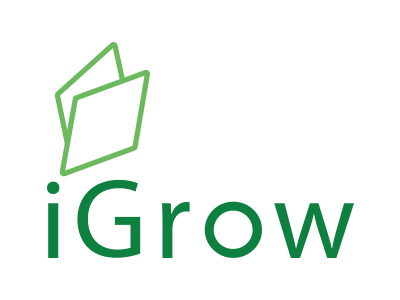
Welcome to iGrow News, Your Source for the World of Indoor Vertical Farming
Quick Guide On Grow Lights
Everyone agrees that knowing how to grow food indoors with grow lights is valuable. It improves your health, brightens your day, calms your nerves, and allows you to do more with your existence.
Introduction
Grow lights are the most important environmental element affecting plant growth and development because the selection of grow lights can have a remarkable effect on the costs, operational costs, and quality of plants in your indoor grow room. This blog describes the physical properties of grow lights. Light sources often used in indoor grow rooms are introduced with a simple clarification of the fundamentals necessary to understand the grow lights. Particular importance is placed on LEDs, which have received extraordinary awareness recently, and on fluorescent lights, which are still commonly used in indoor grow room.
Physical Properties
Light is electromagnetic energy, which is also explained as electromagnetic radiation comprise both visible and invisible wavelengths. The smaller the wavelength, the greater the energy. The wavelength of visible light ranges from 380 to 780 nm, which is what people eyes see.
Visible light is key to plants because it occurs simultaneously with photosynthetically active radiation (PAR, 400-700 nm). For solar radiation, 97% is inside the 280-2800 nm range. In this regard, 43% is visible light, which is practical for plant growth, 4% is ultraviolet, and 53% is infrared, which make heat.
Only electric lights are used in indoor grow rooms. Light has two opposed properties: it can be noticed as a wave phenomenon and it also acts as separate particles called photons. A photon is the smallest particle of light, or a single quantum of light. Light varies in at least three dimensions: quantity, quality, and duration.
When electric lights are used in a indoor grow room, the lighting cycle, which affects plant growth and development, can be willingly changed. Light effects plants in two ways: providing energy or a quantum source and acting as an information medium.
While an energy source, the photons of light, is caught by plants and a part (up to 10%) of photons caught by plants is converted to chemical energy (carbohydrates) through photosynthesis. Almost all of the light energy or photons caught by plants is converted into heat energy.
Light Sources
Till recently, most of the light sources used for indoor grow rooms were fluorescent lights and high-intensity discharge (HID) lights. Till just a decade ago, LEDs were used almost exclusively for research on plant cultivation, but are now being used as a light source for commercial plant cultivation in indoor grow rooms because of their fast price decline and quick improvement in luminous efficacy, which is a measure of how efficiently an electrical lamp produces visible light.
LEDs
LEDs offer advantages over fluorescent and HPS lights: they are strong; produce a stable output; are long lived, compact, and lightweight; turn on right away; and allow the light output to be easily controlled with a light source consist of several color types of LEDs. Benefit of using LEDs as a light source for indoor grow rooms is that LEDs offer great flexibilty for making various light environments compared to conventional lights. A light source having a few types of LEDs with different peak wavelengths can produce light of which the spectral radiant inconstancy can be varied with time. The biggest disadvantage of using LEDs for indoor grow rooms is the high beginning cost for a set of LED lights, compared to conventional lights.
Fluorescent Lights
Fluorescent lights offer no direct advantage over other lights including LEDs. Tubular fluorescent lights are the most suitable light source at present for indoor grow room when taking into account all the factors of bulb and luminaire prices, rated life, luminous efficacy, ready availability, and lighted bulb temperature. A tubular fluorescent light normally consists of a glass tube coated inside with a fluorescent material (phosphor), two tungsten electrodes at the two inside ends that are coated with an electron emissive material, a tiny amount of mercury, and low vapor pressure inert gas (mainly argon) enclosed in the glass.
High-Intensity Discharge (HID)
HIDs are a type of electrical gas discharge light, which generates light by means of an electric arc between tungsten electrodes sheltered inside a translucent or transparent fused quartz or fused alumina arc tube. HID lights make more visible light per unit of electric power adsorbed than fluorescent lights, since a larger proportion of their radiation is visible light in contrast to infrared. Yet, the lumen output of HID lighting can lower by up to 70% over 10,000 burning hours.
If you enjoyed this, you might also enjoy this blog on lighting:
Tags: quickguide growlights leds fluorescent highintensity discharge indoorgrowroom
The 7 Reasons Indoor Vertical Farming Is Sustainable
The 7 Reasons Indoor Vertical Farming Is Sustainable
Indoor Vertical Farms Everywhere
The 7 Reasons Indoor Vertical Farming Is Sustainable:
1) Reduction of the Carbon footprint in food production.
2) Reduction in Carbon footprint moving food 1,500 miles (on average) from production to consumers.
3) Removal of Fertilizer runoff into the water system.
4) Removal of Pesticides from the environment.
5) No wastage of water.
6) Growing can use 100% renewable energy.
7) Greater consumer health from the increased nutritional quality of the vegetables. Some other benefits:
The need for GMOs disappears
Everything can be 100% organic
Food costs will go down
Reduction in the use of fertilizer Indoor Vertical Farming Is Sustainable Farming.
The big food retailers want sustainability.
I gave a talk at FMI (Food Marketing Institute) a few months back on the same topic. All of North America's top retailers were in the room. The next big Sustainability change needs to be in fertilizers. The largest thing in fertilizer is Nitrogen.
Man-made Nitrogen is created using the Haber–Bosch process, which currently burns about 5% of the world's natural gas.
Nitrogen can be created naturally by growing and processing legumes.
Moving to Indoor Vertical Farming frees land that can be used to grow legumes naturally for Nitrogen.
A massive win-win.
BrightFarms Named to Inc. Magazine’s Top 10 Most Successful Startups in Food List
BrightFarms Named to Inc. Magazine’s Top 10 Most Successful Startups in Food List
Company aims to build local greenhouse farms in every major U.S. metro
New York (December 11, 2017) – BrightFarms has been named to Inc. Magazine’s list of the top 10 most successful startups in the food and beverage industry. Featured among brands such as Halo Top and Chef’s Cut Real Jerky, BrightFarms was the only fresh produce brand to make the list.
The company has grown by more than 1,800 percent in the last three years with the development of greenhouse farms for leading retailers like Ahold-Delhaize and Roundy’s (Kroger). Earlier this year, Inc. Magazine ranked BrightFarms number 235 on their list of the 500 fastest-growing private companies in America.
To support the growth, the company has recruited a number of key leaders from the food industry, including Vice President of Sales Dean Martel, former sales executive at Fresh Express; Vice President of Marketing Abby Prior and Vice President of Operations Josh Norbury, formerly with Bimbo Bakeries, among several others.
“Our rapid growth stems from the enormous consumer demand for locally grown produce” said BrightFarms CEO Paul Lightfoot. “We’re developing the next phase of growth for our company and plan to enter every major metropolitan market across the country.”
BrightFarms operates three commercial greenhouse farms in Rochelle, IL.; Culpeper, VA.; and Bucks County, PA., with another under construction in Wilmington, Ohio. The company plans to open another 10-15 greenhouses in the next three years.
For more information, visit www.brightfarms.com.
About BrightFarms
BrightFarms grows local produce, nationwide. BrightFarms finances, builds, and operates local greenhouse farms in partnership with supermarkets, cities, capital sources, and vendors, enabling it to quickly and efficiently eliminate time, distance, and costs from the food supply chain. BrightFarms’ growing methods, a model for the future of scalable, sustainable local farming, uses far less energy, land, and water than conventional agriculture. Fast Company recognizes BrightFarms as “One of World’s 50 Most Innovative Companies” and one of the “Top 10 Most Innovative Companies in Food” in the world. New York (December 11, 2017) – BrightFarms has been named to Inc. Magazine’s list of the top 10 most successful startups in the food and beverage industry. Featured among brands such as Halo Top and Chef’s Cut Real Jerky, BrightFarms was the only fresh produce brand to make the list.
AeroFarms and Dell Team Up to Revolutionize Farming with IoT
AeroFarms and Dell Team Up to Revolutionize Farming with IoT
By Ken Briodagh 2017
Recently, I had the opportunity to visit the future of farming in Newark, New Jersey, thanks to Dell and AeroFarms. AeroFarms is a future agriculture company building indoor, vertical farms that use “aeroponics” to generate yields that are 120 times more productive per acre, per year than a traditional, outdoor farm. Aeroponics is a system of farming which uses no dirt, and only very little water, combined with nutrients, to grow plants. Dell is helping AeroFarms monitor growing conditions, perform analytics and identify harvest quality.
AeroFarms has said it is trying to transform agriculture using technology to build more sustainable, more environmentally responsible and higher producing farms throughout the world, with a focus on local, meaning within 100 miles of the eater. It is currently operating several farms and selling leafy greens to a variety of major retailers, including the largest farm in the world, measured by amount of produce grown per acre, according to the company.
The farms are established on major distribution routes and near population centers in order to stay local, while the indoor nature of the growing spaces are designed to defy traditional growing seasons by enabling local farming at commercial scale all-year round. The produce is monitored using Dell technology from seed to package, so each can be traced for quality control and improvement. Meanwhile, each farm is using 95 percent less water than field farmed-food and with yields 130 times higher per square foot, each year.
“AeroFarms is redefining agriculture combining world-class expertise for horticulture, engineering, food safety, nutrition, and data science to set a new standard for product quality and production,” said David Rosenberg, Co-Founder and CEO, AeroFarms. “We are as much a capabilities company as we are farmers, utilizing science and technology to achieve our vision of totally-controlled agriculture. We have worked closely with Dell Technologies to develop the tools to wirelessly track and monitor our product throughout the growing process from seed to package. Dell Technologies understands our IoT infrastructure and integration needs, and we see the opportunity to collaborate on additional solutions as we build our indoor vertical farms in major cities around the world.”
