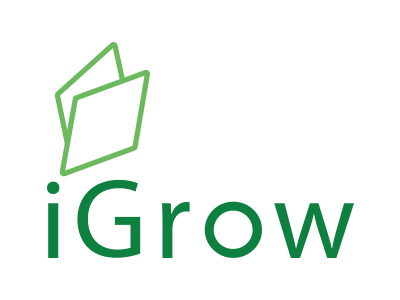
Welcome to iGrow News, Your Source for the World of Indoor Vertical Farming
A Farm In Shipping Containers Grows In Brooklyn
It's farm to table with a twist. A parking lot in Brooklyn isn't the first place you'd expect to see spinach and arugula sprouting up but here they are. Hydroponic vertical farms are growing crops inside 10 steel shipping containers in the same neighborhood where Jay Z grew up
A Farm In Shipping Containers Grows In Brooklyn
POSTED:FEB 21 2017 06:50PM EST
NEW YORK (FOX 5 NEWS) - It's farm to table with a twist. A parking lot in Brooklyn isn't the first place you'd expect to see spinach and arugula sprouting up but here they are. Hydroponic vertical farms are growing crops inside 10 steel shipping containers in the same neighborhood where Jay Z grew up.
But that is not where the cool factor ends. Square Roots takes things one step further by sending a farmer to your office with snack-sized bags of salad the same day the greens are harvested.
Square Roots CEO Tobias Peggs thought up the idea with co-founder Kimball Musk, brother of entrepreneur and innovator Elon Musk. The duo raised $3 million in seed capital to build out this campus, and recruited 10 young farmer entrepreneurs from a pool of 500 to work for a year. The idea is to grow their own careers with Square Roots and in turn help the company grow, too.
A farm in shipping containers grows in Brooklyn
Square Roots aims to expand to 20 metropolitan areas by 2020.
Urban Farmers Grow Crops in Brooklyn Parking Lot
Urban Farmers Grow Crops in Brooklyn Parking Lot
- ERIC GIRARD
- February 21, 2017
Square Roots farmers grow crops in 10 steel shipping containers converted into hydroponic farms.
Square Roots first broke ground by financing and mentoring local entrepreneurs who are growing tasty, nutritious greens in, of all places, a Brooklyn parking lot. Now it’s taking things a step further — right to your New York City office.
Lunch, anyone?
The new “Farm to Local, by Square Roots” initiative delivers snack-size bags of salad greens to workplaces. It already has subscribers at Vice Media and Kickstarter, said Square Roots CEO and cofounder Tobias Peggs.
“Your farmer will literally come to your desk and drop off same-day-harvested greens,” he said.
These farms aren’t your traditional sprawling upstate acreage tended by laborers or a guy on a tractor in bib overalls. Set up near where Jay Z grew up, they’re 10 steel shipping containers converted into hydroponic vertical farms, meaning crops grow in tower formation with recycled water and without soil.
Inside the LED-lit modular containers are rows of panels sprouting pesticide-free plants in a controlled climate — so freezing temperatures and snow pose no problem. Each container produces an annual harvest equivalent to an estimated two acres of land.
Square Roots raised seed financing to build the campus, which cost more than $100,000. Then, 10 young farmers were chosen from more than 500 applicants for a yearlong stint that started in November.
One of them is Electra Jarvis, 27, an Alphabet City resident who grows kale, mustard greens, and Salanova lettuce and is working on cilantro.
“At farmers markets, people are always impressed with the shelf-life and the taste,” said Jarvis, who had been a master’s student in sustainable environmental systems at Pratt Institute and interned with a hydroponic research and development company and an urban farming consulting firm.
The farmers work about 30 hours per week, splitting their time between working on the crops and sales, Peggs said.
“They build a big network of mentors and learn how to build a sustainable business,” said Peggs, whose background is in technology. “Then they are in an incredible position to go off on their own entrepreneurial journey.”
Germination of the idea
Peggs, 44, arrived in the U.S. in 2003 from the United Kingdom. A few years later, he met Kimbal Musk (whose brother is the entrepreneur Elon Musk). Musk, a chef, had cooked for firefighters at ground zero after 9/11. “That’s when he began to see the power of real food and its ability to strengthen communities,” Peggs said.
Peggs and Musk worked together in social media analytics, until Musk broke his neck in a skiing accident and, “realizing life can be short,” shifted his focus to The Kitchen, a farm-to-table restaurant group that started in Colorado, Peggs said. In 2014, the duo began developing the idea for Square Roots.
“What we saw was that millions of people, especially in our biggest cities, were at the mercy of industrial food,” Peggs said. “This is high-calorie, low-nutrient food, shipped in from thousands of miles away. The results are awful, from childhood obesity to adult diabetes to a total loss of community around food.”
For example, Peggs said, a supermarket apple may have been traveling for nine months and is coated in wax. “You think you’re making a healthy choice, but in that time the nutrients have broken down, and you’re basically eating a ball of sugar.”
Square Roots aims to expand to 20 metropolitan areas by 2020.
Until then, in Brooklyn, they’re growing mainly leafy greens (spinach, arugula, chard) and herbs (basil, shiso). Peggs believes berries and tomatoes could follow.
“At the end of the day, if the food doesn't taste amazing, no one will buy it,” Peggs said. “So we focus every day on making sure the food tastes amazing. And it does.”
Nation’s First ‘Sustainable Urban Agrihood’ Being Built In Detroit
An effort has launched in Detroit to build something unique: what they’re calling “America’s First Sustainable Urban Agrihood.”
Nation’s First ‘Sustainable Urban Agrihood’ Being Built In Detroit
February 21, 2017 10:38 AM
DETROIT (WWJ) – An effort has launched in Detroit to build something unique: what they’re calling “America’s First Sustainable Urban Agrihood.”
The centerpiece is a vacant three-story building near Brush Street and East Grand in Detroit. In addition, it includes a two-acre urban farm, 200-tree fruit orchard, children’s sensory garden, water harvesting cistern, and more.
“(It is) formerly an apartment complex that we purchased in the tax auction of 2011,” explained Tyson Gersh, with the Michigan Urban Farming Initiative.
“It is the physical center of our agricultural campus that we’ve been operating in Detroit’s north-end neighborhood…An urban residential development strategy. You position a working farm as the centerpiece of a large development, and we sort of see our agricultural campus as collectively that centerpiece.”
The urban farm grows more than 300 produce varieties annually, according to MUFI. The fresh vegetables are provided for free to about 2,000 households, churches, food pantries and others within two-square miles of the farm.
If successful, the new building will offer educational, nutritional, and other programs. MUFI also has plans for a new healthy food cafe, which will be located next to the community center and will also contain a commercial kitchen.
To help complete the project, Auburn Hills-based BorgWarner is kicking in $10,000. But Gersh said they’re turning to the public and the state in hopes of raising the rest.
They have until Sunday, April 2 to raise another $40,000 to qualify for a matching grant through the Michigan Economic Development Corporation’s (MEDC) Public Spaces Community Places program.
For project details and to donate via an online crowd-funding campaign, visit this link.
Here's What Success In Building Local Food Systems Looks Like
Here's What Success In Building Local Food Systems Looks Like
This article is part of Michigan's Agricultural Future, a series of stories about Michigan’s agricultural economy. It is made possible with funding from the Michigan Department of Agriculture and Rural Development. Read more stories in the series here.
Ten small Upper Peninsula farms are U.S.Department of Agriculture (USDA) food safety certified. About $250,000 in local food products purchased by U.P. schools, hospitals, and restaurants. Hundreds of individuals educated on the benefits of local food, and a strong, growing distribution network to connect local farms with local buyers.
These successes are all the work of the Upper Peninsula Food Exchange, an effort spearheaded by the Marquette Food Co-op with grant backing from the Michigan Department of Agriculture and Rural Development.
The co-op applied for and received, grant funds totaling $165,000 through the Center for Regional Food Systems at Michigan State University in November 2012. The goal was to put the money to the best uses possible, building and strengthening the U.P.'s local food systems and networks. And that's just what they did.
Along with the co-op, two other main partners, MSU Extension in Sault Ste. Marie and the Western Upper Peninsula Health Department in the five westernmost U.P. counties, Marquette Food Co-op began work to connect local food systems, from farms to restaurants, all across the U.P.
Matt Gougeon, general manager of the Marquette Food Co-op, says as soon as the co-op started looking at ways to bring local food initiatives together, they linked up with Michelle Walk at MSU Extension in the eastern Upper Peninsula.
"We realized a lot of what she was doing and what we were doing dovetailed nicely," he says.
At times, says Gougeon, there were major challenges involved. The U.P. has a harsh climate and limited food production, the geographic differences from one end of the peninsula to the other are large, and then there's the lack of connection to lower Michigan food distribution networks. The grant allowed the partners to zero in on those problems and take steps to address them.
Their work started with education. To increase awareness of local and regional food, the partners conducted a series of local food summits out of which came the idea to create three regional cold storage sites -- east, central and west -- to make distribution easier to commercial and institutional buyers such as hospitals, schools, universities, and restaurants.
The cold storage, or aggregation sites, as they're called in food network terms, allow small farmers to deliver their products to one site. Large clients can pick up an order from several different small farms at once, rather than arrange for separate transport and delivery from each individual farm to each client.
The next step was to create the online U.P. Food Exchange website -- a virtual ordering system and marketplace for the sale of all those local farm products. Once the infrastructure was in place, the online market made food distribution even easier by overcoming obstacles for small farms and automating the invoicing system across the board.
"Small farmers put their available inventory up for sale to institutional clients," Gougeon explains. "A hospital or university can go to the site and place orders, then farmers see these orders, can fill them, and deliver them to physical food exchange aggregation sites."
The U.P. Food Exchange website is not set up for sales to individuals, says Gougeon, but local farmer's markets in cities and towns across the U.P. are already filling that market need well.
To learn about transport issues, the co-op conducted a study of existing distribution channels and trucking routes so they could develop a workable plan to connect with companies that already distribute food throughout the U.P. The goal was to create a self-sustaining local food network for the region.
"It would have been cost-prohibitive for just the co-op or MSU to do any of this by themselves," Gougeon says. "What we have now are lots of people talking to each other, trying to pull the oars in the same direction."
The results have been good. In 2015, upwards of $250,000 in food moved through the online U.P. Food Exchange. Gougeon says the plan is to continue to increase that number. Part of making that happen is getting more institutional and commercial food buyers trained and educated on how to access and use local food. There's a continuing need for farmers to list inventory and for online buyers to use the marketplace, he says.
"There's a lot of interest in local and regional food, but part of this work is helping purchasers understand it's not just clicking a button and the food appears," says Gougeon. Seasonal, or a limited supply of specific foods, and the possibility of changing costs from month-to-month, can present obstacles to institutional markets. But, Gougeon says, education on how money spent locally improves the economic conditions of the region and other benefits of buying local and regional food products, has helped convince big clients to buy in.
"Sometimes, it's just getting them to use some local foods, instead of looking for everything locally," Gougeon says. "If they can get just a few, like local potatoes, that's still good."
Another major part of the grant went to educating farmers about food safety, which was an important step toward getting U.S. Department of Agriculture certification, called Good Agricultural Practices, or GAP.
The MDARD grant funding allowed the co-op to connect with the USDA and the education-focused Wallace Foundation to organize funding for an ambitious new pilot project called Group GAP, which would make it easier for small farms to achieve food safety certification.
