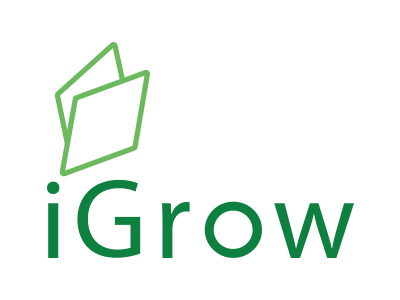
Welcome to iGrow News, Your Source for the World of Indoor Vertical Farming
Sustaining Communities Through Urban Agriculture
Sustaining Communities Through Urban Agriculture
- Erica Quinlan AgriNews Publications
- Nov 16, 2017
Plaut
INDIANAPOLIS — Urban agriculture is about more than just the number of farms in a city. It’s a way of viewing the entire food system, from farm to grocery store.
Karen Plaut, the interim dean of Purdue University’s College of Agriculture, discussed urban ag during a dinner hosted by Marion County Farm Bureau.
“Only 314 people are employed in the farm sector in Marion County,” she said. “But, as many of our FFA students have heard, if you eat, if you wear clothes — most of us are involved in agriculture or farming at some level.
“The university defines urban agriculture as the growing, processing and distribution of food crops and animal products by and for the local community within an urban environment.
“There’s a huge opportunity for careers in agriculture.”
Plaut listed several ways that Indianapolis shows what urban agriculture has to offer.
Urban Ag Certificate Program
“It’s a year-long program with 25 learning modules,” Plaut said. “It’s a hybrid format including online and in-person activities. The program has been in place for one year.
“The goal is to give in-depth instruction for urban, organic crop production all the way from farm design and harvest. Soil health, irrigation and pests are all important issues for an urban garden, just like a larger farm.”
Learn more about the certificate program at:www.purdue.edu/dffs/urbanag/programs/urban-ag-certificate.
Urban Bike Tour
“This year, 114 cyclists went on a bike tour to different urban farms,” Plaut said. “They stopped and looked at each farm, and in the evening, they brought it home by using produce from local farms to have dinner.
Made-in-Toronto Devices Aim to Make Indoor Gardening Simple
Aamar Khwaja is the founder of Modgarden, a modular indoor farming system, and his mission is to enable people to produce enough food to yield a salad a day.
Modgarden founder Aamar Khwaja | Samuel Engelking
One of the joys of summer is stepping out into the backyard or balcony and snipping a few leaves of fresh herbs or greens and adding them to dinner. Then winter comes and destroys all of the plant-growing fun.
But if one local entrepreneur has his way, city-dwellers will be growing healthy food year-round in their homes.
Aamar Khwaja is the founder of Modgarden, a modular indoor farming system, and his mission is to enable people to produce enough food to yield a salad a day.
The Modgarden was born out of Khwaja’s own personal need. After decades on Wall Street, he was chronically sick. When changing his diet resulted in improved health, he decided to grow his own food, which seemed impossible in his Toronto home.
“The food system is broken,” says Khwaja. “Any food can be labelled natural but still be sprayed with pesticides. I wanted to change that. After staring at a wall in my kitchen I thought, ‘Wouldn’t it be great to grow something there?’”
He began researching urban farming and vertical gardening and struck upon the idea of creating his own system, which uses mineral-rich living soil and is app-enabled.
Khwaja enlisted Toronto-based sustainable architect Heather Dubbeldam, whose firm is designing a rooftop farm for a client that includes an orchard.
The Modgarden is smooth and sleek, more like a fetching piece of furniture than a productive garden. With three sizes, ranging from desktop to floor model, all of which are stackable, it has flexibility to fit small spaces. He already has a great deal of interest and expects the units to be on the market in mid-2018. Prices range from $799 to $1,199 (though pre-launch online discounts are $450-$750).
The Modgarden is part of a growing movement catering to indoor food production, one driven by health consciousness and sustainability.
Food-oriented products already on the market are typically hydroponic and range from small objects to large, custom builds. For smaller spaces, there are systems like Click & Grow, which comes in three tabletop sizes with stylish light arms, as well as two wall farm units. Miracle-Gro offers a system called Aerogarden.
The Urban Cultivator is akin to a wine fridge and installed under a counter in place of cabinets. Even IKEA has an indoor gardening system, Krydda/Växer, though it’s not yet available in Canada.
Then there are aquaponics systems, like HiGarden or Grove, which incorporate fish and wetlands to make self-sustaining, closed ecosystems. Water from the fish tank is fed up to the plants and then filters from the plants through a wetland layer for purification before returning to the tank.
At a glance, these devices appear complicated. But as Leon Wasser, VP of business development for Toronto-based HiGarden, says, “All you need to add is air and fish food.”
HiGarden’s VIGA systems range from a mini tabletop and 12- and 24-inch desktop models, to those designed for building lobbies and indoor community farms. (Prices for consumer models run from $499 to $1,119.)
HiGarden founder, Phil Fung, is a leading LEED (Leadership in Energy and Environmental Design) advisor, so his approach includes improving the sustainability of buildings.
HiGarden founder Phil Fung | Courtesy of HiGarden
While HiGarden’s ambitions include working with schools, long-term-care facilities and northern Canadian food deserts, the company is also conscious of growing consumer demand.
“Younger people in condos don’t have easy access to green space,” says Wasser. “This is something that could be transformative – bringing a [garden] oasis into your home can be really beneficial, health-wise.”
So far, most home-sized systems are best suited for microgreens, leafy greens, small vegetables, peas, beans and herbs.
Of course, when people think of growing herbs indoors, a different variety comes to mind.
With federal legislation legalizing marijuana, including growing at home, coming in July 2018, that other herb is on the radars of Modgarden and HiGarden.
HiGarden has already designed a four-pot prototype of the VIGA in anticipation of the four-plant growing limit the law will allow, but beyond that, no modifications have been made, largely because weed is still illegal.
The challenge with retrofitting existing units is that while you don’t need to lock up basil, you’ll want to keep cannabis away from kids. Security and sufficient airflow – not to mention the fact that marijuana is notoriously finicky to keep alive – are chief concerns.
Khwaja is researching modifications for Modgarden but says that, for the moment anyway, his focus is on “feeding people.”
To date, only a few growing units are purpose-built for pot and are still in prototype or early-market stages – or sold out.
Grobo, developed in Waterloo, is a tall, discreet growing box that would look lovely in a living room and boasts security features like a locking door, fluid glass to mask contents, and air filtration. And WeeGro, used by licensed medical marijuana growers, is also customizable to allow users to disguise or display as desired.
Whether growing herbs or herb, the demand is strong and consumers primarily want simplicity.
“If it’s easy, they’ll do it,” says Heather Dubbeldam. “If it’s complicated, they won’t.”
If Randy Rowe’s experience is any indication, consumer demand for cannabis-centric systems is high.
He’s the president of Grow Up Cannabis Conference & Expo, which had its inaugural show in October in Niagara Falls. It drew around 4,000 people, many of whom were interested in growing their own.
Rowe says anyone who comes out with a consumer product that can grow everything in one box will hit the mark.
“That said, growing marijuana is an art. To be able to grow your own is hard,” he says. “It’s why you don’t see people growing their own tobacco.”
Back at Modgarden, Khwaja is finalizing the product for a spring 2018 launch.
“This is the appliance of the future,” he says, before comparing it to a fool-proof (if less sustainable) kitchen gadget. “I see this as the Keurig of fresh salads.”
Skywell to Design and Build Sustainable On-Campus Indoor Farms for Foxconn
Skywell to Design and Build Sustainable On-Campus Indoor Farms for Foxconn
LOS ANGELES, -- Skywell, a leading US water technology company, has been selected by Foxconn, one of the world’s largest manufacturing companies, to design and build a fully sustainable indoor vertical farm that will be integrated into the manufacturing facilities at Foxconn’s Wuhan, China Campus. The futuristic indoor farm will be entirely solar powered and its crops will be nourished exclusively by water generated by Skywell’s sustainable “air water” technology.
The new indoor farms, the latest of Foxconn’s green CSR initiatives, will produce high-quality vegetables and fruits, which will improve the variety and enhance the nutrition of employee meals provided at Foxconn’s on-campus cafeterias.
“Sustainability is a core pillar of Foxconn’s corporate strategy, and we are committed to investing in green, socially responsible innovation,” said Mark Chien, a Foxconn Senior Executive Vice President. “Because our people are the absolute foundation of our company, it is inspiring to be able to pursue a corporate initiative that will not only enhance the workplace, but also be respectful of the environment.”
According to Mr. Chien, since 2008, Foxconn has launched several green initiatives that have resulted in a significant decrease in carbon emissions and reduced water waste. By leveraging Skywell’s sustainable “air water” technology, Foxconn is hoping to enhance the working environment in its corporate facilities and showcase Skywell’s revolutionary technology and potential for the rest of the corporate world.
