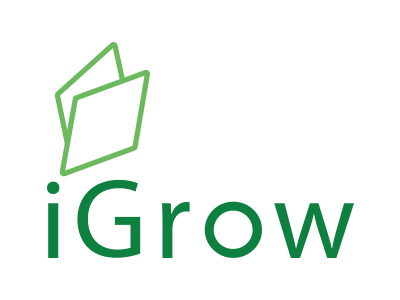
Welcome to iGrow News, Your Source for the World of Indoor Vertical Farming
USA: VIDEO: Veteran Finds Peace, Purpose In Unique Kind of Farming
John Miller's routine may seem a bit "scaled-down" compared to his former life as a combat soldier. Miller spends much of his time in a 40-foot-long shipping container converted into a hydroponic farm field. Hydroponics involves growing plants without soil.
KENTUCKY
August 2, 2021
LOUISVILLE, Ky. — As John Miller prepared to leave the Air Force, the combat veteran admits he had no idea what he was going to do next.
What You Need To Know
John Miller served 14 years in the Air Force
The Louisville resident is the owner of Falls City Farms
Miller has found peace and purpose in hydroponic farming
In the future, Miller hopes to expand and employ fellow veterans
John Miller's routine may seem a bit "scaled-down" compared to his former life as a combat soldier. Miller spends much of his time in a 40-foot-long shipping container converted into a hydroponic farm field. Hydroponics involves growing plants without soil.
A close-up of Miller's baby kale. (Spectrum News 1/Jonathon Gregg)
“In essence, we sell a lot of things what we would consider baby," Miller explained. Little white turnips is just one crop of many growing inside Falls City Farms. “Right now I’m just pulling off the plug to turnips and then clean up any of the leaves."
The Iraq War combat veteran grows, prunes, packages, and sells a variety of greens to Louisville restaurants, online and at local markets.
“Here is our wasabi arugula, this is one of our fresh herbs, our dill, this would be our romaine trio," Miller said while touring his indoor farm.
Scaled-down? Maybe, but the hydroponic farm has helped Miller overcome what can be a sizable challenge for soldiers adapting to life after service.
“I got into this post-military, trying to find my next thing because I didn’t know what I was going to do when I got out," Miller said.
Miller served 14 years in the Air Force. His wife Amy is still active with 17 years to her credit. In his pursuit to figure out the next chapter of his life, Miller learned about hydroponic farming from a marine veteran in San Diego.
Falls City Farm grows a lot of produce in just 320 square feet. (Spectrum News 1/Jonathon Gregg)
His operation encompasses 320 square feet and boasts 6,600 individual plant spaces. Crops grow thanks to a sophisticated watering system and good-old-fashioned artificial sunlight.
“Because we are in a shipping container, the plants and the crops don’t get any of the big yellow sun outside so we have to create that inside," he said. "So we do LED lighting because it is better from an energy standpoint as well as heat."
Miller has lots of time and enough room to think about his life as a soldier and his new career as a farmer.
“If I am being frank with you, I miss being surrounded by other airmen and folks I used to lead," he said. "But it is calming to be in here with the plants and at the end of the day, that’s one of the reasons I chose this path.”
He was after peace and a purpose, and now his purpose includes bringing other veterans aboard.
“A lot of veterans, as we know, suffer from trying to find that next mission. Hopefully, one day soon be able to bring fellow veterans in here to teach them the art of farming through hydroponics to help them find peace and purpose as well," Miller said.
At first, Falls City Farms may appear to be a small operation, it’s only until you spend time on the inside do you see all the big ideas growing.
“I fell in love with the sense of a day’s accomplishment of work, a sense of comfort of being inside a greenhouse," Miller said.
VIDEO: Freight Farm To Teach Youth About Sustainable Agriculture
by Nicole Weaving
July 24th, 2021
To View The Video, Please Click Here
Freight Farm to teach youth about sustainable agriculture (Photo Credit: NTV News)
LINCOLN, Neb. — Beyond School Bells is partnering with the Bay in Lincoln for a new after-school program that will teach students about sustainable ag technology.
"We really see Freight Farm as kind of that key, climate-change impervious tool that young people need to know about as we face an uncertain future," said Jeff Cole, Network Lead for Beyond School Bells.
An old shipping container in the parking lot of the Bay has been transformed in a self-contained hydroponic farm.
Using red and blue LED lights, this Freight Farm, known as the Greenery, creates a climate-controlled environment, where the plants grow vertically without a need for soil.
"We enrich the water with nutrients that would normally be in the soil," said Colton Harper, Organizing Manager for the Greenery. "And then in these grow walls, we've got spickets that come right through these foam and it's directly onto the roots of the plants."
According to Harper, there are currently about 6,000 plants growing in the Freight Farm, but at full capacity, it can hold 13,000 plants between the seeding area and that walls. That would produce the equivalent of a 2.5-acre farm year-round.
"Even in the winter, if there are shortages anywhere, we can turn on a dime, 7-week grow cycle and be able to provide those crops for local markets," said Harper.
The Greenery arrived in Lincoln in April, and Harper has led to two teams to get it up and running. They are currently preparing for their first harvest with items like basil, lettuce and radishes.
"We're at about Week 7, and in 2-3 weeks, we'll have our produce at a farmer's market," said Harper.
After a few more grow cycles, the program will open to local students to teach them all aspects of sustainable farming.
"From the electrical side, the growing, the programming, computer science to the irrigation, the HVAC system, there's so many elements," said Harper. "And we're particularly well-placed with the Bay and their digital design area of focus, the students will also be able to design the packaging, design the labeling, so it's really a full-circle, interdisciplinary opportunity for the students to get involved."
The Greenery plans to hold a Harvest Party to celebrates the farm's success in the coming weeks.
Projected Water Scarcity Prompts Need For Farming Ingenuity
Emerging technologies are quickly trying to find ways to get the most bang for each drop of water. Efficiencies have been identified, including vertical hydroponic farming, which drastically reduces the amount of water needed to grow crops
Posted by chrismichlewicz
July 31, 2021
The common refrain that freshwater is the next gold is ringing true as drastic changes in our climate are resulting in greater competition and a need for more efficient water uses, especially in the agricultural industry.
National Geographic points out that while the amount of fresh water on the planet has remained fairly constant over time — continually recycling through the atmosphere and back into our oceans, lakes, and rivers — the global population has exploded in the last century. This means that competition for a clean supply of water for drinking, cooking, bathing, and sustaining life intensifies every year. There is only so much water to go around.
Essentially, when taking saltwater into account, only about .007 percent of the Earth’s water supply is usable for the planet’s 6.8 billion (and counting) people, National Geographic says.
The vast majority of freshwater — about 70 percent by most estimates — is used for agriculture, and when you consider that feeding a planet of 9 billion people in 2050 will require an estimated 50 percent increase in agricultural production and a corresponding 15 percent increase in water withdrawals, the future becomes a lot clearer, according to World Bank.
Without proper governance, there is likely to be increased competition for water between sectors and an escalation of water crises of various kinds, triggering emergencies in a range of water-dependent sectors, according to a U.N. report.
Emerging technologies are quickly trying to find ways to get the most bang for each drop of water. Efficiencies have been identified, including vertical hydroponic farming, which drastically reduces the amount of water needed to grow crops. FarmBox Foods, a Colorado company that builds automated hydroponic farms inside repurposed shipping containers, has set its sights on creating a tangible shift in the approach to farming.
FarmBox Foods’ innovative, closed-watering system only uses 3-5 gallons of water per day and, almost as important, it does not contribute to groundwater contamination the way that traditional farming does. Furthermore, one farm is able to produce the same yield as 2 – 2.5 acres of farmland on an annual basis.
“Our container farms are built in such a way that it takes only a fraction of the amount of water to grow that same amount of produce,” said Rusty Walker, CEO of FarmBox Foods.
Climate change is projected to increase the number of water-stressed regions and exacerbate shortages in already water-stressed regions. It’s those regions that will realize the most benefit from vertical hydroponic farming and more efficient water usage in general.