"One of the barriers to small farmers entering institutional markets is getting food safety certifications," says Gougeon. "We worked on this concept called Group GAP. It was hard for small, multiple-product farms to get certified." The GAP program generally is designed for larger, one-crop farms.
Using the Group Gap, farmers shared resources and management systems. The group of small farmers also shared the costs of the required federal audits. In 2015, 16 small U.P. farms signed on as pilot project participants to test the guidelines and process for Group GAP certification that the co-op and its partners had hammered out.
During the pilot, the farmers got assistance with audits, record-keeping, and formal food safety training. At the end of the pilot, 10 of the 16 farms were GAP certified, a big step in their ability to sell their food products.
"Once the farm attains that certification, they're good to go to sell their products pretty much anywhere," says Gougeon.
The Michigan Group GAP Network is now working on extending the process developed in the pilot program to more Michigan small farms.
Phil Britton, a former Marquette Co-op staffer now working at Cherry Capital Foods in Traverse City, was instrumental in writing those Group GAP guidelines, and now works with the Michigan-wide network. "He's taken what was learned and the whole system we developed and is applying it to groups of small farms in lower Michigan," says Gougeon.
The goal is to eventually get all small Michigan farms Group GAP certified, perhaps audited by random selection each year, with all the farms sharing the cost of the audit, something that's typically a major burden for a small farm on its own. If that can be accomplished, Gougeon says, "it would be a tremendous boon to getting food into regional markets. That barrier would then be gone for everyone."
Overall, the MDARD grant was used to remove obstacles at the local, regional and state levels, obstacles like certification processes, lack of infrastructure, and lack of knowledge. In the case of the U.P. Food Exchange, removing the obstacle of the need for ongoing funding has been key. The end goal is to make the network self-sustaining.
"The food exchange was set up for anyone to use it," says Gougeon. "It's a shared structure, not owned by the co-op. That's why we brought in all our partners and created it as a resource for anyone to be able to find small farmers in the U.P."
Other funding is, in fact, now carrying the exchange, including a grant from the Sault Ste. Marie Tribe of Chippewa Indians that connects Marquette Food Co-op and MSU Extension resources to tribal members and their greater communities through classes on working with local food and connections with tribal food networks.
Gougeon says there have been "huge gains" since the food exchange came into existence and the network is setting the stage for further food systems development.
There's also been an impact on local policy and planning. A new committee, the Central U.P. Food Policy Committee, was formed as part of the grant work and it has developed an educational document for municipalities to use in infrastructure, policy, and zoning and planning decisions. They hope the result will be more informed decisions regarding local food networks and lowering obstacles to farmers and buyers.
In the meantime, the Marquette Food Co-op, MSU Extension, small farms, the Western U.P. Health Department all can be tapped for their expertise through their connections with the U.P. Food Exchange, which in turn helps the exchange become a self-sustaining resource.
"There's been significant development in a network of agencies, growers, businesses, all connected in a way they weren't before the grant took place," Gougeon says
The exchange and its related networks have grown and strengthened local food systems. The impact is one that should improve the future of the Upper Peninsula for years to come.
Kim Eggleston is a Marquette, Michigan-based freelance writer and editor.
Farming Meets High Tech When Natural History Museum Kicks Off Food Lecture Series
FEB 19, 2017
Become a Member | Ad-Free Login
Farming Meets High Tech When Natural History Museum Kicks Off Food Lecture Series
By KATHY STEPHENSON | The Salt Lake Tribune
First Published Feb 18 2017 12:24PM • Last Updated Feb 18 2017 10:19 pm
They say you can't fool nature, but hundreds of "nerd farmers" around the globe are tapping technology to control climate and create the perfect conditions for growing food.
They are doing it with a personal food computer created by Caleb Harper and his team in the Open Agriculture Initiative at the Massachusetts Institute of Technology. Harper, the principal investigator and director of the lab, leads a diverse group of engineers, architects and scientists in the development of future food systems.
Their climate-controlled box, which can sit on a tabletop, has a computer brain and sensors that allow users to manipulate temperature, carbon-dioxide levels, humidity, light and pH. The plants are grown in minimal amount of water — no soil — using hydroponics.
Anyone, in any part of the world, can grow food, no matter the season, said Harper. Imagine growing water-loving tropical fruits in the middle of the Utah desert or sun-loving summer berries in the midst of a harsh winter.
Harper will talk about this blending of agriculture and technology Tuesday, when he kicks off the Natural History Museum of Utah's annual lecture series. Food is the theme of the five presentations, which include a keynote address by TV personality, chef and author Andrew Zimmern. Tickets for his talk go on sale Wednesday. (See box for details.)
Harper's lecture is free but requires a reservation.
There are nearly 400 "nerd farmers" around the globe who have built personal food computers — using Open Ag's open-source technology — collecting and sharing data with other users, Harper said.
"Every food computer that comes online, whatever they grow is recorded and in the future can be replayed as many times as we want," he said.
Farmers create their own growing "recipe" such as programming in more light or less humidity to see what happens. "As people explore, we are decoding that plant and getting a clearer map of a plant's ability to express itself," he said. "It's pretty phenomenal."
Eventually, Harper hopes the data can be used to create economically viable farms — possibly in shipping containers — that can be placed anywhere to create "hyperlocal food production."
"We need better food-supply chains, which are notoriously complex," he said. "This technology could be a new tool in the chain."
Interest in the personal food computers has grown beyond just the research stage, so Harper recently formed the nonprofit Open Agriculture Foundation, which will protect the open-source data and intellectual property and foster the growing community of farmers.
Harper and Utah entrepreneur Daniel Blake also have started Fenome, a small business that has begun assembling kits the community can buy that have everything needed to build a personal food computer.
The Fenome lab in West Valley City also houses large indoor growing tents, where Blake and the staff experiment with varieties of plants, learning which ones grow best in the personal food computer environments.
The personal food computers have other applications, as well. Many schools are using them to teach about biology, botany and climate change as well as coding, computer programming and engineering.
And Blake recently returned from Jordan, where he visited Azraq, a camp for refugees of the Syrian civil war. He said the United Nations World Food Organization is interested in food computer systems that could help supply at least a portion of the food to those living in the camps. Currently, all food and water are shipped.
"We are in the beginning stages of the process," Blake said, "but food computers could be deployed anywhere, especially harsh environments where food security is a problem."
Indoor Farms of America Brings Customers The Most Innovative Farm Management Platform Available With Award Winning Agrilyst
Indoor Farms of America announces today that all of its vertical aeroponic farms, from the most productive container farms in the world, known as GrowTrucks, to the highest yield indoor farms for warehouse or greenhouse applications, will now come standard with the award winning farm intelligence platform from Agrilyst.
Indoor Farms of America Brings Customers The Most Innovative Farm Management Platform Available With Award Winning Agrilyst
LAS VEGAS, Feb. 17, 2017 /PRNewswire/ — Indoor Farms of America announces today that all of its vertical aeroponic farms, from the most productive container farms in the world, known as GrowTrucks, to the highest yield indoor farms for warehouse or greenhouse applications, will now come standard with the award winning farm intelligence platform from Agrilyst.
“In our desire to bring our customers the best-in-breed for each component of our farms, we recognized that Agrilyst has developed the most comprehensive tool we have studied for effectively managing an indoor farm,” says David Martin, CEO of Indoor Farms of America.
With data tools that help the farm operator easily focus on creating the highest yields from their farm, all managed from a thoughtfully laid out Dashboard, the Agrilyst platform makes the most of the farm on a daily basis.
“Every element of the farm, along with the business side, was taken into consideration by the team at Agrilyst,” states Martin, “and the team at Agrilyst is thrilled to have joined with us in the implementation of their amazing product within our farm offerings.”
“The ability to collect data in real time, analyze that data, display it in a way that the user receives the most benefit from, and to then have that translate into an action plan to guide the farmer to successful yields and harvests, while controlling costs, well, we believe our operators will greatly appreciate that,” said Martin.
In an impressive debut, Agrilyst won the TechCrunch Disrupt competition in September of 2015, and now has a solid amount of time with real world farms under their belt, operating using the Agrilyst platform.
According to Allison Kopf, CEO of Agrilyst, “We are excited to have been chosen as the platform to help make every farm sold by Indoor Farms of America the best it can be,” and “we look forward to working with their team and customers.”
Indoor Farms of America has a showroom with demonstration farms operating in Las Vegas, Nevada where their patented vertical aeroponic equipment is on display, including a container farm, with a primary model that has over 6,800 plant sites in standard configuration, over double the nearest competitor in the container farm segment.
“Our farms represent tremendous value to the purchaser, offer a superior R.O.I. potential than anything else on the market, and with the addition of the Agrilyst platform, our farmers now have the upper hand in total farm management,” stated Martin.
Each week the company hosts business owners, growers, and farm managers from around the U.S. and the world who want to see for themselves the equipment that can grow more crops in any given space that any other brand or type of equipment in the world.
“We will now have the Agrilyst platform operating and on display for our potential farmers to see first-hand, at the first of March, and we are excited for this addition to our end to end indoor farm solution,” according to Ron Evans, President of Indoor Farms of America.
For more information, visit the company website at indoorfarmsamerica.com
This press release was written by Indoor Farms of America and is shared in its original form. For more information on Agrilyst, please visit: www.agrilyst.com.
Urban Farming Insider: With Glenn Behrman, Founder CEA Advisers, The Plant Shed, and Greentech Agro
Glenn Behrman first started the Plant Shed in the 1970's, and has been involved with urban agriculture for over 40 years. We caught up with Glenn to discuss many topics, including his personal story, container farming versus vertical farming, and what is wrong with today's perception of urban farming
Urban Farming Insider: With Glenn Behrman, Founder CEA Advisers, The Plant Shed, and Greentech Agro
Glenn Behrman first started the Plant Shed in the 1970's, and has been involved with urban agriculture for over 40 years. We caught up with Glenn to discuss many topics, including his personal story, container farming versus vertical farming, and what is wrong with today's perception of urban farming.
UV:
Can you tell us a little bit about CEA Advisors and what you guys are working on now and how you got started? What is your background in the urban farming industry?
Glenn:
My career started in the foliage industry in the early '70s. When I first started there was no such thing as a real foliage industry. It was houseplants but (at the time) there was no such thing as houseplants. You know what I mean? There was no Home Depots and no aquaculture and no LED lights. There was no real marketing channel. It was a fragmented industry.
It was ripe for disruption. When I went into it, I had no experience and no real insight. I had nothing. I had no money. I had no education. I just knew it was a good idea and I just spent the next 25 years putting one foot in front of the other and building up a business that was a very substantial business that was one of the first real category killers before the term really existed.
The houseplant industry: A precursor to urban farming
UV:
That company (that dealt houseplants) was different than CEA Advisors? Did it have a different name?
Glenn:
Yeah, that was called The Plant Shed. It was in New York City. It was nine stores. I had an import division. I started traveling to the Philippines and Thailand and China back in the '70s and importing various lawn and garden products for sale in my own
stores.
The last store that I had in New York City, before I retired and sold the business, was 21,000 square feet. It was in a location that now could probably be, and I'm not exaggerating, now in New York City, would probably be $100,000 per month to rent.
UV:
These were primarily nonedible plants though, right?
