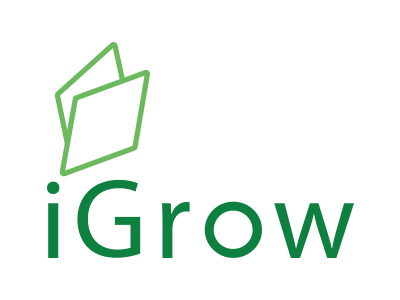
Welcome to iGrow News, Your Source for the World of Indoor Vertical Farming
Green Sense Farms Builds Bridges By Exporting Know-How
Green Sense Farms Builds Bridges By Exporting Know-How
Tony V. Martin
A Portage company has brought new meaning to the phrase, east meets west, by exporting its indoor food-growing technology to China.
Green Sense Farms, of Portage, last year partnered with Star Global Holdings, of the People's Republic of China, to begin building a network of indoor vertical farms that use Phillips LED grow lights to grow produce.
The first farm was built in August in the city of Shenzhen in southern China's Guangdong Province and will serve the Shenzhen area.
Future plans call for building a network of some 20 farms in Bejing, Shanghai and Chengdu to provide fresh, chemical-free produce to major cities in China, said Green Sense Farms CEO Robert Colangelo.
"We're exporting our technology. Food is a bridge-builder. When feeding people, you rise above the political," Colangelo said.
Being able to grow food indoors is something that is new to China but very much needed, given that 80 percent of the aquifer in that country is affected by industrial output from factories.
"So even getting clean water is a challenge," Colangelo said.
By growing a variety of greens and herbs geared to the palate of the Chinese, Green Sense Farms can increase food security and help feed the Chinese people in an environmentally friendly way, Colangelo said.
"It's fun to be part of it. Rarely do you get to be part of something like this," Colangelo said.
Green start
Green Sense Farms started its first indoor growing operation in AmeriPlex at the Port business park in Portage in March 2014. Arugula, cilantro, kale, peas, lettuce and other crops are grown for markets within an average distance of 75 miles, guaranteeing freshness.
The 20,000-square-foot facility — hailed by Popular Science magazine as one of the year's 100 Greatest Inventions in 2014 — produces a large volume of crops year-round in a small footprint, a fraction of the size of a field farm and using much less land, water and fertilizer.
Most of its customers are restaurants, grocers and produce sellers, including Whole Foods, Strack & VanTil and Meijer.
Green Sense Farms is one of just a couple of commercial indoor vertical farms in the state, said Lyndsay Ploehn, a Purdue Extension educator for agriculture and natural resources based in Porter County.
"And Green Sense Farms is one of the first to take their technology to another country," Ploehn said. "They're not traditional farmers. They are kind of thinking out of the box."
Indoor vertical farms are a supplement to traditional outdoor farming, both Ploehn and Colangelo agree.
"It's not going to replace traditional farming. They're not taking away farmland, but are using abandoned buildings to grow food, and land is expensive to produce what they are producing," Ploehn said.
And there have been traditional greenhouse-type businesses in the past that have grown a variety of vegetables and other produce.
"It (vertical farming) isn't new. What's new is the scale they're doing it in," Ploehn said.
The first China farm is expected to produce 750,000 to 1 million heads of lettuce and about 1.5 million leafy greens per year. It's a production level slightly less than the Portage facility, but it's still the start of making a beneficial change in China's food production, Colangelo said.
First there's the population the farm can potentially serve.
Green Sense is starting out in an area of China that has about 50 million people in a 50-mile radius. And after the first farm, there are plans for many more in the area.
"The expansion possibilities are unlimited in China," Colangelo said.
And there's also the quality of product the farm will be growing. China's dense population and large industrial climate has taken away farmland and highly polluted the air, water and soil. By growing produce in vertical towers, Green Sense needs little space compared to a traditional farm, Colangelo said.
Expansion plans
Green Sense is expanding elsewhere, too. Green Sense is partnering with Ivy Tech Community College on a $3 million, 20,000-square-foot farm to be built at 250 E. Sample St. in South Bend.
"We like to be innovative and do things to improve the community and make it more sustainable," Colangelo said.
Green Sense will oversee the farm, but Ivy Tech students will work there in an earn-to-learn setup. Students also will earn credit toward related degrees from the college.
Colangelo's future goals include expanding operations in the United States, Scandinavia and Canada.
Another long-term goal is to spin off a biopharmaceutical business that grows plant proteins using non-GMO seeds that can be synthesized into vaccines and medicine.
Colangelo is a Chicago-area native who has authored books on the environment.
The idea for the indoor urban garden went through many iterations. Colangelo worked with Phillips as a technology partner on lighting and conducted research with Purdue University.
People have been experimenting with vertical farms since the 1980s, Colangelo said. In the case of Green Sense Farms, Colangelo and others integrated and modified an existing system and arrived at a successful product.
"It's ours," Colangelo said.
Colangelo received both his master’s and bachelor’s degrees in earth science from Northeastern Illinois University.
Colangelo spent much of his career in the environmental field, including working with the National Brownfield Association to come up with ideas to clean up the environment.
During his work and research in large cities such as Chicago and New York, the topics of producing food and vertical farming continued to surface.
"We came up with the methodology, and the rest is history," Colangelo said.
Global Vertical Farming Market- Bright Farms, FarmedHere, Garden Fresh Farms, Gotham Greens
Global Vertical Farming Market- Bright Farms, FarmedHere, Garden Fresh Farms, Gotham Greens
Market.Biz Leading Research Firm has added latest report on “Global Vertical Farming Market by Manufacturers, Regions, Type and Application, Forecast to 2021".
By Parnika Paul -
January 13, 2017
The Vertical Farming market report covers forecast and analysis for the Vertical Farming market on a global and regional level. The Vertical Farming industry report provides historic data of 2015 along with a Vertical Farming market forecast from 2015 to 2021 based on Vertical Farming industry volume and Vertical Farming revenue (USD Million). The Vertical Farming includes drivers and restraints for the Vertical Farming market along with the impact they have on the demand over the forecast period. Additionally, the Vertical Farming market report includes the study of opportunities available in the Vertical Farming market on a global level.
The Vertical Farming market report discusses in details about the vendor landscape of the Vertical Farming market. The Vertical Farming Industry has been analyzed on the basis of Vertical Farming market attractiveness and investment feasibility. The Vertical Farming report lists the key players in the Vertical Farming market and provides crucial information about them such as business overview, revenue segmentation, and product offerings. Through SWOT analysis, the Vertical Farming industry report analyses the Vertical Farming market growth of the key players during the forecast horizon.
In Vertical Farming Market report, all the segments have been analyzed based on present and Vertical Farming market future trends and the Vertical Farming market is estimated from 2015 to 2021. In this Vertical Farming report, regional segmentation covers the Vertical Farming industry current and forecast demand for North America, Europe, Asia-Pacific, Latin America and the Middle East and Africa.
Get sample research report at https://market.biz/report/global-vertical-farming-market-gir/25651/#requestforsample
This report segments the global Vertical Farming industry as follows:
Global Vertical Farming Market: Manufacturers Segment Analysis
1 AeroFarms
2 Beijing IEDA Protected Horticulture
3 Bright Farms
4 FarmedHere
5 Garden Fresh Farms
6 Gotham Greens
7 Green Sense Farms
8 Green Spirit Farms
9 Home Town Farms
10 Indoor Harvest
11 Infinite Harvest
12 Lufa Farms
13 Metro Farms
14 Mirai
15 Sky Vegetables
16 Vertical Harvest
17 Uriah’s Urban Farms
18 UrbanFarmers
19 Urban Crops
20 Urban Barns
21 TruLeaf
22 Sundrop Farms
23 Spread
24 Sky Greens
25 SCATIL
26 Podponics
27 Plantagon
28 Metropolis Farms
29 Kingpeng
30 Harvest Urban Farms
31 GreenLand
32 Greener Roots Farm
33 Farmbox
34 Ecopia Farms
35 CityFarm
36 Brooklyn Grange
37 Atlantic Beach Urban Farms
38 Alegria Fresh
39 Agro Strategies
Global Vertical Farming Market: Type Segment Analysis
1. Lighting
2. Hydroponic Component
3. Climate Control
4. Sensors
Global Vertical Farming Market: Regional Segment Analysis
1. North America (USA, Canada and Mexico)
2. Europe (Germany, France, UK, Russia and Italy)
3. Asia-Pacific (China, Japan, Korea, India and Southeast Asia)
4. South America, Middle East and Africa
Report on (Global study on Vertical Farming industry) mainly covers 13 Chapters to deeply display the global Vertical Farming market.
Chapter I, to explain Vertical Farming market Intro, product extent, market summary, market opportunities, market threat, market driving force;
Chapter II, to examine the top manufacturers of Vertical Farming market, with sales, revenue, as well as price of Vertical Farming, in 2015 and also 2016;
Chapter III, to display the Vertical Farming market’s affordable circumstance amongst the top key players, with sales, Vertical Farming market revenue and share in 2015 and also 2016;
Chapter IV, to reveal the worldwide Vertical Farming market by areas, with sales, revenue and market share of Vertical Farming, for each region, from 2011 to 2016;
Chapter V, VI, VII & VIII, to analyze the key regions of Vertical Farming market, with sales, revenue and also market share by manufacturers countries in these regions;
Chapter IX and X, to reveal the Vertical Farming market by type as well as application, with sales Vertical Farming market share as well as growth price by type, application, from 2011 to 2016;
Chapter XI, Global Vertical Farming market forecast, by regions, type and also application, with sales as well as revenue, from 2016 to 2021;
Chapter XII and also XIII, to describe Vertical Farming market sales network, suppliers, investors, suppliers, appendix and also data resource.
Browse More Related Category Research Reports at: https://market.biz/reporttype/market-research/
Blue Planet Consulting 2016 Annual Report
visit blueplanet.consulting in your browser today and learn more
Blue Planet Consulting 2016 Annual Report
- Published on January 11, 2017
Henry Gordon-Smith
Urban Agriculture Consultant
2016 was a year of notable growth for Blue Planet Consulting. For one, we successfully acquired over 15 new client projects, many of which have already been fulfilled to completion. Servicing these clients has strengthened our core team with relevant skills and experience to keep Blue Planet Consulting (BPC) on the forefront of building a thriving urban agriculture industry.
Further keeping our team in the catbird seat of the industry is our continued management of both Sky Vegetables and Stonebridge Farms. Managing these commercial farms for our partners has supplied BPC with more of the relevant knowledge and experience to be able to provide our clients with data-driven and first-hand operator insights. Our involvement with these facilities proved highly useful in multiple client engagements in 2016. Typical urban agriculture problems surrounding waste, labor, energy, sales, and marketing are being overcome by our growing team every day.
Related: Blue Planet Consulting 2015 Annual Report
Another major 2016 development for BPC is that my blog, the Agritecture platform has signed an agreement to be added into the Blue Planet family. This move has diversified BPC’s capabilities, giving the company access to quickly communicate to a growing community of urban agriculture professionals. Agritecture’s strong audience growth in 2016 gives me confidence that BPC will continue to develop its ability to influence the industry. This partnership also allows us to grow the amount and quality of knowledge we share through the platform as we have now hired our first employee: Community Manager Andrew Blume.
2016 was a year where BPC sharpened the methodology we use to help our clients overcome the challenges of developing urban agriculture businesses. Whether those challenges are zoning complexity, site and crop selection issues, recruiting strategies, yields and waste calculations, or implementing a new sales strategy for your product – BPC has likely serviced clients with similar issues facing your team.
