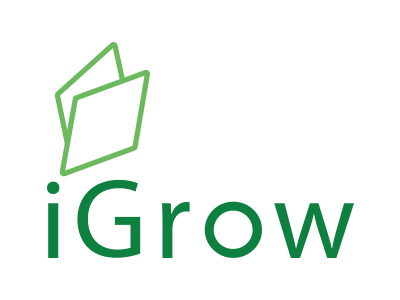
Welcome to iGrow News, Your Source for the World of Indoor Vertical Farming
Shenandoah Growers Opens Texas Indoor Production Facility
Shenandoah Growers Opens Texas Indoor Production Facility
July 13 , 2017
Virginia-based organic culinary herb grower and producer Shenandoah Growers (SGI) claims it is “set to transform the distribution of highly perishable produce”.
Through a proprietary combination of automated greenhouses and indoor LED vertical grow rooms to produce more than 30 million certified organic plants per year, SGI has now brought a third indoor growing facility online.
The new facility, located in Texas, is the latest component of SGI’s innovative hub-and-spoke farming and distribution system, and only the most recent step in the company’s three-year, multi-million-dollar nationwide expansion of indoor farming.
The group claims the system is quickly scalable for market growth, allowing Shenandoah Growers to “locally deliver certified organic superior flavor and shelf life at a fraction of the capital cost of other indoor farms”.
“This indoor farm, and the two others in our system, are critical elements of how Shenandoah Growers is transforming the way perishable produce is grown and distributed,” SGI CEO Timothy Heydon said in a release.
“With the integration of our modular indoor growing technology into our existing national footprint, we can grow amazing certified organic produce that delivers fresh flavor to consumers in a sustainable way, minimizing inputs of water, bio-media, land resources, and food miles.
“We are proud to be a part of transforming agriculture production and distribution for the future.”
SGI’s Rockingham, Virginia farm complex serves as the eastern hub of a nationwide growing system, and with a farming and supply chain platform spanning the country, the group claims its indoor farms cover the Mid-Atlantic, Midwest and South Central market.
The group continues the expansion of its farms, greenhouses and the implementation of an indoor farming hub and spoke system on the West Coast, with completion expected in 2018.
Lettuce That’s Head and Shoulders Above The Rest: Real Dirt
Lettuce That’s Head and Shoulders Above The Rest: Real Dirt
Quality soil is the secret to Greenbelt’s irresistible, award-winning lettuces.
Ian Adamson, president of Greenbelt Microgreens, and head grower Alice Farris show off their totally organic lettuces that have won an Agri-food Award of Excellence from the Ontario government. (SONIA DAY)
By SONIA DAY | Fri., June 23, 2017
Let us talk about lettuce.
The truth is, I’ve wimped out. I no longer grow any. The likes of Lactuca sativa got banished from my garden, because infuriating intruders kept beating me to the punch.
Caterpillars, earwigs, rabbits, groundhogs, birds, deer . . . They all dropped by. Plus, of course, slugs, scores of those slithery, slimy horrors that sneak in after dark. And chomp, chomp. The next morning, fantasies of fresh salad fixings vanished — faster than ice cream in a heat wave.
There was also the bothersome business of bolting. Just about every lettuce variety I tried went whoosh, like a rocket into space, if the temperature soared suddenly in spring (which unfortunately happens a lot, in our yo-yo climate.)
And although we home gardeners love to kid ourselves that our misshapen, nibbled, less-than-perfect produce is still fine to eat, (because hey, didn’t we grow it organically, from non-GMO seeds?) some just isn’t. Elongated stalks and past-their-prime leaves of a bolted lettuce head taste so bitter, I once spat them out at the dining table.
Yet I love lettuce. And like everyone, I worry about questionable residues left behind on specimens sold at the supermarket. So good news: there’s a new Canadian outfit that produces such tasty, fresh, totally organic lettuce, I have no qualms about not growing my own anymore.
Greenbelt Microgreens came on the scene about a year ago, started by a former landscaper named Ian Adamson. And he’s sure done his homework. Eco-conscious himself, he decided to figure out exactly what modern consumers would like to see in salad greens — and the results certainly push all the right buttons.
Greenbelt’s lettuces (plus pea greens and a variety of microgreens) are grown locally in greenhouses, like so much of what we eat today. Yet they’re not hydroponically raised, with chemical nutrients added to the water around the roots. Instead, these lettuces develop in their own individual small pots filled with soil — just like out in the garden. Does that make flavour better? I think so.
Nebraska Man’s Mushroom Growing Hobby Becomes A Business
Fence Post courtesy photo |
Nebraska Man’s Mushroom Growing Hobby Becomes A Business
At a farmers market in Lincoln, Neb., Ash Gordon talks to consumers about mushroom varieties.
They look like sculptures: mushrooms with exotic names like Lion's Mane and Blue Oyster. And they flourish inside a nondescript warehouse located near the airport in Grand Island, Neb. Nebraska Mushroom is an indoor farm where unusual varieties of the fungi are pampered and fussed over from colonization to harvest.
Ash Gordon is the mushroom man.
"The varieties we grow are different than what you normally find at the grocery store," said Gordon, the founder of Nebraska Mushroom. "They have different flavors and textures. Everybody can find a mushroom they like because there are so many options."
Growing up in Nebraska, Gordon spent time as a boy foraging for mushrooms along the Platte River near his Grand Island home. He even bought a mushroom field guide from the Audubon Society to bolster his hobby.
As an adult, Gordon worked as a kidney dialysis technician. Then, at age 27, he developed arthritis that was painful and debilitating. Research into the healing properties of mushrooms led him to include more mushrooms in his diet through tinctures, extracts and teas. With other lifestyle changes, his arthritis symptoms eased and his mushroom hobby grew into a business.
For Gordon, growing mushrooms is both a science and an art. He follows strict procedures to colonize and produce a mushroom, lessons learned by reading books and studying information found on the internet. The art of growing mushrooms has developed through trial and error.
"There's a lot of science in it but I would say the art is in manipulating the conditions so that the mushroom knows it's time to fruit, and then will produce for us," Gordon said.
COLONIZATION
The process begins with mycelium, a culture of mushroom tissue stored in a tube called a slant. A pea-sized piece of mycelium is transferred to a petri dish to colonize. The resulting mushroom culture is mixed with sterilized grain and eventually transferred to bags of sawdust.
One pea-sized piece of mycelium makes about eight grain jars. One jar translates into five master bags and each master bag expands into 30 bags of substrate, where the mushrooms begin to fruit.
The bags are moved to greenhouse-like structures where they begin to react to their environment in different ways. The grow rooms are warm and humid, but the air conditioning runs year round. Even in the winter, Gordon said the mushrooms generate so much heat as they grow they can actually start to cook if the temperature gets too high.
The growing process varies according to the mushroom. Gordon cuts holes in the bags of Oyster mushrooms, allowing them to recognize the fresh air and begin to grow out of the bags. Shitakes go through a more dramatic fruiting process.
"The Shitake mushrooms go through a popcorn stage where they really bubble up and blister. They break through the bags and turn completely brown," Gordon said. "The Oysters stay white the whole time."
Mushrooms also have different personalities: They can be small and delicate or troublesome and finicky. For example, Gordon keeps close watch on a particular strain of Shitake mushroom because if he overfeeds it, the mushroom starts to make mutants. If the bag isn't flipped over, the mushrooms start growing down, under the racks. In general, Gordon said, the mushroom "can be a pain sometimes."
AFTER THE HARVEST
After harvesting the mushrooms, Gordon packages the crop for sale at farmer's markets, grocery stores and co-ops. He also supplies a few restaurants with his fresh mushrooms.
Summer is the busiest time for Gordon. The mushrooms grow so fast, he goes through periods where he is constantly harvesting. Late nights in the greenhouse are followed by early mornings at the farmer's market. In spite of the long hours, Gordon enjoys introducing consumers to mushrooms. He sees a strong future for mushroom farming because consumers are more interested in buying fresh food and they want to know more about where their food comes from and how it's grown.
"The best part is people's reactions," he said. "They don't realize how many types of edible mushrooms there are, the different colors and textures. I like talking to the public and educating people about the mushrooms and how to use them."
Gordon never stops learning and thinking about what's next. He produces and sells mushroom extracts and dried mushrooms. Leftover mushroom substrate is dumped in a pile where, over time, a rich compost develops that can be used to improve the quality of soil for vegetable gardens. Gordon wants to expand his business to include creating products that will help other farmers get into the mushroom business, from providing information to selling mushroom cultures.
"People are interested but maybe they don't have the space or the time or the knowledge," Gordon said. "I'd like to give people more affordable, easier options to help them get started." ❖
— Mary Jane Bruce is a freelance reporter for The Fence Post. She can be reached at mbruce1@unl.edu, or on Twitter @mjstweets.
Alliance Greenhouse Uses Geothermal Heat To Produce All Year Long
Alliance Greenhouse Uses Geothermal Heat To Produce All Year Long
- TORRI BRUMBAUGH Staff Intern | torri.brumbaugh@starherald.com
- Jun 10, 2017
Russ Finch shows off his tango mandarins, a hybrid that contains no seeds.
Torri Brumbaugh/ Star Herald
ALLIANCE — Members of the Nebraska Master Gardener Program anxiously wait as Alliance’s Russ Finch cuts an orange. While the excitement for a simple orange seems strange, this orange is different. It is a 3-year-old orange that Finch grew in his own backyard.
Finch was simply a mail carrier and farmer in Alliance, until 45 years ago when he started experimenting with heating houses with geothermal heat. Fifteen years later, he began using the geothermal heat to improve greenhouses.
Geothermal heat produces heat from the ground. A singular heat source dispenses heat into a tubing system that runs under the ground of the greenhouse. The heat is constantly circulating and reused to create the perfect environment for the greenhouse. This means that in Finch’s greenhouses, he can grow any tropical or subtropical plant that he wants.
