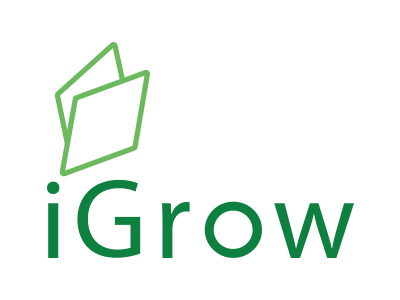
Welcome to iGrow News, Your Source for the World of Indoor Vertical Farming
Affinor Growers Highlights Accomplishments in Fiscal Year End and Outlines Future Plans
Affinor Growers Highlights Accomplishments in Fiscal Year End and Outlines Future Plans
Vancouver (Canada), July 17 2017 - Affinor Growers (CSE:AFI, OTC:RSSFF, Frankfurt:1AF) (“Affinor” or the “Corporation”) is pleased to provide our shareholders with a summary of the Company's accomplishments in the past year and Affinor's plans for the current year.
Affinor's fiscal year end was May 31, 2017. Our ultimate goal continues to focus on becoming the leading technology developer and supplier of vertical farming equipment dramatically increasing the economics of farming, improving food security and increasing agriculture production for high value crops. With the help of our strategic partners and our technical team, Affinor's immediate plans include continuing the development and commercialization of our patented technology and equipment, validation through third party partners, proving revenue models, and crop diversification.
Over the last year, Affinor has focused on strawberry development as fresh strawberries account for 80% of the total strawberry production in North America valued at $2.6 billion annually with several industry challenges making traditional strawberry growing an ongoing concern for long term viability. Affinor will continue to grow and harvest strawberries with our beta prototypes installed at the University of Fraser Valley throughout the summer, fall and winter of 2018. The focus will continue on standardizing crop models and determining best practices for commercialization. Other notable achievements over the last fiscal year included testing cannabis on a small 4 level vertical growing tower to determine if the high value crop can be utilized with the technology, increasing yields and production per square foot, with initial success.
Affinor's goal over the next year is to shift from a development to an operational company focusing on generating revenue from vertical tower sales, license agreements and introducing new agriculture technologies. Our revenue models will include selling systems to growers resulting in a margin on the equipment, license fees, and collecting royalties on the revenues from production; as well as potentially using the equipment ourselves to grow and sell crops.
Project updates:
Commercial Farm in Abbotsford
Affinor expects to commission 32 towers in a commercial farm in Abbotsford British Columbia in late 2017 capable of growing over 21,000 plants. The facility will be one of our first license holders to commercially produce products using Affinor technology. We have partnered with a large strawberry producer in California that will supply the strawberry plants and help oversee the initial growing with an "On-Farm Test Agreement" executed March 27, 2017 (see news release "Affinor Growers Signs an "On-Farm Test Agreement" with California Berry Company")
Beta Prototype Testing Update
Two 4 level beta prototype towers were installed installed in April, 2016, and December, 2016, at the University of the Fraser Valley (“UFV”) Surrey BC location in the agriculture research greenhouse (see news release Dec 6 2016, "Affinor Installs Second Tower at the Agriculture Research Demonstration Greenhouse BioPod Initiative"). One tower holds 128 strawberry plants within 100 square feet and the other 256 within 100 square feet. All crop model information, data, procedures and harvest quality is being documented to help prove operational and financial assumptions, revenue models, and best practices to standardize commercialization. The protocols and developed methods will help catalyze the commercial farm in Abbotsford when ready.
Affinor's next objective is to produce strawberries throughout the winter with customized LED supplemental lighting for fruiting crops and diversify the crop trials with kale during the fall 2017.
Affinor and Cannabis Production
As cannabis becomes more established in North America, cost effective commercial production and greenhouse systems will be needed to improve production. Affinor sees this as an opportunity to diversity our technology into other markets with high value crops and be the first vertical system actively growing cannabis in Canada. Our first trial growing cannabis was completed in February 2017, with a grower in Mission BC (see news release Feb 27 2017 "Affnor Growers Installs Vertical Farming System for Medical Cannabis in Mission BC") with encouraging results within four months (see news release May 29 2017 "Affinor Growers Completes Initial Medical Cannabis Growth Trial with 200% Production Increase.") Affinor will continue to test cannabis, furthering yields and output by developing new crop models for short, high producing cannabis plants specific to the needs of the technology, at licensed sites. We are negotiating with cannabis growers throughout North America to help facilitate a larger pilot plant cannabis growth trial.
BC Tree Seedlings Development.
Affinor executed a research and development license agreement to develop vertical growing systems to mass produce high quality, high stress resistance seedlings for the BC forestry market (see news release May 22 2017 "Affinor Growers Signs and "On-Site Test Agreement" to Develop Vertical Farming with Coniferous Tree Seedling"). 259 million trees were planted in 2016 with 266 million planned for 2017. Reforestation and silviculture are a large and growing market throughout North America requiring new technological solutions to keep up with demand.
License Agreements and Sales
Affinor has signed several license agreements throughout the fiscal year with various companies to use our technology based on our beta prototype concepts and preliminary production results. Each license agreement has the potential to generate significant equipment sales, long term royalties, ownership options and joint venture partnerships. For a complete list, please visit our website. We are also under license agreement negotiations with several international companies looking to build commercial facilities throughout the Caribbean, Europe, and Middle East.
For More Information, please contact:
Jarrett Malnarick, President and CEO
contact@affinorgrowers.com
About Affinor Growers Inc.
Affinor Growers is a publicly traded company on the Canadian Securities Exchange under the symbol ("AFI"). Affinor is focused on growing high quality crops such as romaine lettuce, spinach, strawberries using its vertical farming techniques. Affinor is committed to becoming a pre-eminent supplier and grower, using exclusive vertical farming techniques.
On Behalf of the Board of Directors
AFFINOR GROWERS INC.
"Jarrett Malnarick"
President & CEO
The CSE has not reviewed and does not accept responsibility for the adequacy or accuracy of this release.
FORWARD LOOKING INFORMATION
This News Release contains forward-looking statements. The use of any of the words "anticipate", "continue", "estimate", "expect", "may", "will", "project", "should", "believe" and similar expressions are intended to identify forward-looking statements. Although the Company believes that the expectations and assumptions on which the forward-looking statements are based are reasonable, undue reliance should not be placed on the forward-looking statements because the Company can give no assurance that they will prove to be correct. Since forward-looking statements address future events and conditions, by their very nature they involve inherent risks and uncertainties. These statements speak only as of the date of this News Release. Actual results could differ materially from those currently anticipated due to a number of factors and risks including various risk factors discussed in the Company's disclosure documents which can be found under the Company's profile on www.sedar.com. This News Release contains "forward-looking statements" within the meaning of Section 27A of the Securities Act of 1933, as amended, and Section 21E the Securities Exchange Act of 1934, as amended and such forward-looking statements are made pursuant to the safe harbor provisions of the Private Securities Litigation Reform Act of 1995.
SoftBank Invests in Largest Ever Agtech Deal, a $200m Series B For Indoor Ag Startup Plenty
Indoor vertical farming company agtech investment to date. Just one month after the grower acquired indoor agPlenty has raised $200 million in a Series B round of funding, the largest
SoftBank Invests in Largest Ever Agtech Deal, a $200m Series B For Indoor Ag Startup Plenty
**UPDATE: Added comments from S2G Ventures managing director Sanjeev Krishnan, AeroFarms CEO David Rosenberg***
**UPDATE: Added comments from Plenty CEO Matt Barnard, and AgFunder CEO Rob Leclerc**
Indoor vertical farming company Plenty has raised $200 million in a Series B round of funding, the largest agtech investment to date.
Just one month after the grower acquired indoor agriculture hardware company Bright Agrotech, this round was led by Japan’s SoftBank Vision Fund, a $93 billion, multi-stage tech fund.
Affiliates of Louis M. Bacon, the founder of Moore Capital Management, also joined the round alongside existing investors including Innovation Endeavors, Bezos Expeditions, Chinese VC DCM, Data Collective, and Finistere Ventures.
Plenty uses a vertical growing plane to grow leafy greens in a 52,000 square foot South San Francisco facility. The Series B — which takes total funding for the startup to $226 million — will fuel further expansion and more farms.
One agtech venture capitalist said that Plenty had a pre-money valuation of $500 million, but Plenty CEO Matt Barnard would not confirm this figure. The same venture capitalist said that if that figure was true, the valuation would be “crazy” for a company that appears to be pre-revenue.
But Plenty’s Barnard is confident about Plenty’s “aggressive” expansion plans to improve food quality globally. This expansion will include building farms in Japan, China, and the Middle East, as well as the US.
“This is an enormous investment, which is a testament to the strength of the founders and the strong conviction from Vision Fund in making bets that are true to its mandate,” said Rob Leclerc, CEO of AgFunder. “Plenty is a young company, so there’s going to be a lot of work for their economics to catch up to the valuation, but if they succeed, this will have looked cheap.”
Barnard offered no specific timeline or number of farms in the near-term, saying that the company prefers to announce new locations when all relevant partners are in place. Further, he did not confirm any retail partners for his South San Francisco farm. But he did say that Japan is a priority. “It is one of our top priorities not only because SoftBank is a partner, but there are some specific needs that we plan to fill,” said Barnard.
The CEO said that Plenty used its $1.5 million seed and $24.5 million Series A rounds of financing to prove to investors that the company had the capability to deliver “vegetables and fruits” as good or better than what is currently on the market.