“Our atmospheric water generating technology shares many similarities with nature’s 'water cycle' by condensing and filtering naturally occurring and plentiful atmospheric water vapor into clean and fresh water,” said Ron Dorfman, CEO of Skywell. “Skywell 'air water' is generated with a carbon footprint much lower than alternative water sources due to the absence of pumping, plastics, packaging or shipping.”
Mr. Dorfman added that “When Foxconn became aware of our work with drinking water and indoor sustainable agriculture, Foxconn’s management immediately expressed interest in exploring various ways that our technology and know-how could be become a part of Foxconn’s CSR platform.”
“The implementation of these indoor farms continues our ongoing efforts to enhance the well-being of our employees in innovative ways,” said Mr. Chien. “We have high hopes for the scalability of the Skywell technology in connection with other socially responsible and sustainable initiatives in our facilities.”
Mr. Chien indicated that once the pilot project at the Wuhan campus is successfully operational, Foxconn will consider incorporating indoor vertical farms throughout its other Chinese and international facilities.
For media inquiries please contact Tyler Barnett PR at 323.937.1951.
Vertical Farm Under Construction At New RiNo Development
Construction is underway on the company’s first greenhouse, a 7,000-square-foot structure at the new S’park development on the corner of 25th and Lawrence streets.
Vertical Farm Under Construction At New RiNo Development
KATE TRACY NOVEMBER 16, 2017
Altius Farms will have 340 tower gardens in its greenhouse. (Altius Farms)
Sally Herbert is looking for higher ground in RiNo.
Instead of a penthouse with mountain views or a rooftop bar, the Air Force veteran and GS1 executive plans to grow lettuce. And this farm requires some vertical.
Dissatisfied with Denver’s urban agriculture and farming, Herbert founded Altius Farms with the goal of growing produce on a footprint that spreads up, not out.
Construction is underway on the company’s first greenhouse, a 7,000-square-foot structure at the new S’park development on the corner of 25th and Lawrence streets.
Herbert said the greenhouse, with 340 aeroponic garden towers, could produce 75,000 pounds of lettuce, herbs or other leafy greens annually at full capacity. Aeroponics is the process of growing plants without soil.
“We will produce over 10 times the yield of conventional farming,” she said. “We use 10 percent of the water and 10 percent of the space.”
The greenhouse is set to open in spring 2018.
Herbert said she hopes nearby restaurants will account for most of sales. The produce prices will be comparable to other locally sourced products, and Herbert thinks restaurant owners would pay more for the freshness.
“If I can deliver every day or every other day to a restaurateur, they’re really happy,” she said.
Sally Herbert in front of the under-construction S’Park development. (Kate Tracy)
Plans call for the remainder of produce to be sold through CSAs – community support agriculture – to nearby residents.
Lettuce and arugula will be the greenhouse’s main crops, but the company also plans to grow celery, edible flowers and bok choy, and can grow custom produce by request.
Unlike Infinite Harvest, another local Denver vertical farm, Altius will not use LED lighting or a shared water system.
“We’re not sharing water from tower to tower,” Herbert said, adding that will reduce the number of waterborne pathogens to the produce.
Herbert, a graduate of the University of Colorado and Colorado State University, was an executive of barcode company GS1 until four years ago, when she moved back to Colorado.
She served on the board of nonprofit Veterans to Farmers, where she first learned about vertical farm technology.
Herbert said more than $500,000 has been invested in the project, a mix of her own capital, a bank loan and money from other backers. She plans to hire six veterans to run the greenhouse.
Altius looked at two other sites, near the Stanley Marketplace and in Westminster, before settling on the property at 25th and Lawrence.
It is leasing the greenhouse, above the future site of sushi restaurant Uchi, from S’Park developer Westfield. It’s next door to 99 condos and townhomes priced between $300,000 and $900,000.
Rendering of Altius Farms, bottom left, in the under-construction S’Park development. (Altrius Farms)
About the author: Kate TracyView all posts by Kate Tracy
Kate Tracy is a BusinessDen reporter who covers nonprofits, startups and the outdoors industry. She is a graduate of Corban University. Email her at kate@BusinessDen.com.
Winter Doesn't Faze 87,000-Square-Foot Aquaponics Farm in St. Paul
Winter Doesn't Faze 87,000-Square-Foot Aquaponics Farm in St. Paul
Three-plus months after debuting in its new, vastly larger location, Urban Organics continues to expand.
By Amelia Rayno Star Tribune | NOVEMBER 22, 2017
ELIZABETH FLORES • LIZ.FLORES@STARTRIBUNE.COM
Pentair and Urban Organics are partners in this 87,000-square-foot indoor fish and produce farm in the old Schmidt brewery that provides greens and seafood for grocery stores, co-ops and restaurants.
“There’s no seasonal affective disorder in here,” said Dave Haider, who founded Urban Organics along with his wife, Kristen Koontz Haider, and with Chris Ames and Fred Haberman. “It just makes sense — not just from an environmental standpoint but also from a food safety standpoint. It’s sustainable, it’s consistent and it’s a local option.”
Three-plus months after debuting in its new, vastly larger location, Urban Organics continues to expand its operation — with the capacity to churn out 7,000 pounds of fish a week (up from a mere 100 pounds per week at its first location) along with about 10,000 pounds of produce (up from 250 pounds).
And with a warehouse full of 25,000-gallon tanks and skyward-reaching trays of lettuce, kale, Swiss chard, arugula, basil and parsley, Urban Organics — which the WateReuse Association just named 2017 agricultural project of the year, a national award — is doing so in a very green way.
Here’s how it works: The fish provide the nutrients necessary to grow the plants. The plants, in turn, act as a filter to improve the water quality for the fish. Reusing the water over and over again allows Urban Organics to use just a fraction of what conventional farming would require.
As for the finished products? The fish is mostly nabbed by restaurateurs — Fish Guys handles the distribution, to places like Birchwood Cafe and Spoon and Stable. And the greens are boxed up into nine different salad blends and sold to various grocery stores and co-ops. Even with the great increase in production, Haider said, they’re struggling to fill the overwhelming number of requests.
“We’re cautiously optimistic,” he said. “But we’ve had so much support from the local community. Right now we can’t even come close to keeping up with the demand.”
Indoor Farming Feeding Hundreds Each Day in Connecticut
November 1, 2017,
MERIDEN, Conn. (WTNH) — Indoor farming is underway in the state of Connecticut thanks to a group of young entrepreneurs.
Trifecta Ecosystems Incorporated has just fully filled out its new downtown Meriden aquaponics facility with thousands of plants growing in about 12 inches of water vertically and on a flat surface.
This historic facility is a massive former ball-bearing plant that they fully transformed.
CEO Spencer Curry says never in his wildest imagination did he expect to be in this kind of start-up business because he had been a Latin and philosophy major, but here he is and his company is thriving.
“We can feed about 300 people per week…An 11-ounce container which is like that large container at Whole Foods,” Curry stated.
“This is lettuce in a vertical grow tower,” Curry explained. “You’re actually seeing them hang vertically like that and that allows us to get more plants per square feet.”
Curry showed us other growing methods as well.
“This is actually another style of growing called deep water culture and this is the style we choose for our actual commercial farm in Meriden,” he said. “We use a high-efficiency LED grow lights from Fluence which is a company that we are working with for our commercial farm here.”
Curry said his business is mostly growing kale, lettuce, salad greens, cooking greens and herbs.
“Our model is about building our own network of farms and integrating that with both the existing farms that are out there and new farms that our clients are starting,” Curry said. “We honestly see Connecticut as primed to be a nationwide leader in indoor and controlled environment agriculture, but we also see our company as a much larger company than just the state. We want to develop our model here in Connecticut and make Connecticut really the de facto state in the nation to look toward controlled environment agriculture or CEA. We want to build the city that feeds itself and we want that to start here in Connecticut.”
Curry’s company works a lot with schools, so if you want to grow some greens vertically in your classroom, get in touch with them.
It grows right out of a fish tank, you farm fish and plants together.
You can suscribe to the greens right out of their farm in Meriden. It’s located at 290 Pratt Street.
To find out more, go to www.trifectaecosystems.com.
A Jeff Bezos-Backed Vertical Farm is Coming to the Seattle Area
Indoor farming startup Plenty is building its first full-scale farm in the Seattle area. Plenty snagged $200 million in Series B funding in July from investors including SoftBank's Vision Fund, Alphabet (Nasdaq: GOOGL) Chairman Eric Schmidt and Amazon (Nasdaq: AMZN) founder and CEO Jeff Bezos' Bezos Expeditions.
A Jeff Bezos-Backed Vertical Farm is Coming to the Seattle Area
Plenty will open a 100,000-square-foot indoor farm in Kent in the first half of 2018.
By Casey Coombs – Staff Writer, Puget Sound Business Journal
Nov 3, 2017
Indoor farming startup Plenty is building its first full-scale farm in the Seattle area.
