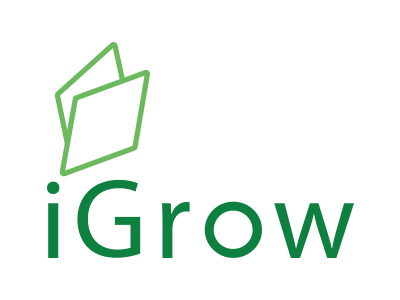
Welcome to iGrow News, Your Source for the World of Indoor Vertical Farming
Urban Farming Insider: Penny McBride, Founder Vertical Harvest Jackson Hole
We caught up with Penny McBride, founder of Vertical Harvest Jackson Hole, to discuss the challenges of running a commercial urban farm, why the best greenhouse engineers are from Europe, and much more!
Urban Farming Insider: Penny McBride, Founder Vertical Harvest Jackson Hole
We caught up with Penny McBride, founder of Vertical Harvest Jackson Hole, to discuss the challenges of running a commercial urban farm, why the best greenhouse engineers are from Europe, and much more!
Introduction
Jackson, Wyoming is home to one of the world’s first vertical greenhouses located on a sliver of vacant land next to a parking garage.
This 13,500 sq. ft. three-story stacked greenhouse utilizes a 1/10 of an acre to grow an annual amount of produce equivalent to 5 acres of traditional agriculture.
Vertical Harvest sells locally grown, fresh vegetables year round to Jackson area restaurants, grocery stores and directly to consumers through on-site sales. Vertical Harvest replaces 100,000 lbs of produce that is trucked into the community each year.In addition to fresh lettuce and tomatoes, Vertical Harvest produces jobs, internships and educational opportunities.
The greenhouse employs 15 individuals with intellectual and physical disabilities. Click here to learn more about our employment model.
Source: Mountain Magazine
Interview
UV: Can you talk about how Vertical Harvest started and your experience with that and how you got into the arena and kind of the background story?
Penny: Sure. I had been working as a consultant on a couple of different community projects...this was back when the pine bark beetle epidemic started and the forest service was looking for a lot of different ways to utilize biomass. That's where I kind of got a baseline understanding of what was possible from the biomass side.
Then from the greenhouse side, I was working with a team of experts that was hired to look at building a year-round greenhouse to be heated with biomass.
Unfortunately the project didn't happen, largely because this was around 2008
when the economy tanked. The people that I was working with had worked on greenhouse projects that were kind of functioning as community centers also. Mostly one was, it's in Boston, and it was helping to employ women, single mothers, and train them.
It was really exciting to me to see what was possible. My background does come
from this desire to create businesses and community enhancement projects that
really are tied to more than just one thing. It's not only a business, but it's
also a business that creates food and is just a much more circular model.
Around that time, I got a call from a case manager who is the person who actually is our employment facilitator now. She called asking if I had jobs for any of her clients, with any of these projects that I was spearheading.
I didn't think I did, but what it did spur me to do was start looking at the possibility of an urban center greenhouse. A greenhouse where people who couldn't drive could get to work by taking public transportation, something that seems a little more core to the community.
I started holding stakeholder meetings to see who might be interested. Really I thought it would be more of a community run greenhouse and not the business that it is today. That's really where (Vertical Harvest Jackson) kind of got its early legs.
UV: Could you talk about how you gained the technical side of (urban and vertical farming)? Some people are looking to grow something on their kitchen counter and some people have larger aspirations, but (either way) they (often) don't know where to start.
Penny: You know, I grew up on a farm and a ranch in Colorado. Not that that made me a hydroponic expert by any means, but I did kind of understand these plants and growing because the farm was started by my grandfather and it so it was really something I understood inherently to a certain degree.
But through the consulting work that I had been doing, I knew this man Paul Sellew, whose family started Backyard Farms, which was at the time the second largest hydroponic tomato producer in the U.S., and it was in Maine.
I knew that Paul had a really great greenhouse engineer. I also knew that this man was hard to get a hold of because he was very busy. I kind of pitched the early concept to Paul, and he was like "Okay, well I think that you seem to have a pretty good desire at least, even though the concept perhaps was half-baked." That's where we got a hold of Thomas Larssen.
I had initially hired my co-founder Nona just to do decent design work for me, basically some rendering. We presented our early renderings to Paul, and those are what he passed along to Thomas, and Thomas eventually came to visit us and really refined what we were looking at because we were looking at basically every kind of growing system under the sun at that point, even aeroponics, which seemed really far-fetched, and it's not far-fetched now. It's amazing how far the industry has come in eight years, it's pretty incredible actually.
I did things like take a hydroponics short course in the University of Arizona. We knew that we needed a head grower, and even though there were plenty ofpeople who have taught themselves how to be growers, everybody emphasizes the key to success is a good grower. We would hear things like "Oh, tomatoes are an art," and "Lettuce is more of a science,"and things like that.
UV: If somebody asked you where would you find a kind of elusive or talented greenhouse engineer now, where would you suggest looking ?
Penny: I do get that question often. The interesting thing is, a lot of the
sales groups (for urban farming equipment) now have developed so much now that they have expertise in their own team, like if you look at Hort Americas, they have their own test greenhouse. They can really basically engineer a greenhouse for you.
UV: You're talking about the companies that you might hire to develop your system for you?
Penny: Right. so a lot of the sales people kind of have greenhouse expertise on their side now. Does that make sense? A lot of the greatest experience comes from Europe because historically that's where so many of the greenhouses and the long history comes from.
UV: Is that because of the limited space there, or what is the reason?
Penny: Yeah. I think in the Netherlands, so much of their farmland was, they had to create their farmland and a lot of it was under water and they had limited space.
I think originally a lot of them were growing flowers and turned to food production also and so they've just been at indoor growing for longer than we have.
I was talking to somebody from Mexico and they were saying that the U.S. has not been responsible for their own food production for years. We've relied on other countries for our food production for such a long time that we haven't really cultivated this expertise.
Now quickly schools are changing, like the University of Arizona has a great
program and Colorado State are developing stronger indoor growing programs because they realize that it is the future.
I think it's just because we (the United States) went to monocrops that were all about the production of food for fuel and other things like that, and we weren't necessarily focusing on food production because it was so cheap for us to import food.
UV: What do you think are the hallmarks of (a greenhouse engineer) who's experienced? Is it just a body of experience, or is it like an expertise in the certain crop that you're trying to work with?
Penny: I do think that if somebody actually has a science background in plants, they
actually understand the science of growing plants (that is important).
I think because now there are certainly a lot of people who just learn about growing and don't learn about horticulture. I have to say that if you can find somebody who has both of those things, it's definitely very beneficial because plant pathology is so
much a part of it, you know because plants are, they're living things and so to say that you understand growing might be fine if you've actually maybe spent
years learning how to grow. I won't discredit those people at all.
It's like a chef. A chef is not made necessarily because he's gone to culinary school, but a chef is made because he maybe has some good experience just cooking.
Experience is another thing because you can't necessarily just take somebody out of school and expect them to run a whole facility, because there's a lot to it, you know? There are control systems. There's understanding temperature that may be something you would only learn on the job.
UV: Can you talk about some of the everyday challenges from an overall facility management side?
You obviously have your day-to-day challenges, like you mentioned temperature or what not, but then you also might have overarching challenges, like market dynamics
Can you talk about your insights and what you've learned since you guys have been in operation,and how you guys have improved both in the "whole forest" view, but also the"tree" view as well.
Penny: For us, since our system was so new and they've (the components) been built in a factory and they actually hadn't operated under growing conditions, there were a lot of kinks to be worked out as you can imagine.
Those were kind of the initial (set backs). Then were was learning about the building itself because I'm sure any new greenhouse has to kind of get to know and to grow into the skin of what their building is and adapt to that.
Then for us, it was even specific plants because we have a living wall, living three-story wall inside. Within this three-story system, the climate goes from very hot on the bottom very cool, I mean very hot on the top to very cool on the bottom.
There are challenges like that. It's not because we have a unique labor force that was an interesting thing to figure out too because I think any business has to figure out how to make sure their employees are where they should be according to their strengths.
Then things that we didn't really aspire to be maybe, like a delivery company even though it's something that everybody thinks is really simple, but adapting to delivering and packaging, I think that was one of the most shocking things for us, like the cost of packaging and the time and correct way to package. We had a lot to learn when we jumped into this.
UV: How would you summarize, or what would be your key points on packaging? For example, how much should people be budgeting for their packaging, common mistakes with packaging, or what are the mistakes that you made that you kind of shot yourself in the foot with?
Penny: We had to laugh because when we started, we had like five different sizes of boxes to ship our produce. It was ridiculous. I think we definitely overstocked on things and under stocked other things like, "oh this label's very pretty but we didn't think about how long it would actually take to put on the clam shell", and things like that.
I remember one day, just laughing at myself thinking "Oh my god, this lettuce is the most pampered lettuce that is going to this restaurant."
Realizing that what you're creating is, of course you fall in love with it and it seems like this living and breathing thing (the produce), but maybe it is like this microclimate that you're creating. It means so much as somebody who was with it from the start.
But what you have to remember is that it's a system. I think looking at it holistically as much as you can to make sure that you think of everything, and having to flow together is so important.
UV: I know you mentioned working with restaurants. It seems like selling whatever you're growing (as an urban farmer) to a restaurant is a very stereotypical kind of cliché kind of marketing channel as far as the main customer or the urban farming output.
Can you talk about what you think, in your experience, people don't understand about marketing and selling the stuff you produce on your urban farm, whether it's a very small amount to a guy down the street, or maybe it's retailers. What do you think are some major misconceptions that have to do with the actual commercialization like after you've grown something, after it's high quality, after it meets the spec of some customer?
Penny: I think the important thing to think about that we didn't probably understand would be so challenging, is to make sure that once it's in the store it might be on the shelf for three or four days, and understanding how to ensure that it looks good over that time period is really, really important.
It might be a little different for a restaurant because typically you can take things to a restaurant and it seems to last more because a lot of the lettuces we take are live.
I think it's just a little more challenging on the grocery store's shelf to make sure that things can stay looking fresh for a while on the shelf.
UV: Can you discuss the pros and cons of a couple of different (marketing and distribution) channels,whether it's restaurants or retail, some people might also be doing farmers'markets, etc?
