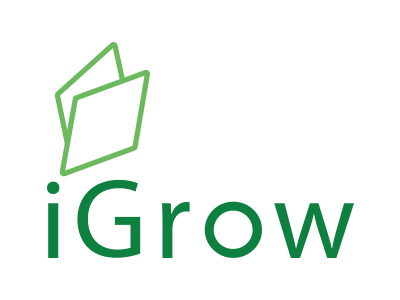
Welcome to iGrow News, Your Source for the World of Indoor Vertical Farming
Greenhouse Technology Could Be The Future of Food
Greenhouse Technology Could Be The Future of Food
Published: Jan. 17, 2018 • By Trent Knoss
Professor Ronggui Yang (left) and Assistant Professor Xiaobo Yin. Photo by Glenn J. Asakawa / University of Colorado Boulder
CU Boulder engineers have received a $2.45 million grant from the U.S. Department of Agriculture (USDA) to develop a scalable, cost-effective greenhouse material that splits sunlight into the photosynthetically efficient light and repurposes inefficient infrared light to aid in water purification. The material can also split the light streaming into greenhouses into rays that plants can use more efficiently.
The four-year research program could yield next-gen technology capable of solving food, energy and water security challenges posed by global population growth and climate change.
The study, administered under the USDA and National Science Foundation’s Innovations at the Nexus of Food, Energy and Water Systems (INFEWS) program, will be led by researchers from CU Boulder’s Department of Mechanical Engineering in collaboration with Michigan State University’s Department of Horticulture and Department of Mechanical Engineering.
“We are excited to work on a project that addresses one of the most important global challenges with our multidisciplinary colleagues at CU and MSU,” said Ronggui Yang, a professor of mechanical engineering who will lead the team.
Greenhouses have been used since the 1960s and remain the standard for effective plant productivity compared to open-field agriculture. But the structures carry high energy costs, requiring tremendous amounts of energy for heating, ventilation, electrical lighting and water for evaporative cooling. By the year 2050, current greenhouse capabilities will likely be unable to keep up with worldwide human consumption, making an increase in productivity an urgent mandate.
Under normal conditions, plants only use around 50 percent of incoming sunlight for photosynthesis while the remaining half goes unused.
“The new CU Boulder technology will take the form of a semi-translucent film that splits incoming light and converts the rays from less-desired green wavelengths into more desirable red wavelengths, thus increasing the amount of photosynthetically efficient light for the plant with no additional electricity consumption,” said Xiaobo Yin, an assistant professor of Mechanical Engineering and Materials Science and Engineering at CU Boulder.
The thin engineered material can be applied directly to the surface of greenhouse panels. The technology also makes use of the photosynthetically ineffective light by redirecting it to aid in solar-driven water purification.
“The near-infrared wavelengths can help clean brackish wastewater, allowing it to be recirculated in an advanced humidification-dehumidification interface and further reducing the greenhouse’s energy footprint,” said Yang, an American Society of Mechanical Engineers Fellow.
The innovation could help improve U.S. agricultural competitiveness and lead to new best practices for greenhouse systems in different climates, especially in arid regions with limited freshwater availability where crops cannot be grown profitably.
The technology expands on the researchers’ previous successful efforts to develop a suite of scalable engineered materials that can cool structures and improve solar panel efficiency, among other applications.
The researchers plan to create a pilot greenhouse facility to test the material’s properties over the course of multiple tomato production cycles and, later, expand the test to leafy greens such as lettuce and herbs.
A New Report on SSL’s Energy-Saving Potential in Horticultural Applications
A New Report on SSL’s Energy-Saving Potential in Horticultural Applications
DOE has just released a report that examines the energy-saving potential of LED lighting in horticultural applications. All three main categories of indoor horticulture were investigated: supplemented greenhouses, which use electric lighting to extend the hours of daylight, supplement low levels of sunlight on cloudy days, or disrupt periods of darkness to alter plant growth; non-stacked indoor farms, where plants are grown in a single layer on the floor under ceiling-mounted lighting; and vertical farms, where plants are stacked along vertical shelving to maximize grow space, and the lighting is typically mounted within the shelving units.
