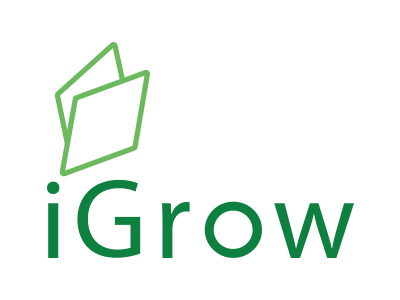
Welcome to iGrow News, Your Source for the World of Indoor Vertical Farming
Lumileds Addresses Industry Growth With LUXEON 3030 HE Plus Horticulture
The new LEDs are engineered for robust sulfur protection – critical for long and stable lifetime in warm and humid environments
Broad spectrum white LEDs are widely available
San Jose, CA – February 2, 2021 – Lumileds today announced immediate high quantity availability of its LUXEON 3030 HE Plus Horticulture LEDs. Based on the company’s leading 3030 LED portfolio and characterized for horticulture, the new options offer high PPF/W, broad-spectrum white light that enables grow lights that are productive and economical.
“In horticulture applications growers are looking for time tested, top performance and reliability, the LUXEON 3030 HE Plus Horticulture delivers the photons that enable consistent and high growth output with the highest of efficiencies,” said Mei Yi, Product Manager.
The new LEDs are engineered for robust sulfur protection – critical for long and stable lifetime in warm and humid environments – and are specified for horticulture at 65mA and Tj= 25°C with CCTs from 2200K to 6500K and CRI of 70, 80 or 90. When matched with LUXEON Deep Red and Far Red options a complete horticulture illumination solution is at hand.
LUXEON 3030 HE Plus Horticulture is available in manufacturing quantities today. It offers a 0.1V forward voltage bin, quadrant color bin inside 3SDCM, and a maximum drive current of 480mA. Detailed product information can be found at https://lumileds.com/3030Horticulture.
About Lumileds
For automotive, mobile, IoT, and illumination companies that require innovative lighting solutions, Lumileds is a global leader employing more than 7,000 team members operating in over 30 countries. Lumileds partners with its customers to push the boundaries of light.
To learn more about our portfolio of lighting solutions, visit lumileds.com.
For further information, please contact:
Steve Landau, Director Marketing Communications
+1 408 710 4090
Elevated Vertical Farming: Vaisala Sensors And The Story of Fifth Season
“When you don’t have to worry about outdoor conditions, you have the benefit of going vertical. We can grow plants year-round in urban areas close to the dense part of a city,” said Fifth Season Cofounder and CTO/COO Brac Webb
Vertical farming is looking up – quite literally. No sun, no soil, no vast expanse of land? No problem. At least not for indoor vertical farming company Fifth Season.
“When you don’t have to worry about outdoor conditions, you have the benefit of going vertical. We can grow plants year-round in urban areas close to the dense part of a city,” said Fifth Season Co-founder and CTO/COO Brac Webb
Every minute, we’re collecting Vaisala sensor data to measure and maintain the conditions most important for plant growth and using that information to build something special.
-Brac Webb, Fifth SeasonUsing a sophisticated mix of artificial intelligence (AI), sensors, data modeling and robotics, Fifth Season’s technology tends to each plant’s individual needs at high levels of efficiency and precision. But sensors and their data play the most pivotal role. “The plants are telling us exactly what they want. We just have to adjust to that,’ said Webb. “Every minute, we’re collecting Vaisala sensor data to measure and maintain the conditions most important for plant growth and using that information to build something special.”
Background
The story of Fifth Season is very much the story of the American Dream.
The startup began with three friends and entrepreneurs: cofounders Brac Webb, Austin Webb, and Austin Lawrence. Originally founded in 2016 as RoBotany Ltd., the company was incubated at Carnegie Mellon University’s (CMU) Swartz Center for Entrepreneurship.
“We really started as a tech company and looked at the vertical farming problem at first and wondered what we can do to help solve some tech problems there,” Webb said. “Much of our evolution is due to the advances of HVAC sensors and LED lights. We already had the programming. So, we said, heck, let’s just do the whole thing.”
Fifth Season is now a 60,000-square-foot, solar-powered vertical farm in the Pittsburgh borough of Braddock, PA. The company’s 25,000 square-foot grow room is equipped with 40 different robots and has 12 levels with more than 125,000 square feet of production capacity. Compared to conventional produce, which can travel thousands of miles by truck or plane, fresh produce grown in local vertical farms need only travel a few miles to reach consumers. The company produces an assortment of leafy greens, arugula, and spinach as well as ready-to-eat salads that are sold to a local clientele including Giant Eagle and numerous other retailers. They have also launched a Direct-To-Consumer model on their website.
The company uses its small army of 40 robots to streamline almost every aspect of the vertical growing operation, including storage, retrieval, harvesting, integrated pest, and disease management, scouting, seeding, media packaging, and more, according to Webb. Humans are minimally involved in the process, mostly to coordinate the robotic army to execute specific growing recipes or other tasks – which also cuts labor costs from 40% in traditional farms to just 20%.
“We have cutting-edge technology - not using traditional methods, using more of a robotics approach - and a ton of data collection with Vaisala sensors, not only for closed-loop control but also for alerting us to changes in plant growth or the environment,” Webb said.
Industry Overview
Total control of the growing environment – 24/7/365 – in small spaces governed by known and emerging technologies are farming’s oft-cited competitive advantages over other types of farming. Vertical farming also is known for efficient resource management. For example, with its hydroponics approach, growing plants in a solution of water and nutrients, Fifth Season uses 97% less land and up to 95% less water than traditional farming.
Vertical farming attempts to take the uncertainties of agriculture – pests, sunlight, soil, etc. – and makes them controllable through various combinations of AI, artificial light, sensor monitoring, climate control systems, etc. Crops are stacked in layers or rows sometimes 20 to 30 feet high. LED lights are used by all vertical farms to create a specific light recipe for each plant, giving the greens the exact spectrum, intensity, and frequency needed for photosynthesis. LEDs offer several benefits, such as: exceptional color range, longevity, low radiated heat, and energy-efficiency. They can also be recycled and don’t contain any toxic compounds or elements like mercury. Different types of crops prefer different types of lighting. For example, leafy greens and vegetative crops prefer light towards the blue side of the spectrum; whereas fruiting and flowering crops may need something more along the red spectrum.
Vaisala Sensors
The peace of mind factor is huge. You get that from Vaisala.... I never once questioned the reading that I’m getting, or that it will be just as consistent tomorrow.
-Brac Webb, Fifth Season
So, why Vaisala? “The peace of mind factor is huge. You get that from Vaisala. If we have issues with our growing environments, all our plants can die. I mean, it could kill our business,” Webb said. “I never once questioned the reading that I’m getting, or that it will be just as consistent tomorrow. But, more than that, it was also the support we received to quickly integrate your technology into our engineering and get everything up and running fast,” Webb added. In fact, tightly controlling and monitoring light, humidity, CO2, and the temperature is critically important to Fifth Season. So, data, data, data….
“We have, gosh, probably 360 of Vaisala’s HMP110 humidity and temperature probes and 36 GMP252 CO2 probes distributed throughout the entire growing environment. It’s not just about gathering data in real-time. With post-analysis of big data, we can review the growth history of those plants and learn something about them. We may learn, for example, what we thought was the best growing environment for those plants to achieve optimal conditions for taste, quality, and yield isn’t the best after all,” Webb said. “And we can course-correct.”
Future
As the world’s population expands, projected to reach 9 billion by 2050, so too does the amount of fruits and vegetables needed to sustain it. There is only so much farmland to accommodate the increase in fresh food required for life. The U.S. Department of Agriculture, investors, and entrepreneurs alike are acknowledging vertical farming as having the potential to strengthen the global food system. And startups like Fifth Season, backed by significant venture capital, are paving the way to deliver new solutions that efficiently deliver fresh and healthy food to people.
