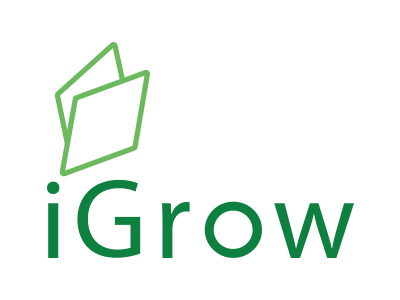
Welcome to iGrow News, Your Source for the World of Indoor Vertical Farming
The Future of Food: Why Farming Is Moving Indoors
A car park opposite the infamous New York City housing estate where rapper Jay-Z grew up seems an unlikely place for an agricultural revolution. Ten shipping containers dominate a corner of the Brooklyn parking area, each full of climate control tech, growing herbs that are distributed to local stores on bicycles. This is urban farming at its most literal
By Russell Hotten BBC News, New York
August 22, 2019
Tobias Peggs says the fledgling industry is still developing the right business models. SQUARE ROOTS
A car park opposite the infamous New York City housing estate where rapper Jay-Z grew up seems an unlikely place for an agricultural revolution.
Ten shipping containers dominate a corner of the Brooklyn parking area, each full of climate control tech, growing herbs that are distributed to local stores on bicycles. This is urban farming at its most literal.
The containers are owned by Square Roots, part of America's fast-expanding vertical farming industry, a sector run by many tech entrepreneurs who believe food production is ripe for disruption.
The world's best basil reputedly comes from Genoa, Italy. Square Roots grows Genovese seeds in a container that recreates the city's daylight hours, humidity, Co2 levels - and all fed hydroponically in nutrient-rich water.
"Rather than ship food across the world, we ship the climate data and feed it into our operating system," says co-founder Tobias Peggs.
High costs
An artificial intelligence expert, Mr Peggs founded Square Roots with investor Kimball Musk (Elon's brother) two years ago. They've signed a deal with one of America's big distribution companies, Gordon Food Service, to locate herb-growing containers at some its 200 warehouses.
He says the deal represents everything about indoor farming's potential: locally grown, quick-to-market, fresh produce that can be harvested year-round and is free of pesticides and harsh weather.
Bowery is set to open its third industrial-sized indoor farm. BOWERY FARMING
"Indoor farming can answer many of the questions being asked by today's consumers about the provenance, sustainability and health of the food they eat," he says.
Jeffery Landau, director of business development at Agritecture Consulting estimates the global value of the vertical farming market will rise to about $6.4bn by 2023, from $403m in 2013, with almost half that attributed to growth in the US.
Despite the sector's high costs and limited food range, the potential is not lost on investors. Recently, AeroFarms, a producer of lettuce and other leafy greens, raised $100m, including from Ingka Group, Ikea's parent company. Bowery Farming raised $90m in a funding round backed by Google Ventures and Uber boss Dara Khosrowshahi.
Plenty, another major US player, raised funds from Softbank chief executive Masayoshi Son and former Google head Eric Schmidt. The company has ambitions to build hundreds of vertical farms in China. In the UK, food delivery and robotics company Ocado is investing in indoor farming.
But there have also been failures. "Vertical farms are a highly intensive capital expenditure," says Mr Landau. "Your lighting system will be one of your highest capital costs." And then there's ventilation, air conditioning, irrigation and harvesting. "Make a mistake and you will have one costly upgrade on the horizon," he adds.
Mr Peggs chose a modular system based around shipping containers because he says it is quickly scalable according to demand. "We can put a herb farm in new city for less than $500,000 and be growing within two months. We just press the 'basil button' - or mint, or tarragon - and the box configures itself to grow in optimum climate conditions."
In neighbouring New Jersey, however, Bowery Farming, takes a different approach. The five-year-old company runs industrial-sized farms. Outside one huge, grey windowless warehouse a heat haze shimmers off the concrete. It's a sharp contrast to the chilly interior where an aroma of fresh farm produce hits you immediately.
Robots
Produce is grown on trays stacked ceiling-high to maximise acreage. Everything from the automatic seeding machine to harvesting is run by Bowery's proprietary operating system (OS) which controls light, adjusts water nutrients and takes camera images of each plant to monitor its health.
"The OS is our central nervous system. There are millions of data points," says founder Irving Fain. "The artificial intelligence is constantly learning and predicting how to produce the best quality product."
Irving Fain hopes to soon start producing radishes and turnips commercially. Michael BACA Image
Running the farm manually would be difficult, he says. Staff operate things from computer screens and iPads. In the cavernous farm room itself, the only sound is robots moving the shelves.
Growing food indoors has been around for decades, but the industry got a kick-start from advances in the performance of lower cost LED lighting. Combine that with robotics, innovations and AI, and you have an industry that Mr Fain says is both viable and scalable.
"The big question was, how can we grow in large volumes at a consistently high quality? Suddenly, the economics changed," he says. "We can grow 365 days a year - a major departure from thousands of years of agriculture. Unlike outdoor farming, our yield is virtually 100% guaranteed."
Vertical farmers talk with a zeal you'd expect of entrepreneurs with tech world backgrounds. With population growth and climate change putting pressure on food production, they think they may have answers.
Square Roots' herbs are delivered to customers by bike. SQUARE ROOTS
But this highlights one of the industry's limitations. You can't feed the world on leafy greens. That said, for Mr Fain, if Bowery only ever grew lettuce or kale, "it's still a win". But his ambitions are greater. Bowery is growing radishes and turnips that he expects to come to market with two years.
Square Roots hopes to soon start commercial production of beetroots and strawberries, and is experimenting with so-called heirloom produce from rare and long-forgotten seeds.
Carbon footprint
Mr Peggs says: "It makes sense to grow perishable produce in the same neighbourhood as the consumer - stuff that doesn't travel well. A lot of produce - tomatoes, strawberries - are grown for travel, not for taste. It doesn't make sense to vertically farm food with a long shelf life."
But different produce presents different challenges, says Mr Landau. Where plants are concerned, not all light is created equal. Fruiting and flowering crops such as tomatoes, strawberries and peppers have different needs.
QR codes on the food packaging can tell customers the history of the produce. SQUARE ROOTS
"Lights for these types of crops will generally be more expensive, require more electricity, and produce more heat, meaning additional cooling," says Mr Landau. "Harvesting these crops can be a significant operational cost."
But it is being done. In the US, Oishii vertically farms the much-prized Japanese Omakase strawberry year-round. And Farm One produces more than 200 products, including 34 edible flowers. Plenty is experimenting with watermelons. As technology costs fall and R&D intensifies, the crop variety will expand.
That may also ease criticism of the industry's carbon footprint. In the artificial light versus sunlight debate, the latter often has the upper hand. But, then, indoor farmers point to the transportation costs and waste in traditional agriculture.
For the moment, Mr Landau says, the carbon footprint concerns are valid, although he expects indoor farms to increasingly draw on renewable energy.
"And when you look at markets located in extreme climate environments or island nations where they import a majority of food, indoor farming could be a viable option," he says.
Mr Peggs stresses that industry is still young are trying to work out the right business models and direction. The entrepreneurs don't agree on everything, though they certainly agree on this: vertical farming has the potential to transform global food production as we know it.
Kimbal Musk’s Goal: Grow Fresh Food In Containers In Every American City
Musk’s newest venture — alongside his co-founder Tobias Peggs — combines food and technology to empower the next generation of farmers. Square Roots is a seed-to-sales urban farm, connecting people in cities to locally grown whole foods. The farm also runs a farmer-training program, which creates opportunities for more people to become urban farmers.
August 22, 2019
Kimbal Musk | SUSAN FRANCE
Standing out in Boulder is not an easy thing to do. From famed world athletes to politicians, the city has its share of notable residents, but when a 6-foot-4-inch man wearing a cowboy hat walks around town, people notice. Some know who he is; some don’t. It’s Kimbal Musk, food entrepreneur and owner of The Kitchen restaurant chain.
Musk’s newest venture — alongside his co-founder Tobias Peggs — combines food and technology to empower the next generation of farmers. Square Roots is a seed-to-sales urban farm, connecting people in cities to locally grown whole foods. The farm also runs a farmer-training program, which creates opportunities for more people to become urban farmers.