Russ Finch leads members of the Nebraska Master Gardener Program into a newly builty greenhouse.Torri Brumbaugh/ Star Herald
His personal greenhouse is filled with numerous plants, nine varieties of southern grapes, pomegranates, 13 types of citrus fruit and much more. His citrus fruits include Eureka lemons, Meyer’s lemons, Cara Cara oranges, Tango mandarins and Washington naval oranges.
At 78-feet long, Finch’s greenhouse is 24 years old and the first one he created.
Around three years ago, Finch began to sell the frames, systems and equipment for his geothermal greenhouses with his business, Greenhouse in the Snow.
Compared to his personal greenhouse, the new greenhouses are much more efficient.
The new greenhouses are at least 96 feet long. They also include shelves on one wall to grow ground vegetables and fruit. The other side of the greenhouse is often designated for trees.
“We just put everything in it to see if it’ll grow, and almost everything did,” says Finch.
Finch’s geothermal greenhouses appear to be much more efficient than the standard greenhouse.
To run his personal greenhouse, it costs Finch up to 85 cents a day. Other geothermal greenhouses, like the one at Alliance High School, cost up to 97 cents a day. A geothermal greenhouse only costs around $200 to run in the winter, compared to the $8,000 it would cost with a regular greenhouse.
In his greenhouses, Finch can also produce more product than planting outside.
A greenhouse can produce 14 tomatoes to every one tomato that average farming produces, while with other crops it is often 50-1, Finch said. Weather is a big factor in this because greenhouses have a controlled environment.
Here is a prototype of Russ Finch's newer greenhouses.
Torri Brumbaugh/ Star Herald
The profit produced by the geothermal greenhouses is a great benefit as well.
Finch said, “Each tree needs an 8-foot circle and will produce 125 pounds of fruit. If a pound is usually $3.50 at a farmers market, that makes each 8-foot circle worth $430.”
According to Finch, most young people do not want to get into agriculture because they believe it is too expensive. Little do they know, a single 3-year-old tractor with four-wheel drive is the same cost as putting up nine of Finch’s greenhouses. So for those looking to get into agriculture, Finch highly suggests going geothermal.
Member of the Nebraska Master Gardener Program get the opportunity to explore one of Russ Finch's newer greenhouses outside of Alliance, Nebraska.
Torri Brumbaugh/ Star Herald
Greenhouses are efficient cost wise, but the newer greenhouses also include a key to helping with the extinction of bees.
Finch showcased an Australian beehive called Flow Hive. The hive would replace common beehives and take away the need for smokers, a device used to calm bees. Within Flow Hive, the hexagonal cells are already formed, so the bees do not need to create them with wax.
When the honey needs to be taken from the beehive, a key is used to break the cells and drain the honey. Finch claims that the new beehives would help kill less bees and hopefully, help the bee from coming extinct.
Finch has sold about 38 greenhouses and almost all of them have been used for commercial purposes. Nine states — including Alaska, South Dakota, Wyoming and Kansas — now have Finch’s greenhouses, along with two greenhouses in Canada.
The Federal Aviation Administration has just given the go for a greenhouse to be built at the Western Nebraska Regional Airport in Scottsbluff. The greenhouse will be used by the North Platte Natural Resources department. It is estimated that the greenhouse will be put in place in late spring.
With the success of Greenhouse in the Snow, Finch is very hopeful for the possibilities. He is trying to spread his geothermal heat across the globe to countries like Australia, Belgium, Croatia, Denmark, Greece and South Africa.
According to Finch, all of the Midwest’s table citrus could be grown locally in greenhouses.
Lemons grow in Russ Finch's greenhouse.
Torri Brumbaugh/ Star Herald
For more information on purchasing a geothermal greenhouse, contact Finch at greenhouseinthesnow.com.
BIG Envisions Multi-Purpose Biomass Power Plant in Sweden
BIG Envisions Multi-Purpose Biomass Power Plant in Sweden
As you find yourself filled with curiosity, peering through the windows of a geodesic dome, its aesthetic value goes unchallenged. However, its level of functionality in relation to indoor agriculture remains questionable. Amidst the uncertainty on the validity of such structures, Bjarke Ingels Group (BIG) envisioned their scheme for a “biomass cogeneration plant” within a geodesic dome for the city of Uppsala, Sweden. During the colder months, the power plant will employ technologies with the potential to generate energy by converting biomass waste into heat, electricity, and biofuels through combustion or other conversion methods. It will serve to entertain in the summertime.
The transparency of the enclosure is an inviting aspect of the power plant that is typically nonexistent in this kind of facility - it communicates a rare level of public education and community engagement for this typology. Although still in the idea phase, it’s an exciting vision of how future energy production might look.
The city of Uppsala invited BIG to design a biomass cogeneration plant that would offset its peak energy loads throughout the fall, winter and spring as part of an international competition (ultimately won by Liljewall Arkitekter). Home to Scandinavia’s oldest university and landmark Uppsala cathedral, the plant proposal’s biggest challenge was to respect the city’s historic skyline.
Considering the project’s proposed seasonal use, BIG envisioned a dual-use power plant that transcends the public perception; in the summer months, the “crystalline” proposal was designed to transform into a venue for festivals during the peak of tourism.
“By harnessing the economies of scale associated with greenhouse structures it is possible to provide a 100% transparent enclosure to provide the future massive silhouette on Uppsala’s skyline with an unprecedented lightness while allowing the citizens to enjoy educational glimpses of what happens within. Rather than the conventional, alienating hermetic envelope of traditional power plants, the crystalline volume serves as an invitation for exploration and education. The next generation of creative energy.”
“BIG’s design proposal fuses two conventional industrial archetypes into an unconventional hybrid: the plant and the greenhouse. Both have been developed to provide a rational and efficient form of enclosure to massive industrial facilities: for manufacturing and agriculture respectively,” stated the practice in a press release.
CONTENT SOURCE FROM HERE ARCHDAILY
Tagged: #greenhouse #dome #geodesic dome #biomass #power plant #bjarkeinglesgroup #sweden #cogeneration #venue #festivals #energy production #sustainability #hybrid #architecture #bjarke ingels
Indoor Farming Plus Made In USA LED Grow Lights: Profile 1.8
Indoor Farming Plus Made In USA LED Grow Lights: Profile 1.8
GREENandSAVE Staff
Posted on Thursday 29th June 2017
This is one of the profiles in an ongoing series covering next generation agriculture. We are seeing an increased trend for indoor farming across the United States and around the world. This is a positive trend given that local farming reduces adverse CO2 emissions from moving food long distances. If you would like us to review and profile your company, just let us know! Contact Us.
Company Profile: Gotham Greens
Here is a great example of an urban farm with greenhouse locations on rooftops of New York City and Chicago.
Here is some of the “About Us” content: Gotham Greens’ pesticide-free produce is grown using ecologically sustainable methods in technologically-sophisticated, 100% clean energy powered, climate-controlled urban rooftop greenhouses. Gotham Greens provides its diverse retail, restaurant, and institutional customers with reliable, year-round, local supply of produce grown under the highest standards of food safety and environmental sustainability. The company has built and operates over 170,000 square feet of technologically advanced, urban rooftop greenhouses across 4 facilities in New York City and Chicago. Gotham Greens was founded in 2009 in Brooklyn, New York and is privately held.
Our flagship greenhouse, built in 2011, was the first ever commercial scale greenhouse facility of its kind built in the United States. The rooftop greenhouse, designed, built, owned and operated by Gotham Greens, measures over 15,000 square feet and annually produces over 100,000 pounds of fresh leafy greens. The greenhouse remains one of the most high profile contemporary urban agriculture projects worldwide.
Here is the link to learn more: http://gothamgreens.com/.
To date, the cost of man made lighting has been a barrier for indoor agriculture. A new generation of LED lighting provides cost effective opportunities for farmers to deliver local produce. Warehouses and greenhouses are both viable structures for next generation agriculture. Here is one example of next generation made in USA LED grow light technology to help farmers: Commercial LED Grow Lights.
Farms On the Fringe: New Takes On America’s Farming Tradition
Farms On the Fringe: New Takes On America’s Farming Tradition
These six farmers have found innovative ways to grow plants in today’s climate, whether in corn country or coal country, with fish tanks or smartphones.
August 01, 2017 Tracie McMillan
How do you feed a hotter, drier, more inequitable world? A new generation of American farmers are coming up with answers that rarely resemble the cornstalks and cattle pens of mainstream agriculture.
Today’s American farmers are less white. They’re also increasingly experimental. Even as our biggest farms get bigger, small producers are innovating in countless ways as they grapple with the serious questions that face our food system. Some prioritize making high-quality food affordable to folks on minimum wage and accessible in places where fresh produce is scarce; others are learning how to farm with far less water on drought-prone fields. They may be discovering hidden super fruits, reinvigorating coal country, or bringing urban farming to the mountains. Here are six who will change your mind about what it means to farm.
Fish Farming on Dry Land
Ouroboros Farms
Half Moon Bay, California
Chard grown in Ouroboros’s aquaponics system reveals its colorful roots.
Courtesy of Ouroboros Farm
When the recent six-year drought hit California, most farmers were screaming for water. Here’s one who wasn’t: Ken Armstrong, owner of Ouroboros Farms in the Bay Area. And that is more than a little strange—because for Armstrong, water is actually a growing medium. He specializes in aquaponics, a system of raising fish and vegetables in tandem.
Armstrong founded the farm in 2012 after watching a YouTube video about Will Allen, a MacArthur Grant–winning urban farmer in Milwaukee. Inspired, he gathered some potential partners and attended a four-day workshop in Florida, then went home and got to work. Today, Ouroboros’s greenhouses sit on a sliver of land, just one-third of an acre. Nutrient-rich water from the farm’s 9,000 gallons of fish tanks circulates out through neighboring “raft beds,” which hold floating frames with sprouting greens whose roots are suspended in water, and through “medium beds,” which use clay pebbles to filter and disperse water for the vegetables. The roots take up the nitrogen from the fish, and clean water circulates back into the tanks.
