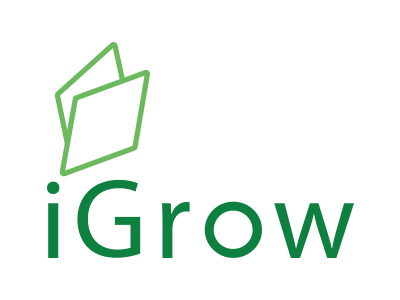
Welcome to iGrow News, Your Source for the World of Indoor Vertical Farming
VIDEO: Indoor Microfarming: Benefits, Costs, And Profits
Microfarms are versatile. They can be created in any small room like shipping containers, bedrooms, and garages
Indoor microfarming is a trendy alternative to outdoor farming.
Outdoor, or field, farming is declining as land costs and soil erosion make it increasingly harder to start a farm. In its place, small indoor farms are popping up to meet increasing demand for locally produced food.
Did you know small farms produce more than 70 percent of the world’s food?
Microfarms are versatile. They can be created in any small room like shipping containers, bedrooms, and garages.
In this article, you’ll learn all about indoor microfarms including its benefits, costs, and how to profit from one.
Basics of Indoor Microfarming
Indoor microfarming refers to small-scale farms in urban or suburban areas.
The ability to control environmental factors like lighting, humidity, and temperature is the biggest advantage that indoor farming has over outdoor farming.
Indoor alternatives to field farming, like greenhouses, have been around for thousands of years, but it wasn’t until the 1970s that controlled environment farms emerged.
Farmers use a variety of different systems to grow plants indoors. Aquaponics, hydroponics, and aeroponics are a few of the most popular systems after using traditional soil.
Aquaponics refers to using fish to grow plants. In these systems, fish fertilize water that’s fed to the plants. The plants in turn purify the water, which is fed back into the fish tanks.
Hydroponic systems grow crops by watering plants with a nutrient-rich solution. Instead of soil, plants are grown in a nutrition-less growing medium that allows plants to absorb the nutrients from the water easier than if they were grown in soil.
In aeroponic systems, plants are grown with their roots exposed in highly misted environments. The mist is created using a nutrient solution.
We use hydroponic systems to cultivate crops in our Pure Greens container farms, which are made out of shipping containers.
Indoor microfarms are often started using spare space like an unused basement, guest room, or garage in the farmer’s home. But they can also be started in any small, indoor area like a shipping container.
The ability to use a small space to grow produce is only one of indoor microfarming’s many benefits.
Benefits of Indoor Microfarming
Indoor microfarming is beneficial because it fills demand for certain produce while saving money and stress.
As far as selling goes, demand for locally produced food across the United States is increasing.
Nielsen, a data and measurement firm, found that 48% of consumers prefer ingredients and food that have been produced locally.
Indoor microfarming fills this demand by being produced in the center of commercial areas, guaranteeing locality.
Purchasing land or buildings big enough for large-scale operations is expensive. Indoor microfarming allows people to use the buildings they already live in to start growing.
Capital expenses are also lower because you don’t have to purchase new land. Plus, equipment isn’t as expensive for microfarms due to availability of ready-for-installation systems and “Do It Yourself” (DIY) tutorials.
With smaller capital expenses comes a lower stakes environment.
When you’ve put less money into a project, there’s less pressure to succeed. Feel free to experiment with systems and crop types to find what works best for your farm.
Indoor microfarming also allows you to develop a local customer base and specialize in a niche market.
Having already secured customers and perfected a crop will help when you’re ready to expand.
Indoor microfarming also allows restauranteurs to grow their own produce onsite, reducing food waste by being able to harvest only what’s needed rather than buying in bulk. Customers will also appreciate the fresher tasting food!
Another benefit of indoor microfarming systems is that there isn’t just one way to do it.
Microfarming Systems
Because microfarming can be done using virtually any size of space, there’s a wide variety of systems to pick from.
Our Pure Greens container farms are an excellent choice for those with yard space for a 40 foot shipping container.
Our farms come outfitted with a recirculating hydroponic system, providing a low water consumption rate, and an automated controlled environment system that can be monitored via your smartphone.
For farmers with less space to work with, there are a few smaller purchasable and DIY options out there as well.
Ready-to-use hydroponic systems can be purchased online or from a local hydroponic equipment store.
One popular DIY hydroponic system for beginners is the Kratky method.
The Kratky method is easy as it doesn’t require pumps or changing the nutrient solution. In this system, plants are placed in a netted pot with a growing medium, such as coconut coir or clay balls, and then placed into a reservoir filled with water and nutrient solution.
While this method is good for farmers with very little experience, it’s only effective for growing leafy greens. Anything with flowers or fruits will need a more involved process.
The Kratky method also requires close attention to the water’s pH levels because it’s not replaced or adjusted during the grow cycle.
Aeroponic systems are also buildable but require a little bit more expertise with construction. Plants grown in these systems receive maximum nutrients.
But aeroponic systems are less common than hydroponic systems when it comes to home-growing because they require special attention to nutrient ratios and pH levels, making them not very beginner-friendly.
Scott Dekarske of Wet-Werk Hydroponics in Memphis, TN, and Master Gardener, Stephan Leonard, show how to assemble an inexpensive aeroponics system.
Aquaponic systems are a good choice for people interested in fish farming. If you raise healthy enough fish, you can sell them along with your produce.
Keep in mind aquaponic systems require more maintenance than hydroponic or aeroponic systems and they’re a little trickier.
With these systems you have to keep both the fish and the plants happy. Doing so requires finding the delicate balance of water flow between the two.
Deciding on which system to use can be tricky, but your expenses will depend heavily on the system you decide to use.
Indoor Microfarming Costs
Capital and operating expenses of indoor microfarming varies depending on the type of system and size of the operation.
The first expense is going to be buying the system itself or any materials needed to construct it. You may need to purchase tubs, pumps, and pipes.
You’ll also need to purchase light fixtures, so your plants have a light source to use for photosynthesis. During photosynthesis, plants absorb energy from light to produce glucose out of carbon dioxide and water.
There are plenty of LED lights in the market aimed specifically toward growing plants. Look for bulbs with high efficiency to conserve energy usage.
Because indoor microfarming typically relies on artificial light rather than sunlight, energy costs can be high. A 2017 survey of indoor farms found that small farms spent about $3.45 per square foot on energy alone, which was about 12% of the total budget.
Take into consideration water usage as well. Systems like recirculating hydroponics and aeroponics use considerably less water than aquaponic and soil-based systems.
Hydroponic and aeroponic systems typically require 4 gallons of water per square foot per year. Meanwhile, aquaponic systems use about 10 gallons of water per square foot per year.
Be sure to also factor in any fish costs such as a tank, food, and the animals themselves when using aquaponic systems.
Once your indoor microfarm is ready to grow, you’ll need to buy planting materials.
Planting expenses will be recurring so be sure to keep them in mind while budgeting. Purchase seeds, growing mediums, and nutrient solution online or in stores.
Growing mediums and nutrient solutions replace soil in hydroponic and some aeroponic systems. The growing medium acts as support for the plants’ roots while the solution provides essential nutrients for strong, healthy plants.
While indoor microfarming can be costly, there are plenty of strategies for growing your business.
Profiting from your Microfarm
The first step to making a profit from indoor microfarming comes before you even plant a single crop: Research.
Find demand for a product in the local market that isn’t being met. Meet with potential customers like chefs, grocery stores, and farmers’ market patrons and ask what they’d like to be able to purchase fresh.
Focus on growing specialty crops rather than common produce like lettuce.
Specialty crops can be things that are out of season, hard to grow in your climate, or something trendy such as microgreens or adaptogens.
Consider selling your products at farmers’ markets, to vendors, to wholesale distributors, and to local restaurants.
The number of farmers’ markets in the country has tripled since 2000, making it an easy choice for finding customers.
Research popular farmers’ markets in your area and learn how to set up shop. Keep in mind that some markets will charge a fee to set-up a booth.
Alternatively, approach a different produce vendor and let them sample your product. If all goes well, they will sell your product for you!
Find a middleman by selling to wholesale distributors. Distributors will find shops to sell your products for you, giving you more time to focus on growing.
Or sell your produce directly to local restaurants.
Research chefs who focus on crafting dishes using locally sourced greens. Set up an appointment with chefs to pitch your business to them and be sure to bring along your best samples.
Try to establish a rapport with the restaurant. Find out whether they’d prefer a range of products or a specific good.
After you’ve established your clientele, your indoor microfarm will blossom.
Now that you’re familiar with indoor microfarming, it’s time to get started.
Visit our website or call us at 602–753–3469 to learn more about how you can start your own container farm.
WRITTEN BY
Pure Greens Arizona LLC
Tags: Vertical Farming Indoor Farming Farming Farming Technology
Pure Greens’ container-based grow systems offer a variety of interior layouts, sizes, and options so customers can create a farm that meets their needs.
Urban Crop Solutions Appoints Commercial Representative For Asian Market
Urban Crop Solutions and BAF signed a representation agreement for the East and South-East Asian markets
Urban Crop Solutions and BAF signed a representation agreement for the East and South-East Asian markets. The collaboration fits with Urban Crop Solutions' vision for global expansion and allows for local customer service in one of the fastest-growing countries in the Asia-Pacific region.
BAF is an Aggrotech company based in Singapore which has extensive experience and network in the Agri and aqua industry in Asia and beyond. The company has also built a strong network and business track record in the region and will provide as a perfect match to operate as an agent for Urban Crop Solutions in what is called the strategic gateway for Europe to the Southern parts of Asia.
NOSH visiting an Urban Crop Solutions ‘FarmPro’ container
Kenneth Tay, Chief Executive Officer at BAF, explains: “Based on my many years of experience in the aggrotech industry, I can see a great synergy between my business and the state-of-the-art solutions that Urban Crop Solutions provides. I believe that this technology will also play a critical role towards food security goals in the region.”
For a start, BAF has already procured its first customer, NOSH Produce, a high tech start-up in the indoor vertical farming industry who has put in a purchase order for an Urban Crop Solutions ‘FarmPro’ for their very first plant production site in Singapore. This will be Singapore’s first fully automated container farm that sets to grow local herbs for the high-end retail market and restaurants. The container farm will not only have a commercial purpose but will also serve as a demonstration facility for interested buyers.
NOSH & BAF and Urban Crop Solutions closing the deal
According to Brecht Stubbe, global sales director at Urban Crop Solutions: “With this opportunity to work with BAF and NOSH, we can demonstrate the economically viable model of our vertical farming solutions in the Asia-Pacific region”
The collaboration between Urban Crop Solutions, BAF & NOSH Produce came to fruition in the beginning of January 2020. The ‘FarmPro’ is set to be operational in May 2020.