The company recently began growing at its ninth farm, located at its new global headquarters in Newark, NJ. AeroFarms also has additional grow sites in development in multiple US states and on four continents.
Agriculture like this, as enabled by IoT technology, is likely to represent the future of farming in the future, and is likely to be one of the many ways that IoT will improve and enhance society moving into the future.
Ken Briodagh is a writer and editor with more than a decade of experience under his belt. He is in love with technology and if he had his druthers would beta test everything from shoe phones to flying cars.
Edited by Ken Briodagh
Author Info
Former Polartec Plant to Become "Industrial Innovation Hub"
The industrial facility that once housed the Polartec textile plant is in for a makeover. On Saturday, its new owner — California-based real estate broker Jitender Makkar — welcomed city and state officials onto the factory floor to unveil his plans for the facility, which he has given a new moniker: IndusPAD.
Former Polartec Plant to Become "Industrial Innovation Hub"
METHUEN/LAWRENCE — The industrial facility that once housed the Polartec textile plant is in for a makeover.
On Saturday, its new owner — California-based real estate broker Jitender Makkar — welcomed city and state officials onto the factory floor to unveil his plans for the facility, which he has given a new moniker: IndusPAD.
The facility, which includes two buildings on a 14.5-acre lot on the Lawrence/Methuen city lines, had been put up for auction this spring and sold for $5.35 million.
Makkar said he intends to subdivide the facility and attract multiple mixed-use tenants to what he envisions as a "take off and landing pad" for young entrepreneurs and innovators.
This is Makkar's first East coast investment.
After starting his career in New Delhi, India in construction and architectural design, Makkar relocated to California in 2000 and became involved in real estate investment and sales, according to Purnima Dey, director of public relations and community outreach for IndusPAD, and Makkar's fiance.
"We envision the opportunity of inspired entrepreneurs in our property," he said. "Our team aims to work strategically and diligently to build something memorable."
The first business to open will be a 30,000 square foot vertical farming facility, growing organic produce, said Makkar, in a partnership with Dutch indoor agriculture company Beyond Organic.
"With that, we hope to expand it within in the next couple of years to a much larger facility, which can create maybe 30, 40, 50 new technology jobs," said Makkar.
He thanked both Lawrence Mayor Daniel Rivera and Methuen Mayor Stephen Zanni for their support, and highlighted Zanni's vision to bring "the jobs of the future" to the region.
"Mayor Stephen Zanni is really the spirit behind what we have planned," said Makkar. "He is the man who has given me the vision to run rather than walk."
"Almost everybody said the biggest challenge we will have is in subdividing this facility, is in creating the option to bring in multiple tenants," said Makkar. "They all saw it was used for one vertical use, and it was hard to transform. What I saw in it was possibilities of a different kind. I saw in it the possibility of somebody from MIT, somebody from Mass. University (sic) to take their projects, take advantage of the infrastructure here, and make it their journey."
Polartec fleece was manufactured in the facility until last year, when Polartec LLC laid off more than 200 workers and moved its operations to Tennessee. When the facility was put up for auction, the listing indicated Polartec had invested more than $6.2 million in the property.
"This brings not only jobs to the Merrimack Valley and beyond, but more importantly it brings about a sustainable company," said Zanni. "A lot of companies come and go, as the company that was here, Polartec moved out to Tennessee and actually moved part of their operations to China. This is an operation that will go over a lifetime."
Methuen Community Development Director Bill Buckley said no other tenants have signed on with IndusPAD yet, but he was aware of some local interest.
"I think you might see some more traditional industrial tenants initially, that might not fit the vision of innovation," he said.
With nearly 600,000 feet of space in the facility, IndusPAD certainly has room to grow.
State Senator Barbara L'Italien welcomed IndusPAD as "the next chapter in this glorious footprint that was Polartec."
"It sounds like there's going to be some innovation, a place for innovation for ideas for allowing small businesses to be able to begin their dreams and launch, and we know what that has done for Boston area, so we welcome that in the city of Methuen and the city of Lawrence."
Subway Operator Tokyo Metro Embarks In New Direction: Hydroponic Vegetable Farming
Under the name "Tokyo Salad," the company is growing lettuce, assorted salad greens, and even herbs at a facility approximately a seven-minute walk from Nishi-kasai Station on the Tokyo Metro Tozai Line.
Subway Operator Tokyo Metro Embarks In New Direction: Hydroponic Vegetable Farming
December 10, 2017 (Mainichi Japan)
A factory worker checks a hydroponic romaine lettuce plant at Tokyo Metro Co.'s cultivation center in Tokyo's Edogawa Ward on Nov. 17, 2017. (Mainichi)
Subway operator Tokyo Metro Co. is bringing its ideology of "safe and secure" to an unlikely place -- farming.
Under the name "Tokyo Salad," the company is growing lettuce, assorted salad greens, and even herbs at a facility approximately a seven-minute walk from Nishi-kasai Station on the Tokyo Metro Tozai Line. The cultivation warehouse Metro vegetable center is located under the elevated train tracks of the line.
The airtight space is held to strict hygienic conditions, and neither fertilizer nor soil is used, with the seven rows of plants instead grown hydroponically. Frill lettuce, basil, along with rare finds such as Lollo Rosso (red coral lettuce) and red kale are found among the 11 varieties regularly grown, with roughly 400 plants reportedly growing on a given day.
The cultivation is completely man-made and mechanized. Seeds are placed on a sponge with tweezers, and the young seedling is raised until the leaves spread out, at which time it is moved to a more spacious area. LEDs shed light on the plants for 16 hours a day and the liquid nutrients are cycled through the system 24/7. It takes roughly three to five weeks for a plant to reach maturity, and there is barely any loss.
The strict hygienic conditions inside of the Tokyo Metro Co.'s cultivation center in Tokyo's Edogawa Ward. (Mainichi)
The leaves are not bitter or astringent, and the leaves are soft all the way to the exterior of the plant. They can be preserved for a long period of time, and because no chemical fertilizers were used to grow them and they never touched soil, the entire plant can be eaten without being washed.
So-called plant factories like this are the focus of efforts by the Ministry of Agriculture, Forestry and Fisheries to expand safe provision of products like vegetables, high productivity and job creation. According to the ministry, the number of cultivators using artificial lights has tripled from 2011 to 197 locations as of February 2017.
Tokyo Metro entered the market to make use of idle land as a new business venture, and built the cultivation facilities in unused warehouses. The operation is a joint project with group company Metro Development Co., which began sales of the lettuce and other products in April 2015.
The element of surprise and the mismatch between subways and vegetables have stirred up quite a reaction. Last spring, a lunch course featuring the products was introduced at The Strings by Intercontinental Tokyo hotel. Even the dessert included ingredients from Tokyo Salad, and because of an overwhelming positive response, the hotel introduced a dinner course this summer as well.
"Dishes where a lot of attention is paid to a single ingredient are very popular," says 47-year-old hotel food and beverage manager Tetsuya Tanigawa. "The ideology and the story behind the product is the deciding factor."
Tokyo Metro overseer Remi Takahara, 33, continued to visit the vegetable plant for the six months she was visiting potential business partners that would use Tokyo Salad vegetables since the factory operation began. "I never thought that I would be growing vegetables when I joined a railway company," she said, reflecting on the trial and error process that led to the subway operator's greens' cultivation.
Vertical Farming is on The Rise In Abbotsford British Columbia
Vertical Farming is on The Rise In Abbotsford
Construction on one of B.C.'s First Vertical Farms will be complete next October
December 9, 2017
While the method of building farms vertically becomes more popular, Kent Mullinix of KPU’s Institute for Sustainable Food Systems worries it may be a step in the wrong direction.
As the effects of climate change and overpopulation become more and more apparent, traditional farming methods seem less likely to provide long-term sustainability for our planet.
One potential method of addressing this problem is with a concept called “vertical farming,” which packs more agriculture into a smaller land area by building upwards, much like a densely inhabited high-rise condo. Next October, Abbotsford will become home to one of the few vertical farms in British Columbia when construction on a 10-acre farm at 34240 Page Road is completed.
Nick Brusatore, CEO of the farm’s developer, Vertical Designs Ltd., says that the project will consist of 32 towers, each 20 feet tall and housed in a 35-foot tall building. The farm is estimated to cost between $2.5 and $2.7 million.
The company has partnered with Affinor and a California strawberry farm for what Brusatore calls an “on-farm test agreement,” or a trial run after which, if all parties are satisfied, production will increase significantly.
Organic strawberries will be the sole product grown at the Abbotsford facility, and through a contract signed with Discovery Organics, all of the strawberries have already been sold.
“We expect to produce probably the best strawberry on the planet,” says Brusatore.
He is unsure where exactly his strawberries will end up, but says that he would be surprised if the first batch makes it outside the city. Eventually, though he hopes to “produce all the strawberries for Canada” from the Abbotsford location.
“We’ve got a problem right now,” says Brusatore, referring to the state of local and global agriculture. “We’ve got a food shortage, we’ve got a water shortage, and we’ve got no governance as to the pesticide use and the way things are manipulated through labels.”
According to Brusatore, the Abbotsford vertical farm will produce zero water waste, require zero pesticides, and will utilize the land 10 times per square foot more efficiently than conventional farming techniques.
Despite the possible benefits of this technology-based farming system, Director of the Institute for Sustainable Food Systems at KPU Kent Mullinix believes that vertical farming is a step in the wrong direction.
“It’s about money. It’s not about feeding the world,” says Mullinix. “It’s really appropriate for the cultivation of just a few high-end crops like salad greens and some more valuable vegetables, so it’s really primarily a system to satisfy high-end markets with very high-end production methods. It’s the antithesis of sustainability if you ask me.”
