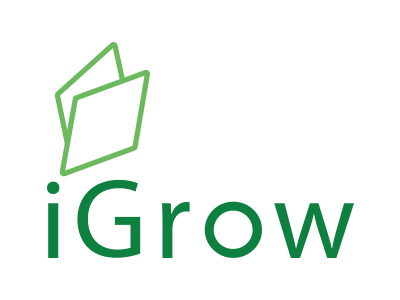
Welcome to iGrow News, Your Source for the World of Indoor Vertical Farming
Underground Air-Raid Shelter Feeding London Restaurants
Underground Air-Raid Shelter Feeding London Restaurants
An old World War II shelter in Clapham, which could protect up to 8,000 people from Nazi German bombs, consists of two large tunnels that were intended to one day become an extension of the London Underground
LONDON, Sept 28, 2017 — Under an anonymous back street in south London lies a vast underground air-raid shelter that has been turned into a pioneering urban farm supplying supermarkets and restaurants in the capital.
The World War II shelter in Clapham, which could protect up to 8,000 people from Nazi German bombs, consists of two large tunnels that were intended to one day become an extension of the London Underground.
That never happened and the shelter lay abandoned for 70 years until two entrepreneurs, Steven Dring and Richard Ballard, decided to grow broccoli, coriander, fennel and a host of other vegetables as so-called micro leaves, also known as micro herbs, grown from seedlings but harvested early when the first leaves form.
“We need to create these new fertile spaces” to meet increased demand from a growing global population, Dring told AFP on a visit to the “Growing Underground” site — some 33 metres below the road.
Staff wear protective clothing and there is a strong smell of vegetables and humidity in the shelter.
The vegetables are grown with hydroponics, using nutrient solutions in a water solvent instead of soil.
The technique can also be used to grow a wide range of produce including tomatoes and baby peppers, Dring said.
Day and night
The only other ingredient required is light.
The tunnels have no natural light and are illuminated with pink LEDs, giving them a futuristic look.
The intensity of the light changes to imitate daylight, but with one major difference — the lights are dimmed during the day and shine brightest at night, as electricity is cheapest then.
“We predominantly grow micro herbs, which are standard herbs, from different seeds.
The site of an underground air-raid shelter which has been turned into the urban farm project, ‘Growing Underground’ is pictured in Clapham, south London. – PHOTOS: AFP
“But what we do is we grow them to a very small stage, before the first true leaves start to come out,” Dring said.
Under an anonymous back street in south London lies a vast underground air-raid shelter that has been turned into a pioneering urban farm supplying supermarkets and restaurants in the capital
The micro herb broccoli takes between three and five days to grow before being packaged up in the shelter and sent off.
Fans enthuse about the intensity of the flavours of the produce.
Vegetables in this underground farm in London are grown with hydroponics, using nutrient solutions in a water solvent instead of soil
Customers include Marks and Spencer which offers the produce in some of its supermarkets, several stalls at London’s Borough Market and many restaurants — helped by the patronage of celebrity chef Michel Roux Jr of Le Gavroche.
‘Quality, flavour’
Dring and Ballard latched onto the concept of vertical farming — producing food in vertically stacked layers — which was developed by US biologist Dickson Despommier in his 2010 book The Vertical Farm: Feeding the World in the 21st Century.
The operation takes up some 200 metres of the 1,000 metres available in the air-raid shelter tunnel, half for growing while the other half is used for packaging.
Their request to use the air-raid shelter in Clapham was eagerly taken up by the owners of the space, London’s public transport company.
This type of farming is “100 times cheaper” than setting up an urban farm on the surface, Dring said.
Their customers say they are happy with the result.
“I think the story is fantastic,” said Charlie Curtis, an agronomist at Marks and Spencer supermarket chain.
'Growing Underground' urban farm customers include Marks and Spencer, stalls at London's Borough Market and many restaurants—helped by the patronage of celebrity chef Michel Roux Jr. of Le Gavroche
“I think we all love to think that our food is grown locally to us but I think also the product sells itself. The quality is fantastic and the flavour is like something I’ve never had before,” she said.
No unpredictable weather
Experts say vertical and urban farming could be ways not only of facing up to population growth but also growing urbanisation worldwide as well as climate change.
Nottingham University’s Centre for Urban Agriculture said on its website that urban farms create jobs, reduce transport costs and pollution as well as offering an “opportunity to develop technologies”.
The “Growing Underground” project sends its data on humidity, temperature and plant growth to Cambridge University to try and improve efficiency.
“What these guys are doing is modelling for us which one is the optimum environment for each product,” Dring said.
Every day is the same in the underground farm and there are no seasons, or unpredictable British weather.
“We have a lot more control than usual growers... When in the winter days it’s cold under the glass, it will take you 25 days to grow red mustard. It will always take us 10 days to grow red mustard,” Dring said.
He added: “There’s nothing that stands as a major challenge, apart from building a farm underneath London.” — AFP
Vertical Farming: A Big Leap Towards Sustainable Farming
Modern day vertical farming includes controlled environment agriculture technology i.e. CEA technology. All other environmental factors can be controlled using this technique. Techniques such as augmentation of sunlight by artificial lightning and by metal reflectors are also used for producing a similar greenhouse-like effect.
Vertical Farming: A Big Leap Towards Sustainable Farming
26/9/2017
Vertical farming is the technique of producing food in stacked layers or on vertically inclined surfaces which comprises of new automated farms. It requires less natural dependency and helps in reducing the dependency and cost of skilled labourers, weather conditions, soil fertility or high water usage.
Modern day vertical farming includes controlled environment agriculture technology i.e. CEA technology. All other environmental factors can be controlled using this technique. Techniques such as augmentation of sunlight by artificial lightning and by metal reflectors are also used for producing a similar greenhouse-like effect.
Vertical farms is a pesticide-free technique which requires much less input than traditional farming methods and gives much more output.
Farms embedded with this technique uses artificial lighting systems that facilitate enhanced photosynthesis. LEDs are placed near plants to impart specific wavelengths of lights for more photosynthesis. This enhances productivity.
‘Aeroponic mist’ is another technique used which helps in supplying the proper amount of oxygen and other soil nutrients. This makes the nature of growth more robust. Some of the major advantages of this farming techniques are as follows
Reliable harvest: No existence of the term ‘seasonal crops’. Irrespective of sunlight, pests or extreme temperature, these farms can easily meet the demand of contractors anytime.
Minimum overheads – Nearly 30% profitability can be obtained through this growing technique.
Low energy usage – Use of computerized LEDs by giving proper wavelength reduces energy to a great extent. Low labour costs – Fully automated technique so no skilled labours are required.
Low water usage – Controlled transpiration technique are used. It requires only 10% of the water usage of traditional technique. Reduced washing and processing – No pests control required. Reduces the cost of damage washing.
Reduced transportation costs – Can be established in any location. This reduces the cost of transportation and usage.
Increased growing area – Enables cost effective farming and provides nearly 8 times more productivity. Maximum crop yield – Irrespective of other geographic factors this technique gives maximum yield.
A wide range of crops – Growth of crop are maintained by an intensive database which enables them to grow a wide range of crops such as Baby spinach, Baby rocket, Basil, Tatsoi, Leaf lettuce.
Fully integrated technology – All environmental factors are closely monitored and are maintained in an optimal range.
Optimum air quality
Optimum nutrient and mineral quality
Optimum water quality
Optimum light quality
All these technologies used leads to a dramatic shift in plant growth rates and their yields.
Vanilla The Next Hydroponic Cash Crop?
Extreme weather events like Enawo are becoming increasingly common, especially if hurricane season in the United States was any indicator this year. Yet, vertical farms, which can be situated in more mellow outdoor climates while dialing in the perfect conditions for indoor growing, might be uniquely positioned to produce these crops in spite of those weather events.
Vanilla The Next Hydroponic Cash Crop?
Posted on September 25, 2017
The best vertical farming crops are high value, difficult to grow crops that have a strong local market. Have recent events and their ongoing impact created a new contender for the top spot?
- The market
- The need
- How to grow hydroponically
We’ve covered niche spice crops for hydroponics, as well as rare plants before, but we’ve never looked at this issue in light of current events. ThisMarch, Cyclone Enawo, the strongest tropical storm to hit Madagascar since 2004, tore through the country, killing more than 80 people and doing millions of dollars in damage to one of the country’s premier exports: vanilla.
In 2015, Madagascar was estimated to have produced 3,914 tonnes out of a global total of 8,294 tonnes, projected U.N. data showed.
As a result of the cyclone, global vanilla prices have jumped 300%, cresting $600/kg – and it was already the world’s second most expensive price after saffron.
Extreme weather events like Enawo are becoming increasingly common, especially if hurricane season in the United States was any indicator this year. Yet, vertical farms, which can be situated in more mellow outdoor climates while dialing in the perfect conditions for indoor growing, might be uniquely positioned to produce these crops in spite of those weather events.
So, is there an opportunity for vertical farmers and hydroponic growers to step in?
Growing Vanilla Hydroponically
Vanilla is a member of the orchid family (Orchidaceae) and much of the knowledge for growing those is applicable here. It can be grown hydroponically with the right media – inert, sterilized, coarse, free draining – such asexpanded clay, pumice, etc. It needs less nutrients than other vegetable crops though there isn’t a real consensus about what ppms/EC is best. I’ve seen recommendations for EC .5.