Barnard, who was introduced to SoftBank by an existing investor, confirmed that in addition to leafy greens, Plenty has successfully grown strawberries, but would not confirm any other crops. He told Bloomberg that cucumbers are on the way as well.
What Plenty has yet to demonstrate is the ability to operate at scale.
Said Barnard, “Operating any farm, anywhere is extremely difficult and requires a lot of diligence, processes, people, and systems. The thing that is hard about investing is that at some point someone has to invest in scale before the scale is there and SoftBank is both visionary and courageous.”
Sanjeev Krishnan of S2G Ventures said that despite the large sums raised, vertical farming is unlikely to be dominated by one name.
“This investment shows the potential of the sector. Indoor agriculture is a real toolkit for the produce industry. There is no winner takes all potential here. I could even see some traditional, outdoor growers do indoor ag as a way to manage some of the fundamental issues of the produce industry: agronomy, logistics costs, shrinkage, freshness, seasonality and manage inventory cycles better. There are many different models that could work and we are excited about the platforms being built in the market.”
In addition to Plenty’s global expansion, this round will go toward hiring in computer science, machine learning, mechanical engineering, crop science, biology among others.
“By combining technology with optimal agriculture methods, Plenty is working to make ultra-fresh, nutrient-rich food accessible to everyone in an always-local way that minimizes wastage from transport,” said Masayoshi Son, Chairman & CEO of SoftBank Group Corp. “We believe that Plenty’s team will remake the current food system to improve people’s quality of life.”
Plenty claims to use 1 percent of the water and land of a conventional farm with no pesticides or synthetic fertilizers. Like other large soilless, hi-tech farms growing today, Plenty says it uses custom sensors feeding data-enabled systems resulting in finely-tuned environmental controls to produce greens with superior flavor.
The SoftBank Vision fund invests no less than $100 million checks in deals across internet-of-things, AI, robotics, infrastructure, telecoms, biotech, fintech, mobile apps and more.
Existing fund investments and recent deals include Indian fintech unicorn Paytm, virtual reality Improbable Worlds, China’s Uber killer Didi Chuxing, and global connectivity company OneWeb.
SoftBank Vision Fund’s managing director, Jeffrey Housenbold, will join the Plenty Board of Directors.
Plenty’s Series B pushes microbial crop input products company Indigo off the top position for the largest agtech deal on record;Indigo raised a $100 million Series C round last year, just months after raising a $56 million Series B.
Today’s deal is also far larger than any other in the indoor ag space; SunDrop Farms, the Australian greenhouse operator, raised $100 million from global private equity group in 2014. The closest in the vertical farming space is AeroFarms, which recently announced $34 million of a $40 million Series D round bring it’s fundraising total to more than $100 million.
Said AeroFarms CEO David Rosenberg, “This is a monster raise, and ultimately competition can be good for the industry to drive further advancement.”
Plenty raised $1.5 million in seed funding and a $24.5 million Series A round, both in 2016. The startup’s other investors are Innovation Endeavors , Bezos Expeditions , Finistere Ventures, Data Collective, Kirenaga Partners, DCM Ventures, and Western Technology Investment.
*Additional reporting by Louisa Burwood-Taylor*
Square Roots Is Looking For Its Next Class of Urban Farmers
Square Roots doesn’t just offer a crash course in the mechanics of urban farming. After the farms yield their first harvests a few weeks into the program, participants are expected to begin making sales. They receive guidance from program mentors in creating sustainable business plans.
Jul. 19, 2017 9:55 am
One of Square Roots' vertical hydroponic farms. | (Photo courtesy of Square Roots)
Square Roots Is Looking For Its Next Class of Urban Farmers
The program equips participants to launch their own food businesses in a matter of months.
By April Joyner / CONTRIBUTOR
Square Roots, the urban farming accelerator based in the Pfizer Building, is taking applications for its second cohort of resident entrepreneurs. The next round of the program will begin in October.
The 13-month program includes access to the distinctive shipping-container farms, made by Boston-based Freight Farms, that participants use to grow food. Participants pay a $5,000 deposit to cover operating expenses for the first three months, but those funds are returned to them at the end of the program. To help front those costs, participants can apply for microloans through the Department of Agriculture, with which Square Roots has partnered.
Square Roots doesn’t just offer a crash course in the mechanics of urban farming. After the farms yield their first harvests a few weeks into the program, participants are expected to begin making sales. They receive guidance from program mentors in creating sustainable business plans. Members of Square Roots’ first class, for instance, have devised a variety of sales strategies for their products, from setting up shop in greenmarkets to courting the CrossFit crowd. The accelerator does not take equity in the participants’ resultant businesses, though it does take a percentage of their sales.
Applications for Square Roots’ second program are due July 31.
Vertical Farming May Be About To Take Off
Vertical Farming May Be About To Take Off
20 Jul, 2017 5:00am
Vertical farming at Cofco's Intelligent Farm in Beijing.
NZ Herald
As nations endeavour to produce higher-value crops and land availability becomes ever more scarce, looking forward is beginning to mean looking up for the most plugged in farmers.
A report earlier this year from Global Market Insights suggested the market size for vertical farming would exceed US$13 billion (NZ17.7b) by 2024.
The technology involves stacked layers of produce in an indoor, controlled environment - often skyscrapers, but also warehouses and even disused bomb shelters in one case. This means farms can be found in urban areas and food may be produced in some of the least traditionally agrarian economies.
For example, Singapore has been a leader in the development of vertical farming as it attempts to reduce its dependency on overseas food sources despite the challenge of being just 720 square kilometres in size.
New Zealand does not face such challenges in terms of land mass. However, Jason Wargent, Associate Professor at Massey University and Chief Science Officer of BioLumic (a start-up that develops yield-stimulating light treatments for agricultural crops, and which has vertical farming on its radar) says New Zealand could still profit from the technology.
"One of the clearest opportunities for New Zealand is in the development of technology, which may support indoor farming system development, and have world-wide value," says Wargent. "New Zealand has a great ag-innovation landscape and developing cross-sector ag-innovation, that may be applicable or originally aimed at indoor, is a win-win for New Zealand."
Jaskirat Matharu last year wrote a research paper on the topic from an architectural perspective, and suggests New Zealand farmers should be exploring the technology too.
"I believe that vertical farming in New Zealand is not needed at this stage," says Matharu.
"Having said that, we should not wait to become a dense country for vertical farming to be used."
"It's more about being future-proof and laying the groundwork for the future. Like with most new things, society needs to educated for it to be taken seriously and it needs to happen sooner rather than later."
SoftBank Vision Fund Leads $200 Million Bet on Indoor Farms
SoftBank Vision Fund Leads $200 Million Bet on Indoor Farms
By Selina Wang
July 19, 2017, 8:00 AM CDT July 19, 2017, 9:02 AM CDT
Masayoshi Son is betting on San Francisco startup Plenty
The investment will help Plenty expand around the world
Masayoshi Son has discovered a green thumb.
The SoftBank Group Corp. chief’s Vision Fund is leading a $200 million investment in Silicon Valley startup Plenty, which says it has cracked the code on growing crops indoors super efficiently. Other participants in the round include Moore Capital Management founder Louis Bacon as well as existing backers such as DCM Ventures and funds that invest on behalf of Alphabet’s Eric Schmidt and Amazon’s Jeff Bezos.
Plenty vertical farming | Source: Plenty
This is Son’s first big bet on agricultural disruption and something of a departure from his recent investments in giant startups like office-space startup WeWork Cos. and Chinese ride-hailing provider Didi Chuxing, but he was attracted by Plenty’s potential to help boost food production near big cities.
“We believe Plenty’s team will remake the current food system to improve people’s quality of life,” Son said in an emailed statement.
Matt Barnard, Plenty’s co-founder, is scheduled to appear Thursday in Tokyo at SoftBank World, the company’s annual two-day event aimed for customers and suppliers. In previous years, Son has shared the stage with Alibaba Group Holding Ltd. co-founder Jack Ma and the company’s Pepper robot.
Son’s backing could give a big boost to vertical farming, a much-hyped concept that so far has failed to revolutionize crop production. In recent years several companies including Atlanta-based Podponics, Vancouver’s LocalGarden and Chicago-area FarmedHere have shut down indoor farms because they weren’t economically viable.
’Plant Factories’ Churn Out Clean Food in China’s Dirty Cities
Barnard, who grew up on a commercial farm in Wisconsin, founded Plenty in 2014 with Nate Storey, a crop scientist who previously started another indoor farm. Plenty does things differently from its rivals. Where most grow plants on shelves like a tall dresser, Plenty uses 20-foot-tall columns from which the plants jut horizontally; picture poles lined up in rows, carpeted in plants from top to bottom. Nutrients and water drip down the columns. Plenty scientists also figured out how to more cheaply remove excess heat emitted by the LED grow lights–a problem Barnard says tripped up other operations.
The company says it can cultivate many more crops per square foot than competitors and uses less energy because the plant food is mostly gravity-fed rather than pumped. “Because we work with physics, not against it, we save a lot of money,” Barnard says. An internet-connected system delivers specific types of light, air composition, humidity and nutrition, depending on which crop is being grown. Plenty says it can yield up to 350 times more produce in a given area than conventional farms -- with 1 percent of the water.
During a recent visit to the company’s facility in San Francisco, the columns are covered in heirloom varietals of purple Siberian kale, red leaf lettuce, sorrel and special species of basil and chives. Barnard says these are more nutritious and flavorful varieties than the mass-produced seeds that were bred to survive the vagaries of commercial production. The company selects which plants to grow based on taste tests with consumers and professional chefs. (A sampling during the tour confirms that the produce is tastier than store-bought.)
