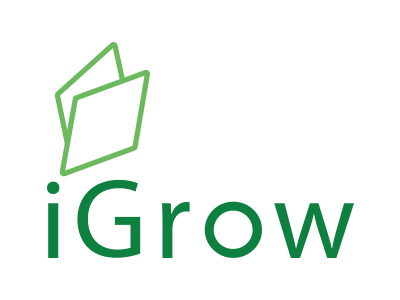
Welcome to iGrow News, Your Source for the World of Indoor Vertical Farming
The Current State of Indoor Farm Economics
THE CURRENT STATE OF INDOOR FARM ECONOMICS
Our sibling company, Contain Inc, is providing the white paper that will be provided in hard copy exclusively to participants in this week’s Indoor Ag-Con. Ahead of that, they have provided us with a sneak peak of its contents:
Contain Inc is an alternate finance company focused on the indoor agriculture market. It solves one of indoor farmers’ most pressing issues as it cuts initial farm build costs by 80% by utilizing 3-5 year equipment leases. As a provider of capital to the industry, Contain Inc has a keen interest in better understanding how and why indoor farms are successful. Its team spends a good deal of time attempting to understand the drivers of farm economics, and it is this theme that we cover in the white paper that will be released at Indoor Ag-Con this week.
What’s the Current State of Indoor Farm Economics?
THIS BLOG POSTING PROVIDES AN EXCERPT FROM THE CONTAIN INC WHITE PAPER THAT WILL BE RELEASED AT INDOOR AG-CON ON MAY 2-3, 2018
The greatest criticism of indoor farms has long been that they are not economically viable, and – in the view of some – never will be. Professor Albright of Cornell University created the most often cited criticism of industry economics, arguing in 2014, that widespread adoption of controlled environment agriculture would increase the cost of certain foods beyond market acceptance. The failure of some of the first generation of North America’s indoor farms seemed to confirm this skepticism, even though most fast-growing young industries are characterized by high startup failure rates.
Yet, software firm Agrilyst found that just over half of respondents to their survey of indoor farms said they operated profitably, and market forces are driving more towards this benchmark. New technologies, falling costs for existing technologies, economies of scale, and better access to capital, along with time itself, all have a part to play.
What do we Know so Far?
As it is young as a commercial industry, we are only beginning to see trends in indoor farm economics. For example, there is some evidence that longer standing farms are more likely to be profitable than newer ones, though there is likely to be some survivorship bias in the data. All else being equal, larger farms are more profitable than smaller ones.
One of the long-observed aspects of agriculture is that it’s a cyclical industry, contributing to booms and busts throughout history. From an economist’s perspective, one of the attractions of indoor agriculture is that it offers the possibility of a less cyclical way of farming. Though the industry is too young for any trend to have developed, theoretically, the steady income stream from indoor farms – which harvest daily rather than periodically – should aid in smoothing long-observed farm business cycles.
To inform our work at Contain Inc, we have developed a proprietary model of the exogenous factors – influences that are not in the control of the grower – that impact indoor farm economics. In this multivariate model, the two indicators proving the greatest significance with p-values < .05 are industrial rents and population density, each of which are location-dependent variables. Consequently, our current “top ten most favorable” indoor farm locations are biased towards larger urban conurbations. We note that this model is dynamic and that we moderate it frequently as we capture new data.
What Trends are Driving Farm Economics?
We see indoor farm economics continuing to improve as:
Moore’s Law is at work in the industry – Indoor farming is benefiting from falling capital expenditure costs, particularly for LED lighting. As LED prices have fallen by 85% in the last five years, they are forecast to fall from over 60% of capex costs in 2011 to under 15% by 2026.[1]
Automation & AI – Growers are increasingly adapting automation to improve nursery, harvesting and post-harvesting operations, improving yields and cutting costs as a consequence.
Plant Genomics – Indoor farmers are turning their attention to breeding seeds that are designed to work better in indoor systems to provide higher yields, better taste and better nutrition.
Lower Cost of Capital – As funding options like lease financing from Contain Inc become more prevalent, growers can afford larger, more efficient farms. As indoor agriculture becomes more mainstream, we anticipate that average interest rates will fall as lenders recognize the lower risk inherent in the practice. Better insurance rates, such as those offered by Contain Inc’s collaboration with InterWest Insurance will also help to reassure lenders that indoor agriculture is bankable.
Beyond the technical and scientific barriers that indoor growers, academics and equipment suppliers break each day, better and more nuanced understanding of the economic factors that underpin indoor agriculture can help to drive the industry further towards profitability. This remains an important aspect of Contain Inc’s mission to support indoor growers.
JOIN US AT THE 6TH ANNUAL INDOOR AG-CON ON MAY 2-3, 2018
REGISTER TODAY
U.S.: Leading Indoor Farming Companies Create Food Safety Coalition
U.S.: Leading Indoor Farming Companies Create Food Safety Coalition
April 11, 2018
Leading Controlled Environment Agriculture (CEA) companies have joined together to establish the first food safety coalition for the sector.
The group’s first meeting will be during the United Fresh co-located 2018 Expos taking place June 25-27 in Chicago, where they will begin to develop the coalition’s structure and food safety standards.
CEA growers including BrightFarms, AeroFarms, and Little Leaf Farms have joined the coalition as founding members, with numerous others expected to join in the coming months.
The development is backed by both the United Fresh Produce Association and the Produce Marketing Association (PMA).
“There is a real need for a group of this kind that enables the industry to combine their collective learning to develop and advance food safety practices,” said United Fresh vice president of food safety & technology, Dr. Jennifer McEntire.
“We frequently get questions from CEA growers with food safety in mind and this coalition will serve as a resource to not only these growers but to all companies in the industry.”
PMA chief science and technology officer, Bob Whitaker, Ph.D., said that collaboration between the companies will advance food safety not just for CEA growers but the fresh produce industry as a whole.
“They ask good questions about how to ensure their particular practices produce safe products and have demonstrated they are willing to learn from and share ideas on risk- and science-based food safety with their open agriculture counterparts,” he said.
AeroFarms CEO David Rosenberg said: “We take food safety very seriously and are proud to help lead this effort to elevate this critical topic not only for CEA growers, but also the industry overall including our retailer partners and ultimately the consumer.”
The CEA produce industry is primarily made up of brands using hydroponic, aeroponic or aquaponic methods. All CEA produce organizations are invited to join the coalition to help shape the model and standard of food safety to protect consumer health.
Those who wish to join are asked to email: ceafoodsafety@gmail.com
Photo: BrightFarms
AEssenseGrows Announces International Indoor Farming Symposium in Shanghai
AEssenseGrows, an ag-tech company specializing in automated aeroponic platforms for high-yield plant production, announced today a symposium featuring leaders in commercial indoor agriculture. Co-sponsored by AEssenseGrows and the Shanghai Academy of Agricultural Sciences (SAAS), the 2018 International Indoor Plant Factory Symposium will run June 12-15 at the Blue Palace Hotel in Jiading, Shanghai.
AEssenseGrows Announces International Indoor Farming Symposium in Shanghai
Co-Sponsored by AEssenseGrows and the Shanghai Academy of Agricultural Sciences, the June Event Brings Together Global Leaders in Indoor Commercial Cultivation
NEWS PROVIDED BY AEssenseGrows
SUNNYVALE, Calif., April 9, 2018 /PRNewswire/ -- AEssenseGrows, an ag-tech company specializing in automated aeroponic platforms for high-yield plant production, announced today a symposium featuring leaders in commercial indoor agriculture. Co-sponsored by AEssenseGrows and the Shanghai Academy of Agricultural Sciences (SAAS), the 2018 International Indoor Plant Factory Symposium will run June 12-15 at the Blue Palace Hotel in Jiading, Shanghai.
AEssenseGrows Announces 2018 International Indoor Plant Factory Symposium in Shanghai
The symposium brings together some of the world's leading experts in commercial indoor cultivation for an exchange of ideas and information about the latest innovations, technologies, and research in the field. The primary focus will be on technology to grow greens and fruit, though topics may also touch upon growing grains and plants for herbal medicines.
"There have been many recent advances in indoor farming, and this symposium will serve as a forum to discuss how they can be deployed commercially to benefit our communities," said Robert Chen, president and CEO of AEssenseGrows. "By joining with the SAAS, we are delivering an event that will be of value to all agriculture professionals who recognize the potential indoor farming presents for businesses and--more importantly--society."
Keynote presentations include:
- "The present and future of the plant factory with artificial lighting," by Professor Toyoki Kozai, president of the Japan Plant Factory Association, Japan
- "Tomorrow's city will be self-sustaining," by Dr. Dickson Despommier, emeritus
- professor, Columbia University, United States
- "The transforming power of vertical farming—global trends and local impacts," by Christine Zimmermann-Loessl, chairwoman of the Association for Vertical Farming, Germany
- "A total solution and innovation for smart plant factory with artificial lighting," by Dr. Huafang Zhou, vice president of AEssenseGrows, United States
- "Grow light recipes and study of artificial lighting for plants," by Professor Shaohua Li, Institute of Botany, Chinese Academy of Sciences, China
Detailed information about the symposium can be found at www.plantfactorysymposium.com. The deadline for submitting abstracts for presentations and posters is April 30.
In addition to the symposium, AEssenseGrows will hit the road in May, demonstrating its advanced grow systems at major conferences in the United States. The Sunnyvale, Calif., startup will demonstrate its AEtrium system and Guardiantm Grow Manager software at:
- Indoor Ag-Con, May 2-3 at the Las Vegas Convention Center
- MJBizConNEXT, May 9-11 at the New Orleans Morial Convention Center
The company will also participate in the NCIA annual Lobby Days, May 21 to 23 in Washington, D.C.
To meet with an AEssenseGrows representative at one of the shows, contact Phil Gibson at pgibson@aessensegrows.com.
AEssense Corp. (pronounced "essence") founded in 2015, is a precision AgTech company based in Sunnyvale, CA.
AEssenseGrows provides accelerated plant growth SmartFarm platforms and software automation delivering pure, zero pesticide, year-round, enriched growth to fresh produce and medicinal plant producers globally.
With AEssenseGrows, you can precisely control your production operations at your fingertips from anywhere in the world.
Phil Gibson
AEssenseGrows
669.261.3086
pgibson@aessensegrows.com
SOURCE AEssenseGrows
FreshBox Farms Names Randy Frederick National Accounts Director
FreshBox Farms Names Randy Frederick National Accounts Director
MILLIS, MA – April 4, 2018 – FreshBox Farms, among the nation’s most efficient vertical farming operations, has named Randy Frederick its National Accounts Director.
His goal will be to build profitable business partnerships with key customers in the Grocery, Wholesale Produce, Food Service and Restaurant retail channels.
“We’re delighted to have Randy on board. He brings a wealth of knowledge about what national corporations consider in choosing locally grown greens,” says FreshBox Farms CEO Sonia Lo.
Mr. Frederick most recently was Vice President of National Sales for Freight Farms, responsible for account development in the grocery, restaurant, and wholesale produce channels. He also served in various capacities with SteadyServ Technologies, which focused inventory, order management, and business intelligence systems to serve the needs of the beer industry.
In addition, he was sales director with MHQ, one of the top up-fitters of municipal vehicles in the US and served in various sales and marketing positions with MillerCoors.
FreshBox Farms’ sustainable indoor growing enclosures use no soil, very little water, a rigorously-tested nutrient mix and LED lighting to produce the freshest, cleanest, tastiest produce possible. Unlike lettuce and other produce that are frozen and spend weeks being transported to local stores, FreshBox Farms’ greens are harvested, packaged, and shipped within hours to local grocers.
All FreshBox Farms products are kosher and non-GMO certified, grown without pesticides, herbicides, or fungicides. The greens are also GAP (Good Agricultural Practices)-certified by the Massachusetts Department of Agricultural Resources, which identifies locally sourced products grown, harvested and processed in using practices that are safe, sustainable and don’t harm the environment.
For more information on where to buy FreshBox Farms’ products, visit www.freshboxfarms.com
##
Motorleaf Uses AI to Predict Crop Yields for Indoor Farmers & Greenhouse Growers
Between unpredictable weather, pests, and degrading soil quality, farming is an extremely difficult way to make a living. Indoor farming, though less weather-dependent, carries its own set of burdens.
Motorleaf Uses AI to Predict Crop Yields for Indoor Farmers & Greenhouse Growers
April 16, 2018
"Republished with permission of The Spoon", Read the original article at The Spoon
Photo: Motorleaf
Share on Facebook Tweet on Twitter
Between unpredictable weather, pests, and degrading soil quality, farming is an extremely difficult way to make a living. Indoor farming, though less weather-dependent, carries its own set of burdens.
Montreal-based startup Motorleaf wants to lighten the lift for indoor farmers by improving crop yield predictions and optimizing growing conditions. The company hopes that their software, which CEO and co-founder Ally Monk likens to a “virtual agronomist,” will take the uncertainty out of farming.