Among the challenges of growing vanilla hydroponically (besides the lack of good information), vanilla is a climbing plant climbing plant, so you will need to provide supports for the aerial roots to attach to. It is also reliant on hand pollination if you aren’t growing in its natural habitat, an extremely labor intensive practice.
Finally, it’s a long term investment as you won’t even start seeing the plants reduce until their third year of growth:
Yield info taken from this outdoor cultivation guide
Take a look at the video below to get a glance inside a an existing vanilla farm and the amount of hand labor farming this crop takes (hand pollination! *buzzers won’t work).
So now that we have an idea of what growing vanilla looks like, let’s take a look at some instructions from a popular online growing forum:
“Here’s Vanilla 101. Aside from being trees, coffee and cacao are pretty ” easy ” to grow.
I start vanilla as a 2 foot vine cutting tied onto a 6 foot bamboo tripod tucked into a 1 gallon nursery pot filled with orchid bark/peat/perlite media in bright shade ( 1500 – 3000 fc ) . If going from a bare vine cutting, trim 1-2 leaves off the lower end and insert into media past the last trim point. ( No need for rooting compound. )
Depending on your humidity, mist the entire vine ( up to ) a few times daily with water for a month or so. ( In the 80s with an RH at 90% here, I mist once a day. ) Mist with a weak nutrient solution every week. The media should be kept very lightly moist. ( I just let the overspray from misting the vine take care of it. ) The cutting will put out roots into the media and you should see new leaf growth in a few weeks. If you have a growing tip ( uncut end ) on your cutting, it will start to grow out. Otherwise, the plant will initiate a new tip. This causes the vine section above that point ( usually the last before the end of the cutting ) to dry out and drop off, allowing the new tip to begin growing out. Startling but normal.
The orchid starts in media but predominantly uses the aerial roots to feed as it matures. A 300 ft long, 3/4″ diameter vine can grow out of a 3 gallon pot full of moist pine bark. Aeroponic / nutrient misting systems are essentially how commercial orchid nurseries grow millions of plants per acre and work quite well for vanilla. An ebb flow tank is likely to be too wet for the media bound roots and does not readily address the majority of the plant’s root system.
At about 3 years, the vine is capable of flowering. If it does, vanilla pod production requires hand pollination within a 6-8 hour window of the flower opening ( and they only open once ) .
If pollination is successful, the pod will fully form in about 2 months. It takes another 6 – 9 months to cure/age the pod to produce those chemicals we associate with vanilla. The orchid typically lives about 15 years.”
Conclusion
While hard to grow, vanilla is a highly profitable crop with some of the key characteristics that make it valuable for vertical farming cultivation. If more people experiment with this type of cultivation, it’s fair to assume that knowledge will increase and costs will come down, making it even more competitive.
Like saffron, because of the high labor costs, it is unlikely that cultivation of this crop will move primarily to the countries that are leading the way in vertical farming any time soon.
However, as changing weather patterns affect agriculture around the world, the adaptability of vertical farming may prove beneficial for continuing to produce vanilla and other expensive plants.
Leafy Green Machine Growing Garden-Fresh Veggies At CHS
Leafy Green Machine Growing Garden-Fresh Veggies At CHS
Vegetables grow in verticle towers, maximizing space in the growing unit.
9/27/2017
Indoor facility first in state at public school
By ETHAN SHOREY, Valley Breeze Managing Editor
CUMBERLAND – A modified shipping container capable of producing a football field’s worth of vegetables every seven weeks now stands outside the kitchen door at Cumberland High School.
The Leafy Green Machine, as it’s called, will bring fresh vegetables to the plates of students at CHS and across the school district, making Cumberland the first public school district in Rhode Island to boast such a facility, according to those who will run it.
Shauna Spillane, food service director for local provider Sodexo, said the hydroponic growing facility is essentially like a “smart home” for food, a “really awesome” facility that keeps vegetables in ideal growing conditions at all times. When it gets too hot in the growing container, the LED lights shut off and the AC comes on. Only the amount of light needed for photosynthesis is used. Air quality is constantly monitored and controlled.
The money to purchase the grow box from Boston-based Freight Farms came out of the food service budget.
Sodexo will manage the growing and picking of vegetables for daily use, but students will be invited to participate in the process. CHS administrators eventually hope to have an agriculture pathway at the school, teaching students about sustainable growing and horticulture.
The Leafy Green Machine, or LGM, allows a variety of crops to be grown regardless of weather conditions, providing students with year-round access to local and fresh produce. Vegetables are grown in vertical rows, requiring minimal water and electricity to flourish. Water drips from overhead spouts onto strips, going down vertical columns to give vegetables exactly the amount that they need. The water then falls into a trough, where it is pumped out.
Gina Rodriguez, food service manager for Sodexo, said employees have typically struggled a bit to put fresh vegetables on the table all winter. Last year was particularly bad, as vegetables often had to be thrown out because they didn’t last, she said.
With the LGM, workers will “pick today for tomorrow,” said Rodriguez. Vegetables typically start losing nutrients the moment they’re picked, she said. The difference will be noticeable in the vegetables picked from the LGM, as they’ll taste better, be a brighter green, and provide more nutrition for students. Because the container is insulated and climate-controlled (about 65 degrees), the entire system uses just five gallons of water a week.
Sodexo currently uses about 200 pounds of leafy greens, mostly for salads, across all schools in Cumberland, including at Blackstone Valley Prep charter school, said Rodriguez. The vegetables harvested from the LGM will be used to supplement the supply.
The entire plant-to-harvest process takes about seven weeks, meaning it can be done several times in a year.
Optimized to grow lettuce, herbs or greens such as kale or Swiss chard, the LGM will initially grow kale and Romaine lettuce at CHS. Spillane said adding something like basil changes the dynamics inside the LGM, because growing the herb calls for slightly different conditions.
The Farmhand App makes farming easier by monitoring, controlling and tracking the indoor farm remotely. Rolling racks allow workers to move the plants for easier access.
Though the LGM is a rarity at public high schools, a number of colleges in New England, including Clark University in Worcester, Mass., have them.
Over the course of a year, the 320-square-foot LGM can grow the same amount of food as about 2 acres of land. Freight Farms, which produces the LGM, promotes its product as a way to grow food in almost any condition all around the world.
The inside of a Leafy Green Machine shows the full operation of vertical gardens, bathed in LED light.
Shauna Spillane, left, and Gina Rodriguez, of Sodexo Food Service, show off the new Green Leafy Machine outside the door of the kitchen at Cumberland High School. The former storage container will be used to grow vegetables for the school’s food service. (Breeze photo by Ethan Shorey)
Did You See AeroFarms On ABC's The Chew?
Did You See AeroFarms On ABC's The Chew?
Click here to watch AeroFarms, the sustainable farming company behind Dream Greens, on The Chew!
The Dream Team is incredibly proud of the positive impact that our indoor farming company, AeroFarms, is having on our community.
Did you know that our local baby greens also grow in the student dining hall of Philip's Academy Charter School in Newark, NJ? Philip's Academy students have been growing, harvesting and enjoying fresh, hyper-local baby greens for the past seven years from their AeroFarms school farm.
Last week, we had the privilege of hosting the incredible Chef Mario Batali at Philip's Academy Charter School, who shared our story on ABC's The Chew! If you missed it, you can watch the full episode here.
Chef Mario also cooked up a healthy, wholesome arugula penne pasta dish with the Philip's Academy students, using our freshly-harvested peppery arugula. You can make it too - check out the full recipe here on our blog! And don't forget about our recipe section on DreamGreens.com for more flavorful, healthy dishes.
“I’ve got news for you, the future is delicious and it is now!” - Chef Mario Batali
Antarctica Is Getting A Farm That Can Grow Produce Even When It's -100 Degrees Fahrenheit Outside — Take A Look
But engineers at the German Aerospace Center (GAC) will soon build a high-tech farm that will allow Antarcticans to harvest produce.
Antarctica Is Getting A Farm That Can Grow Produce Even When It's -100 Degrees Fahrenheit Outside — Take A Look
German Aerospace Center scientist Paul Zabel inside Eden-ISS.DLR German Aerospace Center
Antarctica's nonstop winters make it impossible to grow food outdoors. Fruits and vegetables are instead shipped long distances from overseas, just a few times per year.
But engineers at the German Aerospace Center (GAC) will soon build a high-tech farm that will allow Antarcticans to harvest produce.
The farm will feature a year-round greenhouse that can grow food for researchers at the Neumayer III polar station on the Ekstrom Ice Shelf.
Called the Eden-ISS, the farm exists inside a climate-controlled shipping container. The greenhouse relies ona technique called vertical farming, in which food grows on trays or hanging modules under LEDs instead of natural sunlight.
Take a look at the farm, which will come to Antarctica in October, below.
Before the Eden-ISS shipping container farm debuts in Antarctica, the GAC is testing growing fruits and vegetables at its headquarters in Bremen, Germany.
The Eden-ISS in Bremen, Germany.DLR German Aerospace Center
The 135-square-foot farm can grow all sorts of produce indoors. Harvesting food outdoors is impossible in Antarctica due to its endless winters.
DLR German Aerospace Center
The only way to get produce to McMurdo, the US station where the majority of Antarctic researchers stay, is by ship or plane. In January, a shipment of dried and frozen food is delivered, and during summer, planes come with fresh food around once a week, according to Atlas Obscura.
GAC scientist Paul Zabel will move with the farm to Antarctica, where he will grow fruits and vegetables under 42 LED lamps.
