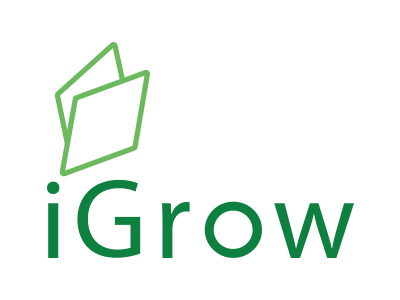
Welcome to iGrow News, Your Source for the World of Indoor Vertical Farming
Containerized Vertical Farming Company Freight Farms Secures $15 Million
Freight Farms — a global innovation leader of containerized vertical farming — announced that it has raised $15 million in Series B funding
By Noah Long ● February 15, 2020
Freight Farms — a global innovation leader of containerized vertical farming — announced that it has raised $15 million in Series B funding
Freight Farms — a global innovation leader of containerized vertical farming — announced that it has raised $15 million in Series B funding led by Ospraie Ag Science. Spark Capital also participated in the round. Including this funding round, the company has raised over $28 million.
“It’s a big step forward for the industry when financial markets recognize and champion the value of creating a distributed food system,” said Freight Farms CEO Brad McNamara. “Aligned on mission-driven growth as a team, there is a massive opportunity before us to scale across global markets, propelling meaningful technology that’s already doing good.”
Freight Farms’ Greenery is able to produce over 500 varieties of crops like calendula at commercial scale year-round using 99.8% less water than traditional agriculture. Four rows of the company’s panels on a flexible moving rack system are able to house more than 8,000 living plants at once thus creating a dense canopy of fresh crops.
This round of funding will be used for advancing the Freight Farms’ platform through continued innovation with new services designed to benefit its growing global network of farmers and corporate partners. And this investment follows the announcement of Freight Farms’ strategic national partnership with Sodexo to grow food onsite at educational and corporate campuses nationwide and will support ongoing contributions to collaborative research projects and partnerships.
“Freight Farms has redefined vertical farming and made decentralizing the food system something that’s possible and meaningful right now, not in the ‘future of food,'” added Jason Mraz, President of Ospraie Ag Science. “Full traceability, high nutrition without herbicides and pesticides, year-round availability – these are elements that should be inherent to food sourcing. Freight Farms’ Greenery makes it possible to meet this burgeoning global demand from campuses, hospitals, municipal institutions and corporate businesses, while also enabling small business farmers to meet these needs for their customers.”
Launched in 2010 by McNamara and COO Jon Friedman, Freight Farms debuted the first vertical hydroponic farm built inside an intermodal shipping container called the Leafy Green Machine with the mission of democratizing and decentralizing the local production of fresh, healthy food. And this innovation, with integral IoT data platform farmhand, launched a new category of indoor farming and propelled Freight Farms into the largest network of IoT-connected farms in the world.
Freight Farm’s 2019 launch of the Greenery raised the industry bar, advancing the limits of containerized vertical farming to put the most progressive, accessible, and scalable vertical farming technology into the hands of people of diverse industry, age, and mission.
“With the Greenery and farmhand, we’ve created an infrastructure that lowers the barrier of entry into food production, an industry that’s historically been difficult to get into,” explained Friedman. “With this platform, we’re also able to harness and build upon a wider set of technologies including cloud IoT, automation, and machine learning, while enabling new developments in plant science for future generations.”
Freight Farms has been an integral part of scientific and academic research studies in collaboration with industry-leading organizations, including NASA (exploring self-sustaining crop production) and Cold Spring Harbor Laboratory (exploring the integration of CRISPR seed genetics and vertical farming to create commercial opportunity).
The company’s customers hail from education, hospitality, retail, corporate, and nonprofit sectors across 44 states and 25 countries, and include independent small business farmers — who distribute to restaurants, farmers’ markets, and businesses such as Central Market, Meijer, and Wendy’s
Shipshape Urban Farms $1 Million Financing, K Dale Speetjens Submitted Nov 29 D Filing
Shipshape Urban Farms is based in Alabama. The firm’s business is Agriculture. The form D was signed by K Dale Speetjens President and CEO. The company was incorporated in 2019
Posted by Jean Kramer on November 29, 2019
Shipshape Urban Farms Financing
Shipshape Urban Farms, Inc., Corporation just had published form D announcing $1 million equity financing. This is a new filing. Shipshape Urban Farms was able to sell $150,000 so far. That is 15.00 % of the round of financing. The total offering amount was $1 million. The offering form was filed on 2019-11-29. The reason for the financing was: unspecified. The fundraising still has about $850,000 more and is not closed yet. We have to wait more to see if the offering will be fully taken.
Shipshape Urban Farms is based in Alabama. The firm’s business is Agriculture. The form D was signed by K Dale Speetjens President and CEO. The company was incorporated in 2019. The filler’s address is: 600 Clinic Drive, Mobile, Al, Alabama, 36688. Kenneth Dale Speetjens is the related person in the form and it has the address: 600 Clinic Drive, Mobile, Al, Alabama, 36688. Link to Shipshape Urban Farms Filing: 000179551019000001.
Analysis of Shipshape Urban Farms Offering
On average, firms in the Agriculture sector, sell 63.30 % of the total offering amount. Shipshape Urban Farms sold 15.00 % of the offering. The financing is still open. The average fundraising size for companies in the Agriculture industry is $287,000. The offering was 47.74 % smaller than the average of $287,000. Of course, this should not be seen as negative. Firms raise funds for a variety of reasons and needs. The minimum investment for this financing is set at $1. If you know more about the reasons for the fundraising, please comment below.
What is Form D? What It Is Used For
Form D disclosures could be used to track and understand better your competitors. The information in Form D is usually highly confidential for ventures and startups and they don’t like revealing it. This is because it reveals the amount raised or planned to be raised as well as reasons for the financing. This could help competitors. Entrepreneurs usually want to keep their financing a ‘secret’ so they can stay in stealth mode for longer.
Why Fundraising Reporting Is Good For Shipshape Urban Farms Also
The Form D signed by K Dale Speetjens might help Shipshape Urban Farms, Inc.’s sector. First, it helps potential customers feel safer to deal with a firm that is well-financed. The odds are higher that it will stay in the business. Second, this could attract other investors such as venture-capital firms, funds, and angels. Third, positive PR effects could even bring leasing firms and venture lenders.
Market Data by TradingView
Farms Inside Shipping Containers Could Grow More Local Produce
Instead of trucking vegetables across the country, one company wants to help food service providers grow food right where they are, no matter how little experience or land they have
The Crops Grow Vertically Under LED Lights
Tuesday, February 18, 2020
Four rows of panels on a flexible moving rack system house more than 8,000 living plants at once, creating a dense canopy of fresh crops. (Photo: Courtesy of Freight Farms)
Instead of trucking vegetables across the country, one company wants to help food service providers grow food right where they are, no matter how little experience or land they have.
“That’s at corporate campuses, university campuses, health care facilities,” says Brad McNamara, CEO of Freight Farms. The company sells what it calls the Greenery.
“It’s a 320-square-foot shipping container like you would see on a boat, a train, a truck, outfitted with an automated growing system,” he says, “to grow about 3.5 acres worth of produce with no pesticides, no herbicides, and about 98.5% less water.”
Inside the Greenery, plants grow vertically, with their roots in a nutrient solution instead of soil. Sensors, pumps, and LED lights automatically maintain ideal growing conditions, so you don’t have to be an expert to start farming.
“You plug it in and you’re growing the same day,” McNamara says.
As the climate changes and the world’s population grows, McNamara says it makes sense to farm in a way that produces more food with fewer resources and less transportation.
“Instead of making more bigger farms,” he says, “We make hundreds, then thousands, then millions of people into independent successful farmers where they live and work.”
Reporting credit: Stephanie Manuzak/ChavoBart Digital Media.
US: South Carolina - Vertical Roots Hits The Road In Their Lettuce Localmotive, Spreading The Good Word of Hydroponics
The hydroponic growing system is simple - nutrient-filled water replaces traditional soil in order to grow the plant, and for the first time since we started tilling land farmers can grow crops without the soil beneath their feet
The technology of planting crops has revolutionized over the years.
The hydroponic growing system is simple — nutrient-filled water replaces traditional soil in order to grow the plant, and for the first time since we started tilling land, farmers can grow crops without the soil beneath their feet.
Hydroponic container grower Vertical Roots is taking one of their shipping container farms on the road — they're hitting the streets with the Lettuce Localmotive, teaching people about the process of growing lettuce. They'll be making stops at Publix and Greenwise Markets across the country.
RELATED Tiger Corner Farms produces full-scale, aeroponic crops in recycled shipping containers: The Future of Farming
Unlike traditional farms, the Vertical Roots' containers grow plants vertically indoors without soil, with the plants obtaining all their nutrition from water and their light energy from powerful LED lights.
During tour stops, guests will get a hands-on experience with seeding lettuce, learn how technology manages the growing process, and get schooled about all the benefits of this alternative way of farming.
The first stop of the tour is at Vertical Root's home base — Charleston. Check them out at the Daniel Island Publix this Sat. Feb. 15 from 10 a.m.-4p.m.
A Belly Ache Can lead To A Trip To The Urgent Care. E. coli Poisoning Lands You In The Emergency Room
The FDA has called little attention to the surge in E. coli outbreaks from leafy green vegetables. It has been slow to investigate or publicize risks and did not disclose one outbreak to the public until the Globe contacted agency officials about reports of E. coli poisonings
Dietitian Determined To Save Salads!
February 12, 2020
Written by Dr. Jenna Bell, RD VP of Nutritional Science at Crop One
Crop One is the world’s largest scalable, completely controlled, vertical farming company. Our Greater Boston brand is FreshBox Farms.