To do this, Motorleaf first gathers data on the grow environment through machine vision, agricultural sensors, and historical information. It then applies algorithms and AI to help farmers determine the adjustments they need to make to the indoor grow environment to optimize their crop. Which means farmers can monitor CO2 levels, light spectrum, and other atmospheric conditions remotely through wireless devices or laptops.
Customers can opt to install Motorleaf’s own hardware (a suite of IoT-enabled sensors), though they can also just connect the Motorleaf’s software to the farm’s existing pre-installed hardware to measure and remotely adjust environmental inputs. Its interoperability makes Motorleaf an easy tool for larger greenhouse operations, ones who already have their own monitoring hardware in place, to install. “At the end of the day, we are a software company,” said Monk.
Motorleaf isn’t the only company helping indoor farmers help manage the lifecycle of their crop. In fact, it’s not even the only company which sees itself as a “virtual agronomist.” What sets it apart, however, is its ability to predict crop yield. Monk claims that Motorleaf is the first company to use AI and machine learning to increase the accuracy of yield estimations.
This is a lot more important than an average person (read: the author) might think. Commercial greenhouses pre-sell produce before their harvest based on estimations given by agronomists — though they’re not always accurate. It’s extremely difficult to guarantee the quantity or quality of their crop before it’s harvested, and miscalculations can lead to loss of profits for both the buyer and producer and also generate huge amounts of food waste.
Motorleaf claims that their software can cut yield prediction error by more than half — at least for some crops. Monk explained that each plant needs its own specialized software for yield prediction, likening farming to a recipe. “Maybe they think there’s a right recipe to growing kale; they need this many nutrients, this much light,” he explained. “We very strongly disagree with that. We think that any farming protocol needs to be dynamic, because if something happens in a greenhouse — which happens all the time — why would you stay rigid? You have to adapt.”
So far, their AI has only been proven to work for estimating tomato yield. However, they’re also deploying algorithms for peppers and silently developing technology for five other crops.
Photo: Motorleaf.
I was surprised to learn that indoor farming environments could be so volatile. After all, that’s the whole point of bringing them indoors, right? Apparently, not so. Monk explained that variable factors like sunlight, outside air temperatures, and human error can all affect greenhouse conditions. Even the plants themselves can do unexpected things that can affect their climate change.
Motorleaf got $100,000 Canadian dollars from the FounderFuel accelerator in the summer of 2016, and later that month Motorleaf raised $850,000 (US) for their seed round of funding. The startup is currently working with clients in Canada, USA, South Africa, South America, Mexico, Holland, Poland, New Zealand and the UK, and aims to be in Spain, France and Germany by early 2019.
Monk concluded our call with what he called “a crazy thought,” one he had when he saw celebrity-branded color palettes. “Why can’t I have a Jamie Oliver taste palette? Why can’t I buy a radish that’s the exact kind he likes to cook with?“ he asked. Farmers could use Motorleaf’s software to manipulate crops into having a certain taste and look, one that would be specific to, and branded by, celebrity chefs. Consumers could purchase produce that had the same taste profile as those preferred by their favorite chefs, and even integrate them into those chef’s recipes.
In the age of celebrity-branded meal kits and baking mixes, this idea isn’t too far-fetched. We’ve even seen companies like Bowery use AI to tweak the flavor, taste, and color of fruits and vegetables.
Motorleaf hasn’t started developing any of this technology yet, but Monk used it chiefly as an example to show how AI can open up “a whole slew of possibilities” for farming. He hopes that one of its applications will be to take the unpredictability out of farming, and put the power back in the hands of the growers.
Next Generation In-Home Robotic Gardening System, Herbot, Now Available on Kickstarter
Next Generation In-Home Robotic Gardening System, Herbot, Now Available on Kickstarter
Entrepreneurs from University of Washington's Global Innovation Exchange Unveil the World's First Artificial Intelligent Indoor Home Garden
NEWS PROVIDED BY farm 4.0
April 05, 2018
SEATTLE, April 5, 2018 /PRNewswire/ -- The future of in-home gardening is here. Recently launched on Kickstarter by farm 4.0, Herbot is a line of indoor robots that automate the process of home gardening and empower the next generation of urban farmers through affordable and sustainable organic agriculture.
Harness the power of Artificial intelligence to grow any plants you want. No green thumbs required. Just pop in a pod, and let Herbot take care of the rest.
With Herbot, anyone can grow anything, anywhere, anytime. It's as simple as that. Using precise sensors, climate-control technology, advanced hydroponics and intelligent growing algorithms, Herbot automates the process of growing fresh produce, medicinal herbs and flowers with the ease of pressing a button.
Each Herbot device leverages Artificial Intelligence to automate the plant cultivation process from seed to harvest. "With Herbot's automatic gardening capabilities, we hope to help those who might never have grown food before by giving them the resources and confidence to become urban farmers and join the growing movement for all-natural, hyper-local food," said Talha Sabri, CEO, farm 4.0.
Getting started with Herbot is easy. All you have to do is plug in the preseeded net pods, insert the nutrient solution, add some water to the hydroponic reservoir and select a plant algorithm using the simple-to-use, educational companion app: Herbot OS.
Three variations of Herbot are currently being made available via Kickstarter: the compact and affordable Herbot Mini, the sophisticated and high-precision Herbot Pro and Herbot Grande, with advanced growing technologies and an elongated growing space. Herbot's proprietary DIY "Seedling" Kits enable anyone with the desire to build their own automated hydroponic growing system to customize their device to meet the specifications they desire, leveraging pre-designed sensors, electronics and schematics.
For more information about Herbot, please visit www.herbot.io, the Kickstarter page or follow new developments from the brand on Instagram.
About farm 4.0:
farm 4.0 is а socio-technological enterprise striving to make agri-tech innovation affordable for underserved consumer segments, while also contributing to high-impact social-welfare projects around the world. "farm 4.0's first venture, Herbot, is more than just a line of products, but the first step towards developing the technology, network and infrastructure necessary to scale to larger solutions in automated agriculture," said Ben Keller, Chief Global Development Officer, farm 4.0.
The farm 4.0 team is currently developing shipping-container-turned-IoT-climate-controlled-farms at the Global Innovation Exchange and is in talks about a potential partnership with innovative technology companies in Seattleincluding Microsoft to ship them to areas across the Middle East, Africa and Asia, which are affected by malnutrition and where conventional farming methods are impractical due to climate change and water shortages.
Press Kit: https://drive.google.com/drive/folders/1dW4rofJ-M193FC4jpzCcI8Bh-b6aCaqf
Press Contacts
Jacques-Laurent Tiktin Misha Savvateev
Chief Marketing Officer Chief Operations Officer
jacques.tiktin@farm40.tech misha@farm40.tech
(914) 255-6905 (206) 371-3878
Related Images
control-your-plants-from-your.png
Control your plants from your pocket.
The Herbot App not only makes gardening more accessible and engaging, it makes Herbot a truly intelligent, fun-to-use product. To make getting started easy, you can choose from our tested plant-growing algorithms or build your own recipe to experiment.
herbot-ai-powered-indoor-gardening.png
Herbot: AI-Powered Indoor Gardening Robot
Harness the power of Artificial intelligence to grow any plants you want. No green thumbs required. Just pop in a pod, and let Herbot take care of the rest.
herbot-grande.png
Herbot Grande:
Herbot Grande takes Pro to the next level with inclusion of a smell-preventing carbon filter, C02 dosing, air control system, insulated glass windows & performance cover that allow for a much wider variety of produce! With its precise climate control system, Grande is ideal for growing larger plants & can grow almost anything from tropical plants to medicinal herbs! Grande starts at a $300 pledge
herbot-pro.png
Herbot Pro
The Herbot system feeds, waters and provides light to your plants, making it possible for anyone to grow any plants they wish, regardless of climate, space, time limitations or level of gardening experience.
SOURCE farm 4.0
Fishers Startup Says Its Indoor Veggie Farms Can End Hunger
Fishers entrepreneur is bringing farms into the kitchen. And the garage. And the closet. And anywhere else at home one might have room indoors for small planters of lettuce, carrots or tomatoes.
Fishers Startup Says Its Indoor Veggie Farms Can End Hunger
John Tuohy, john.tuohy@indystar.com
April 6, 2018
FacebookTwitterGoogle+LinkedIn
This veggie farm fits in your apartment
A Fishers entrepreneur is bringing farms into the kitchen. And the garage. And the closet. And anywhere else at home one might have room indoors for small planters of lettuce, carrots or tomatoes.
Jonathan Partlow, founder of Aggressively Organic, sells small hydroponic plant growing systems that don’t need sunlight, dirt or pesticides and are grown indoors using just water, nutrients and LED lamps.
Partlow says he has the modest of goal of ending hunger. And he’s being taken very seriously.
The bioscience company last month won two awards at the SXSW (South-by-Southwest) convention in Austin, Texas, the first contestant to win both the Food+City Challenge Prize and the People’s Choice Award.
“One of our biggest goals is to end food insecurity within our lifetime,” said Partlow, 49, an Indiana University graduate from Anderson. “We had to create a system that anyone could afford and use.”
Partlow started Aggressively Organic at Launch Fishers, the tech- and app-focused shared workspace that in just a few years has paved the way for several successful startups.
Now, Aggressively Organic is preparing to move into its own 40,000-square-foot building at 9160 Ford Circle later this month, where it will grow 6 million plants each year. It hopes to hire 200 employees within five years and have 42 indoor farms of various sizes across the country.
The concept is the same as hydroponic systems, also known as vertical farming, that are sprouting around the country and grow crops indoors year-round in controlled settings. But unlike those farms, in which thousands of shelves are stacked in large warehouses for wholesale distribution, Aggressively Organic’s plants are tailored for the individual, with the plants grown in cardboard, flower pot-sized containers.
“They are cheap and so easy a kindergarten student can learn it,” Partlow said. “In fact, we have taught kindergartners to use it in Fishers schools.”
Schoolchildren and various Indiana 4-H clubs already are learning the system, and there are plans to distribute the plants to food banks. More broadly, Aggressively Organic launched a crowdfunding campaign to send 50,000 plants to Puerto Rico to aid Hurricane Maria victims.
The plants need only 16 ounces of water and a patented nutrient mixture that permits them to grow rapidly for harvesting in about 30 to 60 days. Replenishing leafy plants, such as arugula and kale, grow fastest and can be plucked and eaten for weeks. But even cherry tomatoes grow quickly and can last a couple of growth cycles.
“I’ve been eating from the same head of lettuce for a month,” Partlow said.
The plants, which include herbs like basil, can be kept anywhere in the house where there’s extra space. They also take a minimum of supervision.
A built-in advantage to Aggressively Organic’s individual system, compared to large systems, is that each box and plant is self-contained. So, a flaw in the balance of nutrients in a water-recirculating system won’t affect an entire supply of plants, said Chris Chick, Aggressively Organic’s plant physiologist.
Chris Chick, Fishers, helps run Aggressively Organic, a new start-up in Fishers that plans to have about 40,000 square feet of hydroponic growing space, Fishers, Wednesday, April 4, 2018. The company has a system that lets people easily grow their own food in a small household space. (Photo: Robert Scheer/IndyStar)
“Each of the different vegetables has its own nutrient solution, so they aren’t sharing a common one,” Chick said. “If something were to go wrong, you throw away the individual plant, not all of them.”
Ultimately, Aggressively Organic will offer memberships in which subscribers can pay a yearly fee to order six packs of plants, then switch them out after they have been eaten after two or three growth cycles, like dropping off empty bottles for the milkman.
Vertical farms are becoming more common in urban areas as a way to provide locally produced vegetables on a large scale that don't need to be shipped thousands of miles, from California or Arizona, where 94 percent of lettuce is grown. Chick said vegetables lose most of their nutrients within 24 hours after being picked.
Lettuce at Aggressively Organic, a new start-up in Fishers that plans to have about 40,000 square feet of hydroponic growing space, Fishers, Wednesday, April 4, 2018. The company has a system that lets people easily grow their own food in a small household space. (Photo: Robert Scheer/IndyStar)
This week at the company's new headquarters in Fishers, Chick displayed a plant that had been growing for about 35 days that was bursting with two dozen ripe cherry tomatoes from a cardboard box. Broccoli leaves, about a foot long, flowed from a larger box measured about a foot in length. A bite of arugula offered a sharp, peppery flavor much more succinct than the bagged product bought in the supermarket.
"It's picked fresh, so it still has all its flavor," Chick said.
Jeff Barranco, 39, a member of the Anderson school board, who has a small 1.4-acre traditional farm, began growing Aggressively Oganic’s plants in his garage last October. He now has 1,000 plants, including bok choy, tomatoes, hot peppers, basil and lettuce and plans to sell the produce at an Anderson farmer’s market this summer.
“It really is a plug in and play type of system,” Barranco said. “You don’t need a lot of knowledge about farming.”
Barranco keeps the plants in a 8-by-10-foot tent in the garage and spends about $100 a month on electricity for the LED lights. Besides that, little maintenance is necessary.
Barranco said he will tear off some basil or lettuce for salads at dinner and can taste the difference from supermarket-bought food.
“It has a much better taste, it’s fresher and really nice to have right here,” he said.