German Aerospace Center scientist Paul Zabel.DLR German Aerospace Center
Since the farm is climate-controlled, it can grow crops year-round in a place where temperatures can plummet as low as -100 degrees Fahrenheit.
DLR German Aerospace Center
As Modern Farmer notes, some sub-Arctic regions are experiencing somewhat of an agricultural boom, due partly to climate change.
Over the past 100 years, Arctic temperatures have increased at nearly twice the global average, making it possible to grow crops in once-desolate places like Yellowknife in Canada and Greenland.
In order to help the plants thrive, the researchers pump in extra carbon dioxide and set the temperature at 75 degrees Fahrenheit.
DLR German Aerospace Center
The LEDs are tuned to red and blue wavelengths — the optimal light frequencies for growing produce.
DLR German Aerospace Center
The crops are stacked on trays. Every few minutes, they receive a spritz of nutrient-rich mist.
DLR German Aerospace Center
The researchers plan to grow between 30 and 50 different species, including leafy greens, peppers, strawberries, radishes, and tomatoes, as well as herbs like basil and parsley.
DLR German Aerospace Center
In July, the team grew its first cucumber, which measured 96 grams and 14 centimeters long, inside Eden-ISS.
DLR German Aerospace Center
In February, the GAC built the farm's platform by crane in Antarctica. Everything else will arrive next month.
DLR German Aerospace Center
The larger goal of the Eden-ISS project is to create a system that allows GAC astronauts to harvest food in space.
DLR German Aerospace Center
If the researchers can perfect a growing process for Antarctica's harsh climate, they may stand a chance at growing on Mars or the moon.
DLR German Aerospace Center
Urban Farming Startup Raises $1.5m To Curb Singapore’s Reliance On Imported Food
Urban Farming Startup Raises $1.5m To Curb Singapore’s Reliance On Imported Food
- Terence Lee
Sep 26, 2017
L to R: Praise Phuan, head of sales and marketing at Packet Greens, Melvyn Yeo, director of Trirec. Image credit: Trirec.
Packet Greens, a Singapore-based startup which couples hydroponics technology with automation to make urban farming more efficient, has raised US$1.5 million in funding from government-related venture capital firm SPRING SEEDS Capital and cleantech-focused fund Trirec.
The company employs vertical farming – racks of crops stacked on top of one another – to improve land-use efficiency. It delivers precise dosages of nutrients and water to crops to minimize wastage. The plants are bathed in LED lights in a tightly controlled environment, eliminating the use of pesticides.
It currently grows 51 types of crops in a 167 square-meter farm – slightly larger than the roomiest three-bedroom apartments in Singapore. It claims to be able to grow five times the crops on the same amount of land compared to traditional farms, and in half the time.
It is aiming to further lower its costs. “Down the road, Packet Greens’ ambitions is to ultimately be able to sell its produce at a price that can be competitive to the wholesale price,” says Trirec co-founder Melvyn Yeo. “Packet Green’s pricing strategy is currently pegged at retail-minus.”
That means it charges wholesalers a certain percentage less than retail price.
“While our operations are not sized at scale for the cost to compete against the traditional imported produce – since Packet Green is still a start-up – our experience has shown us that we are able to achieve a viable costing down strategy.”
Packet Greens tells Tech in Asia that its revenue is forecasted to exceed US$74,000 this year, triple of 2016.
The startup sells its crops directly to consumers online. It also supplies them to restaurants, hotels, and online retailers. It plans to expand locally for three to five years before looking abroad.
Trirec is an investor in Sunseap, a major clean energy solutions provider in Singapore that is valued at US$221 million.
Singapore imports 90 percent of its food, according to a 2015/2016 annual report by the Agri-Food & Veterinary Authority of Singapore. It aims to reduce the country’s reliance on imports and has designed a number of schemes to achieve it.
Converted from Singapore dollors. US$1 = S$1.35.
Are Vegetable Flats The Future?
Are Vegetable Flats The Future?
The most densely populated island in the world is Macau. In the Chinese state, 600,000 people are packed together on 30 km2, making the population density practically 20,000/km2. That figure is much lower in the Netherlands. On average, 500 people live on a square kilometre here. In Dronten, in the centre of the Noordoostpolder, that number is even lower. Inhabitants there have to share their square with just 121 people. Yet the Staay Food Group chose to not build a 3,000 m2 greenhouse, but a much more expensive vertical farm of 900 m2. What inspired them to do that? And is vertical farming becoming more popular globally?
The world population is increasing, we’re all moving to cities, and we attach more and more value to high-quality food, grown safely. The trends cannot be ignored and all indicate the same: a growing demand for vegetables, grown at or near to the place of consumption. But how should that be realised? After all, space in cities is limited. Vertical cultivation systems are seen as the solution increasingly often. By working in a controlled environment and on multiple layers, an enormous amount of food can be produced on a small surface. A minimum amount of water and fertiliser is used. Moreover, the cultivation is clean, the chance of contamination is small, and little knowledge is necessary to run farms like these: computers calculate and adjust the cultivation. And, perhaps most importantly, there’s complete control over climate and light. The crops are grown without outside influences and contaminations, and the production area is sterile.
Japanese nurseries
A number of large, vertical farms have been set up in Japan in recent years. The company Mirai was one of the first. After the earthquake and tsunami of 2011, they saw an increase in demand for safe food, while supply was low. They decided to open a vertical farm in the stricken area. “We wanted to support the region, and to show we can grow food anywhere in the world,” the entrepreneurs said. Since 2013, they’ve grown lettuce on an area of 2,300 m2. Thanks to the 15 floors they work on and the time it takes the lettuce to grow (30 days, compared to 50-60 in the open air), 10,000 heads of lettuce leave the farm now every day. They are sent to restaurants, small retailers and smaller selling places. By now they also have a branch in Hong Kong and two smaller projects in Mongolia: in the south of the Gobi Desert and one in Ulanbataar.
Container cultivations for regional sales
Vertical farms have also been founded outside of Japan. In the United States, numerous projects, or rather small projects, have been started. Entrepreneurs, who don’t have their origin in the fresh produce or horticultural sector, but who did spot a hole in the market, are starting the local production of vegetables. They choose small greenhouses in which they grow lettuce in chutes, or they start growing in containers using LED lighting.
By now, an entire industry has come into existence here as well. Various parties supply ready-made cultivation containers. One of the best known buyers of these is Kimbal Musk, brother of Paypal and Tesla founder Elon Musk. Kimbal purchased as many as 20 cultivation containers, and blogs about the importance of growing near, and being in contact with, the final user. In 2016, his Leafy Green Machine was placed in a residential care home in Deventer. That way, growing leafy vegetables also has a social function.
The container cultivations are completely different projects than the vertical farms that have been producing vegetables on a larger scale for two years now. The 12 metres of growing surface of Leafy Green Machine is not in any way related to the project started in an old steel company in Newark last year. Nursery AeroFarms has a surface of 0.6 hectares, and is 9 metres high. Because of that, food can be grown on as many as 12 floors. The company grows more than 200 types of vegetables: kale, bok choi, watercress, aragula, and so on. The company harvests and sends their ‘Dream Greens’ brand products to important foodservice companies such as The Compass Group, ShopRite, WholeFoods and FreshDirect daily, and they employ about 120 people.
Expensive and energy-intensive?
Is this the future of cultivating? Will we all eat food grown in cultivation factories soon? “How can a vertical farm solve the problem of world hunger? Can we feed the world with just green leafy vegetables and culinary herbs?” These questions were asked in Venlo in June, during the Vertical Farming Congress. The participants don’t really see it that way, either. For vertical farming, sales are an important part of the company. “You must have your objective in mind when starting a vertical farm,” says Jan Westra from Priva. “Are you starting a farm in the city from a social standpoint, or is it the wish of the government to give a new boost to existing buildings? Or do you want to grow food in an inaccessible location such as the South Pole? You can grow practically anywhere with vertical farming, but there’s a great number of factors that decide whether you’ll make a profit or not: from utility costs to marketing.” Dutch horticultural suppliers agree with that. Due to all of the techniques necessary, vertical farming is quite an investment. But precisely that investment offers major opportunities, Marc Kreuger explains. He is in charge of innovations for Here, There & Everywhere, supplier of vertical farming. “Because you have control of everything, and the entire cultivation can be predicted in advance, you also know the exact price per kilo needed,” he says. According to his calculations, growing tomatoes, cucumbers and bell pepper is commercially interesting.
Addition to greenhouses
Dutch company Certhon also invested in growing vegetables in a cultivation system devoid of natural daylight. This summer, they harvested their first bell peppers from their growing cell Plantyfood. Certhon is originally a greenhouse builder. “We focus on the customer and on ensuring they get a profitable system,” Manager Hein van der Sande explains. “We look for the best cultivation method per region. Sometimes that’s a greenhouse and sometimes it’s a system without daylight. It depends on the circumstances.” Moreover, he has also noticed many similarities between the two. “Looking at technical set up of a greenhouse, with three screens and climate computers, the step to containers isn’t all that large. The difference is between glass versus sandwich panels. It’s true sunshine is free, but in certain conditions it can also be an enemy, in the Middle East, for example. You then have to make decisions and calculations and look at the customer’s wishes.”