Aquaponic farmers Jessica Patton and Ken Armstrong at Ouroboros’s farm stand
Courtesy of Ouroboros Farm
The system, says Armstrong, produces mature lettuce more quickly than soil planting and uses less water, too. The monthly output of 12,500 heads of lettuce requires about 8,000 gallons of water—a little less than two-thirds a gallon per head, as opposed to 12 gallons on traditional California farms. And output is constant, allowing his fraction of an acre to match the annual production of five acres of soil.
Armstrong says he launched Ouroboros to prove that the method could work commercially. He sells greens and other vegetables to local restaurants, and an on-site farm stand offers direct sales, with salad mix going for $4 to $5 for an 8-ounce bag. He also hosts training programs and farm tours and consults with new growers looking to run commercial aquaponics operations.
“Being able to bring high-quality, nutritious food closer to urban areas is going to be one of the agricultural paradigm shifts for the future,” he says. “I think more and more it’s going to be popping up.”
Mountainside Urban Farming
Tassinong Farms
Crested Butte, Colorado
Tassinong Farm utilizes a hydroponic system housed in repurposed shipping containers to grow vegetables year-round in the harsh Colorado climate.
Courtesy Tassinong Farms
Local food in Crested Butte, Colorado, has long been a summer-only affair. For residents, there has been little choice in the matter: tucked into the Rocky Mountains at 8,900 feet, Crested Butte doesn't exactly offer optimal growing conditions. Its night temperatures drop below freezing nine months of the year. But Kate Haverkampf saw a way around this obstacle. She launched Tassinong Farm, a year-round hydroponic facility housed in repurposed shipping containers, in December 2015. “It was such a difficult task to get fresh local food year-round,” says the former tech consultant. When her husband, who works in logistics, ran across a story about farming in containers, she was sold: “I just decided to make that my job.”
Inside four containers, which Haverkampf bought from a supplier aptly known as Freight Farms, LED lights illuminate shelves of plants rooted in a growing medium made from recycled plastic bottles. With a smartphone-enabled tracking system, Haverkampf can monitor her crops closely. If the nutrient mix gets out of balance in the irrigation water, she can swipe and tap to fix it, even from across the country. Because there is no soil, there is no need for herbicides to control weeds. There’s little need for pesticides, either, in this tightly controlled indoor growing space. Haverkampf’s biggest cost is electricity—the lights run 18 hours a day—so this year she’s exploring her options for solar.
Kate Haverkampf, owner of Tassinong Farms
Courtesy of Tassinong Farms
Perhaps most important for an arid place like Colorado, water usage is minimal. Agriculture accounts for 80 percent of water usage in the United States, and a typical pound of lettuce requires 34 gallons of water. At Tassinong, says Haverkampf, each container uses about 15 gallons a day—roughly equivalent to a quick shower―or 105 gallons weekly. At peak, this turns into about 60 pounds of greens a week—less than 2 gallons per pound.
Today the shipping containers churn out greens ranging from lacinato kale and purple spinach to romaine lettuces and lemony sorrel. They end up in salads and atop burgers at five local restaurants and are sold at a local food co-op. Haverkampf also takes individual online orders, and later this summer she’s opening a farm stand.
“I’m trying to prevent all of these miles and miles of driven produce,” Haverkampf says. With the new shop, “I like to think that people will come more often and know they can get their greens when they need them.”
Superfruit in the Heartland
Sawmill Hollow
Missouri Valley, Iowa
Andrew Pittz of Sawmill Holllow Farm carries aronia berry seedlings.
Nati Harnik/AP
If you think about the typical Iowa farm, you might picture rows of corn and soy; the state leads the nation in both. But Andrew Pittz, a sixth-generation Iowa farmer, is not typical. At his family’s Sawmill Hollow Farm, the fields are covered with certified organic aronia berries.
The project began in the 1990s, when Pittz’s mom and dad decided to branch out from the corn and soy both their parents had grown and began cultivating a berry farm. When Andrew graduated from Texas A&M with an agricultural degree and a passion for organic farming, he returned to the family homestead on the rolling hills of the Missouri Valley with a vision: he wanted to be part of “a rural renaissance, and create more farmers,” he says. To do that, he knew, he’d need to grow crops that both yield income and preserve land.
Aronia berry bush
Flickr
The key to specializing in aronia, says Pittz, has been figuring out how to market the berries, which are highly astringent and bitter when fresh. The farm sells aronia jelly and syrup, aronia salsa, and even a spiced meat marinade, sold online and during on-site events like an annual Aronia Berry Festival. The berries also have one of the highest antioxidant ratings of any fruit, according to the Journal of Agriculture and Food Chemistry, making them desirable to consumers enthusiastic about so-called superfoods (a designation, it must be noted, met with less enthusiasm by health experts).
But above all, says Pittz says, he’s chosen to stick with aronia because it makes sense for the environment. The plant is native to Iowa and grows readily on his farm without irrigation. Between the bushes, a carpet of native grasses fixes nitrogen in the soil and boosts yield, limiting the need for chemicals. It’s a winning combination for the local turf, which is made of fertile but highly erodible soil called loess. Pittz points out that farmers planting annual grain crops like corn inadvertently increase erosion each time they pull out plants, turn over fields, and replant. Aronia berries, on the other hand, are perennials, so both the roots and the soil around them stay put.
And that, says Pittz, sums up his favorite trait of the aronia berry: “It is meant to grow here.”
Planting Justice
Soul Fire Farm
Grafton, New York
Leah Penniman, co-director of Soul Fire Farm
Capers Rumph (circa 2014)
Rocky hillsides don’t get much play in agricultural daydreams. But when Leah Penniman and Jonah Vitale-Wolff laid their eyes on the thin, rock-strewn soil of Grafton, just outside Albany, New York, they decided to go all in. They applied soil remediation methods they had learned on urban farms and began contouring the hillside, removing rocks, planting crop rows, and even building a house. Five years later, in 2011, they opened shop at Soul Fire Farm, a CSA-only family farm focusing on environmental justice and supporting Albany’s low-income communities of color. They look beyond Albany, too, and run an agricultural training workshop, the Black and Latinx Farmers Immersion, which draws aspiring farmers of color from around the country.
Soul Fire’s CSA offers its 100 customers weekly one-bushel boxes selected from the farm’s 70 crops, which include beets, cucumbers, squash, corn, tomatoes, and peppers, among other veggies. All are grown without synthetic chemicals, and the farmers rely on compost to boost productivity, says Penniman. At the heart of the program is a careful sliding fee scale that can drop as low as zero for struggling families, and a doorstep delivery service to make sure everyone has easy access.
Participants in Black Latinx Farmers Immersion harvest cilantro at Soul Fire Farm.
Capers Rumph (circa 2014)
That focus on accessibility comes in part from personal experience. When Leah and Jonah’s two children were very small, the family lived in a neighborhood where getting high-quality, fresh food meant walking to a farm CSA a couple of miles away. It was, says Leah, “really unfair as an expectation [of what was necessary] to feed families well.” So when the time came to start their own CSA, Penniman and Vitale-Wolff made access a priority.
Many of the couple’s customers share that concern. Francine Godgart, a married mother of two who works at the local hospital, chooses to pay extra every week to keep the costs down for low-income members. “It’s very expensive to eat organically,” she says. “I think it’s important for people who don’t have those resources to be able to be included.”
Re-energizing Coal Country
Fiber Flame/Pumpkin Vine Creek Farm
Paint Lick, Kentucky
A customer chooses Kentucky-grown kenaf.
Jdeg Video & Photo
The hilltops of Kentucky have seen some tough times. More than 500 mountaintop removal sites dot the state’s Appalachian landscape, bringing with them a host of environmental problems: increased dust and toxins, contaminated water, and buried streams. And now that coal is on its way out, questions arise: How do you deal with all that degraded land? And is there a way for residents to make a living off it?
One entrepreneurial farmer, Robin Richmond Mason, has an answer: kenaf, a relative of hemp, okra, and cotton. Native to Africa, the plant has long been used for its fibers and is already cultivated in several states. Moreover, Mason says, it’s unlikely to spread, kudzu-like, since a shorter growing season means that it is harvested, or dies, before it goes to seed.
Working with researchers at a local commercial lab, Mason discovered kenaf is a potent source of fuel, burning longer and hotter than conventional firewood—a bonus in rural areas, where wood heat is common. (In 23 Kentucky counties, more than 10 percent of homes rely on wood heat, according to statistics from the state’s Energy and Environment Cabinet.) One log of firewood tops out at 4,800 BTUs and burns for two or three hours, but a log made of compressed kenaf silage, Mason says, can provide 7,500 BTUs and will burn for four hours. The firewood alternative also helps ease the pressure on standing forests wrought by the harmful biomass industry.
Robin Richmond Mason of Fiber Flame/Pumpkin Vine Creek Farm
Jdeg Video & Photo
Mason wants the mountaintop removal sites “to be restored to Eden” and sees kenaf as an initial way to boost plant life there. “Let’s work toward the very best possible remediation plan. But unless there is economic motivation, I don’t see those developing.”
Last year’s initial run—farmed on an ex-miner’s land and hauled out by a trucker who worked for years with coal—was so successful that this year Mason has expanded to four growing sites across Kentucky. The biggest is at a former tobacco farm in the central part of the state that has dedicated 100 acres to kenaf. Judging by the yield from prior test plantings, Mason expects about five tons per acre. All of it will feed into Mason’s line of Fiber Flame products, including a sextet of logs sold with matches and instructions. She calls it a Pit Kit, and it’s currently being sold in local Whole Foods stores.