“The more we learn, the more we can improve vertical farming,” Webb said, jokingly adding: “If only we can get to the point that the computer could taste the plant.”
The story of Fifth Season is just beginning.
“We’d like to replicate these hyper-local farms. So, it isn’t just about solving the problems of having fresh produce available in Pittsburgh and making sure we can run it here. This farm is a product that we want to be able to deploy in multiple locations all over the United States, all over the world at some point, you know. That’s our grand vision.”
For Fifth Season and Webb, there’s also an underlying humanitarian goal of vertical farming that transcends business.
“As a person and an engineer, I always like reading about how (US President) Thomas Jefferson thought agriculture and engineering are intertwined: that agriculture is humanity’s first and foremost engineering problem to solve. You’re helping create jobs in that local area and we have seen how important that is to the economy. Thanks to the technology from Vaisala, you can create an environment that is perfect for the plants and help people too.”
For more information, please Contact Us.
Download the complete Customer Story below.
Elevated vertical farming: Vaisala sensors and the story of Fifth Season
Boost Operational Efficiencies With Lighting Control System
Signify has expanded its GrowWise Control System, allowing for higher levels of automation and reducing manual labor and operational costs
"Signify’s expanded GrowWise Control System helps growers boost operational efficiencies. This allows for full dimming for Philips toplighting compact in greenhouses. Besides, it enables growers to plan and automate light recipes one year ahead and to control the grow lighting through their climate computer or greenhouse management system. This will result in lower manual labor costs and improved operational efficiency," the company announces.
Signify has expanded its GrowWise Control System, allowing for higher levels of automation and reducing manual labor and operational costs. This can be achieved by automating the lighting planning for their crop’s full growth cycle, up to one year ahead. The software tool brings dynamic lighting to greenhouses and vertical farms and fits seamlessly with modern climate computers and greenhouse management systems. This enables growers to automatically adjust light levels to maintain consistent levels on cloudy days, save energy on sunny days and simulate sunrise and sunset throughout the day or season.
Growers, like the Italian vertical farm, Planet Farms, and the Belgium greenhouse, De Glastuin, are already using the expanded system providing additional value within their growing facility.
“Using the GrowWise Control System is ideal for us,” says Luca Travaglini, co-founder of Planet Farms. “We want to automate as many aspects of our operations as possible to become more cost efficient. Now we can easily create custom light recipes and set them to run year-round to provide the right light recipe with the right light intensity at the right time throughout the crop’s growth cycle. By automating our full light strategy during the growth cycle, for the whole year, we can run our operations very efficiently and keep our manual labor costs low. That makes it easier for us to maintain consistent quality as we scale up our production.”
The demand for the GrowWise Control System is increasing for greenhouse applications as well. “The lighting can be used much more efficient, since it gives us the flexibility to reduce light levels at any moment we need to,” says Wouter de Bruyn, owner at De Glastuin. Lettuce grower De Glastuin is using the GrowWise Control System to control the Philips GreenPower LED toplighting compact grow lights via its climate control system. “The climate computer is equipped with a daylight sensor that sends actual light measurements to the GrowWise Control System so we can adapt our light levels automatically to ensure an even light level throughout the day and season. This results in a continuous high-quality crop. In case the electricity is the limiting factor, we are still able to use the LEDs evenly for the whole greenhouse in a lesser intensity.”
“Dynamic lighting in a greenhouse is the next step in improving the cost-efficiency and quality for the cultivation process,” says Udo van Slooten, Business leader Horticulture LED solutions at Signify. “It allows growers to effortlessly maintain a consistent level of light throughout the day to produce the best possible crops. The system compensates for cloudy weather and creates a more controlled growing environment for your crop.”
Understanding The Key Tech Required In Vertical Farming
Staff Reporter Jan 25, 2021
Vertical farming involves; growing crops indoors under artificial temperature and lighting conditions. This technology focuses on increasing productivity in small places. It utilizes soil-free methods like aeroponics, aquaponics, and hydroponics. Read on to understand the main tech you need for your vertical farm.
(Photo : Valcenteu Wikimedia Commons)
Lighting systems
Covered agriculture, which is the traditional method of farming uses HPS (High-Pressure Sodium) vapor lamps. These units generate a warm light, which appears as an orange-yellow glow in areas with many glasshouses. LED technologies have evolved, becoming more energy-efficient and cheaper.
LED vertical farming lighting dictates the next generation controlled environment agriculture (CEA). While HPS lamps generate orangey-yellow light, LEDs can be designed to generate light in any color or combination of choice. Today, more LED lights are specially designed for the CEA industry.
Researchers are working with manufacturers to manufacture crop-specific lights to enhance photosynthesis, guarantee crop quality, and boost yield production. When growing crops in an indoor environment without a natural or external light source, the quality and quantity of artificial vertical farming lighting for your crops is critical.
Heating, Ventilation and Air Conditioning (HVAC)
Controlling the heating, ventilation, and air conditioning is crucial in managing a vertical farm. Remember, the HVAC can influence the yield, health, and quality of your crops. Smart regulating systems are crucial for the management and maintenance of ventilation, temperature, and humidity. Installing smart enabled HVAC systems that can be incorporated into a general control system is critical.
Nutrients
Controlled environment agriculture allows farmers to regulate the frequency, levels, and nutrients they use on the crops. Commercial nutrient mixes are not only readily available but are also easy to use for your vertical farm. However, you can improve the quality of your crops and increase production with a crop-specific nutrient mix. Research and knowledge help you produce efficient nutrient mixtures for your vertical farm.
Control Systems
Control systems audit, and manage all elements of a controlled environment. Doing so allows the farmer to make proper decisions for crop-specific growing conditions. Advanced control systems give farmers crucial data on crop health, development, and the environment.
With this data, the farmer can develop different features of the growing conditions. Further, control systems facilitate the implementation of nutrient mixes and light that can change throughout growing, light intensity, and delivery of supplementary C02 (carbon dioxide).
Future vertical farms should come with integrated control systems and inline crop monitoring systems to facilitate disease management. These components will help boost conditions, enhance energy-efficiency, and increase yield.
Growing Systems
Vertical farming involves various hydroponic systems, making soil and other growing media unnecessary. Farmers can use different substrates, as seen below.
NTF (Nutrient Film Technique)
The NTF comprises narrow troughs or channels where flowing small amounts of nutrient and water solution drains to the bottom of the troughs. This process creates a thin film. Plants are hanged over the trough in net containers. They receive small amounts of the nutrient solution often per day.
The fine nutrient film solution facilitates watering of the rear of the roots without getting soaked. The top part of the roots stays dry and consumes oxygen. The nutrient film technique is ideal for baby greens, salads, leaves, strawberries, and herbs.
Flood and Ebb System
The flood and ebb system is also known as drain and flood. It involves the use of trays filled with a nutrient solution for a few minutes before the water drains. The plant roots are swayed around the nutrient solution. Using flood like circumstances allows the plants to consume nutrients and oxygen, making them healthy and strong. The flood and ebb system is ideal for producing microgreens.
Finally
Vertical farming allows farmers to grow crops throughout the year, and this facilitates maximum crop production. This technology does not rely on the weather. You can grow your crops with the help of LED lighting. Apart from being eco-friendly, vertical farming allows you to farm within limited spaces, as is the case in cities.
Valoya Announces Departure of CEO
The company will continue to execute its strategy of bringing high quality, research-based horticultural LED lighting solutions to its crop science, medicinal plant and vertical farming customers globally
Valoya's CEO, Mr. Lars Aikala will leave the company in early 2021, by which time he will have served it from its founding, a total of 12 years. A search for the new Chief Executive Officer is undergoing. The company will continue to execute its strategy of bringing high quality, research-based horticultural LED lighting solutions to its crop science, medicinal plant and vertical farming customers globally.
