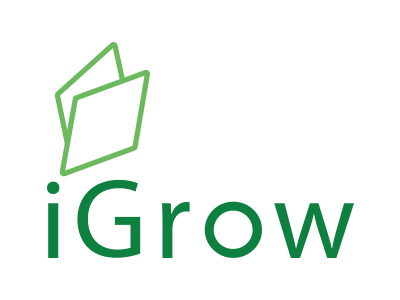
Welcome to iGrow News, Your Source for the World of Indoor Vertical Farming
Lorhill Farms Near New Hamburg is Spearheading Sustainable Agriculture With Vertical Vegetables
The year-round, hydroponic vegetables make up the popular Lorhill Greens Boxes. The fresh vegetable boxes can be purchased online and are delivered to customers’ doors to reduce the long-distance transportation impact
by Lisa Hagen for the Independent New Hamburg Independent
Tonia Streicher stands among Lorhill Farm’s vertically grown, hydroponic vegetables. The plants take up a fraction of the space of tradition row planting and use 90 percent less water. - Lisa Hagen
A surge in “eating local”, as well as a generation of farmers looking to produce food in a sustainable manner has given rise to farmers switching to methods that are better for the environment and their livestock. Lorhill Farms, just west of New Hamburg, is one of the vanguard spearheading sustainable agriculture.
Lorhill Farms was formerly a dairy farm, but as the fourth generation of the Wagler family took over the homestead, the business branched into several, environmentally conscious departments. Tyler and Maegan Wagler Scheerer look after the market gardens, landscape business, and poultry divisions; Dwayne and Tonia Streicher oversee indoor hydroponics and beef and pork production; and original owners Larry and Pat Wagler consult in all areas including a spiritual retreat on the farm.
At the forefront is the family’s hydroponic, vertical farming operation. Housed in their former milking building, the indoor garden, affectionally nicknamed the I-Farm, grows salad vegetables and herbs in a closed-loop environment.
“In a closed loop, we are able to control what comes in and out of the area,” explained Tonia Streicher. “Growing vegetables vertically takes up a fraction of the space of conventional, row farming and because we’re closed loop, we use 90 percent less water which we then recycle. The only energy spent is on lights and we are moving towards solar panels soon.”
Another aspect to a closed-loop is that no pesticides are required as few insects find their way into the sealed room. The few that do are caught in the old fashion way, on specialized, adhesive paper. As the plants are “no-till” they take no nutrients from the soil. Over tilling is known to strip the land. In contrast, the no-till system constantly adds to the soil’s health as old plants are composted.
The year-round, hydroponic vegetables make up the popular Lorhill Greens Boxes. The fresh vegetable boxes can be purchased online and are delivered to customers’ doors to reduce the long distance transportation impact. In the summer, market garden vegetables are added to the selection for the “choose what you want” boxes which, like all their packaging is compostable or recyclable. The outdoor vegetables are pesticide-free as beneficial insects are employed to ward off unwanted pests. Lorhill herbs will be available at the New Hamburg Sobeys in the near future
Lorhill beef, pork, poultry, and egg production also adopts all-natural processes. Livestock are treated responsibly and are pasture-raised with no hormones and no antibiotics.
“My kids name nearly all the animals,” said Streicher. “I want them to have a relationship and respect with them so the animals and kids feel safe. We give the livestock the best lives we can.”
This philosophy includes keeping cows and calves together until the young ones significantly mature.
Innovative Hamilton Company 80 Acres Farms Impresses Ohio Agriculture Leader
State Assistant Director of Agriculture Tim Derickson launched Ohio Agriculture Week on Monday in a surprising location: inside an industrial park building within Hamilton’s city limits, where he saw a future of farming
03-10-20
By Mike Rutledge, Staff Writer
HAMILTON — State Assistant Director of Agriculture Tim Derickson launched Ohio Agriculture Week on Monday in a surprising location: inside an industrial park building within Hamilton’s city limits, where he saw a future of farming.
At the 80 Acres Farms building, Derickson and others watched as a powerful orange-and-blue robotic arm lifted large trays of plants from inside climate-controlled containers into a bin on rollers as part of one of the world’s most high-tech agricultural operations, all located indoors.
“When I think of a farm, a building like this does not come to mind,” said Derickson, of Hanover Twp., whose family had a multiple-generation tradition of dairy farming.
READ MORE: Hamilton’s 80 Acres Farms expands size and influence with new facility, NYC exhibit
Derickson recalls when 17 families in Butler County in the 1980s owned dairy farms. Now the number is a small fraction of that, he said.
For many of the dairy farms, “It simply became a thing where it’s just not profitable, and you work an awful lot,” Derickson said.“It’s a gamble every year,” Derickson said. Among other things, “You’ve got to hope and pray for weather to cooperate.”
That isn’t the case inside several 80 Acres locations across the country, where tomatoes, strawberries, lettuce, grapes, and culinary herbs, among many other crops, can be grown even when there’s a foot of snow outside.
80 Acres is constructing a 70,000-square-foot building in Hamilton Enterprise Park, next to the existing research facility Derickson toured. That building will be able to produce between 1.5 million and 2 million pounds of crops a year — equal to production from 100 acres of farmland.
80 Acres CEO and co-founder Mike Zelkind said his crops taste better and are fresher than competitors. With strawberries the company grows elsewhere, “I bite into it, you guys would all smell it,” because it’s so juicy and full of flavor, he said.
One thing 80 Acres is not trying to do is compete with local farmers, Zelkind emphasized. It does not grow things that area farmers are raising during their growing seasons.
The company during 2019 decided to locate its headquarters in Hamilton, inside the city-government building.
Outdoors across Butler County, 41.5 percent of the county’s total land is used in farming — mainly as cropland, with some pastureland and woodland agricultural uses.
In 2017, the last time an agricultural census was taken, 123,916 acres in the county were dedicated to farming. That was down 12.8 percent from 142,128 in 1997, largely because of housing subdivisions and other developments making use of what was farmland, Kif Hurlbut of the U.S. Department of Agriculture’s Great Lakes Regional Office, and Derickson said.
By far, soybeans and corn are Butler County’s largest cash crops, earning $18.7 million and $16.5 million, respectively, in 2017. Behind them were hogs and pigs, at $6.1 million; and cattle and calves, at just under $6 million; nurseries and greenhouses, $2.9 million, and milk at $1 million.“Technology enables a completely different form of agriculture,” Zelkind told Derickson and others during a tour of one of two company growing operations in Hamilton.
They are pesticide-free operations where people like grower supervisor Tim Brodbeck, 22, control the amount of light, water and nutrients going to plants within various “grow zones” within shipping-container-sized boxes.
The company prides itself on environmentally friendly practices, such as recycling of water and the nutrients it contains.
Controlling all aspects of growing, the company can produce crops with “much higher quality, much better carbon footprint, much cleaner product — the nutritional value is unparalleled,” Zelkind said.
Hydroponic Growers Defend Their Use of Organic Label From Outside The Courtroom
A federal civil action brought by soil-using organic growers does not name any of the hydroponic growers they want to prevent from using USDA’s organic label
By Dan Flynn on March 11, 2020
A federal civil action brought by soil-using organic growers does not name any of the hydroponic growers they want to prevent from using USDA’s organic label.
But that does not mean hydroponic growers are going to remain silent as the litigation proceeds against Secretary of Agriculture Sonny Perdue and other USDA officials.
The lawsuit was filed on March 2 against USDA by the Center for Food Safety and several prominent organic growers. Hydroponic growers, represented by the Coalition for Sustainable Organics (CSO) said the CFS roll-out was misleading.
Current policy as determined by Secretary Perdue permits hydroponic growers to use the official USDA organic seal. Perdue gets advice on such issues from the National Organic Standards Board, an appointed body that meets twice a year.
Lee Frankel, the executive director of the CSO, said the press release and legal complaint “contains incorrect information regarding the final 2017 NOSB vote on whether to recommend making hydroponics, containers, and aquaponic systems as prohibited practices.”
Frankel said the NOSB voted in the majority to reject that proposal. “It is false to state that USDA ignored the NOSB proposal when in fact the NOSB vote indicated that the majority of NOSB supported the existing USDA policy,” he added.
The CFS-led Plaintiffs in the lawsuit charge that current policy permitting hydroponics to use the USDA certified organic seal violates the Organic Foods Production Act (OFPA). That’s because standards for implementing the act encourage organic growers to “foster soil health.”
Frankel says the CSO “is saddened by the latest attempts by the Center for Food Safety and their allies to limit fair competition and organic supplies in the market through legal action.”
“It is disappointing to see groups target pioneering organic farmers that use the most appropriate organic growing methods adapted to their site-specific conditions on their farms to meet the needs of consumers,” Frankel said.
Hydroponics has been called the “indoor agriculture evolution” by USDA, with the potential to offer a food safety advantage for growing lettuce and other leafy greens. Hydroponics grows plants in water using specific mineral nutrient solutions, not soils.
Frankel says his members are committed to the integrity of organic standards and the organic label. He says the groups behind the lawsuit failed to convince NOSB members that hydroponic and container production should be prohibited and there was significant industry debate by the organic community.
Frankel says the CFS “is seeking to eliminate public input to achieve their goals of restricting competition to drive up the price of organics for organic consumers to allow favored producers to increase their profit margins.”
While Perdue’s most recent decision favoring hydroponics occurred on June 6, 2019, the USDA policy is not new. “Growers using containers adhere to the USDA organic standards under the National Organic Program (NOP) and have been allowed to grow certified organic produce since the initiation of the nOP more than 25 years ago,” Frankel added.
Federal Magistrate Judge Laurel Beeler with U.S. District Court for Northern California is hearing the case.
Sylvia Wu, senior attorney for CFS, says “federal organic law unequivocally requires organic production to promote soil fertility.” And CFS Executive Director says “healthy soil is the foundation of organic farming.”