In the report below, we showcase some of our work in 2016, from client engagements to industry events and partnerships we have supported. These activities depict how we have helped entrepreneurs and large companies navigate the uncharted waters of planning, implementing, and operating their urban agriculture business.
Thank you for your time and interest in our company’s 2016 endeavors. On behalf of my whole team, I wish you a warm, healthy, productive, 2017!
Sincerely,
Our 2016 Client Engagements
We conducted a feasibility study for Rob Laing, CEO of Farm.one and helped turn his brilliant idea of growing rare culinary herbs in Manhattan into a reality. We assisted Farm.one with crop selection, site selection, design, and economic analysis. We even assisted with the installation of Farm.one. We also helped Rob recruit his head grower, the talented David Goldstein. We are happy to hear that Farm.one is expanding its operations to another facility in 2017!
The Child Development Services Corporation (CDSC) is one of the only food banks with a vertical farm within it, providing fresh and clean produce to Clinton Hill residents in need. The farm was originally installed by Boswyck Farms 5 years ago and was in need of a retrofit. We assisted CDSC with a retrofit of the lighting, plumbing, and nutrient dosing systems. We also made the vertical farm more ergonomic for its users. CDSC benefitted from an updated management manual of the farm we developed as well as a training we conducted for their volunteers.
A large Chinese manufacturer wanted to explore how converting some of its facilities into a “green campus” could improve worker health and wellbeing. We provided a rapid concept development service including sketching out four interventions to their existing facilities that would improve oxygen within the factories, provide some produce for consumption, and improve overall well being. The final results were a set of renderings which we pitched to some of the companies executive team who continue to discuss the possibility of developing the green campus in 2017.
Our storefront office in Brooklyn certainly catches the eyes of pedestrians passing by. Josh Smith is a local resident and world-renowned artist that saw the +FARM in our window and ask us to design a custom system for his basement. We consulted with Josh what he wanted to grow and designed a system that fit his space and budget. Now Josh and his wife can enjoy leafy greens and microgreens year-round from their home.
Another community group in Brooklyn that has a system originally set up by Boswyck Farms requested our services to update the system. We advised them on means to improve their management of the farm and also recommended certain equipment upgrades.
This organization serves special needs students and families in New Jersey. We conducted a feasibility study on the costs and benefits of converting an unused ~3,000 sf warehouse into a commercial vertical farm for the purposes of generating additional revenue for the school. Our team completed design of the farm and even conducted focus groups with local residents to determine crop selection and packaging choices. The Reed leadership and board are considering funding options and partnerships to develop the vertical farm in the near future.
Global LED Company
We were hired by a global LED manufacturer to conduct market research and analysis to understand the potential for a new product they were considering developing. Our team developed a thorough document reviewing the potential for the product, target customers, pricing, and marketing strategy recommendations.
We assisted Brooklyn’s newest urban farmers and its only urban agriculture accelerator Square Roots launch their first campus. Our primary contributions were on recruiting, curriculum development, and horticulture planning. Now, many of our team serve as mentors to the 10 entrepreneurs that are growing real food in shipping containers in Brooklyn. Read more about Square Roots here.
Grownex USA chose us to help them launch their brand and new product Salad Wall at NYC AgTech Week. We were happy to assist them by building their first US website, social media accounts, and marketing strategy. We also displayed their system in our office getting them their first customer as a result of the exposure we provided them. Grownex is growing its sales to the US market in 2017 and Blue Planet Consulting is excited to continue to help them share their unique product Salad Wall with the US market.
Phillips Programs (Phase II)
Two years after helping our first client Phillips Programs in Maryland install a hydroponics learning lab (pictured), we were able to help them design their next phase: an additional six vertical microgreens systems. For this project we partnered with our local contacts at Modernature and co-designed cultivation systems that were appropriate for the Programs’ special needs students. Phase II of the Phillips’ Growing Futures Program is set to launch in Spring 2017.
BMoreAg
Also in Maryland, this client is interested in making a big impact on jobs and food security in Baltimore. We are assisting this client with concept development for now and eventually a full feasibility study. The plan is to convert a large vacant lot into a productive mix of vertical farming and greenhouse operation with an on-site market.
We are very excited to be working with Goler CDC, one of Winston-Salem, North Carolina’s well known community groups. Our role in their latest project is to provide a comprehensive feasibility study on converting a vacant lot into a series of greenhouses. This project is currently in progress with the site visit complete and crop selection underway. We will be providing Goler CDC with everything they need to get the project moving forward including equipment selection, economic analysis, management planning, and recruiting. The project is set to break ground in 2017.
Global Investor
We provide a benchmarking and case study report to a global investor interested in understanding the ins and outs of vertical farming. The list was comprehensive and included both case study data and analysis from our team of consultants and the investment climate of the emerging vertical farming industry.
Entrepreneur in Dubai
CJ is a young Dubai-based Indian entrepreneur looking to launch a model for vertical farming in Mumbai, India. We are developing a vertical farming concept for CJ that considers the opportunities and challenges of the local market and climate. Crop selection, pre-sqf costs, and a pitch deck are in progress to help CJ raise money for his unique vertical farming idea.
2016 Agritecture Workshops
In 2016 we conducted three Agritecture workshops:
· Fresno, CA (Feb)
· London, UK (June)
· Boston, MA (Dec)
These three 2016 workshops have brought the total number of Agritecture workshops to seven (7). Agritecture workshops match interdisciplinary teams of architects, growers, entrepreneurs, engineers, marketers, designers, and sustainability managers together for a shared mission: to develop a viable “agritecture” concept for the host city.
The Agritecture Design Workshops comprise of three teams, each matched with the goal of demonstrating creativity, sustainability, and feasibility when integrating agriculture into cities. On-site mentors from Blue Planet Consulting guide participants through urban agriculture project planning, hydroponic agriculture, and sustainability.
In the past, Agritecture Workshops were typically planned in partnership with the Association for Vertical Farming. For the Boston Agritecture Workshop, and for future workshops, this will no longer be the case. The AVF has indicated they will seek to develop their own proprietary workshop series, although they may still occasionally promote future Agritecture workshops.
We would like to thank our main sponsors for the three 2016 workshops included the following companies:
Agritecture also began offering sponsored content packages in 2016. These packages helped innovative companies showcase their products or services to our audience of 30,000+ vertical and urban farming enthusiasts. Contact Andrew@agritecture.com for more information on how you can reach our primarily millennial and gen-X audience.
2016 Milestones
January
- Hired new Engineer Jeffrey Landau
- Acquired new client Farm.one
- Visited the first installed Growtainer in NYC
- Completed DIY vertical farming kits for 2016 client Bergen Academies
February
- Hosted Agritecture Workshop in Fresno, California
- Attended GFIA conference in Abu Dhabi
- Attended FarmTek CEA Workshop
- Acquired new client CDSC
- Acquired new client Foxconn
- Became an Autodesk Entrepreneur Impact Partner
March
- Attended U of A CEAC Short Course
- Attended and Spoke at Thought For Food Summit in Zurich, Switzerland
April
- Attended Indoor Ag Con
- Participated in Urban Agriculture Roundtable with Brooklyn Borough President’s Office
- Acquired new client Los Surres
- Acquired new client Reed Academy
- Initiated the California Urban Agriculture Collective
- Attended Food + Future CoLab event @ IDEO in Boston
- Acquired new client Josh Smith
May
- Attended Silicon Valley AgTech Conference
- Spoke at first AgroHack conference in Puerto Rico
- Acquired new client Global LED Manufacturer
- Hired West Coast Representative David Ceaser
June
- Sponsored AVF Summit 2016
- Conducted first international Agritecture Workshop in London, England
July
- Acquired new client Square Roots Urban Growers
August
- Acquired new client Grownex USA
- Hired Djavid Abraham as our new Lead Systems Designer
September
- Participated in 2nd annual NYC AgTech Week
- Acquired new client Global Investor
- Started phase II for client Phillips Programs
- Hired MIT CityFarm veteran Elaine Kung to join our team as a designer
October
- Spoke at the Canadian Greenhouse Conference, offering the first talk on Vertical Farming to ever be featured at the event.
- Attended Chicago LED Magazine Event
- Attended and spoke at Fluence Bioengineering PhotoX event in Austin, TX
- Attended LARTA Institute Urban Agriculture event in Los Angeles
- Whitehouse announces our DIY vertical farming system +FARM on its website
November
- Hired Andrew Blume to join our team as our Community Manager for Agritecture.com
- Spoke at Building Success event sponsored by Microdesk in San Francisco
- Acquired new client Goler CDC
- Attended Seedstock Grow Local OC event
December
- Acquired new client based in Dubai
- Launched Aglanta: the South’s first CEA conference together with the Mayor’s Office of Atlanta and with platinum level sponsor, Southern Company
Our 2017 Strategy & Outlook
2016 was a big year for proving that Blue Planet Consulting’s methodology and team are capable of meeting industry challenges. Our acquisition of high-profile customers such as Foxconn, Square Roots, and Southern Company are evidence that as urban agriculture becomes more mainstream in 2017, BPC will play a role in assisting more high-profile organizations to enter the space successfully.
While we are ecstatic to have worked with these influential customers, we are also proud that we continued our practice of servicing school and institutional clients at a reduced rate. We’re excited to continue working for these small niche customers and adding more value to their installations with the introduction of the +FARM in 2017. We work with these clients because corporate social responsibility is a major motivating factor for our team. Thus, we fully intend to continue devoting resources to communities and clients of all shapes and sizes in 2017.
I can’t think of a more perfect example of how we will engage with big and small, business and education, industry and community, then the Aglanta Conference on February 19th, 2017. Aglanta will be organized by BPC, the Mayor’s Office of Atlanta, and by the conference’s platinum level sponsor, Southern Company. Alongside these entities will be Aglanta’s keynote speaker, Stephen Ritz, who is the undisputed champion of growing in schools.
I encourage you to purchase tickets to Aglanta here or contact me to get your company involved. There are still some exciting opportunities to exhibit or sponsor the event!
Only a crystal ball with tell us exactly how urban agriculture will manifest in 2017. While there are challenges and risks, we are confident that this is the year lucrative and impactful businesses will emerge. If you intend to pioneer and develop alongside the industry, we encourage you to contact us to see how we can work together to turn your growing aspirations into growing operations.
Request your urban agriculture, greenhouse, or vertical farming feasibility study here.
Vertical Farming May Not Feed The World, But Could Empower Cities
Vertical Farming May Not Feed The World, But Could Empower Cities
BY LISA NIKOLAU ON 11 JANUARY 2017
Aware of population growth’s growing impact on global food security, many agricultural experts are debating the use of vertical farming – and its ability to feed the world – but don’t deny its potential in urban agriculture.
Vertical farming is a relatively new term that, at its core, simply means growing more food in smaller spaces. Instead of having a single layer of crops over a large land area, for example, stacks of crops climb upward, typically in highly controlled indoor environments.
The method usually grows crops without soil or natural light. It’s dramatically different from how humans grew food just a few decades ago, but has the potential to produce drastically higher yields with significantly less space.
For humanitarians, the idea is tantalizing. The world’s population is exploding at an exponential rate, stressing the need to find ways to feed people without further destroying the planet. Proponents say vertical farming uses less water and fossil fuel than outdoor farming and eliminate agricultural runoff, all while providing fresh and local food.
As the concept garners both attention and legitimacy, vertical farms are already popping up in Seattle, Houston, New York and Milwaukee, as well as Linköping, Sweden. Some enthusiasts have even considered the rise in vertical farming the “third green revolution.”
Whether the model can be used among the rural poor – where the bulk of the world’s food is grown, in countries with highest food insecurity – is still up for debate.
