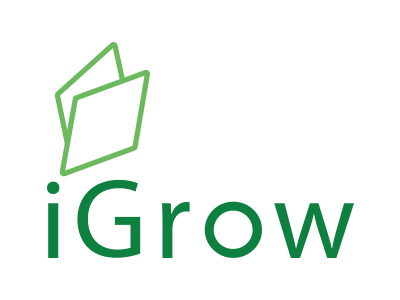
Welcome to iGrow News, Your Source for the World of Indoor Vertical Farming
What Will 2017 Bring For Indoor Ag?
What Will 2017 Bring For Indoor Ag?
JANUARY 4, 2017 NICOLA KERSLAKE
Editor’s Note: Nicola Kerslake is the founder of Newbean Capital, a registered investment adviser that manages early stage venture capital mandates and that has a particular interest in indoor agriculture. It owns the Indoor Ag-Con events business as well as an indoor agriculture alternate financing business Contain that is currently in pilot stage. The next Indoor Ag-Con event will be held in Singapore on January 24-25, 2017.
Here Kerslake offers some predictions for the indoor agriculture industry in 2017.
For all of the year’s many horrors, 2016 was a banner year for indoor agriculture, the practice of growing crops in hydroponic, aquaponic and aeroponic systems in greenhouses, warehouses, and containers. The fledgling industry saw record investment fueling a wave of new indoor farm builds, innovative business models, and technology introductions.
Highlights included the launch of Square Roots, a Kimbal Musk-backed social-benefit endeavor to incubate new urban farmers utilizing Freight Farms’ container farms, and the inauguration of Aerofarms’s long-anticipated Camden, NJ vertical farm. The latter is notable because it uses aeroponics — misting plant roots with a nutrient-rich solution, rather than submerging them in water – and this is typically considered a trickier technology to implement commercially than the more common hydroponics. The upside is, in theory at least, more efficient growing. Both Freight Farms and AeroFarms raised equity from private investors during 2016, contributing to the $50m+ raised from private investors in the US last year.
We expect to see accelerating activity in 2017 thanks to better economics and more farm and technology launches. Here are six ‘big themes’ for the year ahead:
1. The First of the Mega Farms
Indoor farms run the gamut from a basic home-built set up using equipment bought at Home Depot to custom engineered 100,000 ft2 facilities. With a few notable exceptions – such as those growing for the pharmaceutical industry – the US market has mostly used vertical farms to date; mid-sized farms that stack growing racks to maximize space in a warehouse or repurposed building.
Their cooler cousin is the ‘plant factory,’ a term coined in Japan to describe multi-layer growing in clean room conditions using increasingly sophisticated monitoring and control systems to optimize growing conditions. These are large-scale operations, “farming as manufacturing.” The Japanese company, 808FACTORY, has its own data server running at its plant factory, for example. Plant factories are commonplace in the more advanced Asia market – Japan has more than 200, China more than 80 – and we expect them to become a feature of the US one in 2017. For instance, Japanese plant factory company Spread has publicly discussed its search for US partners, while Middle Eastern greenhouse company Pegasus Agriculture leased a large parcel of land in Florida in 2016, though the latter will more likely be used for next-gen greenhouses than for plant factories.
Funded by low-key rounds or by overseas parent companies, new mega-farmers are typically shyer than the likes of BrightFarms or AeroFarms. A few will eventually discuss their work in public, but the majority will stay on the downlow, focused on the complex business of adapting new crops to indoor systems or applying machine learning techniques to improve yields.
2. Indoor Ag goes Mainstream
When we first got involved with the indoor agriculture industry nearly six years’ ago, we spent a good deal of our time explaining the sector to other investors. The vast majority saw it as too small, too niche and too risky to be of interest. A combination of time, technology advances, and a halving of the price of the LED lights — they make up around half of a farm’s capex — has made a big difference. The attention paid to legal cannabis has also helped; its newfound respectability has a halo effect for other crops grown in indoor farms. Now, we receive a couple of inbound calls a week from new investors looking to get into the sector, one of the reasons that we have authored five white papers on various aspects of the industry.
In turn, this influences the kinds of companies that become involved in the sector. Recently, big box retailer Target announced its plans to test in-store vertical farms in the spring, and telecoms major Ericsson demoed an aquaponics project utilizing its IOT-based controls. We expect to see more “big names” announcing their involvement in indoor agriculture this year, whether that’s large produce buyers, technology providers, or long-established farming majors diversifying their growing techniques.
3. IoT Everything
Given the controlled environment in which they operate, indoor farms are well suited to the application of ‘big data’ techniques and a range of startups are joining established industry players in introducing these. Agriculture control majors – Argus Controls, Hortimax, Priva – benefit from long histories of working with customer data, and others are taking innovative approaches to pilot new products. For example, New Zealand-based Autogrow raised a sub-$5m round in 2016 to create an open platform for its controls products and TechCrunch Disrupt winner Agrilyst launched a greenhouse management platform. Up next, we expect to see machine learning-based approaches launching commercially.
4. In-Home Growing
Ubiquitous furniture retailer IKEA has been rolling out an in-home hydroponic range recently and is about to see competition from a wave of in-home growing startups. Some examples of the next generation include SkyDeck graduates Verdical and app-controlled Grobo. We expect that those that gain market traction will be looking for seed and A rounds in 2017, following in the footsteps of an earlier wave of strategic and VC-backed in home systems, such as Scott’s Miracle Grow’s AeroGardens and Upfront Ventures’ Grove Labs.
5. The Crickets are Coming
As alternative proteins – plant-based meat, insects – become commercially available, we anticipate that indoor agriculture will be a part of figuring out the supply chain for these approaches. For instance, cricket farmers, including equipment provider Bitwater Farms, super-angel backed Tiny Farms and Thailand’s Eco Insect Farming, are already adopting and adapting indoor farming techniques.
6. But It Won’t All Be Roses…
A high business failure rate is one of the characteristics of startups, and indoor agriculture is far from immune. This is especially true for the mid-sized vertical farms that make up the bulk of the US market, some of which have yet to hit a scale or figure out a business model that allows for a decent operating profit. If the trajectory of analogous industries – such as solar – is anything to go by, some will merge, others will pivot to new business models, and some will fail. While wretched for the hard-working farmers involved, we view these failures as a necessary part of the industry’s rapid growth. Private and VC investor-backed indoor farmer PodPonics, for instance, shuttered its Atlanta, GA, farm this year to focus on its Middle East technology operations, and we expect to see more of the same as indoor agriculture matures.
By the end of 2017, we expect to see a larger, and stronger, US indoor agriculture industry, able to benefit from a wider variety of technologies and anchored by the beginnings of its own plant factory revolution.
Planned Vertical Farm in East Baltimore Aims To Train Ex-Offenders
Baltimore Business Journal
Morgan Eichensehr Reporter
Planned Vertical Farm in East Baltimore Aims To Train Ex-Offenders
A Canadian agriculture technology company is partnering with CBO Financial Inc. and Volunteers of America Chesapeake to develop a $6 million indoor urban farm in East Baltimore, part of a new program to give workforce training to ex-offenders.
Arcturus Growthstar Technologies Inc. signed a letter of intent last month to lease 25,000 square feet from local nonprofit Volunteers of America Chesapeake at one of its centers at 5000 E. Monument St. Part of the building will be renovated to accommodate Arcturus’ "controlled environment agriculture" technology, which uses LED lights to grow plants indoors on vertically-stacked levels. The farm will vertically grow produce like lettuce, basil, cilantro and oregano.
And though the company is involved with marijuana growing efforts in other markets like Florida, Russell Snyder, CEO of Volunteers of America Chesapeake, said that will not be part of the Baltimore operation.
The renovation is expected to be finished in 2018.
Volunteers of America Chesapeake currently uses the building as a residential re-entry center to help ex-offenders rejoin society and the workforce after serving prison sentences. The new partnership will be utilized to provide workforce development opportunities for residents of the re-entry program — the center serves about 150 residents at a time — in the area of urban farming, Snyder said.
"The job training and jobs created by this social enterprise will allow the resident to gain a skill that can be applied in the workplace once they successfully leave our program," he said. "VOAC is all about empowering individuals who have struggled in life to be independent and inspire hope in a new direction with their lives."
Columbia-based CBO Financial Inc. is helping to arrange financing for the project. Financing will be sought through the federal New Markets Tax Credit program, a $65 billion program designed to incentivize private investment in low-income communities.
The Baltimore farming operation is expected to serve as a model for expansion of Arcturus' technologies and training programs across the country and one of several projects Arcturus, CBO and Volunteers of America will work on together going forward.
William Gildea, CEO of Arcturus, said if the program is successful, it could serve as a bellwether for other public-private partnerships within the urban farming industry.
“Our goal was always to create impactful social and corporate programs that are mutually beneficial for all involved, from the community, to the company and our shareholders," he said in a statement. "Partnering with Volunteers of America Chesapeake and CBO Financial puts us in the position to achieve that goal.”
Morgan is a reporter for the Baltimore Business Journal. She covers technology, education and health care.
