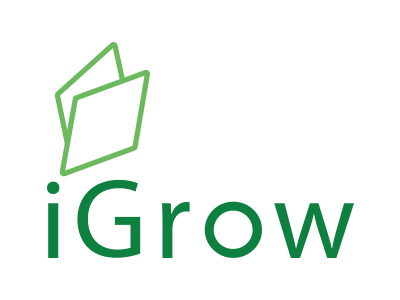
Welcome to iGrow News, Your Source for the World of Indoor Vertical Farming
West Warwick, Rhode Island High School Goes Hydroponic
Sodexo and the school department teamed up to purchase “The Leafy Green Machine,” which is now in operation on the high school campus. The only other school-operated Leafy Green Machine in Rhode Island is located at Cumberland High School.
Kendra Port/klolio@ricentral.com | Sep 21, 2018
West Warwick High School is now the second school in the state to have an indoor hydroponic farm on-campus after purchasing "The Leafy Green Machine" from Freight Farms with the help of Sodexo earlier this year. The Leafy Green Machine is a 40 foot shipping container repurposed into a hydroponic, climate controlled farm. Photo Courtesy Freight Farms
WEST WARWICK –– The West Warwick School District is no stranger to leading the way in educational innovations, and thanks to a partnership with their food service provider, Sodexo, West Warwick High School is now the second high school in the state to implement a campus hydroponic farm from Freight Farms
Sodexo and the school department teamed up to purchase “The Leafy Green Machine,” which is now in operation on the high school campus. The only other school-operated Leafy Green Machine in Rhode Island is located at Cumberland High School.
The Leafy Green Machine, created by Freight Farms, is essentially a “farm-in-a-box.” It’s a 40-foot shipping container outfitted with all of the tools and equipment necessary to run a productive hydroponic indoor farm. The system uses 90 percent less water than traditional farming methods and requires no soil, fertilizer or other planting materials to produce fresh, crisp and flavorful plants year round in a temperature controlled environment.
Hydroponics is the cultivation of plants by placing roots in liquid nutrients rather than soil. There are different types of hydroponic systems, and the Leafy Green Machine uses two — drip irrigation and ‘ebb and flow’. The plants are placed on a vertical growing medium, or tower, and the farm’s emitters drip water and nutrients onto the crops, which trickles down to the roots.
Any water that isn’t consumed by the plants flows to the bottom and is recirculated back into the plants. The farm uses only five gallons of water per day. The plants are surrounded by LED lighting to provide the optimal wavelengths of light required for photosynthesis.
The machine also has a seeding station, a shallow trough with enough space to hold up to 12 trays of seedlings. The trough gets filled with water and is allowed to drain several times a day. Using the “farmhand” platform, farmers, or in this case school staff, can get real time data from sensors and in-farm cameras and even remotely control the farm from their phones.
Right now staff and teachers are working on a crop of rex and butterhead lettuce planted in mid August that they eventually hope to be able to harvest and use for school lunches. According to Freight Farms, the farm should be able to produce up to 150 pounds of produce per week. It is expected to put out around 500 full heads of lettuce a week; 60 to 100 pounds per week of hearty greens or 35 to 80 pounds per week of herbs.
West Warwick High School Science Teacher Hailey Windsor gave a brief presentation to school faculty and staff Wednesday afternoon to talk about ways they can implement the Leafy Green Machine into their curriculum. She said that although the food produced in the farm can’t technically be classified as “organic” because of strict regulations, there are still no pesticides are used, and she’s willing to bet what they grow is still better than your typical store-bought produce in terms of chemicals.
According to West Warwick Public Schools Director of Education Reform, Compliance and IT, Jim Monti, the Leafy Green Machine is really an extension of something the school district is already doing in its elementary schools - creating and maintaining hydroponic farms in the second grade elementary school classrooms. It’s all part of the district’s effort to provide more experiential learning opportunities to students.
“Every grade two classroom has tower gardens that fit right in with this,” said Monti. “We’re trying to get the kids in science all the time. Their system is a smaller version of this Leafy Green Machine.”
Monti said the farm is “quite prolific” and claims it can generate enough produce to fill Gillette Stadium over the course of a year.
“I think there’s a lot we could end up doing with this,” he said.
Sodexo and the school department plan on holding a formal harvest celebration some time next month. Their goal is to eventually have the farm produce enough to supply all of the district’s schools with produce.
Follow Kendra Port on Twitter @kendrarport
How To Stay Pest-Free In A Modular Farm
Any conventional farmer will tell you that losing crops to pests is one of their main concerns. You may be surprised to hear that it’s no different in a Modular Farm. The good news is that Modular Farms uses tried and true methods to both prevent and eradicate infestations should they occur.
Modular Farms Research Scientist & Plant Health Specialist Kevin Jakiela has encountered and dealt with most infestations you can think of from fungus gnats to spider mites. He’s seen it all.
“Our Vestibule Module is a great first line of defense against pests. A clean room for visitors and farmers leads to laboratory-like sanitation. The second line of defense would be maintaining good farm practices including regular cleaning of reservoirs, irrigation lines, seed trays, workstation and towers. It’s also essential to supervise the cultivar’s back canopy to ensure there’s no wilting plant matter or restricted air flow.”
Based on Kevin’s research, the likelihood of unwelcome pests entering a farm is substantially lower with a Vestibule Module present. If used correctly, and combined with good clean farm practices, a Modular Farm will be pest-free.
The Vestibule Module
The Vestibule Module works as a bridge unit add-on allowing farmers to walk from one module to another without altering the controlled temperature in each. Farmers can operate in different areas without stepping outside. This creates a climate barrier for crops by keeping outside air pollution and pests away from crops, resulting in a more uniform and productive crop yield.
Minimizing non-farmer foot traffic and having all visitors pass through the vestibule module will help to eliminate outside contaminants.
Pest control in a Modular Farm
Biological Pest Control: This approach involves introducing predatory insects to consume and eradicate targeted pests. Examples include Nematodes, Ladybugs and Midges. Biological insecticides would also fall into this category.
Mechanical Pest Control: This approach uses hands-on methods when an infestation is too extreme to manage by gradual change. Techniques include handpicking, traps (e.g. sticky traps), using barriers and vacuuming to prevent further breeding.
Cultural Pest Control: The utilization of mechanical pest control applied at a certain stage in the pest’s life cycle. The goal is to target and remove during a weakened stage to interrupt further growth.
Chemical Pest Control: The use of pesticides. This method is discouraged as we operate within a closed loop environment. If pesticides are used, the internal ecosystem could be permanently altered or destroyed.
For more information:
Freight Farmer Q&A: Bee's Greens Company
8 Questions with Lizzy Porter of Bee's Greens Company!
We caught up with Lizzy of Bee's Greens Co. to learn more about her island farm in Waipahu, Hawaii!
One of the best things of being part of the Freight Farms team is talking to our farmers and hearing about their successes, customers, and challenges as they pursue a variety of container farming ventures. They are a wealth of information, so we're sharing some of their stories with you!
“As an island in the middle of the Pacific, importing comes at great environmental and food quality cost.” — Lizzy Porter
Freight Farms: What’s the story behind your Freight Farms project?
Lizzy Porter: My Freight Farms project was born from an interest in the future and emerging exponential technologies, and developed into what it is today after learning about contemporary food issues in Hawaii. I learned about Freight Farms while on a path of learning about how existing big industries could be decentralized and democratized. I began to understand more about current food insecurity issues in Hawaii - where more than 80% of food is imported; where arable land can be hard to come by; where tropical weather can surprisingly and significantly impact a growing season.
As an island in the middle of the Pacific, importing comes at great environmental and food quality cost. With the Freight Farms technology in mind, I found there was an opportunity to participate in a futuristic pursuit while helping with contemporary issues. Not to mention, I was pretty ready for an excuse to move to a beautiful tropic island. Thus, Bee’s Greens Company, operating in Hawaii for Hawaii, came to be.
FF: What, if any, was your experience with farming before becoming a Freight Farmer?
LP: Not much! I had a personal vertical hydroponic gardening system before becoming a Freight Farmer, but would not say I had experience with farming, let alone on a commercial scale. However, I grew up very comfortable with life sciences and technology so was ready for the challenge. I also believe that success often comes from delegating to others whose strengths complement your own - so was confident that if I was struggling, I could always find someone or a team with different skills and experiences to make the project thrive.
Lizzy with her brother and dad, who help her out at the farm!
“The support of my family, the Freight Farms team, and the Freight Farms community has been absolutely instrumental in helping me overcome challenges of getting started and finding my footing.”
— Lizzy Porter
FF: What reaction do you typically get from people when you tell them what you do for a living?
LP: Surprise and genuine interest! I love that my answer is not traditional, whether I’m talking to someone on a corporate path, in the agricultural field, or pretty much any other avenue. It usually makes for a fun conversation about the future, unconventional passions, and potential solutions to contemporary issues - and inevitably ends up with looking us looking a dates to schedule a tour of the farm.
