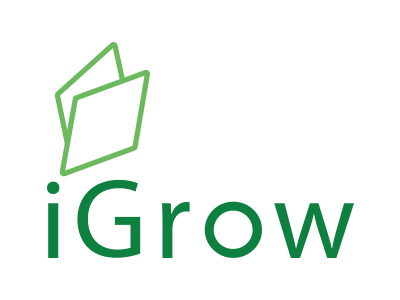
Welcome to iGrow News, Your Source for the World of Indoor Vertical Farming
Urban Crop Solutions Was Awarded The Public Choice Award on The European Finals of The FoodNexus Challenge
Urban Crop Solutions Was Awarded The Public Choice Award on The European Finals of The FoodNexus Challenge
Urban Crop Solutions was awarded the Public Choice Award on the European finals of the FoodNexus Challenge on Wednesday evening December 13th. Fifteen companies from 8 different EU countries were competing during a three-day event in Wageningen (NL) for the European FoodNexus Challenge Award. The expert audience consisting of academic, corporate and venture capital people selected Urban Crop Solutions during a live closing event.
FoodNexus is a European consortium of international food companies and leading knowledge institutions that strives to create a robust and sustainable European Food System.
Fifteen finalists were selected for the European final in Wageningen (NL) out of over 470 applications from European companies. During the past three day event, a boot camp was organized for the European Finalists so that they could work together with R&D and Innovation Managers from corporate partners in facilitated workshops. The goal was to prepare all parties for collaboration projects on e.g. co-development of the startup or scale up’s technology or international marketing and sales. More than 300 people attended the closing night on Wednesday and were able to vote at the end of the event for the Public Choice Award. Representatives of the corporate partners (Unilever, Nutreco, FrieslandCampina, and Ahold), as well as other managers from international corporations, the academic community, and private equity investors, were present during this final session. Prince Constantijn of The Netherlands joined a panel on Corporate-Startup engagement during this event.
“This award is a very important international recognition for our team and for our realizations in the last year. During the past three days, we felt great support for our business model. The feedback that we received from corporate experts makes us believe even more that indoor vertical farming solutions have a great potential worldwide to optimize supply chains and plant production in many industries”, says Maarten Vandecruys, CEO of Urban Crop Solutions. Brecht Stubbe, Global Sales Director of Urban Crop Solutions adds “Our global approach and our focus on automated and robotized systems were very much liked by the European audience during the event. We should leverage this Award and increase our presence in the world even faster. The last weeks we have felt a lot of international traction for our systems”
Urban Crop Solutions develops tailor-made plant growth installations for its clients. These systems are turnkey, robotized and able to be integrated into existing production facilities or food processing units. Urban Crop Solutions also has its own range of standard growth container products. Being a total solution provider, Urban Crop Solutions can also supply seeds, substrates, and nutrients for clients that have limited or no knowledge or experience with farming. Currently, the company has developed plant growing recipes for more than 200 varieties of crops that can be grown in closed environment vertical farms. These recipes (ranging from leafy greens, vegetables, medicinal plants to flowers) are developed specifically for indoor farming applications and sometimes exclusively for clients by its team of plant scientists. Urban Crop Solutions has started activities in Miami (Florida, US) in 2016 and is soon to open a division in Japan.
New Vertical Farming System Being Franchised
New Vertical Farming System Being Franchised
December 13, 2017
Written by Ted Tennison
Crops include micro-greens and leafy greens.
Dec. 13, 2017, Leduc, Alta. – Western Canada’s grocery and food service industries are eagerly waiting for the final commissioning of Trusted Freshness™ Ltd. Canada’s newest vertical farming enterprise. The 37,000 sq. ft. growing facility in Leduc is going through the final steps before launching its commercial operation.
The Trusted Freshness facility provides a controlled indoor urban environment capable of growing a wide assortment of produce including micro greens, leafy greens and vine crops. Many of the crops can be grown and harvested within a seven to 30-day cycle, providing fresh produce year round.
The local availability of produce ensures that the nutritional benefits of the produce are not reduced by long transportation hauls, which is the case with the produce imported from southwestern U.S. and Mexico.
“Our franchise approach to vertical farming provides our franchisees with tremendous flexibility in how they can operate their business,” says Jim Schroeder, Trusted Freshness CEO and chief marketing officer. “The franchisee may wish to simply invest in a Trusted Freshness vertical farming module and have the management of the unit out-sourced or operate their franchise themselves.”
The Trusted Freshness franchise business model enables investors to operate their individual growing enterprises in a co-located facility, while at the same time taking advantage of shared core services such as hands-on training, germination, packaging, distribution and marketing of their produce.
“The demand for Trusted Freshness produce is significant,” says Schroeder. “Since word got out about our vertical farming facility, we have been approached by numerous groups interested in purchasing our freshly-grown produce. Grocery retailers, the food service industry and even individual chefs are looking for that specific herb or micro-green that will give them an extra advantage in their culinary offering.”
“We are delighted with the continued interest our Trusted Freshness operation is receiving from the local business community, the rest of Canada and other parts of the world,” says Schroeder. “We are already investigating additional locations that would be a great fit for a Trusted Freshness operation.”
“With the world-wide market for vertical farming operations projected to be worth a minimum of $3.88 billion U.S. by 2020, this is certainly the time for entrepreneurs and investors to take a look at a Trusted Freshness franchise,” says Schroeder.
For more information on Trusted Freshness™ Ltd. visit www.trustedfreshness.com or contact Trusted Freshness CEO Jim Schroeder at 780.690.8985, email: jim@trustedfreshness.com
What’s It Like to Be a Vertical Farmer?
What’s It Like to Be a Vertical Farmer?
As the Shift Manager for Farm.One’s Tribeca farm, Tom Rubino juggles early mornings, a fast pace, and a high attention to detail. Here’s how he does it.
You’ve probably seen enough videos and photos of vertical farms: Racks and racks, levels and levels within LED-lit warehouses, growing ‘perfect’ produce year-in, year-out. You might see a white-jacketed figure in the distance, tiny against the equipment. The focus is firmly on the technology, not the people.
What’s more, it’s especially hard to find out what it’s really like to work on an indoor farm, because many companies are extremely secretive — hardly letting anyone past their air-curtained doors.
But don’t let that fool you. Like any other business, urban farms live or die on their people. And real people work in them, like Tom.
Tom Rubino, Farm.One Tribeca
Farm.One is kind of unusual in the world of vertical farms. Most grow just a few crops — normally bulk salad greens. Instead, we grow hundreds of rare herbs, edible flowers and micros (581 at last count) for chefs in some of the best restaurants in New York. Often our product is the last thing a chef puts on the plate, and the first thing a customer sees.
Our leaves and flowers, on a dish by Ronny Emborg for Atera
Our farms are very small (Tribeca is just over 1,200 square feet, and our farm at the Institute of Culinary Education is around 300). But we use the latest LED lights and hydroponics to grow year-round in the heart of the city, giving us an outsized level of production for such a tiny space.
As Shift Manager for Farm.One’s new farm in Tribeca, Tom oversees all day-to-day operations from seed to harvest. The buck stops with Tom.
Tom has always had a love for food and how it’s grown
A Love of Food & Farming
“I spent five months on a family farm in Sicily — and it was the time of my life. It was a huge farm, over 500 acres, growing wheat, almonds, olives, grapes and more—kind of the opposite to this! I’d also done a lot of gardening at my house, starting with a small window box and progressing to a 10x20' planter on the roof, growing common herbs.
“I just feel very at peace when I’m around plants.
“It makes me very happy to see a plant through from germination to the point you harvest it — it’s real satisfaction. And to see someone using it in a dish is even better.
Early Mornings
AtFarm.One, mornings start early — often around 6:30am—as we harvest everything on the day of delivery. Tom likes to get a head start.
“I open up the farm early. This is my chance to get ahead of the day, prepping everything for the beginning of people‘s shifts.
“I’ll have a look at the harvest, and print out the harvest tickets [Farm.One uses our own ticketing system, a little bit like a restaurant] — if there’s anything I think one person will harvest better than someone else, faster than someone else, I’ll assign them that ticket.
Running two farms 15 minutes walk from each other is … interesting, logistically. Tom has to stay on top of this, and any special instructions.
“I’ll have a look at what we need from ICE versus here. I’ll try to get ahead of the harvest, looking at what customers need what, and any special packing or cutting requirements ahead of time before it gets busy. In my mind the harvest is finalized at 8am — ready for everyone to come in.
Thai Red Stem Basil
Unlike most farms, Farm.One plants seeds almost every day of the week — so that our customers get the perfect leaf size for their product.
For example, many microgreens are grown for just 12 or 14 days, meaning that even one day off can mean a product isn’t right.
This means every day has a mixture of planting, transplanting and harvesting, as well as general farm maintenance tasks.
“I’ll look at the planting schedule too — so that I know at what point during the harvest I can peel people off the harvest and onto planting so that we get everything done in time.
“We usually have a big planting scheduled. The key is getting everything prepped—seeds, medium, everything before the full effort starts. We’ll have Farm Hands coming in at different times — either starting their shift or from ICE, so it’s key to be ready. I’m constantly corresponding with our Head of Operations if we are short on something or there are last-minute changes.
“When I get the planting underway, I can think about what I need to do, either re-allocating space in the system, receiving consumables.
“On a busy day, there are also unexpected things happening. New orders, problems with a particular crop. Being able to jump in and troubleshoot problems, being flexible is important.
Important qualities
Tom talks through some of the essential traits you need to succeed on a busy indoor farm.
“Anticipation—you’re not always going to know before there is a problem, but you need to think about what you might do if there is one, and be ready for different things to happen. You want to see a few moves ahead and be ready for a variety of scenarios.
