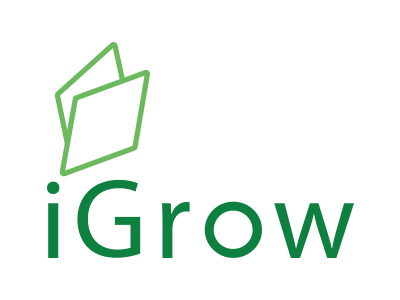
Welcome to iGrow News, Your Source for the World of Indoor Vertical Farming
Dairy Container Costs "Going Crazy"
The skyrocketing cost of shipping containers is hitting the margins of Victorian pulse, grain, dairy and meat processors and exporters
30 Jul 2021
Andrew Miller
CONTAINER PAIN: Wimpak, Minyip, general manager James French says margins are being squeezed by the price of containers.
The skyrocketing cost of shipping containers is hitting the margins of Victorian pulse, grain, dairy and meat processors and exporters.
Thomas Elder Markets analyst Andrew Whitelaw said containers (boxes) were used to export pulses, grains, meat, and wool from Victoria.
"The box market has gone crazy this year," Mr. Whitelaw said.
Rates were at their highest since 2001, with the cost of hiring a 40-foot container to export products to India now sitting at $4000, (A$7700).
That compared with the first week in June 2019 when the rate was US$1300.
The top five agricultural containerized export destinations are China, Japan, the USA, Vietnam, and South Korea.
READ MORE: Rising port costs being passed back to the farmer
Port of Melbourne figures show wheat accounts for 10 percent of all agricultural exports, with hay, chaff and fodder coming in a close second.
Other cereals, barley, lentils, and chickpeas comprise nearly 20 percent of all exports.
Dried milk and processed dairy products make up more than 12pc of exports.
Huge demand
Mr. Whitelaw said part of the problem was the huge demand for containers, from Chinese manufacturers.
"Everyone seems to have much more disposable income, and most of the western world isn't able to spend that money on leisure or travel activities," Mr Whitelaw said.
"This has resulted in huge volumes and gadgets and gizmos shipped out of China."
Sea freight broker Anchor Logistics director Bob Brittles said a combination of factors had resulted in supply and demand pressures.
The blockage of the Suez Canal, when the Ever Given ran aground earlier this month, had a massive effect.
"When the Ever Given was freed, 350 ships followed her through and dumped about 350,000 containers in Europe and just after that there were unloading delays in China.
"Those delays held up 650,000 containers."
He said the Australian market was serviced by about 12 major shipping lines.
"They have been influenced by the coronavirus situation and closures of various ports, over the last year and a half."
That had resulted in congestion and delays in unloading in many south-east Asian ports, which was contributing to the container shortages.
"The containers are in the wrong place, the ships are in the wrong place," Mr Brittles said.
Rising prices
Grain cleaning and packing service Wimpak, Minyip, general manager James French said container prices to ship to most overseas ports had risen dramatically.
"The Bangladesh rates are very similar to India and the shipping lines are making a move (on prices) every four to six weeks," Mr. French said.
He said grower pricing might have to reflect the freight cost.
"Normally we are putting work on, six to eight weeks out, but we are struggling to do that, knowing what our freight rates are going to be," he said.
"It makes us more reluctant to buy more product when we don't know what the price will be at the other end."
READ MORE: Food-grade container shortages hitting Victorian exporters hard
Burra Foods exports most of its dairy products and chief executive Stewart Carson said there was a direct container cost, as well as timing and availability.
"You might have a vessel booked to leave on Friday, then you're told the vessel won't be available until Tuesday or Wednesday," Mr. Carson said.
"What do you do with that container? In some cases, you have to put it on power, which costs you money."
Mr. Carson said the company carried the cost or sought to recoup it from the market.
"Everyone is paying a competitive milk price, you can't say sorry I'll pay 10 cents less because the container price has gone up," Mr. Carson said.
Companies could not pass the cost back to the farmer, which was only right.
"I think that's great, it gives an assurance to the farmer," he said.
He said Burra was in the same position as all other processors.
Southern Grain Storage director Campbell Brumby said his company was fortunate that his company had finished its export program before the price increases hit.
"I was speaking to a colleague who was paying $1750 for a box to a particular destination, and was now looking at $4250 if they can get the container," he said.
He put the price increase down to the state government's lease of the Port of Melbourne.
"We've been doing containers for about 10 years and when we first started, charges were negligible," he said.
"Since the lease was sold to DP World, the rates have gone through the roof - we just have to pay them and the market absorbs the cost.
"As long as all our competitors and all the people we are trying to trade with are working on the same cost basis, the market tends to absorb it.
"Whether its pulses or cereals, the market will be the market."
Innovation Consulting Community Team Proposes Sustainable Farming Container At ISU
In just a few months, a team of motivated students put together a proposal to implement a shipping container farm on Illinois State’s campus
Evan Linden April 15, 2020
NOTE: The photos in this story were taken before travel restrictions from coronavirus (COVID-19) were in place.
In just a few months, a team of motivated students put together a proposal to implement a shipping container farm on Illinois State’s campus.
“Self-motivation is impressive to employers,” said Marketing Professor Dr. Peter Kaufman, one of the founders of the Innovation Consulting Community (ICC). “Most students are taught one discipline in school, but world problems are interdisciplinary.”
Kaufman and others founded the ICC in 2016 to provide students with hands-on experiences outside their classes. Each year, teams of students are matched with clients at companies and nonprofit organizations to help solve a current issue they are facing. “It’s a unique experience to tackle both profit and nonprofit projects,” said Kaufman. “This experience helps students enhance their skills all around and helps our clients find solutions.”
This year, the ICC assigned 14 projects to 90 students representing 24 majors. One group of four students tackled an increasingly pressing issue: sustainable farming.
The students assembled in late October, mentored by Elisabeth Reed, director of the Office of Sustainability, and Dr. David Kopsell, assistant chair of and professor in the Department of Agriculture. Ryan Strange, a senior from Bloomington double majoring in business administration and small business management, led the team and collaborated with fellow students Joe Kennedy, Madison Steines, and Joe Quigley.
The project was inspired by the Boston company Freight Farms, urban agriculture innovators who create farms in shipping containers. Kopsell, who is familiar with growing systems, was brought in by Kaufman to be a horticulture mentor.
“I shared some of the ideas that I’d always wanted to investigate, and one that he really liked was the idea of writing a grant for a containerized growing system,” said Kopsell.
From there, the team focused on analyzing the benefits of a containerized growing system on campus.
“Our project was a feasibility study of the purchase of one of these units,” said Strange. “The unit itself is the technology necessary for hydroponic farming, and all of that goes inside an old freight container.”
The inside of a shipping container farm located in Champaign.
To see one of these units in action, the group visited a current model located at the University of Illinois at Urbana-Champaign. “The director there was a tremendous help,” said Strange. “He gave us many details about operations and risk management.”
The team spent weeks finding the right contacts and establishing relationships in order to gather information for the project. “We built this huge network of different partnerships that helped us find out how we would finance this unit,” said Strange.
According to Strange, the purchase of one of these units would cost $120,000, with recurring costs adding up to around $40,000 a year.
“I think the cost is within the reach of a grant program,” said Kopsell. “These containers can operate year-round and provide great teaching and learning tools.”
Most importantly, the containers are both efficient and sustainable. Each container system can produce as much as one acre of field production —up to 13,000 plants depending on the crop. The efficient drip irrigation system uses five gallons of water per day, which is marginally less than a field.
“This is really the forefront of innovation in terms of agricultural production,” said Strange. “It’s going to cut back on a lot of the carbon emissions from transporting the food. It’s really going to cut back on costs also because most of the costs for food come from transportation.”
If installed on campus, the container system could be located next to the South University Street Garage.
Strange’s team presented its project at ICC’s annual symposium. In adherence with social distancing requirements, the symposium took place via Zoom on April 10.
Strange and his team noted that the ICC experience greatly benefited them as professionals. “It opens up a lot of doors and you have to teach yourself a lot,” said Strange. “Our mentors were definitely there for help, but it was mostly our group that set up all of the meetings and held ourselves to the deadlines. All of those things are fundamental skills that you’ll need when you move on to the professional workforce.”
Reed and Kopsell were impressed by the group’s work ethic and commitment.
“This student group was very well organized and stayed on task throughout the entire semester,” said Reed. “They communicated well with each other.”
“For me, this project represents the best of Illinois State University,” said Kopsell. “It allows students to find their passion and provides them an avenue to learn how to overcome challenges, solve problems, and make a difference.”
Students interested in participating in the Innovation Consulting Community for the next academic year can email innovationconsulting@IllinoisState.edu for more information.
Lead Photo: The ICC team visits a shipping container farm in Champaign. Pictured from left to right: Ryan Strange, Joe Quigley, Madison Steines, James Smith, Phoebe Naylon, Brennan Douglas, Alicia Chiakas, Aviv Zelniker, Max Snyderman, Bill Bagby with Central Illinois Produce, Dr. Eric Godoy, and Joe Kennedy
Filed Under Agriculture Center for Community Engagement and Service Learning College of Business Office of Sustainability
Are Container Farms The Solution To The Coronavirus Food Supply Problem?
As people run to grocery stores to stock up on food and supplies during a time of quarantine, the $899 billion restaurant industry is collapsing, raising questions about the economic security of the nation’s food supply industry in the time of COVID-19
April 13, 2020
As people run to grocery stores to stock up on food and supplies during a time of quarantine, the $899 billion restaurant industry is collapsing, raising questions about the economic security of the nation’s food supply industry in the time of COVID-19.
Dairy farms are already seeing the effects of nationwide school and restaurant closures in the wake of the coronavirus.
About one half of the normal demand for dairy has disappeared since the start of the United States’ social isolation period.
As a result, dairy farmers have had to throw out thousands of pounds of excess milk.
The agricultural side of the farming industry faces similar threats.
Food distributors and wholesalers are scrambling to redirect products from restaurants and other affected businesses to grocery stores.
But grocery stores desire different things than restaurants and schools, making it difficult to fully solve the problem.
Meanwhile, farm suppliers are racing to ship out fertilizers, seeds, and chemicals before the deadly virus disrupts the truck delivery industry.
Without these essential supplies, agriculture farmers won’t be able to produce enough food to meet demand in the States, especially as trade with other countries decreases.
The result could be a wide-scale food shortage.