Plenty snagged $200 million in Series B funding in July from investors including SoftBank's Vision Fund, Alphabet (Nasdaq: GOOGL) Chairman Eric Schmidt and Amazon (Nasdaq: AMZN) founder and CEO Jeff Bezos' Bezos Expeditions.
Expected to open in the first half of 2018 in Kent, Plenty's farm will employ a workforce of indoor farming engineers, organic growers and operations experts.
“Seattle’s emphasis on delicious, healthy food and energy and water efficiency makes the area a natural fit for our next Plenty farm,” Plenty CEO and co-founder Matt Barnard said. “At nearly 100,000 square feet, Seattle will be home to our first full scale farm and help set the standard by which our global farm network makes locally-grown, backyard-quality produce accessible to everyone. We’re excited about what’s next and look forward to building the Seattle team.”
The produce will be available to local Seattle and Vancouver BC-area consumers beginning in mid-2018.
Using LED lighting, micro-sensors and big data processing, the company's indoor farming technology aims to help solve global fresh produce shortages.
Plenty farms use one percent of the water and fraction of the land of conventional agriculture.
Plenty’s first field-scale farm is located in South San Francisco and will start delivering produce to local Bay Area customers within hours of harvest by the end of 2017.
The Microsoft (Nasdaq: MSFT) Redmond headquarters campus features similar lettuce-growing technology:
“Seattle’s emphasis on delicious, healthy food and energy and water efficiency makes the area a natural fit for ou
Microsoft grows hydroponic lettuce in Redmond
Mark Freeman, senior manager of global dining services at Microsoft, stands with lettuce growing in a hydroponic pyramids in Building 121's Cafe 121 on Microsoft's campus in Redmond.
NOSB Votes Not To Ban Hydroponics From Organic Certification
A longtime organic tomato farmer believes this could effectively be the beginning of “divorce proceedings” between the organic movement and the USDA’s National Organic Program.
The U.S. National Organic Standards Board (NOSB) has controversially voted against banning hydroponic and aquaponic crops being eligible for organic certification, in a move that has provoked strong opinions from the sector’s stakeholders.
The vote took place last week as part of the advisory board’s fall meeting in Jacksonville, Florida, which was open to the public and involved a range of testimonies given to the 15-member board.
The board voted to prohibit aeroponic agriculture – which grows plants suspended in the air with their roots exposed – but did not pass motions to ban hydroponics, a method that cultivates plants in water-based nutrient solutions, or aquaponics which combines hydroponic systems with farmed fish operations.
A U.S. Department of Agriculture (USDA) spokesperson told Fresh Fruit Portal the NOSB had heard two days of testimony that were mostly focused on the three production systems.
“The Board did not come to an agreement on any recommendations about the certification of hydroponic or aquaponic production systems. Both systems remain eligible for Organic Certification,” she said.
“The Board passed a proposal to recommend prohibition of aeroponics systems in organic production. Certification of aeroponic operations also remains allowed while USDA considers the Board’s work on this topic.”
Organic pioneers have typically argued that including hydroponic crops in the National Organic Program (NOP) undermines the integrity of the label and that nurturing the fertility of the soil is a fundamental aspect of the farming method.
Meanwhile, those on the other side of the debate have held that there should be no issue including hydroponics as long as farming inputs are organic.
Maintaining the status quo
Organic Trade Association (OTA) farm policy director Nate Lewis said that this vote essentially maintained the status quo for the vast majority of the industry.
“All these systems have been allowed in organic since 2002, so I think the outcome – with the exception of aeroponics – shouldn’t really change the reality for many producers,” he said, explaining that organic aeroponics represented a tiny proportion of the sector.
He said the OTA would have supported the motion to ban hydroponics – as it did in 2010 when the NOSB recommended prohibiting the production method – if the definition of the production system had remained unchanged.
However, he said that as the Crops Subcommittee had revised the definition and coupled it with proposed standards for organic container production – which involves raising plants in containers filled with a mixture of organic matter, water and nutrients – the association, therefore, did not support it this time around.
It should be noted that despite the NOSB previously voting to recommend hydroponics be banned from organic certification – albeit at a time when the hydroponic industry was far less developed than today – the advice was not upheld by regulator the NOP.
Lewis also commented that among the OTA’s members were those who strongly supported organic certifications for hydroponics and those who strongly opposed them, but said there was a “significant segment” of membership in the middle who thought entirely water-based systems shouldn’t be allowed but container production should be, with appropriate guidelines and standards.
Banning would have been “irresponsible”
United Natural Foods vice president of policy and industry relations Melody Meyer said it was positive to see so many members of the organic community come out to participate in last week’s event, but believed the decision left the sector “deeply divided”.
“I was present in Jacksonville to witness one of the most divided NOSB meetings to date.I believe they made the right decision not to prohibit these out-of-soil production methods,” she said.
“It would have put hundreds of growers out of business, taken valuable supply away from organic consumers and squelched innovation in our movement.”
Meanwhile, the head of the Recirculating Farms Commission, which represents hydroponic and aquaponic growers, also believed the NOSB had made the right decision in not prohibiting the two production methods.
The entity’s executive director Marianne Cufone said that as many products from these farms already carried a USDA Organic label, it would have been “irresponsible and confusing” for consumers and farmers to withdraw it now.
“By siding with current science and recognizing that existing law purposely leaves the door open for various farming methods, the NOSB is sending a critical message that sustainability and innovation are valuable in U.S. agriculture,” she said in a statement.
“These goals are at the center of the nationwide local food movement and spur growth of urban and rural farms alike, by a wide range of people. Inclusiveness is important in our food system.
“The Board did vote to prohibit use of aeroponics in USDA Organic production and indicated they would discuss what type of label hydroponic and aquaponic USDA Organic certified products would display.”
The financial factor?
In support of the motions to ban the three production methods, Mark Kastel of farm policy watchdog group the Cornucopia Institute said the industry had effectively created “two organic labels”.
“One label is all about integrity and production and that impacts the nutritional flavor and quality of the food (found at farmers’ markets, CSAs, co-ops and other local retailers). The other is all about profit,” he said.
“What has made the organic industry financially attractive is the fact that consumers are willing to pay a premium for food produced to a different environmental and animal husbandry model.”
He also believed that part of the “organic story” had been about economic justice for family farmers, and that industrial-scale hydroponic production is a stark disconnect from that.
“The industry, in throwing their weight around the regulatory arena at the USDA, in appealing to Congress when that doesn’t work, is poised to kill the golden goose. A loss of consumer goodwill will impact all players, large and small – growers, distributors and retailers.”
The Cornucopia Institute is now engaging with its outside legal counsel to investigate filing a federal lawsuit, he said.
Dave Chapman, a longtime organic tomato grower with a farm in Vermont, said he was “dismayed” by the result of the vote and that it was a “great disappointment”.
“The fact that it was a close vote is a sign of how much the whole process of the National Organic Program has been compromised. It should have been consensus that hydroponics should not be certified as organic,” he said.
“That was the last vote of the same body seven years earlier when there was just one descending vote. What happened in seven years that suddenly reversed the definition of organic? I would say what happened was a lot of money.
“There was no new scientific evidence. I think the market was invaded by some large companies that were making hundreds of millions of dollars and that is what changed the conversation.”
Chapman also emphasized that the organic movement and the NOP were two different things, and believed last week’s vote may result in some profound changes in the future.
“I think that this vote was basically the beginning of divorce proceedings. The NOP is of course going to continue, and the organic movement is going to continue, but I think they’re not going to continue together.
“If consumers become aware that most of the tomatoes – and soon I suspect most of the berries, cucumbers, pepper, lettuce and basil – they’re buying in the store that’s certified organic is in fact hydroponic, they’re going to become further disheartened and stop using organic certification for the basis of how they find good food to buy.
“I think that most likely we will see the creation of one or many alternative labels to the USDA, because the USDA is failing. Of course, this is going to be a lot of work and very confusing, but I really don’t know what other choice there is.”
Cornell Group Explores Future of Indoor Farming
Known as controlled environment agriculture (CEA), the systems combine greenhouse environmental controls such as heating and lighting with hydroponic and soilless production, enabling year-round production of fresh vegetables.
R.J. Anderson/Cornell Cooperative Extension
Doctoral student Jonathan Allred, center, leads a tour of Cornell greenhouses in November.
Cornell Group Explores Future of Indoor Farming
By Jill Monti | November 21, 2017
R.J. Anderson/Cornell Cooperative Extension
Hydroponic tomatoes growing in a Cornell greenhouse.
Indoor farming entrepreneurs and experts came to Cornell in early November with a goal: leverage the innovation at the College of Agriculture and Life Sciences to create viable businesses for local vegetables and produce grown indoors.
Known as controlled environment agriculture (CEA), the systems combine greenhouse environmental controls such as heating and lighting with hydroponic and soilless production, enabling year-round production of fresh vegetables. The process extends the growing season through a range of low-tech solutions – such as row covers and plastic-covered tunnels – to such high-tech solutions as fully automated glass greenhouses with computer controls and LED lights.