“It’s a rush on busy days. When everything goes smoothly, you can be going through huge quantities of tickets and look back at the end of the shift to see a lot of product done, and that’s very rewarding. But that only happens if you’re thinking in advance.
“We’re always looking for new ways to improve, and figuring out the most efficient ways to do things. Not necessarily the fastest, but the correct way.
Food adventures
“Igrew up in a family where eating was a huge business. We start Thanksgiving at around 11:30 in the morning, and have like a nine-course meal! A constant steady stream of food throughout the day. Some of my best memories from my childhood are from waking up and smelling my mom’s garlic for breakfast. Eating is a very social thing, it’s about enjoyment, very much about pleasure and having a good time.
I’ll often tell a waiter when I go into a restaurant ‘We’re going to be here a while, and we’re going to have fun!’.
“I like all different cuisines, and my fiancée and I get a lot of pleasure out of it.
What’s it like visiting a restaurant where you’ve grown the product yourself?
Since starting at Farm.One, Tom has visited our customers like Daniel, Butter, Mission Chinese Food and Le Turtle.
“That is a lot of fun! The first thing I ever ate in a restaurant from this farm was nasturtium, when I was at Butter. My girlfriend ate most of it while I was texting David (Farm.One’s Head Horticulturalist) about it! The second was Le Turtle — and that’s where we got the full experience; Chef Victor hit us with a lot of things that we grow. He did it on purpose, I know!
“I try everything growing often on the farm so I know how it’s doing, but one of the plants I tasted rarely before was Bull’s Blood. On that occasion, at Le Turtle it stood out though, because we had had a nightmare with a lot of failed batches of that product — getting just two trays-worth out of 6 planted trays by painstakingly picking through it for what felt like hours. So when I saw it on a dish at Le Turtle I had to laugh— that was definitely the fruits of my labor! It tasted that much better.
What’s the best part of the job?
“It’s a lot of fun to visit restaurants, but it’s even better to hear from Sales the compliments we’ve had from chefs. I take a lot of pleasure from giving chefs the best product possible. So when I hear back from chefs, it gives me a huge amount of satisfaction.
Tom deep in the Nepitella
Any advice for wannabe urban farmers?
“Patience and persistence. Despite all the work we put in to systematize and automate, at the ground level it’s a very exact science.
“The smallest of details can throw off germination and maturation of any plant. A tray of Dragon’s Tongue might dry out if you have a slightly elevated side of a tray. Flood height might vary. New trays don’t always fit perfectly with the old trays. Even a few millimeters can make a difference sometimes.
“Attention to detail is vital. I’m meticulous. It’s the only way you can have success with this kind of farm. Constantly adjusting and improving as a farmer and pushing that back to the business is essential.
While automation and software helps, a close eye ensures nothing slips through the gaps.
“I love the challenge and I enjoy the work. I don’t mind the extra effort. You have to have a love for it, and an ability to learn from your mistakes.
Find out more about our farming team and how they work with the overview video below, narrated by Head of Operations, Dana.
Inspired? You can now own a piece of Farm.One at http://farm.one/invest.
How Is Our Culture Changing The Way We Eat?
One trend that has been gaining popularity across the country with a variety of people, including millennials, is locally sourced produce.
How Is Our Culture Changing The Way We Eat?
Marissa Peretz, CONTRIBUTOR
Opinions expressed by Forbes Contributors are their own.
Photo courtesy of Local Roots
What does the farm of the future look like?
Whether you have landed your dream job or are just starting your career, lunch and dinner provide a way to bond, network, and share wisdom with friends and teammates. Breakfast can offer the same camaraderie, for those of us who wake up before the sun does. Back in college, our schedules were flexible and the nearest farmer’s market was generally within hiking distance.
As we entered the workforce with longer work hours than previous generations and full podcast length commute times, we considered the time it takes to shop in a large grocery store and the limited options of most chain restaurants. We craved easier, healthier, and more sustainable options which is why locally sourced produce and meal delivery services are such a huge trend.
We also know that when we buy food from local sources, it creates jobs and benefits our local economy. So the question is: where are we getting our food?
Dinner in the city fresh from a local, sustainable farm
One trend that has been gaining popularity across the country with a variety of people, including millennials, is locally sourced produce. One way to find local produce is to join a Community Supported Agriculture (CSA) program. These services often deliver produce to your door (or to your friend’s door if you decide to split a box). When you reduce the number of steps between when produce is freshly picked and when you place it in your fridge, your food retains more vitamins and minerals.
Some companies even help connect employees with CSAs. “There are CSA programs connected with each of our office locations (Providence (HQ), New York, and San Francisco),” said restaurant management platform Upserve'sVP of Talent, Alaina Restivo. “Through these programs, employees can order fresh produce or dairy from local farms to be delivered right to the office, making it easy to eat healthy at home as well as at work. By supporting these CSAs, we’re able to promote a just and sustainable food system in our communities.”
One option includes Imperfect Produce, a service that delivers fruit and vegetables that did not meet cosmetic standards for grocery stores at a lower price. “I just signed up for bi-weekly deliveries,” said Megan Palmer, Public Relations Director, ZeroCater. “Definitely makes it easier to complete my shopping list but also forces me to switch things up.”
Matt Vail, Founder & COO of Local Roots sees this local trend growing much stronger. His company is a Los Angeles based indoor farming startup that uses shipping containers to create an optimal growing environment for produce and co-locates them with retail distribution centers to produce longer lasting, fresh food.
The 7 Reasons Indoor Vertical Farming Is Sustainable
The 7 Reasons Indoor Vertical Farming Is Sustainable
Indoor Vertical Farms Everywhere
The 7 Reasons Indoor Vertical Farming Is Sustainable:
1) Reduction of the Carbon footprint in food production.
2) Reduction in Carbon footprint moving food 1,500 miles (on average) from production to consumers.
3) Removal of Fertilizer runoff into the water system.
4) Removal of Pesticides from the environment.
5) No wastage of water.
6) Growing can use 100% renewable energy.
7) Greater consumer health from the increased nutritional quality of the vegetables. Some other benefits:
The need for GMOs disappears
Everything can be 100% organic
Food costs will go down
Reduction in the use of fertilizer Indoor Vertical Farming Is Sustainable Farming.
The big food retailers want sustainability.
I gave a talk at FMI (Food Marketing Institute) a few months back on the same topic. All of North America's top retailers were in the room. The next big Sustainability change needs to be in fertilizers. The largest thing in fertilizer is Nitrogen.
Man-made Nitrogen is created using the Haber–Bosch process, which currently burns about 5% of the world's natural gas.
Nitrogen can be created naturally by growing and processing legumes.
Moving to Indoor Vertical Farming frees land that can be used to grow legumes naturally for Nitrogen.
A massive win-win.
AeroFarms and Dell Team Up to Revolutionize Farming with IoT
AeroFarms and Dell Team Up to Revolutionize Farming with IoT
By Ken Briodagh 2017
Recently, I had the opportunity to visit the future of farming in Newark, New Jersey, thanks to Dell and AeroFarms. AeroFarms is a future agriculture company building indoor, vertical farms that use “aeroponics” to generate yields that are 120 times more productive per acre, per year than a traditional, outdoor farm. Aeroponics is a system of farming which uses no dirt, and only very little water, combined with nutrients, to grow plants. Dell is helping AeroFarms monitor growing conditions, perform analytics and identify harvest quality.
AeroFarms has said it is trying to transform agriculture using technology to build more sustainable, more environmentally responsible and higher producing farms throughout the world, with a focus on local, meaning within 100 miles of the eater. It is currently operating several farms and selling leafy greens to a variety of major retailers, including the largest farm in the world, measured by amount of produce grown per acre, according to the company.
The farms are established on major distribution routes and near population centers in order to stay local, while the indoor nature of the growing spaces are designed to defy traditional growing seasons by enabling local farming at commercial scale all-year round. The produce is monitored using Dell technology from seed to package, so each can be traced for quality control and improvement. Meanwhile, each farm is using 95 percent less water than field farmed-food and with yields 130 times higher per square foot, each year.
“AeroFarms is redefining agriculture combining world-class expertise for horticulture, engineering, food safety, nutrition, and data science to set a new standard for product quality and production,” said David Rosenberg, Co-Founder and CEO, AeroFarms. “We are as much a capabilities company as we are farmers, utilizing science and technology to achieve our vision of totally-controlled agriculture. We have worked closely with Dell Technologies to develop the tools to wirelessly track and monitor our product throughout the growing process from seed to package. Dell Technologies understands our IoT infrastructure and integration needs, and we see the opportunity to collaborate on additional solutions as we build our indoor vertical farms in major cities around the world.”
The company recently began growing at its ninth farm, located at its new global headquarters in Newark, NJ. AeroFarms also has additional grow sites in development in multiple US states and on four continents.
Agriculture like this, as enabled by IoT technology, is likely to represent the future of farming in the future, and is likely to be one of the many ways that IoT will improve and enhance society moving into the future.
Ken Briodagh is a writer and editor with more than a decade of experience under his belt. He is in love with technology and if he had his druthers would beta test everything from shoe phones to flying cars.
Edited by Ken Briodagh
Author Info
Underground Farm Pays Rent in Heat It Supplies to Building Above
12-08-17
Underground Farm Pays Rent in Heat It Supplies to Building Above
Vertical farms have been touted as a way to feed a rapidly urbanizing world population (I've waxed poetic about them myself.) Critics of the trending technology, however, contend that these energy-intensive hubs are too costly and perhaps impractical to maintain.
Sure, the naysayers have a point, but what if vertical farms did more than just feed mouths? In Stockholm, Sweden, the Plantagon CityFarm located in the basement of the iconic DN-Skrapan building in the Kungsholmen district has a whole other purpose besides nourishing the office workers on site—the farm also recycles its heat to warm the offices above.