Labor is also threatening agriculture as many field workers cannot afford to take time off, increasing potential for rapid spread throughout farms.
It’s a problem threatening to cause a significant labor shortage, lowering production and contributing to a potential food shortage.
Experts predict that our food security this fall and next year will be determined by how well these next harvests go.
With shortages in the food supply comes price gouging, leaving the world’s most vulnerable even more so.
The price of global food staples such as wheat and rice are already rising worldwide. Meanwhile, egg prices reached a record high in the US, as grocery stores reported a demand of six times the normal amount.
With more and more people facing unemployment and economic insecurity due to the effects of the global pandemic, increased food prices can make food insecurity worse.
Food security refers to the ability to obtain affordable, nutritious food.
In 2018, 5.6 million households in the US had very low food security.
Plus, as safety concerns skyrocket, consumers are becoming more conscious of how many hands have touched the food they’re about to take home and eat.
As a result, at-home solutions are seeming more appealing.
Since the beginning of March, Google searches for words related to “gardening” and “hydroponics” have increased.
In this time of uncertainty, small-scale indoor farming, like container farms, could prove to be an emergency solution.
Container farms are small indoor farms built inside of repurposed shipping containers.
They have the potential to easily provide food to urban areas, which tend to have the highest populations of food-insecure households, as they don’t require any farmland, only electricity, water, and internet connections.
Container farms also won’t be too affected by labor problems, as they’re fairly self-sufficient, meaning it doesn’t require too many laborers to ensure a bountiful harvest.
Higher tech containers, like our Pure Greens Container Farms, use controlled environment agriculture technology that’s automated and controllable through a smartphone app.
This allows for a more hands-off approach than traditional agriculture.
It also means the growing environment simulates perfect conditions for crops, resulting in more consistent and reliable yields.
Container farms are also able to yield quite a lot while being compact in size, which could help ease some of the burden of a global food shortage.
We’ll have to wait to see how well the agriculture industry adjusts to the pandemic, but it’s worth it to be proactive by looking into possible solutions as soon as possible.
If you’re interested in learning more about starting your own container farm, visit our website or call us at 602–753–3469 to get started!
WRITTEN BY Pure Greens Arizona LLC
Pure Greens’ container-based grow systems offer a variety of interior layouts, sizes, and options so customers can create a farm that meets their needs.
Tags: Container Farming Farming Covid 19
Clawson Greens Supplies This Snowy Tourist Town With Local Produce, Year-Round
Dave Ridill of Clawson Greens shares his farming unique experiences farming in snowy Tetonia, Idaho.
March 17, 2020
Dave Ridill of Clawson Greens shares his farming unique experiences farming in snowy Tetonia, Idaho.
Dave Ridill from Clawson Greens has made the impossible possible: in an area with a growing season that lasts less than three months (and is known for avalanches!), he has created a thriving year-round farming business that keeps surrounding restaurants flush with fresh greens even in the snowiest weather.
Download our interview with Dave to hear about his experiences!
CLAWSON GREENS WEBINAR
Or, keep reading to a re-cap of the webinar and Q&A with Dave.
Photo by Camrin Dengel, Teton Valley Magazine
Freight Farms: What’s the story behind your Freight Farms project?
Photo by Camrin Dengel, Teton Valley Magazine
Dave Ridill: Long story, short–my neighbors discovered Freight Farms while doing consulting work for Yosemite National Park. They were putting together a proposal for Yosemite to cut down on transportation costs and offer a new plan for food options inside the park. Yosemite didn’t end up going with their bid, so they approached me about starting a hydroponic farm business together. At the time, I was in the process of moving to Boston to go to paramedic school. However, after visiting Freight Farms, I decided to leave the Fire Department, where I was working at the time, and become a lettuce farmer.
FF: Who do you sell to and how do you do it?
DR: Our business model was focused on the restaurants in both Teton Valley and Jackson Hole, Idaho. The restaurant industry in our tourist town is booming. Despite highs and lows with seasonality, restaurants were the main focus in the inception of Clawson Greens.
We also tried a direct to consumer route (CSA) and the local natural food store. Due to time and labor increase, the CSA was not as profitable. We also have a very strong farmers market in both Teton Valley and Jackson so there was never a plan to try and compete with our local farmers. With an 85 day growing season, the local organic farmers already have a very short growing/selling season so adding another vendor to that market would just dilute an already competitive and small market. Our focus was on a market that no other local grower could tap into, year-round tourism.
“Our focus was on a market that no other local grower could tap into, year-round tourism.”
— Dave Ridill
FF: Do you find that customers are willing to pay more for your premium product?
DR: This question reminds me of a meeting with the restaurant manager of our local pub. We sat down and looked over a year’s worth of invoices from his distributors and the price fluctuation that the seasons had. We also looked at his total costs after he factored in waste due to buying in bulk to get the best pricing. With price changes and waste, my higher-priced product that I guarantee was not much more expensive than Sysco.
What I’m trying to say, is chefs will choose fresh local ingredients any day over large scale commercial produce. For them, it’s a selling opportunity: They market it by advertising the local farms/producers on their menus and have servers talk about the local products which are used in the specials. Consumers are willing to pay more for quality and to support local businesses.
“Chefs will choose fresh and local ingredients over large scale commercial produce any day. ”
Photo by Camrin Dengel, Teton Valley Magazine
— Dave Ridill
FF: How do you package your crops?
DR: From the start, Clawson Greens has made a point to not use single-use plastic clamshells or plastic bags. We use compostable corn-based bags for all our deliveries. On average, I put about 30 mini heads into 23-gallon compostable bags.
FF: What was the most challenging part of becoming a Freight Farmer and how were you able to overcome it?
DR: Becoming a Freight Farmer has many challenges much like starting any new business. There’s a steep learning curve but I enjoyed that process. The hardest part for me was understanding when to expand and how to grow with the business as it expanded. It was easy to transition from a full-time ski patroller to a part-time patrol/part-time farmer. However, as I added farms to grow the business, I found it hard to dive in and become a full-time farmer and business owner.
Being thrown into the deep end of the pool overnight was the hardest and easiest way to become a business owner. When your only option is to sink or swim, you do everything you can to make it work. Failure was never an option so by taking that off the table, you’ve got one direction, forward!
Implementing the ‘Profit First’ system is what really changed Clawson Greens. I went from a business that had money in the business account and was blindly throwing money around to pay bills, payroll and occasionally paying myself, to a business that knows exactly how much money to put towards operational expenses, taxes, owners’ compensation and most importantly, profit!
Photo by Camrin Dengel, Teton Valley Magazine
FF: What’s the best piece of advice you can give to people interested in becoming Freight Farmers?
DR: My advice is to hire the right people and acknowledge that you (the owner and operator) deserve to be paid accordingly.
“You are the one who puts in the most time, works late, lays awake at night thinking about the business.”
— Dave Ridill
This is where the profit-first system comes into play again. Being a farmer is hard, being a business owner is even harder. Being the owner and operator of a Freight Farm is very challenging and making a living at it can be a huge challenge. You can hire great employees but they will never go the extra mile that you the owner does. Over the past few years as an employer I’ve learned that you can teach people skills and procedures, but you can’t teach someone to care about your business. Only you can do that: you are the one who puts in the most time, works late, lays awake at night thinking about the business and at the end of the day, is the one who answers to whether the business is a success or failure. You need to pay yourself accordingly. Don’t start a business to make a living for someone else until you can make a living for yourself. When you are ready to start hiring, find an employee that’s financially invested in the business. Their effort and quality of work has a direct impact on their income
Interested in learning more about Clawson Greens?
Hear how Dave created his thriving farming business in some of the harshest conditions in the U.S. when you sign up for our upcoming webinar!
SIGN UP
Freight Farms Expands Leadership Team with New CEO and Head of Engineering
Tune in to our webinar on March 31st with Freight Farmer Dave Ridill! Hear how he is growing produce for his snowy mountain town, all year long. Register here.
March 24, 2020
Freight Farms positions for new innovation and deepened market reach; cofounder Brad McNamara remains President
March 24, 2020 -- Freight Farms is thrilled to announce that it has hired veteran consumer brand executive Rick Vanzura as CEO who will also join the company’s Board of Directors, while cofounder Brad McNamara will remain as Freight Farms’ President. The company also welcomes automation and robotics specialist Jake Felser as Head of Engineering.
The need to simplify supply chains and ensure reliable access to healthy, traceable food at a local level has become more crucial for communities worldwide. Expansion of Freight Farms’ team follows a year of strong momentum for the company as forward-thinking organizations, particularly at the institutional level, recognize the benefits of a secure, distributed, and transparent food supply. As the company scales for growing demand at speed, expansion of Freight Farms’ leadership is positioned to quicken new extensions of its technology platform and deepen market reach.
“Freight Farms’ innovation addresses issues like urban land scarcity, traceability and the need for hyper-local solutions with speed to market. The current environment demonstrates more than ever the value of Freight Farms’ offerings.”
— Rick Vanzura, CEO of Freight Farms
“What excites me about Freight Farms is the ability to join a passionate, mission-driven business that is already perfectly positioned to address the growing critical need for sustainable, hyper-local food production,” says Vanzura. “Freight Farms has an incredible technology platform as the originator of container farming, as well as a global footprint driving numerous sources of value. Beyond providing a meaningful solution across industries, Freight Farms’ innovation addresses issues like urban land scarcity, traceability and the need for hyper-local solutions with speed to market. The current environment demonstrates more than ever the value of Freight Farms’ offerings.”
Vanzura has driven value for companies from start-up to Fortune 5 across technology, restaurant, retail, and entertainment sectors. With a focus on leveraging innovation and developing new market channels, he led strategy for Panera, General Motors Information Services and GameStop, and as the original CEO of Wahlburgers, he built the company from a single unit into one of America's fastest-growing restaurant brands. Vanzura’s 20 years in President and C-level roles include a decade in food service working with markets central to Freight Farms’ business. He also brings significant international experience to his role, having run Borders Group’s nearly $1 billion international business.
“As co-founders, Jon Friedman and I have taken Freight Farms from an idea to help decentralize the food system to being the leader in containerized vertical farming that’s truly putting the power of hyper-local food production into people’s hands,” said McNamara. “Rick has amplified growth across interconnected industries, and his international experience lends itself to our ongoing global expansion. His personal alignment with Freight Farms’ mission was crucial for us as well—he’s a welcomed addition to the team as we scale.”