“Can vertical farming feed the world? I’ll tell you right now: No it can’t,” said Erik Cutter, founder of California-based urban farm company Alegría Fresh, in an interview with Humanosphere. “It’s too expensive to feed the world.”
According to Cutter, the price tag on the type of vertical farm tower conceptualized by Dickson Despommier – the ecologist credited for modernized the idea of vertical farming – can be upward of $1 billion.
He said such a model might intrigue the elite, but is irrelevant to the majority of the world’s farmers. For them, many agriculturalists say building food security would rely on the adoption of regenerative agriculture – a range of techniques with the aim of restoring soil fertility and sequestering carbon.
In Irvine, Calif., Cutter uses a hydroponic vertical farming system – utilizing coconut fiber instead of soil, and powered by the sun – but is quick to describe its shortcomings. Vertical farms generally have a limited range of crop species, such as leafy greens or herbs, and its energy requirements are debated among critics who say lighting and other necessary equipment have a heavy impact on the climate.
But the biggest problem with vertical farming, Cutter adds, is that there isn’t an economic model to sustain it.
“Really, we have to train thousands of thousands of farmers in this country to farm differently, plus source capital, plus develop a market for that food,” he said. For this reason, he says one of his goals is to create decent-paying jobs in urban agriculture.
Even if it can’t feed the planet, proponents of vertical farming say it could at least work for the world’s cities. One of the largest, AeroFarms in Newark, N.J., appears to have created a sustainable economic model. An in-depth look at the company by the New Yorker explained that its main crop is baby salad greens because its premium price makes the enterprise attractive – and because it’s easy to grow.
If sustainable, such enterprises could help prevent cities from what urban agriculturalists warn is the inevitable: intolerable overcrowding with overwhelmed sanitation systems, housing, water and, of course, food. If the bulk of food production could happen close to these highly concentrated centers, the hope is that urban populations could harbor some control of their food supply.
The Great Indoors
The Great Indoors
You’ve heard of recipes for food, but have you heard of a grow recipe? That’s exactly what Philips Grow Wise is developing with partners such as Grow Up Urban Farms in London. Together they are pioneering city farming in the U.K.
By Pithrika Nair.
Any Smart City vision is incomplete without smart food. The current world population of 7.3 billion is projected to reach 9.7 billion in 2050. Of that population 7.7 billion (80 per cent) are expected to live in cities. The UN Food and Agriculture Organization (FAO) also estimates that farmers will have to produce 70 per cent more food by 2050 to meet the needs of these 9.7 billion. Notwithstanding the fact that the quantity of food produced isn’t a safeguard against world hunger (we currently produce enough food to feed the world’s population, but 795 million people still go hungry due to poverty), there is a pressing need to produce more food, with greater efficiency, and a lower carbon footprint.
A potential answer to the problem of food production is urban indoor agriculture, the growing of crops in a building within or near a city, using artificial light to stimulate photosynthesis. The controlled system helps growers reduce or eliminate pesticides and other chemicals, and its proximity to the end consumer ensures fresher produce with greatly reduced food miles. The quality of the solution is driven by how lighting, climate control, software controls, sensoring and logistics work together.
Kate Hofman and Tom Webster founded Grow Up Urban Farms in 2013 as London’s first commercial urban farm. Housed inside an industrial warehouse, the farm combines aquaculture (fish farming), with hydroponics, the practice of growing plants in a nutrient solution with no soil. This is a symbiotic system with one product, the fish, providing fertilizer for the second product, the plants.
With a year round growing season, the 6,000 sq. foot urban farm produces 20,000 kg of salad greens grown in vertically stacked trays under Philips LED lighting. Researchers at Philips GrowWise Center have developed precise ‘growth recipes’ for each product. Just like a cooking recipe, a growth recipe includes an ingredients list and a method, and Philips provides extensive support in both areas to ensure the end result meets the customers’ exact needs.
The ingredients list is the lighting system itself: the type and number of LEDs and where to place them to deliver the optimal lighting conditions and coverage for the plant type and greenhouse set-up, and the growth system.
The full package includes the technology hardware such as racks and automation and software like climate (temperature, humidity, CO2) as well as plant material, fertilizers and growth media. A ‘growth recipe’ helps farmers to optimise their farm systems for productivity.
According to Gus van der Feltz, director of City Farming at Philips, “Indoor growing systems based on LED lighting can maximise plant photosynthesis, for the most delicious and nutritious vegetables grown in a sustainable manner. Growing crops vertically makes it possible to pack more plants per acre, in a much faster way, than would be possible with a field farm, which means more harvests per year. With little waste, no agricultural run-off and more than 90 per cent reduction in the water used to grow clean and healthy food.”
This hyper-controlled growing environment enables better, faster, tastier, cleaner plants through light recipes, in clean air with no pesticides or crop protection.
At the Philips GrowWise research facility in Eindhoven, growers and plant specialists trial a variety of crops under different lighting and climate conditions for a variety of purposes.
“At Philips, we are teaming up with partners to bring this new innovation to the next level,” says Gus van der Feltz. “We are also looking forward to discovering what else can be achieved through this new form of high-tech horticulture. We have already seen that we can increase the amount of vitamin C in tomatoes, colour lettuce, and affect the taste and smell of basil through the smart use of LED light and growth recipes. And it’s possible to grow different varieties indoors. So we certainly have an interesting future ahead of us.”
Does this mean we’ve found the solution to the population-food-location quandary? Not yet. Although the potential unlocked by the LED technology is promising, urban indoor farming still faces several challenges before it starts producing significant, sustainable, and affordable food on a large scale.
A critic of indoor growing systems, Louis D. Albright, programme director of Controlled Environment Agriculture at Cornell University, estimates the high amount of energy required to provide 100 per cent of the light and heat needed doesn’t result in environmental benefits. He found one kilo of tomatoes farmed indoors produces 11-13 kg of CO2 (2-4 kg CO2 in production and 9kg of CO2 in lighting), while tomatoes farmed and transported from California to New York produced 0.6 kg of CO2 (0.3 Kg of CO2 in Production + 0.3 Kg of CO2 in Transport).
What if that energy came from renewable sources? Bruce Bugbee, director of the Plants, Soils & Climate department at Utah State University says, “If we’re going to use solar panels, we’d need 5.4 acres of solar panels to provide 1 acre of sunlight equivalent.”
Based on the current technology and energy options, it’s high end, expensive crops such as herbs and microgreens that offer the best business options for indoor farming. These are the limitations Jeremy Rifkin pointed out (in his presentation to the government of Catalunya), in attempting to plug smart city solutions into a fossil fuel infrastructure.
In an ideal future, a digitised internet of energy would be able to provide renewable energy at the price and efficiency needed to make indoor urban agriculture a viable production option.
The area where high efficiency agricultural LEDS such as those developed at Philips Grow Wise are able to have the most significant impact is as supplementary lighting in greenhouses.
Brookberries Venlo BV grows and supplies strawberries in Venlo, Netherlands. It previously used incandescent lamps to elongate the strawberry plant and encourage growth, but the sale of many types of incandescent lights was banned in the EU from 1 September 2012.
Owners Marcel Dings and Peter van den Eertwegh used the opportunity to trial different technology options, deciding finally to deploy the Philips GreenPower LED flowering lamp on their farms. This has resulted in a staggering 88 per cent reduction in their energy consumption as well as the ability to start harvesting earlier in the year (February and March, rather than in May).
Improved temperature control is also a big plus for Dutch tomato grower Jami. Its grow recipe combines overhead high-pressure sodium lamps with LED lamps hung among the crop to illuminate the lower parts of the plant. The LED lamps can be placed close to the plants without damaging them but also add a little bit of warmth – which the tomato plants thrive on.
Through the placement and monitoring of the LEDs the temperature in the greenhouse is carefully controlled, lengthening the growing season into an all year production. Jami has seen its energy bills fall by 10 per cent, while yields have risen by 35 per cent. Thus, although its energy consumption is high, urban agriculture also benefits greatly from increased control and efficiency.
Citizens within the smart city communities have the chance to gain an understanding and sense of connection with their food, as well as the chance to eat high quality products which have been naturally optimized through light control. Hofman from Grow Up Urban Farm says, “With the lighting we get really good color across the leaf, really good shape, and a really strong and solid product. Everything is delivered to local customers within 12 hours after harvest.”
Twelve hours from harvest to your plate in the heart of London is a significant step in the direction of smart, sustainable food.
If you enjoyed this, you might wish to look at the following:
Philips Lighting looks to the future
Future innovation has its roots in real life projects that are happening right now
smartcitiesworld.net/news/news/philips-lighting-looks-to-the-future-1129
International Congress on Controlled Environment Ag 2017
May 17 - May 19, 2017
Event Navigation
This second event of its kind, the ICCEA 2017 will continue to be the place to engage, learn and apply the foundations of controlled environment agriculture (CEA) for greenhouse and vertical farm owners and operators.
The many benefits of the ICCEA 2017 include:
Meet and network with like-minded professionals and industry experts from around the world.
Learn the latest in CEA advancements, Ag Tech and growing techniques while acquiring in-depth knowledge on the growing of specific products and crops.
Meet with academics, inventors, innovators, investors, manufacturers and suppliers providing the latest in technology and innovation.
Attend the culturally exciting Gala and Innovations Awards Dinner.
The ICCEA 2017 is an event where attendees will have the opportunity to learn from renowned experts in the applied fields of science, horticulture, lighting, robotics and engineering, from some of the most prestigious universities including Chiba University (Japan), National Taiwan University, the Massachusetts Institute of Technology (MIT), the University of Arizona, Cornell, Michigan State University, Wageningen University (Holland) and many others including the National Aeronautics and Space Administration (NASA).
The FDCEA seeks to make CEA, whether greenhouse or vertical farms, the answer to the future of agriculture with a primary focus on the creation of sustainable and profitable agriculture businesses.
ICCEA 2017 will focus on:
Understanding Technology Used in Producing Greenhouse and Vertically Farmed Produced
Understanding Nutrients used in Hydroponics
Learning the latest research available on controlled environment crops
How LED Grow Lights impact photosynthesis and plant growth
Learning new production techniques
Managing Your CEA Business
Automation and Robotics
Integrated Pest Management Strategies
and more!
Feel-Good Story About The Future of Vertical Farms
Feel-Good Story About The Future of Vertical Farms
There's really nothing not to love about vertical farms -- multi-story hydroponic operations, usually sited in dense urban areas -- they borrow their best tech from the space program, they're water-conserving, they don't have runoff, they're energy efficient, and they're super land-efficient, meaning we don't need to turn forests or wetlands into fields.
The New Yorker's profiles of the inventors of modern vertical farming has the usual New Yorker lyricism and slightly-too-long-ism, and is a little short on technical details, but it left me with a warm glow this morning. It's a good example of bright green tech, the kind of thing we'll need as our population stabilizes at 9 billion -- the alternative being the "de-growth" dystopia that starts with 4-6 billion people somehow departing the planet.
For now, vertical farms focus on selling high-margin/high-ticket baby greens in fancy grocery stores, but its proponents argue that they'll scale up through luxury goods, then Moore's Law their way down to the rest of the world. There's also a curious note about a secret process for misting or steaming the veggies that uses a proprietary and unpatented system that the inventor believes no one will ever be able to figure out, which is a claim that the writer allows to pass without comment, despite its extreme implausibility.