The underground farm, which will start production early next year, stores the heat emitted by the LEDs used to grow veggies and then reuses that energy to heat the property. This stroke of genius allows the venture to pay nothing in rent.
"[The building owner] agreed to give us a free lease for three years, so we don't pay one single Swedish kroner for the room," Plantagon cofounder Hans Hassle told FastCompany. "This is the challenge, very often, for urban farmers: If you really want to grow things in the city, you have to find new business models that actually make the food not too expensive in the end."
FastCompany reported that the system will save the office building 700,000 kilowatt-hours of energy a year, roughly worth three times as much as the previous tenant of the space had paid in rent.
Notably, the office building and the farm will work together symbiotically. "The CityFarm under the DN-Skrapan will provide its surplus heat to the offices and in exchange [receive] CO2 from the people who work there," the developers said.
The farm is expected to produce 100 kilograms of fresh vegetables daily and, like many other indoor farming ventures, it recycles most of its water and does not need to use any herbicides or pesticides.
The Swedish company has a goal of opening a total of ten such facilities in the Stockholm area by 2020, and it has started a crowdfunding campaign for the planned expansion.
"The reason for a crowdfunding campaign is that we believe that people that care about the future of cities, food production and the health of our planet should be given the opportunity to be a part of the solution," said Owe Pettersson, CEO of Plantagon International. "To us, it is important to create and expand together, showing that we are a movement for healthy sustainable food. Together, we can make a difference for safe food production in cities—now and in the future."
Former Polartec Plant to Become "Industrial Innovation Hub"
The industrial facility that once housed the Polartec textile plant is in for a makeover. On Saturday, its new owner — California-based real estate broker Jitender Makkar — welcomed city and state officials onto the factory floor to unveil his plans for the facility, which he has given a new moniker: IndusPAD.
Former Polartec Plant to Become "Industrial Innovation Hub"
METHUEN/LAWRENCE — The industrial facility that once housed the Polartec textile plant is in for a makeover.
On Saturday, its new owner — California-based real estate broker Jitender Makkar — welcomed city and state officials onto the factory floor to unveil his plans for the facility, which he has given a new moniker: IndusPAD.
The facility, which includes two buildings on a 14.5-acre lot on the Lawrence/Methuen city lines, had been put up for auction this spring and sold for $5.35 million.
Makkar said he intends to subdivide the facility and attract multiple mixed-use tenants to what he envisions as a "take off and landing pad" for young entrepreneurs and innovators.
This is Makkar's first East coast investment.
After starting his career in New Delhi, India in construction and architectural design, Makkar relocated to California in 2000 and became involved in real estate investment and sales, according to Purnima Dey, director of public relations and community outreach for IndusPAD, and Makkar's fiance.
"We envision the opportunity of inspired entrepreneurs in our property," he said. "Our team aims to work strategically and diligently to build something memorable."
The first business to open will be a 30,000 square foot vertical farming facility, growing organic produce, said Makkar, in a partnership with Dutch indoor agriculture company Beyond Organic.
"With that, we hope to expand it within in the next couple of years to a much larger facility, which can create maybe 30, 40, 50 new technology jobs," said Makkar.
He thanked both Lawrence Mayor Daniel Rivera and Methuen Mayor Stephen Zanni for their support, and highlighted Zanni's vision to bring "the jobs of the future" to the region.
"Mayor Stephen Zanni is really the spirit behind what we have planned," said Makkar. "He is the man who has given me the vision to run rather than walk."
"Almost everybody said the biggest challenge we will have is in subdividing this facility, is in creating the option to bring in multiple tenants," said Makkar. "They all saw it was used for one vertical use, and it was hard to transform. What I saw in it was possibilities of a different kind. I saw in it the possibility of somebody from MIT, somebody from Mass. University (sic) to take their projects, take advantage of the infrastructure here, and make it their journey."
Polartec fleece was manufactured in the facility until last year, when Polartec LLC laid off more than 200 workers and moved its operations to Tennessee. When the facility was put up for auction, the listing indicated Polartec had invested more than $6.2 million in the property.
"This brings not only jobs to the Merrimack Valley and beyond, but more importantly it brings about a sustainable company," said Zanni. "A lot of companies come and go, as the company that was here, Polartec moved out to Tennessee and actually moved part of their operations to China. This is an operation that will go over a lifetime."
Methuen Community Development Director Bill Buckley said no other tenants have signed on with IndusPAD yet, but he was aware of some local interest.
"I think you might see some more traditional industrial tenants initially, that might not fit the vision of innovation," he said.
With nearly 600,000 feet of space in the facility, IndusPAD certainly has room to grow.
State Senator Barbara L'Italien welcomed IndusPAD as "the next chapter in this glorious footprint that was Polartec."
"It sounds like there's going to be some innovation, a place for innovation for ideas for allowing small businesses to be able to begin their dreams and launch, and we know what that has done for Boston area, so we welcome that in the city of Methuen and the city of Lawrence."
Subway Operator Tokyo Metro Embarks In New Direction: Hydroponic Vegetable Farming
Under the name "Tokyo Salad," the company is growing lettuce, assorted salad greens, and even herbs at a facility approximately a seven-minute walk from Nishi-kasai Station on the Tokyo Metro Tozai Line.
Subway Operator Tokyo Metro Embarks In New Direction: Hydroponic Vegetable Farming
December 10, 2017 (Mainichi Japan)
A factory worker checks a hydroponic romaine lettuce plant at Tokyo Metro Co.'s cultivation center in Tokyo's Edogawa Ward on Nov. 17, 2017. (Mainichi)
Subway operator Tokyo Metro Co. is bringing its ideology of "safe and secure" to an unlikely place -- farming.
Under the name "Tokyo Salad," the company is growing lettuce, assorted salad greens, and even herbs at a facility approximately a seven-minute walk from Nishi-kasai Station on the Tokyo Metro Tozai Line. The cultivation warehouse Metro vegetable center is located under the elevated train tracks of the line.
The airtight space is held to strict hygienic conditions, and neither fertilizer nor soil is used, with the seven rows of plants instead grown hydroponically. Frill lettuce, basil, along with rare finds such as Lollo Rosso (red coral lettuce) and red kale are found among the 11 varieties regularly grown, with roughly 400 plants reportedly growing on a given day.
The cultivation is completely man-made and mechanized. Seeds are placed on a sponge with tweezers, and the young seedling is raised until the leaves spread out, at which time it is moved to a more spacious area. LEDs shed light on the plants for 16 hours a day and the liquid nutrients are cycled through the system 24/7. It takes roughly three to five weeks for a plant to reach maturity, and there is barely any loss.
The strict hygienic conditions inside of the Tokyo Metro Co.'s cultivation center in Tokyo's Edogawa Ward. (Mainichi)
The leaves are not bitter or astringent, and the leaves are soft all the way to the exterior of the plant. They can be preserved for a long period of time, and because no chemical fertilizers were used to grow them and they never touched soil, the entire plant can be eaten without being washed.
So-called plant factories like this are the focus of efforts by the Ministry of Agriculture, Forestry and Fisheries to expand safe provision of products like vegetables, high productivity and job creation. According to the ministry, the number of cultivators using artificial lights has tripled from 2011 to 197 locations as of February 2017.
Tokyo Metro entered the market to make use of idle land as a new business venture, and built the cultivation facilities in unused warehouses. The operation is a joint project with group company Metro Development Co., which began sales of the lettuce and other products in April 2015.
The element of surprise and the mismatch between subways and vegetables have stirred up quite a reaction. Last spring, a lunch course featuring the products was introduced at The Strings by Intercontinental Tokyo hotel. Even the dessert included ingredients from Tokyo Salad, and because of an overwhelming positive response, the hotel introduced a dinner course this summer as well.
"Dishes where a lot of attention is paid to a single ingredient are very popular," says 47-year-old hotel food and beverage manager Tetsuya Tanigawa. "The ideology and the story behind the product is the deciding factor."
Tokyo Metro overseer Remi Takahara, 33, continued to visit the vegetable plant for the six months she was visiting potential business partners that would use Tokyo Salad vegetables since the factory operation began. "I never thought that I would be growing vegetables when I joined a railway company," she said, reflecting on the trial and error process that led to the subway operator's greens' cultivation.
Vertical Farming is on The Rise In Abbotsford British Columbia
Vertical Farming is on The Rise In Abbotsford
Construction on one of B.C.'s First Vertical Farms will be complete next October
December 9, 2017
While the method of building farms vertically becomes more popular, Kent Mullinix of KPU’s Institute for Sustainable Food Systems worries it may be a step in the wrong direction.
As the effects of climate change and overpopulation become more and more apparent, traditional farming methods seem less likely to provide long-term sustainability for our planet.
One potential method of addressing this problem is with a concept called “vertical farming,” which packs more agriculture into a smaller land area by building upwards, much like a densely inhabited high-rise condo. Next October, Abbotsford will become home to one of the few vertical farms in British Columbia when construction on a 10-acre farm at 34240 Page Road is completed.
Nick Brusatore, CEO of the farm’s developer, Vertical Designs Ltd., says that the project will consist of 32 towers, each 20 feet tall and housed in a 35-foot tall building. The farm is estimated to cost between $2.5 and $2.7 million.
The company has partnered with Affinor and a California strawberry farm for what Brusatore calls an “on-farm test agreement,” or a trial run after which, if all parties are satisfied, production will increase significantly.
Organic strawberries will be the sole product grown at the Abbotsford facility, and through a contract signed with Discovery Organics, all of the strawberries have already been sold.
“We expect to produce probably the best strawberry on the planet,” says Brusatore.
He is unsure where exactly his strawberries will end up, but says that he would be surprised if the first batch makes it outside the city. Eventually, though he hopes to “produce all the strawberries for Canada” from the Abbotsford location.