Kimbal Musk, Elon’s Brother, Grows Food In Brooklyn Shipping Containers
"Whereas Elon Musk is determined to colonize space with SpaceX, his brother Kimbal Musk is equally determined to leave the earth behind"
Kimbal Musk, Elon’s Brother, Grows Food In Brooklyn Shipping Containers
by 2Paragraphs in Business Spotlight | January 4, 2017
Whereas Elon Musk is determined to colonize space with SpaceX, his brother Kimbal Musk is equally determined to leave the earth behind. But in Kimbal's case, earth means the soil, not the whole planet. Kimball, a restaurant and sustainable foods entrepreneur and venture capitalist, is helping urban farmers grow soil-free crops -- crops that grow vertically indoors in giant shipping containers, nourished by LED lights and nutrient-rich water instead of earth. Leafy greens, basil and other herbs are the crops.
In the fall, Musk and his business partner Tobias Peggs set up a shipping container farm complex in Brooklyn -- creating small vertical farms that thrive in one of the least bucolic places on earth. Each farm is individually managed by selected farmers/entrepreneurs. The business is called Square Roots, and it's as radical an idea as SpaceX or Tesla -- and like Tesla, it really starts to work if the practice scales. The advantages are tantalizing. The farms are closer to the customer base in New York City. They save transport time and expense. They use less water. They grow year-round. And one container can produce as much in crops as two acres of land. If you want to know more about the kind of food Kimbal and Peggs believe in, check out The Kitchen.
Kimbal Musk — Elon's brother — Just Opened A Shipping Container Farm Compound In New York City
Business Insider
01.04.17
- and Sarah Jacobs
Kimbal Musk — Elon's brother — Just Opened A Shipping Container Farm Compound In New York City
For over a decade, he has run two restaurant chains, The Kitchen and Next Door, which serve dishes made strictly with locally-sourced meat and veggies. In 2011, he started a nonprofit program that has installed "Learning Gardens" in over 300 schools, with the intention of teaching kids about agriculture.
His latest food venture delves into the world of local urban farming.
In early November, Musk and fellow entrepreneur Tobias Peggs launched Square Roots, an urban farming incubator program in Brooklyn, New York. The setup consists of 10 steel shipping container farms where young entrepreneurs work to develop vertical farming startups. Unlike traditional outdoor farms, vertical farms grow soil-free crops indoors and under LED lights.
Six weeks into the 12-month program, just after the entrepreneurs completed their first harvests, Business Insider got a tour of the farms. Take a look below.
View As: One Page Slides
The Square Roots farms sit between an old Pfizer factory and the apartment building where Jay-Z grew up in Brooklyn.
They are vertical farms — everything grows inside 320-square-foot steel shipping containers. Each container can produce about 50,000 mini-heads of lettuce per year.
The USDA gave the Square Roots entrepreneurs small loans to cover preliminary operating expenses. Other investors include Powerplant Ventures, GroundUp, Lightbank, and FoodTech Angels.
On four parallel walls, leafy greens and herbs sprout from soil-free growing beds filled with nutrient-rich water. Instead of sunlight, they rely on hanging blue and pink LED rope lights.
About the size of the standard one-car garage, each shipping container can produce the same amount of crops as two acres of outdoor farmland.
Musk and Peggs chose Square Roots’ first class of 10 young entrepreneurs from over 500 applications. Peggs says they represent the next generation of farmers — though not all came to NYC with farming experience.
Before Josh Aliber, 24, moved from Boston to Brooklyn to join Square Roots, he had never farmed. Now he’s starting up his own specialty herb business and running a vertical farm.
Earlier this year, while Aliber was recovering from a concussion, he learned about urban farming from a podcast. He started researching it from his bed, and found out about the Square Roots program.
His shipping container farm runs on 10 gallons of recycled water a day, which is less than the average shower’s worth.
Aliber can monitor everything from the oxygen level to the humidity — which affects the plants’ taste and texture — using “the computer panel” near the door and sensors in the growing beds. If he wants a tropical or northeastern climate, he can control that too.
Aliber is selling his specialty herbs and basil primarily to upscale Italian and pizza restaurants in NYC.
All of the Square Roots farmers sold their first harvests at a recent local farmer’s market.
Though the program, he has had the opportunity to work with numerous mentors, including Tom Colicchio, a restaurateur and judge from “Top Chef."
“Yes, I have the ability to make money, but yes, I also have the ability to change the world,” he says.
Another 27-year-old farmer, Electra Jarvis, comes to Square Roots three days per week. On Wednesdays, she spends four hours meticulously placing 800 seeds inside small troughs.
Two weeks later, she transplants them to the walls. “We should be growing closer to us in cities,” she says.
Aliber, Jarvis, and the other eight entrepreneurs are not just learning how to grow plants, but also how to grow their businesses. A large part of the program is learning about branding and “how to tell our stories,” Jarvis says.
The larger goal of Square Roots, Musk tells Business Insider, is to create “a real food revolution.”
In the late ‘90s, following the tech boom, the Musk brothers moved from South Africa to Silicon Valley. They invested in X.com, which later merged with PayPal and was acquired by eBay.
Kimbal Musk has known Peggs, who previously worked on tech startups sold to Walmart and Adobe, for a decade. Before Square Roots, they worked together at The Kitchen, where Peggs served as the "President of Impact" and helped expand the chain to new cities.
When asked how his experience in tech translates to running a vertical farming accelerator, Peggs says the two fields share the same motivation.
“You learn how to execute impossible dreams. This was all just a Powerpoint presentation six months ago,” says Peggs, pointing to the farms behind him.
“Today’s consumer wants to know they are supporting companies that are doing something good for the world,” Peggs says. “This not just a Brooklyn foodie trend.”
The world’s largest vertical farm, Aerofarms, launched this year in Newark, New Jersey. In late 2015, urban farming company Gotham Greens opened the world’s largest rooftop farm in Chicago.
Square Roots hopes to expand to 20 cities by 2020.
Vertical farms can grow all year, using significantly less water and space than outdoor farms.
Critics of vertical farms point out that the LEDs drain a lot of electricity. Peggs says Square Roots is exploring how the farmers can switch to solar power in the future, since electricity is the biggest cost for the farms.
Kimbal Musk — Elon's brother — Just Opened A Shipping Container Farm Compound In New York City.
Square Roots will build offices inside the Pfizer factory in the coming months. In its past life, the building produced ammonia, a chemical that’s sprayed on plants and became vital to the industrial food system after WWI.
In 2017 and beyond, sustainable food startups will do business there. “It’s an act of poetic justice,” Peggs says.
Copyright © 2017 Business Insider Inc. All rights reserved. Registration on or use of this site constitutes acceptance of our Terms of Service, Privacy Policy, and Cookie Policy.
To Grow Community and Jobs of the Future, Suburbanite Launches Vertical Farming Enterprise in Detroit
After spending time with street children in Brazil as part of a missionary trip, Jeff Adams, founder of Detroit, Michigan-based urban vertical farming enterprise Artesian Farms, felt compelled to change his community. “If we can go 7,000 miles to work with young people we won’t see again, what can we do in our own backyard?
To Grow Community and Jobs of the Future, Suburbanite Launches Vertical Farming Enterprise in Detroit
January 3, 2017
Trish Popovitch
After spending time with street children in Brazil as part of a missionary trip, Jeff Adams, founder of Detroit, Michigan-based urban vertical farming enterprise Artesian Farms, felt compelled to change his community. “If we can go 7,000 miles to work with young people we won’t see again, what can we do in our own backyard?”
13 years ago Adams moved from the suburbs of Detroit to the urban neighborhood of Brightmoor—roughly four square miles on the outskirts of Detroit full of abandoned homes and derelict industrial buildings.
“My wife and I sold our house in the suburbs and moved to the Brightmoor neighborhood in the city of Detroit. What I noticed was in our community there was a lack of jobs for people who are 18 to 30 years old that had some limited skills and limited availability to transportation to get to a job,” says Adams. “I started looking for opportunities to employ people. I set up a business incubator and started looking around to see what we could do.”
What Adams discovered is what many have found in the rehabilitated Motor City – a well established urban farming movement with support from local businesses and city officials that was growing jobs and revitalizing communities. Adams wanted more opportunities like that for the neighborhood of Brightmoor.
After researching the state of urban agriculture in the city and determining that seasonal jobs wouldn’t cut the mustard, Adams bought a warehouse in August of 2014, unoccupied since 1998, on a local industrial complex and set up the shell of a indoor vertical hydroponics farm. “We set up this business as a social enterprise, a limited liability corporation with the social cause of employing people who are difficult to employ, bringing blighted structures back to life and making a vibrant opportunity for our neighborhood,” says Adams.
By March of 2014, the warehouse was renovated enough to set up shop. The farm sits inside a 7,000 square feet warehouse. Using artificial light and seven 20 foot high vertical towers and racked trays, Adams’ workers produce around 75 pounds of lettuce and kale a week, and approximately 40 pounds of basil per week. Adams has recently received funding to install an additional 35 vertical growing systems in the rest of the space, which will serve to increase output as well as his customer base.
Adams sells to local businesses, mostly restaurants and grocery stores. With some proactive self promotion and good old fashioned cold calling, he managed to get Artesian Farms produce into a regional chain with 15 stores as well as one local branch of Whole Foods. One growing contract took an hour while another took 18 months to negotiate. For Adams it’s about having the right product and understanding how to sell your company’s narrative.
