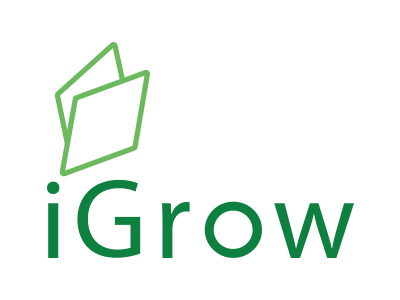
Welcome to iGrow News, Your Source for the World of Indoor Vertical Farming
Food Strategist & Brand Builder Joins FreshBox Farms Advisory Board
Food Strategist & Brand Builder Joins FreshBox Farms Advisory Board
Former Starbucks VP Recognized for Innovations and R&D Strategies
MILLIS, MA – June 26, 2017 – Food strategist and recognized brand builder Dr. Mary Wagner has joined FreshBox Farms’ advisory board.
Wagner, who has worked with brands including Starbucks, Mars, Taco Bell and General Mills, will be focusing on product/business development and strategy for one of the nation’s most profitable modular vertical farms.
“We are very pleased to have someone with Dr. Wagner’s experience and record of success among our advisors,” says FreshBox Farms CEO Sonia Lo. “As a Senior Vice President at Starbucks, Mary built a culture of innovation, and she is recognized for her work in food quality and safety as well as her ability to build brands and create successful strategies that foster innovation.”
FreshBox Farms uses sustainable growing enclosures that use no soil, very little water, a rigorously-tested nutrient mix and LED lighting to produce the freshest, cleanest, tastiest produce possible. FreshBox Farms’ non-GMO certified products go from harvest to the grocer’s produce section in hours, rather than days, and it is the only greens grower -- hydroponic or conventional -- in Massachusetts to be certified kosher.
“As one of only two commercial vertical farms in the US that are gross margin positive, FreshBox Farms continues to innovate and continues to be an industry leader, and we look forward to Mary’s wise counsel as we continue to be a success story in this advanced, technologically-sophisticated food industry,” says Lo.
“Indoor hydroponic farming in the US has amazing growth potential -- no pun intended,” says Wagner. “Forecasters believe that over the next 10 years, 50% of all greens will be harvested indoors through some form of hydroponic growing, and I am eager to work with Sonia and her team on research and innovation that will keep FreshBox Farms an industry leader.”
As Senior Vice President at Starbucks, Wagner was responsible for creating global food and beverage products and solutions for Starbucks and its Evolution Fresh and Teavana brands. She led the effort to create Global Centers of Excellence for R&D, Quality and Regulatory in US, Asia and Europe, with the aim of offering innovative locally relevant products in key markets outside the U.S.
She also created a “stage/gate” product development priority process that focused resources and energy on innovations that had the highest return. The result was improved time to market and an increase in more meaningful new product launches.
Wagner recently founded MK Wagner and Associates, a global food science management consulting firm that specializes in R&D strategic leadership.
About FreshBox Farms, The Thoughtful Choice
Each time consumers go shopping, they make a variety of decisions. “The Thoughtful Choice” is knowing that FreshBox Farms’ produce will always be the best option for their health, happiness, and the planet. Founded in 2013, FreshBox Farms is an entrepreneurial company with a mission of producing non-GMO certified, fresh, healthy, and pure produce for local markets through industry leading and sustainable vertical farming. Its technology and values have received global attention with interest from European, Middle Eastern and Asian markets. To learn more about FreshBox Farms, please visit www.freshboxfarms.com.
With Urban Grit and Pink Lights, London Warehouse Farms Fish and Greens
With Urban Grit and Pink Lights, London Warehouse Farms Fish and Greens
By Reuters
PUBLISHED: 20:00 EDT, 26 July 2017 | UPDATED: 20:00 EDT, 26 July 2017
By Lin Taylor
LONDON, July 27 (Thomson Reuters Foundation) - Inside a warehouse in industrial southeast London, farmed tilapia swim in blue tubs filled with pristine water, ready to be sold to trendy restaurants across the capital.
In an adjacent room, under pink LED lights and controlled temperatures, shoots of salad leaves and herbs grow on recycled carpet fibre fertilised with the fish waste. In this cavernous, windowless space more suited to a nightclub than a farm, the greens are stacked on metal shelves stretching to the ceiling.
It's a far cry from traditional British farms that sprawl across acres of land. But for Kate Hofman, who co-founded GrowUp Urban Farms in 2013, producing food in this 6,000 square feet building in Beckton was not only clever and cost-effective, it was also a sustainable way to feed people in the city.
"Sometimes people have an idealised idea of how their food is being produced. In their head, they think that farmer Joe tends to his field with his hoe and grows his heads of lettuce," the 32-year-old told the Thomson Reuters Foundation.
"We're trying to show that you can have an industrialised food system ... but you can do it in a way that's sustainable," said Hofman, who launched Britain's first commercial aquaponic farm - a system that uses fish waste to fertilise crops, which in turn filtrate the water used to farm the fish.
Rich and poor countries alike are tasked with creating sustainable and inclusive cities by 2030 under global development goals agreed in 2015 - and sorting out how cities are fed is a crucial part of that challenge, experts say.
As two thirds of the global population are forecast to live in cities by 2050, compared with about half now, urban planners and policymakers are increasingly looking to agriculture in towns and cities as a solution to provide nutritious food.
CLOSER AND FRESHER
Land used for farming in cities and the areas around them equals the size of the European Union, a recent study said, while others estimate some 800 million urban farmers provide up to 20 percent of the world's food.
Unlike imported produce, food from city farms and gardens travels less, reducing production costs, waste and fuel use.
"Because (urban farms) are in proximity to an urban population, they can see for themselves where their food is coming from. This has a benefit in terms of education and reconnecting food with the consumer," said Makiko Taguchi, an urban agricultural expert at U.N. Food and Agricultural Organization (FAO).
Having your food come from sources close by is also crucial if supply is disrupted by civil unrest or extreme weather in the rural areas that still supply most of the world's food.
Hofman said Britain's huge appetite for salad leaves and herbs, and the fact that most of it is imported, were key reasons why she decided to grow such plants in her warehouse.
"It makes sense to grow crops like these close to people so you can get it to consumers more quickly - they're fresher, they last longer in the fridge, they're less likely to go to waste," said Hofman, who sells 200,000 bags of salad each year to local food retailers and restaurants.
Hofman also sells 4 tonnes (4000 kg) of fish each year and believes the ethical farming of fish provides a sustainable source of protein, especially at a time when nearly 800 million people worldwide do not have enough to eat, according to FAO.
Though Hofman doesn't think urban farming could ever replace existing food production systems, she hopes to pioneer ways to scale up the output of urban farms.
"It's terrifying. There's so much unknown in the model that we're trying to do. There are so many challenges that we're trying to overcome," Hofman said.
"But it offers a really exciting opportunity for people to engage with the idea of farming as something that can be sustainable and high-tech."
(Reporting by Lin Taylor @linnytayls, Editing by Lyndsay Griffiths. Please credit the Thomson Reuters Foundation, the charitable arm of Thomson Reuters that covers humanitarian issues, conflicts, global land and property rights, modern slavery and human trafficking, women's rights, climate change and resilience. Visit http://news.trust.org to see more stories)
Follow us: @MailOnline on Twitter | DailyMail on Facebook
Grow Your Salad in Your Closet With The GrowChef Hydroponic Garden
GrowChefis a small indoor garden that promises to let you harvest a full pot of greens every day. Because why pay $15 for a salad when you can just make your own fresher version?
Grow Your Salad in Your Closet With The GrowChef Hydroponic Garden
By Lulu Chang — Posted on July 25, 2017 12:20 pm
WHY IT MATTERS TO YOU
Who needs a supermarket when you have GrowChef? This indoor hydroponic garden will let you make salad more often.
The nearest farmer’s market? Your kitchen. Thanks to the GrowChef, you can enjoy the goodness of fresh farm produce, even in the midst of an urban jungle. Heralded as the “ultimate hydroponic food generator,” the GrowChefis a small indoor garden that promises to let you harvest a full pot of greens every day. Because why pay $15 for a salad when you can just make your own fresher version?
Designed to live just about anywhere in your home, no matter how cramped your space may be, the GrowChef can be hung on a wall, set on a floor or a window sill, or even hidden away in a closet. Because of its three-color LED illumination, this little garden creates enough light on its own so you don’t have to worry about placing it in a sunny spot. And while it measures just 24 inches long, 30 inches tall, and 12 inches wide, it claims to produce the same harvest as a three-meter long garden bed.
Of course, because this is a 21st-century invention, the GrowChef comes with an app that allows you to monitor the progress of your plants. And given that you can grow up to 51 plants at once, that’s a lot of monitoring. Luckily, you don’t have to worry about potting any of these plants, as there’s no soil involved. There’s just nutrient solution and vermiculite, the former of which you replenish once a month.
The three tiers of the GrowChef correspond with three stages of growth for your plants. When you’ve just slid new pods into their slots, they go to the very top, where they’ll receive the most light. As they begin to grow, they can be moved to the second tier, where they can continue to develop. And finally, when they’re almost ready for harvest, you can move them to the bottom tier, which really gives the plants room to blossom.