For more information:
Urban Crop Solutions
Grote Heerweg 67, 8791 Beveren-Leie (Waregem), Belgium
800 Brickell Avenue 1100 Suite, Miami (FL 33131), USA
+32 56 96 03 06
info@urbancropsolutions.com
sales@urbancropsolutions.com
urbancropsolutions.com
Publication date: Thu 26 Mar 2020
Freight Farms Expands Leadership Team with New CEO and Head of Engineering
Tune in to our webinar on March 31st with Freight Farmer Dave Ridill! Hear how he is growing produce for his snowy mountain town, all year long. Register here.
March 24, 2020
Freight Farms positions for new innovation and deepened market reach; cofounder Brad McNamara remains President
March 24, 2020 -- Freight Farms is thrilled to announce that it has hired veteran consumer brand executive Rick Vanzura as CEO who will also join the company’s Board of Directors, while cofounder Brad McNamara will remain as Freight Farms’ President. The company also welcomes automation and robotics specialist Jake Felser as Head of Engineering.
The need to simplify supply chains and ensure reliable access to healthy, traceable food at a local level has become more crucial for communities worldwide. Expansion of Freight Farms’ team follows a year of strong momentum for the company as forward-thinking organizations, particularly at the institutional level, recognize the benefits of a secure, distributed, and transparent food supply. As the company scales for growing demand at speed, expansion of Freight Farms’ leadership is positioned to quicken new extensions of its technology platform and deepen market reach.
“Freight Farms’ innovation addresses issues like urban land scarcity, traceability and the need for hyper-local solutions with speed to market. The current environment demonstrates more than ever the value of Freight Farms’ offerings.”
— Rick Vanzura, CEO of Freight Farms
“What excites me about Freight Farms is the ability to join a passionate, mission-driven business that is already perfectly positioned to address the growing critical need for sustainable, hyper-local food production,” says Vanzura. “Freight Farms has an incredible technology platform as the originator of container farming, as well as a global footprint driving numerous sources of value. Beyond providing a meaningful solution across industries, Freight Farms’ innovation addresses issues like urban land scarcity, traceability and the need for hyper-local solutions with speed to market. The current environment demonstrates more than ever the value of Freight Farms’ offerings.”
Vanzura has driven value for companies from start-up to Fortune 5 across technology, restaurant, retail, and entertainment sectors. With a focus on leveraging innovation and developing new market channels, he led strategy for Panera, General Motors Information Services and GameStop, and as the original CEO of Wahlburgers, he built the company from a single unit into one of America's fastest-growing restaurant brands. Vanzura’s 20 years in President and C-level roles include a decade in food service working with markets central to Freight Farms’ business. He also brings significant international experience to his role, having run Borders Group’s nearly $1 billion international business.
“As co-founders, Jon Friedman and I have taken Freight Farms from an idea to help decentralize the food system to being the leader in containerized vertical farming that’s truly putting the power of hyper-local food production into people’s hands,” said McNamara. “Rick has amplified growth across interconnected industries, and his international experience lends itself to our ongoing global expansion. His personal alignment with Freight Farms’ mission was crucial for us as well—he’s a welcomed addition to the team as we scale.”
“Rick has amplified growth across interconnected industries, and his international experience lends itself to our ongoing global expansion.”
— Brad McNamara, President of Freight Farms
“The potential is extraordinary,” Vanzura added, “I’m excited to be working with Brad, Jon and the team on the spectacular opportunities ahead, all while doing our part to help build a better, more sustainable food system for all.”
Jake Felser, former VP of Engineering for eatsa (now Brightloom), has also joined the Freight Farms team as Head of Engineering. With teams across hardware and software, Felser led robotics R&D and the development of eatsa’s shelf-style pickup system from conception to deployment across the company’s network of partners. Prior to eatsa, Felser was Senior Engineer and Product Manager at Cooper Perkins and has worked in hydraulics, refrigeration, structural optimization, design for development, and agriculture for companies including Blue Origin, Promethean Power Systems, and AGCO. With a passion for sustainable development, Felser is focused on automation, IoT, and machine learning-based integrations for Freight Farms growing technology portfolio.
Company growth, including ten new roles across all departments in Q1, also follows Freight Farms’ recent launch of the Greenery. Nearly 100 have been adopted by customers in 9 countries to date, bringing Freight Farms’ global footprint to more than 300 container farms around the world. The innovation also spurred interest from Sodexo in a strategic national partnership to grow food onsite at educational and corporate campuses nationwide and new investment from Ospraie Ag Science.
How Greenhouse Yields Compare To Container Farms
As the agriculture industry searches for more sustainable alternatives to field farming, greenhouses remain the most popular solution, making up 47% of the indoor farming industry in the United States
March 10, 2020
As the agriculture industry searches for more sustainable alternatives to field farming, greenhouses remain the most popular solution, making up 47% of the indoor farming industry in the United States.
Greenhouse popularity is also on the rise worldwide.
A 2019 statistical survey found that more than 1.2 million acres worth of vegetable-growing greenhouses were in use globally, an increase of 223% since 1980.
But they aren’t the only indoor farming option out there.
In this article, you’ll learn about how typical greenhouse yields compare to our Pure Greens container farms.
Let’s start with a little bit of background info.
Greenhouses are structures with glass or clear roofs that are used for cultivating plants. They range in size from small backyard sheds to massive commercial farms.
Greenhouses utilize a variety of crop growing systems. Most use typical soil methods planting in boxes, pots, or raised garden beds. Others use soil-less growing solutions such as hydroponic and aeroponic systems.
Other types of indoor farms include vertical, container, and deep water culture (DWC) systems.
What sets greenhouses apart from these other indoor farms is the use of glass or clear plastic roofing and sides to provide plants with natural sunlight. Other indoor farms rely on artificial light.
Growing indoors has plenty of advantages over outdoor farming. For example, indoor farming allows for highly controlled environments, creating near-perfect growing conditions for plants.
Greenhouses and container farms both offer the ability to control factors such as humidity and temperature and help prevent damage from weather, pests, and diseases. As a result, plants are healthier and can be grown at any time, no matter the season.
Our Pure Greens farms made from repurposed shipping containers are fully controllable from your smartphone!
Soil-based greenhouses are subject to similar space restrictions as field farms because plants need to have enough room for their roots to grow.
Hydroponic systems deliver water and nutrients directly to roots so that plants don’t have to spread. Therefore, our hydroponic container farms yield more per square foot than traditional greenhouse yields.
Using traditional soil methods, each lettuce crop would have to be placed 10 to 16 inches apart, meaning only six to 18 lettuce plants would be able to grow in a 16-square-foot row.
Using our hydroponic technology, we’re able to fit 36 lettuce plants in one row! That’s at least three times as many.
But lettuce takes up a lot of space in both types of farms. Herbs like rosemary and sage are much easier to grow in bulk in our hydroponic container farms than they are in soil-using greenhouses.
In soil, rosemary and sage plants need to be spaced a couple of feet apart. If we were to follow that rule in one of our 16-square-foot rows, we’d only be able to grow four plants total.
We grow 90 rosemary or sage plants in one row!
Thai basil crops need to be spaced 12 to 18 inches apart. Like sage and rosemary, we easily fit 90 Thai basil plants in just one of our rows. Farmers who use soil can only grow 16 max in the same space.
This means our hydroponic farms yield at least 5.6 times as much basil per square foot than a traditional soil greenhouse yields in just one grow cycle.
It’s clear that our container farms come out on top when it comes to yield.
If you’d like to learn more about maximizing your production with one of our farms, reach out to us on our website or give us a call at 602.753.3469.
WRITTEN BY
Pure Greens Arizona LLC
Pure Greens’ container-based grow systems offer a variety of interior layouts, sizes, and options so customers can create a farm that meets their needs.
Coronavirus Pandemic Highlights Vital Need For Vertical Farms In World Cities
Although the sources and sourcing of food in North America and Western Europe are currently generally secure, what might soon become a prodigious concern is that their workers in the production, distribution and retail segments of the food supply chain may eventually succumb to coronavirus infection
MARCH 25, 2020
by Professor Joel Cuello, Ph.D.
Image modified from Martin Sanchez/Unsplash
The speed with which the coronavirus outbreaks in Asia, Europe, and North America metastasized into a full-blown global pandemic — catching many world governments by surprise and with little preparation — underscores just how our world today is highly interconnected and how, in order to contain and stem the surging pandemic, temporary disconnection from the physically-networked world by cities, regions and even entire nations has become an urgent imperative.
With confirmed coronavirus cases globally now exceeding 370,000 and the number of deaths surpassing 16,000, many world cities have become throbbing epicenters of the surging pandemic. Accordingly, various countries, states, and cities have enforced lockdown or stay-at-home orders with drastic measures including banning public gatherings, restricting restaurants to take-out and delivery only, and closing schools, bars, theaters, casinos and indoor shopping malls, among others.
Such orders, or their looming possibility, have consequently intensified the panic-buying urges of consumers for food and household essentials particularly in North America and Western Europe, giving occasions for daily photos of empty grocery-store shelves splashed ubiquitously from across news networks to social media platforms. The availability of food in North America and Western Europe during the ongoing coronavirus pandemic, however, remains generally secure, at least in the near term of the pandemic.
Food Sourcing
New York City, for instance, normally has food supply amounting to approximately 8.6 million tonnes (19 billion pounds) annually as purveyed by a network of regional and national food distributors, which then is sold at about 42,000 outlets across the city’s five boroughs, according to a 2016 study sponsored by the city.
Over half of the outlets are made up of approximately 24,000 restaurants, bars, and cafes through which consumers access almost 40 percent of the city’s food by volume annually. The rest of the outlets are chain supermarkets, bodegas, and online grocery stores. The study reported that the city’s annual food supply feeds over 8.6 million city residents, over 60 million tourists plus daily commuters in the hundreds of thousands from the tri-state area of New York, New Jersey, and Connecticut.
With millions of tourists and commuters now staying away from the city, however, and with the city’s hotels at just 49 percent occupancy for the week ending March 14, an excess of the food supply is readily available for diversion into the city’s grocery stores and other retailers to meet the surge in demand by local residents. In the case of Germany, the country imports food that accounts for nearly 8 percent of its US$1.3 Trillion imported goods in 2018. Germany procures from abroad about 3 million tonnes of fresh vegetables annually — with cucumbers and tomatoes accounting for 40 percent of the import volume — at a value of around 3.5 billion Euros, mainly from the Netherlands and Spain. Indeed, approximately 30 percent of the 2.6 million tonnes of exported Dutch-grown fresh vegetables go to Germany.