“You have this product that people consume, but you also have this background story about growing local and what it means to the city of Detroit. It makes for a compelling combination of good food with a social cause behind it and people gobble that up,” says Adams. “Our branding is all about growing in Detroit for ‘goodness’ sake.’ It’s a great product offering great services to our community.”
Adams introduced his product to the local community on Earth Day last year, gathering locals to celebrate and experience their growing unit’s food. The positive feedback provided the farm with early momentum. Artesian Farms also markets through the local farmers’ markets.
Currently Artesian Farms has two full-time workers, one part-time, and Adams. Having felt the brunt of the mass layoffs in Michigan on a personal level after leaving his job in tech after 30 years, Adams can relate to many of the social and emotional stresses his workers and the locally unemployed face and feel. “There are a lot of issues that go along with hiring under resourced folks. I tell people as long as you can read and follow directions you can do this job. It’s a great way to make a salary.”
Artesian Farms is very aware of the potential issues facing urban employees such as lack of transportation, child care, and background checks that prevent many people from making a fresh start or finding gainful employment. Adams offers his employees a salaried wage and accommodates their scheduling needs as much as possible.
Just recently, Adams installed 15 additional growing towers although they are not yet active. “Now is the time for us to go out and create the volume to fill that up,” says Adams. “Then as we fill this up, then we will look for another space in Detroit to be able to continue that growth.”
Indoor Harvest Corp and Alamo CBD Enter Into Discussions to Combine and Ultimately Create Medical Cannabinoids Pharmaceutical Group
Indoor Harvest Corp and Alamo CBD Enter Into Discussions to Combine and Ultimately Create Medical Cannabinoids Pharmaceutical Group
January 03, 2017 13:39 ET | Source: Indoor Harvest Corp
HOUSTON, Jan. 03, 2017 (GLOBE NEWSWIRE) -- Indoor Harvest Corp (OTCQB:INQD), through its brand name Indoor Harvest®, is a full service, state of the art design-build engineering firm for the indoor and vertical farming industry. The Company provides production platforms, mechanical systems and complete custom designed build outs for both greenhouse and building integrated agriculture grows.
The Company is pleased to announce it has entered into discussions to acquire 100% of the member interests in Alamo CBD, LLC. (“Alamo”), a Texas Limited Liability Company. Upon closing of the acquisition, it is intended that Indoor Harvest shareholders would retain 40% and Alamo shareholders would retain 60%, of the total issued and outstanding common stock of Indoor Harvest. It is contemplated that at or subsequent to the acquisition of Alamo by Indoor Harvest, Indoor Harvest will spin-off its vertical farming operations including its produce and engineering, procurement and construction related operations to Indoor Harvest shareholders at the closing of the acquisition. The Company’s remaining cannabis related assets, agreements, intellectual property and operations will remain with Indoor Harvest/Alamo.
Alamo has signed an agreement with Vyripharm Enterprises, LLC. ("Vyripharm"), a Delaware limited liability company, to form a Joint Venture for pharmaceutical cannabinoids research (“Joint Venture”). Under the proposed joint venture with Vyripharm, Alamo will provide pure medical cannabis oil/product to Vyripharm in order to provide specific chemical profiles needed for Vyripharm’s research and patient treatments. It is planned that Alamo will, as a result of the acquisition by Indoor Harvest described above, have the right to Indoor Harvest’s patent pending biomanufacturing platform which it will then use in connection with the planned Joint Venture. The Joint Venture’s business plan is to develop specific process IP to achieve specific chemical profiles to treat various medical conditions such as epilepsy or PTSD, custom tailored to each patient.
It is anticipated that a condition precedent to the closing of the acquisition will be that Indoor Harvest must raise sufficient capital to repay all existing Company debt and pay for the expenses necessary to complete the spin-off of its vertical farming operations and to complete the proposed acquisition, currently anticipated to be approximately $1,000,000 in the aggregate. John Choo, Chief Executive Officer of Indoor Harvest noted, “The acquisition and spin-off transaction currently contemplated would, if all aspects of the transaction are effected as currently planned, complete Indoor Harvest’s previously announced plan to separate our cannabis and produce related operations.”
Chad Sykes, founder and Chief Innovation Officer of Indoor Harvest, added, “It will be the aspiration of our Company after acquisition of Alamo and thus becoming a joint venture partner with Vyripharm Biopharmaceuticals, to become a leader in the medical cannabinoids pharmaceutical space. Our aeroponic biomanufacturing platform allows for very precise control of plant expression, which allows a producer to create repeatable, consistent chemical profiles. We believe that unlike the small number of pharmaceutical groups operating in cannabis today, which use less precise cultivation methods and isolate certain chemical compounds, we can harness the benefits of the full entourage effect through the actual cultivation process. The planned Joint Venture that we’ll become part of our acquisition of Alamo has the potential to leverage our individual entities’ IP, agreements and relationships and would position us to become a major part of a serious player in the pharmaceutical space and medical cannabis research.”
Alamo’s current business plan is to use ten (10) acres of land, to include water rights, in La Vernia, Wilson County, Texas, to construct a 17,500 square foot cannabidiol pharmaceutical production facility. Alamo plans to seek a license to operate their facility under the Texas Compassionate Use Act. The Texas Compassionate Use Act (Senate Bill 339) was signed by Gov. Greg Abbott and became effective June 1, 2015. The bill requires the Department of Public Saftey (“DPS”) to create a secure registry of physicians who treat epilepsy for the purpose of prescribing low-THC cannabis to patients who have been diagnosed with intractable epilepsy. In addition, the bill requires DPS to license at least three dispensing organizations by Sept. 1, 2017. In addition to plans to file an application to operate under the Texas Compassionate Use Act, Alamo also plans to file an application with the DEA and register to become an authorized producer of medical cannabis and medical cannabis extracts for pharmaceutical research and clinical trials within the United States.
Vyripharm has advised us as follows: It is a biopharmaceutical company with a goal of improving clinical management through diagnosis and treatment with botanicals, synthetic pharmaceuticals and drug delivery systems. Vyripharm is reformulating its patented In-Situ Hydrogel, N4 Technology and Oligosaccharide (Dual Agent) Technology to develop applications in combination with medical cannabinoids for nuclear imaging and treatment for neurologic disorders including, but not limited to, post-traumatic stress disorder, epilepsy, acute/chronic disorders, cancers, metabolic disorders, and microbiome. Vyripharm is working diligently to prepare and file a range of new patent applications covering what it has described to us as being breakthrough work on medical cannabinoids (synthetic/natural).
Dr. Elias Jackson, Vyripharm’s Director of Scientific Public Relations said, “Early studies have shown a positive impact on certain resistant forms of cancer. We are carefully analyzing these results before we formally release this data. Based on the strength of these early studies, we believe that medical cannabis will play a vital role in the treatment regimen addressing a range of cancers, and that Texas and the Texas Medical Center could become a focal point for this important research.” Vyripharm has entered into sponsored research agreements for its core platforms with the University of Texas Medical Branch Galveston, The University of Texas Health Science Center at Houston – Institute of Molecular Medicine Sponsored Research and The University of Texas M.D. Anderson Cancer Center. There is also an agreement with the National Institute of Drug Abuse and has pending agreements with Baylor College of Medicine and the VA Hospital in Houston, TX.
Cynthia Cortez, Alamo’s Marketing Director said “Alamo together with Indoor Harvest after the planned acquisition transaction and through the Joint Venture will have complete control over the entire grow process to ensure consistent high quality medical cannabis. Utilizing Indoor Harvest’s state-of-the-art cultivation process will maintain a clean product for patients. In addition, Alamo looks forward to working with Vyripharm to provide what is intended to be high-quality medical cannabis for their research and development studies. We believe that Vyripharm, Indoor Harvest and Alamo share the same goal of becoming recognized as the global leaders in comprehensive cannabis product testing, certified pure cannabis oil, and evaluating the efficacy of certified pure cannabis in humans.”
Alamo and Indoor Harvest are currently completing customary due diligence and it is expected a definitive acquisition agreement will be agreed upon on or before February 15, 2017. We understand that Alamo and Vyripharm are also completing customary due diligence regarding the proposed Joint Venture which the parties expect to complete a definitive agreement prior to the closing of our acquisition of Alamo.
Consistent with the SEC’s April 2013 guidance on using social media outlets like Facebook and Twitter to make corporate disclosures and announce key information in compliance with Regulation FD, Indoor Harvest is alerting investors and other members of the general public that Indoor Harvest will provide weekly updates on operations and progress through its social media on Facebook, Twitter and YouTube. Investors, potential investors and individuals interested in our company are encouraged to keep informed by following us on Twitter, YouTube or Facebook.
ABOUT ALAMO CBD
Alamo CBD, LLC is dedicated to producing high quality CBD products in service to the patients of South Texas. The company is based in the San Antonio metropolitan area and was founded by a qualified team consisting of a pharmacist, a neuropsychologist, a microbiologist, a horticulturalist, and a dietitian. For more information, please visit http://www.alamocbd.com.