Call IndyStar reporter John Tuohy at (317) 444-6418. Follow on Twitter and Facebook.
Nebullam: Indoor Farming
What started seven years ago as a way to address food security, production and sustainability led to 13 different prototypes and a model farm near Nevada. And if all goes according to plan in 2018, Nebullam will have a second model farm near Ames and additional capital to help send a product to market by 2019.
Nebullam: Indoor Farming
Lettuce that was grown and harvested last Friday from inside the Nebullam model farm near Nevada. Photo courtesy of Clayton Mooney
For the founders of Nebullam, they hope 13 is a lucky number.
What started seven years ago as a way to address food security, production and sustainability led to 13 different prototypes and a model farm near Nevada. And if all goes according to plan in 2018, Nebullam will have a second model farm near Ames and additional capital to help send a product to market by 2019.
The Ames-based agtech startup pairs high-pressure aeroponic technology and software to grow different types of leafy greens indoors.
The company was founded by Clayton Mooney and Danen Pool, who first met while attending Indian Hills Community College. They stayed in contact and three years ago, Pool contacted Mooney to run a business idea by him.
“He started tinkering on hydroponic systems which led into aeroponic systems,” Mooney said of Pool. “He was very intrigued by the early research NASA had done on aeroponic systems back in the 80’s. Throughout the first half-dozen prototypes, he (Pool) was able to grow tomatoes, basil and lettuce varieties. One winter, he took tomatoes into his coworkers and got great feedback.”
Aeroponics is a method of growing plants in a water-based, nutrient-rich solution without using soil. And when those tomatoes—that were grown indoors—tasted like they were from the garden, a business idea formed.
It was no longer a hobby.
“We thought our original business model was to go around Iowa, set up in warehouses, grow leafy greens and get them into grocery stores,” Mooney explained. “The more feedback we received, it really came back to the technology and that was more interesting to scale than just the production side.”
Mooney said along with Pool and third co-founder Mahmoud Parto, they realized the industry needs to be automated.
“Eventually you need an indoor, vertical farm producing at full capacity without any human interaction,” Mooney says. “We are trying to bring it to the forefront so if we have to trail blaze a little bit, we’re ready.”
To fund Nebullam, Mooney said they raised a “friends and family” round of investment last year and received some funding from through the Iowa State Ag Startup Engine last year when they were going through the program. Nebullam also received a $25,000 loan from the Iowa Economic Development Authority.
This year Mooney said they hope to raise $1 million by the end of June.
Fewer parts, fewer problems
With high-pressure aeroponic expertise and startup experience, Nebullam was looking for a partner who had a background in software and automation.
Mooney said that’s when Nebullam hired Parto, who has helped implement software and automate as many of the processes between germination and harvest as possible.
“From there we’ve considered ourselves a 50 percent hardware and 50 percent software company,” Mooney says.
In total there are six employees working for Nebullam in some capacity, with interns to be hired this summer. Mooney said the team should reach ten people.
Nebullam partnered with LongView Farms in Nevada to create a 300 square foot model farm.
“Hardware is tough and the more pieces you have in a product, the more that can go wrong,” Mooney explains. “In our model farm location, we have just under 5,000 parts total. And that’s across four growing units.”
But Mooney said they’ve streamlined the process to get it to 5,000 parts.
“For the 13th prototype that was our entire focus, how do you reduce the required labor?” Mooney asks. “We think we’ve figured that out. We see ourselves as a technology provider to new, indoor growers.”
He said the hardware, software and inputs such as nutrients and seeds are bundled into a monthly price. And over an 18-24 month contract, the grower pays off the hardware and reoccurring revenue comes from seeds, nutrients and an annual licensing fee for the software.
Mooney said they are in negotiations for a second model farm that would be nearly 1,500 square feet and serve as a showcase for potential customers.
“Do we see corn and soybeans being grown aeroponically? Not at this time,” Mooney says. “But leafy greens, herbs, micro greens, flowers and cannabis, we feel pretty good about those segments.”
How GLASE Is Promoting The Development And Adoption of Energy-Efficient Lighting And Control Technologies In The CEA Industry
The Greenhouse Lighting and Systems Engineering (GLASE) consortium is a public-private partnership to integrate advanced energy-efficient LED lighting with improved environmental controls for more efficient and sustainable greenhouse production.
How GLASE Is Promoting The Development And Adoption of Energy-Efficient Lighting And Control Technologies In The CEA Industry
The Greenhouse Lighting and Systems Engineering (GLASE) consortium is a public-private partnership to integrate advanced energy-efficient LED lighting with improved environmental controls for more efficient and sustainable greenhouse production. The consortium is led by Cornell University’s Controlled Environment Agriculture group and the Center for Lighting Enabled Systems and Applications (LESA) at Rensselaer Polytechnic Institute (RPI) and is supported by the New York State Energy Research and Development Authority (NYSERDA).
GLASE principal investigator Neil Mattson explains lighting trial to some of the attendees at the Cornell CEA Advisory Board Meeting November 3.
GLASE research integrates advances in LED light engineering, plant photobiology, carbon dioxide enrichment and systems control to dramatically reduce the energy cost and carbon footprint of horticultural lighting. GLASE is creating intelligent systems that can be easily tailored to the needs of specific greenhouse crops, providing unparalleled flexibility for the grower. This new consortium will include lighting manufacturers, growers, trade groups, produce buyers, agriculture lighting engineers, researchers, and government agencies, as well as researchers at Cornell, Rensselaer and other academic partners.
GLASE builds on prior lighting and agricultural energy control systems work sponsored by NYSERDA. To ensure new energy-efficient technologies are adopted within the greenhouse industry, GLASE will make its advanced systems capabilities broadly accessible through extensive educational outreach and training opportunities.
U.S. Rep. Steve Chabot Visits 80 Acres Farms
April 16, 2018
Steve Chabot with the local 80 Acres Team
U.S. Rep. Steve Chabot Visits 80 Acres Farms
April 16, 2018
Cincinnati, OH: Today, U.S. Rep. Steve Chabot, who has represented Ohio's First Congressional District for 20 years visited 80 Acres Farms, an indoor farm located in his native city of Cincinnati. Rep. Chabot currently serves as Chairman of the House Committee on Small Business. He has made small business growth and job creation a top priority throughout his career. “They’re the engine of our economy. Cincy startups fuel not only my hometown’s local economy-but our nation’s,” Chabot tweeted earlier this week.
Chabot toured the facility, which houses microgreen, leafy green and culinary herb grow-zones as well as the first in the world, completely controlled environment, indoor vine crop room that supplies cucumbers and tomatoes to local retailers and restaurants.
Steve Chabot with CEO, Mike Zelkind and President, Tisha Livingston
80 Acres Farms is an indoor farming company that grows the highest quality fruits and vegetables in an energy efficient, modular environment. These farms use 97% less water and yield 100 times more than traditional farming with ZERO pesticides while operating year-round. 80 Acres was created to make a difference in our communities by providing affordable, fresh, local food. The founders’ passion for sustainably growing more nutritious, great tasting food for the communities we live in developed into 80 Acres Farms.
80 Acres Farms currently operates an equipment manufacturing facility in Granite Falls, NC, as well as 2 R&D Centers in Mobile, AL and Springdale, AR and fully-operational indoor vertical farms in Cincinnati, OH, Springdale, AR and Granite Falls, NC.
For additional information:
The Princeton Vertical Farming Project
The Princeton Vertical Farming Project (PVFP), located in Moffett Laboratory, was launched by Dr. Paul Gauthier, an associate research scholar in plant physiology and environmental plant metabolism in the geosciences department.
The project is funded by the High Meadows Fellowship through the Office of Sustainability as part of the Campus as Lab initiative.
The Princeton Vertical Farming Team, lead by Paul Gauthier, has been steadily growing since the project’s start in the spring of 2017. The team consists of faculty, students, and members of the Office of Sustainability. Coming from a wide range of academic backgrounds, the students on the team were all drawn to PVFP for different reasons, and continue to expand the potential of the vertical farm as a hub for student research and activity. Meet the team and learn about the many ways students and faculty have gotten involved in the project.
Paul discusses sustainability in his research with the Office of Sustainability. Read the interview »
MEET THE TEAM
Paul Gauthier
I am an Associate Research Scholar in the Department of Geosciences at Princeton University. I obtained my PhD from the University of Paris Sud in plant physiology and plant metabolism. I am broadly interested in the regulation of leaf carbon balance and the relation source-sink in the whole plant from the molecular to the ecosystem scale. In the past few years, my interest for the challenges associated with food security has grown and I see vertical farming as a way to answer a growing demand for healthier and tastier vegetables. The development of this project is an opportunity to answer new questions related to the impact of vertical farms on the environment and find new solutions to make them more affordable and sustainable.
Jesenia Haynes (’18)
My name is Jesenia Haynes and I am in the class of 2018 studying Ecology and Evolutionary Biology with a certificate in Environmental Studies. I enjoy learning about all aspects of biology, but recently I have been focusing more on sustainable agriculture. In the future I hope to work both domestically and internationally to promote sustainable agriculture and ecological conservation.
Rozalie Czesana (’18)
I am a senior at Princeton majoring in the Woodrow Wilson school with certificates in Environmental and Urban Studies. Because of my interest in sustainable development and food, I got involved in the Vertical Farming project right in the initial, planning stages. So far my role has revolved mainly around establishing connections across campus and raising awareness about the project, for example by working with Forbes College and Terrace F. club, where I coordinated a parallel study in the greenhouse. In the near future I am excited about exploring the scalability of the farm, particularly its potential use in nearby food deserts such as Trenton.
Aamir Zainulabadeen (’18)
I am currently a senior in the Computer Science department and I’m working on Princeton’s Vertical Farming Project for my senior thesis. The goal of my project is to develop a software/hardware system that automates certain aspects of the farm – data collection, feedback cycles, and data analysis. I’m mainly interested in this project because sustainable agriculture is a key issue for addressing climate change. The great thing about software is that it may be repeatedly used at low cost, so I hope that my thesis will be useful not only for Princeton’s Vertical Farming Project but also for anyone else interested in sustainable agriculture.
Seth Lovelace (’20)
I am a Sophomore in Princeton’s Mathematics Department, and am from New Orleans, Louisiana. I originally grew up in rural California, and grew up growing fruit on an acre and a half of land. As such, seeing both city life and country life growing up, I’ve always had a strong connection to sustainability. As part of the Vertical farm, I am analyzing nutrient uptake by plants, and how this nutrient uptake changes over time. I hope that this will allow for me to optimize the manner in which we supply nutrients to plants in a vertical farm environment. My background is very quantitative, and I hope to bring a rigorous and methodical perspective to the farm, increasing the quality of food through the components that make them up.
Kyra Gregory (’19)
My name is Kyra Gregory, I’m in the Department of Art & Archeology, Program 2 with a certificate in Gender and Sexuality Studies. I work for the Office of Sustainability as a Communications Assistant and have always had a passion for environmental science and sustainability. My job for the Vertical Farming Project is to design and manage the website and blog the progress of the farm.
Natalie Grayson (’20)
My name is Natalie Grayson and I am in the class of 2020 planning to study Ecology and Evolutionary Biology with a certificate in Environmental Studies. I am newly interested in the field of sustainable agriculture and I think that vertical farms will be playing a larger and larger role in this. I have been managing the day to day aspects of the farm thus far, but I have been planning to begin conducting some additional research at the farm.
Allison Huang ’21
As Farm Manager, I upkeep and monitor the farm’s overall progress, which is really an excuse to watch the plants grow and change in their ‘intuitive’ way. In the future, I hope to conduct research on how fluctuations in pH and nutrient availability translate to a more controlled, artificial environment like the Vertical Farm. I am a first-year student and a prospective Woody Woo major.
Tupperware And Techshot Develop Plant Growth Chamber For NASA
Tupperware And Techshot Develop Plant Growth Chamber For NASA
An improved system for growing plants in space, developed for NASA by Tupperware Brands and Techshot is expected to launch to the International Space Station (ISS) April 2 aboard a commercial SpaceX Dragon cargo capsule from Florida's Cape Canaveral Air Force Station.
Mizuna growing inside plant growth chambers developed for NASA by Tupperware and Techshot. Six of the chambers are visible inside a Veggiemini-greenhouse at the Kennedy Space Center.
Since 2014, astronauts aboard the ISS have been growing a variety of leafy vegetables and colorful flowers inside the Vegetable Production System, otherwise known as the 'Veggie' facility. NASA is always seeking to improve upon existing technologies, while reducing its need for resources, such as crew time. In an effort to reduce the frequency that an astronaut must water plants growing in space, Dr. Howard Levine and his colleagues at the NASA Kennedy Space Center (KSC) began exploring new design concepts for the component of Veggie that holds the root structure of the plants - the so-called 'plant pillows'. Research at KSC led to a semi-hydroponic design concept dubbed the Passive Orbital Nutrient Delivery System (PONDS).
