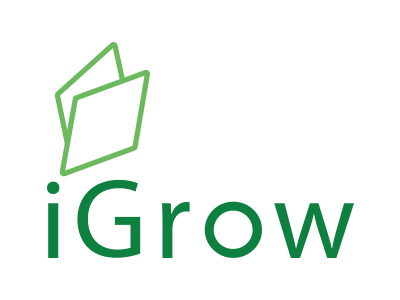
Welcome to iGrow News, Your Source for the World of Indoor Vertical Farming
Vertical Farms: The Height of Sustainability In A Post-COVID World
Vertical farms are innovative soil-based indoor farms that bring production of food to the location where it is consumed: supermarkets, local distribution sites, and restaurants
Among the many indelible images of the COVID-19 crisis have been the photos of mountains of surplus produce rotting in fields while millions of Americans go hungry. Urban areas are especially hard hit as supply chains are disrupted due to coronavirus fallout.
Vertical farms are innovative soil-based indoor farms that bring production of food to the location where it is consumed: supermarkets, local distribution sites, and restaurants.
Vertical Field, an Israeli start-up, has a container up and running at a Poughkeepsie, New York, restaurant and arriving soon at Evergreen supermarket in Monsey, N.Y. Its global clientele for its next-gen vertical farming systems includes Facebook, Intel, Apple, Isrotel, Microsoft, and many more.
Benefits include:
Consistent Supply
Reduced Inventory Waste
Less Human Handling
More Sterile Environment
Modular, expandable, and moveable farm
Bug-free and pesticide-free – healthy, fresh, and clean produce
Uses 90% less water
For more information:
Vertical Field
www.verticalfield.com
Innovation Consulting Community Team Proposes Sustainable Farming Container At ISU
In just a few months, a team of motivated students put together a proposal to implement a shipping container farm on Illinois State’s campus
Evan Linden April 15, 2020
NOTE: The photos in this story were taken before travel restrictions from coronavirus (COVID-19) were in place.
In just a few months, a team of motivated students put together a proposal to implement a shipping container farm on Illinois State’s campus.
“Self-motivation is impressive to employers,” said Marketing Professor Dr. Peter Kaufman, one of the founders of the Innovation Consulting Community (ICC). “Most students are taught one discipline in school, but world problems are interdisciplinary.”
Kaufman and others founded the ICC in 2016 to provide students with hands-on experiences outside their classes. Each year, teams of students are matched with clients at companies and nonprofit organizations to help solve a current issue they are facing. “It’s a unique experience to tackle both profit and nonprofit projects,” said Kaufman. “This experience helps students enhance their skills all around and helps our clients find solutions.”
This year, the ICC assigned 14 projects to 90 students representing 24 majors. One group of four students tackled an increasingly pressing issue: sustainable farming.
The students assembled in late October, mentored by Elisabeth Reed, director of the Office of Sustainability, and Dr. David Kopsell, assistant chair of and professor in the Department of Agriculture. Ryan Strange, a senior from Bloomington double majoring in business administration and small business management, led the team and collaborated with fellow students Joe Kennedy, Madison Steines, and Joe Quigley.
The project was inspired by the Boston company Freight Farms, urban agriculture innovators who create farms in shipping containers. Kopsell, who is familiar with growing systems, was brought in by Kaufman to be a horticulture mentor.
“I shared some of the ideas that I’d always wanted to investigate, and one that he really liked was the idea of writing a grant for a containerized growing system,” said Kopsell.
From there, the team focused on analyzing the benefits of a containerized growing system on campus.
“Our project was a feasibility study of the purchase of one of these units,” said Strange. “The unit itself is the technology necessary for hydroponic farming, and all of that goes inside an old freight container.”
The inside of a shipping container farm located in Champaign.
To see one of these units in action, the group visited a current model located at the University of Illinois at Urbana-Champaign. “The director there was a tremendous help,” said Strange. “He gave us many details about operations and risk management.”
The team spent weeks finding the right contacts and establishing relationships in order to gather information for the project. “We built this huge network of different partnerships that helped us find out how we would finance this unit,” said Strange.
According to Strange, the purchase of one of these units would cost $120,000, with recurring costs adding up to around $40,000 a year.
“I think the cost is within the reach of a grant program,” said Kopsell. “These containers can operate year-round and provide great teaching and learning tools.”
Most importantly, the containers are both efficient and sustainable. Each container system can produce as much as one acre of field production —up to 13,000 plants depending on the crop. The efficient drip irrigation system uses five gallons of water per day, which is marginally less than a field.
“This is really the forefront of innovation in terms of agricultural production,” said Strange. “It’s going to cut back on a lot of the carbon emissions from transporting the food. It’s really going to cut back on costs also because most of the costs for food come from transportation.”
If installed on campus, the container system could be located next to the South University Street Garage.
Strange’s team presented its project at ICC’s annual symposium. In adherence with social distancing requirements, the symposium took place via Zoom on April 10.
Strange and his team noted that the ICC experience greatly benefited them as professionals. “It opens up a lot of doors and you have to teach yourself a lot,” said Strange. “Our mentors were definitely there for help, but it was mostly our group that set up all of the meetings and held ourselves to the deadlines. All of those things are fundamental skills that you’ll need when you move on to the professional workforce.”
Reed and Kopsell were impressed by the group’s work ethic and commitment.
“This student group was very well organized and stayed on task throughout the entire semester,” said Reed. “They communicated well with each other.”
“For me, this project represents the best of Illinois State University,” said Kopsell. “It allows students to find their passion and provides them an avenue to learn how to overcome challenges, solve problems, and make a difference.”
Students interested in participating in the Innovation Consulting Community for the next academic year can email innovationconsulting@IllinoisState.edu for more information.
Lead Photo: The ICC team visits a shipping container farm in Champaign. Pictured from left to right: Ryan Strange, Joe Quigley, Madison Steines, James Smith, Phoebe Naylon, Brennan Douglas, Alicia Chiakas, Aviv Zelniker, Max Snyderman, Bill Bagby with Central Illinois Produce, Dr. Eric Godoy, and Joe Kennedy
Filed Under Agriculture Center for Community Engagement and Service Learning College of Business Office of Sustainability
World’s First Vertical Farming Congress
The first Vertical Farming World Congress will be held from 22nd to 24th September at London’s Heathrow Airport
By urbanagnews
April 8, 2020
The first Vertical Farming World Congress will be held from 22nd to 24th September at London’s Heathrow Airport. Eminent industry-leading speakers have confirmed their participation from North America, the Middle East, and Asia as well as Europe. The chosen theme is ‘Shaping Food’s Future’.
“Vertical farming really can help shape the future of food production,” explained Richard Hall, Chairman of the food and drink experts Zenith Global and the event’s organizer. “By being indoors and with completely controlled conditions, there are no floods, droughts, winds or pesticides. You can grow 30 crops a year locally, right next to a supermarket or city distribution centre. Growing to perfection in a stress-free environment means greater freshness, better nutrition and a longer storage life.”
Topics on the program include: market opportunity; an industry leadership panel; strategic alternatives between aeroponic, aquaponic and hydroponic systems; technology briefings ranging from lighting and robotics to overall system design; a nutrition briefing; a funding panel; and key innovator
case studies.
Among the speakers are:
Industry leaders, such as AeroFarms, Intelligent Growth Solutions, Jones Food Company, Root AI and Square Roots
Association heads from Germany and Japan
Investment experts from Ashfords, S2G Ventures and Innovate UK
Technology developers, including GE and Wageningen University.
There will also be a visit to Vertical Future’s vertical farm operation in East London and a reception with vertically farmed fresh produce tasting.
The event has also attracted sponsorship from GE, LED lighting experts, and YesHealth, which has pioneered vertical farming in Taiwan.
Full program details and booking information are available at www.zenithglobal.com/events/vfwc2020 or contact the events team at events@zenithglobal.com.
Freight Farms Expands Leadership Team with New CEO and Head of Engineering as Business Scales to Meet Growing Global Interest in Decentralized Food Production
Freight Farms, the global innovation leader of containerized vertical farming with the world’s largest network of IoT-connected farms, announces today that it has hired veteran consumer brand executive Rick Vanzura as CEO who will also join the company’s Board of Directors, while cofounder Brad McNamara will remain as Freight Farms’ President
Freight Farms Produce March 27, 2020
BOSTON — Freight Farms, the global innovation leader of containerized vertical farming with the world’s largest network of IoT-connected farms, announces today that it has hired veteran consumer brand executive Rick Vanzura as CEO who will also join the company’s Board of Directors, while cofounder Brad McNamara will remain as Freight Farms’ President. The company also welcomes automation and robotics specialist Jake Felser as Head of Engineering.
The need to simplify supply chains and ensure reliable access to healthy, traceable food at a local level has become more crucial for communities worldwide. Expansion of Freight Farms’ team follows a year of strong momentum for the company as forward-thinking organizations, particularly at the institutional level, recognize the benefits of a secure, distributed, and transparent food supply. As the company scales for growing demand at speed, expansion of Freight Farms’ leadership is positioned to quicken new extensions of its technology platform and deepen market reach.