ABOUT VYRIPHARM BIOPHARMACEUTICALS
Vyripharm is a biopharmaceutical firm focused on natural products, regulatory testing, pharmaceutical drug development, data storage, monitoring technology, development of imaging agents, and drug delivery systems. The aim of Vyripharm is to improve clinical management through diagnosis and treatment with botanicals, synthetic pharmaceuticals, and drug delivery systems.
ABOUT INDOOR HARVEST CORP
Indoor Harvest Corp, through its brand name Indoor Harvest®, is a full service, state of the art design-build engineering firm for the indoor farming industry. Providing production platforms and complete custom designed build outs for both greenhouse and building integrated agriculture (BIA) grows, tailored to the specific needs of virtually any cultivar. Our patent pending aeroponic fixtures are based upon a modular concept in which primary components are interchangeable. Visit our website at http://www.indoorharvest.com for more information about our Company.
FORWARD LOOKING STATEMENTS
This release contains certain “forward-looking statements” relating to the business of Indoor Harvest and its subsidiary companies, which can be identified by the use of forward-looking terminology such as “estimates,” “believes,” “anticipates,” “intends,” expects” and similar expressions. Such forward-looking statements involve known and unknown risks and uncertainties that may cause actual results to be materially different from those described herein as anticipated, believed, estimated or expected. Certain of these risks and uncertainties are or will be described in greater detail in our filings with the Securities and Exchange Commission. These forward-looking statements are based on Indoor Harvest’s current expectations and beliefs concerning future developments and their potential effects on Indoor Harvest. There can be no assurance that future developments affecting Indoor Harvest will be those anticipated by Indoor Harvest. These forward-looking statements involve a number of risks, uncertainties (some of which are beyond the control of the Company) or other assumptions that may cause actual results or performance to be materially different from those expressed or implied by such forward-looking statements. Indoor Harvest undertakes no obligation to publicly update or revise any forward-looking statements, whether as a result of new information, future events or otherwise, except as may be required under applicable securities laws.
Contacts: Indoor Harvest Corp CINO, Mr. Chad Sykes 713-410-7903 ccsykes@indoorharvest.com
Vertical Farming Campaign Kicks Off
LAFAYETTE, Ind. — Austin Kasso, executive director of Red Giant Union, has a towering vision for Greater Lafayette's food production and consumption future, and the vision is vertical, so to speak
Vertical Farming Campaign Kicks Off
Emma Ea Ambrose , eambrose@jconline.com4:10 p.m. EST January 2, 2017
LAFAYETTE, Ind. — Austin Kasso, executive director of Red Giant Union, has a towering vision for Greater Lafayette's food production and consumption future, and the vision is vertical, so to speak.
On Monday Red Giant Union, a charity to further urban agriculture, in partnership with local startup Hydro Grow, launched a campaign to raise $30,000 to start a vertical farm in downtown Lafayette called The Tower Farms.
The vision is to take over a space at 419 North 3rd Street and install vertical tower growers that will generate fresh produce to supply the juice and salad bar that will operate at the same location.
The long term goal is to convert this space into a place where local chefs, food entrepreneurs and farmers can innovate and collaborate on issues of food security and sustainability.
“We transport most of our produce from Arizona and California, which in this day and age is not necessary anymore because we have the means and infrastructure to grow our own produce within our community,” Kasso said.
Kasso said he thinks Lafayette is ready for a vertical tower farm and doesn’t anticipate any issues fundraising the capital required to start the endeavor.
“Lafayette is ready for this. … It’s all about finding ways to engage the community,” he added.
Roughly 300 people are involved with the campaign in some fashion, according to Kasso, and he expects those numbers to grow.
The campaign goal is to raise 75 percent of the funds within two weeks and be fully funded within the month. From that point, it will take two months to set up the farm space.
Projects like this have been successful elsewhere in the country, Kasso said, referencing the Green Bronx Machine project, which takes urban agriculture techniques to children in Bronx school systems.
Urban farming practices, Kasso said “creates economic growth, healthier minds and bodies and an overall healthier community.”
The campaign went live on crowdfunding website Barnraiser and Kasso said they are still looking for corporate partners and sponsors in the community.
Call J&C reporter Emma Ea Ambrose at 765-431-1192. Follow her on Twitter: @emma_ea_ambrose.
Major Vertical Farm Operator Builds Productivity, Scale and Scope
Climate change, water scarcity and a soaring global population are among the key reasons why vertical indoor farming is taking off around the world. Here at www.freshfruitportal.com we recently visited one such facility belonging to U.S.-based AeroFarms, and learned about the extensive international growth plans for its ‘game-changing’ proposition
Major Vertical Farm Operator Builds Productivity, Scale and Scope
January 03 , 2017
Climate change, water scarcity and a soaring global population are among the key reasons why vertical indoor farming is taking off around the world. Here at www.freshfruitportal.com we recently visited one such facility belonging to U.S.-based AeroFarms, and learned about the extensive international growth plans for its ‘game-changing’ proposition.
One could be forgiven for thinking they had come to the wrong location when arriving at AeroFarm’s 30,000-square foot vertical farm in Newark, New Jersey. The unassuming building had operated as a paintball and laser tag arena prior to the company acquiring it, with much of the old business’ artwork still on display outside.
Upon entry I am met with a humid waft of fresh leafy greens, rows upon rows of LED-covered vegetables, and the company’s chief marketing officer Marc Oshima.
AeroFarms started out in 2004 in upstate New York selling to the Ithaca Farmers Market, and has since invested heavily in its R&D and technology.
Over the years it has built and operated numerous vertical farms while continuing to optimize its technology, and has grown more than 250 vegetable varieties.
I am told around 10-15 types of leafy greens are grown at this facility – its eighth in the company’s history. The vegetables have an extremely short crop cycle of just 12-16 days, while using 95% less water than conventional growing methods and no pesticides.
The seeds are germinated and grown on a cloth made from recycled BPA-free plastic bottles and then loaded into one end of the production row.
Over the course of their growing cycle they are moved further down the row, receiving specific intensities and spectrums of light and a nutrient mist sprayed in precise amounts onto the roots hanging below the cloth. Many factors like temperature, humidity, and Ph and CO2 levels are also closely monitored and modified.
“Everything has been measured down to the micron of the misting droplet. This is really taking farming to a whole other level of precision and performance,” Oshima says.
He explains AeroFarm’s technological developments are happening at such a pace that while just one year ago the vertical farm was around 75-times more productive than an open field farm – due to aspects like crop cycle and density – that figure has now shot up to 130 times.
No dressing needed
The various greens I am given to sample pack a flavor punch – a focus of the company’s R&D process. From baby Bok choy to Ruby Streak mustard greens to baby kale and arugula, each item’s flavors are strongly accentuated.
“No dressing is needed for these. What’s been exciting is that the key taste makers like top chefs say they feel like their pallets are being woken up again,” Oshima says.
“At the end of the day we’re a technology company, but we’re also a food company passionate about how we can change behavior. You have to make it taste good – that’s how you change consumption and how you get opportunities to be able to expand category.”
The short crop cycle afford the R&D team ample learning opportunities to optimize the taste and production technology.
“Out in the field you may only have one harvest a year, so you have to get it right. But here we have around 30 harvests a year, or 30 learning opportunities,” Oshima says.
He adds there are more employees with PhDs in the company than just about any other farming operation, and that staff includes the likes of a chief science officer, a chief technology officer, and an Oxford University-educated chief operating officer with a deep background in operating large-scale controlled growing environments.
“It’s a symbiotic relationship between our growing system, environment and product. At the end of the day it’s biology, but it’s also about how we mange and optimize that. And because it’s all our own technology, we understand very clearly how to optimize for these different characteristics.”
The products are sold to retailers within around 50 miles, including ShopRite – one of New York’s leading supermarket chains – and foodservice companies including the Compass Group, one of the world’s leading foodservice operators.
Local schools and restaurants are also supplied, and every week the production facility opens up its doors for local residents to buy from its farm stand.
Oshima says having a connection with the local communities in which AeroFarms operates is important to the company and its ethos of responsibility.
“We think a lot about our local footprint – serving the local communities and hiring locally. Over 40% of our team here lives in Newark, and over 85% live within 15 miles, so there’s a tremendous connection with the community overall.”
A couple of years ago the New York Times hailed the Newark vertical farm as helping to drive the revival of the Ironbound local area, which has been troubled over recent decades with severe economic and social issues.
An ambitious pipeline
With AeroFarms having invested a significant amount of time and money optimizing its business model and production operations, the organization is now in the midst of a major expansion, both in the U.S. and overseas.
Half a mile away from its Newark operation I visited, AeroFarms is building what is claimed to be the largest vertical farm in the world, which will also serve as its global headquarters.
I am given a sneak peek of the 70,000-square-foot operation in a former steel mill, which has started production and is due for its first sales in the first quarter of 2017.
With 35 rows and 12 levels of vertically growing leafy greens, the farm’s growing capacity is far higher than any other facility, and is complete with full automatization for the harvesting and packaging process.
Despite the impressive size of that farm, Oshima tells me soon it will no longer be the biggest, as the company rapidly rolls out major new projects in other locations.
“Our whole focus as a company has been local – thinking how do we disrupt what is often a very complex supply chain involving produce that is grown remotely?”