Old Farm, New Tricks
Santa Cruz Farm and Greenhouses
Española, New Mexico
Don Bustos, organic farmer and owner of Santa Cruz Farm and Greenhouses
Gabriella Marks
There aren’t many farmers in the United States who can lay claim to their land the way Don Bustos can. His family’s been farming a patch of New Mexico for three centuries, and today he and his nephew still use the ancient community system of water ditches, called acequias, to feed their crops. And just as his parents did before him, much of what Bustos grows is sold within a 25-mile radius of his farm. But those traditions are only a foundation for this most modern of family farmers.
When Bustos left a construction career to return to the farm in the 1980s, the easy choice was to grow the staples that his parents had grown: crops like corn, potatoes, chilies, and squash. Instead he decided to try something different and set his sights on high-value organic crops, aimed at farmer’s markets and public schools. He began transforming his humble inheritance—three and a half acres across the road from a desolate stretch of federal public land—into something not just environmentally, but also financially, sustainable.
Santa Cruz Farm and Greenhouses, New Mexico
Gabriella Marks
Today Bustos grows nearly six dozen varieties of fruits and vegetables year-round using a series of low-tech greenhouse structures, known as hoop houses, and a solar water heater. In any given month, it might be arugula or strawberries, salad mix or green chilies. Going solar, he says, made a huge difference in his livelihood. Not only did his energy costs plummet, from $750 a month to 7 cents a day, but the hoop houses “let us create income 12 months a year instead of trying to risk everything for 3 or 4 months.”
His market savvy has helped earn Bustos wide acclaim, including a 2015 James Beard Foundation Leadership Award. He’s also been recognized for his passionate activism on behalf of small and sustainable farmers who fall outside the conventional image of American growers. Bustos has advocated for female farmers and farmers of color in both Washington, D.C., and New Mexico; created a farmer training program that also connects small growers with public school cafeterias; and supported the state’s acequia system, which dates from the 1600s.
That history, says Bustos, is part of what makes New Mexico, where nearly one-third of farmers are Hispanic, special. “We’re not inventing anything new,” he says, with regard to his growing practices and local base of customers. “That’s all been done by our ancestors."
onEarth provides reporting and analysis about environmental science, policy, and culture. All opinions expressed are those of the authors and do not necessarily reflect the policies or positions of NRDC. Learn more or follow us on Facebook and Twitter.
AppHarvest Selects SUNSET To Re-Ignite Coal Country
AppHarvest Selects SUNSET To Re-Ignite Coal Country
Pikeville, KY– Aug 1, 2017 – Jonathan Webb’s vision of bringing a renewed economic boom to the Appalachians looks to be bright. Wisely he has brought in the industry pioneer and expert to launch his mountain top greenhouse in the heart of America.
Agricultural startup AppHarvest, and Mastronardi Produce Ltd., North America’s leading grower and distributor of specialty and commodity greenhouse produce that operates under the SUNSET® brand, today announced that they have partnered to help develop high-tech greenhouses in the Kentucky and West Virginia Appalachian region.
“We are very excited to be partnering with AppHarvest and to support their plan of bringing high-tech greenhouse jobs to this Appalachian region and fresh, local year round produce to key markets,” said Paul Mastronardi, President and CEO of Mastronardi Produce. “AppHarvest shares our passion for developing local communities and our commitment to providing “fresh from the farm” produce to our customers that we believe is critically important to our success.”
AppHarvest Founder and CEO, Jonathan Webb, said his team is committed to bringing the high-tech greenhouse industry to the heart of coal country and believes that Mastronardi is the perfect partner. "We believe that Mastronardi Produce has the most talented and successful greenhouse team in the world and their SUNSET® brand is one of the top brands in produce today. Our partnership with them will set us up for success and allow us to build a scalable model in the region.”
“Jonathan has identified terrific pieces of land to erect the facilities and secured enormous support throughout the region. His dedication to this project is unmatchable.” Mastronardi stated.
About SUNSET® SUNSET® is a pioneer and industry leader in the gourmet greenhouse industry that grows and markets nationally recognized brands such as the Campari®, Zima®, Angel Sweet® and Kumato® brand tomatoes. Family owned and employee managed for over 60 years, SUNSET® prides itself on producing consistently flavorful gourmet tomatoes, peppers and cucumbers. Click here to access more SUNSET® news releases.
Over 10,000 jobs have been lost in Eastern Kentucky since the decline of coal. “The spirit of the region is unmatched and we want to work alongside those hardworking men and women,” Webb said. “Our goal is to provide economic development and opportunity for this region.”
The first project announced is in Eastern Kentucky on top of a reclaimed coal mine site and will be a 1.8 million square ft state of the art glass greenhouse. Webb stated that “as a gateway between the Midwest and South, Kentucky’s borders lie within a day’s drive of 65 percent of the US population and income. Building near these markets will significantly reduce transportation costs and will provide a much need local produce option for these regions.” Mastronardi will be the exclusive marketer for AppHarvest.
About Mastronardi Produce
Founded in the 1940s, Mastronardi Produce is a family-run business that is the largest vertically- integrated producer and distributor of Greenhouse-grown produce in North America. The Company, whose produce is packed under the SUNSET® brand, sources, grows, packages, and distributes over 50 of the most flavorful, award-winning varieties of non-GMO verified greenhouse-grown tomatoes, cucumbers, peppers, and other non-GMO verified products (including organics) on a year round basis. The Company’s nationally recognized specialty brands include the Campari®, Zima® Angel Sweet® and Kumato® tomatoes. Mastronardi’s proprietary rights to varietals, national distribution footprint, large grower network and industry-leading food safety and traceability programs have positioned the Company to be the produce supplier of choice for customers and end-consumers. For more information, please visit Mastronardi’s website at sunsetgrown.com.
About AppHarvest
AppHarvest is bringing Appalachia into the next generation of agriculture. The core of AppHarvest is built around a vision of employing the strong spirited individuals of the region. The startup is developing large-scale hi tech greenhouses growing fresh vegetables for local communities in the US. AppHarvest will be able to to deliver fresh produce to the Northeast, Southeast and Midwest of the US within a day's drive. For more information visit AppHarvest.co.
Grow Up Here: These Cool Vertical Greenhouses Are Local And Fit Right In Your Home
Grow Up Here: These Cool Vertical Greenhouses Are Local And Fit Right In Your Home
The future of growing technology in Northern Ontario is here
Greenhouses Canada designs, builds, sells and grows produce with game changing vertical aeroponic equipment. If you have as little as 20 square feet (sq ft) to spare, Greenhouses Canada can help you create a vertical growing space that will grow crops even in the middle of winter. (Facebook/Greenhouses Canada)
By Candice Morel
The desire to purchase locally grown produce is something many residents of Northern Ontario share. Unfortunately, local produce is scarce during the northern winter and many are forced to purchase imported fruits and vegetables.
As a community, we deserve to know where our food comes from and how far it has traveled. The less your food travels from farm to table, the more nutrient content it maintains, making local growing the obvious solution for nutrient-dense fresh produce.
Greenhouses Canada aims to address this issue by making local crops available year-round in Northern Ontario, even in your own home.
This local company combines energy-efficient building technology with a passion for food security to revolutionize how communities access fresh food year-round in Northern Ontario.
They design, build, sell and grow produce with game changing vertical aeroponic equipment. If you have as little as 20 square feet (sq ft) to spare, Greenhouses Canada can help you create a vertical growing space that will grow crops even in the middle of winter.
Aeroponic vertical growing techniques include the most innovative indoor agriculture equipment on the market. Plants are placed in a vertical panel surface while their roots hang in the air. They are then misted with nutrient rich water directly on the root area of the plant allowing crops to grow significantly faster than traditional growing methods while using less water.
Greenhouses Canada’s aeroponic growing equipment can grow anything from leafy green vegetables to strawberries and flowers. With more produce being tested daily, the possibilities of this technology are endless. The system will also produce high crop yield with little to no farming experience.
After years of research and development, Greenhouses Canada has created the proper recipe for year-round produce growing in all climates. The company will provide training on the growing equipment to those choosing to get started with vertical farming. No matter the size of your project or amount of experience, Greenhouses Canada create an indoor farm that will allow the public to directly contribute to food sustainability and security in Northern Ontario.
For those who prefer not to grow their own crops, but wish to support locally and ecologically grown produce, there is The Innovation Center. The Innovation Center is a commercial-sized greenhouse that will produce approximately 20,000 plants a week available for sale locally.
The centre is currently under construction in Espanola and is expected to be completed by late fall. At any given time, there will be approximately 120,000 plants growing at various stages in all seasons.
The crops produced by The Innovation Center will be available for sale in various food markets in Northern Ontario, including both big and small grocery stores. When you see the Greenhouses Canada logo, you can trust the produce was grown ethically, locally, and transported responsibly and directly after harvest.
You can also keep your eyes out for The Greenhouses Canada Grow Truck, which will be arriving shortly in Sudbury. This truck will include 15 fully functioning aeroponic panels that are growing food fresh daily for consumption. The truck is 26 feet long, wheelchair accessible and will produce 4,875 plants per month.
If you want a taste of Greenhouses Canada, head out to Frubar’s new location and try a wheatgrass shot, or keep an eye out for the Greenhouses Canada logo at Eat Local, or in The Wellness Boxes.
For more information on Greenhouses Canada visit the website and follow us on Facebook for more updates.
Morel is a public relations professional passionate about sustainable solutions and food security in the North. She is currently the marketing and communications director at Greenhouses Canada.
This Queens Warehouse With a Rooftop Produce farm is Sold As Part of a $78 Million Deal
This Queens Warehouse With a Rooftop Produce farm is Sold As Part of a $78 Million Deal
A rendering of the renovated warehouse at 184-60 Jamaica Ave. in Hollis - Courtesy of Madison Realty Capital.