“What excites me about Freight Farms is the ability to join a passionate, mission-driven business that is already perfectly positioned to address the growing critical need for sustainable, hyper-local food production,” says Vanzura. “Freight Farms has an incredible technology platform as the originator of container farming, as well as a global footprint driving numerous sources of value. Beyond providing a meaningful solution across industries, Freight Farms’ innovation addresses issues like urban land scarcity, traceability and the need for hyper-local solutions with speed to market. The current environment demonstrates more than ever the value of Freight Farms’ offerings.”
Vanzura has driven value for companies from start-up to Fortune 5 across technology, restaurant, retail, and entertainment sectors. With a focus on leveraging innovation and developing new market channels, he led strategy for Panera, General Motors Information Services and GameStop, and as the original CEO of Wahlburgers, he built the company from a single unit into one of America’s fastest-growing restaurant brands. Vanzura’s 20 years in President and C-level roles include a decade in food service working with markets central to Freight Farms’ business. He also brings significant international experience to his role, having run Borders Group’s nearly $1 billion International business.
“As cofounders, Jon Friedman and I have taken Freight Farms from an idea to help decentralize the food system to being the leader in containerized vertical farming that’s truly putting the power of hyper-local food production into people’s hands,” said McNamara. “Rick has amplified growth across interconnected industries, and his international experience lends itself to our ongoing global expansion. His personal alignment with Freight Farms’ mission was crucial for us as well—he’s a welcomed addition to the team as we scale.”
“The potential is extraordinary,” Vanzura added, “I’m excited to be working with Brad, Jon and the team on the spectacular opportunities ahead, all while doing our part to help build a better, more sustainable food system for all.”
Jake Felser, former VP of Engineering for eatsa (now Brightloom), has also joined the Freight Farms team as Head of Engineering. With teams across hardware and software, Felser led robotics R&D and the development of eatsa’s shelf-style pickup system from conception to deployment across the company’s network of partners. Prior to eatsa, Felser was Senior Engineer and Product Manager at Cooper Perkins and has worked in hydraulics, refrigeration, structural optimization, design for development, and agriculture for companies including Blue Origin, Promethean Power Systems, and AGCO. With a passion for sustainable development, Felser is focused on automation, IoT, and machine learning-based integrations for Freight Farms growing technology portfolio.
Company growth, including ten new roles across all departments in Q1, also follows Freight Farms’ recent launch of the Greenery. Nearly 100 have been adopted by customers in 9 countries to date, bringing Freight Farms’ global footprint to more than 300 container farms around the world. The innovation also spurred interest from Sodexo in a strategic national partnership to grow food onsite at educational and corporate campuses nationwide and new investment from Ospraie Ag Science.
About Freight Farms
Founded in 2010, Freight Farms debuted the first vertical hydroponic farm built inside an intermodal shipping container—the Leafy Green Machine—with the mission of democratizing and decentralizing the local production of fresh, healthy food. Now with the Greenery and integral IoT data platform, farmhand®, its technology empowers people anywhere in the world to grow more than 500 varieties of pesticide and herbicide-free produce, from leafy greens and herbs to root vegetables and vine crops, with 99.8% less water—onsite, year-round. Freight Farms’ network of IoT-connected container farms is the largest in the world, with more than 300 operating in 25 countries and 44 U.S. states. Customers range from small business farmers to the corporate, hospitality, retail, education, and nonprofit sectors.
To learn more, please visit freightfarms.com,
How Greenhouse Yields Compare To Container Farms
As the agriculture industry searches for more sustainable alternatives to field farming, greenhouses remain the most popular solution, making up 47% of the indoor farming industry in the United States
March 10, 2020
As the agriculture industry searches for more sustainable alternatives to field farming, greenhouses remain the most popular solution, making up 47% of the indoor farming industry in the United States.
Greenhouse popularity is also on the rise worldwide.
A 2019 statistical survey found that more than 1.2 million acres worth of vegetable-growing greenhouses were in use globally, an increase of 223% since 1980.
But they aren’t the only indoor farming option out there.
In this article, you’ll learn about how typical greenhouse yields compare to our Pure Greens container farms.
Let’s start with a little bit of background info.
Greenhouses are structures with glass or clear roofs that are used for cultivating plants. They range in size from small backyard sheds to massive commercial farms.
Greenhouses utilize a variety of crop growing systems. Most use typical soil methods planting in boxes, pots, or raised garden beds. Others use soil-less growing solutions such as hydroponic and aeroponic systems.
Other types of indoor farms include vertical, container, and deep water culture (DWC) systems.
What sets greenhouses apart from these other indoor farms is the use of glass or clear plastic roofing and sides to provide plants with natural sunlight. Other indoor farms rely on artificial light.
Growing indoors has plenty of advantages over outdoor farming. For example, indoor farming allows for highly controlled environments, creating near-perfect growing conditions for plants.
Greenhouses and container farms both offer the ability to control factors such as humidity and temperature and help prevent damage from weather, pests, and diseases. As a result, plants are healthier and can be grown at any time, no matter the season.
Our Pure Greens farms made from repurposed shipping containers are fully controllable from your smartphone!
Soil-based greenhouses are subject to similar space restrictions as field farms because plants need to have enough room for their roots to grow.
Hydroponic systems deliver water and nutrients directly to roots so that plants don’t have to spread. Therefore, our hydroponic container farms yield more per square foot than traditional greenhouse yields.
Using traditional soil methods, each lettuce crop would have to be placed 10 to 16 inches apart, meaning only six to 18 lettuce plants would be able to grow in a 16-square-foot row.
Using our hydroponic technology, we’re able to fit 36 lettuce plants in one row! That’s at least three times as many.
But lettuce takes up a lot of space in both types of farms. Herbs like rosemary and sage are much easier to grow in bulk in our hydroponic container farms than they are in soil-using greenhouses.
In soil, rosemary and sage plants need to be spaced a couple of feet apart. If we were to follow that rule in one of our 16-square-foot rows, we’d only be able to grow four plants total.
We grow 90 rosemary or sage plants in one row!
Thai basil crops need to be spaced 12 to 18 inches apart. Like sage and rosemary, we easily fit 90 Thai basil plants in just one of our rows. Farmers who use soil can only grow 16 max in the same space.
This means our hydroponic farms yield at least 5.6 times as much basil per square foot than a traditional soil greenhouse yields in just one grow cycle.
It’s clear that our container farms come out on top when it comes to yield.
If you’d like to learn more about maximizing your production with one of our farms, reach out to us on our website or give us a call at 602.753.3469.
WRITTEN BY
Pure Greens Arizona LLC
Pure Greens’ container-based grow systems offer a variety of interior layouts, sizes, and options so customers can create a farm that meets their needs.
The Philadelphia Zoo Is Running A Farm Inside A Converted Shipping Container
Tua lives at the Philadelphia Zoo, the first zoo in the country with its own on-site vertical garden used to grow leafy greens for its animals. And she loves the produce they’re feeding her
by Brianna Baker, For The Inquirer, March 4, 2020
Kristen Waldren, director of strategic initiatives at The Philadelphia Zoo, walks through the zoo's new "Cropbox" — a vertical farm being used to grow plants that are harvested to feed animals. MARGO REED
If you’re a fan of homegrown arugula and mustard greens, you just may have the same taste as Tua, a 27-year-old Sumatran orangutan.
Tua lives at the Philadelphia Zoo, the first zoo in the country with its own on-site vertical garden used to grow leafy greens for its animals. And she loves the produce they’re feeding her.
The garden is located in a retrofitted shipping container in the Urban Green, the zoo’s open-air food marketplace. A mural, by Philly-based environmental artist and activist Eurhi Jones, transforms the front of the shipping container into a colorful collage of the animals who’ll chow down on the vegetation.
But the real beauty is inside, where stacked, tidy shelves hold rows of plants that are grown hydroponically, in nutrient-rich water instead of soil. LED lights, a substitute for sunlight, shine 18 hours a day. Farm operators use a mobile app to remotely control the container’s light, temperature, and humidity levels.
Kristen Lewis-Waldron, director of strategic initiatives at the zoo, said the vertical farm is far more sustainable than bringing in food from outside sources. It uses 70% to 90% less water than traditional farming, has no need for pesticides or herbicides, and cuts greenhouse gas emissions out of the equation since no motor-powered transportation is necessary to get the food to the zoo.
“It really kind of creates this farm-to-table [model] — in this case, shipping container-to-exhibit,” she said of the project, which is in a pilot phase.
Want to know what's going on in Philly? Find out about upcoming concerts, shows, and other events with our weekly newsletter.
Lewis-Waldron is short on farming experience but knows a thing or two about feeding animals. She landed her first role at the zoo 23 years ago as a nutrition intern. She went on to work for, and eventually lead, the zoo’s conservation department, before transitioning to her current position. Growing greens for the animals makes her feel like she’s come full circle, she said.