AeroFarms occupies three other buildings in Newark aside from the main vertical farm, on Rome Street. At 400 Ferry Street, it has a thirty-thousand-square-foot space whose most recent previous use was as a paintball and laser-tag entertainment center called Inferno Limits. The graffiti-type spray-painted murals and stylized paintball splatters of that incarnation still cover the walls. AeroFarms’ headquarters—sometimes referred to as its “world headquarters”—are in this building, some of which is taken up by a multiple-row, eight-level vertical farm that glows and hums. Technicians in white coats who wear white sanitary mobcaps on their heads walk around quietly. Some of these workers are young guys who also have mobcaps on their beards. The salad greens, when you put on coat and mobcap yourself and get close enough to peer into the trays, stand in orderly ranks by the thousands, whole vast armies of little watercresses, arugulas, and kales waiting to be harvested and sold. For more than a year, all the company’s commercial greens came from this vertical farm.
Nobody in the building appears to have an actual office. Employees are distributed in more or less open spaces here and there. In a dim corner of the area with the vertical farm, where the fresh, florist-shop aroma of chlorophyll is strong, young graduates of prestigious colleges confab around laptop screens that show photos of currently germinating seeds and growing leaves. Folding tables burgeon with cables, clipboards, and fast-food impedimenta. David Rosenberg, the C.E.O., who hired Ingrid Williams last year, is the boss. This distinction is hard to notice, because he looks more or less like anybody else.
What Will 2017 Bring For Indoor Ag?
What Will 2017 Bring For Indoor Ag?
JANUARY 4, 2017 NICOLA KERSLAKE
Editor’s Note: Nicola Kerslake is the founder of Newbean Capital, a registered investment adviser that manages early stage venture capital mandates and that has a particular interest in indoor agriculture. It owns the Indoor Ag-Con events business as well as an indoor agriculture alternate financing business Contain that is currently in pilot stage. The next Indoor Ag-Con event will be held in Singapore on January 24-25, 2017.
Here Kerslake offers some predictions for the indoor agriculture industry in 2017.
For all of the year’s many horrors, 2016 was a banner year for indoor agriculture, the practice of growing crops in hydroponic, aquaponic and aeroponic systems in greenhouses, warehouses, and containers. The fledgling industry saw record investment fueling a wave of new indoor farm builds, innovative business models, and technology introductions.
Highlights included the launch of Square Roots, a Kimbal Musk-backed social-benefit endeavor to incubate new urban farmers utilizing Freight Farms’ container farms, and the inauguration of Aerofarms’s long-anticipated Camden, NJ vertical farm. The latter is notable because it uses aeroponics — misting plant roots with a nutrient-rich solution, rather than submerging them in water – and this is typically considered a trickier technology to implement commercially than the more common hydroponics. The upside is, in theory at least, more efficient growing. Both Freight Farms and AeroFarms raised equity from private investors during 2016, contributing to the $50m+ raised from private investors in the US last year.
We expect to see accelerating activity in 2017 thanks to better economics and more farm and technology launches. Here are six ‘big themes’ for the year ahead:
1. The First of the Mega Farms
Indoor farms run the gamut from a basic home-built set up using equipment bought at Home Depot to custom engineered 100,000 ft2 facilities. With a few notable exceptions – such as those growing for the pharmaceutical industry – the US market has mostly used vertical farms to date; mid-sized farms that stack growing racks to maximize space in a warehouse or repurposed building.
Their cooler cousin is the ‘plant factory,’ a term coined in Japan to describe multi-layer growing in clean room conditions using increasingly sophisticated monitoring and control systems to optimize growing conditions. These are large-scale operations, “farming as manufacturing.” The Japanese company, 808FACTORY, has its own data server running at its plant factory, for example. Plant factories are commonplace in the more advanced Asia market – Japan has more than 200, China more than 80 – and we expect them to become a feature of the US one in 2017. For instance, Japanese plant factory company Spread has publicly discussed its search for US partners, while Middle Eastern greenhouse company Pegasus Agriculture leased a large parcel of land in Florida in 2016, though the latter will more likely be used for next-gen greenhouses than for plant factories.
Funded by low-key rounds or by overseas parent companies, new mega-farmers are typically shyer than the likes of BrightFarms or AeroFarms. A few will eventually discuss their work in public, but the majority will stay on the downlow, focused on the complex business of adapting new crops to indoor systems or applying machine learning techniques to improve yields.
2. Indoor Ag goes Mainstream
When we first got involved with the indoor agriculture industry nearly six years’ ago, we spent a good deal of our time explaining the sector to other investors. The vast majority saw it as too small, too niche and too risky to be of interest. A combination of time, technology advances, and a halving of the price of the LED lights — they make up around half of a farm’s capex — has made a big difference. The attention paid to legal cannabis has also helped; its newfound respectability has a halo effect for other crops grown in indoor farms. Now, we receive a couple of inbound calls a week from new investors looking to get into the sector, one of the reasons that we have authored five white papers on various aspects of the industry.
In turn, this influences the kinds of companies that become involved in the sector. Recently, big box retailer Target announced its plans to test in-store vertical farms in the spring, and telecoms major Ericsson demoed an aquaponics project utilizing its IOT-based controls. We expect to see more “big names” announcing their involvement in indoor agriculture this year, whether that’s large produce buyers, technology providers, or long-established farming majors diversifying their growing techniques.
3. IoT Everything
Given the controlled environment in which they operate, indoor farms are well suited to the application of ‘big data’ techniques and a range of startups are joining established industry players in introducing these. Agriculture control majors – Argus Controls, Hortimax, Priva – benefit from long histories of working with customer data, and others are taking innovative approaches to pilot new products. For example, New Zealand-based Autogrow raised a sub-$5m round in 2016 to create an open platform for its controls products and TechCrunch Disrupt winner Agrilyst launched a greenhouse management platform. Up next, we expect to see machine learning-based approaches launching commercially.
4. In-Home Growing
Ubiquitous furniture retailer IKEA has been rolling out an in-home hydroponic range recently and is about to see competition from a wave of in-home growing startups. Some examples of the next generation include SkyDeck graduates Verdical and app-controlled Grobo. We expect that those that gain market traction will be looking for seed and A rounds in 2017, following in the footsteps of an earlier wave of strategic and VC-backed in home systems, such as Scott’s Miracle Grow’s AeroGardens and Upfront Ventures’ Grove Labs.
5. The Crickets are Coming
As alternative proteins – plant-based meat, insects – become commercially available, we anticipate that indoor agriculture will be a part of figuring out the supply chain for these approaches. For instance, cricket farmers, including equipment provider Bitwater Farms, super-angel backed Tiny Farms and Thailand’s Eco Insect Farming, are already adopting and adapting indoor farming techniques.
6. But It Won’t All Be Roses…
A high business failure rate is one of the characteristics of startups, and indoor agriculture is far from immune. This is especially true for the mid-sized vertical farms that make up the bulk of the US market, some of which have yet to hit a scale or figure out a business model that allows for a decent operating profit. If the trajectory of analogous industries – such as solar – is anything to go by, some will merge, others will pivot to new business models, and some will fail. While wretched for the hard-working farmers involved, we view these failures as a necessary part of the industry’s rapid growth. Private and VC investor-backed indoor farmer PodPonics, for instance, shuttered its Atlanta, GA, farm this year to focus on its Middle East technology operations, and we expect to see more of the same as indoor agriculture matures.
By the end of 2017, we expect to see a larger, and stronger, US indoor agriculture industry, able to benefit from a wider variety of technologies and anchored by the beginnings of its own plant factory revolution.
UAE Innovators Invited to Present Game-Changing Solutions at Global Forum for Innovations in Agriculture
UAE Innovators Invited to Present Game-Changing Solutions at Global Forum for Innovations in Agriculture
Open call for innovations to join fight in feeding growing population, improve agricultural productivity in MENA
Cutting edge businesses, start-ups, researchers, scientists and entrepreneurs of the UAE are being encouraged to present their game-changing agricultural innovations to an influential audience who have the ability to take their solutions to the next level and help tackle food security.
The Global Forum for Innovations in Agriculture (GFIA) is the world’s influential event for the future of sustainable agriculture. The two-day event returns to Abu Dhabi in March 2017 and the Call for Innovations is now open for anyone who believes they can help make a difference to the way in which farmers and growers work and produce food in the MENA region.
From pioneering entrepreneurs to established businesses, more than 300 innovators have presented their solutions and technologies on stage in front of thousands of investors, food producers, retailers, government delegations, scientists and NGOs since the launch of GFIA in 2014.
Facing water scarcity supply and limited availability of fertile land, the Middle East heavily relies on food imported from abroad and the UAE, Egypt as well as Saudi Arabia are among the top fifteen global importers of food, according to a 2015 World Trade Organisation report.
While The Global Food Security Index, developed by the Economist Intelligence Unit (EIU) in partnership with DuPont, indicates that the MENA region made improvements in food affordability, availability, quality and safety between 2014 and 2015, the progressing impacts of climate change will pose new challenges to the region with its soaring population.
According to Alpen Capital's 2013 GCC Food Industry Report, the region will require 49.1 million tonnes of food per year by the end of 2017 with the UAE leading as the largest consumer at 1,486kg per capita annually.
To address this demand, the private sector in partnership with governments should be actively seeking innovative solutions that tackle food security, nutrition and distribution challenges.
“We’re seeking applications from budding entrepreneurs, innovators and practically anyone who has an idea they think can challenge conventional methods of agricultural farming,” said Nicola Davison, GFIA Event Director.
“We’re especially encouraging those from Abu Dhabi and the wider UAE community to come forward. Now is the time to share your ideas and innovations that can help farmers improve productivity in our region in a sustainable way and help to counter global hunger through pioneering developments in sustainable agriculture.”
All entries should be made online at www.innovationsinagriculture.com before the 31August 2016 deadline, and will be judged by a network of international partners including Anterra Capital, McKinsey, the University of Wageningen, CGIAR and the University of Arizona.
The programme for next year’s event will cover the entire agricultural spectrum, with a particularly strong focus on themes most relevant to the MENA region including climate-smart agriculture, disease and pest management, salt water agriculture, water management, ICT solutions and organic agriculture.
New features to the show include an expanded livestock area, a start-up pavilion to help emerging ag-tech companies meet potential investors, an AgriFood Leaders Forum and a Demo Zone where exhibitors will give live and practical demonstrations of their products and systems.
Speakers from the 2016 edition included His Excellency Dr Thani bin Ahmed Al Zeyoudi, Minister of Climate Change and Environment, His Excellency Rashed Mohammed Khalfan Al Shariqi from Abu Dhabi Food Control Authority, Aidan Cotter from the Irish Food Board, Mamadou Biteye from the Rockefeller Foundation in Kenya, and Haydar Alsahtout from the Arabian Shrimp Company in Saudi Arabia.
“Earlier this year, more than 6,000 visitors from 96 countries descended upon Abu Dhabi to take part in dozens of presentations and panel discussions uniquely designed to tackle world hunger and food security in the face of climate change and resource scarcity,” added Davison.
“We saw more than 80 game-changing innovations for agriculture presented on stage and many of these innovators have met investors, science partners and technology buyers to take their innovations to the next level.
“This year, we plan to present even more solutions and technologies that have the ability to influence the way in which food is produced. We have to collaborate if we are to feed 9 billion people by 2050 while facing the challenges caused by changing climate.”
US: Food Retailer Starts With On-Site Production in Growtainer
"In 2016 we saw the successful Growtainer launch in the UK and the expansion of their European presence at a Spanish biotechnological giant. CEA Advisors & Growtainers® promises, even more, global excitement in Indoor Farming and Controlled Environment Agriculture in 2017"
US: Food Retailer Starts With On-Site Production in Growtainer
In 2016 we saw the successful Growtainer launch in the UK and the expansion of their European presence at a Spanish biotechnological giant. CEA Advisors & Growtainers® promises even more global excitement in Indoor Farming and Controlled Environment Agriculture in 2017.