Spend a few days bent over, writhing in abdominal pain and you’ll understand how serious foodborne illnesses can be. It may even require a trip to urgent care. Experience an outbreak of E. coli O157:H7 from salad greens and you may be among hundreds heading to the ER.
E. coli poisoning can be life-threatening.
What is E. coli, anyway?
Straight out of the Center for Disease Control (CDC):
“Escherichia coli (abbreviated as E. coli) are bacteria found in the environment, foods, and intestines of people and animals. E. coliare a large and diverse group of bacteria. Although most strains of E. coli are harmless, others can make you sick. Some kinds of E. coli can cause diarrhea, while others cause urinary tract infections, respiratory illness and pneumonia, and other illnesses.”
To be crystal clear — we’re talking about fecal contamination. Poo in food. Bird, cow, human, someone’s poop.
As a registered dietitian, I swear by colorful salads of leafy greens with favorite fruits, veggies, seeds, nuts and proteins atop. Making that recommendation sans lettuce feels blasphemous and unfulfilling. But given the pace at which the outdoor-grown romaine industry reports bacterial outbreaks, food safety threatens our salad fixings.
Break out bacteria
Over the past few years, romaine has been hit hard by outbreaks of bacterial contamination — especially from the strain, E. coli O157:H7. The most recent string of outbreaks is considered “under control” by the CDC and Food and Drug Administration (FDA), but the final count as of January 13, 2020, is 167 individuals reported in the US.
“Reported” is a key word here because how many times have you called the CDC or the FDA when you were sick?
Lettuce + E. coli is not a new thing
Several years ago (2013), a scientific investigation of a decade-worth of data on hospitalizations and deaths attributed to food commodities (including seafood, farm animals and plants) revealed that among the 17 commodities, more illnesses were associated with leafy vegetables (2.2 million [22%]). Illnesses associated with leafy vegetables were the second most frequent cause of hospitalizations (14%) and the fifth most frequent cause of death (6%).¹
A 2020 piece in the Boston Globe written by venerated reporter, Christine Haughney Dare-Bryan, traced the tracks of the recent outbreaks and illuminated the grimness with a family’s horrific experience with E. coli poisoning in their two-year-old son. In the article, Haughney Dare-Bryan reflects on the quick response from then commissioner of the FDA, Scott Gottlieb:
…[Gottlieb] tweeted to a startled nation that they should stop eating romaine lettuce just two days before Thanksgiving 2018.
E. coli fatigue
However the seriousness, history shows that someone hit the snooze button. Despite the number of updates and investigations, CDC and the FDA can’t seem to get ahead of it. Haughney explains:
Despite the growing number of outbreaks, the agency remains protective of the growers, taking little enforcement action and sometimes shielding growers suspected of causing outbreaks from bad publicity. Consider:
The FDA has called little attention to the surge in E. coli outbreaks from leafy green vegetables. It has been slow to investigate or publicize risks and did not disclose one outbreak to the public until the Globe contacted agency officials about reports of E. coli poisonings. FDA officials insist they planned to disclose the early fall 2019 outbreak all along.
The FDA has not punished any farm or distributor in connection with the seven outbreaks traced to lettuce since 2017 even though federal law prohibits the sale of contaminated foods. The agency concluded that three of the outbreaks were linked to a single California lettuce grower but declined to release the name.
The FDA staff monitoring lettuce production is just a small fraction of that detailed to the federal oversight of beef: There are 614 FDA field investigators responsible for leafy greens compared to 7,068 workers overseeing beef for the Department of Agriculture. Congress recently gave the FDA $8 million to better handle outbreaks, but the agency doesn’t want to talk about the state of its staffing. When the Globe tried to examine just how understaffed the agency is, officials redacted hundreds of pages of records discussing their internal problems.
The agency relies almost entirely on voluntary cooperation from the lettuce industry, an approach that has brought about some safety improvements. But FDA has asked relatively little of the industry and recently delayed implementing rules aimed at preventing E. coli contamination of irrigation water until 2022.
What do we do now?
From one salad enthusiast to another, or one mom to another, or one PhD/dietitian to consumer (take your pick): there is a safer way to grow your lettuce and eat it too.
We can grow indoors. Out of the soil and away from questionable water, weather disruption messes and “run-off” contaminants (think poop).
I found my safe salad environment when I met and started working for CROP ONE.
How do I know it’s safe?
Concealed, confined, enclosed, controlled, secured, safe, protected — all synonyms for Crop One’s modular growing rooms (“mods”). Mods are protected by double door entryways with fancy sliding doors like at the supermarket and a vestibule. Anyone who enters is fully gloved and covered in stylish lab wear (no, not stylish).
Pictured: The most stylish lab wear in Massachusetts
I should add here that because our plants are protected from the world, we don’t need or use any type of -cide (pesticides, herbicides or fungicides), nor do we deal with pests, insects, rain, contaminated water or other farm’s fertilizer or chemicals. We’re free from all that stuff you’re trying to stay free from.
Pure, clean, filtered — water and air. Each mod is carefully controlled for contaminants, chemicals, heavy metals, and other unwanted impurities through a multi-step, quality-controlled purification system.
FreshBox KVH Kosher Certified romaine lettuce.
Two words: Kosher. Certified.
If you’re not familiar with the process by which produce is certified Kosher, visualize microscopes, tweezers, fastidious inspectors, etc. KVH Kosher certification officers perform comprehensive inspections to ensure that Crop One/FreshBox Farms’ produce is free of all pests and insects.
The salad solution.
Crop One can keep your salad safe. Miraculously, along with safety, our modular enclosures are scalable and sustainable in any climate, on very little land, with barely any water compared to traditional farms (about 95–99% less water required), but we’ll save that for another conversation.
Jenna A. Bell, PhD, RD, joined the Crop One team in September 2019 as the VP of Nutritional Science to be part of the global food supply solution.
References:
Painter JA, Hoekstra RM, Ayers T, et al. Attribution of Foodborne Illnesses, Hospitalizations, and Deaths to Food Commodities by using Outbreak Data, United States, 1998–2008. Emerging Infectious Diseases. 2013;19(3):407–415. doi:10.3201/eid1903.111866.
Haughney Dare-Bryan C. Green Alert. Boston Globe. Last accessed January 30, 2020: https://edition.pagesuite.com/popovers/dynamic_article_popover.aspx?artguid=a497f64d-df30-4f48-b026-10aadc66901b&appid=1165
WRITTEN BY
Crop One Holdings
We grow the cleanest, healthiest greens for anyone, anywhere in the world. Our sustainable vertical farms are free from chemicals and climate-proof.
Hamilton’s 80 Acres Farms To Grow Tons of Tomatoes On New York City’s Fifth Avenue
Hamilton-based 80 Acres Farms will grow tomatoes on one of the busiest streets in New York outside the Solomon R. Guggenheim Museum. The grow is part of “Countryside, The Future,” the Guggenheim’s new exhibition in collaboration with Rem Koolhaas, which opens to the public Feb. 20, and runs through Aug. 14
February 21, 2020
By Eric Schwartzberg, Staff Writer
HAMILTON —
80 Acres Farms will grow tomatoes on one of the busiest streets in New York outside the Solomon R. Guggenheim Museum.
The grow is part of “Countryside, The Future,” the Guggenheim’s new exhibition in collaboration with Rem Koolhaas, which opens to the public today and runs through Aug. 14.
Along with its commercial partner’s Infinite Acres and Priva Holding BV, 80 Acres Farms will grow cherry tomatoes in an indoor grow area right outside the museum on Fifth Avenue.
80 Acres Farms is a leader in indoor growing for retailers such as Kroger, Jungle Jim’s International Market, Whole Foods, Dorothy Lane Markets, and Giant Eagle.
MORE: ‘The perfect home’: Why 80 Acres chose Hamilton to move its headquarters and create 125 jobs
People in New York will be able to look through a large window in the indoor farm to view a crop of fresh tomatoes being grown continuously during the next six months. The first tomatoes grown will be ready for harvesting and consumption by late March.
The “Countryside, The Future” exhibition will examine political forces, social issues, and environmental factors altering landscapes across the world, including traditional farmlands.
“We believe that what we are doing is about the future of food,” said Mike Zelkind, chief executive officer of 80 Acres Farms. “We are changing the way fruits and vegetables are grown and harvested locally then delivered to grocers the very next day. There is an enormous market and consumer appetite around the world for produce that our crop scientists and other food experts have been perfecting during the past five years.”
MORE: Dilapidated Hamilton building transforms into an industry-changing grow facility
Zelkind said 80 Acres’ participation in the “Countryside, The Future” exhibition will allow New York residents and visitors to experience how “the freshest, tastiest locally-grown tomatoes” can be grown year-round indoors in one of the busiest cities in the world.
For the Guggenheim exhibition, 80 Acres Farms, Infinite Acres, and its Priva partners have collaborated on the 700-square-foot grow center, which is expected to grow 50,000 tomatoes in six months. Additional tomatoes will be donated to City Harvest, a New York City food rescue organization that recovers excess food and distributes it to people in need.
MORE: Hamilton’s large indoor growing operation is so advanced they want it around the world
Last year saw a massive year of growth for 80 Acres. It opened its automated facility on Enterprise Drive, a facility that grows leafy vegetables, herbs and strawberries, then a downtown Hamilton location on South 2nd St. that grows vine crops, including tomatoes, cucumbers, and peppers.
The company also launched Infinite Acres, an independent joint venture aimed at providing large-scale indoor farming facilities worldwide. The venture also includes UK-based Ocado Group, one of the world’s largest dedicated online grocery retailers, and Netherlands-based Priva Holding BV, a leading provider of technology solutions, services, and automation systems to horticultural and other industries.