As for the soil-using organic growers who are Plaintiffs in the lawsuit, price competition from hydroponic growers is causing economic damages, according to their complaint.
(To sign up for a free subscription to Food Safety News, click here.)
Tags: Center for Food Safety (CFS), Coalition for Sustainable Organics (CSO), hydroponics, Lee Frankel, National Organic Standards Board
House-Builder Moves Into Indoor Farming
A Property Firm That Failed to Secure Funding For a Residential Development Has Decided to Turn its Attention to Farming – Or, More Specifically, Hydroponics
A Property Firm That Failed to Secure Funding For a Residential Development Has Decided to Turn its Attention to Farming – Or, More Specifically, Hydroponics
AIM-listed developer Trafalgar Property plans to diversify into hydroponic vertical farming and is looking for opportunities. It is in early-stage discussions with a potential hydroponics operator who could benefit from Trafalgar’s property expertise.
Hydroponics has existed since the 1950s. It is a form of controlled environment agriculture, where crops are grown undercover. It is a water-based growth system in which a nutrient solution is pumped around reservoirs in which plant roots grow directly. In vertical farming, crops are cultivated in vertically stacked levels in buildings, under artificial lights, without soil or natural sunlight. It requires less land and less water (since the water is all recycled) than traditional agriculture – and it is all organic as it needs no pesticides or fungicides.
It is battery farming for veg. And Trafalgar sees it as an opportunity.
Trafalgar New Homes is a regional residential property developer focused on Kent, Surrey, and Sussex, focusing on small sites of up to a dozen units – a scale that is too small for large developers, but too big for jobbing builders.
In March 2018 it acquired Trafalgar Retirement to develop assisted living and extra care schemes for the older residents. But difficulties obtaining finance led to the loss of its first development opportunity in that sector. This prompted the board to look around.
It has identified hydroponic food production, which requires significant property investment and expertise, as an area for investment. It is asking shareholders to stump up £2m to fund its new hydroponics venture.
Trafalgar cites a report that predicts the global vertical farming market will grow from $2.2bn in 2018 to $12.8bn by 2026. Other investors in hydroponics include Amazon's Jeff Bezos and Google's Eric Schmidt. Ocado entered the market in 2019 when it took a majority stake in Europe's largest vertical farm.
Got a story? Email news@theconstructionindex.co.uk
How Long Can The Novel Coronavirus Survive On Surfaces And In The Air?
A New Study Shows That SARS-CoV-2 Can Linger in The Air For Hours And On Some Materials For Days
March 19, 2020
AT A TIME when many people have taken to washing hands and sanitizing the objects they hold dear—frequently—a pesky question has loomed. How long does the SARS-CoV-2 virus stick around? A new paper in the New England Journal of Medicine, one of the first to examine the lifespan of the virus on common surfaces, offers some answers.
Like the common cold, Covid-19 spreads through virus-laden droplets of moisture released when an infected person coughs, sneezes or merely exhales. A team of researchers, including scientists from America’s National Institute of Allergy and Infectious Diseases, simulated how an infected individual might spread the virus in the air and on plastic, cardboard, stainless steel and copper. They then measured how long the virus remained infectious in those environments.
They found that SARS-CoV-2 stays more stable on plastic and steel than on cardboard or copper. Traces of the virus were detected on plastic and steel up to three days after contamination. SARS-CoV-2 survived on cardboard for up to one day. On copper, the most hostile surface tested, it lasted just four hours (see chart). In the air, the team found that the virus can stick around for at least three hours. In the air, as elsewhere, the virus’s ability to infect people diminished sharply over time. In the air, for instance, its estimated median half-life—the time it takes for half of the virus particles to become inactive—was just over an hour. And the levels of the virus that do remain in the air are not high enough to pose a risk to most people who are not in the immediate vicinity of an infected person.
These findings are likely to assuage some fears. Homebound consumers worried about contagion from cardboard delivery boxes may have less to worry about the next time Amazon rings (unless they are used to same-day delivery). At the same time, the findings will amplify concerns about airborne transmission, which some experts had not considered possible. The research may change the way medical workers interact with infected patients, who with close contact may transmit the virus onto protective gear.
Why the virus can survive longer on some surfaces rather than others still remains something of a mystery. Maybe it has to do with the consistency of the object playing host to the virus. Cardboard, of course, is much more porous than steel, plastic or copper. But the authors noted that there was more variation in their experiment for cardboard than for other surfaces, and the results should be interpreted with caution. No doubt consumers are used to treating their surroundings that way by now.
PODCAST: Honolulu's First Vertical Farm: MetroGrow Hawaii
They produce specialty crops, like herbs, corn shoots, butter lettuce, and an extra-salty ice plant, using hydroponics and aeroponics
We interview Kerry Kakazu, a plant scientist who started MetroGrow Hawaii.
They produce specialty crops, like herbs, corn shoots, butter lettuce, and an extra-salty ice plant, using hydroponics and aeroponics. Learn why chefs love their produce and what some of the challenges are when building a vertical farm in Hawaii.
LISTEN TO PODCAST
March 2020
InFarm’s High-Tech Vertical Farms Head to Canadian Grocery Stores
InFarm is bringing its in-store vertical farming systems to Empire supermarkets across Canada, according to a press release from Empire. The partnership will launch this coming spring and put InFarms’s high-tech farm pods in stores across that country, including at Empire subsidiaries Sobeys, Thrifty Foods, and Safeway Canada
InFarm is bringing its in-store vertical farming systems to Empire supermarkets across Canada, according to a press release from Empire. The partnership will launch this coming spring and put InFarms’s high-tech farm pods in stores across that country, including at Empire subsidiaries Sobeys, Thrifty Foods, and Safeway Canada.
Berlin-based InFarm, which raised $100 million in June of 2019, has struck multiple deals with grocery store chains around the world over the last several months, including Irma in Denmark, M&S in the UK, and Kroger stores in the U.S. The company is one of many startups developing vertical and/or indoor farming solutions meant to shorten the food supply chain by growing greens closer to food stores.
With InFarm, that means growing those leafy greens and herbs inside the produce section of stores. The company’s indoor farms come in the form of enclosed pods that use the hydroponic grow method, meaning plant roots are submerged in a nutrient-enriched water supply and no soil is involved. Cloud-based software controls the temperature, watering schedule, and light and humidity levels of the farms, adjusting those elements based on plant type.
There are two major benefits to this in-store approach to vertical farming. Zero pesticides are used in the grow process, and greens can be harvested onsite, reducing carbon emissions since food doesn’t have to be transported to the store from a distribution center.
Better-tasting greens is another one of InFarm’s claims. By precisely adjusting light, temperature, water levels, and other elements, vertical farmers can create ideal growing “recipes” for each plant type meant to bring out the optimal amount of flavor.
Many vertical farming companies make this claim, along with those about reduced water usage and carbon footprint. What the indoor ag industry needs next is more public data backing these claims up. With other companies — notably Square Roots and Freight Farms — striking deals of their own to get vertical farms closer to food stores, more hard numbers will be needed to show us when, where, and how these high-tech farms can be most useful in the overall food system.
InFarm will launch a range of herbs at two Safeway stores in Vancouver this spring, according to the press release, and Empire will also put farms in stores across seven Canadian cities.
How An Unlikely Farmer Is Plotting The Future of Food
In a nondescript former root beer plant, tucked behind the Curtain & Bath Outlet off Main Street in Millis, Massachusetts, FreshBox Farms is growing the future of food
By: Dan Morrell; photographed by Scott Nobles
In a nondescript former root beer plant, tucked behind the Curtain & Bath Outlet off Main Street in Millis, Massachusetts, FreshBox Farms is growing the future of food.
The FreshBox facility bears no resemblance to our cultural renderings of a farm; not only is there no soil, but every attempt is made to contain the risk that such outside organic matter could introduce. Visitors are asked to dip the soles of their shoes into a shallow plastic water bath, so as to limit contamination by pathogens and insects. Entry into one of the facility’s 15 growing units—8' x 40' metal boxes resembling shipping containers—necessitates a white cap and a lab coat. The units feature a double-door protocol that requires the exterior door to be closed before a second internal door can be opened. In the far corner of the building, a larger-scale model of the growing unit features an entry foyer with a ventilation system that cycles the air every few seconds and a secondary system designed to blow out any pathogens or insects that might have snuck past earlier garrisons.
All of this security is in place to protect—sans pesticides—the racks of Styrofoam-like growing beds inside the units, which are filled with leafy greens and fed by precisely tuned LED lights. An intricate digital system measures the room’s temperature and the CO2 levels inside the units every 30 seconds, adjusting as necessary; another delivers computer-calculated nutrients and water through the plant beds. These precision systems allow the facility to use about 1 percent of the water required by traditional farming counterparts while producing the equivalent of a 400-acre farm in just 27,000 square feet of space. It’s as if nature has been stripped of its variability and cranked all the way up.
Which is exactly the kind of tech upgrade the world food system needs to be given our increasingly insecure ecosystem, says Sonia Lo (MBA 1994), CEO of Crop One Holdings, which owns and operates the FreshBox brand. Sitting in FreshBox’s makeshift conference room—a long table, chairs, and a monitor, surrounded by four very high stacks of the white foam growing racks—she lays out the challenge. Climate change and its progenies, drought and flooding, are threatening traditional agricultural systems. And even when those systems work, they still rely on carbon-intensive shipping supply chains that move food thousands of miles from where it is grown to the tables where it is consumed. The global population is rising, with the United Nations projecting it to swell to 9.7 billion from its current 7.7 billion by 2050. “We also have to solve the calorie deficiency that we’re going to confront by 2050 on this planet,” she says. “We have to produce 70 percent more calories than we produce today to feed that population.”