“We’ve got a problem right now,” says Brusatore, referring to the state of local and global agriculture. “We’ve got a food shortage, we’ve got a water shortage, and we’ve got no governance as to the pesticide use and the way things are manipulated through labels.”
According to Brusatore, the Abbotsford vertical farm will produce zero water waste, require zero pesticides, and will utilize the land 10 times per square foot more efficiently than conventional farming techniques.
Despite the possible benefits of this technology-based farming system, Director of the Institute for Sustainable Food Systems at KPU Kent Mullinix believes that vertical farming is a step in the wrong direction.
“It’s about money. It’s not about feeding the world,” says Mullinix. “It’s really appropriate for the cultivation of just a few high-end crops like salad greens and some more valuable vegetables, so it’s really primarily a system to satisfy high-end markets with very high-end production methods. It’s the antithesis of sustainability if you ask me.”
Instead of investing in vertical farms, Mullinix argues that the key to sustainability is a decentralized, ecologically-focused network of regional food systems that create local economies and jobs.
Mullinix is also concerned that the proliferation of vertical farming will lead to valuable agricultural land being paved over.
In response, Brusatore argues that vertical farms can be developed on contaminated land that is no longer ideal for conventional farming. He acknowledges that vertical farming is mostly suitable for low-growing plants like kale, lettuce, and strawberries, but says that the project is nevertheless a progressive step for the future of agriculture.
“If we don’t try, if we don’t press these issues, we’re just going to fail for sure,” he says. “I’m excited for Abbotsford …. It’s going to be absolutely amazing and people are going to be blown away by this once it’s up.”
Although it is a capital-intensive project to launch, he points out that, once built, the equipment on the farm will be long-lasting and will require little maintenance.
After the farm is completed and the method is proven successful, Brusatore expects that there will be a significant increase in capital investment in vertical farming, creating a positive effect on the local economy.
Menasha's Fork Farms is Changing The Face of Farming -- And Helping Schools, Pantries
Menasha's Fork Farms is Changing The Face of Farming -- And Helping Schools, Pantries
Maureen Wallenfang, USA TODAY NETWORK-Wisconsin
Nov. 13, 2017
Down on the "farm." Fork Farms' operation has 16 indoor growing modules in Menasha. Here, Stewart McLain, operations manager, left; Alex Tyink, co-founder, center; and Gil Shaw, farm manager, right, stand in front of growing modules.
(Photo: USA TODAY NETWORK-Wisconsin)
MENASHA - This isn’t your father’s farm.
Or anyone’s vision of a farm, really, outside of a science fiction novel.
This “farm” of indoor plastic growing modules looks like it came off a spaceship.
Fork Farms is a small, young, agriculture technology company that manufactures plastic hydroponic growing modules.
Inside each one, ruffled rows of lettuce grow vertically without a speck of soil or sunlight.
Fork Farms grows lettuce around LED lights inside a module. (Photo: Dan Powers/USA TODAY NETWORK-Wisconsin)
Fork Farms moved into its current home at 1101 W. Midway Road this spring and ? 16 indoor growing machines. It's in a former flooring store just west of Appleton Road near Piggly Wiggly in Menasha.
Prior to this, inventor Alex Tyink operated out of his apartment and garage. He’s spent eight years working on the modules while holding down a day job. He's never taken a dime from the company and has operated on a slim investment of less than $20,000 gathered from family and friends.
“I believe in food. I know that sounds corny,” said Tyink, 30. “I felt better when I started eating good food instead of burgers and fries. A simple thing can make so much of a difference in our lives.”
He went to school to become an opera singer, not an engineer, so he said the years tinkering were spent learning, evolving and experimenting to get the system right.
Since 2009, he has made 28 different prototypes and invested thousands of hours into the venture.
Social service
Working on the growing machines satisfied his desire to create something that mattered, he said.
Growing fresh produce this way can make healthy food more accessible and create a connection between kids and food.
“Our mission is to put these in food deserts and low-income schools,” he said. “The social service side is very important to me. I never want to lose that.”
Tyink co-founded the company with his father, Steve Tyink, who is vice president of business innovation at Miron Construction, and John Brogan, CEO of Bank of Kaukauna.
His two employees have taken equity before paychecks. Commercial Horizons gave him a sweet lease on the building.
Fork Farms is a limited liability company owned by a group of 14 people, including employees Gil Shaw and Stewart McLain.
Shaw was formerly hydroponics manager at Riverview Gardens and is now farm manager here. McLain, formerly a music teacher in Seattle, is operations manager.
Shaw said the opportunity to join Fork Farms was too good to pass up.
“It’s one of the most innovative systems out there. It’s in a class of its own,” Shaw said.
“This is a real game changer because of its water use, efficiency and space. The potential of this is extraordinary. It can revolutionize arid land growing.”
Fork Farms' growing system already has one patent and two more pending.
Growing modules
The company's first 20 growing modules have been sold to schools, food pantries and individuals.
Local schools include Mount Olive Lutheran School, Fox Valley Lutheran High School, Appleton North High School and New Directions Learning Community in Kaukauna.
At North, the machine was purchased with a grant from the Appleton Education Foundation.
"We love having our machine in the classroom," said Matt Hechel, North's alternative education coordinator. "We have a few students who have taken charge of being our main gardeners."
"I like learning about the hydroponic system and am really surprised how easy it is to grow our produce right in our classroom," said J.T. Zubich, one of the students in charge of the module. "It would be cool if every classroom was able to do this."
Students have eaten salads in the classroom from their harvest. Students and staff have taken lettuce home.
“It’s an improvement on the traditional school garden model,” Tyink said. “It’s highly productive in growing food and makes a nutritional difference in schools. We’re improving the quality of lunch lines.”
Besides making and selling the growing modules, Fork Farms grows lettuce in its Menasha headquarters and sells it to several hotels and a caterer. Its first and largest buyer has been the Best Western Premier Bridgewood Resort Hotel in Neenah.
"We use their Fox Valley blend of lettuces for lunch buffets and catering, and their buttterhead lettuce for weddings and corporate events," said Ryan Batley, food and beverage director. "What's so great about it is that it's local. It stays fresher than anything else we're getting. It's very clean and crisp. A great product. The cost is a little higher, but we think it's money well-spent."
Batley said they use whole butterhead lettuce heads on each plate for weddings.
"One bride called us back and said her guests were still commenting on it weeks later. She said 'I never thought people would remember the salad,'" Batley said.
For-profit/nonprofit partnership
Tyink’s day job is director of programming at Feeding America Eastern Wisconsin. He previously field tested his growing machines while working at Goodwill Industries of North Central Wisconsin.
Feeding America now provides ancillary support to Fork Farms in what Tyink calls a “for-profit/nonprofit partnership.”
While Fork Farms is a for-profit business, he said it’s “mission-driven” to educate and feed people.
Growing modules cost $3,500. Feeding America provides education, training and a year’s worth of supplies for an additional $1,500.
Each vertical module can grow 288 plants in a four-by-four-foot space, Shaw said. Each machine can grow 15 to 20 pounds of lettuce in three to four weeks.
Indoor farming has been in the national news recently with the large-scale Plenty operation, a Jeff Bezos-backed indoor farm now expanding into the Seattle area.
But at the same time, some indoor farms have struggled.
FarmedHere, for example, closed its indoor hydroponic growing operation near Chicago earlier this year, reportedly because of high labor and energy costs.
At Fork Farms, Tyink keeps a watchful eye on costs and is in the gener8tor’s gBETA accelerator coaching program for startups.
He said it’s self-sustaining and he hasn’t taken a bank loan.
One of the keys, he said, was keeping energy costs low with LED growing lights.
“All of my research started with energy efficiencies," he said. “We’re running at a higher resource efficiency rate.”
“We kept small and kept capitalization small. We haven’t gone after venture capital because we wanted to know what we had before we made promises.”
Kids Speak on Vertically Building a Sustainable Future
Kids Speak on Vertically Building a Sustainable Future
NOVEMBER 13, 2017 URBAN AG NEWS
Originally published in Issue 14
By Lea S. Singer (7th grader)
At the New York Sun Works’ Youth Conference on June 2, 2016, building a sustainable future was the shared topic. So many ideas were presented on how the kids of this generation could help build a better, healthier future for themselves. The passion shared with all who attended was inspiring, and made you want to start a mini hydroponics system in your kitchen the minute you left the conference.
Among the numerous people who spoke, ranging in age from 10- to 15- years old, three guest speakers attended. One of them, Dr. Dickson Despommier, from The Vertical Farm, shared the newest way of growing food—VIG.
One of the guest speakers at the conference was Dr. Dickson Despommier from The Vertical Farm who discussed vertically integrated growing (VIG).
VIG stands for vertically integrated growing, which looks exactly like it sounds. The plants are lined up in rows vertically, against a wall, as opposed to taking up space on the floor. This way of modifying plant growing systems for space efficiency could very well be the standard farming technique of the 21st century.
According to Dr. Despommier, many producers have already adapted this growing technique, using it to grow an abundance of vegetables, including tomatoes, spinach, and kale.
One grocery store that was shown during his presentation had a VIG setup in the store so that customers could simply cut off the leaves they desired from the extremely fresh plants, bag it, pay for their produce, and cook it for dinner the same day it was cut. This is one of the many examples Dr. Despommier showed the audience during his presentation. By the end of his presentation, it’s safe to say attendees were all convinced of the VIG’s efficiency and reliability as a new mass production growing technique.
Another VIG benefit, the free floor space leaves plenty of room for jetpacking and hoverboard riding, which will come in handy in 2050.
Lea S. Singer is a 7th grade student and aspiring writer at the Manhattan School for Children, PS333.