Meanwhile, approximately 80 percent of the United Kingdom’s food and food ingredients are imported. The U.K. imports approximately 2.4 million tonnes of fresh vegetables each year from Spain (33 percent), the Netherlands (28 percent), France (10 percent) and from various parts the world (29 percent).
Access to Food
Although the sources and sourcing of food in North America and Western Europe are currently generally secure, what might soon become a prodigious concern is that their workers in the production, distribution and retail segments of the food supply chain may eventually succumb to coronavirus infection. In such events, coupled with the potential for lockdown bureaucracies to slow down the flow of cargo between countries and between cities, severe delays in delivery — or real delivery shortages — could well become an actual possibility.
Local Vertical Farms
The coronavirus pandemic lockdowns have laid bare if fortuitously, the crucial importance of partial local food production in or around world cities in the context of urban resilience. The following salient features of vertical farms have become especially significant toward buttressing a city’s resilience in the event of a pandemic lockdown:
(1) Local — production of safe and fresh produce can take place within the lockdown zone, obviating the hurdles and perils of going in and out of the red zone;
(2) Automation-Amenability — impact of severe labor shortage which can be expected as the pandemic surges as well as direct physical contact between workers and fresh produce can be significantly minimized or eliminated;
(3) Controlled-Environment — infection risks to both workers and crops are significantly reduced through clean and controlled operations;
(4) Modular Option — crops may be grown in modular production units, such as shipping containers, which may be conveniently transported to neighborhoods located either farther away or in areas of stricter isolation; and,
(5) Reliability — Dependability, and consistency of high-yield and high-quality harvests throughout the year is virtually guaranteed independently of season and external climate conditions.
Fortunately for New York City, even as it sources most of its fresh vegetables from California and Arizona, the New York greater area now serves as host to the highest concentration in the United States of commercial urban vertical farms — including Aerofarms, Bowery Farming, Bright Farms, Farm.One, Square Roots and Gotham Greens, among others — that operate as controlled-environment farms year-round and independently of the variable effects of climate and geography. While conventional outdoor farming can produce three vegetable harvests per year, some of these vertical farms can achieve up to 30 harvests annually.
New York City and other world cities could certainly use more vertical farms.
Indeed, the urban planning and design of every world city should incorporate vertical farms, in and/or around it, not only for promoting food security — but for fostering disaster resilience as well. During a pandemic when a temporary period of social distancing between cities and nations becomes critically necessary, vertical farms can serve as helping outposts of resilience for cities and regions on lockdown as they brave the onslaught of the pandemic until it runs its course and duly dissipates — at which time the enfeebled ties of cooperation between cities, states and nations across the globe can once again be mended and made even stronger than before. Thus, not only locally, but in fact also globally, vertical farms can serve as helping vanguards of protection for all of our communities.
Dr. Joel L. Cuello is Vice-Chair of the Association for Vertical Farming (AVF) and Professor of Biosystems Engineering at The University of Arizona. In addition to conducting research and designs on vertical farming and cell-based bioreactors, he also teaches “Integrated Engineered Solutions in the Food-Water-Energy Nexus” and “Globalization, Sustainability & Innovation.” Email cuelloj@email.arizona.edu.
Indoor Micro Farming: Benefits, Costs, And Profits
Indoor micro-farming is a trendy alternative to outdoor farming. Outdoor, or field, farming is declining as land costs and soil erosion make it increasingly harder to start a farm. In its place, small indoor farms are popping up to meet the increasing demand for locally produced food
March 7, 2020
Indoor micro-farming is a trendy alternative to outdoor farming.
Outdoor, or field, farming is declining as land costs and soil erosion make it increasingly harder to start a farm. In its place, small indoor farms are popping up to meet the increasing demand for locally produced food.
Did you know small farms produce more than 70 percent of the world’s food?
Micro farms are versatile. They can be created in any small room like shipping containers, bedrooms, and garages.
In this article, you’ll learn all about indoor micro-farms including its benefits, costs, and how to profit from one.
Basics of Indoor Micro farming
Indoor micro-farming refers to small-scale farms in urban or suburban areas.
The ability to control environmental factors like lighting, humidity, and temperature is the biggest advantage that indoor farming has over outdoor farming.
Indoor alternatives to field farming, like greenhouses, have been around for thousands of years, but it wasn’t until the 1970s that controlled environment farms emerged.
Farmers use a variety of different systems to grow plants indoors. Aquaponics, hydroponics, and aeroponics are a few of the most popular systems after using traditional soil.
Aquaponics refers to using fish to grow plants. In these systems, fish fertilize water that’s fed to the plants. The plants, in turn, purify the water, which is fed back into the fish tanks.
Hydroponic systems grow crops by watering plants with a nutrient-rich solution. Instead of soil, plants are grown in a nutrition-less growing medium that allows plants to absorb the nutrients from the water easier than if they were grown in soil.
In aeroponic systems, plants are grown with their roots exposed in highly misted environments. The mist is created using a nutrient solution.
We use hydroponic systems to cultivate crops in our Pure Greens container farms, which are made out of shipping containers.
Indoor micro-farms are often started using spare space like an unused basement, guest room, or garage in the farmer’s home. But they can also be started in any small, indoor area like a shipping container.
The ability to use a small space to grow produce is only one of indoor micro-farming’s many benefits.
Benefits of Indoor Micro farming
Indoor micro-farming is beneficial because it fills the demand for certain produce while saving money and stress.
As far as selling goes, demand for locally produced food across the United States is increasing.
Nielsen, a data and measurement firm, found that 48% of consumers prefer ingredients and food that have been produced locally.
Indoor micro-farming fills this demand by being produced in the center of commercial areas, guaranteeing locality.
Purchasing land or buildings big enough for large-scale operations are expensive. Indoor micro-farming allows people to use the buildings they already live in to start growing.
Capital expenses are also lower because you don’t have to purchase new land. Plus, equipment isn’t as expensive for microforms due to the availability of ready-for-installation systems and “Do It Yourself” (DIY) tutorials.
With smaller capital expenses comes a lower-stakes environment.
When you’ve put less money into a project, there’s less pressure to succeed. Feel free to experiment with systems and crop types to find what works best for your farm.
Indoor micro-farming also allows you to develop a local customer base and specialize in a niche market.
Having already secured customers and perfected a crop will help when you’re ready to expand.
Indoor micro-farming also allows restauranteurs to grow their own produce onsite, reducing food waste by being able to harvest only what’s needed rather than buying in bulk. Customers will also appreciate the fresher tasting food!
Another benefit of indoor micro-farming systems is that there isn’t just one way to do it.
Micro farming Systems
Because micro-farming can be done using virtually any size of space, there’s a wide variety of systems to pick from.
Our Pure Greens container farms are an excellent choice for those with yard space for a 40-foot shipping container.
Our farms come outfitted with a recirculating hydroponic system, providing a low water consumption rate, and an automated controlled environment system that can be monitored via your smartphone.
For farmers with less space to work with, there are a few smaller purchasable and DIY options out there as well.
Ready-to-use hydroponic systems can be purchased online or from a local hydroponic equipment store.
One popular DIY hydroponic system for beginners is the Kratky method.
The Kratky method is easy as it doesn’t require pumps or changing the nutrient solution. In this system, plants are placed in a netted pot with a growing medium, such as coconut coir or clay balls, and then placed into a reservoir filled with water and nutrient solution.
While this method is good for farmers with very little experience, it’s only effective for growing leafy greens. Anything with flowers or fruits will need a more involved process.
The Kratky method also requires close attention to the water’s pH levels because it’s not replaced or adjusted during the growing cycle.
Aeroponic systems are also buildable but require a little bit more expertise with construction. Plants grown in these systems receive maximum nutrients.
But aeroponic systems are less common than hydroponic systems when it comes to home-growing because they require special attention to nutrient ratios and pH levels, making them not very beginner-friendly.
Aquaponic systems are a good choice for people interested in fish farming. If you raise healthy enough fish, you can sell them along with your produce.
Keep in mind aquaponic systems require more maintenance than hydroponic or aeroponic systems and they’re a little trickier.
With these systems, you have to keep both the fish and the plants happy. Doing so requires finding the delicate balance of water flow between the two.
Deciding on which system to use can be tricky, but your expenses will depend heavily on the system you decide to use.
Indoor Micro farming Costs
Capital and operating expenses of indoor micro-farming varies depending on the type of system and size of the operation.
The first expense is going to be buying the system itself or any materials needed to construct it. You may need to purchase tubs, pumps, and pipes.
You’ll also need to purchase light fixtures, so your plants have a light source to use for photosynthesis. During photosynthesis, plants absorb energy from light to produce glucose out of carbon dioxide and water.
There are plenty of LED lights in the market aimed specifically toward growing plants. Look for bulbs with high efficiency to conserve energy usage.
Because indoor micro-farming typically relies on artificial light rather than sunlight, energy costs can be high. A 2017 survey of indoor farms found that small farms spent about $3.45 per square foot on energy alone, which was about 12% of the total budget.
Take into consideration water usage as well. Systems like recirculating hydroponics and aeroponics use considerably less water than aquaponics and soil-based systems.
Hydroponic and aeroponic systems typically require 4 gallons of water per square foot per year. Meanwhile, aquaponic systems use about 10 gallons of water per square foot per year.
Be sure to also factor in any fish costs such as a tank, food, and the animals themselves when using aquaponic systems.
Once your indoor micro-farm is ready to grow, you’ll need to buy planting materials.
Planting expenses will be recurring so be sure to keep them in mind while budgeting. Purchase seeds, growing mediums, and nutrient solutions online or in stores.
Growing mediums and nutrient solutions replace the soil in hydroponic and some aeroponic systems. The growing medium acts as a support for the plants’ roots while the solution provides essential nutrients for strong, healthy plants.
While indoor micro-farming can be costly, there are plenty of strategies for growing your business.
Profiting from your Microfarm
The first step to making a profit from indoor micro-farming comes before you even plant a single crop: Research.
Find demand for a product in the local market that isn’t being met. Meet with potential customers like chefs, grocery stores, and farmers’ market patrons and ask what they’d like to be able to purchase fresh.
Focus on growing specialty crops rather than common produce like lettuce.
Specialty crops can be things that are out of season, hard to grow in your climate or something trendy such as microgreens or adaptogens.
