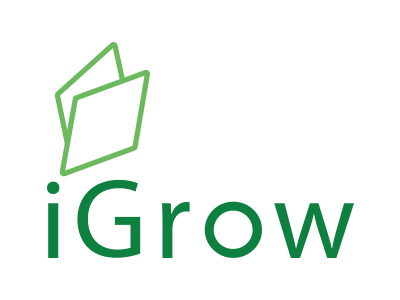
Welcome to iGrow News, Your Source for the World of Indoor Vertical Farming
AR Systems Develops New Automation and Control Systems for Indoor Agriculture Industry
AR Systems Develops New Automation and Control Systems for Indoor Agriculture Industry
System provides comprehensive control for automated farms, one of the fastest growing segments in AgTech
NEWS PROVIDED BY AR Systems
LOS ANGELES, Dec. 21, 2017 /PRNewswire/ -- AR Systems (www.automatedretailingsystems.com), a technology provider of systems that power automated retailing systems, self-service kiosks, and automated farming, unveiled their newest comprehensive control integration for the indoor agriculture market.
AR Systems also announced that it is the exclusive provider of automated control technologies to Grow Pod Solutions, a leading California-based developer of indoor container-based farms. AR Systems provides the farming control software, its proprietary Bipolar Ionization system, fertigation scheduling, and full-time surveillance. The system is fully automated and allows operators to monitor the cultivation process from anywhere in the world.
Shannon Illingworth, Chief Innovation Officer at AR Systems, said that the company has the most innovative and reliable automated farming control technologies in the world.
"Automated farming in portable shipping containers provides a practical solution to so many challenges," he said. "Our proprietary controls allow for the cultivation of a wide variety of plants, fruits, and vegetables, virtually anywhere in the world."
AR Systems also provides data and insight into the cultivation process. Data does two things for a farm: it helps growers increase yields and drives down operational costs. But even more importantly, data helps farmers drive up top-line revenue. According to Agrilyst, data can help farms increase revenue by more than 20%. How? Insights drive better optimization, varietal selection, growth speed, irrigation adjustments, and more.
According to global market insights, indoor farming is a $14.8 billion per year industry, and that doesn't count another$6.7 billion from the cannabis industry.
"This market is growing rapidly because it allows anyone to grow for profit or for humanitarian efforts. AR Systems is proud to be a technology leader and provide the systems that form the backbone of this impressive industry."
About AR Systems
AR Systems is a developer of premium automation technologies that power retailing solutions, self-service kiosks, and indoor farming.
Connect with AR Systems:
Call AR Systems at (951) 465-7700
Email the company at info@automatedretailsystems.com
Visit the website at www.automatedretailingsystems.com
Facebook: www.facebook.com/automatedretailsystems
SOURCE AR Systems
Related Links: http://www.automatedretailingsystems.com
Leafy Green Machine From Freight Farms Brings Sustainable Food To Schools
Freight Farms is a Boston-based startup that takes refrigerated shipping containers and repurposes them as indoor hydroponic gardens.
December 6th, 2017 by Steve Hanley
Freight Farms is a Boston-based startup that takes refrigerated shipping containers and repurposes them as indoor hydroponic gardens. Each sustainable food growing unit is known as a Leafy Green Machine. Its footprint is smaller than the end zone of a football field, yet it is capable of growing as much food each year as a traditional farm the size of an entire football stadium — about 1.7 acres. Because the whole operation is contained in a standard-size shipping container, food can be grown anywhere a container will fit.
On December 4, Freight Farms held a presentation for Rhode Island educators at the Cumberland High School in Rhode Island, where one of its Leafy Green Machines was installed at the beginning of the school year. It takes about 4 months to get each unit fully productive. Harvesting of the first vegetables has just begun, with more sustainable food being planted every week.
The cafeteria staff from Sodexo prepared a delicious and nutritious lunch using the vegetables grown just outside the door of the kitchen. I particularly enjoyed the vegetarian breakfast cups, and the meatless Portuguese kale soup was delicious. I had second helpings of both.
Freight Farms has been in business for about two years and is always updating its systems to make them more efficient. The container is completely refurbished on the outside and repainted in bright green and white. Inside, everything is immaculate, with workstations in the front and four vertical growing racks in the rear. Once everything is set up, it takes only about 20 hours a week to run the farm and tend to the 9,000 plants inside. Work schedules can be prepared weeks, months, or even years in advance.
Freight Farms uses LED lighting exclusively. Not only is it energy efficient, but it also provides the light in the visible red and blue spectrum plants need to thrive, along with a smidgen of ultraviolet and infrared. Water usage is closely monitored, with almost every drop accounted for. Each week, only about one gallon a day is consumed.
The growing process begins with a seedling tray about 18″ long and 12″ wide. It is separated into 200 small compartments with a bit of soil in each one. One seed goes into each compartment, then the tray is watered with a special cocktail of nutrients customized to each variety of plant being grown. Then it is covered and placed on a shelf underneath the preparation area. After two weeks, the seedling tray is moved to the middle shelf, where the bottom is immersed in nutrient-infused water.
Two weeks after that, the sprouted seedlings are transferred by hand to vertical growing racks that attach to an overhead rail system that shuttles them back to the growing area in the rear. When the plants are finished growing, the growing rack is moved back to the front work station for harvesting. The whole process is largely automated and can be monitored and controlled remotely using a dedicated smartphone app developed by Freight Farms called “farmhand.” Each Leafy Green Machine can grow up to 4 tons of fresh vegetables every year.
Because each Leafy Green Machine is fully insulated, only about 120 kWh of electricity per week is needed for heating and cooling and to run the lights and pumps — about the same amount a family of four uses. The temperature inside is maintained at 60ºF. Andrew McCue of Freight Farms says Leafy Green Machines go about their business of producing fresh, sustainably grown food whether the outside temperature is below freezing or over 100 degrees.
Only half the growing space inside the container in the parking lot at Cumberland High School is being used at present. But there are several more seedling trays that are almost ready for transfer to the growing racks and the first vegetables are ready for harvest. The students at the school will be involved in the growing process, helping to make sustainability an integral part of their studies. The produce grown outside will be incorporated into the meals served in the school cafeteria by Sodexo.
During the presentation on December 4, principals from 5 other area high schools were on hand to sample the food and learn more about the Freight Farms’ Leafy Green Machines. Perhaps more of the brightly painted containers will soon be appearing in surrounding communities, bringing fresh, locally grown food to school lunch rooms and teaching young people about sustainable living.
Photos by the author.
Local Roots to Deploy More Than 100 TerraFarms in 2018
Local Roots has announced that its next-generation TerraFarm has achieved cost parity with traditional farming, according to a press release. In response to demand for its produce from corporate customers, acceptance to the UN World Food Programme and membership in the Creative Destruction Lab with the world’s top technologists, Local Roots also announces it will deploy more than 100 new TerraFarms in 2018 and hire 150 new team members.
Local Roots to Deploy More Than 100 TerraFarms in 2018
The company was also accepted into the UN World Food Programme and Creative Destruction Lab.
December 18, 2017
LOS ANGELES -- Local Roots has announced that its next-generation TerraFarm has achieved cost parity with traditional farming, according to a press release. In response to demand for its produce from corporate customers, acceptance to the UN World Food Programme and membership in the Creative Destruction Lab with the world’s top technologists, Local Roots also announces it will deploy more than 100 new TerraFarms in 2018 and hire 150 new team members. The company already has top talent from Amazon, Boeing, Tesla, The Carlyle Group and Hollandia.
A Better than Organic Farm in a Modular Box
Built inside upcycled 40’ shipping containers, Local Roots’ TerraFarms grow better than organic produce year-round in nearly any geography, using 99 percent less water, no pesticides and at the same cost as traditional farms, according to the release. Leveraging the best of plant science and engineering, Local Roots has created a proprietary system that is the optimal environment for plants to flourish. As a result, these high-tech TerraFarms yield ultra-nutrient produce that is equivalent to five acres of farmland or 4,000 heads of lettuce every 10 days, 600 times more produce than the equivalent footprint of an outdoor farm.
Local Roots has a unique modular approach that enables it to quickly deploy and scale large numbers of TerraFarms at or near corporate customers’ large food distribution centers. This approach allows Local Roots produce to last nearly two weeks longer than traditional produce, a compelling offering for an industry suffering from 52 percent spoilage rates, according to the release.
“Spoilage and food waste are major issues and not just for retailers since the costs are passed onto consumers too,” said Eric Ellestad, co-founder and CEO of Local Roots. “What we are doing is not a thought experiment. We are advancing agricultural technology to solve major problems in today’s food supply chain and we’re deploying a solution that already works.”
Working with the United Nations and AI Leaders to Improve Global Health
Local Roots announces today that it has been selected by the UN World Food Programme to field test its TerraFarms in emergency and development contexts. The vertical farming company is driven by a mission to improve global health by building a better food system and this program is critical towards fulfilling this purpose.
Local Roots also announces today that they have been accepted to work with some of the brightest minds in technology through the Artificial Intelligence (AI) program at the University of Toronto’s Creative Destruction Lab. Local Roots is already using machine learning, computer vision and AI to develop the future of farming. Through CDL, the Local Roots team will work with leaders in AI to apply this bleeding edge of technology to agriculture.
Lastly, Local Roots is partnering with a major U.S. retailer for a large-scale deployment of its TerraFarms and details will be announced early next year. Existing Local Roots customers are Tender Greens, and Mendocino Farms. Local Roots has already raised $10.5 million to date from FoodTech Angels; Jerome Metivier, Managing Director, PepsiCo Ventures; Sequel Capital Management; Green Planet Global and others. Local Roots’ Series A financing is expected to close early 2018.
Throughout 2018, Local Roots will add more than 150 team members in the Greater Los Angeles area mostly focused on plant scientists, engineers and production experts. To help scale the company, Local Roots has brought on Marissa Peretz, founder of Silicon Beach Talent and a former Tesla recruiting leader who helped Tesla grow from approximately 200 employees to thousands.