“Valoya has come a long way from when we founded it in 2009. We now have a unique position in the market with our research-based, proven horticultural lighting solutions, which are appreciated by our customers globally. Our innovations and over 600 plant trials have enabled us to pioneer this market for more than a decade. We have built an international patent portfolio of 100+ granted patents, which demonstrates and protects our innovation. Our amazing team and our great resellers serve our customers in more than 50 countries with commitment and dedication.”, says Mr Aikala. He continues “Naturally we have also had to overcome several challenges during the years. The latest one, COVID-19 has again proven that the team strongly pulls together to win. I am very proud of the fact that in these challenging times we managed to deliver revenue growth in 2020 and more importantly we also exceeded our profitability targets. Valoya now has a strong foundation and I am sure Valoya’s future will be very bright.”
The change comes from Lars’s desire to go back to the intensity, thrills and challenges of creating new business. The Board of Directors and Lars agree that now is a good time to make the change. To ensure a smooth transition, Mr Aikala will continue working as CEO until a successor is in place.
"With his passion, relentless drive and unique expertise Lars made Valoya into the great company it is today. On behalf of the Board of Directors and the owners, I would like to extend sincere and best thank you to Lars for his very valuable contribution to Valoya's development", says Christer Härkönen, Chairman of the Board at Valoya.
About Valoya
Valoya is a provider of high end, energy-efficient LED grow lights for use in crop science, vertical farming and medicinal plants cultivation. Valoya LED grow lights have been developed using Valoya's proprietary LED technology and extensive plant photobiology research. Valoya's customer base includes numerous vertical farms, greenhouses and research institutions all over the world (including 8 out of 10 world’s largest agricultural companies).
Additional information:
Valoya Ltd, Finland
Tel: +358 10 2350300
Email: sales@valoya.com
Web: www.valoya.com
Facebook: https://www.facebook.com/valoyafi/
Twitter: https://twitter.com/valoya
Tips To Reduce Vertical Farm Costs
Light Science Technologies offers a bespoke solution that helps growers to achieve maximum yield while saving costs and energy
There are a number of key variables to consider when setting up your own vertical farm that calls for considerable financial clout. Light Science Technologies offers a bespoke solution that helps growers to achieve maximum yield while saving costs and energy.
The rising AgriTech start-up offers the first of two features offering tips to help you to reap optimum results and high returns.
Tip 1: Location, location, location
While you don’t need as much land as traditional growing, finding the right location for your vertical farm is crucial. The wrong location can prove a costly mistake, so do your homework before committing. Do you have the right local infrastructure in place to get your product to your buyer as efficiently as possible? Can you source enough electricity? How much does water cost in this county compared to the next one over?
Tip 2: Minimize energy costs
However, energy-efficient your operation is, you’re still going to use a huge amount of electricity every year. The most cost-effective solution might be to create your own renewable energy. That isn’t possible for all sites, but even micro-generation could help to bring your OPEX down.
Tip 3: Engage the experts
Let’s be frank: vertical farming is no small subject. Start building relationships as early as possible with people who know everything on it, from lighting and data to botany.
Tip 4: Balance OpEx and CapEx costs
Think big picture in terms of cost. Spending more initially could reap rewards later on. For instance, heavier investment in technology in order to automate seeding, feeding, watering and harvesting will require a greater initial outlay, but a far smaller workforce; labour costs can easily account for over 50% of a vertical farm’s OpEx.
According to CambridgeHOK, a small vertical farm with minimal automation costs around £1,000 per square metre to set up. A large farm with full automation will cost in the region of £3,000 per square metre. You’ll also need to factor in OPEX differences to the growing system you choose (hydroponic, aeroponic, and/or aquaponic).
Tip 5: Don’t cut corners
Buy wisely. Avoid gambling on cheaper products, such as mass-produced imported lighting. Ensure major costs come with decent guarantees and support in place should anything go wrong.
Cutting corners now could cause repercussions later down the line, and not just in maintenance and replacement costs. Cheaper options could spell inflexibility, killing your vertical farm’s true potential.
6. Choose your crops carefully
There are pros and cons to different types of crops. Quick-growing plants tend to be cheaper to grow, resulting in an abundance of product. However, some slower-growing crops, such as medicinal cannabis, can earn you far more per plant. Some crops require less energy. Others take up less space so you can pack more in. Fastidious research and number crunching will help you to choose the best option for your own vertical farm.
Tip 7: Know your audience
Assuming there’s a market for what you’re growing is where you could fall short. Many vertical farmers focus on fast-growing salad crops. In an optimized environment, you could end up producing 30 tonnes of salad a day. But can you guarantee sales of lettuce through the depths of winter? Potentially, this could either mean considerable wastage or letting part of your vertical farm sit idle for weeks on end, which will mean diminishing returns.
Sound planning and organization from the start is essential and will enable you to factor in a different crop switch every few months with flexible lighting systems if required.
For more information:
Light Science Tech
Claire Brown, PR Consultant
claire.brown@lightsciencetech.com
www.lightsciencetech.com
Publication date: Fri 8 Jan 2021
Year-Round Under-Glass Herb Cultivation In The Heart of Berlin
ECF Farmsystems uses innovative LED lighting solutions from Fluence for today’s herb cultivation in the heart of Berlin
Urban Farming Using LEDs From Fluence by OSRAM
ECF Farmsystems uses innovative LED lighting solutions from Fluence for today’s herb cultivation in the heart of Berlin. An innovative urban farm, ECF Farm Berlin (ECF Farmsystems) uses techniques for greenhouse and vertical cultivation of basil. The farm also uses aquaponics to naturally fertilize the crops, the produce of which then goes to Rewe, Germany's second-largest supermarket chain.
Less space and more production is the name of the game at ECF Farmsystems: comprehensive lighting solutions, from growing to greenhouse culture, enable the year-round production of uniform, aromatic basil plants.
Modern agriculture thanks to LED lighting / Image: Osram
Urban cultivation from seed to finished product
On-site propagation on VertiCCs, a racking system for vertical cultivation developed by ECF Farmsystems, increases production by 35% with the same footprint and optimized supply chain from seed to finished product.
The system also ensures consistent, uniform products. This is because ECF Farmsystems completely controls the entire growing cycle with less pest infestation and more accurate yield forecasting. In addition, the VYPR lighting systems offer higher-quality light spectra compared to conventional lamp systems. In addition, thanks to VYPR solutions, greenhouse growing is no longer seasonal, as efficient crop lighting provides uniform plants with consistent productivity, regardless of local weather.
With Fluence's RAZR Series, ECF Farmsystems achieves more effective operations and a 35% increase in production without the need for new construction or remodeling. By expanding vertical growing in the plant nursery, which eliminates the need to invest in additional growing space/facilities, ECF Farmsystems saves important emission costs. Propagation on VertiCCs systems with RAZR exposure allows ECF Farmsystems to control the entire growth cycle, better manage pests, and now calculate yields more accurately.
The new RAZR module will be available in January 2021.
For more information:
fluence.science/webinars
https://en.ecf-farm.de/
https://www.osram.com/os/applications/horticulture-lighting/index.jsp
Publication date: Thu 7 Jan 2021
Certhon's First Results of Indoor Strawberries Trial
Martin Veenstra, Indoor Farming specialist at Certhon: “This way of growing strawberries is unique because all grow parameters can be precisely controlled during the entire growth cycle
Martin Veenstra, Indoor Farming specialist at Certhon: “This way of growing strawberries is unique because all grow parameters can be precisely controlled during the entire growth cycle. From start to finish. This ensures optimum quality, yield, and fruit sizes, independent of the growing season. All grown without any pesticides and with a choice of both traditional as well as organic nutrients.”
The Certhon Innovation Centre consists of multiple indoor farms equipped with state of the art systems for LED lighting, climate control, CO2 dosing and irrigation systems which are all managed by Certhon's farm control system. In these farms, many crop trials are conducted for the indoor growing of a wide variety of plants, ranging from leafy greens to many vegetables and soft fruit. We would like to share exciting results of our trials with growing strawberries in our indoor farming system.
