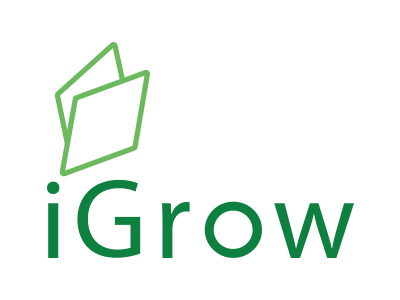
Welcome to iGrow News, Your Source for the World of Indoor Vertical Farming
'Acute' Pallet Shortages Putting Fresh Produce Supply At Risk
The shortages are "acute," according to United Fresh Produce Association’s letter to the industry in a news release
A Pallet Shortage Is Affecting
The Produce Industry In Many Ways
By AMY SOWDER
May 19, 2021
Severe pallet shortages are inflicting a widespread effect on the produce industry — including the availability of produce to consumers.
The shortages are "acute," according to United Fresh Produce Association’s letter to the industry in a news release.
The association detailed a multitude of issues that are impacting pallet availability, including:
Efforts of wholesalers, distributors and retailers to ensure sufficient inventory of non-perishables given previous pandemic-related impacts;
Availability of lumber to repair and build new pallets;
The escalating price of lumber when it is available;
Nonperishable inventory dwell time increase; and
Lack of available trucks to relocate pallets.
“The lack of pallets is adding stress to a supply chain that is already facing significant challenges, which include a lack of available trucks and shipping containers, ongoing labor challenges, fluctuating fuel costs, pandemic-related challenges, and a pending shortage of resin used to make reusable containers and pallets,” according to the release. “At this time, expectations are that the pallet shortage will continue for months, perhaps for the balance of 2021 – all at a time when many North American produce items are just beginning seasonal harvests and shipments.”
Listen to United Fresh’s John Hollay discuss this pallet issue with retail and Produce Market Guide editor Ashley Nickle in our Tip of the Iceberg podcast episode.
The issue has a wide and deep scope of negative impacts, according to United Fresh:
The shortage of lumber and wood products has increased the cost of raw lumber 200% to 350% and is making the cost of wood pallets increase incrementally;
In one example, in the past few weeks, pallet costs have increased more than 400%, if the pallets are even available, and often they are not;
One farmer was told by one pallet supplier that they are not taking any new customers due to an inability to fill even existing customer demand;
Companies are forced to bring pallets from other jurisdictions, thereby incurring border and transportation costs; and
Pallets are being held in-house due to delayed and canceled orders from pallet services, leading to higher storage charges and increased congestion within operations.
Company leaders along the supply chain need to collaborate to balance organizational goals relative to overall availability of goods with availability of food.
“If there is not a concerted effort across the supply chain to ensure pallet availability for shipment of produce, there is little doubt that it will be very difficult, if not impossible, for the grower-shipper community to meet buyer, and ultimately consumer, demand for produce,” according to United Fresh.
Also, growers and shippers are trying to comply with pallet requirement specifications, but this is even more challenging.
United Fresh’s stance is that temporary modifications or exceptions to pallet requirements — as long as those exceptions don’t jeopardize safety — would help greatly until this pallet shortage is resolved.
All partners in the supply chain should have regular conversations with their pallet suppliers to understand the situation and pallet inventories and availability, according to the release.
“We welcome the opportunity to work collaboratively with all parties within the supply chain to mitigate the impacts of the current shortages and will reach out to stakeholders to identify a path forward that provides solutions to this increasingly disruptive threat and enables the continued flow of goods,” according to United Fresh.
Learn more details with this interview.
Lead Photo courtesy Michael Gaida/Pixabay
AppHarvest’s Mega-Indoor Farm Offers Economic Alternative To Coal Mining For Appalachia
AppHarvest is taking advantage in the new wave of high-tech agriculture to help feed a growing population and increase domestic work opportunities in a sustainable manner.
Inside AppHarvest's 60 acre state-of-the art indoor farm in Morehead, KY.
In the first year of business, Jonathan Webb and his growing team at AppHarvest are riding high on what he calls the “third wave” of sustainable development: high-tech agriculture, following the waves of solar energy and electric vehicles. Since launching the concept in 2017, Webb and AppHarvest have raised more than $150 million in funding while building and opening one of the largest indoor farms in the world on more than 60 acres near the Central Appalachian town of Morehead, Kentucky.