“We select stuff that people love because we have the freedom to do that because our supply chain is so short and simple,” Barnard says. “The field doesn’t have that option. It has to grow things that can survive 3,000 miles in a truck. That’s why the field grows iceberg lettuce.”
Skeptics of vertical farms note that they are best suited to growing leafy produce. “Rooting and fruiting” vegetables like carrots, beets, tomatoes, peppers, eggplants and cucumbers are harder to grow under such circumstances and hence more costly. Barnard says Plenty is working on growing cucumbers. So far, most of the startup’s plants are donated to food banks or used for consumer tests, including at a Google campus kitchen. Plenty will start distribution in the San Francisco Bay Area this year. International expansion is the next step and that’s where Son comes in.
A few months ago DCM Ventures co-founder David Chao introduced Barnard to the SoftBank chairman and CEO in California. The meeting was supposed to take 15 minutes but ended up lasting 45 because Son was excited about Plenty’s vision. Two weeks later, Barnard and Chao flew to Tokyo for another meeting with Son, who was skeptical at first, Chao says, but ended up sold on Plenty’s prospects.
“Ever since the Egyptian period, farming has been done one way: flat on the ground, outdoors,” Chao says. “But with indoor farming Masa realizes it’s revolutionary.”
Masayoshi Son | Photographer: Akio Kon/Bloomberg
Son is particularly interested in how Plenty can help nations grow sufficient food to support the population. His Vision Fund backers include sovereign wealth funds from the Middle East, where drought, population growth and a lack of arable land are fueling concerns about food shortages and political instability. Japan, Son’s home country, imports much of its own food and lost farmland after the nuclear power accident six years ago. Sonny Ramaswamy, director of the National Institute of Food and Agriculture at the U.S. Department of Agriculture, says indoor farming will play a significant role in easing shortages of green vegetables.
Chao says the $200 million Vision Fund investment will be used mostly to help Plenty expand domestically and internationally. Eventually, the company hopes to erect pre-fabricated farms outside major cities around the world. SoftBank has extensive connections around the world, Chao says, and wants “to help Plenty expand very quickly, particularly in China, Japan and the Middle East.”
Dickson Despommier, a Columbia professor who wrote “The Vertical Farm: Feeding the World in the 21st Century,” says indoor farming will never completely replace conventional outdoor agriculture but will supplement a growing portion of certain kinds of produce.
“In places where there is no ready access to what they’re growing, then they can corner the market,” he says. “If they do it where the price is right and the demand is right, there’s no reason why they couldn’t go wander into the sunset laughing as they go.”
3 Lessons Learned About Vertical Farming At Cultivate'17
3 Lessons Learned About Vertical Farming At Cultivate'17
Henry Gordon-Smith's presentation offered insight into an emerging industry.
July 16, 2017
On Sunday July 16, the first full day of Cultivate'17, leading vertical farming expert and consultant Henry Gordon-Smith presented for one hour about vertical farming, trends in the industry and what makes businesses fail or succeed in the space. Here are three things we learned from his presentation.
1. Younger citizens are heavily involved in vertical farming's growth.
According to Gordon-Smith, the average age of the U.S. farmer is 58. It is becoming increasingly common, he says, for younger people to not take over their parents' farms and seek out less demanding jobs in more urban areas. As a result — in addition to a nationwide push for local food — young people are making the push for sustainable, vertical farming in metropolises across the United States.
2. Vertical farming is still in its infancy.
At the beginning of his presentation, Gordon-Smith said that seven years ago when he started seeking out information on vertical farming, there were no vertical farms in North America. And, he says, despite a significant amount of funding being put into the industry, it still has a long ways to go before becoming widely used and a part of every urban city in the U.S., if not globally.
Gordon-Smith also noted that Defense Advanced Research Projects Agency (DARPA), a federal agency whose goal is to use technology to improve national security, built a commercial-sized vertical farm to grow tobacco and make vaccines for the military.
3. Cities are prioritizing urban agriculture.
Part of Gordon-Smith's current work to help cities like Los Angeles, New York and Baltimore — as well as companies like Amazon — to add vertical farming to their environment. He says cities are starting to view the sustainable, space-saving production methods of vertical farming to create "green class" jobs and increase food supply in dense urban areas. One success story: Atlanta, which has member's of the mayor's team focused solely on implementing urban agriculture and hosts an event each year called Aglanta that discusses urban food production and its role in shaping the city's future.
Kimbal Musk — Elon's Brother — Is Running A Shipping-Container Farm Compound In New York City
Kimbal Musk — Elon's Brother — Is Running A Shipping-Container Farm Compound In New York City
Cofounder Tobias Peggs outside the Square Roots shipping container farms in Brooklyn, New York. Sarah Jacobs
Kimbal Musk, the brother of Tesla CEO Elon Musk, is trying to change the way we eat by creating what he calls a "real-food revolution."
For over a decade, Kimbal Musk has run two restaurant chains, The Kitchen and Next Door, which serve dishes strictly made with locally sourced meat and veggies. Since 2011, his nonprofit program has installed so-called Learning Gardens in over 300 schools to teach kids about agriculture.
Musk's latest food venture delves into the world of local urban farming.
In early November, he and fellow entrepreneur Tobias Peggs launched Square Roots, an urban-farming incubator program in Brooklyn, New York. The setup consists of 10 steel shipping-container farms where young entrepreneurs work to develop vertical-farming startups. Unlike traditional outdoor farms, vertical farms grow soil-free crops indoors and under LED lights.
On Tuesday, Square Roots opened applications for its second season, which will start in October and last 13 months.
"Graduates are uniquely positioned to embark on a lifetime of real food entrepreneurship — with the know-how to build a thriving, responsible business," Musk wrote on Medium. "The opportunities in front of them will be endless."
Six weeks into the first season, just after the entrepreneurs completed their first harvests, Business Insider got a tour of the farms. Take a look:
The Square Roots farms in Brooklyn sit between an old Pfizer factory and the apartment building where Jay-Z grew up. Sarah Jacobs
Everything grows inside 320-square-foot steel shipping containers. Each container can produce about 50,000 mini-heads of lettuce a year. Sarah Jacobs
The US Department of Agriculture gave the Square Roots entrepreneurs small loans to cover preliminary operating expenses. Other investors include Powerplant Ventures, GroundUp, Lightbank, and FoodTech Angels.
On four parallel walls, leafy greens and herbs sprout from soil-free growing beds filled with nutrient-rich water. Instead of sunlight, they rely on hanging blue and pink LED rope lights. Sarah Jacobs
About the size of the standard one-car garage, each shipping container can produce the same amount in crops as two acres of outdoor farmland.
Musk and Peggs chose Square Roots’ first class of 10 entrepreneurs from over 500 applications. Peggs said they represented the next generation of farmers — though not all had previous farming experience.
Sarah Jacobs
In early 2016, while Aliber was recovering from a concussion, he learned about urban farming from a podcast. He started researching it from his bed and found out about the Square Roots program.
Sarah Jacobs
Before Josh Aliber, 24, moved from Boston to Brooklyn to join Square Roots, he had never farmed. Now he's starting up a specialty herb business and running a vertical farm. Sarah Jacobs
His shipping container farm runs on 10 gallons of recycled water a day, which is less than an average shower's worth.
Sarah Jacobs
Aliber can monitor everything from the oxygen level to the humidity — which affects the plants' taste and texture — using the "computer panel" near the door and sensors in the growing beds. If he wants a tropical or northeastern climate, he can control that, too.
Sarah Jacobs
All of the Square Roots' farmers sold their first harvests at a local farmers market.
Aliber is selling his specialty herbs and basil primarily to upscale Italian and pizza restaurants in NYC.
Sarah Jacobs
All of the Square Roots' farmers sold their first harvests at a local farmers market.
Through the program, Aliber has had the opportunity to work with numerous mentors — Square Roots has 120 so far.
Sarah Jacobs
"Yes, I have the ability to make money," Aliber said, "But yes, I also have the ability to change the world."
Sarah Jacobs
Electra Jarvis, another 27-year-old farmer, usually comes to Square Roots three days a week. On Wednesdays, she spends four hours meticulously placing 800 seeds inside small troughs.
Mary Wetherill
Two weeks later, she transplants them to the walls. "We should be growing closer to us in cities," she said.
Mary Wetherill
Aliber, Jarvis, and the other eight entrepreneurs are not just learning how to grow plants, but also how to grow their businesses. A large part of the program is learning about branding and "how to tell our stories," Jarvis said.
In the late '90s, after the tech boom, the Musk brothers moved from South Africa to Silicon Valley. They invested in X.com, which later merged with PayPal and was acquired by eBay.
Sarah Jacobs
Kimbal Musk has known Peggs, who had worked for a decade on tech startups that eventually sold to Walmart and Adobe. Before Square Roots, they worked together at The Kitchen, where Peggs served as the "president of impact" and helped expand the chain to new cities.
When asked how his experience in tech translated to running a vertical-farming accelerator, Peggs said the two fields shared the same motivation. "You learn how to execute impossible dreams," he said. "This was all just a PowerPoint presentation six months ago."
Sarah Jacobs
Square Roots hopes to expand to 20 cities by 2020. "Today's consumer wants to know they are supporting companies that are doing something good for the world," Peggs said. "This not just a Brooklyn foodie trend."
Sarah Jacobs
The world's largest vertical farm, AeroFarms, launched last year in Newark, New Jersey. In late 2015, the urban-farming company Gotham Greens opened the world's largest rooftop farm in Chicago.