Consider selling your products at farmers’ markets, to vendors, to wholesale distributors, and to local restaurants.
The number of farmers’ markets in the country has tripled since 2000, making it an easy choice for finding customers.
Research popular farmers’ markets in your area and learn how to set up shop. Keep in mind that some markets will charge a fee to set-up a booth.
Alternatively, approach a different produce vendor and let them sample your product. If all goes well, they will sell your product for you!
Find a middleman by selling to wholesale distributors. Distributors will find shops to sell your products for you, giving you more time to focus on growing.
Or sell your produce directly to local restaurants.
Research chefs who focus on crafting dishes using locally sourced greens. Set up an appointment with chefs to pitch your business to them and be sure to bring along your best samples.
Try to establish a rapport with the restaurant. Find out whether they’d prefer a range of products or a specific good.
After you’ve established your clientele, your indoor micro-farm will blossom.
Now that you’re familiar with indoor micro-farming, it’s time to get started.
Visit our website or call us at 602–753–3469 to learn more about how you can start your own container farm.
Vertical Farming Indoor Farming Farming Farming Technology
WRITTEN BY
Pure Greens Arizona LLC
Pure Greens’ container-based grow systems offer a variety of interior layouts, sizes, and options so customers can create a farm that meets their needs.
THE ARCTIC CIRCLE - This Greenhouse In A Sea Can In Gjoa Haven Is Powered by Wind And Solar Energy
Betty Kogvik and Susie Kununak are making sure those little fruits — which will mark the second harvest from the community's new agricultural research station — have all the warmth and light they need, despite the dark winter outside
'It was so fresh, not like what we get in the store,' says technician at shipping container research station
Beth Brown - CBC News
These sea cans in Gjoa Haven are actually a new research station and grow pod used for growing vegetables. The solar and wind-powered project is called Naurvik, which means, the growing place. (Submitted by Thomas Surian)
In a sea can outside Gjoa Haven, Nunavut, there are rows of ripening cherry tomatoes working to grow from green to red.
Betty Kogvik and Susie Kununak are making sure those little fruits — which will mark the second harvest from the community's new agricultural research station — have all the warmth and light they need, despite the dark winter outside.
The two women are technicians, or guardians, for a new wind and solar-powered greenhouse that the Kitikmeot community named "Naurvik." That means "the growing place" in Inuinnaqtun.
The first harvest, of lettuce, grew in around four weeks. It was given to Gjoa Haven elders who have played a large role as advisors for the Naurvik project, which is led by the not-for-profit group, the Arctic Research Foundation.
One elderly lady even danced with joy when she got her lettuce.- Betty Kogvik"It was so fresh, not like what we get in the store. Sometimes when we get [lettuce] in the stores it is almost rotten. The ones we harvested are really fresh and tasty," Kogvik said. "One elderly lady even danced with joy when she got her lettuce."
Agriculture could grow new economy
The research station is built of two sea cans (shipping containers brought up on the summer sealift), two windmills and a row of solar panels. It has a generator for backup when the wind and sun both fall short.
It's on a hill, near a bay, in a place that elders said gets a lot of wind, and is only a few minutes ride by snowmobile from town.
Naurvik technician Betty Kogvik harvests the first lettuce grown in the sea can greenhouse in Gjoa Haven. (Submitted by the Arctic Research Foundation)
Every day, the technicians, including Kogvik's husband Sammy, spend time monitoring the station. The current harvest only uses a quarter of what the station could grow. Come summer, they want to run a trial growing cloudberry and blueberry plants, and other tundra plants used for medicine and tea.
"At the beginning, it was really confusing," Kogvik said. "We didn't know what to do, but we've got the hang of it now."
In the spring, Sammy says he wants to travel to Taloyoak to help that community start its own version of the Naurvik grow pod.
For the Arctic Research Foundation, the focus of Naurvik is on improving food insecurity, and on researching how to most efficiently grow food in remote and harsh environments, said project lead Adrian Schimnowski.
But it's also meant to foster the economy. Schimnowski said he'd like to see a local product grown to a scale where it's ready for export. For now, he's working to be able to employ and train students, as well as community-based technicians.
The Arctic Research Foundation is calling its new Naurvik greenhouse project in Gjoa Haven the most northern agriculture pod to be powered by wind and solar electricity. (Submitted by Thomas Surian)
The foundation is funding the program with help from Agriculture and Agri-Food Canada, the National Research Council of Canada, and the Canadian Space Agency.
"It's a mini, mobile research station. We can add as we expand," said Schimnowski. "It's directed by the wishes of the community."
Space agency looks to Gjoa Haven
Because Naurvik is working on more efficient technology to grow vegetation in an environment it usually wouldn't survive in, that same research can also be used to help scientists understand how to grow food in harsh environments — like space.
"We are hoping to find strategies that could help astronauts grow food in space," Christian Lange, head of exploration strategic planning with the Canadian Space Agency, said in a news release. Research from "extreme or remote environments," like Gjoa Haven, could be part of that, he said.
This crop of potted cherry tomato plants are thriving under LED grow lights. They will be the second kind of plant harvested at the Naurvik grow pod in Gjoa Haven. (Submitted by the Arctic Research Foundation)
The research station itself is built to be hyper-efficient, project lead Schimnowski said.
"It's very narrow and tight, similar to what it would be like in a spaceship, but everything is well organized and everything has purpose."
While gardening isn't an Inuit tradition, using the land to care for and store food is. Elders who are working with Naurvik said using the green energy to run the research station made them think of a community freezer, the kind built into the ground. Those elders said the hill near the station could be used to build a traditional freezer.
"When I first heard of [the project] I thought it would never work up here," Gjoa Haven elder Peter Akkikungnaq is quoted in the news release. "Not in this 40 below zero. Now I know anything is possible if you have the right idea ... I had a taste of the vegetation. It was fresh."
Vertical Farming: The Advantages of Growing Up, Not Out
Vertical farming refers to growing crops in multiple vertical layers in controlled indoor environments, such as repurposed buildings, growth chambers and even shipping containers
We share this planet with more than 7 billion people, and the UN forecasts that by 2050 we will need to feed over 9.7 billion. If you’re like me, you’re wondering what we can do to scale farming to meet the needs of the future. That’s where vertical farming comes in, along with innovative technologies that make growing up, not out, a more viable option.
by Ali Ahmadian, CEO Heliospectra
Vertical farming refers to growing crops in multiple vertical layers in controlled indoor environments, such as repurposed buildings, growth chambers, and even shipping containers. While growing crops in the greenhouse have its own merits, depends on the crop and technology used vertical farming has advantages over single-layer crops grown in a field or greenhouse:
Vertical farming enables growers to optimize their costs per square meter and produce more within the same footprint. A vertical format could potentially produce a harvest that is 3- to 4-times larger (or more!) than a field the same size could produce.
Vertical farming is done in an automated, controlled environment, which eliminates many of the risks involved with traditional field farming. Variables such as seasonal weather and environmental issues are taken out of the mix to produce a thriving crop year-round – no matter what’s happening outdoors.
Crop yields are standardized in vertical farming, with every harvest cycle producing the same quantity, quality, flavor and appearance that customers expect.
Vertical farming enables growers to meet changing market demands, by easily introducing new crops or varieties based on consumer or retail preferences.
Due to its smaller footprint, vertical farming is a viable and environmentally sound solution for feeding cities. The UN predicts that close to 70% of the population will be living in urban areas by 2050. To reduce the carbon footprint of our food, we need to think of ways to bring food production closer to the dining table. A LCA is necessary to weigh in such decision making.
While we continue to build larger and larger cities to accommodate our growing population, arable farmlands will be pushed further out. Vertical farming can ensure our cities have plentiful locally grown food – food that has a predictable harvest, optimizes costs per square meter, looks beautiful, fresh and tastes delicious.
Source: LinkedIn
Publication date: Fri 6 Mar 2020
Freight Farms Announces New Horticultural Funding From Ospraie Ag Science
A Series B venture round of $15 million will allow Freight Farms to invest in plant science, add features to its software control platforms, and expand the customer base for its vertical farms housed in shipping containers
Mar 2nd, 2020
A Series B venture round of $15 million will allow Freight Farms to invest in plant science, add features to its software control platforms, and expand the customer base for its vertical farms housed in shipping containers.
Vertical-farm supplier Freight Farms has received $15M in Series B funding from investment first Ospraie Ag Science for its all-in-one, shipping-container-based agriculture model. (Photo credit: Image courtesy of Freight Farms.)
Shipping-container-based, vertical-farm manufacturer Freight Farms has announced that it received $15 million in Series B venture funding from investment firm Ospraie Ag Science. Freight Farms will use the investment to further optimize its Farmhand software platform, invest in plant science, and expand the customer base for its LED-lit Greenery container farms.
Freight Farms originally branded its container farms The Leafy Green Machine but has since simplified the product name to The Greenery. A Greenery farm includes everything a grower needs to launch a hydroponic farm all integrated into a shipping container. The outfitted Greenery container includes LED lighting, plumbing for nutrient supply, climate, and environmental control, and the Farmhand software to automate the operation of the farm.
The idea of a shipping container for a vertical farm is not a new one. For example, we covered a Dallas grocery store that uses a shipping-container farm to grow some produce right outside the store’s back door. And we covered a Los Angeles area farm using shipping containers right in the downtown metropolitan area back in 2016.
Freight Farms, however, brings unique aspects to its business both in the science behind Greenery and in the company’s business model. Taking the business model first, Freight Farms is specifically in the business of selling turnkey farms. Some other players have vacillated between selling technology and operating as growers.
The configuration of the Freight Farms product is also unique. When we first covered vertical farming back in 2016, the term was primarily utilized to describe growing operations where horizontal trays of plants were stacked in layers vertically to more fully utilize a space, especially for crops such as leafy greens and herbs where there is not much space needed between layers and where LEDs that don’t radiate heat can be placed in close proximity to the plant canopy.
We have since seen other concepts. Plenty, for example, is based in California’s Silicon Valley Area, has received more than 200 million in funding from well-known investors such as Amazon’s Jeff Bezos, and utilizes a system where plants are placed horizontally into the growing structure but run continuously in a vertical row from floor to ceiling.
Freight Farms partitions its systems in the close confines of the shipping container. There is a dedicated area where horizontal racks are used in the initial stages of sprouting. But later plants are transplanted into a vertical row structure where nutrients can drip from the top of each vertical row of plants and unused nutrient is recaptured at the bottom of each row.