A peacock at the Philadelphia Zoo walks past the "Cropbox," a converted shipping container being used to grow plants being used to help feed the animals. MARGO REED
To launch the project, she enlisted the services of CropBox (which is also what the zoo calls the vertical farm), a North Carolina company that provides all the equipment customers need, including the shipping container, and helps set up the system.
Lewis-Waldron also consulted with industry experts, including those who operate their own vertical farms, to learn best practices and how to troubleshoot technical challenges. All in all, the preparation process took about a year.
In its nine months of operation, the CropBox has fed 20 animal species with its microgreens. It produces 275 pounds of leafy greens a month, which is only 10 percent of the zoo’s monthly requirement. But that number, Lewis-Waldron said, will grow once the pilot year concludes and the project is expanded.
“You can take over a vacant warehouse or vacant building and convert it,” she said. “You could take six of these and make a dent in the requirements of our collection.”
The CropBox also benefits the zoo economically by replacing a collection of food it would otherwise purchase.
But perhaps most importantly, the greens grown in the vertical farm are rich in nutrients. The zoo takes animals’ diets very seriously and even employs a full-time nutritionist. By feeding leafy greens to the animals, the zoo is keeping their health in shape.
Still, that doesn’t mean the greens are every species’ favorite snack. Just like humans, animals have unique palates. And the current variety growing in the CropBox — a stir-fry mix that includes arugula and mustard greens — isn’t always a crowd-pleaser.
“It’s got a little kick to it, a little bit of spice. Our emus were a little hesitant,” Lewis-Waldron said. “But our monkeys, langurs, apes, gorillas, orangutans, tortoises absolutely love it. So it’s interesting, and we’ll continue to test out different types of greens.”
Brianna Baker, For The Inquirer
80 Acres Farms Will Grow Tomatoes On Fifth Avenue In Guggenheim Exhibition
Based in Hamilton, Ohio, 80 Acres Farms is a leader in technology-assisted indoor growing and a multi-farm operator marketing a wide variety of freshly picked vegetables and fruits to retailers such as Giant Eagle, Kroger, Whole Foods, Jungle Jim’s and Dorothy Lane Markets
80 Acres Farms will grow tomatoes on one of the busiest streets in New York City outside the Solomon R. Guggenheim Museum as part of the Guggenheim’s new exhibition in collaboration with Rem Koolhaas, “Countryside, The Future.”
Along with its commercial partners Infinite Acres and Priva Holding BV, 80 Acres Farms will grow cherry tomatoes in an indoor grow module right outside the museum on Fifth Avenue.
Based in Hamilton, Ohio, 80 Acres Farms is a leader in technology-assisted indoor growing and a multi-farm operator marketing a wide variety of freshly picked vegetables and fruits to retailers such as Giant Eagle, Kroger, Whole Foods, Jungle Jim’s and Dorothy Lane Markets.
The company was founded by veteran food industry executives Mike Zelkind and Tisha Livingston, who are supported by a deep team and a board of directors representing executive and leadership experience at leading food, healthcare and other companies.
Window on tomato production
People in New York will be able to look through a large window in the indoor farm to view a crop of fresh tomatoes being grown continuously during the next six months under precise LED lighting and other controlled conditions.
The first tomatoes will be ready for harvest by late-March.
The grow module will demonstrate how indoor farming can benefit the world through growing fresh, pesticide-free food near populations, anywhere in the world while using fewer natural resources.
The “Countryside, The Future” exhibition will examine political forces, social issues and environmental factors altering landscapes across the world, including traditional farmlands.
80 Acres Farms is a founding member of the Infinite Acres partnership venture, along with Netherlands-based Priva Holding BV, a leading provider of technology solutions, services and automation systems to horticultural and other industries; and Ocado Group, one of the world’s largest dedicated online grocery retailers, operating its own grocery and general merchandise retail businesses.
That partnership is now building large-scale, fully automated indoor farms in the U.S., Asia and Europe.
“We believe that what we are doing is about the future of food. We are changing the way fruits and vegetables are grown and harvested locally then delivered to grocers the very next day,” Zelkind said.
“There is an enormous market and consumer appetite around the world for produce that our crop scientists and other food experts have been perfecting during the past five years,” he said. “Our participation in this exhibition will allow New York residents and visitors to experience how the freshest, tastiest locally grown tomatoes can be grown year-round indoors in one of the busiest cities in the world.”
700-square-foot grow center
For the Guggenheim exhibition, 80 Acres Farms, Infinite Acres, and Priva Holding have collaborated on the 700-square-foot grow center and all of the state-of-the art ag-technology within it.
While in operation for the next six months outside the Guggenheim, the Infinite Acres grow module is expected to grow 50,000 tomatoes.
Additional tomatoes will be donated to City Harvest, a New York City food rescue organization that safely recovers excess food and distributes it to people in need.
“Countryside, The Future” will be open to the public through Aug. 14.
This Brooklyn Farm Company Is Training A New Generation of Urban Farmers
In old shipping containers, the shoots of a new way of urban farming are starting to emerge, which could help meet the demand of a growing urban population
February 7, 2020, by World Economic Forum
(Credit: Unsplash)
This article is brought to you thanks to the collaboration of The European Sting with the World Economic Forum.
Author: Kate Whiting, Senior Writer, Formative Content
The average age of an American farmer is 57.5 years.
Just under 70% of the world’s population will live in urban areas by 2050.
Square Roots is teaching young city farmers how to grow food sustainably.
Among the high-rise buildings and concrete sidewalks of Brooklyn, there’s a quiet green revolution taking place.
In old shipping containers, the shoots of a new way of urban farming are starting to emerge, which could help meet the demand of a growing urban population.
Square Roots is an indoor urban farming company, which not only grows food sustainably without soil but is teaching a new generation of farmers how to do it too.
“We realized there were tens of thousands of young people who were as passionate about changing the food system as we were, but just didn’t know how to get started,” says Tobias Peggs, CEO of Square Roots.
Feeding the future
Square Roots is tackling several issues in one go: the need to use less water and other resources in agriculture, the aging of farmers, the global population rise and, in particular, the growing urban population.
Farmers in the US aren’t getting any younger, with an average age at 57.5, according to census data, up 1.2 years from 2012.
A new way of farming. Image: WWF/Netflix
And it’s a similar story in other places around the world. In Kenya, the average farmer is 60. In Japan, 67.
By 2050, 68% of the world’s population is expected to live in urban areas, so that’s where much of the focus of food growing will need to be.
“Younger generations are really interested in making sure we’re all eating healthy food that’s nutritious and grown in sustainable ways, but they’re less interested in living in the middle of the country,” says Peggs.
The future of farming
The Next-Gen Farmer Training Program teaches would-be farmers how to grow leafy greens in a high-tech hydroponic system that it says uses up to 95% less water than traditional farms.
They study plant science, to find out what’s happening at a molecular level as the plant grows, they learn about the business side and engage with the local community and agriculture ecosystems.
Food
What is the World Economic Forum doing to help ensure global food security?
Two billion people in the world currently suffer from malnutrition and according to some estimates, we need 60% more food to feed the global population by 2050. Yet the agricultural sector is ill-equipped to meet this demand: 700 million of its workers currently live in poverty, and it is already responsible for 70% of the world’s water consumption and 30% of global greenhouse gas emissions.
New technologies could help our food systems become more sustainable and efficient, but unfortunately, the agricultural sector has fallen behind other sectors in terms of technology adoption.
Launched in 2018, the Forum’s Innovation with a Purpose Platform is a large-scale partnership that facilitates the adoption of new technologies and other innovations to transform the way we produce, distribute and consume our food.
With research, increasing investments in new agriculture technologies and the integration of local and regional initiatives aimed at enhancing food security, the platform is working with over 50 partner institutions and 1,000 leaders around the world to leverage emerging technologies to make our food systems more sustainable, inclusive and efficient.
Learn more about Innovation with a Purpose’s impact and contact us to see how you can get involved.
Each shipping container at the company’s campus in Brooklyn’s Bed-Stuy neighborhood can produce up to 45kg of fresh basil, chive or mint leaves per week, which is grown without pesticides and uses data to optimize flavor and nutrition.
“Successful companies in the 21st century have to be doing well – and doing good at the same time,” says Peggs.
“We’re growing food and selling food, that’s how we make money. But we’re doing that in a sustainable way, which is better for the planet and we’re empowering the next generation of leaders in urban farming.”
MEXICO: Grow Food Anywhere! The Mexican Startup That Innovates In Agriculture
A Mexican startup is offering the possibility of growing vegetables within the city in a healthy enclosed space and harvesting up to 100 times more than normal.
A Mexican startup is offering the possibility of growing vegetables within the city in a healthy enclosed space and harvesting up to 100 times more than normal.
Juan Succar and Jorge Lizardi, graduates of the Tec de Monterrey Leon campus, created the Verde Compacto company, which follows the new global trend of urban and vertical agriculture. This type of agriculture is ideal for supermarkets, restaurants, hotels and real estate developments.
Verde Compact obtained third place in the Heineken Green Challenge at the entrepreneurship festival, INCmty, as one of the ventures to follow in 2020, according to Entrepreneur in Spanish.