Penny: I just think it depends on the size of your greenhouse or your farm. Obviously packaging, part of this is that it adds another element. But then again, it can be much more simple to sell to a restaurant partner.
I know that a lot of people think that restaurants can be fickle, but we've been so fortunate in that our restaurant partners are really very supportive.
People do need to look at the added costs of when you take your product to a grocery store, you do have to invest in packaging and your brand and all of things that I think people underestimate.
The whole distribution question is a whole other challenge too.
UV: Obviously your business has like a social responsibility element, but it's also for profit. Can you talk about that decision and maybe how you came to that decision, but also maybe the ramifications of that? I mean, would you have done it differently, or how do you think it turned out?
Penny: I think for me personally, we are starting a non-profit arm to support our educational arm because we're a production greenhouse but we're also a greenhouse that has a lot of learning going on both in that we bring people in and that we're learning ourselves about this whole new growing system.
I've always wanted it to be just a business. It's a struggle because I think the challenge is that I think it's too easy to criticize something that is a charity sometimes or it's too easy not to believe in it as a solution.
Forus, we have relied heavily on the generosity of grants and donations to get where we are, and investors that have a lot of understanding about what it takes to get started.
Maybe that's just part of being an entrepreneur too and being in an innovative company. I'm sure a lot of innovative companies go through the same sort of financial challenges and they have to have similar support in one way or the other. I guess in the end it doesn't matter. I'm not sure I'm happy that we're able to be a part of a community in a larger way,that we do have educational programs and that we are able to bring in, and most bring in people from the community, and most greenhouses can't do that because of tax pressures and things like that that it brings in.
UV: What's your favorite fruit or vegetable?
Penny: My favorite fruit or vegetable? I love apples.
UV: What's the best advice that you received when you were building Vertical Harvest Jackson or when you were learning the ins and outs of operating this type of facility, like the one you have in Vertical Harvest, or it could even be not related to anything, it could be generalized advice, like what's the best advice you think you've ever gotten?
Penny: I mean, it's so cliché but I think people just say, don't underestimate how much capital you have to have on hand for startups, and I really thought we would avoid that, but it does. It takes more money than you think to get through those early phases.
UV: Do you think that amplifies for like an urban farming company, or do you think it's the same across all company types?
Penny: Not necessarily. But I think the thing that I have learned the most, is that you really have to be honest with yourself, honest with yourself and everybody else. I think that's the easiest thing not to do.
I think a lot of startups are afraid to be honest with themselves because they put so much hard work into it and they don't want to talk about the pitfalls or to be honest about what might be kind of lurking in the shadow. That is what's going to give you a hard time.It really will. I mean, it's something we all have a hard time being, and it's just honest about what the challenge of the day is, or really is that financial really as honest as you think it should be, or are those productions really ...go back and revisit all of your numbers with as many experts as you can.
UV: Obviously Vertical Harvest had a decent amount of press coverage and you probably have gotten a good amount of exposure from that over the years. What do you think is something that a lot of people don't understand about your company or like a misconception that you would like other people to know?
Penny: I've never thought about that. I feel like ... Imean, I don't know if it's a misconception, but I do think, and maybe people don't realize that the time that was put into starting this greenhouse.
It was a monumental effort. Something like this is not for the weak at heart at all.It's scary, and it's hard work and things don't turn out the way you want them to. There's a lot that goes around. It's very life-changing. I don't think it's all like a bed of roses and that. Of course we're smiling on the pictures, but let me tell you. It's not easy.
Thanks Penny!
Future Of Food: How Under 30 Edenworks Is Transforming Urban Agriculture
JUN 1, 2017 @ 03:45 PM
Future Of Food: How Under 30 Edenworks Is Transforming Urban Agriculture
Tim Pierson
Jason Green, 27, and Matt LaRosa, 23, are the CEO and Construction Manager of Edenworks.
When Matt LaRosa joined Edenworks in early 2013, he was a college freshman who still hadn't even picked a major. But when he overheard CEO Jason Green at a pitch competition explain his plan to transform industrial buildings into high-tech farms, he immediately abandoned his own pitch and pitched himself to Green instead. The duo, along with cofounder Ben Silverman, went on to create the self-regulating aquaponic system that now supplies microgreens and fish to Brooklyn and landed them on this year's 30 Under 30 Social Entrepreneurs list.
The Edenworks HQ is not exactly where one would expect to find fresh produce and fish. Located in the Bushwick area of Brooklyn, the company sits atop a metalworking shop belonging to a relative of Green. Their office looks like a typical young startup: all eleven employees crowded in one room with computer screens occupying almost every surface. But upstairs across a narrow walkway is where the magic really happens: an 800 square foot greenhouse, custom built by LaRosa, housing fish tanks, vertically stacked panels of microgreens, and a sanitary packaging unit. Though admittedly cramped, the company says their size has made the team significantly more lithe than larger industrial agriculture operations.
"Being a startup, you have a ton of room to break things and iterate very quickly," LaRosa told Forbes. "We're so nimble with changing our prototypes... we have something different than anywhere else in the entire world."
Currently, about 95% of leafy greens consumed in the US are grown in the desert regions of California and Arizona. Most of these products are grown for mass production and durability in transport, rarely for quality or sustainability. Urban farms have cropped up as way to provide growing metropolises with fresher produce in a way that is better for the environment.
The Edenworks model differentiates itself from other urban farms in that it is a complete, aquaponic ecosystem. Waste from the tilapia fish is used as a natural and potent fertilizer for the microgreens planted on vertically stacked power racks. They have no need for synthetic fertilizers or pesticides that can diminish the nutritional quality of produce.
"The water table is falling every year, there's a huge amount of money invested in pumping water out of the ground and irrigating, and inefficiency in the supply chain where a lot of product gets wasted or left in the field," explained Green, a former bio-engineer and Howard Hughes research fellow. "We eliminate all of that waste."
A common phrase in the office is turning factories into farms instead of farms into factories, and many of their design challenges have been combated by embracing the industrial nature of the location. Indoor farms are often criticized because they can't make use of the natural processes used in traditional farming. But the team has invested in studying ancillary industries to find the lowest cost and highest return methods of mimicking the natural processes, like using custom LED lighting to emulate sunlight.
The research has paid off. In the current iteration, Edenworks is able to harvest, package and reach consumers within 24 hours. By cutting down on transport and prioritizing quality over durability, the greens are also up to 40% more nutrient dense than traditional produce.
For now, their largest barrier is clear: space. With $2.5 million in funding to date, their tiny greenhouse has managed to consistently service the local Whole Foods with two varietals of microgreens. In the winter of 2018 though, they plan to move to a space 40 times the size and simultaneously roll out five additional product lines across the NYC area.
The plans for the new building have been delayed a few times, but with LaRosa graduating NYU last month and joining the team full time, Green is confident they are on track to hit their deadline. The larger facility will be the result of years of planning that will incorporate new technology that will allow them to become even more efficient and competitive in the market.
"What we've developed is a huge amount of automation that will allow us to bring the cost down for local indoor grown product into price parity with California grown product, and that's really disruptive," says Green. "If we want to move the needle on where food comes from in the mass market, it has to be cost competitive. We want to be the cost leader, we want to bring the cost down."
Innovative Thinking and Technology: The Key to Solving Global Problems
Innovative Thinking and Technology: The Key to Solving Global Problems
Austin Belisle - June 1, 2017
This blog was guest-written by Brandi DeCarli, Founding Partner of Farm from a Box. She’ll be guest-speaking during the “Global Problem Solvers Who are Guardians of Our Planet” session of the Women Rock-IT series on June 15th.
Every aspect of our modern-day lives has been impacted by technology. From cloud and robotics to digital currency and drones, our lives are inextricably tied to the technology that surrounds us. While farming may not be the first thing that comes to mind when thinking of technology, it has played a key role in changing the face of agriculture and our global food system.
In the past 50 years, the Green Revolution has pushed to increase crop yields through large-scale intensification of single crops. Advances in mechanized farming allowed for larger and larger acreage to be farmed. By focusing on the large-scale intensification of a single crop, the natural checks and balances that diverse ecosystems provide were no longer in place.
To maintain production, it required heavy use of fertilizers and pesticides, which has directly impacted soil fertility and ecosystems around the globe. Now, with 40% of our agricultural soil degraded and 70% of our freshwater resources being gulped up by agriculture, it is clear that our current approach is not sustainable.
While advances in technology have enabled global agricultural production to increase with our growing population, those gains came at an unprecedented environmental cost. As we work to feed a growing global population, the environmental pressures will continue to increase.
By 2050, the world’s population is expected to grow by more than two billion people. Half will be born in Sub-Saharan Africa, and another 30 percent in South and Southeast Asia. Those regions are also where the effects of climate change are expected to hit hardest.
So, how can make sure that the growing need for food worldwide is met in an ecologically sustainable way? And what role can technology play? The opportunity may be in shifting our focus from mass production to production by the masses.
An estimated 70% of the world’s food comes from small, rural farms that are no bigger, on average, than two acres. And despite the increase in large-scale industrialized farms, small, rural farms are still the backbone of our global food supply. But these rural areas are often the most vulnerable to the effects of climate change.
The challenges of drought, degraded soil, and inefficient and labor-intensive methods contribute to and exacerbate low and unreliable crop production. Without access to the infrastructure or technologies that can support a productive farm, farmers will either struggle with low yields, depend on chemical inputs that further deplete the soil, or rely on outside aid.
This is where Farm from a Box comes in.
Farm from a Box works to bridge the “access” gap by providing a complete, off-grid toolkit for sustainable, tech-powered agriculture. Built from a modified shipping container, each unit contains a complete ecosystem of smart farm technologies to enhance agricultural productivity; from renewable power and micro-drip irrigation to Information and Communications Technology equipment.
Designed as the “Swiss-Army knife” of farming, this mobile infrastructure provides all the tools needed to support a two-acre farm. By empowering farmers to grow and sustain food production at the community level, we build greater resilience to climate shocks, boost livelihoods, and help bridge the access gap by making healthy food locally available.