Iconic kitchen and housewares company Tupperware Brands, and Techshot Inc., a commercial space enterprise, partnered to further develop the concept and manufacture spaceflight-qualified PONDS plant growth units for use aboard the ISS. Up to six can be installed in Veggie at one time. Like the plant pillows, the PONDS devices are single-use items, which can be discarded after the plants are grown and harvested on orbit. However, unlike the plant pillows, PONDS can also be returned, refurbished, and reflown in space.
The seven PONDS modules launching on SpaceX mission CRS-14 in April comprise three variations on a common design. Four black "opaque" modules will grow red romaine lettuce, the same lettuce that has been grown previously in the Veggie facility. The two "shrouded" modules, also growing red romaine lettuce, each includes a clear window and a removable cover that allows astronauts to periodically observe root growth in the hydroponic reservoir. One "clear" module, which does not contain a plant, will be used to perform testing and videography to characterize the movement of water within the reservoir while in space.
Six more modules are expected to launch in May from Wallops Island, Virginia, aboard a commercial Orbital ATK Cygnus cargo spacecraft. These six will grow another leafy vegetable called Mizuna. Both sets of hardware will provide a validation of the device's performance, in advance of its use in a comprehensive research campaign by NASA scientists in November.
Tupperware applied its deep knowledge and longstanding success of design for manufacturability, injection molding, and food-safe construction materials to yield a system that utilizes capillary forces and unusual internal geometries to replace gravity. The result is a product that is expected to provide plants grown in space with a near functionally-equivalent growing environment to their terrestrial counterparts.
"Tupperware products have included smart technology features for nearly 70 years," said Tupperware Brands Vice President of Research and Innovation David Kusuma. "Our product evolution goals have always been to meet today's needs for consumers, whether that includes microwaveable grills or food processors that require no electricity; we are proud to now say that this includes sustainable vegetation growth in space. This has been one of our most exciting and unique collaborations, and we are honored to have worked alongside NASA and Techshot on the advancement and success of the PONDS project."
With nearly 30 years of experience developing equipment for human spaceflight, Techshot assisted with requirements management, safety, verification and integration tasks, and some light manufacturing and assembly. It also provided Tupperware designers with access to subject matter experts in areas such as low-gravity fluidics.
"It's been great working closely with the talented teams of engineers, designers and scientists at NASA and Tupperware on the project," said Dave Reed, Techshot's PONDS project manager and the company's director of launch operations. "And while it's always a thrill watching new hardware launch into space, seeing the first crop of PONDS-grown lettuce harvested aboard the ISS will be the real payoff after more than a year of hard work."
For more information:
www.Techshot.space
www.tupperwarebrands.com
Publication date: 3/28/2018
Benjamin Vidmar About 7 months ago
At least that’s the idea behind Benjamin Vidmar's domed ambition — a lone greenhouse in the heart of one of the coldest and northerliest towns on Earth.
This Chef Built An Urban Farm In The Arctic
(And he's wondering why you haven't started one yet.)
March 15, 2018
If you build it, tomatoes, onions, maybe even some chillies will come. Even when the weather outside is downright, well, chilly.
At least that’s the idea behind Benjamin Vidmar's domed ambition — a lone greenhouse in the heart of one of the coldest and northerliest towns on Earth.
Vidmar's lonely greenhouse is rich with produce all year-long thanks to seasonal crop swaps that take advantages of conditions. (Photo: NBC News/YouTube)
Of course, those chillies don’t quite prosper in winter, when the town of Longyearbyen, on Norway’s Svalbard archipelago shivers to the tune of minus 20 degrees Celsius (minus 4 F).
So Vidmar temporarily downsizes his dream — and plants microgreens.
It all adds up to an unlikely oasis. Vidmar, a transplant from Florida who came to the area as a chef, provides the town with its only locally grown produce. Until he founded Polar Permaculture Urban Farm, everything from vegetables to eggs, had to be flown into the region. The situation left the Longyearbyen dwellers paying exorbitant prices for basic food, which was often exposed to the vagaries of flight conditions.
Vidmar and his son are working to change that precarious paradigm by tailoring their harvest according to the rhythm of the North. So, for example, the Svalbard summer and the 24 hours of sunlight it brings is ideal for tomatoes and onions. But the ever-dark winter calls for a change-up to tiny plants, like sprouts, that don’t need to bask in all that summer sun.
Benjamin Vidmar about 7 months ago
When tapping into the ebb and flow of that challenging climate — the greenhouse is just 650 miles from the North Pole — Vidmar may have had a little help from the downright meditative silence of his surroundings.
"The sad part (in America) is you work so hard and you still have to worry about money," he tells the Thomson Reuters Foundation. "Then you come here and you have all this nature. No distraction, no huge shopping centers, no billboards saying, 'buy, buy, buy.'"
The Svalbard peninsula, on the other hand, chills to a more practical mantra: brrr, brrr, brrr….
In fact, the town of Longyearbyen — with is another 650 miles from mainland Norway — stares into Nature’s frozen face every day. Along with that of the occasional polar bear. The peninsula is home to nearly 3,000 types of the animals, compared to some 2,000 people who inhabit the town.
But in that frozen ground, an even bigger idea may be taking root. If Vidmar can feed much of a community from this citadel of sustainability, what’s stopping the rest of us?
"We're on a mission … to make this town very sustainable,” he tells the Thomson Reuters Foundation. "Because if we can do it here, then what's everybody else's excuse?"
While there is a burgeoning movement to build community gardens in U.S. cities, many parts of the country remain woefully dependent on produce that’s trucked or flown in from other parts.
The situation is still a sight better than countries like Nepal, Kenya and Sudan — consistently ranked among the most vulnerable to food security issues.
We may never get a chance to sample the chillies from Vidmar’s unlikely garden. But his greenhouse, high atop the world, offers a shining beacon of what's possible when we nurture a little earth, even if it’s in the ice cold heart of the Arctic.
Related on MNN:
Kimbal Musk's garden dream is growing
Related topics: Gardening, Sustainable Gardening
Billionaire Launches Hydroponics Startup
Los Angeles-based Sensei plans to build 10 greenhouses, totaling 200,000 square feet, on the Hawaiian island of Lanai. Ellison owns 98 percent of the island.
Billionaire Launches Hydroponics Startup
Billionaire Oracle Corp. co-founder Larry Ellison this week launched his latest startup, which will focus on automated, hydroponic indoor food production.
Los Angeles-based Sensei plans to build 10 greenhouses, totaling 200,000 square feet, on the Hawaiian island of Lanai. Ellison owns 98 percent of the island.
He unveiled the startup this week, promising that it would focus on building products and experiences to “empower you to grow well.”
Sensei said its first farm is hydroponic, powered by Tesla solar and uses minimal amounts of water. The startup says it’s growing food from “original seeds,” suggesting they’ll eschew genetically-modified plants in favor of heirloom varieties.
On Lanai, Ellison’s goal is to grow high-quality food, helped by software automation, and sell it locally, undercutting the more expensive produce imported daily. He says agriculture is one of the last major industries that has remained largely unchanged by software.
“Lanai is step No. 1,” Ellison told the Star-Advertiser at the time. “We think we can transform agriculture.”
Ellison launched Sensei with David Agus, a bestselling author, University of Southern California professor and serial entrepreneur. He’s also the founding director of USC’s Lawrence J. Ellison Institute for Transformative Medicine.
Agus treated late Apple CEO Steve Jobs, who remained close friends with Ellison up until his death in 2011.
The company lists three open positions on its website, notably a postdoctoral researcher who will be tasked with designing “plant experiments and associated protocol and research methodology.” It adds: “Travel to Hawaii will be required.”
The company’s day-to-day operations are being led by Daniel Gruneberg, who cofounded San Francisco-based events software startup Zozi, which was acquired by Peek last year.
Gruneberg told TechCrunch the company will soon begin selling food to restaurants and stores under the Sensei Farms brand. In his interview last year, Ellison said he expected Sensei to be profitable in its first year.
Click here to read the original article at Silicon Valley Business Journal.
Photo credit: Hartmann Studios via Flickr, Creative Commons Attribution.
03/21/2018 - Silicon Valley Business Journal
New Facility To Grow Year-Round Lettuce
22nd March 2018, London
New Facility To Grow Year-Round Lettuce
Two British companies are pairing up to create an "innovative" hydroponics facility which will increase shelf life for UK consumers
A new UK hydroponics facility for growing green leaf salad all year round will aim to give British shoppers longer shelf life.
Lincolnshire-based design firm Arctica is assisting growers H20-ganics to build an innovative location with controlled clean room environment, free from pests or pathogens, scheduled for completion at the end of the year.
Arctica director Niall McQuitty said the facility will provide longer lasting lettuce to UK retailers. Once established, the system will be used to grow a full range of green salads and herbs for sale in supermarkets.
McQuitty said: “Green leaf salad is normally grown outside. The clock starts ticking on the product’s shelf life as soon as it is harvested. Green leaf coming from other markets – such as Spain – takes 24 hours to transport to processing facilities in the UK. It can take up to three days from picking to packing which means, by the time it’s in the shops, it has lost up to half its shelf life.
“Cleaning the leaf also has an impact on the quality of the produce. Washing, drying, mixing, bagging and transport all require care because the leaf is fragile and prone to damage – which also reduces shelf life. H20-ganics creates a high care environment in which to grow the leaf that removes most of these stages from the process. It can be harvested, cleaned and packed without losing quality, thereby increasing its shelf life.”
H20-ganics’ Nick Bateman added: “H2O-ganics produce is not grown in soil but produced in a fully controlled clean environment, which keeps out pests and pathogens, while maintaining the optimum conditions for plant growth.
“Using our controlled environment approach to agriculture and clean room technology, we are able to produce a consistent specification of product 365 days of the year, without the use of pesticides.”
Lincolnshire-based design firm Arctica is assisting growers H20-ganics to build an innovative location with controlled clean room environment, free from pests or pathogens, scheduled for completion at the end of the year.
Arctica director Niall McQuitty said the facility will provide longer lasting lettuce to UK retailers. Once established, the system will be used to grow a full range of green salads and herbs for sale in supermarkets.
McQuitty said: “Green leaf salad is normally grown outside. The clock starts ticking on the product’s shelf life as soon as it is harvested. Green leaf coming from other markets – such as Spain – takes 24 hours to transport to processing facilities in the UK. It can take up to three days from picking to packing which means, by the time it’s in the shops, it has lost up to half its shelf life.
“Cleaning the leaf also has an impact on the quality of the produce. Washing, drying, mixing, bagging and transport all require care because the leaf is fragile and prone to damage – which also reduces shelf life. H20-ganics creates a high care environment in which to grow the leaf that removes most of these stages from the process. It can be harvested, cleaned and packed without losing quality, thereby increasing its shelf life.”
H20-ganics’ Nick Bateman added: “H2O-ganics produce is not grown in soil but produced in a fully controlled clean environment, which keeps out pests and pathogens, while maintaining the optimum conditions for plant growth.
“Using our controlled environment approach to agriculture and clean room technology, we are able to produce a consistent specification of product 365 days of the year, without the use of pesticides.”
Lincolnshire-based design firm Arctica is assisting growers H20-ganics to build an innovative location with controlled clean room environment, free from pests or pathogens, scheduled for completion at the end of the year.
Arctica director Niall McQuitty said the facility will provide longer lasting lettuce to UK retailers. Once established, the system will be used to grow a full range of green salads and herbs for sale in supermarkets.
McQuitty said: “Green leaf salad is normally grown outside. The clock starts ticking on the product’s shelf life as soon as it is harvested. Green leaf coming from other markets – such as Spain – takes 24 hours to transport to processing facilities in the UK. It can take up to three days from picking to packing which means, by the time it’s in the shops, it has lost up to half its shelf life.
“Cleaning the leaf also has an impact on the quality of the produce. Washing, drying, mixing, bagging and transport all require care because the leaf is fragile and prone to damage – which also reduces shelf life. H20-ganics creates a high care environment in which to grow the leaf that removes most of these stages from the process. It can be harvested, cleaned and packed without losing quality, thereby increasing its shelf life.”
H20-ganics’ Nick Bateman added: “H2O-ganics produce is not grown in soil but produced in a fully controlled clean environment, which keeps out pests and pathogens, while maintaining the optimum conditions for plant growth.
“Using our controlled environment approach to agriculture and clean room technology, we are able to produce a consistent specification of product 365 days of the year, without the use of pesticides.”
Lincolnshire-based design firm Arctica is assisting growers H20-ganics to build an innovative location with controlled clean room environment, free from pests or pathogens, scheduled for completion at the end of the year.
Arctica director Niall McQuitty said the facility will provide longer lasting lettuce to UK retailers. Once established, the system will be used to grow a full range of green salads and herbs for sale in supermarkets.
McQuitty said: “Green leaf salad is normally grown outside. The clock starts ticking on the product’s shelf life as soon as it is harvested. Green leaf coming from other markets – such as Spain – takes 24 hours to transport to processing facilities in the UK. It can take up to three days from picking to packing which means, by the time it’s in the shops, it has lost up to half its shelf life.