After more than a year of meetings with the Produce Marketing team at a major US food retailer, the first custom built for onsite production Growtainer® has been delivered and will begin production in Q1, 2017. “We spent over a year discussing the retailer’s concerns and objectives and when I was sure we were all on the same page we began the design and manufacturing process” said Glenn Behrman, founder of Greentech Agro LLC and CEA Advisors LLC.
Growtainers® have come a long way from those first two prototype models built about 4 years ago and recently donated to Texas A & M Agrilife Research Center in Dallas. LED costs have come down and their efficiency has improved. "Our understanding of the critical importance of the growing environment and the need for intuitive control systems has increased. We’re collaborating with more industry experts in all areas that are critical to the development of a well-balanced successful production environment”.
According to Behrman, increasing global awareness of indoor local vertical production has been the driver in the laser focused pursuit of new, modern and sustainable indoor farming practices. "On site production in the Growtainer® to produce the freshest, unique, gourmet leafy greens and herbs for their customers at the retail level is the objective of the retail partner. They are the first in the nation to train their team members in a food safety compliant, climate controlled, LED lit multi-layer vertical indoor production environment. "
"CEA Advisors is proud to be working with a forward-thinking food retailer that is committed to innovation and focused on food safety, unique products and the customer experience” said Behrman.
For this project, CEA collaborated with a McKinney Texas based water management firm, whose team assisted in the design and installation of a state of the art irrigation system. "The container modifications were carried out by the largest and most experienced group in the USA. North America’s leading horticultural supplier of goods and services provides their expert and ongoing consultation to the project, as well."
The state of the art 53’ custom built Growtainer® has a separate utility area and provides 480 square feet of climate controlled vertical production space, specially designed for maximum efficiency and food safety compliance. Besides having a dedicated proprietary technology for ebb and flow irrigation installed, these Growracks® are also equipped with energy efficient LED production modules, specifically designed for multilayer cultivation. The irrigation system is divided into separate zones to provide flexibility and allow a wide variety of production of crops at various growth stages. Behrman worked closely with the irrigation engineers to design a sophisticated control system. The proprietary irrigation system is constantly monitored and any corrections to EC or PH are made immediately. Every irrigation event is perfect for the plants optimum growth.
For more information on this and other exciting innovations in Indoor Vertical Farming
visit www.growtainers.com or email gb@cea-advisors.com
Publication date: 1/2/2017
A barely-used high-tech food-growing and production line is to be pressed into greater service: making soup for Wigan’s homeless and needy. Wigan University Technical College is the proud owner of Britain’s only “vertical farm” and process hall
College Vertical Farm to Help Feed Homeless
Saturday 31 December 2016
A barely-used high-tech food-growing and production line is to be pressed into greater service: making soup for Wigan’s homeless and needy. Wigan University Technical College is the proud owner of Britain’s only “vertical farm” and process hall.
When installed three years ago they were to be used to train up would-be engineers to learn the entire food creation process from seed to container.
But the UTC has struggled to attract the desired number of students to date to get it all running very often. There are plenty of other plans from millionaire backer Martin Ainscough, whose brainchild the UTC was, in order to turn round the college’s fortunes.
But his first mission is to help the borough’s neediest. Students, helped by Groundwork Trust Prince’s Trust participants and experts will grow and process various foods to produce around 60 gallons of soup a week: or, to put it in drinkable sizes, around 500 half-litre pouches.
And Mr Ainscough intends to the give the soup, free of charge, to the Wigan-based charity The Brick. Some of it will be given out free to the homeless, some will be sold at discount at its food banks and also given to volunteers. Mr Ainscough, who recently received a CBE for his services to charity and is a major supporter of the Prince’s Trust and the neighbouring Wigan Youth Zone, said he was keen to forge partnerships.
He added: “The vertical farm is a great piece of machinery. They are used a lot abroad already, but this is the only one in this country and it has been a great shame that it hasn’t been put to use more often since it was installed. “With this in mind I want it to be used to make soup for a charitable cause and there are few more deserving than The Brick. “I think businesses, charities and those in training should work together far more often. “We put the equipment to good use, we educate people and we help those less fortunate.
The farm can grow the equivalent of two acres of greenhouse produce.” Mr Ainscough said that some of the produce for the soup will come from the My Life charity project at Standish (which he also founded) and talks were under way with other organisations to sponsor the UTC to produce the vegetables.
Kathleen Pitt, chief executive of Queen’s Hall Action on Poverty which runs The Brick, said: “Martin Ainscough is keen to get this soup facility up and running and we are equally keen to receive the soup! It would be given out at the food bank at the Brick in Rowbottom Square. “We also have a kitchen and we provide a lunch for the people who work with us.
We have a community warehouse where we help people to learn how to get into employment and we have a kitchen and cafe there too. We could also sell the soup in our charity shop.
We cannot wait for the project to start.” Colin Greenhalgh, programme director, employment and skills at the Groundwork Trust, said: “We run a Prince’s Trust programme, part of which includes a community project which benefits the local community. This soup production idea links up perfectly with the UTC.
It helps them develop new skills and confidence and that looks good on a CV and it is good to give something back to society. “Initially it would be young people learning about food production and distributing the soup. But in the longer term it might also be about growing produce as well because we run a number of community allotments and gardens. This idea is perfect for the community project and it’s right on our doorstep.”
Growlife Inc Updates On Contract Extension
Growlife Inc one of the country’s most renowned indoor farming service providers, reported that the Board of Directors have given its nod to extend Marco Hegyi’s employment for another two years after discussions
DECEMBER 30, 2016
Growlife Inc Updates On Contract Extension
Growlife Inc (OTCMKTS:PHOT) one of the country’s most renowned indoor farming service providers, reported that the Board of Directors have given its nod to extend Marco Hegyi’s employment for another two years after discussions.
Hegyi has led Growlife back to active trading platform from the Gray Sheet, effectively maintained strong and constructive associations with customers, shareholders and suppliers, and helped company to continue operating through its most challenging times. Therefore, with this extended contract, the company will maintain management stability for the following two years under Hegyi’s leadership.
Mr. Hegyi joined Growlife back in 2013 as the firm’s President. In April 2014, the U.S. SEC temporarily suspended the firm’s stock from trading for 10 days. The suspension reason was given as questions that have been asked about the accuracy and acceptability of information in the market and possibly manipulative transactions in PHOT’s shares.
Later that year, the Commission detained and indicted four outside folks for mismanagement of PHOT stock. However, the commission didn’t file any charges against PHOT. As the CEO, Hegyi secured the necessary funding to maintain businesses, worked through the Commission procedure and closed a 22-month journey to start active trading.
Hegyi mentioned that Growlife is a great company, everything from its staff to its clients and investors, with a thrilling future that merits to benefit from the mounting demand for indoor farming. The upcoming vote is just one factor that can noticeably increase company’s market size and product demand.
There are numerous expansion opportunities for company, from serving large viable cultivation clients and caregivers to the developing home indoor cultivators, all who want the equipment, provisions and expertise that Growlife delivers. Also, strong and dependable financing partners, purchases, up-listing to OTCQB, service plans and increased associations, can boost greater growth. They are still lagging from closing what was planned.
The Indoor Harvest
The Indoor Harvest
Posted Dec. 29th, 2016 by Robert Arnason
For Randy King, the argument for indoor farming in Canada is just common sense.
For one, Canada is a northern country with long winters.
Two, during those long winters almost all fruit and vegetables in Canadian grocery stores are imported from Central America, Mexico or California.
Three, wouldn’t it be better if Canadians grew their own fruits and veggies?
“I think this is the way of the future for growing produce in northern regions,” said King, co-owner of West Grow Farms, a company with plans to build an indoor farm near Edmonton.
“In order to gain food sovereignty, we need to step out of the box and revolutionize how we approach growing produce…. Relying on other countries to feed us in the winter time, I’m not certain that’s going to be sustainable.”
In 2016, King and his business partner, Jim Philpott, signed a licensing deal with Indoor Farms of America, a company from the United States, to its technology.
Indoor Farms of America has developed a proprietary method to grow fruits and vegetables inside based on a technique called aeroponics.
Plants are grown without soil in aeroponics. The suspended roots are misted with nutrient-rich water.
Proponents of aeroponics say it can grow greens such as kale and spinach, or herbs like basil and sage, without the use of pesticides.
Large scale indoor farms, or vertical farms, are already growing produce in cities across North America.
- This year AeroFarms of Newark, New Jersey, built a 70,000 sq. foot vertical farm in a former steel mill. When fully operational, it will likely be the largest vertical farm in the world.
- The word “vertical” is used to describe indoor farms because trays of plants are typically stacked inside the building, reaching toward the ceiling.
- Chicago may have the most vertical farms of any major city in North America. It’s sometimes described as America’s urban farming capital.
- In Canada, dozens of companies are planning to construct or are building indoor farms, but it’s difficult to know how many are in operation.
King, who operates a couple of construction companies, became aware of the concept when a client asked him to design an indoor farm.
The project may have stalled, but it sparked King’s interest.
“You look at the nutritional value of a head of lettuce that’s been in transit for a couple of weeks, it’s probably diminished to the (point) where we’re eating straw,” said King, who grew up on a farm near Edmonton.
Supporters say vertical farms may revolutionize agriculture because plants grown indoors mature more quickly and can be harvested 10, 15 or 20 times annually, rather than two or three times a year for outdoor crops.
True believers go further. They say indoor agriculture will save the world.
“If vertical farming in urban centres becomes the norm, then one anticipated long-term benefit would be the gradual repair of many of the world’s damaged ecosystems through the systematic abandonment of farmland,” said Dickson Despommier, author of The Vertical Farm and host of the Urban Agriculture podcast. “The re-growth of hardwood forests could play a significant role in carbon sequestration and may help reverse current trends in global climate change.”
But environmental groups say vertical farms use an incredible amount of energy on artificial lights.
“Producing America’s annual vegetable crop (not counting potatoes) in vertical systems under lights would require well over half of the electricity this country generates every year,” wrote Stan Cox of The Land Institute, a group that supports sustainable agriculture, in Salon magazine.
King confirmed that lights are the biggest cost and challenge of indoor farming. Optimizing lighting for maximum growth is complex and the cost of LED lights can run into the millions.
But if growers get the lighting right, indoor farming can produce a huge quantity of leafy greens and other vegetables.
“We can get 157,000 plant sites in 3,200 sq. feet,” King said.
Based on West Grow’s trials, plants can reach maturity in about 22 days. Which means 15 growing cycles per year.
Once he has a handle on the lighting, King hopes to begin construction of the indoor farm early next year, in a warehouse in the Edmonton area. The 12,000 sq. foot facility will also have a store, so customers can buy produce at the site.
The plan is to start out with leafy greens and herbs. Then, expand into tomatoes, cucumbers and other veggies.
King is convinced that Albertans want to buy locally grown veggies year round.
“Talking to our potential customers … the grocers, they’re extremely excited,” King said. “They’re more than committed to buying local, fresh produce, 365 days of the year.”
King hopes the indoor farm will be producing greens and herbs by June of 2017.
About Glenn Behrman
About - Glenn Behrman
Glenn is a native of New York City and has been involved in the horticulture industry for over 45 years. From a small retail store in New Haven, over the next 20 years Glenn built the business into a regional success, a high volume chain of retail stores and wholesale foliage distribution centers, including a lawn and garden import division. Glenn owned and operated garden centers from New York City to Philadelphia, foliage nurseries in Florida, orchid nurseries in Thailand and tree farms and nurseries in Vietnam. After selling his U.S. based business interests to devote more time to his Asian ventures, Glenn relocated to Bangkok, Thailand in 1994. Glenn has acted as a grower, broker and exporter of young plants and orchids and has introduced new ornamental plant varieties from Asia to growers worldwide. In addition to years of senior level day to day business management and operations, his experience further extends to designing and constructing thousands of square feet of nurseries and greenhouses.