By Robert Pozarycki | rpozarycki@qns.com
- Thursday, July 27, 2017 | 12:30 PM
Two warehouses in Hollis — including one topped with an urban produce farm — have been sold for $78 million, and the new owners have big plans to update both buildings, it was announced on Thursday.
Madison Realty Capital announced that it partnered with Artemis Real Estate Partners to purchase the industrial buildings located at 184-10 and 184-60 Jamaica Ave. from Rodless Properties LLC.
The adjacent structures house a number of commercial and manufacturing tenants including Gotham Greens, which has a 60,000 square foot greenhouse atop 184-60 Jamaica Ave. Gotham Greens uses the site to hydroponically grow leafy greens for sale to restaurants and consumers throughout New York City.
As with most real estate transactions, location was a prime factor in the acquisition, according to Josh Zegen, co-founder and managing principal of Madison Realty Capital. Jamaica Avenue is one of Queens’ busiest thoroughfares, and the warehouses are about a mile from downtown Jamaica. The buildings are also within walking distance of the Hollis Long Island Rail Road station.
“With the growing importance placed on expedient last mile delivery, today’s industrial sector tenants require proximity to population centers,” Zegen said. “We believe strongly that the combination of the site’s ideal location on Jamaica Avenue and our planned significant capital improvements will make this an attractive choice to numerous warehousing, distribution and manufacturing users throughout the city.”
Both Madison Realty Capital and Artemis plan “to upgrade both buildings including enhancing the building envelope, mechanical infrastructure and elevators, and capitalize on the increasing demand” from various industrial and commercial tenants “looking for quality industrial stock within the increasingly supply-constrained NYC market.”
According to PropertyShark, the building at 184-60 Jamaica Ave. encompasses 287,240 square feet, while the structure at 184-10 Jamaica Ave. has 226,605 square feet of space. Each building is five stories tall has an assessed value in excess of $11.3 million.
The buildings also have 12 loading docks and more than 100 parking spaces within a 30,000 square foot parking lot, Madison Realty Capital noted.
Madison Realty Capital has made $6 billion in investments across the city since its foundation in 2004, with holdings in the multi-family, retail, office, industrial and hotel sectors. Artemis has more than $2.5 billion of investor capital tied into various partners in the real estate industry.
Biomimetic Architecture
Daniel Christian Wahl Glocal educator, activist and consultant, generalized in whole systems design and transformative innovation for regenenerative cultures | Jul 23, 2017
Biomimetic Architecture
Through its infinite complexity, nature is an instructive and inspirational influence that can expand the aesthetic horizons of the building arts and confirm the inalienable right of humanity to try to salvage a place on this planet before it’s too late. The mission now in architecture, as in all human endeavour, is to recover those fragile threads of connectedness with nature that have been lost for most of this century. The key to a truly sustainable art of architecture for the new millennium will depend on the creation of bridges that unite conservation technology with an earth-centric philosophy and the capacity of designers to transform these integrated forces into a new visual language.
— James Wines (2000: 237)
There are countless examples of architects taking inspiration from biology. The Uluru- Kata Tjuta Cultural Centre in Australia, designed by Gregory Burgess Architects, mimics the interwoven bodies of two battling snakes. Foster & Partner’s Swiss Re Headquarters in London, known as the ‘Gherkin’, is a 40-storey tower inspired by marine organisms called ‘glass sponges’. These suck in water at the bottom and expel it at the top to filter nutrients; the building’s ventilation system mimics this flow.
Many other internationally recognized architects often rely on zoomorphic inspiration for the designs, processes and concepts that shape their buildings. Other internationally recognized architects who frequently rely on zoomorphic inspiration for the designs, processes and concepts that shape their buildings are Santiago Calatrava, Michael Sorkin, Frank Gehry, Renzo Piano, and Nicholas Grimshaw (Martin, 2004; Aldersey-Williams, 2003).
One of the domes of the Eden Project (designed by Michael Pawlyn) — Source
While many of them are inspired by natural and biological forms, Michael Pawlyn’s approach to biomimicry in architecture is to focus on what he can learn from biological processes to make buildings more efficient by modelling nature’s closed-loop, renewable energy, no-waste systems in the design of buildings (2011).
Michael Pawlyn
In helping to design the indoor environments for the Rainforest and Mediterranean biome exhibitions at the famous Eden Project, Pawlyn learned a lot about how water and energy cycle through natural ecosystems and how processes and functions in ecosystems are integrated and interlocking to create synergies. His design for the ‘Sahara Forest Project’ (Figure 16) makes use of such biomimicry thinking.
The bold proposal aims not only to generate large amounts of renewable energy based on concentrated solar power and to desalinate large amounts of seawater. It integrates these functions through the use of seawater-cooled greenhouses for the horticultural cultivation of food and biomass, creating a long-term strategy to reverse desertification and regenerate productive ecosystems where the Sahara Desert borders the sea.
The project is on its way to implementation. A pilot test and demonstration centre has been built in Qatar in collaboration with two giant fertilizer companies, the Norwegian Yara ASA and its Qatari joint-venture partner Qafco. It would be good to keep in mind that in the long term the fertilizers used in such a facility will also have to be produced from renewable sources and with renewable energy. Nevertheless, this experiment at scale will give us many opportunities to learn. It will teach us how to ask the right questions in an attempt to re-green the world’s deserts.
Figure 16: Reproduced with the permission of the Sahara Forest Project Foundation
Growing vegetables and biomass in the desert with external fertilizer inputs, but also using renewable energy and innovative desalination and horticulture approaches, can be considered a Horizon 2 stepping-stone technology, offering us important opportunities to innovate even more closed-loop systems that are based, as much as possible, on organic fertilizers and on-site nutrient cycling.
Conventionally, human-made systems tend to be fossil-fuel dependent, linear and wasteful, mono-functional and engineered towards maximising one goal. Here the aim is to pursue a different paradigm — that is demonstrated by mature ecosystems which run on current solar income, operate as zero waste systems, are complex and interdependent, and have evolved toward an optimised overall system. The Pilot Project will demonstrate concentrated solar power, seawater-cooled greenhouses, evaporator hedges creating conditions for restorative agriculture, halophyte cultivation and algae production in an interdependent cluster that achieves significant increases in productivity for all elements of the system.
— Michael Pawlyn (2014)
Human beings, as expressions of life-generating-conditions-conducive-to-life, are capable of creating designs that are both restorative and regenerative. We can go beyond simply not doing any harm and start to regenerate health, resilience and thriving communities everywhere. This is the promise of biologically and ecologically inspired design and architecture.
The Eastgate Centre is a multi-storey office building in the Zimbabwean capital Harare. It uses a passive cooling system inspired by the way termites (Macrotermes michaelseni) cool their mounds. Mick Pearce and engineers at Arup designed the building to use only a tenth of the energy normally needed to cool a building of this size in the hot African climate (Biomimicry 3.8, 2014b). The Swedish architect Anders Nyquist of EcoCycleDesign applied a similar termite ventilation to the Laggarberg School in Timrå, Sweden.
Andres Nyquist on Termite Ventilation applied to an eco-retrofit of an old school
The visionary architect and writer Jason McLennan, a Buckminster Fuller prize winner and Ashoka Fellow, created the Living Building Challenge in 2006 as a new kind of building certification system that goes beyond international or national standards like LEED or BREAM and sets a standard for regenerative architecture based on biologically inspired and ecologically informed design. There are currently 192 projects on four continents spanning a range of building types. The ‘Living Building Challenge 3.0’ challenges us to ask some fundamental questions about architecture and design:
What if every single act of design and construction made the world a better place?
What if every intervention resulted in greater biodiversity; increased soil health; additional outlets for beauty and personal expression; a deeper understanding of climate, culture and place; a realignment of our food and transportations systems; and a more profound sense of what it means to be a citizen of a planet where resources and opportunities are provided fairly and equitably?
— International Living Future Institute (2014: 7)
Jason McLennan
McLennan’s vision is to take what has already been learned through previous versions of the Living Building Challenge and incorporate these insights and new questions within the framework of the Living Future Challenge. McLennan regards the Living Future Challenge as “an opportunity to rethink and redesign all our systems and provide a vision for a truly regenerative society” (Living Future Institute Australia, 2014). He is a driving force in the transition towards a regenerative culture who has inspired architects around the world to take up his challenge to create buildings conducive to life.
[This is an excerpt of a subchapter from Designing Regenerative Cultures, published by Triarchy Press, 2016.]
Film Studio, Hydroponic Lab Are Among $3.7 Million in Improvements For Astoria Public Schools
Students at P.S. 84 and I.S. 126 will receive $160,000 for hydroponic science labs. They’ll learn about hydroponics, a method that allows people to grow plants in a water-based solution rather than soil. Students will also learn how biology, agriculture, technology and nutrition intersect.
Film Studio, Hydroponic Lab Are Among $3.7 Million in Improvements For Astoria Public Schools
P.S. 84 and I.S. 126 will receive funding for hydroponic labs from Councilman Costa Constantinides. Photo via Shutterstock
By Angela Matua | amatua@qns.com | Friday, July 28, 2017 | 2:15 PM
Public schools in Astoria will receive millions for infrastructure improvements and new additions like a film studio and science lab.
Councilman Costa Constantinides and Queens Borough President Melinda Katz announced that they are allocating nearly $3.7 million to the School Construction Authority for a number of enhancements.
Young Women’s Leadership School of Astoria at 23-15 Newtown Ave. will receive $375,000 for a new educational film studio. P.S. 300 at 28-37 29 St. will receive a new science lab with a $500,000 allocation from Katz and $300,000 will go toward renovating the bathrooms at I.S. 141.
“I am proud to have partnered with Borough President Katz to invest almost $3.7 million in our most important resource, our children,” Constantinides said. “Our investment this year includes more advanced technology and studying tools. New and improved school infrastructure will help encourage students to spend more time studying and learning while enjoying their overall school experience.”