FF: How did you find customers to buy your produce?
Just one fun farmers market sign!
Photo: Bees Greens Co. on Instagram
LP: We’ve found our customers through farmers markets! We sell the majority of our greens to both patrons of the markets as well as other vendors at the markets. Other customers have come through by looking for like-minded companies.
FF: What’s your favorite crop to grow and why?
LP: My favorite crop is probably the Butterhead Rex. It is well loved here but doesn’t normally grow year-round, so the communities I serve are familiar with it and excited to see it when they hadn’t expected to. It’s also just the right amount of tender and beautiful.
“With the global culture and awesome technology that we have in 2018, it is unrealistic and uncreative to just decide that a society can only have the food that grows well traditionally in that location.”
— Lizzy Porter
Photo: Bees Greens Co. on Instagram
FF: What’s the most pressing issue in food and agriculture that you’d like to see solved?
LP: On a personal and local level, I think a very pressing issue is food security in Hawaii. 80% or more of food is imported to the islands from 3000 miles away, which means quality loss, environmental costs, and an economic loop that is not benefiting the local community as it could. The challenge is that, because the imported produce is produced in very large commercial scales, it can remain cheaper than fresh, low impact, local food.
With the global culture and awesome technology that we have in 2018, it is unrealistic and uncreative to just decide that a society can only have the food that grows well traditionally in that location. Things like the Freight Farms’ LGM provides a great opportunity for global selections of locally produced, consistent, high-efficiency, low impact goods.
We completely agree with Lizzy! Check out our blog, Freight Farming Over Freight Shipping: Bringing Local Back to the Island for more insights into the problems island communities face today.
Lizzy working in her farm–you'd never know she didn't have any previous growing experience!
FF: What was the most challenging part of becoming a Freight Farmer and how were you able to overcome it?
LP: The most challenging part of this project was moving into a field that was relatively new to me, having never been involved in commercial farming before. The support of my family, the Freight Farms team, and the Freight Farms community has been absolutely instrumental in helping me overcome challenges of getting started and finding my footing. Now that we’ve been operational for a while, that support has been epically supplemented by the help and knowledge of great employees, and getting to share our stoke and passion with our customers and community.
“Passion is contagious, and I’ve found the best way to keep the stoke is to share it! ”
— Lizzy Porter
FF: What’s the best piece of advice you can give to people interested in becoming Freight Farmers?
LP: Passion is contagious, and I’ve found the best way to keep the stoke is to share it! A new business venture can at times be a grind, but if you can find the pieces of being a Freight Farmer that are most interesting to you – i.e. the parts that blow your mind - those are what you want to hang onto and share with others to blow their minds in turn. A significant amount of my sales and new connections have come from when I get on a roll, talking about how cool the system is, and why it’s important for now and for the future. Sharing my excitement and having it reflected back to me has been endlessly inspiring and motivating.
Does It Make Economic Sense For You To Install Grow Lights?
Posted on 09/27/2018
Written by David Kuack, HortAmericas.com
The Lighting Approaches to Maximize Profits (LAMP) project aims to determine how growers can maximize their return on investment when considering installing grow lights.
As light emitting diodes (LEDs) become more efficient and more affordable, an increasing number of greenhouse and plant factory growers will consider installing LED luminaires to light their crops. In the case of greenhouse growers, these luminaires would provide light to supplement natural sunlight. For plant factory growers, production depends entirely on the light provided by an artificial light source including LEDs, high pressure sodium or metal halide luminaires.
According to University of Georgia horticulture professor Marc van Iersel, the electricity for supplemental lighting in a greenhouse accounts for 20-30 percent of variable costs. In the case of plant factories which rely solely on artificial light, the electricity cost accounts for 50-60 percent of the variable costs.
van Iersel is heading up a $5 million, four-year research project that will focus on enabling growers to maximize the return on their lighting investment. Funding for the Lighting Approaches to Maximize Profits (LAMP) project is being provided by the USDA National Institute for Food and Agriculture Specialty Crop Research Initiative. The team that has been assembled to work on the project includes 15 university researchers, an advisory panel of greenhouse and plant factory growers and industry consultants.
“The job of the advisory grower panel is to make sure that the research that we do is actually what they need,” van Iersel said. “These are growers who will directly benefit from the research. We are also working with consultants who represent a big section of the industry. We are looking to them to help disseminate the information generated by the research to the industry.
“The research is looking to determine how growers can maximize their return on investment. There has been a lot of research done on how to grow plants with LED lights. We know growers can produce plants with lights. But what we don’t really know is how can growers make the most money doing it.”
Focused on LEDs
van Iersel said most of the project’s research will focus on the use of LEDs with some economic comparison to high pressure sodium (HPS) lamps.
“LEDs are clearly the lights of choice for the future,” he said. “Where we are interested in comparing LEDs and HPS is in regards to the economics. LEDs are more efficient, but they are also more expensive. Is the extra cost of LEDs worth it or are some growers actually better off paying less in capital expense for HPS lamps and more for the electricity to operate them? That is not a simple question to answer.
“There really hasn’t been a big price drop in LEDs. What LED manufacturers have done is rather than lowering the price, they have focused on making the LEDs better. Newer LED lights have hundreds of individual diodes in them. That is one way to help make the lights more efficient. But obviously they are putting more hardware in the lights. In older LED lights there were fewer individual diodes that went into a single light. The diodes were expensive. Now that the diodes are relatively cheap the manufacturers are putting in more of them so that the lights are more efficient. There seems to be a race among manufacturers to try to make the most efficient LED light possible. Right now it seems like the focus is more on creating a more efficient light than on creating a cheaper light.”
van Iersel said LED light manufacturers can easily match the light intensity of HPS lamps.
“What the LED manufacturers typically do with more diodes is run the diodes at only a fraction of their full power,” he said. “That makes the diodes more efficient. If an LED operates at 50 percent of its maximum power, it is substantially more efficient than running it at full power.”
Using supplemental light efficiently
One area that van Iersel is particularly interested in studying is making sure that growers provide supplemental light when plants are best able to efficiently use the light.
“LEDs are fully dimmable and can be dimmed instantaneously,” he said. “LEDs can very easily be programmed to respond to ambient light levels. One of the things that we are working on is designing systems that dim automatically as the sunlight level increases.
“With LEDs it’s more than turning them off and on, it’s dimming them. We have a system where we are calculating every second how much light to provide and how much to dim or brighten the LEDs. That is not possible to do with HPS.”
van Iersel said most LEDs are already dimmable.
“Every LED light is dimmable, it’s just a matter of using the right driver, which provides the power to the LEDs,” he said. It is very easy to incorporate into the lights. What I would hope is going to ultimately happen is growers are going to demand this kind of technology when they look at LEDs and the manufacturers have no choice than to provide it.”
van Iersel said another area of interest with the research is using the light spectrum as a way to manipulate quality.
“This could be accomplished with either the red:blue ratio or the amount of far red that is incorporated into the spectrum,” he said. “We also want to look at how the light is actually delivered to the plants. Right now, at least with ornamentals, growers look at the daily light integral (DLI) that is required to grow a particular crop. There are some clear indications that if the DLI is spread out over a longer photoperiod, for example, 20 hours instead of 14 hours, with the same amount of light over the entire day that more growth occurs with the longer photoperiod. This would be a lower instantaneous light level, but the same amount of light over the course of the entire day. This would allow growers to purchase fewer lights.”
Simplifying growers’ choices
van Iersel said one of outcomes of the research project is to be able to provide growers with a simple to use calculator that allows them to figure out if supplemental lighting will actually pay back in their particular production situation.
“If we can prevent growers from buying lights if they are not going to realize a return on investment that is going to be a good thing,” he said. “If they do decide that they want to use supplemental light, what makes more sense? Is it better to purchase HPS or LEDs? Which lights are going to offer a better return on investment? We hope to develop spreadsheets and some of this information will be incorporated into the Virtual Grower software program that is available free to growers.”
Current, powered by GE, Arize Lynk LED grow lights are being used by mGardens in its vertical farm in Gorham, Kan.
van Iersel also said some of the information that has been incorporated into the proposed horticultural lighting label is going to be required for the calculations.
“The lighting companies typically provide this information already, specifically the efficacy of the lights. Every reputable lighting manufacturer will be able provide this information. After the LAMP research is completed, growers should be able to look at the label information from different lighting companies and run some scenarios to tell them which lights are the most cost effective for them. It is really difficult right now for growers to decide whether or not to light and what kind of lighting is cost effective. It depends on a number of factors including where they’re located, their electricity prices, the crops they’re producing and how well those crops respond to supplemental light. Unfortunately, currently there is a lot of information that needs to go into doing these calculations. This has hampered the adoption of LED lights because growers can’t determine if they can pay for them.
“Once the research is done, the only numbers growers should need to plug in are basically the profit margins on their crops. Hopefully we will be able to provide them with the rest of the information they need to determine whether installing lights makes sense financially.”
