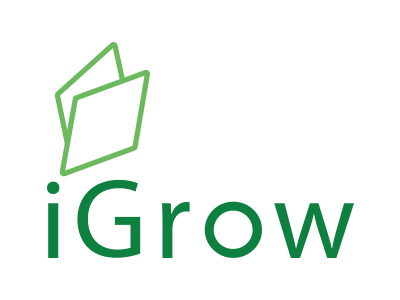
Welcome to iGrow News, Your Source for the World of Indoor Vertical Farming
Logistics Industry Will See Improved Connectivity, Efficiency And Security With Blockchain
MTI, in conjunction with Agility Sciences, have today released a white paper detailing the deployment of their Container Streams system in a supply chain environment. The results of the pilot have been verified by scientists at the University of Copenhagen and maritime technology leaders at Blockchain Labs for Open Collaboration (BLOC).
Jody Cleworth - Marine Transport International
Logistics Industry Will See Improved Connectivity, Efficiency And Security With Blockchain
A successful pilot program delivered by logistics technology company Marine Transport International (MTI) has demonstrated that the logistics industry will see improved connectivity, efficiency and security thanks to blockchain.
MTI, in conjunction with Agility Sciences, have today released a white paper detailing the deployment of their Container Streams system in a supply chain environment. The results of the pilot have been verified by scientists at the University of Copenhagen and maritime technology leaders at Blockchain Labs for Open Collaboration (BLOC).
Jody Cleworth, CEO of Marine Transport International, comments: “The results of this successful pilot demonstrate the strengths of blockchain technology when deployed to link the various actors in the supply chain. We are confident that firms throughout the logistics industry will see a broad spectrum of benefits stemming from blockchain deployment.
"We will need to be able to communicate between multiple block chains and work interoperatively. We have already created some work to do this so that we can communicate between multiple devices, blockchains and legacy systems so it would be one single version of communication between the blockchains.
“A blockchain-enabled supply chain is highly resilient to cyber attack – a copy of the essential shipping data is stored on each node on a decentralised network, meaning that even if one node is compromised, the data is safe nevertheless.
Karim Jabbar, from the Department of Computer Science at the University of Copenhagen, added: “This pilot demonstrates the great potential for distributed ledger technologies to be used in improving supply chain processes. The Container Streams system is unique in the fact that it does not require the complete replacement of existing systems - instead, MTI’s solution allows complete interoperability with existing legacy infrastructure. The logistics industry as a whole can expect better visibility, connectivity and cost savings as a result of distributed ledger adoption.”
Cleworth goes on the say that the cost entry is quite low, it is more about having the right people with the right skills to get this done.
"A conservative estimate is a cost saving of 90%. In the shipping and logistics industry we are very good with new regulations and milestones, putting in an end-perfect way of managing it: 'This is what it is going to cost me to manage a specific milestone'.
The cost saving here comes through the automation of data, you have all these different data silos which have data locked in them or which is not being communicated in an effective way. Smart contact takes the data from those different points and processes it, removing the requirement for human beings to interact with it. We are able then to process that data and format it, whether is it a new system or an old system we can use a blockchain to do that work for us reducing admin costs."
"What people find difficult to get over is that you have your local sales force and internal reporting system to put in numbers and data and using that to augment the outcome or create a spreadsheet, blockchain will actually do this job based on existing parameters so the programmability of the technology.
This can be applied in the food supply chain, firstly to guarantee provenance, "You know where the product has come from and where it is going to. Transactions become frictionless, we can remove the amount of paper work which is required in terms of moving that data between parties. There are a lot of certificates and regulations in terms of what gets exported to where. Regulatory bodies would normally only follow up regulations when it is necessary. With data entering the blockchain the regulators would be able to follow it up based on specific parameters, they would be able to read those contracts or certificates in real-time.
Effectively what we have done with our white paper is to pull in data as soon as that container starts loading, growers can record specific yields for each commodity and enter photos etc. along with all the weather data to attest to the quality of product which consumers are buying. This data entering process can continue along the chain whether it is to a coldstore or to be processed or straight to the retailer, you can follow the chain the whole way through. The management of that data would be automated based on data coming into the system from different points.
"When we have discussions with food producers they want to unlock that data source which is coming into the blockchain to prove the provenance and certification of those goods. This system would also take away inefficiencies in the supply chain and allow more 'just in time' deliveries, doing away with bulk delivery discounts.