Freight Farms said its 328-ft2 container can produce equivalent vegetables to a two-acre outdoor plot. And the container farm uses less than five gallons of water per day. For Freight Farms, the mission is solving the looming issue of feeding a growing global population. “With the Greenery and Farmhand, we’ve created an infrastructure that lowers the barrier of entry into food production, an industry that’s historically been difficult to get into,” said Jon Friedman, Freight Farms COO. “With this platform, we’re also able to harness and build upon a wider set of technologies including cloud IoT, automation, and machine learning, while enabling new developments in plant science for future generations.”
And make no mistake that controlled environment agriculture farming is becoming big business. We recently ran an article that discussed the investment capital coming into the market. Clearly, Ospraie sees an opportunity in the container concept. Freight Farms says it has sold farms into 44 states and 25 countries.
“Freight Farms has redefined vertical farming and made decentralizing the food system something that’s possible and meaningful right now, not in the future of food,” said Jason Mraz, president of Ospraie Ag Science. “Full traceability, high nutrition without herbicides and pesticides, year-round sourcing – these are elements that should be inherent to food sourcing. Freight Farms’ Greenery makes it possible to meet this burgeoning demand globally for campuses, hospitals, municipal institutions, and corporate businesses, while also enabling small business farmers to meet these demands themselves for their customers.”
US: New Jersey - Hope Cahill Starts As Coordinator At Hydroponic Farm
A hydroponic farm, in the middle of a municipal center? Well, it all started in 2016, when Robbinsville Mayor Dave Fried found out about hydroponic farming in freight containers
By Lois Levine
March 1, 2020
A hydroponic farm, in the middle of a municipal center? Well, it all started in 2016, when Robbinsville Mayor Dave Fried found out about hydroponic farming in freight containers.
“He loved the idea and thought it would be beneficial to the township in terms of feeding programs and education on how to grow greens and learn more about nutrition,” said Kevin Holt, recreation manager for the Robbinsville Township.
Hope Cahill, the new coordinator of Robbinsville’s hydroponic farm, holds some of the farm’s yield.
Now, the farm has a new coordinator—Hope Cahill, who took over for original caretaker Kyle Clement in January.
“We can grow anything that is a leafy green,” Cahill said. “Here we are growing butterhead, oak leaf, and lollo lettuce, as well as spring mix.”
The farm also grows some herbs, basil, and cilantro. Cahill, 25, is certified in aquaponics, an off-breed of hydroponics.
After graduating high school, she got certified in a variety of different areas of agriculture, and before taking this position working as a naturalist at various garden centers, as well as with the Monmouth County Park system. Born and raised in Tinton Falls, Cahill will be soon moving to Freehold.
Hydroponic farming is farming done without soil. Plants typically get all their nutrients from the soil. In hydroponic farming, however, nutrient-rich water takes the place of the soil, enriching the seedlings as they grow into fully mature plants and watering them at precise times through a computerized system.
With the system that the Robbinsville Township purchased, known as the Leafy Green Machine, lettuces and herbs are grown in a vertical hydroponic farm that lives within a recycled, refrigerated, insulated, custom-built shipping container.
Between the nutrient-rich water and light energy from powerful LEDs, greens can be independent of the need for land, climate and season, growing in a modular design that is also mobile and can theoretically live anywhere.
The container consists of insulation, where it maintains an average internal temperature of 70 degrees Fahrenheit in extreme climates; climate control, built with an integrated “economizer” that saves energy by drawing in cool outside air when appropriate and also doubling as an intake fan; a dehumidifier to maintain optimal humidity levels and decreasing the farms overall water consumption; airflow ducts, consisting of two fans that distribute cool carbon dioxide enriched air evenly; and a carbon dioxide regulator with a safety shut-off feature, providing plants with exactly the right amount of carbon dioxide needed for photosynthesis.
In addition, the greenery’s LED lights provide the plants with the best quality light at its most efficient point. The LED boards are designed to emit only particular wavelengths of red and blue light, which are the colors that plants are able to absorb most easily for photosynthesis (red light is essential for stem and leaf growth, while blue light helps develop thick stems and dark green foliage).
Just as it is in nature, Cahill and her team start with the seeds, which begin in a flowing hydroponic system and are placed into compressed peat moss, known as grow plugs. The peat-moss plugs act as a sponge for absorbing nutrient-rich water. The seeds soak for 10 minutes, are covered with a humidity dome and sit under grow lights for about a week.
At that point, the seeds have become sprouts, with small roots, short stems, and a few young leaves. They then move up to the next level, a flow troth, where the roots “get completely soaked,” Cahill said. Now actual seedlings, taller and sturdier than they had been, with a secure root system, the plants sit in that troth for another two weeks, getting consistent water and light to develop strong stems needed to support the plant’s weight later in its life cycle.
After this time period, the seedlings are harvested and transplanted into the main cultivation area, where they are now in the towers, growing vertically for the first time. The roots, which are still in the peat-moss grow plugs, are wedged into stiff foam panels, which provide firm support, with the plant facing outward towards the LED light, encouraging the leaves to grow. Here, in this final destination, they spend from two to five weeks until they are ready for their harvest..
A view of the produce inside of the shipping container that houses Robbinsville’s hydroponic farm
“It is a continual cycle of putting new lettuce and herbs in, taking grown ones out,” Cahill said.
Every week, the team has something to harvest.
“What is nice about the system is that it is computerized so that plants get exactly the nutrients it needs at the right time,” Cahill said. “Sensors on the computer know when they might need nitrates or some other nutrient.”
Freight Farm, the company that built the hydroponic farm equipment, also developed an app that can be used via a person’s iPhone or desktop computer to keep an eye on all sensor data.
Holt admits he did not know much about hydroponic farming until Fried asked him to look into purchasing a machine.
“I did a ton of research on what hydroponic farming is, to educate myself, and then looked into what companies are out there to make these container farms,” he said. “We talked to a lot of companies, and decided on Freight Farm, out of Boston. At the time, they told us we were the only municipality they had ever sold a freight farm container to.”
Once Cahill and Holt have the finished products, the lettuce and herbs get donated back to the Robbinsville Senior Center.
“We also give some of the produce to Meals on Wheels, and also Mercer Street Friends, who disperse it to schools,” Cahill said. “They distribute it to about a dozen schools in the Trenton area.”
And how does the finished product taste?
“It is honestly the best lettuce you can ever eat,” Holt said. “You really can see and taste the difference between this produce and the produce you buy in a supermarket.”
It looks good and feels good, too, Cahill said.
“Before we distribute it, we take care to remove any brown or damaged leaves,” she said. “There are, of course, no pesticides, no chemicals that the greens were treated with, so it is very safe and very clean.”
Both Cahill and Holt rave about how green and fresh the lettuce is, “with so much more taste to it than what you get in the stores, which by comparison, tastes so bland,” Holt said.
Since starting the farm at the municipal center in 2017, companies have come through to see the set-up, expressing interest in buying machines for themselves. Holt said the township has also hosted schools and colleges, as well as field trips and local education programs.
“Our mission is to grow, educate and unite: we grow the lettuce, give it away, educate the community about how hydroponic farming works, and unite people by asking them to volunteer or hold events, which is a catalyst for bringing people together,” Holt said. “This has been a huge win-win for the community.”
Cahill said she is always seeking volunteers and visitors, as well.
To schedule a tour or for more information, visit robbinsville.net/recreation or send an email to hcahill@robbinsville.net.
US: Texas - Personal Growth As Well As Leafy Greens Thrive in San Antonio Nonprofit’s New Hydroponic Farm
A group of people crowded around a shipping container in the parking lot of the San Antonio Clubhouse, a community and resource center for adults with mental illness. Inside the 40-foot long container is a hydroponic farm, which produces as many crops as a three-acre farm, simply with water and lights
March 7, 2020
A group of people crowded around a shipping container in the parking lot of the San Antonio Clubhouse, a community and resource center for adults with mental illness.
Inside the 40-foot long container is a hydroponic farm, which produces as many crops as a three-acre farm, simply with water and lights.
But the best part of Clubhouse Grows — the new indoor water-based, high-tech farm — isn’t that it sprouts an abundance of leafy greens. It’s that it also serves as a recovery-oriented volunteer opportunity for the people the nonprofit serves.
“We are working together as a Clubhouse community on this farm,” said Mark Stoeltje, the executive director of San Antonio Clubhouse. “It is providing meaningful work for our members, but it is also providing a product.”
Clubhouse Grows, which was unveiled Friday, was made possible with a $100,000 grant from Impact San Antonio, a women’s philanthropic non-profit that awards grants to local organizations.
Jennifer Bennett, president of Impact SA, said one of the reasons the group chose to award Clubhouse a grant was “because of the multilayered benefits that it delivers to the community.”
“A lot of our citizens who have mental health challenges do not get the degree of support that they need to help them live lives that feel good to them,” Bennett said. “Clubhouse is really unique to doing that in our community.”
The plants in the 320-square-foot freight container do not rely on soil. Instead, they grow on 88 black foam and metal panels, which have water pumped through them. Powerful LED red and blue lights that emulate the sun are on 18 hours a day. And the climate-controlled space remains stable between 65 and 68 degrees.
“The extra sunlight, combined with the fact that it’s never cloudy and we don’t have to worry about different seasons, really helps accelerate the plants’ growth,” said Brandon Wagner, a staff member and project lead for Clubhouse Grows.
On ExpressNews.com: South San Antonio elementary students growing food with a larger goal in mind
Crops planted include five types of lettuce, kale, beets, arugula, basil, oregano, and even some flowers.
Wagner, who has been prepping the new farm and working with it for around a month, said he has found it to be very therapeutic.
“You zone out and just concentrate on the work,” he said. “You are planting 300, 400 or up to 500 seeds at a time, so there is a very meditative workflow.”
While the farm only uses about 25 gallons of water a month, Wagner said, it can grow 550 small and crisp heads of lettuce alone each week.
“I love lettuce, but that is more lettuce than we can eat,” Stoeltje said.
So, in addition to using the produce at the Clubhouse facility, the organization plans to donate some to local non-profits.
Stoeltje said while healthy eating is important, the farming process — seeding, maintaining, relocating and harvesting crops — is also a chance for Clubhouse members to work hard, work together, hone new skills, reach goals and ultimately feel a sense of accomplishment.
San Antonio Clubhouse, which was founded in 2003, operates under a national model that's based on the belief that everyone deserves to be part of a caring community and has talents to share.
The non-profit helps its more than 2,000 members gain work experience through volunteering at the center, job training, résumé building, job-search assistance and advocating to potential employers.
