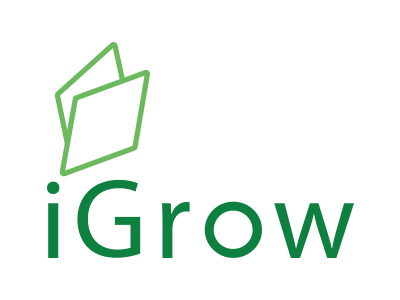
Welcome to iGrow News, Your Source for the World of Indoor Vertical Farming
Nine High-Tech Farms In Singapore Awarded Nearly $40 Million To Ramp Up Food Production
The amount was made available through the "30x30 Express" grant launched by the SFA on April 17 this year. The aim of the grant was to meet 30 percent of Singapore's nutritional needs with food produced locally by 2030
SEP 9, 2020
Shabana Begum
SINGAPORE - Nine urban farms have been offered a total of $39.4 million by the Singapore Food Agency (SFA) as part of efforts to support the growth of local agrifood enterprises and ramp up local food production over the next six to 24 months.
The amount was made available through the "30x30 Express" grant launched by the SFA on April 17 this year. The aim of the grant was to meet 30 percent of Singapore's nutritional needs with food produced locally by 2030.
More than 40 proposals were received by May 29, the closing date for proposals, and SFA said that the nine selected incorporated highly productive farming systems that could be constructed and implemented quickly to achieve high production levels.
All the proposals were assessed based on benchmarks such as productivity, project feasibility, economic viability, and the farms' capabilities.
SFA had to increase its original $30 million budget for the grant to close to $40 million to support the nine companies' proposals, said the agency in a press release on Wednesday (Sept 9).
Seven of the nine companies have accepted the SFA offer.
They are vegetable farms ComCrop, Green Harvest, I.F.F.I, LivFresh, Genesis One Tech Farm and VertiVegies, and egg farm Chew's Agriculture.
The funds will go towards projects such as building additional greenhouses, leveraging technology and automation to reduce manpower, and bringing artificial intelligence to high-tech farms.
SFA said the companies awarded the grant will be able to tap it to defray costs while accelerating their expansion.
For instance, I.F.F.I will set up a mega high-tech indoor vegetable farm that depends on AI to monitor the growth of its leafy greens, along with an advanced environmental control system to ensure optimum yield all year round. The farm will also use an innovative water treatment system that reduces the amount of bacteria in the crops and extends the shelf life of its produce.
Ms. Grace Fu, Minister for Sustainability and the Environment, said: "While we continue to plan to tackle our long-term challenges, we also need to respond swiftly to the immediate global food supply challenges posed by the Covid-19 pandemic.
"Supporting our agri-food industry and augmenting their production capabilities remains a key strategy in strengthening Singapore's food supply resilience," she added.
Singapore Food Agency (SFA) has awarded close to $40 million of funding to nine companies to help them adopt technology to ramp up local food production. This marks another significant step towards reaching our goal of fulfilling 30% of our nutritional needs through local sources by 2030.
The “30x30 Express” grant was launched in April this year to accelerate our efforts to strengthen food security. The COVID-19 pandemic and its adverse impact on global supply chains, has underscored the importance of local food production as a buffer against supply disruptions. With Singapore importing more than 90% of our food, we are particularly vulnerable to fluctuations in the global food supply, which can stem from diseases, trade tensions, or climate change.
I visited two of the awarded companies, ComCrop and I.F.F.I, and was impressed by how they have integrated technological innovation into their farming. ComCrop’s vegetables are grown using NFT hydroponics system, which requires 90% less water and nutrients compared to traditional soil-based farming. I.F.F.I leverages AI farming systems integrated with IoT monitoring to achieve optimum growing conditions all year around. The grant will provide them with an added boost to adopt highly productive farming systems to ramp up production over the next 6 to 24 months.
Let us play our part to strengthen food security by supporting our local farmers! Do lookout for the SG Fresh Produce logo and give local produce a try when you go on your next groceries shopping trip!
Farms in Singapore can tap on SFA's existing Agriculture Productivity Fund (APF), which aims to help them modernize and adopt advanced farming systems, as well as co-fund the test-bedding of technologies.
Enterprise Singapore has also set aside over $55 million to help local agriculture and aquaculture companies build new capabilities and innovate to grow more with less.
SFA has also urged consumers to buy local.
"We urge consumers to support our local farms and buy local produce, which can be identified easily by our new SG Fresh Produce logo," said Mr. Lim Kok Thai, SFA chief executive officer.
Lead photo: Minister for Sustainability and the Environment Grace Fu with ComCrop CEO Peter Barber during a visit to the farm
TOPICS: AGRICULTURE AND FARMING MINISTRY OF SUSTAINABILITY AND THE ENVIRONMENT AWARDS AND PRIZES
AgriTech - A Hotspot For Investments
In recent times, AgriTech or AgTech solutions are gaining their popularity factor because individuals and entities alike, are becoming increasingly aware of the efficiency technology adds to their daily processes, which otherwise would have been tasking to follow through with. The ‘revolutionary’ factor has been highlighted in the AgTech space and hence, it has caught the eyes of investors and big corporations
AgriTech - The Sought After Technology Breakthrough
In recent times, AgriTech or AgTech solutions are gaining their popularity factor because individuals and entities alike, are becoming increasingly aware of the efficiency technology adds to their daily processes, which otherwise would have been tasking to follow through with. The ‘revolutionary’ factor has been highlighted in the AgTech space and hence, it has caught the eyes of investors and big corporations.
AgTech represents that specific niche category of technology buffs that intermingle the age-old occupation of agriculture with the new age specs and wonders of technology.
The specifics of Agronomic Processes:
The agronomic processes encompass diverse solutions in every step, ranging from the sowing of seeds to the harvesting of crops. The processes comprise of integrated resolutions to enhance efficiency within agricultural organizations, along with benefiting smallholder and marginal farmers.
AgriTech, breaking barriers and records:
The upward curve of investments and profitability within the industry does not seem like it would dip anytime soon, with a continuous maturity, breaking barriers, and records. Since 2013, funding within the AgTech sector has increased by roughly a whopping 370%. According to an AgFunder report, specifically, startup investments bucked global venture capital markets across all sectors to $4.7 billion in 2019. The 695 deals were carried out across 940 unique investors.
COVID-19 comes into play:
Similar growth cannot be expected for the remainder of 2020, due to Coronavirus governing industries across all business streams. However, there is less chance of the investments cutting to a freefall wherein they would dip way lower than initially expected. New investment projects may be put on hold, however, ongoing funding is expected to be perennial.
Localizing our viewpoint, we notice that most of these investments are still being carried out within the United States. However, investments in India continue to rise at a rapid rate, representative of a two-way flow (up-stream as well as down-stream) of funding, again highlighting the maturity of the sector.
The reasoning:
WHY? Every action has an equal and opposite reaction. Sir Isaac Newton was well aware of the specifics of investment and the network within which it functions. Our world is at a point today, where overpopulation is a severe problem in various countries, along with the overall population set to increase by 30% over the next 35 years, according to Global-Engage.com. According to a report conducted by FAO, agricultural production will have to increase by 60-70% to feed the world population by 2050. To work towards an increase in the production of food, along with keeping a tap on the factor of ‘sustainability’, it is essential and integral to adopt smart farming and smart agricultural practices, allowing processes and outcomes to become more efficient in the long run.
The Need for Emerging Trends:
The importance of utilizing ‘big data’ and ‘predictive analytics’ to counteract the issues faced by farmers daily is now more than ever. They will allow farmers to achieve and maybe even surpass their targets for the seasons, resulting in an influx of productivity. In a survey conducted with farmers, 60% mentioned that precision farming is an influential trend to look towards for a structural and foundational change in the way daily practices take place. With the risk of climate change looming overhead at all times, it is crucial to understand the essential need to channel funds towards projects that solve difficult and foreseen problems.
The Agricultural 4.0 wave:
Today, 25-30% of all food produced is wasted, which incurs a social, economic, and environmental cost of $2.5 trillion annually. An outdated supply chain with no digital integrations or climate-smart advisory results in around 20% of the crops produced in developed countries being left in the field itself. To spark a change and make a difference, socially conscious investors who look to profitability as well, view the AgTech sector as a gold mine, essentially killing two birds with one stone.
AgriTech today is an area that is ripe for innovation with limits imposed solely due to constraints in terms of available capital. When this constraint is counteracted, creativity applied to AI and food production will be ten-fold.
Sanjay Borkar
Founder, CEO of FarmERP
USA (CA) - Iron Ox Raises $20 Million To Grow Robotic Greenhouse Operations
The funding will be used to open additional robotic growing facilities in California and other parts of the U.S., according to company co-founder and CEO Brandon Alexander
Khari Johnson @kharijohnson
September 9, 2020
Robotics farming company Iron Ox today announced the close of a $20 million funding round. The funding will be used to open additional robotic growing facilities in California and other parts of the U.S., according to company co-founder and CEO Brandon Alexander. The funding will also be used to hire additional machine learning and robotics experts as well as growers and scientists who work with plants.
“We’re now competing on price with field farms, but we think we can do even better and take this to more people,” he said.
Iron Ox employs a 1,000-pound mobile transport system roughly the size of a car to move trays of growing vegetables and tend to plants using a robotic grasper while computer vision systems monitor the plant growth cycle. The semi-autonomous system still relies on humans for a part of its seeding, pruning, and inspection process, Alexander said, but the goal is for Iron Ox to someday be fully autonomous.
While startups like Bowery practice indoor vertical farming in urban facilities near New York and Baltimore, Iron Ox has turned its focus toward greenhouse farming since the company was founded in 2015 as a way to lower energy costs. Earlier this year, Iron Ox opened its first greenhouse, a 10,000-square foot facility in Gilroy, California, the company’s second location. Iron Ox currently provides produce to 15 Whole Foods stores in the San Francisco Bay Area.
Though Gilroy is known as the garlic capital of the world, Iron Ox does not currently grow any garlic. Instead, the company focuses on leafy green vegetables like lettuce and some herbs.
Alexander said Iron Ox’s biggest challenge is how to use data collected by sensors to train AI systems that produce higher yields at lower costs.
“I would say in agriculture as a whole it’s not just collecting data, it’s not just taking an image, but it’s actually how do you include that data into the decision making process?” Alexander said. “I would say that is the biggest challenge in ag is how do you respond to these each individual plants and the variety and all these little variables.”
The $20 million funding round was led by Pathbreak Ventures with participation from Crosslink Capital, Amplify Partners, Eniac Ventures, R7 Partners, Tuesday Ventures, and At One Ventures. Iron Ox is based in San Carlos, California. The company currently has 30 employees and has raised $45 million to date.
Field farming today is still the most efficient way to grow produce. However, concern about shrinking field yields and instability due to climate change has spurred interest in indoor farming. In 2018, international teams from companies like Microsoft and Tencent competed against each other to find out who could grow the highest yield of cucumbers inside a greenhouse using AI and automation. (Spoiler: The Microsoft team won.)
In other AI and agriculture news, last month the startup iFarm raised $4 million for its AI-driven urban farming solution, and in June the startup Burro began rolling out its autonomous farm robot in southern California to assist in grape harvesting.
Image credits: Iron Ox
"Spend Less Time On Your Controls, But More Quality Time With Your Plants"
Practical insights from the Autonomous Greenhouse Challenge
When your team wins the Autonomous Greenhouse Challenge, you may safely call yourself an expert on autonomous cultivation. René Beerkens, who's been with Hoogendoorn Growth Management for twenty years, and Evripidis Papadopoulos, who worked as a Data & Algorithm specialist for Hoogendoorn during the challenge and is now back to LetsGrow.com as a Researcher & Data Analyst, were both involved with winning team AuTomatoes, and from the Hoogendoorn headquarters, they shared some of their insights with growers.
Plant Empowerment
At the heart of Hoogendoorn's holistic approach, René explains, is the concept of Plant Empowerment, which evolved from Next Generation Growing. "We're not only a technical supplier, but also spend an awful lot of time on research and development", René introduces his company.
