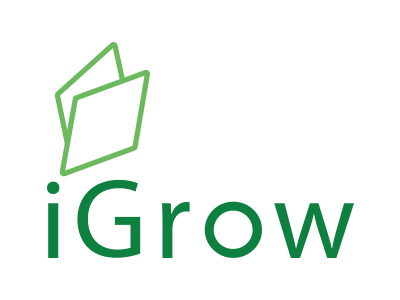
Welcome to iGrow News, Your Source for the World of Indoor Vertical Farming
The 'ekofarmer' by Exsilio Is A Pop-Up Urban Farm For City Streets
Wouldn’t it be great if you could have fresh, locally grown produce, from the comfort of a city? it’s no surprise that urban farming has become popular in recent years, with city slickers attempting to grow fruits and vegetables in backyard gardens, on rooftops, or even indoors using hydroponic systems.
The 'ekofarmer' by Exsilio Is A Pop-Up Urban Farm For City Streets
Wouldn’t it be great if you could have fresh, locally grown produce, from the comfort of a city? it’s no surprise that urban farming has become popular in recent years, with city slickers attempting to grow fruits and vegetables in backyard gardens, on rooftops, or even indoors using hydroponic systems. while all of these solutions are only possible on a small scale, finnish start up exsilio oy is making urban farming possible for whole cities with their modular pop-up farms. just as pop-up shops or cafes, the ekofarmer pod be easily set up in the middle of town, sprouting cost effective crops to grow fresh food for everyone.
images courtesy of exsilio oy
branded as a ‘resource-efficient urban farming chamber,’ the ekofarmer combines high-tech solutions with the easiness and safety of locally produced healthy and clean ecological food. the 13-meter long module forms a closed ecosystem, which needs only electricity and water to function. the levels of humidity, water and carbon dioxide inside can be adjusted to produce optimum yield and the best possible flavor. the neat little module is carbon-neutral, transferable, and can be placed almost anywhere without taking up a whole lot of space.
the shipping container-shaped chamber enables restaurants, businesses owners and small-scale farmers to use efficient and profitable urban farming methods. exsilio oy estimate each module can produce approximately 55,000 pots of salad per year–around 3 times more than the amount that could be produced in a greenhouse, since cultivated plants are located on multiple floors within the farm.
farmers can use the module to grow their own choice of herbs, salads, seedlings, and even non-food plants. ‘our solution is ideal for example for restaurants and institutional kitchens wanting to produce their own ingredients,’ explains Thomas Tapio, CEO of exsilio. ‘the modules also serve as an excellent option for farmers to replace their traditional greenhouses.’
beatrice murray-nag I designboom jun 27, 2017
Indoor Ag Means Safer Conditions For Farm Workers
“Farm workers will no longer have to work with the risk of pesticide drift,” says Sonia Lo, CEO of FreshBox Farms, the nation’s largest modular vertical farm.
Indoor Ag Means Safer Conditions For Farm Workers
Vertical farm CEO says growing greens without pesticides, herbicides and other harmful chemicals one of many pluses of this booming industry
One of the potential benefits of the booming indoor farming industry is safer working conditions for the people who grow and harvest our food.
“Farm workers will no longer have to work with the risk of pesticide drift,” says Sonia Lo, CEO of FreshBox Farms, the nation’s largest modular vertical farm.
California regulators continue to debate how to best protect farm workers from harmful pesticides and herbicides, but when it comes to food grown indoors, in digitally controlled locations, it’s a moot point.
FreshBox Farms, like other Digital Distributed Agriculture (DDA) operations, uses sustainable growing enclosures, no soil, very little water, a rigorously-tested nutrient mix and LED lighting to produce the freshest, cleanest, tastiest produce possible.
“No pesticides or other harmful chemicals are used, so that means a safer working environment,” says Lo. “Conventional growers try to control and contain the chemicals sprayed on fields, but the fact is, in many cases, those chemical can contaminate groundwater, and air, not to mention expose field workers to harmful substances.”
The leafy greens market in the US is $6 billion to $9 billion per year, but over the next 10 years, industry observers believe that over 50% of traditional growing operations will go indoors and into some form of DDA. As a result, industry watchers are predicting the creation of more than new 100,000 jobs.
"Unlike other high-tech industries, Digital Agriculture offers entry level jobs, with career path prospects, to unskilled labor,” says Lo. “It pays well and is in a pleasant indoor, climate-controlled environment. Anyone who is willing to work hard can get ahead in this industry."
Green Machine: Madar Farms’ Plug-and-Play Harvests
Green Machine: Madar Farms’ Plug-and-Play Harvests
Dubai start-up has ambitious plans to provide Gulf food security by combining technology and hydroponics
Photos Credit: Clint Egbert/Gulf News
Andrew Staples, Chief Business Reporter | Gulf News | DUBAI | Published: 18:33 July 29, 2017
The Arab world struggles to feed its population. In the Gulf Cooperation Council (GCC) nations, arable lands accounts for just 1 per cent of the total land, yet agriculture and irrigation use more than 50 per cent of the water supply. And still the GCC imports 90 per cent of its food.
That’s the starting point for Dubai start-up Madar Farms’ ambitious plans to develop sustainable agriculture within the GCC by combining latest hydroponics techniques with high-tech control.
“I think we all know that we have a problem here in the region,” said Madar Farms co-founder and CEO Abdul Aziz Al Mulla. “But I think the scale and imminence of the problem is what really scared me. Over the last 20 years we’ve lost the majority of our water resources.
“We’re not talking about a problem that’s going to hit us now. We’re talking about in 10 years, 20 years. But at the same time intervention is so large scale and takes such a large period of time to actually convert that I felt a very strong need that something had to be done now. Something at a large scale.”
Ultimately, the start-up, which began operations in February, wants to build a fully automated robotic hydroponics farm. Right now, it’s operating three units built into re-used 20-foot shipping containers at its headquarters in Warsan 3, near Dubai Municipality’s nursery, and is on its fourth harvest.
Container hydroponics isn’t a new development, Al Mulla is quick to point out. It’s already been used successfully in other parts of the world.
“We always tell people there’s no magic in hydroponics,” said Al Mulla, a Kuwaiti entrepreneur who began getting interested in food security while working for consultancy McKinsey. “Everyone thinks it’s some kind of new technology. It’s not. It’s all the same, It’s just the delivery mechanism and it’s how accessible you make it that’s the differentiating factor.”
What’s new is combining container hydroponics with a mobile app that maximises efficiency by monitoring crop growth and advising workers in necessary tasks to ensure consistent growth and maximum yield. It will also help Madar monitor and manage hundreds of containers — among their retail models are options for customers to have Madar maintain containers for them, or to store and manage them. The app will be produced in English, Arabic, Hindi, Urdu and Tagalog.
Combining the two allows Madar to grow crops using less than 1 per cent of the water used in traditional methods, and do to so in a manner that makes the process easy and consistent. At the moment they’re concentrating on producing leafy greens such as lettuce, cabbage, herbs, and intend to add legumes and berries in the near future.
“You want people to convert from unsustainable farming habits to sustainable farming habits, but not only that, you want to produce a higher quality produce and all the spiel that comes with that. In order to encourage them to do so, you need to make it as accessible as possible to drive adoptability.”
Madar’s three operating units have served as a proving ground for the concept of a plug and play solution for its small team, who are quick to point out that their background is in business, not agriculture. “We don’t want someone to have an agricultural background. We want them to be able to do it if they know nothing about farming, and we want them to be able to do it consistently and in a standardised fashion. And we want them to be able to upscale as fast as possible.”
Come September, Madar will begin distributing units to customers; they already have orders to carry them through to year-end.
Each container will sell for between $85,000 and $95,000, depending on requirements (Madar is still refining the assembly process to bring costs down). Al Mulla estimates return on investment for each container at between four and seven years, depending on the cost of electricity.
They’re looking into building smaller units in re-used aircraft cargo containers, suitable for installation in restaurants.
The containers have considerable power requirements, which form a significant proportion of operating costs.
But Al Mulla is clear the containers are a stepping stone to a larger platform; they help increase awareness of the method and build the market, but will not solve the problem he is concerned with.
“When we talk about food security, which is our long-term aim, you have to produce a quantity of food, but the right mixture of food of high quality to feed and entire population. That’s our long-term goal and it’s what we’re going to get to. Growing leafy greens isn’t going to get us there.”
Madar’s next phase is a large-scale automated hydroponics factory. They intend to break ground in the third quarter of 2018.
“We take out the labour aspect completely. This automates using robots for transplanting, harvesting and packaging in a 40,000 square foot plant where we can grow 3,000 kilogrammes a day.”
That too is small scale compared to the target if food security for the region, but Al Mulla envisages a chain of plants, producing not only leafy greens but wheat, root crops and fruit. He’s looking also into automated fish farming.
Food Hygiene
Madar operates a strict sanitary process in its hydroponics containers. Al Mulla dons surgical gloves before handling equipment, and asks Gulf News’ reporter and photographer to don face masks and refrain from touching anything.
This is not only a matter of avoiding contamination of the plants, but of standardising the conditions, and the nutrient-laden water flowing through the stone-wool and cotton holders in which the plants grow.
Since there’s no spraying, and fertilisers are delivered through the roots, the sanitised conditions mean the plants can be eaten directly, without washing — something Al Mulla happily demonstrates back in his office as he offers around a pair of freshly harvested lettuces.
In fact, he says, washing the plants actually decreases their cleanliness; tap water is dirtier than they are (though still, of course, perfectly safe).
'Grow Food On Mars': LA Startups Tackle Climate Change With Inventive Solutions
'Grow Food On Mars': LA Startups Tackle Climate Change With Inventive Solutions
Dozens of startups are inventing ways to keep LA cool with products and services that aim to avert environmental disaster – and yield profits
The entrance to Laci’s La Kretz Innovation Campus, which mentors local startups. Photograph: Los Angeles Cleantech Incubator
Rory Carroll in Los Angeles | @rorycarroll72
Tuesday 18 July 2017 07.00 EDT
Drought, floods, wildfires and heat waves – climate change and extreme weather events are wreaking havoc in California, especially in Los Angeles. The city has recently baked in record temperatures with a long, hot summer still stretching ahead.