Addressing a problem with that kind of span requires scaling beyond the 8' x 40' units—and beyond Millis. “The modular unit that’s going into Dubai will be three times the size of this,” says Lo, motioning to the larger-scale model in the back left corner of the facility. In June 2018, Crop One won a bid to provide leafy greens to Emirates Airlines’ flight catering company, and it is in the midst of building a 130,000-square-foot facility in Dubai that they expect to produce three tons of greens a day. It’s an almost unfathomable amount of daily production, but Lo puts it in perspective. “A single fast-food restaurant chain uses 300 million pounds a year of leafy greens alone,” she says. “A one-ton-a-day farm produces 740,000 pounds a year. So even if we built a 50-ton-a-day farm, you’re still only producing 240 million pounds a year. You would serve one customer.”
That 50-ton-a-day mark is a real goal, says Lo, and the Dubai farm will be a big proof of concept. And while any company’s world-saving ambitions can resemble Silicon Valley–like hype, Lo stresses that there’s a path, and the first step was figuring out how to most effectively grow lettuce in climate-controlled shipping containers in this former root beer plant. “We’re doing this in a very logical, road-mapping way. We’re not trying to bend the laws of physics. We are trying to enhance control. We’re trying to grow 365 days a year. We’ve been growing every day since February of 2015, which is pretty remarkable for any farmer to be able to say. We have not stopped growing even one day, you know?”
“We’re not trying to bend the laws of physics. We are trying to enhance control. We’re trying to grow 365 days a year.”
Lo is an admittedly unlikely farmer. She grew up as the daughter of Korean diplomats, a life that provided her with a multitude of international addresses and seven languages. And while growing up in fully staffed ambassadorial residences and being transported in limousines with darkened windows and little flags on the hood seems strange in retrospect, the multicultural upbringing had an impact that Lo has only recently come to realize.
About six years ago, Lo met a neurologist who was fascinated by her early experience with languages. “I would love to study you because the way that your neural networks have been formed must be so different—because you were really substantively multilingual before you were seven,” the doctor told her. “The implications of that are problem-solving, so you’re probably going to be able to see two or three solutions around something in a way that other people don’t.” The other benefit, the neurologist noted, was creativity. While Lo never saw herself as a creative person, she did seem to have a knack for seeing overlooked connections between ideas and then visualizing and building maps to explain those correlations.
These cartography skills have proved vital to her career. In the late 1990s, Lo was working on innovation and ventures for a media company in London when she realized that the industry was due for disruption. In a meeting with the CEO, Lo drew him a network diagram of what the future infrastructure of TV distribution was going to look like. “It’s all going to be bits and bytes,” she told him. Lo would later help stitch together some 200 European internet cafés to build a digital media platform; when the entrepreneurial bug bit soon after, Lo built a Groupon-like platform that helped smaller companies get product discounts.
That startup, eZoka, was pulling in £1 million a month until outside investment was derailed by the attacks of September 11, 2001. She spent a year cleaning up the aftermath. Exhausted and bruised, she decided to step away from business, attending culinary school and becoming a private chef in London for two years. (Lo donated all her earnings to charity and coauthored a book during that time, Dining with Dictators, which was part political satire and part cookbook.)
Lo returned to business in 2004, starting Chalsys, an investment and advisory practice that helps large companies avoid the pitfalls of corporate venturing. And it was through this company that she met a German investor who would become an initial Chalsys coinvestor and, eventually, one of the firm’s partners. In 2012, Phil Strause (MBA 1967), a former boss from an early career stint at Deloitte, sent Lo a business plan for a vertical farming company. She forwarded it on to the German investor, whose family, it so happened, had major European agriculture holdings. “You know, this is really interesting,” he told Lo. “Because if the unit economics of this thing turns out to be even remotely true, it’s the future of food.”
Lo’s interest was piqued. She knew almost nothing about farming and had always just trusted that the Western world’s food supply was safe and reliable. But as she dug into the research, she began to realize how wasteful, unsafe, and unreliable it really was. Conventional agriculture was facing substantive infrastructure problems while the cost of the tech solutions to address these issues was declining rapidly. It was a recipe for revolution.
But what Crop One needed was one of Lo’s maps. After their initial investment in April of 2013, Lo describes the business as “failing to launch.” There was a leadership deficit and a business model that hadn’t accounted for returning investor capital—which included a significant investment from the Chalsys partner to whom she’d initially forwarded the business plan. “By the end of 2013, we reached the point where I confronted either writing it off and writing off my friend and benefactor’s money—or I was going to pull the nose up.”
Lo stepped in as CEO in July 2014. She built out the team, including hiring Chief Scientific Officer Deane Falcone, an expert plant biologist from the University of Massachusetts, to start defining the science side. “I was trying to figure out the technology road mapping for an industry that didn’t have a road map and, in fact, wasn’t an industry,” she says. But she also changed the mindset. “I was asking ‘Why is this an investable industry? Why is this a world-class company? How do we get it to be on the world stage?’ And that’s really the big fundamental shift.”
Lo focused on three factors for growing in her first few years at Crop One: lowering costs, enhancing yield, and segregating risk.
In her first 18 months, the company worked to reduce the cost of the growing units from $560,000 to $43,000. To boost production, they leaned heavily on Falcone’s expertise, allowing him time to test and tweak the inputs—temperature, CO2 levels, water, LED spectrums—to determine optimal growing conditions for the various greens. This focus on nailing the plant science, says Lo, was a differentiator, though one she didn’t immediately grasp. “I have enough experience in technology that I thought, ‘I totally see this hardware being commoditized.’ ” But she soon realized that it wasn’t the racks and tubs and trays that would separate them—anyone could buy those at their local hydroponics store. “But very few people can grow at the density and with the specificity that we can,” says Lo. The risk issue was addressed with what she refers to as the facility’s “triple defense system,” which includes the shoe bath, the growing units’ double-door protocol, and the lab coats. Better defenses mean decreased loss and, therefore, higher yields.
By the fall of 2015, FreshBox had six production units and was distributing its leafy greens to the local Roche Bros. supermarket chain, filling plastic clamshells with kale and spring mix on-site. Originally occupying only 24,000 square feet of the warehouse, it expanded to take over the facility’s entire 43,000 square feet. “What surprised us was the take-up and the demand, the kind of hunger for the product,” says Lo. More than 90 percent of the country’s leafy greens are produced in Arizona or California, according to the states' Leafy Green Marketing Agreement, and transportation to New England can take weeks; FreshBox being able to offer Massachusetts consumers a locally grown product not subject to the region’s cruel winters has proved to be a boon to the brand.
The addition of more modular units also allowed the company to grow different types of greens, enhancing R&D and commercial growth. This diversity came into play when they were bidding for the Emirates contract. Up against a very capable Japanese company that was already producing some 1,700 pounds a day, Crop One boasted 24 plant varieties to the Japanese company’s 4.
The Emirates farm is scheduled to have its first harvests this year, and plans for national expansion are now underway. Crop One will only be a minority owner in these new farms, says Lo, noting that the farming aspect of the business is very capital intensive. But they’ve pursued a project financing model rather than venture financing. “Project financiers are not starry-eyed venture capitalists,” she says. “They’re not romantic at all.” They want to see cash flow and mitigated risk, not hockey-stick returns. “We believe that in every technological disruption you have to have hand-in-hand capital model disruption and business model disruption because you don’t reinvent an industry unless all of those things coalesce. This is the wholesale replacement of agricultural infrastructure, right?”
“Gigafarms we’re defining at 50 tons a day. We hope to build our first gigafarm in the next five years, which is pretty ambitious.”
Deciding on future locations, Lo says, will come down to costs—energy and labor, chief among them—and existing local sources. Meaning, on the latter, can they grow anything there outdoors? “So in the Middle East, definitively not, right? You really have to bend the laws of physics to grow stuff there. Northern Europe—doesn’t grow very much, good prices, high labor, reasonable green energy, right?” The US Midwest has solid energy options and population density. There’s great hydroelectric power in New York, so the Northeast could work. The Southeast too. “When we look out across the United States, we would map against the major retailers’ distribution center network,” says Lo, meaning they’d build a farm at these centralized locations—23 of them to be exact. “We see a minimum of 23 megafarms.”
A megafarm? “Somewhere between 1 and 10 tons [of production] a day,” says Lo. “Gigafarms we’re defining at 50 tons a day. We hope to build our first gigafarm in the next five years, which is pretty ambitious. That’s our sort of moonshot goal.”
But she can see it pretty clearly. Twelve megafarms in Northern Europe, maybe one or two gigafarms. Russia would make sense. The Middle East is almost there.
Another ultimate goal, says Lo, is carbon neutral—vertical farms set up next to, say, a giant solar field or a wind farm. “We look at the industry, and it’s pretty clear you can’t put a sustainable label on yourself unless you solve the energy piece of it—and we don’t see our competitors doing that,” she says.
Crop One is also exploring decarbonization models, pairing with power companies to feed its CO2 to their plants. “We have people who are rocket scientists”—literally—“who are looking at this for us and doing the energy analysis. I touch base with them every couple of months just to say, ‘So tell me, if we were to approach power plants about being their carbon sink, who would we go to?’ They know who we would go to.”
Lo has the coordinates; she sees the path. “I think it is a tangible, known goal in which we have known steps.”
Vertical farming is still far from mainstream, but Lo notes its profile began to rise a few years ago, thanks to a marquee investment: In July 2017, Softbank’s Vision Fund led a $200 million funding round into Plenty, a San Francisco–based vertical farming startup. “That really moved the needle,” she says.
Don Goodwin, the founder and president of produce consulting firm Golden Sun Marketing—and a longtime attendee of the School’s Agribusiness Seminar—has closely tracked the industry’s ascent. He estimates that there’s some $2 billion invested in the space right now, with money flowing in from VCs, sustainable private equity funds, and billionaires like Eric Schmidt and Jeff Bezos, who also contributed to that July 2017 Plenty funding round.
“We look at the industry, and it’s pretty clear you can’t put a sustainable label on yourself unless you solve the energy piece of it.”