For Webb, who grew up in the area and has a background in solar energy and other large-scale sustainable projects, AppHarvest is both a homecoming and a high-profile, purpose-driven venture that addresses the need for additional production to feed a growing population and reduce imported produce.
Webb’s vision for AppHarvest was inspired in part by a National Geographic article on sustainable farming in the Netherlands, where indoor growing is part of a national agriculture network that relies on irrigation canals and other innovations. He traveled across the Atlantic Ocean to see the farmers in action, then decided it was a venture he wanted to pursue — in his home state of Kentucky, where the coal industry is in decline and unemployment levels are on the rise.
“Seeing that the world needs 50% to 70% more food by 2050, plus seeing that we’ve shifted most of our production for fruits and vegetables down to Mexico — produce imports were tripled in the last 10 to 15 years,” he says. “I would go to a grocery store, pick up a tomato, and it could be hard, discolored. That’s because it’s been sitting for two weeks on a semi truck, being bred for transportation. So first it was seeing the problem, then asking, ‘How do we solve the problem?’”
As part of my research on purpose-driven businesses and stakeholder capitalism, I recently talked with Webb about AppHarvest’s whirlwind initial year in business, successful investor fundraise, plans to go public, and B Corp Certification.
Good for Business, Good for Community
Jonathan Webb, founder and CEO of AppHarvest
“Where we’re doing what we’re doing is incredibly important. One of our biggest competitive advantages, frankly, is doing it here,” he says. “Some of the hardest-working men and women are the people in this region that power the coal mines, and all we’re trying to do is tap into that and harness that passion. It’s good for our business, but it's good for communities.”
The location has been central to AppHarvest’s benefit in another way, Webb says, as local enthusiasm for the project enabled swift construction that likely would’ve been a challenge in some other regions.
“It's all about economies of scale. We have to build a really big facility to get our costs on materials down so that we can compete with products that are being imported into the country from Mexico,” he says. “We built one of the largest facilities in about a year, so speed and scale are definitely advantages for the company, and a lot of that’s possible based on where we’re operating here in this region.”
While the Bluegrass State has been a good home for AppHarvest, Webb wants the business to be a resource for nearby communities and a beneficial workplace for residents.
“A fundamental part of the way we’re building and growing this company is that every entry-level employee gets full health care, full benefits, living wage, paid time off. So we’re not just creating jobs, we’re creating a lifestyle for your career path,” he says. “We want to see people with high school degrees in this region grow with the company and be assistant growers and head growers three, four years from now. I know this region, and I know what people can do here. Those are the success stories that I look forward to having happen.”
Creating Positive Stakeholder Impact
Producing needed food and building a stronger workforce aren’t the only goals at AppHarvest; Webb says growing produce sustainably, with minimal impact on the environment, also is paramount.
“We’re land constrained in the world, and water constrained. And we have to grow a lot more food and use fewer resources,” he says. “It’s simple in theory; it’s complex in scale. Just the fact that the place is so big is what makes this challenging. But we’re collecting rainwater on the roof and using it directly on the root of the plants. We’re growing hydroponically, and as a result we can use 90% less water than open field agriculture.
“The way we treat water and handle water and how we use rainwater efficiently is the really biggest driver of resiliency long term for us.”
In building a business to have a positive impact on workers, community, and environment, Webb also created a company that is a natural fit for the B Corporation community made up of businesses that achieve a certification based on how well they incorporate all stakeholders into their policies and practices.
“The impact side of this is incredibly important. We didn’t chase certifications,” he says. “We just did the right things: We’re paying a living wage, we're offering health care. It’s the right way to do business. And as a result, we get a huge ROI on our dollar.”
Thanks to its bottom-line success and future promise, AppHarvest has found favor with investors, including Martha Stewart and venture capitalists; and is part of a growing cohort of businesses with a social purpose that are finding traction in the public markets. The company announced in September that it’s going public through a combination with special purpose acquisition company Novus Capital Corp. (Nasdaq: NOVS).
“Why are we going public now? Because full transparency in agriculture is desperately needed,” Webb says. “We want the people who buy our fruits and vegetables to also have the ability to buy into our company. We want the record. We want the institutional rigor. It’s hard to have this spotlight this early, but it’s making us stronger.”
Christopher Marquis, Contributor