That partnership is now building large-scale, fully automated indoor farms in the United States, Asia and Europe.
It also inked a deal to moved its headquarters from Cincinnati to Hamilton and was granted a tax credit for committing to create 125 new jobs and investing at least $26.9 million.
MORE: Innovative Hamilton indoor growing company part of a worldwide deal to supply food
Brick Street Farms Will Open A Pop-Up Market In A St.Pete Warehouse Next Month
Brick Street Farms, a St. Pete-based urban farming and produce company, comes into 2020 ablaze in change now its “cultivation hub” is set to debut at the end of this year
C/O BRICK STREET FARMS
A temporary spot to cop your fresh kale and spinach.
FEB 6, 2020
Brick Street Farms, a St. Pete-based urban farming and produce company, comes into 2020 ablaze in change now its “cultivation hub” is set to debut at the end of this year. Renovations to Brick Streets' market location—located at 2001 Second Ave. S. in St. Petersburg—have shut it down its market temporarily, so a Brick Street pop-up market will soon open in its production warehouse in St. Petersburg’s Grand Central District (at the corner of 3rd Avenue S. and 22nd Street, to be exact.)A press release says that the warehouse pop-up market hopes to open in March and will sell Brick Street's prized fresh produce as soon as doors are open.
This cultivation hub, which is still in the beginning stages of construction, will allow Brick Street Farms to increase production in order to satisfy high-demand. St. Pete’s Urban Canning Co. will also rebrand itself into the “Brick Street Canning Company” and sell canned and pickled goods out of the Brick Street Farms complex when it opens at the end of 2020. Until the cultivation hub opens, this warehouse space will be home to the Thrive Program—which allows consumers to buy or lease the shipping container farms that the Brick Street team manufactures.
Keep your eyes peeled for the opening of this warehouse pop-up market in the Grand Central Warehouse district by following Brick Street Farms on Instagram.
Want to know everything going on with Tampa Bay's food and drink scene? Sign up for our Bites newsletter.
Container Farms Bring Fresh Vegetables To Remote Canadian Community
Over 1,000 kilometres northeast of Yellowknife sit two steel shipping containers that are changing how we understand and respond to food production challenges in Canada’s North, and in other harsh and isolated locations
Over 1,000 kilometers northeast of Yellowknife sit two steel shipping containers that are changing how we understand and respond to food production challenges in Canada’s North, and in other harsh and isolated locations.
These containers have been retrofitted into a research station in Gjoa Haven, Nunavut, where the local community is working with government researchers and a non-profit organization to understand what is needed to create local food sources, clean energy generation, resilient building materials, scalability and adaptability to local needs, and even job opportunities and training.
The local community of Gjoa Haven has named the initiative Naurvik, which means “growing place.” It is a first-of-its-kind venture in Canada’s North, being built and adapted on-site.
Listening closely to Gjoa Haven Elders and community members, the Arctic Research Foundation, Agriculture and Agri-Food Canada, the National Research Council of Canada, and the Canadian Space Agency are actively collaborating on the design and testing of this green energy-powered controlled environment production unit for growing plants in Canada’s North. The community is deciding what plants they want to grow. It’s then up to the research partners to figure out how to adapt the research to their needs, and to train community partners to operate and maintain the system in the harsh and remote location.
“When I first heard of [the project] I thought it would never work up here. No. Not in this 40 below zero. Now I know anything is possible if you have the right idea... I had a taste of the vegetation. It was fresh”, said Peter Akkikungnaq, Gjoa Haven Elder.
By actively working with the local community, and tailoring solutions to their needs, Naurvik is creating a roadmap of how to deliver effective programs, infrastructure, and research in Canada’s North. By integrating resilience and adaptability into the design, the goal is that the model will be able to respond to needs in other harsh and isolated locations, not only in Canada’s North but also on space missions.
“The Canadian Space Agency is looking at innovative solutions to food production challenges that are common to astronauts on deep-space missions and people on Earth living in remote or extreme environments, such as the northern community of Gjoa Haven. While working towards to help with the development of advanced, robust designs for a terrestrial food production system, we are hoping to find strategies that could help astronauts grow food in space”, said Christian Lange, Head of Exploration Strategic Planning, Canadian Space Agency.
While the project is in its early stages, it’s hoped that by 2025 a community-led, renewable energy-powered plant food production system will be fully operational in Gjoa Haven. It will serve as a scalable blueprint for collaborative partnerships and co-designed projects in the Arctic and will be a focal point for innovative research and educational opportunities.
“This is an effective, novel approach to community-driven collaboration with science institutions in Canada’s North, and that’s the reason why it has been so successful. It will generate research for the benefit of all Canadians while also producing tangible benefits for Gjoa Haven and, eventually, other communities throughout the Arctic”, Adrian Schimnowski, CEO, Arctic Research Foundation, comments.
For more information:
Arctic Research Foundation
www.arcticfocus.org
Publication date: Mon 10 Feb 2020
Can You Fit A 2-Acre Garden In A Shipping Container?
As the bustling streets of Brooklyn, New York rumble nearby, most passersby have no idea there’s a bountiful garden just steps away
WRITTEN BY SAM BURNS
As the bustling streets of Brooklyn, New York rumble nearby, most passersby have no idea there’s a bountiful garden just steps away. It may have something to do with the fact that this garden’s not in a field or in someone’s lawn but in a parking lot, with acres and acres of fresh food growing inside shipping containers!
When people can’t go to the farm, why not bring the farm to the people? That’s what Square Roots is doing by growing fresh, nutritious food in cities to feed the communities around them.
Tucked away inside your everyday shipping container is the equivalent of a two-acre farm. Leaves from a variety of herbs and greens line the walls in columns, as purple lights shine on them and young farmers are hard at work tending to their needs. Let’s take a look at how this all works and what it means for our future with food!
Courtesy of Square Roots
As we face growing populations and changing climates, our ability to grow enough food to support everyone’s health remains in question. But this fascinating look into the future of food with Square Roots gives us the inspiration to keep pushing the barriers on our definitions of what “farming” is, where it happens, and who does it.
On a mission to bring nutritious food to people living in the city and counteract the nutrient loss that happens in our typical food system (when produce is shipped many, many miles), Square Roots is perfecting a sustainable model of farming that can change what we can eat in our growing cities.
To give us an introduction to their work, here’s BEME News:
Dive deeper into Square Roots!
Square Roots has sure been up to a lot in the two years since that video was released! Not only are they continuing their awesome Next-Gen Farmer Training Program to help young people get started in the industry, but they’ve also taken major steps to increase the transparency of information about our food and access to it with some amazing new launches!
Since Square Roots has data collection and technology in their DNA, they’ve decided to let the public in on it. In late 2018, they started putting QR codes on the back of all of their produce packaging so consumers can read the life story of their food; where it was grown, when, how, and by whom! Think about that: when was the last time you knew who picked that bag of spinach you just plucked off the shelf? Or what sort of environment it’s coming from? Square Roots Transparency Timeline lifts the curtain on the stories of our food system and hands the consumer more power. (Read more about their Transparency Timetable here!)
Last year, Square Roots opened its first farm campus outside of New York City!
Gordon Food Service, one of the United States’ leading foodservice providers, has signed on to have Square Roots campuses of indoor farms built on or around their distribution and retail centers around the country. Square Roots wrote in their blog that:
“It’s been exciting for us to witness a company as large as Gordon Food Service move so fast to address the increasing consumer demand for locally-grown food. It’s also very clear that Gordon Food Service takes its role as a responsible member of the food supply chain seriously. They recognize that, at their scale, adoption of innovative solutions like Square Roots can drive significant positive change throughout the entire foodservice industry.”
We couldn’t agree more! When the goliaths in any industry shift their practices, they can begin a huge ripple effect. And this first farm is surely a big one. Read more about the farm–which they opened in September 2019 (congrats, y’all!)–in this blog post!
You can learn more about Square Roots by visiting their website or touring one of their farms in person! And subscribe to their blog to receive updates from them directly in your inbox. (They post great stuff! I highly suggest taking a look.)
View of the Square Roots Brooklyn Farm Campus | Courtesy of Square Roots
Can you imagine what it’d be like if your family had access to fresh food all year round?
How would that impact your lives? As our societies and populations have grown steadily over the years, it seems like we’ve been scrambling to establish a food industry that can accommodate our needs. But something else has been happening as humanity grows: our innovations have adapted. We’ve developed new technologies and uncovered more secrets from the natural world, meaning, we have an immensely better grasp on how plants grow and the tools needed to help them. Every year inches us closer and closer to a solution.
Square Roots is a really great piece of the puzzle, but of course, they aren’t the only ones using their knowledge to make a dent in this problem.
What can you do?
Well first, if you live in New York City you can use this locator to see if Square Roots is selling their produce at a market near you. (And make sure you scan those neat QR codes on the back of their produce—they’ll give you all of the information about who grew the food and where it comes from!)
But for the rest of us without a shipping container garden in a parking lot nearby, what can we do? I’ll just give you one piece of advice (and trust me, I’m giving it to myself as well): grow a plant inside! Any plant! Basil, thyme, spinach, tomatoes, strawberries, I don’t care. If you can avoid buying one product at the market, that’s a great start. Plus, you’ll know exactly where that wonderful basil on your hunk of mozzarella came from. This article can give you some ideas.
If that doesn’t seem like something that’s possible, there are also great directories to find farmer’s markets and CSA’s near you! A simple Google search should suffice in pulling up your local options. But for those living in the United States, the Department of Agriculture’s farmer’s market and CSA directories are a really great resource. Just click those respective links and enter your zip code to see what’s happening near you!