The recipients of those funds vary, says Goodwin. “There’s a number of reasons people come into the space. We have the small local operator who has a vision and a past, and wants to change the way people eat,” he notes. “And then we have these ‘big idea’ guys like Crop One.” Those businesses, he notes, are “trying to create a sustainable investment strategy, not only from traditional economic terms but also from societal terms.”
Which means that growing locally in a vertical farm allows FreshBox to compete on price and mission. Here’s how that works, Goodwin explains: “If [the lettuce] is grown in Massachusetts, I can put it on [a grocery store’s] dock at the same price or lower than if you grow it in California and truck it across the country. And so I get all that benefit of the freight. I get the shelf life that you’ve given up—the seven or eight days to get there by truck. And I get the whole sustainability message because of food miles.”
While she gets the business model and consumer appeal, Mary Shelman (MBA 1987), former director of HBS’s Agribusiness Program, is slightly wary of the world-saving aspirations of vertical farming. She’s heard entrepreneurs discuss how they can manipulate the LED lighting to create arugula with different flavor profiles, for example, even varying the spiciness. “But at the end of the day, how much does arugula really help if we have to feed nearly 10 billion people?”
Which isn’t to say that Shelman thinks there is no value in it. “I think we can learn things from their systems—because they have the ability to do controlled experiments—that we can then take outside or in more traditional, controlled-environment agriculture,” she says, “and use that in those systems that are lower capital cost.”
Chief among vertical farming’s costs is energy. “It’s the industry’s dirty little secret,” says Lo. So noticeable is indoor farming’s drain on a local grid, she notes, that law enforcement used to monitor spikes in electricity demand to find illegal marijuana growers.
The energy costs are improving, plus Crop One is constantly refining its design to increase efficiency, adds Deane Falcone. Scaling up will be a big help. He contrasts the climate system they use for the larger model in the corner of the facility to the individual systems on the independent units. “It’s like if you had a 10-bedroom house: Would you have 15 window air conditioners, or would you have a central air-conditioning system?”
Driving down costs is important because Lo ultimately wants this model to be cheap enough to be a solution for the developing world. “I do not want to be in a carbon-intensive industry; I want to be producing a nutritionally relevant meal, and I do not want to only be in the business of feeding rich people,” she says.
But if vertical farming is going to feed the world, it will also need to expand beyond lettuce and kale. Wheat and corn are unlikely, says Lo, but rice could eventually be a possibility. “Two-thirds of the world population’s staple diet includes rice,” she notes. But there’s perhaps an even greater opening here: Andrew D. Ive (MBA 1997), former managing director of the Food-X accelerator and founder of Big Idea Ventures, says that the meat-production model that much of the world still relies on is wildly inefficient at producing protein. “It basically takes nine calories of energy or input to get one calorie out,” says Ive. “Whereas if you’re producing a plant-based material, it’s closer to one-to-one. It also doesn’t require the same land use, it doesn’t require the same water use, et cetera. So leafy greens are great, but if you’re thinking about how to supply food for the 9 billion, then you’re really, really focusing more on other protein sources and other kinds of plant-based sources.”
This plant-based protein movement is fast becoming mainstream. Even the McDonald’s in the shopping center across Main Street from FreshBox Farms could be offering meatless burgers soon: The fast-food chain recently announced a trial partnership with Beyond Meat, whose products are made in part from yellow peas. So, yes, says Lo, getting to the point where her farms could grow yellow peas and soybeans—a crucial ingredient of the plant-based Impossible Whopper, Burger King’s early market entrant—would be ideal. The ongoing food revolution needs a parallel farming revolution to succeed.
Lo is on it. Crop One, she says, is researching these and other high-protein plants and investigating how her farms can produce products that can provide the world with necessary subsistence while also absorbing carbon dioxide at a higher rate.
“That will cause an explosion of take-up,” says Lo. “Because, again, we can’t continue on the trajectory that we’ve been on. We just can’t.”
Someone has to do something, even if that someone is a first-time farmer trying to build a global revolution in an old root beer plant in small-town New England.
Topics: Agribusiness-Plant-Based AgribusinessInnovation-Disruptive InnovationLeadership-Leading Change
INDIA: The Changing Face of Urban Food System: UrbanKissan
The majority of the World’s future population will live in urban areas in the near future as we witness a mass migration to the cities due to climate impact, related health hazards and associated risks. Feeding the planet ’s population will be one of humanity's greatest challenges by 2050
12 March 2020
The majority of the World’s future population will live in urban areas in the near future as we witness a mass migration to the cities due to climate impact, related health hazards and associated risks. Feeding the planet ’s population will be one of humanity's greatest challenges by 2050. Current food systems in cities are being challenged because they fail to provide permanent and reliable access to adequate safe, local, diversified, fair, healthy and nutrient-rich food to host over half the world’s population. The world at present produces more food than ever before, yet dietary diversity is declining and food insecurity is on the rise.
Food is an effective entry point to improve a city’s resilience. Currently, food production is responsible for almost 25% of global greenhouse gas emissions, and poorly managed fertilization exacerbates pollution of the air, ground, and water. We need to imagine an improved food production system grounded in better use of resources. This will involve moving to a circular economy, particularly in towns and cities. Faced with the acceleration of these tendencies and determined to bring about a reinvention of food policies, urban agriculture is emerging as one driver for this new-look approach. Cities need to explore various opportunities in developing sustainable food systems. Many interesting platforms are reworking on the need for Urban Agriculture and City Region Food Systems.
The Agriculture Industry becomes a complicated place with technologies and marketing tools and techniques that are launched almost on a daily basis. At this juncture how does one feel to step into a farm and purchase greens fresh in an Urban farm and buy it at costs lower than ever thought possible?
UrbanKisaan, the Vertical Farming Startup that puts quality first, has debuted its 3000 sqft new-age urban farm and retail store in Manikonda, Hyderabad. Here, customers can walk into the retail store, harvest fresh and clean products of their choice which are grown in the indoor farm which is on the other side of a glass wall. Urbankissan redefines the category ’Fresh
’!India’s First Urban Retail Farm and Store “Urbankissan” is now open in Hyderabad!
Walk-in, Pick your produce, Harvest on the spot and Walk out with the freshest cleanest produce there is. Grown locally and sustainably, we grow fresh produce that is beyond organic and like no other urban Kissan will change the shopper behavior where consumers are increasingly shifting their purchases to more experience-oriented retail locations in urban areas. Urban Kissan is inspiring a trend of having an indoor farm and a store in the same location and this will necessitate the immediate availability of Good Quality Vegetables within the vicinity of Urban areas for the urban consumers. This will also enable urban consumers in having the choice of vegetables at much lesser prices.
While Interacting with Vihari Kanikollu, CEO of Urban Kissan he eloquently explains the concept of Urbankisaan to be a full stack of plant science and food production technology — a sustainable, high-tech, high-efficiency, automated indoor vertical farm that can produce delicious, nutritious food at massive scale for lower costs than ever before thought possible. Urbankisaan brings together the unified design of a complete large-scale farm that maximizes the applications of energy, process control, and big data, along with with with advanced plant science to create maximum flavor, better shelf life, and ultra-clean food at incredible yields. By combining the latest plant science with these technologies, Urbankisaan farms are ideally optimized to produce yields of delicious, nutrient-rich food at a lower cost. ● 1.75 Acres produce grown in 2,000 Sq. Ft ● 30 days from seedling to harvest ● 365 harvests per year ● The shop and the farm are divided and the shop if of 500 sq ft and the farm of 2000 sq ft.
Urbankissan thereby plans to build a series of indoor vertical farms across India and will grow pesticide-free produce with 95 % less water and requiring less than 1% of the land needed for outdoor farms thereby saving 2,16,000 liters of water per farm per month. Vihari reiterates the Supply Chain’s approach to decentralize F&V production and distribution by being inside and close to the consumption centers (cities). By cutting down thousands of food miles, the produce is in consumers’ hands within hours of harvest, not days or weeks as is now. They harvest at the peak of taste and quality versus harvesting early for transportation. As and when the product gets finished in the shop they harvest more according to the need.UrbanKisaan has been recently funded by Ycombinator in Winter 2020 batch and has gone on to raise further.
Vertical Farming: The Advantages of Growing Up, Not Out
Vertical farming refers to growing crops in multiple vertical layers in controlled indoor environments, such as repurposed buildings, growth chambers and even shipping containers
We share this planet with more than 7 billion people, and the UN forecasts that by 2050 we will need to feed over 9.7 billion. If you’re like me, you’re wondering what we can do to scale farming to meet the needs of the future. That’s where vertical farming comes in, along with innovative technologies that make growing up, not out, a more viable option.
by Ali Ahmadian, CEO Heliospectra
Vertical farming refers to growing crops in multiple vertical layers in controlled indoor environments, such as repurposed buildings, growth chambers, and even shipping containers. While growing crops in the greenhouse have its own merits, depends on the crop and technology used vertical farming has advantages over single-layer crops grown in a field or greenhouse:
Vertical farming enables growers to optimize their costs per square meter and produce more within the same footprint. A vertical format could potentially produce a harvest that is 3- to 4-times larger (or more!) than a field the same size could produce.
Vertical farming is done in an automated, controlled environment, which eliminates many of the risks involved with traditional field farming. Variables such as seasonal weather and environmental issues are taken out of the mix to produce a thriving crop year-round – no matter what’s happening outdoors.
Crop yields are standardized in vertical farming, with every harvest cycle producing the same quantity, quality, flavor and appearance that customers expect.
Vertical farming enables growers to meet changing market demands, by easily introducing new crops or varieties based on consumer or retail preferences.
Due to its smaller footprint, vertical farming is a viable and environmentally sound solution for feeding cities. The UN predicts that close to 70% of the population will be living in urban areas by 2050. To reduce the carbon footprint of our food, we need to think of ways to bring food production closer to the dining table. A LCA is necessary to weigh in such decision making.