Instead of investing in vertical farms, Mullinix argues that the key to sustainability is a decentralized, ecologically-focused network of regional food systems that create local economies and jobs.
Mullinix is also concerned that the proliferation of vertical farming will lead to valuable agricultural land being paved over.
In response, Brusatore argues that vertical farms can be developed on contaminated land that is no longer ideal for conventional farming. He acknowledges that vertical farming is mostly suitable for low-growing plants like kale, lettuce, and strawberries, but says that the project is nevertheless a progressive step for the future of agriculture.
“If we don’t try, if we don’t press these issues, we’re just going to fail for sure,” he says. “I’m excited for Abbotsford …. It’s going to be absolutely amazing and people are going to be blown away by this once it’s up.”
Although it is a capital-intensive project to launch, he points out that, once built, the equipment on the farm will be long-lasting and will require little maintenance.
After the farm is completed and the method is proven successful, Brusatore expects that there will be a significant increase in capital investment in vertical farming, creating a positive effect on the local economy.
SproutsIO
SproutsIO
SproutsIO is another tech company looking to make food more personal. The compact smart microgarden system lives in your home and includes everything you need to grow fresh produce year round without the mess of soil.
The SproutsIO device features a high efficiency LED lamp head, a basin that combines hydroponic and aeroponic technologies, and sensors that monitor both the environment and the plant’s health. The type of light and its duration is automatically determined by the type of produce you are growing, as is the irrigation schedule, and the data from the sensors is used to continuously update the system as needed.
The seeds themselves are contained in easy-to-switch-out sIO refills, and users can order from amongst the 16 types available on the company’s website. The SproutsIO app gives the grower the opportunity to personalized the flavor of their produce through tweaks to its growing environment, too, so not only are they growing produce in their home, they’re growing produce they know they’ll enjoy eating.
Menasha's Fork Farms is Changing The Face of Farming -- And Helping Schools, Pantries
Menasha's Fork Farms is Changing The Face of Farming -- And Helping Schools, Pantries
Maureen Wallenfang, USA TODAY NETWORK-Wisconsin
Nov. 13, 2017
Down on the "farm." Fork Farms' operation has 16 indoor growing modules in Menasha. Here, Stewart McLain, operations manager, left; Alex Tyink, co-founder, center; and Gil Shaw, farm manager, right, stand in front of growing modules.
(Photo: USA TODAY NETWORK-Wisconsin)
MENASHA - This isn’t your father’s farm.
Or anyone’s vision of a farm, really, outside of a science fiction novel.
This “farm” of indoor plastic growing modules looks like it came off a spaceship.
Fork Farms is a small, young, agriculture technology company that manufactures plastic hydroponic growing modules.
Inside each one, ruffled rows of lettuce grow vertically without a speck of soil or sunlight.
Fork Farms grows lettuce around LED lights inside a module. (Photo: Dan Powers/USA TODAY NETWORK-Wisconsin)
Fork Farms moved into its current home at 1101 W. Midway Road this spring and ? 16 indoor growing machines. It's in a former flooring store just west of Appleton Road near Piggly Wiggly in Menasha.
Prior to this, inventor Alex Tyink operated out of his apartment and garage. He’s spent eight years working on the modules while holding down a day job. He's never taken a dime from the company and has operated on a slim investment of less than $20,000 gathered from family and friends.
“I believe in food. I know that sounds corny,” said Tyink, 30. “I felt better when I started eating good food instead of burgers and fries. A simple thing can make so much of a difference in our lives.”
He went to school to become an opera singer, not an engineer, so he said the years tinkering were spent learning, evolving and experimenting to get the system right.
Since 2009, he has made 28 different prototypes and invested thousands of hours into the venture.
Social service
Working on the growing machines satisfied his desire to create something that mattered, he said.
Growing fresh produce this way can make healthy food more accessible and create a connection between kids and food.
“Our mission is to put these in food deserts and low-income schools,” he said. “The social service side is very important to me. I never want to lose that.”
Tyink co-founded the company with his father, Steve Tyink, who is vice president of business innovation at Miron Construction, and John Brogan, CEO of Bank of Kaukauna.
His two employees have taken equity before paychecks. Commercial Horizons gave him a sweet lease on the building.
Fork Farms is a limited liability company owned by a group of 14 people, including employees Gil Shaw and Stewart McLain.
Shaw was formerly hydroponics manager at Riverview Gardens and is now farm manager here. McLain, formerly a music teacher in Seattle, is operations manager.
Shaw said the opportunity to join Fork Farms was too good to pass up.
“It’s one of the most innovative systems out there. It’s in a class of its own,” Shaw said.
“This is a real game changer because of its water use, efficiency and space. The potential of this is extraordinary. It can revolutionize arid land growing.”
Fork Farms' growing system already has one patent and two more pending.
Growing modules
The company's first 20 growing modules have been sold to schools, food pantries and individuals.
Local schools include Mount Olive Lutheran School, Fox Valley Lutheran High School, Appleton North High School and New Directions Learning Community in Kaukauna.
At North, the machine was purchased with a grant from the Appleton Education Foundation.
"We love having our machine in the classroom," said Matt Hechel, North's alternative education coordinator. "We have a few students who have taken charge of being our main gardeners."
"I like learning about the hydroponic system and am really surprised how easy it is to grow our produce right in our classroom," said J.T. Zubich, one of the students in charge of the module. "It would be cool if every classroom was able to do this."
Students have eaten salads in the classroom from their harvest. Students and staff have taken lettuce home.
“It’s an improvement on the traditional school garden model,” Tyink said. “It’s highly productive in growing food and makes a nutritional difference in schools. We’re improving the quality of lunch lines.”
Besides making and selling the growing modules, Fork Farms grows lettuce in its Menasha headquarters and sells it to several hotels and a caterer. Its first and largest buyer has been the Best Western Premier Bridgewood Resort Hotel in Neenah.
"We use their Fox Valley blend of lettuces for lunch buffets and catering, and their buttterhead lettuce for weddings and corporate events," said Ryan Batley, food and beverage director. "What's so great about it is that it's local. It stays fresher than anything else we're getting. It's very clean and crisp. A great product. The cost is a little higher, but we think it's money well-spent."
Batley said they use whole butterhead lettuce heads on each plate for weddings.
"One bride called us back and said her guests were still commenting on it weeks later. She said 'I never thought people would remember the salad,'" Batley said.
For-profit/nonprofit partnership
Tyink’s day job is director of programming at Feeding America Eastern Wisconsin. He previously field tested his growing machines while working at Goodwill Industries of North Central Wisconsin.
Feeding America now provides ancillary support to Fork Farms in what Tyink calls a “for-profit/nonprofit partnership.”
While Fork Farms is a for-profit business, he said it’s “mission-driven” to educate and feed people.
Growing modules cost $3,500. Feeding America provides education, training and a year’s worth of supplies for an additional $1,500.
Each vertical module can grow 288 plants in a four-by-four-foot space, Shaw said. Each machine can grow 15 to 20 pounds of lettuce in three to four weeks.
Indoor farming has been in the national news recently with the large-scale Plenty operation, a Jeff Bezos-backed indoor farm now expanding into the Seattle area.
But at the same time, some indoor farms have struggled.
FarmedHere, for example, closed its indoor hydroponic growing operation near Chicago earlier this year, reportedly because of high labor and energy costs.
At Fork Farms, Tyink keeps a watchful eye on costs and is in the gener8tor’s gBETA accelerator coaching program for startups.
He said it’s self-sustaining and he hasn’t taken a bank loan.
One of the keys, he said, was keeping energy costs low with LED growing lights.
“All of my research started with energy efficiencies," he said. “We’re running at a higher resource efficiency rate.”
“We kept small and kept capitalization small. We haven’t gone after venture capital because we wanted to know what we had before we made promises.”
Kids Speak on Vertically Building a Sustainable Future
Kids Speak on Vertically Building a Sustainable Future
NOVEMBER 13, 2017 URBAN AG NEWS
Originally published in Issue 14
By Lea S. Singer (7th grader)
At the New York Sun Works’ Youth Conference on June 2, 2016, building a sustainable future was the shared topic. So many ideas were presented on how the kids of this generation could help build a better, healthier future for themselves. The passion shared with all who attended was inspiring, and made you want to start a mini hydroponics system in your kitchen the minute you left the conference.
Among the numerous people who spoke, ranging in age from 10- to 15- years old, three guest speakers attended. One of them, Dr. Dickson Despommier, from The Vertical Farm, shared the newest way of growing food—VIG.
One of the guest speakers at the conference was Dr. Dickson Despommier from The Vertical Farm who discussed vertically integrated growing (VIG).
VIG stands for vertically integrated growing, which looks exactly like it sounds. The plants are lined up in rows vertically, against a wall, as opposed to taking up space on the floor. This way of modifying plant growing systems for space efficiency could very well be the standard farming technique of the 21st century.
According to Dr. Despommier, many producers have already adapted this growing technique, using it to grow an abundance of vegetables, including tomatoes, spinach, and kale.
One grocery store that was shown during his presentation had a VIG setup in the store so that customers could simply cut off the leaves they desired from the extremely fresh plants, bag it, pay for their produce, and cook it for dinner the same day it was cut. This is one of the many examples Dr. Despommier showed the audience during his presentation. By the end of his presentation, it’s safe to say attendees were all convinced of the VIG’s efficiency and reliability as a new mass production growing technique.
Another VIG benefit, the free floor space leaves plenty of room for jetpacking and hoverboard riding, which will come in handy in 2050.
Lea S. Singer is a 7th grade student and aspiring writer at the Manhattan School for Children, PS333.
“The NY Sun Works conference was a great opportunity to learn about new ways to use sustainable science and how it works. Sustainable science is very important because, if we keep going without it, it will not be good for us. The conference gave new possibilities, new ways and new approaches on how to save our world.”