He says the crop’s high quality has led to interest from international retailers. Supplying to them from afar would mean going against the company’s focus on supplying locally, but inquiries have served as a strong indicator of the level of demand out there.
“It’s opened our eyes about a completely different part of a business opportunity. Our core focus though is about how do we serve the local communities that we have, and what we want to do is build responsible farms in all the major cities around the world.”
The next two major projects in the pipeline in the U.S. are in Camden, in southern New Jersey, and Buffalo, in upstate New York, and development is underway to roll out new projects in overseas locations.
“Our CEO just got back from China last week where he was for development talks, and then there are other markets we are looking at as well,” he says.
“We’ve had a working demonstration farm in Saudi Arabia since 2011, to show we are able to grow in different challenging environments. So the GCC [Gulf Cooperation Council] countries are an option, and we also have development in Africa and northern Europe, along with a tremendous amount of interest in the U.S.”
Aspects relating to the weather, climate change, pest pressure, water scarcity, food safety and urban density were all among the issues addressed by AeroFarms when decided where to establish new projects.
The entity has been working closely with Goldman Sachs and Prudential Financial on project financing for its farms.
“Each farm in and of itself has the right kind of economic profile that an investor like Goldman Sachs looks for, and they’re very much interested in being part of the next farm and the next farm,” he said.
The company had earlier mentioned its plans to carry out 25 projects over the next five years, and while Oshima explains this figure may end up being higher or lower than estimated due to varying sizes of the operations, he emphasized there was an ‘ambitious pipeline’ based on demand.
“Our organization is very much set up in terms of building the next farm,” he says, adding the operation and technology are very easy to deploy.
“We’re just trying to have very measured growth so that we can make sure we execute and deliver what we think is a game-changing proposition.”
Urban Farming Org Transforms 9 Empty Greenhouses to Tackle Food Insecurity and Grow Meaningful Jobs
Urban Farming Org Transforms 9 Empty Greenhouses to Tackle Food Insecurity and Grow Meaningful Jobs
January 2, 2017 | Vanessa Caceres
When Lynchburg, Virginia resident Paul Lam’s beloved garden was destroyed inadvertently in 2003, residents rallied around him to find a new space. With the help of community members, Lam, who is disabled, eventually found a seven-acre site with nine empty greenhouses on it that had been the home of a large rose supplier.
The farm site needed a bit of rehab, so a call was put out for volunteers. Hundreds showed up from local area schools and universities to help clean it up. From this community outpouring for Lam, Lynchburg Grows, a nonprofit urban farming organization whose dual mission is to increase access to healthy food in the community and provide meaningful jobs to individuals with disabilities, was born.
Lynchburg Grows cultivates 54 raised beds that grow tomatoes, greens, and the occasional specialty item. The raised beds are 90 to 100 feet long and 3 feet wide. They are of varying depth–some are about a half-foot deep for lettuce and others are deeper for root veggies. The organization can grow greens year-round and is especially known for its spring mix, says Farm Manager Shelly Blades. Items that fare well in the heat, such as okra, grow prominently in the summer. The greenhouses are neither heated nor cooled, and that affects what they can produce at certain times of the year.
Much of the produce grown in the greenhouses is destined for distribution to the residents of Lynchburg, a designated food desert in which nearly 24% of the population lives in poverty and where 18% of residents are not sure where their next meal will come from, says Blades.
To help further alleviate this food insecurity, in 2015, Lynchburg Grows in collaboration with Live Healthy Lynchburg launched a mobile produce delivery service called Veggie Van. The van now makes deliveries to 10 locations in the city, three days a week, and through a partnership with USDA SNAP program accepts WIC and EBT card payments. Lynchburg Grows leaders worked with area churches to map out the places most in need of healthy food access.
In addition to selling affordable produce via the Veggie Van, Lynchburg Grows also supplies about five area restaurants, and maintains a summer CSA with about 90 members and a winter CSA made up of approximately 40 members. Any leftover produce is donated to local food banks and homeless shelters.
Although there’s an interest in higher quality food among Lynchburg chefs and residents, the foodie scene in town is not as developed as in bigger cities. So, Blades and others on staff often find themselves introducing “designer veggies,” such as Hakurei turnips. Blades became familiar with such specialty items while working as a garden coordinator for Harlem Children’s Zone in New York City before coming to Lynchburg about a year ago.
She feels that the farmers and staff at Lynchburg Grows should relish their role in educating others—be it top area chefs or everyday residents—about produce items as it solidifies their role as a food and nutrition resource in the area.
Lynchburg Grows employs 11 people, three of whom are full-time. All but two employees live with disabilities and came to Lynchburg Grows from local placement agency, Stand up, Inc., which specializes in vocational training programs. Some of the employees are in wheelchairs, while others have Down syndrome, or are capable of performing farm work, but have trouble with logic. Job coaches from the placement agency often work beside them. The jobs that they do include caring for plants, bagging lettuce, and cleaning. “We like to find what works for one person and help them become an expert at it,” says Blades.
US: Food Retailer Starts With On-Site Production in Growtainer
"In 2016 we saw the successful Growtainer launch in the UK and the expansion of their European presence at a Spanish biotechnological giant. CEA Advisors & Growtainers® promises, even more, global excitement in Indoor Farming and Controlled Environment Agriculture in 2017"
US: Food Retailer Starts With On-Site Production in Growtainer
In 2016 we saw the successful Growtainer launch in the UK and the expansion of their European presence at a Spanish biotechnological giant. CEA Advisors & Growtainers® promises even more global excitement in Indoor Farming and Controlled Environment Agriculture in 2017.
After more than a year of meetings with the Produce Marketing team at a major US food retailer, the first custom built for onsite production Growtainer® has been delivered and will begin production in Q1, 2017. “We spent over a year discussing the retailer’s concerns and objectives and when I was sure we were all on the same page we began the design and manufacturing process” said Glenn Behrman, founder of Greentech Agro LLC and CEA Advisors LLC.
Growtainers® have come a long way from those first two prototype models built about 4 years ago and recently donated to Texas A & M Agrilife Research Center in Dallas. LED costs have come down and their efficiency has improved. "Our understanding of the critical importance of the growing environment and the need for intuitive control systems has increased. We’re collaborating with more industry experts in all areas that are critical to the development of a well-balanced successful production environment”.
According to Behrman, increasing global awareness of indoor local vertical production has been the driver in the laser focused pursuit of new, modern and sustainable indoor farming practices. "On site production in the Growtainer® to produce the freshest, unique, gourmet leafy greens and herbs for their customers at the retail level is the objective of the retail partner. They are the first in the nation to train their team members in a food safety compliant, climate controlled, LED lit multi-layer vertical indoor production environment. "
"CEA Advisors is proud to be working with a forward-thinking food retailer that is committed to innovation and focused on food safety, unique products and the customer experience” said Behrman.
For this project, CEA collaborated with a McKinney Texas based water management firm, whose team assisted in the design and installation of a state of the art irrigation system. "The container modifications were carried out by the largest and most experienced group in the USA. North America’s leading horticultural supplier of goods and services provides their expert and ongoing consultation to the project, as well."
The state of the art 53’ custom built Growtainer® has a separate utility area and provides 480 square feet of climate controlled vertical production space, specially designed for maximum efficiency and food safety compliance. Besides having a dedicated proprietary technology for ebb and flow irrigation installed, these Growracks® are also equipped with energy efficient LED production modules, specifically designed for multilayer cultivation. The irrigation system is divided into separate zones to provide flexibility and allow a wide variety of production of crops at various growth stages. Behrman worked closely with the irrigation engineers to design a sophisticated control system. The proprietary irrigation system is constantly monitored and any corrections to EC or PH are made immediately. Every irrigation event is perfect for the plants optimum growth.
For more information on this and other exciting innovations in Indoor Vertical Farming
visit www.growtainers.com or email gb@cea-advisors.com
Publication date: 1/2/2017
3 Of The Most Inspiring Farm Startups of 2016
3 Of The Most Inspiring Farm Startups of 2016
Posted by Amy Storey on December 30, 2016
Starting a farm isn't easy. And yet we've seen hundreds overcome the challenges of starting a farm and do it. Now they're providing fresh, nutritious food to their communities in ways that we truly admire.
But we haven't forgotten what it took to get there.
As we look forward on a new year of farming, we wanted to bring you some great examples and other resources to help you start your journey!
Each of these businesses launched a farm this year or helped feed their communities in other ways. Learn about how they did it, what kept them going, and follow them for current updates on their farms.
Triple Threat's The Farm - Aurora, Illinois
Nearly a year ago, Nick Marasco with Triple Threat Mentoring installed a ZipFarm in a Chicago warehouse with the dream of using it to enrich the community and train under-resourced youth.
After 12 months, we're glad to say that the farm is doing just that!
The ZipFarm is an indoor hydroponic farm used as a turnkey solution to problems like climate constraints, construction difficulty, and inconsistent yield. Nick chose the ZipFarm because in addition to these, the equipment allows him to work and train others in the farm. You can read more about the mentoring program here.
The example to follow: Like every farmer, Nick went through a learning curve during the first months of growing. Rather than see an insurmountable challenge, Nick saw new ways to teach and learn, and embraced it. This has made him a better farmer! Nick advises other farmers to do the same.