An integrated view on water, the biosphere, and environmental flows is necessary to devise sustainable agricultural and economic systems that will allow us to decelerate climate change, protect us from extremes and adapt to the unavoidable at the same time, the U.N. says.
The automated hydroponic farms have a secondary benefit, as they can grow pine trees that contribute to the overall health of the environment by helping reduce the amount of carbon dioxide in the atmosphere. One container farm from FarmBox Foods can grow 35,000 tree saplings per year.
For more information, go to www.UNwater.org or www.FarmBoxFoods.com.
Posted by chrismichlewicz on July 31, 2021 in Arapahoe County Business, Douglas County, Douglas County Business, Featured, Greenwood Village Business
Tagged #farmboxfoods, agriculture, cleanwater, Colorado, containerfarm, containerfarming, environment, farmboxfoods, freshwater, indoorag, indoorfarming, UN, Water, waterscarcity, watershortage, watersupply, waterusage
USA - VIDEO: Could Hydroponic Farms In Shipping Containers Promote Water Conservation?
Dozens of red leaf lettuce heads grew without ever seeing the actual light of day with the help of Freight Farms "ag tech," a repurposed shipping container, and students from La Sierra University
JULY 21, 2021
RIVERSIDE, Calif. — Dozens of red leaf lettuce heads grew without ever seeing the actual light of day with the help of Freight Farms "ag tech," a repurposed shipping container and students from La Sierra University. One of the students was Max Proebstle, who never thought he would find a personal interest in hydroponic farming.
"As soon as you transplant them into the growth panels after about a week, they're already like a full head of lettuce; it's pretty amazing to see," the graduate student said.
What You Need To Know
More than 20 La Sierra students are working together to study hydroponic farming inside a repurposed shipping container
The Freight to Table program used Freight Farms "ag-tech" to grow leafy greens with the help of high-intensity lights, circulating water, and plant nutrients
The system uses at least 90% less water than traditional farming, according to La Sierra University project director Marvin Payne
The program will utilize harvested crops in the university dining halls and provide locally sourced produce for the surrounding area
Proebstle and about 20 other students have been volunteering their time inside the repurposed shipping container turned indoor hydroponic farm on campus. This method of growing crops replaces the need for soil with plant nutrients, artificial light, and recirculating water. After working with the new tech system, Proebstle believes it could be a game-changer for the future of farming.
"If you have a connection to a water system and electricity, you can basically grow produce sustainably and organically, anywhere and anytime," he said.
The Enactus team on campus recently harvested more than 500 heads of red leaf lettuce, with more on the way. The program is helping students get a hands-on approach in STEM and agriculture while also introducing them to a way to create their urban farms in the future.
Project Director Marvin Payne, who oversees the Freight to Table program on campus, explained that this model allows hydroponic farms to be placed just about anywhere for year-round harvesting.
"The entire footprint of this container is basically 320 square feet, and so with this, you can turn out thousands of plants in a fairly short period of time," he said.
The tech allows growers to monitor nutrient levels, production and light schedules remotely. Since it's inside a container, the amount of artificial daylight for the crops can be increased to about 16 hours each day. Doing so means more growth but also a higher electricity output.
As drought conditions worsen, at least 94% of California is considered to be in a severe drought. There will be more pressure on the farming industry for water conservation, and this model — according to Payne — uses at least 90% less water.
"You are using electricity, but we're getting creative in producing electricity these days, and it uses only a very small fraction of the water that any traditional farming is going to use," he said.
After plucking the leafy greens from growth panels inside the controlled agriculture environment, Proebstle and the team have brought their harvest from a hydroponic farm to the table with a new passion for farming.
"In my personal life, I can totally see this being a part of my life, something that I'll be interested in and involved in for the rest of my life," Proebstle said.
Until then, the Enactus team at La Sierra University will continue exploring how this growing method could bring sustainability and locally sourced produce where it's needed most.
Central Minnesota Research Project Growing Kale Indoors
The project is a partnership with Todd-Wadena Electric Cooperative, Central Lakes College, Lakewood Health System, Great River Energy and the Electrical Power Research Institute
The project is a partnership with Todd-Wadena Electric Cooperative, Central Lakes College, Lakewood Health System, Great River Energy, and the Electrical Power Research Institute.
Written By: Rebecca Mitchell
July 21, 2021
Central Lakes College research analyst Noah Boetler shows a panel of kale plants in the Sota Grown pod during a virtual tour on July 13, 2021. Rebecca Mitchell/Pioneer Journal
STAPLES, Minn. — A community research project in Staples involving indoor gardens is set to continue growing.
The hydroponics project started in 2020 with Great River Energy, Todd-Wadena Electric Cooperative, and the Electrical Power Research Institute hoping to learn new technology and increase access to fresh produce. And even with kale as the chosen plant, local organizations rooted for the success of the hydroponics pod. The pod, planted at the Central Lakes College Staples campus, is a shipping container with room for 5,820 kale plants.
“I didn’t know how things were going to grow in here, it’s kind of a weird concept with there being no sunlight and things like that, so just seeing it go from a little seed to your big plant and harvesting it, I think that has been the coolest aspect,” CLC research analyst Noah Boelter shared with Minnesota educators in a virtual tour on July 13.
The partnership is called "'Sota Grown" and has helped develop a fully enclosed hydroponic container for growing fresh plants all year long — to supplement existing agriculture practices in communities across the state.
The pod, equivalent to one acre of crops, is a supplement to traditional farming, not a replacement, as TWEC member service manager Allison Uselman said. Although kale is the focus of the two-year project, the team has experimented with growing basil, swiss chard, lemon balm, and chives. Romaine lettuce, butterhead lettuce, and salad mixes are next on the list — and after a year of only kale, Boelter is excited for the new opportunities.
Each kale seed, planted by hand, starts in the nursery before being transplanted to vertical panels. The kale takes 12 weeks to reach maturity. The team of four staff members and interns plant and transplant on Wednesdays and harvest on Mondays.
“Kale is pretty forgiving, which is very fortunate for us,” Boelter said after sharing about a frozen pump during the winter. The kale wilted and bounced back in a matter of days. The team is also learning about flooding and nutrient dosing in the pod.
With the expected growth of indoor agriculture, Uselman said electrical companies will need to prepare for the change. For example, the pod uses the most energy when most other customers could have off-peak rates. The light and water systems run from 4 p.m. to 8 a.m. daily. The kale is watered for five minutes every 45 minutes. The electricity is about $600 a month.
“It’s education with students, it’s giving back and feeding our communities, and Todd-Wadena has the opportunity then to research all the electrical side of things and really understand this industry before it grows to a larger state,” Uselman said.
The pod’s water usage depends on the humidity levels outside, with the most water used in the winter — about 10.5 gallons every day—and about five gallons a day in the summer. The two water tanks deliver water above the panels and water behind the plants. There are also several different nutrients added, such as one to adjust pH levels.
“In the summertime, the pod does not use a whole lot of water because the HVAC unit has a dehumidifier built into it and that’s recirculating around a gallon of water an hour that gets dumped back into the pod, so it’s really efficient in the summer,” Boelter explained. “But when it’s winter, the air is so dry that’s when we use the most water.”
The indoor pod means the ability to regulate the temperature, which is a cool 65-68 degrees and having no pesticides or herbicides used on the plants since most bugs remain outside. There are some drain flies due to the algae.
The red LED lights in the Sota Grown pod at Central Lakes College are the only source of heat. The lights and water run from 4 p.m. to 8 a.m. daily. Rebecca Mitchell/Pioneer Journal, July 2021
As for sunlight, the LED lights are the only heat source in the pod, as Boelter said, though it is also insulated. The red and blue lights support stem growth and leaf density.
The process yields about 20 pounds of kale a week — and on a record week 43 pounds — or over 1,000 pounds as of July 5. All of the kale is donated to Lakewood Health System, who shares the kale through the Food Farmacy and Hilltop Regional Kitchen. The Kitchen uses the kale in specific meals for those who have tested positive for COVID-19 and people being discharged from the hospital. People can also receive free kale at the summer farmer’s market on Thursdays.
As Lakewood’s Community Health Coordinator, Amy Wiese works with about 70-100 bags of kale a week to find where it can best be served. She said the kale lasts about two weeks in the fridge.
