chick, Fishers, helps run Aggressively Organic, a new start-up in Fishers that plans to have about 40,000 square feet of hydroponic growing space, Fishers, Wednesday, April 4, 2018. The company has a system that lets people easily grow their own food in a small household space. (Photo: Robert Scheer/IndyStar)
“Each of the different vegetables has its own nutrient solution, so they aren’t sharing a common one,” Chick said. “If something were to go wrong, you throw away the individual plant, not all of them.”
Ultimately, Aggressively Organic will offer memberships in which subscribers can pay a yearly fee to order six packs of plants, then switch them out after they have been eaten after two or three growth cycles, like dropping off empty bottles for the milkman.
Vertical farms are becoming more common in urban areas as a way to provide locally produced vegetables on a large scale that don't need to be shipped thousands of miles, from California or Arizona, where 94 percent of lettuce is grown. Chick said vegetables lose most of their nutrients within 24 hours after being picked.
Lettuce at Aggressively Organic, a new start-up in Fishers that plans to have about 40,000 square feet of hydroponic growing space, Fishers, Wednesday, April 4, 2018. The company has a system that lets people easily grow their own food in a small household space. (Photo: Robert Scheer/IndyStar)
This week at the company's new headquarters in Fishers, Chick displayed a plant that had been growing for about 35 days that was bursting with two dozen ripe cherry tomatoes from a cardboard box. Broccoli leaves, about a foot long, flowed from a larger box measured about a foot in length. A bite of arugula offered a sharp, peppery flavor much more succinct than the bagged product bought in the supermarket.
"It's picked fresh, so it still has all its flavor," Chick said.
Jeff Barranco, 39, a member of the Anderson school board, who has a small 1.4-acre traditional farm, began growing Aggressively Oganic’s plants in his garage last October. He now has 1,000 plants, including bok choy, tomatoes, hot peppers, basil and lettuce and plans to sell the produce at an Anderson farmer’s market this summer.
“It really is a plug in and play type of system,” Barranco said. “You don’t need a lot of knowledge about farming.”
Barranco keeps the plants in a 8-by-10-foot tent in the garage and spends about $100 a month on electricity for the LED lights. Besides that, little maintenance is necessary.
Barranco said he will tear off some basil or lettuce for salads at dinner and can taste the difference from supermarket-bought food.
“It has a much better taste, it’s fresher and really nice to have right here,” he said.
Call IndyStar reporter John Tuohy at (317) 444-6418. Follow on Twitter and Facebook.
Billionaire Larry Ellison to Launch Hydroponic Farm Business on His Private Hawaiian Island
Billionaire Larry Ellison to Launch Hydroponic Farm Business on His Private Hawaiian Island
By Daisy Prince
March 26, 2018
Larry Ellison ILLUSTRATION: GETTY IMAGES
Software giant Larry Ellison leapt into the health/sustainability arena with the launch last week of a new company, Sensei, a network of hydroponic farms in Lanai, Hawaii.
“As a society, we’ve become so detached from knowing our food, knowing where it comes from and why we eat what we eat,” said cancer specialist Dr. David Agus, who worked with Ellison to develop the company.
“With Sensei we hope to increase transparency and restore our relationship with food,” Agus, the founding director of the University of Southern California’s Lawrence J. Ellison Institute for Transformative Medicine, said in a recent statement from Sensei.
Sensei Farms will start with 10 greenhouses, each measuring 200,000 square feet, with the expectation they will yield 1.7 million pounds of produce annually, Oracle founder Ellison told the Honolulu Star Advertiser in an interview. That amount is more than enough to supply Lanai, the private Hawaiian island that Ellison bought 98% of in 2012 for $300 million.
The plan is to farm fruits and vegetables from seeds imported from around the world and sell them in Hawaii, which imports about 85% of its food, according to the Sensei statement.
The first crops are Black Trifele tomatoes and Komatsuna mustard greens, grown hydroponically, meaning the plants are grown in water rather than soil.
This method only requires about 10% of the water needed for conventional farming methods and doesn’t use any harmful chemicals, according to the statement. Sensei will use Tesla solar panels for its greenhouses. Sensei will use software and technology to monitor the nutritional value of the crops and collect data on the yield so that researchers can maximize the nutrient and taste potential.
“For so long, agriculture has been one of the least digitized industries,” Daniel Gruneberg, Sensei’s president, said in a statement. “Now, we can combine software, sensors and robotics to make giant leaps in sustainable farming and perhaps, more importantly, the quality of our food.”
Movement To Strengthen 'Organic' Label Pushes For New Standards At Vermont Meeting
A rally in Thetford back in 2016 criticized the USDA's move to allow vegetables raised hydroponically to be labeled as "organic." Now a movement has formed to strengthen the organic label | REBECCA SANANES / VPR FILE
For a group of farmers and consumers around the country, the term "organic" just doesn't go far enough. They say the U.S. Department of Agriculture has weakened standards for food that is supposed to be raised organically.
And so they’re meeting in Vermont this week to come up with a new label that they argue will show that the food has been produced in ways that protect the environment and animal welfare.
Thetford farmer David Chapman raises organic tomatoes on his Long Wind Farm. It’s what he’s done since 1984. But he spends a lot of time these days helping organize what he calls the "Real Organic” movement.
“I would say the national organic program is just failing miserably at the one thing that they were asked to do, which was to protect the integrity and the transparency of the food supply between the organic farmers and the people who want to buy organic food, organically grown food,” Chapman says.
Chapman’s activism kicked into full gear last year when the USDA allowed vegetables raised hydroponically – without soil – to be labeled organic.
"I would say the national organic program is just failing miserably at the one thing that they were asked to do, which was to protect the integrity and the transparency of the food supply between the organic farmers and the people who want to buy organic food, organically grown food." — David Chapman, Long Wind Farm
And then this month, the USDA rejected Obama-era animal welfare rules that would have required chickens in large-scale organic egg operations to have access to the outdoors. Chapman says farms are known as “concentrated animal feeding operations,” or CAFOs, now dominate the organic egg market — and for one reason:
“The primary influencer on this process is money,” he says.
Both decisions from the USDA, Chapman says, came after heavy pressure from businesses hoping to capture the price premium organic food earns in the market.
“All told, between CAFOs and ‘hydros,’ we’re probably talking about $2 billion in annual sales of CAFO/hydro production that is being certified as organic,” he says.
Enter the “Real Organic” movement, which Chapman is helping organize. A group of farmers and consumers is meeting in Fairlee this week to come up with new standards that Chapman hopes will bring the organic label back to its roots.
“I go to the store, and I buy food — I buy vegetables, I buy milk, eggs,” he says. “Unless I know the farm, I certainly can’t count on the USDA label to let me know whether or not that was produced in the soil, in a soil-based system for the animals, or whether it was produced in a factory.”
From Vermont Edition: Organic Standards At A Crossroads [Nov. 21, 2017]
But the movement has its skeptics.
Grace Gershuny is a pioneer in organic agriculture. She helped develop Vermont’s first organic standards and then worked for the feds developing the national standards.
“I don’t think that the solution to their complaints lies in another label,” she says.
Gershuny would like to see organic food more available – and more affordable. She worries that “real” organic products would be expensive and would serve only an elite, privileged market.
“A lot of people can’t afford to buy organic food,” she says. “And a lot of people don't have access to local, you know, righteously grown 'real' organic, or however you want to label it.”
Gershuny instead wants better enforcement of organic standards.
“I think that the solution isn't to add on another layer of rules, but to help see that the rules that exist are enforced,” she says.
And a group representing Vermont's organic farmers also has some concerns. Noel Dehne is the certification director for the Northeast Organic Farming Association of Vermont. In her ideal scenario, the "Real Organic" movement would push USDA to strengthen its national standards.
"We need to be really careful not to devalue the current organic label, because the majority of organic farmers are meeting the regulations." — Noel Dehne, NOFA-VT
“We need to be really careful not to devalue the current organic label,” Dehne says, “because the majority of organic farmers are meeting the regulations.”
Dehne also worries consumers could get confused by the profusion of new labels on food. But Chapman says consumers are already confused.
“It won’t be our label that’s creating the confusion,” Chapman says. “What’s creating the confusion is that the USDA is redefining organic to mean something very different.”
The USDA did not respond to a request for comment.
Chapman says the group meeting this week in Vermont hopes to come up with new standards — and a name for a new label — over the next two days.
Vermont Sen. Patrick Leahy is credited with initiating the national organic program through legislation he sponsored in 1990. His staff has been following the "Real Organic" movement but did not say whether the senator supports the new label.
In a statement, Leahy said:
"I know the Vermonters who are leading this national effort and they care deeply and are working hard to protect organic agriculture. For my part, I will continue working to keep USDA Organic strong and to reverse some of the damage to the meaning of organic that has been done in recent years. That is why I fought to increase the funding for the National Organic Program by $3 million in the recent Omnibus spending package to provide USDA with sufficient funds for fraud detection and proper oversight."
Disclosure: NOFA-VT is a VPR underwriter.
South Bronx Social Entrepreneur Henry Obispo Creates a Green Revolution and Sustainable Design, in Collaboration With Suny Farmingdale Students, for BORN JUICE
South Bronx Social Entrepreneur Henry Obispo Creates a Green Revolution and Sustainable Design, in Collaboration With Suny Farmingdale Students, for BORN JUICE
Born Juice is a plant-based Eatery and Juice bar coming this Summer
April 14, 2018 | Source: Born Juice
South Bronx Social Entrepreneur Henry Obispo creates a Green Revolution and sustainable design, in collaboration with Suny Farmingdale Students, for BORN JUICE
Mr. Henry Obispo
Volodymyr Zadorozhnyy (satorial studios)
NEW YORK, April 14, 2018 (GLOBE NEWSWIRE) -- Henry Obispo, a social entrepreneur who has set his future in building the first ever cold-pressed juice bar and plant-based eatery in the Bronx, NY with the help of SUNY Farmingdale Department of Urban Horticulture and Design.
Raised in the Bronx and born in the Dominican Republic, Henry Obispo is a product of a rich cultural topography, a community organizer, and an activist.
Mr. Obispo wanted to take it upon himself to find solutions to the oppressive realities around health in his community, considered one of the largest food deserts and the poorest congressional district in the United States.
After implementing a grant from the USDA, where Mr. Obispo looked for solutions to the food desert realities, access to food became a focal point and an obsession for Henry to create solutions for those social ills. The passion that Mr. Obispo has for his community has prompted Mr. Obispo to dream big and start a business which will benefit everyone in the Bronx.
The 14 students led by Professor Stevie Famulari of Farmingdale Department of Urban Horticulture and Design started designing the space which can be found at 2500 Third Avenue in Mott Haven. Each of the students will design and develop a green concept integrating green technology to promote sustainability.
This space will soon become "Born Juice", a juice bar & Plant-based eatery in the Bronx, which will serve fresh pressed juices, smoothies, vegan bowls, and express casual healthy foods. We all know that juices cleanse the body and is a temporary break from eating solid foods. Fresh juices from fruits and vegetables nourishes the body and is another way of detox which can recharge, rejuvenate and renew the system. The Bronx community has been missing this very important factor in their daily lives. Mr. Obispo has seen this ongoing situation for decades and decided to fill in the blanks.
Mr. Obispo focuses on creating a hyperlocal system, where food is grown and harvested by local youth, used and produced in food served to the community by a local workforce, in the quest to reverse many of the health disparities in one of the largest food deserts in the country.
Mr. Obispo states, "We want a model where you have sustainability, and not just in the food. Everything will be from local gardens, local farmers, and hydroponics, and there will be sustainability in the interior designs, too.”
Born Juice is a revolutionary project because of its zero-carbon footprint model. Born Juice is expected to incorporate green technology in the form of hydroponic gardens to grow the food, which is later harvested for their cold-pressed juices and food.
This project will educate the local youth about urban farming and hyper-local systems to empower the local population riddled with health disparities and awaken them to a new green reality, operating in their own neighborhood.
To learn more about the Born Juice project, please visit: http://www.bornjuice.com/
Contact Info:
Contact Name: Henry Obispo
Born Juice
2500 3rd Ave, Bronx
NY10454
www.bornjuice.com
info@bornjuice.com
Instagram: @bornjuice
US: Non-Hydroponic Organic Label In The Making
US: Non-Hydroponic Organic Label In The Making
With a new extra-organic label, a group of Vermont growers want to distinguish their organic production from the USDA certified organic production, i.e. hydroponically grown produce.
It was only last week that Olivier Brailly with French company Groupe MGD opted for a new label addition to close the gap between conventional and organic: pesticide-free. Now American growers opt for a fourth one: Real Organic. Most notable part of it is the importance of keeping the soil in organic. "We are creating a label we can trust", the initiators say.