Led by Neil Mattson, director of Cornell CEA and associate professor in theSchool of Integrative Plant Science, Cornell has become a world leader in CEA research. In early November, the Cornell CEA Advisory Council, which was formed in 2015 to expand the retail and food service markets for products grown using CEA, hosted on campus more than 80 entrepreneurs and stakeholders from across the Northeast to discuss the state of the indoor farming industry, urban agriculture, supermarket trends and new technology.
At the conference the group announced the formation of the Controlled Environment Agriculture Global Association, an organization to foster growth, understanding and sharing ideas related to controlled environment agriculture and associated industries.
Erico Mattos, executive director of the newly formed Greenhouse Lighting and Systems Engineering (GLASE) consortium, presented his vision to advance CEA by bringing together expertise from industry and academia to create solutions.
“The CEA Advisory Council meeting provided a great opportunity to connect with key players from the different segments of the CEA supply chain in New York. I was impressed with the quality and quantity of the ongoing initiatives in this area supported by Cornell University professors and staff members and the level of engagement from the industry members,” Mattos said.
Mattos said private companies and public research from Cornell offer collaborative opportunities that can advance the CEA industry.
Cornell graduates from the CEA program have been in high demand from companies who wish to leverage their skills and knowledge. Little Leaf Farms, a leader in indoor lettuce production founded by Paul Sellew ’79 and based in Devens, Massachusetts, has hired numerous graduates.
“These talented individuals have provided immediate contributions to our business,” said Tim Cunniff, Little Leaf Farms executive vice president of sales and marketing. “It is exciting to see how Cornell is expanding its commitment in controlled environment agriculture to include the business of running a CEA operation. Cornell is in an excellent position to advance a scalable local food movement, and all of us at Little Leaf Farms are excited to be part of the process.”
Paul Brentlinger, who served on the grower panel and is the second-generation owner of CropKing, said his business and Cornell “have similar outlooks on the future generations of farmers, and we support Cornell as much as we can with their goal of educating the next generation of CEA operators.”
Laura Biasillo, agricultural economic development specialist at Cornell Cooperative Extension (CCE) of Broome County, said: “CCE is the ‘boots on the ground,’ providing everything from technical assistance to the business planning, cost analysis and financing needed by startups and business that are expanding.”
The conference attracted participants from traditional agricultural businesses interested in adding CEA to existing operations, to individuals with significant business experience, to those not yet in agriculture.
“The diverse perspectives made the conversations highly engaging, and building a network for this emerging New York ag sector was one of the key benefits of the conference,” said Aileen Randolph, outreach and communications manager of the New York Farm Viability Institute. “Now it’s up to the participants to do the hard work of utilizing this information for their specific business planning process.”
Jill Monti is technical lead at the Cornell Institute for Food Systems Industry Partnership Program.
STORY CONTACTS
George Lowery
Sensors Applied to Plant Leaves Warn of Water Shortage
Forgot to water that plant on your desk again? It may soon be able to send out an SOS.
MIT engineers have created sensors that can be printed onto plant leaves and reveal when the plants are experiencing a water shortage. This kind of technology could not only save neglected houseplants but, more importantly, give farmers an early warning when their crops are in danger, says Michael Strano, the Carbon P. Dubbs Professor of Chemical Engineering at MIT and the senior author of the new study.
“This appears to be the earliest indicator of drought that we have for agricultural applications,” Strano says. “It’s hard to get this information any other way. You can put sensors into the soil, or you can do satellite imaging and mapping, but you never really know what a particular plant is detecting the water potential.”
Strano has already begun working with a large agricultural producer to develop these sensors for use on crops, and he believes that the technology could also be useful to gardeners and urban farmers. It may also help researchers develop new ways to engineer drought-resistant plants, he says.
Volodymyr Koman, an MIT postdoc, is the lead author of the paper, which appears in the Nov. 8 online edition of the journal Lab on a Chip.
Printable sensors
When soil dries out, plants slow down their growth, reduce photosynthetic activity, and suffer damage to their tissues. Some plants begin to wilt, but others show no visible signs of trouble until they have already experienced significant harm.
The new MIT sensor takes advantage of plants’ stomata — small pores in the surface of a leaf that allow water to evaporate. As water evaporates from the leaf, water pressure in the plant falls, allowing it to draw water up from the soil through a process called transpiration.
Plant biologists know that stomata open when exposed to light and close in darkness, but the dynamics of this opening and closing have been little studied because there hasn’t been a good way to directly measure them in real time.
“People already knew that stomata respond to light, to carbon dioxide concentration, to drought, but now we have been able to monitor it continuously,” Koman says. “Previous methods were unable to produce this kind of information.”
To create their sensor, the MIT researchers used an ink made of carbon nanotubes — tiny hollow tubes of carbon that conduct electricity — dissolved in an organic compound called sodium dodecyl sulfate, which does not damage the stomata. This ink can be printed across a pore to create an electronic circuit. When the pore is closed, the circuit is intact and the current can be measured by connecting the circuit to a device called a multimeter. When the pore opens, the circuit is broken and the current stops flowing, allowing the researchers to measure, very precisely, when a single pore is open or closed.
By measuring this opening and closing over a few days, under normal and dry conditions, the researchers found that they can detect, within two days, when a plant is experiencing water stress. They found that it takes stomata about seven minutes to open after light exposure and 53 minutes to close when darkness falls, but these responses change during dry conditions. When the plants are deprived of water, the researchers found that stomata take an average of 25 minutes to open, while the amount of time for the stomata to close falls to 45 minutes.
“This work is exciting because it opens up the possibility of directly printing electronics onto plant life for long-term monitoring of plant physiological responses to environmental factors, such as drought,” says Michael McAlpine, an associate professor of mechanical engineering at the University of Minnesota, who was not involved in the research.
Drought alert
For this study, the researchers tested the sensors on a plant called the peace lily, which they chose in part because it has large stomata. To apply the ink to the leaves, the researchers created a printing mold with a microfluidic channel. When the mold is placed on a leaf, ink flowing through the channel is deposited onto the leaf surface.
The MIT team is now working on a new way to apply the electronic circuits by simply placing a sticker on the leaf surface. In addition to large-scale agricultural producers, gardeners and urban farmers may be interested in such a device, the researchers propose.
“It could have big implications for farming, especially with climate change, where you will have water shortages and changes in environmental temperatures,” Koman says.
In related work, Strano’s lab is exploring the possibility of creating arrays of these sensors that could be used to detect light and capture images, much like a camera.
The research was funded by the U.S. Department of Energy, the Swiss National Science Foundation, and Singapore’s Agency for Science, Research, and Technology.
Amazon's Jeff Bezos Invests in Vertical Produce Farming Company Plenty
, according to a report from getting into the fresh produce businessA new investment by Jeff Bezos has the man behind the Amazon Whole Foods buyout Business Insider
Amazon's Jeff Bezos Invests in Vertical Produce Farming Company Plenty
Nov. 6th, 2017
SOUTH SAN FRANCISCO, CA - A new investment by Jeff Bezos has the man behind the Amazon Whole Foods buyout getting into the fresh produce business, according to a report from Business Insider. Bezos reportedly has taken his place alongside the likes of Eric Schmidt of Alphabet, SoftBank Vision, and DCM Ventures to get in on the ground floor of Bay Area-based vertical farming startup, Plenty.
With the new investors signing on, Plenty announced it will now open a 100,000-square-foot farm in Kent, Washington, where the startup hopes to grow pesticide-free, “backyard quality,” fresh fruits and vegetables for consumers in the Seattle and Vancouver, B.C., areas. This second farm marks the first occasion Plenty will grow beyond its home in South San Francisco.
A plenty vertical farm
Business Insider reports that Plenty’s new farm will grow 4.5 million pounds of greens annually, which, according to the USDA, is enough to feed around 183,600 Americans. Set to come online in spring 2018, Plenty’s twist on the classic produce farm means that all of its crops will grow on glowing, LED-lit, 20-foot-tall towers, taking all soil, pesticides, and even natural sunlight out of the growing equation. Those of us in the biz know this is called indoor vertical farming and allows for a climate-controlled, year-round growing option.
In Seattle, Plenty has said it will begin growing leafy greens and herbs first, but will later expand to fruits, such as strawberries, tomatoes, and watermelons. CEO and Co-Founder Matt Barnard told Business Insider the company will begin selling in 2018 under it’s newly achieved organic certification and may be even looking at delivery as one option for distribution.
Matt Barnard, CEO, Plenty
Seattle’s emphasis on delicious, healthy food and energy and water efficiency makes the area a natural fit for our next Plenty farm,” said Barnard in a press release. “At nearly 100,000 square feet, Seattle will be home to our first full-scale farm and help set the standard by which our global farm network makes locally-grown, backyard-quality produce accessible to everyone. We’re excited about what’s next and look forward to building the Seattle team.”