It is the new normal: climate models predict the number of extreme heat days, defined as more than 95F, will triple by the middle of the century.
Little wonder Hollywood is churning out desert dystopias in films such as Mad Max: Fury Road and The Bad Batch.
Reality, however, has an overlooked subplot: geeks are inventing ways to keep LA cool – and possibly mint fortunes in the process.
Dozens of startups have turned the city and nearby regions into a laboratory for products and services which they hope will avert environmental disaster and yield business models replicable across the globe, even beyond.
“We would welcome opportunities for off-planet growing,” said Brandon Martin, vice president of business development of Local Roots, which turns shipping containers into hydroponic farms. “We’d love to be the first company to grow food on Mars.”
He was completely serious. Engineers from Elon Musk’s Space X have studied how the company uses sensors, algorithms and machine learning to transform 40ft containers into the equivalent of three to five acres of farmland while using 97% less water.
“We want to be a billion-dollar company as soon as possible,” said Kipp Stroden, another Local Roots executive. “We’d like to feed at least a billion people in the next 10 years.”
Time will tell if that is hubris but it reflects the confidence of startups which think solving some of LA’s environmental challenges will open other markets in a heating planet.
“LA is essentially a giant opportunity to demonstrate their technologies,” said Mike Swords, vice president of government relations for Los Angeles Cleantech Incubator (Laci), a public-private nonprofit which mentors startups. “If you can demonstrate that your company can help solve problems here there’s a good chance you will export it to other urban areas around the world.”
Kipp Stroden at the entrance to one of Local Roots’s container farms. Photograph: Rory Carroll for the Guardian
LA’s biggest climate challenges were extreme heat and drought and increased fires, said Matt Petersen, who was the city’s first chief sustainability officer before recently taking over the reins at Laci. “Trees are job number one, and cool surfaced roofs and streets are key strategies as well,” he said.
LA’s mayor, Eric Garcetti, has set bold targets to reduce the so-called urban heat island effect, improve air quality and ease congestion. Voters approved two measures which will generate $150bn in the next decades – a sum exceeding Franklin Roosevelt’s New Deal, according to some estimates – to replace traffic gridlock, a major source of heat and pollution, with cleaner transport and shaded, pedestrian-friendly sidewalks.
“It’s a city that has taken the climate change challenge seriously,” said Adrienne Alvord, western states director of the Union of Concerned Scientists.
California’s governor, Jerry Brown, and the state legislature, meanwhile, champion a cap-and-trade programme and ever more ambitious renewable energy targets – big-spending rebuffs to the Trump administration’s environmental policies.
The result is an El Dorado of subsidies, favorable rules and fast growing markets for cleantech companies.
“It has the attributes of a gold rush,” said Mike Hopkins, CEO of Ice Energy, which makes air conditioning units that store energy and can cool homes without using electricity. “It’s a bit of a wild west, the rules are still being formed. Those who innovate and take risks, win.”
A potential big winner is GuardTop, an asphalt coating manufacturer which makes CoolSeal, a reflective street surface which can reduce temperatures by more than 10F. It is being piloted around LA.
You can see other green technology on display even before entering Laci’s La Kretz Innovation Campus, a 3.2-acre site in LA’s downtown arts district.
The car park boasts a canopy of solar panels which feed a microgrid supplying a third of the campus’s energy needs. A bioswale collects and recycles rainwater. Amid the Teslas and other vehicles sits a triple-function generator which can turn biomass, including banana peels and coconut shells, into electricity, heat or cool air. A “living wall” of 2,100 plants looms over the reception.
The incubator was founded in 2011 with money from the federal government, the city and the Los Angeles Department of Water and Power (DWP), and moved to this campus in 2015. It has outposts in Silicon Valley and Northridge and plans to open one in Mexico City.
“We want to bring the best cleantech companies from around the world, especially startups, and help them grow,” said Swords, the spokesman. “This level of coaching and mentoring is an incredible deal. Every single one of the companies plans to scale. They hope to sell their products all over the world.”
In return, he said, LA and its water and power utility will get the chance to acquire technology to combat climate change.
The DWP has a tradition of thinking big: a century ago it siphoned water from the Owens Valley to LA, a controversial rerouting fictionalized in Roman Polanski’s Chinatown.
Mike Swords, at the LA Cleantech Incubator’s ‘living wall’. Photograph: Rory Carroll for the Guardian
Laci will survive even if the Trump administration ends federal funding, which was important but not essential, said Swords.
The buzz on the Laci campus was unmistakable. Pick My Solar, which helps householders choose solar panels, has grown from five to 30 employees in a year. “With the heatwaves and brownouts people are thinking a lot about energy,” said Kyle Graycar, a company analyst.
Green Commuter, another company, says it is the US’s first all-electric vanpool. “We reduce the cost of commuting, the amount of traffic and CO2 emissions,” said Bart Sidles, as he drove one of the company’s Tesla SUVs up Alameda Street.
River LA, one of the incubator’s nonprofits, is also feeling emboldened: it has been tasked with helping to spend $100m in water bond money to transform the Los Angeles River, in places a sorry trickle, into a lush waterway.
Torrential winter rains ended California’s drought but Local Roots, the farming company, believes continued water shortages plus a growing population and pressure to reduce transport costs will make their container farms a common sight in parking lots across the US and beyond. One container can produce 4,000 heads of butterhead lettuce every 10 days using just 25 gallons of water daily, said Stroden, the executive.
Jonathan Parfrey, executive director of the nonprofit Climate Resolve, cautioned that LA will inevitably heat up. “We could all turn into vegans driving electric vehicles and we’d still see this.”
Low-income residents will suffer most – several studies have shown the inequitable impact. Poorer neighborhoods near the coast such as Compton will enjoy relative coolness but be vulnerable to gentrification, potentially pushing residents to the city’s hotter, eastern side, said Parfrey.
Even so, he was optimistic. Technologies were getting cheaper and smarter. “The antidote to climate despair is working on solutions.”
Urban Farming 2.0: From Plow Beams to Leafy Green Machines
Urban Farming 2.0: From Plow Beams to Leafy Green Machines
SEARCH FOR SOLUTIONS
A new generation of urban farmers is leaving dirt behind and turning shipping containers into tech-driven vertical farms.
Shane Witters Hicks/Staff
Shane Witters Hicks | Staff
JULY 26, 2017 BOSTON—Shawn Cooney swings open the door of 320-square-foot industrial shipping container to reveal a futuristic setting: hundreds of edible plants growing in vertical columns, fed by the energy from strings of neon red and blue LED lights. Nutrient-infused water cascades from ceiling spigots down through artificial root systems in the growing towers. The temperature inside feels like a comfortable spring day – about 70 degrees F., with a touch of humidity. There isn’t a speck of dirt anywhere.
Welcome to the new urban farm.
This shipping container is one of four that comprise Corner Stalk Farm run by Mr. Cooney and his wife in the heart of Boston. Once the cargo holds for exhaust-spewing 18-wheelers, these discarded freight vessels have been transformed into units known as Leafy Green Machines outfitted with state-of-the-art growing technology by a company called Freight Farms. Now they help farmers turn out crops of lettuce and herbs at a rapid pace.
In the past, urban farmers have eked a living from food grown in greenhouses, reclaimed brownfields, vacant lots, or rooftop farms. But with these new kinds of urban crops – grown using what’s known as controlled-environment agriculture, or CEA – farmers leverage technology to break free from the seasonal and climatic limitations that bind traditional crops. As a result, these farmers enjoy longer growing seasons and more plentiful harvests – a hopeful promise for urban communities looking to boost access to fresh produce.
“To think that you don’t have to worry about whether it’s going to rain, or whether the sun is too bright because you flick a switch and you know how much light you have, you know how much water is being supplied ... that would take a lot of the stress out of agriculture,” says Joel Gruver, associate professor and director of Western Illinois University's research and demonstration farm.
Getting fresh food into urban centers has proved to be a persistent and growing problem. By 2050, 66 percent of the world’s more than 9 billion people will live in cities, predicts the United Nations. While some cities offer farmers’ markets and have worked to open more grocery stores in so-called food deserts, these farmer-entrepreneurs are searching for solutions that will not only grow fresh food within city limits but also mitigate some of the environmental effects of traditional farming.
“People want real food. And increasingly people live in the city. So there has been – unsurprisingly – a lot of innovation and investment in urban farming in the last handful of years,” says Tobias Peggs, co-founder and chief executive officer of Square Roots Urban Growers in Brooklyn, N.Y. Upon launching, the company received more than 500 applicants for 10 farmer slots from those wanting to take up the challenge.
Easing An Environmental Burden
Small-scale sustainable farming and organic practices have long sought to lessen the environmental impacts of monocropping and pesticide reliance, but CEA has a significant advantage: the ability to scale up without significantly increasing its ecological footprint. The vertical farming market is expected to quadruple from its $1.5 billion market value in 2016 to $6.4 billion in 2023, according to a recent report by Allied Market Research.
In San Francisco, agrotech company Plenty boasts a 51,000-square-foot warehouse that leverages machine learning to optimize plant growth.
Nate Storey, Plenty’s co-founder and chief science officer, says the environmental benefits gained by fusing technology and food production make large-scale CEA a no-brainer.
“We have no runoff, we have no erosion, we have few, if any, pests, we don’t need to use many of the pesticides, we don’t have any soil to sterilize, we don’t have any intensive irrigation, we use a fraction of the water,” he explains. “There are just not a whole lot of reasons not to do this.”
Unlike other large-scale food producers who must optimize their goods for long truck rides and shelf lives, indoor growers located closer to customers can instead prioritize food quality, such as flavor and “mouth feel,” as Dr. Storey puts it.