“This is the perfect project for us because we are founded on two principles,” Stoeltje said, “meaningful relationships and rewarding work.”
sara.cline@express-news.net
Sara Cline
Follow Sara on: https://www.facebook.com/sara.cline.5494SaraLCline
Sara Cline is a staff writer for the San Antonio Express-News through the Hearst Fellowship Program.
She previously worked at the Times Union under the program. She also worked at the Brockton Enterprise, in Massachusetts, as a general assignment reporter. She has also contributed to newspapers and magazines in Arizona, Massachusetts and Rhode Island.
Sara graduated from the University of Arizona in 2016 with a B.A. in journalism.
Past Articles from this Author:
CropKing Partners With Urban Crop Solutions To Grow Vertical Container Farm Showcase
CropKing, a full-service hydroponic company located in Lodi, OH, specializing in controlled-environment agriculture and hydroponic growing, will operate the Urban Crop Solutions’ FarmPro vertical container farm as a showcase, continued research, and testing facility
March 4, 2020
CropKing and Urban Crop Solutions have announced plans to collaborate on a controlled-environment agriculture project in the U.S., leveraging the extensive hydroponic experience of CropKing with the high-quality controlled-environment technology in vertical farming of Urban Crop Solutions.
CropKing, a full-service hydroponic company located in Lodi, OH, specializing in controlled-environment agriculture and hydroponic growing, will operate the Urban Crop Solutions’ FarmPro vertical container farm as a showcase, continued research, and testing facility. The first FarmPro container arrives in March at the Lodi headquarters, where CropKing will start testing it with the help of in-house plant scientists.
“We are excited to be working with Urban Crop Solutions and for the opportunity to validate the effectiveness of automated container farming,” said CropKing President Paul Brentlinger in a press release from Urban Crop Solutions. “
Their personal and custom-made approach could fulfill the needs of many clients. The shipping container system offers advantages like climate control, irrigation system, and automated growing process, which has captured our interest for the past few years.”
Urban Crop Solutions, a turn-key solutions provider that offers biological know-how in the indoor vertical farming industry, recently celebrated its 5th anniversary and already has 28 active projects across the world. In the last five years, it has developed more than 200 plant growing recipes, for a variety of industries, through its in-house research center.
Paulina Murrath, Business Development Manager of Urban Crop Solutions, will serve as a point of contact for the North American market at the company’s offices in Miami, FL.“
It’s a great honor to start a collaboration with CropKing and Paul Brentlinger, who is a controlled-environmental agriculture expert with extensive knowledge of growing high-quality food products,” Murrath said in the press release. “CropKing shares the same values that we consider as important, like bringing higher yields, nutritional value, food security, local production, and consumption, to different industries. That’s why we believe our collaboration will be rewarding.
”The Vertical Farming Industry Needs Proven Technology
CropKing will put the FarmPro vertical container through a rigorous testing process, which includes assessing items such as plant pathology and system yield, as well as validating the true return on investment (ROI) of the unit, according to Brecht Stubbe, Global Sales Director at Urban Crop Solutions.
The FarmPro vertical container CropKing will receive is a fully automated and climate-controlled 40-foot freight container with a four-layer, state-of-the-art growing system for leafy greens and herbs. The insulated container includes features such as climate control and an irrigation system, continuous monitoring, custom-made LEDs, a handling area and technical room, as well as online crop and process management. Plants grow in a nutrient film technique (NFT) hydroponic system.“
Technological failures and resulting bankruptcies have been a problem in the vertical farming industry,” Stubbe says. “With CropKing’s 30 years of experience in the greenhouse industry, we can prove that this technology and our growing recipes can provide the ROI to growers. We don’t want this technology to fail for our clients.”
Collaboration a Strong Match for Exploring New Markets, Including Floriculture
This collaboration is only phase one for CropKing and Urban Crop Solutions. Stubbe says the companies hope to work together on more projects to explore new markets and opportunities in the vertical farming sphere
.Urban Crop vertical farming technology is already being used for research into medical plants for compound extraction. On the floriculture side, Stubbe says Urban Crop Solutions is currently conducting some promising research in Belgium. The latest growth trials with strawberries, for example, resulted in sweet fruits with a Brix value averaging between 11 and 16.“
They are growing azaleas at the trialing facility and now to a very high extent can control the temperature and bring crops just to the point of flowering, which helps increase their shelflife when they go to retail,” Stubbe says. “This type of technology could allow flowers to be grown across the globe, instead of shipped internationally to supply those markets.”
When asked about how the unit might be integrated into a controlled-environment greenhouse operation, Stubbe said he sees several applications and benefits, two being maximizing germination space with multilayer growing and eliminating risk factors involved with plant handling. For people growing in high tunnels or the field, the unit could help them diversify their operation into new crop segments. A grower could also use the unit to provide products locally on a year-round basis.
Janeen Wright is managing editor for Greenhouse Grower. You can email her at jwright@meistermedia.com. See all author stories here.
Paris Mayor: It's Time For a '15-Minute City'
Paris needs to become a “15-minute city.” That’s the message from the manifesto of Mayor Anne Hidalgo, who is seeking re-election this March
FEBRUARY 18, 2020
During the city's transit strike in December, Parisians got a taste of what being a more foot- and bike-oriented city would feel like. Philipe Lopez/AFP via Getty Images
In her re-election campaign, Mayor Anne Hidalgo says that every Paris resident should be able to meet their essential needs within a short walk or bike ride.
Paris needs to become a “15-minute city.” That’s the message from the manifesto of Mayor Anne Hidalgo, who is seeking re-election this March. Hidalgo has been leading a radical overhaul of the city’s mobility culture since taking office in 2014 and has already barred the most polluting vehicles from entry, banished cars from the Seine quayside and reclaimed road space for trees and pedestrians. Now, she says, Paris needs to go one step further and remodel itself so that residents can have all their needs met—be they for work, shopping, health, or culture—within 15 minutes of their own doorstep.
Even in a dense city like Paris, which has more than 21,000 residents per square mile, the concept as laid out by the Hidalgo campaign group Paris en Commun is bold. Taken at a citywide level, it would require a sort of anti-zoning—“deconstructing the city” as Hidalgo adviser Carlos Moreno, a professor at Paris-Sorbonne University, puts it. “There are six things that make an urbanite happy,” he told Liberation. “Dwelling in dignity, working in proper conditions, [being able to gain] provisions, well-being, education, and leisure. To improve the quality of life, you need to reduce the access radius for these functions.” That commitment to bringing all life’s essentials to each neighborhood means creating a more thoroughly integrated urban fabric, where stores mix with homes, bars mix with health centers, and schools with office buildings.
Paris en Commun has created a diagram to illustrate the concept of what should be available within 15 minutes of “Chez Moi” (home).
Paris en Commun’s 15-minute city concept. From the top, clockwise, the headings read: Learn, Work, Share and Re-Use, Get Supplies, Take the Air, Self-Develop and Connect, Look After Yourself, Get Around, Spend, and Eat Well. (Paris en Commun)
This focus on mixing as many uses as possible within the same space challenges much of the planning orthodoxy of the past century or so, which has studiously attempted to separate residential areas from retail, entertainment, manufacturing, and office districts. This geographical division of uses made sense at the dawn of the industrial era when polluting urban factories posed health risks for those living in their shadows. Car-centric suburban-style zoning further intensified this separation, leading to an era of giant consolidated schools, big-box retail strips, and massive industrial and office parks, all isolated from each other and serviced by networks of roads and parking infrastructure. But the concept of “hyper proximity,” as the French call it, seeks to stitch some the these uses back together, and it’s driving many of the world’s most ambitious community planning projects.
Barcelona’s much-admired “superblocks,” for example, do more than just remove cars from chunks of the city: They’re designed to encourage people living within car-free multi-block zones to expand their daily social lives out into safer, cleaner streets, and to encourage the growth of retail, entertainment, and other services within easy reach. East London’s pioneering Every One Every Day initiative takes the hyper-local development model in a slightly different direction, one designed to boost social cohesion and economic opportunity. Working in London’s poorest borough, the project aims to ensure that a large volume of community-organized social activities, training and business development opportunities are not just available across the city, but specifically reachable in large number within a short distance of participants’ homes.
Meanwhile, in Portland, Oregon, walking-distance-limited neighborhood planning is seen as central to climate action: The city aims to cover 90 percent of the city in so-called “20-minute neighborhoods,” where all basic needs—with the exception of work—can be reached within a third of an hour of walking time. In Australia, Melbourne rolled out a similar pilot in 2018.
Hidalgo’s aspirations for Paris build on this idea, but with a local twist. The goal travel time is reduced to 15 minutes, but bike journeys can count. And while it likewise underlines the importance of stores and doctors, it also includes cultural activities and workplaces within its central aspirations.
In Paris, this isn’t necessarily such a tall order. The mayor oversees only the 2.2 million residents of the city’s heavily populated historic core, which already enjoys some of the use-mixing that the 15-minute-city concept encourages, thanks to its pre-industrial roots. Paris would have an easier time with the concept than say, sprawling Melbourne, where more radical residential densification may be in order.
Paris en Commun’s manifesto sketches out some details for what this future walkable, hyperlocal city would look like. More Paris road space would be given up to pedestrians and bikes, with car lanes further trimmed down or removed. Planning would try to give public and semi-public spaces multiple uses—so that, for example, daytime schoolyards could become nighttime sports facilities or simply places to cool off on hot summer nights. Smaller retail outlets would be encouraged—bookstores as well as grocery stores—as would workshops making wares using a “Made in Paris” tag as a marketing tool. Everyone would have access to a nearby doctor (and ideally a medical center), while sports therapy facilities would be available in each of the city’s 20 arrondissements.
To improve local cultural offerings, public performance spaces would be set up, notably at the “gates” of Paris — the large, currently car-dominated squares around the inner city’s fringe which once marked entry points through the long-demolished ramparts. Finally, Paris would be populated by a network of “citizen kiosks”—booths staffed by city employees that would offer not just information, but also community cohesion services. Think places where you can drop off and pick up keys, join a local club or buy compost for your balcony plants.
Paris en Commun provides some glimpses of what this more self-sufficient, neighborhood-oriented city might look like. The (imaginary) triangular intersection below resembles the current state of many in Paris; there’s some public pedestrian space, but it remains hemmed in by cars, both mobile and parked, and genuinely safe space for pedestrians is limited.