The initiative follows the NOSB's recent decision to have hydroponic and aquaponic farms remain eligible for the USDA Organic Certification - allowing products from these farms to carry the USDA Organic label. According to a group of farmers and advocates united under the name 'Real Organic Project', the USDA certification 'loses the meaning of organic'. They fight for another label, excluding hydroponic farming and large livestock farms that don’t pasture their animals.
"It has not been a good year for the National Organic Program", Dave Chapman, organic tomato grower and partner of the project, writes on the website. "Since the November NOSB (National Organic Standards Board) meeting in Jacksonville failed to prohibit HYDRO, the organic community has gone through a period of questioning and searching. We are wrestling with the basic question, 'Can we trust the USDA to protect organic integrity?'"
The Real Organic Standards Board is formed by several farmers including several fruit and vegetable growers like Eric Sideman, Linley Dixon, Dave Chapman, and Paul Muller, Jennifer Taylor, Jim Gerritsen and other industry representatives, including Alan Lewis, with health food store chain Natural Grocers. "We feel that something must be done. We want to help clear up the confusion the NOP failures have created for people trying to support traditional organic farming", the explanation continues on their website.
"We are not trying to destroy the USDA label. Rather we are trying to save it. We have already worked for many years to build an organic label that people can trust. Without such transparency, we all lose."
In this video, uploaded last November by The Northeast Organic Farming Association of Vermont, David Chapman explains why he believes the integrity of the USDA organic seal is at risk
Their work will involve a number of efforts, starting with the creation of a new “Add-On” label. "It will use USDA certification as a base, but it will have a small number of critical additional requirements. These will differentiate it from the CAFOs, HYDROs, and import cheaters that are currently USDA certified."
Read more about the Real Organic Project here.
Publication date: 4/13/2018
More than 100 jobs coming to Breathitt County, Kentucky
More than 100 jobs coming to Breathitt County, Kentucky
By WYMT News Staff |
March 29, 2018
BREATHITT CO., Ky. (WYMT) - Startup indoor farming company Hydroponic Farms USA plans to invest more than $44.5 million into Breathitt County and bring in over 100 new jobs.
Governor Matt Bevin made the announcement Thursday, saying the business will provide 121 full-time jobs.
Hydroponic Farms USA plans to construct a new facility on a reclaimed mine in Jackson. The facility will use hydroponic and aeroponic technology to grow leafy greens, tomatoes, peppers and other produce.
Company leaders say they will break ground after the land is purchased and the permits are approved. The jobs will include leadership, production and post-production roles.
“It has been our administration’s mission to provide better job opportunities in every part of our state, and this investment is evidence that we are achieving that goal. We are truly grateful for this vote of confidence in the commonwealth. Hydroponic Farms USA will be a great fit for the Jackson community, and continues the economic momentum that is building in Eastern Kentucky," said Governor Bevin.
The farming company is working with major retailers and wholesalers to secure contracts to supply customers with fresh produce all year round.
Tim Davis, a managing member of Hydroponic Farms USA, said this.
“Appalachia has much to offer the world in terms of natural beauty and abundant resources, but what really makes this place special is its people. We knew the moment we set foot in Breathitt County, that this was not only a perfect place to build our business, but also a place we could proudly call home. Our investors have been humbled by the overwhelming support of Kentucky’s state and local government representatives. Moving forward, we are committed to building positive relationships with all of our new neighbors in Breathitt County and doing our part to create real opportunities for people. With the agronomic and technological expertise provided by our partners at Green Ag Technologies, we are proud to bring the future of farming to the area and make a significant impact on the produce industry.”
US (AR): Students Develop Hydroponic System For Non-Profit Farm
US (AR): Students Develop Hydroponic System For Non-Profit Farm
Laura Gray and Sarah Gould, both pursuing their bachelor's degrees in biological engineering at the University of Arkansas, did not anticipate that their participation in the 2017 Social Innovation Challenge would turn into a year-long thesis project. But that's exactly what has happened; the two juniors are working with Tri Cycle Farms to implement their proposal, developed in the fall semester during the annual competition, for a hydroponics system to improve Tri Cycle Farms' ability to address food insecurity in Northwest Arkansas.
Led by Rogelio Garcia-Contreras, director of social innovation, the initiative is part of the Office of Entrepreneurship and Innovation. Its purpose is to allow students, faculty and staff to connect with local organizations that are tackling social and environmental issues within the community. Once a year, the Social Innovation Initiative hosts a Social Innovation Challenge, in which students partnering with an organization can partake in a competition to present entrepreneurial, market-based, viable, and sustainable solutions to problems posed by the organization.
From left, Laura Gray, Don Bennett and Sarah Gould at Tri Cycle Farms. Photo by Abigail Grossman
Jennie Popp is the associate dean of the Honors College and co-chair of the Service Learning Initiative. She has helped to organize and formalize service learning through the Initiative at the University of Arkansas. "Service learning gives the students real-world experience to test the knowledge they learn in the classroom. It can also lead to internships and job offers from the organizations with whom the students work," said Popp. Popp has also served as a judge for the Social Innovation Challenge for the past two years. She describes the challenge as being extremely beneficial to students who are looking to make a change in the community while having the opportunity to discover an important, worthwhile thesis topic.
When asked why the challenge piqued her interest, Gould answered, "I like to get involved and stay busy. Laura and I were really excited about all the projects listed in the informational email, so we set up a meeting with Rogelio to learn more about the challenge." Gould and Gray described that activism, nonprofit involvement, and the idea of having the opportunity to learn not only about how to physically structure the project, but also how to look at it from an economic perspective, were all reasons why they wanted to join the challenge.
Gould and Gray partnered with the non-profit Tri Cycle Farms, located on Garland Avenue in Fayetteville. Tri Cycle Farms is a community farm working to address food insecurity by growing food and teaching others how to grow food. "One in four children in the state of Arkansas are food insecure," said Don Bennett, founder of Tri Cycle Farms. Bennett said that once he learned this, he began doing research into the food system in Washington County. "I found a purpose," he said. Tri Cycle Farms redistributes about 50 tons of food per week and works to teach garden and farming education to people within the community.
Gould and Gray chose to partner with Tri Cycle Farms because they believed that with their engineering background, they could implement a hydroponics system within a greenhouse, also known as a hydro-house, to improve crop yields and reduce water usage. "Tri Cycle Farms does a lot of community activism and wants to use the hydro-house as not only an effective way to grow plants but also as an educational opportunity for students," said Gray. Once the hydroponics greenhouse is finished, Bennett would like to call it the "Seed-to-Sell Learning Project." He wants the house to provide opportunities for student groups and interns to obtain service learning hours from working in the hydroponics house and helping it develop.
Gray and Gould both emphasized the value of the Social Innovation Challenge in getting their project launched.
"We knew, regardless of the challenge outcome, we wanted to continue our work with Tri Cycle Farms," said Gould. "While we did discover this project as our thesis, the reward of finishing it is so much more than us, or our thesis. It has such a lasting impact on the community."
When asked how the challenge helped them in their professional experience and with their personal growth, Gray answered, "Being engineering students, we are not exposed to very much business. It forced us to think more about the economic side of things. We went from having zero experience to having the opportunity to apply so many concepts we learned to the real world."
Gould and Gray continue to work on the hydroponics greenhouse system for Tri Cycle Farms, which will be used as a service learning project for future students when it is complete. The two students are also able to continue working towards their thesis project while helping the community.
"Although Laura and Sarah did not win the Social Innovation Challenge, they have demonstrated success by making a commitment and a connection to our organization," said Bennett. "In the end, Tri Cycle Farms won. Laura and Sarah have committed over a year and a half to this project."
Source: University of Arkansas
Publication date: 3/29/2018
IndoorFarming Company Bringing News Jobs To Breathitt County, Kentucky
Indoor Farming Company Bringing News Jobs To Breathitt County, Kentucky
By Morgan Henry
March 29, 2018
FRANKFORT, Ky. (WTVQ)-Governor Matt Bevin announced Thursday that startup indoor farming company Hydroponic Farms USA will invest more than $44.5 million in Eastern Kentuckys Breathitt County and create 121 jobs with the construction of a new facility on a reclaimed mine in Jackson.
Bevin says “The announcement of 121 full-time jobs in Breathitt County is wonderful news for Eastern Kentucky and its skilled workforce. It has been our administrations mission to provide better job opportunities in every part of our state, and this investment is evidence that we are achieving that goal. We are truly grateful for this vote of confidence in the commonwealth. Hydroponic Farms USA will be a great fit for the Jackson community, and continues the economic momentum that is building in Eastern Kentucky.”
Hydroponic Farms USA will build a nearly 42-acre facility with 35.5 acres of production space. The facility will use hydroponic and aeroponic technology to grow leafy greens, tomatoes, peppers and other produce. The 121 jobs will include leadership, production and post-production roles. Company leaders plan to break ground following their land purchase and approval of permits.
Tim Davis, the managing member of Hydroponic Farms USA, says “Appalachia has much to offer the world in terms of natural beauty and abundant resources, but what really makes this place special is its people. We knew the moment we set foot in Breathitt County, that this was not only a perfect place to build our business, but also a place we could proudly call home. Our investors have been humbled by the overwhelming support of Kentucky's state and local government representatives. Moving forward, we are committed to building positive relationships with all of our new neighbors in Breathitt County and doing our part to create real opportunities for people. With the agronomic and technological expertise provided by our partners at Green Ag Technologies, we are proud to bring the future of farming to the area and make a significant impact on the produce industry.”
Hydroponic Farms USA says it is working to develop and implement advanced hydroponic and aeroponic technology and innovation. To do so, the company formed a partnership with Oz Agribusiness Projects and Investments Ltd. and Green Ag Technologies LLC to manage and operate the facility.
Hydroponic Farms USA will follow a similar business model to Kentucky Fresh Harvest, which broke ground in Lincoln County in January 2017 and also is managed by OAPI. Currently, the company is working with major retailers and wholesalers to secure contracts to supply their customers with fresh produce year-round.
Kentucky Commissioner of Agriculture Ryan Quarles says the project is a good fit within the commonwealths evolving agricultural profile.
Kentucky has a long tradition of being a leader when it comes to agricultural innovation, Commissioner Quarles said. Whether it is no-till corn, industrial hemp or hydroponic farms like this one, Kentucky agriculture continues to thrive. Todays announcement is the result of the hard work done by Governor Bevin and Think Kentucky to attract new and exciting businesses to our old Kentucky home.
In addition, Hydroponic Farms can receive resources from the Kentucky Skills Network. Through the Kentucky Skills Network, companies can receive no-cost recruitment and job placement services, reduced-cost customized training and job training incentives. In fiscal 2017, the Kentucky Skills Network provided training for more than 120,000 Kentuckians and 5,700 companies from a variety of industry sectors.
Billionaire Launches Hydroponics Startup
Los Angeles-based Sensei plans to build 10 greenhouses, totaling 200,000 square feet, on the Hawaiian island of Lanai. Ellison owns 98 percent of the island.
Billionaire Launches Hydroponics Startup
Billionaire Oracle Corp. co-founder Larry Ellison this week launched his latest startup, which will focus on automated, hydroponic indoor food production.
Los Angeles-based Sensei plans to build 10 greenhouses, totaling 200,000 square feet, on the Hawaiian island of Lanai. Ellison owns 98 percent of the island.
He unveiled the startup this week, promising that it would focus on building products and experiences to “empower you to grow well.”
Sensei said its first farm is hydroponic, powered by Tesla solar and uses minimal amounts of water. The startup says it’s growing food from “original seeds,” suggesting they’ll eschew genetically-modified plants in favor of heirloom varieties.
On Lanai, Ellison’s goal is to grow high-quality food, helped by software automation, and sell it locally, undercutting the more expensive produce imported daily. He says agriculture is one of the last major industries that has remained largely unchanged by software.
“Lanai is step No. 1,” Ellison told the Star-Advertiser at the time. “We think we can transform agriculture.”
Ellison launched Sensei with David Agus, a bestselling author, University of Southern California professor and serial entrepreneur. He’s also the founding director of USC’s Lawrence J. Ellison Institute for Transformative Medicine.
Agus treated late Apple CEO Steve Jobs, who remained close friends with Ellison up until his death in 2011.
The company lists three open positions on its website, notably a postdoctoral researcher who will be tasked with designing “plant experiments and associated protocol and research methodology.” It adds: “Travel to Hawaii will be required.”
The company’s day-to-day operations are being led by Daniel Gruneberg, who cofounded San Francisco-based events software startup Zozi, which was acquired by Peek last year.
Gruneberg told TechCrunch the company will soon begin selling food to restaurants and stores under the Sensei Farms brand. In his interview last year, Ellison said he expected Sensei to be profitable in its first year.
Click here to read the original article at Silicon Valley Business Journal.
Photo credit: Hartmann Studios via Flickr, Creative Commons Attribution.