The company is also the main contractor for the vertical farm Fresh-Care Convenience in Dronten. Lettuce is grown in the climate rooms on nine layers. “It is the largest in Europe, but it’s still just a test set-up,” Rien Panneman said during the royal visit in June. “But if it does as is expected, we’ll definitely expand on this method of growing food, both regionally and internationally. At first we’ll have a capacity of 6,000-7,000 kilos per week, but we already have a weekly demand of 120,000 kilos. Early 2018 we’ll decide whether to expand the cultivation or not. And other regional cultivation companies can join us in that.”
Staay Food Group used the vertical farm mostly to become independent of the Southern European cultivation. “We currently get our lettuce from Southern Europe during part of the year. Disadvantages of this are the changeable climate and the long transportation distances. When we get lettuce from our own vertical farms, it’ll be fresher, no pesticides will have been used, and quality will be stabler. Furthermore, the cultivation is sustainable, the use of water can be reduced ten times. And we can plan much better. When we plant on day 1, we can harvest on day 30. The first heads of lollo bionda, lollo rosso, rocket and frisée lettuce will therefore be marketed this year.”
Publication date: 9/26/2017
Grand Rapids Micro-Farm Turns Shipping Container Into Year-Round Crop Bonanza
Grand Rapids Micro-Farm Turns Shipping Container Into Year-Round Crop Bonanza
By STATESIDE STAFF • September 25, 2017
Crops grow in the Green Collar Farms, a converted shipping container.
BRIAN HARRIS / FACEBOOK
Since mankind first began growing crops, the farmer's enemies have been drought, wind, wild temperature swings: curve balls served up by Mother Nature.
Brian Harris is turning out an array of green produce, protected from the elements, in a converted freight container that sits near downtown Grand Rapids.
He calls this a “hydroponic vertical micro-farm,” officially named Green Collar Farms.
A friend tipped Harris off to a wave of urban farming in Florida. He started by assembling a variety of containers and spaces in order to grow crops.
Currently, Harris’s farm is located in a freight converter. “It’s literally an oceangoing, refrigerated shipping container,” said Harris. “This one was built in 2004 and retired I think last year. It’s an insulated 40-foot by eight-foot by nine-foot box that just happens to hold almost two acres of crop.”
The container is growing cold crops right now, including a number of leafy greens.
Hydroponics is promising for farmers. Its reliance on recycling allows the farmer to be conservative with water. “We use about ten percent of what a typical soil farm would use,” said Harris. Growth can occur year-round, since the farm is wholly contained in an insulated space. That means that crop cycles can continue without waiting for the warmer months.
Nutrition studies indicate little difference from field-grown crops and hydroponics, said Harris, and hydroponics may prove to be better for consumers. Since field crops often have to consume their own energies, like sugar, they end up being more bitter and chewy. In hydroponic farms, nutrients simply come to the plants, so the crops don’t have to build roots.
Harris sees a bright future for a hydroponics franchise: “You could place these containers throughout an urban area where they would serve the local restaurants,” said Harris. He’s looking to expand his farm into a warehouse. “A 10,000-square-foot facility would produce 65-70 acres of crops, every seven weeks.”
Fresh Produce Grows Big Results For Akron Startup
Vigeo Gardens, which grows its crops in an indoor, highly controlled, chemical-free environment in downtown Akron and delivers its products fresh to area restaurants, grocery stores and food distributors, had about $23,000 in sales the first year. In year two, sales were $250,000, and they are on pace to be at least $750,000 in 2017, said Vincent Peterson, the company's chief executive officer.
September 24, 2017
Fresh Produce Grows Big Results For Akron Startup
By BETH THOMAS HERTZ
Photo by Shane Wynn for Crain's
Vigeo Gardens principals, from left, Vincent Peterson, Mark Preston and Jacob Craine stand in front of some o the company’s hydroponic growing racks. The pinkish hue in the room comes from the red and blue lightbulbs used for growing.
A downtown Akron company that was started in late 2014 by two young men who wanted to be part of the restaurant industry without giving up all of their nights and weekends has seen explosive growth in the demand for its fresh-grown basil, lettuce and microgreens.
Vigeo Gardens, which grows its crops in an indoor, highly controlled, chemical-free environment in downtown Akron and delivers its products fresh to area restaurants, grocery stores and food distributors, had about $23,000 in sales the first year. In year two, sales were $250,000, and they are on pace to be at least $750,000 in 2017, said Vincent Peterson, the company's chief executive officer.
"We believe the facility could yield $2 million to $3 million in sales once it is fully operational," said Jacob Craine, chief marketing officer.
The huge growth is the result of matching good science with innovative ideas and hard work. Craine said he, Peterson and Mark Preston, chief operating officer, routinely put in 80 to 100 hours a week.
This journey all started when Craine, 26, and Peterson, 25, friends since kindergarten, grew their first crop of microgreens in Craine's basement in 2014.
"Everyone thought we were crazy, but we had been working in the restaurant industry for a number of years and really enjoyed it, and wanted to find a way that we could stay in the industry without working the off-schedule from the rest of the world that most people in the restaurant industry do," Craine explained.
Their initial idea was to develop a line of microgreens for people who were in particular need of the high-nutrient boost they provide, such as chemotherapy patients.
"But we quickly found out that it takes a lot to get into the hospital market, so we switched gears for the moment and have been focusing on the culinary industry, which is something that we knew," he said.
Initially, they called the company Plantscription, but changed it to Vigeo Gardens in 2015. Vigeo means to thrive in Latin, not just survive, Craine pointed out.
"That's kind of the motto of our company," he said.
To get out of Craine's basement, the pair moved into the Akron Global Business Accelerator, where they connected with Preston, 27, who has an aerospace engineering degree from Ohio State University and experience in the hydroponics industry. His skills helped create their first vertical "rack," a platform on which they grow their crops, in a 1,000-square-foot space.
The trio was then able to raise funding from a private investor and add five more racks, but they were still uncertain if their idea was scalable. Clearly it was, though, as six months later, in August 2016, they moved to even larger space — 6,000 square feet on the third floor of the accelerator that now holds 37 racks. This was funded through the same private investor as well as a bank loan. Craine estimates that the two steps represent a combined investment of about $400,000.
Just over a year later, this expansion is now in the "finishing touches" phase. Most racks are operational, and the few remaining dormant ones are being activated as needed to meet demand.
Today, the company has six full-time employees and several part-time workers, mostly farming jobs and one sales position, in addition to the three partners.
Products
Craine said that the primary thing that sets Vigeo's products apart is that the company sells their basil and eight types of lettuce "live." They are harvested in the morning and delivered to customers with the root structures still intact the same day.
"It's as fresh as you can get," he said.
They also grow about 20 types of microgreens.
He said such freshness is hard to obtain from other sources.
"When you go to the grocery store and you buy lettuce that's been packaged and shipped here from California, it's at least a week to two weeks old," he explained.
Equally appealing to customers is the lack of chemicals on the crops, which is possible because they grow indoors.
"We don't do any spraying. Everything we grow is non-GMO," he said.
Another big advantage of being inside is that the company is able to produce the same consistency year-round, he said.
The lack of the climate variables brings productivity advantages, too. By maximizing the efficiencies of their growing system, such as using custom LED lights designed by Preston and making their own nutrient solutions and strictly controlling the relative humidity of the room, they have been able to effectively cut three weeks off the growing cycle of basil and two weeks off the growth cycle of lettuce.
This lets them produce a few extra cycles a year and provides them with four to five harvests per week.
"We have been in business for two-and-a-half years, but we have had as many crop cycles as farmers that have been in business for 10 to 20 years," Craine said.
Vigeo's client list includes about 35 to 40 restaurants in Northeast Ohio, including Dante Boccuzzi Akron, where Craine previously worked, and Jonathon Sawyer's Trentina and Greenhouse Tavern, as well as several in Columbus.
The company also sells to several major distributors, such as US Foods and Sirna & Sons, plus to all of the Mustard Seed stores, and 26 of the Heinen's stores, including the four in Chicago.
Vigeo also began a pilot program with Giant Eagle this month, with the goal of moving into all of the grocer's Market District stores in the area.
Boccuzzi said he thinks there was a real need for a company like Vigeo in this area. He previously purchased such produce from an out-of-state company, but is happier with the greater freshness the local company can provide for his several area restaurants.
"They produce a good quality, consistent product that lasts a long time since they are so close," he said.
He said he is glad to support his former employee, Craine, and finds Vigeo is willing to work with him on his product needs.
"They are young people who work very hard," he said. "I appreciate that today."
Craine said Vigeo's future growth plans include a desire to refurbish old factories such as the one that houses the Akron accelerator into high-efficiency vertical farms. It also may build a greenhouse here to grow products that aren't amenable to the indoor facility, such as tomatoes and peppers.
It also wants to apply its technology to growing medical marijuana in a facility in Akron through another corporate entity it has created, Vita Est, LLC. That facility this month received a conditional use permit from Akron City Council that will allow it to proceed if the state grants it a license.
"We believe our knowledge base on controlled agriculture is transferable to the production of high-quality medical marijuana," Peterson said.
Craine stressed that the companies would be completely separate, but the trio declined to comment further on the plans.
Ikea Is Bringing A Pop-Up Vertical Farm To London
According to Wikipedia: ‘Vertical farming is the practice of producing food and medicine in vertically stacked layers, vertically inclined surfaces and/or integrated in other structures (such as in a skyscraper, used warehouse, or shipping container).
Ikea Is Bringing A Pop-Up Vertical Farm To London
Lisa Bowman for Metro.co.uk | Wednesday 20 Sep 2017 5:01 pm
(Credit: SPACE10/Cover Images)
If you’re into the future of food, then everyone’s favourite Swedish furniture lords have a treat for you.