“Cleaning the leaf also has an impact on the quality of the produce. Washing, drying, mixing, bagging and transport all require care because the leaf is fragile and prone to damage – which also reduces shelf life. H20-ganics creates a high care environment in which to grow the leaf that removes most of these stages from the process. It can be harvested, cleaned and packed without losing quality, thereby increasing its shelf life.”
H20-ganics’ Nick Bateman added: “H2O-ganics produce is not grown in soil but produced in a fully controlled clean environment, which keeps out pests and pathogens, while maintaining the optimum conditions for plant growth.
“Using our controlled environment approach to agriculture and clean room technology, we are able to produce a consistent specification of product 365 days of the year, without the use of pesticides.”
Lincolnshire-based design firm Arctica is assisting growers H20-ganics to build an innovative location with controlled clean room environment, free from pests or pathogens, scheduled for completion at the end of the year.
Arctica director Niall McQuitty said the facility will provide longer lasting lettuce to UK retailers. Once established, the system will be used to grow a full range of green salads and herbs for sale in supermarkets.
McQuitty said: “Green leaf salad is normally grown outside. The clock starts ticking on the product’s shelf life as soon as it is harvested. Green leaf coming from other markets – such as Spain – takes 24 hours to transport to processing facilities in the UK. It can take up to three days from picking to packing which means, by the time it’s in the shops, it has lost up to half its shelf life.
“Cleaning the leaf also has an impact on the quality of the produce. Washing, drying, mixing, bagging and transport all require care because the leaf is fragile and prone to damage – which also reduces shelf life. H20-ganics creates a high care environment in which to grow the leaf that removes most of these stages from the process. It can be harvested, cleaned and packed without losing quality, thereby increasing its shelf life.”
H20-ganics’ Nick Bateman added: “H2O-ganics produce is not grown in soil but produced in a fully controlled clean environment, which keeps out pests and pathogens, while maintaining the optimum conditions for plant growth.
“Using our controlled environment approach to agriculture and clean room technology, we are able to produce a consistent specification of product 365 days of the year, without the use of pesticides.”
Lincolnshire-based design firm Arctica is assisting growers H20-ganics to build an innovative location with controlled clean room environment, free from pests or pathogens, scheduled for completion at the end of the year.
Arctica director Niall McQuitty said the facility will provide longer lasting lettuce to UK retailers. Once established, the system will be used to grow a full range of green salads and herbs for sale in supermarkets.
McQuitty said: “Green leaf salad is normally grown outside. The clock starts ticking on the product’s shelf life as soon as it is harvested. Green leaf coming from other markets – such as Spain – takes 24 hours to transport to processing facilities in the UK. It can take up to three days from picking to packing which means, by the time it’s in the shops, it has lost up to half its shelf life.
“Cleaning the leaf also has an impact on the quality of the produce. Washing, drying, mixing, bagging and transport all require care because the leaf is fragile and prone to damage – which also reduces shelf life. H20-ganics creates a high care environment in which to grow the leaf that removes most of these stages from the process. It can be harvested, cleaned and packed without losing quality, thereby increasing its shelf life.”
H20-ganics’ Nick Bateman added: “H2O-ganics produce is not grown in soil but produced in a fully controlled clean environment, which keeps out pests and pathogens, while maintaining the optimum conditions for plant growth.
“Using our controlled environment approach to agriculture and clean room technology, we are able to produce a consistent specification of product 365 days of the year, without the use of pesticides.”
Lincolnshire-based design firm Arctica is assisting growers H20-ganics to build an innovative location with controlled clean room environment, free from pests or pathogens, scheduled for completion at the end of the year.
Arctica director Niall McQuitty said the facility will provide longer lasting lettuce to UK retailers. Once established, the system will be used to grow a full range of green salads and herbs for sale in supermarkets.
McQuitty said: “Green leaf salad is normally grown outside. The clock starts ticking on the product’s shelf life as soon as it is harvested. Green leaf coming from other markets – such as Spain – takes 24 hours to transport to processing facilities in the UK. It can take up to three days from picking to packing which means, by the time it’s in the shops, it has lost up to half its shelf life.
“Cleaning the leaf also has an impact on the quality of the produce. Washing, drying, mixing, bagging and transport all require care because the leaf is fragile and prone to damage – which also reduces shelf life. H20-ganics creates a high care environment in which to grow the leaf that removes most of these stages from the process. It can be harvested, cleaned and packed without losing quality, thereby increasing its shelf life.”
H20-ganics’ Nick Bateman added: “H2O-ganics produce is not grown in soil but produced in a fully controlled clean environment, which keeps out pests and pathogens, while maintaining the optimum conditions for plant growth.
“Using our controlled environment approach to agriculture and clean room technology, we are able to produce a consistent specification of product 365 days of the year, without the use of pesticides.”
Lincolnshire-based design firm Arctica is assisting growers H20-ganics to build an innovative location with controlled clean room environment, free from pests or pathogens, scheduled for completion at the end of the year.
Arctica director Niall McQuitty said the facility will provide longer lasting lettuce to UK retailers. Once established, the system will be used to grow a full range of green salads and herbs for sale in supermarkets.
McQuitty said: “Green leaf salad is normally grown outside. The clock starts ticking on the product’s shelf life as soon as it is harvested. Green leaf coming from other markets – such as Spain – takes 24 hours to transport to processing facilities in the UK. It can take up to three days from picking to packing which means, by the time it’s in the shops, it has lost up to half its shelf life.
“Cleaning the leaf also has an impact on the quality of the produce. Washing, drying, mixing, bagging and transport all require care because the leaf is fragile and prone to damage – which also reduces shelf life. H20-ganics creates a high care environment in which to grow the leaf that removes most of these stages from the process. It can be harvested, cleaned and packed without losing quality, thereby increasing its shelf life.”
H20-ganics’ Nick Bateman added: “H2O-ganics produce is not grown in soil but produced in a fully controlled clean environment, which keeps out pests and pathogens, while maintaining the optimum conditions for plant growth.
“Using our controlled environment approach to agriculture and clean room technology, we are able to produce a consistent specification of product 365 days of the year, without the use of pesticides.”
Lincolnshire-based design firm Arctica is assisting growers H20-ganics to build an innovative location with controlled clean room environment, free from pests or pathogens, scheduled for completion at the end of the year.
Arctica director Niall McQuitty said the facility will provide longer lasting lettuce to UK retailers. Once established, the system will be used to grow a full range of green salads and herbs for sale in supermarkets.
McQuitty said: “Green leaf salad is normally grown outside. The clock starts ticking on the product’s shelf life as soon as it is harvested. Green leaf coming from other markets – such as Spain – takes 24 hours to transport to processing facilities in the UK. It can take up to three days from picking to packing which means, by the time it’s in the shops, it has lost up to half its shelf life.
“Cleaning the leaf also has an impact on the quality of the produce. Washing, drying, mixing, bagging and transport all require care because the leaf is fragile and prone to damage – which also reduces shelf life. H20-ganics creates a high care environment in which to grow the leaf that removes most of these stages from the process. It can be harvested, cleaned and packed without losing quality, thereby increasing its shelf life.”
H20-ganics’ Nick Bateman added: “H2O-ganics produce is not grown in soil but produced in a fully controlled clean environment, which keeps out pests and pathogens, while maintaining the optimum conditions for plant growth.
“Using our controlled environment approach to agriculture and clean room technology, we are able to produce a consistent specification of product 365 days of the year, without the use of pesticides.”
Lincolnshire-based design firm Arctica is assisting growers H20-ganics to build an innovative location with controlled clean room environment, free from pests or pathogens, scheduled for completion at the end of the year.
Arctica director Niall McQuitty said the facility will provide longer lasting lettuce to UK retailers. Once established, the system will be used to grow a full range of green salads and herbs for sale in supermarkets.
McQuitty said: “Green leaf salad is normally grown outside. The clock starts ticking on the product’s shelf life as soon as it is harvested. Green leaf coming from other markets – such as Spain – takes 24 hours to transport to processing facilities in the UK. It can take up to three days from picking to packing which means, by the time it’s in the shops, it has lost up to half its shelf life.
“Cleaning the leaf also has an impact on the quality of the produce. Washing, drying, mixing, bagging and transport all require care because the leaf is fragile and prone to damage – which also reduces shelf life. H20-ganics creates a high care environment in which to grow the leaf that removes most of these stages from the process. It can be harvested, cleaned and packed without losing quality, thereby increasing its shelf life.”
H20-ganics’ Nick Bateman added: “H2O-ganics produce is not grown in soil but produced in a fully controlled clean environment, which keeps out pests and pathogens, while maintaining the optimum conditions for plant growth.
“Using our controlled environment approach to agriculture and clean room technology, we are able to produce a consistent specification of product 365 days of the year, without the use of pesticides.”
Lincolnshire-based design firm Arctica is assisting growers H20-ganics to build an innovative location with controlled clean room environment, free from pests or pathogens, scheduled for completion at the end of the year.
Arctica director Niall McQuitty said the facility will provide longer lasting lettuce to UK retailers. Once established, the system will be used to grow a full range of green salads and herbs for sale in supermarkets.
McQuitty said: “Green leaf salad is normally grown outside. The clock starts ticking on the product’s shelf life as soon as it is harvested. Green leaf coming from other markets – such as Spain – takes 24 hours to transport to processing facilities in the UK. It can take up to three days from picking to packing which means, by the time it’s in the shops, it has lost up to half its shelf life.
“Cleaning the leaf also has an impact on the quality of the produce. Washing, drying, mixing, bagging and transport all require care because the leaf is fragile and prone to damage – which also reduces shelf life. H20-ganics creates a high care environment in which to grow the leaf that removes most of these stages from the process. It can be harvested, cleaned and packed without losing quality, thereby increasing its shelf life.”
H20-ganics’ Nick Bateman added: “H2O-ganics produce is not grown in soil but produced in a fully controlled clean environment, which keeps out pests and pathogens, while maintaining the optimum conditions for plant growth.
“Using our controlled environment approach to agriculture and clean room technology, we are able to produce a consistent specification of product 365 days of the year, without the use of pesticides.”
Lincolnshire-based design firm Arctica is assisting growers H20-ganics to build an innovative location with controlled clean room environment, free from pests or pathogens, scheduled for completion at the end of the year.
Arctica director Niall McQuitty said the facility will provide longer lasting lettuce to UK retailers. Once established, the system will be used to grow a full range of green salads and herbs for sale in supermarkets.
McQuitty said: “Green leaf salad is normally grown outside. The clock starts ticking on the product’s shelf life as soon as it is harvested. Green leaf coming from other markets – such as Spain – takes 24 hours to transport to processing facilities in the UK. It can take up to three days from picking to packing which means, by the time it’s in the shops, it has lost up to half its shelf life.
“Cleaning the leaf also has an impact on the quality of the produce. Washing, drying, mixing, bagging and transport all require care because the leaf is fragile and prone to damage – which also reduces shelf life. H20-ganics creates a high care environment in which to grow the leaf that removes most of these stages from the process. It can be harvested, cleaned and packed without losing quality, thereby increasing its shelf life.”
H20-ganics’ Nick Bateman added: “H2O-ganics produce is not grown in soil but produced in a fully controlled clean environment, which keeps out pests and pathogens, while maintaining the optimum conditions for plant growth.
“Using our controlled environment approach to agriculture and clean room technology, we are able to produce a consistent specification of product 365 days of the year, without the use of pesticides.”
Lincolnshire-based design firm Arctica is assisting growers H20-ganics to build an innovative location with controlled clean room environment, free from pests or pathogens, scheduled for completion at the end of the year.
Arctica director Niall McQuitty said the facility will provide longer lasting lettuce to UK retailers. Once established, the system will be used to grow a full range of green salads and herbs for sale in supermarkets.
McQuitty said: “Green leaf salad is normally grown outside. The clock starts ticking on the product’s shelf life as soon as it is harvested. Green leaf coming from other markets – such as Spain – takes 24 hours to transport to processing facilities in the UK. It can take up to three days from picking to packing which means, by the time it’s in the shops, it has lost up to half its shelf life.
“Cleaning the leaf also has an impact on the quality of the produce. Washing, drying, mixing, bagging and transport all require care because the leaf is fragile and prone to damage – which also reduces shelf life. H20-ganics creates a high care environment in which to grow the leaf that removes most of these stages from the process. It can be harvested, cleaned and packed without losing quality, thereby increasing its shelf life.”
H20-ganics’ Nick Bateman added: “H2O-ganics produce is not grown in soil but produced in a fully controlled clean environment, which keeps out pests and pathogens, while maintaining the optimum conditions for plant growth.
“Using our controlled environment approach to agriculture and clean room technology, we are able to produce a consistent specification of product 365 days of the year, without the use of pesticides.”
Lincolnshire-based design firm Arctica is assisting growers H20-ganics to build an innovative location with controlled clean room environment, free from pests or pathogens, scheduled for completion at the end of the year.
Arctica director Niall McQuitty said the facility will provide longer lasting lettuce to UK retailers. Once established, the system will be used to grow a full range of green salads and herbs for sale in supermarkets.