Additionally, Local Roots is expanding into a spacious 165,000 square feet manufacturing and headquarter facility in Vernon, Calif., 15 times larger than its original space. The first facility will remain focused on R&D and product development. January 2018 marks the start of manufacturing for the more than 100 new TerraFarms in the new location. To scale the farms, Local Roots has hired manufacturing talent such as a former rocket and spacecraft manufacturing and engineering director to design the systems and processes for the mass production of the TerraFarm. Local Roots engineers and plant scientists have created the next generation TerraFarm that is more efficient, productive and cost-effective than other indoor farms. Local Roots’ proprietary system of lights, software, airflow, automation, and controls give plants the perfect balance of light and nutrients to make them as healthy as possible while also unlocking their yield potential. The TerraFarms’ modular design allows Local Roots to quickly test and revise new designs and operating practices more economically than traditional indoor farms.
With an additional 2.5 billion people expected to live on planet earth by 2050, along with increased environmental stresses, productive farmland shrinking and a population migrating to cities, efficient urban farms have the opportunity to help feed the world.
High-Tech Shipping Crates, Precision Technology Poised To Revolutionize Urban Ag
December 19, 2017
Image credit: Freight Farms
Between a growing global population — which is estimated to reach 9.5 billion by 2050 — rapid urbanization and climate change, shifting agricultural to a more sustainable model is essential for safeguarding the future of our food system. Startups in the United States and Singapore are ready to rise to the challenge, championing food sustainability through new technologies and infrastructure solutions designed with urban environments in mind.
Reconnecting consumers with their food is a critical component of future-fitting the food system, but heading straight to the source — farms themselves — isn’t always an option. To close the gap, Boston-based startup Freight Farms developed the Leafy Green Machine (LGM), a refrigerated shipping container repurposed as an indoor hydroponic food growing unit.
The 40-foot containers can be installed just about anywhere — schools, corporate campuses, restaurants, hospitals, retail stores, etc. — and are capable of growing between two to four tons of produce a year (as much as a 1.7-acre farm). The controlled environment eliminates the need for herbicides and pesticides, and the system uses 90 percent less water than traditional farming methods — approximately one gallon per week.
What’s more, Leafy Green Machines use only about 120 kWh of electricity a week — the same as a family of four — to run its heating, cooling, lighting and irrigation systems. A smartphone app is used to monitor and control the growing process. In total, it only takes around 20 hours a week to care for the 9,000 plants housed within the LGM.
High schools in Rhode Island have begun exploring the idea of adding Leafy Green Machines to their campuses in an effort to incorporate fresh, organic produce into their school lunch offerings and teach students about sustainable food production. Cumberland High School has already installed one of the systems. According to Clean Technica, students will be involved in the maintenance of the farm and Sodexo will serve the farm-fresh food in the school cafeteria. Similar projects have also been rolled out at the Boston Latin School, Georgia State University, Stonybrook University and UMASS Dartmouth.
Leafy Green Machines are also being deployed by small businesses and soil farmers: The system is at the heart of Houston-based startup Acre in Box, which supplies kale and lettuces to local restaurants, and helped Karma Farm in Monkton, MD diversify its crops and expand its operations. The farm now supplies local farm-to-table restaurants in the Baltimore area with fresh and local produce.
Meanwhile, a new food sustainability accelerator in Singapore is helping startups bring their sustainable food solutions to scale.
A joint initiative of social impact startup incubator UNFRAMED and the Croeni Foundation, an environmental NGO, Makanpreneur is a four-month holistic training program that offers startups tackling food sustainability challenges comprehensive support from seasoned entrepreneurs and industry experts, training, funding and networking opportunities to develop sustainable food alternatives.
Two of the four startups selected for the program are focusing their efforts on enhancing food-system resiliency in Singapore via local production and precision technology.FarmX is harnessing the power of blockchain and IoT to create a precision farming technology that allows farmers to communicate with their plants. Sensors collect real-time data on temperature, humidity, soil moisture and nutrients, which farmers can access on their smartphones. The data can then be used to help urban growers increase productivity, reduce costs and reduce the likelihood of crop failure. Ecolution is also using precision agriculture technologies to take polyculture farms to the next level by boosting productivity and competitive advantage.
The Makanpreneur accelerator program will run until 28 March 2018, when participating startups will present their ideas to an audience of key players in the food industry and impact investment space. Winners will receive up to $10,000 in funding from the Croeni Foundation to scale their solutions.
Launched in 2006, Sustainable Brands has become a global learning, collaboration, and commerce community of forward-thinking business and brand strategy, marketing, innovation and sustainability professionals who are leading the way to a better future. We recognize that brands today have… [Read more about Sustainable Brands]
Container Farming, Sense and Nonsense
Container Farming, Sense and Nonsense
December 22, 2017
Ed van der Post
Small Hydroponics system specialist
Container farming is the cultivation of products in a container, which is adapted in such a way that the weather conditions are overcome and fully is equipped with the most efficient hydroponics cultivation system possible. Container farming is hot. The superlatives will fly you over if you look for them. But is that right? Here is a critical view of this new way of vegetable growing.
The question we have to ask is whether the rise of container farming is a realistic technological development or only suitable for an exclusive crop of lettuce. It is time to puncture unrealistic expectations and to talk honestly about the possible advantages and disadvantages of this trend. I hope that through this article, which has arisen after research of the various sites, the exchange of experiences with people in various countries and stories that I have heard from all over the world, which I will give you an as objective as possible picture of the real place that container farming could take in the future of food shortage.
When you look at the market for the supply of container systems, there are a number of companies that stand out. The best known are: Freight Farms, Smart Greens, CropBox, Modular Farms, Alesca Life and Agritom. The last company is more focused on fodder systems (grass cultivation). More unknown: Growtainer®, Madar Farms, Harvestsquared, BoxXLand, Urban Crop Solutions and Sprout Stack. The American containers are generally the best known. I think they owe this to their aggressive market approach with many promises. (you will find more companies and data on our website)
It is striking that containers for container farming are not cheap. Unfortunately, most companies are not transparent about their prices and other information. But if you have enough money you can even have a container with your own name made as the Belgians have done with FARMPRO in cooperation with the company Urban Crop Solutions.
In the Netherlands, we also have container farming. For example, there is the Dutch initiative of Patrick Stoffer (Freight Farms container), which now tries out one of these containers under the name Growlocal. He has shared his experiences with us. His vegetables mainly go to the residential and care center Humanitas in Deventer. Albert Heijn (grocer) and De Bakker Barendrecht (Urban Crop Solutions container) have also placed one for the headquarters of Ahold Delhaize in Zaandam. Only that will be a publicity stunt rather than a contribution to our world food issue, I think.
Some Figures
There is a lot of talk about the comparison with the yield of a container and traditional agriculture. For example, every 40ft sea container would yield the annual equivalent of three to five hectares of agricultural land. And in a container you could grow plants at least six times faster than on a conventional farm. Let's look at the real numbers (numbers are averages).
- fact 1. A 40ft container has a capacity of 66 m3. The length is 11.95, the width 2.33 and the height 2.37 meters.
- fact 2. Lettuce on open ground yields (8 to) 12 crops of m2 and can be harvested twice a year.
- Lettuce under glass yields an average of 20 corps of lettuce per m2, with an average of 5 harvests/year.
- Lettuce under glass based on hydroponics yields 70 corps / m2 and 8 to 9 harvests per year.
- Lettuce in the modern automated environment produces 100 corps per m2, times 9 harvests.
- fact 3. The cost of a corp of lettuce is about 24 cents.(in Holland) The purchase price around 36 cents and the sales price between € 0.80 and € 1.00
- fact 4. The weight of lettuce lies on average between 200 and 350 gr. (depending on the species).
- fact 5. The yield per hectare of open ground is 10,000 x 12 heads x 2 = 240,000 heads per year is 48 tons;
- The yield per hectare under glass is 10,000 x 20 x 5 = 1,000,000 heads = 200 tons;
- The yield per hectare automated is 10,000 x 100 x 9 = 9,000,000 heads = 1800 tons.
Now we are going to look at the container. Nearly all 40 ft containers reach a yield of between 27,000 and 40,000 heads of lettuce per year (see our website). This corresponds to a maximum of 1/6 hectares of traditional agriculture (so no three or five hectares as stated!). The yield is, of course, dependent on various factors, but also how you define a head of lettuce. To begin with, every head of lettuce needs a certain space. The more space there is for storage, movement and processing, the less space for the lettuce. I always made this comparison when organizing a fair: every visitor needs at least 1.5 m2. So you can calculate very quickly how many visitors there can be at an exhibition: width times length of the aisles and visitor spaces (+, of course, the time of visit included). Every trade fair organizer will charge more for the promotional activities than reality, which will look suspiciously like the calculation of the number of heads of lettuce. Because here too you are bound by a number of laws. An adult lettuce plant needs a space of at least 30x30x30cm (= 27,000cm3). So when you have a container 100% full you can have 2444 plants in it. Then you have no aisle, no distance from lighting to plant, no picking or processing place, no room for electricity, pump, etc. And every cm3 counts. According to the builders of the container farms, the number of plants varies between 2700 and 3500 plants per container. Apparently, they have devised a trick to reduce the amount of space per head of lettuce. You can also see this in practice. A vertical system has 13 plants per row. That would mean that you have to go up to 4 meters from my dimensions. But the height of a container is only 2.37 meters. So the plants only have a distance of 18 cm instead of 30. In traditional agriculture, this is 25 to 30 cm. The size of a small head of lettuce is between 15 and 20 cm. In principle, they are always bigger. In other words, the growth margin, the number of heads of lettuce per m2, is limited in comparison with water cultivation and agriculture. In addition, the yield is further increased by accelerating and optimizing the growth process. And here: the pops lettuce is a fact!
Now let's assume the yield that is feasible according to the container builders, is 27 to 40,000 heads per year. Then you come to 74 to 110 heads per day. A store pays about 36 cents, that's between 26 and 40 euros per day or 780 to 1200 euros per month. That is of course not the profit, but the turnover. The purchase of the container and the system, the soil to set it up, the electricity, the water, the seed, the growth substances, the maintenance and the labor costs are not included. If you could sell the heads directly to the consumer, which is of course much more work, for a price of one euro each, your gross turnover at 80 heads per day is 2400 euro per month.
Negative Sides
- A container farm is not cheap. Although they do not all mention their price, the price is approximately between 75 and 120,000 euros. That is 25 to 40 million euros per hectare. For one-tenth of that money you have a modern greenhouse, with a price of about 2.5 to 4 million euros per hectare;
- The electricity costs of a container are considerable. Again, the companies prefer not to mention what their containers consume on electricity. But assuming the amount of LED lamps you can assume that the energy consumption is around 35000 kWh per year (equal to the consumption of more than 10 households). Depending on the country in which you live, these costs will reduce your profit much or very much. In the Netherlands, it amounts to more than € 7,000 per year or € 600 per month.