Glenn:
Yeah, just houseplants, just ornamental plants for beautifying people's homes. It's funny because I kind of remember the first day, or the first time after Home Depot entered the market ... I remember for the first time telling somebody, "Look (now) plants are basically disposable." You put something in this corner in your living room and it looks beautiful for six months, and then it could die so you throw it away and you buy a new one.
You know what I mean? The whole industry, it went from a beautiful to ... It went from a living thing to a piece of furniture.
Glenn:
(Eventually) we started importing orchids from Thailand. We built a big nursery and a big plant brokerage business there. Then in 1994, I just sold everything and moved to Thailand.
UV:
What was the thinking behind that?
Glenn:
I just had enough. I had enough money. I had enough.Things were changing. Ikea was in the plant business. Home Depot was doing a big job. Rents in New York City were unbelievable. It wasn't fun anymore.
The Early Days of Urban Farming
UV:
How did you move from the foliage, as you say, to the more edible type stuff?
Glenn:
What happened was, while I was living in Thailand I became the landscape project manager for a casino project in Vietnam. It was a 500 acre site that was just sand. It had to be completely landscaped as a five star hotel.
As that project was coming to a close, I went to China to Hortiflorexpo, which is an event that's held every year in China. You know, like a horticulture exposition.
On my way back I read about a company in Holland that was starting to do research on indoor farming, using LED lighting, climate control and all that kind of stuff. I immediately went to Holland to meet with those people.
After we met I immediately tried to buy the U.S. rights to that company.
After seeing their technology. The seed for indoor farming was planted in my head. I went back home to Thailand. We had a big home and a farm and all that there. I told my wife, "You know what, we're moving back to America. I am going to get involved
with this new technology- take everything that I've learned and everything that
I've done and all the connections that I have, and I'm going to pursue this." That's what I did.
The beginning of GreenTech Agro
UV:
Did you start a new company at point, back in the States?
Glenn:
We started a new company called GreenTech Agro.
UV:
Okay, and then you eventually sold that company and then started CEA Advisors or is that company still around?
Glenn:
That company's still around. It's kind of dormant now. It's not doing anything one way or another. I had a partner in that company, he was just a silent partner.
Eventually I bought out the partner and started CEA Advisors, used it to pursue the highest and best use for vertical farming, rather than to concentrate on the Growtainer concept. In other words, I felt that containers and indoor farming had a lot more potential than just container farming.
Vertical Farming vs Container Farming
UV: You saw more potential in the vertical stacking inside of the container as opposed to just growing one level in the container? Why?
Glenn: No, in other words, what I am trying to say is, the first few years was spent strictly growing in containers and developing a system to grow in containers.
As I started to work out the problems associated with container growing, or container based production, I started realizing that this was not really the highest and best use for (controlled atmosphere) technology.
Problems With Urban Farming Container Growing
UV: What are some of those problems (with container growing)?
Glenn: Well, air circulation, humidity, climate control, an effective irrigation system. A container is not the best. For example, it's 10 feet high.
How many vertical levels can you put in there? How much production can
you put in there really without crowding the plants? There are some people,
they advertise that they can grow 45 plants per square foot.
Glenn: That's fantasy. This business, so much of it is hype. So much of it is bad information to people that don't know any better. It's difficult to really tell the truth,
whether it is good for you or not. People believe what they want to believe.
Understanding "plants per square foot" based off plant type
UV:
Does the plants per square foot ... Does that change based off of the type of plant? Are you talking about a best case scenario?
Glenn:
Well of course. You could sprout seeds at 45 seeds per square foot. You can't grow plants at 45 plants per square foot. A head of lettuce, for example, as it grows, it needs more space.
Glenn:
If I wanted to promote an untrue economic model, I would turn around and say, there are 216 seed cell trays that are 1.5 square feet, and tell people they can grow a hundred plants per square foot.
UV:
That's not even close?
Glenn:
It's not true. It's not true and it's not real and it's not economic. It's not based on any integrity. In other words it's based on just feeding. It's telling people what they want to hear.
Reliable urban farming brands to know
UV:
What are some of the brands in the industry as far as lighting or fertilizer or what not, that you view as, they've been high quality for a long time?
They're dependable. Somebody wants to get a top-notch system and get
really great lights. What are some of the companies they should be looking at?
Glenn:
It's not necessarily that ... In other words the criteria for let's say lighting, for example, which is a very very crowded market. First of all, the lighting is only ... All of the components are really based on what crop you want to produce, or what your
economic model is, or what your business model is.
In other words, listen I think Philips makes a good light for certain applications. I think Heliospectra makes a good light for certain applications. I think even Fluence ... I know it's Fluence, they make a good light. Every light is got to be matched through
the crop that you're trying to produce. Every fertilizer, in other words ... The whole key to successful vertical farming is about balance. It's not about any one particular product. It's that all the products work together and in conjunction with each other.
Knowing Variety and Desired Characteristics Before Growing
UV:
How do you go about finding that balance? For example, loose leaf lettuce, how would you view that balance?
What would be some of the best components for those, just because I know that's
a pretty popular crop?
Glenn:
Again, you're talking about lettuce. Are you talking about full heads? Are you talking about cut-leaf? Are you talking about ... You know what I mean? In other words there's so many ...
Listen, I get calls from people and they tell me, "Well I want to grow
lettuce." I'm like, "Okay, great." I then have ten more questions to ask them. In other words, lettuce is not generic. Lettuce is ... There's a hundred different varieties.
Are you growing something that's green? Are you growing something that's got red in it? Is the color important? Is the weight important? Do you have a post harvest facility? It's not all that simple. Everybody thinks it's that simple. It's not.
What Urban Farming Beginners Should Think About Before Growing:
UV:
Those are some of the considerations that people should be thinking about- some of the stuff that you just mentioned like the color, the weight, the facility after, the post harvest facility. Are there any other things that ...
Glenn:
Who's your customer, in other words, your packaging costs? Are you selling to restaurants? Are you selling to ... Listen the container, a 40 foot container is too big for a farmers market and too small for a supermarket.
UV:
Right, so that's more of a restaurant type fit, is what you're saying, or that's not what you're saying.
Glenn:
Right but then a 40 foot container could sell to a restaurant is a recipe for disaster.
UV:
Why is that?
Glenn:
An economic disaster because you're never ... They're never going to consume everything you produce.
UV:
Then they'll presumably ... You're saying that they may order from you every week, but the size of the order will be different.
Glenn:
Yeah, well of course. In other words, you're producing every day. You know what I mean? I feel bad for some of these people that have no business model. They're going to be under constant pressure to sell what they've created.
Understanding your urban farming business model:
UV:
How do you at least start? Obviously it may be a complicated total solution, but how do you at least start to address the bread and butter of the business model. What do you view as the fundamentals of that, addressing some of the problems we've been
talking about?
There might be a mismatch between demand and your supply. Managing the unit cost, how do you really look at that, just at least to get started? I know there's a lot of intricate details.
Glenn: This is a business just like any other business. You follow me? You really have to do your homework. The truth of the matter is that, again you are dealing with a market that doesn't ... They have good intentions.
You know what I mean. They don't realize how complicated it really is.
UV: You're talking about the buyers?
Glenn:
I'm talking about the growers, the customers, the indoor farm ... The Facebook ... The farmers that learned about this from social media. Learned about this from talking to their friends. They have an interest in pursuing this type of business model.
UV:
You're talking about people who
are actually growing the stuff or trying to.
Glenn:
Not growing it, but trying to.
UV:
Yeah, okay. You're saying they have good intentions but ...
Glenn: They don't realize how complicated of a process that it really is. In other words, let me tell you something. I'll give you an example. This is just my own opinion okay?
The Flaw of Remotely Monitoring Farms
Glenn:
People promote the idea that their farms can be remotely monitored. I don't think that you should run your business from Starbucks.
You follow me? I think that in order to be a farmer, you need to get up in the morning and go to your farm - whether it's in a container or a greenhouse or a warehouse or wherever it is.
You need to get yourself up to a level where you have a checklist every day of things that you do, and you do every one of those things. You follow me - so that you get to a point where in the first minute you walk in and you look around, you know what's going on. You follow me? A latte, and adjusting your humidity is nonsense.
UV:
Right. The issue with that is, from what I'm getting from what you're saying is, it may not all happen in one day, but slowly but surely you will get out of touch with what's going on.
Glenn:
You will get out of touch or get in touch. In other words if you understand that you're not ... Listen this is not a technology business. This is food production.
You follow me? That's really the bottom line. You need to put it in the right perspective and approach it for what it really is.
The Value of Data in Urban Farming
UV:
What do you think of the whole argument about collecting data on growing? A lot
of these companies that will, like as you mentioned, allow you to monitor stuff
remotely, will say there's a lot of value in the data of the growing and how
that they can use that data to make improvements in the future. How do you view
the value of that? Do you agree with that? Do you disagree with that? Do you
think that's a similar concept to ... It clashes with the idea of going every
day, or what do you think of the data aspect?
Glenn:
Honestly I haven't figured
that one out yet, for an honest answer. I don't know. I guess maybe as an old
timer in this industry, I look at things in a more traditional sense. I don't
feel that ... You know what I mean? I think that business should be run in a
cash flow positive manner.
Glenn:
I see young people today who's
business model is getting funding. That's their destination.
UV:
You're talking about specifically in the space or just in general?
Glenn:
I think in general. I don't follow other spaces. You know what I mean? I got to tell you. Somebody said it the other day on a trip overseas. They said, "The one thing we see about you, and based on everything you're doing and saying, is that you live this
business."
I'm involved with projects all over the world. I hear a lot of different perspectives. I speak to a lot of very intelligent people. I try to pay attention to everything that everyone says, take it seriously. Like I said, I pay attention to people, from young, old, in the business, not in the business. I try to compute it all, where it all fits in. I think that there's not enough focus on really building this as an industry.
Why Designing A Food System for 2050 in 2017 Is A Mistake
Glenn:
It's (urban farming) too fragmented. It's being approached from too many different levels, in too many different ways. I think that people to some degree, have lost sight in the fact that this is food production. I'll give you an example. People talk about the
population explosion and feeding the world in 2050.
Glenn:
I've got to tell you, my honest opinion is that ... First of all, we don't have any idea what people are going to be eating in 2050. There's a lot of technology involved with food production, meatless meat and egg-less eggs. There's a lot of stuff like that
going on. I believe that it's very possible that the solution to the food
crisis that's coming in 2050 ... They may not find the solution until 2049.
UV:
Yeah, that would not be surprising to me.
Glenn:
I think that the issues that need to be focused on right now are the issues that need to be focused on right now. I wouldn't use that as a motivation for building a business.
Rapid Fire Questions
UV:
A couple more short answer questions, rapid fire questions, what I like to call
them ... What are some specific crops that you see getting trendy?
Do you see any trends and stuff that people are asking you about or stuff that's getting more popular with restaurants or what not?
Glenn:
That's really a question of creativity. You know what I mean. Edible flowers are interesting- different, unique, gourmet, smaller quantities of higher value, more unique products. It also depends on again, on your market, on your economics, on your ... In other words, trendy is great. Can you make money with it?
UV:
(What about) Assuming that the trendy thing will touch a better margin or have higher demand?
Glenn:
Again, you can grow the trendy item. Can you sell it? Can you grow the trendy item in a vertical farm?
How much does it cost you to set up that facility to produce that product? You know
what I mean? This is all about business. It's all about economics. While something might be trendy, it may not be possible to produce in an efficient, profitable manner.