A plenty vertical farm
To date, after Bezos’ contribution, Plenty has raised $226 million, which Barnard said will help the company fund new farms around the world in order to drive down prices and costs.
Will the Amazon leader move further into fresh produce investments as he seems to be keeping a watchful eye on the food industry? AndNowUKnow will keep you apprised with the latest.
Philips Lighting To Install its First LED Grow Light Project in New Zealand at Gourmet Mokai
Philips Lighting To Install its First LED Grow Light Project in New Zealand at Gourmet Mokai
November 21, 2017
Eindhoven, The Netherlands - Philips Lighting (Euronext: LIGHT), the world leader in lighting, today announced it has signed its first LED grow light project in New Zealand with Gourmet Mokai Ltd to improve the quality and cost efficiency of growing its popular Campari cocktail tomatoes.
Gourmet Mokai Ltd is part of the New Zealand Gourmet group of companies and sells premium fruits and vegetables to local markets and in Australia, Japan and Southeast Asia. The new LED grow lighting will be installed in January 2018 in a 4,500 square meter greenhouse at the facility in Mokai on the North Island, known for its sophisticated eco-friendly growing practices.
"Over the years, our LED technologies have helped tomato growers across the globe produce better quality fruit and higher yields, with more control over their growing climate," said Udo van Slooten, Business Leader Horticulture at Philips Lighting. "We feel privileged to be participating with New Zealand Gourmet, a leader in its field, and look forward to showing other growers in the region what we are doing at this location."
Gourmet Mokai Ltd is a joint venture of New Zealand Gourmet and two New Zealand Maori trusts, and it uses naturally occurring underground geothermal steam for heating. The Campari tomatoes are grown under glass using a hydroponic type method. The LED system chosen combines Philips GreenPower LED toplighting with GreenPower LED interlighting.
"We expect several benefits from the LED grow lights. We are using an optimal spectrum for plant growth and crop management, based on the LED light recipe specified by Philips Lighting's horticultural team. We also hope to improve the taste, vitamin C content and shelf life of our product with the LED grow lights," said Roelf Schreuder, Production Director Protected Crops at New Zealand Gourmet. "At the same time, we expect to reduce our operating costs and gain more control over the growing climate as the LEDs produce hardly any heat."
According to Schreuder, Gourmet Mokai must first learn how to grow tomatoes under LED lights and evaluate how it affects their heating set-up, CO2 supply, irrigation management and pollination. "We release bumblebees to pollinate our crops. However, when there's no daylight and the lighting system is on, the beehives have to be closed and the bees can no longer pollinate the crops. The lights will be connected with the existing Hoogendoorn climate computer system which will also control the opening and closing of the bumblebee boxes and CO2 supply."
Several parties are collaborating to make this project a success, including Philips Lighting, RTF Climate, Agrolux, Zonda Beneficials and Hoogendoorn Automation with the iSii Next Generation System equipped with a special LED light module software package.
For further information, please contact:
Philips Lighting - Horticulture LED Solutions
Daniela Damoiseaux, Global Marcom Manager Horticulture
Tel: +31 6 31 65 29 69
E-mail: daniela.damoiseaux@philips.com
www.philips.com/horti
About Philips Lighting
Philips Lighting (Euronext: LIGHT), the world leader in lighting products, systems and services, delivers innovations that unlock business value, providing rich user experiences that help improve lives. Serving professional and consumer markets, we lead the industry in leveraging the Internet of Things to transform homes, buildings and urban spaces. With 2016 sales of EUR 7.1 billion, we have approximately 34,000 employees in over 70 countries. News from Philips Lighting is located at the Newsroom, Twitter and LinkedIn. Information for investors can be found on the Investor Relations page.
3D Printed Connectors Make This Startup's Sustainable Indoor Garden Grow
3D Printed Connectors Make This Startup's Sustainable Indoor Garden Grow
by Sarah Saunders | November 22, 2017, | 3D Design, 3D Printing, Business
The first time we planted a garden in our backyard, I couldn’t get enough of watching the vegetables grow. I would go out in the yard and gently move aside the leaves to get a glimpse of the tiny green beans that were getting bigger every day. We had an abundance of tomatoes that year – so much that the cages were starting to bend from the weight. At the time, I had friends who lived in an apartment and were unable to garden outside, so they grew tomatoes indoors in one of those hanging garden set-ups. Hexagro Urban Farming, an Italian startup, is working to innovate urban farming, and this same kind of hanging garden, using 3D printing technology.
The Milan-based startup works to develop scalable, sustainable and sharing economy-based solutions, so customers can improve their production and supply of fresh, healthy, home-grown food. Last month, Hexagro launched a crowdfunding campaign on the Katana platform, which runs through New Year’s Eve, for its sustainable Living Farming Tree – an attractive, maintenance-free indoor garden, complete with 3D printed connectors.
The Living Farming Tree aims to bring nature from the outside to the inside of any workplace, like businesses, hotels, and restaurants, where its air-cleaning plants and healthy vegetables can enhance the well-being of the people there.
Irish 3D printing company Wazp, which worked with IKEA this summer on its first mass-produced 3D printed collection of home objects, also announced a partnership with the Hexagro startup for the Living Farming Tree, in order to provide a sustainable, socially responsible solution that could work in the catering industry.
“This partnership is a notable example of how 3d printing can facilitate innovative companies, like Hexagro, scale; by enabling stock-purchasing to be critically managed at the early stage of a business, so that essential capital is not tied up in stocks, while also giving a long-term option for commercial production,” said Wazp Product Development Manager Daniel Barrett. “Working with the Hexagro team is an exciting opportunity for us, to be a part of a new and innovative approach to a more sustainable farming future for countries around the world, which will be a global success.”
The Living Farming Tree is available in three size options:
- 4 Module Kit with 24 vases
- 7 Module Kit with 42 vases
- 13 Module Kit with 78 vases
The connectors for the modules are 3D printed, so that the design of the Living Farming Tree system is adaptable, modular, and scalable – thus making it possible for any person to bring nature into their own space, whether it’s at work or home.
L-R) Hexagro Urban Farming Team: Felipe Hernandez, Alessandro Grampa, Milica Mladenovic, Arturo Montufar
“We are glad to have found a partner that can help us in developing our 3D printed parts for prototyping and early fulfillment,” said Alessandro Grampa, CMO and Business Development at Hexagro. “This will allow us to maintain a dynamic product development, adapting to customer needs and feedback. Thanks to Wazp high-quality technology, we can provide our clients with the best modular and scalable farming systems adaptable to any of their indoor environments.”
By utilizing 3D printing technology to manufacture the module connectors, they can be scaled up to increase production, making the system adaptable to different kinds of crops; they also have a modular design, so the system can be customized to fit in any space. The system includes an automated monitoring device, which uses data analysis and dedicated crop planning software to adapt the Living Farming Tree to individual environmental conditions; it also comes with LED lights and an automatic irrigation system. According to the startup, the best crops for the Living Farming Tree include herbs like basil, mint, and oregano, and leafy green vegetables like kale, spinach, and lettuce.
This isn’t the first time we’ve seen 3D printing technology used to augment urban gardens, and by taking advantage of the benefits that 3D design and scalable production that Wazp’s supply chain solution offers, Hexagro will be able to bring the Living Farming Tree to the market faster, while also improving the system by listening to, and implementing, customer feedback and needs.
Speaking of customers, there are still super early bird rewards left on the Living Farm Tree’s Katana campaign – a pledge of €549 (a 30% discount from the retail price) will get you one of the first small configurations of the system, which includes a water pump, nutrient container, monitoring system, irrigation system, four LED lamps, four farming modules, 11 3D printed global connectors, and one app, with included user credentials.
The Living Farm Tree has been shortlisted for the Katana Opencircle Project, part of the European Union’s Horizon 2020 initiative.
Let us know what you think about this, and other 3D printing topics, at 3DPrintBoard.com or share your thoughts in the Facebook comments below.
Spider Webs and Succulents Inspire This Water-Collection Startup
The system designed by NexLoop combines biomimetic principles inspired by cribellate orb weaver spider webs, dwarf honey bees, mycorrhizal fungi and crystalline ice plants (pictured).
The core team behind NexLoop, a biomimicry venture, has been collaborating on its nature-inspired water collection technology for almost two years. But the first time the three entrepreneurs met in person was in mid-October in California, when their idea won the $100,000 grand prize in the Biomimicry Global Design Challenge.
"We have tons of people who are excited about pilots around the world," said C. Mike Lindsey, who hails from Brooklyn, New York, and aspires to a career in urban agriculture. "That's the main goal now: To see what it can do in various climates, and how it can scale."
His partners, who started the project, are Jacob Russo, a Carnegie Mellon-educated architect working toward his masters in international design in Stuttgart, Germany; and Anamarija Frankic, an expert in biomimicry who splits her research work between Boston and Zadar, Croatia.