For independent CEA farmers, starting up a controlled environment for indoor growing doesn’t come cheap. A Freight Farms unit costs $85,000 and the annual operating costs range between $8,000 and $16,500. But Cooney of Corner Stalk Farm, who bases the size of his crop on customer demand, explains that similarly sized outdoor farms are pressured to overproduce during short growing seasons.
“Their losses are much higher. So that’s why it comes out to be about the same,” he says. Moreover, other farms may spend a fortune on transportation and land. Taking up about 1/34th of an acre, Cooney’s lettuce farm can have a marketable yield that’s about the equivalent of 8 acres of traditional farmland yield, according to Freight Farms. And the indoor environment allows for a continual harvest.
But without the government subsidies that larger farms receive, greens grown within shipping containers will inevitably cost more than most supermarket greens.
“A bag of our Square Roots greens costs about as much as a Starbucks [coffee],” admits Mr. Peggs. He is quick to add that the enhanced sense of community fostered through farmer-customer relationships makes the price worthwhile.
“Customers come to the farm and hangout – we have a big window on the farm, so everyone can see what’s going on. It’s all about total transparency in the food-supply chain,” Peggs says.
But is High-Tech Food ‘Natural’?
The benefits of CEA may be tantalizing, but Dr. Gruver of Western Illinois University foresees potential difficulties for the burgeoning industry. Controlled-environment agriculture depends upon those who can operate and fix the technology. In other words, finding someone who can troubleshoot a malfunctioning LED system may prove more difficult than finding someone who can repair a tractor, for example.
And while local food and connections to the farmers who grow it have proven to be profitable in urban markets, not everyone embraces the idea of food grown exclusively in an artificial environment.
“I think with any high-tech approach, there is a general concern that it’s not natural,” says Gruver. “There’s more potential for unforeseen, unintended consequences.”
Urban tech growers are well aware of this perception.
“We’re sensitive to that,” responds Storey of Plenty. “We’re really focused on how do we show people that this new growing environment is something that is important for our food supply.”
Before indoor farmers can dominate the urban food arena, however, they’ll need to grow more than lettuce and herbs. The larger the plant, the more energy it costs to grow it, and this energy is currently expensive.
But based on the rapid pace of innovation and technology, Peggs predicts large, affordable produce may not be far off. He thinks his Square Roots entrepreneurs will figure out how to grow sustainable strawberries within 18 months.
“Imagine a farmer traipsing through 2 feet of snow to deliver you a box of freshly harvested, locally grown strawberries in the middle of a New York winter,” he says. “In the near future everyone will have local food and they will know your farmer.”
Make High Quality Food A Stable of The Culture
For today’s modern corporate campus, Freight Farms provides the opportunity to seamlessly integrate sustainable food production into current operations to make high-quality food a staple of the culture. Each farm offers a unique flexibility to create tailored programs to meet the specific needs of our clients. It becomes a powerful tool for promoting wellness, sustainability, and innovation while building an active community and fostering a culture of social responsibility and creativity.
Here are 7 ways to improve your corporate campus with the Leafy Green Machine:
Champion social responsibility: Companies seeking to reduce their carbon footprint are using the Leafy Green Machine (LGM) to offer great food at a low environmental cost. Google, the internet giant notorious for offering free breakfast, lunch, and dinner for their more than 20,000 employees, is growing produce in an LGM on their campus in Mountain View as part of their farm-to-table initiative.
Demonstrate your commitment to sustainability: Incorporating the Leafy Green Machine system into current operations is a way to showcase your business's commitment to sustainability through more environmentally-sound sourcing practices. Each farm acts as an immediate solution to shorten the food supply chain, thereby cutting fuel emissions, increasing transportation costs, and dramatically reducing the carbon footprint of any food operation. The innovative climate technology and energy-efficient growing equipment allows businesses to grow their own produce 365 days a year, regardless of the outside climate. The closed-loop hydroponic system uses over 90% less water than traditional agriculture, significantly reducing the environmental impact of food production.
Actively promote nutrition, health, and wellness: Today’s industry leaders recognize the importance of equipping employees with the tools and resources to help them lead successful, healthy lives both in and out of the workplace. Food has become a core component of every strategy, as more companies seek to provide the freshest, healthiest foods available to their staff. By equipping them with the right information, they are able to make more informed choices that support their health and in turn the health of the larger community.
Be an advocate for innovative technology and creativity: The Leafy Green Machine gives businesses and their food service teams the opportunity to explore new, innovative approaches to food production and provides a platform for education and engagement throughout each step of the process. Producing fresh food directly on campus with the latest growing technology makes it easy to captivate employees and facilitate a dialogue around food. Campus chefs have the ability to choose what to grow and how to incorporate it into their menus. Produce is grown on-site, and brought directly into the kitchens after harvest, ensuring employees get the freshest, most nutritious food available.
Serve up the freshest food for your employees year-round: Chef Kevin Gibbons of UMass Dartmouth is growing a variety of lettuces of herbs in the Leafy Green Machine on campus. In a recent interview, he told us, “we can harvest lettuce at 10:00 am and serve it for lunch later that day.” It doesn't get fresher than that!
Educate your employees about the food supply chain: Use the Leafy Green Machine as a tool to facilitate engagement and inspire change by providing employees with the opportunity to interact with food in a new way. Increase participation and collaboration by bringing transparency to operations and educating employees on the journey their food takes from farm to table.
Cut costs: Sourcing fresh produce and herbs during the winter months can be expensive. The Courtyard Marriott Grappone Conference Center in Concord, New Hampshire is growing lettuce, kale, spinach, arugula, and basil. Steve Duprey, the owner of the hotel, reported that during the winter months they are now able to produce basil at 1/10 of the cost of wholesale prices.
If you'd like to learn more about how Freight Farms is helping farmers grow food in regions across the United States, Canada, Europe, and the Caribbean reach out to us here.
FREIGHT FARMER Q&A: KARMA FARM
Jon Shaw has his roots in organic, soil-based farming. He has been an avid organic vegetable grower since he was a student in high school, and in 2009, after 45 years of gardening experience, Jon transformed his hobby into a career and launched Karma Farm
JUNE 8, 2017
6 Questions With Jon and Nathaniel Shaw of Karma Farm
One of the best parts of being part of the Freight Farms team is talking to our freight farmers and hearing about their successes, their businesses, their customers, and their challenges. They are a wealth of information, so now we are sharing some of their stories with you!
Jon Shaw has his roots in organic, soil-based farming. He has been an avid organic vegetable grower since he was a student in high school, and in 2009, after 45 years of gardening experience, Jon transformed his hobby into a career and launched Karma Farm. Located in Maryland, this family run farm decided to extend their growing season through the use of a hoop house, and now a Leafy Green Machine (LGM), which is run by Jon's son, Nathaniel. In addition to running a farm stand CSA, the Shaws provide area farm-to-table restaurants with leafy greens grown in the LGM year-round. With over 40 years of gardening and farming experience, Jon is a wonderful addition to our Freight Farmer community. We recently spoke with Jon and Nathaniel about the transition from traditional farming to hydroponics.
Freight Farms (FF): What, if any was your experience with farming before becoming a Freight Farmer?
Jon Shaw (JS): I started organic gardening in high school (circa 1972) and I have been growing vegetables ever since. Eight years ago, I decided to take a portion of my horse farm and turn it into commercial vegetable production.
FF: How did you find customers to buy your produce?
JS: We found many of our current customers our first summer when we grew too many tomatoes in our family garden and I decided I would go into town (Baltimore) to a few restaurants to give away samples or possibly sell them. Providing samples of our produce and explaining the breadth of our product line to chefs is still the main method we use to bring in new restaurants. Our customer base has also grown significantly from word of mouth as chefs tend to change jobs frequently.
FF: What is one small change everyone can make in their daily lives to make a big difference in our food system?
JS: Eat less meat and more vegetables.
“I was motivated to become a Freight Farmer because of my desire to turn our family farm into a sustainable business.”
FF: What’s the best part of being a Freight Farmer?
Nathaniel Shaw (NS): I’ve only been a Freight Farmer for a few months, but so far, the best things about it are bringing local chefs into the LGM to touch and taste the greens we are growing inside and seeing their surprise and excitement about the bold tastes and textures it can produce. Working with local chefs to find new greens and develop products that best utilize the advantages of the LGM has been an amazing process and one that I’m most excited to continue.
FF: What motivated you to become a farmer?
NS: I was motivated to become a Freight Farmer because of my desire to turn our family farm into a sustainable business. In recent years, we have worked to supply our restaurant customers with produce more consistently using row covers and hoop-houses, but our off-season production has remained slim. Our LGM gives us the ability to sustain a broader product line throughout the year and sustain our revenue and employee base over the winter.
FF: Which individuals, groups, and communities do you strive to reach and why have you chosen to get involved with these groups?
NS: We primarily target chefs at Farm-to-Table restaurants. The reason for this is that we love to grow beautiful and unusual produce and sell to chefs at mid to higher end restaurants that specialize in utilizing local ingredients. The restaurant community in nearby Baltimore is thriving and has grown with the farm as well.
Make sure to follow Karma Farm on Facebook and Instagram to check out pictures of Little Shaw (top dog in change) as well as beautiful shots from the farm!
If you'd like to learn more about how Freight Farms is helping farmers grow food in regions across the United States, Canada, Europe, and the Caribbean reach out to us here.
Square Roots Is Looking For Its Next Class of Urban Farmers
Square Roots doesn’t just offer a crash course in the mechanics of urban farming. After the farms yield their first harvests a few weeks into the program, participants are expected to begin making sales. They receive guidance from program mentors in creating sustainable business plans.
Jul. 19, 2017 9:55 am
One of Square Roots' vertical hydroponic farms. | (Photo courtesy of Square Roots)
Square Roots Is Looking For Its Next Class of Urban Farmers
The program equips participants to launch their own food businesses in a matter of months.
By April Joyner / CONTRIBUTOR
Square Roots, the urban farming accelerator based in the Pfizer Building, is taking applications for its second cohort of resident entrepreneurs. The next round of the program will begin in October.