The councilman, who is the chair of the committee on environmental protection, allocated $1.1 million for solar panels at P.S.122. It will be the first school in Astoria to install solar panels.
Students at P.S. 84 and I.S. 126 will receive $160,000 for hydroponic science labs. They’ll learn about hydroponics, a method that allows people to grow plants in a water-based solution rather than soil. Students will also learn how biology, agriculture, technology and nutrition intersect.
Nearly $900,000 was allocated to update technology in all Astoria public schools and $200,000 will upgrade the lunchroom at P.S. 122. Originally constructed as a gymnasium, the walls of the cafeteria consist of exposed brick and concrete, amplifying loud sounds.
“Queens has some of the best schools in the state, but to continue their success our schools need to have first-class facilities that will enable our children to reach their full potential,” Katz said in a statement. “This capital investment of millions of dollars will go a long way toward ensuring our kids learn in facilities with modern laboratories and studios, with up-to-date technology and with the quality playground space.”
Artemis Takes on The World
We’re currently helping indoor farmers get to profitability and beyond in 8 markets around the world.
Artemis Takes on The World
It’s no secret — the indoor farming market is huge… and growing! As Allison detailed in this blog post, indoor farms in the US produce over $21B in revenue annually. And the US only represents 0.2% of the global greenhouse vegetable market. This is the the same industry that is aggressively growing to help increase food production by 70% to feed 9B people by 2050.
Global Expansion
Artemist has set out to provide the world’s best management software from its inception. In order to be the world’s best, you have to be a global company. Within just a few months of our launch, we were proud to support incredible customers in South America, Sri Lanka, Canada, and the United States.
We’re not stopping there — we’re excited to announce that in addition to continuing to add customers in our existing markets, this month we’ve entered new markets, adding customers in Europe, the Middle East, and Asia!
Supporting Customers
The biggest challenge any growing company faces in adding new customers is supporting them while keeping existing customers both excited and engaged. Over the past month we’ve introduced a new onboarding process to ensure customers see value from Day 1 as well as easier ways for our customers to use our software. We’ve also welcomed Regina Bellows to our team as our dedicated Customer Success Manager.
Managing customers across so many time zones can lead to sleepless nights. One of the things I love about Artemis is everyone here is customer-obsessed. We take turns monitoring support channels all hours of the day and night so a customer never feels like they’re left in the dark when they run into a question. I think it’s probably one of our customers’ favorite things about us.
Let’s Chat!
While we’re excited with our progress to-date, we’re not stopping here. We continue to be excited about how we can use data to evolve one of the world’s largest legacy industries. I’d love to understand more about your farm, your challenges, and how we can help you solve your problems with data. Please email me at jschmitz@agrilyst.com or call at +1 646–719–0304.
Take-aways
The global greenhouse market is large and growing.
Agrilyst is growing along with the market, now working with clients across four continents.
We‘re keeping a close eye on support to ensure our customers are getting the most out of their software investment.
Artemis is the virtual agronomist powering the horticulture industry. We invite you to join the #DigitalHorticulture movement on social media and share your stories of farm innovation.
If you enjoyed this story, tune in for more here and be sure to check out our website: https://artemisag.com/
Indigenous Hydroponics System A Boon For Organic Farming
Agrico, a private local Qatari agricultural development company established in 2011 with the aim of helping Qatar achieve food security, operates a 120,000sqm (12 hectare) organic farm in Al Khor. Its first production was in May 2012.
Agrico managing director Nasser Ahmed al-Khalaf at his organic hydroponics farm in Al Khor. PICTURE: Joey Aguilar
Indigenous Hydroponics System A Boon For Organic Farming
July 25 2017 10:15 PM | QATAR | Joey Aguilar
A local farm in Qatar has developed a highly sophisticated hydroponics system capable of producing various types of organic vegetables and fruits in a bid to help the country achieve food security, it is learnt.
Organic eggplants at the 120,000sqm hydroponics farm in Al Khor
Speaking to Gulf Times, Agrico managing director Nasser Ahmed al-Khalaf said they made a lot of modifications in hydroponics farming to produce an all-organic fresh produce to meet the growing demand in Qatar.
Agrico, a private local Qatari agricultural development company established in 2011 with the aim of helping Qatar achieve food security, operates a 120,000sqm (12 hectare) organic farm in Al Khor. Its first production was in May 2012.
“The Asians, European or Western people have not developed a system that would be suitable for this area, especially for Qatar,” he stressed. “What we did is to develop our own system which is suitable for our environment.”
The local farm owner noted that vegetable-exporting countries in Asia, Europe, and America have the technology and knowhow in their region but inapplicable in the Gulf.
Al-Khalaf explained that regions with winter seasons such as Europe, especially those in the northern part, only have heating systems.
But in Qatar, he said they developed a cooling system that can reduce the temperature inside the greenhouse down to 16 degrees, depending on the variety of vegetables and fruits.
Some varieties need 16, 18 or 20 degrees, during a certain time of the day, for the plant to give the right texture, size, and taste, among others.
“Our vegetables they can last for a month on shelf without changing,” he said, adding that they can produce an average of 6 tonnes daily during the summer, which is 30% less compared to their production in the winter. The farm plans to produce more in the near future.
With this technology, he said Qatar has become one of the largest producers of organic vegetables in the world using what he described as a very promising and one-of-its-kind hydroponics technology.
Agrico Organic Farm in Al Khor produces 14 types of tomatoes.
“As long as you are providing the right temperature, right humidity, right amount of light (sun radiation), right fertiliser, and right amount of water, then you can grow anything,” al-Khalaf added. “I guarantee that all types of vegetables can be grown, I have tried this myself and we have been successful on this.”
Agrico has started growing five types of fruits, including papaya and lemon (experimental stage). It expects the plants to bear fruits in a year or two.
As Agrico products continue to supply more than 150 supermarkets and small outlets in Qatar, he said “there will be a lot of surprises soon.”
“We are going to produce root crops, fresh leaf and herbs such as coriander, parsley, green onion, basil, and mint, among others,” he said, adding that producing iceberg lettuce and other types, carrots, potatoes, and white onion, in the next few months.
While Qatar currently imports various types of fresh vegetable and fruits from European, Asian, and American countries, he expressed confidence that the country will soon achieve self-sufficiency.
He noted that even before the economic blockade imposed by the Saudi-led group on June 5, Qatar already has plans to import fresh produce in the future.
System suitable for livestock, poultry, fish farming
Apart from vegetables and fruits, local farm owner Nasser Ahmed al-Khalaf said the cooling system they developed is also suitable for livestock, poultry and fish farming.
“It is an integrated system, we take advantage of the vegetable greenhouses and in between we cool an empty wasted area using the cold air that comes out from the greenhouse,” he added.
Al-Khalaf explained that they harness this cold air, which comes out of the greenhouse, for testing an area of his farm for growing fruits. This can bring down the temperature from 45 degrees, for example, to 27 degrees in an open field.
The system, from temperature, humidity to sun radiation and water irrigation, has to be monitored round-the-clock seven days a week, according to the farm owner.
“Even if I am abroad I get a warning from my mobile phone if any abnormality happens,” he noted.
Greenhouses In The Arctic Will Reduce Food Insecurity In Canada's North
Greenhouses In The Arctic Will Reduce Food Insecurity In Canada's North
Growing North’s Greenhouse in Naujaat, Nunavut. Image: Growing North
Jul 26 2017, 10:41am
Greenhouses grow food at a fraction of what it would normally cost.
In Nunavut, in Canada's Arctic, shoppers pay $12.44 for for a kilogram of celery, almost four times more than the $3.38 national average, and $6.90 for a kilogram of potatoes. It's just one of many examples of food inaccessibility in the region, which severely affects 18.5 percent of Nunavut households, a problem the government is addressing by investing $13.8 million per year to support isolated Northern communities.
To address this problem, not-for-profit Growing North built a greenhouse in the Inuit hamlet of Naujaat in September 2015 to increase accessibility to fresh food.
The greenhouse produced 13,250 lbs of food last year for the local community of 1,082 people, an amount that "could feed just over 50 percent of the Naujaat population Health Canada's daily recommended amount of produce," explained Stefany Nieto, co-founder of Growing North. With the success of the Naujaat greenhouse, the organization is expanding to Arviat, Nunavut's third-largest community, in August.
"It is completely unacceptable that many northern and Indigenous families cannot afford to put healthy food on the table," the Office of the Minister of Indigenous and Northern Affairs Canada told Motherboard in an email. In an effort to "support families and hunters - and improve access to country foods," in 2016, the Canadian government invested an additional $64.5 million over five years, and $13.8 million per year ongoing, and have now expanded full subsidies to an additional 37 isolated northern communities. Investments in local greenhouses could help grow fresh food and make it more accessible.
Bright Agrotech's ZipFarm System. Image: Bright Agrotech
Growing North is exploring alternative and sustainable ways of feeding Canada's north by using some of the latest in vertical farming techniques.
What was a once far-fetched idea is now a sustainable option for providing food to a growing population. Vertical farming allows farmers to have a 365-day season without having to use pesticides or worry about traditional farming concerns like sunlight, rain, or drought.
Over the last ten years, a number of companies have popped up around the world using old warehouses and other unconventional urban spaces to grow fresh produce. Many of these farms operate in densely populated places like China, Japan, Belgium, and the United States. The largest floor-to-ceiling farm is currently in New Jersey at nearly 70,000 square feet. And the phenomenon is only going to get bigger. By some estimates, the vertical farming industry is projected to be worth USD $13 billion by 2024.
Bright Agrotech, a Wyoming startup, allows small urban and suburban farmers to grow crops through its vertical hydroponic farming systems. Hydroponic refers to soilless growing, in which the plants are grown using only nutrient-rich water. The water flows across the root structure and is taken up by the plants. Bright Agrotech's systems, which focus on greens and herbs is being used in Growing North's Naujaat greenhouse.