03/21/2018 - Silicon Valley Business Journal
Hydroponics: The Future of Agriculture
Hydroponics: The Future of Agriculture
— By Jescilia Karayamparambil & R N Bhaskar | Mar 14, 2018
Mumbai : In one of the many offices of HiMedia Laboratories in Mumbai, there is a lab that is working on basic research relating to plants – as an aid to promote hydroponics. Hydroponics, or vertical farming, is not a new concept. But the techniques that are being adopted in hydroponics are improving every day. HiMedia has now opted to create another company – Higronics – to focus on providing plant-specific nutrients.
In some ways, HiMedia is an unusual company. It has focussed on the study of the structure, physiology, genetics, pathogenicity, ecology, and taxonomy of microorganisms in a simulated growth environment and has enabled researchers to isolate the typical behaviour of microbes that affects humans in different ways. Today, with a turnover of over Rs 500 crore, it is one of the top three brands in microbiology in the world. It has been in the forefront of assisting microbiological research by providing essential culture media that are easy to use, safe, and comparable with world standards.
It is with this background that it decided to focus on food, through the development of plant nutrients, which would be immensely useful for hydroponic farms. Dr. Vishal G Warke, from the promoter family, believes that “the area of hydroponics requires continuous research and development for it to become the future of farming. “
Unlike conventional farming, hydroponics uses little soil but uses cocopeat – coconut fibre and vermiculture – during the growth phase of the plant. Thereafter, it allows the plants to grow in a soil-less environment, thus taking away 70 percent of pests from the agri-system. This is because over 70 percent of all pests are soil based – including weeds. The absence of pest allows for significantly less use of pesticides. Thus you have healthier plants, using less water and hardly any pesticides. Moreover, while conventional agriculture believes that sunlight is important, hydroponics works on the principle that what plants need is spectrum – particularly blue and red – and not sunlight. Using LED lamps, they create an environment where the plant gets all that it needs for growth in a controlled and healthy manner. Hydroponics thus reduces the chances of crop failures due to drought, thanks to the minimal use of water.
With the vision of providing excellence at the doorstep, HiMedia Biosciences began its journey about 35 years ago. Today, the company has an ambitious target to provide a one-stop solution for farmers looking for soil-less farming. Recalling the plight of farmers, Warke said, “The idea to conduct a research on hydroponics developed merely as a CSR thought. But after understanding the functions of hydroponics, we realized that it needs to reach out to a larger number of farmers.” With CSR, the scope of expansion is limited.
There is a great divide among farmers in India— while some are rich, there are some who are trying to make their ends meet, he said. He pointed that while rich farmers are getting richer with passing day, the small and marginalized ones are taking suicidal route.
“This is where we want to come in,” stated Warke, whose company is famous player in developing microbiology products. The rich farmers fail to transfer the technology to marginalized farmers, he added. “We would like farmers to allow one-fourth of the land they have to be developed for hydroponics. That would allow farmers to de-risk themselves from dependence on just one crop to offering high-quality crops in a carefully managed controlled environment.” Hydroponics with soil-less farming is immensely popular in South Korea where more than half the crop is produced using these techniques.
According to recent reports by MarketInsightsReport, the global hydroponics market is expected to grow at a CAGR of 6.5 percent during the period between 2018 and 2023. In 2016, it was estimated to have crossed $2,120.35 crore. Even though the report brands Europe as the largest market, it goes on to predict Asia-Pacific region, second largest market for hydroponics, to grow at a steady pace.
Higronics, product specialist, Manish Raut stated there are 50 plus hydroponic companies out there. However, we have a clear vision to become a one-stop destination for all hydroponic needs. He said that 2016-formed company has conducted research and development (R&D) with over 350 crop-types and have derived some productive conclusion. Raut revealed that the company shows positive results with leafy veggies and some fruits like strawberry and its variants, for vertical farming. Globally, major veggie production via hydroponic is of tomato, lettuce and leafy vegetables, pepper, cucumber, others.
HiMedia is currently working on developing other modules: “We are working on a various spectrum of light to understand how the vegetables and fruits react to different lights.” Warke believes that this temperature-controlled atmosphere will prove successful for exotic vegetables and also flowers.
Warke strongly believes that hydroponics would be a perfect marriage between industries and agriculture. He advocates the need to de-risk the farmers by introducing various methods and increase profitability which is the need of the hour. Hydroponics would also reduce the loss of agri-produce as the market will be very close to the consumers. Of course, this will require state support. And that is why he has gone around explaining to people why the future of farming will have to be hydroponics – using less land, water, and pesticides, yet ensuring higher output. With climate change, unseasonal rains, and the quest for food without pesticides, hydroponics could be the solution for the future.
New Facility To Grow Year-Round Lettuce
22nd March 2018, London
New Facility To Grow Year-Round Lettuce
Two British companies are pairing up to create an "innovative" hydroponics facility which will increase shelf life for UK consumers
A new UK hydroponics facility for growing green leaf salad all year round will aim to give British shoppers longer shelf life.
Lincolnshire-based design firm Arctica is assisting growers H20-ganics to build an innovative location with controlled clean room environment, free from pests or pathogens, scheduled for completion at the end of the year.
Arctica director Niall McQuitty said the facility will provide longer lasting lettuce to UK retailers. Once established, the system will be used to grow a full range of green salads and herbs for sale in supermarkets.
McQuitty said: “Green leaf salad is normally grown outside. The clock starts ticking on the product’s shelf life as soon as it is harvested. Green leaf coming from other markets – such as Spain – takes 24 hours to transport to processing facilities in the UK. It can take up to three days from picking to packing which means, by the time it’s in the shops, it has lost up to half its shelf life.
“Cleaning the leaf also has an impact on the quality of the produce. Washing, drying, mixing, bagging and transport all require care because the leaf is fragile and prone to damage – which also reduces shelf life. H20-ganics creates a high care environment in which to grow the leaf that removes most of these stages from the process. It can be harvested, cleaned and packed without losing quality, thereby increasing its shelf life.”
H20-ganics’ Nick Bateman added: “H2O-ganics produce is not grown in soil but produced in a fully controlled clean environment, which keeps out pests and pathogens, while maintaining the optimum conditions for plant growth.
“Using our controlled environment approach to agriculture and clean room technology, we are able to produce a consistent specification of product 365 days of the year, without the use of pesticides.”
Lincolnshire-based design firm Arctica is assisting growers H20-ganics to build an innovative location with controlled clean room environment, free from pests or pathogens, scheduled for completion at the end of the year.
Arctica director Niall McQuitty said the facility will provide longer lasting lettuce to UK retailers. Once established, the system will be used to grow a full range of green salads and herbs for sale in supermarkets.
McQuitty said: “Green leaf salad is normally grown outside. The clock starts ticking on the product’s shelf life as soon as it is harvested. Green leaf coming from other markets – such as Spain – takes 24 hours to transport to processing facilities in the UK. It can take up to three days from picking to packing which means, by the time it’s in the shops, it has lost up to half its shelf life.
“Cleaning the leaf also has an impact on the quality of the produce. Washing, drying, mixing, bagging and transport all require care because the leaf is fragile and prone to damage – which also reduces shelf life. H20-ganics creates a high care environment in which to grow the leaf that removes most of these stages from the process. It can be harvested, cleaned and packed without losing quality, thereby increasing its shelf life.”
H20-ganics’ Nick Bateman added: “H2O-ganics produce is not grown in soil but produced in a fully controlled clean environment, which keeps out pests and pathogens, while maintaining the optimum conditions for plant growth.
“Using our controlled environment approach to agriculture and clean room technology, we are able to produce a consistent specification of product 365 days of the year, without the use of pesticides.”
Lincolnshire-based design firm Arctica is assisting growers H20-ganics to build an innovative location with controlled clean room environment, free from pests or pathogens, scheduled for completion at the end of the year.
Arctica director Niall McQuitty said the facility will provide longer lasting lettuce to UK retailers. Once established, the system will be used to grow a full range of green salads and herbs for sale in supermarkets.
McQuitty said: “Green leaf salad is normally grown outside. The clock starts ticking on the product’s shelf life as soon as it is harvested. Green leaf coming from other markets – such as Spain – takes 24 hours to transport to processing facilities in the UK. It can take up to three days from picking to packing which means, by the time it’s in the shops, it has lost up to half its shelf life.
“Cleaning the leaf also has an impact on the quality of the produce. Washing, drying, mixing, bagging and transport all require care because the leaf is fragile and prone to damage – which also reduces shelf life. H20-ganics creates a high care environment in which to grow the leaf that removes most of these stages from the process. It can be harvested, cleaned and packed without losing quality, thereby increasing its shelf life.”
H20-ganics’ Nick Bateman added: “H2O-ganics produce is not grown in soil but produced in a fully controlled clean environment, which keeps out pests and pathogens, while maintaining the optimum conditions for plant growth.
“Using our controlled environment approach to agriculture and clean room technology, we are able to produce a consistent specification of product 365 days of the year, without the use of pesticides.”
Lincolnshire-based design firm Arctica is assisting growers H20-ganics to build an innovative location with controlled clean room environment, free from pests or pathogens, scheduled for completion at the end of the year.
Arctica director Niall McQuitty said the facility will provide longer lasting lettuce to UK retailers. Once established, the system will be used to grow a full range of green salads and herbs for sale in supermarkets.
McQuitty said: “Green leaf salad is normally grown outside. The clock starts ticking on the product’s shelf life as soon as it is harvested. Green leaf coming from other markets – such as Spain – takes 24 hours to transport to processing facilities in the UK. It can take up to three days from picking to packing which means, by the time it’s in the shops, it has lost up to half its shelf life.
“Cleaning the leaf also has an impact on the quality of the produce. Washing, drying, mixing, bagging and transport all require care because the leaf is fragile and prone to damage – which also reduces shelf life. H20-ganics creates a high care environment in which to grow the leaf that removes most of these stages from the process. It can be harvested, cleaned and packed without losing quality, thereby increasing its shelf life.”
H20-ganics’ Nick Bateman added: “H2O-ganics produce is not grown in soil but produced in a fully controlled clean environment, which keeps out pests and pathogens, while maintaining the optimum conditions for plant growth.
“Using our controlled environment approach to agriculture and clean room technology, we are able to produce a consistent specification of product 365 days of the year, without the use of pesticides.”
Lincolnshire-based design firm Arctica is assisting growers H20-ganics to build an innovative location with controlled clean room environment, free from pests or pathogens, scheduled for completion at the end of the year.
Arctica director Niall McQuitty said the facility will provide longer lasting lettuce to UK retailers. Once established, the system will be used to grow a full range of green salads and herbs for sale in supermarkets.
McQuitty said: “Green leaf salad is normally grown outside. The clock starts ticking on the product’s shelf life as soon as it is harvested. Green leaf coming from other markets – such as Spain – takes 24 hours to transport to processing facilities in the UK. It can take up to three days from picking to packing which means, by the time it’s in the shops, it has lost up to half its shelf life.
“Cleaning the leaf also has an impact on the quality of the produce. Washing, drying, mixing, bagging and transport all require care because the leaf is fragile and prone to damage – which also reduces shelf life. H20-ganics creates a high care environment in which to grow the leaf that removes most of these stages from the process. It can be harvested, cleaned and packed without losing quality, thereby increasing its shelf life.”
H20-ganics’ Nick Bateman added: “H2O-ganics produce is not grown in soil but produced in a fully controlled clean environment, which keeps out pests and pathogens, while maintaining the optimum conditions for plant growth.
“Using our controlled environment approach to agriculture and clean room technology, we are able to produce a consistent specification of product 365 days of the year, without the use of pesticides.”
Lincolnshire-based design firm Arctica is assisting growers H20-ganics to build an innovative location with controlled clean room environment, free from pests or pathogens, scheduled for completion at the end of the year.
Arctica director Niall McQuitty said the facility will provide longer lasting lettuce to UK retailers. Once established, the system will be used to grow a full range of green salads and herbs for sale in supermarkets.
McQuitty said: “Green leaf salad is normally grown outside. The clock starts ticking on the product’s shelf life as soon as it is harvested. Green leaf coming from other markets – such as Spain – takes 24 hours to transport to processing facilities in the UK. It can take up to three days from picking to packing which means, by the time it’s in the shops, it has lost up to half its shelf life.
“Cleaning the leaf also has an impact on the quality of the produce. Washing, drying, mixing, bagging and transport all require care because the leaf is fragile and prone to damage – which also reduces shelf life. H20-ganics creates a high care environment in which to grow the leaf that removes most of these stages from the process. It can be harvested, cleaned and packed without losing quality, thereby increasing its shelf life.”
H20-ganics’ Nick Bateman added: “H2O-ganics produce is not grown in soil but produced in a fully controlled clean environment, which keeps out pests and pathogens, while maintaining the optimum conditions for plant growth.