Currently, Square Roots farmers grow a variety of fresh herbs in indoor, vertical farms inside containers, right in the heart of Brooklyn. They hand-harvest, self-package and deliver to retail stores across New York City. The herbs are non-GMO and pesticide-free, developed through human-centered farming technology that surrounds farmers with data, insights and tools so they can grow high-quality food, all year-round, using the fewest resources possible.
The system uses a water-efficient hydroponic growing system within vertical modular farms in shipping containers, which means there is no need for pesticides. Plus, Musk says, it requires about one-tenth the amount of water compared to traditional gardening.
Musk started to really think about urban gardening 16 years ago when he opened The Kitchen in Boulder alongside partner and chef Hugo Matheson. According to Musk, they worked with local farmers from the beginning because the food simply tasted better. Along the way, they ended up learning about the sustainability ethos and how much local farmers care about the land, as well as how important it was to have local food production.
The idea behind Square Roots, Musk says, was to create something that would enable the best quality herbs while empowering young farmers to grow food in the city.
“Most of our young farmers are in big cities,” Musk says. “They are not in the countryside.”
But every new technology comes with a cloud of doubts and skepticism, and Square Roots is not immune. Critics have questioned whether or not Square Roots will require more fossil fuel energy to grow food inside, as well as the limits to the type of food that can be produced without soil, and the unrealistic possibility of feeding millions of people with a technology that cannot produce food for the masses.
Musk says that Square Roots’ electricity consumption is mitigated because the containers use electricity at night when power plants have excess energy.
“The energy is being produced anyway,” Musk says. “The farms don’t pull more energy from the grid, which allows us to get electricity at a much lower price.”
For farmer Maxwell Carmack, a Square Roots graduate, the future of vertical farming seems promising. Aware of the critics, he says the carbon footprint of the transportation and refrigeration costs currently in use to move food across the country is worse than the electricity needed to run the indoor farms. Still, he is looking forward to incorporating sustainable energy production technologies to the industry of vertical farming to take it to the “next step.”
While critics may think it will be impossible to feed cities out of containers, Carmack, an engineer who decided to stay on with Square Roots after graduating the program, is excited to prove them wrong.
“I spend my time making all of the marginal gains that can add up,” he says. “In fact, in the past year we’ve doubled the production. I see improvement every day. In the end, as an engineer, I care about what might be possible and not what might not.”
Since its founding two and half years ago, the Square Roots program has graduated 30 people, and many graduates have taken the path of entrepreneurship, from rooftop garden installations to catering. And it’s expanding, as urban farmers in Grand Rapids, Michigan, will soon start producing fresh herbs as well.
Musk says the ultimate goal over the next 10 years is to have Square Roots systems in every U.S. city and to graduate around a thousand new urban food farmers, while continuing to improve the technology. While he’s aware that Square Roots can’t feed America alone, he hopes it’s the start of a vertical revolution with its roots in Boulder.
LAST CALL: Become A Next-Gen Farmer In Brooklyn, New York
Applications are open for the fourth season of the Next-Gen Farmer Training Program on our Brooklyn farm campus
Applications are open for the fourth season of the Next-Gen Farmer Training Program on our Brooklyn farm campus. We’re looking for passionate and dedicated people to become integral members of our farm team. No experience is necessary, just the drive and excitement to jump in and start growing.
Apply now until August 23
Our next monthly farm tour will be on Tuesday, August 20 at 5:30 pm— if you’re in NYC next week, stop by and say hello!
Meet the current cohort of Next-Gen Farmers, taste our hyper-local herbs, and see the farms first-hand. More info + RSVP.
Fresh Out of The Box
Shipping containers, the vectors of globalisation that were forged in the first instance to ferry goods thousands of miles around the earth, are now being used to grow fresh produce that will be consumed in their immediate vicinity
Wednesday 14th August 2019, London
As interest in urban farming continues to grow, modular, closed-loop production units could spark a horticultural revolution
A growing phenomenon that is reshaping fresh produce supply chains. Shipping containers, the vectors of globalisation that were forged in the first instance to ferry goods thousands of miles around the earth, are now being used to grow fresh produce that will be consumed in their immediate vicinity. What’s more, having made international markets more accessible to all, the containers now house technology so advanced that even someone with the most basic, rudimentary knowledge of horticulture can control and oversee the cultivation within.
Excitement about the potential of urban farming continues to build, with the idea of producing closer to market – using fewer resources and arguably boosting quality in the process – attracting plenty of interest, not to mention investment. Earlier this year, Italian start-up Planet Farms unveiled a plan to build Europe’s largest and most advanced vertical farm by spring 2020 in Cavenago, halfway between Milan and Bergamo. The farm will eventually extend across 9,000m2 and supply 40,000 packs of residue-free produce per day.
It’s a trend that is by no means confined to Europe or North America. In Shanghai, a group called Orisis is working with joint venture Infinite Acres – comprising British online retailer Ocado, Dutch horticultural tech specialist Priva and US plant science firm 80 Acres Farms – to build what it says will be the city’s first indoor vertical farm, producing lettuce and other leafy greens.
However, it’s the arrival of closed-loop, container-based systems, which theoretically allow anyone to become a grower, that could really revolutionise this area of the fresh produce business. In June 2019, furniture retail giant Ikea revealed it was preparing to harvest its first hydroponically grown lettuces and serve them to customers at two of its in-store restaurants in Helsingborg and Malmö. The vegetables are grown under led lights inside specially retrofitted shipping containers using a so-called circular farming system developed by partner company Bonbio. Days later, Swedish supermarket chain ICA announced a similar venture at its Maxi Högskolan store in Halmstad, between Gothenburg and Helsingborg, using a container system called Greenery configured by Boston-based vertical farming start-up Freight Farms.
In this exclusive interview, fresh focus tech speaks to Freight Farms co-founder Brad McNamara about the company’s recent dramatic growth, about the trends he says are driving that expansion and about a future that might eventually see fresh produce cultivation become something that practically anyone with access to a laptop or smartphone can manage and control.
Brad, can you tell us what inspired you and co-founder Jon Friedman to create Freight Farms?
Brad McNamara: We were originally looking at how we could bring food production closer to the urban centre. We were looking at greenhouses, but really it came down to a better way to create accessibility and transparency in the food system. So for us, the idea was to move away from the constraints of a rooftop greenhouse to a more user-friendly model that allows a wider population to grow locally in a particular place. That’s really where it all came from.
Were you involved in horticulture in any way prior to that?
BM: Not specifically, although I had been growing on my own for some time. I got an undergrad degree from Northeastern University in Boston, then an MBA in sustainability and environmental science. Jon’s background was industrial design, so the two kind of married well. The big thing for us was, when we first started the market potential for local, transparent, sustainable, chemical-free was just at the beginning. Everybody was talking about it, but no-one had a solution for how to produce in those ways while increasing the quality and consistency of the supply chain.
The business you created, was it a fairly large operation from the start?
BM: No, at the start it was Jon and I plus a small team, very much your classic startup, starting in a simple parking lot. We knew we needed to build the technology from the ground up with the market and the farmer in mind, and we knew it had the potential to empower anyone to grow food anywhere. We built our first prototypes in 2012 and went into commercial manufacturing in 2014.
To whom did you show this original proof of concept?
BM: Well, anyone that would look in the early days! What we did was grow a wide variety of crops to test the stability and the flexibility of the system, as well as some of the concepts within it. I was constantly bringing people from the produce industry by, so we made a lot of connections with cold supply chain, produce distributors, regional specialists, as well as some of the markets around us. We talked to a lot of the wholesalers and asked them, ‘Is this product ready? or ‘Is this crop specifically what you would look for, or maybe something different?’ That was really the guiding light, to know what the market would accept. The feedback was phenomenal. Much of the time they would say ‘this is fresher, brighter, crisper than anything I’m getting now’ and they got very excited about that.
Were there any areas in which you needed to improve?