During his time in Asia, in addition to his horticulture business, he has been involved in other ventures including an internet start-up which he founded and then sold to a Singapore investment group (www.theglobalgrocer.com) and the production of postage stamps for the Lao government (SEA Philatelic Group, Inc). He has also served as a Special Advisor to H.E. Sar Sambath, former Cambodian Ambassador to the United Nations. In 2011 he left his position as Landscape Project Manager for the $4.5 billion Ho Tram Strip project, consisting of 5 five star resorts and two Las Vegas style casinos in Vung Tau, Vietnam, to return to the United States to devote his full time and energy as co-founder and President of GreenTech Agro LLC. Glenn and his wife currently reside in Dallas where he manages the day to day operations of GreenTech Agro LLC and CEA Advisors LLC. Based at Texas A & M University Agrilife Research Center, Glenn works full time on the design, development and fabrication of the Growtainer™ containers, Growrack™ rack systems, Growtroller™ control systems and provides Consulting services to international clients on the development of innovative investment grade indoor farming projects
More Urban Farms Sprouting With USDA's Help
More Urban Farms Sprouting With USDA's Help
Farming, a largely rural activity, is moving to the cities, as urban farms continue to grow with help from the federal government.
As Business Insider reports, the U.S. Department of Agriculture each year provides millions of dollars to rural farmers, but the same is starting to be said for urban farms.
According to greensgrow.org, urban farming is just what it sounds like – growing or producing food in a city or heavily populated town or municipality.
In 2016, the USDA funded a dozen urban farms and in 2017, even more money is expected to go toward rooftop farms, greenhouses and warehouses in urban settings.
One of the USDA’s programs geared specifically for urban farming is the Microloan program, which offers funding up to $50,000. Since 2013, 23,000 loans worth $518 million have been awarded through the program. About 70 percent have gone to urban farmers.
The USDA also published an “Urban Agriculture Toolkit” this year that is full of advice about how to launch a greenhouse or rooftop farm, and tips about how to apply for loans.
While most USDA grants and loans go to rural farms, but is making efforts at giving urban farmers equal opportunities and recently set up an office in New York City – a departure from the norm, as most of the USDA’s 2,200 offices are in rural states like Missouri, Texas and Iowa.
These initiatives, as Business Insider reports, underscore a growing movement within the USDA to support local food systems and look beyond rural agriculture.
Urban farmers provide a way to meet a growing need for a growing global population.
In 2016, Business Insider reports, Aerofarms was launched inside a 70,000-square-foot warehouse in Newark, New Jersey, making it the largest vertical farm. In 2015, Gotham Greens, the world’s largest rooftop farm, was started in Chicag
Premier Indoor Agriculture Conference Returns to Singapore For An Expanded Indoor Ag-Con Asia On January 24-25, 2017
Premier Indoor Agriculture Conference Returns to Singapore For An Expanded Indoor Ag-Con Asia On January 24-25, 2017
Indoor Ag-Con Asia features plant factory & vertical farming leaders such as Prof. Kozai of Chiba University, 808FACTORY, Autogrow, Kajima Corporation, MIRAI & Pegasus Agriculture.
SINGAPORE, SG (PRWEB) DECEMBER 29, 2016
Indoor agriculture is one of the fastest-growing industries in Asia as consumer demand for “clean food” benefits this form of farming that uses few pesticides and shields crops from environmental pollution. Indoor Ag-Con – the premier industry conference – will be returning to Singapore for the second year on January 24-25, 2017 to discuss the prospects for this increasingly important contributor to the global food supply chain.
The two-day seminar will be hosted at the Marina Bay Sands, Singapore, and is tailored toward corporate executives from the technology, investment, vertical farming, greenhouse growing, and food and beverage industries, along with hydroponic, aquaponic and aeroponic startups and urban farmers.
The event will consist of keynotes from industry leaders and extended networking breaks, along with an exhibition hall. More than 20 confirmed speakers include Professor Kozai of Chiba University, author of ‘The Plant Factory’, and executives from 808FACTORY, Autogrow, Intravision, Kajima Corporation, MIRAI, Pegasus Agriculture, and Urban Crops. “Our speakers will cover topics as diverse as automation for plant factories and financing an indoor agriculture startup” commented Nicola Kerslake, founder of Newbean Capital, the event’s host. Participants will receive an exclusive hard copy of the newest edition in our popular white paper series, which is sponsored by Pegasus Agriculture and will be the first published on global indoor agriculture policy. Agriculture technology companies, suppliers and automation companies will have the chance to meet and mingle with leading vertical farmers and commercial greenhouse operators at a drinks party on the first evening of the event. The platinum sponsor for the event is Lighting Science Group, and other sponsors include Autogrow, Kennett Township, Microsoft BizSpark, Pegasus Agriculture, Upgrown Farming and Urban Crops.
Beginning farmers, chefs and entrepreneurs can win passes to the event through the Nextbean program, which awards a limited number of complimentary passes to the event to those who have been industry participants for less than two years. Applications are open through December 31, 2016 at Indoor Ag-Con’s website. The program is supported by Newbean Capital, the host of Indoor Ag-Con, and Kennett Township, a leading indoor agriculture hub that produces half of the US’s mushrooms.
In the lead up to the main event, Indoor Ag-Con has partnered with Startup Weekend Singapore to add an indoor agriculture theme to a Startup Weekend on January 20-22, 2017, and will host a VIP reception with local fresh salad restaurant chain SaladStop!.
Indoor Ag-Con has also hosted events in Las Vegas, NV and New York, NY in the past year, and will host its first event in Dubai – in partnership with greenhouse major Pegasus Agriculture – in November 2017. Since it was founded in 2013, Indoor Ag-Con has captured an international audience and attracted some of the top names in the business. Events have welcomed over 1,500 participants from more than 20 countries.
Newbean Capital, the host of the conference, is a registered investment advisor; some of its clients or potential clients may participate in the conference. The Company is ably assisted in the event’s production by Rachelle Razon, Sarah Smith and Michael Nelson of Origin Event Planning, and by Michele Premone of Brede Allied.
2nd Annual Indoor Ag-Con Asia
Date – January 24-25, 2017
Place – Marina Bay Sands, Singapore
Exhibition Booths – available from US$1,599 at indoor.ag
Registration – available from US$349 at indoor.ag
Features – Two-day seminar, with keynote speakers, an exhibition hall, an after-party, and VIP reception
For more information, please visit http://www.indoor.ag/asia or call +1.775.623.7116 in the US and +65.3159.1305 in Singapore
Designing An Aquaponic Unit
Designing An Aquaponic Unit
Summary
Aquaponics is the integration of recirculating aquaculture and hydroponics in one production system. In aquaponics, the aquaculture effluent is diverted through plant beds and not released to the environment, while at the same time the nutrients for the plants are supplied from a sustainable, cost-effective and non-chemical source. This integration removes some of the unsustainable factors of running aquaculture and hydroponic systems independently. The technology presented in this document, provides a description of the concept of aquaponics and an overview of the three most common methods of aquaponics being utilized at present. In addition, the factors to consider when selecting a site for an aquaponic unit and the components essential for any method of aquaponics are described in details in this document.
Description
Introduction:
Aquaponics is a technique that combines hydroponics and aquaculture in a single system that cultivates plants in recirculated aquaculture water (Figure 1).
Hydroponics is the most common method of soil-less culture (growing agricultural crops without the use of the soil), which includes growing plants either on a substrate or in an aqueous medium with bare roots. The substrate provides plant support and moisture retention. Irrigation systems are integrated within these substrates, thereby introducing a nutrient solution to the plants’ root zones. This solution provides all of the necessary nutrients for plant growth.
Aquaculture is the captive rearing and production of fish and other aquatic animal and plant species under controlled conditions The four major categories of aquaculture include open water systems (e.g. cages, longlines), pond culture, flow-through raceways and recirculating aquaculture systems (RAS). A RAS is the most applicable method for the development of integrated aquaculture agriculture systems because of the possible use of by-products and the higher water nutrient concentrations for vegetable crop production.
Aquaponics is a form of integrated agriculture that combines two major techniques, aquaculture and hydroponics. In one continuously recirculating unit, culture water exits the fish tank containing the metabolic wastes of fish. The water first passes through a mechanical filter that captures solid wastes, and then passes through a biofilter that oxidizes ammonia to nitrate. The water then travels through plant grow beds where plants uptake the nutrients, and finally the water returns, purified, to the fish tank. The biofilter provides a habitat for bacteria to convert fish waste into accessible nutrients for plants. These nutrients, which are dissolved in the water, are then absorbed by the plants. This process of nutrient removal cleans the water, preventing the water from becoming toxic with harmful forms of nitrogen (ammonia and nitrite), and allows the fish, plants, and bacteria to thrive symbiotically. Moreover, the converted fish waste provides all of the fertilizer required by the plants. Thus, all the organisms work together to create a healthy growing environment for one another, provided that the system is properly balanced.
Aquaponics is a technique that has its place within the wider context of sustainable intensive agriculture, especially in family-scale applications. It offers supportive and collaborative methods of vegetable and fish production and can grow substantial amounts of food in locations and situations where soil-based agriculture is difficult or impossible. Aquaponics is most appropriate where land is expensive, water is scarce, and soil is poor. Deserts and arid areas, sandy islands and urban gardens are the locations most appropriate for aquaponics because it uses an absolute minimum of water.
Aquaponic systems are expensive because they require the installation of a full aquaculture system and a hydroponic system. Despite this, units can be designed and scaled to meet the skill and interest level of many farmers. Aquaponics is quite adaptable, and can be developed with local materials and domestic knowledge, and to suit local cultural and environmental conditions. It will always require a dedicated and interested person, or group of persons, to maintain and manage the system on a daily basis.
Types of aquaponic units:
a) Media Bed Technique (MBT):
Media-filled bed units are the most popular design for small-scale aquaponics. This method is strongly recommended for most developing regions. These designs are efficient with space, have a relatively low initial cost and are suitable for beginners because of their simplicity. In media bed units, the medium is used to support the roots of the plants and also the same medium functions as a filter, both mechanical and biological. There are many designs for media beds, and this is probably the most adaptable technique. Moreover, recycled materials can easily be repurposed to hold the media and the fish (Figure 2).
b) Nutrient Film Technique (NFT):
The NFT is a hydroponic method using horizontal pipes each with a shallow stream of nutrient-rich water flowing through it. Plants are placed within holes in the top of the pipes, and are able to use this thin film of nutrient-rich water. This technique is far more complicated and expensive than media beds, and may not be appropriate in locations with inadequate access to suppliers. It is most useful in urban applications, especially when vertical space or weight-limitations are considerations. In addition, this technique requires separate mechanical and biofiltration components, in order to respectively remove the suspended solids and oxidize the dissolved wastes (ammonia to nitrate) (Figure 3).
c) Deep Water Culture (DWC):
The DWC method involves suspending plants in polystyrene sheets, with their roots hanging down into the water. This method is the most common for large commercial aquaponics, growing one specific crop (typically lettuce, salad leaves or basil), and is more suitable for mechanization. On a small-scale, this technique is more complicated than media beds, and may not be suitable for some locations, especially where access to materials is limited. As in the NFT, separate mechanical and biological filters are needed (Figure 4, and 5).