— Nate Hajdu, 7th grader and member of NY Sun Works Youth Conference Press Team
NY Sun Works is a non-profit organization that builds innovative science labs in urban schools. Through their Greenhouse Project Initiative they use hydroponic farming technology to educate students and teachers about the science of sustainability. www.nysunworks.org
Could Indoor Farming Help Address Future Food Shortages?
By 2050, Earth’s population is expected to rise to 10 billion, while the resources on the planet continue to shrink. Researchers in the Netherlands are experimenting with one way to feed more people with less: growing crops indoors.
Could Indoor Farming Help Address Future Food Shortages?
November 11, 2017
By 2050, Earth’s population is expected to rise to 10 billion, while the resources on the planet continue to shrink. Researchers in the Netherlands are experimenting with one way to feed more people with less: growing crops indoors. NewsHour Weekend’s Ivette Feliciano takes a look at how indoor farming could shift our relationship with food.
Megan Thompson:
The United Nations estimates that by the year 2050, the world’s population will grow from today’s 7.5 billion people to nearly 10 billion. And as natural resources like farmland and water become scarce, feeding everyone will become an even greater challenge. In tonight’s Signature Segment, NewsHour Weekend’s Ivette Feliciano reports on how there might a solution well underway in the Netherlands. This story is part of our ongoing series, “Peril and Promise – the challenge of climate change.”
Ivette Feliciano:
Just south of The Hague, in the Westland region of the Netherlands, miles upon miles of greenhouses are spread across the landscape. They’ve been built by Dutch farmers as part of a 20-year movement by the country to pursue sustainable agriculture by growing indoors.
Dutch farmer Hans Zwinkel grows tomatoes in two greenhouses that cover 20 acres of land. His annual harvest of two-and-a-half million pounds of tomatoes is more than double the average yield of an outdoor farm.
Hans Zwinkel:
The plant started over there as a small plant, stands about five meters, six meters further.
Ivette Feliciano:
Zwinkel and growers like him achieve high yields by controlling the climate and water for their crops under glass. Filtration systems allow them to collect and recycle the plants’ water supply. Crops receive direct sunlight — supplemented as needed by artificial light — and are protected from unpredictable weather events and insects, which almost completely eliminates the use of chemical pesticides.
Hans Zwinkel:
It’s nice to see the plants grow. You–it gives you energy.
Ivette Feliciano:
These growing techniques have helped foster an indoor growing boom in the Netherlands. Greenhouses now produce 35 percent of the country’s vegetables–despite occupying less than one percent of its farmland.
The Netherlands’ Wageningen University has led much of the research on how to best grow crops indoors. Leo Marcelis–a professor at the university–says that in the era of climate change, the Dutch agricultural revolution needs to move beyond greenhouses, which still rely on some outside forces like sunlight.
Leo Marcelis:
We wanted to control the production process, that we can control the yield, the quality, that we can give guarantees towards the consumers. Although we can control a lot we’re still dependent on the outdoor conditions. So the next step would be to have a further control. So we can, in fact, guarantee how much produce we will have tomorrow or on any date of the — of the year, of a guaranteed quality.
Ivette Feliciano:
Marcelis is now experimenting with indoor vertical farming–growing plants stacked on shelves to maximize space–and completely cut-off from the outside. As in many greenhouses, water for the plants is drained, collected, and reused, reducing their dependence on an outside water source. And instead of sunlight, the researchers use LED's — light bulbs that can replicate solar light in a variety of colors and intensities.
Leo Marcelis:
Whether we are growing tomatoes, whether it’s about getting fruits, or whether it’s a lettuce or leafy vegetables. You can imagine that you want a different type of plant. And that may require therefore a different light. With LEDs, we can also put them in between the plants. And that’s very good. Because usually there is maybe too much light on the top, but insufficient at the bottom. So we can have a much better distribution of the light in the plant.
But growing indoors isn’t cheap. Marcelis says a quarter of the expenses for indoor growers in the Netherlands relate to construction–something farmers who grow in fields don’t have to worry about. Then there’s the energy costs of round-the-clock climate control and artificial lighting. But Marcelis says a key advantage to indoor farming is that by creating ideal growing conditions and maximizing space, it can produce much higher yields, in some cases, up to 350 times the yield of a conventional farm of the same size.
Leo Marcelis:
What really matters is if the income is larger than the cost. So if the investment costs are high, and also the other costs are high, well, if the income is then also very high, then it is about the balance.
Ivette Feliciano:
Marcelis says one important part of their work is developing techniques that can be replicated anywhere, even in arid climates like the Middle East or sub-Saharan Africa. The United Nations estimates as the world’s population grows, global food demand will rise 70 percent by 2050, even as the amount of water and farmable land shrinks due to the global warming.
The Netherlands is already doing its part to feed the world. Propelled by indoor farming, it’s become the second biggest food exporter in the world, accounting for nearly 90 billion dollars last year. This is all the more astounding given that the Netherlands is less than one-percent the size of the United States, the world’s number one food exporter, where indoor farming is also gaining a foothold.
Here in Kennett Township, Pennsylvania, mushroom growers have been practicing indoor farming for over a hundred years, and today produce half the U.S. mushroom crop.
An hour outside Philadelphia, this small community of eight thousand people harvests half a billion pounds of mushrooms every year — all of it indoors and at a low cost of about one dollar per pound.
Chris Alonzo:
We invested nine years ago into a Dutch-style farm.
Ivette Feliciano:
Chris Alonzo owns this indoor farm that uses the vertical farming methods seen in the Netherlands.
Chris Alonzo:
We put in aluminum shelving instead of wooden beds, we invested in equipment which made the job less labor intensive. We have heat in the room, air conditioning in the room, and air flow. And we use those tools to make sure that the room environment is specifically controlled for what the mushroom likes.
Ivette Feliciano:
Using these techniques, Alonzo’s facility alone is responsible for more than one percent of the nation’s mushroom crop — growing 11 million pounds of mushrooms a year — protected from potentially harsh outdoor conditions.
Chris Alonzo:
The only day we take off is Christmas. And the consumer wants fresh produce year-round. So we’re able to meet the needs to have locally grown produce all year-round. As opposed to some crops where they’re only grown seasonally.
This is our environmental control unit…
Ivette Feliciano:
Alonzo says the difficulty with indoor farming–as with outdoor farming–is finding the balance between your harvest’s revenue and its expenses.
Chris Alonzo:
Mushrooms has been sustainable for– for generations. However, land is – is — affordable, because Mother Nature provides rain, Mother Nature provides sun. Growing indoors is very capital intensive. You have the building, you have the infrastructure, you have energy costs. But if you can maximize productivity and having consistent quality year-round, yes, it’s economically viable, but the margins are still very tight.”
Ivette Feliciano:
Most indoor farmers can’t grow at the same scale as mushroom farmers in Kennett Township. But where they — and some venture capitalists — see the future of indoor agriculture lying is in small-scale urban production in areas with no farming industry of their own.
Matt Barnard:
The place where we’re stepping in now is to serve demand that is unmet.
Ivette Feliciano:
Three-thousand miles west of Alonzo’s farm, indoor farming pioneer Matt Barnard heads a major agriculture project in San Francisco called “plenty.” Its farm is a retrofitted former warehouse, now with walls of fresh vegetables that stretch for 100-thousand square feet.
Currently, it grows leafy greens like spinach and kale–the easiest and most affordable crops to grow indoors–but it will soon start growing tomatoes and strawberries as well. The plants grow directly out of vertical columns. Similar to Dutch researchers, the company also uses l-e-d lighting, water recycling, and climate control.
No genetically modified seeds or pesticides are used in production. Instead, it’s the environment that’s modified, carefully crafted around each type of plant to give them the ideal conditions for growing.
Matt Barnard:
The advantages that we find are because of that control– we, for example, don’t have to use pesticides. Instead of using 15 gallons of water to produce one head of lettuce, we use less than one-fifth of a gallon to produce that same head of lettuce. So we’re saving a significant amount of water. We can actually influence the way the food tastes by making sure it has exactly the right nutrient recipe, the right light recipe, the right water recipe.
Ivette Feliciano:
Plenty hopes to become an industry leader in indoor farming. The company recently received 200 million dollars of private funding, which it plans to spend on building farms in the ten most populous American cities and hundreds more worldwide.
But, as in the Netherlands, plenty has to overcome certain challenges — the upfront cost of building or retrofitting indoor spaces suitable for farming…and the energy costs of indoor lighting and climate control.
But Matt Barnard believes that the advances that have been made in indoor agriculture will make it a key player in feeding the world’s ever-growing population.
Matt Barnard:
We’ve added, you know, six billion people since the tractor came around, and so we believe this is one of the core innovations that’ll help us, you know, serve the next two to three billion people that we add to the planet.
Peril and Promise is an ongoing series of reports on the human impact of, and solutions for, Climate Change. Lead funding for Peril and Promise is provided by Dr. P. Roy Vagelos and Diana T. Vagelos. Major support is provided by Marc Haas Foundation.
Indoor Agriculture Brand Fresh Farms of America Launching in the Las Vegas, Nevada Market
Indoor Agriculture Brand Fresh Farms of America Launching in the Las Vegas, Nevada Market
NEWS PROVIDED BY: Indoor Farms of America
December 4, 2017
LAS VEGAS, Dec. 4, 2017, /PRNewswire/ -- Fresh Farms of America, announces today the first farm under the brand name, located in Las Vegas, Nevada. The local operation is named Vegas Fresh Farms, and is on track to serve and sell its first customers with locally grown, fresh-harvested daily produce in the dynamic market of Las Vegas, starting January, 2018.
The Fresh Farms of America brand exclusively utilizes the propriety vertical aeroponic equipment from leading R&D and equipment manufacturer Indoor Farms of America, which is headquartered in Las Vegas.