- Working conditions are not ideal. Since every cm3 is important, you see that the workspace is kept to a minimum. Jokingly you can also say that the work is not reserved for people with a strong stature. The container must always be closed in most weather conditions, so you are in an enclosed space with artificial light. You must therefore also not be claustrophobic.
- Nutrients. Some container companies have also devised a way of not limiting profit by only selling the container. They prefer to make you dependent on them for a long time. They can do this by developing food systems that only they have. You are then obliged to continue to take it. Sometimes you also see that growth media systems have been specially made for their container. Prices are not known. But even without this strangulation, you will have to feed your plants.
- There is a restriction in the number of vegetables. The current breeding containers are focused on high-quality, fast-growing crops that require only a small area and a high turnover rate, such as lettuce, basil, and other salad products. Slower growing vegetables are not profitable at all.
When you look at all aspects, you see that the purchase of the container and the construction of water and electricity cables already require a substantial investment and that, in addition, ongoing costs such as land rent, taxes, energy, seeds, growth mediums, and nutrients put the profits under considerable pressure. In fact, we have to conclude that the exploitation of a container as a production location is not profitable, on the contrary: it is quite loss-making. You must have at least four containers and work 80 hours per week to make it profitable. Or sell each head of lettuce for € 4,
Remember that container farming cannot actually be about how much production you can put into a room. It is about bringing food closer to the people and maximizing production as a function to recoup the resources and labor that you invest. But not at all costs. So while container parks have the potential to make a fundamental contribution to bring food closer to the market, the people who exploit these container farms must be able to survive in order to make an impact.
Positive Sides
Containerfarming certainly also has advantages over other types of cultivation.
- In terms of sustainability, the reuse of containers is, of course, perfect. They are easy to transport and the containers themselves are cheap and there are many. The 40ft containers, in particular, are popular (but an old container is far from being a container farm).
- Another positive aspect of a container is that it can be placed in impossible places. You only need an area of 12 by 2.5 meters. Although they have forgotten to mention that you have to take into account that most containers require a perfectly flat surface (level) in order to function properly. So putting it in your backyard can be difficult.
- Another advantage of a container is that you can quickly start your own business and no special building is needed (probably a building permit). This means that a modern city farmer or a company in the city can easily put a container behind their restaurant or even in a parking space.
- The most obvious advantage of any form of gardening in a container, whether it is flowers, grass or vegetables, is the possibility to grow them in places where a normal garden cannot be realized. Such as in case of lack of ground or lack of clean soil.
- The distance from production to the customer is minimal.
- The transport of vegetables to the local market also prints the foodprint.
Conclusion
Container farming is a piece of technology that is not unique in itself. There are sufficient locations and initiatives in the world in closed spaces that use the same techniques. You must, therefore, ask yourself whether an existing location is not more suitable in a city to bring food production closer to the customer. (roof farming) Container farming does have the technology and the potential to grow relatively many vegetables on a small surface, only: at the expense of what? It is certainly not a feasible sustainable initiative given the costs. For the time being, I can not find a place in the world that would justify container fueling when it comes to solving our "world food problem" or for a sustainable future. There are many cheaper systems in a city to solve this "problem". You can always approach us about this.
Ed van der Post
www.hydroponics-nederland.nl
Thank You and Next Steps From The Coalition For Sustainable Organics
Thank You and Next Steps From The Coalition For Sustainable Organics
Eighteen months ago, the outlook for hydroponic, aquaponic, and containerized growing methods in the National Organic Program looked bleak. A small, yet vocal, minority in the organic sector had mounted a campaign within the National Organic Standards Board (NOSB) to prohibit these production methods from organic certifications despite a lack of scientific basis to do so. Through the hard work and dedication of CSO’s Board and member companies, we were able to launch a strategic advocacy plan to push back against this unfair and arbitrary effort. After three failed votes in the NOSB, our place in the organic industry is safe for now but more work is needed to ensure the continued success of these systems.
As the NOSB considers additional potential regulations that may impact your on-farm practices, we must remain vigilant in our efforts to educate policymakers on the integrity and sustainability of your production systems. The CSO still needs you as a member to fight the good fight and ensure a sustainable future in the U.S. organic industry for farmers incorporating containers in their operations. Please fill out the linked application form today to join the CSO.
The CSO is closely monitoring the following additional potential threats to hydroponic, aquaponics and containerized growing methods:
1) Some Certifiers Continue to Refuse to Certify Legitimate Organic Operations: In spite of the recent NOSB votes rejecting proposals to prohibit container, hydroponic, and aquaponic production tools used by organic growers, widespread inconsistencies remain between USDA-authorized certifiers. Many certifiers are defying USDA regulations and refusing to certify operations incorporating containers beyond their use for nursery stock. Other certifiers will certify growers using certain types of substrate, but not growers using Nutrient Film Technique or Floating Raft Systems regardless of the fact they have created complex, living biological systems to cycle nutrients in an organic manner.
2) NOSB’s Next Steps for Containers Remains Unknown: At the close of the November 2017 NOSB meeting, the Board released a draft agenda indicating a plan to continue to pursue additional recommendations to revise USDA’s organic standards related to containers including potential regulations on new labeling requirements and the reuse and recycling of containers. This remaining uncertainty hurts growers and producers looking to make investments and upgrades.
3) Groups Opposed to Organic Certification for Containers Threaten Legal Action: After their latest setback at the NOSB, our opponents are now planning to file legal action against the USDA over the current certification policy that does allow for container production systems. Specifically, they claim that the Organic Foods Production Act of 1990 and as amended REQUIRES that crops must be grown in the soil. The CSO stands ready to defend the rights and interests of its members.
4) Voluntary “Regenerative Organic” Label Efforts Move Forward: The Rodale Institute is leading efforts to create a new and at this time voluntary, label currently taking the name of Regenerative Organics. This label would exclude containers from participation. Groups like the Organic Consumers Association are coalescing around this effort. Details of that standard can be found here. The idea is to add specific requirements for soil management including tillage practices as well as social justice and animal welfare elements that are not part of the current USDA standard.
Your Help Is Needed
The CSO needs your continued participation in efforts to safeguard your rights to select the most appropriate growing methods in your organic operations. Our opponents continue to push Congress to pass restrictions on our operations and will only ramp up their efforts after their defeat at the NOSB.
Actions to take:
Join CSO if you have not done already. Our sustained efforts on behalf of the hydroponic, aquaponics and container industry in Washington, DC rely on dues from farming operations like yours.
Contact your elected officials to make sure that they see this issue as being important to their district or state. You are a key to humanizing the issue for them. Some examples of ways to engage include:
- Send a version of the draft letter below.
- Offer a tour of your operations to the Member or staff.
- Visit Washington, DC to see your Member of Congress. If you are a member of CSO our team in will coordinate meetings on your behalf.
Please forward any notes and the contact information you gathered during the visit to Lee Frankel at info@coalitionforsustainableorganics.org.
You can find the contact information for your Member of Congress and Senatorat the highlighted links.
Thanks for your help.
Sample Letter to email or fax
The Honorable XXXXXX
United States House of Representatives or United States Senate
Local Address
Date
Dear Representative XXXXXX,
As your constituent, I am writing to invite you to visit our farming operation to learn more about the use of hydroponic/container/aquaponic cultivation to grow certified organic produce for our community.
Our company grows [list your products here] in [city of facility/farm] and employs XXX people. In addition, we are perfecting our growing methods to expand our line into more and more fresh produce items. Our current production is helping to make fresher produce available to our community and alleviating food deserts in the area. We achieved certification under the U.S. Department of Agriculture and take pride in meeting all the necessary requirements under the law to meet this incredibly high standard.
You may be aware that, over the last few years, USDA’s advisory committee on organic agriculture, the National Organic Standards Board (NOSB), has been considering multiple proposals to revoke the existing organic certifications for growers using hydroponic methods to produce fresh vegetables, herbs, and fruit. While the latest proposal was defeated by an 8 to 7 vote, the NOSB continues to examine ways to limit our ability to maintain our organic certification through their insistence that only farms that look like theirs should carry the organic label.
This is an unnecessary and burdensome action that will significantly impact our livelihood, jobs in your district, and reduce the availability and accessibility of fresh organic produce. If the use of these innovative and practical growing techniques is limited, our company will no longer be permitted to continue to produce certified organic fresh produce, and our economic potential will be significantly impacted.
I look forward to welcoming you to our operation to demonstrate our use of these techniques to help meet the rising consumer demand for organic produce.
Thank you for your consideration. You can contact me at [email address] or by phone at [phone number].
Respectfully,
Your Name
Farm/Operation Name
Town Sees Big Future In Small, Hydroponic Box 'Farm'
November 29, 2017
The Leafy Green Machine after its arrival in Robbinsville. (Provided photo)
By Kevin Shea
For NJ.com
The town of Robbinsville says they're the first municipality in New Jersey to take delivery of a portable, hydroponic box farm from which they plan to grow leafy greens.
The farm - located in a 40-foot metal shipping container and can produce an assortment of lettuce, kale and herbs - arrived Tuesday from the Boston company Freight Farms. It's called a Leafy Green Machine.
It's the future, Robbinsville says: the "vertical" farm can pump out leafy greens all year round without the worry of weather or the need for soil or pesticides from a 320-square-foot space. Hydroponics is the science of growing plants in nutrient-rich water.
And it's also a nod to the township's rural, farming past, the town says.
Kevin Holt, the town's recreation activities coordinator, says the box farm - which cost $104,000 - will aid Robbinsville and residents in three ways.
A peek inside the box farm. (Provided photo)
First, the town plans to grow lettuce and other greens and supply township programs, like the senior center, where the box will reside, and Meals on Wheels.
In the near future, the town plans to partner with nonprofits or organizations that aid the needy or hungry with low-cost produce.
Then, Holt says, the town plans to start a community share garden and sell greens to residents, maybe with a set monthly fee or something similar. "And that will help offset the cost," he said.
Plans are still in the works, Holt said.
In addition to lettuce, the farm has the capability to make mustard greens, Asian greens, endive and herbs like basil, cilantro, dill, mint, oregano, thyme and parsley, the town said.
The grand plan, town spokesman John Nalbone said, is to pay off the box in five to seven years. "That's the goal," he said.