The AquaWeb incorporates lessons on how nature captures, stores and distributes water in a novel new design that enables urban farms to feed our growing populations.
Russo and Frankic met at a workshop in New York, and pulled in Lindsey when they began exploring food-related applications. Their concept combines research associated with architecture, agriculture and materials.
The trio's invention, AquaWeb, mimics the way that natural systems capture, store and distribute water — not just rainwater, but ambient moisture such as fog. NexLoop believes that the approach initially will be useful in helping container farms or indoor vertical farms to become more self-sufficient. In theory, the system could have broader approaches, such as amplifying rooftop rainwater harvesting and storage for large buildings — but that's not the current focus of their pilot work.
NexLoop
The AquaWeb module is a multifunctional biomimetic system to integrate water capture, filtration, storage and distribution into food production building envelopes such as greenhouses and container farms.
"The Ray of Hope Prize judges were impressed by NexLoop's push to further their design — making it more locally attuned, more energy-efficient and decentralized — by looking to living organisms for design clues every step of the way," said Megan Schuknecht, director of the design challenge. "The result is functional and beautiful, as well as resilient, and a great example of regenerative biomimetic design. We are all looking for ways to make our cities more resilient to the effects of climate change. The AquaWeb incorporates lessons on how nature captures, stores and distributes water in a novel new design that enables urban farms to feed our growing populations reliably and affordably using locally available resources."
The contest is run by three nonprofits: the Biomimicry Institute and Bioneers (both focused on identifying innovative technologies that could be part of solutions to address climate change); and the Ray C. Anderson Foundation (named for the late Interface Carpet founder and sustainability pioneers), which funds projects around the world. The main award, the "Ray of Hope," is meant to help the winners move toward commercializing their idea.
A convergence of biomimetic principles
AquaWeb's design actually combines several ideas. The water capture mechanisms are inspired by cribellate orb weaver spider webs, which are "engineered" to collect fog out of the air; the storage concepts mimic the approaches used by drought-tolerant succulents (such as the crystalline ice plant) to hold on to water; and the trio studied the ways that certain mycorrhizal funghi, such as the Jersey cow mushroom, distribute water to the entire plant structure.
They also have been busy borrowing from bees: Each module of the system is shaped as a hexagon, like a hive structure. They can be stacked together depending on the required application — a stacked pair measures 16 inches tall by 18.5 inches wide. "They can be scaled up or down depending on the needs of who we are working with," Russo said.
In theory, the system could have broader approaches, such as amplifying rooftop rainwater harvesting and storage for large buildings.
The NexLoop team will be collecting data on several areas during the next phase of its pilot tests. For one thing, it will study how the system performs in a variety of climates — including very arid regions in Hawaii, Morocco, and Africa. They also will evaluate how materials and fabrics affect how much water can be collected.
In simulations where water is sprayed onto the system, AquaWeb captures about 50 percent, according to NexLoop's early test results — or about 2,000 milliliters per square meter of fog. Right now the prototype can store about five liters of water per unit. The team estimates it would take about 20 units to support a shipping container.
Aside from systems that could be added to a rooftop or onto the structure of a greenhouse, NexLoop is studying ways that these ideas could be incorporated directly into building envelopes — offering multiple functions with minimal material additions.
Who knows? Perhaps it could provide the foundation for decentralized water systems that support a variety of functions across next-generation buildings. For now, NexLoop will get busy proving its concept.
Topics: Tags:
Solar Greenhouses Generate electricity and Grow Crops at The Same time, UC Santa Cruz Study Reveals
Electricity-generating solar greenhouses are outfitted with transparent roof panels embedded with magenta luminescent dye that absorbs light and transfers energy to narrow photovoltaic strips, where electricity is produced. A new study shows that this novel technology, which has the potential to take greenhouses offline, didn't interfere with plant growth or production.
Plants grown in this "smart" greenhouse fared as well or better than plants grown in conventional greenhouses. (Photo by Nick Gonzales)
The first crops of tomatoes and cucumbers grown inside electricity-generating solar greenhouses were as healthy as those raised in conventional greenhouses, signaling that "smart" greenhouses hold great promise for dual-use farming and renewable electricity production.
"Plants are sensitive not just to the intensity of light but also to color," says Michael Loik. "But it turns out the plants grow just as well."(Photo by Nick Gonzales)
"We have demonstrated that 'smart greenhouses' can capture solar energy for electricity without reducing plant growth, which is pretty exciting," said Michael Loik, professor of environmental studies at the University of California, Santa Cruz, and lead author on a paper that appears in the current issue of the American Geophysical Union's journal Earth's Future.
Electricity-generating solar greenhouses utilize Wavelength-Selective Photovoltaic Systems (WSPVs), a novel technology that generates electricity more efficiently and at less cost than traditional photovoltaic systems. These greenhouses are outfitted with transparent roof panels embedded with a bright magenta luminescent dye that absorbs light and transfers energy to narrow photovoltaic strips, where electricity is produced. WSPVs absorb some of the blue and green wavelengths of light but let the rest through, allowing the plants to grow. WSPV technology was developed by coauthors Sue Carter and Glenn Alers, both professors of physics at UC Santa Cruz, who founded Soliculture in 2012 to bring the technology to market.
Loik's team monitored photosynthesis and fruit production across 20 varieties of tomatoes, cucumbers, lemons, limes, peppers, strawberries, and basil grown in magenta glasshouses at two locations on campus and one in Watsonville, California.
"Eighty percent of the plants weren’t affected, while 20 percent actually grew better under the magenta windows," said Loik. Tomatoes and cucumbers are among the top greenhouse-produced crops worldwide, he said.
In additional experiments, small water savings were associated with tomato photosynthesis inside the magenta glasshouses. "Plants required 5 percent less water to grow the same amount as in more conventional glasshouses," he said.
"I thought the plants would grow more slowly, because it's darker under these pink panels. The color of the light makes it like being on the Red Planet," said Loik. "Plants are sensitive not just to the intensity of light but also to color. But it turns out the plants grow just as well."
Reducing the energy consumed by greenhouses has become a priority as the global use of greenhouses for food production has increased six-fold over the past 20 years to more than 9 million acres today—roughly twice the size of New Jersey, according to Loik. "It's big and getting bigger," he said. "Canada relies heavily on greenhouses for vegetable production, and their use is growing in China, too." Plastic greenhouses are becoming popular for small-scale commercial farming, as well as for household food production, he added.
Greenhouses use electricity to control temperature and power fans, lights, and other monitoring systems. "This technology has the potential to take greenhouses offline," said Loik, who specializes in climate change, plant physiology, water resources, and sustainable technologies. Cost per panel of WSPV technology is 65 cents per watt—about 40 percent less than the per-watt cost of traditional silicon-based photovoltaic cells.
"If greenhouses generate electricity on site, that reduces the need for an outside source, which helps lower greenhouse gas emissions even more," said Loik. "We're moving toward self-sustaining greenhouses."
Additional coauthors include Catherine Wade, who participated as a graduate student, Carley Corrado, who participated as a postdoctoral researcher, and undergraduates David Shugar and Devin Jokerst, all of UC Santa Cruz; and Carol Kitayama, senior grower at Kitayama Brothers Growers.
Valoya Launches a New Line of State-of-the-Art LED Grow Lights
Valoya Launches a New Line of State-of-the-Art LED Grow Lights
Since its entrance to the LED grow lights market in 2009 Valoya has been dedicated to producing the highest quality horticultural LED lights for its customers which include 8 out of 10 world’s largest agricultural companies. Countless crop science companies, research institutes, universities, vertical farms etc are equipped with Valoya’s existing series (L, C, B and R). The range is now complemented with a new a line that brings significant improvements and pushes the LED grow lights industry forward.
The BX-Series is the next evolution step of the existing B-Series, the high intensity bar shaped luminaires widely used in growth chambers and similar applications demanding high light intensity. With the intensity of up to 2,1 µmol/W and a dimming feature these luminaires can produce the micromole output for the widest range of plants. The spectra include Valoya’s already available, patented wide-spectra such as NS1 (sunlight spectrum widely used in research) and AP673L (vegetative growth spectrum, widely used by vertical farmers and other growers). These adhere to Valoya's Spectrum Quality Standards which define the permitted wavelength variations among production batches as well as over time of the fixtures' usable life. This is a quality guarantee for researchers and growers ensuring them that the spectrum will remain consistent with minimal variation over a long period of time as well as when they acquire luminaires produced in more recent batches. The BX-Series, like all Valoya products, has been designed with GMP compliant production facilities in mind.