McQuitty said: “Green leaf salad is normally grown outside. The clock starts ticking on the product’s shelf life as soon as it is harvested. Green leaf coming from other markets – such as Spain – takes 24 hours to transport to processing facilities in the UK. It can take up to three days from picking to packing which means, by the time it’s in the shops, it has lost up to half its shelf life.
“Cleaning the leaf also has an impact on the quality of the produce. Washing, drying, mixing, bagging and transport all require care because the leaf is fragile and prone to damage – which also reduces shelf life. H20-ganics creates a high care environment in which to grow the leaf that removes most of these stages from the process. It can be harvested, cleaned and packed without losing quality, thereby increasing its shelf life.”
H20-ganics’ Nick Bateman added: “H2O-ganics produce is not grown in soil but produced in a fully controlled clean environment, which keeps out pests and pathogens, while maintaining the optimum conditions for plant growth.
“Using our controlled environment approach to agriculture and clean room technology, we are able to produce a consistent specification of product 365 days of the year, without the use of pesticides.”
Lincolnshire-based design firm Arctica is assisting growers H20-ganics to build an innovative location with controlled clean room environment, free from pests or pathogens, scheduled for completion at the end of the year.
Arctica director Niall McQuitty said the facility will provide longer lasting lettuce to UK retailers. Once established, the system will be used to grow a full range of green salads and herbs for sale in supermarkets.
McQuitty said: “Green leaf salad is normally grown outside. The clock starts ticking on the product’s shelf life as soon as it is harvested. Green leaf coming from other markets – such as Spain – takes 24 hours to transport to processing facilities in the UK. It can take up to three days from picking to packing which means, by the time it’s in the shops, it has lost up to half its shelf life.
“Cleaning the leaf also has an impact on the quality of the produce. Washing, drying, mixing, bagging and transport all require care because the leaf is fragile and prone to damage – which also reduces shelf life. H20-ganics creates a high care environment in which to grow the leaf that removes most of these stages from the process. It can be harvested, cleaned and packed without losing quality, thereby increasing its shelf life.”
H20-ganics’ Nick Bateman added: “H2O-ganics produce is not grown in soil but produced in a fully controlled clean environment, which keeps out pests and pathogens, while maintaining the optimum conditions for plant growth.
“Using our controlled environment approach to agriculture and clean room technology, we are able to produce a consistent specification of product 365 days of the year, without the use of pesticides.”
Lincolnshire-based design firm Arctica is assisting growers H20-ganics to build an innovative location with controlled clean room environment, free from pests or pathogens, scheduled for completion at the end of the year.
Arctica director Niall McQuitty said the facility will provide longer lasting lettuce to UK retailers. Once established, the system will be used to grow a full range of green salads and herbs for sale in supermarkets.
McQuitty said: “Green leaf salad is normally grown outside. The clock starts ticking on the product’s shelf life as soon as it is harvested. Green leaf coming from other markets – such as Spain – takes 24 hours to transport to processing facilities in the UK. It can take up to three days from picking to packing which means, by the time it’s in the shops, it has lost up to half its shelf life.
“Cleaning the leaf also has an impact on the quality of the produce. Washing, drying, mixing, bagging and transport all require care because the leaf is fragile and prone to damage – which also reduces shelf life. H20-ganics creates a high care environment in which to grow the leaf that removes most of these stages from the process. It can be harvested, cleaned and packed without losing quality, thereby increasing its shelf life.”
H20-ganics’ Nick Bateman added: “H2O-ganics produce is not grown in soil but produced in a fully controlled clean environment, which keeps out pests and pathogens, while maintaining the optimum conditions for plant growth.
“Using our controlled environment approach to agriculture and clean room technology, we are able to produce a consistent specification of product 365 days of the year, without the use of pesticides.”
Lincolnshire-based design firm Arctica is assisting growers H20-ganics to build an innovative location with controlled clean room environment, free from pests or pathogens, scheduled for completion at the end of the year.
Arctica director Niall McQuitty said the facility will provide longer lasting lettuce to UK retailers. Once established, the system will be used to grow a full range of green salads and herbs for sale in supermarkets.
McQuitty said: “Green leaf salad is normally grown outside. The clock starts ticking on the product’s shelf life as soon as it is harvested. Green leaf coming from other markets – such as Spain – takes 24 hours to transport to processing facilities in the UK. It can take up to three days from picking to packing which means, by the time it’s in the shops, it has lost up to half its shelf life.
“Cleaning the leaf also has an impact on the quality of the produce. Washing, drying, mixing, bagging and transport all require care because the leaf is fragile and prone to damage – which also reduces shelf life. H20-ganics creates a high care environment in which to grow the leaf that removes most of these stages from the process. It can be harvested, cleaned and packed without losing quality, thereby increasing its shelf life.”
H20-ganics’ Nick Bateman added: “H2O-ganics produce is not grown in soil but produced in a fully controlled clean environment, which keeps out pests and pathogens, while maintaining the optimum conditions for plant growth.
“Using our controlled environment approach to agriculture and clean room technology, we are able to produce a consistent specification of product 365 days of the year, without the use of pesticides.”
Lincolnshire-based design firm Arctica is assisting growers H20-ganics to build an innovative location with controlled clean room environment, free from pests or pathogens, scheduled for completion at the end of the year.
Arctica director Niall McQuitty said the facility will provide longer lasting lettuce to UK retailers. Once established, the system will be used to grow a full range of green salads and herbs for sale in supermarkets.
McQuitty said: “Green leaf salad is normally grown outside. The clock starts ticking on the product’s shelf life as soon as it is harvested. Green leaf coming from other markets – such as Spain – takes 24 hours to transport to processing facilities in the UK. It can take up to three days from picking to packing which means, by the time it’s in the shops, it has lost up to half its shelf life.
“Cleaning the leaf also has an impact on the quality of the produce. Washing, drying, mixing, bagging and transport all require care because the leaf is fragile and prone to damage – which also reduces shelf life. H20-ganics creates a high care environment in which to grow the leaf that removes most of these stages from the process. It can be harvested, cleaned and packed without losing quality, thereby increasing its shelf life.”
H20-ganics’ Nick Bateman added: “H2O-ganics produce is not grown in soil but produced in a fully controlled clean environment, which keeps out pests and pathogens, while maintaining the optimum conditions for plant growth.
“Using our controlled environment approach to agriculture and clean room technology, we are able to produce a consistent specification of product 365 days of the year, without the use of pesticides.”
Lincolnshire-based design firm Arctica is assisting growers H20-ganics to build an innovative location with controlled clean room environment, free from pests or pathogens, scheduled for completion at the end of the year.
Arctica director Niall McQuitty said the facility will provide longer lasting lettuce to UK retailers. Once established, the system will be used to grow a full range of green salads and herbs for sale in supermarkets.
McQuitty said: “Green leaf salad is normally grown outside. The clock starts ticking on the product’s shelf life as soon as it is harvested. Green leaf coming from other markets – such as Spain – takes 24 hours to transport to processing facilities in the UK. It can take up to three days from picking to packing which means, by the time it’s in the shops, it has lost up to half its shelf life.
“Cleaning the leaf also has an impact on the quality of the produce. Washing, drying, mixing, bagging and transport all require care because the leaf is fragile and prone to damage – which also reduces shelf life. H20-ganics creates a high care environment in which to grow the leaf that removes most of these stages from the process. It can be harvested, cleaned and packed without losing quality, thereby increasing its shelf life.”
H20-ganics’ Nick Bateman added: “H2O-ganics produce is not grown in soil but produced in a fully controlled clean environment, which keeps out pests and pathogens, while maintaining the optimum conditions for plant growth.
“Using our controlled environment approach to agriculture and clean room technology, we are able to produce a consistent specification of product 365 days of the year, without the use of pesticides.”
Lincolnshire-based design firm Arctica is assisting growers H20-ganics to build an innovative location with controlled clean room environment, free from pests or pathogens, scheduled for completion at the end of the year.
Arctica director Niall McQuitty said the facility will provide longer lasting lettuce to UK retailers. Once established, the system will be used to grow a full range of green salads and herbs for sale in supermarkets.
McQuitty said: “Green leaf salad is normally grown outside. The clock starts ticking on the product’s shelf life as soon as it is harvested. Green leaf coming from other markets – such as Spain – takes 24 hours to transport to processing facilities in the UK. It can take up to three days from picking to packing which means, by the time it’s in the shops, it has lost up to half its shelf life.
“Cleaning the leaf also has an impact on the quality of the produce. Washing, drying, mixing, bagging and transport all require care because the leaf is fragile and prone to damage – which also reduces shelf life. H20-ganics creates a high care environment in which to grow the leaf that removes most of these stages from the process. It can be harvested, cleaned and packed without losing quality, thereby increasing its shelf life.”
H20-ganics’ Nick Bateman added: “H2O-ganics produce is not grown in soil but produced in a fully controlled clean environment, which keeps out pests and pathogens, while maintaining the optimum conditions for plant growth.
“Using our controlled environment approach to agriculture and clean room technology, we are able to produce a consistent specification of product 365 days of the year, without the use of pesticides.”
Lincolnshire-based design firm Arctica is assisting growers H20-ganics to build an innovative location with controlled clean room environment, free from pests or pathogens, scheduled for completion at the end of the year.
Arctica director Niall McQuitty said the facility will provide longer lasting lettuce to UK retailers. Once established, the system will be used to grow a full range of green salads and herbs for sale in supermarkets.
McQuitty said: “Green leaf salad is normally grown outside. The clock starts ticking on the product’s shelf life as soon as it is harvested. Green leaf coming from other markets – such as Spain – takes 24 hours to transport to processing facilities in the UK. It can take up to three days from picking to packing which means, by the time it’s in the shops, it has lost up to half its shelf life.
“Cleaning the leaf also has an impact on the quality of the produce. Washing, drying, mixing, bagging and transport all require care because the leaf is fragile and prone to damage – which also reduces shelf life. H20-ganics creates a high care environment in which to grow the leaf that removes most of these stages from the process. It can be harvested, cleaned and packed without losing quality, thereby increasing its shelf life.”
H20-ganics’ Nick Bateman added: “H2O-ganics produce is not grown in soil but produced in a fully controlled clean environment, which keeps out pests and pathogens, while maintaining the optimum conditions for plant growth.
“Using our controlled environment approach to agriculture and clean room technology, we are able to produce a consistent specification of product 365 days of the year, without the use of pesticides.”
Lincolnshire-based design firm Arctica is assisting growers H20-ganics to build an innovative location with controlled clean room environment, free from pests or pathogens, scheduled for completion at the end of the year.
Arctica director Niall McQuitty said the facility will provide longer lasting lettuce to UK retailers. Once established, the system will be used to grow a full range of green salads and herbs for sale in supermarkets.
McQuitty said: “Green leaf salad is normally grown outside. The clock starts ticking on the product’s shelf life as soon as it is harvested. Green leaf coming from other markets – such as Spain – takes 24 hours to transport to processing facilities in the UK. It can take up to three days from picking to packing which means, by the time it’s in the shops, it has lost up to half its shelf life.
“Cleaning the leaf also has an impact on the quality of the produce. Washing, drying, mixing, bagging and transport all require care because the leaf is fragile and prone to damage – which also reduces shelf life. H20-ganics creates a high care environment in which to grow the leaf that removes most of these stages from the process. It can be harvested, cleaned and packed without losing quality, thereby increasing its shelf life.”
H20-ganics’ Nick Bateman added: “H2O-ganics produce is not grown in soil but produced in a fully controlled clean environment, which keeps out pests and pathogens, while maintaining the optimum conditions for plant growth.
“Using our controlled environment approach to agriculture and clean room technology, we are able to produce a consistent specification of product 365 days of the year, without the use of pesticides.”
Lincolnshire-based design firm Arctica is assisting growers H20-ganics to build an innovative location with controlled clean room environment, free from pests or pathogens, scheduled for completion at the end of the year.
Arctica director Niall McQuitty said the facility will provide longer lasting lettuce to UK retailers. Once established, the system will be used to grow a full range of green salads and herbs for sale in supermarkets.
McQuitty said: “Green leaf salad is normally grown outside. The clock starts ticking on the product’s shelf life as soon as it is harvested. Green leaf coming from other markets – such as Spain – takes 24 hours to transport to processing facilities in the UK. It can take up to three days from picking to packing which means, by the time it’s in the shops, it has lost up to half its shelf life.
“Cleaning the leaf also has an impact on the quality of the produce. Washing, drying, mixing, bagging and transport all require care because the leaf is fragile and prone to damage – which also reduces shelf life. H20-ganics creates a high care environment in which to grow the leaf that removes most of these stages from the process. It can be harvested, cleaned and packed without losing quality, thereby increasing its shelf life.”
H20-ganics’ Nick Bateman added: “H2O-ganics produce is not grown in soil but produced in a fully controlled clean environment, which keeps out pests and pathogens, while maintaining the optimum conditions for plant growth.
“Using our controlled environment approach to agriculture and clean room technology, we are able to produce a consistent specification of product 365 days of the year, without the use of pesticides.”