For more information:
Jody Cleworth
Marine Transport International
jody@askmti.com
Publication date: 8/30/2017
Author: Nichola Watson
Copyright: www.freshplaza.com
Autogrow Launches Jelly - The First Indoor-Agricultural SDK
Autogrow Launches Jelly - The First Indoor-Agricultural SDK
31 August 2017, Auckland, New Zealand:
Autogrow has launched the first indoor-agricultural SDK (Software Development Kit), opening the door for a new revolution in the industry.
Called Jelly, this first SDK will form part of a group of software Autogrow will provide publicly on the world leading development platform Github.
'Jelly is the first step in raising agtech to the next level. For us this is about building a community for a new generation of growers who love to grow and hack the tech,' says Darryn Keiller, CEO of Autogrow.
'We are opening the door for 3rd parties to access our technology programmatically which has never been done in our industry and is just the beginning as we work our way towards our open source initiative.'
Traditionally agricultural providers utilise proprietary products and services which leave little flexibility for the growers to create their own solutions or connect them with existing infrastructure. Autogrow's move will provide their customers access to the programmable layer of Autogrow's Intelli product range. Other future products will follow suit.
'Growing crops is no longer just about dirt and seeds - it's about tech and data. The most successful and sustainable growers embrace technology and utilise every opportunity to understand their growing environments,' explains Mr Keiller.
'Technology has a huge role to play in future food production but we can only really do that if we create an open environment where everyone is pushing hard to design better, more innovative solutions - regardless of who owns the IP.'
Darryn Keiller - CEO (left), Jeffrey Law - Chief Technology Officer (right)
Autogrow's Chief Technology Officer, Jeffrey Law, is the driving force behind Jelly and the various solutions the research and development team are currently creating.
'We came up with the name Jelly as it reflects that early incubation stage where everything is flexible, you can mould it in any configuration, it comes in different variations, and of course it's quite tasty,' says Mr Law.
'For us it's like a play area where we get to experiment and come up with original ideas. The biggest difference here is that we are opening the door to the play room and welcoming in anyone who wants to revolutionise the agricultural industry.'
Autogrow will monitor the progress of their Jelly SDK with availability via Github from 6 September 2017 - https://github.com/AutogrowSystems/go-jelly
About Autogrow
Established in 1994, Autogrow (www.autogrow.com) is committed to creating original ideas for agriculture - and making them a reality.
With a global headquarters in Auckland, New Zealand, and growers and resellers in over 39 countries, Autogrow provides growers with affordable, accessible and easy-to-use innovation - 24/7, anywhere in the world.
By leveraging the power of technology, data science and plant biology through a team of software designers, engineers and crop science experts - Autogrow continues to push innovation boundaries to gain the best result for the growers.
MEDIA QUERIES
Autogrow
Kylie Horomia, Communications Manager
(e) Kylie.horomia@autogrow.com
(m) +6421 733 025
Dole And Driscoll's Join IBM Blockchain
Dole And Driscoll's Join IBM Blockchain
A group of leading companies across the global food supply chain today announced a major blockchain collaboration with IBM intended to further strengthen consumer confidence in the global food system.
The consortium includes Dole, Driscoll's, Golden State Foods, Kroger, McCormick and Company, McLane Company, Nestlé, Tyson Foods, Unilever and Walmart, who will work with IBM to identify new areas where the global supply chain can benefit from blockchain.
Every year, one-in-ten people fall ill - and 400,000 die - due to contaminated food. Many of the critical issues impacting food safety such as cross-contamination, the spread of food-borne illness, unnecessary waste and the economic burden of recalls are magnified by lack of access to information and traceability.
It can take weeks to identify the precise point of contamination, causing further illness, lost revenue and wasted product. For example, it took more than two months to identify the farm source of contamination in a recent incidence of salmonella in papayas.
Blockchain is ideally suited to help address these challenges because it establishes a trusted environment for all transactions. In the case of the global food supply chain, all participants - growers, suppliers, processors, distributors, retailers, regulators and consumers - can gain permissioned access to known and trusted information regarding the origin and state of food for their transactions.
This can enable food providers and other members of the ecosystem to use a blockchain network to trace contaminated product to its source in a short amount of time to ensure safe removal from store shelves and stem the spread of illnesses.