"The Dutch have a vast history of experience growing plants, mostly by trial and error", he continues. Having learned the laws of physics and completed a lot of research on plant development, growers have moved on from trial and error to a data-driven approach.
Data-driven
This begs the question: why data-driven growing? "We lack experts in the field", René says, "investors want a quick return on investment (they want to invest in something that works from the start), but the main thing is, we want to leave planet Earth in a better way than we found it, using less resources."
The Autonomous Greenhouse Challenge was a perfect opportunity to put this data-driven approach to the test. Using a variety of sensors that measured things like air temperature, humidity, CO2, EC and root temperature, plant temperature, and light levels, a range of data was collected, which was all gathered in one central place so the team could access it wherever they were.
This team featured members from various disciplines, who met once a week. The dashboard, built on the LetsGrow.com platform and customized for Hoogendoorn, helped them analyze data and make the appropriate decisions. As Evripidis puts it, this allows you to "save time for yourself, and due to the holistic approach you find space for further optimization."
Results
The main attraction of the webinar was, of course, the results that participation in the challenge yielded. Using a data-driven strategic approach, the team built their strategies based on historical data from outside conditions. During the challenge, the AI system made adjustments to accommodate the changing circumstances, as can be seen in the below graph showing the ratio temperature radiation (RTR).
"You can't be at your computer daily," Evripidis explains, "so the algorithm made changes automatically, based on feedback from the crop."
It may sound scary to give your precious crops into the hands of an autonomous computer, but the holistic approach taken by team AuTomatoes at least provides the grower with the peace of mind that they can actually see the crop, even when they're not in the greenhouse. The slide below shows how that looks in the dashboard.
René explains that you can also make time-lapses with the dashboard and compare day by day development with the pictures, which is arguably better comparing than just looking at the plants in the greenhouse, because changes in the crop become more noticeable.
Data Driven Operational approach
The next graph shows two identical days with the outside temperature and wind speed the same. In the first day (on the left), the temperature fluctuates a lot, as Evripidis points out. On the second day, the temperature doesn't fluctuate so much, thanks to an intervention in ventilation from the autonomous system, which is of course more favorable to the crop.
While growers are fully focused on ventilation or temperature, Evripidis explains how they came up with VO control. "We keep the windows as closed as possible to trap humidity, so that the temperature is not too high, stomata will remain open, and photosynthesis is maximized. If you trap humidity, you also trap CO2, so it's a win-win situation." With VO control it's not necessary to work with P-band anymore. Growers can set five setpoints, the rest will be done automatically.
René and Evripidis also discussed how the autonomous cultivation system dealt with irrigation and assimilates during the challenge. More about the former can be found in this article from Godfrey Dol on HortiDaily, and Hoogendoorn shared some information on realizing an optimized assimilates balance in this article.
Quality time
In conclusion, it can be said that a grower can do much more based on data. "We had a grower who had never grown tomatoes in the Netherlands, and he did quite well using just data", René shares, telling growers that they can "spend less time on your controls, but more quality time with your plants."
As Evripidis puts it: "We're trying to assist, not take over - we make the car, you drive the car." Or to use another metaphor, as René did: "A plane can fly itself, but the pilot still has to know what happens in the background. We can do a lot with data, but we're still dealing with organisms that are much cleverer than us - they've evolved for millions of years, we are just catching up in the last few years."
For more information:
Hoogendoorn Growth Management
info@hoogendoorn.nl
www.hoogendoorn.nl
Publication date: Mon 7 Sep 2020
Author: Jan Jacob Mekes
© HortiDaily.com
Could Urban Agriculture Feed The Cities of The Future?
Vertical farms, rooftop farms and computer-controlled growing environments are an emergent phenomenon in cities around the world, which are eager to take advantage of the many benefits of urban agriculture
03 Sep 2020
By Agency
Vertical farms, rooftop farms, and computer-controlled growing environments are an emergent phenomenon in cities around the world, which are eager to take advantage of the many benefits of urban agriculture.
Drawing on new technologies and enthusiasm for locally sourced organic produce, these promising initiatives have raised hopes for greater sustainability that will reduce the environmental impact of cities and agricultural production required to meet the needs of their citizens.
However, the question remains: will urban farms be able to produce enough food to make cities self-sufficient?
The vast majority of fruit and vegetables sold in cities are picked before they are ripe, and are produced using intensive farming methods, which do extensive damage to the environment.
In contrast, urban agriculture offers the hope that we will one day be able to meet the global challenge of feeding cities in a much more sustainable manner. At the same time, it also provides a solution to the need for high-quality and locally sourced fresh food.
Recent successes in the field speak for themselves, notably the US$4mil (RM16.6mil) in funding raised by IFarm, which provides software and technology to the vertical farming sector.
The Helsinki-based company manages heavily automated indoor farms in which produce is grown in vertically stacked beds with a host of technologies that include a wide range of sensors, computer vision, and machine learning.
It currently has some 50 farms that are in development and is hoping to manage one million square meters of vertical farms and provide support for 500 different crops by 2026.
Is food self-sufficiency within reach?
It could be, notably with regard to vertical farms and certain crops. A recent publication in the interdisciplinary scientific journal PNAS has drawn attention to the potential of vertical farming to generate enormous yields of wheat.
Researchers have calculated, on the basis of theoretical values for the growth of wheat under optimal conditions, that a 10-story building on a one-hectare site could provide up to 1,940 tonnes of wheat per year, 600 times more than the average yield from traditional agriculture.
One of the reasons for this is because vertical farming provides conditions that would allow for five harvests per year instead of one. With the added advantages of doing away with the need for herbicides and pesticides, low water use, and land depletion, vertical farms may well fulfill their promise.
Questions remain about the viability of projects
However, as it stands, urban farms are very expensive to set up, and only a very few are actually profitable. Taking advantage of their situation in cities, most of those that are now operating are sustained by revenue from sources other than food production: notably income generated by cultural events, workshops, and renting plots to private individuals. – AFP Relaxnews
Related stories:
Community farm brings residents together
Getting ready for Agriculture 4.0
Lead photo: Urban agriculture is increasingly common in cities. This picture shows one of six farms created by the New York City Housing Authority in Brooklyn, New York. Photo: Leticia Barboza/AFP
TAGS / KEYWORDS: Urban Farming , Food Security , Vertical Farming , Rooftop Farms
IDTechEx Identifies Innovative Companies Changing The Face of Vertical Farming
Vertical farming, the practice of growing crops indoors under tightly controlled conditions, is continuing to expand rapidly
Sep 02, 2020
BOSTON, Sept. 2, 2020,/PRNewswire/ -- Vertical farming, the practice of growing crops indoors under tightly controlled conditions, is continuing to expand rapidly. By using LED lighting tailored to the exact needs of the crop, alongside advanced hydroponic growing systems, and growing crops in vertically stacked trays, vertical farms can achieve yields hundreds of times higher than the same area of traditional farmland.
Investors and entrepreneurs alike are excited about the potential of vertical farming to revolutionize the global food system and some vertical farming companies have raised dizzying amounts of money. Plenty, a San Francisco-based start-up, and the most well-funded vertical farm, has raised $401 million in funding, with backers including SoftBank, Alphabet Chairman Eric Schmidt, and Amazon CEO Jeff Bezos. Fellow US start-ups AeroFarms and Bowery Farming are not far behind, with $238 million and $167.5 million in funding, respectively.
While there has been much attention on these companies and their exploits, there are dozens of other companies in the industry developing their own approaches to vertical farming. Here, we explore some of the most innovative vertical farming start-ups, based on the recent IDTechEx report, "Vertical Farming 2020-2030".
Freight Farms
Freight Farms is a Boston-based vertical farming company that manufactures "container farms", vertical farming systems installed into 40' mobile containers. Alongside its container farms, Freight Farms provides the farmhand software, a hydroponic farm management, and automation platform that also connects users with other Freight Farms customers. Container farms have many advantages - they are easy to transport, compact, and relatively cheap to set up in comparison to other vertical farming systems. Container farms are often turnkey systems, too, meaning that they require much less experience and expertise to operate than either a factory-scale vertical farm or indeed a traditional farm.
Freight Farms recently released its most advanced container farming system, the Greenery, which it believes is the most advanced container farming system in the world. The Greenery is a turnkey system that uses an array of sensors to continuously monitor the growing conditions inside the farm, with the farmhand software automatically making adjustments and planning watering cycles in order to provide the optimum environment for growing crops and allowing users to control their Greenery remotely from a smartphone.
80 Acres – Collaboration, Food Experience
Despite their potential, many vertical farming start-ups have struggled over the years with the labor costs and power requirements for running a high-tech indoor farm. This has often forced producers to sell their crops at a much higher price than conventionally farmed leafy greens. Additionally, many founders of vertical farming companies have little experience in the food industry and can struggle with the day-to-day realities of running a food production industry.
80 Acres is an Ohio-based vertical farming start-up aiming to overcome these challenges by constructing the world's first fully automated indoor farm. The company was founded in November 2015 by Tisha Livingston and Mike Zelkind, who between them have over 50 years' experience in the food industry. Collaboration is also important to 80 Acres. The company believes that vertical farming is a very multidisciplinary field, requiring collaboration between partners who are experts in their own discipline. Signify (formerly Philips Lighting) developed the LEDs used in the facility and Dutch greenhouse automation company Priva developed the control and fertigation systems, with 80 Acres using its experience in food to bring the system together and integrate the technology.
The company currently operates a 75,000 square foot facility in Hamilton, a suburb of Cincinnati, which is set to expand to 150,000 square feet in summer 2020 following a $40 million investment from Virgo Investment Group. When completed, 80 Acres claims this facility will be the world's first fully automated indoor farm. The farm will be automated from seeding to growing to harvesting, using robotics, artificial intelligence, data analytics, and around-the-clock monitoring sensors and control systems to optimize every aspect of growing produce indoors.
Jones Food Company
Jones Food Company is a British vertical farming start-up that operates Europe's largest vertical farm out of a warehouse in Scunthorpe, UK. It was founded in 2016 by James Lloyd-Jones and Paul Challinor, who wanted to build the largest vertical farming facility that they could in order to help overcome some of the operational problems plaguing the industry and bring vertical farming to the mainstream. After visiting several vertical farms in Japan, they decide that the only way to make vertical farming a success is to focus on scale and automation.
Jones Food Company focuses on maximizing automation and robotics in their facility to minimize operating costs, with its facility being modeled on a car factory, with the growing process resembling a production line - over the 25-day growing period, plants move from one end of the facility to another. Much of the work is done by machines, helping to reduce labor costs. Harvesting is carried out by bespoke machines and the heavy lifting is performed by a robot called Frank. This focus on automation means that only six employees are required to operate the Scunthorpe facility.
Jones Food Company has partnered with UK online grocery company Ocado, which currently owns about 70% of the business. Through this partnership, Jones Food Company is aiming to set up vertical farms next to Ocado's grocery depots, meaning that fresh produce could be delivered to shoppers within an hour of being picked.
Infarm
Infarm is a Berlin-based start-up that sells modular, hydroponic vertical farms for growing leafy greens and herbs in supermarkets, schools, and offices. A single two-square meter unit can grow 8,000 plants in a year, with the company claiming its farms use 95% less water than soil-based farms, take up 99.5% less space, use zero chemical pesticides, need 90% less transportation, and use 75% less fertilizer.
Infarm has partnered with several major supermarkets across Europe, where it has currently deployed over 500 farms in stores and distribution centers. The company is also beginning to expand in the USA, having recently partnered with Kroger to trial its indoor farms in two QFC stores in Seattle. In the UK, it has partnered with supermarket chain Marks & Spencer, which is trialing in-store urban farming in seven locations in London, growing Italian basil, Greek basil, Bordeaux basil, mint, mountain coriander, thyme, and curly parsley.