“I’m delighted to bring people a new original opportunity to have fresh herbs on your plate every day,” said founder Viktor Pjatnitski of the hydroponic garden. “GrowChef helps you to eat healthier, [and] reduce your shopping list and expenses. After two and a half years of experiments, we’ve figured out how to perfect the hydroponic farm to constantly provide you with ready-to-eat plants.”
You can pre-order the GrowChef now from Kickstarter for $210, with an estimated shipment date of March 2018.
Urban Farming 2.0: From Plow Beams to Leafy Green Machines
Urban Farming 2.0: From Plow Beams to Leafy Green Machines
SEARCH FOR SOLUTIONS
A new generation of urban farmers is leaving dirt behind and turning shipping containers into tech-driven vertical farms.
Shane Witters Hicks/Staff
Shane Witters Hicks | Staff
JULY 26, 2017 BOSTON—Shawn Cooney swings open the door of 320-square-foot industrial shipping container to reveal a futuristic setting: hundreds of edible plants growing in vertical columns, fed by the energy from strings of neon red and blue LED lights. Nutrient-infused water cascades from ceiling spigots down through artificial root systems in the growing towers. The temperature inside feels like a comfortable spring day – about 70 degrees F., with a touch of humidity. There isn’t a speck of dirt anywhere.
Welcome to the new urban farm.
This shipping container is one of four that comprise Corner Stalk Farm run by Mr. Cooney and his wife in the heart of Boston. Once the cargo holds for exhaust-spewing 18-wheelers, these discarded freight vessels have been transformed into units known as Leafy Green Machines outfitted with state-of-the-art growing technology by a company called Freight Farms. Now they help farmers turn out crops of lettuce and herbs at a rapid pace.
In the past, urban farmers have eked a living from food grown in greenhouses, reclaimed brownfields, vacant lots, or rooftop farms. But with these new kinds of urban crops – grown using what’s known as controlled-environment agriculture, or CEA – farmers leverage technology to break free from the seasonal and climatic limitations that bind traditional crops. As a result, these farmers enjoy longer growing seasons and more plentiful harvests – a hopeful promise for urban communities looking to boost access to fresh produce.
“To think that you don’t have to worry about whether it’s going to rain, or whether the sun is too bright because you flick a switch and you know how much light you have, you know how much water is being supplied ... that would take a lot of the stress out of agriculture,” says Joel Gruver, associate professor and director of Western Illinois University's research and demonstration farm.
Getting fresh food into urban centers has proved to be a persistent and growing problem. By 2050, 66 percent of the world’s more than 9 billion people will live in cities, predicts the United Nations. While some cities offer farmers’ markets and have worked to open more grocery stores in so-called food deserts, these farmer-entrepreneurs are searching for solutions that will not only grow fresh food within city limits but also mitigate some of the environmental effects of traditional farming.
“People want real food. And increasingly people live in the city. So there has been – unsurprisingly – a lot of innovation and investment in urban farming in the last handful of years,” says Tobias Peggs, co-founder and chief executive officer of Square Roots Urban Growers in Brooklyn, N.Y. Upon launching, the company received more than 500 applicants for 10 farmer slots from those wanting to take up the challenge.
Easing An Environmental Burden
Small-scale sustainable farming and organic practices have long sought to lessen the environmental impacts of monocropping and pesticide reliance, but CEA has a significant advantage: the ability to scale up without significantly increasing its ecological footprint. The vertical farming market is expected to quadruple from its $1.5 billion market value in 2016 to $6.4 billion in 2023, according to a recent report by Allied Market Research.
In San Francisco, agrotech company Plenty boasts a 51,000-square-foot warehouse that leverages machine learning to optimize plant growth.
Nate Storey, Plenty’s co-founder and chief science officer, says the environmental benefits gained by fusing technology and food production make large-scale CEA a no-brainer.
“We have no runoff, we have no erosion, we have few, if any, pests, we don’t need to use many of the pesticides, we don’t have any soil to sterilize, we don’t have any intensive irrigation, we use a fraction of the water,” he explains. “There are just not a whole lot of reasons not to do this.”
Unlike other large-scale food producers who must optimize their goods for long truck rides and shelf lives, indoor growers located closer to customers can instead prioritize food quality, such as flavor and “mouth feel,” as Dr. Storey puts it.
For independent CEA farmers, starting up a controlled environment for indoor growing doesn’t come cheap. A Freight Farms unit costs $85,000 and the annual operating costs range between $8,000 and $16,500. But Cooney of Corner Stalk Farm, who bases the size of his crop on customer demand, explains that similarly sized outdoor farms are pressured to overproduce during short growing seasons.
“Their losses are much higher. So that’s why it comes out to be about the same,” he says. Moreover, other farms may spend a fortune on transportation and land. Taking up about 1/34th of an acre, Cooney’s lettuce farm can have a marketable yield that’s about the equivalent of 8 acres of traditional farmland yield, according to Freight Farms. And the indoor environment allows for a continual harvest.
But without the government subsidies that larger farms receive, greens grown within shipping containers will inevitably cost more than most supermarket greens.
“A bag of our Square Roots greens costs about as much as a Starbucks [coffee],” admits Mr. Peggs. He is quick to add that the enhanced sense of community fostered through farmer-customer relationships makes the price worthwhile.
“Customers come to the farm and hangout – we have a big window on the farm, so everyone can see what’s going on. It’s all about total transparency in the food-supply chain,” Peggs says.
But is High-Tech Food ‘Natural’?
The benefits of CEA may be tantalizing, but Dr. Gruver of Western Illinois University foresees potential difficulties for the burgeoning industry. Controlled-environment agriculture depends upon those who can operate and fix the technology. In other words, finding someone who can troubleshoot a malfunctioning LED system may prove more difficult than finding someone who can repair a tractor, for example.
And while local food and connections to the farmers who grow it have proven to be profitable in urban markets, not everyone embraces the idea of food grown exclusively in an artificial environment.
“I think with any high-tech approach, there is a general concern that it’s not natural,” says Gruver. “There’s more potential for unforeseen, unintended consequences.”
Urban tech growers are well aware of this perception.
“We’re sensitive to that,” responds Storey of Plenty. “We’re really focused on how do we show people that this new growing environment is something that is important for our food supply.”
Before indoor farmers can dominate the urban food arena, however, they’ll need to grow more than lettuce and herbs. The larger the plant, the more energy it costs to grow it, and this energy is currently expensive.
But based on the rapid pace of innovation and technology, Peggs predicts large, affordable produce may not be far off. He thinks his Square Roots entrepreneurs will figure out how to grow sustainable strawberries within 18 months.
“Imagine a farmer traipsing through 2 feet of snow to deliver you a box of freshly harvested, locally grown strawberries in the middle of a New York winter,” he says. “In the near future everyone will have local food and they will know your farmer.”
Aquaponics Operation Tests Cayman’s Potential
Aquaponics Operation Tests Cayman’s Potential
Canadian company aims to fulfill Cayman’s leafy vegetable demand
By Kayla Young | July 25, 2017
While Cayman’s natural barriers may inhibit its agricultural potential, a Canadian farming operation is betting on transforming the islands into a potential aquaponics site.
Alberta-based NutraPonics is evaluating plans to set up a 6,000-square-meter (64,580-square-foot) growing bed in Grand Cayman that director Tim Goltz anticipates will satisfy 80 percent of the local leafy greens market.
“We can blow the top off it and really surprise people. We can make Cayman a global leader,” Mr. Goltz said.
“Indoor vertical farming in and of itself is probably one of the hottest investment spaces in the world right now,” Mr. Goltz said.
The company’s aquaponics systems operate in a fully enclosed, high-density growing environment. Tilapia kept in tanks produce byproducts that are then filtered to create nitrate-rich water. These nutrients are filtered to the vertical growing area, where plants sit under LED lighting.
Pesticides unnecessary
The enclosed nature of the growing method eliminates the need for fertilizers, pesticides and other chemicals.
The setup aims to minimize operating costs and maximize food production. Mr. Goltz estimates a 6,000-square-meter growing bed would produce enough leafy greens to feed 60,000 people.
Vertical stacks allow the NutraPonics system to grow more food in less space.
He noted that shoppers in Cayman depend on high-cost imports routed from farms in North and Central America. While Cayman’s grocers and restaurants already receive a limited supply of local produce, including some grown using hydroponics, Mr. Goltz hopes NutraPonics will be able to supplement supply and offer an alternative to imports.
The perishable leafy greens are particularly sensitive to long journeys, which creates an extra headache for supermarkets, Mr. Goltz said. Temperature fluctuations, delays on the tarmac and other disruptions can all compromise shelf life.
“Grocers have a real logistical and structural problem unless someone can figure out how to grow the volume they require,” Mr. Goltz said.
After meeting with grocers in November, Mr. Goltz said aquaponics could solve many of their supply-chain problems. He contends vertical, indoor farming could provide a local solution.
He expects the operation would require around 40 local employees.
Vertical stacks allow the NutraPonics system to grow more food in less space.