BM: Well, once we got the plants in their mouths, there weren’t really any doubts left. You know when you eat something and it’s really good? I think in the early days it was more about general education in the market, in terms of growing crops indoors, hydroponics and all of the more technical pieces which by now have been more established. On the institutional side, the concept of needing to supply more locally grown food was not something we had to explain. They were getting hammered by their customers to provide higher quality, locally sourced, clean, healthy and consistent produce.
Brad McNamara (left) with Freight Farms co-founder Jon Friedman
Around 2012, there was a lot of talk about vertical farming as a concept that might eventually see production centres constructed as entire buildings in cities. Were you aware of this trend bubbling away?
BM: We were right there at the early stage of vertical farming, so we had the benefit of building systems while seeing those conceptual drawings of space-age technology. That was great, because it was almost like watching a sci-fi movie while you’re doing it in real life. Some of those concepts did apply but we had that functional knowledge we needed to satisfy.
Many people at the time said it was science fiction, but we kept very quiet about the fact that we were already accomplishing it with our unit. That made us feel like we were on to something. We were early enough that we were growing, we had customers and we had market insight. Technology for technology’s sake wasn’t going to serve our customers appropriately.
With any transition to a new technology, there can be resistance from certain quarters. Did you encounter any concerns about bringing traditional horticulture into an urban, indoor environment?
BM: What people want to understand is about traceability – where exactly did it come from, who grew it, how was it grown. That’s been the driving question in the conversation, and less about whether it’s grown in soil or not. Indoor-grown, whether in a greenhouse, warehouse or decentralised module is pretty much mainstream at this point.
The full interview with Brad McNamara of Freight Farms is published in Fruitnet's annual fresh produce technology supplement Fresh Focus Tech.
To order your copy, contact subscriptions@fruitnet.com or +44 20 7501 0311.
Part two of this interview will be published on Monday 26 August.
Dave Riddell Grows Greens In A Storage Container
Riddell grew up in Needham, Massachusetts outside Boston. Both his mom and his aunt were passionate gardeners. His fascination began early with the plant world. He graduated from the University of Maine after a course of study that included communications and forest recreation management
August 7, 2019
Owner Dave Ridill holds a tower of growing lettuce inside his hydroponic farm, housed in an upcycled, 40-foot shipping container in Tetonia, Idaho. Riddell has been in business for three years and grows a variety of hardy greens like lettuce, Swiss chard, arugula and others. It happens 365 days a year.
Greens sprout from towers in Riddell’s hydroponic farm at Clawson Greens.
REBECCA NOBLE / NEWS&GUIDE photos
It was quite a while back, actually, that my dear friend Ken retired from Grand Targhee Resort’s ski patrol and moved to Salt Lake City. It was then that he told me it would be a good idea for me to become acquainted with his fellow patroller, Dave Riddell. Ridill had started a new business, Clawson Greens, growing greens inside shipping containers in Tetonia, Idaho. Now just how unlikely is that scenario?
Ridill and I spoke on the phone a few times before I met him, with me repeatedly promising it would be soon that I would come check out his scene. Around Christmas time of 2017 we met while he was delivering his beautiful produce to Hand Fire Pizza as I was interviewing the chef and manager for a column. Hand Fire serves one simple and delicious salad. It is made of Clawson Greens.
Ridill grew up in Needham, Massachusetts outside Boston. Both his mom and his aunt were passionate gardeners. His fascination began early with the plant world. He graduated from the University of Maine after a course of study that included communications and forest recreation management.
One college spring break Riddell accompanied his brother and some friends to Jackson Hole to ski. While in the neighborhood he applied for a summer job at Grand Targhee on the wilderness crew of the U.S. Forest Service in the Jedediah Smith Forest. That continued until 2018, when Clawson Greens began consuming more of his time.
That winter of 2007 Ridill started a winter job of as ski patroller at Grand Targhee that he still enjoys. He was later a bike patrolman for six years but, after breaking his back in four places, he decided that job was not for him. He also worked as part of Teton County, Idaho’s fire department.
In 2016 he was about to attend paramedic school in Boston when his neighbors approached him with an outlandish proposal. They had discovered a company that used shipping containers to grow food in a controlled environment. They loved the idea and yet believed it more appropriate for someone much younger than they were to embark on such project of that scope. Thus they shared the idea with their favorite neighbor.
Ridill became more intrigued and educated about the possibilities. There are countless shipping containers all over the planet. Many are abandoned or fallen into disuse. Why not repurpose, up-cycle these already existing units in a productive manner?
Ridill connected with Freight Farms. As fate would have it, the founder of the company grew up a couple miles from Ridill’s family home. They went to the same high school although five years apart. It was as if it was meant to be.
After he returned from training with Freight Farms the first shipping container grow room arrived at its final home in Tetonia, Idaho. In the winter of 2017 Ridill had his first restaurant customer.
It’s simple to check out Freight Farms’ website online. It is amazing to look at the possibilities of the future of farming and food, though it’s much more impressive in person.
The system uses a fraction of the water used in most agriculture. The drip irrigation waters the vertical tube, and it all recycles. The environment is temperature and humidity controlled for a growing season of 52 weeks a year. Beautiful organic produce is available mud- and insect-free using no pesticides.
It is an eight-week process from planting the seeds in tiny plugs to harvesting the heads of greens with their root ball attached. The variety of plants ranges from red-veined sorrel and wasabi arugula to rainbow chards and many lettuce varieties. All are vibrantly alive and remain in excellent condition for use for a couple weeks. As chefs plan their seasonal menus, Ridill provides specialty greens in a timely fashion.
There are now three grow room containers that supply 10 local restaurants. Last winter the customers at Phoenix and Dragon were impressed enough that they requested greens for home use. Eric and Zarina Sakai, who own Phoenix and Dragon, put together a little CSA. Ridill brought greens and everyone was happy. I hope they do it again next winter. It is true that the salads at the restaurant are particularly tasty. The small plate of summer rolls and their KFC, or Korean Fried Chicken, sent me into a dreamy state the other evening. Their summer schedule serves lunch Monday through Friday and dinner Tuesday through Saturday.
Ridill has not become a paramedic and yet he is caring for our health in a different way. It’s pretty exciting. 
Where to find Clawson Greens
The Phoenix and the Dragon
Hand Fire Pizza
Forage Bistro & Lounge (Driggs, Idaho)
Butter Cafe (Victor, Idaho)
Citizen 33 Brewery (Driggs)
Warbirds Cafe (Driggs)
Huntsman Springs (Driggs)
Royal Wolf (Driggs)
Branding Iron Cafe (Bondurant)
Visit ClawsonGreens.com or FreightFarms.com for more information.
Bru, who cooks for private clients, writes about the valley’s talented chefs.
US: Applications Open For Brooklyn’s Next-Gen Farmer Training Program
Square Roots is an urban farming company with a mission to bring local, real food to people in cities around the world by empowering next-gen leaders in urban farming
Square Roots | 08.05.19
The fourth season of the Square Roots Next-Gen Farmer Training Program at our Brooklyn farm campus starts October 2019. Applications will be open August 5 through August 23 at 11:59 pm EST. Apply now.
This year’s cohort of Square Roots Next-Gen Farmers harvesting hyper-local basil in the climate-controlled farms on our Brooklyn farm campus
Shaping a New Food System
The food system is changing rapidly all around us. People are increasingly demanding healthy, locally-sourced food. At the same time, technology is enabling entirely new systems to grow delicious food in the middle of cities, all year long. And young, diverse change-makers are now finding their place in an ever-evolving agriculture industry. There’s never been a more exciting time to forge a new career in farming. The opportunities to contribute to the real food revolution are endless. The big question is: how do you get started?
The Square Roots Next-Gen Farmer Training Program
Square Roots is an urban farming company with a mission to bring local, real food to people in cities around the world by empowering next-gen leaders in urban farming. Our Next-Gen Farmer Training Program is at the heart of what we do—providing an accessible pathway to the forefront of urban agriculture for more young farmers. Our farmers grow a variety of fresh and flavorful greens and herbs in indoor, vertical farms, right in the heart of cities. Our produce is non-GMO, pesticide-free, and hand-harvested.