The company's business model is based around an "agriculture-as-a-service" model. The modular farms remain the property of Infarm, which receives income per harvested plant. Infarm then coordinates with clients such as retailers and takes care of the farm including installation, cultivation, harvesting, and maintenance. Aside from the regular visits by service personnel to plant new plants, the farms are controlled remotely. This modular, data-driven, and distributed approach — a combination of big data, IoT, and cloud analytics — sets Infarm apart from competitors. From a price point, Infarm is attractive for supermarkets, which get a better product at the same price. In addition, the plants, especially herbs, are harvested fresh, preserving color, smell, flavor, and nutrients.
For more information about the vertical farming industry and the innovative companies operating within the space, please see the recent IDTechEx report, "Vertical Farming 2020-2030", www.IDTechEx.com/VertFarm or for the full portfolio of related research available from IDTechEx please visit www.IDTechEx.com/Research.
IDTechEx guides your strategic business decisions through its Research, Consultancy, and Event products, helping you profit from emerging technologies. For more information on IDTechEx Research and Consultancy, contact research@IDTechEx.com or visit www.IDTechEx.com.
CubicFarms Announces Sale of Control Rooms To Global Agtech Leader, Terramera
In June, CubicFarms offered its Control Room system for sale to growers requiring complete control over the growing environment that is so crucial for high crop yields and quality
VANCOUVER, BC, AUGUST 31, 2020 – CubicFarm® Systems Corp. (TSXV:CUB) (“CubicFarms” or the “Company”) is pleased to announce the sale of three Control Rooms to Terramera, a global agtech leader transforming how food is grown and the economics of agriculture. Terramera is a British Columbia-based company on a mission to reduce global synthetic pesticide use 80 percent by 2030 with its revolutionary Actigate™ technology platform, named a 2020 World-Changing Idea by Fast Company.
In June, CubicFarms offered its Control Room system for sale to growers requiring complete control over the growing environment that is so crucial for high crop yields and quality. Each CubicFarms Control Room is assembled inside a proprietary stainless steel, fully insulated growing chamber with the option to customize features such as lighting, automated irrigation, and nutrient delivery, providing full climate control for temperature, humidity, and carbon dioxide levels. The system has a variety of sensors available, all of which can be remotely monitored and controlled.
Dr. Travis Good, Terramera’s Chief Technology Officer commented, “We required a closed space with precise controls to isolate each environmental variable and produce uniform, plentiful and high-quality plants for our research. CubicFarms’ Control Room system is an ideal solution and helps us scale our Actigate™ technology with the goal of dramatically reducing the use of synthetic pesticides in agriculture.”
CubicFarms CEO Dave Dinesen commented, “We are pleased to call Terramera a customer as we share the same strategic investor, Ospraie Ag Science, and vision to transform how food is grown with the use of leading-edge technology. Terramera is a natural fit for a synergistic partnership in the future as both companies look to develop our machine learning and AI capabilities to further advance our respective technologies.”
Photos: The CubicFarms Control Room, complete with LED light fixtures, an automated heating, cooling and ventilation system, and wired environmental controls.
Neither the TSX Venture Exchange nor it’s Regulation Services Provider (as that term is defined in the policies of the TSX Venture Exchange) accepts responsibility for the adequacy or accuracy of this release.
About CubicFarm® Systems Corp.
CubicFarm Systems Corp. (“CubicFarms”) is a technology company developing and deploying technology to feed a changing world. Its proprietary technologies enable growers around the world to produce high quality, predictable crop yields. CubicFarms has two distinct technologies that address two distinct markets. The first technology is its patented CubicFarms™ system, which contains patented technology for growing leafy greens and other crops. Using its unique, undulating-path growing system, the Company addresses the main challenges within the indoor farming industry by significantly reducing the need for physical labour and energy, and maximizing yield per cubic foot. CubicFarms leverages its patented technology by operating its own R&D facility in Pitt Meadows, British Columbia, selling the system to growers, licensing its technology, and providing vertical farming expertise to its customers.
The second technology is CubicFarms’ HydroGreen system for growing nutritious livestock feed. This system utilizes a unique process to sprout grains, such as barley and wheat, in a controlled environment with minimal use of land, labour and water. The HydroGreen system is fully automated and performs all growing functions including seeding, watering, lighting, harvesting, and re-seeding – all with the push of a button – to deliver nutritious livestock feed without the typical investment in fertilizer, chemicals, fuel, field equipment and transportation. The HydroGreen system not only provides superior nutritious feed to benefit the animal, but also enables significant environmental benefits to the farm.
About Terramera
Terramera is a global agtech leader fusing science, nature, and artificial intelligence to transform how food is grown and the economics of agriculture in the next decade. With its revolutionary Actigate™ technology platform, which was recognized by Fast Company as a 2020 World Changing Idea, Terramera is committed to reducing the global synthetic pesticide load 80% by 2030 to protect plant and human health and ensure an earth that thrives and provides for everyone. The privately-held, venture-backed company was founded in 2010 and has grown to include a world-class bench of engineers, scientists, advisors, and investors. Terramera is headquartered in Vancouver, British Columbia, with integrated operations in Canada, the US, and India that include research labs, a greenhouse and farm, and more than 240 patents in its global IP portfolio. For more information, please visit terramera.com
Cautionary statement on forward-looking information
Certain statements in this release constitute "forward-looking statements" or "forward-looking information" within the meaning of applicable securities laws, including, without limitation, statements with respect to CubicFarms’ future partnership with Terramera; and the development of machine learning and AI capabilities by CubicFarms. Such statements involve known and unknown risks, uncertainties, and other factors which may cause the actual results, performance, or achievements of CubicFarm Systems Corp., or industry results, to be materially different from any future results, performance, or achievements expressed or implied by such forward-looking statements or information including the Company obtaining the approval of the Offering from the TSX Venture Exchange. Such statements can be identified by the use of words such as "may", "would", "could", "will", "intend", "expect", "believe", "plan", "anticipate", "estimate", "scheduled", "forecast", "predict", and other similar terminology, or state that certain actions, events, or results "may", "could", "would", "might", or "will" be taken, occur, or be achieved.
These statements reflect the Company's current expectations regarding future events, performance, and results and speak only as of the date of this news release. Consequently, there can be no assurances that such statements will prove to be accurate and actual results and future events could differ materially from those anticipated in such statements. Except as required by securities disclosure laws and regulations applicable to the Company, the Company undertakes no obligation to update these forward-looking statements if the Company's expectations regarding future events, performance, or results change.
Information contact:
Kimberly Lim
VP, Corporate Communications & Investor Relations
Mobile: 236.858.6491
Office: 1.888.280.9076
Email: kimberly@cubicfarms.com
“If We Really Want To Make A Change, We Should Intensively Invest In Innovation and Technique In Africa”
Christine Zimmerman discusses vertical farming trends
Christine Zimmerman Discusses Vertical Farming Trends
Vertical farming is a rapidly growing industry, and there are many challenges and opportunities. In this interview with Christine Zimmermann-Loessl, Chairwoman at the Association for Vertical Farming, she discusses the latest trends and developments within the vertical farming sector worldwide.
What are the latest trends within vertical farming?
Zimmermann-Loessl stated that there is a very clear trend in automation and fully automated systems. Especially in the USA, Japan, and Europe. “The main trend here is that we see robotics and AI machine learning that will even play a bigger role than it does now. Another trend is scaling, as people start to understand the necessity of vertical farming. I still hear from the majority of greenhouse growers, to have a fully automated greenhouse, the vertical farmers say: no we can be more efficient and it can be much more controlled. However, there are so many input factors that cannot be perfectly controlled in a greenhouse. In order to have reliable minimal resources and yield, vertical farming is a better solution.”
Zimmermann stated that once the energy problem issue is solved, they can connect the issue with solar and teach students about it in the AVF demonstration center. Using solar is possible and there are the costs to have the proof of concept.
Have you seen positive developments in vertical farming regarding COVID-19?
As there are strict hygiene standards, higher than in any other farm, there is a very clean environment. “We are beyond ahead COVID-19 measurements and this needs to be communicated even better.” According to Zimmermann, a great advantage of indoor farming the high hygiene standards. Working with a hygiene room quality and improving these standards. “We have seen a lot of growth, also at the AVF as we gained 11 members. Start-ups have the ambition to grow out of that start-up phase.”
She also notes that vertical farming has had more understanding of politics and politicians, but also on a national- and municipal level. They understand that there is a need to secure the future, being less dependent on external factors. “We had to communicate all these advantages even better. The majority doesn’t know them yet and we have to improve that”, she adds.
What is the quickest growing country in terms of vertical farming techniques?
“That’s a tough question. I think that in Germany really took off in the past two years. We have Fraunhofer Institute in Aachen with two brand new systems that haven’t been on the market before with that high level of innovation. The Orbiplant, from Fraunhofer, shows how economical VF can be today. It is built from material on the market for automation or transport systems highly automated and allows cheap production prices. Another company, Lite+Fog, where I see innovation at a level of experience with a new system design and water-saving fog for the roots instead of hydroponics.
Zimmermann continues that Japanese farming company Spread, its Techno farm, is really the state of the art. It’s a proven operation and they produce for the market. “However, Orbiplant and Lite+Fog are still in a demo size compared to the commercial farms of SPREAD and the fully on-demand farms now. We have a differentiation to make between these three.”
And in terms of newly constructed farms?
"I have visited Farminova, Turkey, and it’s very interesting to see how in such an agricultural country a company takes on the innovative food business. Cantek Turkey, the owner Hakan Karaca decided to go into vertical farming and built a system in one of his warehouses, near Antalya, to bring the topic forward. They see the need for sustainability and innovation.” Zimmermann said that Italy is also becoming an interesting country for vertical farming. Companies such as Planet Farms and Ono Exponential Farms that have fully automated new constructions. “People need to build up their trust in technology and the produce from it. In Europe, they have a prejudice against artificial environment by technology, but in Asian countries such as Japan and Singapore they don’t. They’re much more open to it, also in the new farming technology because it offers safe, fresh, local products. They see the shrinking traditional farming in their countries and growing imports."
Are we at a maturity stage in vertical farming yet?
“Not at all. When we started we were in an infant stage. Now we are at age 12 to 14. From an age perspective, we are not mature enough yet. It would be really good to have official government backing. Not just money-wise, but also policy-wise. We want more agriculture sustainable methods. One of these is indoor vertical farming. Once that statement comes, it would help VF implementation a lot.”
Why do you think that governments haven’t done that yet?
“It’s all about the necessity. ‘Why do we need it? We have greenhouses. We have industrial agriculture. Now, with severe droughts, even in Europe, more politicians see the need. I am part of the dialog forum for the 'Future of Agriculture', where all major stakeholders gather in Berlin twice a year. I get to meet all the associations from traditional farming and few of them have heard of vertical farming. Not to talk about embracing, saying it could be a part of agriculture production. However, it’s still a long way to go for communication, marketing, and raising awareness.
"We need more innovation- and vertical farming centers around the cities and rural areas to enable our hands-on learning and demonstration. If we do that, farmers will see it and understand it better. We start with the farmers. More young people are coming in the industry. We will rely on vertical farming systems to maintain reliable food production. It will play a major role if we want to protect the ecosystem when we have over 10 billion people on this planet.”
What would you address as the most frequent struggles within the industry?
“Investment is still a major struggle. Either banks don’t understand the business model of high-tech farms, because they have only know traditional agriculture business models. Or investors don’t have a sufficient understanding of vertical farming. They want a quick ROI and don’t know that they need patience. So, in order to find the right investor and money, it’s not that easy. If you want to scale, you have to have a proof of concept. But more money is needed to go to that next level.
"It ‘seems easier’ in the USA and Asia. Looking at the UAE, which is taking off with vertical farming, partially because the government is supporting it now too. Their food supply chain is in the hand of a couple of people and they were used to importing all food. It takes time to build a new food chain and trust in new suppliers."
In what underdeveloped countries do you see the most potential for vertical farming?
“Absolutely, we just founded our regional chapter by our team. We cannot serve the interest in India anymore, so we decided to have a local team there. It’s taking off like crazy. Now, we have two members in Africa and we get at least two requests per week. In South Africa, it can be seen that there’s a lot of equipment development. Which gives them the highest level of technology compared to the rest of Africa.