With its own off-grid power, Farm from a Box can act as its own micro-grid in remote locations; drip irrigation helps save water and stabilize crops through drought conditions while also extending the growing season; internal cold-storage helps keep crops fresher longer, reducing post-harvest loss by 80%; Wi-Fi connectivity improves information access and exchange; and a cloud-based IoT system helps monitor production and efficiencies.
By introducing micro-irrigation, we can extend the growing season and better support a wide variety of crops throughout the year, while lowering the amount the water used by applying it directly to the plant. The off-grid power array and storage provide a reliable energy source to power the pump, move the water through the irrigation lines, cool the internal cold storage area, and support the charging of auxiliary needs.
We have also connected each unit with Wi-Fi capabilities and a complete IoT system to improve operational efficiency, optimize water and energy use, and provide guidance on farm management and market information. Because we have integrated sensors on all of the primary systems, we can monitor and control the performance of the system, and also set alerts for when a component dips below or exceeds certain levels.
Let me give you an example of how this applies in a real-world situation. We recently teamed up with the United Nations World Food Programme Tanzania and WFP’s Innovation Accelerator to support food and nutrition security for refugee and host communities. Our Farm from a Box system will be used to increase the availability of nutritious crops, provide low-cost agricultural commodities and, through increased production, boost the income levels for both refugees and the surrounding host communities.
Because the farm is operating in a remote location in eastern Tanzania, information becomes a vital component to ensuring the system is working as it should be, and the farmers have the data they need to know what is happening and why. Through our cloud-based IoT system, both the community and the WFP has open access to see how much energy the solar panels are producing, how much water is being used, and if the overall system is functioning properly.
Now, technology for the sake of technology isn’t a standalone solution; how it is utilized in overall value creation is where we find the real impact. By marrying technology with small-scale regenerative farming practices, we can improve soil quality, reduce dependence on outside inputs, conserve water, and build up nutrients.
Techniques like composting, crop rotation and diversification, cover cropping, and no-till practices nurture the soil’s fertility and help produce a healthier crop. By shifting our focus from industrialized agriculture to local organic agriculture, we can potentially convert carbon from a greenhouse gas into a food-producing asset.
Farm from a Box is just one of many innovations that are working to empower smallholder farmers with sustainable solutions; there are vertical farm systems, small farm robots that automate field work, drones that use near-infrared and thermal sensors to “see” how plants are doing. Technological innovations like these can help us achieve better health, well-being, and equity throughout our planetary system as a whole.
But we need creative solutions, and sometimes that requires thinking outside of the box. I don’t come from a technological background, nor does my business partner, but we saw a problem and thought, “There must be a better way.” We all have the power to change our world for the better. Food is something that connects us all and has a direct impact on our everyday lives and environment.
When we first set out to start Farm from a Box, our intention was to create a mobile infrastructure that could provide people with the tools they need to grow their own nutritious food. Over time, that idea has grown; we now see Farm from a Box as a tool that could transform local production and nutritional security globally.
Whether it is a local school, community group, or remote village in an underdeveloped country, smallholder farmers are the ecological gatekeepers to building a more sustainable and equitable food supply. Technology has the potential to help solve the intractable problems facing humanity and will continue to play an increasingly vital role in global food security and planetary health. But it will require innovative thinking from all of us to achieve it.
Freight Farms Lands $7.3M As Agriculture Meets Data & Automation
June 6th, 2017
Investors have planted $7.3 million in Freight Farms to help the Boston-based startup bring its micro-farms to more places around the globe—and potentially even beyond.
The investors in the Series B round include return backer Spark Capital, also based in Boston. The news was first reported by the Wall Street Journal on Monday. Freight Farms’ total venture capital haul now exceeds $12 million, according to SEC filings.
The company sells shipping containers filled with hydroponic farming systems that can grow a variety of lettuces, herbs, and other greens. The system is designed to operate with minimal hands-on work by humans. It employs LED lights and automated watering and fertilizing technology. Operators can monitor the farm through a live camera feed, and they can use an app to control the climate within the shipping container and shop for growing supplies. The company has said the system uses less water than traditional farming methods, and because it’s housed inside a shipping container, it doesn’t require pesticides or herbicides.
Freight Farms has deployed more than 100 of these farming systems across the U.S. and in several countries. Customers include urban farmers, traditional farms, produce distributors, and universities.
The startup was formed in 2010 by Brad McNamara and Jon Friedman, who previously worked on rooftop hydroponic gardens.
Freight Farms is trying to take advantage of the growing interest in local food sourcing, as its shipping containers can be set up close to where food gets sold or consumed. It also aims to enable year-round food production in challenging locales—think the snowy mountains of Colorado, or even space. Freight Farms and Clemson University are working on a NASA-funded project exploring ways to grow food in harsh climates and, potentially, deep space.
Freight Farms also fits with trends in agriculture around automation and using digital tools. That’s a key reason why Spark made another investment.
“Modular, Internet-connected, and highly automated commercial farms will play an important role in bringing local and affordable produce to communities all over the world,” Spark’s Todd Dagres and John Melas-Kyriazi wrote in a blog post about the new investment. “Value will accrue to those who own the technology layer of this farming stack (hardware + software) as data and automation become increasingly important drivers of low-cost production.”
Agricultural technology companies are taking various approaches to indoor farming. Like Freight Farms, Atlanta-based PodPonics sells tech-enabled mini-farms inside shipping containers. Businesses such as New York-based BrightFarms and Harrisonburg, VA-based Shenandoah Growers produce food inside greenhouses. And startups like Grove and SproutsIO, two Boston-area firms, sell micro-farming systems to consumers for growing food inside their homes.
An Urban Farm Grows In Brooklyn
Tue Jun 6, 2017 | 8:12am EDT
An Urban Farm Grows In Brooklyn
By Melissa Fares | NEW YORK
Erik Groszyk, 30, used to spend his day as an investment banker working on spreadsheets. Now, he blasts rapper Kendrick Lamar while harvesting crops from his own urban farm out of a shipping container in a Brooklyn parking lot.
The Harvard graduate is one of 10 "entrepreneurial farmers" selected by Square Roots, an indoor urban farming company, to grow kale, mini-head lettuce and other crops locally in the Bedford-Stuyvesant neighborhood of Brooklyn.
For 12 months, farmers each get a 320-square-foot steel shipping container where they control the climate of their own farm. Under pink LED lights, they grow GMO-free greens all year round.
Groszyk, who personally makes all the deliveries to his 45 customers, said he chooses certain crops based on customer feedback and grows new crops based on special requests.
"Literally the first day we were here, they were lowering these shipping containers with a crane off the back of a truck," said Groszyk. "By the next week, we were already planting seeds."
Tobias Peggs launched Square Roots with Kimbal Musk, the brother of Tesla Inc (TSLA.O) Chief Executive Elon Musk, in November, producing roughly 500 pounds of greens every week for hundreds of customers.
"If we can come up with a solution that works for New York, then as the rest of the world increasingly looks like New York, we'll be ready to scale everywhere," said Peggs.
In exchange for providing the farms and the year-long program, which includes support on topics like business development, branding, sales and finance, Square Roots shares 30 percent of the revenue with the farmers. Peggs estimates that farmers take home between $30,000 and $40,000 total by the end of the year.
The farmers cover the operating expenses of their container farm, such as water, electricity and seeds and pay rent, costing them roughly $1,500 per month in total, according to Peggs.
"An alternative path would be doing an MBA in food management, probably costing them tens of thousands if not hundreds of thousands of dollars," Peggs said, adding that he hopes farmers start companies of their own after they graduate from the program.
Groszyk harvests 15 to 20 pounds of produce each week, having been trained in artificial lighting, water chemistry, nutrient balance, business development and sales.
"It's really interesting to find out who's growing your food," said Tieg Zaharia, 25, a software engineer at Kickstarter, while munching on a $5 bag of greens grown and packaged by Groszyk.
"You're not just buying something that's shipped in from hundreds of miles away."
Nabeela Lakhani, 23, said reading "Fast Food Nation: The Dark Side of the All-American Meal" in high school inspired her to change the food system.
Three nights per week, Lakhani assumes the role of resident chef at a market-to-table restaurant in lower Manhattan.
"I walk up to the table and say, 'Hi guys! Sorry to interrupt, but I wanted to introduce myself. I am Chalk Point Kitchen's new urban farmer,' and they're like, 'What?'" said Lakhani, who specializes in Tuscan kale and rainbow chard.
"Then I kind of just go, 'Yeah, you know, we have a shipping container in Brooklyn ... I harvest this stuff and bring it here within 24 hours of you eating it, so it's the freshest salad in New York City.'"
(Reporting by Melissa Fares in New York; Additional reporting by Mike Segar in New York; Editing by Dan Grebler)
5 Things To Know About Urban Organics Aquaponics Farm
5 Things To Know About Urban Organics Aquaponics Farm
Monday, June 5, 2017 by Mecca Bos in Food & Drink
Urban Organics aquaponics farm now has two locations in St. Paul
Many years ago, I stood with Dave Haider in a nearly empty grain silo at the old Hamm’s Brewery staring at a blue pool.
He had big dreams. One day, wife Kristen called him into the room, where she was watching TV.
“Look,” she said, and pointed. On the screen was an aquaponics farm, a closed-loop system for farming fish and produce. The fish enrich the water, the water is filtered through the root systems of the plants, and both are eventually edible for humans.
“You should do that.”
“OK,” said Haider.
And thus began their journey, along with partners Fred Haberman and Chris Ames, to implement Urban Organics aquaponics farm. The Hamm’s Brewery was their first location, and a second is now up and running in the Historic Schmidt Brewery. They’ve come a long way since a single pool in a silo.
Five things to know about the Twin Cities largest aquaponics farm:
1. Urban Organics greens are now available for purchase, including green and red kale, arugula, bok choy, green and red romaine, swiss chard, and green and red leaf lettuces. Get them at Hy Vee supermarkets in Eagan and Savage and at Seward, Wedge, and Lakewinds co-ops.
Want to taste the fish? Get it at Birchwood Cafe. The Fish Guys (local fish wholesaler led in part by Tim McKee) will be distributing Urban Organics fish, so watch for it at stores and restaurants in the coming months (more info on the fish below).
2. The farm was recently featured in The Guardian as a Top 10 innovative “next-gen” urban farm. Urban Organics was noted for using only 2 percent of the water used in conventional agriculture, and for its mission to prove the viability of aquaponics systems overall.