Lincolnshire-based design firm Arctica is assisting growers H20-ganics to build an innovative location with controlled clean room environment, free from pests or pathogens, scheduled for completion at the end of the year.
Arctica director Niall McQuitty said the facility will provide longer lasting lettuce to UK retailers. Once established, the system will be used to grow a full range of green salads and herbs for sale in supermarkets.
McQuitty said: “Green leaf salad is normally grown outside. The clock starts ticking on the product’s shelf life as soon as it is harvested. Green leaf coming from other markets – such as Spain – takes 24 hours to transport to processing facilities in the UK. It can take up to three days from picking to packing which means, by the time it’s in the shops, it has lost up to half its shelf life.
“Cleaning the leaf also has an impact on the quality of the produce. Washing, drying, mixing, bagging and transport all require care because the leaf is fragile and prone to damage – which also reduces shelf life. H20-ganics creates a high care environment in which to grow the leaf that removes most of these stages from the process. It can be harvested, cleaned and packed without losing quality, thereby increasing its shelf life.”
H20-ganics’ Nick Bateman added: “H2O-ganics produce is not grown in soil but produced in a fully controlled clean environment, which keeps out pests and pathogens, while maintaining the optimum conditions for plant growth.
“Using our controlled environment approach to agriculture and clean room technology, we are able to produce a consistent specification of product 365 days of the year, without the use of pesticides.”
Lincolnshire-based design firm Arctica is assisting growers H20-ganics to build an innovative location with controlled clean room environment, free from pests or pathogens, scheduled for completion at the end of the year.
Arctica director Niall McQuitty said the facility will provide longer lasting lettuce to UK retailers. Once established, the system will be used to grow a full range of green salads and herbs for sale in supermarkets.
McQuitty said: “Green leaf salad is normally grown outside. The clock starts ticking on the product’s shelf life as soon as it is harvested. Green leaf coming from other markets – such as Spain – takes 24 hours to transport to processing facilities in the UK. It can take up to three days from picking to packing which means, by the time it’s in the shops, it has lost up to half its shelf life.
“Cleaning the leaf also has an impact on the quality of the produce. Washing, drying, mixing, bagging and transport all require care because the leaf is fragile and prone to damage – which also reduces shelf life. H20-ganics creates a high care environment in which to grow the leaf that removes most of these stages from the process. It can be harvested, cleaned and packed without losing quality, thereby increasing its shelf life.”
H20-ganics’ Nick Bateman added: “H2O-ganics produce is not grown in soil but produced in a fully controlled clean environment, which keeps out pests and pathogens, while maintaining the optimum conditions for plant growth.
“Using our controlled environment approach to agriculture and clean room technology, we are able to produce a consistent specification of product 365 days of the year, without the use of pesticides.”
Lincolnshire-based design firm Arctica is assisting growers H20-ganics to build an innovative location with controlled clean room environment, free from pests or pathogens, scheduled for completion at the end of the year.
Arctica director Niall McQuitty said the facility will provide longer lasting lettuce to UK retailers. Once established, the system will be used to grow a full range of green salads and herbs for sale in supermarkets.
McQuitty said: “Green leaf salad is normally grown outside. The clock starts ticking on the product’s shelf life as soon as it is harvested. Green leaf coming from other markets – such as Spain – takes 24 hours to transport to processing facilities in the UK. It can take up to three days from picking to packing which means, by the time it’s in the shops, it has lost up to half its shelf life.
“Cleaning the leaf also has an impact on the quality of the produce. Washing, drying, mixing, bagging and transport all require care because the leaf is fragile and prone to damage – which also reduces shelf life. H20-ganics creates a high care environment in which to grow the leaf that removes most of these stages from the process. It can be harvested, cleaned and packed without losing quality, thereby increasing its shelf life.”
H20-ganics’ Nick Bateman added: “H2O-ganics produce is not grown in soil but produced in a fully controlled clean environment, which keeps out pests and pathogens, while maintaining the optimum conditions for plant growth.
“Using our controlled environment approach to agriculture and clean room technology, we are able to produce a consistent specification of product 365 days of the year, without the use of pesticides.”
Lincolnshire-based design firm Arctica is assisting growers H20-ganics to build an innovative location with controlled clean room environment, free from pests or pathogens, scheduled for completion at the end of the year.
Arctica director Niall McQuitty said the facility will provide longer lasting lettuce to UK retailers. Once established, the system will be used to grow a full range of green salads and herbs for sale in supermarkets.
McQuitty said: “Green leaf salad is normally grown outside. The clock starts ticking on the product’s shelf life as soon as it is harvested. Green leaf coming from other markets – such as Spain – takes 24 hours to transport to processing facilities in the UK. It can take up to three days from picking to packing which means, by the time it’s in the shops, it has lost up to half its shelf life.
“Cleaning the leaf also has an impact on the quality of the produce. Washing, drying, mixing, bagging and transport all require care because the leaf is fragile and prone to damage – which also reduces shelf life. H20-ganics creates a high care environment in which to grow the leaf that removes most of these stages from the process. It can be harvested, cleaned and packed without losing quality, thereby increasing its shelf life.”
H20-ganics’ Nick Bateman added: “H2O-ganics produce is not grown in soil but produced in a fully controlled clean environment, which keeps out pests and pathogens, while maintaining the optimum conditions for plant growth.
“Using our controlled environment approach to agriculture and clean room technology, we are able to produce a consistent specification of product 365 days of the year, without the use of pesticides.”
Lincolnshire-based design firm Arctica is assisting growers H20-ganics to build an innovative location with controlled clean room environment, free from pests or pathogens, scheduled for completion at the end of the year.
Arctica director Niall McQuitty said the facility will provide longer lasting lettuce to UK retailers. Once established, the system will be used to grow a full range of green salads and herbs for sale in supermarkets.
McQuitty said: “Green leaf salad is normally grown outside. The clock starts ticking on the product’s shelf life as soon as it is harvested. Green leaf coming from other markets – such as Spain – takes 24 hours to transport to processing facilities in the UK. It can take up to three days from picking to packing which means, by the time it’s in the shops, it has lost up to half its shelf life.
“Cleaning the leaf also has an impact on the quality of the produce. Washing, drying, mixing, bagging and transport all require care because the leaf is fragile and prone to damage – which also reduces shelf life. H20-ganics creates a high care environment in which to grow the leaf that removes most of these stages from the process. It can be harvested, cleaned and packed without losing quality, thereby increasing its shelf life.”
H20-ganics’ Nick Bateman added: “H2O-ganics produce is not grown in soil but produced in a fully controlled clean environment, which keeps out pests and pathogens, while maintaining the optimum conditions for plant growth.
“Using our controlled environment approach to agriculture and clean room technology, we are able to produce a consistent specification of product 365 days of the year, without the use of pesticides.”
Lincolnshire-based design firm Arctica is assisting growers H20-ganics to build an innovative location with controlled clean room environment, free from pests or pathogens, scheduled for completion at the end of the year.
Arctica director Niall McQuitty said the facility will provide longer lasting lettuce to UK retailers. Once established, the system will be used to grow a full range of green salads and herbs for sale in supermarkets.
McQuitty said: “Green leaf salad is normally grown outside. The clock starts ticking on the product’s shelf life as soon as it is harvested. Green leaf coming from other markets – such as Spain – takes 24 hours to transport to processing facilities in the UK. It can take up to three days from picking to packing which means, by the time it’s in the shops, it has lost up to half its shelf life.
“Cleaning the leaf also has an impact on the quality of the produce. Washing, drying, mixing, bagging and transport all require care because the leaf is fragile and prone to damage – which also reduces shelf life. H20-ganics creates a high care environment in which to grow the leaf that removes most of these stages from the process. It can be harvested, cleaned and packed without losing quality, thereby increasing its shelf life.”
H20-ganics’ Nick Bateman added: “H2O-ganics produce is not grown in soil but produced in a fully controlled clean environment, which keeps out pests and pathogens, while maintaining the optimum conditions for plant growth.
“Using our controlled environment approach to agriculture and clean room technology, we are able to produce a consistent specification of product 365 days of the year, without the use of pesticides.”
Lincolnshire-based design firm Arctica is assisting growers H20-ganics to build an innovative location with controlled clean room environment, free from pests or pathogens, scheduled for completion at the end of the year.
Arctica director Niall McQuitty said the facility will provide longer lasting lettuce to UK retailers. Once established, the system will be used to grow a full range of green salads and herbs for sale in supermarkets.
McQuitty said: “Green leaf salad is normally grown outside. The clock starts ticking on the product’s shelf life as soon as it is harvested. Green leaf coming from other markets – such as Spain – takes 24 hours to transport to processing facilities in the UK. It can take up to three days from picking to packing which means, by the time it’s in the shops, it has lost up to half its shelf life.
“Cleaning the leaf also has an impact on the quality of the produce. Washing, drying, mixing, bagging and transport all require care because the leaf is fragile and prone to damage – which also reduces shelf life. H20-ganics creates a high care environment in which to grow the leaf that removes most of these stages from the process. It can be harvested, cleaned and packed without losing quality, thereby increasing its shelf life.”
H20-ganics’ Nick Bateman added: “H2O-ganics produce is not grown in soil but produced in a fully controlled clean environment, which keeps out pests and pathogens, while maintaining the optimum conditions for plant growth.
“Using our controlled environment approach to agriculture and clean room technology, we are able to produce a consistent specification of product 365 days of the year, without the use of pesticides.”
New Whole Foods Cultivates Mini Mushroom Farm In Produce Section
New Whole Foods Cultivates Mini Mushroom Farm In Produce Section
New Jersey location touts “freshest possible” produce
Gloria Dawson | Mar 26, 2018
When designing the new Whole Foods location in Bridgewater, N.J., the company created an expansive produce department and carved out space for something a bit different: a mushroom farm.
"We think the farm will add a level of innovation and intrigue that customers will find very interesting,” said Chris Manca, Whole Foods Market’s local program coordinator for the Northeast region. “These mushrooms will also be the freshest possible produce that you can buy, and we know our shoppers will be excited about that.”
The farms are the creation of Smallhold, a new company out of Brooklyn, N.Y. The company’s mini farms can be found in a handful of restaurants, but Whole Foods is the first retail partner. The farm in the Bridgewater location will produce about 120 pounds of mushrooms every week, but the farms can be much smaller depending on need, said Adam DeMartino, co-founder and COO of Smallhold. “Essentially, we need as little as 4 feet by 2 feet square footage,” he said. “It depends on how muchyou're going to sell.” Whole Foods hopes to install another farm in one of the company’s Brooklyn locations later this year.
Whatever the size, Smallhold’s vertical farm units are meant to be seen, said DeMartino. “It's a glowing box. It has lights in it. It attracts the eye. It attracts people to the produce aisle. And kids love it.”
Manca agrees. “The growing unit is so unique and beautiful that people will inevitably be very drawn to it,” he said. “Our job will be to educate people about what we are doing, and we expect they will be very interested in purchasing some of the mushrooms to take home and try.”
Logistically, the mushrooms are initially grown in nearby farms, including one run by Smallhold, and brought to the mini farm during the last stage of growth. Once the mushrooms are ready, a store or Smallhold employee bags the mushrooms and puts them on nearby shelves where customers can grab them. Smallhold’s technology monitors the environment and gathers data on temperature and humidity. The company can also gather market data and see which mushrooms are selling. At the Whole Foods location in New Jersey, the farm is growing three different kinds of oyster mushrooms – yellow, blue and pink.
Smallhold started with mushrooms, in part, because “we looked for high-margin, high-output crops, and mushrooms were the natural ones to land on,” said DeMartino. Mushrooms are also tricky to transport and have a short shelf life, both problems the mini farms eliminate. These benefits afford retailers the ability to price their mushrooms at a lower price per pound, DeMartino said.
“This is a direction that not just produce, but food in general is moving,” he said. “There's definitely a renewed focus on healthy produce, there's definitely a desire for local, but we need to make that affordable. And basically, that's what we offer. In addition, [you get] the marketing value of having produce grown on-site.”
DeMartino said the company plans to expand to other retail locations and beyond.
“Our goal is to start with Whole Foods, but the applications for this, because it's a remotely operated farm, reach beyond even groceries stores,” he said. “We see these as being useful in many applications, for instance, where people don't have arable land. And so, the ultimate goal of Smallhold is to get the price of local produce down to an affordable price for people.”
Contact Gloria Dawson at gloria.dawson@knect365.com
Follow her on Twitter: @gloriadawson
GrowLife, Inc. Launches Line of Eco-Friendly Products to Meet Growing Demand for Sustainability in Indoor Cultivation Practices
GrowLife, Inc. Launches Line of Eco-Friendly Products to Meet Growing Demand for Sustainability in Indoor Cultivation Practices
March 14, 2018
KIRKLAND, Wash.--(BUSINESS WIRE)--GrowLife, Inc. (PHOT) (“GrowLife” or the “Company”), one of the nation’s most recognized indoor cultivation product and service providers, today announced the launch of a new line of sustainable eco-friendly products for the indoor cultivation market. These new products will allow GrowLife’s customers to play a role in providing a greener economic footprint compared to traditional indoor cultivation methods while remaining efficient on output and profitability.