Fresh Farms of America grows a wide variety of crops indoors
"This new brand of indoor farm operation represents the best in the industry for farm performance, using any metric," statesDavid Martin, CEO of Indoor Farms of America. "Over the next month, we will announce multiple new locations of farms operating under the Fresh Farms of America brand. This brand will quickly become the leading brand of fresh, locally grown produce, accessible by consumers in markets across the U.S. and Canada."
Fresh Farms of America uses the vertical aeroponics of Indoor Farms of America
"Consumers want to know where their food is coming from, they want to know it is the best they can serve their families in terms of purity and nutrition, and the Fresh Farms of America brand exemplifies that," says Martin. "Our produce is grown with no pesticides, no herbicides, is Non-GMO, and is quite frankly, beyond organic."
"Chefs from the best restaurants in Las Vegas continually visit the farm at Indoor Farms of America and say how excellent the produce tastes, how the aroma of our herbs is beyond comparison, and how the texture and structure of the plants is simply superior, and how they appreciate the wide variety of fresh produce we can grow. We think the U.S. consumer will really enjoy having this level of quality, and at prices that are more competitive than organic at this time."
Ron Evans, President of Indoor Farms of America, says, "The owners of this local Las Vegas farm are committed to making this a world class operation, which local Southern Nevada residents will really enjoy. Having access to an abundant supply of leafy greens, herbs, strawberries, peppers and tomatoes is something to get excited about, especially when they are grown in your neighborhood."
The farm will provide direct access to local consumers, the freshest, most purely grown produce they can find. The owners are committed to providing meaningful jobs to veterans and disadvantaged young adults from the community. "When we discussed how important this farm is for the local community in the area of reaching out to at-risk young people, we knew they have a great vision for this farm," states Martin.
According to Martin, "We are putting in place what will be the nations' premiere brand of indoor farm that can operate 12 months out of the year, provide outstanding investment returns without peer, and make the strongest impact on easily accessible, locally grown food across North America."
Leading indoor agriculture R&D and manufacturer, Indoor Farms of America, has a showroom with demonstration farms operating in Las Vegas, Nevada and in multiple locations in Canada, and in South Africa, where their world class vertical aeroponic equipment is on display.
CONTACT:
David W. Martin, CEO • 187031@email4pr.com • IndoorFarmsAmerica.com
4000 W. Ali Baba Lane, Ste. F Las Vegas, NV 89118
(702) 664-1236 or (702) 606-2691
SOURCE Indoor Farms of America
Herbs From the Underground
Herbs From the Underground
Farm One just opened an indoor rare herb and flower garden in a TriBeCa basement and many prominent chefs are flocking to it.
By ALYSON KRUEGER | DEC. 6, 2017
In the basement of a loft-style building in TriBeCa that houses a vet, a dog swimming pool, an eye-and-ear infirmary, and a two-Michelin-starred restaurant, there is a working farm.
Farm One is a hydroponic facility, which means that the plants do not grow in soil. Many of these farms are located indoors, in controlled environments, with artificial lighting.
The new two-room space, which opened in November in a former cycling studio for high-altitude training and an old storage area, is only 1200 square feet. There is no fresh air or natural light; there is not even a window. Yet the venue can grow around 580 varieties of rare herbs and flowers (200 at a time) that supply New York’s top restaurants. Le Turtle,Le Coucou, Mission Chinese Food, and The Pool get regular deliveries from Farm One, sometimes several times a week.
“I wouldn’t want to pay for a space with great retail frontage,” said Robert Laing, the farm’s chief executive and founder. “All we need is a floor drain, water, power, temperature control, and the ability to seal the space so bugs don’t get in.” The farm does deliberately bring in a few types of insects that are beneficial for plants, like ladybugs. “You can buy them on Amazon,” he said.
Katherine Chester, a farm hand at Farm One, harvests for a morning delivery.CreditSarah Blesener for The New York Times
Seeds are planted in materials like coconut husks and are put in a tray so water and nutrients can circulate below them. LED lights above simulate the sun. Growing time is not long; many plants, like microgreens, are ready in a little over a week.
People who find it weird to eat food grown in a basement have no reason to worry, said Neil Mattson, associate professor and greenhouse extension specialist at Cornell University. “There is nothing icky about it. Plants don’t care whether they get light from the sun or the lamps. It’s the same thing.”
Matthew Hyland, the chef and owner of Pizza Loves Emily, a client of Farm One, agreed. “A hydroponic garden in general is an amazing thing,” he said. “It’s lit nicely; it smells good in there; the temperature is nice; everything about it is very pleasing.”
The plants grow on shelves that can be expanded or contracted like the stacks in a university library (this setup almost doubles the growing space.) On one level there might be anise hyssop, an herb with tiny lavender-colored flowers and square stems that tastes strongly of mint and licorice. On another, mustard green, a plant that tastes a lot like spicy horseradish. The colors are so diverse and vibrant that the head horticulturalist, David Goldstein, has taken to arranging them on trays for parties.
From top: Amazon neon cherry dianthus and neon rose magic dianthus; edible flowers; nasturtium leaves; and anise hyssop flowers. Farm One can grow some 580 varieties of rare herbs and flowers. CreditSarah Blesener for The New York Times
Mr. Laing, a British-Australian entrepreneur with a sharp sense of humor, can walk around the farm and tell you exactly what every variety is and to whom it is being delivered. “This is my favorite,” he said, pulling off a leaf of papalo. “Crush it up a little bit in your hand and smell it first — there is cilantro, citrus peel. It’s super fresh and quite grassy.” He paused. “I never want to sell software again.”
In a previous life, Mr. Laing worked in Japan, where he started a translation software company. After eight years he turned his attention to his true passion: food. He took culinary classes and visited farmers’ markets across the world, discovering many rare herbs he had never heard of along the way. “And I was someone I thought knew about food,” he said. So he started researching ways to bring these herbs to chefs.
Farm One grew out of this research. In April 2016 the new company started growing products at a small indoor farm at the Institute of Culinary Education, also in Lower Manhattan, on Liberty Street. By August, the farm had its first client: Daniel Boulud’s Daniel. By the end of the summer, the herbs had sold out, which led Farm One to open a second location this fall, at 77 Worth Street.
For $50, New Yorkers can take a tour of the farm, tasting dozens of rare flowers while sipping a glass of prosecco, and they are given a box of herbs to take home. Farm One also offers seminars on the basics of hydroponics, and any herbs and flowers not snapped up by chefs are available for purchase through its website. Mr. Laing is discussing bringing the farm to other cities.
The harvest room at Farm One. CreditSarah Blesener for The New York Times
Mr. Laing attributes the farm’s success to two factors: Rare products and low overhead. “Pluto basil can be sold for $40 a pound as opposed to $10 to $15 for regular basil,” he said. And since the farm is small, the cost of expensive LED lights is minimized. Larger hydronic farms like FarmedHerein Chicago have had to close.
Farm One is also poised to cash in on the Instagram-driven food world, where chefs are willing to pay extra money for novelty items like rare herbs and flowers. Mr. Hyland, for example, is besotted by pluto basil. “They are really beautiful looking on a pizza with the little leaves everywhere,” he said. “Customers know it’s a custom-made product.”
Atera, the restaurant upstairs at 77 Worth, brings certain customers down to the farm for tours. It also offers one course in which the chef, tableside, dresses a dish with the herbs sourced from the basement. “Everyone gets pretty excited,” said Matthew Abbick, the restaurant’s general manager.
Farm One is not the only place chefs can procure these herbs; chef farms or wholesalers in California or Ohio ship a variety of rare products across the country. However, New York chefs like that the greens at Farm One are grown locally and haven’t been sitting in a warehouse or delivery truck for days. “Farm One snips the herbs in the morning for an afternoon delivery,” said Victor Amarilla, the executive chef at Le Turtle. “I actually see my delivery guy walking up now. I see him twice a week.” Farm One boasts on its website that delivery is just a 30-minute bike ride away from 90 percent of the restaurants in the city.
At Atera, a restaurant housed in the same building as Farm One, there is a course in which the chef, tableside, dresses a dish with the herbs sourced from the basement. CreditSarah Blesener for The New York Times
There are also the environmental benefits. The farm recycles and reuses water, purging it every three weeks, which minimizes waste. But there are downsides. Studies show that in general, the environmental costs of lighting and heating indoor farms are significantly higher than shipping something across the country that’s been grown in the California sun. “We know it’s an issue and we are working on it with things like getting more efficient LED lights,” Mr. Mattson said.
Other insiders say that hydroponic farming is essential, especially as climate change makes growing seasons volatile and unreliable. “One of the most important things people will need to do over the next 100 years with climate change is bring food creation and cultivation back to cities where people are moving,” said Dan Nelson, an entrepreneur in Brooklyn who is researching the urban agriculture movement and who took a Farm One seminar on hydroponics. “That’s my humanity-level thesis,” he added.
The New York City Council is currently exploring Bill 1661, a piece of legislation to define urban agriculture and bring about industry standards that will help it advance.
The main concern of chefs, though, is having ingredients they can cook with today. And many are applauding Farm One’s contribution to their operations.
“New York has the greatest summer vegetables and fruits and leafy greens, and in the winter, we are in a real dead zone,” said Mr. Hyland. “Having a product year round that we can really be proud of, would be a great win for New York City food.”
Affinor Growers Reduces Cost of Tower Technology By 30%
Affinor Growers Reduces Cost of Tower Technology By 30%
Cost reductions resulted from several growing tests. New design also allows for organic certification
Vancouver (Canada), December 6 2017 - Affinor Growers (CSE:AFI, OTC:RSSFF, Frankfurt:1AF) (“Affinor” or the “Corporation”), is pleased to announce several design improvements have resulted in a 30% reduction in overall cost and optimized growing conditions.
30% Tower Cost Reduction
Over the summer and during various grow-trial testing periods, Affinor took the opportunity to redesign certain aspects of the tower technology with the goal to reduce overall cost by 20%, improve plant resource availability and versatility. New ideas were conceived and prototyped with our supplier located in Port Coquitlam. By reducing the number of parts and simplifying various fabrications, the overall financial objective was exceeded with a total cost saving of 30% per tower.