While we continue to build larger and larger cities to accommodate our growing population, arable farmlands will be pushed further out. Vertical farming can ensure our cities have plentiful locally grown food – food that has a predictable harvest, optimizes costs per square meter, looks beautiful, fresh and tastes delicious.
Source: LinkedIn
Publication date: Fri 6 Mar 2020
Lawsuit Demands USDA Stop Certifying Hydroponic Foods as 'Organic'
Hydroponics is a type of farming or gardening that uses water (rather than soil) as a growth medium for a variety of fruits, vegetables, herbs, and other plants—including cannabis. Hydroponic growth can be accomplished indoors with the addition of commercially available lighting, nutrients, and other materials
Dirt Farmers Want The Feds To Stack The Deck in Their Favor.
BAYLEN LINNEKIN | 3.14.2020
(Rodrigo Reyes Marin/ZUMA Press/Newscom)
Earlier this month, a group of organic farmers and advocates sued the U.S. Department of Agriculture (USDA) over the agency's certification of some hydroponic produce as "organic." The suit seeks to bar the USDA from awarding its organic seal to hydroponically raised foods.
Hydroponics is a type of farming or gardening that uses water (rather than soil) as a growth medium for a variety of fruits, vegetables, herbs, and other plants—including cannabis. Hydroponic growth can be accomplished indoors with the addition of commercially available lighting, nutrients, and other materials.
The suit was filed by the Center for Food Safety (CFS)—a "litigious" California-based nonprofit that boasts nearly a million members—along with a handful of organic farmers and the Maine Organic Farmers & Gardeners Association. CFS petitioned the USDA early last year, asking the agency to develop rules that would prohibit organic certification of hydroponic operations. The agency denied the petition in June.
The suit alleges that the USDA's actions fly in the face of the 1990 law that established the agency's authority over the labeling of organic foods. That argument hinges in large part on the language around fostering soil fertility in the 1990 law, the Organic Foods Production Act (OFPA), which gave rise to the USDA's certification program. Under the law, which refers to "soil" only a handful of times, farmers must have in place an "organic plan [which] shall contain provisions designed to foster soil fertility, primarily through the management of the organic content of the soil." A farmer raising crops she wishes to market under the USDA's organic seal must submit its organic plan to a certifying body such as Oregon Tilth.
That group, the nation's first organic certifying body, was established in the early 1970s. The word "tilth" refers to soil quality.
"Organic farmers and consumers believe that the Organic label means not just growing food in soil, but improving the fertility of that soil," says Andrew Kimbrell, executive director of the Center for Food Safety, in a release announcing the lawsuit. "USDA's loophole for corporate hydroponics to be sold under the Organic label guts the very essence of 'Organic.'"
According to the handful of farmers who are part of the lawsuit—and who grow a host of organic fruits and vegetables, many of them having done so for decades—they're facing stiff competition from (typically) larger hydroponic farmers, who incur lower costs to grow the same food and can, therefore, offer more value to consumers for the same products.
What exactly is "organic"? For regulatory purposes, the term refers as much to what doesn't go into producing a particular food as what does go into it. As I explained in a 2016 column, under USDA rules the term "organic" refers to foods that are produced 1) "without excluded methods;" 2) " using allowed substances;" and 3) under the oversight of a USDA-authorized organic certifying agent.
The hydroponic-organic fight dates back to at least 2010, according to Food Dive, a news website that has a helpful chronology on the fight.
As I detailed in 2016, the Cornucopia Institute, which promotes organic foods, had recently filed a complaint with the USDA over hydroponic organics.
TOP ARTICLES1/5After a State-Authorized Medical Marijuana Patient Had an EpilepticSeizure and Crashed Her Car, Police Arrested Her for Driving With 'Marijuana in Her System
"It's not hard to make the case that soil is as central to the concept of 'organic' as any other idea or thing," I wrote. "On the other hand, it's also not hard to make the case that soil isn't central to the concept of what is and isn't organic. While most of our food is grown in soil, only a small percentage of that food is 'organic' under USDA rules. In other words, whether or not food is grown in soil tells us little that's useful about whether that food is 'organic' or not."
When I last wrote about this issue, the Boston Globe editorial board had just weighed in on the debate over hydroponics and organics. Step off, the paper told the USDA.
"It would be better for the authorities to focus on ensuring the safety of food and the accuracy of label information about things like nutrition and allergens, while letting consumers figure out for themselves what organic means to them," write the Globe's editors.
That latter point is so important—and something USDA rules simply don't allow for. It's also just one of the many flaws inherent in the USDA's oversight of organic food. For example, I detail the arguments of several leading supporters of organic foods who are also leading critics of the USDA's organic labeling program in my book, Biting the Hands that Feed Us: How Fewer, Smarter Laws Would Make Our Food System More Sustainable
If CFS and its fellow plaintiffs lose, then the result will likely be more innovation, more competition, and lower costs for consumers. The USDA's organic seal has very little integrity to begin with. Allowing hydroponic crops to be certified as organic—while not as welcome as would be getting the USDA out of the organic-labeling business altogether—won't damage that integrity any further.
BAYLEN LINNEKIN is a food lawyer, scholar, and adjunct law professor, as well as the author of Biting the Hands that Feed Us: How Fewer, Smarter Laws Would Make Our Food System More Sustainable (Island Press 2016).
ORGANIC FOODDEPARTMENT OF AGRICULTUREREGULATIONFOOD LABELING
Is Vertical Farming The Future of Agriculture?
To address these issues of resource scarcity and loss, many scientists and innovators have been hard at work to come up with a solution
MARCH 14, 2020
To address these issues of resource scarcity and loss, many scientists and innovators have been hard at work to come up with a solution. A viable option that has come up is controlled environment agriculture, or weather or climate-proof farming, or vertical farming. This is increasingly being utilized in urban centers, arid zones, and some populous Asian countries.
This kind of farming is done in vertical rack systems as opposed to conventional farming. Oda has successfully experimented with this technology in arid zones and urban centers in Beijing.
His company has successfully used an abandoned shipment container to grow vegetables in the dry climate of Dubai.
Vertical farming is finding more acceptance commercially with innovations in efficiency and affordability, says Oda.
So how does this vertical farming work?
A lot of artificial elements are introduced to take the place of sunlight, water, etc. LEDs are used to provide energy in place of sunlight. Nutrients are pumped directly into the root zones of the vegetables, which are recyclable, for plant growth. Hydroponics and aeroponics systems are used for efficiency. Soil substitutes like polyurethane sponges, biodegradable peat moss, and even inorganic materials like perlite and clay pellets are used.
Racking systems can be16 to 14 stories high. A sophisticated automation and monitoring system is used to increase productivity, efficiency, and consistency of the food.
The benefits of indoor vertical farming are many. There is year-round production, which is of consistent quality, and one can be assured of a certain quantifiable output. It is great in terms of resource efficiency. Water, fertilizers and land use goes down by almost 99 percent in this type of farming. Moreover, as the system is weatherproof, the need for fertilizers is nil.
The produce can be made totally chemical-free. It gives 350 times more food per square meter than conventional farming. It will shorten the supply chain and maintain the nutritional content as the growth centers will be near urban and city centers. Also, such type of farming can be seamlessly integrated into the urban landscape with the utilization of underused civic structures, office corners, etc.
Considering the advantages, you may wonder why there is no widespread adoption of the method. The reason being it is a very energy-intensive program. Also, the variety of vegetables produced like this is limited. The cost of production is still very high for it to be widely adopted. For a better energy solution, higher efficient LED lights are being developed. Another option is to use laser lights for plant growth. Fiber optics cables to channelize sunlight to the facility in daylight hours is also another option.
Vertical farming may be the solution to an imminent water and food crisis that the world is facing. The biggest advantage is it will give equitable access to nutritional food to the most underprivileged, too once it becomes a common practice and is widely accepted. Still, a lot needs to be done before it becomes a shared reality.
Stuart Oda has floated his own vertical farming company called Alesca Life.
TAGS: AGRICULTURE, INDOOR VERTICAL FARMING, VERTICAL FARMING
GreenTech Americas Program Focuses On 2 Main Themes
During GreenTech Americas fifty Mexican and international speakers will present various topics for ‘crop optimization in protected horticulture’ and ‘strategic themes focused on business and investment’
By urbanagnews
February 21, 2020
Press Release – During GreenTech Americas fifty Mexican and international speakers will present various topics for ‘crop optimization in protected horticulture’ and ‘strategic themes focused on business and investment’. The objective is to present trends, knowledge and new solutions to all levels of professionals in the horticultural industry of Latin America. The show and program will be held from March 24 to 26, 2020, at the Congress Center, Querétaro Mexico.
Program
Within the framework of this event, a program of conferences and panels is developed with 2 main themes 1: Crop optimization
and 2: Business and investment. A few of the many highlights are:
Saber Merismailli, CEO of Ecoation, talks about “How artificial intelligence can help us grow clean food. And how early detection of issues can increase the revenue in your greenhouse”;
Chris Higgins, Hort Americas, tells you all you want to know about vertical farms. “Do vertical farms build stronger plants? How will the vertical farming industry develop and how does it impact you?”;
Peter Hendriks, director of LetsGrow.com, gives an update about big data. “Big data is no longer a stranger. How can you implement it to your business?”;
“The world’s population is growing and with it the demand for raw materials. However, the supply of crucial raw materials is limited”. A delegate of The World Bank explains the importance of Circular Economy, trends and developments for a sustainable future;
Héctor Manuel Cotero, Dummen Orange, discusses the trends in high-quality flower production. “What are the latest technologies and trends in this industry?’.
Experts and panel leaders
To name a few of the experts who will participate:
Erik J. Plaisier, Agricultural Counsellor for Mexico and Cuba, Nature and Food Embassy of the Netherlands;
Aldo Mares, President of the National Association of Exporters of Berries, Aneberries;
Oscar Woltman de Vries, General Director of Hortinvest Mexico;
Ricardo Martínez, Director General de Asesores en Invernaderos;
Alfonso Torres, Director General, Koppert Mexico, Koppert Biological Systems;
Edison Torrado León, Founder of Naturavisión;
Mauricio Revah, CEO, United Farms;
Paul Arkesteijn, Product Manager & Consultant, Ludvig Svensson;
Remy Matt, Manager, Cultilene;
Rene Beerkens, Consultant, Hoogendoorn.