Other eco-friendly perks of the Urban Organics aquaponics system: they do not rely on herbicides, pesticides, or chemical fertilizers, and raising fish indoors takes pressure off oceans and wild-caught species.
More food raised in urban centers means less food traveling in from far-flung places. Urban Organics calls its product “hyper-local.”
3. The numbers: The 87,000 square foot Schmidt farm aims to provide 275,000 pounds of fresh fish and 475,000 pounds of organically grown produce per year.
Currently, the farm is at 30 percent capacity for produce, and they project being at full capacity by fall. Getting their Arctic Char and Atlantic Salmon to a harvestable size of eight to 10 pounds will take another 11 to 20 months.
4. If you happen to find yourself at a HealthPartners hospital, you might wind up eating Urban Organics food from your patient meal tray, cafeteria salad bar, or grab-and-go retail kiosk.
5. Part of the Urban Organics mission statement is to grow fresh food in urban “food deserts,” which would not otherwise have access to locally produced food. And with an indoor system, they can do it year-round, even in the dead of a St. Paul winter.
For more information on Urban Organics: urbanorganics.com
(Toggle around in their website. It’s kinda fun.)
700 Minnehaha Ave. E., St. Paul
543 James Ave. W.
Biosphere's Vertical Gardens Will Provide Produce For Public
Biosphere's Vertical Gardens Will Provide Produce For Public
- By Tom Beal Arizona Daily Star
- Apr 18, 2017
Food crops are coming back to Biosphere 2, but they won’t be planted in the 3 acres under glass at the University of Arizona research facility in Oracle.
A company named Civic Farms plans to grow its leafy greens under artificial lights in one of the cavernous “lungs” that kept the Biosphere’s glass from imploding or exploding when it was all sealed up.
The lungs, which equalized the air pressure in the dome, are no longer needed now that the Biosphere is no longer sealed. The west lung will be transformed into a “vertical farm” that will train LED lights on stacked racks of floating plants whose roots draw water and nutrients from circulating, fortified water.
A variety of leafy greens and herbs such as kale, arugula, lettuce and basil will be packaged and sold to customers in Tucson and Phoenix, said Paul Hardej, CEO and co-founder of Civic Farms.
He also expects to grow high-value crops, such as microgreens, Hardej said.
Hardej said the company plans to complete construction and begin growing by the end of the year.
Civic Farms’ contact with the UA allows for half the 20,000-square-foot space to be devoted to production, with areas given over to research and scientific education.
The UA will lease the space to Civic Farms for a nominal fee of $15,000 a year. In return, the company will invest more than $1 million in the facility and dedicate $250,000 over five years to hire student researchers in conjunction with the UA’s Controlled Environment Agriculture Center.
Details of branding haven’t been worked out, said UA Science Dean Joaquin Ruiz, but don’t be surprised to find Biosphere Basil turning up in your salad soon.
Hardej said the “brands” established by the UA were lures for his company.
“The UA itself has a brand recognition throughout the agricultural industry and specifically the Controlled Environment Agriculture Center. They have a lot of respect worldwide.”
“Also, the Biosphere itself is a great story,” he said.
“The original intent was to develop a self-sustaining, controlled environment where people could live, regardless of outside conditions.
“In a way, this is a fulfillment of the original purpose,” he said.
Hardej said he recognizes the irony of growing food in artificial light at the giant greenhouse. He is convinced, however, that growing plants with artificial lighting can become as economical as growing them in sunlight.
“Decades ago, greenhouses were very innovative. It felt like it allowed the farmer to control the environment. It did not control the light and also the temperature differentials.”
Hardej said indoor growing allows you to control all the variables — the water, the CO2 levels, the nutrients and the light. “Farming is much more productive and much more predictable than in a greenhouse,” he said.
You can’t stack plants on soil, or even in a greenhouse, he said. “A vertical farm can be 20 to 100 times more productive. The overall direction globally is indoors,” he said.
Indoor agriculture is still a sliver of overall crop production, said Gene Giacomelli, director of the UA’s Controlled Environment Agriculture Center (CEAC) and most indoor operations are greenhouses.
“Vertical farms” account for a small portion of that sliver, but are a fast-growing segment for growing high-value crops with a level of control over the environment that can’t be attained elsewhere, he said.
“Theoretically, we should be able to control everything,” he said.
Murat Kacira, a UA professor of agricultural-biosystems engineering, is already working on systems to do that in a lab at the CEAC center on North Campbell Avenue, where he grows leafy greens and herbs under banks of LED lights. He can control the wavelengths of light, temperature, humidity, the mix of oxygen and carbon dioxide and the nutrients available to the plants.
Those variables can be tuned to improve the yield, quality and nutritional value of the plants being grown. He is developing sensor systems that allow the plants to signal their needs.
A lot of questions remain, said Giacomelli. Different plants require different inputs. Young plants have different needs than mature ones.
Air handling is a tricky problem, he said. Air flow differs between the bottom and top racks and at different locations of a given rack of plants.
It will take “more than a couple years” to figure it all out, said Giacomelli.
Kacira said the Civic Farms installation “is a really complementary facility to the research going on under glass.”
He expects the Biosphere to become a “test bed” for more research on the nexus of food, water and energy.
Ruiz said that “nexus” is the direction for research at the Biosphere for the coming decade.
Partnership Brings Fresh, Eco-Friendly Produce to Area Hospitals, Clinics
Partnership Brings Fresh, Eco-Friendly Produce to Area Hospitals, Clinics
Published May 30, 2017 at 7:00 am
Lakeview Hospital Nutrition Services employee Kristal Anderson with a fresh delivery of Urban Organics salad greens to the hospital kitchen. (Submitted photo)
An new partnership between Urban Organics and four HealthPartners hospitals and clinics in the St. Croix Valley has made it simpler for patients and health care staff to be eco-friendly.
Urban Organics is an organic aquaponic farm in St. Paul.
Under the partnership — which Lakeview Health believes to be the first of its kind in Minnesota between a health system and an aquaponic farm — salad greens are provided by Urban Organics, which has converted an old brewery in St. Paul into one of the first USDA-certified organic aquaponic farms in the country. Urban Organics delivers organic salad greens to each of the four participating HealthPartners hospitals or clinics within 24 hours of harvest.
Aquaponics is a farming method where fish and plants help each other grow, with the aim of mimicking what happens organically in nature. Aquaponics uses 2 percent of the water used in conventional farming, and produce can be grown and harvested year-round.
“It’s something that people can trust,” said Urban Organics co-founder Kristen Haider of the farm’s produce. “It’s coming from a reliable source. It’s local, the produce is organic and we’re using a sustainable method of farming. It’s a different way of looking at it.”
The pilot project at Lakeview Hospital (Stillwater), Hudson Hospital & Clinic, Westfields Hospital & Clinic (New Richmond, Wis.) and Stillwater Medical Group has been received well, according to Lakeview.
“Fresh and sustainably grown foods are an important part of our commitment to health,” said Ted Wegleitner, CEO and President of Lakeview Hospital. “We were excited about this opportunity to partner with Urban Organics to provide these delicious, nutritious salad greens in our patient meals and our campus cafeterias. The feedback we’ve heard from patients and employees confirmed that this was a good decision.”
Urban Organics salad greens have been used in patient meals and cafeteria salad bars since December. A trial retail option – Greens To Go – offering patients, employees and visitors the chance to purchase 5 oz take-home containers of the salad blends went live this month after a successful trial in March.
Pentair, Urban Organics Open Aquaponics Farm In Old Schmidt Brewery
Pentair, Urban Organics Open Aquaponics Farm In Old Schmidt Brewery
One of Nancy Espinosa's jobs at Urban Organics is placing plants into their pods to continue growing. About 475,000 pounds of organic greens will be produced.
— Elizabeth Flores, Star Tribune.
By DEE DEPASS , STAR TRIBUNE
June 04, 2017 - 2:00 PM
Urban Organics worker Lee Scoggins flicked a cup of powder into a large blue pool and watched as 50,000 tiny salmon, each the size of a paper clip, darted toward dinner inside the newly converted old Schmidt Brewery plant in St. Paul.
The 8-week-old fish that will grow into 10-pound beauties over the next year were introduced to an enthusiastic crowd Thursday as part of the grand opening of Urban Organics' and Pentair's second indoor fish and produce farm, one of the largest commercial aquaponics facilities in the world.
Waste produced by 150,000 fish will help fertilize produce grown on aqua beds on the other side of the facility. The estimated $12 million project — certified as an organic farm by the U.S. Department of Agriculture — boasts 87,000 square feet and is 10 times larger than Urban Organics' and Pentair's first facility, which opened in the converted Hamm's brewery in St. Paul in 2014.
"It's a very exciting time for us," Dave Haider, who founded Urban Organics with his wife, Kristen, and Fred Haberman and Chris Ames, told the crowd at the opening. "Six years ago, my wife said, 'You know. We should open a [aquaponics] farm. We could do that.' "
The key was an unlikely pairing with Pentair, a $5 billion Wall Street stronghold, that almost didn't happen.
"At first, [Haider] wouldn't return my calls," said Bob Miller, chief financial officer of Pentair's aquatic water system business.
Haider sheepishly smiled. "It's true," he said.
Then Miller emphasized in a voice message that Pentair is a filtration expert that could probably help the tiny Urban Organics company with a host of equipment and engineering solutions. Pentair also wanted to prove fish and produce aquaponics farms are viable commercial concerns that can solve food shortage problems, Miller said.
With an added boost from the city of St. Paul, the partners were on their way to creating their new business.
The partnership works, Miller said, because both entities are committed to finding farming techniques that use less water and energy, and protein that is free of antibiotics and pesticides.
Urban Organics will use Pentair's advanced pumps, filters, aerators, mineralization systems and more at the Schmidt site to raise 275,00 pounds of Atlantic salmon and arctic char fish each year. About 475,000 pounds of organic greens including kale, bok choy and arugula also will be produced. The new operation should be at full capacity next year.
The new facility broadens Urban Organics' product offerings. The existing tiny Hamm's building raises striped bass and tilapia and grows basil, kale, watercress and Swiss chard.