UV:
What's your favorite fruit or vegetable?
Glenn:
I don't know. What's my favorite vegetable? I would say spinach.
UV:
Spinach?
Glenn:
For growing or for eating?
UV:
I don't know, is it different?
Glenn:
Well growing ... Well for eating I like spinach because it's got a lot of different ways it can be prepared.
My favorite food for eating is probably fresh mozzarella. Very fresh mozzarella.
UV:
Just by itself or ...
Glenn:
Yeah.
UV:
All right well what about for growing?
Glenn:
My favorite product for growing is got to be just anything unique and unusual.
UV:
Okay, what's one example.
Glenn:
Minutina.
UV:
Minutina?
Glenn:
Yeah, minutina.
UV:
What is ... I'm not familiar
with that. What is that?
Glenn:
It's a green that originally comes from Europe. It's an addition to a salad, nice, crispy, delicious green that actually grows very well in an indoor environment.
UV:
Like arugula?
Glenn:
No, it's not. It's like ... I don't even know how to describe it. Look it up. It's a really interesting product. It's pretty rare and not easily available.
UV:
Okay, for sure. If people want to find out more about you or what you're working on now, what's the best place for them to go, just the website?
Glenn: Yeah, let them start at the website. The Growtainers' (Growtainers.com) website we keep up-to-date.
UV:
Thanks Glenn!
There Are Acres of Leafy Greens Inside These Shipping Crates On An Old St. Petersburg Junkyard
There Are Acres of Leafy Greens Inside These Shipping Crates On An Old St. Petersburg Junkyard
Friday, February 17, 2017 10:48am
ST. PETERSBURG — The would-be farmers bought three transoceanic refrigerated shipping containers, just a little dinged up, for $6,500 each.
Shannon O'Malley and Bradley Doyle had them hauled to a distressed property they purchased on Second Avenue S and painted them a vibrant green. The green of John Deere tractors and regimented rows of farm crops.
Because this is what they were building: A farm. Brick Street Farms.
The property had been used as a junk yard and asphalt dump for years. They hauled 57 loads of trash away on a 50-yard dump truck. It took eight months to clean and level the property before they could bring in their three slightly used shipping containers, two rows of picnic tables and a tall fence to discourage the lookie-loos.
You can't blame the loos for looking. This is Pinellas County's first and only commercial-size, indoor, hydroponic farm. These three upcycled containers have the ability to grow the equivalent of 6 acres of traditionally farmed leafy greens, herbs and edible flowers, using a minimum of water and no pesticides, herbicides or fungicides.
There is no dirt, there are no bugs and produce is delivered "plate ready" to the Vinoy, Brick & Mortar, Rococo Steak, Souzou, Stillwaters Tavern and BellaBrava, all in St. Petersburg. O'Malley aims to sell everything she produces within five miles of Brick Street Farms.
In this era of locavore fever, you can't get much more local than that.
Indoor, hydroponic, vertical farms are popping up in urban spaces around the globe. A dwindling amount of arable land due to industrialization, urban sprawl and climate pressures, coupled with population growth (9 billion people predicted on Earth by 2050!), has led many people to think creatively about our food supply.
Farmer Dave Smiles launched a 24,000-square-foot warehouse in Tampa in 2015 doing similar indoor vertical farming. In the same year in Newark, New Jersey a steel-supply company was taken over by a new indoor-agriculture company called AeroFarms, filling it with 70,000-square-feet of vertical kale, bok choi, watercress and such. In January, the New Yorker ran an exuberant article about the future of urban farming without soil or natural light.
But it's not easy: The nation's largest indoor farm, FarmedHere, which opened in 2013 in an abandoned warehouse in Bedford Park, Ill., closed its 90,000-square-foot facility in January. While CEO Nate Laurell didn't say precisely what had gone awry, it is clear that growing large enough to offset equipment, energy and labor costs proved tricky.
There are, O'Malley says, considerable costs to running the operation, but she declined to say what the farm's ongoing costs are.
"Hydroponics aren't new, this technology isn't new and all the technology we used is 'off the shelf,'" said O'Malley, 35, who recently quit her job at Duke Energy to work the farm full time. Doyle, 37, still works in information technology at Duke Energy.
Here's how it works. Each container is its own climate, kale in the one on the right, herbs in the middle one and heirloom lettuces on the left. There are three inches of insulation, plus reflective roofing to keep things cool, plus air conditioning (lettuces like it chilly, around 60 degrees). Everything is grown from non-GMO heirloom seeds, spending two weeks in the seedling area before each tiny root plug is transplanted to a white vertical tower, fitted into a mesh of recycled food-safe plastic.
The plant lives in the tower for three to five weeks, with recirculated water running down a felt wicking strip to feed the plants.
Strips of red and blue Phillips high-efficiency LED lights provide the sunshine (although because electricity is cheaper at night, the plants "daytime" is in the evening. From there, it gets complicated. Computers take readings of the plants every seven minutes — pH levels get adjusted, CO2 levels are tweaked, plant nutrients are measured in electrical conductivity and there's special air circulation for proper "plant transpiration."
According to O'Malley, this kind of indoor vertical farming uses one tenth the water of traditional farming and a tenth of the fuel (a traditional farm uses fuel to run the equipment and deliver product, for an indoor farm fuel costs are all electricity).
So how does all this high-tech food taste?
Glorious. Basil leaves as big as a catcher's mitt (well, a kid's mitt), rainbow chard and lacinato kale. Pea shoots and micro kohlrabi, arugula and red amaranth. The Vinoy is using a special mix of Brick Street lettuces in their salads and Rococo Steak will host a farm-to-table dinner at the farm on Feb. 25.
"It's a much more consistent product and a much cleaner product because it's not grown in dirt," says Jeffrey Jew, the executive chef at Stillwaters Tavern and BellaBrava. "It's super cool what they're doing. I know at the beginning Shannon was looking for chefs and restaurants to sell to. But now they're pretty much maxed out."
It's true. O'Malley and Doyle are looking to buy more containers, their goal seven across and stacked two deep. They don't envision doing a community supported agriculture subscription in which consumers buy a share of a farm, a popular model for more traditional farms. But they do sell direct to the public on Tuesday and Thursday evenings and Saturday afternoons.
They spend a lot of their time explaining what they're doing. No, they're not growing cannabis. No, it's not U-pick. No, it's not open to the public. And it's not a garden. It's not a laboratory.
It's a farm. You just have to think inside the box.
Contact Laura Reiley at lreiley@tampabay.com or (727) 892-2293. Follow @lreiley.
Farmed Here Asset Sale Set for February 23rd
This past month, we at Agritecture syndicated this open letter from Paul Hardej (originally published on the Association for Vertical Farming newsletter) about the closure of the 90,000 sq ft. FarmedHere Facility in Bedford Park, IL
Farmed Here Asset Sale Set for February 23rd
This past month, we at Agritecture syndicated this open letter from Paul Hardej (originally published on the Association for Vertical Farming newsletter) about the closure of the 90,000 sq ft. FarmedHere Facility in Bedford Park, IL.
Upon sharing this news, we received a flood of questions in regards to how and why this happened. This gave us the idea to moderate the panel, An Examination of Shuttered Vertical Farms at the upcoming Aglanta Conference. Paul Hardej will be a participant on that panel.
Since that time, we have been contacted by the assignees charged with liquidated FarmedHere’s assets, and they requested we publish information about the sale which will take place at 2:00 p.m. on Feb. 23rd 2017 at the offices of Rally Capital Services, LLC, 350 N. LaSalle St., Suite 1100, Chicago, IL.
The FarmedHere assets will be sold in either one or two lots at the Assignee’s discretion, and include both tangible and intangible assets including the domain name, patents, social media accounts, trade secrets, grow beds, 1,200 gallon tanks, office furniture and more.
More information about the lots and assets for sale can be found below:
Assignee’s Return of Bids Sale
FarmedHere, LLC
6700 S. Sayre Ave.
Bedford Park, IL 60638
SALE OF ASSETS: On Thursday, February 23, 2017 Howard B. Samuels, not individually, but solely as Assignee for the Benefit of Creditors (the “Assignee”) of FarmedHere, LLC (“FarmedHere”), intends to sell his right, title and interest in and to certain tangible and intangible assets (the “Assets”). The Assets sold or to be sold will be offered only as two separate lots. The Assets to be sold in Lot 1 include but are not limited to trademarks, copyrights, patents, trade secrets, trade dress, and any other known or unknown intellectual property related to FarmedHere or its business, including but not limited to specifically: The domain www.farmedhere.com (to the extent assignable) as well as all farmedhere.com email addresses (to the extent assignable), all FarmedHere social media accounts including but not limited to Twitter, Facebook, Instagram and Pintrest (to the extent assignable); United States Trademark Reg. Nos. 5026385 and 4292224, all UPC codes, Ceres software platform, all trade secrets related to organic growing; Certain other tangible Assets including but not limited to equipment owned by FarmedHere related to the physical production of salad dressings. A complete and detailed list of Lot 1 can be viewed by contacting the Assignee.
The Assets to be sold in Lot 2 include but are not limited to certain tangible Assets utilized for indoor vertical growing of a variety of vegetables or other botanicals, including 168 growing beds, ten 1,200 gallon tanks, approximately 3,500 growing trays, office furniture and fixtures and other items used for indoor vertical growing. A complete and detailed list of Lot 2 can be viewed by contacting the Assignee. FarmedHere was established in August 2011 to operate as a sustainable indoor farming operation supplying year round local greens for public consumption.
On January 17, 2017, Howard B. Samuels, not individually but solely as Assignee for the Benefit of Creditors of the Debtor, received and accepted an Asset Purchase Agreement (“APA”) for Lot 1 for the Assignee’s right, title and interest in and to certain Assets of the Debtor’s tangible and intangible operating assets and rights of any and every kind, used or usable in the Debtor’s business, subject to all liens, claims and encumbrances of record, as a single lot as provided and further detailed in the APA, for a purchase price of Forty Thousand Dollars ($40,000.00). The APA for Lot 1 also details excluded assets and other terms and conditions. Upon request, the Assignee will furnish to a qualified purchaser, after execution of a confidentiality agreement, a complete list of the Assets and a copy of the fully executed APA.
Lot 2 Assets will be sold as a single lot, or at the Assignee’s discretion, in separate lots. All Assets will be sold “AS IS, WHERE IS” with all faults and without any express or implied representations or warranties whatsoever, including, without limitation, warranties of merchantability, quiet enjoyment or fitness for a particular purpose or as to the title, value or quality of the Assets. The Assignee reserves the right, on or prior to the Date of Sale, to modify, waive or amend any terms or conditions of the Sale or impose any other terms or conditions on the Sale, and, if the Assignee deems appropriate, to reject any bids or continue the Sale (whether for all of the Assets or separate lots) without prior notice.
TERMS & CONDITIONS: An Assignee’s Return of Bids Sale (the “Sale”) for the Assets of FarmedHere identified in Lot 1 and Lot 2 will take place on Thursday, February 23, 2017 at 2:00 p.m. at the offices of Rally Capital Services, LLC, 350 N. LaSalle St., Suite 1100, Chicago, IL. The Assets will be offered as single lots or in separate lots as determined by the Assignee on an “AS IS” and “WHERE IS” basis.