DOE utilized data from U.S. agriculture and horticulture censuses, as well as catalog and product specification databases for horticultural lighting products, and interviewed growers, utilities, lighting manufacturers, retailers, and other industry experts.
Among the findings:
- Based on current performance, LED lighting offers 24% to 30% reduction in electricity consumption per ft2 of grow area for each of the three categories.
- Non-stacked indoor farms employ the most energy-intensive lighting, with incumbent technology using about 60W/ft2 and LED lighting 41.8 W/ft2.
- Of the three categories of indoor horticulture, vertical farms have seen the highest adoption of LED lighting, which comprises 66% of all lighting in that application, while LED products make up only 2% of the lighting in supplemented greenhouses and 4% of the lighting in non-stacked indoor farms.
- In 2017, horticultural lighting installations in the U.S. consume a total of 5.9 terawatt hours (TWh) of electricity per year, which is equivalent to 61 trillion Btu (tBtu) of source energy consumption. Of this 5.9 TWh, 89% comes from lighting in non-stacked indoor farms, 10% from supplemental lighting in greenhouses, and 1% from lighting in vertical farms.
- If all horticultural lighting today was converted to LED technology, annual horticultural lighting consumption would be reduced to 3.6 TWh, or 37 tBtu, which represents energy savings of 40%, or $240 million.
For the complete findings, download the full report.
Helping Small-Scale Operations Develop A Recipe For Horticultural Lighting Success
Helping Small-Scale Operations Develop A Recipe For Horticultural Lighting Success
December 19, 2017
By Jeff Mastin
Venntis Technologies LLC
During the Emerging Applications track at Strategies in Light (SIL), co-located with The LED Show and Lightspace California in Long Beach, CA, Venntis Technologies biologist Jeff Mastin will explore the landscape of modern farming on the smaller scale, with a presentation on the economics of equipping a small indoor/vertical farm and how such operations can leverage the qualities of LED-based horticultural lighting. Mastin explains the appeal of close-to-consumer growing operations, but notes that a smaller operation will naturally need a different approach than a mass commercial grower. In the presentation “Small-scale vertical farming success recipes: Horticultural lighting reports from the field,” he will address a Michigan-based grower as a case study for analyzing the horticultural lighting needs of localized vertical farms with specific crop and usage objectives. Here Mastin looks at the prospects and exciting opportunities for both the grower community and the solid-state lighting (SSL) industry in expanding this horticultural niche. — Carrie Meadows
Where does our food come from? Three generations ago, this question had much simpler and well-known answers. Most food was derived from family gardens and family farms. Organic, local, sustainable, hydroponic, aeroponic, vertical-farming, container farming, etc. — these terms were not in our vocabulary with the absence of a dozen ways to buy lettuce at the local grocery store. After recent decades of urbanization, population growth, climate care (or lack thereof), and both geographic and relational disconnect from our food sources, vertical farms are an exciting new approach to shorten these distances in fascinating new ways with the help of recent technological advancements. Most foundational to the ability to move some types of farming indoors into dense, highly productive spaces is the advancement of LED-based horticultural lighting technology to make it possible to grow without the Sun and have a chance at economic viability.
Lighting as a Platform Part I: What It Is and Why You Should Care
In the world of the smart building, smart has real meaning. Creating buildings whose performance is optimised with respect to a variety of goals and which meet the increasingly challenging demands of building and energy efficiency regulations is a tough job these days. Energy use must be minimised and operating costs kept low.
Brought To You By LED - Bluetooth Feed
Related: 10 Things to Love about Strategies in Light 2018
LEDs Magazine will continue its countdown to Strategies in Light with more industry insights here at ledsmagazine.com. You can find details on the conference program, speakers, exhibitors, and more at strategiesinlight.com.