With the two facilities, Urban Organics will serve customers across the Midwest, including the Fish Guys, Hy-Vee, Lunds & Byerlys and Co-Op Partners Warehouse in St. Paul.
"We are very excited about this partnership ... and have heard a lot of great feedback from both our patients and employees," said Ted Wegleitner, president and CEO of HealthPartners' Lakeview Health System in Stillwater.
Tracy Singleton, owner of the 22-year-old Birchwood Cafe, said she was "thrilled" to hear about Urban Organics.
"It's been hard to find fish that fits our parameters for sustainable ingredients" that are free of antibiotic, mercury, PCB and overfishing concerns, she said.
Haider and co-founder Ames said their method uses 2 percent of the water usually consumed by traditional agriculture.
"Our local market will get the benefit of our fish and greens, but there will also be a worldwide benefit as we continue to learn from this model and apply its lessons to other locations in the future," Haider said.
Dee DePass • 612-673-7725
Nabeela Lakhani: I’m Taking Action To Create Solutions
Nabeela Lakhani: I’m Taking Action To Create Solutions
Square Roots, a new urban farming accelerator located in Brooklyn, New York, is producing as much food as a 20-acre farm without using any soil. The-five month-old company puts hydroponic growing systems in old, repurposed shipping containers. Each container is capable of producing roughly two acres of food, without the use of pesticides or GMOs. Each container only uses eight gallons of water per day. That’s less than your morning shower.
Nabeela Lakhani is a food entrepreneur at Square Roots specializing in Tuscan Kale and Rainbow Chard. She was one of 10 farmers chosen out of an application pool of 500 for Square Root’s inaugural launch. Food Tank had a chance to speak with Nabeela about her background, current work, and thoughts on approaching solutions in the food system.
Nabeela with her kale at Square Roots. Credit: Nabeela Lakhani
Food Tank (FT): How did you get involved with Square Roots?
Nabeela Lakhani (NL): I’ve always been interested in food and my passion and my purpose has always been around the food industry and the food system. I went to school for public health and nutrition thinking that was going to be the way I made whatever impact I wanted in the food industry, but then as I was going through school I started to realize nutrition was highly clinical and medical. We were looking at treating diseases with medical and nutrition therapy, diseases that could be prevented if we nourished our populations better. We should have been looking at how our food system was prioritizing certain crops over others and how food is distributed in our country. What would happen if we looked at food before it gets to the body, food before it gets to the community? When I discovered that food production and food distribution was what I wanted to pursue I just kind of started telling everyone in my networks that that was what I was now interested in. I used to just tell people, ‘I want to be a farmer I want to be a farmer!’ I was having a hard time getting my foot in the door in urban agriculture because I had no experience; my experience was all health and nutrition related. But I did have a lot of start-up experience so I was really excited about Square Roots. It put the startup experience that I had with the agriculture experience I wanted.
FT: Can you explain how Square Roots works?
NL: We use a standard shipping container, just a regular truck, and it is repurposed to accommodate a hydroponic system. You have these towers lined up inside and the towers are essentially the farm field where everything grows. You control all the elements that a plant needs to grow and you can optimize those elements for that plant’s growing experience, which is then going to reflect heightened taste, heightened freshness, heightened nutritional content. You can even control the nutrient levels that go into the water. And then you’re also controlling the temperature, the climate, the humidity, the CO2 level; you can literally recreate an environment to grow something. For example, if you visited Italy one summer in 2006 and you the best-tasting basil you’ve ever in your life, you could look up the climate and the weather patterns for that time that you were there and recreate that climate inside this container. Another really cool thing is we have a really low water usage, so we use 70 percent less water than conventional farming. This whole container, if you really pack it in, can grow almost two acres worth of food in just that standard shipping container space. It runs on eight gallons of water a day, which is less than your shower.
FT: Are you the first farmers to grow food in a shipping container?
NL: No, actually the containers we use are bought by manufactured by a company called Freight Farms. Their business is to manufacture these containers and then they sell them to customers like us. They have these containers in multiple countries across the world already.
FT: Who is your customer base?
NL: Right now, our customers are mostly adults, although one of my customers is a bunch of NYU students. One of the channels that a lot of farmers are exploring now is farm to local membership, which is basically a weekly delivery to a local community hub. We found that offices are really good for this, because there’s already a community feeling around them. You’re already in a team and you already know the people, so it’s easier to mobilize people and get bigger hubs out of office spaces. That’s one channel that’s really taking off and we’re delivering to places like Adobe and the New York Times building. It’s picking up pretty fast.
Nabeela surveying a wall of produce. Credit: Nabeela Lakhani.
FT: What are you guys growing right now?
NL: Mostly just leafy greens. With hydroponics it is possible to grow fruits and vegetables and one of our farmers is actually experimenting with carrots and radishes and things like that, but given the way the Square Roots program is set up, which is we get this container for one year and we get to build a business out of it, it makes sense to grow whatever makes the most economic sense. If leafy greens take four weeks to grow and yield really high then I’m going to grow that.
FT: What plans does Square Roots have for the future?
NL: Right now we’re based in New York City, but the goal is to get to 20 cities by 2020. Square Roots’ mission is to create an army of young food entrepreneurs who are equipped with experience using technology and building a viable business model. Before I started at Square Roots I felt like I never knew what kind of step I could take or what kind of impact I could have. Revolutionizing the food industry seems so colossal. But now it’s like, ‘No, I’m actually taking action and I can create my own solutions in the future.’ I now have the experience of building a sustainable business and running a business responsibly and impact fully.
Kids Who Grow Vegetables, Eat Vegetables
Kids who grow vegetables are more likely to want to eat them. A recent report by Cornell University found that salad consumption increased by 400% when kids had been involved in growing the ingredients.
Kids Who Grow Vegetables, Eat Vegetables
May 31, 2017 | Posted by Nathan Littlewood | Uncategorized | 0 comments
Kids who grow vegetables are more likely to want to eat them. A recent report by Cornell University found that salad consumption increased by 400% when kids had been involved in growing the ingredients. But here’s the challenge; who has the time to go shopping for pots, soil, gloves, buckets, seeds and a watering can only to have the kids lose interest a week later and have the plants die. Not to mention the inevitable mess involved. No thanks!
Urban Leaf may have just the answer you need. The World’s Smallest Garden turns a bottle into a self-watering garden in seconds. The device allows plants to water themselves for up to a month at a time using the water from the bottle, and when the water level gets low — top up is easy.
The product relies on capillary action to lift water up to the seed. As the seedling sprouts it sends roots down into the bottle. The nice thing about growing in a bottle is that kids can observe the entire process — roots and all! One of the many benefits of growing your own food indoors is that you know exactly where it came from and how it was produced — with no nasty pesticides or sprays.
The process of decorating the bottle can even be made into a cool craft project. We’ve seen users decorating their bottles with paint, ribbons, buttons and much more. If that sounds a bit much, there’s a bunch of people on Etsy who sell decorated bottles that are ready to go!
So while the kids are busy learning about recycling, repurposing, biology, plants, nutrition and health all mom and dad have to worry about is ensuring there’s an adequate supply of empty bottles around the house. How hard can that be?
Urban Leaf is currently launching the World’s Smallest Garden on a crowd funding site called Kickstarter. By making a pledge toward the campaign you’d be helping get the project off the ground.
About Nathan Littlewood
Nate Littlewood is the Co-Founder and CEO of Urban Leaf
Indoor Farms of America Sales Growth Escalates
Indoor Farms of America Sales Growth Escalates
By News Release May 24, 2017 | 8:24 am EDT
Indoor Farms of America is pleased to announce that sales through the first four months of 2017 have exceeded the entire year of 2016, when the company first sold its patented vertical aeroponic indoor farm equipment.
According to company CEO David Martin, "During 2016, our first year selling our equipment, we enjoyed what we consider a very solid year for launching our unique vertical farming equipment, and 2017 has already eclipsed that in dollar volume and diversity of farms being sold, built and delivered."
Indoor Farms of America two story display at 2017 Indoor AgCon Las Vegas
GrowTruck Container Farm Display at 2017 Indoor AgCon Las Vegas
The company sold numerous smaller farm packages and container farms during 2016, many of which were considered "pilot farms," to allow potentially large warehouse farm operators to get a feel for this amazing vertical equipment, prior to making larger commitments.
"We knew when we introduced the equipment throughout the previous year, it would somewhat be a year of "tire kickers," and we were overwhelmed at the positive response to our total farm solutions. Those tire kickers are now converting into sold larger farms, as we continue to see positive crop growing results by folks across the U.S. and in key international markets."
Indoor Farms of America spent several years designing and developing its patented ultra high yield vertical aeroponic equipment. The firm manufactures a robust line of aeroponic products, including the world's most productive containerized farms, for deployment in any area of the world that has real need for such a unique small farm platform that produces commercial quantities of fresh produce in an manner superior to any other container farm manufacturer.
Other "turn-key" complete farm packages were specifically developed for fully scalable indoor farm applications to drive down initial capital costs as well as the ongoing operational costs. This focus combines to provide the operator with the single most cost-effective indoor agriculture equipment available in the world.
Ron Evans, company President, stated it this way: "We received numerous affirmations throughout 2016 from third party growers using our farm technology that it delivers on what we promise in overall farm performance. We are committed to the concept that if you are going to own and operate an indoor farm, it should provide you a very sound financial return."
"So many farm platforms that Ron and I analyzed in the early R&D phase back in 2013 and 2014, we believed were doomed to financial failure due to poor design with off the shelf 30 year old growing technology that was not innovative. We recognized that if those marginally profitable operators made errors in execution, they would not survive. It was our mandate internally to develop a complete farming solution that would transcend anything on the market, and we achieved that", stated Martin.
New sales by the company for 2017 to date include numerous locations around the U.S., as well as other countries, as the company continues on a path of rolling out the products in key markets that will benefit dramatically from truly locally grown fresh produce.
"We have sold our first farm for Alaska, destined for Juneau in the next couple months. As well, we have sold our first farm for the GCC region, destined for Dubai. This farm will change the landscape for food production in the Middle East." stated Martin. "Further developments include complete farms sold for multiple regions of Canada, including Alberta, Manitoba and Ontario provinces, and that region is about to explode with growth in the use of our farm solution."