For more: Marc van Iersel, University of Georgia, Department of Horticulture, Athens, GA 30602; (706) 583-0284; mvanier@uga.edu; http://hortphys.uga.edu/personnel/van-iersel.html; https://www.facebook.com/HortLAMP.
This article is property of Hort Americas and was written by David Kuack, a freelance technical writer in Fort Worth, TX.
Posted in News
Tagged Ag Tech, Indoor Ag, LED, LED grow light research, LED Grow Lights
Antarctica Greenhouse Produces Cucumbers, Tomatoes And More in Mars-Like Test
By Elizabeth Howell, Space.com Contributor | September 24, 2018
DLR researcher Paul Zabel poses with kohlrabi harvested from the EDEN ISS Antarctic greenhouse. Credit: DLR
Fresh vegetables on Mars, anyone?
An Antarctic greenhouse known as EDEN ISS not only survived the polar night but emerged from it with a harvest for local researchers, thus providing hope that future Mars colonists could also enjoy fresh food during their time on the Red Planet, German Aerospace Center (DLR) officials said in a statement.
Regularly withstanding temperatures below minus 40 degrees Fahrenheit (minus 40 degrees Celsius), the greenhouse provided herbs, lettuce and other vegetables to 10 people who were riding out the winter in the remote station, called the Alfred Wegener Institute's Neumayer Station III. It's the first time the greenhouse operated through the winter. [How Living on Mars Could Challenge Colonists (Infographic)]
"After more than half a year of operation in Antarctica, the self-sufficient greenhouse concept appears to be effective for climatically demanding regions on Earth, as well as for future manned missions to the moon and Mars," DLR officials said in the statement.
"The harvests are now so plentiful that some of it does not always make it straight to the table, and we now have the luxury of spreading out our consumption of some refrigerated lettuce and herbs over several days," Paul Zabel, a DLR researcher who works with EDEN ISS, said in the statement. "The overwintering team members are always looking forward to their next fresh meal."
A thermotransport box sits in front of the Antarctic greenhouse EDEN ISS, which tests the ability to grow food in Mars-like conditions. Credit: DLR
The haul included 170 lbs. (77 kilograms) of lettuce, 112 lbs. (51 kg) of cucumbers, 64 lbs. (29 kg) of tomatoes, 26 lbs. (12 kg) of kohlrabi, 20 lbs. (9 kg) of herbs and 11 lbs. (5 kg) of radishes.
All of the crops were produced in a cultivated area measuring just 140 square feet (13 square meters). However, the peppers and strawberries failed to produce a harvest, likely due to pollination issues, according to the statement.
While Zabel tended to the planets when possible, stormy conditions in Antarctica often prevented him from walking the quarter mile or so (about 400 m) outdoors to the greenhouse. In those cases, a control center in Bremen, Germany, took over for as long as three consecutive days.
When conditions allowed, Zabel could perform urgent repairs, such as fixing a screw that came loose in the thermal system.
The path to EDEN ISS in the Antarctic. Credit: DLR
Other tasks for Zabel included looking at the quality of the harvest, picking up microbiological samples and checking on the systems (light, temperature regulation, and air supply enriched by nutrients and carbon dioxide). His responsibilities even included reporting on how the fresh food improved the health of his team members.
"We greatly value and enjoy the fact that regularly fresh salad, herbs and vegetables from the greenhouse enrich our diet. The positive effect is noticeable," Bernhard Gropp, Neumayer Station III manager, said in the same statement. Without the fresh produce, the crew would have to live on freeze-dried supplies until the next flight to Antarctica in October, DLR officials noted.
The EDEN ISS project website also provides regular updates to the public, including photos of the individual boxes that are taken every day. You can follow the project at DLR.de/EDEN-ISS or by using the hashtag #MadeInAntarctica on Twitter.
Follow us @Spacedotcom, Facebook and Google+. Original article on Space.com.
Farming In A Box Comes To Downtown Holyoke
By PAUL TUTHILL • 2018
A new project in urban agriculture is launching this week in western Massachusetts.
Community farmers and college students will grow produce inside two shipping containers that have been outfitted with hydroponic farming technology and set up on a vacant lot in downtown Holyoke. It is a pilot project which, if successful, could help satisfy a demand for locally grown food year-round and create jobs.
The container farm project is a joint venture of the city of Holyoke, Holyoke Community College, and the grassroots urban agriculture organization Nuestras Raices. MassDevelopment provided $208,000 to pay for the project through the agency’s Transformative Development Initiative, which is intended to promote economic growth in the state’s Gateway Cities.
Lettuce and herbs will be grown to be sold to local stores and restaurants. Each of the 40-foot-long containers can grow as much produce in a year as an acre of farmland.
"We have local farms in Holyoke, but I think it is great to try this type of farming and bring the community into it as well," said Alina Daveledzarova of Westfield , whohas been hired as the container farm manager.
The goal is to grow and sell enough product for the container farm to become self-supporting after two years, according to Insiyah Mohammad Bergeron, manager of the Holyoke Innovation District.
"So we are really excited, but we are treating it as a big experiment," said Bergeron. "It is an emerging but very expensive technology, so we want accessiblity and equity to be a big part of the project."
Staffing at the container farm will be a mix of HCC students, who will receive course credits for their work, and community members who be paid as apprentices. The staff will turn over about every three months.
Kate Maiolatesi, who heads the sustainable studies programs at HCC, said some of her students will be interns at the container farm.
"They are in a program learning about how to farm and this is an opportunity for them to see what more of an urban farm setting is," said Maiolatesi. " They also are looking for employment and there is growing interest in this kind of farming verus land farming, so we thought it would be a great program to be involved in."
For Nuestras Raices, which operates a 30-acre farm in Holyoke and a network of community gardens, the appeal of the container farm is to able to grow produce year round, says Hilda Roque, the organization’s executive director.
"This came as a blessing because we will be able to grow food during the winter time," said Roque.
The container farm is next to the new HCC MGM Culinary Arts Institute which opened earlier this year in a converted former mill building.
Urban Farming Flourishes In Paris
Sidney Delourme and Sarah Msika, winners of a public call for urban-farming projects in Paris, on the future site of one of the biggest urban farms in France. (Cultivate)
City of Lights is one of the least green among major cities; some Parisians want to change that
September 18, 2018
PARIS—Sidney Delourme gets really passionate when showing pictures of his ambitious project. For now, it is just a huge rooftop in Paris overlooking rails and old towers with the Montmartre hill in the background, but his drawings show plans for green and wooden spaces.
The 31-year-old is developing a huge urban farm in the heart of Paris, which is often cited for its lack of green space compared to its large population size. A study by MIT’s Sensible City Lab published in January found that Paris is the least green city among 10 major cities studied.
An employee of urban farming start-up Aeromate checks on vegetables and aromatic herbs growing on the rooftop of a building owned by French public transport group RATP, as part of a rooftop farming project in Paris on Aug. 24, 2017. (Benjamin Cremel/AFP/Getty Images)
People like Delourme want to change that. With his working-partner and co-founder Sarah Msika, they are in the process of securing further funding to turn the rooftop of a former railway site into an innovative urban farmcovering 7,000 square meters (1.7 acres).
The duo intend to plant purple basil, chocolate mint, ancient lettuce, and edible flowers in the farm. The facility will have many innovative features, including a greenhouse that gets its heat from a data center located below, hydroponics cultures—a method of growing plants in water rather than in soil—and space for permaculture. Plans are also in place to include a store to sell some of the produce, as well as areas for educational activities.
Samples of Oyster mushroom grown by urban farming company La boîte à Champignon in the basement of a supermarket in Paris. (La boîte à Champignon)
“It will be the biggest urban farm in France and Europe when it opens, hopefully in the third quarter of 2019,” Delourme said.
It will be one of the biggest, at least. There are other similar projects under development in France, among them a project to develop a 10,000-square-meter (2.5 acres) urban farm on the rooftop of a large logistic platform in Ivry-sur-Seine in the south of Paris.
A Boom
There has been a dramatic increase in urban farming in France over the past few years.
“I remember that two years ago, when we started to get organized and worked with Agroparitech—a prestigious French school and research center in life science and agronomy—we were only seven project developers,” said Grégoire Bleu, co-founder and president of the French Association of Urban Farming (AFAUP).
Grégoire Bleu (L), CEO of La Boîte à Champignons and president of the French Association of Professional Urban Farming, talks with fellow company co-founder Arnaud Ulrich in their office at Les Grands Voisins in Paris. (Alexia Luquet/Special to The Epoch Times)
“Today, we can estimate that there are anywhere between 200 to 300 projects under development,” he added.
Bleu said the figures only account for professional projects, meaning those that have at least one full-time employee. To get closer to the real number of sizeable urban farming projects, he said the figure has to be doubled to account for those that may not have full-time employees. That doesn’t even include the not-for-profit and smaller-scale initiatives such as community gardens, which are much larger in number.