“Rick has amplified growth across interconnected industries, and his international experience lends itself to our ongoing global expansion.”
— Brad McNamara, President of Freight Farms
“The potential is extraordinary,” Vanzura added, “I’m excited to be working with Brad, Jon and the team on the spectacular opportunities ahead, all while doing our part to help build a better, more sustainable food system for all.”
Jake Felser, former VP of Engineering for eatsa (now Brightloom), has also joined the Freight Farms team as Head of Engineering. With teams across hardware and software, Felser led robotics R&D and the development of eatsa’s shelf-style pickup system from conception to deployment across the company’s network of partners. Prior to eatsa, Felser was Senior Engineer and Product Manager at Cooper Perkins and has worked in hydraulics, refrigeration, structural optimization, design for development, and agriculture for companies including Blue Origin, Promethean Power Systems, and AGCO. With a passion for sustainable development, Felser is focused on automation, IoT, and machine learning-based integrations for Freight Farms growing technology portfolio.
Company growth, including ten new roles across all departments in Q1, also follows Freight Farms’ recent launch of the Greenery. Nearly 100 have been adopted by customers in 9 countries to date, bringing Freight Farms’ global footprint to more than 300 container farms around the world. The innovation also spurred interest from Sodexo in a strategic national partnership to grow food onsite at educational and corporate campuses nationwide and new investment from Ospraie Ag Science.
Coronavirus Pandemic Highlights Vital Need For Vertical Farms In World Cities
Although the sources and sourcing of food in North America and Western Europe are currently generally secure, what might soon become a prodigious concern is that their workers in the production, distribution and retail segments of the food supply chain may eventually succumb to coronavirus infection
MARCH 25, 2020
by Professor Joel Cuello, Ph.D.
Image modified from Martin Sanchez/Unsplash
The speed with which the coronavirus outbreaks in Asia, Europe, and North America metastasized into a full-blown global pandemic — catching many world governments by surprise and with little preparation — underscores just how our world today is highly interconnected and how, in order to contain and stem the surging pandemic, temporary disconnection from the physically-networked world by cities, regions and even entire nations has become an urgent imperative.
With confirmed coronavirus cases globally now exceeding 370,000 and the number of deaths surpassing 16,000, many world cities have become throbbing epicenters of the surging pandemic. Accordingly, various countries, states, and cities have enforced lockdown or stay-at-home orders with drastic measures including banning public gatherings, restricting restaurants to take-out and delivery only, and closing schools, bars, theaters, casinos and indoor shopping malls, among others.
Such orders, or their looming possibility, have consequently intensified the panic-buying urges of consumers for food and household essentials particularly in North America and Western Europe, giving occasions for daily photos of empty grocery-store shelves splashed ubiquitously from across news networks to social media platforms. The availability of food in North America and Western Europe during the ongoing coronavirus pandemic, however, remains generally secure, at least in the near term of the pandemic.
Food Sourcing
New York City, for instance, normally has food supply amounting to approximately 8.6 million tonnes (19 billion pounds) annually as purveyed by a network of regional and national food distributors, which then is sold at about 42,000 outlets across the city’s five boroughs, according to a 2016 study sponsored by the city.
Over half of the outlets are made up of approximately 24,000 restaurants, bars, and cafes through which consumers access almost 40 percent of the city’s food by volume annually. The rest of the outlets are chain supermarkets, bodegas, and online grocery stores. The study reported that the city’s annual food supply feeds over 8.6 million city residents, over 60 million tourists plus daily commuters in the hundreds of thousands from the tri-state area of New York, New Jersey, and Connecticut.
With millions of tourists and commuters now staying away from the city, however, and with the city’s hotels at just 49 percent occupancy for the week ending March 14, an excess of the food supply is readily available for diversion into the city’s grocery stores and other retailers to meet the surge in demand by local residents. In the case of Germany, the country imports food that accounts for nearly 8 percent of its US$1.3 Trillion imported goods in 2018. Germany procures from abroad about 3 million tonnes of fresh vegetables annually — with cucumbers and tomatoes accounting for 40 percent of the import volume — at a value of around 3.5 billion Euros, mainly from the Netherlands and Spain. Indeed, approximately 30 percent of the 2.6 million tonnes of exported Dutch-grown fresh vegetables go to Germany.
Meanwhile, approximately 80 percent of the United Kingdom’s food and food ingredients are imported. The U.K. imports approximately 2.4 million tonnes of fresh vegetables each year from Spain (33 percent), the Netherlands (28 percent), France (10 percent) and from various parts the world (29 percent).
Access to Food
Although the sources and sourcing of food in North America and Western Europe are currently generally secure, what might soon become a prodigious concern is that their workers in the production, distribution and retail segments of the food supply chain may eventually succumb to coronavirus infection. In such events, coupled with the potential for lockdown bureaucracies to slow down the flow of cargo between countries and between cities, severe delays in delivery — or real delivery shortages — could well become an actual possibility.
Local Vertical Farms
The coronavirus pandemic lockdowns have laid bare if fortuitously, the crucial importance of partial local food production in or around world cities in the context of urban resilience. The following salient features of vertical farms have become especially significant toward buttressing a city’s resilience in the event of a pandemic lockdown:
(1) Local — production of safe and fresh produce can take place within the lockdown zone, obviating the hurdles and perils of going in and out of the red zone;
(2) Automation-Amenability — impact of severe labor shortage which can be expected as the pandemic surges as well as direct physical contact between workers and fresh produce can be significantly minimized or eliminated;
(3) Controlled-Environment — infection risks to both workers and crops are significantly reduced through clean and controlled operations;
(4) Modular Option — crops may be grown in modular production units, such as shipping containers, which may be conveniently transported to neighborhoods located either farther away or in areas of stricter isolation; and,
(5) Reliability — Dependability, and consistency of high-yield and high-quality harvests throughout the year is virtually guaranteed independently of season and external climate conditions.
Fortunately for New York City, even as it sources most of its fresh vegetables from California and Arizona, the New York greater area now serves as host to the highest concentration in the United States of commercial urban vertical farms — including Aerofarms, Bowery Farming, Bright Farms, Farm.One, Square Roots and Gotham Greens, among others — that operate as controlled-environment farms year-round and independently of the variable effects of climate and geography. While conventional outdoor farming can produce three vegetable harvests per year, some of these vertical farms can achieve up to 30 harvests annually.
New York City and other world cities could certainly use more vertical farms.
Indeed, the urban planning and design of every world city should incorporate vertical farms, in and/or around it, not only for promoting food security — but for fostering disaster resilience as well. During a pandemic when a temporary period of social distancing between cities and nations becomes critically necessary, vertical farms can serve as helping outposts of resilience for cities and regions on lockdown as they brave the onslaught of the pandemic until it runs its course and duly dissipates — at which time the enfeebled ties of cooperation between cities, states and nations across the globe can once again be mended and made even stronger than before. Thus, not only locally, but in fact also globally, vertical farms can serve as helping vanguards of protection for all of our communities.
Dr. Joel L. Cuello is Vice-Chair of the Association for Vertical Farming (AVF) and Professor of Biosystems Engineering at The University of Arizona. In addition to conducting research and designs on vertical farming and cell-based bioreactors, he also teaches “Integrated Engineered Solutions in the Food-Water-Energy Nexus” and “Globalization, Sustainability & Innovation.” Email cuelloj@email.arizona.edu.
THE ARCTIC CIRCLE - This Greenhouse In A Sea Can In Gjoa Haven Is Powered by Wind And Solar Energy
Betty Kogvik and Susie Kununak are making sure those little fruits — which will mark the second harvest from the community's new agricultural research station — have all the warmth and light they need, despite the dark winter outside
'It was so fresh, not like what we get in the store,' says technician at shipping container research station
Beth Brown - CBC News
These sea cans in Gjoa Haven are actually a new research station and grow pod used for growing vegetables. The solar and wind-powered project is called Naurvik, which means, the growing place. (Submitted by Thomas Surian)
In a sea can outside Gjoa Haven, Nunavut, there are rows of ripening cherry tomatoes working to grow from green to red.
Betty Kogvik and Susie Kununak are making sure those little fruits — which will mark the second harvest from the community's new agricultural research station — have all the warmth and light they need, despite the dark winter outside.
The two women are technicians, or guardians, for a new wind and solar-powered greenhouse that the Kitikmeot community named "Naurvik." That means "the growing place" in Inuinnaqtun.
The first harvest, of lettuce, grew in around four weeks. It was given to Gjoa Haven elders who have played a large role as advisors for the Naurvik project, which is led by the not-for-profit group, the Arctic Research Foundation.
One elderly lady even danced with joy when she got her lettuce.- Betty Kogvik"It was so fresh, not like what we get in the store. Sometimes when we get [lettuce] in the stores it is almost rotten. The ones we harvested are really fresh and tasty," Kogvik said. "One elderly lady even danced with joy when she got her lettuce."
Agriculture could grow new economy
The research station is built of two sea cans (shipping containers brought up on the summer sealift), two windmills and a row of solar panels. It has a generator for backup when the wind and sun both fall short.
It's on a hill, near a bay, in a place that elders said gets a lot of wind, and is only a few minutes ride by snowmobile from town.
Naurvik technician Betty Kogvik harvests the first lettuce grown in the sea can greenhouse in Gjoa Haven. (Submitted by the Arctic Research Foundation)
Every day, the technicians, including Kogvik's husband Sammy, spend time monitoring the station. The current harvest only uses a quarter of what the station could grow. Come summer, they want to run a trial growing cloudberry and blueberry plants, and other tundra plants used for medicine and tea.
"At the beginning, it was really confusing," Kogvik said. "We didn't know what to do, but we've got the hang of it now."
In the spring, Sammy says he wants to travel to Taloyoak to help that community start its own version of the Naurvik grow pod.
For the Arctic Research Foundation, the focus of Naurvik is on improving food insecurity, and on researching how to most efficiently grow food in remote and harsh environments, said project lead Adrian Schimnowski.
But it's also meant to foster the economy. Schimnowski said he'd like to see a local product grown to a scale where it's ready for export. For now, he's working to be able to employ and train students, as well as community-based technicians.
The Arctic Research Foundation is calling its new Naurvik greenhouse project in Gjoa Haven the most northern agriculture pod to be powered by wind and solar electricity. (Submitted by Thomas Surian)
The foundation is funding the program with help from Agriculture and Agri-Food Canada, the National Research Council of Canada, and the Canadian Space Agency.