With two other operations under way in Saskatoon and White Horse, Canada, NutraPonics hopes to prove its model can operate under the most hostile growing environments. Once a Cayman facility takes off, Mr. Goltz envisions moving beyond leafy greens to a range of hothouse vegetables, including strawberries, tomatoes, sweet and hot peppers and cucumbers.
“Our ultimate goal is to become kings of the strawberry empire in the Caribbean,” Mr. Goltz said.
Investment interest
While it has been difficult to attract international partners to the company’s Edmonton facility, Mr. Goltz said entrepreneurs in Singapore, Dubai and Oman have already shown interest in Cayman’s potential. He expects the islands’ natural beauty and tax neutrality will be a draw for investors.
NutraPonics’ operations in Cayman would fall under two branches, the vertical aquaponics facility, and a separate corporation for global development.
In the long term, Mr. Goltz hopes to turn the Cayman facility into a showcase for sustainable agriculture, where tourists and schoolchildren can learn about farming.
The company is evaluating a West Bay property owned by the National Trust for the project but has not finalized a lease on the land.
Mr. Goltz said his team is in the fundraising stage and meeting with potential partners.
Tanks of tilapia produce byproducts that then nourish plants in the growing house.
This Vertical Farm Wants To Be An Agriculture Company, Not A Tech Company
- 07.12.17 | Updated: 07-26-17
This Vertical Farm Wants To Be An Agriculture Company, Not A Tech Company
The FreshBox model centers around shipping containers. [Photos: courtesy FreshBox Farms]
FreshBox Farms is going big by focusing on harvests, not proprietary growing systems.
As the indoor farming industry has taken off in the last several years–over the next 10 years, indoor farming is expected to account for 50% of leafy green production, and grow to a $42 billion industry–it’s become apparent that it’s as much about technology as it is about agriculture. Bowery, a new startup operating out of an old warehouse building in Kearney, New Jersey, developed a sensor-based proprietary technology, called BoweryOS, specifically to support the venture by determining necessary nutrient levels, as well as when crops are ready for harvesting. And in South San Francisco, Plenty is growing produce via a tech-supported vertical farming model that has already received $26 million from tech investors like Bezos Expeditions and Innovation Endeavors.
For FreshBox Farms, an indoor farm operational since 2015 at an old factory site in Millis, Massachusetts, around 30 miles outside of Boston, the technology is important–it is, after all, what enables the greens to grow–but it’s not sacred. “We’re equipment agnostic,” Sonia Lo, the CEO of Crop One Holdings, FreshBox’s parent company, tells Fast Company. “There are people out there doing great work to perfect lights, trays, control systems, nutrient dosing systems–we focus on growing as much as possible.” This almost brusque approach, Lo says, has enabled FreshBox Farms to become one of just two commercial indoor farming ventures in the U.S. that is gross-margin positive. The other is the Newark, New Jersey-based AeroFarms, which grows up to 2 million pounds of produce per year.
Earlier this year, Matt Barnard, CEO of Plenty, told Fast Company that “small-scale growing in 2017 is not a profitable enterprise.” He was referring to the fact that indoor farming startups, which, since the boom began within the last five years, have a track record of failure. FarmedHere, a Chicago-based venture, intended to expand nationally but instead went bankrupt earlier this year, citing the difficulty of maintaining financial equilibrium. PodPonics and LocalGarden, ventures based respectively in Atlanta and Vancouver, similarly failed; the business tensions derived from the high cost of technology, and the relatively small return on investment from output and distribution. Given the hefty price tag of developing proprietary growing technologies, not to mention renting pricey urban land, underwhelming harvests (which are common among startups still tinkering with their growing systems) can be financially devastating.
But with the cost of technology (for instance, LED lights, sensor technology, and smartphones, all of which are necessary for indoor farming) falling, and interest in local produce continuing to increase, Lo believes FreshBox Farms has hit on a sweet spot with its growing strategy. The company spends less money growing more product than any other indoor farm in the country, and Lo attributes that to FreshBox’s approach to technology, and easily scalable farm setup.
The FreshBox model centers around shipping containers (hence the name of the farm). At the farm in Massachusetts, which currently serves 37 supermarkets in the Boston region, each of FreshBox’s 12 commercial products, whether it be kale, arugula, or chard, is grown with hydroponics in its own shipping container; the farm currently houses 15, along with one “Mod”–a modular unit equivalent to nine containers. Conditions inside each container are optimized for each product, but the network as a whole is governed and monitored by the same technology system. By growing crops in separate containers, Lo says, FreshBox can focus on optimizing yield for each product.
The modular system, Lo says, is really what has enabled FreshBox to become profitable just 23 months after launching two years ago. “Because we’re modular, we’re not waiting for a whole farm to be built out to create revenue,” Lo says. “Once we have a box or two on the ground, we’re growing.” FreshBox can have a farm up and running, and selling, within 12 weeks.
The current FreshBox Farm configuration in Massachusetts produces a quarter ton of produce per day, but Lo emphasizes that as the company continues to iterate on the technology it uses and the size of the containers themselves, that number will likely increase. Currently, FreshBox is growing the equivalent of as much as 19 acres of produce in 320 square feet; as FreshBox verticalizes further, that efficiency will grow. “Real estate is a square-foot venture,” Lo says, “But we’re dealing in cubic feet.” Meaning that once FreshBox secures a plot of land on which to operate, they can continue stacking shipping containers higher and higher, and maximizing output. The containers on the farm are not yet stacked, but that’s a next step, Lo says.
Even as other indoor farming companies struggle with expansion, Crop One Holdings has locked in nine new locations for the next generation of FreshBox Farms. The majority will be in the northeast, and, like the Millis farm, located outside the urban center to cut down on property rental costs. And the focus, Lo says, will remain on productivity and profit–not necessarily for profits sake, but to ensure that fresh produce can become more available. “There are a ton of urban farmers out there who are talking about how they’re on the cutting edge of technology and measuring 20,000 data points,” Lo says. “But we’ve never fallen in love with the science. We’re all about: What is the yield? Are we actually growing things? Are we selling every leaf?”
Over the next five years, FreshBox is aiming to reach 25 farms across the U.S., each of which will produce between one and three tons of produce per day. The company will continue to iterate and switch out technology as it grows, and as more efficient systems become available. “I don’t think you should be in this industry unless you’re planning to be big,” Lo says.
Indoor Farms of America Bridges the Gap with Traditional U.S. Agriculture in Landmark Farm Sales
"With the sale of these farms, which will be up and running in the great state of Indiana in about 90 days from today, our company has achieved the first stage of the plans to have large scale indoor farming adopted by the very folks who have kept us fed in this country since its inception, and that is the traditional farmer," stated David Martin, CEO of Indoor Farms of America.
Indoor Farms of America Bridges the Gap with Traditional U.S. Agriculture in Landmark Farm Sales
NEWS PROVIDED BY | Indoor Farms of America
Indoor Farms of America corporate Farm Manager Anthony Randolph grows beautiful greens in the vertical aeroponics from IFOA.
LAS VEGAS, July 25, 2017 /PRNewswire/ -- In what is a watershed transaction and a continuance of plans to integrate world-class indoor agriculture equipment into traditional farming, Indoor Farms of America announces that it has sold the first two "warehouse" style farms to Co-Alliance, LLP one of the largest, oldest and most respected major locally owned Farmer Cooperatives in the United States.
Unlike all other commercial scale Indoor Farm equipment, Indoor Farms of America patented equipment does not require ladders or skylifts to operate, and grows 40 plant sites per square foot in just 8 feet of ceiling height.
"With the sale of these farms, which will be up and running in the great state of Indiana in about 90 days from today, our company has achieved the first stage of the plans to have large scale indoor farming adopted by the very folks who have kept us fed in this country since its inception, and that is the traditional farmer," stated David Martin, CEO of Indoor Farms of America.
"Co-Alliance has been investigating several companies and the equipment available for the indoor agriculture space for some time," states Darren Radde, Business Development Manager at Co-Alliance. "Our team understands quality equipment, and after reviewing numerous growing platforms, we believe the equipment developed and manufactured by Indoor Farms of America will provide our Farmer Members with a viable means of supplementing their income, allowing them to farm new crops all year long, and be within 30 minutes to 2 hours delivery time to any major market they can serve from their existing farm."
John Graham, CFO of Co-Alliance, said: "When we visited with the team at Indoor Farms of America, they expressed to us that while their indoor growing equipment was designed to be superior in performance to anything else in the world, which makes them very 'disruptive' in that space, Ron and Dave have a real desire to see existing traditional farmers embrace the technology."
Graham went on to say, "This means our farmers can take advantage of all our existing channels to market, our inherent ability to be close to those markets, which means our farmers can deliver fresh produce every day of the year from their farms. When the fields are covered in snow, they can produce income for their families. We like that."
The first of the two farms will be owned and operated by a long-time family farming operation, who have an existing building as part of their farming operation in central Indiana, that will be converted to state-of-the-art indoor growing facility at pretty minimal expense.