(Nicolas Bascop/Paris en Commun)
After a superblock-style transformation, several neighborhood streets have been stripped of cars and no longer act as through-routes. This frees up room for new public space, with a small park at one end and a produce garden for residents at the other. New trees, green roofs and balconies, and a fountain would help mitigate the heat island effect and make the area a more pleasant place to linger. Meanwhile, the crossing space has ballooned in size, providing greater priority for pedestrians.
(Nicolas Bascop/Paris en Commun)
In December, transit strikes in Paris in protest of national pension reform gave Parisians an accidental taste of what a 15-minute-city future would look like, at least in terms of the hugely enlarged volume of cyclists on the city’s roads while bus and Metro service was halted. At some points during the strikes (which are still ongoing), bikes started to outnumber cars by two to one—a premonition of what might be to come.
Still, piecing together an entire modern working city around this 15-minute rubric would pose a challenge. In addition to its residents, central Paris attracts vast numbers of tourists who must be fed, housed and transported from neighborhood to neighborhood. Millions more commute into the city for work on regional transit from the vast greater Paris metro area. The people living in self-sufficient squares like the one above might find their rents rise along with the charm. And Paris can’t be transformed into a city that solely serves the needs of affluent locals.
Just how Hidalgo would execute the infrastructural changes required remains to be seen. She appears well-positioned to stay in City Hall: She’s leading in the polls (and one of her rivals has pulled out of the race after a sex scandal). Her office has not announced any specific budget or timetable for the 15-minute city concept, which remains perhaps more of a rough blueprint for the future than an imminent makeover, should she be re-elected in March. As a rethink of the way cities should be planned—and exactly who they should serve, and how—it’s an idea that other cities are likely to watch with great interest.
About the Author
Feargus O'Sullivan @FEARGUSOSULL
Feargus O'Sullivan is a contributing writer to CityLab, covering Europe. His writing focuses on housing, gentrification and social change, infrastructure, urban policy, and national cultures. He has previously contributed to The Guardian, The Times, The Financial Times, and Next City, among other publications.
How To Start A Container Farm Business
Using stacked farming to produce food in vertical spaces, vertical farming is an attractive option to traditional methods of farming, opening more opportunities for year-round freshly grown and locally accessed food
Have You Ever Wondered How To Start A Container Farm Business?
Vertical farming continues to grow with increased interest for both beginners and seasoned professional farmers. In this guide, Pure Greens helps new growers navigate the business side of container farming, with helpful steps to get started, such as:
How to create customer personas
Investment planning and funding
How to grow and harvest your crops
How to sell and brand your container farm business
Check Out The Guide Here
Darragh McCullough: Vertical Farming Is All The Rage, But The Downsides Will Limit Its Potential
There are so many stories about this tech that you would be forgiven for thinking that there is going to be a vertical farm at every traffic light next time you make it into the city
What grows up, must come down: Vertical farming presents interesting possibilities, but it has its limits
Darragh McCullough
February 20, 2020
Vertical farming is all the rage. It makes great click-bait by combining key buzz words: 'technology' in the form of new LED lighting; 'novelty' food that some celebrity chef can shout about producing beside their New York restaurant, and 'sustainability' courtesy of zero food miles and a low carbon footprint.
Your phone's news feed is probably similar to my own.
There are so many stories about this tech that you would be forgiven for thinking that there is going to be a vertical farm at every traffic light next time you make it into the city.
But beyond the low-energy LED lights in colours tailored to turbo-charge plant growth even in the depths of winter, you realise that we've had vertical farms for decades.
More recently, I've seen production in tunnels and glass take on vertical formats. Modern glasshouses are now so tall that each line of tomatoes or peppers is tended to via nifty little scissor lifts. I see the same trend in tunnels, with 4m high tunnels now standard in new soft fruit set-ups.
When I visited the Farmony vertical farm in Ballycoolin, west Dublin for Ear to the Ground this year, we all had to gown up before being allowed access to the growing unit.
It might have appeared a bit over-the-top given that we were just stepping into a converted refrigerated truck container that has a few pumps, fans and extra sockets fitted.
But by manipulating every single aspect of this growing environment - and maintaining near-sterile conditions - the people behind Farmony claim that their 80 square metre unit can produce the same amount as a 5ac field. That's a 250-fold increase in the productivity per square metre, which is impressive by any measure.
Farmony is focusing on the unit's ability to grow leafy salads and herbs, especially the baby and micro-leaved versions that are so beloved of chefs and foodies.
Normally these are flown in from places like Africa, Israel and further afield at this time of year when it's just impossible to grow them commercially here in tunnels or glass.
The beauty about using refrigerated truck containers is that they are insulated, allowing the grower to maintain ideal temperatures at a relatively low cost.
They are also pretty secure and mobile so that they can be parked anywhere there's room for a truck container.
The idea is that they'll pop up in carparks, basements, and office block roofs, regardless of whether that's in baltic Belfast or boiling Beirut.
Farmony claims that the €87,000 price tag is a snip given that the herbs the container is capable of producing would pay that off after all costs in about two years.
The downsides? The unit should be able to work well for produce that is 95pc water and has a short growth cycle of just 1-3 weeks. These plants don't need a lot of heat and light to get to a saleable point. But if you wanted to grow a more carbohydrate-dense food - like any root crop, or even a strawberry where only a small fraction of the plant that you've poured light and heat energy into ends up being saleable - the calculations start to unravel.
And, much and all as we should be reducing our calorie intake, there's only so much salad that a body can take.
We'll certainly see more of the LED light tech being incorporated into existing production systems like tunnels and glass, and there are interesting possibilities for old mushroom tunnels to be repurposed as salad units.
But there's a lot to be said still for good old-fashioned horizontal farming.
Indo Farming
8 Keys To Getting Funding Through Contain
Figuring out financing is one of the big challenges every new indoor farmer faces. Like death and taxes, it’s nearly inevitable. According to research from software provider Artemis, indoor farmers’ greatest challenge is finding funding
February 28, 2020
Figuring out financing is one of the big challenges every new indoor farmer faces. Like death and taxes, it’s nearly inevitable. According to research from software provider Artemis, indoor farmers’ greatest challenge is finding funding.
Contain’s mission is to change that, and in our work using tech to better connect growers to vendors and lenders, we always get the same question: how do you up your odds of securing equipment leases? Well, we’ve got answers.
We put together this guide to help anyone considering working with Contain up their odds of funding. We hope it helps demystify the funding process in general, too.
1. Where are you based?
We work with growers across the U.S. and Canada, but our best lender coverage is in the lower 48.
2. How long have you been farming?
We work with lots of startup farms. They’re great. But those with at least a two-year history of operations are more appealing to lenders. They’re viewed as a safer bet. Occasionally, lenders are willing to consider the track record of a different kind of business as you finance your farm.
3. Is your farm profitable?
Naturally, lenders prefer to work with profitable farms. That said, they also understand that increasing a farm’s scale will transform its economics, too. Don’t count yourself out if you’re still building towards the black.
4. What lease size are you looking for?
For a startup farm, we’ve found that it’s best to start small, sell out your produce and then scale to meet your customers’ demand. A common mistake we see is new growers trying to launch with a large setup, more than $1 million in equipment. Lenders rarely back farms like this at the get-go.
5. How much deposit will you put down?
Lenders generally want at least 20% down, and up to 50%. Of course, higher deposits often mean lower interest rates and, generally, better funding odds.
6. Do you have other collateral?
Lenders like to see other collateral for the lease, such as land or an existing property—especially if you’re a new grower. It’s not always necessary, but it definitely helps.
7. Do you have agreements with customers?
We know that most farmers sell produce without a prior written agreement but — at least where it makes sense for your business — lenders always appreciate letters of intent or even letters of support from customers. No bank has ever been mad because it got too many documents vouching for you.
8. How does your credit look?
A good credit rating with no recent bankruptcies usually translates into better leasing offers.
So that’s what you need to get started! Want to calculate your own odds of finding lease-funding? Take our quiz here.
Photo credit: Steve took it on VisualHunt.com / CC BY-NC-SA
Tags: Startup Funding Agriculture Sustainability Small Business
WRITTEN BY
Nicola Kerslake
We’re Contain Inc. We use data to improve access to capital for indoor growers, those farming in warehouses, containers & greenhouses.
Elon Musk's Brother Wants To Transform Farming
Vertical farming is an indoor farming method in which crops are grown in stacked layers, often without soil. The practice is becoming more popular and important as urban populations grow dramatically and available farmland decreases
February 28, 2020
New York (CNN Business)Plant-based foods are all the rage right now, and vertical farms are capitalizing on the trend.
Vertical farming is an indoor farming method in which crops are grown in stacked layers, often without soil. The practice is becoming more popular and important as urban populations grow dramatically and available farmland decreases.
While vertical farming isn't a new concept, these eco-friendly indoor farms are now rapidly expanding.
Elon Musk's younger brother, Kimbal Musk, who was named "Global Social Entrepreneur" of the year by the World Economic Forum in 2017, started Square Roots, an indoor urban farming company based in Brooklyn, in 2016. Square Roots' mission is to bring fresh, local food to cities around the world by empowering younger generations to participate in urban farming.
"When I was a kid, the only way I could get my family to sit down and connect was by cooking the meal," Musk, co-founder and executive chairman of Square Roots, told CNN Business in an email.
Kimbal Musk teaches students how to plant a vegetable garden in California.
"Getting involved with the internet, especially in the late '90s, was very exciting and I wouldn't change anything about those experiences, but my passion has always been food," Musk said. "The moment Elon and I sold Zip2, our first internet company, I knew I wanted to pursue food and become a trained chef." He moved to New York and enrolled at the International Culinary Center.
Musk said the company plans to open a Square Roots "Super Farm" — with 25 climate-controlled shipping containers, cold storage, biosecurity infrastructure and everything else needed to run a vertical farm at scale — in less than three months.
Since its inception, Square Roots has grown more than 120 varieties of crops, including greens, vegetables, and strawberries.
The company isn't the first of its kind. Startups like Silicon Valley's Plenty, which was founded in 2013 and is backed by Jeff Bezos, are also beginning to dominate the space.
"Environmentalists, urban farmers, architects, agronomists, and public health experts, among others, have been joining this mini-revolution as they partner to work out a way to salvage a food-scarce, ultra-urbanized future," Kheir Al-Kodmany, a professor of sustainable urban design at the University of Illinois at Chicago, said in a report.
It involves various techniques, such as hydroponics, which uses mineral nutrient solutions in a water solvent; aquaponics, which uses aquatic creatures -- such as fish and snails -- and cultivates plants in water; and aeroponics, which grows plants in the air.