Vertical farms can grow crops all year, using significantly less water and space than outdoor farms.
Sarah Jacobs
Critics of vertical farms say that the LED lights drain a lot of electricity. Peggs said Square Roots was exploring how the farmers could switch to solar power in the future, since electricity is the program's biggest cost.
Sarah Jacobs
Square Roots' lights are on only in the evening and night, although other vertical farms run theirs 24/7.
Square Roots recently built offices inside the Pfizer factory. In its past life, the building produced ammonia, a chemical sprayed on plants that became vital to the industrial food system after World War I.
The building is populated by sustainable-food startups. "It's an act of poetic justice," Peggs said.
Sarah Jacobs
Deptford Has Its First Vertical Farm And It Could Hold The Key To Our Urban Future
Published by Bdaily Editor Billy Woodon 07 JUL 2017
Deptford Has Its First Vertical Farm And It Could Hold The Key To Our Urban Future
#London #Funding #Agriculture #Innovation #Technology
A new vertical farm has opened its doors in Deptford housed within a previously disused warehouse.
Tech startup Vertical Future has launched the new farm, which is both the company and Deptford’s first vertical farm, just months after the company was established and sealed a six-figure funding package from HSBC.
In what is the first of a number of planned farms operating under the MiniCrops brand, the farm has been developed as part of The Artworks’ new Creekside development and will provide the local community and businesses with sustainably grown fresh produce.
Vertical farms have really begun to take off in the last ten years, with installations popping up in urban areas across the world with many touting the technique as holding the key to our future food supply while at the same time delivering a number of environmental and health benefits.
Its proponents argue that the technology can deliver more produce than traditional farming or greenhouses, and use less water to boot.
Locating the farms in urban locations can also help to cut down on delivery miles thus reducing emissions and helping to combat poor air quality, while crops can be grown year round regardless of season or weather.
Founders of Vertical Future, Jamie and Marie-Alexandrine Burrows said in a statement that their planned network of London sites will do more than just provide crops and produce, but also provide community outreach and engagement projects to help tackle some of our most pressing urban problems.
They said: “We want to make cities a better place for our children, and our urban initiatives are long-term responses to the ongoing issues of urbanisation.
“All signs following our launch have been positive and launching MiniCrops is our first real milestone as a new business.
“We want to promote fast but sustainable growth that will make a real impact on our local communities around each site.”
Crops at Vertical Future’s first MiniCrops site in Deptford. / Image: Vertical Futures
As part of its outreach work, the startup recently launched its mobile health app which links users with health and social opportunities in London, and the business is also developing its own air pollution device.
The vision for its Deptford site also stretches to local events with plans to host regular educational talks about sustainable food for local schools and at risk groups from Lewisham and its surrounding boroughs.
Lucy Wynn, HSBC’s Area Director for South London, said: “We are delighted to be able to support Vertical Future with these exciting first steps into making our cities a healthier place to live.
“We are passionate about projects that benefit the local community and with our funding Jamie and Marie have been able to turn their ideas into a reality.”
Vertical Farming Is Officially Coming to Grocery Stores
Vertical Farming Is Officially Coming to Grocery Stores
IN BRIEF:
German startup Infarm is putting modular, vertical farms directly into grocery stores, giving customers the ability to pick fresh crops and drop them straight into their grocery baskets.
IN-STORE FARMING
Fresh produce is the best produce, and nothing could be fresher than crops you’ve just harvested. To that end, Berlin-based startup Infarm wants to give consumers direct access to freshly grown produce by putting vertical farms in grocery stores.
While vertical farming isn’t exactly a new idea, Infarm’s approach is undoubtedly fresh. Rather than your typical indoor vertical farming, the company utilizes a modular approach for their go-to-market strategy. This allows them to do vertical farming on a smaller but easily expandable scale.
Infarm’s produce won’t be found stored in large warehouses. It will be in places that are frequented by customers, such as grocery stores, shopping malls, and even in restaurants. You’d see the crop, pick out the produce that’s ripe for harvest, and place it in your grocery basket.
“When we presented our idea three or four years ago, people looked at us as though we [had] lost our mind,” Infarm co-founder Erez Galonska told TechCrunch. “We are the first company in the world that has put vertical farming in a supermarket.”
GOOD FOR YOUR HEALTH AND THE ENVIRONMENT
Infarm’s modular vertical farms help promote a healthier lifestyle. Urban-dwellers won’t have a hard time getting their fresh supply of greens, and Infarm makes sure that their crops are, indeed, fresh. Each module is monitored by sensors, connected to an internet-controlled irrigation and nutrition system.
“The system is smart. It can guide you where to harvest and can notify you when the produce needs to be harvested, and this is your part in the game,” Galonska explained. “Machine learning can help us understand and predict future problems.”
Aside from this, vertical farming also helps eliminate waste and promotes self-sufficient food production directly in cities. It reduces the negative environmental impacts associated with more traditional farming methods — i.e., the use of pesticides — while providing people with the freshest crops. It’s a futuristic agricultural solution.
References: TechCrunch, Infarm
WRITTEN BY - AUTHOR Dom Galeon - EDITOR Kristin Houser
Freight Farms Builds Farms In Shipping Containers, And NASA Wants To Launch Them To Space
This Boston-based sustainable agriculture company grabbed NASA's attention along with Elon Musk's brother, Kimbal.
Getty Boston Globe
July 7, 2017
If we built farms in space, they'd look nothing like the vast wheat fields of Kansas. But they just might look something like urban farms being used today—modular closed-loop hydroponic farms, actually. These compact, efficient grow houses could be the life-giving answer to keeping astronauts fed, a solution The Martian's Mark Watney could only dream of. The idea is less science fiction than you might think, too.
Freight Farms, based in Boston, is trying to revolutionize the global food system with its Leafy Green Machines. These shipping containers filled with racks of planted crops, grow lights, and environmental control systems can be installed anywhere in the world and make fresh produce available in even the densest urban neighborhoods.
Although Freight Farms initial intentions were much more down to Earth, the company inadvertently built a prototype farm that NASA wants to study for future applications on other planets. And NASA isn't the only one. Google and modern farming entrepreneurs including Kimbal Musk, brother to Martian hopeful Elon Musk, have also shown interest in the project.
A single Leafy Green Machine (LGM) can house the equivalent of roughly two acres of produce. One LGM can produce an astonishing 1,000 heads of restaurant-ready lettuce a week, and restaurants like B.Good in Boston are taking advantage of fresher, less expensive produce grown in their own backyard LGMs.
"The demand now is farm to table. It's all about local," co-founder Jon Friedman told Popular Mechanics. "Which is great for summer for select geographies, but for the rest of the year, that isn't possible." Boston winters have as little as 3 hours of daylight, and the massive snow load would ruin the delicate frames of most modular indoor farm prototypes. Friedman calls the shipping containers "magnificent structures for their thermal properties" as well as for their robust structural integrity and easy-to-manage unit size.
With this compelling proof-of-concept on Earth, Freight Farms and Clemson University recently received a grant from NASA to develop the next generation of off-the-grid systems using as many renewables as possible with an ultimate goal of providing "life support for human exploration of deep space." Future LGMs could be even more self-regulating as Freight Farms looks to incorporate technologies like water capture from the ambient air and automatic compost systems. Eventually, Freight Farms would like to build LGMs that are entirely autonomous and run on 100 percent renewable energy.
A NASA concept image with an indoor Mars farm that looks something like the inside of a Leafy Green Machine. NASA
The NASA grant—under the agency's research initiative, "Closed-Loop Living System for Deep-Space ECLSS with Immediate Applications for a Sustainable Planet"—is designed to help Freight Farms advance their LGM technology to the point that the space agency could adapt the farms and launch them into space. In addition to providing food for astronauts, NASA wants to work with Freight Farms to study the production of proteins and medicines, develop lightweight containers with inflatable materials or 3D printing, and ultimately design a similar system to the LGM that could be incorporated into "space exploration vessels."
Freight Farms' largest customer on this planet, however, is Brooklyn-based Square Roots Grow, founded by Kimbal Musk and Tobias Peggs. Square Roots operates a whole parking lot full of LGM units for local growers and entrepreneurs. Because the containers are self-contained, they can program the simulated daytime hours inside the farms to run at night when energy costs are lower. It's a sustainable system that has legs.
"My hope is that we are in every metro area in America as fast as we can get there," Musk told Popular Mechanics in an email.
The inside of a Leafy Green Machine.Freight Farms
Beyond fresh greens, Freight Farm founders Jon Friedman and Brad McNamara say that it's also popular to grow radishes, edible flowers, peppers, tomatoes, and pumpkins. What's more, given the closed-loop system of a LGM, it can sustain the crops on just 10 gallons of water a day. The efficiencies of Leafy Green Machines are an astonishing 90 percent improvement over traditional farming, according to the USDA.
Maintaining a single LGM takes roughly 20 hours per week. That's only 10 hours per acre, per week. To sustain the plants, columns of hanging LED strips with blue and red diodes in the grow lights require an average of between 90 and 110 kWh per day—about the equivalent of 3 average U.S. households. Many LGMs are outfitted with solar panels as well to minimize the required energy input.
Freight Farms' LGMs are currently operating across America, Canada, Europe, and Japan. Atlantic island nations are among the first in the developing world do adopt the technology in an effort to become more food-independent. These areas are heavily reliant on imports, and even though they have tropical climates, food production is difficult. The result is high prices and low variety from imported produce. Pilot projects are currently sprouting up throughout the Middle East and Africa as well. And yes, the units can be shipped out on trucks, freighters, and railroads, traveling anywhere you can send an intermodal container—so basically anywhere in the world.