Within the realm of vertical farming, besides both strong proponents and objectors, there is also a wide spectrum of approaches. Vertical farmers can grow in soil, hydroponically, or aeroponically; use pallet rack shelving or vertical towers with plants growing horizontally; invest in various levels of control of humidity, CO2, isolation from potential pests; establish operations in abandoned warehouses or new facilities; and focus on “simpler” crops like leafy greens and herbs or break metaphorical ground on potentially higher value crops. For the Feb. 14 Strategies in Light session, we will of course focus on the various options and opportunities related to the critical lighting component of vertical farms, with an emphasis on how the scale of the vertical farm may impact horticultural lighting choices.
Garden manager Christy Kaledas has established indoor vertical farming operations that utilize LED horticultural lighting for the Black Pearl restaurant in Ann Arbor, MI.
Understandably, the most press is given to the largest vertical farming entities such as Plenty, which has raised at least $260 million to date with visions of large vertical farms on the outskirts of every major city. However, your local news might also have shared a story recently about a garage, basement, classroom, or industrial space that is now growing microgreens, leafy greens, or herbs for local restaurants, groceries, and farmers’ markets. In many cases, these are self-funded and driven by conversations with local chefs regarding exactly what they’d like to be adding to their menu next. The specifics of how these grow operations are set up are dictated by budget, physical space constraints, and information sources. Many of these growers are coming out of non-horticultural career paths and are learning from blogs, books, university extension offices, equipment suppliers, and other sources.
Related: Strategies in Light tracks send strong signals about lighting prospects
For the largest-scale vertical farmers, lighting technology is often developed in-house to lower costs. Facilities are large enough to justify multiple lighting approaches where experience, curiosity, or a physical constraint makes it worthwhile. These can include lights of various intensities and spectra. However, for smaller-scale vertical farmers, developing their own horticultural lighting is not an option. Furthermore, changes in their operation as they grow, changing customers, and the completely unforeseen places a premium on versatility within their lighting source. At any scale, upfront costs and operating costs are extremely important as lighting can represent a very large proportion of both costs. Furthermore, lighting performance will have a drastic impact on growth quality and quantity.
An example to be discussed in detail at Strategies in Light will be Black Pearl Gardens. The Black Pearl restaurant recruited its garden manager, Christy Kaledas, to begin growing microgreens and other crops for the restaurant in 2014. The small vertical farm began in Christy’s basement until the restaurant basement was ready, and has since expanded to include a warehouse facility for increased production space. The aforementioned need for versatility resulted in early setups using soil-filled trays, simple and adjustable wire shelving, and TotalGrow Broad Grow Spectrum LED lamps on flexible socketed cords, which could be configured to match the various setups that fit in the basements. The modular, individual lights with an all-purpose growing spectrum also allow the ability to adjust lighting concentrations as needed for different crops and production schedules. Most of this equipment is still used in the new spaces, though not necessarily in the same configuration. Besides multiplying shelving quantities, Black Pearl Gardens has experimented with varying degrees of success with hydroponic systems, higher-powered lighting over more spacious grow ponds, and other variations on its base system.
Black Pearl Gardens’ operations have since expanded into the restaurant basement (shown) and an additional warehouse facility equipped with TotalGrow Broad Grow Spectrum LED lamps with flexible configurations for various crops and growing schedules.
The combination of entrepreneurial aptitude, a great culture for selling high-quality and high-value crops in Ann Arbor, MI, successful horticultural lighting, and other growing techniques are consistent with the stories of other successful small-scale vertical farmers who seek to bring the farm closer to the consumer.
JEFF MASTIN is chief biologist for Venntis Technologies, a specialist in custom spectra, volumetric LED lighting, and custom output pattern lighting, and a finalist in the 2017 LEDs Magazine Sapphire Awards.
Why LED Lighting is Ideal For Indoor Farming
According to data from National Geographic, the sun radiates enough energy in 15 minutes to equal energy consumption of the entire world for ONE YEAR.