Boasting an Ingress Protection rating of IP67 the BX-Series is entirely dust and humidity resistant and can even withstand water submersion. These fixtures are passively cooled without fins thus they do not accumulate dirt over time and can be easily cleaned and if needed sterilized with harsh chemicals like peroxide, alcohol etc. Another innovation that the BX-Series brings are the GORE-TEX components in its end-caps that push the hot air and moisture out of the luminaire preventing condensation and overheating. This means the luminaires can function in high temperatures (up to 40°C / 104°F) and thus the LED chips inside last longer than in a typical LED grow light. Furthermore, their high Impact Protection (IK) rating (IK08) makes them robust and allows them to keep functioning consistently even when getting dropped or hit. All of this comes in an only 2,6 kg / 5.7 lb heavy luminaire that consumes 132 Watts (model BX120).
These are heavy duty, research grade luminaires designed to produce high and uniform light output over a long period of time. Combined with Valoya’s patented spectra and the support of a team of photobiologists, BX-Series is a smart choice of LED grow lights.
To learn more about the BX-Series, please download the brochure.
About Valoya Oy
Valoya is a provider of high end, energy efficient LED grow lights for use in crop science, vertical farming and medicinal plants cultivation. Valoya LED grow lights have been developed using Valoya's proprietary LED technology and extensive plant photobiology research. Valoya's customer base includes numerous vertical farms, greenhouses and research institutions all over the world (including 8 out of 10 world’s largest agricultural companies).
Additional information:
Valoya Oy, Finland
Tel: +358 10 2350300
Email: sales@valoya.com
Web: www.valoya.com
Facebook: https://www.facebook.com/valoyafi/
Twitter: https://twitter.com/valoya
Autogrow Launches Cloud Application To Grow Anywhere And On Any Device
Global ag-tech company Autogrow has further revolutionized indoor agriculture with an API-enabled cloud application giving growers access to grow anywhere, on any operating system and viewed on any device.
Autogrow Launches Cloud Application To Grow Anywhere And On Any Device
22 November 2017, San Francisco, U.S.
Global ag-tech company Autogrow has further revolutionized indoor agriculture with an API-enabled cloud application giving growers access to grow anywhere, on any operating system and viewed on any device.
“With our growers now in 40 countries; our new IntelliGrow application can seamlessly support their crop production via the cloud, giving them the ability to access their Intelli controllers, change and set new data points and monitor and manage their crops – from anywhere and on any device,” says CEO Darryn Keiller.
The ability to control the devices remotely is due to the IntelliGrow API (Application Programming Interface) that Autogrow created for the IntelliDose and IntelliClimate control systems.
“Our IntelliGrow utilizes an open API which means it can integrate with any third-party systems including lighting, HVAC, sensors and machine vision systems,” explains Chief Technology Officer Jeffrey Law.
“We have also ensured enterprise-level data security of our cloud platform for peace of mind. We have had a great core group of growers as beta testers, so we have designed IntelliGrow with growers, and for growers.”
Alongside real-time data, IntelliGrow also captures unlimited historical data enabling data-driven decision making. Current language features on the user interface have also been enabled for English and Chinese with Spanish and Arabic rolling out over the next few months, reflecting Autogrow’s core customer markets of the Americas, Asia, Middle East and North Africa, Australia and New Zealand.
"Being cloud-based, we enable a significantly better, more flexible and highly scalable growing experience. Growers have historically been tethered to their growing operations and we're now removing the need to be physically present onsite. Not only that, we're empowering them with real-time data, so they're more informed, more agile to changes in their growing environment, enabling better crop management and more profitable operations," notes Mr. Keiller.
To find out more about IntelliGrow visit www.autogrow.com/intelligrow
Amazon’s Seattle Campus Is Using Data Center Next Door As A Furnace. It’s Pretty Neat
Using “waste heat” from digital infrastructure to stay warm downtown.
Amazon’s Seattle Campus Is Using A Data Center Next Door As A Furnace. It’s Pretty Neat
Using “waste heat” from digital infrastructure to stay warm downtown.
Updated by David Roberts@drvoxdavid@vox.com Nov 22, 2017
The hippest new technology: big pipes carrying hot water. Jordan Stead/Amazon
Retail giant Amazon has a rather mixed reputation among progressives, to say the least. There are ongoing debates about its labor practices and its ruthless competitive tactics, which have driven competitor after competitor out of business. Among environmentalists, opinion is also divided — some argue that online shopping (and shipping) has accelerated wasteful consumer culture, others that it has reduced the carbon footprint of shopping that was going to happen anyway.
Putting those broader disputes aside, there is one area where the company is making substantial and undeniable progress. After years of what could charitably be called benign neglect, Amazon has recently moved aggressively toward corporate sustainability.
It plans to have 15 rooftop solar systems, with a total capacity of around 41 MW, deployed atop fulfillment centers by the end of this year, with plans to have 50 such systems installed by 2020.
Amazon was the lead corporate purchaser of green energy in 2016. That year, it also announced its largest wind energy project to date, the 253 MW Amazon Wind Farm Texas. Overall, the company says, it has “announced or commenced construction on wind and solar projects that will generate a total of 3.6 million megawatt hours (MWh) of renewable energy annually.”
(Of particular interest to Vox nerds: The company also signed on to an amicus brief in support of Clean Power Plan, Obama’s signature climate policy, which the Trump administration wants to kill.)
But what recently caught my eye is the clever way that Amazon’s giant new campus in downtown Seattle will keep its occupants warm in the winter — a pleasingly low-tech solution that sits squarely at the intersection of several of my enduring obsessions: the importance of smart design, the benefits of urban density, and the need for electrification of the power system.
Juicy! Let’s take a look.
Hot water is so hot right now
Amazon is building a giant four-block campus in downtown Seattle’s Denny Triangle, which will eventually encompass five towers and five million square feet. This schematic is fromGeekwire (which has its own excellent story on Amazon’s project).
That’s a lot of space to heat during the dreary Pacific Northwest winters.
Good fortune! Just across 6th Avenue from Doppler Tower is the 34-story Westin Building Exchange, a regional telecom “carrier hotel” that houses computer and server hardware for some 250 telecom and internet companies. About 70 percent of the building is occupied by data centers.
All that hardware creates an enormous amount of heat. Lacking any better options, Westin has been venting that heat into the Seattle air, through giant cooling towers, at considerable expense.
Waste heat, meet heat consumer.
Amazon and the co-owners of the Westin — Seattle’s Clise Properties and San Francisco’s Digital Realty Trust — struck a deal: Amazon would buy some of the Westin’s waste heat.
As winter approaches, an innovative heat source will be keeping our Seattle headquarters warm. #greenenergyhttp://amzn.to/2j2t8pI
The technology is impressive at this scale, but conceptually, it’s pretty simple. Water circulates in PVC pipes throughout the Westin, gathering heat. It is then sent beneath the street (city waivers had to be granted to cross public rights of way, a huge problem for waste-heat projects historically) to Doppler tower.
Beneath Doppler, a series of large heat exchangers run the Westin’s warm water next to cool water from Amazon, heating it up (exchanging the heat). That warmed water is around 65 degrees, so it is run through a series of five heat-reclaiming chillers to raise the temperature to 130 degrees (also reducing the volume of water).
Amazon’s five big chillers, chilling.
That hot water is then circulated beneath the floors of the campus buildings via radiant heating systems, providing more than three-quarters of the heating required by the campus, at about four times the energy efficiency of a comparable HVAC system.
The cooled water then returns to the basement to gather more heat, and lo, the cycle continues.
Westin’s building manager told the Seattle Times that the building generates the heat equivalent of about 11 megawatts per day. During winter, Amazon will siphon off about 5 megawatts of that.
In effect, Westin is replacing Amazon’s need for natural gas boilers to heat the water, which would have run close to a million dollars annually in fuel and maintenance costs. Another way of looking at it: the system will allow Amazon to avoid the purchase of some 4 million kilowatt-hours of electricity a year.
What’s more, the data center is a rock-solid, reliable source of heat; it is guaranteed to always be running (unless the grid goes down). Amazon has a couple of efficient natural gas boilers for backup, but at least over the past two winters, it says they have rarely been run.
In exchange, during the winter, Amazon’s campus is serving as a giant cooling tower for the Westin, substantially reducing its cooling bill — and paying for the privilege.
It is, to risk cliché, a win-win.
To pull all this off, Amazon and Clise had to create an “ecodistrict” (navigating a thicket of city bureaucracy). The coolest part is that there’s lots more heat to use, so there’s no reason the district couldn’t be extended to more Amazon buildings, or to surrounding buildings.
An aerial view of Amazon’s Doppler Tower and Meeting Center (with its green roof). Note the “biospheres,” which will be filled with plants. (Amazon)
Old technology with intriguing new applications
There’s nothing new about “district heating” — i.e., heating multiple buildings using a single source and a network of pipes. The concept dates all the way back to the Roman Empire. In the Industrial Era, such systems were frequently used to exploit the heat from small in-city power plants. A number of modern cities, from Paris to Tokyo to Vancouver, BC, have district heating systems in use today, fueled by everything from biomass to sewer water to solid waste incineration.
What is somewhat novel about Amazon’s arrangement is the use of an electricity consumer — a data center — as the heat source. (Waste heat from data centers is used in other places, though Amazon says this is the first contract between a data center and a heat consumer with different owners.)
