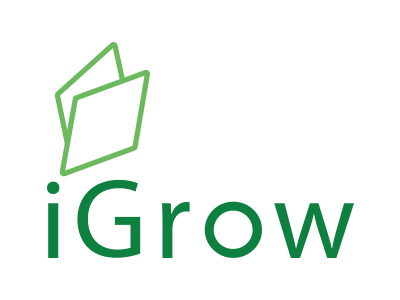
Welcome to iGrow News, Your Source for the World of Indoor Vertical Farming
CubicFarms Leverages Its Expertise In Controlled-Environment Agriculture And Announces Launch of new Control Room System And Sale To Career Field Farmer And Entrepreneur
CubicFarms’ Control Room is assembled inside its proprietary stainless steel, fully insulated growing chamber with the option to customize features such as lighting, automated irrigation and nutrient delivery, and full climate control for temperature, humidity and carbon dioxide levels
VANCOUVER, BC, JUNE 18, 2020 – CubicFarm® Systems Corp. (TSXV:CUB) (“CubicFarms” or the “Company”) is pleased to announce the launch of its new Control Room system for sale to growers looking to grow crops more efficiently by controlling every aspect of the growing environment.
CubicFarms’ Control Room is assembled inside its proprietary stainless steel, fully insulated growing chamber with the option to customize features such as lighting, automated irrigation, and nutrient delivery, and full climate control for temperature, humidity, and carbon dioxide levels. The system has a variety of sensors available, all of which can be remotely monitored and controlled.
Photo: Inside a CubicFarms Control Room, complete with LED light fixtures, an automated heating, cooling and ventilation system, and wired environmental controls.
The Control Room enables growers to have complete control over the growing environment that is so crucial for high yields and quality – a capability especially well suited for research and development purposes. The temperature, humidity, lighting, and airflow can be properly calibrated to suit crop requirements.
“We are pleased to launch a new product that allows growers to conduct their own growing trials inside a controlled-environment chamber. We’ve had numerous inquiries for this kind of solution and are pleased to be able to support our customers with this technology. We see good market potential for this solution that helps growers fine-tune the optimal environmental parameters for growing crops indoors,” commented CubicFarms CEO Dave Dinesen.
“We are confident that once growers experience the consistency and quality of yields achieved in the Control Room, they will seek to automate growing inside our Fresh Produce system, which is essentially the Control Room plus motorized rows of trays containing crops that follow a patented path inside the chamber to ensure all sides of the crop are evenly bathed in light to maximize growth.”
CubicFarms control rooms can be placed inside an existing warehouse or greenhouse to serve as controlled-environment growing chambers to test and develop crop varieties. They can also be placed outside in many environments. It is well-suited for many types of growers, including:
Photo: CubicFarms control rooms being installed at the customer’s site.
Greenhouse growers and vertical farmers who have a need to hold larger plants in an environment separate from their existing facility. As an example, a hemp grower who would like to hold the mother plant used for cloning in an ideal environment;
Growers in the floral or nursery industry who need to hold plants or bulbs at a specific temperature or humidity; and
Growers undertaking research activities that require different environmental controls than their typical growing space.
CubicFarms announces first sale and installation of control rooms to BC-based field farmer and food entrepreneur
The Company is pleased to announce that it has sold three control rooms to a customer in British Columbia. The control rooms were recently installed at the customer’s site. The customer, an experienced field farmer, and consumer packaged foods expert, plans to engage in controlled-environment growing trials of various crops that have traditionally been grown in the field. Mr. Dinesen added: “I’m very excited that CubicFarms can support our customers by leveraging technology we already have, but in this unique way. Our customers never cease to amaze me in how creative and inspiring they are when looking to grow their businesses.”
Neither the TSX Venture Exchange nor it’s Regulation Services Provider (as that term is defined in the policies of the TSX Venture Exchange) accepts responsibility for the adequacy or accuracy of this release.
About CubicFarm® Systems Corp.
CubicFarm Systems Corp. (“CubicFarms”) is a technology company that is developing and deploying technology to feed a changing world. Its proprietary technologies enable growers around the world to produce high-quality, predictable crop yields. CubicFarms has two distinct technologies that address two distinct markets. The first technology is its patented CubicFarm™ System, which contains patented technology for growing leafy greens and other crops. Using its unique, undulating-path growing system, the Company addresses the main challenges within the indoor farming industry by significantly reducing the need for physical labor and energy, and maximizing yield per cubic foot. CubicFarms leverages its patented technology by operating its own R&D facility in Pitt Meadows, British Columbia, selling the System to growers, licensing its technology and providing vertical farming expertise to its customers.
The second technology is CubicFarms’ HydroGreen System for growing nutritious livestock feed. This system utilizes a unique process to sprout grains, such as barley and wheat, in a controlled environment with minimal use of land, labor, and water. The HydroGreen System is fully automated and performs all growing functions including seeding, watering, lighting, harvesting, and re-seeding – all with the push of a button – to deliver nutritious livestock feed without the typical investment in fertilizer, chemicals, fuel, field equipment, and transportation. The HydroGreen System not only provides superior nutritious feed to benefit the animal but also enables significant environmental benefits to the farm.
Cautionary statement on forward-looking information
Certain statements in this release constitute "forward-looking statements" or "forward-looking information" within the meaning of applicable securities laws, including, without limitation, statements with respect to the market potential of the Control Room system and system capabilities. Such statements involve known and unknown risks, uncertainties, and other factors including evolving market conditions, which may cause the actual results, performance, or achievements of CubicFarm Systems Corp., or industry results, to be materially different from any future results, performance, or achievements expressed or implied by such forward-looking statements or information including the Company obtaining the approval of the Offering from the TSX Venture Exchange. Such statements can be identified by the use of words such as "may", "would", "could", "will", "intend", "expect", "believe", "plan", "anticipate", "estimate", "scheduled", "forecast", "predict", and other similar terminology, or state that certain actions, events, or results "may", "could", "would", "might", or "will" be taken, occur, or be achieved.
These statements reflect the Company's current expectations regarding future events, performance, and results and speak only as of the date of this news release. Consequently, there can be no assurances that such statements will prove to be accurate and actual results and future events could differ materially from those anticipated in such statements. Except as required by securities disclosure laws and regulations applicable to the Company, the Company undertakes no obligation to update these forward-looking statements if the Company's expectations regarding future events, performance, or results change.
Kimberly Lim
VP, Corporate Communications & Investor Relations
Mobile: 236.858.6491
Office: 1.888.280.9076
Email: kimberly@cubicfarms.com
From Macau's Casinos To a Kallang Farm: The Gaming Industry Professional Who Now Grows Baby Spinach
His indoor hydroponics farm, Artisan Green, specializes in growing baby spinach. The 3,200 sq ft farm is located in Kallang in central Singapore, with its entire set-up costing Mr. Poh slightly under a million-dollar
Mr Ray Poh founded Artisan Green in 2018. (Photo: Artisan Green)
23 May 2020
SINGAPORE: For five years, Mr. Ray Poh mingled with high rollers in Macau, which has been dubbed the gambling capital of the world.
It was a lucrative career filled with opportunities to travel frequently. But in 2015, Mr. Poh gave all of that up.
“I did think about making it a career,” said Mr. Poh, who had studied in Australia since the age of 12. “But I think at the end of the five years, I realized that I’d been away for most of my life from my mum, who was back in Singapore. That was one of the main factors (that led me to leave).”
It took him a year to completely leave the industry, but by 2016, Mr. Poh had decided on a very different career path: Urban farming.
His indoor hydroponics farm, Artisan Green, specializes in growing baby spinach. The 3,200 sq ft farm is located in Kallang in central Singapore, with its entire set-up costing Mr. Poh slightly under a million dollars.
Although Artisan Green was founded in 2018, a year before Singapore announced its ’30 by 30’ goal to produce 30 percent of Singapore’s nutritional needs locally by 2030, it is part of an increasing wave of indoor farms looking to use sustainable methods to grow to produce locally.
In April, the Ministry of Environment and Water Resources announced a S$30 million 30x30 Express grant for the agri-food industry to speed up the production of commonly consumed food items like eggs, vegetables, and fish.
READ: COVID-19 pandemic highlights importance of strengthening Singapore's food security, say experts
READ: Interest in urban farming sprouts amid COVID-19 outbreak
A FAMILY BUSINESS
While casino gaming was never something he had been interested in, a chat with his mother post-graduation was enough to convince Mr. Poh to enter the family business.
“I was thinking of entering the banking industry, but the thought of being behind a desk didn’t appeal to me much. So we were having a discussion and she said, why don’t you give this a try. Your father needs some help in the company, perhaps you can go out and see what you can do,” he said.
Initially, he did business development with his father’s manufacturing company, developing products such as slot machines. As he became more involved in product design, so his interest in the industry grew, he said.
The exterior of Artisan Green. (Photo: Artisan Green)
After a year, his boss convinced him that he ought to head to Macau to advance his understanding of the industry, which turned out to be a fruitful experience.
“I think at the very start when I first went there, I didn’t know anything or anyone in Macau, so the main thing I did was to network around. I met a lot of good people, and at the same time, obviously, you meet people that are not so good.