However, the aquaponic DWC units can be designed without a filtration system. These units carry a very low stocking density of fish (i.e. 1–1.5 kg of fish per m3 of fish tank), and then rely mainly on the plant root space and the interior area of the canals as the surface area to house the nitrifying bacteria. Simple mesh screens capture the large solid waste, and the canals serve as settling tanks for fine waste. The advantage -of this method is the reduction in initial economic investment and capital costs, while at the same time eliminating the need for additional filter containers and materials, which can be difficult and expensive to source in some locations (Figure 6).
Consideration while designing an aquaponic unit:
1. Site Selection:
Be sure to choose a site that is stable and level. Some of the major components of an aquaponic system are heavy, leading to the potential risk of the legs of the system sinking into the ground. This can lead to disrupted water flow, flooding or catastrophic collapse. Find the most level and solid ground available. Concrete slabs are suitable, but do not allow any components to be buried, which can lead to tripping hazards. If the system is built on soil, it is useful to grade the soil and put down material to mitigate weeds. In addition, place concrete or cement blocks under the legs of the grow beds to improve stability. Stone chips are often used to level and stabilize soil locations. Moreover, it is important to place the fish tanks on a base; this will help to provide stability, protect the tank, allow for plumbing and drains on the tank bottom, and thermally isolate it from the ground.
a) Exposure to wind, rain and snow:
Extreme environmental conditions can stress plants and destroy structures. Strong prevailing winds can have a considerable negative impact on plant production and can cause damage to stems and reproductive parts. In addition, strong rain can harm the plants and damage unprotected electrical sockets. Large amounts of rain can dilute the nutrient-rich water, and can flood a system if no overflow mechanism is integrated into the unit. Snow causes the same problems as heavy rain, with the added threat of cold damage. It is recommended to locate the system in a wind-protected zone. If heavy rains are common, it may be worth to protect the system with a plastic-lined hoop house, although this may not be necessary in all locations.
b) Exposure to sunlight and shade:
Most of the common plants for aquaponics grow well in full sun conditions; however, if the sunlight is too intense, a simple shade structure can be installed over the grow beds. Some light sensitive plants, including lettuce, salad greens and some cabbages, will bolt in too much sun, go to seed and become bitter and unpalatable. Other tropical plants adapted to the jungle floor such as turmeric and certain ornamentals can exhibit leaf burn when exposed to excessive sun, and they do better with some shade. On the other hand, with insufficient sunlight, some plants can have slow growth rates. This situation can be avoided by placing the aquaponic unit in a sunny location. If a shady area is the only location available, it is recommended that shade-tolerant species be planted.
On the contrary, the fish do not need direct sunlight. In fact, it is important for the fish tanks to be in the shade or covered with a removable shading material that is placed on top of the tank. However, where possible, it is better to isolate the fish tanks using a separate shading structure. This will prevent algae growth and will help to maintain a stable water temperature during the day. Moreover, fish tanks are vulnerable to predators. Using shade netting, tarps or other screening over the fish tanks will prevent all of these threats.
c) Access to utilities:
In site selection, it is important to consider the availability of utilities. Electric outlets are needed for water and air pumps. These outlets should be shielded from water and equipped with a residual-current device (RCD) to reduce the risk of electrical shock. Moreover, the water source should be easily accessible, whether it is municipal water or rain collection units. Similarly, consider where any effluent from the system would go. Although extremely water efficient, aquaponic systems occasionally require water changes, and filters and clarifiers need to be rinsed. It is convenient to have some soil plants located nearby that would benefit from this water. The system should be located where it is easy for daily access because frequent monitoring and daily feeding are required. Finally, consider if it is necessary to fence the entire section. Fences are sometimes required to prevent theft and vandalism, animal pests and for some food safety regulations.
2. Water quality in aquaponics:
Water is the life-blood of an aquaponic system (Figure 7). It is the medium through which plants receive their nutrients andfish receive their oxygen. It is very important to understand water quality and basic water chemistry in order to properly manage aquaponics.
There are five key water quality parameters for aquaponics: dissolved oxygen (DO), pH, water temperature, total nitrogen concentrations and hardness (KH). Each organism in an aquaponic unit has a specific tolerance range for each parameter of water quality. The tolerance ranges are relatively similar for all three organisms, but there is need for compromise and therefore some organisms will not be functioning at their optimum level.
Ideal parameters for aquaponics as a compromise between all three organisms
Water testing is essential for maintaining good water quality in the system. This starts from the selection of the water source: rainwater, aquifer water, tap water. Continue to test and keep records of the following water quality parameters each week: pH, water temperature, nitrate and carbonate hardness. Ammonia and nitrite tests should be used especially at system start-up and if abnormal fish mortality raises toxicity concerns.
3. Essential components of an aquaponic unit:
a) Fish tank
Fish tanks are a crucial component in every unit. As such, fish tanks can account for up to 20 percent of the entire cost of an aquaponic unit. Although any shape of fish tank will work, round tanks with flat bottoms are recommended. The round shape allows water to circulate uniformly and transports solid wastes towards the centre of the tank by centripetal force.
It is recommended to use strong inert plastic or fibreglass tanks, because of their durability and
long life span. If using plastic containers, make sure that they are UV-resistant because direct sunlight can destroy plastic. In general, low-density polyethylene (LDPE) tanks are preferable because of their high resistance and food-grade characteristics. Other options include second hand containers, such as bathtubs, barrels or intermediate bulk containers (IBCs). It is very important to make sure that the container has not been used previously to store toxic material. Contaminants, such as solvent-borne chemicals, will have penetrated into the porous plastic itself and are impossible to remove with washing.
Regarding the tank color, white or other light colours are strongly advised as they allow easier viewing of the fish in order to easily check behaviour and the amount of waste settled at the bottom of the tank. White tanks will also reflect sunlight and keep the water cool. Alternatively, the outside of darker coloured tanks can be painted white. All fish tanks should be covered. The shade covers prevent algae growth. In addition, the covers prevent fish from jumping out (often occurs with newly added fish or if water quality is sub-optimal), prevent leaves and debris from entering, and prevent predators such as cats and birds from attacking the fish. Often, agricultural shading nets that block 80–90 percent of sunlight are used. The shade cloth can be attached to a simple wooden frame to provide weight and make the cover easy to remove.
b) Sump tank
The sump tank is a water collection tank at the lowest point in the system; water always runs downhill to the sump. This is often the location of the submersible pump. Sump tanks should be smaller than the fish tanks, and should be able to hold between one-fourth and one-third of the volume of the fish tank. For ebb-and-flow type media beds, the sump needs to be large enough to hold at least the entire volume of water in the grow beds. External sump tanks are mainly used in media bed units; however, for DWC units the actual hydroponic canal can be used as a sump tank / pump house also.
On the other hand, very small units with fish tanks up to 200 litres can simply pump water from the fish tank to the grow beds, from where water trickles back down into the fish tank. In this case the use of a sump tank is not required.
c) Filtration system
Some level of filtration is essential to all aquaponics, although fish stocking density and system design determines how much filtration is necessary. Mechanical filters separate solid wastes which are then removed from the system to prevent toxic gases from being released by harmful bacteria that feed on accumulated solid wastes. Moreover, the wastes can clog systems and disrupt water flow, causing anoxic conditions to the plant roots. For aquaponics, mechanical filtration is arguably the most important aspect of the design.
There are several types of mechanical filters. The simplest method is a screen or filter located between the fish tank and the grow bed. This screen catches solid wastes, and needs to be rinsed often. Similarly, water leaving the fish tank can pass through a small container of particulate material, separate from the media bed; this container is easier to rinse periodically. These methods are valid for some small-scale aquaponic units, but are insufficient in larger systems with more fish where the amount of solid waste is relevant. There are many types of mechanical filters, including sedimentation tanks, radial-flow clarifiers, sand or bead filters and baffle filters; each of them can be used according to the size of solid wastes that needs to be removed. For small-scale aquaponics, clarifiers or radial swirl filters are the most appropriate filters.
Biofiltration is the conversion of ammonia and nitrite into nitrate by living bacteria. Most fish waste is not filterable using a mechanical filter because the waste is dissolved directly in the water, and the size of these particles is too small to be mechanically removed. Therefore, in order to process this microscopic waste an aquaponic system uses microscopic bacteria. The biofilter is installed between the mechanical filter and the hydroponic containers. Many types of media can be used, including purpose-designed plastic pieces, volcanic gravel, plastic bottle caps, nylon shower poufs, netting, polyvinyl chloride (PVC) shavings and nylon scrub pads.
The media beds themselves act as both mechanical filters and biofilters when using this technique, but additional mechanical filtration is sometimes necessary for higher fish densities (15 kg/m3). In a unit without the media beds, such as in NFT and DWC units, standalone filtration is necessary.
d) Aeration system
Another required component for aquaponics is aeration. Fish and plants need oxygen to breath, and nitrifying bacteria need adequate access to oxygen in order to oxidize the ammonia. One easy solution is to use air pumps, placing the air stones at the bottom of the container. This ensures that all the living organisms have constantly high and stable dissolved oxygen (DO) concentrations.
Venturi siphons are another technique to increase the DO levels in aquaponics. Venturi siphons use a hydrodynamic principle that pulls in air from the outside (aspiration) when pressurized water flows with a faster speed through a pipe section of a smaller diameter. As the water in the main pipe is forced through the narrower section, it creates a jet effect.
e) Water movement
Water movement is fundamental for keeping all organisms alive in aquaponics. As mentioned before, the flowing water moves from the fish tanks, through the mechanical separator and the biofilter and finally to the plants in their media beds, pipes or canals, removing the dissolved nutrients. If water movement stops, the most immediate effect will be a reduction in DO and accumulation of wastes in the fish tank.
It is recommended to use a standard pump as the heart of an aquaponics unit. Most commonly an impeller-type submersible water pump is used. When installing an aquaponic unit, be sure to place the submersible pump in an accessible location because periodic cleaning is necessary.
Airlifts are another technique of lifting water. They use an air pump rather a water pump. Air is forced to the bottom of a pipe within the fish tank, bubbles form and burst, and during their rise to the surface the bubbles transport water with them.
Some aquaponic systems have been designed to use human power to move water. Water can be lifted in buckets or by using pulleys, modified bicycles or other means. A header tank can be filled manually and allowed to slowly drain throughout the course of the day. These methods are only applicable for small systems, and should only be considered where electricity is unavailable or unreliable.
f) Plumbing materials
Every system requires a selection of PVC pipe, PVC connections and fittings, hoses and tubes. These provide the channels for water to flow into each component. Bulkhead valves, uniseals, silicone sealant and Teflon tape are also needed. In addition, some general tools are needed such as hammers, drills, hand saws, electric saws, measuring tapes, pliers, channel-locking pliers, screwdrivers, levels, etc. One special tool is a hole-saw and/ or spade bit, which is used in an electric drill to make holes up to 8 cm, necessary for inserting the pipes into the fish tanks and filters, as well as for making holes in the PVC or polystyrene grow beds in NFT and DWC systems.
Make sure that the pipes and plumbing used in the system have never previously been used to hold toxic substances. It is also important that the plumbing used is of food-grade quality to prevent possible leaching of chemicals into the system water. It is also important to use pipes that are black and/or non-transparent to light, which will stop algae from growing.
g) Water testing kits
Simple water tests are a requirement for every aquaponic unit. Colour-coded freshwater test kits are readily available, fairly economical and easy to use, and thus these are recommended.
These can be purchased in aquarium stores or online. These kits include tests for pH, ammonia, nitrite, nitrate and water hardness (GH and KH). Be sure that the manufacturers are reliable and that the expiration date is still valid.
Other methods include digital meters or test strips. If using digital meters for pH or nitrate, be sure to calibrate the units according to the manufacturer’s directions. A thermometer is necessary to measure water temperature. In addition, if there is risk of saltwater in the source water, a cheap hydrometer, or a more accurate but more expensive refractometer, is worthwhile.