“Using our controlled environment approach to agriculture and clean room technology, we are able to produce a consistent specification of product 365 days of the year, without the use of pesticides.”
Lincolnshire-based design firm Arctica is assisting growers H20-ganics to build an innovative location with controlled clean room environment, free from pests or pathogens, scheduled for completion at the end of the year.
Arctica director Niall McQuitty said the facility will provide longer lasting lettuce to UK retailers. Once established, the system will be used to grow a full range of green salads and herbs for sale in supermarkets.
McQuitty said: “Green leaf salad is normally grown outside. The clock starts ticking on the product’s shelf life as soon as it is harvested. Green leaf coming from other markets – such as Spain – takes 24 hours to transport to processing facilities in the UK. It can take up to three days from picking to packing which means, by the time it’s in the shops, it has lost up to half its shelf life.
“Cleaning the leaf also has an impact on the quality of the produce. Washing, drying, mixing, bagging and transport all require care because the leaf is fragile and prone to damage – which also reduces shelf life. H20-ganics creates a high care environment in which to grow the leaf that removes most of these stages from the process. It can be harvested, cleaned and packed without losing quality, thereby increasing its shelf life.”
H20-ganics’ Nick Bateman added: “H2O-ganics produce is not grown in soil but produced in a fully controlled clean environment, which keeps out pests and pathogens, while maintaining the optimum conditions for plant growth.
“Using our controlled environment approach to agriculture and clean room technology, we are able to produce a consistent specification of product 365 days of the year, without the use of pesticides.”
Lincolnshire-based design firm Arctica is assisting growers H20-ganics to build an innovative location with controlled clean room environment, free from pests or pathogens, scheduled for completion at the end of the year.
Arctica director Niall McQuitty said the facility will provide longer lasting lettuce to UK retailers. Once established, the system will be used to grow a full range of green salads and herbs for sale in supermarkets.
McQuitty said: “Green leaf salad is normally grown outside. The clock starts ticking on the product’s shelf life as soon as it is harvested. Green leaf coming from other markets – such as Spain – takes 24 hours to transport to processing facilities in the UK. It can take up to three days from picking to packing which means, by the time it’s in the shops, it has lost up to half its shelf life.
“Cleaning the leaf also has an impact on the quality of the produce. Washing, drying, mixing, bagging and transport all require care because the leaf is fragile and prone to damage – which also reduces shelf life. H20-ganics creates a high care environment in which to grow the leaf that removes most of these stages from the process. It can be harvested, cleaned and packed without losing quality, thereby increasing its shelf life.”
H20-ganics’ Nick Bateman added: “H2O-ganics produce is not grown in soil but produced in a fully controlled clean environment, which keeps out pests and pathogens, while maintaining the optimum conditions for plant growth.
“Using our controlled environment approach to agriculture and clean room technology, we are able to produce a consistent specification of product 365 days of the year, without the use of pesticides.”
Lincolnshire-based design firm Arctica is assisting growers H20-ganics to build an innovative location with controlled clean room environment, free from pests or pathogens, scheduled for completion at the end of the year.
Arctica director Niall McQuitty said the facility will provide longer lasting lettuce to UK retailers. Once established, the system will be used to grow a full range of green salads and herbs for sale in supermarkets.
McQuitty said: “Green leaf salad is normally grown outside. The clock starts ticking on the product’s shelf life as soon as it is harvested. Green leaf coming from other markets – such as Spain – takes 24 hours to transport to processing facilities in the UK. It can take up to three days from picking to packing which means, by the time it’s in the shops, it has lost up to half its shelf life.
“Cleaning the leaf also has an impact on the quality of the produce. Washing, drying, mixing, bagging and transport all require care because the leaf is fragile and prone to damage – which also reduces shelf life. H20-ganics creates a high care environment in which to grow the leaf that removes most of these stages from the process. It can be harvested, cleaned and packed without losing quality, thereby increasing its shelf life.”
H20-ganics’ Nick Bateman added: “H2O-ganics produce is not grown in soil but produced in a fully controlled clean environment, which keeps out pests and pathogens, while maintaining the optimum conditions for plant growth.
“Using our controlled environment approach to agriculture and clean room technology, we are able to produce a consistent specification of product 365 days of the year, without the use of pesticides.”
Lincolnshire-based design firm Arctica is assisting growers H20-ganics to build an innovative location with controlled clean room environment, free from pests or pathogens, scheduled for completion at the end of the year.
Arctica director Niall McQuitty said the facility will provide longer lasting lettuce to UK retailers. Once established, the system will be used to grow a full range of green salads and herbs for sale in supermarkets.
McQuitty said: “Green leaf salad is normally grown outside. The clock starts ticking on the product’s shelf life as soon as it is harvested. Green leaf coming from other markets – such as Spain – takes 24 hours to transport to processing facilities in the UK. It can take up to three days from picking to packing which means, by the time it’s in the shops, it has lost up to half its shelf life.
“Cleaning the leaf also has an impact on the quality of the produce. Washing, drying, mixing, bagging and transport all require care because the leaf is fragile and prone to damage – which also reduces shelf life. H20-ganics creates a high care environment in which to grow the leaf that removes most of these stages from the process. It can be harvested, cleaned and packed without losing quality, thereby increasing its shelf life.”
H20-ganics’ Nick Bateman added: “H2O-ganics produce is not grown in soil but produced in a fully controlled clean environment, which keeps out pests and pathogens, while maintaining the optimum conditions for plant growth.
“Using our controlled environment approach to agriculture and clean room technology, we are able to produce a consistent specification of product 365 days of the year, without the use of pesticides.”
Lincolnshire-based design firm Arctica is assisting growers H20-ganics to build an innovative location with controlled clean room environment, free from pests or pathogens, scheduled for completion at the end of the year.
Arctica director Niall McQuitty said the facility will provide longer lasting lettuce to UK retailers. Once established, the system will be used to grow a full range of green salads and herbs for sale in supermarkets.
McQuitty said: “Green leaf salad is normally grown outside. The clock starts ticking on the product’s shelf life as soon as it is harvested. Green leaf coming from other markets – such as Spain – takes 24 hours to transport to processing facilities in the UK. It can take up to three days from picking to packing which means, by the time it’s in the shops, it has lost up to half its shelf life.
“Cleaning the leaf also has an impact on the quality of the produce. Washing, drying, mixing, bagging and transport all require care because the leaf is fragile and prone to damage – which also reduces shelf life. H20-ganics creates a high care environment in which to grow the leaf that removes most of these stages from the process. It can be harvested, cleaned and packed without losing quality, thereby increasing its shelf life.”
H20-ganics’ Nick Bateman added: “H2O-ganics produce is not grown in soil but produced in a fully controlled clean environment, which keeps out pests and pathogens, while maintaining the optimum conditions for plant growth.
“Using our controlled environment approach to agriculture and clean room technology, we are able to produce a consistent specification of product 365 days of the year, without the use of pesticides.”
Lincolnshire-based design firm Arctica is assisting growers H20-ganics to build an innovative location with controlled clean room environment, free from pests or pathogens, scheduled for completion at the end of the year.
Arctica director Niall McQuitty said the facility will provide longer lasting lettuce to UK retailers. Once established, the system will be used to grow a full range of green salads and herbs for sale in supermarkets.
McQuitty said: “Green leaf salad is normally grown outside. The clock starts ticking on the product’s shelf life as soon as it is harvested. Green leaf coming from other markets – such as Spain – takes 24 hours to transport to processing facilities in the UK. It can take up to three days from picking to packing which means, by the time it’s in the shops, it has lost up to half its shelf life.
“Cleaning the leaf also has an impact on the quality of the produce. Washing, drying, mixing, bagging and transport all require care because the leaf is fragile and prone to damage – which also reduces shelf life. H20-ganics creates a high care environment in which to grow the leaf that removes most of these stages from the process. It can be harvested, cleaned and packed without losing quality, thereby increasing its shelf life.”
H20-ganics’ Nick Bateman added: “H2O-ganics produce is not grown in soil but produced in a fully controlled clean environment, which keeps out pests and pathogens, while maintaining the optimum conditions for plant growth.
“Using our controlled environment approach to agriculture and clean room technology, we are able to produce a consistent specification of product 365 days of the year, without the use of pesticides.”
Lincolnshire-based design firm Arctica is assisting growers H20-ganics to build an innovative location with controlled clean room environment, free from pests or pathogens, scheduled for completion at the end of the year.
Arctica director Niall McQuitty said the facility will provide longer lasting lettuce to UK retailers. Once established, the system will be used to grow a full range of green salads and herbs for sale in supermarkets.
McQuitty said: “Green leaf salad is normally grown outside. The clock starts ticking on the product’s shelf life as soon as it is harvested. Green leaf coming from other markets – such as Spain – takes 24 hours to transport to processing facilities in the UK. It can take up to three days from picking to packing which means, by the time it’s in the shops, it has lost up to half its shelf life.
“Cleaning the leaf also has an impact on the quality of the produce. Washing, drying, mixing, bagging and transport all require care because the leaf is fragile and prone to damage – which also reduces shelf life. H20-ganics creates a high care environment in which to grow the leaf that removes most of these stages from the process. It can be harvested, cleaned and packed without losing quality, thereby increasing its shelf life.”
H20-ganics’ Nick Bateman added: “H2O-ganics produce is not grown in soil but produced in a fully controlled clean environment, which keeps out pests and pathogens, while maintaining the optimum conditions for plant growth.
“Using our controlled environment approach to agriculture and clean room technology, we are able to produce a consistent specification of product 365 days of the year, without the use of pesticides.”
Lincolnshire-based design firm Arctica is assisting growers H20-ganics to build an innovative location with controlled clean room environment, free from pests or pathogens, scheduled for completion at the end of the year.
Arctica director Niall McQuitty said the facility will provide longer lasting lettuce to UK retailers. Once established, the system will be used to grow a full range of green salads and herbs for sale in supermarkets.
McQuitty said: “Green leaf salad is normally grown outside. The clock starts ticking on the product’s shelf life as soon as it is harvested. Green leaf coming from other markets – such as Spain – takes 24 hours to transport to processing facilities in the UK. It can take up to three days from picking to packing which means, by the time it’s in the shops, it has lost up to half its shelf life.
“Cleaning the leaf also has an impact on the quality of the produce. Washing, drying, mixing, bagging and transport all require care because the leaf is fragile and prone to damage – which also reduces shelf life. H20-ganics creates a high care environment in which to grow the leaf that removes most of these stages from the process. It can be harvested, cleaned and packed without losing quality, thereby increasing its shelf life.”
H20-ganics’ Nick Bateman added: “H2O-ganics produce is not grown in soil but produced in a fully controlled clean environment, which keeps out pests and pathogens, while maintaining the optimum conditions for plant growth.
“Using our controlled environment approach to agriculture and clean room technology, we are able to produce a consistent specification of product 365 days of the year, without the use of pesticides.”
Lincolnshire-based design firm Arctica is assisting growers H20-ganics to build an innovative location with controlled clean room environment, free from pests or pathogens, scheduled for completion at the end of the year.
Arctica director Niall McQuitty said the facility will provide longer lasting lettuce to UK retailers. Once established, the system will be used to grow a full range of green salads and herbs for sale in supermarkets.
McQuitty said: “Green leaf salad is normally grown outside. The clock starts ticking on the product’s shelf life as soon as it is harvested. Green leaf coming from other markets – such as Spain – takes 24 hours to transport to processing facilities in the UK. It can take up to three days from picking to packing which means, by the time it’s in the shops, it has lost up to half its shelf life.
“Cleaning the leaf also has an impact on the quality of the produce. Washing, drying, mixing, bagging and transport all require care because the leaf is fragile and prone to damage – which also reduces shelf life. H20-ganics creates a high care environment in which to grow the leaf that removes most of these stages from the process. It can be harvested, cleaned and packed without losing quality, thereby increasing its shelf life.”
H20-ganics’ Nick Bateman added: “H2O-ganics produce is not grown in soil but produced in a fully controlled clean environment, which keeps out pests and pathogens, while maintaining the optimum conditions for plant growth.
“Using our controlled environment approach to agriculture and clean room technology, we are able to produce a consistent specification of product 365 days of the year, without the use of pesticides.”
Lincolnshire-based design firm Arctica is assisting growers H20-ganics to build an innovative location with controlled clean room environment, free from pests or pathogens, scheduled for completion at the end of the year.
Arctica director Niall McQuitty said the facility will provide longer lasting lettuce to UK retailers. Once established, the system will be used to grow a full range of green salads and herbs for sale in supermarkets.
McQuitty said: “Green leaf salad is normally grown outside. The clock starts ticking on the product’s shelf life as soon as it is harvested. Green leaf coming from other markets – such as Spain – takes 24 hours to transport to processing facilities in the UK. It can take up to three days from picking to packing which means, by the time it’s in the shops, it has lost up to half its shelf life.