Freight Farms
And it's not just restaurants or remote islands that have opted for the Leafy Green Machine. Institutions around America are harnessing the power of these units not only for food but also for educational purposes. Corporate campuses like Google were eager early adopters. Schools including the University of Michigan and UMass Dartmouth are using the LGMs as part of their curriculum to teach students about sustainable agriculture.
The benefit of distributed small farms is that they're vastly more sustainable than larger options in terms of conserving land and minimizing transport. Between production and shipping, the global food system accounts for about one-third of all human-induced greenhouse gas emissions. It also helps that the local produce passes through fewer hands, which means more affordable food. "The most exciting thing about Square Roots and urban farming is getting back to knowing our farmer and trusting our food again," says Musk.
With Leafy Green Machines spreading across the world, it might not be too long until NASA builds the very first variant—the Leafy Red Machine, perhaps?—and launches it to Mars.
Ivy Tech, Green Sense Partner On Vertical Farm In South Bend
Ivy Tech, Green Sense Partner On Vertical Farm In South Bend
Ivy Tech to partner on vertical farm
Photos/BECKY MALEWITZ
SOUTH BEND — Ivy Tech Community College and Green Sense Farms have entered into a partnership to build a 20,000-square-foot “vertical farm” on land transferred by the college to the Portage-based grower on Sample Street in South Bend.
The announcement ends two years of speculation about the project, which also involves the city of South Bend. A ceremonial ground-breaking is set for Wednesday.
According to a press release, the state-of-the-art, $3 million to $4 million facility will be utilized for workforce training so that students better understand future opportunities in farming.
Courses will begin as non-credit or “through” courses complementing other programs while the school develops a curriculum for the program, and students will receive training in transferable skills for areas such as food service, retail and industrial maintenance.
Ivy Tech, for its part, will gain access to the vertical farming labs without the large-scale investment needed to acquire equipment, the release states.
“It's a working commercial farm, meaning we will be providing produce every day to the community, and it's a hands-on training center,” said Robert Colangelo, founder and CEO of Green Sense.
Items such as micro-greens, baby greens, lettuces and herbs will be grown at the facility to support local markets, restaurants and colleges, Colangelo said, including Martin's Super Market, the University of Notre Dame, the Morris Inn, Café Navarre, Four Winds Casino and Sodexo, the food service provider for Memorial Hospital and Saint Mary's College.
The facility will employ 10 students every six months in “earn to learn” roles, Colangelo said, plus five full-time employees who will earn $30,000 to $50,000 per year. The students will work 20 hours per week and gain hands-on experience in all aspects of the business.
Students who are interested in the retail or food service sides of the industry will train with the partner organizations as well, Colangelo said, with opportunities to work for those organizations afterward.
“The plan is that they graduate job-ready so that they've got real hands-on skills,” he said. “And more importantly, the much-needed soft skills that employers are looking for.”
Colangelo said he is working with Mike Keen, director of the Center for a Sustainable Future at Indiana University South Bend, to develop a curriculum for the course so students can earn credit for it and professional certification.
They're also working to develop some sort of criteria for the selection of the students, he said, likely to include an interview. “It's not just education,” he said. “Some of it will come down to personality, drive and interest.”
Founded in 2014, Green Sense Farms grows leafy greens in stacking, vertical towers, 365 days a year. The company uses automated computer controls to provide the precise amount of light, nutrients, water, temperature and humidity for the plants so they can be harvested year-round.
The process provides greater yield per unit of space than traditional farming because it allows for growing and harvesting year-round. A typical facility allows for 20 to 30 harvests per year depending on the crop, Colangelo said.
The company opened its first farm in Portage in 2014. It also designed and built a farm in Shenzhen, China, for its operating partner StarGlobal A. And it is preparing to break ground on a third facility in Las Vegas.
“We have about 10 farms in the pipeline being developed in the next six months,” Colangelo said. “And I think once news hits that we're doing this training center, we'll see a lot of colleges and universities want to emulate this.”
The facility here, financed, in part, with a $700,000, low-interest Industrial Revolving Loan from the city, will be at 250 E. Sample St., on the south side of the street, directly west of Ivy Tech's Sample Street location.
It will consist of space to germinate the seeds and grow, package, store and ship the plants, plus office space and an enclosed corridor for students and tour groups to observe the operation, Colangelo said.
Design-wise, the structure will be a steel-frame building with a front-facing brick facade made to match the adjacent Ivy Tech building in look and color, he said.
“It will be the nicest thing on the block,” he said.
Once up and running, the facility will provide fresh, organic produce to local stores, restaurants and food-service providers on a daily basis, Colangelo said. “Most of the stuff from the farm takes days to get from the farm to the table,” he said. “We're going to be able to do that in hours, so it's fresh.”
He said they're also hoping to deliver produce “live” with the roots still on the plant, “because as soon as you cut a plant and harvest it, it starts to decay and lose nutritional value.”
According to Ivy Tech South Bend Chancellor Thomas Coley, the school is approved to offer agricultural courses but never has, “and this seemed to be a very promising way to provide training for a market that seems to be growing fairly well.”
“And it could tie into other related programs in biotechnology or hospitality or even hospitality,” Coley said. “Or even, because it's technologically driven, industrial maintenance and other related areas.”
Colangelo said he hopes to break ground on the project in the coming weeks or months, with a completion date of next June.
He said, “I feel like we're setting a model here for how government, academia and business can work together to train the new, modern workforce.”
574-235-6187
@ErinBlasko
Staying Competitive With New Edible Crops
Staying Competitive With New Edible Crops
Greenhouse Management highlights ice plant and purslane, new opportunities in produce, with Dr. Richard Fu, president of of the Connecticut-based agriculture technology company Agrivolution.
June 28, 2017
Patrick Williams
Ice plant has a unique crunchy texture, and a briny, yet lemony flavor.
Photo courtesy of Dr. Richard Fu
By taking advantage of new lighting technologies and experimenting with unique produce offerings such as ice plant and purslane, ornamental growers can effectively move into the produce space, says Dr. Richard Fu, president of Agrivolution, a Connecticut-based agriculture technology company.
After hearing him speak at Indoor Ag-Con in Las Vegas this past May, Greenhouse Management recently spoke with Fu to learn more about these new opportunities in the produce market. If you would like to know more about growing produce in a controlled environment, subscribe to sister publication Produce Grower magazine at bit.ly/2sxThRU
Greenhouse Management: What does Agrivolution do?
Richard Fu: Agrivolution is a supplier of controlled environment agriculture [CEA] equipment, mostly in LED products at this moment.
We also engage in consultation works for our clients in setting up a vertical farm and greenhouse lighting. We have been doing this for a couple years now, and we hope to establish ourselves further here in North America.
GM: At Indoor Ag-Con, you discussed ice plant as a crop that is becoming more popular in Asia and that can offer opportunities for indoor growers in the United States. Can you explain what ice plant is, and why more growers in the United States should consider growing it?
RF: One of the challenges, I think, in any kind of farming, is a product differentiation. Even though there is certainly a large demand for lettuce and kale and basil and so on, there is only so much you can produce while somebody else is going to do that same thing. Eventually, you’re going to be competing on the price amongst the other growers. Even in a remote area, you’re still going to be competing against others, including much lower-priced imported field-grown produce from California.
Conventional crops are very seasonal also, to some extent. Price fluctuation is very unpredictable sometimes — it depends on the geographical location and climate, obviously. But in the majority of the markets in the U.S., you have to compete with the California and Mexico produce, and locally, you may be competing with other greenhouses or vertical farms. The demand may be there, but the margin may not be the greatest.
Dr. Richard Fu
Photo courtesy of Dr. Richard Fu
We believe by differentiating and offering unique products, you control the supply and pricing. The advantage of a controlled environment is that you can grow crops others cannot in certain locations. Ice plant is a succulent that is considered to be a unique crop and new to the market, so people are very curious but it is hard to grow steadily in a field. It has unique crunchy texture and briny, but lemony flavor. And it has some nutritional benefits compared to lettuce. Those are some of the unique attributes of ice plant and that makes it a good introductory crop, especially for vertical farming growers. In greenhouses, it might be a little bit harder to grow ice plant because of the temperature management, but if you are able to maintain the temperature within a certain range, then ice plant definitely can be a crop to consider as well.
In addition to that, as I mentioned about the nutritional side of it, ice plant contains a rich amount of inositol, which is a substance that helps to reduce insulin resistance, so that can help people with prediabetic conditions and PCOS, or polycystic ovary syndrome. Also, it’s rich in beta-Carotene and vitamin K. We were able to take this crop, and through a controlled environment agriculture technique, enhance the level of d-pinitol concentration and extract it to turn into a supplement. So there was a secondary value-added product that we were able to produce from ice plant. Those are some of the interesting things we can do through CEA that we were promoting at Indoor Ag-Con.
Purslane contains rich amounts of Super Omega-3 and alpha-linolenic fatty acids.
Photos courtesy of Dr. Richard Fu
GM: Purslane is another crop you mentioned. It has Omega-3 fatty acids and antioxidants, and it aids in cancer prevention and allergy control. Are you currently working with that crop?
RF: Yes. Well, I’m not directly working with this crop, but the company in Japan — the company that I partner with — is involved with it, and they have developed a technique to use this crop, which is known to contain rich amounts of Super Omega-3 and alpha-linolenic fatty acids, into a secondary supplement product, which helps to alleviate allergies.
GM: Is that something that greenhouses or controlled environment growers could grow in the United States?