As I mentioned, this sits right at the intersection of three of my enduring obsessions.
First, it represents enormous energy savings with relatively old and reliable technology — it’s just water run through pipes. What produced the savings was not some whiz-bang tech innovation, but simple design. Cities produce enormous amounts of waste heat and then import enormous amounts of energy to warm themselves. It’s kinda crazy. Smarter design could help close that loop, reducing the need for imports, reducing emissions, and bringing more of a city’s energy management under its own control.
Second, along the same lines: cities! Cities are everything this century. State, provincial, and national governments are often captured by rural or corporate interests, creating substantial status quo bias. In cities, however, constant change is a fact of life and governments are at least somewhat more nimble — and that’s especially true when it comes to experimentation and innovation around the clean-energy transition. The more cities can generate and manage their own energy, the less hostage they are to state and national policy shifts.
With that in mind, why not bring more highly energy-intensive operations — not just data centers, but, oh, indoor farms, or marijuana grow operations — into dense urban areas? They have traditionally been built in the hinterlands, where land and power are cheap, but if they could make a substantial second income selling their waste heat, they might be able to justify urban locations.
That would reduce shipping supply lines. It would bring tax-paying, profit-making industrial facilities that don’t pollute into urban boundaries and budgets. It could potentially reduce urban HVAC bills, if the facilities are hooked up to district heating systems. And it would give cities more direct control over their energy fate.
Indoor farming generates lots of waste heat. Plenty
Third: Amazon explicitly decided against an electricity-based heating system, instead opting for hydroponic (fluid-circulating) system, which must draw on local sources of heat. Is this an exception to my “electrify everything” mantra?
Yes and no. Mostly no. The key difference here is that the local source of heat is itself electrical — a data center. So in that sense, Amazon is using electricity for heat. In fact, it is helping Seattle use its electricity more efficiently, getting more work out of the same kWh.
The expert community is divided on the possibility, or advisability, of moving all HVAC to electricity (like heat pumps). It would require an enormous amount of capital and produce an enormous new electricity load. Limitations on both probably mean that we’ll need zero-carbon HVAC alternatives that still draw on heated water or combusted fuel, which can substitute more easily in retrofits of today’s buildings.
Perhaps some of that fuel can itself come from electricity — it is increasingly possible tosynthesize liquid fuels that way. But a great deal of the heated water can come from existing and planned sources of waste heat, preferably drawing on electrical sources.
Making sunlight and CO2 into methane and other liquid fuels. MIT
If electricity is zero carbon, then all subsequent derivatives, from waste heat to synthetic liquid fuels, will be zero carbon as well. That is the magic of clean electricity.
Better design, urban density, and electrification all require far-seeing investment
There’s a telling line in Amazon’s blog post on this project:
Because of the up-front investment to build it, the ecodistrict isn't currently delivering heat that's any cheaper compared to a typical system, according to [Mike Moriarty, the Senior Engineering Manager who leads operations and maintenance for campus], but “the price of electricity is only going to go up.”
This is like so many clean-energy technologies: The upfront investment is high relative to the alternatives, but it pays back many times over throughout its life.
As Amazon adds buildings to the system — and maybe someday, as Seattle expands the system beyond Amazon’s campus — the savings will pile up ever higher, eventually dwarfing the upfront investment.
A robust district energy system could save Seattle money for a hundred years. Again, it’s just pipes with water, a technology that has stood the test of time. All that’s needed is policy coordination and good design.
Whatever its other sins, Amazon has shown itself willing to make patient investments; that’s why it keeps growing but never makes much profit. It invests for the long term.
Almost more than anything, it is that mentality — the willingness to sink upfront investment into long-term savings — that can move corporations (and society) toward sustainability. For that reason alone, I hope this project pays off for Amazon.
And I hope Amazon carries the lesson over to its next headquarters.
IKEA Wants ‘Radical Change’ For its Food Business to Promote Sustainability
Another area of change could be in growing its own produce through vertical farming. The company recently invested inAeroFarms, the New Jersey-based indoor farming group.
IKEA Wants ‘Radical Change’ For its Food Business to Promote Sustainability
NOVEMBER 8, 2017 | LOUISA BURWOOD-TAYLOR
“The horsemeat scandal made us take inventory of our food business,” Michael la Cour, managing director of IKEA Food Services, told an audience at the Sustainology Summit in New York on Tuesday.
While IKEA is best known for its furniture, which apparently uses 1% of the world’s timber, the retailer also has a well-known food retail business, including in-store restaurants selling its famous meatballs and marketplaces selling over 180 Swedish food products. This sideline food business sells a cool €2 billion ($2.3 billion) of food per year and serves 650 million customers, making it Sweden’s biggest restaurant by default, said la Cour.
Turning its attention to the provenance of its meat amid the horsemeat scandal — which started in the UK in 2013 but spread to other parts of Europe, including Sweden, and even the US when retailers such as Tesco realised there was horsemeat in their beef products — brought other challenges within the food system into the spotlight for IKEA, according to la Cour, such as food waste.
“It was a great opportunity for us to take responsibility for what we serve, where we source it, and who we partner with,” said la Cour.
Some key changes at IKEA in the wake of this deep dive into their supply chain included introducing the veggie meatball in April 2015 as well as taking Coca-Cola and Pepsi products off the menu in favor of Swedish fruit waters.
“Our veggie meatballs have a significantly lower carbon footprint than the meat alternatives, and are actually priced lower too; we need to move to a more plant-based diet,” said la Cour. “Everything we do is driven by sustainability design. It’s at the core of what we do and not a bi-thought.”
Referencing a conversation about the sustainability of insect-based protein compared to meat, la Cour added “I don’t know if the future is a crispy bug ball, but I know we are going to work with lots of different partners to bring changes to our food business.”
The company’s interest in edible insects is more than just lip service too, since Israeli fruit fly farm and insect protein startup Flying SpArk joined IKEA’s first boot camp and startup accelerator in September.
Another area of change could be in growing its own produce through vertical farming. The company recently invested inAeroFarms, the New Jersey-based indoor farming group.
Speaking to AgFunderNews on the sidelines of the conference, la Cour said it might be possible for stores to grow food on-site using this technology. He was set to visit AeroFarms later this week to explore opportunities.
However the company incites change at its stores and within its supply chain, la Cour said it is not wasting any time.
“We don’t need gradual change but radical change and we are willing to challenge our business model to get there,” he said. But he admitted that it still may take time to get consumers to catch up when it comes to some shifts, such as going totally vegetarian at some point.
Three Startups That Wowed Jack Ma And Won Alibaba's Backing
Three Startups That Wowed Jack Ma And Won Alibaba's Backing
November 22, 2017
PHOTO: BLOOMBERG
[HONG KONG] After hearing 600 pitches spanning fintech and robotics to healthy ageing, three startups will share US$3 million in backing from an entrepreneurs fund set up by billionaire Jack Ma.
Jumpstarter, a competition for new ideas and products similar to TechCrunch Disrupt, has the backing of Mr Ma's Alibaba Group Holding Ltd, which unveiled its HK$1 billion (S$173.4 million) fund in 2015 to support startups.
A shortlist of six candidates made the final pitches on Tuesday, getting eight minutes to talk about their products and then four minutes of questioning by the judging panel. Among the criteria used to decide winners were innovation, community impact and market potential.
The winners:
Cuttingedge Medtech Ltd: Robot doctors may not be science fiction anymore. A team of robotic and medical imaging graduates is building specialised surgical robots for orthopedics, neural surgery and oral implants. The vision is personalised care with minimal invasive surgery.
Farm66 Investment Ltd: The company is joining the increasingly hot field of hydroponics and vertical farming as companies try to alleviate a global food crisis with sustainable agriculture. Combining indoor farming with fish ponds, this startup has already won a couple of awards from local industry associations.
En-Trak Hong Kong Ltd:This four-year-old startup targets commercial buildings with a connected device platform to help manage power use. En-Trak says it can pull in data from existing meters to manage consumption and lower costs while also lowering carbon emissions, with customers already including Hong Kong Stock Exchange and Fuji Xerox.
The other finalists:
BeeInventor: Trying to bring a technology solution to an old-fashioned industry, BeeInventor has built a cloud-based platform for communication among construction workers. Its Dasloop product fits over the helmets worn on building sites and monitors body temperatures, warns of potential collisions and provides video feeds. It can also connect to gas detectors or a flashlight.
Viewider: This startup aims to help merchants on e-commerce sites pick the best site to sell on. Viewider builds search and market research tools that help online merchants suss out global e-commerce services such as eBay or Amazon, register products for sale and price their wares accordingly.
Human Washer Ltd: Like a car wash for people. This startup offers the Sit & Shower, a device that enables the elderly and mobility impaired to bathe with automated soaping, temperature control, 13 surrounding water jets and air drying. The company says the device also cleans itself.
BLOOMBERG