Dole, Driscoll's, Golden State Foods, Kroger, McCormick and Company, McLane Company, Nestlé, Tyson Foods, Unilever, Walmart and others are now coming together with IBM to further champion blockchain as an enabling technology for the food sector. Together they will help identify and prioritize new areas where blockchain can benefit food ecosystems and inform new IBM solutions. This work will draw on multiple IBM pilots and production networks in related areas that successfully demonstrate ways in which blockchain can positively impact global food traceability.
"Unlike any technology before it, blockchain is transforming the way like-minded organizations come together and enabling a new level of trust based on a single view of the truth," said Marie Wieck, general manager, IBM Blockchain. "Our work with organizations across the food ecosystem, as well as IBM's new platform, will further unleash the vast potential of this exciting technology, making it faster for organizations of all sizes and in all industries to move from concept to production to improve the way business gets done."
New IBM Blockchain Platform
Beyond food supply chain applications, blockchains are now being used to transform processes and streamline transactions for everything from flowers, real estate and trade finance, to education, insurance and medical services.
To accelerate this adoption, IBM is introducing the first fully integrated, enterprise-grade production blockchain platform, as well as consulting services, that will allow more organizations to quickly activate their own business networks and access the vital capabilities needed to successfully develop, operate, govern and secure these networks. The IBM Blockchain Platform is available via the IBM Cloud.
The platform builds off of the successful blockchain work IBM has delivered to more than 400 organizations, incorporating insights gained as IBM has built blockchain networks across industries including financial services, supply chain and logistics, retail, government and health care.
Extensively tested and piloted, the platform addresses a wide range of enterprise pain points, including both business and technical requirements around security, performance, collaboration and privacy that no other blockchain platform delivers today. It includes innovation developed through open source collaboration in the Hyperledger community, including the newest Hyperledger Fabric v1.0 framework and Hyperledger Composer blockchain tool, both hosted by the Linux Foundation.
The integrated platform allows multiple parties to jointly develop, govern, operate and secure blockchain networks to help enterprises accelerate blockchain adoption.
Features of the IBM Blockchain Platform include:
Govern - The platform offers all participating members a level of control, while preventing any one member from having exclusive control. A new class of democratic governance tools is designed to help improve productivity across the organizations using a voting process that collects signatures from members to govern member invitation distribution of smart contracts and creation of transactions channels. By quickly onboarding participants, assigning roles and managing access, organizations can begin transacting via the blockchain.
Operate –The platform is underpinned by an architecture that operates more than 55% of today's global transactional systems. It is the first offering available to allow updates to be made to the network while it is running without any downtime. Running in the IBM Cloud, it offers protection from insider credential abuse, protection from malware and hardware encryption key protection. IBM claims their Blockchain Platform provides the highest-level commercially available tamper resistant FIPS140-2 level 4 protection for encryption keys.
The IBM Blockchain Platform offers a range of pricing options, starting at $0.50 per hour, to support rapid adoption for networks of all sizes. To support blockchain ecosystems among different organizations, the cost of the network can be shared across all network members.
Strengthening Trust Across the Global Food Supply Ecosystem
In parallel trials in China and the U.S., IBM and Walmart recently demonstrated that blockchain can be used to track a product from the farm through every stage of the supply chain, right to the retail shelf, in seconds instead of days or weeks.
These trials also demonstrated that stakeholders throughout the global food supply chain view food safety as a collaborative issue, rather than a competitive one, and are willing to work together to improve the food system for everyone.
"As an advocate for greater transparency in the food system to benefit customers, Walmart looks forward to expanding on our initial work by collaborating with others to accelerate exploration on how this technology can be used as a more effective food traceability and food safety tool," said Frank Yiannas, vice president, food safety, Walmart.
"Blockchain technology enables a new era of end-to-end transparency in the global food system – equivalent to shining a light on food ecosystem participants that will further promote responsible actions and behaviors. It also allows all participants to share information rapidly and with confidence across a strong trusted network. This is critical to ensuring that the global food system remains safe for all."
"IBM has deep experience and a commitment to business processing and security needs, which are exactly the skill sets needed to bring blockchain to full maturity for food safety and all associated transactions," said Guilda Javaheri, chief technology officer. As a customer and partner with IBM for more than forty years, Golden State Foods is pleased to collaborate with IBM and this group of trusted food companies."
"Safety is a key value for Kroger, and our partnership with IBM positions us to explore and test blockchain technology as a solution for enhanced food safety across our business," said Howard Popoola, Kroger's vice president of Corporate Food Technology and Regulatory Compliance. "Food safety is a universal priority for food retailers and companies. It's not a competitive advantage; it benefits our customers to have greater transparency and traceability in the supply chain."