"It's a mini, mobile research station. We can add as we expand," said Schimnowski. "It's directed by the wishes of the community."
Space agency looks to Gjoa Haven
Because Naurvik is working on more efficient technology to grow vegetation in an environment it usually wouldn't survive in, that same research can also be used to help scientists understand how to grow food in harsh environments — like space.
"We are hoping to find strategies that could help astronauts grow food in space," Christian Lange, head of exploration strategic planning with the Canadian Space Agency, said in a news release. Research from "extreme or remote environments," like Gjoa Haven, could be part of that, he said.
This crop of potted cherry tomato plants are thriving under LED grow lights. They will be the second kind of plant harvested at the Naurvik grow pod in Gjoa Haven. (Submitted by the Arctic Research Foundation)
The research station itself is built to be hyper-efficient, project lead Schimnowski said.
"It's very narrow and tight, similar to what it would be like in a spaceship, but everything is well organized and everything has purpose."
While gardening isn't an Inuit tradition, using the land to care for and store food is. Elders who are working with Naurvik said using the green energy to run the research station made them think of a community freezer, the kind built into the ground. Those elders said the hill near the station could be used to build a traditional freezer.
"When I first heard of [the project] I thought it would never work up here," Gjoa Haven elder Peter Akkikungnaq is quoted in the news release. "Not in this 40 below zero. Now I know anything is possible if you have the right idea ... I had a taste of the vegetation. It was fresh."
The Philadelphia Zoo Is Running A Farm Inside A Converted Shipping Container
Tua lives at the Philadelphia Zoo, the first zoo in the country with its own on-site vertical garden used to grow leafy greens for its animals. And she loves the produce they’re feeding her
by Brianna Baker, For The Inquirer, March 4, 2020
Kristen Waldren, director of strategic initiatives at The Philadelphia Zoo, walks through the zoo's new "Cropbox" — a vertical farm being used to grow plants that are harvested to feed animals. MARGO REED
If you’re a fan of homegrown arugula and mustard greens, you just may have the same taste as Tua, a 27-year-old Sumatran orangutan.
Tua lives at the Philadelphia Zoo, the first zoo in the country with its own on-site vertical garden used to grow leafy greens for its animals. And she loves the produce they’re feeding her.
The garden is located in a retrofitted shipping container in the Urban Green, the zoo’s open-air food marketplace. A mural, by Philly-based environmental artist and activist Eurhi Jones, transforms the front of the shipping container into a colorful collage of the animals who’ll chow down on the vegetation.
But the real beauty is inside, where stacked, tidy shelves hold rows of plants that are grown hydroponically, in nutrient-rich water instead of soil. LED lights, a substitute for sunlight, shine 18 hours a day. Farm operators use a mobile app to remotely control the container’s light, temperature, and humidity levels.
Kristen Lewis-Waldron, director of strategic initiatives at the zoo, said the vertical farm is far more sustainable than bringing in food from outside sources. It uses 70% to 90% less water than traditional farming, has no need for pesticides or herbicides, and cuts greenhouse gas emissions out of the equation since no motor-powered transportation is necessary to get the food to the zoo.
“It really kind of creates this farm-to-table [model] — in this case, shipping container-to-exhibit,” she said of the project, which is in a pilot phase.
Want to know what's going on in Philly? Find out about upcoming concerts, shows, and other events with our weekly newsletter.
Lewis-Waldron is short on farming experience but knows a thing or two about feeding animals. She landed her first role at the zoo 23 years ago as a nutrition intern. She went on to work for, and eventually lead, the zoo’s conservation department, before transitioning to her current position. Growing greens for the animals makes her feel like she’s come full circle, she said.
A peacock at the Philadelphia Zoo walks past the "Cropbox," a converted shipping container being used to grow plants being used to help feed the animals. MARGO REED
To launch the project, she enlisted the services of CropBox (which is also what the zoo calls the vertical farm), a North Carolina company that provides all the equipment customers need, including the shipping container, and helps set up the system.
Lewis-Waldron also consulted with industry experts, including those who operate their own vertical farms, to learn best practices and how to troubleshoot technical challenges. All in all, the preparation process took about a year.
In its nine months of operation, the CropBox has fed 20 animal species with its microgreens. It produces 275 pounds of leafy greens a month, which is only 10 percent of the zoo’s monthly requirement. But that number, Lewis-Waldron said, will grow once the pilot year concludes and the project is expanded.
“You can take over a vacant warehouse or vacant building and convert it,” she said. “You could take six of these and make a dent in the requirements of our collection.”
The CropBox also benefits the zoo economically by replacing a collection of food it would otherwise purchase.
But perhaps most importantly, the greens grown in the vertical farm are rich in nutrients. The zoo takes animals’ diets very seriously and even employs a full-time nutritionist. By feeding leafy greens to the animals, the zoo is keeping their health in shape.
Still, that doesn’t mean the greens are every species’ favorite snack. Just like humans, animals have unique palates. And the current variety growing in the CropBox — a stir-fry mix that includes arugula and mustard greens — isn’t always a crowd-pleaser.
“It’s got a little kick to it, a little bit of spice. Our emus were a little hesitant,” Lewis-Waldron said. “But our monkeys, langurs, apes, gorillas, orangutans, tortoises absolutely love it. So it’s interesting, and we’ll continue to test out different types of greens.”
Brianna Baker, For The Inquirer
US: New Jersey - Hope Cahill Starts As Coordinator At Hydroponic Farm
A hydroponic farm, in the middle of a municipal center? Well, it all started in 2016, when Robbinsville Mayor Dave Fried found out about hydroponic farming in freight containers
By Lois Levine
March 1, 2020
A hydroponic farm, in the middle of a municipal center? Well, it all started in 2016, when Robbinsville Mayor Dave Fried found out about hydroponic farming in freight containers.
“He loved the idea and thought it would be beneficial to the township in terms of feeding programs and education on how to grow greens and learn more about nutrition,” said Kevin Holt, recreation manager for the Robbinsville Township.
Hope Cahill, the new coordinator of Robbinsville’s hydroponic farm, holds some of the farm’s yield.
Now, the farm has a new coordinator—Hope Cahill, who took over for original caretaker Kyle Clement in January.
“We can grow anything that is a leafy green,” Cahill said. “Here we are growing butterhead, oak leaf, and lollo lettuce, as well as spring mix.”
The farm also grows some herbs, basil, and cilantro. Cahill, 25, is certified in aquaponics, an off-breed of hydroponics.
After graduating high school, she got certified in a variety of different areas of agriculture, and before taking this position working as a naturalist at various garden centers, as well as with the Monmouth County Park system. Born and raised in Tinton Falls, Cahill will be soon moving to Freehold.
Hydroponic farming is farming done without soil. Plants typically get all their nutrients from the soil. In hydroponic farming, however, nutrient-rich water takes the place of the soil, enriching the seedlings as they grow into fully mature plants and watering them at precise times through a computerized system.
With the system that the Robbinsville Township purchased, known as the Leafy Green Machine, lettuces and herbs are grown in a vertical hydroponic farm that lives within a recycled, refrigerated, insulated, custom-built shipping container.
Between the nutrient-rich water and light energy from powerful LEDs, greens can be independent of the need for land, climate and season, growing in a modular design that is also mobile and can theoretically live anywhere.
The container consists of insulation, where it maintains an average internal temperature of 70 degrees Fahrenheit in extreme climates; climate control, built with an integrated “economizer” that saves energy by drawing in cool outside air when appropriate and also doubling as an intake fan; a dehumidifier to maintain optimal humidity levels and decreasing the farms overall water consumption; airflow ducts, consisting of two fans that distribute cool carbon dioxide enriched air evenly; and a carbon dioxide regulator with a safety shut-off feature, providing plants with exactly the right amount of carbon dioxide needed for photosynthesis.
In addition, the greenery’s LED lights provide the plants with the best quality light at its most efficient point. The LED boards are designed to emit only particular wavelengths of red and blue light, which are the colors that plants are able to absorb most easily for photosynthesis (red light is essential for stem and leaf growth, while blue light helps develop thick stems and dark green foliage).
Just as it is in nature, Cahill and her team start with the seeds, which begin in a flowing hydroponic system and are placed into compressed peat moss, known as grow plugs. The peat-moss plugs act as a sponge for absorbing nutrient-rich water. The seeds soak for 10 minutes, are covered with a humidity dome and sit under grow lights for about a week.
At that point, the seeds have become sprouts, with small roots, short stems, and a few young leaves. They then move up to the next level, a flow troth, where the roots “get completely soaked,” Cahill said. Now actual seedlings, taller and sturdier than they had been, with a secure root system, the plants sit in that troth for another two weeks, getting consistent water and light to develop strong stems needed to support the plant’s weight later in its life cycle.
After this time period, the seedlings are harvested and transplanted into the main cultivation area, where they are now in the towers, growing vertically for the first time. The roots, which are still in the peat-moss grow plugs, are wedged into stiff foam panels, which provide firm support, with the plant facing outward towards the LED light, encouraging the leaves to grow. Here, in this final destination, they spend from two to five weeks until they are ready for their harvest..
A view of the produce inside of the shipping container that houses Robbinsville’s hydroponic farm
“It is a continual cycle of putting new lettuce and herbs in, taking grown ones out,” Cahill said.
Every week, the team has something to harvest.
“What is nice about the system is that it is computerized so that plants get exactly the nutrients it needs at the right time,” Cahill said. “Sensors on the computer know when they might need nitrates or some other nutrient.”
Freight Farm, the company that built the hydroponic farm equipment, also developed an app that can be used via a person’s iPhone or desktop computer to keep an eye on all sensor data.
Holt admits he did not know much about hydroponic farming until Fried asked him to look into purchasing a machine.
“I did a ton of research on what hydroponic farming is, to educate myself, and then looked into what companies are out there to make these container farms,” he said. “We talked to a lot of companies, and decided on Freight Farm, out of Boston. At the time, they told us we were the only municipality they had ever sold a freight farm container to.”
Once Cahill and Holt have the finished products, the lettuce and herbs get donated back to the Robbinsville Senior Center.
“We also give some of the produce to Meals on Wheels, and also Mercer Street Friends, who disperse it to schools,” Cahill said. “They distribute it to about a dozen schools in the Trenton area.”
And how does the finished product taste?
“It is honestly the best lettuce you can ever eat,” Holt said. “You really can see and taste the difference between this produce and the produce you buy in a supermarket.”