Phil Brewer, VP of Marketing at Co-Alliance, sees new opportunities for member farmers to have a major impact on the "locally grown" food movement, never seen before. "By bringing scale production of a variety of crops such as premium herbs, for example, to within a very short distance of the actual consumption of those products, we are able to deliver on two fronts. First, the consumer wins by having truly fresh, locally grown and high quality products available to them from local farmers they know and trust. Second, our farmers win, as they are now able to operate during the cold winter season when the fields are out of operation. This creates meaningful additional income for themselves."
After seeing a solid first year in sales of its game-changing vertical aeroponic farm equipment, Indoor Farms of America is on a path to more than quadruple first year sales in 2017, which is year two.
"The largest food-related companies in the world are working with us at this point. They have compared every aspect of every available indoor platform and come back to us. We designed, patented with multiple patents, and now build a fundamentally and economically sound indoor farming product that scales to as large as may be required, anywhere in the world. Nothing grows in quantities that are even close to our equipment, in terms of robust, healthy, clean and nutritious produce," states Martin.
According to company President Ron Evans, "We have seen traditional farmers who purchased our equipment last year respond with praise for our equipment and how it performs. This year we are seeing them buy larger farms. When you get compliments from a farmer that operates 5,000 acres for a living, yet understands the real need and place for this in his own operation, the light bulb goes on for him and those around him."
Room To Grow More Local Veggies At Panasonic's Farm
Room To Grow More Local Veggies At Panasonic's Farm
PUBLISHED - JUL 10, 2017, 5:00 AM SGT | Updated July 25, 2017
S'pore Farm Now Yields 40 Varieties, Aims to More Than Double Production
Consumers here can look forward to more home-grown leafy greens from Panasonic, which plans to expand its high-tech indoor vegetable farm and more than double its production by next year.
The Japanese electronics giant is also looking into cultivating seasonal fruit usually grown in temperate climates.
It runs a 1,154 sq m indoor farm, about the size of 11/2 soccer fields, at Panasonic Factory Solutions Asia-Pacific's premises in Jalan Ahmad Ibrahim.
The farm produces up to 40 crop varieties, amounting to 81 tonnes of vegetables annually.
Plans are under way to increase farm size to 1,710 sq m, which will allow it to produce up to 180 tonnes at optimum capacity. The cultivated varieties include mizuna, oba, leafy lettuce, mini red radish, Swiss chard and baby spinach.
Mr Paul Wong, managing director of Panasonic Singapore, said the company embarked on vertical farming as a viable and efficient means of producing vegetables in a limited space.
Mr Wong said: "We started with eight types of crops. Through constant research and development, we now produce 40 varieties of leafy greens and we want to expand that list with seasonal fruits.
"Increasing our overall crop production is also in line with our goal to contribute to Singapore's food security through a stable local supply of leafy greens."
Latest figures from the Agri-Food and Veterinary Authority (AVA) show that last year, 11,300 tonnes of vegetables were locally produced, which accounts for 12 per cent of the total vegetable supply. Singapore imports over 90 per cent of its food supply.
Mr Melvin Chow, group director of AVA's Food Supply Resilience Group, said local food production provides a crucial buffer in the event of disruptions in overseas food supply.
The AVA encourages the use of technology that can help local farms optimise land use, boost capability and raise production.
Mr Chow said: "The most important step is for our industry to adopt a progressive mindset and improve productivity."
Panasonic's indoor vegetable farm was the first of its kind to be licensed by the AVA in 2013.
It utilises both soil cultivation and hydroponics. No pesticides are used. Seeding and potting are automated, which doubles productivity compared with traditional farming methods. An intelligent lighting system using LED lights helps to accelerate plant growth.
Through a system of automated irrigation, controlled temperature, humidity and carbon dioxide, the farm is able to increase crop growth and achieve a high yield rate of 95 per cent.
The farm is also licensed by the AVA to process salads. Panasonic produces three ready-to-eat salad mixes, which are sold at major supermarkets. It also supplies vegetables to hotels, restaurants and catering companies.
Japanese restaurant chain Ootoya placed its first order of vegetables with Panasonic in 2014.
Mr Yusuke Shimizu, 39, managing director of Ootoya Asia-Pacific, said: "Our customers... complimented us on the freshness and some even asked us where to buy the vegetables."
Ootoya orders an average of 150kg of vegetables from Panasonic every month for its three outlets. Mr Shimizu said: "Freshness is a priority at our restaurants and Panasonic supplies us with vegetables that are harvested on the same day."
A version of this article appeared in the print edition of The Straits Times on July 10, 2017, with the headline 'Room to grow more local veggies at Panasonic's farm'.
$200M Invested For a Global Network of Indoor Farms? That’s Plenty
$200M Invested For a Global Network of Indoor Farms? That’s Plenty
Frank Vinluan | July 21st, 2017 | @frankvinluan | @xconomy | Email
Agtech startup Plenty has reeled in $200 million in financing as the company presses forward on its plans to build a global network of indoor vertical farms.
Softbank Vision Fund of Japan led the Series B funding round for South San Francisco, CA-based Plenty. The round included investments from affiliates of Louis Bacon, the founder of Moore Capital Management, as well earlier investors Innovation Endeavors, Bezos Expeditions, DCM, Data Collective, and Finistere Ventures.
The founders of Plenty say they aim to site their farms near major cities. By growing plants vertically, these farms can produce more food from a smaller footprint while also shortening the supply chain to reach consumers. The company also says these facilities will use sensors and software to optimize growing conditions, avoid the use of crop chemicals, and conserve water—savings that help keep the produce affordable. Plenty CEO Matt Barnard toldBloomberg News that the company’s goal is to provide food priced to fit everyone’s budget.
“That’s the thing that’s hardest to do,” Barnard said. “Now that we’ve accomplished those milestones, we’re looking to scale.”
Plenty has plenty of company in the indoor farming space. In June, New York-based Bowery raised $20 million in its Series A round, four months after announcing its seed round of financing. Bowery CEO Irving Fain hinted at ambitions to build its indoor farms around the world but in the near term, he said the funding will support the construction of at least one additional indoor farm in the New York area. Last year, New York-based BrightFarms raised $30.1 million in a Series C round to bankroll expansion of its indoor farms across the country.
Indoor farming investments have heated up in recent years; the category accounted for $247 million invested in 43 deals last year, according to a report from online investment marketplace AgFunder. But Plenty’s latest round appears to be the biggest agtech investment ever. The $200 million round tops the $100 million Series C round of Boston agricultural microbials startup Indigo a year ago in what AgFunder calculated was previously the largest-ever agtech investment.
Softbank has a lot of money to invest in agtech and elsewhere. In May, the fund announced it had closed on $93 billion in committed capital, a sum that it expected would reach $100 billion. At the time, Softbank said it would seek investments of $100 million or more as it builds a portfolio diversified across technology sectors and geographies. The fund said it is looking to invest in companies “that seek to enable the next age of innovation.”
Plenty has also been a dealmaker in the indoor farming space. Last month, the company acquired Laramie, WY-based Bright Agrotech, a maker of vertical farming equipment. No financial terms were disclosed for that deal but at the time it was announced, Bright Agrotech CEO Chris Michael wrote in a blog post that his company’s technology would help Plenty “build field-scale vertical indoor farms around the world.”
Among the technologies that Plenty gained in the Bright Agrotech deal is the ZipGrow Hydroponic Tower. These towers use gravity to feed nutrient-rich water to plants grown in a vertical plane. Barnard told Bloomberg that using gravity saves energy compared to the energy-consuming systems of other farms that pump nutrients to plants.
Plenty has not yet said where it plans to build its farms, nor has the company set a timeline for bringing produce to the market. Other than the Bright Agrotech facilities, Plenty’s only disclosed location is its 51,000-square-foot warehouse in South San Francisco.
ZipFarm photo by Plenty subsidiary Bright Agrotech.
Frank Vinluan is editor of Xconomy Raleigh-Durham, based in Research Triangle Park. You can reach him at fvinluan [at] xconomy.com Follow @frankvinluan
Living Greens Farm Quadruples Its Vertical Food Growing Operation In Rice County
Next month, the company will add 30 systems to help grow more lettuce, microgreens and herbs in Faribault.
Living Greens Farm Quadruples Its Vertical Food Growing Operation In Rice County
- GUNNAR OLSON golson@faribault.com
- Jul 24, 2017
Head Grower Michelle Keller, left, and Chairman/President Dana Anderson stand in front of rows of food being grown at Living Greens Farm in Faribault. Currently, the business is quadrupling its output with the addition of 30 more growing machines. (Gunnar Olson/Daily News)
From butter lettuce to arugula microgreens, Living Greens Farm specializes in growth. In August, the company will undergo some growth itself, quadrupling its size in its Faribault facility.
Currently, Living Greens Farm houses 10 growing systems in its Faribault Industrial Park facility. These systems grow food products vertically and indoors without the use of herbicides or pesticides. According to its own estimates, the company uses 200 times less land and 95 percent less water than traditional farming.
Next month, the company will add 30 systems to help grow more lettuce, microgreens and herbs in Faribault.