“What I did was learn what to do and what not to do. It was a very good experience,” he said.
Being new to the industry also meant that people did not take him seriously. Mr. Poh had to work hard to brush up his knowledge on the casino gaming industry by doing research, reading industry magazines, and making friends who could teach him – skills which would later put him in good stead to enter a completely different industry.
CONTRIBUTING TO SUSTAINABILITY
When he told his family that he wanted to move out of casino gaming, they were supportive of his decision, said Mr. Poh.
“I think from the business aspect of things, it was more of a diversification. I’ve always thought that agriculture is something that’s evergreen. People will always need to eat. Whereas casino gaming is something like the entertainment sector,” he said, adding that he wanted to “do something more to contribute to the sustainability segment”.
“At first I thought about doing landscaping, but I didn’t really want to go back to study more. So I thought farming might be an easy way in.
“But I was very wrong about how easy it was. After doing the research, I quite naively thought that I would do this for about a year and network around, meet more people, and then move into landscaping. But it just took me down towards farming all the way,” he said.
Artisan Green has 120 growing racks, with six layers in each rack. (Photo: Artisan Green)
Just like when he started out in Macau, Mr. Poh had “zero knowledge” of the agriculture sector, and people also did not take him seriously when he started.
“I knew I had to build up my knowledge from ground-up again,” he said.
He attended courses and conferences, forged relationships with people in the industry, watched Youtube videos, and built prototypes.
Building the prototypes gave him the confidence to decide that he wanted to build his entire farm from scratch. After leasing space from Mapletree and procuring all his supplies and tools, Mr. Poh set himself to work as the main contractor of his own farm.
Save for the electrical wiring and the plumbing, Mr. Poh put the entire 3,200 sq ft farm together with his own hands over the course of three months.
“When I was building the farm, I was there from 9 am to 10 pm. I’d only eat one meal a day during the building because I didn’t want to waste time. So I would only eat one really huge brunch and then just work the entire day in the farm,” he said.
It was challenging work, as he did all the sawing, drilling, and lifting and even suffered a back injury from hunching over and moving around too much. While he admitted that he should have gotten a partner to build the farm with him in hindsight, Mr. Poh said that the process was necessary.
“Now that I’ve gone through this, I can safely say that I know pretty much everything in the farm. I’ve sourced for every single piece of equipment by myself which makes it even easier for me to understand other people’s systems.
“I can look at other people’s systems, I can derive how it’s built, how it’s done, and that experience isn’t something you can get from reading books or watching tutorials online,” he said.
WHAT KEEPS HIM GOING
Even with his extensive research, his lack of science and engineering knowledge posed challenges for him.
“I didn’t really do chemistry, so that was kind of hard to pick up, and I knew that I needed to get the foundational knowledge of farming in terms of the science aspect to be able to do well in it,” he said, as science was an integral part of farming.
He also had to engage professional engineers to help him ensure the farm was built well.
This was in addition to the time he had to sacrifice in those early months, when he was just starting out, with many weekends spent at the farm just to make sure that everything was running well.
And even with the farm up and running, the team also ran into other problems, such as nutrient deficiency issues for their spinach.
Artisan Green's team packing spinaches. (Photo: Artisan Green)
But what kept Mr. Poh going was his desire to “see the final product”.
“And we’re quite proud of what we’ve done with this current farm. We’ve had people from the industry – from the US, Europe – coming to visit us and they were quite impressed with the farm we’ve built. They told that it was comparable to some of the more advanced overseas farms as well.
“Hearing that gives us the motivation and a stronger belief in what we do.”
FUTURE PLANS
In the short-term, Artisan Green hopes to scale up its production from its current 30kg to 250kg of vegetables per week.
Although Malaysia’s Movement Control Order has temporarily disrupted the farm’s supply of equipment which they require to scale up, Mr. Poh is hoping to at least double the farm’s output by the end of the “circuit breaker” period and to hit 100kg per week by the end of the quarter.
In the longer-term, Mr. Poh is also looking to build his second farm – this time bigger, and with a wider variety of crops. But rather than growing specialty crops, Mr. Poh said he now wants to start growing crops such as Chinese cabbage, which he says there is a bigger demand for in Singapore.
“The next farm will have to be more automated, from end-to-end. That’s what our future goal is: to build the second farm and also to grow different crops, not just baby spinach, and work towards something where we can fulfill the whole ’30 by 30’ vision by the Government,” he said.
Source: CNA/cc
Tagged Topics
10 Crops You Can Grow At Home: Hydroponic Growing
Hydroponic growing is a method of growing plants in nutrient enriched water – just water and nutrients. There’s no soil involved; instead, nutrition is added directly to the water, to make up for what the plants would normally receive from the soil
Growing your own fruit and vegetables at home may be something you’ve considered before, but if you’ve hesitated because of the space the plants will take up or the mess it will make in your home, the good news is that neither of these things needs to stop you. Whether you have no floor space to spare, can’t grow outdoors, or simply don’t consider yourself green-fingered, it’s never been easier to grow your own crops at home.
What is Hydroponic Growing?
Hydroponic growing is a method of growing plants in nutrient-enriched water – just water and nutrients. There’s no soil involved; instead, nutrition is added directly to the water, to make up for what the plants would normally receive from the soil. Many plants will root and grow in something as simple as a glass jar, but you can make your hydroponic system as big or as little as you want.
What can I grow?
You can grow a massive variety of vegetables hydroponically so it really depends on what your favorites are.
Here’s a list of ten common fruit and veggies to get you started:
Lettuce
Probably the most common vegetable to be hydroponically grown, it’s not unusual to find people placing the head of a used lettuce into a glass or jar filled with water and leaving it to regrow. It really is that simple! You can harvest the lettuce as it grows, meaning you can have crispy lettuce leaves to add to your salads or sandwiches without affecting later harvests.
Spinach
As with many leafy vegetables, spinach also grows well in hydroponic systems. It is a cool plant, meaning it does not require much light and likes cool to warm temperatures so storing it near a window is the best option to ensure your spinach flourishes. You can harvest spinach all at once, or tear off some leaves as and when you need it.
Tomatoes
Whether you think of the tomato as a fruit or a vegetable, you can definitely grow it without soil. Many types of tomatoes take well to hydroponic systems, including traditional and cherry tomatoes. Whichever variety you grow, tomatoes require a lot of light. The good news is that, as they are a vine and can be trained to grow upwards, they only require a small amount of ground space.
Cucumber
Given enough space and support, cucumbers will grow abundantly in a hydroponic system – which is no surprise given that it is a water-loving fruit. Cucumber vines grow vertically, so it’s important to ensure they have some sort of structure or support to hold them up.
Peppers
Similar to tomatoes, peppers require lots of light and warm conditions. There are a few varieties or pepper that take well to hydroponic growing, but some of the best are Jalapeno, Habanero, Nairobi, and Fellini.
Celery
Celery is a great way to snack healthy, as well as being a great addition to soups, stir-fries, and stews. The fastest way to grow celery at home is to use the base of the last bunch you had from the grocery store. Simply place the celery on a plate of room temperature water until you see new growth from the roots, and then you can transplant it into your hydro system – even if that just means placing it into a tall glass which can support the celery as it grows.
Radishes
Radishes are one of the easiest vegetables to grow, thriving in cool conditions, and not requiring much light. They are usually harvested within a month, meaning you can have multiple harvests in a year. That being said, if radishes are kept constantly and persistently soaked, rot can become an issue, so make sure it’s the roots that are kept in water, rather than the radish itself.
Spring Onions
When it comes to spring onions, you can use the ends of a shop-bought onion and place it in a glass to allow for regrowth, or you can start them from bulbs. The bulbs and roots will sit down in the water, whilst the leafy green stems will rise upward: this makes it possible to grow a lot in a small amount of space.
Kale
Kale is another leaf that is easy to grow in a hydroponic system; in fact, it has been farmed hydroponically for years. The crop grows relatively quickly, and will happily regrow if you only harvest a couple of leaves at a time.
Strawberries
As strawberries enjoy wet conditions, they actually thrive in a hydroponic system; they provide bigger fruits than when grown in soil and can provide harvest all year round. Using a hydroponic system also means that strawberry plant containers can be stacked vertically, saving you floor space.
Hydroponic growing is becoming more popular due to the fact that in can be done from anywhere and doesn’t need to take up a lot of space. It’s a great way to get the satisfaction of growing your own crops, without needing a large gardening space.
We at the Nick Greens Grow Team understand that not everyone has the space to grow their own crops, but the joy of hydroponics is the simplicity of the process. Want to learn more about growing plants in water systems? Stay up-to-date with our weekly blog articles, and subscribe to our YouTube channel to learn more.
#hydroponics #hydroponicsystem #hydroponicsfarm #hydroponicsvegetables #hydroponicsstarwberry #hydroponicscelery #hydroponicsradish #hydroponicskale #hydroponicsgrowing #hydroponicsfarming #growfoodwithhydroponics #growingfoodathome #hydroponicgrowing #hydroponicfarming #hydroponicfarm #hydroponicsfarm #growathome #growfoodathome
The Race Is on To Grow Crops In The Sea And Feed Millions of People
With the quality of arable land declining and seawater encroaching on fertile cropland, researchers are trying to find a way to make crops grow in seawater
With the quality of arable land declining and seawater encroaching on fertile cropland, researchers are trying to find a way to make crops grow in seawater
17 June 2020
Chen Hanquan / WIRED
In December 2015, as representatives from United Nations member states were finalizing what would become the Paris Agreement on climate change, Duncan Cameron stood before a crowd of delegates and warned them about an environmental catastrophe happening right beneath their feet.