About GreenTech Americas
GreenTech Americas is a spin-off of GreenTech Amsterdam with the goal to meet the needs of regional growers, breeders, and suppliers. GreenTech Americas will enable a greater exchange of knowledge, experiences, and success stories of the horticultural industry from Mexico and its region. The show is organized by RAI Amsterdam and Tarsus México. Please find more information and to register at www.greentech.nl.
About GreenTech Amsterdam
GreenTech Amsterdam will be held Monday 8 – Wednesday 10 June 2020. The exhibition is a global meeting place for all horticultural technology professionals. GreenTech focuses on the early stages of the horticultural chain and the current issues growers face. All Dutch front runners, greenhouse builders and suppliers are present. Last year a total of 12,489 professionals from 114 countries visited GreenTech Amsterdam.
Inside The Change: How Hamilton’s 80 Acres Works On The Front Lines of Farming
He’s not knocking lifelong farmers, but Mike Zelkind, CEO and co-founder of 80 Acres Farms, says the 20-something growers working for him in some ways have the experience of 5o-year-old traditional farmers
By Mike Rutledge, Staff Writer
03-14-20
HAMILTON — He’s not knocking lifelong farmers, but Mike Zelkind, CEO, and co-founder of 80 Acres Farms says the 20-something growers working for him in some ways have the experience of 5o-year-old traditional farmers.
That’s because they grow crops every month of the year, and may grow 17 crop cycles in a year, instead of one or two, because in the completely enclosed indoor growing environments, there are no off seasons to slow the crops down.
Using video monitors and other devices, they can see how plants grow differently when the humidity drops by 3 percent, or temperatures are 1 degree higher.
And with crops growing in such rapid succession, “They’ll see all these little things that if you’re growing a crop now and you’re growing it again in a year, you’re not going to remember all that,” he said.80 Acres, co-founded by Zelkind and Tisha Livingston, is at a technological frontier of completely enclosed indoor farming, where pesticides are not needed or used, where adjustable LED light replaces the sun, and things like temperatures are completely controlled. Universities all over are studying various aspects of what 80 Acres and other companies are doing.
Meanwhile, 80 Acres is raising “fireworks tomatoes” and other crops that are very flavorful — the kind you buy at a roadside farm stand on a good day. And does so even through Ohio winters.“We’re learning every day with this. That’s the fun part of the job. That’s what attracts the Timmys, the Megans, the Haleys,” he said, naming three Hamilton employees, “because this is how they think. They grew up with video games, playing with joy sticks.”He and his workers don’t compete against Ohio farmers: They don’t grow things that nearby farms are producing in-season. In fact, Zelkind says the company employees some farmers during their off-seasons, and works with farmers to help them better market their products and better get their fruits and vegetables into stores more profitably.
READ MORE: Ohio agriculture leader visits future of farming in Hamilton
With the fruits and other crops, 80 Acres grows in Hamilton and elsewhere, water use is way less than is needed outdoors. Where lettuce or leafy greens might use 650,000 gallons for certain production outdoors, they can use less than 20,000, he said.
About 90 percent of the water plants drink in through their roots they respire into the environment. The containers surrounding each 80 Acres “growing zone” recapture that evaporated water and condense it. It is run through ultraviolet filters and other systems, the nutrients in the water are measured and supplemented with nutrients that the plants consumed.“We can show you on tomatoes where our yields are 2-3 times what any greenhouse will get you,” said Zelkind, who has decades in the food-growing industry, as does his co-founder, Tisha Livingston, company co-founder and CEO of sister company Infinite Acres, based in the Netherlands.
80 Acres, which last year decided to locate its headquarters on the 7th floor of Hamilton’s city building, has about 130 employees nationwide and more than 40 in Hamilton.
The company’s growers mix the art of experimentation with the science of indoor agriculture. In one artistic twist, its growers strategically stress their plants to stir different flavors.
When growing things like tomatoes or grapes outdoors, “there’s all these random stresses,” Zelkind said. “That’s why sometimes you have the most incredible, phenomenal crops.”When it’s too wet, too dry, too sunny or too cold, plants naturally create phytochemicals and secondary metabolites as defense mechanism, which make them more healthy for people to eat, and also add flavors.“We can get a grape to fruit in eight months, instead of three years,” he said. “We do that in Arkansas.”Indoor growers also could replicate the grape-growing conditions of France, down to the fabled Mistral winds that many believe improve grapes.“If I know what you want the wind to be, and if I know what nutrients you want, then we can duplicate it completely,” he said. “Absolutely.”
The company now operates six indoor “farms: in Alabama, Arkansas, North Carolina, Cincinnati and two in Hamilton (on South Second Street and in a 10,000-square-foot research-and-development farm in the city’s Enterprise Park industrial park).
Next to that building, the company is building a $10-million-plus, 70,000-square-foot building that will take the best of the company’s other procedures to create a larger commercial-scale indoor farm.
Within five years, Zelkind hopes to have more than 20 indoor farms.
The company’s current “grow zones” have sometimes been in shipping containers that are used for cargo on ships and trains, because those canisters were sturdy, inexpensive, and could be retrofitted easily. Grow zones at the new Hamilton building, to open this year, will be larger. The increased production volume should allow the company to lower prices from organic levels to closer to prices for conventional crops.
Dennis Chrisman, vice president of Dayton-area Dorothy Lane Market gourmet stores, said 80 Acres has “some great combos that offer some great flavors, especially when they mix in some microgreens in their salad mixes. I think they’ve got powerful flavor.”Customers especially “love the Queen City mix. For those that are regulars with them, I think that’s one of their best options,” he said.
Rather than choosing seeds, like far-away farmers must, that create plants that are durable during transportation, Zelkind asks his seed providers for those producing their best-tasting fruits, but that were too temperamental for the outdoors.
Chieri Kubota, a professor of controlled environment agriculture at Ohio State University, said a big advantage of 80 Acres’ approach on raising food for local markets is it reduces the supply chain between it and markets, eliminating fuel waste, transportation time and distribution costs.
Rather than California lettuce spending two weeks being shipped here, the kind grown in Hamilton can be in stores within hours.
Rebecca Haders, the company’s vice president for marketing and creative, said it is worth it for customers to pay more for such products, because, “some of our salads can last 21, 28 days if they’re in the right conditions. You’re giving the shelf life to the customer, versus the truck.”80 Acres has been featured in such publications as Techweek, and in 2018 won the North Carolina Manufacturing Extension Partnership’s leadership award for Manufacturing Excellence.
Although its completely-enclosed-agricultural systems can be expensive to create, limiting their ability to be used for many crops, such farming also has potential to reduce droughts and famines by putting farms inside cities and using far less water than traditional cultivation. There’s also no fertilizer runoff into rivers.
Tim Brodbeck, a 22-year-old grower from Norwood who has been with the company three years, said: “It’s coming to work with a purpose. I love coming to my job every day, and every day is just another step toward feeding the world and feeding the people who don’t have the access to this food.”
INDIA: These Urban Farming Startups Are Going The Extra Mile To Bring Organic Food To Your Table
With new technologies like hydroponics and vertical farming, these startups are helping people grow produce in small urban spaces
With new technologies like hydroponics and vertical farming, these startups are helping people grow produce in small urban spaces.
By Suman Singh
11th Mar 2020
The Green Revolution in the 50s and 60s may have allowed our farmers to better their yields, but it also brought with it the evils of using pesticides and chemical fertilizers.
Urban farming
Over the years, they have been incorporated into conventional farming methods, bringing with them a host of problems. They are not only found to be toxic to humans by increasing the risk of getting cancers, but they also cause pollution, degradation of soil and water, and poison domestic animals.
Now, many farmers and urban-dwellers have switched to organic farming or urban farming. According to the International Federation of Organic Agriculture Movements (IFOAM),
“Organic agriculture is a production system that sustains the health of soils, ecosystems, and people. It relies on ecological processes, biodiversity, and cycles adapted to local conditions, rather than the use of inputs with adverse effects.”
Just a few years back, farming in cities would have been thought to be impossible. But new technologies like hydroponics and vertical farming have made growing produce in small urban spaces possible.
Here are six urban farming startups which are going the extra mile to bring sustainable farming practices in India:
UGF Farms
Started by Linesh Narayan Pillai in 2017, Urban Green Fate (UGF) Farms converts unused spaces into live food gardens. Live food gardens are built in a way that they do no structural damage to buildings. The Mumbai-based startup sends residents microgreens (vegetable greens after they’ve produced first leaves) in pots, to grow them in organic coco peat as opposed to heavy soil. All a user needs to do is cut the greens from the live plant as and when they need them.
Further, UGF also helps to address issues of starvation, malnutrition, food contamination, and food insecurity by collaborating with schools as well as corporates that work for underprivileged communities as part of their CSR initiatives.
UGF Farms
Since its inception, the startup has planted over 10,000 kg of microgreens. It has also educated 4,000 people over 150 workshops across multiple locations in Delhi and Mumbai about the importance of growing food in their homes and going organic.
Back2basics
Back2basics is the brainchild of S Madhusudhan. Started in 2015, it is an organic farm spread across close to 200 acres around Bengaluru, producing high-quality organic fruits and vegetables.
Run by a father-daughter duo, Back2basics supplies produce to grocery chains, retailers, organic stores, and gated communities in Bengaluru. Its produce is also exported to organic food supply chains and retailers in other parts of the world.
Back2basics
The startup deals in more than 90 varieties of seasonal produce in four categories – fruits, vegetables, greens, and exotics. It has reserved almost three to four acres for customers who wish to visit the farm and try their hand out in agriculture.