Results
Yields vary off course per strawberry variety, but at least a minimum of 26 up to 30 kg per m² per year with a consistent BRIX of 8 or higher is now available to every grower. Also, fruit sizes are much more consistent compared to open field or even greenhouse growing.
"At Certhon, we focus on the consistent and uniform top quality of the produce with an improved shelf life. In addition to optimizing the yield, we also put a strong emphasis on minimizing the power consumption for lighting and climate control. Also reducing water consumption is a strong focus point."
Martin: “We are continuously improving our trials and see even more potential in the very near future. Besides strawberries, we are also testing with tomatoes, lettuce, and raspberries.”
For more information:
Certhon
ABC Westland 555
P.O. Box 90
2685 ZH Poeldijk
The Netherlands
Tel: +31 174 22 50 80
Fax: +31 174 22 50 81
www.certhon.com
5 Jan 2021
Signify Adds Artechno To Its Philips Horticulture LED Partner Network To Lower Bar For Future Vertical Farmers
“Partnering with Signify is a logical choice for us,” said Art van Rijn, Owner of Artechno
January 4th, 2021
Signify Chooses Artechno As its New Philips
Horti LED Partner For The Unique Modular
Turnkey Vertical Farming Solutions That it Provides
· Lowers bar for growers and entrepreneurs to start a new vertical farm
· Helps to automate the production process for diverse crops from seed to harvest
Eindhoven, Netherlands – Signify (Euronext: LIGHT), the world leader in lighting, has signed a partnership agreement with Artechno, global provider of scalable Automated Vertical Farming systems, to make it easier for growers and entrepreneurs to start a state-of-the-art vertical farm using Philips GreenPower LED lighting. Artechno, headquartered in De Lier, the Netherlands, is an engineering company that develops and realizes unique automated cultivation systems based on hydroponic substrates for clients across the globe.
“Partnering with Signify is a logical choice for us,” said Art van Rijn, Owner of Artechno. “We’re a winning combination as we offer our customers the highest efficiency and highest reliability, while Signify provides energy-efficient lighting solutions that perform 24/7, 365 days a year. Together this will help our customers to grow tasty, high-quality produce year-round.”
Artechno has channeled 100+ years of combined experience in horticulture into its flagship product, Automated Vertical Farming, or AVF+. It offers a fully automated solution for producing a variety of crops from seed to harvest. Artechno has automated all processes to ensure low labor costs and consistent crop production. AVF+ is a modular system that can be customized to the needs of the crop, available space, or desired production volume. Growers and entrepreneurs can start with a few key components and scale up their automation and operation as they grow.
“We’re proud to expand our partnership network with the knowledge and expertise of Artechno,” said Udo van Slooten, Business Leader Horticulture at Signify. “They share our values of innovation, quality and reliability. This partnership will help us lower the barriers for growers and entrepreneurs who are considering a vertical farm by enabling us to offer Philips GreenPower lighting within fully modular and automated systems for every aspect of their operations.”
Signify continues to expand its horticulture partner network, further demonstrating its commitment to lead the horticulture industry as the innovative LED lighting systems provider for the indoor farming industry.
--- END ---
For further information, please contact:
Global Marcom Manager Horticulture at Signify
Daniela Damoiseaux
Tel: +31 6 31 65 29 69
E-mail: daniela.damoiseaux@signify.com
About Signify
Signify (Euronext: LIGHT) is the world leader in lighting for professionals and consumers and lighting for the Internet of Things. Our Philips products, Interact connected lighting systems and data-enabled services, deliver business value, and transform life in homes, buildings, and public spaces. With 2019 sales of EUR 6.2 billion, we have approximately 37,000 employees and are present in over 70 countries. We unlock the extraordinary potential of light for brighter lives and a better world. We achieved carbon neutrality in 2020, have been in the Dow Jones Sustainability World Index since our IPO for four consecutive years, and were named Industry Leader in 2017, 2018 and 2019. News from Signify is located at the Newsroom, Twitter, LinkedIn and Instagram. Information for investors can be found on the Investor Relations page.
How 4 Young Vertical Farming Visionaries Built A Thriving Business In Just 3 Years
Recently, in one of our most popular webinars of all time, Wihelmsson fired us up with Ljusgårda’s amazing story – building a thriving modern farm in what was once a factory, by “replacing the tractor with lights and the shovel with an iPad.”
An enthusiastic evangelist for modern vertical farming, Wihelmsson explained, “We took the concept of farming outdoors and brought it indoors, creating a controlled ecosystem where we can grow under optimal conditions year-round. We have a facility here of 7,000 sq meters.
Article from | Heliospectra
It all began in 2017 when three friends, Magnus Crommert, Cristoffer Barath and Erik Lundgren decided to try modern indoor farming. Our own Plant & Light Expert, Ida Fällström, remembers when Magnus visited our Göteborg office, introduced us to his team’s vision of modern farming, and left with an ELIXIA LED grow light under his arm. With that LED grow light, he started to conduct tests in his garage while the rest of the business took form, including bringing on a young business visionary, Andreas Wihelmsson, as partner and CEO. Fast forward to today, and their operation has grown to become Ljusgårda AB, a successful and sustainable climate certified farm in Tibro, Sweden.
Recently, in one of our most popular webinars of all time, Wihelmsson fired us up with Ljusgårda’s amazing story – building a thriving modern farm in what was once a factory, by “replacing the tractor with lights and the shovel with an iPad.” An enthusiastic evangelist for modern vertical farming, Wihelmsson explained, “We took the concept of farming outdoors and brought it indoors, creating a controlled ecosystem where we can grow under optimal conditions year-round. We have a facility here of 7,000 square meters. A year from now, we will have outgrown this facility and we will begin building the next one.” He continued, “If someone would have told me years ago that I would be growing salad for a living, I would have thought they were joking. Yet today thousands of families are eating our salad every week.”
What are the secrets to Ljusgårda’s overwhelming success? Here are 5 key things we learned in our webinar about starting a successful vertical farm:
5 Habits of a Highly Successful Vertical Farm
1. Quality Comes First
Wihelmsson commented that “More than 70% of all the fruits and vegetables Sweden eats are imported from other countries.” This leads not only to higher emissions, but it also negatively affects plant quality and nutrients due to the transportation time. Because indoor vertical farming enables Ljusgårda to grow locally, they always get their products to store within 24 hours of harvest to retain quality and nutrition.
2. Give Your Customers What They Really Want (Not What You Think They Want)
Ljusgårda produces salad greens, including lettuce and arugula, for Swedish tables year-round. Wihelmsson noted, “When it comes to making a produce buying decision in Sweden, 7 out of 10 people say that one of the most important factors is that it's Swedish. Sustainability and price are also very important. We provide a great tasting Swedish product that is sustainable, and we sell it at roughly the same price as imported products.”
When it comes to giving customers what they want on an individual crop level, Ljusgårda is able to use LED grow lighting and intelligent controls to influence every phase of plant growth, from biomass development to finish and flavour. Wihelmsson commented, “One very interesting experience we had was with our rocket salad, the first product we launched. I remember our initial tryouts and it tasted terrible.” He laughed, “We were by far growing the worst tasting rocket salad in the world, but we became better. We developed a good product with a robust peppery flavour, and we went to grocery stores for people to try it. Their polite reactions were that it was okay, so we knew that we had it dead wrong. We progressed by altering our rocket salad’s flavour through lighting control and conducting countless in-house and in-store taste tests.”
Wihelmsson continued, “We realized that Swedes didn’t want a traditional strong rocket salad. They wanted a mild one. We have a term in Sweden, Lagom, which relates to balance – not too little, not too much. We ended up producing a milder rocket and outsold all other products in that store.” He concluded, “You don't always know what the customer actually wants until you test in person and can see their reaction. If in the future customers demand a spicier rocket salad, we can achieve that with our flexible LED lighting. We have the ability to control taste, nutrition, quality, colour, biomass, almost everything – because light has a huge effect on the plants. You just first need to figure out what your customer wants in their food.”