“The NY Sun Works conference was a great opportunity to learn about new ways to use sustainable science and how it works. Sustainable science is very important because, if we keep going without it, it will not be good for us. The conference gave new possibilities, new ways and new approaches on how to save our world.”
— Nate Hajdu, 7th grader and member of NY Sun Works Youth Conference Press Team
NY Sun Works is a non-profit organization that builds innovative science labs in urban schools. Through their Greenhouse Project Initiative they use hydroponic farming technology to educate students and teachers about the science of sustainability. www.nysunworks.org
Could Indoor Farming Help Address Future Food Shortages?
By 2050, Earth’s population is expected to rise to 10 billion, while the resources on the planet continue to shrink. Researchers in the Netherlands are experimenting with one way to feed more people with less: growing crops indoors.
Could Indoor Farming Help Address Future Food Shortages?
November 11, 2017
By 2050, Earth’s population is expected to rise to 10 billion, while the resources on the planet continue to shrink. Researchers in the Netherlands are experimenting with one way to feed more people with less: growing crops indoors. NewsHour Weekend’s Ivette Feliciano takes a look at how indoor farming could shift our relationship with food.
Megan Thompson:
The United Nations estimates that by the year 2050, the world’s population will grow from today’s 7.5 billion people to nearly 10 billion. And as natural resources like farmland and water become scarce, feeding everyone will become an even greater challenge. In tonight’s Signature Segment, NewsHour Weekend’s Ivette Feliciano reports on how there might a solution well underway in the Netherlands. This story is part of our ongoing series, “Peril and Promise – the challenge of climate change.”
Ivette Feliciano:
Just south of The Hague, in the Westland region of the Netherlands, miles upon miles of greenhouses are spread across the landscape. They’ve been built by Dutch farmers as part of a 20-year movement by the country to pursue sustainable agriculture by growing indoors.
Dutch farmer Hans Zwinkel grows tomatoes in two greenhouses that cover 20 acres of land. His annual harvest of two-and-a-half million pounds of tomatoes is more than double the average yield of an outdoor farm.
Hans Zwinkel:
The plant started over there as a small plant, stands about five meters, six meters further.
Ivette Feliciano:
Zwinkel and growers like him achieve high yields by controlling the climate and water for their crops under glass. Filtration systems allow them to collect and recycle the plants’ water supply. Crops receive direct sunlight — supplemented as needed by artificial light — and are protected from unpredictable weather events and insects, which almost completely eliminates the use of chemical pesticides.
Hans Zwinkel:
It’s nice to see the plants grow. You–it gives you energy.
Ivette Feliciano:
These growing techniques have helped foster an indoor growing boom in the Netherlands. Greenhouses now produce 35 percent of the country’s vegetables–despite occupying less than one percent of its farmland.
The Netherlands’ Wageningen University has led much of the research on how to best grow crops indoors. Leo Marcelis–a professor at the university–says that in the era of climate change, the Dutch agricultural revolution needs to move beyond greenhouses, which still rely on some outside forces like sunlight.
Leo Marcelis:
We wanted to control the production process, that we can control the yield, the quality, that we can give guarantees towards the consumers. Although we can control a lot we’re still dependent on the outdoor conditions. So the next step would be to have a further control. So we can, in fact, guarantee how much produce we will have tomorrow or on any date of the — of the year, of a guaranteed quality.
Ivette Feliciano:
Marcelis is now experimenting with indoor vertical farming–growing plants stacked on shelves to maximize space–and completely cut-off from the outside. As in many greenhouses, water for the plants is drained, collected, and reused, reducing their dependence on an outside water source. And instead of sunlight, the researchers use LED's — light bulbs that can replicate solar light in a variety of colors and intensities.
Leo Marcelis:
Whether we are growing tomatoes, whether it’s about getting fruits, or whether it’s a lettuce or leafy vegetables. You can imagine that you want a different type of plant. And that may require therefore a different light. With LEDs, we can also put them in between the plants. And that’s very good. Because usually there is maybe too much light on the top, but insufficient at the bottom. So we can have a much better distribution of the light in the plant.
But growing indoors isn’t cheap. Marcelis says a quarter of the expenses for indoor growers in the Netherlands relate to construction–something farmers who grow in fields don’t have to worry about. Then there’s the energy costs of round-the-clock climate control and artificial lighting. But Marcelis says a key advantage to indoor farming is that by creating ideal growing conditions and maximizing space, it can produce much higher yields, in some cases, up to 350 times the yield of a conventional farm of the same size.
Leo Marcelis:
What really matters is if the income is larger than the cost. So if the investment costs are high, and also the other costs are high, well, if the income is then also very high, then it is about the balance.
Ivette Feliciano:
Marcelis says one important part of their work is developing techniques that can be replicated anywhere, even in arid climates like the Middle East or sub-Saharan Africa. The United Nations estimates as the world’s population grows, global food demand will rise 70 percent by 2050, even as the amount of water and farmable land shrinks due to the global warming.
The Netherlands is already doing its part to feed the world. Propelled by indoor farming, it’s become the second biggest food exporter in the world, accounting for nearly 90 billion dollars last year. This is all the more astounding given that the Netherlands is less than one-percent the size of the United States, the world’s number one food exporter, where indoor farming is also gaining a foothold.
Here in Kennett Township, Pennsylvania, mushroom growers have been practicing indoor farming for over a hundred years, and today produce half the U.S. mushroom crop.
An hour outside Philadelphia, this small community of eight thousand people harvests half a billion pounds of mushrooms every year — all of it indoors and at a low cost of about one dollar per pound.
Chris Alonzo:
We invested nine years ago into a Dutch-style farm.
Ivette Feliciano:
Chris Alonzo owns this indoor farm that uses the vertical farming methods seen in the Netherlands.
Chris Alonzo:
We put in aluminum shelving instead of wooden beds, we invested in equipment which made the job less labor intensive. We have heat in the room, air conditioning in the room, and air flow. And we use those tools to make sure that the room environment is specifically controlled for what the mushroom likes.
Ivette Feliciano:
Using these techniques, Alonzo’s facility alone is responsible for more than one percent of the nation’s mushroom crop — growing 11 million pounds of mushrooms a year — protected from potentially harsh outdoor conditions.
Chris Alonzo:
The only day we take off is Christmas. And the consumer wants fresh produce year-round. So we’re able to meet the needs to have locally grown produce all year-round. As opposed to some crops where they’re only grown seasonally.
This is our environmental control unit…
Ivette Feliciano:
Alonzo says the difficulty with indoor farming–as with outdoor farming–is finding the balance between your harvest’s revenue and its expenses.
Chris Alonzo:
Mushrooms has been sustainable for– for generations. However, land is – is — affordable, because Mother Nature provides rain, Mother Nature provides sun. Growing indoors is very capital intensive. You have the building, you have the infrastructure, you have energy costs. But if you can maximize productivity and having consistent quality year-round, yes, it’s economically viable, but the margins are still very tight.”
Ivette Feliciano:
Most indoor farmers can’t grow at the same scale as mushroom farmers in Kennett Township. But where they — and some venture capitalists — see the future of indoor agriculture lying is in small-scale urban production in areas with no farming industry of their own.
Matt Barnard:
The place where we’re stepping in now is to serve demand that is unmet.
Ivette Feliciano:
Three-thousand miles west of Alonzo’s farm, indoor farming pioneer Matt Barnard heads a major agriculture project in San Francisco called “plenty.” Its farm is a retrofitted former warehouse, now with walls of fresh vegetables that stretch for 100-thousand square feet.
Currently, it grows leafy greens like spinach and kale–the easiest and most affordable crops to grow indoors–but it will soon start growing tomatoes and strawberries as well. The plants grow directly out of vertical columns. Similar to Dutch researchers, the company also uses l-e-d lighting, water recycling, and climate control.
No genetically modified seeds or pesticides are used in production. Instead, it’s the environment that’s modified, carefully crafted around each type of plant to give them the ideal conditions for growing.
Matt Barnard:
The advantages that we find are because of that control– we, for example, don’t have to use pesticides. Instead of using 15 gallons of water to produce one head of lettuce, we use less than one-fifth of a gallon to produce that same head of lettuce. So we’re saving a significant amount of water. We can actually influence the way the food tastes by making sure it has exactly the right nutrient recipe, the right light recipe, the right water recipe.
Ivette Feliciano:
Plenty hopes to become an industry leader in indoor farming. The company recently received 200 million dollars of private funding, which it plans to spend on building farms in the ten most populous American cities and hundreds more worldwide.
But, as in the Netherlands, plenty has to overcome certain challenges — the upfront cost of building or retrofitting indoor spaces suitable for farming…and the energy costs of indoor lighting and climate control.
But Matt Barnard believes that the advances that have been made in indoor agriculture will make it a key player in feeding the world’s ever-growing population.
Matt Barnard:
We’ve added, you know, six billion people since the tractor came around, and so we believe this is one of the core innovations that’ll help us, you know, serve the next two to three billion people that we add to the planet.
Peril and Promise is an ongoing series of reports on the human impact of, and solutions for, Climate Change. Lead funding for Peril and Promise is provided by Dr. P. Roy Vagelos and Diana T. Vagelos. Major support is provided by Marc Haas Foundation.
Indoor Agriculture Brand Fresh Farms of America Launching in the Las Vegas, Nevada Market
Indoor Agriculture Brand Fresh Farms of America Launching in the Las Vegas, Nevada Market
NEWS PROVIDED BY: Indoor Farms of America
December 4, 2017
LAS VEGAS, Dec. 4, 2017, /PRNewswire/ -- Fresh Farms of America, announces today the first farm under the brand name, located in Las Vegas, Nevada. The local operation is named Vegas Fresh Farms, and is on track to serve and sell its first customers with locally grown, fresh-harvested daily produce in the dynamic market of Las Vegas, starting January, 2018.