To be a qualified purchaser for Lot 1, a party must post a cash deposit (the “Deposit”) in the form of a cashier’s check, certified check or wire transfer in the amount of Ten Thousand Dollars ($10,000), made payable to and delivered to the Assignee one day prior to the Sale. All bidding for the Assets shall be conducted in the same room with the identity and bid terms of all bidders fully disclosed and on the record as recorded by a court reporter. Any subsequent overbids for the Assets will be determined by the Assignee at the Auction; provided, however, the Assignee reserves the right to change the minimum bid from time to time during the Sale. At the conclusion of the Asset sale, the Assignee shall declare on the record which bid has been declared the highest and best bid and accepted, for the Assets and shall recite the terms of the winning bid into the record with the concurrence of the prevailing bidder. The balance of the purchase price for the Assets must be paid to the Assignee in available funds within twenty-four (24) hours. If the successful bidder fails to pay the balance of his or her successful bid for the Assets, then its Deposit will be forfeited and the Assets may, at the Assignee’s option, be sold to the next highest bidder without prejudice to or waiver of the Assignee’s rights and remedies against the defaulting highest bidder. The Assignee reserves the right to adjourn the Sale from time to time without further notice except as announced at the auction. The Assignee further reserves the right to determine the qualifications of any bidder, including the ability to close the transaction on the terms and conditions referenced herein.
The Assets sold or to be sold are being sold as a single lot “As Is” and “Where Is” and with no express or implied warranties, representation, statements or conditions of any kind including but not limited to warranties of merchantability or fitness for a particular purpose and are to be sold in accordance with the terms and provisions set forth above. Assignee is not transferring or selling herein any leased property, whether real or personal, whether evidenced by a true lease or a capital lease (unless the capital lessor so consents).
For more information on Lot 1 and Lot 2 or to arrange for an inspection of the Assets, please contact the Assignee.
Assignee
Howard B. Samuels, Esq. • David N. Missner, Esq.
Jeffrey D. Samuels
Rally Capital Services, LLC
350 N. LaSalle St., Suite 1100
Chicago, IL 60654
(312)645-1975
info@rallyllc.com
GE Lighting Horticultural LED Lights Are Specifically Designed for Controlled Environment Agriculture
GE Lighting Horticultural LED Lights Are Specifically Designed for Controlled Environment Agriculture
GE Lighting has introduced LED grow lights for use in greenhouses, vertical farms, tissue culture labs and growth chambers.
BEDFORD, TX (PRWEB) FEBRUARY 15, 2017
GE Lighting has been offering horticultural LED lights to the North American market since 2011.
“GE had been marketing horticultural LED lights in Japan prior to introducing them to the United States,” said Sharee Thornton, Product Manager at GE Lighting. “The reason for not introducing them sooner was the U.S. horticulture market was just starting to work with LEDs and GE was still developing the products specific to this market. We currently have three LED products that we are actively selling in the North American market and have additional products that are expected to come out during 2017. These would include interlighting and toplighting products.
“We have customers who operate vertical farms that are asking for a toplighting product. We are developing toplighting products for both vertical farms and for greenhouses.”
Horticultural LED grow lights
GE Arize Life
The primary application of the GE Arize Life LED light fixture is as a replacement for fluorescent lights typically found in tissue culture labs, growth chambers and testing labs. The fixture is available as a 2-, 4- and 8-foot light bar.
“This fixture has an integrated power supply, is IP66 rated and UL wet rated, which means it’s splash proof and easy to clean,” Thornton said. “If the fixture is used in a high moisture environment, it is easy to wipe clean. The operating temperature can be from 0ºC-40ºC (32ºF-104ºF). The fixtures can be daisy-chained from end to end or they can be daisy-chained with a jumper cable.”
Thornton said the Life fixture, which has a 5-year limited warranty, previously had a L80 of 36,000 hours. She stated GE has updated the fixture to a L90 of 36,000 hours.
“This means at 36,000 hours a grower will still have 90 percent of the fixture light intensity available,” she said. “Other fixtures on the market are at L70 at 35,000 or 25,000 hours. That means at either 35,000 or 25,000 hours a grower is going to get 70 percent of the light intensity. A grower would have to replace the fixture if he loses 25-30 percent of the light intensity. Within that time period at 90 percent a grower may not have to replace the GE light fixture depending on what he is growing.”
Thornton said replacement of the fixtures will depend on where they are used.
“If the fixtures are used in a vertical farm where they account for 100 percent of the supplemental light the plants are receiving, those are usually operated 16-18 hours per day,” she said. “The lights won’t be operating 24 hours because the plants have to have some time to rest. At a rate of 16 hours of light, seven days a week, the fixtures would run approximately 5,000 hours per year. The life expectancy of the fixtures would be around seven years.
“This is what we typically see with some of our other applications. That is why we are able to offer a longer life expectancy. GE has been doing this with its other products. We know how to mechanically and electronically put the products together and run them at a higher efficiency in order to get a longer life. For growers who are using the lights for propagation rather than for a vertical farm, the life expectancy could be even longer if the lights aren’t run as often or as long.”
GE Arize Lynk
Side-by-side the Lynk and Life light bar fixtures look identical. The GE Arize Lynk fixture is available as a 4- and 8-foot light bar with plans to release a 2-foot bar in 2017.
“The biggest difference between the two fixtures is the light intensity,” Thornton said. “The Lynk fixture can be used with vertical farms, in greenhouses, and growth chambers. Like the Life fixture, Lynk is IP66 rated and UL wet rated so it can be cleaned very easily. The Lynk fixtures can also be daisy chained from end-to-end. It has an independent driver so there is no additional driver required. There is also a plug so that it can be hot wired or it can be plugged in.”
Thornton said because the Lynk and Life fixtures are lightweight, weighing less than 5 pounds, they are easy to install with mounting clips.
“The mounting clips are attached with fasteners and then the fixtures are attached to the clips,” she said. “It is a very easy and fast installation. Hort Americas has done a video showing how easy the fixtures are to install.”
Thornton said GE offers similar light spectrums for both the Lynk and Life fixtures.
“We have a reproductive spectrum, a vegetative and a balance. It depends on the goals of the growers,” she said. “The purple light is the ideal light for photosynthesis. Some growers want all purple and then they will move the crop out to harvest it. Others want white light so that they don’t have to move the product around. A grower can have a balanced pink, a balanced purple and a balanced white.
“The reproductive spectrum with a higher red content is for the grower who wants to promote flowering and fruiting. The light spectrum for vegetative growth, which has a higher blue content, is for the grower looking at size or selling the product by the pound. If a grower really doesn’t know what light spectrum he wants or wants a spectrum for both reproductive and vegetative, he can choose the balanced spectrum of red and blue. The balance is the more common spectrum chosen because growers want both or don’t know and want to see what happens with the balanced spectrum. If the balanced spectrum doesn’t produce a beefy enough plant then the grower will look at the vegetative spectrum. Or if the plant didn’t flower or fruit as well as expected, then the grower would use the reproductive spectrum.”
Thornton said the Lynk fixture puts out about twice as much light as the Life fixture.
“A 4-foot reproductive Life fixture produces about 43.2 micromoles per second (μmol/s),” she said. “A 4-foot Lynk fixture produces 82.9 μmol/s. So it’s almost double. There would be a similar difference for the 8-foot fixtures too. An 8-foot reproductive Life fixture produces about 86.3 μmol/s and an 8-foot Lynk fixture is around 181.5 μmol/s.
“We have seen a lot of the 8-foot fixtures used in vertical farms. Because of the insulation and they are so easy to clean, it is a lot easier to install the 8-foot fixtures. A lot of the vertical racks have five 8-foot sections so it works out perfect for the 8-foot light fixtures.”
GE Arize™ Greenhouse Pro LED Flowering Lamp
The GE Arize Greenhouse Pro is for photoperiodic control. It is set up on a BR30 platform.
“This bulb’s main application is to primarily control photoperiod and flowering in greenhouses,” Thornton said. “The light intensity of this bulb is 17.8 μmol/s. It is not as intense as the Arize light bar fixtures, but for its application it is very competitive with similar bulbs on the market. Its life expectancy is L90 at 10,000 hours. It is 90 percent at 10,000 hours.
“We have some trials going on at Michigan State University and expect to have some results coming out this year so that we can help growers use this bulb efficiently.”
Robots Meet Indoor Farming
The goal: to produce 30,000 heads of lettuce a day initially using LED lighting and hydroponic technology a 47,300-square-foot facility near Kyoto, SPREAD, an agriculture technology company, is creating a massive, automated, indoor „vertical farm”—and the special ingredient is the use of robots
Robots Meet Indoor Farming
The goal: to produce 30,000 heads of lettuce a day initially using LED lighting and hydroponic technologyIn a 47,300-square-foot facility near Kyoto, SPREAD, an agriculture technology company, is creating a massive, automated, indoor „vertical farm”—and the special ingredient is the use of robots. The goal: to produce 30,000 heads of lettuce a day initially using LED lighting and hydroponic technology, a method of growing plants without soil, using mineral nutrient solutions in a water solvent, and with produce on multiple rows of shelving, stacked one on top of the other.
But robotic systems will do much of the work growing and producing the crops, from watering to harvesting. „The farm will be as robotically automated as possible,” says Frank Tobe, editor of The Robot Report. For example, cranes will deliver seedlings to small robots, which will then transplant the sprouts to grow beds. The company expects the facility to be operational by mid-2017 and to construct and operate 20 new factories over the next five years, in addition to selling the system for others to use in their own facilities, according to Tobe.
Robots and indoor farms
While SPREAD is billing its new facility as the world’s largestplant factory, around the world, an increasing number of other growers and technology companies are using indoor farms, also known as controlled environmental agriculture, rather than the conventional outdoor variety, to grow produce and other greenery. Although still in its infancy, in some cases, they’re experimenting with vertical indoor operations, relying on hydroponic or other non-soil based methods; in others, they’re applying advanced technology to greenhouses.
See also: The farm tech revolution
The key to efficiency, however, is the use of automation, especially robots, as a vital part of the system. The technology does repetitive, tedious tasks usually performed by humans, like constantly rotating containers to get the right amount of sun, for example, or placing items on a conveyer belt. „Robots are perfectly suited for this type of task,” says Tobe.
There are many advantages to robotic indoor systems, from the ability to grow food throughout the year, without being affected by weather variations, to a dramatically reduced use of water and lower labor costs. It’s also a more sustainable type of production that has the potential to boost locally grown, fresher produce.
„Our aim is to build robotic greenhouses in order to allow for cheaper, local and sustainable produce.. „ That’s the goal for Brandon Alexander, co-founder of Iron Ox, a Silicon Valley startup building a robotic environment for greenhouses growing lettuce and other leafy greens. He can’t reveal too many details, but, he says, „Our aim is to build robotic greenhouses in order to allow for cheaper, local and sustainable produce. The goal is fully automated crop production.”
Partial robotics
For now, most systems incorporate robots in part of the process, with other machines and human workers taking care of other aspects of production.
Take Egatic, a company in Odense, Denmark, that is developing a new system in partnership with a grower of herbs and small flowers to take items from a greenhouse to be packed and shipped. It uses a mix of robots, people and other automated equipment. For example, a conveyer belt transports herbs from the greenhouse to a packing area. Workers place herbs in boxes put together by what CEO Mars Nychel calls „erector machines”, but robots place the boxes onto pallets.