RF: Yes, if there are growers in the U.S. that are interested, then ice plant and purslane certainly can be an introductory edible crops, in CEA, especially.
GM: What advice do you have for greenhouse ornamental growers entering the produce space?
RF: Whether to grow leafy greens such as lettuce and kale or flowering crops such as tomatoes and peppers is dependent on the geographical location, but the produce segment is definitely an option greenhouse growers should be considering because the local food movement is strong today. I think that’s a great opportunity, except as I mentioned before, no matter what industry you may be in, you want to have a certain competitive advantage, and having differentiating products like ice plants will definitely help to maintain your competitive edge over other growers. And you can still grow conventional crops like lettuce and kale and so on, but you want to mix a unique crop or two into your offering. Microgreens are becoming popular crops, so that’s a good option as well. But you need to find products that have high value and high margin to survive in the environment that’s becoming very crowded.
The other thing is, consumers are looking for produce year-round, so you want to be able to supply crops in demand. In order to maintain a competitive edge, your production needs to be year-round with CEA when the demand is year-round. From a CEA perspective, the challenge is to control your environmental parameters in order to grow crops at a steady production rate — especially in greenhouses where the advantage is that you take advantage of free natural light, but the disadvantage is that you’re dependent on the natural light. If you’re in a climate zone where you have shorter daylight in winter, that becomes very disadvantageous because your crop efficiency — production efficiency — can be cut in half in some cases compared to summer. So you definitely want to consider adding supplemental lighting. There are several lighting choices, but LED lighting is definitely one good option.
The other way to keep the edge is to consider adding a seedling incubator, which can promote the growth in the early stages of crop production so you have very healthy seedlings of, for example, tomatoes and peppers. Even in winter months, your crops will have an early start, and then transition into greenhouses as healthy and strong plants. Those are some of the things that you can definitely consider to maintain your competitiveness.
An Alaskan Wants To Put A Lettuce Tower In Every Elementary School In America
An Alaskan Wants To Put A Lettuce Tower In Every Elementary School In America
- Author: Erica Martinson
Lettuce flourishes in a hydroponic grow tower in Sen. Lisa Murkowski’s office recently in Washington, D.C. (Erica Martinson / Alaska Dispatch News)
WASHINGTON — Last month, Bernie Karl flew down to Washington, D.C., and installed a hydroponic grow tower in Sen. Lisa Murkowski's office. Next, he wants to hit every public school in Alaska.
Karl, who owns Chena Hot Springs northeast of Fairbanks, has a mission: He wants to teach kids how to feed their families using cheap, easily obtained materials.
Karl's daughter has a tower at her house — hers grows strawberries and cherry tomatoes, he said. In Murkowski's office, the tower grows only lettuce — enough to feed a family of six.
And for a few weeks now, the senator's staffers have been picking their own salad greens off the tower of orange Home Depot buckets in the corner of her office lobby in the Hart Senate Office Building.
Karl is well known to Murkowski as well as to other political bigwigs in Alaska. Murkowski, Sen. Dan Sullivan and Gov. Bill Walker routinely show up at his renewable-energy fair each August.
So it's not entirely surprising to see the tower appear in Murkowski's office, after he touted its earliest iteration at last summer's Chena Hot Springs energy fair.
"Our goal is to get one in every school in Alaska and every school in America by the end of next year — to teach third- and fourth-graders that everyone can be responsible for growing their own food," Karl said in an interview.
More than 98,000 public schools operated in the United States in the 2013-14 school year, according to the National Center for Education Statistics. More than 67,000 of them were elementary schools.
"The problem is that things are so expensive. But they don't need to be. So we decided that we would come up with something that you could go to any Home Depot and buy," Karl said.
The tower in Murkowski's office is the 3.0 version of Karl's efforts, along with others at his employee-owned Chena Hot Springs Resort, where they grow food for the staff and guests.
That tower is getting its own upgrades. On June 27, Murkowski's husband, Verne Martell, arrived in her office with a wax plumbing ring and set about tweaking a previous fix. Martell was working on quieting the sound of running water that plagued the two employees who sit at desks in the lobby, greeting visitors and answering phones.
Karl said Friday he had just sent an extra light to Martell, an upgrade for a side of the tower that wasn't growing as well as the rest.
Karl is a boisterous man — the kind of guy who has big ideas and even bigger plans. Currently, he's hoping to get a meeting with the top brass at Home Depot — he said Murkowski had kindly put in a call for him.
He's hoping to convince them to offer Saturday classes on building the tower at stores nationwide. And he wants the company to sponsor "one for every school in America."
Karl is in the process of patenting his invention — called "Lettuce Grow for Free" — but he doesn't plan to make money off it. He wants to give the plans away. And he encourages others to improve upon them.
"We're building a fourth prototype right now … that uses a little less material, gets it down a few more dollars."
Karl also hopes that school programs run by Future Farmers of America and 4-H will start programs in schools.
"I want them to help replant the world," he said of the youth agricultural organizations.
This fall, an elementary school in Fort Yukon will get Alaska's first school-based grow tower, Karl said. They were the first to ask for one, he said.
See the plans here: The Chena Grow Tower Project
About this Author
Erica Martinson is Alaska Dispatch News' Washington, DC reporter, and she covers the legislation, regulation and litigation that impact the Last Frontier. Erica came to ADN after years as a reporter covering energy at POLITICO. Before that, she covered environmental policy at a DC trade publication and worked at several New York dailies
LumiGrow Brings Smart Horticultural Lighting to Cultivate'17
Cultivate ’17, North America’s largest horticultural tradeshow is set to use the entirety of the newly expanded and renovated Greater Columbus Convention Center (GCCC). AmericanHort’s Cultivate’17, July 15-18 in Columbus, OH, is the horticulture industry’s renowned professional development event with the largest all-industry trade show. AmericanHort estimates about 10,000 attendees, more than 125 educational sessions and close to 700 exhibitors.
LumiGrow Brings Smart Horticultural Lighting to Cultivate'17
LumiGrow Lights Up Farming at Cultivate ’17 Tradeshow
Greater Columbus Convention Center, Ohio – July 14, 2017 – Cultivate ’17, North America’s largest horticultural tradeshow is set to use the entirety of the newly expanded and renovated Greater Columbus Convention Center (GCCC). AmericanHort’s Cultivate’17, July 15-18 in Columbus, OH, is the horticulture industry’s renowned professional development event with the largest all-industry trade show. AmericanHort estimates about 10,000 attendees, more than 125 educational sessions and close to 700 exhibitors.
Trade show attendees interested in learning about lighting strategies, LED applications and spectral science research are invited to visit the Discovery Café Smartfarm, attend the LumiGrow Cultivate Live session and stop by the LumiGrow exhibit booth.
As part of the $140 million conference center expansion and renovation, the GCCC will showcase a new onsite indoor vertical farm. The newly constructed indoor Smartfarm at the center’s Discovery Café is lit with LumiGrow LEDs and utilizes a hydroponic farming system built by Bright Agrotech, a vertical farming company. Restaurant chef’s will exercise their culinary creativity with hyperlocal ingredients grown from the Smartfarm.
Tradeshow attendees looking for a grower’s perspective on LED lighting strategies are invited to attend the LumiGrow Cultivate Live session on Monday July 17 between 1:45 PM – 2:15 PM. Steve Stasko, Orangeline Farms, and Marco de Leonardis, Freeman Herbs, will discuss how they use adjustable spectrum technology to apply advanced LED lighting strategies to positively impact profits for their greenhouse operations.
Growers, operators and industry professionals looking for a deeper conversation about smart horticultural lighting strategies are invited to visit LumiGrow at exhibit booth 2326.
Cultivate ’17 is set to define the green industry’s upcoming trends, technology and business best practices in horticulture.
About LumiGrow Inc.
LumiGrow, Inc., the leader in smart horticultural lighting, empowers growers and scientists with the ability to improve plant growth, boost crop yields, and achieve cost-saving operational efficiencies. LumiGrow offers a range of proven grow light solutions for use in greenhouses, controlled environment agriculture and research chambers. LumiGrow solutions are eligible for energy-efficiency subsidies from utilities across North America.
LumiGrow has the largest horticultural LED install-base in the United States, with installations in over 30 countries. Our customers range from top global agribusinesses, many of the world’s top 100 produce and flower growers, enterprise cannabis cultivators, leading universities, and the USDA. Headquartered in Emeryville, California, LumiGrow is privately owned and operated. For more information, call (800) 514-0487 or visit www.lumigrow.com.
Media Contact
Brandon Newkirk
bnewkirk@lumigrow.com
510-709-4437
Berlin Startup To Plant Mini Vertical Farms In Supermarkets
The idea of growing fresh local produce in supermarkets has seen a large amount of progress – it was announced earlier in April that Europe’s first commercial vertical farm had begun construction in Dronten.
Berlin Startup To Plant Mini Vertical Farms In Supermarkets
Berlin based startup Infarm intends to distribute smart vertical farming systems to supermarkets, providing customers with the option to hand-pick fresh vegetables and herbs, whilst simultaneously reducing food mileage and transport emissions.
The idea of growing fresh local produce in supermarkets has seen a large amount of progress – it was announced earlier in April that Europe’s first commercial vertical farm had begun construction in Dronten.
Infarm’s hydroponic vertical farms are adaptable and self-regulating – they can be stacked according to space requirements, and they are also monitored to ensure optimal conditions for the plants.
Additionally, these hydroponic systems not only decrease agricultural water usage, but they also reduce wastage and minimise energy usage from transportation and refrigeration, making them an incredibly sustainable option.