"We're excited about the possibilities that come with this technology and are glad to collaborate with IBM and others," said Scott Stillwell, Ph.D., senior vice president of food safety and quality assurance for Tyson Foods. "Producing safe food is critical to our business; it appears blockchain can help provide trust not only about the origin of food, but also about how that food moved through the supply chain."
For more information:
Holli Haswell
IBM
Tel: +1 720 396 5485
www.ibm.com/blockchain/
Seattle-Based iUNU Raises $6 Million To Launch LUNA
Seattle-Based iUNU Raises $6 Million To Launch LUNA
Turning Commercial Greenhouses Into Predictable, Demand-Based Manufacturers
iUNU (“you knew”) has raised $6 million from 2nd Avenue Partners, Initialized Capital, Fuel Capital, Liquid 2 Ventures, and others, to bring large scale, computer vision-based, industrial manufacturing process and inventory management to the commercial greenhouse market.
"This solution turns greenhouses into data driven manufacturing plants. It is both a seriously practical and crucial commercial application of AI to a fundamental industry,” says Alexis Ohanian of Initialized Capital.
Building detailed models of individual plants
Following three years of development and testing in large scale commercial operations, LUNA combines computer vision and machine learning technologies to continuously build detailed models of individual plants, unique among millions, throughout the day. Using high resolution and 3D imagery, as well as real-time bioinformatics, LUNA monitors even the most minute changes in health of individual plants, giving growers the precise knowledge they need for proactive management.
“When we saw how differentiated LUNA is from the other solutions in this space, we knew we had to invest in iUNU,” said Liquid 2 Ventures in a statement (Joe Montana, Mike Miller, and Michael Ma). “LUNA provides a truly comprehensive understanding of each plant’s health and growth, focused on the plant’s actual performance, not just the environment around it. Closing the control loop has the potential to change the equation of the economics of commercial-scale, indoor horticulture.”
Greenhouse growers must deal with pests, diseases and other environmental threats to plants. The struggle is quantifiable: up to 20 percent of fruits and vegetables go to waste before they have even left the farm — and that number can be even higher for delicate ornamentals. At the same time, growers are under relentless pressure from retailers to deliver consistently on quantity and quality. While technologies such as sensors and cloud computing offer incremental relief to growers, LUNA offers a solution that enables greenhouses to operate as modern, demand-based, information-driven, manufacturing facilities.
Model crop and timelapse comparison
Empowering growers
“We have built a customer focused, plant-first solution with LUNA that does more than just improve a grower’s reaction time to problems,” said Adam Greenberg, CEO of iUNU. “We reject the premise that ‘reactive mode’ is the natural state for growers. With the right technology, thoughtfully applied, we can give them better computer driven visibility, greenhouse operations can be as precise, proactive, and predictable as modern manufacturing. We are empowering growers to see and control more.”
LUNA begins to learn, and remember, the moment her cameras and sensors are first installed in your greenhouses, giving growers historical records of every detail of every plant in the system, as well as live information – everything they need to make the decisions to run their business, all in one place.
Contact: John Murray
iUNU | Tel: 202-821-2219 | pr@iunu.com | www.iunu.com
Growlink Announces Strategic Partnership With Modular Farms
Growlink Announces Strategic Partnership With Modular Farms
Growlink Grow Controllers to be used in Modular Farms Container Farms
DENVER, CO (PRWEB) AUGUST 16, 2017
Modular Farms
We wanted a strong technology partner that would meet our needs for a reliable, easy-to-use farm, and Growlink provides that.
Growlink, a Denver-based technology company, announced today that it has formed a strategic partnership with Brampton, Ontario-based Modular Farms, to integrate its cloud-based grow controllers into their modular farm systems.
“We’re excited for this partnership with Modular Farms,” said Ted Tanner, CEO of Growlink. “Modular Farms has the potential to lengthen growing seasons, reduce local food insecurity, and stabilize a farmer’s income stream. We share their goals of bringing smart, fresh, local food to communities worldwide.”
Modular Farms began selling its farm systems in November 2016. Instead of repurposing shipping containers, Modular Farm Systems are built from the ground up from composite, rust-resistant panels and are larger than traditional shipping containers at 40’ x 10’ x 10’. The larger size allows for better spacing between plans and lights and greater airflow. Every unit comes with two intensive days of training and 24/7 support.