It produces products that are 100 percent organic. The producer has full control over the colour and texture of the greens, making them healthier and tastier.
Pindfresh
After returning from New York where he worked as a banker, Somveer Singh Anand, much like UGF Farms' Linesh, found it impossible to source organic food in India.
To address this concern, Somveer developed indoor hydroponic technology suitable for Indian climatic conditions and started Pindfresh in 2016 in Chandigarh. The startup sets up indoor and outdoor hydroponic plants for people who want to farm using the technology across India.
Pindfresh
The lighting, humidity, and temperature are controlled all the time for these microgreens to grow. And to that effect, Pindfresh manufactures quality controlled pipes, lights, and all the necessary equipment required to set up a hydroponic plant.
Growing Greens
Former Infosys employees Hamsa V and Nithin Sagi partnered to start a hydroponic farm, Growing Greens. The Bengaluru-based B2B startup grows and sells microgreens, salad leaves, sprouts, edible flowers, and herbs to high-end restaurants in the city.
Growing Greens
These microgreens, which are about one to three inches tall, are mostly used to decorate and garnish food. They have concentrated nutrient levels that can be almost 40 times higher than the normal-sized produce.
The duo did thorough research by talking to various chefs to understand their requirements before venturing into the business.
Started in 2012 on a small terrace, the startup is currently farming on four acres of land, which it plans to expand to 10 acres.
Herbivore Farms
Not many 24-year-olds would choose to ditch well-paying jobs and take up farming. But after paying a visit to Auroville in Puducherry in 2017, Mumbai-based Joshua Lewis and Sakina Rajkotwala were inspired by musician and organic farmer Krishna Mckenzie who started Solitude Farm with the aim of “honouring Mother Nature through local food.”
Herbivore Farms
The duo got down to business with Herbivore Farms, Mumbai’s first hyperlocal, hydroponic farm. Today, the farm is spread across 1,000 sq ft and grows 2,500 plants. It sells fresh, organic vegetables to customers across Mumbai from its temperature-controlled indoor setting.
The vegetables are grown in a clean, sterile environment, with zero pesticides. As compared to conventional farming methods, the setup consumes up to 80 percent less water to grow the produce due to “recirculating irrigation system.”
Harvested vegetables are delivered to the customers’ homes within hours, maintaining their freshness, nutrition, and flavour.
(Edited by Kanishk Singh)
The Value of Third-Party Verification For Horticultural Lighting
Horticultural lighting comprises the largest percentage of power demand in controlled environment agriculture (CEA) facilities for fruit and vegetable production
By urbanagnews
February 24, 2020
By Leora Radetsky
The US vertical farming market is projected to reach $3 billion by 2024, exhibiting a compound annual growth rate of over 24 percent, according to a February 2019 report. Another report, by the US Department of Energy’s Office of Energy Efficiency and Renewable Energy, put the annual electricity consumption of US horticultural lighting installations at 5.9 terawatt hours – equal to the annual usage of about 550,000 US households, and projected that to increase 15 to 25 percent annually.
Horticultural lighting comprises the largest percentage of power demand in controlled environment agriculture (CEA) facilities for fruit and vegetable production. A 2019 study by Toronto’s Independent Electricity System Operator (IESO) found, for example, that “a lit vegetable greenhouse consumes 10 times as much electricity as an unlit vegetable greenhouse, with essentially all the additional electricity used for lighting”.
Clearly, getting a handle on facility efficiency, including horticultural lighting, is a must-have if individual states and the US as a whole hope to rein in carbon emissions and meet energy reduction goals. This increase in electricity usage comes as states, provinces, and cities across North America are confronting the impacts of climate change and working to reduce – not grow – greenhouse gas (GHG) emissions from the electrical generation sector. In the US, 23 states and the District of Columbia have adopted specific GHG reduction targets. Massachusetts law, for example, requires the state to reduce GHG emissions by 80 percent below 1990 levels by 2050, and California is under a statutory mandate to cut emissions by 40 percent below 1990 levels by 2030.
The good news is there are reliable, third-party lighting and safety standards to help indoor farmers make the leap from old-school lighting to state-of-the-art light-emitting diodes (LEDs) that use a fraction of the electricity and are increasingly effective for growing a variety of crops. Perhaps even better for farmers is the availability of a new industry-wide benchmark for horticultural lighting and a growing list of qualified products that are third-party certified to meet it.
More about the benchmark later – first, it’s useful to walk through the various lighting and safety standards specific to horticultural lighting.
Most lighting fixtures in the North American market go through rigorous inspection by certified labs. The first part of the check is for safety. An official UL safety standard tailored for the unique challenges of the greenhouse environment was recently released (UL 8800, the Standard for Horticultural Lighting Equipment and Systems). This standard and similar safety certifications at other major labs address wiring, environmental conditions, ingress protection, and worker safety related to prolonged photobiological exposure to the eyes and skin. Growers should always ask a lighting fixture manufacturer about safety certification specifically for horticultural environments.
Next on the standards checklist for horticultural lighting fixtures is performance testing. This often happens at the same labs that do safety testing but is designed to verify efficacy, output, spectrum, and other important performance variables. Commercial labs are certified for specific standards so that a test on a fixture is repeatable at any other lab certified to the same standard. This performance testing results in a report summarizing items such as photosynthetic photon flux (PPF), input power (watts), photosynthetic flux efficacy (PPE, measured in μmol/J or micromoles of photosynthetic photons per joule of electrical input power), and spectral content (flux per nanometer (nm) between 400 and 700 nm).
Then, there are flux maintenance standards for LEDs (such as IES LM-80 and IES TM-21) that help make sure the photosynthetic light output of LED products degrades at an acceptable rate to make a grower’s investment worthwhile. The testing and calculation methods that go into these standards were painstakingly developed through a consensus of knowledgeable lighting stakeholders. A key difference between general lighting and plant lighting, however, is how flux maintenance is measured and benchmarked – the bar is significantly higher for plants compared to people since their metabolism and growth are dependent on the light spectrum and amount.
Against this backdrop of standards and testing, lighting and related technologies are quickly evolving. For indoor growers, questions abound – from how long a fixture will last and whether a manufacturer’s claims about efficacy are accurate to the effectiveness of various wavelengths for growing particular crops. The tests described above produce a lot of important information, but it takes an informed reader to analyze and use it to select appropriate horticultural lighting. This is where our organization, the DesignLights Consortium (DLC), comes in. Through our Horticultural Lighting Program, the DLC strives to make the process of vetting lighting products easier, freeing up growers to focus on their core business.
Horticultural lighting specification is a relatively recent addition to the DLC’s work. The organization was founded in the early days of LED lighting to help electric utilities compare different lighting factors and reports to inform their energy efficiency rebate/incentive programs for commercial and industrial electric customers. The DLC began serving as a central clearinghouse for setting energy efficiency and other product performance minimum standards, and for evaluating products against those standards. Then and now, lighting products that pass review qualify for an online qualified products list (QPL) that utilities use to quickly and accurately incentivize high-performing products.
Back to the benchmark mentioned earlier, the goal of the DLC’s new minimum performance standards for horticultural light fixtures is to accelerate the adoption of new energy-saving LED fixtures in controlled agriculture environments. To be on the new DLC Horticultural QPL, an LED fixture must have a PPE of 1.9 micro mol/J, which means it will be at least 10 percent more efficacious than the best non-LED alternative – a 1,000-watt double-ended high-pressure sodium (HPS) fixture. It also must have a Q90 of 36,000 hours (the number of hours before the photon flux output depreciates to 90 percent), and its driver and fan (if included) must have a rated life of at least 50,000 hours.
Importantly, every product is listed online in a searchable, filterable database to help growers and controlled environment agriculture facility designers quickly narrow their options. For example, in a retrofit, a grower might know what PPF is needed from each fixture but might also need to stay within a power budget to avoid rewiring circuits. The DLC’s Horticultural QPL can be filtered to quickly find and compare conforming products.
For utilities and horticultural lighting users alike, trusted, third-party verification holds the same value as it does in other industries. It plays a critical role in ensuring the integrity of a growing array of products – providing assurance that an independent party has done the legwork and is vouching that a fixture can do the job and save electricity.
As the IESO study referenced above noted, horticultural lighting standards developed by the DLC, as well as the American Society of Agricultural and Biological Engineers, “should help to build trust between growers and lighting manufacturers and suppliers regarding performance information as LED technology continues to mature”.
Just over a year since it was unveiled, the DLC’s Horticultural QPL contains 58 products from 18 manufacturers, and additional products are reviewed and added regularly. We’re confident this growing roster of third-party certified products is expanding the options for farmers and providing a greater level of assurance about product performance, leading to quicker and wider adoption of advanced, energy-efficient horticultural lighting technology.
Leora Radetsky (lradetsky@designlights.org) is a Senior Lighting Scientist at the DesignLights Consortium.
Armela Brings Fresh Perspective To Farming In UAE
Armela Farms, an expert in hydroponic farming and the largest producer of water-grown lettuce in the UAE, now has a production capacity of 1.6 million lettuce heads – the equivalent of 330 tonnes per year
March 15, 2020
ABU DHABI
Armela Farms, an expert in hydroponic farming and the largest producer of water-grown lettuce in the UAE, now has a production capacity of 1.6 million lettuce heads – the equivalent of 330 tonnes per year.
As an innovator in the large-scale commercial production, packing and distribution of lettuce and kale, Armela Farms utilizes cutting-edge hydroponic growing technology, on-site storage, packing, and local distribution methods to redefine local food supply, the company said.
By producing natural, eco-friendly, locally grown, farm-fresh, 100% pesticide-free products, Armela Farms continuously reaffirms its commitment to feeding people in cities in a way that is positive for the environment.
The UAE is globally renowned for blending the core values of its agricultural history with the latest innovations and technologies. The Ministry of Climate Change and Environment has prioritized increasing the use of hydroponic farms, cooling and climate control technologies to overcome the historical problems of scarcity of water resources and arable land, soil salinity, difficult environmental conditions, and typically high production costs. Consequently, Armela Farms is striving to perfect the process and become the industry standard in UAE, it said.