Vertical farming allows for the locating of food production close to, and within, urban areas, where food consumption is concentrated.
Infarm, who recently raised €4 million in funding, have already planted their modular vertical farms in a Metro Cash & Carry, and plan to install them in German supermarket chain EDEKA.
Investors are increasingly interested in approaches to growing fresh food locally, and smart startups such as Infarm are proving a good place to start.
To receive similar news articles, sign up to our free newsletter here.
40-foot Shipping Container Farm Can Grow 5 Acres of Food With 97% Less Water
The 40-foot containers house hydroponic farms that only draw on five to 20 gallons of water each day to grow produce like lettuce, strawberries, or kale.
40-foot Shipping Container Farm Can Grow 5 Acres of Food With 97% Less Water
by Lacy Cooke
Communities that have to ship in fresh food from far away could start getting local produce right from their parking lots or warehouses thanks to Local Roots‘ shipping container farms. The 40-foot containers house hydroponic farms that only draw on five to 20 gallons of water each day to grow produce like lettuce, strawberries, or kale. Popping up all around the United States, these scalable farms “grow far more produce than any other indoor farming solution on the market” according to co-founder Dan Kuenzi. Local Roots is even talking with SpaceX about using their farms in space.
Local Roots’ 40-foot shipping container farms, called TerraFarms, grow produce twice as fast as a traditional farm, all while using 97 percent less water and zero pesticides or herbicides. They can grow as much food as could be grown on three to five acres. They’re able to do this thanks to LED lights tuned to specific wavelengths and intensities, and sensor systems monitoring water, nutrient, and atmospheric conditions.
Related: Pop-up shipping container farm puts a full acre of lettuce in your backyard
The process from setup to first harvest takes only around four weeks. TerraFarms can be stacked and connected to the local grid. CEO Eric Ellestad said in a video 30 million Americans live in food deserts, and their farms could be placed right in communities that most need the food.
Los Angeles is already home to a farm with several shipping containers, and a similar one will be coming to Maryland this year. It could offer local food like strawberries in January.
And Local Roots’ technology could one day allow astronauts to consume fresh produce in space. Their growing systems could offer a food source on long-term, deep space missions. Ellestad told The Washington Post, “The opportunities are global and intergalactic at the same time.”
Vine to Cart: Grocery Stores Use New Tech To Create In Store Farms
Vine to Cart: Grocery Stores Use New Tech To Create In Store Farms
July 13, 2017
While the demand for organic and sustainable agriculture is growing across the globe, the future of fresher produce might be picking it right at the supermarket.
A startup out of Berlin called Infarm is currently working on an “indoor vertical farming” system with the capacity to grow any kind of fruit, vegetable or herb. Multiple sensors monitor the plants’ health and connected data lets the system know when to irrigate and feed the crops, creating individual ecosystems. In addition to creating idyllic growing environments for each plant, the system is smart, providing the opportunity for experts to analyze and collect data to optimize growth and flavor and potentially predict problems in the future.
“We are able to develop growing recipes that tailor the light spectrums, temperature, pH, and nutrients to ensure the maximum natural expression of each plant in terms of flavor, colour, and nutritional quality,” Osnat Michaeli, co-founder of Infarm, explained in an interview with TechCrunch.
Although vertical farming is already a familiar concept to agriculture, what makes Infarm so unique is their ability to do small-scale vertical farming in customer-facing situations. The company has already found major success after placing systems in Metro Group locations, one of the biggest wholesalers in Europe, and are now being approached by other grocers that want to do the same. Instead of growing produce outside on traditional farms and dealing with the supply chain to deliver it to each store, grocers could invest in InFarm and allow customers to harvest food right from the vine. In an era where grocery stores are trying to remain more relevant to consumers who often shop online for dry goods, InFarm helps grocers turn into a next gen farmers market with fresh from the plant produce.
Investors have also noticed the potential within Infarm as the company recently closed a €4 million funding round which included Berlin’s Cherry Ventures, Impact investor Quadia, London’s LocalGlobe, Atlantic Food Labs, design consultant Ideo, Demand Analytics and others.
Philips Lighting Develops a New Growth Recipe to Reach Seven Times The Average "Vitamin C" Content in Arugula
Philips Lighting (Euronext Amsterdam ticker: LIGHT), a global leader in lighting, today announced that its GrowWise Research Center has produced a vitamin C-rich arugula with seven times higher vitamin C[1] content than the published USDA value of 15 mg/100 gr.
Philips Lighting Develops a New Growth Recipe to Reach Seven Times The Average "Vitamin C" Content in Arugula
July 10, 2017
Eindhoven, The Netherlands – Philips Lighting (Euronext Amsterdam ticker: LIGHT), a global leader in lighting, today announced that its GrowWise Research Center has produced a vitamin C-rich arugula with seven times higher vitamin C[1] content than the published USDA value of 15 mg/100 gr. The vitamin C-rich arugula was grown in a trial in collaboration with the Dutch Wageningen University and Research, and Maastricht University, using a new growth recipe under Philips LED lighting in a vertical farming environment with no daylight.
The results of this trial prove that it is possible to add functional ingredients to a food like arugula in a natural way by simply growing it differently. Retailers and growers can apply specific Philips growth recipes using LED technologies to meet the growing demand for functional foods from health-conscious consumers. Since vitamin C is one of the markers of shelf life, the higher vitamin C levels in the arugula at harvest may also help retailers extend the green’s shelf life. In addition to vitamin C, other healthy compounds are shown to be influenced by the growth recipe.
“The results of this trial reveal that not only can we boost the yield of a crop, but we can also influence the taste and growth characteristics of a crop by changing the growth recipe. A Philips growth recipe provides parameters for growing a crop that include the light level, spectrum, intensity, required uniformity, position and time, as well as climate conditions like temperature, humidity, CO2 levels and nutrition,” said Udo van Slooten, business leader for Philips Lighting’s horticultural lighting business. “This achievement confirms the tangible benefits that our research at Philips GrowWise Center is delivering for growers and retailers as they look to meet specific consumer needs like optimized smell, taste and flavor to differentiate themselves in their markets.”
Light Influences Nitrate Level
The arugula grown under the LED lighting with the new Philips growth recipe showed a very low nitrate level while having a high yield. Lower nitrate levels also have higher sugar levels and a milder taste. The leaves grown under the LED lighting scored between five and eight on the Brix index, which correlates with a higher perception of sweetness in sensory tastes. The low nitrate levels achieved in this trial are considerably lower than those set by the European Union, which range from 7000 mg/kg to 6000 mg/kg). This low-nitrate arugula would help retailers in Poland, Russia and Finland, specifically, meet the growing demand for low-nitrate foods from consumers in these countries. By using another growth recipe, it is also possible to grow a high vitamin C arugula with a high nitrate content for consumers willing to use high rich nitrate content as a health benefit without affecting the production of other nutritious compounds.
The trial was carried out at the Philips GrowWise Center in Eindhoven, the largest vertical farming research facility of its kind, in cooperation with Wageningen University and Research for plant science and shelf life, and Maastricht University on Health Food innovation, both in the Netherlands. The arugula crop was tested in four different lighting situations with three different LED lighting combinations and one artificial light source that mimicked the sun and/or HPS lighting. The effects of high blue and high far red wavelengths were also studied to determine their impact on shelf life and nutrient content of the harvested greens.
For a comprehensive guide on how to grow arugula, at home, click here:
For further information, please contact:
Philips Lighting, Horticultural LED Lighting, Nederland
Daniela Damoiseaux
Tel: +31 6 31 65 29 69
E-mail: daniela.damoiseaux@philips.com
www.philips.com/horti
Hydroponic Paradox: Saving Water With Water
Hydroponic Paradox: Saving Water With Water
June 6, 2017
by Mary Allen
The local food movement has deep roots in urban centers, but the juxtaposition of urbanites’ locavore enthusiasm with the shortage of arable land in cities raises the question: how local is local enough? In terms of geography, there is no consensus or regulation around what “local food” should be. Depending on your definition (or marketing strategy), the term could refer to anything from food produced in your own backyard to food produced 100 miles away or simply within the state.
Community gardens and urban farming are obvious—if partial—answers to this paradox. And while urban farming is nothing new, there’s no denying that in recent years, rooftops gardens, vertical farms, and the like have become increasingly seductive to enterprising young farmers. Consumers, the media, and even investors are climbing on board with new urban farming initiatives as 21st century innovation pushes the limits of how and where food is grown.
This hydroponically grown basil has never touched soil or seen sunlight. | Image Source: @plantnasty
Hydroponic farming, a system in which plants are grown without soil and are nourished instead by a mineral solution, has enjoyed a groundswell of entrepreneurial energy in particular. As hydroponics are well suited to indoor spaces and environments that would otherwise be unfit for plant life, city centers are primed for the proliferation these wunderkind farms.
From the sweeping Alexander Ranch greenhouse in California and Bowery’s warehouse farm in New Jersey, to the intimate indoor Farm.One nestled at the heart of the Manhattan’s Institute of Culinary Education and the shipping container farms of Square Roots in a parking lot in Brooklyn, hydroponic farms of all shapes and sizes are cropping up across the country. The hyperlocality they offer to city-dwellers means not only that the food travels fewer miles, thus reducing the transportation footprint, but that the produce can be harvested and delivered on the same day.
Baby kale and butterhead lettuce from the behemoths Gotham Greens and Bowery can be found in grocery stores. Square Roots farmers hand-deliver their greens to offices around New York City. Farm.One, which is a specialty grower of microgreens and garnishes, serves high-end chefs and restaurants from just a subway ride away. With greens being among the most perishable of produce, this rapid delivery is especially attractive from a food waste reduction standpoint. Hydroponics becomes a compelling alternative to soil-based urban farming practices in light of its unique sustainability solutions.