The towers have an estimated useful life of 20 years so a 30% reduction allows farmers to amortize the reduced cost at a lower rate and reap more financial benefits from the optimized growing conditions.
Organic Certification Potential
In parallel, the new design improvements upgrade the tower to allow growers to be certified as compliant for organic certification under current Canadian regulations pertaining to the amount of volume and depth of organic soil required per plant as well as improved light penetration by introducing a new tiered level approach. Improved versatility was achieved by designing a universal growing arm that now fits custom plastic inserts to maximize density during the plant growing cycle and accommodate different types of plants.
Jarrett Malnarick, President & CEO, commented, "We are very happy about the design improvements that occurred over the last several months and believe our growing technology can offer cost-effective solutions to a variety of markets. These improvements will allow organic certification and enhanced growing environments for fresh fruit, produce and cannabis plants as well as offer versatility within the plant's life cycle or types of product to be grown.”
For More Information, please contact:
Jarrett Malnarick, President, and CEO
contact@affinorgrowers.com
About Affinor Growers Inc.
Affinor Growers is a publicly traded company on the Canadian Securities Exchange under the symbol ("AFI"). Affinor is focused on growing high-quality crops such as romaine lettuce, spinach, strawberries using its vertical farming techniques. Affinor is committed to becoming a pre-eminent supplier and grower, using exclusive vertical farming techniques.
On Behalf of the Board of Directors
AFFINOR GROWERS INC.
"Jarrett Malnarick"
President & CEO
The CSE has not reviewed and does not accept responsibility for the adequacy or accuracy of this release.
FORWARD-LOOKING INFORMATION
This News Release contains forward-looking statements. The use of any of the words "anticipate", "continue", "estimate", "expect", "may", "will", "project", "should", "believe" and similar expressions are intended to identify forward-looking statements. Although the Company believes that the expectations and assumptions on which the forward-looking statements are based are reasonable, undue reliance should not be placed on the forward-looking statements because the Company can give no assurance that they will prove to be correct. Since forward-looking statements address future events and conditions, by their very nature they involve inherent risks and uncertainties. These statements speak only as of the date of this News Release. Actual results could differ materially from those currently anticipated due to a number of factors and risks including various risk factors discussed in the Company's disclosure documents which can be found under the Company's profile on www.sedar.com. This News Release contains "forward-looking statements" within the meaning of Section 27A of the Securities Act of 1933, as amended, and Section 21E the Securities Exchange Act of 1934, as amended and such forward-looking statements are made pursuant to the safe harbor provisions of the Private Securities Litigation Reform Act of 1995.
Something Fishy About Downtown Toronto’s Waterwheel Farms
Something Fishy About Downtown Toronto’s Waterwheel Farms
With aquaponic farming, the root systems of plants grow directly through pipes into water.
TORONTO • Arts & Life • Food
Solutions to growing local produce may be as close as Queen Street West
By Katherine ForteDecember 4th, 2017
When you think farm you may not think of downtown Toronto, but Alec Wheeler is trying to change that perception.
His Waterwheel Farms uses aquaponic techniques to grow leafy greens and herbs in the facility near Queen Street West and Dufferin Street. The farm employs fish and microbes to grow the plants, which in turn filter the water for the fish – no soil required.
“It looks a little ‘labby’ in here but this is the identical ecosystem you’d find in a lake,” Wheeler said during a recent tour for the Toronto Observer. “You have fish, you feed them, they produce waste, the waste feeds the plants and just as importantly, the plants then filter the water for the fish. It’s a closed loop cycle.”
At Waterwheel Farms, instead of aquatic plants, they are growing crops for human consumption.
“So that’s aquaponics in a nutshell. It’s a living ecosystem between fish, microbes, and plants.”
Aquaponic farming is a closed loop cycle in which the fish act as the fertilizer for plants. The environment is similar to a lake. (WATERWHEEL FARMS)
Wheeler began a small aquaponics farm in his apartment five years ago, when he got tired of his store-bought greens going rotten too quickly. All of his education on aquaponics farming came from research and translating knowledge gained from growing up on his family’s open-field farm in Northern Ontario. He works as a financial analyst for a renewable energy provider. He jokingly refers to himself as “a renewable energy crusader by day and an urban farmer revolutionist by night.”
In May 2017, Wheeler expanded from his apartment to a 1,000 square foot research facility and farm. On-site at there are two tanks containing 400 tilapia fish who aid in growing Bok Choy, arugula, sorrel, spinach, lettuce and Waterwheel Farms’ most popular product, their tender kale. Anyone can purchase their fresh produce by visiting on Saturdays.
The seeds start their life cycle in peat moss. When they’ve grown to the point where their roots are the appropriate length they’re transplanted into pipes with running water where they have more room to flourish. The vegetables grow under different kinds of lights, at controlled temperatures that mimic the longest summer day in Toronto, for optimal growing conditions.
“Because we are indoors we’re controlling the lighting and heating and all that kind of stuff. In Toronto we are at the 43 latitude. Our longest day is just shy of 16 hours. We have these lights timed so they run on 16-hour cycles,” Wheeler said. “We can get, like, seventeen harvests for certain plants as opposed to the one or two you’d get traditionally.”
Waterwheel Farms doubles as a research facility. Founder Alec Wheeler experiments with different colours in the light spectrum to see which yield the best plant growth. (KATHERINE FORTE)
Wheeler finds that aquaponic farms have the ability to provide farmers with more, using less space.
“In traditional agriculture – nothing against it – you’ll read on the packet it says plant every 18 inches or whatever, it’s mainly because there’s a limited amount of nutrients in that soil and those plants are competing for those nutrients. With aquaponics it’s more of a smorgasbord for the plants because the nutrients are coming to the plants. So you can pack them in closer and produce more food and faster,” Wheeler said.
He boasts that his lettuces grow in 20 days, rather than three months.
Plentiful crops aren’t the only benefit of aquaponic farming. Since crops are grown indoors, they’re resistant to poor weather and climate change. The closed-loop system also uses 90 percent less water than traditional agriculture. The only water that leaves the system is what’s used by the plants, and the fish are edible, as well as the vegetables.
There’s no need to worry about toxins from the fish poop or harmful pesticides either. Just like in nature anything toxic in the fish waste or water would “crash the system” according to Wheeler. The same can’t be said about many methods of traditional open-field farming. Though crops can flourish with chemicals in the ecosystem, these chemicals often run off into our rivers and lakes.
Wheeler thinks his style of urban agriculture could change the way Toronto eats, and its impact on our lives could be huge. More people don’t have their own aquaponic farms due to lack of awareness, he believes.
“Like everything, there’s an education barrier. “ Wheeler said. “That’s kind of why we have the facility here so that people from Toronto and in Toronto can come and see the farm.”
That education barrier and lack of awareness is exactly why Rhonda Teitel-Payne and the other members of Toronto Urban Growers celebrated the first Urban Agriculture Day, on Sept. 15, 2017. Farms and gardens, including Waterwheels, opened their doors for tours, and urban farmers from Toronto got together to host a week of events.
What began as a community of urban farmers became Toronto Urban Growers in 2008. The group helps potential city-based farmers and gardens locate resources and connect to each other, so they can share tips, tricks, and anecdotes.
“We started to realize one of the biggest barriers we had in terms of getting projects going was lack of awareness of what urban agriculture is and what it can do and what it’s capable of,” Teitel-Payne said. “We thought that Urban Agriculture Day would be a great way both to celebrate and build that urban agriculture community in Toronto but also to get out the message of ‘Hey look what we can do when we’re growing food in the city. Let’s do more of it.’”
According to Teitel-Payne, urban farming can have more of an effect on us than just what’s on our plate. While Toronto probably couldn’t be self-sufficient when it comes to agriculture (some of the most optimistic statistics estimate we could only produce 10 per cent of our own food), there are other changes that could come with bringing some of the farm to the city.
Not only is diversifying our food sources a bonus, but Teitel-Payne finds that food connects us in different ways to different issues. That connection through food and urban agriculture could empower others to become more vocal on a number of issues.
“Food is that pathway into greater action.” Teitel-Payne said. “What comes out of that is people saying ‘There’s something about our neighbourhood we wanna change.’ Whether it be climate change, political action, access to food, or income or transit, there’s a whole constellation of issues that food touches.”
So where do we start?
Both Teitel-Payne and Wheeler agree condos could hold some potential for the future.
“Let’s start having a discussion with the developers and owners and let’s start cutting out a portion of the space for each condo to have it’s own farm,” Wheeler said. “The condominium right next to us has a beautiful and massive grocery store in it. Well, let’s just add to it. Rather than them having to ship in their food, let’s have it produced on site.”
Until then, Wheeler and Teitel-Payne hope that when people see urban agriculture in action it’ll inspire them to get on board.
“I envision it being a snowball effect,” said Wheeler. “You plant a couple of seeds and let it grow.”
from research and translating knowledge gained from growing up on his family’s open-field farm in Northern Ontario. He works as a financial analyst for a renewable energy provider. He jokingly refers to himself as “a renewable energy crusader by day and an urban farmer revolutionist by night.”
About this article:
By: Katherine Forte
Posted: Dec 4 2017 12:16 pm
Edition: Toronto
Filed in: Arts & Life • Food
Multimedia: Photos
Tagged: alec wheeler • aquaponic farming • Food • gardening • lettuce • tilapia •Toronto • toronto urban farm • Toronto urban growers • waterwheel farms
Vertical Farming is Amazon’s Next Bold Step
Associate Consultant at Bain & Company | Los Angeles | Harvey Mudd ’17 | lakshayakula.com
Nov 4, 2017
Vertical Farming is Amazon’s Next Bold Step
An artist’s (i.e. my) impression
Vertical farming complements Amazon’s business model, the Whole Foods acquisition, Jeff Bezos’s ambitions, and Amazon’s capabilities — it’s only a matter of time until Amazon pours money into vertical farming.