The basic aquaponic system works in a wide range of conditions, and units can be designed and scaled to meet the skill and interest level of many farmers. However, its success is derived from the appropriate selection of the locations while considering its limitations, the maintenance and management of the system on a daily basis by a motivated farmer or group of farmers..
There is a wide variety of aquaponic designs, ranging from high-tech to low-tech, and from high to reasonable price levels. The three most common methods of aquaponics and their management are described in the following technologies:
1. Designing an Aquaponic unit
2. Media Bed Aquaponic Unit - Step by Step Description
3. Nutrient Film Aquaponic Unit – Step by Step Description
4. Deep Water Culture Aquaponic Unit – Step by Step Description
5. Management of the Aquaponic Systems
See also
Management of the Aquaponic Systems
Deep Water Culture Aquaponic Unit – Step by Step Description
Nutrient Film Aquaponic Unit – Step by Step Description
Media Bed Aquaponic Unit - Step by Step Description
Further reading
Small-scale aquaponic food production - Integrated fish and plant farming (FAO, 2014): http://www.fao.org/3/a-i4021e/
7 rules-of-thumb to follow in aquaponics: http://www.fao.org/zhc/detail-events/en/c/320156/
Keywords
Category
Region
Created date
Wed, 03/06/2015 - 16:19
Source(s)
Fisheries and Aquaculture Department (FI) in FAO
Fisheries and aquaculture have the capacity – if supported and developed in a regulated and environmentally sensitive manner – to contribute significantly to improving the well-being of poor and disadvantaged communities in developing countries and to achievement of several of the Millennium Development Goals, especially those related to poverty reduction and food and nutrition security, environmental protection and biodiversity. As part of a long-term strategy, the FAO Fisheries and Aquaculture Department (FI) is envisioning a world in which responsible and sustainable use of fisheries and aquaculture resources makes an appreciable contribution to human well-being, food security and poverty alleviation. In this regard, FI works towards strengthening global governance and the managerial and technical capacities of members and to lead consensus-building towards improved conservation and utilization of aquatic resources. The activities of FI reflect the main FAO mandate of managing knowledge and information, assuring a global neutral forum for Members and providing technical assistance at national, regional and global levels.
In addition, the FAO Fisheries and Aquaculture Department undertakes capacity development activities for marine and inland fisheries as well as aquaculture. These include training at different levels, preparation of training and extension materials for general or targeted training, awareness raising through workshops, and collaboration with partner training institutions. The FI is also involved in the development of appropriate technical guidelines and the promotion of participatory approaches in sustainable and responsible aquatic resources management, including gender aspects.
The Aquaculture Branch of FI (FIAA) is particularly responsible for providing technical assistance towards sustainable and responsible aquaculture development and management in support of improving food and nutrition security and alleviating poverty, globally.
The Products, Trade and Marketing Branch (FIAM) of the Fisheries and Aquaculture Department of FAO, assists FAO member countries on all aspects related to post-harvest. FIAM provides technical assistance in areas such as marketing, trade, handling and processing and preservation of fish products, food safety and nutrition. As such, FIAM supports activities along the value chain aiming at a sustainable supply of fish and fishery products in the market, while securing greater benefits for actors in the value chain. FIAM has broad experience in the field of promotion fish consumption, through the dissemination of knowledge on the nutritional value of fish and fishery products, including the promotion of good hygienic practices at any level of the supply chain (on board canoes/vessels, landing sites, aquaculture farms, factories and sales points). Local fishermen and processors are assisted to adapt best practices in order to reduce food losses and waste, and to promote an optimal use of their fishery by-products, improving their returns, minimizing the environmental impacts and contributing to food security. Finally, as fish and fishery products are among the most traded food commodities worldwide, FIAM coordinates the implementation of Globefish, a programme collecting and disseminating information on markets and fish trade. Globefish produces a number of publications including fish price reports (European Fish Price Report), market studies (GLOBEFISH Research Programme) and trend analysis (GLOBEFISH Highlights).
Contacts:
Contact person:
Aquaculture Branch of the Fisheries and Aquaculture Policy and Resource Division
Contact email:
Contact person:
Alessandro Lovatelli (Aquaculture Branch)
Contact email:
Contact person:
Aina Randrianantoandro (Products, Trade and Marketing Branch)
Contact email:
Aina.Randrianantoandro@fao.org
Web:
Country:
Italy
Concrete Farms
Concrete Farms
What if you could pluck lettuce, cucumber and tomato from the rooftop farm in your residential building to prepare a salad that is fresh and pesticide free? And that, too, from plants grown without the use of soil?
Well, it could be a common sight in the near future. The Food and Agriculture Organization (FAO) of the United Nations estimates that by 2050, agriculture production must increase by 70 per cent to feed the ever-increasing population. India will be one of the world's top food importers if we do not try out every futuristic technology that can increase productivity by using less water and less or no soil, apart from reducing health risks to near zero.
Rising demand for fresh and pesticide-free horticultural produce for perennially-swelling urban population all over the world is resulting in the introduction of new farming techniques. These include soil-less techniques such as Hydroponics, Aeroponics and Aquaponics that will redefine commercial agriculture.
Vijay S Yelmalle, who runs a Mumbai-based start-up, Center for Research in Alternative Farming Technologies, says as greenhouse technology has had limited success in India, farming without soil is the best way to use our fast-expanding urban spaces. The best part is that mass adoption of this new technology is easier than we think
Soil plays a key role in growth of plants. It supports the plant, provides it nutrients, and holds moisture, organic matter and bacteria. Well-ploughed land means good oxygen circulation to the root zone. The new techniques provide all these things to the plants without using soil as the medium.
The word Hydroponics is derived from two Greek words, 'Hydro' (water) and 'Ponics' (to labour); so, it means putting water to work. In this, the roots of the plant are either submerged in water or in sterile and inert material. The nutrient salts are provided by dissolving them in the water. These salts are natural substances purified by fractional crystallisation, making them technically inorganic. There are different methods that suit specific plant varieties. While Nutrient Film Technology and Deep Water Culture are commonly used for green vegetables, Substrate-Based Hydroponics is often deployed to grow vines of tomato, cucumber, etc.
Commercial Hydroponics farms are usually set up over more than one hectare for optimum use of resources. The Hydroponics technology ensures consistent taste, shape and colour of the produce. The yield is high and predictable and free from soil-borne diseases. Besides, unlike the traditional open farms, commercial soil-less farms are immune from environmental changes. They also use almost 90 per cent less water. Further advancements in artificial lighting, ways to provide nutrients, pest management and building the systems vertically could multiply the yield of Hydroponics farms to tens of times the traditional farming yield.
In Aeroponics, plant roots are suspended in the air, and moisture and nutrients are provided through foggers. This provides most oxygen to the roots, making the plants grow faster and produce more. Aquaponics, on the other hand, involves replacement of nutrient salts with water from aquaculture, a method of growing a lot of fish in a small area. In other words, it finds a solution to the biggest challenge of aquaculture - the generation of ammonia from fish excreta, whose high concentration can be toxic - by allowing bacteria strains to convert ammonia into nitrites (also toxic to the fish) and to nitrates (less toxic to the fish). Nitrates, a major nutrient for the plants, are taken up by the plant roots. The water so cleaned is used for aquaculture.
Vertical/Urban Farming
Vertical farms are located in the centre of cities where space is available at a premium. These are built over a smaller carpet area but designed to grow vegetables in multiple layers. These farms generally employ the Aeroponics technique but Hydroponics and Aquaponics are used as well. Reduction in carbon footprint (vegetables are transported over hundreds of kilometres, adding carbon to the environment), conservation of water (sometimes condensed water from air-conditioning units is used), freshness/safety of the produce, and premium prices are the common considerations behind vertical farming. Worldwide many enthusiasts and agripreneurs are running successful vertical farms with more and more innovative ideas. There is no limit to these farms. They can go as high as you can pump water and access the place, either yourself or through a robot. The Association for Vertical Farming (AVF), an international NGO, is working with many farms to spread the technology. From Middle East to South-East Asia to Japan to USA to Europe, commercial soilless farms are producing quality and insecticide- and chemical-free produce. South Asia, however, has been slow in adopting these new technologies.
Scenario in India
India's protected cultivation (soil-based greenhouse) farming has had limited success due to wrong adaption of technology. Soilless farming being more advanced, most investors are reluctant to try it at a commercial scale. A few successful greenhouse farmers are trying the substrate-based Hydroponics to grow tomato, capsicum and cucumber and becoming successful. The major hurdle in the success of soil-based greenhouse farming, and even in soilless farming, is experience, knowledge and skills. But the scenario is changing fast. Under the initiative of the government of India, universities have started skill-based degree programmes for urban and rural youths. One such course, a degree in Greenhouse Management, is being offered by Ramnarain Ruia College in the heart of Mumbai. Much of the workforce trained in greenhouses is ready to venture into commercial soilless farms. Many agriculturists who are looking after huge commercial soilless farms are also ready to relocate to India if appropriate opportunity is provided
Modular Farms Newsletter #5
2016 has been an incredible year of growth for Zipgrow, Modular Farms,
Upstart Farmers and the entire hydroponic food industry
Modular Farms Newsletter #5
This year in Brampton the ugly head of winter has reared itself a little earlier than we hoped. On the bright side, it's given us extra motivation to spend more time working within the heavily insulated walls of our Modular Farm. And for good reason, as we have begun donating our weekly harvests to the Daily Bread Food Bank in Etobicoke.
Since November 23rd, the Daily Bread team has been working tirelessly to ensure that this year's holiday food drive feeds as many hungry Canadians as possible. To date, they have amassed over 200,000 pounds of food, but they still have a long way to go. Their goal this season is 1.5 million pounds and if we all pitch in a little extra food we have no doubt that they'll get there!
We'd like to sincerely thank everyone who made the trip to our office last month to participate in our inaugural open house event. It was a pleasure to see such an intelligent and curious group of like-minded individuals interacting and sharing ideas; we hope that you all had as much fun attending the event as we did hosting it. We also made sure to videotape a portion of the event for those who couldn't be there physically, which you can watch by clicking here.
Back inside the office things are more exciting than ever. For starters, we recently added a new member to our team - Kamil - who has given us a much-needed boost in our engineering efforts. Under his guidance, our first round of Primary Modules will be making their way off the assembly line and into the hands of our customers in early 2017, followed by our Macro and Vestibule Module prototypes. Also, as you can see from the above gif, our Master Farmer Kevin has been skillfully pollinating and nurturing our first generation of office-grown Strawberry and Cherry Tomato plants, which we are excited to announce are getting close to being harvestable!
In addition to hosting clients and friends, we also had the pleasure of welcoming in a class of inquisitive young pupils and teachers from the St. Joan of Arc Secondary School in Mississauga. The students had already been operating their own classroom hydroponic and aquaponic system for a while and we were blown away by their level of understanding and appreciation for Zipgrow technology and our Modular Farm. When the students left that day, our team breathed a sigh of relief knowing that the next generation of Canadian hydroponic farmers are already blossoming, and will be well equipped to face the food scarcity challenges that the future holds for both our country and the rest of the world.
2016 has been an incredible year of growth for Zipgrow, Modular Farms, Upstart Farmers and the entire hydroponic food industry. More than ever, people have become conscious of the need for sustainable farming practices that are close to home. More importantly, these same people have begun taking it upon themselves to act as a force for change in their own communities. We are proud and grateful to be in a position to empower, educate and support people like you, and we can't wait to see what we can all accomplish together in 2017.
Happy holidays from all of us here at Modular Farms. We wish you nothing but health, happiness, and success in the new year!