A soil biologist and co-director of the University of Sheffield’s Institute for Sustainable Food, Cameron had long known that the amount of farmland capable of growing nutrient-rich crops was shrinking, but he didn’t know how fast. For the previous year, Cameron’s team had analyzed the scattershot data available on arable land loss, and what they found was disturbing: in the past four decades, the world lost up to one-third of its arable land to soil degradation and resulting erosion. Without alternatives, already fragile agricultural systems are on the verge of collapse, raising the prospect of a world filled with farms that can’t grow enough food.“
It’s quite a terrifying amount,” Cameron says. “We hear that we can solve a lot of these problems in terms of food insecurity by wasting less and getting more efficient, but that isn't going to give us everything we need.” Now, an emerging group of startups and researchers are convinced that answers to the impending food crisis may not lie on land at all – instead they’re looking to the ocean and to feed future populations with crops grown on floating farms and fed by seawater.
These ambitious initiatives target a thorny mess of environmental and humanitarian issues — freshwater and land scarcity, global hunger, crop security, and agriculture’s enormous carbon footprint amongst others — but the scientific and logistical challenges they face are enormous. In a field where there are few easy answers, one problem looms above all others: what do we do about all the salt?
Soil scientists and farmers have waged war against salt for decades. As sea levels rise, salt levels are creeping up in the rivers and underground aquifers that irrigate fields – particularly those low-lying areas close to vast river deltas. Across the world, farmland is drying out which raises salt levels and interferes with nutrient uptake and damages tissues. Excessive salt causes massive global crop loss — an estimated £21.7 billion each year — and that's expected to increase as factors like sea level rise and higher-intensity weather events driven by climate change push ocean water further into farmland, hitting the poorest coastal communities hardest.
Once there, salt requires significant resources to remove from soil — the most common methods involve large amounts of freshwater, which is already scarce for an estimated four billion people worldwide — sending researchers on a long-running race to find staple crops that can grow despite constantly increasing salinity. Several countries including China, India, the Netherlands, and the United Arab Emirates have developed crop varieties that can withstand some soil salinity, but the real white whale is a staple crop that can thrive regardless of how much seawater is thrown at it.
“In principle, it could be done, but it's complicated,” says Exequiel Ezcurra, a plant ecologist at the University of California, Riverside who studies desert and ocean ecosystems. Ezcurra says that creating seawater-tolerant crops would require at least one, and possibly both, of the basic biological mechanisms plants like black mangroves have adapted to survive in salty waters. One mechanism is freshwater filtration in the roots, which for staple crops would require fundamentally altering the root’s dermal tissue to keep salt out. The other is specialised glands in the leaves that excrete salt as the plant pumps seawater throughout its system.
Changing a staple crop to have either mechanism is a challenge so big, many researchers aim for far more modest gains in salt tolerance and aren’t yet gunning for crops that grow in straight seawater. Plant breeders have been working on salt-resistant crops for decades but in rice – a crop notoriously sensitive to salinity – even the most salt-resistant varieties can’t cope with anything like the saltiness of seawater. “I'm not saying that nobody will be able to do it. Probably somebody will at some point,” Ezcurra says. “I simply have never seen a patent or anybody being able to do that” now.
Luke Young and Rory Hornby filed for a provisional patent in February for a technology they believe will break the seawater tolerance barrier. Young and Hornby are the cofounders of Agrisea, a Canadian startup that’s working to develop gene-edited salt-tolerant crops with the goal of soon growing them in floating farms placed in sea-flooded plains or anchored directly in the ocean.
Agrisea’s proposed method involves first isolating stem cells from crops like rice, then using CRISPR gene editing technology to insert a DNA sequence specialised to the plant. The sequence targets one of eight different genes, each chosen because the only place in nature where all eight are “switched on” is in plants that have naturally adapted saltwater tolerance. The sequence alters how the gene expresses, then stem cells are grown into a full plant that produces its own seeds armed with the newly edited gene. Follow the same process for editing the remaining seven genes, and the Agrisea team says you’ll have a plant that can grow in the salty sea without fertiliser, freshwater, or pesticides.
Many researchers have edited single genes for salt tolerance, but editing a gene network is an approach Young and Hornby say are unique to Agrisea. But they’re not at the finish line yet. Thus far, Young and Hornby are working to grow rice plants in water one-third the salinity of seawater and plan to have small farms floating off the shores of Kenya and Grand Bahama Island by the end of the year. Young says that he’s confident the process will work because similar strategies have been used in the past to gene edit plants for other traits and “because I'm not proving something, I'm copying something. I'm copying what nature has already been able to do.
”Julia Bailey-Serres, director of the Center for Plant Cell Biology at the University of California, Riverside, studies crop resilience and the molecular physiology of rice. She says that researchers routinely edit plants to knock out a gene’s function, but editing in a way that changes specific amino acids, which likely would be required for growing crops in the ocean, has only been done by a few researchers worldwide and not yet for the purposes of salt tolerance. That more granular type of editing will become more feasible in the future, she says, ”but I don't know if that’s going to be in two years or 10 years.”Bailey-Serres adds that she would be excited to see Agrisea succeed and that any tolerance increases beyond one-third ocean salinity would be a huge win in places like Vietnam and Bangladesh where rice paddies are bombarded with seawater.
Agrisea’s approach to arable land scarcity relies on cracking the salt tolerance problem, but other teams are opting to sidestep the issue entirely. Floating farms that reduce demand for arable land have long been key to survival in many non-Western nations. These crops thrive in freshwater bodies — like Myanmar’s Inle Lake, which locals have relied on for food possibly since as early as the nineteenth century — in buoyant beds that bob along the surface as monsoons and floods sweep through. Floating farms have also gained interest in Western cities. Over the last few years, research groups and architectural firms in the UK, Spain, and Italy amongst others have produced designs for floating vertical farms and greenhouses that suck up seawater from the outside and desalinate it to nourish hydroponic crops grown inside.
These projects push crops out into the ocean, but Yanik Nyberg’s strategy is to bring the ocean in. Instead of making new space for crops offshore, Nyberg’s Scotland-based company Seawater Solutions takes degraded coastal farmland, seeds it with naturally salt-tolerant herbs like samphire and sea blite, then floods the area by removing seawalls or pumping in water from the ocean to create an artificial salt marsh. In this new wetland ecosystem, crops grow without fertilisers, pesticides, or freshwater. They also hold soil in place, preventing erosion, and feed on nitrates and carbon, both of which over-accumulate in waters near human populations due to factors like agricultural runoff and CO2 emissions. A solar-powered irrigation system recycles the remediated water back to its original source.
WEBINAR: Agritecture And Indoor Ag-Conversations To Present "Megatrends In Indoor Farming" - June 24 @ 2 PM EST
Indoor Ag-Con, LLC is pleased to announce “MegaTrends In Indoor Farming,” the latest topic to join its new Indoor Ag-Conversations monthly free webinar series
“MEGATRENDS IN INDOOR FARMING’ WEBINAR “
ON JUNE 24, 2020 @ 2 PM EST
LAS VEGAS (June 9, 2020) – Indoor Ag-Con, LLC is pleased to announce “MegaTrends In Indoor Farming,” the latest topic to join its new Indoor Ag-Conversations monthly free webinar series. Hosted by Agritecture Consulting, this panel discussion will cover megatrends in food, agtech, and vertical farming. Scheduled for Wednesday, June 24 at 2 pm EST, the program will be moderated by Agritecture Founder & CEO, Henry Gordon-Smith, and include panelist Menachem Katz, former head of WeWork Food Labs. Additional panelists to be announced soon.
“From Covid-19 to climate change to food security concerns, there are a number of factors accelerating megatrends shaping the indoor agriculture marketplace,” said Nancy Hallberg, co-owner, Indoor Ag-Con. “We’re excited to have Henry Gordon-Smith and his expert panel share their insights into these key trends and the opportunities they can offer for our growers, suppliers, and other industry members.”
Indoor Ag-Con LLC, producers of the premier event for the indoor vertical farming industry, created the new Indoor Ag-Conversations series to share content originally planned for its May 2020 in-person annual conference that was postponed due to the Covid-19 pandemic. During the 60-minute webinar, Gordon-Smith and his panelists will take a deep dive into some of the megatrends impacting indoor vertical farming, including plant-based proteins and other consumer-driven food demands, automation/artificial intelligence, urban farming/local food, food security and more. Indoor Ag-Conversation webinars are free to industry members. To register for the upcoming June 24, 2020 session, visit www.indoor.ag/webinar. Indoor Ag-Conversations presenters include:
Moderator Henry Gordon-Smith is a sustainability strategist focused on urban agriculture, water issues, and emerging technologies. His firm, Agritecture Consulting, primarily helps entrepreneurs with vertical farming feasibility studies, recruiting, and systems design. He serves on the advisory board of numerous AgTech startups, including Smallhold and Foodshed.io.; serves on the board of directors for the not-for-profit food access organization Teens for Food Justice in NYC; has spoken on the topic of urban agriculture in 4 continents; and has been interviewed about urban and vertical farming for the WSJ, Futurism, Men’s Health, Bloomberg, The Atlantic, Arabian Business, CNBC, and many more media outlets.