Why LED Lighting is Ideal For Indoor Farming
According to data from National Geographic, the sun radiates enough energy in 15 minutes to equal energy consumption of the entire world for ONE YEAR.
The sun is so powerful that it was worshiped by ancient cultures.
So how is it possible to have lighting for growing plants indoor that is actually more efficient than the sun?
And why is it often a shade of purple???
Why is LED lighting is ideal for indoor growing?
Ancient cultures worshiped the sun due to its life giving power (source)
The idea that plants need exposure to daylight for perfect growing conditions has persisted during the sustained growth of indoor farming in the past several decades.
But, as numerous researchers (and an increasingly large amount of growers) have realized, the concept of sunlight as a necessity is, in fact, a flat out myth.
Why?
Read on to find the step-by-step explanation for how LED lighting is revolutionizing indoor growing, and more!
In the rest of the article we will discuss:
1) Why Purple (a.k.a. blue-red LEDs?
2) LED Lighting vs Daylight
3) PROS and CONS of LED Grow Lights
Ready?
Let's get started!
Why Purple (a.k.a. blue-red) LEDs?
The technical answer, in a nutshell, is related to the spectrum of color present in different types of light. While good 'ol sunlight contains a variety of color spectra (think rainbows), it turns out that plants only need specific color spectra to grow properly.
What colors work best?
According to urban farming research on the way plants respond to light, the blue-red spectra is ideal for plant growth.
The reason for this is because chlorophyll, which plays a central role in plant growth and photosynthesis, responds primarily to "peak" spectra in the blue and red ranges, or 450 nanometer and 650 nanometer wave lengths respectively.
Some research has also experimented with using other forms of light in urban agriculture growing settings, often yellow LED spectra, to alter plant traits such as color, texture, and increased shelf life.
With a consumer base increasingly enamored by rare and interesting varieties of common fruits and vegetables, concepts such as red or yellow carrots can be marked up as exotic items or at the very least add some extra zest for small-scale urban farmer.
Plant growth does not require the full spectra present in daylight (via Illumitex)
LED Lighting vs Daylight
Sunlight, in fact, is inefficient in many ways when it comes to optimizing small-scale, urban agriculture.
For one, the heat generated by the sun can be damaging to plants and can have an adverse effect on shelf life immediately post harvest.
This "heat effect" caused by sunlight is even further amplified when the plants are closely packed, as is often the case in urban farming.
In contrast to sunlight, LED lights are known for transferring nearly undetectable amounts of heat onto plants, and the bulbs themselves are even often cool to the touch. The result?
Urban farms with LED lighting can have more closely packed arrangements for maximum efficiency. These arrangements would not be possible in normal agricultural environments without compromising the health of the plants.
Besides the decreased heat transfer, LED lighting is a cheaper alternative to traditional lighting sources that emulate daylight conditions.
Although there is often a higher upfront cost with LED lighting, the best way to view the cost-savings of LED lighting for urban farming is as a long-term investment.
This is because LED lighting has a much higher energy efficiency over time compared to other urban farming lighting technologies such as halogen or compact fluorescent (CFL).
As a quantitative example, average CFL lighting options on the market will have approximately 1/3 the lifespan of LED lighting options, with similar lighting strengths (Look for 12-16 W / 800-1000 Lumens)
Plants, due to the presence of chlorophyll necessary for photosynthesis, respond mainly to red and blue color spectra (via NPR)
Pros and Cons of LED Grow Lights
PROS
1) LED's use WAY less electricity:
Most LED grow lights use 40% - 50% of the wattage of other lighting sources, like high pressure sodium lights or fluorescent.
2) Less airflow needed
It is a simple fact that for indoor growing, proper ventilation is required.
According to this post from Epic Gardening, ventilation for indoor growing helps prevent at least:
- Excess Moisture
- Proliferation of Pests
- Weakening of Plant Stems
Now, can you guess the #1 cause of heat in an indoor growing environment?
That's right: Grow lights.