"We see a lot of the need to train farmers and really implement vertical farming in Africa. We just received new proposals from Cameroon to train 1200 farmers on vertical farming in the Northwest. So far, our partner in Cameroon has built the center already and we only need the equipment yet and training can start. It’s great to see what they do. If we really want to make a change, we should intensively invest in innovation and technology in Africa. We can grow forest there, instead of turning more land into agriculture and reduce CO2 even more. They are willing to do that and know what they need. It’s not up to us to tell them what they do. If AVF would have the financial power, we’d be there tomorrow to help them."
Where do you see the most positive reactions towards vertical farming?
"In Asia, we can find mature markets, especially in Singapore and Japan. People are willing to buy and understand the concept. China is an important market from a global perspective. A lot of projects in vertical farming are happening there, but the government policy to protect traditional agriculture has such a big importance for the government. Therefore, it’s very tricky to launch vertical farming in the right way. They have megacities and over 1.3 bln people so the demand is huge. But, they only have 12% of land and so there are many opportunities for farming. However, there’s a huge challenge for vertical farming as it’s very hard to implement it on a bigger scale."
For more information:
Association for Vertical Farming
Christine Zimmermann-Loessl, Chairwoman
czl@vertical-farming.net
www.vertical-farming.net
Publication date: Wed 26 Aug 2020
Author: Rebekka Boekhout
© HortiDaily.com
How Can Crop Production Data Advance The Controlled Environment Agriculture Industry?
The Controlled Environment Agriculture Open Data project aims to advance controlled environment research, machine learning, and artificial intelligence through the collection and dissemination of crop production data
The Controlled Environment Agriculture Open Data project aims to advance controlled environment research, machine learning, and artificial intelligence through the collection and dissemination of crop production data.
by By David Kuack
There is a considerable amount of data being generated by both private companies and university researchers when it comes to controlled environment crop production. This data is being generated for ornamentals, food crops, and cannabis. One of the questions about all this data is whether it is being used to its maximum potential to benefit the horticulture industry.
“Data has become a big topic in the horticulture industry with university researchers and private companies,” said Erico Mattos, executive director of the Greenhouse Lighting and Systems Engineering (GLASE) consortium. “People can identify with the challenges and opportunities with the amount of data that is being generated. However, we don’t yet have a centralized repository and a standard methodology for storage to allow us to explore and exploit this data.”
The formation of the Controlled Environment Agriculture Open Data (CEAOD) project aims to promote crop production data sharing from universities and private companies to accelerate CEA research.
Addressing the data proliferation
In 2018 during the North Central Extension & Research Activity–101 (NCERA-101) meeting members of this USDA-organized committee discussed what should be done with the extensive amount of data being generated by controlled environment researchers. Ohio State University professor Chieri Kubota proposed the formation of a sub-committee to address the need to develop guidelines for sharing data generated by controlled environment agriculture researchers.
“Dr. Kubota initiated the discussion about the need for a centralized platform to store data collected from controlled environment research,” Mattos said. “A task force was formed that included Chieri, Kale Harbick at USDA-ARS, Purdue University professor Yang Yang, Melanie Yelton at Plenty and myself. Since the task force was formed Ken Tran at Koidra and Timothy Shelford at Cornell University have also become members of the task force.
“We started discussing how we could make use of all this data. Researchers in the United States collect a huge amount of data. All of the environmental data such as temperature, relative humidity and carbon dioxide and light levels in controlled environment research is collected. There is also a biological set of data which includes plant biomass and fruit yield.”
Mattos said there is also a great deal of research data generated and collected by private companies that is not shared with the horticulture industry.
“With the advancement in sensors and environmental controls, the capability now exists that this data can be collected,” he said. “With the advancements in computing power, this data can be used to start new applications and new tools that haven’t been available before. However, in order to do this, we have to have access to a large amount of data. That’s why the task force thought it would be good to create a repository where researchers and private companies could share the data following a specific format. This data could then be used in the advancement of machine learning and artificial intelligence applications to optimize crop yields in commercial CEA operations.”
An increasing number of funding agencies and organizations, including USDA, are requiring researchers include information about their data management plans in their grant proposals.
Need for collecting and organizing data
Mattos said university researchers see the value in creating a centralized database.
“There are probably millions of data points when you consider how many researchers are doing research in the U.S.,” he said. “Historically these researchers have not been required to share their data. However, an increasing number of funding agencies and organizations, including USDA, are requiring that researchers share their data. If researchers apply for a grant from USDA, they are required to include information about their data management plans in their grant proposals.
“Researchers see the value of sharing this data, but this is not a common practice which involves allocating time and resources. This means someone on their research team would have to organize and share the data. There are probably millions of data points (big data) when you consider how many horticulture researchers there are in the U.S.”
Creating a central database
Based on the need for collecting and organizing the controlled environment research data that is being generated, the task force established the Controlled Environment Agriculture Open Data (CEAOD) project [https://ceaod.github.io/]. The project aims to promote data sharing to accelerate CEA research.
The CEAOD website provides guidelines on how to upload the data. The task force developed the guidelines, which include three sets of data that can be uploaded to the website.
“One set is environmental data, including environmental controlled parameters such as temperature, carbon dioxide, relative humidity, and ventilation,” he said. “These data points are usually collected automatically by sensors. Another set of data is biological data, which is usually collected by humans. These biomass production yield parameters include shoot and root biomass and plant height and weight. The final document is the metadata which are descriptions of the experimental setups and data sets. It is a file that explains the experiments. It describes how the experiments were done.
“There is a certain format that is recommended to be followed to upload the data on the CEAOD website. The step-by-step process is listed on the website. There are no restrictions on which crops the data can be submitted. Our goal is to establish a platform to host a large number of crop production data sets to allow for the development of machine learning and artificial intelligence algorithms aimed at improving crop production efficiency.”
Leading by example
This winter GLASE will have a student collecting and organizing environmental and biological research data.
“The data will be uploaded to the CEAOD database and we will be documenting these activities,” Mattos said. “We will create a guideline of recommendations. We also plan to work with researchers from other institutions to demonstrate how the data can be organized and uploaded to create awareness and how to use the database.
“We hope this initial GLASE contribution will incentivize other researchers to share their data and will facilitate the uploading process. Access to the CEAOD database is free. It is an open platform and anyone can contribute to the development of this database tool.”
Once research data is collected and available for dissemination, the equipment used to produce controlled environment crops will be able to optimize the environmental conditions for a wide variety of crops, including lettuce, tomatoes, and cannabis.
Benefits to the horticulture industry
Mattos said private companies would also benefit from the collection of data and creating a centralized database.
“These companies need more data because it would allow them to analyze the data to develop new products and identify new markets,” he said. “Unfortunately, many of these companies don’t want to share their data. They are very proprietary about their data. They see that collecting and analyzing this data can put them ahead of their competition.
“Many private companies see the need for more data and how it can be valuable but are unwilling to share their own data. But like in other industries there are early adopters. I believe there will be companies that step up and will share their data with the horticulture industry. Hopefully, industry people will be willing to contribute and work on this database as well.”
Mattos said one of the big applications with this project is related to machine learning and artificial intelligence.
“With these applications, large sets of data are needed in order to create baselines,” he said. “Using the data, machines can be taught. Currently, growers’ production knowledge and opinion are more accurate for growing crops than artificial intelligence predictions. Growers are still more reliable, but it is just a matter of time before the use of big data and artificial intelligence will be able to match the growers in regards to optimizing growth.
“We are trying to develop this platform between the growers and controlled environment researchers and the machine learning/data computer scientists. I’m not sure the controlled environment researchers have grasped the potential that is available. We are not using this technology. Establishing this platform, as we collect and disseminate the data, there is real potential to help the advancement of the horticulture industry.”
For more: Erico Mattos, Greenhouse Lighting and Systems Engineering (GLASE), (302) 290-1560; em796@cornell.edu.
More info on CEAOD
Want to learn more about the Controlled Environment Agriculture Open Data project? Then check out these two upcoming events.
Aug. 4, 2-3 p.m. EDT
GLASE webinar: Controlled Environment Agriculture Open Data project. Presented by Erico Mattos, executive director of GLASE, and Kenneth Tran, founder of Koidra LLC.
Aug. 13, 10:30 a.m.-12 p.m. EDT
American Society for Horticultural Science presentation: The Promise of Big Data and New Technologies in Controlled Environment Agriculture. Presented by Erico Mattos.
David Kuack is a freelance technical writer in Fort Worth, Texas; dkuack@gmail.com.
GERMANY: "Dry-Fog is The Next Generation of Aeroponics"
Lite+Fog can replace heavy steel racks with unique fabric, which separates the root zone from the growing zone and allows farmers to grow with any substrate
Lite+Fog, a Berlin-based company, started focusing on dry-fog systems as they noticed many benefits from it. "Dry-fog is the next generation of aeroponics. I started working on indoor farms for more than ten years. Because I did a lot of mushroom farming, I began to work with dry-fog and realized that it is a great way to feed plants. So we are now able to ultimately reduce the typical costs of Vertical Farming by around 80% and even triple the energy efficiency", states Martin Peter, Co-founder, and CEO of Lite+Fog.
Lite+Fog can replace heavy steel racks with unique fabric, which separates the root zone from the growing zone and allows farmers to grow with any substrate. "The system is a realization of work that originally started with urban farming projects, where I built many prototypes and tested a lot of approaches, especially vertical column-based farming technologies. The system as we plan it right now, however, has been developed over the last year."
Efficiency There is a lot of interest from farmers based in Israel, India, and the UK, all with different purposes. Compared to other systems, the Lite+Fog system dramatically reduces the costs in production, maintenance, and labour. The company is planning to have a pilot farm constructed by next year. "We are still on the lookout for potential pilot partners, strategic investors, and research institutes which are interested in joining this new generation of Vertical Farming. Bringing the efficiency up and lowering the costs is the most important thing to transform this vital technology into the mass-market application it has to be", says Martin.
Standardized farms
"We want to become a core technology supplier for indoor farms. As the technique has proven to be successful, we are now upscaling, and engineering the larger versions of our prototype farms. So we're connecting with suppliers and core industries in Germany and elsewhere, to create an important industrial network, able to satisfy the demand we expect in the future.
We plan on delivering at least 60 bigger farms per year during the next five years. Very simply put, we create a big box where seeds enter at one end and plants come out at the other. Eventually, we want to focus on standardizing these farms, as this would significantly improve cost efficiency and comparability. These are both essential factors for research and marketability", Martin states.
The concept design of Lite+Fog's 1000m2 footprint farm creating more than 45.000 m2 of growing surface for greens and berries
Benefits
"Dry-fog enables plants to be better nourished and improves growth by up to 20%. This way of growing is also practically weightless, so you can completely reimagine the architecture of farms - which we make great use of. Improving the efficiency of indoor farms is about how many square meters of growing space you generate in a given volume. Our approach is focusing on that primarily.
In addition to that, with no clogging nozzles, less maintenance, and easier central production, dry-fog is the next step of indoor farming. And that's why we are so much more cost-efficient than other approaches which are not vertical but multilayer horizontal farms anyway. We develop a true vertical "food-reactor".
The state-of-the-art spray nozzles typically used in vertical farms, which directly spray water on the plant roots, are bound to clog up as they are using a salty solution. These now outdated systems need to be cleaned and maintained all the time - and are reliably unreliable in the long run. However, dry-fog does barely weigh anything, doesn't need nozzles, and is therefore much cheaper and easy to use. "
Challenges
However, "fogponics" also has its challenges. As there is no growing medium, you have to be extra aware of the temperature of the root zone and on the complex system delivering the fog to the roots. Also, the droplet size has to be adjusted for bigger nutrients that are essential for some crops. But "these 'difficulties' can easily be mitigated if you adapt a bit - and that's what we are researching currently," says Martin.