Plus, the town will offer the Leafy Green Machine as an educational tool to schools, and for community engagement and volunteer opportunities, Nalbone said.
"Growing our own food that is healthy and nutritious, with an eye on partnering with organizations such as Meals on Wheels, is a wonderful concept," Mayor Dave Fried said in a statement.
"We really want our seniors and children to take part in this ground-breaking program and learn about futuristic farming," Fried said. "Hydroponics is the way of the future, and we are proud to be on the cutting edge as the first municipality to purchase and operate a Freight Farms hydroponic system."
Kyle Clement, who graduated from Rutgers University recently, where he studied plant science graduate, will spearhead the program for the town, with the title, hydroponic farm coordinator.
"Food connects everyone," Clement said. "Today, people are becoming more and more invested in understanding where their food comes from, and we want to give everyone the chance to explore that."
Kevin Shea may be reached at kshea@njadvancemedia.com. Follow him on Twitter@kevintshea. Find NJ.com on Facebook.
This Shipping Container Is A High-Tech Growing Machine | Editorial
The township recently laid claim to being the first New Jersey municipality to take delivery of a portable, hydroponic box farm. It's basically a 40-foot-by-80-foot metal shipping container that has been converted into a high-tech growing machine.
12-07-17
By Times of Trenton Editorial Board
Robbinsville is thinking inside the box as a way to go green.
The township recently laid claim to being the first New Jersey municipality to take delivery of a portable, hydroponic box farm.
It's basically a 40-foot-by-80-foot metal shipping container that has been converted into a high-tech growing machine.
Plants are grown in nutrient-rich water that requires no soil. Indoor lighting takes the place of sunlight to produce the photosynthesis needed to grow leafy green vegetables. An added advantage is that plants can be grown year-round in a temperature-controlled environment that is regulated by computer software. And no pesticides are needed to raise fresh organic food.
The box farm, called a Leafy Green Machine, is made by Freight Farms, a Boston company, and costs $104,000, according to Kevin Holt, Robbinsville's recreation activities coordinator.
He sees a bright future for the box farm. Initially, the town plans to grow lettuce and other greens for the benefit of township programs, such as Meals on Wheels and the senior center, where the box will be set up.
Town sees big future in small, hydroponic box 'farm'
The box farm - located in a portable shipping container - can grow lettuce, leafy greens and kale
Once food production is up and running, Holt expects it will produce nutritious greens such as lettuce, mustard greens, Asian greens, endive and an assortment of herbs for nonprofits and other organization that feed the needy.
The hope is that the township will eventually start a community share garden and sell greens to residents to help pay for the initial investment. If all goes according to plan, the township will pay off the farm box in five to seven years.
Robbinsville is breaking new ground with this food-growing experiment. If it is successful, it will pave the way for other towns and organizations to follow its example.
The beauty of a self-contained food growing system is that it can be placed in just about any urban lot, where it can produce about 1,000 heads of lettuce a week, according to box farm manufactures.
Imagine what this could mean for "food deserts," poor areas where fresh, healthy vegetables at reasonable prices are scarce.
Of course, this small-space farming is no panacea for solving world hunger, but it certainly could put a dent in it, especially if scaled up to bigger proportions.
Robbinsville is starting out small, but it is paving the way for a possible food revolution.
Bookmark NJ.com/Opinion. Follow on Twitter @NJ_Opinion and find NJ.com Opinion on Facebook.
Containerized Growing System For The Coldest Weather
Getting fresh produce in remote northern parts of Canada has been costly because of the increased logistics for delivery, but now an Ottawa-based company has created a way provide these communities access to growing fresh vegetables year round.
Containerized Growing System For The Coldest Weather
Year-round produce for Canada’s most northern communities
Getting fresh produce in remote northern parts of Canada has been costly because of the increased logistics for delivery, but now an Ottawa-based company has created a way provide these communities access to growing fresh vegetables year round. “We started developing our technology with the specific idea of working with northern communities, helping them produce their own food,” says Corey Ellis, chief executive officer and co-founder of The Growcer, “meaning we were working in some of the harshest conditions in the world: minus 50 minus 60 degrees Celsius.”
The containerized Growing Systems are actually suitable for any climate he says. The system is built within new 40-foot shipping containers and combines hydroponic technology with precision climate controls to enable northerners to easily grow fresh produce. The system is automated and monitored remotely.
Plug and play
The container is delivered, gets plugged and is essentially ready to start growing things. “When they start their project we already have an idea of what they want to grow, in what quantities and built that into the system so that when it arrives all it needs is a fill up of water with a hose, plugged into a power outlet and they’re growing,” says Ellis.
Modular system
Each of the units can be plugged together to create larger growing capacity. One unit grows enough produce to feed 110 people. Ellis says this allows communities to start using one system, which generates income for them and they can invest down the road for another container and add it to the main unit.
Cost and consumption benefits
The minute the system arrives a community can start producing food locally – which would be more affordable than having produce shipped from the southern Canadian regions. Ellis says it can also have an impact on the diets of people within these communities. “We’re trying to figure out how to leverage our technology to help people have better behaviours with regards to their diet. The big question for us in northern communities is how can we help promote traditional diets and use fresh produce as a supplement to those traditional foods as opposed to trying to assimilate them to southern culture.” There’s also the benefit of creating more jobs for locals for management of the system itself. Ellis says they’re also looking at additional opportunities for value add, such as processing.
No farming knowledge required
Much like you’d expect, there isn’t a single farmer in town, unless Ellis says if they get lucky to find someone who’s lived more south or grew up on a farm and moved up north later in life. But, the vast majority of the residents don’t understand what goes on behind the scenes when it comes to growing their food. “We had to make this a very user friendly approach and product for them to pick it up quickly,” he says. The Growcer works one on one with the people who buy the units. Ellis and his team fly out to the community and walk them through the process of operating the units. “The outcome we’re looking for is a profitable business (for them), something that could last for many years and maintain employment in the community and make some money for the local individuals who own it.”
Produce can be grown in remote, desolate conditions.
Variety of commodities grown
So far a wide variety of crops have been grown; Ellis has counted about 40 different vegetables have been grown in the container (eggplant, cucumbers, tomatoes, chilli peppers, and bell peppers). “We usually start them off with a basic set of crops that we know will do well. Ie: lettuces, herbs. They can experiment too if they choose.” Lots of Asian greens are popular, including bok choy and pak choi. “People are wanting to grow what they can’t currently get from the south and then work their way into niches in terms of what their community wants.” The produce is most often made available through subscription models, selling direct to residents or through farmer’s markets. Strawberries are in beta testing.
The technology has great potential for other climates as well. “We’re not just working with northern communities, we’re working with some southern communities and on the international level as well. But our focus remains on the north.”
For more information:
Corey Ellis
The Growcer
Ph 1-833-GROWCER
Publication date: 11/13/2017
Author: Rebecca D Dumais
Copyright: www.freshplaza.com
What’s On The Menu at Food Dudes? Kale Grown in Their Backyard
What’s On The Menu at Food Dudes? Kale Grown in Their Backyard
The Food Dudes are partnering with a Brampton company that creates indoor farming systems, allowing restaurants to use hyperlocal produce in their menus.
Modular Farms president Aaron Spiro grows kale inside his mobile farm with infra red lights. (VINCE TALOTTA / TORONTO STAR)
By AINSLIE CRUICKSHANKStaff Reporter
Nov. 6, 2017
Inside an inconspicuous white container tucked in the corner of a parking lot behind an east-end catering company, infrared lights and a vertical hydroponics system will soon produce up to 68 kilograms of kale a week.
Once harvested, that kale will be carried across the alley to The Food Dudes’ bustling kitchen and transformed into something delicious.
“They can start guaranteeing their customers that any kale on the menu was not only grown locally but was literally harvested less than half an hour before people are eating it, which is pretty amazing,” said Aaron Spiro, the president of Modular Farms.
Over the last four years the Brampton-based company has developed an indoor farming system housed in 40-foot containers made of insulated composite steel panels that they say can grow food in any climate.
They aren’t cheap though. It would cost close to $150,000 to purchase the “primary module” like the one at The Food Dudes. But rather than owning and operating its own module, the catering company has an agreement with Modular Farms to purchase 100 per cent of the module’s produce.
While Modular Farms’ units that have been purchased can now be found in a handful of locations across North America, including Calgary and Sudbury, this is the first in Toronto — but Spiro said it won’t be the last. He’s hoping to see more Modular Farms pop up throughout the city, either purchased outright or through similar partnerships like the one with the Food Dudes.
“Our goal is really to replace as much food as possible with locally sourced options. When it comes to restaurants and caterers, it’s about putting the farms as close to them as possible,” said Spiro, who’s also managing the indoor farm at The Food Dudes.
Modular Farms vertical hydroponics system will soon produce up to 68 kilograms of kale a week.
Karen Landman, a professor at the University of Guelph who studies urban agriculture, said these container systems can make a “real contribution.”
“There’s certainly room for that kind of production in an urban environment,” she said, adding it contributes opportunities for learning, community engagement and chances to get high-value crops like herbs as fresh as possible.
The Food Dudes’ creative director Brent McClenahan said they’d like to have four units in the back parking lot giving them access to a variety of produce year round.
“We’ve partnered with Modular Farms because we recognize that urban agriculture is a local solution to an increasing environmental problem,” he said in a statement.
“As we move into the future and our cities continue to strain the surrounding lands and resources, hyper-local food sourcing will play a crucial role in defining our capacity and approach to feeding our communities.”
Aaron Spiro, president of Modular Farms, poses outside an inconspicuous white container in the corner of a parking lot, which contains his mobile kale farm.
While The Food Dudes currently get most of their produce from the Ontario Food Terminal, Toronto’s main produce distribution centre, they’re planning to eventually source all of it from either organic farms or hyperlocal hydroponics.
The indoor farm out back is just one step toward that goal.
Inside, awash in red light, Spiro takes one of the vertical towers from the wall and lays it on a shiny metal work bench. He pulls a tray of seedlings from the shelf below and pries one of the peat moss plugs free. Today it’s ready to be transplanted into the tower and in about three weeks it will be ready for harvest.
A computer system manages the climate and nutrient dosing to maximize plant growth.
“Kale, it’s a very hardy plant, you can really pump the nutrients into it and it grows quite extensively,” he said.
In the future, the company’s hoping to offer learning opportunities for the public.