It looks good and feels good, too, Cahill said.
“Before we distribute it, we take care to remove any brown or damaged leaves,” she said. “There are, of course, no pesticides, no chemicals that the greens were treated with, so it is very safe and very clean.”
Both Cahill and Holt rave about how green and fresh the lettuce is, “with so much more taste to it than what you get in the stores, which by comparison, tastes so bland,” Holt said.
Since starting the farm at the municipal center in 2017, companies have come through to see the set-up, expressing interest in buying machines for themselves. Holt said the township has also hosted schools and colleges, as well as field trips and local education programs.
“Our mission is to grow, educate and unite: we grow the lettuce, give it away, educate the community about how hydroponic farming works, and unite people by asking them to volunteer or hold events, which is a catalyst for bringing people together,” Holt said. “This has been a huge win-win for the community.”
Cahill said she is always seeking volunteers and visitors, as well.
To schedule a tour or for more information, visit robbinsville.net/recreation or send an email to hcahill@robbinsville.net.
80 Acres Farms Will Grow Tomatoes On Fifth Avenue In Guggenheim Exhibition
Based in Hamilton, Ohio, 80 Acres Farms is a leader in technology-assisted indoor growing and a multi-farm operator marketing a wide variety of freshly picked vegetables and fruits to retailers such as Giant Eagle, Kroger, Whole Foods, Jungle Jim’s and Dorothy Lane Markets
80 Acres Farms will grow tomatoes on one of the busiest streets in New York City outside the Solomon R. Guggenheim Museum as part of the Guggenheim’s new exhibition in collaboration with Rem Koolhaas, “Countryside, The Future.”
Along with its commercial partners Infinite Acres and Priva Holding BV, 80 Acres Farms will grow cherry tomatoes in an indoor grow module right outside the museum on Fifth Avenue.
Based in Hamilton, Ohio, 80 Acres Farms is a leader in technology-assisted indoor growing and a multi-farm operator marketing a wide variety of freshly picked vegetables and fruits to retailers such as Giant Eagle, Kroger, Whole Foods, Jungle Jim’s and Dorothy Lane Markets.
The company was founded by veteran food industry executives Mike Zelkind and Tisha Livingston, who are supported by a deep team and a board of directors representing executive and leadership experience at leading food, healthcare and other companies.
Window on tomato production
People in New York will be able to look through a large window in the indoor farm to view a crop of fresh tomatoes being grown continuously during the next six months under precise LED lighting and other controlled conditions.
The first tomatoes will be ready for harvest by late-March.
The grow module will demonstrate how indoor farming can benefit the world through growing fresh, pesticide-free food near populations, anywhere in the world while using fewer natural resources.
The “Countryside, The Future” exhibition will examine political forces, social issues and environmental factors altering landscapes across the world, including traditional farmlands.
80 Acres Farms is a founding member of the Infinite Acres partnership venture, along with Netherlands-based Priva Holding BV, a leading provider of technology solutions, services and automation systems to horticultural and other industries; and Ocado Group, one of the world’s largest dedicated online grocery retailers, operating its own grocery and general merchandise retail businesses.
That partnership is now building large-scale, fully automated indoor farms in the U.S., Asia and Europe.
“We believe that what we are doing is about the future of food. We are changing the way fruits and vegetables are grown and harvested locally then delivered to grocers the very next day,” Zelkind said.
“There is an enormous market and consumer appetite around the world for produce that our crop scientists and other food experts have been perfecting during the past five years,” he said. “Our participation in this exhibition will allow New York residents and visitors to experience how the freshest, tastiest locally grown tomatoes can be grown year-round indoors in one of the busiest cities in the world.”
700-square-foot grow center
For the Guggenheim exhibition, 80 Acres Farms, Infinite Acres, and Priva Holding have collaborated on the 700-square-foot grow center and all of the state-of-the art ag-technology within it.
While in operation for the next six months outside the Guggenheim, the Infinite Acres grow module is expected to grow 50,000 tomatoes.
Additional tomatoes will be donated to City Harvest, a New York City food rescue organization that safely recovers excess food and distributes it to people in need.
“Countryside, The Future” will be open to the public through Aug. 14.
Paris Mayor: It's Time For a '15-Minute City'
Paris needs to become a “15-minute city.” That’s the message from the manifesto of Mayor Anne Hidalgo, who is seeking re-election this March
FEBRUARY 18, 2020
During the city's transit strike in December, Parisians got a taste of what being a more foot- and bike-oriented city would feel like. Philipe Lopez/AFP via Getty Images
In her re-election campaign, Mayor Anne Hidalgo says that every Paris resident should be able to meet their essential needs within a short walk or bike ride.
Paris needs to become a “15-minute city.” That’s the message from the manifesto of Mayor Anne Hidalgo, who is seeking re-election this March. Hidalgo has been leading a radical overhaul of the city’s mobility culture since taking office in 2014 and has already barred the most polluting vehicles from entry, banished cars from the Seine quayside and reclaimed road space for trees and pedestrians. Now, she says, Paris needs to go one step further and remodel itself so that residents can have all their needs met—be they for work, shopping, health, or culture—within 15 minutes of their own doorstep.
Even in a dense city like Paris, which has more than 21,000 residents per square mile, the concept as laid out by the Hidalgo campaign group Paris en Commun is bold. Taken at a citywide level, it would require a sort of anti-zoning—“deconstructing the city” as Hidalgo adviser Carlos Moreno, a professor at Paris-Sorbonne University, puts it. “There are six things that make an urbanite happy,” he told Liberation. “Dwelling in dignity, working in proper conditions, [being able to gain] provisions, well-being, education, and leisure. To improve the quality of life, you need to reduce the access radius for these functions.” That commitment to bringing all life’s essentials to each neighborhood means creating a more thoroughly integrated urban fabric, where stores mix with homes, bars mix with health centers, and schools with office buildings.
Paris en Commun has created a diagram to illustrate the concept of what should be available within 15 minutes of “Chez Moi” (home).
Paris en Commun’s 15-minute city concept. From the top, clockwise, the headings read: Learn, Work, Share and Re-Use, Get Supplies, Take the Air, Self-Develop and Connect, Look After Yourself, Get Around, Spend, and Eat Well. (Paris en Commun)
This focus on mixing as many uses as possible within the same space challenges much of the planning orthodoxy of the past century or so, which has studiously attempted to separate residential areas from retail, entertainment, manufacturing, and office districts. This geographical division of uses made sense at the dawn of the industrial era when polluting urban factories posed health risks for those living in their shadows. Car-centric suburban-style zoning further intensified this separation, leading to an era of giant consolidated schools, big-box retail strips, and massive industrial and office parks, all isolated from each other and serviced by networks of roads and parking infrastructure. But the concept of “hyper proximity,” as the French call it, seeks to stitch some the these uses back together, and it’s driving many of the world’s most ambitious community planning projects.
Barcelona’s much-admired “superblocks,” for example, do more than just remove cars from chunks of the city: They’re designed to encourage people living within car-free multi-block zones to expand their daily social lives out into safer, cleaner streets, and to encourage the growth of retail, entertainment, and other services within easy reach. East London’s pioneering Every One Every Day initiative takes the hyper-local development model in a slightly different direction, one designed to boost social cohesion and economic opportunity. Working in London’s poorest borough, the project aims to ensure that a large volume of community-organized social activities, training and business development opportunities are not just available across the city, but specifically reachable in large number within a short distance of participants’ homes.
Meanwhile, in Portland, Oregon, walking-distance-limited neighborhood planning is seen as central to climate action: The city aims to cover 90 percent of the city in so-called “20-minute neighborhoods,” where all basic needs—with the exception of work—can be reached within a third of an hour of walking time. In Australia, Melbourne rolled out a similar pilot in 2018.
Hidalgo’s aspirations for Paris build on this idea, but with a local twist. The goal travel time is reduced to 15 minutes, but bike journeys can count. And while it likewise underlines the importance of stores and doctors, it also includes cultural activities and workplaces within its central aspirations.
In Paris, this isn’t necessarily such a tall order. The mayor oversees only the 2.2 million residents of the city’s heavily populated historic core, which already enjoys some of the use-mixing that the 15-minute-city concept encourages, thanks to its pre-industrial roots. Paris would have an easier time with the concept than say, sprawling Melbourne, where more radical residential densification may be in order.
Paris en Commun’s manifesto sketches out some details for what this future walkable, hyperlocal city would look like. More Paris road space would be given up to pedestrians and bikes, with car lanes further trimmed down or removed. Planning would try to give public and semi-public spaces multiple uses—so that, for example, daytime schoolyards could become nighttime sports facilities or simply places to cool off on hot summer nights. Smaller retail outlets would be encouraged—bookstores as well as grocery stores—as would workshops making wares using a “Made in Paris” tag as a marketing tool. Everyone would have access to a nearby doctor (and ideally a medical center), while sports therapy facilities would be available in each of the city’s 20 arrondissements.
To improve local cultural offerings, public performance spaces would be set up, notably at the “gates” of Paris — the large, currently car-dominated squares around the inner city’s fringe which once marked entry points through the long-demolished ramparts. Finally, Paris would be populated by a network of “citizen kiosks”—booths staffed by city employees that would offer not just information, but also community cohesion services. Think places where you can drop off and pick up keys, join a local club or buy compost for your balcony plants.
Paris en Commun provides some glimpses of what this more self-sufficient, neighborhood-oriented city might look like. The (imaginary) triangular intersection below resembles the current state of many in Paris; there’s some public pedestrian space, but it remains hemmed in by cars, both mobile and parked, and genuinely safe space for pedestrians is limited.
(Nicolas Bascop/Paris en Commun)
After a superblock-style transformation, several neighborhood streets have been stripped of cars and no longer act as through-routes. This frees up room for new public space, with a small park at one end and a produce garden for residents at the other. New trees, green roofs and balconies, and a fountain would help mitigate the heat island effect and make the area a more pleasant place to linger. Meanwhile, the crossing space has ballooned in size, providing greater priority for pedestrians.
(Nicolas Bascop/Paris en Commun)
In December, transit strikes in Paris in protest of national pension reform gave Parisians an accidental taste of what a 15-minute-city future would look like, at least in terms of the hugely enlarged volume of cyclists on the city’s roads while bus and Metro service was halted. At some points during the strikes (which are still ongoing), bikes started to outnumber cars by two to one—a premonition of what might be to come.