People also receive kale recipes for new ways to enjoy the vegetable. Wiese enjoys massaging the kale to break down the bitterness and then eating it in a salad. Other favorites are kale chips and soups.
“We just see the benefits of this project and recognize the positive impact that healthy food can have on individuals and in the community,” Wiese said. The organizations also hope to address local food deserts. “It’s really amazing that we are able to provide fresh produce all year with this pod” even with snow on the ground for six months of the year.
The seeds grown and sown in the community have finished their process with new seeds set to germinate, grow to maturity, and be harvested and packaged in four to eight hours for their short drive up the road.
Photo: 1 - The kale seeds are planted in peat moss plugs and stored in the nursey for three weeks before being transplanted to the indoor panels. The planting process takes about an hour. Submitted photo
Photo: 2 - The shipping container contains an acre of kale growing hydroponically with LED lights. Photo courtesy Todd-Wadena Electric Coop
Photo: 3 - Each section has 22 panels with space for 5,820 kale plants or the resemblance of one acre of crops. Rebecca Mitchell/Pioneer Journal, July 2021
Earth911 Podcast: Freight Farms’ Jake Felser On Hydroponic Agriculture & Container Farming
Earth911 talks with Jake Felser, chief technology officer at Freight Farms, about the company’s “complete farming system inside a box.”
By Earth911
JULY 14, 2021
Earth911 talks with Jake Felser, chief technology officer at Freight Farms, about the company’s “complete farming system inside a box.” It’s a very big box that includes climate controls and monitoring systems to make farming easy for anyone to do. Freight Farms builds and delivers shipping containers converted into highly efficient hydroponic farms that use LED lighting to grow and deliver fresh produce year-round.
Jake discusses the cost of getting started, how many people are needed to run the farm, and how the built-in automation helps farmers plan a profitable business. Grocers, restaurants, communities, and small farms are using Freight Farms installations at 350 farms in 49 states and 32 countries. The company says most of its customers are new to agriculture and operate right in the urban and rural communities they serve.
Jake Felser, CTO at Freight Farms, visits Sustainability in Your Ear to talk about automated hydroponic gardening in shipping containers.
Growing and distributing vegetables locally is one of the most effective ways to lower our society’s carbon footprint. While agriculture contributes about 10% of the U.S. greenhouse gas emissions each year, the majority of that is from raising animals. By increasing our consumption of locally grown vegetables, we can improve local health and reduce overall emissions from transportation. It’s not easy to grow food in most cities using traditional methods. The introduction of container farms and vertical farming inside buildings can reshape food deserts and create economic opportunities.
To learn more, visit FreightFarms.com.
Subscribe to Sustainability in Your Ear on iTunes and Apple Podcasts.
Follow Sustainability in Your Ear on Spreaker, iHeartRadio, or YouTube
Tags: container farming, Freight Farms, hydroponics, reinventing agriculture
USA - ALABAMA: Auburn College of Agriculture Using High-Tech Shipping Containers To Grow Produce For Campus Dining
Unique ‘Vertical’ Farms part of Planned 16-Acre Transformation Garden On Campus
High-tech Horticulture
Unique ‘Vertical’ Farms part of Planned 16-Acre Transformation Garden On Campus
June 10, 2021
Josh Woods | College of Agriculture
Recycled shipping containers have gained popularity in recent years, being converted into everything from houses to small stores—but the Auburn University College of Agriculture, in partnership with Campus Dining, is using them as self-contained “vertical” farms to grow produce to serve to students.
In April, the college acquired two Freight Farms shipping containers that have been converted into technologically advanced hydroponic growing stations in which plants grow vertically indoors without soil, getting their nutrition from water and light energy from powerful LEDs.
Now, the farms are producing the first crop of lettuce.
“This is state of the art,” said Desmond Layne, head of the Department of Horticulture. “We're talking growing from seed to fork in four to six weeks, depending on whether it is lettuce, arugula or another vegetable crop that can grow in there. And we can produce 15 times as much per year as we could outside in the same exact spot.”
Associate Professor of Horticulture Daniel Wells taught a vertical farming course this spring and leads operations of the vertical farms.
Wells said the containers are outfitted with a complete climate control system, which includes air conditioning and humidity control. Because they are highly insulated, the system ensures the same climate 365 days a year.
The converted containers also have an elaborate lighting system, giving all the light the plants need from two color LEDs.
“We can do any number of colors of lights,” he said. “But it turns out for photosynthesis, plants use mostly red and blue light. What’s neat about that is you can cut out a lot of the other color spectrum, creating far less heat energy. That's very efficient. It means more of the energy used is turned into light than heat.”
The containers also allow for controlled carbon dioxide levels, which accelerates plant growth.
“Ambient CO2, what you and I are exposed to every day, is about 400 ppm [parts per million],” he said. “And that’s fine, plants can grow there. But if we boost the CO2 to 1,000 ppm, they’ll grow faster. And because we’re containing the CO2, the plants can really use it. And it’s not dangerous for humans at all.”
Wells and Director of Dining and Concessions Glenn Loughridge first initiated a partnership between the College of Agriculture and Campus Dining five years ago through the Auburn Aquaponics Project, which uses hydroponics and aquaculture technologies to provide a system in which nutrient-laden wastewater from fish production is used as a food source for plant growth. Today, fish from this effort are served in dining facilities on the Auburn campus.
The new vertical farms build on that effort.
“We're in the process of finishing a $26 million dining hall in the center of campus,” Loughridge said. “It has always been foremost in my mind that we would have the opportunity to feature produce grown here on campus in that dining hall. In our biggest location, our biggest asset, we want to bring our A-game.
“This is hyper-local, on-campus sourcing,” he added. “Can you imagine being a potential student coming to tour, seeing where these products are grown, and then going to eat there? It’s incredible. We truly believe this elevates our dining experience.”
The converted shipping containers were manufactured by Freight Farms, a Boston-based company operating in 45 states and 28 countries.
“There are a few different companies out there doing this,” Layne said. “But Freight Farms is the most sophisticated. They’re the ones who have both the best product on the market and the largest production of these containers. It’s really a best-case scenario.”
Adam Lenhard, a rising senior majoring in biological agricultural technology management, said Wells’ course has been one of the most influential courses he’s taken at Auburn.
“It has been very helpful, not just in preparation for the arrival of the freights, but also in learning all about new hydroponic technologies and growing techniques,” Lenhard said. “Post-graduation, I plan to continue to work with these types of indoor, LED hydroponic systems. My primary goal after college is to normalize urban hydroponic farming, provide large, consistent yields of fresh vegetables and provide food to those in need who do not have as much access to fresh produce.”
Transformation Garden
The vertical farms are located on the College of Agriculture’s planned 16-acre Transformation Garden on the south end of the university’s campus, near the intersection of Lem Morrison Drive and Duncan Drive. The goal of the garden is to encompass every aspect of plant-based agriculture, including everything from fruits and vegetables to ornamentals to grow crops and more.
The Transformation Garden will showcase new technology and the history of agriculture, as it envelops Auburn’s Old Rotation, a single-acre research plot created in 1896. Continuously since that year, the historic landmark has been the site for testing and advancing transformative ideas that are now commonplace—ideas like crop rotation, cover crops, and low- and no-till farming.
(Written by: Kristen Bowman)
HELP DEVELOP THE TRANSFORMATION GARDEN
To help develop the new Transformation Garden, you can give online or contact Phillip Cowart, College of Agriculture director of development, at poc0001@auburn.edu or 334-844-1198.
Auburn University is a nationally ranked land grant institution recognized for its commitment to world-class scholarship, interdisciplinary research with an elite, top-tier Carnegie R1 classification, life-changing outreach with Carnegie’s Community Engagement designation and an undergraduate education experience second to none. Auburn is home to more than 30,000 students, and its faculty and research partners collaborate to develop and deliver meaningful scholarship, science and technology-based advancements that meet pressing regional, national and global needs. Auburn’s commitment to active student engagement, professional success and public/private partnership drives a growing reputation for outreach and extension that delivers broad economic, health and societal impact.