From data centers to organic kale
Amazon is well known for investing in bold, new technologies and businesses. Here’s a list of some of their noteworthy moves:
- In 1997, Amazon set the stage for their logistics network by building theirfirst two fulfillment centers in Seattle and Delaware
- In 2006, Amazon launched Amazon Web Services (AWS); today, as Google is to search, AWS is to the cloud
- Later in 2006, Amazon became a logistics provider by offering Fulfillment by Amazon
- In August 2007, Amazon launched AmazonFresh, starting their ongoing journey to become a grocery provider
- A couple months later 2007, Amazon entered hardware and brought e-readers to the masses by introducing the Kindle
- In 2012, Amazon made a significant step in automated warehouses by acquiring Kiva Systems for $775M
- In 2014, Amazon brought the Amazon ecosystem into the living room, with the home assistant Alexa (and the smart speaker it runs on, Echo)
- This year, Amazon acquired Whole Foods for a whopping $13.7B
At first, it seems like there’s very little in common among Amazon’s ventures. There’s no connection between data centers and organic kale. But there’s method to the madness. A simple business model underlies Amazon’s success.
The Amazon model
For a venture to fit into Amazon’s business model (i.e. the Amazon model), it only needs to have three characteristics:
- High fixed costs with huge economies of scale
- Have Amazon as the first and best customer
- Can be modularized, to offer infrastructural components to third-parties
Here’s how it works. Amazon invests in a new venture with high fixed costs and economies of scale. It can justify their initial investment and provide scale because Amazon’s existing businesses will be a customer of the new venture. The services are modularized to third-parties, increasing scale and decreasing costs, making the new services even more attractive, further increasing scale and feeding a virtuous and unrelenting cycle.
Here’s a diagram of the model. Note that growth is central to the model.
Supposedly drawn by Bezos on a napkin; also resembles a fried egg (Source: Stratechery)
AWS is the best example of the Amazon model at work. AWS is distant from Amazon’s core e-commerce business. For one, the former is B2B whereas the latter is consumer-facing. With conventional goggles, it’s difficult to see why Amazon launched AWS or why AWS has become so wildly successful. With the lens of the Amazon model, we can understand the beauty of AWS.
Let’s see how AWS fits those three characteristics from earlier:
- Cloud services is an industry defined by high fixed costs with huge economies of scale. It’s expensive to build the infrastructure and buy servers at first, but once that’s done, adding the marginal customer is practically free.
- Amazon.com was the first and best customer of AWS. Amazon.com benefits from free web services and AWS gets a jump-start with the initial scale.
- AWS may be the most modularized service in existence — I counted 124 products across 22 categories. It’s so modularized that any company can use its products, from fast-growing startups to multibillion dollar companies to the CIA.
To summarize, AWS started with Amazon.com as a customer, justifying the initial investment in AWS and providing initial scale. It was then modularized for 3rd parties, increasing scale, which AWS used to invest in more capabilities and reach more businesses, further increasing scale and decreasing costs. Today, AWS is in a league of its own in terms of market share and leadership.
AWS’s market share, execution and vision are unmatched by competitors (Sources: Synergy Research Group & Gartner)
The Amazon model is precisely why AWS is so successful. If you want to learn more about the Amazon model, I’d recommend reading Ben Thompson’s blogStratechery (particularly this one).
Making sense of Whole Foods
I promise to get to vertical farming soon, but first, we need to understand why Amazon acquired Whole Foods. The most common explanations are: 1. AmazonFresh will benefit from selling Whole Foods products 2. Amazon can use Whole Food’s urban, retail space, and 3. Amazon Prime can synergize with Whole Foods’s loyal and affluent customer base. These explanations are reasonable but they misunderstand Amazon’s strategy.
Ben Thompson wrote an excellent explanation for how the Whole Foods acquisition ties into Amazon’s business model. In it, he details how the acquisition is effectively Amazon purchasing a customer to provide scale for their grocery efforts.
Amazon’s food delivery service, AmazonFresh has floundered for the past decade. It hasn’t expanded beyond a few urban centers, nor has it given traditional grocery stores a run for their money. The problem is that AmazonFresh fails criteria #2 of the Amazon model — have Amazon as the first and best customer. As a result, AmazonFresh has never built the scale to become competitive.
With the Whole Foods acquisition, AmazonFresh is re-positioning itself as “Amazon Grocery Services” (AGS). The parallelism with AWS is intentional. AGS’s first, large customer is Whole Foods. With this initial scale, AGS will be competitive and Amazon can justify investing in AGS. AGS will modularize and offer services to other grocery stores, restaurants and customers. With increased scale, costs will go down and AGS will become more competitive.
But Amazon isn’t about being competitive. Amazon is about being dominant. In order for AGS to be dominant, AGS needs a technological advantage over its competitors. This key differentiating factor will be vertical farming.
Vertical Farming’s perfect fit for Amazon
Vertical farming comes in many flavors and forms. For Amazon, I envision warehouses near population centers producing greens and herbs. These warehouses will be highly controlled environments, optimized to produce maximum yields.
Currently, vertical farms like these not economical because of high energy costs for artificial lighting. I’m expecting Amazon to be the one to solve this problem and take vertical farming off the ground. And in case Amazon is looking for a name, I have an idea — “Amazon Vertical Farming” (AVF).
Why boils down to three reasons:
- AVF synergizes well with AGS
Both services cater to urban locales and will scale in lockstep. It’s a perfect union. AVF gives AGS a competitive advantage and improves AGS’s scale. Whole Foods will be AVF’s first and best customer. AVF can be modularized by using AGS to sell produce to other grocery stores, households and restaurants. AVF may not be as perfect of a fit for the Amazon model as AWS, but it’s still a great fit. - Amazon has the know-how for vertical farming
To execute successfully, vertical farming will require developments on both the technological and supply-chain fronts. Amazon is the only player with both. Amazon Robotics can automate much of vertical farming and Amazon Logistics can deliver the product to customers. - CEO and Founder Jeff Bezos wants to
To be honest, this is probably the most important reason of the three. Bezos has personally invested in the vertical farming startup Plenty twice: once in a Series A round in 2016, and again in a Series B round in July 2017 just after the Whole Foods acquisition. Clearly Bezos is a believer in vertical farming.
He also has a track record for taking risks. He launched the experimental drone-delivery services Prime Air and created the spaceflight company Blue Origin. Taking a risk with vertical farming wouldn’t be out of character for him.
Most importantly, what more could the third-richest person on Earth want to do than solve one of the biggest problems facing the planet? Agricultural pollution and food waste are pressing issues. With vertical farming, Bezos can make a significant step forward for humanity in addressing these problems.
What’s next?
How Amazon will enter vertical farming is up to debate. It’s possible that Amazon will enter a partnership with Plenty, the vertical farming start-up Bezos has already invested in. I personally believe Amazon will be much more ambitious and acquire Plenty. It’s also possible that Amazon will develop vertical farming capabilities independently, but I find that unlikely given Bezos’s existing investment in Plenty.
Google searching amazon vertical farming as of 09/25/2017, for future reference
Regardless of how Amazon enters vertical farming, one thing is certain. At the time of writing, Google searching “amazon vertical farming” brings up vertical farming products sold on Amazon, including this book and this indoor vertical garden. The 7th link down is the first one to discuss Bezos’s investment in Plenty. With certainty, I can promise that those search results will change significantly in just the next year or so.
Thanks to Rohan Nagpal for the conversations that led to this piece and reviewing my drafts. This really was a collaborative effort. Thanks, bud.
Rensselaer Polytechnic Institute Study
Rensselaer Polytechnic Institute Study Demonstrates that Both High Yields and Nutritional Quality of Leafy Greens Can Be Achieved With LUXEON SunPlus Lime LEDs
In a comparison study, Rensselaer researchers determined that LUXEON SunPlus Lime + Purple and Green + Purple LEDs provided beneficial growth spectra, resulting in high crop yield and high levels of antioxidants important to human health.
San Jose, CA – December 5, 2017 – The results of a controlled horticulture lighting study conducted by the NSF funded Center for Lighting Enabled Systems and Applications (LESA) at Rensselaer Polytechnic Institute (RPI, Troy, NY), have been released. The study, utilizing a variety of commercial LEDs, compared the effectiveness of different LEDs on the growth of red lettuce Rouxai. The best combined yield and antioxidant concentrations in the lettuce was observed using LUXEON SunPlus Series LEDs. “Comparing the growth results using different combinations of LEDs shows that the spectra that performed best for yield (fresh weight), anthocyanin and chlorophyll concentrations were the LUXEON SunPlus Lime + Purple and Green + Purple LEDs from Lumileds,” said LESA’s Dr. Tessa Pocock, a global expert on light and plant physiology. “Green light is necessary for crop growth and the specific wavelengths within the green region matters.” This work is also part of the Greenhouse Lighting and Systems Engineering (GLASE) Consortium operated by LESA and Cornell University and funded by the New York State Energy Research and Development Authority (NYSERDA) that is examining the most effective way to add green light to horticultural fixtures.
“Growers today are experimenting with various LEDs to arrive at the best color combinations for their crops. The LESA study indicates that such experimentation is paying off because a common, nutrient-rich crop can be produced with excellent yield,” said Jennifer Holland, Product Line Director of the LUXEON SunPlus Series. The study demonstrated that a light spectrum like the combination of LUXEON SunPlus Lime and Purple, which contains a certain ratio of royal blue, green, deep red and far red components, is beneficial to growth optimization.
For details of the study, see here: www.lumileds.com/uploads/702/WP34-pdf
To learn more about the LUXEON SunPlus Series including the new Far Red and Deep Red LEDs, see www.lumileds.com/horticulture
About Lumileds
For automotive, mobile, IoT and illumination companies who require innovative lighting solutions, Lumileds is a global leader employing more than 9,000 team members operating in over 30 countries. Lumileds partners with its customers to push the boundaries of light.