Still, piecing together an entire modern working city around this 15-minute rubric would pose a challenge. In addition to its residents, central Paris attracts vast numbers of tourists who must be fed, housed and transported from neighborhood to neighborhood. Millions more commute into the city for work on regional transit from the vast greater Paris metro area. The people living in self-sufficient squares like the one above might find their rents rise along with the charm. And Paris can’t be transformed into a city that solely serves the needs of affluent locals.
Just how Hidalgo would execute the infrastructural changes required remains to be seen. She appears well-positioned to stay in City Hall: She’s leading in the polls (and one of her rivals has pulled out of the race after a sex scandal). Her office has not announced any specific budget or timetable for the 15-minute city concept, which remains perhaps more of a rough blueprint for the future than an imminent makeover, should she be re-elected in March. As a rethink of the way cities should be planned—and exactly who they should serve, and how—it’s an idea that other cities are likely to watch with great interest.
About the Author
Feargus O'Sullivan @FEARGUSOSULL
Feargus O'Sullivan is a contributing writer to CityLab, covering Europe. His writing focuses on housing, gentrification and social change, infrastructure, urban policy, and national cultures. He has previously contributed to The Guardian, The Times, The Financial Times, and Next City, among other publications.
This Brooklyn Farm Company Is Training A New Generation of Urban Farmers
In old shipping containers, the shoots of a new way of urban farming are starting to emerge, which could help meet the demand of a growing urban population
February 7, 2020, by World Economic Forum
(Credit: Unsplash)
This article is brought to you thanks to the collaboration of The European Sting with the World Economic Forum.
Author: Kate Whiting, Senior Writer, Formative Content
The average age of an American farmer is 57.5 years.
Just under 70% of the world’s population will live in urban areas by 2050.
Square Roots is teaching young city farmers how to grow food sustainably.
Among the high-rise buildings and concrete sidewalks of Brooklyn, there’s a quiet green revolution taking place.
In old shipping containers, the shoots of a new way of urban farming are starting to emerge, which could help meet the demand of a growing urban population.
Square Roots is an indoor urban farming company, which not only grows food sustainably without soil but is teaching a new generation of farmers how to do it too.
“We realized there were tens of thousands of young people who were as passionate about changing the food system as we were, but just didn’t know how to get started,” says Tobias Peggs, CEO of Square Roots.
Feeding the future
Square Roots is tackling several issues in one go: the need to use less water and other resources in agriculture, the aging of farmers, the global population rise and, in particular, the growing urban population.
Farmers in the US aren’t getting any younger, with an average age at 57.5, according to census data, up 1.2 years from 2012.
A new way of farming. Image: WWF/Netflix
And it’s a similar story in other places around the world. In Kenya, the average farmer is 60. In Japan, 67.
By 2050, 68% of the world’s population is expected to live in urban areas, so that’s where much of the focus of food growing will need to be.
“Younger generations are really interested in making sure we’re all eating healthy food that’s nutritious and grown in sustainable ways, but they’re less interested in living in the middle of the country,” says Peggs.
The future of farming
The Next-Gen Farmer Training Program teaches would-be farmers how to grow leafy greens in a high-tech hydroponic system that it says uses up to 95% less water than traditional farms.
They study plant science, to find out what’s happening at a molecular level as the plant grows, they learn about the business side and engage with the local community and agriculture ecosystems.
Food
What is the World Economic Forum doing to help ensure global food security?
Two billion people in the world currently suffer from malnutrition and according to some estimates, we need 60% more food to feed the global population by 2050. Yet the agricultural sector is ill-equipped to meet this demand: 700 million of its workers currently live in poverty, and it is already responsible for 70% of the world’s water consumption and 30% of global greenhouse gas emissions.
New technologies could help our food systems become more sustainable and efficient, but unfortunately, the agricultural sector has fallen behind other sectors in terms of technology adoption.
Launched in 2018, the Forum’s Innovation with a Purpose Platform is a large-scale partnership that facilitates the adoption of new technologies and other innovations to transform the way we produce, distribute and consume our food.
With research, increasing investments in new agriculture technologies and the integration of local and regional initiatives aimed at enhancing food security, the platform is working with over 50 partner institutions and 1,000 leaders around the world to leverage emerging technologies to make our food systems more sustainable, inclusive and efficient.
Learn more about Innovation with a Purpose’s impact and contact us to see how you can get involved.
Each shipping container at the company’s campus in Brooklyn’s Bed-Stuy neighborhood can produce up to 45kg of fresh basil, chive or mint leaves per week, which is grown without pesticides and uses data to optimize flavor and nutrition.
“Successful companies in the 21st century have to be doing well – and doing good at the same time,” says Peggs.
“We’re growing food and selling food, that’s how we make money. But we’re doing that in a sustainable way, which is better for the planet and we’re empowering the next generation of leaders in urban farming.”
A Belly Ache Can lead To A Trip To The Urgent Care. E. coli Poisoning Lands You In The Emergency Room
The FDA has called little attention to the surge in E. coli outbreaks from leafy green vegetables. It has been slow to investigate or publicize risks and did not disclose one outbreak to the public until the Globe contacted agency officials about reports of E. coli poisonings
Dietitian Determined To Save Salads!
February 12, 2020
Written by Dr. Jenna Bell, RD VP of Nutritional Science at Crop One
Crop One is the world’s largest scalable, completely controlled, vertical farming company. Our Greater Boston brand is FreshBox Farms.
Spend a few days bent over, writhing in abdominal pain and you’ll understand how serious foodborne illnesses can be. It may even require a trip to urgent care. Experience an outbreak of E. coli O157:H7 from salad greens and you may be among hundreds heading to the ER.
E. coli poisoning can be life-threatening.
What is E. coli, anyway?
Straight out of the Center for Disease Control (CDC):
“Escherichia coli (abbreviated as E. coli) are bacteria found in the environment, foods, and intestines of people and animals. E. coliare a large and diverse group of bacteria. Although most strains of E. coli are harmless, others can make you sick. Some kinds of E. coli can cause diarrhea, while others cause urinary tract infections, respiratory illness and pneumonia, and other illnesses.”
To be crystal clear — we’re talking about fecal contamination. Poo in food. Bird, cow, human, someone’s poop.
As a registered dietitian, I swear by colorful salads of leafy greens with favorite fruits, veggies, seeds, nuts and proteins atop. Making that recommendation sans lettuce feels blasphemous and unfulfilling. But given the pace at which the outdoor-grown romaine industry reports bacterial outbreaks, food safety threatens our salad fixings.
Break out bacteria
Over the past few years, romaine has been hit hard by outbreaks of bacterial contamination — especially from the strain, E. coli O157:H7. The most recent string of outbreaks is considered “under control” by the CDC and Food and Drug Administration (FDA), but the final count as of January 13, 2020, is 167 individuals reported in the US.
“Reported” is a key word here because how many times have you called the CDC or the FDA when you were sick?
Lettuce + E. coli is not a new thing
Several years ago (2013), a scientific investigation of a decade-worth of data on hospitalizations and deaths attributed to food commodities (including seafood, farm animals and plants) revealed that among the 17 commodities, more illnesses were associated with leafy vegetables (2.2 million [22%]). Illnesses associated with leafy vegetables were the second most frequent cause of hospitalizations (14%) and the fifth most frequent cause of death (6%).¹
A 2020 piece in the Boston Globe written by venerated reporter, Christine Haughney Dare-Bryan, traced the tracks of the recent outbreaks and illuminated the grimness with a family’s horrific experience with E. coli poisoning in their two-year-old son. In the article, Haughney Dare-Bryan reflects on the quick response from then commissioner of the FDA, Scott Gottlieb:
…[Gottlieb] tweeted to a startled nation that they should stop eating romaine lettuce just two days before Thanksgiving 2018.
E. coli fatigue
However the seriousness, history shows that someone hit the snooze button. Despite the number of updates and investigations, CDC and the FDA can’t seem to get ahead of it. Haughney explains:
Despite the growing number of outbreaks, the agency remains protective of the growers, taking little enforcement action and sometimes shielding growers suspected of causing outbreaks from bad publicity. Consider:
The FDA has called little attention to the surge in E. coli outbreaks from leafy green vegetables. It has been slow to investigate or publicize risks and did not disclose one outbreak to the public until the Globe contacted agency officials about reports of E. coli poisonings. FDA officials insist they planned to disclose the early fall 2019 outbreak all along.
The FDA has not punished any farm or distributor in connection with the seven outbreaks traced to lettuce since 2017 even though federal law prohibits the sale of contaminated foods. The agency concluded that three of the outbreaks were linked to a single California lettuce grower but declined to release the name.
The FDA staff monitoring lettuce production is just a small fraction of that detailed to the federal oversight of beef: There are 614 FDA field investigators responsible for leafy greens compared to 7,068 workers overseeing beef for the Department of Agriculture. Congress recently gave the FDA $8 million to better handle outbreaks, but the agency doesn’t want to talk about the state of its staffing. When the Globe tried to examine just how understaffed the agency is, officials redacted hundreds of pages of records discussing their internal problems.
The agency relies almost entirely on voluntary cooperation from the lettuce industry, an approach that has brought about some safety improvements. But FDA has asked relatively little of the industry and recently delayed implementing rules aimed at preventing E. coli contamination of irrigation water until 2022.
What do we do now?
From one salad enthusiast to another, or one mom to another, or one PhD/dietitian to consumer (take your pick): there is a safer way to grow your lettuce and eat it too.
We can grow indoors. Out of the soil and away from questionable water, weather disruption messes and “run-off” contaminants (think poop).
I found my safe salad environment when I met and started working for CROP ONE.
How do I know it’s safe?
Concealed, confined, enclosed, controlled, secured, safe, protected — all synonyms for Crop One’s modular growing rooms (“mods”). Mods are protected by double door entryways with fancy sliding doors like at the supermarket and a vestibule. Anyone who enters is fully gloved and covered in stylish lab wear (no, not stylish).
Pictured: The most stylish lab wear in Massachusetts
I should add here that because our plants are protected from the world, we don’t need or use any type of -cide (pesticides, herbicides or fungicides), nor do we deal with pests, insects, rain, contaminated water or other farm’s fertilizer or chemicals. We’re free from all that stuff you’re trying to stay free from.
Pure, clean, filtered — water and air. Each mod is carefully controlled for contaminants, chemicals, heavy metals, and other unwanted impurities through a multi-step, quality-controlled purification system.