Martin added, "We have sold our first large scale farm for Africa, destined for the country of Botswana. We have had a farm in operation in Johannesburg for many months, and our distributor there reports how amazed potential customers are with the robust growing they experience with our vertical aeroponics platform."
The company has spent thousands of hours developing new crops beyond leafy greens. Evans stated: "Leafy greens were the easy part, and ours does that better than anything else. We have proven out growing of certain varieties of cherry tomatoes, strawberries, peppers, peas and beans for proteins, and we are now working on specialty root crops like heirloom carrots and baby potatoes. We know a well-rounded garden approach is what many folks want to see, not just leafy greens, and we are rapidly developing those for commercial scale."
Indoor Farms of America has a showroom with demonstration farms operating in Las Vegas, Nevada and in multiple locations in Canada, and in South Africa, where their patented vertical aeroponic equipment is on display and receiving amazing reviews by industry leaders.
Des Moines Power Brokers Want to Build Massive Greenhouses Downtown
Des Moines Power Brokers Want to Build Massive Greenhouses Downtown
Joel Aschbrenner , jaschbrenn@dmreg.com
Published 5:40 p.m. CT May 25, 2017 | Updated 10:59 a.m. CT May 26, 2017
A group of business leaders want to build a string of greenhouses on the south side of downtown. They call it the Des Moines Agricultural Corridor.
(Photo: Special to The Register)
New York architect Mario Gandelsonas helped reshape Des Moines when he laid out his vision for the city nearly 30 years ago. That vision ultimately led to the development of the Western Gateway, construction of the Principal Riverwalk and resurrection of the East Village.
Now, Gandelsonas is back in town promoting his latest idea, one he says is equally ambitious.
A group led by Gandelsonas and local venture capitalist Jim Cownie wants to build a string of massive greenhouses and vertical farms along the railroad tracks on the south side of downtown. They’re calling it the Des Moines Agricultural Corridor. If fully realized, the project would span the length of downtown.
“The dream is all the way from Meredith Corp. to the state Capitol,” Cownie said.
Cownie hopes to get buy-in from local players like Hy-Vee, DuPont Pioneer, MidAmerican Energy and Iowa State University. The urban farms could feed the desire for locally grown food, provide produce for area farmers markets, grocery stores and restaurants, and offer research space for Iowa State students and agriculture companies, he said.
Gandelsonas sees the project as a cultural symbol. It would provide the urban core with a link to the state’s farming roots and showcase Des Moines as a hub for innovative agriculture, he said.
“The idea is not just to build a greenhouse,” he said. “The idea goes deeper than that. It relates to identity, to health, to education. So it is really a grand idea.”
Far-fetched? Maybe.
At this point, the Des Moines Agricultural Corridor is little more than an idea. No land has been acquired. No money has been raised. And it’s unclear who would own and operate the indoor farms.
Cownie thinks it could take 20 years and tens of millions of dollars to complete.
But after working behind the scenes for a few years, Cownie and Gandelsonas are beginning their campaign to drum up support.
They've pitched it to local companies. Officials from MidAmerican and Hy-Vee told The Register they're listening but they've made no commitments.
Cownie and Gandelsonas held meetings Wednesday and Thursday with City Council members and other power brokers.
Buy Photo
Mario Gandelsonas shows plans for the Des Moines Agricultural Corridor, a string of massive greenhouses on the south side of downtown Des Moines. Gandelsonas, a New York architect, and a group of local business leaders are trying to drum up support for the idea. (Photo: Joel Aschbrenner/The Register)
In Cownie’s penthouse office overlooking the East Village on Wednesday, Gandelsonas explained to Councilwoman Christine Hensley how the greenhouses, lit with bright colors, would create a “river of light” visible to people flying into the city.
Hensley, Des Moines’ longest serving city council member, whose ward includes downtown, said she would be apt to support the project if the greenhouses operated as a for-profit entity that pays property taxes.
“The city has demonstrated that if we get the right people behind projects such as this, there is no question we will get it done,” she said.
The goal is to start with one half-acre greenhouse. Those involved said they don't know the exact cost. Ballpark: $5 million.
Cownie thinks the best location is a piece of city-owned land near 12th and Mulberry streets, on the southwest side of downtown.
A group of local business leaders is promoting the idea of building a string of massive greenhouses along they railroad tracks on the south side of downtown Des Moines. The idea, called the Des Moines Agricultural Corridor, is the brainchild of Mario Gandelsonas, the New York architect who created the vision for several Des Moines redevelopment projects including the Western Gateway and the Principal Riverwalk. (Photo: Special to The Register)
The first step, Cownie said, would be to come to an understanding with city leaders. He wants the city to challenge him to raise the money for the first greenhouse, and if he does the city, in return, would offer the land for free.
“We need to demonstrate to the city that it would be good public policy to make available the site to start this process,” he said.
If the first greenhouse is a successful model, it could be replicated down the railroad corridor on undeveloped sites.
Cownie hesitated to put a timeframe on the project — he’s been burned by such promises in the past — but others involved in the proposal said they want to harvest crops within five years.
More: 13 of downtown Des Moines' craziest ideas – good and bad
The project will depend on acquiring land. Most of the property along the rail line is privately owned.
That includes land where Cownie has a stake. He recently partnered with the city to offer five square blocks on the east bank of the Des Moines River as a site for a new federal courthouse. It is one of four proposed courthouse locations and includes several blocks for private development.
Gandelsonas said the greenhouses would make nearby properties more valuable by providing a buffer between the rail line. His plan also calls for a pedestrian corridor along the greenhouses with a recreational trail and landscaping.
The idea is not entirely new. Gandelsonas pitched a farming corridor nearly 10 years ago during a city planning process. The original idea was an avenue of outdoor crops stretching across downtown to showcase Iowa agriculture.
Mario Gandelsonas in Des Moines in 1989. A New York architect, Gandelsonas helped create a vision for the city that led to the create of the Western Gateway and the Principal Riverwalk. (Photo: Register file photo)
Among movers and shakers in Des Moines, Gandelsonas has a fervent following. The Argentina-born, Paris-educated architect came to city in the late 1980s and helped craft the Des Moines Vision Plan, a blueprint for revitalizing the city.
Over the years, he has proposed some of the city’s most audacious projects.
One idea called for massive apartment complexes built in the shape of letters on the north side of downtown. He also dreamed of carving back the Des Moines River banks so City Hall and the World Food Prize would stick out on peninsulas.
But Gandelsonas is also credited with some of the city's biggest successes. He had the vision to demolish roughly 10 blocks of aging buildings and car dealerships on the west side of downtown to make room for a park. The project drew scoffs from skeptics and backlash from preservation advocates, but the development of the Western Gateway ultimately led to the construction of the Pappajohn Sculpture Park and hundreds of millions of dollars of office development from Nationwide, Wellmark and Kum & Go.
Asked if the Des Moines Agricultural Corridor is even more ambitious, Gandelsonas said: “It feels as impossible as the idea for Gateway Park... It is quite an undertaking, but I view it as important to accomplish this.”
Why now?
Jim Cownie (Photo: Register file photo)
Cownie, 72, and Gandelsonas, 78, say they’re getting older so it’s now or never.
And downtown has the momentum to support it, Gandelsonas said.
It also helps that a compatible idea is gaining steam. Iowa State officials and local business leaders are working on a proposal to create a year-round, indoor market inside Kaleidoscope at the Hub, an aging downtown shopping center.
Iowa State’s Courtney Long, who is overseeing the idea, said the greenhouses could provide produce for the indoor market and collaborate in other ways. Long has been meeting with the greenhouse backers for about a year to discuss the project.
“I think it’s interesting and unique," she said. "There is nothing like it."
To lead the greenhouse effort, Cownie is considering Bill Menner, a consultant who recently served as a state director for the U.S. Department of Agriculture.
A group of local business leaders is promoting the idea of building a string of massive greenhouses along they railroad tracks on the south side of downtown Des Moines. The idea, called the Des Moines Agricultural Corridor, is the brainchild of Mario Gandelsonas, the New York architect who created the vision for several Des Moines redevelopment projects including the Western Gateway and the Principal Riverwalk. (Photo: Special to The Register)
Menner said there could be USDA grants or government loans available for the Des Moines Agricultural Corridor.
And there are good models to learn from, he said. A group in Cleveland recently opened a 3.25-acre urban greenhouse, though it sits in a more industrial area, not in the heart of downtown.
Menner sees the greenhouse development as a way to bridge the urban-rural divide that has grown amid water lawsuits, bitter politics and rural population loss.
“By placing urban agriculture in the center of a metropolitan area, you’re actually building a bridge to the producers and the folks who make a living (in agriculture) while at the same time creating access to locally grown foods,” he said.
Fresh Veggies Grown Close to Home, Without Pesticides — And Without Dirt
Fresh Veggies Grown Close to Home, Without Pesticides — And Without Dirt
Civic Farms touts having “pioneered the vertical farming industry.” The company says its proprietary growing systems, licensed patented technologies, and optimized processes for cultivation and harvesting processes maximize the efficiency and efficacy of growing indoors.
TUCSON (CN) – An ambitious project of emerging agricultural technologies that produce food without soil is taking shape at Biosphere 2, the University of Arizona’s research complex north of Tucson.
Civic Farms, an Austin-based company, this summer will start building a vertical farm in one of two 20,000-square-foot domes – or “lungs” – that regulated pressure inside a sealed glass structure during experiments to study survivability in the 1990s.
The company will invest $1 million to renovate the Biosphere’s west lung, unused for years, and outfit the space with stacked layers to grow soil-free plants in nutrient-laden circulating water under artificial lights.
At full capacity, the vertical farm will produce 225,000 to 300,000 lbs. a year of leafy greens and herbs such as lettuce, kale, arugula and basil, said Paul Hardej, CEO and co-founder of Civic Farms.
“Biosphere itself is a fantastic facility and food production is a big part of what it was originally intended to do,” he said.
As the world population continues to rise, particularly in cities, along with consumer interest in the origins of food, vertical farming is gaining traction as a commercially viable way to increase crop production in a fully controlled indoor environment.
“People want know what they eat and what’s in their food and how healthy and good it is for them,” Hardej said. “Growing food in city centers or close to city centers where people live makes perfect sense.”