To learn more about our portfolio of lighting solutions, visit lumileds.com.
For further information, please contact:
Kevin Lucido
Senior Director of Global Marketing Communications
Lumileds
+1 650 576 3864
Kevin.Lucido@lumileds.com
This Company Wants To Solve The World's Hunger Problem. Here's How
Plenty, a new San Francisco–based startup, hopes to step up to that plate. The Jeff Bezos–backed endeavor, which has raised $200 million to date, is dedicated to bringing healthy food to everyone in the world, thanks to a unique system of vertical farms. Plenty, a new San Francisco–based startup, hopes to step up to that plate. The Jeff Bezos–backed endeavor, which has raised $200 million to date, is dedicated to bringing healthy food to everyone in the world, thanks to a unique system of vertical farms
This Company Wants To Solve The World's Hunger Problem. Here's How
November 9, 2017
While we love bringing you functional recipes and sharing the latest in superfood trends, it's hard to ignore the fact that some people simply don't have access to the most basic elements of healthy food. In line with our newly shared You. We. All. mission, it's abundantly clear that if some—many—of us can't find or purchase healthy food, the system isn't working for all of us, and something needs to change.
Plenty, a new San Francisco–based startup, hopes to step up to that plate. The Jeff Bezos–backed endeavor, which has raised $200 million to date, is dedicated to bringing healthy food to everyone in the world, thanks to a unique system of vertical farms. Vertical farming is the perfect antidote to many of the problems that plague the modern agricultural world: It doesn't require land (it goes up, not out); soil (which is often depleted of nutrients from over-farming); sunlight (special low-energy UV lamps are used); or pesticides (Plenty will seek official organic certification within the next calendar year). While vertical farming is incredibly effective in all types of environments, it's especially change-making in urban regions, where thousands of gallons of fuel are typically used to ship produce from more far-flung farms (the time in transit significantly reduces the nutrient contents of produce as well), and countries with environments that don't typically lend themselves to agriculture (many mountainous and desert regions). Vertical farming crops can yield up to 530 times more than typical fields, a huge boon when it comes to quickly getting vegetables to the world's ever-expanding population.
The company has opened two vertical farms thus far, in the Bay Area and Wyoming, with plans for a third to debut in Seattle in spring 2018. The new warehouse is twice as large as the company's first and will grow 4.5 million pounds of greens annually—enough to feed nearly 200,000 Americans. With its large investment, the company hopes to eventually have a vertical farm in every major city in the world.
While there is speculation about the company's future plans—rumors include direct-to-consumer delivery done by robots, among other things—one thing is certain: Plenty is poised to quickly revolutionize the way the world eats.
Liz Moody is the senior food editor at mindbodygreen. She's contributed to Glamour, Women's Health, Food & Wine, goop, and many other publications and is the woman behind the...
Urban Agriculture Just Got Serious! Plantagon Is Building 10 Underground City Farms In Stockholm – And Locals Are Invited To Join In…
Plantagon CityFarm® is a new concept for using empty premises for resource efficient and sustainable food production in cities. The first plant is located under Stockholm’s iconic “DN Skrapan” in Kungsholmen, and the goal is to have ten production facilities for indoor production in the Stockholm area by 2020.
Urban Agriculture Just Got Serious! Plantagon Is Building 10 Underground City Farms In Stockholm – And Locals Are Invited To Join In…
Press Release • Dec 01, 2017
Plantagon is building 10 underground city farms in Stockholm – and locals are invited to join in…
STOCKHOLM, SWEDEN (December 1, 2017) – We hear a lot about smart sustainable innovations coming from Sweden, from turning rubbish into fuel, recycling excess heat from data centres, geothermals etc… Swedish pioneers Plantagon, are now taking on sustainable city farming on an industrial scale.
Plantagon CityFarm® is a new concept for using empty premises for resource efficient and sustainable food production in cities. The first plant is located under Stockholm’s iconic “DN Skrapan” in Kungsholmen, and the goal is to have ten production facilities for indoor production in the Stockholm area by 2020. Now the public is invited to a crowdfunding campaign on the Fundedbyme Investor Platform to support the expansion.
"The reason for a crowdfunding campaign is that we believe that people that care about the future of cities, food production and the health of our planet should be given the opportunity to be a part of the solution. To us, it is important to create and expand together, showing that we are a movement for healthy sustainable food. Together, we can make a difference for safe food production in cities - now and in the future", says Owe Pettersson, CEO of Plantagon International.
The goal of the campaign is to reach between 3.5 and 7.5 million kronor. The minimum amount to participate is set at SEK 1,000. All who participate will get a blueprint for a home-growing system if they would like to start cultivating at home. For all who participate at the level of SEK 10,000 or more, a private guided tour and your own harvest of vegetables and herbs inside the facility are included. Read more about the campaign here: www.fundedbyme.com/plantagon
Collaborators in the project include Samhall (a state-owned company with a mandate to create work that furthers the development of people with functional impairment causing reduced working capacity), ICA Maxi Lindhagen (a very local supermarket store), and world-renowned chef Pontus Frithiof with the restaurant, Pontus Tidningspressen, in the same building.
Ten units by 2020
"The first unit in the DN house is already fully funded and under construction. We aim to sign contracts on plant number two and three in March 2018 to start these in December 2018. Then we continue with plant four and five. The goal is that we have ten facilities running in Stockholm by 2020", says Owe Pettersson.
Plantagon CityFarm Stockholm is part of Plantagon Production Sweden AB, a subsidiary of Plantagon International AB. CEO of the new production company is Owe Pettersson, who is also CEO of Plantagon International AB.
Plantagon's technology for industrial indoor and urban cultivation is a response to the need for new solutions for sustainable food production that can provide for the growing urban population around the world while maximizing the use of unused urban spaces. Cultivation takes place in a controlled environment without any forms of chemical pesticides. Plantagon CityFarm® saves 99 percent of water consumption compared with traditional agriculture and carbon dioxide emissions are reduced to almost zero, while 70 percent of the energy used is reused to heat the offices in the DN House. By saving and reusing resources, production costs are significantly reduced.
What does Urban Agriculture really mean?
For Plantagon, it means that it must be sustainable environmentally, sustainable for society and also economically sustainable. Many players in food tech talk about urban agriculture or city farming, but no one has managed to cover all three goals. Delivering locally and using smart energy systems minimizes costs as well as emissions. Large-scale production using efficient cultivation systems while training the future farmers through Samhall, Plantagon plans on taking urban agriculture to the next level and developing the industry globally.
Please go to investment page for more information
Contacts
Carin Balfe Arbman, Communications Manager, Plantagon, tel. +46-70-633 35 08, carin.balfe-arbman@plantagon.com
Anna Karlsson, Press Contact, Manifest Stockholm, +46-735-20 28 80,anna@manifeststockholm.se
Plantagon International is a world-leading pioneer within the field food security and CSR – combining urban agriculture, innovative technical solutions and architecture – to meet the demand for efficient food production within cities; adding a more democratic and inclusive governance model.
www.plantagon.com www.plantagon.org
Kent To Get Large, Indoor Organic Produce Farm
Kent To Get Large, Indoor Organic Produce Farm
- By Steve Hunter
- Friday, November 10, 2017
Once known decades ago for its many fields of greens as the “Lettuce Capital of the World,” Kent’s about to get its first large indoor organic produce farm.
Plenty, a San Francisco-based firm whose investors include Jeff Bezos, founder of Amazon.com and Kent’s Blue Origin aerospace manufacturer, announced plans this month to open a 100,000-square-foot facility next year near the Amazon Fresh grocery delivery service site along 84th Avenue South.
“Seattle’s emphasis on delicious, healthy food and energy and water efficiency makes the area a natural fit for our next Plenty farm,” said Matt Barnard, CEO and co-founder of Plenty, in a media release. “At nearly 100,000 square feet, Seattle will be home to our first full-scale farm and help set the standard by which our global farm network makes locally grown, backyard-quality produce accessible to everyone. We’re excited about what’s next and look forward to building the Seattle team.”
Plenty’s farm is expected to open in the first half of next year with about 50 employees, including indoor farming engineers, organic growers, and operations experts. Produce grown will be available to Seattle and Vancouver British Columbia area consumers beginning in mid-2018.
“This is a grow we can all get behind,” Ben Wolters, city economic and community development director, said to the City Council at its Tuesday meeting, in reference to the city’s ban against marijuana businesses. “They grow organic produce with LED lights, and yield 350 times what a field of similar size would produce.”
The indoor farm will produce about 4.5 million pounds of greens annually and grow 300 types of produce year-round, Wolters said.
The location near Amazon Fresh, which opened its Kent warehouse this year, makes for a natural connection.
“The idea is Amazon Fresh will buy from here and then ship it out as part of your order,” Wolters said. “They can harvest produce within hours of your order.”
As the amount of domestic acreage that produces affordable fresh fruit and vegetables shrinks while labor and land costs sustain their perpetual rise, Plenty’s expansion is critical to making local, hyper-fresh and organic produce available and affordable for people everywhere, company officials said.
Plenty’s farms, which the company is developing in or near communities around the world, will deliver industry-leading yields of local, backyard-quality produce that’s completely GMO and pesticide-free while remaking agriculture to be both predictable and perpetual given the demands of 7.3 billion people worldwide. Plenty officials say the farms give plants the perfect environment for amazing flavor, use 1 percent of the water and a tiny fraction of the land of conventional agriculture.
The company’s first field-scale farm is in South San Francisco and will start delivering produce to local Bay Area customers within hours of harvest by the end of this year.
“It’s very cutting edge, and the technical and business magazines are covering it,” Wolters said. “It highlights Kent where innovation and opportunity can thrive.”