Do you have any other tips? Share with us on Twitter or Facebook!
Stay open to new possibilities!
Sam
“No problem can be solved from the same level of consciousness that created it.” —Albert Einstein
Freight Farms Raises $15M in Series B funding Led By Ospraie Ag Science
Freight Farms, the containerized vertical farming company, announced that it has raised $15 million in Series B funding led by Ospraie Ag Science, an investment firm committed to supporting sustainable solutions that improve the quality of life for both farmers and society
Freight Farms, the containerized vertical farming company, announced that it has raised $15 million in Series B funding led by Ospraie Ag Science, an investment firm committed to supporting sustainable solutions that improve the quality of life for both farmers and society. The investment round, which received participation from existing investor Spark Capital, brings the company's total funding to more than $28 million.
Proceeds from the Series B fundraise will be used to advance the technical potential of Freight Farms’ platform through continued innovation, with new services designed to benefit its growing global network of farmers and corporate partners. The investment follows the announcement of Freight Farms’ strategic national partnership with Sodexo to grow food onsite at educational and corporate campuses nationwide and will support ongoing contributions to collaborative research projects and partnerships.
“Freight Farms has redefined vertical farming and made decentralizing the food system something that’s possible and meaningful right now, not in the ‘future of food,’” said Jason Mraz, President of Ospraie Ag Science. “Full traceability, high nutrition without herbicides and pesticides, year-round availability – these are elements that should be inherent to food sourcing. Freight Farms’ Greenery makes it possible to meet this burgeoning global demand from campuses, hospitals, municipal institutions, and corporate businesses, while also enabling small business farmers to meet these needs for their customers.”
“It’s a big step forward for the industry when financial markets recognize and champion the value of creating a distributed food system,” added Brad McNamara, Freight Farms CEO. “Aligned on mission-driven growth as a team, there is a massive opportunity before us to scale across global markets, propelling meaningful technology that’s already doing good.”
Founded in 2010 by CEO Brad McNamara and COO Jon Friedman, Freight Farms debuted the first vertical hydroponic farm built inside an intermodal shipping container—the Leafy Green Machine—with the mission of democratizing and decentralizing the local production of fresh, healthy food. This innovation, with integral IoT data platform farmhand, launched a new category of indoor farming and propelled Freight Farms into the largest network of IoT-connected farms in the world. Freight Farm’s 2019 launch of the Greenery raised the industry bar, advancing the limits of containerized vertical farming to put the most progressive, accessible, and scalable vertical farming technology into the hands of people of diverse industry, age, and mission.
“With the Greenery and farmhand, we’ve created an infrastructure that lowers the barrier of entry into food production, an industry that’s historically been difficult to get into,” said Jon Friedman, Freight Farms COO. “With this platform, we’re also able to harness and build upon a wider set of technologies including cloud IoT, automation, and machine learning, while enabling new developments in plant science for future generations.”
For more information:
Talia Pinzari
Tel: +1 (781) 635-6392
Email: talia@pinzaripr.com
www.freightfarms.com
Publication date: Wed 12 Feb 2020
Partnership Brings Container Farms To Students Across The U.S.
Freight Farms and Sodexo have partnered to bring hydroponic vertical farming technology to schools and universities across the U.S. The collaboration will usher in the implementation of Freight Farms’ Greenery container farms to campuses across the U.S., enabling the onsite growth of fresh, traceable produce year-round
Freight Farms and Sodexo have partnered to bring hydroponic vertical farming technology to schools and universities across the U.S. The collaboration will usher in the implementation of Freight Farms’ Greenery container farms to campuses across the U.S., enabling the onsite growth of fresh, traceable produce year-round.
“Students, institutions, and corporate businesses want healthy, safe, and delicious food, and they want it sourced as sustainably as possible. Sodexo is proud to use and support the latest agricultural technology to create meaningful food system change," said Kenny Lipsman, Director of Produce Category for Sodexo. “Our partnership with Freight Farms allows us to grow nutritious, superior-quality food on-site for our clients, just steps from the kitchens and serveries.
As part of Sodexo’s Better Tomorrow Commitments, developed in accordance with the United Nations’ Sustainable Development Goals, this technology allows for traceability, reductions in food waste, and year-round crop consistency.”
Co-founder and CEO of Freight Farms Brad McNamara, continued, “Sodexo’s commitment to offer onsite food production to its customers helps accelerate food system decentralization — leading the charge for better sourcing practices at an institutional level. Sodexo’s adoption of Freight Farms on-site programming will demonstrate to their customers and client communities the positive impact hyper-local food production can have on priorities from nutrition and food safety to emissions reduction.”
For more information:
Freight Farms
www.freightfarms.com
Sodexo
www.sodexo.com
Publication date: Wed 29 Jan 2020
Are Indoor Agriculture and Vertical Farming Growing Up?
In the US alone, the vertical farming market is projected to reach values of around $3 billion by 2024. Globally, the predicted value is $6.4 billion by 2023, with both figures growing at a similar rate of 24% CAGR
About Chris Sworder
Urban agriculture and vertical farming, are they viable? There are question marks on efficiency, availability of useful and reasonably priced real estate, and demand for the leafy greens and herbs that are most often the crop of choice. That said, there are several high-profile companies in the U.S. that have been around for several years, e.g. AeroFarms, Plenty, and Bowery, which have raised a total of over $400M. Alongside these farm developers, we are seeing more indoor agriculture-specific technology (see iUNU’s $7.5M Series A in February for an example).
Indoor farming is attractive
In the US alone, the vertical farming market is projected to reach values of around $3 billion by 2024. Globally, the predicted value is $6.4 billion by 2023, with both figures growing at a similar rate of 24% CAGR.
Vertical farming’s value propositions include; a controlled environment, less water use, no pesticides, controlled fertilizer use, easier automation, optimized growing conditions and high-density output that can be placed in or near urban demand. In an agriculture system that will need to support another 3.25 billion people in urban environments over the next thirty years, the high volume of investment in this sector is understandable. In order to support the investment required these farms have focused on high-value greens and herbs and the ability to provide a consistent predictable volume of produce all year round. Reduced water use is particularly important in markets such as EMEA where this is a more expensive input or in areas with often restricted supply but large demand such as Southern Spain or California.
Food safety is an increasingly valuable part of vertical farming, as food born illness is estimated to cost the US economy $15.6 billion per year. There have been two high profile outbreaks of E. coli in romaine lettuce in the US in the last 12 months related to washing practices. Vertical farms are controlled growing environments, and dirt-free, therefore no washing is required. As a high-value, short shelf-life, leafy-green this is a key market for vertical farming.
Underlying technologies are maturing
There are three technologies used in vertical farming; hydroponics, aeroponics, and aquaponics.
Hydroponics is the most popular method, accounting for around 70% of installed capacity, as it is the least expensive system to build, and the water substrate system is easiest to control.
Aeroponics is next, with a nutrient-rich mist substrate that feeds plants. It is generally a more expensive system to install, but water use is 40% lower than hydroponics and 95% lower than field farming. Leading installers include AeroFarms and Living Greens.
Aquaponics incorporates fish farming into the hydroponic substrate to take advantage of natural feeding and waste cycles to produce nutrients for the crops. Leaders in aquaponics include BIGH and Superior Fresh.
Indoor cultivation systems arranged by commercial development
Many of these companies have either adapted existing components or created their own. New specialized component suppliers such as Inno-3B are developing more complex automation systems, which they describe as having a high ‘unit of production per dollar of automation spent.’ The company also water cools the LEDs, providing a longer expected life.
Beyond technologies – exploring business models
Vertical farms can have many more harvests per year than traditional farming methods. For a leafy green, this can mean up to thirty harvests per year compared to five or six. This lends itself to a subscription-based model. Growing Underground, a vertical farmer based in an old air-raid shelter in south London has this arrangement with high-end restaurateurs as well as selling to retailers like Waitrose and Whole Foods. This can be extended to farming-as-a-service, as fast-growing cycles allow vertical farmers to plant crops at a client’s request, ensuring a buyer for produce before a seed is planted.
Existing food distributors are integrating vertical farmers in their supply chain, the partnership between Square Roots and Gordon Food Service is one example. The startup has agreed to build farming facilities in shipping containers located on or near Gordon Food Service distribution centers. For vertical farms, finding customers for high-value produce and having the logistics network to deliver has been a stumbling block – this partnership solves that problem. Similarly, Bonbio recently teamed up with IKEA to build container farms on IKEA sites to serve produce to the homeware chain’s restaurants.
Getting vertical farm produce to the consumer has also been taken to a logical conclusion – put the farm in front of the customer. Infarm has developed a system that can be installed in grocery stores, shopping malls, and restaurants, while Vertical Harvest has built the market and farm right where fresh produce was hard to come by. Click & Grow (an IKEA portfolio company) has put the hydroponic farm in the home with a smart home-growing kit.
Freight Farms has developed a turnkey hydroponics farm in a shipping container called the Greenery. Twenty have sold so far for $104,000, with price varying according to customization. The company estimates that ROI ranges from 2.5 to 3 years depending on the market. With the company’s hardware in place, it sells Farmhand, it’s farming services platform, offering farm management as well as sales of farm input. Freight Farms are keen to point out that the farmer is not tied to buying inputs from Freight Farms. It is also continuing to sell produce it grows itself in select locations. This model aims to reduce the need for large project financing rounds to build out capacity, creating a hardware + software model for expansion.