For more information:
Lite+Fog GmbH
Martin Peter, Co-Founder, and CEO
Marienburger Str. 8
10405 Berlin
martin.peter@liteandfog.com
www.liteandfog.com
Publication date: Fri 17 Jul 2020
Author: Rebekka Boekhout
© HortiDaily.com
CANADA: Space-Age Tech Will Take Farming To New Heights in Welland
Intravision Group has shone a light on everything from cannabis to planet simulators, spanning across Kuwait, McMaster University, and the European Space Agency. Now, through Intravision Greens Niagara, its tech is taking veggies to new heights in Welland
Vertical Farming Facility Aims to Produce 1-Million Pounds of Produce
Intravision Group has shone a light on everything from cannabis to planet simulators, spanning across Kuwait, McMaster University, and the European Space Agency. Now, through Intravision Greens Niagara, its tech is taking veggies to new heights in Welland.
Starting in Norway, Intravision made its progression across the pond to the University of Guelph's Controlled Environment Systems Research Facility. In collaboration with the university, they honed in on how isolated plants in a hyper-controlled environment responded to everything from lighting spectrum, to airflow movements.
While the technology applies to plants grown in space, the fundamentals behind it aren’t rocket science.
Modern farming has drastically evolved to give farmers more control over their crops, but outside in the field, nature still has the upper hand.
Move the entire growing process inside into a controlled environment, and suddenly you have control over everything. For Intravision Greens, it’s a bit like getting to play God.
"It's a low-tech approach to a high-tech challenge," says Nic Keast, a senior project manager with Intravision. "You're growing plants, plants grow themselves, let's give them the right conditions and let them do their thing."
Non-GMO, certified and sterile seeds are planted in-house. Every stage of the plant’s growth, from germination to harvesting, is dialed in; from what spectrum of light the plant gets, to the temperature and amount of air circulated over a plant, to the spacing in a tray.
By the time produce makes its way out the door, there’s a traceable log of its entire journey.
Plants start off on the lower level of a vertical farming system and as they mature, they’re moved up higher. It’s a constant cycle of maturing plants moving up, replaced by seeds below.
Intravision Greens Niagara’s Neville D’Souza, one of the operation’s executive directors, said without insects to worry about, there won’t be pesticides or herbicides used; leafy greens like basil and arugula, are sent out the door ready-to-eat; and the facility will use significantly less land and water than a conventional farm.
Inside the 20,000 square-foot facility, one-acre of leaf cover will be grown, producing around 1-million pounds of plants, according to D’Souza.
Undeniably, there’s a lot of work and money going into only one acre, but Keast stresses it’s all about getting the most out of a bit of space.
The Welland facility, now being built, is based off of a pilot plant in Toronto where the concept was tested on a small scale.
For their produce to compete with commercial-scale productions, they’ll eventually have to scale, says Keast. There’s the potential for an additional two acres — by knocking down a few walls, they can replicate their current setup.
D’Souza says they aren’t trying to compete with local farms though. Their interest lies in the GTA market, where he says most produce is imported.
"What we are going to produce here, represents just two to give percent of what is imported, so that is what we are looking at, and the farmers are growing for three or four months, this is growing the other nine months when stuff is imported ... this is import substitution, and so it compliments what the farmer is growing and not treading on his toes," D'Souza said.
This past Friday, some of Intravision’s 2,340 lighting units were being installed above roller racks that will eventually hold plant trays. Keast and D’Souza point out that robotics, framing, the water system, harvesting equipment, and a future conveyor system are all locally sourced.
D’Souza claims that an operation like theirs will be the first in the world, and believes as the technology becomes more viable, there will be more vertical farms to compliment traditional ones.
It’s still early stages, and D’Souza admits it’s an ambitious goal, but he hopes for the operation to be up and running by the fourth quarter of this year, and sees an expansion within 24 months.
Photo Credits:
A vertical farming system is seen at an upcoming Intravision Greens Niagara facility in Welland on July 17, 2020.
A vertical farming system is seen at the “We the Roots” pilot plant in Toronto, in this undated photo provided by Intravision Light Systems. - Photo provided: Intravision Light
A vertical farming system is seen at an upcoming Intravision Greens Niagara facility in Welland on July 17, 2020. - Jordan Snobelen/Torstar
Controlled Environment Agriculture Open Data (CEAOD) Project
The use of Machine Learning and Artificial Intelligence techniques could provide CEA researchers and commercial growers an opportunity to optimize crop production efficiency and unveil new methods to improve production yield
Date: August 4, 2020
Time: 2 p.m. - 3 p.m. EDT
Presented by: Erico Mattos, GLASE Director, and Kenneth Tran, Koidra
Click Here to Register
Controlled Environment Agriculture (CEA) is a data-driven scientific discipline. In CEA operations all the environmental parameters are monitored and controlled to provide optimal conditions for crop growth. Recent technological advancements made the use of sensors and controls more accessible to CEA growers allowing them to precisely adjust these parameters.
The use of Machine Learning and Artificial Intelligence techniques could provide CEA researchers and commercial growers an opportunity to optimize crop production efficiency and unveil new methods to improve production yield. However, there is a lack of a centralized repository and a standard methodology for data sharing.
Join GLASE Director Erico Mattos and Koidra CEO Kenneth Tran on this GLASE Webinar to learn about the Controlled Environment Agriculture Open Data (CEAOD) project. This initiative aims to promote data sharing to accelerate Controlled Environment Agriculture (CEA) research through the establishment of a free centralized platform for the CEA community. Researchers and commercial growers are welcome to join and learn more about it.
Kenneth Tran was part of the winning team at the first International Autonomous Greenhouse Challenge held at Wageningen University in 2018. The team defeated four other international teams, consisting of experts in the field of Artificial Intelligence (AI) and horticulture. Erico Mattos is working with Cornell University and Rensselaer Polytechnic Institute Researchers to develop a guideline for data collection and upload to the CEAOD project.
Is The Future of Farming Indoors?
The global population is predicted to reach 9.7 billion by 2050, and to feed everyone, it’s estimated that global food production will need to increase by up to 70% in the next 30 years
July 14, 2020
Brian Kateman Contributor
I write about sustainable and ethical technology and consumer trends.
The global population is predicted to reach 9.7 billion by 2050 and to feed everyone, it’s estimated that global food production will need to increase by up to 70% in the next 30 years.
There are many challenges to overcome before fears of a worldwide food shortage can be allayed, including rising temperatures and more frequent droughts caused by global warming. These obstacles are making traditional farming methods increasingly inefficient and unpredictable.
Traditional farming has also been hit hard by the COVID-19 pandemic. According to the FAO, border closures, quarantines and disruptions to supply chains are limiting some people's access to food, especially in countries hit hard by the virus or already affected by high levels of food insecurity.
There’s an emerging consensus that the agriculture industry needs to adapt to use less water and chemicals, make crops less vulnerable to changes in the climate, and produce more reliable yields. Part of the answer may lie in the emerging start-ups growing produce in indoor environments, where growing conditions can be better managed.
The indoor farming technology market was valued at $23.75 billion in 2016, and is projected to reach $40.25 billion by 2022. Yields are typically much higher than traditional farming methods. Crops from indoor farming are grown in three dimensions, rather than two – and can be grown all year round, independent of external weather conditions.
Square Roots next-generation farmers growing basil. CRAIG VANDER LENDE
One of Square Roots’ indoor farms, for example, produces the same amount of food as a two- or three-acre farm annually, just from 340 square feet. This yield is achieved by growing plants at 90 degrees, and by using artificial intelligence (AI) to ensure the environment is optimal for each specific plant, including the day and night temperatures and amount of CO2 needed.
“Our indoor farms are living biosystems, constantly adapting to maintain optimal climates for growing specific crops. We’re then able to understand how changes in the climate can impact yield taste and texture,” says Tobias Peggs, Square Roots’ chief executive.
Not only could indoor farming help adapt to a warming planet, but it has the potential to help slow down climate change by being more sustainable – using less water and producing fewer emissions. While estimates vary widely, according to the United States Environmental Protection Agency, agriculture accounted for 10% of all greenhouse gas emissions in 2018; it is also highly dependent on, and a pollutant of, water.
Square Roots’ pop-up farms are built in shipping containers in cities, often in parking lots. They serve local communities, which means reduced emissions compared to traditional agriculture, which often involves transporting food much further. For example, it has 10 farms in Brooklyn that serve 100 retail stores all within five miles of the farm.
At the Plenty headquarters in South San Francisco, leafy greens use up one percent of the land and five percent of the water compared to traditional outdoor farms, says Matt Barnard, the start-up’s Chief Executive Officer, and Co-Founder.
AeroFarms’ indoor farm in New Jersey grows greens including baby kale, baby arugula, and baby watercress using 95% less water than conventional agriculture on just one percent of the land required. The crops grow under LED light with no pesticides and a fraction of the fertilizer used on traditional farms.
AeroFarms environmentally-controlled indoor farms can grow all year round independent of climate and ... [+] AEROFARMS
Marketing director Alina Zolotareva says being able to produce have ready-to-eat produce that doesn’t require rinsing helps to reduce water usage.
“This is a transformational innovation for agriculture at large,” she says, “as access to fresh water for growing food is one of the most pressing challenges of our time.”
As well as fewer miles and less water, indoor farming doesn’t require pesticides. This is better for the environment and human health as it eliminates the risk of water contamination due to run-off, and is in line with increasing consumer demand for non-GMO produce.
Plenty eliminates the need for pesticides with LED lights, which are synced with the crop’s growth, Barnard says, to provide the ideal spectrums and exposure and minimize energy usage.
“Our sensor system ensures each plant gets exactly the amount of purified water it needs, and any excess water is recycled through a closed-loop irrigation system resulting in greatly reduced water consumption and zero waste,” he says.
Nanobubbles super-saturates the water with oxygen, making the plant roots healthier. This promotes ... [+]
MOLEAER
Other farms are using nanobubble technology, such as Moleaer, which has allowed more than 100 indoor farms to connect their irrigation systems to generators that provide oxygen via sub-micron gas-containing cavities to the plant’s roots to provide chemical-free water. These nanobubbles result in healthier roots, more resilient plants, and increasing crop yields, says Nick Dyner, CEO of Moleaer.
“Our oxygen transfer efficiency provides the most cost-effective solution to elevate oxygen levels in the water, which in turn promotes beneficial bacteria and root development,” he says.
The company is also working on a new NASA-approved space farming research project, exploring how astronauts on the International Space Station can grow their own food in microgravity using nanobubble technology.
There are concerns that it’s an expensive investment, but Dyner says Moleaer has various systems so it’s accessible to all sizes of indoor farms, high- and low-tech. Some products do, however, require growers to connect an external source of oxygen, which must come from a gas supply company or an onsite oxygen generator, which Moleaer provides.
“In many cases, traditional farmers may have more to gain by using our technology, since the capital investment is significantly less than the most advanced growing technologies available today, which are often out of a typical farmer’s budget,” Dyner says.
“Nanobubble technology is a cost-effective, chemical-free, and scalable solution that allows growers to increase crop yields and shorten cultivation time - which will be much needed to feed our growing population in the future.”
Peggs says Square Roots is also focused on ensuring its technology makes farming an accessible career path for young people who live in urban areas.
“If you’re a new young farmer at Square Roots, our app will guide you through what to do; what’s growing, what state is in it, what do we need to do today based on where things are in the growth cycle. Through our app and our training program we’re able to bring new people into our team, even folks with zero horticulture experience, and get them ready to go in about six weeks.”
Indoor farming is putting the youth back in agriculture. PLENTY
But despite being an emerging option for youth in the city, Barnard predicts most will remain traditional farmers.
“The world still needs the field and will need the field forever. We support the field by growing in addition to the field. Over time, [indoor] farming systems will become more accessible and affordable. Both field and indoor farming will be necessary to support global food demand.”