The 13-month program includes access to the distinctive shipping-container farms, made by Boston-based Freight Farms, that participants use to grow food. Participants pay a $5,000 deposit to cover operating expenses for the first three months, but those funds are returned to them at the end of the program. To help front those costs, participants can apply for microloans through the Department of Agriculture, with which Square Roots has partnered.
Square Roots doesn’t just offer a crash course in the mechanics of urban farming. After the farms yield their first harvests a few weeks into the program, participants are expected to begin making sales. They receive guidance from program mentors in creating sustainable business plans. Members of Square Roots’ first class, for instance, have devised a variety of sales strategies for their products, from setting up shop in greenmarkets to courting the CrossFit crowd. The accelerator does not take equity in the participants’ resultant businesses, though it does take a percentage of their sales.
Applications for Square Roots’ second program are due July 31.
Agricool Raises $9.1 Million To Grow Fruits And Vegetables In Containers
Agricool Raises $9.1 Million To Grow Fruits And Vegetables In Containers
Posted Jul 11, 2017 by Romain Dillet (@romaindillet)
French startup Agricool is using containers to grow strawberries around big cities. The company just raised a $9.1 million (€8 million) funding round from Jacques-Antoine Granjon, Thibault Elziere as well as existing investors Henri Seydoux and Daphni.
The great thing about growing fruits in containers is that you can control everything. The company tweaks the temperature, humidity, CO2 level, color spectrum and day/night cycle to get the most out of the strawberries.
For instance, the company wanted to find the perfect LEDs to provide the right shade of light. It bought dozens of LEDs and tried them all, but even the best LED model was disappointing. Agricool ended up hiring someone to design its own LED with a specific shade.
Another interesting example, if you want to imitate the real world, you turn the lights on and off and on again every 24 hours. But do strawberries really need a 24-hour day cycle? Maybe 22 hours are enough and strawberries end up growing more quickly.
In order to do this, Agricool now has a warehouse outside of Paris where it can A/B test all these things using refrigerated rooms. Then, it can manufacture containers tailored to Agricool’s needs — think about it as the concept cars of containers. The company has produced 6 prototypes over the last 12 months.
But that was just step one. Agricool wants to go from concept cars to industrialized processes. Eventually, Agricool wants to outsource the production of those containers and put them around big cities globally.
This summer, the startup is going to put five containers around Paris. One in Bercy, another one next to Vente-Privée’s office, another one on Asnière’s market, etc.
“At first they tell you that strawberries are not going to have a great taste with LEDs, but they like them when they try them,” co-founder and CEO Guillaume Fourdinier told me. “Then they tell you that you can’t scale production, but you scale. And then they tell you you can’t distribute and now we’re going to distribute.”
A 250g pack of strawberries is going to cost €4. On average, Fourdinier says that organic strawberries coming from France cost around €6.70 for 250g.
The main reason why those strawberries are cheaper is because you don’t have to pay middlepersons. There’s no importing company, transportation company, central purchasing, supermarket, etc. Agricool grows strawberries where end customers are going to buy them.
“Our challenge is to find an industrial model that lets us grow quickly from 1 to 1,000 containers,” Fourdinier said. In order to do this, Agricool could eventually become a franchise. The company would focus on research & development, containers and branding, while partners would manage those containers and sell fruits and vegetables.
While the strawberry market is huge, the company is also thinking about producing common vegetables and fruits, such as lettuce, tomatoes, cucumbers, zucchinis and bell peppers. The same model can be used across all those vegetables.
“We want to build the biggest brand for fruits and vegetables,” Fourdinier said. “No pesticide, a lot of flavor, no GMO, harvested and sold on the same day.”
This Shipping-Container Farm Could Someday Solve The Food Desert Problem
This Shipping-Container Farm Could Someday Solve The Food Desert Problem
By Maura Judkis July 7, 2017
The inside of one of Local Roots’ shipping container farms. (Courtesy of Local Roots)
There’s a farm opening soon in Laurel, Md., that can grow strawberries in January. It could grow rare tropical fruits from Asia and Central America on our native soil. It could produce custom-designed lettuce, more peppery or sweet. It’s a hydroponic farm in a shipping container, and its owners hope it could eventually put an end to food deserts, including our biggest one: outer space.
Local Roots, a California company, has created an indoor farm that can turn any produce into local produce, anywhere. They grow fruits and vegetables in shipping containers that are stacked in old warehouses or parking lots, which can either be connected to the grid or, eventually, powered by solar energy. Local Roots has designed the custom growing technology and hardware, and it owns and operates the farms, selling its produce to restaurants and food distributors under its own brand. The fact that the company is vertically integrated differentiates it from other container farming systems, like Freight Farm, which sells their containers to others, including novice farmers.
[Want to get more people to eat their veggies? Make them sound like they’re bad for you.]
“You can start to bring that farm into communities that historically had to import their food due to geography, climate, weather, soil or light.” chief executive Eric Ellestad said.
Every 40-foot shipping container can yield the annual equivalent of three to five acres of farmland. Ellestad says his company can grow plants twice as fast as a conventional farm while using 97 percent less water.
Here’s how they do it: Every farm is hydroponic, meaning the plants are grown in nutrient-rich water instead of soil. Leftover water is recirculated, so each container only uses between 5 to 20 gallons each day. They also use sensors to keep tabs on how the plants are growing, and can give them exactly the nutrients they need at that phase in the growing cycle, speeding it up. It’s “almost a growing algorithm in some ways,” Ellestad said. “You can use that software platform to drive that farm as efficiently as possible.”
Included in that are LED lamps that give the plants exactly the right wavelengths of light they need to grow and which can bring out certain qualities in their appearance and flavor. Chlorophyll, the molecule that causes photosynthesis in plants, absorbs red and blue light, so the farms usually look pink or purple. With its rows of lights and repetition, a container farm that was on display at the South by Southwest conference in March felt a bit like stepping into a Yayoi Kusama infinity room.
A Local Roots farm at South by Southwest (Maura Judkis/TWP)
When they tool around with different growing conditions, they can bring out certain qualities in their produce — the same way that terroir gives grapes grown in California a different taste than ones grown in France.
[“Souping," birch water and Gochujang: 9 up-and-coming food trends]
“You can sit down and say, ‘What do you want your lettuce to taste like? Do you want it to be more peppery?’ ” Ellestad said. “Especially with basil, you can really accentuate some of those flavors. You can really sit down and co-design a product with a chef.”
All of the produce is grown organically, and there’s little risk of the types of E. coli scares that pop-up in conventional farming. “Occasionally a fly will get in, and that’s as serious as it gets,” Ellestad said.
Another key fact: Local Roots has figured out how to make the farm efficient enough that it can sell produce at a comparable cost to conventionally-grown fruits and veggies.
A Local Roots container farm on the move. (Courtesy of Local Roots)
“If you can only sell produce to affluent customers in the Northeast, then that’s a fantastic business but you’re not really going to change how the food system functions for most Americans,” Ellestad said.
They already have a farm of several dozen containers up and running in Los Angeles, and later this year, they’re bringing one to D.C. It will be located in Laurel because it’s adjacent to Coastal Sunbelt Produce, a major food distributor in the area that has partnered with Local Roots. Co-locating the farms means that they won’t have to worry about transportation time or costs — which also means the produce will be selected for its flavor, rather than its hardiness, as many vegetables that must travel long distances are.
“We’re pretty excited about the freshness, just having it grown about as local as it can get,” said Jason Lambros, vice president of purchasing for Coastal Sunbelt. “We can be a neat place for them to experiment and grow anything we can dream of, because we have the customers for it.”
The flexibility and scalability of the farms has huge implications for food deserts, a term for communities that have many fast food restaurants, but few places to purchase fresh, nutritious food. Once Local Roots has scouted a location and set up a farm, its first harvest can take place only four weeks later. The company could drop a farm in the middle of Alaska, where a bag of lettuce can cost nearly $6, or in famine-stricken South Sudan, or here in Anacostia, where there are only three full-service grocery stores in Ward 3.
[The next big march in Washington should be for food, celebrity chefs say]
So why don’t they? It’s about having the infrastructure to distribute the food properly, Ellestad said.
“I think simply helicoptering a farm into a food desert could be part of the solution,” Ellestad said. “We would want to partner with the groups that are already working in that community … we can’t operate in isolation. The food system is far too complex and localized.”
For example, they could put a container farm in a neighborhood with few amenities and sell their produce to corner stores, but if the corner stores don’t have refrigerated cases for produce, it would rot. They are currently seeking partners that work in food deserts, as well as literal ones — “In the Middle East, there’s obviously huge food-supply-chain issues in those areas,” he said. Container farms could be a solution for disaster relief after earthquakes, floods or humanitarian crises.
But they’re also looking a bit further. The company is talking to aerospace manufacturer Space X because these types of growing systems could one day be used to feed astronauts on long-term missions to other planets. “The opportunities are global and intergalactic at the same time,” said Ellestad.
For now, they’re going to begin growing lettuce, herbs and microgreens in the area, while expanding to other cities in the United States. And as efficient as indoor growing is, Ellestad doesn’t think it will replace good, old-fashioned rain, sun and soil.
40-foot Shipping Container Farm Can Grow 5 Acres of Food With 97% Less Water
The 40-foot containers house hydroponic farms that only draw on five to 20 gallons of water each day to grow produce like lettuce, strawberries, or kale.
40-foot Shipping Container Farm Can Grow 5 Acres of Food With 97% Less Water
by Lacy Cooke
Communities that have to ship in fresh food from far away could start getting local produce right from their parking lots or warehouses thanks to Local Roots‘ shipping container farms. The 40-foot containers house hydroponic farms that only draw on five to 20 gallons of water each day to grow produce like lettuce, strawberries, or kale. Popping up all around the United States, these scalable farms “grow far more produce than any other indoor farming solution on the market” according to co-founder Dan Kuenzi. Local Roots is even talking with SpaceX about using their farms in space.