Only one person is needed on the assembly line, with a part-time employee supervising. The company will start testing out the new system this year, according to Nychel. Next step: adding flowers to the process.
Lettuce is not like a car
Using robotics in indoor farming is complicated, however. Perhaps the thorniest problem is the variability of each, say, head of lettuce. „It’s not like you’re making a car and every item is the same,” says Alexander. Thus, robots must be programmed to be able to grab, remove and transplant things that are not exactly the same shape.
According to Nychel, his company has been working on a system since 2007 with a client that uses greenhouses to grow tomatoes. The goal is for robots to pick the tomatoes automatically. But the company has struggled with creating a robot able to pick the produce using a sufficiently gentle touch, as well as grab plants that aren’t a standard size. They’re also using vision systems to allow robots to discern whether each tomato is the right color to be picked.
He figures it should take another 18 months or so to finish the project. „It’s been quite a task,” he says. „But, there will be very high demand when it’s done.”
Ultimately, robotic experts predict that robotic indoor farming systems won’t replace conventional methods. Instead, they’ll serve as supplements–enhancing agriculture grown the old-fashioned way with a more efficient, sustainable and weather-resistant method for producing crops.
The contents or opinions in this feature are independent and may not necessarily represent the views of Cisco. They are offered in an effort to encourage continuing conversations on a broad range of innovative technology subjects. We welcome your comments and engagement.
We welcome the re-use, republication, and distribution of „The Network” content. Please credit us with the following information: Used with the permission of http://thenetwork.cisco.com/.
Another Look At GreenGro Technologies Inc
Another Look At GreenGro Technologies Inc (OTCMKTS:GRNH)
By Alex Carlson / in Momentum Stocks, Sector Watch, Stocks / Tuesday, 14 Feb 2017 05:48 AM
GreenGro Technologies Inc (OTCMKTS:GRNH) has traded fairly flat so far this year. The stock has not made the big moves like it did in 2016 when we saw the stock run from $.0171 to just under $.16 a share. With the stock trading on either side of the $.10 level, we’re taking another look at GRNH.
First up, a little background on the company. GreenGro describes itself as “a world class provider of eco-friendly green technologies with specific domain expertise in indoor and outdoor agricultural science systems serving both the consumer and commercial farming markets. It brings together community and commerce through the growth and distribution of healthy, nutritious foods and vital medicines backed by science and technology. Customers include restaurants, community gardens, small and large scale commercial clients. Greengro Technologies also provides design, construction and maintenance services to large grow and cultivation operations and collectives in the medical and recreational marijuana sectors.”
Last week, the company signed a definitive agreement on a ten-acre, $25 million Greengro hydroponic indoor farm project with Global Renewable Resources LLC, a new startup specializing in sustainable technologies and renewable energy. The agreement calls for GRR to purchase a Glass Greenhouse Franchise marketed by Greengro subsidiary BP Gardens, Inc. The project will utilize advanced technology and production methods from Greengro’s newly acquired subsidiary Biodynamics. The GRR Glass Greenhouse Franchise includes a turnkey greenhouse facility powered by renewable energy and designed to annually produce millions of pounds of a large variety of organic, pesticide-free hydroponically grown vegetables and fruits.
Last month, GRNH completed the acquisition of a 55% majority interest in Biodynamics LLC. Biodynamics provides high-tech, hydroponic vertical farms. As a result of the merger, Biodynamics CEO Timothy Madden became the new COO of GreenGro Technologies. He will be managing the ten-acre, $25 million Greengro hydroponic indoor farm project with Global Renewable Resources, LLC along with other Greengro mergers and acquisitions currently in progress. CEO James Haas said:
“By combining Greengro’s business operations with Biodynamics’ superior indoor vertical farming technology, Greengro will be able to offer one of the highest producing and most energy-efficient turnkey systems on the market, at a competitive price. Our research shows that Biodynamics’ ‘smart’ vertical farming technology is arguably among the world’s best, and we expect to make strong inroads into new markets as a result of this deal.”
Earlier this month, GRNH launched GenoBreeding that will look to bring new cannabis varieties to market through new plant breeding technologies. This initiative from Greengro is in keeping with the cannabis industry’s increasing reliance on genetics – heredity and the variation of inherited characteristic in plants – to help growers create better, more powerful and sometimes personalized commercial cannabis strains that share desirable inherited characteristics. Greengro’s GenoBreeding group is focused on developing breeding tools such as molecular markers to enable breeding decisions and processes to achieve top-tier plant performance in a sustainable manner.
Last November, GRNH unveiled a new 5k sq ft fully equipped industrial glass greenhouses for the produce and cannabis markets. Measuring 19 ft. in height, 30 ft. in width and 170 ft. in length, these high-capacity greenhouses provide 5,037 square feet of technologically advanced climate controlled cultivation and harvesting space. The structure of a Greengro Technologies greenhouse is built with nearly two-inch tempered glass and erected with a customized aluminum frame. The turnkey operational setup consists of a Cooling Pad and Fan System designed to regulate temperatures through an efficient circulation system. The ventilation assemblage is driven by a motorized and galvanized hot-dipped rack-and-pinion arrangement, optimizing stability. CEO James Haas said:
“We are very pleased to be bringing this immense, advanced greenhouse offering to the marketplace. Our continuing discovery of technologies suited for lucrative new fields of trade will broaden our footprint in both the consumer and commercial markets alike, strengthening our ability to further capitalize on our unique operating advantages, particularly as local demand escalates with the opening of the new recreational cannabis market while other areas throughout the country embrace medical marijuana provisions.”
Currently trading with a market cap of $27 million, GRNH has been more active on the news front, but that has not moved the needle on the stock price in 2017. Once some of its latest deals translates into higher revenues, we believe GRNH’s share price will start moving again. We will be updating our subscribers as soon as we know more. For the latest updates on GRNH, sign up below!
Disclosure: We have no position in GRNH and have not been compensated for this article.
The Future of Agriculture Is Already Here
The Future of Agriculture Is Already Here
2/13/2017
A robot that grafts seedlings. Fleets of remote-controlled, self-regulating greenhouses. Organic rice that’s grown entirely by drones.
Even for those of us on the bleeding edge of U.S. farming trends, the coupling of technology and agriculture often exists on the outskirts of what seems fathomable — or even practical.
Sure, we’ve heard about agricultural drones in theory, but that still seems light years away. And indoor, vertical farms that grow plants aeroponically (without sunlight, water or soil)? Judging by the amount of media attention surrounding a soon-to-open aeroponics facility in New Jersey, the practice continues to hold a science fiction-like fascination.
In Japan, though, these kinds of agri-tech innovations are already readily employed — if not downright common — across the country.
At the 2016 Agri World Expo just outside of Tokyo, over 55,000 companies from across Japan and Southeast Asia have gathered to showcase the latest and greatest in farming technology — and I’m in the middle of it all. A veritable three ring circus of flashing flights, wheeling machinery and tiny bowls of free snacks, the event is something of a sensory overload, with enough newfangled bells and whistles confound any old-fashioned notions of where agriculture is headed.
Rural populations across Japan have been in decline for decades, with younger generations casting off the countryside for the lure of city lights and leaving aging farmers with no other choice than to simply watch their land — and craft — whither. Instead, as urban populations have boomed, Japan has seen a massive push towards metropolis-adjacent indoor farming and other forms of argi-tech that can exist within high-density communities. Growing crops so close to the people who will eat them, advocates suggest, means that they are both fresher and healthier when they reach the consumer.
But the technological innovations on the horizon in Japan go far beyond LED-supported lettuce. Behemoth farm drones lay splayed out like metallic, aerial spiders at multiple booths, and salespeople tittered excitedly about how drone farming — especially when it comes to organic crops — means plants can flourish in a more stabilized, consistent fashion. Constant monitoring and an eagle-eye view, it seems, are key.
The rise of drone-based farming has also opened a new career path for many Japanese.
One of the surest signs that technology and agriculture are pairing off for the long-haul is the buy-in of Japan’s telecommunications giant, Nippon Telegraph and Telephone Corporation (or NTT, for short). With an annual revenue of 11 trillion yen, NTT is the granddaddy of Japanese telephones, retaining their oligopolistic grip on landlines nationwide while constantly pivoting into new areas of information technology in order to keep up with younger, nimbler companies. Increasingly, this means investing in Artificial Intelligence for farmers.
“A lot of our community-based research and design goes into trying to help farmers through new inventions,” a company representative says as he hands me a tiny can of fresh vegetable juice. “We’re looking for ways to make farming more productive.”
At the Agri World Expo, NTT’s booth magnetizes crowds, as women in cow-print dresses mingle among drone-explainer videos, oohing and ahhing. The company’s piece de resistance, though, is Scarecrow: an adorable, teddy bear-sized “personal robot” with big, Disney princess eyes and an “S” emblazoned on its chest.
Scarecrow might be small, but its purpose is mighty: the robot has the ability to remotely control an entire farm. One input from the farmer, and Scarecrow can connect via satellite with plant-fertilizing drones, or operate farm machinery with a single instruction. Since it’s constantly getting feedback and input from the fields, the new technology has the potential to streamline farm operations while serving as a singular point of data retention and collection from season-to-season.
“New technologies are a lot more efficient,” says a representative of E-Minori, a fledgling company which uses sensors to alert farmers if their greenhouse conditions fall below peak standards. “In the past, farmers would only have their experiences and intuition to know if temperatures or humidity inside their greenhouses was off — and they can’t be there all the time. Now, it can be dealt with automatically.”
This also means ensuring that nature doesn’t have the chance to wreak havoc, either. Between plant-eating pests, see-sawing temperatures and the threat of natural disasters like tsunamis and earthquakes, farming that’s tightly controlled — and, yes, indoors — means that no matter what’s going on in the actual dirt, plants will continue to flourish inside their perfectly-regulated, safe bubbles.
“Indoor farming is the way of now, and the way of the future, because it’s not impacted by the temperature,” a man from Clean Farm — a soil-free, water-free aeroponics company that calls itself a “flexible plant factory” — notes. “It is completely isolated from the outside.”
And while, in the U.S., worries about the impact of hazardous materials on crops is a catch-all concern, in Japan, the impetus feels even more urgent in the wake of the 2011’s nuclear plant meltdown in FukushiRama, which resulted in the radioactive contamination of all farmland, groundwater and soil for hundreds of miles. In turn, the promise of disease-free, pollutant-free produce means that families are a natural target audience for the products from many agri-tech companies. Images of toddlers gleefully biting into a fistful of LED-supported spinach are littered across company advertising, and “safe eating” (which is a few standard deviations beyond the concept of organic-only “clean eating”) has become rhetorical dogma.
Larger profits are a major boon, too. Using indoor systems, farmers are able to tinker with seasonality by growing traditionally summer-only crops in the winter (and vice-versa) to sell for higher prices.
“In the wintertime, the sun sets at 5 p.m., which means growing conditions aren’t good,” the BioSun associate notes. “Using indoor systems, farmers can make produce grow faster — and sell faster — because the sunlight and seasons don’t matter, which means they can make more money.”
Still, there are perhaps a few kinks to work out.
After sampling some coriander grown using an indoor vertical system, a colleague of mine noted that while it tasted great, the plant — which is usually quite fragrant — had no smell.