Latest Newsroom Articles
CubicFarms Announces Closing of $25.3 Million Equity Financing
This financing allows us to fully capitalize on our accelerating sale pipeline growth and market-leading R&D program.”
CubicFarm Systems announced today the closing of its previously announced bought deal equity offering of common shares of the company. The net proceeds from the offering of approximately C$23.8 million will be used to support CubicFarms’ continued global growth, research, and development efforts to optimize machine yields, automation, and functionality, expand addressable crop varieties, and for working capital and other general corporate purposes.
Pursuant to the offering, the company issued a total of 18,740,742 common shares at a price of C$1.35 per common share for gross proceeds to the company of C$25,300,001, which includes the exercise, in full, by the underwriters of the over-allotment option granted by the company to purchase an additional 2,444,445 common shares at a price of C$1.35 per common share.
“We are thrilled by the overwhelming support by our global institutional shareholders, like Handelsbanken, and their confidence in our vision,” said Dave Dinesen, Chief Executive Officer, CubicFarms. “The strong demand for this bought deal financing allowed us to upsize and fully allocate the over-allotment option with the closing of $25.3 million. This financing allows us to fully capitalize on our accelerating sale pipeline growth and market-leading R&D program.”
CubicFarms completes previously announced debt reduction
CubicFarms also announced that further to its news release dated May 3, 2021, the company has completed its previously announced issuance to Business Development Bank of Canada of 128,205 common shares of the company at a deemed price of $1.56 per common share.
“We’re pleased to work with our long-term lending partner on reducing the debt associated with our C$2.5 million growth capital loan with more favorable terms for the Company,” said Dave Dinesen, CEO, CubicFarms. “This demonstrates continued confidence in our ongoing development and the growth of the Company.”
CubicFarms approves grant of options
The Company also announced today that its board of directors has approved the grant of 700,000 stock options to certain directors and officers of the company pursuant to the company’s stock option plan. The options have an exercise price of $1.47 per share, vest as to one-third n each of 12, 24, and 36 months from the date of grant, and have a 5-year term. The grant of the options is subject to the approval of the TSX Venture Exchange.
For more information:
CubicFarms
1-888-280-9076
info@cubicfarms.com
www.cubicfarms.com
Publication date: Fri 4 Jun 2021
USA - COLORADO: Sedalia-Based FarmBox Foods Sending Container Farms All Over The World
FarmBox Foods’ short-term goals include partnering with institutions that help provide the biggest possible impact for the most people, including food banks, schools, and hospitals
Posted by Chris Michlewicz
May 28, 2021
With increasingly unpredictable weather patterns impacting crops and a continuing global food crisis affecting millions, a Colorado company is using tech-based indoor farming to make sure no one goes without a reliable, secure source of nutrient-rich food.
FarmBox Foods, based in Sedalia, has spent the last four years developing automated farms in shipping containers to grow organic leafy greens, culinary herbs, tomatoes, and now pine tree seedlings. The company also has a first-of-its-kind gourmet mushroom farm that produces around 400 pounds of mushrooms per week.
The mission-driven company is focused on helping feed those living in food deserts while empowering local communities and providing jobs and educational opportunities. FarmBox Foods’ patented vertical hydroponic watering systems use 90% less water than traditional farms and yield the equivalent of 2 – 2.5 acres of farmland. The repurposed shipping containers that house these systems can be placed virtually anywhere in the world — from island nations to college campuses to the frozen reaches of Alaska — and produce food year-round.
The fully controlled enclosed growing environment is protected from pests and pathogens, which reduces and can eliminate entirely the need for pesticides, allowing people to harvest and eat untainted farm-fresh produce. Setting up containers in or near populated areas also reduces food waste, as the food is able to get to the table more quickly and can better retain its nutritional value.
“The real mission in this whole thing is to be able to feed the world in places that ordinarily wouldn’t be able to grow food,” said Rusty Walker, CEO of FarmBox Foods.
FarmBox Foods’ short-term goals include partnering with institutions that help provide the biggest possible impact for the most people, including food banks, schools, and hospitals.
Learn more at www.farmboxfoods.com.
Posted in Arapahoe County, Douglas County, Douglas County Business, Douglas County Front, Featured, Jefferson County, South Jeffco
Tagged agtech, climatecontrolledfarming, Colorado, coloradobusiness, containerag, containerfarms, eatorganic, farmboxfoods, farmboxfoodscolorado, farming, farmtotable, fooddeserts, foodinequality, foodinsecurity, foodsecurity, growyourownfood, indoorfarming, indoorfarms, mushroomcultivation, mushroomfarm, mushrooms, organic, sedalia, urbanfarming, verticalhydroponicfarm, verticalhydroponics
About the Author: Chris Michlewicz
USA - KENTUCKY: Elliott County High School Receives New Container Farm Through AppHarvest
The curriculum provided by AppHarvest will cover topics such as high-tech growing and an introductory course on local food systems and food resiliency
May. 29, 2021
SANDY HOOK, Ky. (WSAZ) - Some students at Elliott County High School will soon be able to help grow food -- not only for themselves but for the entire region.
The Elliott County High School container farm is the fourth addition to AppHarvest’s program in 2021 and the sixth educational container farm to date.
The container farm program was launched in 2018 and demonstrates AppHarvest’s ongoing commitment to cultivating interest in high-tech farming as it seeks to create America’s AgTech capital from inside Appalachia. Each retrofitted shipping container acts as a hands-on agricultural classroom for students, allowing them to grow and provide fresh leafy greens to their classmates and those in need in their communities.
AppHarvest has opened container farms in Eastern Kentucky at Madison Central High School in Richmond; Breathitt High School in Jackson; Shelby Valley High School in Pikeville; and Rowan County Senior High School and AppHarvest’s flagship farm at Rockcastle County High School in Morehead.
Elliott County High School’s container farm includes space to grow up to 2,760 seedlings and 2,960 mature plants, all at once in a nutrient film technique (NFT) system. NFT is a water-saving system in which plant roots are continuously fed all necessary water and nutrients by a shallow stream, also called “film.” Excess water drains to a holding tank and is then recirculated. This system of high-tech growing sets the Elliott County container apart from AppHarvest’s other educational containers, which have operated hydroponically and vertically.
“One of our goals at AppHarvest is to build an AgTech capital right here in Appalachia,” said Jonathan Webb, AppHarvest Founder, and CEO. “We want to see communities across the region use technology to bring farms to life. And in five years from now, it’ll be leaders from these very programs coming to us with ideas on how we continue to evolve and change agriculture.”
Makayla Rose, Elliott County High School agriculture teacher, will lead the newest container program.
The curriculum provided by AppHarvest will cover topics such as high-tech growing and an introductory course on local food systems and food resiliency.
“This is exciting. Some students who might not like to get in the dirt have a different way of growing vegetables,” said Garret Barker, president of Elliot County’s FFA chapter. “It’s different than my farm at home. It doesn’t depend on outside factors like the rain. It’s all controlled by an app.”
Lead Photo: Elliott County High School receives new container farm through AppHarvest (Kimberly Keagy/ WSAZ)
Brick Street Farms Expands Through Florida and East Coast
“We really wanted to bring food production to the point of consumption, so we’re focused on embedding our farms in urban areas,” says Shannon O’Malley, CEO, and co-founder of Florida-based container farming company, Brick Street Farms
"We Are As Much A
Technology Company
As We Are A Farm Operator”
“We really wanted to bring food production to the point of consumption, so we’re focused on embedding our farms in urban areas,” says Shannon O’Malley, CEO, and co-founder of Florida-based container farming company, Brick Street Farms.
The company was founded by Shannon and her husband Bradley, who combined her expertise in electrical engineering with his background in software development to design their own shipping container farms.
According to Shannon, a major differentiator of Brick Streets Farms is that the company manufactures and operates its own shipping container farms.
Brick Street Farms Hubs
Brick Street Farms has recently secured a significant investment from Lykes Brothers, which is reportedly one of the largest and longest-running private agricultural companies in the United States. During the official announcement last week, the financial investment will be used to aggressively expand Brick Street Farms hubs, which are the combination of container farms with a retail front in densely populated areas.