Paris Leading the Trend
Bleu himself is co-founder and CEO of an urban-farming company, La Boîte à Champignons, with multiple operations between Paris and Rennes in the region of Brittany.
“The trend is everywhere in France. From what I know, 45 percent of the projects are based in Paris and 55 percent outside. Cities such as Marseille, Lyon, Rennes, Lille, Strasbourg are very dynamic, but I must admit the phenomenon, at least regarding its news coverage, started in Paris,” Bleu explained.
Inside one a “cooltainer” close to Bercy in Paris, where the start-up Agricool grows strawberries (Alexia Luquet/Special to The Epoch Times)
Delourme concurs: “Paris has been the driver of the movement.” Their rooftop project won a major urban-farming competition in February, one of several introduced by Paris Mayor Anne Hidalgo under an initiative called Parisculteurs.
“Paris has a very structured approach: They started with auditing all underexploited or empty public buildings, and within three years, they had prepared a hundred sites so that they could accommodate urban farms,” said Delourme.
The Parisculteurs jury panel that chooses the award-winners boasts many experts, including the internationally-renowned Italian architect and urban planner Stefano Boeri, who designed the famous Bosco Verticale, or vertical forest, in Milan.
A conceptual image of the iconic Tour Montparnasse in Paris after renovations with a greenhouse at the top. (Nouvelle AOM)
There are more initiatives to encourage urban farming in Paris as well, including incentives for construction projects.
“Since 2016 in Paris, city planning rules have been allowing us to construct beyond the maximum height limitations only if we build an agricultural greenhouse,” said Frédéric Chartier, who co-founded the architecture studio Chartier Dalix along with his wife Pascale.
Their firm is part of the Nouvelle AOM consortium, which won the bid to oversee a 300-million-euro ($350 million) project to renovate the iconic Tour Montparnasse skyscraper ahead of the 2024 Paris Olympic Games. Part of their design is a 59-foot-high biosphere greenhouse on top of the skyscraper to grow vegetables, which will partly be consumed by occupants of the building.
Once done, Tour Montparnasse would become the highest urban farm in Paris, visible from different locations in the city. “A strong symbol,” Dalix said.
Frédéric Chartier, co-founder of Chartier Dalix Studio, in his Paris office. He is reading the booklet presenting one of his delivered projects incorporating urban farming, the Biodiversity School and Gymnasium at Boulogne Billancourt, near to Paris. (Alexia Luquet/Special to The Epoch Times)
It’s no surprise to Dalix that the City of Lights is leading the trend in urban farming.
“Paris is one of the most densely populated cities in the world, with few green areas, so it makes sense that people want to reverse the situation.”
Still, business-focused urban farms in the Paris area currently account for just 5 percent of total urban cultivated areas, according to Maison de l’Agriculture Urbaine—or the House of Urban Farming. The vast majority of the farms are driven by non-profit projects, a gap that points out the largest challenge for taking urban farming to the next level: creating a profitable business.
Successful Business Models
According to Bleu, efficient business models still need to be developed further for urban-farming companies to prosper.
Bleu said their own secret for success lies in employing circular economy principles, such as re-using waste and unused urban residue in their operations.
Vegetables and aromatic herbs being grown on the rooftop of a building owned by French public transport group RATP, as part of a rooftop farming project by urban farming start-up Aeromate in Paris on Aug. 24, 2017. (Benjamin Cremel/AFP/Getty Images)
For example, they use coffee grounds to cultivate oyster mushrooms in the basement of a supermarket, and offer their products to nearby supermarkets and restaurants. They further diversify their operation by selling growing kits that can be ordered online, and offer educational kits for school students.
This is what Bleu calls “an ecosystemic approach” to urban farming: their project aims at reconciling social, economic, and environmental issues through different initiatives such as recycling urban waste, air purification through green space, the creation of social unity using the economic cycle, and providing educational programs for children.
“Our cities are in a poor condition from an ecosystemic perspective. So what matters to us is to understand how we can cleverly integrate urban metabolism,” he said.
Agricool
One of France’s urban farming startups that has succeeded in attracting millions in funds is Agricool, which grows fruit and vegetables in containers.
Agricool founders Guillaume Fourdinier and Gonzague Gru, 31 and 30 years old, respectively, and both sons of traditional farmers, managed to turn a personal challenge into a promising business venture in three years.
Guillaume Fourdinier, CEO and co-founder of Agricool, in his La Courneuve office, near Paris, in front of a “cooltainer,” dedicated to research and development. (Alexia Luquet/Special to The Epoch Times)
The initiative started when Fourdinier broke his leg and decided to kill time by challenging himself to grow strawberries in his apartment. Today, their startup employs 53 full-time employees, and has raised 12 million euros ($14 million) from private investors, a first in French urban-farming history.
Agricool uses refurbished shipping containers—called cooltainers—to grow strawberries using hydroponic methods, specially designed LEDs, air conditioning, and bumblebees for pollination.
“We collect strawberries every morning except Sundays and then we supply our distributors, all located in the neighborhood, and some supermarkets and gourmet food shops,” Charlotte Mignol, a “co-oltivator” at Agricool, said while completing her daily harvest in a white jumpsuit to follow hygienic precautions.
The company has built four operating boxes in Paris region and wants to build more in the near future and expand to other types of products such as tomatoes.
Fourdinier touts their company as an environmentally responsible organization. “By purchasing and eating this type of strawberry—GM [genetically modified]—free, pesticide-free, transport-free—instead of a basket full of GM [strawberries grown with] pesticide and [requiring] transportation, don’t you think it makes sense for the environment and for your health?”
Currently, the company sells an average of 200 boxes of strawberries a day, which is not yet enough to turn a profit. But Fourdinier is confident that their business model will work.
“It can be summed up in a single word: sales-volume.” They have set an objective to be profitable by 2021.
Feeding Cities?
Fourdinier’s ambition for urban farming isn’t limited to his operations alone. He believes urban farming could one day supply one-third of the nation’s produce needs.
“Can urban farms feed our cities? I believe they can,” Fourdinier said enthusiastically.
Bleu is more conservative in his assessment.
“In France, urban farming is still more focused on projects driven by associations that tend to meet local needs and create social unity,” he said.
For him, there is no competition between rural and urban farming. “It’s like a bear being scared of a hamster,” he said.
In his assessment, food produced by urban farming is still very negligible, and will remain that way, except for niche products such as high-quality mushrooms or micro-green projects.
But he raises a question: “Can Parisians—city people in general—afford not to have agricultural areas downtown? I don’t think so.”
Record Harvest At Antarctic Greenhouse
77 kilograms fresh lettuce, 51 kilograms cucumbers, 29 kilograms tomatoes
The Antarctic greenhouse EDEN ISS has weathered the polar night – as well as Antarctic storms and temperatures below minus 40 degrees Celsius – in its practical test under the direction of the German Aerospace Center (Deutsches Zentrum für Luft- und Raumfahrt; DLR). It has been yielding herbs, lettuce and freshly harvested vegetables to the 10-member overwintering crew in the Alfred Wegener Institute’s Neumayer Station III for the first time since the beginning of 2018.
After more than half a year of operation in Antarctica, the self-sufficient greenhouse concept appears to be effective for climatically demanding regions on Earth, as well as for future manned missions to the Moon and Mars.
DLR researcher Paul Zabel is overcoming challenges, as well as acquiring knowledge from cultivating plants under such harsh conditions. To the overwintering team, the fresh greens are a welcome change during their long-term isolation. Zabel reported on his experiences in a live transmission from Antarctica on 13 September 2018.
Plenty of lettuce and tomatoes, few peppers, and no strawberries yet
“The harvests are now so plentiful that some of it does not always make it straight to the table, and we now have the luxury of spreading out our consumption of some refrigerated lettuce and herbs over several days,” Zabel says. “The overwintering team members are always looking forward to their next fresh meal.” Indeed, the lettuce, tomatoes, cucumbers and herbs thrive especially well under the conditions of 21 degrees Celsius and 65 percent relative humidity in the greenhouse. Seventy-seven kilograms of lettuce, 51 kilograms of cucumbers, 29 kilograms of tomatoes, 12 kilograms of kohlrabi, five kilograms of radishes and nine kilograms of herbs have been grown and harvested on a cultivation area of about 13 square metres.
“What astonished us was the failed harvest for peppers and strawberries,” Zabel says. The pepper and strawberry plants grow quickly in Antarctica as well, but the artificial pollination causes some problems, whereby only a few fruits or – in the case of strawberries – none at all have been produced. EDEN ISS Project Manager Daniel Schubert adds: “The pepper plants bore ample fruit during the greenhouse trial run in Bremen last year. This shows how important and instructive the greenhouse’s extreme test under Antarctic conditions is.”