Square Roots Next-Gen Farmers harvesting, packing, and sharing hyper-local herbs in Brooklyn, New York
This October, Square Roots launches the fourth season of our Next-Gen Farmer Training Program at our Bed-Stuy farm campus in Brooklyn, New York. We’re looking for passionate and dedicated future farmers to join our team. No farming experience is necessary—just the dedication and excitement to jump in and start learning.
Similar to traditional farmer apprenticeships, the Next-Gen Farmer Training Program is a full-time job, in which farm skills are learned through hands-on training and application of skills in a production environment. This is complemented by curriculum focusing on plant science, controlled-environment agriculture, and leadership in farming. Skill-building related to successful farm management is emphasized throughout the program, including but not limited to observation, problem solving, troubleshooting, interpersonal communications, management skills, and cultivating trust. After initial training in our modular, hydroponic growing systems, farmers are responsible for growing quality food on a consistent basis to meet customer demand—with the guidance of our expert Farm Management Team. Farmers are also integral to customer-focused marketing and community events, as we bring local, real food to local customers, all year round.
The experience gained in one year with the Next-Gen Farmer Training Program might take several years to develop in a traditional farmer apprenticeship. And while many people enroll in degree programs to study agriculture, plant science, or related fields, there are only a handful of places to study emerging and innovative types of agriculture, such as urban or controlled-environment agriculture. Our program provides an accelerated pathway into the sector and prepares farmers for roles as leaders in urban farming—without having to pay tuition. Over the past three years, alumnae/i have gone on to start their own urban farms, join forwarding-thinking agriculture companies and organizations, and move into permanent positions on the Square Roots Team.
The Future of Food
The future of our food system is in the hands of our farmers. Through collaboration, open minds, and full transparency, Square Roots believes that we can shift to a system that brings value to people, the planet, and the economy. This shared value system drives our Next-Gen Farmer Program: and now we want you to join us as we play our part in the real-food revolution.
The fourth season of the Next-Gen Farmer Training Program at our Brooklyn farm campus in New York starts in October 2019. Applications will be open from August 5 through 23, and more information can be found on the Square Roots website via www.squarerootsgrow.com/program.
Learn more about our Next-Gen Farmer Training Program.
Why Shipping Container Farming?
The local food trend isn't going away anytime soon, but as demand increases, traditional farmers and restaurants are faced with the challenge of providing fresh, hyper-local food year-round
Local Food Is Here To Stay
The local food trend isn't going away anytime soon, but as demand increases, traditional farmers and restaurants are faced with the challenge of providing fresh, hyper-local food year-round.
Since the advent of the grocery store, customer's have become accustomed to an endless summer regarding the variety of produce available on store shelves regardless of where they live. In order to feed the rising demand for local food, as well as meet the nutritional needs of a growing population, methods of indoor farming are a large part of the solution designed to meet increasing demand created by the local food movement.
There are a variety of approaches to growing crops in indoor environments including home growing, retrofitting warehouses, rooftop farming, and of course, container farming. If you want to learn more about the advantages and disadvantages of these practices, read our article on Comparing Different Indoor Farming Methods. But in this article, we are going to focus on what makes freight farming so accessible to new farmers, no matter where they're located.
An (extremely) brief history lesson
The number of farms producing the food we eat here in the United States has dropped by roughly 70% since the 1930's, leaving the majority of the food we eat grown by giant corporations, often shipped from hundreds or even thousands of miles away. Despite this trend, however, consumers' appetite for local food is growing. In 2014, local foods generated nearly 12 billion in sales and are expected to double by 2019. While the "local" label conjures up images of small farms, pastoral scenes, or perhaps even urban farming operations, the reality is, big box retailers are elbowing their way into the space and capitalizing on the trend.
Studies show that only about one-third of small farms has a designated successor in the family, in part because many young people are unwilling to make the significant financial investment in an industry that requires them to work long hours and has a somewhat antiquated reputation.
Container farming can work for anyone
The Leafy Green Machine at Google's Campus in Mountain View, CA.
At Freight Farms, we're committed to lowering the barriers to entry for small farmers by decreasing the start-up cost of farming and increasing the productivity on a per-square-foot basis. Furthermore, the automation inside the farm makes container farming less labor intensive than traditional agriculture and other indoor growing techniques, meaning that you have more time to grow the business side of your operation or pursue your other interests and entrepreneurial endeavors.
Container farming works well in both urban and rural settings and can function as a stand-alone business, or be an accessory to your existing farm or restaurant, making it easier for both small businesses and institutions to incorporate truly sustainable practices. It's a great learning tool, plus it can feed your employees, guests, or students.
Although some of our farmers come from farming backgrounds, many freight farmers are new to the industry. Part of our mission here at Freight Farms is to provide both the hardware and software solutions to simplify the hydroponic growing process, so that any company, individual or organization can grow fresh produce year-round no matter what their technical or farming experience might be.
“I just remember when we harvested our first round of produce the pride that our department felt – none of us are farmers! – in knowing that we made this happen ”
— Lenore Musick, Executive Director, Sustainability Initiatives at Georgia State.
A complete farming system inside a box
Unlike other indoor growing methods, the Greenery comes fully assembled to allow you seamlessly kickstart your farm and get growing.
Turnkey: The Greenery is a complete hydroponic growing system in a box. Meaning, freight farmers can perform every farm-related task from seeding to harvesting and packaging right inside the container!
Climate Controlled: Intuitive climate controls automatically respond to air and water sensors inside the farm to ensure an ideal growing environment for your crops.
Automated: Inside each farm is a central brain that is programmed to automatically adjust all the components inside the farm so that it's creating the perfect environment. That means the climate is managed by the Greenery, enabling farmers to focus on growing the crops and their business.
Remote Monitoring and Control: The farmhand® mobile application allows our freight farmers to remotely monitor and control the climate components inside the farm such as the lights, temperature, and humidity, so they can know what's going on inside the farm, even when they're not there.
Scaleable: The modular and stackable design of the Greenery allows you to quickly scale up your farming operation or start a new business from scratch.
Tech Businesses Seek To Shatter Stereotypes About Women In Farming
When Oluwayimika Angel Adelaja-Kuye started Nigeria’s first vertical farming company she already had years of experience advising governments under her belt - yet as a woman, she still struggled to be taken seriously
Reuters . Rome | July 06,2019
When Oluwayimika Angel Adelaja-Kuye started Nigeria’s first vertical farming company she already had years of experience advising governments under her belt - yet as a woman, she still struggled to be taken seriously. ‘In the beginning, even my staff, when they first come on board, are more likely to listen to my husband before me,’ said the founder of Fresh Direct Nigeria, which grows vegetables hydroponically - farming in water instead of soil. ‘These challenges make you hungrier,’ she told the Thomson Reuters Foundation. Women make up nearly half the global workforce in farming, but many say their contribution has long gone unrecognised, particularly in developing countries.
Adelaja-Kuye is among a small but growing group of women entrepreneurs who are helping to change that, many using new technologies to produce food in more sustainable ways. The 35-year-old, who started farming in the heart of the Nigerian capital Abuja in 2015 and uses shipping containers, said she wanted to support those who did not conform to the stereotype of the poor, uneducated subsistence farmer. Four of the six staff at her farm are young women who previously worked as household help.
‘I want young people to see agriculture as a solution for them, one that makes good money,’ she said. ‘If I’m changing the narrative of who a farmer is, I’m happy with that.’
She has that in common with Awa Caba, a computer scientist who co-founded a platform for Senegalese women farmers to sell their produce online. Caba’s company Sooretul - meaning ‘it’s not far’ - sells more than 400 products from about 2,800 rural women online. ‘My background is not agriculture,’ she said. ‘But it’s more sensitive for me to use my knowledge as a woman to target underprivileged groups, and give them more access and income. ‘My vision is to have a pan-African e-commerce platform where you can find different agricultural products produced by women in Africa.’