Click here to Zoom the photo. (Photo courtesy of Brick Street Farms)
According to Shannon, this expansion will begin in west-central Florida then expand to the east coast. From these hubs, Brick Street Farms will also introduce home delivery and will support restaurant partners located within 50-100 miles of the hubs. Already in 272 Publix supermarkets, Brick Street Farms will continue this partnership and plans to expand into additional product categories.
Building a resilient, multi-channel sales strategy
Brick Street Farms was first developed in 2015, and during its early years, the company predominantly sold its products to restaurants and directly to customers. However, the pandemic-induced shutdown in 2020 resulted in the loss of 70% of Brick Street Farms’ clients due to restaurant closures. As Shannon explains, Brick Street Farms was already selling its products in the GreenWise section at Publix supermarkets, which is reportedly the largest employee-owned supermarket chain in the US. This partnership allowed Brick Street Farms to quickly pivot following the mandated closure of restaurants.
“In the same month that Florida went into lockdown, grocery stores saw an incredible jump in demand so we were able to quickly pivot and provide our vegetables to grocery stores within a week. We are currently in 272 Publix stores and are working to expand into west-central Florida,” says Shannon. The state of Florida has since reopened and Brick Street Farms was able to bring back its previous accounts and sign new ones, according to Shannon.
Brick Street Farms also has its own gourmet market located at the farm that is open six days per week. Consumers can shop either on-site or online, with contactless delivery available. Shannon also explains that the company has adopted a unique twist to community-supported agriculture. By subscribing to a farm membership, consumers receive a discount and support the recently approved non-profit, Desert Farms Foundation.
“We established Desert Farms Foundation to help us bring container farms to food deserts within the United States. With a farm membership, 1% of the proceeds go to Desert Farms Foundation to really support community agriculture,” explains Shannon.
Thrive Containers
“Our containers are under the name Thrive Containers, which is wholly owned by Brick Street Farms. Our containers are the equivalent of 2-3 acres of traditional farmland. They use very little water, are energetically efficient, produce very little waste and use no chemicals. Since our products are wash-free, our customers get the benefits of long-lasting produce,” explains Shannon.
According to Shannon, Brick Street Farms is as much an agtech company as it is a farm operator. The company decided to establish Thrive Containers as its own entity within Brick Street Farms in order to differentiate between the food production and manufacturing aspect of the company. “When people see Brick Street Farms, we want them to think of butterhead lettuce, basil and our other vegetables,” notes Shannon.
Thrive Containers does not sell its container farms to third parties, but instead continuously improves the farm design for current and future installations. As Shannon explains, the company focuses on designing intelligent systems that can adjust to indoor and outdoor environmental conditions. Thrive containers have more than 120 sensors in and around the farm to monitor and respond to ambient temperature, humidity, carbon dioxide, vapor pressure deficit, etc.
Brick Street Farms and Thrive Containers work closely, with the engineers and designers having all undergone farmer training to ensure that the systems designed truly respond to the needs of Brick Street Farms’ growers.
Why Florida?
While warm and sunny Florida may seem ideal for outdoor agriculture, Shannon explains that soil conditions make soil-based agriculture somewhat difficult. She says that Florida soils are rather degraded and sandy, lack nutrients and lack natural bacteria, meaning farmers need to spend significant time and effort on rebuilding soils. Also, water sources are highly saline because of our position at level, near the coast, and with a low water table. Finally, the lack of winter makes it difficult to regulate pest cycles.
Lead photo: Co-founders Brad Doyle and Shannon O’Malley
For more information:
Madeline McNaughton, Head of Business Development
Brick Street Farms
madeline@brickstreetfarms.com
www.brickstreetfarms.com
Publication date: Thu 27 May 2021
Author: Rebekka Boekhout
© VerticalFarmDaily.com
AmplifiedAg Increases Better Fresh Farms Production 50% With New Indoor Farm And AmpEDGE Operating System
AmplifiedAg hydroponic container farm and technologies increased leafy green production over 50% for Better Fresh Farms
By AmplifiedAg
May 6, 2021
AmplifiedAg hydroponic container farm and technologies increased leafy green production over 50% for Better Fresh Farms.
AmplifiedAg, Inc. is an agtech visionary on a mission to provide global access to safe food. (PRNewsfoto/AmplifiedAg)
CHARLESTON, S.C., May 6, 2021 /PRNewswire/ -- AmplifiedAg, Inc.®, holistic indoor farming leader with a mission to provide global access to safe food, has increased leafy green production over 50% for Metter, Georgia-based Better Fresh Farms with its automated hydroponic container farm and AmpEDGE™ proprietary Operating System.
AmplifiedAg farms sustainably grow consistent yields of 800-1000 pounds of full head leafy greens per harvest every 3 weeks.
Founded in 2016 by Grant Anderson, Better Fresh Farms is expanding its hyperlocal produce throughout Georgia with the addition of its first AmplifiedAg farm, the company's exclusive producer of leafy greens.
Anderson said, "Our AmplifiedAg farm replaced two existing models that were fairly inefficient for our goals. The new system has optimized our production in the same square footage,"
"The software is going to help us get our arms around the whole operation; there's nothing out there really like it," added Anderson. "To have tracking processes that follow produce from growth all the way through to the sale is huge. It's been cumbersome up until now, and it will save us money in the long run to have one efficient system instead of multiple programs."
AmpEDGE uniquely combines farm production and business management for an end-to-end system. 24/7 environment controls, detailed analytics, and traceability features allow farmers to easily optimize crop growth, mitigate risk, while also tracking sales forecasts, revenue streams, and daily operations. Multi-tenant software with data-driven learning capabilities, AmpEDGE can operate any type of controlled environment.
"We grow 52 weeks a year in Georgia where the majority of the time weather is extremely hot and humid," added Grant. "We're constantly trying to adapt our systems to work in an environment that they weren't designed for. AmplifiedAg understands how to adapt their containers to different weather."
Manufactured from upcycled shipping containers, AmplifiedAg's enterprise-scale farms are built to the highest global food safety certifications. The resilient architecture allows for farming in any region regardless of resources and climate. A compact 320-square feet container design promotes ultimate segmentation and risk mitigation for reliable production.
AmplifiedAg farms sustainably grow consistent yields of 800-1000 pounds of full head leafy greens per harvest every 3 weeks. The company deploys farms 70% faster and at a fraction of the cost of other CEA implementations
"This has given us a chance to start exploring larger and more legitimate sales opportunities," added Anderson.
David Flynn is the General Manager of AmplifiedAg and leader behind the company's farm and technology production. He and his team have built and deployed over 180 farm containers that services farms across the country. This includes AmplifiedAg's Vertical Roots hydroponic container farm, with produce in nearly 1,500 stores nationwide.
"We've spent the last five years developing a platform that proves our technology and shipping container farms can be used to operate a profitable produce business at scale," said Flynn.
"We're excited to share our technologies and farms with other indoor farming experts like Grant and Better Fresh Farms, and continue to refine the indoor farming process for the future."
Learn more at www.amplifiedaginc.com.
US: TEXAS - Awty Unveils Carbon-Neutral Container Farm Thanks to Sustainability Grant From Green Mountain Energy Sun Club
Incorporating a container farm into Awty’s current operations and curriculum reinforces the school’s commitment to sustainability while providing a real-life example of environmentally sound sourcing practices to their international student body
Source: GREEN MOUNTAIN ENERGY
05/03/21
Teachers and students alike at The Awty International School are excited about the possibilities a carbon-neutral container farm brings to their campus. Awty received a $135,000 sustainability grant from the Green Mountain Energy Sun Club to implement the container farm that now provides fresh produce to the school’s cafeteria and hands-on education for students through a newly formed urban farming elective class. The school installed a 20-foot hydroponics shipping container, a 20-foot aquaponics shipping container, and a 14.4-kilowatt solar system with 48 panels to power both containers to achieve the carbon-neutral status.