Greenhouse technology in extreme conditions
Quite often, a storm prevents Zabel from making the 400-metre outdoor trip from the Neumayer Station III to the greenhouse. Under these circumstances, the control centre in Bremen takes complete responsibility for monitoring the plants and supervising the greenhouse. However, this has been necessary on no more than three consecutive days so far, so Zabel has been able to do a good job of ensuring that the plants receive continuous care. The importance of his presence on site has been demonstrated repeatedly at times when the greenhouse technology has run into difficulties under the extreme conditions and urgent assistance has been needed. “On one occasion, for example, I had to go to the greenhouse quickly because a screw had come loose in the thermal system, and the lamp cooling was no longer sufficiently ensured.” Small repairs like these are hardly foreseeable and teach the researchers about the greenhouse concept and how to make its design more robust in future.
“It is important for us to be able to react when there are complications with the existing tools and resources on site. After all, the sound operation of a greenhouse on the Moon and Mars would be essential for survival,” says Schubert, the Project Manager. Forty different experiments are currently running in the greenhouse. This means a lot of work for Zabel, as he extensively analyses the cultivation of vegetables. His tasks include taking regular microbiological samples, examining the precise quality of the harvest, and periodically checking all systems, such as light, temperature regulation, and the nutrient- and carbon dioxide-enriched air supply. He also documents how fresh food is affecting the health of the overwintering team members.
Sharing the fun live with strawberries and peppers, and providing tips
Gaining insights into Antarctic plant cultivation has so far been reserved for the international researchers on the project, but everyone will have this opportunity in the future. “Until now, we in the control centre have received daily images of the individual plants through 32 cameras in the greenhouse. The researchers involved have access to these images and can provide the relevant tips,” Schubert says. “Now, we are opening these plant images to the public via an online tool on the EDEN ISS project website. Anyone who is interested can take part live in our vegetable cultivation in the Antarctic.” Every day, photos of the individual plant cultivation boxes are automatically taken at a specific time and under special lighting conditions. These images are then transmitted to the mission control centre in Bremen and made available online. The plant growth can be followed via an interactive timeline. In this way, people can interactively participate in a technology that will become more important in the future.
Positive effect is noticeable
Eberhard Kohlberg from the Alfred Wegener Institute, who is the logistics manager for the Neumayer Station III and has been a member of the overwintering crew on several occasions, says how pleasant it is to have a garden with lettuce and herbs just around the corner: “Otherwise, the menu just consists of long-life products from the freezer and storage room.” Only at the end of October 2018 will the first supply aircraft be able to provide the overwintering team with fresh food items from the outside world once again. Neumayer III station manager Bernhard Gropp adds: “We greatly value and enjoy the fact that regularly fresh salad, herbs and vegetables from the greenhouse enrich our diet. The positive effect is noticeable.” The last part of the winter is particularly challenging for the crew, as they gradually have to switch back to normal operation with many people at the station.
For more information:
EDEN ISS
Freight Farms Unveils Onsite Vertical Farming Service
September 12, 2018
Your average institution, be it a schools, company, hospital, or university, typically doesn’t have the space or cash to consider an indoor farming initiative, even if it would mean putting fresher, more local greens into cafeterias and dining halls. That’s an issue Freight Farms looks to solve with the release of its new service Grown, which was just announced today.
The Boston, MA-based company is already known for its Leafy Green Machines, which are 40-square-foot shipping containers that hold vertical farms. These farms are climate controlled and use LEDs as well as a closed-loop hydroponic irrigation system to nurture crops throughout their entire lifecycle. Like most other vertical farming systems, the technology platform powering Freight Farms’ containers automates much of the work (and guesswork) of growing and harvesting greens.
Grown, unveiled today, is less product than service, as Freight Farms installs the Leafy Green Machine then manages the lifecycle of crops on an ongoing basis. Once the Machine, aka the shipping container with the farm inside, is installed, the customer doesn’t have to do much besides decide which crops to grow and what to do with the produce once its harvested (e.g., serve it in the company cafeteria). No additional staff (or land, for that matter) is needed, as Freight Farms monitors climate, water usage, and all other aspects of the indoor farming process. (This is different from, say, Freight Farms’ relationship with vertical farming startup Square Roots, who use the Leafy Green Machine but have their own farmers to care for the greens.)
The Grown package starts at $5,000/month, and includes replenishing supplies, maintenance, cleaning, 24/7 farm monitoring, and all farming operations, including seeding, transplanting, and harvesting. Customers can also add, for an extra fee, services like marketing and branding as well as on-campus educational programs.
Freight Farms already counts a few universities and several small-business farmers among its customers, and also has a presence in Europe. But they’re one of many in the indoor agriculture space, each with a slightly different focus. Agrylist raised $1.5 million earlier this year, though it’s focus is on larger farms (10,000 square feet up to five acres). Farmshelf brings smaller setups directly into restaurants and retail outlets. Crop One and Emirates Flight Catering are in the midst of building what they claim will be the world’s largest vertical farm.
The Grown service could really set Freight Farms apart, though, particularly if it manages to bring vertical farming and fresh greens into places it might not otherwise go, like schools or smaller companies. In fact, Freight Farms told The Spoon that a major focus right now is “the existing interest in on-site, year-round local sourcing methods especially in the school dining/university education sector.” So there’s also a real opportunity for a vertical farming company to align itself with a mission that’s about more than selling products at farmers markets to those with disposable income.
Consider the current initiatives to get more local, fresh produce into NYC public schools: Thanks to a non-profit called GrowNYC, over 50 percent of those public schools now have gardens. But accessing and using them depends in part on the weather, and as any New Yorker knows, the weather out here is horrible about half the time. By working with programs like GrowNYC, Freight Farms could theoretically expose an entirely new audience to vertical farming, not to mention provide them with year-round greens.
The company is already thinking in that direction. In the K–12 and higher education sectors, Freight Farms said they’ve seen a 63 percent increase “from those who strongly want to integrate the farms (to provide hyper-local produce for meals, as well as provide a great platform for education around nutrition and sustainability) – but haven’t had the capacity to do so.”
The launch of Grown has at least set on the discussion table the idea that we can expand our thinking around where and when everyone, not just tech employees, can get their hands on the kind of nutrition they need.
Share this:
Related
Indoor Urban Agriculture Is Growing Up Thanks to These Cities June 22, 2018In "Ag Tech"
Crop One Holdings and Emirates Are Building the World's Largest Vertical Farm June 26, 2018In "Ag Tech"
Innovative Approaches Bringing Urban Farming To Cities Across The Globe July 18, 2017In "Ag Tech"
Freight Farms Announces 'Grown,' The World's First On-Site Vertical Farming Service
Freight Farms Announces 'Grown,' The World's First On-Site Vertical Farming Service
New service can seamlessly integrate with any foodservice operation or support year-round CSA programs--no farmland or additional staff required
NEWS PROVIDED BY Freight Farms
BOSTON, Sept. 12, 2018 /PRNewswire/
Freight Farms, the leading innovator of smart hydroponic software and containerized growing environments, today announces the addition of Grown by Freight Farms, an on-site vertical farming service, to its product line. With Grown, Freight Farms will not only install its signature hydroponic farm—the Leafy Green Machine™—on site, but staff a designated farmer to operate, monitor, and maintain the farm completely.
Joshua Fiagbedzi, one of the first Grown farmers, packs farm shares mere minutes after harvest. More than 50 customers will enjoy his crop, grown by a farmer they know, transported just 100 yards from farm to fork.
By eliminating the need to train staff for farming, Grown can immediately integrate with any foodservice operation, employer amenity package, or produce supply chain. Clients choose what to grow, and how that produce will be distributed within their organization. Ease of integration makes Grown ideal for corporations, universities, residential communities, hospitals, and other clients committed to food transparency and wellness.
Farming in a controlled environment means clients can depend on consistent costs and quality year-round, regardless of season. Leafy Green Machines can be installed mere steps from the plate, drastically reducing food-miles. They consume just five gallons of water per day or less, and require no major construction to deploy.
"Our mission with Grown is to provide a solution to institutions that see the immense value of local produce, and would rethink their sourcing methods if challenges like personnel and facilities management were reduced," says Brad McNamara, CEO and Co-Founder of Freight Farms.
The Grown program is already supplying B.GOOD, a Boston-based farm-to-table restaurant chain, with lettuce for its popular Cousin Oliver Burger. Meanwhile, 3D design software company Dassault Systèmes enjoys a thriving CSA program for employees at its Waltham, MA campus.
"Since Google installed their Leafy Green Machine in 2014, institutions all over the world have used them to promote involvement and education around nutrition, sustainability, and technology," says Jon Friedman, Freight Farms COO and Co-Founder. "Now, by removing the burden of managing those farms internally, we hope to reach more people than ever."
Freight Farms is currently accepting new Grown clients in New England, with plans to roll out nationwide in 2019.
Average Grown packages start at $5,000 / mo., which includes custom crop scheduling, maintenance, supply replenishment, 24/7 farm monitoring, and all farming operations, such as seeding, transplanting, and harvesting. Add-ons range from marketing and branding services, to in-farm educational events and on-campus CSA programs.
To learn more, visit FreightFarms.com/Grown.