Head Grower Michelle Keller, left, and Chairman/President Dana Anderson stand in front of rows of food being grown at Living Greens Farm in Faribault. Currently, the business is quadrupling its output with the addition of 30 more growing machines. (Gunnar Olson/Daily News)
In 15 to 17 cycles per year, Living Greens Farms harvests about 1,500 plants per cycle. Lettuce, microgreens and herbs each have different grow times, but the company’s 10 patents for its traversing misting system help Living Greens grow food in a shorter time frame.
According to Dana Anderson, chairman and president of Living Greens Farm, the company uses aeroponics to grow the plants quickly.
“We feel aeroponics is the fastest and most disease-resistant way to grow,” he said.
Once the expansion is complete and production begins in September, Living Greens Farm will be one of the “largest indoor farms in the world,” Anderson said.
Getting to that point, however, was a tall task. Development of its traversing misting system took five years and $5 million to complete. While just one part of the equation, Living Greens Farm’s invention was pivotal to the company’s success.
“We didn’t invent aeroponics,” Anderson said. “But we invented how to commercialize it.”
The person tasked with doing the day to day growing is Michelle Keller, the head grower at Living Greens Farm and a four-year master grower.
Keller works with two other individuals that make up the current staff, which she said she expects to grow to six or seven employees once the 30 additional machines are added to the operation.
In the current operation, the plants are first grown outside of the machines before they are placed into the rows under the misting system technology.
“It maximizes the space,” she said. “But it still gives the plants the room they need to grow.”
Growing in Rice County
When the expansion is complete, the earliest stages of growth will occupy the current space, while plants will grow in the 30 new machines in the next room in the latter stages.
The Faribault business is built on a series of high-tech innovations and also contributes to Faribault’s community of growers and agriculture.
For Faribault Area Chamber of Commerce and Tourism Marketing Director Nort Johnson, Living Greens Farm fits into a growing market.
“Locally grown, homegrown, organic foods are growing in popularity,” he said. “Living Greens Farms is at the very front edge of that. They use no herbicides or pesticides and they do it all in house.”
Johnson also has a particular interest in biomes, or the natural growth within one’s habitat. In Living Greens Farm, Johnson sees the opportunity for people in Rice County to take advantage of their own biome.
“In the big picture of sustainability, the more you can produce and manage within your own biome, the less dependent that you can be in a world economy,” he said.
From the growing rows of Living Greens Farm, its products are distributed locally in Faribault and Northfield at the Smoqhouse, Hy-Vee, Just Foods Co-op, Carleton College and Tanzenwald Brewing.
While those businesses now benefit from Living Greens’ operations in Rice County, it almost didn’t happen here. According to Anderson, former Faribault Mayor John Jasinski and current Economic and Community Development Director Deanna Kuennen were instrumental in bringing Living Greens to Faribault, where they will now expand.
“They were really welcoming and supporting,” he said. “That was the difference for us. That’s why we chose Rice County over Dakota or Hennepin counties.”
Make High Quality Food A Stable of The Culture
For today’s modern corporate campus, Freight Farms provides the opportunity to seamlessly integrate sustainable food production into current operations to make high-quality food a staple of the culture. Each farm offers a unique flexibility to create tailored programs to meet the specific needs of our clients. It becomes a powerful tool for promoting wellness, sustainability, and innovation while building an active community and fostering a culture of social responsibility and creativity.
Here are 7 ways to improve your corporate campus with the Leafy Green Machine:
Champion social responsibility: Companies seeking to reduce their carbon footprint are using the Leafy Green Machine (LGM) to offer great food at a low environmental cost. Google, the internet giant notorious for offering free breakfast, lunch, and dinner for their more than 20,000 employees, is growing produce in an LGM on their campus in Mountain View as part of their farm-to-table initiative.
Demonstrate your commitment to sustainability: Incorporating the Leafy Green Machine system into current operations is a way to showcase your business's commitment to sustainability through more environmentally-sound sourcing practices. Each farm acts as an immediate solution to shorten the food supply chain, thereby cutting fuel emissions, increasing transportation costs, and dramatically reducing the carbon footprint of any food operation. The innovative climate technology and energy-efficient growing equipment allows businesses to grow their own produce 365 days a year, regardless of the outside climate. The closed-loop hydroponic system uses over 90% less water than traditional agriculture, significantly reducing the environmental impact of food production.
Actively promote nutrition, health, and wellness: Today’s industry leaders recognize the importance of equipping employees with the tools and resources to help them lead successful, healthy lives both in and out of the workplace. Food has become a core component of every strategy, as more companies seek to provide the freshest, healthiest foods available to their staff. By equipping them with the right information, they are able to make more informed choices that support their health and in turn the health of the larger community.
Be an advocate for innovative technology and creativity: The Leafy Green Machine gives businesses and their food service teams the opportunity to explore new, innovative approaches to food production and provides a platform for education and engagement throughout each step of the process. Producing fresh food directly on campus with the latest growing technology makes it easy to captivate employees and facilitate a dialogue around food. Campus chefs have the ability to choose what to grow and how to incorporate it into their menus. Produce is grown on-site, and brought directly into the kitchens after harvest, ensuring employees get the freshest, most nutritious food available.
Serve up the freshest food for your employees year-round: Chef Kevin Gibbons of UMass Dartmouth is growing a variety of lettuces of herbs in the Leafy Green Machine on campus. In a recent interview, he told us, “we can harvest lettuce at 10:00 am and serve it for lunch later that day.” It doesn't get fresher than that!
Educate your employees about the food supply chain: Use the Leafy Green Machine as a tool to facilitate engagement and inspire change by providing employees with the opportunity to interact with food in a new way. Increase participation and collaboration by bringing transparency to operations and educating employees on the journey their food takes from farm to table.
Cut costs: Sourcing fresh produce and herbs during the winter months can be expensive. The Courtyard Marriott Grappone Conference Center in Concord, New Hampshire is growing lettuce, kale, spinach, arugula, and basil. Steve Duprey, the owner of the hotel, reported that during the winter months they are now able to produce basil at 1/10 of the cost of wholesale prices.
If you'd like to learn more about how Freight Farms is helping farmers grow food in regions across the United States, Canada, Europe, and the Caribbean reach out to us here.
Can Digital Farming Be A Success?
Can Digital Farming Be A Success?
Susan Martinez, 20th July 2017
Farmers in the United States are constantly struggling to make ends meet. Part of the problem is the logistics involved in getting products from farm to table, but one company is looking to circumvent the process by creating a fully automated farming distribution center right outside many cities. A private firm Bowery Founds is attempting to automate the farming process and reduce the costs of distribution by using technology to grow products.
The Demand for Organic Products
Demand for organic products continue to grow. Protein demand has skyrocketed during the past year. According to the US Department of Agriculture, the number of organic chickens slaughtered have increased nearly 3-fold in the past 12-months. Organic produce demand has grown significantly, as consumer look for non-genetically modified foods.
Organic Prices are High
The problem that consumers face is the high cost of organic products. For example, the retail price for organic corn is nearly 4-times the cost of conventional corn. This is for several reasons including the cost to farming corn, the time it takes to receive certification which takes 3-years to growth grains, and the loss of crop due to pests.
Additionally, fraudulent organic products have been flooding into the United States which has help satiate demand, and cap prices. The recent detection of fraudulent organic grains, which include corn, soybeans and wheat from Turkey in the U.S. drove the Organic Trade Association to form a task force to detect fraudulent activity. Certifiers of organic products are now asking traders to show that there is certification back from the original farms that produced the products.
A Weaker Dollar Makes Imports Expensive
In addition, a weaker dollar in the forex markets make imports more expensive to purchase in the United States. If the dollar continues to move lower if the Federal Reserve keeps interest rates on hold for the balance of 2017, consumers will turn to domestic products to feed strong demand.
Technology at the Farm
One of the ways Bowery believes they can circumvent some of these issues is to grow most of the crops indoors using LED lights. While the USDA has not ruled yet on whether hydroponic growth can be considered organic, there is demand for this product. In the last decade, the costs of LED lights have dropped nearly 85%, while the efficiency of these lights has surged. LED lights can be used to grow plants, making these farms very efficient.
Additionally, there are now software programs that can analyze a plant and specifically determine what is needed to create a better product. In real-time, algorithms can evaluate the soil and water as well as analyze a plants DNA. The algorithms are constantly changing givIng produce the best chance to flourish.
Most of the farms will be right outside major cities, at most 20-miles from a major metropolitan urban center. This will provide for lower distribution costs, and reduce spoilage that is due to transportation. Farm to table will become much more efficient and given the robust demand, this technology driven approach could be successful.
Vertical Farming Tour Visits Delval Programs
Vertical Farming Tour Visits Delval Programs
Chris Filling, hydroponics greenhouse manager, leads a tour of DelVal's greenhouses during an educational tour conducted by the state Department of Agriculture. Delaware Valley University photo
DOYLESTOWN, Pa. — As interest in vertical farming continues to grow, the Pennsylvania Department of Agriculture has been conducting an educational tour for its urban agriculture partners featuring hydroponics and aquaponics programs in Pennsylvania.
Delaware Valley University was the first stop on the tour, which kicked off Tuesday in the Philadelphia area.