“Cleaning the leaf also has an impact on the quality of the produce. Washing, drying, mixing, bagging and transport all require care because the leaf is fragile and prone to damage – which also reduces shelf life. H20-ganics creates a high care environment in which to grow the leaf that removes most of these stages from the process. It can be harvested, cleaned and packed without losing quality, thereby increasing its shelf life.”
H20-ganics’ Nick Bateman added: “H2O-ganics produce is not grown in soil but produced in a fully controlled clean environment, which keeps out pests and pathogens, while maintaining the optimum conditions for plant growth.
“Using our controlled environment approach to agriculture and clean room technology, we are able to produce a consistent specification of product 365 days of the year, without the use of pesticides.”
Lincolnshire-based design firm Arctica is assisting growers H20-ganics to build an innovative location with controlled clean room environment, free from pests or pathogens, scheduled for completion at the end of the year.
Arctica director Niall McQuitty said the facility will provide longer lasting lettuce to UK retailers. Once established, the system will be used to grow a full range of green salads and herbs for sale in supermarkets.
McQuitty said: “Green leaf salad is normally grown outside. The clock starts ticking on the product’s shelf life as soon as it is harvested. Green leaf coming from other markets – such as Spain – takes 24 hours to transport to processing facilities in the UK. It can take up to three days from picking to packing which means, by the time it’s in the shops, it has lost up to half its shelf life.
“Cleaning the leaf also has an impact on the quality of the produce. Washing, drying, mixing, bagging and transport all require care because the leaf is fragile and prone to damage – which also reduces shelf life. H20-ganics creates a high care environment in which to grow the leaf that removes most of these stages from the process. It can be harvested, cleaned and packed without losing quality, thereby increasing its shelf life.”
H20-ganics’ Nick Bateman added: “H2O-ganics produce is not grown in soil but produced in a fully controlled clean environment, which keeps out pests and pathogens, while maintaining the optimum conditions for plant growth.
“Using our controlled environment approach to agriculture and clean room technology, we are able to produce a consistent specification of product 365 days of the year, without the use of pesticides.”
Lincolnshire-based design firm Arctica is assisting growers H20-ganics to build an innovative location with controlled clean room environment, free from pests or pathogens, scheduled for completion at the end of the year.
Arctica director Niall McQuitty said the facility will provide longer lasting lettuce to UK retailers. Once established, the system will be used to grow a full range of green salads and herbs for sale in supermarkets.
McQuitty said: “Green leaf salad is normally grown outside. The clock starts ticking on the product’s shelf life as soon as it is harvested. Green leaf coming from other markets – such as Spain – takes 24 hours to transport to processing facilities in the UK. It can take up to three days from picking to packing which means, by the time it’s in the shops, it has lost up to half its shelf life.
“Cleaning the leaf also has an impact on the quality of the produce. Washing, drying, mixing, bagging and transport all require care because the leaf is fragile and prone to damage – which also reduces shelf life. H20-ganics creates a high care environment in which to grow the leaf that removes most of these stages from the process. It can be harvested, cleaned and packed without losing quality, thereby increasing its shelf life.”
H20-ganics’ Nick Bateman added: “H2O-ganics produce is not grown in soil but produced in a fully controlled clean environment, which keeps out pests and pathogens, while maintaining the optimum conditions for plant growth.
“Using our controlled environment approach to agriculture and clean room technology, we are able to produce a consistent specification of product 365 days of the year, without the use of pesticides.”
Lincolnshire-based design firm Arctica is assisting growers H20-ganics to build an innovative location with controlled clean room environment, free from pests or pathogens, scheduled for completion at the end of the year.
Arctica director Niall McQuitty said the facility will provide longer lasting lettuce to UK retailers. Once established, the system will be used to grow a full range of green salads and herbs for sale in supermarkets.
McQuitty said: “Green leaf salad is normally grown outside. The clock starts ticking on the product’s shelf life as soon as it is harvested. Green leaf coming from other markets – such as Spain – takes 24 hours to transport to processing facilities in the UK. It can take up to three days from picking to packing which means, by the time it’s in the shops, it has lost up to half its shelf life.
“Cleaning the leaf also has an impact on the quality of the produce. Washing, drying, mixing, bagging and transport all require care because the leaf is fragile and prone to damage – which also reduces shelf life. H20-ganics creates a high care environment in which to grow the leaf that removes most of these stages from the process. It can be harvested, cleaned and packed without losing quality, thereby increasing its shelf life.”
H20-ganics’ Nick Bateman added: “H2O-ganics produce is not grown in soil but produced in a fully controlled clean environment, which keeps out pests and pathogens, while maintaining the optimum conditions for plant growth.
“Using our controlled environment approach to agriculture and clean room technology, we are able to produce a consistent specification of product 365 days of the year, without the use of pesticides.”
Lincolnshire-based design firm Arctica is assisting growers H20-ganics to build an innovative location with controlled clean room environment, free from pests or pathogens, scheduled for completion at the end of the year.
Arctica director Niall McQuitty said the facility will provide longer lasting lettuce to UK retailers. Once established, the system will be used to grow a full range of green salads and herbs for sale in supermarkets.
McQuitty said: “Green leaf salad is normally grown outside. The clock starts ticking on the product’s shelf life as soon as it is harvested. Green leaf coming from other markets – such as Spain – takes 24 hours to transport to processing facilities in the UK. It can take up to three days from picking to packing which means, by the time it’s in the shops, it has lost up to half its shelf life.
“Cleaning the leaf also has an impact on the quality of the produce. Washing, drying, mixing, bagging and transport all require care because the leaf is fragile and prone to damage – which also reduces shelf life. H20-ganics creates a high care environment in which to grow the leaf that removes most of these stages from the process. It can be harvested, cleaned and packed without losing quality, thereby increasing its shelf life.”
H20-ganics’ Nick Bateman added: “H2O-ganics produce is not grown in soil but produced in a fully controlled clean environment, which keeps out pests and pathogens, while maintaining the optimum conditions for plant growth.
“Using our controlled environment approach to agriculture and clean room technology, we are able to produce a consistent specification of product 365 days of the year, without the use of pesticides.”
Lincolnshire-based design firm Arctica is assisting growers H20-ganics to build an innovative location with controlled clean room environment, free from pests or pathogens, scheduled for completion at the end of the year.
Arctica director Niall McQuitty said the facility will provide longer lasting lettuce to UK retailers. Once established, the system will be used to grow a full range of green salads and herbs for sale in supermarkets.
McQuitty said: “Green leaf salad is normally grown outside. The clock starts ticking on the product’s shelf life as soon as it is harvested. Green leaf coming from other markets – such as Spain – takes 24 hours to transport to processing facilities in the UK. It can take up to three days from picking to packing which means, by the time it’s in the shops, it has lost up to half its shelf life.
“Cleaning the leaf also has an impact on the quality of the produce. Washing, drying, mixing, bagging and transport all require care because the leaf is fragile and prone to damage – which also reduces shelf life. H20-ganics creates a high care environment in which to grow the leaf that removes most of these stages from the process. It can be harvested, cleaned and packed without losing quality, thereby increasing its shelf life.”
H20-ganics’ Nick Bateman added: “H2O-ganics produce is not grown in soil but produced in a fully controlled clean environment, which keeps out pests and pathogens, while maintaining the optimum conditions for plant growth.
“Using our controlled environment approach to agriculture and clean room technology, we are able to produce a consistent specification of product 365 days of the year, without the use of pesticides.”
Lincolnshire-based design firm Arctica is assisting growers H20-ganics to build an innovative location with controlled clean room environment, free from pests or pathogens, scheduled for completion at the end of the year.
Arctica director Niall McQuitty said the facility will provide longer lasting lettuce to UK retailers. Once established, the system will be used to grow a full range of green salads and herbs for sale in supermarkets.
McQuitty said: “Green leaf salad is normally grown outside. The clock starts ticking on the product’s shelf life as soon as it is harvested. Green leaf coming from other markets – such as Spain – takes 24 hours to transport to processing facilities in the UK. It can take up to three days from picking to packing which means, by the time it’s in the shops, it has lost up to half its shelf life.
“Cleaning the leaf also has an impact on the quality of the produce. Washing, drying, mixing, bagging and transport all require care because the leaf is fragile and prone to damage – which also reduces shelf life. H20-ganics creates a high care environment in which to grow the leaf that removes most of these stages from the process. It can be harvested, cleaned and packed without losing quality, thereby increasing its shelf life.”
H20-ganics’ Nick Bateman added: “H2O-ganics produce is not grown in soil but produced in a fully controlled clean environment, which keeps out pests and pathogens, while maintaining the optimum conditions for plant growth.
“Using our controlled environment approach to agriculture and clean room technology, we are able to produce a consistent specification of product 365 days of the year, without the use of pesticides.”
Lincolnshire-based design firm Arctica is assisting growers H20-ganics to build an innovative location with controlled clean room environment, free from pests or pathogens, scheduled for completion at the end of the year.
Arctica director Niall McQuitty said the facility will provide longer lasting lettuce to UK retailers. Once established, the system will be used to grow a full range of green salads and herbs for sale in supermarkets.
McQuitty said: “Green leaf salad is normally grown outside. The clock starts ticking on the product’s shelf life as soon as it is harvested. Green leaf coming from other markets – such as Spain – takes 24 hours to transport to processing facilities in the UK. It can take up to three days from picking to packing which means, by the time it’s in the shops, it has lost up to half its shelf life.
“Cleaning the leaf also has an impact on the quality of the produce. Washing, drying, mixing, bagging and transport all require care because the leaf is fragile and prone to damage – which also reduces shelf life. H20-ganics creates a high care environment in which to grow the leaf that removes most of these stages from the process. It can be harvested, cleaned and packed without losing quality, thereby increasing its shelf life.”
H20-ganics’ Nick Bateman added: “H2O-ganics produce is not grown in soil but produced in a fully controlled clean environment, which keeps out pests and pathogens, while maintaining the optimum conditions for plant growth.
“Using our controlled environment approach to agriculture and clean room technology, we are able to produce a consistent specification of product 365 days of the year, without the use of pesticides.”
Lincolnshire-based design firm Arctica is assisting growers H20-ganics to build an innovative location with controlled clean room environment, free from pests or pathogens, scheduled for completion at the end of the year.
Arctica director Niall McQuitty said the facility will provide longer lasting lettuce to UK retailers. Once established, the system will be used to grow a full range of green salads and herbs for sale in supermarkets.
McQuitty said: “Green leaf salad is normally grown outside. The clock starts ticking on the product’s shelf life as soon as it is harvested. Green leaf coming from other markets – such as Spain – takes 24 hours to transport to processing facilities in the UK. It can take up to three days from picking to packing which means, by the time it’s in the shops, it has lost up to half its shelf life.
“Cleaning the leaf also has an impact on the quality of the produce. Washing, drying, mixing, bagging and transport all require care because the leaf is fragile and prone to damage – which also reduces shelf life. H20-ganics creates a high care environment in which to grow the leaf that removes most of these stages from the process. It can be harvested, cleaned and packed without losing quality, thereby increasing its shelf life.”
H20-ganics’ Nick Bateman added: “H2O-ganics produce is not grown in soil but produced in a fully controlled clean environment, which keeps out pests and pathogens, while maintaining the optimum conditions for plant growth.
“Using our controlled environment approach to agriculture and clean room technology, we are able to produce a consistent specification of product 365 days of the year, without the use of pesticides.”
Lincolnshire-based design firm Arctica is assisting growers H20-ganics to build an innovative location with controlled clean room environment, free from pests or pathogens, scheduled for completion at the end of the year.
Arctica director Niall McQuitty said the facility will provide longer lasting lettuce to UK retailers. Once established, the system will be used to grow a full range of green salads and herbs for sale in supermarkets.
McQuitty said: “Green leaf salad is normally grown outside. The clock starts ticking on the product’s shelf life as soon as it is harvested. Green leaf coming from other markets – such as Spain – takes 24 hours to transport to processing facilities in the UK. It can take up to three days from picking to packing which means, by the time it’s in the shops, it has lost up to half its shelf life.
“Cleaning the leaf also has an impact on the quality of the produce. Washing, drying, mixing, bagging and transport all require care because the leaf is fragile and prone to damage – which also reduces shelf life. H20-ganics creates a high care environment in which to grow the leaf that removes most of these stages from the process. It can be harvested, cleaned and packed without losing quality, thereby increasing its shelf life.”
H20-ganics’ Nick Bateman added: “H2O-ganics produce is not grown in soil but produced in a fully controlled clean environment, which keeps out pests and pathogens, while maintaining the optimum conditions for plant growth.
“Using our controlled environment approach to agriculture and clean room technology, we are able to produce a consistent specification of product 365 days of the year, without the use of pesticides.”