FreshBox KVH Kosher Certified romaine lettuce.
Two words: Kosher. Certified.
If you’re not familiar with the process by which produce is certified Kosher, visualize microscopes, tweezers, fastidious inspectors, etc. KVH Kosher certification officers perform comprehensive inspections to ensure that Crop One/FreshBox Farms’ produce is free of all pests and insects.
The salad solution.
Crop One can keep your salad safe. Miraculously, along with safety, our modular enclosures are scalable and sustainable in any climate, on very little land, with barely any water compared to traditional farms (about 95–99% less water required), but we’ll save that for another conversation.
Jenna A. Bell, PhD, RD, joined the Crop One team in September 2019 as the VP of Nutritional Science to be part of the global food supply solution.
References:
Painter JA, Hoekstra RM, Ayers T, et al. Attribution of Foodborne Illnesses, Hospitalizations, and Deaths to Food Commodities by using Outbreak Data, United States, 1998–2008. Emerging Infectious Diseases. 2013;19(3):407–415. doi:10.3201/eid1903.111866.
Haughney Dare-Bryan C. Green Alert. Boston Globe. Last accessed January 30, 2020: https://edition.pagesuite.com/popovers/dynamic_article_popover.aspx?artguid=a497f64d-df30-4f48-b026-10aadc66901b&appid=1165
WRITTEN BY
Crop One Holdings
We grow the cleanest, healthiest greens for anyone, anywhere in the world. Our sustainable vertical farms are free from chemicals and climate-proof.
Hamilton’s 80 Acres Farms To Grow Tons of Tomatoes On New York City’s Fifth Avenue
Hamilton-based 80 Acres Farms will grow tomatoes on one of the busiest streets in New York outside the Solomon R. Guggenheim Museum. The grow is part of “Countryside, The Future,” the Guggenheim’s new exhibition in collaboration with Rem Koolhaas, which opens to the public Feb. 20, and runs through Aug. 14
February 21, 2020
By Eric Schwartzberg, Staff Writer
HAMILTON —
80 Acres Farms will grow tomatoes on one of the busiest streets in New York outside the Solomon R. Guggenheim Museum.
The grow is part of “Countryside, The Future,” the Guggenheim’s new exhibition in collaboration with Rem Koolhaas, which opens to the public today and runs through Aug. 14.
Along with its commercial partner’s Infinite Acres and Priva Holding BV, 80 Acres Farms will grow cherry tomatoes in an indoor grow area right outside the museum on Fifth Avenue.
80 Acres Farms is a leader in indoor growing for retailers such as Kroger, Jungle Jim’s International Market, Whole Foods, Dorothy Lane Markets, and Giant Eagle.
MORE: ‘The perfect home’: Why 80 Acres chose Hamilton to move its headquarters and create 125 jobs
People in New York will be able to look through a large window in the indoor farm to view a crop of fresh tomatoes being grown continuously during the next six months. The first tomatoes grown will be ready for harvesting and consumption by late March.
The “Countryside, The Future” exhibition will examine political forces, social issues, and environmental factors altering landscapes across the world, including traditional farmlands.
“We believe that what we are doing is about the future of food,” said Mike Zelkind, chief executive officer of 80 Acres Farms. “We are changing the way fruits and vegetables are grown and harvested locally then delivered to grocers the very next day. There is an enormous market and consumer appetite around the world for produce that our crop scientists and other food experts have been perfecting during the past five years.”
MORE: Dilapidated Hamilton building transforms into an industry-changing grow facility
Zelkind said 80 Acres’ participation in the “Countryside, The Future” exhibition will allow New York residents and visitors to experience how “the freshest, tastiest locally-grown tomatoes” can be grown year-round indoors in one of the busiest cities in the world.
For the Guggenheim exhibition, 80 Acres Farms, Infinite Acres, and its Priva partners have collaborated on the 700-square-foot grow center, which is expected to grow 50,000 tomatoes in six months. Additional tomatoes will be donated to City Harvest, a New York City food rescue organization that recovers excess food and distributes it to people in need.
MORE: Hamilton’s large indoor growing operation is so advanced they want it around the world
Last year saw a massive year of growth for 80 Acres. It opened its automated facility on Enterprise Drive, a facility that grows leafy vegetables, herbs and strawberries, then a downtown Hamilton location on South 2nd St. that grows vine crops, including tomatoes, cucumbers, and peppers.
The company also launched Infinite Acres, an independent joint venture aimed at providing large-scale indoor farming facilities worldwide. The venture also includes UK-based Ocado Group, one of the world’s largest dedicated online grocery retailers, and Netherlands-based Priva Holding BV, a leading provider of technology solutions, services, and automation systems to horticultural and other industries.
That partnership is now building large-scale, fully automated indoor farms in the United States, Asia and Europe.
It also inked a deal to moved its headquarters from Cincinnati to Hamilton and was granted a tax credit for committing to create 125 new jobs and investing at least $26.9 million.
MORE: Innovative Hamilton indoor growing company part of a worldwide deal to supply food
Container Farms Bring Fresh Vegetables To Remote Canadian Community
Over 1,000 kilometres northeast of Yellowknife sit two steel shipping containers that are changing how we understand and respond to food production challenges in Canada’s North, and in other harsh and isolated locations
Over 1,000 kilometers northeast of Yellowknife sit two steel shipping containers that are changing how we understand and respond to food production challenges in Canada’s North, and in other harsh and isolated locations.
These containers have been retrofitted into a research station in Gjoa Haven, Nunavut, where the local community is working with government researchers and a non-profit organization to understand what is needed to create local food sources, clean energy generation, resilient building materials, scalability and adaptability to local needs, and even job opportunities and training.
The local community of Gjoa Haven has named the initiative Naurvik, which means “growing place.” It is a first-of-its-kind venture in Canada’s North, being built and adapted on-site.
Listening closely to Gjoa Haven Elders and community members, the Arctic Research Foundation, Agriculture and Agri-Food Canada, the National Research Council of Canada, and the Canadian Space Agency are actively collaborating on the design and testing of this green energy-powered controlled environment production unit for growing plants in Canada’s North. The community is deciding what plants they want to grow. It’s then up to the research partners to figure out how to adapt the research to their needs, and to train community partners to operate and maintain the system in the harsh and remote location.
“When I first heard of [the project] I thought it would never work up here. No. Not in this 40 below zero. Now I know anything is possible if you have the right idea... I had a taste of the vegetation. It was fresh”, said Peter Akkikungnaq, Gjoa Haven Elder.
By actively working with the local community, and tailoring solutions to their needs, Naurvik is creating a roadmap of how to deliver effective programs, infrastructure, and research in Canada’s North. By integrating resilience and adaptability into the design, the goal is that the model will be able to respond to needs in other harsh and isolated locations, not only in Canada’s North but also on space missions.
“The Canadian Space Agency is looking at innovative solutions to food production challenges that are common to astronauts on deep-space missions and people on Earth living in remote or extreme environments, such as the northern community of Gjoa Haven. While working towards to help with the development of advanced, robust designs for a terrestrial food production system, we are hoping to find strategies that could help astronauts grow food in space”, said Christian Lange, Head of Exploration Strategic Planning, Canadian Space Agency.
While the project is in its early stages, it’s hoped that by 2025 a community-led, renewable energy-powered plant food production system will be fully operational in Gjoa Haven. It will serve as a scalable blueprint for collaborative partnerships and co-designed projects in the Arctic and will be a focal point for innovative research and educational opportunities.
“This is an effective, novel approach to community-driven collaboration with science institutions in Canada’s North, and that’s the reason why it has been so successful. It will generate research for the benefit of all Canadians while also producing tangible benefits for Gjoa Haven and, eventually, other communities throughout the Arctic”, Adrian Schimnowski, CEO, Arctic Research Foundation, comments.
For more information:
Arctic Research Foundation
www.arcticfocus.org
Publication date: Mon 10 Feb 2020
US: Florida - Making Microgreens A Household Word
In The Box, which is a completely retrofitted shipping container, Rodriguez sustainably grows an assorted variety of herbs and microgreens, using a minimal amount of water, energy, and soil
January 30, 2020
These broccoli microgreens are 40 to 50 times higher in nutritional value than the conventional form of broccoli. LOIS KINDLE PHOTOS
Farmer Seeks To Make Microgreens
A Household Word
By LOIS KINDLE
Eco-farmer Dario Rodriguez shows the container he uses to sell a variety of microgreens he sustainably grows at The Box Eco-Farm in Ruskin.
Dario Rodriguez wants the whole world to know about the nutritive value of microgreens, but for now, he’ll settle for South Shore and surrounding areas. LOIS KINDLE PHOTOS
The owner of Sustainable Eco-System LLC began his quest to make organic microgreens more mainstream by establishing The Box Eco-Urban Farm and setting it up at the Circle Pond Tiny Home Community in Ruskin last December.
In The Box, which is a completely retrofitted shipping container, Rodriguez sustainably grows an assorted variety of herbs and microgreens, using a minimal amount of water, energy, and soil.
“(The Box) allows for the maximum production of highly nutritional food in the smallest amount of space,” he said. “That’s what makes us eco-farmers.”
As part of his sustainability mission, Rodriguez sells only locally to individuals, restaurants, nutritionists, and chefs. His service area is South Shore, Brandon and some parts of south Tampa.
“To avoid the use of fossil fuels, I would rather place another box in Wesley Chapel, for example, rather than make deliveries there,” said Rodriguez, 49. “We do not ship what we grow.”
Microgreens are green, tiny vegetables with high concentrations of flavor and nutritional value. For example, broccoli microgreens are 40 to 50 times higher in nutritional value than the conventional form of broccoli, Rodriguez said.
Rodriguez’s wife, Iliana, helps him sell microgreens at the Firehouse Cultural Center in Ruskin.
Currently, he is growing broccoli, basil, red cabbage, peas, cilantro, arugula, parsley, kale, radish, sunflower, wheatgrass, and fennel Greek and mustard kohlrabi – all as microgreens. About 48 veggies can be grown as microgreens, Rodriguez said.
“When you buy microgreens from us, I like to tell you about their nutrients and health benefits, which have been acknowledged by the FDA,” he said.
The farmer also likes to tell you about their uses.
“Microgreens can be used in salads, sandwiches and as a topping for soups, pasta, eggs, and rice,” he said. “You don’t cook them; they’re tender without heat.”
Although Rodriguez and The Box are new to the area, he already has many satisfied customers.