Panelist Menachem Katz has 20 years of food industry experience in roles ranging from operations to technology and logistics to culinary. He started his career as an Executive Chef, first at Artichoke Restaurant in Tel Aviv, and then at 1868, a restaurant chain in Jerusalem that he co-founded. From there he served as Executive Chef for multiple companies; co-founded and led Culinary & Operations at Goodmeal, a delivery startup; led operations and expansion at Kettlebell Kitchen; and most recently, served as Head of WeWork Food Labs.
More details on the upcoming Megatrends session, as well as access to the recording of the June 3 series launch session - "United Fresh Presents Produce Trends & New Business Opportunities For Indoor Growers Emerging From The Covid-19 Pandemic," and other programs joining the new Indoor Ag-Conversations series, can all be found at www.indoor.ag/webinar.
ABOUT INDOOR AG-CON LLC
Founded in 2013, Indoor Ag-Con touches all sectors of the business, covering produce, legal cannabis, hemp, alternate protein, and non-food crops. In December 2018, three event industry professionals – Nancy Hallberg, Kris Sieradzki, and Brian Sullivan – purchased Indoor Ag-Con LLC, setting the stage for further expansion of the events globally. For more information, visit: www.indoor.ag
ABOUT AGRITECTURE
Agritecture is a global urban agriculture consulting firm, whose mission is to empower impact-driven organizations to develop feasible urban farming solutions, turning their business ideas into practical and sustainable realities. Agritecture has completed more than 100 consulting projects in over 20 countries, working with a range of clients including entrepreneurs, real estate developers, educational non-profits, corporate food- & agri-businesses, and city agencies. Agritecture’s popular blog and social media presence have a total digital following of 100,000. www.agritecture.com
Indoor Ag-Con, 950 Scales Road, Building #200, Suwanee, GA 30024, United States
Creating A Business Based on Hydroponics And Agricultural Technology
Fork Farms is a leader in hydroponics and agricultural technology-based here in the Fox Cities. Listen to Alex Tynik, founder and president explain how they have developed the products and organization needed to enable individuals and organizations to produce low cost, high-quality food
June 14, 2020
PLAY EPISODE
Featured Guest:
Alex Tyink, Fork Farms
101 W Edison Ave
Suite 224
Appleton, WI 54915
Email: info@forkfarms.com
Direct: 920.515.0730
Toll-Free: 877.886.7736
BizTalk Air Date: June 6, 2020
Fork Farms is a leader in hydroponics and agricultural technology-based here in the Fox Cities. Listen to Alex Tynik, founder and president explain how they have developed the products and organization needed to enable individuals and organizations to produce low cost, high-quality food.
Fork Farms has built a national and international reputation in just five years and theirs is a story that will inspire others thinking about creating a social enterprise balancing business results and improving society.
Business PlanningFinanceMotivationSales & MarketingStrategic Management
"After Summing Up All Production Costs, The Plants Cost Less Than 0.25$, Which is 2% of The Total Sum of Normal Farmers"
The growing process is fully automated, except for harvesting. “We purposely chose moveable walls, so when our containers are installed, people with disabilities can participate during projects.”
Cost-Effective Growing
We’re working with high efficiency LED lights and cooling systems, which basically are our only costs. Therefore, our produce is way cheaper than with traditional farming. ”After summing up all production costs, the plants cost less than 0.25$, which is 2% of the total sum of normal farmers”, Tony English, Founder and Visionary of FarmBox Foods says. If a grower spends 2 cents more per plant, they can deliver organic produce with FarmBox Foods growing containers. The seeding process starts in organic fiber where organic nutrients are used. Next to that you can use filtered water and cultivation without pests. But it’s all up to the grower what plants they choose.”
The seedling table
Self-Sanitizing Farm
The growing process is fully automated, except for harvesting. “We purposely chose moveable walls, so when our containers are installed, people with disabilities can participate during projects.” The company uses peat moss plugs for the seedling table, alongside an ebb and flow system. “When the plants are two inches high, they’re transferred to the grow walls. When one batch is harvested, a new one goes in immediately to maintain a constant production cycle,” English adds. These containers are maintenance-friendly and self-sanitizing. The grow towers are cleaned with ozone, a bacteria and disease killing gas. “It works better than bleach or other commonly used sanitizing agents.” When watering the plants, ozone is added into the nutrient solution, allowing the grow walls to clean themselves.
The moveable grow walls
New Designs
The system development took about a year to complete; during this time, FarmBox Foods designed a grow tube which solved all the problems that they came across during the R&D phase. The team is currently testing and researching new crops and designs. The R&D prototype has been sold and is now in use in Georgia. “We build our containers one at a time, and when we think of doing something better, we apply it. For now, we have three containers placed, but we’re looking into manufacturers around the States to speed up the production process.”
The Self-Sanitizing Farm
“We were actually going to build containers for homeless people for the major US cities, as there’s a big shortage of fresh produce, especially for those who won’t have access to them. We bought land and designed a hydro system. When they told us it would take up to 5 years before they would even look at our proposal. It would have been insane to wait for that approval. Well, we had a great hydro system thus why not move them inside a shipping container that we can provide to homeless shelters, churches, and anyone who could grow food for the people who need it the most?” The start-up supplies fully-automated containers for vegetable farming in the US.
Increasing Demand
FarmBox noticed an increasing demand as a result of the COVID-19 pandemic. They now have a major hospital chain buying their farms. “We have a system suitable for schools, and at first we were donating them to schools. We are not going to do that anymore as we’re too busy with fulfilling the demand for our containers farms.”
For more information:
FarmBox Foods Tony English, CEO and Founder
tony@farmboxfoods.com
www.farmboxfoods.com
Publication date: Tue 16 Jun 2020
Author: Rebekka Boekhout
© HortiDaily.com
Bowery Farming Debuts New Lettuce Variety
Bowery Farming, per a press release, announced its newest leafy greens launch, Bowery Crispy Leaf Lettuce (Crispy Leaf). A reinvigorated version of iceberg lettuce that is refreshing and simple, Crispy Leaf boasts a bold color and satisfying crunch
Posted by Chris Manning | June 3, 2020 | Produce Grower
Bowery Farming, per a press release, announced its newest leafy greens launch, Bowery Crispy Leaf Lettuce (Crispy Leaf). A reinvigorated version of iceberg lettuce that is refreshing and simple, Crispy Leaf boasts a bold color and satisfying crunch. The much-anticipated product, which goes from harvest to shelf in just a few days, will be available in the produce aisle at over 250 grocery stores and specialty markets in the Tri-State area and Mid-Atlantic region beginning in June 2020. Crispy Leaf will also be available through Bowery’s online partners, including Amazon Fresh, Peapod and Hungryroot.
"With unparalleled flavor and crunch in every bite, we're confident that Crispy Leaf has the potential to disrupt the traditional iceberg market," said Carmela Cugini, EVP of Sales, Bowery Farming. “Crispy Leaf is one of the most in-demand leafy greens from Bowery based on current retailer orders. We've had to ramp up production to meet retail demand,” continued Cugini. “Early feedback from buyers indicates Crispy Leaf is poised to change the way consumers interact with lettuce by introducing a completely new sensory experience to the category."
Crispy Leaf is grown locally at Bowery’s commercial farms in Kearny, New Jersey, and White Marsh, Maryland, and has zero pesticides. The mild and versatile green is the ideal base for salads and grain bowls and serves well as a culinary garnish.
Looking Up: Vertical Farms Fill Produce Supply Chain Lag During Pandemic
The great panic buying of 2020 revealed the time it takes for food to go from farm to shelves. The curtain was pulled back on something the shopper rarely thinks about — supply chain logistics
By Jesse Klein | Green Biz | June 11, 2020
The great panic buying of 2020 revealed the time it takes for food to go from farm to shelves. The curtain was pulled back on something the shopper rarely thinks about — supply chain logistics. As grocery store shelves emptied, the problem wasn’t necessarily lack of food but a drastic shift in demand that caused traditional distribution engines to sputter.
For example, lettuce takes between 30 and 45 days to grow in a field farm. According to a 2001 study by the Leopold Center for Sustainable Agriculture, traditionally grown lettuce travels about 2,000 miles to get to Chicago grocery stores. So by the time prepackaged greens are bought by consumers, that produce can be almost two weeks old. These long lead times caused those empty shelves in March.
Vertical farms have struggled to become a major force in the grocery market. Their products are usually limited to leafy greens, and the high labor costs have made turning a profit challenging for many. But the pandemic clarified their role within a more sustainable food system. Vertical farms, with their hyperlocality and ability to quickly grow new crops, can step in to fill retail shelves when traditional farms falter.