Mexican technology for a worldwide trend
Urban agriculture is growing in the world and already accounts for 15% of all agriculture, according to UN data. The UN Food and Agricultural Organization (FAO) itself is promoting this alternative, although there were not so many options in Mexico.
Verde Compacto ensures that, unlike other similar foreign companies, they are the first to use only Mexican technology, which makes them pioneers in Latin America.
Growing food in enclosed spaces
Urban agriculture goes hand in hand with vertical agriculture, which allows sowing in enclosed spaces and at various height levels, thus maximizing space.
Verde Compacto launched Huvster, an intelligent vegetable growing system in a recycled trailer container. The system allows growing up to 200 times more vegetables per square meter with less water.
Fully Automated
The container has a system that circulates the water and an LED-lights system in the germination zone that simulates the conditions needed by the seeds to grow.
The plants are located in vertical towers and are watered via drip irrigation. Here, they grow until they are harvested. "The system has sensors that measure CO2 levels, ambient humidity, and temperature," Juan stated.
Characteristics
According to the company founders, this option also has these advantages:
It has an intelligent system for measuring and controlling temperature, humidity, irrigation, and other aspects of vegetable cultivation via hydroponics.
It allows having savings of 90% in water, and 80% in fertilizers when compared to a traditional method.
The system measures the plants' nutrition levels and regulates them so that they all grow at the same speed.
It decreases the risks of having pests.
It can produce, for example, an average of 730 lettuces per month, or 20 kilos of oregano, coriander, or other herbs per month, as well as 30 to 35 kilos of vegetables.
It can also impact agribusiness in several ways, avoiding distribution costs if installed near consumers.
In addition, the vegetables can be grown at any time of the year.
The company stood out in INCmty
Verde Compacto became one of the leading startups at INCmty, Tec de Monterrey's entrepreneurship festival.
This venture was also part of the Heineken Green Challenge, an initiative that recognizes companies that innovatively solve problems in Mexico, where it achieved third place in the 2019 edition.
Source: tec.mx
Publication date: Tue 7 Jan 2020
Top 7 Vertical Farming Companies
Vertical farming refers to the practice of producing fruits and vegetables or cannabis vertically, in stacked layers, perhaps on many floors inside a building, using artificial lights instead of the sun, and a whole range of relatively new technologies
Written by: GP Solutions
Vertical farming refers to the practice of producing fruits and vegetables or cannabis vertically, in stacked layers, perhaps on many floors inside a building, using artificial lights instead of the sun, and a whole range of relatively new technologies.
The three main reasons why it’s a much-discussed topic now is because:
There are a number of startup companies emerging in the sector and attracting tens of millions of dollars in investment; and more people live in cities than do in rural areas, a global trend which seems irreversible, and this means that the demand for fresh produce will increase in urban areas, and bringing the production closer to the consumer would make sense.
Vertical farming provides a low-cost, turnkey method to start farming. This is especially useful in the cannabis industry where traditional greenhouses require land that could cost many millions of dollars.
Some of these technologies have been available for some time, decades even, but they were probably too expensive in the past to make vertical farming a viable business proposition.
The key technologies in vertical farming include:
Perception Technologies – cameras and other sensors which can monitor for colour and other factors, such as disease;
Artificial Intelligence – which can process the data from the sensors and formulate solutions;
Automated and Even Autonomous Mechatronics – robots and other automated machines which pick the produce when it is ready for market, or apply cures to ailments during their growing.
The above list is a very simple breakdown of the fundamental technologies that will be required to, basically, reduce to a minimum or even eliminate the need for human involvement.
If vertical farms are run like traditional greenhouses, there would be too much human input required and it probably would not be profitable.
It’s the new automation technologies that will make it work.
Carnegie Mellon University is among a number of organizations which have developed integrated systems for vertical farming. CMU’s version is called ACESys, short for Automation, Culture, Environment, and Systems Model for Vertical Farming.
An academic paper probably worth checking out is called Advances in greenhouse automation and controlled environment agriculture: A transition to plant factories and urban agriculture.
In their introduction to the paper, the authors note: “Greenhouse cultivation has evolved from simple covered rows of open-fields crops to highly sophisticated controlled environment agriculture facilities that projected the image of plant factories for urban farming.
“The advances and improvements in CEA have promoted the scientific solutions for the efficient production of plants in populated cities and multi-story buildings.”
So the interest in the field is strong and most people seem to think it’s a viable business proposition.
And to underline the positivity about the sector, Research and Marketsforecasts the vertical farming market will grow to a value of $3 billion by 2024, from virtually nothing now.
In some sectors, such as marijuana production, indoor farming is providing a strong foundation for healthy profits.
COMPANIES FOCUS ON VERTICAL FARMING
It’s a very new business sector, so this list is subject to change:
1. AEROFARMS
This company has won many plaudits for its operation and uses its own patented “aeroponic technology… to take indoor vertical farming to a new level of precision and productivity with minimal environmental impact and virtually zero risks”.
The company has raised at least $138 million in funding since launch in 2004, according to CrunchBase. Some of its backers are quite impressive, as this article in Ag Funder News reports.
The term “aeroponic farming” refers to the process of growing plants in an air or mist environment without the use of soil or any earth-like material, which is known as “geoponics.”
Aeroponic systems enable the production of plants using 95 percent less water, which is what AeroFarms says it does.
2. GP SOLUTIONS
GP Solutions developed “GrowPods” – finely tuned, automated, transportable and scalable micro-farms that have been shown to grow all types of crops, including cannabis, at a faster rate than conventional means of agriculture.
GrowPods allow cultivation to take place year-round, which maximizes ROI. The systems are sealed from outside pathogens, contaminants, pesticides, and chemicals, and produce clean and robust crops.
The company has licensed its technology to Micro Lab Farms for the cannabis market only. The Pods from Micro Lab Farms differ slightly from the regular GrowPods from GP Solutions in that they have been specifically tuned for the production of cannabis.
Micro Lab Farms recently announced the development of a cannabis complex in Southern California that will hold many of the aforementioned GrowPods – some of which are being made available to farmers, businesses, and entrepreneurs looking to quickly enter the California cannabis market (the largest in the world).
GP Solutions also has a line of remarkable new proprietary soil mixtures, which contain no animal products. This is critical because many other soils and additives can contain harmful pathogens and contaminants that can cause crops to become tainted or fail rigorous testing.
The company is traded on the OTC stock exchange (ticker: GWPD) and is growing at a rapid pace (pardon the pun).
3. PLENTY
Like the other big vertical farming companies on this list, Plenty is another one that retails its produce, which includes kale and other greens, as well as some exotic herbs.
Plenty is probably the biggest company in terms of the amount of money it has raised in funding – approximately $226 million, according to CrunchBase.
4. BOWERY FARMING
You’d think any farming startup of any kind would steer clear of everything that’s genetically modified, but the fact that Bowery makes a point of saying it uses “zero pesticides and non-GMO” seeds might suggest that some vertical farming companies don’t have the same ideas.
Having raised more than $140 million in investment since inception in 2015, Bowery has carefully developed a distribution network in the US. Its leafy greens are available to buy in Whole Foods Market and Foragers. It also supplies a number of restaurants and sells online.
It doesn’t look like Bowery supplies its platform to other companies, even though some might be interested in its claims, such as: 95 percent less water usage than traditional agriculture; 100 times more productive on the same amount of land; and from harvest to shelf “within a few days”.
5. BRIGHTFARMS
Another of the big-money startups, BrightFarms has so far raised more than $112 million since its establishment in 2010, according to CrunchBase.
But unlike some of the other big companies, it isn’t into aeroponics as much. It seems more interested in hydroponics, which refers to growing plants with water, or, to be more accurate, mineral nutrient solutions in a water solvent.
6. GOTHAM GREENS
This company is one of many which have started up in the New York area. Strange to say it about such a new sector, but the market for vertical farming produce may be saturated – in that city at least.
Gotham Greens has so fair raised at least $45 million since its launch in 2011. It has four production-scale facilities, in New York City and in Chicago, and plans for more in several other states.
And, like BrightFarms, it’s more of a proponent for the hydroponic growing method, although it may well eventually mix it all up and try different approaches in different facilities.
7. IRON OX
This company appears to use robotics perhaps more than the others, in the picking process at least, and claims to operate fully autonomous indoor farmings. It too is a proponent of hydroponics, and is a retail-oriented company.
Its products are similar to the others’ – leafy greens such as lettuce and kale or things like that. It’s one of the newer startups on the list so a lot might change.
Iron Ox has only recently started supplying its products to local markets in California. The company has so far raised over $6 million in funding, according to CrunchBase.
US: Georgia State University - Freight Farms - Leafy Green Machine
Just yards behind Piedmont North, the Leafy Green Machine is a fully functional hydroponic farm built inside a shipping container. Configured for the immediate growth of a variety of crops such as lettuce, kale, spinach and other herbs, its innovative climate technology and growing equipment allow for the perfect environment 365 days a year
Freight Farms
Just yards behind Piedmont North, the Leafy Green Machine is a fully functional hydroponic farm built inside a shipping container. Configured for the immediate growth of a variety of crops such as lettuce, kale, spinach and other herbs, its innovative climate technology and growing equipment allow for the perfect environment 365 days a year.