Follow Triple Threat Mentoring on Twitter or Instagram for more info.
American Heartland Acres - Stem, North Carolina
Matt Marsh and his family started American Heartland Acres with a strong belief that farming had to change and with the confidence that he could help do it.
Many farmers around the Marsh's were ill equipped for changing markets, and suffering from issues like rising prices of inputs. They had slipped into a way of life that was sacrificial rather than passion-driven. Matt knew this had to change. The cost of farming couldn't be greater than the benefits.
Using space- and labor-efficient technology and by approaching his craft pragmatically, Matt has crafted a farming model that allows him to feed his family and enjoy his profession as a basil farmer. He's known as the "basil guy" in the North Carolina towns of Stem and Durham.
The example to follow: "Due diligence" is a term thrown around a lot when planning a business, but it sometimes gets diluted with overuse. Matt is a great example of what due diligence ought to look like. He researched (and researches) his methods, hustles to form connections to potential clients, and constantly looks for ways to improve his farm.
Follow AH Acres on Instagram or Facebook for more info.
Green Wolf Vertical Farm - Panhandle, Texas
Marre Seleska started Green Wolf Vertical Farm in Panhandle, Texas after discovering that an indoor ZipGrow farm could not only trump the capricious Texas weather, but offer fresh food to a high-demand community.
Now Marre can hardly keep up with demand from her clientele, which consists mostly of farmer's market folks, chefs (who Marre sees as food artists hungry for quality supplies), and a soon-to-be CSA group.
The example to follow: When Marre saw opportunity ripe in her community, she took it. She has the ambition necessary for a small farmer and the hustle to back it up!
About Glenn Behrman
About - Glenn Behrman
Glenn is a native of New York City and has been involved in the horticulture industry for over 45 years. From a small retail store in New Haven, over the next 20 years Glenn built the business into a regional success, a high volume chain of retail stores and wholesale foliage distribution centers, including a lawn and garden import division. Glenn owned and operated garden centers from New York City to Philadelphia, foliage nurseries in Florida, orchid nurseries in Thailand and tree farms and nurseries in Vietnam. After selling his U.S. based business interests to devote more time to his Asian ventures, Glenn relocated to Bangkok, Thailand in 1994. Glenn has acted as a grower, broker and exporter of young plants and orchids and has introduced new ornamental plant varieties from Asia to growers worldwide. In addition to years of senior level day to day business management and operations, his experience further extends to designing and constructing thousands of square feet of nurseries and greenhouses.
During his time in Asia, in addition to his horticulture business, he has been involved in other ventures including an internet start-up which he founded and then sold to a Singapore investment group (www.theglobalgrocer.com) and the production of postage stamps for the Lao government (SEA Philatelic Group, Inc). He has also served as a Special Advisor to H.E. Sar Sambath, former Cambodian Ambassador to the United Nations. In 2011 he left his position as Landscape Project Manager for the $4.5 billion Ho Tram Strip project, consisting of 5 five star resorts and two Las Vegas style casinos in Vung Tau, Vietnam, to return to the United States to devote his full time and energy as co-founder and President of GreenTech Agro LLC. Glenn and his wife currently reside in Dallas where he manages the day to day operations of GreenTech Agro LLC and CEA Advisors LLC. Based at Texas A & M University Agrilife Research Center, Glenn works full time on the design, development and fabrication of the Growtainer™ containers, Growrack™ rack systems, Growtroller™ control systems and provides Consulting services to international clients on the development of innovative investment grade indoor farming projects
Senator Stabenow Introduces Urban Agriculture Act of 2016
Senator Stabenow Introduces Urban Agriculture Act of 2016
This fall, U.S. Senator Debbie Stabenow announced plans to introduce the Urban Agriculture Act of 2016, legislation that would support urban farming initiatives and increase access to healthy food. “Urban agriculture is steadily growing in cities and towns across Michigan and across our country, creating new economic opportunities and safer, healthier environments,” said Senator Stabenow. “The Urban Agriculture Act will continue this momentum by helping urban farmers get started or expand their business, so they can sell more products and supply more healthy food for their neighbors.”
Michigan's urban agriculture leaders are hopeful that the Act will increase the number of urban farms in Michigan and around the country. “We have an abundance of available land in Detroit and groups like D-Town Farms are putting it to productive use in a way that promotes good health and economic opportunity,” said Detroit Mayor Mike Duggan. “I hope that Sen. Stabenow's bill will help efforts like this expand and allow others to follow in their footsteps." Malik Yakini, Executive Director of the Detroit Black Community Food Security Network, commented, “As we rethink how we provide food in an environmentally sustainable way for an increasingly urban population, urban agriculture is an important component. Growing food closer to centers of population-density not only provides people with fresher, more nutrient-rich foods but also reduces the carbon released into the atmosphere by transporting food long distances. Finally, urban agriculture, and the associated businesses needed to support it, helps local economies to thrive. We appreciate Senator Stabenow's awareness of the great importance and potential of urban agriculture.”
Specifically, the bill would create new economic opportunities through agriculture cooperatives, encouraging rooftop and vertical farms, and invest millions of dollars for cutting-edge research to explore market opportunities and technologies for lowing energy and water needs. It would also provide new financial tools and support for urban farmers by expanding farm loan programs, providing affordable risk management tools to protect against crop losses, and create a new urban ag office at USDA. Furthermore, it invests $5 million for the development of community gardens, expands resources for technical and financial support to test and clean up contaminated soils and creates a pilot program for urban composting.
More Urban Farms Sprouting With USDA's Help
More Urban Farms Sprouting With USDA's Help
Farming, a largely rural activity, is moving to the cities, as urban farms continue to grow with help from the federal government.
As Business Insider reports, the U.S. Department of Agriculture each year provides millions of dollars to rural farmers, but the same is starting to be said for urban farms.
According to greensgrow.org, urban farming is just what it sounds like – growing or producing food in a city or heavily populated town or municipality.
In 2016, the USDA funded a dozen urban farms and in 2017, even more money is expected to go toward rooftop farms, greenhouses and warehouses in urban settings.
One of the USDA’s programs geared specifically for urban farming is the Microloan program, which offers funding up to $50,000. Since 2013, 23,000 loans worth $518 million have been awarded through the program. About 70 percent have gone to urban farmers.
The USDA also published an “Urban Agriculture Toolkit” this year that is full of advice about how to launch a greenhouse or rooftop farm, and tips about how to apply for loans.
While most USDA grants and loans go to rural farms, but is making efforts at giving urban farmers equal opportunities and recently set up an office in New York City – a departure from the norm, as most of the USDA’s 2,200 offices are in rural states like Missouri, Texas and Iowa.
These initiatives, as Business Insider reports, underscore a growing movement within the USDA to support local food systems and look beyond rural agriculture.
Urban farmers provide a way to meet a growing need for a growing global population.
In 2016, Business Insider reports, Aerofarms was launched inside a 70,000-square-foot warehouse in Newark, New Jersey, making it the largest vertical farm. In 2015, Gotham Greens, the world’s largest rooftop farm, was started in Chicag
No Sunlight, No Soil, No Problem: Vertical Farms Take Growing Indoors
No Sunlight, No Soil, No Problem: Vertical Farms Take Growing Indoors
New Jersey company seeks to build world's largest vertical farm inside old steel mill near the airport
By Steven D'Souza, CBC News
Posted: Dec 28, 2016 5:00 AM ET
Steven D'Souza
CBC News New York
Steven D'Souza is a Gemini-nominated journalist based in New York City. He has reported internationally from the papal conclave in Rome and the World Cup in Brazil, and he spent eight years in Toronto covering stories like the G20 protests and the Rob Ford crack video scandal.
Related Stories
- Food of the future: Bugs, seaweed and vertical farms
- St. Stephen possible home for country's largest aquaponics vertical farm
- Farming in the city: aquaponics farm comes to Montreal
- Stuck-in-the-mud Koreans help Manitoba First Nation grow fresh veggies
- Innovator wants to test fish aquaponics facility in Yukon
Inside a windowless warehouse once used for paintball, with planes heading to nearby Newark airport overhead, an industrial park in New Jersey seems an unlikely place to find fresh locally grown produce.
With LED lights standing in for the sun, and cloth replacing soil, the plants grown at AeroFarms are not your typical greens.
"This is fully controlled agriculture and allows us to understand plant biology in ways that, as humans, we've never achieved," said AeroFarms CEO and co-founder David Rosenberg, standing in front of rows of kale, arugula, lettuce and other leafy greens.
This is a vertical farm — a facility that looks like it jumped off the page of a science-fiction novel instead of an agriculture textbook.
Here seeds are woven into a mesh cloth made of recycled materials. Trays of plants are stacked one on top of the other in long rows. LED lamps provide the light, while water and nutrients are sprayed in a mist to the roots as they dangle below — a process called aeroponics.
"We give the plants what they want, when they want it, how they want it," Rosenberg said.
World's largest vertical farm
The company is currently building what's been described as the world's largest industrial vertical farm, with food grown 12 levels high inside a two-million-square-foot space, which the company says will produce two million pounds of food a year. It's set to open next year.