They also want to bring in students from schools such as Durham College, the University of Guelph and Niagara College, which have pre-existing horticulture programs, to learn about their system and hydroponic food production.
How to Feed a Hungry City
How to Feed a Hungry City
How does Toronto's garden grow? With fish farms, rooftop planters and vegetable patches all in a row. The city has become a leader in urban agriculture, but there's worry public awareness is lagging as new projects struggle to take root
Steven Bourne, co-founder of Ripple Farms Inc., inspects some of the fish his team uses to create nutrient-rich water to fertilize plants in their aquaponic lab on Seneca College’s campus on Wednesday.
PHOTOS BY CHRISTOPHER KATSAROV/THE GLOBE AND MAIL
NOVEMBER 3, 2017 | CHARLIE FRIEDMANN | SPECIAL TO THE GLOBE AND MAIL
"Do you want to feed the fish?" Not an everyday question inside a shipping container. But here within Ripple Farms' home on the campus of Toronto's Seneca College it's routine, and without awaiting an answer, Steven Bourne – one of the co-founders of the local aquaponics start-up – swiftly hands over a carefully measured container of organic fish feed.
"Sprinkle it over the top," Mr. Bourne says and, within seconds, scores of tilapia dart to the surface seeking their lunch. "We feed them really good food, so our fish are happy and that means our plants are happy," he says, beaming with pride.
This modified shipping container is Ripple's second pilot project in the city, following its inaugural farm at Evergreen Brickworks. The ground floor is filled with a large fish tank, along with a system of pumps and filters that provide nutrient-rich water to the greenhouse set atop the shipping container, feeding plants such as arugula, Swiss chard, kale, basil and mint. The system not only produces extremely healthy crops, but creates no waste beyond rich fertilizer that is later used in traditional soil farming.
Because of this remarkable sustainability and the capacity to produce food year-round, many point to aquaponics farms such as Ripple's as the future, but aquaponics is hardly alone in the urban farming landscape. Urban agriculture as a whole is on the rise in Toronto – this year, the mayor's office recognized Toronto's first Urban Agriculture Day on Sept. 15, marking a milestone for the city's growing community of practitioners. That community includes entrepreneurial farms such as Ripple, as well as traditional backyard gardens, community gardens, school gardens, rooftop farms, backyard chickens and more. Even before this year's recognition by Mayor John Tory, Toronto had been hailed as a leader in the field thanks to the GrowTO Urban Agriculture Action Plan unanimously approved by City Council in 2012 to provide a framework for encouraging the growth of urban agriculture.
But while this is viewed as a global model for city planning, local experts caution that not all is rosy in Toronto's gardens, as a number of projects have recently stalled due to lagging approvals and other challenges.
Brandon Hebor, co-founder of Ripple Farms Inc., inspects the growing lights of an aquaponics lab. Ripple currently sells its produce to high-end chefs.
"Torontonians have long grown in their backyards and continue to do so, but it's mostly been under the radar," notes Joe Nasr of the Centre for Studies in Food Security at Ryerson University and a co-ordinator of Toronto Urban Growers (TUG). "What's new is this attention to the fact it exists and that it has a place in the city, and that the city can help it prosper."
TUG has brought together a diverse group of civilian stakeholders since 2009, with the goal of increasing the availability of healthy and sustainable food grown, processed and sold in Toronto. Through networking meetings, public forums, and lobbying, the group has done just that, and – working with the Toronto Food Policy Council (TFPC) – was largely behind efforts to bring Toronto's Urban Agriculture Day to fruition.
Experts explain that supporting urban agriculture citywide is crucial because projects such as community gardens or larger-scale operations such as Black Creek Community Farm not only provide access to healthy and affordable food but offer skills and job training.
"I'm very keen on urban agriculture," Lori Stahlbrand, chair of the TFPC, says. "There are so many ways you can address health, nutrition, social inclusion, the environment and economic development, all using food." In contrast to the civilian TUG, the food-policy council is directly embedded in city government. "We were the first food-policy council in a major city in the world," Ms. Stahlbrand says. "There are now several hundred, but the key to what makes ours different is that I'm a permanent staff of the City of Toronto."
Established in 1991 as a subcommittee of the Toronto Board of Health, the TFPC focuses on the city's food policy as a whole, a large part of which includes strategies for increasing urban agriculture.
Many point to aquaponics farms such as Ripple’s as the future.
This year's first Urban Agriculture Day was preceded by a week of tours around the city led by TUG and the TFPC, seeking to expose some of the ways urban agriculture can result in healthy, low-cost food, engagement of isolated communities such as seniors and people living with mental illness, as well as promising entrepreneurial ventures.
"We're starting to encounter the problem that because people don't know what urban agriculture is, they're more likely to say no to projects," says Rhonda Teitel-Payne, another TUG co-ordinator, on the importance of the tours. Other events included public forums, workshops and a harvest dinner at Black Creek Community Farm with some of Toronto's top chefs.
Located in one of Toronto's poorest neighbourhoods, Black Creek Community Farm has quickly become a model for other cities. "The vision was to look at how this farm can play a role in food security in the Jane and Finch community – doing this from a community-development perspective, ensuring community members are part of the decision making," Leticia Boahen, Black Creek's director, says.
The farm addresses food security by providing access to farmland and discounted fresh produce to low-income families in the area, but a major part of its program is about education and engagement.
Brandon Hebor, left, and Steven Bourne. This modified shipping container is Ripple’s second pilot project in the city, following its inaugural farm at Evergreen Brickworks.
The benefits of education and food literacy continually come up when speaking with urban-agriculture experts. Local organizations such as FoodShare have long tried to address this issue, with programs of school nutrition and the goal of a food-growing garden in every school.
"It's a terrific idea," Ms. Stahlbrand says. "Programs where students are engaged and learning food-growing skills train them in real skills, make them employable in the food system – and they also learn so much about good eating."
Postsecondary schools are becoming more involved, with entire programs now dedicated to food studies. And local universities and colleges are beginning to implement gardens on empty spaces or campus rooftops. Seneca's partnership with Ripple Farms is just one such example. The farm will be operated by students and the school will partner on related educational programs with Ripple's founders, Mr.Bourne and Brandon Hebor – themselves recent graduates of Seneca's Green Business Management program.
Ripple Farms is a for-profit business but it's run as a social enterprise. "There's a big shift happening with our generation," Mr. Bourne explains. "My metrics aren't how much money is going into my pocket at the end of the day, it's how many people do I feed? I will make money, but it's not my main impact measure."
The company currently sells mainly to high-end chefs because of limited production, but that will soon change. Ripple recently received government loans that will be used to build a 10,000-square-foot farm in Toronto that can produce 250,000 pounds of fresh produce a year – the equivalent of feeding approximately 55,000 people three meals a day.
Steven Bourne inspects some of the herbs that Ripple Farms has been growing.
Ripple has been using tilapia in its system, as almost all aquaponics farmers do, but more local species such as trout and catfish are being considered. This would then provide a sustainable source of high-quality local fish in addition to the fresh produce. Among those interested are local restaurants such as Montgomery's, which has purchased some of Ripple's herbs and vegetables.
Focusing on seasonal, local ingredients was always essential for Kim Montgomery-Rawlings and her husband, chef Guy Rawlings, but the pair wanted to think locally beyond the menu when they opened their first restaurant last summer. "Guy and I always said we wanted to make a restaurant that wasn't just a restaurant," Ms.Montgomery-Rawlings says. "It's an opportunity to get involved with the community, meet new people, branch out and share ideas."
While researching local food issues, Ms. Montgomery-Rawlings was introduced to TUG and the TFPC and immediately began attending meetings – eventually becoming an elected member of the TFPC. Montgomery's is also a local leader in featuring seasonal and local products; in addition to local produce purchased from others, it maintains a rooftop garden of its own, built in self-watering containers.
In fact, the idea of adding container gardens to empty lots around the city is one theTFPC's Ms. Stahlbrand is especially fond of. In Vancouver, Sole Food Street Farms has been successful at growing 25 tonnes of food a year while transforming empty lots and employing dozens of members of the city's poorest neighbourhoods.
Having Ms. Stahlbrand as a permanent city employee through the food policy council is undoubtedly beneficial, but if Toronto hopes to follow the lead of other cities and adopt projects such as these, many suggest another city staff member dedicated to urban agriculture is needed.
The ground floor of Ripple Farms is filled with a large fish tank, along with a system of pumps and filters that provide nutrient-rich water to the greenhouse set atop the shipping container.
One promising large-scale project that has run up against challenges involves building community farms within underused hydro corridors. Such farms would be a new hybrid model meshing community gardens with farmers' markets, creating economic development to support low-income communities. With soil and electromagnetic tests completed by Toronto Public Health nearly four years ago, city staff got on board and have backed the program. Unfortunately, gaining final approval from Hydro One has been more onerous and expensive than expected, as more than $100,000 raised from Toronto Public Health and private grants has been put into Hydro's site-assessment processes. Supporters believe they're close to clearing the final hurdle. "If we finally do get these farms in the ground, it's going to be amazing," Ms. Teitel-Payne says. "The space is there, the communities desperately need the farms and it will be a chance to test out new urban-farming models."
New entrepreneurs are also cropping up, large developers such as the Daniels Corporation have shown interest in building rooftop farms and members of city government and community organizers are increasingly advocating for the benefits urban-agriculture projects. "The solutions are out there, we just need to work on convincing people that this can be done here," Ms. Stahlbrand says. "It's definitely time for the next big step in Toronto and because of the structure we have, I don't see a reason why it won't happen."
How To Grow 40,000 Heads of Lettuce In A Shipping Container
How To Grow 40,000 Heads of Lettuce In A Shipping Container
Nov 19, 2017
Lettuce grows inside a converted shipping container at Tiger Corners Farms in Summerville. Tony Bertauski/Provided | Tony Bertauski
The weather is always perfect at Tiger Corner Farms.
Using the cozy interiors of shipping containers, the facility in Summerville farms indoors. By retrofitting 320 square feet of storage, they convert open space into a highly productive aeroponic farm. Seed to harvest, they can produce nearly 4,000 heads of lettuce in five weeks. That’s almost 13 heads of lettuce per square foot and a little more than 40,000 per year. How do they do it?
The answer is in the air.
Farming traditionally requires land. In urban areas, farming is nearly impossible where space is limited and expensive. Food often is shipped in from rural farms. What about all the space above the ground?