"Nunavut has the highest rate of food insecurity in Canada," Nieto told Motherboard in an interview. The organization estimates the price reductions on fresh produce grown in their greenhouses to be anywhere from 50 to 70 percent, depending on whether the produce is sold to local grocers or sold directly to consumers through places like the farmer's market.
"You can face food insecurity even living in a city like downtown Toronto if there is not a grocery store for miles around," explained Ben Canning, co-founder of Growing North.
Food inaccessibility persists in northern Canada, in large part, due to the cost of getting food to the region. Fresh food has to be flown in from the south. Each community faces its own challenges. Some are only accessible by road and not by air, which adds time and money. "Whether it's food or construction goods that need to shipped in, the farther north you go, the longer the supply chain gets and the more it costs. Even a lot of our food consumed in Toronto is shipped in. To get to the North, they spend an extra two weeks in cargo freights, craters, and planes," said Canning.
Growing North's current greenhouse is 75 percent hydroponic and 25 percent soil-based agriculture. The hydroponic system can grow any herb as well as greens like lettuce, kale, collard greens and swish chards. The agricultural side grows vegetables like radishes, potatoes, and carrots.
But the cost to construct these systems is extremely high—much higher than soil-based farming. For example, the 1300-square-foot dome shaped greenhouse in Naujaat cost Growing North about $100,000. For poor communities, especially in developing countries, vertical farming can be unaffordable. In addition to the initial costs, there are other ongoing expenses related to paying tech-savvy workers needed to run the farms. Currently, Growing North is working on lowering that cost through in-house research and development which would make project implementation in smaller communities with limited access to funds, possible.
Still, local greenhouses may be a viable answer to the problem of food accessibility in the north.
NatureFresh Farms Mobile Greenhouse Pushes Past Heat
NatureFresh Farms Mobile Greenhouse Pushes Past Heat
By Kate Walz July 2017
Two people check out the mobile greenhouse education center. The mobile greenhouse also has a live bumblebee eco-system.Photo by NatureFresh Farms
NatureFresh Farms mobile greenhouse tour (#GreenInTheCity) is continuing across the Midwest despite the heat.
The mobile greenhouse, which has done almost 50 events since mid-April, teaches consumers how greenhouse vegetables are grown.
“The mobile greenhouse has not only been a conversation starter but a difference maker in how we connect with our customers,” Ray Wowryk, director of business development of the Leamington, Ontario, greenhouse company, said in a news release.
The Greenhouse Education Center (GEC) is a 38-foot mobile unit equipped with fruit bearing plants and a live bumblebee eco-system.
“We care about the future of fresh and all that it entails; we need to collectively increase fresh produce consumption,” Wowryk said in the release. “NatureFresh can help do that with the GEC and by getting front and center with consumers, we share our story to help inform them of the value of greenhouse vegetables.” Knowing who grows what you buy is important, understanding how it’s grown is just as important if not more.”
Five college students are serving as brand ambassadors at each event, conducting event day operations and interacting with retail partners. The group has varied backgrounds including agribusiness, environmental science, marketing and biology.
“We are able to immediately impact consumers purchasing decisions at store level with the knowledge we share about how we grow greenhouse vegetables,” said Cole Burkholder, a third-year environmental science major from Ohio State University. “The look on people’s faces when we explain the greenhouse growing process and they see the live plants with real fruit, it’s priceless. You kind of see that ‘a-ha’ moment in their eyes. We’ve even had customers show us their shopping carts when leaving to show us the tomatoes or bell peppers they have purchased because of our conversation.”
This is the third mobile greenhouse tour, which has completed more than 200 events since its inception, including events at retail stores, summer camps, schools and community fairs. The 2017 tour will end Nov. 12 at the Royal Agriculture Winter Fair in Toronto, Ontario.
Philips Lighting Begins Largest LED Horticultural Lighting Project In The World
Philips Lighting Begins Largest LED Horticultural Lighting Project In The World
2017
LED grow lights will illuminate greenhouses occupying an area the size of 40 soccer pitches
Project indicative of trend for large-scale horticultural LED lighting projects supporting domestically grown produce
Eindhoven, the Netherlands – Philips Lighting (Euronext Amsterdam ticker: LIGHT), a global leader in lighting, today announced that it will provide LLC Agro-Invest, Russia’s most innovative greenhouse produce company, with LED grow lights to support cultivation of tomatoes and cucumbers in greenhouses covering an area of more than 25 hectares (equivalent in size to about 40 soccer pitches). The project, which is the largest LED horticultural lighting project ever undertaken, will enable year-round growing, help boost yields - especially in the winter - and will save 50 percent on energy costs compared to conventional high-pressure sodium lighting. The project also underlines a global trend for large-scale LED horticultural lighting implementations that can support demand for locally grown produce.
Philips Lighting is working with Dutch partner Agrolux and Russian installer, LLC ST Solutions, which will equip greenhouses in Lyudinovo, Kaluga Oblast, 350 km south west of Moscow, during the next three months. Philips Lighting will provide ‘light recipes’ optimized for growing tomatoes and cucumbers, training services and 65,000 1.25m long Philips GreenPower LED toplights and 57,000 2.5m long Philips GreenPower LED interlights. Laid end to end, they would stretch 223 km, the equivalent of crossing the English Channel from Dover to Calais more than five times.
“We have a reputation for innovation on a large scale and LED grow lights are definitely the future. They deliver the right light for the plant, exactly when and where the plant needs it the most, while radiating far less heat than conventional lighting. This allows us to place them closer to the plants,” said Irina Meshkova, Deputy CEO and General Director, Agro-Invest. “Thanks to this technology we will be able to increase yields in the darker months of the year, and significantly reduce our energy usage,” she added.
“This LED horticultural project is the largest in the world. It will reduce the electricity consumed to light the crop by up to 50 percent compared with conventional horticultural lighting and uses light recipes designed to boost quality and crop yields by up to 30 percent in the dark period of the winter,” said Udo van Slooten, business leader for Philips Lighting’s horticultural lighting business. “Our grow lights are the perfect supplement to natural daylight so that crops can be grown efficiently throughout the year. The project also highlights a growing international trend to replace imports with domestically grown produce, reducing food miles and ensuring freshness,” he added.
About Agro-Invest
LLC Agro-Invest is Russia’s most innovative greenhouse produce company. Its 43 hectare modern greenhouse complex grows more than 15 varieties of vegetables with an annual production capacity of 25,000 tons. The company acts ecologically, collecting rainwater to water the plants which are pollinated by bees from special beehives within the greenhouse complex. The latter helps improve harvests by 20-25 percent. Protection of the plants is undertaken by natural biological methods. Since 2016, Agro-Invest has sold and marketed its produce under the “Moyo Leto.” trademark. The company works with all the federal trade networks in the Russian Federation and is expanding its operations.
About Agrolux
Agrolux is a worldwide supplier of assimilation lighting for horticulture. It is one of the biggest dealers in Philips LED horticultural lighting worldwide. It distinguishes itself based on advice, service and quality. It also produces its own luminaires and exports them to clients worldwide. The company's broad knowledge, extensive experience and innovative technology, make it stand out as a leader in the horticulture sector. It combines good, honest advice with the fast and dependable delivery of lighting luminaires and parts. Established in 2002, Agrolux has grown in size and production numbers annually. Its employees come from diverse sectors within horticulture and offer a wealth of practical experience, providing the best advice and most efficient lighting for horticulture.
For more information on Philips horticultural lighting: www.philips.com/horti
For further information, please contact:
Philips Lighting, Global Media Relations
Neil Pattie
Tel: +31 6 15 08 48 17
Email: neil.pattie@philips.com
Philips Lighting Horticulture LED Solutions
Daniela Damoiseaux
Tel: +31 6 31 65 29 69
Email: daniela.damoiseaux@philips.com
About Philips Lighting
Philips Lighting (Euronext Amsterdam ticker: LIGHT), a global leader in lighting products, systems and services, delivers innovations that unlock business value, providing rich user experiences that help improve lives. Serving professional and consumer markets, we lead the industry in leveraging the Internet of Things to transform homes, buildings and urban spaces. With 2016 sales of EUR 7.1 billion, we have approximately 34,000 employees in over 70 countries. News from Philips Lighting is located at http://www.newsroom.lighting.philips.comand on Twitter via @Lighting_Press.
MSU Students Launch Local Food Business Made From Campus Grown Foods
MSU Students Launch Local Food Business Made From Campus Grown Foods
Look for Land Grant Goods products this summer on campus.
July 20, 2017 by Kendra Wills, Michigan State University Extension
Land Grant Good founders, Alex Marx (left) and Bethany Kogut (right). Photo credit: Land Grant Goods
For anyone who finds themselves around the Brody Halls at Michigan State University, whether they be an incoming resident, staff, family member, or simply someone in the neighborhood, it may be beneficial to know that this location site offers their own handmade goods straight from the Bailey GREENhousecommunity garden located next to Bailey Hall in the Brody Complex, west of the Kellogg Center. Stop by to help support this student-run organization.
Since Michigan State University opened its doors in 1855, it has always been dedicated to education and to agriculture. In fact, it was originally called “the Agriculture College of the State of Michigan.” Which is why, to this day, you will see various gardens, hoop houses, open fields, and an overall beautiful landscape when touring the campus. As the school continues to build on to this campus, as you can see in the future visions they have set for the year 2020, MSU will continue to embrace the university’s agricultural heritage.
With this in mind, various students studying agriculture, sustainability, and education have decided that the Brody Halls, which is secluded from much of campus, needed their own greenhouse. With MSU having such a large agriculture department, and Brody Halls being located several miles away from the MSU Student Organic Farm and other MSU agricultural production facilities, it created a barrier for students living in these halls to be exposed to the culture of farming. Luckily, the Bailey GREENhouse enables students living on campus to be involved in agriculture without having to travel far distances.