About Freight Farms
Founded in 2010, Boston-based Freight Farms has established itself as the leader in the containerized agriculture industry. With its flagship product, The Leafy Green Machine™, the company was the first to integrate smart, hydroponic, vertical farming into an intermodal freight container. To date, Freight Farms' global customer base includes more than 200 farms across 38 states and 13 countries.
For more information, please visit FreightFarms.com, Instagram, or Facebook.
Coming to Englewood: Kimbal Musk's Square Roots Urban Farm In Shipping Containers
Tobias Peggs, CEO of Square Roots Urban Growers, speaks about urban farming outside one of the Square Roots shipping containers on April 25, 2017 in New York. The startup says its hydroponic system can grow more than 50 pounds of greens per container per week. (Don Emmert / AFP/Getty Images)
Greg TrotterContact ReporterChicago Tribune
There’s another Musk brother with big plans for Chicago.
Kimbal Musk, younger brother of Tesla founder Elon Musk, is planning on bringing his Brooklyn, N.Y.-based Square Roots urban farm to Englewood on about 3 acres of city-owned property behind Whole Foods Market at 62nd and Green streets. Square Roots grows leafy greens in a hydroponic system inside repurposed shipping containers, yielding more than 50 pounds of greens per container each week, according to the startup’s website.
Kimbal Musk, brother of Tesla founder Elon Musk, is co-founder of Square Roots, a New York urban farm. (Michael Tercha / Chicago Tribune 2017)
Craig Huffman of Ascendance Partners, developer on the project, confirmed Wednesday that Square Roots would be one of the anchor tenants of the second phase of the Englewood Square development, which is expected to break ground next year. The first phase, which included Whole Foods Market, Starbucks and Chipotle, opened to much fanfare in 2016.
Square Roots would have offices in the vacant firehouse behind Whole Foods. Huffman’s also in talks with Folkart Management, the restaurant group led by chef Matthias Merges, to open a barbecue restaurant in the firehouse.
Huffman otherwise declined to answer questions, saying it was too early.
“We are working around the clock to finalize our funding and then bring this project to life, which can help build new and exciting partnerships for Englewood through this unique entrepreneurial venture,” Huffman said in a subsequent emailed statement. “We believe Square Roots will support the momentum established by phase one by bringing more foot traffic and investment to Englewood.”
Square Roots, an urban farming concept inside shipping containers, is coming to Englewood. (Don Emmert / AFP/Getty Images)
Musk couldn’t be reached for comment. His automatic email reply said he was “off grid.”
Musk’s spokeswoman Courtney Walsh didn’t respond to emails and calls.
It’s not yet known how much the city might offer in tax incentives to help finance the project’s second phase. The first $20 million phase of Englewood Square received about $10.7 million in city subsidies.
Grant Klinzman, spokesman for Mayor Rahm Emanuel, said he couldn’t answer that question at this point.
“This is an important project and we are working hard with the community and developer to finalize the vision and make it a reality. We will have more to share later this year, but it’s a priority for the mayor and the city and reflects Englewood’s strong future,” Klinzman said in an email.
Square Roots greens are grown by entrepreneurs in a yearlong program and sold locally, according to its website. The company was founded by Musk and CEO Tobias Peggs, who was formerly CEO of Aviary, the photo editing program.
Community organizers in Englewood said they were excited by the farm’s potential to provide opportunities and fresh greens to Englewood residents, while also attracting people from other parts of the city. Square Roots will fit the “Whole Foods vibe” of the neighborhood, which is also home to the well-established Growing Home urban farm.
“It will serve as a kind of tourist attraction,” said Perry Gunn, executive director of Teamwork Englewood, a community nonprofit aimed at improving the quality of life in Englewood. “People will wonder, ‘What is this concept? Let me see and touch it.’”
Asiaha Butler, president of the nonprofit Resident Association of Greater Englewood, traveled to Brooklyn in November to see the Square Roots farm. Initially, she had concerns about adding shipping containers to what has become a vibrant retail area. But that changed as she saw the farms firsthand and learned more about how the business fosters entrepreneurship.
“When you open the doors, that’s when you’re like — whoa,” Butler said. “I was like, OK, now I get it. This is going to be a draw for Englewood.”
Butler commended Huffman’s “tenacity and willingness to do something different” in trying to get the second phase of the Englewood Square development off the ground. Despite some of the progress in Englewood in recent years, it’s still difficult to lure retailers to a neighborhood that’s had longtime struggles with poverty and violence, Butler said.
Both Butler and Gunn said they’d been involved in ongoing conversations with Huffman and potential tenants on the project.
The younger Musk, known for his philanthropy and trademark cowboy hat, has previous investments in Chicago. After receiving a $1 million grant from Emanuel in 2012, Musk’s nonprofit Big Green — formerly called The Kitchen Community — has built more than 120 learning gardens in Chicago Public Schools. Musk is also co-owner of The Kitchen, a farm-to-table restaurant in River North.
Last month, Emanuel selected older brother Elon Musk’s The Boring Co. to design a new high-speed transit option to O’Hare International Airport from downtown.
Twitter @GregTrotterTrib
Hydroponic “Farm” In A Shipping Container In Concord
by David Brooks | Aug 22, 2018
Magenta LED lights help many crops grow. Photo: Freight Farms
Time has taken its toll on Concord’s most unusual “farm,” the hydroponic trailer that has provided lettuce to a Marriott hotel for almost five years, but fans of high-tech leafy greens needn’t fret – a replacement is on its way.
“It needed to be rehabbed quite a bit. It required a lot of babysitting,” said owner Steve Duprey. “Rather than rehab it, which would cost $20,000 or $25,000, we decided it was better to sell it and buy a new one.”
The system was built by Freight Farms, a Boston-based agricultural technology firm. When it arrived in Concord in November 2013 bearing the snazzy name Leafy Green Machine, it was the first of its kind in New Hampshire.
Since then, said Christopher Snow, product marketer for Freight Farms, more than 200 Leafy Green Machines have been installed in all 50 states and 13 countries. The cost is $85,000 plus installation.
The Leafy Green Machine consists of a refurbished 40-foot shipping container, weighing about 7 ½ tons. Inside are vertical racks holding plants that grow under LED lighting, often of a magenta color to maximize photosynthesis, fed by nutrients in a liquid bath. The company says it can grow a wide variety of crops, from greens to edible flowers to root vegetables.
Indoor farming often uses much less water than growing outdoors, as well as much less pesticides because of the controlled environment. It, however, comes with other issues – for example, the lack of insects makes pollination difficult. A major benefit is the ability to grow fresh vegetables in urban environments where it can be hard or expensive to get them from traditional farms.
Duprey said the trailer produced about 100 to 150 heads of lettuce a week for the Courtyard Marriott hotel and adjacent Grappone Conference Center.
“We go through that much, if we have an event, in a day sometimes. So it’s a nice addition but it doesn’t fulfill our full needs,” he said.
Duprey said he was looking for other sources and pointed to Lef Farms in Loudon, which grows greens hydroponically inside greenhouses.
Hydroponic ‘Farm’ In A Trailer Getting An Upgrade At Concord Hotel
By DAVID BROOKS
Monitor staff
August 21, 2018
Time has taken its toll on Concord’s most unusual “farm,” the hydroponic trailer that has provided lettuce to a Marriott hotel for almost five years, but fans of high-tech leafy greens needn’t fret – a replacement is on its way.
“It needed to be rehabbed quite a bit. It required a lot of babysitting,” said owner Steve Duprey. “Rather than rehab it, which would cost $20,000 or $25,000, we decided it was better to sell it and buy a new one.”
The system was built by Freight Farms, a Boston-based agricultural technology firm. When it arrived in Concord in November 2013 bearing the snazzy name Leafy Green Machine, it was the first of its kind in New Hampshire.
Since then, said Christopher Snow, product marketer for Freight Farms, more than 200 Leafy Green Machines have been installed in all 50 states and 13 countries. The cost is $85,000 plus installation.
The Leafy Green Machine consists of a refurbished 40-foot shipping container, weighing about 7 ½ tons. Inside are vertical racks holding plants that grow under LED lighting, often of a magenta color to maximize photosynthesis, fed by nutrients in a liquid bath. The company says it can grow a wide variety of crops, from greens to edible flowers to root vegetables.
Indoor farming often uses much less water than growing outdoors, as well as much fewer pesticides because of the controlled environment. It, however, comes with other issues – for example, the lack of insects makes pollination difficult. A major benefit is the ability to grow fresh vegetables in urban environments where it can be hard or expensive to get them from traditional farms.
Duprey said the trailer produced about 100 to 150 heads of lettuce a week for the Courtyard Marriott hotel and adjacent Grappone Conference Center.
“We go through that much, if we have an event, in a day sometimes. So it’s a nice addition but it doesn’t fulfill our full needs,” he said.
Duprey said he was looking for other sources and pointed to Lef Farms in Loudon, which grows greens hydroponically inside greenhouses.