Grönska Stadsodling is the operator of one of Europe’s largest vertical farms and has developed the hardware it grows with from the ground-up. The company was born from the work of two engineering-minded founders. Their growing system includes a proprietary LED system which, Grönska claims, out-performs the off-the-shelf options available. The company aims to be cost-competitive with greenhouses, and eventually conventional growers. To get there Grönska believes the cost of automation will be a factor as vertical automation is easier than over the large footprint of a greenhouse. Combined with balancing energy costs, price of land, production scale, and matching product to market demand, there is plenty to balance in defining a vertical farm business model.
In trying to create an effective business model, Grönska Stadsodling has learned a lot about competing with the established brands. The first challenge is to reach cost parity with traditional methods of farming. The next challenge is particular to food; it is difficult to draw customers’ attention from a familiar and trusted branded, even when their product sits side-by-side on the supermarket shelf. The decades of marketing and trust, and associated cost, of establishing that customer base requires large marketing and branding budgets. While this is not insurmountable, another route may be to white label produce and sell to wholesalers to prevent these costs.
Who’s investing?
Investors in vertical farms are not what you would expect. There are the agriculture and food-focused investors, such as Wheatsheaf Investments (AeroFarms) or Finistere Ventures (Plenty, BioLumic), but the majority are generalists, and there is a noticeable lack of food and agricultural industry incumbents. No large agricultural OEM such as a John Deere, CNH, AGCO, or others, have placed a bet in vertical farming. However, IKEA, a food, logistics, and homewares company, has invested in Click & Grow and AeroFarms’ latest round, giving an insight into where food will be grown and who will be growing it in the future. We expect to see more agricultural corporate direct interest into these companies in the coming year.
Keep an eye on
In order to answer the question of long-term viability, we will need to keep up with the market’s response to the following questions:
Will vertical farms stay focused on niche produce and markets?
Do they compete against rooftop farms that have lower energy costs and provide a wider range of produce?
Will they compete against greenhouse farms that benefit from cheaper real estate, but must ship produce long distances to the urban markets and have higher costs of automation?
For In-Store Farms To Succeed, Finding The Right Balance Is Key
High-tech growing operations promise to efficiently supply retailers with greens. But the bigger payoff may be in offering shoppers a bit of food theatre
High-tech growing operations promise to efficiently supply retailers with greens. But the bigger payoff may be in offering shoppers a bit of food theater.
Credit: Jeff Wells
AUTHOR: Lauren Stine
Feb. 6, 2020
To appeal to consumers' growing desire for transparency and to know where their food came from, retailers across the country have brought local products into their aisles. They've also created informational web pages, integrated with nutrition apps and encouraged suppliers to tell their story to customers.
With 95% of consumers saying they'll pay more for locally grown products and 21% saying they eat local at least twice a week, though, companies are feeling the pressure to up the ante. Some, like Kroger and Whole Foods, have taken that step by bringing high-tech produce farms into their aisles — a budding movement that's made possible by advancements in growing technology.
Discover how to improve engagement among hourly employees by providing predictability and flexibility.
“Across the indoor farming industry, there have been dramatic decreases in cost when it comes to the physical hardware, advanced LED lighting and technology platforms automating a lot of the growth cycle,” Alexander Olsen, founder of automated mini-farm purveyor Babylon Micro-Farms, told Grocery Dive.
As more and more retailers discuss shifting center store operations online and accentuating the store perimeter, miniature produce farms promise to offer a supply line as well as a touch of food theater.
“We are also seeing a lot of traditional goods that grocers stock being purchased online and it’s freeing up a lot of space in-store,” Olsen said.
Retailers have been bringing cultivation to their stores for several years now. As early as 2012, Rouses sought to dazzle shoppers with an aeroponic garden on the rooftop of one of its New Orleans store locations. Hy-Vee and H-E-B's Central Market stores have also experimented with growing operations, with the latter adding a 53-foot modified shipping container full of greens to one of its Dallas stores.
Whole Foods has established a few different store growing operations. In 2018, it added an in-store mushroom growing display inside its Bridgewater, New Jersey store. The system was provided by Smallhold, a Brooklyn-based indoor farming company that also sells its mushrooms to local restaurants. A few years earlier, the chain partnered with urban greenhouse operator Gotham Greens to open a growing facility on top of a Brooklyn store location.
Credit: Kroger
The trend has gained momentum in Europe and Japan. Founded in 2013, Berlin-based InFarm has placed its in-store farms, which grow leafy greens, herbs, and vegetables, in hundreds of European stores, while Amazon Fresh sells its produce in Germany, France, and Switzerland. Last year, the company raised $100 million in Series B funding.
InFarm recently made its U.S. debut with two Kroger-owned QFC stores in Seattle and will bring its sprigs of kale, mint, cilantro, and dill to 13 more banner locations this year. The greens are initially planted at a nearby distribution center before being transferred to the store, where each plant's growth is monitored remotely by the company. The price points for the greens are competitive at $2.99 per bunch.
Grocery Dive reached out to Kroger and Whole Foods for comment but did not hear back by press time.
InFarm has lofty ambitions for its in-store farms, hoping to significantly impact grocery and restaurant supply chains, according to co-founder and CMO Osnat Michaeli.
“By growing produce on-demand and as close to possible to where it’s consumed, retailers are able to reduce food waste and sunk costs typically linked to industrial farming,” Michaeli wrote in an email to Grocery Dive. “We find that when retailers are able to understand the value, quality and flexibility of our business model they are more than enthusiastic to enter into conversations to explore our farms.”
Retail attraction or real action?
Although in-store farm displays and gardens are attractive additions, farming is no small feat even at a micro-scale.
“I think this trend is going to be closer to food theater and closer to a niche that engages the public and excites them about fresh produce,” Neil Mattson, associate professor at Cornell’s School of Integrative Plant Science, told Grocery Dive. Through his research, Mattson specializes in controlled environment agriculture systems such as hydroponics.
Operating an in-store farm is not for the novice beginner, he adds, noting that a retailer or its farming partner will have to allocate employees to monitoring the in-store farm to ensure it’s working properly. This requires intensive training, adds labor hours and could take the employee away from other tasks that still need doing.
If an in-store farm is not operating properly, the plants could fall victim to unsightly mold, disease and other issues that would make the display unappetizing to shoppers. Should a situation like this arise, the plants must be stripped out immediately and all surfaces must be sanitized, leaving an empty display, said Mattson.
Even for high-tech farming systems that are remotely monitored, Mattson has concerns about long-term success.
"Plants are biological systems so sometimes they don’t grow as fast as you think they should or some other factor becomes limiting and you have to adjust," he explained.
Credit: Pixabay
Mattson also questions whether an in-store farm could supply enough produce to be more than just an interesting display for consumers. Produce sales in the U.S. totaled $60.8 billion during 2018, representing a 1.7% increase over the prior year. The input costs for indoor farming systems, namely water, and around-the-clock electricity to power LED lights, are also substantial barriers even for large-scale indoor growing operations.
“It’s hard to foresee this producing the quantities of produce at the price points needed to become the widespread way that most Americans would buy their lettuce," Mattson said. "I think it is an expensive way to grow produce in a supermarket.”
High-tech farming operations have struggled to overcome high costs in the past, but the new crop of companies like InFarm and Babylon claim their systems are much more cost-effective and scalable.
To the extent that a retailer could overcome these challenges, benefits to having an in-store farm would include cutting out distributors and other middlemen, who often hike up the price of produce, and increasing store traffic, Mattson said. He believes the success of in-store farms may depend on balancing production needs and efficiency with the desire to amuse consumers.
Mattson said a larger-scale operation like Whole Foods' rooftop farm in Brooklyn offers the benefits of a customer draw with a more viable supply line. In recent years, retailers have also turned to large greenhouse and vertical farming operations to supply stores. Gotham Greens operates greenhouses in five states while BrightFarms operates greenhouses in four states and supplies to retailers like Giant Food, Acme and Food Lion.
Finding the middle ground
For Brooklyn-based grower and Whole Foods partner Smallhold, providing mushrooms first and in-store farms second has been a recipe for success. The duo behind the operation started out in a shipping container offering locally grown mushrooms to restaurants. They began asking their buyers whether they could fit a mini mushroom farm on-site and were encouraged enough to start modeling a prototype.
Whole Foods Local Forager Elly Truesdell ate lunch at a Vietnamese restaurant where one of Smallhold’s mushroom farms is located and promptly contacted the company to see about locating one at a Whole Foods store, according to co-founder Adam DeMartino.
“We didn’t intend to start a produce brand, it just sort of happened and a lot of that was because of Whole Foods,” DeMartino told Grocery Dive.
Today, Smallhold maintains mini mushroom farms in restaurants and retail locations, including two Whole Foods stores. It also sells mushrooms under a branded label.
Smallhold visits retail locations where its mini-farms are located once a week to swap out materials and harvest mushrooms. To achieve the volume that a retailer like Whole Foods demands, the company breaks up the growth process, completing the final stages, or fruiting, in-store. Mushrooms have an advantage over other crops grown indoors because of the high weight per square foot that mushrooms usually yield, according to DeMartino.
“Is it right for everyone? I’m not sure. That’s why it’s not the only thing we do,” co-founder Andrew Carter added. “How we look at it is we are offering a bunch of different tools to accomplish the task of getting mushrooms into the hands of everyone in the U.S. and hopefully the world. One of these tools is increasing the visibility of farming by growing on-site.”
The Shipping Container Farm That's The Way of The Future
Recycled shipping containers have been used for many things in their second life, from swimming pools and restaurants to classrooms and emergency hospitals. Now, with a global population hurtling towards almost 10 billion people by 2050, they may also be the farms of the future
CALLAN BOYS
Jan 26, 2020
Sprout Stack CEO Hugh McGilligan inside a shipping container farm. Photo: James Brickwood
Recycled shipping containers have been used for many things in their second life, from swimming pools and restaurants to classrooms and emergency hospitals. Now, with a global population hurtling towards almost 10 billion people by 2050, they may also be the farms of the future.