Guests toured the University’s hydroponics and aquaponics greenhouses to see how DelVal is preparing students for these industries.
In hydroponics, growers use soilless systems for more precise control of inputs. In aquaponics, fish provide nutrients for plants in a soilless system.
These systems allow growers to produce food in unconventional places, using less space and resources.
“The hydroponics and aquaponics industries have tremendous potential to help solve pressing challenges, such as how to feed a growing population with limited resources,” said Chris Tipping, DelVal’s interim dean of agriculture and environmental sciences.
“At DelVal, we’re educating our students about these industries, and we’re also reaching out into the larger community to partner with other educational programs,” Tipping said. “There’s a real sense of excitement about hydroponics and aquaponics in Pennsylvania.”
Scott Sheely, special assistant for workforce development for the state Department of Agriculture, was part of organizing the tour.
“As schools, government officials and businesses look at ways to apply the technology to grow food in cities, there has been a demand for education on urban agriculture,” Sheely said.
“The Pennsylvania Department of Agriculture invited its urban agriculture partners to join it in visiting sites across Pennsylvania to learn more about this technology and how it is being used in the region,” he said.
“DelVal was chosen as a stop because the university is investing in research and education in hydroponics and aquaponics,” Sheely said.
DelVal President Maria Gallo and Tipping addressed the group.
DelVal is currently building a new specialization in hydroponics and aquaponics within its established Department of Plant Science, thanks to the support of DelVal trustee Kate Littlefield.
“This support was used to renovate two greenhouses as well as to provide the opportunity to create the first endowed professorship in DelVal history,” Tipping said. “This professor will lead the program.”
The tour also visited sites in Lancaster on Wednesday and Harrisburg on Thursday. Other stops included W.B. Saul High School, Metropolis Farm, Aero Development, Garden Spot Village, Steelton-Highspire High School, Ladder & Vine and Messiah College.
For Additional Information, please click on the link below:
3 Urban Farming Companies On The Fast Track To Success
3 Urban Farming Companies On The Fast Track To Success
One of the beauties of urban farming is that it can be implemented on both a small scale by individual urban dwellers as well as large commercial scale, supplying surrounding communities with locally sourced urban farmed goods.
These 3 companies, running urban farming operations at the commercial scale in some of the worlds largest cities, are urban agriculture enterprises to watch out for, if you have not seen their products on the shelf of your local grocery store, you may see them soon!
1. Metropolitan Farms (Chicago)
Despite opening less than a year ago (Fall 2015), Metropolitan farms has been years in the making. CEO Benjamin Kent had been developing the concept for quite some time before launching the 10,000+ sq ft facility that is Metropolitan farms today.
Metropolitan farms' specialty? Aquaponic farming - and lots of it. The rapidly growing company is on pace to produce approximately 100,000 heads of lettuce annually.
The best part? With close proximity to clients, metro farms can get their products to clientele as quickly and as freshly as possible, a common benefit to the urban farming approach.
But lettuce isn't the only output of Metropolitan farms, they also produce the urban farming staple herb basil along with over a tonne of fish annually produced by the hydroponic cycle.
2. Bright Farms (Washington D.C. , Chicago, and others)
Bright Farms also focuses on greenhouse style urban farming, but thus far has built larger urban agriculture facilities on the outskirts of urban centers. Currently, the company has over a quarter million square feet in cumulative growing space, and has raised over $25MM cumulatively to expand their urban farming operations.
The production output potential of some of Bright Farms' new facilities is also staggering to say the least. The Chicago facility, according to CEO Paul Lightfoot, will have the capability to produce upwards of one million pounds of urban farmed produce annually to customers at large retail grocers such as Mariano's.
Bright Farms' isn't slowing down either - according to CEO Lightfoot, the company, which originally started as a non-profit but has now switched to for-profit, has plans to expand by opening over 15 new urban farming locations in the near future.
3. Gotham Greens (New York, Chicago)
With over 150,000 sq ft cumulatively in facilities spanning across New York City and Chicago predominantly, Gotham Greens is stiff competition for companies like the aforementioned Bright Farms in what has now become a crowded space in commercial urban large-scale farming.
The secret sauce of Gotham Greens may lie in its highly technical approach to their growing systems, which utilize advanced computer algorithms to manage growing conditions with more efficiency than human farmers possibly could.
Investors are starting to buy in also, with Gotham Greens having raised over $30 MM in venture funding to date, they are without question a trending agricultural technology startup and the proof is in the pudding in terms of traction - Gotham has picked up high profile clients such as Whole Foods.
With the urban agricultural landscape expanding so rapidly (and it is expanding quite rapidly, urban agriculture is now practiced by over 800 million peopleworldwide, or over 10% of the world population, according to the FAO), these three companies will be in the center of the a rapidly swelling market.
Both commercial enterprises such as these as well as individuals practicing urban farming could lead to unprecedented prevalence and reliance on urban farming in the not so distant future.
Kind LED Grow Lights - The Best Grow Lights
The conversation about the best grow lights, whether HID or LED lights, continues to be a hot topic. With the quickly emerging hydroponic and vertical farming movement, the conversation now expands further than HID vs LED and begs the question of which LED light is the best grow light.
Kind LED Grow Lights - The Best Grow Lights
Growers Worldwide Acknowledge That LED Lights Are The Best Grow Lights— And The Future Of Indoor Growing.
Kind LED Grow Lights are the best grow lights for all considerations.
The conversation about the best grow lights, whether HID or LED lights, continues to be a hot topic. With the quickly emerging hydroponic and vertical farming movement, the conversation now expands further than HID vs LED and begs the question of which LED light is the best grow light.
There are many factors to consider when choosing the best grow light– spectrum, cost, wattage, PAR output, lumens, electrical safety, enclosure type & size, plant type, yield, and ventilation to name a few.
Kind LED Grow Lights have been designed with a proprietary 12 bandwidth spectrum with UV and IR, comprised of 3 watt diodes that run at 650mA spectrum for growth and/or flowering, and don’t waste any energy emitting large amounts of spectral ranges that plants don’t use, making them the best grow lights for the entire plant lifecycle.
In comparison, other LED grow lights run at 500mA with only a 6 bandwidth spectrum and HIDs are designed to a specific portion of the full light spectrum. This means that HID users must purchase multiple HID lights to compliment both the vegetative and flowering stages and compete with Kind LED Grow Lights for the title of best grow lights.
Kind LED Commercial Grow Lights challenge the standard of high-performance horticulture lighting technology, redefining consumer expectations of the best grow light, having passed the extremely stringent safety requirements needed to earn a certification from respected UL Laboratories.
In comparison, certifications for HID and LED grow lights are extremely rare. Yet, for commercial grow operations, electrical safety certification is an absolute requirement.
Kind LED Grow Lights use 40% less power than HIDs. With a cost savings of roughly $420/ month (over $5,000 during the course of its 50,000 hour lifetime), and no need for extra inline fans, ducting, or AC units (roughly another $3600 plus costs of electricity), the highest yields (1.4 grams per watt, while, for example, the HID Gavita came in at about .84 grams per watt), UL electrical safety certification for commercial grows, and lifetime customer, technical, and grow support, Kind LED Grow Lights are the best grow lights for all considerations.
About Kind LED Grow Lights:
KIND LED Grow Lights are the industry leader in indoor LED grow lights. KIND LED consulted with hundreds of professional hydroponic and soil growers to rigorously research and develop their cutting edge LED indoor grow light technology that has since revolutionized the indoor growing industry.
For more information about Kind LED Grow Lights click here.
PRWEB) JULY 2017
A Behind-the-Scenes Look at Europe’s Huge New Vertical Farm
GrowWise is a vertical farming research facility, and in conjunction with Dutch fresh food distributor Staay Food Group, it’s laying the groundwork for the first commercial vertical farm in Europe, slated to open north-east of Amsterdam in a town called Dronten later this year.
A Behind-the-Scenes Look at Europe’s Huge New Vertical Farm
July 20, 2017
The Eindhoven High Tech Campus, a 90-minute train ride south of Amsterdam, consists of two rows of nondescript mid-rise office buildings on either side of a wide, tree-lined road. In typical Dutch fashion, there’s more parking for bikes than cars, and the campus is flanked by stretches of neatly-maintained green fields and canals.
The place doesn’t have an especially high-tech feel to it. But on the third floor of a building near the end of the road, a division of Philips Lighting called GrowWise is using technology to tackle a crucial question: what are we going to eat once there are over nine billion people on Earth?
GrowWise is a vertical farming research facility, and in conjunction with Dutch fresh food distributor Staay Food Group, it’s laying the groundwork for the first commercial vertical farm in Europe, slated to open north-east of Amsterdam in a town called Dronten later this year.
During a tour of GrowWise, I spoke with Gus van der Feltz, Global Director of City Farming, about the ins and outs of vertical farms and the opportunities and challenges the field will face in coming years.
No Sun + No Soil = Organic Plants?
Since the beginning of growing food, sunlight, water, and soil have been essential ingredients. If you take away two of these most basic of inputs, how do plants grow?