“I bought four boxes last week: salad mix, broccoli, arugula, and radish,” said Dee Hood of Ruskin. “I use them on salads, and they’re so good, I just cut and eat them on their own.
“My teenage granddaughter and her boyfriend had some for lunch and loved them,” Hood continued. “I knew they were good for you, but I had no idea they would taste so good.”
Wheat grass, foreground is one of many microgreens Rodriguez currently grows in The Box.
Rodriguez uses high-density seeds in an organic growing medium like jute. In The Box, he’s able to control all of the production parameters: temperature, airflow and the humidity content of the air. The urban farm has a capacity of 720 10-inch by 20-inch trays of microgreens.
Rodriguez and his family moved to Ruskin from Argentina in 2016, when one of his three daughters began studying international business at the University of Tampa.
“We came as a two-year adventure,” said Rodriguez, who earned a master’s degree in global sustainability in 2018 from the University of South Florida. “But we’ve been here almost four years now, so we’ve decided to stay.”
He has invested $124,000 thus far between the Ruskin location and another at Fat Beet Farm in Oldsmar, where he grows mushrooms.
This is the completely retrofitted shipping container Rodriguez located at the Circle Pond Tiny Home Community in Ruskin to grow his microgreens. The Box allows him to produce the maximum amount of highly nutritional food in the smallest amount of space.
Rodriguez sells his microgreens for $3 per box, which is well below what you’d pay at a commercial establishment, and because they’re grown in an organic medium you can harvest as needed and they last longer.
Every Friday, you can find him set up at the Firehouse Cultural Center from 11 a.m. to 2 p.m. Microgreens can be preordered, paid for and picked up there.
To do so, call 813-416-5444, email sustainableecosystems@gmail.com or visit www.sustainablemicrogreens.net.
Facebook Twitter Share
Partnership Brings Container Farms To Students Across The U.S.
Freight Farms and Sodexo have partnered to bring hydroponic vertical farming technology to schools and universities across the U.S. The collaboration will usher in the implementation of Freight Farms’ Greenery container farms to campuses across the U.S., enabling the onsite growth of fresh, traceable produce year-round
Freight Farms and Sodexo have partnered to bring hydroponic vertical farming technology to schools and universities across the U.S. The collaboration will usher in the implementation of Freight Farms’ Greenery container farms to campuses across the U.S., enabling the onsite growth of fresh, traceable produce year-round.
“Students, institutions, and corporate businesses want healthy, safe, and delicious food, and they want it sourced as sustainably as possible. Sodexo is proud to use and support the latest agricultural technology to create meaningful food system change," said Kenny Lipsman, Director of Produce Category for Sodexo. “Our partnership with Freight Farms allows us to grow nutritious, superior-quality food on-site for our clients, just steps from the kitchens and serveries.
As part of Sodexo’s Better Tomorrow Commitments, developed in accordance with the United Nations’ Sustainable Development Goals, this technology allows for traceability, reductions in food waste, and year-round crop consistency.”
Co-founder and CEO of Freight Farms Brad McNamara, continued, “Sodexo’s commitment to offer onsite food production to its customers helps accelerate food system decentralization — leading the charge for better sourcing practices at an institutional level. Sodexo’s adoption of Freight Farms on-site programming will demonstrate to their customers and client communities the positive impact hyper-local food production can have on priorities from nutrition and food safety to emissions reduction.”
For more information:
Freight Farms
www.freightfarms.com
Sodexo
www.sodexo.com
Publication date: Wed 29 Jan 2020
The Shipping Container Farm That's The Way of The Future
Recycled shipping containers have been used for many things in their second life, from swimming pools and restaurants to classrooms and emergency hospitals. Now, with a global population hurtling towards almost 10 billion people by 2050, they may also be the farms of the future
CALLAN BOYS
Jan 26, 2020
Sprout Stack CEO Hugh McGilligan inside a shipping container farm. Photo: James Brickwood
Recycled shipping containers have been used for many things in their second life, from swimming pools and restaurants to classrooms and emergency hospitals. Now, with a global population hurtling towards almost 10 billion people by 2050, they may also be the farms of the future.
Founded by Francisco Caffarena and Michael Harder in 2016, Sprout Stack is Australia's only commercial vertical farm. The Brookvale-based start-up utilizes shipping containers to grow greens for independent grocers using methods more productive than traditional farming, says chief executive Hugh McGilligan.
"Vertical farming is also called controlled environment agriculture," he says. "Lighting in the containers is designed to optimize plant growth in vertical stacks, and we have sensors constantly measuring temperature, humidity and carbon dioxide levels which can be adjusted as needed. Because there's no birds, pests or fungus, we don't need to use herbicides or pesticides either."
Salad greens under light optimised to encourage plant growth. Photo: James Brickwood
Instead of soil, Sprout Stack uses the husk byproduct of commercial coconut production to hydroponically grow salad greens such as lettuce, kale, mizuna, and pea tendrils. One shipping container can produce 2500 head of lettuce a week, which is a rate of about 30 percent faster than traditional agriculture.
"Carbon footprint wise, we use 95 percent less water than traditional farming, too," says McGilligan. "By only selling to local businesses, our food miles are also reduced. We're not carbon neutral yet, but we will be at scale."
Sprout Stack supplies Harris Farm Markets and independent grocers including Manly Food Co-Op and Harbord Growers. With an aim to double output by the end of summer, the company moved to a larger warehouse in October and increased its container count from three to five.
Sprout Stack's shipping container farms can produce 2500 head of lettuce a week. Photo: James Brickwood
McGilligan says Sprout Stack is now on track to ship its first container farm to Melbourne in 2021.
"We've spent the past 18 months honing our production techniques so we can clone the business and shift it to other cities around Australia," he says. "We will always be about local food for local communities."
To assist in its expansion, Sprout Stack has partnered with the University of New South Wales. Both are members of the Future Food Systems Co-operative Research Centre, a partially government-funded body that aims to optimize the productivity of food systems.
"The university is helping us look at ways we can introduce robotics and boost production by four to five times over the next year or so," says McGilligan.
Professor Sami Kara of the UNSW school of mechanical and manufacturing engineering says he was excited to work with Sprout Stack after seeing similar farms in Singapore and recognizing their potential to feed a growing population.
"By 2050, 70 percent of the world's population will be living in an urban area," he says. "We will also need to produce 70 percent more food to feed that population.
Coconut husk used to grow Sprout Stack's lettuce. Photo: James Brickwood
"We can keep producing food in large quantities, far away from the majority of people, and shipping it with a massive transportation footprint. Or, we can grow food in the cities where the yield is high, the environmental footprint is low, and customers receive food that's fresher, more nutritious and delicious."
Kara stresses that vertical farming is not trying to compete with traditional farming, but offers an additional solution to the population problem. "In order to provide the world's food requirements by 2050, we're going to need many different types of production models," he says.
McGilligan supports this view and recognizes the importance of Australia's agricultural economy.
"We're not short on arable land in this country, so I understand this kind of venture may look a little bit threatening and odd compared to traditional farming," he says. "However, I firmly believe many more people will be eating vertically grown food in the future."
The Booming Indoor Gardening Movement
LG’s indoor farm appliance is an example of how a built-in, columned indoor garden using lighting, temperature and water control can change the way consumers obtain their kitchen ingredients
Sarah Buckley
22/01/2020
The booming indoor gardening movement, prominently explored at CES 2020 earlier this year, is allowing consumers to grow their greens indoors, all year-round.
LG’s indoor farm appliance is an example of how a built-in, columned indoor garden using lighting, temperature and water control can change the way consumers obtain their kitchen ingredients.
LG’s offering of all-in-one seed packages and a growth monitoring app makes the one-stop-shop capable of feeding a family of four with home-grown produce.
The appliance replicates optimal outdoor conditions by matching the temperature inside the insulated cabinet to the time of day.
The LED lights, air circulation, and wick-based water management system allows the produce to quickly grow, alongside the automated gardening solution’s non-circulating water supply technology.
The core technology, which evenly distributes the precise water required for the plant’s to healthily flourish, prevents algae and odors for a hygienic, green enclosure.
Much like LG, n.thing, a South Korean agriculture start-up has developed ‘planty cube’ which is an automated vertical farming system, to a more elaborate effect – allowing consumers to maintain crops from anywhere, at any time.
Cubes, blocks, cells – the hydroponic farm, presented in a shipping container, has each square evenly stacked with rows of shelves of plants.
A computerized system controls the environment by monitoring the plants’ health, adjusting the environment accordingly.
These alternatives to glasshouse production are presenting solutions to production, health, convenience, pollution, water-use, but most notably, are finally brought to the consumer’s arena.
IKEA Wants All Restaurants To Be Self-Sufficient in Herbs and Lettuce
Many IKEA customers like to grow their own fruit and vegetables. "What if we could do the same?" they wondered at the Swedish retail chain
Many IKEA customers like to grow their own fruit and vegetables. "What if we could do the same?" they wondered at the Swedish retail chain.
The company is testing smallscale urban farms, exploring whether they can become self-sufficient in some of the fresh produce used in IKEA restaurants.
Container farms
In FY18, they grew their own herbs and lettuces in small-scale urban farms in Sweden and Switzerland. In FY19, they extended the tests, installing medium-scale container farms with romaine and frisée lettuces outside the IKEA Malmö and IKEA Helsingborg stores in Sweden. The farms use hydroponic technology and operate in a circular way, with food waste from the store used to create a nutrient solution to feed the lettuces.
Promising results
Early results show the container farms produced enough to supply the in-store restaurants with all the lettuce they need. Since they’re grown onsite, the lettuce can be used almost straight away, meaning they’re fresher, tastier and contain more nutrients. They also grow faster, with less water and waste than conventional farming and without the use of pesticides and herbicides. A life-cycle assessment shows that when the urban farm is powered by renewable energy, the carbon footprint of the lettuce is 30% smaller than the ones we would usually use. IKEA is planning to extend urban farming so that they become self-sufficient in herbs and lettuce across all store restaurants.
Cost-cutting
The main challenge is that the produce IKEA uses is currently more expensive than a conventionally farmed alternative. They’ve already made progress on reducing these costs, and they’re continuing to find ways to improve efficiency. Ingka Investments has also invested in two urban farming businesses in the USA and Estonia to support development of the industry.
For more information, check out the Ingka Group Sustainability Report.
Publication date: Fri 31 Jan 2020