Founded by Francisco Caffarena and Michael Harder in 2016, Sprout Stack is Australia's only commercial vertical farm. The Brookvale-based start-up utilizes shipping containers to grow greens for independent grocers using methods more productive than traditional farming, says chief executive Hugh McGilligan.
"Vertical farming is also called controlled environment agriculture," he says. "Lighting in the containers is designed to optimize plant growth in vertical stacks, and we have sensors constantly measuring temperature, humidity and carbon dioxide levels which can be adjusted as needed. Because there's no birds, pests or fungus, we don't need to use herbicides or pesticides either."
Salad greens under light optimised to encourage plant growth. Photo: James Brickwood
Instead of soil, Sprout Stack uses the husk byproduct of commercial coconut production to hydroponically grow salad greens such as lettuce, kale, mizuna, and pea tendrils. One shipping container can produce 2500 head of lettuce a week, which is a rate of about 30 percent faster than traditional agriculture.
"Carbon footprint wise, we use 95 percent less water than traditional farming, too," says McGilligan. "By only selling to local businesses, our food miles are also reduced. We're not carbon neutral yet, but we will be at scale."
Sprout Stack supplies Harris Farm Markets and independent grocers including Manly Food Co-Op and Harbord Growers. With an aim to double output by the end of summer, the company moved to a larger warehouse in October and increased its container count from three to five.
Sprout Stack's shipping container farms can produce 2500 head of lettuce a week. Photo: James Brickwood
McGilligan says Sprout Stack is now on track to ship its first container farm to Melbourne in 2021.
"We've spent the past 18 months honing our production techniques so we can clone the business and shift it to other cities around Australia," he says. "We will always be about local food for local communities."
To assist in its expansion, Sprout Stack has partnered with the University of New South Wales. Both are members of the Future Food Systems Co-operative Research Centre, a partially government-funded body that aims to optimize the productivity of food systems.
"The university is helping us look at ways we can introduce robotics and boost production by four to five times over the next year or so," says McGilligan.
Professor Sami Kara of the UNSW school of mechanical and manufacturing engineering says he was excited to work with Sprout Stack after seeing similar farms in Singapore and recognizing their potential to feed a growing population.
"By 2050, 70 percent of the world's population will be living in an urban area," he says. "We will also need to produce 70 percent more food to feed that population.
Coconut husk used to grow Sprout Stack's lettuce. Photo: James Brickwood
"We can keep producing food in large quantities, far away from the majority of people, and shipping it with a massive transportation footprint. Or, we can grow food in the cities where the yield is high, the environmental footprint is low, and customers receive food that's fresher, more nutritious and delicious."
Kara stresses that vertical farming is not trying to compete with traditional farming, but offers an additional solution to the population problem. "In order to provide the world's food requirements by 2050, we're going to need many different types of production models," he says.
McGilligan supports this view and recognizes the importance of Australia's agricultural economy.
"We're not short on arable land in this country, so I understand this kind of venture may look a little bit threatening and odd compared to traditional farming," he says. "However, I firmly believe many more people will be eating vertically grown food in the future."
Can Vertical Farming Ever Become Mainstream?
The nascent vertical-farming industry is growing and gaining prominence among investors and governments that recognize the potential in a world where land availability for producing fresh food is fast diminishing, especially in countries with increasing urban populations
By Simon Harvey | 28 January 2020
Infarm's systems deployed in M&S
Amid the growing concerns about climate change and feeding the world's increasing population, especially in urban conurbations in developing countries, Simon Harvey investigates whether vertical farming – growing fresh produce in a controlled environment – can become well-established in the market.
The nascent vertical-farming industry is growing and gaining prominence among investors and governments that recognize the potential in a world where land availability for producing fresh food is fast diminishing, especially in countries with increasing urban populations.
Singapore is a prime example of an economy with a limited landmass for agricultural farming, leaving the city-state reliant on imports to feed its expanding population and turning to new technologies such as vertical farming and cell-grown meat. And with much of Singapore dominated by skyscrapers, it is cultivating fresh food on window ledges and rooftops of commercial and residential buildings in self-contained growing units.
But vertical farming as its name implies may be a bit misleading, which is why it also carries the designation of urban or indoor farming, or, what the chief executive of UK government-backed CHAP (Crop Health and Protection) prefers to call controlled-environment farming. As well as growing produce in stacked shelf-style units, it also takes the form of using redundant shipping containers known as 'cooltainers' and abandoned subway tunnels, employing the most-widely used hydroponics and aeroponics technologies – at least currently – without the need for soil and fields.
And it's not just space that's one of the primary factors driving the interest but also the advantage of being able to produce fresh produce like leafy greens year-round, so avoiding extreme weather events – an important element given the increasing concerns over global warming and the environmental impact of intense farming. And urban-farming methods don't use pesticides either.
Vertical farming is also applauded for using 90% less water – estimates do vary but are at least that level – than conventional techniques because it can be recycled and recirculated. The technology has also been touted as a potential means of cutting retailers' food waste, and, because the growing systems can be located nearer to the consumer, is claimed to potentially reduce the carbon footprint. It also opens the door to cultivating a broader range of crop varieties, many of which have died out due to commercial or viability reasons.
More importantly, perhaps, from a commercial perspective, the technology provides greater yields because the growers can control the nutrient inputs, which, it is claimed, in turn, provides fresher and better quality produce, as well as improved nutrition for the consumer.
Evolving from niche markets
However, a major drawback for many vertical-farming operators revolves around energy use and cost because most of the systems employ LED lighting, although tech firms are investing in NPD and more efficient devices. There's also the aspect of raising the capital to fund the required technology and research and development, and to make it commercially viable and profitable.
Vertical farming is also currently limited to fresh leafy vegetables, soft fruits and herbs, although, that said, it's not regarded by those in the industry as a method destined to replace arable farming. And new food choices such as tomatoes are slowly emerging.
The intensifying interest in the cannabis market – for medicinal, and in some cases, recreational use – might just arguably be the pick-me up to inject more momentum into the vertical-farming sector, an area still difficult to quantify in terms of size because of the split between the companies cultivating the produce and those supplying the technologies, according to CHAP. But can urban farming become mainstream?
"I think it definitely will. I think it will go into niche markets to start with like the micro greens, leafy greens and then the higher-value foods, so there's definitely a market now for high-value nutrition foods coming through," Fraser Black, the CEO of CHAP, tells just-food.
CHAP, which is part of the UK's Agri-Tech strategy, and Innovate UK, a government-backed innovation agency, have teamed up to open a center called The Innovation Hub for Controlled Environment Agriculture (IHCEA), based in Dundee, Scotland.
Black continues: "The consumer view of what they eat and how they eat it is definitely helping fuel this whole area. It's not going to be mainstream arable, it's not going to be cereals, but, as we drive down the price and improve varieties, it will become more mainstream. I think it's going to be a companion rather than a competitor to existing farming.
"A lot of the technology, we suspect, will start to be driven not by salads and leafy greens but by the cannabis boom that's happening in the States and in other places. A lot of the technology that will be used in that will transfer over into the consumable-food market as well. And clearly then driving down the cost.
"You have a combination of entrepreneurs, growers, investors, technologists, biologists, and physicists all working together to see how do we work this effectively and scale-up."
Venture-capital backing
Research from US-based MarketsandMarkets.com suggests the global vertical-farming sector could reach almost US$6bn in value over the next two years, from around $1.5bn in 2016.
There are a myriad of firms already involved around the globe, including in the US, Europe and Asia.
Infarm, based in Berlin, has drawn venture capital for its vertical-farming technology targeted at retail and foodservice channels. UK retailer Marks and Spencer recently installed systems from Infarm for fresh herbs – basil, mint, parsley, and coriander – in seven stores across London, joining other European retailers such as Edeka and Intermache using the company's technology.
Announcing the development last September, M&S said: "Each in-store farm unit uses 95% less water and 75% less fertilizer than traditional soil-based agriculture and is capable of producing the equivalent of 400 square meters of farmland, resulting in a more sustainable use of natural resources and ensuring zero-pesticide use."
M&S declined to comment for this article but Paul Willgoss, director of food technology, said in September: "We operate as part of a complex global food-supply chain and want to understand the emerging technologies that could help provide more sustainable solutions, whilst also delivering fantastic products with exceptional taste, quality and freshness for our customers."
Infarm is seeking to expand its own services across the whole food chain as innovation in the sector accelerates.
"We are sensitive to the fact that the Infarm approach to vertical farming is only one way to tackle the urgent agricultural and ecological challenges of our time," says Osnat Michaeli, co-founder and head of marketing. "Solving these challenges will require innovation and collaboration across the entire industry to generate a lasting impact.
"Over the next several years we are building a farming-as-a-service model that will be capable of delivering the technology, processes and expertise to enable an entire ecosystem of partners – from distribution centres to food manufacturers, from schools to hospitals and beyond – to participate in making cities truly self-sufficient in their food production."
Agricool in Paris has also secured funding from investors, including Danone Manifesto Ventures, the investment arm of the French dairy giant. The company started out growing strawberries in an apartment building in the capital before switching to cooltainers, and is now also present in Dubai, another major food importer.
Guillaume Fourdinier, the founder and CEO of Agricool, agrees with others in the vertical-farming sector that it will take five years before the market becomes more mainstream. However, as an example of the growth potential, he tells just-food Agricool's systems are currently in five supermarkets in Paris, which will increase to 25 in the next three months.