Ikea are bringing a pop-up vertical farm to Shoreditch, as part of the London Design Festival.
Researchers from the SPACE10 lab at the Lokal pop-up want to show the general public that delicious, fresh food can be grown right in your home, using a hydroponics farming system.
It’s basically soil-less farming – crops are grown indoors using artificial lights and computerised automation that grows food optimised for freshness, nutrients, and taste.
They say it makes food production smarter and more efficient as their system can grow vegetables three times faster than traditional methods, with 90% less water, less waste, and without the need for soil and sunlight in a much more space-efficient footprint.
The indoor system has computerised automation (Credit: SPACE10/Cover Images)
So how does it work?
Modified LED lights allow for year-round indoor growing and smart sensors allow for machine learning so that healthier food can be grown faster while the data is fed into Google Home.
Essentially, you can ask your plants how they’re doing, and they can let you know.
The creators hope it will help kids and adults learn more about sustainable food, and they also promise that the system will be run solely on renewable energy in the future.
The vertical farming system (Credit: SPACE10/Cover Images)
What is vertical farming?
According to Wikipedia: ‘Vertical farming is the practice of producing food and medicine in vertically stacked layers, vertically inclined surfaces and/or integrated in other structures (such as in a skyscraper, used warehouse, or shipping container).
‘The modern ideas of vertical farming use indoor farming techniques and controlled-environment agriculture (CEA) technology, where all environmental factors can be controlled.
‘These facilities utilise artificial control of light, environmental control (humidity, temperature, gases…) and fertigation.
‘Some vertical farms use techniques similar to greenhouses, where natural sunlight can be augmented with artificial lighting and metal reflectors.’
The pop-up features a futuristic salad bar that provides meals of hydroponic microgreens, topped with delicious locally sourced ingredients.
There will also be ‘Grow Your Greens’ workshops for kids to learn how to grow their own take-away plant hydroponically, until it turns into a delicious green.
‘Food Preservation’ workshops will teach visitors how to use fermentation to preserve food and minimise waste.
Growing food at the vertical farm (Credit: SPACE10/Cover Images)
The farm is located at 31 New Inn Yard, London EC2A 3EY.
It’s open between 10am – 9.30pm until September 23.
Find out more here.
Go eat some futuristic food, people!
How Can New York Meet the Challenges of Urban Agriculture?
How Can New York Meet the Challenges of Urban Agriculture?
SEPTEMBER 21, 2017 LOUISA BURWOOD-TAYLOR
On the final day of AgTech Week in New York City, a panel of local experts got together to think about how the city can embrace, promote and foster urban agriculture.
New York is one of the leading cities in the US for urban agriculture, with a plethora of initiatives from hobby community gardens to commercial rooftop farms to high-tech indoor vertical farms. But there is still a long way to go until the city provides wannabe urban growers with the support they need to make locally grown produce a permanent and significant part of the city’s food supply.
Before the panel commenced, Henry Gordon-Smith, a celebrity in New York’s urban agriculture scene and founder of consultancy and content businesses Agritecture and Blue Planet Consulting (now Agritecture Consulting), set the scene by offering some insights into how other cities in the world make a success of their urban agriculture initiatives.
In Cuba, for example, 3.2 tonnes of organic food was grown in urban farms in 2002. Individuals are incentivized economically to grow food, but there are also rules around what they can grow in each location, depending on what else is being grown nearby to ensure diversity in the food supply.
Japan’s weekend farming program brings families out of the city and into the surrounding countryside to help grow food, connecting them with the source of their food and providing them some often needed respite from city life. There are also programs to get their help at indoor grow operations too.
And in Canada, urban farmer Curtis Stone has borrowed or rented unused land to produce food at scale, making the most of untapped resources in the city, and rules around vacant real estate lots.
“How can we have our own brand and approach to urban agriculture in New York City?” he asked the audience.
What are the main challenges for urban agriculture in New York and what can the city do to alleviate them
1. Access to Land and Space
This can be a real inhibitor at the early days of a project, but also when the operator wants to scale, moving from 1,000 sq ft to 10,000 sq ft is very difficult, said Gordon-Smith.
The difficulties mainly lie in permitting and the delays inherent in the system. There is also lack of available information about the availability of space for urban farms.
Gordon-Smith and Tatiana Pawlowski, a law clerk at Braverman Greenspan and expert in zoning laws, blamed permitting challenges to a lack of understanding in the department of buildings about urban agriculture. “The department does not know how to handle an application for an urban farm. The zoning code itself is very hard to read and it’s very long. It hasn’t been updated since 1962 and the phrase urban agriculture doesn’t exist! There is some brief talk about raised truck beds and community gardens, but the law is very silent on what exactly can and can’t be done.”
Gordon-Smith added: “There is a lot of interpretation of code needed before permits can be awarded, but for operations, timing is critical to get investment as investors won’t support a project if you can’t secure a space.”
There is also a lack of concrete, and available data and information about where vacant spaces might be and how they’re utilized, or not.
“People might not know that technically farming is allowed in commercial and industrial districts,” Pawlowski said.
What Can NYC Do?
Create a well-organized, centralized place for all data and information about finding and securing space in New York that’s readily accessible.
“Modernize and organize the information available so it’s readily accessible for urban farmers, particularly small-scale scale community residents,” said Tatiana.
None of the panelists suggested this outright, but it sounds like the city could do with updating its zoning laws too!
Rafael Espinal, council member for Bushwick and East New York, agreed that urban farming initiatives were struggling to get seed funding they need because investors are afraid to invest in a city which has “not yet taken a leading role in recognizing the work that’s being done in this area.” He added that he has introduced a bill to “force the city to sit down and take a year to figure out what challenges we’re seeing for urban agriculture in terms of zoning or incentives as the city must get engaged at that level.”
2. Access to Basic Talent
Finding entry level talent, with some training in food safety and other relevant skills, is very challenging, according to all the panel members. It also represents a significant portion of an urban operation’s cost base.
What Can NYC Do?
Gordon Smith suggested that the city could develop a training program to help develop a diverse skillset among potential workers to strengthen the urban ag industry, but that there might need to be a financial incentive attached to it, particularly as labor is one of the leading operational costs of urban farming.
Alex Highstein, corporate development at AeroFarms, which is based in New Jersey, said New Jersey has some initiatives like this. “We work with the New Jersey Economic Development Authority. They have a program called Grow NJ which gives us tax incentives for hiring, and we’re also working with the city of Newark to source labor from fantastic places like the veterans program, and the re-entry program. They help train them, particularly where there are big gaps in knowledge such as around food safety.”
3. Lack of Awareness About Benefits of Local Food
Governments do not put local food first, which limits the ability to promote urban agriculture among the population to bring new talent and expertise to the sector.
Highstein agreed that people in New York “often lack a connection to what they’re eating; if we could spread the idea that this food was grown the next street over, those people would value their food more.”
What Can NYC Do?
Work with industry, incubators, and farms to spread those ideas around the importance and value of locally grown food.
“We need more carrot to get groups involved and excited about promoting urban agriculture to help it accelerate,” said Gordon-Smith.
4. Energy Costs and Carbon Footprint
There is a certain amount of resistance to indoor farming from some quarters of the city, namely around the high use of electricity to light and heat indoor farming facilities, and therefore the potential for added pollution. Developments in LED lighting are aiming to increase efficiency, but it’s a significant cost-base, economically and carbon emissions-wise.
Council member Espinal said: “We get lots of emails from people who are against expanding urban ag as they say it will require more power and create more plumes. There is not enough green energy produced, pushing reactors to create more power to feed indoor farm lighting.”
What Can NYC Do?
“We need to continue pushing for ’80×50′, which is a New York pledge to reduce greenhouse gas emissions by 80% by 2050,” said Espinal. “But to do this the city needs to change the grids to accept solar and wind energy.”
Highstein also suggested incorporating hydroelectrical energy.
Panelists argued that protesters also need to be better educated about the environmental benefits of urban agriculture, something the local government could help with.
“People forget about the benefits of outdoor rooftop farming and the amazing effect it has on mitigating the heat island effect, where black tar rooftops create heat, requiring more energy to cool buildings down,” said Pawlowski. A green roof can bring temperatures down by a couple of degrees, which is significant, and not only fits with the 80×50 plan but is also good for air quality.”
Harrison Hillier, hydroponics manager at Teens For Food Justice said that just looking at energy consumption was only part of the broader picture, pointing to the food security indoor operations can bring in the face of natural disasters, and the reduction in the use of harmful chemicals and pollutants causing negative ecological impacts across the country.
Food Pioneers Regenerate Cities
Urban Organics opened the doors of its first aquaponics farm, built inside an old Minnesota brewery, in 2014. The venture was backed by global water firm Pentair, which fitted out the Hamm’s Brewery site with an innovative water filtration system and industry leading reuse technologies
Food Pioneers Regenerate Cities
Staff reporter | 15th September 2017
An urban food pioneer is transforming abandoned buildings in Minnesota into breeding grounds for sustainable fish and organic greens.
Urban Organics opened the doors of its first aquaponics farm, built inside an old Minnesota brewery, in 2014. The venture was backed by global water firm Pentair, which fitted out the Hamm’s Brewery site with an innovative water filtration system and industry leading reuse technologies. And the pair have built on that relationship with the regeneration of Minnesota’s Schmidt brewery, which will be able to supply ‘275,000 lbs. of fresh fish and 475,000 lbs. of produce per year to the surrounding region’ this year. The ‘USDA-certified-organic farm’ extends Urban Organics reach as it begins to expand a business with tech that could have a global impact.