The science behind this seems like a strange, and almost unsettling, development. How can an herb lose one of its most notable characteristics simply by being grown indoors? If LED farms cause such a dramatic shift in the actual chemical make-up of the plant through their modifications, it seems like a potentially slippery slope. Seeing the concern in my face, a company representative nervously brushed it off as a good thing, chalking up the fragrance-free herb to the fact that it lacked the acidity typical of plants grown in soil.
Reassurances aside, there’s no doubt in my mind that the company will soon be going back to the drawing board on this issue, figuring out yet another new way to use technology as both a progressive tool and problem-solver in the world of agriculture.
Atlanta To Host Agriculture Conference
Atlanta To Host Agriculture Conference
- Leslie Johnson
- For the AJC
4:49 p.m Monday, Feb. 13, 2017 Metro Atlanta / State news
Relationships built at the inaugural Aglanta Conference on Feb. 19 could help the city meet its goals of bringing local healthy food within a half mile of 75 percent of all Atlanta residents by 2020, said the city of Atlanta’s urban agriculture director, Mario Cambardella.
Urban and controlled environment agriculture innovation will be featured during the conference, which will take place at Georgia Railroad Freight Depot.
The purpose of Aglanta is to assist in Atlanta’s growth as a central hub in the nation’s annual $9 billion indoor farming industry, the city said in an announcement. Participants will include restaurateurs, grocers, architects, entrepreneurs, technologists, business owners and urban farmers for networking, sharing of best practices and making partnerships. The conference will include workshops and lectures, and cover urban agriculture business models and technologies, with a focus on vertical and indoor farming.
Information: https://www.aglanta.org/
The Vertical Farm: A Chat with Dickson D. Despommier, Ph.D.
By the year 2050, nearly 80% of the earth’s population will live in urban centers and that number will have increased by about 3 billion people in the interim – a big challenge and opportunity to feed. One emergent model is indoor farming, aka, vertical farming
The Vertical Farm: A Chat with Dickson D. Despommier, Ph.D.
February 10, 2017
By the year 2050, nearly 80% of the earth’s population will live in urban centers and that number will have increased by about 3 billion people in the interim – a big challenge and opportunity to feed. One emergent model is indoor farming, aka, vertical farming.
Columbia professor Dickson D. Despommier, Ph.D., (now emeritus) at Columbia University Medical School authored “The Vertical Farm: Feeding the World in the 21st Century,” published in 2010, and is credited with mainstreaming the term vertical farming.
At its most basic, the process refers to growing crops in vertically stacked beds in a controlled environment, without natural light or soil as Despommier describes here:
Sustainable Brands spoke with Despommier about the adoption of this model today.
“The idea has not been in the public domain for more than ten years,” he said. “It requires a heavy investment and creativity to invent the methods and to create social buy-in. It’s been quite rapid depending on how you define it. The idea smoldered in Japan for ten years and then Fukushima occurred and countries went ballistic as the people of Japan were not buying food grown there thinking it was contaminated.
“An indoor food industry was a solution and the Japanese government supported it. Indoor farming spread in the country and Toshiba and Panasonic were enlisted by the government of Japan to become leaders in indoor farming. These two giants had some downsizing in their own factories due to competition in other sectors that affected their ability to keep pace with the growth of electronics industry. Warehouses not being used were converted to indoor growing systems. Japan has embraced indoor/vertical farming.
“Singapore lacks land but is rich. They want to control food safety and sovereignty. Before urban farming there were no options. Panasonic has large indoor farms in Singapore and six others are being built to fulfill expanding demand.
“Taiwan has 50 vertical farms. They have little land to farm on a mountainous island with a tropical climate. Korea built and experimental farm in 2010 and the Mayor of Seoul announced in the last six months that every building can accommodate an addition for vertical farming. There are 30 million people in Seoul now and they’re importing foods but want to be in control.
“Here in the US, farmers in the Midwest have a winter problem and can’t deliver fresh greens as easily – fresh greens as in picked today – so what arrives is three weeks old and 40% is thrown out from refrigerators as it rots.
“There are 30 or so indoor farms centered around Chicago in abandoned warehouses – many no higher than a single story, single greenhouses – but they must be higher than one story to qualify as vertical farms. Companies like Sears, Kmart and Walmart who have such buildings can get tax breaks to repurpose them for farming but these stories don’t make the radar screen of the public, they don’t usually make the headlines.”
Despommier and his students figured out that a space like Floyd Bennett Field, former airport-turned-park on Jamaica Bay in Brooklyn, could provide enough vegetables and rice to feed every person living in New York City in the year 2050 – along with medicinal plants, and herbs and spices for five different traditional cuisines.
SB asked is this an extensible model?
“Every situation for establishing an indoor farm is predicated on supply and demand,” Despommier said. “Most cities in the US north of the Mason Dixon - the weather division – are going to run out of fresh green vegetables in winter.
“It’s amazing how important they are to restaurants and even fast-food chains as accoutrements – it’s a huge output that needs a reliable source and from that perspective, every city has space but a different set of priorities. You have to be clever in dealing with real estate agents etc.”
“Empty warehouses are a prime target for the establishment – every Mayor has relics from industrial movements and habits developed by Kmart and Costco and Sears. Corporations overextended. Starbucks has gigantic warehouses out of reach of a city for property taxes, several thousand sq. feet, intergowing vegetables like tomatoes and green beans. They’re not hard to grow but you need demand.”
Since your book was published, what changes do you perceive in consumer and business attitudes towards sustainable agriculture?
“There’s been a gradual transition from the Currie and Ives view of farming of the 1910’s and 20’s and then the 30’s drought trashed the Midwest, followed by WWII – and then, as depicted in the “Grapes of Wrath,” a favorite book, what happened next was a generation displaced by climate change who moved to CA. How ironic that CA is in its seventh year of drought and even the weather coming isn’t going to help as it’s coming in the wrong place to solve the problem. The problem continues.
“Moving to dairy farms, out of CA’s total $70 billion agricultural initiative, half is dairy farming. Dairy farmers in Europe are growing food for cattle indoors. No bales of hay, real cow food, and they grow it on demand, enough to raise 300 head of dairy cattle on oats barley grain from plants that stand just six inches tall with a tangled root system – crops in trays – which is then inverted and the root system falls out and that cattle feed is the Häagen-Dazs or Jerry Garcia flavor for them, they love it. You don’t need a lot of room and continuous growth for six weeks yields enough for 300 head of cattle.”
Despommier is hopeful we’ll get it right before we’ve exhausted the planet’s patience and resources but cautions, “humans are born with capacity to creativity and environmental destruction. We do it creatively, use our creativity in ways that damage the planet. Eventually the reality that what we’re doing with environmental encroachment will sink in.”
Today in the U.S., there are vertical farms in Seattle, Detroit, Houston, Brooklyn, Queens and near Chicago.
AeroFarms in Newark, New Jersey is one of the largest with a main crop of
baby salad greens, “vast armies of little watercresses, arugulas, and kales waiting to be harvested and sold. For more than a year, all the company’s commercial greens came from this vertical farm.”
“It’s still hovering at lever of industrial radar screens,” said Despommier, “but it’s a big industry waiting to happen – and the grow-light industry is huge, all that equipment, but it needs to be cobbled together.”
The building now leased by AeroFarms used to be Grammer, Dempsey & Hudson headquarters in 1929 when in an average year, the steel-supply company shipped about twenty thousand tons of steel. When the vertical farm there today is in full operation, soon, they expect to ship more than a thousand tons of greens each year.
Sheila Shayon, President of Third Eye Media, is a senior media executive with twenty five plus years in television and new media including expertise in programming, production, broadband, start-up models, creative and branding strategies, digital content and social networking.
City of Atlanta to Host inaugural “Aglanta Conference”
The City of Atlanta will host its inaugural “Aglanta Conference” to showcase urban and controlled environment agriculture innovation in the City of Atlanta
City of Atlanta to Host inaugural “Aglanta Conference”
February 10, 2017 Valerie Morgan Local News, more news0
The City of Atlanta will host its inaugural “Aglanta Conference” to showcase urban and controlled environment agriculture innovation in the City of Atlanta.
The Mayor’s Office of Sustainability has partnered with Blue Planet Consulting, a firm specializing in urban agriculture projects, to bring together restaurateurs, grocers, architects, entrepreneurs, technologists, business owners and urban farmers to network, share best practices and establish partnerships. The conference will take place on Feb. 19 at the Georgia Railroad Freight Depot, and aims to help foster Atlanta’s growth as a central hub in the nation’s annual $9 billion indoor farming industry.
“We are excited about the inaugural Aglanta Conference and expect more than 200 industry leaders to attend,” said Mario Cambardella, the City of Atlanta Urban Agriculture Director. “The City of Atlanta recognizes the positive health and community outcomes of urban agriculture and will use this conference to foster relationships and partnerships which can ultimately help us meet our goals of bringing local, healthy food within a half-mile of 75 percent of all Atlanta residents by year 2020.”
In December 2015, Mayor Kasim Reed appointed Cambardella as the city’s first ever Urban Agriculture Director. Atlanta is one of a few cities in the nation with an Urban Agriculture Director, dedicated to working on food access generating policy, advocacy, and development. The Aglanta Conference will create an environment for participants to engage with a local, national and international audience. Through workshops, lectures, and networking sessions, the conference will cover issues across the spectrum of urban agriculture business models and technologies, with a particular focus on the emerging field of vertical and indoor farming.
During the conference, the Mayor’s Office of Sustainability will spotlight local champions already doing incredible work growing food as means of ecological restoration, social cohesion, cultural preservation, economic development and biopharmaceutical development.Partners for the conference include the Georgia Department of Economic Development, Georgia Power, Indoor Farms of America and Tower Farms.
To learn more about the conference or to register, visit: https://www.aglanta.org/
Buy Infinite Harvest's Greens at Nooch and Company Headquarters
Denver-based vertical farm Infinite Harvest has big plans to take its produce-growing capabilities to outer space. In the meantime, it could help a lot of people here on Earth
Buy Infinite Harvest's Greens at Nooch and Company Headquarters
THURSDAY, FEBRUARY 9, 2017 AT 5:48 A.M.
BY LAURA SHUNK
You can now buy Infinite Harvest's Bibb lettuce for use in salads at home.
Denver-based vertical farm Infinite Harvest has big plans to take its produce-growing capabilities to outer space. In the meantime, it could help a lot of people here on Earth. As we reported in our feature story about the company last week, it grows some really tasty lettuce and microgreens.
At the time, you could only find Infinite Harvest products at local restaurants, tucked into salads and sprinkled as garnish on finished dishes or cocktails. But now the company has introduced two ways to purchase its produce for your own home-cooking purposes.
RELATED STORIES
Infinite Harvest has started supplying Nooch Vegan Market, a small retail shop at 10 East Ellsworth Avenue. At the moment, that store is just stocking Bibb lettuce, but the Infinite Harvest team says it may eventually bring on microgreens, too.
If it's microgreens you're after, you're in luck: Starting this weekend, Infinite Harvest will also sell to consumers directly out of its warehouse at 5825 West Sixth Avenue, Frontage Road North, Unit 3B in Lakewood. It's offering fresh-cut living Bibb lettuce plus two-ounce packages of thirteen different varieties of microgreens, including Genovese basil, micro-arugula and micro-pea tendrils.