“You can think of a vertical farm as a black box,” van der Feltz said. “We look at it as an integrated system, trying to create vegetables in a closed environment.”
Before going into said ‘black box’—otherwise known as the growth rooms—we slip light blue covers over the soles of our shoes and sanitize our hands. These are minor protective measures, and they don’t prevent pathogens from entering the chamber. “If we were going into the actual growth facility we’d need to put on full protective gear,” van der Feltz said.
Outside the growth room is a winding, humming network of pipes, screens, and dials. Van der Feltz pulls back a large sandwich panel door, and when we step inside, the air is noticeably warmer and more humid. It smells like a farm, except without the manure, and it feels a little like being on a spaceship—trays of plants are stacked four levels high, hundreds of blue and red pinpoints of light beaming down on them from above. The light on the bottom two levels is white, while the top two give off a purplish glow.
We have to raise our voices to talk over the hum of the regulators. Solar light, van der Feltz explains, is spread across a spectrum ranging from UV to infrared. In photosynthesis, red and blue wavelengths of light interact with chlorophyll to help form glucose and cellulose, the structural material in cell walls.
LEDs can reproduce this effect, and can do it faster than the sun; time from seed to harvest at GrowWise is 30-40 days, as compared to 60-65 days in a typical greenhouse, according to van der Feltz.
“What we’ve done with LEDs is optimize the conditions for growth. There are elements of sunlight that plants don’t use as efficiently, and those can be reduced or taken out,” van der Feltz said. One of those elements is heat—when I wave a hand under the lights, they feel no warmer than the rest of the room.
The crops need different intensities of light as they pass through stages of growth, and they’re constantly monitored by sensors and software that tweak their conditions as necessary. Van der Feltz explains that triggering the right combination of processes in photosynthesis, in combination with other growth factors, can also create desired effects. “With the right lighting conditions we can make lettuce turn purple or red. We can make strawberries sweeter,” he said.
Each plant sits in a thimble-sized container of sterilized coconut bark, which serves as a substrate for germination and root development. From there the roots extend into shallow troughs of nutrient-rich water—the plants are constantly in water rather than being periodically sprayed or on a timed drip, making this hydroponic farming.
Food And The Future
The Dronten facility will be 900 square meters (9,680 square feet), with a total cultivation area of 3,000 square meters (32,290 square feet).
Though this pales in comparison to the biggest vertical farm in the world—AeroFarms’ 70,000-square-foot facility in Newark, New Jersey—it will be the largest in Europe. Outside Europe and the US, vertical farms also exist in Japan, Korea, Singapore, and Canada, and a facility much larger than Aerofarms is planned in Shanghai.
It’s no coincidence most of these farms are near big, densely-populated cities. The UN’s 2014 World Urbanization Prospects report predicts population growth and urbanization will add 2.5 billion people to the world’s big cities by 2050. That’s a whole lot of people who’ll be buying all their food rather than producing any of it.
Agricultural yields, then, will have to increase significantly, and since much of the world’s farmable land is already being farmed, we’ll need to get a bit more resourceful with our food supply.
Right now, vertical farming is still expensive—a bag of GrowWise lettuce costs more than a bag of organic lettuce, which costs more than a bag of regular lettuce—and it requires a lot of energy; those LED bulbs aren’t lighting themselves.
But continued research and investment will gradually drive prices down, and as ironic as it sounds, vertical farms will eventually get all their energy from solar panels.
This will leave us with an organic growing method that requires no fertilizer or pesticides, produces no agricultural runoff or other pollution, uses a fraction of the water traditional farms use (same goes for land), and yields consistent harvests year-round, even in extreme or unusual weather.
“You can create optimal growing conditions for the crop and you don’t need to wash it,” van der Feltz said. “The washing process damages the leaves and causes them to decay faster. Having the growth facility nearby decreases travel time and means the food will be fresher.”
The Consumer’s Still King
As rosy as this all sounds, it doesn’t mean people will embrace vertically-farmed food with open arms. Food is a sensitive topic many consumers take very seriously; if we are, in fact, what we eat, people may not love the idea of eating food that, for all its merits, is grown under decidedly artificial conditions.
As we stood peering at the neatly glowing rows of plants, van der Feltz reached out, plucked one from its roots, and handed it to me. “Try it,” he said. So I did. I tasted the green-leaf lettuce and the basil. Both seemed to have a stronger flavor and aftertaste than the store-bought greens I’m used to, though it was nothing I’d have noticed had I not been aware of what I was eating.
Van der Feltz recognizes widespread adoption of vertically-farmed food may be a challenge. “We understand some people may feel uneasy about food grown with no sunlight,” he said. Consumer education will play a key role in getting people comfortable with purchasing and eating LED-grown greens.
At the same time, though, food preferences are shifting, and for the better as far as vertical farming is concerned. “In the Western world there’s a growing demand for convenience products that have already been washed and are ready to use,” van der Feltz explained.
His confidence in GrowWise’s products, for one, is unwavering. “We test our produce regularly for pathogens and nutritional quality, and each time the results are excellent,” he said. “They serve this lettuce here in our cafeteria. I take it home to my family. My kids love it.”
Image Credit: Vanessa Bates Ramirez
Plenty Attracts Largest-Ever Agriculture Technology Investment Led by the SoftBank Vision Fund to Solve Global Fresh Produce Shortages
Plenty Attracts Largest-Ever Agriculture Technology Investment Led by the SoftBank Vision Fund to Solve Global Fresh Produce Shortages
Investment will drive deployment of global, large-scale indoor farm network to deliver radically fresher, affordable food to local communities everywhere
July 19, 2017 10:00 AM Eastern Daylight Time
SOUTH SAN FRANCISCO, Calif.--(BUSINESS WIRE)--Plenty, the leading field-scale indoor farming company remaking the global food system, announced today a $200 million Series B funding round led by the SoftBank Vision Fund, making it the largest agriculture technology investment in history. In connection with the investment in Plenty, the SoftBank Vision Fund’s Managing Director, Jeffrey Housenbold, will join the Plenty Board of Directors.
“Fruits and vegetables grown conventionally spend days, weeks, and thousands of miles on freeways and in storage, keeping us all from what we crave and deserve — food as irresistible and nutritious as what we used to eat out of our grandparents’ gardens”
Plenty is using proven plant science and patented technologies to build a new kind of indoor farm that uses cutting-edge LED lighting, micro-sensor technology, and big data processing to deliver higher-quality produce for pricing as good or better than what consumers pay today. The world has run out of economically viable, arable land for many fresh fruit and vegetable crops. This investment will support building out Plenty’s global, hyper-yield farm network and support its mission of solving the increasingly critical need to make fresh produce available and affordable for people everywhere.
“Fruits and vegetables grown conventionally spend days, weeks, and thousands of miles on freeways and in storage, keeping us all from what we crave and deserve — food as irresistible and nutritious as what we used to eat out of our grandparents’ gardens," said Matt Barnard, CEO and co-founder of Plenty. “The world is out of land in the places it’s most economical to grow these crops. After a decade of development driven by one of our founders, our technology is uniquely capable of growing hyper-organic food with no pesticides nor GMOs while cutting water consumption by 99 percent, making locally-grown produce possible anywhere. We’re now ready to build out our farm network and serve communities around the globe.”
"By combining technology with optimal agriculture methods, Plenty is working to make ultra-fresh, nutrient-rich food accessible to everyone in an always-local way that minimizes wastage from transport," said Masayoshi Son, Chairman & CEO of SoftBank Group Corp. "We believe that Plenty's team will remake the current food system to improve people's quality of life."
Plenty’s farms, which the Company plans to build near the world’s major population centers, will deliver industry-leading yields of the freshest, best-tasting local produce that’s completely GMO- and pesticide-free, all while transitioning agriculture to a predictable and perpetual model. Plenty farms maintain a perfect growing environment, use one percent of the water and a tiny fraction of the land of conventional agriculture, while delivering produce to local grocery shelves within hours of harvest.
The Series B funding round was led by the SoftBank Vision Fund, with participation from affiliates of Louis M. Bacon, the founder of Moore Capital Management, LP, and existing investors including Eric Schmidt’s Innovation Endeavors, Bezos Expeditions, DCM, Data Collective and Finistere.
About Plenty
Plenty is a new kind of farm for a new kind of world. We’re on a mission to bring local produce to people and communities everywhere by growing the freshest, best-tasting fruits and vegetables, while using one percent of the water, less than one percent of the land, and none of the pesticides, synthetic fertilizers, or GMOs of conventional agriculture. Our field-scale indoor farms combine the best in American agriculture and crop science with machine learning, IoT, big data, climate creation technology and the extraordinary flavor and nutritional profiles of heirloom seed stock, enabling us to grow the food nature intended — while minimizing our water and energy footprint. Based in San Francisco, Plenty is currently building out and scaling its operations to serve people around the world.
Indoor Farming Plus Made In USA LED Grow Lights: Profile 1.18
Indoor Farming Plus Made In USA LED Grow Lights: Profile 1.18
E-mailRSS
GREENandSAVE Staff | Posted on Thursday 20th July 2017
This is one of the profiles in an ongoing series covering next generation agriculture. We are seeing an increased trend for indoor farming across the United States and around the world. This is a positive trend given that local farming reduces adverse CO2 emissions from moving food long distances. If you would like us to review and profile your company, just let us know! Contact Us.