After launching the company in August 2016, the Armela team has spent more than two years in Research and Development regarding the best techniques, varieties of produce and optimum climate conditions, before celebrating its first harvest in August 2018. Since then, the team has advanced its process to achieve over 250% of an increase in production and is currently finalizing the opening of a new facility for Q1 2021, which will boast over 3 hectares of fully automated advanced lettuce farm, making the largest commercial hydroponic project in the UAE.
At Armela Farms, produce is delivered immediately upon harvesting, with no or minimum storage or shipping time, to provide customers with produce that is fresher, tastier and more nutritious, while lasting longer. As the topic of food security becomes more prevalent across the GCC, these fantastic new technologies are going to make access to affordable and nutritious food easier for everyone.
Avir Shah, CEO and co-founder of Armela Farms, states: “Our mission is to sell hydroponic produce that is of high quality and high nutritional value, to maximize consumer benefits towards healthy living in the United Arab Emirates.”
Rachana Shah, director and co-founder at Armela Farms, adds: “Most people maybe don’t realize is that locally produced harvest, and, in particular, commercial hydroponics farming, provide not only better quality products, but also a cheaper price tag to benefit the customer, be it, retailers or consumers.” -
TradeArabia News Service
Empire Partners With Infarm To Bring Innovative And Sustainable In-Store Farms To Select Sobeys, Safeway And Thrifty Foods Stores
"Our partnership with Empire builds upon our vision to grow a resilient ecosystem that can help feed people living in cities around the world by 2050, while improving the environmental footprint of our food," said Erez Galonska , co-founder and CEO of Infarm
CNW Group March 9, 2020
National partnership to deliver fresh farmed and harvested in-store produce
STELLARTON, NS, March 9, 2020,/CNW/ - Empire's family of brands is partnering with Infarm, one of the world's most advanced and fastest-growing in-store farming platforms, to grow and harvest a range of fresh produce in select Sobeys, Safeway and Thrifty Foods stores across Canada. Each vertical farming unit is a stand-alone ecosystem, enabled by machine learning and AI technology, that creates the optimum environment required for plants to flourish.
"Our goal at Empire is to be the fastest-growing and most innovative retailer in Canada. As we strive to achieve that goal, we continuously seek out first-to-market opportunities," said Niluka Kottegoda, Vice President Customer Experience, Sobeys Inc. "Our partnership with Infarm is unique in Canada and offers our customers a world-leading urban farming solution. The products we will offer in-store are unique to customers in urban communities. We're excited to test and learn with our customers along the way."
Launching this Spring, the first fresh produce harvests will include a range of herbs at two Safeway stores in Vancouver, 8475 Granville Street and 2733 West Broadway. Empire will place farms in stores across seven cities in Canada, ( Calgary, Edmonton, Halifax, Toronto, Vancouver, Victoria, Winnipeg ) growing millions of hyper-local plants for our customers.
"Our partnership with Empire builds upon our vision to grow a resilient ecosystem that can help feed people living in cities around the world by 2050 while improving the environmental footprint of our food," said Erez Galonska, co-founder and CEO of Infarm. "For example, through vertical farming, we can introduce plants to markets that were previously unavailable because they were too delicate to be transported. We're proud to partner with Empire to share the Infarm revolution with Canadians."
The in-store farms produce fresh, nutritious and flavourful produce all year round without the use of chemical pesticides. The vertical farms use 95 percent less water, 90 percent less transportation and 75 percent less fertilizer than industrial agriculture.
How it works:
Infarm has developed the world's most advanced, sustainable, easily scalable and rapidly deployable modular farms.
Each in-store farm has a controlled energy-friendly environment designed to bring out the natural flavour and properties of each plant.
The plants are all grown in-store, dramatically reducing carbon emissions that result from transportation.
The individual farms are connected and remotely controlled from a central farming platform that gathers up-to-the-minute information about the growth of each plant and learns, adjusts and improves the growing conditions.
About Empire
Empire Company Limited (EMP-A.TO) is a Canadian company headquartered in Stellarton, Nova Scotia . Empire's key businesses are food retailing, through wholly-owned subsidiary Sobeys Inc., and related real estate. With approximately $25.6 billion in annualized sales and $13.8 billion in assets, Empire and its subsidiaries, franchisees, and affiliates employ approximately 123,000 people.
About InFarm
Founded in 2013 by Osnat Michaeli and the brothers Erez and Guy Galonska, Infarm combines highly efficient vertical farms with IoT technologies and Machine Learning, to offer an alternative food system that is resilient, transparent, and affordable. The company distributes its smart modular farms throughout the urban environment to grow fresh produce for the city's inhabitants. With cutting edge R&D, patented technologies, and a leading multi-disciplinary team, Infarm was founded on a visionary mission: helping cities become self-sufficient in their food production while significantly improving the safety, quality, and environmental footprint of our food. Infarm currently operates across Denmark, France, Germany, Luxembourg, the United Kingdom, the United States and Switzerland where it has deployed more than 500 farms in stores and distribution centres.
Infarm (CNW Group/Empire Company Limited)
SOURCE Empire Company Limited
Freight Farms Announces New Horticultural Funding From Ospraie Ag Science
A Series B venture round of $15 million will allow Freight Farms to invest in plant science, add features to its software control platforms, and expand the customer base for its vertical farms housed in shipping containers
Mar 2nd, 2020
A Series B venture round of $15 million will allow Freight Farms to invest in plant science, add features to its software control platforms, and expand the customer base for its vertical farms housed in shipping containers.
Vertical-farm supplier Freight Farms has received $15M in Series B funding from investment first Ospraie Ag Science for its all-in-one, shipping-container-based agriculture model. (Photo credit: Image courtesy of Freight Farms.)
Shipping-container-based, vertical-farm manufacturer Freight Farms has announced that it received $15 million in Series B venture funding from investment firm Ospraie Ag Science. Freight Farms will use the investment to further optimize its Farmhand software platform, invest in plant science, and expand the customer base for its LED-lit Greenery container farms.
Freight Farms originally branded its container farms The Leafy Green Machine but has since simplified the product name to The Greenery. A Greenery farm includes everything a grower needs to launch a hydroponic farm all integrated into a shipping container. The outfitted Greenery container includes LED lighting, plumbing for nutrient supply, climate, and environmental control, and the Farmhand software to automate the operation of the farm.
The idea of a shipping container for a vertical farm is not a new one. For example, we covered a Dallas grocery store that uses a shipping-container farm to grow some produce right outside the store’s back door. And we covered a Los Angeles area farm using shipping containers right in the downtown metropolitan area back in 2016.
Freight Farms, however, brings unique aspects to its business both in the science behind Greenery and in the company’s business model. Taking the business model first, Freight Farms is specifically in the business of selling turnkey farms. Some other players have vacillated between selling technology and operating as growers.
The configuration of the Freight Farms product is also unique. When we first covered vertical farming back in 2016, the term was primarily utilized to describe growing operations where horizontal trays of plants were stacked in layers vertically to more fully utilize a space, especially for crops such as leafy greens and herbs where there is not much space needed between layers and where LEDs that don’t radiate heat can be placed in close proximity to the plant canopy.
We have since seen other concepts. Plenty, for example, is based in California’s Silicon Valley Area, has received more than 200 million in funding from well-known investors such as Amazon’s Jeff Bezos, and utilizes a system where plants are placed horizontally into the growing structure but run continuously in a vertical row from floor to ceiling.
Freight Farms partitions its systems in the close confines of the shipping container. There is a dedicated area where horizontal racks are used in the initial stages of sprouting. But later plants are transplanted into a vertical row structure where nutrients can drip from the top of each vertical row of plants and unused nutrient is recaptured at the bottom of each row.
Freight Farms said its 328-ft2 container can produce equivalent vegetables to a two-acre outdoor plot. And the container farm uses less than five gallons of water per day. For Freight Farms, the mission is solving the looming issue of feeding a growing global population. “With the Greenery and Farmhand, we’ve created an infrastructure that lowers the barrier of entry into food production, an industry that’s historically been difficult to get into,” said Jon Friedman, Freight Farms COO. “With this platform, we’re also able to harness and build upon a wider set of technologies including cloud IoT, automation, and machine learning, while enabling new developments in plant science for future generations.”
And make no mistake that controlled environment agriculture farming is becoming big business. We recently ran an article that discussed the investment capital coming into the market. Clearly, Ospraie sees an opportunity in the container concept. Freight Farms says it has sold farms into 44 states and 25 countries.
“Freight Farms has redefined vertical farming and made decentralizing the food system something that’s possible and meaningful right now, not in the future of food,” said Jason Mraz, president of Ospraie Ag Science. “Full traceability, high nutrition without herbicides and pesticides, year-round sourcing – these are elements that should be inherent to food sourcing. Freight Farms’ Greenery makes it possible to meet this burgeoning demand globally for campuses, hospitals, municipal institutions, and corporate businesses, while also enabling small business farmers to meet these demands themselves for their customers.”
2020 GLASE Summit - CANCELLED
GLASE will host its annual Summit in Leamington, Ont. Canada. Participants will discuss the latest GLASE research innovations, the CEA market trends and connect with Canadian greenhouse growers
2020 GLASE Summit
Leamington, Ont. Canada
Best Western Plus Conference Center
March 26 - 27, 2020
GLASE will host its annual Summit in Leamington, Ont. Canada. Participants will discuss the latest GLASE research innovations, the CEA market trends and connect with Canadian greenhouse growers.
Over 60% of Ontario's greenhouses can be found in Leamington/Kingsville area. With the largest concentration of greenhouses in North America (nearly 2,000 acres under cover) Leamington host some of the largest CEA facilities in Canada and US.
To learn more about it please contact GLASE director Erico Mattos at em796@cornell.edu