The Fresh Farms of America brand exclusively utilizes the propriety vertical aeroponic equipment from leading R&D and equipment manufacturer Indoor Farms of America, which is headquartered in Las Vegas.
Fresh Farms of America grows a wide variety of crops indoors
"This new brand of indoor farm operation represents the best in the industry for farm performance, using any metric," statesDavid Martin, CEO of Indoor Farms of America. "Over the next month, we will announce multiple new locations of farms operating under the Fresh Farms of America brand. This brand will quickly become the leading brand of fresh, locally grown produce, accessible by consumers in markets across the U.S. and Canada."
Fresh Farms of America uses the vertical aeroponics of Indoor Farms of America
"Consumers want to know where their food is coming from, they want to know it is the best they can serve their families in terms of purity and nutrition, and the Fresh Farms of America brand exemplifies that," says Martin. "Our produce is grown with no pesticides, no herbicides, is Non-GMO, and is quite frankly, beyond organic."
"Chefs from the best restaurants in Las Vegas continually visit the farm at Indoor Farms of America and say how excellent the produce tastes, how the aroma of our herbs is beyond comparison, and how the texture and structure of the plants is simply superior, and how they appreciate the wide variety of fresh produce we can grow. We think the U.S. consumer will really enjoy having this level of quality, and at prices that are more competitive than organic at this time."
Ron Evans, President of Indoor Farms of America, says, "The owners of this local Las Vegas farm are committed to making this a world class operation, which local Southern Nevada residents will really enjoy. Having access to an abundant supply of leafy greens, herbs, strawberries, peppers and tomatoes is something to get excited about, especially when they are grown in your neighborhood."
The farm will provide direct access to local consumers, the freshest, most purely grown produce they can find. The owners are committed to providing meaningful jobs to veterans and disadvantaged young adults from the community. "When we discussed how important this farm is for the local community in the area of reaching out to at-risk young people, we knew they have a great vision for this farm," states Martin.
According to Martin, "We are putting in place what will be the nations' premiere brand of indoor farm that can operate 12 months out of the year, provide outstanding investment returns without peer, and make the strongest impact on easily accessible, locally grown food across North America."
Leading indoor agriculture R&D and manufacturer, Indoor Farms of America, has a showroom with demonstration farms operating in Las Vegas, Nevada and in multiple locations in Canada, and in South Africa, where their world class vertical aeroponic equipment is on display.
CONTACT:
David W. Martin, CEO • 187031@email4pr.com • IndoorFarmsAmerica.com
4000 W. Ali Baba Lane, Ste. F Las Vegas, NV 89118
(702) 664-1236 or (702) 606-2691
SOURCE Indoor Farms of America
Affinor Growers Reduces Cost of Tower Technology By 30%
Affinor Growers Reduces Cost of Tower Technology By 30%
Cost reductions resulted from several growing tests. New design also allows for organic certification
Vancouver (Canada), December 6 2017 - Affinor Growers (CSE:AFI, OTC:RSSFF, Frankfurt:1AF) (“Affinor” or the “Corporation”), is pleased to announce several design improvements have resulted in a 30% reduction in overall cost and optimized growing conditions.
30% Tower Cost Reduction
Over the summer and during various grow-trial testing periods, Affinor took the opportunity to redesign certain aspects of the tower technology with the goal to reduce overall cost by 20%, improve plant resource availability and versatility. New ideas were conceived and prototyped with our supplier located in Port Coquitlam. By reducing the number of parts and simplifying various fabrications, the overall financial objective was exceeded with a total cost saving of 30% per tower.
The towers have an estimated useful life of 20 years so a 30% reduction allows farmers to amortize the reduced cost at a lower rate and reap more financial benefits from the optimized growing conditions.
Organic Certification Potential
In parallel, the new design improvements upgrade the tower to allow growers to be certified as compliant for organic certification under current Canadian regulations pertaining to the amount of volume and depth of organic soil required per plant as well as improved light penetration by introducing a new tiered level approach. Improved versatility was achieved by designing a universal growing arm that now fits custom plastic inserts to maximize density during the plant growing cycle and accommodate different types of plants.
Jarrett Malnarick, President & CEO, commented, "We are very happy about the design improvements that occurred over the last several months and believe our growing technology can offer cost-effective solutions to a variety of markets. These improvements will allow organic certification and enhanced growing environments for fresh fruit, produce and cannabis plants as well as offer versatility within the plant's life cycle or types of product to be grown.”
For More Information, please contact:
Jarrett Malnarick, President, and CEO
contact@affinorgrowers.com
About Affinor Growers Inc.
Affinor Growers is a publicly traded company on the Canadian Securities Exchange under the symbol ("AFI"). Affinor is focused on growing high-quality crops such as romaine lettuce, spinach, strawberries using its vertical farming techniques. Affinor is committed to becoming a pre-eminent supplier and grower, using exclusive vertical farming techniques.
On Behalf of the Board of Directors
AFFINOR GROWERS INC.
"Jarrett Malnarick"
President & CEO
The CSE has not reviewed and does not accept responsibility for the adequacy or accuracy of this release.
FORWARD-LOOKING INFORMATION
This News Release contains forward-looking statements. The use of any of the words "anticipate", "continue", "estimate", "expect", "may", "will", "project", "should", "believe" and similar expressions are intended to identify forward-looking statements. Although the Company believes that the expectations and assumptions on which the forward-looking statements are based are reasonable, undue reliance should not be placed on the forward-looking statements because the Company can give no assurance that they will prove to be correct. Since forward-looking statements address future events and conditions, by their very nature they involve inherent risks and uncertainties. These statements speak only as of the date of this News Release. Actual results could differ materially from those currently anticipated due to a number of factors and risks including various risk factors discussed in the Company's disclosure documents which can be found under the Company's profile on www.sedar.com. This News Release contains "forward-looking statements" within the meaning of Section 27A of the Securities Act of 1933, as amended, and Section 21E the Securities Exchange Act of 1934, as amended and such forward-looking statements are made pursuant to the safe harbor provisions of the Private Securities Litigation Reform Act of 1995.
Something Fishy About Downtown Toronto’s Waterwheel Farms
Something Fishy About Downtown Toronto’s Waterwheel Farms
With aquaponic farming, the root systems of plants grow directly through pipes into water.
TORONTO • Arts & Life • Food
Solutions to growing local produce may be as close as Queen Street West
By Katherine ForteDecember 4th, 2017
When you think farm you may not think of downtown Toronto, but Alec Wheeler is trying to change that perception.
His Waterwheel Farms uses aquaponic techniques to grow leafy greens and herbs in the facility near Queen Street West and Dufferin Street. The farm employs fish and microbes to grow the plants, which in turn filter the water for the fish – no soil required.
“It looks a little ‘labby’ in here but this is the identical ecosystem you’d find in a lake,” Wheeler said during a recent tour for the Toronto Observer. “You have fish, you feed them, they produce waste, the waste feeds the plants and just as importantly, the plants then filter the water for the fish. It’s a closed loop cycle.”
At Waterwheel Farms, instead of aquatic plants, they are growing crops for human consumption.
“So that’s aquaponics in a nutshell. It’s a living ecosystem between fish, microbes, and plants.”
Aquaponic farming is a closed loop cycle in which the fish act as the fertilizer for plants. The environment is similar to a lake. (WATERWHEEL FARMS)
Wheeler began a small aquaponics farm in his apartment five years ago, when he got tired of his store-bought greens going rotten too quickly. All of his education on aquaponics farming came from research and translating knowledge gained from growing up on his family’s open-field farm in Northern Ontario. He works as a financial analyst for a renewable energy provider. He jokingly refers to himself as “a renewable energy crusader by day and an urban farmer revolutionist by night.”
In May 2017, Wheeler expanded from his apartment to a 1,000 square foot research facility and farm. On-site at there are two tanks containing 400 tilapia fish who aid in growing Bok Choy, arugula, sorrel, spinach, lettuce and Waterwheel Farms’ most popular product, their tender kale. Anyone can purchase their fresh produce by visiting on Saturdays.
The seeds start their life cycle in peat moss. When they’ve grown to the point where their roots are the appropriate length they’re transplanted into pipes with running water where they have more room to flourish. The vegetables grow under different kinds of lights, at controlled temperatures that mimic the longest summer day in Toronto, for optimal growing conditions.
“Because we are indoors we’re controlling the lighting and heating and all that kind of stuff. In Toronto we are at the 43 latitude. Our longest day is just shy of 16 hours. We have these lights timed so they run on 16-hour cycles,” Wheeler said. “We can get, like, seventeen harvests for certain plants as opposed to the one or two you’d get traditionally.”
Waterwheel Farms doubles as a research facility. Founder Alec Wheeler experiments with different colours in the light spectrum to see which yield the best plant growth. (KATHERINE FORTE)
Wheeler finds that aquaponic farms have the ability to provide farmers with more, using less space.
“In traditional agriculture – nothing against it – you’ll read on the packet it says plant every 18 inches or whatever, it’s mainly because there’s a limited amount of nutrients in that soil and those plants are competing for those nutrients. With aquaponics it’s more of a smorgasbord for the plants because the nutrients are coming to the plants. So you can pack them in closer and produce more food and faster,” Wheeler said.
He boasts that his lettuces grow in 20 days, rather than three months.
Plentiful crops aren’t the only benefit of aquaponic farming. Since crops are grown indoors, they’re resistant to poor weather and climate change. The closed-loop system also uses 90 percent less water than traditional agriculture. The only water that leaves the system is what’s used by the plants, and the fish are edible, as well as the vegetables.
There’s no need to worry about toxins from the fish poop or harmful pesticides either. Just like in nature anything toxic in the fish waste or water would “crash the system” according to Wheeler. The same can’t be said about many methods of traditional open-field farming. Though crops can flourish with chemicals in the ecosystem, these chemicals often run off into our rivers and lakes.