The new product line was strategically curated by the Company’s expert growing consultancy team to offer products that are not only high quality and affordable, but also offer significantly decreased environmental impacts compared to traditional products.
The product line, which features products from all categories of indoor growing, includes items such as lighting, nutrients and growing mediums, climate control devices, and overall plant care products. The Company saw an unmet need in the indoor cultivation market, which faces consistent criticism for its environmental footprint, for high-quality, sustainable products that yield similar output results as traditional products. The Company understands the demand for these types of products will continue to increase as end consumers’ demand for green practices increases following national trends toward sustainability.
“GrowLife is committed to offering its customers innovative technologies and products that help them to achieve maximum efficiency and profitability while satisfying their end consumers,” said GrowLife CEO Marco Hegyi. “The launch of this product line assists in that commitment by offering a sustainable solution with all of the efficient production benefits our customers expect. These green products will enable our customers to make the important shift to more sustainable indoor growing practices that will garner more trust from their customers while preparing them for any further regulatory and social obligation placed on this industry with respect to sustainability.”
In addition to the product line, the Company will offer eco-friendly growing tips and resources to its customers through its renowned support and education platform. For more information on the GrowLife ECO line or to purchase products, please visit Shopgrowlife.com/ECO.
For more information about GrowLife Inc., please visit the company’s website.
About GrowLife, Inc.
GrowLife, Inc. (PHOT) aims to become the nation’s largest cultivation service provider for cultivating organics, herbs and greens and plant-based medicines. Our mission is to help make our customers successful. Through a network of local representatives covering the United States and Canada, regional centers and its e-Commerce team, GrowLife provides essential goods and services including media, industry-leading hydroponics and soil, plant nutrients, and thousands more products to specialty grow operations. GrowLife is headquartered in Kirkland, Washington and was founded in 2012.
Contacts
Public Relations
CMW Media
Cassandra Dowell, 858-264-6600
cassandra@cmwmedia.com
www.cmwmedia.com
or
Investor Relations
info@growlifinc.com
Resources To Help Become A Microgreens Grower
Resources To Help Become A Microgreens Grower
March 20, 2018
"May I ask any recommendations or tips on what direction I should go to start learning how to become a microgreens grower."
This question inspired us to write this blog post. Ladies and gentlemen, the Master Grower has turned on the Fasten Seat Belt sign. If you haven’t already done so, please stow your carry-on luggage underneath the seat in front of you or in an overhead bin. Make sure you're seat belt is tightened. You won’t regret missing out on this! We promise.
Microgreen Garden: Indoor Grower's Guide To Gourmet Greens
by Mark Mathew Braunstein
"No matter where you live or what season, you can be a successful microgreens gardener. By growing microgreens, you gain access to fresh, delectable, organic, and homegrown greens year round. And all you need to start your indoor garden are seeds, soil or coco coir, water, and access to a sunny window or grow lights." pg.4
Storing Your Microgreens
"One of the wonderful things about growing microgreens is that it's often possible to harvest the greens as you're ready to eat them. When this isn't the case, refrigerate whatever you don't plan to eat immediately.
The best way to store clipped microgreens is in a food-safe plastic container with a lid. If necessary, It's okay to store microgreens in a bag if you handle the greens and bag gently. Set refrigerator's thermostat close to the freezing point and you'll keep your harvest fresh for two weeks or longer. Make sure you store microgreens dry to touch.
If you grow microgreens in repurposed containers (such as pints or half pints), you can refrigerate the microgreens, soil, container, and all if the greens are ready but you're not quite ready to eat them. After one week, the soil may need some soaking, after which the greens will remain fresh for yet another week. This is one of several conveniences that container growing offers over tray growing." pg.35
Water From The Bottom
The technique of watering microgreens from below is adapted from a method used by large scale microgreens farmer, who deliver their uncut crops to restaurants and markets still in their seedling containers.
The microgreens continue to grow in the restaurant and the marketplace and they do so without becoming moldy. Avoiding mold is the main goal of bottom watering. Water your microgreens whenever the top of the soil feels dry,
usually once daily for half pint containers and every other day for pint containers, which are deeper. pg.46
Microgreens: A Guide To Growing Nutrient Packed Greens
by Eric Frank
"Over the past twenty years, interest in local, fresh and organic food has been on the rise. There has been a rejuvenation of the small farm and a renewal of appreciation for fresh vegetables. The revival of the farmers market, the inception of the CSA model (Community Supported Agriculture), and the overall movement towards clean, whole foods has been extraordinary and is
continuing to grow. People are rediscovering the importance of fresh, locally grown food. This movement has shown that it's not just for the affluent, not only for those interested in farming but for the whole of the population and future generations." pg.2
Seeds
Quality seeds are another integral part of growing microgreens. Factors that'll affect the viability of your seeds are storage, handling, age, and seed source. If you sow one thousand seeds, the difference between a 95 percent germination rate and a 50 percent germination rate is quite noticeable. It can be disheartening to have gone through the effort of sowing and caring for your trays only to see a small percentage of your seeds come up.
When it comes to storing and handling your seeds, you'll want to keep them cool and dry. Avoid great
fluctuation in temperature and moisture. During hot, humid summer days, be mindful not to leave them in the sun or let them get caught in a summer thunderstorm. Properly caring for your seeds will maintain their viability for longer period of time. pg.22
Scissors For Harvesting
We find that scissors are most effective tool for harvesting microgreens. Buy a separate pair solely for the use of harvesting is not a bad idea that way they stay sharp and clean and make cutting easy. Having a couple of different sizes of scissors can be helpful for cutting different varities and densities of microgreens as well. The most important thing here is sharpness. Once your scissors begin to dull. you can either buy new pair or sharpen your existing pair. Making a clean cut through the stem is one important component to the longevity of your microgreens. The less cell damage done during the harvest, the longer they'll hold. Once scissors are allowed to dull, they'll start to tear the stems of the microgreens versus making a clean cut. If stored for later use, you may notice deterioration and discoloration at the bottom of the stem where they have been poorly cut.
If you enjoyed this, you might also enjoy these post:
"Questions about urban farming"
LumiGrow Honored with Sapphire Award for Using Light to Change the Agricultural Model
LumiGrow Honored with Sapphire Award for Using Light to Change the Agricultural Model
Emeryville, CA, March 13, 2018
On February 14, 2018, the Sapphire Awards Gala Dinner celebrated the most innovative companies in the solid-state lighting (SSL) industry by naming the fourth annual LED Magazine Sapphire Award winners. The event, held in Long Beach, CA aboard the RMS Queen Mary, recognized the most innovative LED-centric technologies across the lighting industry. LumiGrow was delighted to receive a Sapphire Award for Best Horticultural Lighting Solution of the year.
“With LEDs, the story was long about energy efficiency, but when history is written it will be about photometrics and form factor. LEDs enable all new experiences in light,” said Maury Wright, Editor-in-Chief of LEDs Magazine. “Our Sapphire Awards winners exemplify that eventuality with innovation that is simply amazing relative to products from one year ago.”
The LumiGrow Smart Lighting Solution led the pack for data-centric innovations fundamentally changing the industry. The smart horticultural lighting solution begins with LED fixtures that are dynamically adjustable for light intensity, spectrum, and photoperiod. The fixtures are then integrated with Wi-Fi modules used to control the fixtures by zone from any smartphone, tablet, or computer. This level of dynamic control is used to deploy advanced horticultural lighting strategies built to improve crop quality, achieve higher crop yields (in some cases up to 40% without any additional energy-usage required), and elicit desired crop characteristics by customizing plant morphology, color, flavor, and nutrition.
The next level of the solution comes when plugging LumiGrow Light Sensor Modules into the fixtures. The light sensors analyze sunlight within the greenhouse and report data back to the Wireless Control System. The LumiGrow system will then learn cloud-cover and lighting patterns to adjust the LumiGrow fixtures and automatically deliver ideal lighting conditions year-round. Growers can then access the LumiGrow software interface to gain better understanding of their lighting performance. seasonal sunlight conditions, and power-usage by monitoring daily and historical lighting charts to track both sunlight and supplemental LED light levels at the crop.
"The agricultural industry is now seeing the value that advanced data-centric technologies can have when meeting rapidly increasing demands for a growing world population. For the last ten years we’ve been deploying smart horticultural lighting solutions, advancing a new field of science to create value where it wasn’t possible before. We already have over 8,000 smart fixtures in the cloud. Now we’re just making our solution as automated and easy-to-use as possible to support growers worldwide.” says LumiGrow CEO, Shami Patel.
A panel of 27 independent judges chose the LumiGrow Smart Horticultural Lighting Solution from a group of numerous finalists, which included the category's 2017 incumbent. The judges are chosen from industry and consultancy roles to ensure that each entry is fairly evaluated by multiple experts. All judges were carefully screened to verify that there were no possible conflicts of interest in the process and ensure that the best and most innovative solutions were recognized.
About LumiGrow Inc.
LumiGrow, Inc., the leader in smart horticultural lighting, empowers growers and scientists with the ability to improve plant growth, boost crop yields, and achieve cost-saving operational efficiencies. LumiGrow offers a range of proven grow light solutions for use in greenhouses, controlled environment agriculture and research chambers. LumiGrow solutions are eligible for energy-efficiency subsidies from utilities across North America.
LumiGrow has the largest horticultural LED install-base in the United States, with installations in over 30 countries. Our customers range from top global agribusinesses, many of the world’s top 100 produce and flower growers, enterprise cannabis cultivators, leading universities, and the USDA. Headquartered in Emeryville, California, LumiGrow is privately owned and operated.
For more information, call (800) 514-0487 or visit www.lumigrow.com
Billionaire Larry Ellison Is Teaming Up With Steve Jobs' Former Doctor To Launch A Mysterious Wellness Company On His Private Island
Kimberly White / Getty Images
Billionaire Larry Ellison Is Teaming Up With Steve Jobs' Former Doctor To Launch A Mysterious Wellness Company On His Private Island
Billionaire Larry Ellison is teaming up with Steve Jobs' former doctor to create a mysterious new wellness company.
- The company, called Sensei, will start with food grown and harvested on Lanai, the Hawaiian island Ellison owns.
- Eventually, Sensei will also offer other practical goods and services aimed at helping people live healthier, longer lives.
The Hawaiian island of Lanai is billionaire Larry Ellison's oyster.
After purchasing the island for $300 million in 2012, the Oracle founder has now announced plans to transform it into a giant experiment for his new business — a mysterious consumer wellness company aimed at giving people simple, practical solutions for living more healthily.
The new company, called Sensei, was announced by company president Daniel Gruneberg during a 10-minute pitch at the Fortune Brainstorm Health conference in Laguna Niguel, California.
Ellison owns and operates two Four Seasons resorts on the 90,000-acre island.
Gruneberg, an East Coast native who founded a travel startup that was acquired last year, sat down with Business Insider to discuss some of Sensei's details, which are still sparse.
Sensei is starting its journey into health with food. The company will begin growing produce on Lanai with heirloom, organically-farmed fruits and vegetables like Black Trifele tomatoes and Komatsuna mustard greens.
The company will use hydroponics and solar power (via a partnership with Tesla) to slash energy and water usage, which it claims will be only a fraction of what other farms use. The food will be sold to restaurants and eventually to retailers under the Sensei Farms brand.
"We'll tell you the story about the produce," Gruneberg said.
A no-nonsense approach to health
The son of a nutritionist and graduate of Fordham University, Gruneberg struggled for years with his weight and a general feeling of being unwell.
Last year he met Ellison and David Agus, the company's other co-founder and a Los Angeles-based cancer doctor. Agus also co-chaired the conference where Gruneberg delivered the new company's pitch.
The idea of offering up practical health advice was naturally appealing to Gruneberg.
Shutterstock
"People have a really hard time caring about their future selves," Gruneberg told Business Insider.
Agus, meanwhile, has made a reputation for himself as a celebrity doctor who once treated Steve Jobs.
He has a no-nonsense approach to general health and wellbeing which involves eating fish; skipping shortcuts like vitamins, juices, and detoxes; and incorporating regular exercise, along with positive psychology and meditation, into daily life. All of these staples are generally regarded as the best ways to quickly and immediately improve health.
Given the strong role of diet in overall wellness, it makes sense that Agus' new company is focusing first on food.
Although Sensei's initial offerings will be focused on fruits and vegetables, Ellison has previously discussed the idea of farming fish on the island, as well using aquaponics — an alternative to traditional farming which, like hydroponics, uses less water and fewer resources.
Pineapple Island has a long history
Ellison is not the first wealthy white man to use Lanai as a farming hub.
In 1922, American industrialist James Drummond Dole purchased most of the island and recruited laborers from the Philippines and Japan who worked long, hard days earning low wages. By 1930, their labor allowed Lanai to export 65,000 tons of pineapples a year, earning the island the nickname "Pineapple Island." Some of their descendants still live on the island; many work in the service industry.
But many of them have emigrated elsewhere.