But here's the catch:
LEDs generate far less heat than all other types of grow lights. As a result, less ventilation is needed to prevent excess moisture, pest problems, and other ventilation related issues.
From an economic perspective, smaller fans cost less than larger fans, so your ventilation investment requirement with LED grow lights will typically be lower than with other types of grow lights.
Additionally, the on-going electricity cost of powering fans is also eliminated.
3) Less Heat
As we have already discussed above (#2), LEDs generate far less heat than other grow lights.
Now, the reason why LED's generate less heat is because they emit far less infrared heat as output.
Other types of grow lights like high pressure sodium and metal halide grow lights emit enormous amounts of infrared heat - over half of the wattage that powers an HPS or MH light is instantly lost as heat.
Bottom line?
LEDs are far more efficient and produce far less heat.
4) EXTREMELY long life
LED's grow lights are as close to immortal as grow lights get:
They typically have at least 50,000 hours of usable life, which is nearly 6 years of continuous use.
If you are utilizing the lights on a 50% on /50% off schedule (common benchmark), this is over 11 years of shelf life.
5) No need to purchase reflector equipment to improve efficiency
HPS/MH systems often require use reflectors to help re-capture light that was not directed toward plants and instead illuminates walls and ceiling.
LED's have superb directional focus and therefore reflectors are not necessary.
6) Stackability
Because LED's have so much lower heat emission, they can be placed closer to the plants.
The result of this is that the ability to "stack" plants in a growing space is possible.
This is potentially the most exciting benefit of using LEDs: the potential to double the production output (or triple, or 4x, etc) without changing the area of the growing space.
Now, one consideration to remember is that the height of the growing space is a factor.
However, this type of stacking functionality is just not doable with other types of grow lights.
Cons
1) Upfront Cost
LED's will commonly be at least 2x more expensive then many other types of grow lights.
The return on investment may pay off over time with less energy use, replacement cost, and less investment in other previously needed equipment like fans and reflectors.
See how the economics compare with the case study from Diffen above.
2) Heavy
The component of an LED grow light that makes it heavy is the heat sink, which helps absorb excess generated heat.
As a rule of thumb, a quality LED grow light will have 10 square inches of heat sink space per LED watt.
If you do the math, you will see that this heat sink space adds up VERY quickly and adds a lot of weight.
The result of this is that investment to support the weight of LED grow lights is often a good idea, *especially* if you are stacking layers into a vertical farming stylesystem.
3) Technology Still Developing
As far as commercial indoor growing, LED technologies have not been around for very long (less than 10 years).
Previously lighting methods have included High Pressure Sodium and Metal Halidelighting.
One risk with LED lights is that they are understood less thoroughly than other types of grow lights, which have been studied for several decades.
What does this mean?
Essentially, the support and knowledge base for LED grow lights is far more limited than other types of grow lights.
However, where there is a knowledge gap, there is also opportunity...
4) "Purple" Color
The purplish color that most LED grow lights will generate can be problematic beyond just being annoying:
How?
This color of lighting presents a couple real challenges that can become huge problems:
- Pest damage is harder to identify with LED grow lights
- Nutritional deficiencies, such as yellow under-nourishment and black rot, are more difficult to identify
- Potential danger to YOUR eyes without proper protection. As detailed in this article from Electronics Weekly, the potential to damage your vision with LED lights is very real, and protective eyeware is best practice
Solution: Inspecting plants being grown with LED grow lights is best done using an alternate source of light, such as a fluorescent bar. Most commercial LED operations will inspect plants with fluorescent lights at least once every 10 days.
In Summary
So, why does all of this information matter? In an urban farming environment where space and resources may be limited, optimizing lighting will often be a winning strategy for best urban farming results.
- Red and Blue light (purple when combined) are optimal for plant growth in tightly packed, urban farming style conditions
- LED lighting has several advantages over daylight or other lighting alternatives, such as cheaper pricing over time and reduced heat transferred onto plants
- Experimentation with other color spectra with LEDs such as Yellow LEDs can cause changes in urban farming crop flavor, color, and other aesthetic characteristics.