3. Control Your Light to Optimize Your Production
An intelligent LED lighting strategy can help you achieve your crop goals. We have worked with Ljusgårda to accelerate their production of arugula and reduce their production time by 19%, by making adjustments to their lighting strategies. Wihelmsson commented, “For us, light control is very important to our production. If we look at our collaboration with Heliospectra, we chose to go with ELIXIA LEDs because we needed maximum flexibility. The other reason was their positive effect on reducing power consumption.”
Ljusgårda has also found that flexible LEDs can help them control risk and even save crops. Wihelmsson noted, “Now that we have been running this farm for a few years, we’ve come to see that our flexible lights can actually be used to compensate for human errors or things like the water tank failing or other issues. In such cases, we have been able to change the spectrum to recovery lighting. Our LED lighting has meant a lot to us and the flexibility has been extremely important.”
4. Automate Step by Step (and Plan Several Steps Ahead)
Wihelmsson talked about the company’s approach to automation, “We had to redesign the system to be able to get it automated step by step and growing-wise it's been working. For us most steps in production will be semi-automated, leveraging a machine but with human beings still involved, while other steps will be fully automated.”
He cautioned, “You need to do the math and see where automation makes economic sense for you. Our approach is to look at what takes up the most labour, what is most costly in the whole economic calculation, and address it. We also run the numbers to plan ahead. For example, we are preparing some processes for automation, but we won't automate them until production volumes hit certain critical numbers. Overall, it’s best to take it one step at a time, starting with a semi-automated approach.”
5. Keep it Simple and Learn from Others
Rather than focusing on the high-tech aspects of their operation, Ljusgårda found that their consumers responded better to a simpler, more straightforward message. Wihelmsson commented, “We know that our consumers want local produce, and so it says three times on the bag that our salad is from Sweden. We keep our messaging and packaging simple, ensuring people know that we are passionate about growing great tasting, nutritious, and sustainable food that they can eat in good conscience year-round. This simple, positive message has helped put our bag salad in the top three in each and every store, and it’s even number one in several of them.”
If you are interested in starting your own vertical farming operation or taking your farm to the next level, Wihelmsson suggested that you try to learn from others who have succeeded. He commented, “We have something we like to call common farmer sense. It's a direct translation from Swedish, and it basically consists of us questioning all the solutions that are out there and always telling ourselves not to reinvent the wheel. See if any industry or any other grower has already taken an approach you want to try. Take a look at it, learn from it, and then start growing from there.”
Watch the entire webinar here.
The content & opinions in this article are the author’s and do not necessarily represent the views of AgriTechTomorrow
Valoya Appoints A VP Sales North America
Valoya continues its growth trajectory with the addition of VP Sales North America, Mr. Wes Eaton. With extensive experience in horticulture and business development, Mr. Eaton will be tasked with driving Valoya’s growth in the North American market even further
Valoya continues its growth trajectory with the addition of VP Sales North America, Mr. Wes Eaton. With extensive experience in horticulture and business development, Mr. Eaton will be tasked with driving Valoya’s growth in the North American market even further.
Eaton’s horticulture industry experience is extensive, and his track record is impressive. Having worked in sales of two horticultural LED lighting companies he has a deep understanding of the horticulture lighting applications as well as the competitive landscape in North America. His experience prior to this includes working as a controlled environment agriculture consultant and developing meters and sensors for fertigation and control systems. He thus brings a deep understanding of the market and growers’ needs to the company.
In this role, he will be responsible for driving sales in crop science, cannabis cultivation, vertical farming, and greenhouse applications. Additionally, he will further develop Valoya’s North American reseller network within the cannabis market, as well as establish a local team. In meeting Valoya’s ambitious growth goals he will closely collaborate with existing customers, research partners, and distributors, to enable wider access to Valoya’s high-end LED solutions within the N.American market.
“Valoya’s ongoing commitment to deliver research-based, high-end lighting solutions is commendable. I am excited and honored to join the team and empower growers across North America to drive their plant performance to industry-leading results” says Eaton.
"We have been operating in North America since 2011 and it has always been a very important part of our business. Wes will build on this foundation to take us to the next level with his excellent experience and in-depth insight of the market", comments Mr. Lars Aikala, CEO and Co-Founder of Valoya.
Contact Mr. Eaton at – wes.eaton (at) valoya.com
About Valoya
Valoya is a provider of high-end, energy-efficient LED grow lights for use in crop science, vertical farming, and medicinal plant cultivation. Valoya LED grow lights have been developed using Valoya's proprietary LED technology and extensive plant photobiology research. Valoya's customer base includes numerous vertical farms, greenhouses, and research institutions all over the world (including 8 out of 10 world’s largest agricultural companies).
Additional information:
Valoya Ltd, Finland
Tel: +358 10 2350300
Email: sales@valoya.com
Web: www.valoya.com
Facebook: https://www.facebook.com/valoyafi/
Twitter: https://twitter.com/valoya
HortiPower Helps You Make Your HPS Lights Smarter
Several greenhouses are choosing hybrid lighting in which they combine LED lights and HPS lights. An issue with hybrid lighting however is that HPS lights are often not individually controllable, but rather by the whole row or group
A commonly used connector in horticulture is the Wieland rst20i3. Both HPS lights and LED grow lights are using this in the greenhouse and vertical farm.
Several greenhouses are choosing hybrid lighting in which they combine LED lights and HPS lights. An issue with hybrid lighting however is that HPS lights are often not individually controllable, but rather by the whole row or group.
With the HortiPower timer, growers are now able to turn the individual HPS lights on and off. The timer has a wifi-chip on board and supports max. 16 amp which means up to 6 grow lights of 600W with 230V.
The timer is controllable with MQTT protocol through the Amazon Web Services (AWS). Power measurement is possible as well.
The timer gives growers the ability to really choose which lights should turn on or off. Growers may use sensors and climate computers to make that decision for them and automation is possible through an API.
Watch a short intro here.
HortiPower | Right Light. Better Growth
HortiPower makes plant-centric lighting solutions for tissue culture, vertical farms and greenhouses.
For more information:
HortiPower
CANADA: Sustainable Agriculture With LED Lighting
GoodLeaf opened it’s fully commercialized, a state-of-the-art vertical farm in Guelph in 2018. This after many years of research at its pilot farm that opened in Truro, Nova Scotia in 2015
11-12-2020 | Philips Lighting
CANADA, Ontario, Guelph- GoodLeaf opened it’s fully commercialized, a state-of-the-art vertical farm in Guelph in 2018. This after many years of research at its pilot farm that opened in Truro, Nova Scotia in 2015.
We wanted a partner that could help us scale the business. ''
-Jeff McKinnon, Chief Financial Officer and Vice President | Photo Courtesy of Philips Lighting
The Challenge
For GoodLeaf it’s all about sustainability. The facility incorporated innovations to enable the use of sustainable farming practices to execute on expectional product quality. With lighting being a primary component, GoodLeaf had specific needs they expected from a lighting solution and provider. The envisioned lighting solution needed to provide scalability whilst being energy efficient. GoodLeaf was looking for a true partner.
The LED lighting solution
“We’ve been using the Philips products since Generation one back in 2013; we did a lot of testing against the T5 light bulb. The Production Module Gen 1 performed well, they held up over time compared to competitors, using them ever since”, says Jeff McKinnon, CFO and VP at GoodLeaf. Over time GoodLeaf worked with 12 different providers of LED lights but in Signify found the partner they were looking for to move forward and to scale their business.
For their 45000 SQF multilayer growing facility in Guelph, Goodleaf installed Philips GeenPower LED production modules. The light recipe was designed in collaboration with the Truleaf design team and engineers together with the plant specialists of Signify. The installed lighting system delivers optimal lighting uniformity.