Sarah Nolet, who works as a consultant to the agricultural technology industry, said more and more women were getting involved in the growing sector. ‘When you take agriculture, it’s male dominated, and tech is often male dominated,’ said Nolet, the Sydney-based chief executive of AgThentic, which consults on innovation in food and farming. ‘So you would think AgTech would be worse. But we actually see, especially in Australia, a lot of female founders starting AgTech companies.’ Globally, women make up 43 per cent of the agricultural workforce, but they tend to have less access to land, credit, technical advice and quality seeds, according to the International Fund for Agricultural Development (IFAD).
If women farmers had the same access to resources as men, they could increase yields by 20 per cent to 30 percent, the UN Food and Agriculture Organization (FAO) has said. But much depends on having the right role models. ‘We have to change mindsets and show women in lucrative, high-value markets, with access to technology, and innovation,’ said Tacko Ndiaye, the FAO’s senior gender officer.
In 2018, companies working on food and agricultural technology globally raised a record $16.9 billion, according to AgFunder, a San Francisco-based online investment platform for these businesses.
Yet estimates based on available gender information show only 4 per cent of that went to start-ups with one or more female founders, said Louisa Burwood-Taylor, head of media & research at AgFunder.
‘However you slice the data, there’s clearly a very big gap in the level of female entrepreneurship in food and agriculture technology,’ she said. ‘The reasons for this gap are broad including educational and investment biases, so we are investigating how they can be overcome.’
Benjamina Bollag, who co-founded Britain-based Higher Steaks with stem cell scientist Stephanie Wallis, is among those who did receive funding - at least $200,000 since setting up 18 months ago.
Higher Steaks hopes to bring laboratory-grown pork to consumers within the next three years.
Several companies are seeking to produce cell-based meat, promising less waste and dramatically fewer greenhouse gas emissions than livestock, but most are focusing on beef or poultry.
Bollag said being a woman in a male-dominated industry had its difficulties, but added, ‘there are times when it was helpful too, where people were like, ‘actually, we want to diversify so we will pick you’.’
Ensuring women’s voices are heard in farming was a key motivation for Rose Funja, whose company uses aerial surveillance to help farmers in Tanzania avoid crop losses to insects, disease and other pests.
Funja, one of the country’s only female drone pilots, said she made a point of going to farms in person because that was the best way to meet the women who worked on cultivating the crop while the men tended to focus on sales.
‘They let me know what their actual needs are and how these technologies can help them. So we have been able to have very good conversations with them as compared to men,’ she said.
‘They (the women) say they feel safe to talk to another woman about their needs.’
📣 Last Call For Applications To Become An Urban Farmer in Grand Rapids, MI! 🌱
No farming experience is necessary—just the dedication and excitement to jump in and start learning.
Become a Next-Gen Farmer
This September, Square Roots launches the first season of our Next-Gen Farmer Training Program at our Michigan farm campus in Grand Rapids, and we’re looking for ten passionate future farmers to join the team. No farming experience is necessary—just the dedication and excitement to jump in and start learning.
This is the last call for applications, so if you know someone who would be a perfect fit, forward away!
Applications are open until July 12 at 11:59 pm EST.
Apply Now!
Korean Smart Farm Heads For Abu Dhabi
A Korean artificial farming technology developer has sent its first "farm" to the Middle East, boosting the start-up's global competitiveness in the promising industry
2019-07-08
By Ko Dong-hwan
A Korean artificial farming technology developer has sent its first "farm" to the Middle East, boosting the start-up's global competitiveness in the promising industry.
"Planty Cube," a white, 12.2-meter container created by n.thing, was shipped to Abu Dhabi from Busan Port in South Gyeongsang Province, on July 6, the Seoul-based company told The Korea Times.
Inside the module-type smart farm in the shape of a shipping container are multi-stacked rows of water troughs on both sides. Small pots called "Pickcells" can be slotted on each trough where seeds of whatever farmers want can be sown. The plants can then grow without human hands, with a computerized system controlling the environment from temperature to humidity and disease elements.
The maneuver happens in a control room outside the container. The room oversees inside all Planty Cubes, remotely changing the isolated spaces' conditions automatically and manually, based on each plant's "recipe" data.
The latest export to the United Arab Emirates city will first grow romaine lettuce. It will diversify its crops based on distribution data from the city's markets. The cultivated crops, from salads to herbs, will then be distributed to fresh vegetable markets.
Inside Planty Cube, the isolated environment's temperature, humidity and disease elements can be remotely controlled from outside. Courtesy of n.thing
"Those who influence the Middle Eastern smart farm markets quickly will eventually lead the industry on a global scale," said n.thing strategy officer Han Seung-soo.
"No smart farmer has yet stood tall in the region. We will move fast and aggressively to make our name known in the industry."
The Middle East, where many smart farm companies from different countries have ventured, has been supporting the industry because growing vegetables there in traditional methods is difficult because of the hot desert climate and a shortage of farm land and water.
In March this year, n.thing CEO Leo Kim signed a partnership with a major Korean conglomerate and then with an international trader in Abu Dhabi to mass-produce the cubes and auxiliary system parts.
Established in 2014, n.thing's smart farm modules can be linked to each other, making it easy for users to increase or decrease the capacity of their farm businesses. The company said the convenience differentiated the product from factory-type smart farms that could only be vertical.
Lead Photo: n.thing's "Planty Square" was transported to Busan Port on June 20 for export to Abu Dhabi, the United Arab Emirates, the following month. Courtesy of n.thing
aoshima11@koreatimes.co.kr More articles by this reporter
Grand Rapids, Michigan, Square Roots Starts Farmer Training Program in September
Square Roots is looking for 10 passionate and dedicated future farmers to join the team as it launches in September the first season of its Next-Gen Farmer Training Program at the Grand Rapids, Mich., farm campus at Gordon Food Service headquarters.
Amy Sowder July 3, 2019
Square Roots is looking for 10 farmers-in-training. ( Courtesy of Square Roots )
Square Roots is looking for 10 passionate and dedicated future farmers to join the team as it launches in September the first season of its Next-Gen Farmer Training Program at the Grand Rapids, Mich., farm campus at Gordon Food Service headquarters.
No farming experience is necessary, just the dedication and excitement to jump in and start learning, according to a news release.
Square Roots is an urban farming company with a mission to bring local food to people in cities around the world with next-gen leaders in urban farming. The training program provides an accessible pathway to the forefront of urban agriculture for more young farmers.
In March, Square Roots announced a partnership with Gordon Food Service to bring its farms and training program to their distribution centers across the continent, according to the release.
During the year-long program, similar to traditional farmer apprenticeships, farmers learn skills through curriculum focused on plant science, controlled environment agriculture, business and leadership, as well as hands-on learning by doing the tasks.
After initial training in the modular, hydroponic growing systems, farmers are responsible for growing quality food on a consistent basis to meet customer demand, with the guidance of an expert farm management team. Farmers are also integral to customer-focused marketing and community events.
For more information, visit www.squarerootsgrow.com/program.
Related Topics: Greenhouse Michigan Training Produce
These Tech Start-Ups Are Changing What It Means To Farm
Feeding a rapidly expanding population without depleting the Earth’s finite resources, is one of the major challenges of the 21st century
The future of farming? Image: REUTERS/Ilya Naymushin
01 Jul 2019
Briony Harris Senior Writer, Formative Content
This article is part of the Annual Meeting of the New Champions
Feeding a rapidly expanding population without depleting the Earth’s finite resources, is one of the major challenges of the 21st century.
These four entrepreneurs - who have all been selected as the World Economic Forum’s Technology Pioneers for 2019 - have a vision to transform the way we farm in order to help feed the world.
Mini-farms in underground parking lots
In an abandoned car park in downtown Beijing, trays and trays of planting beds are stacked on top of each other.
This is a mini-farm, right in the heart of the city, and it supplies nearby hotels with lettuce, celery, herbs, kale and other green vegetables.
“It’s no longer impossible to grow food where people work and live”, says Stuart Oda, who co-founded the agriculture start-up Alesca Life in 2013, referring to the amount of disused urban infrastructure available, including things such as old shipping containers.
LEDs provide the light, and mineral nutrients are added to water instead of soil. Internet-linked devices monitor humidity, acidity levels and the amount of dissolved oxygen in the water, allowing such variables to be adjusted to increase yields.