LEAFY GREEN MACHINE
Ready, set, grow. Want to try our freshly-grown produce? Stop by Miss Demeanor’s or Centennial Café to try some on your salad or sandwich.
About Our Leafy Green Machine:
Seeds begin in the nursery area, where they germinate and grow into little seedlings.
In this area, plants grow in a shallow trough that periodically floods and drains with the nutrient-rich water solution.
This area holds up to 3,600 plants at one time.
After three weeks in the seedling station, the sprouts will grow into a sturdier leafy green. The plants are transplanted into vertical growing towers that hang from the ceiling.
This method creates a high-density growing environment and maximizes the cubic footage in the container.
Emitters drip nutrient-rich water down the vertical grow tower using only 10 gallons of water daily to grow more than 4,500 plants.
The water that isn’t consumed by the plant flows out the bottom of the tower and is then recirculated right back to the water tank.
As sunlight is important during photosynthesis, the windowless farm is equipped with LED lighting that mimics the sun’s natural light via growth-optimized blue and red hues.
There are 128 lighting strips running about 18 hours per day to maximize the growth cycle, with the lights turned off to give plants time to rest and during peak hours.
US: Florida - Making Microgreens A Household Word
In The Box, which is a completely retrofitted shipping container, Rodriguez sustainably grows an assorted variety of herbs and microgreens, using a minimal amount of water, energy, and soil
January 30, 2020
These broccoli microgreens are 40 to 50 times higher in nutritional value than the conventional form of broccoli. LOIS KINDLE PHOTOS
Farmer Seeks To Make Microgreens
A Household Word
By LOIS KINDLE
Eco-farmer Dario Rodriguez shows the container he uses to sell a variety of microgreens he sustainably grows at The Box Eco-Farm in Ruskin.
Dario Rodriguez wants the whole world to know about the nutritive value of microgreens, but for now, he’ll settle for South Shore and surrounding areas. LOIS KINDLE PHOTOS
The owner of Sustainable Eco-System LLC began his quest to make organic microgreens more mainstream by establishing The Box Eco-Urban Farm and setting it up at the Circle Pond Tiny Home Community in Ruskin last December.
In The Box, which is a completely retrofitted shipping container, Rodriguez sustainably grows an assorted variety of herbs and microgreens, using a minimal amount of water, energy, and soil.
“(The Box) allows for the maximum production of highly nutritional food in the smallest amount of space,” he said. “That’s what makes us eco-farmers.”
As part of his sustainability mission, Rodriguez sells only locally to individuals, restaurants, nutritionists, and chefs. His service area is South Shore, Brandon and some parts of south Tampa.
“To avoid the use of fossil fuels, I would rather place another box in Wesley Chapel, for example, rather than make deliveries there,” said Rodriguez, 49. “We do not ship what we grow.”
Microgreens are green, tiny vegetables with high concentrations of flavor and nutritional value. For example, broccoli microgreens are 40 to 50 times higher in nutritional value than the conventional form of broccoli, Rodriguez said.
Rodriguez’s wife, Iliana, helps him sell microgreens at the Firehouse Cultural Center in Ruskin.
Currently, he is growing broccoli, basil, red cabbage, peas, cilantro, arugula, parsley, kale, radish, sunflower, wheatgrass, and fennel Greek and mustard kohlrabi – all as microgreens. About 48 veggies can be grown as microgreens, Rodriguez said.
“When you buy microgreens from us, I like to tell you about their nutrients and health benefits, which have been acknowledged by the FDA,” he said.
The farmer also likes to tell you about their uses.
“Microgreens can be used in salads, sandwiches and as a topping for soups, pasta, eggs, and rice,” he said. “You don’t cook them; they’re tender without heat.”
Although Rodriguez and The Box are new to the area, he already has many satisfied customers.
“I bought four boxes last week: salad mix, broccoli, arugula, and radish,” said Dee Hood of Ruskin. “I use them on salads, and they’re so good, I just cut and eat them on their own.
“My teenage granddaughter and her boyfriend had some for lunch and loved them,” Hood continued. “I knew they were good for you, but I had no idea they would taste so good.”
Wheat grass, foreground is one of many microgreens Rodriguez currently grows in The Box.
Rodriguez uses high-density seeds in an organic growing medium like jute. In The Box, he’s able to control all of the production parameters: temperature, airflow and the humidity content of the air. The urban farm has a capacity of 720 10-inch by 20-inch trays of microgreens.
Rodriguez and his family moved to Ruskin from Argentina in 2016, when one of his three daughters began studying international business at the University of Tampa.
“We came as a two-year adventure,” said Rodriguez, who earned a master’s degree in global sustainability in 2018 from the University of South Florida. “But we’ve been here almost four years now, so we’ve decided to stay.”
He has invested $124,000 thus far between the Ruskin location and another at Fat Beet Farm in Oldsmar, where he grows mushrooms.
This is the completely retrofitted shipping container Rodriguez located at the Circle Pond Tiny Home Community in Ruskin to grow his microgreens. The Box allows him to produce the maximum amount of highly nutritional food in the smallest amount of space.
Rodriguez sells his microgreens for $3 per box, which is well below what you’d pay at a commercial establishment, and because they’re grown in an organic medium you can harvest as needed and they last longer.
Every Friday, you can find him set up at the Firehouse Cultural Center from 11 a.m. to 2 p.m. Microgreens can be preordered, paid for and picked up there.
To do so, call 813-416-5444, email sustainableecosystems@gmail.com or visit www.sustainablemicrogreens.net.
Facebook Twitter Share
Partnership Bringing Vertical Farming Opportunity To U.S. Colleges
Many colleges and universities are getting access to some of the most advanced hydroponic vertical farming technology around, thanks to a partnership between vertical-farming innovator Freight Farms and food/facilities management company Sodexo
January 29, 2020
Many colleges and universities are getting access to some of the most advanced hydroponic vertical farming technology around, thanks to a partnership between vertical-farming innovator Freight Farms and food/facilities management company Sodexo. The collaboration will usher in the implementation of Freight Farms’ 320-square-foot Greenery containers on campuses, enabling the onsite growth of fresh, traceable produce year-round.
The hope is that having food that would travel zero food miles will help reduce these schools’ environmental impacts. In a news release, the companies said the benefits include:
Food miles and waste reduction
Food is harvested steps from the plate, eliminating food miles
Harvested onsite, food lasts significantly longer, reducing spoilage waste
The Greenery uses 99.8 percent less water than traditional agriculture, and in some humid areas, operations can be water-positive
Peak freshness and nutrition, year-round
Unlike food that has to travel great distances between harvest and plate, freshness and nutrient density does not degrade during transit
Pesticides won’t be used
The farms grow at commercial scale and maintain the perfect environmental conditions every day of the year
Safety, transparency, and data-driven traceability
The hydroponic container farms are soil-free and are decentralized from the mass supply chain
Campus communities can get to know their own farmers and witness every growing stage of their food
Proprietary IoT technology, farmhand, tracks produce from seed to plate, even down to the hour
Student and employee engagement
Schools can choose to integrate their farms into interactive curricula across disciplines like science and technology, agriculture, nutrition, business, and social impact
Corporate businesses can integrate their onsite farms into employee wellness and benefit programs
Freight Farms’ customers are located in 25 countries and 44 U.S. states and range from small business farmers to corporate, hospitality, retail, education, and nonprofit sectors. To date, 35 educational and corporate campuses use Freight Farms’ technology, and together with Sodexo, implementation will rapidly expand across the U.S.
Images courtesy of Freight Farms
For In-Store Farms To Succeed, Finding The Right Balance Is Key
High-tech growing operations promise to efficiently supply retailers with greens. But the bigger payoff may be in offering shoppers a bit of food theatre
High-tech growing operations promise to efficiently supply retailers with greens. But the bigger payoff may be in offering shoppers a bit of food theater.
Credit: Jeff Wells
AUTHOR: Lauren Stine
Feb. 6, 2020
To appeal to consumers' growing desire for transparency and to know where their food came from, retailers across the country have brought local products into their aisles. They've also created informational web pages, integrated with nutrition apps and encouraged suppliers to tell their story to customers.
With 95% of consumers saying they'll pay more for locally grown products and 21% saying they eat local at least twice a week, though, companies are feeling the pressure to up the ante. Some, like Kroger and Whole Foods, have taken that step by bringing high-tech produce farms into their aisles — a budding movement that's made possible by advancements in growing technology.
Discover how to improve engagement among hourly employees by providing predictability and flexibility.
“Across the indoor farming industry, there have been dramatic decreases in cost when it comes to the physical hardware, advanced LED lighting and technology platforms automating a lot of the growth cycle,” Alexander Olsen, founder of automated mini-farm purveyor Babylon Micro-Farms, told Grocery Dive.
As more and more retailers discuss shifting center store operations online and accentuating the store perimeter, miniature produce farms promise to offer a supply line as well as a touch of food theater.