Under an agreement with the university, Civic Farms will grow crops in half the space it will lease for $15,000 annually. Research and scientific education will comprise the other half and the company will contribute $250,000 over five years for those efforts.
“We envision that a portion of the lung will be open and accessible to the public so people can come in see how and what it is to have a vertical farm,” said John Adams, the Biosphere’s deputy director.
Civic Farms touts having “pioneered the vertical farming industry.” The company says its proprietary growing systems, licensed patented technologies, and optimized processes for cultivation and harvesting processes maximize the efficiency and efficacy of growing indoors.
The Biosphere already draws nearly 100,000 annual visitors to expansive grounds originally intended to showcase a self-sustaining replica of Earth, or Biosphere 1.
Set on a 40-acre campus against the backdrop of the rugged Santa Catalina Mountains, the Biosphere’s 91-foot steel-glass structure serves as a global ecology laboratory enclosing an ocean, mangrove swamp, rain forest, savanna and coastal desert.
In the early 1990s, a crew of scientists was locked inside the sealed structure in privately funded scientific experiments designed to explore survivability with an eye toward space colonization. Problems with the experiments and management disputes eventually halted the highly public venture.
The University of Arizona took over the property, about 30 miles north of Tucson in the town of Oracle, in 2011.
The Biosphere’s Adams views the planned vertical farm as a good fit for research initiatives.
“For the next 10 years, Biosphere’s focus is very much on food, energy, water – and the nexus,” he said.
Civic Farms’ Hardej said the university’s myriad resources were strong incentives for his company’s new enterprise in Arizona. A big plus are the concepts being developed at the university’s Controlled Environment Agriculture Center on North Campbell Avenue, where scientist Murat Kacira grows leafy crops indoors under LED lights.
“There’s so much interest in this technology platform because it provides the capability to grow food with consistency,” Kacira, a professor of agricultural-biosystems engineering, said of vertical farm systems.
Inside the lab where lettuce and basil grow in hydroponic beds under the glow of blue and red LED lights, Kacira and his students monitor the conditions in which seedlings mature.
“The environment is fully controlled in terms of providing temperatures needed, or humidity needed, carbon dioxide or the light intensity or the quality needed for the plant production,” Kacira said.
Not being at the mercy of Mother Nature makes vertical farms more productive than conventional farms, as well as more efficient at using natural resources such as water, he said. “You’re circulating it inside the environment, so the efficiency is much higher.”
Still, Kacira said, the technology is energy-intensive, given the use of artificial lights and the need to condition the environment. And although large-scale commercial operations are relatively rare, he said, advances in scientific research and the high-tech industry are making it a feasible platform to help supplement food production in cities.
“Our food transportation is coming from long distances, and by the time it gets to the consumer, especially leafy crops, the freshness may not be there,” Kacira said.
Vertical farms are a relatively new concept that hold great potential, Hardej said it. With a projected global population of 9.5 billion, mostly urban, by 2050, he views vertical farms as an increasingly important part of the world’s food system.
His own vertical farm aims to provide the Tucson and Phoenix markets with high-quality produce grown sustainably and without pesticides, Hardej said.
In time, he plans to incorporate more energy-efficient solutions into his operation.
“For commercial scale, those technologies still need to be perfected,” he said.
His company plans to begin growing the leafy greens by year’s end.
Seeds Of Change: Mini Gardens Help Drive The Growth Of Food At Home
Seeds Of Change: Mini Gardens Help Drive The Growth Of Food At Home
May 31, 2017 11:59 AM ET
KRISTEN HARTKE
Seedsheets are made of weed-blocking fabric, a thick layer of soil and dissolvable pods full of organic seeds.
Courtesy of Seedsheet
The short, but intense, growing season in Vermont might be a drawback for some, but for native son Cam MacKugler, it has turned out to be the key to developing his container garden kit startup, Seedsheet.
"Up here in Vermont," says MacKugler, "we don't have a lot of time to grow our food, so the goal is to get as much as you can as quickly as possible."
A house-sitting stint on a co-worker's farm in 2012 is what inspired MacKugler, an architect working in sustainable design in Middlebury, a small town in western Vermont. "I was paid with access to the backyard garden," he says, "and I was looking at the companion planting [an agricultural system for maximizing space and crop productivity] and how well it was designed — the arrangement of tomatoes and basil and zucchini. The idea for Seedsheet almost immediately came to me."
Sketching out the concept with crayons that were handy in the farmhouse, MacKugler was intrigued by the idea of foolproof gardening that would appeal to people living in cities with little or no outdoor space, but who still wanted the experience of harvesting their own crops.
When MacKugler first came up with the concept of Seedsheet, he sketched out the concept with crayons that were handy in the farmhouse where he was inspired by the garden.
Courtesy of Seedsheet
As MacKugler says, "We're kind of the Blue Apron of agriculture. It's not meal delivery, it's farm delivery."
A 2017 gardening industry survey produced by GardenResearch.com shows that 1 in 3 U.S. households now produces something edible at home, whether it's a pot of herbs on the windowsill or a raised-bed kitchen garden. In fact, consumer interest in growing food has translated to a $1 billion increase in sales in just five years, surpassing sales for flower gardening.
It's that all-important 18- to 34-year-old demographic — millennials — who are driving much of that growth, says Michelle Simakis, editor of Garden Center Magazine.
"Some millennials did not grow up gardening with their parents, so they aren't necessarily gardening as a hobby or to beautify their homes like previous generations did," says Simakis. "They are planting vegetables and fruit because they want to know where their food comes from and are interested in cooking with produce that's better than what they can find in stores."
As a millennial himself, MacKugler's instinct for the Seedsheet concept is all about making that "Green Acres" dream come true, but within the confines of modern urban living. His instincts are proving correct: 100 percent of Seedsheet customers live in cities, from Washington, D.C., to San Francisco.
"Most people here in Vermont think we're crazy, but that's because they've been raised as gardeners and don't see the need for this kind of product," he says.
His original concept involved spacing different types of seeds within two layers of dissolvable film, which were placed on top of soil and then watered. MacKugler had it tested by friends and family, who liked the basic idea — except for the weeds that sprouted alongside the seedlings, making it difficult to know what needed to be plucked. A new design using a 12-inch circle of recyclable weed-blocking fabric dotted with four or eight dissolvable pods filled with organic seeds and a thin layer of soil solved the weed problem.
"Companies in the lawn and garden industry are aware they need to provide products that guarantee ease and success for first-time gardeners," says Paul Cohen, research director of gardenresearch.com. Noting that he'd seen MacKugler demonstrating his product on a recent episode of the budding-entrepreneur reality TV show Shark Tank, Cohen says, "I expect to see a lot more of these types of products in the future."
MacKugler is particularly mindful of making first-time gardeners feel successful. "Our main goal is to choose varieties that will grow really quickly. We're figuring out which plants can grow together and reach maturity around the same time so people can coordinate cooking meals around the harvest."
MacKugler and his team focus on fast-growing varietals like Glacier tomatoes, while Ruby Streaks mustard greens and Valentine's Day radishes can be ready to eat in about a month.
Seedsheets are recipe-focused. For example, the one for hot sauce includes seeds for cayenne peppers, red carrots, Napoli carrot and purple bunching onions.
Courtesy of Seedsheet
"You can grow a lot of food in a small amount of space," asserts MacKugler. "People will say, 'You can't grow tomatoes in a bucket,' but it's actually very easy."
Indeed, besides MacKugler's kits, Simakis notes there are already a variety of other options popping up in the small garden marketplace. Both IKEA and Miracle-Gro offer countertop units, while would-be gardeners with a little more space can opt for LED-powered, indoor hydroponic growing kits. But she also sees that the millennial interest in growing food may be tied to loftier goals.
"Making gardening easy is important, but I think more companies are starting to promote the importance of gardening to help the environment, and generally speaking, the millennial generation is drawn to causes," she says.
For MacKugler, his own interest in sustainable design and supporting the local community means sourcing organic seeds and relying on the expertise of an important segment of the nearby population: farmers.
Because Vermont's farmers are typically out of work during the winter and early spring until planting season starts, they are becoming the biggest asset for his young company, where everything from custom machinery to seed assembly procedures needs to be built from the ground up. And with up to 600 kits being made per hour, MacKugler says, "We're selling more kits now than we actually have people in our town."
Curating seeds specifically for recipes has also been an important focus for MacKugler, highlighting another millennial trend: home cooking. A recent survey by online grocer Peapod shows that millennials are now twice as likely to cook at home than baby boomers, but they are more in need of inspiration than older, more experienced cooks. The "Hot Sauce Seedsheet" is one recipe-based kit designed to feed that need, with four seed varieties that grow together in a standard 12-inch pot: the Ring-O-Fire Cayenne Pepper, Dragon Red Carrot, Napoli Carrot and Purple Bunching Onions. The kit comes with recipes for spicy carrot juice and, of course, hot sauce.
"Our goal is to cultivate an understanding of how gardening works," says MacKugler. "Everyone should be able to call themselves a gardener, no matter where they live."
AeroFarms Raises $34m of $40m Series D from International Investors for Overseas Expansion
AeroFarms Raises $34m of $40m Series D from International Investors for Overseas Expansion
MAY 30, 2017 LOUISA BURWOOD-TAYLOR
US indoor agriculture group AeroFarms has raised over $34 million, according to a Securities & Exchange Commission Filing. The funding is the first close of a targeted $40 million Series D round.
AeroFarms grows leafy greens using aeroponics –- growing them in a misting environment without soil –- LED lights, and growth algorithms.
The round takes AeroFarms’ total fundraising efforts to over $130 million since 2014, according to AgFunder data, including a $40 million debt facility from Goldman Sachs and Prudential.
AeroFarms attracted new, international investors in this latest round, including Meraas, the investment vehicle of Sheikh Mohammed bin Rashid, vice president of the United Arab Emirates and the ruler of Dubai.
The round marks the first investment for ADM Capital’s new growth stage agriculture-focused Cibus Fund, and global asset management firm Alliance Bernstein also invested. Existing investors Wheatsheaf Investments from the UK and GSR Ventures from China also joined the round.