Benefits
As a branded producer, GoodLeaf Farms produces and packs fresh, nutritious, and pesticide-free micro and baby greens year-round for Canadian consumers. They expect to grow and harvest approximately 1 million pounds of fresh produce per year at their automated growing facility in Guelph. Plant specialists of GoodLeaf and Signify meet monthly to discuss optimizing their crop growth recipe. As part of the partnership, GoodLeaf has greatly improved the predictability of its fresh produce. In addition, Signify and GoodLeaf worked together to obtain a sizable utility rebate from the company’s hydro provider in Ontario. McKinnon said, “The partnership with Signify has been very advantageous to GoodLeaf. We will work with them on a go-forward basis and very much look forward to that”.
GreenPower LED Production Module Static Grow Light
A static module for multilayer applications with the ideal light recipe for higher yield, better quality, higher propagation success rates, and year-round production. Suitable for multilayer, indoor cultivation of leafy greens, microgreens, and herbs.
Source: Philips Lighting
Header photo: Screenshot from GoodLeaf Farm video on youtube
GE Current Expands Horticulture Distribution Network To Support Indoor Growers Across Eurasia
Current’s Lucalox and Arize lighting solutions are available now. Customers can contact their local distribution partner for more information and advice on the best Current solution for their individual greenhouse set-up
GE Current, a Daintree company, has signed three new distribution partnership agreements with Agro Top Garden, Helle-Tech Oy, and Vitro HTS to make its full Lucalox HPS and Arize LED portfolio available to more greenhouse growers across Europe and Asia. The deals inked will provide growers focusing on horticulture, floriculture, and the burgeoning medicinal cannabis market, with easier access to leading lighting technologies, whether they rely on traditional HPS or are looking to transition over to low-energy LEDs to meet net-zero carbon goals.
Malcolm Yare, Business Development Manager for Horticulture at Current, commented, “There are all sorts of variables that combine to create the most productive greenhouse environment, from location and surrounding geography, to weather patterns and the type of crop grown. We want to ensure that greenhouse growers have access to the perfect lighting for their unique set-up. By expanding our network of distribution partners, we can ensure that growers receive expert, localised advice and support to ensure that they get the right Current system to maximise their yields and grow their businesses.”
Agro Top Garden is now the exclusive European distributor of Current’s Lucalox HPS lighting to the medicinal plant market, as well as being a master distributor of the company’s Arize LED portfolio. With a depth of broad horticultural experience, Agro Top Garden advises customers on the best growing media and fertilisers for their flowering plants. Now, with Current’s broad portfolio at its disposal, the company will also be able to advise cannabis growers on the most appropriate, low-energy lighting technology to nurture high-quality, abundant harvests every time.
Based in Finland, Helle-Tech Oy provides a range of greenhouse products, up to complete turn-key installations. With more than 30 years’ team experienced in building greenhouses all over Europe and Russia, Helle-Tech Oy partners with its customers throughout every stage of planning and installation, followed by close support and counsel, in order to maximize the potential of each greenhouse. With more growers looking to reduce their energy bills and carbon footprint, Helle-Tech Oy is expecting to guide many more customers through the transition from HPS to LED lighting in 2021, working with Current’s lighting experts to maintain yields and income throughout the process.
Vitro HTS is based at the heart of Eurasia, in Antalya, Turkey, and is focused on supporting growers across Turkey, Georgia, Armenia, and Azerbaijan. With new investments in horticulture and floriculture across the region, Vitro HTS is ideally positioned to support new market entrants and existing growers with Current’s state-of-the-art lighting systems that reduce energy consumption and costs, whilst boosting revenue.
Current’s Lucalox and Arize lighting solutions are available now. Customers can contact their local distribution partner for more information and advice on the best Current solution for their individual greenhouse set-up.
For more information:
www.gecurrent.com
agrotopgarden.de
www.helle-tech.fi
www.vitrohts.com
1 Dec 2020
New OEM -Agreement For Shelf-And-Lighting Panels For Industrial Vertical Farming
The strategic partnership between Senmatic and LED iBond is based on Senmatic’s in-depth knowledge of LED grow lights and software solutions for industrial vertical farming and LED iBond’s unique LED technology platform
Danish-based companies Senmatic and LED iBond International have entered a strategic OEM-partnership for delivery of shelves with built-in grow light to advance the industrial vertical farming industry – a production method globally foreseen to gain currency among producers in the future.
Senmatic and LED iBond International have entered a strategic partnership for OEM delivery of shelves with built-in grow light to be included in Senmatic’s offering of industrial vertical farming solutions. In vertical farming you utilize the cubic meters by planting in layers rather than the square meters, as traditionally done with row upon row of plants and crops.
The new vertical farming shelves are based on LED iBond’s patented lighting fixture, which combines superior cooling characteristics and minimal space requirements with a high carrying capacity.
Photo by: LED iBond
The strategic partnership between Senmatic and LED iBond is based on Senmatic’s in-depth knowledge of LED grow lights and software solutions for industrial vertical farming and LED iBond’s unique LED technology platform.
- We have more than 40 years of experience with indoor plant production. We will combine LED iBond’s super-slim and energy-efficient shelf-and-lighting panels with our controllers and software to create a multifunctional vertical farming solution with best-in-class growth conditions for industrial indoor horticulture. This new partnership with LED iBond will further contribute to our growth in the vertical farming market, so we are very pleased indeed for this opportunity to join forces with LED iBond, says Mads Nychel, CEO at Senmatic.
The joint vertical farming offering is planned to launch at the end of Q4 2020.
WEBINAR: The Importance of Light Quality In CEA Systems
Spectrum has an important impact on plant growth, morphology, and development. Plants have evolved a sophisticated photoreceptor system capable of perceiving small changes on the light spectrum
Date: November 19, 2020
Time: 2 p.m. - 3 p.m. EDT
Presented by: Ricardo Hernandez (NCSU)
Click Here to Register
Spectrum has an important impact on plant growth, morphology, and development. Plants have evolved a sophisticated photoreceptor system capable of perceiving small changes on the light spectrum. Plants use spectral changes as information to adapt and increase survival and reproduction. Therefore, by understanding plant-light interactions, we are able to use light as a tool to change plant responses to meet human needs. This presentation will outline the importance of light quality and provide examples of the commercial applicability of spectral manipulation.
Dr. Ricardo Hernandez is an assistant professor at North Carolina State University focused on Controlled Environment Agriculture research and teaching (https://ceh.cals.ncsu.edu/). He has worked in the field of spectral optimization for over 10 years. In addition to his academic appointment, Ricardo is also a co-founder of two start-ups focused on the use of controlled environment technology and strategies to produce young plants.
Special thanks to our Industry partners
Join today
If you have any questions or would like to know more about GLASE, please contact its executive director Erico Mattos at em796@cornell.edu
The 5 Best LED Grow Lights To Use For Indoor Plants And Greenhouse Growing
Grow lights mimic natural sunlight and utilize the correct color spectrum to encourage photosynthesis to help plants grow indoors
The best grow lights allow us to garden indoors and in our greenhouses throughout the year. Grow lights mimic natural sunlight and utilize the correct color spectrum to encourage photosynthesis to help plants grow indoors. LED grow lights are energy-efficient, long-lasting, and have the full light spectrum, and we’ll cover the best LED grow lights in this article for indoor and greenhouse growing. This article will cover the best grow lights to use for indoor and greenhouse growing.
Kind LED Grow Light K5 Series This is one the best LED grow lights for indoor plants because of its grow light spectrum. This provides plants with a wide range of lights to optimize their growth and lets you grow all kinds of crops year-round. You can use these LED lights for hydroponic and indoor growing.
MD Lighting LED Grow Light This LED lighting system is set up like a lamp and allows for LED replacement bulbs for long-lasting use. It uses the right wavelengths to help encourage and promote plant growth. The grow light is easy to adjust and move to ensure all parts of the plant are receiving an equal amount of sunlight. It’s energy-efficient and saves money on electric bills.