Lincolnshire-based design firm Arctica is assisting growers H20-ganics to build an innovative location with controlled clean room environment, free from pests or pathogens, scheduled for completion at the end of the year.
Arctica director Niall McQuitty said the facility will provide longer lasting lettuce to UK retailers. Once established, the system will be used to grow a full range of green salads and herbs for sale in supermarkets.
McQuitty said: “Green leaf salad is normally grown outside. The clock starts ticking on the product’s shelf life as soon as it is harvested. Green leaf coming from other markets – such as Spain – takes 24 hours to transport to processing facilities in the UK. It can take up to three days from picking to packing which means, by the time it’s in the shops, it has lost up to half its shelf life.
“Cleaning the leaf also has an impact on the quality of the produce. Washing, drying, mixing, bagging and transport all require care because the leaf is fragile and prone to damage – which also reduces shelf life. H20-ganics creates a high care environment in which to grow the leaf that removes most of these stages from the process. It can be harvested, cleaned and packed without losing quality, thereby increasing its shelf life.”
H20-ganics’ Nick Bateman added: “H2O-ganics produce is not grown in soil but produced in a fully controlled clean environment, which keeps out pests and pathogens, while maintaining the optimum conditions for plant growth.
“Using our controlled environment approach to agriculture and clean room technology, we are able to produce a consistent specification of product 365 days of the year, without the use of pesticides.”
Lincolnshire-based design firm Arctica is assisting growers H20-ganics to build an innovative location with controlled clean room environment, free from pests or pathogens, scheduled for completion at the end of the year.
Arctica director Niall McQuitty said the facility will provide longer lasting lettuce to UK retailers. Once established, the system will be used to grow a full range of green salads and herbs for sale in supermarkets.
McQuitty said: “Green leaf salad is normally grown outside. The clock starts ticking on the product’s shelf life as soon as it is harvested. Green leaf coming from other markets – such as Spain – takes 24 hours to transport to processing facilities in the UK. It can take up to three days from picking to packing which means, by the time it’s in the shops, it has lost up to half its shelf life.
“Cleaning the leaf also has an impact on the quality of the produce. Washing, drying, mixing, bagging and transport all require care because the leaf is fragile and prone to damage – which also reduces shelf life. H20-ganics creates a high care environment in which to grow the leaf that removes most of these stages from the process. It can be harvested, cleaned and packed without losing quality, thereby increasing its shelf life.”
H20-ganics’ Nick Bateman added: “H2O-ganics produce is not grown in soil but produced in a fully controlled clean environment, which keeps out pests and pathogens, while maintaining the optimum conditions for plant growth.
“Using our controlled environment approach to agriculture and clean room technology, we are able to produce a consistent specification of product 365 days of the year, without the use of pesticides.”
Lincolnshire-based design firm Arctica is assisting growers H20-ganics to build an innovative location with controlled clean room environment, free from pests or pathogens, scheduled for completion at the end of the year.
Arctica director Niall McQuitty said the facility will provide longer lasting lettuce to UK retailers. Once established, the system will be used to grow a full range of green salads and herbs for sale in supermarkets.
McQuitty said: “Green leaf salad is normally grown outside. The clock starts ticking on the product’s shelf life as soon as it is harvested. Green leaf coming from other markets – such as Spain – takes 24 hours to transport to processing facilities in the UK. It can take up to three days from picking to packing which means, by the time it’s in the shops, it has lost up to half its shelf life.
“Cleaning the leaf also has an impact on the quality of the produce. Washing, drying, mixing, bagging and transport all require care because the leaf is fragile and prone to damage – which also reduces shelf life. H20-ganics creates a high care environment in which to grow the leaf that removes most of these stages from the process. It can be harvested, cleaned and packed without losing quality, thereby increasing its shelf life.”
H20-ganics’ Nick Bateman added: “H2O-ganics produce is not grown in soil but produced in a fully controlled clean environment, which keeps out pests and pathogens, while maintaining the optimum conditions for plant growth.
“Using our controlled environment approach to agriculture and clean room technology, we are able to produce a consistent specification of product 365 days of the year, without the use of pesticides.”
Lincolnshire-based design firm Arctica is assisting growers H20-ganics to build an innovative location with controlled clean room environment, free from pests or pathogens, scheduled for completion at the end of the year.
Arctica director Niall McQuitty said the facility will provide longer lasting lettuce to UK retailers. Once established, the system will be used to grow a full range of green salads and herbs for sale in supermarkets.
McQuitty said: “Green leaf salad is normally grown outside. The clock starts ticking on the product’s shelf life as soon as it is harvested. Green leaf coming from other markets – such as Spain – takes 24 hours to transport to processing facilities in the UK. It can take up to three days from picking to packing which means, by the time it’s in the shops, it has lost up to half its shelf life.
“Cleaning the leaf also has an impact on the quality of the produce. Washing, drying, mixing, bagging and transport all require care because the leaf is fragile and prone to damage – which also reduces shelf life. H20-ganics creates a high care environment in which to grow the leaf that removes most of these stages from the process. It can be harvested, cleaned and packed without losing quality, thereby increasing its shelf life.”
H20-ganics’ Nick Bateman added: “H2O-ganics produce is not grown in soil but produced in a fully controlled clean environment, which keeps out pests and pathogens, while maintaining the optimum conditions for plant growth.
“Using our controlled environment approach to agriculture and clean room technology, we are able to produce a consistent specification of product 365 days of the year, without the use of pesticides.”
Lincolnshire-based design firm Arctica is assisting growers H20-ganics to build an innovative location with controlled clean room environment, free from pests or pathogens, scheduled for completion at the end of the year.
Arctica director Niall McQuitty said the facility will provide longer lasting lettuce to UK retailers. Once established, the system will be used to grow a full range of green salads and herbs for sale in supermarkets.
McQuitty said: “Green leaf salad is normally grown outside. The clock starts ticking on the product’s shelf life as soon as it is harvested. Green leaf coming from other markets – such as Spain – takes 24 hours to transport to processing facilities in the UK. It can take up to three days from picking to packing which means, by the time it’s in the shops, it has lost up to half its shelf life.
“Cleaning the leaf also has an impact on the quality of the produce. Washing, drying, mixing, bagging and transport all require care because the leaf is fragile and prone to damage – which also reduces shelf life. H20-ganics creates a high care environment in which to grow the leaf that removes most of these stages from the process. It can be harvested, cleaned and packed without losing quality, thereby increasing its shelf life.”
H20-ganics’ Nick Bateman added: “H2O-ganics produce is not grown in soil but produced in a fully controlled clean environment, which keeps out pests and pathogens, while maintaining the optimum conditions for plant growth.
“Using our controlled environment approach to agriculture and clean room technology, we are able to produce a consistent specification of product 365 days of the year, without the use of pesticides.”
How Urban Farmers Are learning To Grow Food Without Soil Or Natural Light
How Urban Farmers Are learning To Grow Food Without Soil Or Natural Light
February 13, 2018
Mandy Zammit/Grow Up, Author provided
Author
- Silvio Caputo
Senior Lecturer, University of Portsmouth
Disclosure statement
Silvio Caputo does not work for, consult, own shares in or receive funding from any company or organization that would benefit from this article, and has disclosed no relevant affiliations beyond their academic appointment.
Partners
University of Portsmouth provides funding as a member of The Conversation UK.
Growing food in cities became popular in Europe and North America during and immediately after World War II. Urban farming provided citizens with food, at a time when resources were desperately scarce. In the decades that followed, parcels of land which had been given over to allotments and city farms were gradually taken up for urban development. But recently, there has been a renewed interest in urban farming – albeit for very different reasons than before.
As part of a recent research project investigating how urban farming is evolving across Europe, I found that in countries where growing food was embedded in the national culture, many people have started new food production projects. There was less uptake in countries such as Greece and Slovenia, where there was no tradition of urban farming. Yet a few community projects had recently been started in those places too.
Today’s urban farmers don’t just grow food to eat; they also see urban agriculture as a way of increasing the diversity of plants and animals in the city, bringing people from different backgrounds and age groups together, improving mental and physical health and regenerating derelict neighbourhoods.
Many new urban farming projects still struggle to find suitable green spaces. But people are finding inventive solutions; growing food in skips or on rooftops, on sites that are only temporarily free, or on raised beds in abandoned industrial yards. Growers are even using technologies such as hydroponics, aquaculture and aquaponics to make the most of unoccupied spaces.
Something fishy
Hydroponic systems were engineered as a highly space and resource efficient form of farming. Today, they represent a considerable source of industrially grown produce; one estimate suggests that, in 2016, the hydroponic vegetable market was worth about US$6.9 billion worldwide.
Hydroponics enable people to grow food without soil and natural light, using blocks of porous material where the plants’ roots grow, and artificial lighting such as low-energy LED. A study on lettuce production found that although hydroponic crops require significantly more energy than conventionally grown food, they also use less water and have considerably higher yields.
Growing hydroponic crops usually requires sophisticated technology, specialist skills and expensive equipment. But simplified versions can be affordable and easy to use.
They grow up so fast. Mandy Zammit/Grow Up, Author provided
Hemmaodlat is an organisation based in Malmö, in a neighbourhood primarily occupied by low-income groups and immigrants. The area is densely built, and there’s no green space available to grow food locally. Plus, the Swedish summer is short and not always ideal for growing crops. Instead, the organisation aims to promote hydroponic systems among local communities, as a way to grow fresh food using low-cost equipment.
The Bristol Fish Project is a community-supported aquaponics farm, which breeds fish and uses the organic waste they produce to fertilise plants grown hydroponically. GrowUp is another aquaponics venture located in an East London warehouse – they grow food and farm fish using only artificial light. Similarly, Growing Underground is an enterprise that produces crops in tunnels, which were originally built as air raid shelters during World War II in London.
The next big thing?
The potential to grow food in small spaces, under any environmental conditions, are certainly big advantages in an urban context. But these technologies also mean that the time spent outdoors, weathering the natural cycles of the seasons, is lost. Also, hydroponic systems require nutrients that are often synthesised chemically – although organic nutrients are now becoming available. Many urban farmers grow their food following organic principles, partly because the excessive use of chemical fertilisers is damaging soil fertilityand polluting groundwater.
To see whether these drawbacks would put urban growers off using hydroponic systems, my colleagues and I conducted a pilot study in Portsmouth. We installed small hydroponic units in two local community gardens, and interviewed volunteers and visitors to the gardens. Many of the people we spoke to were well informed about hydroponic technology, and knew that some of the vegetables sold in supermarkets today are produced with this system.
A simplified hydroponic frame in Portsmouth. Silvio Caputo/University of Portsmouth, Author provided
Many were fascinated by the idea of growing food without soil within their community projects, but at the same time reluctant to consume the produce because of the chemical nutrients used. A few interviewees were also uncomfortable with the idea that the food was not grown naturally. We intend to repeat this experiment in the near future, to see how public opinion changes over time.
And while we don’t think hydroponic systems can replace the enjoyment that growing food in soil can offer, they can save water and produce safe food, either indoors or outdoors, in a world with increasingly scarce resources. Learning to use these new technologies, and integrating them into existing projects, can only help to grow even more sustainable food.
As with many technological advancements, it could be that a period of slow acceptance will be followed by rapid, widespread uptake. Perhaps the fact that IKEA is selling portable hydroponic units, while hydroponic cabinets are on the market as components of kitchen systems, is a sign that this technology is primed to enter mainstream use.
Hydroponics Are A Soil-Less Marvel
Image courtesy of Tim Durham
Hydroponics Are A Soil-Less Marvel
AGDAILY | March 22, 2018
Durham, North Carolina:
Whoever coined the proverb “necessity is the mother of all invention” wasn’t kidding. I’m frequently astounded by the ability of farmers to scrounge together ideas and improvise solutions. Some are one-time creations to get out of a bind, while others have more staying power — perhaps leading to the creation of new implements or farming techniques. Occasionally, necessity prompts the rediscovery of old approaches (making them chic once again) or even births the next wave in farming. Hydroponics is a classic example of ingenuity — one poised to make an indelible mark on today’s food system.
But what is hydroponics? My fav franchise “Star Trek” makes periodic references to a “hydroponics bay” on starships and starbases. Let’s run with that. If I were to suggest that one of the following isn’t necessary to grow plants in the infinite expanse of space, which would it be? Water, air, soil, or light?
Hydroponic (and Earthling) devotees scoff at your soil requirement. As long as a plant has some way to keep itself anchored and upright — and nutrition can be delivered exclusively through a liquid diet of fertilizer water — soil is expendable. That’s the simple definition. The sciencey definition is a medium that lacks cation exchange capacity (CEC). Basically, growing the plant in something that has no ability to attract and hold onto essential nutrients floating around in the water. CEC is beneficial because it prevents valuable nutrients from simply washing out of the root zone and out of “pickup contention” by the roots after every rainfall.