“Our system allows us to automate all of the major points of human error that could lead to a loss of crop,” Oda says.
Stuart Oda shows his container farms to the UAE’s minister for food security . | Image: Stuart Oda
The proximity of the mini-farms to the customers means that the produce is fresh, and reduces transport and packaging.
Alesca Life has signed an agreement to distribute 1,000 container farms across the Middle East, Africa, China, and North America.
Oda’s decision to launch his company was prompted by the change he could see happening all around him in China, including rapid urbanization, population growth and land degradation of traditional farms.
“There’s a real sense of urgency to dealing with these challenges and I want to dedicate all my productive years, including my passion and my youth, to addressing them,” he says.
2. Finding a market for ugly fruit and veg
Christine Moseley has witnessed massive food waste at first hand.
During the harvest of romaine lettuce, Moseley watched as 25% of each plant was put into uniform packaging, while the rest was discarded.
“I knew then we had a broken food system. It was my ‘aha’ moment and I vowed not to stop until I found a way for that produce to be utilized for consumption,” she told Forbes.
That was when she decided to start Full Harvest, a B2B platform to sell rather than waste unsightly or unwanted fruit and veg.
Roughly one-third of the food produced in the world for human consumption every year — approximately 1.3 billion tonnes — gets lost or wasted, according to the Food and Agricultural Organization of the UN.
In the US alone, 9 billion kilos of ‘ugly’ and surplus produce are wasted each year simply due to the cosmetic standards of grocery stores.
Supermarkets often only buy perfect produce
Image: Reuters/Ngwyen Huy Khan
Full Harvest connects food companies with trucking firms and farms so that they can make use of the imperfect and surplus produce.
This not only makes good use of the food, it also stops water being wasted and limits carbon dioxide emissions from agriculture.
3. Preventing waste with NASA’s hyperspectral imaging
Hyperspectral imaging sees information on parts of the electromagnetic spectrum that human eyes cannot. That means it can test the freshness of food - from beef steaks to avocados - without even touching it.
The technology - first developed by NASA for aerial imaging - detects the internal quality and chemical composition of food products.
ImpactVision then uses machine-learning techniques to assess the quality of the product, providing food companies with real-time information about their stock.
With an avocado, for example, the images can determine the fruit’s ripeness and reject any rotten ones. Previous systems have depended on sampling - and then wasting - fruits.
“Using advanced imaging and machine learning, we help food companies learn about the quality of their food products non-invasively, providing real-time continuous data,” says ImpactVision’s CFO Rachael Gan.
“That leads to optimized decision-making during processing that in turn reduces waste.”
Can you tell which avocado is ripe without touching . Image: REUTERS/Siphiwe Sibeko
ImpactVision is now working with several leading food producers and supermarkets in the US and believes the data it gathers has the power to transform food supply chains in the same way as GPS transformed navigation.
As food quality control is digitized, this new technique could also help spot contamination and prevent costly food recalls at a later date.
Have you read?
4. More productive seeds
“Seeds are the heroes of modern agriculture. If we improve seeds, then we determine how much land, how much water, how much fertilizer will be used,” says Ponsi Trivisvavet, CEO of Inari Agriculture. “We can solve these major environmental problems by going back to the root cause - the seed.”
Image: FAO
Inari operates a seed foundry where a plant’s genes are edited - some genes may be knocked out, others inserted and others fine-tuned. "Everything we do would probably happen naturally over the next 1,000 years or so,” says Trivisvavet. “We’re just speeding up that process.”
Three changes were simultaneously carried out on tomato plant seeds in order to grow the size of the branch, increase the number of flowers and expand the size of the fruit. This led to an increase of productivity of more than 90%, something which has never happened before in the history of crop development, according to Trivisvavet.
The same technology is being used for soybeans, where the genes of the seed are being edited to increase the number of pods per node, and the number of seeds per pod.
Inari’s seed foundry uses AI-powered computuational crop design to understand the genomes of the crop and how they interact with each other.
“The gene editing itself is easier than identifying where the changes need to be made,” Trivisvavet says. “AI tells us where the changes need to be.”
Among the areas being worked on is making crops more drought-resistant and less dependent on fertilizer.
“We’re working out how to feed the world without starving the planet,” Trivisvavet says.
“If we can grow food with less inputs, then we can return land to nature and lighten the ecological footprint of farming.”
Written by Briony Harris, Senior Writer, Formative Content
The views expressed in this article are those of the author alone and not the World Economic Forum.
40-foot Shipping Container Farm Can Grow 5 Acres of Food With 97% Less Water
The 40-foot containers house hydroponic farms that only draw on five to 20 gallons of water each day to grow produce like lettuce, strawberries, or kale
by Lacy Cooke
Communities that have to ship in fresh food from far away could start getting local produce right from their parking lots or warehouses thanks to Local Roots‘ shipping container farms. The 40-foot containers house hydroponic farms that only draw on five to 20 gallons of water each day to grow produce like lettuce, strawberries, or kale. Popping up all around the United States, these scalable farms “grow far more produce than any other indoor farming solution on the market” according to co-founder Dan Kuenzi. Local Roots is even talking with SpaceX about using their farms in space.
Local Roots’ 40-foot shipping container farms, called TerraFarms, grow produce twice as fast as a traditional farm, all while using 97 percent less water and zero pesticides or herbicides. They can grow as much food as could be grown on three to five acres. They’re able to do this thanks to LED lights tuned to specific wavelengths and intensities, and sensor systems monitoring water, nutrient, and atmospheric conditions.
Related: Pop-up shipping container farm puts a full acre of lettuce in your backyard
The process from setup to first harvest takes only around four weeks. TerraFarms can be stacked and connected to the local grid. CEO Eric Ellestad said in a video 30 million Americans live in food deserts, and their farms could be placed right in communities that most need the food.
Los Angeles is already home to a farm with several shipping containers, and a similar one will be coming to Maryland this year. It could offer local food like strawberries in January.
And Local Roots’ technology could one day allow astronauts to consume fresh produce in space. Their growing systems could offer a food source on long-term, deep space missions. Ellestad told The Washington Post, “The opportunities are global and intergalactic at the same time.”
Images via Local Roots Facebook
Agriculture, carousel showcase, Eat & Drink, Gardening and Plants, News
Hydroponic Lettuce Farm Offers Room To Grow
By JESSE ADCOCK
JADCOCK@ADIRONDACKDAILYENTERPRISE.COM
PUBLISHED: MAY 12, 2019
A column of lettuce is ready to receive transplants at Dandelion Farms in Saranac Lake.
JESSE ADCOCK/ADIRONDACK DAILY ENTERPRISE
Aurora White, owner of Dandelion Farms in Saranac Lake.
SARANAC LAKE — Inside a 40-foot cargo container at the old village landfill site near McKenzie Pond Road, Aurora White transplants lettuce into columns under the glow of fuchsia grow lights. Hundreds of lettuce transplants grow vertically inside the container, hanging from dozens of columns, gravity fed by tubes full of water and green and orange nutrients.
She calls this place Dandelion Farms, even though she mainly grows lettuce.
Last April, the Saranac Lake village Board of Trustees approved a lease for the container, and last month, they approved a one-year lease extension, for $1.
After a year on site, White’s hydroponic cargo container farm is growing and selling about 25 to 30 pounds of lettuce a week.
“Right now we’re harvesting about 400 to 500 plants a week,” White said. “We could do probably twice as much as we do now.”
In order to double her yield, all she needs is more regular customers.
White said she and Master Grower Jennie Evans spend about 10 hours a week at the facility, otherwise monitoring and adjusting the inside environment from an app on their phones.
The temperature remains around 68 degrees while the plants are active and about 59 degrees during the plants’ rest period.
“The trailer is rated down to negative 40,” White said. “So this last winter was kind of the testing period. We wanted to see if it was really rated down to negative 40, and it worked.”
The operation uses about five gallons of water per day — as both the air conditioning system and dehumidifier recycle fluid from the air.
Water is the one thing they’ve got to bring into the site. White said they haul in a 300-gallon tank every three months or so. They paid to get the electricity hooked up last April.