"We are a really critical part of this food supply chain, and we can fill a gap when there is a crisis," said Shireen Santosham, head of strategic initiatives at Plenty, which sells vegetables at 20 locations around the San Francisco Bay area.
Location always has been a core part of the vertical farm appeal and business model. During the pandemic, many have taken advantage of the fact that their growing operations often use abandoned warehouses in urban areas and therefore are much closer to retail stores.
Fifth Season Connection, a vertical farm that leverages robotic technology, operates a 600,000-square-foot vertical farm in the food deserts of Pittsburgh. Its chief category officer, Grant Vandenbussche, called me from inside his delivery truck. He was delivering that day’s produce to grocery stores a mere 24 hours after the greens were picked. His company has seen a 50 percent increase in orders over the past few months, even as its restaurant market has dwindled.
"We have fantastic retail partners that we have really leaned on," he said. "Our partnerships have allowed us to get more onto the shelves and expand our offerings."
The consumer also benefits from the quick turnaround time, especially during the pandemic. According to Vandenbussche, vertical farm greens typically last longer after purchase because they haven’t been out of the dirt for as long as traditional produce. So when every trip to the grocery store feels like a risk, shoppers are looking for products that will last longer than a few days.
According to AeroFarms, its advantage has been the ability to produce baby greens in a third of the time of traditional farms, typically 12 days. AeroFarms operates four vertical farms in New Jersey harvesting almost 2 million pounds of produce a year using aeroponic mist instead of traditional irrigation, resulting in 95 percent less water usage than a traditional farm. According to Marc Oshima, co-founder and marketing director of AeroFarms, most field farms don’t have the nimbleness to respond to a quick change in market demand.
"Because we are inside, we are able to grow all year round," he said. "We can pivot as needed and adjust to the marketplace. We plant, seed and harvest for our customers based on their orders. That allows us to be very customer- and market-driven in how we grow."
Plenty has seen a threefold increase in demand from its retailers since the start of March. The pandemic opened up opportunities with new retail partners for Plenty because the stores were experiencing a disruption in supply chain and looking for alternative means of keeping shelves full, according to executives.
"[The increase in demand] came from both our existing stores as well as from additional stores that called us up and said, ‘Hey, we are having trouble keeping our shelves stocked, could you add some volume with us?’" said Roger Kirkpatrick, director of business development at Plenty.
Plenty was able to meet the demand as it already was gearing up its volume for placement in new stores but coronavirus accelerated the pace, Kirkpatrick said.
Vertical farms are hoping to capitalize on this moment. Shelves empty of a consumer's habitual brands help force consumers over the initial barrier of trying a new product such as those sold by Plenty. Once people do try Plenty's produce, according to Kirkpatrick, they tend to stick with the brand. So even as panic buying has calmed down, Plenty has seen its demand stay level, he said.
And even though the Centers for Disease Control and World Health Organization guidelines agree COVID-19 is unlikely to be passed through food contamination, vertical farms are using consumers’ increased awareness of the food supply chain to push their product as a safer and better alternative.
"[Consumers] will continue to gravitate towards local clean options because, now more than ever, they're thinking about where is my food coming from, who is touching it and how has it been processed," Vandenbussche said.
Kalera and University of Florida LED Lighting Study Sheds New Light on Cost-Effective Modes of Increasing Nutritive Value in Lettuce
Today, technology-driven vertical farming company Kalera announced the publication of a new study, “Effect of End-of-Production High-Energy Radiation on Nutritional Quality of Indoor-Grown Red-Leaf Lettuce,” conducted in partnership with the University of Florida Institute of Food and Agricultural Sciences
The New Study Reveals Exciting Findings For Both Consumers and
Vertical Farming Industry Practices
June 04, 2020, | Source: Kalera
ORLANDO, Fla., June 04, 2020 (GLOBE NEWSWIRE) -- Today, technology-driven vertical farming company Kalera announced the publication of a new study, “Effect of End-of-Production High-Energy Radiation on Nutritional Quality of Indoor-Grown Red-Leaf Lettuce,” conducted in partnership with the University of Florida Institute of Food and Agricultural Sciences. The Kalera-sponsored study found that by using high-energy LED lighting prior to harvest, red-leaf lettuce significantly increases the production of antioxidants and especially of anthocyanins, compounds in plants that may offer health-promoting benefits by protecting cells from free radicals — exciting news for health-conscious consumers. By only using high-energy LED lighting for the last few days before harvest, both yield and quality could be maximized indoors, indicating promising and cost-effective future practices for the vertical farming industry.
The entire study can be read here.
Representative plants at harvest after exposure to EOP treatments
While numerous studies have evaluated the effect of high-energy light as a means to increase nutritional quality of lettuce grown in vertical farms, most research has focused on providing constant light quality or quantity throughout the production cycle, which typically reduces yield or increases production costs. In this new University of Florida study, Dr. Celina Gómez, Assistant Professor of Controlled Environment Horticulture at the University of Florida, who led the study, evaluated the use of end-of-production (EOP) high energy light as a cost-effective, pre-harvest practice that can allow growers to manipulate product quality and increase market value of lettuce without negatively affecting yield.
“Dr. Toma approached me to discuss the possibility of leading the study, which resulted in exciting findings for the vertical farming industry and consumers of healthy produce alike. The objective of the study was to compare growth and accumulation of secondary metabolites such as antioxidants from two popular red-leaf lettuce cultivars grown indoors and exposed to different strategies of EOP high-energy lighting. In general, EOP with blue or high-intensity lighting increased anthocyanin content and antioxidant capacity,” noted Dr Gómez. “Considering potential implications on production costs, EOP with additional blue light is an effective strategy to increase the quality of indoor-grown red-leaf lettuce plants.”
“Given the positive effects of pre-harvest light treatments on nutritional value and marketability of red-leaf lettuce cultivars, vertical farms like Kalera offer tremendous opportunities to deliver fresh, high-quality produce to local markets. This is just one example of what vertical farming can do,” noted Dr. Cristian Toma. “By investing in new developments in science and technology, Kalera is positioning itself as a leader in the vertical farming space and as an expert in the ag-tech revolution. This new research reflects the importance of constantly educating our company, our customers, and our industry on best practices, even as we continue to expand and grow into new markets.”
The new study is being released shortly after Kalera announced its expansion into Atlanta, GA, with its newest facility. Kalera opened its second Orlando, Florida indoor vertical farm in March. While Kalera’s Orlando farm is currently the highest production volume vertical farm in the Southeast, the new Atlanta facility will be more than double the size while generating over 70 jobs for the local community. As was the case in Orlando, Kalera is able to quickly open its newest growing facility in Atlanta with its proprietary technology as a result of a streamlined design and construction process, further illustrating its ability to rapidly scale and expand its vertical farms. The Atlanta facility is the third indoor vertical farm in Kalera’s portfolio and will soon be joined by more in the United States and abroad.
About Kalera
Kalera is a technology driven vertical farming company with unique growing methods combining optimized nutrients and light recipes, precise environmental controls, and cleanroom standards to produce safe, highly nutritious, pesticide-free, non-GMO vegetables with consistent high quality and longer shelf life year-round. The company’s high-yield, automated, data-driven hydroponic production facilities have been designed for rapid rollout with industry-leading payback times to grow vegetables faster, cleaner, at a lower cost, and with less environmental impact.
About UF/IFAS
The mission of the University of Florida Institute of Food and Agricultural Sciences (UF/IFAS) is to develop knowledge relevant to agricultural, human and natural resources and to make that knowledge available to sustain and enhance the quality of human life. With more than a dozen research facilities, 67 county Extension offices, and award-winning students and faculty in the UF College of Agricultural and Life Sciences, UF/IFAS brings science-based solutions to the state’s agricultural and natural resources industries, and all Florida residents.
Media Contact:
Elka Karl
Phone: 510-508-7328
Email: elka@dadascope.com
Microgreens Launched By Vertical Farmer April Sun
Just in time for this year’s winter season, vertical farmer April Sun launched its range of sustainably grown microgreens from its new commercial-sized micro-farming facility in Melbourne
Food & Beverage | June 4, 2020
Just in time for this year’s winter season, vertical farmer April Sun launched its range of sustainably grown microgreens from its new commercial-sized micro-farming facility in Melbourne.
With a philosophy of true sustainability and paired with cutting-edge technology, the local farm wants to provide the community with a range of nutrient-packed microgreens available year-round to their nearby community.
Co-founder Darren Nichol, April Sun visionary of Australia’s cleanest and highest nutritional food supply who has a wealth of knowledge due to his agricultural background, says, “This is a particular focus of the Darebin Council. They have an actual goal to increase food production within its municipality.”
These super foods are grown without pesticides and utilise 95 percent less water than traditional farming methods due to a hydroponic based (closed loop) watering system. Co-founder Ty Dickson, April Sun technologist and facility designer, said this system guarantees the plants do not receive too little or too much water.
“The watering targets each individual plant or root system and is drained back to the holding tanks,” he said. “Traditional farming methods would see water being lost to the ground and you would use more water to achieve the same level of fertigation without the ability to recapture the excess.”
With custom-spectrum lights developed in-house, the microgreens are grown in their ideal conditions, allowing for year-round production and minimal waste.