Tiger Corner Farms grows more than 40,000 heads of lettuce a year inside shipping containers in Summerville. Tony Bertauski/Provided | Tony Bertauski
Tiger Corner Farms has taken an innovative approach to vertical farming. Recycling empty shipping containers, they’ve created mobile farms that can be functional in any environment.
The process starts on a simple flood rack. Seeds are planted in coconut fiber plugs. Trays are flooded with a nutrient solution 10 minutes each day. Two weeks after seeding, seedling are plugged into hollow panels where they will grow for another three weeks. Matured lettuce is then harvested, roots and all, with no soil to wash off.
They use an alternative method of growing called aeroponics. Hydroponics grows crops in a soiless environment where roots bathe in a flowing nutrient solution. In aeroponics, roots dangle in a humid, nutrient-rich atmosphere rather than liquid. At Tiger Corner Farms, two hollow panels hang from the ceiling of a storage container. Plants are grown on both sides. The newest design has a capacity of 3,160 plants with an increased quality of product due to an improved design of locally sourced panels.
Every 10 minutes, nutrient solution is misted over the roots inside the panels. The excess solution drains to a reservoir to be recycled. An average of 10 gallons of water is used daily. Hydroponics and aeroponics require vigilant monitoring of nutrient solution. While this can be time consuming, Tiger Corner Farms has fully automated this process by adapting warehouse management software to adjust nutrient levels, pH and other environmental parameters. This system not only reduces manual labor, it tracks every crop from seed to harvest.
The shipping container is a closed system that relies completely on LED lights mounted on all sides of the panels. The light spectrum is optimized for plant growth. LEDs generate very little heat, which reduces the need to cool the container.
Besides the need for artificial light, another side effect of the closed system is carbon dioxide. Photosynthesis requires sunlight, water and carbon dioxide to manufacture glucose, or sugar. Inside the container, carbon dioxide levels drop to approximately a quarter of atmospheric levels. A propane burner is used to boost carbon dioxide and increase photosynthesis and growth.
A nutrient solution is misted over the roots of lettuce plants every 10 minutes inside shipping containers in Summerville. Tony Bertauski/Provided | Tony Bertauski
Once the crop is harvested, the growing panels are powerwashed and sterilized before the next planting. Crops often are rotated so that only a quarter of the container’s capacity is harvested. This reduces the demand on maintenance and delivery.
Of course, this self-contained system relies on power. Any failure in the system, whether power or a component, will alert the manager via phone or other means. In the meantime, generators keep the system running.
While Tiger Corner Farms builds the containers, Vertical Roots is the local company using them to grow and distribute the products. Currently, they provide for the Dorchester District 2 school cafeterias as well as more than 50 restaurants sourced by Grow Food Carolina.
Ashley Ridge High School in Summerville has a container on site where horticulture students assist in growing the crop. The Citadel also operates a container to provide food for the cafeteria.
Tiger Corner Farms sees its product as a way of filling a need for local produce in an urban environment. This self-contained farm can be operational in most areas and grow a variety of leafy greens and herbs.
Tony Bertauski is a horticulture instructor at Trident Technical College. To give feedback, e-mail him at tony. bertauski@tridenttech.edu.
Freight Farms Expands Reach to Asia
Company Announces Partnership with Everlane to Equip Saitex Denim Factory with Leafy Green Machines ™
NEWS PROVIDED BY | Freight Farms
BOSTON, Nov. 21, 2017 /PRNewswire/ --
Freight Farms today announced Everlane as a new corporate partner, who plans to purchase and launch three Leafy Green Machines™ at Saitex, their LEED-certified denim factory in Ho Chi Minh City, Vietnam. Everlane is a San Francisco-based retailer known for its commitment to radical transparency and high quality, ethically-made basics. Everlane will be placing the farms at Saitex to provide its workers with two healthy meals a day. This project is made possible by Everlane's Black Friday Fund, an annual initiative which uses Black Friday sales to improve the lives of workers at factories like Saitex.
Everlane's contribution addresses the rampant use of unregulated pesticides in Vietnam, which has severely degraded soil health and water quality. As a result, existing sources of local agriculture leave Saitex's employees at risk to exposure to dangerous chemicals.
"Since 2014, the Black Friday Fund has allowed us to invest in projects that give back to the workers at our factories," saidMichael Preysman, founder, Everlane. "This year, we are excited to partner with Freight Farms to build a farm that will provide the workers at Saitex two healthy meals per day that are pesticide free and grown in the cleanest way possible."
"We're thrilled to empower Everlane and Saitex to grow fresh and clean lettuce for their workers. The container's controlled environment enables anyone to grow produce at a commercial scale without the need for pesticides or herbicides, and with very little water consumption," said Brad McNamara, co-founder, Freight Farms.
About Freight Farms: Founded in 2010 in Boston, Freight Farms has established itself as the leader in the agriculture technology industry. The company was the first to bring farming into a shipping container to create their flagship product: The Leafy Green Machine™. To date, there are over 160 farms in operation in the U.S., Canada, the Caribbean, Dubai, and Europe. For more information about Freight Farms, visit www.freightfarms.com/media-kit.
About Everlane: Everlane launched online-only in November 2011 with the mission to provide consumers with well-designed, high-quality clothing and accessories at an approachable price point. Simultaneously, Everlane encourages consumers to stay informed and educated on product origins. By cutting out the middleman and sharing the true cost and markup of each product, they have become distinguished leaders in the transparent retail space, and a disruptor of the luxury clothing industry. Everlane currently works with 25 factories and employs 100 people at offices in San Francisco and New York City.
SOURCE Freight Farms
Related Links
Everlane Is Using Black Friday Sales To Bring Farm-Fresh Food To Garment Workers
In a new move, Everlane is partnering with Freight Farms, a Boston-based ag-tech startup that makes ready-to-go hydroponic farms in shipping containers, to bring three of their Leafy Green Machines to the Saitex International factory in Ho Chi Minh City, Vietnam, which makes Everlane’s denim clothing.
By Andrew Amelinckx on November 22, 2017
There's a farm in that shipping container. Freight Farms
Everlane, a San Francisco-based e-commerce clothing retailer known for ethical, sustainable fashion and transparent pricing, is using its Black Friday sales to provide container farms—and farm-fresh produce—for its garment workers in Vietnam.
The fashion industry is pretty well known for having a crappy record when it comes to sustainability and ethical issues—things like wasting natural resources and not paying garment workers a living wage. But Everlane has made sustainability a priority, working with ethical factories around the world and being super transparent about what it costs the company to make its clothes (even going so far as offering “Choose What You Pay” pricing that labels how much goes to cover manufacturing costs vs company profit).
In a new move, Everlane is partnering with Freight Farms, a Boston-based ag-tech startup that makes ready-to-go hydroponic farms in shipping containers, to bring three of their Leafy Green Machines to the Saitex International factory in Ho Chi Minh City, Vietnam, which makes Everlane’s denim clothing. And the company is using money its Black Friday sales to fund the effort, which is part of its ongoing program to improve the lives of its workers.
What Is The Leafy Green Machine?
We’ve written about Freight Farms a few times since the company launched back in 2011. It’s Leafy Green Machine comes in a 40-foot-long upcycled shipping container and is operated remotely via smartphone by a computer system that controls temperature, moisture, humidity, and nutrient levels in the hydroponic system. The LGM uses LED lights for its vertical grow towers, doesn’t require pesticides or herbicides, and uses about 90 percent less water than conventional farming the same crops, according to the company.
The inside of one of the Leafy Green Machines. Freight Farms
The container farms will be used to supply the cafeteria that serves the 3,900 employees at the LEED-certified denim factory (LEED means the facility meets stringent environmental requirements having to do with energy and natural resource conservation). Everlane reps tell Modern Farmer the container farms will be used for growing lettuce, herbs and root vegetables—like onions, carrots, and radishes—with a portion of space reserved for experimenting with tomatoes and other crops. The three LGMs, depending on what vegetables are being grown, can produce somewhere in the range of 1,500 heads of lettuce, 135 to 240 pounds of herbs, and 180 to 300 pounds of leafy greens—a week. That comes to between six and 12 tons of produce a year. The farms, which cost around $75,000 each, are scheduled to be delivered this coming spring.
Everlane decided on this project due to the widespread unregulated use of highly toxic pesticides in Vietnam’s farming sector and wanted to provide pesticide-free produce for the garment workers there, according to the company.
With Vertical Farms, Food Banks Are Growing Their Own Produce to Fight Hunger
With Vertical Farms, Food Banks Are Growing Their Own Produce to Fight Hunger
Vertical farms allow food banks to grow their own produce with high-tech systems in an effort to fight food insecurity year-round.
The Community Food Bank of Oklahoma’s Growtainers. Photo courtesy of Growtainers.
BY JODI HELMER | Technology, Urban Agriculture
11.17.17
When temperatures dip below zero, it’s too cold for farmers to grow fresh produce in Tulsa.
Until spring, almost all of the fresh fruits and vegetables distributed through the Community Food Bank of Eastern Oklahoma are imported from warmer climes like Mexico and California. Those donations are few and far between, often leaving the food bank distributing non-perishable items such as canned tomatoes, peanut butter, and pasta instead of fresh foods. To address this gap, the food bank started to grow its own greens, ensuring a stable supply of fresh, locally-grown produce for its clients.
“Our priority is getting healthy foods to the people that need them, but getting donated produce has been a big challenge for us—and having fresh produce is even tougher in the winter months,” said John McCarthy, the food bank’s director of community incentives.
Inside the Community Food Bank of Oklahoma’s vertical farm. (Photo courtesy Growtainers)
In 2016, the food bank installed a vertical farm—an indoor, temperature-controlled environment where food is grown in stacked towers under LED lights. The two 40-foot by 8-foot shipping containers that make up the operation were upfitted into indoor hydroponic farms by Growtainers, one of several manufacturers of vertical farm systems. The containers are designed to produce up to 1,800 heads of lettuce and other leafy greens every 45 days—regardless of the time of year.
“We harvest greens in the morning, and they’re available in the afternoon, producing a really nice product we can count on,” McCarthy said.
Farming is generally not commonplace among food banks. Feeding America, a nonprofit, nationwide network of food banks, reports that only 29 of its 200 members operate farms and distribute that produce to food insecure and low-income clients. And this is mostly because land is expensive to acquire or lease; growing food is time- and labor-intensive and requires specialized knowledge; and many food banks choose instead to focus their efforts on the logistics of getting food to people in need.