White said the operation is about halfway to profitability. With their regular sales, they pay for the trailer itself but not the utilities and the staff.
Currently, she said her two largest and regular customers are the Adirondack Medical Center and Fiddlehead Bistro, both in Saranac Lake.
“It has really allowed us to incorporate more fresh greens year round without going to the commercial lettuces that you traditionally see in the off-growing seasons here,” said Carl Bowen, Adirondack Health’s director of nutritional and environmental services. “It has helped us stabilize our menus with fresh vegetables all year long.”
That’s why White said she started researching the idea. She wanted to find a way to grow fresh greens throughout the year. That led her to the cargo container from Freight Farms.
“Right now we grow lettuce and arugula and spinach,” White said. “Once we get those things down, because we’re still in a learning phase, then we’ll probably bring in some herbs and start growing some herbs.”
It all starts in a small plug of peat and adhesive.
“That’s the only growing medium it needs throughout the whole life cycle of the plant,” White said.
Once large enough to be transplanted, White and Evans place the plants into columns, sandwiched between two bars of foam. The plants then grow sideways and are watered and fed from the top the of the column.
Bowen said that because of how the lettuce is grown, it makes it easier to process at AMC.
“When we received their samples and tried them, they were beautiful products,” Bowen said. “There’s not even any dirt to worry about because of how it’s grown. It comes in clean, we rinse it again, and that’s it.”
Additionally, the lettuce columns can be arranged with different blends.
“We can actually customize a person’s blend,” White said. “Fiddlehead Bistro gets what’s called an ovation blend. So we take all the different lettuces, and we mix them all together. And when we harvest we have a custom blend of salad.”
In 2018, Dandelion Farms also sold some of its greens at the Saranac Lake Farmers Market.
EDEN ISS Mobile Test Facility Remains In Antarctica
The first EDEN ISS Antarctic mission (February – November 2018) aimed at advancing controlled environment agriculture technologies for plant cultivation in extreme conditions, applicable to both terrestrial earth and space exploration. In April 2019, the EU-funded project comes to a complete close with all research concluded, providing definitive results. Due to the advantages this unique learning platform offers, it has been decided to extend research missions into 2021.
Partner institutions German Aerospace Center (DLR) and Alfred Wegener Institute for Polar and Marine Research (AWI), operators of the German Antarctic research center Neumayer Station III, will keep the analogue facility in operation for a minimum of two years until 2021, enabling two more isolation phases. Between January and February 2019, the facility was updated with repairs made to all subsystems where required. A complete cleaning of the greenhouse was performed preparing the facility for future research and analogue testing.
Researchers interested in taking advantage of the highly isolated conditions of Antarctica, remote monitoring and communication system, and/or the high-functioning systems architecture of the EDEN ISS Mobile Test Facility are invited to contact Dr. Daniel Schubert to submit research proposals.
In April 2019, the EU-funded project comes to a close with first phase research concluded, providing definitive results. During the Antarctic mission, a significant amount of fruits and vegetables were produced in the Future Exploration Greenhouse and were a great benefit to the over-wintering crew at the Neumayer Station III. A large amount of plant and microbiological samples from within the greenhouse have been preserved and are currently being tested by project partners for determining further the quality and safety of the cultivated fruits and vegetables.
The EDEN ISS Mobile Test Facility is comprised of two standard shipping containers fitted-out to accommodate a Future Exploration Greenhouse, a service section, a climatic buffer zone, and all the required subsystems for operating a controlled-environment greenhouse (including an LED Illumination System, Atmosphere Management System & Thermal Control System, a Nutrient Delivery System, and Plant Health Monitoring system, and an all-in-one hardware and software platform for monitoring and controlling all equipment and for communications between the Mission Control Centre in Bremen).
For more information:
EDEN ISS
eden-iss.net
Publication date: 5/2/2019
Trending: Are Shipping Container Farms The Future of The Industry?
BY LUKIE PIETERSE ON APRIL 19, 2019
Could shipping containers be the future of farming? According to Cleveland Containers in the UK, they can. The company states that shipping containers could provide an answer to the rapid demand for local produce.
According to the company, the trend for local food has risen over the last few years and as a result, the demand for local produce is showing no signs of slowing down. With this in mind, farmers are being forced to get creative in how they can deliver the volume needed for local supermarkets, whilst still keeping hold of the nutritional value in its fruit and veg.
So, how could container farms shape the future of the industry? Johnathan Bulmer, Managing Director of Cleveland Containers, explains.
“Many are unaware that containers can be fitted with heating and water systems, as well as gas and electrics and therefore offer a whole host of benefits for crops and farmers alike.”
“Creating your own farming space inside a container enables you to grow crops all year round and once modified, allows you to control growing conditions such as climate, soil quality and heat and light exposure.”
Read the full article in Future Farming here
Related article: Indoor farming technology market to grow to $ 40.25 billion
Swedish Supermarket Opens Onsite Container Farm
It's The Third Container Farm Made By US Manufacturer
US container farm manufacturer Freight Farms has built and opened a new container farm at a Swedish supermarket through their Scandinavian distributor Futufarm. Located in Halmstad Sweden, Freight Farms customer ICA Maxi Högskolan is one of ICA Gruppen's 1,300 grocery stores in the country. This month, the store began harvesting a range of hydroponically-grown greens for shoppers from the 'Leafy Green Machine' container farm, bringing the number of Freight Farms' container farms in Sweden to three.
"We're excited to be the first ICA Maxi store to implement an onsite farm," said Rikard Hillarp, owner ICA Maxi Högskolan. "By growing crops just steps from our shelves, we're able to offer our customers what are truly the freshest greens possible."
On March 29, the group kicked off its launch with a Harvest Festival for customers, selling produce and offering free samples of the newly-harvested greens and a Q&A with store employees Max Rydberg and Douglas Klang, now the newest onsite farmers.
ICA Maxi Freight Farm exterior
Transport to the store and capacity
The Leafy Green Machine destined for the Swedish supermarket began life in the United States where it was built by Freight Farms in Massachusetts. It was trucked to New York City from where it was shipped to Europe, before making its journey to the ICA Maxi store by truck and placed into position by a crane. The company says this farm can produce up to two acres worth of produce.
"Freight Farms' containerized farming technology allows ICA Maxi Högskolan to create and maintain the optimal growing conditions to harvest produce year-round using less than 5 gallons of water per day," Freight Farms said in a release. "Beyond the store's initial offering of butterhead lettuce, spinach, and herbs, the farm's integrated IoT data platform, farmhand, will also allow the store to grow non-native crops otherwise unavailable in the region, regardless of seasonal limitations in Sweden's Nordic climate."
ICA Maxi Högskolan is Freight Farms' third container farm in Sweden, and the company said there is anticipation to scale.
ICA Maxi store employees
Scandinavia ideal setting for container farms
With winters being rather cold and offering limited daylight, Scandinavia is restricted in what it can produce locally, especially outside the summer months. Freight Farms also noted that consumers in the region are known for their penchant for sustainable and environmentally-friendly solutions to a range of situations. In fact, IKEA made an announcement last month, stating that it would begin growing lettuce on site for its staff soon, suggesting that it may later sell it to paying customers if all goes well. However, this trial is only for lettuce and ICA Maxi's new farm is fully operations and consists of several varieties which are all available to customers. Therefore, Freight Farms wants to highlight the benefits of having food grown locally.
"Freight Farms' technology is especially helpful in Sweden, where our short growing seasons can limit crop availability throughout the year and increase our reliance on imported produce," added Hillarp. "We're now able to shorten the distance food travels to get to our customers from 2,000 kilometers to just 30 meters."
Max Rydberg and Douglas Klang - the new "onsite farmers"
Futufarm's Chairman, Harrie Rademaekers, noted that the potential for container farms in Nordic countries is great, pointing out that much of the produce consumed in the region originates from overseas. "Even though we have access to greens all year round, only 50 percent of the crops we consume are grown in the region," he observed. "In general we are very dependent on imported crops from Holland and Spain, which is not very sustainable. Nordic consumers are very focused on locally-grown and this fact builds a strong case for local container farms serving local food stores, restaurants, hotels, schools and so forth. Our climate is changing and water supplies are becoming more precious, which will force us to find new methods of farming. Food tech solutions will helps us, and in this case, Freight Farms' hydroponic technology can provide a climate-controlled farming solution that helps us save 95 percent more water than traditional agriculture."