Phlizon 1200W LED Grow Light The Philzon 1200W is one of the best LED grow lights for indoor plants and greenhouse growing. This grow light system doesn’t use a reflector in order to reduce heat emissions for plant protection. It’s known for generating less heat, being energy efficient, which is a cost-effective solution for electric bills. There are two light switches: VEG (blue and white LED light) which is used to promote young vegetative growth, and BLOOM (red and white LED) to promote flowering and blooming in the plants. The full spectrum of light can be found in this grow light to ensure your plants get the necessary nutrients.
HAUS Bright LED Grow Light Bulb These bright LED growing light bulbs provide a full spectrum of light that will help you grow your plants indoors all year round. It’s easy to install since it’s a light bulb and you can hang it anywhere! Only 20w of power is used, but it still produces 1200 lumens to keep your plants healthy.
Aceple Small LED Grow Light This LED grow light is perfect for small plants like succulents or potted plants. This Aceple grow light is one of the best LED grow lights for indoor plants and you can set it up at your office or wherever you may have a small assortment of plants. It provides red and blue lighting, which is essential for healthy leaves and blooming.
Want to learn more about the best LED grow lights for indoor plants and greenhouse gardening? Join our microgreens class to learn the basics about everything there is to know about microgreen and indoor growing. If you can’t sign up for our class, subscribe to our weekly blog and Youtube channel for weekly updates!
#bestledgrowlightsforindoorplants #bestgrowlight #indoorgrowlight #growinglight #growlight #bestgrowlights
Unleashing The Potential of Indoor Sole-Source LEDs on Tomato Production
Enlightening collaboration between Heliospectra and the University of Tokyo
Enlightening Collaboration Between Heliospectra And The University of Tokyo
Heliospectra announced a collaboration with the Institute for Sustainable Agro-ecosystem Services (ISAS), the University of Tokyo. In an effort to redefine and unleash the potential of indoor tomato production, this will be a joint research project with the University’s Institute for Sustainable Agro-ecosystem Services (ISAS), in collaboration with Associate Professor Wataru Yamori at the Agricultural Biology and Biogeochemistry Group, and Heliospectra Japan.
With the average age of Japanese farmers reaching 67 years old and younger generations migrating to cities, traditional farming is facing a crisis. This is forcing the country to investigate new ways to produce food. Plant factories are scaling to meet consumer food demand, mainly in vegetable cultivation in both solar and artificial light environments, and the industry is growing. Japan already has approximately 200 lettuce factories using artificial light, and that number is expected to double by 2025. However, to-date, plant factories have been unsuccessful in cultivating light-hungry vine crops such as tomatoes in indoor artificial light. Heliospectra and the University of Tokyo want to challenge this.
Working together, they are looking to build a business model for Japan’s plant factories and PFAL (Plant Factory with Artificial Lighting) organizations for indoor tomato cultivation. In the University lab, the Professor and his students will be using Heliospectra’s MITRA linear, the horticulture market’s first truly modular LED light. Designed by growers for growers, MITRA is a solution for high-light crops, with high-intensity light output and electrical efficacy of up to 2.8 µmol/J.
“We are very excited to be a part of this research together with Dr. Yamori and the ISAS at the University of Tokyo. Over the years, Heliospectra has conducted research on light’s effect on tomatoes in indoor facilities with great results,” comments Yasuhiro Suzuki, General Manager of Heliospectra Japan. “We now look forward to further expanding our knowledge and developing more effective indoor cultivation of tomatoes for commercial use. We look forward to collaborating with the university and sharing with the world our knowledge of growing tomatoes indoors.”
For more information:
Heliospectra
info@heliospectra.com
www.heliospectra.com
Publication date: Thu 29 Oct 2020
Increasing Lettuce Leaves' Fresh Weight by Light Treatments
Italian researchers dove into the matter and trialed three spectra to see what the effects would be on the crop and what the potential is for growing vegetables at your house
While red light is widely considered the visible spectral region with higher effects on photosynthesis, the amount of blue required for different species is an ongoing question. Italian researchers dove into the matter and trialed three spectra to see what the effects would be on the crop and what the potential is for growing vegetables at your house.
By Mattia Accorsi PhD (1); Federico Carotenuto PhD (2)
1) Biologist2) Researcher CNR IBIMET Florence
Light-spectrum manipulation
The research deepen the enhancement of the nutraceutical components in indoor primary production through only the light-spectrum manipulation. To achieve the experimental results was built, in collaboration with the Department of Agronomical Sciences (University of Bologna), an integrated and automated indoor prototypal growing system. In the prototype different state-of-the-art LED lighting lamps prepared ad hoc by C-LED (www.c-led.it) are compared in order to pinpoint the best spectral characteristics for food production as well as the most energy-efficient solution.
Material and methods: Sampling Location, hydroponic system, and plant material
Indoor growing system was divided into three sectors separated by a non-reflective opaque membrane. Each sector held two draining trays with 8 pots each containing a 50:50 perlite-vermiculite growing medium. The automated irrigation system dispensed 30” of irrigation each three hours from 6:00 to 22:00 (local time) and again at 2 am. A 200 liters tank, refilled weekly, was used as the water reservoir. To the irrigation water were added a series of nutrients. Room temperature was regulated at 18 ± 2 °C between 8 am and 20 pm, and at 16 ± 2°C between 20 pm and 8 am, by the building HVAC system. Each sector (i.e.: each of the three columns with three shelves each) had a specific light spectrum supplied by different LED lamps. Each shelf (i.e.: each row of the scaffolding) contained one of the three varieties of lettuce (Lactuca sativa L.): var. Maravilla de Verano, var. Lollo Rosso, and var. Crispa. In this way, each variety was illuminated by the three different spectra, therefore generating nine combinations between variety and lightning.
Agronomical and morphological determination
Determinations on the number of leaves, LAI, and growth rate were conducted weekly for the entire duration of the plants’ growth since the transplanting (Zink and Yamaguchi, 1962). Plants’ biomass in fresh weight (FW) and dry weight (DW) production were analyzed at harvesting time. Values of electroconductivity (EC) and pH of water tank and drainage was checked three times per week with a conductometer model Basic 30 (Crison instrument, Barcelona, Spain). The content of nitrogen in the leaf tissues was measured weekly utilizing a Yara N-Tester (Oslo, Norway), taking thirty measurement per plant. Vegetables’ yield was related to the lamps’ energetic consumption in order to evaluate the energy use efficiency (EUE) and expressed as g kW-1.
Figure: Morphology of three lettuce varieties (Meravilla de Verano, Crispa and Lollo Rosso), treated with three light spectra at 200 PPFD. Picture acquired at harvesting time (30 DAT). Effects on color intensity (green index) and pigment composition will be deepen in next article.
Biochemical determination
At harvesting time, 30 days after transplanting, a portion of leaf tissues of different theses were collected and stored in polyethylene bags at -20°C until processed. Extraction and quantification of total phenolic and flavonoid contents was conducted as described in Piovene et al. (2014). Antioxidant capacity was determined with the 1,1-diphenyl-2-picrylhydrazyl (DPPH) method as described by Floegel et al. (2011), in order to evaluate the additive and synergistic effects of all antioxidants rather than the effects of single compounds (Brighenti et al., 2005; Puchau et al., 2009).
In all lettuce varieties, leaves’ fresh weight was significantly increased by light treatments. Thesis A (110±34g) and C (112±42g) determined a better production in respect to B (90±34g) as shown in figure. Between three lettuce varieties, at 30 days after transplanting (DAT), Meravilla de Verano showed the highest fresh biomass production with 135±28 grams per plant while Crispa and Lollo Rosso varieties had a production of 104±31g and 72±25g respectively. Dry: Fresh biomass ratio (DFr) revealed opposite trend with respect to total fresh food production: treatment B showed higher DFr with values of 1.34±0.15. These values were significantly different in respect to A (1.25±0.12 ) and C (1.10±0.98).