Local Roots’ 40-foot shipping container farms, called TerraFarms, grow produce twice as fast as a traditional farm, all while using 97 percent less water and zero pesticides or herbicides. They can grow as much food as could be grown on three to five acres. They’re able to do this thanks to LED lights tuned to specific wavelengths and intensities, and sensor systems monitoring water, nutrient, and atmospheric conditions.
Related: Pop-up shipping container farm puts a full acre of lettuce in your backyard
The process from setup to first harvest takes only around four weeks. TerraFarms can be stacked and connected to the local grid. CEO Eric Ellestad said in a video 30 million Americans live in food deserts, and their farms could be placed right in communities that most need the food.
Los Angeles is already home to a farm with several shipping containers, and a similar one will be coming to Maryland this year. It could offer local food like strawberries in January.
And Local Roots’ technology could one day allow astronauts to consume fresh produce in space. Their growing systems could offer a food source on long-term, deep space missions. Ellestad told The Washington Post, “The opportunities are global and intergalactic at the same time.”
Launching Of Its Start-Up: Agricool Prepares Its Meeting With The Public
Launching Of Its Start-Up: Agricool Prepares Its Meeting With The Public
NICOLAS RAULINE Le 30/05 à 01:00
Strawberries that grow in Agricool containers require neither pesticides nor GMOs and consume 90% less water compared to a conventional crop. - Photo Tony Trichanh
A part of the future of agriculture is perhaps taking shape, at this moment, in the heart of an industrial zone in La Courneuve. It is there, in the suburbs of Paris, in Seine-Saint-Denis, that Agriculture has set up its quarters. It must be said that the start-up needed space to grow its strawberries . Since its creation less than two years ago, its young founders, neither farmers nor agronomists, but themselves sons of peasants, claim to want to revolutionize the sector with a new process. They recycled containers, arranged them for deployment of strawberry walls, separated from LED lighting walls. Temperature, humidity, light ... Everything is measured, controlled. With one goal: "get the best taste in the end". Subjective, The objective? "When we test 10,000 people, subjectivity no longer exists," says Guillaume Fourdinier, co-founder of Agricool. "In our approach, we wanted to eliminate all certainties. This is why we constantly test the sugar content, the vitamin content and so on. If tomorrow we realize that changing the culture temperature by one degree has a positive impact on taste and nutritional value, we will do it. Everything is possible. In containers you can even create shorter days! " We wanted to remove all certainties. This is why we constantly test the sugar content, the vitamin content and so on. If tomorrow we realize that changing the culture temperature by one degree has a positive impact on taste and nutritional value, we will do it. Everything is possible. In containers you can even create shorter days! " We wanted to remove all certainties. This is why we constantly test the sugar content, the vitamin content and so on. If tomorrow we realize that changing the culture temperature by one degree has a positive impact on taste and nutritional value, we will do it. Everything is possible. In containers you can even create shorter days! "
READ ALSO
For example, in the 1,500 square meters of warehouses and offices owned by Agricool in La Courneuve, developers, agronomists, workers who build containers, electrical engineers and plant physiologists are active. The strawberries are never far, measured, observed, tasted permanently ... "We were able to build a unique team," welcomes Guillaume Fourdinier. After the recent € 4 million fundraiser (led by Daphni), the workforce grew to thirty-three . And everything is done internally. Even the LEDs: no solution of the market was really adapted to strawberries, the young shoot decided to create his own. It also disposed of hives,
"Reasonable" Rates
The advantages of the developed technique are manifold. The start-up does not use GMOs or pesticides and consumes 90% less watercompared to a conventional crop, in particular because the water used to irrigate the plants is recovered under the vertical walls. And above all, Agricool wants to reduce the distance between the place of production and the place of consumption , to "twenty kilometers at the most" . "This is the paradox of" organic ", adds Guillaume Fourdinier. Since there are fewer production sites, we travel more kilometers to deliver, with all the consequences that may have on the environment. " The start-up do not short a label behind which it could,
After the R & D phase, Agricool is preparing to face the public. The first strawberries will go on sale in early July. Nearly 8,000 people are already registered . A wait that could put Agricool in a position of strength, but the young shoot wants to keep prices reasonable. "We are doing this so that we consume better and that quality is accessible to all," repeats the young entrepreneur. It therefore ensures that the price will, on average, be 15 to 20% lower than that of organic products .
7 Tons of Strawberries Per Year Per Container
At full throttle, the start-up estimates that it will be able to deliver 7 tons of strawberries per year and per container, ie 800 trays per week . "The market is huge," explains Guillaume Fourdinier. To produce 20% of all strawberries consumed by Parisians, we would need 600 containers. " To achieve one day, on this scale, Agricool wants to put its containers available to all those interested: companies, new" urban farmers "... After his first container to Bercy Park, removed from the start-up Has installed one on the site of Vente-privée in Saint-Denis . Another will follow at the entrance of Station F, the start-up campus created by Xavier Niel . "But it will be necessary to fill in a complete specifications , " says Guillaume Fourdinier. "Farmers" will need to be trained, and then engage, for example, to sell locally .
HELLO
Let's take off !
Agricool is a crazy bet : building the future of farming.
Since the launch in 2015, our team works day and night to get there.
Today we need you.
You who are 3000% behind our mission.
We prepared a video to present the project.
Take a look at it. Share it on your social networks.
It's time to introduce our mission to the world ! ️
We also took the opportunity to redo our website.
To discover it is here.
We Are Building A Farm Out of Shipping Containers in Downtown Mobile
We Are Building A Farm Out of Shipping Containers in Downtown Mobile
JULY 2, 2017
“We are building Shipshape Urban Farms, eight hydroponic farms, on St. Michael Street in downtown Mobile. The whole space is the equivalent of a 20-acre farm on less than 1/4 of an acre and over 56,000 plants can grow at once. We will harvest nearly 9,000 heads of lettuces, herbs, leafy greens, and small vegetables a week and the growing season is 365 days a year. The farm is built from repurposed shipping containers because shipping containers were developed in Mobile in the 1950’s. The first harvest will be the end of November or the first of December. We can also host garden parties and events there.
Baldwin County was all farmland when I was a kid and now it is track houses. We are creating a way to take farmland back in a very small space by growing vertically instead of horizontal and using three-dimensional space. We have also taken out environmental pressures by using LED lighting and drip irrigation systems so plants don’t have to grow in soil. Everything is dense and the root structure sits in a permeable mesh. The water recycles through, it gets to the bottom and goes back up again, so we use the equivalent of 10 gallons of water a day. That is 90 percent less water than a traditional farm. We will be non-GMO and won’t use any pesticides
We will also grow herbs on a vertical wall that is about 700 square feet. We are doing an annual CSA, which is Community Supported Agriculture, and people can buy a share of a crop. It is a way to keep food local and support farmers.
Angela and I have been working on this for nearly two years. I have a background in landscape architecture and urban planning and she has a background in horticulture and she researched hydroponics. I worked for the Bloomberg team and went to work for Auburn as an adjunct professor then we started Shipshape. I am an Iraq war vet and this will have a certification for Homegrown Heroes, certifying this farm is produced by a veteran family. Starting a business is stressful and financing is challenging. It took a while to get our first dollar and show the banks that Mobile wants this. People can support it now by signing up for the CSA.
“This farm has been the focal point of all of our conversations the last two years. We had to figure out how to do bring this to Mobile. We are lucky that our backgrounds compliment each other.”
“We plan to sell to restaurants downtown, farmers markets, and directly to the consumer through CSAs. A lot of the local restaurant owners are interested. Nothing that is worth doing comes easy. Several years ago, people thought we were crazy to live downtown, now everyone thinks it is amazing and asks how they can get an apartment. It is cool to be in Mobile at this time. We are 20 years too late to hit the big cities like Seattle and Austin but you can make a” big difference here. Downtown Mobile two years from now is going to be a very different place from where it is today. It is totally different than it was two years ago.”
“We talked about going to a big city where it would be easy to start this farm, but we wanted to stay here and bring it home. We would like to expand it to other areas on the Gulf Coast.I look forward to seeing our name on a chalkboard outside of a restaurant. It gives me chills thinking about it.”
“Science brought us together. We met in a Biology lab at Faulkner. I walked into class late and she was sitting in the front row. I sat next to her because I thought she was cute.”
“We started as study buddies. I am sure we made the people behind us want to throw up. We were taking night classes and the labs were long. We had the highest grades in the class because studying was an excuse to be together. I guess it worked.”
(You can support Shipshape Urban Farms by joining their CSA)
Urban Crop Solutions Collaborates With Albert Heijn (Ahold Delhaize) & Bakker Barendrecht
Urban Crop Solutions Collaborates With Albert Heijn (Ahold Delhaize) & Bakker Barendrecht
Climate change, the global lack of arable land and the fact that more and more people are living in cities are a real challenge for the daily supply of fresh and healthy food for retail companies.
As an innovative and progressive retail company Albert Heijn, member of the global retail group Ahold Delhaize, is always seeking to work with partners using the most advanced cultivation methods, for the benefit of their customers. As a major vegetable and fruit supplier for Albert Heijn, Bakker Barendrecht plays a significant role in this process. The past three days Urban Crop Solutions (UCS), a specialist and reference as a global total solution provider in the fast emerging world of indoor vertical farming, teamed up with Albert Heijn and Bakker Barendrecht
Already more than a decade ago Albert Heijn has acknowledged the importance of sustainable cultivation methods. At the same time, their supplier for herbs, Tuinderij Bevelander, has begun to produce chives with hydroponic systems. Nowadays, the customer can still buy these chives produced on water at Albert Heijn. The implementation of this innovative cultivation method is becoming more accessible, due to the increasing technological developments. UCS is playing a key role in making indoor vertical farming systems more accessible. The agtech company develops tailored plant growth installations (PlantFactory), has its own range of standard growth container products (FarmFlex and FarmPro) and has an in-house team of plant biologists which develops plant growth recipes to grow a wide range of crops in these installations.