An AeroFarms' worker waters seeds freshly planted in a special cloth used to grow the plants. In vertical farming, the cloth replaces traditional soil and LED lights replace sunlight. (CBC News)
The pitch is enticing: locally grown food in any climate, year-round. In AeroFarms' case, they say they use 95 per cent less water, no pesticides and don't produce any of the waste that comes with industrial agriculture.
"We can take the exact same seeds that are out in the field that may take 30 to 45 days to grow, [and] we can grow it in 12 to 16 days by creating the perfect environment," said Marc Oshima, AeroFarms' chief marketing officer.
Problems with power
Indoor farming isn't a new concept. Farms across Canada are attempting similar concepts, trying to extend growing seasons and bringing fresher produce to colder climates.
But critics like Bruce Bugbee, a professor of crop physiology at Utah State University, say using artificial light to replace sunlight is still the biggest problem.
"I know how much electricity goes into the electric lights," he said, adding the cost doesn't include carbon emissions created from generating the power.
Then there's the problem of the light quality.
"To me, sunlight is still the gold standard for nutritional quality and they're aspiring to get it as good as the crops grown in sunlight," Bugbee said.
Big-ticket investors
Rosenberg says the company is using energy-efficient lighting and only grows the most cost-effective vegetables, focusing on micro-greens, instead of other vegetables like tomatoes, cucumbers or other larger produce.
Their efforts have won the support of big-name investors, like Goldman Sachs and Prudential, which have provided funding for the more than $30 million US project. One estimate projects that the vertical farming industry will grow to be worth as much as $6 billion US by 2022.
With computer models, data points and mechanical engineers working beside plant scientists and crop physiologists, Oshima says the operation is less farm, more tech startup.
"We like to think of ourselves as the Apple of farming, so the growing towers are really the hardware, the growing recipes for each of the variety is really the software."
A matter of taste
Another knock against indoor and vertical farms is the question of taste. Can plants grown in unnatural environments replicate the taste and texture of outdoor- and soil-grown plants?
To answer that, the company invited Marion Nestle — a professor of nutrition, food studies and public health at New York University — to tour their facility. Nestle was a skeptic.
"I rolled my eyes," she said, describing the initial invitation. "Why are we doing this when you can grow vegetables really beautifully in soil? What's the problem all of this technology is trying to solve?"
AeroFarms says it treats its plants with specific types of light, which allows for more efficient photosynthesis. But critics say the excessive use of electricity makes the operation less green than it appears. (Steven D'Souza/CBC News)
But Nestle says she's now a convert, after tasting samples of the produce AeroFarms sells to local grocery stores, making it available to nearby schools and the community.
"They taste a lot better than the microgreens we get in New York that have sometimes been on the road for a week."
Whether AeroFarms' crops are as nutritious as traditional produce, Nestle can't say; the nutrients the company feeds its plants is a closely kept secret.
While AeroFarms pitches its methods as a way to disrupt traditional farming, save water and provide access to fresh produce in urban areas underserved by grocery stores, Bugbee says vertical farming — and the more expensive produce it grows — won't solve the world's food problems.
"It will provide terrific food for people that can afford it, but they shouldn't be saying they'll save the planet."
Concrete Farms
Concrete Farms
What if you could pluck lettuce, cucumber and tomato from the rooftop farm in your residential building to prepare a salad that is fresh and pesticide free? And that, too, from plants grown without the use of soil?
Well, it could be a common sight in the near future. The Food and Agriculture Organization (FAO) of the United Nations estimates that by 2050, agriculture production must increase by 70 per cent to feed the ever-increasing population. India will be one of the world's top food importers if we do not try out every futuristic technology that can increase productivity by using less water and less or no soil, apart from reducing health risks to near zero.
Rising demand for fresh and pesticide-free horticultural produce for perennially-swelling urban population all over the world is resulting in the introduction of new farming techniques. These include soil-less techniques such as Hydroponics, Aeroponics and Aquaponics that will redefine commercial agriculture.
Vijay S Yelmalle, who runs a Mumbai-based start-up, Center for Research in Alternative Farming Technologies, says as greenhouse technology has had limited success in India, farming without soil is the best way to use our fast-expanding urban spaces. The best part is that mass adoption of this new technology is easier than we think
Soil plays a key role in growth of plants. It supports the plant, provides it nutrients, and holds moisture, organic matter and bacteria. Well-ploughed land means good oxygen circulation to the root zone. The new techniques provide all these things to the plants without using soil as the medium.
The word Hydroponics is derived from two Greek words, 'Hydro' (water) and 'Ponics' (to labour); so, it means putting water to work. In this, the roots of the plant are either submerged in water or in sterile and inert material. The nutrient salts are provided by dissolving them in the water. These salts are natural substances purified by fractional crystallisation, making them technically inorganic. There are different methods that suit specific plant varieties. While Nutrient Film Technology and Deep Water Culture are commonly used for green vegetables, Substrate-Based Hydroponics is often deployed to grow vines of tomato, cucumber, etc.
Commercial Hydroponics farms are usually set up over more than one hectare for optimum use of resources. The Hydroponics technology ensures consistent taste, shape and colour of the produce. The yield is high and predictable and free from soil-borne diseases. Besides, unlike the traditional open farms, commercial soil-less farms are immune from environmental changes. They also use almost 90 per cent less water. Further advancements in artificial lighting, ways to provide nutrients, pest management and building the systems vertically could multiply the yield of Hydroponics farms to tens of times the traditional farming yield.
In Aeroponics, plant roots are suspended in the air, and moisture and nutrients are provided through foggers. This provides most oxygen to the roots, making the plants grow faster and produce more. Aquaponics, on the other hand, involves replacement of nutrient salts with water from aquaculture, a method of growing a lot of fish in a small area. In other words, it finds a solution to the biggest challenge of aquaculture - the generation of ammonia from fish excreta, whose high concentration can be toxic - by allowing bacteria strains to convert ammonia into nitrites (also toxic to the fish) and to nitrates (less toxic to the fish). Nitrates, a major nutrient for the plants, are taken up by the plant roots. The water so cleaned is used for aquaculture.
Vertical/Urban Farming
Vertical farms are located in the centre of cities where space is available at a premium. These are built over a smaller carpet area but designed to grow vegetables in multiple layers. These farms generally employ the Aeroponics technique but Hydroponics and Aquaponics are used as well. Reduction in carbon footprint (vegetables are transported over hundreds of kilometres, adding carbon to the environment), conservation of water (sometimes condensed water from air-conditioning units is used), freshness/safety of the produce, and premium prices are the common considerations behind vertical farming. Worldwide many enthusiasts and agripreneurs are running successful vertical farms with more and more innovative ideas. There is no limit to these farms. They can go as high as you can pump water and access the place, either yourself or through a robot. The Association for Vertical Farming (AVF), an international NGO, is working with many farms to spread the technology. From Middle East to South-East Asia to Japan to USA to Europe, commercial soilless farms are producing quality and insecticide- and chemical-free produce. South Asia, however, has been slow in adopting these new technologies.
Scenario in India
India's protected cultivation (soil-based greenhouse) farming has had limited success due to wrong adaption of technology. Soilless farming being more advanced, most investors are reluctant to try it at a commercial scale. A few successful greenhouse farmers are trying the substrate-based Hydroponics to grow tomato, capsicum and cucumber and becoming successful. The major hurdle in the success of soil-based greenhouse farming, and even in soilless farming, is experience, knowledge and skills. But the scenario is changing fast. Under the initiative of the government of India, universities have started skill-based degree programmes for urban and rural youths. One such course, a degree in Greenhouse Management, is being offered by Ramnarain Ruia College in the heart of Mumbai. Much of the workforce trained in greenhouses is ready to venture into commercial soilless farms. Many agriculturists who are looking after huge commercial soilless farms are also ready to relocate to India if appropriate opportunity is provided
In Kakaako, A Growing Urban Farm Reaches New Heights
"Between the high rise buildings and industrial warehouses, a farm is the last thing you’d expect to find in urban Kaka‘ako. But one business is creating a space for growing food in an unexpected"
In Kakaako, A Growing Urban Farm Reaches New Heights
Between the high rise buildings and industrial warehouses, a farm is the last thing you’d expect to find in urban Kaka‘ako. But one business is creating a space for growing food in an unexpected
From the outside, this looks like just another building in Honolulu’s developing neighborhood of Kaka‘ako. But step inside a door on the second floor and you’re greeted with stacks of red and green lettuce glowing under rows of LED lights. This is Hawai‘i’s first indoor vertical farm.
“This is an ice plant, or crystal lettuce,” said Kerry Kakazu, the owner and operator of MetroGrow Hawai‘i. “It gives a little bit of a salty taste, nice as a garnish with poke or oysters.”
His love of technology and plants led him to research the growing field of vertical farming.
“Vertical farming just means it’s grown indoors and in multiple levels,” said Kakazu. “People have done vertical farming that’s soil based, but most of it is hydroponics.”
Kakazu uses a method he calls aeroponics, where the roots are suspended in air and bathed in a nutrient-rich mist, instead of soaking in water or planted in soil. This environment gives Kakazu more control of his crops. And since it’s indoors, he doesn’t have to worry about weather, pests and other agricultural challenges.