But vertical farms—with manufacturers’ promises of producing large amounts of food in a small footprint through high-tech, plug-and-play growing operations—could bring about a shift in food banks’ willingness to grow their own food. Unlike greenhouses, which can lack light and temperature control, thereby limiting the growing season, vertical farms might offer food banks the ability to grow food year-round.
With the National Organic Standards Board recently making the controversial recommendation that hydroponic and aeroponic systems be eligible to earn organic certification, vertical farms are poised to reach new levels of popularity. And though there is no data on the number of food banks operating vertical farms, several appear to be experimenting with the high-tech approach.
Cultivating the Right Approach for the Climate
One of the biggest arguments against food banks getting into the vertical-farming business is simply that these systems are pricey. The Community Food Bank of Eastern Oklahoma paid $140,000 for its two Growtainers, securing a grant from the Morningcrest Healthcare Foundation to purchase the vertical farms. It costs an additional $680 per month for electricity to power them.
For nonprofits, cost can be a barrier and, in some locations, indoor farms are an unnecessary expense. The learning curve can also be steep and most food banks rely on volunteer labor to handle maintenance and harvesting, often with training from the manufacturers of the vertical systems.
The climate was the main reason the Surrey Food Bank, the second-largest food bank in British Columbia, installed a vertical farm from Living Garden Foods at one of its four locations earlier this year. The wall-mounted towers grow produce in eight rows; fresh lettuce and kale are harvested every six weeks, allowing the food bank to provide fresh greens for up to 80 families at its Cloverdale location.
“A lot of food banks have outdoor community gardens, but this is a new thing, and we think it’s working well,” said Feezah Jaffer, the food bank’s executive director.
The Surrey Food Bank’s vertical farm system. (Photo © Pixel Perfect Photography)
Still, some food banks growing food in warmer climates are continuing to grow outside. San Antonio Food Bank, for example. operates a 75-acre farm and an urban orchard with 170 fruit trees, distributing produce to clients in 16 counties across Texas. The conventional farming plots grow everything from onions and potatoes to watermelons and cantaloupe, helping the food bank achieve its mission to provide fresh, healthy foods to those in need.
Because of the success of the farms, Patrick Brennan, manager of facilities and agricultural initiatives at the San Antonio Food Bank, has no immediate plans to add vertical farming to the agricultural operations.
“In more extreme climates, growing indoors is a more attractive option,” Brennan explained. “We do get temperature fluctuations and occasional freezes, so vertical farming might be in our future, but for now we have the ability in Central Texas to decrease costs by growing produce traditionally.”
Working Through the Growing Pains
For food banks where the climate isn’t as friendly to outdoor farming, vertical farms may hold promise. Given their positive experience with vertical farming, Surrey Food Bank in B.C. is hoping to install similar systems at the bank’s three other sites as well. While farmers donate apples, pears, cherries, and other locally grown fruits and vegetables to the food bank, those donations often fall short of demand, requiring the food bank to allocate part of its budget to purchase fresh produce. All together, produce comprises 45 percent of the food the bank distributes.
Before expanding the farming effort, however, Jaffer wants to address some of the challenges facing the current operation.
First harvest in the Community Food Bank of Oklahoma’s Growtainers. (Photo courtesy Growtainers)
Less than six months into production, volunteers at the Surrey Food Bank are still figuring out how to maximize the farm’s output. Some of the greens failed to grow, and others went to seed too fast. Additionally, varieties like Swiss chard grew well, but clients were unfamiliar with the greens or disliked their flavor. As volunteers gained experience with the vertical towers, production problems became less common and surveying families about what kinds of greens they prefer helped the food bank tweak its crop mix so no greens went uneaten.
The Community Food Bank of Eastern Oklahoma also adjusted its approach based on feedback from clients and experience with the vertical growing system. In addition to experimenting with growing tomatoes in one of its Growtainers, the food bank reduced output of non-nutrient-dense greens such as butter lettuce, romaine, and mesclun in favor of growing more kale and spinach—and teaching clients on how to prepare it by offering recipes—to maximize the nutritional value, and reduce waste.
Jaffer at the Surrey Food Bank believes asking clients about their preferences helps provide a sense of ownership in the harvest and increases their willingness to add fresh greens to their food baskets.
“There have been growing pains, but the more we learn these lessons, the bigger of a success it becomes,” she said. “We think food banks need to evolve to meet the needs of our clients, and embracing vertical farming technology is one way we can do that.”
Indoor Farm Grows Produce In Outer Space
Indoor Farm Grows Produce In Outer Space
The plant cultivation technology will help provide food for crew members on board the International Space Station.
6 Nov 2017
Most people take the ability of walking to the supermarket to buy food for granted, but that simply isn’t a possibility for many who are based – quite literally – in the middle of outer space. Engineers at the German Aerospace Center (GAC) saw this gap in the market and created the EDEN ISS project, which aims to advance controlled environment agriculture technologies beyond the state-of-the-art. EDEN ISS is a 4-year project under the European Union‘s Research and Innovation Action program Horizon 2020. The goal of the project is to develop safe food production for on-board the International Space Station (ISS) and for future human space exploration vehicles and planetary outposts.
The project will develop an advanced nutrient delivery system, a high performance LED lighting system, a bio-detection and decontamination system, and food quality and safety procedures and technologies. A mobile container-sized greenhouse test facility will be built to demonstrate and validate different key technologies and procedures necessary for safe food production within a semi-closed system. The plant cultivation technologies will initially be tested in a laboratory setting. The next phase will see the high-tech greenhouse container shipped to the German Neumayer Station III in Antarctica, which will begin crop cultivation experiment in December.
Technology has placed itself in the middle of those who are in need of a service and the creation of the required service, with nothing seeming impossible. The mobility of the less able in poverty-stricken countries, for example, has been tackled by one company, who created an all-terrain wheelchair, while the Finnish government has teamed up with a startup tohelp refugees with their finances. How has technological advances in the past 12 months boosted your business’ operations?
Website: www.eden-iss.net
Contact: www.eden-iss.net/index.php/contact
What’s On The Menu at Food Dudes? Kale Grown in Their Backyard
What’s On The Menu at Food Dudes? Kale Grown in Their Backyard
The Food Dudes are partnering with a Brampton company that creates indoor farming systems, allowing restaurants to use hyperlocal produce in their menus.
Modular Farms president Aaron Spiro gows kale inside his mobile farm with infra red lights. (VINCE TALOTTA / TORONTO STAR)
By AINSLIE CRUICKSHANK Staff Reporter
Mon., Nov. 6, 2017
Inside an inconspicuous white container tucked in the corner of a parking lot behind an east-end catering company, infrared lights and a vertical hydroponics system will soon produce up to 68 kilograms of kale a week.
Once harvested, that kale will be carried across the alley to The Food Dudes’ bustling kitchen and transformed into something delicious.
“They can start guaranteeing their customers that any kale on the menu was not only grown locally but was literally harvested less than half an hour before people are eating it, which is pretty amazing,” said Aaron Spiro, the president of Modular Farms.
Over the last four years the Brampton-based company has developed an indoor farming system housed in 40-foot containers made of insulated composite steel panels that they say can grow food in any climate.
They aren’t cheap though. It would cost close to $150,000 to purchase the “primary module” like the one at The Food Dudes. But rather than owning and operating its own module, the catering company has an agreement with Modular Farms to purchase 100 per cent of the module’s produce.
While Modular Farms’ units that have been purchased can now be found in a handful of locations across North America, including Calgary and Sudbury, this is the first in Toronto — but Spiro said it won’t be the last. He’s hoping to see more Modular Farms pop up throughout the city, either purchased outright or through similar partnerships like the one with the Food Dudes.
“Our goal is really to replace as much food as possible with locally sourced options. When it comes to restaurants and caterers, it’s about putting the farms as close to them as possible,” said Spiro, who’s also managing the indoor farm at The Food Dudes.
Modular Farms vertical hydroponics system will soon produce up to 68 kilograms of kale a week.
Karen Landman, a professor at the University of Guelph who studies urban agriculture, said these container systems can make a “real contribution.”
“There’s certainly room for that kind of production in an urban environment,” she said, adding it contributes opportunities for learning, community engagement, and chances to get high-value crops like herbs as fresh as possible.
The Food Dudes’ creative director Brent McClenahan said they’d like to have four units in the back parking lot giving them access to a variety of produce year round.
“We’ve partnered with Modular Farms because we recognize that urban agriculture is a local solution to an increasing environmental problem,” he said in a statement.
“As we move into the future and our cities continue to strain the surrounding lands and resources, hyper-local food sourcing will play a crucial role in defining our capacity and approach to feeding our communities.”
Aaron Spiro, president of Modular Farms, poses outside an inconspicuous white container in the corner of a parking lot, which contains his mobile kale farm.
While The Food Dudes currently get most of their produce from the Ontario Food Terminal, Toronto’s main produce distribution centre, they’re planning to eventually source all of it from either organic farms or hyperlocal hydroponics.
The indoor farm out back is just one step toward that goal.
Inside, awash in red light, Spiro takes one of the vertical towers from the wall and lays it on a shiny metal work bench. He pulls a tray of seedlings from the shelf below and pries one of the peat moss plugs free. Today it’s ready to be transplanted into the tower and in about three weeks it will be ready for harvest.
A computer system manages the climate and nutrient dosing to maximize plant growth.
“Kale, it’s a very hardy plant, you can really pump the nutrients into it and it grows quite extensively,” he said.
In the future, the company’s hoping to offer learning opportunities for the public.
They also want to bring in students from schools such as Durham College, the University of Guelph and Niagara College, which have pre-existing horticulture programs, to learn about their system and hydroponic food production.
‘Farm in a Box’ Could Protect Food Supplies After Extreme Weather Events
‘Farm in a Box’ Could Protect Food Supplies After Extreme Weather Events
Boston-based Freight Farms has developed what it calls the Leafy Green Machine, a method for vertical, hydroponic farming inside a shipping container.
BY MOLLY FOSCO | OCTOBER 16, 2017
Vertical and hydroponic farming has gained popularity in recent years. And with the frequency and intensity of some extreme weather events on the rise, innovative techniques offer enticing solutions to some agricultural problems.
Boston-based company Freight Farms is offering one approach: It’s helping people grow food inside shipping containers 365 days a year, no matter the weather conditions.