UCS has joined forces with Albert Heijn and Bakker Barendrecht in order to promote this high-tech method of cultivating. A FarmFlex container was strategically placed in front of the headquarters of Ahold Delhaize in Zaandam (The Netherlands) where the past three days employees could visit this mobile indoor vertical farming system. Global Sales Director, Brecht Stubbe and Chief Technical Officer, Dr. Oscar Navarrete were on-site to provide detailed information.
“The past 3 days were a very intense experience”, explains Brecht Stubbe, responsible for Urban Crop Solutions for this project, “Working together with these well reputed cultivator and retailer group confirms our view that our solutions will definitely be part of the solution to meet with the ambitions of our partners to supply their customers daily with fresh and healthy food.”
Sun Bandit Produces Solar Hot Water In Sub-Zero Temperatures to Heat Dwellings and Grow Fresh Produce North of the Arctic Circle
Sun Bandit Produces Solar Hot Water In Sub-Zero Temperatures to Heat Dwellings and Grow Fresh Produce North of the Arctic Circle
Freeze-Resistant Properties Allow World’s First Certified PV-Powered Solar Water Heating System to Heat Water, Channel Stored Energy to Feed Radiant Wall and Floor Heating and Extend Growing Season for Hydroponically Produced Fresh Vegetables In Sub-Zero Temperatures
The world's first solar hydroponic trailer to grow fresh produce north of the Arctic Circle.
LAFAYETTE, COLORADO (PRWEB) JUNE 23, 2017
Next Generation Energy’s Sun Bandit celebrated the Summer Solstice by shedding light on the first off-grid photovoltaic (PV) solar water heating solution to heat water, channel stored energy into radiant heating and hydroponically grow fresh vegetables in sub-zero temperatures -- NORTH of the Arctic Circle.
Freezing temperatures are no longer a barrier to solar hot water production.
The 26-foot Solar Hydroponic Trailer manifesting this innovation is located in the enterprising village of Kotzebue, Alaska, the hub of 11 Native Alaskan villages in the state’s Northwest Arctic Borough. Kotzebue is 26 miles north of the Arctic Circle, in the Land of the Midnight Sun. It’s an inspiring time to celebrate the power of solar energy -- and Sun Bandit’s expanded solar applications.
The Solar Hydroponic Trailer is the brainchild of Ingemar Mathiasson and solar thermal veteran Mark Houston, founder and CEO of Anchorage-based The Comforts of Home, LLC. A Passive House Institute (PHIUS)-certified* contractor/energy rater, Houston has been advising clients on energy conservation and alternative energy concepts for 30 years.
“For the first time, we can keep the trailer at 74 degrees in sub-zero temperatures, which allows growing to begin as early as March,” said Houston. “We are collecting solar energy, converting it to heat, and running it through a glycol-based radiant floor and wall panel that provides all of the heat we need to grow a bounty of fresh produce in often-dark, bitter-cold conditions for about nine months of the year.”
The project was inspired when Mathiasson, the energy coordinator representing the Inupiat village of Kotzebue, asked Houston to build a sustainable, cost-effective solution to keep a trailer warm enough to grow fresh vegetables throughout the year.
It’s a tall task, as temperatures in Kotzebue swing from a bitter 40 degrees below zero in winter to a chilly 54 degrees Fahrenheit in the summer. Even during the summer, it’s simply not warm enough to sustain a large community garden. With an average daily temperature of 21.8 degrees Fahrenheit, the best ‘vehicle’ to consistently serve the village with fresh produce was a hydroponic trailer.
The desire to grow fresh vegetables in many remote areas of Alaska isn’t new; Alaskans import up to 95% of their food. Houston says there are companies shipping hydroponic growing containers to Alaska, but they’re overly-sophisticated for the market. They have rotating racks and a bevy of bells and whistles. And they use oil, which can run from $6 to $11 a gallon, depending on the location. Not only is oil expensive for many Alaskans (it has to be refined and then delivered by ship or flown to remote villages), it is finite. It can be a long wait for a delivery truck trekking across the tundra to replenish one’s fuel reservoir – or any household goods for that matter.
Kotzebue had tried using oil to heat their hydroponic trailer, but when it came time to ventilate the space to eliminate water vapor emitted by the plants, the ventilation systems (sometimes as rudimentary as simple fans) rid the trailer of moisture, but took the heat as well, fostering less than ideal growing conditions.
To solve the heat loss problem, Houston introduced a Minotair Air Source Heat Pump (ASHP) to remove unwanted moisture and contaminants and replenish the trailer with fresh outdoor air. Before leaving the trailer, the ASHP heats the stale, damp exhausting air to 150 degrees. The heated air blends with fresh incoming air (whose temperatures can be as low as 40 degrees below zero), warming it to 66 degrees Fahrenheit before returning it to the growing area. This is a critical process, as air colder that that would damage or kill the plants.
When village elders got wind of Sun Bandit, they asked Houston to conceive of a cleaner concept using Sun Bandit as the primary heat source. “They didn’t need anything fancy. They just wanted a place they could reliably grow things. And they wanted to heat it without using oil,” Houston said. “Burning oil (and the cash that goes with it) wasn’t working for them.”
By integrating Sun Bandit’s solar electric hybrid water heating and storage solution with hydronic heating hybridized with a Sanden Air Source Heat Pump and air sealing with urethane foam, Houston has delivered a lower cost, oil-free innovation that provides fresh vegetables year-round in a difficult growing climate – and with a reduced carbon footprint.
Seven to eight months of the nine-month Solar Hydroponic Trailer growing season will be supported using free solar hot water and radiant heat from stored Sun Bandit energy. Sun Bandit optimizes energy production with an arsenal of built-in back-up options for days when the sun doesn’t shine. In off-grid situations, Sun Bandit solar hybrid water heaters can be configured with a small wind turbine or battery backup to heat water and – as the Kotzebue project illustrates -- support radiant floor heating and hydroponics. Sun Bandit is equipped to use grid-fed electricity when solar is not available as well. View a detailed slide presentation of Houston’s solution by clicking here.
Sun Bandit was selected for this project because it performs where old-school solar water heating systems can’t, eliminating fluids, leaks, pump stations, overheating, stagnation, freezing and the complicated installation and maintenance issues that can plague traditional mechanical solar water heating systems.
“The exciting takeaway here is that freezing temperatures are no longer a barrier to solar hot water production -- even in extreme conditions,” said Next Generation Energy CEO Dave Kreutzman. See Sun Bandit’s white paper on “Redefining Solar Hot Water Efficiency” by clicking here.
As a small business owner, installer and energy rater, Houston sees the broader market potential for Sun Bandit-centered solar hot water and heating solutions in homes; he's already working with clients eager to begin.
“I’ve been in this business for decades. The Kotzebue project demonstrates that PV-powered Sun Bandit is a much better product to use in colder regions: it’s simple, low-maintenance and it can be installed in one third the time. It’s really the only one that works in the coldest, darkest of climates. And in its solar heating applications, Sun Bandit is four times more efficient than regular electric heat,” Houston said. “At the end of the day --- particularly the longest day of the year -- people don’t want to have to fix things in freezing temperatures. They just want them to work. That is where Sun Bandit shines.”
About Next Generation Energy's Sun Bandit® : Sun Bandit is a trademark-registered, patented product innovation of Colorado-based Next Generation Energy (NGE®), whose expertise in PV, solar thermal and off-grid system design and engineering have been delivering high-performing, money-saving renewable energy solutions to commercial, utility-scale, governmental, individual and multi-family housing interests for over 30 years. Learn more by calling 877-NGE-4SUN – or visit http://www.ngeus.com. Find Sun Bandit at http://www.sunbandit.us.
Indoor Farming Plus Made In USA LED Grow Lights: Profile 1.1
Indoor Farming Plus Made In USA LED Grow Lights: Profile 1.1
GREENandSAVE Staff
Posted: Monday. 12th June 2017
This is one of the profiles in an ongoing series covering next generation agriculture. We are seeing an increased trend for indoor farming across the United States and around the world. This is a positive trend given that local farming reduces adverse CO2 emissions from moving food long distances. If you would like us to review and profile your company, just let us know! Contact Us.
Company Profile: Tiger Corner Farms Manufacturing
Here is a great example of a company specializing in aeroponics.
Here is some of the “About Us” content: We’re a team of builders, growers, geeks, problem solvers, foodies, parents, engineers and enthusiasts designing farm systems that transform the way we eat. Our aeroponic container farms were born from a dream that every individual deserves access to healthy food—and that dream starts right here at our home in South Carolina. Our mission is to create container farm systems that power healthier, sustainable communities. Housed in recycled shipping containers, the TCFM aeroponic farm system is customized with an innovative cloud-based control system that allows growers 24-hour, 365-day monitoring of each plant from seed to sale and the ability to adjust any farm system setting from any computer, tablet, or mobile device. A single farm can be grown in any climate, in any location, using 98% less water than traditional farming—a healthy, fresh, and sustainable approach to achieving bountiful harvests in a small space. Tiger Corner Farms Manufacturing is locally owned and operated in Summerville, SC.
Here is the link to learn more: http://tigercornerfarmsmfg.com/
To date, the cost of man made lighting has been a barrier for indoor agriculture. A new generation of LED lighting provides cost effective opportunities for farmers to deliver local produce. Warehouses and greenhouses are both viable structures for next generation agriculture. Here is one example of next generation made in USA led grow light technology to help farmers:
Engineers Use Shipping Containers For New Spin on Ancient Practice, Hydroponics
Engineers Use Shipping Containers For New Spin on Ancient Practice, Hydroponics
By Staff Reports - 6/8/17 6:27 PM
INDIANAPOLIS — Hydroponics — growing crops in water only, without soil — dates back to the first century, in the Roman Empire.
But four millennials working out of a barn just east of Indianapolis are putting a new spin on the old farming technique. And they’re using a surprising space for it.
During an educational outreach mission that took him through South Africa, Chris Moorman came up with a novel idea for refrigerated shipping containers.