Incorporating a container farm into Awty’s current operations and curriculum reinforces the school’s commitment to sustainability while providing a real-life example of environmentally sound sourcing practices to their international student body. The farm serves to demonstrate how to reduce the carbon footprint of a food operation by shortening the supply chain and reducing fuel emissions. The innovative container farm and solar-powered equipment provides Awty a year-round steady supply of fresh produce, regardless of the outside climate. The closed-loop hydroponic system also uses 98 percent less water than traditional agriculture, significantly reducing the environmental impact of food production.
“While our school community has already started to reap the benefits from the farm, one of our many goals for the container project is sharing what we have achieved with others,” stated Robert Sload, STEAM coordinator at The Awty International School. “As an international school, we certainly want to help other international, national, and local schools introduce their communities to the wonderful community-wide lessons this project provides. A larger goal is to deconstruct our efforts and refashion a much simpler and cost-effective model that could be recreated anywhere with a particular eye to school communities located in food deserts.”
Green Mountain Energy, the nation’s longest-serving renewable energy retailer, founded Sun Club in 2002 to advance sustainability by partnering with nonprofit organizations engaged in meaningful work to support the communities the company serves. Awty is one of more than 130 projects to receive a sustainability grant since Sun Club’s founding. The grants are awarded to nonprofits seeking to implement projects promoting renewable energy, energy efficiency, resource conservation, and environmental stewardship.
“Green Mountain Energy’s goal with Sun Club grants is to promote sustainability in the community, and we were excited about this project from the start as it amplifies the message to future generations through education,” said Mark Parsons, vice president, and general manager of Green Mountain Energy. “Container farming will allow Awty students the opportunity to explore innovative new approaches to food production. Farming fresh produce directly on campus powered by solar energy makes it easy to captivate students and facilitate a dialogue around farming and solar energy at the same time.”
The respect of self, of individuals, and of the environment, and the importance of contributing to the community, are the fundamental principles of Awty’s sustainability program. The program’s mission is to reduce the school’s environmental impact and become more sustainable while inspiring and challenging students to come up with innovative solutions to environmental problems. Initiatives like composting, recycling, collecting water from HVAC units, and working toward becoming a zero-waste school have allowed the school to become a Bronze Award recipient of the Eco-Schools program, an international organization that accredits schools demonstrating a commitment to sustainability.
Tags: Indoor & Vertical Farming, Processing & Supply Chain | Containers
What Is A Container Farm?
A container farm is usually a vertical farming system built inside a shipping container. The benefits of placing a farm within a container, rather than a building, are that it is transportable and can be squeezed into existing spaces, such as in car parks or on farmland
30-04-2021 LettUs
Container farming, vertical farming, indoor farming… What do they all mean? Are they all the same thing? In this blog, we’re going to explain exactly what a container farm is and what the benefits of growing crops in this way are.
The controlled environment agriculture club
Controlled environment agriculture (CEA) is a term for using different technologies to grow food indoors. In CEA, these technologies ensure the best growing conditions and protection for specific crops. This is slightly different to just indoor farming - by nature, indoor farms simply protect crops from external forces such as weather and pests. A container farm would be an example of CEA, as would other indoor farms such as vertical farms and high-tech commercial greenhouses.
A container farm is usually a vertical farming system built inside a shipping container. The benefits of placing a farm within a container, rather than a building, are that it is transportable and can be squeezed into existing spaces, such as in car parks or on farmland.
Since it is classified as a temporary structure, you typically don’t need planning permission for a shipping container. This can be particularly useful for those who rent their farmland. However, there are always exceptions and the necessary checks should always be made before making arrangements. As long as there is level ground, access to electricity, water & wifi, a shipping container can fit into a range of different settings.
Serving communities, big or small
Since they’re easy to transport, container farms can be easily deployed as and when they are needed. This means they could be used for research or social-impact projects, without needing to build a permanent facility. Shipping containers are also modular, which means multiple containers can be used to build a larger facility and businesses can scale their operations appropriately. They also have the potential to be bedded into existing container parks - these are dotted around the UK and are usually shipping containers made up of independent shops, cafes, and restaurants. One container farm could supply fresh produce to all of these.
In this way, container farms have the potential to be a positive disruptor within our food supply networks and strengthen our local food security by reducing our dependence on imported produce. Food waste and carbon caused by food transportation would also be reduced by strategically placing containers in key locations within communities.
The DROP & GROW container farm
LettUs Grow’s container farms are powered by aeroponic technology. This is a soil-less system that uses a nutrient-dense mist to irrigate crops - boosting oxygen levels and encouraging healthy root stock. Whilst hydroponic container farms are more common, DROP & GROW uses aeroponics to optimise crop health and increase growth rates.
Our container farms have also been designed with the grower in mind. DROP & GROW:24 includes a separate preparation area, providing ample space for the grower to do their job. Our farms have also been designed to be easy to maneuver within and check on your crops.
Celebrating vertical farming technology
DROP & GROW wasn’t designed to be inconspicuous. Quite the opposite! We think urban farming, new technologies and feeding local communities is something to shout about, so a DROP & GROW on your site is an opportunity to start a conversation and encourage your customers to learn more about the benefits of vertical farming.
If you want to take a positive step towards a more sustainable and resilient food supply chain in the UK, then talk to LettUs business development team about why a container farm might be in the right choice for you. Find out more...
Source and Photo Courtesy of LettUs Grow
ZipGrow Expands To New Facility, Inks Deal With Sodexo
ZipGrow has expanded its footprint, moving from leased premises to its own building at the corner of Cumberland and Seventh Street
April 9, 2021
By Bob Peters
Cornwall Ontario – ZipGrow has expanded its footprint, moving from leased premises to its own building at the corner of Cumberland and Seventh Street.
The new building more than doubles the amount of space available to the manufacturer of the world’s most installed vertical hydroponic equipment.
“Demand for our products continues to soar,” says Eric Lang, President of ZipGrow. “The new building allows us to be more efficient while at the same time giving us room to grow in the future.”
Growth is on the menu at ZipGrow, with the company launching an innovative partnership with Sodexo to introduce sustainable growing systems to facilities throughout Canada and the United States.
“Having been installed throughout the world over the past decade, our system enables growers, both big and small, to access fresh produce no matter where they are located”, explains Mr. Lang. “We are excited to move ahead with this new partnership with Sodexo. Together we will be able to introduce sustainable food to Sodexo locations throughout North America.”
ZipGrow technology is a patented system that utilizes both hydroponic growing systems and vertical planes to maximize production volume within a small footprint. Primarily growing leafy greens such as lettuce and kale, along with herbs and small fruiting crops such as strawberries, ZipGrow systems will be installed in Sodexo locations including educational institutions, conference facilities, and corporate food service centers.
“This new partnership with ZipGrow not only enables us to reduce our carbon emissions of distance traveled for food source, onsite food waste, and packaging requirements, but also to introduce innovative technology to our facilities and team members”, said Normand St-Gelais, Director of Corporate Responsibility, Sodexo Canada.
About ZipGrow
ZipGrow is an international leader in indoor, vertical farming technology. The company’s flagship product, the ZipGrow Tower, is a core component of many of the world’s most innovative farms; from indoor hydroponic warehouses to vertical aquaponic greenhouses and high-density container farms.
Categorized in: Business, Community, Environment, General, News
Vertical Growing Solutions That Are Easily Multiplied Increasing The Management Scale of Each Grower
GrowSpec offers three main products, each with numerous product lines contained therein. These three products include LED grow lights, vertical grow systems, and container farms
GrowSpec is an indoor farming equipment supplier established in 2015. GrowSpec offers three main products, each with numerous product lines contained therein. These three products include LED grow lights, vertical grow systems, and container farms. According to GrowSpec CEO Alvis Ma, these products can be used to produce a variety of crops indoors.
LED Grow Lights
GrowSpec offers six different types of LED lighting: AgriSpec, AgriBar, Sun Ray, Panel, SlimSpec, and Quantum. According to the company’s website, AgriSpec is a high-performance top-lighting solution with dimmable capabilities to allow growers to transition from vegetative to regenerative growth (i.e., flowering). The lights’ slim configuration enables installation in low rooms, racking systems, etc. While AgriBar and Sun Ray are both advertised as applicable for greenhouses as well as indoor farms, Panel is more specifically designed for indoor growing as the wide panels are somewhat wide for greenhouse use yet provide high light uniformity for indoor environments.