“We started this venture as social entrepreneurs who wanted to figure out how to bring a reliable source of healthy foods into areas that had to rely on food transported in from far away,” explained Dave Haider, co-founder of Urban Organics. “It turned out that our wild idea also made a lot of sense to a community hungry for organic, sustainably-raised food, and to other innovators around the world who had been asking the same questions we were. By collaborating with Pentair, we’re able to contribute beyond our immediate region—we’re able to test and perfect the technologies that will make a global impact advancing the field of large-scale commercial aquaponics.”
Farming in the city is a growing trend. By 2022 it is estimated the vertical farming market will be worth more than $6 billion. And America is leading the way. Aero Farms is making progress with its vision to combat the ‘global food crisis with technology’. While an urban food accelerator in the heart of New York, Square Roots, led by entrepreneur Kimbal Musk, is helping innovators take forward their ideas for developing indoor farming businesses – inside shipping containers located in Brooklyn.
The Farms Of The Future Are Here – But There's A Catch
This new type of farming, dubbed "urban farming," requires significantly less acreage and energy. Simply put, urban farms grow or produce food in a city or heavily populated area using unorthodox methods.
The Farms Of The Future Are Here – But There's A Catch
By CASEY WILSON, Associate Editor, Money Morning • September 21, 2017
The farms of the future use absolutely no soil and 95% less water.
Yes, you read that right. No soil – at all.
This new type of farming, dubbed "urban farming," requires significantly less acreage and energy. Simply put, urban farms grow or produce food in a city or heavily populated area using unorthodox methods.
Urban farming takes many forms, using many different methods. Some urban farms are strictly vertical farms, which means the plants grow upright on walls. Some are aeroponic, which means the plants grow in an air or mist environment.
Urban farms are so efficient, just half an acre can yield the same (and in some cases, more) harvest than over 10 acres of traditional farmland.
No wonder these urban farms are sprouting up all over the country. There's at least one urban farm in almost every major city today. In some cities, like New York City, there are more than 20.
But here's the downside…
Urban farming isn't something average investors and traders can directly invest in, and likely won't be for a while.
You see, most urban farming ventures get their funding from venture capitalists. For example, AeroFarms Corp., one of the largest urban vertical farming companies, just secured $20 million for its latest indoor farm all from one round of venture funding.
And the company has not made any plans to go public as of yet. Instead, the company is planning to work with Goldman Sachs Group Inc. (NYSE: GS) and Prudential Financial Inc. (NYSE: PRU) to raise more than $70 million over the next five years in order to build 25 new farms – a 177% increase from the 14 farms it has now.
Still, there's a way for investors to profit from this burgeoning technology. Check out the video below…
Bosses Of Google And Amazon Back Plenty In plan To Bring High-Tech Farm Warehouses To Feed Britain
Bosses Of Google And Amazon Back Plenty In plan To Bring High-Tech Farm Warehouses To Feed Britain
Danny Fortson, San Francisco
September 24 2017, 12:01am, The Sunday Times
Plenty plans to open farm warehouses globally, in the cities that are home to at least 1m peopleALAMY
An indoor-farming start-up backed by Amazon’s Jeff Bezos and Eric Schmidt, chairman of Google parent Alphabet, plans to bring its high-tech farm warehouses to Britain by 2019.
Plenty raised $200m ($148m) in a funding round led by SoftBank Vision Fund, the $100bn mega-fund created by Saudi Arabia and Japan’s SoftBank. Bezos and Schmidt, who invested in a previous financing, also contributed.
The San Francisco company is in the midst of bringing in more investors to bankroll an aggressive global rollout. Chief executive Matt Barnard wants to open “farms” in the 500 cities around the world with at least 1m people, with that expansion arriving in Britain as soon as 2019.
Plenty’s giant warehouses — where plants are grown in 20ft towers with lighting, temperature, water and pests controlled and managed with artificial intelligence — promise to dramatically improve efficiency and output compared with normal farms.
Barnard claimed lettuce can be grown with less than 1% of the water required in a traditional operation. High energy costs are offset by locating warehouses in or near city centres, doing away with the need for long-haul transport that accounts for up to 40% of the price for fruit and veg.
He said: “What’s going to be stunning for people is the speed at which much of what they eat will be grown.”
Danny in the Valley podcast: Plenty’s Matt Barnard: “You’re eating year-old apples”
Modern Farmers: Modern Farmers: The Future of Farming Is Sprouting Up Where You'd Least Expect It
It's not just a potential antidote to the unsustainable machine of industrial agriculture. It's also a new frontier for the culinary world, and you're about to reap the benefits.
Go Inside the Farms | Photo: Bowery
Beneath one of NYC's best restaurants, down a hallway you could find only if you knew where to go, rows of heady, hydroponic herbs, sticky with residue, grow under LED lights. Across the East River, in an old factory, a small lab of growers tinker with their own seedlings, while a greenhouse just two miles away grows its own special line of potent plants.
No, we're not talking about weed—although in many ways, the, ahem, budding industry helped pave the way here. We're describing the field of indoor farming, much of it hydroponic, catering to home cooks and restaurant chefs, that's growing at an incredible clip around the country. And it's booming where you'd least expect it: none other than New York City.
It's not just a potential antidote to the unsustainable machine of industrial agriculture. It's also a new frontier for the culinary world, and you're about to reap the benefits.
Just ask Tom Colicchio, an investor in Bowery Farming, a seven-month-old hydroponic vertical farm, which just recently started selling greens to tristate area Whole Foods. The chef calls the company the "new paradigm for farming," one that he's "really excited about." At his new Downtown NYC restaurant, Temple Court (previously Fowler & Wells), the Top Chef judge garnishes crudo with Bowery's wasabi arugula—a spicy green bursting with flavor. Or ask Claus Meyer, an adviser at Brooklyn Navy Yard-based start-up Farmshelf, or Alex Guarnaschelli, who sources from newcomer Farm.One, which has spaces at the Institute of Culinary Education and underneath the restaurant Atera in Tribeca. Each one of these chefs is a champion for the undeniable advantage of indoor farming: fresh, unique and local produce available all year round.
Andrew Whitcomb, executive chef at Norman | Photo: Farmshelf
Exact methods vary, but generally speaking, hydroponic farms grow greens, herbs and flowers in soilless containers under LED lights in highly controlled climates. That means 365 days of ideal growing conditions, with efficient water use and minimal waste. They're also often stacked vertically, which cuts down on the need for square footage. Some farms, like Edenworks in Brooklyn, use fish and aquatic life to feed their ecosystems, while others, like AeroFarms, don't use hydroponics at all but rely on a specifically crafted aeroponic mist.
It might sound unnatural, but these farms are actually growing their goods without the use of herbicides or pesticides. Bowery cofounder Irving Fain implores skeptics to rethink what organic really means, pointing out that "organic standards were written at a time when a lot of the technology we have access to today didn't even exist."
And then there's the magic word: local. These indoor farms are able to grow and sell within mere miles of the restaurants or homes to which they're catering, no matter the season.
As Great Northern Food Hall's Jonas Boelt—who works with Farmshelf—explains, "Back in Denmark, my team and I would go forage for ingredients daily. As that is impossible in New York City, harvesting Farmshelf herbs is the next best thing."
When you look at it this way, it makes sense that NYC and the surrounding area, against all odds, has become a major hub for ag tech. The high demand from the most competitive dining scene in the country, coupled with the short growing season, actually makes for quite fertile ground. Add to that the great public transportation, Farm.One CEO Robert Laing points out, and distribution becomes even more sustainable.
Though the space may seem crowded, every company has a distinct mission. AeroFarms and Edenworks focus on large-scale production, boxing greens to sell at the supermarket. Bowery does the same but also works with Colicchio to expand its culinary partnerships.
Farmshelf builds units to put into restaurants—like the Great Northern Food Hall and Brooklyn's Norman—hotels, corporate cafeterias and eventually home kitchens, "putting the technology into the hands of the consumer and bringing the farm right into the building," as cofounder/CRO Jean-Paul Kyrillos says.
Unique greens growing at Farm.One in TriBeCa | Photo: Farm.One
Then there's Farm.One, which focuses on providing restaurants with rare and fresh ingredients, selling to some of the hottest spots in NYC. Think Mission Chinese, Daniel, Atera, Pizza Loves Emily, Le Turtle, Locanda Verde, The Pool and The Grill.
"In general, they're buying things that are normally the last thing that a chef puts on the plate and the first thing the customer sees," Laing says of a list of herbs and flowers that may be unrecognizable to even the proudest foodie. Multiple kinds of sorrel and basil are just the beginning. (Pizza Loves Emily is fond of the Pluto basil, while the blue spice basil's vanilla notes would compliment any dessert.) There's also papalo, a limey herb from Central Mexico that's great for cutting the fat on rich dishes, as well as medicinal-tasting yarrow and sweet anise hyssop. Farm.One even grows something called cheese plant, which tastes just as funky as it sounds.
Beyond the accessibility to fresh or rare plants—and the intense flavor that comes along with them—another culinary win for these farms is that they guarantee chefs a certain amount of predictability and control, Boelt points out. Among the many reasons chef Tim Hollingsworth of L.A.'s Otium values his vertical garden—albeit an outdoor one—is for the control it gives him over a plant's different growing phases. For example, he can use nasturtium flowers one week or harvest them early for their capers another week.