(David Brooks can be reached at 369-3313 or dbrooks@cmonitor.com or on Twitter @GraniteGeek.)
Grow Pod Solutions Offers Alternative As Fast Food Companies Shift Sourcing to Indoor Farms
PRESS RELEASE PR Newswire
Aug. 21, 2018
CORONA, Calif., Aug. 21, 2018 /PRNewswire/ -- As the fast food industry realizes the need to move to sourcing their products from indoor farms, Grow Pod Solutions - a leading agtech company and developer of portable automated farms - is the perfect solution for companies that are seeking a higher quality crop that can be grown year-round.
For example, according to the Wall Street Journal, Wendy's is removing the risk factors associated with outdoor agriculture and unpredictable weather and providing itself with a constant supply of fresh produce by switching to indoor farming.
Wendy's action mirrors the growing trend to source food locally. Not only do consumers like the idea of supporting local farms, but businesses are also welcoming local suppliers as a way to improve quality, cut costs, and increase margins.
Wendy's says that it expects to see social and environmental benefits from the shift as well, including the reduction of pesticides.
Grow Pod Solutions provides an ideal system for companies like Wendy's: Grow Pods are transportable and can be placed virtually anywhere. The system is scalable and units can be stacked to create giant automated farms. Grow Pods have low energy requirements, patented water and air filtration, spectral tuned lighting, and a perfectly balanced sealed environment that eliminates the need for pesticides.
George Natzic, president of Grow Pod Solutions, said that in addition to fast food companies, he expects to see increased interest in automated farms from the grocery industry.
"Today, many grocery stores will have a section of organic produce," Natzic commented. "But imagine the consumer response when grocers offer fresh produce grown right next to their building."
"Even organic produce needs to be picked early to survive transportation to distribution centers and stores," Natzig added. "But with Grow Pod, you can pick a tomato at the height of its flavor and freshness, and have it in the store within minutes."
Grow Pods are made in the USA. The company's automated indoor farms allow businesses, community groups, and entrepreneurs to grow healthy, contaminant-free produce, anywhere, year-round.
For information, visit: www.growpodsolutions.com or call (855) 247-8054.
Connect:
Email: info@growpodsolutions.com
Website: www.growpodsolutions.com
Facebook: facebook.com/GrowPodTechnology
Twitter: @GrowPodSolution
Media:
Innovation Agency
310-571-5592
www.inov8.us
hello@inov8.us
View original content:https://www.prnewswire.com/news-releases/grow-pod-solutions-offers-alternative-as-fast-food-companies-shift-sourcing-to-indoor-farms-300700081.html
SOURCE Grow Pod Solutions
The Components of Personal Container Farming
Author: Jonathan Tsai
Author: Jonathan Tsai, from Duramax Trusscore
Indoor agriculture has been gaining popularity as compact and versatile opportunities like container farming is making its way into the market. Container farming allows modern farmers to grow without owning a large amount of land. A school can add a new garden on their asphalt yards or a chef can grow fresh ingredients behind the restaurant. Fresh food can be quickly accessed wherever it is needed due to the mobility of container farming. It is even easier to start now that you can purchase from a manufacturer or make it your own DIY project.
The basic requirements in container farming are the container box, lighting system, water pump system, a water-resistant wall liner, and an HVAC unit. The container box is often inexpensive to obtain. Shipping companies prefer to get rid of their damaged containers because they are more expensive to repair than to replace. You can bid for a 20 ft container online and it can go from $1,000 and up. Some important ones to note are the tunnel containers that are open on both ends, open side containers that open from the side, refrigerated containers that keep temperatures low, and insulated containers meant to keep temperatures high.
LED lighting systems allow access to optimal plant growth any time of the day and in areas of the world with less sunlight. In terms of cost, there are a wide variety of LED light options to choose from in every price range. It ultimately depends on the plant you are trying to grow and its needs. One of the factors of the lighting system is the relation to growth and light intensity. It is known that the brighter the lights are, the faster plants grow; however, this also means more heat is radiated.
If the container does not have the right temperature controls, farmers sacrifice plant growth to keep the lighting at appropriate levels. Depending on the location of the container farm, you may need cooling or heating systems. Plants thrive in a warm and humid environment but it is important to have ventilation to keep temperatures from rising too high. There are many ways to ventilate a container including fans, using underground air through a pipe or a mini-split. For a 20 ft container with an area roughly 150 ft, a 9000 BTU mini-split goes for around $600.
An irrigation drip system is a very efficient way to water crops. This system reduces water usage by 90 percent compared to outdoor farming. The cost is inexpensive ranging as low as $30 for a drip system, and $250 for a water pump. The two main factors when picking a water pump should be the Gallons Per Hour (GPH) and PSI water pressure. These metrics will vary as a number of plants, plant size, plant type, and temperature change. It is important to note that the water pressure is associated with the height of the drip system.
Humidity can cause corrosion and rot to walls that are made of wood or metal. Wall Liner that is water resistant, easy to clean and lightweight is important when it comes to building out a container farm. Duramax Trusscore PVC is a great option to use as it is waterproof and seamless. The installation of these panels require no other materials and interlock with each panel. Material that is lightweight allows for cheaper freight expense. In a 20ft container, with a wall surface area of around 440 sq ft, these panels would be roughly $1000 not including the savings in installation and labor.
Overall, there are many manufacturers that offer a turn-key operation complete with equipment and systems. These prices can range from economical to costly as performance increases and additional attributes are applied. Constructing your own container farm can be a fairly simple and inexpensive. Always consider the location, environment, and plant necessities when comparing which components you need to invest more in.
To get more details about the specifications of Duramax Trusscore for your project, please visit us at:
www.duramaxpvcpanels.com/resources/
The Growcer Installs Hydroponics System On University of Ottawa Campus
The Growcer cofounder Corey Ellis.
BY: Craig Lord
Aug 21, 2018
ORGANIZATIONS: The Growcer University of Ottawa
The Growcer has returned to its University of Ottawa roots, this time installing its hydroponics system on campus to contribute to the cafeteria’s produce supply.
The Ottawa-based hydroponics startup installed one of its converted shipping containers on campus in front of Fauteux Hall Tuesday. Produce grown inside will be sold directly to Chartwell, the post-secondary institution’s food supplier.
Students eating at the on-campus cafeteria, then, will be eating food grown by one of the University of Ottawa’s own startups. The Growcer got its start at the school’s Enactus program, a social entrepreneurship initiativeNow graduated, co-founder Corey Ellis and his partner Alida Burke were first inspired to start the Growcer during a trip to Nunavut. There, they saw first-hand the demand for food security in Canada’s North.
Ellis recently told Techopia Live that the Growcer’s goal is to enable any community in Canada to be more more self-reliant when it comes to food.
“We can do a lot with the technology we have now to allow any community, not only in northern Canada, but in Canada in general, to be more self-reliant. So I’d love to see a Growcer system in every major city in Canada,” he said.
A retrofitted shipping container with a carbon dioxide-and-water-based hydroponics system inside is enough to sustainably grow plants and vegetables in northern communities, or for that matter, during an Ottawa winter. The local firm worked with MadeMill at Bayview Yards to develop the latest generation of its prototype.
Container Farms: A New Type of Agriculture
August 20, 2018
A forklift truck picks up a container at the Freight Farms production facility. (Freight Farms)
Innovators within the produce industry are breaking the boundaries of food production — by growing crops not in fields, but in recycled shipping containers.
This modern twist on farming is designed to bypass some of the challenges and restrictions that farmers traditionally have faced, such as extreme weather, pests and limited growing seasons.
By overcoming these limitations, farming operations are capable of producing more food and growing certain crops in regions that otherwise would have had to import them.
By growing this food locally, suppliers are able to cut out the long travel distances often necessary to transport these foods to certain markets.
According to Jeff Moore, vice president of sales at produce supplier Tom Lange Co., shorter travel distances provide numerous benefits, such as fresher product, reduced transportation costs, less waste and fewer empty shelves at markets.
The use of innovative farming methods also is being pushed in Canada. Grocery retailer Loblaw Companies Ltd. announced plans to spend $150 million more each year with Canadian farmers by 2025. As part of that effort, the company pledged to help farmers implement growing techniques that will enable them to produce fruits and vegetables in Canada that the country has traditionally imported.
Freight Farms and Tiger Corner Farms are two companies that are growing produce in shipping containers through the use of hydroponics and aeroponics — methods of growing plants without the use of soil.
Freight Farms is working with NASA to find ways to grow produce in space. (Freight Farms)
Both companies use nutrient-rich water as a substitute for soil, but beyond that, their container farms are quite different.
Tiger Corner Farms’ farming units consist of five shipping containers; four are used for farming and the fifth one is used as a working station where the plants germinate and as a post-harvest station.
Tiger Corner Farms, based out of Summerville, S.C., is a family company that began with the combined interest of Stefanie Swackhamer, the general manager, and her dad, Don Taylor.