The filing also revealed that AeroFarms had renamed its holding company to Dream Holdings, as part of its move from an LLC to a C-Corp, referencing its new retail brand Dream Greens. The Dream Greens brand hit the shelves of ShopRite, Whole Foods, FreshDirect, and Newark chain Seabras in February. Before that, the business was selling its greens into food service under the AeroFarms brand.
AeroFarms’ global list of investors is representative of its plans to expand globally, David Rosenberg, CEO, told AgFunderNews.
“We want to expand domestically and overseas, and we are excited about the potential for Meraas to help us expand into that region,” he said.
AeroFarms is not the only group to consider building indoor farms in the Middle East; Pegasus Agriculture Group, is a hydroponics-based indoor ag company that is based in Abu Dhabi, with facilities across the Middle East and North Africa. Egyptian Hydrofarms is another local example, and Indoor Farms of America recently made its first farm sale in the region.
AeroFarms also wants to add to its 120-strong team of plant biologists, pathologists, microbiologists, mechanical engineers, system engineers, data scientists and more. In particular, the company wants to add team members to its research & development department, with a view to improving the quality and operating costs of the business, according to Rosenberg. “This is where the data science and software platforms we’re using can really pull the business together.”
AeroFarms just completed construction of its ninth indoor farm, with four in New Jersey including its state-of-the-art 69,000 square foot flagship production facility in Newark. It also has plans to build in the Northeast of the US.
For more about AeroFarms, read our earlier interview with CEO David Rosenberg here.
Cloud Controlled Mini-Farms | AUDIO Interview - Smallhold
Cloud Controlled Mini-Farms | AUDIO Interview - Smallhold
31 May 2017
Very soon, grocery stores will be cloud-controlled mini-farms with shelves of growing produce -- according to the co-founders of the Brooklyn startup Smallhold. Hear how their ideas for vertical farming could impact your home, your supermarket and even outer space.
Click Above for Audio
We farm for you by growing produce 3/4 of the way and then deliver it to miniature vertical farm units (the size of shelving units) at your place of business to be harvested onsite as fresh, local food.
Smallhold gives you a networked farm, complete with sensors, climate control mechanisms, and hydroponics. Our horticulturalists run the farm from afar, growing for you right up until you pick and serve your produce.
From Slaughterhouse To Vertical Farm: The Plant Is Innovating In Sustainability And The Circular Economy
From Slaughterhouse To Vertical Farm: The Plant Is Innovating In Sustainability And The Circular Economy
May 30, 2017 Chuck Sudo, Bisnow, Chicago
In 1906, Upton Sinclair’s “The Jungle” depicted the harsh conditions workers toiled under inside the slaughterhouses of the Union Stock Yard and Packingtown. A century later, this area that gave Chicago its brawny identity as “hog butcher for the world” is now home to several new food businesses focusing on sustainability, and The Plant in Back of the Yards is its epicenter.
Chuck Sudo/Bisnow - The Plant, a vertical farm in Back of the Yards, was once a slaughterhouse.
This 94K SF former slaughterhouse was abandoned and slated for demolition when John Edel — through his company Bubbly Dynamics — bought it in 2010 and slowly repurposed the building into a vertical farm and food production business committed to a "circular economy," a closed loop of recycling and material reuse. Today, the Plant is home to several businesses where the waste stream from one business is repurposed for use by another business elsewhere in the building.
Chuck Sudo/Bisnow
Whiner Beer Co. brews its beer at The Plant and opened a taproom whose bar, tables and chairs were made from reclaimed wood.
The Plant’s tenants are a who’s who of local food producers. Pleasant House Bakery is a popular company that bakes breads, desserts and Yorkshire-style meat pies that are sold wholesale at farmers markets and at Pleasant House’s Pilsen pub. Arize Kombucha distributes nearly 500 gallons of fermented probiotic tea monthly to area grocery stores. Four Letter Word Coffee, a boutique coffee roaster, has a roastery on the second floor. Whiner Beer Co. specializes in Belgian-style ales and operates a taproom inside the Plant. Justice Ice makes crystal-clear ice for use by Chicago’s best bars and restaurants for their cocktails. The Plant also has an outdoor farm, an indoor aquaponic farm that grows an average of five pounds of greens a week, an indoor tilapia farm and hatchery, a mushroom farm capable of growing 500 pounds of oyster mushrooms a month, and an apiary for making honey.
Chuck Sudo/Bisnow
The Plant has an outdoor farm and an indoor aquaponics farm on the basement level.
Chuck Sudo/Bisnow
With all of that happening, waste is bound to pile up. And the Plant repurposes over 90% of the waste byproducts created by its tenants. Waste from the fish farm and carbon dioxide from kombucha production is used to fertilize the greens in the aquaponics farm, which in turn filters the water that goes back to the tilapia farm. Spent grain from the brewery is used to feed the fish and for Pleasant House’s baking purposes. The Plant’s tenants even repurpose as many building materials as possible. The bar, tables and seating inside Whiner Beer Co.’s taproom was made from reclaimed wood. Pleasant House uses scrap wood to fire its ovens. Sections of the former slaughterhouse's hanging rooms (where beef and pork were processed assembly line-style and aged) are now bathrooms that comply with the Affordable Care, and other sections are being rebuilt into an information center that will open in the fall.
Chuck Sudo/Bisnow
The Plant is in the process of installing a digestible aerator that will produce methane and fertilizer for The Plant's internal uses and outside uses.
The linchpin in the Plant's circular economic model is a 100-foot-long anaerobic digester. This machine is capable of breaking down biodegradable material without oxygen to create methane gas to power the Plant's electrical generation systems, algae and duckweed to feed the tilapia, produce enough process heat for use by the brewery, coffee roaster and baker, and make fertilizer for the outdoor farms. The digester is capable of producing 2.2 million BTUs of biogas. On a smaller level, the Plant is also experimenting with making biobriquettes, a hockey puck-sized brick of biomass from spent grain and coffee chaff, that can be used as fuel in the bakery's ovens instead of wood.
The Plant's circular economy has the possibility of being adapted on a larger scale. A French food engineer and Brazilian urban engineer spent their internships at the Plant analyzing material flows in order to create methodologies to determine if the Plant's closed loop system can be used for developing more efficient urban ecosystems and sustainable cities.
Related Topics: The Plant, Bubbly Dynamics, John Edel, union stock yard, packingtown, Chicago stockyards, Chicago sustainability, Chicago adaptable reuse
AeroFarms To Open World’s Largest Indoor Farm In Camden
AeroFarms To Open World’s Largest Indoor Farm In Camden
By Gillian Blair - May 30, 2017
Credit: AeroFarms
AeroFarms will soon surpass itself as the world’s largest indoor vertical farm with a second and larger New Jersey location in Camden. Set to be operational by 2018, Farm No. 10 will be 78,000 square feet on the 1500 block of Broadway. They are still working on the design of the facility and will need to gain local zoning approvals, but the biggest victory was already won when AeroFarms LLC was awarded an $11.14 million grant in tax incentives by the New Jersey Economic Development Authority.
Farm No. 9 in Newark, New Jersey, is currently the world’s largest indoor vertical farm based on annual growing capacity and where, in a converted steel mill, they harvest up to 2 million pounds a year. AeroFarms is able to germinate seeds in 12 to 48 hours–a process that typically takes 8 to 10 days–and focuses on growing leafy greens like baby kale and arugula and packaging under the name “Dream Greens” for distribution locally in North Jersey and Manhattan. Farm No. 10 in Camden will supply South Jersey and Philadelphia.
The greens are grown “aeroponically,” meaning the roots grow downward, dangle in the air, and are misted with water and minerals. And the process dispenses with premium elements like land and water: “We can grow on one acre what would normally take 130 acres on a field farm. And we use 75 percent less water [than hydroponics],” said Co-founder and CEO David Rosenberg.
AeroFarms has come far since Farm No. 1 in a converted kayak shop in Ithaca, New York, where Ed Harwood, an associate professor in the Cornell University School of Agriculture, became interested in growing things without the elements that grow things: soil, sunlight, a lot of water. Now Co-founder and Chief Scientific Officer, his biggest breakthrough was developing the root mister that doesn’t clog. Also developed for this practice of vertical farming is a cloth made of recycled soda bottles on which the seeds germinate and through which the roots grow downward.
Even the lighting is specially calibrated and everything is monitored electronically. AeroFarms recently won a “vision” award at the Global Food Innovation Summit in Milan which was an especially exciting honor as it recognizes “the coolest vision of how the world should work,” said Mr. Rosenberg.
The tax incentives enabling AeroFarms to open their second facility in Camden are part of the Grow New Jersey Assistance Program Grants which incentivize businesses to relocate or start-up in economically challenged areas, infusing the local economy, workforce, and property with capital, opportunities, and improvements.
Have something to add to this story? Email tips@jerseydigs.com. Stay up-to-date by following Jersey Digs on Twitter and Instagram, and liking us on Facebook.
La Bajada Urban Youth Farm Grows Good In West Dallas
La Bajada Urban Youth Farm Grows Good In West Dallas
POSTED 5:39 PM, MAY 21, 2017, BY TIM ROBERTS
DALLAS — Nothing like a Sunday afternoon brunch, with a great purpose. The La Bajada Urban Youth Farm hosted its first ever “Farm to Community Brunch” with local chefs providing the meal and all the proceeds going to help La Bajada, a community garden in West Dallas.
“These youth interns get paid to come work on this farm and grow food and then we share the food with the community,” said Elizabeth Dry, the executive director of Promise of Peace Gardens who works with the La Bajada Urban Youth Farm.
Yeah, it gives them a hands on, outdoors education they wouldn’t otherwise get.
“Coming here I’m not really used to being outdoors with the nature so learning how to plant and grow different seeds and getting my hands dirty was new to me,” said Grace Zamora, one of the students. “So it was difficult but I’m having a lot of fun doing it.”
And for these kids there’s an even bigger purpose than learning how to farm and making a little extra cash.
“I see all of us as great leaders and it’s up to us to change how people see West Dallas,” another student, Jave Garcia, said. “It isn’t a place of crime, it isn’t a place of violence, it’s a place where normal people live and have great dreams and they try to aspire to their dreams and make them come true.”
Just goes to show there’s a lot more growing in this garden in the middle of the city than just plants.