Nevertheless, Fourdinier emphasises the financial cost of getting an urban-farming business going and the efforts that go into R&D, an area in which 50 of the company's 85 staff are engaged. Fourdinier says Agricool has raised EUR30m (US$33.2m) in funding and "we are only just starting".
"It's a lot of effort and money and investment to make it profitable," he says. "We are basically inventing a new industry. This is something that will change the next 100 years of agriculture but it will take time for sure."
"We think we will be able to show that it's really profitable to grow indoors"
In the UK, Saturn Bioponics, located in the city of Birmingham and setting up farms in the local greenbelt area, uses hydroponic technology to grow fruit and leafy salad vegetables such as pak choi, lettuce and strawberries, and also herbs. The company uses natural light, growing produce in greenhouses. It has been backed by Innovate UK through project financing and grants, and is also assisting Shockingly Fresh in Scotland.
Saturn chief executive Alex Fisher says the company is engaged in projects not only in the UK, but also in France, Romania and Japan. He argues main stumbling block in getting vertical farming off the ground is finance because of the cost of technology and R&D, before a venture can get to the commercialisation stage and start delivering profits.
"We do see it going mainstream," Fisher tells just-food. "It's all about money in the end. It's been very much about de-risking it technically, proving it financially and then getting people to adopt it on a large scale. And that's been our journey over nearly ten years. Probably, you will see the market exploding on our end in about five years."
Like Black at CHAP, Fisher says urban farming was never intended to compete with the well-established agrarian sector, which is much larger by comparison Agricool's Fourdinier points out the technology isn't suitable for crops such as cereals and potatoes, which tend to have a longer shelf-life, particularly as the sector is geared toward providing the freshest produce in closer proximity to the consumer.
Fisher adds when asked to quantify the size of the market: "You are talking many tens of billions or even hundreds of billions of dollars per annum in farm-gate crop values. Your lettuce, strawberries, herbs – it's huge – obviously that's a drop in the ocean for agriculture overall but it's still very significant values. As we move into other areas that number will expand."
Major breakthrough in five years
Saturn is also exploring aromatic products, botanical-type products, brassica and other soft fruits.
Black says the main driver behind vertical farming is commercial, although Agricool's Fourdinier tags on the environmental aspect, too. Both believe China and India will embrace the technology to feed their growing populations, especially with vast numbers relocating to the big cities from rural areas. And, with the mistrust among Chinese consumers over the food they eat, greens and herbs grown in indoor and controlled environments might be one solution to quell concerns over pollution, adds Fourdinier.
"I think in the next five years you are going to see some major breakthroughs. You've already got big companies investing in this. You've also got an investment community eager to get involved," says Black. "There's huge interest in making this work and being able to have this combination of what is fresh produce 365 days a year. It has to be in a fashion that is cost-effective and provides value to the consumer, and we are definitely heading in that direction.
"You are going to see the US grow, partly because of the growth in cannabis and the use of medicinal and recreational cannabis. I think you will see the rest of the world follow quickly behind it because of the convenience factor."
Looking at the UK's vertical-farming market, Saturn's Fisher says it's a hard nut to crack when farmers generally in the country are struggling. If they are to venture into the sector, the Government needs to improve access by offering grants or other incentives because farmers are already highly leveraged with debt to take on the extra capital.
"If what you are looking for is for the farmer to progress you need to take the risk out of the adoption of new technologies. That's a huge thing," he says. "Access to finance in general is very difficult for farmers. So it's very hard for them to borrow money for new tech and stuff like that."
Shockingly Fresh is developing five vertical-farming sites, one in Scotland and four in England, using technology from Saturn. Fisher is also part of the company's team.
Garth Bryans, the director at Shockingly Fresh, says the sector needs to compete on price per kilogram with traditional farming to bring in the investment for the industry to expand and suggests the UK government should offer some form of tax incentives for large-scale systems to attract capital.
He says there are benefits, too, in terms of imports with Brexit on the horizon.
"We should note that with Brexit approaching, vertical farming significantly increases the UK season and will reduce reliance on imported leafy veg from mainland Europe in the early spring and late summer 'shoulder months'," he tells just-food. "If tariffs come in, this could make vertical farms even more compelling.
"The UK alone imports over GBP1bn ($1.3bn) of green leafy veg per year, providing a very significant market for systems that can compete with traditional crops on price whilst providing a much better quality crop closer to the point of supply."
More broadly, Fourdinier highlights the benefits to the consumer in terms of the nutritional content of foods grown in a controlled environment in close proximity, and says they need educating to fully understand the advantages.
He adds, for example, that 50% of the vitamins in fruit are lost after five days storage, arguing vertical farming is all about being "fresher, the nutritional value and taste, and also consumers know where their food is coming from".
While the market is limited in terms of product selection, Fourdinier says it's natural to start off with the "easy ones" as other vegetables tend to be more complex and the nascent industry would need to develop the appropriate technologies. However, he sees tomatoes, peppers and courgettes coming through.
"We have to invent a lot of new technologies to make it profitable and you have to be productive to become mass market," Fourdinier explains. "It's the same as electric cars. We think we will be able to show that it's really profitable to grow indoors and that you get more sustainable food by doing so in large cities."
Freight Farms and Sodexo Announce Strategic National Partnership to Grow Food Onsite at School Campuses Across the U.S.
With sustainability and transparency in mind, partnership will enable year-round on-campus food production at university and K-12 educational institutions and other national Sodexo clients
With sustainability and transparency in mind, partnership will enable year-round on-campus food production at university and K-12 educational institutions and other national Sodexo clients
BOSTON, Jan. 29, 2020 / PRNewswire
Freight Farms, the global innovation leader of containerized vertical farming, and Sodexo, the world leader of integrated food, facilities management and organizational quality of life services, have partnered to bring the most advanced hydroponic vertical farming technology to schools and universities across the country. The collaboration will usher in the implementation of Freight Farms' Greenery container farms to campuses across the U.S., enabling the onsite growth of fresh, traceable produce year-round that's pesticide and herbicide-free and sourced with zero food miles.
With Freight Farms’ Greenery onsite, educational and corporate campuses will be able to grow more than 500 varieties of crops, like Salanova Green Butter Lettuce, at commercial scale year-round.
As awareness of key issues in food safety, health and wellness, and environmental sustainability continue to rise with increased urgency, this strategic partnership reflects Freight Farms' and Sodexo's shared vision to enable real, measurable change in food sourcing for educational and corporate institutions.
"Students, institutions, and corporate businesses want healthy, safe, and delicious food, and they want it sourced as sustainably as possible. Sodexo is proud to use and support the latest agricultural technology to create meaningful food system change, said Kenny Lipsman, Director of Produce Category for Sodexo. "Our partnership with Freight Farms allows us to grow nutritious, superior-quality food on-site for our clients, just steps from the kitchens and serveries. As part of Sodexo's Better Tomorrow Commitments, developed in accordance with the United Nations' Sustainable Development Goals, this technology allows for traceability, reductions in food waste, and year-round crop consistency."
Co-founder and CEO of Freight Farms Brad McNamara, continued, "Sodexo's commitment to offer onsite food production to its customers helps accelerate food system decentralization — leading the charge for better sourcing practices at an institutional level. Sodexo's adoption of Freight Farms on-site programming will demonstrate to their customers and client communities the positive impact hyper-local food production can have on priorities from nutrition and food safety to emissions reduction."
With the largest network of connected farms in the world, Freight Farms' customers are located in 25 countries and 44 U.S. states, and range from small business farmers to corporate, hospitality, retail, education, and nonprofit sectors. To date, 35 educational and corporate campuses use Freight Farms' technology, and together with Sodexo, implementation will rapidly expand across the U.S.
By integrating Freight Farms' 320 square foot Greenery onto campus, Sodexo's customers will reap numerous benefits, including:
Food miles and waste reduction
Food is harvested steps from the plate, eliminating food miles
Harvested onsite, food lasts significantly longer, reducing spoilage waste
The Greenery uses 99.8% less water than traditional agriculture, and in some humid areas, operations can be water-positive
Peak freshness and nutrition, year-round
Unlike food that has to travel great distances between harvest and plate, freshness and nutrient density does not degrade during transit
Crops are never exposed to pesticides or herbicides
The farms grow at commercial scale and maintain the perfect environmental conditions every day of the year
Safety, transparency, and data-driven traceability
The hydroponic container farms are soil-free, a common carrier of E. coli, as well as decentralized from the mass supply chain
Campus communities can get to know their own farmers and witness every growing stage of their food
Proprietary IoT technology, farmhand, tracks produce from seed to plate, even down to the hour
Student and employee engagement
Schools can choose to integrate their farms into interactive curricula across disciplines like science and technology, agriculture, nutrition, business, and social impact
Corporate businesses can integrate their onsite farms into employee wellness and benefit programs
About Freight Farms
In 2012, Freight Farms debuted the first vertical hydroponic farm built inside an intermodal shipping container—the Leafy Green Machine—with the mission of democratizing and decentralizing the local production of fresh, healthy food. Now with the Greenery and integral IoT data platform, farmhand®, Freight Farms has the largest network of connected farms in the world, with global customers in 25 countries and 44 U.S. states ranging from small business farmers to corporate, hospitality, retail, education, and nonprofit sectors. To learn more, please visit freightfarms.com, or visit us on Instagram, Twitter, or Facebook.
About Sodexo North America
Sodexo North America is part of a global, Fortune 500 company with a presence in 72 countries. Sodexo is a leading provider of integrated food, facilities management and other services that enhance organizational performance, contribute to local communities and improve quality of life for millions of customers in corporate, education, healthcare, senior living, sports and leisure, government and other environments daily.