“We are also seeing a lot of traditional goods that grocers stock being purchased online and it’s freeing up a lot of space in-store,” Olsen said.
Retailers have been bringing cultivation to their stores for several years now. As early as 2012, Rouses sought to dazzle shoppers with an aeroponic garden on the rooftop of one of its New Orleans store locations. Hy-Vee and H-E-B's Central Market stores have also experimented with growing operations, with the latter adding a 53-foot modified shipping container full of greens to one of its Dallas stores.
Whole Foods has established a few different store growing operations. In 2018, it added an in-store mushroom growing display inside its Bridgewater, New Jersey store. The system was provided by Smallhold, a Brooklyn-based indoor farming company that also sells its mushrooms to local restaurants. A few years earlier, the chain partnered with urban greenhouse operator Gotham Greens to open a growing facility on top of a Brooklyn store location.
Credit: Kroger
The trend has gained momentum in Europe and Japan. Founded in 2013, Berlin-based InFarm has placed its in-store farms, which grow leafy greens, herbs, and vegetables, in hundreds of European stores, while Amazon Fresh sells its produce in Germany, France, and Switzerland. Last year, the company raised $100 million in Series B funding.
InFarm recently made its U.S. debut with two Kroger-owned QFC stores in Seattle and will bring its sprigs of kale, mint, cilantro, and dill to 13 more banner locations this year. The greens are initially planted at a nearby distribution center before being transferred to the store, where each plant's growth is monitored remotely by the company. The price points for the greens are competitive at $2.99 per bunch.
Grocery Dive reached out to Kroger and Whole Foods for comment but did not hear back by press time.
InFarm has lofty ambitions for its in-store farms, hoping to significantly impact grocery and restaurant supply chains, according to co-founder and CMO Osnat Michaeli.
“By growing produce on-demand and as close to possible to where it’s consumed, retailers are able to reduce food waste and sunk costs typically linked to industrial farming,” Michaeli wrote in an email to Grocery Dive. “We find that when retailers are able to understand the value, quality and flexibility of our business model they are more than enthusiastic to enter into conversations to explore our farms.”
Retail attraction or real action?
Although in-store farm displays and gardens are attractive additions, farming is no small feat even at a micro-scale.
“I think this trend is going to be closer to food theater and closer to a niche that engages the public and excites them about fresh produce,” Neil Mattson, associate professor at Cornell’s School of Integrative Plant Science, told Grocery Dive. Through his research, Mattson specializes in controlled environment agriculture systems such as hydroponics.
Operating an in-store farm is not for the novice beginner, he adds, noting that a retailer or its farming partner will have to allocate employees to monitoring the in-store farm to ensure it’s working properly. This requires intensive training, adds labor hours and could take the employee away from other tasks that still need doing.
If an in-store farm is not operating properly, the plants could fall victim to unsightly mold, disease and other issues that would make the display unappetizing to shoppers. Should a situation like this arise, the plants must be stripped out immediately and all surfaces must be sanitized, leaving an empty display, said Mattson.
Even for high-tech farming systems that are remotely monitored, Mattson has concerns about long-term success.
"Plants are biological systems so sometimes they don’t grow as fast as you think they should or some other factor becomes limiting and you have to adjust," he explained.
Credit: Pixabay
Mattson also questions whether an in-store farm could supply enough produce to be more than just an interesting display for consumers. Produce sales in the U.S. totaled $60.8 billion during 2018, representing a 1.7% increase over the prior year. The input costs for indoor farming systems, namely water, and around-the-clock electricity to power LED lights, are also substantial barriers even for large-scale indoor growing operations.
“It’s hard to foresee this producing the quantities of produce at the price points needed to become the widespread way that most Americans would buy their lettuce," Mattson said. "I think it is an expensive way to grow produce in a supermarket.”
High-tech farming operations have struggled to overcome high costs in the past, but the new crop of companies like InFarm and Babylon claim their systems are much more cost-effective and scalable.
To the extent that a retailer could overcome these challenges, benefits to having an in-store farm would include cutting out distributors and other middlemen, who often hike up the price of produce, and increasing store traffic, Mattson said. He believes the success of in-store farms may depend on balancing production needs and efficiency with the desire to amuse consumers.
Mattson said a larger-scale operation like Whole Foods' rooftop farm in Brooklyn offers the benefits of a customer draw with a more viable supply line. In recent years, retailers have also turned to large greenhouse and vertical farming operations to supply stores. Gotham Greens operates greenhouses in five states while BrightFarms operates greenhouses in four states and supplies to retailers like Giant Food, Acme and Food Lion.
Finding the middle ground
For Brooklyn-based grower and Whole Foods partner Smallhold, providing mushrooms first and in-store farms second has been a recipe for success. The duo behind the operation started out in a shipping container offering locally grown mushrooms to restaurants. They began asking their buyers whether they could fit a mini mushroom farm on-site and were encouraged enough to start modeling a prototype.
Whole Foods Local Forager Elly Truesdell ate lunch at a Vietnamese restaurant where one of Smallhold’s mushroom farms is located and promptly contacted the company to see about locating one at a Whole Foods store, according to co-founder Adam DeMartino.
“We didn’t intend to start a produce brand, it just sort of happened and a lot of that was because of Whole Foods,” DeMartino told Grocery Dive.
Today, Smallhold maintains mini mushroom farms in restaurants and retail locations, including two Whole Foods stores. It also sells mushrooms under a branded label.
Smallhold visits retail locations where its mini-farms are located once a week to swap out materials and harvest mushrooms. To achieve the volume that a retailer like Whole Foods demands, the company breaks up the growth process, completing the final stages, or fruiting, in-store. Mushrooms have an advantage over other crops grown indoors because of the high weight per square foot that mushrooms usually yield, according to DeMartino.
“Is it right for everyone? I’m not sure. That’s why it’s not the only thing we do,” co-founder Andrew Carter added. “How we look at it is we are offering a bunch of different tools to accomplish the task of getting mushrooms into the hands of everyone in the U.S. and hopefully the world. One of these tools is increasing the visibility of farming by growing on-site.”
The Booming Indoor Gardening Movement
LG’s indoor farm appliance is an example of how a built-in, columned indoor garden using lighting, temperature and water control can change the way consumers obtain their kitchen ingredients
Sarah Buckley
22/01/2020
The booming indoor gardening movement, prominently explored at CES 2020 earlier this year, is allowing consumers to grow their greens indoors, all year-round.
LG’s indoor farm appliance is an example of how a built-in, columned indoor garden using lighting, temperature and water control can change the way consumers obtain their kitchen ingredients.
LG’s offering of all-in-one seed packages and a growth monitoring app makes the one-stop-shop capable of feeding a family of four with home-grown produce.
The appliance replicates optimal outdoor conditions by matching the temperature inside the insulated cabinet to the time of day.
The LED lights, air circulation, and wick-based water management system allows the produce to quickly grow, alongside the automated gardening solution’s non-circulating water supply technology.
The core technology, which evenly distributes the precise water required for the plant’s to healthily flourish, prevents algae and odors for a hygienic, green enclosure.
Much like LG, n.thing, a South Korean agriculture start-up has developed ‘planty cube’ which is an automated vertical farming system, to a more elaborate effect – allowing consumers to maintain crops from anywhere, at any time.
Cubes, blocks, cells – the hydroponic farm, presented in a shipping container, has each square evenly stacked with rows of shelves of plants.
A computerized system controls the environment by monitoring the plants’ health, adjusting the environment accordingly.
These alternatives to glasshouse production are presenting solutions to production, health, convenience, pollution, water-use, but most notably, are finally brought to the consumer’s arena.
Freight Farms And Sodexo Are Bringing Vertical Farming to U.S. Schools
In North America alone, Sodexo serves over 13,000 client sites, many of them school cafeterias and university dining halls
Freight Farms, a major player in the world of containerized vertical farms, announced today a partnership with food service and facilities management company Sodexo. Together, the two aim to bring Freight Farms’ hydroponic vertical farms into school campuses across the U.S., according to a press release sent by Freight Farms
In North America alone, Sodexo serves over 13,000 client sites, many of them school cafeterias and university dining halls. The new partnership means Boston-based Freight Farms will be able to implement its Greenery container farms in more locations. At the moment, the company has 35 of these farms set up at educational and corporate campuses. The Sodexo partnership will expand that number “rapidly,” according to the press release, as the two companies implement more farms at both K-12 schools and university campuses that are Sodexo customers.
The 320-sq-foot Greenery farm uses hydroponics to grow leafy greens and herbs inside climate-controlled shipping containers. Users control watering and nutrient schedules and access data on their plants via the company’s proprietary Farmhand software, which can be accessed via the user’s smartphone. The idea is to equip growers with a turnkey offering they can flip on from anywhere in the world and use to grow food with relatively little hassle.
For schools in particular, that means outfitting students and teachers with not just freshly harvested food for the cafeteria but also potential new curriculum around technology, agriculture, and business, if students are allowed to work directly with the farms. Co-founder and CEO of Freight Farms Brad McNamara told me last year that the Greenery “allows us the opportunity to not only feed a demographic and teach them how to farm.”