With so many culinary perks, it's no wonder that the ag tech industry is taking off, with ambitious chefs going all in. Whether you're dining out or cooking at home, the variety of fresh and local produce is only going to get better as these farms grow, elevating the possibilities for your plate and palate—and making the watered-down, mass-harvested produce you're used to tasting even more bland. "I can't even buy herbs from the supermarket anymore," Laing says. You're next.
This month, join us as we go all in on Peak Season, taking full advantage of the bumper crop of cozy recipes, market ingredients, wine trends and entertaining gear to help you live your best fall.
5 Profitable Urban Farming Questions With Metropolis Farms
5 Profitable Urban Farming Questions With Metropolis Farms
Jack Griffin, President of Philadelphia-based vertical farming company Metropolis Farms, is known for his passionate support of the burgeoning indoor agriculture industry, whether that’s founding an industry association or representing the industry in Congress. We’re looking forward to hearing about his wide-ranging plans at Indoor Ag-Con Philly, and caught up with him ahead of that to hear more about his indoor agriculture world view.
1. Metropolis Farms has become a leader in the Philadelphia vertical farming scene. How did the farm come about?
Six years ago, I was working as the president of a merchant bank on Wall Street. Two very prominent Philadelphians came to our firm for a 25 million dollar investment to start an indoor vertical farm. After an enormous amount of due diligence I realized none of the existing farms were actually economically viable. They only thing they could grow was baby lettuce (basically crunchy water). There technical and scientific claims were a joke, and their financial projections had more in common with a game of three card monte then tier one financials. But the idea kept me up at night because economically sustainable indoor farms could not only produce food, medicine and energy, but would also create explosive local economies. If I could help build this new potential industry, cities would generate large amounts of green collar jobs to supply the existing demand while chase out the poverty and crush food deserts as a collateral consequence. It was on my mind constantly until one day I left Wall St to work on this problem myself. I made a giant list of everything that was wrong. I self-funded the research and dove in. It was a lot of work and a lot of what I call failing forward. We started on the “Mark1” about 5 years ago and here we are today with a solid commercial system at “Mark26”.
2. At Metropolis Farms, you take a ‘low tech, low cost’ approach to vertical farming. What’s the thinking behind that?
First off, we are definably not low tech. Our systems are actually among the most sophisticated in the industry. The difference is that they are designed to go up rapidly, and be operated and maintained simply with minimal training by people with high school educations instead of folks with PhDs and Master Degrees. We removed the over engineered complexity and excessive costs, not the technology. For indoor farming to truly become an industry, we need the technology to be accessible to everyone that wants grow, that means community groups and non-profits, not rich white men and cannabis farmers. We call it democratizing the technology. It has to cost less to build, grow more in less space, and it absolutely has to grow more than just baby lettuce and microgreens… We need to grow substantial nutrient dense foods to be taken seriously. Our mission is to make it possible for everyone that wants to farm to have access. That’s how we build the future.
3. You recently presented to Congress on urban agriculture. What did you learn from that experience?
While it was a positive experience, I learned that we as an emerging industry really need to step up our game. Right now, the organic farming lobby is trying to do everything it can to stop indoor farming from obtain organic status. In addition, the USDA’s current agriculture bill excludes Urban and Indoor farms from getting the same USDA funding that rural communities get. This is clearly a form of discriminatory redlining. Last year I was offered fifty million in USDA B&I funding, but only if I left the city for a rural community, because USDA B&I funding regulations actually excludes cities from funding. So I founded the National Urban Farmers Association and I am fighting to change the next agriculture bill so that city farmers have equal access to money that rural famers enjoy. We aren’t asking for a handout, just equal access. Today with almost zero funding cities like Philadelphia only have about 8 acres of urban farming. But back in 1944 city farms then called victory gardens produced over 40% of all the fresh fruits and vegetables in the United States. The difference is that back then urban farmers had access to the same funding that rural farms had. Now Urban farmers get nothing. This needs to change, and we as an industry need to stand up and change it.
4. What new tech developments in vertical farming are you most excited about implementing in your farm?
We are in final trials on a new lighting technology that reduces our cost of full spectrum lighting by about 25% (and no it’s not an LED). It also reduces the cost of direct energy use by a little over 30% and indirectly removes about 2,000 BTU’s per light for a massive savings on BTU management. Considering we already use 40% less energy than other vertical farms, this is a huge reduction. This new technology is incredibly disruptive to existing technologies and everyone’s going to want it, except of course the people making the current equipment in China, Taiwan and Japan. We plan on creating even more American green collar jobs by manufacture them at our Philadelphia factory. If all goes well, I’m actually considering showing it at the conference.
5. If you were starting out and had $1,000 to spend on an indoor farm and free space in your Mom’s basement, what farm equipment would you buy?
For either food or Cannabis, I would buy two ceramic lights and mount them in a reflective hood. Then I would add a light mover with a pair of hangers mounted on a 4 ft. piece of super strut to get better coverage and yield. Philips makes a great bulb for about $100.00 per bulb with a hood and digital ballasts that’s around $500.00. A light mover and strut should run less than $200.00. Then I would use “Roots Organic Original Soil” brand and some plane old plastic pots and saucer. Plus a good dry fertilizer for a top feed. I would recommend one of the “Down to Earths” brand dry fertilizer…they are excellent. Then get to work. This rig will grow flowing plants year round, but would be quite effective on leafy greens as well. Don’t let the low wattage fool you, these lights are powerful and full spectrum so don’t go super close to the canopy or you are going to burn your plants.
SEE JACK SPEAK AT INDOOR AG-CON PHILLY ON OCTOBER 16, 2017
Minnesota: Sustainable Indoor Vertical Farming In Action
Minnesota: Sustainable Indoor Vertical Farming In Action
Wisconsin State Farmer | Published 5:04 p.m. CT Sept. 16, 2017
(Photo: Associated Press)
ST. PAUL, MN - The Midwest has long been a major source of innovation when it comes to feeding the world, so it’s no wonder that the same state where Nobel Peace Prize winning agronomist Norman Borlaug was educated is now delivering on the promise of urban indoor aquaponics.
The St. Paul, Minnesota company Urban Organics, which uses aquaponics to raise fish and grow leafy greens, has already proven the viability of an idea that’s been getting national attention: year-round indoor farming. In fact, Urban Organics has been so successful in its pioneering approach that it recently added a second larger location to meet skyrocketing local demand for its fresh arctic char and salmon, and organic greens including bok choy, kale, lettuce, arugula, chard, and spinach.
In a sector of the food industry seeing substantial growth of new entrants, Urban Organics offers a highly differentiated approach to vertical farming that addresses market demand for both local and organic produce and protein.
Unlike typical hydroponic farming operations, the Company can supply produce that is USDA-certified organic by using solids produced in its fish culturing system as the nutrient source for the produce. Using natural waste products from one system as the primary input of another has substantial economic advantages and represents a far more environmentally sustainable and resource conservative approach to urban food production.
In 2014, the company opened its first indoor urban aquaponics farm inside an old St. Paul brewery complex — the former Hamm’s Brewery. Its 8,500 sq. ft. became home to a fully-operational farm which housed four 3,500 gallon fish tanks with 4,000 hybrid striped bass plus herbs and leafy greens—one of the largest and most advanced aquaponics facilities in the country. Local, national and international interest followed; England’s The Guardian called the farm one of 10 innovative concepts from around the world.
The Hamm’s farm proved the concept, as area restaurateurs and grocers demanded more ultra-fresh, ultra-local product than the location could provide. Global water company Pentair, with its main U.S. offices in Minnesota, was an early supporter of the Hamm’s location — designing, engineering and installing the innovative system with its water filtration and reuse technologies.
After the success of the Hamm’s location, Pentair and Urban Organics joined forces and expanded to a larger space in another unused urban brewery building—the 87,000 square foot Schmidt complex, which is in the middle of a revitalization including artists’ condos and a planned food hall.
That new Urban Organics Schmidt brewery location opened earlier this summer. Its 87,000 sq. ft. are home to 14 fish tanks and 50, 5-tier towering racks of greens, and when it reaches full capacity later this year, it will provide 275,000 lbs. of fresh fish and 475,000 lbs. of produce per year to the surrounding region.
The USDA-certified-organic farm has created jobs, brought life back into abandoned buildings, provided a global model for indoor aquaponics farming, and done it all without the use of pesticides - and while using significantly less water than traditional methods to grow produce.
“We started this venture as social entrepreneurs who wanted to figure out how to bring a reliable source of healthy foods into areas that had to rely on food transported in from far away,” said Dave Haider, co-founder of Urban Organics. “It turned out that our wild idea also made a lot of sense to a community hungry for organic, sustainably-raised food, and to other innovators around the world who had been asking the same questions we were. By collaborating with Pentair, we’re able to contribute beyond our immediate region - we’re able to test and perfect the technologies that will make a global impact advancing the field of large-scale commercial aquaponics.”
Urban farming is an extremely competitive endeavor, but Urban Organics continues to add products and customers. Earlier this summer, the farm rolled out nine different types of packaged greens and salads, now distributed through regional coops and grocery chains. And by next summer, arctic char growing in its tanks will be ready for harvest. Local health care provider HealthPartners, the largest consumer-governed health care organization in the nation, is now including Urban Organics greens in patient meals and serving them in its cafeterias. And restaurants, like Birchwood Café, are serving the greens as well.