Produce — and lots of it — could be grown in them, he surmised after a casual conversation with a local resident that somehow turned to the topic of uses for discarded shipping containers.
After concluding his overseas mission and a five-year tour as a Wall Street stock broker, Moorman decided to build a business on the unusual idea.
An acre’s worth of produce can be harvested from a 40-foot shipping container outfitted with his company’s high-tech system, according to the 30-year-old Bedford native.
These days, hydroponics is most often conducted in a greenhouse, but that involves high construction costs and building permits.
Moorman’s company, Greenfield-based Rubicon Agriculture, offers a self-contained, fully enclosed hydroponics unit, called an AgroBox, for $75,000. A higher-yield model costs $82,000.
Heads of lettuce in Rubicon’s AgroBox mature in less than half the time as those grown outside in a field.
“I’ve seen a lot of hydroponics operations, but I’ve never seen or heard of one using a shipping container,” said Robert Rode, lab manager of Purdue University’s AquaCulture Research Lab.
Rubicon’s founders’ backgrounds are as unique as their ideas. None of them have farmed.
Moorman, who graduated from Purdue University with an economics degree and is Rubicon’s CEO, spent his early career as a commodities trader before discovering his passion for sustainable agriculture during a year-long sojourn through several developing countries.
Moorman’s younger brother, Erik, 26, served as a nuclear engineer in the U.S. Navy. Serving on the USN Newport News, he learned about closed-circuit water systems in agriculture.
Jesse Robbins, 26, who, like the Moorman brothers, is from Bedford, and Pat Burton, 28, a Greenfield native, previously worked with automation technology in manufacturing that they now apply to the growing process. Both graduated from Purdue with electrical engineering degrees.
“We’re an eclectic group, but we all have vital skills we bring to the table,” Moorman said.
Initially, they had difficulty finding financing.
“We were a bunch of guys who never grew anything,” looking for funding to start an agricultural company, Moorman said with a laugh.
Eventually, the founders started the firm with $60,000 from their own pockets.
The company, which launched in July 2015, is approaching profitability, Moorman said.
Built-in Advantages
Rubicon’s system has several advantages, he said. It’s “easily movable with a semitruck and a winch. You can put it anywhere.”Also, because the containers are refrigerated, “they have a great insulation rating,” Moorman said, making temperature control — critical for maximum hydroponics production — easier and more efficient.
An added plus for Rubicon is that it can buy the containers — after they’ve made myriad trips across the globe — for pennies on the dollar.
About 2,500 plants can be placed on each unit’s floor-to-ceiling tiered shelving and, with only a water and electrical hookup, growers can control conditions inside a Rubicon unit with “pinpoint precision,” Moorman said. The key, he added, is a data-collection system that allows growers to monitor conditions for optimal growth.
“If I can’t act on the data, the data is just noise,” Moorman said. “Having our system is all about actionable data.”
Driven by Mitsubishi control components, the system is akin to those used in advanced manufacturing, he said.
Rubicon’s units are outfitted with LED lights and a system that controls light spectrum and wavelength, a climate control unit that tightly monitors and controls oxygen and carbon dioxide levels, and a hydration system that recirculates water with a precise mix of nutrients and a carefully set pH balance. Moorman boasts that Rubicon’s system uses only 10 percent as much water as traditional farming.
“One of the best parts of our system is, it doesn’t require pesticides or herbicides,” Moorman said. “It’s completely organic.”
But hydroponics comes with serious challenges, said Darin Kelly, who operates Good Life Farms in Eminence.
The technique “is technical and not simple,” said Kelly, who grows crops traditionally and through hydroponics. “You’ve got to worry about plumbing, slope, pressure and measuring nutrients. You become a plumber; you become an electrician.”
With Rubicon’s system, zoning can be a concern, too, Moorman admitted. Since this is a new concept, local zoning officials are still working out the regulations.
Rubicon’s system is best suited for predictably growing plants that don’t stretch upward too much or have lots of inedible biomass, like corn. Plants like snap peas, kale, basil, oregano, spinach, cilantro and lettuce are ideal.
Moorman said a head of lettuce grown in the field takes more than 60 days to mature — but only 24 in Rubicon’s unit. By using phased growing, Moorman said, farmers using Rubicon’s system can produce 500 heads of lettuce weekly year-round from a single 320-square-foot container unit.
“For a space that small, that type of production is really super,” Purdue’s Rode said. “It may even be optimistic. But if they can achieve that, it’s very, very good.”
Educational Component
Moorman has been working to get his system in the hands of several Hoosier high schools, including Shortridge High School in Indianapolis, another in southern Indiana, and one in Omaha, Nebraska. He said it’s a great teaching tool.“We’re going to have a generation of farmers that don’t live on farms,” Moorman said.
But the technology can go beyond farming.
It’s the same as that used “to make an intake manifold,” he said. “There’s a real workforce-development part of this.”
He predicted Rubicon’s portable system will also be key in furthering the farm-to-table movement and could help solve the problem of food deserts — neighborhoods, often low-income, that are more than a mile from a grocery store.
“The average American meal travels more than 1,500 miles from farm to plate,” Moorman said. “Of all the produce consumed in the U.S., 50 percent of it is grown in California, where there is a major water shortage. Those aren’t sustainable trends.
“We’re taking something — a shipping container — that has been bringing food to you in a more traditional sense and putting it back to work growing food right in your local neighborhood.”
No Aquaponics
One field Moorman has no interest in is aquaponics, a system not quite as old as hydroponics, but nevertheless one that has been around several centuries. In aquaponics, Rode said, producers have to balance two ecosystems that aren’t always compatible.Aquaponics operations use controlled ponds — often indoors — to raise fish, usually a hardy species like tilapia. The plants draw from the bionutrients in the fish ponds. The upside to aquaponics: Operators can sell both fish and crops. But Rode said establishing conditions that both the fish and crops can thrive in is tough.
“The fish and plants often prefer different pH levels and water temperatures,” he said.
Moorman said there’s plenty to harvest with the more manageable hydroponics. The U.S. hydroponics industry is projected to hit $9 billion by 2020, according to multiple sources. Moorman said Indiana can nab $2 billion of that, pointing out that Indiana and the four surrounding states spend $20 billion on produce annually.
“We think there’s an opportunity for Indiana to be a powerhouse of produce,” Moorman said. “But that opportunity comes with a lot of education. ”
With Shipping Container, Fidelis Greens Fuses Technology, Farming
With Shipping Container, Fidelis Greens Fuses Technology, Farming
Credit: Josh Mandell, Charlottesville Tomorrow
Fidelis Greens aims to sell its fresh and sustainably produced microgreens to farm-to-table restaurants in Central Virginia year-round. From left: Kyle McCrory, Andre Ortiz, Joel Shindeldecker
Fidelis Greens, an agricultural startup near Crozet, is located on a picturesque 154-acre farm. But most of its work is confined to a much smaller space.
The company grows tiny, flavorful microgreens inside a repurposed steel shipping container, including arugula, amaranth, mustard greens and a "spicy mix" of several varieties.
The business aims to sell its fresh and sustainably produced microgreens to farm-to-table restaurants in Central Virginia year-round, giving chefs a local alternative to greens shipped from California and Mexico during the winter.
Joel Shindeldecker, who leads the company's marketing and sales, said the shipping container's hydroponic growing system can equal the output of a 2.5-acre plot of land, but requires much less water and allows for more consistent quality.
Fidelis Greens harvested its first microgreens earlier this year and has plans to share its open-source approach to indoor, "vertical" farming. They will be joined in the Charlottesville-area market by Freight Farms, a Boston-based startup that is bringing shipping container growing units to the Barracks Road and 29th Place shopping centers.
Fidelis Greens co-founder Randy Caldejon said his company has designed a simple, low-cost model for shipping container farms, while using computer technology to perfect the growing process.
"I'm fascinated by ways that farmers can optimize productivity and sustainability with software and machine learning," he said.
Caldejon previously co-founded nPulse Technologies, a network security firm that was acquired by FireEye in 2014 for more than $60 million.
Caldejon now supervises Fidelis Farm & Technologies, an incubator for agricultural startups at his Albemarle County estate. Fidelis Greens is the incubator's first venture and the startup has five team members who serve the company in multiple roles.
Kyle McCrory, an Albemarle native, brought expertise in industrial design and horticulture to the company. After graduating from Virginia Tech in 2010, McCrory started his career at Gotham Greens, which operates several large greenhouses in New York City and Chicago.
Credit: Josh Mandell, Charlottesville Tomorrow
Fidelis Greens currently specializes in four kinds of microgreens: arugula, amaranth, mustard greens and a “spicy mix” of several varieties.
"It was a great experience to be part of one of the pioneers in this field," he said. "I wanted to bring what I learned back home."
Fidelis Greens' shipping container farm became fully operational in mid-March, when many traditional farmers in Virginia feared a late winter storm could jeopardize the upcoming growing season.
Andre Ortiz said Fidelis Greens spent a few thousand dollars on a shipping container that had only gone through one voyage, even though heavily used containers can be purchased for much less.
The team insulated the container with spray foam, and built a hydroponic growing system out of materials that can be found at most hardware stores.
The container currently has six shelves installed on one side of the container that fit a total of 216 standard gardening trays. Shindeldecker said the company hopes to add six more shelves to the other wall.
Once seeds sprout into microgreens in seven to 10 days, Fidelis Greens delivers trays of live greens to restaurants that chefs can clip and serve as needed. The reusable trays avoid the waste generated by plastic clamshell packaging.
Shindeldecker said one of Fidelis Greens' strengths is the shipping container's automated climate control system, which combines open-source computer hardware and software with additional programming by Caldejon.
Caldejon's software automatically adjusts the container's air conditioning unit and fans to keep the temperature in the container constant at 77 degrees during the day, and 65 at night. It reads data from sensors placed throughout the container to regulate humidity, vapor pressure deficit and carbon dioxide levels.
Fidelis Greens staffers usually spend no more than two hours tending to the greens each day. They can monitor and adjust the growing conditions online when they are away from the farm.