Still, vertical farming has yet to prove itself in terms of scale and economics. Part of determining the success of the Freight Farms-Sodexo partnership will lie in getting more data on how well the vertical farms function in an institutional environment. Many vertical farms geared towards institutional levels of food production promise simple “plug in and grow” solutions. Not all of them deliver as promised.
And beyond basic functionality of the farms, we also need more information about whether or not its truly cost-effective to bring these farms into schools and cafeterias in place of greens transported across the country. Will the reduction in water usage and food waste translate into money saved for these institutions? Freight Farms noted in the press release that in some parts of the country, those using the Greenery can actually make their operations water positive. We don’t, however, have any numbers on how beneficial being water positive is to these organizations’ overall margins, and if it offsets, say, the electricity required to run the farms.
This isn’t the first food-tech-focused initiative Sodexo has embarked on in the recent past. In 2019, the company partnered with Starship to bring wheeled food delivery robots to college campuses in the U.S. The company also launched an Impossible Burger menu at 1,500 of its U.S. locations.
Sodexo’s sheer reach (it’s a multi-national corporation with services all over the world) gives it a certain amount of influence over the educational sector’s meals many others wouldn’t have. If the partnership with Freight Farms can showcase both the health and economical benefits from hyper-local, hyper-traceable, longer-lasting greens onsite, it could open the door to more schools and institutions considering some form of indoor farming onsite.
Related
US: Montgomery, AL - Local Restaurant Farms Out of Shipping Container For Fresher Produce
They say necessity is the mother of all invention. For a Montgomery restaurant group, a shipping container turned out to be the solution to their problem
Freight Farm Up And Running
In Midtown Montgomery
By Jennifer Horton | January 16, 2020
MONTGOMERY, Ala. (WSFA) - They say necessity is the mother of all invention. For a Montgomery restaurant group, a shipping container turned out to be the solution to their problem.
Eric Rivera is the executive chef for Vintage Hospitality, which runs Vintage Year and Vintage Café. He was struggling to find fresh, sustainable lettuce options for his restaurants.
“We found that importing all the stuff from California or from Florida, we would get these lettuces after they’ve been harvested for days and sometimes almost a week by the time we get to them,” Rivera explained. “The product goes bad really fast costs a lot of money to replace that product with other product, it’s just not that quality that we were looking for.”
Enter the Freight Farm, an unassuming shipping container housed in the heart of Old Cloverdale - only steps from his restaurants. The 320 square-foot farm is equipped to grow up to 4 tons of produce a year, according to the manufacturer. It runs on power and minimal water consumption, a stark contrast to the water needed to farm traditional row crops.
“We can control all the elements and control the growth cycles,” he explained. “No rain, no hail, we’re not exposed to any elements.”
Which means they can grow a variety of greens year-round while decreasing the carbon footprint of cross-country supply chains and the threat of lettuce recalls.
“We feel like that it’s our responsibility in the restaurant industry not only provide healthy, nutritious food; but that is done in a socially conscious way as well,” stated Rivera.
US: Boston, Freight Farms Goes To School
Farming is a club activity for the school’s high school students, who can go in during their free time
On local campuses, the repurposed shipping containers aren’t just used for growing food, they’re helping teach valuable lessons about science, social justice, and the humanities
By Andrea Pyenson Globe correspondent,
January 14, 2020
A student harvests lettuce at Rivers School in Weston.
STEPHEN PORTER FOR THE BOSTON GLOBE (CUSTOM CREDIT)
Inside the big white shipping container parked behind a classroom building on the campus of the Rivers School in Weston, it smells like a verdant field on a warm spring day, with a degree of humidity that is completely at odds with the cold, dry air outside.
A variety of lettuces, herbs, and a smattering of other vegetables grow on vertical towers in adjustable rows. The sixth-grade students who maintain the school’s Freight Farm cycle through in groups of four to reap the bounty of work they started at the beginning of the 2019-2020 academic year. The first harvest day was in late October.“
They all love to come in here,” says Emily Poland, who teaches eighth-grade science and is the farm director at this independent school for grades 6 through 12. The Freight Farm and related projects are built into the sixth-grade curriculum, incorporating humanities, social justice, and science, among other subjects. Students spend time there once a week planting, cleaning, and harvesting. Farming is a club activity for the school’s high school students, who can go in during their free time.
The Freight Farms container at the Rivers School.
STEPHEN PORTER FOR THE BOSTON GLOBE (CUSTOM CREDIT)
Based in Boston, Freight Farms manufactures technologically advanced hydroponic farming systems. In 320-square-foot, climate-controlled shipping containers, users can grow up to 13,000 plants at a time, vertically, without soil. The company was founded in 2010 by Brad McNamara and Jon Friedman. Several area schools, among them Rivers, Boston Latin School, and Worcester State University, are using the farms to grow food for their own communities, for their neighbors, and as educational tools.
For Poland, managing the farm was a natural extension of her teaching. “I like to create a curriculum. I care about food. I like to be outside,” she says. One of the sixth-graders’ annual activities, which combines academics with community service, is cooking a meal for the Natick Open Door at St. Paul’s Episcopal Church. These are hosted every week and attended primarily by seniors. Poland explains that planning the meal incorporates math skills because the students have to scale recipes to feed up to 45 people. And naturally, they use their own greens in the salads.
The students run a farmers market in the spring. And this year they are maintaining a (very micro) CSA, which one parent won in an auction. The school’s chef, Michael Clancy, also gets involved, using the students’ produce in the dining room, and helping them cook with what they grow — so far this year they have made pesto and herb vinaigrette. “Their pride is really amazing,” he says.
Boston Latin, a public exam school for grades seven through 12, acquired its farm in 2013 after students in the Youth Climate Action Network won the $75,000 prize in the Global Green Schools Makeover Competition. Farming is a student-run after-school activity here, under the guidance of eighth-grade history and civics teacher Cate Arnold, whose evident affection for her students appears to be reciprocal.
Though roughly 70 students have signed up as student farmers, there is a smaller core group that farms regularly, with an even smaller leadership team that is trained by Freight Farms. At the beginning of each academic year, the leaders meet to plan what they will grow, who will work to train new students, and organize schedules. They keep track of chores on a whiteboard in the farm.
Addy Krom, a junior, notes of the farm, “You can come in, it’s a whole different environment. All the stress from school [goes] away.” Adds sophomore Azalea Thompson, “This makes locally grown food more accessible to the city.” The students give the food they grow to faculty members, bring some home, and are working to create a CSA. With Arnold’s help, they are also trying to reestablish a more consistent connection to a food pantry in Jamaica Plain, where a former Boston Latin parent, recently deceased, used to deliver their greens.
At Worcester State, Mark Murphy, associate director of dining services, oversees the Freight Farm, which sits outside of Sheehan Hall, the school’s newest dormitory and site of its main cafeteria. Rich Perna, former director of dining, made the decision to purchase the farm five years ago, says Murphy, “to bring hyperlocal produce to the campus.
”Murphy has been responsible for the farm for the last two years. An employee of Chartwells, which has the contract for all of the school’s food services, he grows almost all of the greens for the cafeteria, as well as for alumni catering events, and the salad bar in the food court in the building next door. “I’m learning from trial and error,” he says.
At full capacity, Murphy explains, the farm produces about two acres’ worth of crops. He is constantly looking for different varieties of lettuce that will appeal to the students and is currently “trying to figure out a gourmet mix.” In addition to three varieties of lettuce, he grows kale, rainbow Swiss chard, parsley, and basil. He coordinates with the cafeteria’s cooks, telling them what he is growing so they can plan menus to incorporate the farm’s production.
Though WSU students are not currently working in the farm Murphy says he promotes the fact that most of the greens in the cafeteria are grown right outside the door. And, he says, “We’re trying to get the word out to get students involved.”
Through a partnership with the Worcester Public Schools and its program that helps young adults with differences transition from school to the workforce, Murphy has three part-time helpers/trainees. Once a week three students, who have completed high school with a certificate, come (often with a job coach from the program) to seed, plant, harvest, and clean. Murphy is in the process of hiring one of the students, who has aged out of the program. She “has a lot of passion for the farm,” he says.“I never thought we’d be growing food inside a container,” Murphy says. “I think it may become a necessity someday.”
Andrea Pyenson can be reached at apyenson@gmail.com.
Brick Street Farms To Construct Cultivation Hub, Increase Production In St. Pete
Backed by proprietary technology developed by Brad and Shannon, Brick Street Farms is now able to produce the equivalent of 2-3 acres of agriculture per shipping container
OWNERS OF BRICK STREET FARMS, BRAD DOYLE AND SHANNON O’MALLEY
For some reason, I can never keep plants alive. Maybe I don’t water them enough. Or perhaps I water them too much! Could it be the amount of light I expose them to? You know what, it’s probably due to my cats eating the leaves off every plant I’ve ever owned. Either way, I’ve never been able to provide the perfect environment for green life to thrive. And back in 2015, Shannon O’Malley and Brad Doyle were having similar troubles. But for them, the problem was the Florida heat.