Company Profile: Metropolis Farms
Here is a great example of a large scale vertical indoor farm growing vegetables and herbs.
Here is some of the “About Us” content: We are urban-vertical farmers with over 15 years of indoor growing experience. We grow great tasting, wholesome herbs and vegetables, inside city buildings year-round. We grow the highest-quality food without pesticides, herbicides, or many of the other health risks that impact the food that reaches your table. We harvest and deliver our fresh produce the same day to local stores and restaurants. We can also make our fresh herbs and vegetables available by next-day air to restaurants and home gourmets nationwide. Our South Philadelphia Location is the first vertical farm in Philadelphia in addition to being the first vertical farm ever built on a second floor.
Our proprietary Revolution Vertical Farming Technology ™ is ultra-efficient, environmentally-responsible and commercially scalable. Our farms are highly-adaptive and virtually eliminate many of the health business and environmental risks that make conventional and greenhouse farming so expensive. Our farms can operate profitably for both smaller-artisan farms (Flash Farms) as well as large-scale operations (Super Farms). Our farming systems use 95 to 98 percent less water and 82 percent less energy than traditional farms. Our cost-effective technology allows us to grow more than an acre of produce in a 36 square feet of space, over 1,200 times the herbs and vegetables of an outdoor farm per square foot. We bring great food, good jobs and opportunities to local communities.
Instead of focusing on creating the world’s largest vertical farm. Our focus is on creating the world’s most efficient, cost effective and consequently productive local farms. It seems like every few months the media announces yet another proposed “World’s Largest Vertical Farm”. To date exactly none of these projects have ever fulfilled their promises. Our technology produces the most food, at the lowest cost, of both capital and operational expense, while maintaining the highest taste and nutritional values. Our goal is to grow both farms and farmers nationwide.
Here is the link to learn more: http://www.metropolisfarmsusa.com.
To date, the cost of man made lighting has been a barrier for indoor agriculture. A new generation of LED lighting provides cost effective opportunities for farmers to deliver local produce. Warehouses and greenhouses are both viable structures for next generation agriculture. Here is one example of next generation made in USA LED grow light technology to help farmers: Commercial LED Grow Lights.
Indoor Farming Operation Being Built At Ivy Tech South Bend
Indoor Farming Operation Being Built At Ivy Tech South Bend
By Mark Peterson | Posted: Wed 6:22 PM, Jul 19, 2017
SOUTH BEND, Ind. (WNDU) - A farm is being built on Ivy Tech’s South Bend campus at a cost of up to $4 million.
The farm will span just 20,000 square feet because all the growing will take place indoors, hydroponically, under L.E.D. lights. It was somewhat ironic that the soil ceremoniously overturned during groundbreaking ceremonies today won’t be used to grow a thing.
“We are at the tip of the spear of a brand new industry, we're leaders in an emerging market,” said Green Sense Farm’s Founding Farmer Robert Colangelo. “We’re like Steve Jobs making computers in your garage. This field is just at the beginning of the beginning.”
The Green Sense search to find an academic partner for the project was not an easy one. “We went to a number of four year institutions looking to transform farming at agricultural schools but hit walls of bureaucracy and Chancellor Coley took a risk, he saw that there was a real need to train students with two year degrees to work in the produce food service and agricultural sectors.”
Chancellor Coley refers to the leader at Ivy Tech South Bend, Dr. Thomas Coley: “They set up a real live production and then our students get to train in a live production that's a very unique arrangement, it’s probably one, if not few in the country that would have this kind of partnership.”
And the partnering doesn’t end there. The facility’s produce production capacity has already been purchased by a half dozen entities including Martin’s Super Markets.
“When you harvest produce it starts dying and losing its nutritional value as soon as it’s cut,” said Colangelo. “So if it travels from the west coast to the Midwest it could take three days, so it’s less nutritious. If it’s harvested and it’s at your table in hours, because it’s locally grown it’s much more nutritious and you can see that in the taste and in the color of the produce as well as the shelf life, it’ll last much longer.”
On July 19, 2017, Green Sense Farms and Ivy Tech Community College broke ground on a 20,000 square-foot indoor vertical farm which will be an innovative workforce training center for the next generation of farmers as it grows produce for local customers in a year-round, sustainable farm. On hand to celebrate were representatives from Green Sense Farms, Ivy Tech, the City of South Bend, as well as the customers who will use produce from the farm. Pictured are (left to right): Robert Colangelo, Founding Farmer/CEO for Green Sense Farms; Donte Shaw, Executive Chef for Café Navarre; Kenneth Acosta, General Manager for Sodexo; Patrick Dahms, Executive Chef for Morris Inn at University of Notre Dame; Pipe Halpin, Customer Relations for Green Sense Farms; Dr. Thomas G. Coley, Chancellor for Ivy Tech South Bend; Dr. Sue Ellspermann, President of Ivy Tech Community College; Craig Lewkowitz, Vice President of Culinary Operations for Four Winds Casinos.
The list of sponsors also includes the wing of Sodexo and serves the St. Mary’s Campus: “No, I don’t think dirt farms are doomed, so this is just something else that’s different. You’ve got limited growing products that are in there you know, more on the lettuces the micro greens, the enhanced flavors of herbs, stuff like that, but you aren’t going to able to take corn and wheat and all that other stuff out of the system,” said Sodexo General Manager Kenneth Acosta.
FREIGHT FARMER Q&A: KARMA FARM
Jon Shaw has his roots in organic, soil-based farming. He has been an avid organic vegetable grower since he was a student in high school, and in 2009, after 45 years of gardening experience, Jon transformed his hobby into a career and launched Karma Farm
JUNE 8, 2017
6 Questions With Jon and Nathaniel Shaw of Karma Farm
One of the best parts of being part of the Freight Farms team is talking to our freight farmers and hearing about their successes, their businesses, their customers, and their challenges. They are a wealth of information, so now we are sharing some of their stories with you!
Jon Shaw has his roots in organic, soil-based farming. He has been an avid organic vegetable grower since he was a student in high school, and in 2009, after 45 years of gardening experience, Jon transformed his hobby into a career and launched Karma Farm. Located in Maryland, this family run farm decided to extend their growing season through the use of a hoop house, and now a Leafy Green Machine (LGM), which is run by Jon's son, Nathaniel. In addition to running a farm stand CSA, the Shaws provide area farm-to-table restaurants with leafy greens grown in the LGM year-round. With over 40 years of gardening and farming experience, Jon is a wonderful addition to our Freight Farmer community. We recently spoke with Jon and Nathaniel about the transition from traditional farming to hydroponics.
Freight Farms (FF): What, if any was your experience with farming before becoming a Freight Farmer?
Jon Shaw (JS): I started organic gardening in high school (circa 1972) and I have been growing vegetables ever since. Eight years ago, I decided to take a portion of my horse farm and turn it into commercial vegetable production.
FF: How did you find customers to buy your produce?
JS: We found many of our current customers our first summer when we grew too many tomatoes in our family garden and I decided I would go into town (Baltimore) to a few restaurants to give away samples or possibly sell them. Providing samples of our produce and explaining the breadth of our product line to chefs is still the main method we use to bring in new restaurants. Our customer base has also grown significantly from word of mouth as chefs tend to change jobs frequently.
FF: What is one small change everyone can make in their daily lives to make a big difference in our food system?
JS: Eat less meat and more vegetables.
“I was motivated to become a Freight Farmer because of my desire to turn our family farm into a sustainable business.”
FF: What’s the best part of being a Freight Farmer?
Nathaniel Shaw (NS): I’ve only been a Freight Farmer for a few months, but so far, the best things about it are bringing local chefs into the LGM to touch and taste the greens we are growing inside and seeing their surprise and excitement about the bold tastes and textures it can produce. Working with local chefs to find new greens and develop products that best utilize the advantages of the LGM has been an amazing process and one that I’m most excited to continue.
FF: What motivated you to become a farmer?
NS: I was motivated to become a Freight Farmer because of my desire to turn our family farm into a sustainable business. In recent years, we have worked to supply our restaurant customers with produce more consistently using row covers and hoop-houses, but our off-season production has remained slim. Our LGM gives us the ability to sustain a broader product line throughout the year and sustain our revenue and employee base over the winter.
FF: Which individuals, groups, and communities do you strive to reach and why have you chosen to get involved with these groups?
NS: We primarily target chefs at Farm-to-Table restaurants. The reason for this is that we love to grow beautiful and unusual produce and sell to chefs at mid to higher end restaurants that specialize in utilizing local ingredients. The restaurant community in nearby Baltimore is thriving and has grown with the farm as well.
Make sure to follow Karma Farm on Facebook and Instagram to check out pictures of Little Shaw (top dog in change) as well as beautiful shots from the farm!
If you'd like to learn more about how Freight Farms is helping farmers grow food in regions across the United States, Canada, Europe, and the Caribbean reach out to us here.