Image courtesy of Tim Durham
You could argue that the few fields of beach sand at my family farm are technically hydroponic. Sand is an inert medium that provides a temporary residence for water (and the nutrients dissolved in them). In other words, sand is arguably not true “soil” because it has no CEC! Real soil has CEC mojo, compliments of clay and organic matter. To improve the poor hand that we’ve been dealt back home, we’ve been spreading leaves and manure to boost the organic matter content of our aspiring sandy soil.
But that’s in the field. Most interest centers on hydroponic systems in controlled environments — and there are many flavors! If you’ve ever been to Disney World, specifically Epcot’s “Living with the Land” pavilion, you’ve seen them in action.
Granted, that’s a high-tech approach. At Florida’s ECHO, a faith-based demonstration farm and training center that combats global hunger, I’ve seen enviable stands of plants grown in kiddie pools filled with pine cones or aluminum cans wrapped in old socks. These act as a makeshift mulch. The bottom of the pools are lined with old carpet that wicks up nutrient solution slow trickled from an upside down barrel with a hole poked in the top. ECHO stresses a concept called “appropriate technology” — leveraging what a developing country already has on hand for maximum impact. And one can repurpose nearly any non-agricultural real estate for family-scale farming!
Plants certainly don’t know the difference between a high or low-tech approach. The roots meander where they need to go to get their “RDA” of nutrients. In a soil setting, roots absorb nutrients dissolved in water (in soil pores) anyway, so why not eliminate the middleman?
The hydroponic setup at my college straddles soil-less simplicity and sophistication. Compliments of a Virginia Tobacco Region Revitalization Commission grant, we have a 30-by-60-foot climate controlled greenhouse equipped with nutrient film technique (NFT) benches to grow specialty lettuce. A custom fertilizer recipe is mixed in water, pumped from a reservoir, and trickled into growing channels (which resemble shallow gutters). Lids on the tops have small spaces to seat plants. The roots dangle down, where they wick up their liquid feed. It’s like an IV for plants. Whatever feed isn’t used is recycled. We can accommodate nearly 1,100 romaine and bibb lettuce plants at a given time. I plant on a weekly staggered basis, just like in the field. And I get to indulge my experimental chops by working with students to tweak things like fertilizer and lighting to optimize production.
Image courtesy of Tim Durham
There’s something to be said for the glorious reductionism of hydroponics — taking the guesswork out of conventional farming. At the same time, it’s renegotiating conventions. Previously, I’ve pondered the unsubstantiated hype surrounding vertical farming (which typically uses some variant of hydroponics). But it’s not the underlying technique that’s questionable — it’s the sheer scale, capital investment, and voodoo energetics of such an endeavor. Small scale is much more reasonable. And it’s already paying dividends. Already, the campus hydroponic facility has begun to supply the dining hall with a portion of its needs, provide faculty and staff with farm fresh lettuce as part of a wellness initiative, and supply local food banks with nearly a half ton of fresh produce.
Is traditional “dirt farming” a goner? Hardly. But war weary farmers might welcome an infusion of predictability as well as an alternative revenue stream to diversify and manage risk. In a short 20 years, hydroponics has graduated from a curiosity to niche market up-and-comer.
Tim Durham’s family operates Deer Run Farm — a truck (vegetable) farm on Long Island, New York. As an agvocate, he counters heated rhetoric with sensible facts. Tim has a degree in plant medicine and is an Assistant Professor at Ferrum College in Virginia.
U.S.: Gotham Greens Breaks Ground On Second Chicago Greenhouse
U.S. urban agricultural company Gotham Greens has broken ground on its second Chicago greenhouse, as it continues its rapid expansion in the country.
The 140,000-square-foot facility is in the Pullman neighborhood, which is also where the company’s existing Chicago rooftop greenhouse is located.
The new facility will produce vegetables and herbs year-round for local retailers, restaurants, and institutional foodservice customers.
On Thursday Mayor Rahm Emanuel joined Gotham Greens founders Viraj Puri and Eric Haley and community leaders in Pullman to break ground on what will be the city’s largest agricultural greenhouse.
It is expected to create 60 permanent and 70 construction jobs.
“Gotham Greens’ decision to double down and build a second greenhouse is a vote of confidence in Chicago and another sign of the economic renaissance underway in the historic Pullman community,” Mayor Emanuel said.
“Pullman’s historic past is matched only by its growing economic resurgence today, thanks to partners like Gotham Greens.”
Using modern growing methods that include hydroponics, evaporative cooling systems and renewable energy resources, the US$12.6 million complex is expected to produce approximately 30 times the yield of conventional agriculture per acre while using 10% of the water.
Gotham Greens said the expansion reflects its success growing and selling premium quality produce year-round in technologically advanced indoor farms.
Besides its Pullman locations, Gotham Greens currently owns three greenhouses in New York City and has “several facilities in development in other US cities”.
The company employs over 160 people and partners with community organizations to support job training, wellness, and environmental education programs in both Chicago and New York.
“Thanks to the leadership and hard work of Mayor Emanuel, Alderman Beale, the City of Chicago, CNI, and all of our community partners, Pullman has been a great place to innovate and do business,” Puri said.
“We’re producing millions of pounds of fresh produce annually for national and local grocery stores and foodservice operators across Chicagoland, far exceeding our expectations. This is the ideal time for us to expand our presence in the Midwest, and Pullman is the ideal place for us to do so.”
In Pullman the company currently operates a 75,000-square-foot greenhouse on the roof of the nearby Method Products factory, which opened in 2015.
The 6.2-acre project site of the new greenhouse was occupied until 2008 by a Ryerson Steel plant and later acquired by Pullman Park LLC.
Chicago Neighborhood Initiatives plans to acquire and prepare the site for US$3.68 million and subsequently sell the property to Gotham Greens, which will complete the greenhouse’s vertical construction. Approximately US$3.4 million in Tax Increment Financing assistance for the site preparation work is pending City Council approval.
Larry Ellison And Dr. David Agus Unveil Their Hydroponic Farming Start-Up.
Larry Ellison And Dr. David Agus Unveil Their Hydroponic Farming Start-Up.
Larry Ellison is the founder of Oracle and the 10th-richest man on the planet, according to Forbes. Dr. David Agus is a best-selling author and physician whose clients included Steve Jobs and Sumner Redstone.
Of all the companies the two could have started together, they’ve chosen an unusual approach: a hydroponic farming start-up focused on creating more healthful food.
Their new business, Sensei, formally unveiled itself Monday afternoon, wading into an industry that has become increasingly popular among investors.
Silicon Valley Start-up Plenty raised $200 million from SoftBank’s $100 billion Vision Fund. Bowery Farming, whose vegetables are now sold in a few grocery stores in New York City, has collected money from the likes of Google’s venture arm and General Catalyst.
Sensei is focused more on wellness. While the company ultimately plans to expand into an array of businesses, its initial focus is on hydroponic farming, using software and sensors to monitor growing conditions. (Its first farm is on Lanai, the Hawaiian island of which Mr. Ellison owns roughly 98 percent.)
Sensei’s first batch of crops includes Black Trifele tomatoes and Komatsuna mustard greens, with its yardstick for production being nutrition per acre.
“So far, the conversation in agriculture has been dominated by productivity: How much food can we grow in a square foot. But scale is just part of the equation,” Dr. Agus said in a statement. “To properly nourish the world, we need to consider how nutritious that food is. This is where Sensei is focused.”
Its first customer is Hawaii, which imports the majority of its food. Sensei said that it can provide the state fresh food within 24 hours of harvesting, compared with over a week for imported vegetables.
But the company is also eager to tout its tech bona fides. Its farm runs off solar power provided by Tesla panels. And it claims to use just 10 percent of the water used in traditional farming methods.
“For so long, agriculture has been one of the least digitized industries,” Daniel Gruneberg, Sensei’s president, said in a statement. “Now, we can combine software, sensors and robotics to make giant leaps in sustainable farming and perhaps, more importantly, the quality of our food.”
— Michael de la Merced
There's New Life At The Former Buffalo China Factory
There's New Life At The Former Buffalo China Factory
By Maura Christie | March 17, 2018
In 2003, Buffalo China was shut down abruptly because of competition overseas. A couple years after, Kevin Callahan, Managing Partner of Hayes Place Management Group, purchased the former factory with a vision to restore it to what it once was.
"It was hard walking around because peoples' lives were here and I was the only one in here. And it was eerie, you know there were generations of people that had worked here and it just stopped in an instant," he said. "I'd like to see people use it and be here, it's exciting to see hundred or a thousand people here on an individual day using the building. It's been here since 1903 and I'd like to bring as much life back to it as possible."
The 285,000 square foot building is already being used by five local companies, including Callahan's company, 716 China, which sells off the 350,000 plates that was left behind. Some products are original while others are printed with a special roaming buffalo design.
In addition, there's also Buffalo Curling Club, a cryptocurrency mine, hydroponics farming and a women operated distillery. Some of the businesses even teaming up with their products. Yoga Pants Distillery using the wheatgrass grown on site from Growtech to make their vodka.
"The distillery was really a result of growing microgreens and the wheatgrass in the containers outside. And you know, what're you gonna do with this product. And we were going to do either one of two things we were gonna make doggie biscuits or we were gonna make booze," Callahan said.
He said people in the area are excited to have something exciting happening near them.
"This side of town doesn't get a lot of attention for the development so yeah they're super excited especially a lot of former employees and people that grew up with their parents or grandparents working here, they come in and they go to the curling club or come into the store, and it just brings back a lot of memories for people."
This Local AGTech Startup Wants You To Forget Everything You Know About Farming
This Local AGTech Startup Wants You To Forget Everything You Know About Farming
By Andrew Moore
March 15, 2018
In November 2016, Tyger River Smart Farm constructed a 13,000-square-foot greenhouse and 3,500-square-foot harvesting facility on 30 acres in Greer. The expansion has increased the farm’s production capacity tenfold. Photo by Will Crooks.
Industrial agriculture has allowed farmers to maximize the potential yield of their crops for centuries. But it has done so at a major cost to the environment — a cost characterized by a steady decline in soil productivity, reduced water quality, elevated levels of carbon dioxide, habitat loss, and more.
Unfortunately, the negative consequences of industrial agriculture are set to worsen in the coming decades as the national population grows and urban sprawl continues to swallow large swaths of productive farmland. The American Farmland Trust, a group working to promote healthier farming practices, estimates that 24 million acres of agricultural land have been developed since 1982.
As a solution, an increasing number of entrepreneurs are turning to controlled-environment agriculture (a combination of engineering, plant science, and computer-managed greenhouse control technologies) to optimize plant growing systems, plant quality, and production efficiency.
One company that’s leveraging the power of CEA is Tyger River Smart Farm.
The Greer-based operation grows a variety of lettuces, chard, kale, and basil through the use of hydroponics — the method of cultivating plants without soil by instead using a nutrient-rich solution to deliver water and minerals to their roots.
“I don’t have a problem with people who adhere to conventional farming methods,” said Ryan Oates, owner and founder of Tyger River Smart Farm. “But I do think growing crops with hydroponics is more beneficial to both the consumer and the environment.”
Growing a business
Despite being the first person in his family to farm, Oates is no stranger to plants.
Oates studied plant biology at Clemson University and conducted numerous research projects at the Genomics Institute. He then enrolled at Miami University in Ohio to pursue a graduate degree in plant molecular biology but decided to drop out after becoming disenchanted with academia.
Upon his return to the Palmetto State, Oates spent several years as a financial planner in his father’s business. He then worked in commercial cabinetry for nearly a decade. In 2012, Oates stumbled onto the concept of hydroponic farming and decided to install a system in an existing greenhouse behind his parents’ home in Duncan.
“My mom loves to garden, so she built the greenhouse as a hobby,” Oates said. “But she was no longer using it, so I thought I would give hydroponics a try. It just seemed like something I would enjoy doing as a full-time job.”
Ryan Oates
Oates eventually outfitted his mother’s 1,300-square-foot greenhouse with fans, an evaporative cooling system, a propane heater, overhead LED lights, and hydroponics equipment. He officially launched Tyger River Smart Farm in August 2013. But the new venture didn’t come without challenges, according to Oates. A power outage, for instance, stopped the flow of water for about two hours and decimated about 70 percent of his crop. Oates outfitted the greenhouse with a generator shortly after.
Following the first harvest in February 2013, Oates had to give away most of his produce to neighbors due to a lack of customers. But then Tyger River Smart Farm was accepted into the TD Saturday Market in downtown Greenville. The market, which runs on Main Street on Saturday mornings from May 6 through Oct. 28, has become a signature event since its launch in 2002 and typically features more than 75 vendors that sell farm-fresh produce, baked goods, meats, cheeses, seafood, and other specialty foods.
“We owe a lot of our success to the TD Saturday Market,” Oates said. “The market not only helped us sell our produce that summer. It also helped us get our name out there and gain new customers.”