Discussion: Light characteristics and physiological implications
An increasing interest in indoor growing within the urban area is reflected in a multiplication of commercial solutions making use of soilless systems and precision agriculture techniques (Massa et al., 2008; Poulet et al., 2014; Specht et al., 2014). Differently to artificial lighting technologies such as HPS and fluorescent lamps, LED lighting allows a concrete energy saving and to choose the light spectrum for specific purposes (Ilieva et al., 2010). Continuous advancements in LED technology, allow in-depth research on physiology and biochemistry of plants, two-sector of botany strictly correlated with the quality and quantity of the incident light (Horton, 2000; Poulet et al., 2014).
While red light is widely considered the visible spectral region with higher effects on photosynthesis, the amount of blue required for different species is an ongoing question. Red wavelengths (600-700nm) contain the peak absorption of chlorophyll around 660nm (Massa, 2008). Photosystem I (PSI) and photosystem II (PSII) intercept photons respectively around 650nm (PSII) and 700nm (PSI) (Schopfer and Brennicke, 2010). Blue wavelengths (400-500nm) revealed a variety of important morphological (Blaaw and Blaauw-Jansen, 1970; Cosgrove, 1981), and physiological (Schwartz and Zeiger, 1984; Kinoshita et al., 2001; Horrer 2016; Wang et al., 2016) effects.
In this project, all three light spectra integrate a low percentage (8-19%) of green light. These wavelengths were added to continue the work of Piovene (2015) that identified a specific combination of BRr and green for stimulation of biomass production and nutraceutical characteristics. Other works in literature in mentioned green wavelengths for positive effects towards functional compounds content (Samuolienė et al., 2012) and physiological response to photosynthetic light (Kim et al., 2005; Johkan et al., 2012).
How light spectra influenced food production
This study did not identify the correlation between the percentage of green light and biomass production or nutraceutical characteristics (statistical data not shown) contrary to what stated by the work of Kim et al. (2005) who found positive influence in biomass production with the addition of 24% of green light. Anyway, green light, especially if added to the only red and blue LED, completes the visible spectrum and hence helped in the aesthetic presentation of the plants which appeared less purplish-gray and more natural. Therefore, the latter effect of green light within a growing spectrum, would help in better fitting the plant in the indoor living environment for human purposes and ease the identification of disease onset (Massa et al., 2008).
Figure: Study of LED C-LED lamps in collaboration with an italian university. Range of PAR, UV and Far-red are deeply analizyed in product prototyping process.
The food production has shown significant differences between lettuce varieties and light spectra. Taking into consideration only the lettuce varieties, Meravilla de Verano showed the best yield in respect to Crispa and Lollo Rosso. Light spectra, on the other hand, confirmed that the optimal ratio between red and blue has great relevance in influencing crop yield. While a certain quantity of blue light is necessary for a proper physiological balance (Yoro et al., 2001), this study showed that lower BRr has a positive influence on food productivity across lettuce varieties in accordance with previous researches (Wang et al., 2016). In general, it seems that the optimal BRr is somewhat species-specific since, for example, leafy aromatic vegetables showed better biomass production with a higher percentage of blue wavelengths (Piovene et al., 2015; Abiusi et al., 2013). On the other hand, strawberry showed an improvement of vegetative growth when the red percentage was higher than blue, although compensated by a background white light (Samuoliené et al., 2010)
In fact, many researches points out how plants require a complex spectrum that may include green: this parameter increase the difficulty to choose the “correct” light recipe, considering a number of factors such as specific species-varieties- phonological stage requirements (Wang et al., 2016; Kim et al., 2005).
Nutraceutical implications
Different studies described how BRr influences nutraceutical properties in vegetables grown in indoor condition (Bantis et al., 2015; Piovene et al., 2015). Correlation between polyphenols and flavonoids content with antioxidant capacities has been documented (Dudonne´ et al., 2009; Samaniego Sanchez et al., 2007; Puchau et al., 2009). Polyphenols have an important antioxidant capacity determined by their ability to act as radical scavengers (Carter et al., 2006; Fardet, 2010). In nature, polyphenols are generally accumulated in plant tissues as response to external factors (Loaiza-Velarde et al., 1997). In indoor controlled growing system water, nutrition and microclimate are generally optimized: a particular light spectrum may therefore improve nutraceutical properties through photochemical induction and may, therefore, have a dramatic importance for human nutrition.
The three-light theses tested in this project revealed significant effects on the functional compounds such as phenolics and flavonoids, as well as the antioxidant activity. These data confirm previous works conducted with LED light manipulation (Piovene et at., 2015). In this work, antioxidant activity showed), an attitude of blue light to improve the antioxidant properties of lettuce (Figure 8) with a good correlation coefficient (R2=0.776). This is in accordance with previous researches that correlated the amount of flavonoids and antioxidant activity with blue light stimulation (Ebisawa et al., 2008; Kojima et al., 2010; Ouzounis et al., 2016). Blue light revealed also to be effective in increasing chlorogenic acid (Awada et al., 2001), that has higher antioxidant activity than carotenoids and tocopherols (Rice-Evans et al., 1997).
Fresh food possesses significant amounts of antioxidant and, due to its regular consumption, highly contributes in providing dietary antiradical protection (Deng et al., 2013; Harasym and Oledzki, 2014). Generally, fresh fruits have higher level of total polyphenols, total flavonoids and antioxidant capacity than vegetables (Chun et al., 2005) but, due to the higher consumption of vegetable the antioxidant uptake may be much lower. In epidemiologic studies (Chun et al., 2005) the daily nutraceutical uptake may be estimated at 129mg for TPC and 17mg for TFC.
The indoor experimental structure tested in this study guaranteed a certain TPC and TFC production. Considering the average consumption of 0.27 Kg d-1 person-1 (Leclercq et al., 2009; USP-BO 2013) is possible assert that indoor soilless system lighted with all LED spectrum allowed an average uptake of 6% of TPC and 6.2% of TFC.
Figure: Fresh weight of yield (g plant-1) correlated with Blue:Red ratio highlighted with empty circles (○); Antioxidant activity (DPPH) correlated with Blue:Red ratio highlighted with full circles (●).
Read more on the indoor food production sustainability and the conclusion of the research here.
Lead photo: Figure: Experimental vertical farming system realized in C-LED headquarters. Lettuce varieties at 30 DAT (harvesting time). From right to left: spectra thesis A, B and C. From top to bottom lettuce varieties: Lollo Rosso, Meravilla de Verano and Crispa
27 Oct 2020
New OEM-Agreement For Shelf-And-Lighting Panels For Vertical Farming
Senmatic and LED iBond International have entered a strategic partnership for OEM delivery of shelves with built-in grow light to be included in Senmatic’s offering of industrial vertical farming solutions
Senmatic and LED iBond International have entered a strategic partnership for OEM delivery of shelves with built-in grow light to be included in Senmatic’s offering of industrial vertical farming solutions. The new vertical farming shelves are based on LED iBond’s patented lighting fixture, which combines superior cooling characteristics and minimal space requirements with a high carrying capacity.
The strategic partnership between Senmatic and LED iBond is based on Senmatic’s in-depth knowledge of LED grow lights and software solutions for industrial vertical farming and LED iBond’s unique LED technology platform.
"We have more than 40 years of experience with indoor plant production. We will combine LED iBond’s super-slim and energy-efficient shelf-and-lighting panels with our controllers and software to create a multifunctional vertical farming solution with best-in-class growth conditions for industrial indoor horticulture. This new partnership with LED iBond will further contribute to our growth in the vertical farming market, so we are very pleased indeed for this opportunity to join forces with LED iBond," says Mads Nychel, CEO at Senmatic.
Rolf H. Sprunk-Jansen, CEO of LED iBond, adds: "The new partnership with Senmatic marks LED iBond’s commercial entry into the industrial vertical farming market. With their vertical farming technology and their global network of 40 dealers, Senmatic is an ideal partner for us, bringing our LED panel technology into play in an emerging industry with huge growth potential. The agreement with Senmatic makes us even more confident that LED iBond’s financial outlook is well within reach."
The joint vertical farming offering is planned to launch at the end of Q4 2020.
For more information:
Senmatic
Publication date: Tue 20 Oct 2020