As for job creation, rapid climate change will put millions of traditional farmers out of business, but vertical farmers won't be affected, according to microbiologist Dickson Despommier, an emeritus professor of public and environmental health at Columbia University.
Although vertical farming was first introduced in the early 1900s, it was recently popularized by Despommier. More than 20 years ago, he began teaching a class at Columbia called Medical Ecology.
Despommier spent a decade growing crops indoors with his students. "Ten years ago, there were no vertical farms," he said, noting that LED grow lights have vastly improved farming efficiency over the last five years, making indoor growing cheaper and more reliable.
Basil growing at the Square Roots farm in Brooklyn.
"People want local food because they've lost trust in the industrial food system that ships in high calorie, low nutrient food from thousands of miles away with little transparency as to who grew the food and how," said Peggs, the Square Roots CEO.
At the same time, the world population is growing and urbanizing rapidly. Peggs said climate change is threatening existing supplies of food, forcing the industry to figure out new ways to grow food quickly.
Peggs is optimistic about raising money for vertical farming. "A lot of smart money and capital is entering the space," he said. "The quality of food that can now be produced in these indoor systems is at least on par with the best organic field-grown food you can buy."
Despommier said that cities will eventually be able to grow "all they can eat" from indoor farms located within city limits. "If an outdoor farm fails, the farmer has to wait until next year to start again, he said. "Indoor farms fail too, but the indoor farmer can start again within weeks."
Freight Farms Is Now More Green
Freight Farms runs a network of smart farms across 44 states and 25 countries. Each smart farm called a “Greenery” is housed in a 320 -sq.-ft. hydroponic shipping container
The Boston startup that builds automated farm systems in shipping containers raised $15M in a Series B round led by New York City-based Ospraie Ag Science, which invests in agtech companies. Existing investor Spark Capital also participated in the round, which brings the company’s total funding to more than $28M.
Freight Farms runs a network of smart farms across 44 states and 25 countries. Each smart farm called a “Greenery,” is housed in a 320-sq.-ft. hydroponic shipping container. These vertical farming containers are all linked to the startup’s data platform, Farmhand.
The startup’s customers range from food distributors and grocery stores to educational institutions and corporate campuses. In the past, the company has worked with the Compas Group, Google and Federal Realty Investment Trust.
The 10-year-old startup claims its farms can grow more than 500 varieties of crops at a commercial scale by using 99.8% less water than traditional agriculture.
Read more: Freight Farms Raises $15M in Series B For New Partnerships and Expansion
CubicFarm Systems Announces Its Largest Sale To Date - A 100-Machine Commercial-Scale Vertical-Farming System in Surrey, BC
The Company has a current backlog at C$24.7 million representing 144 machines under deposit and awaiting installation - demonstrating continued sales momentum due in part to the growing demand for its systems. The current backlog is anticipated to be recognized in revenue in mid-2020 to mid-2022
March 2, 2020
VANCOUVER, BC / ACCESSWIRE / March 2, 2020, / CubicFarm® Systems Corp. (TSXV: CUB) ("CubicFarms" or the "Company") is pleased to announce that it has finalized an agreement for the sale of 100 CubicFarms growing machines, and received a deposit in the amount of C$1.2 million from a commercial grower and agricultural product wholesaler based in the province of British Columbia, Canada. The customer had previously provided a deposit for a 12-machine system and now has applied its deposit toward this revised order for 100 machines.
The 100-machine system represents a total of C$16.5 million in sales revenues to the Company, and is expected to be installed in two phases in Surrey, BC. The first phase, consisting of the installation of 26 growing machines and an irrigation system, is planned for installation this year, with the remaining machines planned for installation by mid-2022.
The Company has a current backlog at C$24.7 million representing 144 machines under deposit and awaiting installation - demonstrating continued sales momentum due in part to the growing demand for its systems. The current backlog is anticipated to be recognized in revenue in mid-2020 to mid-2022.
The sale represents CubicFarms' largest to date, following on its 21-machine sale to a customer in Montana, USA - its largest sale in the US - and its 23-machine sale to a customer in Calgary, Canada.
Due to the close proximity of the customer's Surrey site to CubicFarms' headquarters, CubicFarms will provide a turn-key solution to the customer, by facilitating and managing site preparation and installation of the CubicFarms system - leveraging the experience the Company has gained from its R&D and production facility in Pitt Meadows, BC.
CubicFarms CEO Dave Dinesen commented: "We are extremely encouraged by the growth in sales we've enjoyed and the trend toward increasingly larger facilities. It reflects the demand emerging around the world for commercial-scale growing technology. Once installed, the system in Surrey will be one of the world's largest automated vertical-farming systems.
"We are excited to be working with our customer, an established multi-industry group with investments and operations in the agriculture, technology and health space. Our customer understands the importance of using technology to significantly improve yields in an environmentally sustainable manner, and we look forward to helping them scale up production of fresh local vegetables for their market in southwest British Columbia and beyond.
"We are also pleased to receive ongoing feedback from our existing machine customers about the quality of produce from our systems and the resulting growth in demand for that produce."
Concurrent with the 100-machine sale, CubicFarms has entered into a Shareholders' Agreement with the customer and its associated companies with respect to a joint venture entity that will own and operate the 100-machine venture. As consideration for CubicFarms' 20% ownership in the joint venture, the Company will provide approximately C$342,000 in the form of a zero-interest loan.
Neither the TSX Venture Exchange nor it’s Regulation Services Provider (as that term is defined in the policies of the TSX Venture Exchange) accepts responsibility for the adequacy or accuracy of this release.
About CubicFarm® Systems Corp.
CubicFarm Systems Corp. ("CubicFarms") is a technology company that is developing and deploying technology to feed a changing world. Its proprietary technologies enable farmers around the world to grow high-quality, predictable crop yields. CubicFarms has two distinct technologies that address two distinct markets. The first technology is its patented CubicFarm™ System, which contains patented technology for growing leafy greens and other crops. Using its unique, undulating-path growing system, the Company addresses the main challenges within the indoor farming industry by significantly reducing the need for physical labor and energy, and maximizing yield per cubic foot. CubicFarms leverages its patented technology by operating its own R&D facility in Pitt Meadows, British Columbia, selling the System to farmers, licensing its technology and providing industry-leading vertical farming expertise to its customers.
The second technology is CubicFarms' HydroGreen System for growing nutritious livestock feed. This system utilizes a unique process to sprout grains, such as barley and wheat, in a controlled environment with minimal use of land, labor, and water. The HydroGreen System is fully automated and performs all growing functions including seeding, watering, lighting, harvesting, and re-seeding - all with the push of a button - to deliver nutritious livestock feed without the typical investment in fertilizer, chemicals, fuel, field equipment, and transportation. The HydroGreen System not only provides superior nutritious feed to benefit the animal but also enables significant environmental benefits to the farm.
Information contact
Kimberly Lim
kimberly@cubicfarms.com
Phone: +1-236-858-6491
www.cubicfarms.com
Cautionary statement on forward-looking information
Certain statements in this release constitute "forward-looking statements" or "forward-looking information" within the meaning of applicable securities laws, including, without limitation, statements with respect to the anticipated benefits to the customer; timing and the completion of machine installation by mid-2022; benefits to the Company of the sale; the anticipated revenue recognition in mid-2020 to mid-2022; and the joint venture that will own and operate the 100-machine venture. Such statements involve known and unknown risks, uncertainties, and other factors which may cause the actual results, performance, or achievements of CubicFarm Systems Corp., or industry results, to be materially different from any future results, performance, or achievements expressed or implied by such forward-looking statements or information. Such statements can be identified by the use of words such as "may", "would", "could", "will", "intend", "expect", "believe", "plan", "anticipate", "estimate", "scheduled", "forecast", "predict", and other similar terminology, or state that certain actions, events, or results "may", "could", "would", "might", or "will" be taken, occur, or be achieved.
These statements reflect the company's current expectations regarding future events, performance, and results and speak only as of the date of this news release. Consequently, there can be no assurances that such statements will prove to be accurate and actual results and future events could differ materially from those anticipated in such statements. Except as required by securities disclosure laws and regulations applicable to the company, the company undertakes no obligation to update these forward-looking statements if the company's expectations regarding future events, performance, or results change.
SOURCE: CubicFarm Systems Corp
Harvest Fresh Canteen Vegetables On-Site
In schools and universities in America, the catering and service provider Sodexo plans to produce fresh vegetables all year round via indoor farming. To this end, the company is cooperating with the US hydroponics provider Freight Farms. The salad should grow vertically in containers on campus
by Frauke Brodkorb-Kettenbach
February 15, 2020
In the container greenery of the US company Freight Farms, Sodexo grows fresh vegetables for its cafeterias directly on campus. CAROLINE KATSIROUBAS / FREIGHT FARMS
In schools and universities in America, the catering and service provider Sodexo plans to produce fresh vegetables all year round via indoor farming. To this end, the company is cooperating with the US hydroponics provider Freight Farms. The salad should grow vertically in containers on campus.
Over 500 vegetables, such as Salanova Green Butter Salad (pictured), can be grown on a commercial scale in Freight Farm’s containers with 320 square meters of vertical acreage - regardless of the season and without pesticides or herbicides. Delivery routes are also eliminated with this type of vegetable cultivation.
Save resources
With the cooperation, Sodexo is pursuing its strategy of operating as sustainably as possible and at the same time being precisely informed about the origin of its food for customers in the education segment.
In addition, students could monitor the stages of growing their food. For example, schools could integrate hydroponic farming into interactive curricula or school subjects such as technology, agriculture, nutrition, and economics, according to Freight Farms' approach. The vertical farming provider also sees similar advantages for employees when using the containers in companies.
CAROLINE KATSIROUBAS / FREIGHT FARMS
So far, vegetables grow in freight farm containers in 25 countries and 44 states in the US - in small and medium-sized businesses, hospitals, as well as in retail and non-profit organizations, the information says. 35 school facilities now work with the hydroponics system. By working with Sodexo, the number should grow rapidly.
SODEXO, USA
Sodexo USA offers building management and catering services to schools, universities, hospitals, senior citizens' communities, venues, and other key industries. The parent company Sodexo Quality of Life Services, with headquarters in Issy-les-Moulineaux, France, was founded in 1966. According to its own statements, the group offers Benefits and Rewards Services and Personal and Home Services daily for 100 million people in 72 countries. In 2019, it had an annual turnover of 22 billion euros with 460,000 employees worldwide. The portfolio includes reception, security, maintenance and cleaning services, catering, facility management, restaurant, and gift vouchers and fuel passes for employees.