Some leafy greens produced in the container farm
"By removing the miles between the food source and consumers, produce maintains nutrient density and stays fresh for far longer, significantly reducing food waste for both retailers and consumers," said Freight Farms' CEO Brad McNamara.
"Our team innovated the technology to empower individuals and businesses all over the world to decentralize the food system in meaningful ways specific to their local community or environment," he concluded. "We're thrilled to work with industry leaders like Rikard Hillarp and retailers like ICA Maxi, who together have the forward-thinking vision and reach to disrupt the grocery industry internationally."
For more information:
www.freightfarms.com
For Indoor Ag Startup Freight Farms, Competing With The Mass Market Produce Industry Was Never The Plan
Indoor agriculture, a generalized term used to refer to farms inside structures such as greenhouses, container farms, and multi-level warehouse operations housing thousands of rows of plant space, has been touted as a way to meet the demand for local food, help consumers learn more about food production, and provide a fresher source of produce with fewer food miles.
But some are skeptical about the scalability of an inherently localized industry and whether it will ever truly compete with traditional mass market produce, especially when it comes to container farming where production is housed in an old shipping container.
“The confines of the retrofit shipping container make it inherently inefficient compared to other forms of CEA (controlled environment agriculture) and therefore the audience for container grown produce will be a highly niche one over the long term,” agriculture consultant Peter Tasgal recently wrote in the AgFunderNews guest post What is the Future of Container Farming?
Tasgal also noted that there are significant costs involved with container farming, including retrofitting the box, labor, and the cost of power for the LED lights. He concludes that container farming is at least four times as expensive per pound to produce leafy greens in a container compared to traditional farming methods.
“There is technological innovation that will improve the efficiency of container farming, but I don’t see anything on the horizon that will allow container-grown produce to compete with the quick turning leafy greens sold at your local grocery store or those sold by wholesale distributors,” Tasgal wrote.
Did you know that AgFunder is one of the most active agrifood tech investors?
We are democratizing access to venture capital. Learn how you can invest with us.
Funding for novel farming systems like indoor agriculture and insect farming dropped between 2018 and 2017 according to AgFunder’s AgriFood Tech Funding Report 2018, which you can download here, raising $596 million. There were 17% fewer deals and only two of those deals were over $100 million after US vertical farming operation Plenty closed a record-breaking $200 million round in 2017.
Different Routes to Market
Indoor ag companies’ route-to-market approaches differ just as much as their approaches to cultivating produce under a roof. Some companies like BrightFarms and Bowery, for example, are offering packaged salads to local retailers to compete with traditional supermarket produce offerings.
But for Boston-based Freight Farms, however, competing with grocery store produce was never the plan.
Founded by Brad McNamara and Jonathan Friedman, Freight Farms has been a longstanding player in the container farming space, raising over $12 million in venture capital funding to-date, including backing from accelerator group Techstars, Right Side Capital Management, Spark Capital, Morningside Group, and The Startup Playbook author Will Herman.
As many startups often say, the idea is to disrupt existing markets, not necessarily to conquer them. For a startup that spends most of its time thinking about how to grow food inside a box, its technology is based on thinking outside of the traditional produce cultivation box.
“They compare container farming to the iceberg lettuce industry. We are not interested in that market,” Friedman told AgFunderNews. “We are interested in a distributed food system and some of the incredible changes that are happening throughout the whole food system like ugly produce, food waste, yield maximization. The entire system is in flux and that’s exciting.”
Introducing Greenery, the Leafy Green Machine 2.0
Freight Farms offers a ready-made shipping container called the Leafy Green Machine (LGM) that can be placed in a wide variety of locations including dense metropolitan areas. It just launched its newest product, Greenery, which is the first deviation from the LGM model.
Within the same 320-square-foot space as the LGM, Greenery boasts 70% more growing space and new IoT technology driven at improving yield, efficiency, and automation. With its real-time transparency feature, a single head of romaine can be traced back through every growing stage to the exact hour its seed was planted. It also features recipes that allow farmers to replicate ideal environmental conditions for specific crops like non-native produce. It supports a variety of crops beyond greens, as well, including tomatoes and root vegetables.
The University of Georgia has already purchased two Greenery containers. An independent farmer operating WhyNot Farms, which supplies pasture-raised meat to chefs in North Carolina and Tennessee, also made a purchase.
Although the duo has been pleased with the LGM’s success, Greenery was developed in response to their clientele’s feedback and ever-changing needs. Freight Farms has diverse users throughout the world, including schools, hospitals, NGOs, corporations, and private owners who develop niche businesses offering locally grown produce to restaurants and chefs in the area.
“The joys of standardizing something is that you get a lot of feedback. We have a network of 200 farmers around the world including Guam, Puerto Rico, Europe, and UAE. When we talk about greenhouse farming or traditional farming, no one farms the same way so it’s hard to collect these metrics,” Friedman says. “We looked at workflow considerations and where operators were spending the most time such as fixing things or having to remove a column to replace a part.”
“We benefited from having hundreds of customers in all these varied segments but at the end of the day, there is overlap among what they want, like more yield, fewer operating costs, flexibility, and customization. Our core, bread-and-butter customers are small business entrepreneurs,” McNamara told AgFunderNews. “And because we had experience developing four generations of the LGM, we were able to move faster and to save development dollars because we had real experience. Something John and I talk about all the time is human centric design. When it came to Greenery’s design process, it was equal parts human and plant-centric.”
Tech Developments
Some of the biggest differences between the LGM and Greenery have to do with workflow and appearance. Greenery has mobile LED light boards and grows rows that are both adjustable. This allows farmers to grow a larger variety of crops and makes it easier to maneuver through the grow rows.
“After the fourth evolution of the LGM, there was a significant design jump to increase yield, bring in new tech, and to hit the metrics that all of our customers want, which are things like increased yield and improved workflow,” Friedman adds. “One of the bigger things we ran into is that we felt like we had exhausted as much of the off-shelf tech as we could. We realized we had to go back to the beginning and build from the ground up.”
As a testament to its outside-the-box ethos, NASA selected Freight Farms for a Small Business Technology Transfer grant to fund work with Clemson University exploring how to grow food in extreme climates. NASA is hoping that Freight Farms can help create an off-grid crop production unit that would help facilitate deep space exploration.
It’s a Dynamic Time for Agriculture
As far as the future of container farming, McNamara and Friedman want to remind people that the industries are not static entities, especially when they are so heavily focused on technological innovation.
“What frustrates us is that articles are written as if everything is in a static state. We are in a dynamic time for indoor agriculture. If you could have told us back in 2010 how things would be today, it would have been beyond our wildest dreams,” McNamara says.
“With LGM and Greenery, we offer a new way of growing to build a distributed food system, which is exciting to us. You can lower the bar to entry for agriculture with this technology, making it possible for people who want to get into this professionally but who don’t want to build a warehouse or who don’t have a background in ag,” says Friedman. “If they want to grow their own brand or have a private label deal for a restaurant, we want to give them the tools to achieve that and to bring the other half of the world into farming and agriculture.”
GP Solutions (OTC: GWPD) Innovative Indoor Farming Technology Addressing Billion Dollar Opportunities
March 29, 2019 admin CEO Interview, Consumer
GP Solutions (OTC: GWPD) Interview with Shannon Illingworth, chairman and founder discussing the company’s GrowPod turnkey indoor organic farming solution, which uses re-purposed shipping containers, and optimized environmental controls. Shannon explains how GrowPod’s address a multi-billion market opportunity.
Shannon Illingworth, Chairman & Founder
GP Solutions (OTC: GWPD) Interview with Shannon Illingworth, chairman and founder discussing the company’s GrowPod turnkey indoor organic farming solution, which uses re-purposed shipping containers, and optimized environmental controls