Viraj Puri, Co-Founder, and CEO of Gotham Greens, a pioneer in urban indoor agriculture that operates over 500,000 square feet greenhouses in 5 U.S. states, echoes this sentiment: “Growing produce indoors certainly has an increasing role to play in the future of sustainable food production. While indoor farming may not represent the future of all fresh produce production, for certain types of crops such as tomatoes, cucumbers, leafy greens, and herbs, it will become more prevalent. Customers are increasingly recognizing the reliability, consistency, and high quality of greenhouse-grown produce that’s grown in close proximity to large population centers using fewer natural resources. Other agricultural commodities like grains or fruits or root vegetables, however, can’t yet be produced.”
However, Dyner predicts that, eventually, the majority of agriculture will move to indoors, in vertical farms— the practice of growing crops in vertically stacked layers—in urban areas.
“These settings enable traditional farming to shift to controlled growing conditions, using new technology and automation, and reducing the risk of exposure to harsh climate conditions,” he says.
Plenty's goal is to build vertical farms in urban hubs and distribute each farm’s harvest locally ... [+]
PLENTY
Start-ups like Square Roots, Plenty, and AeroFarms currently practice vertical farming, which is a form of indoor farming that relies on artificial lighting such as LEDs instead of drawing on natural sunlight.
Other indoor farming companies like Gotham Greens grow produce in high-tech glass-clad greenhouses that primarily rely on natural sunlight for plant photosynthesis. According to Puri: “vertical farming is a more nascent technology within the indoor farming sector and the costs of running a vertical farm with artificial lighting and air conditioning is currently not as cost-effective as relying on natural sunlight in greenhouses.”
Gotham Greens takes a different approach, relying on natural sunlight rather than the artificial ... [+]
GOTHAM GREENS AND JULIE MCMAHON
“Greenhouse indoor farming technology has been in operation globally for 20 to 30 years and is proven to be commercially viable. That being said, the costs around artificial lighting and other vertical farming technologies have been coming down significantly in the past few years,” he adds.
Nonetheless, indoor farm technology start-ups, broadly speaking, don’t see themselves as disruptive, but as being on the same side of traditional farms, for the wider cause.
“The common enemy is the industrial food system, shipping food from one part of the world to the other, rather than locally produced food,” Peggs says.
Indoor farms don’t work in competition with each other, either; they work collaboratively by forming a network that shares data. For example, AeroFarms is collecting data on a research project with the non-profit Foundation for Food & Agriculture Research to understand the sensory and nutritional characteristics of leafy greens for the benefit of the entire agriculture industry.
However traditional and AI-based indoor farming work together in the future, there’s little doubt that indoor farming is helping to meet the needs of a growing global population and support traditional farming, which is both at the mercy of and exacerbating a warming planet. Only one method will find itself in space – but there’s space for them both.
I am co-founder and president of the Reducetarian Foundation, a nonprofit organization dedicated to reducing consumption of animal products.
Lead Photo: The world’s current agricultural practices are unsustainable, and indoor farming may offer solutions ... [+] PLENTY
Vertical Farms Fill a Tall Order by Emeritus Professor of Public Health and Microbiology at Columbia University, Dr Dickson Despommier
The Covid-19 pandemic has disrupted agricultural production and supply chains around the world. Farmers have often struggled to get their food to distant markets, and sharp shifts in demand have repeatedly forced them to dump crops
Indoor crops grown by high-tech methods are on the rise as the Covid-19 pandemic spurs interest in food security for cities.
Stacked trays of greens growing at the Newark, N.J., facility of AeroFarms.
PHOTO: BRYAN ANSELM FOR THE WALL STREET
By Dickson Despommier
July 25, 2020
The Covid-19 pandemic has disrupted agricultural production and supply chains around the world. Farmers have often struggled to get their food to distant markets, and sharp shifts in demand have repeatedly forced them to dump crops. Avoiding such logistical problems is one of the chief advantages of vertical farms, a new approach to agriculture that aims to grow food closer to population centers.
Over the past 10 years, hundreds of such indoor farms have sprouted up around the globe, mostly in the larger cities of industrialized countries. They occupy multistory buildings in which crops are grown in water or in misted air instead of soil, with LED lights in place of sunlight, in a controlled and largely automated environment.
Building more vertical farms in cities is especially timely because of the expected effects of the pandemic on urban office towers. Moody’s Analytics REIS now projects office vacancies to rise to 19.3% in the 82 largest metropolitan areas by the end of the year, up from 16.8% last year, and then to continue rising. In June, 82% of employers surveyed by market-research firm Gartner, Inc. said that they would allow employees to work from home permanently. Indoor farms can occupy some of the abandoned or underused office space created by these trends.
So far, vertical farms have mostly grown and sold leafy greens and herbs—the easiest food crops to grow indoors and to harvest year-round. They are competitive against conventional farms because their crops don’t have to travel far and are free of pesticides and other soil contaminants.
Strictly controlled conditions enable vertical farms to bypass the unpredictable variations of weather and soil.
As demand rises, however, vertical farms are poised to add a number of other crops that can be grown effectively indoors. These include root vegetables (potatoes, radishes, carrots, celery), vine vegetables (green beans, tomatoes, peppers), and bush fruits (blueberries, blackberries, raspberries). Such an expansion could eventually result in a significant shift of agriculture to cities, where 60% of the world’s population now lives.
Vertical farms are no longer some futuristic fantasy. Well-established, efficient hydroponic and aeroponic methods have been paired with newer technology such as high-performance LED grow lights. Artificial intelligence now often controls the instruments that automatically deliver nutrients and provide optimal lighting for each crop.
The strictly controlled conditions inside vertical farms enable them to bypass the unpredictable variations of weather and soil and to exclude the heavy metals and other elements so common in traditional agriculture. Such control also allows endless experimentation to develop the best-tasting produce and most efficient ways of growing. And when pollination is required, bumblebees do the job quite nicely, just as they do outdoors.
Creating and maintaining that environment takes big startup costs for technology and ongoing costs for energy. But the efficiency of such farms allows nearly 95% of indoor seedlings to be grown to maturity and harvested, according to Gene Giacomelli, professor of biosystems engineering at the University of Arizona. By contrast, the survival rate for outdoor crops, from planting to harvest, vary from 90% in good years to 70% or less in drought or flood years. The latter have been increasing because of climate change, with record-high temperatures often accompanied by extreme weather patterns.
On multiple floors of a single building, layers of vertical fields can be harvested in phases to provide year-round crops. Since the farms are close to their target consumers, spoilage and damage from shipping are greatly reduced. Eventually, such farms could provide healthier produce options in under-served neighborhoods that have been described as “food deserts.”
One of the largest and earliest commercial outfits, AeroFarms of Newark, N.J., was started by an agronomist in a defunct paintball arena in 2004. After several false starts, it flourished in 2014 with the help of $200 million in startup funding from the city and private firms. AeroFarms relocated to 70,000 square feet in Newark’s Ironbound district and won contracts with local restaurants, supermarkets and school lunch programs. It has since added larger facilities of 150,000 square feet in Danville, Va., and 90,000 in Abu Dhabi. The company supplements its 72 staff with local personnel trained to work in various phases of crop production.
Infarm, founded in Israel in 2013 and now based in Berlin, operates differently, exporting its model directly to supermarkets. (I serve, without pay, on its science advisory board and as a paid advisory board member for another firm.) It provides in-store, automated hydroponic growing systems. Each store selects its own mix of greens and herbs, and consumers are encouraged to choose, taste, and harvest from a menu growing right in front of them. The original startup employed a retrofitted 1955 Airstream trailer as its mobile crop production vehicle. Now it employs more than 400 people in 40 countries, mostly in Europe. It sells through, among others, Kroger grocery stores on the West Coast and Marks and Spencer in London.
There are many other vertical-farm startups backed by venture capital and expanding in Europe and the U.S., as well as on the Arabian peninsula, where they can provide an alternative to hot, arid conditions. But other firms have failed, or have canceled expansion plans, as they struggle to manage their costs and compete in local markets. And vertical farms aren’t likely to gain a competitive advantage over conventional farming when it comes to important commodities such as fruits grown in orchards or grains grown in vast fields. Both are possible to raise in vertical indoor settings, but so far, their yields are too low and seasonal to be economical.
Would more food crops grown indoors in cities be a helpful trend in agriculture, or not? Join the conversation below.
The pandemic has sparked new demand for the industry. San Francisco-based vertical farm Plenty says that a significant increase in shipments has sped up its effort to diversify crops. The company has already experimented with strategies to add items such as tomatoes and strawberries.
Covid-19 has been a harbinger of longer-term problems in food security for our cities. One answer may come from growing more of our food just down the street.
—Dr. Despommier is emeritus professor of public health and microbiology at Columbia University and the author of “The Vertical Farm: Feeding the World in the 21st Century.”
US: Vacant For Five Years, A Former Target in Calumet City Gets New Life As An Indoor Vertical Farm Growing Greens For The Chicago Area
The 135,000-square-foot building in the River Oaks shopping center will house stacks of trays growing kale, arugula and other leafy greens under artificial lights. A retail shop on-site will sell the produce to the community and invite people in to learn about how indoor farming works
CHICAGO TRIBUNE | JUL 15, 2020
Jake Counne, founder of Wilder Fields, is seen July 14, 2020, inside an empty Target he plans to convert to an indoor farm, in Calumet City. (Brian Cassella / Chicago Tribune)
A former Target that’s been sitting vacant in Calumet City for five years will be reborn as an indoor vertical farm producing locally grown greens for the Chicago area.
The 135,000-square-foot building in the River Oaks shopping center will house stacks of trays growing kale, arugula and other leafy greens under artificial lights. A retail shop on-site will sell the produce to the community and invite people in to learn about how indoor farming works.
Once at full capacity, Wilder Fields will employ 80 people and produce 25 million heads of lettuce a year that will be available in grocery stores across the region, said founder Jake Counne. Wilder Fields is the new name of the company, which previously was called Backyard Fresh Farms.
The property was exactly what Counne envisioned when he set out to repurpose existing buildings as indoor farms to supply fresh produce to cities far from the growing fields of California and Arizona.
An empty Target that Jake Counne, founder of Wilder Fields, plans to convert to an indoor farm in Calumet City. (Brian Cassella / Chicago Tribune)
As retail giants close stores, a trend that’s been exacerbated by the COVID-19 pandemic, Counne hopes to put the buildings they leave behind to sustainable use.
“We think this is very repeatable,” said Counne, who was a real estate investor before he became an agricultural entrepreneur. “There is a huge amount of vacant anchor retail space.”
Calumet City, which borders Chicago’s southern edge, acquired the building from Target and will lease it to Wilder Fields for 12 months, Counne said. After that, he plans to purchase the property from the city.
Counne expects to break ground by the end of this year and have the first phase of the redevelopment completed by early next year. After operating at a smaller scale to work out the kinks, Counne plans to finish developing the site by 2023. A group of investors is funding the first phase of the project. He declined to say how much funding he has received.
Produce grown locally indoors has gained popularity with consumers in recent years for environmental and quality reasons. It uses less land and water than traditional agriculture and travels far shorter distances, so the product is fresher and lasts longer when it gets into consumers’ hands. Growing year-round in controlled environments also cuts down on waste and contamination and avoids the challenges of unpredictable weather.
The Chicago area is home to several greenhouses that sell greens commercially, including Gotham Greens in Chicago’s Pullman neighborhood and BrightFarms in Rochelle, both of which have recently expanded. But vertical farms, which use artificial light rather than sunlight, have struggled to succeed at a large scale.
Counne believes he can make it profitable with lower-cost automation, which he has been testing at a small pilot facility at The Plant, a food business incubator in Chicago’s Back of the Yards neighborhood.
He’s developed robotics to reduce the amount of time workers spend climbing ladders to tend to plants. For example, an automated lift collects trays of ready plants and brings them to an assembly line of workers for harvest. He’s also developed a system of cameras and artificial intelligence software that prompts the environment to automatically adjust to optimize growing conditions.
Jake Counne, founder of Wilder Fields, on July 14, 2020. (Brian Cassella / Chicago Tribune)
Wilder Fields’ pricing will be in line with greenhouse-grown lettuces, which typically retail at $2.99 to $3.99 for a clamshell.