Vertical Grow Systems
GrowSpec also designs a number of vertical grow systems, all consisting of racks with integrated power supply, control system, and PVC trays so that each 4’x 8’ tray can be managed independently. Among these product lines in VertiDrip, a modular rack consisting of GrowSpec’s lighting, drip irrigation, airflow system, power supply, and touchscreen controls. The company’s VertiGro follows similar principles. GrowSpec’s main grow system, which was previously featured in IGrow (Combining Hydroponic And Aeroponic In Vertical Farming — iGrow) is VertiAero, which uses aeroponic technology. According to Alvis, VertiAero is patent pending in both the United States and Europe and offers various savings to growers.
“VertiAero reduces operational costs by 40%. In terms of electricity, we use 30% less. With nutrients, we save 85% because we use aeroponics rather than soil, so the root area is sealed and water losses are reduced. Our vertical grow systems are designed to optimize farm’s operation, they can match up with different irrigation systems so as to meet growers’ different preferred cultivation skills, and easily multiplied increasing the management scale of each grower,” explains Alvis.
Moreover, Alvis explained that having an integrated ventilation system in every rack of GrowSpec’s vertical grow systems helps to decrease plant disease.
“With inadequate ventilation, some plants will have diseases like powdery mildew or botrytis. But if you have full ventilation and every leaf can be blown with air, you will seldom have those diseases,” says Alvis.
Alvis also explained that the racks are space-efficient by both having an adjustable height and by being horizontally mobile using a mechanical assist. This, according to Alvis, allows growers to fit more racks into a grow room.
Container Farms
GrowSpec’s third product offering is container farms, which are equipped with GrowSpec’s vertical grow systems. According to Alvis, GrowSpec’s container farms are ideal both for production and for research as the conditions are highly modifiable and allow growers to test various things.
“If people want to do research, they can use this container to do so. They can set up irrigation, lighting, temperature of the root zone, temperature of the canopy, light intensity, etc. It is the perfect toy for them.”
Efficiency and scalability as priorities
Across GrowSpec’s three product types (LEDs, vertical grow systems and container farms), the company has emphasized improved resource use efficiency and scalability so that growers can easily increase production over time.
“For installation, we design our systems in modules so that they are very easy to install. It is a complex system yet easy to install. And it is scalable. It is easy to design the grow room because every rack is independent. The rack height is also customizable, and the power is integrated so that there is one main cable per rack, this allows requires the systems to be easy to maintenance ” explains Alvis.
GrowSpec also reports increased crop productivity by allowing growers to produce seven crops per year rather than four crops in traditional farming systems.
For more information:
OurCrowd, Waterfund Launch New Water Investment Platform
Waterfund committed $50 million of capital to the OurCrowd managed portfolio, with an initial investment completed in Plenty, Inc., a vertical farming leader
Waterfund committed $50 million of capital to the OurCrowd managed portfolio, with an initial investment completed in Plenty, Inc., a vertical farming leader.
By ZEV STUB MARCH 22, 2021
Future Crops will set up a farm to grow vertical agriculture in the UAE. (photo credit: Courtesy)
OurCrowd and Waterfund said Monday they will build a dedicated investment portfolio of 15 leading water and agricultural technology companies. Waterfund committed $50 million of capital to the OurCrowd managed portfolio, with an initial investment completed in Plenty, Inc., a vertical farming leader.
The companies also announced that they are jointly working on a water-focused financial product platform called Aquantos, which they said will "pioneer the issuance of Blue Bonds and other innovative water investment products." “We are working to issue Blue Bonds that can be both climate bonds-certified and backed by sovereign or sub-sovereign borrowers," said Scott Rickards, CEO of Waterfund.
"This new financial tool and others are being designed to enable water projects in the Middle East to acquire leading technologies to address water scarcity in a fundamentally new way.” Sustainable investing assets now total more than $30 trillion globally, with 34% growth over the past two years, According to Morgan Stanley research cited by the companies. In the United States alone, $12 trillion is sustainably invested, they added.“In 2016, the Paris Agreement heightened interest in green bonds; in the years since, we’ve seen a spike in companies, municipalities, sovereigns, and banks issuing green bonds.
We expect that demand for next-generation water-oriented bond products will see similar growth,” Rickards said. “The Abraham Accords present a huge opportunity to bring new water and agricultural technology to the water scarcity challenges of the entire Middle East," said Jon Medved, Founder & CEO of OurCrowd. "Alongside Waterfund, it is our mission to invest in and help build game-changing technology companies. We are excited to be working together with Waterfund to drive more private capital to address the critical challenges of water."
AUSTRALIA: VIDEO - Shipping Container Farms: Check Out This Craze In Modified Containers
Greenhouses, hydroponics, and mushroom farms – converted shipping containers can produce protein and vegetables for all your needs
Greenhouses, hydroponics, and mushroom farms – converted shipping containers can produce protein and vegetables for all your needs. Even if you’re not an environmentalist, there are business opportunities to be had in delivering extremely fresh food to people in urban environments like Brisbane. Given the changing climate and topsoil loss we are facing, shipping container farms could well be an answer to these issues.
Over the years in the Gateway Gazette, we have published a number of stories that look at producing food in converted shipping containers. Reflecting on what we have published and looking at the detail of what can be done, let’s consider the possibilities that come with shipping container farms.
Open Top Container Greenhouse
One of the most cost-effective ways of using a shipping container as a food-producing unit is by attaching a glass top to an open-top shipping container.
In this video, Urban Farm Units looked at the concept of a greenhouse-container. An open-top 20-foot container would have a greenhouse attached to the top with shelving units directly under the glass. This allows photosynthesis to take place in the normal way.
Seedlings can be started in the lower part of the unit, which is warmed by the light and heat from the outside.
One step down from slapping a greenhouse on top of an open-top container would be to use a flat rack container and to have the greenhouse on the base (Gateway Containers can supply both open-top and flat rack containers).
The concept is an improvement on the one in the video, as long as you keep the greenhouse within the dimensions of a 20ft standard or high-cube container, it would be possible to lift and move the container farm from place to place.
This might be useful where you have an agreement with property developers or a council to use vacant plots of land in a city for agriculture. When the site is ready to be developed you can stick it all on a truck and move it to the next plot.
The concept of a shipping container greenhouse is:
Cheap to buy
Mobile
And often won’t need planning permission for a permanent site
Could this be something you’d consider? Contact us at Gateway Containers to discuss your needs!
Mushie Container Farm!
Image source: King Oyster Mushrooms Facebook
In 2019 we reported how Belgrave, Vic-based John Ford has developed a shipping container mushroom farm. This could produce protein for people as an alternative to meat or for anyone who loves the taste of freshly cut shrooms.
Mushrooms of any kind don’t store well and are best eaten as soon as possible after cutting. This is why having a mushroom farm close to restaurants could be a money-spinner.
This requires no modification from a basic shipping container, you could even install the racking inside the container yourself.
In their lifecycle, mushroom mycelium live out of sight of the world until they are stressed and get the impression that they are facing death. When stressed they flower to produce spores – those flowers are the mushrooms that many of us love to eat.
A shipping container is perfect to take advantage of such a lifecycle. Logs or other media are infected with the mycelium and left to rot for a certain time. By altering the environmental conditions, so you deliberately stress the fungi and they flower.
In our article, we reported how John Ford is producing mushroom species that are famed for their delicate taste but don’t travel well at all – shiitake and oyster mushrooms. As a sideline to his main income as a marine biologist restoring seagrass habitats near Belgrave, he produces freshly cut shrooms for local people and restaurants.
For you as an entrepreneur, mushroom growing would require buying a used shipping container and setting it up as a mushroom farm. If you are planning an urban mushroom container farm, you can take advantage of the fact that you can treat the container as a mobile unit and not as a permanent base. Shipping containers are also pretty inexpensive to buy and convert.
Hydroponics – The Rolls Royce of Shipping Container Farms
Image source: ABC
The hydroponics concept is highly developed for the use of fresh food and can be set up for high density vegetable farming in shipping containers. This requires a fair bit more modification than the two systems we describe above.