Luckily, the couple found a solution to their woes. When they took their plants inside and put lights on them, the plants flourished. Brad and Shannon didn’t know it yet, but this revelation would end up being the seed that would sprout into an agricultural movement in Downtown St. Pete. After extensive research, the duo realized they could use their backgrounds in computer engineering and IT skills to build indoor hydroponic farms.
HUMBLE BEGINNINGS: BRICK STREET FARMS FIRST THREE CONTAINER FARMS
And so in January 2016, the duo purchased an overrun junkyard at 2001 2nd Avenue South in the Warehouse Arts District for $125,000 to house their new venture — Brick Street Farms. After months of environmental inspections, permitting and zoning obstacles, and electrical and plumbing issues, Brick Street Farms kicked off their first grow cycle inside three 320 square-foot shipping containers in October 2016.
Backed by proprietary technology developed by Brad and Shannon, Brick Street Farms is now able to produce the equivalent of 2-3 acres of agriculture per shipping container. The farm cultivates a variety of leafy greens including heads of bibb, butterhead and romaine lettuce, kale, basil, and rainbow chard.
Best of all, the growing process uses no dirt, no pesticides and much less water than traditional farming. Needless to say, their concept caught the attention of many local residents, and restaurants, such as the Vinoy, Oak & Ola, Oxford Exchange, and Pacific Counter.
For the past three years, Brick Street Farms has been feverishly trying to keep up with production. “When we started, we really just thought we’d be a wholesale production facility to grow and sell to restaurants, and maybe grocery stores,” says O’Malley. "But the level of interest and inquiries we get from everyone from chefs to elementary schools, we realized we couldn’t be closed off to the public.”
INSIDE ONE OF BRICK STREET’S HYDROPONIC SHIPPING CONTAINER FARMS
This year will be Brick Street Farm’s biggest yet. After bringing on a few investment partners in late 2019, the hydroponic farm will begin construction on a community-focused grow facility and will also dramatically ramp up production to satisfy demand from a new Publix partnership.
The current farm, located at 2001 2nd Avenue South, will be transformed into the Brick Street Cultivation Hub, which will include an expanded market, more container farms, a commissary kitchen, a beautiful courtyard, and pop-up event space.
RENDERING OF THE BRICK STREET CULTIVATION HUB AT 2001 2ND AVENUE SOUTH IN THE WAREHOUSE ARTS DISTRICT OF ST. PETERSBURG
Right now there are four container farms on site, but once the Cultivation Hub is complete, there will be a total of ten, stacked two high. Not only will Brick Street continue to grow lettuces, kales, and herbs, but they’ll be expanding into other products, such as tomatoes and strawberries.
“People always laugh at us, but one product we can grow exceptionally well in the containers is strawberries,” says O’Malley. “We haven’t sold them because we live in the strawberry capital of the world, but ours are phenomenal so we are going to give them a try and see if people want them.”
The largest addition to the property will be a new 6,500 square foot mixed-use building. The first floor will contain a 1,800 square foot farm-to-table market featuring greens grown on-site, as well as items from other local farms, like dairy, fruits, and vegetables, which cannot be grown in Brick Street’s shipping containers.
Additionally, the market will carry sustainable products from other local businesses, such as baked goods, health and beauty items, apothecary products, grab-and-go meals, beer and wine, and much more. Well-known local companies like St Pete Ferments, Nightshift Wax Company, Mother Kombucha, and Sunny Culture will also be available at the market.
A coffee concept will be located in the center of the Cultivation Hub. “It’ll be a full-time community space serving coffee, beer and wine,” says O’Malley. “Customers can relax in the beautifully landscaped courtyard, connect to the wifi and just hang out.” Two local coffee companies are currently in negotiations to lease the space.
An existing 416 square foot building will be converted into a commissary kitchen. This will be the new home of Brick Street Canning Company, helmed by Illene Sofranko, founder of The Urban Canning Company, which recently closed up shop. “We will be revising all of her core products and introducing an all-new line of products as well,” says O’Malley.
When Sofranko isn’t using the space, it’ll be rented out to local food makers. A few local restaurants will be hosting pop-up events at Brick Street, including Greenstock, Pete’s General, and Top Chef alum Jeffrey Jew, whose new St. Pete restaurant, Lingr on 6th St, opens this Spring.
“The Cultivation Hub will be dog-friendly and kid-friendly,” says O’Malley. “It’s just going to be a multi-functional property centered on food.” Construction begins in February and is tentatively scheduled to open in November.
If the Cultivation Hub wasn’t exciting enough, Brick Street Farms has also leased a warehouse on 22nd Avenue South that will serve as a manufacturing facility as well as house all farming operations while the Cultivation Hub is under construction.
BRICK STREET FARMS RECENTLY STARTING SELLING AT A PUBLIX SUPERMARKET IN LAKELAND, FL. AS PRODUCTION INCREASES, BRICK STREET PRODUCE WILL BE AVAILABLE IN ST. PETE & TAMPA
Brick Street Farms recently started selling their greens at a Publix Supermarket in Lakeland, the grocery chain’s test market. Feedback has been stellar and Publix is interested in expanding the partnership. “We have been selling 12 times their projected volume,” says O’Malley. “As our production grows, we will begin expanding to more cities.” Brick Street Farms is slated to hit St. Pete Publix stores in early March followed by Tampa and Central Florida thereafter.
With interest from Publix and a growing list of wholesale partners, the 22nd Avenue South warehouse will serve as a farming container assembly line. “It’ll be like a car plant,” says O’Malley. “We have an entire construction crew ready to begin building the farm containers.”
The goal is to build 60 containers in 2020 and an additional 100 in 2021. So if Brick Street’s goal is met, they’ll be operating around 170 container farms or the equivalent of 340 to 510 acres of agriculture by the end of 2021.
BRICK STREET FARMS RED LEAF LETTUCE
So, where will all of these container farms live? Everywhere! One of the core tenants of Brick Street Farms is to decentralize farming. In other words, the Tampa market will be served by Brick Street farm containers in Tampa, and Orlando produce will come from farm containers in Orlando.
“We have been overwhelmed by the response from the community, both from individual households as well as our restaurant accounts,” says O’Malley.
At St. Pete Rising, we couldn’t be more excited for Shannon O’Malley, Brad Doyle and the future of Brick Street Farms, a true homegrown local business. Be sure to follow them on Facebook and Instagram to stay up to date on well their produce will hit St. Pete shelves and for the debut of the Brick Street Cultivation Hub at 2001 2nd Avenue South.
CES 2020: The Planty Cube Aims to Make Vertical Farming More Modular And Automated
Like other vertical farms out there, the Planty Cube environment contains rows and shelves of planters stacked inside a shipping container
While many questions remain around exactly what role vertical farming will play in the future of agriculture, there are a few things we can count on with certainty. These indoor farms will become more and more automated over time, as well as modular. They will also be more user-friendly to the average consumer or small business, something evident by the number of indoor farming offerings at CES 2020 this week.
Among those offerings is the Planty Cube, a smart hydroponic indoor farm made by a Seoul, South Korea-based IoT company called n.thing. The grow system is modular enough to work in a number of different settings, from an apartment to a cafeteria, and automated enough that pretty much anyone can operate it.
Like other vertical farms out there, the Planty Cube environment contains rows and shelves of planters stacked inside a shipping container. Plants rely not on soil and human hands cultivating them, but instead on a computerized system that delivers the right “recipe” of nutrients, water, and light from LEDs to help photosynthesis. Humans have little involvement with the actual plants during the grow process. Most of the work on the farm, such as adjusting the LEDs, controlling temperature and humidity, and monitoring plant health, is done by the Planty Cube system, which uses sensors to collect data on the plants and can be controlled remotely by a smartphone.
Leo Kim, n.thing’s CEO, came up with the idea for the farm after creating an IoT-enabled smart pot called “Planty.” From there, the company developed the Planty Square, a modular system made up of multiple capsules called Pickcells, each roughly two inches in width, length, and depth, that contain the seeds of each plant. Users can connect multiple Squares (“like a Lego block,” says Kim) to grow larger crops, and enough of these put together make up the Planty Cube farm.
The Planty Cube system relies heavily on data from farming logs, which are fed back into a database known as the CUBE Cloud and analyzed with AI to help farmers determine optimal growing conditions for each crop. As the user adds more Squares to the farm with new and different crops, this real time, cloud-based system makes it easier for the user to manage the overall farm, even remotely.
While a number of companies now operate automated vertical farms that grow leafy greens, most of these (Kalera, Plenty, Intelligent Growth Systems) are better suited to large warehouse settings that produce millions of heads of lettuce. Planty Cube’s modular and user-friendly nature make it a more apt candidate for places like schools, hospital cafeterias, and university dining halls — all locations that would benefit from having freshly harvested greens onsite.
Planty Cube nabbed a Best of Innovation award for CES this year. If you’re currently milling about the show floor in Vegas, drop by n.thing’s booth to see the Planty Cube in action.