After initially building the container farms using other control systems, Modular Farms soon realized they would not fit the needs of their customers. “We were disappointed by the performance and limited functionality of other systems,” said Eric Amyot, CEO of Modular Farms. “We needed a new solution.” After reviewing all of the options available, Modular Farms selected Growlink to be its technology partner. The Growlink modular platform uses a variety of sensors and switching modules to monitor and control the environment and nutrient system, which growers can access from their smartphones using the Modular Farms App.
The App, available in the Apple App store and Google Play, connects to the Growlink Grow Controllers and allows users to monitor sensor data in real time, view real-time video, and control any connected devices. Users can set up rules including sensor triggers, timers, and schedules to automate the grow process.
“We wanted a strong technology partner that would meet our needs for a reliable, easy-to-use farm, and Growlink provides that,” said Amyot. “Our Modular Farms Systems ship with the Growlink technology fully installed, customized for our customers’ planting needs.”
About Growlink
Growlink’s mission is to deliver an elegant and affordable way to control and automate lighting, climate, fertigation and irrigation systems. The Denver-based company focuses on creating well-designed, tightly integrated hardware and software that allow users to see, monitor and control their farm from anywhere. Visit http://www.growlink.com for more information and follow us on Facebook, Twitter and Instagram.
About Modular Farms
Launched in 2015, Modular Farms Co. is a Canadian agriculture company that provides first-of-its-kind engineered farming units designed for multiple terrains, weather conditions and a focus on plant health. Each Modular Farms unit is fully-manufactured in Brampton, Ontario and is capable of producing fresh, healthy produce virtually anywhere in the world and in any climate, exceeding the qualities and quantities of those grown in shipping containers. Current modules include Primary, Macro, and Vestibule, with Water, Storage, Energy and Sprout modules in development. The Modular Farms App allows users to monitor sensor data in real time, view real-time video and control any connected devices. Users can set up sensor triggers, timers, and schedules to automate the grow process directly from their smartphones. By partnering with world-leading experts in LED lighting, plant health sciences and indoor agriculture, Modular Farms brings unprecedented opportunity for expansion and growth in the agricultural industry. Visit http://www.modularfarms.co for more information and follow Modular Farms on Facebook, Twitter and Instagram.
Artemis Takes on The World
We’re currently helping indoor farmers get to profitability and beyond in 8 markets around the world.
Artemis Takes on The World
It’s no secret — the indoor farming market is huge… and growing! As Allison detailed in this blog post, indoor farms in the US produce over $21B in revenue annually. And the US only represents 0.2% of the global greenhouse vegetable market. This is the the same industry that is aggressively growing to help increase food production by 70% to feed 9B people by 2050.
Global Expansion
Artemist has set out to provide the world’s best management software from its inception. In order to be the world’s best, you have to be a global company. Within just a few months of our launch, we were proud to support incredible customers in South America, Sri Lanka, Canada, and the United States.
We’re not stopping there — we’re excited to announce that in addition to continuing to add customers in our existing markets, this month we’ve entered new markets, adding customers in Europe, the Middle East, and Asia!
Supporting Customers
The biggest challenge any growing company faces in adding new customers is supporting them while keeping existing customers both excited and engaged. Over the past month we’ve introduced a new onboarding process to ensure customers see value from Day 1 as well as easier ways for our customers to use our software. We’ve also welcomed Regina Bellows to our team as our dedicated Customer Success Manager.
Managing customers across so many time zones can lead to sleepless nights. One of the things I love about Artemis is everyone here is customer-obsessed. We take turns monitoring support channels all hours of the day and night so a customer never feels like they’re left in the dark when they run into a question. I think it’s probably one of our customers’ favorite things about us.
Let’s Chat!
While we’re excited with our progress to-date, we’re not stopping here. We continue to be excited about how we can use data to evolve one of the world’s largest legacy industries. I’d love to understand more about your farm, your challenges, and how we can help you solve your problems with data. Please email me at jschmitz@agrilyst.com or call at +1 646–719–0304.
Take-aways
The global greenhouse market is large and growing.
Agrilyst is growing along with the market, now working with clients across four continents.
We‘re keeping a close eye on support to ensure our customers are getting the most out of their software investment.
Artemis is the virtual agronomist powering the horticulture industry. We invite you to join the #DigitalHorticulture movement on social media and share your stories of farm innovation.
If you enjoyed this story, tune in for more here and be sure to check out our website: https://artemisag.com/