Wheeler thinks his style of urban agriculture could change the way Toronto eats, and its impact on our lives could be huge. More people don’t have their own aquaponic farms due to lack of awareness, he believes.
“Like everything, there’s an education barrier. “ Wheeler said. “That’s kind of why we have the facility here so that people from Toronto and in Toronto can come and see the farm.”
That education barrier and lack of awareness is exactly why Rhonda Teitel-Payne and the other members of Toronto Urban Growers celebrated the first Urban Agriculture Day, on Sept. 15, 2017. Farms and gardens, including Waterwheels, opened their doors for tours, and urban farmers from Toronto got together to host a week of events.
What began as a community of urban farmers became Toronto Urban Growers in 2008. The group helps potential city-based farmers and gardens locate resources and connect to each other, so they can share tips, tricks, and anecdotes.
“We started to realize one of the biggest barriers we had in terms of getting projects going was lack of awareness of what urban agriculture is and what it can do and what it’s capable of,” Teitel-Payne said. “We thought that Urban Agriculture Day would be a great way both to celebrate and build that urban agriculture community in Toronto but also to get out the message of ‘Hey look what we can do when we’re growing food in the city. Let’s do more of it.’”
According to Teitel-Payne, urban farming can have more of an effect on us than just what’s on our plate. While Toronto probably couldn’t be self-sufficient when it comes to agriculture (some of the most optimistic statistics estimate we could only produce 10 per cent of our own food), there are other changes that could come with bringing some of the farm to the city.
Not only is diversifying our food sources a bonus, but Teitel-Payne finds that food connects us in different ways to different issues. That connection through food and urban agriculture could empower others to become more vocal on a number of issues.
“Food is that pathway into greater action.” Teitel-Payne said. “What comes out of that is people saying ‘There’s something about our neighbourhood we wanna change.’ Whether it be climate change, political action, access to food, or income or transit, there’s a whole constellation of issues that food touches.”
So where do we start?
Both Teitel-Payne and Wheeler agree condos could hold some potential for the future.
“Let’s start having a discussion with the developers and owners and let’s start cutting out a portion of the space for each condo to have it’s own farm,” Wheeler said. “The condominium right next to us has a beautiful and massive grocery store in it. Well, let’s just add to it. Rather than them having to ship in their food, let’s have it produced on site.”
Until then, Wheeler and Teitel-Payne hope that when people see urban agriculture in action it’ll inspire them to get on board.
“I envision it being a snowball effect,” said Wheeler. “You plant a couple of seeds and let it grow.”
from research and translating knowledge gained from growing up on his family’s open-field farm in Northern Ontario. He works as a financial analyst for a renewable energy provider. He jokingly refers to himself as “a renewable energy crusader by day and an urban farmer revolutionist by night.”
About this article:
By: Katherine Forte
Posted: Dec 4 2017 12:16 pm
Edition: Toronto
Filed in: Arts & Life • Food
Multimedia: Photos
Tagged: alec wheeler • aquaponic farming • Food • gardening • lettuce • tilapia •Toronto • toronto urban farm • Toronto urban growers • waterwheel farms
Vertical Farming is Amazon’s Next Bold Step
Associate Consultant at Bain & Company | Los Angeles | Harvey Mudd ’17 | lakshayakula.com
Nov 4, 2017
Vertical Farming is Amazon’s Next Bold Step
An artist’s (i.e. my) impression
Vertical farming complements Amazon’s business model, the Whole Foods acquisition, Jeff Bezos’s ambitions, and Amazon’s capabilities — it’s only a matter of time until Amazon pours money into vertical farming.
From data centers to organic kale
Amazon is well known for investing in bold, new technologies and businesses. Here’s a list of some of their noteworthy moves:
- In 1997, Amazon set the stage for their logistics network by building theirfirst two fulfillment centers in Seattle and Delaware
- In 2006, Amazon launched Amazon Web Services (AWS); today, as Google is to search, AWS is to the cloud
- Later in 2006, Amazon became a logistics provider by offering Fulfillment by Amazon
- In August 2007, Amazon launched AmazonFresh, starting their ongoing journey to become a grocery provider
- A couple months later 2007, Amazon entered hardware and brought e-readers to the masses by introducing the Kindle
- In 2012, Amazon made a significant step in automated warehouses by acquiring Kiva Systems for $775M
- In 2014, Amazon brought the Amazon ecosystem into the living room, with the home assistant Alexa (and the smart speaker it runs on, Echo)
- This year, Amazon acquired Whole Foods for a whopping $13.7B
At first, it seems like there’s very little in common among Amazon’s ventures. There’s no connection between data centers and organic kale. But there’s method to the madness. A simple business model underlies Amazon’s success.
The Amazon model
For a venture to fit into Amazon’s business model (i.e. the Amazon model), it only needs to have three characteristics:
- High fixed costs with huge economies of scale
- Have Amazon as the first and best customer
- Can be modularized, to offer infrastructural components to third-parties
Here’s how it works. Amazon invests in a new venture with high fixed costs and economies of scale. It can justify their initial investment and provide scale because Amazon’s existing businesses will be a customer of the new venture. The services are modularized to third-parties, increasing scale and decreasing costs, making the new services even more attractive, further increasing scale and feeding a virtuous and unrelenting cycle.
Here’s a diagram of the model. Note that growth is central to the model.
Supposedly drawn by Bezos on a napkin; also resembles a fried egg (Source: Stratechery)
AWS is the best example of the Amazon model at work. AWS is distant from Amazon’s core e-commerce business. For one, the former is B2B whereas the latter is consumer-facing. With conventional goggles, it’s difficult to see why Amazon launched AWS or why AWS has become so wildly successful. With the lens of the Amazon model, we can understand the beauty of AWS.
Let’s see how AWS fits those three characteristics from earlier:
- Cloud services is an industry defined by high fixed costs with huge economies of scale. It’s expensive to build the infrastructure and buy servers at first, but once that’s done, adding the marginal customer is practically free.
- Amazon.com was the first and best customer of AWS. Amazon.com benefits from free web services and AWS gets a jump-start with the initial scale.
- AWS may be the most modularized service in existence — I counted 124 products across 22 categories. It’s so modularized that any company can use its products, from fast-growing startups to multibillion dollar companies to the CIA.
To summarize, AWS started with Amazon.com as a customer, justifying the initial investment in AWS and providing initial scale. It was then modularized for 3rd parties, increasing scale, which AWS used to invest in more capabilities and reach more businesses, further increasing scale and decreasing costs. Today, AWS is in a league of its own in terms of market share and leadership.
AWS’s market share, execution and vision are unmatched by competitors (Sources: Synergy Research Group & Gartner)
The Amazon model is precisely why AWS is so successful. If you want to learn more about the Amazon model, I’d recommend reading Ben Thompson’s blogStratechery (particularly this one).
Making sense of Whole Foods
I promise to get to vertical farming soon, but first, we need to understand why Amazon acquired Whole Foods. The most common explanations are: 1. AmazonFresh will benefit from selling Whole Foods products 2. Amazon can use Whole Food’s urban, retail space, and 3. Amazon Prime can synergize with Whole Foods’s loyal and affluent customer base. These explanations are reasonable but they misunderstand Amazon’s strategy.
Ben Thompson wrote an excellent explanation for how the Whole Foods acquisition ties into Amazon’s business model. In it, he details how the acquisition is effectively Amazon purchasing a customer to provide scale for their grocery efforts.
Amazon’s food delivery service, AmazonFresh has floundered for the past decade. It hasn’t expanded beyond a few urban centers, nor has it given traditional grocery stores a run for their money. The problem is that AmazonFresh fails criteria #2 of the Amazon model — have Amazon as the first and best customer. As a result, AmazonFresh has never built the scale to become competitive.
With the Whole Foods acquisition, AmazonFresh is re-positioning itself as “Amazon Grocery Services” (AGS). The parallelism with AWS is intentional. AGS’s first, large customer is Whole Foods. With this initial scale, AGS will be competitive and Amazon can justify investing in AGS. AGS will modularize and offer services to other grocery stores, restaurants and customers. With increased scale, costs will go down and AGS will become more competitive.
But Amazon isn’t about being competitive. Amazon is about being dominant. In order for AGS to be dominant, AGS needs a technological advantage over its competitors. This key differentiating factor will be vertical farming.
Vertical Farming’s perfect fit for Amazon
Vertical farming comes in many flavors and forms. For Amazon, I envision warehouses near population centers producing greens and herbs. These warehouses will be highly controlled environments, optimized to produce maximum yields.
Currently, vertical farms like these not economical because of high energy costs for artificial lighting. I’m expecting Amazon to be the one to solve this problem and take vertical farming off the ground. And in case Amazon is looking for a name, I have an idea — “Amazon Vertical Farming” (AVF).
Why boils down to three reasons:
- AVF synergizes well with AGS
Both services cater to urban locales and will scale in lockstep. It’s a perfect union. AVF gives AGS a competitive advantage and improves AGS’s scale. Whole Foods will be AVF’s first and best customer. AVF can be modularized by using AGS to sell produce to other grocery stores, households and restaurants. AVF may not be as perfect of a fit for the Amazon model as AWS, but it’s still a great fit. - Amazon has the know-how for vertical farming
To execute successfully, vertical farming will require developments on both the technological and supply-chain fronts. Amazon is the only player with both. Amazon Robotics can automate much of vertical farming and Amazon Logistics can deliver the product to customers. - CEO and Founder Jeff Bezos wants to
To be honest, this is probably the most important reason of the three. Bezos has personally invested in the vertical farming startup Plenty twice: once in a Series A round in 2016, and again in a Series B round in July 2017 just after the Whole Foods acquisition. Clearly Bezos is a believer in vertical farming.