“We use a combination of specific wavelengths of blue, red, far red and full spectrum light to stimulate the chlorophyll A and B of the plants, while giving the right signals to ensure proper colour, increased nutrients through stress and, above all, a very healthy plant,” Dickson said.
“We are a non-single use plastics company; we opt for PLA compostable packaging. Our facility uses the highest efficiency components and equipment available. We do run on electricity, although we are engaging in using 100% renewables, and are in preliminary talks with the Darebin Council to implement 100kW of solar panels on our warehouse roof.” said Dickson.
In traditional farming, external factors such as drought, pollution, soil erosion and more can impact crop success. However, the world of vertical farming is “most often done indoors in a controlled environment”, he adds. “Vertical farming when done sustainably has less impact on the environment, there are significant reductions in water usage, land usage, gas usage and many other resources. This is all achieved whilst controlling the indoor growing environment with minimal impact to it outside.”
“By controlling every factor in the plant’s environment, you end up with a high-quality product on a number of levels,” said Nichol.
“We can grow to a timeline and the removal of variables such as the weather allows us to more accurately forecast and grow to our customers’ demands. This can reduce the amount of waste and also increase consistency of supply to customers. This is a huge problem for traditional farming and is the cause for the large price jumps and shortages of produce on the market.”
To see more, click here.
Growing Up: The Rise of Vertical Food Production
Vertical farming is a novel food production system that doesn’t require arable land, but instead makes use of derelict spaces in an urban environment. Instead of growing crops the traditional way, in fields, utilizing the sun or greenhouses, vertical farming grows crops by stacking them vertically, in cities, utilizing UV lights
Today the population of the world is approximately 7.8 billion, and it is predicted to grow by another 2 billion people by 2050. Arable land is continuously lost due to industrial development and urbanization, and as such the increasing food demand of the growing population alongside the decreasing of arable land is an enormous challenge. There is thus a need for realistic strategies for implementing novel food production systems around the world. Could the answer lie in vertical farming?
What is Vertical Farming?
Vertical farming is a novel food production system that doesn’t require arable land, but instead makes use of derelict spaces in an urban environment. Instead of growing crops the traditional way, in fields, utilizing the sun or greenhouses, vertical farming grows crops by stacking them vertically, in cities, utilizing UV lights. This method of indoor farming meets all seventeen requirements of the UN’s Sustainable Development Goals. These goals are a plan to attain a better and more sustainable future for the world’s population and address current global challenges. Furthermore, vertical farming also incorporates all of the Urban Future program’s ten tracks, who believe that cities are key to a sustainable future for our planet.
Furthermore, it has been proposed that rooftop greenhouses be developed in schools in Barcelona, Spain. It is believed that schools can play an important role in environmental sustainability and the Institute of Environmental Sciences and Technology in Barcelona has developed a procedure to install rooftop greenhouses in compact cities. The implementation of urban agriculture proposals supports the development of novel methods for environmental sustainability in our ever-growing world.
How Does it Work?
There are three main models for vertical farming:
Hydroponics, where plants are grown in a nutrient-rich basin of water.
Aeroponics, where crops’ roots are periodically sprayed with a mist containing water and nutrients.
Aquaponics, which involves breeding fish to help cultivate bacteria that is used for plant nutrients.
Aeroponics uses less water overall but is technically more complicated. Interestingly, the water used in hydroponics can be recycled several times after it has evaporated from the plant and recaptured from the humid air.
Pros and Cons of Vertical Farming
Vertical farming is able to yield more crops per square meter than traditional farming or greenhouses can. Furthermore, vertical farming is not weather or season dependent, and as such year-round crop production is possible. Vertical farming also uses 70-95% less water than traditional methods and as the crops are produced in a well-controlled indoor environment it is possible to eliminate the use of chemical pesticides and grow organic crops with a faster harvesting method. This is key, as one of the biggest problems with fresh vegetables is the time it takes between harvest and consumption. A faster harvesting times could mean that more vitamins and nutrients are also maintained within the produce.
Vertical farming is a relatively new venture and as such, the financial and economic feasibility remains uncertain. Yet several vertical farming companies have been set up in the past decade utilizing old warehouses and disused factories with structures to grow vegetables and herbs. One certain disadvantage is the initial cost of real estate in cities, which could impede the viability of urban locations. In addition, labor costs in cities tend to be higher. Although, maybe most impeding is the total dependence on power for lighting, maintenance of temperature, and humidity, and as such the loss of power for just one day could see a significant loss in production.
Conclusion
Vertical farming has the ability to provide fresh and safe food in sufficient quantities, independent of climate and location. Today, we are well aware of climate change and the immediate need to change our current way of life, as such vertical farming and food production has the potential to become a necessary solution in global food production.
References
The United Nations. Sustainable Development Goals. https://www.un.org/sustainabledevelopment/sustainable-development-goals/
Urban Future Programme’s Ten Tracks. https://www.urban-future.org/about/
What You Should Know About Vertical Farming. https://www.thebalancesmb.com/what-you-should-know-about-vertical-farming-4144786
Association for Vertical Farming. https://vertical-farming.net/
How Vertical Farming Reinvents Agriculture. http://www.bbc.com/future/story/20170405-how-vertical-farming-reinvents-agriculture
Nadal A et al. (2018) Rooftop greenhouses in educational centers: A sustainability assessment of urban agriculture in compact cities. Science of The Total Environment. Jun 1;626:1319-1331
Research For Workforce Development in Controlled Environment Ag: What Makes a Successful Indoor Farm Manager?
As indoor agriculture has grown, finding, training, and retaining a skilled workforce has emerged as an important challenge to the industry. A unique combination of plant production, tech troubleshooting, and innovation is needed among employees managing these operations
By urbanagnews
June 8, 2020
As indoor agriculture has grown, finding, training, and retaining a skilled workforce has emerged as an important challenge to the industry. A unique combination of plant production, tech troubleshooting, and innovation is needed among employees managing these operations.
What are the critical skill sets, and how can we create a larger pipeline of individuals trained in these skills so that they can contribute to CEA business success?
At Cornell University, a group led by Professor Anu Rangarajan (Director, Small Farms Program) seeks to provide answers as part of a National Science Foundation-funded research project on CEA Viability in Metro Areas.
Rangarajan’s team has conducted extensive research to date in order to understand the workforce needs of the hydroponics industry, including greenhouses and indoor vertical farms—and the research continues.
With the long-term goal of creating robust curricula for training CEA employees in mind, a team from Cornell University conducted many in-depth interviews with professional CEA growers in 2018 and 2019.
The team then organized a workshop, in consultation with The Ohio State and Agritecture Consulting, that invited a focus group of CEA operations managers to model in detail the diverse activities that they perform on the job.
The resulting chart is a detailed, peer-reviewed list of duties (responsibilities) and tasks (activities, skills) that describe the work of the expert Indoor Farm Operations Manager.
The chart is currently being reviewed by peer growers worldwide, who are asked to verify how important each skill is, and how frequently it is conducted.
Based on this input, the Indoor Farm Operations Manager chart will be used as a starting point for prioritizing future CEA training modules. After that, a deeper analysis of key individual skills will be conducted in order to translate the foundational research into a teachable vocational curriculum.
Right now, however, Rangarajan’s team is actively seeking more responses to the verification survey.
“We need your help,” she emphasizes, speaking to professional CEA growers. “We want to learn your priorities for a CEA curriculum that will enhance the skills of current or future employees.”
The survey takes approximately thirty minutes to complete and can be completely anonymously. CEA growers who complete the survey will also be provided with an Amazon gift card for $25 as a token of appreciation, although they must provide their names and email addresses in order to receive this gift.
To take the survey, register here. The Cornell team will send a survey link directly from Qualtrics.
As Rangarajan notes, “Grower input will help us prioritize the core education and training relevant to indoor agriculture,” helping provide the industry with the skilled workforce it will need to scale.
For more information about this study regarding the future of the CEA workforce, please contact project lead Anu Rangarajan (ar47@cornell.edu) or research associate Wythe Marschall (wmarschall@fas.harvard.edu).
Elon Musk’s Brother, Kimbal, Is Pretty Accomplished Himself
Based in Brooklyn, New York, Square Roots has developed and installs “modules” — hydroponic farms in reclaimed shipping containers that can grow certain non-GMO vegetables around the clock and without pesticides. Today they are producing mint, basil, other herbs, and leafy greens
08 Jun 2020 by Jasmine Stone in Berry & Donaldson, Business, Elon Musk, Lifestyle, Partners
[imagesource: @kimbalmusk / Instagram]
When your older brother is Elon Musk, you probably get used to growing up in somebody else’s shadow.
Just over a year separates Elon and Kimbal Musk (above left), with the former grabbing headlines in the wake of SpaceX’s successful launch of astronauts to the International Space Station.
Makes a nice change from some of his other headline-grabbing antics, but let’s chat about Kimbal.
In 2016, he co-founded Square Roots with CEO Tobias Peggs, to grow non-GMO crops in reclaimed shipping containers.