Unlike the Urban Farm Units company, several companies have managed to survive over the years selling their hydroponic container farm businesses to entrepreneurs and restaurants around the world.
Modular Farms is a company we featured in our blog originally based in Canada, but who recently set up shop over here in Australia. According to their website, they “design and manufacture container farm systems that can be used to grow food in most locations on earth.”
These systems strive to get around some of the issues we face here. Cities like Brisbane get far too much water sometimes and then face droughts for years on end. The Australian Food Services News reported, “With a focus on sustainability, Modular Farms’s hydroponic, closed-loop system uses 95% less water than a typical outdoor farm.”
Topsoil erosion is a problem, especially in prolonged droughts when it gets blown away as dust. Hydroponics use media like rock wool and even used mattresses to house the plants’ root systems and feed them nutrients via a watering system.
With our ever more extreme climate, food often has to be imported into cities from hundreds or thousands of miles away. A hydroponic container farm can enable you to grow many vegs very close to markets and restaurants.
This has been observed by global homewares retail giant IKEA, which in 2019 announced it was piloting growing vegetables in its stores for use at its restaurants. We reported, “While selling hydroponic indoor growing equipment to customers, IKEA is feeding its staff with lettuce and other vegetables grown in a container outside its Malmö and Helsingborg stores.”
Image source: ABC
There are a few downsides to hydroponics. Firstly, while some types of plants are happy enough growing in hydroponics – the simpler ones producing leaves and flowers (like broccoli!) – others aren’t so happy, such as cassava, wheat, and potatoes.
The next big issue is that for a high-intensity farm, not unlike factory farming chickens, you need to be ultra-clean in your production as the arrival of a destructive disease or fungus could wipe you out very quickly.
Container Fish Farm Too?
In theory, it is possible to run a fish farm connected to the hydroponics container farm, with you largely feeding the fish and collecting their feces and other waste to feed the plants. The plants would clean the fishes’ water and make it habitable for them as reed beds do in nature. This a concept that is in development but hasn’t caught on commercially yet.
How Can Gateway Containers Help?
We can provide and convert an insulated container for you to get started with and advise you how to best make further additions without compromising the overall structure.
If any or all of these ideas have caught your interest – or you just know about these concepts and need a shipping container to make it possible – then get in touch with us today to discuss your needs!
Posted on February 22, 2021
By Mark FinneganOtherShipping ContainerModified Shipping ContainersLeave a comment
Providing A Sustainable Growing Solution For Farmers, Using Renewable Energy in Container Farming
Recently, Freight Farms and Arcadia have partnered to provide Freight Farms' U.S. customers with access to clean energy for their everyday operations
“The past year has really proved our proposition as it has never been proven before,” says Rick Vanzura, CEO at FreightFarms. “The pandemic put a huge focus on supply chain security, local food access, and how to handle disruption to a supply chain, and we saw that having a modular farming solution that can be put next to people where they need food fits in perfectly. Some segments have suffered, while our farms have proven to be a great solution.” The company has seen demand going up, with 2020 being a record year: Freight Farms tripled revenue versus the prior year and set a record for orders.
Recently, Freight Farms and Arcadia have partnered to provide Freight Farms' U.S. customers with access to clean energy for their everyday operations. With this partnership, Freight Farms and Arcadia are taking strides to align their respective industries, moving indoor farming into a more sustainable future. Freight Farms’ customers can now connect the utility for their container farm to Arcadia to match 100% of the farm’s electrical usage with clean energy.
Tackling sustainability pillars
“We already have a number of current farmers that have signed up with the Arcadia energy offering. It was a really important milestone for us as sustainability has been a core mission since the founding of the company.” Rick identifies the sustainability pillars in farming as soil conservation, water conservation, food miles, and energy usage. “At Freight Farms, we have always performed very strongly in the first three categories. Our farms have no effect on soil; they use very little water (5 gallons/day, or 19 L/day), and they reduce food miles significantly, sometimes to zero. What remained for us to solve and why the Arcadia partnership is so crucial is energy,” Rick notes.
Before the Arcadia partnership, energy was the only unsolved part of the sustainability pillars Freight Farms hadn’t tackled yet. The recent partnership has given access to clean energy to all small business farmers. “With the presence of clean energy, we believe there hasn’t been a more sustainable farming solution similar to this one before.
Freight Farms looks at sustainability through the triangle of labor, yield, and power. They are increasing the output per unit of input. According to Rick, Freight Farms is far down the road in the development of greater efficiencies in their farms, focusing on optimizing for yield per unit of power and continuing to research renewable energy options. Rick says that “Everybody’s success is a collective success as we’re all relying on the industry as a whole... We’re all bound by this mission to create a more sustainable planet. Therefore, anything we can do in our own small way, we’re ready to do.”
Improving farm efficiency
On the product side, the company is doing updates to everything. “We made our farms more efficient, delivering value in several aspects, working on different renewable energy in all forms. The ROI has never been better than this farm, because of the intersection of output and efficiency gains. As we’re big believers in helping the industry as a whole for good, our ultimate goal is to be NET zero ultimately.”
While Freight Farms customers already span 46 U.S. states and 32 countries, Rick believes that the company will expand into more locations this year. This growth is stimulated by recent investment and team expansion. “By the end of 2021, we’re expecting to be in every US state and several other countries. Ospraie Ag Science led our last fundraising round, where they invested heavily in our ability to do research. Therefore, we’ve added lots of strength to the team over the last year.”
Collaborations
As a plug of vertical farming, Freight Farms is collaborating with MIT sustainability lab students together on a project. The project is about working in conjunction with the government, and public- and private partnerships around sustainability. “The goal is to be part of something where brilliant people are willing to donate their time and energy. This is just one example of many where people want to pitch in and help as we all want to have a more sustainable planet,” Rick notes.
“We’re not trying to solve for renewable energy on a location by location basis. That would be the route to go with today, but it’s a solution limited to the United States as of now,” Rick affirms. Freight Farms is always on the lookout for partners worldwide where its services can be made available.
For more information:
Rick Vanzura, CEO
Freight Farms
+1 877 687 4326
info@freightfarms.com
www.freightfarms.com
Publication date: Wed 17 Mar 2021
Author: Rebekka Boekhout
© VerticalFarmDaily.com
GrowGroup IFS Introduces Their Own Grow Container Systems GCS 40HQ
The GCS 40HQ is available in different models. All models are in a 40ft container and includes LED technology, climate computers with remote control, and extensive control on water, temperature, humidity, CO2, and lighting
March 12, 2021
GrowGroup IFS Introduces Their Own Grow Container Systems GCS 40HQ
GrowGroup IFS introduces the GrowGroup Grow Container Systems “GCS 40HQ” for small container cluster farms, research & development, schools & universities, and pilots for new indoor farms. With this new solution now GrowGroup IFS can support also small farms in an accessible way with their unique and full approach including support with the operation through their partners GaaS Wageningen and Hoogendoorn Growth Management.
Grow Container Systems “GCS 40HQ”
The GCS 40HQ is available in different models. All models are in a 40ft container and includes LED technology, climate computers with remote control, and extensive control on water, temperature, humidity, CO2, and lighting. The basic model has a very low entry-level and is upgradeable on different levels. The client can choose for example for an upgrade to the highest quality of climate computers of partner Hoogendoorn Growth Management or the highest quality of LED technology of Signify. The client can even choose for the support with the operation through partner GaaS Wageningen.
“We support the bigger farmers with our unique and full approach on indoor farming for some time already but noticed also that smaller farmers, in particular, have a great need for this. That’s why we launch our own GCS solution right now, so all farmers can use the newest technology of indoor farming for year-round cultivation all over the world”, John Breedveld, CEO GrowGroup IFS.
GaaS Wageningen
Partner GaaS Wageningen from the Netherlands has access to a pool of more than 200 agricultural specialists. Its core business is supporting the operation of high-tech indoor farms from the small ones as the container farms up to the large ones as the big indoor factories. They have high knowledge of indoor farming and sharing their knowledge with the farmers by supporting and training them but also with schools and universities.