Though its first products will be standards like spring mix, spinach and basil, the plan is to also sell more unique varieties that people may not have tasted before. Among those Counne tested during his pilot were spicy wasabi arugula, tart red sorrel and horseradish-tinged red mizuna.
Counne is proud that his first farm is bringing fresh vegetables and jobs to an area that needs both. Parts of Calumet City are in a food desert.
Counne will be hiring for a variety of positions, from harvesters to software engineers to executives. He plans to implement a training program that will allow people to move from entry-level roles to positions managing the computer algorithms.
Alexia Elejalde-Ruiz
Alexia Elejalde-Ruiz covers the food industry for the Chicago Tribune's business section. Prior beats include workplace issues, the retail sector and lifestyle features, plus stints at RedEye, the Daily Herald and the City News Service. Alexia grew up in Washington, D.C., and has her degree in international relations from Brown University.
VIRTUAL SUMMIT: Connecting Technology & Business To Create Healthy, Resilient Food Systems - July 23, 2020
By sharing best practice from around the globe, and facilitating new connections and collaborations, the summit offers an invaluable platform to develop new business and accelerate projects across the Indoor AgTech ecosystem
The Indoor AgTech Innovation Summit is going virtual! This year’s summit will be live online on July 23, 2020, providing an essential opportunity for the industry to meet, network, https://indooragtechnyc.com/, and exchange ideas at this critical time for our industry.
The world’s leading farm operators, food retailers, and investors will present live, before hosting virtual discussion groups on the emerging trends and technologies that will shape your business as we emerge from the current crisis into a redesigned food system:
Key Themes:
· Finding Growth in Crisis: Responding to a Rapidly Changing Food Landscape
· Scaling Up: Co-locating Food Production and Distribution Centers
· Enhancing Nutritional Value: Towards a Perfect Plant Recipe
· Optimizing Seeds for Indoor Agriculture: Breeding a Competitive Advantage
· Analytics and the Cloud: Digital Integration to Optimize Indoor Agriculture
· Robotics: Developing a Contactless Food System
· Energy Consumption: Driving Efficiency and Economic Viability
· Financing Growth: Can Capital Keep Pace with Industry Demand?
· Consumer Awareness: How to Build a “Holistic” Indoor Brand
All participants can schedule video 1-1 meetings with potential partners and clients throughout the summit, and for an extended period before and after the sessions.
By sharing best practice from around the globe, and facilitating new connections and collaborations, the summit offers an invaluable platform to develop new business and accelerate projects across the Indoor AgTech ecosystem.
Summit website: https://indooragtechnyc.com/
Registration:
- One summit pass Indoor AgTech: $195.00
- Start-Up pass: $95.00 / Please contact jamie.alexander@rethinkevents.com to enquire about the criteria to qualify for special rates.
The Future of Food: Inside The World's Largest Urban Farm – Built on a Rooftop
On top of a striking new exhibition hall in the southern 15th arrondissement of Paris, the world’s largest urban rooftop farm has started to bear fruit. Strawberries, to be precise: small, intensely flavoured and resplendently red
In Paris, urban farmers are trying a soil-free approach to agriculture that uses less space and fewer resources. Could it help cities face the threats to our food supplies?
Urban farming on a Parisian rooftop. Photograph: Stéphane de Sakutin/AFP/Getty Images
08 Jul 2020
On top of a striking new exhibition hall in the southern 15th arrondissement of Paris, the world’s largest urban rooftop farm has started to bear fruit. Strawberries, to be precise: small, intensely flavoured and resplendently red.
They sprout abundantly from cream-coloured plastic columns. Pluck one out to peer inside and you see the columns are completely hollow, the roots of dozens of strawberry plants dangling into thin air.
From identical vertical columns nearby burst row upon row of lettuces; near those are aromatic basil, sage, and peppermint. Opposite, in narrow, horizontal trays packed not with soil but coco coir (coconut fibre), grow heirloom and cherry tomatoes, shiny aubergines, and brightly coloured chards.
“It is,” says Pascal Hardy, surveying his domain, “a clean, productive and sustainable model of agriculture that can in time make a real contribution to the resilience – social, economic and also environmental – of the kind of big cities where most of humanity now lives.
And look: it really works.”Hardy, an engineer, and sustainable development consultant, began experimenting with vertical farming and aeroponic growing towers – as those soil-free plastic columns are known – on his Paris apartment block roof five years ago.
This space is somewhat bigger: 14,000 sq metres, the size (almost exactly) of two football pitches. Coronavirus delayed its opening by a couple of months, but Nature Urbaine, as the operation is called, is now up and running, and has planted roughly a third of the available space.
Already, the team of young urban farmers who tend it have picked, in one day, 3,000 lettuces and 150 punnets of strawberries. When the remaining two-thirds of the vast rooftop of Paris Expo’s Pavillon 6 are in production, 20 staff will harvest up to 1,000kg of perhaps 35 different varieties of fruit and vegetables, every day.“
We’re not ever, obviously, going to feed the whole city this way,” cautions Hardy. “In the urban environment you’re working with very significant practical constraints, clearly, on what you can do and where. But if enough unused space – rooftops, walls, small patches of land – can be developed like this, there’s no reason why you shouldn’t eventually target maybe between 5% and 10% of consumption.”
Nature Urbaine is already supplying local residents, who can order fruit and veg boxes online; a clutch of nearby hotels; a private catering firm that operates 30 company canteens in and around Paris; and an airy bar and restaurant, Le Perchoir, which occupies one extremity of the Pavillon 6 rooftop.
Nature Urbaine. Photograph: Magali Delporte/The Guardian
Perhaps most significantly, however, this is a real-life showcase for the work of Hardy’s flourishing urban agriculture consultancy, Agripolis, which is currently fielding inquiries from around the world – including in the UK, the US, and Germany – to design, build and equip a new breed of soil-free inner-city farm.“The method’s advantages are many,” he says. “First, I don’t know about you, but I don’t much like the fact that most of the fruit and vegetables we eat have been treated with something like 17 different pesticides, or that the intensive farming techniques that produced them are such huge generators of greenhouse gases.“I don’t much like the fact, either, that they’ve travelled an average of 2,000 refrigerated kilometres to my plate, that their quality is so poor, because the varieties are selected for their capacity to withstand that journey, or that 80% of the price I pay goes to wholesalers and transport companies, not the producers.”
Produce grown using this soil-free method, on the other hand – which relies solely on a small quantity of water, enriched with organic nutrients, minerals and bacteria, pumped around a closed circuit of pipes, towers and trays – is “produced up here, and sold locally, just down there. It barely travels at all,” Hardy says.“It uses less space. An ordinary intensive farm can grow nine salads per square metre of soil; I can grow 50 in a single tower. You can select crop varieties for their flavour, not their resistance to the transport and storage chain, and you can pick them when they’re really at their best, and not before.”
No pesticides or fungicides are needed, no soil is exhausted, and the water that gently showers the plants’ roots every 12 minutes is recycled, so the method uses 90% less water than a classic intensive farm for the same yield. The whole automated process can be monitored and controlled, on site or remotely, with a tablet computer.
Urban farming is not, of course, a new phenomenon. The mayor of Paris, Anne Hidalgo, aims eventually to have at least 100 hectares of rooftops, walls and facades covered with greenery – including 30 hectares producing fruit and vegetables.
A programme called Les Parisculteurs invites local groups to come up with suitable projects for up to a dozen new sites every year.Inner-city agriculture is booming from Shanghai to Detroit and Tokyo to Bangkok. Strawberries are being grown in disused shipping containers; mushrooms in underground carparks. Not all techniques, however, are environmentally friendly: ultra-intensive, 10-storey indoor farms that have sprung up in the US rely on banks of LED lighting and are major consumers of energy, Hardy says.
Aeroponic farming, he says, is “virtuous”. The equipment weighs little, can be installed on almost any flat surface, and is cheap to buy: roughly €100 to €150 per sq metre. It is cheap to run, too, consuming a tiny fraction of the electricity used by some techniques.
Aeroponic farming is ‘virtuous’, says Pascal Hardy. Photograph: Magali Delporte/The Guardian
Produce grown this way typically sells at prices that, while generally higher than those of classic intensive agriculture, are lower than soil-based organic growers. In Paris, Nature Urbaine should break even, Hardy estimates, some time next year – a few months later than planned because of the pandemic
.There are limits to what farmers can grow this way, of course, and much of the produce is suited to the summer months. “Root vegetables we cannot do, at least not yet,” he says. “Radishes are OK, but carrots, potatoes, that kind of thing – the roots are simply too long. Fruit trees are obviously not an option. And beans tend to take up a lot of space for not much return.”
But Agripolis runs a smaller test farm, on top of a gym and swimming pool complex in the 11th arrondissement, where it experiments with new varieties and trials new techniques. A couple of promising varieties of raspberries are soon to make the transition to commercial production.
Urban agriculture is not the only development changing the face of farming. As with almost every other sector of the economy, digitisation and new technologies are transforming the way we grow food.
Artificial intelligence (AI) and the internet of things are beginning to revolutionise farming, from driverless, fully automated farm machinery that can sow seeds and fertilise and water soil with maximum precision to systems that monitor exactly how healthy individual animals are and how much they are producing (a concept known as the “connected cow”).
Other AI systems analyse satellite and remote ground sensor data, for example, to monitor plant health, soil condition, temperature and humidity and even to spot potential crop diseases.
Drones, too, have multiple potential uses on farms. With the world’s bee population in steep decline due to global heating, pesticides, and other factors, drones are increasingly being used to pollinate crops fields and fruit orchards. To avoid wasting pollen by wafting it randomly at crops, or the damage to individual flowers caused by drones rubbing against them, scientists in Japan have developed a system in which a drone uses what can only be described as a bubble gun to blow balls of specially formulated liquid containing pollen at individual blossoms.
With global food production estimated to need to increase by as much as 70% over the coming decades, many scientists believe genetic editing, which has already been used to create crops that produce higher yields or need less water to grow, will also have to play a bigger role.
The technique could help build plant and animal resistance to disease, and reduce waste. For example, with methane known to be a stronger greenhouse gas than carbon dioxide, research is under way into the stomach bacteria of cows in the hope that tweaking animals’ gut microbes may eventually allow them to produce not just more meat, but also less gas.
Seating at Le Perchoir. Photograph: Magali Delporte/The Guardian
Urban farming of the kind being practised in Paris is one part of a bigger and fast-changing picture. “Here, we’re really talking about about building resilience, on several levels – a word whose meaning I have come to understand personally,” says Hardy, pointing to the wheelchair he has been forced to use since being injured by a falling tree.
“That resilience can be economic: urban farming, hyper-local food production, can plainly provide a measure of relief in an economic crisis. But it is also environmental: boosting the amount of vegetation in our cities will help combat some of the effects of global heating, particularly urban ‘heat islands’.”
Done respectfully, and over time, inner-city agriculture can prompt us to think differently both about cities, by breaking down their traditional geography of different zones for working, living and playing, and about agriculture, by bringing food production closer into our lives. “It’s changing paradigms,” says Hardy.
VIDEO: Home Hydroponics: Tech Trend Or The New Victory Garden?
Home gardening is experiencing a renaissance spurred by the Covid-19 pandemic. Facing anxiety surrounding food security and the need for hobbies during quarantine, close to 20% of Americans have reported taking up gardening as a result of the pandemic. Seed sales have soared to unprecedented level
Jun 30, 2020
Rob Girling Contributor
Co-Founder of Artefact, a purpose-driven strategy, and design company dedicated to responsible design. I am a designer passionate about mitigating the negative impact of technology and maximizing the positive.
Home gardening is experiencing a renaissance spurred by the Covid-19 pandemic. Facing anxiety surrounding food security and the need for hobbies during quarantine, close to 20% of Americans have reported taking up gardening as a result of the pandemic. Seed sales have soared to unprecedented levels.
An indoor vertical hydroponic system by Gardyn. COURTESY OF GARDYN.