While the warehouse store will be open from 8 a.m. until noon on Saturday and Sunday, you'll need to order in advance: E-mail info@infinite-harvest.com with your list and specify a pick-up time during the open window. Lettuce is $4 per head, while microgreens are $9 per package; Infinite Harvest requests a $12 minimum order.
If shelf life is a selling point for you, know that my Bibb lettuce lasted nearly two weeks in my fridge, and I imagine my microgreens would have, too, had I not eaten them within, like, sixteen nanoseconds.
If you'd rather try Infinite Harvest's produce in a composed dish, many restaurants around town are using it. Here are the most consistent buyers:
American Grind at Avanti, The Way Back, Jax Fish House, Grind Kitchen + Watering Hole, Il Porcellino, Blue Agave Grill, Brasserie Ten Ten, STK Denver, Machete, Ocean Prime, Shells and Sauce, Cerebral Brewing, Washington Park Grille, Edge at the Four Seasons, Ameristar Casino (Black Hawk), Mackenzie’s Chophouse (Colorado Springs), Odyssey Gastropub (Colorado Springs), Locality (Fort Collins) and 4th Street Chophouse (Loveland).
Freight Farms Revolutionizing Farm-To-Fork System
Usually the concept of farm-to-fork is designed to keep locally-grown produce out of shipping containers, but one company is working with local farmers to do just the opposite
By Patrick Lantrip
February 08, 2017
Usually the concept of farm-to-fork is designed to keep locally-grown produce out of shipping containers, but one company is working with local farmers to do just the opposite.
The Leafy Green Machine, developed by Boston-based Freight Farms, is a virtual farm-in-a-box that converts used shipping containers into year-round hydroponic farms, which can be monitored and controlled with your smartphone.
Each unit equates to a two-acre farm in terms of annual production, but is packed into a 40’ x 8’ x 9.5’ space and can be operated year-round regardless of geographic location or climate.
“It provides a pretty cool story thinking about these shipping containers that have previously transported cold goods across the globe and now they’re just in one place growing food,” Caroline Katsiroubas, Freight Farms marketing director said.
When its two founders, Brad McNamara and Jon Friedman, started the company they were originally looking into urban rooftop farming and how to make it economically viable, but after about a year of research, they decided that it was a little bit too cost intensive and time intensive.
The plans were eventually altered for shipping containers and the first prototype was built in 2012.
“Now at this point we have over 100 farms located across the globe,” Katsiroubas said. “A lot of them are small business that have just started and they are selling to their local farmers market, local restaurants or are starting farm stands or CSAs.”
In addition the United States, Freight Farms has operations in Canada, Japan and parts of Europe.
“We’re hoping to be all across the globe soon, because there is a definitely a need from it everywhere,” Katsiroubas said.
However, she noted that the company plans of bring strategic with its growth as not spread itself too thin.
“Our first and foremost priority would be the success of our farmers,” she said.
In Savannah, Ga., Grant Anderson is one such farmer.
Anderson, who was raised by his grandparents in rural Georgia, has been around farming his whole life, but said he never saw it as a viable business model. Since his grandfather owned 90 acres of land and leased most of it out to local farmers, Anderson said he saw many of the farmers’ struggles first-hand.
“I saw what temperamental weather can do to a farmer’s production and their income stream,” Anderson said. “I never really thought it was a stable career path even though it is something that a lot of folks around me did.”
Anderson eventually went to Georgia Tech, and obtained a business degree with the hopes of one day starting his own company.
For six years Anderson worked in finance as an auditor and portfolio manager, before taking a corporate job with Equifax in Atlanta.
However, Anderson said he wasn’t happy with his career trajectory and eventually returned home after the birth of his son and took a job as an administrator with the local board of education.
Once day, Anderson read an article in CNN Money that would change his life about a Boston couple with no agriculture experience who became highly-successful urban farmers through Freight Farms.
“I thought that agriculture is a part of my life even though it’s not something that I actually chose for a career path,” Anderson said. “It just sparked a curiosity.”
Anderson said there were a lot of positives around the idea of local food production and the lack of local food producers.
“The more I looked into it the more interested I became,” he said. “With my background I felt like I could viably operate that business and I also enjoy the hands-on work of growing plants, which I do for my own family over the summer in our backyard.”
Though Anderson has only been container farming for only four months, he is already having success at the local farmer’s market and is now working to build a rapport with local chefs to grow his customer base.
“It’s not something that I think is really popular right out of the gate in South Georgia,” Anderson said. “A lot of people do local dirt farming, so that fact that I am farming is not really a novel idea, but getting people to understand that this is in a shipping container, we can do it year-round and we can grow it vertically up the walls – people are just dumbfounded when they look in these things.”.
Freight Farms converts refurbished shipping containers into hydroponic farms that yield as much produce in a year as two acres of land.
Brad McNamara and Jon Friedman have helped farmers launch more than 100 container farms across the globe since they built the first Leafy Green Machine prototype in 2012.
The Future of Food - Community Development Field Trip
The Future of Food - Community Development Field Trip
Food and agriculture endeavors that focus on community development in cities -- from community gardens and urban farms to workforce development programs -- play an essential role in enhancing food security, educating citizens about where there food comes from, and strengthening food equity.
To learn firsthand about the impact of community development ventures on the future of food, Seedstock has organized the 'Future of Food – Community Development Field Trip’. Scheduled for March 17, 2017 in Los Angeles, CA, the field trip will include lectures from experts in the fields of community gardening, urban farming, and food justice, and visits to the following sites:
1. L.A. Kitchen - Founded by Robert Egger in 2013, L.A. Kitchen is located in a 20,000 sq. ft., two–level processing kitchen, in NE Los Angeles. L.A. Kitchen operates Strong Food, a wholly owned, for-profit subsidiary that hires training program graduates and competes for food service contracts, with an emphasis on opportunities to serve healthy senior meals. By purchasing and reclaiming cosmetically imperfect fruits and vegetables, which would otherwise be discarded, and using them to train and create culinary jobs for unemployed men and women, L.A. Kitchen makes scratch-cooked, healthy meals for the community.
This tour will sell out. Discounted Early Bird Special Tickets are available for a limited time here: http://seedstockfieldtrip.eventbrite.com.
2. Edendale Grove Parish Garden is part of the Seeds of Hope program, which is a ministry of the Episcopal Diocese of Los Angeles that seeks to help congregations, communities, and schools turn unused land into productive gardens and orchards to provide healthy and fresh food in areas of need across the county. Edendale Grove farm is situated on a previously vacant lot next to the Cathedral Center of St. Paul in Echo Park. The lot has been transformed into a parish garden that supplies fresh produce to local families as well as the essential ingredients to create sacramental oil and bread for the church.
This tour will sell out. Discounted Early Bird Special Tickets are available for a limited time here: http://seedstockfieldtrip.eventbrite.com.
3. Lavender Hill Urban Farm - Lavender Hill is a key project of the Los Angeles Community Garden Council, which manages 40 community gardens in Los Angeles County. Comprised of four and half acres of land, Lavender Hill Farm is located alongside the 110 freeway near Chinatown in Los Angeles, directly behind the Solano Canyon Community Garden. It was launched to provide meaningful work for ex-cons, former addicts, and at-risk teenagers.
To purchase early bird tickets, please visit: http://seedstockfieldtrip.eventbrite.com
A farm-to-fork lunch will be hosted and prepared by the staff at
Select Confirmed Speakers include:
- Tim Alderson - Executive Director of Seeds of Hope
- Julie Beals - Executive Director of the Los Angeles Community Garden Council
- Robert Egger - Founder and CEO of L.A. Kitchen
For sponsorship opportunities, please send inquiries to: sponsor@seedstock.com
It’s The Middle Of Winter, Do You Know Where Your Arugula Is Being Grown?
It’s The Middle Of Winter, Do You Know Where Your Arugula Is Being Grown?
By LIZ REID • 1 HOUR AGO
Pure Sky Farms CEO Austin Webb wore a black apron over his dress shirt as he served samples to costumers at the grand opening of the new Whole Foods Market in Upper St. Clair in January.
“This is micro and petite arugula that we have right here, covered in olive oil and lava salt,” he told a customer. “Then we have cilantro with a tortilla chip.”
The customer opted for the arugula, which Webb explained was harvested that very morning.
RoBotany CEO Austin Webb tells customers about his company's produce at the grand opening of the South Hills Whole Foods Market on Wednesday, January 25, 2017.
The concept of vertical farming has been around for more than a century. The idea is to grow a lot more food with a lot less space, water and waste. Plants are grown in trays that are stacked vertically, sometimes several stories tall.
“The roots are hanging down below the trays basically suspended in air and then they get the nutrient rich water which replace soil,” Webb said.
Every 10 minutes, the misters kick on for two-and-a-half seconds. Blue and red LEDs provide just the right color of light to optimize growth.
As high-tech as all this sounds, it’s fairly standard for the vertical farming industry. But Webb said there’s still one part of the process ripe for automation.
“A lot of what you see out there is a lot of folks growing manually,” Webb said. “If they're going 25 or 30 feet in the air they're using ladders and scissor lifts to go up and get the plants.”
RoBotany is developing robots that do the work humans are currently doing, which Webb said will be a huge space saver.
In addition to robots, the company is developing data analytics that will help them optimize for nutrition and taste. Webb noted that traditional farmers often have to optimize for pest resistance and shelf stability, but Pure Sky greens will be grown indoors and harvested the same day they’re put on grocery store shelves.
“It’s a lot cooler to be able to optimize for the nutrients and the taste of a plant and be focusing on if you really want sharp tasting cilantro or mild cilantro,” Webb said.
RoBotany’s current prototype is a much smaller version of what they hope to soon build. Its footprint is just 50 square feet, and they can produce about one pound of greens a day. Because this version is so small, they don’t actually need to use the robots they’ve built to place the trays of seedlings and move them back down to ground level when it’s time to harvest.
But with a 2,000 square footprint, RoBotany’s version two protoype will allow the team to further test their technology. It will be housed in the same South Side warehouse where the company plans to build its full scale, 20,000-square-foot farm.
What will make their farm different than existing vertical farms is that they won’t need aisles wide enough for scissor lifts or even for people. They won’t really even need humans to interact with the plants at all between germination and harvest.
Webb said this is the future of farming and envisions automated indoor farming increasingly supplementing traditional farming. But he said there are still a lot of issues to figure out. Right now, most indoor vertical farms focus on greens and herbs, because they’re pretty hardy and don’t grow very tall. Growing grain, a staple in human and livestock diets alike, is a much bigger challenge.
It’s also important to note that the vertical farming industry doesn’t directly address the biggest problem with current food systems.
“We don’t actually have a food shortage worldwide,” said Tony Miga, master of sustainability at Chatham University’s Eden Hall campus. “It is not a supply issue, it’s a distribution issue.
Miga said the biggest problem with current food systems is access, on both a global and local level. But he said urban agriculture, made greener and more efficient by companies like RoBotany, does have a role to play.
“I think it's finding ways to empower communities to be able to produce their own food at some level,” Miga said.
Webb said ideally, his company’s technology could be used to bring fresh produce to food deserts. But the company is still in its infancy, and right now they’re focused on scaling up production, and bringing hyper local produce to Pittsburgh shoppers. Pure Sky Farms' produce is planned to hit Whole Foods South Hills shelves later this month.
Webb said a future goal is to create Pure Sky Farms franchises, with local owners using RoBotany’s technology to bring fresh produce to customers across the country.
The Associated Press contributed to this report.