- There are many pros and cons to using LED grow lights. In general, LEDs are far more efficient than other types of grow lights in many aspects, however they are more expensive and still relatively new as far as large scale commercial use goes.
Questions, comments, feedback? Follow us @urbanvineco
Major Green Technology Breakthrough! Metropolis Farms Unveils A New Device That Reduces Electric Cost by 60% and Disrupts The Entire Industry
On 10/16, President of Metropolis Farms Jack Griffin unveiled and demonstrated this new ballast technology at Indoor Ag Con alongside Pennsylvania's Secretary of Agriculture, Russel C. Redding. We are working on plans to manufacture these ballasts in Philadelphia and estimate they will be available in 2018.
Major Green Technology Breakthrough! Metropolis Farms Unveils A New Device That Reduces Electric Cost by 60% and Disrupts The Entire Industry
October 17, 2017
Do you know what a lighting ballast is? Chances are, if you're not involved in a trade that deals with lighting, you probably don't.
You're probably reading this because you saw a headline about a massively disruptive technology that reduces electric costs by 60%. This might be puzzling to some, since most folks don't even know about ballasts in the first place.
Well, we're here to tell you that lighting ballasts are one of the most important technological devices that very few people know about. And we have developed a ballast that can make a significant impact on the amount of energy the world uses.
There are two paths to travel to get the world to a more sustainable future:
1. Increase the percentage of power generated by renewable energy sources
and/or
2. Decrease the amount of energy consumed
We are attacking this problem on the consumption side of the equation. This new technology dramatically decreases the amount of energy that is needed to power most lights. (By the way, we are attacking this problem on the production side too, check out the world's first solar powered indoor farm we're building in South Philadelphia.)
But before we dive into this new breakthrough, since most folks don't know what a ballast is, let's start with the basics.
In the simplest of terms, a ballast's responsibility is to ensure lights work properly and don't burn out immediately.
In more defined terms, per the National Lighting Product Information Program, a "ballast regulates the current to lamps and provides sufficient voltage to start the lamps. Without a ballast to limit its current, a lamp connected directly to a high voltage power source would rapidly and uncontrollably increase its current draw. Within a second the lamp would overheat and burn out. During lamp starting, the ballast must briefly supply high voltage to establish an arc between the two lamp electrodes. Once the arc is established, the ballast quickly reduces the voltage and regulates the electric current to produce a steady light output."
Ballasts are connected to all fluorescent, compact fluorescent, HID, and many commercial LED lights. Regarding LEDs, ballasts are called drivers, but they are effectively the same thing. So whenever you're out and about, know that almost all of the lights you see in commercial or public spaces are connected to a ballast.
Lighting accounts for 53% of electric usage in U.S. retail buildings. And ballasts are the bridge that enables that power consumption.
In 2016, the U.S. Energy Information Administration estimates about 279 billion kilowatthours (kWh) of electricity were used for lighting by the residential sector and commercial sector in the United States. That's 279 million megawatts and does not account for public buildings or streetlamps.
So lighting is responsible for a massive amount of energy that is consumed.
Beyond the statistics that are directly related to powering the lights, more energy is used by HVAC systems to combat the excessive BTUs (heat) that lighting systems generate. This is a particularly sensitive issue when the temperature needs to be highly regulated, like in an indoor vertical farm.
Currently in our vertical farms, we are using 315W ceramic metal halide bulbs and we have 1 ballast for 1 bulb. For every bulb in our hydroponic farms, there's a ballast regulating the energy necessary for the light to work properly.
That's typical for most big lighting systems. For example, in another sector, each streetlamp you see illuminated at night is connected to a ballast.
All that said, you're now probably wondering: what's this development that will change the world?
Well, it's a new ballast. A more efficient ballast. One that brings unprecedented breakthroughs in ballast technology.
Here are two facts that will show why this is not hyperbole:
1) This new ballast will reduce total energy consumption in our indoor farms by 60%.