Namely, it is remarkably water efficient. Seventy percent of humans’ water usage is allocated to farming and animal agriculture. Nitrate-ladened fertilizer runoff from traditional agriculture is also one of the main causes of water pollution, catalyzing algae blooms that ultimately create dead zones in our rivers, lakes, and oceans. In hydroponics, water is continuously recycled, making these systems anywhere from 90 to 98 percent more water efficient than traditional farming while eliminating fertilizer runoff. Needless to say, this drastic improvement in water efficiency makes hydroponic farming especially interesting in places like California where water is in short supply.
Hydroponic farming can be tremendously space efficient, too. In an interview with the Natural Gourmet Institute, Gotham Greens’ Nicole Baum enthusiastically notes, “Our half acre rooftop farm on top of Whole Foods Market in Brooklyn actually produces that of a 10 acre soil based farm!” Even more impressively, Bowery asserts that it produces over one hundred times more food than a traditional farm on the same footprint of land.
Part of the reason that hydroponic farms are able to grow so much more is that the plants have continuous ideal growing conditions—just the right temperature, just the right light, with no hungry animal intruders and no winter. The clean, climate controlled environments also eliminate the need for pesticides and insecticides. For the odd pest that does wander in, farmers enlist beneficial insects, such as ladybugs, to keep the peace. Being pesticide-free is a point of pride for Farm.One, Square Roots, Gotham Greens, and Bowery alike, something Bowery refers to as “post-organic.”
Rock wool is made from spun fibers of molten rock. This is one medium that hydroponic farmers use in lieu of soil to germinate seeds. | Image Source: @plantnasty
And here we encounter the discomfort hydroponic farming engenders among the soil-loyalists in the good food movement. A central tenant of organic farming is to “feed the soil, not the plant.” With hydroponics, of course, there is no soil, just plants—and manufactured mineral solution. The long term viability of an entirely human-fabricated growing environment is a big question mark for many. So while the notion of “post-organic” produce may thrill the food tech enthusiasts, strong advocates of pre-agroindustrial sustainable farming practices balk at the idea of food grown in plastic containers with artificial light.
Despite its water-saving potential, indoor hydroponic farming poses its own sustainability risks. These operations rely on LEDs, which stay on approximately 18 hours per day. Does drastically reducing water usage and water pollution justify the carbon footprint of all that electricity? It’s a question that hydroponic farmers are already taking into consideration. Farm.One, for instance, purchases carbon offsets to help mitigate this environmental cost.
But then there’s the actual cost. For all its efficiencies, hydroponics is a capital intensive process in a highly competitive market. A small bag of greens from Square Roots is $5. As Square Roots Cofounder and CEO Tobias Peggs explained at the monthly open house, the heavier a plant is—the more biomass it has—the more costly it is to grow. At this point in the game, hydroponic growers are focusing on greens. Fruits, vegetables, and tuber roots are not quite financially viable. But as the technology continues to improve, the price points continue to drop.
According to Rob Laing, CEO and founder of Farm.One, the price of LEDs is roughly halving every four years. Farm.One keeps their profit margins viable by selling high-end microgreens and garnishes, but Laing is hopeful that, “in five years time people can use the techniques that we’re using and similar equipment to grow lettuce and kale underneath a bodega.” Peggs is even more sanguine: “We think, two years from now, we’ll be able to economically grow strawberries, tomatoes, and blueberries as well.”
Technology is not the only thing setting hydroponics on the fast track to improvement; robust data collection is supercharging production capacity. Modern hydroponic farms are outfitted with sensors to monitor the plants, water, air, and light, and the farmers are growing not just crops but databases of information about how different factors influence flavor and plant health.
Farm.One's Red Rubin Basil, Saltwort, Red Veined Sorrel & Stems | Image Source: @farm.one
With different light recipes and nutrients, farmers can adjust certain variables to bring out different flavors. Some farms are even using machine learning to integrate and deploy these learnings. It’s a prospect that is remarkable to some and off-putting to others. As Dan Barber said in a conversation with co-founder of Square Roots Kimbal Musk at the Food for Tomorrow conference, “When Kimbal says you can dial in the flavor and colors you want, I don’t know that I want that kind of power,” Barber said. “I’d rather have a region or environment express color and flavor.” Agree to disagree perhaps. New Yorkers might not be as enthused about the taste of the subway expressing itself in their salad greens.
So what role will hydroponics play in the future of food? “People on both sides of the issue tend to overstate how big hydroponic farming is going to be,” Laing told Food Future Co. “It’s part of the solution.” He reminds us that hydroponics works well for greens but not at all for crops like wheat or corn. It can’t replace pig farms (leave that to Memphis Meats). It can’t replace olive groves. What hydroponics can do, however, is expand the possibilities for local food in urban spaces. It has many promising implications for sustainable food production. It may even serve as a more viable on-ramp for the next generation of farmers. Who knows? At the rate technology and data are changing the world, we really may be able to buy a locally grown, freshly harvested strawberry in the dead of winter from the corner bodega.
Farmers Grow A New Stream of Revenue Through Vertical Farming
Farmers Grow A New Stream of Revenue Through Vertical Farming
Combining hydroponic techniques with new timer control innovations
In January, the open fields of Harvard, IL, a far northwestern suburb of Chicago, are biting and bone-chilling. Inside Kirk Cashmore’s barn, it is a fair 72 degrees F, the perfect temperature for producing leafy heads of lettuce through vertical hydroponics, the practice of water-based gardening with vertically stacked shelving in a controlled environment.
Since 2011, Kirk Cashmore has been the only for-profit vertical hydroponic farmer in Northern Illinois. His pesticide- and chemical-free lettuce is served at a popular, Green-certified restaurant, Duke’s Alehouse and Kitchen, in nearby Crystal Lake, IL, and sold at biweekly basket drops along the North Shore and in the Madison, WI metro area.
“Working for my grandfather as a big acre farmer for many years taught me how things worked. I always knew I wanted to be a farmer, but wanted to take a different approach to it. I didn't have the capital or the money to buy big acres to start a traditional farm, so I went around the Midwest and looked at farms that were growing hydroponically and figured out how to start my own,” said Cashmore.
A Growing Industry
According to a recent market research report, the vertical farming market is estimated to be valued at 5.8B U.S. dollars by 2022, growing at a Compound Annual Growth Rate (CAGR) of 24.8% between 2016 and 2022. Factors driving growth of the vertical farming market include generating high quality food without the use of pesticides, less dependency on the weather for production, a growing urban population, an increase in the year around production of crops, and reduced impact on the environment.
“The beauty of hydroponic farming is there really is no downtime… I have assets throughout the whole winter and am the only game in town when it comes to winter production of lettuce, Swiss chard, kale, and all the small greens that can be harvested hydroponically,” he remarked. None of his yield is ever wasted. Unsold, yet still edible, greens are donated to a local food pantry and wilted or damaged heads are sent to the compost bin.
Inside Cashmore’s 3,500 square foot building, three vertically stacked shelves, built from recycled materials, provide room for up to 4,000 heads of lettuce. Each shelf grows approximately 1,200 heads, or about five heads per square foot, which Cashmore reports is the number to beat in the world of vertical hydroponics. With room in his barn to still expand out- and upwards, Cashmore has the potential to harvest nearly 8,000 heads.
Plants are seeded in rockwool, a lava-like medium that allows for more oxygen than does soil or water, and an ebb and flow pumping system supplies water to the roots. Cashmore checks pH levels daily.
Winter in the Midwest means long periods of grey, cloudy skies. An electronic timer ensures lights remain on based on the amount of sun, typically 16 hours a day, 7 days a week. Relying on the timer to turn lights on and off as needed gives Cashmore – a one-man show – the freedom to tend to other business without worrying. “Timers are very important for turning lights and fans on and off,” stated Cashmore. “Having an electronic timer makes this an automated sport, so I can have more time with my family and friends. It gives me more time to not have to work.”
He also believes that ensuring a good supply of oxygen is absolutely vital to growing success. Floating rafts of lettuce -- or any system where roots are permanently soaked in water -- offer little available oxygen since the solubility of oxygen in water is remarkable low. Cashmore monitors how much oxygen his roots have and uses an ozone system to kill bacteria, control oxygenation, and keep the water sanitized. This has eliminated the need to use chemicals such as chlorine or hydrogen peroxide.
“I find that if something is worth doing, it's worth doing right. As a father of three little girls, I have no tolerance for chemicals going home and into my kids’ mouths. I want to make the best produce that I can for my family, my clients and my friends,” he explained.
Organically Grown Produce That’s Bug-Chemical-and Pesticide-Free
One of the biggest benefits of hydroponic farming is the superb quality of the produce. Plants don’t spend any time outside in the wind, dirt or the rain; they grow in a controlled environment that is bug-, chemical- and pesticide free. This creates greens with an unmatched body and texture. As more and more people buy organic and seek out locally grown produce, demand is certain to grow. Cashmore envisions remaining profitable and productive by adding more capacity to double or triple lettuce headcount and growing a variety of other vegetables in the winter.
“From school field trips to other farmers and private citizens, there’s an increasingly large interest in my hydroponics facility. I hope to see more vertical hydroponic farms popping up in the area over the next decade.”
Do you have a budding interest in vertical hydroponic farming? Learn more with an in-depth look at Kirk Cashmore’s farm.