The company employs 160,000 people at 13,000 sites in all 50 U.S. states and Canada and indirectly supports tens of thousands of additional jobs through its annual purchases of $19 billion in goods and services from small to large businesses. Sodexo is committed to supporting diversity and inclusion and safety while upholding the highest standards of corporate responsibility and ethical business conduct. In support of local communities across the U.S., in 2018, Sodexo contributed over 159,500 in volunteer hours, and since 1996, the Stop Hunger Foundation has contributed nearly $34.5 million to help feed children in America impacted by hunger.
Founded in 2010, Boston-based Freight Farms has established itself as the leader in the containerized agriculture industry. With its flagship product, The Leafy Green Machine™, the company was the first to integrate smart, hydroponic, vertical farming into an intermodal freight container.
To date, Freight Farms’ global customer base includes individual clients and corporations, universities, non-profits, municipalities, and restaurants.
(PRNewsfoto/Freight Farms)
View original content to download multimedia:
SOURCE Freight Farms
AgroTech Shipping Container Farming Systems For Indoor Organic Farming
Grow Pod Solutions is an AgroTech shipping container farming systems for indoor organic farming. Their desire is to provide sustainable, reliable, and result-oriented modular farming to feed the next generations
February 3, 2020
With this modern farming technology innovation, anyone can farm leafy greens, herbs, and spices for personal consumption and sales. The modular farming also guarantees high yield and no bacteria or disease, in a controlled environment.
As the population of the world grows, food security remains one of the biggest challenges to human survival and proper nutrition. Traditional farming methods alone can’t deliver all the food needed, as it is prone to negative effects that can stunt growth.
Grow Pod Solutions is an AgroTech shipping container farming systems for indoor organic farming. Their desire is to provide sustainable, reliable, and result-oriented modular farming to feed the next generations.
Everything about the farm is automated including soil, water, temperature, humidity, etc. These modular farms are also not affected by disease and there are no pesticides, so the food is 100% of quality and nutrient.
Now, anyone can grow their food for personal consumption or sell the produce for profit.
To learn more, please visit here.
Grow Pods are designed to offer farmers an unmatched yield in a highly controlled farming environment. For each pod, farmers will be able to grow a considerable amount of vegetables like 2,000 heads of lettuce which equates to about 70,000 dollars of yearly revenue.
Leafy greens are in high demand these days because they are rich in nutrients and people are becoming more conscious about living healthy. However, growing them in the open is a pain. They are exposed to too much or not enough water, pathogens, bacteria and diseases, pests, human and animal contamination, and unfavorable weather.
However, with the Grow Pods, farmers don’t have to worry about any such issues. The pods are focused mainly on leafy greens and every 55 days the users can harvest and use or sell. The pods can grow quite a number of leafy green varieties like carrots, lettuce, cabbage, even spice, and herbs.
Grow Pod Solutions is working with universities, farmers, and distributors, local farmers, and outdoor markets, and essentially anyone that sells directly to consumers and interested in getting into farming.
With the help of soil scientists, Grow Pod Solutions has been able to develop its own soil that is pathogen-free and clean. So, they are able to provide both Hydroponic Based farming and soil-based and custom based farming that guarantee quality and high yield.
Existing farming and new entrepreneurs are welcomed to join Grow Pod’s community of growers. They are exposed to try new lines of soil and nutrients, so they can become successful in the indoor environment farming.
Grow Pod Solutions was created out of the desire to deliver quality leafy greens that are free of pesticides and contamination. With their superior and automated technology, they will be able to provide farmers with greater farm yield that promises high profitability.
For more information, please visit https://www.growpodsolutions.com/.
RELATED ITEMS: AGRICULTURE, AGROTECH, CABBAGE, CARROTS, CONTAINER, FARMING, FOOD, GROW POD SOLUTIONS, HERBS, INDOOR, LETTUCE, ORGANIC, SHIPPING, SPICE, SYSTEMS, TECHNOLOGY
IKEA Wants All Restaurants To Be Self-Sufficient in Herbs and Lettuce
Many IKEA customers like to grow their own fruit and vegetables. "What if we could do the same?" they wondered at the Swedish retail chain
Many IKEA customers like to grow their own fruit and vegetables. "What if we could do the same?" they wondered at the Swedish retail chain.
The company is testing smallscale urban farms, exploring whether they can become self-sufficient in some of the fresh produce used in IKEA restaurants.
Container farms
In FY18, they grew their own herbs and lettuces in small-scale urban farms in Sweden and Switzerland. In FY19, they extended the tests, installing medium-scale container farms with romaine and frisée lettuces outside the IKEA Malmö and IKEA Helsingborg stores in Sweden. The farms use hydroponic technology and operate in a circular way, with food waste from the store used to create a nutrient solution to feed the lettuces.
Promising results
Early results show the container farms produced enough to supply the in-store restaurants with all the lettuce they need. Since they’re grown onsite, the lettuce can be used almost straight away, meaning they’re fresher, tastier and contain more nutrients. They also grow faster, with less water and waste than conventional farming and without the use of pesticides and herbicides. A life-cycle assessment shows that when the urban farm is powered by renewable energy, the carbon footprint of the lettuce is 30% smaller than the ones we would usually use. IKEA is planning to extend urban farming so that they become self-sufficient in herbs and lettuce across all store restaurants.
Cost-cutting
The main challenge is that the produce IKEA uses is currently more expensive than a conventionally farmed alternative. They’ve already made progress on reducing these costs, and they’re continuing to find ways to improve efficiency. Ingka Investments has also invested in two urban farming businesses in the USA and Estonia to support development of the industry.
For more information, check out the Ingka Group Sustainability Report.
Publication date: Fri 31 Jan 2020
US: Minnesota - Shipping Container To Grow Year-Round Veggies At CLC
The project consists of an insulated shipping container outfitted with a complete hydroponic growing system able to provide numerous Minnesotans with fresh, leafy greens year-round. Partners include Todd-Wadena Electric Cooperative, Lakewood Health System, Great River Energy, the Electric Research Power Institute and CLC
By: Brainerd Dispatch | Jan 18th, 2020
A crane places a 'Sota Grown hydroponic growing system at its new home on the Central Lakes College Staples campus. The system will produce year-round leafy greens. Submitted photo
STAPLES — Central Lakes College’s Ag and Energy Center in Staples is the new home of ‘Sota Grown, a collaborative indoor agriculture container farm project.
The project consists of an insulated shipping container outfitted with a complete hydroponic growing system able to provide numerous Minnesotans with fresh, leafy greens year-round. Partners include Todd-Wadena Electric Cooperative, Lakewood Health System, Great River Energy, the Electric Research Power Institute and CLC.
Following the installation of the container farm, CLC students will receive hands-on training to plant, maintain and harvest the growing crops, the first of which will be kale, ready to be harvested 10 weeks from planting. The kale will then be delivered to Lakewood for its Food Farmacy program that feeds more than 600 people monthly.
Great River Energy, Todd-Wadena Electric Cooperative and Electric Research Power will collect data throughout the process for electricity load planning, technology evaluation, and beneficial rate design analysis.
“Efficiencies with indoor food production and hydroponics will be critical as we look to feeding a growing global population that will surpass 9 billion in a few decades,” Keith Olander, CLC dean of agriculture studies, said in a news release.
The ‘Sota Grown project is part of a national indoor crop production demonstration effort that looks at how using efficient electricity, technology, plant sciences, and control solutions to create microclimates can produce ideal conditions for plant growth, yield, quality, and consistency.
Growing produce locally for area communities will also reduce the distance to market — a significant factor for Todd and Wadena counties since they are impacted by food deserts — thereby reducing net greenhouse gas emissions. Leafy greens generally travel an average of 2,000 miles before reaching a store, according to the release.
A ribbon-cutting event where the public will be able to view and tour the container farm will be this spring.
Those interested in following the process from seedlings to the first harvest can do so on the ‘Sota Grown Facebook page.
The Planty Cube is A Vertical Farming System Assembled Like LEGO Bricks
Agriculture IoT startup n.thing has developed ‘planty cube,’ an automated vertical farming system that allows users to maintain crops at any time and from anywhere. the system connects like LEGO bricks with a modular design made up of multiple capsules called pickcells that contain the seeds of each plant
jan 14, 2020
Agriculture IoT startup n.thing has developed ‘planty cube,’ an automated vertical farming system that allows users to maintain crops at any time and from anywhere. the system connects like LEGO bricks with a modular design made up of multiple capsules called pickcells that contain the seeds of each plant.
images courtesy of n.thing
to demonstrate its potential, n.thing has developed a smart hydroponic farm that uses the planty cube design. shaped like a shipping container, it is made of stacked rows and shelves of planters on each wall with each pickcell roughly two inches in width, length, and depth. after seeds are sown through their smart seed capsules, a computerized system controls the environment by monitoring plant health and adjusting the LEDs, temperature, and humidity, accordingly. the planty cube system, which uses sensors to collect data on the plants, can also be controlled via a smartphone, presenting the unique opportunity to farm remotely.
the grow system can work in a number of different settings, from an apartment to a cafeteria, and is automated enough that plants can thrive without constant human attention. the ease of use also makes it simpler for clients who want to start vertical farming businesses, to increase the size of their farm at low-costs, over longer periods of time, and in line with their individual business growth.
a number of companies are developing vertical farming concepts including LG who launched its own indoor vertical farm at CES 2020. unlike glasshouse production, which relies on sunlight, vertical farming makes use of led lighting to provide different wavelengths of light, according to crop and growth stage need. these high-tech units are being presented as the solution to many of the challenges facing traditional production methods, such as pollution and water use.