Based in Brooklyn, New York, Square Roots has developed and installs “modules” — hydroponic farms in reclaimed shipping containers that can grow certain non-GMO vegetables around the clock and without pesticides. Today they are producing mint, basil, other herbs and leafy greens. The company made CNBC’s 2019 Upstart 100 list…
Image: https://squarerootsgrow.com/
The modules, which employ software-controlled LED lighting and irrigation systems, can be set up in the parking lot of a grocery store or even inside a large warehouse or industrial building, enabling a food maker to access fresh ingredients locally for use in their dishes or packaged products.
Kimbal, who also serves on the board at Tesla and SpaceX, says that whilst they’re currently working on providing food for people here on Earth, the same farming technology “can and will be used on Mars”.
While freight containers are working hard to grow veggies, their former life saw them shipping goods around the world, which is no mean feat, either.
South African-owned shipping logistics company Berry & Donaldson knows all about the business of moving goods and has been handling every step of the complicated process for more than 50 years, but they’re happy to leave the veggie-growing game to Kimbal and his team at Square Roots.
The company also hopes to inspire more people to become farmers, running a Next-Gen Farmer Training Program aimed at teaching city dwellers about agriculture.
During the COVID-19 pandemic, Square Roots has also provided hundreds of kilograms of produce to Rethink Food NYC, an organization that provides nutrient-rich food to the needy, all of which was grown in its Brooklyn shipping container.
For Kimbal, it’s quite a pivot from how he originally cut his teeth. In a recent profile on 5280, his journey was summarised as follows:
In 1999, after the $307 million sale of Zip2—which he’d founded with his brother—Musk left Silicon Valley to train at the French Culinary Institute in New York City (now known as the International Culinary Center).
Image: Chris & Ruth Photography
Kimbal [above, with Elon, sister Tosca, and mother Maye back in 2018] ended up in Colorado two years later with his first wife, artist Jen Lewin. That he had moved into the “food space,” as he calls it, and eventually turned one Boulder restaurant into a formidable chain of locally sourced eateries across the country made him something of a star in the industry.
Whilst the pandemic has seen some of his restaurant empire take a real hit, Kimbal still seems in good spirits.
You can read the rest of that interview here.
Not a bad set of accomplishments for the Musk family, with Tosca running a streaming service called Passionflix, as well as having producer credits on more than 30 movies.
U.S. Department of Agriculture Secretary Sonny Perdue Visits Kalera
On Monday, June 8th, technology-driven vertical farming company Kalera welcomed Secretary of Agriculture Sonny Perdue to its Orlando facility
Perdue Visits Kalera For a Behind-The-Scenes Tour With Top Kalera Executives
June 09, 2020, | Source: Kaleraphoto-release
Secretary of Agriculture Sonny Perdue (l) stands next to Kalera CEO Daniel Malechuk (r) during a visit to the vertical farm's Orlando facility.
ORLANDO, Fla., June 09, 2020 (GLOBE NEWSWIRE) -- On Monday, June 8th, technology-driven vertical farming company Kalera welcomed Secretary of Agriculture Sonny Perdue to its Orlando facility. Secretary Perdue was greeted by Kalera’s top executives, including CEO Daniel Malechuk and CTO Cristian Toma, who, along with other staff members, escorted him on a private tour of the facility’s proprietary technology, providing a glimpse at the future of farming. Key takeaways included how Kalera:
eliminates the use of chemicals and removes exposure to pathogens through cleanroom technology.
is able to supply an abundance of produce locally, eliminating the need to travel long distances when shipping perishable products.
ensures the highest quality and freshness by delivering product to customers within hours of harvest rather than days or weeks
Is able to reduce water consumption by 95% compared to field farming.
During the tour, Perdue was able to sample the lettuce Kalera grows at the Orlando facility. Some of his positive reflections about the tour can be read in this Fox 35 Orlando news piece, “USDA Secretary visits Central Florida hydroponic farm, calls it a 'very innovative food production system'.”
Kalera recently announced its new Atlanta facility, which will open in early 2021. While Kalera’s Orlando farm, which Perdue visited on Monday, is currently the highest production volume vertical farm in the Southeast, the new Atlanta facility will be more than double the size and generate approximately 75 jobs for the local community. As was the case in Orlando, Kalera is able to quickly open its newest growing facility in Atlanta as a result of a streamlined design and construction process, further illustrating its ability to rapidly scale and expand its vertical farms.
After the tour, Daniel Malechuk, CEO of Kalera, addressed Secretary Perdue in front of assembled employees and press, saying, “Thank you very much on behalf of the Kalera staff for your time, and visiting us to discuss the future of agriculture, which is clean, healthy, sustainable, local and fresh. We look forward to helping the US stay on the cutting edge of agricultural innovation and feeding a hungry world with fewer natural resources.”
In addition to its R&D center, Kalera opened its first commercial vertical farm, the HyCube growing center, on the premises of the Orlando World Center Marriott to bring fresh, local produce to the hotel’s visitors and customers. In March this year, it announced the opening of its second facility in Orlando. The Atlanta facility is the third farm in Kalera’s portfolio, and will soon be joined by more in the United States. Kalera is currently sold in over 160 Publix stores.
About Kalera
Kalera is a technology-driven vertical farming company with unique growing methods combining optimized nutrients and light recipes, precise environmental controls, and cleanroom standards to produce safe, highly nutritious, pesticide-free, non-GMO vegetables with consistently high quality and longer shelf life year-round. The company’s high-yield, automated, data-driven hydroponic production facilities have been designed for rapid rollout with industry-leading payback times to grow vegetables faster, cleaner, at a lower cost, and with less environmental impact.
Kalera’s shares are traded on NOTC, a marketplace for unlisted shares managed by NOTC AS, which is owned 100% by Oslo Børs ASA, the Oslo Stock Exchange.
Further information about the company may be found at www.kalera.com and www.kalera.com/investor along with an introductory Kalera film: www.youtube.com/watch?v=2Crpph9w0hE
Kalera Contact:
Daniel Malechuk, CEO
Phone: +1 407 574 2382
Email: dmalechuk@kalera.com
Is Pontus A Technology or Agriculture Company?
Not long ago, nor very far away, my Company, Vancouver-based Green Oasis Foods developed the CEVAS™ (Closed Environment Vertical Aquaponics System); arguably the most advanced soil-less organic growth system developed to date
By Steve R McArthur, Partner, Founder & CTO of Pontus Water Lentils | February 26, 2020
Both, actually!
Not long ago, nor very far away, my Company, Vancouver-based Green Oasis Foods developed the CEVAS™ (Closed Environment Vertical Aquaponics System); arguably the most advanced soil-less organic growth system developed to date. Our main consideration was to build a closed-loop Aquaponics system that ensured there was no way for contaminants to enter the growth chain. The resulting efficiency and product quality as a result are quite startling, almost like having a built-in anti-malware program for crop growth.
Good Things Come in Threes
All ’ponic’ grow systems have unique benefits and challenges. Still all markedly increase yields and, to varying degrees, lowers the use of power and water. Each also can be set up to be custom complementary systems. Green Oasis’ CEVAS™ is a hybrid aquaponics system currently being used by Green Oasis and Pontus Water Lentils, the latter owning an exclusive worldwide license to the technology.
Full disclosure, I am also CTO of Pontus Water Lentils. Ultimately, through an agreement with Amwolf, Pontus plans to obtain a public listing in approximately Q2/2020.
Before that, we plan to crowdfund through FrontFundr for $1.5 million and a like amount in a sponsored Private Placement. We plan to use the initial funds to build a 10,000 square foot grow facility. It might be useful to define the main types of soil-less grow systems.
Let’s Translate the Main Types of ‘Ponic’s
Aquaponics: A symbiotic relationship with the system; housing fish producing waste to provide crop nutrients
Hydroponics: Continuous water system, but nutrients are added to the growth media that replaces soil
Aeroponics: is a variation of hydroponics, but instead of using a grow bed filled with media, the plants are instead suspended, with roots facing a sprinkler system connected to the main nutrient reservoir.
The difference between a standard Aquaponics system and CEVAS™ is analogous to a Prius versus a Tesla, with the latter having a much more efficient with less impact on the environment. We decided it made sense to start with Water Lentils as the first crop as its grow characteristics and high market price are very attractive.
We are Reinventing Agriculture™
I sincerely believe that our system brings a fundamental and profound change to growing soil-less crops successfully and in greater numbers than other methods. Here are some key points:
CEVAS™
A combination of the best of both Hydro- and Aquaponics
Completely closed-loop system customized by Green Oasis
Utilizes state of the art, data-driven analytics
Optimize machine learning and artificial intelligence to produce superior and consistent crops
Uses 5% of the water of traditional agriculture
CO2 captured and recycled
Symbiotic air exchange
Bio Security systems to remove all possible contaminants from any human interaction
Solids filtration
Biodigestion; fish waste turned into plant nutrient through aerobic digestion
The Pontus Water Lentils farming practice was created in Vancouver Canada and is licensed Worldwide
For more information visit: https://pontuswaterlentils.com/
Shenandoah Growers - Bringing Nature Indoors
At Shenandoah Growers, we believe in the power of technologically-controlled indoor environments to sustainably transform the future of fresh produce. As the only large scale USDA Certified Organic soil-based indoor growing system in the United States, we are passionate about leveraging cutting-edge science and technological innovation to ensure that our customers receive the freshest, healthiest, most affordable organic produce possible year-round.