Brad McNamara and Jon Friedman started Freight Farms in 2010 with the goal of making it easier for anyone to grow food on a commercial scale. “We really focused on putting farming into the hands of regular people so that you can have a manageable footprint but still produce at a commercial level,” McNamara, the company’s CEO, told Seeker. “We were really inspired by what’s becoming possible with new technology and the fact that no one had changed their thinking yet from big agriculture and large-scale farms.”
McNamara and Friedman wanted to create something small that could still produce large crop yields. The result is the Leafy Green Machine, a produce farm that operates inside a shipping container that is forty feet long, eight feet wide, and nine and a half feet high. The LGM uses a vertical, hydroponic farming method that allows leafy greens like kale, lettuce, and cabbage, as well as herbs like basil, mint, and oregano, to be harvested once a week, year round. It grows 2-4 tons of produce annually using less than 10 gallons of water per day. Its water, air, and nutrient inputs can be monitored and controlled remotely using a software called "farmhand."
The LGM costs about $85,000 and around $13,000 to operate annually. Freight Farms offers financing options, as well as video tutorials and two-day, in-person trainings at their Boston headquarters on how to operate an LGM.
“The LGM is a really good tool for existing farmers to take some of the pressure off their farm infrastructure … and their native lands,” McNamara said.
Freight Farms is among other large and small companies embracing small-scale, vertical and hydroponic farming techniques. Metropolis Farms will open a solar-powered, 660-acre, indoor farm in Philadelphia next month, growing broccoli, strawberries, tomatoes, and lettuce in a 100,000-square-foot warehouse year round. And Ikea is developing a hydroponic farming system that will allow the furniture retailer to grow and harvest its own veggies in-house.
“We’ve had multiple waves of innovation within agriculture and to me this is just the next frontier that needs to be created,” McNamara said.
RELATED: Urban Farming Isn't a Game Changer When It Comes to Carbon Emissions
The Leafy Green Machine came in very handy when Hurricane Harvey destroyed crops across dozens of counties around Houston, Texas. Employees at Acre in a Box, a Houston-based hydroponic farm that uses the LGM, couldn’t get to their farm for several days after the storm due to flooding. However, because they were monitoring their crops remotely with the Farmhand app, all the plants remained intact.
“Eventually they were able to go in and harvest, and right as the restaurants they work with started to open, they were the only ones who could provide them with produce,” McNamara said.
In light of the recent, severe hurricanes like Harvey and raging, deadly wildfires in California, McNamara believes the LGM could be invaluable after future, extreme weather events.
“It’s always been an exciting use case for us, you know, the ability to take an area that’s been decimated by these increasing, more extreme climate events and allow it to bounce back,” he said. “If you look at what’s happening in Puerto Rico, their priorities are water, electricity, and food, and the traditional farming sector might take years to come back. But what do you do in the meantime?”
He added, “Everything we’ve built since the beginning, from the hardware to the software side of the business, has been to make it easier and more efficient for people to grow food where ever they are.”
Antarctic Farm Could One Day Journey to Mars
Antarctic Farm Could One Day Journey to Mars
BY TRACY STAEDTER POSTED OCT 13, 2017
Illustration of the shipping-container greenhouse that'll be providing fresh produce to Antarctic residents from February 2018 to December 2018. LSG
Antarctica is no place for a tomato. But starting in January 2018, researchers at the German Antarctic research station, Neumayer III, will begin growing not only tomatoes but also lettuces, herbs, peppers, cucumbers, swiss chard, radishes and even strawberries inside a climate-controlled shipping container. Although other indoor gardens have existed in Antarctica, the EDEN ISS Mobile Test Facility will be the most advanced indoor farm on the continent — an experiment meant to push the limits of indoor agriculture, so that the technology can hold up for a long mission to Mars.
"Some of my colleagues like to say, 'It's no longer your grandmother's garden anymore,'" says Matthew Bamsey, a research associate at DLR, also known as the German Aerospace Center, and a member of the EDEN ISS team, a multipartner project focused on developing plant cultivation technologies for future use in space.
Out on the Ekström Ice Shelf in the Atlantic sector, the greenhouse will stand against Antarctica's frigid temperatures, the long dark winter and extremely low humidity. From the outside it's a simple structure, just two 20-foot (6-meter) shipping containers placed end to end. But inside, it's a high-tech oasis capable of producing 661 pounds (300 kilograms) of produce annually. To give you an idea of how much that is, in 2013, the average U.S. person consumed 272 pounds (123 kilograms) of fruits and vegetables.
Fine-tuning the operation for space is one of the main goals of the project.
"We don't want an astronaut working 16 hours a day in the greenhouse," he says.
The experiment will allow them to figure out just how much time is needed to tend the garden. Over the next year, they'll get closer to that answer.
The indoor garden is based on a soil-free growing system called aeroponics. The system, first invented in the 1920s but advanced by NASA in the 1990s, is extremely water-efficient, using 98 percent less water than soil-based gardens. Plants grow in trays on racks, with their roots suspended within a protected chamber that prevents light from entering. At regular intervals, the hanging roots are spritzed with a fine water and nutrient-rich mist. Any water not taken in by the roots is captured and recirculated.
The Future Exploration Greenhouse pictured here (not in Antarctica) is the area where the plants grow in the EDEN ISS Mobile Test Facility. The greenhouse has 135 square feet (12.5 square meters) available for cultivation | BRUNO STUBENRAUCH
Sensors monitor the nutrient levels and provide data to a computer that analyzes the mix and adjusts it according to the plants being grown and their stage of growth. Cameras monitor the plant's growth, while other sensors capture temperature, humidity and carbon dioxide levels, which are fed to a computer that keeps the ideal levels precisely tuned. Air filters keep the environment free of bacteria and fungus, while an ultraviolet light helps sterilize the air and kill any organism not caught in the filter. Because of the sterile environment, neither insecticides nor pesticides are required.
The plants grow beneath LED lights that illuminate the leaves in blue, red and white light, which when mixed together, bathe the room in pinkish-violet sci-fi glow, says Bamsey. The lights shine for 16 hours a day and then turn off for eight hours to simulate night.
As of this writing, the greenhouse, comprising two shipping containers, is making its way by ship to Cape Town, South Africa, where it will be transferred to another ship bound for Antarctica, and due to arrive on Dec. 24, 2017. Bamsey and several of his colleagues, including DLR scientist Paul Zabel, will be there to meet the shipment and oversee its transport by tracked vehicle approximately 12 miles (20 kilometers) across the ice shelf. Bamsey says the shipping containers will be placed end to end atop an 8.2-foot (2.5-meter) tall platform that will prevent the greenhouse from becoming buried in snow. One shipping container, named the Future Exploration Greenhouse, houses the plants and the other, the Service Section, contains the control systems that keep them alive.
As this drawing shows, the greenhouse will be split into three separate sections: a cold porch/airlock, a service section and the actual greenhouse | LSG
All of the DLR scientists, including Bamsey, will return home after seven weeks, with the exception of Zabel, who will stay behind at Neumayer III, along with nine other researchers. There, Zabel will keep an eye on the greenhouse, which will sit about (1,312 feet) 400 meters away from the main station. Along with making sure all of the systems are running smoothly, he'll prune the plants, harvest them when they're ready and take samples that will be sent back to partner research labs. Having some interaction with the plants provides a psychological benefit, says Bamsey. And even though a fully autonomous system is possible, the engineers likely will not design one. Previous research has shown that for people stationed in remote areas like Antarctica, tending to plants, interacting with them and just observing them improves a person's state of mind.
Bamsey referred to a 2013 South Korean study, conducted after an indoor garden was installed at the King Sejong Station on Antarctica. It found that 83 percent of station crew members found the fresh produce to be "very helpful" or "somewhat helpful" to their mental health.
The psychological benefits of having greenery in Antarctica goes back to the 1902 Discovery Expedition of the continent, led by Robert Falcon Scott, where some of the crew members grew cress and mustard in the ship's ward under natural light, says Bamsey. In some of the crewmen's journal entries, they talk of the plants, the energy and time they took to care for them and the boost to morale they provided.
"Some of the crew members and explorers of that time talk about how this was the first green material they had eaten in two years," says Bamsey.
The greenhouse has funding until the end of 2018. Produce samples will be sent back to labs in Europe to test for their nutritional value and if all goes well, the researchers will be back again for another frigid growing season.
Made in the Lowcountry: Tiger Corner Farms
SUMMERVILLE, SC (WCBD)– Growing over 4500 plants in a 40 foot box may sound unbelievable. At Tiger Corner Farms they do it every month.
“Every single scientific discipline that I can think of is wrapped up into one box,” says chief engineer Evan Aluise.
It’s a partnership between nature and technology, and it all happens in recycled shipping containers. The innovative farm is operated by 3 sister companies.
One of those companies is Vertical Roots. A horticulture start up in charge of growing and harvesting the plants. Although they have experimented with many different plants, right now they primarily grow lettuce. They produce 7 different kinds.
Co-founder and operator, Matt Daniels, says they yield around 15 harvests a year.
“Right now we’re producing collectively 4000 heads a week, for the public and for Dorchester District 2 schools.”
It could be thanks to the perfect growing climate, the 20 second bursts of nutrient infused water, or the LED panels providing peak amounts of chlorophyll A and B.
All levels are monitored and regulated by a computer program, which was coded by the third sister company, Boxcar Central.
The aeroponic technology is manufactured by Tiger Corner Farms, a company in its infancy, but one with big goals.
“The container that we were in does not look like the next, or the next […] we’re continually evolving into a better product,” says Aluise.
The container itself also goes through a major transformation. It arrives as a bare bones shipping container at the end of its previous life. In two and a half weeks it will be revived and ready for a new purpose.
The crew installs insulation, shelving and a state of the art air conditioning unit. Then they install the technology that will power the project.
Stefanie Swackhamer, general manager of Tiger Corner Farms says watching the containers arrive never gets old. She and her father created the company after she saw a need for healthier food and farming population that is aging.
“It’s a big problem that we aren’t locally sourcing food and eating healthy food on a daily basis,” says Swackhamer.
She is a former Stall High School Teacher. Now her farm provides produce to schools in Dorchester County, and the aeroponic containers are used to teach students.
“We’re teaching kids about technology, we’re getting them excited about agriculture, and we are hopefully creating future farmers that would not have otherwise existed.”
To learn more about the company, you can head to their website: http://tigercornerfarmsmfg.com/