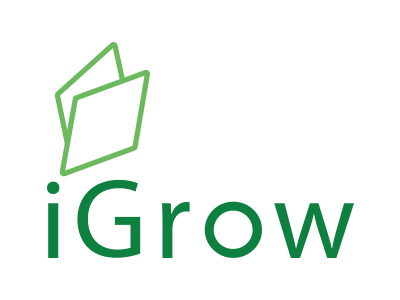
Welcome to iGrow News, Your Source for the World of Indoor Vertical Farming
Delivering The Optimal Growing Parameters
“Especially in the pharmaceutical or supplemental industry, you need an extremely strict batch control that leaves no room for variation,” says Dr Alexis Moschopoulos, Managing Director at Grobotic Systems.
The Grobotic Systems team shows off an early prototype Grobotic chamber. From left to right: Gareth Coleman (Software Developer), Richard Banks (Chief Technology Officer), Dr Alexis Moschopoulos (Managing Director), and Andrew Merson (Mechanical Engineer). Credit: UKRI.
Growing a new variety
Indoor farming has numerous growing parameters to take into account. Particularly when growing a new variety, all variables should be perfected in order to reach an optimum yield. In an indoor space, experimenting with these environmental parameters might, however, seem tricky. But what about trying out this environment in a smaller setting, such as an experimental growth chamber?
Alexis is fully aware of the challenges that vertical farmers face. The environmental control needs to be as precise as possible, as the effect of different light spectra or nutrients may have a significant impact on crop yield and quality. With this challenge in mind, Grobotic Systems brings a new solution to the market: a compact and highly instrumented growth chamber. “It’s an experimental chamber rather than a farming chamber. Therefore, you won’t use it to grow vegetables, but you can use it to identify which growing parameters are best suited to your crops,” Alexis says.
The Grobotic Systems team outside their workshop in Sheffield, England. From left to right: Dr Alexis Moschopoulos, Richard Banks, Andrew Merson, and Gareth Coleman. Credit: UKRI.
On your desk or under your bench
According to Alexis, the chamber fits on your desk or under your bench. It can apply any environmental condition preferred, including light spectra and temperature. Internet connection via the growth chambers allows users to monitor plants on their cellphones via integrated cameras and other sensors inside the chamber.
Another advantage of the chambers’ size is that they can be stacked in an array, adjusting variables in each chamber. In this way, a multi-variable experiment can help users identify which environment works most optimally for their intended crop. “When using a large cultivation room, it is hard to split the room into different temperatures. A smaller cultivation space, such as our growth chambers, can be placed anywhere, just like a personal computer. Moving away from the large expensive capital equipment and machinery to small and stackable experimental chambers saves a lot of space and money.”
Alexis first came up with the concept of the growth chamber during his PhD and postdoctoral work in plant genetics. Several prototypes are currently being used at research institutes and start-up companies. Grobotic Systems is working on a more advanced growth chamber that will be launched in the summer of 2021: “We are integrating feedback from the deployed prototypes into the design of the advanced chamber, and we will start marketing the advanced chamber later this year.”
Richard Banks designs a control system circuit board for an early prototype Grobotic chamber. Credit: UKRI.
Large-scale farms
Not only new farmers can benefit from running small-scale experiments in a growth chamber, but also large-scale, established farms, since the chamber allows them to experiment with new varieties, creating the optimal yield. This will in turn enable them to upscale their production. “Not all farmers like to invest their time in carrying out experiments, as some trust that the vertical farming technologies they buy will always work for them. However, in the end it could save them a lot of money. No one needs to use productive farm space to do the experiments, just a few manageable boxes can suffice.”
Gareth Coleman works on the chamber imaging and control systems. Credit: UKRI.
For more information:
Grobotic Systems
Dr Alexis Moschopoulos, Managing Director alexis@groboticsystems.com
www.groboticsystems.com
Author: Rebekka Boekhout
© VerticalFarmDaily.com
Signify’s Expanded GrowWise Control System Helps Growers Boost Operational Efficiencies
Signify has expanded its GrowWise Control System, allowing for higher levels of automation and reducing manual labor and operational costs
Signify has expanded its GrowWise Control System, allowing for higher levels of automation and reducing manual labor and operational costs. This can be achieved by automating the lighting planning for their crop’s full growth cycle, up to one year ahead. The software tool brings dynamic lighting to greenhouses and vertical farms and fits seamlessly with modern climate computers and greenhouse management systems. This enables growers to automatically adjust light levels to maintain consistent levels on cloudy days, save energy on sunny days and simulate sunrise and sunset throughout the day or season.
Growers, like the Italian vertical farm, Planet Farms, and the Belgium greenhouse, De Glastuin, are already using the expanded system providing additional value within their growing facility.
“Using the GrowWise Control System is ideal for us,” says Luca Travaglini, co-founder of Planet Farms. “We want to automate as many aspects of our operations as possible to become more cost efficient. Now we can easily create custom light recipes and set them to run year-round to provide the right light recipe with the right light intensity at the right time throughout the crop’s growth cycle. By automating our full light strategy during the growth cycle, for the whole year, we can run our operations very efficiently and keep our manual labor costs low. That makes it easier for us to maintain consistent quality as we scale up our production.”
The demand for the GrowWise Control System is increasing for greenhouse applications as well. “The lighting can be used much more efficient, since it gives us the flexibility to reduce light levels at any moment we need to,” says Wouter de Bruyn, owner at De Glastuin. Lettuce grower De Glastuin is using the GrowWise Control System to control the Philips GreenPower LED toplighting compact grow lights via its climate control system. “The climate computer is equipped with a daylight sensor that sends actual light measurements to the GrowWise Control System so we can adapt our light levels automatically to ensure an even light level throughout the day and season. This results in a continuous high-quality crop. In case the electricity is the limiting factor, we are still able to use the LEDs evenly for the whole greenhouse in a lesser intensity.”