As Covid-19 highlights, the precarious supply chain that supports our modern lifestyles and the benefit of more self-sufficiency, hydroponics – a method of growing plants without traditional soil, using water-based, nutrient-dense solutions – is emerging as the latest trend in smart home devices. Advances in hydroponic food-growing technology and LED lighting have reached a point where smart devices can take some of the labor, land, and expertise of traditional gardening out of the equation. Make no mistake that “real” gardening requires deep knowledge and effort to yield nutritional and emotional benefits; however, technology can now help laypeople experiment with growing fresh, nutritious food in their homes.
While home hydroponic systems are more effective, easy to use, and aesthetically pleasing than ever, there is a long way to go before the promise of sustainable, accessible food for all comes to fruition. Who wins and who loses in the smart food ecosystem and just how sustainable are these services? Let’s look at the design of three leading home hydroponics systems and the broader impact of such “smart growing”.
Home Hydroponics Leading the Pack
Gardyn, Rotofarm and Click & Grow are three of the leading “smart growing” entrants that promise attractive, no-hassle, indoor hydroponic systems.
The Gardyn system consists of three vertical artificial “stems” where up to 30 plants can grow at once. These stems are rooted in a sturdy, oval-shaped base reservoir where water, pumps and electronics are discretely hidden under a wooden lid. Two vertical aluminum bars hide the latest-generation LED lights that focus their attention on the plants and dissipate heat effectively. Gardyn comes with an AI assistant app that monitors and manages temperature, humidity, and light.
The most sculptural of the leading home hydroponic systems, the Bace Rotofarm is a jaw-droppingly gorgeous object with a supporting app component. Using a rotating circular drum, it slowly turns up to eight plants around an LED hub, compressing 5.5 feet of growing space into just 15 inches and eliminating gravitational penalty to help plants grow faster. Despite winning several design awards for its science-fiction-turned-reality aspiration, the Rotofarm will not launch until 2021 and its price remains a mystery.
A more economical home hydroponics system comes in the form of the Click & Grow Smart Garden. With three- and nine-plant growing options, the Click & Grow design concept looks vaguely like a carrying basket with an end-to-end handle that cleverly hides LED lights. Click & Grow is unique in its scaled design, allowing customers to stack Smart Gardens together to create a compact food growing system. Like the others, the system has a companion app to track growing schedules and help troubleshoot.
Improving Access to Produce, at a Cost
There is great opportunity for home hydroponics to improve education and access to healthy produce for those who live in food deserts or do not have access to nutritious food. Yet, so far, smart growing systems target tech-savvy, mostly affluent people living in high-density urban communities.
No matter the brand, existing home hydroponics systems command a hefty price tag. The Click & Grow system ranges from $99 for three plants to $599 for a 27-plant system, while the Gardyn kit starts at $799 with a monthly fee of $69 for 240 seed plants. Each plant might produce up to five yields before it needs replacing – that’s a lot of money for leafy greens, fresh herbs, and a handful of fruit.
These products make big claims about sustainability, healthy living, and a reliable food ecosystem, but don’t provide sufficient practical value for communities who could benefit the most from home hydroponics. One hopes that the pricing of these new systems reflects the enormous startup costs of building their business. Perhaps subsequent generations and scale can reduce the unit costs, like what has occurred in the electric vehicles market.
Lowering Environmental Impact
Dirt, when combined with growing chemicals, is responsible for significant water pollution in traditional farming. Rather than using soil, most home hydroponics systems call for compostable refill cubes similar to espresso pods. Each cube includes seeds planted in the company’s patented “growing medium” – in other words, artificial soil consisting of natural materials designed to hold water and nutrients more efficiently than regular dirt. Unlike espresso pods, these cubes are made from compostable corn-based plastic that can be thrown in the yard waste.
Gardyn's compostable "yCubes" are made up of rockwool and corn. COURTESY OF GARDYN.
The essential trade-off with indoor hydroponics is foregoing the free light-bulb in the sky: the sun. Depending on the amount of natural light available in a home, an LED hydroponic system uses significant electricity that adds to energy consumption and utility bills.
Nevertheless, growing food through hydroponics reduces reliance on industrial agro-farming with its heavy reliance on chemicals, fresh water, and the transportation infrastructure needed to get from production to table.
A Victory Garden Redux
Smart growing and home hydroponics is an exciting new trend in consumer hardware. While early entrants to the market feel more proof-of-concept than robust products or services, I predict that this category of products will improve quickly and become commonplace in homes of all types, expanding into other types of gardening and food production beyond leafy greens alone.
Although smart gardens may not yet be as impactful as the victory gardens that produced nearly 40% of vegetables in the US during World War II, there is significant opportunity for home hydroponics reduce dependence on an easily disrupted global food infrastructure while also easing individual environmental impact and increasing access to fresh, healthy produce.
I am a designer passionate about mitigating the negative impact of technology and maximizing the positive. I co-founded Artefact, a purpose-driven strategy and design company dedicated to responsible design. I have worked across the tech industry in various leadership roles at IDEO, Apple, Sony, and Microsoft. I also co-founded the SAAS resource management software 10000ft, acquired by Smartsheet in 2019
I am a designer passionate about mitigating the negative impact of technology and maximizing the positive. I co-founded Artefact, a purpose-driven strategy and design company dedicated to responsible design. I have worked across the tech industry in various leadership roles at IDEO, Apple, Sony, and Microsoft. I also co-founded the SAAS resource management software 10000ft, acquired by Smartsheet in 2019
Rob Girling
Indoor Agtech Virtual Innovation Summit July 23, 2020
By sharing best practice from around the globe, and facilitating new connections and collaborations, the summit offers an invaluable platform to develop new business and accelerate projects across the Indoor AgTech ecosystem
We Are Proud To Be A Marketing Partner
Save 10% With Discount Code iGROW10
Major names join speaker line-up for virtual summit
We are thrilled to announce the first speakers confirmed for the 2020 virtual Indoor AgTech Innovation Summit on July 23.
They'll share critical intelligence on how the indoor farming industry is shaping the agri-food landscape, and redesigning food systems to meet consumer demand for fresh produce.
VIEW SPEAKER LINE-UP
Hear from and connect with international thought leaders including:
WHAT ARE OUR EXPERTS SAYING?
"Instead of shutting down, we implemented South Korean-style measures for our warehouse, farm, and office. Then, we launched a new nationally distributed product that allows folks to grow mushrooms at home rather than travel to the grocery store."
Andrew Carter, CEO, SMALLHOLD
"COVID-19 has raised awareness about the prospects for automation such as machines working in packing houses and indoor environments. I think it’s fair to say that humans can be relieved of those tasks."
Elyse Lipman, Director of Strategy, LIPMAN FAMILY FARMS
"Given current pressures on the U.S. food system, one thing is clear: the importance of strengthening our country’s food supply chain through decentralized, regional supply chains."
Viraj Puri, CEO and Co-Founder, GOTHAM GREENS
READ MORE INSIGHTS FROM OUR SPEAKERS>>
Secure your place at Indoor AgTech and save 10% with discount code iGROW10
and connect with the world’s leading farm operators, food retailers, and investors for a jam-packed day full of 1-1 video meetings, live panel sessions, and interactive roundtable discussion groups.
BOOK NOW WITH CODE iGROW10
We look forward to welcoming you online.
Best wishes,
Oscar Brennecke
Conference Producer
Indoor AgTech Innovation Summit
+44 (0)1273 789 989
oscar.brennecke@rethinkevents.com
THANKS TO OUR PARTNERS
Platinum Partner:
Marketing and Media Partners:
BioLumic Appoints Steve Sibulkin as CEO
“An exceptionally sustainable agriculture innovator tackling complex farming challenges, BioLumic is at a critical juncture as it prepares for the immense opportunities ahead and the rigors of global commercialization,” noted Dr. Adrian Percy, BioLumic Chairman of the Board and CTO of UPL Ltd.
Proven Ag and Tech Leader to Drive Photogenics Company’s Continued Product Development Efforts and Global Growth
New York, NY and Palmerston North, New Zealand — June 8, 2020 —BioLumic Ltd. (“BioLumic”), the leader in using plant photogenics to unlock the genetic potential of seeds and seedlings, today announced the appointment of Steve Sibulkin as Chief Executive Officer. Based on decades of experience in the agriculture and technology industries, Sibulkin will lead the company’s global expansion and accelerate its UV light treatment innovation based on the groundbreaking BioLumic photogenics platform.
“An exceptionally sustainable agriculture innovator tackling complex farming challenges, BioLumic is at a critical juncture as it prepares for the immense opportunities ahead and the rigors of global commercialization,” noted Dr. Adrian Percy, BioLumic Chairman of the Board and CTO of UPLLtd. “With a proven track record building industry-leading ag and tech companies, Steve will help BioLumic move faster and deepen relationships with key partners while accelerating the company’s ability to bring its innovations to the market.”
Sibulkin joins BioLumic from Yara International, where he led enterprise sustainability, partnership, and digital initiatives after the company acquired the precision agriculture company he co-founded, Agronomic Technology Corp (ATC), in 2017. As the CEO of ATC, Sibulkin commercialized and grew the Adapt-N nitrogen recommendation solution, which was originally developed by a team at Cornell University. Under his leadership, ATC conducted over one billion simulations, expanded its product portfolio, signed enterprise partners, and became an industry-standard with growers, agriculture industry leaders, and sustainably focused organizations. Before joining Yara, Sibulkin was a multi-time CEO, entrepreneur, and strategic advisor, and held leadership positions at Sapient, Ogilvy & Mather, and Mainspring.
“BioLumic’s discoveries around plant signaling responses harness the natural genetic potential of seeds and seedlings for yield improvement, disease resistance, and the ability to withstand environmental stress — all without requiring additional inputs or genetic modification. This is a huge win for farmer profitability, the food, and agriculture supply chain and the environment,” said Sibulkin. “BioLumic perfectly aligns with the movement toward more resilient and productive agriculture, and the opportunity to accelerate the growth of this transformative technology is one I couldn’t resist.”
Rooted in more than a decade of research into UV light treatments in plants and spun out from Massey University in New Zealand, BioLumic’s proven technology offers seed producers and growers new opportunities to grow more valuable and sustainable crops. Its scientifically validated photogenics platform uses a combination of artificial intelligence and precise light treatments to activate the natural plant signaling response to UV light, triggering plant growth that enhances crop yield, crop quality, drought tolerance, and natural disease and pest resistance.
“Our proprietary technology cultivates stronger, healthier plants to meet rising food demands, and we are ready to focus on commercialization and building a global footprint,” added Dr. Jason Wargent, founder and chief science officer. ”A respected leader in sustainable agriculture, Steve’s wealth of experience leading cross-disciplinary teams around new categories of product innovation will help drive the adoption of our novel light treatments in the global ag marketplace.”
Positive outcomes from produce such as broccoli, lettuce, strawberries, and tomatoes have accelerated the development of BioLumic’s high-quality seed and plant treatment innovations for indoor farming, row crops like soybeans, and high-value crops like cannabis. BioLumic is actively growing its team to support the acceleration and expansion of its UV light treatment initiatives.
“With recent trials showing the extensibility of this novel technology across crops, we know growers around the globe will see improved profit from their seed and seedling investments,” added Sibulkin. “Our next step involves deepening our partnerships with seed companies, seed dealers, sustainability-focused organizations, and enterprises that have aligned interest in utilizing and expanding this technology.”
Sibulkin earned a B.A. in political science from UCLA and an MBA from Kellogg Graduate School of Management, where he graduated with Beta Gamma Sigma distinction and co-founded the Net Impact Chapter. He currently resides in New York City.
About BioLumic
BioLumic harnesses the power of ultraviolet (UV) light to empower growers and seed producers around the globe. BioLumic’s pioneering technology activates natural mechanisms in seeds and seedlings that increase plant growth, vigor, and natural defense mechanisms — resulting in increased yields at harvest without the use of chemical input or genetic modification. Backed by top Ag investors, BioLumic is headquartered in New Zealand and is actively growing its presence in North America.
To learn more, visit www.biolumic.com.