Tyger River Smart Farm has since become a vendor at the Greer Farmers Market and Hub City Farmers Market in Spartanburg, according to Oates.
The farm also sells fresh produce to a variety of local restaurants and grocers, including the Swamp Rabbit Café and Grocery in Greenville, Tandem Creperie and Coffeehouse in Travelers Rest, The Farmer’s Table in Spartanburg, Stella’s Southern Bistro in Simpsonville, Cribbs Kitchen in Spartanburg, Restaurant 17 in Travelers Rest, Adam’s Mobile Market in Easley, and GB&D in the Village of West Greenville.
Farming as a science
As the farm’s reputation and customer base continued to grow over the years, Oates realized that Tyger River Smart Farm would need to scale to survive.
In November 2016, Oates expanded his operation by constructing a 13,000-square-foot greenhouse and 3,500-square-foot harvesting facility on 30 acres in Greer. The expansion has increased the farm’s production capacity tenfold, according to Oates.
Oates said the new greenhouse relies heavily on automation. The facility features natural gas heaters, recirculating fans, exhaust fans, mechanical vents, and an evaporative cooler that aids in controlling the temperature and humidity. It also features a retracting shade system that helps with temperature control and light levels.
“Traditional farming isn’t easy,” Oates said. “But our CEA system requires us to monitor our plants on a real-time basis and watch how they react to different conditions. It’s much more process-oriented, so all the automation really helps.”
He added that the farm’s greenhouse uses carbon dioxide generators, which enrich the surrounding air if the levels become low, and more than 100 LED lights, which provide supplemental lighting during the winter months when solar light levels are too low for growing crops. It also uses an environmental controller, which is responsible for sensing environmental conditions and integrating all of the equipment through computer logic to produce a consistent environment year round.
As for growing the produce, Tyger River Smart Farm employs a Nutrient Film Technique (NFT) system, a soilless technique that bathes the roots of the plants in water infused with carefully monitored nutrients.
Tyger River Smart Farm uses over 100 LED lights to provide plants with supplemental lighting during the winter months when solar light levels are too low for growing crops. Photo by Will Crooks.
Oates typically begins the process by purchasing seeds from Johnny’s Selected Seeds in Maine or Paramount Seeds in Florida. The seeds are then germinated in a propagation room, which is completely enclosed and controlled with central heat and air.
After basking in the pink glow of LED lights for one to two weeks, the seedlings are relocated into nursery channels in the greenhouse, which sits on a well and 600-gallon underground tank. The water from the tank is then mixed with nutrients and sent down the channel, where it flows over the roots of the plants. Excess water is then collected at the end of the channels and returned to the water tank.
The nutrient water is then pumped from the main storage tanks back into the plastic channels, according to Oates. Thus, no water or nutrients is ever wasted. The same environmental controller in the greenhouse is responsible for maintaining optimum nutrient and pH levels in the storage tanks.
When the produce is harvested, it is packaged and sold with the roots in order to maintain the plant’s lifespan and nutritional value. During the peak of the season, Oates harvests between 8,000 and 9,000 plants a week, but he continues to produce plants all year round.
“The best part about hydroponics is that I get to harvest plants during the winter months when other farms are buried under the snow,” Oates said. “It definitely helps me stay ahead of the competition.”
The farm’s hydroponic system also has various environmental benefits, according to Oates. About 1,500 square feet of the greenhouse, for instance, is dead space reserved for an insect screen, which allows the farm to not use any toxic pesticides, insecticides, or herbicides during the growing process. And the recirculation process from the farm’s NFT system uses about one-tenth of the water a traditional farm usually uses. And since soil is not used, there is no chance of contamination through runoff.
Tyger River Smart Farm also utilizes various methods to conserve energy. Last year, for instance, Oates purchased and installed a large solar array behind the greenhouse that’s capable of producing enough electricity to power the entire operation.
Planning for the future
While hydroponic farming can be more lucrative than traditional farming and beneficial to the environment, it can also be challenging. Plants, for instance, require over a dozen essential nutrients that must be administered according to species, growth stage, and local conditions, such as water hardness.
“Hydroponic farmers have to understand how plants and nutrients interact in order to be successful,” Oates said. “We use a lot of automation, but we’re still dealing with living things that react to the environment. Luckily, I have a background in plants and can tell pretty quickly whether or not I need to make an adjustment to the system.”
Oates has hired three full-time employees since launching the farm in 2012, but he still spends up to 70 hours a week tending to plants in the greenhouse. “Hydroponics is a double-edged sword,” he said. “We get to farm year-round, which gives us a leg-up on the competition. But we don’t really get vacations or holidays because we have to get the work done when the plants demand it.”
Tyger River Smart Farm grows a variety of lettuces, chard, kale, and basil through the use of hydroponics — the method of cultivating plants without soil by instead using a nutrient-rich solution to deliver water and minerals to their roots. Photo by Will Crooks.
The industry forecast, however, makes all the hard work worthwhile, according to Oates.
The U.S. hydroponic industry has grown consistently the past five years and is projected to continue into 2022, according to market research group IBISWorld. Industry revenue rose 3.4 percent to a total of $848 million the past five years ending 2017. Its outlook declined to a yearly rate of 0.2 percent until 2022.
Oates hopes to reach new customers in the coming years by selling produce through local distributors. The farm has already partnered with a wholesale distributor to sell basil at numerous Ingles supermarkets across the Upstate and Western North Carolina.
He also plans to expand the farm by constructing another 13,000-square-foot greenhouse in 2019. “It will just be an addition to what we have now,” Oates said. “We really want to become an industrial operation, and we’re pretty close to that now, but this addition will pretty much complete that transition.”
Aramark Deal Spurs Lettuce Dream Growth
A lot more than hydroponic produce has been growing these days at Lettuce Dream, a local non-profit greenhouse that provides vocational training for post-high school young adults coping with cognitive and developmental disabilities.
Aramark Deal Spurs Lettuce Dream Growth
- By TONY BROWN | Staff writer
-
- Mar 10, 2018
Diners fill up their plates Friday over the noon hour during the second annual Taste O’ Green salad luncheon fundraiser for Lettuce Dream, a local non-profit greenhouse that provides vocational training for post-high school young adults coping with cognitive and developmental disabilities
MARYVILLE, Mo. — A lot more than hydroponic produce has been growing these days at Lettuce Dream, a local non-profit greenhouse that provides vocational training for post-high school young adults coping with cognitive and developmental disabilities.
On Friday, the organization hosted its second annual Taste O’ Green salad luncheon in the Maryville First United Methodist Church fellowship hall, where Director Charlie Clodfelter was on hand to offer an impressive list of accomplishments posted by Lettuce Dream over the past several months.
Scores of area residents attended the self-serve luncheon, which from late morning through mid-afternoon offered diners a tasty assortment of salads, wraps, fruit dishes, and desserts.
Most of the dishes on offer were made from produce grown at the Lettuce Dream complex near the intersection of East First Street and the U.S. Highway 71 bypass.
Clodfelter said the greenhouse’s current line-up of crops, which are sold to area restaurants, grocery stores, and food-service operations, include romaine lettuce, butterhead lettuce, Salanova, basil and pak choi, a variety of cabbage associated with China and other Asian countries.
The inventory of fresh-grown greenstuff is proving attractive to a growing list of Lettuce Dream customers, Clodfelter said, including Aramark, the food-service vendor for Northwest Missouri State University.
Aramark’s coming on board as a major customer — the company currently purchases 54 percent of Lettuce Dream’s total crop output — followed Lettuce Dream’s acquisition of a Good Agricultural Practices certificate through the U.S. Department of Agriculture.
The regulatory designation that means the greenhouse has implemented traceability and sanitation practices, including worker training, designed to ensure its produce is grown and distributed under safe and healthy conditions.
Clodfelter said the arrangement with Aramark means Lettuce Dream is providing Northwest’s Campus Dining operation with 200 pounds of nutrition-rich romaine lettuce each week.
Other businesses on the organization’s customer roster include Hy-Vee supermarkets in Maryville and St. Joseph, the Dusty Trails wild-game restaurant in Rock Port and the employee cafeteria operation at Maryville’s Kawasaki Motors manufacturing plant.
The influx of customers, Clodfelter said, means Lettuce Dream is seeking to raise around $5,000 in grant funds and donations to pay for a new nursery bay, which could raise the greenhouse’s production volume by nearly 90 percent without construction of additional cultivation space.
“In a year’s time we’ve come a long way on all fronts,” Clodfelter said.
Other Lettuce Dream developments include efforts that could lead to client referrals through the Developmental Disabilities Division of Missouri’s Department of Mental Health.
The cost of training, placement and other services offered to those clients, Clodfelter said, could then be billed to Medicaid, creating an additional revenue stream.
Current Lettuce Dream clients receive all services free of charge, a practice Clodfelter said would continue for trainees not covered by the DMH referral program in the event it is ultimately approved.
Additional vocational offerings available through the non-profit include paid internships for qualified clients at the local Pizza Ranch restaurant.
Lettuce Dream currently serves nine clients working through a progressive series of vocational training modules. Clodfelter said three people have completed the program, one of whom is self-employed. The remaining two graduates both hold jobs in the private sector.
Staff writer Tony Brown can be reached at tbrown@maryvilledailyforum.com or by calling the newspaper at 660.562.2424.
Tags:
Northwest Missouri State University
Foolproof Growing Tips For Microgreens
Foolproof Growing Tips For Microgreens
February 27, 2018
Ever feel like growing microgreens is a bit like being stuck in a blizzard? We promise that these foolproof tips will help you out a lot. Growing microgreens doesn't have to be brain science. It should be like strolling on a tropical island with no worry in the world. Easier said than done, right? We sure wish that someone would've told us these tips when we were first attempting to harvest.
Water Quality
At the start of a microgreens crop, a hydroponic system is filled with water. Water is continually being lost from the system, mainly through the leaves of the microgreens crop by a process known as transpiration. The volume of water in the system is, however, maintained constant by the automatic replacement of the water that is lost. This is achieved by a float valve in the catchment tank, which allows water to flow into the microgreens system from an external source as required. This makeup water will normally contain dissolved substances in it. The nature and quantity of the substances in solution in the water will differ by locality. If these substances are not removed from the water by the microgreens crop plants at a faster rate than they are being supplied in the makeup water, then their concentration in the recirculating water in the microgreens system will increase, until a concentration of one ion will be reached at which growth is adversely affected, and eventually a toxic concentration will occur. The best water for growing microgreens is rainwater or water condensed from the moisture-laden air. Water from these two sources has virtually no dissolved substances in it. Consequently, there is no build-up of excess ions coming into a hydroponic installation with the makeup water.
Filtration
Very little filtration should be required in a microgreen hydroponic system. If the makeup water does not contain solid particles in suspension, and if the method of supporting the young microgreens plants does not release solid particles into the recirculating solution, then filtration will not be necessary. The only precaution to take would be to site the inlet of the circulation pump in the catchment tank, as far as possible from any solution returning from the microgreens hydroponic system to the tank, and also near the surface of the solution in the tank. the tank will act as a sedimentation tank and the solution recirculated by the pump will thus be drawn from the clear solution near the surface. Yet, if there is a problem with solid particles in suspension, a course filter should be fitted over the outlet end of the catchment pipe so that the returning solution discharges into the tank through the filter.
Root Death
In a microgreens crop, the root system can be inspected readily. Consequently, if any roots should die. their demise is quickly seen and observed in all its tragedy. Roots are so basic. If too many roots should die, will not the whole microgreens plant die? In soil grown microgreens crop, the death of roots cannot be seen. The phenomenon of root death has been most extensively studied in tomatoes. Three english research workers at the Chestnut Experiment Station (Leonard, Head and Cooper) in the 50s, using glass sided inspection trenches dug besides rows of soil grown tomatoes, recorded the root growth visible through the glass. All three workers studied plants from December sowing dates, because at the time, most commercial tomato crops in southern England were not sown before December. They all reported a sudden and marked loss of roots in the month of May; from 50% to 90% of the roots visiblein the glass panel suddenly died and decomposed. The phenomenon was given the name of the 'May Check', because there was also a reduction in the growth rates of the tops of the plants.
Without these tips, you'd possibly be stuck in These tips are foolproof. If you follow these basic guidelines you can't possibly go wrong. These are the essentials needed to grow microgreens. Remember consistency is key!
If you enjoyed this, you might also enjoy these post:
February 23, 2018
Facts about the microgreens grow system
February 20, 2018
Supercharge your hydroponics setup
February 16, 2018
February 13, 2018
Key health benefits of microgreens
February 9, 2018
Beginners guide to plant nutrition
February 6, 2018
Understanding water pH in hydroponics
February 1, 2018
January 29, 2018
Understanding coco coir as a grow medium
Tags: microgreens growing microgreens growing tips hydroponic system