“Dynamic lighting in a greenhouse is the next step in improving the cost-efficiency and quality for the cultivation process,” says Udo van Slooten, Business leader Horticulture LED solutions at Signify. “It allows growers to effortlessly maintain a consistent level of light throughout the day to produce the best possible crops. The system compensates for cloudy weather and creates a more controlled growing environment for your crop.”
For more information about the GrowWise Control System and our Philips-banded horticulture lighting, visit our horticulture pages.
Or please contact:
Global Marcom Manager Horticulture at Signify
Daniela Damoiseaux
Tel: +31 6 31 65 29 69
E-mail: daniela.damoiseaux@signify.com
About Signify
Signify (Euronext: LIGHT) is the world leader in lighting for professionals and consumers and lighting for the Internet of Things. Our Philips products, Interact connected lighting systems and data-enabled services, deliver business value and transform life in homes, buildings and public spaces. With 2019 sales of EUR 6.2 billion, we have approximately 37,000 employees and are present in over 70 countries. We unlock the extraordinary potential of light for brighter lives and a better world. We achieved carbon neutrality in 2020, have been in the Dow Jones Sustainability World Index since our IPO for four consecutive years and were named Industry Leader in 2017, 2018 and 2019. News from Signify is located at the Newsroom, Twitter, LinkedIn and Instagram. Information for investors can be found on the Investor Relations page.
VIDEO: How To Optimise Plant Growth In Vertical Farms
Lisanne Meulendijks, Researcher at Delphy Improvement Centre, Mike Zelkind. Cofounder and CEO 80 Acres Farms and Mariska Dreschler discuss the latest insights in Vertical Farming
Back to overview Print webpage
VIDEO: How to optimise plant growth in a vertical farm
08 September 2020
GreenTech
Lisanne Meulendijks, Researcher at Delphy Improvement Centre, Mike Zelkind. Co-founder and CEO 80 Acres Farms and Mariska Dreschler discuss the latest insights in Vertical Farming.
Climate control in vertical farms
What have we learned from the transition from conventional farming to vertical farming
What should you optimize in your vertical farm
Difference between horticulture and a vertical farm
The impact of wind and lights
Plant processes, how can you optimize this in vertical farms
Which innovations are needed in vertical farming
The necessity of interdisciplinary approaches to reach common goals in vertical farming
You can watch the video, or listen to the audio on one of our podcast platforms »
Share your horticulture stories with us
Do you have an innovation, research results or other interesting topics you would like to share with the international horticulture industry? The GreenTech website and social media channels are a great platform to showcase your stories!
Please contact our Brand Marketing Manager Murkje Koopmans.
Are you a GreenTech exhibitor?Make sure you add your latest press releases to your Company Profile in the Exhibitor Portal for free exposure.
+31 (0)6 264 34 601
First Indoor Basil Harvested In Delphy Improvement Center
Meulendijks has been working on the development of practical cultivation knowledge for Vertical Farms. Growth factors such as climate, light and irrigation can easily be varied in the test chambers.
The first batch of indoor-grown basil was harvested at the Delphy Improvement Centre. Since May, Lisanne Meulendijks has been working on the development of practical cultivation knowledge for Vertical Farms. Growth factors such as climate, light and irrigation can easily be varied in the test chambers.
Because of this flexibility, experiments can be conducted to see how cultivation in a Vertical Farm can be optimized. The focus is on analyzing the plant’s growth process. In a Vertical Farm, the plant influences its own growing environment relatively strongly which creates a microclimate around the crop that deviates from the controlled climate in the chamber.
Lisanne in the climate chamber
Cultivation factors
The degree of exchange between these climates depends on the design of the Vertical Farm. In order to fully utilize the potential of a Vertical Farm, optimization of the growth recipes should be based on this principle, because it is ultimately the microclimate that controls the growth of the plant.
By approaching the research from this angle and looking at the effect of the different cultivation factors on the plant, it is possible to formulate growing advice that is specific for different Vertical Farming facilities.
Light intensity
The first experiment looked at the effect of increasing light intensity on the growth of basil, in combination with testing different types of substrate. By using sensors on and around the plant, the growth was closely monitored and could be linked to the microclimate between the crop and the macro climate in the cell. This led to interesting and tasty first results, says Lisanne.
Investigating business questions
The graph shows the relation between increasing light intensity and annual production: the more light, the steeper the curve, the faster the plants growth. The fact that the plant grows faster with more light is of course nothing new.
What makes these results interesting is that each growth curve can be expressed in a formula and the error margin around the curves is small, Lisanne explains. This is because the growing conditions within a Vertical Farm are completely under control. Cultivation practices can then be optimized using the formulas behind these kind of curves.
It becomes possible to formulate answers to questions such as: “How does an investment in extra light affect my yield? How many days after germination is best to harvest to maximize my yield?”
These are important business aspects for production. "Through our application-oriented research, we develop knowledge that responds to these kinds of practical questions."
Fresh weight of the basil plotted as a function of light intensity and days after germination.
This experiment is part of the Fieldlab Vertical Farming South Holland project. This project has in part been made possible by the European Fund for Regional Development of the European Union and a contribution from the Province of South Holland.
For more information:
Delphy
www.delphy.nl
Publication date: Wed 15 Jul 2020