2) We will use 1 ballast to power 8 bulbs.
These results are being verified by a major university's lighting laboratory and certified by a CPA firm.
If you don't understand the game-changing ramifications of those statements, please keep reading!
The most common argument against indoor farming or vertical farming is that it requires too much energy to produce diverse crops. And in light of that argument (pun intended), we've already developed vertical farming systems that can grow diverse crops while still using less energy than other indoor farms that only grow leafy greens, and we have shown that these systems can produce profitable results for farmers.
Now with this new ballast, the energy argument can be totally put to bed. The equation has completely changed and by making these ballasts available to everyone, all indoor vertical farms will be able to reduce their energy consumption dramatically. All businesses and cities will be able to reduce their energy consumption dramatically.
We recently wrote a post on the topic of legal cannabis and how it's going to change the world. We said that due to the technologies being researched and developed to grow cannabis better, there will be emerging technologies that are backwards compatible and enable us to grow foodbetter.
But this technology takes it a step further. By focusing efforts on how to grow anything in a more energy efficient way, a technology was discovered that will enable every industry to operate using less energy.
With our old ballasts, the bulbs in our hydroponic systems required 3 amps and 315W to power them. With this new ballast, they only need 1 amp and 110W. That is far less energy used by the most efficient LED lights, and we still produce full spectrum light so our plants thrive.
This was me after being told how these ballasts work:
Below are a few other features of this new ballast breakthrough that changes the game:
There's a massive heat reduction at the bulb from 400 degrees to 150 degrees, which significantly reduces energy cooling loads.
Remember the Superbowl when the power went out and the lights couldn't be turned on for 34 minutes? That happened because the ballasts and bulbs needed time to cool down and recalibrate the energy flowing into the bulbs. With our new ballast, those lights could have been turned on right away.
Before, a ballast could only power a certain kind of light. For example, one type of ballast could power fluorescents, another could power HIDs, while another powers LEDs. This new ballast can power any kind of bulb, simultaneously.
As mentioned earlier, this one ballast can power multiple high usage lights.
And as nature goes, there are indirect consequences from a technological advancement. It just so happens that in this case, we are extremely excited about one consequence in particular.
Since 1 ballast will effectively replace 8, the economics work in such a way that we will be manufacturing these ballasts in the United States.
We are already working on plans to build a Philadelphia-based manufacturing facility that will provide a significant amount of living-wagejobs to local Philadelphians.
Beyond the manufacturing jobs, there will be a significant amount of work for electricians everywhere as we envision this new technology becoming the norm. Building owners will be able to retrofit their existing light systems with these new ballasts and immediately decrease the amount of energy they use.
To review, this technology can help decrease electric usage by 60%. Considering the 279 billion kWh used for just lighting in the residential and commercial sectors, and that the average residential price per kWh is 12.99 cents, saving over 167 billion kWh is the same as saving over $21.7 billion. Indoor farming for cannabis alone accounts for 1% of the entire country's energy usage, at $6 billion annually, and that number will continue to climb as more states legalize cannabis.
If these ballasts are installed everywhere, think of what $22+ billion could be spent on!
On 10/16, President of Metropolis Farms Jack Griffin unveiled and demonstrated this new ballast technology at Indoor Ag Con alongside Pennsylvania's Secretary of Agriculture, Russel C. Redding. We are working on plans to manufacture these ballasts in Philadelphia and estimate they will be available in 2018. From there, we believe this new ballast will become the new standard not only in indoor vertical farming, but in all commercial lighting. This will have an immense impact on the amount of energy that is used for lighting by decreasing the energy consumed immediately upon installation. This will help the world transition to a more sustainable future. And this will create living-wage jobs in the U.S.
We are incredibly excited about this new breakthrough and hope that you are on board as well. The times they are a changing and indoor agriculture is here to stay, here to create positive change, and here to revamp the broken food system. Join us for the journey.
Let's get lit.
For more information on Metropolis Farms and to see where we plant our roots, read about us here.