Started By Four Friends, Triton Foodworks grows 700 Tonnes Of Organic Food Without Soil
Started By Four Friends, Triton Foodworks grows 700 Tonnes Of Organic Food Without Soil
- HEMA VAISHNAVI | 28 AUGUST 2017
Foraying into urban farming, a group of friends have set up a green enterprise that is based on hydroponics.
There is growing concern in urban and semi-urban areas about the dangers of the pesticide-ridden food that is sold in the market.
Following the Green Revolution in the mid-1960s, the use of pesticides in India has increased. Although the period saw the boom in agriculture like never before, the flip side of this revolution has left the country consuming poisonous food. Food production in large quantities at the cost of their health has made people wary and look for alternatives.
In the confines of an urban setting, four youngsters from Delhi are venturing into hydroponics to provide an organic and healthier option for the urban populace.
Hydroponics is the method of growing plants in a water-based, nutrient-rich medium, without the use of soil. This method essentially cuts down the amount of water being used compared to the method in which plants are grown in soil. In some cases, up to 90 percent less water is used in the hydroponics method compared to the traditional soil-based agriculture — a boon for water-starved urban areas. One can plant four times the number of crops in the same space as soil farming.
An experiment in urban farming
Triton Foodworks started as an experiment in urban farming in the September of 2014 by four friends — Deepak Kukreja, Dhruv Khanna, Ullas Samrat, and Devanshu Shivnani.
In early 2014, Ullas was exploring ways to develop his agricultural land in Mohali for his mother, who suffers from ILD, a degenerative disorder of the lungs. When the doctors told him that life on a farmhouse would in fact be counterintuitive for his mother due to dust and other issues related to farming, he became obsessed with finding a way to farm in a clean and hygienic manner.
Dhruv, who was in Singapore at the moment working on his tech startup, wanted to come back to India and start something here. On a catch-up call, the two got discussing how much fun it would be to start a business together; especially something that made sense economically and ecologically. Following a lot of research, they zeroed in on hydroponic farming, something that connected with both of them. Dhruv visited a few hydroponic farms in Singapore to see firsthand how it works. Ullas met Deepak online while researching on hydroponics. The team quickly realised that to make this thing big, they needed a formal structure and a financial disciple — which is when Devanshu was roped in.
“We were just a bunch of friends who wanted to do something in the space of food and agriculture. We were very excited by the opportunities of rooftop farming and farming within the limits of the city. We did a pilot to grow strawberries in Sainik Farm of Delhi. We used an open system with vertical towers to grow eight tonnes of strawberries out of 500 sqm of land. Eventually, we decided against setting rooftop farms due to feasibility issues. Instead, we set up full scale, commercial farms in the outskirts of cities,” says 38-year-old Deepak, technical Co-founder, who takes care of the farming aspect of the business.
Like any bootstrapped startup, Triton Foodworks also faced a huge number of issues at every step. Their farm at the Sainik Farm was demolished by the Municipal Corporation of Delhi (MCD) because the team refused to pay a bribe.
“We went to the Delhi government to ask for some sort of help in setting up farms in Delhi; we were called ‘food terrorists’ to our face. Quite a few vendors still owe us money for our early projects, something which is a huge issue in this industry. We had no previous data to map our progress against, no previous players who could be used as a yardstick in the field,” says 27-year-old Devanshu, who takes care of the finances and the financial modelling for the business.
Taking hydroponics ahead
“Toxic food is the biggest issue we are trying to resolve. People don’t realise how toxic their food really is. We don’t use chemical pesticides for our plants. The second issue is the fact that we are running out of land and water to grow food. Lastly, we are addressing the problem of traceability, consistency and, by extension, accountability in farming. You buy a bag of chips and you can trace it back to the field in which the potatoes were grown, but if you pick up a tomato from your vegetable vendor, there is no way to know where it came from, who harvested it, when was it harvested, and what all did he put in it to grow. We are teaching people to ask these questions by offering them answers even before they realise this information is important,” says 27-year-old Dhruv, who looks after operations and marketing.
The team relies on Ayurvedic recipes and bio control to fight off pests and other infections, as an alternative to pesticides and insecticides. The team grows the same amount of food grown under conventional farming with just about one-eighth of the area and using 80 percent less water.
The team has successfully set up more than 5 acres of hydroponic farms across three locations in India. The strawberry farm in Mahabaleshwar grows 20 tonnes of strawberries a year and a 1.25 acres facility in Wada district of Maharashtra that produces about 400 tonnes of tomatoes, 150 tonnes of cucumbers, 400 heads of spinach, and over 700 bunches of mint.
Triton also operates an acre facility in Shirval, Pune that grows tomatoes and cucumbers, which are used to feed farmers’ markets in Pune. The team also advises companies in Hyderabad, Manesar and Bengaluru that are interested in incorporating hydroponics.
Triton currently has over 200,000 sqft of area under hydroponic cultivation in various locations in the country. Using hydroponics, it produces more than 700 tonnes of residue-free fruits and vegetables every year.
“Our systems enable us to save around 22 crore litres of water per year as compared to traditional agriculture. In terms of volume, our vertical systems grow food comparable to 10,00,000 sqft of land when using traditional agriculture methods, which translates into a saving of more than 800,000 sqft of land to grow the same amount of food. Since our farms are located within a 100-km radius from cities, our produce carries lesser food miles,” says 27-year-old Ullas.
The team is currently in the process of setting up stalls in farmers’ markets in Pune and Mumbai.
"Towards The Green Revolution"
"Towards The Green Revolution"
2017
The vertical cultivation system aponix: The height and thus the number of planting areas of the tonne superstructures are variable. Photo: Manticore IT GmbH
Marco Tidona works as a software developer. A coincidence led him to become acquainted with the Urban Farming scene in New York. Now Tidona aponix - a vertical cultivation system for horticulture - is launching on the market, which should bring production and consumer closer together. TASPO Online spoke with the resourceful entrepreneur.
How to design a vertical cultivation system for horticulture as a software developer?
When in 1999 the Neue Markt and the Internet really started, I became a service provider. Today, I am again ready to start a new market, but this time with a product for the Vertical Urban Farming sector. In 2014, I placed an aquaponic circuit with 4,000 liters of water and 100 tilapia in private, underestimating the amount of plants that would have been necessary to balance the ever-higher concentration of nitrate in the plant.
At this time there was no simultaneously affordable, usable and vertically flexible solution on the young urban farming market. On top of that, I spent one day in New York City by chance and got an unprecedented insight into the state of the urban farming scene and the farming operations. After seeing more professional production sites and looking at the existing value chains from cultivation to harvesting through logistics to consumption by the consumer, I soon realized that we are heading towards a green revolution more purposefully.
What is the difference between aponix and common vertical systems?
There are several differences and specifically vertical systems are very different. Each system has its own strengths and weaknesses, which should be looked at and compared against one another before purchase. In case of doubt, we recommend that you first carry out a practical test. The mission of aponix is o simplify the cultivation of hyperlocal edible plants in 3D. A) for the commercial user of an urban farm with lean processes, b) the ambitious hobby grower and c) the "prosumers" - the consumers who produce some of their own food and, if necessary, have no garden.
The height and thus the number of planting areas of the tonne superstructures are variable. The barrels are constructed from similar lego-like components with different plant adapters. No fixed installations such as tables or rack systems are required. Everything is mobile, modular and scalable. In principle one can understand the system of aponix as a kit, with which one can configure many different urban solutions. In the summer, additional elements are added that can be used to assemble substrate-based tonnages, which can then be used as a raised-bed alternative for the balcony or also as a gray-water filter. We show these examples on our website.
How are the plants supplied with nutrients? How many plants fit into such a system?
In the earthless version one can work with mineral or organic fertilizer - hydroponics or aquaponics. In the summer, additional parts are added, with which one can build a ground-based version. For the groundless version, we usually sell the variant with a height of 12 ring segments. Each ring segment provides 12 2-inch mesh head racks, thus accommodating 144 herb or salad plants. A tonne has a diameter of 57 centimeters.
The height of the barrels can be changed at any time. Irrigation by means of sprinkler and gravity works independently of the height always over a lid. It is possible to combine several tonnes into a production line and manage the reservoir centrally or operate a single tonne.
What is the advantage for horticultural companies using this system?
If we want to move the production closer to the end user (= hyperlocal) in order to get the average 1,500 "food miles" in the existing value chain to zero and thus offer the end user significantly more diversity, freshness and nutrients, the mounting surfaces become significantly. In decentralized distributed urban micro-farms, it will be important to operate cultural areas of less than 1,000 square meters profitably.
This is only possible with a high plant density and a competitive offer. The freshness, sustainability of the production and the absence of herbicides / pesticides will, among other things, be the key for the mature consumer to pay a small extra charge compared to the standard merchandise from the supermarket and the discounters. It feeds on the highest nutrient level and with the greatest pleasure.
What about the renaming process during the project phase? Was the conflict with another product from the same industry or a "foreign" industry?
Originally we had called ourselves 'ponix' in the prototype phase and had a fish symbol around the logo. Shortly thereafter, a company from Austria came onto the market with the name 'Ponix Systems'. Since in most cases alphabetical sorting is carried out, we have made the renaming easy here, and a 'a' has been hanged, and from the fish on the occasion a lying "infinite 8" is made as a sign for the upcoming Circular Economy.
Created by TASPO Online