He also has a track record for taking risks. He launched the experimental drone-delivery services Prime Air and created the spaceflight company Blue Origin. Taking a risk with vertical farming wouldn’t be out of character for him.
Most importantly, what more could the third-richest person on Earth want to do than solve one of the biggest problems facing the planet? Agricultural pollution and food waste are pressing issues. With vertical farming, Bezos can make a significant step forward for humanity in addressing these problems.
What’s next?
How Amazon will enter vertical farming is up to debate. It’s possible that Amazon will enter a partnership with Plenty, the vertical farming start-up Bezos has already invested in. I personally believe Amazon will be much more ambitious and acquire Plenty. It’s also possible that Amazon will develop vertical farming capabilities independently, but I find that unlikely given Bezos’s existing investment in Plenty.
Google searching amazon vertical farming as of 09/25/2017, for future reference
Regardless of how Amazon enters vertical farming, one thing is certain. At the time of writing, Google searching “amazon vertical farming” brings up vertical farming products sold on Amazon, including this book and this indoor vertical garden. The 7th link down is the first one to discuss Bezos’s investment in Plenty. With certainty, I can promise that those search results will change significantly in just the next year or so.
Thanks to Rohan Nagpal for the conversations that led to this piece and reviewing my drafts. This really was a collaborative effort. Thanks, bud.
This Company Wants To Solve The World's Hunger Problem. Here's How
Plenty, a new San Francisco–based startup, hopes to step up to that plate. The Jeff Bezos–backed endeavor, which has raised $200 million to date, is dedicated to bringing healthy food to everyone in the world, thanks to a unique system of vertical farms. Plenty, a new San Francisco–based startup, hopes to step up to that plate. The Jeff Bezos–backed endeavor, which has raised $200 million to date, is dedicated to bringing healthy food to everyone in the world, thanks to a unique system of vertical farms
This Company Wants To Solve The World's Hunger Problem. Here's How
November 9, 2017
While we love bringing you functional recipes and sharing the latest in superfood trends, it's hard to ignore the fact that some people simply don't have access to the most basic elements of healthy food. In line with our newly shared You. We. All. mission, it's abundantly clear that if some—many—of us can't find or purchase healthy food, the system isn't working for all of us, and something needs to change.
Plenty, a new San Francisco–based startup, hopes to step up to that plate. The Jeff Bezos–backed endeavor, which has raised $200 million to date, is dedicated to bringing healthy food to everyone in the world, thanks to a unique system of vertical farms. Vertical farming is the perfect antidote to many of the problems that plague the modern agricultural world: It doesn't require land (it goes up, not out); soil (which is often depleted of nutrients from over-farming); sunlight (special low-energy UV lamps are used); or pesticides (Plenty will seek official organic certification within the next calendar year). While vertical farming is incredibly effective in all types of environments, it's especially change-making in urban regions, where thousands of gallons of fuel are typically used to ship produce from more far-flung farms (the time in transit significantly reduces the nutrient contents of produce as well), and countries with environments that don't typically lend themselves to agriculture (many mountainous and desert regions). Vertical farming crops can yield up to 530 times more than typical fields, a huge boon when it comes to quickly getting vegetables to the world's ever-expanding population.
The company has opened two vertical farms thus far, in the Bay Area and Wyoming, with plans for a third to debut in Seattle in spring 2018. The new warehouse is twice as large as the company's first and will grow 4.5 million pounds of greens annually—enough to feed nearly 200,000 Americans. With its large investment, the company hopes to eventually have a vertical farm in every major city in the world.
While there is speculation about the company's future plans—rumors include direct-to-consumer delivery done by robots, among other things—one thing is certain: Plenty is poised to quickly revolutionize the way the world eats.
Liz Moody is the senior food editor at mindbodygreen. She's contributed to Glamour, Women's Health, Food & Wine, goop, and many other publications and is the woman behind the...
Kent To Get Large, Indoor Organic Produce Farm
Kent To Get Large, Indoor Organic Produce Farm
- By Steve Hunter
- Friday, November 10, 2017
Once known decades ago for its many fields of greens as the “Lettuce Capital of the World,” Kent’s about to get its first large indoor organic produce farm.
Plenty, a San Francisco-based firm whose investors include Jeff Bezos, founder of Amazon.com and Kent’s Blue Origin aerospace manufacturer, announced plans this month to open a 100,000-square-foot facility next year near the Amazon Fresh grocery delivery service site along 84th Avenue South.
“Seattle’s emphasis on delicious, healthy food and energy and water efficiency makes the area a natural fit for our next Plenty farm,” said Matt Barnard, CEO and co-founder of Plenty, in a media release. “At nearly 100,000 square feet, Seattle will be home to our first full-scale farm and help set the standard by which our global farm network makes locally grown, backyard-quality produce accessible to everyone. We’re excited about what’s next and look forward to building the Seattle team.”
Plenty’s farm is expected to open in the first half of next year with about 50 employees, including indoor farming engineers, organic growers, and operations experts. Produce grown will be available to Seattle and Vancouver British Columbia area consumers beginning in mid-2018.
“This is a grow we can all get behind,” Ben Wolters, city economic and community development director, said to the City Council at its Tuesday meeting, in reference to the city’s ban against marijuana businesses. “They grow organic produce with LED lights, and yield 350 times what a field of similar size would produce.”
The indoor farm will produce about 4.5 million pounds of greens annually and grow 300 types of produce year-round, Wolters said.
The location near Amazon Fresh, which opened its Kent warehouse this year, makes for a natural connection.
“The idea is Amazon Fresh will buy from here and then ship it out as part of your order,” Wolters said. “They can harvest produce within hours of your order.”
As the amount of domestic acreage that produces affordable fresh fruit and vegetables shrinks while labor and land costs sustain their perpetual rise, Plenty’s expansion is critical to making local, hyper-fresh and organic produce available and affordable for people everywhere, company officials said.
Plenty’s farms, which the company is developing in or near communities around the world, will deliver industry-leading yields of local, backyard-quality produce that’s completely GMO and pesticide-free while remaking agriculture to be both predictable and perpetual given the demands of 7.3 billion people worldwide. Plenty officials say the farms give plants the perfect environment for amazing flavor, use 1 percent of the water and a tiny fraction of the land of conventional agriculture.
The company’s first field-scale farm is in South San Francisco and will start delivering produce to local Bay Area customers within hours of harvest by the end of this year.
“It’s very cutting edge, and the technical and business magazines are covering it,” Wolters said. “It highlights Kent where innovation and opportunity can thrive.”
Why Some Young Workers Are Leaving White-Collar Jobs for Farming
Why Some Young Workers Are Leaving White-Collar Jobs for Farming
December 4, 2017 | Gina Belli
There was a time in the United States when it was very common to work as a farmer. In 1820, 72 percent of the workforce was employed in “farm occupations.” By the late 1980s, that figured had fallen to just about 2 percent.
The industry is aging, too. According to the Labor Department, today the median age of farmers in the U.S. is 55.9 years old. But, that might be starting to change. These days, a growing number of young workers are going into farming, and they’re often leaving behind desk jobs to do it.
Farmers Are Getting Younger
The number of farmers aged 25 to 34 increased 2.2 percent between 2007 and 2012, according to the latest U.S. Department of Agriculture data, per the Chicago Tribune. This is only the second time in 100 years that the number of farmers under the age of 35 has increased. These young people are already starting to have a real impact on this challenging industry.
“There’s real power in the young people and what they’re bringing to this, and to the agriculture, which is a tedious, tiresome, labor-intensive, and low-wage industry,” Henry Gordon-Smith of Blue Planet Consulting told Civil Eats.
There aren’t enough young farmers in this new generation to replace the ones who are retiring. But, the shift could “contribute to the growth of the local food movement and could help preserve the place of midsize farms in the rural landscape,” according to the Chicago Tribune article.
The number of farmers aged 25 to 34 increased 2.2 percent between 2007 and 2012.CLICK TO TWEET
They Aren’t Your Grandfathers’ Farmers
Many of these young farmers didn’t grown up on farms, as farmers often did in years past. Perhaps that’s why they’re open to doing things a little differently. This group is far more likely to grow organically, operate small farms, diversify crops or animals and to be involved in community supported agriculture (CSA) programs and farmers markets.
Other young farm workers are finding work in places like warehouse farms. Indoor agriculture, which utilizes techniques like vertical farming, hydroponics and aquaponics, is expanding in areas in and around cities.
“Food jobs have steadily left our cities for the past 100 years, and local food demand is driving production that is now bringing some of these jobs back to the communities in which their food is produced,” Paul Lightfoot, CEO of BrightFarms, told Civil Eats. “This has no downside for urban markets—it only increases jobs and economic activities.”
What They’re Leaving Behind
Perhaps these young farmers aren’t just moving toward rural farms but also away from office life, and the workday grind that goes with it. Of course, farming is unbelievably hard work. But, it’s a very different kind of experience than what workers encounter in white-collar employment.
“I wanted to have a positive impact, and that just felt very distant in my other jobs out of college,” 32-year-old farmer Liz Whitehurst told the Chicago Tribune. “In farming, on the other hand, you make a difference. Your impact is immediate.”
More than 50 percent of millennials say they would take a pay cut in order to find work that’s aligned with their values. And, 75 percent say they feel that businesses are focused on their own agendas not on improving society. One way to reconcile this is to leave office life behind and blaze a new trail.
Some of these young workers have even been bold enough to leave city life behind and try their hand at rural midsize farming. They might not have the numbers to replace the farmers who came before them, but they might revolutionize our agricultural system just the same.
Do You Know What You're Worth?
Tell Us What You Think
How do you think farming in the U.S. will change in the years to come? We want to hear from you! Leave a comment or join the discussion on Twitter.