This idea was put in motion in 2012, joining with the Residential Initiative for the Study of the Environment (RISE). The Bailey GREENhouse produces a wide variety of greens, tomatoes, herbs, mushrooms and even an apiary they have created themselves. The amount of components being produced in such a small area between the dorm halls is impressive and is all student-grown.
Bailey GREENhouse crops were originally used only for the residential dining halls and the State Room restaurant in the Kellogg Center, but the students knew they could take their successes further. They launched Land Grant Goods in 2015, with a goal to promote locally-made products to the community.
Today, using a mobile certified kitchen inside of a trailer parked at the MSU Student Organic Farm, the students process their jams. They sell the honey made from the apiary, and make teas from GREENhouse herbs. Overall, they have shown that they can work to make their small space as productive as possible by thinking about various value-added products that can be created.
For anyone who finds themselves visiting this site, seek out the students running this operation. This group of passionate individuals welcome all those interested in learning more about how they run their business, and will talk with excitement about the work they do and the new projects they have lined up. This may only be the start for these students, but in order to achieve these goals they will need a support system to do it.
Michigan State University Extension supports commercial agricultural producers and food businesses. For more information about launching a food business or seeking business counseling services, please contact the MSU Product Center at (517) 432-8750.
This article was published by Michigan State University Extension. For more information, visit http://www.msue.msu.edu. To have a digest of information delivered straight to your email inbox, visit http://www.msue.msu.edu/newsletters. To contact an expert in your area, visit http://expert.msue.msu.edu, or call 888-MSUE4MI (888-678-3464).
Do-It-Yourself Farmer Grows Strawberries In The Air
The system has a number of advantages. Elevated strawberries stay warmer than strawberries in the ground, which means a relatively long season, from November through April. And the plants grow downward, so the berries are easy to harvest. Outdoor strawberry farms yield about 12 tons of strawberries per acre; hanging strawberry plants in greenhouses yield three times as much.
Do-It-Yourself Farmer Grows Strawberries In The Air
July 18, 201712:50 PM ET
SHAINA SHEALY
An elevated strawberry farms in the West Bank city of Tulkarum, funded by a USAID program.
Shaina Shealy for NPR
Hezam Kittani didn't want U.S. handouts to help him grow strawberries.
He wanted to be a do-it-yourself berry farmer — and to teach others to follow in his footsteps.
Strawberries were barely grown in the West Bank, where Kittani lives, before 2009. Today they're a 250-ton yearly crop. And that's because of $705,358 in grants from USAID for farmers in this "lower middle income region" (as classified by the World Bank).
The USAID money offered a helping hand for farmers to set up a new way to grow the fruits — in hanging planters where pests can't get to them as easily as on the ground and with "a computerized automated drip irrigation system that accurately measures the optimum amount of water needed." The berries grow in a mix of perlite and peat moss.
The system has a number of advantages. Elevated strawberries stay warmer than strawberries in the ground, which means a relatively long season, from November through April. And the plants grow downward, so the berries are easy to harvest. Outdoor strawberry farms yield about 12 tons of strawberries per acre; hanging strawberry plants in greenhouses yield three times as much.
Hezam Kittani (left), the do-it-yourselfer who created his own aerial strawberry system, and Mustafa Barakat, the Palestinian Ministry of Agriculture's strawberry expert.
Shaina Shealy for NPR
But Kittani thinks there's a big disadvantage to the current setup. He doesn't want local farmers to rely on foreign aid. He wants them to succeed — to help themselves and the economy — without outside help. That's why Kittani set out to design a version of the USAID elevated strawberry system that Palestinian farmers could easily (and inexpensively) replicate themselves.
He began watching YouTube videos and doing trial-and-error experiments to find a system that farmers could pay for themselves and that would still yield lots of berries. First, Kittani built planters from the same plastic boards used in USAID-assisted strawberry farming, but the process was labor-intensive, Kittani says. "It was hard to construct because you have to cut it in pieces and find how to stick it together."
One video suggested sewage pipes as planters. So Kittani bought pipes, drilled holes in them and lined them with plastic cups full of strawberry plants. But the pipes ended up costing more than the plastic boards.
Kittani kept experimenting. Eventually he settled on wooden beams wrapped with white plastic sheets — the cheapest materials he found. "I try to make it more practical and easy to construct to train neighbors how to do it," he says.
Kittani fills his channels with soil he calls "ideal," a mix of coconut shells, peat moss and foam balls. He learned about it on a video series on the University of Arizona website.
The biggest challenge was building a computer-based irrigation system similar to the expensive USAID model. Kittani asked his daughter's high school science teacher for advice; she told him about a market that sold irrigation timers for around $30 each. He taught himself how to code and programmed a computer with similar nutrient and water measurements as the USAID system. The result was a $500 automated irrigation computer, about a third of the cost of the USAID model.
USAID's objective is the same as Kittani's: to boost the local economy, create jobs and make Palestinian agriculture globally competitive. In response to Kittani's project, a USAID spokesperson said the organization applauds innovation and is pleased that an entrepreneur is trying to develop a new system: "Our goal is to make this program self-sustaining so that farmers will be able to do this work in the future without USAID's assistance."
Strawberries and almonds (pictured, raw) are popular crops in the West Bank.
Shaina Shealy for NPR
Kittani is still fine-tuning his strawberry operation. He's working with local researchers to develop a strawberry plant tissue culture, a technique used to grow whole plants from plant cells. And Kittani recently rigged a smartphone app that's connected to a device in the soil to track irrigation and pH levels. He's researching solar panels and wants to install internet using local SIM cards instead of a wireless router so farmers without internet or electricity can send and receive information from smartphones.
"It's called smart irrigation," Kitanni says. He pauses. "No," he continues. "We will call it smart farming."
This year marked the first full strawberry harvest in Kittani's backyard. Five farmers have come to him for advice. None of them have replicated his strawberry system from scratch, but they are asking him how to make their farms more affordable and resource-efficient.
And the strawberry is just the beginning, Kittani says. Next up: "We need to study the pineapple."
Shaina Shealy is an American journalist living in Jerusalem. Her work focuses on religion, community development and women's health. Find her on twitter @shainashealy
FREIGHT FARMER Q&A: KARMA FARM
Jon Shaw has his roots in organic, soil-based farming. He has been an avid organic vegetable grower since he was a student in high school, and in 2009, after 45 years of gardening experience, Jon transformed his hobby into a career and launched Karma Farm
JUNE 8, 2017
6 Questions With Jon and Nathaniel Shaw of Karma Farm
One of the best parts of being part of the Freight Farms team is talking to our freight farmers and hearing about their successes, their businesses, their customers, and their challenges. They are a wealth of information, so now we are sharing some of their stories with you!
Jon Shaw has his roots in organic, soil-based farming. He has been an avid organic vegetable grower since he was a student in high school, and in 2009, after 45 years of gardening experience, Jon transformed his hobby into a career and launched Karma Farm. Located in Maryland, this family run farm decided to extend their growing season through the use of a hoop house, and now a Leafy Green Machine (LGM), which is run by Jon's son, Nathaniel. In addition to running a farm stand CSA, the Shaws provide area farm-to-table restaurants with leafy greens grown in the LGM year-round. With over 40 years of gardening and farming experience, Jon is a wonderful addition to our Freight Farmer community. We recently spoke with Jon and Nathaniel about the transition from traditional farming to hydroponics.
Freight Farms (FF): What, if any was your experience with farming before becoming a Freight Farmer?
Jon Shaw (JS): I started organic gardening in high school (circa 1972) and I have been growing vegetables ever since. Eight years ago, I decided to take a portion of my horse farm and turn it into commercial vegetable production.
FF: How did you find customers to buy your produce?
JS: We found many of our current customers our first summer when we grew too many tomatoes in our family garden and I decided I would go into town (Baltimore) to a few restaurants to give away samples or possibly sell them. Providing samples of our produce and explaining the breadth of our product line to chefs is still the main method we use to bring in new restaurants. Our customer base has also grown significantly from word of mouth as chefs tend to change jobs frequently.
FF: What is one small change everyone can make in their daily lives to make a big difference in our food system?
JS: Eat less meat and more vegetables.
“I was motivated to become a Freight Farmer because of my desire to turn our family farm into a sustainable business.”
FF: What’s the best part of being a Freight Farmer?
Nathaniel Shaw (NS): I’ve only been a Freight Farmer for a few months, but so far, the best things about it are bringing local chefs into the LGM to touch and taste the greens we are growing inside and seeing their surprise and excitement about the bold tastes and textures it can produce. Working with local chefs to find new greens and develop products that best utilize the advantages of the LGM has been an amazing process and one that I’m most excited to continue.
FF: What motivated you to become a farmer?
NS: I was motivated to become a Freight Farmer because of my desire to turn our family farm into a sustainable business. In recent years, we have worked to supply our restaurant customers with produce more consistently using row covers and hoop-houses, but our off-season production has remained slim. Our LGM gives us the ability to sustain a broader product line throughout the year and sustain our revenue and employee base over the winter.
FF: Which individuals, groups, and communities do you strive to reach and why have you chosen to get involved with these groups?
NS: We primarily target chefs at Farm-to-Table restaurants. The reason for this is that we love to grow beautiful and unusual produce and sell to chefs at mid to higher end restaurants that specialize in utilizing local ingredients. The restaurant community in nearby Baltimore is thriving and has grown with the farm as well.
Make sure to follow Karma Farm on Facebook and Instagram to check out pictures of Little Shaw (top dog in change) as well as beautiful shots from the farm!
If you'd like to learn more about how Freight Farms is helping farmers grow food in regions across the United States, Canada, Europe, and the Caribbean reach out to us here.