Through Grow Food Carolina, a nonprofit organization focused on preserving farming in South Carolina, Tiger Corner Farms has partnered with two other companies: Vertical Roots and Boxcar Central. Tiger Corner Farms manufactures farming units from recycled shipping containers, Boxcar Central works on the automation of the hardware and software used for these container farms, and Vertical Roots deals with the production of the produce.
With Tiger Corner Farms’ shipping container farmsshipping container farms, Vertical Roots can increase food production. Having 13 farms in total, Vertical Roots is able to produce about 40,000 heads of lettuce in about half the time it would take a traditional farm.
Vertical Roots sells its produce to grocery stores such as Whole Foods and Harris Teeter.
Vertical Roots is able to produce about 40,000 heads of lettuce in about half the time it would take a traditional farm (Tiger Corner Farms)
For Vertical Roots, founded by Andrew Hare and Matt Daniels, working with Tiger Corner Farms was a no-brainer.
“Providing cleaner, fresher, better access to food was something all four of us were wanting to do. They wanted to provide jobs and educate people on the importance of sustainable agriculture, and we wanted to do the same thing,” said Hare, Vertical Roots’ general manager. “We wanted to bring transparency and education and empowering our community in knowing where their food comes from and how important the freshness and quality is.”
Meanwhile, Boston-based Freight Farms offers a hydroponic “farm in a box,” dubbed the Leafy Green Machine, built entirely inside a single 40-foot shipping container.
The company, founded in 2010 by Brad McNamara and Jon Friedman, also offers a farming service and mobile app, Farmhand, to aid farmers in monitoring their farms.
Freight Farms’ customers range from individual farmers to universities and corporations.
One of those customers is Kim Curren of Shaggy Bear Farm in Bozeman, Mont., which provides local restaurants with leafy greens that aren’t grown in the region.
Someday, hydroponic farming might even play a role in space exploration and colonization.
Freight Farms is working with NASA and Clemson University to improve the efficiency of its farming units in the hopes of eventually using them in space.
Joshua Summers is one of the professors at Clemson that worked on the project. Professors Cameron Turner and John Wagner and students Doug Chickarello, Malena Agyemang and Amaninder Singh Gill also worked on the project.
Lettuce grows inside a climate-controlled container farm from Tiger Corner Farms. (Tiger Corner Farms)
In order to enable the farming units to work in space, the Clemson team is focusing on making it a closed-loop system by looking at thermal and electrical loads of the LED lights as well as the heating, ventilation and air conditioning unit.
While working on this project, there is one major issue that Summers said needs to be taken into consideration.
“One of the major issues in moving into space is gravity. As you move away from gravity, a lot of their growing patterns are based on plants growing in a specific way,” Summers said. “Now you don’t know exactly how they are going to grow, so it’s going to be a bit more random, so we have to change some of the geometric layout to make it more efficient in terms of volume.”
Clemson, NASA and Freight Farms are working on a new proposal to continue this project.
Through its work with individual farmers as well as organizations such as NASA, Freight Farms is taking steps toward its goal of empowering anyone to grow food anywhere.
More Articles About:
US: Indoor Agtech Producer Providing Lease-Back Program
United Opportunities, the developer of an exclusive program that allows individuals to take ownership positions in the AgTech market, announced that manufacturing of its high-tech growing environments has commenced. The company's advanced indoor cultivation Pods are being manufactured in Southern California and will be available for delivery by end of summer.
The company is selling these high-tech growing Pods with a unique lease-back program that allows Pod owners to receive quarterly payments while United Opportunities manages the unit and handles the cultivation, sales and distribution.
Each Pod is a self-contained cultivation system, equipped with proprietary technology, patented air and water filtration systems, and specially tuned lighting.
Jack Boyle, CEO of United Opportunities, created the company because of the explosion in the AgTech sector - and specifically in the indoor farming sector.
"The AgTech industry is not only one of the fastest growing sectors in the world, but it is also creating a profound change in how and where crops are grown, distributed and sold," Boyle said. "We are at the tip of an agricultural revolution that will impact billions of lives worldwide."
United Opportunities has developed a "Pod Farm" in California where the first 1,000 units will be placed. Owners of the units will receive a guaranteed 20% yield, paid on a quarterly basis.
For more information:
United Opportunities
(800) 379-4052
Publication date: 8/10/2018
Growtainer® 20’ Micro Greens Factory
CEA Advisors is pleased to offer our 20’ fully equipped Growtainer®, a highly engineered modular vertical production environment optimized to produce high-value Micro Greens for growers wishing to market Hyper-Local specialty products to consumers, chefs, and restaurants.
Each 20’ fully insulated GrowtainerTM has been substantially modified by the removal of the container doors, the installation of an end mounted man door and the installation of an insulated wall with a door inside the container to create a separate utility area, epoxy flooring throughout and a climate-controlled production area. The utility area creates a barrier against climate fluctuations and prevents pest and disease contamination in the production chamber.
Each chamber is optimized for Micro Greens production with a vertical rack system which contains 5 vertical production levels. Each level contains 3 10” wide x 12’ long NFT Crop King Gutters for a total of 360 linear feet of production equaling a potential harvest of 108 “1020” growers trays per week. Each level contains 3 to 4 energy efficient crop-specific, full-spectrum LED fixtures for optimum growth.
Each GrowtainerTM comes complete with our automatic Hydroponic system for water monitoring, automatic dosing, and nutrient recirculation. The production chamber air-conditioned and includes Humidistat controlled vents and hi-cfm Fans to maintain an even temperature and relative humidity for optimum growth. Each chamber comes equipped with an organic CO2 system. Increases in CO2 typically result in higher yields and increased growth and reproduction, provided other growth factors like light, and temperature are controlled.
Over the past 8 years CEA Advisors has designed and manufactured custom built 40’, 45’ and 53’ shipping containers which have been specifically modified to provide the optimum controlled environment for growing or researching a wide range of horticultural and agricultural products. Our custom built commercial Growtainers® are in use worldwide for many different clients, including food manufacturers, growers, pharmaceutical manufacturers, researchers, government agencies, universities, food banks, schools and supermarkets.
Unlike other container farm manufacturers in the market today, we have always avoided making any unrealistic claims about yield and profitability. Our results have consistently generated a higher yield in a shorter time than all conventional production methods. Recently we’ve developed a collaboration with Crop King, a well-known manufacturer of Hydroponic systems to create an affordable, crop specific Growtainer® to produce Micro Greens for sales to Chef’s, restaurants, caterers, grocery retailers etc.
We believe that even an inexperienced farmer, using our system can generate a substantial profit with a minimal investment. The system requires approximately 30 hours per week of labor for production and delivery, it’s modular so you can increase production as you increase sales and you can produce any of the hundreds of varieties of Micro Greens in demand by Chefs everywhere.
Our 20’ Growtainers® for MicroGreen Production are priced from $65,000 and are fully equipped and Plug & Play, all you need is a flat surface and utility hookups, such as power and water, seeds, substrate and fertilizer and you’re in business.
Based on our conservative calculations, a $65,000 investment can return as much as $50,000 per year in revenue.
For Additional Information:
Contact us by email at gb@cea-advisors.com
Or visit our website at:
www.microgreens.growtainers.com
Future of Farming Is Rooting Itself In Central Oregon
A sustainable, shipping container 'vertical farm'
By: Lauren Melink
July 26, 2018
Around the Bend Farms
BEND, Ore. - There’s a new farm in Central Oregon, and it’s a bit different from your standard homestead.
It’s called Around the Bend Farms. And for now, you’ll find it in a laboratory at OSU-Cascades.
Around the Bend Farms CEO, Ben Marsh describes it like this: "It's definitely not your archetypal farmer who is in a field, sweating in 95-degree weather with a big combine. Our combine is a computer or a micro-controller."
Around the Bend, Farms is a non-profit organization that’s partnered with OSU-Cascades to create a personal food computer.
"What that means is that the computer can tell this thing, 'OK, I need you to turn on a light.' And this thing goes 'All right,' and turns on a light," Marsh said.
The farm is a sustainable "vertical farm" that after being programmed with the correct grow recipe, runs on its own.
"We’re controlling the heating, the cooling, the air movement, the lighting, temperature," Marsh said
The goal is to eventually build computer-run, sustainable, vertical farms inside shipping containers.
Lance Porter is an energy systems engineering graduate involved in the project. He thinks the computer farm will attract a different type of farmer.
"The newer generations really want to be more involved in where their food comes from and especially involved in how it’s made and how it’s produced," Porter said
Executive research associate Makena Whitaker said this unique kind of farming will hopefully keep people coming back.
"It’s more fun if you make farming fun and interesting. People will stick around," Whitaker said.
Around the Bend Farms also hopes to create a sense of community around growing food.
"Food was always a family endeavor and a community-based endeavor, and we want to kind of get back to that," Marsh said.
Around the Bend, Farms is in its early stages of development, but already they’ve tripled the size of their crop and hope to have a shipping container farm in Bend within two years.