“This shows that you can do this kind of farming,” he said. “I don’t know if this would ever be enough to supply a large amount of food, like a more traditional farm. But for specialty crops or to grow things that are hard to grow outdoors, I think this is an ideal setup.”
Kakazu started MetroGrow Hawai‘i in 2014. He produces about 100 heads of lettuce a week and a couple dozen containers of microgreens. His clients range from high end restaurants in Chinatown to an herbology store that buys medicinal plants grown by Kakazu.
He’s looking to expand out of his 800 square foot space, but has run into challenge other urban dwellers are familiar with: high rents.
“That’s the one thing with urban food. There’s so much competition for the space, so costs can be high,” Kakazu explained. “Whether it can continue to survive this way, or if it has to be subsidized, somebody’s going to have to want food grown in the urban core. So we’ll have to see.”
Kakazu said eventually he’d like to be able to grow enough produce to feed the flow of residents who are moving into his neighborhood.
Space Age Farm: Chef Grows Hydroponic Greens In Upcycled Shipping Container In Bonner, Montana
Space Age Farm: Chef Grows Hydroponic Greens In Bonner, Montana
Jennifer Stackpole’s indoor farm looks like something out of a sci-fi movie.
Using a pre-assembled hydroponic vertical growing system inside a converted freight container at the Bonner mill site, Stackpole is growing tender crisp greens for local restaurants, stores and markets even as the temperature dips well below freezing throughout the dark Montana winter months.
Requiring only 10 gallons of water a day, red and blue LED lights, and a complex nutrient delivery and cooling system, Stackpole can produce the same amount of lettuce, kale, wasabi arugula and other leafy greens that ordinarily would take up two acres of farmland.
There is no need for soil, as each seed is inserted into a pre-made plug. Once they sprout, they're put into 256 hanging towers where nutrients and water drip down into a growing medium made from recycled polyethylene terephthalate (PET) bottles.
Stackpole calls her startup Wicked Good Greens, and she plans to purchase a second upcycled shipping container farm – nicknamed the Leafy Green Machine – from the same company where she got her first one, Freight Farms out of Boston. She paid to have it shipped here, but all it needs is to be hooked up to electricity and a garden hose, and she can grow more than 5,000 heads of lettuce at one time.
She also will be able to supply restaurants with a huge array of specialty herbs and crops such as tatsoi, basil, short French radishes and edible flowers.
“You’ve never seen anything like it,” Stackpole says as she demonstrates how she works the computer console that controls everything. “This is space age stuff.”
Because the air temperature and nutrients are regulated, and the plants get an even amount of light for 18 hours a day, the greens grow incredibly fast and without flaws.
“There’s no stress to the plants at all,” she said. “There’s no bugs or weather issues that affect most things that grow in the dirt. It produces these big, beautiful heads of lettuce. Everything’s dialed in.”
As a chef herself who operates Balsamroot Catering Co., Stackpole said that she understands what kitchen managers want. The unblemished greens don’t have to be heavily cleaned or processed, and there’s no brown spots or ridges. That saves time in the kitchen. As more and more customers demand farm-to-table, locally sourced food options, Stackpole is betting on an eager market.
“So we don’t have to eat stuff from Mexico or California that’s been sprayed and gassed and is all withered by the time it gets here,” she said. “When the chef receives these greens, they’ll still be alive so they have a very long shelf life, over two weeks. Timing can be everything to a chef because freshness delivers flavor, texture and aesthetics.” She said they will also appreciate the predictability and variety that her operation will offer.
Stackpole lives in Potomac and once ran the kitchen at the Montana Island Lodge on Salmon Lake. She took a two-day course in Boston to learn how to operate the machine.
There’s a constant workflow process she goes through to keep things moving so that the Leafy Green Machine is constantly producing. Certified organic seeds are planted in the seedling bay using tweezers and a chef’s funnel. After a week on the germination shelf, they get moved to the seedling trough for two weeks until being transferred to the towers for harvest.
A new crop will be ready each week, and she already has a list of customers lined up. Stackpole admits that many people ask her if the machine would be good for growing another type of green – marijuana – but she says that plant doesn’t grow well vertically and she’s not interested.
USDA Urban Agriculture Toolkit
USDA Microloans, a program that offers funding up to $50,000, is specifically geared toward urban farmers. Established in 2013, the program has awarded 23,000 loans worth $518 million to farms in California, Connecticut, and Massachusetts. Though it is open to all farmers, urban farmers often apply for it because it offers the money on a smaller scale than other programs. Seventy percent (or about 16,100 of those loans) have gone to new farmers, many of them in cities.
USDA Urban Agriculture Toolkit
The US Government Is Loaning Millions Of Dollars To Jumpstart Urban Farming
The US Government Is Loaning Millions Of Dollars To Jumpstart Urban Farming
Electra Jarvis, a 27-year-old urban farming entrepreneur who is part of the Square Roots program in Brooklyn, New York. Mary Wetherill
Every year, the US Department of Agriculture devotes millions of dollars to farmers in rural areas.
The government is increasingly starting to offer assistance to urban farms, too.
In 2016, the USDA funded a dozen urban farms, the highest number in history, Val Dolicini, the administrator for the USDA Farm Services Agency, tells Business Insider.
In 2017, he expects the USDA to funnel even more money toward farms on rooftops, in greenhouses, and in warehouses.
USDA Microloans, a program that offers funding up to $50,000, is specifically geared toward urban farmers. Established in 2013, the program has awarded 23,000 loans worth $518 million to farms in California, Connecticut, and Massachusetts. Though it is open to all farmers, urban farmers often apply for it because it offers the money on a smaller scale than other programs. Seventy percent (or about 16,100 of those loans) have gone to new farmers, many of them in cities.
"Urban farmers are not looking to form 10,000 acres in Missouri, but perhaps in an indoor container on a parking lot next to old factory," Dolcini says.
In 2016, nine young farmers participating in a vertical farming accelerator program called Square Roots, founded by entrepreneurs Kimbal Musk (Elon's brother) and Tobias Peggs, became the first urban farmers to receive microloans in New York.
Farmers selected for Square Roots grow their crops inside climate-controlled, LED-lit shipping containers. The Square Roots farmers used their loans to cover the costs of seeds and operating expenses before their first harvests, Peggs says.
Entrepreneur Tobias Peggs outside Square Roots, a vertical farming startup accelerator in Brooklyn, New York.Sarah Jacobs
Peggs and Musk worked with the USDA to streamline the 2016 microloan application, which will make it even easier for urban farmers to gain funding in the future.
Dolcini says the agency wants to take advantage of people's experiences in other fields, or those who might be making an industry change (One of the Square Roots farmers used to be an accountant, and others are recent university graduates). The program also now allows grantees to use the loan for non-traditional farm equipment (think LEDs instead of tractors), which is beneficial for urban farmers.
Earlier in 2016, the USDA also published an "Urban Agriculture Toolkit," which includes advice about how to launch a greenhouse or rooftop farm, and how to apply for loans.
"The funding process made it impossible, or certainly extremely difficult, to complete if you were an urban farmer," Peggs says. "'Question 1: how big is your field?' is hard to answer if you don't have one."
The majority of USDA grants and loans still go to rural farms, but the agency is making an active effort to give urban farmers equal opportunities. Dolcini says these efforts were highlighted under the Obama administration, with the launch of the Know Your Farmer, Know Your Food campaign in 2009. It's easier to meet your farmer, he adds, when they grow in your own city.
"We've d one a lot of work in the Obama administration to open doors wider to urban farmers," Dolcini says. "The Square Roots farmers represent the tip of the iceberg into our foray into regional foods and giving folks greater access to the USDA who previously haven't had access."
Though Dolcini is leaving his position in January, he is optimistic that the USDA will still support urban farming under the Trump administration.
"We have demonstrated to the nation that our investments in microloans and conservation grants have really paid off, and we have made business case for them," he says. "It will be hard to un-do the success we've had."
Agriculture was not a significant part of Trump's platform. But his agricultural advisors and potential picks for the Secretary of Agriculture may hint at what his presidency could mean for the future of urban farming. A number have emphasized rural farming in their work. Some have also have advocated for industrial farming, a process in which food is produced on a huge scale in rural areas.
The USDA currently has 2,200 offices, the majority of which are located in rural states, like Missouri, Iowa, and Texas. In winter 2016 , Dolcini says the USDA hired NYC's first urban agriculture specialist, who will coordinate farm efforts in Brooklyn.
These initiatives underscore a growing movement within the USDA to support local food systems and look beyond rural agriculture.
"The global population is expected to be 9 billion by 2050. We really need to pull every farm into finding solutions for that — not just folks out in the Midwest who grow the lion's share of food but also those in urban agriculture," he says.
Though the modern local agriculture movement sprouted up in the late '90s, it has grown rapidly in cities in recent years. Today, urban farmers are not just growing a few tomatoes on rooftops, they're moving toward commercial production.
In 2016, the world's largest vertical farm, Aerofarms, launched inside a 70,000-square-foot warehouse in Newark, New Jersey. Brooklyn-based urban farming company Gotham Greens opened the world's largest rooftop farm in Chicago in late 2015.
"It seems like there's a new innovation every day in agriculture," Dolcini says.