Working with (not against) nature to create an optimal environment for plants to thrive
What Sets Us Apart?
At Shenandoah Growers, we believe in the power of technologically-controlled indoor environments to sustainably transform the future of fresh produce. As the only large scale USDA Certified Organic soil-based indoor growing system in the United States, we are passionate about leveraging cutting-edge science and technological innovation to ensure that our customers receive the freshest, healthiest, most affordable organic produce possible year-round. With twelve growing locations across the country, we couldn’t be prouder to provide organic, local produce to over 18,000 stores every day.
Why Indoor Controlled Agriculture?
There’s nothing quite like the great outdoors—at Shenandoah Growers, we know there’s something better. Our LED-powered indoor bioponic growing platform increases yields and reduces waste, enabling us to make fresh herbs available year-round across the country. Plus this proprietary system is environmentally conscious, conserving water and land, and avoiding harmful pesticides.
How Do We Do It?
Some call it “Know-How”. We call it “Grow-How”
Our proprietary bioponic growing process mimics nature but enhances it with carefully controlled temperatures, light levels, humidity, and water exposure. And because we use just what we need to keep our plants healthy and no more, we conserve valuable environmental resources and set our industry up for a sustainable future.
VIDEO: Vertical Farming: The Only Way Is Up
Just like we've grown accustomed to living in compartments stacked directly on top and beside each other so too are lettuce and herbs
by Jasmine Reimer
Trends - /March 2, 2020
Just like we've grown accustomed to living in compartments stacked directly on top and beside each other so too are lettuce and herbs.
Agriculture is going vertical. Why? Because it saves water, increases efficiency, and provides us with fresh, local produce.
Vertical farming is the practice of producing food on upright surfaces. Instead of farming in a field, vertical farming grows plants stacked in layers, in structures like shipping containers or warehouses.
If this seems like an insignificant shift, unlikely to produce much effect, consider this: by 2050 the world's population is expected to grow by another 2 billion people.
Feeding everyone will be challenging. Vertical farming could be a solution.
What is vertical farming?
Assembled layer by layer under candy-colored lights, vertical farming has become an increasingly popular way for food producers to reduce costs related to space and energy consumption while increasing growth rates and nutrient values.
Of the many companies that are testing out this innovative farming method, Urban Crops uses a conveyor-like system to hold baby plants under LED ultraviolet lights. Their system is automated and relies on technology to program lighting and growing conditions specific to each species. And because they don't heat up, the bulbs can be placed closer to the leaves to encourage optimal light absorption.
In addition to not having to maintain an entire plot of land, Urban Crops boasts that vertical farming yields more crops per square meter than traditional farming or greenhouses. It also grows plants faster and can be used year-round. In theory, vertical farming can be practiced anywhere, which means that water-restricted locations can still harvest produce. Vertical farming uses up to 95% less water than traditional methods.
As Urban Crops' Chief Executive Maartin Vandecruys points out:
“Basically… every day is a summer's day without a cloud in the sky."
CES 2020: LG are launching exciting new indoor gardening technology.
While vertical farming could be the future of large-scale agriculture, companies like Urban Crops are also hoping that non-farming folk like yourself will be interested in investing in DIY versions. Because, while it makes sense to grow salad greens and edible flowers, trying to grow other foods like wheat for bread isn't yet an option: “At 10 cents a kilowatt-hour, the amount of energy it would take to produce wheat would [translate to] something like $11 for a loaf of bread," states, Vandecruys. Nonetheless, vertical farming could mean big changes in the way you think about “local" produce.
Vertical farming helps reduce the amount of questions for the consumer including its provenance, growing conditions and harvest date.
Data is useless unless you put it to work
Around the world, data-driven technologies are being used to keep indoor farming afloat. Detailed, real-time data collected via artificial intelligence, location services and IoT technology is used to analyze and produce better feeding models and optimal configurations, i.e. the concentration and scheduling of light and ratio of nutrients. Most recent is IoT company n.thing's Planty Cube, launched at this year's CES 2020.
Leo Kim, n.thing's CEO, came up with the idea for Planty Cube after creating an IoT-enabled smart pot called “Planty Square."
Planty Cube is a smart hydroponic vertical farm that relies on data from farming logs, which are fed back into a database called the “Cube Cloud" and analyzed with AI to help farmers determine optimal growing conditions. As the user adds more Planty Cubes to the vertical farm, this real-time, cloud-based system makes it easier for the grower to manage the overall farm, even remotely.
But even prior to sowing seeds, technology can help vertical farmers and consumers alike.
Automation, tracking and AI technology also opens up the potential to locate farms in urban, industrial, and even domestic spaces that can produce crops all year round.
This has the possibility to truly change the way cities source food. Most urban supermarkets are supplied from distributors around the world. Local indoor farms could decrease reliance on imports and reduce carbon emissions from transportation.
In the future, I hope to see supermarkets filled with vertical farms of their own.
The ups and downs of growing up
The vertical farming industry is booming. However, there are realities to consider before growing on a professional scale:
What are you growing and for whom?
Before you invest, do some market research. Get a sense of who your customers will be and your price point. Basically, if you can't sell it, you shouldn't grow it.
What is your distribution plan?
How will you physically get your produce to your customers? Find out who your end customers are and keep your farm as close to them as possible. Being local is an integral component to your success but this may present further challenges such as high cost of land, poor soil quality, and resource restrictions.
Will your building meet your needs?
Remember, indoor farming requires substantial amounts of power: lighting, pumps, HVAC, automation equipment, fans, computers etc. Not all buildings are equipped with the type of electricity you require. And if you're serious about getting into the vertical farming industry, you need to plan for future expansions.
Fortunately, vertical farming is being supported by more than just salad-starved individuals like me; location services and tracking technology are helping farmers retain high yields and prepare for the future.
Phytoponics - Deep Water Culture (DWC) Hydroponic Growing Systems
Phytoponics designs and manufactures Deep Water Culture (DWC) hydroponic growing systems for supply to commercial produce growers
MAKING FRESH PRODUCE ABUNDANT AND MORE SUSTAINABLE
Phytoponics designs and manufactures Deep Water Culture (DWC) hydroponic growing systems for supply to commercial produce growers.
Our mission is to realize and promote the sustainable benefits of hydroponic agriculture at scale through the global deployment of our Deep Water Culture substrate-less growing solutions.
Phytoponics has taken an ancient hydroponic method and we have adapted and evolved it for use at scale by designing a range of Deep Water Culture (DWC) growing modules containing nutrient solutions which are kept oxygenated by built-in aerators.
Plants are located in the growing module and the roots of the plant are suspended in the water which has the crop specific nutrient recipe and the correct amount of dissolved oxygen.
The growing modules are serviced by a computerized nutrient control system that maintains the nutrient and pH at optimum levels whilst also irrigating the rootzone of the plants according to a carefully designed inlet and drain duty cycles.
All Phytoponics' Deep Water Culture solutions are configured around proprietary designed and patent protected grow modules which enable fully controlled soilless growing conditions without the need for additional substrates such as rockwool or coconut coir, but with the additional ability to apply unique root zone management to the crop.
We have developed a range of Deep Water Culture hydroponic growing solutions that are suitable for large scale commercial crop production, tested and refined to deliver high quality taste and yields for vine tomatoes, cucumbers, peppers, with recent trials on soft fruits.
Our DWC approach uses less water and produces less waste than other traditional methods of hydroponics for example drip irrigation using rockwool or coir substrates. As such Phytoponics offers a more sustainable means of growing produce, something that will be increasingly preferred by consumers and retail produce buyers.
Our customers, whom we prefer to think of as partners, are typically large scale commercial growers who are looking to take advantage of the efficiency and sustainability benefits we can help them deliver at better or comparable cost to incumbent growing techniques.
For more information, please visit: https://phytoponics.com/
UAE Based Company ‘Smart Acres’ to Launch Hydroponic Vertical Farming in 2020
In the efforts to push the country’s agriculture to new heights, a company named ‘Smart Acres’ will be launching a new Hydroponic Vertical Farm, which is anticipated to come in the third quarter of 2020
Nikita Arya 7 June 2020
United Arab Emirates (UAE) has been putting countless efforts in boosting agriculture in the country. The country is creating its presence in the global market with its outstanding marketing of fresh local produce. In the efforts to push the country’s agriculture to new heights, a company named ‘Smart Acres’ will be launching a new Hydroponic Vertical Farm, which is anticipated to come in the third quarter of 2020. This new hydroponic plant will be set up in Abu Dhabi and the company aims to expand it all over the country in the following years.
Smart Acres has designed the system using IoT-based technology, which will help the growers in monitoring and growing produce with the consumption of fewer resources. The hydroponics usually generate high quality of crops, and with IoT based technology, the growers could easily grow their produce.
Another unique differentiating thing about the farm is that all the plants are going to be stacked vertically. In vertical farms, the crops are stacked into one another, which creates room for more saplings. The environment needs to be controlled with no natural sunlight or soil. The nutrients are dissolved in the water-based solvent and reach the plants through roots. Roots are generally kept in the water-based system but can also be kept in other solids, which again will contain the necessary nutrients to help the plants grow.