McCrory said the company is in a "fast-paced learning mode," finding new ways to improve the quality of the product and distributing samples to restaurants in Crozet and Charlottesville.
Six restaurants have committed to regular deliveries from Fidelis Greens this summer, Shindeldecker said.
Kardinal Hall, a restaurant and beer garden in Charlottesville, uses Fidelis Greens' arugula as a garnish for salads and sausages.
"Putting a little arugula in everything is so 'in' right now," said Allison Hurt, Kardinal Hall's marketing manager. "We are all about trying new things, especially when they are locally made."
Kardinal Hall chef Jeffery Burgess said he has been using one or two trays of the arugula each week. "I think it's a great product," he said.
Caldejon said he will keep the design of Fidelis Greens' shipping container farm in the public domain, and hopes to publish a construction manual later this year so other organizations and individuals can replicate it.
Caldejon said military veterans, especially those suffering from post-traumatic stress disorder, could benefit from the opportunity to start their own shipping container farm.
Caldejon, Ortiz and fellow co-founder James Edward King are veterans of the U.S. Marine Corps. The Marines motto, "Semper Fidelis," inspired the name of their company.
"It opens up an opportunity [for veterans] to be gainfully self-employed in an environment with relatively low stress," Caldejon said.
"High-tech can be intimidating, but we are incorporating technology in a way that makes it more approachable," McCrory said.
The Fidelis Greens team includes three veterans of the U.S. Marine Corps, whose flag flies above the shipping container farm. Credit: Josh Mandell, Charlottesville Tomorrow.
Innovative Thinking and Technology: The Key to Solving Global Problems
Innovative Thinking and Technology: The Key to Solving Global Problems
Austin Belisle - June 1, 2017
This blog was guest-written by Brandi DeCarli, Founding Partner of Farm from a Box. She’ll be guest-speaking during the “Global Problem Solvers Who are Guardians of Our Planet” session of the Women Rock-IT series on June 15th.
Every aspect of our modern-day lives has been impacted by technology. From cloud and robotics to digital currency and drones, our lives are inextricably tied to the technology that surrounds us. While farming may not be the first thing that comes to mind when thinking of technology, it has played a key role in changing the face of agriculture and our global food system.
In the past 50 years, the Green Revolution has pushed to increase crop yields through large-scale intensification of single crops. Advances in mechanized farming allowed for larger and larger acreage to be farmed. By focusing on the large-scale intensification of a single crop, the natural checks and balances that diverse ecosystems provide were no longer in place.
To maintain production, it required heavy use of fertilizers and pesticides, which has directly impacted soil fertility and ecosystems around the globe. Now, with 40% of our agricultural soil degraded and 70% of our freshwater resources being gulped up by agriculture, it is clear that our current approach is not sustainable.
While advances in technology have enabled global agricultural production to increase with our growing population, those gains came at an unprecedented environmental cost. As we work to feed a growing global population, the environmental pressures will continue to increase.
By 2050, the world’s population is expected to grow by more than two billion people. Half will be born in Sub-Saharan Africa, and another 30 percent in South and Southeast Asia. Those regions are also where the effects of climate change are expected to hit hardest.
So, how can make sure that the growing need for food worldwide is met in an ecologically sustainable way? And what role can technology play? The opportunity may be in shifting our focus from mass production to production by the masses.
An estimated 70% of the world’s food comes from small, rural farms that are no bigger, on average, than two acres. And despite the increase in large-scale industrialized farms, small, rural farms are still the backbone of our global food supply. But these rural areas are often the most vulnerable to the effects of climate change.
The challenges of drought, degraded soil, and inefficient and labor-intensive methods contribute to and exacerbate low and unreliable crop production. Without access to the infrastructure or technologies that can support a productive farm, farmers will either struggle with low yields, depend on chemical inputs that further deplete the soil, or rely on outside aid.
This is where Farm from a Box comes in.
Farm from a Box works to bridge the “access” gap by providing a complete, off-grid toolkit for sustainable, tech-powered agriculture. Built from a modified shipping container, each unit contains a complete ecosystem of smart farm technologies to enhance agricultural productivity; from renewable power and micro-drip irrigation to Information and Communications Technology equipment.
Designed as the “Swiss-Army knife” of farming, this mobile infrastructure provides all the tools needed to support a two-acre farm. By empowering farmers to grow and sustain food production at the community level, we build greater resilience to climate shocks, boost livelihoods, and help bridge the access gap by making healthy food locally available.
With its own off-grid power, Farm from a Box can act as its own micro-grid in remote locations; drip irrigation helps save water and stabilize crops through drought conditions while also extending the growing season; internal cold-storage helps keep crops fresher longer, reducing post-harvest loss by 80%; Wi-Fi connectivity improves information access and exchange; and a cloud-based IoT system helps monitor production and efficiencies.
By introducing micro-irrigation, we can extend the growing season and better support a wide variety of crops throughout the year, while lowering the amount the water used by applying it directly to the plant. The off-grid power array and storage provide a reliable energy source to power the pump, move the water through the irrigation lines, cool the internal cold storage area, and support the charging of auxiliary needs.
We have also connected each unit with Wi-Fi capabilities and a complete IoT system to improve operational efficiency, optimize water and energy use, and provide guidance on farm management and market information. Because we have integrated sensors on all of the primary systems, we can monitor and control the performance of the system, and also set alerts for when a component dips below or exceeds certain levels.
Let me give you an example of how this applies in a real-world situation. We recently teamed up with the United Nations World Food Programme Tanzania and WFP’s Innovation Accelerator to support food and nutrition security for refugee and host communities. Our Farm from a Box system will be used to increase the availability of nutritious crops, provide low-cost agricultural commodities and, through increased production, boost the income levels for both refugees and the surrounding host communities.
Because the farm is operating in a remote location in eastern Tanzania, information becomes a vital component to ensuring the system is working as it should be, and the farmers have the data they need to know what is happening and why. Through our cloud-based IoT system, both the community and the WFP has open access to see how much energy the solar panels are producing, how much water is being used, and if the overall system is functioning properly.
Now, technology for the sake of technology isn’t a standalone solution; how it is utilized in overall value creation is where we find the real impact. By marrying technology with small-scale regenerative farming practices, we can improve soil quality, reduce dependence on outside inputs, conserve water, and build up nutrients.
Techniques like composting, crop rotation and diversification, cover cropping, and no-till practices nurture the soil’s fertility and help produce a healthier crop. By shifting our focus from industrialized agriculture to local organic agriculture, we can potentially convert carbon from a greenhouse gas into a food-producing asset.
Farm from a Box is just one of many innovations that are working to empower smallholder farmers with sustainable solutions; there are vertical farm systems, small farm robots that automate field work, drones that use near-infrared and thermal sensors to “see” how plants are doing. Technological innovations like these can help us achieve better health, well-being, and equity throughout our planetary system as a whole.
But we need creative solutions, and sometimes that requires thinking outside of the box. I don’t come from a technological background, nor does my business partner, but we saw a problem and thought, “There must be a better way.” We all have the power to change our world for the better. Food is something that connects us all and has a direct impact on our everyday lives and environment.
When we first set out to start Farm from a Box, our intention was to create a mobile infrastructure that could provide people with the tools they need to grow their own nutritious food. Over time, that idea has grown; we now see Farm from a Box as a tool that could transform local production and nutritional security globally.
Whether it is a local school, community group, or remote village in an underdeveloped country, smallholder farmers are the ecological gatekeepers to building a more sustainable and equitable food supply. Technology has the potential to help solve the intractable problems facing humanity and will continue to play an increasingly vital role in global food security and planetary health. But it will require innovative thinking from all of us to achieve it.
Freight Farms Lands $7.3M As Agriculture Meets Data & Automation
June 6th, 2017
Investors have planted $7.3 million in Freight Farms to help the Boston-based startup bring its micro-farms to more places around the globe—and potentially even beyond.
The investors in the Series B round include return backer Spark Capital, also based in Boston. The news was first reported by the Wall Street Journal on Monday. Freight Farms’ total venture capital haul now exceeds $12 million, according to SEC filings.
The company sells shipping containers filled with hydroponic farming systems that can grow a variety of lettuces, herbs, and other greens. The system is designed to operate with minimal hands-on work by humans. It employs LED lights and automated watering and fertilizing technology. Operators can monitor the farm through a live camera feed, and they can use an app to control the climate within the shipping container and shop for growing supplies. The company has said the system uses less water than traditional farming methods, and because it’s housed inside a shipping container, it doesn’t require pesticides or herbicides.
Freight Farms has deployed more than 100 of these farming systems across the U.S. and in several countries. Customers include urban farmers, traditional farms, produce distributors, and universities.
The startup was formed in 2010 by Brad McNamara and Jon Friedman, who previously worked on rooftop hydroponic gardens.
Freight Farms is trying to take advantage of the growing interest in local food sourcing, as its shipping containers can be set up close to where food gets sold or consumed. It also aims to enable year-round food production in challenging locales—think the snowy mountains of Colorado, or even space. Freight Farms and Clemson University are working on a NASA-funded project exploring ways to grow food in harsh climates and, potentially, deep space.
Freight Farms also fits with trends in agriculture around automation and using digital tools. That’s a key reason why Spark made another investment.
“Modular, Internet-connected, and highly automated commercial farms will play an important role in bringing local and affordable produce to communities all over the world,” Spark’s Todd Dagres and John Melas-Kyriazi wrote in a blog post about the new investment. “Value will accrue to those who own the technology layer of this farming stack (hardware + software) as data and automation become increasingly important drivers of low-cost production.”
Agricultural technology companies are taking various approaches to indoor farming. Like Freight Farms, Atlanta-based PodPonics sells tech-enabled mini-farms inside shipping containers. Businesses such as New York-based BrightFarms and Harrisonburg, VA-based Shenandoah Growers produce food inside greenhouses. And startups like Grove and SproutsIO, two Boston-area firms, sell micro-farming systems to consumers for growing food inside their homes.